Что такое дефектоскопия и неразрушающий контроль
Что такое дефектоскопия и неразрушающий контроль | КазЭкспертПромОставить онлайн-заявку
+7 727 222 333 2
+7 777 7 9999 19
г. Алматы, ул. Менжинского, 55/16,
[email protected]
- Главная
- Блог
- Что такое дефектоскопия и неразрушающий контроль
21.10.2019
Общие сведения
Дефектоскопия — это процесс, позволяющий обнаруживать изъяны в различных конструкциях с помощью современного оборудования. Под этим термином также понимаются разработка методов контроля, приборов; обработка данных, получаемых с дефектоскопов.
Дефекты появляются абсолютно во всех материалах по нескольким причинам:
- эксплуатация в суровых условиях;
- динамическая нагрузка;
- несовершенство технологии получения материала;
- линейное расширение.
Одно из направлений, в котором востребована дефектоскопия, — это промышленная безопасность компаний.
Методы
Известно, что дефекты ведут к изменению физических параметров изделия, конструкции: плотности, электропроводности, упругости и т.д. Исследование этих параметров и является основой многих современных методов дефектологии, которые бывают:
-
Визуальными. При исследовании внутренних поверхностей, глубоких полостей используют призматические трубки с миниосветителями, лазеры, миниатюрные видеокамеры. Осмотр может также происходить с помощью увеличительного стекла или без каких-либо приспособлений.
Визуальный способ позволяет обнаруживать поверхностные дефекты: трещины, щели, плены — от 0,1 мм до десятков микрон.
- Рентгеновскими. Плотность материала влияет на поглощение им рентгеновских лучей. Выявляются скрытые дефекты: трещины, раковины, инородные вещества, неоднородность. Интенсивность излучения регистрируется фотографически, визуально, электронно-оптическим, ионизационным способами. Такое проведение дефектоскопии оправдано при изучении материала небольшой толщины — стали до 80 мм и легких сплавов до 250 мм.
-
Радиоактивными. Принцип такой же, как и у рентгеновских. Используется гамма-излучение радиоактивных изотопов металлов (кобальта, иридия). Преимущество таких методов — простота, компактность аппаратуры, незаменимой в полевых условиях и при изучении труднодоступных участков конструкций.
Радиоволновыми. Позволяют находить поверхностные дефекты (преимущественно неметаллических материалов).
Используется санти- и миллиметровый диапазон. Методы помогают исследовать тонкие металлические листы, проволоку, толщину защитных, диэлектрических покрытий.
- Инфракрасными. Здесь используется нагрев материала. Дефекты изменяют тепловой поток, который регистрируется теплочувствительным принимающим устройством.
-
Магнитными. Исследуются ферромагнитные материалы. При этом используется в качестве индикатора магнитный порошок или его суспензия. При намагничивании материала порошок оседает на дефективных участках. Магнитографический способ предполагает использование специальной магнитной пленки, накладываемой на изделие. Он помогает обнаруживать трещины на глубине до 2мм.
Феррозондовый метод основан на изменении тока, регистрируемом осциллоскопом, при прохождении прибором через дефектный участок. Он позволяет исследовать участки до 20мм. Контроль и отбраковка изделий таким методом могут быть автоматизированы.
-
Электроиндуктивными. Принцип заключается в использовании переменного магнитного поля. Датчиком регистрируется изменение вихревых токов. На показания прибора влияют: электропроводность, магнитопроницаемость, размеры изделия, неоднородность его структуры.
Датчики токовихревых дефектоскопов представляют собой катушки индуктивности. Методы поддаются автоматизации.
-
- Трибоэлектрическими. Принцип заключается в изменении ЭДС, которая возникает при трении материалов различного рода. Один из материалов принят за эталон.
-
Электростатическими. Методы основаны на использовании электростатического поля, в которое помещается изделие. Они подходят для исследования металлов и неметаллов.
Исследуемый предмет покрывают тонким слоем мела из распылителя с эбонитовым наконечником. Положительно заряженные частицы мела указывают на неоднородность изделия, скапливаясь в дефективных местах.
- Ультразвуковыми. Здесь используется регистрация упругих колебаний, которые в неоднородной среде распространяются по-разному.
Заключение
В обучение по промышленной безопасности может входить умение работать с приборами, дефектоскопами, позволяющими проводить неразрушающий контроль. Важно уметь обрабатывать полученные данные.
Возврат к списку
Ультразвуковая дефектоскопия
Что такое ультразвуковая дефектоскопия и для чего она нужна. Эхо-импульсный, эхо-зеркальный и теневой методы. Достоинства и недостатки ультразвуковой дефектоскопии.
Содержание статьи
Что такое ультразвуковая дефектоскопия?
Ультразвуковая дефектоскопия представляет собой совокупность методов неразрушающего контроля, использующих для нахождения дефектов в изделиях ультразвуковые волны. Полученные данные затем анализируются, выясняется форма дефектов, размер, глубина залегания и другие характеристики.
Позволяет надёжно и эффективно проверять качество стального литья, сварных соединений, литых заготовок. Применяется при изготовлении и эксплуатации железнодорожных рельс, частей авиационных двигателей, трубопроводов в атомных реакторах и контроля иных ответственных изделий. Самый совершенный инструмент диагностики — дефектоскоп на фазированных решетках.
Ультразвуковые преобразователи к содержанию
В промышленности металлы, как правило, проверяют ультразвуком с частотой в диапазоне от 0,5 МГц до 10 МГц. В определённых случаях сварные швы обследуют волнами, имеющими частоту до 20 МГц. Благодаря этому можно выявлять дефекты весьма небольшого размера. Объекты значительной толщины, в частности отливки, поковки, сварные соединения, сделанные электрошлаковой сваркой, а также металлы крупнозернистого строения, например, чугун и некоторые виды стали проверяют ультразвуком с низкими частотами.
Пьезоэлектрическими преобразователями называются приборы, которые возбуждают и принимают ультразвуковые волны.
Совмещённые преобразователи имеют в своём составе пьезоэлемент, который может в один момент времени испускать ультразвук, а в следующий принимать.
В раздельно-совмещенных аппаратах один пьезоэлемент является источником ультразвуковых волн, а другой их улавливает.
В раздельных пьезоэлемент служит либо генератором, либо приёмником ультразвука.
В контактных преобразователях ультразвуковые волны излучаются в исследуемый объект через тонкую прослойку жидкости.
В иммерсионном устройстве его поверхность и изделие разделены слоем жидкости, во много раз превышающим длину волны. Для этого образец помещают в иммерсионную ванну, применяют струю воды и т.д.
В контактно-иммерсионном преобразователе имеется специальная ванна с эластичной мембраной, контактирующей с проверяемым изделием.
В бесконтактных установках ультразвуковые колебания возбуждаются с помощью различных физических эффектов через воздушный промежуток. Их чувствительность уступает преобразователям других типов в десятки тысяч раз.
Способы контроля с помощью ультразвука к содержанию
Эхо-импульсный способ самый широко распространённый и простой. Преобразователь излучает зондирующие сигналы и сам же регистрирует отражённые дефектами эхо-сигналы.
По временному интервалу между посылаемыми сигналами и эхо можно узнать, где и на какой глубине находится дефект, а по амплитуде сигнала – каковы его размеры. К достоинствам данного способа следует отнести:
К достоинствам данного способа следует отнести:
- Возможность провести проверку с использованием только одного преобразователя;
- Хорошо находит внутренние дефекты;
- Очень точно определяет местонахождение дефекта.
Основные его недостатки это:
- К поверхностным отражателям помехоустойчивость оставляет желать лучшего;
- Отражённый сигнал слишком сильно зависит от того, как ориентирован дефект;
- Нельзя контролировать акустический контакт, когда преобразователь перемещается по проверяемому объекту, потому что эхо на участках без дефектов отсутствует.
Эхо-зеркальный метод нуждается в двух преобразователях. Их располагают по одну сторону проверяемого изделия так, чтобы один прибор мог улавливать сигнал излучаемый другим. В приёмник поступает ультразвук, отражённый от дефекта и от донной поверхности.
К недостаткам следует отнести необходимость менять через определённые промежутки времени расстояние между преобразователями.
Теневой метод требует доступа преобразователей к проверяемому изделию с двух сторон, причём устройства обязаны находиться на одной акустической оси. О присутствии в объекте дефекта судят по серьёзному снижению амплитуды принимаемого сигнала либо его полному исчезновению. Основные достоинства подобного метода это: хорошая помехоустойчивость и низкая зависимость амплитуды сигнала от ориентации дефекта.
Преимущества и недостатки ультразвуковой дефектоскопии к содержанию
Ультразвуковой контроль в промышленности используется с 50 годов прошлого века. В то время инструментами для диагностики сварных соединений и обнаружения других дефектов на трубопроводах служили ламповые дефектоскопы и УЗК преобразователи на основе пьезокерамических элементов. За прошедшие более чем 60 лет накоплен богатый опыт применения ультразвукового контроля, появились новые цифровые дефектоскопы и новые методы неразрушающего контроля.
Плюсы ультразвуковой дефектоскопии
| Недостатки ультразвукового контроля
|
Все публикации
Другие публикации
3 причины добавить в свой арсенал зонд с внутренним рабочим каналом
Коммерческие авиакомпании имеют сжатые сроки для выполнения тех или иных задач, поэтому техническое обслуживание выполняется строго по графику, и начинается с оснащения команды необходимыми инструментами визуального контроля. Читайте о трех причинах добавления в свой арсенал зонда с внутренним рабочим каналом.
C-скан развёртка в УЗ ФР для контроля коррозии и расслоений
Принцип C-скан развёртки, который используется для контроля коррозии и расслоений отводов трубопроводов.
C-скан развёрстка — это двухмерное представление данных, которое представляет собой вид сверху, изображение плоскости объекта контроля на выбранном участке глубины.
IQ FireWatch — эффективное решение для предотвращения природных пожаров
Обеспечение пожарной безопасности — одна из главных задач государства. Лучший способ не допустить природный пожар — предупредить его, найти очаг возгорания на стадии задымления и принять меры по тушению. Мы знаем, как предотвратить природные пожары на ранней стадии и у нас есть для этого проверенное решение.
