ДЕФЕКТОСКОПИЧЕСКИЕ МАТЕРИАЛЫ — МегаЛекции
Капиллярный дефектоскопический материал применяют при капиллярном неразрушающем контроле и используют для пропитки, нейтрализации или удаления избытка проникающего вещества с поверхности и проявления его остатка с целью получения первичной информации о наличии несплошности в объекте контроля.
Дефектоскопические материалы выбирают в зависимости от требований, предъявляемых к объекту контроля, его состояния и условий контроля. Их укомплектовывают в целевые наборы, в которые входят полностью или частично взаимообусловленные совместимые дефектоскопические материалы, приведенные ниже.
Набор дефектоскопических материалов — взаимозависимое целевое сочетание дефектоскопических материалов: индика-торного пенетранта, проявителя, очистителя и гасителя.
Индикаторный пенетрант (пенетрант) И — капиллярный дефектоскопический материал, обладающий способностью про-никать в несплошности объекта контроля и индицировать их.
Очиститель от пенетранта (очиститель) М — капиллярный дефектоскопический материал, предназначенный для удаления индикаторного пенетранта с поверхности объекта контроля самостоятельно или в сочетании с органическим растворителем или водой.
Гаситель пенетранта (гаситель) Г — капиллярный дефекто-скопический материал, предназначенный для гашения люминесценции или цвета остатков соответствующих индика-торных пенетрантов на поверхности объекта контроля.
Проявитель пенетранта (проявитель) П — капиллярный дефектоскопический материал, предназначенный для извлечения индикаторного пенетранта из капиллярной полости несплош-ности с целью образования четкого индикаторного рисунка и создания контрастирующего с ним фона.
Специализированные составы, предназначенные для выявления поверхностных дефектов методами капиллярной дефектоскопии, имеют следующие условные групповые обозначения.
И — цветные пенетранты, имеющие характерный цветовой тон при наблюдении в видимом излучении,
l — люминесцентные пенетранты, излучающие свет под воздействием длинноволнового ультрафиолетового излучения.
И3 — люминесцентно-цветные пенетранты, имеющие характерный цветовой тон при наблюдении в видимом излучении и люминесцирующие под воздействием длинно-волнового ультрафиолетового излучения.
Ц — химические активные пенетранты, предназначенные для химического взаимодействия с соответствующими проявителями для образования специфического индикаторного следа, меняющего цвет, способность люминесцировать или образовывать продукты реакции, дающие информацию о наличии несплошностей.
И5 — ахроматические пенетранты, которые под воздействием видимого излучения дают черное или серое показание.
И6 — прочие пенетранты.
М1 — органические очистители.
Mj — водяные очистители
М3 — прочие очистители
Г — гасители ленетанта.
П — порошковые проявители, сорбционные, представляющие собой сухой, преимущественно белый мелкодисперсный сорбент, поглощающий ленетрант.
П2 — суспензионные проявители, сорбционные, представляющие собой белый сорбент, диспергированный в летучих растворителях, воде или быстросохнущих смесях, поглощающие пенетрант.
П3 — красочные проявители (лаки), диффузионные, состоящие из пигментированного или бесцветного быстросохнущего жидкого раствора, связывающие, поглощающие пенетрант.
П4 — пленочные проявители, диффузионные, представляющие собой бесцветную или белую накладную пленку с проявляющим липким слоем, поглощающим пенетрант.
П5 — прочие проявители.
Очистители и гасители в зависимости от характера взаимодействия с индикаторным пенетраитом подразделяют на растворяющие, самоэмульгирующие и эмульгирующие при внешнем воздействии.
Индикаторные пенетранты подразделяют в зависимости от физического состояния и светоколористических признаков.
В зависимости от физических свойств бывают различные пенетранты.
Магнитный пенетрант является суспензией, частицы твердой фазы которой имеют ферромагнитные свойства, а жидкий носитель представляет собой молекулярную или коллоидную дисперсию люминофора, красителя или другого индикатора,
Электропроводящий пенетрант имеет нормированную электрическую проводимость.
Ионизирующий пенетрант испускает ионизирующее излучение. Поглощающий пенетрант поглощает ионизирующее излучение.
Комбинированный пенетрант сочетает свойства двух или более индикаторных пенетрантов.
По технологическим признакам пенетранты можно разделить следующим образом.
Органосмываемый пенетрант смывается с поверхности объекта контроля органическими безводными антикорро-зионными составами: растворителями, маслами или их смесями.
Водосмываемый пенетраит смывается водой или водосодержащими составами.
Пенетрант последующего эмульгирования образует эмульсию в воде, очищающей поверхность объекта контроля, после его предварительного взаимодействия с очистителем от пенетранта или ПАВ.
Обесцвечивающий пенетрант, особенность которого заключается в том, что люминесценция или цвет его уничтожается специально подобранным гасителем.
Проявители подразделяют в зависимости от состояния.
Проявитель разделяют в зависимости от характера взаимодействия его с индикаторным пенетрантом.
Химически пассивный проявитель не меняет колористические свойства индикаторного пенетранта.
Рекомендации по контролю качества материалов
Данные рекомендации распространяются на материалы для капиллярной дефектоскопии и контроля параметров .
Плотность вещества определяется как отношение массы т к объему т.е. = М/ V. Пикнометрический метод. Плотность определяется при температуре 20 °С и указывается в г/см3.
Вязкость — это свойство жидкого вещества к восприятию сдвигающего напряжения t, вызываемого деформацией сдвига и зависящего от градиента среза D.
Кинематическая вязкость — это отношение динамической вязкости t\ к плотности р, т.е. v = ц /р. Она определяется на конечных точках соответствующего температурного диапазона и выражается в м 2 /с.
Применяют капиллярный вискозиметр по Уббелоде на температурный диапазон 10 — 100 °С, а также вискозиметр с падающим шариком по Хапплеру на температурный диапазон — 60 +150 °С.
Поверхностное натяжение — это напряжение на поверхности, стремящееся уменьшить данную поверхность. Оно измеряется в Н/м при температуре 20° С. Применяют тензиометр с пластиной, дугой или кольцом.
Смачиваемость — это адгезия жидкости на поверхности твердого тела, т.е. образование малого контактного угла (< 90° ) между поверхностью жидкости и поверхностью твердого тела, В случае полного смачивания этот контактный угол равен 0° .
Плоская пластина из стекла, стали, алюминия, латуни площадью 100 х 100 мм тщательно очищается, например, щелочным промывочным средством, при помощи целлюлозной бумаги с использованием трихлорэтилена, этилалкоголя, ацетона или окунанием в ацетон, обезжиривается и сушится. Шероховатось шлифованных или имеющихся в состоянии поставки металлических пластин должна составлять по показателю Ra = 3 — 5 мкм. На середину горизонтально установленной пластины наносится 0,04 мл пенетранта и определяется средний диаметр смачиваемой площади (в качестве меры смачиваемости) в зависимости от времени.
Проникающая способность — это свойство пенетрантов к проникновению в капиллярные несплошности. Скорость проникновения пенетрантов может быть определена приближенно путем сложения двух мерительных плиток, при помощи стяжного устройства устанавливается щель шириной в несколько мкм. На верхнюю сторону щели напыляется проявитель, а на нижнюю сторону наносится капля пенетранта. Измеряется время от момента нанесения пенетранта до первых признаков окраски проявителя.
Выявляемость дефектов указывает на то, какой определенный наименьший поверхностный дефект (например, ширина трещины) еще визуализируется данным набором материалов. Она определяется на естественных или искусственных дефектах при температуре 20° С, причем необходимо применять установленную заводом-изготовителем технологию контроля. Для испытаний используют стандартные образцы.
Образец выполняют из измерительных плиток так, что последние образуют калиброванную клинообразную капиллярную щель, как описано выше при испытании проникающей способности пенетранта.
Пластана из азотированной стали, деформированная шариком.
Изготовляется пластина из азотируемой стали размерами 50 х50 х 3 мм, поверхность которой шлифуется так, чтобы шероховатость составила Ra = 3 — 4 мкм. В середине сверлят проходное отверстие диаметром 5 мм, фаска с обеих сторон 60 °. После этого пластина азотируется (глубина азотирования 0,2-0,7 мм), очищается от окалины мелкой шлифовальной бумагой и кладется на стальное кольцо (внутренний диаметр 30 мм, высота 25 мм, наружный диаметр около 60 мм). На противоположной стороне 20-миллиметровый стальной шар вдавливается с помощью испытательной машины в отверстие силой около 2—3 кН, пока треск не укажет на образование трещин в зоне растяжения. Трещины измеряют под микроскопом. Путем повторного надавливания на переднюю или обратную сторону плитки можно управлять раскрытием трещин. Ширина трещины определяется с помощью растрового сканирующего, электронного микроскопа при необходимом увеличении. Глубина трещин определяется по поперечным шлифам.
Методика испытания(рисунок1):
· предварительная очистка и обезжиривание ацетоном или спиртом с применением ультразвукового воздействия;
· сушка нагреванием на электроплите;
· нанесение пенетранта в течение 10 мин;
· промежуточная очистка с помощью волокон целлюлозы и заданного очистителя, вытереть насухо;
· нанесение проявителя, который должен действовать не менее 15 мин;
· визуальный осмотр количества, длины, конфигурации трещин и фона;
· фотографирование.
