Как нарезать резьбу в чугуне метчиком
Резьбовое соединение является основным способом соединения деталей. При изготовлении своими руками любого приспособления из металла возникает необходимость самостоятельного нарезания резьбы. Нарезка позволяет своими руками сформировать резьбу в различных отверстиях.
На практике приходится иметь дело с различными материалами, которые отличаются по своим свойствам. Нарезка должна учитывать особенности материала. Существуют определенные правила, выработанные годами, которые позволяют качественно выполнить нарезание резьбы разных размеров и видов.
Особенности строения метчиков
Метчик, относящийся к группе слесарно-токарных режущих инструментов, имеет форму стержня, на котором выполнен режущий элемент. Он предназначается для нарезания внутренней резьбы, то есть внутри отверстия в различных материалах, а также для восстановления поврежденной внутренней резьбы.
Набор металлорежущего инструмента: а — сверла, б — зенкеры, в — развертки, г — метчики, д — плашки.
Инструменты состоят из рабочей и хвостовой частей. В свою очередь, рабочая часть делится на заборный (режущий) и калибрующий участок. Режущий участок ответствен за основную функцию метчика — нарезание резьбы, и, чаще всего, имеет конусную форму. Он обладает зубьями в виде резцов, размещенных по окружности. Калибрующий участок выполняет задачу окончательного формирования. Он выполнен в виде цилиндра с зубьями, являющимися продолжением зубьев режущего участка. Этот участок значительно длиннее заборного. Рабочая часть в продольном направлении разрезана канавками, которые предназначены для формирования резцов и вывода стружки. В метчиках диаметром до 22 мм выполняется три канавки. Устройства специального назначения могут изготавливаться без канавок. Канавки могут быть прямыми или винтообразными.
Хвостовая часть имеет форму цилиндра. На конце участка выполнен квадрат для установки в крепежный инструмент. В этой части выбивается маркировка по диаметру. С помощью хвостовика инструмент фиксируется в ручном держателе или патроне станка.
Основные виды метчиков
По способу использования метчики делятся на два типа — ручные и машинные. Первые устанавливаются в ручных держателях (воротках) и предназначены для нарезания внутренней резьбы вручную. Машинные крепятся в специальные держатели для патронов токарного станка.
По виду резьбы, нарезаемой метчиком, они делятся на несколько видов. Метрический предназначен для нарезания наиболее распространенной метрической резьбы. Трубный формирует внутреннюю резьбу на трубах, а также усиленную в отверстиях металлических деталей. Дюймовый — это устройство для специальной дюймовой резьбы, а также конусообразной. Специализированные гаечные метчики изготавливаются из очень прочной стали (Р6М5) и имеют особую форму хвостовиков.
Кроме того, метчики подразделяются на одиночные и комплектные. Комплектные применяются для того, чтобы резать в несколько заходов. Комплект может содержать два метчика — чистовой и черновой; или три метчика — черновой, средней обработки и чистовой. Комплектность указывается на хвостовой части инструмента. Метчики в комплекте отличаются по форме зуба: у чернового зуб имеет трапециевидную форму; у среднего — треугольник с закругленной вершиной; у чистового — треугольник с острой вершиной.
Основные параметры
Нарезание резьбы метчиком.
В общем случае нарезать резьбу — это значит изготовить выступ на внутренней поверхности отверстия так, чтобы он образовал винтовую линию. Такой выступ, как и вся резьба, характеризуется следующими основными параметрами: угол подъема винтообразной линии, шаг, вид профиля выступа и угол подъема профиля, наружный и внутренний диаметр. Кроме того, принято выделять еще глубину, определяемую по наружному и внутреннему диаметрам.
По направлению резьба может быть правой, когда винтообразный выступ поднимается против часовой стрелки, и левой, когда направление подъема выступа совпадает с движением часовой стрелки. По форме профиля выступа выделяются два основных типа: резьба с прямоугольным профилем и с треугольным профилем. Существуют еще специальные формы профиля, но они в бытовых условиях практически не применяются.
Основной является метрическая резьба. Такой профиль представляет собой треугольник с углом профиля 60º. По шагу метрическая делится на резьбу с крупным шагом и с мелким шагом. Пример полного обозначения метрической резьбы — М10х1-6Н. Обозначение нужно понимать следующим образом:
Таблица выбора метчиков для нарезания резьбы.
- М — метрическая резьба;
- 10 — номинальный диаметр;
- 1 — шаг резьбы;
- 6Н — пределы допуска отклонений размеров.
При нормальном (крупном шаге) обозначение сокращается (например, М10). В случае левой резьбы, вводится обозначение LH.
Вторым по распространенности в быту является трубный цилиндрический тип. Профиль представляет собой треугольник с углом при вершине 55º. Такой тип используется при соединении труб и цилиндров, где нужна повышенная герметичность соединения. Трубная цилиндрическая резьба обозначается буквой G с указанием диаметра в дюймах.
Упорная резьба основана на трапециевидном профиле с углами наклона с одной стороны 3º, с другой — 30º. В обозначение входит буква S, диаметр и шаг.
Выбор подходящего метчика
Схема нарезания внешней и внутренней резьбы.
Вначале выбирается тип метчика по виду резьбы и ее назначению (форма профиля, шаг резьбы, допуски). По требованиям (классу) точности определяется, следует ли применить одинарный метчик или необходим комплект. Кроме того, метчики выпускаются с различной чистотой обработки их режущего элемента, что влияет на точность нарезания профиля резьбы.
Материал, в котором надо нарезать резьбу, влияет на выбор метчика. Так, следует учитывать передний угол заточки зубьев. Он составляет для стали — 5-10º, для медных сплавов — 0-5º, для алюминия и сплавов — 25-30º. Устройства могут изготавливаться из обычных сталей, высокопрочных сталей или высокопрочными напайками, что должно учитываться при рассмотрении того, материал какой прочности обрабатывается.
Основной выбор делается по диаметру отверстия, в котором производится нарезание внутренней резьбы. Диаметр метчика должен быть немного меньше диаметра отверстия. Так, для метрической резьбы М20 (диаметр метчика 20 мм) диаметр отверстия составляет 19 мм. При метрической резьбе, если нет особых требований, то выполняется стандартный шаг. Например, резьба М4 — шаг 0,7 мм; М5 — 0,8 мм; М10 — 1,5 мм; М12 — 1,75 мм и т.д.
Инструмент для крепления
Схемы нарезания резьбы плашками.
Для того чтобы обеспечить нарезание резьбы, метчику необходимо придать вращательное движение с приложением усилия. Эту функцию выполняет ручной держатель — вороток. Он обеспечивает вертикальное крепление инструмента и возможность приложения значительной нагрузки за счет рычагов. Стандартная конструкция воротка содержит узел крепления метчика и удлиненные ручки, при помощи которых можно вращать приспособление вручную с усилием.
Крепление устройства осуществляется двумя способами. Одна из конструкций воротка состоит из двух частей. При сочленении этих частей внутри формируется отверстие для установки метчика. Обе части сближаются на регулируемое расстояние, которое устанавливается винтами. Второй вариант предусматривает единую конструкцию воротка с отверстием по центру. Метчик вставляется в это отверстие и зажимается 3-4 стопорными винтами. Ручки воротка выполнены с обеих сторон. Длины ручек могут составлять 15-25 см.
Подготовка к нарезанию
Нарезка внутренней резьбы начинается с просверливания нужного отверстия — сквозного или глухого. Главное условие: отверстие должно быть меньше диаметра резьбы. При сверлении отверстия рекомендуется выбирать сверло из следующего условия:
- при резьбе М3 — диаметр сверла 2,5 мм;
- при М4 — 3,4 мм;
- при М5 — 4,2 мм;
- при М6 — 5 мм;
- при М8 — 6,7 мм;
- при М10 — 8,4 мм.
Если необходимо нарезать большую резьбу, то диаметр отверстия определяется приблизительно умножением диаметра резьбы на 0,8.
Отверстие для нарезания внутренней резьбы делается на сверлильном станке или электродрелью. В последнем случае заготовка зажимается в тиски. Необходимо следить, чтобы сверло направлялось строго вертикально. На верхней кромке отверстия снимается фаска для облегчения входа метчика. Ее можно сделать сверлом большего диаметра или напильником.
Нарезка резьбы метчиком
Деталь, в которой просверлено отверстие для внутренней резьбы, закрепляется в тиски так, чтобы фаска на отверстии находилась вверху. Ось отверстия должна расположиться строго перпендикулярно столу. Метчик надежно закрепляется в гнезде воротка и вертикально вводится в фаску отверстия заготовки. Держась обеими руками за ручки воротка, метчик прижимают к детали и вращают по часовой стрелке. Вращение производится плавно и равномерно с легким нажимом. Так делается два оборота вперед. Затем производится поворот на половину оборота назад (против часовой стрелки).
При нарезании резьбы болт нужно закреплять.
При нарезке резьбы необходимо периодически охлаждать инструмент. Рекомендуется использовать следующие вещества: при работе с алюминием и его сплавами — керосин, с медью — скипидар, со стальными деталями — эмульсию. Для таких металлов, как бронза или чугун, охлаждающие смазки можно не применять.
Нарезку внутренней резьбы метчиком лучше всего производить комплектными метчиками. Вначале нарезается черновая резьба. Потом аналогично пропускают средний метчик, и только потом резьба окончательно формируется с помощью чистового. Исключение из процесса какого-либо метчика не приведет к заметному ускорению процесса, но значительно ухудшит качество работы.
Основные правила нарезки
Внутренняя резьба метчиком должна делаться с обязательным соблюдением определенных правил. В случае нарезания в длинных отверстиях, в глухих отверстиях, в алюминии или меди, метчик нужно временами извлекать наружу, а отверстие тщательно прочищать от частиц металла.
Нарезку рекомендуется производить полным комплектом устройства. Средний и чистовой вначале проворачиваются в отверстии вручную без закрепления в воротке и только после этого закрепляются в нем и прогоняются с легким усилием. Резьба внутри глухих отверстий нарезается длиной, большей расчетной длины резьбы на длину режущего участка метчика.
Введение метчика в отверстие необходимо тщательно контролировать по вертикали.
Через каждые три оборота воротка следует проверять вертикальность угольником.
Обязательно используется охлаждающая жидкость.
При нарезке могут возникнуть характерные дефекты, за появлением которых необходимо пристально следить. Шероховатая или неравномерная резьба появляется при недостаточном охлаждении или перекосе метчика. Неполное формирование профиля может проявиться при неправильном просверливании отверстия. По той же причине могут происходить перекосы направления и поломки инструмента.
Необходимый инструмент
Для нарезания резьбы метчиком понадобится следующий инструмент:
- набор метчиков;
- вороток;
- тиски;
- электродрель;
- набор сверл;
- плоскогубцы;
- отвертка;
- напильник;
- наждачная бумага;
- штангенциркуль;
- угольник.
При изготовлении своими руками различных приспособлений не удастся обойтись без резьбовых соединений. Нарезка метчиками является важнейшим этапом таких работ. При выполнении определенных правил ее можно произвести самостоятельно.
Автор: 1-vip, 6 декабря 2012 в Разговоры
Рекомендованные сообщения
Создайте аккаунт или войдите в него для комментирования
Вы должны быть пользователем, чтобы оставить комментарий
Создать аккаунт
Зарегистрируйтесь для получения аккаунта. Это просто!
Войти
Уже зарегистрированы? Войдите здесь.
Сейчас на странице 0 пользователей
Нет пользователей, просматривающих эту страницу.
Автор: stroitelinfo · Опубликовано 01.02.2014 · Обновлено 08.11.2018
Нарезаем резьбу метчиком. Самый элементарный и часто встречающийся вариант скрепления деталей – резьбовое соединение. Казалось бы, что сделать его самостоятельно не составит никакого труда. На самом деле, правильная нарезка резьбы метчиком требует соблюдения многих правил, в противном случае качественного соединения в последующем не получится, а то и вовсе резьба не удастся или придет в негодность используемый инструмент. Как нарезать резьбу метчиком самостоятельно.
Подбор инструмента
Некачественное орудие труда – некачественная работа. Использование старых затупившихся или проржавевших метчиков или плашек чревато изломом их в процессе работы и плохой резьбой на детали. Помимо уже давно непригодных инструментов нужно избегать и тех, что непригодны с самого начала. К ним относятся все дешевые варианты неизвестного происхождения.
Помимо качества важен также их размер, а именно соотношение размеров используемого сверла и отверстия для него. Высчитать необходимые параметры можно благодаря формуле, но для облегчения этого процесса приведены примеры с точным соотношением:
- метрическая резьба М2 – диаметр сверла (метчика) 1,6 мм;
- м. р. М2,5 – д. с. 2,2 мм;
- м. р. М3 – д. с. 2,5 мм;
- м. р. М4 – д. с. 3,3 мм;
- м. р. М5 – д. с. 4,2 мм;
- м. р. М6 – д. с. 5 мм;
- м. р. М8 – д. с. 6,7 мм;
- м. р. М10 – д. с. 8,3 мм.
Смазка деталей
Этот момент очень важен, ведь благодаря нему используемый инструмент прослужит в разы дольше. Помимо этого он уменьшает вероятность поломки сверла внутри отверстия и снижает температуру разогретых кромок метчика. Но при выборе смазки обязательно нужно учитывать материал деталей, на которые наносится резьба:
- сталь, латунь – льняное масло;
- алюминий – керосин;
- медь – скипидар;
- бронза, чугун – без использования СОЖ (смазочно-охлаждающая жидкость).
В качестве смазки не рекомендуется использовать минеральные либо машинные масла. Их состав не позволяет мягко скользить поверхности метчика или плашки, поэтому резьба получится с шероховатостями.
Как нарезать резьбу метчиком: нарезка внутренней резьбы
О главных нюансах уже сказано, теперь можно перейти непосредственно к тому, как нарезать резьбу метчиком или плашкой. Пошагово этот процесс выглядит следующим образом:
Зажимаем в тисках обрабатываемую деталь.
Просверливаем отверстие под дальнейшую нарезку внутренней резьбы.
При помощи сверла, диаметр которого на несколько миллиметров больше планируемой резьбы, наносим фаску на край отверстия. Она необходима для более легкого вхождения метчика, а также для облегчения процесса ввинчивания винта в готовое изделие.
Вставляем в вороток (устройство для крепежа метчиков и плашек) черновой метчик.
Наносим на режущую часть смазку.
Вставляем в отверстие метчик и делаем три оборота.
После первых трех оборотов, делаем один оборот в обратную сторону. Таким образом, мы ломаем получающуюся в процессе нарезки стружку и она не будет мешать качественному и ровному нанесению резьбы.
Если отверстие в детали сквозное, необходимо сделать так, чтобы передняя часть метчика вышла полностью с обратной стороны. Не сделав этого, мы рискуем получить незаконченную резьбу.
Слом режущей части метчика в глухом отверстии
Если конец обломившейся детали полностью «утоплен» в отверстии, достать его будет очень сложно. Но поднабравшись терпения этого сделать все-таки реально. Вам потребуется парафин, продолговатая и тонкая деревянная палочка, азотная кислота. Парафином смазываем обрабатываемую деталь (защищаем от воздействия кислоты). Конец палочки смачиваем кислотой, просовываем его в отверстие и смазываем режущие кромки метрика. Как нарезать резьбу метчиком
Необходимо продолжать процедуру до тех пор, как края начнут расплавляться. После этого обломок либо выбивают молотком с обратной стороны детали, либо выковыривают пинцетом.
Как нарезать резьбу сметчиком: нарезка внешней резьбы
Взяв необходимую деталь, зажимаем ее в тиски. С одной стороны напильником делаем небольшую фаску, смазываем эту сторону маслом, керосином или скипидаром (в зависимости от материала).