Неразрушающая дефектоскопия
Проведение дефектоскопии материалов и конструкций необходимо для определения их качества, а также прочности и долговечности. Отказ от проведения дефектоскопии приводит к печальным последствиям, таким как обнаружение брака в изготовленных конструкциях и материальным издержкам, связанным с этим. Проведение же дефектоскопии, напротив, поможет обнаружить брак ещё на этапе производства и устранить проблему, избежав ненужных затрат.
Преимущества неразрушающей дефектоскопии
Одно из немаловажных преимуществ кроется в технологии проведения контроля. Неразрушающая дефектоскопия позволяет определить наличие, вид и размер дефектов, не повреждая конструкцию или изделие. Это, в свою очередь, сводит к минимуму затраты.
Кроме того, большинство методов неразрушающей дефектоскопии имеют высокую точность определения при затрате минимума времени и усилий на саму процедуру.
Методы неразрушающей дефектоскопии
— Ультразвуковая дефектоскопия.
Дефекты определяются в местах изменения направления ультразвуковых волн, генерируемых специальным оборудованием. Включает в себя пять методов исследования, различающихся по технологии исполнения и степени точности результатов. Востребованный и универсальный способ неразрушающего контроля.
— Рентгенодефектоскопия.
Методика основана на свойствах предметов поглощать рентгеновские лучи. Дефекты обнаруживаются в местах ослабления поглощения. Преимущества метода – мобильность и возможность выявлять недостатки даже в изделиях большой толщины.
— Радиодефектоскопия.
Подходит только для контроля металлических изделий малой толщины, большей частью применяется для дефектоскопии неметаллов.
— Инфракрасная дефектоскопия.
Отличный метод для обнаружения проблем изделий в процессе работы. За счёт их нагрева и излучения инфракрасных волн становятся видимы дефекты изделия.
— Магнитная дефектоскопия.
Простой метод обнаружения. Индикатором расположения при таком контроле становится магнитный порошок, который оседает в местах неравномерного рассеивания электромагнитного поля.
— Электростатическая дефектоскопия.
Основана на свойствах электростатического поля. Детали обрабатываются меловым порошком с положительным зарядом, и по неравномерности его расположения определяются дефекты.
— Капиллярная дефектоскопия.
Контрастное вещество, которым обрабатывается поверхность изделия, проникает в трещины под воздействием сил капиллярности. После вещество-индикатор обрисовывает контуры дефекта, извлекая частицы контрастного вещества.
— Термоэлектрическая дефектоскопия.
Чаще используется для определения марки материала, из которого изготовлена конструкция.
— Электроиндуктивная дефектоскопия.
Основана на возбуждении вихревых токов переменным магнитным датчиком. Фиксируется поле, противоположное возбуждаемому, и по этим показателям обнаруживается место.
Как обнаружить раковины и непропаи в металлических конструкциях
О качестве металлических конструкций говорит их прочность, антикоррозийные качества, способность выполнять такие функции, как теплопроводность, электропроводность и пр. Дефекты, которые появляются в процессе изготовления паяных изделий – это поры, раковины, непропаи, трещины, шлаковые и флюсовые включения.
Оценка качества паяных изделий проводится с помощью двух методов контроля: разрушающего и неразрушающего.
Неразрушающий метод предполагает использование разного оборудования. Дефектоскопия проводится с использованием:
— рентгеноскопа;
— ультразвукового дефектоскопа.
Кроме этого, практикуют внешний осмотр, магнитное исследование и капиллярный метод.
Рентгенодефектоскопия
Радиационная дефектоскопия проводится согласно ГОСТу 20426-75.
Радиографический осмотр применяют для выявления внутренних дефектов в паяных изделиях – трещин в шве, паяном металле, пор, непропаев. Принцип рентгенодефектоскопии основан на способности рентгеновских лучей проходить через толщу материала и поглощаться им в разной степени в зависимости от степени плотности.
Прежде чем приступить к диагностике, сотрудник осуществляет зачистку изучаемого участка и близлежащих мест. Для проведения процедуры рентгеновскую трубку располагают таким образом, чтобы пучок попадал на шов под прямым углом. На другой стороне конструкции расположена кассета с рентгеновской пленкой. Время диагностики зависит от качества пленки, толщины и фокуса. О наличии изъянов будут свидетельствовать темные пятна на чувствительной фотопленке после ее проявления.
Ультразвуковой метод
Ультразвуковая дефектоскопия помогает обнаружить отклонения, которые образуются в процессе отражения волн от границ сред с разными свойствами.
Ультразвуковой источник подает сигнал, который отражается при достижении конца сплава. Если на его пути встречается дефект, то это отражается на волне. Прибор в обязательном порядке фиксирует такую находку. С помощью ультразвука определяют природу недостатка. Дефектоскопия с использованием ультразвуковой аппаратуры позволяет выявить изъян на поверхности и в глубине металлической конструкции. Метод применим для всех видов металлов, за исключением чугуна.
Диагностика сварных швов проводится несколькими методами (разрушающий и неразрушающий способ).
Неразрушающий способ предполагает механическое или иное влияние на сварное соединение, чтобы узнать имеются ли дефекты. Однако при этом часть или полностью сваренная область утрачивает конструктивные качества. Поэтому большим спросом пользуются неразрушающие методы контроля.
Чтобы узнать, имеются ли у сварного шва проблемы, эксперты просвечивают предмет рентгеновскими лучами, которые проникают сквозь элементы из металла и попадают на фотопленку. Готовый снимок покажет все. Проникающие лучи в силе выявить включения, поглощенные металлом, газовые поры, смещения свариваемых кромок, непровары.
Перед просвечиванием исследования участок и близлежащая плоскость тщательно очищается. Если имеются внешние дефекты, диагностика не проводится, поскольку ее задача заключается в определении скрытых.
Принцип радиационного исследования следующий: рентгеновская трубка располагается таким образом, чтобы пучок рентгеновского излучения попадал на соединение под прямым углом. С другой стороны исследуемого элемента располагается кассета с рентгеновской пленкой. После диагностики, пленка проявляется и таким образом, получают результаты.
Если обнаруживается дефект, принимается решение, относительно допуска или переделки исследуемого элемента с учетом нормативной документации. На основе установленных регламентов и инструктажа определяются вхождения погрешностей в установленные для изучаемого изделия нормы.
Капиллярный неразрушающий контроль
Когда предстоит задача выявить поверхностные и сквозные дефекты в объектах и определять расположение, прибегают к методам неразрушающего контроля. Один из них предполагает проведение капиллярной дефектоскопии.
Для этого метода используется индикаторное вещество. Оно смачивает поверхность объекта контроля и проникает внутрь. На основе следов делаются выводы о наличии и месте локализации. Индикаторные линии свидетельствуют о наличии трещин, царапин, точки – о порах.
Преимущество капиллярной дефектоскопии перед другими методами заключается в том, что она помогает контролировать объекты, которые имеют любые размеры и формы. Применим метод для исследования изделий из черных и цветных металлов, сплавов, пластмассы, керамики. Спросом пользуется капиллярный контроль, когда узнают о наличии недостатков в сварных стыках.
Этапы проведения капиллярного контроля
Проводится в 5 этапов:
- Очистка поверхности. На начальном этапе проводят очистку поверхности от следов грязи с помощью воды или органической жидкости, чтобы краситель проник в имеющиеся дефекты. Затем поверхности дают подсохнуть.
- Нанесение красителя. Пенетрант распределяется на поверхность посредством кисти или погружением объекта контроля в ванну на полчаса.
- Устранение излишков пенетранта. Избыток удаляется салфеткой, промыванием водой. Используется специальный очиститель. Сам пенетрант удаляется с поверхности контроля, но не из полости дефекта. После этого поверхность протирается салфеткой или подсушивается путем подачи струи воздуха.
- Нанесение проявителя. Как только просушка окончена, на поверхность исследуемого объекта равномерно наносится слой проявителя.
- Выявление возможных дефектов. Завершающий этап следует после окончания процесса проявки. Контроль помогает выявить индикаторные следы. Интенсивность их окраски говорит о глубине и ширине раскрытия. Чем бледнее цвет, тем незначительнее дефект. О наличии глубоких трещин свидетельствует яркая окраска. Как только объекты будут зафиксированы, проявитель смывают с помощью воды или очистителя.
Материалы для цветной дефектоскопии подбирают с учетом требований, которые предъявлены к исследуемому объекту.
Как проводится магнитная дефектоскопия деталей
Метод магнитоскопии проводится с целью выявить трещины, раковины, поры в поверхностных слоях изделий, которые выполнены из металла. Применим он также и для выявления ферромагнитных включений в элементах из неферромагнитных материалов.
Для определения нарушений сплошности металла используются методы, принцип которых заключается в исследовании магнитных полей рассеяния вокруг них после намагничивания. В областях дефектов магнитный поток перераспределяется, характер магнитного поля рассеяния изменяется.
Часто используемый способ магнитной дефектоскопии предполагает применение магнитного порошка или суспензии. Вещество распределяется на намагниченный элемент. Частички порошка, которые проникли в области магнитных полей рассеяния, оседают на изделиях возле мест, где находятся дефекты.
Ширина полоски, на которой оседает порошковое средство, превышает ширину раскрытия. По этой причине их удается обнаружить без устройств. Метод, при котором используется магнитный порошок, помогает обнаруживать области и контуры нарушений сплошности металла, находящиеся на поверхности исследуемых изделий и на глубине до 2-3 мм. Намагничивание контролируемых изделий, нанесение на них специального средства и дальнейшее размагничивание с помощью магнитных дефектоскопов.
Выявление дефектов
Если в исследуемых элементах допустима различающаяся ориентировка, потребуется продольное и циркулярное намагничивание. Первый метод предполагает пропуск тока через зажатый между контактными площадками контролируемый объект. Он считается основным методом магнитной дефектоскопии. К продольному прибегают, если в контролируемом объекте обнаруживаются поперечные дефекты. Зависит от геометрических данных. Четко видны те, которые имеют большую высоту и находятся на незначительной глубине.
Оседание магнитного порошка позволяет диагностировать проблему. При трещинах, которые возникли при термической обработке (закалочные), и ковочных, порошок выпадает в осадок в виде резких ломаных линий.
О флокенах сигнализируют искривленные линии. При этом слой осевшего порошка будет плотным. Волосовины диагностируют по оседанию порошка в виде прямых или изогнутых тонких черточек. Для таких интенсивность оседания средства будет меньшей, нежели та, которая обнаруживается при трещинах поперечных разрезов таких дефектов.
