Электроды для сварки алюминия дуги E4043 — алюминиевого сплава электрода — продукция
Описание
Краткие сведения
- Место происхождения: Чжэцзян, Китай (материк)
- Фирменное наименование: Океан сварки
- Номер модели: E4043
- Материал: Алюминий / алюминиевый сплав
- Длина: 300-500 мм
- Рабочий ток: 50-240А
- Сварочный ток: 2.5 мм V, OH 50-80
- Рабочая температура: 60-90, 90-120, 120-150
- Диаметр: 2.0 мм, 2,5 мм, 3.2 мм, 4,0 мм
- Применение: Сварка алюминиевых материалов
Упаковка и доставка
Упаковка Подробности: |
Размер: 2,5 мм X 300 мм (упаковка: 1.0 кг/внутренней коробки 1 тонна / поддон) Размер: 3.2 мм X 350 мм (упаковка: 1.0 кг/внутренней коробки 1 тонна / поддон) Размер: 4,0 мм X 400 мм (упаковка: 1.
Детали поставки:
в течение 25 дней после подтверждения
Технические характеристики
алюминиевый электрод
Стандарт: АРМ
Сертификаты: ISO CE
OEM является приемлемым
Алюминиевый электрод сварки AWS E4043
Технические характеристики
Сплав: 4043 КТР соответствует сертификации: А5.3 AWS
Класс: E4043 ASME SFA А5.3
Сплава: E4043 КТР
Требования к химическому составу AWS
SI = 4.5-6.0 Zn = 0,10 Макс
Fe = 0,80 Макс Ti = 0,20 Макс
Cu = 0,30 = 0,0008 Макс Макс
Mn = 0,05 max Al = остаток
MG = 0,05 max другой = 0,05 каждого — 0,15 max всего
Хранение химический состав % (типичное)
Si = 5,00 Cu = 0,20
TI = 0.11 Аль = баланс
Рекомендуемая операция сварки стержней
Параметры сварного шва зависит от диаметра, материал сварного шва и положение сварки, включая толщину опорной плиты.
Применение
КТР E4043 является покрытием электрод предназначен для обслуживания сварки алюминиевых и алюминиевых сплавов, таких как 5454, 5154, 6052, 6063, 700 серия.-Выбор присадочного металла алюминия главным образом зависит от свойств основного металла
быть достигнуто и сварочной техники. Пост сварки трещин, коррозии и поведение при повышенной температуре также должны приниматься во внимание. Крекинг обычно можно минимизировать путем выбора наполнителя металла выше содержание сплава, то основной металл.
Тестирование продукта
Строго контроля продукции гарантируют качество нашей продукции.
Преимущества
1. меньше брызг
2. легко перезабастовка
3. меньше смога
4. хорошо от шлака, эффективность высокая осаждения
Детали пакета:
1. 1 кг/ПВХ или ПВХ/5 кг поле (термоусадочная пленка + ПВХ окно)
2. 4 коробки ПВХ (20kgs) / картон
3. 50 carton(1 ton)/поддон
4.

5. Доставка: Обычно готовые товары в течение 8 до 25 дней.
О нас
1. Мы являемся Линь Dayang сварочный материал Co., Ltd., один из ведущих производственных предприятий в Китае,
специализируется в создании расходных материалов как сварочные электроды, сварочная проволока, 20 лет.
2. профессионального производства группы, линейки продуктов, опыт технических экспертов, которые участвуют в этой отрасли
около 20 лет у нас есть профессиональные линии для сварки электродом E306-16 теперь.
Процедуру
1. лучшее ценовое предложение
2.on время доставки
3. строгий контроль качества
4. самый полный и самый внимательный сервис
Применение
Транспортные средства, мост техника, Машиностроение,
стальные конструкции, Доставка, производство, строительство и контейнеров.
Hot Tags: Электроды для сварки алюминия дуги,E4043, алюминиевого сплава электрода
|
Электрод алюминиевого электролизера (варианты)
Область техники, к которой относится изобретение
Изобретение относится к устройствам, используемым при электролитическом получении алюминия, в частности к вертикальным или наклонным электродам электролизера для электролитического получения алюминия из оксида алюминия, растворенного в расплавленном электролите, а именно к катодам или катодным частям биполярного электрода.
Применение вертикальных или наклонных смачиваемых катодов, а также биполярных электродов в новых конструкциях алюминиевых электролизеров позволяет уменьшить удельный расход энергии производства алюминия благодаря уменьшению межполюсного расстояния (МПР) между электродами, а также увеличить производительность электролизеров в расчете на единицу занимаемой ими площади. Разработка новых конструкций электролизеров с вертикальными или наклонными электродами сдерживается среди прочего отсутствием технологичных, экономически эффективных и технически реализуемых смачиваемых алюминием электродов электролизера, которые могут быть использованы в качестве вертикальных или наклонных смачиваемых катодов или в качестве катодной части биполярных электродов. Для этого такие электроды должны иметь высокую электропроводность, механическую прочность, трещиностойкость и стойкость к воздействию алюминия и расплавленного электролита при температуре до 1000°C. Кроме того, необходимо, чтобы соединение этих электродов с металлическим токоотводом по технологичности, надежности и электросопротивлению было сравнимо со сварным контактом между металлическими материалами. Трудность обеспечения сочетания всех этих свойств обуславливает отсутствие в настоящий момент работоспособных смачиваемых алюминием электродов и примеров промышленной реализации новых более эффективных конструкций электролизеров для получения алюминия.
Уровень техники
В настоящее время наиболее подходящим материалом для смачиваемого алюминием катода считается чистый диборид титана (TiB2) (Kvande Н. Inert electrodes in aluminium electrolysis cells // Light metals. — 1999. — P. 369-376). Обусловлено это уникальным сочетанием способности противостоять взаимодействию с электролитом и алюминием (Wendt Н.; Dermeteik S. Erosion of sintered titanium diboride cathodes during cathodic aluminium deposition from lithium chloride/aluminium chloride melts // J. Appl. Electrochem. — 20. — 1990. — P. 438-441), хорошей стойкости к окислению (Tampieri A., Landi Е., Bellosi A. On the oxidation behaviour of monolithic titanium diboride and alumina-TiB2 and silicon nitride-TiB2 composites // J. Therm. Anal. — 38 (12). — 1992. — P. 2657-2668) и смачиваемости алюминием. Как правило, большинство добавок к TiB2, улучшая те или иные свойства, отрицательным образом сказываются на химической стойкости композиции по отношению к расплавленному алюминию (Odegard R. On the formation and dissolution of aluminium carbide in aluminium cells // Aluminium. — 64. — 1988. — P. 84-86).
Известен смачиваемый катод из диборида титана (патент US 4308114, С25С 3/06, опубл. 29.12.1981) с содержанием 96% диборида титана, который получают прессованием при температуре более 2000°C. Известен смачиваемый катод из диборида титана с металлическими добавками (заявка на выдачу патента на изобретение US 2012/0222964, С25С 7/02, опубл. 06.09.2012), которые добавляются в количестве от 0,01 до 0,75 мас. % для спекания диборида титана при температурах 1400-2100°C. Учитывая высокую стоимость диборида титана, а также технологические трудности, обусловленные необходимостью спекать катоды при температурах около 2000°C, такие методы изготовления смачиваемых катодов для промышленной практики не применимы. Последнее обуславливает применение композиционных материалов на основе диборида титана.
Известны керамические композиционные материалы B4C-TiB2-TiC (патент RU 2143411, C04B 35/563, опубл. 27.12.1999), TiB2-SiC (международная заявка WO 2013/089886, С25С 3/06, С25С 2/07, опубл. 20.06.2013) для изготовления смачиваемых катодов.
Недостатками таких материалов являются технологические трудности, связанные с высокой температурой спекания, низкая стойкость к ударным и изгибающим механическим нагрузкам, высокая стоимость и меньшая электропроводность по сравнению с чистым диборидом титана. Кроме того, трудно обеспечить электрический контакт металлических катодных токоотводов с такими материалами, сравнимый по надежности и электросопротивлению со сварными контактами между металлическими материалами.
Известны композиционные материалы TiB2-C, из которых могут быть изготовлены смачиваемые алюминием катоды или смачиваемые покрытия углеродных катодов (патент RU 2418888, С25С 3/08, опубл. 20.05.2011). В частности, согласно патенту US 3400061, С25С 3/08, опубл. 03.09.1968, дренируемый катод изготавливают путем смешивания углеродсодержащего наполнителя, 10-20% связующего и 10-80% диборида титана или другого смачиваемого алюминием тугоплавкого соединения, который позволяет снизить межполюсное расстояние и расход электроэнергии электролизеров для получения алюминия. Полученный катод формуют и затем обжигают при температуре 900-1800°C.
Недостатком таких материалов, является то, что для обеспечения достаточной прочности вертикальных катодов и пропускания через них постоянного электрического тока большой величины, они должны иметь большую толщину. Поэтому такие катоды имеют большие габаритные размеры, массу и стоимость. Кроме того, трудно обеспечить электрический контакт металлических катодных токоотводов с такими катодами, сравнимый по надежности и электросопротивлению со сварными контактами между металлическими материалами.
Известны смачиваемые композиционные материалы, содержащие смачиваемый алюминием компонент и оксидный компонент, такой как, оксид алюминия (международная заявка WO 8902423, С25С 3/08, опубл. 23.03.1989; патент US 4717692, С25С 3/08, опубл. 05.01.1988; патент RU 2371523, С25С 3/08, опубл. 27.10.2008; патент US 5753163, С25С 3/08, опубл. 19.05.1998; патент RU 2412283, С25С 3/08, опубл. 24.02.2010).
Недостатком таких материалов является их низкая электропроводность и стойкость к термоудару. Кроме того, трудно обеспечить электрический контакт металлических катодных токоотводов с такими материалами, сравнимый по надежности и электросопротивлению со сварными контактами между металлическими материалами.
Известны композиционные материалы смачиваемых катодов, выполненные из инертной к алюминию керамической матрицы, заполненной алюминием (патент US 4560448, С25С 3/08, опубл. 24.12.1985; патент US 4600481, С25С 3/08; опубл. 15.07.1986; патент US 4650552, С25С 3/06, опубл. 17.03.1987; патент RU 2281987, С25С 3/08, опубл. 20.08.2006).
Недостатком таких смачиваемых электродов является то, что матрица композиционного материала выполнена из керамики, и поэтому они плохо противостоят термоудару, ударным и изгибающим механическим нагрузкам, которые могут иметь место при промышленном использовании катодов. Кроме того, трудно обеспечить электрический контакт металлических катодных токоотводов с такими катодами, сравнимый по надежности и электросопротивлению со сварными контактами между металлическими материалами.