В плашкодержатель вставляем и фиксируем плашку. Приставляем плашку к нужному концу трубы и в нужном нам направлении медленно вращаем одной рукой, второй рукой обязательно прижимаем верх плашки к трубе.
Когда плашка прочно села на трубу, проверьте ее перпендикулярность трубе, возьмитесь за плашкодержатель обеими руками и сделайте 3-4 оборота вперед, а потом пол оборота назад.
При нарезке внешней резьбы есть один нюанс, во время последних витков не делайте вращение назад, это позволит гайке прочно зафиксироваться на трубе.
Обратите внимание, свеженарезанную резьбу не стоит трогать голыми руками, на ней могут быть очень острые заусеницы и есть большая вероятность пореза.
Информация на заметку : Клупп для нарезки резьбы , Как крепить анкерный болт
youtube.com/embed/xKnc9ungzyc?rel=0″/>
Нарезка резьбы в чугуне
Ремонт резьбового отверстия (восстановление повреждённой резьбы)
Наша компания не занимается восстановлением резьбы. Данная статья служит исключительно для ознакомления с процессом восстановления резьбы. В наших магазинах вы можете купить футорки (резьбовые вставки) , сверла , метчики , наборы для восстановления резьбы .
Информация предназначена для лиц, производящих ремонт в условиях личного гаража, и автосервисов. В соответствии с этим выстроен текст и даны рекомендации. Применение данного метода на производственных предприятиях предполагает использование специфических инструментов и устройств, и другой технологии.
Способ восстановления резьбы
Повреждённую резьбу можно полностью восстановить по следующей технологии:
1. Рассверлить резьбовое отверстие до диаметра, указанного в приведённой ниже таблице
2. Нарезать в нём резьбу особого профиля специальным метчиком
3. Ввернуть в полученную резьбу спиральную ремонтную вставку (футорку из прочной нержавеющей стали, с помощью специального инструмента.
После такой операции резьба становится более прочной, чем первоначальная в исправном состоянии. Этот эффект особенно заметен, когда резьба выполнена в мягком материале, например, алюминии. При срыве болта (шпильки) в резьбовой вставке эффект “закусывания” отсутствует. Сорванный болт (шпильку) можно легко вывернуть.
Посмотрите видео, как используется резьбовая вставка
Какие возможности есть у резьбовых вставок
Особенно актуален этот способ для восстановления резьбовых отверстий в корпусных деталях автомобильных двигателей, например, свечного отверстия. Резьба под свечу становится очень прочной и надёжной.
Резьбовая вставка вкручена
Резьбовая вставка вкручена
Если сорвана резьба под шпильку , иногда рассверливают её, и нарезают резьбу следующего размера. В таком случае приходится применять ступенчатую шпильку неизвестного происхождения, сомнительного качества. Да и не всякую ступенчатую шпильку найдёшь в нужный момент. Если же отремонтировать отверстие с применением резьбовой вставки , остаётся возможность применить штатную, фирменную шпильку.
Ещё одно применение ремонтных резьбовых вставок – в латунных гайках выхлопного коллектора . Получается гайка, совмещающая очень прочную резьбу и свойство не «пригорать» к шпилькам.
Владельцам некоторых иномарок стоит обратить внимание и на возможность замены резьбы М12 х 1,5 на резьбу М12 х 1,25. Нередко случается, что болт с такой резьбой повреждён, а найти его в розничной сети в вашем городе практически невозможно (в нашем магазине есть такие болты ). Токарь приличный болт не выточит, т.к. резьба на заводских болтах формируется давлением (накаткой), что обеспечивает необходимую прочность. А на токарном станке резьба получается резцом, при этом волокна стального прутка перерезаются и витки резьбы не могут нести необходимой нагрузки.
Если заменить резьбу в корпусной детали на более распространённую в России М12 х 1,25 , появляется возможность подобрать болт необходимых размеров и прочности в ассортименте Российских и Европейских производителей автомобильного крепежа, представленных в нашем каталоге.
Видео – как работает резьбовая вставка, демонстрация
Какие инструменты применяются при восстановлении резьбы
№ п/п | Размеры восстанавливаемой резьбы | Диаметр сверла |
1 | М5 х 0,8 | 5,2 |
2 | М6 х 1 | 6,3 |
3 | М8 х 1 | 8,3 |
4 | М8 х 1,25 | 8,4 |
5 | М10 х 1 | 10,25 |
6 | М10 х 1,25 | 10,4 |
7 | М10 х 1,5 | 10,5 |
8 | М12 х 1,25 | 12,25 |
9 | М12 х 1,5 | 12,5 |
10 | М12 х 1,75 | 12,5 |
11 | М14 х 2 | 14,5 |
12 | М14 х 1,5 | 14,5 |
13 | М14 х 1,25 (под свечу) | 14,25 |
Для ремонта свечного отверстия рекомендуется метчик ступенчатый. Он центрируется в старом отверстии своей заходной частью, и сразу нарезает новую резьбу, минуя операцию рассверливания.
Ступенчатый метчик существенно уменьшает риск порчи свечного отверстия, но он заметно дороже обычного.
Для удлинения метчика при ремонте глубоко утопленного свечного отверстия можно использовать обычную торцовую двенадцатигранную головку на 10 с соответствующим инструментом.
3. Шпиндель (инструмент для вворачивания вставки)
Рабочая часть шпинделя похожа на резьбовую часть болта, с зацепом на торце.
Вставка представляет собой спираль ромбовидного профиля.
На одном конце её имеется поводок, за который вставка вращается шпинделем.
Вставки имеют разные длины.
Описание технологии восстановления резьбы
Внимание: эта технология применяется для ремонта резьбовых отверстий в бытовых, гаражных условиях.
1. Рассверлить отверстие. Периодически вынимать сверло из отверстия и обмакивать его конец в ёмкость с моторным маслом. Желательна минимальная скорость вращения сверла.
2. Нарезать метчиком резьбу под вставку. В процессе работы необходимо постоянно подавать в зону резания моторное масло, например из медицинского шприца, особенно при работе с алюминием. Иначе резьба может получиться «рваной», шероховатой, а на метчик налипнет алюминий.
Если отверстие глухое — вместо моторного масла лучше применить смазку, например Литол. Ею нужно обмазать рабочую часть метчика, чтобы стружка не сыпалась в отверстие, а прилипла к метчику.
3. Промыть полученную резьбу керосином.
4. Надеть вставку на шпиндель, ввести в зацепление поводок и зацеп.
Нужно иметь в виду, что вставка несколько больше шпинделя, она не сидит на нём плотно, а свободно болтается. При вкручивании в отверстие вставка сжимается и тем самым закрепляется в отверстии. Вставку вворачивать до тех пор, пока её задний конец не углубится в отверстие на 1/4 шага резьбы. После этого вывернуть шпиндель и отломить поводок вставки, надавив на него подходящим стержнем. Для этого на витке за поводком имеется риска, по которой и отломится поводок. Примечание:При использовании ступенчатого метчика пункт 1 исключается.
Наша компания не занимается восстановлением резьбы. Данная статья служит исключительно для ознакомления с процессом восстановления резьбы. В наших магазинах вы можете купить футорки (резьбовые вставки) , сверла , метчики , наборы для восстановления резьбы.
Нарезание внутренней резьбы. Подготовка отверстий под резьбу заключается в соответствующем выборе диаметра сверла, которым будет просверливаться отверстие под нарезание резьбы.
Отверстие, в котором нарезают резьбу метчиком, должно быть чистым, т. е. просверлено, обработано зенкером или же проточено. При нарезании резьбы материал частично выдавливается, поэтому диаметр сверла должен быть несколько больше, чем внутренний диаметр резьбы.
Металлы твердые и хрупкие дают меньшие изменения величины отверстие при нарезании резьбы, чем металлы мягкие и вязкие. Если просверлить под резьбу отверстие диаметром, точно соответствующим внутреннему диаметру резьбы, то материал, выдавливаемый при нарезании, будет давить на зубья метчика, отчего они нагреваются и к ним прилипают частицы металла. Резьба может получиться с рваными нитками, а в некоторых случаях возможна поломка метчика.
При сверлении слишком большого диаметра резьба получится неполной. Для определения диаметра сверла под метрическую резьбу следует руководствоваться табл. 26.
Таблица 26 Диаметр сверления отверстия под нарезание метрической резьбы при обработке чугуна и бронзы, стали и латуни
В случае отсутствия таблиц размер диаметра отверстия под резьбу можно вычислить по формуле D= d-1,6t,
где D – диаметр отверстия, мм;
d – диаметр нарезаемой резьбы, мм; t – глубина резьбы, мм. Размеры воротка для закрепления метчика при нарезании резьбы подбираются в зависимости от диаметра нарезаемой резьбы. Примерная длина воротка может быть определена по формуле
где D – диаметр резьбы.
После подготовки отверстия под резьбу и выбора воротка заготовку закрепляют в тисках и вставляют вертикально (без перекоса) в ее отверстие черновой метчик; а затем, прижимая левой рукой, правой поворачивают вороток вправо до тех пор, пока он не врежется на несколько ниток в металл и не займет устойчивое положение, после чего вороток с метчиком берут Обеими руками и вращают (рис. 152, а).
Рис. 152. Прием нарезания резьбы метчиком (а) и плашкой (б)
В целях облегчения работы вороток с метчиком вращают не все время по направлению часовой стрелки, а один-два оборота вправо и пол-оборота влево и т. д. Благодаря такому возвратно-вращательному движению метчика стружка ломается, получается короткой (дробленой), а процесс резания значительно облегчается.
Мы продолжаем рассматривать технологии восстановления сорванной резьбы в различных узлах и агрегатах, как автомобильной техники, так и в промышленном оборудовании. В первой части «Методы восстановления резьбы свечного колодца» мы начали обсуждать методику ремонта и разобрали преимущества, и недостатки представленных вариантов, как можно восстановить резьбу в головке под свечу зажигания.
Во второй части нашего обзора, будут в общих чертах рассмотрены способы восстановление различных резьбовых отверстий на практике.
И так, давайте разберемся, что делать если сорвал резьбу. Какие способы ремонта применяют различные ремонтные предприятия.
В ремонтном производстве применяют следующие способы восстановление резьбы:
- заварка отверстий с последующей нарезкой резьбы;
- установка ввертыша;
- сверление отверстий и нарезка резьбы на новом месте;
- обработка отверстия и нарезание резьбы увеличенного размера;
- применение полимерных материалов;
- установка резьбовой спиральной вставки.
Восстановление резьбы с применением сварки
Заварка резьбового отверстия с последующим нарезанием резьбы. Во всех случаях при заварке резьбовых отверстий сначала удаляют старую поврежденную резьбу путем рассверливания. В стальных деталях заварку отверстий производят газовой или электродуговой сваркой в защитных средах. Заварку в чугунных деталях производят газовой или электродуговой сваркой с общим или местным нагревом или в холодном состоянии. В качестве присадочного материала или электродов при горячей заварке применяют чугунные прутки с повышенным содержанием кремния, поршневые кольца из серого чугуна, электроды ЦЧ-4, ОЗЧ-1, МНЧ-1. Место заварки обрабатывают заподлицо с основным металлом, сверлят отверстие и нарезают резьбу в алюминии или чугуне номинального размера. Однако применение сварочных процессов вследствие большой зоны термического влияния приводит к появлению отбела, трещин и короблений детали, изменению структуры основного металла. Прочность восстановленной резьбы ниже новой.
Для заварки отверстий в алюминиевых деталях двигателя наибольшее применение получила аргонно-дуговая сварка специальными электродами из алюминиевой проволоки марки АК. Недостаток применения сварочных способов для, того чтобы восстановить резьбу в алюминии — активное поглощение расплавленным алюминием газов, что приводит к образованию пор в наплавленном слое. Большая усадка остывающего алюминия часто приводит к образованию трещин. От себя можем добавить, чтобы восстановить внутреннюю резьбу, например на блоке цилиндров двигателя, то необходимо произвести снятие детали и произвести дальнейший ее ремонт, что финансово будет не совсем выгодно.
Как восстановить сорванную резьбу используя футорки
Как восстановить резьбу в отверстии используя футорку (рис.1). Установка ввертыша может применяться, при восстановление резьбы если конструкция детали позволяет увеличивать отверстия. Этот способ ремонта резьбы трудоемок, стоимость ремонта высокая.
Сверление резьбового отверстия и нарезание резьбы на новом месте можно применять только для отдельных групп алюминиевых и чугунных деталей, у которых расположение резьбовых отверстий может быть изменено без нарушения взаимозаменяемости соединения (ступицы колеса, барабаны, фланцы) и способ ремонта резьбовых отверстий на ремонтный размер влечет за собой введение увеличенного размера и дополнительной обработки сопряженной детали.
Как восстановить внутреннюю резьбу спиральными вставками
За последние годы на ремонтных предприятиях для ремонта резьбовых отверстий широко распространен способ установки резьбовых спиральных вставок. Отечественный и зарубежный опыт изготовления спиральных вставок показал, что наилучшие результаты при восстановление резьбы, достигнуты при использовании нержавеющей стали.
рис.2 резьбовая вставка helicoil
Спиральные резьбовые вставки серийно изготавливают из проволоки с жесткими производственными допусками (рис.3). В таком виде спиральные вставки представляют строго концентрические внутренние и наружные резьбы.
Восстановленная резьба в чугуне имеет высокую износостойкость, обусловленную применением высококачественного материала спиральных вставок и наличием гладких поверхностей проволоки.
Сорванная резьба, отремонтированная обладает повышенной антикоррозионной стойкостью, исключающей возможность заедания резьб болтов и шпилек в результате атмосферных условий, так как отсутствует контактная коррозия в резьбовом соединении.
рис.4 восстановленная резьба
Такие резьбы имеют достаточный запас прочности при наличии термических напряжений, поскольку концентрированно подверженные тепловым напряжениям резьбовые соединения эффективно защищены от заедания и пригорания, образования окислов и окалин.
Как нарезать резьбу метчиком — пошаговая инструкция
Нарезаем резьбу метчиком
Самый элементарный и часто встречающийся вариант скрепления деталей – резьбовое соединение. Казалось бы, что сделать его самостоятельно не составит никакого труда. На самом деле, правильно нарезать резьбу метчиком требует соблюдения многих правил, в противном случае качественного соединения в последующем не получится, а то и вовсе резьба не удастся или придет в негодность используемый инструмент.
Подбор инструмента
Некачественное орудие труда – некачественная работа. Использование старых затупившихся или проржавевших метчиков или плашек чревато изломом их в процессе работы и плохой резьбой на детали. Помимо уже давно непригодных инструментов нужно избегать и тех, что непригодны с самого начала. К ним относятся все дешевые варианты неизвестного происхождения.
Помимо качества важен также их размер, а именно соотношение размеров используемого сверла и отверстия для него. Высчитать необходимые параметры можно благодаря формуле, но для облегчения этого процесса приведены примеры с точным соотношением:
- метрическая резьба М2 – диаметр сверла (метчика) 1,6 мм;
- м. р. М2,5 – д. с. 2,2 мм;
- м. р. М3 – д. с. 2,5 мм;
- м. р. М4 – д. с. 3,3 мм;
- м. р. М5 – д. с. 4,2 мм;
- м. р. М6 – д. с. 5 мм;
- м. р. М8 – д. с. 6,7 мм;
- м. р. М10 – д. с. 8,3 мм.
Смазка деталей
Этот момент очень важен, ведь благодаря нему используемый инструмент прослужит в разы дольше. Помимо этого он уменьшает вероятность поломки сверла внутри отверстия и снижает температуру разогретых кромок метчика. Но при выборе смазки обязательно нужно учитывать материал деталей, на которые наносится резьба:
- сталь, латунь – льняное масло;
- алюминий – керосин;
- медь – скипидар;
- бронза, чугун – без использования СОЖ (смазочно-охлаждающая жидкость).