Магнитный неразрушающий контроль
Принцип магнитных исследований конструкций состоит в том, что возможные изъяны в намагниченном металле приводят к искажению магнитных силовых линий. Появление их объясняется тем, что дефекты в виде пор, раковин, трещин или включений отличаются сильными магнитными свойствами, нежели металл, который их окружает. Чтобы обнаружить и узнать размеры искажения магнитных силовых линий прибегают к разным способам.
— Использование компаса
Простой из них предполагает исследование посредством компаса. Стрелка устройства, которое подносят к изучаемому металлическому изделию, будет располагаться вдоль направления силовых линий магнитного поля. Если перемещать компас металлического стержня и приближать его дефекту, который невозможно обнаружить невооруженным глазом, магнитная стрелка отклонится, что будет свидетельствовать о наличии изъяна на этом участке. Стоит учесть, что способ обнаружения дефектов посредством компаса характеризуется низкой чувствительностью, поэтому он не подходит для автоматического контроля.
— Магнитная дефектоскопия
Магнитная порошковая дефектоскопия позволяет выявить дефект по магнитному полю рассеяния ферро-магнитных частиц вокруг него. Такой метод считается одним из надежных и при этом не предполагает каких-либо сложностей в проведении. С его помощью можно узнать о наличии трещин и прочих дефектов на поверхности металла и в глубинных слоях. Метод контроля проводится поэтапно. На первом этапе происходит намагничивание метала. Второй этап предполагает нанесение магнитных порошков.
В качестве магнитных порошков применяют измельченные ферромагнитные порошки, которые отличаются высокой магнитной проницаемостью. Могут быть представлены в сухом или жидком виде. Прежде чем порошок будет нанесен на поверхность, ее очищают от окалины и ржавчины. Для очистки используется пескоструйный аппарат либо проволочная щетка. Применяют также метод шлифовки.
Если на поверхности имеются дефекты, порошковый рисунок получается плотным, надежно сцепляется с металлом и имеет четкие контуры. Когда изъян находится в глубине металла, рисунок получается не столь плотным. Однако по виду рисунка можно узнать о характере дефекта и место его расположении. При исследовании дефектов, которые находятся на некоторой глубине от поверхности, используют порошок в сухом виде.
Выбор техники для магнитно-порошковой диагностики осуществляется в зависимости от вида намагничивающего тока, условий, характера и цели исследований, а также от типа и состояния, используемых магнитных порошков. Если диагностике подвергаются мелкие изделия из стали, сварные швы, прибегают к использованию оборудования, установленного в специальных лабораториях. Когда предстоит задача проверить качество больших стальных конструкций и сварных узлов, используется магнитный дефектоскоп и другие установки.
В нашей испытательной строительной лаборатории проводятся все виды неразрушающей дефектоскопии конструкций и изделий. У нас вы можете получить точный результат в кратчайшие сроки. Используем только современное сертифицированное оборудование. Исследования осуществляет обученный и опытный персонал. Кроме того, стоимость наших услуг вас точно порадует.
Дефектоскопия рельсов и железнодорожных путей.
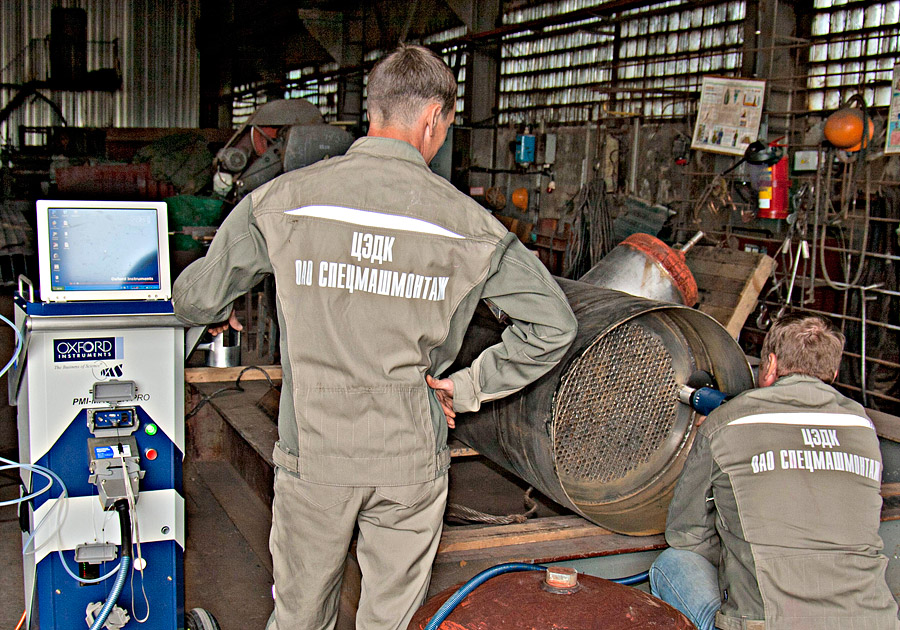
Главная / Виды работ / Ультразвуковая дефектоскопия рельсов и железнодорожных путей
Дефектоскопия рельсов
Дефектоскопия рельсов: общие сведения
При непрерывной эксплуатации железнодорожных путей верхнее строение пути приходит в негодность. Рельсы в пути постоянно работают на сопротивление силам, возникающим от движущихся колес поездов и на температурные напряжения. В результате рельсы подвергаются излому.
В данном случае специалисты полагаются на дефектоскопию рельсов с помощью специальной техники, так как визуально определить в каком месте рельса появился дефект, невозможно. Последствием излома рельса в большинстве случаев является сход подвижного состава. И хуже всего, если им окажется, например, цистерна с опасным грузом.
Ультразвуковая дефектоскопия рельсов
Единственный способ, позволяющий выявить дефект в рельсе на ранней стадии и предупредить его излом, является ультразвуковая дефектоскопия рельсов.
Сейчас существуют методы неразрушающего контроля, позволяющие обнаруживать дефекты в металлических изделиях используя импульсы ультразвуковых колебаний, один из них регулярно используется на ЖД транспорте и называется ультразвуковая дефектоскопия. С её помощью можно достоверно и быстро выявить скрытые дефекты, не повреждая и не разрушая исследуемый объект.
Железнодорожная дефектоскопия нужна при использовании старогодных рельсов и стрелочных переводов. Она позволяет отбраковать дефектные рельсы, а дефектоскопия стрелочного перевода поможет подобрать по-настоящему качественный старогодный стрелочный перевод, еще до укладки в путь, экономя ресурсы предприятия.
Преимущества дефектоскопии
Главными преимуществами данного метода являются:
- отсутствие повреждений и нарушений целостности на исследуемом образце;
- высокая достоверность при низкой цене;
- возможность исследования в любое время года.
Как известно, ультразвуковая дефектоскопия — это надежный способ обнаружения даже минимальных дефектов в самых разных металлических изделиях. Ультразвуковая дефектоскопия пути еще используется для контроля:
- элементов стрелочных переводов;
- сварных стыков на рельсах.
Контроль состояния рельсов и металлических элементов стрелочных переводов при помощи ультразвуковой дефектоскопии
Ультразвуковое исследование возможно проводить в любое время года, оно не разрушает и не повреждает исследуемый образец, что является его главным преимуществом. Так же можно выделить достоверность исследования при низкой стоимости.
При визуальном методе контроля при всем желании можно выявить лишь наружные дефекты (сколы, выбоины, трещины, вмятины, коррозийные повреждения и пр.). Но известно, что в рельсах постоянно идёт развитие дефектов 1-й, 2-й и 5-й групп (так называемые, контактно-усталостные), обнаружить большую часть которых визуально невозможно, например, расположенные в местах болтовых соединений под стыковыми накладками.
Здесь на помощь приходит железнодорожная дефектоскопия стрелочных переводов и рельсов.
Ультразвуковая дефектоскопия, пока остается самым актуальным и часто единственно действенным способом предотвращения аварийных моментов на ЖД транспорте от излома рельсов, наступающего вследствие скрытых дефектов. Дефектоскопия железнодорожная также является надежным способом контроля над деталями стрелочных переводов и сварными стыками рельсов.
Прозвучивание рельса любого вида дает возможность выявлять на ранней стадии подавляющую часть опасных дефектов в районе головки, шейки и подошвы рельса, которые могут развиваться в нем со временем. В процессе контроля устанавливается код дефекта и его местоположение в рельсе.
Дефектоскопия рельсов осуществляется методом неразрушающего контроля и определяет:
- нарушения однородности структуры;
- однородность материала;
- места поражения коррозией;
- несоответствие начальному химическому составу;
- отклонения в размере и другие дефекты.
Дефекты рельсов и их выявление
Подробно о видах дефектов, причинах их появления и основных способах выявления, а также правила эксплуатации можно узнать в классификации дефектов рельсов НТД/ЦП-1-93.
У каждого дефекта существует свой код. По коду обнаруженного дефекта определяют меры по его устранению. Все дефекты можно разделить на 2 группы, дефектные (ДР) и остродефектные (ОДР):
- Дефектные рельсы – элементы верхнего подвижного пути, служебные свойства которых снизились, но еще обеспечивают безопасное движение поездов. Иногда уже необходимо вводить ограничение скорости движения составов и дополнительный контроль.
- Остродефектный рельс — рельс, представляющий прямую угрозу безопасному движению так как в любой момент, возможно, его разрушение под движущимся составом или даже сход колес с рельса. Если дефектоскопия показала подобную проблему, остродефектный рельс немедленно меняют на новый или старогодный рельс.
Рельсовая дефектоскопия железнодорожного подъездного пути является неотъемлемой частью путевых работ и ведения путевого хозяйства. Результаты дефектоскопной проверки рельсов дают возможность планировать работы в объемах текущего содержания пути и капитальные работы.
Особенно важно понимать это людям, ответственным за процесс перевозки опасных грузов. Экономия на данном виде работ ложна и себя не оправдывает.
Дефектоскопия пути
Ультразвуковая дефектоскопия ЖД пути
Истинная польза для предприятия от ультразвукового контроля (дефектоскопии) железнодорожного пути в том, что она помогает своевременно выявить опасные скрытые дефекты в рельсах. Они впоследствии могут привести к изломам рельсов и деталей стрелочных переводов и аварийному сходу подвижного состава.