Из патента CN 103304239, C04B 35/58, опубл. 18.09.2013, известен способ изготовления смачиваемого керметного композиционного материала на основе TiB2, который включает смешивание композиционных частиц TiB2-Al2O3, оксидных и металлических добавок, формование и спекание смеси в инертной атмосфере. Согласно изобретению, композиционные частицы TiB2-Al2O3 получают путем смешивания частиц 60-90% TiB2 и 10-40% золя Al2O3, прокаливания полученной смеси при 900-1000°C и последующего дробления спеченного материала. В качестве оксидной добавки используют оксид алюминия, оксид магния, шпинель AB2O4, титанат алюминия, оксид титана или сочетание нескольких из них, где A — один из элементов Ni, Mg, Co, Zn, Cu, Li и Fe или их сочетание; а B — по крайней мере один из элементов Fe, Al, Co, Mn, Cr и Ge. Содержание оксидной добавки 5-25%. В качестве металлической добавки используют 0,5-10% Ni, Fe, Cu, Ti, Co, Cr, Mo, Mn или их сочетание. Формование производят посредством прессования, вибропрессованием или холодным изостатическим прессованием с давлением, 200-300 МПа, 250-400 МПа и 80-150 МПа, соответственно. Спекание производят при 1250-1600°C в течение 120-480 мин, причем на начальной стадии при температуре 800-1200°C спекание выполняют в условиях вакуума с остаточным давлением 10-2-1 Па, а потом в атмосфере инертного газа с давлением 0,8×105 Па, используя Ar, N2 высокой чистоты или их комбинацию с содержанием O2 около 100 мг/м3.
Недостатком этого смачиваемого композиционного материала является то, что его структура состоит в основном из керамической матрицы с высоким содержанием оксидов. Из-за этого материал имеет низкую электропроводность и стойкость к ударным и изгибающим механическим нагрузкам. Кроме того, между катодами из этого материала и металлическими проводниками трудно обеспечить надежный электрический контакт.
Известны способы нанесения керамических композиционных материалов на углеродные основы, которые превосходят керамические материалы по электропроводности, прочности и стойкости к термоудару, а кроме того, упрощают задачу создания контакта с металлическим токоотводом. Например, известны покрытия на основе диборида титана, наносимые на углеродные катоды алюминиевых электролизеров (международная заявка WO 9320027, С25С 3/08, опубл. 14.10.1993; патент CN 1807693, С25С 3/08, опубл. 26.07.2006; патент RU 2518032, С25С 3/06, опубл. 10.06.2014; патент RU 2135643, С25С 3/06, опубл. 17.08.1999). Недостатками этих покрытий является применение основы из углеродсодержащих материалов, которые для обеспечения достаточной прочности и пропускания через них постоянного электрического тока большой величины, должны иметь большую толщину. Поэтому такие катоды имеют большие габаритные размеры и массу. Кроме того, трудно обеспечить электрический контакт металлических катодных токоотводов с такими катодами, сравнимый по надежности и электросопротивлению сварным контактам между металлическими материалами.
Также известны способы нанесения покрытий на основе диборида титана на металлическую основу (патент US 3827954, C25D 3/66; опубл. 06.08.1974; US 3697390, C25D 9/08, опубл. 10.10.1972; международная заявка WO 9320027, С25С 3/08, опубл. 14.10.1993). Благодаря металлической основе смачиваемые алюминием электроды с такими покрытиями будут иметь высокую электропроводность и стойкость к механическим и ударным нагрузкам и могут быть легко приварены к металлическим проводникам для обеспечения надежного электрического контакта. Однако, в случае появления дефектов покрытий, таких как, трещины, расслоения и поры, алюминий будет проникать к основе и взаимодействовать с ней. Это приведет к разрушению основы и загрязнению получаемого алюминия. Кроме того, нанесенное покрытие имеет значительно меньший коэффициент термического расширения (КТР), чем металлическая основа и поэтому при нагреве покрытие будет растрескиваться и отслаиваться от основы.
Известны способы формирования на поверхности тугоплавких металлов диффузионных слоев боридов (борирование) и карбидов (цементация). Например, в патенте RU 2452798, C25D 11/26, опубл. 10.06.2012, предложен способ получения покрытия из диборида титана гальванической поляризацией титана в расплавленной эвтектической смеси хлоридов цезия и натрия, содержащей от 0,2 до 2,0 мас. % оксида бора при температуре 810-840 K в атмосфере аргона.
Наиболее близким аналогом (прототипом) заявленного технического решения по технической сущности и достигаемому результату является известный из международной заявки WO 2008132590, С25С 3/08, опубл. 06.11.2008, смачиваемый алюминием катод, который состоит из основы, выполненной из тугоплавкого металла: молибдена или вольфрама, а на ее поверхности находится интегрированный в основу слой карбида этого тугоплавкого металла. Карбидная поверхность является рабочей поверхностью катода, на которой выделяется алюминий или является промежуточным слоем для покрытия из смачиваемой алюминием керамики, на котором выделяется алюминий. Согласно изобретению основа катода может содержать 50-100 мас. % тугоплавкого металла, 0,1-30 мас %. кремния, 0,1-10 мас. % алюминия, 0,1-20 мас. % углерода. Карбидный слой на поверхности основы может быть получен диффузионным насыщением углеродом (цементацией) поверхности основы и имеет толщину не менее 0,01 мм. На поверхность карбидного слоя может быть нанесено покрытие из тугоплавкого керамического вещества, включающего по меньшей мере одного из боридов титана, хрома, ванадия, циркония, гафния, ниобия, тантала, молибдена, церия, никеля и железа. Покрытие может также содержать добавки, улучшающие смачивание алюминием, которые могут быть выбраны из оксидов или частично окисленных следующих металлов: железо, медь, кобальт, никель, цинк, марганец и их комбинации. Покрытие может быть получено путем нанесения суспензии частиц тугоплавкого вещества и улучшающих смачивание добавок в неорганическом полимерном и/или коллоидном связующем.
Недостатком технического решения по наиболее близкому аналогу является использование в качестве основы молибдена или вольфрама, т. к. они имеют высокую стоимость и их сложно приварить к металлическим проводникам для обеспечения надежного электрического контакта. Кроме того, они имеют низкую стойкость к окислению и при использовании в качестве основы подвешиваемых сверху вертикальных или наклонных катодов могут окисляться на незащищенных электродах, выступающих из расплавленного электролита. Также молибден и вольфрам по сравнению с распространенными конструкционными и жаростойкими сталями обладают высокой хрупкостью и, следовательно, имеют низкую стойкость к механическим и ударным нагрузкам. Помимо этого, высокая плотность молибдена и вольфрама приводит к значительному увеличению массы катодов, что нежелательно с точки зрения материалоемкости катодов и нагрузки на элементы конструкции электролизера.
Раскрытие изобретения
Общими признаками наиболее близкого аналога (прототипа) и предлагаемых смачиваемых алюминием электродов является то, что на их основу нанесен защитный смачиваемый алюминием слой поверхностного покрытия на основе тугоплавкой керамики. Как и в прототипе, смачиваемый алюминием электрод может быть использован в качестве наклонного или вертикального катода электролизеров для получения алюминия электролизом расплавленных солей при температуре ниже 960°C.
Задачей изобретения является разработка конструкции смачиваемых алюминием электродов электролизера для электрохимического получения алюминия, сочетающих высокую коррозионную стойкость, характерную для керамических материалов и высокую электропроводность, технологичность и экономичность, характерную для металлических материалов.
Техническим результатом является решение поставленной задачи, а именно, повышение стойкости основы электрода к окислению, снижение массы электродов, повышение прочности и стойкости смачиваемых алюминием электродов алюминиевого электролизера к ударным и механическим нагрузкам, а также обеспечение надежного сварного контакта смачиваемого алюминием электрода и металлического проводника (токоотвода).
Заявляемый технический результат по первому варианту изобретения достигается за счет того, что основа электрода выполнена из композиционного материала, в состав которого входит электропроводная смачиваемая алюминием и стойкая к алюминию и электролиту тугоплавкая керамика с ее содержанием в композиционном материале от 5 до 90 мас. % и металл или сплав с температурой плавления выше 1000°C, образующий при взаимодействии с алюминием тугоплавкие интерметаллиды. Технический результат по второму варианту изобретения достигается за счет того, что основа электрода с поверхностным покрытием из тугоплавкой керамики выполнена металлической — из стали или другого металла или металлического сплава, который может быть, в частности, жаропрочным и жаростойким, с нанесенным на поверхность основы промежуточного слоя из композиционного материала, в состав которого входит электропроводная смачиваемая алюминием и стойкая к алюминию и электролиту тугоплавкая керамика с ее содержанием в композиционном материале от 5 до 90 мас. % и металл с температурой плавления выше 1000°C или сплав с температурой плавления выше 1000°C, которые образуют при взаимодействии с алюминием тугоплавкие интерметаллиды.
Достижение технического результата обусловлено тем, что непосредственно под поверхностным покрытием из тугоплавкой керамики располагают основу или промежуточный слой, выполненные из композиционного материала, в состав которого входит электропроводная смачиваемая алюминием и стойкая к алюминию и электролиту тугоплавкая керамика и металл или сплав с температурой плавления выше 1000°C, образующие при взаимодействии с алюминием тугоплавкие интерметаллиды. В случае нарушения целостности поверхностного покрытия из тугоплавкой керамики, расплавленный алюминий достигнет композиционного материала, содержащего металл или сплав с температурой плавления выше 1000°C, образующий при взаимодействии с алюминием тугоплавкие интерметаллиды. Тугоплавкие интерметаллиды, образующиеся при взаимодействии металла, содержащегося в композиционном материале, с алюминием создают защитную прослойку, существенно замедляющую дальнейшее проникновение алюминия в тело электрода и его разрушение. Этим, а также высокой стойкостью к алюминию и электролиту входящей в состав композиционного материала тугоплавкой керамики, обусловлена повышенная стойкость предложенного композиционного материала к расплавленному алюминию. Одновременно изобретение вследствие использования композиционного материала заявленного состава, располагающегося под поверхностным покрытием электрода, позволяет улучшить прочность электрода к ударным и механическим нагрузкам, снизить массу электрода, а также обеспечить возможность надежного сварного контакта электрода и токоотвода вследствие наличия металлической составляющей в композиционном материале.
Изобретение представлено частными случаями его конструктивного исполнения.
При изготовлении основы из металлического сплава используют конструкционную углеродистую сталь или жаропрочные и жаростойкие стали и сплавы с температурой плавления выше 1000°C.
При изготовлении основы из композиционного материала в качестве металла с температурой плавления выше 1000°C, образующего при взаимодействии с алюминием тугоплавкие интерметаллиды, используют по меньшей мере один из следующих металлов: железо, никель, марганец, титан, тантал, цирконий, хром, ниобий, кобальт, ванадий, и/или по меньшей мере один из сплавов этих металлов.
В качестве тугоплавкой керамики в составе композиционного материала используют бориды и/или карбиды титана, циркония, ниобия, тантала, вольфрама, молибдена, бора (только карбиды) и их смеси.
