распространена ультразвуковая дефектоскопия сварных швов и соединений
Содержание:
- Ультразвуковая дефектоскопия
- Анализ сварных швов
- Дефектоскопия стыков трубопроводов
- Внутритрубная проверка
В течение длительного периода использования, трубопроводы попадают под негативное внешнее и внутреннее воздействие окружающей среды. В итоге – металл деградирует, на нем образуются коррозийные образования, появляются трещины и сколы, и другие типы дефектов. Казалось бы, при создании проекта трубопровода используя современные технологии, должна быть обеспеченна полная защита магистральных коммуникаций.
Но, к сожалению, исключить в полной мере возникновение повреждений невозможно. Чтобы небольшие дефекты не превратились в серьезную проблему, используют различные виды контроля.
Одним из них, который не предусматривает вывода в ремонт магистральной системы — является дефектоскопия трубопроводов.
Этот метод диагностики получил широкое распространение. Его применение позволяет выявить следующие виды дефектов:
- потеря уровня герметичности;
- потеря контроля состояния напряженности;
- нарушение сварных стыков;
- разгерметизация сварных швов другие параметры, которые ответственны за надежное функционирование магистралей.
Проверять таким образом можно:
- теплосеть;
- газоподающую сеть;
- нефтепроводы;
- водоподающие трубопроводы и др.
Дефектоскопия на 100% способна выявить недостатки и предупредить серьезные аварии. Методы поиска дефектов постоянно усовершенствуются, обновляется оборудование, и испытываются новые модели дефектоскопов. Плюс ко всему этому проводятся различные анализы для того, что бы в последствие улучшить работу средств.
Ультразвуковая дефектоскопия
Ультразвуковая дефектоскопия трубопровода впервые была предоставлена Соколовым С.Я. в 1928 году. Она создана на основе изучения передвижения ультразвуковых колебаний, которые находились под контролем дефектоскопа.
Описывая принцип работы этих устройств, необходимо отметить, что волна звука не меняет направление своего передвижения в среде, имеющем одинаковую структуру. Когда среда разделяется удельным акустическим препятствием, то получается отражение волны.
Видео: Магнитопорошковая дефектоскопия сварных швов
Магнитный контроль — Магнитопорошковая дефектоскопия
Смотрите это видео на YouTube
Чем выше количество таких препятствий, тем больше волн будет отражена от границы, которая разделяет среду. Возможность обнаружить небольшие дефекты отдельно один от другого определяет длина звуковой волны. А она при этом зависима от того, насколько часты звуковые колебания.
Многообразные задачи, стоящие при проведении ультразвуковой дефектоскопии, привели к тому, что появились большие возможности этого способа поиска неисправностей. Из них выделяют пять основных вариантов:
- Эхо – локация.
- Теневой метод.
- Зеркально-теневой.
- Зеркальный.
- Дельта – способ.
Приборы современного производства для ультразвуковой проверки оснащают несколькими возможностями измерения одновременно. И делают это в разных сочетаниях.
Эти механизмы отличаются очень высокой точностью, в результате остаточное пространственное разрешение и достоверность итогового вывода о дефективности трубопровода или его деталей получается максимально правдивым.
Ультразвуковой анализ не приносит повреждений исследуемой конструкции, и дает возможность провести все работы с максимально быстро и без вреда человеческому здоровью.
Ультразвуковая дефектоскопия — это доступная во всех отношениях система контроля мест соединения и швов. То, что в основе этого метода положена высокая возможность проникновения ультразвуковых волн сквозь металл.
Анализ сварных швов
Дефектоскопия сварных швов трубопроводов является обязательной процедурой перед запуском в эксплуатацию магистральных коммуникаций, особенно проходящих под землей.
В любой конструкции сварной шов являлся слабым местом, по этим причинам их качество всегда должно быть под контролем. На сварных швах лежит важная ответственность – они определяют герметичность и качество готового сооружения в целом.
Суть различных подходов для анализа таких стыков состоит в оценке тех или других физических свойств, характеризующих надежность и прочность трубопровода. Дефектоскопия определяет не только размер дефектов, но и оценивает качественное состояние швов. В эту оценку входит:
- показатель прочности;
- возможность противостоять коррозийным образованиям;
- степень пластичности;
- структура металла шовного соединения и области возле него;
- количество о габариты дефекта.
