Сварные соединения макро- и микроструктура
Сварные соединения, выполненные сваркой плавлением, можно разделить на несколько зон, отличающихся химическим составом, макро- и микроструктурой и другими признаками сварной шов, зону сплавления, зону термического влияния и основной металл (рис. 13.1). Сварной шов характеризуется литой макроструктурой металла. Ему присуща первичная микроструктура кристаллизации, тип которой зависит от условий кристаллизации щва (см. гл. 12). [c.490]Химический состав стали, макро- и микроструктура и размеры аустенитного зерна в шве и ЗТВ — главные факторы, определяющие механические свойства, склонность к образованию холодных трещин и сопротивляемость хрупким разрушениям этих зон сварного соединения. [c.527]
Металлографические исследования проводят для определения структуры основного металла и сварных соединений аппарата. Исследуя структуру металла сварного соединения, можно установить правильность выбора режимов сварки, типа электродов, флюсов, присадочного металла и других факторов, определяющих качество сварного шва, а также выявить дефекты шва и установить причины их образования.
Для исследования структуры сварных соединений были вырезаны и изготовлены поперечные макро- и микрошлифы. Фотографии типичной макро- и микроструктуры сварного шва, зоны термического влияния и основного металла приведены в ранее опубликованной работе [5]. Никаких отклонений от нормы, за исключением незначительной микропористости по границам зерен в участках зоны термического влияния, непосредственно прилегающих к зоне сплавления в сварных соединениях, выполненных ЭЛС, не обнаружено (рис. 1). [c.315]
Контроль сварных соединений паровых котлов и трубопроводов осуществляется путем внешнего осмотра механических испытаний образцов, вырезанных из контрольных пластин, из контрольных стыков труб или из самих изделий просвечивания рентгеновскими или гамма-лучами ультразвуковой дефектоскопии исследования макро- и микроструктуры и гидравлического испытания.
Механические испытания и изучение макро- и микроструктуры сварных соединений относятся к разрушающим методам контроля. Методика механических испытаний должна учитывать условия эксплуатации изделия. В ряде случаев механические испытания проводятся на стендах, имитирующих условия работы изделия. Однако чаще испытания проводятся на стандартных образцах. Это позволяет сравнить между собой результаты испытаний свойств соединений, полученных в различных условиях или различными сварщиками (например, при аттестации сварщиков). При механических испытаниях определяют предел прочности металла на растяжение, усталостную прочность при знакопеременных нагрузках, пластичность металла по предельному углу загиба и относительному удлинению образца при растяжении, ударную вязкость, твердость. Методика и обработка результатов механических испытаний определены государственными стандартами.
Как и зачем проверяют макро- и микроструктуру сварных соединений [c.

Определение макро- и микроструктуры сварного соединения, а также химический состав различных участков сварного соединения определение механических свойств сварного шва [c.85]
В атласе описаны методы металлографии, способы приготовления шлифов для макро- и микроанализа, приведены сведения о количественном и качественном анализе структур. Широко представлены макро- и микроструктуры сварных соединений углеродистых, среднелегированных и высоколегированных сталей, чугуна и цветных металлов, выполненных различными способами сварки плавлением н давлением. Даны иллюстрации структур сварных соединений разнородных металлов, структур плакирующих слоев, зон сплавления и зон термического влияния при наплавке, а также структур, образующихся при термической резке. Показана возможность металлографического анализа для объяснения причин разрушения сварных соединений. [c.4]
По сравнению с металлографическим анализом металлов, при исследовании макро- и микроструктуры сварных соединений, особенно из разнородных металлов, возникают дополнительные трудности, обусловленные неоднородностью структуры различных участков сварного соединения и связанные с выбором реактивов для травления шлифов.
При металлографических исследованиях изучаются характер разрушения образцов (вид излома), макро- и микроструктура сварного шва и зоны термического влияния. Кроме этого, на шлифах для металлографических исследований определяют твердость различных зон сварного соединения. [c.159]
Металлографические исследования позволяют определить структуру металла сварного соединения, что дает возможность судить о правильности выбора режима сварки, типа электродов и других факторов, характеризующих качество сварного шва, а также выявить дефекты и установить причины их образования. Производят исследования макро- и микроструктуры металла. В первом случае исследуется макроструктура металла [c.252]
Металлографические исследования сварных соединений заключаются в анализе макро- и микроструктуры мет-лча. [c.380]
Контроль качества сварных соединений паровых котлов и трубопроводов осуществляют внешним осмотром механическими испытаниями образцов, вырезанных из контрольных пластин, из контрольных стыков труб или из самих изделий просвечиванием рентгеновскими или гамма-лучами ультразвуковой или цветной дефектоскопией исследованием макро-и микроструктуры гидравлическим испытанием.
Данный вид контроля включает исследование макро- и микроструктуры и осмотр изломов сварных соединений. [c.690]
МАКРО- И МИКРОСТРУКТУРА СВАРНОГО СОЕДИНЕНИЯ [c.133]
Испытания на свариваемость с определением технологических свойств материалов механические испытания металлографические исследования макро- и микроструктуры сварного соединения проверка стойкости металла шва против межкристаллитной коррозии определение сплошности металла шва физическими методами контроля [c.689]
Металлографические исследования сварных швов проводят путем засверливания шва сверлом, диаметр которого на 3 мм больше ширины шва. Просверленное место травят специальными растворами. Отверстие рассматривают невооруженным глазом или с помощью лупы. Для контроля наиболее ответственных сварных соединений из изделий вырезают контрольные пластины и исследуют их макро- и микроструктуры. [c.138]
Металлографические, исследования. Рассмат-))иваемые ниже два метода исследований сварного соединения на межкристаллитную коррозию, к сожалению, не дают исчерпывающей характеристики качества сварного шва. Во многих случаях для точного определения всех дефектов сварки испытаниям на устойчивость против межкристаллитной коррозии должно сопутствовать исследование макро- и микроструктуры шва и зоны термического влияния.
[c.152]
Макро- и микроструктура сварного соединения [c.140]
Металлографическое исследование макро- и микроструктуры сварного соединения [c.339]
Металлографический контроль швов состоит в исследовании макро- и микроструктуры и осмотре изломов сварных соединений. [c.136]
Металлографический метод контроля сварных соединений состоит в исследовании макро- и микроструктуры сварного шва и околошовной зоны (зоны термического влияния).
[c.134]
МАКРО- И МИКРОСТРУКТУРА МЕТАЛЛОВ И СВАРНЫХ СОЕДИНЕНИЙ [c.97]
При наличии дефектов и повреждений, превышающих требования НТД, и изменении свойств металла, выходящих за пределы ТУ, проводят оценку фактической нагруженности объекта и уточненные расчеты прочности элементов конструкции согласно [30, 31, 35, 36, 45, 49, 88, 97, 99, 100, 101, 110, 129, 130] с учетом имеющихся дефектов и повреждений, изменений свойств металла и режимов нагружения. При этом уточняют механизмы повреждений и ПТС, устанавливают определяющие ПТС и критерии предельного состояния. Основные ПТС дефекты в сварных соединениях несплошности в основном металле оборудования коррозионные повреждения трещины в основном металле и сварных соединениях толщина стенки оборудования и его элементов твердость эрозионный и кавитационный износы водородное и коррозионное растрескивания деформация оборудования или его элементов. Дополнительными ПТС являются механические характеристики металла оборудования и его элементов химический состав характеристики макро- и микроструктуры коэффициенты запаса прочности.
Механические свойства сварных соединений близки к свойствам основного металла. Недостаток сварки — получение крупнозернистой макро- и микроструктуры, понижающей пластические свойства. Улучшают свойства термической обработкой. Техника и технология сварки сплавов принципиально не отличаются от сварки технического титана. [c.140]
Сварные соединения хромомолибденованадиевых сталей снижают свою жаропрочность вследствие появления мягкой прослойки на участке зонь термического влияния, нагреваемом при сварке в межкритическом интервале температур. Наличие этой мягкой прослойки, иногда называемой белой полоской [82], может приводить (п. 7) к снижению уровня длительной прочности и пластичности, вызывая преждевременное разрушение сварного стыка. Макро- и микроструктуры разрушения такого рода в тройнике высокого давления из стали 12Х1МФ, проработавшем 17 тыс. ч при температуре 565° С, показаны на рис. 103. Возникшая трещина имеет межзеренный характер и расположена преимущественно на участке межкритического интервала на расстоянии 2 мм от границы сплавления.
Сварные соединения аппаратов можно рассматривать как наиболее заселенные дефектами. К дефектам сварных соединений (табл. 3.2) относят разного рода отклонения от установленных норм и технических требований, которые уменьшают прочность и эксплуатационную надежность сварных соединений и могут привести к разрушению всей консфук-ции. Наиболее часто встречаются дефекты формы и размеров сварных швов, дефекты макро- и микроструктуры, деформа ции и коробление сварных конструкций. [c.130]
Оценка качества сварного шва по макро- и микроструктуре производится в соответствии с требованиями технических условий и Правил Котлонадзора на сварные соединения. Согласно этим требованиям трещины и непровары в сварных швах котлострои-
[c.273]
Поставленные задачи решались путем проведения экспериментальных исследований физико-механических и электрохимических характеристик металла и определения малоцикловой коррозионно-усталостной долговечности сварных соединений. При этом были использованы стандартные методы определения механических свойств, микротвердости, макро- и микроструктуры металла, а также оригинальные методики изучения коррозионных и механохими-ческих свойств сварных соединений. [c.5]
В третьей главе приведены результаты исследований макро- и микроструктуры, механических свойств, макро- и микротвердости сварных соединений, а также определены значения скорости коррозии сварных соединений, выполненных электродами марок УОНИ 13/55(Б), МР-З(Р), Е4303, Е5015. [c.12]
На шлифованных поверхностях образцов (шлифах) оценивают макро- и микроструктуру. Для лучшего выявления структуры шлифы обрабатывают (травят) специальными реактивами. Макрошлифы рассматривают без увеличения или при небольшом увеличении с помощью лупы. При этом выявляют глубину проплавления, зоны сварного шва, наличие дефектов, скопления серы и фосфора. Для изготовления микрошлифов поверхность дополнительно полируют. После этого изучают поверхность шлифа под микроскопом без травления при увеличении примерно в 100 раз для выявления трещин, непрова-ров (непропаев), пор, неметаллических включений, пережога (неисправимый дефект структуры сталей — окисление границ зерен при нагреве до температуры выше 1300 «С). Затем для выявления более мелких дефектов и особенностей микроструктуры отдельных зон сварного или паяного соединения шлифы протравливают специальными реактивами, состав которых и режимы травления зависят от материала образца, и изучают под микроскопом при увеличении в
[c.343]
Для контроля качества сварных соединений при этих испытаниях широко используют металлографические исследования макро- и микроструктуры, химический анализ основного металла и металла шва, а также неразрушаюище методы контроля.