Бориды и карбиды в композиционном материале могут быть получены в процессе изготовления электрода путем добавления бора и углерода в металл или сплав, которые входят в состав композиционного материала.
Тугоплавкая керамика в композиционном материале находится в виде частиц с размером 1-1000 мкм, при этом частицы равномерно распределены по всему объему материала.
Основа электрода может быть изготовлена литьем или самораспространяющимся высокотемпературным синтезом (CBC-синтезом) или методом порошковой металлургии.
По второму варианту изобретения на основу, выполненную из углеродистой стали или жаропрочного и жаростойкого металлического сплава, нанесен промежуточный слой композиционного материала с содержанием тугоплавкой керамики от 5 до 90 мас. % и металла или сплава с температурой плавления выше 1000°C, образующих при взаимодействии с алюминием тугоплавкие интерметаллиды. Промежуточный слой расположен между основой металлического сплава и поверхностным покрытием на основе тугоплавкой керамики, т.е. поверхностное покрытие нанесено на промежуточный слой.
В качестве материала поверхностного покрытия, наносимого на основу, как для первого варианта, так и для второго варианта изобретения может быть использован композиционный материал с содержанием тугоплавкой керамики более 90 мас. % или тугоплавкая керамика.
Для второго варианта изобретения в качестве материала промежуточного слоя, наносимого на основу электрода, используют композиционный материал с содержанием тугоплавкой керамики от 5 до 90 мас. %), а также металла или сплава с температурой плавления выше 1000°C, образующих при взаимодействии с алюминием тугоплавкие интерметаллиды. В частном случае выполнения электрода по второму варианту на промежуточный слой может быть нанесен дополнительный слой композиционного материала с большим содержанием тугоплавкой керамики, чем ее количество в промежуточном слое. Дополнительных слоев может быть один или более, причем вследствие наличия дополнительного слоя обеспечена возможность создать последовательное увеличение содержания тугоплавкой керамики в композиционном материале каждого дополнительного слоя в направлении от основы к поверхностному покрытию, например, начиная от (5-90) мас. % до величины более 90 мас. % (но менее, чем в поверхностном покрытии) при обязательном наличии в этом композиционном материале металла или сплава с температурой плавления выше 1000°C, образующих при взаимодействии с алюминием тугоплавкие интерметаллиды. Как еще один частный вариант исполнения изобретения, промежуточный слой может быть выполнен в виде одного слоя с постепенным увеличением содержания тугоплавкой керамики в композиционном материале в направлении от основы к поверхностному покрытию. В этом случае содержание тугоплавкой керамики в композиционном материале промежуточного слоя, вблизи поверхностного покрытия может содержать более 90 мас. % тугоплавкой керамики и собственно, являться поверхностным покрытием, т.е. плавно переходить в поверхностное покрытие.
Суммарная толщина промежуточного слоя и слоя поверхностного покрытия, как правило, составляет 0,5-10 мм.
В частном случае выполнения изобретения, под смачиваемым алюминием поверхностным покрытием из тугоплавкой керамики или на основе тугоплавкой керамики находится насыщенная углеродом поверхность основы или промежуточного слоя.
Электрод может представлять собой катод или катодную часть биполярного электрода.
Для обеспечения повышенной стойкости указанных композиционных материалов к расплавленному алюминию необходимо, чтобы входящий в их состав металл или сплав имел температуру плавления выше 1000°C и при взаимодействии с алюминием образовывал тугоплавкие интерметаллиды. По этому критерию, а также для снижения стоимости этих материалов в качестве компонентов композиционных материалов, образующих с алюминием тугоплавкие интерметаллиды, выбраны металлы: железо, никель, марганец, титан, тантал, цирконий, хром, ниобий, кобальт, ванадий и/или сплавы, включающие по меньшей мере один из следующих металлов: железо, никель, марганец, титан, тантал, цирконий, хром, ниобий, кобальт, ванадий.
Для обеспечения высокой электропроводности, смачиваемости алюминием, снижения коэффициента термического расширения (КТР) композиционных материалов и для увеличения химической стойкости указанных композиционных материалов в их состав должна входить электропроводная смачиваемая алюминием и стойкая к алюминию и электролиту тугоплавкая керамика. Это могут быть бориды и карбиды титана, циркония, ниобия, тантала, бора (только карбиды) и их смеси. Размер частиц тугоплавкой керамики в композиционном материале может варьироваться в широком диапазоне от 1 до 1000 мкм или в более узком диапазоне, находящемся внутри упомянутого диапазона от 1 до 1000 мкм. Распределение частиц по размерам должно быть равномерным по объему материала, что обеспечивается известными технологическими приемами.
Частицы боридов и карбидов в материале могут быть получены путем добавления бора и углерода в металлическую компоненту. В процессе нагрева при изготовлении изделий из таких материалов в них будут идти реакции между металлами и бором и углеродом с образованием соответствующих боридов и карбидов. Известные технологии позволяют получить композиционный материал с высокой степенью равномерности распределения частиц боридов и карбидов по объему изделия.
Содержание частиц керамики в этих материалах может варьироваться в широких пределах. При содержании в композиционном материале поверхностного покрытия тугоплавкой керамики в количестве менее 90 мас. % металлическая основа может загрязнять получаемый алюминий и поэтому композиционные материалы с содержанием тугоплавкой керамики менее 90 мас. % следует использовать только в качестве основы и/или промежуточных слоев покрытий смачиваемых алюминием элементов. Как покрытие основы такой материал использовать нецелесообразно.
При содержании керамики более 90 мас. % композиционные материалы можно применять непосредственно в качестве поверхностного покрытия смачиваемых алюминием электродов, т.к. они становятся аналогичными покрытиям на основе тугоплавкой керамики.
При содержании тугоплавкой керамики менее 5 мас. % композиционные материалы становятся близки по свойствам к металлическим сплавам и поэтому не могут служить для нанесения на них покрытий на основе тугоплавкой керамики. Такие материалы нецелесообразно использовать в качестве материала основы без покрытия композиционным материалом, в котором содержание керамики более 5%, или в качестве материала промежуточного слоя в силу их слабого сцепления с поверхностным покрытием на основе тугоплавкой керамики, риска разрушения покрытия при нагреве из-за различия в КТР подложки и покрытия и низкой стойкости к алюминию и электролиту такого материала
Основа электродов из композиционных материалов с предлагаемым содержанием тугоплавкой керамики от 5 мас. % до 90 мас. % может быть изготовлена любыми известными методами (литье, CBC-синтез, порошковая металлургия и т.п.).
Высокая электропроводность и прочность материала позволяют уменьшить толщину основы, а относительно низкий КТР таких материалов позволяет наносить на них любыми известными способами более устойчивые к алюминию и смачиваемые им покрытия на основе тугоплавкой керамики, такой как бориды и карбиды титана, циркония, ниобия, тантала, вольфрама, молибдена, бора (только карбиды). При этом близость КТР керамических покрытий на основе тугоплавкой керамики и композиционных металлокерамических материалов предотвращает разрушение покрытий при нагреве катодов до температуры электролиза.
Для снижения стоимости смачиваемых алюминием электродов их основа может быть выполнена из известных конструкционных, жаропрочных и жаростойких сплавов с температурой плавления выше 1000°C, образующих при взаимодействии с алюминием тугоплавкие интерметаллиды. При этом для защиты основы электрода от алюминия и электролита на нее необходимо нанести поверхностное покрытие на основе тугоплавкой керамики, такой как бориды и карбиды титана, циркония, ниобия, тантала, бора (только карбиды), вольфрама, молибдена, в т. ч. описанные выше композиционные материалы с содержанием тугоплавкой керамики более 90 мас. % или поверхностное покрытие из чистой тугоплавкой керамики. При использовании в качестве материала основы конструкционных, жаропрочных и жаростойких металлов и сплавов для предотвращения разрушения покрытия из-за различия КТР основы и покрытия на основу необходимо предварительно нанести промежуточный слой описанного выше композиционного материала с содержанием тугоплавкой керамики от 5 до 90 мас. %, т.к. чем больше содержание тугоплавкой керамики, тем ближе КТР композиционного материала к КТР поверхностного покрытия на основе тугоплавкой керамики или из тугоплавкой керамики. Поэтому промежуточный слой может быть выполнен из композиционного материала, в котором, как указано выше, содержание тугоплавкой керамики плавно увеличивается в направлении от основы к покрытию. Как вариант, на промежуточный слой может быть нанесен дополнительный слой с содержанием керамики более 90%, но менее, чем содержание керамики в поверхностном покрытии.
Соответственно увеличенное содержание керамики вблизи поверхностного покрытия и уменьшение ее содержания вблизи основы из металла снижает риск разрушения на границе «основа — промежуточное покрытие» и «промежуточный (или дополнительный) слой поверхностное покрытие».
Нанесение поверхностного покрытия на промежуточный слой, нанесенный на основу из конструкционной углеродистой стали или жаропрочных и жаростойких сплавов, может быть выполнено любыми известными способами (газотермическое напыление, пайка, нанесение паст и красок с последующим спеканием и т.д.). Суммарная толщина промежуточного слоя и поверхностного покрытия электрода, как указывалось выше, может варьироваться в диапазоне 0,5-10 мм.
Для улучшения стойкости электродов к алюминию и улучшения сцепления поверхностного покрытия и основы из композиционного материала или поверхностного покрытия и промежуточного слоя из композиционного материала, поверхность основы или промежуточного слоя под смачиваемым алюминием поверхностным покрытием на основе тугоплавкой керамики или из тугоплавкой керамики может быть насыщена углеродом.
Способы насыщения углеродом (цементация) поверхности металлических материалов, содержащих железо, тугоплавкие металлы и сплавы известны и применяются в производстве для повышения твердости и износоустойчивости поверхностей изделий. Насыщение углеродом поверхности металлической или композиционной основы, или композиционного промежуточного слоя (или дополнительного слоя, наносимого поверх промежуточного) позволит сформировать на них слой, обогащенный карбидами металлов, входящих в состав основы или промежуточного слоя, а именно, имеющегося в композиционном материале по меньшей мере одного из следующих металлов: железо, никель, марганец, титан, тантал, цирконий, хром, ниобий, кобальт, ванадий, и/или имеющегося в композиционном материале как минимум одного из сплавов на основе перечисленных металлов. В связи с тем что карбиды являются тугоплавкой керамикой, очевидно, что в результате цементации будет улучшена стойкость основы, промежуточного и/или дополнительного слоя к алюминию и адгезия к ним поверхностного покрытия электрода на основе тугоплавкой керамики.