Способ ультразвукового исследования – это один из основных методов выявления дефектов на сварных швах.
Видео: Обзор дефектоскопа магнитопорошкового
Обзор дефектоскопа магнитопорошкового МД-6
Смотрите это видео на YouTube
Дефектоскопия сварных соединений трубопроводов имеет следующие преимущества.
- Быстрое проведение ревизии.
- Высокая точность исследования.
- Небольшая стоимость.
- Абсолютная безвредность для человека.
- Мобильность используемых для проверки устройств.
- Возможность выполнять проверку качества функционирующего трубопровода.
Самая простая процедура дефектоскопии – это визуальный осмотр. Визуально — измерительный способ позволяет на основе первых полученных результатов при внешнем осмотре определить наличие многих дефектов.
С помощью данного осмотра проверяют уровень качества готовых сварных стыков. Этот вид исследования применяют независимо от других типов контроля. Чаще всего он является очень информативным, и кроме этого, он самый дешевый.
Этим методом выявляют отклонения от номинальных размеров. При этом поверхность трубопровода тщательно очищают от грязи, металлических брызг, ржавых образований, окалины, масла и прочих загрязнений.
В зону внимания попадают сварные швы и прилегающая к ним зона. Все найденные на этом этапе недостатки устраняют до выполнения иных способов дефектоскопии.
Например, заметно выраженные различия в высоте сварного шва свидетельствуют о том, что дуга во время сварочных работ прерывалась.
На период проверочных мероприятий такие стыки рекомендуют обработать 10% раствором азотной кислоты. Если будут заметны грубые геометрические нарушения, то это свидетельствует о нарушении качества сварного шва.
Видео: В видео представлен краткий обзор ультразвуковых приборовTG 110-DL, Avenger EZ
Смотрите это видео на YouTube
Преимущества данного метода исследования следующие:
- Чаще всего на такую операцию нужно немного времени.
- Небольшая стоимость проверки.
- Безопасность данной процедуры для человеческого здоровья.
- Можно проверить действующий трубопровод.
Ну и куда же без недостатков:
- Возможность разрушающего действия.
- Потребность в спецреактивах и иных расходных материалах.
- Опытные образцы после этого процесса не всегда подлежали восстановлению.
Дефектоскопия стыков трубопроводов
Дефектоскопия соединений трубопроводов – это довольно ответственный процесс, который начинают только после того, как сварной шов готовый. Место состыковки должно остыть и его необходимо очистить от загрязнений.
Еще одним методом проверки является цветная дефектоскопия трубопроводов, ее по-другому называют капиллярный контроль. В основе данной проверке лежит капиллярная активность жидкости. Поры и потрескавшиеся образования создают сетку в стыке.
Когда они контактируют с жидкостью, то они просто пропускают ее сквозь себя. Такой способ дает возможность обнаружить скрытие проблемные образования. Проводят такую процедуру в соответствии к ГОСТу 1844-80.
Часто для этого вида поверки применяют магнитную дефектоскопию. В ее основу положили такое явление, как электромагнетизм. Возле проверяемой зоны механизм создает магнитное поле. Его линии свободно проходят сквозь металл, но когда присутствует повреждение, то линии теряют ровность.
Видео: Проведение внутритрубной диагностики магистральных трубопроводов
Проведение внутритрубной диагностики
Смотрите это видео на YouTube
Чтобы зафиксировать полученное изображение, используют магнитографическую или магнитопорошковую дефектоскопию. Если применяют порошок, то его накладывают сухим или в виде влажной массы (в нее добавляют масло). Порошок станет скапливаться только в проблемных местах.
Внутритрубная проверка
Внутритрубная дефектоскопия магистральных трубопроводов – это самый эффективный вариант обнаружения проблем, основанный на прогоне по системе труб спецустройств.
Ими стали внутритрубные дефектоскопы, с установленными специальными приборами. Эти механизмы определяют конфигурационные особенности поперечного сечения, выявляют вмятины, утончения и коррозийные образования.