Полученную дефектоскопическую информацию используют во время текущего содержания пути, а также для определения сроков и объема ремонта. А самое главное, с помощью ультразвуковой дефектоскопии можно планировать выделение финансовых средств для обслуживания путевого хозяйства, как на текущий, так и на следующий год.
Периодичность проведения рельсовой дефектоскопии
РОСТРАНСНАДЗОР требует — дефектоскопия подъездных железнодорожных путей должна проводиться:
- не реже 2-х раз в год на ЖД путях предприятий, занимающихся перевозками опасных грузов;
- минимум 1 раз в год на подъездных путях прочих организаций.
Проверки проводятся на основании следующих документов: согласно Приказа № 2ЦЗ МПС РФ от 25.02.1997 г., Закона № 17-ФЗ от 10.01.2003 г. и Инструкции по текущему содержанию ЖД пути ЦП-774 от 01.07.2000 г.
Необходимость проведения дефектоскопии железнодорожных путей очевидна.
Затраты на проведение работ по дефектоскопии пути и предупреждение аварий на железной дороге незначительны и несоизмеримы с калькуляцией затрат собственника путей по ликвидации последствий схода.
Дефектоскопия железнодорожных путей в России
Компания ООО «Трудовой десант» более 7 лет выполняет дефектоскопию железнодорожных подъездных путей и дефектоскопию стрелочных переводов на всей территории России.
Мы имеем в наличии все необходимое для проведения железнодорожной дефектоскопии: собственную аттестованную лабораторию неразрушающего контроля, полностью укомплектованные дефектоскопные тележки и высококвалифицированный штат сотрудников с многолетним опытом работы.
youtube.com/embed/lsyO-o3081Y?rel=0″ frameborder=»0″>Получить более подробную консультацию специалиста по рельсовой дефектоскопии, или заказать обследование пути, можно по телефону в Санкт-Петербурге 8 (812) 640-30-00.
Пусть путь к вашему успеху будет ровным!
Капиллярный контроль, цветная дефектоскопия, капиллярный метод неразрушающего контроля
По умолчаниюПо имени (A — Я)По имени (Я — A)По цене (возрастанию)По цене (убыванию)По рейтингу (убыванию)По рейтингу (возрастанию)По модели (A — Я)По модели (Я — A)
12255075100
Очиститель AEROPEN-KD LR-1
Очиститель Aeropen-KD LR-1 на основе бензина подходит для черных и цветных металлов. Очиститель обес..
790 р.
Подробнее
Очиститель Helling U87
Очиститель U87 Helling для капиллярного контроля относится к серии НОРД-ТЕСТ (Nord-Test). Это эколог..
922 р.
Подробнее
Очиститель Sherwin DR-60
Очиститель Sherwin DR-60 предназначен для подготовки поверхности к проведению капиллярного контроля,. .
878 р.
Подробнее
Пенетрант AEROPEN-KD RF-1
Пенетрант Aeropen-KD RF-1 красного цвета, хорошо смывается водой и растворителем. Подходит для черны..
887 р.
Подробнее
Пенетрант Helling U88
Пенетрант Helling U88 серии Nord-Test — Это экологически безопасный пенетрант, хорошо смывается вод..
930 р.
Подробнее
Показано с 1 по 12 из 18 (всего 2 страниц)
Капиллярная дефектоскопия — это метод дефектоскопии, основанный на проникновении определенных контрастных веществ в поверхностные дефектные слои контролируемого изделия под действием капиллярного (атмосферного) давления, в результате последующей обработки проявителем повышается свето- и цветоконтрастность дефектного участка относительно неповрежденного, с выявлением количественного и качественного состава повреждений (до тысячных долей миллиметра).
Существует 2 метода капиллярной дефектоскопии:
- люминесцентный (флуоресцентный) метод капиллярной дефектоскопии
- цветной метод капиллярной дефектоскопии
В основном по техническим требованиям или условиям необходимо выявлять очень малые дефекты (до сотых долей миллиметра) и идентифицировать их при обычном визуальном осмотре невооруженным глазом просто невозможно. Использование же портативных оптических приборов, например увеличительной лупы или микроскопа, не позволяет выявить поверхностные повреждения из-за недостаточной различимости дефекта на фоне металла и нехватки поля зрения при кратных увеличениях.
В таких случаях применяют капиллярный метод контроля.
При капиллярном контроле индикаторные вещества проникают в полости поверхностных и сквозных дефектов материала объектов контроля, в последствие образующиеся индикаторные линии или точки регистрируются визуальным способом или с помощью преобразователя.
Контроль капиллярным методом осуществляется в соответствии с ГОСТ 18442-80 “Контроль неразрушающий. Капиллярные методы. Общие требования.”
Главным условием для обнаружения дефектов типа нарушения сплошности материала капиллярным методом является наличие полостей, свободных от загрязнений и других технических веществ, имеющих свободный доступ к поверхности объекта и глубину залегания, в несколько раз превышающую ширину их раскрытия на выходе. Для очистки поверхности перед нанесением пенетранта используют очиститель.
Назначение капиллярного контроля (капиллярной дефектоскопии)
Капиллярная дефектоскопия (капиллярный контроль) предназначена для обнаружения и инспектирования, невидимых или слабо видимых для невооруженного глаза поверхностных и сквозных дефектов (трещины, поры, непровары, межкристаллическая коррозия, раковины, свищи и т.д.) в контролируемых изделиях, определение их консолидации, глубины и ориентации на поверхности.
Применение капиллярного метода неразрушающего контроля
Капиллярный метод контроля применяется при контроле объектов любых размеров и форм, изготовленных из чугуна, черных и цветных металлов, пластмасс, легированных сталей, металлических покрытий, стекла и керамики в энергетике, ракетной технике, авиации, металлургии, судостроении, химической промышленности, при строительстве ядерных реакторов, в машиностроении, автомобилестроении, электротехники, литейном производстве, медицине, штамповке, приборостроении, медицине и других отраслях. В некоторых случаях этот метод является единственным для определения технической исправности деталей или установок и допуск их к работе.
Капиллярную дефектоскопию применяют как метод неразрушающего контроля также и для объектов из ферромагнитных материалов, если их магнитные свойства, форма, вид и расположение повреждений не позволяют достигать требуемой по ГОСТ 21105-87 чувствительности магнитопорошковым методом или магнитопорошковый метод контроля не допускается применять по техническим условиям эксплуатации объекта.
Капиллярные системы также широко применяются для контроля герметичности, в совокупности с другими методами, при мониторинге ответственных объектов и объектов в процессе эксплуатации. Основными достоинствами капиллярных методов дефектоскопии являются: несложность операций при проведение контроля, легкость в обращение с приборами, большой спектр контролируемых материалов, в том числе и немагнитные металлы.
Преимущество капиллярной дефектоскопии в том, что с помощью несложного метода контроля можно не только обнаружить и индентифицировать поверхностные и сквозные дефекты, но и получить по их расположению, форме ,протяженности и ориентации по поверхности полную информацию о характере повреждения и даже некоторых причинах его возникновения (концентрация силовых напряжений, несоблюдение технического регламетна при изготовлении и пр. ).
В качестве проявляющих жидкостей применяют органические люминофоры — вещества, обладающие ярким собственным излучением под действием ультрафиолетовых лучей, а также различные красители и пигменты. Поверхностные дефекты выявляют посредством средств, позволяющие извлекать пенетрант из полости дефектов и обнаруживать его на поверхности контролируемого изделия.
Параметр «чувствительность» в капиллярном методе дефектоскопии
Чувствительность капиллярного контроля – способность выявления несплошностей данного размера с заданной вероятностью при использовании конкретного способа, технологии контроля и пенетрантной системы. Согласно ГОСТ 18442-80 класс чувствительности контроля определяют в зависимости от минимального размера выявленных дефектов с поперечными размером 0,1 — 500 мкм.
Выявление поверхностных дефектов, имеющих размер раскрытия более 500 мкм, капиллярными методами контроля не гарантируется.
Класс чувствительности | Ширина раскрытия дефекта, мкм |
I | Менее 1 |
II | от 1 до 10 |
III | от 10 до 100 |
IV | от 100 до 500 |
Физические основы и методика капиллярного метода контроля
Капиллярный метод неразрушающего контроля (ГОСТ 18442-80) основан на проникновении внутрь поверхностного дефекта индикаторного вещества и предназначен для выявления повреждений, имеющих свободный выход на поверхность изделия контроля. Метод цветной дефектоскопии подходит для обнаружения несплошностей с поперечными размером 0,1 — 500 мкм, в том числе сквозных дефектов, на поверхности керамики, черных и цветных металлов, сплавов, стекла и другие синтетических материалов. Нашел широкое применение при контроле целостности спаек и сварного шва.
Цветной или красящий пенетрант наносится с помощью кисти или распылителя на поверхность объекта контроля. Благодаря особым качествам, которое обеспечиваются на производственном уровне, выбор физических свойств вещества: плотности, поверхностного натяжения, вязкости, пенетрант под действием капиллярного давления, проникает в мельчайшие несплошности, имеющие открытый выход на поверхность контролируемого объекта.
Проявитель, наносимый на поверхность объекта контроля через относительно недолгое время после осторожного удаления с поверхности неусвоенного пенетранта, растворяет находящийся внутри дефекта краситель и за счет взаимного проникновения друг в друга “выталкивает” оставшийся в дефекте пенетрант на поверхность объекта контроля.
Имеющиеся дефекты видны достаточно четко и контрастно. Индикаторные следы в виде линий указывают на трещины или царапины, отдельные цветовые точки — на одиночные поры или выходы.
Цветная дефектоскопия (капиллярный контроль) сварных швов. ПВК контроль и дефектоскопия сварных соединений
- Главная
- Услуги
- Капиллярный метод – цветная дефектоскопия
Заказать звонок
ПО «Волгоградский Завод Резервуарных Конструкций» предлагает услугу по цветной дефектоскопии сварных швов. Наше предприятие владеет специальными материалами и оборудованием для оказания данной услуги, а так же квалифицированными специалистами в данной области неразрушающего контроля.
