Π‘ΡΡΠΎΠ΅Π½ΠΈΠ΅ Π²Π΅ΡΠ΅ΡΡΠ²Π°. ΠΠΎΠ»Π΅ΠΊΡΠ»Ρ. ΠΠΈΡΡΡΠ·ΠΈΡ Π² Π³Π°Π·Π°Ρ , ΠΆΠΈΠ΄ΠΊΠΎΡΡΡΡ ΠΈ ΡΠ²Π΅ΡΠ΄ΡΡ ΡΠ΅Π»Π°Ρ . ΠΠ·Π°ΠΈΠΌΠ½ΠΎΠ΅ ΠΏΡΠΈΡΡΠΆΠ΅Π½ΠΈΠ΅ ΠΈ ΠΎΡΡΠ°Π»ΠΊΠΈΠ²Π°Π½ΠΈΠ΅ ΠΌΠΎΠ»Π΅ΠΊΡΠ»
46. ΠΠ°ΠΌΠ½ΠΈ ΠΌΠ°Π»ΠΎΡΠΆΠΈΠΌΠ°Π΅ΠΌΡ, Π½ΠΎ ΠΌΠ΅ΡΠ°Π»Π»Ρ (Π΄Π°ΠΆΠ΅ ΠΎΡΠ΅Π½Ρ ΠΏΠ»ΠΎΡΠ½ΡΠ΅) Ρ ΠΏΠΎΠΌΠΎΡΡΡ ΠΌΠΎΡΠ½ΠΎΠ³ΠΎ ΠΏΡΠ΅ΡΡΠ° ΡΠ΄Π°Π΅ΡΡΡ ΡΠΆΠ°ΡΡ Π΄ΠΎ 0,75 ΠΎΡ Π½Π°ΡΠ°Π»ΡΠ½ΠΎΠ³ΠΎ ΠΎΠ±ΡΠ΅ΠΌΠ°. ΠΠΎΡΠ΅ΠΌΡ Π²ΠΎΠ·ΠΌΠΎΠΆΠ½ΠΎ ΡΠ°ΠΊΠΎΠ΅ ΡΠΈΠ»ΡΠ½ΠΎΠ΅ ΡΠΆΠ°ΡΠΈΠ΅?
ΠΠ°Π½Π½ΠΎΠ΅ ΡΠ²ΠΎΠΉΡΡΠ²ΠΎ ΠΎΠ±ΡΡΠ»ΠΎΠ²Π»Π΅Π½ΠΎ ΠΎΡΠΎΠ±Π΅Π½Π½ΠΎΡΡΡΠΌΠΈ ΡΡΡΠΎΠ΅Π½ΠΈΡ ΠΊΡΠΈΡΡΠ°Π»Π»ΠΈΡΠ΅ΡΠΊΠΎΠΉ ΡΠ΅ΡΠ΅ΡΠΊΠΈ ΠΌΠ΅ΡΠ°Π»Π»ΠΎΠ².
47. Π ΡΡΠ΅ΠΊΠ»ΡΠ½Π½ΡΡ Π±ΡΡΡΠ»ΠΊΡ Π½Π°Π»ΠΈΠ»ΠΈ Π²ΠΎΠ΄Ρ ΠΈ ΠΏΠΎΠΌΠ΅ΡΡΠΈΠ»ΠΈ Π΅Π΅ Π² ΠΌΠΎΡΠΎΠ·ΠΈΠ»ΡΠ½ΡΡ ΠΊΠ°ΠΌΠ΅ΡΡ. Π§ΡΠΎ ΠΏΡΠΎΠΈΠ·ΠΎΠΉΠ΄Π΅Ρ Ρ Π±ΡΡΡΠ»ΠΊΠΎΠΉ ΠΈ ΠΏΠΎΡΠ΅ΠΌΡ?
ΠΠΎΠ΄Π° Π² Π±ΡΡΡΠ»ΠΊΠ΅ Π·Π°ΠΌΠ΅ΡΠ·Π½Π΅Ρ, ΡΠ²Π΅Π»ΠΈΡΠΈΡΡΡ Π² ΠΎΠ±ΡΠ΅ΠΌΠ΅, ΠΈ Π±ΡΡΡΠ»ΠΊΠ° Π»ΠΎΠΏΠ½Π΅Ρ.
48. ΠΠ΅Π½ΡΠ΅ΡΡΡ Π»ΠΈ Π²ΠΌΠ΅ΡΡΠΈΠΌΠΎΡΡΡ ΡΠΎΡΡΠ΄ΠΎΠ² ΠΏΡΠΈ ΠΈΠ·ΠΌΠ΅Π½Π΅Π½ΠΈΠΈ ΠΈΡ
ΡΠ΅ΠΌΠΏΠ΅ΡΠ°ΡΡΡΡ?
ΠΠ΅Π½ΡΠ΅ΡΡΡ
49. ΠΡΠ»ΠΈΡΠ°ΡΡΡΡ Π»ΠΈ ΠΌΠΎΠ»Π΅ΠΊΡΠ»Ρ Π²ΠΎΠ΄Ρ Π² Π³ΠΎΡΡΡΠ΅ΠΌ ΡΠ°Π΅ ΠΎΡ ΠΌΠΎΠ»Π΅ΠΊΡΠ» Π²ΠΎΠ΄Ρ Π² Ρ
ΠΎΠ»ΠΎΠ΄Π½ΠΎΠΌ Π»ΠΈΠΌΠΎΠ½Π°Π΄Π΅?
ΠΠ΅ ΠΎΡΠ»ΠΈΡΠ°ΡΡΡΡ
50. Π‘ΡΠΎΠΈΡ Π»ΠΈ Π½Π°Π»ΠΈΠ²Π°ΡΡ ΠΏΠΎΠ»Π½ΡΠΉ ΡΠ°ΠΉΠ½ΠΈΠΊ Π²ΠΎΠ΄Ρ, Π΅ΡΠ»ΠΈ Π² Π½Π΅ΠΌ Π½ΡΠΆΠ½ΠΎ Π²ΡΠΊΠΈΠΏΡΡΠΈΡΡ Π²ΠΎΠ΄Ρ?
ΠΠ΅ ΡΡΠΎΠΈΡ, ΡΠ°ΠΊ ΠΊΠ°ΠΊ ΠΏΡΠΈ ΡΠ²Π΅Π»ΠΈΡΠ΅Π½ΠΈΠΈ ΡΠ΅ΠΌΠΏΠ΅ΡΠ°ΡΡΡΡ Π²ΠΎΠ΄Π° ΠΌΠΎΠΆΠ΅Ρ ΠΏΡΠΎΠ»ΠΈΡΡΡΡ.
51. ΠΠ°ΠΊ Π½Π°Π·ΡΠ²Π°Π΅ΡΡΡ ΡΠΈΠ·ΠΈΡΠ΅ΡΠΊΠΎΠ΅ ΡΠ²Π»Π΅Π½ΠΈΠ΅, Π±Π»Π°Π³ΠΎΠ΄Π°ΡΡ ΠΊΠΎΡΠΎΡΠΎΠΌΡ ΠΌΠΎΠΆΠ½ΠΎ Π·Π°ΡΠ°Π»ΠΈΠ²Π°ΡΡ ΠΎΠ²ΠΎΡΠΈ Π½Π° Π·ΠΈΠΌΡ? ΠΠ°ΠΊ ΠΏΡΠΎΠΈΡΡ
ΠΎΠ΄ΠΈΡ ΠΏΠ΅ΡΠ΅Ρ
ΠΎΠ΄ ΡΠΎΠ»ΠΈ ΠΈΠ· Π²ΠΎΠ΄Ρ Π² ΠΎΠ²ΠΎΡΠΈ ΠΏΡΠΈ Π·Π°ΡΠΎΠ»ΠΊΠ΅?
ΠΠΈΡΡΡΠ·ΠΈΡ. ΠΠΎΠ»Π΅ΠΊΡΠ»Ρ ΡΠΎΠ»ΠΈ ΠΏΡΠΎΠ½ΠΈΠΊΠ°ΡΡ Π² ΠΏΡΠΎΡΡΡΠ°Π½ΡΡΠ²ΠΎ ΠΌΠ΅ΠΆΠ΄Ρ ΠΌΠΎΠ»Π΅ΠΊΡΠ»Π°ΠΌΠΈ ΠΎΠ²ΠΎΡΠ΅ΠΉ.
52. Π‘ΠΈΠ»ΡΠ½ΠΎ Π·Π°Π²ΠΈΠ½ΡΠ΅Π½Π½ΡΡ ΠΊΡΡΡΠΊΡ Π±Π°Π½ΠΊΠΈ Π»Π΅Π³ΡΠ΅ ΠΎΡΠ²ΠΈΠ½ΡΠΈΡΡ, Π΅ΡΠ»ΠΈ Π΅Π΅ ΠΏΠΎΠ΄ΠΎΠ³ΡΠ΅ΡΡ. ΠΠΎΡΠ΅ΠΌΡ?
ΠΠ°Π³ΡΠ΅ΡΠ°Ρ ΠΊΡΡΡΠΊΠ° ΡΠ²Π΅Π»ΠΈΡΠΈΡΡΡ Π² ΠΎΠ±ΡΠ΅ΠΌΠ΅.
53. ΠΡΠ»ΠΈ ΠΏΠ΅ΡΠ΅Π½Π΅ΡΡΠΈ Π½Π°Π΄ΡΡΡΠΉ Π²ΠΎΠ·Π΄ΡΡΠ½ΡΠΉ ΡΠ°ΡΠΈΠΊ ΠΈΠ· ΡΠ΅ΠΏΠ»Π° Π² Ρ
ΠΎΠ»ΠΎΠ΄, ΡΡΠΎ ΠΏΡΠΎΠΈΠ·ΠΎΠΉΠ΄Π΅Ρ Ρ Π΅Π³ΠΎ ΠΎΠ±ΡΠ΅ΠΌΠΎΠΌ? ΠΠΎΡΠ΅ΠΌΡ?
Π¨Π°ΡΠΈΠΊ ΡΠΌΠ΅Π½ΡΡΠΈΡΡΡ. Π§Π°ΡΡΠΈΡΡ Π²ΠΎΠ·Π΄ΡΡ
Π° Π²Π½ΡΡΡΠΈ Π±ΡΠ΄ΡΡ Π΄Π²ΠΈΠ³Π°ΡΡΡΡ ΠΌΠ΅Π΄Π»Π΅Π½Π½Π΅Π΅.
54. ΠΠΎΡΡΡΠΈΠ΅ ΡΡΠ΅ΠΊΠ»ΡΠ½Π½ΡΠ΅ ΡΡΠ°ΠΊΠ°Π½Ρ Π½Π΅ ΡΠ΅ΠΊΠΎΠΌΠ΅Π½Π΄ΡΠ΅ΡΡΡ Π²ΡΡΠ°Π²Π»ΡΡΡ Π΄ΡΡΠ³ Π² Π΄ΡΡΠ³Π°. ΠΠΎΡΠ΅ΠΌΡ?
ΠΡΡΡΠ²ΡΠΈΠ΅ ΡΡΠ°ΠΊΠ°Π½Ρ ΡΠΌΠ΅Π½ΡΡΠ°ΡΡΡ, ΠΈ ΠΈΡ
ΡΠ»ΠΎΠΆΠ½ΠΎ Π±ΡΠ΄Π΅Ρ Π²ΡΠ½ΠΈΠΌΠ°ΡΡ Π΄ΡΡΠ³ ΠΈΠ· Π΄ΡΡΠ³Π°.
55. ΠΠΎΡΠ΅ΠΌΡ ΡΠ»ΠΎΠΆΠ΅Π½Π½ΡΠ΅ Π²ΠΌΠ΅ΡΡΠ΅ ΡΡΠ΅ΠΊΠ»Π° ΡΡΡΠ΄Π½ΠΎ ΡΠ°Π·ΡΠ΅Π΄ΠΈΠ½ΠΈΡΡ?
ΠΠ΅ΠΉΡΡΠ²ΡΡΡ ΡΠΈΠ»Ρ ΠΌΠΎΠ»Π΅ΠΊΡΠ»ΡΡΠ½ΠΎΠ³ΠΎ ΠΏΡΠΈΡΡΠΆΠ΅Π½ΠΈΡ.
56. ΠΡΠΈΠΆΠΌΠΈΡΠ΅ ΠΏΠΎΠΏΠ»ΠΎΡΠ½Π΅Π΅ Π΄Π²Π΅ Π΄Π΅ΡΠ΅Π²ΡΠ½Π½ΡΠ΅ Π»ΠΈΠ½Π΅ΠΉΠΊΠΈ. ΠΠ΅Π³ΠΊΠΎ Π»ΠΈ ΠΈΡ
ΡΠ°Π·ΡΠ΅Π΄ΠΈΠ½ΠΈΡΡ? ΠΠ±ΡΡΡΠ½ΠΈΡΠ΅ Π½Π°Π±Π»ΡΠ΄Π°Π΅ΠΌΠΎΠ΅ ΡΠ²Π»Π΅Π½ΠΈΠ΅.
ΠΠ΅Π³ΠΊΠΎ. ΠΠ·-Π·Π° Π½Π΅ΡΠΎΠ²Π½ΠΎΡΡΠ΅ΠΉ Π½Π° ΠΏΠΎΠ²Π΅ΡΡ
Π½ΠΎΡΡΡΡ
Π»ΠΈΠ½Π΅Π΅ΠΊ ΠΈΡ
Π½Π΅ ΡΠ΄Π°Π΅ΡΡΡ ΡΠ±Π»ΠΈΠ·ΠΈΡΡ Π½Π° ΡΠ°ΠΊΠΎΠ΅ ΡΠ°ΡΡΡΠΎΡΠ½ΠΈΠ΅, Π½Π° ΠΊΠΎΡΠΎΡΠΎΠΌ ΡΠ°ΡΡΠΈΡΡ ΠΌΠΎΠ³ΡΡ ΠΏΡΠΈΡΡΠ³ΠΈΠ²Π°ΡΡΡΡ Π΄ΡΡΠ³ ΠΊ Π΄ΡΡΠ³Ρ.
57. ΠΠΎΠ»ΠΎΠΆΠΈΡΠ΅ Π² ΡΡΠ°ΠΊΠ°Π½ ΠΊΡΡΠΏΠΈΠ½ΠΊΡ ΠΌΠ°ΡΠ³Π°Π½ΡΠΎΠ²ΠΊΠΈ, Π° Π·Π°ΡΠ΅ΠΌ ΠΎΡΡΠΎΡΠΎΠΆΠ½ΠΎ Π½Π°Π»Π΅ΠΉΡΠ΅ Π² Π½Π΅Π³ΠΎ Π²ΠΎΠ΄Ρ. Π§ΡΠΎ Π²Ρ Π½Π°Π±Π»ΡΠ΄Π°Π΅ΡΠ΅? ΠΠ°ΠΊ Π½Π°Π·ΡΠ²Π°Π΅ΡΡΡ ΡΡΠΎ ΡΠ²Π»Π΅Π½ΠΈΠΉ?
ΠΠ°ΡΠ³Π°Π½ΡΠΎΠ²ΠΊΠ° ΡΠ°ΡΡΠ²ΠΎΡΡΠ΅ΡΡΡ Π² Π²ΠΎΠ΄Π΅. ΠΠΈΡΡΡΠ·ΠΈΡ.
58. ΠΠΎΠ·ΡΠΌΠΈΡΠ΅ Π΄Π²Π΅ ΡΠ°ΡΠΊΠΈ. ΠΠ°ΠΏΠΎΠ»Π½ΠΈΡΠ΅ ΠΈΡ
Π²ΠΎΠ΄ΠΎΠΉ ΠΈ ΠΎΡΡΠΎΡΠΎΠΆΠ½ΠΎ ΠΏΠΎΠ»ΠΎΠΆΠΈΡΠ΅ Π½Π΅ΡΠΊΠΎΠ»ΡΠΊΠΎ ΠΊΡΡΠΏΠΈΠ½ΠΎΠΊ Π»ΠΈΠΌΠΎΠ½Π½ΠΎΠΉ ΠΊΠΈΡΠ»ΠΎΡΡ. ΠΠ΄Π½Ρ ΡΠ°ΡΠΊΡ ΠΎΡΡΠ°Π²ΡΡΠ΅ Π½Π° ΡΡΠΎΠ»Π΅, Π° Π²ΡΠΎΡΡΡ ΠΏΠΎΠΌΠ΅ΡΡΠΈΡΠ΅ Π² Ρ
ΠΎΠ»ΠΎΠ΄ΠΈΠ»ΡΠ½ΠΈΠΊ. Π§Π΅ΡΠ΅Π· Π½Π΅ΠΊΠΎΡΠΎΡΠΎΠ΅ Π²ΡΠ΅ΠΌΡ ΠΏΠΎΠΏΡΠΎΠ±ΡΠΉΡΠ΅ Π²ΠΎΠ΄Ρ. ΠΠ±ΡΡΡΠ½ΠΈΡΠ΅ Π½Π°Π±Π»ΡΠ΄Π°Π΅ΠΌΠΎΠ΅ ΡΠ²Π»Π΅Π½ΠΈΠ΅.
Π’Π΅ΠΏΠ»Π°Ρ Π²ΠΎΠ΄Π° Π±ΠΎΠ»Π΅Π΅ ΠΊΠΈΡΠ»Π°Ρ, ΡΠ°ΠΊ ΠΊΠ°ΠΊ Π΄ΠΈΡΡΡΠ·ΠΈΡ Π² ΡΠ΅ΠΏΠ»ΠΎΠΉ Π²ΠΎΠ΄Π΅ ΠΏΡΠΎΡΠ΅ΠΊΠ°Π΅Ρ Π±ΡΡΡΡΠ΅Π΅.
59. Π‘Π»ΠΈΡΠΊΠΎΠΌ ΡΠΎΠ»Π΅Π½ΡΡ ΡΡΠ±Ρ ΠΌΠΎΠΆΠ½ΠΎ ΠΏΠΎΠ»ΠΎΠΆΠΈΡΡ Π½Π° Π½Π΅ΠΊΠΎΡΠΎΡΠΎΠ΅ Π²ΡΠ΅ΠΌΡ Π² Π²ΠΎΠ΄Ρ ΠΏΡΠΈ ΠΊΠΎΠΌΠ½Π°ΡΠ½ΠΎΠΉ ΡΠ΅ΠΌΠΏΠ΅ΡΠ°ΡΡΡΠ΅, ΠΈ ΡΡΠ±Π° ΡΡΠ°Π½Π΅Ρ ΠΌΠ΅Π½Π΅Π΅ ΡΠΎΠ»Π΅Π½ΠΎΠΉ. ΠΠΎΡΠ΅ΠΌΡ?
Π§Π°ΡΡΡ ΡΠΎΠ»ΠΈ ΠΈΠ· ΡΡΠ±Ρ ΡΠ°ΡΡΠ²ΠΎΡΠΈΡΡΡ Π² Π²ΠΎΠ΄Π΅.
60. ΠΠ° ΡΠ»ΠΈΡΠ΅ Π²Π±Π»ΠΈΠ·ΠΈ Ρ
Π»Π΅Π±ΠΎΠ·Π°Π²ΠΎΠ΄Π° ΡΡΠ²ΡΡΠ²ΡΠ΅ΡΡΡ Π·Π°ΠΏΠ°Ρ
Ρ
Π»Π΅Π±Π°. ΠΠΎΡΠ΅ΠΌΡ?
ΠΡΠΎΠΈΡΡ
ΠΎΠ΄ΠΈΡ Π΄ΠΈΡΡΡΠ·ΠΈΡ Π³Π°Π·ΠΎΠ².
61. ΠΠΎΠ·Π»Π΅ ΠΊΠΎΠ½Π΄ΠΈΡΠ΅ΡΡΠΊΠΎΠΉ ΡΠ°Π±ΡΠΈΠΊΠΈ ΠΎΠ±ΡΡΠ½ΠΎ ΠΏΠ°Ρ
Π½Π΅Ρ Π²Π°Π½ΠΈΠ»ΡΡ ΠΈ ΡΠΎΠΊΠΎΠ»Π°Π΄ΠΎΠΌ. ΠΠ±ΡΡΡΠ½ΠΈΡΠ΅ ΡΡΠΎ ΡΠ²Π»Π΅Π½ΠΈΠ΅, ΠΈΡΠΏΠΎΠ»ΡΠ·ΡΡ ΠΏΠΎΠ½ΡΡΠΈΠ΅ ΠΎ ΠΌΠΎΠ»Π΅ΠΊΡΠ»Π°Ρ
.Β
ΠΠΎΠ»Π΅ΠΊΡΠ»Ρ Π²Π°Π½ΠΈΠ»ΠΈ ΠΈ ΡΠΎΠΊΠΎΠ»Π°Π΄Π° ΠΏΠ΅ΡΠ΅Π½ΠΎΡΡΡΡΡ ΠΈΠ· ΠΎΠ±Π»Π°ΡΡΠΈ Π²ΡΡΠΎΠΊΠΎΠΉ ΠΊΠΎΠ½ΡΠ΅Π½ΡΡΠ°ΡΠΈΠΈ Π² ΠΎΠ±Π»Π°ΡΡΡ Π½ΠΈΠ·ΠΊΠΎΠΉ ΠΊΠΎΠ½ΡΠ΅Π½ΡΡΠ°ΡΠΈΠΈ.
62. ΠΡΡΠ½ΠΎ ΠΎΡ ΠΉΠΎΠ΄Π° Π½Π° ΡΠΊΠ°Π½ΠΈ ΠΌΠΎΠΆΠ½ΠΎ ΠΏΡΠΎΠ³Π»Π°Π΄ΠΈΡΡ Π³ΠΎΡΡΡΠΈΠΌ ΡΡΡΠ³ΠΎΠΌ, ΠΈ ΠΎΠ½ΠΎ ΠΈΡΡΠ΅Π·Π½Π΅Ρ. ΠΠΎΡΠ΅ΠΌΡ?
ΠΠΎΠ΄ ΠΈΡΠΏΠ°ΡΡΠ΅ΡΡΡ.
63. ΠΠΎΡΠ΅ΠΌΡ ΠΏΡΠ»Ρ ΡΠ°Π΄ΠΈΡΡΡ Π΄Π°ΠΆΠ΅ Π½Π° ΠΎΠ±ΡΠ°ΡΠ΅Π½Π½ΡΠ΅ Π²Π½ΠΈΠ· ΠΏΠΎΠ²Π΅ΡΡ
Π½ΠΎΡΡΠΈ?
ΠΠ° ΡΡΠ΅Ρ ΠΌΠ΅ΠΆΠΌΠΎΠ»Π΅ΠΊΡΠ»ΡΡΠ½ΠΎΠ³ΠΎ ΡΠΎΠ΅Π΄ΠΈΠ½Π΅Π½ΠΈΡ.
64. ΠΠΎΡΠ΅ΠΌΡ ΠΏΡΠΈ ΡΠ²Π°ΡΠΊΠ΅ ΠΌΠ΅ΡΠ°Π»Π»ΠΎΠ² Π½Π΅ΠΎΠ±Ρ
ΠΎΠ΄ΠΈΠΌΠ° ΠΎΡΠ΅Π½Ρ Π²ΡΡΠΎΠΊΠ°Ρ ΡΠ΅ΠΌΠΏΠ΅ΡΠ°ΡΡΡΠ°?
ΠΠ΅ΡΠ°Π»Π» Π½Π΅ΠΎΠ±Ρ
ΠΎΠ΄ΠΈΠΌΠΎ ΡΠ°ΡΠΏΠ»Π°Π²ΠΈΡΡ.
65. Π£ ΡΠ»Π°ΠΊΠΎΠ½ΡΠΈΠΊΠ° Π΄Π»Ρ Π΄ΡΡ
ΠΎΠ² ΡΡΠ°ΡΠ΅Π»ΡΠ½ΠΎ ΡΠ»ΠΈΡΡΡΡ Π³ΠΎΡΠ»ΡΡΠΊΠΎ ΠΈ ΠΏΡΠΎΠ±ΠΊΡ Π² ΠΌΠ΅ΡΡΠ΅ ΠΈΡ
ΡΠΎΠΏΡΠΈΠΊΠΎΡΠ½ΠΎΠ²Π΅Π½ΠΈΡ. ΠΠΎΡΠ΅ΠΌΡ?
Π§ΡΠΎΠ±Ρ ΡΠ»Π°ΠΊΠΎΠ½ Π·Π°ΠΊΡΡΠ²Π°Π»ΡΡ ΠΏΠ»ΠΎΡΠ½Π΅Π΅, Π½Π΅ Π΄Π°Π²Π°Ρ Π·Π°ΠΏΠ°Ρ
Ρ ΠΏΡΠΎΠ½ΠΈΠΊΠ½ΡΡΡ Π½Π°ΡΡΠΆΡ.
66. ΠΠ΅Π»ΡΠ΅ ΠΏΠΎΡΠ»Π΅ ΡΡΠΈΡΠΊΠΈ, Π²ΡΠ²Π΅ΡΠ΅Π½Π½ΠΎΠ΅ Π½Π° ΠΌΠΎΡΠΎΠ·, ΠΏΠΎΡΠ»Π΅ Π·Π°ΠΌΠ΅ΡΠ·Π°Π½ΠΈΡ ΡΡΡΠ΄Π½ΠΎ ΡΠ°Π·Π³ΠΈΠ±Π°Π΅ΡΡΡ. ΠΠΎΡΠ΅ΠΌΡ?
ΠΡΡΠ°ΡΠΊΠΈ Π²ΠΎΠ΄Ρ Π² Π±Π΅Π»ΡΠ΅ ΠΏΡΠ΅Π²ΡΠ°ΡΠ°ΡΡΡΡ Π² Π»Π΅Π΄.
67. ΠΠΎΡΠ΅ΠΌΡ ΠΏΡΠΈ ΠΎΠ΄ΠΈΠ½Π°ΠΊΠΎΠ²ΠΎΠΉ ΡΠ΅ΠΌΠΏΠ΅ΡΠ°ΡΡΡΠ΅ Π΄ΠΈΡΡΡΠ·ΠΈΡ Π² ΠΆΠΈΠ΄ΠΊΠΎΡΡΡΡ
ΠΈΠ΄Π΅Ρ ΠΌΠ΅Π΄Π»Π΅Π½Π½Π΅Π΅, ΡΠ΅ΠΌ Π² Π³Π°Π·Π°Ρ
?
Π§Π°ΡΡΠΈΡΡ Π²ΠΎΠ·Π΄ΡΡ
Π° Π΄Π²ΠΈΠΆΡΡΡΡ Π±ΡΡΡΡΠ΅Π΅, ΡΠ΅ΠΌ ΡΠ°ΡΡΠΈΡΡ Π²ΠΎΠ΄Ρ.
68. ΠΠΎΡΠ΅ΠΌΡ ΡΠ°Π·Π±ΠΈΡΡΠ΅ Π²Π°Π·Ρ Π½Π΅ Β«ΡΡΠ°ΡΡΠ°ΡΡΡΡΒ» ΠΎΠ±ΡΠ°ΡΠ½ΠΎ, ΠΊΠ°ΠΊ Π±Ρ ΡΠΈΠ»ΡΠ½ΠΎ ΠΌΡ Π½Π΅ ΠΏΡΠΈΠΆΠΈΠΌΠ°Π»ΠΈ Π΄ΡΡΠ³ ΠΊ Π΄ΡΡΠ³Ρ ΠΎΡΠΊΠΎΠ»ΠΊΠΈ?
ΠΠ·-Π·Π° Π½Π΅ΡΠΎΠ²Π½ΠΎΡΡΠ΅ΠΉ Π½Π΅ ΡΠ΄Π°Π΅ΡΡΡ ΠΈΡ
ΡΠ±Π»ΠΈΠ·ΠΈΡΡ Π½Π° ΡΠ°ΠΊΠΎΠ΅ ΡΠ°ΡΡΡΠΎΡΠ½ΠΈΠ΅, Π½Π° ΠΊΠΎΡΠΎΡΠΎΠΌ ΡΠ°ΡΡΠΈΡΡ ΠΌΠΎΠ³ΡΡ ΠΏΡΠΈΡΡΠ³ΠΈΠ²Π°ΡΡΡΡ Π΄ΡΡΠ³ ΠΊ Π΄ΡΡΠ³Ρ.
69. ΠΠΎΡΠ΅ΠΌΡ ΡΠ°Π·ΠΎΡΠ²Π°Π½Π½ΡΠΉ ΠΏΠ»Π°ΡΡΠΈΠ»ΠΈΠ½ ΠΌΠΎΠΆΠ½ΠΎ ΡΠΎΠ΅Π΄ΠΈΠ½ΠΈΡΡ ΠΎΠ±ΡΠ°ΡΠ½ΠΎ Π² ΠΎΠ΄ΠΈΠ½ ΠΊΡΡΠΎΠΊ?
Π‘ΡΡΡΠΊΡΡΡΠ° ΠΏΠ»Π°ΡΡΠΈΠ»ΠΈΠ½Π° ΠΏΠΎΠ·Π²ΠΎΠ»ΡΠ΅Ρ ΠΏΡΠΈΠ±Π»ΠΈΠ·ΠΈΡΡ Π΅Π³ΠΎ ΠΌΠΎΠ»Π΅ΠΊΡΠ»Ρ Π½Π°ΡΡΠΎΠ»ΡΠΊΠΎ, ΡΡΠΎ ΠΏΡΠΈΡΡΠΆΠ΅Π½ΠΈΠ΅ ΠΌΠ΅ΠΆΠ΄Ρ Π½ΠΈΠΌΠΈ Π²ΠΎΡΡΡΠ°Π½Π°Π²Π»ΠΈΠ²Π°Π΅ΡΡΡ.
70. ΠΠΎΡΠ΅ΠΌΡ ΠΏΡΠ»Ρ Ρ ΠΌΠ΅Π±Π΅Π»ΠΈ ΡΡΡΡΠ°Π½ΡΠ΅ΡΡΡ ΠΌΠΎΠΊΡΠΎΠΉ ΡΡΡΠΏΠΊΠΎΠΉ Π»ΡΡΡΠ΅, ΡΠ΅ΠΌ ΡΡΡ
ΠΎΠΉ?
ΠΠΎΠ΄Π° ΡΠ²ΡΠ·ΡΠ²Π°Π΅Ρ ΠΌΠΎΠ»Π΅ΠΊΡΠ»Ρ ΠΏΡΠ»ΠΈ Ρ ΡΡΡΠΏΠΊΠΎΠΉ, Π·Π°ΠΏΠΎΠ»Π½ΡΡ ΠΏΡΠΎΠΌΠ΅ΠΆΡΡΠΊΠΈ ΠΌΠ΅ΠΆΠ΄Ρ ΠΌΠΎΠ»Π΅ΠΊΡΠ»Π°ΠΌΠΈ.
71. ΠΠΎΡΠ΅ΠΌΡ ΠΏΠΎΡΠ»Π΅ ΠΏΠ»Π°Π²Π°Π½ΠΈΡ Π½Π° ΡΠ΅Π»ΠΎΠ²Π΅ΡΠ΅ΡΠΊΠΎΠΌ ΡΠ΅Π»Π΅ ΠΎΡΡΠ°ΡΡΡΡ ΠΊΠ°ΠΏΠ΅Π»ΡΠΊΠΈ Π²ΠΎΠ΄Ρ?
ΠΠΎΠ»Π΅ΠΊΡΠ»Ρ ΠΆΠΈΠ΄ΠΊΠΎΡΡΠΈ ΠΏΡΠΈΡΡΠ³ΠΈΠ²Π°ΡΡΡΡ ΠΊ ΡΠ΅Π»Ρ ΡΠΈΠ»ΡΠ½Π΅Π΅, ΡΠ΅ΠΌ Π΄ΡΡΠ³ ΠΊ Π΄ΡΡΠ³Ρ.
72. ΠΠΎΡΠ΅ΠΌΡ Π½Π° ΡΡΡΠΊΠ°Ρ
ΠΆΠ΅Π»Π΅Π·Π½ΠΎΠ΄ΠΎΡΠΎΠΆΠ½ΡΡ
ΡΠ΅Π»ΡΡΠΎΠ² ΠΎΡΡΠ°Π²Π»ΡΡΡ ΠΏΡΠΎΠΌΠ΅ΠΆΡΡΠΊΠΈ, Π° Π½Π΅ ΡΠΎΠ΅Π΄ΠΈΠ½ΡΡΡ ΠΈΡ
ΠΏΠ»ΠΎΡΠ½ΠΎ?
Π Π΅Π»ΡΡΡ ΡΠ²Π΅Π»ΠΈΡΠΈΠ²Π°ΡΡΡΡ ΠΈ ΡΠΌΠ΅Π½ΡΡΠ°ΡΡΡΡ Π² Π·Π°Π²ΠΈΡΠΈΠΌΠΎΡΡΠΈ ΠΎΡ ΡΠ΅ΠΌΠΏΠ΅ΡΠ°ΡΡΡΡ.
73. ΠΠΎΡΠ΅ΠΌΡ ΡΠ΅Π»Π΅Π³ΡΠ°ΡΠ½Π°Ρ ΠΏΡΠΎΠ²ΠΎΠ»ΠΎΠΊΠ° ΠΏΡΠΎΠ²ΠΈΡΠ°Π΅Ρ Π»Π΅ΡΠΎΠΌ Π±ΠΎΠ»ΡΡΠ΅, ΡΠ΅ΠΌ Π·ΠΈΠΌΠΎΠΉ?
ΠΠ΅ΡΠΎΠΌ ΠΏΡΠΎΠ²ΠΎΠ»ΠΎΠΊΠ° ΡΠ°ΡΡΠΈΡΡΠ΅ΡΡΡ.
74. Π§ΡΠΎΠ±Ρ Π²ΡΠ½ΡΡΡ ΠΏΠ»ΠΎΡΠ½ΠΎ Π·Π°ΡΠ΅Π²ΡΡΡ ΡΡΠ΅ΠΊΠ»ΡΠ½Π½ΡΡ ΠΏΡΠΎΠ±ΠΊΡ, Π½Π°Π΄ΠΎ Π½Π° ΡΠ»Π°Π±ΠΎΠΌ ΠΎΠ³Π½Π΅ Π½Π°Π³ΡΠ΅ΡΡ ΡΠ½Π°ΡΡΠΆΠΈ Π³ΠΎΡΠ»ΡΡΠΊΠΎ ΡΠΊΠ»ΡΠ½ΠΊΠΈ. ΠΠΎΡΠ΅ΠΌΡ ΡΡΠΎ Π½Π°Π³ΡΠ΅Π²Π°Π½ΠΈΠ΅ ΠΌΠΎΠΆΠ΅Ρ ΠΏΠΎΠΌΠΎΡΡ Π΄Π΅Π»Ρ?
ΠΠΎΡΠ»ΡΡΠΊΠΎ ΡΠ²Π΅Π»ΠΈΡΠΈΡΡΡ.
75. ΠΡΠΈ Π»ΠΈΡΡΠ΅ ΡΠ°ΡΠΏΠ»Π°Π²Π»Π΅Π½Π½ΡΠΉ ΡΡΠ³ΡΠ½ Π²ΡΠ»ΠΈΠ²Π°ΡΡ Π² ΡΠΎΡΠΌΡ, Π² ΠΊΠΎΡΠΎΡΡΡ
ΠΎΠ½ ΠΈ Π·Π°ΡΡΡΠ²Π°Π΅Ρ. ΠΠΈΡΡΠ΅ ΠΏΡΠΎΠΈΠ·Π²ΠΎΠ΄ΡΡ ΠΏΡΠΈ ΡΠ΅ΠΌΠΏΠ΅ΡΠ°ΡΡΡΠ΅ ΠΎΠΊΠΎΠ»ΠΎ 1300Β°. ΠΠ°ΡΠ΅ΠΌ ΡΠΎΡΠΌΡ Π΄Π΅Π»Π°ΡΡ Π±ΠΎΠ»ΡΡΠ΅, ΡΠ΅ΠΌ Π±ΡΠ΄Π΅Ρ ΡΠ°ΠΌ ΠΏΡΠ΅Π΄ΠΌΠ΅Ρ?
ΠΡΠΈ ΠΎΡΡΡΠ²Π°Π½ΠΈΠΈ ΠΎΠ±ΡΠ΅ΠΌ Π΄Π΅ΡΠ°Π»ΠΈ ΡΠΌΠ΅Π½ΡΡΠΈΡΡΡ ΠΈ Π΄Π΅ΡΠ°Π»Ρ Π±ΡΠ΄Π΅Ρ ΠΏΡΠΎΡΠ΅ Π²ΡΠ½ΡΡΡ ΠΈΠ· ΡΠΎΡΠΌΡ.
76. ΠΠΎΠΆΠ½ΠΎ Π»ΠΈ ΡΠ΄Π΅Π»Π°ΡΡ ΡΠ΅ΡΠΌΠΎΠΌΠ΅ΡΡ, ΠΈΡΠΏΠΎΠ»ΡΠ·ΡΡ Π΄Π»Ρ Π΅Π³ΠΎ Π½Π°ΠΏΠΎΠ»Π½Π΅Π½ΠΈΡ ΠΊΠ΅ΡΠΎΡΠΈΠ½?
ΠΠΎΠΆΠ½ΠΎ, Π½ΠΎ Π΅Π³ΠΎ ΠΏΠΎΠΊΠ°Π·Π°Π½ΠΈΡ Π±ΡΠ΄ΡΡ Π½Π΅ ΡΠΎΡΠ½ΡΠΌΠΈ.
77. Π§ΡΠΎΠ±Ρ Π²ΡΠ²Π΅ΡΠ½ΡΡΡ ΡΡΠ°ΡΡΠΉ Π·Π°ΡΠΆΠ°Π²Π΅Π²ΡΠΈΠΉ Π²ΠΈΠ½Ρ, ΠΊ Π΅Π³ΠΎ Π³ΠΎΠ»ΠΎΠ²ΠΊΠ΅ ΠΏΠΎΠ΄Π½ΠΎΡΡΡ Π½Π°Π³ΡΠ΅ΡΡΠΉ ΠΏΠ°ΡΠ»ΡΠ½ΠΈΠΊ, ΠΊΠΎΡΠΎΡΡΠΌ Π½Π°Π³ΡΠ΅Π²Π°ΡΡ Π²ΠΈΠ½Ρ. ΠΠΎΠ³Π΄Π° Π²ΠΈΠ½Ρ ΠΎΡΡΡΠ½Π΅Ρ, ΠΎΠ½ Π»Π΅Π³ΠΊΠΎ Π²ΡΠ²ΠΈΠ½ΡΠΈΠ²Π°Π΅ΡΡΡ. ΠΠ°ΠΊ ΠΎΠ±ΡΡΡΠ½ΠΈΡΡ ΡΡΠΎ ΡΠ²Π»Π΅Π½ΠΈΠ΅?
ΠΠΈΠ½Ρ ΡΠ½Π°ΡΠ°Π»Π° ΡΠ²Π΅Π»ΠΈΡΠΈΡΡΡ, Π° Π·Π°ΡΠ΅ΠΌ ΡΠΌΠ΅Π½ΡΡΠΈΡΡΡ ΠΈ Π΅Π³ΠΎ Π±ΡΠ΄Π΅Ρ Π»Π΅Π³ΠΊΠΎ Π²ΡΠ²ΠΈΠ½ΡΠΈΡΡ.
78. ΠΠΎΡΠ΅ΠΌΡ ΠΈΠ· ΠΏΠΎΠ»Π½ΠΎΠ³ΠΎ ΡΠ°ΠΉΠ½ΠΈΠΊΠ° Π²ΠΎΠ΄Π° ΠΏΡΠΈ Π½Π°Π³ΡΠ΅Π²Π°Π½ΠΈΠΈ Π²ΡΠ»ΠΈΠ²Π°Π΅ΡΡΡ, Ρ
ΠΎΡΡ ΠΎΠ±ΡΠ΅ΠΌ ΡΠ°ΠΉΠ½ΠΈΠΊΠ° ΠΏΡΠΈ Π½Π°Π³ΡΠ΅Π²Π°Π½ΠΈΠΈ ΡΠΎΠΆΠ΅ ΡΠ²Π΅Π»ΠΈΡΠΈΠ²Π°Π΅ΡΡΡ?
ΠΠΎΠ΄Π° ΡΠ°ΡΡΠΈΡΡΠ΅ΡΡΡ ΡΠΈΠ»ΡΠ½Π΅Π΅, ΡΠ΅ΠΌ ΠΌΠ΅ΡΠ°Π»Π».
79. Π‘Π»Π΅Π΄ΡΠ΅Ρ Π»ΠΈ Π·ΠΈΠΌΠΎΠΉ ΠΏΠΎΠΊΡΠΏΠ°ΡΡ ΠΏΠΎΠ»Π½ΡΠΉ Π±ΠΈΠ΄ΠΎΠ½ ΠΊΠ΅ΡΠΎΡΠΈΠ½Π°, Π΅ΡΠ»ΠΈ Π΅Π³ΠΎ ΠΏΡΠΈΡ
ΠΎΠ΄ΠΈΡΡΡ Ρ
ΡΠ°Π½ΠΈΡΡ Π΄ΠΎΠΌΠ° Π² ΡΠ΅ΠΏΠ»ΠΎΠΌ ΠΏΠΎΠΌΠ΅ΡΠ΅Π½ΠΈΠΈ?
ΠΠ΅ ΡΡΠΎΠΈΡ. Π ΡΠ΅ΠΏΠ»ΠΎΠΌ ΠΏΠΎΠΌΠ΅ΡΠ΅Π½ΠΈΠΈ Π΅Π³ΠΎ ΠΎΠ±ΡΠ΅ΠΌ ΡΠ²Π΅Π»ΠΈΡΠΈΡΡΡ.
80. ΠΠ°ΡΠ΅ΠΌ ΠΆΠ΅Π»Π΅Π·Π½ΡΡ ΡΠΈΠ½Ρ, Π½Π°Π΄Π΅Π²Π°Π΅ΠΌΡΡ Π½Π° ΠΎΠ±ΠΎΠ΄ ΠΊΠΎΠ»Π΅ΡΠ° ΡΠ΅Π»Π΅Π³ΠΈ, ΠΊΡΠ·Π½Π΅Ρ ΠΏΠ΅ΡΠ΅Π΄ Π½Π°Π΄Π΅Π²Π°Π½ΠΈΠ΅ΠΌ ΡΠΈΠ»ΡΠ½ΠΎ Π½Π°Π³ΡΠ΅Π²Π°Π΅Ρ?
ΠΡΠΈ ΠΎΡΡΡΠ²Π°Π½ΠΈΠΈ ΡΠΈΠ½Π° ΡΠΌΠ΅Π½ΡΡΠΈΡΡΡ ΠΈ Π±ΡΠ΄Π΅Ρ Π±ΠΎΠ»Π΅Π΅ ΠΏΠ»ΠΎΡΠ½ΠΎ Π΄Π΅ΡΠΆΠ°ΡΡΡΡ Π½Π° ΠΊΠΎΠ»Π΅ΡΠ΅.