Таким образом, предлагаемое техническое решение характеризуется тем, что основа смачиваемого алюминием электрода изготовлена из конструкционной стали или металлического сплава и/или композиционного материала, которые обладают меньшей плотностью и более высокой прочностью, и стойкостью к ударным и механическим нагрузкам, чем вольфрам и молибден, использованные в ближайшем аналоге. Кроме того, основа, изготовленная из конструкционной, стали или металлического сплава, покрытого промежуточным слоем из композиционного материала, или изготовленная композиционного материала, имеет более высокую стойкость к окислению, и ее легко соединить с металлическим токоотводом сваркой. Стойкость к алюминию и электролиту смачиваемых элементов с такой основой обеспечивается путем нанесения смачиваемых алюминием поверхностных покрытий на основе тугоплавкой керамики или из тугоплавкой керамики. По этой причине заявленные смачиваемые алюминием электроды имеют преимущество с точки зрения материалоемкости, стоимости и технологичности применения в качестве наклонного или вертикального катода электролизеров для получения алюминия электролизом расплавленных солей при температуре ниже 960°C.
Поскольку известные вертикальные или наклонные биполярные электроды включают катодную часть, к которой предъявляются те же требования, что и к смачиваемому катоду, электроды, согласно обоим вариантам изобретения, могут быть использованы не только в качестве наклонного или вертикального катода, но и в качестве катодной части вертикальных или наклонных биполярных электродов в электролизерах для получения алюминия электролизом расплавленных солей.
Краткое описание чертежей
Сущность предлагаемого технического решения поясняется схематичным изображением фрагментов сечения смачиваемых алюминием электродов для предложенных вариантов их конструктивного исполнения (фиг. 1 и фиг. 2). На чертежах показан прилегающий к поверхности фрагмент сечения электродов, т.к. размеры электродов и их форма могут быть выбраны произвольно.
На фиг. 1 представлен первый вариант исполнения электродов с основой 2 из композиционного материала с содержанием тугоплавкой керамики от 5 до 90 мас. %.
На фиг. 1(А) показан электрод с основой 2 из композиционного материала с содержанием керамики от 5 до 90% и покрытием 3 на основе тугоплавкой керамики.
На фиг. 1(В) показан электрод с основой 2 из композиционного материала с содержанием тугоплавкой керамики от 5 до 90 мас. %, поверхность 4 которого насыщена углеродом и на нее нанесено покрытие 3 на основе тугоплавкой керамики.
На фиг. 2 представлен второй вариант исполнения электродов с основой из металлического сплава 1 и промежуточным слоем композиционного материала 2.
На фиг. 2(А) показан электрод с основой из конструкционной стали или металлического сплава 1, на который нанесен слой композиционного материала 2 с содержанием тугоплавкой керамики от 5 до 90 мас. % и покрытие на основе тугоплавкой керамики 3.
На фиг. 2(В) показан электрод с основой 1 из конструкционной стали или металлического сплава, поверхность 4 которой насыщена углеродом и на нее нанесено покрытие 3 на основе тугоплавкой керамики. В данном случае насыщенная углеродом поверхность стали или сплава играет роль промежуточного слоя между основой и покрытием.
На фиг. 2(С) показан электрод с основой 1 из конструкционной стали или металлического сплава, на который нанесен промежуточный слой 2 композиционного материала с содержанием тугоплавкой керамики от 5 до 90 мас. %), поверхность 4 которого насыщена углеродом и на нее нанесено покрытие 3 на основе тугоплавкой керамики.
Осуществление изобретения
Пример 1 характеризует изобретение по первому варианту. Для изготовления смачиваемого алюминием электрода в качестве заготовки основы 2 использовали пластину из композиционного материала 80% мас. Fe — 20% мас. TiB2, с габаритными размерами 94×77×10 мм. К пластине методом электродуговой сварки был приварен прут из нержавеющий стали, который выполнял роль токоотвода. Далее для образования поверхностного покрытия на поверхность заготовки смачиваемого электрода наносилась суспензия керамических частиц TiB2 в растворе фенолформальдегидной смолы. Нанесенное покрытие просушивалось 1 час при комнатной температуре, затем 1 час при температуре 150°C. Таким образом, на поверхности смачиваемого алюминием электрода был сформирован слой поверхностного покрытия 3 толщиной 1,5 мм, состоящий из диборида титана (93 мас. %) и фенолформальдегидной смолы (7 мас. %).
Схематично сечение электрода, изготовленного в соответствии с примером 1, показано на фиг. 1(A).
Изготовленный таким образом образец испытывали в качестве вертикального катода при электролизе с двумя вертикальными электродами в корундовом контейнере диаметром ПО мм и высотой 220 мм, помещенном в охранный графитовый тигель. В качестве анода использовали медную пластину с габаритами 115×80×5 мм. Катод погружали в расплав так, чтобы сварной контакт с токоотводом оставался выше уровня электролита. Анод был полностью погружен в расплав. Анодная и катодная плотности тока составили 0,5 A/см2, температура электролиза — 850°C.
Через несколько минут после пуска напряжение установилось в диапазоне 4,63÷4,65 B и затем изменялось незначительно. Длительность испытания составила 24 ч. В результате испытания было установлено, что поверхность изготовленного согласно изобретению электрода — катода хорошо смочилась алюминием и не имела признаков разрушения. Геометрические размеры катода сохранились. Масса катодного алюминия составила 350,2 г. Выход по току в расчете на чистый алюминий составил 70%. Загрязнение металла железом — основным компонентом металлической основы катода составило менее 0,1 мас. %.
Пример 2 характеризует изобретение по второму варианту. Для изготовления смачиваемого алюминием электрода использовали металлическую основу из конструкционной стали Ст 3 с габаритными размерами 100×70×5 мм. Металлическая (стальная) основа имела хвостовик для приварки к нему металлического токоотвода. Для образования промежуточного слоя к основе 1 методом высокотемпературной пайки на первом этапе прикреплялись пластины из пеноферроникеля толщиной 3 мм. Удельная пористость пеноферроникеля составляла 60 PPI. Пористая металлическая основа на поверхности основы пропитывалась суспензией керамических частиц TiB2 в растворе фенолформальдегидной смолы для получения композиционного материала промежуточного слоя. На следующем этапе для образования поверхностного покрытия сверху наносился слой этой же суспензии, толщиной около 1 мм. Далее заготовка электрода с нанесенным поверхностным покрытием просушивалась 1 час при комнатной температуре, затем 1 час при температуре 150°C. Для спекания покрытия образцы прокаливали 3 ч при температуре 800°C в засыпке из активированного угля. Таким образом, на поверхности металлической (стальной) основы был сформирован слой композиционного материала, состоящего из матрицы из ферроникеля и распределенных в ней частиц диборида титана, и слой поверхностного покрытия 3 на основе тугоплавкой керамики. Содержание тугоплавкой керамики в композиционном материале промежуточного слоя составило около 80 мас. %.
Схематично сечение электрода, изготовленного в соответствии с примером 2, показано на фиг. 2(А).
Изготовленный таким образом образец испытывали в качестве вертикального катода при электролизе с двумя вертикальными электродами в корундовом контейнере диаметром 110 мм и высотой 220 мм, помещенном в охранный графитовый тигель. В качестве анода использовали медную пластину с габаритами 100×70×3 мм. Анод и катод погружали в расплав так, чтобы уровень электролита над ними составлял около 1 см. Анодная и катодная плотности тока составили 0,5 А/см2, температура электролиза — 850°C.
Через несколько минут после пуска напряжение установилось в диапазоне 5,36÷5,41 B и затем изменялось незначительно. Длительность испытания составила 24 ч. В результате испытания было установлено, что поверхность катода хорошо смочилась алюминием и не имела признаков разрушения. Геометрические размеры катода сохранились. Масса катодного алюминия составила 365,3 г. Выход по току в расчете на чистый алюминий составил 75%. Загрязнение металла железом — основным компонентом металлической основы катода составило менее 0,1 мас. %.
Другие электроды, изготовленные с использованием металлической основы из конструкционной стали Ст3, согласно вариантам, изображенным на фиг. 2B и 2C, показали аналогичные результаты.
Пример 3 характеризует частный случай выполнения изобретения по первому варианту с цементацией поверхности композиционного материала основы. При изготовлении смачиваемого алюминием электрода в качестве заготовки основы 2 использовали пластину из композиционного материала 80 мас. % Fe — 20 мас. % TiB2, с габаритными размерами 96×81×10 мм. Пластину обработали методом твердофазной цементации, целью которой было диффузионное насыщение поверхностного слоя 4 образца углеродом. В качестве карбюризатора применялась смесь, состоящая из 80% древесного угля и 20% кальцинированной соды. Цементация проводилась в течение 10 часов в герметичном корундовом контейнере при температуре 900°C. Затем к пластине из композиционного материала методом электродуговой сварки был приварен прут из нержавеющий стали, который выполнял роль токоотвода. Далее на поверхность заготовки смачиваемого элемента наносилась суспензия керамических частиц TiB2 в растворе фенолформальдегидной смолы. Основа 2 электрода просушивалось 1 час при комнатной температуре, затем 1 час при температуре 150°C. Таким образом, на поверхности смачиваемого алюминием электрода был сформирован слой поверхностного покрытия 3 толщиной 2 мм, состоящий из диборида титана (93 мас. %) и фенолформальдегидной смолы (7 мас. %).
Схематично сечение электрода, изготовленного в соответствии с примером 3, показано на фиг. 1(B).
Изготовленный таким образом образец испытывали в качестве вертикального катода при электролизе с двумя вертикальными электродами в корундовом контейнере диаметром ПО мм и высотой 220 мм, помещенном в охранный графитовый тигель. В качестве анода использовали медную пластину с габаритами 114×79×4,4 мм. Катод погружали в расплав так, чтобы сварной контакт с токоотводом оставался выше уровня электролита. Анод был полностью погружен в расплав. Анодная и катодная плотности тока составили 0,5 А/см2, температура электролиза — 850°C.
Через несколько минут после пуска напряжение установилось в диапазоне 5,95÷6,05 B и затем изменялось незначительно. Длительность испытания составила 24 ч. В результате испытания было установлено, что поверхность катода хорошо смочилась алюминием и не имела признаков разрушения. Геометрические размеры катода сохранились. Масса катодного алюминия составила 360 г. Выход по току в расчете на чистый алюминий составил 65%. Загрязнение металла железом — основным компонентом металлической основы катода составило менее 0,1 мас. %.
Полученные результаты свидетельствуют о том, что предлагаемый смачиваемый алюминием электрод является стойким к окислению, к алюминию и электролиту, обладает высокой электропроводностью, обеспечивает надежный электрический контакт между смачиваемым алюминием элементом и токоотводом.
ESABESAB — мировой лидер в производстве сварочных материалов и оборудования. телефон: +7 (812) 334-07-70 Электроды ESAB(6 из 120) См. все(120)
Проволока ESAB(6 из 110) См.![]()
Прутки ESAB(6 из 48) См.![]()
Оборудование ESAB(6 из 25) См. все(25)
Аксессуары ESAB(6 из 50) См. все(50)
| ||||||||||||||||||||||||||||||||
© 2003-2021, ООО «ЭЛЕКТРОД.РУ«, тел. +7 (812) 334-07-70 |
Электроды для сварки алюминия, и что необходимо знать?