[c.179]
Металлографические исследования находят широкое применение при контроле качества сварных соединений. Металлографический анализ проводогг для исследования макро- и микроструктуры сварного шва, зоны сплавления, зоны термического влияния и основного металла при различных испытаниях на свариваемость, а также на эта- [c.214]
Металлографические исследования сварных соединений прово дят для контроля макро- и микроструктуры металла [13, 23—25 27], а также для выявления внутренних дефектов (трещин, по, непроваров, шлаковых и неметаллических включений снижающих прочность сварного соединения, и участков со струк турой металла, отрицательно влияющей на надежность и безо пасность эксплуатации. [c.166]
При исследовании сварного соединения определяют химический состав основного и нанлавленного металла твердость металла по поперечному сечению механические свойства при комнатной и рабочей температурах макро- и микроструктуры по поперечному сечению сварного соединения (для стали 20 структурно-свободный графит следует выявлять металлографическим способом) размер и характер обнаруженных дефектов посредством последовательной шлифовки и травления поперечных макротемплетов.
[c.229]
При металлографических исследованиях контролируется вид излома (образца), макро-и микроструктура сварного соединения. По излому выявляют поры, шлаковые включения, непровары и трещины. Для контроля макроструктуры шва из сварного соединения вырезают образцы, из которых изготавливают специальные макро-шлифы. По макрошлифам определяют трещины, внутренние непровары, скопления серы и фос ра. При проверке микроструктуры сварного соединения пользуются микроскопами с увеличением от 50 до 2000 раз и более. С этой целью из сварных соединений изготавливают так называемые микрошлифы. Микрострукт ура (микроанализ) сварного шва позволяет выявить такие дефекты, как микропоры, непровары, перегрев, пережог и др. [c.178]
Для оценки качества сварного соединения исследуют его макро- и микроструктуру. Для определения макростр -ктуры сварного соединения по его поперечному сечению вырезается образец, поверхность которого проходит травление. После травления на поверхности шва выступают его слои. Дефекты
[c.98]
Проведенные исследования макро- и микроструктуры клее-сварных соединений показывают, что строение литого металла ядра доброкачественной точки, выполненной сваркой по слою клеев ЭПЦ и К 153, ничем не отличается от строения ядра точки, выполненной без клея. Микроструктура ядра включает две зоны наружную, состоящую из столбчатых кристаллбв, и внутреннюю— из равноосных кристаллов. [c.104]
Diex — Металлографические исследования металла
Металлографическое исследование строения металлов и сварных соединений
Металлография исследования – это комплекс испытаний и аналитических мероприятий, направленный на изучение макроструктуры и микроструктуры металлов, исследование закономерности образования структуры и зависимостей влияния структуры на механические, физико – механические, электрические и другие свойства металла.
Металлографические методы исследования металлов и сварных
соединений позволяют определить размеры, форму и взаимное расположение кристаллов,
а также неметаллические включения, трещины, раковины, поры, свищи и т. д.
Различают макроскопический и микроскопический методы изучения строения металлов. Макроскопический метод — исследование строения металлов и сварных соединений невооруженным глазом или с применением лупы, дающей увеличение в 5—30 раз. Макроанализ дает возможность выявлять раковины, шлаковые включения, нарушение сплошности металла, трещины и другие дефекты строения сплава, химическую и структурную неоднородность.
Микроскопический анализ металлов заключается в исследовании их структуры с помощью оптического или электронного микроскопов, на специально подготовленных образцах. Методами микроанализа определяют форму и размеры кристаллических зерен, обнаруживают изменения внутреннего строения сплава под влиянием термической обработки или механического воздействия на сплав, микротрещины и многое другое.
Так как все металлы непрозрачны, то их строение можно
исследовать на изломах или специально подготовленных шлифах. Исследование строения
методом фактографии по изломам часто применяют при анализе причин разрушения
деталей машин, аппаратов и элементов стальных конструкций. Макроструктурный
метод используется также для ориентировочного определения глубины закаленной
зоны инструментальных сталей, глубины цементованного слоя и т. д.
Изучение макроструктуры металла обычно проводят на специально
подготовленных шлифах. В этом случае деталь или изделие разрезают. Поверхность,
которую необходимо исследовать, тщательно обрабатывают под плоскость на
металлорежущем станке. Если деталь разрезали при помощи газовой горелки, то
необходимо снимать весь слой металла, в котором произошло изменение структуры в
результате нагрева пламенем горелки. Обычно глубина этого слоя для сталей,
применяемых в котло- и турбиностроении, не превышает 10—12 мм. Затем
поверхность следует отшлифовать на плоско-шлифовальном станке и наждачной
бумагой. Для выявления структуры металла его необходимо подвергнуть травлению.
В процессе травления кристаллы растворяются с различной скоростью, так как они
по-разному ориентированы относительно исследуемой поверхности. Свойства же
кристаллов, в том числе и растворимость в химических реактивах, разные в
разных направлениях. Границы между кристаллами содержат повышенный процент
примесей, поэтому они растворяются быстрее кристаллов. Иногда травлением
получают различную окраску структурных составляющих сплава. Поэтому в
результате травления можно получить четкую картину кристаллического строения
металла.
Травитель сильнее разъедает трещины, закатанные плены, пористые участки и слабее — основной металл.
В теплотехнике принято исследовать макроструктуру сварных
соединений паропроводов, по которым транспортируется перегретый пар с
температурой выше 450° С независимо от давления и трубопроводов, по которым
транспортируется вода или насыщенный пар при температуре свыше 120° С и
давлении более 8 Мн/м2 (80 am). Контроль макроструктуры сварных соединений
обязателен также для остальных элементов парового котла, работающих при
температуре стенки свыше 450° С и независимо от температуры стенки при давлении
свыше 4 Мн/м2 (40 am).
В процессе металлографического исследования выявляют макро- и микроскопические дефекты сварного шва: непровары, трещины, поры, шлаковые включения, а также устанавливают структуру металла.
Образец для металлографического исследования вырезают из сварного соединения- поперек оси шва. Образец должен включать в себя как шов, так и зону термического влияния.
Трещины в основном металле шва, несварившиеся слои, крупные шлаковые включения, непровар сверх нормы не допускаются. Непровар не должен превышать при односторонней сварке без подкладного кольца 15% толщины стенки; если толщина стенки превышает 20 мм — не более 3 мм.
Допускаются видимые невооруженным глазом мелкие поры и шлаковые
включения в количестве не более пяти штук на 1 см2 площади
поперечного сечения шва. Максимальный линейный размер отдельного дефекта по
наибольшей протяженности не должен быть более 1,5 мм, а сумма максимальных
линейных размеров всех дефектов — не более 3 мм.
Микроскопический анализ строения металлов и сварных соединений позволяет наблюдать непосредственно их строение при увеличении до 2000 раз. Обычно пользуются увеличением от 100 до 800 раз.
Изучение структуры металла проводят при помощи микроскопа в отраженном свете. Образец металла тщательно обрабатывают под плоскость на металлорежущем станке, шлифуют и полируют. После такой подготовки он отражает лучи как зеркало. На нетравленом шлифе видны трещинки, поры, неметаллические включения. Чтобы выявить границы зерен и отдельные структурные составляющие, шлиф травят. Для травления микроструктуры стали и сварных соединений часто применяют 3—5%-ный раствор азотной кислоты в спирте.
Исследования и фотографирование микроструктуры проводят с
помощью специального стационарного металлографического микроскопа. На фото 1, а
показан микроскоп Neophot 2 представляющий собой, инвертированный фотомикроскоп отраженного
света, предназначенного для металлографической микроскопии. С
компьютеризированной системой воспроизведения результатов.
На тепловых электростанциях необходимо проводить контроль за структурой металла паропроводов как в исходном состоянии, так и после различных сроков эксплуатации. Такой контроль осуществляют по образцам, вырезанным из паропровода, при помощи переносных микроскопов, устанавливаемых непосредственно на паропроводе, а также при помощи оттисков.
В случае использования двух последних способов отпадает необходимость в вырезке для металлографических исследований образцов из паропровода. Подготавливается шлиф непосредственно на трубе (на объекте исследования). Окалина и поверхностный обезуглероженный при термической обработке слой металла глубиной 0,5—1 мм снимаются при помощи переносного наждачного круга, который приводится во вращение от пневматического или электрического привода.
Подготовка микрошлифа: обработка поверхности проводится
последовательно тремя кругами: крупнозернистым электрокорундовым, мелкозернистым
электрокорундовым с вулканитовой связкой и войлочным или фетровым, покрытым
пастой ГОИ на половине круга по ширине. Если отсутствует мелкозернистый круг,
то тонкую шлифовку проводят при помощи шкурки вручную. При переходе от одного
круга на другой направление обработки меняется на 90°. При этом легче выводятся
риски от предыдущего круга. При полировке пастой ГОИ ее остатки снимаются
чистой половиной войлочного или фетрового круга.
Подготовленная поверхность шлифа обезжиривается ватным тампоном, смоченным этиловым спиртом.
Травление проводят чаще всего 4%-ным раствором азотной кислоты в спирте. Для лучшего выявления микроструктуры процесс полировки и травления обычно повторяют несколько раз.
Подготовленный таким образом шлиф можно изучать либо непосредственно на объекте при помощи переносного оптического микроскопа, либо, сняв слепок со шлифа и исследуя уже его при помощи стационарного микроскопа, в лаборатории.
Имеется переносной металлографический микроскоп типа ММУ-3У
(фото 2), позволяющий проводить исследования микроструктуры при увеличении до
400 раз.
Для снятия слепков со структуры чаще всего используют
полистирол. Его размягчают при помощи бензола, в котором он легко растворяется.
На кусочек полистирола в виде кубика со стороной 10—20 мм или цилиндра такого
же диаметра и высоты кисточкой наносят бензол. Им смачивают только ту грань или
торец, которые в дальнейшем прижмут к предварительно подготовленному шлифу.
Между моментом нанесения бензола и прижатием кусочка полистирола должно пройти
3—5 секунд. За это время полистирол успеет размягчиться. Далее кусочек
полистирола плотно прижимают к шлифу и выдерживают в течение 5— 10 сек при
помощи миниатюрного ручного пресса или рукой. Затем он прилипает к шлифу. Его
оставляют в таком положении на 1,5— 2 ч. За это время полистирол затвердевает,
а кусочек легко отделяется рукой. Оттиск должен просохнуть и окончательно
затвердеть, после чего его помещают на металлографический микроскоп. Методика
исследования оттиска на металлографическом микроскопе ничем не отличается от
методики исследования обычного шлифа. Для исследования оттисков удобно
использовать косое освещение.
При исследовании причин разрушения различных деталей в процессе эксплуатации образцы для анализа вырезают вблизи места разрушения и в отдалении от него, чтобы можно было определить наличие каких-либо отклонений в строении металла. Кроме того, изучают структуру в продольном и поперечном направлениях.