81. ΠΡΠ»ΠΈ ΡΠΊΠ»Π΅ΠΏΠ°ΡΡ ΠΆΠ΅Π»Π΅Π·Π½ΡΡ ΠΈ ΠΌΠ΅Π΄Π½ΡΡ ΠΏΠΎΠ»ΠΎΡΠΊΠΈ ΠΎΠ΄ΠΈΠ½Π°ΠΊΠΎΠ²ΠΎΠ³ΠΎ ΡΠ°Π·ΠΌΠ΅ΡΠ° ΠΈ Π·Π°ΡΠ΅ΠΌ Π½Π°Π³ΡΠ΅ΡΡ ΠΈΡ
, ΡΠΎ Π²ΡΡ ΠΏΠ»Π°ΡΡΠΈΠ½ΠΊΠ° ΠΈΠ·ΠΎΠ³Π½Π΅ΡΡΡ. ΠΠΎΡΠ΅ΠΌΡ?
ΠΠΎΡΡΡΠΈΡΠΈΠ΅Π½ΡΡ ΡΠ°ΡΡΠΈΡΠ΅Π½ΠΈΡ ΠΆΠ΅Π»Π΅Π·Π° ΠΈ ΠΌΠ΅Π΄ΠΈ ΡΠ°Π·Π½ΡΠ΅.
82. ΠΠ° Π±Π»ΡΠ΄ΡΠ΅ Ρ Π²ΠΎΠ΄ΠΎΠΉ ΠΏΠΎΡΡΠ°Π²ΠΈΠ»ΠΈ ΠΎΠΏΡΠΎΠΊΠΈΠ½ΡΡΡΠΉ Π³ΠΎΡΡΡΠΈΠΉ ΡΡΠ°ΠΊΠ°Π½. ΠΠΎΡΠ΅ΠΌΡ ΡΠ΅ΡΠ΅Π· Π½Π΅ΠΊΠΎΡΠΎΡΠΎΠ΅ Π²ΡΠ΅ΠΌΡ Π²ΠΎΠ΄Π° Π²Π½ΡΡΡΠΈ ΡΡΠ°ΠΊΠ°Π½Π° Π±ΡΠ΄Π΅Ρ ΡΡΠΎΡΡΡ Π²ΡΡΠ΅, ΡΠ΅ΠΌ Π² Π±Π»ΡΠ΄ΡΠ΅ (ΡΠΈΡ. 10)?
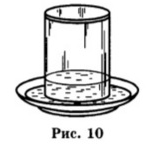
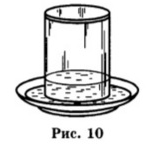
Π‘ΡΠ°ΠΊΠ°Π½ ΠΎΡΡΡΠ½Π΅Ρ. Π£ΠΌΠ΅Π½ΡΡΠΈΡΡΡ Π΅Π³ΠΎ ΠΎΠ±ΡΠ΅ΠΌ. ΠΠ±ΡΠ΅ΠΌ Π²ΠΎΠ΄Ρ Π² Π½Π΅ΠΌ ΠΎΡΡΠ°Π½Π΅ΡΡΡ ΠΏΡΠ΅ΠΆΠ½ΠΈΠΌ.
83. ΠΠΎΡΠ΅ΠΌΡ Π³Π»ΡΠ±ΠΎΠΊΠΈΠ΅ ΠΏΡΡΠ΄Ρ Π½Π΅ ΠΏΡΠΎΠΌΠ΅ΡΠ·Π°ΡΡ Π΄ΠΎ Π΄Π½Π°?
ΠΠ»ΠΎΡΠ½ΠΎΡΡΡ Π»ΡΠ΄Π° ΠΌΠ΅Π½ΡΡΠ΅ ΠΏΠ»ΠΎΡΠ½ΠΎΡΡΠΈ Π²ΠΎΠ΄Ρ, ΡΠ΅ΠΏΠ»ΠΎΠΏΡΠΎΠ²ΠΎΠ΄Π½ΠΎΡΡΡ Π»ΡΠ΄Π° ΠΏΠ»ΠΎΡ
Π°Ρ, ΠΏΠΎΡΡΠΎΠΌΡ Π³Π»ΡΠ±ΠΎΠΊΠΈΠ΅ Π²ΠΎΠ΄ΠΎΠ΅ΠΌΡ Π½Π΅ ΠΏΡΠΎΠΌΠ΅ΡΠ·Π°ΡΡ Π΄ΠΎ Π΄Π½Π°.
84. ΠΠΎΠΆΠ½ΠΎ Π»ΠΈ Π΄Π΅Π»Π°ΡΡ ΡΠ΅ΡΠΌΠΎΠΌΠ΅ΡΡΡ, Π²Π·ΡΠ² Π²ΠΌΠ΅ΡΡΠΎ ΠΏΠΎΠ΄ΠΊΡΠ°ΡΠ΅Π½Π½ΠΎΠ³ΠΎ ΡΠΏΠΈΡΡΠ° ΠΏΠΎΠ΄ΠΊΡΠ°ΡΠ΅Π½Π½ΡΡ Π²ΠΎΠ΄Ρ?
ΠΠ΅Ρ.
Π£ΡΠ΅Π±Π½ΠΎ-ΠΌΠ΅ΡΠΎΠ΄ΠΈΡΠ΅ΡΠΊΠΈΠΉ ΠΌΠ°ΡΠ΅ΡΠΈΠ°Π» ΠΏΠΎ ΡΠΈΠ·ΠΈΠΊΠ΅ (7 ΠΊΠ»Π°ΡΡ) ΠΏΠΎ ΡΠ΅ΠΌΠ΅: ΠΠ°Π΄Π°ΡΠΈ 7 ΠΊΠ»Π°ΡΡ ΠΏΠΎ ΡΠ΅ΠΌΠ΅ «Π‘ΡΡΠΎΠ΅Π½ΠΈΠ΅ Π²Π΅ΡΠ΅ΡΡΠ²Π°. ΠΠΈΡΡΡΠ·ΠΈΡ»
ΠΠΎ ΡΠ΅ΠΌΠ΅: ΠΌΠ΅ΡΠΎΠ΄ΠΈΡΠ΅ΡΠΊΠΈΠ΅ ΡΠ°Π·ΡΠ°Π±ΠΎΡΠΊΠΈ, ΠΏΡΠ΅Π·Π΅Π½ΡΠ°ΡΠΈΠΈ ΠΈ ΠΊΠΎΠ½ΡΠΏΠ΅ΠΊΡΡ
Π Π΅ΡΠ΅Π½ΠΈΠ΅ Π·Π°Π΄Π°Ρ ΠΌΠ΅ΡΠΎΠ΄ΠΎΠΌ ΠΠ»ΡΡΠ΅Π²ΡΡ ΡΠΈΡΡΠ°ΡΠΈΠΉ. ΠΠΎΠ½ΡΡΠΎΠ»ΡΠ½Π°Ρ ΡΠ°Π±ΠΎΡΠ° β1. 7-ΠΎΠΉ ΠΊΠ»Π°ΡΡ.» ΠΠ»ΠΎΡΠ½ΠΎΡΡΡ Ρ Π°ΡΠ°ΠΊΡΠΈΠ΅ΡΠΈΠ·ΡΠ΅Ρ Π²Π΅ΡΠ΅ΡΡΠ²ΠΎ». «ΠΡΡ ΠΈΠΌΠ΅Π΄ΠΎΠ²Π° ΡΠΈΠ»Π°»..ΠΠΈΡΡΠ°Π½ΡΠΈΠΎΠ½Π½ΡΠΉ ΠΊΡΡΡ ΠΏΠΎΠ²ΡΡΠ΅Π½ΠΈΡ ΠΊΠ²Π°Π»ΠΈΡΠΈΠΊΠ°ΡΠΈΠΈ «ΠΠ°ΠΊ Π½Π°ΡΡΠΈΡΡΡΡ ΡΠ΅ΡΠ°ΡΡ Π·Π°Π΄Π°ΡΠΈ ΠΏΠΎ ΡΠΈΠ·ΠΈΠΊΠ΅ (ΠΎΡΠ½ΠΎΠ²Π½Π°Ρ ΡΠΊΠΎΠ»Π°).ΠΠΎΠ΄Π³ΠΎΡΠΎΠ²ΠΊΠ° ΠΊ ΠΠΠ». Π ΡΠΊΠΎΠ»ΡΠ½ΠΎΠΌ ΠΊΡΡΡΠ΅ ΠΎΠ³ΡΠΎΠΌΠ½ΠΎΠ΅ ΠΊΠΎΠ»ΠΈΡΠ΅ΡΡΠ²ΠΎ Π·Π°Π΄Π°Ρ, ΠΊΠΎΡΠΎΡΡΠ΅ ΠΌΠΎΠΆΠ½ΠΎ ΡΠ³ΡΡΠΏΠΏΠΈΡΠΎΠ²Π°ΡΡ Π²ΠΎΠΊΡΡΠ³ Π½Π΅ΡΠΊ…
Π Π΅ΡΠ΅Π½ΠΈΠ΅ Π·Π°Π΄Π°Ρ ΠΌΠ΅ΡΠΎΠ΄ΠΎΠΌ ΠΠ»ΡΡΠ΅Π²ΡΡ ΡΠΈΡΡΠ°ΡΠΈΠΉ. ΠΠΎΠ½ΡΡΠΎΠ»ΡΠ½Π°Ρ ΡΠ°Π±ΠΎΡΠ° β1. 7-ΠΎΠΉ ΠΊΠ»Π°ΡΡ.» ΠΠ»ΠΎΡΠ½ΠΎΡΡΡ Ρ Π°ΡΠ°ΠΊΡΠΈΠ΅ΡΠΈΠ·ΡΠ΅Ρ Π²Π΅ΡΠ΅ΡΡΠ²ΠΎ». «ΠΡΡ ΠΈΠΌΠ΅Π΄ΠΎΠ²Π° ΡΠΈΠ»Π°»..ΠΠΈΡΡΠ°Π½ΡΠΈΠΎΠ½Π½ΡΠΉ ΠΊΡΡΡ ΠΏΠΎΠ²ΡΡΠ΅Π½ΠΈΡ ΠΊΠ²Π°Π»ΠΈΡΠΈΠΊΠ°ΡΠΈΠΈ «ΠΠ°ΠΊ Π½Π°ΡΡΠΈΡΡΡΡ ΡΠ΅ΡΠ°ΡΡ Π·Π°Π΄Π°ΡΠΈ ΠΏΠΎ ΡΠΈΠ·ΠΈΠΊΠ΅ (ΠΎΡΠ½ΠΎΠ²Π½Π°Ρ ΡΠΊΠΎΠ»Π°).ΠΠΎΠ΄Π³ΠΎΡΠΎΠ²ΠΊΠ° ΠΊ ΠΠΠ». Π ΡΠΊΠΎΠ»ΡΠ½ΠΎΠΌ ΠΊΡΡΡΠ΅ ΠΎΠ³ΡΠΎΠΌΠ½ΠΎΠ΅ ΠΊΠΎΠ»ΠΈΡΠ΅ΡΡΠ²ΠΎ Π·Π°Π΄Π°Ρ, ΠΊΠΎΡΠΎΡΡΠ΅ ΠΌΠΎΠΆΠ½ΠΎ ΡΠ³ΡΡΠΏΠΏΠΈΡΠΎΠ²Π°ΡΡ Π²ΠΎΠΊΡΡΠ³ Π½Π΅ΡΠΊ…
Π Π΅ΡΠ΅Π½ΠΈΠ΅ Π·Π°Π΄Π°Ρ ΠΌΠ΅ΡΠΎΠ΄ΠΎΠΌ ΠΠ»ΡΡΠ΅Π²ΡΡ ΡΠΈΡΡΠ°ΡΠΈΠΉ. ΠΠΎΠ½ΡΡΠΎΠ»ΡΠ½Π°Ρ ΡΠ°Π±ΠΎΡΠ° β1. 7-ΠΎΠΉ ΠΊΠ»Π°ΡΡ.» ΠΠ»ΠΎΡΠ½ΠΎΡΡΡ Ρ Π°ΡΠ°ΠΊΡΠΈΠ΅ΡΠΈΠ·ΡΠ΅Ρ Π²Π΅ΡΠ΅ΡΡΠ²ΠΎ». «ΠΡΡ ΠΈΠΌΠ΅Π΄ΠΎΠ²Π° ΡΠΈΠ»Π°»..ΠΠΈΡΡΠ°Π½ΡΠΈΠΎΠ½Π½ΡΠΉ ΠΊΡΡΡ ΠΏΠΎΠ²ΡΡΠ΅Π½ΠΈΡ ΠΊΠ²Π°Π»ΠΈΡΠΈΠΊΠ°ΡΠΈΠΈ «ΠΠ°ΠΊ Π½Π°ΡΡΠΈΡΡΡΡ ΡΠ΅ΡΠ°ΡΡ Π·Π°Π΄Π°ΡΠΈ ΠΏΠΎ ΡΠΈΠ·ΠΈΠΊΠ΅ (ΠΎΡΠ½ΠΎΠ²Π½Π°Ρ ΡΠΊΠΎΠ»Π°).ΠΠΎΠ΄Π³ΠΎΡΠΎΠ²ΠΊΠ° ΠΊ ΠΠΠ». Π ΡΠΊΠΎΠ»ΡΠ½ΠΎΠΌ ΠΊΡΡΡΠ΅ ΠΎΠ³ΡΠΎΠΌΠ½ΠΎΠ΅ ΠΊΠΎΠ»ΠΈΡΠ΅ΡΡΠ²ΠΎ Π·Π°Π΄Π°Ρ, ΠΊΠΎΡΠΎΡΡΠ΅ ΠΌΠΎΠΆΠ½ΠΎ ΡΠ³ΡΡΠΏΠΏΠΈΡΠΎΠ²Π°ΡΡ Π²ΠΎΠΊΡΡΠ³ Π½Π΅ΡΠΊ…
ΠΡΠΊΡΡΡΡΠΉ ΡΡΠΎΠΊ ΠΏΠΎ Ρ ΠΈΠΌΠΈΠΈ Π² 8 ΠΊΠ»Π°ΡΡΠ΅ ΠΏΠΎ ΡΠ΅ΠΌΠ΅ : Π Π΅ΡΠ΅Π½ΠΈΠ΅ ΡΠ°ΡΡΠ΅ΡΠ½ΡΡ Π·Π°Π΄Π°Ρ ΠΏΠΎ ΡΠ΅ΠΌΠ΅ «ΠΠΎΠ»ΠΈΡΠ΅ΡΡΠ²ΠΎ Π²Π΅ΡΠ΅ΡΡΠ²Π°. ΠΠΎΠ»Ρ».Π Π΅ΡΠ΅Π½ΠΈΠ΅ ΡΠ°ΡΡΠ΅ΡΠ½ΡΡ Π·Π°Π΄Π°Ρ ΠΏΠΎ ΡΠ΅ΠΌΠ΅ » ΠΠΎΠ»ΠΈΡΠ΅ΡΡΠ²ΠΎ Π²Π΅ΡΠ΅ΡΡΠ²Π°. ΠΠΎΠ»Ρ.»…
ΠΡ/Ρ «Π Π΅ΡΠ΅Π½ΠΈΠ΅ ΡΠΊΡΠΏΠ΅ΡΠΈΠΌΠ΅Π½ΡΠ°Π»ΡΠ½ΡΡ Π·Π°Π΄Π°Ρ Π½Π° ΡΠ°ΡΠΏΠΎΠ·Π½Π°Π²Π°Π½ΠΈΠ΅ ΡΠ°ΡΡΠ²ΠΎΡΠΎΠ² Π²Π΅ΡΠ΅ΡΡΠ² ΠΈ ΠΎΠΏΡΠ΅Π΄Π΅Π»Π΅Π½ΠΈΠ΅ ΠΈΡ ΠΊΠ°ΡΠ΅ΡΡΠ²Π΅Π½Π½ΠΎΠ³ΠΎ ΡΠΎΡΡΠ°Π²Π°» 9 ΠΊΠ»Π°ΡΡΠ Π°Π±ΠΎΡΠ° ΡΠ°ΡΡΠΈΡΠ°Π½Π° Π½Π° ΡΡΠ΅Π½ΠΈΠΊΠΎΠ² 9 ΠΊΠ»Π°ΡΡΠ°, ΠΏΠΎΡΡΠΎΠΌΡ ΡΠΎΠ΄Π΅ΡΠΆΠΈΡ ΠΏΠΎΠ΄ΡΠΎΠ±Π½ΡΡ ΠΈΠ½ΡΡΡΡΠΊΡΠΈΡ Π²ΡΠΏΠΎΠ»Π½Π΅Π½ΠΈΡ ΡΠΊΡΠΏΠ΅ΡΠΈΠΌΠ΅Π½ΡΠ°Π»ΡΠ½ΡΡ Π·Π°Π΄Π°Ρ…
ΠΡΠΎΠ³ΠΎΠ²Π°Ρ ΡΠ°Π±ΠΎΡΠ° ΠΏΠΎ ΠΊΡΡΡΡ ΠΏΠΎΠ²ΡΡΠ΅Π½ΠΈΡ ΠΊΠ²Π°Π»ΠΈΡΠΈΠΊΠ°ΡΠΈΠΈ Β«Π‘ΠΈΡΡΠ΅ΠΌΠ° ΡΠ°ΡΡΠ΅ΡΠ½ΡΡ Π·Π°Π΄Π°Ρ ΠΏΠΎ Ρ ΠΈΠΌΠΈΠΈΒ»: Β«Π‘ΠΈΡΡΠ΅ΠΌΠ° ΡΠ΅ΡΠ΅Π½ΠΈΡ Π·Π°Π΄Π°Ρ Π½Π° Π½Π°Ρ ΠΎΠΆΠ΄Π΅Π½ΠΈΠ΅ ΡΠΎΡΠΌΡΠ» Π²Π΅ΡΠ΅ΡΡΠ²Β».ΠΡΠΈΠ²ΠΎΠ΄ΠΈΡΡΡ ΠΈΡΠΎΠ³ΠΎΠ²Π°Ρ ΡΠ°Π±ΠΎΡΠ° ΠΏΠΎ ΠΊΡΡΡΡ ΠΏΠΎΠ²ΡΡΠ΅Π½ΠΈΡ ΠΊΠ²Π°Π»ΠΈΡΠΈΠΊΠ°ΡΠΈΠΈ «Π‘ΠΈΡΡΠ΅ΠΌΠ° ΡΠ°ΡΡΡΡΠ½ΡΡ Π·Π°Π΄Π°Ρ ΠΏΠΎ Ρ ΠΈΠΌΠΈΠΈ»: «Π‘ΠΈΡΡΠ΅ΠΌΠ° ΡΠ΅ΡΠ΅Π½ΠΈΡ Π·Π°Π΄Π°Ρ Π½Π° Π½Π°Ρ ΠΎΠΆΠ΄Π΅Π½ΠΈΠ΅ ΡΠΎΡΠΌΡΠ» Π²Π΅ΡΠ΅ΡΡΠ²»….
ΠΠ΅ΡΠΎΠ΄ΠΈΡΠ΅ΡΠΊΠ°Ρ ΡΠ°Π·ΡΠ°Π±ΠΎΡΠΊΠ° ΡΡΠΎΠΊΠ° ΠΏΠΎ ΡΠΈΠ·ΠΈΠΊΠ΅ Π½Π° ΡΠ΅ΠΌΡ «ΠΠ²ΠΈΠΆΠ΅Π½ΠΈΠ΅ ΡΠ°ΡΡΠΈΡ Π²Π΅ΡΠ΅ΡΡΠ²Π°. ΠΠΈΡΡΡΠ·ΠΈΡ. ΠΡΠΎΡΠ½ΠΎΠ²ΡΠΊΠΎΠ΅ Π΄Π²ΠΈΠΆΠ΅Π½ΠΈΠ΅. Π‘ΠΈΠ»Ρ Π²Π·Π°ΠΈΠΌΠΎΠ΄Π΅ΠΉΡΡΠ²ΠΈΡ ΠΌΠΎΠ»Π΅ΠΊΡΠ»»ΠΠΎΠ½ΡΠΏΠ΅ΠΊΡ ΡΡΠΎΠΊΠ° ΠΏΠΎ ΡΠ΅ΠΌΠ΅: Π΄Π²ΠΈΠΆΠ΅Π½ΠΈΠ΅ ΡΠ°ΡΡΠΈΡ Π²Π΅ΡΠ΅ΡΡΠ²Π°. ΠΠΈΡΡΡΠ·ΠΈΡ.ΠΡΠΎΡΠ½ΠΎΠ²ΡΠΊΠΎΠ΅ Π΄Π²ΠΈΠΆΠ΅Π½ΠΈΠ΅. Π‘ΠΈΠ»Ρ Π²Π·Π°ΠΈΠΌΠΎΠ΄Π΅ΠΉΡΡΠ²ΠΈΡ ΠΌΠΎΠ»Π΅ΠΊΡΠ». Π Π°ΡΠΊΡΡΠ²Π°Π΅Ρ ΠΏΠΎΠ½ΡΡΠΈΡ Π±ΡΠΎΡΠ½ΠΎΠ²ΡΠΊΠΎΠ³ΠΎ Π΄Π²ΠΈΠΆΠ΅Π½ΠΈΡ, Π΄ΠΈΡΡΡΠ·ΠΈΠΈ (Π² ΡΠ΅ΠΌ ΡΠ°Π·Π»ΠΈΡΠΈΡ), ΠΎΡΡΠ°ΠΆΠ΅Π½Ρ ΠΏΡΠΈΠΌΠ΅ΡΡ, Π³Π΄Π΅…
Π§ΡΠ³ΡΠ½Π½ΠΎΠ΅ Π»ΠΈΡΡΠ΅: ΡΠΏΠΎΡΠΎΠ±Ρ ΠΎΡΠ»ΠΈΠ²ΠΊΠΈ, ΠΈΠ½ΡΡΡΡΠΌΠ΅Π½ΡΡ
Π‘ΠΏΠ»Π°Π² ΠΆΠ΅Π»Π΅Π·Π°, Π² ΠΊΠΎΡΠΎΡΠΎΠΌ ΡΠΎΠ΄Π΅ΡΠΆΠΈΡΡΡ Π±ΠΎΠ»Π΅Π΅ 3% ΡΠ³Π»Π΅ΡΠΎΠ΄Π°, Π½Π°Π·ΡΠ²Π°Π΅ΡΡΡ ΡΡΠ³ΡΠ½ΠΎΠΌ. ΠΠ΅ΡΠ°Π»Π» ΠΎΠ±Π»Π°Π΄Π°Π΅Ρ Π²ΡΡΠΎΠΊΠΎΠΉ ΠΆΠΈΠ΄ΠΊΠΎΡΠ΅ΠΊΡΡΠ΅ΡΡΡΡ ΠΈ ΡΠ²Π΅ΡΠ΄ΠΎΡΡΡΡ, Π±Π»Π°Π³ΠΎΠ΄Π°ΡΡ ΡΠ΅ΠΌΡ Π·Π°ΠΏΠΎΠ»Π½ΡΠ΅Ρ ΡΠΎΡΠΌΡ Ρ ΠΊΠΎΠ½ΡΠΈΠ³ΡΡΠ°ΡΠΈΠ΅ΠΉ Π»ΡΠ±ΠΎΠΉ ΡΠ»ΠΎΠΆΠ½ΠΎΡΡΠΈ. Π§ΡΠ³ΡΠ½Π½ΠΎΠ΅ Π»ΠΈΡΡΠ΅ ΡΠΏΠΎΡΠΎΠ±Π½ΠΎ Π΄Π»ΠΈΡΠ΅Π»ΡΠ½ΠΎΠ΅ Π²ΡΠ΅ΠΌΡ Π½Π°Ρ ΠΎΠ΄ΠΈΡΡΡΡ Π½Π° ΠΎΡΠΊΡΡΡΠΎΠΌ Π²ΠΎΠ·Π΄ΡΡ Π΅, Π½Π΅ ΠΏΠΎΠ΄Π²Π΅ΡΠ³Π°ΡΡΡ ΠΊΠΎΡΡΠΎΠ·ΠΈΠΈ ΠΈ ΡΠ°Π·ΡΡΡΠ΅Π½ΠΈΡ.
Π’Π΅Ρ Π½ΠΎΠ»ΠΎΠ³ΠΈΡ ΠΏΡΠΎΠΈΠ·Π²ΠΎΠ΄ΡΡΠ²Π° ΡΡΠ³ΡΠ½Π° Π±ΡΠ»Π° ΠΎΡΠ²ΠΎΠ΅Π½Π° Π΅ΡΠ΅ Π² 17 Π²Π΅ΠΊΠ΅. ΠΠ· Π½Π΅Π³ΠΎ ΠΈΠ·Π³ΠΎΡΠ°Π²Π»ΠΈΠ²Π°Π»ΠΈ ΠΏΠ΅ΡΠΈΠ»Π° ΠΌΠΎΡΡΠΎΠ², ΡΠΊΡΠ»ΡΠΏΡΡΡΡ, ΡΠ΅ΡΠ΅ΡΠΊΠΈ Π΄Π»Ρ ΠΊΠ°ΠΌΠΈΠ½ΠΎΠ² ΠΈ ΠΊΠΎΠ»ΠΎΡΠ½ΠΈΠΊΠΈ Π² ΠΏΠ΅ΡΠΈ. ΠΡΠΎΡΡΠ°Ρ ΡΠ΅Ρ Π½ΠΎΠ»ΠΎΠ³ΠΈΡ ΡΠΎΡΠΌΠΎΠ²ΠΊΠΈ ΠΈ Π²ΡΠΏΠ»Π°Π²ΠΊΠΈ ΠΏΠΎΠ·Π²ΠΎΠ»ΡΠ΅Ρ Π»ΠΈΡΡ ΡΡΠ³ΡΠ½ Π² ΠΏΡΠΎΠΌΡΡΠ»Π΅Π½Π½ΡΡ ΠΌΠ°ΡΡΡΠ°Π±Π°Ρ ΠΈ Π΄ΠΎΠΌΠ°ΡΠ½ΠΈΡ ΡΡΠ»ΠΎΠ²ΠΈΡΡ .

ΠΠ±ΡΠΈΠ΅ ΡΠ²ΠΎΠΉΡΡΠ²Π° ΡΡΠ³ΡΠ½Π°
Π§ΡΠ³ΡΠ½ ΠΏΡΠΎΠΈΠ·Π²ΠΎΠ΄ΡΡ Π² Π΄ΠΎΠΌΠ΅Π½Π½ΡΡ ΠΏΠ΅ΡΠ°Ρ . Π’Π΅ΠΌΠΏΠ΅ΡΠ°ΡΡΡΠ° Π½Π°Π³ΡΠ΅Π²Π° ΠΎΡ Π³ΠΎΡΠ΅Π½ΠΈΡ Π³Π°Π·Π° ΠΈ ΡΠ³ΠΎΠ»ΡΠ½ΠΎΠΉ ΠΏΡΠ»ΠΈ ΠΏΠΎΠ²ΡΡΠ°Π΅ΡΡΡ. Π ΡΠ΅Π·ΡΠ»ΡΡΠ°ΡΠ΅ ΠΏΠΎΠ»ΡΡΠ°ΡΡ 2 ΡΠΈΠΏΠ° Π²ΡΡΠΎΠΊΠΎΡΠ³Π»Π΅ΡΠΎΠ΄ΠΈΡΡΡΡ ΡΠΏΠ»Π°Π²ΠΎΠ²:
- ΠΏΠ΅ΡΠ΅Π΄Π΅Π»ΡΠ½ΡΠΉ;
- Π»ΠΈΡΠ΅ΠΉΠ½ΡΠΉ.
ΠΠ΅ΡΠ΅Π΄Π΅Π»ΡΠ½ΡΠΉ ΡΠΏΠ»Π°Π², Π² ΠΎΡΠ½ΠΎΠ²Π½ΠΎΠΌ Π±Π΅Π»ΡΠΉ, ΠΎΡΠ΅Π½Ρ ΡΠ²Π΅ΡΠ΄ΡΠΉ. ΠΠ½ ΡΠΎΠ΄Π΅ΡΠΆΠΈΡ ΡΠ³Π»Π΅ΡΠΎΠ΄ Π² ΡΠ²ΡΠ·Π°Π½Π½ΠΎΠΉ ΡΠΎΡΠΌΠ΅, Π½Π° ΠΈΠ·Π»ΠΎΠΌΠ΅ Π·Π΅ΡΠ½ΠΎ Π±Π΅Π»ΠΎΠ³ΠΎ ΡΠ²Π΅ΡΠ°. ΠΡΠ΅Π½Ρ ΡΠ²Π΅ΡΠ΄ΡΠΉ, ΡΠ΅ΠΆΡΡΠΈΠΌ ΠΈΠ½ΡΡΡΡΠΌΠ΅Π½ΡΠΎΠΌ Π½Π΅ ΠΎΠ±ΡΠ°Π±Π°ΡΡΠ²Π°Π΅ΡΡΡ. ΠΡΠΏΠΎΠ»ΡΠ·ΡΠ΅ΡΡΡ ΠΊΠ°ΠΊ ΠΎΡΠ½ΠΎΠ²Π½ΠΎΠ΅ ΡΡΡΡΠ΅ Π΄Π»Ρ ΠΏΠΎΠ»ΡΡΠ΅Π½ΠΈΡ ΡΡΠ°Π»Π΅ΠΉ ΡΠ°Π·Π»ΠΈΡΠ½ΡΡ ΠΌΠ°ΡΠΎΠΊ.
ΠΡΡΠ°Π»ΡΠ½ΡΠ΅ Π²ΠΈΠ΄Ρ ΡΡΠ³ΡΠ½Π°: ΡΠ΅ΡΡΠΉ, ΠΊΠΎΠ²ΠΊΠΈΠΉ, Π²ΡΡΠΎΠΊΠΎΠΏΡΠΎΡΠ½ΡΠΉ. ΠΠ½ΠΈ ΠΈΠΌΠ΅ΡΡ Π²ΡΡΠΎΠΊΡΡ ΠΆΠΈΠ΄ΠΊΠΎΡΠ΅ΠΊΡΡΠ΅ΡΡΡ, ΠΈΡΠΏΠΎΠ»ΡΠ·ΡΡΡΡΡ Π΄Π»Ρ ΠΈΠ·Π³ΠΎΡΠΎΠ²Π»Π΅Π½ΠΈΡ Π΄Π΅ΡΠ°Π»Π΅ΠΉ ΠΌΠ΅ΡΠΎΠ΄ΠΎΠΌ Π»ΠΈΡΡΡ Π² ΡΠΎΡΠΌΡ Ρ ΠΏΠΎΡΠ»Π΅Π΄ΡΡΡΠ΅ΠΉ ΠΎΠ±ΡΠ°Π±ΠΎΡΠΊΠΎΠΉ ΡΠ΅Π·Π°Π½ΠΈΠ΅ΠΌ. Π’Π²Π΅ΡΠ΄ΠΎΡΡΡ Π·Π½Π°ΡΠΈΡΠ΅Π»ΡΠ½ΠΎ Π²ΡΡΠ΅, ΡΠ΅ΠΌ Ρ Π½Π΅Π·Π°ΠΊΠ°Π»Π΅Π½Π½ΡΡ ΡΡΠ°Π»Π΅ΠΉ. ΠΡΡΠΎΠΊΠΎΠ΅ ΡΠΎΠΏΡΠΎΡΠΈΠ²Π»Π΅Π½ΠΈΠ΅ ΡΡΠΈΡΠ°Π½ΠΈΡ. Π Π½Π΅Π΄ΠΎΡΡΠ°ΡΠΊΠ°ΠΌ ΠΎΡΠ½ΠΎΡΠΈΡΡΡ Ρ ΡΡΠΏΠΊΠΎΡΡΡ, Π½ΠΈΠ·ΠΊΠΈΠΉ ΠΏΡΠ΅Π΄Π΅Π» ΡΠΎΠΏΡΠΎΡΠΈΠ²Π»Π΅Π½ΠΈΡ Π½Π° ΠΈΠ·Π³ΠΈΠ± ΠΈ ΠΊΡΡΡΠ΅Π½ΠΈΠ΅.
ΠΠΎΠ²ΠΊΠΈΠΌ Π½Π°Π·Π²Π°Π»ΠΈ ΡΡΠ³ΡΠ½ Π·Π° ΠΎΡΠ½ΠΎΡΠΈΡΠ΅Π»ΡΠ½ΠΎ Π²ΡΡΠΎΠΊΡΡ ΠΏΠ»Π°ΡΡΠΈΡΠ½ΠΎΡΡΡ ΠΈ ΡΡΡΠΎΠΉΡΠΈΠ²ΠΎΡΡΡ ΠΊ Π΄ΠΈΠ½Π°ΠΌΠΈΡΠ΅ΡΠΊΠΈΠΌ Π½Π°Π³ΡΡΠ·ΠΊΠ°ΠΌ. ΠΠ½ ΠΏΡΠΎΡΠ½Π΅Π΅ ΡΠ΅ΡΠΎΠ³ΠΎ, Π±Π»Π°Π³ΠΎΠ΄Π°ΡΡ ΠΊΠΎΠΌΠΏΠ°ΠΊΡΠ½ΡΠΌ Ρ Π»ΠΎΠΏΡΠ΅Π²ΠΈΠ΄Π½ΡΠΌ Π²ΠΊΠ»ΡΡΠ΅Π½ΠΈΡΠΌ Π³ΡΠ°ΡΠΈΡΠ°, ΡΠ°ΡΠΏΠΎΠ»ΠΎΠΆΠ΅Π½Π½ΡΠΌ ΠΌΠ΅ΠΆΠ΄Ρ Π·Π΅ΡΠ΅Π½. Π£ Π²ΡΡΠΎΠΊΠΎΠΏΡΠΎΡΠ½ΠΎΠ³ΠΎ ΡΠΏΠ»Π°Π²Π° Π³ΡΠ°ΡΠΈΡ ΠΈΠΌΠ΅Π΅Ρ ΡΠ°ΡΠΎΠΎΠ±ΡΠ°Π·Π½ΡΡ ΡΠΎΡΠΌΡ. ΠΡΡΠ°Π»ΡΠ½ΡΠ΅ Π²ΠΈΠ΄Ρ ΡΡΠ³ΡΠ½Π° ΡΠΎΠ΄Π΅ΡΠΆΠ°Ρ ΡΠ²ΠΎΠ±ΠΎΠ΄Π½ΡΠΉ ΡΠ³Π»Π΅ΡΠΎΠ΄ Π² Π²ΠΈΠ΄Π΅ ΠΏΠ»Π°ΡΡΠΈΠ½ Π³ΡΠ°ΡΠΈΡΠ° ΠΏΠΎ Π³ΡΠ°Π½ΠΈΡΠ°ΠΌ Π·Π΅ΡΠ΅Π½ ΠΈ ΠΎΡΠ½ΠΎΡΠΈΡΠ΅Π»ΡΠ½ΠΎ Π»Π΅Π³ΠΊΠΎ Π»ΠΎΠΌΠ°ΡΡΡΡ. ΠΠ° ΡΠ°ΠΌΠΎΠΌ Π΄Π΅Π»Π΅ Π½ΠΈΠΊΠ°ΠΊΠΎΠΉ Π²ΠΈΠ΄ ΡΡΠ³ΡΠ½Π° ΠΊΠΎΠ²Π°ΡΡ Π½Π΅Π»ΡΠ·Ρ.
ΠΡΠΈ ΠΎΠ±ΡΠ°Π±ΠΎΡΠΊΠ΅ ΡΡΠ³ΡΠ½Π° ΡΠ΅Π·Π°Π½ΠΈΠ΅ΠΌ Π½Π° ΠΌΠ°Π»ΠΎΠΉ ΠΏΠΎΠ΄Π°ΡΠ΅ ΠΈ ΡΠΊΠΎΡΠΎΡΡΠΈ ΠΏΠΎΠ»ΡΡΠ°Π΅ΡΡΡ ΠΏΠΎΠ²Π΅ΡΡ Π½ΠΎΡΡΡ Ρ Π²ΡΡΠΎΠΊΠΎΠΉ ΡΠΈΡΡΠΎΡΠΎΠΉ. Π Π°Π·ΠΌΠ΅ΡΡ Ρ ΡΠΎΡΠ½ΠΎΡΡΡΡ Π΄ΠΎ 0,02 ΠΌΠΌ.
ΠΡΠΎΠΈΠ·Π²ΠΎΠ΄ΡΡΠ²ΠΎ ΡΡΠ³ΡΠ½Π°
ΠΡΠΈ Π·Π°ΠΏΡΡΠΊΠ΅ Π΄ΠΎΠΌΠ΅Π½Π½ΠΎΠΉ ΠΏΠ΅ΡΠΈ Π² Π½Π΅Π΅ ΠΏΠΎΡΠ»ΠΎΠΉΠ½ΠΎ Π·Π°ΡΡΠΏΠ°ΡΡ ΠΊΠΎΠΊΡ ΠΈ Π°Π³Π»ΠΎΠΌΠ΅ΡΠ°Ρ β ΠΎΠ±ΠΎΠ³Π°ΡΠ΅Π½Π½Π°Ρ ΠΆΠ΅Π»Π΅Π·Π½Π°Ρ ΡΡΠ΄Π° Ρ ΡΠ»ΡΡΠΎΠΌ. Π‘Π½ΠΈΠ·Ρ ΡΠ΅ΡΠ΅Π· ΡΠΎΡΡΡΠ½ΠΊΠΈ Π²Π΄ΡΠ²Π°Π΅ΡΡΡ ΠΊΠΈΡΠ»ΠΎΡΠΎΠ΄, ΠΏΠΎΠ΄ΠΎΠ³ΡΠ΅ΡΡΠΉ Π³Π°Π·. Π ΠΏΡΠΎΡΠ΅ΡΡΠ΅ ΡΠ³ΠΎΡΠ°Π½ΠΈΡ ΡΠ³Π»Ρ ΠΏΡΠΎΠΈΡΡ ΠΎΠ΄ΠΈΡ Ρ ΠΈΠΌΠΈΡΠ΅ΡΠΊΠΎΠ΅ ΠΏΡΠ΅Π²ΡΠ°ΡΠ΅Π½ΠΈΠ΅ Π΅Π³ΠΎ Π² Π΄Π²ΡΠΎΠΊΠΈΡΡ ΡΠ³Π»Π΅ΡΠΎΠ΄Π° CO2, Π·Π°ΡΠ΅ΠΌ Π² ΠΎΠΊΠΈΡΡ β CO, ΠΊΠΎΡΠΎΡΠ°Ρ ΠΎΠΊΠΈΡΠ»ΡΠ΅Ρ ΠΆΠ΅Π»Π΅Π·ΠΎ, Π²ΡΠ΄Π΅Π»ΡΡ Π΅Π³ΠΎ ΠΈΠ· ΡΡΠ΄Ρ ΠΈ Π΄Π΅Π»Π°Ρ ΡΠ²Π΅ΡΠ΄ΡΠΌ.
ΠΠΎΠΌΠ΅Π½Π½ΡΠΉ ΠΏΡΠΎΡΠ΅ΡΡ Π½Π΅ΠΏΡΠ΅ΡΡΠ²Π½ΡΠΉ. Π ΡΠ΄Π° ΠΈ ΡΠ»ΡΡ Π΄ΠΎΠ±Π°Π²Π»ΡΡΡΡΡ ΡΠ΅Π³ΡΠ»ΡΡΠ½ΠΎ. ΠΠΎΠ³Π΄Π° ΡΠΊΠ°ΠΏΠ»ΠΈΠ²Π°Π΅ΡΡΡ ΠΎΠΏΡΠ΅Π΄Π΅Π»Π΅Π½Π½ΠΎΠ΅ ΠΊΠΎΠ»ΠΈΡΠ΅ΡΡΠ²ΠΎ ΡΡΠ³ΡΠ½Π°, Π΅Π³ΠΎ Π²ΡΠΏΡΡΠΊΠ°ΡΡ Π² ΠΊΠΎΠ²Ρ, Π·Π°ΡΠ΅ΠΌ ΡΠ°Π·Π»ΠΈΠ²Π°ΡΡ ΠΏΠΎ ΡΠΎΡΠΌΠ°ΠΌ. ΠΠΈΠ΄ΠΊΠΈΠΉ ΡΠ»Π°ΠΊ ΠΏΡΠ΅Π΄ΠΎΡΠ²ΡΠ°ΡΠ°Π΅Ρ ΠΎΠΊΠΈΡΠ»Π΅Π½ΠΈΠ΅ ΡΠ°ΡΠΏΠ»Π°Π²Π»Π΅Π½Π½ΠΎΠ³ΠΎ ΠΌΠ΅ΡΠ°Π»Π»Π°. ΠΠ³ΠΎ ΡΠ»ΠΈΠ²Π°ΡΡ ΠΏΠΎΡΠ»Π΅ ΡΡΠ³ΡΠ½Π° ΡΠ΅ΡΠ΅Π· Π»Π΅ΡΠΎΠΊ, ΡΠ°ΡΠΏΠΎΠ»ΠΎΠΆΠ΅Π½Π½ΡΠΉ Π²ΡΡΠ΅, ΠΈ Π²ΡΠ²ΠΎΠ·ΡΡ Π·Π° ΠΏΡΠ΅Π΄Π΅Π»Ρ ΡΠ΅Ρ
Π°. Π Π΄Π°Π»ΡΠ½Π΅ΠΉΡΠ΅ΠΌ ΠΈΡΠΏΠΎΠ»ΡΠ·ΡΡΡ ΠΊΠ°ΠΊ ΡΡΡΡΠ΅ Π΄Π»Ρ ΠΏΡΠΎΠΈΠ·Π²ΠΎΠ΄ΡΡΠ²Π° ΡΠ΅ΠΌΠ΅Π½ΡΠ° ΠΈ Π² ΡΡΡΠΎΠΈΡΠ΅Π»ΡΡΡΠ²Π΅.