Рисунок 1 — Последовательность операций при капиллярном контроле
Существуют следующие методы контрастного капиллярного контроля:
Рекомендуемые страницы:
Воспользуйтесь поиском по сайту:
Дефектоскопические материалы — Справочник химика 21
Для локальной капиллярной дефектоскопии хорошо зарекомендовал себя аэрозольный способ нанесения дефектоскопических материалов. Особенностью этого способа является использование малогабаритных баллонов, содержащих фреон для нанесения и хранения материалов (индикаторных жидкостей, очищающих составов и проявляющих лаков и суспензий). Этот способ удобен для контроля в цеховых условиях, резко повышая его производительность. Вместе с тем использование аэрозольного способа позволяет экономно расходовать специальные дефектоскопические материалы, повышает культуру работы с одновременным улучшением качества контроля. [c.173]Обработка дефектоскопическими материалами составляет основную часть процесса контроля. Пропитку пенетрантом выполняют погружением в ванну, намазыванием кистью. Очень удобный способ распыления из аэрозольного баллона. Во всех случаях пенетрант оставляют на поверхности на 10—20 мин для лучшего его проникновения в полость дефектов. Существуют способы интенсификации пропитки, например воздействие мощными ультразвуковыми колебаниями, повышенным давлением. Пропитка в вакууме способствует удалению воздуха из полости дефекта и более глубокому проникновению пенетранта. [c.59]
Оценка качества изображения. При этом смотрят, нет ли фона, не покрытых проявителем участков, отслаивания проявителя, следов пыли. Если такие недостатки обнаружены, обработку дефектоскопическими материалами повторяют после прогрева изделия до 40—50°С. [c.62]
Расход дефектоскопических материалов зависит от качества поверхности контролируемого объекта, ее расположения, консистенции материалов, способа их нанесения. Расход пенетранта 0,3— [c.63]
Требования техники безопасности при проведении капиллярного контроля указаны в ГОСТ 18442—80. Некоторые легколетучие и токсичные (хотя и слабо) дефектоскопические материалы требуют хорошей вентиляции помещения или участка, где проводят контроль, а также применения спецодежды, в частности резиновых перчаток, фартуков. Дефектоскопические материалы держат в плотно закрытой таре. Отходы производства регенерируют, сливают в сборники или сжигают. Соблюдают также противопожарные требования и меры безопасности при работе с электрооборудованием. [c.63]
Чувствительность капиллярного контроля в большой степени зависит от качества и правильности подбора дефектоскопических материалов, поэтому они проходят предварительную проверку. Смачиваемость и вязкость пенетранта проверяют по диаметру и времени растекания капли на поверхности материала контролируемого объекта. Индикаторные способности проверяют по сравнению с некоторыми стандартными растворами. Для этого 10%-ный раствор пенетранта в растворителе набирают в пробирку и визуально сравнивают его цветовой, яркостный контраст или способность люминесцировать в ультрафиолетовых лучах со стандартным раствором в таких же пробирках. Кроме того, смотрят, не расслаивается ли пенетрант в пробирке, нет ли в нем взвешенных частиц, измеряют его плотность, температуру кипения и воспламенения., [c.65]
Изготовленные таким образом образцы аттестуют. Определяют ширину и длину отдельных трещин измерительным микроскопом и вносят их в формуляр образцов. К формуляру прилагают фотографию образца с индикациями дефектов, их хранят в футлярах, предохраняющих их от загрязнения. Обычно в лаборатории имеют образцы рабочие для повседневного использования и контрольные для решения арбитражных вопросов. Стандартные образцы используют не только для проверки дефектоскопических материалов на эффективность совместного применения, но также для определения правильной технологии (времени пропитки, проявления), аттестации дефектоскопистов и определения общей чувствительности контроля. [c.66]
Общее время, необходимое для контроля относительно небольшого объекта типа турбинной лопатки, 0,5—1,1 ч в зависимости от дефектоскопических материалов и требований по чувствительности. Затраты времени (мин) распределяются следующим образом подготовка к контролю [c.69]
Необходимость применения мероприятий техники безопасности для предотвращения вредного воздействия на организм некоторых дефектоскопических материалов и интенсивного УФ-облучения. [c.69]
В третьей книге рассмотрены общие вопросы капиллярного метода контроля терминология физика капиллярных явлений классификация, назначение, свойства и характеристики дефектоскопических материалов капиллярного контроля классификация, назначение и рекомендации по использованию тест-объектов. Приведены сведения об источниках ультрафиолетового излучения для люминесцентного капиллярного контроля. Описана технология капиллярного контроля промышленных изделий. Освещены вопросы компьютерного количественного анализа результатов капиллярного контроля. [c.2]
Использованные промасленные обтирочные материалы (ветошь, салфетки) следует складывать в металлический ящик, обязательно опорожняемый по окончании работ. При размещении, хранении, транспортировании дефектоскопических материалов, отходов производства должны соблюдаться требования по защите от пожаров в соответствии с ГОСТ 12.1.004-91. [c.536]
Для локальной капиллярной дефектоскопии хорошо зарекомендовал себя аэрозольный способ нанесения дефектоскопических материалов. [c.594]
Создание автоматических систем оценки результатов контроля требует разработки соответствующих алгоритмов для ЭВМ. Работы ведутся по нескольким направлениям определение конфигурации индикаций (протяженность, ширина, площадь), соответствующее недопустимым д
Дефектоскопические материалы.
Количество просмотров публикации Дефектоскопические материалы. — 478
Фильтрующиеся суспензии являются специфическим видом пенетранта. В жидкий пенетрант добавляют нерастворимый порошок с диаметром частиц 0,01…0,1 мм, обладающий цветовым контрастом или люминесценцией. Порошок не проникает в дефект, а фильтруется и скапливается у ᴇᴦο устья. Такой пенетрант не требует проявления.
В качестве индикаторной жидкости, используемой для контроля материалов с наибольшей пористостью фильтрующимися частицами, можно использовать легкую фракцию нефти. Этот материал является компромиссным с точки зрения стоимости, безопасности, запаха и скорости высыхания.
Для специального применения должна быть использована другая суспергирующая среда. Суспензии могут быть успешно приготовлены в воде, гликолях, тяжелой фракции нефти и спирте. Суспензии на такой жидкой основе, кроме легкой фракции нефти, должны быть специально приготовлены для конкретного применения.
Во всех жидкостях, используемых для контроля фильтрующимися частицами, частицы подбираются нужных размеров и формы.
Для контроля только поверхности рекомендуется люминесцентная контрольная среда с основой из легкой фракции нефти, в которой взвешены ярко-желтые люминесцентные частицы.
В том случае, в случае если стремятся к восстановлению пористого изделия, используется контрольная среда, частицы которой указывают на трещину с поверхности, а цветные красители окрашивают полость трещины так, что контролер может выводить дефект до дна.
Окрашенные, но не люминесцентные дефектоскопические суспензии, также чувствительны при работе на пористых материалах, как и люминесцентные.
Однако они менее заметны на образцах сложной формы или деталях с выемками. Для таких случаев контроля рекомендуется люминесцентный материал. В общем, нелюминесцентные материалы могут быть использованы на объектах простой формы, таких, как кирпичи, кокс и бетон, хотя люминесцентные материалы проще в работе и более надежны.
Среди нерешенных ещё вопросов метода фильтрующихся частиц можно отметить, например, задачу приготовления люминесцентных порошков для суспензий с наперед заданным и достаточно постоянным размером частиц, так как обычный помол не обеспечивает этого постоянства размера частиц и всегда порождает фон.
Для промышленного использования предложена люминесцирующая суспензия, состоящая из трех компонентов˸ измельченного до тонкодисперсного состояния нерастворимого в воде люмогена (светло-желтого или оранжево-краевого) в количестве от 0,5 до 1 г; 0,05…0,5 г поверхностно-активного вещества (ОП-7 или ОП-10) и 1 л воды.
Порошок люмогена размалывается в шаровой мельнице с керамическими шарами, а затем размешивается с небольшим количеством воды и поверхностно-активным веществом до получения сметанообразной консистенции. В дальнейшем полученная смесь разбавляется водой до необходимой пропорции.
Суспензия наносится на контролируемую пористую поверхность с помощью пульверизатора, кисти или кратковременного погружения. Осмотр под ультрафиолетовым светом фокусируемого источника типа ДРШ-260 с фильтром УЭС-6 можно производить через 30…60 сек после нанесения суспензии.
Обозначения дефектоскопических материалов — Студопедия.Нет
В целях унификации обозначения дефектоскопических материалов применяют единую систему индексации.
Таблица 5
Унифицированные обозначения дефектоскопических материалов
Способ обнаружения индикаторного следа | Индикаторный пенетрант (И) | Очиститель пенетранта (М) | Гаситель пенетранта (Г) | Проявитель пенетранта (П) |
Яркостный (Я) | И1…….И09 | М1…….М09 | Г1…….Г09 | П1…….П09 |
Люминесцентный (Л) | И100…..И109 | М100…..М109 | Г100…..Г109 | П100…..П109 |
Цветной (Ц) | И200…..И209 | М200…..М209 | Г200…..Г209 | П200…..П209 |
Люминесцентно-цветной (ЛЦ) | И300…..И309 | М300…..М309 | Г300…..Г309 | П300…..П309 |
Комбинированный, специальные (К) | И400…..И409 | М400…..М409 | Г400…..Г409 | П400…..П409 |
Примеры записи технологии контроля (ГОСТ 18442 –80):
Капиллярный метод проникающих растворов с люминесцентным способом обнаружения, обладающий первым классом чувствительности, использующий пенетрант № 1, проявитель № 1 и очиститель пенетранта № 7:
Л=1- (И1П1М7). (2)
Капиллярный метод фильтрующихся суспензий с цветным способом обнаружения обладающий третьим классом чувствительности, использующий пенетрант № 38:
ФЦ — III- (И38). (3)
Нумерацию дефектоскопических материалов устанавливают в стандартах или технических условиях на конкретный материал.
В последнее время для контроля качества изделий нашел широкое применение аэрозольный способ нанесения дефектоскопических материалов на контролируемую поверхность изделия с использованием аэрозольных баллонов. Дефектоскопические материалы заправлены в баллон вместе с инертным сжиженным газом – хладоном 12 или 22 (фреоном 12 или 22). Известны белорусские материалы: люминесцентный пенетрант ЛЖТ, цветной пенетрант «Пион» в аэрозольных газовых баллончиках.
Наборы дефектоскопических материалов (КД-1, …КД-4) для каждого метода капиллярной дефектоскопии выбирают исходя из требуемой чувствительности, производительности контроля и возможности его автоматизации и механизации, стабильности качества материалов в условиях применения и хранения, химической инертности материалов по отношению к контролируемым изделиям.