1. Результаты макроисследования
(на примере наплавки дистанционное кольцо нижнего отвода реактора, установки каталитического реформинга).
При макроисследовании в наплавке
дистанционного кольца выявлена магистральная трещина глубиной ~ 11мм рис.1, 2.
Раскрытие трещины до 0,19мм. Характер растрескивания трещины показан на рис.3.
Края трещины острые, рваные, что свидетельствует о динамике ее развития.
Трещина в металле наплавки распространяется по всему периметру кольца. Длина
трещины ~2160мм. Из наплавки трещина переходит в основной металл, см. рис. 4.
При определенном насыщении водородом аустенитные коррозионные стали, в нашем
случае наплавка, подвержены водородному охрупчиванию, что объясняет процесс
трещинообразования в металле наплавки.
Излом ударных образцов хрупкий, кристаллический. Согласно «Шкалы изломов» доля хрупкой составляющей в образцах – 100%, сам излом представляет собой однородную поверхность хрупкого разрушения с мелкокристаллическим строением без признаков макропластической деформации см. рис.5.
Рис.1. Растрескивание в наплавке дистанционного кольца. Увеличено в 3 раза.
Рис. 2. Характер трещины в наплавке.
Рис. 3.Внешний вид излома ударного образца.
2. Результаты микроисследования
Характер микроструктуры по линии сплавления
основной металл кольца — наплавка показан на рис. 8. Микроструктура основного
металла кольца, см. рис. 5а отпущенный бейнит + феррит. Линия сплавления
сформирована нормально, см. рис. 5б. В металле наплавки выявлены микротрещины
см. рис.8в. Структура металла наплавки аустенитная, литая, см. рис. 5г.
Микроструктура металла дистанционного кольца по сечению, см. рис.6а, 6б отпущенный бейнит+феррит. Различий в структурах наружной и внутренней поверхности кольца не выявлено. Обезуглероживания либо науглероживания в основном металле дистанционного кольца не выявлено. Межкристаллитной коррозии (МКК) в основном металле кольца и наплавке не выявлено.
Рис. 4. Микроструктура ОМ – наплавка
Рис. 5.Микроструктура ОМ по сечению
Лабораторная работа 2 — Материаловедение — 3 семестр — 2004 — сайт студентов ПС МГТУ
Макроскопический метод исследования строения материалов.
Цель работы — ознакомиться с макроструктурой различных материалов и способами подготовки образцов.
Задание.
1. Изучить и нарисовать макроструктуры слитка и образцов алюминиевых сплавов, отлитых в земляную форму, в кокиль и после модифицирования. Охарактеризовать макроструктуры.
2. Исследовать и нарисовать макроструктуру лопатки турбины. Дать оценку макроструктуры.
3. Нарисовать волокнистое строение макрошлифов деформированного металла. Дать заключение о технологии изготовления и эксплуатационных свойствах изделий.
4. Исследовать качество свварного соединения, выявить общую химическую неоднородность; установить наличие дефектов. Нарисовать макроструктуру с указанием характерных зон и дефектов. Дать заключение о качестве сварного соединения.
5. Исследовать и нарисовать макроструктуру изломов (хрупкого, вязкого, усталостного).
Приборы и материалы: лупа, коллекция макрошлифов, коллекция изломов.
Порядок выполнения работы.
1. Зарисовать макроструктуру образцов, показывающую особенности литого состояния. Сравнить макроструктуру слитка с макроструктурой образцов, отлитых различными методами.
2. Зарисовать макроструктуру образцов с волокнистым строением и сделать вывод о правильности изготовления заготовки.
3. Зарисовать макрошлиф сварного соединения. Определить положение зоны термического влияния, отметить дефекты.
4. Определить различие вязкого и хрупкого изломов.
5. Отметить на рисунке усталостного излома очаг зарождения усталостной трещины и характерные зоны этого вида излома.
Основные теоретические сведения.
Исследование строения материалов невооруженным глазом, а также с помощью лупы или микроскопа при увеличении до 50 раз называют макроскопическим исследованием (макроанализом). Строение материала, изучаемое при макроанализе, называют макроструктурой.
Макроанализ находит применение в промышленности для выявления дефектов строения материалов (трещин, раковин, шлаковых включений и др.), химической и структурной неоднородности в отливках, прокате, поковках, сварных соединениях и т.д., а также для оценки характера разрушенных изделий.
Макроанализ проводят на специально подготовленных образцах — макрошлифах, поверхность которых шлифуют и подвергают травлению реактивами, иногда подогретыми до 70. ..100oC. Кроме того, анализ можно провести непосредственно по виду излома, установив при этом характер разрушения металлического изделия.
Макроанализ литых изделий дает возможность выявить дендритное строение, определить размер, форму зерен, а также различные дефекты (раковины, неметаллические включения, пузыри и др.). Структура отливки зависит от скорости образования центров кристаллизации и скорости их роста, что, в свою очередь, зависит от скорости охлаждения и модифицирования (введения в расплав специальных примесей, ускоряющих процесс образования центров кристаллизации). Чем выше скорость охлаждения и больше дополнительных центров в результате модифицирования, тем меньше зерна в отливке. В слитке металла различают 3 зоны: 1) мелких кристаллов на поверхности, где имеет место высокая скорость охлаждения; 2) столбчатых кристаллов, которые растут нормально к поверхности отвода теплоты; 3) равноосных крупных кристаллов в центре слитка, где скорость охлаждения мала.
При литье в земляную форму скорость охлаждения меньше, чем при литье в металллическую форму (кокиль). Части детали большого сечения охлаждаются медленнее частей деталей тонкого сечения. В результате в одной отливке получаются зоны с мелким и крупным зерном.
При обработке давлением изменяется форма первичных кристаллов, полученных в отливке. Так, при прокатке, ковке, волочении зерна вытягиваются вдоль направления течения металла и превращаются в волокна. В холоднодеформированном металле полученная волокнистая структура сохраняется. После горячего девормирования вместо волокон образуются равноосные зерна в результате рекристаллизации. Однако при горячей обработке давлением большинства сталей неметаллические включения оказываются пластичными и вытягиваются по направлению течения металла в форме волокон и ленточек. Эта форма включений сохраняется при термической обработке, так как включения в металле нерастворимы. Волокнистая структура такой природы выявляется на макрошлифах и после рекристаллизации.
Механические свойства металла с волокнистым строением анизотропны. Поэтому в деталях, работающих при динамических, циклических нагрузках с высоким напряженным состоянием (шестерни, коленчатые валы, шатуны и др.), стремятся получить волокнистую структуру, соответствующую профилю изделия или направлению наибольших напряжений. Волокнистую структуру выявляют методом глубокого травления в 50%-ных растворах кислот (соляной для углеродистой и азотной для легированных сталей), подогретых до 70oC. Это позволяет определить и технологию изготовления детали (обработка давлением или резанием).
Метод глубокого травления применяется и для выявления внутренних и внешних дефектов, нарушающих сплошность металла.
Макроанализ используют и для проведения плавочного контроля, при этом определяются:
1) центральная пористость, поры сосредоточены в центре слитка;
2) общая пористость, поры равномерно распределены по сечению макрошлифа;
3) ликвация примесей;
4) подкорковые пузыри, которые образуются газами, не успевающими выделиться из жидкого металла при его затвердевании;
5) трещины, к которым относятся и так называемые флокены. Чаще всего они встречаются в поковках легированных сталей. Причиной образования флокенов является водород, выделяющийся при фазовых превращениях аустенита.
Методом макроанализа выявляют, кроме того, различные дефекты сварных соединений (поры усадочные и газовые, трещины, шлаковые включения, подрезы, непровар и др.), образовавшиеся вследствие нарушения технологии изготовления этих соединений. Макроанализ используют также для исследования структурной и химической неоднородности металла, возникающей при термической и химико-термической обработке. При этом, исследуя изломы образцов и применяя метод глубокого травления, можно установить глубину закаленного слоя (прокаливаемость), толщину цементованного слоя и др.
Плавочный контроль проводят путем сравнения по баллам поверхности макрошлифов с эталонами согласно ГОСТ (для сплаваов имеются допустимые по каждому виду дефектов баллы).
Для выявления макроструктуры сварных соединений используют метод определения общей химической неоднородности (ликвации), который позволяет установить общий характер распределения элементов по сечению детали. Распределение в стали углерода, фосфора, серы зависит как от их количества, так и от процессов кристаллизации и обработки давлением. Распределение этих элементов влияет на структуру металла и, следовательно, на его свойства. Ликвацию углерода, фосфора и серы выявляют путем травления в 10-15%-ном водном растворе медноаммонийной соли соляной кислоты. При травлении железо переходит с поверхности макрошлифа в раствор, а на его место осаждается медь, которая и предохраняет поверхность металла от воздействия хлористых составляющих реактива. В результате места, обогащенные углеродом, фосфором и серой, оказываются менее защищенными медью и сильнее протравливаются. После снятия слоя меди они выглядят темнее участков с меньшим содержанием этих элементов. В результате травления в сварном соединении четко видны 3 зоны: основного металла, наплавленного металла (собственно сварной шов) и термического влияния. В зоне наплавленного металла будут видны столбчатые кристаллы, направленные нормально к поверхности отвода теплоты.
Макроанализ по виду излома. По характеру разрушения изломы подразделяют на хрупкие, вязкие и усталостные. Хрупкий излом имеет блестящую кристаллическую поверхность, на которой достаточно четко видны зерна опредееленных размеров и формы, так как разрушение происходит без значительной пластической деформации. Хрупкое разрушение может быть межкристаллическим (по границам зерен) и транскристаллическим (по телу зерен). Это наиболее опасный и быстрый вид разрушения, приводящий к преждевременному внезапному отказу деталей в условиях эксплуатации.
Вязкий излом имеет матовую поверхность и обычно волокнистое строение с зернами сильно искаженных размеров и формы, так как разрушение сопровождается значительной пластической деформацией. Вязкий излом менее опасен, чем хрупкий.
При циклических (повторно-переменных) нагрузках материал подвержен усталостному разрушению. Усталостная трещина зарождается обычно на поверхности детали в местах наибольшей концентрации напряжений (галтели, отверстия, надрезы, неметаллические включения и др. ).
Процесс усталостного разрушения достаточно длителен, так как он связан с постоянным накоплением повреждений, развитием и перемещением трещины. В усталостном изломе рассматривают 3 зоны: очаг разрушения; зону усталостного арзрушения с гладкой, ступенчато-слоистой, мелкозернистой, фарфоровидной поверхностью и зону долома со структурой типичной или для хрупкого, или для вязкого излома (в зависимсти от строения и свойств материала). Для фиксирования результатов анализа применяют фотографирование макроструктуры.
Прогнозирование усталостной долговечности сварных соединений от номинальной системы до механики разрушения
https://doi.org/10.1016/j.ijfatigue.2020.105647Получить права и содержание сварные швы в типовых стыках.Показано расчетное определение напряжений в сварных соединениях.