ΠΡΠ΅ΠΈΠΌΡΡΠ΅ΡΡΠ²Π° ΡΡΠ³ΡΠ½Π½ΠΎΠ³ΠΎ Π»ΠΈΡΡΡ
ΠΠ·Π³ΠΎΡΠΎΠ²Π»Π΅Π½ΠΈΠ΅ Π΄Π΅ΡΠ°Π»Π΅ΠΉ ΠΈΠ· ΡΡΠ³ΡΠ½Π° ΡΡΠΎΠΈΡ Π·Π½Π°ΡΠΈΡΠ΅Π»ΡΠ½ΠΎ Π΄Π΅ΡΠ΅Π²Π»Π΅, ΡΠ΅ΠΌ ΡΠ΄Π΅Π»Π°ΡΡ Π°Π½Π°Π»ΠΎΠ³ΠΈΡΠ½ΡΠ΅ ΠΈΠ·Π΄Π΅Π»ΠΈΡ ΠΈΠ· ΡΡΠ°Π»ΠΈ ΠΈΠ»ΠΈ Π±ΡΠΎΠ½Π·Ρ. ΠΠΎΠ²ΡΡΠ΅Π½Π½ΠΎΠ΅ ΡΠΎΠ΄Π΅ΡΠΆΠ°Π½ΠΈΠ΅ ΡΠΎΡΡΠΎΡΠ° Π΄Π΅Π»Π°Π΅Ρ ΡΡΠ³ΡΠ½ ΠΆΠΈΠ΄ΠΊΠΎΡΠ΅ΠΊΡΡΠΈΠΌ. ΠΠ½ Π»Π΅Π³ΠΊΠΎ Π·Π°ΠΏΠΎΠ»Π½ΡΠ΅Ρ Π²ΡΠ΅ ΠΏΡΡΡΠΎΡΡ Π² ΡΠΎΡΠΌΠ΅, Π²ΠΊΠ»ΡΡΠ°Ρ ΠΌΠ΅Π»ΠΊΠΈΠ΅ ΡΠ»Π΅ΠΌΠ΅Π½ΡΡ. ΠΠΎ ΠΊΡΠ°ΡΠΎΡΠ΅ ΠΈ ΡΠ°Π·Π½ΠΎΠΎΠ±ΡΠ°Π·ΠΈΡ ΡΡΠ³ΡΠ½Π½ΡΠ΅ ΡΠ΅ΡΠ΅ΡΠΊΠΈ Π²ΡΠ³Π»ΡΠ΄ΡΡ Π»ΡΡΡΠ΅ ΠΊΠΎΠ²Π°Π½ΡΡ . ΠΠ½ΠΈ ΡΡΡΠΎΠΉΡΠΈΠ²Ρ ΠΊ Π²Π»Π°Π³Π΅, Π½Π΅ ΡΡΠ΅Π±ΡΡΡ ΡΠ΅Π³ΡΠ»ΡΡΠ½ΠΎΠ³ΠΎ ΡΡ ΠΎΠ΄Π°.
ΠΠΈΡΡΠ΅ ΠΈΠ· ΡΡΠ³ΡΠ½Π° ΠΈΠΌΠ΅Π΅Ρ ΡΠ°ΠΌΡΠ΅ ΡΠ°Π·Π½ΡΠ΅ ΡΠΎΡΠΌΡ, ΠΌΠΎΠΆΠ΅Ρ Π΄Π»ΠΈΡΠ΅Π»ΡΠ½ΠΎΠ΅ Π²ΡΠ΅ΠΌΡ Π½Π°Ρ ΠΎΠ΄ΠΈΡΡΡ Π² Π²ΠΎΠ΄Π΅ ΠΈ Π·Π΅ΠΌΠ»Π΅, Π½Π΅Π²ΠΎΡΠΏΡΠΈΠΈΠΌΡΠΈΠ²Ρ ΠΊ Π½ΠΈΠ·ΠΊΠΈΠΌ ΡΠ΅ΠΌΠΏΠ΅ΡΠ°ΡΡΡΠ°ΠΌ. ΠΠ·Π³ΠΎΡΠΎΠ²Π»Π΅Π½ΠΈΠ΅ ΡΡΡΠ± ΠΈ ΡΠΈΡΠΈΠ½Π³ΠΎΠ², ΠΌΡΡΡ, Π²Π΅Π½ΡΠΈΠ»Π΅ΠΉ ΠΈΠΌΠ΅Π΅Ρ ΠΏΡΠΎΡΡΡΡ ΡΠ΅Ρ Π½ΠΎΠ»ΠΎΠ³ΠΈΡ,ΠΏΠΎ ΡΡΠ°Π²Π½Π΅Π½ΠΈΡ Ρ Π΄ΡΡΠ³ΠΈΠΌΠΈ ΠΌΠ°ΡΠ΅ΡΠΈΠ°Π»Π°ΠΌΠΈ.
Π£ΡΠ°Π΄ΠΊΠ° ΡΡΠ³ΡΠ½Π° Π²ΠΎ Π²ΡΠ΅ΠΌΡ ΠΎΡΡΡΠ²Π°Π½ΠΈΡ ΠΏΡΠ°ΠΊΡΠΈΡΠ΅ΡΠΊΠΈ ΠΎΡΡΡΡΡΡΠ²ΡΠ΅Ρ. ΠΡΠΎ ΠΏΠΎΠ·Π²ΠΎΠ»ΡΠ΅Ρ Π΄Π΅Π»Π°ΡΡ ΠΎΡΠ»ΠΈΠ²ΠΊΠΈ Ρ ΠΌΠΈΠ½ΠΈΠΌΠ°Π»ΡΠ½ΡΠΌΠΈ ΠΎΡΡ ΠΎΠ΄Π°ΠΌΠΈ: ΠΌΠ°Π»ΡΠΌΠΈ ΠΏΡΠΈΠ±ΡΠ»ΡΠΌΠΈ, Π±Π΅Π· Π½Π°ΠΊΠΎΠΏΠΈΡΠ΅Π»Π΅ΠΉ. ΠΠ±ΡΠ°Π±ΠΎΡΠΊΠ° Π΄Π΅ΡΠ°Π»Π΅ΠΉ ΡΠ²ΠΎΠ΄ΠΈΡΡΡ ΠΊ ΠΏΡΠΎΡΠΎΡΠΊΠ΅ ΠΏΠΎΡΠ°Π΄ΠΎΡΠ½ΡΡ ΠΌΠ΅ΡΡ.
Π§ΡΠ³ΡΠ½Π½ΡΠ΅ Π²ΡΡΠ»ΠΊΠΈ ΡΡΠ°Π²ΡΡΡΡ Π² ΠΏΠΎΠ΄ΡΠΈΠΏΠ½ΠΈΠΊΠΈ ΡΠΊΠΎΠ»ΡΠΆΠ΅Π½ΠΈΡ Π½Π° Π½ΠΈΠ·ΠΊΠΎΠΎΠ±ΠΎΡΠΎΡΠΈΡΡΡΠ΅ Π²Π°Π»Ρ. ΠΠΌΠ΅Ρ Π²ΡΡΠΎΠΊΡΡ ΠΈΠ·Π½ΠΎΡΠΎΡΡΠΎΠΉΠΊΠΎΡΡΡ ΡΡΠΈΡΠ°Π½ΠΈΠ΅ΠΌ, ΠΎΠ½ΠΈ ΡΠ»ΡΠΆΠ°Ρ Π΄ΠΎΠ»ΡΡΠ΅ ΡΠ°ΡΠΈΠΊΠΎΠΏΠΎΠ΄ΡΠΈΠΏΠ½ΠΈΠΊΠΎΠ² ΠΈ ΡΡΠΎΡΡ Π² Π½Π΅ΡΠΊΠΎΠ»ΡΠΊΠΎ ΡΠ°Π· Π΄Π΅ΡΠ΅Π²Π»Π΅.

Π’Π΅Ρ Π½ΠΎΠ»ΠΎΠ³ΠΈΡ Π»ΠΈΡΡΡ ΠΈΠ· ΡΡΠ³ΡΠ½Π°
ΠΠΈΡΡΠ΅ ΡΡΠ³ΡΠ½Π° ΠΏΡΠΎΠΈΠ·Π²ΠΎΠ΄ΠΈΡΡΡ Π² ΡΡΡΠΎΠ³ΠΎΠΉ ΠΏΠΎΡΠ»Π΅Π΄ΠΎΠ²Π°ΡΠ΅Π»ΡΠ½ΠΎΡΡΠΈ:
- Π·Π°Π³ΡΡΠ·ΠΊΠ° ΡΠΈΡ ΡΡ;
- Π½Π΅ΠΏΡΠ΅ΡΡΠ²Π½ΡΠΉ ΠΏΡΠΎΡΠ΅ΡΡ ΠΏΠ»Π°Π²Π»Π΅Π½ΠΈΡ Π² Π΄ΠΎΠΌΠ΅Π½Π½ΠΎΠΉ ΠΏΠ΅ΡΠΈ;
- Π·Π°Π»ΠΈΠ²ΠΊΠ° Π³ΠΎΡΠΎΠ²ΠΎΠ³ΠΎ ΡΡΠ³ΡΠ½Π° Π² ΠΊΠΎΠ²Ρ;
- ΡΠ°Π·Π»ΠΈΠ²ΠΊΠ° ΠΏΠΎ ΠΏΠΎΠ΄Π³ΠΎΡΠΎΠ²Π»Π΅Π½Π½ΡΠΌ ΡΠΎΡΠΌΠ°ΠΌ;
- ΠΎΡ Π»Π°ΠΆΠ΄Π΅Π½ΠΈΠ΅;
- ΠΎΡΠΆΠΈΠ³;
- ΠΎΡΠΈΡΡΠΊΠ° ΠΎΡ ΠΎΠΊΠ°Π»ΠΈΠ½Ρ.
ΠΡΠΈ ΠΈΠ·Π³ΠΎΡΠΎΠ²Π»Π΅Π½ΠΈΠΈ ΡΡΡΠ± ΠΈ ΠΏΠΎΠ»ΡΡ Π΄Π΅ΡΠ°Π»Π΅ΠΉ ΠΏΡΠΈΠΌΠ΅Π½ΡΡΡ ΡΠ΅Π½ΡΡΠΎΠ±Π΅ΠΆΠ½ΠΎΠ΅ Π»ΠΈΡΡΠ΅. ΠΡΠΈ ΡΡΠΎΠΌ ΡΠΏΠΎΡΠΎΠ±Π΅ Π² Π±ΡΡΡΡΠΎ Π²ΡΠ°ΡΠ°ΡΡΡΡΡΡ ΡΠΎΡΠΌΡ Π·Π°Π»ΠΈΠ²Π°ΡΡ ΡΡΠ³ΡΠ½. ΠΠΎΠ΄ Π΄Π΅ΠΉΡΡΠ²ΠΈΠ΅ΠΌ ΡΠ΅Π½ΡΡΠΎΠ±Π΅ΠΆΠ½ΠΎΠΉ ΡΠΈΠ»Ρ ΠΆΠΈΠ΄ΠΊΠΈΠΉ ΠΌΠ΅ΡΠ°Π»Π» ΡΠ°ΡΡΠ΅ΠΊΠ°Π΅ΡΡΡ ΠΏΠΎ ΠΏΠΎΠ²Π΅ΡΡ Π½ΠΎΡΡΠΈ Π½Π° Π·Π°Π΄Π°Π½Π½ΡΡ ΡΠΎΠ»ΡΠΈΠ½Ρ.
ΠΡΡΠ°Π»ΡΠ½ΡΠ΅ Π΄Π΅ΡΠ°Π»ΠΈ Π·Π°Π»ΠΈΠ²Π°ΡΡ ΠΏΠΎ ΡΠΎΡΠΌΠ΅, ΠΊΠΎΡΠΎΡΠ°Ρ Π·Π°ΡΠ°Π½Π΅Π΅ ΠΈΠ·Π³ΠΎΡΠ°Π²Π»ΠΈΠ²Π°Π΅ΡΡΡ, Π² Π·Π΅ΠΌΠ»Ρ.
ΠΡΠΎΡΠ΅ΡΡ Π»ΠΈΡΡΡ ΠΈΠ· ΡΡΠ³ΡΠ½Π°
ΠΡΠΈ Π½Π°ΠΊΠΎΠΏΠ»Π΅Π½ΠΈΠΈ Π² Π½ΠΈΠΆΠ½Π΅ΠΉ ΡΠ°ΡΡΠΈ ΠΏΠ΅ΡΠΈ Π΄ΠΎΡΡΠ°ΡΠΎΡΠ½ΠΎΠ³ΠΎ ΠΊΠΎΠ»ΠΈΡΠ΅ΡΡΠ²Π° ΠΆΠΈΠ΄ΠΊΠΎΠ³ΠΎ ΠΌΠ΅ΡΠ°Π»Π»Π° ΠΏΡΠΎΠ±ΠΈΠ²Π°ΡΡ Π»Π΅ΡΠΎΠΊ, ΠΈ ΡΠ°ΡΠΊΠ°Π»Π΅Π½Π½Π°Ρ ΠΌΠ°ΡΡΠ° Π»ΡΠ΅ΡΡΡ Π² ΠΊΠΎΠ²Ρ, ΠΈΠ· ΠΊΠΎΡΠΎΡΠΎΠ³ΠΎ ΠΈ ΠΏΡΠΎΠΈΠ·Π²ΠΎΠ΄ΠΈΡΡΡ Π½Π΅ΠΏΠΎΡΡΠ΅Π΄ΡΡΠ²Π΅Π½Π½ΠΎ Π»ΠΈΡΡΠ΅ ΡΡΠ³ΡΠ½Π° Π² ΡΠΎΡΠΌΡ. ΠΠ½ΡΡΡΡΠΌΠ΅Π½Ρ Π΄Π»Ρ ΡΠ°Π·Π»ΠΈΠ²ΠΊΠΈ β ΠΊΠΎΠ²Ρ, ΠΈΠΌΠ΅Π΅Ρ Π²Π½ΠΈΠ·Ρ ΠΎΡΠ²Π΅ΡΡΡΠΈΠ΅ Ρ ΠΏΡΠΎΠ±ΠΊΠΎΠΉ. Π§Π΅ΡΠ΅Π· Π½Π΅Π³ΠΎ ΠΏΡΠΎΠΈΠ·Π²ΠΎΠ΄ΠΈΡΡΡ Π·Π°Π»ΠΈΠ²ΠΊΠ° ΠΌΠ΅Π»ΠΊΠΈΡ Π΄Π΅ΡΠ°Π»Π΅ΠΉ. ΠΠ»Ρ Π³Π°Π±Π°ΡΠΈΡΠ½ΡΡ ΡΡΠΆΠ΅Π»ΠΎΠ²Π΅ΡΠ½ΡΡ ΠΎΡΠ»ΠΈΠ²ΠΎΠΊ, ΠΊΠΎΠ³Π΄Π° Π½Π°Π΄ΠΎ Π±ΡΡΡΡΠΎ Π·Π°ΠΏΠΎΠ»Π½ΠΈΡΡ ΡΠΎΡΠΌΡ, ΠΌΠΎΠ³ΡΡ ΠΈΡΠΏΠΎΠ»ΡΠ·ΠΎΠ²Π°ΡΡ Π½ΠΎΡΠΈΠΊ Π² Π²Π΅ΡΡ Π½Π΅ΠΉ ΡΠ°ΡΡΠΈ ΠΊΠΎΠ²ΡΠ°, Π½Π°ΠΊΠ»ΠΎΠ½ΠΈΠ² Π΅Π³ΠΎ Ρ ΠΏΠΎΠΌΠΎΡΡΡ ΠΊΡΠ°Π½Π°.
ΠΠΎΠ΄Π³ΠΎΡΠΎΠ²ΠΊΠ° ΠΌΠΎΠ΄Π΅Π»Π΅ΠΉ
ΠΠΎΠ΄Π΅Π»ΠΈ ΠΈΠ·Π³ΠΎΡΠ°Π²Π»ΠΈΠ²Π°ΡΡΡΡ ΠΈΠ· ΡΠ°Π·Π»ΠΈΡΠ½ΡΡ ΠΌΠ°ΡΠ΅ΡΠΈΠ°Π»ΠΎΠ². ΠΠ»Ρ ΠΈΠ·Π³ΠΎΡΠΎΠ²Π»Π΅Π½ΠΈΡ ΠΌΠ°Π»ΡΡ ΠΏΠ°ΡΡΠΈΠΉ ΠΈ Π΅Π΄ΠΈΠ½ΠΈΡΠ½ΡΡ Π·Π°Π³ΠΎΡΠΎΠ²ΠΎΠΊ ΠΊΡΡΠΏΠ½ΠΎΠ³Π°Π±Π°ΡΠΈΡΠ½ΡΡ Π΄Π΅ΡΠ°Π»Π΅ΠΉ ΠΈΡΠΏΠΎΠ»ΡΠ·ΡΡΡ Π΄Π΅ΡΠ΅Π²ΠΎ. ΠΠΎΠ΄Π΅Π»Ρ ΠΏΠΎΠ²ΡΠΎΡΡΠ΅Ρ Π½Π°ΡΡΠΆΠ½ΡΡ ΡΠΎΡΠΌΡ Π΄Π΅ΡΠ°Π»ΠΈ Ρ ΠΏΡΠΈΠΏΡΡΠΊΠ°ΠΌΠΈ Π½Π° ΡΡΠ°Π΄ΠΊΡ. Π ΠΌΠ΅ΡΡΠ° ΡΠ°ΡΠΏΠΎΠ»ΠΎΠΆΠ΅Π½ΠΈΡ ΠΎΡΠ²Π΅ΡΡΡΠΈΠΉ Π²ΡΡΠ°Π²Π»ΡΡΡ ΡΡΠ΅ΡΠΆΠ½ΠΈ ΠΈΠ· ΡΠΎΡΠΌΠΎΠ²ΠΎΡΠ½ΠΎΠΉ ΡΠΌΠ΅ΡΠΈ.
Π ΠΊΠ°ΡΠ΅ΡΡΠ²Π΅ ΠΌΠ°ΡΠ΅ΡΠΈΠ°Π»Π° Π΄Π»Ρ ΠΈΠ·Π³ΠΎΡΠΎΠ²Π»Π΅Π½ΠΈΡ ΠΌΠΎΠ΄Π΅Π»Π΅ΠΉ ΠΈΡΠΏΠΎΠ»ΡΠ·ΡΡΡ:
- Π²ΠΎΡΠΊ;
- Π³ΠΈΠΏΡ;
- ΠΏΠ»Π°ΡΡΠΌΠ°ΡΡΡ;
- ΠΏΠ΅Π½ΠΎΠΏΠ»Π°ΡΡ.
ΠΠ»Ρ ΠΈΠ·Π³ΠΎΡΠΎΠ²Π»Π΅Π½ΠΈΡ Π±ΠΎΠ»ΡΡΠΈΡ ΠΏΠ°ΡΡΠΈΠΉ ΠΎΡΠ»ΠΈΠ²ΠΎΠΊ, Π½Π°ΡΠΈΠ½Π°Ρ Ρ Π½Π΅ΡΠΊΠΎΠ»ΡΠΊΠΈΡ ΡΠΎΡΠ΅Π½, ΡΠΎ ΡΠ»ΠΎΠΆΠ½ΠΎΠΉ ΠΊΠΎΠ½ΡΠΈΠ³ΡΡΠ°ΡΠΈΠ΅ΠΉ ΠΈΡΠΏΠΎΠ»ΡΠ·ΡΡΡ ΠΈΠ·Π³ΠΎΡΠΎΠ²Π»Π΅Π½Π½ΡΠ΅ Π½Π° ΡΡΠ°Π½ΠΊΠ°Ρ Π§ΠΠ£ ΠΈ Π΄ΡΡΠ³ΠΎΠΌ ΠΎΠ±ΠΎΡΡΠ΄ΠΎΠ²Π°Π½ΠΈΠΈ ΠΌΠΎΠ΄Π΅Π»ΠΈ ΠΈΠ· Π±ΡΠΎΠ½Π·Ρ, Π»Π°ΡΡΠ½ΠΈ, Π°Π»ΡΠΌΠΈΠ½ΠΈΠ΅Π²ΡΡ ΡΠΏΠ»Π°Π²ΠΎΠ². Π ΡΠ΅Π·ΡΠ»ΡΡΠ°ΡΠ΅ ΠΏΠΎΠ»ΡΡΠ°Π΅ΡΡΡ ΠΎΡΠ»ΠΈΠ²ΠΊΠ° Ρ Π±ΠΎΠ»ΡΡΠΎΠΉ ΡΠΎΡΠ½ΠΎΡΡΡΡ Π½Π°ΡΡΠΆΠ½ΡΡ ΡΠ°Π·ΠΌΠ΅ΡΠΎΠ², Π½Π΅ Π½ΡΠΆΠ΄Π°ΡΡΠ°ΡΡΡ Π² ΠΎΠ±ΡΠ°Π±ΠΎΡΠΊΠ΅.
Π€ΠΎΡΠΌΠΎΠ²ΠΊΠ°
ΠΠΎΠ΄Π΅Π»Ρ Π²ΡΡΠ°Π²Π»ΡΡΡ Π² ΠΌΠ΅ΡΠ°Π»Π»ΠΈΡΠ΅ΡΠΊΡΡ ΡΠΎΡΠΌΡ, ΠΈ ΠΎΡΡΠ°Π²ΡΠ΅Π΅ΡΡ ΠΏΡΠΎΡΡΡΠ°Π½ΡΡΠ²ΠΎ Π·Π°ΠΏΠΎΠ»Π½ΡΡΡ ΠΏΠ΅ΡΡΠ°Π½ΠΎ-Π³Π»ΠΈΠ½ΡΠ½ΠΎΠΉ ΡΠΌΠ΅ΡΡΡ. ΠΠ»Ρ ΠΏΠΎΠ»ΡΡΠ΅Π½ΠΈΡ ΠΏΠ»ΠΎΡΠ½ΠΎΠΉ ΠΎΠ±ΠΎΠ»ΠΎΡΠΊΠΈ ΡΠΌΠ΅ΡΡ ΡΠΏΠ»ΠΎΡΠ½ΡΡΡ Π½Π° Π²ΠΈΠ±ΡΠΎΡΡΠ΅Π½Π΄Π°Ρ ΠΈΠ»ΠΈ ΡΡΡΠ°ΠΌΠ±ΠΎΠ²ΡΠ²Π°ΡΡ ΡΡΡΠ½ΡΠΌ ΠΏΠ½Π΅Π²ΠΌΠΎΠΈΠ½ΡΡΡΡΠΌΠ΅Π½ΡΠΎΠΌ.
ΠΠΎΠ»ΡΡΠΈΠ΅ ΡΠΎΡΠΌΡ Π·Π°ΠΏΠΎΠ»Π½ΡΡΡ Π² Π½Π΅ΡΠΊΠΎΠ»ΡΠΊΠΎ ΡΡΠ°ΠΏΠΎΠ², ΠΏΠΎΠ΄ΡΡΠΏΠ°Ρ ΡΠΌΠ΅ΡΡ. ΠΠ°ΡΠ΅ΠΌ ΠΌΠΎΠ΄Π΅Π»Ρ Π²ΡΠ½ΠΈΠΌΠ°ΡΡ. ΠΠΎΠ²Π΅ΡΡ Π½ΠΎΡΡΡ ΡΠΎΡΠΌΡ ΠΎΠ±ΡΠ°Π±Π°ΡΡΠ²Π°ΡΡ Π°Π½ΡΠΈΠΏΡΠΈΠ³Π°ΡΠ½ΡΠΌ ΡΠΎΡΡΠ°Π²ΠΎΠΌ ΠΈ ΡΡΡΠ°Ρ.

ΠΠ°Π»ΠΈΠ²ΠΊΠ° ΠΌΠ΅ΡΠ°Π»Π»Π°
Π€ΠΎΡΠΌΡ Π²ΡΡΡΠ°Π²Π»ΡΡΡ Π² ΠΎΠ΄ΠΈΠ½ ΡΡΠ΄ Π½Π° ΡΠΏΠ΅ΡΠΈΠ°Π»ΡΠ½ΠΎ ΠΏΠΎΠ΄Π³ΠΎΡΠΎΠ²Π»Π΅Π½Π½ΠΎΠ΅ ΠΌΠ΅ΡΡΠΎ. ΠΠ°Π΄ Π½ΠΈΠΌΠΈ ΡΡΡΠ°Π½Π°Π²Π»ΠΈΠ²Π°ΡΡΡΡ Π»ΠΈΡΠ½ΠΈΠΊΠΈ Π΄Π»Ρ Π·Π°Π»ΠΈΠ²ΠΊΠΈ. ΠΠΎΠ²Ρ Π·Π°Π²ΠΎΠ΄ΠΈΡΡΡ Π½Π°Π΄ ΡΠΎΡΠΌΠ°ΠΌΠΈ ΠΈ Π±ΡΡΡΡΠΎ Π·Π°ΠΏΠΎΠ»Π½ΡΠ΅Ρ ΠΈΡ . ΠΡΠ»ΠΈ ΡΡΠ³ΡΠ½ Π»ΡΠ΅ΡΡΡ Π΄ΠΎΠ»Π³ΠΎ, ΠΎΡΠ»ΠΈΠ²ΠΊΠΈ Π±ΡΠ΄ΡΡ Π½Π΅ΡΠ°Π²Π½ΠΎΠΌΠ΅ΡΠ½ΠΎ ΠΎΡ Π»Π°ΠΆΠ΄Π°ΡΡΡΡ, ΠΌΠΎΠ³ΡΡ ΠΎΠ±ΡΠ°Π·ΠΎΠ²Π°ΡΡΡΡ ΡΠ°ΡΡΠ»ΠΎΠ΅Π½ΠΈΡ ΠΌΠ΅ΡΠ°Π»Π»Π° Π²Π½ΡΡΡΠΈ.
ΠΠ°Π²Π΅ΡΡΠ°ΡΡΠΈΠ΅Β ΠΎΠΏΠ΅ΡΠ°ΡΠΈΠΈ
ΠΠΎΡΠ»Π΅ Π·Π°Π»ΠΈΠ²ΠΊΠΈ ΡΠΎΡΠΌΡ ΠΎΡΡΠ°ΡΡΡΡ Π² ΡΠΌΠ΅ Π΄Π»Ρ ΡΠ°Π²Π½ΠΎΠΌΠ΅ΡΠ½ΠΎΠ³ΠΎ ΠΎΡΡΡΠ²Π°Π½ΠΈΡ Π½Π° 12β60 ΡΠ°ΡΠΎΠ². ΠΡΠΎΠ΄ΠΎΠ»ΠΆΠΈΡΠ΅Π»ΡΠ½ΠΎΡΡΡ ΠΏΡΠΎΡΠ΅ΡΡΠ° Π·Π°Π²ΠΈΡΠΈΡ ΠΎΡ Π½Π°ΠΈΠ±ΠΎΠ»ΡΡΠ΅Π³ΠΎ ΡΠ΅ΡΠ΅Π½ΠΈΡ ΠΎΡΠ»ΠΈΠ²ΠΊΠΈ.
ΠΡΡΡΠ²ΡΡΡ ΡΠΎΡΠΌΡ Π΄ΠΎΡΡΠ°ΡΡ, ΠΎΡΠ²ΠΎΠ±ΠΎΠΆΠ΄Π°ΡΡ Π΄Π΅ΡΠ°Π»Ρ ΠΎΡ ΡΠΎΡΠΌΠΎΠ²ΠΎΡΠ½ΠΎΠΉ ΡΠΌΠ΅ΡΠΈ ΠΈ Π²ΠΌΠ΅ΡΡΠ΅ Π½Π°ΠΊΠΎΠΏΠΈΡΠ΅Π»ΡΠΌΠΈ ΠΈ ΠΏΡΠΈΠ±ΡΠ»ΡΠΌΠΈ ΠΏΠΎΠΌΠ΅ΡΠ°ΡΡ Π² ΡΠ΅ΡΠΌΠΈΡΠ΅ΡΠΊΡΡ ΠΏΠ΅ΡΡ Π½Π° ΠΎΡΠΆΠΈΠ³. ΠΠ΅ΡΠ°Π»Π» Π½Π°Π³ΡΠ΅Π²Π°ΡΡ Π΄ΠΎ 800β°β900β°, Π² Π·Π°Π²ΠΈΡΠΈΠΌΠΎΡΡΠΈ ΠΎΡ ΠΌΠ°ΡΡΡ ΠΎΡΠ»ΠΈΠ²ΠΊΠΈ ΠΈ ΠΌΠ°ΡΠΊΠΈ ΡΡΠ³ΡΠ½Π°. ΠΠ°ΡΠ΅ΠΌ Π²ΡΠ΄Π΅ΡΠΆΠΈΠ²Π°ΡΡ ΠΏΡΠΈ Π·Π°Π΄Π°Π½Π½ΠΎΠΉ ΡΠ΅ΠΌΠΏΠ΅ΡΠ°ΡΡΡΠ΅ Π½Π΅ΡΠΊΠΎΠ»ΡΠΊΠΎ ΡΠ°ΡΠΎΠ². Π§ΡΠ³ΡΠ½ Π²ΠΌΠ΅ΡΡΠ΅ Ρ ΠΏΠ΅ΡΡΡ ΠΌΠ΅Π΄Π»Π΅Π½Π½ΠΎ ΠΎΡΡΡΠ²Π°Π΅Ρ Π΄ΠΎ 300β°. ΠΠ°ΡΠ΅ΠΌ ΠΎΡΠ»ΠΈΠ²ΠΊΡ Π΄ΠΎΡΡΠ°ΡΡ, ΠΈ ΠΎΡ Π»Π°ΠΆΠ΄Π΅Π½ΠΈΠ΅ ΠΏΡΠΎΠ΄ΠΎΠ»ΠΆΠ°Π΅ΡΡΡ Π½Π° Π²ΠΎΠ·Π΄ΡΡ Π΅.
ΠΠΎΡΠ»Π΅ ΠΎΡΠΆΠΈΠ³Π° ΡΡΡΡΠΊΡΡΡΠ° ΡΡΠ³ΡΠ½Π° Π²ΡΡΠ°Π²Π½ΠΈΠ²Π°Π΅ΡΡΡ, ΡΠ½ΠΈΠΌΠ°ΡΡΡΡ Π½Π°ΠΏΡΡΠΆΠ΅Π½ΠΈΡ. Π’Π΅ΠΏΠ΅ΡΡ ΠΎΠ±ΡΠ΅Π·Π°ΡΡΡΡ ΡΠ΅Ρ
Π½ΠΎΠ»ΠΎΠ³ΠΈΡΠ΅ΡΠΊΠΈΠ΅ Π½Π°Π΄ΡΡΠ°Π²ΠΊΠΈ ΠΈ Π΄ΡΡΠ³ΠΈΠ΅ ΡΠ»Π΅ΠΌΠ΅Π½ΡΡ. ΠΡΠΎΠΈΠ·Π²ΠΎΠ΄ΠΈΡΡΡ Π·Π°ΡΠΈΡΡΠΊΠ° ΠΏΠΎΠ²Π΅ΡΡ
Π½ΠΎΡΡΠΈ ΠΎΡ ΠΎΡΡΠ°ΡΠΊΠΎΠ² ΡΠΎΡΠΌΠΎΠ²ΠΎΡΠ½ΠΎΠΉ ΡΠΌΠ΅ΡΠΈ, ΠΎΠΊΠ°Π»ΠΈΠ½Ρ.
Π‘ΠΏΠΎΡΠΎΠ±Ρ Π»ΠΈΡΡΡ Π² Π΄ΠΎΠΌΠ°ΡΠ½ΠΈΡ ΡΡΠ»ΠΎΠ²ΠΈΡΡ
ΠΠΈΡΡΠ΅ ΡΡΠ³ΡΠ½Π° Π² Π΄ΠΎΠΌΠ°ΡΠ½ΠΈΡ
ΡΡΠ»ΠΎΠ²ΠΈΡΡ
Π²ΠΎΠ·ΠΌΠΎΠΆΠ½ΠΎ. Π ΡΠ΅ΡΠ΅Π΄ΠΈΠ½Π΅ 20 Π²Π΅ΠΊΠ° Π² ΠΠΈΡΠ°Π΅ ΠΏΠΎΡΡΠΈ Π½Π° ΠΊΠ°ΠΆΠ΄ΠΎΠΌ ΠΎΠ³ΠΎΡΠΎΠ΄Π΅ ΡΡΠΎΡΠ»ΠΈ ΠΌΠ°Π»Π΅Π½ΡΠΊΠΈΠ΅ ΠΏΠ΅ΡΠΈ ΠΈ ΠΊΠ°ΠΆΠ΄ΡΠΉ ΠΏΡΠΎΠΈΠ·Π²ΠΎΠ΄ΠΈΠ» ΡΡΠ³ΡΠ½Π½ΡΠ΅ Π΄Π΅ΡΠ°Π»ΠΈ.
ΠΠ°Π½Π½Ρ ΠΈΠ»ΠΈ Π΄ΡΡΠ³ΡΡ Π΅ΠΌΠΊΠΎΡΡΡ Ρ ΠΎΡΠ²Π΅ΡΡΡΠΈΠ΅ΠΌ Π²Π½ΠΈΠ·Ρ Π½Π΅ΠΎΠ±Ρ ΠΎΠ΄ΠΈΠΌΠΎ ΠΎΠ±Π»ΠΎΠΆΠΈΡΡ ΠΎΠ³Π½Π΅ΡΠΏΠΎΡΠ½ΡΠΌ ΠΊΠΈΡΠΏΠΈΡΠΎΠΌ, Π·Π°ΠΏΠΎΠ»Π½ΠΈΡΡ Π΅Π΅ ΡΡΠ³ΡΠ½Π½ΡΠΌ Π»ΠΎΠΌΠΎΠΌ, Π΄ΠΎΠ±Π°Π²ΠΈΡΡ ΠΊΠΎΠΊΡ ΠΈ ΡΠ°ΡΠΊΠΈΡΠ»ΠΈΡΠ΅Π»Ρ. ΠΠ°Π³ΡΠ΅Π²Π°ΡΡ ΠΌΠΎΠΆΠ½ΠΎ Π³Π°Π·ΠΎΠ²ΠΎΠΉ Π³ΠΎΡΠ΅Π»ΠΊΠΎΠΉ. ΠΠ°ΠΆΠ½ΠΎ ΠΏΠΎΠΌΠ½ΠΈΡΡ β ΡΠ΅ΠΌ ΠΌΠ΅Π½ΡΡΠ΅ ΠΎΠ±ΡΠ΅ΠΌ, ΡΠ΅ΠΌ Ρ ΡΠΆΠ΅ ΠΊΠ°ΡΠ΅ΡΡΠ²ΠΎ ΠΌΠ΅ΡΠ°Π»Π»Π°.
Π₯ΡΠ΄ΠΎΠΆΠ΅ΡΡΠ²Π΅Π½Π½ΠΎΠ΅ Π»ΠΈΡΡΠ΅ ΠΈΠ· ΡΡΠ³ΡΠ½Π°: ΠΈΡΡΠΎΡΠΈΡ, ΡΠ΅Ρ Π½ΠΎΠ»ΠΎΠ³ΠΈΡ ΠΎΡΠ»ΠΈΠ²ΠΊΠΈ
ΠΠΎ ΠΌΠ΅ΡΠ΅ ΡΠ°Π·Π²ΠΈΡΠΈΡ ΠΌΠ΅ΡΠ°Π»Π»ΠΎΠΎΠ±ΡΠ°Π±ΠΎΡΠΊΠΈ Π»ΡΠ΄ΠΈ ΡΡΠΈΠ»ΠΈΡΡ Π½Π΅ ΡΠΎΠ»ΡΠΊΠΎ ΡΠΎΠ·Π΄Π°Π²Π°ΡΡ ΡΠ°Π·Π»ΠΈΡΠ½ΡΠ΅ Π΄Π΅ΡΠ°Π»ΠΈ ΠΈ ΠΏΡΠ΅Π΄ΠΌΠ΅ΡΡ ΡΠ»ΠΎΠΆΠ½ΡΡ ΡΠΎΡΠΌ, Π½ΠΎ ΠΈ ΡΡΠ°ΡΠ°Π»ΠΈΡΡ ΡΠ΄Π΅Π»Π°ΡΡ ΠΈΡ ΠΊΡΠ°ΡΠΈΠ²Π΅Π΅. Π’Π°ΠΊΠΈΠΌ ΠΎΠ±ΡΠ°Π·ΠΎΠΌ ΡΠ°Π·Π²ΠΈΠ²Π°Π»ΠΎΡΡ Π»ΠΈΡΠ΅ΠΉΠ½ΠΎΠ΅ ΠΈΡΠΊΡΡΡΡΠ²ΠΎ. ΠΠΎ ΠΌΠ΅ΡΠ΅ ΡΠ°Π·Π²ΠΈΡΠΈΡ ΡΠ΅Ρ Π½ΠΎΠ»ΠΎΠ³ΠΈΠΉ Π΄Π΅ΠΊΠΎΡΠ°ΡΠΈΠ²Π½Π°Ρ ΠΎΡΠ΄Π΅Π»ΠΊΠ° ΠΌΠ΅ΡΠ°Π»Π»ΠΎΠΌ ΠΏΡΠ°ΠΊΡΠΈΡΠ΅ΡΠΊΠΈ Π½Π΅ ΠΈΠ·ΠΌΠ΅Π½ΠΈΠ»Π°ΡΡ. ΠΠ΄Π½ΠΎΠΉ ΠΈΠ· ΠΈΠ½ΡΠ΅ΡΠ΅ΡΠ½Π΅ΠΉΡΠΈΡ ΡΠ΅v ΡΠ²Π»ΡΠ΅ΡΡΡ Ρ ΡΠ΄ΠΎΠΆΠ΅ΡΡΠ²Π΅Π½Π½ΠΎΠ΅ Π»ΠΈΡΡΠ΅ ΠΈΠ· ΡΡΠ³ΡΠ½Π°. Π§ΡΠΎΠ±Ρ Π·Π½Π°ΡΡ, ΠΊΠ°ΠΊ ΡΠΊΡΠ°ΡΠΈΡΡ Π΄Π΅ΡΠ°Π»ΠΈ ΠΈΠ»ΠΈ Π³ΠΎΡΠΎΠ²ΡΠ΅ ΠΏΡΠ΅Π΄ΠΌΠ΅ΡΡ, Π½Π΅ΠΎΠ±Ρ ΠΎΠ΄ΠΈΠΌΠΎ ΡΠ°Π·Π±ΠΈΡΠ°ΡΡΡΡ Π² ΠΏΡΠΎΡΠ΅ΡΡΠ΅ ΠΈ ΠΈΡΠΏΠΎΠ»ΡΠ·ΡΠ΅ΠΌΡΡ ΠΌΠ°ΡΠ΅ΡΠΈΠ°Π»Π°Ρ .

ΠΡΡΠΎΡΠΈΡ ΠΈ ΡΡΡΡ ΡΠ΅Ρ Π½ΠΎΠ»ΠΎΠ³ΠΈΠΈ
ΠΡΡΠΎΡΠΈΡ ΡΠ°Π±ΠΎΡΡ ΡΠ΅Π»ΠΎΠ²Π΅ΠΊΠ° Ρ ΠΌΠ΅ΡΠ°Π»Π»ΠΎΠΌ Π½Π°ΡΠΈΠ½Π°Π΅ΡΡΡ Π² 4 ΡΡΡΡΡΠ΅Π»Π΅ΡΠΈΠΈ Π΄ΠΎ Π½Π°ΡΠ΅ΠΉ ΡΡΡ. ΠΠ± ΡΡΠΎΠΌ Π³ΠΎΠ²ΠΎΡΡΡ ΡΠ°Π·Π½ΠΎΠΎΠ±ΡΠ°Π·Π½ΡΠ΅ Π°ΡΡ Π΅ΠΎΠ»ΠΎΠ³ΠΈΡΠ΅ΡΠΊΠΈΠ΅ Π½Π°Ρ ΠΎΠ΄ΠΊΠΈ. ΠΠ΄Π½Π°ΠΊΠΎ ΠΊΠ°ΡΠ΅ΡΡΠ²ΠΎ ΠΈ ΡΠΎΡΠ½ΠΎΡΡΡ ΡΠ°Π±ΠΎΡ Π½Π°ΡΠ°Π»ΠΎ ΠΏΠΎΡΠ²Π»ΡΡΡΡΡ Π²ΠΎ 2 ΡΡΡΡΡΠ΅Π»Π΅ΡΠΈΠΈ. ΠΡΡ Π΅ΠΎΠ»ΠΎΠ³ΠΈΡΠ΅ΡΠΊΠΈΠ΅ Π½Π°Ρ ΠΎΠ΄ΠΊΠΈ ΡΡΠΎΠ³ΠΎ Π²ΡΠ΅ΠΌΠ΅Π½Π½ΠΎΠ³ΠΎ ΠΏΠ΅ΡΠΈΠΎΠ΄Π° ΡΠ²ΠΈΠ΄Π΅ΡΠ΅Π»ΡΡΡΠ²ΡΡΡ ΠΎ ΡΠΎΠΌ, ΡΡΠΎ ΠΈΡΡΠΎΠΊΠΈ ΠΌΠ°ΡΡΠ΅ΡΡΡΠ²Π° ΠΏΡΠΎΡΠ²Π»ΡΡΡΡΡ ΠΈΠΌΠ΅Π½Π½ΠΎ ΡΠΎΠ³Π΄Π°. Π‘ ΡΡΠΎΠ³ΠΎ ΠΌΠΎΠΌΠ΅Π½ΡΠ° ΠΌΠ΅ΡΠ°Π»Π»ΠΎΠΎΠ±ΡΠ°Π±ΠΎΡΠΊΠ° ΡΡΠ°Π½ΠΎΠ²ΠΈΡΡΡ Π½Π΅ ΡΠΎΠ»ΡΠΊΠΎ ΡΠ΅ΠΌΠ΅ΡΠ»ΠΎΠΌ, Π½ΠΎ ΠΈ Π΄Π΅ΠΊΠΎΡΠ°ΡΠΈΠ²Π½ΠΎ-ΠΏΡΠΈΠΊΠ»Π°Π΄Π½ΡΠΌ ΠΈΡΠΊΡΡΡΡΠ²ΠΎΠΌ.