В качестве смазки не рекомендуется использовать минеральные либо машинные масла. Их состав не позволяет мягко скользить поверхности метчика или плашки, поэтому резьба получится с шероховатостями.
Как нарезать резьбу сметчиком — нарезка внутренней резьбы
О главных нюансах уже сказано, теперь можно перейти непосредственно к тому, как нарезать резьбу метчиком или плашкой. Пошагово этот процесс выглядит следующим образом:
Зажимаем в тисках обрабатываемую деталь.
Просверливаем отверстие под дальнейшую нарезку внутренней резьбы.
При помощи сверла, диаметр которого на несколько миллиметров больше планируемой резьбы, наносим фаску на край отверстия. Она необходима для более легкого вхождения метчика, а также для облегчения процесса ввинчивания винта в готовое изделие.
Вставляем в вороток (устройство для крепежа метчиков и плашек) черновой метчик.
Наносим на режущую часть смазку.
Вставляем в отверстие метчик и делаем три оборота.
После первых трех оборотов, делаем один оборот в обратную сторону. Таким образом, мы ломаем получающуюся в процессе нарезки стружку и она не будет мешать качественному и ровному нанесению резьбы.
Если отверстие в детали сквозное, необходимо сделать так, чтобы передняя часть метчика вышла полностью с обратной стороны. Не сделав этого, мы рискуем получить незаконченную резьбу.
Слом режущей части метчика в глухом отверстии
Если конец обломившейся детали полностью «утоплен» в отверстии, достать его будет очень сложно. Но поднабравшись терпения этого сделать все-таки реально. Вам потребуется парафин, продолговатая и тонкая деревянная палочка, азотная кислота. Парафином смазываем обрабатываемую деталь (защищаем от воздействия кислоты). Конец палочки смачиваем кислотой, просовываем его в отверстие и смазываем режущие кромки метрика.
Необходимо продолжать процедуру до тех пор, как края начнут расплавляться. После этого обломок либо выбивают молотком с обратной стороны детали, либо выковыривают пинцетом.
Как нарезать резьбу метчиком — нарезка внешней резьбы
Взяв необходимую деталь, зажимаем ее в тиски. С одной стороны напильником делаем небольшую фаску, смазываем эту сторону маслом, керосином или скипидаром (в зависимости от материала).
В плашкодержатель вставляем и фиксируем плашку. Приставляем плашку к нужному концу трубы и в нужном нам направлении медленно вращаем одной рукой, второй рукой обязательно прижимаем верх плашки к трубе.
Когда плашка прочно села на трубу, проверьте ее перпендикулярность трубе, возьмитесь за плашкодержатель обеими руками и сделайте 3-4 оборота вперед, а потом пол оборота назад.
При нарезке внешней резьбы есть один нюанс, во время последних витков не делайте вращение назад, это позволит гайке прочно зафиксироваться на трубе.
Обратите внимание, свеженарезанную резьбу не стоит трогать голыми руками, на ней могут быть очень острые заусеницы и есть большая вероятность пореза.
Информация на заметку: Клупп для нарезки резьбы , Как крепить анкерный болт
Нарезание резьбы — Диаметры отверстий под резьбу
На точность нарезаемой резьбы влияют три параметра отверстия под резьбу диаметр, длина и перпендикулярность оси отверстия к базе.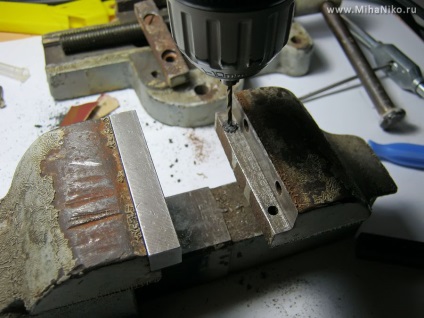
При нарезании резьбы материал детали несколько выдавливается метчиком, и внутренний диаметр резьбы оказывается больше диаметра исходного отверстия. Это обстоятельство учтено в специальных таблицах, по которым выбирают диаметр отверстия под резьбу. Диаметры сверл для обработки отверстий в стальных деталях под нарезание метрических резьб с мелкими шагами приведены в табл. 16. [c.221]
Диаметр отверстия под резьбу должен быть несколько больше внутреннего диаметра резьбы, так как в процессе нарезания резьбы металл деформируется и в результате этого диаметр отверстия уменьшается. Поэтому результат, полученный по приведенной выше формуле, увеличивают на 0,2…0,4 мм при нарезании резьбы в вязких материалах (стали, латуни и др.) и на 0,1…0,02 мм при нарезании резьбы в хрупких материалах (чугуне, бронзе и др.

Диаметры отверстий под резьбу должны обеспечить после нарезания внутренний диаметр резьбы в пределах допусков, предусмотренных стандартом. [c.475]
Большое значение для правильного нарезания резьбы имеет размер отверстия под резьбу. У чугуна он делается равным внутреннему диаметру резьбы, а у вязких материалов он должен быть несколько больше, так как в процессе резания происходит пластическая деформация и подъем металла. В случае заниженного диаметра отверстия может произойти срыв резьбы или поломка метчика. Величина подъема металла зависит от степени его вязкости и поэтому в каждом отдельном случае надо пользоваться данными соответствующих справочников. [c.150]
Нарезание внутренней резьбы в отверстиях. До нарезания резьбы необходимо просверлить отверстие соответствующего диаметра. Правильный выбор диаметра сверла при нарезании резьбы в отверстии имеет большое значение. Если диаметр отверстия слишком велик, резьба получается недостаточно глубокой (неполной) и молдиаметр отверстия под резьбу слишком мал, то при нарезании срывается резьба или ломается метчик.
[c.200]
Сверление отверстий под резьбу. Диаметр отверстия под резьбу должен быть несколько меньше наружного и больше внутреннего диаметра резьбы. Объясняется это тем», что при нарезании резьбы металл выдавливается, отчего диаметр отверстия уменьшается. Чем более тверд и хрупок металл, тем меньше изменяется диаметр отверстия при нарезании резьбы. В отверстии, меньшем нормального, метчик испытывает большее сопротивление резанию, резьба получается с рваными нитками. Если же диаметр отверстия больше нормального, получается неполная резьба. [c.168]
Правильный выбор диаметра отверстия под резьбу имеет большое значение. Если диаметр просверленного отверстия больше, чем необходимо, получается неполная резьба, если диаметр отверстия меньше требуемого, при нарезании срывается резьба или ломается метчик. [c.501]
При нарезании резьбы метчиком увеличение диаметра отверстия под резьбу уменьшает опорную поверхность между витками метчика и гайки, повышает удельное давление на этой поверхности.

Диаметр отверстия под резьбу. В процессе нарезания резьбы метчиком материал гайки слегка вдавливается внутрь, т. е. в направлении к внутреннему диаметру. В результате сказанного, высота резьбы увеличивается на величину подъема. [c.45]
Формула (4), кроме своего прямого назначения, дает возможность решать обратную задачу, т. е., задаваясь конкретными значениями диаметра отверстия под резьбу, можно рассчитать потребное количество метчиков для нарезания резьбы. [c.47]
При нарезании резьбы метчиком увеличение диаметра отверстия под резьбу уменьшает опорную поверхность между витками метчика и гайки и повышает удельное давление на этой поверхности. Возрастание удельного давления может быть весьма значительным и превзойти предел прочности обрабатываемого материала оно приводит к разбиванию резьбы по среднему диаметру. Величина разбивания тем больше, чем больше удельная нагрузка на виток в каждый данный момент, и значительно изменяется в зависимости от твердости обрабатываемого материала.
[c.59]
Большое значение имеет правильный выбор диаметра отверстия под резьбу. Диаметр сверла для отверстия под нарезание резьб выбирают по специальным таблицам (см. табл. 5.5). [c.210]
Номи- нальный диаметр, мм Шаг Р, мм Диаметр отверстия под резьбу Предельное (верхнее) отклонение диаметра Диаметры сверл для получения отверстий под нарезание резьбы [c.221]
Нарезание резьбы — Диаметры отверстий под резьбу 221, 222 [c.319]
Подготовка отверстия под резьбу. При нарезании резьбы метчиками небольшие отверстия обычно нарезают сразу же посла сверления большие отверстия предварительно растачивают. Диаметр отверстия под резьбу должен быть несколько больше внутреннего диаметра резьбы, что необходимо для уменьшения силы резания и предотвращения поломки метчика. Металл нарезаемой гайки под действием силы резания несколько затекает во впадины резьбы (рис. 213). Чем более пластичен металл нарезаемой детали, тем сильнее он течет и, следовательно, те.м больше должен быть диаметр отверстия под резьбу.
[c.184]
Учитывая возможное вспучивание резьбы в процессе ее нарезания, минимальный диаметр отверстия принимают на 0,04 — 0,1 мм больше минимального внутреннего диаметра резьбы. В титане и его сплавах минимальные диаметры отверстий под резьбу должны быть еще больше. [c.659]
Диаметр отверстия под резьбу должен обеспечить высоту профиля резьбы, равную 75 от теоретической. Нарезание резьбы в отверстиях меньшего диаметра значительно увеличивает нагрузку на метчик. Установлено, что при нарезании 100%-ной высоты профиля затрачивается сила резания в 3 раза большая, чем при высоте профиля резьбы, равной 75% при этом прочность резьбы возрастает лишь на 5%. Высота профиля может на.ходиться в пределах от 50 до 83% 75% является средним значением. Чем больше шаг резьбы, тем меньше может быть высота профиля резьбы. Следует иметь в виду, что даже при 50%-ной высоте профиля резьбы прочность резьбового соединения выше прочности тела болта.
[c.541]
Отверстия под резьбу. Диаметр отверстия под резьбу зависит от типоразмера последней и характера обрабатываемого материала. Для нарезания метрической резьбы с = (1 — Кс8, где — диаметр сверла й — номинальный диаметр резьбы Кс — коэффициент (табл. 27). Диаметры расточенных отверстий под нарезание метрических резьб приведены в табл. 28, а трубных цилиндрических — в табл. 29. [c.818]
Диаметр отверстия, подготовленного для нарезания резьбы метчиками, можно определять по правилам, относящимся к подготовке отверстия под нарезание резьбы резцом, и изложенным выше. Правильный выбор диаметра отверстия под резьбу в данном случае имеет особое значение, так как материал витков, деформирующийся в процессе работы метчика, увеличивается в объеме и так защемляет метчик, что вращение его становится затруднительным.

Если диаметр отверстия под резьбу равен внутреннему диаметру резьбы, то материал, выдавливаемый при нарезании, слишком будет давить на зубья метчика, нагревая их. В результате сильного нагрева к зубьям будут прилипать частицы металла. Резьба может получиться с рваными нитками, а в некоторых случаях возможна поломка метчика. Если отверстие под резьбу слишком большое, резьба получится неполной. [c.222]
Диаметры отверстий под резьбу при нарезании ее метчиками выбираются с таким расчётом, чтобы получить внутренний диаметр резьбы после работы метчиков в пределах, предусмотренных ГОСТом. [c.67]
Диаметр отверстия под резьбу должен быть возможно большим. Чем более труднообрабатываемым является металл, в котором нарезается резьба, тем больше должны быть диаметр отверстия и длина сбега (для глухих отверстий) резьбы. По зарубежным данным при нарезании резьбы со 100-процентной высотой профиля затрачивается сила резания в три раза большая, чем при 75-процентной высоте профиля, прочность же резьбы в первом случае лишь на 5% больше, чем во втором. Чем больше шаг резьбы,
[c.324]
Расчет диаметра отверстий для нарезания резьбы с крупным шагом диаметром от 8 до 16 мм приведен в табл. 117. Там же указаны близкие к диаметру отверстия диаметры сверл под резьбу по ГОСТ 885—60. Аналогично могут быть подсчитаны диаметры отверстий под резьбу с мелким шагом. [c.325]
Сверление отверстий под резьбу должно производиться правильно заточенными острыми сверлами. Отверстия под точные резьбы иногда зенкеруют и развертывают. Отверстия для глухих резьб желательно выполнять с проточкой под сбег резьбы. Диаметр отверстия под резьбу должен быть возможно большим. Для особо трудных условий нарезания высота резьбы может быть равна 75% от теоретической. [c.333]
Качество внутренней резьбы зависит от диаметра отверстия под резьбу (диаметр определяют по таблицам), правильного выбора и способа прн.менения смазочного материала (для смазывания применяют тот же смазочный материал, что и прн нарезании резьбы плашками), правильного подбора инструментов. Метчики подбирают комплектно на основе данных чертежа или по резьбомеру.
[c.131]
Диаметр отверстия под резьбу должен быть несколько больше внутреннего диаметра резьбы, так как в процессе нарезания резьбы металл деформируется, что приводит к у.меньшению диаметра отверстия. Поэтому результат, полученный по приведенной выше формуле, следует увеличить на 0,2—0,4 мм при нарезании резьбы в стали, латуни и других вязких материалах, на 0,1—0,2 мм в чугунных, бронзовых и других хрупких материалах. [c.102]
Ответ. Диаметр отверстия под нарезание резьбы МЗО должен составлять 26,15 мм. Диаметры, «отверстий под резьбу, а также диаметры стержней под резьбу даны в табл. 16 и 17. [c.85]
Диаметры стержней под накатывание и нарезание резьб, диаметры отверстий под нарезание резьб, а также выход резьбы (сбеги, недорезы, проточки и фаски) стандартизованы. Кроме того, стандартизованы метки (в виде прорезей) на деталях с левой резьбой.
[c.32]
Применяется только в глухих отверстиях, Оказывает меньшее стопорящее действие, чем у элементов заклинивания. Диаметр цилиндрической цапфы должен быть несколько меньше внутренней резьбы. Угол конуса на конце цилиндрической цапфы должен совпадать с углом заточки сверла для нарезания отверстия под резьбу [c.193]
Диаметры отверстий под нарезание метрической резьбы по ГОСТ 9150—81 с допусками по ГОСТ 16093—81, выполняемых в сером чугуне по ГОСТ 1412—79, [c.289]
Справочные таблицы диаметров заготовок, диаметров сверл и диаметров отверстий под нарезание резьбы разработаны с учетом изложенного выше, а также на основании практических данных машиностроительных заводов, В табл. 192 приведены диаметры стержней под нарезание метрических резьб плашками. [c.311]
Диаметры отверстий под нарезание метрической резьбы [c.317]
GO. Диаметры отверстии под нарезание метрических резьб (по ГОСТ 9150-59) Размеры в мм
[c. 403]
При нарезании резьбы метчиками и плашками материал детали несколько выдавливается, поэтому размер заготовкй нужно брать меньший, чем при нарезании резьбы резцом. Диаметр отверстия под резьбу должен быть равен 75% от теоретического профиля резьбы. Нарезание резьбы в отверстнях меньшего диаметра сильно увеличивает нагрузку на метчик, не оказывая существенного влияния на прочность резьбы. Для большинства резьбовых соединений достаточно, если резьба в гайке соответствует 0,75 ее полной глубины, или [c.136]
Нарезание резьбы в титане и его сплавах. Рекомендуется избегать нарезания глухих или длинных резьб. Длл облегчения процесса резь-бонарезания и уменьшения поломок метчиков увеличивают диаметр отверстий под резьбу. При нарезании резьбы в сквозных отверстиях длиной /> 2d применяют метчики с подточкой зубьев под углом X = 15°. [c.345]
Рекомендации по выбору расположения эубьев метчиков и диаметров отверстий под резьбу при нарезании в сквозных отверстиях
[c. 258]
Нартзание резьбы в титане и его сплавах. Следует избегать нарезания глухих и длинных резьб. Процесс резьбонарезания облегчается с увеличением диаметра отверстия под резьбу. Для сквозных отверстий длиной / > широко применяют метчики с подточкой зубьев под углом X. = 15 . Для (2 6 мм рекомендуются двухканавочные метчики, для (2 > 6 мм — трехканавочные с уменьшенной шириной перьев, чисто шлифованным и. затылованным профилем резьбы. [c.460]
Угол заборного конуса. На практике фактическое число зубьев, осуществляющих процесс резания, будет меньше приведенных выше. На рис. 9, а показано положение первого из двухкомплектных метчиков при нарезании резьбы М1,6. Диаметр отверстия под резьбу для труднообрабатываемых материалов о = 1,30 мм. Первый метчик, имеющий на заборном конусе три режущие нитки, примерно на половину проваливается в отверстие, не производя никакой работы.