Приведены рекомендации для стальных сварных соединений плоских деталей.
Особое внимание уделяется определению усталостной долговечности в соответствии с рекомендациями IIW.
Abstract
В данной статье представлены методы определения усталостной долговечности сварных соединений с особым акцентом на типовые соединения. Показаны возможные методы расчетного определения напряжений в сварных соединениях, начиная от номинальных напряжений по различным предложениям, через структурные напряжения, в том числе типа «горячих точек», до сложнейшей линейной механики разрушения.На этом фоне представлены рекомендации Международного института сварки (МИС) по определению усталостной долговечности сварных стальных соединений плоских деталей в условиях одноосного растяжения-сжатия. Статья посвящена проблеме определения и оценки усталостной долговечности отдельных видов сварных соединений в соответствии с рекомендациями МИС и анализа безопасности сварных конструкций. Исследование показывает, в какой степени простейший метод, основанный на амплитуде номинального напряжения, можно использовать для расчета усталостной долговечности на основе двух выбранных типов соединений с различными коэффициентами асимметрии, R = -1 и 0, и соединений без геометрического надреза. Анализ был основан на стальных сварных соединениях четырех различных материалов. Результаты показывают, что характеристики FAT всегда хорошие, за исключением категории FAT 90, где для более низкой усталостной долговечности мы приближаемся к оценке опасной усталостной долговечности. Для крестообразных соединений типа К модель FAT можно использовать для всех соотношений напряжений. В других случаях такое соответствие не может быть принято. Для категории FAT 90 стыковых соединений X-типа предлагается новая категория FAT ‘134 и новый уклон, m = 5. Для стыковых соединений типа X без надреза предлагается угол наклона m = 12 и новая категория FAT’ 525.
Ключевые слова
Ключевые слова
Усталость Срок службы
Сварное соединение
Удаленное соединение
Механика разрушения
Эффективное напряжение
Структурное напряжение
Номинальный стресс
Рекомендуемая статьи на изделии (0)
© 2020 Авторы. Опубликовано Elsevier Ltd.
Рекомендуемые статьи
Ссылки на статьи
(PDF) Прогноз усталостной долговечности сварных соединений от номинальной системы до механики разрушения
[29] Susmel L, Tovo R.Модифицированный метод кривой Вёлера и Еврокод 3: Точность в
для прогнозирования многоосной усталостной прочности сварных соединений. п. 203–7.
[30] Разер К., Рундальф Дж. Оценка усталости сварных конструкций: практические аспекты
анализа напряжения и оценки усталости. Fatigue Fract Eng Mater Struct
2011;34:177–204.
[31] Мартинссон Дж. Оценка усталости сложной сварной стальной конструкции. Подразделение
Легкие конструкции Департамент авиационной и автомобильной инженерии Королевский
Технологический институт SE-100 44 Стокгольм, TRITA-AVE, vol.02; 2005 [ISBN 91-
2783-968-6].
[32] Данг Ван К., Биньонне А., Фаярд Дж.Л. Оценка сварных конструкций методом структурной многоосной усталости. В: Карпинтери А., де Фрейтас М. , Спаньоли А., редакторы.
Двухосный/многоосевой усталостный излом. Эльзевир; 2003. с. 3–21.
[33] Ниеми Э. Подход структурного напряжения к анализу усталости сварных компонентов –
руководство проектировщика. IIIW-док. XIII-1819-00/XV-1091-01 (окончательный проект). Международный
Институт сварки; 2001.
[34] Ниеми Э. Определение напряжения для анализа усталости сварных компонентов. Abington
(Кембридж): Международный институт сварки, Ambington Publishing; 1995.
[35] Sonsino CM, Kaufmann H, Demofonti G, Riscifuli S, Sedlacek G, Müller C, et al.
Стали высокопрочные в сварном состоянии для легких конструкций,
и пики переменных напряжений. Программа исследований стали ECSC. CSM – Рим, LBF –
Дармштадт; 1999.
[36] Сонсино С.М., Лагода Т.Оценка поведения многоосной усталости сварных соединений
при изгибе и кручении с применением фиктивного радиуса. Int J Fatigue
2004; 26 (3): 265–79.
[37] Seeger T. Stahlbauhandbuch – Band 1, Teil B, Abschnitt «Grundlagen für
Betriebsfestigkeitsnachweise». Дюссельдорф: Stahlbau-Verlagsgesellschaft mbH; 1996.
[38] Neuber H. Kerbspannungslehre – Theorie der Spannungskonzentration. 3-е изд.
Verlag (Берлин): Genaue Berechnung der Festigkeit Springer; 1985.
[39] Neuber H. Über die Berücksichtigung der Spannungskonzentration bei
Festigkeitsberechnungen. Уровень 7: Строительство; 1968. с. 245–51.
[40] Labesse-Jied F, Lebrun B, Petitpas E, Robert JL. Оценка многоосной усталости сварных конструкций
локальным подходом. Эльзевир; 2003. с. 43–62.
[41] Сонсино СМ. Учет допустимых эквивалентных напряжений для расчета на усталость сварных соединений
в соответствии с концепцией напряжения надреза с исходным радиусом
rref=1.00 и 0,05 мм. Сварное слово 2009; 53: R64–75.
[42] Каракас О., Моргенштерн С., Сонсино С.М. Расчет на усталость сварных соединений из деформируемого магниевого сплава
АЗ31 по концепции локальных напряжений с фиктивными радиусами надреза
rf=1,0 и 0,05 мм. Int J Fatigue 2008; 30: 2210–9.
[43] Sonsino CM, Hanselka H, Karakas Ö, et al. Расчетные значения усталостной прочности сварных соединений
деформируемого магниевого сплава AZ31 (ISO-MgAI3Zn1) по номинальному,
конструктивному и надрезному напряжениям в сравнении со сварными соединениями из стали и алюминия
.Weld World 2008; 52:79–94.
[44] Каракас О. Применение метода эффективного напряжения Нейбера для оценки усталостного поведения магниевых сварных швов
. Int J Fatigue 2017; 101: 115–26.
[45] Маруло Г., Баумгартнер Дж., Френдо Ф. Оценка усталостной прочности сварных лазером
тонкостенных соединений из малоуглеродистой и высокопрочной стали. Int J Fatigue
2017; 96: 142–51.
[46] Каракас О., Чжан Г., Сонсино СМ. Метод критического расстояния для оценки усталостной прочности
сварных соединений из магния в отличие от метода эффективного напряжения Нейбера
.Int J Fatigue 2018; 112: 21–35.
[47] Берто Ф. Концепция скругления фиктивных пазов, примененная к V-образным пазам с торцевыми отверстиями
при нагрузке в режиме 3. Int J Fatigue 2012; 38: 188–93.
[48] Лоуренс Ф.В., Маттос Р.Дж., Хигашида Ю., Берк Д.Д. Оценка долговечности сварных швов до образования усталостной трещины. Филадельпия (Пенсильвания): ASTM STP 648, Испытание на усталость сварных деталей
; 1978. с. 134–58.
[49] Сяо З.Г., Ямада К. Метод определения геометрического напряжения для оценки усталостной прочности
стального сварного соединения.Int J Fatigue 2004; 26: 1277–93.
[50] Еврокод 3: Проектирование стальных конструкций – Часть 1-1: Общие правила для зданий.
Брюссель: Европейский комитет по стандартизации; 1992 [ENV 1993-1-1].
[51] Тово Р., Ливьери П. Численный подход к оценке усталости соединений точечной сварки.
Fatigue Fract Eng Mater Struct 2011;34:32–45.
[52] Еврокод 9: Проектирование алюминиевых конструкций – Часть 2: Конструкции, подверженные усталости. Брюссель; 1998 [ENV 1999-2].
[53] Sędek P. Projektowanie konstrukcji narażonych na zmęczenie w ujęciu normy PN-
EN 1993-1-9, Seminarium Pt. Zagadnienia wytrzymałości zmęczeniowej konstrukcji
spawanych – projektowanie, wykonawstwo, badania, Instytut Spawalnictwa.
Гливице; 2007 [на польском языке].
[54] BS 7608:1993 Свод правил по расчету усталости и оценке стальных конструкций.
Лондон: BSI; 1993.
[55] Рекомендации по расчету усталости стальных конструкций Японского общества стали
Construction (JSSC).Технический отчет № 32. Токио: JSSC; 1995.
[56] Американская ассоциация государственных служащих автомобильных дорог и транспорта AASHTO.
Технические характеристики конструкции моста LRFD, 2-е изд.; 1998.
[57] Шведские правила для сварных стальных конструкций. СТБК-Н2. Шведский национальный комитет по стальным конструкциям
; 1974.
[58] Сонсино ВМ. Влияние остаточных напряжений на усталостные характеристики сварных соединений
в зависимости от условий нагружения и геометрии шва. Int J Fatigue 2009; 31: 88–101.
[59] ASTM E 739-91 (1998). Стандартная практика статистического анализа линеаризованных данных усталостной долговечности при напряжении (S-N) и долговечности при деформации (ε–N). В: Ежегодный сборник стандартов ASTM,
vol. 03.01, Филадельфия; 1999.
T. Łagoda and K. Głowacka International Journal of Fatigue 137 (2020) 105647
9
Разрушение сварных соединений, выполненных из сталей HSLA разного уровня прочности
Инженерная механика разрушения 64 (1999) 401±415www.elsevier.com/locate/engfracmech
Разрушение сварных соединений, выполненных из сталей HSLA разного уровня прочности Инослав Рак*, Арпад Трейбер Университет Марибора, Факультет машиностроения ИКГС, Лаборатория сварки ул. Сметанова, 17, 2000 Марибор, Словения Принято 27 августа 1999 г.