Зарубежные фирмы выпускают наборы для капиллярного метода в виде трех препаратов, в которых применяется универсальный очиститель, как для очистки поверхности объекта, так и для снятия пенетранта. На российском рынке появились наборы для капиллярного контроля разных фирм, например ELY (Великобритания) выпускает наборы CHECKMOR, MAGNAFLUX (Англия) – материалы для цветной дефектоскопии SPOTCHECK, SK3-S Kit, люминесцентные материалы ZIGLO; Франция – наборы для цветной дефектоскопии SHERWIN; ARDROX (Германия) наборы для цветной дефектоскопии OVERCHEK, HELLING и т. д., в которые входят проникающие растворы, очистители, проявляющие жидкости в аэрозольных упаковках. Для выборочного оперативного капиллярного контроля небольших поверхностей широко применяется набор фирмы MR® Piccolo/ Фломастер MR® Пикколо-пэн. Набор состоит из красного и флуоресцентного пенетранта MR® 68 C, очистителя MR®88, проявителя белого MR®70.
Аппаратура для капиллярного контроля
Для обнаружения дефектов капиллярными методами контроля применяют дефектоскопы различных типов, состоящие из приборов и вспомогательных средств. В зависимости от функционального назначения и эксплуатационной законченности дефектоскопы включают в себя полностью или частично следующие функциональные устройства подготовки объектов к контролю; обработки объектов дефектоскопическими материалами; выявления дефектов; контроля качества дефектоскопических материалов; контроля ультрафиолетового, видимого, теплового и других используемых излучений, контроля технологических процессов подготовки объектов и обработки их дефектоскопическими материалами.
В комплект дефектоскопа входят баллоны с проникающей жидкостью, проявляющей краской и растворителем для удаления излишков проникающей жидкости в процессе контроля, а также футляр с кистями, эталонный образец со шлифовочными трещинами, малогабаритный краскораспылитель и 7-кратная лупа.
Дефектоскопы изготовляют в следующих исполнениях: переносные, передвижные и стационарные.
По своему технологическому назначению аппаратура и оборудование для капиллярного контроля делится на унифицированные группы:
– КД-10,…КД-19 – стационарные комплексные дефектоскопы – типа КД-10- базовая модель;
– КД-20,…КД-29 – стационарные передвижные для выполнения отдельных операций, например осмотра изделий в УФ излучении, КД-20 – базовая модель;
– КД-30,…КД-39 – переносные ультрафиолетовые облучатели, КД-30 – базовая модель;
– КД-40,…КД-49 – переносные аэрозольные дефектоскопы, КД-40 –базовая модель;
– КД-50,…КД-59 – ряд вспомогательных средств, КД-50 – базовая модель;
– КД-60,…КД-69 – ряд -ультрафиолетовых облучателей с источниками УФ-излучения, КД-60 – базовая модель.
Тип аппаратуры и оборудования выбирают с учетом их размеров и массы, условий и объема работы; требуемой производительности и типа используемых дефектоскопических материалов.
Переносную и передвижную аппаратуру используют в условиях мелкосерийного производства, ремонта и эксплуатации изделий. Наиболее перспективны передвижные аэрозольные комплекты (например КД-40ЛЦ). Их выполняют разборными и при необходимости многократно заряжают с помощью стенда, входящего в состав комплекта.
В условиях крупносерийного производства отливок используют стационарную аппаратуру (например, ЛДА-3, УКЛ-1 с ртутными лампами сверхвысокого давления ДРШ), состоящую из ряда установок и приспособлений для пропитки пенетрантом, мойки, сушки, проявления и осмотра отливок при обычном освещении или ультрафиолетовом излучении.
Дополнительно в необходимых случаях для обнаружения следа дефекта и расшифровки результатов контроля применяют различные средства осмотра (лупы, бинокулярные стереоскопические микроскопы, зеркала) в условиях, обеспечивающих освещенность объекта контроля, соответствующую правилам эксплуатации этих средств.
Контроль качества деталей и сварных соединений изделий при люминесцентном и люминесцентно-цветном методах проводят при облучении их ультрафиолетовыми лучами (УФ-лучи). В качестве источников ультрафиолетовых лучей применяют газоразрядные источники света – специализированные ртутные лампы, а также неспециализированные лампы с приставными светофильтрами.
Для оценки чувствительности дефектоскопических материалов, качества промежуточной очистки и контроля всего капиллярного процесса применяются контрольные образцы. Это металлические пластины с определенной шероховатостью и нанесенными на них нормированными искусственными трещинами (дефектами). Используются отдельные контрольные образцы II или III класса чувствительности, либо комплект из трех контрольных образцов со II и III классом чувствительности (рабочий, контрольный, экспертный).
Например, контрольный образец для оценки чувствительности III класса в соответствии с ГОСТ 18442 – 89, выпускаемый филиалом ФГУП «НИКИМТ» – «ЭКСПЕРТ-ЦЕНТР», изготовляется из стали 40Х13, с одной поверхностной трещиной, шириной раскрытия 20 мкм, длиной 9,6 м.
Для работы с зарубежными пенетрантными наборами выпускаются свои эталоны. Например, контрольный образец JIS Z 2343, который используется для определения чувствительности пенетрантных систем и сравнения двух пенетрантов, один из которых может быть принят за референтный. Состоит из двух тест-панелей, представляющих собой бронзовые пластины 100х35х2, покрытые Ni-Cч-слоем. В Ni-Cч- покрытии изготовлены поперечные трещины, глубина которых соответствует толщине NiCч- покрытия (выпускаются 4 вида с толщиной 10, 20, 30, и 50 мкм). К каждой тест-панели прилагается сертификат. Тест-панели с глубиной трещин 10 мкм, 20 мкм, 30 мкм применяются для контроля чувствительности флуоресцентных пенетрантных систем. Чувствительность контрастных пенетрантных систем определяется с помощью панелей с глубиной трещин 30 и 50 мкм.
Контрольный образец № 2 (TN ISO 3452-3). Представляет из себя тест-панель, которая служит для контроля степени смывания флуоренсцентного пенетранта. Панель состоит из пластины, изготовленной из аустенитной стали, рабочая сторона которой хромирована и имеет четыре ступени шероховатости. Пять звездообразных эталонов трещин, изготовлены методом давления и располагаются на рабочей стороне тест-панели. Для контроля степени смывания флуоресцентного пенетранта используются четыре сегмента с различной степенью шероховатости: 2,5 мкм, 5 мкм, 10 мкм и 15 мкм и расположенные над ними пять звездообразных эталонов трещин.
Эти тест-образцы (контрольные образцы) нельзя использовать для сравнения чувствительности разных пенетрантов. Они являются средством проверки технологии капиллярного контроля по соответствующему классу чувствительности и могут быть использованы применительно только к одной пенетрантной системе.
В настоящее время ведутся работы по автоматизации капиллярного контроля. Для расшифровки результатов контроля создаются автоматические анализаторы изображения.
При массовом производстве ряда изделий необходимо производить проверку каждого изделия. В этих случаях применяют автоматические линии для капиллярного контроля.
Выпускаются модульные линии Magnaflux, серии ZA915 для люминесцентного капиллярного контроля. Предлагаются три стандартных комплектации: ZA-37E для контроля люминсцентными постэмульгируемыми пенетрантами, ZA-37W люминсцентными водосмываемыми пенетрантами, ZA-37S для контроля цветными пенетрантами. В состав этих линий включается разное число модулей в зависимости от цели. Составные части включают в себя бак для пенетранта, бак для предварительной промывки, бак окончательной промывки, бак для эмульгатора-очистителя, сушку горячим воздухом, шторм-камеру для нанесения порошкового проявителя, дренажные лотки, смотровую кабину. Конструкции изготовляются из нержавеющей стали. Дополнительно прилагаются принадлежности, включающие набор тест-образов, испытательных панелей, систему освещения и т. д.
Капиллярный метод неразрушающего контроля (кнк) (капиллярная дефектоскопия)
Капиллярный метод неразрушающего контроля (кнк) (капиллярная дефектоскопия)Этот метод пригоден только для выявления дефектов, проявляющихся на поверхности контролируемого объекта. Он основан на проникновении специальной жидкости — пенетранта — в полости поверхностных и сквозных несплошностей объекта контроля, в извлечении пенетранта из дефектов с помощью проявляющего покрытия и фиксировании пенетранта. Глубина дефектов, обнаруживаемых КНК должна значительно превышать их ширину. Если ширина поверхностного повреждения больше его глубины (риска, царапина), то оно легко заполняется пенетрантом и так же легко удаляется из повреждений. Такие дефекты, как правило, КНК не выявляются.
КНК обычно используют для обнаружения дефектов, не видимых невооруженным глазом. Его абсолютную чувствительность определяют средним раскрытием дефекта типа трещин длиной 3-5 мм. выявляемого с заданной вероятностью.
Индикаторные рисунки, образующиеся при контроле, либо обладают способностью люминесцировать в ультрафиолетовых лучах, либо имеют окраску, вызываемую избирательным поглощением (отражением) части падающих на них световых лучей. Линии индикаторного рисунка имеют ширину от 0.05 до 0.3 мм (на расстоянии наилучшего зрения это соответствует угловой ширине от 15″ до Г30″). яркостный контраст 30-60% и более, а также высокий цветовой контраст. Это значительно выше соответствующих параметров поверхностных дефектов, обнаруживаемых визуально (угловой размер от Г до 10″. яркостный контраст 0-5%. цветовой контраст отсутствует).
При КНК ставятся следующие задачи: обнаружение дефекта, определение направления дефекта относительно конфигурации детали, определение размеров и формы дефекта.
В процессе КНК осуществляется следующая маркировка дефектов;
а — по количеству дефектов: А — одиночные дефекты. Б — множественные дефекты. В — сплошные дефекты:
б — по направлению дефектов:
|| -дефекты, параллельные направлению изделия:
_|_ — дефекты, перпендикулярные направлению изделия;
Z -дефекты, расположенные под углом к направлению изделия.
Основными объектами КНК являются неферромагнитные материалы: лопатки турбин из никелевых сплавов, в том числе авиационных турбин: титановый крепеж для летательных и космических аппаратов: литые детали из цветных металлов для электроники и систем автоматического управления: детали приборов и аппаратов нефтяной и химической промышленности.
КНК позволяет диагностировать объекты контроля любых размеров и форм, изготовленных из чёрных и цветных металлов и сплавов, пластмасс, стекла, керамики, а также других твёрдых неферромагнитных материалов. При этом выявляются такие дефекты, как трещины, пористость, рыхлоты.