Современные электроды для сварки алюминия представляют собой высокотехнологичный сплав, способный производить качественные, неразъемные и долговечные соединения, швы. Для сварки алюминия необходимы именно специальные электроды, поскольку рассматриваемый металл можно отнести к числу тяжело свариваемых.
Общие характеристики
На поверхность алюминия при контакте её с воздухом мгновенно образуется оксидная пленка. Для того чтобы окислы не имели место во время сварки, применяется защитный газ, среда которого служит вытесняющим фактором, отделяющим поверхность металла от воздуха. Электроды по алюминию могут быть различных марок,основные из которых, а также их предназначения заслуживают отдельного внимания.
Маркировки и предназначение:- Электрод по алюминию ОЗА-1 – для сварки, а также плавки деталей, конструкций из алюминия технической частоты;
- Электрод по алюминию марки ОЗА-2 – для заваривания бракованных участков алюминия, наплавки деталей алюминиево-кремнистых сплавов марок АЛ-4, АЛ-9, А-11;
- Электроды для алюминия ОЗАНА-1 – для сварки и наплавки деталей, конструкций, выполненных из алюминия, технической чистоты;
- Сварочные электроды ОЗАНА-2 – для заваривания бракованных участков литья, наплавки деталей из алюминиево-кремнистых сплавов марок АЛ-4, АЛ-9, АЛ-11;
- Сварочные электроды марки УАНА-1 – для сварки сплавов марок АД, АД0, АД00, АД1;
- Электрод по алюминию марки УАНА-2 – для сварки сплавов марок АД31, АД33, АД35, АЛ9, АЛ11, АЛ34;
- Электроды УАНА-3 – для сварки сплавов марок АЛ-2, АЛ4, АЛ30;
- Алюминиевый электрод марки УАНА-4 – для сварки алюминия и сплавов марок АМЦ, АМцС, ММ;
- Электрод марки УАНА-5 – для сварки сплавов марок АМг2, АМгЗ, АМг4, АМг5;
- Электрод по алюминию марки УАНА-6 – для сварки алюминия и сплавов марок АМгЗ, АМг4, АМг5, АМг6.
Прежде чем выполнять сварочные работы, должны обязательно следовать подготовительные работы, включающие в себя обезжиривание рабочих поверхностей, очистку, удаление оксидной пленки. Присадочные алюминиевые материалы, включая вольфрамовый электрод, должны обрабатываться аналогичным способом. Ниже приведен список основных шагов на этапе подготовки поверхностей к обработке.
Этапы подготовки поверхностей к работе:- Обезжиривание и травление деталей;
- Промывка посредством проточной воды;
- Осветление в растворе азотной кислоты;
- Промывка посредством проточной горячей воды;
- Сушка до полноценного удаления влаги.
Алюминиевые электроды плавятся в несколько раз быстрее, нежели стальные. Алюминиевые катоды обрабатывают детали практически непрерывно. Обработка деталей выполняется сварщиком, обладающим соответствующей квалификацией, имеющим специфические навыки, знания. Электроды для производства сварки рассматриваемого металла и его сплавов имеют неоспоримые положительные качества, среди которых особого внимания стоят невысокая цена, эксплуатационная простота.
Производство соединительных работ деталей из алюминия подойдет идеальным образом для полевых условий, а также для применения в частных мастерских. Вольфрамовые электроды способны разрушать оксидную пленку, которая образуется на поверхности данного цветного металла. Электрод должен быть качественным и надежным, так как от его качественных параметров и характеристик по окончании соединительных работ будет зависеть долговечность шва и соединения.
Присадочный материал — предмет повышенного внимания как профессионального сварщика, так и новичка данного ремесла, который оказывает влияние на пластичность шва, его аккуратность и долговечность. Если присадочный материал пользуется спросом на рынке электротехнических товаров — значит, он в большинстве случаев является проверенным и надежным.
к меню ↑О технологии
Технология сварки алюминия посредством катода сначала предполагает подготовку металла к работе. Таким образом, профилируются кромки деталей, после чего производится очистка поверхности материала от загрязнений, оксидных образований. Обработка материала выполняется посредством удаления в специальных щелочных ваннах. Для очистки и удаления поверхности металла и самого катода применяются специализированные растворители органического происхождения. От качества растворителя, которым осуществляется очистка рабочих поверхностей, также очень многое зависит, включая качество сопряжения материалов с присадочным припоем.
С ролью растворителя для очистки обрабатываемых поверхностей успешно справляется Уайт-спирит, либо технический ацетон. Также может использоваться растворитель РС-1, РС-2. Относительно щелочных ванн, то они состоят из 50 г технического тринатрийфосфата, 50 г кальцинированной соды, 30 г стекла в жидком состоянии из расчета на один литр. Стоит отметить, что температура ванны щелочи может равняться пределам 60-70 градусов. Обработка металла производится на протяжении 5 минут.
По окончании очистки алюминия следует удаление оксидной пленки, которую можно снять посредством металлической щетки. После проведения очистки кромок деталей, металл обезжиривается посредством растворителя снова. Прежде чем приступать к работе, понадобится тщательнейшим образом просушить катоды в условиях температуры 200 градусов на протяжении двух часов. Рассматриваемый материал и его сплавы обрабатывается сварочным инвертором, используя специальные электроды.
После подготовительного этапа приступают к соединительным работам, используя электрод, которые производятся в условиях постоянного тока с обратной полярностью. Рабочий параметр принимается из расчета 25-30 А на 1 мм диаметра, который имеет электрод. Для получения надежного, аккуратного и долговечного шва материал разогревается до температуры от 250 до 400 градусов Цельсия (показатель температурного нагрева выбирается, опираясь на диаметр обрабатываемого материала).
к меню ↑Способы
Электрод, применяемый для сварки алюминия, может быть графитовым, вольфрамовым, угольным. Выбор осуществляется, опираясь на диаметр обрабатываемых деталей. Применяются многие виды воздействия на рассматриваемый металл, среди которых ручной электродуговой, автоматический электродуговой, дуговой в среде защитных газов. Каждая методика имеет свои преимущественные стороны, а также недостатки, к тому же может быть использован исключительно при конкретных производственных необходимостях.
Ручная электродуговая сварка производится путем применения штучных катодов специальных марок при постоянном токе обратной полярности. Аргонодуговая обработка деталей выполняется посредством вольфрамового катода, и эта методика считается наиболее оправданной и популярной среди профессиональных рабочих. Распространением пользуется использование инверторных источников питания, с возможностью смены частоты напряжения.
Обработка алюминиевых деталей должна производиться на повышенной частоте, в то время как для заварки дефектов — при пониженной частоте. Полуавтоматический режим предпочтительнее аргонодугового ввиду повышенной степени производительности. Работа в полуавтоматическом режиме выполняется при постоянном токе с положительной полярностью на основном элементе.
Для получения высококачественных, долговечных, а также надежных соединений понадобится определенная квалификация, профессиональный уровень, навыки, с помощью которых удастся добиться аккуратности и долговечности швов. Стоит помнить, что электрод, а также все вспомогательные и основные рабочие элементы должны быть качественными. В противном случае, если пренебрегать общими наставлениями и рекомендациями опытных специалистов, Вы рискуете не получить желаемый итог стараний.
Похожие статьиЭлектроды для сварки алюминия своими руками
Каждому сварщику известно, что сваривание без электродов невозможно, а без качественных электродов невозможно качественное сваривание, поэтому необходимо приобретать качественные сварочные электроды, чтобы производить сваривание на наивысшем уровне. Однако возникают ситуации, когда нет возможности приобрести сварочные электроды, но есть множество подручных средств.Можно ли обойтись без завода-изготовителя сварочных электродов? Давайте узнаем об этом из этой статьи.
Электроды изготавливаются не так и сложно. Для изготовления необходимо подобрать сварочную проволоку подходящего диаметра для создания сварочного электрода. После подбора проволоки, ее необходимо разрубить на куски по 350 миллиметров и зачистить шкуркой. После этого необходимо подготовить обмазку, которая состоит из жидкого стекла (силикатного клея) и растолченного мела.
Для того чтобы покрытие было ровным. Необходимо электродную проволоку погружать в обмазку вертикально и оставлять под верхом чистый конец длиной 30 – 35 миллиметров. После этого электрод следует медленно вынуть и подвесить на веревке для просушивания. После полного высыхания и затвердения Вы получаете полностью рабочие сварочные электроды.
Когда сваривание производится в домашних условиях, то получается удовлетворительный результат при использовании контактного метода сварки алюминия. Данный вид сваривания производится с непрекращающимся оплавлением на электропроводных машинах. Также есть возможность проведения шовного сваривания алюминия, но для этого необходимо машину высокой мощности и со специальными ионными прерывателями. Использование таких методов может быть затруднено в домашних условиях, но некоторые сварщики все-таки пользуются ими.
При сваривании в домашних условиях стоит не забывать о том, что необходимо соблюдать технику безопасности и неукоснительно соблюдать все требования. Первым, на что необходимо обратить внимание, является изоляция всех проводов, которые принимают участие в сварочном процессе и находятся под напряжением.
Проводя сварочные работы у себя дома, требуется использовать перчатки или рукавицы, которые обезопасят Ваши руки от ожогов. От удара электрическим током Вас будут страховать резиновые сапоги. Проводя сварочные работы, требуется обязательно надевать специальную маску, чтобы защитить свое лицо от искр, угольков и ожогов. В помещении, в котором Вы собираетесь проводить сварочные работы ни в коем случае нельзя хранить легковоспламеняющиеся и огнеопасные материалы и предметы.
Если в помещении деревянный пол, то его следует закрыть от воспламенения с помощью металлического листа. Обязательно стоит поставить огнетушитель или ведро с водой возле того места, где Вы собираетесь производить сваривание. По причине возможного образования вредных газов или других опасных для здоровья соединений, требуется регулярно проветривать помещение, в котором Вы производите сваривание.
Сварка алюминия электродом
Алюминий и его сплавы, как и любой другой металл, поддается сварке основными способами сварки, разница заключается в экономической целесообразности того или иного способа, а также в качестве полученного сварного шва. То есть в общем можно сказать, что различают три основных способа сварки алюминия и его сплавов:
- pучная дуговая сварка покрытыми электродами (ММА)
- полуавтоматическая сварка (MIG)
- аргонодуговая сварка (TIG).
Наиболее простой способ сварки – это MMA сварка алюминия и его сплавов или как ее еще называют, ручная дуговая сварка покрытым электродом. Несмотря на все недостатки ручной дуговой сварки алюминия, а именно: плохое формирование сварного шва, пористость и сниженная прочность, значительный процент разбрызгивания, усложненное отделение шлака и т.д., существуют условия, когда ММА сварка просто необходима.
