Чем спаять силумин в домашних условиях
На заметку! Силумин – это сплав алюминия и кремния, который предназначен для создания деталей сложной формы.
Такой металл характеризуется высокими показателями прочности, устойчивостью к коррозийным процессам и износостойкостью.
Сварка силумина при помощи аргоном
Технология сварки силумина практически идентична процессу сваривания алюминия. Она получила название аргонодуговой, поскольку в ней объединились электрическая и газовая сварки. А именно, сварка осуществляется при помощи неплавящегося электрода в защитном аргоном облаке.
Как уже отмечалось, основная функция аргона заключается в защите сплава от процессов окисления. За счет того, что он тяжелее воздуха, он вытесняет воздушные массы из зоны сварки. Еще одна отличительная особенность аргона состоит в том, что он является инертным газом, а значит ни с воздухом, ни с другими газами он ни при каких обстоятельствах не будет вступать в реакцию.
Если вы новичок, и впервые производите сварку силумина в домашних условиях, следует быть очень внимательным и не перегреть газ.
В случае, когда осуществляется сварка на обратной полярности (электрод подсоединяется к плюсу, а заготовленная деталь к минусу), от атомов аргона будут отсоединяться электроды. Таким образом, происходит ионизация газа и он начнет пропускать через себя электроток. Поэтому очень важно довести аргон до нужной температуры, ведь если его перегреть, то своей силой он будет не соединять заготовки из силумина, а начнет их разрушать.
Обратите внимание! Сваривать можно исключительно литейный силумин, в котором находится 5-20% кремния. Если в составе много цинка. То варить такой материал нельзя.
Как произвести сварку силумина
Чтобы сварить силумин нужно прибегнуть к аргонодуговой технологии. Оборудование сконструировано из инвертора, газового баллона, осциллятора и горелки. В горелку монтируется неплавящийся вольфрамовый электрод, силуминовая проволока предстает в качестве присадки.
Перед тем как начать процесс сварки нужно:
- взять наждачку, металлическую щетку или пескоструйную машину и зачистить кромки свариваемых силуминовых деталей,
- затем нужно обработать их химическим составом. Для этого подойдут: бензин или любой растворитель.
Сварка осуществляется на обратной полярности при короткой дуге, поскольку так металл будет лучше плавиться. Присадочную проволоку нужно поместить в зону сварки, там она расплавится и совместится с основным металлом. В результате образуется однородная жидкая масса, которая после того как остынет превратится в монолит.
Чтобы сварной шов получился качественным, важно подавать проволоку перед горелкой и держать ее нужно пол углом. Соблюдайте точность и равномерность подачи проволоки вдоль шва, ведь если подать ее слишком быстро – металл разбрызгается и шов получится кривым.
Осуществляя сварку силумина в домашних условиях, соблюдайте все установленные правила и рекомендации, а именно:
- когда поджигаете электрод, ни в коем случае не касайтесь свариваемых металлических заготовок,
- подаваться газ должен только спустя 15 секунд после того как вольфрамовый электрод разожжется,
- в конце сварочного процесса нельзя прекращать подачу газа, отключать его разрешается лишь спустя 10 секунд после того, как прекратится подача электрической энергии на электрод.
Так, металл будет остывать равномерно.
Достоинства и недостатки аргонодуговой сварки силумина
Данная технология отличается рядом достоинств, среди которых выделяются:
- во-первых, такой способ является практически единственной возможностью соединить силуминовые заготовки,
- во-вторых, при короткой дуге сварочный процесс не займет много времени,
- аргон зарекомендовал себя как надежный защитный элемент, поэтому при соблюдении всех правил сварки, в конечном итоге вы получите прочное соединение,
- сварочный процесс каждый может осуществить в домашних условиях, здесь большую роль сыграет опыт.
Несмотря на большое количество плюсов, есть у такого способа и некоторые недостатки:
- сварку силумина аргоном не рекомендуется проводить на улице, т.к. ветер будет сдувать из зоны сварки защитный газ, поэтому сварочные работы лучше производить в закрытых помещениях,
- для сварки с аргоном нужно обзавестись всем необходимым оборудованием,
- могут возникнуть сложности с настройкой режима сварки,
- в случае применения сварочного трансформатора с большим током, важно дополнительно охладить силуминовые детали.
Подводя итог, стоит отметить, что сварка силумина – достаточно трудоемкий процесс, требующий внимательности и определенных знаний. Для того, чтобы конечный результат был качественным, лучше доверить это дело опытному специалисту.
Периодически сталкиваюсь с разрушением силуминовых элементов. Внешне детали изготовленные из силумина похожи на алюминий, но это только на первый взгляд. Хотя его достаточно легко отличить когда изделие повреждено. Невооруженным гразом можно видеть спекшиеся крупицы порошка. Но, как говорится, надежда умирает, последней. В телефонной книге ищешь номер знакомого аргонщика. Приносишь деталь и после первого «чварка» можно наблюдать кислое лицо этого аргонщика. И вот после очередных повреждений силуминовых деталей уже и не хочется предпринимать попытки обращения к аргонщикам.
И вот я решил погуглить в сети, действительно ли этот самый силумин на сваривается. Для начала заглядываю в википедию, чтобы узнать из чего же состоит этот самый силумин. Его схожесть с алюминием не случайна, посколько это основная составляющая этого сплава. Второй основной элемент это кремний, доля которого составляет от 4 до 22% в зависимости от его марки. Также в состав силумина входит небольшое количество примесей: железо, медь, марганец, титан и прочие. Исходят из того, что процентное соотношение кремния разное, то скорее всего шанс сваривания есть.
Итак, погрузившись в бурные обсуждения интернет-форумов я понял следующее, что сваривать (спаивать) стоит только лишь в том случае, если деталь представляет некую ценность и если она находится под действием определенных нагрузок. В противном случае все ратуют за склеивание деталей силумина.
ОК. Все равно хотелось бы тезисно изложить основные требования к свариванию. Источник Websvarka.ru.
- Использовать только аргон.
- Силумин бывает разный. Надо всегда пробовать. Откровенно китайские изделия не свариваются. Тупо расплавляются. А вот, к примеру, автомобильные детали от известных производителей без проблем поддаются свариванию.
- Для сваривания силумина рекомендуют использовать специальные припои типа Harris-52, НТS-2000, ER 4043. Они предназначены для сваривания алюминия.
- Перед сваркой необходимо детали предварительно разогреть до температуры 220 градусов цельсия. Для более эффективного отвода тепла рекомендуют использовать стальные прокладки. Насколько я понимаю это необходимо для недопущения расплавления силумина.
- Жесткие закрепления стараться избегать во избежаний трещинообразования.
- Перед сваркой попытаться попробовать на тестовом образце.
Теперь что касается склеивания силумина. Прежде чем клеять необходимо тщательно подготовить поверхность. Максимально очистить от грязи и масла. Заранее продумать чем зафиксировать изделия после нанесения клея. Самое распространенный клее — эпокситный. Также многие советуют всяческие пятиминутки. После застывания клея можно армировать места склеивания. Для этих целей подойдет шпатлевка с волоконным наполнителем. Да, если вы надеетесь найти специальный клей для силумина, не теряйте зря время. Но здесь можно пойти по логике сварщиков, которые ищут припои для алюминия. Так и здесь, существуют специальные клеи предназначенные для склеивания алюминия.
Двухкомпонентные клеи COSMOFEN DUO и AL-1. Применяется в строительстве для склеивания алюминиевых элементов окон и дверей.
Вот такой вот краткий анализ в помощь тем, кто ищет способы сваривания и склеивания силумина. Здесь подход должен быть творческий, когда сумма попыток рождает победу.
Рекомендованные сообщения
Создайте аккаунт или войдите в него для комментирования
Вы должны быть пользователем, чтобы оставить комментарий
Создать аккаунт
Зарегистрируйтесь для получения аккаунта. Это просто!
Войти
Уже зарегистрированы? Войдите здесь.
Сейчас на странице 0 пользователей
Нет пользователей, просматривающих эту страницу.
как заказать работу по выгодной цене
Новички часто ошибаются, полагая, что сварка силумина аргоном – это относительно простой процесс, предназначенный для соединения деталей. Однако на практике всегда возникает много трудностей. Во-первых, сплав может окислиться из-за нагрева, в результате это приводит к существенному снижения прочности детали и ухудшению других ее характеристик.
Во-вторых, сам силумин – достаточно сложный в работе металл. Именно поэтому сварка силумина аргоном – наилучший способ. Технология непростая, но вы обязательно должны освоить ее, чтобы изготавливать надежные аккуратные швы.
Сам силумин является сплавом алюминия и кремния. У него превосходные механические свойства, он хорошо поддается литью. Из достоинств можно выделить следующие:
- устойчивость к износу;
- хорошая механическая прочность;
- низкая подверженность коррозии.
Почему именно аргонодуговая сварка?
Достоинств у этого метода масса, пусть он и сложен в освоении и реализации.
- Силумин нагревается в небольшой области. Поэтому деформация свариваемых частей детали минимальна.
- Аргон защищает металл от окисления.
Он вытесняет кислород и исключает его действие на горячий сплав. Сам аргон является инертным газом, который практически не взаимодействует с окружающей средой.
- Используемые технические приемы по отдельности просты и общедоступны. Способ недорогой и практичный.
- Зачастую детали из силумина можно сварить только таким способом.
Недостатки тоже есть, и их необходимо нивелировать. К примеру, сильный ветер однозначно помешает работе, аргон попросту не будет задерживаться в рабочей области. Для дуги большой силы тока нужно охлаждение. К тому же, нужно хорошо разбираться в настройках сварочного аппарата, чтобы получить оптимальные характеристики тока.
Особенности метода
Используется горелка с соплом, откуда подается аргон. Вольфрамовый неплавящийся электрод закрепляется в специальном держателе. Перед началом процесса сварки зачищаются края детали от тугоплавкой окисной пленки.
Сделать это можно разными способами:
- специальным химическим раствором;
- металлической щеткой;
- пескоструйным аппаратом;
- бензином.
При обработке химикатами нужно промыть водой перед началом сварки. В обязательном порядке используется присадочная проволока. Помните, что по своему составу она должна максимально совпадать с исходным материалом.
Электрод в процессе работы должен располагаться максимально близко к свариваемой области, но ни в коем случае не соприкасаться с ней. 2 мм – идеальное расстояние. Вести электрод нужно ровно, подавать проволоку тоже. Зигзагообразные движения недопустимы.
Помните, что быстрая подача проволоки приводит к высокой вероятности появления металлических брызг, а это небезопасно и приводит к ухудшению качества шва. Зажигание дуги осуществляется только бесконтактным методом!
Загрузка…Сварка аргоном маленькой детали в г. Москва
Цена договорная
Сварить (с выездом или пришлю человека) сломавшуюся по сгибу деталь (силумин)
В предложениях указывайте сроки, когда сможете выполнить задание и цену за работу. Жду Ваших предложений!
Когда: , 23:59
Адрес: 6-й Монетчиковский переулок, Москва
Смотрите также:
Хотите найти лучшего мастера по ремонту?
Последние добавленные задания
-
1 000 руб
Установить пилон ( дома )
Установить пилон ( шест для танцев ) !!Нужен мастер со своим перфоратором !!! Есть подробная инструкция / стремянка
Нана улица Савушкина, 125к1, Санкт-Петербург
-
7 000 руб
Обивка входной двери
Есть деревянная дверь: 2500х900.
Требуется сделать на ней новую обивку (белый кожзам) и поставить новую ручку.