При КНК применяют следующие материалы:
1. В качестве пенетранта — различные жидкие растворы, чаше всего на основе керосина, в который добавляются красители или люминофоры, светящиеся под действием ультрафиолетового излучения. Например, пенетрант «А» состоит из 700 мл керосина, 300 мл бензина Б-70. 30 г тёмно-красного красителя. Пенетрант «Е» состоит из керосина (800 мл), бензола (200 мл) и тёмно- красного красителя. Существуют пенетранты. у которых в керосин добавлены ацетон, бензин и краситель, или трансформаторное масло, скипидар и краситель, и ряд других.
Люменисцирующие пенетранты представляют собой смеси органических растворителей, масел, керосина с добавками поверхностно-активных веществ (ПАВ) и люминесцирующих веществ: масел, нефти, норнола, эмульсола и др.
2. Очищающую жидкость, которая предназначена для удаления пенетранта с поверхности контролируемого объекта. В качестве очищающих жидкостей используются вода, вода с добавлением ПАВ. органические растворители, смесь масла с керосином и другие жидкости. Например, масло МК-8-65% объема, толуол — 30%. эмульгатор ОП-7
3. Гаситель, который представляет собой состав для устранения окраски или люминесцентных остатков пенетранта без удаления его с контролируемой поверхности. В качестве гасителей используется, например, вода с кальцинированной содой (гаситель О201). спирт с поверхностно активным веществом ОП-7 (гаситель О300) и другие вещества.
4. В качестве проявляющих веществ — агар-агар, крахмал, порошок окиси магния, суспензия каолина в ацетоне и многие другие материалы, которые адсорбируют пенетрант. проникший в дефекты, и тем самым позволяют фиксировать их на поверхности контролируемого объекта.
Для выполнения КНК применяется следующая аппаратура:
1 — ванны для мойки и насыщения изделия пенетрантом:
2 — шкафы для сушки изделий:
3 — устройства для нанесения пенетранта:
4 — оптические устройства для фиксации дефектов визуально, с помощью фотосъёмок и для облучения пенетранта ультрафиолетовыми лучами в случае применения люминесцирующих веществ.
Проникающую жидкость наносят на предварительно очищенную поверхность деталей, чтобы заполнить полости возможных поверхностных дефектов. Продолжительность контакта жидкости с поверхностью детали зависит от физических свойств жидкости, характера обнаруживаемых дефектов и способа заполнения жидкостью полостей дефектов.
При вакуумном способе деталь помешают в герметичную камеру, из которой откачивают воздух. После подачи проникающей жидкости камеру разгерметизируют. Жидкость заполняет полости дефектов под действием капиллярного и атмосферного давлений. При разрежении около 1 Па выявляются трещины шириной на порядок меньше, чем при капиллярной пропитке.
При компрессионном способе жидкость быстро заполняет полости дефектов под действием капиллярного и внешнего избыточного давлений. При этом достигается более полное заполнение полостей дефектов, однако многие пенетранты изменяют свои свойства при увеличении давления — увеличивается вязкость, ухудшается смачиваемость твердых тел. в результате эффективность способа невелика.
При ультразвуковом способе ускоряется процесс заполнения полостей дефектов, особенно загрязненных. Высокой эффективности способ достигает при использовании пенетрантов средней и высокой вязкости (нориола, шубнкола. смесей масла с керосином), когда направление колебаний совпадает с плоскостью полости дефекта.
Под воздействием статических сил увеличивается ширина раскрытия полости дефектов, улучшаются условия заполнения этих полостей н выявления дефектов ннзковязкимн жидкостями.
При обычных условиях, например, заполнение поверхностных трещин раскрытием 0.002 мм и глубиной происходит за 20 с: такая же трещина глубиной 3 мм полностью заполняется примерно за 40 с.
Скорость заполнения сквозных дефектов зависит от их размеров и конфигурации, время заполнения измеряется секундами.
Индикаторные пенетранты для красок и люминофоров, приготовленные на основе растворителей (керосин, бензин и т.п.). достаточно быстро испаряются. Длительная выдержка пенетранта на контролируемой поверхности может привести к его высыханию и выпадению в виде осадка из частиц красителя или люминофора. Эти частицы, являясь сорбентом, могут привести к извлечению пенетранта из устья дефекта: в результате выявление дефектов при контроле ухудшается. Для предотвращения высыхания можно периодически наносить дополнительно пенетрант. однако это процесс трудоемкий, особенно при контроле больших площадей, поэтому время нахождения пенетранта на контролируемой поверхности обычно ограничено 3-5 мин. После этого индикаторный пенетрант необходимо удалить с поверхности КО.
Способы удаления проникающей жидкости с поверхности выбирают с учетом необходимости сохранения ее в полостях дефектов, а также типа пенетранта. шероховатости поверхности, условий контроля, объема работ и требуемой производительности труда. При локальном контроле условиях в случае использования невысыхающих жидкостей детали протирают ветошью или бумагой. При большом объеме работ или при контроле шероховатых деталей (с чистотой обработки поверхности ниже пятого класса) этот способ непригоден. В этих случаях применяют промывку органическими растворителей!, водой и пр. Для удаления невысыхающих жидкостей применяют обдувку струей песка, дроби, косточковой крошки, опилок и т.п. Гашением устраняется люминесценция или окраска при использовании специальных проникающих жидкостей. При контроле массовых деталей в цеховых условиях применяют комбинированный способ удаления проникающей жидкости с поверхности деталей.
Полноту удаления пенетранта определяют визуально или (при люминисцентном методе) в ультрафиолетовом свете. Оценку считают удовлетворительной, если отсутствует светящийся или окрашенный фон.Если фон обнаружен, для повторной очистки используют очиститель типа O-l или 0-2. При температуре окружающего воздуха ниже 8°С индикаторный пенетрант с поверхности КО снимают бязью, смоченной в спирте. Влагу с поверхности изделия удаляют влажной бязью до полного исчезновения с нее капель воды, после чего поверхность считается подготовленной к следующей операции. Проявитель чаще всего наносят кистью. При этом расход проявителя значительно меньше, чем при нанесении его краскораспылителем, окружающий воздух меньше насыщается вредными для человека парами растворителей и аэрозолей.В цеховых условиях применяют также способ посыпания и способ наложения липких пленок. Затем происходит медленное перемещение мениска в глубь трещины (рис. 4.2) и незначительное увеличение индикаторного следа. Размер индикаторного следа определяется объемом пенетранта. извлеченного из устья трещины, после образования мениска по всей ее протяженности.
Средняя ширина индикаторного следа определяется в основном раскрытием поверхностной единичной трещины. Следовательно, для надежного выявления поверхностных дефектов при проведении технологических операций контроля необходимо обеспечить сохранение пенетранта в устье дефекта от момента нанесения до момента его извлечения из дефекта, поэтому операции по нанесению и удалению проникающей жидкости и нанесению проявителя должны проводиться непосредственно одна за другой с минимальным интервалом времени, не следует допускать длительной сушки поверхности после удаления пенетранта. длительной промывки КО и т.п.
Освещенность исследуемой поверхности должна быть не ниже 50 лк. Контроль проводят в затененном помещении, а в полевых условиях — при местном затемнении. При цветном контроле естественное или искусственное освещение на контролируемом участке должно быть не менее 3000 лк. С поверхностей деталей, прошедших контроль и признанных годными, удаляют проявитель и следы других дефектоскопических материалов одним из перечисленных способов: протиркой, промывкой, анодной обработкой, выжиганием, органическими растворителями.
В некоторых случаях в условиях производства возникает необходимость многократного контроля. Перед повторным контролем проводят полный цикл подготовки изделий, тщательно промывая КО ацетоном, бензином или другими растворителями для удаления остатков дефектоскопических материалов из поверхностных дефектов. Небольшие изделия перед повторным контролем рекомендуется помещать на несколько часов в растворители индикаторного красителя. В качестве иллюстрации влияния первичного контроля на последующие проверки на рис. 4.3 приведены результаты двух серий (каждая по пять раз) контроля образцов из стали, на которых при первичном осмотре было обнаружено 11 единичных трещин.Осмотр контролируемой поверхности, как правило, проводят дважды: через 5-6 мин для обнаружения крупных дефектов и через 25-60 мин для обнаружения мелких. При люминесцентном методе контроля используют ультрафиолетовое излучение с длиной волны Сумма площадей индикаторных следов, обнаруженных на образцах, изменяется в зависимости от числа проведенных ранее испытаний.
Между сериями испытаний образцы помешали на 8-10 ч в растворители индикаторного красителя. Из рис. 4.3 видно, что такая обработка образцов почти полностью исключает влияние загрязнений дефектов остатками дефектоскопических материалов, используемых на предыдущих стадиях контроля.
КНК подразделяется на четыре уровня, как указано в табл. 4.2.
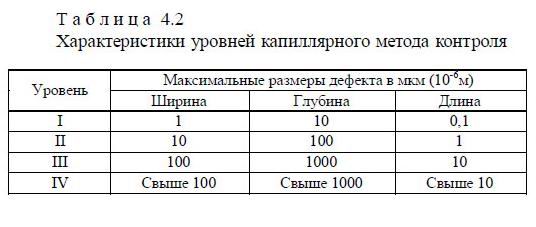
Чувствительность КНК определяется геометрическим к. и оптическим ко факторами: KKHK=f(kr. ko). где f- знак функции.
Геометрический фактор определяется как k=l-y/b, где у— ширина устья дефекта, a b — ширина выделившегося пенетранта. как показано на рис. 4.4.
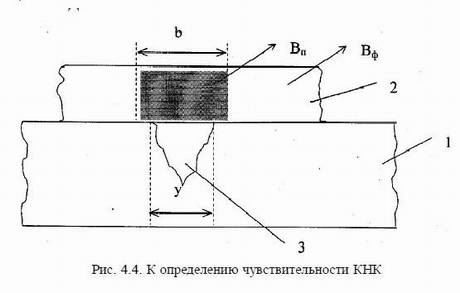
Здесь 1 — контролируемое изделие. 2 — проявитель. 3 — дефект. В6 и Ва — интенсивности света, отражённого от проявителя (фон) и от выделившегося из дефекта пенетранта. Оптический фактор определяется отношением интенсивностей света: ко= В./ Вп .
Приборы для КНК выпускаются серийно. В качестве примеров приведём отечественный прибор ЛДА-3 н прибор США «Тнн-Kq) АФБ». Последний позволяет контролировать в течение часа до 500 лопаток турбин.