Чтобы получить сварной шов надлежащего качества при помощи ручной дуговой сварки, в первую очередь нужно подобрать правильный электрод. Для этого необходимо знать химический состав и физические особенности заготовки, после чего по спецификации производителя подбирается соответствующий электрод. Следует отметить, что электроды, разработанные для сварки чистого алюминия, и электроды для сварки сплавов на его основе значительно отличаются и не являются взаимозаменяемыми. Также нужно помнить, что минимально возможная толщина заготовки при ручной сварке должна быть не меньше, чем диаметр сварочного электрода.
Чтобы улучшить свойства сварного шва, в состав покрытых электродов для сварки алюминия вводят специальные добавки, например:
- марганец (Mn) для повышения коррозионной стойкости;
- кремний (Si) для улучшения текучести металла и его свариваемости
- магний (Mg) для улучшений свариваемости и получения более прочного шва
Особенно следует обратить внимание чистоте поверхности заготовки – чем более качественно подготовлена поверхность заготовки перед сваркой, тем более качественным будет сварной шов. Чистота поверхности влияет на сплавление основного металла з присадочным и на появление пор.
Сварка алюминия покрытым электродом проводится на постоянном токе обратной полярности, то есть к заготовке подводится «-», а к держателю электрода – «+». Такая система подвода тока обусловлена тем, что поверхность заготовки из алюминиевых сплавов всегда покрыта тугоплавкой оксидной пленкой, разрушить которую можно исключительно катодным распылением при сварке на обратной полярности.
Основные проблемы при ручной дуговой сварке алюминия – это высокая текучесть металла, образование тугоплавкой оксидной пленки и высокий коэффициент линейного расширения.
Текучесть расплавленного алюминия очень высока и его очень сложно контролировать в процессе сварки в следствие чего расплав в сварочной ванне может разрушить слой твердого металла и образуется протечка. Чтобы предупредить вытекание расплавленного металла рекомендуется использовать специальные подкладки.
При контакте алюминия и кислорода на поверхности металла образуется плотная оксидная пленка (Al2O3), которая отличается высокой температурой плавления — 2055°С (температура плавления алюминия составляет 660°С) и диэлектрическими свойствами. Поэтому при сварке алюминия необходима тщательная зачистка поверхности деталей и сварка на обратной полярности.
Высокий коэффициент линейного расширения алюминия может привести к появлению трещин или возникновению деформаций детали, потому необходимо постоянно контролировать уровень тепловложений при сварке или же предварительно подогреть детали до 210-300°С. Горячие трещины могут появиться при кристаллизации металла, чтобы предупредить их появление нужно правильно подбирать марку электродов.
1/8 дюйма x 14 дюймов Алюминиевый электрод 521Al 5 фунтов Упаковка
/ {{vm.product.unitOfMeasureDescription || vm.product.unitOfMeasureDisplay}}
{{section. sectionName}}:
{{option.description}}
{{section.sectionName}} Выберите {{section.sectionName}}
.{{styleTrait.nameDisplay}} {{styleTrait.unselectedValue? «»: «Выбрать»}} {{styleTrait.unselectedValue? styleTrait.unselectedValue: styleTrait.nameDisplay}}
- product.brand.name)»> Атрибуты
- Документы
- {{спецификация.nameDisplay}}
- Атрибуты
- Документы
Марка | product.brand.name»/> |
{{attributeValue.valueDisplay}} {{$ last? »: ‘,’}} |
Марка | |
{{attributeValue.valueDisplay}} {{$ last? »: ‘,’}} |
доля
Электронное письмо было успешно отправлено. Электронное письмо не было отправлено, проверьте данные формы.
5/64 дюйма x 10 дюймов Алюминиевый электрод 521Al 2,5 фунта Упаковка
/ {{vm.product.unitOfMeasureDescription || vm.product.unitOfMeasureDisplay}}
{{section.sectionName}}:
{{option.description}}
{{section.sectionName}}
Выберите {{section. sectionName}}
{{styleTrait.nameDisplay}} {{styleTrait.unselectedValue? «»: «Выбрать»}} {{styleTrait.unselectedValue? styleTrait.unselectedValue: styleTrait.nameDisplay}}
- Атрибуты
- Документы
- {{спецификация.nameDisplay}} settings.displayAttributesInTabs && vm.settings.attributesTabSortOrder === ‘DisplayLast’ && (vm.product.attributeTypes.length > 0 || vm.product.brand.name)»> Атрибуты
- Документы
Марка | |
{{attributeValue.valueDisplay}} {{$ last? »: ‘,’}} |
Марка | |
{{attributeValue.valueDisplay}} {{$ last? »: ‘,’}} |
доля
Электронное письмо было успешно отправлено.Электронное письмо не было отправлено, проверьте данные формы.
×Алюминий, металлический электрод, 4 «
Есть вопросы? Обратитесь в службу поддержки клиентов.
406-256-0990 или Живой чат в
- Возраст 8+
- На складе, готово к отправке
- Это нужно быстро? Смотрите варианты доставки в корзине.
Эта полоска имеет ширину 3/4 дюйма и длину 4 дюйма. Весит около 4 граммов. Читать Подробнее
My Science Perks получают не менее $ 0,04 обратно на этот предмет. Войдите или создайте Бесплатный HST Аккаунт для начала зарабатывать сегодня
ОПИСАНИЕ
Эта полоска имеет ширину 3/4 дюйма и длину 4 дюйма. Весит около 4 граммов.
ПРИМЕЧАНИЕ. Фактический продукт может отличаться от представленного на фотографии из-за различий в поставщиках.
БОЛЬШЕ ИНФОРМАЦИИ
ВКЛАДКА С СОДЕРЖАНИЕМ
ТАБЛИЦА ТЕХНИЧЕСКИХ ХАРАКТЕРИСТИК
- Описание продукта
- ЭЛЕКТРИЧЕСКИЙ
- Технические характеристики
- СОДЕРЖАНИЕ
Мы хотим, чтобы этот предмет был живым, когда вы его получите! Следовательно, нам необходимо
знать, когда вы будете дома, чтобы получить его (минимизируя
воздействие стихии). Укажите дату доставки, среда
— Пятница, это минимум 7 дней с сегодняшнего дня.
Физика и инженерия / Электричество и электроника / Статическое электричество
/ физика-инженерия /, / физика-инженерия / электричество-электроника /, / физика-инженерия / электричество-электроника / электроды-статическое электричество /
Мы поняли. Наука может быть беспорядочной. Но продукты и услуги Home Science Tools справятся с этим.
Наши продукты долговечны, надежны и доступны по цене, чтобы доставить вас из полевых условий в лабораторию и на кухню. Они не подведут вас, с чем бы они ни боролись. Будь то (чрезмерно) нетерпеливые молодые ученые из года в год или строгие требования, которые возникают раз в жизни.
И если ваш научный запрос идет не так, как ожидалось, вы можете рассчитывать на помощь нашей службы поддержки клиентов. Рассчитывайте на дружеские голоса на другом конце телефона и советы экспертов в вашем почтовом ящике. Они не будут счастливы, пока вы не станете счастливыми.
Итог? Мы гарантируем, что наши продукты и услуги не испортят ваше научное исследование, каким бы беспорядочным оно ни было.
Вопросы? Свяжитесь с нашей службой поддержки клиентов.
Пруток для дуговой сварки алюминияХорошая функция сварки Производители электродов из алюминиевого сплава E4043 — Электрод из алюминиевого сплава — Продукция
Описание
Краткие сведения
Место происхождения: Чжэцзян, Китай (материк)
Фирменное наименование: Ocean Welding
Номер модели: E4043
Материал: алюминий / алюминиевый сплав
Длина: 300-500 мм
Рабочий ток: 50-240 А
Сварочный ток: 2.5 мм V, OH 50-80
Рабочая температура: 60-90, 90-120, 120-150
Диаметр: 2,0 мм, 2,5 мм, 3,2 мм, 4,0 мм
Применение: сварка алюминия материалы
Упаковка и доставка
Детали упаковки: | Размер: 2,5 мм X 300 мм (упаковка: 1,0 кг / внутренние коробки 1 тонна / поддон) Размер: 3,2 мм X 350 мм (упаковка : 1,0 кг / внутренние ящики 1 тонна / поддон) Размер: 4. |
Сведения о доставке: | в течение 25 дней после подтверждения |
Технические характеристики
алюминиевый электрод
Стандарт: AWS
Сертификаты: CE ISO
OEM приемлемый
Алюминиевый сварочный электрод AWS E4043
Технические характеристики
Сплав: 4043 CTD Соответствует сертификации: AWS A5.3
Класс: E4043 ASME SFA A5.3
Сплав: E4043 CTD
Требования к химическому составу AWS
Si = 4,5 — 6,0 Zn = 0,10 макс.
Fe = 0,80 макс. Ti = 0,20 макс.
Cu = 0,30 макс. Be = 0,0008 макс.
Mn = 0,05 макс. Al = остаток
Mg = 0,03 макс. Другое = 0,05 каждый — всего 0,15 макс.
Химический состав отложений% (типичный)
Si = 5,00 Cu = 0,20
Ti = 0,11 Al = баланс диаметр сварочного материала и положение сварки, включая толщину опорной плиты.
Приложение
E4043 CTD представляет собой электрод с покрытием, предназначенный для ремонтной сварки алюминия и алюминиевых сплавов, таких как серии 5454, 5154, 6052, 6063, 700. — Правильный выбор алюминиевого присадочного металла в основном зависит от свойств основного металла
Достигнутые и Сварочная техника. Также необходимо учитывать растрескивание после сварки, коррозионную стойкость и поведение при повышенных температурах. Растрескивание обычно можно минимизировать, выбирая сплав присадочного металла с более высоким содержанием сплава, чем основной металл.
Тестирование продукции
Строгое тестирование продукции гарантирует качество нашей продукции.
Преимущества
1. Меньшее количество брызг
2. Легкость повторного взрыва
3. Меньше смога
4. Хорошее удаление шлака, высокая эффективность осаждения
Упаковка и доставка
Детали упаковки:
1. Коробка 1 кг / ПВХ или 5 кг / Коробка из ПВХ (термоусадочная пленка + коробка из ПВХ)
2. 4 коробки из ПВХ (20 кг) / коробка
3. Коробка 50 (1 тонна) / поддон
4. По требованию клиентов
5.Доставка: Обычно готовый товар от 8 до 25 дней.
О нас
1. Мы Lin an Dayang Welding Material Co., Ltd., одно из ведущих производственных предприятий в Китае,
специализируется на производстве расходных материалов, таких как сварочные электроды, сварочная проволока, в течение 20 лет.
2. Профессиональная производственная группа, производственная линия, опытные технические специалисты, которые работают в этой отрасли
около 20 лет. Сейчас у нас есть профессиональная производственная линия для сварочного электрода E306-16.
Гарантировано
1. Лучшее ценовое предложение
2. Своевременная поставка
3. Строгий контроль качества
4. Наиболее полное и внимательное обслуживание
Заявка
Транспортные средства, мостостроение, машиностроение,
металлоконструкции, морское производство, строительство и контейнеры.