Петр М. 3-я Фрунзенская улица, Москва
-
Цена договорная
Возведение свайного фундамента
Нужно сделать свайный фундамент под павильон из СИП панелей. Размер павильона 7.9х2 метра
Станислав Л. Климовск, советская площадь
-
Цена договорная
Распил лдсп
Распилить 3 фальшпанели из фасодов икеа
Даша Я.
проспект Энергетиков, 11к3, Санкт-Петербург -
Цена договорная
Подсобный рабочий
Требуется подсобник для сварщика. Подержать, принести, просверлить, забить, отрезать, убрать и т.д. Сборка металлического ограждения с воротами из уголков и сетки-рабицы на теплом складе. Размер ограждения…
Роман Н. микрорайон Птицефабрика, рабочий посёлок Томилино
Проволока / Пруток | Номер сплава по AWS A5.![]() |
Назначение и свариваемые материалы (марки по ГОСТ и ISO) | Российский аналог (ГОСТ 7871-75) ESAB |
АL99.7 | ~ ER 1100, 1070 | Технический алюминий АД00, АД0, АД1, АД, АМц Е1070, Е1050, Е1230, Е1200, E3003 |
Св. А7, OK 18.01 |
АL99.5Ti | 1450 | Технический алюминий Повышенная стойкость к образованию трещин и мелкозернистая структура сварного шва АД00, АД0, АД1, АД, АМц Е1070, Е1050, Е1230, Е1200, E3003 |
Св. А85Т, OK 18.11 |
АLSi 5 | ER 4043 | Алюминий-магний-кремний «Авиаль» Ремонтная сварка литья и поковок из силуминов, содержащих до 7% кремния, в т.ч. АЛ1, АЛ3, АК4, АК6, АК6ч, АК8, Е2014 (слабонагруженные вспомогательные конструкции и автомобильная индустрия) |
Св.![]() |
ALSi12 | ER 4047 | Алюминий-магний-кремний-медь сплавы, содержащие свыше 7% кремния, в т.ч «Силумин» AЛ2, АЛ4, АЛ9, АК9, АК12 (ремонтная сварка литья и поковок) |
~ Св. АК 10 |
ALMg3 | ~ ER 5654, 5754 | Алюминий-магний «Магналий» АМг2, АМг3, Е 5251, Е 5754, Е 5954 (слабонагруженные вспомогательные конструкции) |
Св. АМг 3 |
ALMg 2,7Mn | ER 5554 | Алюминий-магний-марганец «Магналий» АМг2, АМг3, Е 5251, Е 5754, Е 5954 (в основном применяется для изделий, работающих при температурах более 100 °С) |
~ Св. АМг 3 |
АLMg 5 | ER 5356 | Алюминий-магний «Магналий» АМг4, АМг5, Е 5086, Е 5083, Е 5056, АМг2, АМг3, Е 5251, Е 5754, Е 5954 (судостроение, транспортные емкости, железнодорожный и автомобильный транспорт) |
Св.![]() |
АLMg 4,5 Mn | ER 5183 | Алюминий-магний-марганец «Магналий» АМг4, АМг4,5Mц, АМг5, Е 5056, Е 5083 и другие сплавы с содержанием магния менее 5% (изделия стойкие к морской воде, железнодорожный и автомобильный транспорт, емкости для молочной и пивоваренной промышленности, криогенные сосуды) | ~ Св. АМг 5, ОК 18.16 |
АLMg 4,5Mn Zr | 5087 | Алюминий-магний-марганец «Магналий» АМг4, АМг4,5Mц, АМг5, Е 5056, Е 5083 и другие сплавы с содержанием магния менее 5% с повышенной стойкостью против трещин и коррозии (судостроение, транспортные емкости, железнодорожный и автомобильный транспорт) |
Св. 1557 |
AlMg 5Mn | ER 5556 | Алюминий-магний-марганец «Магналий» АМг5, Е 5056, Е 5083 и другие сплавы с содержанием магния менее 5% (высокопрочные конструкции для ВПК и строительной индустрии, транспортные емкости) |
~ Св.![]() |
ALMg 6Zr | — | Алюминий-магний «Магналий» АМг5, АМг6, АМг61, Е 5086, Е 5056 и другие сплавы с содержанием магния менее 5% с повышенной прочностью и коррозионной стойкостью (судостроение, высокопрочные конструкции для ВПК и авиационной промышленности) |
Св. АМг 61, ~ Св. АМг 6, ОК 18.22 |
ALCu 6Mn Zr Ti | ER 2319 | Алюминий-медь-марганец «Дюраль» 1201, 1205, Е 2219, Е 2014, Е 2036 (высокопрочные сварные конструкции с термической обработкой для ВПК и других применений) |
~ Св. 1201 |
Cварка алюминия электродом: оборудование и применяемые материалы
Очень часто сварщики сталкиваются с проблемой, когда необходимо сварить те или иные детали из алюминия, а традиционный способ сварки TIG такого непростого металла как алюминий по некоторым причинам не доступен. Это создает некоторые неудобства, и найти выход из подобных ситуаций порой удается не просто.
Сегодня я буду говорить о сварке алюминия сварочным электродом. Этот способ сильно отличается от методов сварки TIG, MIG-MAG, MMA.
Перед началом работ необходимо удостовериться, какой вид и марку металла требуется сварить. Некоторые металлы и сплавы внешне очень похожи на алюминий. Силуминовые сплавы сварить у вас не получиться. А магний вообще взрывоопасен.
Магний отличить от алюминия не сложно. Нужно сточить напильником небольшое количество стружки с проверяемого металла, и соблюдая элементарные правила ТБ высыпать ее на открытое пламя, магний вспыхнет, а алюминиевая пыль создаст только небольшое количество искр.
Сварочный аппарат должен быть достаточно мощным, и выдавать ток порядка 200 – 250А, и не чувствительным к перепадам электричества в сети. Сейчас это не проблема, можно взять хороший инвертор с соответствующими параметрами.
Сварка будет производиться постоянным током обратной полярности. Мощность сварного тока для работы электродом диаметра 3мм должна быть равна 170 – 190А, электрод 4мм = 200 – 230А.
При сварке металла толщиной до 2мм разделка свариваемых кромок не требуется. Необходимо зачистить наждачной бумагой и обезжирить ацетоном края соединений. Непосредственно перед свариванием требуется прогревать кромки до 280 – 330°С. Кромки металла толщиной свыше 2мм нужно произвести разделку кромок под углом 60°. Далее все действия повторяем, как и при подготовке тонких металлов.
Сам процесс сварки покажется сварщикам, которые варят алюминиевым электродом первый раз немного не обычным. Дугу надо поджигать не чирканьем электрода по металлу, а легким отрывистым ударом, чтобы избежать примерзания электрода к металлу, так как в этом случае осыплется обмазка электрода. Необходимо не упустить момент загорания дуги и стараться удержать ее, что вызовет некоторые затруднения у многих сварщиков, так как электрод 3мм/d сгорает за 3 – 4сек. За это время нужно успеть сориентироваться в ситуации и направить сварную ванну в нужном направлении.
Во время сваривания металла вышеописанным способом выделяется большое количество дыма, и происходит разбрызгивание металла. В сварной ванночке практически невозможно отличить металл от шлака, что в принципе не имеет большого значения, потому как кромки металла свариваются без раковин и свищей. Полученный сварной шов нужно очистить от шлака при помощи ветоши смоченной водой.
При соответствующей квалификации сварщика, сварные швы полученные данным способом сварки положительно проходят тестирование на герметичность, излом, дефектоскопию.
Сварка алюминия покрытыми электродами
Положительные стороны сварки таким способом:
- Отсутствие баллонов.
- Высокая производительность.
- Сварка в любой плоскости.
Недостатки:
- Наличие шлака на шве
- Большое количество дыма
- Разбрызгивание металла.
Сварка алюминия — руководство за 20 минут
Сущность
Определения и сущность диффузной сварки описаны в ГОСТ 19521-74.
Диффузионная сварка производится воздействием давления и нагревом свариваемых деталей в защитной среде. Перед сваркой поверхность детали обрабатывают по 6 классу шероховатости и промывают для обезжиривания ацетоном.
Температура нагрева составляет 0,5 – 0,7 от температуры расплавления металла свариваемых деталей. Высокая температура обеспечивает большую скорость диффузии и большую пластичность деформирования металла. При недостаточной диффузии в сварке используют металлические прокладки (фольга из припоя ВПр7 толщиной 0,1 – 0,06 мм.) или порошок (фтористый аммоний), прокладываемые в месте сварки. Перед сваркой фольгу приваривают к поверхности одной из деталей с помощью контактной сварки. В процессе сварки прокладка расплавляется.
Процесс сварки осуществляется с использованием разных источников нагрева. В основном применяют индукционный, радиационный, электронно-лучевой нагрев, нагрев проходящим током, тлеющим разрядом или в расплаве солей
Сварка протекает при давление в камере – 10−2 мм. рт. ст. или в атмосфере инертного газа (иногда водорода). Вакуум или защитная атмосфера предохраняет свариваемые поверхности от загрязнения.
Сварка производится сжатием деталей с давлением 1 – 4 кгс/мм2. Давление, применяемое при способах сварки без расплавления материалов, способствует разрушению и удалению окисных пленок и загрязнений на поверхности металла, сближению свариваемых поверхностей до физического контакта и эффективного атомного взаимодействия, обеспечению активации поверхностей для протекания диффузии и рекристаллизации. Различается сварка с высокоинтенсивным силовым воздействием (свыше 20 МПа) и сварка с низкоинтенсивным силовым воздействием (до 2 МПа).
Диффузионная сварка походит в две стадии:
- сжатие свариваемых поверхностей, при котором все точки соединяемых материалов сближаются на расстоянии межатомных взаимодействий;
- формирование структуры сварного соединения под влиянием процессов релаксации.
ДИФФУЗИОННАЯ СВАРКА
Диффузионная сварка
осуществляется в твердом состоянии металла при повышенных температурах с приложением сдавливающего усилия к месту сварки. Процесс сварки металла в твердом состоянии при повышенных температурах принципиально протекает так же, как и при холодной сварке. В начальной стадии процесса на линии раздела двух деталей создаются условия для образования металлических связей. Из теории образования сварного соединения при холодной сварке известно, что для возникновения на линии раздела металлических связей необходимо обеспечить тесный контакт свариваемых поверхностей и создать условия для удаления поверхностных пленок окислов, жидкостей, газов и различного рода загрязнений [7, с. 46–56].
Использование повышенных температур при диффузионной сварке приводит к уменьшению сопротивления металла пластическим деформациям. Вследствие этого имеющиеся в зоне действительного контакта выступы на металле деформируются при значительно меньших нагрузках, что облегчает сближение атомов металла на всей площади свариваемой поверхности.
Удаление поверхностных пленок и предупреждение возможности образования их в процессе сварки достигается использованием вакуумной защиты и тщательной предварительной зачисткой свариваемых поверхностей.
Таким образом, первая стадия процесса диффузионной сварки, так же как и холодной сварки, основана на образовании металлических связей на свариваемых поверхностях металлов при нагревании их в вакууме с применением сдавливающего усилия. На второй стадии процесса диффузионной сварки происходят процессы взаимной диффузии атомов свариваемых металлов. Эти процессы приводят к образованию промежуточных слоев, увеличивающих прочность сварного соединения. Однако в некоторых случаях образование промежуточных слоев нежелательно.