Аннотация Обсуждено влияние различий прочности (несоответствия) между металлом шва и двумя основными металлами, а также локальных изменений прочности в пределах зон ЗТВ сварного шва на характеристики вязкости разрушения сварных соединений. Из-за большого глобального несоответствия сварных соединений произошло отклонение разрушения от CGHAZ в сварной шов или основной металл. Это событие произошло в обоих сварных соединениях, выполненных на сталях одинакового и разного уровня прочности. Таким образом, результат не был правильным измерением вязкости разрушения ЗТВ. Значимость методики измерения локального смещения раскрытия вершины трещины также обсуждалась путем сравнения результатов CTOD d5 и британского стандарта dBS. Обсуждены некоторые различия в двух методах, в частности, для ударных сварных соединений CGHAZ, выполненных на сталях одинакового и разного уровня прочности.# 1999 Elsevier Science Ltd. Все права защищены. Ключевые слова: сварные швы; Несоответствие; Зона термического влияния; Смещение раскрытия вершины трещины
1. Введение Многопроходная процедура сварки под флюсом с узким зазором ¯at SAW может быть пригодна для сварки толстых профилей, поскольку выгодное направление нагрева дуги связано с меньшим диапазоном разбавления основного материала и шириной ЗТВ по сравнению с к обычному процессу SAW. Кроме того, узкая разделка разделки под сварку обеспечивает меньшее смещение сварного шва и остаточные напряжения.Этот прием может быть полезен, в частности, при сварке двух сталей разной прочности сварочным материалом, обеспечивающим прочность металла шва (МС)
* Автор, ответственный за переписку: Тел.: +386-62-7670; факс: +386-62-220-7994. 0013-7944/99/$ — см. вступительное сообщение № 1999 Elsevier Science Ltd. Все права защищены. PII: S 0 0 1 3 — 7 9 4 4 ( 9 9 ) 0 0 0 8 5 — 5
402
I. Rak, A. Treiber / Engineering Fracture Mechanics 64 (1999) 401±415
свойств в между.Таким образом, особенно в сварных конструкциях из высокопрочных сталей возникают существенные различия в прочностных свойствах (несоответствие) двух сварных основных материалов (ОМ), отличающихся прочностью, ВМ и обеими зонами термического влияния (ЗТВ). . Целью настоящей работы являлось изучение характеристик текучести и трещиностойкости РО и ЗТВ сварных соединений, выполненных на сталях HSLA одинакового и разного уровня прочности. Различия в механических свойствах различных участков сварного шва будут влиять на развитие зон пластичности и, следовательно, на распределение деформации вокруг вершины трещины во время испытания на вязкость разрушения и, следовательно, могут влиять на значения вязкости разрушения CTOD.Считается, что как свойства несоответствия прочности, так и локальная вязкость разрушения будут контролировать поведение при разрушении сварных соединений, выполненных на сталях одинакового и разного уровня прочности в зависимости от температуры испытаний. В настоящее время проводится обширная работа по пониманию поведения несоответствующих сварных соединений и разработке методологий решения этой проблемы в отношении испытаний на вязкость разрушения и процедур оценки дефектов.
2. Материалы, сварные соединения и методика эксперимента 2.1. Определение механических свойств и коэффициента рассогласования. Использовались промышленные высокопрочные низколегированные (HSLA) стали толщиной 50 мм в закаленном и отпущенном состоянии (Q+T), соответствующие маркам HT50 и HT80. Эти две стали соответствуют европейскому стандарту: сталь EN 10113-2-S355NL и сталь EN 10137-2S690QL1 соответственно. Для сварки стальных купонов была выбрана технология сварки ¯at SAW в узкий зазор, позволяющая получать пересогласованные и несогласованные сварные соединения BM, а также сварное соединение двух сталей разного уровня прочности.Все сварные соединения выполнены одними и теми же сварочными материалами. Технологические характеристики всех изготовленных сварных соединений представлены в таблице 1. Химические составы для ОМ, СМ и сварочной проволоки представлены в таблице 2. Механические свойства подложек и участков СС многопроходных сварных соединений представлены в таблице. 3. В связи с тем, что на каждой стороне РС имеется два разных МО, коэффициент несоответствия прочности М следует определять отдельно между РМ и обеими сторонами сварного соединения (МНТ50 и МНТ80).Механические свойства РМО определяли на цилиндрических стержнях (образцы по DIN 50125) диаметром 5 мм, извлеченных из верхней, средней и прикорневой областей, в направлении оси шва сварного соединения с узким зазором, показанного на рис.
1. Эти данные Таблица 1 SAW ¯ данные процедуры сварки в узкий зазор Температура предварительного нагрева и межпроходная температура (8C)
Напряжение (В)
Ток (А)
Скорость сварки (см/мин)
Время охлаждения Dt8=5 (с)
Подводимая теплота (кДж/см)
0260
33
450
50
022
0 20
I.Rak, A. Treiber / Engineering Fracture Mechanics 64 (1999) 401±415
403
Композиция N (WT%) C
Si
Si
Mn
Cr
CU
CU
MO
0,11 0,07 0,084 0,11
0,28 0,28 0,34 0,32
0.27 0.43 0.32 1.22
0,011 0,012 0,026 0,014
0.003 0,005 0,009 0,007
1.03 0.007
1,03 0,51 0,13 0,23 2,15 2,4
0,23 0,24
0,27 0,27 0,02 ±
0,27 0,27 0,02 ±
0,05
0.256 0,101 0.205
PCM: параметр холодного крекинга.
представляют только механические свойства регионов, из которых были взяты образцы. Предел текучести РМ рассчитывали по формуле syw ˆ 3:15 HV-168, предложенной для РМ [7,11].Измерения твердости WM HV1 с расстоянием 1 мм между отпечатками в трех направлениях по толщине, показанные на рис. 2, дали средние значения распределения коэффициентов несоответствия WM M поперек сварного соединения, как показано в таблице 4. Они могут можно сравнить со значениями в табл. 3. Единственным исключением была очень узкая полоса вблизи линии сплавления на стороне WM сталей с разным уровнем прочности, где коэффициент несоответствия незначительно локально изменился из-за влияния разбавления от основного металла к расплавленной ванне и которые не могут быть определены стандартными цельносварными металлическими цилиндрическими образцами на растяжение.Различия коэффициента несоответствия М также могут быть выявлены для обеих ЗТВ. Эти полосы могут влиять на поведение текучести вблизи вершины трещины и влиять на значение локально измеренного CTOD. Распределение глобального/локального коэффициента несоответствия М, рассчитанного по значениям твердости, показано на рис.
3. Кроме того, целью данного исследования было определение свойств трещиностойкости стальных сварных соединений с одинаковыми и разными уровнями прочности и, следовательно, установление влияние прочности соседней опорной плиты (несоответствие) на ударную вязкость HAZ и WM.Таблица 3 Механические свойства основных материалов разного уровня прочности и металла шва Обозначение
Y.S. (МПа)
U.T.S. (MPA)
Удлинение (%)
CHARPY (J) на ÿ408C
HT80 HT50 WM CAP WM SIDLE WM CORT
690 380 565 595 585
765 490 690 680 665
23.0 33.8 21 24 22
70 300 30 (в 08C) 70 (в 08C)
средний WM
581,6
581.6
678.3
22.39.3
22.3
608 22.08C)A
Несоответствие фантазии MHT80
MHT50
± ± 0 .82 0,86 0,85 Среднее 0,85
1,49 1,57 1,54
M = Y.S.WM/Y.S.BM, M 1 ì условие пересогласования.
1,53
404
И. Рак, А. Трейбер / Engineering Fracture Mechanics 64 (1999) 401±415
был получен путем сравнения экспериментальных результатов CTOD, полученных при измерении локального d5 и стандартных методов оценки вязкости разрушения. Кроме того, особое внимание уделялось предварительному усталостному растрескиванию образцов CTOD, полученных из сварной пластины. Если использовать методику, предписанную существующими стандартами испытаний на ударную вязкость (справедливую для однородных материалов) [1 — 3], то фронт вершины усталостной трещины будет непрямолинейным из-за бимодального распределения остаточных напряжений в направлении толщины и неоднородного распределения твердости по вершина трещины [4,5]. Для преодоления этой проблемы можно использовать модифицированную версию метода высокого R-отношения, так называемого метода GKSS «Step-wise High R-ratio» (SHR) [6].При использовании этого метода и учете наибольшего значения предела текучести РМ достигаются более прямолинейные фронты вершин трещин для полнотолщинных образцов, изготовленных из сварных соединений после сварки.
Рис. 2. Направления измерения макротвердости в WM узкощелевого сварного соединения стали разного уровня прочности.
I. Rak, A. Treiibe / Engineering Mechance Mechanics 64 (1999) 401 ± 415
405
405
Таблица 4 WM и CGHAZ Несовместительный фактор М Определяется из средней твердости INCESATA Недостаточный фактор M CGHAZ
WMHT50
WMHT80
Твердость WM по линии сплавления ÿ0. 15 мм +0,2 мм +1 мм WM средняя линия Средняя твердость 217 223 225 225 M 1,26 1,42 1,42 1,42 0,78 a
CGHAZ +1 мм +0,2 мм ÿ0,15 мм 224 227 274 0,78 0,8 1,14 Y
9:SHT009:SHT ˆ 380 МПа, Y:S:BMHT80 ˆ 690 МПа.
Серия ударных образцов по Шарпи-V и образцы SENB полной толщины были извлечены из сварных соединений. Ударные образцы по методу Шарпи-V были взяты из обоих ОМ, ЗТВ, колпачковых проходов РМ, верхней части РМ (между верхним и средним проходами) и средних проходов РМ. Положения надреза образца показаны на рис.4. Тип образца SENB: B 2B …B ˆ 40 мм). Сквозные усталостные трещины с реальной глубиной трещины а=W00:5 располагались в РК и вблизи линии сплавления, как показано на рис. 1. Температура испытаний составляла -108С; однако некоторые образцы были испытаны также при -208С и +108С. Во время испытаний на механику разрушения применялась методика падения потенциала постоянного тока для мониторинга стабильного роста трещины [8]. Смещение грузовой линии (LLD) было измерено с эталонным стержнем, чтобы свести к минимуму последствия возможных вмятин роликов. Величины CTOD рассчитывали по BS 5762 …dBS† [1] и измеряли непосредственно с помощью калибра-клипсы d5 на боковых поверхностях образца в вершине усталостной трещины на измерительной длине 5 мм [9].
Рис. 3. Глобальный/локальный коэффициент рассогласования М в разнородном сечении сварного шва.
406
I. Rak, A. Treiber / Engineering Fracture Mechanics 64 (1999) 401±415
уровень.
3. Результаты 3.1. Энергия удара по Шарпи Результаты испытаний на удар по Шарпи-V показаны на рис. 5 в виде кривых перехода средняя энергия-температура для различных местоположений надрезов. Самая низкая ударная вязкость по Шарпи была получена для WM в месте сварного шва. Остальной материал WM показывает лучшую ударную вязкость, чем верхний слой, но ниже, чем обе ЗТВ. Оба BM демонстрируют превосходную ударную вязкость, и фактически все данные BM HT50 представляют собой верхнюю полку ударной вязкости. Обе кривые перехода ЗТВ резко уменьшаются по сравнению с исходными кривыми основного материала, особенно при более низком температурном режиме. Температура перехода ЗТВ HT80 показана прибл. ÿ408C …070 Дж) и для HT50 HAZ при ок. Э358С …0160 Дж). Верхняя и средняя температура перехода WM показаны прибл. 08C (070 Дж) и для BM HT80 прибл. М408С ( 0200 Дж), тогда как БМ НТ50 показывает во всем тестируемом районе верхние полочные значения. Различий в энергиях Шарпи-V в HAZ и WM при сравнении сварных соединений, выполненных на сталях HSLA одинакового и разного уровня прочности, не обнаружено. Это является следствием лишь незначительного разбавления на линии сплавления во всех рассмотренных случаях и видно, например, из таблицы 2 химического состава и рис.3.