Основные положения, которые необходимо знать при КНК. следующие.
1. Подготовку изделий к контролю (удаление жидкостей из поверхностных дефектов) можно проводить путем их нагрева или нанося на их поверхность проявитель. При нагреве изделий выше температуры кипения жидкостей происходит удаление жидкости из дефектов за счет образования пузырьков пара. Температура, при которой происходит выброс жидкости из дефекта, зависит от величины раскрытия дефекта. При широких является практически мгновенно. При нагреве изделий ниже температуры кипения жидкости очистка дефектов происходит за счет испарения жидкостей и пленочного массопереноса ее по стенкам дефекта. Нанесение проявителя на контролируемую поверхность обеспечивает удаление жидкости из устья дефектов приблизительно за 20 мин.
2. Размер индикаторного следа от поверхности единичной трещины определяется в основном объемом индикаторного пенетранта. находящегося в устье трещины, поэтому надежное выявление поверхностных дефектов обеспечивается при условии сохранения пенетранта в устье дефекта от момента его нанесения до момента извлечения его из дефекта.
3. Осмотру с целью обнаружения дефекта не подвергаются детали, состояние проявителя в зонах контроля которых затрудняет видимость индикаторных рисунков. Например, при цветовом варианте КНК осмотру не подвергаются детали, если в слое проявителя имеются пятна не удаленной красной проникающей жидкости, пятна и потеки масляно-керосиновой смеси, непокрытые проявляющей краской участки зоны контроля, частицы пыли, ветоши, следы каких-либо посторонних материалов (из-за применения загрязненных инструментов, приспособлений — краскораспылителей, кистей, захватов и др.).
Общий осмотр проводят невооруженным глазом или с применением луп малого увеличения с большим полем зрения 2.
Размер индикаторного следа от поверхности единичной трещины определяется в основном объемом индикаторного пенетранта. находящегося в устье трещины, поэтому надежное выявление поверхностных дефектов обеспечивается при условии сохранения пенетранта в устье дефекта от момента его нанесения до момента извлечения его из дефекта.
3. Осмотру с целью обнаружения дефекта не подвергаются детали, состояние проявителя в зонах контроля которых затрудняет видимость индикаторных рисунков. Например, при цветовом варианте КНК осмотру не подвергаются детали, если в слое проявителя имеются пятна не удаленной красной проникающей жидкости, пятна и потеки масляно-керосиновой смеси, непокрытые проявляющей краской участки зоны контроля, частицы пыли, ветоши, следы каких-либо посторонних материалов (из-за применения загрязненных инструментов, приспособлений — краскораспылителей, кистей, захватов и др.).
Общий осмотр проводят невооруженным глазом или с применением луп малого увеличения с большим полем зрения. При осмотре отыскивают окрашенный или люминесцирующнй индикаторный рисунок, обращая внимание на основные признаки:
— Трещины любого происхождения, волосовины, закаты, неслитнны. непровары. неспаи, плены выявляются в виде четких, иногда прерывистых окрашенных линий различной конфигурации (рис.4.5. 4.6)
— Растрескивание материала, межкристаллнтная коррозия участков поверхности крупнозернистых сплавов проявляются в виде группы отдельных коротких линий или сетки (рис.4.7. б)
— Межкристалльная коррозия участков поверхности мелкозернистых сплавов выявляется в виде пятен, размытых полос:
— Поры, язвенная коррозия, выкрашивание материала, эрозионные повреждения поверхности выявляются отдельными точками, звездочками (рис.4.7, а).
Обнаружение рисунка, соответствующего указанным выше основным признакам, служит основанием для анализа допустимости дефекта по его размеру, положению, характеру.
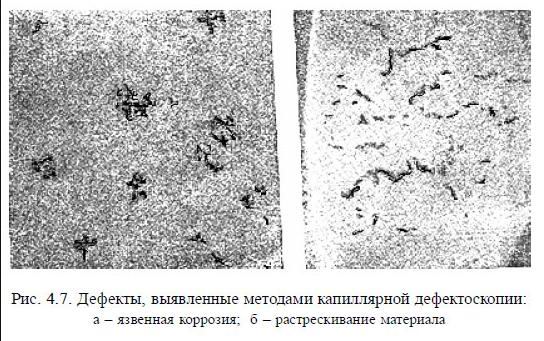
К недостаткам КНК следует отнести высокую трудоемкость контроля при отсутствии механизации; сложность механизации и автоматизации процесса контроля: большую длительность процесса (от 0.5 до 1.5 ч): снижение достоверности результатов при отрицательных температурах, необходимость удаления лакокрасочных покрытий и тщательной предварительной очистки контролируемых деталей: низкую вероятность обнаружения дефектов, перекрытых окисными пленками или сжатых значительными остаточными или рабочими напряжениями в детали: громоздкость стационарного оборудования: вредность некоторых дефектоскопических материалов для персонала и необходимость использования защитных приспособлений и вентиляции: субъективность контроля, зависимость достоверности результатов от умения и состояния контролера: ограниченный срок хранения дефектоскопических материалов, зависимость их свойств от продолжительности хранения и температуры среды.
ПНАЭ Г-7-018-89 Унифицированные методики контроля основных материалов (полуфабрикатов), сварных соединений и наплавки оборудования и трубопроводов АЭУ. Капиллярный контроль
Федеральный надзор России по ядерной и
радиационной безопасности
(Госатомнадзор России)
РУКОВОДСТВА ПО БЕЗОПАСНОСТИ
УНИФИЦИРОВАННЫЕ МЕТОДИКИ
КОНТРОЛЯ
ОСНОВНЫХ МАТЕРИАЛОВ (ПОЛУФАБРИКАТОВ),
СВАРНЫХ СОЕДИНЕНИЙ И НАПЛАВКИ
ОБОРУДОВАНИЯ И ТРУБОПРОВОДОВ АЭУ
КАПИЛЛЯРНЫЙ КОНТРОЛЬ
ПНАЭ Г-7-018-89
Введены
в действие
с 1 июля 1990 г.
Москва
СОДЕРЖАНИЕ
Обязательны для всех министерств, ведомств, организаций и предприятий, осуществляющих проектирование, конструирование, изготовление, монтаж и эксплуатацию оборудования и трубопроводов атомных энергетических установок.
Настоящий документ устанавливает классы чувствительности капиллярного контроля, технологическую последовательность операций при контроле, рецептуру наборов дефектоскопических материалов, требования к контрольным образцам. Методика распространяется на сварные соединения и наплавку, контролируемые в соответствии с требованиями ПНАЭ Г-7-010-89 «Оборудование и трубопроводы атомных энергетических установок. Сварные соединения и наплавки. Правила контроля», и на основные материалы (полуфабрикаты), контролируемые в соответствии с требованиями стандартов и технических условий.
1.1. Капиллярный контроль позволяет обнаружить дефекты, выходящие на поверхность: трещины, поры, раковины, непровары, межкристаллитную коррозию и другие несплошности.
1.2. Поверхностные дефекты обнаруживаются по ярко окрашенным или светящимся индикаторным следам, которые образуются на проявляющем покрытии (проявителе) в местах расположения несплошностей.
1.3. Выявление дефектов, имеющих ширину раскрытия более 0,5 мм, капиллярными методами контроля не гарантируется.
1.4. Контролю капиллярными методами подлежат поверхности изделия, принятые по результатам визуального контроля в соответствии с требованиями действующей нормативной документации. Для сварных соединений и наплавки — в соответствии с требованиями ПНАЭ Г-7-010-89 «Оборудование и трубоп
дефектоскопические+материалы — с английского на русский
1. сущ.1)
а) общ. (регистрационная) запись, помета
to keep [make\] a record — вести записи
See:
б) общ. регистрация, учет, запись, письменная фиксация
record clerk, record keeper — регистратор
record department [room\] — регистратура
Syn:
See:
2)
а) общ. официальный документ, официальная запись, отчет, протокол
Syn:
See:
б) юр. (юридический) документ, письменно зафиксированное свидетельствоto have record — иметь власть [полномочия\] (судить [выносить приговоры\])
в) , общ. учетно-отчетные [регистрационные\] материалы [данные\]
accounting records — бухгалтерская [учетная\] документация
depositary [custodian\] records — документация депозитарных операций
See:
3) , мн. данные, факты; досье, собрание фактов
See:
4)
а) общ. памятник прошлого; исторический документ
б) общ. архив, собрание памятников прошлого
Syn:
5) комп. запись
6)
2. гл.1) общ. записывать, регистрировать
She carefully recorded the events of the meeting. — Она сделала записи о ходе встречи.
2) общ. заносить в список
The clerk recorded their names in the register. — Клерк записал их имена в реестр [список\].
* * *
1) регистрировать, записывать; 2) регистрационные документы.
* * *
• 1) /vt/ делать запись; 2) /vt/ сделать запись; 3) /in passive/ зарегистрированный* * *
Дефектоскопия | Статья о дефектоскопии по The Free Dictionary
— это совокупность методов неразрушающего контроля материалов и изделий с целью выявления дефектов. Он включает в себя разработку методов и аппаратуры (например, дефектоскопов), создание процедур тестирования и обработку данных дефектоскопов.
Различные дефекты — нарушение целостности или однородности материала или отклонение от предписанного химического состава, структуры или размеров — возникают в изделиях в результате несовершенного состояния производственных процессов или эксплуатации в сложных условиях.Дефекты изменяют физические свойства материала (такие как плотность, электропроводность, магнитные и упругие свойства). В основе существующих методов дефектоскопии лежит исследование физических свойств материалов при воздействии рентгеновских лучей; инфракрасные, ультрафиолетовые и гамма-лучи; радиоволны; ультразвуковые колебания; магнитное и электростатическое поля.
Самым простым методом обнаружения дефектов является визуальный метод — невооруженным глазом или с помощью оптических устройств, таких как увеличительные стекла.Специальные трубки с призмами и миниатюрные осветители (диоптрические трубки) и телевизионные трубки используются для исследования внутренних поверхностей, глубоких полостей и труднодоступных мест. Лазеры также используются для тестирования, например, поверхности тонкой проволоки. Визуальная дефектоскопия позволяет обнаруживать только поверхностные дефекты (например, трещины или корки) в металлических изделиях и внутренние дефекты в изделиях из стекла или пластика, прозрачных для видимого света. Минимальный размер дефектов, обнаруживаемых невооруженным глазом, равен 0.1-0,2 мм, или несколько десятков микрон при использовании оптических систем.