Схема процесса диффузионной сварки в вакууме представлена на рис. 9.1. В вакуумной охлаждаемой камере 1 размещают свариваемое изделие 2 и нагреватель 3. Для сдавливания деталей в процессе сварки используют механизм сжатия, состоящий из штока 5 и механизма нагружения 6, шток проходит через вакуумное уплотнение или сильфон 4.
Сварка происходит в вакууме 10–3– 10–5 мм рт. ст. (133·10–3 – 10–5 Н/м2).
После откачки из камеры воздуха изделие нагревают обычно т. в. ч. до температуры сварки. Для получения качественного соединения необходимо обеспечить равномерный нагрев свариваемого изделия по всему сечению.
Усилие сжатия прикладывают после выравнивания температуры и поддерживают постоянным в течение всего процесса. Известны также технологические приемы с меняющимся давлением в процессе сварки. Продолжительность выдержки под нагрузкой зависит от свойств свариваемого металла, величины давления и других факторов и может достигать десятков минут.
Рис. 9.1 – Схема установки для диффузионной сварки в вакууме |
Давление также зависит от свойств металла, температуры сварки и других факторов и изменяется от 0,3 до 10 кгс/мм2 (2,9–98 МН/м2). Обычно при охлаждении деталей сжимающее усилие снимают при достижении температуры 100–400оС (373–673 К). Преждевременное снятие сжимающего усилия при охлаждении деталей в некоторых случаях приводит к разрушению сварного соединения.
Температура нагрева соединяемых деталей в диапазоне 800–1100°С (1073 – 1373 К) влияет на прочность соединения из стали Ст. 50 при различных давлениях. Так, при продолжительности сварки 5 мин, разрежении 10-3 мм рт. ст. (133·10-3 Н/м2) и увеличении температуры с 800 до 900 °С (с 1073 до 1173 К) прочность соединения увеличивается в 2 раза, а при повышении температуры до 1100 °С (1373 К) – в 3 раза. В несколько меньшей степени температура оказывает влияние при давлении 1 кгс/мм2 (9,8 МН/м2). При давлении 2 и 5 кгс/мм2 (19,6 и 49,0 МН/м2) прочность соединения увеличивается лишь до температуры 1000 оС (1273 К). При температуре 1100 °С (1373 К) наблюдается незначительное уменьшение прочности соединения.
При увеличении давления от 0,5 до 2 кгс/мм2 (от 4,9 до 19,6 МН/м2) прочность соединения значительно растет для 800, 900, 1000, 1100оС (1073, 1173, 1273, 1373 К).
Дальнейшее увеличение давления от 2 до 5 кгс/мм2 (от 19,6 до 49,0 МН/м2) сказывается незначительно на прочности соединения. Изменение прочности соединения при увеличении давления до 2 кгс/мм2 (19,6 МН/м2) и выше можно объяснить главным образом увеличением площади фактического контакта между соединяемыми поверхностями.
Повышение температуры при постоянной продолжительности сварки и прочих равных условиях увеличивает прочность соединения. Продолжительность сварки аналогично влияет на все прочностные характеристики.
С увеличением продолжительности сварки прочность сварного соединения растет, увеличение продолжительности сварки сверх оптимального практически не влияет на прочность сварного соединения. Однако чрезмерное увеличение выдержки приводит даже к снижению прочности сварного соединения. Аналогичным образом влияет продолжительность процесса на пластичность, относительное удлинение и ударную вязкость.
Важное значение для проведения диффузионной сварки имеет степень разрежения в вакуумной камере. При температуре 1000° С (1273 К), р
= 2 кгс/мм2 (19,6 МН/м2),
t =
5 мин прочность соединения значительно возрастает с повышением разрежения до 10-1 мм рт. ст. (133·10-1 Н/м2), при дальнейшем повышении разрежения имеет место лишь незначительное увеличение прочности зоны сварки.
Способы подготовки и обработки поверхностей свариваемых деталей оказывают большое влияние на прочность соединения при диффузионной сварке в вакууме. При черновой обработке давление недостаточно для обеспечения высокой прочности сварного соединения.
Сварочные установки.
Сварочные диффузионные установки имеют следующие основные узлы: сварочную камеру, вакуумную систему, механизм давления, приводимый в действие гидравлическим насосом, пульт управления электрической и вакуумной системами.
Величину давления контролируют манометром. Для уменьшения нагрева стенок сварочной камеры на ней имеется водяная рубашка и охлаждаемый промежуточный шток. В качестве источника нагрева в установках обычно используют генератор т. в. ч.
На рис. 9.2 представлена вакуумная система установки СДВУ-6М, которая состоит из сварочной камеры 1 с вентилем 2 для пуска воздуха. К камере через высоковакуумный затвор 3 присоединен паромасляный насос 4.
Предварительное разрежение в системе создается двумя механическими вакуумными насосами 6, которые могут работать как последовательно, так и параллельно, что обеспечивается переключением вентиля. 9 и других вакуумных вентилей 10.
Механические насосы подключают к вакуумпроводам 8 через сильфонные компенсаторы 7. Разрежение в сварочной камере и в патрубке паромасляного насоса замеряется вакуумметрическими датчиками 5.
Для сварки деталей и узлов электровакуумных приборов используют установку А306-04, позволяющую сваривать в вакууме и контролируемой атмосфере при нагреве деталей с помощью т. в. ч. с одновременным прижатием соприкасающихся поверхностей свариваемых деталей.
Рабочая камера имеет диаметр 350 мм и высоту 440 мм. На установке можно сваривать изделия диаметром до 120 мм, высотой до 180 мм.
Усилие сжатия свариваемых деталей достигает 10 тс (198 кН). Максимальная температура нагрева свариваемых деталей 1300 °С (1573 К). Продолжительность сварки регулируют ступенчато в пределах 22–25 мин. Остаточное давление воздуха в камере 2·10-4 мм рт. ст. (266,6·10-4 Н/м2). Воздух из рабочей камеры откачивается вакуумными насосами ВН-2 и Н5С.
На рис. 9.3 показана двухпозиционная установка А306-06, которая предназначена для диффузионной сварки металлических и металлокерамических узлов электровакуумных приборов в вакууме.
Установка состоит из двух блоков, работающих независимо друг от друга. В каждый блок входит вакуумная камера, система откачки, механизм перемещения дна камеры, гидравлическая система, система охлаждения и электроаппаратура, управляющая работой всех узлов.
Механизм сжатия свариваемых деталей – гидравлический с широким диапазоном изменения силы сжатия. Электрическая схема установки обеспечивает дистанционное управление откачкой вакуумных камер, механизмами перемещения дна камер, системой охлаждения. Система откачки, вакуумных камер снабжения электромагнитными вакуумными кранами. Температура нагрева свариваемых деталей поддерживается электронным терморегулятором. Продолжительность сварки задается электронным реле времени.
В отличие от установки типа А306-04 установка А306-06 имеет две рабочие камеры. Это позволяет повысить коэффициент использования высокочастотного генератора и производительность установки.
Основные технические данные установки типа А306-06 аналогичны данным установки А306-04.
Опыт показывает, что диффузионная сварка в вакууме в ряде случаев имеет определенные преимущества. При сварке этим способом металл не доводится до расплавления, что в некоторых случаях дает возможность получить более прочные соединения. Изделия, выполненные диффузионной сваркой, обладают высокой точностью размеров.
Преимущества этого способа состоят также и в том, что он позволяет сваривать разнообразные материалы: например сталь с алюминием, вольфрамом, титаном, металлокерамикой, молибденом; медь с алюминием и титаном; титан с платиной и т. п. Этот способ нашел применение на ряде промышленных предприятий радиоэлектротехники, электронной техники, приборостроения.
Детали и узлы вакуумных приборов сваривают в специальных многопозиционных приспособлениях или оправках из стали 12Х18Н9Т. Приспособления и оправки после их изготовления отжигают во влажном водороде при температуре 900–1000 °С (1173–1273 К), чтобы получить на поверхности термостойкие пленки окиси хрома. Такая пленка исключает возможность сварки детали с приспособлением или оправкой. С этой же целью в некоторых случаях в качестве прокладки между оправкой и деталью используют обезвоженную слюду и керамику.
На рис. 9.4 показаны катод и его детали. Диффузионной сваркой соединены основания катода 1 с рубашкой 3 и диском 4. За один цикл сваривали восемь катодов.
Диффузионная сварка позволяет сваривать заготовки для получения биметаллических листов, состоящих из двух медных дисков, между которыми расположен диск из константана. На установке за одну загрузку сваривают 10 – 15 дисков.
Чтобы избежать приварки биметаллических дисков к прижимным оправкам и между собой, их разделяли прокладками из обезвоженной слюды. После диффузионной сварки из дисков прокаткой изготовляли фольгу, из которой штамповали мембраны для механизмов настройки приборов.
Диффузионная сварка может быть использована для соединения неметаллических материалов. Изготовлены сварные высокотемпературные нагреватели из дисилицид-молибдена для электропечей сопротивления, работающих в окислительной атмосфере при температуре до 1650 °С (1923 К).
Диффузионная сварка в вакууме найдет применение в первую очередь для деталей относительно небольших размеров, предназначенных для работы в сложных условиях, при необходимости получения высокоточных размеров деталей, для изделий из материалов, трудно соединяемых методами сварки плавлением.
Оборудование
Для проведения диффузионной сварки выпускается оборудование, различаемое по степени вакуумирования: с низким вакуумом (до 10-2 мм рт. ст.), со средним вакуумом (10-3…10-5 мм рт. ст.), с высоким вакуумом (свыше 10-5 мм рт. ст.), с защитным газом разной степени давления.
Для нагрева деталей применяют индукционный нагрев токами высокой частоты, электроконтактный нагрев током, радиационный нагрев электронагревателем.
В установках используют гидравлические или механические системы давления. Установки бывают с ручным управлением, полуавтоматические и автоматические с программным управлением. Автоматы применяются в крупносерийном или массовом производстве.
Как устроена диффузионная установка
Комплекс для сварки диффузионным методом включает следующие основные элементы:
- Рабочую камеру. Она изготовлена из металла и предназначена для ограничения рабочей среды, в которой создается вакуум.
- Станину – шлифованную подставку. На нее опирается рабочая камера, вдоль которой она может перемещаться.
- Вакуумный уплотнитель. Является прокладкой между камерой и подставкой.
- Роликовый механизм и прижимной винт. С их помощью осуществляется перемещение камеры вдоль направляющих и фиксация ее на подставке.
- Насос вакуумный. Создает безвоздушное пространство в рабочей зоне.
- Генератор с индуктором. Выступают системой нагрева свариваемых деталей.
- Пуансоны жаропрочные, цилиндры гидравлические и насос масляный представляют механизм сжатия деталей под заданным давлением.
В зависимости от модификации установки диффузионной сварки могут отличаться формой камер и способом их герметизации. Также разными бывают методы разогрева деталей. Могут использоваться радиационные нагреватели, генераторы высоких токов, установки тлеющего разряда, электронно-лучевые нагреватели.
Какой метод лучше всего использовать для сварки алюминия?
Лучший метод для сварки алюминия и его сплавов зависит от области применения соединения. Следующие пункты должны быть включены для рассмотрения, прежде чем принимать решение о сварочном процессе:
- Стоимость (сварочное оборудование, расходные материалы, утилизация отходов, расходы оператора и т. д.)