Π‘ΡΡΡ ΡΠ΅Ρ
Π½ΠΎΠ»ΠΎΠ³ΠΈΠΈ ΠΈΠ·Π³ΠΎΡΠΎΠ²Π»Π΅Π½ΠΈΡ ΡΠΊΡΠ»ΡΠΏΡΡΡ ΠΈΠ· ΡΡΠ³ΡΠ½Π° Π·Π°ΠΊΠ»ΡΡΠ°Π΅ΡΡΡ Π² ΡΠΎΠΌ, ΡΡΠΎ ΠΈΠ·Π½Π°ΡΠ°Π»ΡΠ½ΠΎ ΡΠΎΠ·Π΄Π°ΡΡΡΡ ΠΏΠΎΠ»Π°Ρ ΡΠΎΡΠΌΠ°, Π² ΠΊΠΎΡΠΎΡΡΡ Π·Π°Π»ΠΈΠ²Π°Π΅ΡΡΡ ΡΠ°ΡΠΏΠ»Π°Π²Π»Π΅Π½Π½ΡΠΉ ΠΌΠ΅ΡΠ°Π»Π». ΠΡΠΈ Π·Π°ΡΡΡΠ²Π°Π½ΠΈΠΈ ΠΎΠ½ ΠΏΠΎΠ²ΡΠΎΡΡΠ΅Ρ Π²ΡΠ΅ Π»ΠΈΠ½ΠΈΠΈ, Π³ΡΠ°Π½ΠΈ ΠΈ Π΄Π΅ΡΠ°Π»ΠΈ, ΠΊΠΎΡΠΎΡΡΠ΅ ΠΎΠ±ΡΠΈΡΠΎΠ²Π°Π½Ρ Π² ΠΏΠΎΠ»ΠΎΠΉ ΡΠΎΡΠΌΠ΅. ΠΠΎΠ³Π΄Π° ΠΌΠ΅ΡΠ°Π»Π» Π·Π°ΡΡΡΠ²Π°Π΅Ρ, Π΅Π³ΠΎ ΠΎΡΠ²ΠΎΠ±ΠΎΠΆΠ΄Π°ΡΡ ΠΎΡ ΡΠΎΡΠΌΡ. ΠΠ° ΡΠ΅Π³ΠΎΠ΄Π½ΡΡΠ½ΠΈΠΉ ΠΌΠΎΠΌΠ΅Π½Ρ ΠΎΠ΄Π½ΠΈΠΌ ΠΈΠ· ΠΈΠ·Π²Π΅ΡΡΠ½Π΅ΠΉΡΠΈΡ
Π½Π°ΠΏΡΠ°Π²Π»Π΅Π½ΠΈΠΉ ΡΠ°Π±ΠΎΡΡ Ρ ΡΡΠ³ΡΠ½ΠΎΠΌ ΡΠ²Π»ΡΠ΅ΡΡΡ ΠΊΠ°ΡΠ»ΠΈΠ½ΡΠΊΠΎΠ΅ Π»ΠΈΡΡΠ΅.
ΠΡΠ°ΠΏΡ ΠΈΠ·Π³ΠΎΡΠΎΠ²Π»Π΅Π½ΠΈΡ ΡΠΊΡΠ»ΡΠΏΡΡΡ:
- ΠΠ·Π³ΠΎΡΠ°Π²Π»ΠΈΠ²Π°Π΅ΡΡΡ ΠΎΡΠΈΠ³ΠΈΠ½Π°Π»ΡΠ½Π°Ρ ΡΠΊΡΠ»ΡΠΏΡΡΡΠ° ΠΈΠ· ΠΏΠ»Π°ΡΡΠΈΡΠ½ΡΡ ΠΌΠ°ΡΠ΅ΡΠΈΠ°Π»ΠΎΠ².
- Π‘ΠΎΠ·Π΄Π°ΡΡΡΡ Π»ΠΈΡΠ΅ΠΉΠ½Π°Ρ ΡΠΎΡΠΌΠ° ΠΏΠΎ Π³ΠΎΡΠΎΠ²ΠΎΠΉ ΡΠΊΡΠ»ΡΠΏΡΡΡΠ΅.
- ΠΠ»Π°Π²ΠΈΡΡΡ ΠΈ Π·Π°Π»ΠΈΠ²Π°Π΅ΡΡΡ Π² Π³ΠΎΡΠΎΠ²ΡΠΉ ΡΠ°Π±Π»ΠΎΠ½ ΠΌΠ΅ΡΠ°Π»Π».
- ΠΠΎΡΠ»Π΅ Π·Π°ΡΡΡΠ²Π°Π½ΠΈΡ ΠΌΠ΅ΡΠ°Π»Π»Π° Ρ Π½Π΅Π³ΠΎ ΡΠ½ΠΈΠΌΠ°Π΅ΡΡΡ Π²Π½Π΅ΡΠ½ΠΈΠΉ ΠΊΠ°ΡΠΊΠ°Ρ. ΠΠΎΠ²Π΅ΡΡ Π½ΠΎΡΡΡ Π·Π°ΡΠΈΡΠ°Π΅ΡΡΡ.
Π‘Π»ΠΎΠΆΠ½Π΅Π΅ Π²ΡΠ΅Π³ΠΎ ΠΈΠ·Π³ΠΎΡΠ°Π²Π»ΠΈΠ²Π°ΡΡ ΠΎΡΠ»ΠΈΠ²ΠΊΠΈ Ρ ΠΏΡΡΡΠΎΡΠ°ΠΌΠΈ Π²Π½ΡΡΡΠΈ.
ΠΡΠΏΠΎΠ»ΡΠ·ΡΠ΅ΠΌΡΠ΅ ΠΌΠ°ΡΠ΅ΡΠΈΠ°Π»Ρ
ΠΠ° ΠΏΡΠΎΡΡΠΆΠ΅Π½ΠΈΠΈ Π²ΡΠ΅ΠΉ ΠΈΡΡΠΎΡΠΈΠΈ ΡΠ΅Π»ΠΎΠ²Π΅ΠΊ ΠΈΡΠΏΠΎΠ»ΡΠ·ΠΎΠ²Π°Π» ΡΠ°Π·Π»ΠΈΡΠ½ΡΠ΅ ΠΌΠ΅ΡΠ°Π»Π»Ρ Π΄Π»Ρ Ρ ΡΠ΄ΠΎΠΆΠ΅ΡΡΠ²Π΅Π½Π½ΠΎΠΉ ΠΎΡΠ»ΠΈΠ²ΠΊΠΈ. ΠΠ·Π½Π°ΡΠ°Π»ΡΠ½ΠΎ Π³Π»Π°Π²Π½ΡΠΌΠΈ ΡΠΎΠ΅Π΄ΠΈΠ½Π΅Π½ΠΈΡΠΌΠΈ ΠΌΠ΅ΡΠ°Π»Π»ΠΎΠ² Π΄Π»Ρ Π΄Π΅ΠΊΠΎΡΠ°ΡΠΈΠ²Π½ΠΎΠ³ΠΎ Π»ΠΈΡΡΡ ΡΡΠΈΡΠ°Π»ΠΈΡΡ ΡΠΏΠ»Π°Π²Ρ, Π² ΠΊΠΎΡΠΎΡΡΡ ΠΏΡΠ΅ΠΎΠ±Π»Π°Π΄Π°Π»Π° ΠΌΠ΅Π΄Ρ. ΠΠ°ΡΠΈΠ½Π°Ρ Ρ 19 Π²Π΅ΠΊΠ°, Π½Π°ΡΠ°Π»ΠΈ ΠΈΡΠΏΠΎΠ»ΡΠ·ΠΎΠ²Π°ΡΡΡΡ ΡΠΎΠ΅Π΄ΠΈΠ½Π΅Π½ΠΈΡ Ρ ΠΏΡΠ΅ΠΎΠ±Π»Π°Π΄Π°Π½ΠΈΠ΅ΠΌ ΡΠΈΠ½ΠΊΠ° ΠΈ ΡΠ²ΠΈΠ½ΡΠ°. Π§ΡΠ³ΡΠ½Π½ΠΎΠ΅ Ρ ΡΠ΄ΠΎΠΆΠ΅ΡΡΠ²Π΅Π½Π½ΠΎΠ΅ Π»ΠΈΡΡΠ΅ ΠΏΠΎΡΠ²ΠΈΠ»ΠΎΡΡ ΡΡΡΡ ΠΏΠΎΠ·ΠΆΠ΅. ΠΠ° ΡΠ΅Π³ΠΎΠ΄Π½ΡΡΠ½ΠΈΠΉ ΠΌΠΎΠΌΠ΅Π½Ρ Π² ΡΡΠΎΠΌ ΠΏΡΠΎΡΠ΅ΡΡΠ΅ ΠΈΡΠΏΠΎΠ»ΡΠ·ΡΠ΅ΡΡΡ Π½Π΅ΡΠΆΠ°Π²Π΅ΡΡΠ°Ρ ΡΡΠ°Π»Ρ ΠΈ Π°Π»ΡΠΌΠΈΠ½ΠΈΠΉ.
Π‘Π΅ΡΡΠΉ ΡΡΠ³ΡΠ½
ΠΠΎΠΌΠΈΠΌΠΎ ΠΈΡΠΏΠΎΠ»ΡΠ·ΠΎΠ²Π°Π½ΠΈΡ ΠΆΠ΅Π»Π΅Π·Π° ΠΈ Π±ΡΠΎΠ½Π·Ρ Π² Ρ ΡΠ΄ΠΎΠΆΠ΅ΡΡΠ²Π΅Π½Π½ΠΎΠΌ Π»ΠΈΡΡΠ΅ ΠΈ ΠΈΠ·Π³ΠΎΡΠΎΠ²Π»Π΅Π½ΠΈΠΈ ΡΠ°Π·Π»ΠΈΡΠ½ΡΡ ΠΏΡΠ΅Π΄ΠΌΠ΅ΡΠΎΠ² Π±ΠΎΠ»ΡΡΡΡ ΠΏΠΎΠΏΡΠ»ΡΡΠ½ΠΎΡΡΡ ΠΏΠΎΠ»ΡΡΠΈΠ» ΡΡΠ³ΡΠ½. ΠΠ· Π½Π΅Π³ΠΎ ΠΈΠ·Π³ΠΎΡΠ°Π²Π»ΠΈΠ²Π°Π»ΠΈ ΠΏΡΡΠΊΠΈ, ΡΠ΄ΡΠ°, ΠΏΠ°ΠΌΡΡΠ½ΠΈΠΊΠΈ, ΡΠΎΠ½ΡΠ°Π½Ρ. ΠΠ΄Π½Π°ΠΊΠΎ Π² ΡΠ°Π·Π²ΠΈΡΠΈΠΈ Π΄Π΅ΠΊΠΎΡΠ°ΡΠΈΠ²Π½ΠΎΠ³ΠΎ Π½Π°ΠΏΡΠ°Π²Π»Π΅Π½ΠΈΡ Π² ΠΌΠ΅ΡΠ°Π»Π»ΠΎΠΎΠ±ΡΠ°Π±ΠΎΡΠΊΠ΅ ΡΡΠ³ΡΠ½ ΠΏΠΎΠ»ΡΡΠΈΠ» ΠΏΠΎΠΏΡΠ»ΡΡΠ½ΠΎΡΡΡ ΡΠΎΠ»ΡΠΊΠΎ Π²ΠΎ Π²ΡΠΎΡΠΎΠΉ ΠΏΠΎΠ»ΠΎΠ²ΠΈΠ½Π΅ 19 Π²Π΅ΠΊΠ°.
Π‘Π°ΠΌΡΠΌ ΡΠ°ΡΠΏΡΠΎΡΡΡΠ°Π½ΡΠ½Π½ΡΠΌ ΡΠΏΠ»Π°Π²ΠΎΠΌ ΠΏΡΠΈ ΠΈΠ·Π³ΠΎΡΠΎΠ²Π»Π΅Π½ΠΈΠΈ ΡΠΊΡΠ»ΡΠΏΡΡΡ ΡΠ²Π»ΡΠ»ΡΡ ΡΠ΅ΡΡΠΉ ΡΡΠ³ΡΠ½. ΠΠ½ ΠΎΠ±Π»Π°Π΄Π°Π» ΡΠ°ΠΊΠΈΠΌΠΈ ΠΏΡΠ΅ΠΈΠΌΡΡΠ΅ΡΡΠ²Π°ΠΌΠΈ:
- Π₯ΠΎΡΠΎΡΠ°Ρ ΡΠ΅ΠΊΡΡΠ΅ΡΡΡ Π±Π»Π°Π³ΠΎΠ΄Π°ΡΡ Π΄ΠΎΠ±Π°Π²Π»Π΅Π½ΠΈΡ ΡΠΎΡΡΠΎΡΠ°.
- ΠΠΈΠ·ΠΊΠ°Ρ ΡΡΠΎΠΈΠΌΠΎΡΡΡ ΠΌΠ°ΡΠ΅ΡΠΈΠ°Π»Π°.
- ΠΡΠΈΠ²Π»Π΅ΠΊΠ°ΡΠ΅Π»ΡΠ½ΡΠΉ Π²Π½Π΅ΡΠ½ΠΈΠΉ Π²ΠΈΠ΄.
ΠΠ΄Π½Π°ΠΊΠΎ ΡΠΎΡΡΠΎΡ Π΄Π΅Π»Π°Π» ΠΌΠ΅ΡΠ°Π»Π» Π±ΠΎΠ»Π΅Π΅ Ρ ΡΡΠΏΠΊΠΈΠΌ.
ΠΡΠΈΠΌΠ΅Π½ΡΠ΅ΠΌΡΠ΅ ΠΌΠ΅ΡΠΎΠ΄Ρ
ΠΠ»Π°ΡΡΠΈΡΠ΅ΡΠΊΠΎΠ΅ ΠΈΡΠΊΡΡΡΡΠ²ΠΎ ΠΎΡΠ»ΠΈΠ²ΠΊΠΈ Π½Π΅ ΠΏΠΎΡΠ΅ΡΡΠ»ΠΎ ΠΏΠΎΠΏΡΠ»ΡΡΠ½ΠΎΡΡΡ Ρ ΡΠ΅ΡΠ΅Π½ΠΈΠ΅ΠΌ Π²ΡΠ΅ΠΌΠ΅Π½ΠΈ. ΠΡΠ½ΠΎΠ²Π½ΡΠΌΠΈ ΡΠ΅Ρ Π½ΠΎΠ»ΠΎΠ³ΠΈΡΠΌΠΈ ΡΠ²Π»ΡΡΡΡΡ ΠΎΡΠ»ΠΈΠ²ΠΊΠ° Π² ΡΠΎΡΠΌΡ, ΠΈΠ·Π³ΠΎΡΠ°Π²Π»ΠΈΠ²Π°Π΅ΠΌΡΠ΅ Π² Π·Π΅ΠΌΠ»Π΅ ΠΈΠ»ΠΈ ΠΎΡΠ»ΠΈΠ²ΠΊΠ° ΠΏΠΎ ΡΠΆΠ΅ Π³ΠΎΡΠΎΠ²ΡΠΌ ΠΏΡΠ΅Π΄ΠΌΠ΅ΡΠ°ΠΌ. ΠΠ° ΡΠ΅Π³ΠΎΠ΄Π½ΡΡΠ½ΠΈΠΉ Π΄Π΅Π½Ρ ΡΡΠΈ Π΄Π²Π° ΠΌΠ΅ΡΠΎΠ΄Π° ΠΏΡΠΎΠ΄ΠΎΠ»ΠΆΠ°ΡΡ ΡΠ²ΠΎΡ ΡΠΎΠΏΠ΅ΡΠ½ΠΈΡΠ΅ΡΡΠ²ΠΎ.

ΠΠΈΡΡΠ΅ Π² Π·Π΅ΠΌΠ»Ρ
ΠΠΎΠΆΠ½ΠΎ ΠΎΡΠ»ΠΈΠ²Π°ΡΡ Π±ΡΠ΄ΡΡΠΈΠ΅ ΡΠΊΡΠ»ΡΠΏΡΡΡΡ Π² ΡΠΎΡΠΌΡ ΠΈΠ· Π·Π΅ΠΌΠ»ΠΈ, ΠΏΠ΅ΡΠΊΠ° ΠΈΠ»ΠΈ Π³Π»ΠΈΠ½Ρ. ΠΠ»Π°Π²Π½Π°Ρ Π·Π°Π΄Π°ΡΠ° Π·Π°ΠΊΠ»ΡΡΠ°Π΅ΡΡΡ Π² ΡΠΎΠΌ, ΡΡΠΎΠ±Ρ ΠΏΠΎΠ»ΡΡΠΈΡΡ ΠΎΡΠΏΠ΅ΡΠ°ΡΠΎΠΊ ΠΎΡ ΡΠ°Π±Π»ΠΎΠ½Π° Π½Π° ΡΠΌΠ΅ΡΠΈ. Π Π΄Π°Π»ΡΠ½Π΅ΠΉΡΠ΅ΠΌ Ρ ΠΏΠΎΠΌΠΎΡΡΡ ΡΡΠ°ΠΌΠ±ΠΎΠ²ΠΊΠΈ ΠΈΠ·ΠΌΠ΅Π½ΡΡΡΡΡ Π΅Ρ ΠΊΠ°ΡΠ΅ΡΡΠ²Π°. Π€ΠΎΡΠΌΠΈΡΡΡΡΡΡ ΠΊΠ°Π½Π°Π»Ρ Π΄Π»Ρ Π·Π°ΠΏΠΎΠ»Π½Π΅Π½ΠΈΡ ΡΠΎΡΠΌΡ ΡΠ°ΡΠΏΠ»Π°Π²Π»Π΅Π½Π½ΡΠΌ ΠΌΠ΅ΡΠ°Π»Π»ΠΎΠΌ. ΠΡΠΎΡ ΡΠΏΠΎΡΠΎΠ± ΠΎΡΠ»ΠΈΡΠ°Π΅ΡΡΡ ΡΠ²ΠΎΠ΅ΠΉ ΠΏΡΠΎΡΡΠΎΡΠΎΠΉ ΠΈ Π½ΠΈΠ·ΠΊΠΎΠΉ ΡΠ΅Π±Π΅ΡΡΠΎΠΈΠΌΠΎΡΡΡΡ.
ΠΠΎ Π²ΡΠΏΠ»Π°Π²Π»ΡΠ΅ΠΌΡΠΌ ΠΌΠΎΠ΄Π΅Π»ΡΠΌ
ΠΡΠ΅Π²Π½ΠΈΠΉ ΡΠΏΠΎΡΠΎΠ± Π»ΠΈΡΡΡ, ΠΊΠΎΡΠΎΡΡΠΉ ΠΏΠΎΠ΄ΡΠ°Π·ΡΠΌΠ΅Π²Π°Π» ΠΏΠΎΠ΄ ΡΠΎΠ±ΠΎΠΉ ΠΎΡΠ»ΠΈΠ²ΠΊΡ ΠΏΠΎ ΡΠΎΡΠΌΠ°ΠΌ, ΡΠ½ΡΡΡΠΌ Ρ Π³ΠΎΡΠΎΠ²ΡΡ ΠΏΡΠ΅Π΄ΠΌΠ΅ΡΠΎΠ² ΠΈΠ»ΠΈ ΠΎΡΡΠΆΠΈΡ. ΠΠ»Ρ ΡΠΎΠ·Π΄Π°Π½ΠΈΡ ΡΠΎΡΠΌ ΠΈΡΠΏΠΎΠ»ΡΠ·ΠΎΠ²Π°Π»ΠΈ Π²ΠΎΡΠΊ, ΡΠ΅Π·ΠΈΠ½Ρ, Π³ΠΈΠΏΡ.
ΠΡΠ°ΠΏΡ ΠΏΡΠΎΠ²Π΅Π΄Π΅Π½ΠΈΡ ΡΠ°Π±ΠΎΡ Ρ Π²ΠΎΡΠΊΠΎΠΌ:
- ΠΠ·Π½Π°ΡΠ°Π»ΡΠ½ΠΎ ΡΠΎΠ·Π΄Π°ΡΡΡΡ ΡΠΊΡΠ»ΡΠΏΡΡΡΠ° ΠΈΠ»ΠΈ ΠΏΡΠ΅Π΄ΠΌΠ΅Ρ Ρ ΡΠΎΡΠ½ΡΠΌΠΈ ΡΠ°Π·ΠΌΠ΅ΡΠ°ΠΌΠΈ ΠΈΠ· Π²ΠΎΡΠΊΠ°.
- ΠΠ·Π³ΠΎΡΠ°Π²Π»ΠΈΠ²Π°Π΅ΡΡΡ ΡΠΎΡΠΌΠ°, Ρ ΠΏΠΎΠΌΠΎΡΡΡ Π½Π°Π½Π΅ΡΠ΅Π½ΠΈΡ Π³Π»ΠΈΠ½ΡΠ½ΠΎΠΉ ΡΠΌΠ΅ΡΠΈ Π½Π° ΠΏΠΎΠ²Π΅ΡΡ Π½ΠΎΡΡΡ Π²ΠΎΡΠΊΠ°.
- Π€ΠΎΡΠΌΠ° Π·Π°ΠΏΠ΅ΠΊΠ°Π΅ΡΡΡ Π² ΠΏΠ΅ΡΠΈ Π΄ΠΎ ΠΏΠΎΠ»Π½ΠΎΠ³ΠΎ ΠΎΡΠ²Π΅ΡΠ΄Π΅Π²Π°Π½ΠΈΡ. ΠΠΎΡΠΊ Π²ΡΡΠ΅ΠΊΠ°Π΅Ρ ΠΈΠ· Π½Π΅Ρ ΠΏΠΎ ΠΈΠ·Π½Π°ΡΠ°Π»ΡΠ½ΠΎ ΠΏΠΎΠ΄Π³ΠΎΡΠΎΠ²Π»Π΅Π½Π½ΡΠΌ ΠΊΠ°Π½Π°Π»Π°ΠΌ.
- ΠΠ»Π°Π²ΠΊΠ° ΠΌΠ΅ΡΠ°Π»Π»Π° ΠΈ ΠΏΠ΅ΡΠ΅Π»ΠΈΠ²Π°Π½ΠΈΠ΅ Π΅Π³ΠΎ Π² Π³ΠΎΡΠΎΠ²ΡΡ ΡΠΎΡΠΌΡ.
- Π£Π΄Π°Π»Π΅Π½ΠΈΠ΅ Π²Π½Π΅ΡΠ½Π΅Π³ΠΎ ΠΊΠ°ΡΠΊΠ°ΡΠ° ΠΏΠΎΡΠ»Π΅ Π·Π°ΡΡΡΠ²Π°Π½ΠΈΡ ΠΌΠ΅ΡΠ°Π»Π»Π°.
ΠΠΎΡΠ»Π΅ ΠΈΠ·Π³ΠΎΡΠΎΠ²Π»Π΅Π½ΠΈΡ ΡΠΊΡΠ»ΡΠΏΡΡΡΡ Π΅Ρ ΠΏΠΎΠ²Π΅ΡΡ
Π½ΠΎΡΡΡ Π΄ΠΎΠΏΠΎΠ»Π½ΠΈΡΠ΅Π»ΡΠ½ΠΎ ΡΠ»ΠΈΡΡΠ΅ΡΡΡ ΠΈ ΠΎΠ±ΡΠ°Π±Π°ΡΡΠ²Π°Π΅ΡΡΡ.
Π₯ΡΠ΄ΠΎΠΆΠ΅ΡΡΠ²Π΅Π½Π½ΠΎΠ΅ Π»ΠΈΡΡΠ΅ ΠΈΠ· ΡΡΠ³ΡΠ½Π° Π°ΠΊΡΠΈΠ²Π½ΠΎ ΠΈΡΠΏΠΎΠ»ΡΠ·ΡΠ΅ΡΡΡ Π΄Π»Ρ ΡΠΎΠ·Π΄Π°Π½ΠΈΡ ΡΠΊΡΠ»ΡΠΏΡΡΡ ΠΈ ΡΠ°Π·Π»ΠΈΡΠ½ΡΡ Π΄Π΅ΡΠ°Π»Π΅ΠΉ. ΠΡΠΎΡ ΠΌΠ΅ΡΠ°Π»Π» ΠΎΠ±Π»Π°Π΄Π°Π΅Ρ ΠΌΠ½ΠΎΠΆΠ΅ΡΡΠ²ΠΎΠΌ ΠΏΡΠ΅ΠΈΠΌΡΡΠ΅ΡΡΠ² ΠΈ Π½Π΅Π±ΠΎΠ»ΡΡΠΎΠΉ ΡΠ΅Π½ΠΎΠΉ, Π±Π»Π°Π³ΠΎΠ΄Π°ΡΡ ΡΠ΅ΠΌΡ ΠΎΠ½ ΡΠ΅Π½ΠΈΡΡΡ ΡΡΠ΅Π΄ΠΈ ΠΌΠ°ΡΡΠ΅ΡΠΎΠ² ΠΌΠ΅ΡΠ°Π»Π»ΠΎΠΎΠ±ΡΠ°Π±ΠΎΡΠΊΠΈ.
ΠΠΏΡΠ΅Π΄Π΅Π»Π΅Π½ΠΈΡ Π»ΠΈΡΡΡ Π² Π·Π΅ΠΌΠ»Ρ ΠΠΈΡΠ΅ΠΉΠ½Π°Ρ ΠΏΡΠΎΠ΄ΡΠΊΡΠΈΡ ΠΠΈΡΡΠ΅ Π² ΠΏΠ΅ΡΡΠ°Π½ΡΠ΅ ΡΠΎΡΠΌΡ β ΠΌΠ΅ΡΠΎΠ΄ Π»ΠΈΡΡΡ ΠΌΠ΅ΡΠ°Π»Π»ΠΎΠ² ΠΈ ΡΠΏΠ»Π°Π²ΠΎΠ², ΠΏΡΠΈ ΠΊΠΎΡΠΎΡΠΎΠΌ ΡΠ°ΡΠΏΠ»Π°Π²Π»Π΅Π½Π½ΡΠΉ ΠΌΠ΅ΡΠ°Π»Π» Π·Π°Π»ΠΈΠ²Π°Π΅ΡΡΡ Π² ΡΠΎΡΠΌΡ ΡΠ΄Π΅Π»Π°Π½Π½ΡΡ ΠΈΠ· ΠΏΠ»ΠΎΡΠ½ΠΎ ΡΡΡΠ°ΠΌΠ±ΠΎΠ²Π°Π½Π½ΠΎΠ³ΠΎ ΠΏΠ΅ΡΠΊΠ°. ΠΠ»Ρ ΡΠ²ΡΠ·ΠΈ ΠΏΠ΅ΡΡΠΈΠ½ΠΎΠΊ ΠΌΠ΅ΠΆΠ΄Ρ ΡΠΎΠ±ΠΎΠΉ, ΠΏΠ΅ΡΠΎΠΊ ΡΠΌΠ΅ΡΠΈΠ²Π°ΡΡ Ρ Π³Π»ΠΈΠ½ΠΎΠΉ, Π²ΠΎΠ΄ΠΎΠΉ ΠΈ Π΄ΡΡΠ³ΠΈΠΌΠΈ ΡΠ²ΡΠ·ΡΡΡΠΈΠΌΠΈ ΠΌΠ°ΡΠ΅ΡΠΈΠ°Π»Π°ΠΌΠΈ. ΠΡΡΡ ΡΠ΅ΡΡΡ ΡΠ°Π³ΠΎΠ² Π² ΡΡΠΎΠΌ ΠΏΡΠΎΡΠ΅ΡΡΠ΅: -Π£Π΄Π°Π»ΠΈΡΡ ΠΈΠ· ΠΎΠΏΠΎΠΊΠΈ ΠΌΠΎΠ΄Π΅Π»Ρ ΠΈ ΡΠΎΠ΅Π΄ΠΈΠ½ΠΈΡΡ ΠΏΠΎΠ»ΡΡΠΎΡΠΌΡ. -ΠΠ°ΠΏΠΎΠ»Π½ΠΈΡΡ ΠΏΠΎΠ»ΠΎΡΡΡ ΡΠΎΡΠΌΡ ΡΠ°ΡΠΏΠ»Π°Π²Π»Π΅Π½Π½ΡΠΌ ΠΌΠ΅ΡΠ°Π»Π»ΠΎΠΌ. -ΠΡΠ΄Π΅ΡΠΆΠ°ΡΡ Π·Π°ΡΡΡΠ²Π°ΡΡΠΈΠΉ ΠΌΠ΅ΡΠ°Π»Π» Π² ΠΎΠΏΠΎΠΊΠ°Ρ ΡΠΎΠ³Π»Π°ΡΠ½ΠΎ ΡΠ΅Ρ Π½ΠΎΠ»ΠΎΠ³ΠΈΠΈ. -ΠΡΠ±ΠΈΡΡ ΠΎΡΠ»ΠΈΠ²ΠΊΡ ΠΈ ΠΎΡΠ²ΠΎΠ±ΠΎΠ΄ΠΈΡΡ ΠΎΡ Π»ΠΈΡΠ½ΠΈΠΊΠΎΠ² ΠΈ Π²ΡΠΏΠΎΡΠΎΠ². ΠΠΎ ΡΠ΅ΡΡΠ΅ΠΆΠ°ΠΌ ΠΈ Π»ΠΈΡΠ΅ΠΉΠ½ΡΠΌ ΡΠ΅Ρ
Π½ΠΎΠ»ΠΎΠ³ΠΈΡΠΌ, ΡΠ°Π·ΡΠ°Π±ΠΎΡΠ°Π½Π½ΡΡ
ΡΠ΅Ρ
Π½ΠΎΠ»ΠΎΠ³ΠΎΠΌ ΠΈΠ»ΠΈ ΠΊΠΎΠ½ΡΡΡΡΠΊΡΠΎΡΠΎΠΌ, ΠΎΠΏΡΡΠ½ΡΠΉ ΠΌΠΎΠ΄Π΅Π»ΡΡΠΈΠΊ ΠΈΠ·Π³ΠΎΡΠ°Π²Π»ΠΈΠ²Π°Π΅Ρ ΠΌΠΎΠ΄Π΅Π»Ρ Π΄Π΅ΡΠ°Π»ΠΈ ΠΈΠ· Π΄Π΅ΡΠ΅Π²Π°, ΠΌΠ΅ΡΠ°Π»Π»Π° ΠΈΠ»ΠΈ ΠΏΠ»Π°ΡΡΠΌΠ°ΡΡΡ ΠΈΠ»ΠΈ ΠΏΠ΅Π½ΠΎΠΏΠΎΠ»ΠΈΡΡΠΈΡΠΎΠ»Π°. ΠΠ΅ΡΠ°Π»Π» Π² ΠΏΡΠΎΡΠ΅ΡΡΠ΅ ΠΎΡ
Π»Π°ΠΆΠ΄Π΅Π½ΠΈΡ Π΄Π°ΡΡ ΡΡΠ°Π΄ΠΊΡ, ΠΈ ΠΊΡΠΈΡΡΠ°Π»Π»ΠΈΠ·Π°ΡΠΈΡ ΠΌΠΎΠΆΠ΅Ρ Π±ΡΡΡ Π½Π΅ΠΎΠ΄Π½ΠΎΡΠΎΠ΄Π½ΠΎΠΉ ΠΈΠ·-Π·Π° Π½Π΅ΡΠ°Π²Π½ΠΎΠΌΠ΅ΡΠ½ΠΎΠ³ΠΎ ΠΎΡ
Π»Π°ΠΆΠ΄Π΅Π½ΠΈΡ. Π’Π°ΠΊΠΈΠΌ ΠΎΠ±ΡΠ°Π·ΠΎΠΌ, ΠΌΠΎΠ΄Π΅Π»Ρ Π΄ΠΎΠ»ΠΆΠ½Π° Π±ΡΡΡ ΡΡΡΡ Π±ΠΎΠ»ΡΡΠ΅, ΡΠ΅ΠΌ Π³ΠΎΡΠΎΠ²Π°Ρ ΠΎΡΠ»ΠΈΠ²ΠΊΠ°, Ρ ΠΏΡΠΈΠΌΠ΅Π½Π΅Π½ΠΈΠ΅ΠΌ, ΡΠ°ΠΊ Π½Π°Π·ΡΠ²Π°Π΅ΠΌΠΎΠ³ΠΎ, ΠΊΠΎΡΡΡΠΈΡΠΈΠ΅Π½ΡΠ° ΡΡΠ°Π΄ΠΊΠΈ ΠΌΠ΅ΡΠ°Π»Π»Π°. Π Π°Π·Π»ΠΈΡΠ½ΡΠ΅ ΡΡΠ°Π΄ΠΎΡΠ½ΡΠ΅ ΠΊΠΎΡΡΡΠΈΡΠΈΠ΅Π½ΡΡ ΠΈΡΠΏΠΎΠ»ΡΠ·ΡΡΡΡΡ Π΄Π»Ρ ΡΠ°Π·Π»ΠΈΡΠ½ΡΡ
ΠΌΠ΅ΡΠ°Π»Π»ΠΎΠ². ΠΠΎΠ΄Π΅Π»ΠΈ Π² ΠΏΡΠΎΡΠ΅ΡΡΠ΅ ΡΠΎΡΠΌΠΎΠ²ΠΊΠΈ ΠΎΡΡΠ°Π²Π»ΡΡΡ Π² ΠΏΠ΅ΡΠΊΠ΅ ΠΏΠΎΠ»ΠΎΡΡΠΈ-ΠΎΡΠΏΠ΅ΡΠ°ΡΠΊΠΈ Π² ΡΠΎΡΠΌΠ΅, Π² ΠΊΠΎΡΠΎΡΡΠ΅ ΠΏΠΎΠΌΠ΅ΡΠ°ΡΡ ΡΡΠ΅ΡΠΆΠ΅Π½Ρ ΠΈΠ· ΠΏΠ΅ΡΠΊΠ°. Π’Π°ΠΊΠΈΠ΅ ΡΡΠ΅ΡΠΆΠ½ΠΈ ΠΈΠ½ΠΎΠ³Π΄Π° ΡΡΠΈΠ»ΠΈΠ²Π°Π΅ΡΡΡ ΠΏΡΠΎΠ²ΠΎΠ»ΠΎΡΠ½ΠΎΠΉ Π°ΡΠΌΠ°ΡΡΡΠΎΠΉ, ΠΊΠΎΡΠΎΡΡΠ΅ ΠΈΡΠΏΠΎΠ»ΡΠ·ΡΡΡΡΡ Π΄Π»Ρ ΡΠΎΠ·Π΄Π°Π½ΠΈΡ ΠΏΠΎΠ»ΠΎΡΡΠ΅ΠΉ, ΠΊΠΎΡΠΎΡΡΠ΅ Π½Π΅ ΠΌΠΎΠ³ΡΡ Π±ΡΡΡ ΡΡΠΎΡΠΌΠΈΡΠΎΠ²Π°Π½Ρ ΠΎΡΠ½ΠΎΠ²Π½ΠΎΠΉ ΠΌΠΎΠ΄Π΅Π»ΡΡ, Π½Π°ΠΏΡΠΈΠΌΠ΅Ρ, Π²Π½ΡΡΡΠ΅Π½Π½ΠΈΠ΅ ΠΏΡΠΎΡ
ΠΎΠ΄Ρ ΠΊΠ»Π°ΠΏΠ°Π½ΠΎΠ² ΠΈΠ»ΠΈ ΠΌΠ΅ΡΡΠ° ΠΎΡ
Π»Π°ΠΆΠ΄Π΅Π½ΠΈΡ Π² Π±Π»ΠΎΠΊΠ°Ρ
Π΄Π²ΠΈΠ³Π°ΡΠ΅Π»Π΅ΠΉ. ΠΠΏΠΎΠΊΠΈ Π΄Π»Ρ ΡΠΎΡΠΌΠΎΠ²ΠΎΡΠ½ΡΡ
ΠΌΠ°ΡΠ΅ΡΠΈΠ°Π»ΠΎΠ² ΠΡ
Π»Π°ΠΆΠ΄Π΅Π½ΠΈΠ΅ ΠΌΠ΅ΡΠ°Π»Π»Π° ΠΡΠΎΠΈΠ·Π²ΠΎΠ΄ΡΡΠ²ΠΎ Π Π°Π·ΡΠ°Π±ΠΎΡΠΊΠ° ΡΠ΅Ρ
Π½ΠΎΠ»ΠΎΠ³ΠΈΠΈ Π‘ΠΏΠΎΡΠΎΠ±Ρ Π»ΠΈΡΡΡ Π² Π·Π΅ΠΌΠ»Ρ Π’Π΅Ρ Π½ΠΎΠ»ΠΎΠ³ΠΈΡ ΠΠ‘Π‘ (ΠΆΠΈΠ΄ΠΊΠΎ-ΡΡΠ΅ΠΊΠΎΠ»ΡΠ½Π°Ρ ΡΠΌΠ΅ΡΡ) ΠΡΠ° ΡΠ΅Ρ
Π½ΠΎΠ»ΠΎΠ³ΠΈΡ ΡΠΎΡΡΠΎΠΈΡ Π² ΡΠ»Π΅Π΄ΡΡΡΠ΅ΠΌ: Π’ΠΎΡΠ½ΠΎΡΡΡ Π»ΠΈΡΡΡ Π½Π°ΠΏΡΡΠΌΡΡ ΡΠ²ΡΠ·Π°Π½Π° Ρ ΡΠΈΠΏΠΎΠΌ ΡΠΎΡΠΌΠΎΠ²ΠΎΡΠ½ΠΎΠΉ ΡΠΌΠ΅ΡΠΈ ΠΈ ΡΠΎΡΠΌΠΎΠ²ΠΊΠΈ. Π‘ΡΡΡΠ΅ ΡΠΎΡΠΌΡ ΡΠΎΠ·Π΄Π°ΡΡ Π½Π° ΠΏΠΎΠ²Π΅ΡΡ Π½ΠΎΡΡΠΈ ΠΎΡΠ»ΠΈΠ²ΠΊΠΈ ΠΏΠΎΠ²ΡΡΠ΅Π½Π½ΡΡ ΡΠ΅ΡΠΎΡ ΠΎΠ²Π°ΡΠΎΡΡΡ. ΠΠΎΡΡΠΎΠΌΡ Π»ΠΈΡΡΠ΅ Π² Π·Π΅ΠΌΠ»Ρ ΠΌΠΎΠΆΠ½ΠΎ ΡΡΠ°Π·Ρ ΠΎΡΠ»ΠΈΡΠΈΡΡ ΠΎΡ Π»ΠΈΡΡΡ ΠΏΠΎ ΠΠ‘Π‘ ΠΈ Π₯Π’Π‘. ΠΠΈΡΡΠ΅ Π² ΡΠΎΡΠΌΡ ΠΈΠ· ΠΌΠ΅Π»ΠΊΠΎΠ³ΠΎ ΠΏΠ΅ΡΠΊΠ° Π·Π½Π°ΡΠΈΡΠ΅Π»ΡΠ½ΠΎ ΡΠΈΡΠ΅ ΠΈ ΠΌΠ΅Π½Π΅Π΅ ΡΠ΅ΡΠΎΡ ΠΎΠ²Π°ΡΠΎ. Π’Π΅Ρ Π½ΠΎΠ»ΠΎΠ³ΠΈΡ ΠΠ‘Π‘ ΠΏΠΎΠ·Π²ΠΎΠ»ΡΠ΅Ρ ΠΈΠ·Π³ΠΎΡΠ°Π²Π»ΠΈΠ²Π°ΡΡ ΠΎΡΠ»ΠΈΠ²ΠΊΠΈ Ρ Π³Π»Π°Π΄ΠΊΠΎΠΉ ΠΏΠΎΠ²Π΅ΡΡ Π½ΠΎΡΡΠΈ, ΠΎΡΠΎΠ±Π΅Π½Π½ΠΎ ΠΏΡΠΈ ΠΈΡΠΏΠΎΠ»ΡΠ·ΠΎΠ²Π°Π½ΠΈΠΈ ΠΏΠ»Π°ΡΡΠΈΠΊΠΎΠ²ΡΡ ΠΌΠΎΠ΄Π΅Π»Π΅ΠΉ. Π ΠΎΡΠ΄Π΅Π»ΡΠ½ΡΡ ΡΠ»ΡΡΠ°ΡΡ , Π½Π°ΠΏΡΠΈΠΌΠ΅Ρ ΠΏΡΠΈ Π»ΠΈΡΡΠ΅ ΠΊΠΎΡΠΏΡΡΠ½ΡΡ Π΄Π΅ΡΠ°Π»Π΅ΠΉ, ΠΌΠΎΠΆΠ½ΠΎ ΠΎΠ±ΠΎΠΉΡΠΈΡΡ Π΄Π°ΠΆΠ΅ Π±Π΅Π· ΠΌΠ΅Ρ Π°Π½ΠΈΡΠ΅ΡΠΊΠΎΠΉ ΠΎΠ±ΡΠ°Π±ΠΎΡΠΊΠΈ Π½Π° Π±ΠΎΠ»ΡΡΠΈΡ ΠΏΠΎΠ²Π΅ΡΡ Π½ΠΎΡΡΡΡ β ΡΡΠΎ ΠΏΠΎΠ·Π²ΠΎΠ»ΡΠ΅Ρ ΠΎΡΠ»ΠΈΠ²Π°ΡΡ ΠΊΡΡΠΏΠ½ΠΎΠ³Π°Π±Π°ΡΠΈΡΠ½ΡΠ΅ ΡΡΠ³ΡΠ½Π½ΡΠ΅ Π±Π»ΠΎΠΊΠΈ ΡΠΈΠ»ΠΈΠ½Π΄ΡΠΎΠ². ΠΡΡΠ°ΡΠΊΠΈ ΠΏΡΠΈΠ³ΠΎΡΠ΅Π²ΡΠ΅ΠΉ ΠΊ ΠΎΡΠ»ΠΈΠ²ΠΊΠ΅ ΡΠΎΡΠΌΠΎΠ²ΠΎΡΠ½ΠΎΠΉ ΡΠΌΠ΅ΡΠΈ ΡΠ΄Π°Π»ΡΡΡΡΡ Π΄ΡΠΎΠ±Π΅ΡΡΡΡΠΉΠ½ΠΎΠΉ ΠΎΠ±ΡΠ°Π±ΠΎΡΠΊΠΎΠΉ. Π₯ΠΎΠ»ΠΎΠ΄Π½ΠΎ ΡΠ²Π΅ΡΠ΄Π΅ΡΡΠ°Ρ ΡΠΌΠ΅ΡΡ (Π»ΠΈΡΡΠ΅ Π² Π₯Π’Π‘) Π€ΠΎΡΠΌΠΎΠ²ΠΊΠ° Π₯Π’Π‘ ΠΠΎΡ ΠΎΠΆΠΈΠ΅ ΡΡΠ°ΡΡΠΈ: Π‘Π»Π΅Π΄ΡΡΡΠΈΠ΅ ΡΡΠ°ΡΡΠΈ: |
ΠΡΠ½ΠΎΠ²Π½ΡΠ΅ Π²ΠΈΠ΄Ρ Π»ΠΈΡΡΡ Π΄Π»Ρ ΠΈΠ·Π³ΠΎΡΠΎΠ²Π»Π΅Π½ΠΈΡ ΠΎΡΠ»ΠΈΠ²ΠΎΠΊ armtorg.ru
ΠΠΈΡΡΡ Π² ΠΏΠ΅ΡΡΠ°Π½ΡΠ΅ ΡΠΎΡΠΌΡ
ΠΠΈΡΡΡ Π² ΠΏΠ΅ΡΡΠ°Π½ΡΠ΅ ΡΠΎΡΠΌΡΒ β Π΄Π΅ΡΡΠ²ΡΠΉ, ΡΠ°ΠΌΡΠΉ Π³ΡΡΠ±ΡΠΉ, Π½ΠΎ ΡΠ°ΠΌΡΠΉ ΠΌΠ°ΡΡΠΎΠ²ΡΠΉ (Π΄ΠΎ 75-80Β % ΠΏΠΎ ΠΌΠ°ΡΡΠ΅ ΠΏΠΎΠ»ΡΡΠ°Π΅ΠΌΡΡ Π² ΠΌΠΈΡΠ΅ ΠΎΡΠ»ΠΈΠ²ΠΎΠΊ) Π²ΠΈΠ΄ Π»ΠΈΡΡΡ. ΠΠ½Π°ΡΠ°Π»Π΅ ΠΈΠ·Π³ΠΎΡΠΎΠ²Π»ΡΠ΅ΡΡΡ Π»ΠΈΡΠ΅ΠΉΠ½Π°Ρ ΠΌΠΎΠ΄Π΅Π»Ρ (ΡΠ°Π½Π΅Π΅Β β Π΄Π΅ΡΠ΅Π²ΡΠ½Π½Π°Ρ, Π² Π½Π°ΡΡΠΎΡΡΠ΅Π΅ Π²ΡΠ΅ΠΌΡ ΡΠ°ΡΡΠΎ ΠΈΡΠΏΠΎΠ»ΡΠ·ΡΡΡΡΡ ΠΏΠ»Π°ΡΡΠΈΠΊΠΎΠ²ΡΠ΅ ΠΌΠΎΠ΄Π΅Π»ΠΈ, ΠΏΠΎΠ»ΡΡΠ΅Π½Π½ΡΠ΅ ΠΌΠ΅ΡΠΎΠ΄Π°ΠΌΠΈ Π±ΡΡΡΡΠΎΠ³ΠΎ ΠΏΡΠΎΡΠΎΡΠΈΠΏΠΈΡΠΎΠ²Π°Π½ΠΈΡ), ΠΊΠΎΠΏΠΈΡΡΡΡΠ°Ρ Π±ΡΠ΄ΡΡΡΡ Π΄Π΅ΡΠ°Π»Ρ. ΠΠΎΠ΄Π΅Π»Ρ Π·Π°ΡΡΠΏΠ°Π΅ΡΡΡ ΠΏΠ΅ΡΠΊΠΎΠΌ ΠΈΠ»ΠΈ ΡΠΎΡΠΌΠΎΠ²ΠΎΡΠ½ΠΎΠΉ ΡΠΌΠ΅ΡΡΡ (ΠΎΠ±ΡΡΠ½ΠΎ ΠΏΠ΅ΡΠΎΠΊ ΠΈ ΡΠ²ΡΠ·ΡΡΡΠ΅Π΅), Π·Π°ΠΏΠΎΠ»Π½ΡΡΡΠ΅ΠΉ ΠΏΡΠΎΡΡΡΠ°Π½ΡΡΠ²ΠΎ ΠΌΠ΅ΠΆΠ΄Ρ Π΅Ρ ΠΈ Π΄Π²ΡΠΌΡ ΠΎΡΠΊΡΡΡΡΠΌΠΈ ΡΡΠΈΠΊΠ°ΠΌΠΈ (ΠΎΠΏΠΎΠΊΠ°ΠΌΠΈ). ΠΡΠ²Π΅ΡΡΡΠΈΡ Π² Π΄Π΅ΡΠ°Π»ΠΈ ΠΎΠ±ΡΠ°Π·ΡΡΡΡΡ Ρ ΠΏΠΎΠΌΠΎΡΡΡ ΡΠ°Π·ΠΌΠ΅ΡΡΠ½Π½ΡΡ Π² ΡΠΎΡΠΌΠ΅ Π»ΠΈΡΠ΅ΠΉΠ½ΡΡ ΠΏΠ΅ΡΡΠ°Π½ΡΡ ΡΡΠ΅ΡΠΆΠ½Π΅ΠΉ, ΠΊΠΎΠΏΠΈΡΡΡΡΠΈΡ ΡΠΎΡΠΌΡ Π±ΡΠ΄ΡΡΠ΅Π³ΠΎ ΠΎΡΠ²Π΅ΡΡΡΠΈΡ. ΠΠ°ΡΡΠΏΠ°Π½Π½Π°Ρ Π² ΠΎΠΏΠΎΠΊΠΈ ΡΠΌΠ΅ΡΡ ΡΠΏΠ»ΠΎΡΠ½ΡΠ΅ΡΡΡ Π²ΡΡΡΡΡ ΠΈΠ²Π°Π½ΠΈΠ΅ΠΌ, ΠΏΡΠ΅ΡΡΠΎΠ²Π°Π½ΠΈΠ΅ΠΌ ΠΈΠ»ΠΈ ΠΆΠ΅ Π·Π°ΡΠ²Π΅ΡΠ΄Π΅Π²Π°Π΅Ρ Π² ΡΠ΅ΡΠΌΠΈΡΠ΅ΡΠΊΠΎΠΌ ΡΠΊΠ°ΡΡ (ΡΡΡΠΈΠ»ΡΠ½ΠΎΠΉ ΠΏΠ΅ΡΠΈ). ΠΠ±ΡΠ°Π·ΠΎΠ²Π°Π²ΡΠΈΠ΅ΡΡ ΠΏΠΎΠ»ΠΎΡΡΠΈ Π·Π°Π»ΠΈΠ²Π°ΡΡΡΡ ΡΠ°ΡΠΏΠ»Π°Π²ΠΎΠΌ ΠΌΠ΅ΡΠ°Π»Π»Π° ΡΠ΅ΡΠ΅Π· ΡΠΏΠ΅ΡΠΈΠ°Π»ΡΠ½ΡΠ΅ ΠΎΡΠ²Π΅ΡΡΡΠΈΡΒ β Π»ΠΈΡΠ½ΠΈΠΊΠΈ. ΠΠΎΡΠ»Π΅ ΠΎΡΡΡΠ²Π°Π½ΠΈΡ ΡΠΎΡΠΌΡ ΡΠ°Π·Π±ΠΈΠ²Π°ΡΡ ΠΈ ΠΈΠ·Π²Π»Π΅ΠΊΠ°ΡΡ ΠΎΡΠ»ΠΈΠ²ΠΊΡ. ΠΠΎΡΠ»Π΅ ΡΠ΅Π³ΠΎ ΠΎΡΠ΄Π΅Π»ΡΡΡ Π»ΠΈΡΠ½ΠΈΠΊΠΎΠ²ΡΡ ΡΠΈΡΡΠ΅ΠΌΡ (ΠΎΠ±ΡΡΠ½ΠΎ ΡΡΠΎ ΠΎΠ±ΡΡΠ±ΠΊΠ°), ΡΠ΄Π°Π»ΡΡΡ ΠΎΠ±Π»ΠΎΠΉ ΠΈ ΠΏΡΠΎΠ²ΠΎΠ΄ΡΡ ΡΠ΅ΡΠΌΠΎΠΎΠ±ΡΠ°Π±ΠΎΡΠΊΡ.