I. Rak, A. Treiber / Engineering Fracture Mechanics 64 (1999) 401±415
407
соединение, рис. 4, кривые двух основных металлов BM HT80 и BM HT50 также включены для целей сравнения.
3.2. Вязкость разрушения при CTOD В таблицах 5 и 6 результаты по вязкости разрушения представлены в единицах CTOD(BS) и CTOD(d5). Все измеренные значения d5 скорректированы из-за разницы между средним a0 (из-за фронта усталостной трещины в форме пенни) и положением зажима d5 на обеих сторонах образца в соответствии с предложением в Ref. [10]. Согласно этому предложению использовалась следующая формула для коррекции d5: d5corr: ˆ d5
…W ÿ a0 †rp …W ÿ a0 †rp ‡ a0 ÿ ad5
, где d5 – CTOD, измеренный на боковой поверхности трещины, W – ширина образца, a0 – исходная длина трещины,
…1†
408
И. Рак, А. Трейбер / Engineering Fracture Mechanics 64 (1999) 401±415
их сварных швов Материал/сварной шов (температура испытаний)
Da (мм)
CTOD d5 коррелированный (мм)
CTOD dBS (мм)
Тип d-значение
CTODI Da ˆ 0:2, коррелированный d5
CTODI дБС 0.2 (мм)
a0 измеренная (мм)
ad5 измеренная (мм)
BM-HT80 при ÿ108C при ÿ108C BM-HT50 при ÿ108C при ÿ108C WM-HT80 при ÿ108C при ÿ108C +WM-HT80 при ÿ108C при ÿ108C при ÿ108C ÿ108C при ÿ108C при ÿ108C при ÿ208C HAZ-HT80 при ÿ108C при ÿ108C HAZ-HT50 AT + 108C при ÿ108C на ÿ108C на ÿ108C
1.02 0.51 0.38 2,50 0,11 3.19 0.34 0,22 2.07 2,10 0,07 0,84 0,48 0,89 2.28 2.35 2,62. 2,67 2,67
0,540 0,566 0,334 2,424 2,685 2,525 0,251 0,154 0,098 0,142 2.076 1,367 0,070 1,260 1,066 0,072 0,609 0,312 0,526 1,863 1,841 1,994 2,162 2,280
0,620 0,549 0,376 2,435 2,723 2,667 0,305 0,190 0,125 0,183 2,218 1,521 0,123 1,277 1,260 0,097 0,697 0,346 0,635 2,429 2,362 2,603 2,766 2,712
mmuummucccuucmucmuumu ммм
0,222 0,242 0,233 0,405 0.314 0.281 0,165 ± ± 0,281 0,165 ± 0,218 0,136 ± 0,259 0,227 0,203 0,259 0,227 0,203 0,273 0,241 0,263 0,273 0,286
0,267 0,243 0,265 0,267 0,243 0,265 0,405 0.310 0,289 0,202 ± ± ± 0,247 0.239 ± 0,260 0,190 ± 0,294 0,252 0,247 0,349 0,339 0,376 0,290 0,340
41,6 43,9 41,1 43,4 43,5 42,5 42,0 41,2 41,4 41,6 41,0 41,1 42,5 41,8 41,5 41,9 40,5 41,2 40,6 39,5 40,0 39,4 40,1 39,5
40,4 41,6 40,5 40,0 40,3 40,0 42,0 41,2 41,4 41,6 40,6 40,4 41,5 40,0 40,8 41,1 40,3 40,2 40,2 39,5 40,4 40,4 41,4 40,0
одной и той же БМ, а в табл. 6 представлены значения CTOD для сварного соединения из БМ двух разных уровней прочности. На рис. 6 показаны R-кривые, отражающие наименьшие значения CTOD двух различных по прочности сварных соединений СС по сравнению с BM, R-кривые, а на рис. 7 R-кривые, отражающие наименьшие значения CTOD показаны R-кривые двух различных по прочности сварных соединений ЗТВ в сравнении с БМ. На рис. 8 представлен один из вариантов поведения при разрушении несоответствующих образцов WM, когда траектория вязкого разрушения отклоняется в сторону менее прочного основного металла HT50, а хрупкое разрушение инициируется по линии сплавления на стороне ЗТВ.Кроме того, на рис. 9 представлено медленное распространение трещины на образце, показанном на рис. 8, через РМ, достигающее ИКГАЗ.
I. Rak, A. Treiber / Engineering Fracture Mechanics 64 (1999) 401±415
409
соединение (температура испытания)
Da (мм)
CTOD d5 коррелированный (мм)
CTOD дБS (мм)
CTODI d5 0,2 коррелированный (мм)
CTODI дБS 0.2 (мм)
a0 измеренные (мм)
измеренные (мм)
AD5 (мм)
WM при ÿ108C при ÿ108C при ÿ108C HAZ-HT80 на ÿ108C при ÿ108C при ÿ108C HAZ-HT50 на ÿ108C
2,05 0,06 0 4. 12 0.74 0.63 1.12 0.53 3.18 3.05 3.01 2.68
0.905a 0.083b 0.088b 2.473c 0,392 0,676 0,350 0,323 2,272 2,289 2,651 0,939
1,160 0,098 0,108 2,800 0,640 0,650 1,110 0,690 2,470 2,930 3,040 2,630
± ± ± 0,150 0,175 0,216 0,231 0,187 0,186 0,243 0,273 0,073
0.245 ± ± 0,216 0,319 0,346 0,368 0,383 0,253 0,325 0,377 2,63
40,4 40,1 41,1 36,5 39,8 38,3 38,2 37,5 44,1 37,9 38,1 37,8
40,1 39,8 40,4 38,7 38,9 38,8 38,2 38,7 40,7 38,7 39,5 38,5
Трещина инициации началась в Средний и устойчивый рост трещины WM отклонялся в сторону HT50 BM, но останавливался в WM …dm ). б Начало разрушения в РК и трещина осталась в РК как LBZ …dc ). в Начало разрушения в среднем сечении РВ и устойчивая трещина отклонилась в сторону ВТ50 РВ, прошла РВ и на самом слабом участке ВКГАЗ произошло хрупкое разрушение по линии сплавления …du ).
4. Обсуждение Ожидалось, что глобальное рассогласование перед вершиной трещины будет играть важную роль в характеристиках текучести, зарождении трещины и отклонении разрушения в сварном соединении. Это результат сложных условий несоответствия, которые определяют сварное соединение двух сталей с различной прочностью из-за различной ударной вязкости, микроструктурных свойств вблизи зоны сплавления и оставшихся участков WM и HAZ. 4.1. Ударная вязкость сварного соединения Наименьшая ударная вязкость по Шарпи была получена в области верхней части WM сварного соединения, выполненного на двух сталях с разным уровнем прочности.Эти различия между верхним слоем и наполнителем обусловлены микроструктурой осажденного и повторно нагретого/преобразованного WM, а также разной скоростью охлаждения для покровного и наполняющего слоев. Однако в целом РМ, изготовленные из двух сталей с разным уровнем прочности, показали более низкую ударную вязкость по сравнению с обоими БР, рис. сварные соединения, выполненные на сталях HSLA одинакового и разного уровня прочности. Из этого наблюдения можно сделать вывод, что WM, полученный сваркой SAW в узкий зазор на двух сталях с различной прочностью, будет наиболее чувствительной частью и потенциальной областью для возникновения LBZ.
410
И. Рак, А. Трейбер / Инженерная механика разрушения 64 (1999) 401±415
4.1.1. Вязкость разрушения металла шва Наименьшие значения вязкости разрушения, определенные для РС, сопоставимы как для СС сварных соединений, выполненных на ОМ одного уровня прочности, так и для сварных соединений, выполненных из ОМ разного уровня прочности, см. табл. 4 и 5. Вязкость разрушения поведение определяется локальными свойствами вязкости разрушения WM, и инициирование хрупкого разрушения происходит на границах зерен дендритной микроструктуры WM.В других случаях, когда вязкость разрушения была выше, очевидно, что разрушение инициировалось и распространялось по более прочным участкам ВМ по вязкому механизму роста трещины. В двух оставшихся сварных соединениях из БМ разного уровня прочности разрушение обусловлено более низкими прочностными свойствами стали ВТ50. На рис. 8 показано инициирование вязкого разрушения от фронта усталостной трещины в WM и трещины, отклоненной медленным ростом в сторону BM-HT50. В самой слабой зоне HAZ-ICCGHAZ, до того, как трещина достигла BM-HT50, см.9, хрупкое разрушение произошло по неблагоприятной менее жесткой линии сплавления в ЗТВ. Предполагается, что распространение трещины после зарождения трещины в этом случае определялось более низкими прочностными свойствами HT50 до тех пор, пока не была достигнута область более высокой ударной вязкости HT50 HAZ, где разрушение дополнительно определялось свойствами ударной вязкости, которые были ниже в ICCGHAZ вблизи линии сплавления. Это поведение было подтверждено металлографическим разрезом, представленным на рис. 9. Таким образом, ясно показано, что несоответствие прочности в сочетании с локальными свойствами материала может влиять на характер разрушения.Аналогичное поведение имело место в другом образце, в котором максимальная нагрузка была достигнута до начала хрупкого разрушения и
I. Rak, A. Treiber / Engineering Fracture Mechanics 64 (1999) 401±415
411
при температуре 108С.
Рис.8. Зарождение разрушения в металле шва, медленное отклонение трещины до ВМ HT50 и распространение хрупкого разрушения по линии сплавления.
412
И. Рак, А. Трейбер / Engineering Fracture Mechanics 64 (1999) 401±415
I. Rak, A. Treiber / Engineering Fracture Mechanics 64 (1999) 401±415
413
до того, как рост вязкой трещины достигнет линии сплавления HAZ HT50.Как упоминалось ранее, поведение при разрушении показало высокую вязкость разрушения при CTOD в обоих образцах, как это видно из таблицы 5. Похоже, что удлиненные дендриты обладают высоким сопротивлением распространению разрушения перпендикулярно их удлиненным зернам тела. R-кривые на рис. 6 представляют результаты для значений обоих WM, полученных на HT80 и HT50, по сравнению с двумя BM и WM, полученными на сталях HT80 и HT50 с разным уровнем прочности. Наименьшее значение трещиностойкости CTOD для всех трех РО примерно одинаковое (0.07 мм для WMHT50, 0,098 мм для WMHT80 и 0,083 мм для WM на двух сталях разной прочности) и сильфонное инициирование при Da ˆ 0,2 мм. Как видно из рисунка, только сверхсогласованный WM-HT50 показал некоторое расширение трещины перед разрушением. События инициации хрупкого разрушения обозначены стрелками на рис. 6. С другой стороны, как показано в таблицах 5 и 6, для других образцов преобладают более высокие значения вязкости разрушения. Очевидно, что испытание на CTOD в соответствии с действующими стандартами …a=W00:5† является слишком консервативным для определения оценки трещиностойкости сварных соединений, предусмотренных для сталей HSLA.Этот вывод следует также из того факта, что LBZ может появиться после некоторого количества медленного роста трещины в HT80 BM (рис. 6), несмотря на его высокую ударную вязкость (рис. 5). Оценку сварных соединений (в том числе из сталей разной прочности) удобно проводить путем испытаний широких пластинчатых образцов с более низкими условиями стеснения, приближающимися к сварным соединениям, работающим при их номинальном нагружении. 4.1.2. Вязкость разрушения ЗТВ Средняя вязкость разрушения сварных соединений ЗТВ на сталях одинаковой прочности, представленная в таблице 5 (ЗТВ-HT80, ЗТВ-HT50), имеет тот же порядок величины по сравнению со средней вязкостью разрушения сварных соединений ЗТВ на сталях с разной прочностью.