- Желаемая производительность сварки
- Геометрические ограничения
- Наличие поставщика
- стабильность
- Допуск искажения
- Скорость производства
Преимущества метода
При диффузионной сварке возможно:
- соединять однородные и неоднородные твердые вещества;
- избегать деформации деталей;
- не использовать расходники в виде припоев и флюсов;
- получать безотходное производство;
- не применять сложные системы приточно-вытяжной вентиляции, так как в процессе не образуется вредных паров;
- получать любую площадь зоны контактного соединения, ограниченную только возможностью оборудования;
- обеспечить надежный электрический контакт.
К этому следует добавить отличный эстетический вид готовой детали, которая не требует применения дополнительных операций обработки, таких как удаление сварной окалины, например.
Как сварить алюминий электродом — MOREREMONTA
Особенности сварки алюминия вызывают определенные трудности при соединении этого металла. Разработанные технологии в той или иной степени позволяют с этим бороться и добиваться положительных результатов. Качество сварки алюминия инвертором нельзя сопоставить с аргоннодуговой сваркой или другими технологиями соединениями Al.
Однако в бытовых условиях вряд ли найдется подходящее оборудование. В распоряжении мастера может оказаться максимум домашний сварочный аппарат, будь то инвертор или трансформатор постоянного тока.
Возникают разумные вопросы: возможно ли сварить алюминий инвертором в домашних условиях, как это сделать правильно и какие для этого потребуются материалы?
Что нужно знать сварщику
По заявлениям опытных сварщиков, электросварка этого “крылатого” металла без аргона может быть не хуже аргонной. Те мастера, которые говорят о посредственном качестве сварного шва и плохой свариваемости данным способом либо не варили алюминий электродом вообще, либо неправильно подходили к этому методу.
Обратите внимание на следующие рекомендации:
- Стыковое соединение является наиболее приемлемым. Тавровые и нахлесточные типы сварных соединений стараются избегать из- за большой вероятности затекания шлака в зазоры, который вызывает коррозию.
- После сварки шов промывается водой для удаления шлака;
- Подготовка алюминия перед сваркой обязательна. Удаление оксидной пленки, защита от ее повторного образования;
- Сварка массивных деталей толщиной более 3 мм сопровождается разделкой кромок под углом 60° с V-образной формой.
- Предварительный прогрев Al перед сваркой до 150-250 °C.
Не стоит забывать, что технически чистый алюминий сваривается лучше, чем его сплавы, содержащие магний и марганец (дюралюмилий, силумин).
Именно поэтому следут правильно подойти к выбору сварочных электродов в зависимости от химического состава сплава.
Электроды по алюминию
Наиболее распространенные марки электродов для сварки алюминиевых сплавов: ОЗА-1, ОЗА-2, ОЗАНА-1, ОЗАНА-2, ОК96.20. Стержни электродов изготавливают из сварочной проволоки с нанесением на них покрытий из смеси хлористых и фтористых солей. Толщина покрытия не более 0,3…0,5 мм на сторону.
Рассмотрим более детальное назначение каждого электрода.
- ОЗА-1 − для деталей и конструкций из технически чистого алюминия А0, А1, А2, А3. Сварка с предварительным подогревом по зачищенным кромкам.
- ОЗА-2 – для заварки литьевого брака и наплавки алюминиево-кремнистых сплавов АЛ- 4, АЛ-9, АЛ-11.
- ОЗАНА-1- сваривает технически чистый алюминий толщиной изделий более 10 мм. Предварительный подогрев температурой 250…400 С.
- ОЗАНА-2 – для сплавов АЛ-4, АЛ-9, АЛ-11, наплавки и заварки литьевого брака. Можно использовать в качестве соединительного материала изделий из дюралюминия и силумина.
- ОК96.20 − алюминиево-марганцовистые сплавы АМц; алюминиево-магниевые сплавы АМг2; АМг3; АМг5; АМг6; алюминиево-кремнистые сплавы АЛ-4; АЛ-9; АЛ-11.
Подойдет для дюралюминия
Алюминиевые электроды дороже обычных и очень гигроскопичны, т. е. набирают влагу из окружающего воздуха.
Техника сварки алюминия покрытыми электродами
Сварка алюминия инвертором производится постоянным током обратной полярности, предпочтительно в нижнем положении. Дело даже не в большой текучести алюминия, а в скорости сварки, которая увеличивается в 2-3 раза в сравнении со сталью.
Электрод плавится очень быстро и вы просто не сможете выполнить шов в вертикальном, и уж тем более в потолочном положении.
Важно! Перед сваркой электроды следует прокалить.
Держать электрод следует преимущественно в вертикальном положении или чуть наклоняя . Конец электрода перемещать в направлении шва. Сварка производится в один проход на короткой дуге, без поперечных движений.
Химические элементы обмазки создают повышенное электрическое сопротивление сварочного шва, поэтому создают препятствия при повторном зажигании дуги. Швы стараются делать не длинными.
В случае обрыва дуги, шлаковую корку с кратера и конца электрода следует удалить и перекрыть предыдущий минимум на 1 см во избежание образования пор при заварке кратера.
По завершении сварки сварочный шов обязательно зачистить и промыть водой во избежании коррозии.
Заключение
Ядовитый дым, выделяющийся при сварке, а также дороговизна электродов и их капризность в хранении не сделают данный метод популярнее MIG или TIG. Применяют его, как правило, в тех случаях, где невозможно использование или нецелесообразно использование газового оборудования.
Из алюминия произведено множество конструкций применяемых в устройстве автомобиля. Это могут быть блоки двигателя, коробки передач и элементы кузова. Изготавливают из этого нержавеющего материала различные емкости для промышленных и бытовых нужд. В случае образования трещины или свища заварить проблемное место лучше в среде аргона специальным аппаратом. Но если такой возможности нет, то можно воспользоваться инвертором. Сварка алюминия электродом в домашних условиях требует определенного режима и предварительной подготовки. Используются и специализированные расходные материалы. Как все это осуществить описывается ниже и демонстрируется на дополнительном видео.
Сварочный процесс-трудности работы с материалом
Электрической дугой можно соединять многие виды железа. У нее достаточно высокая температура горения, что позволяет хорошо проплавлять разную толщину пластин и создавать надежные и герметичные соединения. Но сваривать алюминий инвертором сложнее ввиду нескольких специфичных особенностей этого материала.
Первой трудностью являются гигроскопичные свойства алюминия. Материал способен впитывать окружающую влагу и накапливать в себе. Это не проявляется видимым образом на охлажденном изделии, но сразу станет заметно при ведении сварки. Когда зажигается дуга и металл оказывается в зоне повышенной температуры, то влага начинает испаряться с его поверхности, неизбежно попадая в зону сварки. Это приводит к чрезмерным брызгам и помехам при выполнении шва. Чтобы предупредить такое явление, требуется предварительный подогрев изделия горелкой при температуре 150-190 градусов. Во время выполнения процедуры можно увидеть выделение влаги на поверхности.
Еще одной сложностью является оксидная пленка, покрывающая все изделие тонким слоем. Она защищает металл от разрушения в кислотной среде, но существенно мешает свариванию инвертором в домашних условиях. Трудность заключается в огромной разнице температур плавления. Алюминиевый материал плавится при 500 градусах, а его оксид при 2000 градусах. Чтобы устранить этот перепад необходимо зачистить место сварки железной щеткой, дающей доступ к основному металлу.
Взаимодействие с окружающим воздухом способствует образованию пор в структуре шва, что значительно понижает его герметичные свойства. Защита сварочной ванны выполняется подачей аргона в случае TIG, или созданием газового облака от покрытых электродом при сварке инвертором в домашних условиях.
Поскольку чистый алюминий не используется в изделиях, то трудностью для сварки могут быть другие элементы входящие в сплав. Так, марки Ал2 и Ал9 с содержанием силумина от 4 до 13% считаются ограниченно свариваемыми. Такие же показатели имеют марки AMr1 и AMr6, где марганец может добавляться от 2 до 6%. Дюралюминий Д16 относится к трудносвариваемым.
Выполняем сварку: этапы работы
Как сварить алюминий стало понятно после многочисленных попыток и экспериментов. Далее представлены пошаговые действия, позволяющие получить качественное соединение в домашних условиях:
- Если свариваемые пластины имеют толщину более 5 мм, то необходима разделка кромок. Стандартом считается срез краев под 45 градусов, но допускаются и другие значения. Стоит отметить, что чем больше угол разделки, тем шире получится сварочный шов. При толщине пластин более 7 мм между ними требуется технологический зазор в 2 мм. Если рабочим объектом является трещина, то ее необходимо расширить отрезным диском и «болгаркой», иначе шов будет поверхностным.
- Подготовленное изделие необходимо прогреть. Удаление влаги производится пропан-кислородным пламенем. Это может быть резак или обычный баллончик с бытовой горелкой. Нагреть необходимо поверхность до 150 градусов. Проверить это можно специальным аппаратом или визуально по сухому состоянию материала.
- После нагрева быстро осуществляется зачистка оксидной пленки. Для этого подойдет обычная щетка по металлу. Снять тугоплавкий слой важно в начале зоны сварки. Последующее действие будет оказывать электрод, чей состав и температура разъедают оксид, позволяя производить сварку.
- На подготовленном материале ставятся прихватки, фиксирующие свариваемые стороны. Корневой шов необходимо провести ровно, заполнив зазор. Угол относительно свариваемых частей необходим в 90 градусов. Это непривычно для начинающих сварщиков, или тех, кто работал только с углеродистой сталью. Но так расплавляемый металл будет точнее попадать в место соединения. После небольшого остывания поверхности отбивается шлак.
Это происходит довольно трудно, поэтому требуется острый молоточек.
- Последующие слои шва наносятся до того уровня, чтобы заполнить всю толщину материала и создать небольшой валик поверх места соединения.
- Швы ведутся короткой дугой. Чрезмерное увеличение зазора может приводить к обрыву дуги. На конце электрода образуется нагар в виде белого слоя. Это выступающая щелочь. Чтобы продолжить сварку требуется удалить этот диэлектрик.
Электрод при сварке алюминия инвертором плавится быстрее, чем при работе с обычной сталью, поэтому тренировки на нерабочей поверхности помогут привыкнуть руке к сохранению дистанции.
Оборудование и электроды
Сваривание изделий из алюминия можно выполнять обычным инвертором. Аппарат удобен для транспортировки и передвижению на месте. Полярность необходимо выставить так, чтобы в руках сварщика находился «плюс», а на изделие крепился «минус». Потребуется розетка с 220 V.
Электроды необходимы специализированные, например UTP 48, или аналоги. Они бывают различных диаметров и подбираются по толщине металла. Состав расходных материалов тоже имеет гигроскопичные свойства, что требует предварительной просушки для образования качественного соединения. Подходящие режимы для сварки могут быть такими:
Толщина пластин, мм | Диаметр электрода, мм | Сила тока, А |
2 | 2.5 | 50-70 |
3 — 4 | 3.2 | 80-100 |
5 | 4 | 90-130 |
Алюминий позволяет долго служить изделиям. А его сварка в домашних условиях простым инвертором обеспечивает быстрый ремонт важной детали или корпуса. Применяя вышеизложенные рекомендации и приобретя подходящие электроды можно быстро заварить требуемую конструкцию из алюминия.
Алюминиевые конструкции, детали иногда нужно срочно отремонтировать. Имея навыки сварщика, многие самостоятельно заваривают алюминий электросваркой. В домашних условиях качественно выполнить шов не получится. Но как экстренную меру сварку алюминия электродом часто используют. Во время работы с легким металлом нужно учитывать особенности сплавов. Марганец увеличивает окислительную способность, магний улучшает свариваемость, кремний снижает температуру плавления.