ΠΠΎΠ²ΡΠΌ Π½Π°ΠΏΡΠ°Π²Π»Π΅Π½ΠΈΠ΅ΠΌ ΡΠ΅Ρ Π½ΠΎΠ»ΠΎΠ³ΠΈΠΈ Π»ΠΈΡΡΡ Π² ΠΏΠ΅ΡΡΠ°Π½ΡΠ΅ ΡΠΎΡΠΌΡ ΡΠ²Π»ΡΠ΅ΡΡΡ ΠΏΡΠΈΠΌΠ΅Π½Π΅Π½ΠΈΠ΅ Π²Π°ΠΊΡΡΠΌΠΈΡΡΠ΅ΠΌΡΡ ΡΠΎΡΠΌ ΠΈΠ· ΡΡΡ ΠΎΠ³ΠΎ ΠΏΠ΅ΡΠΊΠ° Π±Π΅Π· ΡΠ²ΡΠ·ΡΡΡΠ΅Π³ΠΎ. ΠΠ»Ρ ΠΏΠΎΠ»ΡΡΠ΅Π½ΠΈΡ ΠΎΡΠ»ΠΈΠ²ΠΊΠΈ Π΄Π°Π½Π½ΡΠΌ ΠΌΠ΅ΡΠΎΠ΄ΠΎΠΌ ΠΌΠΎΠ³ΡΡ ΠΏΡΠΈΠΌΠ΅Π½ΡΡΡΡΡ ΡΠ°Π·Π»ΠΈΡΠ½ΡΠ΅ ΡΠΎΡΠΌΠΎΠ²ΠΎΡΠ½ΡΠ΅ ΠΌΠ°ΡΠ΅ΡΠΈΠ°Π»Ρ, Π½Π°ΠΏΡΠΈΠΌΠ΅Ρ ΠΏΠ΅ΡΡΠ°Π½ΠΎ-Π³Π»ΠΈΠ½ΠΈΡΡΠ°Ρ ΡΠΌΠ΅ΡΡ ΠΈΠ»ΠΈ ΠΏΠ΅ΡΠΎΠΊ Π² ΡΠΌΠ΅ΡΠΈ ΡΠΎ ΡΠΌΠΎΠ»ΠΎΠΉ ΠΈΒ Ρ.Π΄. ΠΠ»Ρ ΡΠΎΡΠΌΠΈΡΠΎΠ²Π°Π½ΠΈΡ ΡΠΎΡΠΌΡ ΠΈΡΠΏΠΎΠ»ΡΠ·ΡΡΡ ΠΎΠΏΠΎΠΊΡ (ΠΌΠ΅ΡΠ°Π»Π»ΠΈΡΠ΅ΡΠΊΠΈΠΉ ΠΊΠΎΡΠΎΠ± Π±Π΅Π· Π΄Π½Π° ΠΈ ΠΊΡΡΡΠΊΠΈ). ΠΠΏΠΎΠΊΠ° ΠΈΠΌΠ΅Π΅Ρ Π΄Π²Π΅ ΠΏΠΎΠ»ΡΡΠΎΡΠΌΡ, ΡΠΎ Π΅ΡΡΡ ΡΠΎΡΡΠΎΠΈΡ ΠΈΠ· Π΄Π²ΡΡ ΠΊΠΎΡΠΎΠ±ΠΎΠ². ΠΠ»ΠΎΡΠΊΠΎΡΡΡ ΡΠΎΠΏΡΠΈΠΊΠΎΡΠ½ΠΎΠ²Π΅Π½ΠΈΡ Π΄Π²ΡΡ ΠΏΠΎΠ»ΡΡΠΎΡΠΌ β ΠΏΠΎΠ²Π΅ΡΡ Π½ΠΎΡΡΡ ΡΠ°Π·ΡΡΠΌΠ°. Π ΠΏΠΎΠ»ΡΡΠΎΡΠΌΡ Π·Π°ΡΡΠΏΠ°ΡΡ ΡΠΎΡΠΌΠΎΠ²ΠΎΡΠ½ΡΡ ΡΠΌΠ΅ΡΡ ΠΈ ΡΡΡΠ°ΠΌΠ±ΠΎΠ²ΡΠ²Π°ΡΡ Π΅Ρ. ΠΠ° ΠΏΠΎΠ²Π΅ΡΡ Π½ΠΎΡΡΠΈ ΡΠ°Π·ΡΡΠΌΠ° Π΄Π΅Π»Π°ΡΡ ΠΎΡΠΏΠ΅ΡΠ°ΡΠΎΠΊ ΠΏΡΠΎΠΌΠΎΠ΄Π΅Π»ΠΈ (ΠΏΡΠΎΠΌΠΎΠ΄Π΅Π»Ρ ΡΠΎΠΎΡΠ²Π΅ΡΡΡΠ²ΡΠ΅Ρ ΡΠΎΡΠΌΠ΅ ΠΎΡΠ»ΠΈΠ²ΠΊΠΈ). Π’Π°ΠΊΠΆΠ΅ Π²ΡΠΏΠΎΠ»Π½ΡΡΡ Π²ΡΠΎΡΡΡ ΠΏΠΎΠ»ΡΡΠΎΡΠΌΡ. Π‘ΠΎΠ΅Π΄ΠΈΠ½ΡΡΡ Π΄Π²Π΅ ΠΏΠΎΠ»ΡΡΠΎΡΠΌΡ ΠΏΠΎ ΠΏΠΎΠ²Π΅ΡΡ Π½ΠΎΡΡΠΈ ΡΠ°Π·ΡΡΠΌΠ° ΠΈ ΠΏΡΠΎΠΈΠ·Π²ΠΎΠ΄ΡΡ Π·Π°Π»ΠΈΠ²ΠΊΡ ΠΌΠ΅ΡΠ°Π»Π»Π°.
ΠΠΈΡΡΡ Π² ΠΊΠΎΠΊΠΈΠ»Ρ
ΠΠΈΡΡΡ ΠΌΠ΅ΡΠ°Π»Π»ΠΎΠ² Π² ΠΊΠΎΠΊΠΈΠ»ΡΒ β Π±ΠΎΠ»Π΅Π΅ ΠΊΠ°ΡΠ΅ΡΡΠ²Π΅Π½Π½ΡΠΉ ΡΠΏΠΎΡΠΎΠ±. ΠΠ·Π³ΠΎΡΠ°Π²Π»ΠΈΠ²Π°Π΅ΡΡΡ ΠΊΠΎΠΊΠΈΠ»ΡΒ β ΡΠ°Π·Π±ΠΎΡΠ½Π°Ρ ΡΠΎΡΠΌΠ° (ΡΠ°ΡΠ΅ Π²ΡΠ΅Π³ΠΎ ΠΌΠ΅ΡΠ°Π»Π»ΠΈΡΠ΅ΡΠΊΠ°Ρ), Π² ΠΊΠΎΡΠΎΡΡΡ ΠΏΡΠΎΠΈΠ·Π²ΠΎΠ΄ΠΈΡΡΡ Π»ΠΈΡΡΡ. ΠΠΎΡΠ»Π΅ Π·Π°ΡΡΡΠ²Π°Π½ΠΈΡ ΠΈ ΠΎΡ Π»Π°ΠΆΠ΄Π΅Π½ΠΈΡ, ΠΊΠΎΠΊΠΈΠ»Ρ ΡΠ°ΡΠΊΡΡΠ²Π°Π΅ΡΡΡ ΠΈ ΠΈΠ· Π½Π΅Π³ΠΎ ΠΈΠ·Π²Π»Π΅ΠΊΠ°Π΅ΡΡΡ ΠΈΠ·Π΄Π΅Π»ΠΈΠ΅. ΠΠ°ΡΠ΅ΠΌ ΠΊΠΎΠΊΠΈΠ»Ρ ΠΌΠΎΠΆΠ½ΠΎ ΠΏΠΎΠ²ΡΠΎΡΠ½ΠΎ ΠΈΡΠΏΠΎΠ»ΡΠ·ΠΎΠ²Π°ΡΡ Π΄Π»Ρ ΠΎΡΠ»ΠΈΠ²ΠΊΠΈ ΡΠ°ΠΊΠΎΠΉ ΠΆΠ΅ Π΄Π΅ΡΠ°Π»ΠΈ.
ΠΠΈΡΡΡ Π² ΠΊΠΎΠΊΠΈΠ»Ρ, ΠΊΠΎΠΊΠΈΠ»ΡΠ½ΠΎΠ΅ Π»ΠΈΡΡΡ, ΡΠΏΠΎΡΠΎΠ± ΠΏΠΎΠ»ΡΡΠ΅Π½ΠΈΡ ΡΠ°ΡΠΎΠ½Π½ΡΡ ΠΎΡΠ»ΠΈΠ²ΠΎΠΊ Π² ΠΌΠ΅ΡΠ°Π»Π»ΠΈΡΠ΅ΡΠΊΠΈΡ ΡΠΎΡΠΌΠ°Ρ Β β ΠΊΠΎΠΊΠΈΠ»ΡΡ . Π ΠΎΡΠ»ΠΈΡΠΈΠ΅ ΠΎΡ Π΄ΡΡΠ³ΠΈΡ ΡΠΏΠΎΡΠΎΠ±ΠΎΠ² Π»ΠΈΡΡΡ Π² ΠΌΠ΅ΡΠ°Π»Π»ΠΈΡΠ΅ΡΠΊΠΈΠ΅ ΡΠΎΡΠΌΡ (Π»ΠΈΡΡΡ ΠΏΠΎΠ΄ Π΄Π°Π²Π»Π΅Π½ΠΈΠ΅ΠΌ, ΡΠ΅Π½ΡΡΠΎΠ±Π΅ΠΆΠ½ΠΎΠ΅ Π»ΠΈΡΡΡ ΠΈ Π΄Ρ.), ΠΏΡΠΈ Π»ΠΈΡΡΡ Π² ΠΊΠΎΠΊΠΈΠ»Ρ Π·Π°ΠΏΠΎΠ»Π½Π΅Π½ΠΈΠ΅ ΡΠΎΡΠΌΡ ΠΆΠΈΠ΄ΠΊΠΈΠΌ ΡΠΏΠ»Π°Π²ΠΎΠΌ ΠΈ Π΅Π³ΠΎ Π·Π°ΡΠ²Π΅ΡΠ΄Π΅Π²Π°Π½ΠΈΠ΅ ΠΏΡΠΎΠΈΡΡ ΠΎΠ΄ΡΡ Π±Π΅Π· ΠΊΠ°ΠΊΠΎΠ³ΠΎ-Π»ΠΈΠ±ΠΎ Π²Π½Π΅ΡΠ½Π΅Π³ΠΎ Π²ΠΎΠ·Π΄Π΅ΠΉΡΡΠ²ΠΈΡ Π½Π° ΠΆΠΈΠ΄ΠΊΠΈΠΉ ΠΌΠ΅ΡΠ°Π»Π», Π° Π»ΠΈΡΡ ΠΏΠΎΠ΄ Π΄Π΅ΠΉΡΡΠ²ΠΈΠ΅ΠΌ ΡΠΈΠ»Ρ ΡΡΠΆΠ΅ΡΡΠΈ. ΠΡΠ½ΠΎΠ²Π½ΡΠ΅ ΠΎΠΏΠ΅ΡΠ°ΡΠΈΠΈ ΠΈ ΠΏΡΠΎΡΠ΅ΡΡΡ: ΠΎΡΠΈΡΡΠΊΠ° ΠΊΠΎΠΊΠΈΠ»Ρ ΠΎΡ ΡΡΠ°ΡΠΎΠΉ ΠΎΠ±Π»ΠΈΡΠΎΠ²ΠΊΠΈ, ΠΏΡΠΎΠ³ΡΠ΅Π² Π΅Π³ΠΎ Π΄ΠΎ 200β300Β°Π‘, ΠΏΠΎΠΊΡΡΡΠΈΠ΅ ΡΠ°Π±ΠΎΡΠ΅ΠΉ ΠΏΠΎΠ»ΠΎΡΡΠΈ Π½ΠΎΠ²ΡΠΌ ΡΠ»ΠΎΠ΅ΠΌ ΠΎΠ±Π»ΠΈΡΠΎΠ²ΠΊΠΈ, ΠΏΡΠΎΡΡΠ°Π½ΠΎΠ²ΠΊΠ° ΡΡΠ΅ΡΠΆΠ½Π΅ΠΉ, Π·Π°ΠΊΡΡΠ²Π°Π½ΠΈΠ΅ ΡΠ°ΡΡΠ΅ΠΉ ΠΊΠΎΠΊΠΈΠ»Ρ, Π·Π°Π»ΠΈΠ²ΠΊΠ° ΠΌΠ΅ΡΠ°Π»Π»Π°, ΠΎΡ Π»Π°ΠΆΠ΄Π΅Π½ΠΈΠ΅ ΠΈ ΡΠ΄Π°Π»Π΅Π½ΠΈΠ΅ ΠΏΠΎΠ»ΡΡΠ΅Π½Π½ΠΎΠΉ ΠΎΡΠ»ΠΈΠ²ΠΊΠΈ. ΠΡΠΎΡΠ΅ΡΡ ΠΊΡΠΈΡΡΠ°Π»Π»ΠΈΠ·Π°ΡΠΈΠΈ ΡΠΏΠ»Π°Π²Π° ΠΏΡΠΈ Π»ΠΈΡΡΠ΅ Π² ΠΊΠΎΠΊΠΈΠ»Ρ ΡΡΠΊΠΎΡΡΠ΅ΡΡΡ, ΡΡΠΎ ΡΠΏΠΎΡΠΎΠ±ΡΡΠ²ΡΠ΅Ρ ΠΏΠΎΠ»ΡΡΠ΅Π½ΠΈΡ ΠΎΡΠ»ΠΈΠ²ΠΎΠΊ Ρ ΠΏΠ»ΠΎΡΠ½ΡΠΌ ΠΈ ΠΌΠ΅Π»ΠΊΠΎΠ·Π΅ΡΠ½ΠΈΡΡΡΠΌ ΡΡΡΠΎΠ΅Π½ΠΈΠ΅ΠΌ, Π° ΡΠ»Π΅Π΄ΠΎΠ²Π°ΡΠ΅Π»ΡΠ½ΠΎ, Ρ Ρ ΠΎΡΠΎΡΠ΅ΠΉ Π³Π΅ΡΠΌΠ΅ΡΠΈΡΠ½ΠΎΡΡΡΡ ΠΈ Π²ΡΡΠΎΠΊΠΈΠΌΠΈ ΡΠΈΠ·ΠΈΠΊΠΎ-ΠΌΠ΅Ρ Π°Π½ΠΈΡΠ΅ΡΠΊΠΈΠΌΠΈ ΡΠ²ΠΎΠΉΡΡΠ²Π°ΠΌΠΈ. ΠΠ΄Π½Π°ΠΊΠΎ ΠΎΡΠ»ΠΈΠ²ΠΊΠΈ ΠΈΠ· ΡΡΠ³ΡΠ½Π° ΠΈΠ·-Π·Π° ΠΎΠ±ΡΠ°Π·ΡΡΡΠΈΡ ΡΡ Π½Π° ΠΏΠΎΠ²Π΅ΡΡ Π½ΠΎΡΡΠΈ ΠΊΠ°ΡΠ±ΠΈΠ΄ΠΎΠ² ΡΡΠ΅Π±ΡΡΡ ΠΏΠΎΡΠ»Π΅Π΄ΡΡΡΠ΅Π³ΠΎ ΠΎΡΠΆΠΈΠ³Π°. ΠΡΠΈ ΠΌΠ½ΠΎΠ³ΠΎΠΊΡΠ°ΡΠ½ΠΎΠΌ ΠΈΡΠΏΠΎΠ»ΡΠ·ΠΎΠ²Π°Π½ΠΈΠΈ ΠΊΠΎΠΊΠΈΠ»Ρ ΠΊΠΎΡΠΎΠ±ΠΈΡΡΡ ΠΈ ΡΠ°Π·ΠΌΠ΅ΡΡ ΠΎΡΠ»ΠΈΠ²ΠΎΠΊ Π² Π½Π°ΠΏΡΠ°Π²Π»Π΅Π½ΠΈΡΡ , ΠΏΠ΅ΡΠΏΠ΅Π½Π΄ΠΈΠΊΡΠ»ΡΡΠ½ΡΡ ΠΏΠ»ΠΎΡΠΊΠΎΡΡΠΈ ΡΠ°Π·ΡΡΠΌΠ°, ΡΠ²Π΅Π»ΠΈΡΠΈΠ²Π°ΡΡΡΡ.
Π ΠΊΠΎΠΊΠΈΠ»ΡΡ ΠΏΠΎΠ»ΡΡΠ°ΡΡ ΠΎΡΠ»ΠΈΠ²ΠΊΠΈ ΠΈΠ· ΡΡΠ³ΡΠ½Π°, ΡΡΠ°Π»ΠΈ, Π°Π»ΡΠΌΠΈΠ½ΠΈΠ΅Π²ΡΡ , ΠΌΠ°Π³Π½ΠΈΠ΅Π²ΡΡ ΠΈ Π΄Ρ. ΡΠΏΠ»Π°Π²ΠΎΠ². ΠΡΠΎΠ±Π΅Π½Π½ΠΎ ΡΡΡΠ΅ΠΊΡΠΈΠ²Π½ΠΎ ΠΏΡΠΈΠΌΠ΅Π½Π΅Π½ΠΈΠ΅ ΠΊΠΎΠΊΠΈΠ»ΡΠ½ΠΎΠ³ΠΎ Π»ΠΈΡΡΡ ΠΏΡΠΈ ΠΈΠ·Π³ΠΎΡΠΎΠ²Π»Π΅Π½ΠΈΠΈ ΠΎΡΠ»ΠΈΠ²ΠΎΠΊ ΠΈΠ· Π°Π»ΡΠΌΠΈΠ½ΠΈΠ΅Π²ΡΡ ΠΈ ΠΌΠ°Π³Π½ΠΈΠ΅Π²ΡΡ ΡΠΏΠ»Π°Π²ΠΎΠ². ΠΡΠΈ ΡΠΏΠ»Π°Π²Ρ ΠΈΠΌΠ΅ΡΡ ΠΎΡΠ½ΠΎΡΠΈΡΠ΅Π»ΡΠ½ΠΎ Π½Π΅Π²ΡΡΠΎΠΊΡΡ ΡΠ΅ΠΌΠΏΠ΅ΡΠ°ΡΡΡΡ ΠΏΠ»Π°Π²Π»Π΅Π½ΠΈΡ, ΠΏΠΎΡΡΠΎΠΌΡ ΠΎΠ΄ΠΈΠ½ ΠΊΠΎΠΊΠΈΠ»Ρ ΠΌΠΎΠΆΠ½ΠΎ ΠΈΡΠΏΠΎΠ»ΡΠ·ΠΎΠ²Π°ΡΡ Π΄ΠΎ 10000 ΡΠ°Π· (Ρ ΠΏΡΠΎΡΡΠ°Π½ΠΎΠ²ΠΊΠΎΠΉ ΠΌΠ΅ΡΠ°Π»Π»ΠΈΡΠ΅ΡΠΊΠΈΡ ΡΡΠ΅ΡΠΆΠ½Π΅ΠΉ). ΠΠΎ 45Β % Π²ΡΠ΅Ρ ΠΎΡΠ»ΠΈΠ²ΠΎΠΊ ΠΈΠ· ΡΡΠΈΡ ΡΠΏΠ»Π°Π²ΠΎΠ² ΠΏΠΎΠ»ΡΡΠ°ΡΡ Π² ΠΊΠΎΠΊΠΈΠ»ΡΡ . ΠΡΠΈ Π»ΠΈΡΡΠ΅ Π² ΠΊΠΎΠΊΠΈΠ»Ρ ΡΠ°ΡΡΠΈΡΡΠ΅ΡΡΡ Π΄ΠΈΠ°ΠΏΠ°Π·ΠΎΠ½ ΡΠΊΠΎΡΠΎΡΡΠ΅ΠΉ ΠΎΡ Π»Π°ΠΆΠ΄Π΅Π½ΠΈΡ ΡΠΏΠ»Π°Π²ΠΎΠ² ΠΈ ΠΎΠ±ΡΠ°Π·ΠΎΠ²Π°Π½ΠΈΡ ΡΠ°Π·Π»ΠΈΡΠ½ΡΡ ΡΡΡΡΠΊΡΡΡ. Π‘ΡΠ°Π»Ρ ΠΈΠΌΠ΅Π΅Ρ ΠΎΡΠ½ΠΎΡΠΈΡΠ΅Π»ΡΠ½ΠΎ Π²ΡΡΠΎΠΊΡΡ ΡΠ΅ΠΌΠΏΠ΅ΡΠ°ΡΡΡΡ ΠΏΠ»Π°Π²Π»Π΅Π½ΠΈΡ, ΡΡΠΎΠΉΠΊΠΎΡΡΡ ΠΊΠΎΠΊΠΈΠ»Π΅ΠΉ ΠΏΡΠΈ ΠΏΠΎΠ»ΡΡΠ΅Π½ΠΈΠΈ ΡΡΠ°Π»ΡΠ½ΡΡ ΠΎΡΠ»ΠΈΠ²ΠΎΠΊ ΡΠ΅Π·ΠΊΠΎ ΡΠ½ΠΈΠΆΠ°Π΅ΡΡΡ, Π±ΠΎΠ»ΡΡΠΈΠ½ΡΡΠ²ΠΎ ΠΏΠΎΠ²Π΅ΡΡ Π½ΠΎΡΡΠ΅ΠΉ ΠΎΠ±ΡΠ°Π·ΡΡΡ ΡΡΠ΅ΡΠΆΠ½ΠΈ, ΠΏΠΎΡΡΠΎΠΌΡ ΠΌΠ΅ΡΠΎΠ΄ ΠΊΠΎΠΊΠΈΠ»ΡΠ½ΠΎΠ³ΠΎ Π»ΠΈΡΡΡ Π΄Π»Ρ ΡΡΠ°Π»ΠΈ Π½Π°Ρ ΠΎΠ΄ΠΈΡ ΠΌΠ΅Π½ΡΡΠ΅Π΅ ΠΏΡΠΈΠΌΠ΅Π½Π΅Π½ΠΈΠ΅, ΡΠ΅ΠΌ Π΄Π»Ρ ΡΠ²Π΅ΡΠ½ΡΡ ΡΠΏΠ»Π°Π²ΠΎΠ². ΠΠ°Π½Π½ΡΠΉ ΠΌΠ΅ΡΠΎΠ΄ ΡΠΈΡΠΎΠΊΠΎ ΠΏΡΠΈΠΌΠ΅Π½ΡΠ΅ΡΡΡ ΠΏΡΠΈ ΡΠ΅ΡΠΈΠΉΠ½ΠΎΠΌ ΠΈ ΠΊΡΡΠΏΠ½ΠΎΡΠ΅ΡΠΈΠΉΠ½ΠΎΠΌ ΠΏΡΠΎΠΈΠ·Π²ΠΎΠ΄ΡΡΠ²Π΅.
ΠΠΈΡΡΡ ΠΏΠΎΠ΄ Π΄Π°Π²Π»Π΅Π½ΠΈΠ΅ΠΌ
ΠΠΠ Π·Π°Π½ΠΈΠΌΠ°Π΅Ρ ΠΎΠ΄Π½ΠΎ ΠΈΠ· Π²Π΅Π΄ΡΡΠΈΡ ΠΌΠ΅ΡΡ Π² Π»ΠΈΡΠ΅ΠΉΠ½ΠΎΠΌ ΠΏΡΠΎΠΈΠ·Π²ΠΎΠ΄ΡΡΠ²Π΅. ΠΡΠΎΠΈΠ·Π²ΠΎΠ΄ΡΡΠ²ΠΎ ΠΎΡΠ»ΠΈΠ²ΠΎΠΊ ΠΈΠ· Π°Π»ΡΠΌΠΈΠ½ΠΈΠ΅Π²ΡΡ ΡΠΏΠ»Π°Π²ΠΎΠ² Π² ΡΠ°Π·Π»ΠΈΡΠ½ΡΡ ΡΡΡΠ°Π½Π°Ρ ΡΠΎΡΡΠ°Π²Π»ΡΠ΅Ρ 30β50Β % ΠΎΠ±ΡΠ΅Π³ΠΎ Π²ΡΠΏΡΡΠΊΠ° (ΠΏΠΎ ΠΌΠ°ΡΡΠ΅) ΠΏΡΠΎΠ΄ΡΠΊΡΠΈΠΈ ΠΠΠ. Π‘Π»Π΅Π΄ΡΡΡΡΡ ΠΏΠΎ ΠΊΠΎΠ»ΠΈΡΠ΅ΡΡΠ²Ρ ΠΈ ΡΠ°Π·Π½ΠΎΠΎΠ±ΡΠ°Π·ΠΈΡ Π½ΠΎΠΌΠ΅Π½ΠΊΠ»Π°ΡΡΡΡ Π³ΡΡΠΏΠΏΡ ΠΎΡΠ»ΠΈΠ²ΠΎΠΊ ΠΏΡΠ΅Π΄ΡΡΠ°Π²Π»ΡΡΡ ΠΎΡΠ»ΠΈΠ²ΠΊΠΈ ΠΈΠ· ΡΠΈΠ½ΠΊΠΎΠ²ΡΡ ΡΠΏΠ»Π°Π²ΠΎΠ². ΠΠ°Π³Π½ΠΈΠ΅Π²ΡΠ΅ ΡΠΏΠ»Π°Π²Ρ Π΄Π»Ρ Π»ΠΈΡΡΡ ΠΏΠΎΠ΄ Π΄Π°Π²Π»Π΅Π½ΠΈΠ΅ΠΌ ΠΏΡΠΈΠΌΠ΅Π½ΡΡΡ ΡΠ΅ΠΆΠ΅, ΡΡΠΎ ΠΎΠ±ΡΡΡΠ½ΡΠ΅ΡΡΡ ΠΈΡ ΡΠΊΠ»ΠΎΠ½Π½ΠΎΡΡΡΡ ΠΊ ΠΎΠ±ΡΠ°Π·ΠΎΠ²Π°Π½ΠΈΡ Π³ΠΎΡΡΡΠΈΡ ΡΡΠ΅ΡΠΈΠ½ ΠΈ Π±ΠΎΠ»Π΅Π΅ ΡΠ»ΠΎΠΆΠ½ΡΠΌΠΈ ΡΠ΅Ρ Π½ΠΎΠ»ΠΎΠ³ΠΈΡΠ΅ΡΠΊΠΈΠΌΠΈ ΡΡΠ»ΠΎΠ²ΠΈΡΠΌΠΈ ΠΈΠ·Π³ΠΎΡΠΎΠ²Π»Π΅Π½ΠΈΡ ΠΎΡΠ»ΠΈΠ²ΠΎΠΊ. ΠΠΎΠ»ΡΡΠ΅Π½ΠΈΠ΅ ΠΎΡΠ»ΠΈΠ²ΠΎΠΊ ΠΈΠ· ΠΌΠ΅Π΄Π½ΡΡ ΡΠΏΠ»Π°Π²ΠΎΠ² ΠΎΠ³ΡΠ°Π½ΠΈΡΠ΅Π½ΠΎ Π½ΠΈΠ·ΠΊΠΎΠΉ ΡΡΠΎΠΉΠΊΠΎΡΡΡΡ ΠΏΡΠ΅ΡΡ-ΡΠΎΡΠΌ.
ΠΠΎΠΌΠ΅Π½ΠΊΠ»Π°ΡΡΡΠ° Π²ΡΠΏΡΡΠΊΠ°Π΅ΠΌΡΡ ΠΎΡΠ΅ΡΠ΅ΡΡΠ²Π΅Π½Π½ΠΎΠΉ ΠΏΡΠΎΠΌΡΡΠ»Π΅Π½Π½ΠΎΡΡΡΡ ΠΎΡΠ»ΠΈΠ²ΠΎΠΊ ΠΎΡΠ΅Π½Ρ ΡΠ°Π·Π½ΠΎΠΎΠ±ΡΠ°Π·Π½Π°. ΠΡΠΈΠΌ ΡΠΏΠΎΡΠΎΠ±ΠΎΠΌ ΠΈΠ·Π³ΠΎΡΠΎΠ²Π»ΡΡΡ Π»ΠΈΡΡΠ΅ Π·Π°Π³ΠΎΡΠΎΠ²ΠΊΠΈ ΡΠ°ΠΌΠΎΠΉ ΡΠ°Π·Π»ΠΈΡΠ½ΠΎΠΉ ΠΊΠΎΠ½ΡΠΈΠ³ΡΡΠ°ΡΠΈΠΈ ΠΌΠ°ΡΡΠΎΠΉ ΠΎΡ Π½Π΅ΡΠΊΠΎΠ»ΡΠΊΠΈΡ Π³ΡΠ°ΠΌΠΌΠΎΠ² Π΄ΠΎ Π½Π΅ΡΠΊΠΎΠ»ΡΠΊΠΈΡ Π΄Π΅ΡΡΡΠΊΠΎΠ² ΠΊΠΈΠ»ΠΎΠ³ΡΠ°ΠΌΠΌΠΎΠ². ΠΡΠ΄Π΅Π»ΡΡΡΡΡ ΡΠ»Π΅Π΄ΡΡΡΠΈΠ΅ ΠΏΠΎΠ»ΠΎΠΆΠΈΡΠ΅Π»ΡΠ½ΡΠ΅ ΡΡΠΎΡΠΎΠ½Ρ ΠΏΡΠΎΡΠ΅ΡΡΠ° ΠΠΠ:
- ΠΡΡΠΎΠΊΠ°Ρ ΠΏΡΠΎΠΈΠ·Π²ΠΎΠ΄ΠΈΡΠ΅Π»ΡΠ½ΠΎΡΡΡ ΠΈ Π°Π²ΡΠΎΠΌΠ°ΡΠΈΠ·Π°ΡΠΈΡ ΠΏΡΠΎΠΈΠ·Π²ΠΎΠ΄ΡΡΠ²Π°, Π½Π°ΡΡΠ΄Ρ Ρ Π½ΠΈΠ·ΠΊΠΎΠΉ ΡΡΡΠ΄ΠΎΡΠΌΠΊΠΎΡΡΡΡ Π½Π° ΠΈΠ·Π³ΠΎΡΠΎΠ²Π»Π΅Π½ΠΈΠ΅ ΠΎΠ΄Π½ΠΎΠΉ ΠΎΡΠ»ΠΈΠ²ΠΊΠΈ, Π΄Π΅Π»Π°Π΅Ρ ΠΏΡΠΎΡΠ΅ΡΡ ΠΠΠ Π½Π°ΠΈΠ±ΠΎΠ»Π΅Π΅ ΠΎΠΏΡΠΈΠΌΠ°Π»ΡΠ½ΡΠΌ Π² ΡΡΠ»ΠΎΠ²ΠΈΡ ΠΌΠ°ΡΡΠΎΠ²ΠΎΠ³ΠΎ ΠΈ ΠΊΡΡΠΏΠ½ΠΎΡΠ΅ΡΠΈΠΉΠ½ΠΎΠ³ΠΎ ΠΏΡΠΎΠΈΠ·Π²ΠΎΠ΄ΡΡΠ².
- ΠΠΈΠ½ΠΈΠΌΠ°Π»ΡΠ½ΡΠ΅ ΠΏΡΠΈΠΏΡΡΠΊΠΈ Π½Π° ΠΌΠ΅Ρ ΠΎΠ±ΡΠ°Π±ΠΎΡΠΊΡ ΠΈΠ»ΠΈ Π½Π΅ ΡΡΠ΅Π±ΡΡΡΠΈΠ΅ ΠΎΠ½ΠΎΠΉ, ΠΌΠΈΠ½ΠΈΠΌΠ°Π»ΡΠ½Π°Ρ ΡΠ΅ΡΠΎΡ ΠΎΠ²Π°ΡΠΎΡΡΡ Π½Π΅ΠΎΠ±ΡΠ°Π±Π°ΡΡΠ²Π°Π΅ΠΌΡΡ ΠΏΠΎΠ²Π΅ΡΡ Π½ΠΎΡΡΠ΅ΠΉ ΠΈ ΡΠΎΡΠ½ΠΎΡΡΡ ΡΠ°Π·ΠΌΠ΅ΡΠΎΠ², ΠΏΠΎΠ·Π²ΠΎΠ»ΡΡΡΠ°Ρ Π΄ΠΎΠ±ΠΈΠ²Π°ΡΡΡΡ Π΄ΠΎΠΏΡΡΠΊΠΎΠ² Π΄ΠΎ Β±0,075Β ΠΌΠΌ Π½Π° ΡΡΠΎΡΠΎΠ½Ρ.
- Π§ΡΡΠΊΠΎΡΡΡ ΠΏΠΎΠ»ΡΡΠ°Π΅ΠΌΠΎΠ³ΠΎ ΡΠ΅Π»ΡΠ΅ΡΠ°, ΠΏΠΎΠ·Π²ΠΎΠ»ΡΡΡΠ°Ρ ΠΏΠΎΠ»ΡΡΠ°ΡΡ ΠΎΡΠ»ΠΈΠ²ΠΊΠΈ Ρ ΠΌΠΈΠ½ΠΈΠΌΠ°Π»ΡΠ½ΠΎΠΉ ΡΠΎΠ»ΡΠΈΠ½ΠΎΠΉ ΡΡΠ΅Π½ΠΊΠΈ Π΄ΠΎ 0,6Β ΠΌΠΌ, Π° ΡΠ°ΠΊΠΆΠ΅ Π»ΠΈΡΡΠ΅ ΡΠ΅Π·ΡΠ±ΠΎΠ²ΡΠ΅ ΠΏΡΠΎΡΠΈΠ»ΠΈ.
- Π§ΠΈΡΡΠΎΡΠ° ΠΏΠΎΠ²Π΅ΡΡ Π½ΠΎΡΡΠΈ Π½Π° Π½Π΅ΠΎΠ±ΡΠ°Π±Π°ΡΡΠ²Π°Π΅ΠΌΡΡ ΠΏΠΎΠ²Π΅ΡΡ Π½ΠΎΡΡΡΡ , ΠΏΠΎΠ·Π²ΠΎΠ»ΡΠ΅Ρ ΠΏΡΠΈΠ΄Π°ΡΡ ΠΎΡΠ»ΠΈΠ²ΠΊΠ΅ ΡΠΎΠ²Π°ΡΠ½ΡΠΉ ΡΡΡΠ΅ΡΠΈΡΠ΅ΡΠΊΠΈΠΉ Π²ΠΈΠ΄.
Π’Π°ΠΊΠΆΠ΅ Π²ΡΠ΄Π΅Π»ΡΡΡ ΡΠ»Π΅Π΄ΡΡΡΠΈΠ΅ Π½Π΅Π³Π°ΡΠΈΠ²Π½ΠΎΠ΅ Π²Π»ΠΈΡΠ½ΠΈΠ΅ ΠΎΡΠΎΠ±Π΅Π½Π½ΠΎΡΡΠ΅ΠΉ ΠΠΠ, ΠΏΡΠΈΠ²ΠΎΠ΄ΡΡΠΈΠ΅ ΠΊ ΠΏΠΎΡΠ΅ΡΠ΅ Π³Π΅ΡΠΌΠ΅ΡΠΈΡΠ½ΠΎΡΡΠΈ ΠΎΡΠ»ΠΈΠ²ΠΎΠΊ ΠΈ Π½Π΅Π²ΠΎΠ·ΠΌΠΎΠΆΠ½ΠΎΡΡΠΈ ΠΈΡ Π΄Π°Π»ΡΠ½Π΅ΠΉΡΠ΅ΠΉ ΡΠ΅ΡΠΌΠΎΠΎΠ±ΡΠ°Π±ΠΎΡΠΊΠΈ:
- ΠΠΎΠ·Π΄ΡΡΠ½Π°Ρ ΠΏΠΎΡΠΈΡΡΠΎΡΡΡ, ΠΏΡΠΈΡΠΈΠ½ΠΎΠΉ ΠΎΠ±ΡΠ°Π·ΠΎΠ²Π°Π½ΠΈΡ ΠΊΠΎΡΠΎΡΠΎΠΉ ΡΠ²Π»ΡΡΡΡΡ Π²ΠΎΠ·Π΄ΡΡ ΠΈ Π³Π°Π·Ρ ΠΎΡ Π²ΡΠ³ΠΎΡΠ°ΡΡΠ΅ΠΉ ΡΠΌΠ°Π·ΠΊΠΈ, Π·Π°Ρ Π²Π°ΡΠ΅Π½Π½ΡΠ΅ ΠΏΠΎΡΠΎΠΊΠΎΠΌ ΠΌΠ΅ΡΠ°Π»Π»Π° ΠΏΡΠΈ Π·Π°ΠΏΠΎΠ»Π½Π΅Π½ΠΈΠΈ ΡΠΎΡΠΌΡ. Π§ΡΠΎ Π²ΡΠ·Π²Π°Π½ΠΎ Π½Π΅ΠΎΠΏΡΠΈΠΌΠ°Π»ΡΠ½ΡΠΌΠΈ ΡΠ΅ΠΆΠΈΠΌΠ°ΠΌΠΈ Π·Π°ΠΏΠΎΠ»Π½Π΅Π½ΠΈΡ, Π° ΡΠ°ΠΊΠΆΠ΅ Π½ΠΈΠ·ΠΊΠΎΠΉ Π³Π°Π·ΠΎΠΏΡΠΎΠ½ΠΈΡΠ°Π΅ΠΌΠΎΡΡΡΡ ΡΠΎΡΠΌΡ.