ПВК как вид неразрушающего контроля
Капиллярная дефектоскопия – это метод, основанный на проникновении жидкости с малым поверхностным натяжением внутрь дефектного участка под действием капиллярного эффекта, вследствие этого повышается цветоконтрастность поврежденного участка, по которому можно судить о степени поврежденности соединения.
Данный способ контроля может выявлять:
- холодные и горячие трещины в швах соединения;
- излишнюю пористость сварного шва;
- непровары;
- раковины и др.
Преимущества метода:
- Применим для любых видов металла и сплавов, используемых в конструкциях различного назначения: трубопроводы магистральные, резервуары, силосы и др. объекты из металла. Его применяют даже для выявления дефектов на керамических, стеклянных и пластмассовых изделиях.
- Позволяет определить конкретное расположение дефекта и его размеры.
- Относительно дешевый вид неразрушающего контроля.
- Высокая точность и наглядность, в сравнении с некоторыми другими видами дефектоскопии.
- Не требует затратных подготовительных работ.
- Быстрый и безопасный.
Методы капиллярного контролясварных швов
Различают методы основные и комбинированные. К основному можно отнести контроль, который производится только капиллярным проникновением специальных веществ в соединение. Тогда логично, что к комбинированному методу относят те обследования, где контроль осуществляется двумя и более неразрушающими методами контроля.
Комбинированные методы контроля
Такие методы можно классифицировать в зависимости от способа воздействия на исследуемое соединение.
- Капиллярно-магнитный.
- Капиллярно-радиационный метод излучения.
- Капиллярно-электростатический.
- Капиллярно-радиационный метод поглощения.
- Капиллярно-индукционный.
Материалы для дефектоскопии сварных швов
В современной промышленности для капиллярного контроля ПВКиспользуются специальные составы. Их называют пенетрантами (от англ. penetrant — проникающий). Специальные препараты не только обладают лучшей проникающей способностью, но имеют заметную окраску. Кроме того, в целях объективного контроля, чёткие цветные изображения становятся доступны для фото и видео регистрации. Некоторые виды содержат люминесцентные компоненты. С их помощью в ультрафиолетовом свете становятся заметными и контрастными микроскопические участки, заполненные пенетрантом.
Кроме пенетнрата, который проникает в полости и трещины, применяются и проявители. Это жидкость, которая при контакте с пенетрантом изменяет цвет и становится заметной. Проявители, называемые ещё индикаторами, используют для определения сквозных изъянов сварного шва или для увеличения чёткости изображения дефектных участков.
Для сквозной дефектации, как и в случае с керосином, проявитель наносится на одну сторону шва, а пенетрат — на другую. При наличии сквозной трещины или полости индикаторная жидкость окрасится контрастным цветом.
Индикаторные жидкости для ПВК контроля различаются не только по цвету и способности к свечению, но и по проникающей способности, называемой чувствительностью.
Технология проведения контроля
Для проведения капиллярного контроля сварных соединений методом цветной дефектоскопии необходимо выполнить четыре этапы капиллярного контроля:
- Подготовка рабочего места и осмотр исследуемых поверхностей;
- Очистка обследуемойповерхности;
- Высушивание подготовленной поверхности для получения результатов более высокого качества;
- Нанесение специальных составов индикаторов;
- Выявление дефектовсварки, проведение измерения величина дефекта и его характера;
- Занесение результатов в журнал, отчет, протокол или другой отчетный документ.
При очистке поверхности с нее удаляют пыль, пятна, верхние загрязнения (ржавчина, окалина, краски и др.).
Следует понимать, что очистка может производиться при помощи специальных химических очищающих веществ и только в редких случаях при помощи специального механического оборудования.
Подготовка к проведению капиллярного контроля
Рабочее место должно соответствовать требованиям ОТ, ПТБ и ГОСТ по состоянию окружающей среды, наличию средств защиты, инструментов и препаратов.
Очистка поверхности производится сначала механическим способом, затем растворителем или специальным составом, входящим в комплект индикаторных жидкостей. Часто состав растворителя повышает информативность дефектоскопии, так как учитывает индивидуальные свойства пенетранта и проявителя (поверхностное натяжение, растворимость, вязкость, смешиваемость).
а – имеющийся дефект; б – нанесение пенетранта; в – удаление пенетранта с изделия; г – нанесение проявителя и проявление; 1 – изделие; 2 – дефект; 3 – пенетрант; 4 – проявитель; 5 – след дефекта (окрашенный проявитель).
После подготовки участка приступают к нанесению пенетранта в соответствии с инструкцией по его применению и приступают к ПВК расшифровке. При проведении неразрушающего контроля следует избегать излишних количеств и подтёков — они будут препятствовать формированию чёткой картины локализации дефектов. После нанесения пенетранта, при наличии в комплекте средств индикатора — его наносят сверху или с противоположной стороны в случае выявления только сквозных дефектов.
Скопления пенетранта с прореагировавшим проявителем показывают наличие и величину трещин, пор и непроваров. Для регистрации результатов метода неразрушающего контроля линейные размеры полостей измеряют инструментально.
В ряде случаев требуется регистрация результатов с помощью фотосъёмки и применение измерительных эталонов.
Ограничения методов капиллярной дефектоскопии сварных швов
Капиллярная цветная дефектоскопия — довольно универсальный метод неразрушающего контроля. При соблюдении технологий и применении соответствующих препаратов его можно использовать для любых материалов и видов сварки. Однако у данного способа есть индивидуальные ограничения:
- Пенетрат проникает в капилляры, глубина которых в 10 раз больше их ширины;
- Внутренние дефекты шва методом цветной дефектоскопии не выявляются, если полости и рыхлые участки герметичны;
- Капиллярная дефектоскопия сварных швов не позволяет точно определить глубину полости или трещины;
- При хорошей наглядности и приемлемой точности выявления изъянов, метод не даёт цифровой точности измерения размеров;
- Метод не позволяет определять трещины и поры с линейными размерами менее 0,1 — 0,2 мкм.
В силу указанных причин, для более точного и информативного выявления дефектов, применяют, где это необходимо, другие способы контроля сварных швов.
Контроль капиллярныйс применением керосина
В прежние времена для нахождения дефектов использовали керосин. Эта жидкость широко применялась в быту и технике. Керосин почти не испаряется в обычных условиях, но обладает хорошей проникающей способностью, благодаря низкой вязкости и высокой полярности.
Т.к. керосин бесцветный, то сварщики применяли мел и другие вещества для корректной оценки наличия и величины раковин, трещин и полостей.
Керосиновый способ, благодаря своей простоте и сегодня ещё применяется на практике. Чаще всего такой метод используют для поиска сквозных дефектов резервуаров, работающих под давлением, также используется при испытаниях топливных отсеков или изделий с различными сварными соединениями.
Порядок осмотра и чувствительность при керосиновом способе контроля:
Давление керосина, |
Чувствительность, |
Порядок осмотра при толщине металла, мм |
|
---|---|---|---|
≤ 6 |
6 — 25 |
||
— |
6,6 · 10-2 |
1. |
1. Через 3-5 мин после подачи керосина |
2,9 · 105 |
6,6 · 10-3 |
1. Через 1-2 мин после подачи давления |
1. Через 1-2 мин после подачи давления |
Выделяют четыре виды контроля с помощью керосина:
- Простой керосиновый.
- Керосин с применением вибрации.
- Керосин с использованием вакуума.
- Керосин с применением пневматических свойств.
Простой керосиновый способ заключается в том, что остывшее после сварки соединение с одной стороны красят водной суспензией коалина или мела, после высыхания суспензии, другую сторону смазывают керосином и наблюдают за реакцией.
В керосинопневматическом методе на смоченную керосиновым раствором поверхность направляют струю сжатого воздуха под давлением около 0,4МПа, что повышает чувствительность испытания и ускоряет выявление повреждений.
При керосиновакуумном методе смачиваются швы изделия, устанавливается вакуумная камера, с помощью которой создается перепад давлений воздуха. В результате капиллярное давление вместе с разностью давления воздуха повышает точность результатов испытания.
Керосиновибрационный способ проводится с применением ультразвука. На смоченную керосином поверхность начинают воздействовать ультразвуковыми колебаниями, при это повышается его проникающая способность в соединение и таким образом можно получить более точные результаты.
ПВК контроль сварных соединений на проницаемость
Некоторые изделия с применением сварки должны быть строго герметичны, так как внутри них будут храниться различные жидкие вещества: вода, нефть, горюче-смазочные вещества и др. Поэтому проницаемости швов в данных конструкциях уделяется особое внимание.
Контроль проницаемости зачастую проводится двумя способами: гидравлическим и пневматическим.
Гидравлический способ проверки проницаемости сварных соединений
Емкость, которая должна быть герметичной, заполняется водой или маслом, в ней создается избыточное давление, которое больше стандартного в полтора раза.
Далее в течение 10-30 минут области вокруг сварных швов простукивают молотком со скругленным бойком в расчете на то, что при наличии сквозного дефекта сварки появится течь.
Пневматический способ проверки
В емкость закачивают любой газ до достижения давления в 150% от номинального. После закачки, сварные соединения обрабатываются мыльным раствором. Суть в том, что если, имеются сквозные дефекты в швах, то на поверхности мыльного раствора начнут образовываться пузыри, что наглядно отразит наличие повреждения.
При невозможности закачки газа в бак, шов обдувается под давлением с одной стороны, а с другой обрабатывается мыльным раствором. Если дефект существует, то на растворе вновь появятся пузыри.
Преимущества нашего предприятия в оказании услуги
- Опытный квалифицированный персонал.
- Применение качественных материалов при обследовании.
- Максимально достоверные результаты отчетов.
- Соблюдение норм и требований действующих нормативных документов.
- Консультация в подборе наилучшего метода контроля.
- Мы выполняем обследования в нужные Вам сроки.
Стоимость услуги неразрушающего контроля с применением ПВК
Ценообразование данной процедуры зависит от выбранного метода контроля, количества мест проведения обследования и вида применяемого вещества. Наше предприятие предоставляет качественную услугу по конкурентоспособной на рынке цене.
Заказать услугу
Для заказа проведения обследования можно заполнить онлайн форму, в таком случае, наши сотрудники свяжутся с Вами. Также Вы сами можете позвонить нам по указанным в шапке сайта телефонным номерам. В любом случае, наши сотрудники проконсультирую Вас более подробно о нашей услуге ПВК контроля сварных соединений.