Особенности сварки алюминия электродом
Сварить алюминий электродом без защитной атмосферы не получится. Горячий металл быстро насыщается водородом, шов получается пористым, расплав сильно разбрызгивается, шов получается неровным. Чтобы уменьшить разбрызгивание, металл варят на токе обратной полярности, на деталь подключают минусовую клемму, к держателю подводят плюс. Заготовки предварительно прогревают до +150 – +190°С, чтобы устранить воду, накапливающуюся в порах оксидного слоя.
Возникают трудности из-за оксидной пленки, она расплавляется при +2037°С, алюминий – при +660°С. Перед сваркой оксидный слой зачищают до блеска. Чистота поверхности влияет на качество соединения. У сплавов хорошая теплопроводность, он быстро нагревается, остывает, дает большую усадку, возникают внутренние напряжения, трещины. При сварке металла используют теплоотводящие подкладки. Они поддерживают необходимую температуру. Легкий металл в домашних условиях варят на высоких токах. Электроды выбирают специальные, предназначенные для сварки.
Выбор сварочного аппарата и электродов
Алюминий относится к плохо поддающимся сварке металлам. Сила рабочего тока должна быть в 1,5 раза выше, чем для стали. Сварочный аппарат должен генерировать постоянный ток до 250–300 ампер. Для работы подойдет бытовой аппарат для сварки, работающий от сети 220 В. Можно подобрать выпрямители, трансформаторы или генераторы, но лучше остановить выбор на инверторе, его преимущества:
- высокий КПД, до 95%;
- низкие индуктивные потери;
- снижение расхода тока за счет автоматического отключения;
- аппарат спокойно переносит просадку напряжения в сети;
- поддерживается стабильная дуга, достаточно задеть заготовку;
- есть дополнительные функции;
- небольшие габариты, можно переносить его в любое место.
Легкие сплавы несколькими электродами с солевой обмазкой, образующей шлаковый защитный слой:
- Озана, Озана-2 производства Спецэлектрод;
- ОК 96.20, 96.10, 96.50, шведская компания ESAB;
- УАНА отечественных производителей.
Можно использовать другие расходники, предназначенные для сварки алюминиевого литья и сплавов. Заготовки 2мм варят диаметром 2,5, для 3–4 мм деталей выбирают толщину 3,2; максимальный диаметр стержней – 4
Технология сварки алюминия электродом
В домашних условиях заготовки предварительно зачищают. У деталей, свыше 3 мм, разделывают кромки под углом 45–60°. Чем больше угол, тем качественнее получится шов. Если пластины толще 7 мм, их укладывают с зазором 2 мм. Трещины предварительно выравнивают, углубляют болгаркой, края высверливают, чтобы снять внутренние напряжения.
Как варят алюминий электродами:
- сначала заготовки прихватывают в нескольких местах;
- корневой шов ведут, держа электрод перпендикулярно;
- толстые детали варят в несколько проходов, каждый слой простукивают для снятия окалины;
- наплавочный валик должен выступать на 2-5 мм в зависимости от толщины деталей.
Сваривать алюминий нужно с соблюдением рабочего режима (толщина заготовки, мм/ток, А):
Толщина заготовки, мм
Начинающим сварщикам до выполнения шва нужно потренироваться на нерабочих поверхностях, чтобы привыкнуть держать короткую дугу.
Электросваркой ремонтируют детали, работающие под статической нагрузкой на сжатие. Это не самый эффективный метод ремонта. Швы не выносят скручивания, изгибов, сразу трескаются.
Как металлургический кремний улучшает производство алюминиевых сплавов
Использование металлического алюминия в строительстве значительно выросло за последние несколько десятилетий из-за растущей урбанизации и коммерциализации все более инновационных и адаптивных алюминиевых сплавов.
Алюминиевые сплавы представляют собой химические составы, в которых к чистой алюминиевой основе добавляются элементы. Эти сплавы могут использоваться для многих уникальных промышленных применений благодаря гибкости алюминия в качестве литейного материала.Именно эта гибкость позволила алюминию стать одним из любимых металлов, используемых профессионалами в промышленности.
Алюминиево-кремниевые сплавы, или силумин, как его называют в просторечии, часто используют высокочистый металлургический кремний (98% или выше) для улучшения химических характеристик металла.
Силумин имеет меньший вес, чем обычный алюминий или другие конкурирующие традиционные металлы, такие как сталь или титан. Добавление кремния высокой чистоты к алюминию вызывает более медленное разрушение металла.Это также придает металлу более низкую температуру теплового расширения, улучшая текучесть литейного расплава. Наконец, кремний снижает усадку в процессе затвердевания сплава, добавляя пластичность и прочность.
В автомобильной промышленности, в частности, силумин используется для замены стали в рамах автомобилей. (НАСА)
HPQ Silicon будет использовать собственную технологию PUREVAP ™ для производства кремния металлургического качества, часто используемого в алюминиевых сплавах.Полученный кремний будет иметь чистоту 98% или выше, что позволяет отнести его к металлургическому классу и подготовить его для использования в сплаве.
Алюминиево-кремниевые сплавы стали очень практичным материалом в транспорте и инфраструктуре. В автомобильной промышленности, в частности, силумин используется в качестве замены стали в рамах автомобилей. Сталь может быть более прочной, чем алюминий, но она также невероятно плотная, что утяжеляет кузова транспортных средств и снижает топливную экономичность.
Замена тяжелых металлов на сплав алюминия и кремния может немного снизить долговечность автомобиля, но не настолько, чтобы компенсировать промышленные преимущества снижения веса продукта.Алюминиевые сплавы особенно важны для электромобилей, которые полагаются на легкий вес, чтобы не мешать их батарее и мобильности.
Та же история в авиационной и железнодорожной отрасли. В японских сверхскоростных поездах Синкансэн в качестве основного производственного материала используются алюминиевые сплавы. Более легкий металл снижает аэробное трение, улучшает скорость, снижает затраты на топливо и выбросы парниковых газов. Даже космические корабли используют алюминиевые сплавы из-за очень эффективного соотношения прочности и веса.
Помимо транзита, алюминиевые сплавы используются во всевозможных строительных целях. Алюминий устойчив к коррозии, что делает его идеальным для несущих конструкций. Более легкий вес металла также означает, что фундамент здания не нужно строить на такой глубине, так как требуется меньший вес для поддержки. Металл также относительно термически эффективен.
Рыночные перспективы отрасли алюминиевых сплавов весьма оптимистичны.
Рыночный прогноз, проведенный Global Market Insights, предполагает, что значительный рост неизбежен, а чистая стоимость рынка алюминиевых сплавов к 2024 году превысит 150 миллиардов долларов. Широкий спектр адаптируемых сплавов, глобальная торговая деятельность, рост населения и ускоренная урбанизация будут и впредь способствовать успеху индустрии алюминиевых сплавов.
Это дополнительно подкрепляется существенным преобладанием отрасли в строительстве и транзитной инфраструктуре.
Инновации в отрасли производства алюминиевых сплавов, такие как использование металлического кремния металлургического качества, положительно влияют на рыночные условия во многих смежных отраслях. Повышение качества алюминиевых сплавов побуждает производителей переходить на алюминий для производства более качественных товаров.Эти улучшенные продукты затем предлагают большее удовлетворение потребителям, что еще больше стимулирует спрос на алюминиевые сплавы.
Чтобы проиллюстрировать это на примере: производитель автомобилей переходит с производства автомобилей из стали на силумин, уменьшая вес автомобиля и повышая эффективность использования топлива. Потребители, воспользовавшись сниженными расходами на топливо, приобретают силуминовый автомобиль, что еще больше увеличивает спрос на алюминиевые сплавы.
Металлический кремний высокой чистоты, полученный металлургическим способом из кремния HPQ Silicon , обеспечивает превосходные преимущества для промышленности алюминиевых сплавов.Использование инновационных сплавов поможет обеспечить доминирование алюминиевой промышленности в строительстве на десятилетия вперед.
С 2015 года HPQ Silicon Resources Inc работает над разработкой нового одностадийного процесса производства кремния высокой чистоты (Si) и преобразованием этого Si в наноразмерные порошки Si, которые необходимы производителям аккумуляторов.
(PDF) Силумины: автомобильные сплавы
1 Введение
Сварка трением — это уникальная технология сварки в твердом состоянии, которая особенно полезна при соединении разнородных металлов и сплавов.Сварка трением (FRW) — это процесс сварки в твердом состоянии
, при котором выделяется тепло за счет трения между деталями
, вращающимися относительно друг друга. Усилие осадки
обеспечивает боковой толчок к образцу. Сварка трением — это фактически техника ковки, а не
технически сварка, поскольку плавление составляющих металлов не происходит. Сварка трением
используется с металлами и термопластами в широком спектре авиационных и
автомобильных применений.Сила трения и относительное вращение дают
тепла трения. Таким образом, металл достигает пластичного состояния, и при приложении усилия, достаточного для создания осадки
, получается бездефектное сварное соединение [1].
В последние годы цветные металлы, включая алюминиевые сплавы, привлекают
все большее внимание в связи с их применением в морской, аэрокосмической и автомобильной промышленности.
Желчеотделение. Это связано с их высоким отношением прочности к весу, а также с характеристиками естественного старения
, которые придают большую прочность алюминиевому сплаву
[2].Процесс сварки трением приводит к минимальному образованию хрупких интерметаллических соединений
на границе раздела, так как он осуществляется при высоком давлении, причем
— это короткое время обработки и не в расплавленном состоянии [3]. Это не относится к традиционной сварке
, где большее образование хрупких интерметаллических соединений
с увеличением содержания алюминия приводит к снижению пластичности. Гарсия и др. исследовали
стойкость к питтинговой коррозии в хлоридсодержащих средах.Различные зоны
сварных соединений аустенитных нержавеющих сталей [AISI-304L и AISI-316L]
были исследованы с использованием потенциодинамической анодной поляризации и циклической потенциодинамической поляризации, при этом было сделано заключение, что точечная коррозия свариваемых металлов была
Набольше, чем у основного металла [4]. Bimes et al. изучили поведение точечной коррозии
прямозубого мартенситного шва в хлоридной среде, поддерживая потенциостатический метод
, и представили тот факт, что ЗТВ была наиболее важной зоной для точечной коррозии
и [5].Сплавы AA6061 содержат дисперсионно-упрочненный алюминиевый сплав
, содержащий магний и кремний в качестве основных легирующих элементов,
с небольшим количеством меди и железа. Кроме того, цинк вместе с магнием или магнием
плюс медь и никель развивают различные уровни прочности. Материалы
, содержащие медь и никель, обладают наивысшей прочностью и более 50 лет используются в качестве конструкционного материала
в пищевой промышленности и в самолетах
[6].Среди термообрабатываемых сплавов в семействе 6xxx представлены сплавы средней прочности
, которые обладают высоким уровнем стойкости к общей коррозии. Коррозионная стойкость
приближается к стойкости нетермообрабатываемого сплава [7]. Многие из этих алюминиевых сплавов
используются в щелочных растворах, особенно в атомной промышленности. Следовательно, для исследования коррозионного поведения прослойки Al – Ni – Cu в щелочных условиях
необходимо
. Методы поляризации, такие как потенциодинамическая поляризация, потенциодинамическая поляризация, тиолестница и циклический вольтамперметр, обычно используются для испытаний на коррозию в лабораториях
. Интерметаллическое образование, которое происходит при соединении алюминия и меди
, снижает коррозионную стойкость. Чтобы улучшить коррозию на этом стыке, между алюминием и медью необходимо ввести прослойку из никеля
.