прочность (HAZ-HT80, HAZ-HT50) представлена в таблице 6.Из этих таблиц видно, что ЗТВ HT80 демонстрирует более низкую вязкость разрушения, чем ЗТВ HT50. Это понятно из-за более низкого уровня прочности стали, но более высокой ударной вязкости последней. Некоторые из испытанных образцов не показали хрупкого разрушения до конца испытания. Это является следствием отличной ударной вязкости ВМ и влияния процедуры сварки под флюсом в узком зазоре, при которой подводимое тепло не воздействует на ВМ так, как это происходит при сварке обычных сварных соединений со скошенными кромками (X, V, K-канавки). .Вязкость разрушения ЗТВ при CTOD значительно выше, чем у РМ. Их нижняя полоса ударной вязкости представлена R-кривыми по сравнению с R-кривыми BM на рис. 7. Во всех случаях значительное расширение трещин было обнаружено до того, как произошло разрушение или до достижения максимального значения нагрузки. События, при которых возникла хрупкая неустойчивость, отмечены стрелками, они происходили в основном при распространении трещин более 1,0 мм, как показано на рисунке.
Весьма интересным было поведение образцов HAZ-HT80, взятых из сварных соединений сталей одинакового и разного уровня прочности.При испытаниях в РСМ появлялась локальная хрупкая неустойчивость как следствие зарождения трещины на предварительно растрескавшейся ВТ80 ЦГАЗ, которая сразу переходила медленным ростом на более мягкие недосогласованные РМ. Очевидно, что влияние на вершину трещины более мягких СМ и СТ50 по сравнению с СТ80 было существенным для развития пластической зоны в РМ, поэтому измеренная вязкость разрушения по CTOD не отражает характеристики вязкости разрушения ЗТВ. Сварные соединения HT 80, выполненные на сталях одинаковой и разной прочности.Это видно на рис. 7 для ЗТВ-HT80 сварного шва
414
I. Rak, A. Treiber / Engineering Fracture Mechanics 64 (1999) 401±415
соединения, выполненного на равнопрочной стали и ЗТВ-dHT80 из сварное соединение, выполненное на сталях разного уровня прочности. Характер разрушения обеих R-кривых аналогичен после входа трещины из ЗТВ HT80 в WM. Измеренная вязкость разрушения HAZ-HT50 для сварных соединений, изготовленных из сталей одинаковой и разной прочности, не отражает реальных характеристик ударной вязкости.Разрушение начинается в HAZ-HT50, но сразу же переходит в BM-HT50 из-за превосходящих свойств WM. Свойства несоответствия в сварных соединениях, выполненных на BM с разным уровнем прочности, оказывают заметное влияние на вязкость разрушения ЗТВ из-за отклонения трещины в другие области, чем обе ЗТВ, и значения не отражают вязкость разрушения ЗТВ. Представляется, что испытание CGHAZ на вязкость разрушения следует модифицировать/изменить. Расположение вершины трещины перпендикулярно направлению сварного шва, за несколько миллиметров до линии сплавления на прямой стороне ЗТВ является хорошим решением для определения вязкости разрушения CGHAZ.
5. Выводы Выполнена экспериментальная программа по сравнению прочности и ударной вязкости несогласованных сварных соединений с узким зазором, выполненных на двух сталях HSLA с разным уровнем прочности с использованием одинаковых сварочных материалов. Результаты данной исследовательской работы можно обобщить следующим образом: 1. Благодаря выгодному способу сварки под флюсом в узкий зазор двух ВМ разного уровня прочности диапазон разбавления основного материала по ширине ЗТВ меньше, чем в обычных сварочных процессах.Следствие этого ясно выражается в виде состояния глобального несоответствия прочности. По-видимому, единственным исключением является очень узкая полоса вдоль линии слияния со стороны ВМ, где могут появляться слабые локальные рассогласования. 2. Ударная вязкость WM по Шарпи сварного соединения, выполненного на сталях разного уровня прочности, ниже, чем у БМХАЗ. Наименьшая ударная вязкость выявлена у верхнего слоя WM, где твердость наибольшая и не имеется полезного тепла отпуска от последующих проходов. 3. Вязкость разрушения WM CTOD в сварных соединениях, выполненных на сталях одинакового уровня прочности, достаточно хорошая, но в ряде случаев очень низкая.Очевидно, что инициирование разрушения зависит от угла усталостной трещины к ориентации дендритов и либо вершина трещины отбирает частицы/примеси на границе зерен дендритов, либо находится в матрице зерен.
То же самое может проявиться в сварном соединении, выполненном на сталях разного уровня прочности. Но, при медленном росте трещины, трещина отклоняется в сторону более мягкого БМ. При прохождении трещины через РВ может возникнуть хрупкое разрушение, если вершина трещины достигает зоны ЗБЗ раньше БМ с высокой вязкостью.Кажется, что инициирование и распространение разрушения сложны и могут регулироваться ударной вязкостью и прочностными свойствами вокруг вершины трещины. 4. Вязкость разрушения HAZ CTOD в сварном соединении, выполненном на сталях разного уровня прочности, превосходна по сравнению с вязкостью WM CTOD. Вязкость ЗТВ БМ с более высокой прочностью может быть завышена из-за влияния более мягкого РМ и распространения трещины от ЗТВ перпендикулярно дендритам РМ. То же можно сказать и по вязкости ЗТВ
И. Рак, А.Treiber / Engineering Fracture Mechanics 64 (1999) 401±415
415
ВМ с меньшей прочностью из-за более мягкого ВМ и отклонения трещины от CGHAZ в ВМ. 5. Используемые методы измерения CTOD: CTOD d5, устаревший CTOD dBS5762 или даже новый стандарт BS 7448, часть 2 [11], который также учитывает влияние несоответствия сварных швов, особенно сварных соединений, выполненных на сталях разного уровня прочности. огромные различия в некоторых случаях. Еще раз было показано, насколько важны локальные измерения без необходимости делать выводы из дистанционно измеренных величин.Все измеренные значения CTOD d5 были скорректированы из-за различий между средним значением a0 и длиной поверхностной трещины, где измерялось d5.
Благодарности Эта работа частично финансируется Международным бюро DLR в Бонне (Германия) и Министерством науки и технологий Словении в Любляне. Авторы благодарят Исследовательский центр GKSS, доктора М. Кочака и его коллег за помощь в экспериментальной работе и за комментарии к рукописи. Ссылки [1] BS 5762: 1979. Метод испытания на раскрытие трещин (COD).Британский институт стандартов. [2] АСТМ Е 1290-91. Стандартный метод измерения вязкости разрушения при раскрытии вершины трещины (COD). [3] Европейское общество структурной целостности, рекомендация ESIS по определению сопротивления разрушению пластичных материалов, ESIS P1-92. [4] Schwalbe K-H, Koc°ak M. Механика разрушения сварных конструкций: свойства и применение к компонентам. В: Основная лекция на 3-й Международной конференции по тенденциям в исследованиях в области сварки, 1-5 июня, Гатлинбург, Теннесси, США.1992. [5] Мукаи Ю., Нисимура А. Поведение распространения усталостной трещины в неоднородной области твердости. Труды Японского общества сварщиков 1983; 14:1. [6] Коак М., Зайферт К., Яо С., Лампе Х. Сравнение методов усталостного предварительного растрескивания для испытаний сварных соединений на вязкость разрушения: локальное сжатие и ступенчатое высокое отношение R. В: Koc°ak M, редактор. проц. Междунар. конф. Сварка-90, октябрь 1990 г., Geesthacht, FRG, 1990. с. 307±18. [7] Паргертер Р.Дж. Предел текучести по твердости — переоценка металла шва.Бюллетень исследований в области сварки, ноябрь 1978 г. [8] Швальбе К.
Х., Хеллманн Д. Применение метода электрического потенциала для измерения длины трещины с использованием формулы Джонсона. ЖТЕВА 1981;9(3):218±21. [9] GKSS-Forschungszentrum Geesthacht. ГКСС-Измерительные системы для применения в механике разрушения, 1991. [10] Трейбер А., Рак И. Свойства разрушения несогласованного по прочности сварного соединения с узким зазором. В: Первая конференция ASM по сварке и научным технологиям, Мадрид, Испания, 10-12 марта. 1997. [11] BS 7448 Часть 2.Метод определения KIC, критических значений CTOD и критических значений J сварных швов металлических материалов, 1997.