Силы резания. Исследование силовых зависимостей при нарезании резьбы метчиками в заготовках из жаропрочной стали ЭЯ1Т [97] позволило установить влияние на величину крутящего момента геометрии метчика, скорости резания, диаметра метчика и степени его затупления, а также диаметра отверстия под резьбу. [c.317]
Фиг. 148. Влияние диаметра отверстия под резьбу на величину крутящего момента при нарезании стали ЭЯ1Т метчиками М12 X 1,75. |

Для уменьшения увода отверстий сверление выполняют в два или три перехода. Вначале отверстие центруют или засверлива-ют сверлом, диаметр которого в 2-3 раза меньше требуемого. Для отверстий под резьбу диаметром более 25-30 мм помимо сверления вьшолняют зенкерование или растачивание. Диаметр отверстий под резьбу делают на 0,04…0,1 мм больше внутреннего диаметра резьбы, тем самым учитывают подьем витков, возникающий при нарезании. Рекомендуемые диаметры сверл под резьбу с различным шагом и диаметром приведены в специальных нормативных таблицах. Торцы обрабатьшают с осевой подачей зенковками или подрезными резцами. [c.785]
В отверстиях диаметром 56 мм и более резьбу нарезают с помошью самораскрываю-щихся резьбонарезных головок. Основные нормативные данные (режимы резания, диаметры отверстий под резьбы и т.д.) остаются такими же, как и при нарезании резьбы метчиками. Точность резьбы несколько ниже точности резьбы, полученной шлифованными метчиками, однако поле допуска Нб может быть обеспечено с достаточной стабильностью.
[c.791]
Диаметры отверстий под нарезание дюймовой конической резьбы ио ГОСТу 6111—52, М6х1 конической по ГОСТу 1303—56 [c.151]
На рис. 28 показана схема наладки агрегатного станка с круглым поворотным столом для многопереходной двусторонней обработки с последовательной переустановкой двух Чугунных заготовок корпуса. Позиция / — загрузочно-разгрузочная. Заготовки устанавливают на обработанный ранее торец Б, базируют и закрепляют в правом (п) и левом (л) рабочем приспособлении. Полностью обработанную заготовку из приспособления п снимают и на ее место устанавливают снятую с приспособления л обработанную с одной стороны заготовку, повернув ее на 90°. Освободившееся место приспособления л загружают новой заготовкой. Позиция II, л — фрезерование верхнего торца горизонтальной головкой. Позиции III, л, /К, —фрезерование вертикальной плоскости вертикальной головкой. Позиция V — центрование отверстий под резьбу у обеих заготовок позиция К,л — зенкерование трехступенчатого центрального отверстия вертикальной головкой. Позиция И/, и — сверление отверстия диаметром 18 мм горизонтальной головкой позиция VI,л — развертывание трехступенчатого отверстия вертикальной головкой. Позиция VII — сверление отверстий под резьбу у обеих заготовок позиция VII, л — протачивание трех канавок в верхней части ступенчатого отверстия с помощью копирного патрона, преобразующего осевую подачу шпинделя вертикальной головки в радиальную подачу резца. Позиция VIII — нарезание резьбы в обеих заготовках горизонтальными головками позиция VIII,л — протачивание канавки и снятие фаски в нижней ступени цен-
[c.466]
КАК НАРЕЗАТЬ РЕЗЬБУ МЕТЧИКОМ НА ТРУБЕ [таблица, видео, советы]
[Как нарезать резьбу] — актуальный вопрос, т. к. это основной способ для соединения элементов конструкции.
Сделать это вполне можно вручную с помощью специального приспособления.
Разделяют наружную и внутреннюю резку детали, благодаря которой резьбу можно будет установить в отверстии разного типа.
Способ нарезки зависит от типа материала, с которым вы будете работать.
Особенности процесса, а также описание инструментов, которые для этого нужны, вы найдете в статье, а видео поможет вам справиться с поставленной задачей.
Метчик для нарезки
Метчиком называют слесарно-токарное режущее устройство, сделанное в форме стержня с установленным на нем режущим элементом.
Резчик используют для создания внутренней резьбы в разных металлических деталях, трубе, а также его можно использовать для того, чтобы восстановить поврежденную ранее резьбу.
Резчик имеет рабочую и хвостовую часть. Рабочая часть включает два участка: для резки и для калибровки.
Участок для резки обычно конусообразной формы, он отвечает за непосредственное нарезание резьбы.
На этом участке установлены также резцовые зубья, которые охватывают участок по всей окружности. Участок калибровки отвечает за окончательное формирование детали.
Он выглядит как цилиндр, оснащенный зубьями, и продолжает собой участок для резки.
Он более длинный, а его рабочий элемент разделен канавками, нужными для того, чтобы создавать резцы и выводить стружку.
Количество канавок зависит от размера метчика с клуппом – в устройствах, не превышающих 22 мм, их обычно три. Бывают и специальные метчики, в которых канавки отсутствуют.
В тех устройствах, где они есть, канавки могут иметь прямую, либо винтообразную форму.
Задняя часть метчика имеет цилиндрическую форму, на конце ее находится квадрат, который необходим для возможности фиксации к крепежному инструменту.
Эта часть метчика отвечает за присоединение устройства к ручному держателю или патрону станка.
Метчики с клуппом бывают двух типов: ручной или машинный. Ручные устройства прикрепляются к ручным держателям и предназначены для создания внутренней резьбы.
Машинные аппараты устанавливают на патронные держатели токарных станков.
Перед тем как узнать, как нарезать резьбу метчиком, нужно определиться с ее типом. Резьба, которую можно сделать, может быть разной в зависимости от типа устройства.
Наиболее распространенной формой резьбы является метрическая – ее делают с помощью метрического инструмента.
Для создания резьбы с внутренней стороны водопроводной трубы, а также в трубе отопления, используют специализированные трубные метчики, ими же можно сделать усиленную резьбу в металлических деталях, а не только в элементах отопления.
Для создания конусообразной или дюймовой резьбы, нужно использовать специальный дюймовый метчик, который позволяет делать резьбу наименьшего размера.
Чаще всего можно встретить прочные стальные устройства с клуппом – они наиболее эффективные, прочные и долговечные.
Помимо типа резьбы, метчики отличаются по устройству: они могут быть одиночными или комплектными.
Последние применяют для создания резьбы в несколько заходов. Обычно в комплект входит два метчика, один из которых называют чистовым, а второй – черновым.
В некоторых случаях сюда добавляется еще метчик для средней обработки. Количество деталей в комплекте всегда указано сзади, на части хвоста.
Комплектные метчики не одинаковы, они имеют разные формы зубьев: черновой имеет форму зуба трапеции, средний – треугольную, вершина у которой закруглена, а у чистового – это стандартный треугольник, имеющий острую вершину.
Нарезка резьбы заключается в создании выступа в отверстии, при этом линия выступа должна иметь винтовую форму.
Выступ возле стены в отверстии должен соответствовать заданным параметрам, чтобы резьбу можно было использовать: он должен иметь правильные шаг, подъемный угол, внешний и внутренний диаметр и т.д.
Также важным параметром является глубина, которую определяют, исходя из диаметра резьбы внутри и снаружи на трубе.
Вариантов, как правильно нарезать резьбу, может быть несколько.
Видео:
Направление резьбы в трубе может быть разным, в зависимости от необходимости: она может быть направлена вправо, при этом выступ развивается по часовой стрелке, либо иметь левую направленность, тогда выступ будет следовать против часовой стрелки.
Существует две возможных формы профиля: прямоугольная или треугольная, а также специальные дополнительные формы, но их используют в основном на производстве, и почти никогда в домашних условиях.
Выбор метчика и нарезка
Выбирают метчик в зависимости от резьбы, которая необходима, а также ее назначения (резьба может отличаться по форме профиля, шагу резьбы, допускам).
Для выбора метчика существует таблица, в которой отражены классы точности – в соответствии с ними нужно выбирать, какой тип метчика приобрести – комплект, или же одиночный инструмент.
Важный фактор, из которого стоит исходить при выборе метчика – необходимая точность нарезания профиля.
Разные инструменты имеют разную чистоту обработки резательного элемента, и это тоже нужно учитывать.
Металл, с которым вы будете работать, напрямую влияет на метчик, который для этого понадобится.
На алюминии потребуется угол заточки не менее 25 градусов, на чугуне и меди будет достаточно до 5 градусов, а на стали – до 10 градусов.
Для изготовления самого метчика используют чаще всего обычную или высокопрочную сталь. При выборе нужно ориентироваться на диаметр в отверстии, в котором будет делаться резьба.
Перед созданием резьбы в алюминии, чугуне или другой металлической детали нужно сделать отверстие. Оно может быть сквозным или глухим, в зависимости от необходимости.
Отверстие может иметь любой диаметр, важно только, чтобы оно было меньше, чем будущая резка. Сверло для отверстия лучше всего выбирать, руководствуясь размером резьбы.
Видео:
Существует специальная таблица, где отражен рекомендуемый диаметр сверла в соответствии с размером резьбы, рекомендуется ознакомиться с ней, прежде чем приступать к работе.
Если на чугуне или алюминии требуется сделать крупную резьбу стены, то выбирать диаметр под отверстие следует, умножив диаметр резьбы на 0.8, таким образом, вы получите значение, которое будет максимально возле требуемого размера.
Создание отверстия для внутренней резьбы дается не вручную, а с помощью специального сверлильного станка, либо электродрели.
В случае использования дрели, заготовку нужно предварительно зажать в тиски, чтобы место сверления было точно там, где нужно.
При сверлении сверло должно быть расположено строго вертикально и не отклоняться от заданной плоскости.
Чтобы работать метчиком было проще, с верхней кромки можно снять фаску – тогда устройство будет входить легче.
Сделать это можно с помощью сверла, имеющего больший диаметр, либо напильника. После окончания работ, отверстие нужно очистить от стружки.
Особенно тщательно нужно сделать это в глухом отверстии, иначе нарезать качественно не получится.
Перед сверлением деталь, с которой вы будете работать, нужно плотно закрепить с помощью тисков, при этом фаска должна находиться сверху, а ось сделанного вами отверстия должна быть расположена по отношению к столу перпендикулярно.
Метчик нужно зафиксировать в гнездо воротка, а затем ввести его в фаску заготовочного отверстия. Вводится устройство всегда вертикально.
Видео:
После этого метчик нужно сильно прижать к заготовке (лучше обеими руками) и начать вращать его по направлению часовой стрелки.
Нельзя допускать резких движений или остановок: вращать устройство нужно медленно и равномерно, но при этом работать с нажимом.
Работать метчиком нужно в следующей последовательности: сначала два поворота вперед, затем пол оборота назад и далее снова вперед. Таким методом происходит обработка всего отверстия в трубе.
Во время резки метчик нужно время от времени охлаждать.
Для разных металлов используются разные способы охлаждения: для алюминия будет эффективен керосин, для меди – скипидар, для прочих металлов – специальная эмульсия, а при резке в чугуне охлаждение устройства не требуется.
Для внутренней нарезки лучше всего использовать комплекты метчиков.
Работа происходит следующим образом: сначала нужно сделать черновую резьбу, затем воспользоваться средним метчиком, который пропускается через отверстие, а затем формируется окончательная резка с помощью чистового метчика.
Подобная последовательность является оптимальной для наилучшего качества обработки, поэтому рекомендуется не пропускать никакое из трех устройств, иначе качество резьбы в трубе будет заметно хуже.
Все этапы процесса нарезки вы можете увидеть на видео – в этом процессе нет ничего сложного, самое главное – правильно выбрать диаметр и соблюсти последовательность работ, а также помнить, как работать с тем или иным видом металла.
В этом случае вы получите качественную резьбу в трубе, которую можно будет использовать для соединения любых деталей.
Видео:
Три инструмента для формирования резьбы
Инструменты для накатывания резьбы очень похожи на метчики, но имеют абсолютно иной принцип действия. Все фотографии предоставлены компанией Walter USAФормирование внутренней резьбы обычно выполняется на последней стадии производственного цикла. Это означает, что данный процесс очень важен, так как основная часть расходов на изготовление детали уже инвестирована. Ошибка или брак могут обойтись очень дорого.
Поэтому когда речь заходит о нарезании резьбы, производительность и стоимость инструмента не всегда являются основными факторами. Иногда основное внимание уделяется надежности процесса. Обычно резьбу нарезают одним из трех способов, каждый из которых имеет преимущества применения в различных ситуациях.
Нарезание
Нарезание – наиболее часто используемый процесс, и в 90% случаев для нарезания внутренней резьбы используют именно его. В процессе нарезания используется метчик, который врезается в материал изделия по спиральной конфигурации, необходимой для получения отверстия с резьбой. Конструкция режущего инструмента должна разрабатываться для каждого конкретного диаметра и типа резьбы, а скорость подачи инструмента должна соответствовать шагу резьбы.
Инструмент подается исключительно по оси Z, что делает программирование относительно простым. Но нужно учитывать разнообразие инструментов, которые могут различаться количеством канавок, длиной заборной части, системой допусков, передним и задним углом резца, углом наклона кромки и стандартом хвостовика (например, стандарты немецких организаций DIN или ANSI). Поэтому найти оптимальный дизайн для конкретного применения может стать непростой задачей.
Накатывание
Накатывание – это процесс формирования внутренней резьбы, последние 20 лет развивающийся быстрыми темпами. При накатывании материал выдавливается для придания ему нужной формы. Для накатывания резьбы используется инструмент, похожий на метчик, но имеющий принципиально другую конструкцию и функциональность. Резьба при накатывании получается значительно более прочной, чем при нарезании, потому что при этом изменяется структура материала, находящегося в холодном состоянии, а это повышает твердость заготовки. Более того, в процессе накатывания заготовка не подвергается резке, и, соответственно, не образовывается стружка. Таким образом устраняется одна из основных проблем нарезания – удаление стружки.
Фреза имеет форму резьбы, но диаметр нарезаемой резьбы контролируется станкомОднако накатывание накладывает ограничение на материал, в котором можно сделать резьбу – он должен быть ковкий. Накатывание не используется для обработки таких хрупких материалов, как чугун.
Фрезерование
Фрезерование – это процесс резания материала при помощи вращающегося инструмента, имеющего форму резьбы. Размер фрезы меньше, чем диаметр отверстия, поэтому для нарезания резьбы станок должен вводить фрезу в отверстие, одновременно подавая ее по оси Z и создавая таким образом спиралевидную резьбу.
Обычно для нарезания резьбы инструмент вращается на 360 градусов, однако некоторые производители рекомендуют проходить полные 180 градусов для входа в отверстие и еще 180 градусов для выхода из него. В последнем случае для завершения нарезки инструмент совершит два полных оборота.
Использование фрезы делает программирование станка более сложным, но так как станок частично контролирует точный размер резьбы, настройка ее размера осуществляется путем внесения изменений в программу. При нарезании и накатывании вместо настройки приобретается инструмент нужного размера.