284 E. Ravikumar et al.
Микроструктура и механические свойства легированной и электронно-лучевой обработки поверхности заэвтектического сплава Al-11,1% Si
Аннотация
Эффект электровзрывного легирования в двух режимах с последующей интенсивной импульсной электронно-лучевой обработкой заэвтектического сплава Al-11.Сплав 1% Si (силумин) исследован на изменение его структуры и фазового состава, механических и трибологических свойств. Методами методов растровой электронной микроскопии, электронно-микрозондового и рентгеноструктурного анализа проанализированы изменения структуры, фазового состава и морфологии модифицированной поверхности доэвтектического силумина, подвергнутого комплексной обработке. Оценивается изменение триболого-механических свойств после комплексного энерговложения: микротвердость увеличивается в 3 раза. В 2 раза (2,34 ГПа по сравнению с 0,73 ГПа в литом состоянии) параметр износа (обратный износостойкости) уменьшается в 18–20 раз (с 49⋅10 −4 мм 3 / Н⋅ м до 2,5⋅10 −4 мм 3 / Н⋅м), а коэффициент трения уменьшается в ≈1,5 раза (с 0,55 до 0,36). Выявлено, что комплексный режим обработки практически не влияет на исследуемые свойства, но сильно влияет на фазовый состав модифицированного слоя (содержание твердого раствора на основе алюминия снижается в 2 раза).В 5 раз, а относительное содержание оксида кремния возрастает в ≈2,2 раза). Многофазная субмикро- и нанокристаллическая структура, образующаяся в поверхностном слое, ответственна за изменение износостойкости и микротвердости, а особенности теплового воздействия интенсивным импульсным электронным пучком на поверхность обуславливают уменьшение коэффициента трения.
Ключевые слова
Заэвтектический сплав Al-Si
Электронный пучок
Электровзрывное легирование
Микроструктура
Износостойкость
Микротвердость
Рекомендуемые статьиЦитирующие статьи (0)
© 2019 Авторы. Опубликовано Elsevier B.V.
Рекомендуемые статьи
Цитирующие статьи
Силумин или цинк, что лучше. Создаем дома металлические предметы: силумин
Покупая цветной миксер, очень сложно по оттенку поверхности определить, из какого материала он сделан. Впрочем, эта сложность присутствует и у покупателей хромированных, никелевых и других моделей сантехники, цветное покрытие просто надежнее скрывает исходный материал. Также не всегда можно отличить основной материал миксера по весу, поскольку отдельные производители научились делать штамповки из сплавов, специально утяжеленных свинцом и другими подобными металлами.
Как определить качество смесителя цвета и узнать, из чего он сделан?
В первую очередь следует обратить внимание на точность и правильность формы деталей. Изделия из латуни изготавливают исключительно методом литья, а чаще всего — центробежным. Благодаря такому способу производства количество возможных дефектов литья (впадин, трещин, неровностей поверхности) стремится к минимуму, соответственно, качество смесителя очень высокое. Даже если для корпуса миксера используется деталь из двух половинок, они должны пройти механическую обработку, и стык под покрытием невозможно найти.Недорогие смесители силумина изготавливаются методом штамповки без дополнительной обработки, линия стыка фильеры хорошо видна даже под покрытием.
При выборе также можно ориентироваться на толщину стен (если конструкция модели позволяет это определить). Литые заготовки не могут быть очень тонкостенными, это противоречит принципам технологии производства. Штампованные детали наоборот делаются с минимальной толщиной стенки для экономии материала.
Внутренняя часть смесителя обычно не оцинкована и имеет естественный цвет оригинального материала.Поэтому золотистый оттенок латуни на внутренних поверхностях поможет пользователю определить качество продукта, но и здесь могут быть нюансы — например, сплаву силумина с помощью добавок придают цвет, близкий к цвету латуни.
Итак, при выборе смесителя цвета следует обратить внимание на следующие детали:
- цвет материала на внутренних поверхностях;
- вес продукта;
- толщина стенки;
- наличие хорошо заметных стыков половинок деталей.
Если изделие кажется тяжелым, имеет внутри характерный золотистый оттенок, стенки гладкие или со следами механической обработки и имеют толщину не менее 1 мм, то у вас в руках качественная латунная модель.
Если сомневаетесь, то лучше сравнить несколько моделей из разных ценовых категорий и спросить у менеджера — экономия в этом вопросе может обернуться значительными расходами в дальнейшем, когда хрупкий силуминовый смеситель вызовет «потоп» в квартире.
Основное отличие смесителя для душа от смесителя для ванной в том, что у него нет излива — крана, гусака или излива.Это более компактные изделия, которые оснащены отверстием для подключения душевой лейки и шланга. Обратите внимание, что не все смесители идут в комплекте с душевым набором — их можно приобрести отдельно. Самые популярные смесители — рычажные и двухклапанные.
Смеситель рычажный (для одной руки)
Зарубежные производители смесителей выбирают тумблер как рентабельный. Но наши пользователи предупреждают: рычажные смесители недолговечны. Даже если вы купите смеситель у известной и проверенной компании, срок его службы будет намного меньше, чем обещает гарантия.Ты знаешь почему? Все дело в качестве нашей воды. Он хлорированный и прочный, к тому же в водопровод часто попадает ржавчина, а для изготовления рычажных смесителей используются керамические картриджи, которые очень чувствительны к этим параметрам.
- Тем, кто решил выбрать рычажный смеситель для душа, обязательно нужно позаботиться об основных фильтрах для очистки воды. Причем нужно брать не только «грязеуловители» — фильтры грубой очистки, но и сетчатые, более дорогие, рассчитанные на тонкую очистку (от 3 до 5 мкм).Обойдутся они недешево — около 8000 рублей.
- Внутри рычажного смесителя устанавливаются шариковые или керамические патроны. Если шаровой картридж пришел в негодность, то миксер можно смело выбросить — ремонту не подлежит. Более надежен в эксплуатации керамический картридж Ø 40 мм (максимальный рабочий диаметр), который легко заменяется в случае поломки.
Поэтому тем, кто решил выбрать смеситель с рычагом подачи воды, лучше поискать модель с керамическим картриджем, а не с шаровой.
Cмеситель для душа со смесителем (двуручный)
Для нашей воды удобнее в эксплуатации смесители с резиновыми подушечками. Но вы вряд ли найдете такие модели! Чаще встречаются двухклапанные модели с поворотом крана на 180 градусов, где используются не резиновые, а керамические уплотнители. Если бы были резиновые прокладки, как и у самых простых смесителей для ванны, не было бы проблем с заменой прокладок. Но смесителям для душа приходится выбирать между однорычажными картриджными клапанами и поворотными клапанами с керамическими пластинами.
Что выбрать?
Если вы выбираете между одноручным и двуручным миксером, то предпочтительнее приобретать продукцию первого типа. В случае поломки можно найти к ним комплектующие и заменить картридж, а вот смеситель с двумя кранами и керамическими уплотнителями отремонтировать не получится — придется искать новый смеситель для душа. Та же проблема с одноручными моделями с шариковыми патронами.
Помните, купите смеситель рычажный, если у вас установлены фильтры для очистки воды.
Чтобы отличить латунь от силумина, понадобится …
Важно обратить внимание на материал, из которого изготовлен миксер. Все специалисты однозначно советуют выбирать смесители из латуни (многокомпонентного сплава на основе меди), но вместе с тем предупреждают: 90% сантехнических изделий этой категории — это поддельный силумин (алюминиевый сплав с кремнем).
По внешнему виду простому покупателю сложно отличить смеситель из латуни от дешевого аналога силумина, так как смесители сверху покрыты хромом.Внешне товары практически не отличаются, поэтому ориентируйтесь на следующие критерии:
- Сначала попросите продавца показать вам латунные краны. Возьми их в руки. Если миксер из качественного металла, он тяжелый и увесистый — около 3 кг, если из силумина легкий.
- Во-вторых, загляните внутрь крана — для изделия из латуни она должна быть желтой и гладкой.
Кстати, китайские мастера научились делать смесители из силумина, очень похожие на их латунные аналоги.Поэтому есть еще один критерий, по которому определится материал смесителя:
- Все латунные изделия изготавливаются методом литья, только после этого проходят механическую обработку. Поэтому внутри латунного смесителя нет ни одного стыка, поверхность ровная, неровностей нет. Силуминовые смесители нельзя изготовить методом литья. Этот сплав очень хрупкий, на нем будут видны все стыки и шероховатости. Внимательно осмотрите миксер. Обратите внимание на стыки, шероховатости, вмятины — перед вами не латунь.
- Еще одна подсказка — маркировка. Латунь маркируется буквой «L», силумин — «AL». Эту информацию можно найти в техническом паспорте, где указан материал продукта.
- Смесители выполнены из латуни без каких-либо изысков, излишеств и «цветочков». Технология изготовления не позволяет «гнуть» медный сплав, как порошковый силумин.
Таким образом, чтобы отличить латунь от силумина, нужно внимательно изучить и «пощупать» изделие, ознакомиться с документацией на смеситель.
Наконец
Что касается цены смесителей, то она варьируется от 1000 до 60 000 рублей. Отличия зависят от материала, из которого сделан миксер и где вы его покупаете. В сомнительных местах купите «фирменный» смеситель за 1000-2000 рублей, но гарантии в эксплуатации вам никто не даст. При покупке таких вещей лучше обращаться в специализированные магазины.
- Хорошие отзывы Вы найдете о дорогих немецких (Hansa, Grohe), итальянских (Fari, Fiori), польских (Ferro), чешских (Imprese) смесителях.
- Из средней ценовой категории хвалят Emivi (Италия), Vidima (Болгария) и Mixxen (Испания-Китай).
- Из бюджетных (дешевых) вариантов обратите внимание на смесители Россинка (Россия-Китай), Сантехприбор (Россия), Укрсанлит (Украина).
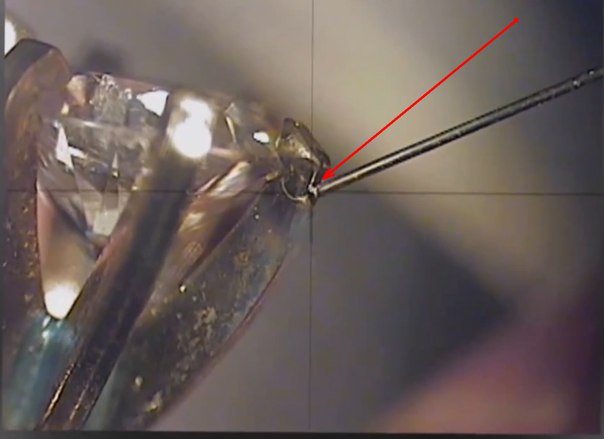
Силумин — это материал, который получают путем соединения алюминия с кремнием. Обладает прекрасными литейными качествами. Отличить мешалку силумин очень легко — для этого достаточно обратить внимание на вес изделия. этот вид легкий.
Преимущества и недостатки смесителей силумина
Популярность смесителей силумина очень высока.К положительным характеристикам этой продукции можно отнести:- устойчивость к коррозии во влажной атмосфере; высокая прочность, износостойкость; выгодная стоимость продукции; современный внешний вид.