Характеристики разрушения разнородных электронно-лучевых сварных соединений между хромомолибденовой сталью и аустенитной сталью AISI 304: AIP Advances: Vol 9, No 4
C. Прочность на растяжение
Виды разрушения сварных образцов с надрезом и без надреза, связанные с РЭМ-изображениями поверхностей излома, показаны на рис. 1. В случае образцов без надреза и с надрезом с глубиной надреза 2 мм разрушение произошло вне сварного шва в БМ КС.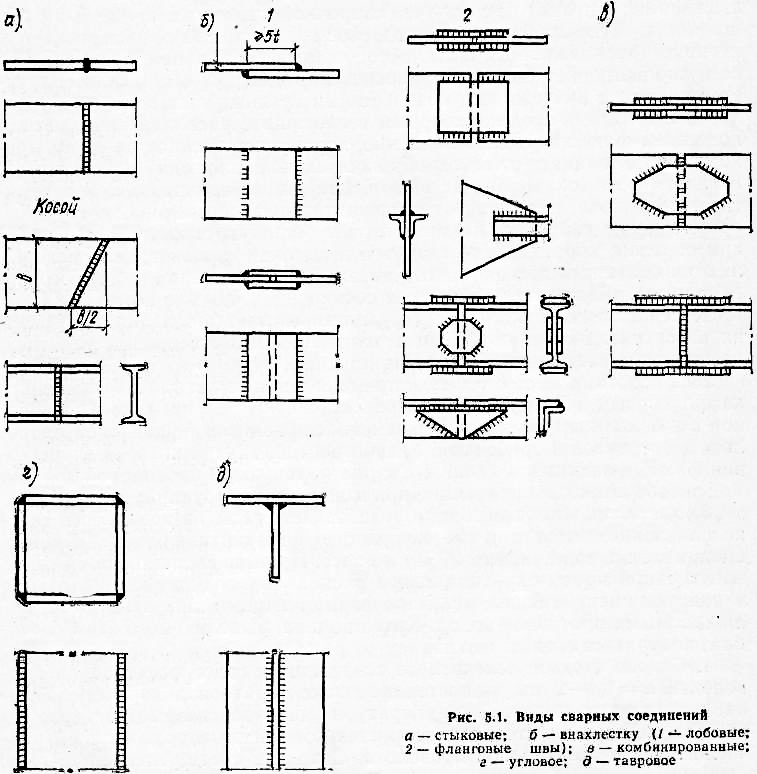

Прогноз усталостной долговечности сварных соединений из мелкозернистой мартенситно-бейнитной стали S960QL и определение очагов трещин
В связи с растущими требованиями, связанными с применением прогрессивных конструкций, в настоящее время развиваются современные процессы проектирования. Одним из важнейших вопросов, рассматриваемых в этих процессах, является правильная конструкция соединений с учетом усталости, чтобы обеспечить заявленный срок службы. В данном исследовании представлен метод прогнозирования усталостной долговечности на основе критерия диапазона допустимых деформаций в корне надреза. Ранее для мягких и углеродистых сталей была разработана привлекательная упрощенная модель прогнозирования усталостной долговечности. Оценка, проведенная в ходе исследования, показала, что этот метод можно использовать и для высокопрочной стали S960QL, характеризующейся совершенно другими свойствами и структурой. Рассмотренная теоретическая модель демонстрирует удовлетворительную корреляцию с экспериментальными данными и надежно описывает усталостную долговечность сварных конструкций.Кроме того, прогнозируемая усталостная долговечность исследуемой стали без сварных швов показывает большую сопоставимость с экспериментальными данными. Оценено предельное значение диапазона деформации в корне надреза. Ниже этого значения деформации усталостная долговечность сварных соединений теоретически бесконечна. Наконец, выявлено влияние дефектов поверхности на зарождение усталостной трещины.
Для отцовского материала очаги растрескивания обнаружены в местах попадания частиц неметаллической окалины. В сварных соединениях усталостные трещины зарождаются по всей длине линии сплавления.
1. Введение
Отдельные элементы более сложных структур соединяются друг с другом в узлах с использованием различных методов. Требования к конструкции определяют, должно ли это соединение быть разборным или постоянным. Неразъемный способ соединения очевиден в случае изготовления больших и сложных конструкций, таких как мосты и другие строительные конструкции, рамы большегрузных транспортных средств, трубопроводные системы или краны, например. Эти типы конструкций требуют выполнения многочисленных соединений, и сварки достаточно для обеспечения оптимальной эффективности изготовления с надлежащим финансовым результатом.Использование сварки позволяет уменьшить толщину конструктивных элементов, уменьшая общий вес конструкции вместе с количеством используемых расходных материалов и, в конечном итоге, влияя на снижение себестоимости изготовления. По этим причинам такая соединительная техника получила широкое распространение. Тем не менее, следует помнить, что стыки являются точками ослабления конструкции и наиболее вероятными местами возникновения разрушения. Вышеупомянутые конструкции эксплуатируются в условиях знакопеременных нагрузок, поэтому основной причиной разрушения прогнозируется усталость.Это явление напрямую связано с изменениями геометрической формы, микроструктуры и распределения напряжений, происходящими в процессе сварки. По этим причинам наибольшая вероятность зарождения трещин находится в непосредственной близости от сварных соединений, где обнаруживаются многочисленные надрезы.
Сложность этого вопроса привела к тому, что до сих пор были разработаны различные методы прогнозирования усталостной прочности и усталостной долговечности. Наиболее популярным является разделение на три основных подхода: стресс-, деформационно-энергетический.
Метод номинального напряжения основан на предположении об общем упругом поведении. Рассчитываются напряжения в рассматриваемом сечении с учетом влияния макрогеометрической формы детали, надрезов и остаточных напряжений. Тем не менее, локальным влиянием сварных соединений на величину напряжения пренебрегают. По причине своей простоты этот метод является наиболее широко используемым подходом к расчету сварных конструкций на усталость [1–5].
В случае, когда номинальные напряжения не могут быть определены с достаточной точностью из-за сложности компонентов, следует использовать метод конструкционных горячих точек.Этот метод учитывает все факторы, приводящие к увеличению напряжения вблизи стыка, и работает путем экстраполяции эталонного значения напряжения на концах сварного шва, при этом эффект градиента напряжения учитывается с помощью специально составленных расчетных кривых [6, 7]. ]. Два или три измерения должны быть реализованы на разных расстояниях от края шва, чтобы вычислить значение напряжения в стыке шва. В случае напряжения, рассчитанного на поверхности пластины, согласно [1], его можно определить с помощью экстраполяции следующих уравнений:
Параметром является толщина рассматриваемой детали и напряжение, измеренное на расстоянии 04 t от носка. Подход с точечным напряжением очень часто используется при анализе методом конечных элементов (МКЭ) сварных компонентов. Более того, разрабатываются новые численные методы, и в связи с этим рассматриваются особые или уникальные структурные случаи [8–12]. Тем не менее, этот подход также недостаточен в более сложных случаях из-за предположения о диапазоне упругих напряжений с линейным изменением. Поэтому сварные соединения этих конструкций рассчитаны на усталость с использованием метода эффективного напряжения надреза [13–19], который является наиболее передовым методом расчета усталости, рекомендованным IIW [1].Этот подход основан на утверждении, что напряжения в дне разделки определяются в закруглении носка/корня шва с фиктивным радиусом 1 мм или 0,5 мм при толщине свариваемой детали более 5 мм и менее соответственно. Идея этого метода заключается в том, что механическое локальное поведение материала на дне надреза аналогично поведению не надрезанного или слегка надрезанного, миниатюрного и аксиально нагруженного образца, извлеченного из этой области [20].
Описанные подходы могут быть успешно применены, если принимается во внимание многоцикловая усталостная прочность при бесконечном сроке службы.Эти экземпляры характеризуются наличием упругих напряжений. Только подход напряжения надреза может быть распространен на диапазон конечного срока службы, где пластические микродеформации вызывают зарождение трещин и их развитие. Влияние пластических деформаций более существенно в области малоцикловой усталости, полученной при высоких и сверхвысоких нагрузках.
В работе представлены результаты исследований по разработке упрощенной модели прогнозирования усталостной долговечности сварных соединений из мелкозернистой высокопрочной конструкционной стали.Первоначально рассматривается вопрос о принятии существующего описания для быстрорежущей стали и распространении его на сварные соединения. Проведена экспериментальная проверка, а также представлены фрактографические исследования зарождения усталостной трещины.
2. Прогнозирование усталостной долговечности
Описание усталостного поведения в малоцикловом диапазоне должно учитывать пластический компонент. Эта решающая причина приводит к тому, что подходы к прогнозированию усталостной долговечности, основанные на деформации и энергии, являются наиболее подходящими по сравнению с методами, основанными на напряжении.Наиболее распространенная формула, описывающая эту взаимосвязь, — это правило расчета Морроу (3):
Вышеприведенное правило определяет зависимость между амплитудой деформации, разделенной на упругую и пластическую составляющие, и соответствующей усталостной долговечностью. Коэффициенты и совместно с показателями степени и определяют при испытаниях на усталость, проводимых в режиме деформации.
Альтернативное упрощенное решение этой проблемы было предложено Мэнсоном [21]: используются только три свойства материала: предел прочности, модуль текучести и пластичность, определяемые как где — процентное уменьшение площади.
Другой вариант соотношений (3) и (4) представляет собой уравнение, разработанное Лангером [22]: где – усталостная прочность при полностью обращенном нагружении.
В публикации [23] авторы предложили новую формулу, разработанную на основе соотношений (3)–(6) с некоторыми изменениями. Во-первых, заменяется в уравнении (6) на 0,55 R m , так как согласно [24] и γ = 0,55 является коэффициентом, зависящим от типа материала. Для стали он равен от 0.4 до 0,55, и на основании результатов, представленных в [23], выбрано максимальное значение. Кроме того, учитывалось и влияние асимметрии цикла. Согласно [24] амплитуда пластической деформации ε apl заменена на среднюю амплитуду пластической деформации ε mapl :
Рассмотренные зависимости разработаны и оценены для углеродистых и мягких сталей с R m < 700 МПа. В случае высокопрочных сталей, имеющих другую микроструктуру и механизм упрочнения, параметр Z следует заменить на Z x = 0.5 Z + 15 [24] . Более того, чтобы определить допустимый диапазон штамма Δ ε на и допустимой усталости жизни N на , частичные факторы безопасности ψ ε и ψ n были наложены, определенные в уравнениях (8). Первое связано с Δ ε a , а второе связано с N f соответственно:
было получено:
2.1. Прогнозирование малоцикловой усталостной долговечности сварных соединений
Для описания прогнозируемой усталостной долговечности сварных соединений был предложен метод деформации с надрезом. Поэтому следует указать значение диапазона упругопластических деформаций в корне надреза Δ ε надреза . В рассматриваемом случае надрез локализуется на линии сплавления шва. Условие малоцикловой усталостной прочности выполняется, если это означает, что деформация не должна превышать предельного значения, определенного для локально измененного материала в месте надреза.Диапазон деформации может быть выражен произведением коэффициента концентрации деформации на номинальный диапазон деформации:
Согласно [23], коэффициент концентрации деформации можно рассчитать по следующей формуле: где — коэффициент концентрации напряжения (вызванный формой сварного шва) , – показатель деформационного упрочнения, – постоянная (равная от 0 до 0,5), – нормированный диапазон номинальных напряжений, – номинальный диапазон напряжений, – коэффициент напряжения при нагрузке.
Диапазон номинальных деформаций рассчитывался по следующей зависимости:
Для определения зависимости, описывающей прогнозируемую усталостную долговечность сварных соединений и с учетом условия (11), уравнение (10) было модифицировано.Прежняя деформация была заменена на Δ ε выемка , и были рассмотрены два новых фактора безопасности, а именно ψ Ff , связанные со степенью неопределенности используемой теоретической модели, и ψ Mf , связанные с чувствительность материала к растрескиванию, связанная с доступностью для наблюдения за сварной конструкцией (15):
3. Экспериментальная методика
3.1. Материалы
Экспериментальная проверка модели прогнозирования усталостной долговечности проведена на мелкозернистой высокопрочной конструкционной стали S960QL.Используемый материал представлял собой лист толщиной 6 мм. Эта сталь производится методом жидкостной закалки и отпуска (Q&T), в результате чего получается бейнитно-мартенситная микроструктура. Результаты, полученные во время измерений химического состава и механические свойства тесты в таблицах 1 и 2.