Фрезерование обычно используется для нарезания резьбы большого диаметра. Однако фрезы уникальной конструкции, называемые сферическими фрезами, могут нарезать резьбу размером UNC1-64 и доступны в качестве стандартного изделия. Отверстие для такой резьбы имеет диаметр 1,5113 мм. В то же время метчики могут нарезать резьбу М1, для этого используется сверло-метчик диаметром 0,7493 мм.
Сравнение надежности процессов
Нарезание – надежный и простой способ создания резьбы. Однако для достижения стабильного результата необходимо выбрать правильный метчик, подходящий для конкретной задачи.
Удаление стружки является основной проблемой, и особенно это касается глухих отверстий. Для ее удаления необходимо выбрать правильную конструкцию метчика. Именно поэтому большинство производителей предлагают широкий выбор метчиков с различной геометрией и конфигурацией.
Еще одну проблему представляет поломка и застревание метчиков в отверстии. Так как головка метчика буквально ввинчивается в заготовку, извлечь сломавшуюся часть или части может быть очень непросто. Для этого может потребоваться дополнительная механическая обработка заготовки или обработка на другом станке, таком как электроэрозионный вырезной станок.
Ассортимент инструментов для накатывания резьбы менее разнообразен, чем ассортимент режущих метчиков, что связано с отсутствием необходимости удалять стружку. По сравнению с метчиками, накатники имеют значительно более широкий стержень, делающий их прочнее.
При поломке накатника его также непросто извлечь из отверстия, но ломаются они реже, в основном благодаря большему диаметру стержня. По сравнению с нарезанием, накатывание сильно ограничено областью применения, типом материалов и размером резьбы. Техническая документация некоторых конструкторских предприятий и даже в масштабах целых отраслей содержит специальные указания, запрещающие накатывать резьбу на изделии.
Это связано с тем, что после накатывания на дне отверстия остается небольшое углубление, называемое за свой внешний вид «рыбий рот». Например, на деталях для медицинской и пищевой промышленности накатывание не допускается, так как в этом маленьком углублении могут размножаться бактерии, а очистить и простерилизовать его непросто. Тем не менее, это углубление никак не влияет на качество резьбы.
Фрезерование является наиболее гибким из трех процессов. Сам инструмент задает только форму и наклон резьбы, поэтому им можно нарезать резьбу любого диаметра – главное, чтобы ее форма и наклон не менялись. Например, при помощи одного инструмента можно нарезать резьбу диаметром 1″-8 и 1½ «-8 по стандарту UN. При этом в размер резьбы можно вносить небольшие изменения, чтобы она соответствовала требуемым допускам, или компенсировать износ инструмента, тем самым продлевая срок его службы.
Диаметр стержня фрезы меньше, чем диаметр метчика или накатника, но фрезерование и не требует инструмента с высокой прочностью. Диаметр инструмента обычно составляет 70-80% диаметра резьбы, инструмент значительно меньше контактирует с заготовкой и, соответственно, на него передается меньший крутящий момент. Даже если инструмент сломался, небольшой диаметр позволяет легко извлечь его из отверстия и после установки новой фрезы продолжить процесс обработки.
Учитывая, что подавляющее большинство резьб выполняется при помощи метчика, этот процесс можно считать эталоном надежности. По сравнению с нарезанием, накатывание считается чуть более надежным, так как в процессе накатывания не образовывается стружка. К тому же накатник имеет больший корпус, чем метчик, и он с меньшей вероятностью сломается в процессе работы. А для обеспечения максимальной надежности оптимальным вариантом является фрезерование.
Применение на практике, пример №1
Не так давно компания Walter USA работала с компанией-производителем плашек из Северного Висконсина. В ходе работы мы пытались установить, будет ли фрезерование лучшей альтернативой нарезанию, которое они на тот момент применяли. Процесс нарезания был нестабилен, инструменты ломались, а срок их службы был неодинаковым. В заготовке из инструментальной стали P-20 твердостью 33-36 HRC требовалось выполнять 30 отверстий с резьбой M30 глубиной 50,8 мм. При 80 об/мин скорость нарезания составляла 7,62 м/мин, и для формирования резьбы требовалось 26 секунд.
После наладки и испытаний фреза сравнялась с метчиком по скорости нарезания. Во время дальнейших испытаний фреза достигла скорости 198,12 м/мин, что уменьшило время нарезания резьбы до 19 секунд. Еще до компенсации износа срок службы фрезы превысил срок службы метчика, который составил 200 заготовок. В итоге, благодаря переходу на фрезерование клиент начал обрабатывать заготовку быстрее, себестоимость обработки отверстий снизилась, а сам процесс стал более надежным и стабильным.
Применение на практике, пример №2
Производственная мастерская из Центрального Иллинойса испытывала затруднения с нарезанием резьбы М-8 в стальном изделии. Чертеж предусматривал наличие резьбы глубиной 17,5 мм в глухом отверстии. Резьба проходила через поперечное отверстие. Материал изделия – литая сталь 17-22 AS твердостью 35-38 HRC. В процессе обработки возникала проблема с удалением стружки, что иногда приводило к поломке инструмента.
Компания Walter USA порекомендовала перейти от нарезания к накатыванию. Клиент не изъявил большого желания менять свой производственный процесс, поэтому компания Walter доставила образцы изделия в Технологический центр г. Уокешо, штат Висконсин, для сравнения процессов нарезания и накатывания.
Результаты испытания были вполне однозначны, но мы не смогли должным образом продемонстрировать качество получаемых деталей и надежность наших инструментов, так как небольшое количество образцов не позволило испытать полный срок службы инструментов. Применение метчиков различных конструкций немного улучшило результат. Удалять стружку стало проще, благодаря тому, что она стала короче и не цеплялась одна за другую. Однако в отверстии все еще оставалось некоторое количество стружки, которое нужно было удалять при помощи дополнительной операции обработки. Очевидно, что при накатывании, которое формирует резьбу, а не нарезает, такая проблема не возникала.
Более того, накатники значительно меньше изнашивались, и это дало основание полагать, что срок их службы будет существенно больше, чем у метчиков.
Основным преимуществом стала производительность. Скорость подачи при нарезании составляла 264,2 мм/мин, а при накатывании – 584,2 мм/мин. Двукратное увеличение скорости подачи позволило сократить время производственного цикла более чем на 50%. При помощи накатывания клиент не только повысил надежность процесса, но также увеличил производительность и срок службы инструментов.
Источник материала: перевод статьи
Triple Threaders,
Cutting Tool Engineering (CTE)
Автор статьи:
Люк Полок (Luke Pollock),
Walter USA LLC
Об авторе: Люк Поллок работает менеджером по продукции (круглые резцы) в компании Walter USA LLC, Уокешо, штат Висконсин.
Нет связанных записей.
Подготавливаем материал для резьбового соединения: как сделать резьбу?
Внутренняя резьба
Для того, чтобы нарезать внутреннюю резьбу, используют метчики. Прежде чем приступить к работе, нужно определить, какой необходим диаметр резьбы. После этого подбирается сверло. Есть таблицы, по которым выбирают сверло нужного диаметра, чтобы нарезать внутреннюю резьбу метчиком. В них указаны диаметры при нарезании в стали. Если необходимо нарезать резьбу в чугуне, дюралюминии или бронзе, применяется сверло размером на 0,1 см в диаметре меньше, чем отмечено в таблице. В табличных данных по внутреннему нарезанию резьбы обозначены небольшие диаметры, исходя из того, что сверлом более 14 мм сложно работать в домашних условиях.Качественному выполнению работы способствует подбор инструмента. Использование ржавых инструментов и тех, которые на протяжении эксплуатации затупились, приведет к поломке и некачественно нарезанной резьбе.
Есть два вида метчиков: машинные и ручные. Первым нарезают резьбу в станке, метчик крепится в патрон токарного станка, второй закрепляют в ручном держателе. Они также разделяются на комплектные и одиночные. Комплект может состоять из двух или трех единиц. На черновых метчиках есть маркировки, выточены ободки. На поверхности метчика чернового режущая часть не очень выражена.
Начинать нарезать резьбу необходимо черновым метчиком. Изготавливаются метчики из инструментальной (9ХС) или быстрорежущей стали (Р6М5, Р18, Р6М5К5, Р6АМ5). Временами случаются поломки инструментов во время работы. Именно поэтому желательно иметь в запасе еще один комплект. Для начала нужно выбрать метчик по резьбе нужного вида и назначения. Согласно требованиям точности определяют, будет ли резьба нарезаться одним метчиком или нужно применять комплект. Главным выбором является определение диаметра резьбы в отверстии.=»text-align:>
Деталь, в которой будет нарезаться резьба, фиксируется в тисках, подобранным сверлом делаем отверстие. Сверло применяется немного меньшего диаметра, чем диаметр резьбы. В целях удобства работы метчиком в сделанном отверстии снимается фаска. Метчик фиксируется в специальном воротке, устанавливается строго перпендикулярно. Рабочая поверхность метчика смазывается маслом, при этом не допускаются резкие движения. Сделав первые три оборота вперед, делается один в обратную сторону, ломая стружку, которая образовалась в процессе нарезки. Нарезая сквозную резьбу, метчик должен выйти на обратную сторону. Стружка снимается по мере ее образования. После работы с черновым переходят к выполнению нарезки чистовым. Все операции проводятся в такой же последовательности, что и черновым метчиком.
Наружная резьба
Резьба наружная нарезается плашкой. Чаще всего этот режущий инструмент имеет форму гайки. Она предназначена как для калибрования, так и для нарезания резьбы наружной. По способу нарезания они бывают двух видов: пластическое деформирование металла и нарезание. Нарезная плашка изготовлена в форме гайки. В ней есть осевые отверстия, которые образуют режущие кромки. Сама режущая часть выглядит в форме конуса, а для отвода стружки на плашке сделаны специальные отверстия.Заготовка закрепляется в тисках. Плашка болтами фиксируется в плашкодержателе. Прежде чем осуществлять нарезание резьбы, заготовку подготавливают путем обтачивания до необходимого диаметра и снимают фаску. Корродированный материал не обрабатывается, потому что плашка на таком материале быстро изнашивается. Режущую часть плашки накладываем на заготовку так, чтобы она ложилась по всей окружности, избегая перекоса. Правая резьба нарезается по часовой стрелке, а левая — против. Нарезается резьба без рывков. Инструмент должен вращаться плавно.
Для получения качественного резьбового соединения деталей нужно строго контролировать недопущение перекосов. Рабочая поверхность плашки во время работы смазывается и удаляется стружка. Смазывают режущую часть разными смазками в зависимости от материала. Наружную резьбу нарезают аналогично внутренней. Для этого плашку закрепляют в плашкодержателе, после чего совершаются повороты: полтора вперед, после чего один назад. Нажимы на ручки воротка делаются одинаковые.
Нарезание резьбы на трубе
Процесс нарезания резьбы на трубе является довольно сложным, особенно для людей, не имеющих опыта в данном деле. Трудности состоят в том, что плашка не имеет направляющих. Отсутствие таковых способствует перекосу и нарезанию некачественной резьбы. Для выполнения качественной работы применяют специальный инструмент, который называется клупп. Он очень удобный, легкий в эксплуатации. Основной причиной удобства управляемости являются специальные направляющие, которыми оборудован этот инструмент. В эти направляющие заводится труба, после чего нужно только крутить клупп. Для облегчения процесса устанавливается трещётка.
Как сверлить и нарезать резьбу в чугуне
, автор C.L. Rease
Кристаллическая структура чугуна варьируется в зависимости от скорости охлаждения стали. Сверление из чугуна отличается от сверления из других типов стали из-за различий в структуре стали. При сверлении прокатной стали материал, просверленный из отверстия, будет двигаться по спирали от наконечника сверла. Чугун выделяет множество мелких металлических стружек. Случайные твердые участки в чугуне могут сломать наконечник сверла, если вы приложите чрезмерное давление на наконечник сверла.Нарезание резьбы в отверстии, просверленном в чугуне, требует осторожности, чтобы не сломать метчики в отверстии, когда вы столкнетесь с твердым местом.
Шаг 1
Найдите размер крепежа, который вам нужно вкрутить в чугун, на диаграмме сверла и метчика. Следуйте линии на диаграмме, представляющей размер крепежа, чтобы определить размер сверла. Например, крепеж с резьбой 1 / 4-20 на таблице сверл и метчиков покажет сверло №7 как идеальный размер для метчика.
Шаг 2
Закрепите сверло из набора в патроне двигателя дрели с регулируемой скоростью.Смажьте сверло смазочно-охлаждающей жидкостью.
Step 3
Просверлите отверстие в чугуне, нажав на спусковой крючок электродвигателя сверла, чтобы поддерживать низкие обороты электродвигателя сверла. Смажьте сверло дополнительной смазочно-охлаждающей жидкостью, если в области сверления появится дым.
Шаг 4
Установите метчик правильного размера в гаечный ключ с Т-образной рукояткой. Смазать кран смазочно-охлаждающей жидкостью.
Шаг 5
Вставьте кончик метчика в просверленное отверстие.Залейте дополнительную смазочно-охлаждающую жидкость вдоль крана и в отверстие. Поверните смесительный ключ по часовой стрелке, чтобы начать пробивать отверстие. Если метчик заедает в отверстии, поверните его на 1/2 оборота против часовой стрелки. Продолжайте чередовать движения по часовой стрелке и против часовой стрелки, пока не получите резьбовое отверстие. Снимите кран с отверстия.
Вверните фиксатор в резьбовое отверстие. Пропустите метчик через отверстие, если застежка не входит в отверстие.
Ссылки
Наконечники
- Просверлите в чугуне меньшее пилотное отверстие для отверстий размером более 3/16 дюйма, чтобы сверло не смещалось.
Вещи, которые вам понадобятся
- Таблица сверл и метчиков
- Набор сверл
- Сверлильный двигатель с регулируемой скоростью
- Смазочно-охлаждающая жидкость
- Набор метчиков
- Ключ для метчика с Т-образной рукояткой
Предупреждения
- Износ защита глаз при сверлении и нарезании резьбы чугуном.
Еще статьи
(PDF) Контроль качества резьбы при нарезании резьбы из чугуна с шаровидным графитом с использованием метчиков из быстрорежущей стали с покрытием TiN
27
[7] W.Э. Хендерер, 1977, «О механике нарезания резьбы резанием», Журнал
Engineering for Industry, Vol 98, 257-262
[8] Догра, А.С., 1999, «Механистическая модель процесса нарезания резьбы с акцентом на
технологические дефекты и геометрия отверстий », магистерская работа, Университет Иллинойса,
Урбана-Шампейн.
[9] Мезенцев, Олег А., ДеВор, Ричард Э., Каппор, Шив Г., 2002, «Прогноз качества резьбы
путем обнаружения и оценки ошибок нарезания резьбы», ASME Journal of
Manufacturing Science and Engineering , Vol.124: 1, стр. 643-650.
[10] О. А. Мезенцев, С. Г. Капур, Р. Э. ДеВор, «Прогнозирование качества резьбы путем обнаружения и оценки неисправностей нарезания резьбы
». Journal of Manufacturing Science
и Engineering 124 (2002) 643-650.
[11] Цао Тэнюнь, Сазерленд Дж. У., 2002, «Исследование характеристик нагрузки на резьбу
посредством механического моделирования и экспериментов», International
Journal of Станки и производство, с. 1527-1538.
[12] Масори О., 1991. Мониторинг процессов обработки с использованием мультисенсорных показаний
, объединенных искусственной нейронной сетью. Журнал технологий обработки материалов.
28 (1-2), 231-240.
[13] Варгезе С., Радхаркришнан В., 1994, Многосенсорный подход к производственному процессу
мониторинг шероховатости поверхности, Журнал технологий обработки материалов,
44 (3-4), 353-362 .