Также есть внутритрубные механизмы, которые созданы для решения конкретных заданий. Например, оборудование, имеющее видео и фотокамеры, инспектирует внутреннюю часть магистрали и определяет степень кривизны и профиль конструкции. Также оно обнаруживает трещины.
Эти агрегаты передвигаются по системе потоком и оснащаются разнообразными датчиками, они накапливают и хранят информацию.
Внутритрубная дефектоскопия магистральных трубопроводов имеет весомые преимущества. Она не выставляет требований ставить устройства, которые ведут систематический контроль.
К сказанному необходимо добавить, что, используя это вид диагностики, можно производить регулярный контроль деформационных изменений по всему участку действующей конструкции с высоким уровнем производительности.
Таким путем можно вовремя установить участок, который несет аварийную угрозу всей системе, и своевременно провести ремонтные работы по устранению неполадок.
Говоря об этом методе, важно заметить, что есть ряд технических трудностей по его внедрению. Основное – он является дорогим. А второй фактор – это наличие устройств только для магистральных трубопроводов с большими объемами.
Видео
Внутритрубная диагностика газопровода
Смотрите это видео на YouTube
По этим причинам этот метод чаще всего применяют для относительно новых газопроводных систем. Внедрить этот способ для других магистралей можно посредством выполнения реконструкции.
Помимо оговоренных технических трудностей, этот метод отличается максимально точными показателями с обработкой проверочных данных.
Для исследования магистральных трубопроводов не обязательно выполнять все процедуры, чтобы убедиться в отсутствии проблем. Каждый участок магистрали можно проверить тем или другим наиболее подходящим способом.
Чтобы выбрать оптимальный вариант проверки нужно оценить, насколько важна ответственность стыка. И уже, исходя из этого, подбирать метод исследования. Например, для домашнего производства часто хватает визуального осмотра или других бюджетных видах проверок.
ультразвуковая проверка сварных швов и труб, как проводится, виды, методы, оборудование
Много трубопроводов, находящихся сегодня в эксплуатации, устарело в плане их длительной службы. Поэтому коррозия швов и уменьшение толщины стенки труб – дело обычное. Чтобы обнаружить недостатки конструкции, используют специальные методы, которые входят в единую систему под названием дефектоскопия трубопроводов.
Общие сведения
Содержание статьи
- 1 Общие сведения
- 2 Подробности
- 2.1 Визуальная
- 2.2 Ультразвуковая дефектоскопия
- 2.3 Магнитная дефектоскопия трубопроводов
- 2.4 Радиационная дефектоскопия трубопроводов
- 2.5 Капиллярная дефектоскопия
- 2.6 Дефектоскопия соединений на проницаемость
- 3 Оборудование для дефектоскопии трубопроводов
- 4 Итоги
Диагностика трубопроводов – это несколько технологий, которые делятся на две основные группы: разрушающие и неразрушающие. При использовании первой производится разрушение стыка двух труб, после которого обследуются кромки соединенных участков на предмет качества и обнаружения дефектов. Такой вариант возможен, если проводится ремонт трубопровода (полная его остановка).
Вторая технология не требует разрушения, что дает возможность проводить контроль на действующих участках. Ее используют сегодня повсеместно, особенно в сфере нефте- и газотранспортировки, плюс ЖКХ. Такая дефектоскопия, именно так называют неразрушающий контроль, проводится для определения дефектов насосных станций, резервуаров разного назначения, на заводах сжиженного газа и прочих предприятиях.
Да, я неоднократно проводил дефектоскопию металлических труб у себя дома.
50%
Нет, впервые слышу.
50%
Проголосовало: 2
Подробности
Существует несколько технологий дефектоскопии трубопроводов. Самая простая из них – визуальный осмотр.
Можно по внешнему виду сварного шва определить – качественный он или нет. Если дефекты стыка не видны, то для их нахождения используют лупу. Раковины, неровности, трещины – все это является изъянами сварного шва, что говорит о низком качестве проведенных сварочных работ.
Этот метод контроля в действующих трубопроводах используют редко. Чаще в качестве дополнения к другим видам. Именно последние являются основой качественно проведенного контроля.