Дефектоскопия в рентгеновских лучах основана на поглощении рентгеновских лучей, которое зависит от плотности среды и атомного номера элементов, образующих материал среды. Наличие таких дефектов, как трещины, пузыри или включения постороннего материала, приводит к тому, что лучи, проходящие через материал (рис. 1), в той или иной степени ослабляются. Регистрируя распределение интенсивности переходных лучей, можно определить наличие и расположение различных неоднородностей в материале.
Рисунок 1 Схема рентгеновского облучения: (1) источник рентгеновского излучения, (2) рентгеновский луч, (3) проверяемая деталь, (4) внутренний дефект детали, (5) рентгеновское излучение изображение за деталью (невидимое для глаза), (6) Регистратор рентгеновских изображений
Интенсивность рентгеновских лучей регистрируется несколькими методами. Для записи статьи на пленку используются фотографические методы. Визуальный метод основан на наблюдении изображения предмета на флуоресцентном экране. Этот метод более эффективен при использовании электрооптических преобразователей изображения.В ксерографическом методе изображения создаются на металлических пластинах, покрытых слоем вещества, на поверхность которого нанесен электростатический заряд. Контрастные снимки получаются на пластинах, которые можно использовать повторно. Метод ионизации основан на измерении интенсивности электромагнитного излучения по его ионизирующему воздействию (например, на газ). В этом случае индикатор может быть размещен на значительном удалении от продукта, что позволяет проводить испытания продуктов, нагретых до высоких температур.
Чувствительность методов рентгеновской дефектоскопии определяется отношением длины дефекта в направлении радиоскопии к толщине детали в этом сечении; для различных материалов она составляет 1-10 процентов. Использование рентгеновской дефектоскопии эффективно только для сравнительно тонких изделий, поскольку проникающая способность рентгеновских лучей незначительно увеличивается с увеличением их энергии. Рентгеновская дефектоскопия применяется для обнаружения пузырей, глубоких трещин и ликворальных включений в стальных литых и сварных изделиях толщиной до 80 мм и в изделиях из легких сплавов толщиной до 250 мм.Для этой цели были созданы промышленные рентгеновские установки с лучистой энергией от 5-10 до 200-400 килоэлектронвольт (кэВ; 1 эВ = 1,60210 x 10 -19 джоулей). Изделия большой толщины (до 500 мм) облучаются сверхжестким электромагнитным излучением с энергией в несколько десятков МэВ, генерируемым в бетатроне.
Гамма-дефектоскопия имеет те же физические принципы, что и рентгеновская дефектоскопия, но используется гамма-излучение, испускаемое искусственными радиоактивными изотопами различных металлов (таких как кобальт, иридий или европий).Для облучения толстых деталей используется лучистая энергия от нескольких десятков кэв до 1-2 МэВ. Этот метод имеет существенные преимущества перед рентгеновской дефектоскопией: сравнительно простое оборудование и компактный источник излучения, что позволяет исследовать труднодоступные части изделий. Более того, этот метод может быть использован, когда рентгеновское обнаружение дефектов затруднено (например, при полевых испытаниях). При работе с источниками рентгеновского и гамма-излучения должна быть обеспечена биологическая защита.
Радиографический контроль основан на проникающих свойствах радиоволн в сантиметровом и миллиметровом диапазонах (микроволны) и позволяет обнаруживать дефекты преимущественно на поверхности изделий, изготовленных из неметаллических материалов.Из-за низкой проникающей способности микроволн возможность радиографического контроля металлических изделий ограничена. Этот метод используется для обнаружения дефектов в листовой стали, стальных стержнях и стальной проволоке во время их изготовления, а также для измерения их толщины или диаметра, толщины диэлектрических покрытий и т. Д. Микроволны от генератора, работающего в непрерывном или импульсном режиме, проникают в продукт через электромагнитные сигналы и, пройдя через усилитель, регистрируются приемником.
Инфракрасная дефектоскопия использует инфракрасные (тепловые) лучи для обнаружения включений, непрозрачных для видимого света.Так называемое инфракрасное изображение дефекта создается переходным, отраженным или собственным излучением исследуемого продукта. Этот метод используется для тестирования изделий, которые нагреваются во время работы: дефектные детали в изделии изменяют тепловой поток. Через изделие проходит поток инфракрасного излучения, и его распределение регистрируется термочувствительным приемником. Неоднородность структуры материалов также может быть исследована методом ультрафиолетовой дефектоскопии.
Магнитная дефектоскопия основана на исследовании искажений магнитного поля, возникающих в местах дефектов изделий из ферромагнитных материалов.Индикатором может служить магнитный порошок (оксид железа или железа) или его суспензия в масле с дисперсностью частиц 5-10 микрон. При намагничивании изделия порошок осаждается в местах дефектов (метод магнитного порошка). Поле рассеяния может быть записано на магнитной ленте, которую прикладывают к исследуемому сечению намагниченного изделия (магнитографический метод). Также используются небольшие датчики (феррозонды), которые при движении по изделию показывают изменения импульса тока в месте дефекта, которые регистрируются на экране осциллографа (метод феррозонда).
Чувствительность метода магнитной дефектоскопии зависит от магнитных характеристик материалов, используемых индикаторов и типов намагничивания продукта. Магнитопорошковый метод позволяет обнаруживать трещины и другие дефекты на глубину до 2 мм; Магнитографический метод используется в первую очередь для испытания сварных швов труб толщиной до 10-12 мм, а также для обнаружения мелких трещин и плохого проплавления. Метод феррозонда лучше всего подходит для обнаружения дефектов на глубине до 10 мм, а в некоторых случаях до 20 мм в изделиях правильной формы.Этот метод позволяет полностью автоматизировать тестирование и отбраковку. Намагничивание изделий осуществляется с помощью магнитных дефектоскопов, которые создают магнитные поля достаточной интенсивности. После тестирования изделия тщательно размагничиваются.
Методы магнитной дефектоскопии используются для исследования структуры материалов (магнитная структурометрия) и измерения толщины (магнитный толщиномер). Магнитная структурометрия основана на определении основных магнитных характеристик материала (коэрцитивная сила, индукция, остаточный магнетизм и магнитная проницаемость), которые обычно зависят от структурного состояния сплава, подвергнутого различным видам термической обработки.Магнитная структурометрия используется для определения структурных компонентов сплава, которые присутствуют в нем в небольших количествах и которые существенно отличаются по своим магнитным характеристикам от основы сплава, а также для измерения таких качеств, как глубина поверхностного упрочнения и поверхностного упрочнения. . Магнитный толщиномер основан на измерении силы притяжения постоянного магнита или электромагнита к поверхности изделия из ферромагнитного материала, на которое нанесен слой немагнитного покрытия; позволяет определить толщину покрытия.
Индуктивная (вихретоковая) дефектоскопия основана на возбуждении вихревых токов переменным магнитным полем датчика дефектоскопа. Вихревые токи создают собственное поле, противоположное по знаку возбуждающему полю. В результате взаимодействия этих полей общее сопротивление катушки датчика изменяется, и это изменение фиксируется индикатором. Показания индикатора зависят от электропроводности и магнитной проницаемости металла, размера изделия и изменений электропроводности, вызванных структурными неоднородностями или нарушениями целостности металла.
Датчики вихретоковых дефектоскопов выполнены в виде индукционных катушек, внутри которых размещаются изделия (сквозные датчики) или которые прикрепляются к изделию (съемные датчики). Использование вихретоковой дефектоскопии позволяет автоматизировать контроль качества проволоки, прутков, труб и секций, движущихся с высокими скоростями при их изготовлении, а также непрерывное измерение размеров. Вихретоковые дефектоскопы могут использоваться для контроля качества термообработки, для оценки загрязнения металлов с высокой проводимостью (таких как медь или алюминий), для определения глубины слоев химической и термической обработки с точностью до 3 процентов. для сортировки определенных материалов, для измерения электропроводности неферромагнитных материалов с точностью до 1 процента и для обнаружения поверхностных трещин глубиной в несколько микрон и размером в несколько десятых миллиметра.
Термоэлектрическая дефектоскопия основана на измерении электродвижущей или термоэлектродвижущей силы, которая возникает в замкнутой цепи при нагревании точки контакта двух разных материалов. Если один из этих материалов принять за эталон, для данной разницы температур между горячим и холодным контактами величина и знак термоэлектродвижущей силы будут определяться химическим составом второго материала. Этот метод обычно используется в тех случаях, когда необходимо определить марку материала, из которого изготовлено промежуточное изделие или конструктивный элемент, а также готовые конструкции.
Трибоэлектрическая дефектоскопия основана на измерении электродвижущей силы, возникающей при трении материалов различной природы. Измеряя разность потенциалов между стандартными материалами и тестируемыми материалами, можно различать типы определенных сплавов.
Электростатическая дефектоскопия основана на использовании электростатического поля, в которое помещается изделие. Для наблюдения за трещинами на поверхности изделий из непроводящих материалов (фарфора, стекла и пластика), а также металлов, покрытых этими материалами, изделие покрывают мелким порошком мела из пульверизатора с эбонитовым наконечником (порошок метод).Таким образом, частицы мела получают положительный заряд. В результате неоднородности электростатического поля частицы мела скапливаются по краям трещин. Этот метод также используется для испытаний изделий из изоляционных материалов. Перед нанесением на них частиц необходимо смочить ионогенной жидкостью.
Ультразвуковая дефектоскопия основана на использовании упругих колебаний, в основном в ультразвуковом диапазоне частот. Нарушение непрерывности или однородности среды влияет на распространение упругих волн в изделии или на условия колебания изделия.Основными ультразвуковыми методами являются эхо, теневой, резонансный и велосиметрический методы (собственно ультразвуковые методы), а также импедансный метод и метод свободных колебаний (акустические методы).