- Π£ΡΠ°Π΄ΠΎΡΠ½ΡΠ΅ ΠΏΠΎΡΠΎΠΊΠΈ, ΠΏΡΠΎΡΠ²Π»ΡΡΡΠΈΠ΅ΡΡ ΠΈΠ·-Π·Π° Π²ΡΡΠΎΠΊΠΎΠΉ ΡΠ΅ΠΏΠ»ΠΎΠΏΡΠΎΠ²ΠΎΠ΄Π½ΠΎΡΡΠΈ ΡΠΎΡΠΌ Π½Π°ΡΡΠ΄Ρ Ρ Π·Π°ΡΡΡΠ΄Π½Π΅Π½Π½ΡΠΌΠΈ ΡΡΠ»ΠΎΠ²ΠΈΡΠΌΠΈ ΠΏΠΈΡΠ°Π½ΠΈΡ Π² ΠΏΡΠΎΡΠ΅ΡΡΠ΅ Π·Π°ΡΠ²Π΅ΡΠ΄Π΅Π²Π°Π½ΠΈΡ.
- ΠΠ΅ΠΌΠ΅ΡΠ°Π»Π»ΠΈΡΠ΅ΡΠΊΠΈΠ΅ ΠΈ Π³Π°Π·ΠΎΠ²ΡΠ΅ Π²ΠΊΠ»ΡΡΠ΅Π½ΠΈΡ, ΠΏΠΎΡΠ²Π»ΡΡΡΠΈΠ΅ΡΡ ΠΈΠ·-Π·Π° Π½Π΅ΡΡΠ°ΡΠ΅Π»ΡΠ½ΠΎΠΉ ΠΎΡΠΈΡΡΠΊΠΈ ΡΠΏΠ»Π°Π²Π° Π² ΡΠ°Π·Π΄Π°ΡΠΎΡΠ½ΠΎΠΉ ΠΏΠ΅ΡΠΈ, Π° ΡΠ°ΠΊΠΆΠ΅ Π²ΡΠ΄Π΅Π»ΡΡΡΠΈΠ΅ΡΡ ΠΈΠ· ΡΠ²ΡΡΠ΄ΠΎΠ³ΠΎ ΡΠ°ΡΡΠ²ΠΎΡΠ°.
ΠΠ°Π΄Π°Π²ΡΠΈΡΡ ΡΠ΅Π»ΡΡ ΠΏΠΎΠ»ΡΡΠ΅Π½ΠΈΡ ΠΎΡΠ»ΠΈΠ²ΠΊΠΈ Π·Π°Π΄Π°Π½Π½ΠΎΠΉ ΠΊΠΎΠ½ΡΠΈΠ³ΡΡΠ°ΡΠΈΠΈ, Π½Π΅ΠΎΠ±Ρ ΠΎΠ΄ΠΈΠΌΠΎ ΡΡΡΠΊΠΎ ΠΎΠΏΡΠ΅Π΄Π΅Π»ΠΈΡΡ Π΅Ρ Π½Π°Π·Π½Π°ΡΠ΅Π½ΠΈΠ΅: Π±ΡΠ΄ΡΡ Π»ΠΈ ΠΊ Π½Π΅ΠΉ ΠΏΡΠ΅Π΄ΡΡΠ²Π»ΡΡΡΡΡ Π²ΡΡΠΎΠΊΠΈΠ΅ ΡΡΠ΅Π±ΠΎΠ²Π°Π½ΠΈΡ ΠΏΠΎ ΠΏΡΠΎΡΠ½ΠΎΡΡΠΈ, Π³Π΅ΡΠΌΠ΅ΡΠΈΡΠ½ΠΎΡΡΠΈ ΠΈΠ»ΠΈ ΠΆΠ΅ Π΅Ρ ΠΈΡΠΏΠΎΠ»ΡΠ·ΠΎΠ²Π°Π½ΠΈΠ΅ ΠΎΠ³ΡΠ°Π½ΠΈΡΠΈΡΡΡ Π΄Π΅ΠΊΠΎΡΠ°ΡΠΈΠ²Π½ΠΎΠΉ ΠΎΠ±Π»Π°ΡΡΡΡ. ΠΡ ΠΏΡΠ°Π²ΠΈΠ»ΡΠ½ΠΎΠ³ΠΎ ΡΠΎΡΠ΅ΡΠ°Π½ΠΈΡ ΡΠ΅Ρ Π½ΠΎΠ»ΠΎΠ³ΠΈΡΠ΅ΡΠΊΠΈΡ ΡΠ΅ΠΆΠΈΠΌΠΎΠ² ΠΠΠ, Π·Π°Π²ΠΈΡΠΈΡ ΠΊΠ°ΡΠ΅ΡΡΠ²ΠΎ ΠΈΠ·Π΄Π΅Π»ΠΈΠΉ, Π° ΡΠ°ΠΊΠΆΠ΅ Π·Π°ΡΡΠ°ΡΡ Π½Π° ΠΈΡ ΠΏΡΠΎΠΈΠ·Π²ΠΎΠ΄ΡΡΠ²ΠΎ. Π‘ΠΎΠ±Π»ΡΠ΄Π΅Π½ΠΈΠ΅ ΡΡΠ»ΠΎΠ²ΠΈΠΉ ΡΠ΅Ρ Π½ΠΎΠ»ΠΎΠ³ΠΈΡΠ½ΠΎΡΡΠΈ Π»ΠΈΡΡΡ Π΄Π΅ΡΠ°Π»Π΅ΠΉ, ΠΏΠΎΠ΄ΡΠ°Π·ΡΠΌΠ΅Π²Π°Π΅Ρ ΡΠ°ΠΊΠΎΠ΅ ΠΈΡ ΠΊΠΎΠ½ΡΡΡΡΠΊΡΠΈΠ²Π½ΠΎΠ΅ ΠΎΡΠΎΡΠΌΠ»Π΅Π½ΠΈΠ΅, ΠΊΠΎΡΠΎΡΠΎΠ΅, Π½Π΅ ΡΠ½ΠΈΠΆΠ°Ρ ΠΎΡΠ½ΠΎΠ²Π½ΡΡ ΡΡΠ΅Π±ΠΎΠ²Π°Π½ΠΈΠΉ ΠΊ ΠΊΠΎΠ½ΡΡΡΡΠΊΡΠΈΠΈ, ΡΠΏΠΎΡΠΎΠ±ΡΡΠ²ΡΠ΅Ρ ΠΏΠΎΠ»ΡΡΠ΅Π½ΠΈΡ Π·Π°Π΄Π°Π½Π½ΡΡ ΡΠΈΠ·ΠΈΠΊΠΎ-ΠΌΠ΅Ρ Π°Π½ΠΈΡΠ΅ΡΠΊΠΈΡ ΡΠ²ΠΎΠΉΡΡΠ², ΡΠ°Π·ΠΌΠ΅ΡΠ½ΠΎΠΉ ΡΠΎΡΠ½ΠΎΡΡΠΈ ΠΈ ΡΠ΅ΡΠΎΡ ΠΎΠ²Π°ΡΠΎΡΡΠΈ ΠΏΠΎΠ²Π΅ΡΡ Π½ΠΎΡΡΠΈ ΠΏΡΠΈ ΠΌΠΈΠ½ΠΈΠΌΠ°Π»ΡΠ½ΠΎΠΉ ΡΡΡΠ΄ΠΎΡΠΌΠΊΠΎΡΡΠΈ ΠΈΠ·Π³ΠΎΡΠΎΠ²Π»Π΅Π½ΠΈΡ ΠΈ ΠΎΠ³ΡΠ°Π½ΠΈΡΠ΅Π½Π½ΠΎΠΌ ΠΈΡΠΏΠΎΠ»ΡΠ·ΠΎΠ²Π°Π½ΠΈΠΈ Π΄Π΅ΡΠΈΡΠΈΡΠ½ΡΡ ΠΌΠ°ΡΠ΅ΡΠΈΠ°Π»ΠΎΠ². ΠΡΠ΅Π³Π΄Π° Π½Π΅ΠΎΠ±Ρ ΠΎΠ΄ΠΈΠΌΠΎ ΡΡΠΈΡΡΠ²Π°ΡΡ, ΡΡΠΎ ΠΊΠ°ΡΠ΅ΡΡΠ²ΠΎ ΠΎΡΠ»ΠΈΠ²ΠΎΠΊ, ΠΏΠΎΠ»ΡΡΠ°Π΅ΠΌΡΡ ΠΠΠ, Π·Π°Π²ΠΈΡΠΈΡ ΠΎΡ Π±ΠΎΠ»ΡΡΠΎΠ³ΠΎ ΡΠΈΡΠ»Π° ΠΏΠ΅ΡΠ΅ΠΌΠ΅Π½Π½ΡΡ ΡΠ΅Ρ Π½ΠΎΠ»ΠΎΠ³ΠΈΡΠ΅ΡΠΊΠΈΡ ΡΠ°ΠΊΡΠΎΡΠΎΠ², ΡΠ²ΡΠ·Ρ ΠΌΠ΅ΠΆΠ΄Ρ ΠΊΠΎΡΠΎΡΡΠΌΠΈ ΡΡΡΠ°Π½ΠΎΠ²ΠΈΡΡ ΡΡΠ΅Π·Π²ΡΡΠ°ΠΉΠ½ΠΎ ΡΠ»ΠΎΠΆΠ½ΠΎ ΠΈΠ·-Π·Π° Π±ΡΡΡΡΠΎΡΡ Π·Π°ΠΏΠΎΠ»Π½Π΅Π½ΠΈΡ ΡΠΎΡΠΌΡ.
ΠΡΠ½ΠΎΠ²Π½ΡΠ΅ ΠΏΠ°ΡΠ°ΠΌΠ΅ΡΡΡ, Π²Π»ΠΈΡΡΡΠΈΠ΅ Π½Π° ΠΏΡΠΎΡΠ΅ΡΡ Π·Π°ΠΏΠΎΠ»Π½Π΅Π½ΠΈΡ ΠΈ ΡΠΎΡΠΌΠΈΡΠΎΠ²Π°Π½ΠΈΡ ΠΎΡΠ»ΠΈΠ²ΠΊΠΈ, ΡΠ»Π΅Π΄ΡΡΡΠΈΠ΅:
- Π΄Π°Π²Π»Π΅Π½ΠΈΠ΅ Π½Π° ΠΌΠ΅ΡΠ°Π»Π» Π²ΠΎ Π²ΡΠ΅ΠΌΡ Π·Π°ΠΏΠΎΠ»Π½Π΅Π½ΠΈΡ ΠΈ ΠΏΠΎΠ΄ΠΏΡΠ΅ΡΡΠΎΠ²ΠΊΠΈ;
- ΡΠΊΠΎΡΠΎΡΡΡ ΠΏΡΠ΅ΡΡΠΎΠ²Π°Π½ΠΈΡ;
- ΠΊΠΎΠ½ΡΡΡΡΠΊΡΠΈΡ Π»ΠΈΡΠ½ΠΈΠΊΠΎΠ²ΠΎ-Π²Π΅Π½ΡΠΈΠ»ΡΡΠΈΠΎΠ½Π½ΠΎΠΉ ΡΠΈΡΡΠ΅ΠΌΡ;
- ΡΠ΅ΠΌΠΏΠ΅ΡΠ°ΡΡΡΠ° Π·Π°Π»ΠΈΠ²Π°Π΅ΠΌΠΎΠ³ΠΎ ΡΠΏΠ»Π°Π²Π° ΠΈ ΡΠΎΡΠΌΡ;
- ΡΠ΅ΠΆΠΈΠΌΡ ΡΠΌΠ°Π·ΠΊΠΈ ΠΈ Π²Π°ΠΊΡΡΠΌΠΈΡΠΎΠ²Π°Π½ΠΈΡ.
Π‘ΠΎΡΠ΅ΡΠ°Π½ΠΈΠ΅ΠΌ ΠΈ Π²Π°ΡΡΠΈΡΠΎΠ²Π°Π½ΠΈΠ΅ΠΌ ΡΡΠΈΡ ΠΎΡΠ½ΠΎΠ²Π½ΡΡ ΠΏΠ°ΡΠ°ΠΌΠ΅ΡΡΠΎΠ², Π΄ΠΎΠ±ΠΈΠ²Π°ΡΡΡΡ ΡΠ½ΠΈΠΆΠ΅Π½ΠΈΡ Π½Π΅Π³Π°ΡΠΈΠ²Π½ΡΡ Π²Π»ΠΈΡΠ½ΠΈΠΉ ΠΎΡΠΎΠ±Π΅Π½Π½ΠΎΡΡΠ΅ΠΉ ΠΏΡΠΎΡΠ΅ΡΡΠ° ΠΠΠ. ΠΡΡΠΎΡΠΈΡΠ΅ΡΠΊΠΈ Π²ΡΠ΄Π΅Π»ΡΡΡΡΡ ΡΠ»Π΅Π΄ΡΡΡΠΈΠ΅ ΡΡΠ°Π΄ΠΈΡΠΈΠΎΠ½Π½ΡΠ΅ ΠΊΠΎΠ½ΡΡΡΡΠΊΡΠΎΡΡΠΊΠΎ-ΡΠ΅Ρ Π½ΠΎΠ»ΠΎΠ³ΠΈΡΠ΅ΡΠΊΠΈΠ΅ ΡΠ΅ΡΠ΅Π½ΠΈΡ ΠΏΠΎ ΡΠ½ΠΈΠΆΠ΅Π½ΠΈΡ Π±ΡΠ°ΠΊΠ°:
- ΡΠ΅Π³ΡΠ»ΠΈΡΠΎΠ²Π°Π½ΠΈΠ΅ ΡΠ΅ΠΌΠΏΠ΅ΡΠ°ΡΡΡΡ Π·Π°Π»ΠΈΠ²Π°Π΅ΠΌΠΎΠ³ΠΎ ΡΠΏΠ»Π°Π²Π° ΠΈ ΡΠΎΡΠΌΡ;
- ΠΏΠΎΠ²ΡΡΠ΅Π½ΠΈΠ΅ Π΄Π°Π²Π»Π΅Π½ΠΈΠ΅ Π½Π° ΠΌΠ΅ΡΠ°Π»Π» Π²ΠΎ Π²ΡΠ΅ΠΌΡ Π·Π°ΠΏΠΎΠ»Π½Π΅Π½ΠΈΡ ΠΈ ΠΏΠΎΠ΄ΠΏΡΠ΅ΡΡΠΎΠ²ΠΊΠΈ;
- ΡΠ°ΡΠΈΠ½ΠΈΡΠΎΠ²Π°Π½ΠΈΠ΅ ΠΈ ΠΎΡΠΈΡΡΠΊΠ° ΡΠΏΠ»Π°Π²Π°;
- Π²Π°ΠΊΡΡΠΌΠΈΡΠΎΠ²Π°Π½ΠΈΠ΅;
- ΠΊΠΎΠ½ΡΡΡΡΠΈΡΠΎΠ²Π°Π½ΠΈΠ΅ Π»ΠΈΡΠ½ΠΈΠΊΠΎΠ²ΠΎ-Π²Π΅Π½ΡΠΈΠ»ΡΡΠΈΠΎΠ½Π½ΠΎΠΉ ΡΠΈΡΡΠ΅ΠΌΡ;
Π’Π°ΠΊΠΆΠ΅, ΡΡΡΠ΅ΡΡΠ²ΡΠ΅Ρ ΡΡΠ΄ Π½Π΅ΡΡΠ°Π΄ΠΈΡΠΈΠΎΠ½Π½ΡΡ ΡΠ΅ΡΠ΅Π½ΠΈΠΉ, Π½Π°ΠΏΡΠ°Π²Π»Π΅Π½Π½ΡΡ Π½Π° ΡΡΡΡΠ°Π½Π΅Π½ΠΈΠ΅ Π½Π΅Π³Π°ΡΠΈΠ²Π½ΠΎΠ³ΠΎ Π²Π»ΠΈΡΠ½ΠΈΠ΅ ΠΎΡΠΎΠ±Π΅Π½Π½ΠΎΡΡΠ΅ΠΉ ΠΠΠ:
- Π·Π°ΠΏΠΎΠ»Π½Π΅Π½ΠΈΠ΅ ΡΠΎΡΠΌΡ ΠΈ ΠΊΠ°ΠΌΠ΅ΡΡ Π°ΠΊΡΠΈΠ²Π½ΡΠΌΠΈ Π³Π°Π·Π°ΠΌΠΈ;
- ΠΈΡΠΏΠΎΠ»ΡΠ·ΠΎΠ²Π°Π½ΠΈΠ΅ Π΄Π²ΠΎΠΉΠ½ΠΎΠ³ΠΎ Ρ ΠΎΠ΄Π° Π·Π°ΠΏΠΈΡΠ°ΡΡΠ΅Π³ΠΎ ΠΌΠ΅Ρ Π°Π½ΠΈΠ·ΠΌΠ°;
- ΠΈΡΠΏΠΎΠ»ΡΠ·ΠΎΠ²Π°Π½ΠΈΠ΅ Π΄Π²ΠΎΠΉΠ½ΠΎΠ³ΠΎ ΠΏΠΎΡΡΠ½Ρ ΠΎΡΠΎΠ±ΠΎΠΉ ΠΊΠΎΠ½ΡΡΡΡΠΊΡΠΈΠΈ;
- ΡΡΡΠ°Π½ΠΎΠ²ΠΊΠ° Π·Π°ΠΌΠ΅Π½ΡΠ΅ΠΌΠΎΠΉ Π΄ΠΈΠ°ΡΡΠ°Π³ΠΌΡ;
- ΠΏΡΠΎΡΠΎΡΠΊΠ° Π΄Π»Ρ ΠΎΡΠ²ΠΎΠ΄Π° Π²ΠΎΠ·Π΄ΡΡ Π° Π² ΠΊΠ°ΠΌΠ΅ΡΠ΅ ΠΏΡΠ΅ΡΡΠΎΠ²Π°Π½ΠΈΡ;
ΠΠΈΡΡΡ ΠΏΠΎ Π²ΡΠΏΠ»Π°Π²Π»ΡΠ΅ΠΌΠΎΠΉ ΠΌΠΎΠ΄Π΅Π»ΠΈ
ΠΡΡ ΠΎΠ΄ΠΈΠ½ ΡΠΏΠΎΡΠΎΠ± Π»ΠΈΡΡΡ ΠΌΠ΅ΡΠ°Π»Π»ΠΎΠ²Β β ΠΏΠΎ Π²ΡΠΏΠ»Π°Π²Π»ΡΠ΅ΠΌΠΎΠΉ ΠΌΠΎΠ΄Π΅Π»ΠΈΒ β ΠΏΡΠΈΠΌΠ΅Π½ΡΠ΅ΡΡΡ Π² ΡΠ»ΡΡΠ°ΡΡ ΠΈΠ·Π³ΠΎΡΠΎΠ²Π»Π΅Π½ΠΈΡ Π΄Π΅ΡΠ°Π»Π΅ΠΉ Π²ΡΡΠΎΠΊΠΎΠΉ ΡΠΎΡΠ½ΠΎΡΡΠΈ (Π½Π°ΠΏΡΠΈΠΌΠ΅Ρ Π»ΠΎΠΏΠ°ΡΠΊΠΈ ΡΡΡΠ±ΠΈΠ½ ΠΈΒ Ρ.Β ΠΏ.) ΠΠ· Π»Π΅Π³ΠΊΠΎΠΏΠ»Π°Π²ΠΊΠΎΠ³ΠΎ ΠΌΠ°ΡΠ΅ΡΠΈΠ°Π»Π°: ΠΏΠ°ΡΠ°ΡΠΈΠ½, ΡΡΠ΅Π°ΡΠΈΠ½ ΠΈ Π΄Ρ., (Π² ΠΏΡΠΎΡΡΠ΅ΠΉΡΠ΅ΠΌ ΡΠ»ΡΡΠ°Π΅Β β ΠΈΠ· Π²ΠΎΡΠΊΠ°) ΠΈΠ·Π³ΠΎΡΠ°Π²Π»ΠΈΠ²Π°Π΅ΡΡΡ ΡΠΎΡΠ½Π°Ρ ΠΌΠΎΠ΄Π΅Π»Ρ ΠΈΠ·Π΄Π΅Π»ΠΈΡ ΠΈ Π»ΠΈΡΠ½ΠΈΠΊΠΎΠ²Π°Ρ ΡΠΈΡΡΠ΅ΠΌΠ°. ΠΠ°ΠΈΠ±ΠΎΠ»Π΅Π΅ ΡΠΈΡΠΎΠΊΠΎΠ΅ ΠΏΡΠΈΠΌΠ΅Π½Π΅Π½ΠΈΠ΅ Π½Π°ΡΡΠ» ΠΌΠΎΠ΄Π΅Π»ΡΠ½ΡΠΉ ΡΠΎΡΡΠ°Π² Π50Π‘50 ΡΠΎΡΡΠΎΡΡΠΈΠΉ ΠΈΠ· 50Β % ΡΡΠ΅Π°ΡΠΈΠ½Π° ΠΈ 50Β % ΠΏΠ°ΡΠ°ΡΠΈΠ½Π°, Π΄Π»Ρ ΠΊΡΡΠΏΠ½ΠΎΠ³ΠΎΠ±Π°ΡΠΈΡΠ½ΡΡ ΠΈΠ·Π΄Π΅Π»ΠΈΠΉ ΠΏΡΠΈΠΌΠ΅Π½ΡΡΡΡΡ ΡΠΎΠ»Π΅Π²ΡΠ΅ ΡΠΎΡΡΠ°Π²Ρ ΠΌΠ΅Π½Π΅Π΅ ΡΠΊΠ»ΠΎΠ½Π½ΡΠ΅ ΠΊ ΠΊΠΎΡΠΎΠ±Π»Π΅Π½ΠΈΡ. ΠΠ°ΡΠ΅ΠΌ ΠΌΠΎΠ΄Π΅Π»Ρ ΠΎΠΊΡΠ½Π°Π΅ΡΡΡ Π² ΠΆΠΈΠ΄ΠΊΡΡ ΡΡΡΠΏΠ΅Π½Π·ΠΈΡ Π½Π° ΠΎΡΠ½ΠΎΠ²Π΅ ΡΠ²ΡΠ·ΡΡΡΠ΅Π³ΠΎ ΠΈ ΠΎΠ³Π½Π΅ΡΠΏΠΎΡΠ½ΠΎΠ³ΠΎ Π½Π°ΠΏΠΎΠ»Π½ΠΈΡΠ΅Π»Ρ. Π ΠΊΠ°ΡΠ΅ΡΡΠ²Π΅ ΡΠ²ΡΠ·ΡΡΡΠ΅Π³ΠΎ ΠΏΡΠΈΠΌΠ΅Π½ΡΡΡ Π³ΠΈΠ΄ΡΠΎΠ»ΠΈΠ·ΠΎΠ²Π°Π½Π½ΡΠΉ ΡΡΠΈΠ»ΡΠΈΠ»ΠΈΠΊΠ°Ρ ΠΌΠ°ΡΠΎΠΊ ΠΠ’Π‘ 32 ΠΈ ΠΠ’Π‘ 40, Π³ΠΈΠ΄ΡΠΎΠ»ΠΈΠ· Π²Π΅Π΄ΡΡ Π² ΡΠ°ΡΡΠ²ΠΎΡΠ΅ ΠΊΠΈΡΠ»ΠΎΡΡ, Π²ΠΎΠ΄Ρ ΠΈ ΡΠ°ΡΡΠ²ΠΎΡΠΈΡΠ΅Π»Ρ (ΡΠΏΠΈΡΡ, Π°ΡΠ΅ΡΠΎΠ½). Π Π½Π°ΡΡΠΎΡΡΠ΅Π΅ Π²ΡΠ΅ΠΌΡ Π² ΠΠΠ Π½Π°ΡΠ»ΠΈ ΠΏΡΠΈΠΌΠ΅Π½Π΅Π½ΠΈΡ ΠΊΡΠ΅ΠΌΠ½Π΅Π·ΠΎΠ»ΠΈ Π½Π΅ Π½ΡΠΆΠ΄Π°ΡΡΠΈΠ΅ΡΡ Π² Π³ΠΈΠ΄ΡΠΎΠ»ΠΈΠ·Π΅ Π² ΡΠ΅Ρ ΠΎΠ²ΡΡ ΡΡΠ»ΠΎΠ²ΠΈΡΡ ΠΈ ΡΠ²Π»ΡΡΡΠΈΠ΅ΡΡ ΡΠΊΠΎΠ»ΠΎΠ³ΠΈΡΠ΅ΡΠΊΠΈ Π±Π΅Π·ΠΎΠΏΠ°ΡΠ½ΡΠΌΠΈ. Π ΠΊΠ°ΡΠ΅ΡΡΠ²Π΅ ΠΎΠ³Π½Π΅ΡΠΏΠΎΡΠ½ΠΎΠ³ΠΎ Π½Π°ΠΏΠΎΠ»Π½ΠΈΡΠ΅Π»Ρ ΠΏΡΠΈΠΌΠ΅Π½ΡΡΡ: ΡΠ»Π΅ΠΊΡΡΠΎΠΊΠΎΡΡΠ½Π΄, Π΄ΠΈΡΡΠ΅Π½ΡΠΈΠ»ΠΈΠΌΠ°Π½ΠΈΡ, ΠΊΠ²Π°ΡΡ ΠΈΒ Ρ.Β Π΄. ΠΠ° ΠΌΠΎΠ΄Π΅Π»ΡΠ½ΡΠΉ Π±Π»ΠΎΠΊ (ΠΌΠΎΠ΄Π΅Π»Ρ ΠΈ ΠΠΠ‘) Π½Π°Π½ΠΎΡΡΡ ΡΡΡΠΏΠ΅Π½Π·ΠΈΡ ΠΈ ΠΏΡΠΎΠΈΠ·Π²ΠΎΠ΄ΡΡ ΠΎΠ±ΡΡΠΏΠΊΡ, ΡΠ°ΠΊ Π½Π°Π½ΠΎΡΡΡ ΠΎΡ 6 Π΄ΠΎ 10 ΡΠ»ΠΎΡΠ². Π‘ ΠΊΠ°ΠΆΠ΄ΡΠΌ ΠΏΠΎΡΠ»Π΅Π΄ΡΡΡΠΈΠΌ ΡΠ»ΠΎΠ΅ΠΌ ΡΡΠ°ΠΊΡΠΈΡ Π·Π΅ΡΠ½Π° ΠΎΠ±ΡΡΠΏΠΊΠΈ ΠΌΠ΅Π½ΡΡΡΡΡ Π΄Π»Ρ ΡΠΎΡΠΌΠΈΡΠΎΠ²Π°Π½ΠΈΡ ΠΏΠ»ΠΎΡΠ½ΠΎΠΉ ΠΏΠΎΠ²Π΅ΡΡ Π½ΠΎΡΡΠΈ ΠΎΠ±ΠΎΠ»ΠΎΡΠΊΠΎΠ²ΠΎΠΉ ΡΠΎΡΠΌΡ. Π‘ΡΡΠΊΠ° ΠΊΠ°ΠΆΠ΄ΠΎΠ³ΠΎ ΡΠ»ΠΎΡ Π·Π°Π½ΠΈΠΌΠ°Π΅Ρ Π½Π΅ ΠΌΠ΅Π½Π΅Π΅ ΠΏΠΎΠ»ΡΡΠ°ΡΠ°, Π΄Π»Ρ ΡΡΠΊΠΎΡΠ΅Π½ΠΈΡ ΠΏΡΠΎΡΠ΅ΡΡΠ° ΠΈΡΠΏΠΎΠ»ΡΠ·ΡΡΡ ΡΠΏΠ΅ΡΠΈΠ°Π»ΡΠ½ΡΠ΅ ΡΡΡΠΈΠ»ΡΠ½ΡΠ΅ ΡΠΊΠ°ΡΡ, Π² ΠΊΠΎΡΠΎΡΡΠ΅ Π·Π°ΠΊΠ°ΡΠΈΠ²Π°Π΅ΡΡΡ Π°ΠΌΠΌΠΈΠ°ΡΠ½ΡΠΉ Π³Π°Π·. ΠΠ· ΡΡΠΎΡΠΌΠΈΡΠΎΠ²Π°Π²ΡΠ΅ΠΉΡΡ ΠΎΠ±ΠΎΠ»ΠΎΡΠΊΠΈ Π²ΡΠΏΠ»Π°Π²Π»ΡΡΡ ΠΌΠΎΠ΄Π΅Π»ΡΠ½ΡΠΉ ΡΠΎΡΡΠ°Π²: Π² Π²ΠΎΠ΄Π΅, Π² ΠΌΠΎΠ΄Π΅Π»ΡΠ½ΠΎΠΌ ΡΠΎΡΡΠ°Π²Π΅, Π²ΡΠΆΠΈΠ³Π°Π½ΠΈΠ΅ΠΌ, ΠΏΠ°ΡΠΎΠΌ Π²ΡΡΠΎΠΊΠΎΠ³ΠΎ Π΄Π°Π²Π»Π΅Π½ΠΈΡ. ΠΠΎΡΠ»Π΅ ΡΡΡΠΊΠΈ ΠΈ Π²ΡΡΠΎΠΏΠΊΠΈ Π±Π»ΠΎΠΊ ΠΏΡΠΎΠΊΠ°Π»ΠΈΠ²Π°ΡΡ ΠΏΡΠΈ ΡΠ΅ΠΌΠΏΠ΅ΡΠ°ΡΡΡΠ΅ ΠΏΡΠΈΠΌΠ΅ΡΠ½ΠΎ 1000 Π΄Π»Ρ ΡΠ΄Π°Π»Π΅Π½ΠΈΡ ΠΈΠ· ΠΎΠ±ΠΎΠ»ΠΎΡΠΊΠΎΠ²ΠΎΠΉ ΡΠΎΡΠΌΡ Π²Π΅ΡΠ΅ΡΡΠ² ΡΠΏΠΎΡΠΎΠ±Π½ΡΡ ΠΊ Π³Π°Π·ΠΎΠΎΠ±ΡΠ°Π·ΠΎΠ²Π°Π½ΠΈΡ. ΠΠΎΡΠ»Π΅ ΡΠ΅Π³ΠΎ ΠΎΠ±ΠΎΠ»ΠΎΡΠΊΠΈ ΠΏΠΎΡΡΡΠΏΠ°ΡΡ Π½Π° Π·Π°Π»ΠΈΠ²ΠΊΡ. ΠΠ΅ΡΠ΅Π΄ Π·Π°Π»ΠΈΠ²ΠΊΠΎΠΉ Π±Π»ΠΎΠΊΠΈ Π½Π°Π³ΡΠ΅Π²Π°ΡΡ Π² ΠΏΠ΅ΡΠ°Ρ Π΄ΠΎ 1000. ΠΠ°Π³ΡΠ΅ΡΡΠΉ Π±Π»ΠΎΠΊ ΡΡΡΠ°Π½Π°Π²Π»ΠΈΠ²Π°ΡΡ Π² ΠΏΠ΅ΡΡ ΠΈ ΡΠ°Π·ΠΎΠ³ΡΠ΅ΡΡΠΉ ΠΌΠ΅ΡΠ°Π»Π» Π·Π°Π»ΠΈΠ²Π°ΡΡ Π² ΠΎΠ±ΠΎΠ»ΠΎΡΠΊΡ. ΠΠ°Π»ΠΈΡΡΠΉ Π±Π»ΠΎΠΊ ΠΎΡ Π»Π°ΠΆΠ΄Π°ΡΡ Π² ΡΠ΅ΡΠΌΠΎΡΡΠ°ΡΠ΅ ΠΈΠ»ΠΈ Π½Π° Π²ΠΎΠ·Π΄ΡΡ Π΅. ΠΠΎΠ³Π΄Π° Π±Π»ΠΎΠΊ ΠΏΠΎΠ»Π½ΠΎΡΡΡΡ ΠΎΡ Π»Π°Π΄ΠΈΡΡΡ Π΅Π³ΠΎ ΠΎΡΠΏΡΠ°Π²Π»ΡΡΡ Π½Π° Π²ΡΠ±ΠΈΠ²ΠΊΡ. Π£Π΄Π°ΡΠ°ΠΌΠΈ ΠΌΠΎΠ»ΠΎΡΠ° ΠΏΠΎ Π»ΠΈΡΠ½ΠΈΠΊΠΎΠ²ΠΎΠΉ ΡΠ°ΡΠ΅ ΠΏΡΠΎΠΈΠ·Π²ΠΎΠ΄ΠΈΡΡΡ ΠΎΡΠ±ΠΈΠ²ΠΊΠ° ΠΊΠ΅ΡΠ°ΠΌΠΈΠΊΠΈ, Π΄Π°Π»Π΅Π΅ ΠΎΡΡΠ΅Π·ΠΊΠ° ΠΠΠ‘.Π’Π°ΠΊΠΈΠΌ ΠΎΠ±ΡΠ°Π·ΠΎΠΌ ΠΏΠΎΠ»ΡΡΠ°Π΅ΠΌ ΠΎΡΠ»ΠΈΠ²ΠΊΡ.
Π ΡΠΈΠ»Ρ Π±ΠΎΠ»ΡΡΠΎΠ³ΠΎ ΡΠ°ΡΡ ΠΎΠ΄Π° ΠΌΠ΅ΡΠ°Π»Π»Π° ΠΈ Π΄ΠΎΡΠΎΠ³ΠΎΠ²ΠΈΠ·Π½Ρ ΠΏΡΠΎΡΠ΅ΡΡΠ° ΠΠΠ ΠΏΡΠΈΠΌΠ΅Π½ΡΡΡ ΡΠΎΠ»ΡΠΊΠΎ Π΄Π»Ρ ΠΎΡΠ²Π΅ΡΡΡΠ²Π΅Π½Π½ΡΡ Π΄Π΅ΡΠ°Π»Π΅ΠΉ.
ΠΡΠΎΡΠ΅ΡΡ Π»ΠΈΡΡΡ ΠΏΠΎ Π²ΡΠΏΠ»Π°Π²Π»ΡΠ΅ΠΌΡΠΌ ΠΌΠΎΠ΄Π΅Π»ΡΠΌ Π±Π°Π·ΠΈΡΡΠ΅ΡΡΡ Π½Π° ΡΠ»Π΅Π΄ΡΡΡΠ΅ΠΌ ΠΎΡΠ½ΠΎΠ²Π½ΠΎΠΌ ΠΏΡΠΈΠ½ΡΠΈΠΏΠ΅:
β’ ΠΠΎΠΏΠΈΡ ΠΈΠ»ΠΈ ΠΌΠΎΠ΄Π΅Π»Ρ ΠΊΠΎΠ½Π΅ΡΠ½ΠΎΠ³ΠΎ ΠΈΠ·Π΄Π΅Π»ΠΈΡ ΠΈΠ·Π³ΠΎΡΠ°Π²Π»ΠΈΠ²Π°ΡΡΡΡ ΠΈΠ· Π»Π΅Π³ΠΊΠΎΠΏΠ»Π°Π²ΠΊΠΎΠ³ΠΎ ΠΌΠ°ΡΠ΅ΡΠΈΠ°Π»Π°.
β’ ΠΡΠ° ΠΌΠΎΠ΄Π΅Π»Ρ ΠΎΠΊΡΡΠΆΠ°Π΅ΡΡΡ ΠΊΠ΅ΡΠ°ΠΌΠΈΡΠ΅ΡΠΊΠΎΠΉ ΠΌΠ°ΡΡΠΎΠΉ, ΠΊΠΎΡΠΎΡΠ°Ρ Π·Π°ΡΠ²Π΅ΡΠ΄Π΅Π²Π°Π΅Ρ ΠΈ ΠΎΠ±ΡΠ°Π·ΡΠ΅Ρ ΡΠΎΡΠΌΡ.
β’ ΠΡΠΈ ΠΏΠΎΡΠ»Π΅Π΄ΡΡΡΠ΅ΠΌ Π½Π°Π³ΡΠ΅Π²Π°Π½ΠΈΠΈ (ΠΏΡΠΎΠΊΠ°Π»ΠΊΠ΅) ΡΠΎΡΠΌΡ ΠΌΠΎΠ΄Π΅Π»Ρ ΠΎΡΠ»ΠΈΠ²ΠΊΠΈ ΡΠ°ΡΠΏΠ»Π°Π²Π»ΡΠ΅ΡΡΡ ΠΈ ΡΠ΄Π°Π»ΡΠ΅ΡΡΡ.
β’ ΠΠ°ΡΠ΅ΠΌ Π² ΠΎΡΡΠ°Π²ΡΡΡΡΡ Π½Π° ΠΌΠ΅ΡΡΠ΅ ΡΠ΄Π°Π»ΡΠ½Π½ΠΎΠ³ΠΎ Π²ΠΎΡΠΊΠ° ΠΏΠΎΠ»ΠΎΡΡΡ Π·Π°Π»ΠΈΠ²Π°Π΅ΡΡΡ ΠΌΠ΅ΡΠ°Π»Π», ΠΊΠΎΡΠΎΡΡΠΉ ΡΠΎΡΠ½ΠΎ Π²ΠΎΡΠΏΡΠΎΠΈΠ·Π²ΠΎΠ΄ΠΈΡ ΠΈΡΡ ΠΎΠ΄Π½ΡΡ ΠΌΠΎΠ΄Π΅Π»Ρ ΠΎΡΠ»ΠΈΠ²ΠΊΠΈ.
ΠΠΈΡΡΡ ΠΏΠΎ Π³Π°Π·ΠΈΡΠΈΡΠΈΡΡΠ΅ΠΌΡΠΌ (Π²ΡΠΆΠΈΠ³Π°Π΅ΠΌΡΠΌ) ΠΌΠΎΠ΄Π΅Π»ΡΠΌ
ΠΠΈΡΡΡ ΠΏΠΎ Π³Π°Π·ΠΈΡΠΈΡΠΈΡΡΠ΅ΠΌΡΠΌ ΠΌΠΎΠ΄Π΅Π»ΡΠΌ (ΠΠΠ) ΠΈΠ· ΠΏΠ΅Π½ΠΎΠΏΠ»Π°ΡΡΠ° ΠΏΠΎ ΠΊΠ°ΡΠ΅ΡΡΠ²Ρ ΡΠ°ΡΠΎΠ½Π½ΡΡ ΠΎΡΠ»ΠΈΠ²ΠΎΠΊ, ΡΠΊΠΎΠ½ΠΎΠΌΠΈΡΠ½ΠΎΡΡΠΈ, ΡΠΊΠΎΠ»ΠΎΠ³ΠΈΡΠ½ΠΎΡΡΠΈ ΠΈ Π²ΡΡΠΎΠΊΠΎΠΉ ΠΊΡΠ»ΡΡΡΡΠ΅ ΠΏΡΠΎΠΈΠ·Π²ΠΎΠ΄ΡΡΠ²Π° Π½Π°ΠΈΠ±ΠΎΠ»Π΅Π΅ Π²ΡΠ³ΠΎΠ΄Π½ΠΎ. ΠΠΈΡΠΎΠ²Π°Ρ ΠΏΡΠ°ΠΊΡΠΈΠΊΠ° ΡΠ²ΠΈΠ΄Π΅ΡΠ΅Π»ΡΡΡΠ²ΡΠ΅Ρ ΠΎ ΠΏΠΎΡΡΠΎΡΠ½Π½ΠΎΠΌ ΡΠΎΡΡΠ΅ ΠΏΡΠΎΠΈΠ·Π²ΠΎΠ΄ΡΡΠ²Π° ΠΎΡΠ»ΠΈΠ²ΠΎΠΊ ΡΡΠΈΠΌ ΡΠΏΠΎΡΠΎΠ±ΠΎΠΌ, ΠΊΠΎΡΠΎΡΠΎΠ΅ Π² 2007 Π³ΠΎΠ΄Ρ ΠΏΡΠ΅Π²ΡΡΠΈΠ»ΠΎ 1,5Β ΠΌΠ»Π½ Ρ/Π³ΠΎΠ΄, ΠΎΡΠΎΠ±Π΅Π½Π½ΠΎ ΠΏΠΎΠΏΡΠ»ΡΡΠ½Π° ΠΎΠ½Π° Π² Π‘Π¨Π ΠΈ ΠΠΈΡΠ°Π΅ (Π² ΠΎΠ΄Π½ΠΎΠΉ ΠΠΠ ΡΠ°Π±ΠΎΡΠ°Π΅Ρ Π±ΠΎΠ»Π΅Π΅ 1,5 ΡΡΡ. ΡΠ°ΠΊΠΈΡ ΡΡΠ°ΡΡΠΊΠΎΠ²), Π³Π΄Π΅ Π²ΡΡ Π±ΠΎΠ»ΡΡΠ΅ Π»ΡΡΡ ΠΎΡΠ»ΠΈΠ²ΠΎΠΊ Π±Π΅Π· ΠΎΠ³ΡΠ°Π½ΠΈΡΠ΅Π½ΠΈΠΉ ΠΏΠΎ ΡΠΎΡΠΌΠ΅ ΠΈ ΡΠ°Π·ΠΌΠ΅ΡΠ°ΠΌ. Π ΠΏΠ΅ΡΡΠ°Π½ΠΎΠΉ ΡΠΎΡΠΌΠ΅ ΠΌΠΎΠ΄Π΅Π»Ρ ΠΈΠ· ΠΏΠ΅Π½ΠΎΠΏΠ»Π°ΡΡΠ° ΠΏΡΠΈ Π·Π°Π»ΠΈΠ²ΠΊΠ΅ Π·Π°ΠΌΠ΅ΡΠ°Π΅ΡΡΡ ΡΠ°ΡΠΏΠ»Π°Π²Π»Π΅Π½Π½ΡΠΌ ΠΌΠ΅ΡΠ°Π»Π»ΠΎΠΌ, ΡΠ°ΠΊ ΠΏΠΎΠ»ΡΡΠ°Π΅ΡΡΡ Π²ΡΡΠΎΠΊΠΎΡΠΎΡΠ½Π°Ρ ΠΎΡΠ»ΠΈΠ²ΠΊΠ°. Π§Π°ΡΠ΅ Π²ΡΠ΅Π³ΠΎ ΡΠΎΡΠΌΠ° ΠΈΠ· ΡΡΡ ΠΎΠ³ΠΎ ΠΏΠ΅ΡΠΊΠ° Π²Π°ΠΊΡΡΠΌΠΈΡΡΠ΅ΡΡΡ Π½Π° ΡΡΠΎΠ²Π½Π΅ 50 ΠΊΠΠ°, Π½ΠΎ ΡΠ°ΠΊΠΆΠ΅ ΠΏΡΠΈΠΌΠ΅Π½ΡΡΡ ΡΠΎΡΠΌΠΎΠ²ΠΊΡ Π² Π½Π°Π»ΠΈΠ²Π½ΡΠ΅ ΠΈ Π»Π΅Π³ΠΊΠΎΡΠΏΠ»ΠΎΡΠ½ΡΠ΅ΠΌΡΠ΅ ΠΏΠ΅ΡΡΠ°Π½ΡΠ΅ ΡΠΌΠ΅ΡΠΈ ΡΠΎ ΡΠ²ΡΠ·ΡΡΡΠΈΠΌ. ΠΠ±Π»Π°ΡΡΡ ΠΏΡΠΈΠΌΠ΅Π½Π΅Π½ΠΈΡ ΠΠΠΒ β ΠΎΡΠ»ΠΈΠ²ΠΊΠΈ ΠΌΠ°ΡΡΠΎΠΉ 0,1β2000Β ΠΊΠ³ ΠΈ Π±ΠΎΠ»Π΅Π΅, ΡΠ΅Π½Π΄Π΅Π½ΡΠΈΡ ΡΠ°ΡΡΠΈΡΠ΅Π½ΠΈΡ ΠΏΡΠΈΠΌΠ΅Π½Π΅Π½ΠΈΡ Π² ΡΠ΅ΡΠΈΠΉΠ½ΠΎΠΌ ΠΈ ΠΌΠ°ΡΡΠΎΠ²ΠΎΠΌ ΠΏΡΠΎΠΈΠ·Π²ΠΎΠ΄ΡΡΠ²Π΅ ΠΎΡΠ»ΠΈΠ²ΠΎΠΊ Ρ Π³Π°Π±Π°ΡΠΈΡΠ½ΡΠΌΠΈ ΡΠ°Π·ΠΌΠ΅ΡΠ°ΠΌΠΈ 40β1000Β ΠΌΠΌ, Π² ΡΠ°ΡΡΠ½ΠΎΡΡΠΈ, Π² Π΄Π²ΠΈΠ³Π°ΡΠ΅Π»Π΅ΡΡΡΠΎΠ΅Π½ΠΈΠΈ Π΄Π»Ρ Π»ΠΈΡΡΡ Π±Π»ΠΎΠΊΠΎΠ² ΠΈ Π³ΠΎΠ»ΠΎΠ²ΠΎΠΊ Π±Π»ΠΎΠΊΠΎΠ² ΡΠΈΠ»ΠΈΠ½Π΄ΡΠΎΠ² ΠΈ Π΄Ρ.