[14] Стейн Дж. Л., Хух К., 2002 «Мониторинг сил резания при токарной обработке: подход на основе модели
», Journal of Manuf.Sci. Eng, Vol. 124, Выпуск 1, 26-32.
[15] Г. Бирн, Д. Дорнфельд, И. Инасаки, Г. Кеттелер, В. Кениг и Р. Тети, Tool
Condition Monitoring (TCM) — Статус исследований и промышленных приложений
, CIRP Annals Технология производства, том 44, выпуск 2, 1995 г.,
Страницы 541-567.
[16] Санджай, К., Нима, М. Л., Чин, К. В., 2005. Моделирование износа инструмента при бурении с помощью статистического анализа
и искусственной нейронной сети.J. обработки материалов и
технологии. 170 (3), 494-500.
[17] Агапиу, Дж. С., 1994 «Оценка влияния высокоскоростной обработки на нарезание резьбы
», Промышленный журнал, Vol. 116, 457-462.
[18] Монтгомери, округ Колумбия (1996), Введение в статистический контроль качества, 3-е издание,
John Wiley & Sons, Нью-Йорк
[19] Джексон, Дж. Э., Руководство пользователя по основным компонентам, Джон Вили & Sons, New
York, 1991
[20] Lorentz, G., 1989, «Анализ главных компонентов в технологии», Анналы CIRP,
Vol. 38.01.1989. С. 107-109.
[21] Мастранджело, К. М., Рунгер, Г. К. и Д. К. Монтгомери (1996) «Статистический
Мониторинг процессов с основными компонентами», Качество и надежность
Engineering International, Vol. 12, No. 3.
[22] Уэбб А., Статистическое распознавание образов, 2-е издание, John Wiley & Sons, New
York, 2003.
[23] Хуберти К.J. Прикладной дискриминантный анализ. John Wiley & Sons, New York,
1994.
[24] Салливан, Дж. Х. и Вудалл, У. Х. (1996). «Сравнение многомерной контрольной диаграммы
для индивидуальных наблюдений». Journal of Quality Tecnology, 28, стр. 398-
408.
Все о нарезании резьбы винтами и болтами: 7 шагов (с изображениями)
Начните с определения правильного размера. Если у вас есть винт или болт, на которые вы нацеливаетесь, посмотрите размер и необходимое отверстие для нарезания резьбы.В Википедии есть хорошая таблица, которая поможет вам определить, какого размера должно быть ваше отверстие. На многих метчиках на боковой стороне крана написано необходимое отверстие.
Просверлите отверстие, стараясь держать его перпендикулярно обрабатываемой детали. Сверлильный станок — отличный способ сделать это. Если у вас под рукой нет дрели, попробуйте использовать приспособление.
Зенковка устья отверстия. Это поможет направить метчик в центр отверстия и облегчит начало процесса нарезания резьбы.
Когда вы будете готовы, вы можете взять ручку крана и крана. Отвинтите его, пока ваш кран не войдет внутрь, и завинтите, пока он не станет плотно, но не настолько, чтобы вы не смогли открыть его снова. Все в меру 🙂
Зажмите заготовку или воспользуйтесь тисками. Вы не сможете удерживать его руками, так как вам понадобятся как для направления, так и для поворота крана.
Нанесите на кран немного жидкости. Проверьте раздел, в котором следует использовать жидкость для вашего материала.
Вставьте кончик крана в отверстие.Держите кран как можно перпендикулярно и прикладывайте давление вниз. Начните медленно поворачивать кран на по часовой стрелке . Зубцы канавок зацепятся, и вы начнете обрезать нити. Каждые несколько оборотов осторожно отключайте кран и убирайте фишки.
Не могу не подчеркнуть: идите медленно и очистите свои фишки . Наиболее частая причина поломки метчика заключается в том, что стружка застревает между метчиком и стенкой отверстия, которое вы пытаетесь продеть. Метчик недостаточно прочен, чтобы выдержать усилие сдвига, и он сломается.Поверьте, вы не хотите, чтобы вам пришлось вытаскивать сломанный метчик из критически необходимой дыры.
Продолжайте этот процесс (скручивание, раскручивание, очистка стружки), пока вы не пройдете весь путь вниз. Нанесите больше жидкости, если вы думаете, что она убежала полностью или вам пришлось стереть ее, потому что вы убирали фишки.
Проверьте отверстие с резьбой, вкрутив соответствующий винт или болт. Если это нестандартный размер отверстия, вам нужно сначала использовать матрицу, чтобы нарезать подходящую резьбу.
|
Проблема | Раствор |
Увеличенный Диаметр поля | |
Неправильно кран | 1.Используйте правильные пределы GH кранов. |
2. Используйте более длинные метчики с фаской | |
Чип упаковка | 1. Используйте метчики со спиральным острием или метчики со спиральными канавками. |
2. Уменьшите количество канавок, чтобы освободить место для стружки. | |
3.Используйте отверстие большего размера. | |
4. При нарезании резьбы в глухом отверстии сделайте отверстия более глубокими или укоротите длина резьбы деталей. | |
5. Используйте подходящую смазку. | |
истирание | 1. Нанесите соответствующую поверхностную обработку, например, оксид пара или TiN. |
2.Используйте подходящую смазку для резки. | |
3. Уменьшите скорость постукивания. | |
4. Используйте правильный угол резания в соответствии с обрабатываемым материалом. | |
5. Используйте отверстие большего размера. | |
Эксплуатация условия | 1.Применяйте правильную скорость нарезания резьбы. |
2. Правильное совмещение метчика и просверленного отверстия. | |
3. Используйте правильную скорость нарезания резьбы, чтобы избежать обрыва или шероховатости резьбы. | |
4. Используйте резьбовую головку для ходового винта. | |
5. Используйте подходящий метчик с подходящей мощностью. | |
6. Избегайте перекоса метчика и просверленного отверстия из-за ослабленного или изношенного шпинделя. держатель. | |
Инструмент условия | 1. Обеспечьте правильный угол индексации канавок на режущей кромке. |
2. Отшлифуйте правильный угол резания и угол фаски. | |
3.Избегайте слишком узкого участка земли. | |
4. Удалите заусенцы при переточке. | |
Проблема | Раствор |
Увеличенный Внутренний диаметр | |
Отверстие размер | 1. Используйте минимальный размер отверстия. |
2.Избегайте конических отверстий. | |
3. Используйте подходящие метчики с фаской. | |
истирание | 1. Нанесите соответствующую поверхностную обработку, например, оксид пара или TiN. |
2. Используйте подходящую смазку для резки. | |
3. Уменьшите скорость постукивания. | |
4. Используйте правильный угол резания в соответствии с обрабатываемым материалом. | |
Проблема | Раствор |
Меньший размер Диаметр поля | |
Неправильно кран | 1. Используйте метчики увеличенного диаметра для резки таких материалов, как медный сплав, алюминий. сплав и чугун. |
2. Используйте метчики увеличенного диаметра для резки трубок, у которых будет «пружина». действие «назад» после постукивания. | |
3. Применяйте правильный угол фаски. | |
4. Увеличьте угол резания. | |
Аварийный резьба | Использование правильная скорость реверса, чтобы избежать повреждения нарезанной резьбы при выходе из дыра. |
Остаток чипсы | 1. Увеличьте производительность резания, чтобы в отверстии не оставалась стружка. |
2. Удалите оставшуюся стружку из отверстия для Калибровочная проверка. | |
Проблема | Раствор |
Меньший размер Внутренний диаметр | |
Отверстие диаметр | Использование максимальный размер сверла. |
Проблема | Раствор |
Рваный / Грубая резьба | |
Фаска слишком короткий | Увеличение длина фаски. |
Неправильно угол резания | Применить правильный угол резки. |
истирание | 1. Используйте метчики с резьбой. |
2. Уменьшите ширину площадки. | |
3. Нанесите поверхностную обработку, например, оксид пара или TiN. | |
4. Используйте подходящую смазку для резки. | |
5.Уменьшите скорость постукивания. | |
6. Используйте отверстие большего размера. | |
7. Обеспечьте правильное выравнивание между краном и работой. | |
Чип упаковка | 1. Используйте метчики со спиральным заострением или метчики со спиральными канавками. |
2. Используйте сверло большего размера. | |
Проблема | Раствор |
Дребезжание на резьбе | |
Тоже бесплатная резка | 1. Уменьшите угол резания. |
2. Уменьшите ослабление резьбы. | |
Инструмент условия | 1.Избегайте слишком узких участков. |
2. Не шлифуйте дно флейты. | |
Проблема | Раствор |
Поломка | |
Неправильно выбор крана | 1. Избегайте скапливания стружки в канавках или на дне отверстия.Используйте спираль метчики с остроконечными или спиральными канавками или метчики без канавок. |
2. Правильно обработайте поверхность, например, оксидом пара или TiN. | |
чрезмерное момент нарезания резьбы | 1. Используйте сверло большего размера. |
2. Попробуйте сократить длину нити. | |
3.Увеличьте угол резания. | |
4. Используйте метчик с большим зазором резьбы и уменьшенной шириной площадки. | |
5. Используйте метчики со спиральным заострением или метчики со спиральными канавками. | |
Эксплуатация условия | 1. Уменьшите скорость постукивания. |
2.Избегайте несовпадения метчика с отверстием и коническим отверстием. | |
3. Используйте плавающий тип держателя для метчиков. | |
4. Используйте держатель для метчиков с регулировкой крутящего момента. | |
5. Избегайте ударов крана по дну отверстия. | |
Инструмент условия | 1.Не шлифуйте дно флейты. |
2. Избегайте слишком узкого участка земли. | |
3. Удалите все изношенные части при переточке канавок. | |
4. Заточите инструмент чаще. | |
Проблема | Раствор |
Скол | |
Неправильно выбор крана | 1.Уменьшите угол резания. |
2. Используйте метчики из быстрорежущей стали другого типа. | |
3. Уменьшите жесткость крана. | |
4. Увеличьте длину фаски. | |
5. Избегайте укладки стружки в канавки или на дно отверстия, используя метчики со спиральными канавками или спиральными заостренными метчиками. | |
Эксплуатация условия | 1. Уменьшите скорость постукивания. |
2. Избегайте перекоса между метчиком и отверстием. | |
3. Избегайте внезапного возврата реверса при нарезании резьбы в глухих отверстиях. | |
4. Избегайте раздражения. | |
5.Используйте отверстия большого размера. | |
Проблема | Раствор |
Износ | |
Неправильно выбор крана | 1. Используйте специально разработанные метчики для нарезания резьбы по термообработанному материалу. |
2. Выберите тип метчика из быстрорежущей стали, который содержит ванадий. | |
3. Нанесите специальную обработку поверхности, например, оксид пара или TiN. | |
4. Увеличьте длину фаски. | |
Эксплуатация условия | 1. Уменьшите скорость постукивания. |
2. Используйте подходящую смазку для резки. | |
3. Избегайте наклепа. | |
4. Используйте отверстие большего размера. | |
Инструмент условия | 1. Отшлифуйте правильный угол резания. |
2. Избегайте снижения твердости в процессе шлифования. |
Покрытия | Бесплатный полнотекстовый | Характеристики резьбонарезания различных покрытий для нарезания резьбы из быстрорежущей стали
1.Введение
Нарезание резьбы — это операция нарезания резьбы, состоящая из гравировки профильной резьбы на предварительно просверленной поверхности, где полученный диаметр немного меньше диаметра резьбы. Эта операция аналогична протяжке с той разницей, что в этой операции зубцы инструмента описывают линейную траекторию, тогда как при нарезании резьбы траектория является винтовой. Тот факт, что, как и при протяжке, при нарезании резьбы каждый активный зуб имеет разную геометрию [1] и, кроме того, инструмент погружается во время резания в предыдущее отверстие, практически без колебаний, делает эту операцию одной из самых сложных для анализа.С другой стороны, нарезание резьбы обычно выполняется, когда деталь практически закончена, и поэтому нарезание резьбы метчиком является операцией с высокой добавленной стоимостью. Вследствие сложности операции и высокой добавленной стоимости заготовки нарезание резьбы является критически важным. операция, которую следует принять во внимание. Однако, как отмечают некоторые авторы, в литературе не так много упоминаний об этом процессе [2]. Высокая сложность операции постукивания — одна из основных причин относительного отсутствия рукописей по теме.Из-за этой сложности модели не всегда успешны.Среди проблем, которые могут быть достигнуты в процессе эксплуатации, наиболее важной является поломка крана внутри отверстия. Это явление иногда приводит к браку детали и, как следствие, к увеличению производственных затрат. Однако бывают случаи, когда заготовку можно восстановить, но в этом случае необходимо удалить сломанный стержень резьбонарезного инструмента, и эта операция увеличивает время изготовления и, следовательно, затраты на производство.Помимо проблемы поломки метчика, есть и другие проблемы, такие как; поломка одного или нескольких зубьев или неизбежный износ инструмента, который, несмотря на то, что он менее серьезен, также необходимо учитывать, чтобы не повредить качество работы.
Хотя для нарезания резьбы некоторых материалов, таких как абразивные отливки, стекловолокно, литейные стали, аустенитные и закаленные стали, метчики обычно выполняются твердосплавными метчиками, чаще всего в качестве подложки используется быстрорежущая сталь (HSS) и, в частности, полученная процессами порошковой металлургии и, следовательно, предметом данного исследования.
С другой стороны, с постепенным и успешным внедрением противоизносных микропокрытий [3,4] большинство инструментов для нарезания резьбы HSS на рынке покрыты очень тонкими пленками материалов, которые значительно улучшают свои свойства, что дает им более низкую коэффициент трения, меньшая способность к химической реакции с материалом заготовки, более высокая стойкость к истиранию и более высокая жаропрочность. В этом случае цель подложки из быстрорежущей стали — быть прочной опорой и способствовать хорошему сцеплению слоев.Оба свойства важны в процессе резки.В данном исследовании представлен анализ поведения трехканальных метчиков из быстрорежущей порошковой стали M12 × 1,5. Метчики представляют собой основные современные покрытия, которые упоминаются в порядке появления на рынке — TiN, TiCN, TiAlN и TiAlN + WC / C, и сравниваются с характеристиками метчиков без покрытия.