Лаборатория дефектоскопии
×
Для поиска определенного термина используйте двойные кавычки. Пример: «искомый термин»
Лаборатория дефектоскопии является подразделением института испытаний и сертификации, которое, как аккредитованная испытательная лаборатория № 1004, предлагает специализированные услуги в области характеризации дефектов материалов и измерения факторов, влияющих на образование дефектов. Используя имеющийся опыт современной науки и техники, можно обеспечить экспертное прогнозирование и предупреждение дальнейшего развития дефекта. Специализированные услуги лаборатории дефектоскопии основаны на многолетнем опыте в области исследований и разработок (НИОКР) полимерных материалов и аналитической науки.
Ссылки / Загрузка
Руководство для клиентов
УСЛУГИ ЛАБОРАТОРИИ ДЕФЕКТОСКОПИИ
- Идентификация характера дефектов
- с использованием специальных методов — термической десорбции ГХ-МС, прямого ввода-МС, пиролизной ГХ-МС, демонстрирующей очень высокий уровень успеха при анализе дефектов
- базовый анализ элементов для отслеживания их концентрации с использованием РФА, ИСП-ОЭС-спектроскопии, ИСП-МС-спектроскопии и ААС
- Науки о хроматографии и разделении, полностью оснащенные современными системами ГХ и ВЭЖХ с использованием нескольких систем ввода и детектирования
- специальные испытания, предлагаемые Лабораторией физических испытаний (испытания на вибрацию, воспламеняемость, испытания на сопротивление, испытания на старение, электростатические испытания)
- Измерение влияющих параметров
- идентификация и оценка параметров, влияющих на возникновение дефектов
- определение дефектов, возникающих в производственном процессе, путем адаптации аналитических условий к запрошенным параметрам
- диагностика, определяющая оптимизацию параметров процесса и предотвращение дефектов
- для обслуживания клиентов в качестве аналитической лаборатории для исследований и разработок (НИОКР)
- Прогнозирование и предотвращение дефектов
- использование научных ресурсов ИТЦ (оборудование, исследователи) вместе с техническими ресурсами клиентов в соответствии с их индивидуальными требованиями может привести к предотвращению дефектов
- сотрудничество с индивидуальными заказчиками с целью определения оптимальных технологических приемов производственного процесса
- консультационные услуги ИТЦ по предотвращению образования дефектов с целью оптимизации будущих технологических затрат
ОБОРУДОВАНИЕ
- газовая хроматография с детектированием FID и MS, жидкостная хроматография с детектированием UV-VIS, флуоресценция, рефрактометр и детектирование по электропроводности
- полностью оборудованная подготовка проб для элементного анализа с помощью кислотного разложения с помощью микроволновой печи
- атомно-абсорбционная спектрометрия
- аналитическая атомная спектрометрия с индуктивно связанной плазмой, сочетающая оптическое детектирование (ИСП-ОЭС) и масс-детектирование (ИСП-МС)
- Рентгенофлуоресцентная спектрометрия с EDX (микроскопом)
- инфракрасная спектроскопия и инфракрасная микроскопия
- УФ-видимая спектроскопия
- гравиметрия, объемный анализ
- микроскопия, анализ изображений
ПРОЧИЕ СОПУТСТВУЮЩИЕ УСЛУГИ
- Услуги аккредитованной испытательной лаборатории № 1004 и № 1004.
3
- Оценка соответствия уполномоченным органом 224 и уполномоченным органом 1023 в соответствии с требованиями постановлений правительства и европейских директив.
- Предоставление лицензий на знаки добровольной сертификации «Безопасные игрушки» и «Качество, сертифицированное ITC»
- Услуги по стандартизации и техническая информация Центра технической стандартизации, специализирующегося на товарах для детей, предоставляются в рамках ИТЦ
- Сертификация систем менеджмента (ISO 9001, ISO 14001, OHSAS 18001)
- Технический осмотр
- Технологическое консультирование
- Услуги по калибровке и метрологические консультации
- Юридические и экспертные услуги в соответствии с Законом № 36/1967 об экспертах и переводчиках
КОНТАКТЫ
Инж. Вера Вилимкова
заведующая лабораторией
Инж. Давид Гребеничек
технический инженер
Почтовый адрес:
Институт испытаний и сертификации, Inc.
Лаборатория аналитической химии и микробиологии
trida Tomase Bati 299, Луки, 763 02 Злин
Чехия
Лицо, ответственное за точность данных: Ing. Вера Вилимкова
дефектоскопия — перевод на немецкий язык – Linguee Кроме того, отдел также предлагает услуги во многих областях моделирования МКЭ, экспериментального анализа напряжений и деформаций
a n d дефектоскопия a s 5 скважина.izm.fraunhofer.de
izm.fraunhofer.de
Darber hinaus beetet die Abteilung ihre Dienstleistungen in einer Vielfalt weiterer Bereiche and — von der FEM-Simulation ber die Experimentelle Spannungs- u nd Dehnungsanalyse hi n zur Defektoskopie.
izm. fraunhofer.de
izm.fraunhofer.de
A l l дефектоскопия a n d разрушающий […]
тестирование может быть проведено по запросу клиента и будет подтверждено автономным
[…]
и аккредитованная лаборатория по испытанию материалов.
astech-hydraulik.com
astech-hydraulik.com
A lle zerstrungsfreien и zer st […]
Prfungen knnen auf Anforderung durchgefhrt und durch ein unabhngiges, akkreditiertes
[…]
Werkstoffprflabor bescheinigt werden.
astech-hydraulik.com
astech-hydraulik.com
Условия в рамках STN и европейских стандартов для испытаний на герметичность и
[. ..]
комп le t e дефектоскопия o f s резервуары для хранения […]
связаны с выполнением строгих требований по
[…]
профессиональная квалификация персонала в области неразрушающего контроля.
environ.sk
environ.sk
Die Bedingungen fr Dichtigkeitsproben и
[…] vollst n dige Дефектоскопия der Ла Гертанкс […]
innerhalb der STN- und EN-Normen erfordern die Einhaltung von strengen Anforderungen
[…]
bezglich der sachkundigen Qualifizierung von Personal, das die zerstrungsfreie Prfung durchfhrt.
environ.sk
environ.sk
Comp le t e дефектоскопия o f s резервуары для сбора [. ..]
в соответствии с действующими стандартами STN и EN, включая испытания на стойкость к утечке гелием.
environ.sk
environ.sk
Vol ls tndi ge Defektoskopie de r Lag er […]
nach den gltigen STN- und EN-Normen, einschlielich der Dichtigkeitsprobe durch Helium.
environ.sk
environ.sk
Трансвертер FVG1 расширяет вихретоковые системы, так что они могут
[…] также можно использовать f o r дефектоскопия o f i […]
компоненты, напр. пластик или стекло- и
[…]
пластик, армированный натуральным волокном.
fitm.de
fitm.de
Das Vorschaltgert FVG1 erweitert handelsbliche Wirbelstromprfsysteme derart, dass sie auch zur zerstrungsfreien Дефектоскопия
[. ..]
in nichtleitenden Bauteilen eingesetzt
[…] werden knne n, wie zum Beis pi el in Kunststoffen […]
sowie in Glas- und Naturfaser- verbundwerkstoffen.
fitm.de
fitm.de
Настоящая программа компании включает в себя собственную продукцию, а также поставки различных деталей и
[…]
узлы для клиентов автомобильной и пищевой промышленности
[…] и фармацевтической промышленности, на железнодорожном транспорте a n d дефектоскопия .
джамп.ск
джамп.ск
Der gegenwrtigen Progamm ist an eigene Produkte so wie an Teile und
[…]
Funktionseinheiten der Kunden in Automobil-,
[. ..]
Lebensmittel — und Farmzeutik- In du strie, Eisenb ah n un d Dfektoskopie o rien 90.erti 90.erti
джамп.ск
джамп.ск
Магнитная часть ic l e дефектоскопия i s b по показаниям […]
возмущений магнитного поля в местах или вблизи дефектов материала.
www.technic-control.com.pl
www.technic-control.com.pl
Магнитище
[…] Fehlerpr f ungen bestehen in de r Такой нах […]
Strungen des Magnetfeldes am Ort oder in der Umgebung eines Materialfehlers.
www.technic-control.com.pl
www.technic-control.com.pl
Ультразвуковой испытательный стенд, используется для
[. ..]
технологический тест в г ( дефектоскопия ) i n […]
многослойной керамики
bam.de
bam.de
Ultraschall-Prfstand, eingesetzt zur
[…] prozessbegleitenden Pr fung (дефектоскопия) in de r Fertigung […]
keramischer Multilayer
bam.de
bam.de
К искусственным источникам излучения относятся, например, медицинское использование ионизирующего излучения (рентгеновское излучение, ядерная медицина), техническое использование ионизирующего излучения (например, радиация TI O N Дефектоскопия , I ND USTRIAL IRSERITION ИСПОЛЬЗОВАНИЕ ИСПОЛЬЗОВАНИЯ ИСПОЛЬЗОВАНИЯ ИСПОЛЬЗОВАНИЯ ИСПОЛЬЗОВАНИЯ ИСПОЛЬЗОВАНИЯ ИСПОЛЬЗОВАНИЯ ИСПОЛЬЗОВАНИЯ ИСПОЛЬЗОВАНИЯ ИСПОЛЬЗОВАНИЯ ИСПОЛЬЗОВАНИЯ ИСПОЛЬЗОВАНИЯ ИСПОЛЬЗОВАНИЯ ИСПОЛЬЗОВАНИЯ. цепная реакция (особенно для выработки электроэнергии) или использование ядерной энергии в военных целях (главным образом атомная бомба).
cez.cz
cez.cz
Zu den Kunstquellen der ionisierenden Strahlung gehren z.B. die medizinische Ausnutzung der Radionuklide und der ionisierenden Strahlung (Rntgen, Nuklearmedizin), die technische Ausnutzung der ionisierenden Strahlung (z.B. Quellen der ionisierenden Strahlung, die in der Defektskopie benutzt werden, Industriebestrahlungsgerte, die z.B. zur Konservierung der Lebensmittel benutzt werden, Wasserstandsanzeiger, Messgerte fr die Messung der Dicke oder der Dichte von Materialien), die Atomenergetik, die bei der Spaltkettenreaktion ausgelsten Energien ausnutzt.
cez.cz
cez.cz
Пожалуйста, нажмите на причину вашего голосования:
- Это не лучший пример для перевода выше.