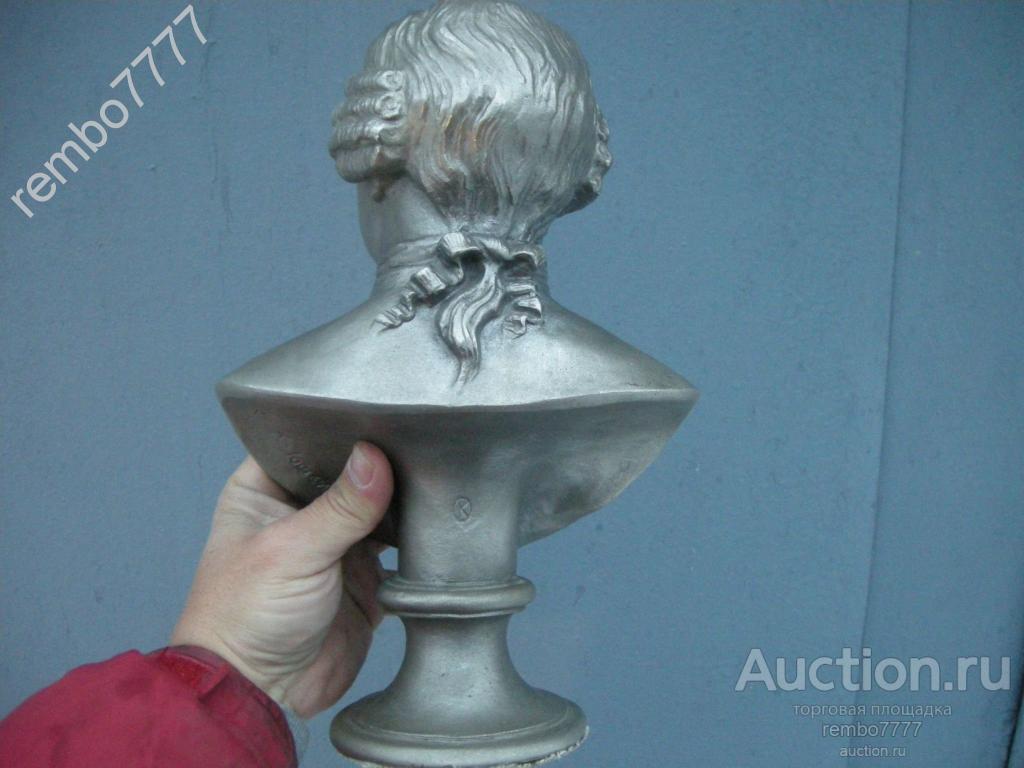
Перед тем, как купить смеситель из силумина, важно помнить, что устройства этого типа имеют определенные недостатки. Например, даже небольшой скачок давления воды в системе может спровоцировать появление трещины на поверхности корпуса. Кроме того, силумин корродирует намного быстрее, чем традиционная латунь. Силумин не совсем долговечен — устройства такого типа часто требуют преждевременной замены.
Покупая цветной миксер, очень сложно по оттенку поверхности определить, из какого материала он сделан. Впрочем, эта сложность присутствует и у покупателей хромированных, никелевых и других моделей сантехники, цветное покрытие просто надежнее скрывает исходный материал. Также не всегда можно отличить основной материал миксера по весу, поскольку отдельные производители научились делать штамповки из сплавов, специально утяжеленных свинцом и другими подобными металлами.
Как определить качество смесителя цвета и узнать, из чего он сделан?
В первую очередь следует обратить внимание на точность и правильность формы деталей. Изделия из латуни изготавливают исключительно методом литья, а чаще всего — центробежным. Благодаря такому способу производства количество возможных дефектов литья (впадин, трещин, неровностей поверхности) стремится к минимуму, соответственно, качество смесителя очень высокое. Даже если для корпуса миксера используется деталь из двух половинок, они должны пройти механическую обработку, и стык под покрытием невозможно найти.Недорогие смесители силумина изготавливаются методом штамповки без дополнительной обработки, линия стыка фильеры хорошо видна даже под покрытием.
При выборе также можно ориентироваться на толщину стен (если конструкция модели позволяет это определить). Литые заготовки не могут быть очень тонкостенными, это противоречит принципам технологии производства. Штампованные детали наоборот делаются с минимальной толщиной стенки для экономии материала.
Внутренняя часть смесителя обычно не оцинкована и имеет естественный цвет оригинального материала.Поэтому золотистый оттенок латуни на внутренних поверхностях поможет пользователю определить качество продукта, но и здесь могут быть нюансы — например, сплаву силумина с помощью добавок придают цвет, близкий к цвету латуни.
Итак, при выборе смесителя цвета следует обратить внимание на следующие детали:
- цвет материала на внутренних поверхностях;
- вес продукта;
- толщина стенки;
- наличие хорошо заметных стыков половинок деталей.
Если изделие кажется тяжелым, имеет внутри характерный золотистый оттенок, стенки гладкие или со следами механической обработки и имеют толщину не менее 1 мм, то у вас в руках качественная латунная модель.
Если сомневаетесь, то лучше сравнить несколько моделей из разных ценовых категорий и спросить у менеджера — экономия в этом вопросе может обернуться значительными расходами в дальнейшем, когда хрупкий силуминовый смеситель вызовет «потоп» в квартире.
Итак, в металлургии есть несколько ипостасей.Сегодня внимание к силумину. Наличие в нем кремния читается из названия. Взято «C» из научного названия. Это записано в таблице с кремнием. Его смешивают с алюминием в основном для упрочнения.
Максимальное содержание кремния в силумине — 15%. Поэтому его внешне сложно отличить от чистого металла. Кремний такой же белесый. Есть небольшое потемнение, больше напоминающее. Правда, на этот нюанс обращают внимание только профессионалы, покупатели.
Плотность кремниевой составляющей силумина выше, чем у алюминия, равна 3.2 грамма на кубический сантиметр. Это означает, что вес кремния больше. Однако в весе сплава 15% кремний не оказывает значительного влияния на вес алюминия. Сплав остается легким и ярким. Общая плотность материала не достигает 3 граммов на кубический сантиметр.
Свойства силумина
Алюминий «Силумин» по свойствам сравнивается с нержавеющим. Герой легче ее. Это одно из немногих отличий и безусловный плюс. В остальном материал силумин практически такой же прочный и устойчивый к коррозии. Оксидная пленка, образующаяся на поверхности в окислительных средах, то есть в присутствии кислорода, защищает сплав от разрушения.
Удельная сила силумина — это его отношение к плотности. Для алюминиево-кремниевого сплава этот показатель близок к 15. Он, как правило, не превышает 17.
Разница незначительная, а масса материалов другая. Учитывая, что удельная прочность показывает, насколько надежной будет конструкция для данного веса, силумин в выигрыше.
Силумин также выигрывает по пластичности. Сплав легко повторяет самые сложные формы, равномерно их заполняя. Со временем отливка силумина упрощает, а значит, снижает стоимость производственных процессов.
Поэтому сделали ставку на сочетание алюминия и кремния. Из силумина делают бюджетные варианты многих товаров для дома. Некоторые из них некачественные, а некоторые уступают прототипам только в. Откуда такая разница?
Свойства силумина имеет ротовой сплав и соответствие требованиям его производства. Основные обозначения для материала 5. Это: AL2, AL3, AL4, AL5 и AL9.
Однако по цифровым обозначениям можно догадаться, что есть и другие. У каждого есть свои плюсы и минусы. Состав силумина далеко не ограничивается только алюминием и кремнием.
Иногда добавляют и марганец с магнием. Иногда ничего не смешивают, просто они не избавляются от примесей, изначально присутствующих в шихте. В этом случае металлический силумин оказывается грязным ,,.
Так что есть претензии к качеству сплава и его пригодности для той или иной сковороды. Однако есть отрасли, где производители не играют в аналогичные игры с силумином. Риски слишком велики. Вместо гневных ответов домохозяек можно натолкнуться на человеческие и государственные выговоры.
Применение силумина
Силумин применяется также в машиностроении и авиастроении. Ставка на алюминиево-кремниевый сплав сделана из-за его легкости.Для воздуха это залог подъема в небо, маневренности.
Для обычных автомобилей вес становится одной из ценовых категорий. За тяжесть придется доплачивать. К тому же массивные разбивают дорожное покрытие. Забота о его качестве вынуждает промышленников и автомобилистов использовать силумин для производства деталей двигателей, поршней, цилиндров и гильз.
Сплав все чаще используется оружейными мастерами. Итак, сварка силумина стала важным этапом в производстве таких пневматических винтовок, как Cuno Melcher, Umarex, Stalker, Crosman и Walther.
Из сплава алюминия с кремнием указанные выше изготавливают, по крайней мере, ствольную коробку, а иногда и все узлы винтовки. В новом дизайне они стали легче и удобнее в обращении.
Силумин — состав прочный, но хрупкий, и это главный недостаток материала. падать с него не желательно. Винтовку необходимо осторожно положить на землю, прислонить к дереву.
Автомобиль может пойти в капитальный ремонт после небольшого удара.Нечаянно брошенная кастрюля треснет. Вероятность, конечно, не 100%, но ее нужно держать.
Несмотря на определенные риски, плавильный силумин заказан для генераторов газотурбинных установок. Они состоят из пластинчатых теплообменников.
Точка плавления силумина при 670 градусах позволяет использовать данный материал. Но в космос нельзя пустить алюминиево-кремниевый сплав. В ракетостроении нужны металлы, которые могут выдерживать тысячи градусов тепла.
Производство силумина
Купить силумин предлагают не только крупные металлургические предприятия, но и небольшие лаборатории. Последние экспериментируют с улучшением производства сплавов.
Стандартный способ получения — смешивание алюминия с кремнием и их плавление. Металлы для шихты добываются из руды. Заглянем в «Банк патентов» и выясним, что силумин можно получить и на основе золы, остающейся на ТЭС страны в виде производственных отходов.
Зола коричневого цвета может быть восстановлена. Все, что вам нужно, это электролизер и. В присутствии последнего происходит реакция. Не секрет, что в золе, помимо кремния и алюминия, есть еще много других компонентов.
Интересно, что они практически не влияют на качество сплава, не имеют существенного значения. В золе слишком много железа. Однако его присутствие в силумине допускается в качестве лигатуры. Феррум по ГОСТу допускается в количестве 0.8-1,5%. Примерно столько в отходах ТЭЦ.
Если промышленники примут на вооружение новый метод производства силумина, давние споры исчезнут. Он состоит из предписанного природой дуэта алюминия и кремния.
Элементы изначально расположены рядом, например, в руде. Однако промышленники сначала тратят деньги на разделение каждого по отдельности, а затем снова тратятся на сплавление их в силумин.
Работа с золой упростит и удешевит производство, и в то же время принесет пользу окружающей среде.Мелкая взвесь в воздухе от работы ТЭЦ донимает жителей многих городов.
Цена на силумин
Цена на силумин в гранулах — около 80 за килограмм. Если вы возьмете полуфабрикат, например, свинью, заплатите 130-180 рублей. То же самое для большинства марок сплавов. Другой вопрос — готовая продукция.
Здесь она может существенно отличаться от себестоимости. Таким образом, казан силумин диаметром около 30 сантиметров стоит более 1000 рублей.Однорычажный смеситель из алюминиево-кремниевого сплава оценивается примерно в 1500 штук.
За гидрораспределитель из силумина просят около 8000 руб. За счетчик газа дают в районе 2000–3500. За 4000 получится купить вибронасос, а за 45 рублей — чаевые.
Вообще, почти все, что можно сделать из металла, делается из силумина. Так что не помешает запомнить название материала, изучить его сильные и слабые стороны.