TiN было первым покрытием, нанесенным на режущие инструменты в 1970-х годах [5]. Это покрытие имеет широкий спектр применения, будучи более дорогим, чем классические покрытия (полученные осаждением оксида в очень горячей атмосфере), но значительно увеличивает срок службы метчика и обычно компенсирует его применение.Это одно из первых покрытий, испытанных на инструментах, сначала на твердосплавных инструментах, а затем на инструментах из быстрорежущей стали. Это покрытие характеризуется низким коэффициентом трения, который снижает тепловыделение во время резки и защищает от адгезии и абразивного износа. Фактически, спустя пятьдесят лет после его появления на рынке и несмотря на существующие более современные покрытия, он все еще применяется сегодня из-за дешевизны. Кроме того, его золотой цвет визуально отражает износ инструмента, что полезно оператору для предотвращения неконтролируемой поломки метчика.Следующим нанесенным покрытием стал TiCN, обладающий большей твердостью и вязкостью разрушения. Последнее свойство обеспечивает устойчивость кромок инструмента к динамическим нагрузкам, что делает его очень подходящим для высокоскоростного и прерывистого резания, где всегда присутствует динамика. Следует особо отметить изменения, произошедшие в последнее время в используемых материалах покрытия и в технологиях. В частности, разработка покрытий на основе Ti, C, N и Al в их различных комбинациях. Введение Al и N придает покрытиям лучшую стойкость к окислению и большую твердость, когда инструмент горячий.Он также снижает остаточные напряжения, тем самым улучшая адгезию слоя к материалу сердцевины. Среди этих новых методов нанесения покрытий выделяются методы напыления и «дугового осаждения», которые позволяют получить структуру зерен с «нано» размером, что позволяет градуировать состав слоя по его толщине [6]. Наиболее часто используемым представителем этих новых слоев в режущих инструментах в целом — и метчиках в частности — является TiAlN, материал с необычайной устойчивостью к высоким температурам, который очень хорошо подходит для обработки деталей из чугуна [7], который является материалом это будет использоваться в этом исследовании.Более новым покрытием является покрытие со смазывающей способностью, которое состоит из нанесения слоев со смазочной способностью [8] на твердые слои, упомянутые выше. Наиболее распространены CBC (покрытия на основе углерода), среди которых DLC (алмазоподобный углерод), WC / Cs (карбид вольфрама / графит) [9,10] и TiC / Cs. Другим видом смазочного покрытия является сульфид молибдена (MoS 2 ), который использовался в деталях космических спутников, где из-за вакуума условия смазывания низкие, и достигаются хорошие результаты.Что касается CBC, WC / C — это тот, который будет использоваться в этом исследовании на подложке TiAlN. Несмотря на не большое количество исследований, посвященных операциям постукивания, необходимо принять во внимание несколько из-за его полезности. В частности, есть два исследования, в которых сплавы Al-Si выпускаются метчиками из быстрорежущей стали. В частности, в первом сплаве 319 Al-Si нарезали метчиками из быстрорежущей стали с алмазным покрытием и без покрытия в качестве эталона. Использование этого покрытия связано с высокими абразивными свойствами, присущими сплавам этого типа.При испытаниях использовалась смазка MQL. Результаты показали, что покрытия являются обязательными для достижения подходящего процесса. С другой стороны, было доказано, что использование MQL (Minimum Quantity Lubrication) помогает избежать прилипания масла [11]. Принимая во внимание это последнее утверждение, другой проанализировал механизмы износа. В данном случае использовались метчики из быстрорежущей стали без покрытия с целью увеличения их износа. Полученные выводы показывают, что истирание и адгезионный износ вызвали серьезное повреждение выступов на скошенной длине метчика [12].Чтобы избежать этих механизмов износа, другие исследования были сосредоточены на влиянии покрытия во время процесса выпуска резьбы. В частности, операции по выпуску резьбы проводились с несколькими покрытиями PVD (физическое осаждение из паровой фазы) на ковком чугуне после закалки (ADI) в Elósegui et al. исследование [13]. В частности, были протестированы AlTiN, AlTiSiN и AlCrSiN. Результаты показывают, что применение шлифовки перед нанесением покрытия на метчики позволило добиться лучшей адгезии пленки к подложке. С другой стороны, метчики для штамповки и нарезки использовались в Pereira и da Silva [14], соответственно, для нарезания резьбы ламинированной углеродистой стали SAE 1045.В данном случае были испытаны покрытия TiCN и TiN. Результаты показывают, что важно учитывать толщину слоя покрытия, но не было установлено, какой вид покрытия или какое значение толщины были наиболее устойчивыми. Последний вопрос был решен в 2019 году Abdoos et al. [15]. В этом исследовании влияние толщины покрытия проверялось на чугуне с компактным графитом (CGI). В данной работе были испытаны покрытия размером ≈4 мкм, ≈5,38 мкм, ≈10 мкм, ≈17 мкм. Результаты показывают, что толщина ≈10 мкм является оптимальным значением для работы с таким материалом.Наконец, Безерра и Коэльо [16] провели несколько испытаний чугуна GG25 с метчиками, покрытыми TiAlN и TiCN. Результаты показывают, что основным механизмом износа была адгезия с последующим истиранием, как это произошло с сплавами Al-Si. Что касается поведения покрытий, то при скорости 30 м / мин представлены аналогичные характеристики. Однако, когда скорость резания была увеличена до 60 м / мин, TiAlN оказался лучшим выбором для обработки этого чугуна, достигнув увеличения срока службы инструмента почти на 60%. Другие работы по теме предоставлены Urbikaín et al.[17], но в данном случае для формирования метчиков. Другой автор также анализирует влияние покрытий на различные геометрии инструмента [18,19,20], анализируя микроструктуру, механические, окислительные и коррозионные свойства покрытий Cr-Al-Si-N [18], композита Mo-Cu-VN. покрытий [19], а также трибологических свойств, стойкости к окислению и токарной обработки многослойных покрытий AlTiN / AlCrSiN [20]. Эта работа направлена на лучшее понимание производительности метчика по сравнению с некоторыми из существующих покрытий, и ее мотивирует поставщик инструмента. Группа НЕКО-Тиволы.Поэтому, принимая во внимание все эти вопросы, в данной работе было проанализировано поведение четырех покрытий при использовании чугунных пластин GG25. В этом случае использовалось сухое нарезание резьбы, чтобы улучшить смазывающие свойства покрытия и в то же время избежать адгезионного износа. Рукопись была структурирована следующим образом: во-первых, была установлена установка машины, на которой был разработан процесс нарезания резьбы, определены геометрия метчика и свойства покрытия (раздел 2). Затем описываются стратегия испытаний, методология износа и выбранные критерии окончания срока службы.Кроме того, представлены результаты экспериментов и анализа износа (раздел 3). Впоследствии обсуждение результатов представлено в соответствии с количественно оцененным износом боковой поверхности каждого из зубьев, сравнивается поведение различных покрытий (Раздел 4), и, наконец, представлены выводы.2. Материалы и методы
Для проведения испытаний используется вертикальный обрабатывающий центр и пластины, в которых предварительно просверлено 2000 отверстий диаметром 10,5 мм сверлом из быстрорежущей стали.Все отверстия проверяются обычным калибром отверстий H7 с проверками «годен» и «непроходен» (мин. Диаметр 10,5 мм и макс. Диаметр 10,518 мм). На рис. 1 показана деталь стяжки, используемой для фиксации и размещения перфорированной пластины на столе.Инструменты для метчиков фиксировались с помощью держателя метчика WIDAFLEX UTS (Fort Mill, SC, США), Ref. UT40, втулка BILZ-M12 (Ostfildern, Германия). Перед каждым испытанием держатель метчика фиксировался с крутящим моментом сцепления примерно 16 Н · м в качестве меры безопасности для предотвращения поломки инструмента для метчика внутри отверстия.
Материал детали — чугун GG25 на пластинах 250 мм × 225 мм и толщиной 20 мм, в которых, как уже упоминалось, ранее были просверлены отверстия диаметром 10,5 мм. В качестве метчика использовался метчик из быстрорежущей стали M12 × 1,5 (HSSEE) с половинным углом входного конуса 10 ° и тремя каналами (см. Рисунок 2a). На рисунке 2b показан осевой вид инструмента для метчика, на котором можно выделить три канала. Номенклатура, используемая для различения различных частей метчика (канавка, резьба, зуб), показана на рисунке 3.Четыре типа покрытий (TiN, TiCN, TiAlN, TiAlN + WC / C), как видно на Рисунке 4, были испытаны в условиях резания V c = 50 м / мин и без использования смазки. Скорость подачи выводится из метрической резьбы (M12 × 1,5), нарезание резьбы (нарезание резьбы) — это только операция с одной степенью свободы, поэтому скорость резания является главной, подавать ведомую. Эти условия резания, которые соответствуют требованиям к производительности поставщика инструмента и промышленным применениям, могут считаться требовательными для этого типа обработки.В этой статье делается попытка проанализировать высокоскоростную обработку железа. Для каждого покрытия использовалось пять метчиков. Покрытия наносились на метчики по технологии PVD. Поставщик покрытия использовал купоны для теста Calo, чтобы оценить толщину покрытия, а также адгезию с помощью теста на царапину. Капли в покрытии удалялись шлифованием в течение нескольких минут (с использованием станка OTEC (Straubenhardt-Conweiler, Германия). Также проверялась округлость режущей кромки, поскольку это подразумевает некоторое изменение характеристик.Таблица 1 иллюстрирует основные параметры покрытий. Поставщик покрытий (Oerlikon Balzers, Antzuola, Испания) измеряет толщину и микротвердость с помощью рентгеновской флуоресценции в соответствии со стандартами DIN ISO 3497 [21] и ASTM B 568 [22] и наноиндентирования в соответствии с ISO. 14577 [23] соответственно. Кроме того, покрытие TiN обеспечивает высокую износостойкость, предотвращает образование наростов режущих кромок из-за холодной сварки лома и обеспечивает более высокое качество поверхности резьбы. Покрытие TiCN имеет более высокую абразивную стойкость, чем предыдущее, и рекомендуется для вязких материалов, литья и сталей с твердостью выше 1000 Н / мм 2 .TiALN идеально подходит для высоконагруженных компонентов, что гарантирует наилучший отвод стружки. Кроме того, он разработан для работы в режиме сухой обработки и в условиях более высоких скоростей резания. Наконец, TiALN + WC / C имеет те же свойства, что и предыдущий, плюс дополнительный слой смазки, чтобы избежать трения между профилем резьбы и зубом метчика.4. Обсуждение
После того, как экспериментальные результаты были проиллюстрированы и проанализированы, а также были обнаружены лучшие характеристики покрытий TiAlN y TiALN + WC / C, следующий раздел — Обсуждение — посвящен сравнению уровня износа этих покрытий и без покрытия. от первого зуба до восемнадцатого.Также рассматриваются результаты износа инструмента на каждом зубе на покрытиях TiN и TiCN. Перед тем, как начать обсуждение, значение резьбы на профиле% A определено пластически на рисунке 3. Однако резьба представляет собой набор из трех зубцов от первой канавки до одной и той же канавки при геликоидальном движении.4.1. Обсуждение результатов для метчиков без покрытия
Во всех испытанных метчиках режущие зубья имеют размер от зуба 1 до зуба 10. Начиная с 13, они находятся в цилиндрической части и, следовательно, являются чистовыми зубьями.Что касается зубьев с номерами 11 и 12, есть три возможности: (а) зубья 11 и 12 могут быть режущими и рыболовными соответственно, (б) они могут быть обоими режущими зубьями или (в) они могут быть обоими чистовыми. Логично, что вероятность нарезания зуба на кромке 11 выше, чем на зубе 12.
На рисунке 14 показано изменение параметра% A для каждого зуба от первого до восемнадцатого зуба для пяти исследованных метчиков без покрытия. Поведение профилей% A одинаково для метчиков без покрытия.Поэтому и для упрощения анализа на рисунке 15 показано среднее значение% A для этих пяти образцов с доверительным интервалом 95%. Сосредоточившись на рисунке 15, значение% A остается ниже 10% в зубах 1, 2 и 3, а также внезапно изменяется на значение менее 20% в зубах 4 и 5, увеличивается до 20% и остается в следующих шести зубах (от 5 до 10). Зуб 11 изнашивается немного больше, чем 30%, а зуб 12 достигает значения 100%. Предположим, что кажется логичным, что в пяти испытанных метчиках без покрытия зуб 11 является режущим (поскольку он сохраняет значения износа предыдущих).Принимая во внимание профиль чистовой резьбы зуба 12, объяснение высокой степени износа зуба 12 может быть следствием износа боковой поверхности зуба номер 11, в результате чего профиль резьбы остается незавершенным и, следовательно, зуб 12 удаляет неразрезанный материал. Этот, как и остальные фрикционные зубья, сильно изнашивается на двух своих углах, и, поскольку его основная кромка очень мала (1/8 шага, то есть 0,18 мм), износ обоих углов (см. Рисунок 11 ) перекрытие, вызывающее высокий относительный износ на поверхности зазора.По мере износа зуба 12 профиль резьбы остается незавершенным, и, следовательно, зуб 13 становится режущей кромкой. Этот износ распространяется по фрикционным зубцам, отвечающим за калибровку резьбы.Несмотря на 100% износ зубьев 12–18, резьба, образованная метчиками без покрытия, была проверена резьбовым калибром «GO / NO-GO», и все резьбы находятся в пределах допусков. Хотя параметр износа% A составляет 100%, количество материала без его удаления из профиля резьбы достаточно мало, чтобы не допустить проникновения резьбового калибра в резьбовое отверстие.Следовательно, зазоры зубьев 12–18 метчиков без покрытия имеют более высокий уровень износа, чем у других метчиков с покрытием. Однако износ неглубокий и, следовательно, резьба правильная.
Этот средний профиль износа метчиков без покрытия является основным профилем износа для сравнения с другими метчиками с покрытием. Кроме того, как упоминалось ранее, для обсуждения результатов износа были выбраны TiAlN и TiAlN + WC / C, поскольку они имеют минимальные уровни износа, как описано в разделе 3.4.2. Обсуждение результатов метчиков с покрытием TiAlN
На рисунке 16 показано различное поведение параметра% A для каждого зуба.Наблюдая схожие формы износа всех метчиков, средний профиль износа рассчитывается для упрощения результатов. Поэтому на Рисунке 10 показаны средние значения% A для пяти метчиков с доверительным интервалом 95%. С учетом значений профиля износа метчиков без покрытия. На Рисунке 15, Рисунок 17 показывает аналогичное поведение до шестого зуба по сравнению с Рисунок 15, потому что средний уровень износа зубьев 1, 2 и 3 близок к 10%, затем уровень износа увеличивается до 20% в зубе 4. и, наконец, это значение сохраняется в зубах 5 и 6.Следовательно, это поведение одинаково для обоих ответвлений. То же самое не происходит со значениями дисперсии, которые явно ниже, чем у непокрытых, наблюдаемых на рисунке 15, особенно тех, которые соответствуют резьбе 2. Продолжая анализ, можно заметить, что между зубцами 6 и 7 происходит еще одно увеличение до тех пор, пока достигая значения более 30%, и это значение сохраняется в зубе 8. В зубах 9 и 10 значения достигают 35% и 40% соответственно. Следовательно, коническая часть метчика имеет примерно одинаковый уровень износа независимо от покрытия, как это видно на Рисунке 13b.В коническо-цилиндрической части процент износа достигает 40%, более 50% и максимального значения 65% в зубах 10, 11 и 12 соответственно. Следовательно, увеличение составляет 30% и 25% от зубцов 9 до 12 и от зубцов 10 до 12 соответственно. Для тех же зубов без покрытия тот же параметр увеличился на 20%, 25% и 100% для зубов 9, 10 и 12 соответственно (см. Рисунок 15). То есть в том же интервале зубцов он показал увеличение на 80% и 75%, соответственно, значения намного выше, чем у 30% и 25% TiAlN.Следовательно, покрытие TiAlN предотвращает развитие сильных градиентов износа, обнаруживаемых в метчиках без покрытия.С другой стороны, это предотвращение образования покрытия на чистовых зубьях сохраняется вдоль цилиндрической части инструмента, потому что износ начинает уменьшаться, более или менее с тем же наклоном, с которым он увеличивался, и дисперсии также уменьшаются по сравнению с зубья 10, 11 и 12. Во всех зубах без покрытия процент износа составляет 100%, а их дисперсия равна нулю, потому что области износа A sp на этих зубах всегда выше контрольной площади A p .Поэтому нет смысла сравнивать оба покрытия, начиная с кромки 12.