- Подсвечиваются неправильные слова.
- Не соответствует моему запросу.
- Не суммировать с оранжевыми записями
- Перевод неправильный или плохого качества.
Большое спасибо за ваш голос!
Вы помогли повысить качество нашего сервиса.
Дефектоскопия – Группа прикладной математики и стохастики
Дефектоскопия, упругость и акустическая эмиссия Наше исследование посвящено точной модели локализации источников акустической эмиссии (АЭ) на реальных сложных твердых телах, содержащих отверстия/препятствия. Подход основан на численном расчете точных геодезических кривых на трехмерных судах, которые могут быть составлены из нескольких параметризованных поверхностей с множеством пересечений. Вместо того, чтобы решать геодезические дифференциальные уравнения при определенных символах Кристоффеля, мы вычисляем наши геодезические численно с помощью методов конечных разностей, Ньютона-Рафсона и итераций с фиксированной точкой. Для более быстрых вычислений нам требуются новые технические усовершенствования и оптимизации. Затем эти методы используются в реальных экспериментах, таких как паровой резервуар.
Мы разрабатываем алгоритмы реального времени, позволяющие классифицировать сигналы акустической эмиссии (АЭ) на конечное число групп, соответствующих физической природе источников АЭ. Классификация может быть основана на спектральных параметрах и неметрических расстояниях, которые не зависят от амплитуд сигналов. Мы хотели бы различать обнаруженные сигналы, излучаемые разными источниками подавленной акустической эмиссии в материалах, а также отделять их от общего шума. Модели, которые оценивают лежащее в основе распределение спектральных параметров, происходят из системы мультимодальных оценок плотности вероятности, например. смеси с конечным распределением или непараметрические ядерные оценки плотности.
Модель гистерезиса Прейзаха-Майергойца (PM) может использоваться для оценки механических свойств гистерезисных материалов. Мы разрабатываем алгоритмическую автоматическую идентификацию плотности вероятности этого пространства PM в классе смесей распределения. Основным инструментом являются стохастические алгоритмы оптимизации (например, имитация отжига) с использованием мер фи-дивергенции. Необходимо определить как новый показатель упругости, так и показатель поврежденности на основе выявленного ПМ-пространства гистеронов гистерезисного материала. Экспериментально измеренные данные свиной кожи и гистерезисных демпферов при циклической нагрузке оцениваются в сотрудничестве с Университетом Гранады.
Сотрудничество
- проф. Серж Дос Сантос (INSA Blois FR): сотрудничество в области БДМ и характеристики материалов
- проф. Антолино Гальего (UGR Granada ES, Департамент прикладной физики): сотрудничество по оценке повреждения демпфера
- Инж. Зденек Пржеворовски, CSc. (УТ АВ ЧР, отдел D 4 – Удары и волны в твердых телах): сотрудничество по измерению эластичности кожи и мониторингу состояния материалов
Члены Вацлав Куш
доцент FNSPE CTU в Праге
(методы на основе дивергенции в упругой дефектоскопии, локализация источника акустической эмиссии, моделирование упругости PM)
Зузана Дворжакова Кандидат наук. студент FNSPE CTU в Праге
(классификация сигналов акустической эмиссии)
Милан ХладаIT, CAS
(методы дефектоскопии, распространение сигналов в материалах, нейронные сети)
Радован Земанмагистрант FNSPE CTU в Праге
(метод источника изображения для описания распространения дисперсионной упругой волны в тонких пластинах)
Erik Dolejšмагистрант FNSPE CTU в Праге
(статистические методы для оценки индекса упругости пространства PM, применение к гасителям землетрясений)
Мартин Ковандамагистрант FNSPE CTU в Праге
(методы глубокого обучения для оценки акустической эмиссии (CNN))
Ян Завадилстудент бакалавриата FNSPE CTU в Праге
(мудрая классификация сигналов АЭ SDDT/MBC/KDE и другие методы машинного обучения)
Выпускники
Петр Галис
(численная оптимизация карт геодезии и локализации в акустической эмиссии)
Colette Kožená
(оценка эластичности/повреждаемости материала при гистерезисе на основе PM)
Михал Завески
(геодезическая итеративная локализация акустических источников; статистическое разделение кластеров в акустике)
Ян Тласкаль
(методы статистической классификации акустической эмиссии)
Шарка Черна (Вейводова)
(нелинейная ультразвуковая томография с обращенными во времени сигналами)
Яна Хабаскова (Папоушкова)
(новые семейства статистических распределений в гистеронном пространстве Прейзаха-Майергойца)
Петр Своитка
(алгоритмы геодезической локализации на сложных поверхностях)
Богумил Поспишил
(локализация микротрещин на основе обнаружения сигнала акустической эмиссии)
Martin Petřík
(локализация микротрещин на основе обнаружения сигнала акустической эмиссии)
Ян Мака
(применение статистических методов для определения точки изменения акустических сигналов)
Важные документы
- Куш В.
и Долейш Э. Оценка индекса эластичности на основе Le Camdivergence и оценки ядерной плотности в пространстве PM. Journal of Physics: Conf Ser, 2021, Volume 1730, 012008, DOI: 10.1088/1742-6596/1730/1/012008
- Кожена, К.; Кусь, В .; Галего, А .; Бенавент-Климан, А., Оценка повреждения демпферов землетрясений на основе модели Прейзаха-Майергойца. Раз в два года Балтийская конференция по электронике (BEC). США: IEEE Computer Society, 2018. с. 1-4. ISBN 978-1-5386-7311-9. DOI: 10.1109/BEC.2018.8600971
- Галис, П.; Кусь, В .; Хлада М., Локализация источника акустической эмиссии на основе точных геодезических кривых (с применением к лейке). В кн.: Применение современного неразрушающего контроля в технике – конф. Труды. Любляна: Словенское общество неразрушающего контроля, 2017. с. 313-319. ISBN 978-961-93537-3-8. SCOPUS: 2-s2.0-85049240591
- Кожена, К., Кус, В., Дос Сантос, С., Эффекты гистерезиса и памяти при старении кожи с использованием идентификации пространственной плотности PM.
Раз в два года Балтийская конференция по электронике (BEC), США: IEEE Computer Society, 2016, стр. 179.-182. ISSN 1736-3705, ISBN 978-1-5090-1393-7. DOI: 10.1109/BEC.2016.7743758
- Кобер, Дж.; Дворжакова, З.; Пржеворовский, З.; Крофта, Дж., Передача с обращением времени: исследование устойчивости акустики с обращением времени в средах с возмущениями геометрии. JASA, Журнал Акустического общества Америки, 2015 г., 138(1), EL49-EL53. ISSN 0001-4966. DOI: 10.1121/1.4922623
- Дворжакова З.; Дос Сантос, С.; Пржеворовский, З.; Куш, В., Пространственная локализация и статистическая классификация нелинейной ультразвуковой сигнатуры в биомеханической среде с использованием новостных методов на основе обращения времени, Международный конгресс по ультразвуку. Сингапур: Research Publishing Services, 2013. стр. 79.6-801. ISBN 978-981-07-5938-4. DOI: 10.3850/978-981-07-5938-4_P0426
Бакалаврские и дипломные проекты для студентов
- Стохастическая обработка сигналов акустической эмиссии – обнаружение, локализация, классификация, гистерезис
- Методы дивергенции и их применение в моделировании упругости материалов и структуры
- Приложение информационных расхождений и достоверной метрики в дефектоскопии, эластичность материала и частичная физика
- Надежный корпус и тестированные статистические гипотезы с применением в дефектоскопии
Использование ультразвукового метода для дефектоскопии повреждений железобетонных колонн
[1]
Fib Model Code 2020. Structural Concrete 20, 860–866, (2019).
[2] П. Конечный, П. Гош, К. Грабова, П. Ленер и Б. Теплы, Эффективная методология оценки устойчивости бетонных смесей. Материалы и конструкции, 2020, 53, гл. 4, ISSN: 1359-5997.
DOI: 10.1617/s11527-020-01535-3
[3] ČSN 73 0038 Оценка и проверка существующих конструкций — Дополнительное руководство. Прага: УНМЗ, (2014).
[4]
Д. С. Адамати, А. Лоренци, Дж.А. Chies, L.C.P. Сильва Фильо, Анализ железобетонных конструкций с помощью скорости ультразвукового импульса: вовлеченный технологический параметр. Том 10, номер 2 (апрель 2017 г.), стр. 358–385. ISSN 1983-195. Доступно по адресу: http://dx.doi.org/10.1590/S1983-41952017000200006.
DOI: 10.1590/s1983-41952017000200006
[5] Г. Конку и Н. Трулли. Определение размеров дефектов бетона с помощью ультразвуковых карт скоростей. Здания 2018, 8(12), 176; https://doi.org/10.3390/buildings8120176.
DOI: 10.3390/buildings8120176
[6]
Proceq: PUNDIT® PL-200 СКОРОСТЬ УЛЬТРАЗВУКОВОГО ИМПУЛЬСА. Швейцария, 2014 г. https://www.proceq.com/uploads/tx_proceqproductcms/import_data/files/Pundit%20PL-2_Sales%20Flyer_English_high.pdf.
[7] ЧСН 73 1371 Неразрушающий контроль бетона – Метод ультразвукового импульсного контроля бетона. Прага: УНМЗ, (2011).
[8] Т.С. Калян и Дж. К. Кишен, Экспериментальная оценка трещин в бетоне по скорости ультразвукового импульса. В материалах Азиатско-Тихоокеанской конференции по неразрушающему контролю APCNDT 2013. (2013).
[9]
А. Вибово и соавт. Измерение глубины трещин железобетонных балок с использованием УПВ. Рекаяса Сипил, т. 8, н. 1, с. стр. 41-46, октябрь 2014 г. ISSN 2502-6348.
[10] М.А. Хабулла, Р. Юсоф и М.Н. Юсов. Оценка работоспособности бетонной конструкции по ширине трещины с помощью УПВ. Журнал инженерных наук и технологий, том 12, специальный выпуск, ISSC’16, апрель (2017 г.).
[11]
Цикрле П. «Значение неразрушающих методов диагностики для обследования сталежелезобетонных конструкций». Брненский технический университет, ВУТИУМ, 2017. Научные труды Брненского технологического университета. ISBN 978-80-214-5464-4.