Самый универсальный метод эхо-сигнала основан на отправке коротких импульсов ультразвуковых колебаний в изделие (рис. 2) и регистрации интенсивности и времени возврата эхо-сигналов, отраженных от дефектов. Для проверки изделия датчик эходефектоскопа сканирует его поверхность. Метод позволяет наблюдать поверхностные и внутренние дефекты различной ориентации.Созданы промышленные установки для испытаний различных типов изделий. Эхо-сигналы можно наблюдать на экране осциллографа или записывать записывающим устройством. В последнем случае повышаются надежность и объективность оценки, а также производительность и воспроизводимость тестирования. Чувствительность эхо-метода очень высока: при оптимальных условиях тестирования на частоте 2-4 мегагерца (МГц) можно наблюдать дефекты, отражающая поверхность которых составляет около 1 кв. Мм.
Рисунок 2 Блок-схема ультразвукового эхо-дефектоскопа: (1) генератор электрических импульсов, (2) пьезоэлектрический преобразователь (селекторная головка), (3) схема приема-усиления, (4) таймер, (5) генератор развертки, (6) катодная трубка. / — начальный сигнал, 8 — обратный поворот дна, а DF — вспышка от дефекта.
При теневом методе ультразвуковые колебания, попадающие в дефект, отражаются в противоположном направлении. О наличии дефекта можно судить по уменьшению энергии ультразвуковых колебаний или по изменению фазы колебаний, которые проходят вокруг дефекта.Метод широко используется для испытания сварных швов и рельсов.
Резонансный метод основан на определении собственных резонансных частот упругих колебаний с частотой 1-10 МГц, возбуждаемых внутри изделия. Таким способом измеряется толщина стенок металлических и некоторых неметаллических изделий. Когда измерения можно проводить только с одной стороны, точность измерений составляет около 1 процента. Кроме того, с помощью этого метода можно обнаружить зоны коррозионного повреждения.Резонансные дефектоскопы используются как для ручного тестирования, так и для автоматизированного тестирования (при записи показаний прибора).
Велосиметрический метод эхо-дефектоскопии основан на измерении изменения скорости распространения упругих волн в зоне расположения дефектов в многослойных конструкциях; его используют для поиска участков нарушения сцепления между металлическими слоями.
Метод импеданса основан на измерении механического сопротивления (импеданса) изделия датчиком, который сканирует его поверхность и возбуждает в ней упругие колебания звуковой частоты.Этот метод позволяет находить дефекты в слоистых и паяных соединениях, а также между тонкой оболочкой и элементами жесткости или наполнителями в многослойных конструкциях. Дефекты площадью 15 кв. Мм и более помечаются сигнализатором и могут быть зафиксированы автоматически.
Метод свободных колебаний основан на анализе спектра свободных колебаний испытываемого изделия при его ударе; его применяют для поиска участков разрыва стыков между элементами многослойных слоистых конструкций значительной толщины из металлических и неметаллических материалов.
Ультразвуковая дефектоскопия, использующая несколько переменных параметров (частотный диапазон, тип волн, условия излучения и способы установления контакта), является одним из наиболее универсальных методов неразрушающего контроля.
Капиллярная дефектоскопия основана на искусственном усилении светового и цветового контраста дефектного участка по сравнению с неповрежденным участком. Методы капиллярной дефектоскопии позволяют невооруженным глазом обнаруживать мелкие поверхностные трещины и другие неоднородности материала, образующиеся при изготовлении и использовании деталей машин.Полости поверхностных трещин заполняются специальными индикаторными веществами (пенетрантами), которые пропитывают их под действием капиллярных сил. Для так называемого люминесцентного метода пенетранты основаны на люминофоре (керосин, , нориол, и другие). Проявитель в виде мелкодисперсного белого порошка (оксида магния или талька), обладающего сорбционными свойствами, наносится на поверхность, очищенную от излишков пенетранта; Благодаря сорбционным свойствам порошка, частицы пенетранта вытягиваются из полостей трещин, показывая контуры трещин и ярко светясь в ультрафиолетовом свете.При так называемом цветовом методе испытания пенетранты изготавливаются на основе керосина с добавлением бензола, скипидара и специальных красителей (например, красной краски). Для испытания изделия с темной поверхностью используется окрашенный люминофором магнитный порошок (магнитолюминесцентный метод), позволяющий легче увидеть мелкие трещины.
Чувствительность методов капиллярной дефектоскопии позволяет видеть поверхностные трещины с раскрытием менее 0,02 мм. Однако использование этих методов ограничено из-за высокой токсичности пенетрантов и проявителей.
Дефектоскопия — это равноправное и неотъемлемое звено технологических процессов, позволяющее повысить надежность продукции. Однако методы дефектоскопии не являются абсолютными, так как на результаты тестов влияет ряд случайных факторов. Об отсутствии недостатков в статье можно говорить лишь с определенной долей уверенности. Надежность тестов повышается за счет автоматизации, совершенствования методов и рационального сочетания нескольких методов. Полезность изделий определяется стандартами качества, которые формулируются на этапе проектирования и разработки технологии производства.Стандарты качества различны для разных типов изделий, для изделий одного типа, которые работают в разных условиях, и даже для различных областей одного и того же изделия, если они подвержены различным механическим, термическим или химическим воздействиям.
Использование дефектоскопа в производственном процессе и при эксплуатации изделий дает большой экономический эффект с точки зрения сокращения времени, затрачиваемого на обработку изделий с внутренними дефектами, а также с точки зрения расхода металла.Кроме того, дефектоскопия играет значительную роль в предотвращении повреждений конструкций, увеличивая их надежность и срок службы.
СПИСОК ЛИТЕРАТУРЫ
Трапезников А.К. Рентгенодефектоскопия . М., 1948.Жигадло, А.В. Контроль деталей метода магнитного порошка . М., 1951.
Таточенко Л.К., Медведев С.В. Промышленная гаммадефектоскопия . Москва, 1955.
Дефектоскопия металлов: Сб.ул ‘. Под редакцией Д. С. Шрайбера. Москва 1959.
Современные мелодии контроля материалов без разрушения . Под редакцией С. Т. Назарова. М., 1961.
Кифер И.И. Испытания ферромагнитных материалов , 2-е изд. Москва-Ленинград, 1962.
Гурвич, А.К. Ультразвуковая дефектоскопия сварнытин в соетии Киев, 1963.
Шрайбер Д.С. Ультразвуковая дефектоскопия . Москва, 1965.
Неразрушающие испытания: Справочник , кн. 1-2.Под редакцией Р. Макмастера. Москва-Ленинград, 1965. (Пер. С англ.)
Дорофеев А.Л. Электроиндуктивная (индукционная) дефектоскопия . Москва, 1967.
Большая Советская Энциклопедия, 3-е издание (1970-1979). © 2010 The Gale Group, Inc. Все права защищены.
.Ультразвуковое обнаружение дефектов и визуализация через реверберационные слои с помощью подпространственного анализа и проецирования
Ультразвуковое обнаружение дефектов и визуализация через реверберирующие слои представляют собой сложные проблемы из-за реверберации, вызванной слоем, и отражений от передней поверхности. Эти нежелательные сигналы представляют собой сильные помехи и маскируют дефектные эхо. В этой статье разработан подход на основе подпространства для удаления или значительного уменьшения нежелательных ревербераций, что позволяет правильно обнаруживать дефекты и формировать изображения.Этот метод использует набор независимых эталонных измерений материала, проходящего через слой, без помех. Если эти измерения недоступны, вместо них используются массивные измерения материала с дефектами. Беспорядок, из-за его высокой силы по сравнению с отражениями дефекта, формирует подпространство, охватываемое собственными векторами, соответствующими доминирующим собственным значениям ковариационной матрицы данных. Подпространство препятствий оценивается и удаляется с использованием ортогональной проекции подпространства. Беспорядок обычно занимает многомерное подпространство, которое зависит от уровня связи, неоднородности материала, шероховатости поверхности и частоты дискретизации измерений.Когда ссылка только на помехи недоступна, методы теории информации используются для оценки размера подпространства помех, так что сигналы помех в достаточной степени подавляются без искажения сигналов дефектов. Эффективность предложенного подхода демонстрируется с использованием моделирования и реальных результатов измерений.
1. Введение
Ультразвуковое обнаружение и визуализация дефектов через слой или экран — сложные проблемы, возникающие при ультразвуковой неразрушающей оценке (NDE).В частности, промышленные материалы часто производятся в виде нескольких слоев, которые создают сильные отражения на границах раздела слоев при воздействии ультразвукового контроля. Эти отражения обычно повторяются в ходе ультразвуковых измерений, вызывая сильные и повторяющиеся модели реверберации [1]. В медицинском ультразвуке прямой доступ к интересующей ткани не всегда возможен, и поэтому ультразвуковые измерения часто выполняются через другую ткань или анатомическую структуру [2].Например, при ультразвуковой визуализации головного мозга для выявления аномалий или опухолей измерения проводятся через череп, который представляет собой сильный сигнал реверберации.
Реверберационные сигналы, индуцированные верхним слоем (т. Е. Экраном визуализации), часто маскируют эхо-сигналы от цели и делают обнаружение и локализацию дефектов материала или аномалий тканей чрезвычайно трудным, если не невозможным. Следовательно, такие сигналы реверберации (которые в дальнейшем также называются помехами реверберации или просто помехами) должны подавляться или в достаточной степени ослабляться, чтобы выявить целевые эхо-сигналы.Большинство существующих подходов к реверберации основано на идеальной модели распространения акустической волны в слоистых средах [1, 3–6]. Например, Saniie и Nagle разработали аналитические модели моделей реверберации, измеренных в многослойной среде [1]. Эти модели используются для классификации эхо-сигналов, связанных с каждым слоем. Метод прогнозирующей деконволюции [7], обычно используемый для подавления реверберации при сейсмических исследованиях, был применен для подавления реверберации ультразвука [3, 4].Этот метод также предполагает, хотя и неявно, идеальную модель распространения, полагаясь на повторяемость шаблонов реверберации. Методы, представленные в [5, 6], предназначены для идентификации реверберационных эхо-сигналов в многослойных средах на основе анализа времени пролета всех возможных эхо-сигналов и сравнения их спектров мощности. В дополнение к идеальным моделям распространения, упомянутым выше, эти методы предполагают наличие неперекрывающихся эхосигналов, пригодных для анализа времени пролета, который требует, чтобы толщина каждого слоя была относительно большой по сравнению с длиной волны эхо-сигнала.Кроме того, существующие подходы часто связаны с ультразвуковыми измерениями в дальней зоне преобразователя и, как таковые, используют методы погружения. Эти методы непрактичны для сценариев полевых испытаний при ультразвуковом неразрушающем контроле, когда только контактные измерения могут выполняться в ближней зоне преобразователя. Проведение контактных измерений через слой дополнительно осложняется проблемами связи и сильными нерегулярными эхо-сигналами от передней поверхности слоя. Образцы реверберации в этих случаях нельзя просто предсказать и удалить из измерений.