Однако дисперсия, соответствующая непокрытию, намного меньше, чем у метчиков с покрытием TiAlN (как можно увидеть, сравнив рисунок 15 и рисунок 17). Эта сильная дисперсия подразумевает низкую надежность покрытия TiAlN, проблему, хорошо известную производителям инструментов с покрытием. Эта худшая надежность объясняется большим разбросом значений срока службы метчиков (таблица 2), влиянием за счет уменьшения значений% A от зубьев 12 до 18 и градиентов в зубцах края метчика.Наконец, существует поразительно низкая корреляция между количеством резьбовых отверстий в конце срока службы и общей площадью износа (A t ) метчиков (площадь под кривой% A-количество зубьев), другими словами , одинаковые метчики (с одинаковым покрытием) в конце срока службы имеют несколько совершенно разные уровни общего износа (см. 1.3 и 4.3 в Таблице 2 и на Рис. 15 и Рис. 17, соответственно).4.3. Обсуждение результатов метчиков с покрытием TiAlN + WC / C
На рисунке 11 показано изменение параметра% A для каждого зуба от первого зуба к восемнадцатому из пяти изученных метчиков.Прежде чем приступить к обсуждению метчиков из TiAlN + WC / C, профили износа этого покрытия аналогичны предыдущим. Таким образом, обсуждение этого вопроса сравнимо с предыдущим разделом при сравнении этого метчика для нанесения покрытия с метчиком без покрытия. В этой части основное внимание уделяется сравнению этого покрытия с предыдущим, поскольку это лучший инструмент для метчиков по сроку службы и уровню износа.
Для упрощения анализа на рисунке 18 показано среднее значение% A для пяти инструментов с доверительным интервалом 95%. Как было замечено ранее, покрытие TiAlN + WC / C априори превосходит TiAlN за счет добавления слой WC / C, который действует как смазка, и чтобы оценить это превосходство [10], оба они будут сравнены ниже.Во-первых, наблюдается впечатляющая разница в поведении в соответствии с таблицей 2, следовательно, оба типа метчиков достигают конца срока службы, определяемого значением крутящего момента 16 Нм, сделав очень разное количество отверстий 272 и 326, покрытых TiAlN + WC / C. и TiAlN соответственно. Этот результат утверждает, что добавление слоя твердой смазки WC / C не только не улучшает, но и ухудшает срок службы метчика, и, следовательно, этот результат противоречит цели, к которой стремятся с помощью слоя.Однако из наблюдений на Рисунке 17 и Рисунке 19 можно сделать вывод, что среднее и дисперсия значений% A покрытия TiAlN намного выше, чем у покрытия TiAlN + WC / C, потому что первое представленное покрытие не имеет слоя смазки. . Этот декремент износа ниже на кромках с 7 по 13 и особенно на чистовых зубьях (цилиндрическая часть).Наконец, WC / C перемещает максимум на один зуб, снижает максимальный пик износа на 30%. Кроме того, у этого покрытия меньше распространение износа вдоль чистовых зубьев.
4.4. Обсуждение результатов по метчикам с покрытием TiN и TiCN
В этом подразделе рассматриваются результаты определения процента средней площади износа% A для метчиков с покрытием TiCN и TiN. На рис. 20 показан износ различных зубьев метчика в конце срока службы инструмента, когда он достигает критерия конца срока службы. Показано среднее значение 5 нажатий на TiCN и 5 ответвлений на TiN. Износ метчиков из TiN аналогичен тому, который наблюдается на инструментах без покрытия (рис. 15), но 100% износ цилиндрических зубцов не наблюдается.С другой стороны, инструменты TiCN показали значения, близкие к наблюдаемым для TiAlN и TiAlN + WC / C, что можно сделать, сравнивая Рисунок 17, Рисунок 19 и Рисунок 20.Зажмите чипы | Производство режущего инструмента
Предоставлено OSG Tap and Die
При правильном применении нарезание резьбы по форме обеспечивает реальные производственные преимущества.
Процесс смещения металла вместо резки называется по-разному. Но, по словам Питера Дженнусо, руководителя разработки приложений OSG Tap, многие профессионалы в области металлообработки, по словам Питера Дженнусо, руководителя разработки приложений для OSG Tap, называют ли это нарезанием резьбы нарезкой, нарезанием резьбы холодной штамповкой, резьбонарезанием, холодной прокаткой, профилированием, накаткой резьбы, нарезанием резьбы на вальцах или нарезанием резьбы холодным валком & Die Inc., Глендейл-Хайтс, штат Иллинойс,
Аль Зайтун, менеджер по маркетингу YG-1 Tool Co., Вернон-Хиллз, штат Иллинойс, согласился с тем, что метчики более приемлемы и понятны. По его оценкам, соотношение количества используемых метчиков к размеру составляет около 100: 1.
Нарезание резьбы резьбы требует материала детали, который действительно может течь для создания профиля резьбы. Материал с пределом прочности на разрыв 160 000 фунтов на квадратный дюйм и максимальной твердостью 36 HRC — это примерно предел для нарезания резьбы по форме, хотя для некоторых материалов доступны метчики с твердостью до 40 HRC.
Резьбовое соединение может быть выполнено из различных металлов, включая алюминий, нержавеющую сталь, углеродистую сталь, титан и никель. Хрупкие материалы, такие как чугун, плохо текут и не поддаются нарезке.
Титан — тоже вызов. «Помимо высокой прочности на разрыв и низкой пластичности, титан имеет очень низкую теплопроводность, что означает, что он не очень хорошо поглощает тепло», — сказал Дженнусо. Он пояснил, что во время операции нарезания резьбы на деталь, метчик и стружку попадает тепло.Поскольку при формовке не образуется стружка, тепло должно поступать в кран или материал. При нарезании резьбы по титану большое количество тепла проникает в инструмент и вызывает преждевременный выход из строя.
Метчики для форм обычно имеют диаметр менее 3⁄4 дюйма или M20. Инструменты большего размера создают большее трение и требуют большей мощности станка.
«Существует также ограничение шага», — сказал Пэт Нелс, менеджер по продукции компании Walter USA LLC, Вокеша, Висконсин, которая предлагает резьбообразователи Protodyn CAP и Protodyn S Synchrospeed.«Резьбу с мелким шагом легче сформировать, потому что меньше материала, который нужно вытеснить. Предел составляет около 10 tpi или 2,5 шага в метрической системе. Если профиль резьбы равен 10 tpi или больше, вы сможете его сформировать ».
Держите чипы
Самым большим преимуществом нарезания резьбы валками является отсутствие стружки, что исключает необходимость обработки стружки, а также всей очистки, технического обслуживания и оборудования, которое она включает.
«Во многих случаях, в зависимости от материала, нарезание резьбы по форме лучше для крупносерийного производства», — сказал Дженнусо из OSG.«Нарезание резьбы может вызвать« птичье гнездо », что означает, что оператор должен останавливать машину, убирать стружку и запускать снова — неоднократно — в течение дня. Метчик формы может работать без присмотра до тех пор, пока не истечет срок службы инструмента; нет необходимости останавливать обработку ».
Нарезание резьбы по форме особенно эффективно для нарезания резьбы в глубоких отверстиях глубиной 3 и более диаметра, когда удаление стружки может оказаться затруднительным.
Предоставлено OSG Tap and Die
Метчик OIL-S-XPFOSG обеспечивает резьбу в прутке из легированной стали 4120, используемой для испытаний.Метчик может применяться в сталях до 40 HRC.
Метчик для формования имеет большее поперечное сечение инструмента, чем сопоставимый метчик. Это означает, что метчики более жесткие и менее подвержены поломке. Метчики Form более стабильны при нарезании резьбы, чем метчики для резки, которые должны иметь большие канавки для удаления стружки. «Если все переменные присутствуют, метчик для форм может прослужить 30, 40 или даже 50 к 1», — сказал Зайтун из YG-1.
Формованные нити также прочнее нарезанных. Согласно Руководству по машинному оборудованию, это связано с тем, что зерна в металле не разрушаются в сформированной нити, а смещенный металл затвердевает.Другими словами, процесс формовки обеспечивает высокую статическую и динамическую прочность резьбы на растяжение из-за деформационного упрочнения.
«Это связано с зернистостью материала», — сказал Дженнусо. «Метчик для форм фактически сжимает эту зернистую структуру для создания профиля резьбы. Это сжатие дает более плотную структуру зерна, поэтому нити становятся прочнее. Режущий метчик нарушает эту структуру зерна, создавая более слабую резьбу ».
Согласно Walter’s Nehls, еще одним преимуществом нарезки форм является «лучшая экономия в производственной среде.При формовке инструмент не так сильно изнашивается, что позволяет нарезать больше резьбы с меньшими затратами на резьбу, чем при использовании метчика ». Он добавил, что нарезание резьбы также позволяет получать резьбу быстрее, чем нарезание резьбы.
Факторы станков
Метчики для формовки, однако, требуют большего крутящего момента при механической обработке, и рабочая опора должна быть более стабильной, чем для метчиков для резки. Согласно Gennuso, нарезание резьбы по форме требует в два-четыре раза большего крутящего момента, чем нарезание резьбы, поэтому станку приходится работать в два-четыре раза тяжелее, чтобы нарезать резьбу.
Требуемый крутящий момент зависит от размера отвода. «Размеры наших метчиков варьируются от M1 до M48, но обычно используются метчики от M3 до M20», — сказал Вольфганг Руфф, вице-президент по техническим вопросам компании KOMET of America Inc., Шаумбург, штат Иллинойс. деталь больше, поэтому у вас уже будет машина большего размера с более высоким крутящим моментом ».
Предоставлено KOMET of America
Вместо полного профиля резьбы нарезание резьбы по форме создает канал или пустоту (полукруглые области на фото) внутри вершины резьбы.
Важно иметь станок, который может не только соответствовать крутящему моменту, но также может работать с требуемой скоростью подачи, необходимой для нарезания резьбы метчиком. «Станок должен обеспечивать жесткое нарезание резьбы», — отметил Томас Шихи, менеджер по разработке приложений, Hardinge Inc., Эльмира, штат Нью-Йорк,
.Станок, способный к жесткому нарезанию резьбы, имеет цикл нарезания резьбы внутри элемента управления, чтобы синхронизировать вращение шпинделя станка с линейным движением оси нарезания резьбы. Это позволяет машине всегда подбирать и поддерживать определенный шаг резьбы.При жестком нарезании резьбы линейное движение оси нарезания резьбы получает сигнал подтверждения от энкодера шпинделя, чтобы гарантировать, что синхронизация сохраняется, а полученная резьба соответствует спецификациям. Часто это позволяет увеличить скорость нарезания резьбы и подачу по сравнению с обычным нарезанием резьбы, тем самым повышая производительность и пропускную способность.
Для станков, не имеющих возможности выполнять жесткое нарезание резьбы, для компенсации доступны инструменты и приспособления. «При нарезании резьбы метчиком на вертикальном обрабатывающем или токарном центре вы можете использовать цанги с ограничением крутящего момента для компенсации ошибок частоты вращения», — сказал Шихи.«У вас также есть резцедержатель для сжатия растяжения, который может обеспечивать как отдачу, так и вытягивание, поэтому вы не рискуете сломаться. Это компенсирует тот факт, что станок нельзя настроить на скорость подачи, необходимую для шага резьбы ».
Предоставлено Уолтером США
Устройство для формирования резьбы Protodyn S HSS-E компании Walter Prototyp для глухих и сквозных отверстий доступно в размерах от M1 до M24.
Ключевым препятствием для нарезания резьбы по форме является то, что формованная резьба не допускается в некоторых отраслях промышленности.«Причина в профиле резьбы сформированной резьбы», — сказал Дженнусо. «Вместо полного профиля резьбы вы получаете небольшой канал или пустоту внутри гребня резьбы, которая может удерживать загрязнения. В таких отраслях, как медицинская и пищевая, существуют строгие правила относительно чистоты, поэтому они не могут принимать нитки с этими каналами ».
Еще одним ограничивающим фактором для нарезания резьбы является то, что просверленное отверстие должно быть намного более точным, чем при нарезании резьбы. Для стандартной резьбы M4 диаметр 0,130 дюйма.Нельс объяснил, что отверстие с допуском +0,005 «/-0,002» является приемлемым, но для формирования метчика с такой резьбой требуется отверстие диаметром 0,1457 дюйма с более жестким допуском ± 0,0012 дюйма.
Согласно Нельсу, если просверленное отверстие слишком велико, не будет достаточно материала для вытеснения, чтобы полностью сформировать резьбу. Если отверстие слишком маленькое, будет слишком много материала для вытеснения, что приведет к поломке детали.
Aerospace — еще одна отрасль, которая может ограничивать прием формовых резьб из-за требований жестких допусков.«Гораздо труднее контролировать размер резьбы с помощью метчика для формования, чем с помощью метчика», — сказал Дженнусо. «Поскольку метчики для формования основаны на собственной эластичности материала для создания резьбы, формованные резьбы немного более восприимчивы к расширению и усадке материала. Это иногда затрудняет соблюдение очень жестких допусков с помощью метчиков для форм. Чтобы компенсировать это, метчики-метчики обычно используют больший предел диаметра шага, чем метчики для резки; например, метчик-20 2B будет использовать предел H6, а метчик-20 2B будет использовать предел H5.”
Хотя все согласны с тем, что в аэрокосмической отрасли есть ограничения на резьбу форм, все не согласны с тем, что это проблема допуска. Те же допуски могут быть достигнуты с помощью метчика, метчика или резьбовой фрезы, согласно KOMET’s Ruff. «Аэрокосмическая промышленность не принимает фасонные резьбы из-за небольшого зазора на кончике резьбы малого диаметра, который может удерживать загрязнения», — сказал он. «Цель в аэрокосмической отрасли — уменьшить загрязнение во всех областях».
Третьи не верят, что загрязнение является проблемой, но указывают, что аэрокосмическая промышленность считает этот зазор или пустоту возможной точкой разрушения.
Охлаждение
Охлаждающая жидкость особенно важна при формировании резьбы, а не на ее нарезке, поскольку для процесса требуется охлаждающая жидкость для отвода тепла и перемещения материала, — отметил Джулиан Уэбб, менеджер по продукции KOMET. По словам Уэбба, резьба, хотя и не идеальна, может быть нарезана всухую, и инструмент не будет легко сломаться, но метчик для формования без СОЖ сломается.
«Существует также разница с охлаждающей жидкостью, в зависимости от того, какой тип материала вырезается», — сказал Уэбб.«Если это более прочный материал, то следует использовать масло. Если это менее прочный материал, подойдет обычная эмульсия ».
Предоставлено KOMET of America
Метчики для профилирования валков MOREX R HSS-EKOMET имеют гибкий корпус для компенсации небольших перекосов, особенно на линиях передачи, и паяные твердосплавные полосы для обеспечения жесткости.
Кроме того, охлаждающая жидкость более важна при формовке, чем при резке, потому что на границе раздела инструмент / заготовка оказывается большее давление.Необходима охлаждающая жидкость, работающая при более высоком давлении. «Если вы используете охлаждающую жидкость на водной основе, тогда вам нужна противозадирная присадка, которая химически не разрушается под высоким давлением», — сказал Зайтун из YG-1. «Если вы не будете использовать масло или противозадирную присадку, это может привести к чрезмерной нагрузке на резьбу и появлению трещин».
Метчики формыимеют некоторые отличия в способе подачи СОЖ. «Проходные краны для СОЖ имеют отверстие в центре крана, через которое СОЖ подается непосредственно в зону формовки.Сплошные метчики имеют канавки, скажем, радиусом от 0,020 дюйма до 0,040 дюйма, которые зашлифованы в самом метчике, чтобы охлаждающая жидкость протекала до дна отверстия », — сказал Дженнусо из OSG. «Независимо от способа доставки, использование охлаждающей жидкости обязательно в виде врезки, чтобы обеспечить эффективную смазку и отвод тепла».
Хотя некоторые еще могут быть незнакомы с отбором форм, в электронной промышленности нет. Автомобильная промышленность также набирает обороты в области нарезания резьбы по форме, особенно для алюминиевых деталей.
Чтобы решить, спросите, поддается ли применение последней части формированию, рекомендует Walter’s Nehls. «У вас есть станок и приспособления для этого, и вы хотите потратить время и силы, чтобы просверлить высококачественное отверстие, необходимое для правильной нарезки резьбы?» CTE
Об авторе: Сьюзан Вудс (Susan Woods) — редактор CTE.