Модифицированные металлы для космической техники производятся за микросекунды — ScienceDaily
Ученые Томского политехнического университета (ТПУ) и Института сильноточной электроники СО РАН разработали метод нанесения износостойких покрытий на металлы с последующим их плавлением. субстраты. Такие модифицированные материалы, благодаря сочетанию легкости, прочности и коррозионной стойкости, могут быть использованы в машиностроении, авиации и космической технике.
Новые материалы на основе алюминия и силумина — сплава алюминия и кремния.
«Эти металлы имеют малый вес, хорошую коррозионную стойкость. Для использования в авиационной и космической технике достаточно изменить их прочностные и трибологические свойства: повысить твердость и износостойкость», — говорит Мария Рыгина, аспирантка кафедры ТПУ. наноматериалов и нанотехнологий.
В качестве покрытий политехники используют титан, нитрид титана и силумин, содержащие 25% кремния. Особенность разработанного метода заключается в том, что покрытие не наносится на подложку, а вплавляется в нее с помощью интенсивного импульсного электронного пучка.Экспериментальные исследования показали, что это привело к увеличению твердости металла почти в шесть раз и износостойкости в три раза.
«Мировые эксперты по материаловедению отмечают, что сейчас основной проблемой является адгезия между покрытием и подложкой. Если покрытие просто нанесено, то его можно легко удалить. Иностранные исследовательские группы ищут решение этой проблемы путем формирования многослойного покрытия. . Однако многослойное напыление занимает много времени.
Предлагаем наплавленное покрытие в подложке: это занимает микросекунды, и адгезия значительно улучшается, — говорит научный руководитель проекта, профессор кафедры наноматериалов и нанотехнологий ТПУ Юрий Иванов.
Формирование покрытий таким методом возможно благодаря специфическим электронно-ионно-плазменным установкам, созданным учеными ИВКЭ СО РАН и ТПУ. По словам разработчиков, установки уникальны и поставляются в Японию, Китай, Канаду.
По словам Марии Рыгиной, модифицированные металлы могут быть использованы для изготовления деталей внутренних механизмов космических аппаратов: именно они самые носимые. В настоящее время этот метод используется при производстве деревообрабатывающих инструментов и деталей для машиностроения.«
История Источник:
Материалы предоставлены Томским политехническим университетом (ТПУ) . Примечание. Содержимое можно редактировать по стилю и длине.
% PDF-1.7
%
496 0 объект
>
endobj
xref
496 127
0000000016 00000 н.
0000003615 00000 н.
0000003843 00000 н.
0000003885 00000 н.
0000003921 00000 н.
0000004387 00000 п.
0000004502 00000 н.
0000004617 00000 н.
0000004732 00000 н.
0000004847 00000 н.
0000004962 00000 н.
0000005077 00000 н.
0000005192 00000 н.
0000005307 00000 н.
0000005422 00000 н.
0000005535 00000 н.
0000005650 00000 н.
0000005765 00000 н.
0000005870 00000 н.
0000005977 00000 н.
0000006085 00000 н.
0000006193 00000 п.
0000006297 00000 н.
0000006405 00000 н.
0000006513 00000 н.
0000006593 00000 н.
0000006673 00000 н.
0000006753 00000 н.
0000006832 00000 н.
0000006912 00000 н.
0000006991 00000 п.
0000007070 00000 п.
0000007148 00000 н.
0000007227 00000 н.
0000007304 00000 н.
0000007383 00000 н.
0000007462 00000 н.
0000007541 00000 н.
0000007620 00000 н.
0000007698 00000 п.
0000007776 00000 н. 0000007854 00000 п.
0000007932 00000 н.
0000008012 00000 н.
0000008092 00000 н.
0000008172 00000 п.
0000008252 00000 н.
0000008332 00000 н.
0000008412 00000 н.
0000008492 00000 п.
0000008572 00000 н.
0000008712 00000 н.
0000008770 00000 н.
0000008827 00000 н.
0000008972 00000 н.
0000009018 00000 н.
0000009052 00000 н.
0000009251 00000 п.
0000009755 00000 н.
0000010506 00000 п.
0000010701 00000 п.
0000010993 00000 п.
0000011214 00000 п.
0000011412 00000 п.
0000011573 00000 п.
0000011783 00000 п.
0000012194 00000 п.
0000012646 00000 п.
0000012864 00000 п.
0000012942 00000 п.
0000014693 00000 п.
0000014903 00000 п.
0000015200 00000 н.
0000015283 00000 п.
0000015961 00000 п.
0000016610 00000 п.
0000016813 00000 п.
0000017109 00000 п.
0000017178 00000 п.
0000017356 00000 п.
0000017717 00000 п.
0000019501 00000 п.
0000019801 00000 п.
0000020171 00000 п.
0000022020 00000 н.
0000023893 00000 п.
0000025517 00000 п.
0000027149 00000 н.
0000027401 00000 п.
0000027753 00000 п.
0000027952 00000 п.
0000028115 00000 п.
0000029754 00000 п.
0000031432 00000 п.
0000037643 00000 п.
0000038053 00000 п.
0000043679 00000 п.
0000044284 00000 п.
0000047312 00000 п.
0000049039 00000 п.
0000049585 00000 п.
0000050718 00000 п.
0000050960 00000 п.
0000051523 00000 п.
0000051863 00000 п.
0000101124 00000 п.
0000130230 00000 н.
0000130774 00000 н.
0000130900 00000 н.
0000182742 00000 н.
0000182781 00000 н.
0000182841 00000 н.
0000182957 00000 н.
0000183037 00000 н.
0000183108 00000 н.
0000183187 00000 н.
0000183266 00000 н.
0000183345 00000 н.
0000183402 00000 н.
0000183709 00000 н.
0000183820 00000 н.
0000183921 00000 н.
0000184041 00000 н.
0000184220 00000 н.
0000184503 00000 н.
0000184782 00000 н.
0000002836 00000 н.
трейлер
] >>
startxref
0
%% EOF
622 0 объект
> поток
x ڜ S] HSa ~ M2, LRFn ٟ ms # Jg3 ctSYhPXu] QWtE] x ە ~ ż} y?} sw
Алюминий или алюминиевые сплавы — список
Алюминиевый сплав — это композиция, состоящая в основном из алюминия, к которому были добавлены другие элементы. Сплав изготавливается путем смешивания элементов, когда алюминий расплавлен (жидкость), который охлаждается, образуя однородный твердый раствор. Остальные элементы могут составлять до 15 процентов сплава по массе. Добавленные элементы включают железо, медь, магний, кремний и цинк. Добавление элементов к алюминию дает сплаву улучшенную прочность, обрабатываемость, коррозионную стойкость, электропроводность и / или плотность по сравнению с чистым металлическим элементом. Алюминиевые сплавы имеют тенденцию быть легкими и устойчивыми к коррозии.
Список алюминиевых сплавов
Это список некоторых важных алюминия или алюминиевых сплавов.
- AA-8000: используется для сборки провода в соответствии с Национальным электротехническим кодексом
- Alclad: алюминиевый лист, изготовленный путем приклеивания алюминия высокой чистоты к высокопрочному материалу сердечника
- Al-Li (литий, иногда ртуть)
- Alnico (алюминий , никель, медь)
- Birmabright (алюминий, магний)
- Дуралюминий (медь, алюминий)
- Хиндалий (алюминий, магний, марганец, кремний)
- Магний (5% магния)
- Магний (оксид магния, алюминий)
- Намбе (алюминий плюс семь других неуказанных металлов)
- Силумин (алюминий, кремний)
- Титанал (алюминий, цинк, магний, медь, цирконий)
- Замак (цинк, алюминий, магний, медь)
- Формы алюминия прочие сложные сплавы с магнием, марганцем и платиной
Идентификация алюминиевых сплавов
У сплавов есть общие названия, но их можно идентифицировать с помощью четырехзначного числа. Первая цифра номера определяет класс или серию сплава.
1xxx — Технически чистый алюминий также имеет четырехзначный цифровой идентификатор. Сплавы серии 1xxx изготовлены из алюминия чистотой 99% или выше.
2xxx — Основным легирующим элементом серии 2xxx является медь. Термообработка этих сплавов повышает их прочность. Эти сплавы прочные и жесткие, но не так устойчивы к коррозии, как другие алюминиевые сплавы, поэтому для использования их обычно окрашивают или покрывают.Самый распространенный авиационный сплав — 2024. Сплав 2024-Т351 — один из самых твердых алюминиевых сплавов.
3xxx — Основным легирующим элементом в этой серии является марганец, обычно с меньшим количеством магния. Самый популярный сплав из этой серии — 3003, работоспособный и умеренно прочный. 3003 используется для изготовления кухонной утвари. Сплав 3004 — один из сплавов, используемых для изготовления алюминиевых банок для напитков.
4xxx — Кремний добавляется в алюминий для получения сплавов 4xxx.Это снижает температуру плавления металла, не делая его хрупким. Эта серия используется для изготовления сварочной проволоки. Сплав 4043 используется для изготовления присадочных сплавов для сварки автомобилей и элементов конструкций.
5xxx — Основным легирующим элементом серии 5xxx является магний. Эти сплавы прочные, свариваемые и устойчивы к морской коррозии. Сплавы 5xxx используются для изготовления сосудов под давлением и резервуаров для хранения, а также для различных морских применений. Сплав 5182 используется для изготовления крышек алюминиевых банок для напитков.Итак, алюминиевые банки на самом деле состоят как минимум из двух сплавов!
6xxx — Кремний и магний присутствуют в сплавах 6xxx. Элементы объединяются, образуя силицид магния. Эти сплавы поддаются формованию, сварке и термообработке. Они обладают хорошей коррозионной стойкостью и средней прочностью. Самый распространенный сплав в этой серии — 6061, из которого изготавливают рамы грузовиков и лодок. Экструзионные продукты серии 6xxx используются в архитектуре и при создании iPhone 6.
7xxx — Цинк является основным легирующим элементом в серии, начинающейся с цифры 7.Полученный сплав поддается термообработке и очень прочен. Важными сплавами являются сплавы 7050 и 7075, которые используются при строительстве самолетов.
8xxx — это алюминиевые сплавы с другими элементами. Примеры включают 8500, 8510 и 8520.
9xxx — В настоящее время серия, начинающаяся с цифры 9, не используется.
Какой алюминиевый сплав самый прочный?
Марганец, добавленный к алюминию, увеличивает его прочность и дает сплав с превосходной обрабатываемостью и коррозионной стойкостью.Самым прочным сплавом из нетермообрабатываемой марки является сплав 5052.
Классификация алюминиевых сплавов
В целом, две широкие категории алюминиевых сплавов — это деформируемые сплавы и литейные сплавы. Обе эти группы подразделяются на термически обрабатываемые и нетермообрабатываемые типы. Около 85% алюминия используется в деформируемых сплавах. Литые сплавы относительно недороги в производстве из-за их низкой температуры плавления, но они, как правило, имеют более низкий предел прочности на разрыв, чем их деформируемые аналоги.
Источники
- Дэвис, Дж. Р. (2001). «Алюминий и алюминиевые сплавы». Легирование: основные сведения . С. 351–416.
- Degarmo, E. Paul; Black, J T .; Козер, Рональд А. (2003). Материалы и процессы в производстве (9-е изд.). Вайли. п. 133. ISBN 0-471-65653-4.
- Кауфман, Джон Гилберт (2000). «Применение алюминиевых сплавов и сплавов». Знакомство с алюминиевыми сплавами и сплавами .ASM International. С. 93–94. ISBN 978-0-87170-689-8.