ΠΠ° 1 ΡΠΎΠ½Π½Ρ Π³ΠΎΠ΄Π½ΠΎΠ³ΠΎ Π»ΠΈΡΡΡ ΡΠ°ΡΡ ΠΎΠ΄ΡΠ΅ΡΡΡ 4 Π²ΠΈΠ΄Π° ΠΌΠΎΠ΄Π΅Π»ΡΠ½ΠΎ-ΡΠΎΡΠΌΠΎΠ²ΠΎΡΠ½ΡΡ (Π½Π΅ΠΌΠ΅ΡΠ°Π»Π»ΠΈΡΠ΅ΡΠΊΠΈΡ ) ΠΌΠ°ΡΠ΅ΡΠΈΠ°Π»ΠΎΠ²:
- ΠΊΠ²Π°ΡΡΠ΅Π²ΠΎΠ³ΠΎ ΠΏΠ΅ΡΠΊΠ°Β β 50Β ΠΊΠ³,
- ΠΏΡΠΎΡΠΈΠ²ΠΎΠΏΡΠΈΠ³Π°ΡΠ½ΠΎΠ³ΠΎ ΠΏΠΎΠΊΡΡΡΠΈΡΒ β 25Β ΠΊΠ³,
- ΠΏΠ΅Π½ΠΎΠΏΠΎΠ»ΠΈΡΡΠΈΡΠΎΠ»Π°Β β 6Β ΠΊΠ³,
- ΠΏΠ»ΡΠ½ΠΊΠΈ ΠΏΠΎΠ»ΠΈΡΡΠΈΠ»Π΅Π½ΠΎΠ²ΠΎΠΉΒ β 10 ΠΊΠ².ΠΌ.
ΠΡΡΡΡΡΡΠ²ΠΈΠ΅ ΡΡΠ°Π΄ΠΈΡΠΈΠΎΠ½Π½ΡΡ ΡΠΎΡΠΌ ΠΈ ΡΡΠ΅ΡΠΆΠ½Π΅ΠΉ ΠΈΡΠΊΠ»ΡΡΠ°Π΅Ρ ΠΏΡΠΈΠΌΠ΅Π½Π΅Π½ΠΈΠ΅ ΡΠΎΡΠΌΠΎΠ²ΠΎΡΠ½ΡΡ ΠΈ ΡΡΠ΅ΡΠΆΠ½Π΅Π²ΡΡ ΡΠΌΠ΅ΡΠ΅ΠΉ, ΡΠΎΡΠΌΠΎΠ²ΠΊΠ° ΡΠΎΡΡΠΎΠΈΡ ΠΈΠ· Π·Π°ΡΡΠΏΠΊΠΈ ΠΌΠΎΠ΄Π΅Π»ΠΈ ΠΏΠ΅ΡΠΊΠΎΠΌ Ρ ΠΏΠΎΠ²ΡΠΎΡΠ½ΡΠΌ Π΅Π³ΠΎ ΠΈΡΠΏΠΎΠ»ΡΠ·ΠΎΠ²Π°Π½ΠΈΠ΅ΠΌ Π½Π° 95-97Β %.
Π¦Π΅Π½ΡΡΠΎΠ±Π΅ΠΆΠ½ΠΎΠ΅ Π»ΠΈΡΡΠ΅ ΠΈ ΡΠ΅Π½ΡΡΠΎΠ±Π΅ΠΆΠ½ΡΠΉ ΠΌΠ΅ΡΠΎΠ΄ Π»ΠΈΡΡΡ
Π¦Π΅Π½ΡΡΠΎΠ±Π΅ΠΆΠ½ΡΠΉ ΠΌΠ΅ΡΠΎΠ΄ Π»ΠΈΡΡΡ (ΡΠ΅Π½ΡΡΠΎΠ±Π΅ΠΆΠ½ΠΎΠ΅ Π»ΠΈΡΡΡ) ΠΈΡΠΏΠΎΠ»ΡΠ·ΡΠ΅ΡΡΡ ΠΏΡΠΈ ΠΏΠΎΠ»ΡΡΠ΅Π½ΠΈΠΈ ΠΎΡΠ»ΠΈΠ²ΠΎΠΊ, ΠΈΠΌΠ΅ΡΡΠΈΡ ΡΠΎΡΠΌΡ ΡΠ΅Π» Π²ΡΠ°ΡΠ΅Π½ΠΈΡ. ΠΠΎΠ΄ΠΎΠ±Π½ΡΠ΅ ΠΎΡΠ»ΠΈΠ²ΠΊΠΈ ΠΎΡΠ»ΠΈΠ²Π°ΡΡΡΡ ΠΈΠ· ΡΡΠ³ΡΠ½Π°, ΡΡΠ°Π»ΠΈ, Π±ΡΠΎΠ½Π·Ρ ΠΈ Π°Π»ΡΠΌΠΈΠ½ΠΈΡ. ΠΡΠΈ ΡΡΠΎΠΌ ΡΠ°ΡΠΏΠ»Π°Π² Π·Π°Π»ΠΈΠ²Π°ΡΡ Π² ΠΌΠ΅ΡΠ°Π»Π»ΠΈΡΠ΅ΡΠΊΡΡ ΡΠΎΡΠΌΡ, Π²ΡΠ°ΡΠ°ΡΡΡΡΡΡ ΡΠΎ ΡΠΊΠΎΡΠΎΡΡΡΡ 3000 ΠΎΠ±/ΠΌΠΈΠ½.
ΠΠΎΠ΄ Π΄Π΅ΠΉΡΡΠ²ΠΈΠ΅ΠΌ ΡΠ΅Π½ΡΡΠΎΠ±Π΅ΠΆΠ½ΠΎΠΉ ΡΠΈΠ»Ρ ΡΠ°ΡΠΏΠ»Π°Π² ΡΠ°ΡΠΏΡΠ΅Π΄Π΅Π»ΡΠ΅ΡΡΡ ΠΏΠΎ Π²Π½ΡΡΡΠ΅Π½Π½Π΅ΠΉ ΠΏΠΎΠ²Π΅ΡΡ Π½ΠΎΡΡΠΈ ΡΠΎΡΠΌΡ ΠΈ, ΠΊΡΠΈΡΡΠ°Π»Π»ΠΈΠ·ΡΡΡΡ, ΠΎΠ±ΡΠ°Π·ΡΠ΅Ρ ΠΎΡΠ»ΠΈΠ²ΠΊΡ. Π¦Π΅Π½ΡΡΠΎΠ±Π΅ΠΆΠ½ΡΠΌ ΡΠΏΠΎΡΠΎΠ±ΠΎΠΌ ΠΌΠΎΠΆΠ½ΠΎ ΠΏΠΎΠ»ΡΡΠΈΡΡ Π΄Π²ΡΡ ΡΠ»ΠΎΠΉΠ½ΡΠ΅ Π·Π°Π³ΠΎΡΠΎΠ²ΠΊΠΈ, ΡΡΠΎ Π΄ΠΎΡΡΠΈΠ³Π°Π΅ΡΡΡ ΠΏΠΎΠΎΡΠ΅ΡΡΠ΄Π½ΠΎΠΉ Π·Π°Π»ΠΈΠ²ΠΊΠΎΠΉ Π² ΡΠΎΡΠΌΡ ΡΠ°Π·Π»ΠΈΡΠ½ΡΡ ΡΠΏΠ»Π°Π²ΠΎΠ². ΠΡΠΈΡΡΠ°Π»Π»ΠΈΠ·Π°ΡΠΈΡ ΡΠ°ΡΠΏΠ»Π°Π²Π° Π² ΠΌΠ΅ΡΠ°Π»Π»ΠΈΡΠ΅ΡΠΊΠΎΠΉ ΡΠΎΡΠΌΠ΅ ΠΏΠΎΠ΄ Π΄Π΅ΠΉΡΡΠ²ΠΈΠ΅ΠΌ ΡΠ΅Π½ΡΡΠΎΠ±Π΅ΠΆΠ½ΠΎΠΉ ΡΠΈΠ»Ρ ΠΎΠ±Π΅ΡΠΏΠ΅ΡΠΈΠ²Π°Π΅Ρ ΠΏΠΎΠ»ΡΡΠ΅Π½ΠΈΠ΅ ΠΏΠ»ΠΎΡΠ½ΡΡ ΠΎΡΠ»ΠΈΠ²ΠΎΠΊ.
ΠΡΠΈ ΡΡΠΎΠΌ, ΠΊΠ°ΠΊ ΠΏΡΠ°Π²ΠΈΠ»ΠΎ, Π² ΠΎΡΠ»ΠΈΠ²ΠΊΠ°Ρ Π½Π΅ Π±ΡΠ²Π°Π΅Ρ Π³Π°Π·ΠΎΠ²ΡΡ ΡΠ°ΠΊΠΎΠ²ΠΈΠ½ ΠΈ ΡΠ»Π°ΠΊΠΎΠ²ΡΡ Π²ΠΊΠ»ΡΡΠ΅Π½ΠΈΠΉ. ΠΡΠΎΠ±ΡΠΌΠΈ ΠΏΡΠ΅ΠΈΠΌΡΡΠ΅ΡΡΠ²Π°ΠΌΠΈ ΡΠ΅Π½ΡΡΠΎΠ±Π΅ΠΆΠ½ΠΎΠ³ΠΎ Π»ΠΈΡΡΡ ΡΠ²Π»ΡΠ΅ΡΡΡ ΠΏΠΎΠ»ΡΡΠ΅Π½ΠΈΠ΅ Π²Π½ΡΡΡΠ΅Π½Π½ΠΈΡ ΠΏΠΎΠ»ΠΎΡΡΠ΅ΠΉ Π±Π΅Π· ΠΏΡΠΈΠΌΠ΅Π½Π΅Π½ΠΈΡ ΡΡΠ΅ΡΠΆΠ½Π΅ΠΉ ΠΈ Π±ΠΎΠ»ΡΡΠ°Ρ ΡΠΊΠΎΠ½ΠΎΠΌΠΈΡ ΡΠΏΠ»Π°Π²Π° Π² Π²ΠΈΠ΄Ρ ΠΎΡΡΡΡΡΡΠ²ΠΈΡ Π»ΠΈΡΠ½ΠΈΠΊΠΎΠ²ΠΎΠΉ ΡΠΈΡΡΠ΅ΠΌΡ. ΠΡΡ ΠΎΠ΄ Π³ΠΎΠ΄Π½ΡΡ ΠΎΡΠ»ΠΈΠ²ΠΎΠΊ ΠΏΠΎΠ²ΡΡΠ°Π΅ΡΡΡ Π΄ΠΎ 95Β %.
Π Π½Π°ΡΠ΅ΠΌ ΠΏΡΠΎΠΈΠ·Π²ΠΎΠ΄ΡΡΠ²Π΅ ΠΈΡΠΏΠΎΠ»ΡΠ·ΡΡΡ ΠΌΠ°ΡΠΈΠ½Ρ Ρ Π³ΠΎΡΠΈΠ·ΠΎΠ½ΡΠ°Π»ΡΠ½ΡΠΌΠΈ ΠΎΡΡΠΌΠΈ Π²ΡΠ°ΡΠ΅Π½ΠΈΡ. Π¨ΠΈΡΠΎΠΊΠΈΠΌ ΡΠΏΡΠΎΡΠΎΠΌ ΠΏΠΎΠ»ΡΠ·ΡΡΡΡΡ ΠΎΡΠ»ΠΈΠ²ΠΊΠΈ Π²ΡΡΠ»ΠΎΠΊ, Π³ΠΈΠ»ΡΠ· ΠΈ Π΄ΡΡΠ³ΠΈΡ Π·Π°Π³ΠΎΡΠΎΠ²ΠΎΠΊ, ΠΈΠΌΠ΅ΡΡΠΈΡ ΡΠΎΡΠΌΡ ΡΠ΅Π»Π° Π²ΡΠ°ΡΠ΅Π½ΠΈΡ, ΠΏΡΠΎΠΈΠ·Π²Π΅Π΄Π΅Π½Π½ΡΠ΅ Ρ ΠΏΠΎΠΌΠΎΡΡΡ ΠΌΠ΅ΡΠΎΠ΄Π° ΡΠ΅Π½ΡΡΠΎΠ±Π΅ΠΆΠ½ΠΎΠ³ΠΎ Π»ΠΈΡΡΡ. Π§ΡΠΎ ΡΠ°ΠΊΠΎΠ΅ ΡΠ΅Π½ΡΡΠΎΠ±Π΅ΠΆΠ½ΠΎΠ΅ Π»ΠΈΡΡΡ?
Π¦Π΅Π½ΡΡΠΎΠ±Π΅ΠΆΠ½ΠΎΠ΅ Π»ΠΈΡΡΠ΅Β β ΡΡΠΎ ΡΠΏΠΎΡΠΎΠ± ΠΏΠΎΠ»ΡΡΠ΅Π½ΠΈΡ ΠΎΡΠ»ΠΈΠ²ΠΎΠΊ Π² ΠΌΠ΅ΡΠ°Π»Π»ΠΈΡΠ΅ΡΠΊΠΈΡ ΡΠΎΡΠΌΠ°Ρ . ΠΡΠΈ ΡΠ΅Π½ΡΡΠΎΠ±Π΅ΠΆΠ½ΠΎΠΌ Π»ΠΈΡΡΠ΅ ΡΠ°ΡΠΏΠ»Π°Π²Π»Π΅Π½Π½ΡΠΉ ΠΌΠ΅ΡΠ°Π»Π», ΠΏΠΎΠ΄Π²Π΅ΡΠ³Π°ΡΡΡ Π΄Π΅ΠΉΡΡΠ²ΠΈΡ ΡΠ΅Π½ΡΡΠΎΠ±Π΅ΠΆΠ½ΡΡ ΡΠΈΠ», ΠΎΡΠ±ΡΠ°ΡΡΠ²Π°Π΅ΡΡΡ ΠΊ ΡΡΠ΅Π½ΠΊΠ°ΠΌ ΡΠΎΡΠΌΡ ΠΈ Π·Π°ΡΠ²Π΅ΡΠ΄Π΅Π²Π°Π΅Ρ. Π’Π°ΠΊΠΈΠΌ ΠΎΠ±ΡΠ°Π·ΠΎΠΌ ΠΏΠΎΠ»ΡΡΠ°Π΅ΡΡΡ ΠΎΡΠ»ΠΈΠ²ΠΊΠ°. ΠΡΠΎΡ ΡΠΏΠΎΡΠΎΠ± Π»ΠΈΡΡΡ ΡΠΈΡΠΎΠΊΠΎ ΠΈΡΠΏΠΎΠ»ΡΠ·ΡΠ΅ΡΡΡ Π² ΠΏΡΠΎΠΌΡΡΠ»Π΅Π½Π½ΠΎΡΡΠΈ, ΠΎΡΠΎΠ±Π΅Π½Π½ΠΎ Π΄Π»Ρ ΠΏΠΎΠ»ΡΡΠ΅Π½ΠΈΡ ΠΏΡΡΡΠΎΡΠ΅Π»ΡΡ ΠΎΡΠ»ΠΈΠ²ΠΎΠΊ (ΡΠΎ ΡΠ²ΠΎΠ±ΠΎΠ΄Π½ΠΎΠΉ ΠΏΠΎΠ²Π΅ΡΡ Π½ΠΎΡΡΡΡ).
Π’Π΅Ρ Π½ΠΎΠ»ΠΎΠ³ΠΈΡ ΡΠ΅Π½ΡΡΠΎΠ±Π΅ΠΆΠ½ΠΎΠ³ΠΎ Π»ΠΈΡΡΡ ΠΎΠ±Π΅ΡΠΏΠ΅ΡΠΈΠ²Π°Π΅Ρ ΡΠ΅Π»ΡΠΉ ΡΡΠ΄ ΠΏΡΠ΅ΠΈΠΌΡΡΠ΅ΡΡΠ², Π·Π°ΡΠ°ΡΡΡΡ Π½Π΅Π΄ΠΎΡΡΠΈΠΆΠΈΠΌΡΡ ΠΏΡΠΈ Π΄ΡΡΠ³ΠΈΡ ΡΠΏΠΎΡΠΎΠ±Π°Ρ , ΠΊ ΠΏΡΠΈΠΌΠ΅ΡΡ:
- ΠΡΡΠΎΠΊΠ°Ρ ΠΈΠ·Π½ΠΎΡΠΎΡΡΠΎΠΉΠΊΠΎΡΡΡ.
- ΠΡΡΠΎΠΊΠ°Ρ ΠΏΠ»ΠΎΡΠ½ΠΎΡΡΡ ΠΌΠ΅ΡΠ°Π»Π»Π°.
- ΠΡΡΡΡΡΡΠ²ΠΈΠ΅ ΡΠ°ΠΊΠΎΠ²ΠΈΠ½.
- Π ΠΏΡΠΎΠ΄ΡΠΊΡΠΈΠΈ ΡΠ΅Π½ΡΡΠΎΠ±Π΅ΠΆΠ½ΠΎΠ³ΠΎ Π»ΠΈΡΡΡ ΠΎΡΡΡΡΡΡΠ²ΡΡΡ Π½Π΅ΠΌΠ΅ΡΠ°Π»Π»ΠΈΡΠ΅ΡΠΊΠΈΠ΅ Π²ΠΊΠ»ΡΡΠ΅Π½ΠΈΡ ΠΈ ΡΠ»Π°ΠΊ.
Π¦Π΅Π½ΡΡΠΎΠ±Π΅ΠΆΠ½ΡΠΌ Π»ΠΈΡΡΡΠΌ ΠΏΠΎΠ»ΡΡΠ°ΡΡ Π»ΠΈΡΡΠ΅ Π·Π°Π³ΠΎΡΠΎΠ²ΠΊΠΈ, ΠΈΠΌΠ΅ΡΡΠΈΠ΅ ΡΠΎΡΠΌΡ ΡΠ΅Π» Π²ΡΠ°ΡΠ΅Π½ΠΈΡ:
- Π²ΡΡΠ»ΠΊΠΈ;
- Π²Π΅Π½ΡΡ ΡΠ΅ΡΠ²ΡΡΠ½ΡΡ ΠΊΠΎΠ»ΡΡ;
- Π±Π°ΡΠ°Π±Π°Π½Ρ Π΄Π»Ρ Π±ΡΠΌΠ°Π³ΠΎΠ΄Π΅Π»Π°ΡΠ΅Π»ΡΠ½ΡΡ ΠΌΠ°ΡΠΈΠ½;
- ΡΠΎΡΠΎΡΡ ΡΠ»Π΅ΠΊΡΡΠΎΠ΄Π²ΠΈΠ³Π°ΡΠ΅Π»Π΅ΠΉ.
ΠΠ°ΠΈΠ±ΠΎΠ»ΡΡΠ΅Π΅ ΠΏΡΠΈΠΌΠ΅Π½Π΅Π½ΠΈΠ΅ ΡΠ΅Π½ΡΡΠΎΠ±Π΅ΠΆΠ½ΠΎΠ΅ Π»ΠΈΡΡΡ Π½Π°Ρ ΠΎΠ΄ΠΈΡ ΠΏΡΠΈ ΠΈΠ·Π³ΠΎΡΠΎΠ²Π»Π΅Π½ΠΈΠΈ Π²ΡΡΠ»ΠΎΠΊ ΠΈΠ· ΠΌΠ΅Π΄Π½ΡΡ ΡΠΏΠ»Π°Π²ΠΎΠ², ΠΏΡΠ΅ΠΈΠΌΡΡΠ΅ΡΡΠ²Π΅Π½Π½ΠΎ ΠΎΠ»ΠΎΠ²ΡΠ½Π½ΡΡ Π±ΡΠΎΠ½Π·.
ΠΠΎ ΡΡΠ°Π²Π½Π΅Π½ΠΈΡ Ρ Π»ΠΈΡΡΡΠΌ Π² Π½Π΅ΠΏΠΎΠ΄Π²ΠΈΠΆΠ½ΡΠ΅ ΡΠΎΡΠΌΡ ΡΠ΅Π½ΡΡΠΎΠ±Π΅ΠΆΠ½ΠΎΠ΅ Π»ΠΈΡΡΡ ΠΈΠΌΠ΅Π΅Ρ ΡΡΠ΄ ΠΏΡΠ΅ΠΈΠΌΡΡΠ΅ΡΡΠ²: ΠΏΠΎΠ²ΡΡΠ°ΡΡΡΡ Π·Π°ΠΏΠΎΠ»Π½ΡΠ΅ΠΌΠΎΡΡΡ ΡΠΎΡΠΌ, ΠΏΠ»ΠΎΡΠ½ΠΎΡΡΡ ΠΈ ΠΌΠ΅Ρ Π°Π½ΠΈΡΠ΅ΡΠΊΠΈΠ΅ ΡΠ²ΠΎΠΉΡΡΠ²Π° ΠΎΡΠ»ΠΈΠ²ΠΎΠΊ, Π²ΡΡ ΠΎΠ΄ Π³ΠΎΠ΄Π½ΠΎΠ³ΠΎ. ΠΠ΄Π½Π°ΠΊΠΎ Π΄Π»Ρ Π΅Π³ΠΎ ΠΎΡΠ³Π°Π½ΠΈΠ·Π°ΡΠΈΠΈ Π½Π΅ΠΎΠ±Ρ ΠΎΠ΄ΠΈΠΌΠΎ ΡΠΏΠ΅ΡΠΈΠ°Π»ΡΠ½ΠΎΠ΅ ΠΎΠ±ΠΎΡΡΠ΄ΠΎΠ²Π°Π½ΠΈΠ΅; Π½Π΅Π΄ΠΎΡΡΠ°ΡΠΊΠΈ, ΠΏΡΠΈΡΡΡΠΈΠ΅ ΡΡΠΎΠΌΡ ΡΠΏΠΎΡΠΎΠ±Ρ Π»ΠΈΡΡΡ: Π½Π΅ΡΠΎΡΠ½ΠΎΡΡΡ ΡΠ°Π·ΠΌΠ΅ΡΠΎΠ² ΡΠ²ΠΎΠ±ΠΎΠ΄Π½ΡΡ ΠΏΠΎΠ²Π΅ΡΡ Π½ΠΎΡΡΠ΅ΠΉ ΠΎΡΠ»ΠΈΠ²ΠΎΠΊ, ΠΏΠΎΠ²ΡΡΠ΅Π½Π½Π°Ρ ΡΠΊΠ»ΠΎΠ½Π½ΠΎΡΡΡ ΠΊ Π»ΠΈΠΊΠ²Π°ΡΠΈΠΈ ΠΊΠΎΠΌΠΏΠΎΠ½Π΅Π½ΡΠΎΠ² ΡΠΏΠ»Π°Π²Π°, ΠΏΠΎΠ²ΡΡΠ΅Π½Π½ΡΠ΅ ΡΡΠ΅Π±ΠΎΠ²Π°Π½ΠΈΡ ΠΊ ΠΏΡΠΎΡΠ½ΠΎΡΡΠΈ Π»ΠΈΡΠ΅ΠΉΠ½ΡΡ ΡΠΎΡΠΌ.
ΠΠΈΡΡΡ Π² ΠΎΠ±ΠΎΠ»ΠΎΡΠΊΠΎΠ²ΡΠ΅ ΡΠΎΡΠΌΡ
ΠΠΈΡΡΡ Π² ΠΎΠ±ΠΎΠ»ΠΎΡΠΊΠΎΠ²ΡΠ΅ ΡΠΎΡΠΌΡ
ΠΠ±ΠΎΠ»ΠΎΡΠΊΠΎΠ²ΡΡ ΡΠΎΡΠΌΡ ΠΏΠΎΠ»ΡΡΠ°ΡΡ ΠΎΠ΄Π½ΠΈΠΌ ΠΈΠ· Π΄Π²ΡΡ ΠΌΠ΅ΡΠΎΠ΄ΠΎΠ². Π‘ΠΌΠ΅ΡΡ Π½Π°ΡΡΠΏΠ°ΡΡ Π½Π° ΠΌΠ΅ΡΠ°Π»Π»ΠΈΡΠ΅ΡΠΊΡΡ ΠΌΠΎΠ΄Π΅Π»Ρ, Π½Π°Π³ΡΠ΅ΡΡΡ Π΄ΠΎ 300Β°Π‘, Π²ΡΠ΄Π΅ΡΠΆΠΈΠ²Π°ΡΡ Π² ΡΠ΅ΡΠ΅Π½ΠΈΠ΅ Π½Π΅ΡΠΊΠΎΠ»ΡΠΊΠΈΡ Π΄Π΅ΡΡΡΠΊΠΎΠ² ΡΠ΅ΠΊΡΠ½Π΄ Π΄ΠΎ ΠΎΠ±ΡΠ°Π·ΠΎΠ²Π°Π½ΠΈΡ ΡΠΎΠ½ΠΊΠΎΠ³ΠΎ ΡΠΏΡΠΎΡΠ½ΡΠ½Π½ΠΎΠ³ΠΎ ΡΠ»ΠΎΡ, ΠΈΠ·Π±ΡΡΠΎΠΊ ΡΠΌΠ΅ΡΠΈ ΡΠ΄Π°Π»ΡΡΡ. ΠΡΠΈ ΠΈΡΠΏΠΎΠ»ΡΠ·ΠΎΠ²Π°Π½ΠΈΠΈ ΠΏΠ»Π°ΠΊΠΈΡΠΎΠ²Π°Π½Π½ΠΎΠΉ ΡΠΌΠ΅ΡΠΈ Π΅Ρ Π²Π΄ΡΠ²Π°ΡΡ Π² Π·Π°Π·ΠΎΡ ΠΌΠ΅ΠΆΠ΄Ρ Π½Π°Π³ΡΠ΅ΡΠΎΠΉ ΠΌΠΎΠ΄Π΅Π»ΡΡ ΠΈ Π½Π°ΡΡΠΆΠ½ΠΎΠΉ ΠΊΠΎΠ½ΡΡΡΠ½ΠΎΠΉ ΠΏΠ»ΠΈΡΠΎΠΉ. Π ΠΎΠ±ΠΎΠΈΡ ΡΠ»ΡΡΠ°ΡΡ Π½Π΅ΠΎΠ±Ρ ΠΎΠ΄ΠΈΠΌΠΎ Π΄ΠΎΡΠΏΡΠΎΡΠ½Π΅Π½ΠΈΠ΅ ΠΎΠ±ΠΎΠ»ΠΎΡΠΊΠΈ Π² ΠΏΠ΅ΡΠΈ (ΠΏΡΠΈ ΡΠ΅ΠΌΠΏΠ΅ΡΠ°ΡΡΡΠ΅ Π΄ΠΎ 400Β°Π‘) Π½Π° ΠΌΠΎΠ΄Π΅Π»ΠΈ. ΠΠΎΠ»ΡΡΠ΅Π½Π½ΡΠ΅ ΠΎΠ±ΠΎΠ»ΠΎΡΠΊΠΎΠ²ΡΠ΅ ΠΏΠΎΠ»ΡΡΠΎΡΠΌΡ ΡΠΊΡΠ΅ΠΏΠ»ΡΡΡ, ΠΈ Π² Π½ΠΈΡ Π·Π°Π»ΠΈΠ²Π°ΡΡ ΠΆΠΈΠ΄ΠΊΠΈΠΉ ΡΠΏΠ»Π°Π². ΠΠΎ ΠΈΠ·Π±Π΅ΠΆΠ°Π½ΠΈΠ΅ Π΄Π΅ΡΠΎΡΠΌΠ°ΡΠΈΠΈ ΡΠΎΡΠΌ ΠΏΠΎΠ΄ Π΄Π΅ΠΉΡΡΠ²ΠΈΠ΅ΠΌ Π·Π°Π»ΠΈΠ²Π°Π΅ΠΌΠΎΠ³ΠΎ ΡΠΏΠ»Π°Π²Π° ΠΏΠ΅ΡΠ΅Π΄ Π·Π°Π»ΠΈΠ²ΠΊΠΎΠΉ ΠΈΡ ΠΏΠΎΠΌΠ΅ΡΠ°ΡΡ Π² ΠΌΠ΅ΡΠ°Π»Π»ΠΈΡΠ΅ΡΠΊΠΈΠΉ ΠΊΠΎΠΆΡΡ , Π° ΠΏΡΠΎΡΡΡΠ°Π½ΡΡΠ²ΠΎ ΠΌΠ΅ΠΆΠ΄Ρ Π΅Π³ΠΎ ΡΡΠ΅Π½ΠΊΠ°ΠΌΠΈ ΠΈ ΡΠΎΡΠΌΠΎΠΉ Π·Π°ΠΏΠΎΠ»Π½ΡΡΡ ΠΌΠ΅ΡΠ°Π»Π»ΠΈΡΠ΅ΡΠΊΠΎΠΉ Π΄ΡΠΎΠ±ΡΡ, Π½Π°Π»ΠΈΡΠΈΠ΅ ΠΊΠΎΡΠΎΡΠΎΠΉ Π²ΠΎΠ·Π΄Π΅ΠΉΡΡΠ²ΡΠ΅Ρ ΡΠ°ΠΊΠΆΠ΅ Π½Π° ΡΠ΅ΠΌΠΏΠ΅ΡΠ°ΡΡΡΠ½ΡΠΉ ΡΠ΅ΠΆΠΈΠΌ ΠΎΡ Π»Π°ΠΆΠ΄Π°ΡΡΠ΅ΠΉΡΡ ΠΎΡΠ»ΠΈΠ²ΠΊΠΈ.
ΠΡΠΈΠΌ ΡΠΏΠΎΡΠΎΠ±ΠΎΠΌ ΠΈΠ·Π³ΠΎΡΠ°Π²Π»ΠΈΠ²Π°ΡΡ ΡΠ°Π·Π»ΠΈΡΠ½ΡΠ΅ ΠΎΡΠ»ΠΈΠ²ΠΊΠΈ ΠΌΠ°ΡΡΠΎΠΉ Π΄ΠΎ 25Β ΠΊΠ³. ΠΡΠ΅ΠΈΠΌΡΡΠ΅ΡΡΠ²Π°ΠΌΠΈ ΡΠΏΠΎΡΠΎΠ±Π° ΡΠ²Π»ΡΡΡΡΡ Π·Π½Π°ΡΠΈΡΠ΅Π»ΡΠ½ΡΠ΅ ΠΏΠΎΠ²ΡΡΠ΅Π½ΠΈΠ΅ ΠΏΡΠΎΠΈΠ·Π²ΠΎΠ΄ΠΈΡΠ΅Π»ΡΠ½ΠΎΡΡΠΈ ΠΏΠΎ ΡΡΠ°Π²Π½Π΅Π½ΠΈΡ Ρ ΠΈΠ·Π³ΠΎΡΠΎΠ²Π»Π΅Π½ΠΈΠ΅ΠΌ ΠΎΡΠ»ΠΈΠ²ΠΎΠΊ Π»ΠΈΡΡΡΠΌ Π² ΠΏΠ΅ΡΡΠ°Π½ΡΠ΅ ΡΠΎΡΠΌΡ, ΡΠΏΡΠ°Π²Π»Π΅Π½ΠΈΠ΅ ΡΠ΅ΠΏΠ»ΠΎΠ²ΡΠΌ ΡΠ΅ΠΆΠΈΠΌΠΎΠΌ ΠΎΡ Π»Π°ΠΆΠ΄Π΅Π½ΠΈΡ ΠΎΡΠ»ΠΈΠ²ΠΊΠΈ ΠΈ Π²ΠΎΠ·ΠΌΠΎΠΆΠ½ΠΎΡΡΡ ΠΌΠ΅Ρ Π°Π½ΠΈΠ·ΠΈΡΠΎΠ²Π°ΡΡ ΠΏΡΠΎΡΠ΅ΡΡ.
ΠΡΠ½ΠΎΠ²Π°Π½ΠΈΠ΅ | ΡΠ΅Ρ Π½ΠΎΠ»ΠΎΠ³ΠΈΡ | Britannica
ΠΠ·Π³ΠΎΡΠΎΠ²Π»Π΅Π½ΠΈΠ΅ ΡΠ΅ΡΠΊΠΎΠ²Π½ΡΡ ΠΊΠΎΠ»ΠΎΠΊΠΎΠ»ΠΎΠ² ΠΠ±Π·ΠΎΡ ΠΈΠ·Π³ΠΎΡΠΎΠ²Π»Π΅Π½ΠΈΡ ΡΠ΅ΡΠΊΠΎΠ²Π½ΡΡ ΠΊΠΎΠ»ΠΎΠΊΠΎΠ»ΠΎΠ² Ρ ΠΎΠ±ΡΡΠΆΠ΄Π΅Π½ΠΈΠ΅ΠΌ ΠΏΡΠΎΡΠ΅ΡΡΠ° Π»ΠΈΡΡΡ. Contunico Β© ZDF Enterprises GmbH, ΠΠ°ΠΉΠ½Ρ Π‘ΠΌ. ΠΡΠ΅ Π²ΠΈΠ΄Π΅ΠΎ Π΄Π»Ρ ΡΡΠΎΠΉ ΡΡΠ°ΡΡΠΈΠΠΈΡΡΠ΅ , ΠΏΡΠΎΡΠ΅ΡΡ Π·Π°Π»ΠΈΠ²ΠΊΠΈ ΡΠ°ΡΠΏΠ»Π°Π²Π»Π΅Π½Π½ΠΎΠ³ΠΎ ΠΌΠ΅ΡΠ°Π»Π»Π° Π² ΠΏΠΎΠ»ΠΎΡΡΡ, ΠΊΠΎΡΠΎΡΠ°Ρ Π±ΡΠ»Π° ΠΎΡΠ»ΠΈΡΠ° Π² ΡΠΎΠΎΡΠ²Π΅ΡΡΡΠ²ΠΈΠΈ Ρ ΡΠ°Π±Π»ΠΎΠ½ΠΎΠΌ ΠΆΠ΅Π»Π°Π΅ΠΌΠΎΠΉ ΡΠΎΡΠΌΡ. ΠΠΎΠ³Π΄Π° ΠΌΠ΅ΡΠ°Π»Π» Π·Π°ΡΠ²Π΅ΡΠ΄Π΅Π²Π°Π΅Ρ, Π² ΡΠ΅Π·ΡΠ»ΡΡΠ°ΡΠ΅ ΠΏΠΎΠ»ΡΡΠ°Π΅ΡΡΡ ΠΎΡΠ»ΠΈΠ²ΠΊΠ° — ΠΌΠ΅ΡΠ°Π»Π»ΠΈΡΠ΅ΡΠΊΠΈΠΉ ΠΎΠ±ΡΠ΅ΠΊΡ ΡΠΎΠΎΡΠ²Π΅ΡΡΡΠ²ΡΡΡΠ΅ΠΉ ΡΠΎΡΠΌΡ. Π ΠΊΠ°ΠΊΠΎΠΉ-ΡΠΎ ΠΌΠΎΠΌΠ΅Π½Ρ Π² ΠΏΡΠΎΡΠ΅ΡΡΠ΅ ΠΈΠ·Π³ΠΎΡΠΎΠ²Π»Π΅Π½ΠΈΡ ΡΠ°ΠΊ ΠΎΡΠ»ΠΈΠ²Π°ΡΡ ΡΠ°ΠΌΡΠ΅ ΡΠ°Π·Π½ΡΠ΅ ΠΌΠ΅ΡΠ°Π»Π»ΠΈΡΠ΅ΡΠΊΠΈΠ΅ ΠΏΡΠ΅Π΄ΠΌΠ΅ΡΡ.
ΠΠΎΠ΄ΡΠΎΠ±Π½Π΅Π΅ ΠΏΠΎ ΡΡΠΎΠΉ ΡΠ΅ΠΌΠ΅
Π‘ΡΠ°Π»Ρ: Π‘ΡΠ°Π»Π΅Π»ΠΈΡΠ΅ΠΉΠ½ΠΎΠ΅ ΠΏΡΠΎΠΈΠ·Π²ΠΎΠ΄ΡΡΠ²ΠΎ
ΠΠΈΡΠ΅ΠΉΠ½ΡΠ΅ Π·Π°Π²ΠΎΠ΄Ρ, ΠΊΠΎΡΠΎΡΡΠ΅ ΡΠ°Π·Π»ΠΈΠ²Π°ΡΡ ΡΡΠ°Π»Ρ Π² ΡΠΎΠ²Π°ΡΠ½ΡΡ ΠΏΡΠΎΠ΄ΡΠΊΡΠΈΡ, Π² ΠΎΡΠ½ΠΎΠ²Π½ΠΎΠΌ ΠΈΡΠΏΠΎΠ»ΡΠ·ΡΡΡ ΠΈΠ½Π΄ΡΠΊΡΠΈΠΎΠ½Π½ΡΠ΅ ΠΏΠ΅ΡΠΈ Π±Π΅Π· ΡΠ΅ΡΠ΄Π΅ΡΠ½ΠΈΠΊΠ° ΠΈΠ»ΠΈ ΡΠ»Π΅ΠΊΡΡΠΎΠ΄ΡΠ³ΠΎΠ²ΡΠ΅ ΠΏΠ΅ΡΠΈ Π΄Π»Ρ ΠΏΠ»Π°Π²ΠΊΠΈ Π»ΠΎΠΌΠ° ….