Среди различных возможных подходов к значительному ослаблению помех при обработке радиолокационных сигналов обычно используется прямое вычитание фонового ответного сигнала, измеренного в пустых эталонных сценах, из ответного сигнала с целями (дефектами) [8]. Однако прямое применение этого метода к практическому подавлению ультразвуковой реверберации оказывается неэффективным из-за значительных вариаций ультразвуковых измерений из-за сцепления, неоднородности материала и шероховатости поверхности.
В этой статье мы предлагаем альтернативный подход, основанный на обучении и проецировании подпространства реверберации. Этот подход был недавно использован в радиолокационных изображениях сквозь стены для удаления помех от стен и улучшения видимости внутренних целей [9, 10], а также в наземных радарах для обнаружения наземных мин [8, 11]. В предлагаемом подходе помехи устраняются путем проецирования принятого сигнала на подпространство, которое ортогонально основанию возможных ответов на помехи.Чтобы построить комплексное подпространство помех для эффективного удаления помех, мы рассмотрим два случая обучения подпространству реверберации, которые представляют интерес для ультразвукового NDE, а именно: (i) обучение подпространству на основе эталонов (в автономном режиме) с использованием набора безупречных измерений реверберации и (ii) обучение подпространству без ссылок непосредственно из данных массива онлайн. Последнее особенно важно при визуализации массивов NDE, когда доступ к исправной реплике недоступен [12]. В первом случае мы используем несколько независимых измерений реверберации из выбранных мест, используя здоровую копию исследуемого материала.Затем мы строим подпространство препятствий, используя модель возмущений на основе сдвига, чтобы учесть изменения, вызванные контактами поверхности, неоднородностью материала и шероховатостью поверхности. Во втором случае мы используем массив физической или синтетической апертуры и формируем подпространство помех, используя пространственную когерентность сигналов реверберации и некогерентность эхо-сигналов дефекта в данных массива. В обоих случаях помехи часто занимают несколько измерений подпространства, в зависимости от уровня связи, неоднородности материала, шероховатости поверхности и частоты дискретизации измерений.Следовательно, размер подпространства препятствий должен быть правильно оценен перед применением ортогональной проекции. Недооценка подпространства помех может привести к недостаточному удалению помех. С другой стороны, особенно во втором случае, когда сигналы дефекта присутствуют в конструкции подпространства помех, переоценка подпространства помех приведет к удалению сигнала дефекта. Чтобы избежать этой проблемы, методы теории информации используются для оценки размера подпространства помех, так что сигналы помех в достаточной степени подавляются, не искажая сигналы дефектов.
Эффективность предложенного метода проверена и продемонстрирована с использованием как моделирования, так и данных реальных экспериментов. Результаты ясно показывают, что сильные помехи могут быть значительно подавлены с помощью предлагаемой техники, основанной на обучении подпространству и ортогональной проекции подпространства. Для сравнения мы также применяем методы вычитания фона и предиктивной деконволюции, которые показывают худшие характеристики по сравнению с предлагаемым методом при наличии нерегулярных вариаций.
Остальная часть документа организована следующим образом.В разделе 2 представлена техника построения и проецирования подпространства помех с использованием безупречных эталонных измерений реверберации. В разделе 3 представлена техника построения и проецирования подпространства помех без опорных точек на основе данных массива преобразователей. В разделе 4 представлены результаты моделирования и экспериментальных методов устранения препятствий в обоих сценариях.
2. Удаление помех с использованием эталонных измерений реверберации
2.1. Предлагаемый метод
Рассмотрим проблему обнаружения дефектов и визуализации через реверберирующий слой, как показано на рисунке 1.Начнем с рассмотрения одного измерения датчика, которое может содержать дефектные эхо, и помехи от реверберации, при наличии аддитивного шума измерения. где шум представляет собой белый гауссовский шум с нулевым средним и не зависит от дефектных эхосигналов и помех от реверберации. Шум измерений обычно не считается серьезным препятствием, поскольку его влияние можно уменьшить путем усреднения по нескольким наблюдениям. Помехи реверберации имеют квазипериодическую природу, затухающую во времени, причем периодичность и степень затухания зависят от толщины и плотности слоя.В идеальных условиях измерения (например, слой погружен в воду в дальнем поле преобразователя) сигнал реверберации от слоя может быть смоделирован как суперпозиция сдвинутых во времени и масштабированных по амплитуде копий эхо-вейвлета импульса преобразователя. , как [1] где обозначает разницу во времени прихода последовательных эхо-сигналов, обозначает коэффициент отражения от пути распространения к слою и обозначает коэффициенты передачи от пути распространения к слою и слоя к пути распространения соответственно.Эту аналитическую модель реверберации можно интерпретировать как наложенные эхо с неизвестными задержками и амплитудами. Кроме того, сигнал реверберации можно оценить с помощью алгоритма оценки максимального правдоподобия [13].
Для контактных измерений, рассматриваемых в этой статье, сигнал реверберации не соответствует идеальной модели по ряду причин. Во-первых, поскольку измерения проводятся в ближнем поле, сильное отражение от передней поверхности (большой взрыв) на границе преобразователь-слой значительно усложняет реверберирующую диаграмму.Во-вторых, сигнал реверберации меняется от одного измерения к другому в зависимости от связи между преобразователем и слоем, а также границы между слоем и исследуемым материалом. С другой стороны, дефектные эхо-сигналы представляют собой краткосрочные сигналы с гораздо меньшей энергией по сравнению с помехами реверберации. Кроме того, в зависимости от местоположения дефекта в материале, возвратное эхо-сигнал имеет более длительное время прихода, чем у отраженных помех. Таким образом, дефектные эхо-сигналы имеют очень низкую корреляцию с помехами реверберации.Наша цель — устранить помехи от реверберации без значительного ослабления дефектных эхо. С этой целью мы используем высокую энергию и низкую корреляционные свойства реверберационных помех по отношению к дефектным эхо.
Чтобы смоделировать помехи реверберации, мы собираем
.FlawExplorer NDT — Dantec Dynamics

FlawExplorer — это портативная, компактная и надежная система контроля лазерной шеарографии для неразрушающего контроля (NDT) и контроля качества композитов и металлических материалов с областями контроля от 10 см 2 до ~ 2 м 2 ( ~ 20 футов 2 ) за один снимок.

Ключ Преимущества
- Очень портативный, простой в установке и готовый к работе за секунды
- Компактная, прочная конструкция с лазерными диодами класса 3R для использования на месте и в полевых условиях
- Эффективный контроль больших площадей с быстрым обнаружением и определением характеристик дефекты
- Визуализация структурной информации композита, такой как перепады слоев, переборки, перекрытия, стыки, стрингеры, ребра и т. д.
- Улучшенные фазовые карты в реальном времени позволяют обнаруживать дефекты в реальном времени без какой-либо пост-обработки.
- Позволяет пользователям непосредственно отмечать дефекты на проверяемых образцах.
- Расширенная фильтрация изображений дает четкие и однозначные результаты.
- Расширенные настраиваемые функции отчетности.
- Дополнительные модули: Интерфейсы для термической, вакуумной или вибрационной нагрузки и автоматизации роботов
Принцип измерения
Laser Shearography — это метод оптических измерений для неразрушающего контроля (NDT) и контроля качества, обычно используемый для композитных и металлических материалов.
.Physical / Case | Масса | 5,6 фунта (2,54 кг) |
Размеры (Ш x В x Г) | 5,75 дюйма. x 9,50 дюйма. х 3,00 дюйма. (146 мм x 241 мм x 76 мм) | |
Рабочая температура | от 14 до 122 ° F (от -10 до 50 ° C) | |
Конструкция корпуса | Алюминиевый корпус, резиновые заглушки | |
Тип разъема | Двойной BNC | |
Клавиатура | Конструкция клавиатуры | Клавиши с тактильной мембранной обратной связью, управление колесом |
Преобразователь | Тип преобразователя | Одиночный, двойной, угловой, контактный, с задержкой |
Диапазон частот | 0.От 5 МГц до 30,0 МГц | |
Длина кабеля | 6 футов (1,83 м) стандартный | |
Источник питания | Источник питания | Одиночный литий-ионный аккумулятор |
Срок службы батареи | 8 часов | |
Дисплей | Тип дисплея | Цветной VGA для чтения на солнце, 60 Гц |
Размер дисплея | 640 x 480 пикселей, 3,40 дюйма. х 4,55 дюйма. (86 мм x 116 мм) | |
Сертификация | Сертификация | Заводская калибровка |
Гарантия | Гарантия | 1 год |
Измерения | Диапазон толщины | 0.01дюйм. до 400000 дюймов (От 0,254 мм до 10160 мм) |
Отображаемые единицы | дюйм / мм | |
Разрешение | 0,01 дюйма. (0,254 мм) | |
Демпфирование | 8 уровней демпфирования 25-375 Ом | |
Задержка | от 0 до 165 дюймов / мкс (от 0 до 4 191,00 мм / мкс) на полном диапазоне | |
Режим отображения | RF, + HW, -HW, FW заполнено или выделено | |
Диапазон скорости материала | 0.От 0490 до 0,9999 дюйма / мкс (от 1,24 до 25,40 мм / мкс) | |
Скорость захвата | ||
Генератор / приемник | от 10 Гц до 5000 Гц, от 50 В до 450 В — пиковые и прямоугольные импульсы | |
Ширина импульса | от 20 нс до 10 000 нс в режиме прямоугольной волны | |
Прирост | 100 дБ | |
Ворота | Контакт, IP-1-й, 1-й-2-й (допускает сквозное покрытие, задержку, барботер, погружение) | |
IP Blocking, IF Blocking, IF-1st, 1st-2nd, Echo Blk, POS или NEG gating | ||
2 дефлектора | ||
Интерфейс | ввода / вывода | USB |
Память | Съемная SD-карта до 2 ГБ |