[12] ЧСН ЕН 1992-1-1 Еврокод 2: Проектирование бетонных конструкций — Часть 1-1: Общие положения и правила для зданий, Прага: ÚNMZ, (2006).
Дефектоскоп исследования, ультразвуковой контроль
StartServiceВращающиеся барабаны Дефектоскоп исследовательский
ЛАБОРАТОРИЯ НЕРАЗРУШАЮЩЕГО КОНТРОЛЯ
Неразрушающие методы контроля представляют собой группу методов исследовательского анализа, которые обеспечивают
информации о материальных свойствах предмета, не лишая его утилитарного
ценности. Первостепенной целью предподготовительных исследований НК является, прежде всего, обнаружение
и оценка дефектов, имеющих характер
материальные разрывы. Применение неразрушающих индикаторов относится
для обоснования в первую очередь соображений безопасности и экономических аспектов невидимой аварии.
Чем ответственнее объект, тем тяжелее последствия внезапного отказа.
Компания ZMP имеет сертификат субподрядчика Польской службы технического
Инспекция. У нас есть возможность проводить исследования методом
ультразвуковой и магнитный контроль при ремонте и модернизации оборудования в
предмет технического осмотра. Современное оборудование и многолетний опыт
при выполнении сервисных работ на многих технических объектах реализуем основные
цель неразрушающего контроля, которая заключается в предоставлении информации о
состояние материала, оборудования, установки или здания на различных стадиях их
срок службы, начиная от изготовления, через сборку и заканчивая эксплуатацией.
МАГНИТНЫЙ МЕТОД КОНТРОЛЯ (МТ)
Метод использует явление рассеяния магнитных частиц, магнитное поле или магнитное поле. проницаемость в местах дефектов. Используя метод МТ, мы можем успешно обнаружены какие-либо дефекты в компонентах, изготовленных в основном из ферромагнитных материалов, которые все конструкционные стали, за исключением высоколегированных сталей (аустенитных).
ПРИМЕНЕНИЕ
Метод МТ используется в основном при исследовании качества различных видов сварных швов. (включая угловой шов). Испытания этого метода можно рассматривать как независимые или в качестве предварительного обследования перед ультразвуковым контролем.
МЕТОД УЛЬТРАЗВУКОВОГО КОНТРОЛЯ (УЗ)
Ультразвуковой контроль использует явление, сопровождающее распространение ультразвука.
волны в материалах. Это наиболее известный и широко используемый метод группы неразрушающего контроля.
Используется методика ультразвукового контроля.
в основном для обнаружения несплошностей материала, расположенных глубоко под поверхностью материала. Дополнительным преимуществом этих исследований является возможность оценка и определение размеров обнаруженных дефектов.
ПРИМЕНЕНИЕ
Из-за концентрации нашего бизнеса в области вращающихся барабанов и бумаги
обслуживание машины, мы специализируемся в основном на неразрушающем контроле
их компоненты. Проводя комплексные испытания элементов вращающихся барабанов, мы
может определить состояние материала элементов, правильная работа которых имеет решающее значение
на безаварийную работу объекта. Испытания проводятся на: открытой передаче
компоненты, валы, ролики и дорожки качения живых колец. Так же делаем УЗИ
замеры толщины сегментов обечайки, определяющие степень ее износа с
возможность дополнительного обнаружения расслоения листа.
Для изучения элементов бумагоделательной машины мы проверяем в основном состояние таких элементов, как
цилиндр/ролик, которые в процессе эксплуатации подвергаются значительным нагрузкам. Расследования
в основном ориентированы на: штифты, головки и болты, соединяющие головки с цилиндром / валом
оболочка. Измеряем также толщину цилиндрической детали из чугуна.
Мы также проводим исследования валов вращающихся машин, таких как вентиляторы, насосы, дробилки.
Что касается других технических средств, мы выполняем исследования валов различных
типы конвейеров; популярны также тесты качества сварки и ультразвуковой
замеры толщины стенок трубопроводов.
Имя пользователя (электронная почта):
Поле электронной почты обязательно.
Пароль:
Требуется пароль. Забыли свой пароль?
Запомните меня
- Документация ЗМП
- Публикации компании
- Интересные реализации
- Ваш аудит онлайн
H. Rohloff — NDT — Неразрушающий контроль
Foma BOHEMIA Ltd., Чешская Республика, производит широкую систему продуктов для промышленной радиографии (FOMA NDT SYSTEM), включающую весь диапазон скоростей неразрушающих пленок INDUX, химические вещества для обработки и другие аксессуары (пленочные просмотрщики, контрольные тесты, смачивающий агент и т. д.) .
INDUX (FOMADUX) — техническая радиографическая пленка, предназначенная для неразрушающего контроля материалов рентгеновским или гамма-излучением. Он предназначен как для ручной, так и для машинной обработки.
INDUX доступен в упаковке для фотолаборатории (IF-папка с чередованием, FW-папка в обертке, NIF-без чередования) или в упаковке для дневного света (вакуумная упаковка со свинцовой фольгой или без нее, а также в рулоне).
ПРОМЫШЛЕННЫЕ РЕНТГЕНОВСКИЕ ПЛЕНКИ
Промышленные рентгеновские пленки INDUX для неразрушающей дефектоскопии поставляются в упаковке для темной комнаты или в упаковке для дневного света в соответствии со стандартом ISO 5655.
Упаковка для фотолаборатории: IF (папка с чередованием), FW (папка в обертке), NIF (пленка без чередования)
Размеры: 6×24, 6×40, 6×48, 10×12, 10×24, 10×40, 10×48, 10×72 и 35×43 см в коробках по 100 листов,
Размеры: 10х20, 18х24, 24х30 и 30х40 см в коробках по 50 листов.
Упаковка Daylight представлена в виде вакуумной упаковки под наименованием Fomapak с фольгой Pb или без нее (DW).
Размеры: 6х10, 6х12, 6х16, 6х20, 6х24, 6х30, 6х40, 6х48, 10х10, 10х12, 10х16, 10х20, 10х24, 10х30, 10х40 и 10х48 см в коробках по 50 листов на 50 листов:
Другие размеры могут быть изготовлены по запросу.
MultiPack (Sandwich) – вакуумная упаковка, содержащая 2 пленки INDUX с разной скоростью. Размеры и скорости вставляемых пленок доступны в соответствии с индивидуальными требованиями заказчика.
Дневная упаковка в рулоне под наименованием FOMADUX ROLLFILM (со свинцовой фольгой или без нее) выпускается шириной 70 мм и 100 мм, длиной 90 м и 150 м. Упаковка: намотана на бумажный сердечник в картонной коробке-дозаторе со свинцовой фольгой, DW – без свинцовой фольги и как BLR (Bulk Load Roll) – голая рулонная пленка (BLR).
ХИМИКАТЫ ДЛЯ ОБРАБОТКИ
Foma BOHEMIA Ltd. производит химические вещества для обработки — ванны для автоматической и ручной обработки промышленных рентгеновских пленок.
Для автоматической обработки рекомендуем жидкие ванны Foma — проявитель FOMADUX LP-D, стартер для проявочной ванны FOMA LP-DS, быстротвердеющий закрепитель FOMADUX FIX Set.
Процедуру ручной обработки рекомендуется завершать применением смачивающего средства ФОТОНАЛ в дополнительной промывочной ванне в концентрации от 20 до 40 мл на 1 л воды.
Приготовление ванн для обработки следует инструкциям, представленным в технических паспортах (технической спецификации).
INDUX можно также обрабатывать в ваннах других производителей, предназначенных для промышленных рентгенографических пленок.
ПРИНАДЛЕЖНОСТИ ДЛЯ НК
В дополнение к материалам для промышленной радиографии Foma BOHEMIA Ltd. предлагает дополнительные продукты, такие как кинопросмотры (FV-2008, FV-2010), цифровые денситометры (MD-10, HD-03), тест для проверки стабильности обработанных рентгеновских пленок (Fomatest THIO), тест для контроля качества процесса обработки (Fomatest SC 981) и другое оборудование для фотолаборатории.
- Пленка Indux
Магнитопорошковая дефектоскопия (испытание MPI) обнаруживает все поверхностные и приповерхностные дефекты типа трещин, которые, в зависимости от их положения и размера, пропорционально влияют на магнитное поле.
MPI, обычно называемый магнитным испытанием (MT), используется в промышленности в качестве метода обеспечения качества для испытания всех ферромагнитных материалов, включая все виды стали и ее сплавов, за исключением аустенитной стали и чугуна. Как правило, надежное обнаружение поверхностных трещин требует, чтобы размеры ширина-глубина-длина соответствовали соотношению: 1: 10: 50.
Обычно самые низкие пределы обнаружения составляют трещину шириной 1 мкм и глубиной трещины 10 мкм.
При намагничивании ферромагнитного материала силовые линии потока магнитного поля проходят через магнитопроводящую среду.
При попадании магнитопроводов в область с низкой магнитной проводимостью (трещина, заполненная воздухом) часть магнитопроводов вытекает из материала и отклоняется наружу и над поверхностью контролируемой детали. Из детали выходит магнитное поле потока рассеяния.
Чтобы показать это внешнее поле рассеяния, частицы железного порошка наносятся в виде сухого порошка или с помощью специального жидкого аппликатора на проверяемую деталь.
Частицы железного порошка притягиваются за счет магнитного эффекта магнитного поля потока рассеяния и, по существу, создают контур порошка — четкий визуальный признак для человеческого глаза.
Для облегчения распознавания рисунка трещин железного порошка основной железный порошок можно окрасить флуоресцентным красителем. Под УФ-светом индикация порошкового рисунка будет усилена за счет подсветки черным светом. Оптимальное обнаружение трещины происходит, когда силовые линии магнитного поля расположены под прямым углом к дефекту. Угол между направлением поля и ожидаемым положением дефекта не должен превышать 30°.
Методы магнитного порошка обычно считаются методами обнаружения поверхностных трещин; однако существует вероятность того, что могут быть указаны приповерхностные дефекты благоприятного положения и адекватного размера. Структура поверхности испытуемого образца оказывает существенное влияние на возможность обнаружения дефектов.
Глубина дефекта должна как минимум вдвое превышать соответствующую шероховатость поверхности.