Π§Π°ΡΠ΅ Π²ΡΠ΅Π³ΠΎ ΡΠΎΡΠΌΡ ΠΈΠ·Π³ΠΎΡΠ°Π²Π»ΠΈΠ²Π°ΡΡΡΡ ΠΈΠ· ΠΏΠ΅ΡΠΊΠ° ΠΈ Π³Π»ΠΈΠ½Ρ; ΠΊΠ΅ΡΠ°ΠΌΠΈΠΊΠ°, ΠΏΠ΅ΡΠΎΠΊ Ρ ΡΠ΅ΠΌΠ΅Π½ΡΠΎΠΌ, ΠΌΠ΅ΡΠ°Π»Π»Ρ ΠΈ Π΄ΡΡΠ³ΠΈΠ΅ ΠΌΠ°ΡΠ΅ΡΠΈΠ°Π»Ρ ΡΠ°ΠΊΠΆΠ΅ ΠΈΡΠΏΠΎΠ»ΡΠ·ΡΡΡΡΡ Π΄Π»Ρ ΡΠΎΡΠΌ. ΠΡΠΈ ΠΌΠ°ΡΠ΅ΡΠΈΠ°Π»Ρ Π½Π°Π±ΠΈΡΡ Π½Π° ΠΏΠΎΠ²Π΅ΡΡ Π½ΠΎΡΡΡ ΡΠΈΡΡΠ½ΠΊΠ° (ΠΎΠ±ΡΡΠ½ΠΎ ΡΠ΄Π΅Π»Π°Π½Π½ΠΎΠ³ΠΎ ΠΈΠ· Π΄Π΅ΡΠ΅Π²Π°, ΠΌΠ΅ΡΠ°Π»Π»Π° ΠΈΠ»ΠΈ ΡΠΌΠΎΠ»Ρ), ΠΊΠΎΡΠΎΡΡΠΉ ΠΎΠ±ΡΠ°Π·ΡΠ΅Ρ ΠΏΠΎΠ»ΠΎΡΡΡ, Π² ΠΊΠΎΡΠΎΡΡΡ Π΄ΠΎΠ»ΠΆΠ΅Π½ Π·Π°Π»ΠΈΠ²Π°ΡΡΡΡ ΡΠ°ΡΠΏΠ»Π°Π²Π»Π΅Π½Π½ΡΠΉ ΠΌΠ΅ΡΠ°Π»Π».Π ΠΈΡΡΠ½ΠΎΠΊ ΡΠ΄Π°Π»ΡΠ΅ΡΡΡ ΠΈΠ· ΡΠΎΡΠΌΡ, ΠΊΠΎΠ³Π΄Π° Π΅Π³ΠΎ ΡΠΎΡΠΌΠ° ΠΌΠΎΠΆΠ΅Ρ Π±ΡΡΡ ΡΠΎΡ ΡΠ°Π½Π΅Π½Π° ΠΌΠ°ΡΠ΅ΡΠΈΠ°Π»ΠΎΠΌ ΡΠΎΡΠΌΡ. Π€ΠΎΡΠΌΡ ΠΎΠ±ΡΡΠ½ΠΎ ΡΠΎΡΡΠΎΡΡ ΠΈΠ· Π΄Π²ΡΡ ΠΏΠΎΠ»ΠΎΠ²ΠΈΠ½, ΠΈ Π΄Π²Π΅ ΠΏΠΎΠ»ΠΎΠ²ΠΈΠ½ΠΊΠΈ ΡΠΎΠ΅Π΄ΠΈΠ½ΡΡΡΡΡ Π²ΠΌΠ΅ΡΡΠ΅ ΠΏΠΎΡΠ»Π΅ ΡΠ΄Π°Π»Π΅Π½ΠΈΡ Ρ Π½ΠΈΡ ΡΠΈΡΡΠ½ΠΊΠ°. Π¨ΡΠΈΡΡΡ ΠΈ Π²ΡΡΠ»ΠΊΠΈ ΠΎΠ±Π΅ΡΠΏΠ΅ΡΠΈΠ²Π°ΡΡ ΡΠΎΡΠ½ΠΎΠ΅ ΡΠΎΠ΅Π΄ΠΈΠ½Π΅Π½ΠΈΠ΅ Π΄Π²ΡΡ ΠΏΠΎΠ»ΠΎΠ²ΠΈΠ½, ΠΊΠΎΡΠΎΡΡΠ΅ Π²ΠΌΠ΅ΡΡΠ΅ ΠΏΠΎΠΌΠ΅ΡΠ΅Π½Ρ Π² ΠΏΡΠ΅ΡΡ-ΡΠΎΡΠΌΡ. ΠΠ°ΡΠ΅ΠΌ ΠΌΠ΅ΡΠ°Π»Π» ΡΠ΅ΡΠ΅Π· ΡΠΏΠ΅ΡΠΈΠ°Π»ΡΠ½ΡΠ΅ Π·Π°ΡΠ²ΠΎΡΡ Π·Π°Π»ΠΈΠ²Π°Π΅ΡΡΡ Π² ΡΠΎΡΠΌΡ ΠΈ ΡΠ°ΡΠΏΡΠ΅Π΄Π΅Π»ΡΠ΅ΡΡΡ ΠΏΠΎ Π½Π°ΠΏΡΠ°Π²Π»ΡΡΡΠΈΠΌ ΠΏΠΎ ΡΠ°Π·Π½ΡΠΌ ΡΡΠ°ΡΡΠΊΠ°ΠΌ ΠΎΡΠ»ΠΈΠ²ΠΊΠΈ. Π€ΠΎΡΠΌΠ° Π΄ΠΎΠ»ΠΆΠ½Π° Π±ΡΡΡ Π΄ΠΎΡΡΠ°ΡΠΎΡΠ½ΠΎ ΠΏΡΠΎΡΠ½ΠΎΠΉ, ΡΡΠΎΠ±Ρ Π²ΡΠ΄Π΅ΡΠΆΠΈΠ²Π°ΡΡ Π΄Π°Π²Π»Π΅Π½ΠΈΠ΅ ΡΠ°ΡΠΏΠ»Π°Π²Π»Π΅Π½Π½ΠΎΠ³ΠΎ ΠΌΠ΅ΡΠ°Π»Π»Π°, ΠΈ Π΄ΠΎΡΡΠ°ΡΠΎΡΠ½ΠΎ ΠΏΡΠΎΠ½ΠΈΡΠ°Π΅ΠΌΠΎΠΉ, ΡΡΠΎΠ±Ρ ΠΎΠ±Π΅ΡΠΏΠ΅ΡΠΈΠ²Π°ΡΡ Π²ΡΡ ΠΎΠ΄ Π²ΠΎΠ·Π΄ΡΡ Π° ΠΈ Π΄ΡΡΠ³ΠΈΡ Π³Π°Π·ΠΎΠ² ΠΈΠ· ΠΏΠΎΠ»ΠΎΡΡΠΈ ΡΠΎΡΠΌΡ; Π² ΠΏΡΠΎΡΠΈΠ²Π½ΠΎΠΌ ΡΠ»ΡΡΠ°Π΅ ΠΎΠ½ΠΈ ΠΎΡΡΠ°Π½ΡΡΡΡ Π΄ΡΡΠ°ΠΌΠΈ Π² ΠΎΡΠ»ΠΈΠ²ΠΊΠ΅.ΠΠ°ΡΠ΅ΡΠΈΠ°Π» ΡΠΎΡΠΌΡ ΡΠ°ΠΊΠΆΠ΅ Π΄ΠΎΠ»ΠΆΠ΅Π½ ΡΠΎΠΏΡΠΎΡΠΈΠ²Π»ΡΡΡΡΡ ΠΏΠ»Π°Π²Π»Π΅Π½ΠΈΡ Ρ ΡΠ°ΡΠΏΠ»Π°Π²Π»Π΅Π½Π½ΡΠΌ ΠΌΠ΅ΡΠ°Π»Π»ΠΎΠΌ, Π° ΠΏΠ΅ΡΠΎΠΊ Π½Π° ΠΏΠΎΠ²Π΅ΡΡ Π½ΠΎΡΡΠΈ ΡΠΎΡΠΌΡ Π΄ΠΎΠ»ΠΆΠ΅Π½ Π±ΡΡΡ ΠΏΠ»ΠΎΡΠ½ΠΎ ΡΠΏΠ»ΠΎΡΠ½Π΅Π½, ΡΡΠΎΠ±Ρ ΠΏΠΎΠ»ΡΡΠΈΡΡ Π³Π»Π°Π΄ΠΊΡΡ ΠΏΠΎΠ²Π΅ΡΡ Π½ΠΎΡΡΡ ΠΎΡΠ»ΠΈΠ²ΠΊΠΈ.
ΠΠ·Π³ΠΎΡΠΎΠ²Π»Π΅Π½ΠΈΠ΅ Π»Π΅ΠΊΠ°Π» Π΄Π»Ρ Π»ΠΈΡΠ΅ΠΉΠ½ΡΡ ΡΠ΅Ρ ΠΎΠ² ΡΡΠ΅Π±ΡΠ΅Ρ ΠΎΡΡΠΎΡΠΎΠΆΠ½ΠΎΡΡΠΈ ΠΈ ΡΠΌΠ΅Π½ΠΈΡ. ΠΠ±ΡΠ°Π·ΡΡ ΡΠ°Π²Π½ΠΎΠΌΠ΅ΡΠ½ΠΎ Π±ΠΎΠ»ΡΡΠ΅, ΡΠ΅ΠΌ ΠΆΠ΅Π»Π°Π΅ΠΌΠ°Ρ ΠΎΡΠ»ΠΈΠ²ΠΊΠ°, ΡΡΠΎΠ±Ρ ΠΊΠΎΠΌΠΏΠ΅Π½ΡΠΈΡΠΎΠ²Π°ΡΡ ΡΡΠ°Π΄ΠΊΡ ΠΏΡΠΈ ΠΏΠ°Π΄Π΅Π½ΠΈΠΈ ΡΠ΅ΠΌΠΏΠ΅ΡΠ°ΡΡΡΡ ΠΈ ΠΏΠ΅ΡΠ΅Ρ ΠΎΠ΄Π΅ ΠΎΡ ΠΆΠΈΠ΄ΠΊΠΎΠΉ ΡΠ°Π·Ρ ΠΊ ΡΠ²Π΅ΡΠ΄ΠΎΠΉ. Π ΠΈΡΡΠ½ΠΊΠΈ ΠΈΠ· ΠΏΠ΅Π½ΠΎΠΏΠΎΠ»ΠΈΡΡΠΈΡΠΎΠ»Π° ΠΎΡΡΠ°ΡΡΡΡ Π² ΡΠΎΡΠΌΠ΅ ΠΈ ΠΈΡΠΏΠ°ΡΡΡΡΡΡ ΠΏΡΠΈ ΠΊΠΎΠ½ΡΠ°ΠΊΡΠ΅ Ρ ΡΠ°Π·Π»ΠΈΡΡΠΌ ΠΌΠ΅ΡΠ°Π»Π»ΠΎΠΌ; Π²ΠΎΡΠΊΠΎΠ²ΡΠ΅ ΠΌΠΎΠ΄Π΅Π»ΠΈ Π²ΡΠΏΠ»Π°Π²Π»ΡΡΡΡΡ ΠΈΠ· ΡΠΎΡΠΌΡ ΠΏΠ΅ΡΠ΅Π΄ Π·Π°Π»ΠΈΠ²ΠΊΠΎΠΉ ΡΠ°ΡΠΏΠ»Π°Π²Π»Π΅Π½Π½ΠΎΠ³ΠΎ ΠΌΠ΅ΡΠ°Π»Π»Π°.ΠΠ΅ΡΠ°Π»Π»ΠΈΡΠ΅ΡΠΊΠΈΠ΅ ΡΠΎΡΠΌΡ ΠΈΡΠΏΠΎΠ»ΡΠ·ΡΡΡΡΡ ΠΏΡΠΈ Π»ΠΈΡΡΠ΅ ΠΏΠΎΠ΄ Π΄Π°Π²Π»Π΅Π½ΠΈΠ΅ΠΌ. Π§Π°ΡΡΠΎ Π²Π½ΡΡΡΠΈ ΠΎΡΠ»ΠΈΠ²ΠΊΠΈ ΡΡΠ΅Π±ΡΠ΅ΡΡΡ ΠΏΡΡΡΠΎΠ΅ ΠΏΡΠΎΡΡΡΠ°Π½ΡΡΠ²ΠΎ; Π² ΡΡΠΎΠΌ ΡΠ»ΡΡΠ°Π΅ Π² ΠΎΠ΄Π½Ρ ΠΈΠ· ΠΏΠΎΠ»ΠΎΠ²ΠΈΠ½ΠΎΠΊ ΡΠΎΡΠΌΡ ΠΏΠΎΠΌΠ΅ΡΠ°Π΅ΡΡΡ ΡΡΠ΅ΡΠΆΠ΅Π½Ρ ΠΈΠ· ΠΌΠ΅Π»ΠΊΠΎΠ³ΠΎ ΠΏΠ΅ΡΠΊΠ°. Π ΡΡΠΎΠΌ ΠΎΡΠ½ΠΎΡΠ΅Π½ΠΈΠΈ ΡΠ°ΠΊΠΆΠ΅ ΠΈΡΠΏΠΎΠ»ΡΠ·ΡΡΡΡΡ ΡΡΠ΅ΡΠΆΠ½Π΅Π²ΡΠ΅ ΡΡΠΈΠΊΠΈ ΠΈΠ· Π΄Π΅ΡΠ΅Π²Π°, ΠΌΠ΅ΡΠ°Π»Π»Π° ΠΈΠ»ΠΈ ΡΠΌΠΎΠ»Ρ.
Π‘ΠΎΠ²ΡΠ΅ΠΌΠ΅Π½Π½ΡΠ΅ Π»ΠΈΡΠ΅ΠΉΠ½ΡΠ΅ ΡΠ΅Ρ Π°, ΡΠΏΠΎΡΠΎΠ±Π½ΡΠ΅ ΠΊ ΠΊΡΡΠΏΠ½ΠΎΡΠ΅ΡΠΈΠΉΠ½ΠΎΠΌΡ ΠΏΡΠΎΠΈΠ·Π²ΠΎΠ΄ΡΡΠ²Ρ, Ρ Π°ΡΠ°ΠΊΡΠ΅ΡΠΈΠ·ΡΡΡΡΡ Π²ΡΡΠΎΠΊΠΎΠΉ ΡΡΠ΅ΠΏΠ΅Π½ΡΡ ΠΌΠ΅Ρ Π°Π½ΠΈΠ·Π°ΡΠΈΠΈ, Π°Π²ΡΠΎΠΌΠ°ΡΠΈΠ·Π°ΡΠΈΠΈ ΠΈ ΡΠΎΠ±ΠΎΡΠΎΡΠ΅Ρ Π½ΠΈΠΊΠΈ, Π° ΠΌΠΈΠΊΡΠΎΠΏΡΠΎΡΠ΅ΡΡΠΎΡΡ ΠΏΠΎΠ·Π²ΠΎΠ»ΡΡΡ ΡΠΎΡΠ½ΠΎ ΡΠΏΡΠ°Π²Π»ΡΡΡ Π°Π²ΡΠΎΠΌΠ°ΡΠΈΠ·ΠΈΡΠΎΠ²Π°Π½Π½ΡΠΌΠΈ ΡΠΈΡΡΠ΅ΠΌΠ°ΠΌΠΈ. ΠΠΎΡΡΠΈΠΆΠ΅Π½ΠΈΡ Π² ΠΎΠ±Π»Π°ΡΡΠΈ Ρ ΠΈΠΌΠΈΡΠ΅ΡΠΊΠΈΡ ΡΠ²ΡΠ·ΡΡΡΠΈΡ ΠΏΡΠΈΠ²Π΅Π»ΠΈ ΠΊ ΡΠΎΠ·Π΄Π°Π½ΠΈΡ Π±ΠΎΠ»Π΅Π΅ ΠΏΡΠΎΡΠ½ΡΡ ΡΠΎΡΠΌ ΠΈ ΡΡΠ΅ΡΠΆΠ½Π΅ΠΉ ΠΈ Π±ΠΎΠ»Π΅Π΅ ΡΠΎΡΠ½ΡΡ ΠΎΡΠ»ΠΈΠ²ΠΎΠΊ.Π’ΠΎΡΠ½ΠΎΡΡΡ ΠΈ ΡΠΈΡΡΠΎΡΠ° ΠΏΠΎΠ²ΡΡΠ°ΡΡΡΡ Π² ΡΡΠ»ΠΎΠ²ΠΈΡΡ Π²Π°ΠΊΡΡΠΌΠ°, ΠΈ Π΄Π°Π»ΡΠ½Π΅ΠΉΡΠ΅Π΅ ΡΠ°Π·Π²ΠΈΡΠΈΠ΅ ΠΎΠΆΠΈΠ΄Π°Π΅ΡΡΡ ΠΎΡ Π»ΠΈΡΡΡ Π² ΡΡΠ»ΠΎΠ²ΠΈΡΡ Π½Π΅Π²Π΅ΡΠΎΠΌΠΎΡΡΠΈ Π² ΠΊΠΎΡΠΌΠΎΡΠ΅.
ΠΠΎΠ»ΡΡΠΈΡΠ΅ ΡΠΊΡΠΊΠ»ΡΠ·ΠΈΠ²Π½ΡΠΉ Π΄ΠΎΡΡΡΠΏ ΠΊ ΠΊΠΎΠ½ΡΠ΅Π½ΡΡ ΠΈΠ· Π½Π°ΡΠ΅Π³ΠΎ ΠΏΠ΅ΡΠ²ΠΎΠ³ΠΎ ΠΈΠ·Π΄Π°Π½ΠΈΡ 1768 Ρ Π²Π°ΡΠ΅ΠΉ ΠΏΠΎΠ΄ΠΏΠΈΡΠΊΠΎΠΉ. ΠΠΎΠ΄ΠΏΠΈΡΠΈΡΠ΅ΡΡ ΡΠ΅Π³ΠΎΠ΄Π½Ρ .ΠΠ°ΡΡΠΈΠ½Π³: ΠΠΆΠ΅ΠΊΠΈ Π₯ΠΎ. ΠΠΈΡΡΠ΅ ο§ ΠΡΠΎΡΠ΅ΡΡ, ΠΏΡΠΈ ΠΊΠΎΡΠΎΡΠΎΠΌ ΠΌΠ°ΡΠ΅ΡΠΈΠ°Π» Π²Π²ΠΎΠ΄ΠΈΡΡΡ Π² ΡΠΎΡΠΌΡ Π² ΠΆΠΈΠ΄ΠΊΠΎΠΌ ΡΠΎΡΡΠΎΡΠ½ΠΈΠΈ, ΠΈ Π΅ΠΌΡ Π΄Π°ΡΡ Π·Π°ΡΠ²Π΅ΡΠ΄Π΅ΡΡ Π²Π½ΡΡΡΠΈ ΡΠΎΡΠΌΡ,
ΠΡΠ΅Π·Π΅Π½ΡΠ°ΡΠΈΡ Π½Π° ΡΠ΅ΠΌΡ: Β«ΠΡΠ»ΠΈΠ²ΠΊΠ°: ΠΠΆΠ΅ΠΊΠΈ Π₯ΠΎ. ΠΡΠ»ΠΈΠ²ΠΊΠ° ο§ ΠΡΠΎΡΠ΅ΡΡ, ΠΏΡΠΈ ΠΊΠΎΡΠΎΡΠΎΠΌ ΠΌΠ°ΡΠ΅ΡΠΈΠ°Π» Π²Π²ΠΎΠ΄ΠΈΡΡΡ Π² ΡΠΎΡΠΌΡ Π² ΠΆΠΈΠ΄ΠΊΠΎΠΌ ΡΠΎΡΡΠΎΡΠ½ΠΈΠΈ, ΠΈ Π΅ΠΌΡ Π΄Π°ΡΡ Π·Π°ΡΠ²Π΅ΡΠ΄Π΅ΡΡ Π²Π½ΡΡΡΠΈ ΡΠΎΡΠΌΡΒ», — ΡΡΠ΅Π½ΠΎΠ³ΡΠ°ΠΌΠΌΠ° ΠΏΡΠ΅Π·Π΅Π½ΡΠ°ΡΠΈΠΈ:
1 ΠΠ°ΡΡΠΈΠ½Π³: ΠΠΆΠ΅ΠΊΠΈ Π₯ΠΎ
2 ΠΠΈΡΡΠ΅ ο§ ΠΡΠΎΡΠ΅ΡΡ, ΠΏΡΠΈ ΠΊΠΎΡΠΎΡΠΎΠΌ ΠΌΠ°ΡΠ΅ΡΠΈΠ°Π» Π²Π²ΠΎΠ΄ΠΈΡΡΡ Π² ΡΠΎΡΠΌΡ Π² ΠΆΠΈΠ΄ΠΊΠΎΠΌ ΡΠΎΡΡΠΎΡΠ½ΠΈΠΈ, ΠΈ Π΅ΠΌΡ Π΄Π°ΡΡ Π·Π°ΡΠ²Π΅ΡΠ΄Π΅ΡΡ Π²Π½ΡΡΡΠΈ ΡΠΎΡΠΌΡ, ΡΠΎΠ·Π΄Π°Π²Π°Ρ Π³ΠΎΡΠΎΠ²ΡΡ Π΄Π΅ΡΠ°Π»Ρ.
3 ΠΠΈΡΡΠ΅ Π² ΠΏΠ΅ΡΡΠ°Π½ΡΠ΅ ΡΠΎΡΠΌΡ ο§ ΠΠΎΠ»ΠΎΡΡΡ, ΠΎΠ±ΡΠ°Π·ΠΎΠ²Π°Π½Π½Π°Ρ ΡΠ·ΠΎΡΠΎΠΌ ΠΈΠ· Π΄Π΅ΡΠ΅Π²Π° ΠΈΠ»ΠΈ ΠΌΠ΅ΡΠ°Π»Π»Π° ο§ Π’ΡΠ΅Π±ΡΠ΅ΡΡΡ ΡΡΠΎΡΠΊ, ΠΏΠΎΡΠΊΠΎΠ»ΡΠΊΡ ΡΠ°ΡΠΏΠ»Π°Π²Π»Π΅Π½Π½ΡΠΉ ΠΌΠ΅ΡΠ°Π»Π» Π΄Π°Π΅Ρ ΡΡΠ°Π΄ΠΊΡ ΠΏΡΠΈ Π·Π°ΡΠ²Π΅ΡΠ΄Π΅Π²Π°Π½ΠΈΠΈ ΠΠ°ΡΠ΅ΡΠΈΠ°Π», ΠΈΡΠΏΠΎΠ»ΡΠ·ΡΠ΅ΠΌΡΠΉ ΠΏΡΠΈ Π»ΠΈΡΡΠ΅ Π² ΠΏΠ΅ΡΡΠ°Π½ΡΠ΅ ΡΠΎΡΠΌΡ: Π½ΠΈΠ·ΠΊΠΎΡΠ΅ΠΌΠΏΠ΅ΡΠ°ΡΡΡΠ½Π°Ρ ΡΡΠ°Π»Ρ, ΡΠΏΠ»Π°Π²Ρ Al, Mg ΠΈ Ni
4 ΠΠΎΠ΄ΡΠ΅ΠΌΠ½ΠΈΠΊ ΠΈΡΠΏΠΎΠ»ΡΠ·ΡΠ΅ΡΡΡ Π΄Π»Ρ ΡΡΠ΅ΡΠ° ΡΡΠ°Π΄ΠΊΠΈ ΡΠ°ΡΠΏΠ»Π°Π²Π»Π΅Π½Π½ΠΎΠ³ΠΎ ΠΌΠ΅ΡΠ°Π»Π»Π° ΠΏΡΠΈ Π΅Π³ΠΎ Π·Π°ΡΠ²Π΅ΡΠ΄Π΅Π²Π°Π½ΠΈΠΈ.Π€ΡΠ½ΠΊΡΠΈΡ ΡΡΠΎΡΠΊΠ° — ΠΏΡΠΎΡΡΠΎ ΠΏΠΎΠ΄Π°Π²Π°ΡΡ ΡΠ°ΡΠΏΠ»Π°Π²Π»Π΅Π½Π½ΡΠΉ ΠΌΠ΅ΡΠ°Π»Π» Π² ΠΏΡΡΡΠΎΡΡ, Π³Π΄Π΅ ΠΏΡΠΎΠΈΡΡ ΠΎΠ΄ΠΈΡ ΡΡΠ°Π΄ΠΊΠ°.
5 ΠΡΠ»ΠΈΠ²ΠΊΠ° Π² ΠΏΠΎΡΡΠΎΡΠ½Π½ΡΡ ΡΠΎΡΠΌΡ Π€ΠΎΡΠΌΠ°: ο§ ΠΠ° ΠΏΠΎΠ΄Π³ΠΎΡΠΎΠ²ΠΊΡ ΡΡ ΠΎΠ΄ΠΈΡ Π½Π΅ΡΠΊΠΎΠ»ΡΠΊΠΎ Π½Π΅Π΄Π΅Π»Ρ ο§ ΠΠ·Π³ΠΎΡΠΎΠ²Π»Π΅Π½Π° ββΠΈΠ· ΡΡΠ³ΡΠ½Π° ο§ ΠΠ΅ΡΠ΅Π΄ Π·Π°Π»ΠΈΠ²ΠΊΠΎΠΉ ΠΏΡΠ΅Π΄Π²Π°ΡΠΈΡΠ΅Π»ΡΠ½ΠΎ Π½Π°Π³ΡΠ΅Π²Π°Π΅ΡΡΡ Π΄ΠΎ 200 Β° C ο§ Π Π°ΡΡΠΈΡΡΠ΅ΡΡΡ Π²ΠΎ Π²ΡΠ΅ΠΌΡ Π·Π°Π»ΠΈΠ²ΠΊΠΈ ο§ ΠΠΎΠ»ΠΎΡΡΡ Π±ΠΎΠ»ΡΡΠ΅ ΠΆΠ΅Π»Π°Π΅ΠΌΡΡ ΡΠ°Π·ΠΌΠ΅ΡΠΎΠ² ΠΠ°ΡΠ΅ΡΠΈΠ°Π», ΠΈΡΠΏΠΎΠ»ΡΠ·ΡΠ΅ΠΌΡΠΉ ΠΏΡΠΈ Π·Π°Π»ΠΈΠ²ΠΊΠ΅ ΠΏΠΎΡΡΠΎΡΠ½Π½ΠΎΠΉ ΡΠΎΡΠΌΡ: Fe, Al, Mg , Π‘ΠΏΠ»Π°Π²Ρ Π½Π° ΠΎΡΠ½ΠΎΠ²Π΅ ΠΌΠ΅Π΄ΠΈ
6 ΠΠΈΡΡΠ΅ ΠΏΠΎΠ΄ Π΄Π°Π²Π»Π΅Π½ΠΈΠ΅ΠΌ ο§ ΠΠΎΠ΄ΠΎΠ±Π½ΠΎ ΠΏΠΎΡΡΠΎΡΠ½Π½ΠΎΠΌΡ Π»ΠΈΡΡΡ Π² ΡΠΎΡΠΌΡ (ΡΠ°Π·Π½ΠΈΡΠ° Π² ΡΠΎΠΌ, ΡΡΠΎ Π² ΡΡΠΎΠΌ ΡΠΈΠΏΠ΅ Π»ΠΈΡΡΡ ΠΈΡΠΏΠΎΠ»ΡΠ·ΡΠ΅ΡΡΡ Π²ΡΡΠΎΠΊΠΎΠ΅ Π΄Π°Π²Π»Π΅Π½ΠΈΠ΅) (ΡΠ°Π·Π½ΠΈΡΠ° Π² ΡΠΎΠΌ, ΡΡΠΎ ΠΏΡΠΈ ΡΡΠΎΠΌ ΡΠΈΠΏΠ΅ Π»ΠΈΡΡΡ ΠΈΡΠΏΠΎΠ»ΡΠ·ΡΠ΅ΡΡΡ Π²ΡΡΠΎΠΊΠΎΠ΅ Π΄Π°Π²Π»Π΅Π½ΠΈΠ΅) ο§ ΠΠΎΠ»ΠΎΡΡΡ ΡΠΎΡΠΌΡ ΠΌΠΎΠΆΠ΅Ρ Π±ΡΡΡ ΠΎΡΠ΅Π½Ρ ΡΠΎΡΠ½ΠΎΠΉ ο§ ΠΡΠ΅Π½Ρ ΡΠ΅Ρ Π½ΠΈΡΠ½Π°Ρ ΠΈ Π²ΡΡΠΎΠΊΠ°Ρ ΠΊΠ²Π°Π»ΠΈΡΠΈΠΊΠ°ΡΠΈΡ ΡΡΠ΅Π±ΡΠ΅ΡΡΡ Π΄Π»Ρ ΡΠΎΠ·Π΄Π°Π½ΠΈΡ ΡΡΠ°ΠΌΠΏΠ°. ΠΠ΅ΡΠ°Π»Π», ΠΈΡΠΏΠΎΠ»ΡΠ·ΡΠ΅ΠΌΡΠΉ ΠΏΡΠΈ Π»ΠΈΡΡΠ΅ ΠΏΠΎΠ΄ Π΄Π°Π²Π»Π΅Π½ΠΈΠ΅ΠΌ: ΡΠΏΠ»Π°Π²Ρ Π½Π° ΠΎΡΠ½ΠΎΠ²Π΅ Π½Π΅ Fe, Al, Mg, Zn, Cu.
7 Π¦Π΅Π½ΡΡΠΎΠ±Π΅ΠΆΠ½ΠΎΠ΅ Π»ΠΈΡΡΠ΅ ο§ ΠΠΌΠ΅Π΅Ρ ΠΏΡΡΠ΄ΠΈΠ»ΡΠ½ΡΡ ΠΊΠ°ΠΌΠ΅ΡΡ ΡΠΎ ΡΠΊΠΎΡΠΎΡΡΡΡ 300-3000 ΠΎΠ± / ΠΌΠΈΠ½ ο§ ΠΡΠ°ΡΠ΅Π½ΠΈΠ΅ ΠΏΡΠΈ Π·Π°Π»ΠΈΠ²ΠΊΠ΅ ΡΠ°ΡΠΏΠ»Π°Π²Π»Π΅Π½Π½ΠΎΠ³ΠΎ ΠΌΠ΅ΡΠ°Π»Π»Π° ο§ Π Π°ΡΠΏΠ»Π°Π²Π»Π΅Π½Π½ΡΠΉ ΠΌΠ΅ΡΠ°Π»Π» ΠΎΡΠ±ΡΠ°ΡΡΠ²Π°Π΅ΡΡΡ Π² ΡΡΠΎΡΠΎΠ½Ρ, Π³Π΄Π΅ ΠΎΠ½ Π·Π°ΡΠ²Π΅ΡΠ΄Π΅Π²Π°Π΅Ρ ο§ ΠΠ·Π³ΠΎΡΠΎΠ²Π»Π΅Π½Π½ΡΠ΅ Π΄Π΅ΡΠ°Π»ΠΈ ΠΈΠΌΠ΅ΡΡ ΠΌΠ΅Π»ΠΊΠΎΠ·Π΅ΡΠ½ΠΈΡΡΡΡ Π²Π½Π΅ΡΠ½ΡΡ ΠΏΠΎΠ²Π΅ΡΡ Π½ΠΎΡΡΡ ΠΈ ΠΏΡΠΈΠΌΠ΅ΡΠΈ Π²ΠΎ Π²Π½ΡΡΡΠ΅Π½Π½Π΅ΠΌ Π΄ΠΈΠ°ΠΌΠ΅ΡΡΠ΅. ΠΠ°ΡΠ΅ΡΠΈΠ°Π», ΠΈΡΠΏΠΎΠ»ΡΠ·ΡΠ΅ΠΌΡΠΉ ΠΏΡΠΈ ΡΠ΅Π½ΡΡΠΎΠ±Π΅ΠΆΠ½ΠΎΠΌ Π»ΠΈΡΡΠ΅: Fe, ΡΡΠ°Π»Ρ, Π½Π΅ΡΠΆΠ°Π²Π΅ΡΡΠ°Ρ ΡΡΠ°Π»Ρ ΠΈ ΡΠΏΠ»Π°Π²Ρ Al, Cu, Ni
8 ΠΡΠ΅ΠΈΠΌΡΡΠ΅ΡΡΠ²Π° ο§ ΠΠΈΡΡΠ΅ Π² ΠΏΠ΅ΡΡΠ°Π½ΡΠ΅ ΡΠΎΡΠΌΡ ο§ ΠΡΠΎΠΈΠ·Π²ΠΎΠ΄ΡΡΠ²ΠΎ ΠΊΡΡΠΏΠ½ΡΡ Π΄Π΅ΡΠ°Π»Π΅ΠΉ ο§ ΠΠΎΠ·ΠΌΠΎΠΆΠ½ΠΎΡΡΡ Π²ΡΠΎΡΠΈΡΠ½ΠΎΠΉ ΠΏΠ΅ΡΠ΅ΡΠ°Π±ΠΎΡΠΊΠΈ ο§ ΠΡΡΡΡΠ°Ρ ΠΏΠΎΠ΄Π³ΠΎΡΠΎΠ²ΠΊΠ° ΠΏΠ΅ΡΡΠ°Π½ΠΎΠΉ ΡΠΎΡΠΌΡ ο§ ΠΠΎΡΡΠΎΡΠ½Π½ΠΎΠ΅ Π»ΠΈΡΡΠ΅ Π² ΡΠΎΡΠΌΡ ο§ ΠΡΡΠΎΠΊΠ°Ρ ΠΏΡΠΎΠΈΠ·Π²ΠΎΠ΄ΠΈΡΠ΅Π»ΡΠ½ΠΎΡΡΡ ο§ ΠΠΈΠ·ΠΊΠ°Ρ ΡΡΠΎΠΈΠΌΠΎΡΡΡ ΠΏΡΠΎΠΈΠ·Π²ΠΎΠ΄ΡΡΠ²Π° Π½Π° Π΅Π΄ΠΈΠ½ΠΈΡΡ
9 ΠΡΠ΅ΠΈΠΌΡΡΠ΅ΡΡΠ²Π° (ΠΏΡΠΎΠ΄ΠΎΠ»ΠΆΠ΅Π½ΠΈΠ΅) ο§ ΠΠΈΡΡΠ΅ ΠΏΠΎΠ΄ Π΄Π°Π²Π»Π΅Π½ΠΈΠ΅ΠΌ ο§ ΠΠΎΠ΄Ρ ΠΎΠ΄ΠΈΡ Π΄Π»Ρ ΠΌΠ°ΡΡΠΎΠ²ΠΎΠ³ΠΎ ΠΏΡΠΎΠΈΠ·Π²ΠΎΠ΄ΡΡΠ²Π° ο§ Π‘ΡΠΎΠΊ ΡΠ»ΡΠΆΠ±Ρ Π΄ΠΎ 500000 ΠΎΡΠ»ΠΈΠ²ΠΎΠΊ ο§ ΠΡΠ΅Π½Ρ Π²ΡΡΠΎΠΊΠ°Ρ ΠΏΡΠΎΠΈΠ·Π²ΠΎΠ΄ΠΈΡΠ΅Π»ΡΠ½ΠΎΡΡΡ ο§ Π¦Π΅Π½ΡΡΠΎΠ±Π΅ΠΆΠ½ΠΎΠ΅ Π»ΠΈΡΡΠ΅ ο§ ΠΡΠ΅Π½Ρ ΠΌΠ΅Π»ΠΊΠΎΠ·Π΅ΡΠ½ΠΈΡΡΠ°Ρ Π²Π½Π΅ΡΠ½ΡΡ ΠΏΠΎΠ²Π΅ΡΡ Π½ΠΎΡΡΡ ο§ Π‘ΡΠΎΠΉΠΊΠΎΡΡΡ ΠΊ Π°ΡΠΌΠΎΡΡΠ΅ΡΠ½ΠΎΠΉ ΠΊΠΎΡΡΠΎΠ·ΠΈΠΈ
10 ΠΠ΅Π΄ΠΎΡΡΠ°ΡΠΊΠΈ ο§ ΠΠΈΡΡΠ΅ Π² ΠΏΠ΅ΡΡΠ°Π½ΡΠ΅ ΡΠΎΡΠΌΡ ο§ ΠΠΎΠ·ΠΌΠΎΠΆΠ½ΠΎ ΠΏΡΠΎΠΈΠ·Π²ΠΎΠ΄ΡΡΠ²ΠΎ Π² ΠΎΠ³ΡΠ°Π½ΠΈΡΠ΅Π½Π½ΡΡ ΠΊΠΎΠ»ΠΈΡΠ΅ΡΡΠ²Π°Ρ ο§ ΠΠ΅ΡΠ°Π»Π» ΠΏΠΎΠΏΠ°Π΄Π°Π΅Ρ Π² ΠΎΡΡ ΠΎΠ΄Ρ Π² ΡΡΠΎΡΠΊΠ΅ ο§ ΠΠΎΡΡΠΎΡΠ½Π½ΠΎΠ΅ Π»ΠΈΡΡΠ΅ ΡΠΎΡΠΌΡ ο§ Π€ΠΎΡΠΌΡ Π·Π°Π½ΠΈΠΌΠ°ΡΡ ΠΌΠ΅ΡΡΠΎ Π΄Π»Ρ Ρ ΡΠ°Π½Π΅Π½ΠΈΡ ο§ ΠΠΈΡΡΠ΅ ΠΏΠΎΠ΄ Π΄Π°Π²Π»Π΅Π½ΠΈΠ΅ΠΌ ο§ Π’ΡΠ΅Π±ΡΠ΅ΡΡΡ ΠΌΠ½ΠΎΠ³ΠΎ Π²ΡΠ΅ΠΌΠ΅Π½ΠΈ Π΄Π»Ρ ΠΏΠΎΠ΄Π³ΠΎΡΠΎΠ²ΠΊΠΈ ΡΠΎΡΠΌΡ ο§ Π¦Π΅Π½ΡΡΠΎΠ±Π΅ΠΆΠ½ΠΎΠ΅ Π»ΠΈΡΡΠ΅ ο§ ΠΠΎΠ΄Ρ ΠΎΠ΄ΠΈΡ ΡΠΎΠ»ΡΠΊΠΎ Π΄Π»Ρ ΠΏΡΠΎΠΈΠ·Π²ΠΎΠ΄ΡΡΠ²Π° ΡΠΈΠ»ΠΈΠ½Π΄ΡΠΈΡΠ΅ΡΠΊΠΈΡ Π΄Π΅ΡΠ°Π»Π΅ΠΉ
.Π Π°ΡΠΏΠ»Π°Π²Π»Π΅Π½Π½ΠΎΠ³ΠΎ Π·ΠΎΠ»ΠΎΡΠ° Π²ΡΠ»ΠΈΠ²Π°ΡΡ Π² ΡΠΎΡΠΌΡ Π΄Π»Ρ ΡΠ»ΠΈΡΠΊΠΎΠ². ΠΠ°Π»ΠΈΠ²ΠΊΠ° ΡΠ°ΡΠΏΠ»Π°Π²Π»Π΅Π½Π½ΠΎΠ³ΠΎ Π·ΠΎΠ»ΠΎΡΠ° Π² ΡΠΎΡΠΌΡ Π΄Π»Ρ ΡΠ»ΠΈΡΠΊΠΎΠ². ΠΡΠ»ΠΈΠ²ΠΊΠ° ΠΌΠ΅ΡΠ°Π»Π»Π° ΠΈΠ»ΠΈ Π·ΠΎΠ»ΠΎΡΠ° Stock Image
ΠΠΎΡ ΠΎΠΆΠΈΠ΅ ΠΈΠ·ΠΎΠ±ΡΠ°ΠΆΠ΅Π½ΠΈΡ
ΠΠΈΡΡΠ΅ Π·ΠΎΠ»ΠΎΡΠ° Π½Π° ΡΠ°Π±ΡΠΈΠΊΠ΅
Π Π°ΡΠΏΠ»Π°Π²Π»Π΅Π½Π½ΠΎΠ΅ Π·ΠΎΠ»ΠΎΡΠΎ
ΠΠ°Π³ΡΠ°Π΄Π° Π·Π° ΠΌΡΠ·ΡΠΊΠ°Π»ΡΠ½ΡΠΉ Π΄ΠΈΡΠΊ Ρ Π·ΠΎΠ»ΠΎΡΠΎΠΉ Π»ΠΈΡΠΎΠΉ ΠΈΠ»ΠΈ ΠΏΠ»Π°Π²Π»Π΅Π½Π½ΠΎΠΉ ΠΏΠ»Π°ΡΡΠΈΠ½ΠΎΠΉ
Π Π°ΡΠΏΠ»Π°Π²Π»Π΅Π½Π½ΡΠΉ Π·ΠΎΠ»ΠΎΡΠΎΠΉ ΡΠ»ΠΈΡΠΎΠΊ Π²Π΅ΡΠΎΠΌ 250 Π³ΡΠ°ΠΌΠΌ Π½Π° ΡΠΎΠ½Π΅ Π΄ΠΎΠ»Π»Π°ΡΠΎΠ²ΡΡ ΠΊΡΠΏΡΡ
Π Π°ΡΠΏΠ»Π°Π²Π»Π΅Π½Π½ΠΎΠ΅ Π·ΠΎΠ»ΠΎΡΠΎ Π² ΡΠΏΠ΅ΡΠΈΠ°Π»ΡΠ½ΠΎΠΉ ΡΠ°ΡΠ΅, ΠΊΡΡΠΏΠ½ΡΠΉ ΠΏΠ»Π°Π½.Π Π°Π±ΠΎΡΠΈΠΉ ΠΏΡΠΎΡΠ΅ΡΡ Π² ΡΠ²Π΅Π»ΠΈΡΠ½ΠΎΠΉ ΠΌΠ°ΡΡΠ΅ΡΡΠΊΠΎΠΉ
Π‘ΠΈΠ±ΠΈΡΡ, Π ΠΎΡΡΠΈΡ — ΡΠ°ΡΠΏΠ»Π°Π²Π»Π΅Π½Π½ΠΎΠ΅ Π·ΠΎΠ»ΠΎΡΠΎ
Π Π°ΡΠΊΠ°Π»Π΅Π½Π½ΠΎΠ΅ ΡΠ°ΡΠΊΠ°Π»Π΅Π½Π½ΠΎΠ΅ ΡΠ°ΡΠΊΠ°Π»Π΅Π½Π½ΠΎΠ΅ Π·ΠΎΠ»ΠΎΡΠΎ Π·Π°Π»ΠΈΠ²Π°Π΅ΡΡΡ Π² ΠΈΠ·Π»ΠΎΠΆΠ½ΠΈΡΡ
Π Π°ΡΠΏΠ»Π°Π²Π»Π΅Π½Π½ΠΎΠ΅ Π·ΠΎΠ»ΠΎΡΠΎ ΡΠ°Π·Π»ΠΈΠ²Π°Π΅ΡΡΡ ΠΈΠ· Π»ΠΈΡΠ΅ΠΉΠ½ΠΎΠ³ΠΎ ΡΠΈΠ³Π»Ρ
Π Π°ΡΠΏΠ»Π°Π²Π»Π΅Π½Π½ΠΎΠ΅ Π·ΠΎΠ»ΠΎΡΠΎ
ΠΊΡΡΠΎΡΠ΅ΠΊ ΡΠ°ΡΠΏΠ»Π°Π²Π»Π΅Π½Π½ΠΎΠ³ΠΎ Π·ΠΎΠ»ΠΎΡΠ°. ΠΠ°ΠΏΠ»Ρ ΡΠ°ΡΠΏΠ»Π°Π²Π»Π΅Π½Π½ΠΎΠ³ΠΎ Π·ΠΎΠ»ΠΎΡΠ°
Π’ΡΠ·Π΅ΠΌΡΡ Π²ΡΠ»ΠΈΠ²Π°ΡΡ ΡΠ°ΡΠΏΠ»Π°Π²Π»Π΅Π½Π½ΠΎΠ΅ Π·ΠΎΠ»ΠΎΡΠΎ Π² ΠΈΡΠΏΠ°Π½ΡΠΊΠΎΠ³ΠΎ ΠΊΠΎΠ½ΠΊΠΈΡΡΠ°Π΄ΠΎΡΠ°
ΠΠΎΠ»ΠΎΡΠ°Ρ ΡΠΎΠ½ΠΎΠ²Π°Ρ ΡΠΎΡΠΎΠ³ΡΠ°ΡΠΈΡ ΠΈΠ· ΡΠ°ΡΠΏΠ»Π°Π²Π»Π΅Π½Π½ΠΎΠ³ΠΎ ΠΌΠ΅ΡΠ°Π»Π»Π°.
Π Π°ΡΠΏΠ»Π°Π²Π»Π΅Π½Π½ΠΎΠ΅ Π·ΠΎΠ»ΠΎΡΠΎ Π·Π°Π»ΠΈΠ²Π°Π΅ΡΡΡ Π² ΡΠΎΡΠΌΡ Π΄Π»Ρ ΡΡΠ°ΡΡΠΈ ΠΡΠ΄Π΄Ρ
ΠΡΠΎΠ²Π΅ΡΠΊΠ° Π·ΠΎΠ»ΠΎΡΠ°
.