Произошла ошибка при установке пользовательского файла cookie
Этот сайт использует файлы cookie для повышения производительности. Если ваш браузер не принимает файлы cookie, вы не можете просматривать этот сайт.
Настройка вашего браузера для приема файлов cookie
Существует множество причин, по которым cookie не может быть установлен правильно. Ниже приведены наиболее частые причины:
- В вашем браузере отключены файлы cookie. Вам необходимо сбросить настройки своего браузера, чтобы он принимал файлы cookie, или чтобы спросить вас, хотите ли вы принимать файлы cookie.
- Ваш браузер спрашивает вас, хотите ли вы принимать файлы cookie, и вы отказались. Чтобы принять файлы cookie с этого сайта, нажмите кнопку «Назад» и примите файлы cookie.
- Ваш браузер не поддерживает файлы cookie. Если вы подозреваете это, попробуйте другой браузер.
- Дата на вашем компьютере в прошлом.
Если часы вашего компьютера показывают дату до 1 января 1970 г., браузер автоматически забудет файл cookie. Чтобы исправить это, установите правильное время и дату на своем компьютере.
- Вы установили приложение, которое отслеживает или блокирует установку файлов cookie. Вы должны отключить приложение при входе в систему или проконсультироваться с системным администратором.
Почему этому сайту требуются файлы cookie?
Этот сайт использует файлы cookie для повышения производительности, запоминая, что вы вошли в систему, когда переходите со страницы на страницу. Чтобы предоставить доступ без файлов cookie потребует, чтобы сайт создавал новый сеанс для каждой посещаемой страницы, что замедляет работу системы до неприемлемого уровня.
Что сохраняется в файле cookie?
Этот сайт не хранит ничего, кроме автоматически сгенерированного идентификатора сеанса в cookie; никакая другая информация не фиксируется.
Как правило, в файле cookie может храниться только информация, которую вы предоставляете, или выбор, который вы делаете при посещении веб-сайта. Например, сайт не может определить ваше имя электронной почты, пока вы не введете его. Разрешение веб-сайту создавать файлы cookie не дает этому или любому другому сайту доступа к остальной части вашего компьютера, и только сайт, который создал файл cookie, может его прочитать.
Новый композитный золото-алюминиевый электрод для применения в нейронной записи и стимуляции в сканерах магнитно-резонансной томографии сверхвысокого поля
.2021 Сен; 49 (9): 2337-2348. DOI: 10.1007 / s10439-021-02779-у. Epub 2021 21 апреля.Принадлежности Расширять
Принадлежности
- 1 Кафедра машиностроения, Университет Миннесоты, Миннеаполис, Миннесота, США.
- 2 Центр исследований магнитного резонанса (CMRR), Радиологический факультет, Университет Миннесоты, Миннеаполис, Миннесота, США.
- 3 Кафедра машиностроения, Университет Миннесоты, Миннеаполис, Миннесота, США. [email protected].
Элемент в буфере обмена
Кори Э. Круттенден и др.Ann Biomed Eng. 2021 сен.
Показать детали Показать вариантыПоказать варианты
Формат АннотацияPubMedPMID
.
Принадлежности
- 1 Кафедра машиностроения, Университет Миннесоты, Миннеаполис, Миннесота, США.
- 2 Центр исследований магнитного резонанса (CMRR), Радиологический факультет, Университет Миннесоты, Миннеаполис, Миннесота, США.
- 3 Кафедра машиностроения, Университет Миннесоты, Миннеаполис, Миннесота, США. [email protected].
Элемент в буфере обмена
Полнотекстовые ссылки Опции CiteDisplayПоказать варианты
Формат АннотацияPubMedPMID
Абстрактный
Традиционные электроды, используемые для нейронной записи и стимуляции, генерируют большие области пустого сигнала (без функционального сигнала МРТ) при использовании в сканерах МРТ сверхвысокого поля (УВЧ). Это является значительным недостатком, когда требуется одновременная запись / стимуляция нейронов и получение сигнала фМРТ, например, для понимания функциональных механизмов глубокой стимуляции мозга (DBS). В данной работе представлен новый нейронный электрод из микропровода золото-алюминий, в котором этот недостаток устранен. Конструкция из золота и алюминия значительно снижает разницу в магнитной восприимчивости между электродом и тканью мозга, что приводит к значительному сокращению областей пропускания сигнала. Образцы золото-алюминиевых микропроводов получены в сверхсильном поле 16.4 Тл и сравнивается с образцами микропровода, содержащего только золото и только алюминий. Во-первых, картирование поля B 0 использовалось для количественной оценки искажений поля при 16,4 Тл и сравнивалось с аналитическими вычислениями на агарозном фантоме. Образцы микропровода золото-алюминий генерировали существенно меньшие искажения поля и потери сигнала по сравнению с образцами только из золота и алюминия при 16,4 Тл с использованием последовательностей градиентного эхо-изображения и последовательностей эхо-планарного изображения.
Затем предложенный золото-алюминиевый электрод был использован для успешной регистрации сигналов потенциала локального поля от коры головного мозга крысы.Недавно предложенный золото-алюминиевый микропроволочный электрод демонстрирует уменьшенные искажения поля и потери сигнала при 16,4 Тл, что также применимо к сканерам МРТ с более низкой напряженностью магнитного поля. Дизайн может быть легко воспроизведен для широкого изучения DBS с помощью МРТ на животных моделях. Кроме того, использование инертных материалов из золота и алюминия открывает новые возможности для применения в имплантатах человека в будущем.
Ключевые слова: Золото-алюминиевые электроды; Артефакты изображения; Сканеры МРТ; Согласованная магнитная восприимчивость; Нервные электроды.
© 2021. Общество биомедицинской инженерии.
Заявление о конфликте интересов
ЗАЯВЛЕНИЕ О КОНФЛИКТЕ ИНТЕРЕСОВ
Часть работы, представленной в этом документе, защищена патентом. Ожидающий рассмотрения патент будет принадлежать Миннесотскому университету, у которого есть стандартное соглашение о распределении роялти с сотрудниками университета на случай, если лицензионные платежи будут получены от лицензирования указанного патента.
Похожие статьи
- Надежные процедуры МРТ с функциональной стимуляцией глубокого мозга у крыс и мышей с использованием вольфрамового микропроволочного электрода, совместимого с МРТ.
Лай Х.Й., Албоу Д.Л., Као Ю.К., Юнс-младший, Ши Й. Lai HY, et al. Magn Reson Med. 2015 Март; 73 (3): 1246-51. DOI: 10.1002 / mrm.25239. Epub 2014 5 мая. Magn Reson Med. 2015 г. PMID: 24798216
- Запись электрокортикографических сигналов человека (ЭКоГ) для нейробиологических исследований и функционального кортикального картирования в реальном времени.
Хилл Нью-Джерси, Гупта Д., Бруннер П., Гундуз А., Адамо М.А., Ритаччо А., Шалк Г. Hill NJ, et al. J Vis Exp. 2012 июня 26; (64): 3993. DOI: 10,3791 / 3993. J Vis Exp. 2012 г. PMID: 22782131 Бесплатная статья PMC.
- Ультрамягкие нейронные электроды из микропровода улучшают интеграцию хронических тканей.
Du ZJ, Kolarcik CL, Kozai TDY, Luebben SD, Sapp SA, Zheng XS, Nabity JA, Cui XT.
Du ZJ и др. Acta Biomater. 2017 15 апреля; 53: 46-58. DOI: 10.1016 / j.actbio.2017.02.010. Epub 2017 6 февраля. Acta Biomater. 2017 г. PMID: 28185910 Бесплатная статья PMC.
- Коррекция артефактов чувствительности, индуцированной металлами, для функциональной МРТ при глубокой стимуляции мозга.
In MH, Cho S, Shu Y, Min HK, Bernstein MA, Speck O, Lee KH, Jo HJ. В MH et al.Нейроизображение. 2017 сентябрь; 158: 26-36. DOI: 10.1016 / j.neuroimage.2017.06.069. Epub 2017 27 июня. Нейроизображение. 2017 г. PMID: 28666879 Бесплатная статья PMC.
- Применение сверхвысокопольной магнитно-резонансной томографии в лечении опухолей головного мозга: метаанализ.
Барретт Т.Ф., Саркисс Калифорния, Диворн Х.А., Ли Дж., Балчандани П.
, Шривастава РК. Барретт Т.Ф. и др.World Neurosurg. 2016 Февраль; 86: 450-65. DOI: 10.1016 / j.wneu.2015.09.048. Epub 2015 25 сентября. World Neurosurg. 2016 г. PMID: 26409071 Обзор.
LinkOut — дополнительные ресурсы
Источники полных текстов
Другие источники литературы
цитировать
КопироватьФормат: AMA APA ГНД NLM
Влияние размера и положения неподключенного алюминиевого электрода на биполярное анодирование в электрическом поле переменного тока
Биполярное анодирование алюминиевых БПЭ на переменном токе различных размеров
Кривые зависимости плотности тока от времени во время биполярного анодирования алюминиевых БПЭ на переменном токе соответствовали результаты нашего предыдущего исследования 20 . Плотность тока рассчитывалась для площади углеродного электрода, подвергшейся воздействию электролита, и площадь открытой поверхности алюминиевого БПЭ не учитывалась (рис. 1). Поскольку угольные управляющие электроды не принимали непосредственного участия в окислительно-восстановительных реакциях на БПЭ, плотность тока оставалась в основном стабильной независимо от размера БПЭ.
На угольных управляющих электродах электролиз воды протекает следующим образом: кислород выделяется на аноде, а водород на катоде, когда на элемент подается достаточно высокое напряжение.{-} \ to {\ text {H}} _ {{2}} $$
(2)
На рис. 2 показана поверхность анодированного образца до и после окрашивания. Поскольку в случае тонких оксидных пленок оценка распределения толщины путем окрашивания была затруднена, время реакции было установлено равным 60 мин, чтобы обеспечить рост достаточно толстой пленки. Специфические интерференционные полосы наблюдались на всех анодированных образцах даже до того, как они были окрашены, независимо от размера БПЭ (рис. 2а). Эти интерференционные картины также наблюдались в нашем предыдущем исследовании 20 .Для сравнения показаны результаты для BPE длиной х = 5 см и шириной х = 1 см, который использовался в качестве стандартного образца в нашем предыдущем исследовании 20 . Когда центр образца был определен как x = 0 см, на каждом BPE наблюдалась картина с линейной симметрией. Этот результат показывает, что толщина сформированной пленки оксида алюминия непрерывно изменялась от центра ( x = 0) к обоим концам ( x ~ ± 2,5 см) поверхности BPE.Несмотря на равноудаленность от центра, наблюдались некоторые расхождения в цвете. Вероятно, это связано с неточностью размещения образца в электрохимической ячейке.
Цифровые фотографии алюминиевых листов (а) после биполярного анодирования переменным током в 10 ммоль дм -3 щавелевая кислота при 20 ° C в течение 60 мин при 60 В и (б) после последующего окрашивания . Длина ( l ) и ширина ( w ) каждого БПЭ варьировались в пределах 1–5 см и 1–3 см соответственно.
Распределение толщины пленки можно косвенно оценить, оценив интенсивность цвета окрашенного образца, поскольку краситель адсорбируется на пористой поверхности, как показано на рис. 2b. Более глубокие цвета указывают на то, что на пористой поверхности адсорбируется больше красителя, что соответствует более толстой пленке. Когда БПЭ с переменной длиной х = 1–5 см и фиксированной шириной х = 1 см были расположены горизонтально в ячейке, площади обоих концов, которые сохраняли металлический блеск, были разными.Короткие БПЭ с l, = 1 и 3 см имели меньшие площади, которые сохраняли металлический блеск, чем БПЭ с l = 5 см. Для BPE с l = 1 см оба конца были относительно темно-синими, а центр был либо бледно-синим, либо не имел синего. Таким образом, был сделан вывод, что центр БПЭ имеет относительно тонкую пористую пленку оксида алюминия из-за низкой адсорбции красителя. Для BPE с l = 3 см, хотя цвет на расстоянии 1 см от центра ( x ~ ± 1 см) был более интенсивным, чем в других областях, оба конца и центр были бледно-голубыми.
В нашем предыдущем исследовании было выполнено наблюдение FE-SEM для непосредственного изучения детальной структуры пленки 20 . На краю БПЭ пленка не была нормальной пленкой анодного пористого оксида алюминия с прямыми порами. Вместо этого были сформированы ламинатные пленки, состоящие из плотно уложенных друг на друга барьерных слоев. Пленки имели минимальную толщину ~ 200 нм по сравнению с другими областями, как показано на рис. S2. Поскольку оцененные межфазные разности потенциалов были самыми высокими на концах, образование водорода подавляло рост пленки во время биполярного анодирования на переменном токе, что приводило к более тонким пленкам оксида алюминия на краю BPE.Следовательно, эти участки не были достаточно окрашены. Подавление анодной реакции (т. Е. Образования анодной пленки) на основе уравнения. (1) в результате катодной реакции согласно формуле. (2) также наблюдалось при обычном анодировании переменным током алюминия 24 .
Для БПЭ с l = 5 см и w = 1–3 см изменение цвета по поверхности было почти одинаковым независимо от ширины. Однако интерференционные полосы показали явный изгиб.Хотя интерференционные полосы были почти параллельны поверхностям ведущих электродов, они не были идеально параллельны и искажались по краям широких образцов (например, w = 2 и 3 см). Это могло быть вызвано эквипотенциальной поверхностью, которая всегда перпендикулярна силовым линиям электрического поля. Если электрическое поле однородно, эквипотенциальная поверхность должна быть плоскостью, перпендикулярной прямой линии, соединяющей ведущие электроды.
Распределение эффективной разности потенциалов на BPE
Для оценки распределения толщины барьерных слоев в пористых пленках оксида алюминия, сформированных на каждом BPE, образцы были разрезаны на 1 × 1 см 2 кусок и повторно анодированы. V j был измерен в пределах 8 мм от центра каждой квадратной детали. Значение V j было записано как среднее значение измеренных значений для каждой детали. Мы подробно описываем принцип оценки и метод повторного анодирования в предыдущих статьях 20,21,22,23 . В j на кривой зависимости напряжения от времени, записанной во время повторного анодирования, должно зависеть от электрического сопротивления алюминиевого БПЭ, которое определяется толщиной барьерного слоя в пористой пленке оксида алюминия.На рис. 3а показана начальная стадия зависимости напряжения от времени для повторного анодирования каждого образца. На рис. 3b показаны графики V j для каждой области BPE с разной длиной l = 1–5 см и фиксированной шириной w = 1 см. V j BPE с l = 5 см и w = 1 см, о котором мы сообщали ранее 20 , также показано для сравнения.
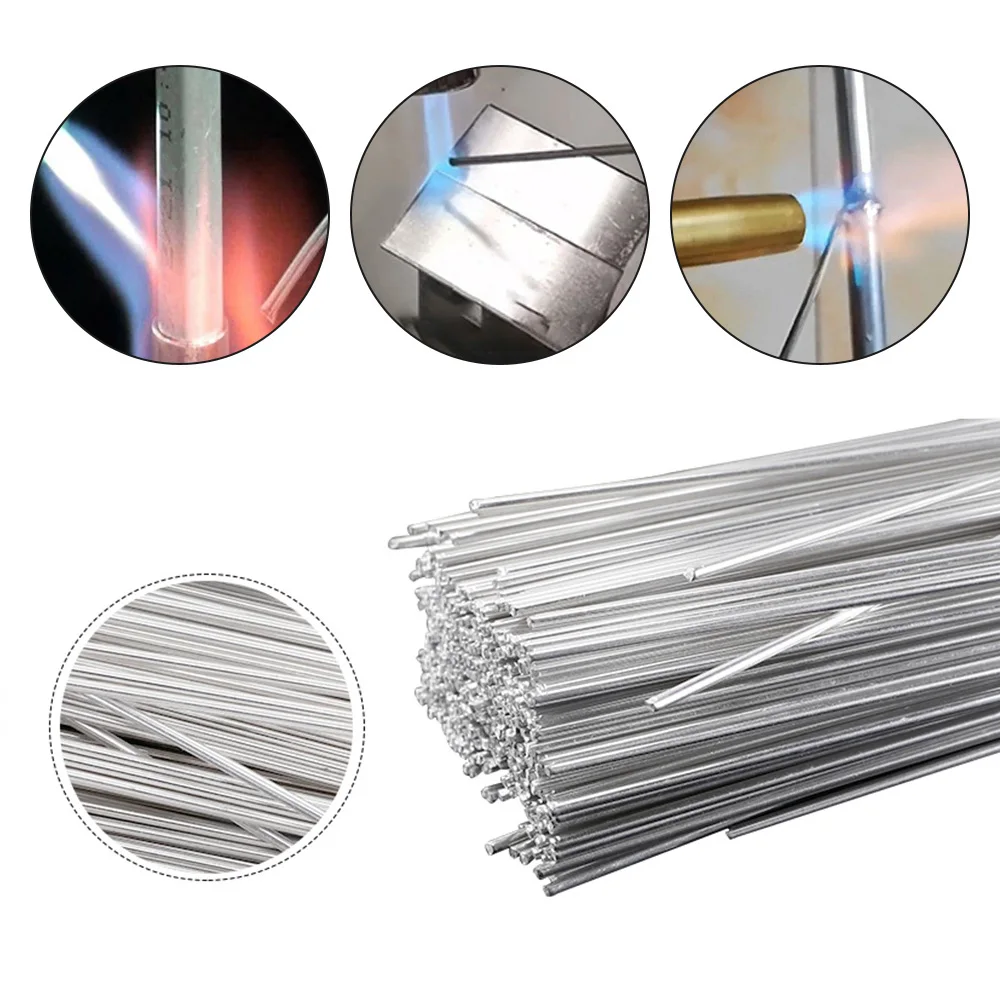
(a) Типичные кривые зависимости напряжения от времени, записанные в разных местах на алюминиевых образцах во время повторного анодирования, и (b) скачок напряжения ( В, j ), построенный как функция удаленность от центра БПЭ.Каждое указанное значение для V j является средним из трех измерений.
BPE с l = 3 см имел V j ~ 10 В на обоих концах ( x = ± 1 см) и ~ 5 В в центре ( x = 0). Это соответствовало ожиданиям, что межфазная разность потенциалов самая высокая на краю. Градиент потенциала от центра к краям поверхности БПЭ был почти линейным. Электрическое сопротивление имело симметричное распределение с центром x = 0 см, что хорошо согласуется с предыдущими результатами для BPE с l = 5 см 20 .Наклоны показывают, что электрическое сопротивление барьерного слоя увеличивается пропорционально приложенной разности потенциалов на поверхности BPE. Если области анодной и катодной реакций равны по размеру, V j не должно быть обнаружено в центре BPE. Однако там было обнаружено электрическое сопротивление, поэтому межфазная разность потенциалов не была нулевой. Это может быть связано с увеличением анодной движущей силы за пределами центра BPE во время биполярного анодирования на переменном токе.
BPE с l = 1 см (т. Е. В центре квадрата) имел V j ~ 1,4 В, что ниже, чем значения для BPE с l = 3 и даже 5 см. в той же позиции (x = 0). Таким образом, на окислительно-восстановительную реакцию явно влияла длина БПЭ. Разница между потенциалами на концах BPE, ∆ V BPE , была оценена с учетом разности потенциалов E 1 :
$$ \ Delta V _ {\ text {BPE}} = E \ раз \ frac {l} {L} $$
(3)
Следовательно, БПЭ с относительно длинным l должен иметь большую ∆ V BPE , а степень поляризации должна увеличиваться. С полем постоянного тока направление поля является простым и фиксированным, поэтому ∆ V BPE можно оценить по длине одного только BPE на основе уравнения. (3). Однако для переменного поля миграция ионов (как анионов, так и катионов) в электролите и перенос электронов в BPE более сложны, поскольку полярность управляющих электродов (то есть направление поля) периодически переключается. Кроме того, поскольку окислительно-восстановительная реакция происходит на левой и правой сторонах BPE одновременно, реакция в центре может быть полностью подавлена для BPE с относительно коротким -1.Другими словами, ожидалось, что ДПЭ с l = 1 см будет иметь самую низкую степень поляризации среди образцов, рассмотренных в этом исследовании.
Одновременная обработка нескольких алюминиевых BPE
Чтобы прояснить важные моменты при одновременной обработке нескольких BPE, положение каждого BPE между ведущими электродами было изменено, как показано на рис. 4a. Для оценки эквипотенциальной поверхности наблюдались специфические интерференционные полосы. На рис. 4 показано положение каждого БПЭ и их внешний вид после биполярного анодирования и окрашивания переменным током.Для всех конфигураций БПЭ наблюдались специфические интерференционные полосы, параллельные поверхностям ведущих электродов. Окраска была почти такой же, как и для BPE того же размера (1 × 1 см 2 ), обработанного отдельно, как показано на рис. 2. Воспроизводимость эксперимента по обработке нескольких BPE была подтверждена, как показано на рис. S3. . Все БПЭ имели значения В, , и менее 2 В, что близко к результату, показанному на рис. 3 (~ 1,4 В).
(a) Схема вида сверху для биполярного анодирования нескольких BPE и (b) цифровых фотографий алюминиевых BPE, записанных после биполярного анодирования на переменном токе в 10 ммоль дм -3 щавелевая кислота при 20 ° C в течение 60 мин при 60 В с последующим окрашиванием.