Основные методы, которые применяются сегодня:
- ультразвуковая дефектоскопия трубопроводов;
- магнитная;
- радиационная;
- капиллярная;
- исследование на проницаемость.
Визуальная
С помощью этого вида контроля можно обнаружить не только внешние дефекты, но и внутренние. К примеру, если шов по высоте и ширине имеет серьезное отклонение, то вероятнее всего в процессе сварки произошло прерывание дуги. А это говорит о том, что внутри шва могут появиться непровары, снижающие качество соединения.
Обнаружить такие изъяны можно так:
- шов очистить от окалины, капель, шлака;
- он дополнительно очищается при помощи спирта;
- на шовный участок наносится азотная кислота – процесс называется травлением;
- с помощью лупы исследуется шов.
Травление делает поверхность металла чистой и матовой. На ней хорошо видны даже мелкие недостатки. Обычно внимание обращают на трещины. Н хорошо видны и пережоги, подрезы, прочие дефекты.
Ультразвуковая дефектоскопия
Это один из точных вариантов дефектоскопии трубопроводов, накопительных сосудов и других конструкций. В основе технологии лежит свойство ультразвука отражаться от поверхностей, а также материалов, которые имеют разную плотность. Если сварочный шов был сделан качественно, то плотность залитого между кромками труб металла будет одинакова по всему объему. И когда проводится ультразвуковая дефектоскопия, то звук пройдет сквозь шов беспрепятственно.
Если внутри металла есть пора или раковина, то внутри них всегда присутствует какой-то газ. Плотность внутри изъяна явно меньше, чем металла. И при прохождении ультразвука сквозь металл на его пути встречается пустота. Звук проходит через газ, ударяется о стенку раковины и возвращается обратно. Именно обратная волна говорит, что внутри шва есть дефект.
Разные пустоты отражают ультразвук по-разному. Это позволяет их классифицировать. То есть это раковина, трещина или что-то другое.
Чисто технически этот метод дефектоскопии трубопроводов представляет собой специальное устройство в виде колец, которые часто называют решетками. Их надевают на трубу, после чего подключают к источнику ультразвука. Кольца передают направленные внутрь волны и принимают отраженные.
Чем больше дефектов внутри металла, тем больше отраженных волн возвращается на приемник устройства дефектоскопии трубопроводов. При этом отличительная особенность каждого дефекта – это длина возвращенной волны.
Есть много задач, которые ставятся перед ультразвуковой дефектоскопией.
Поэтому разработаны несколько эффективных методов, которые сегодня используются для решения каждой:
- теневой;
- зеркальный;
- зеркально-теневой;
- эхолокация;
- дельта-метод.
Сегодня приборы, которыми проводят ультразвуковое исследование трубопроводов, оснащаются разными устройствами в соответствии с требуемыми методами контроля.
Магнитная дефектоскопия трубопроводов
Этот метод основан на электромагнитной индукции (создания магнитного поля в металле сварного шва). Для этого применяется оборудование, которое это поле создает.
Есть две технологии проведения дефектоскопии этого типа:
- При помощи ферромагнитного порошка. Обычно для этого используют железо.
- При помощи ферромагнитной ленты.
В первом случае порошок просто насыпают на участке проведения контроля. Он может быть сухим или смешанным с маслом или керосином. С обратной стороны трубы устанавливается магнит. Если в каком-то месте порошок стал собираться кучками, значит, здесь есть дефект металла.
Во втором случае вместо порошка укладывают специальную ленту. С обратной стороны шва устанавливается прибор, образующий магнитное поле.
Этот способ дефектоскопии трубопроводов может быть использован, если трубы изготовлены из ферромагнитных сплавов (которые притягивают магнит). Цветные металлы, нержавейка аустенитного класса, стали с покрытием из никеля или хрома такому способу контроля не подвергаются.
Радиационная дефектоскопия трубопроводов
Этот метод – обычная рентгеноскопия, где используется компактный рентгеновский аппарат и пленка. Метод дорогой, но самый точный из всех предложенных. При этом рентгеновские лучи опасны для человека.
Капиллярная дефектоскопия
Этот метод основан на свойстве некоторых жидкостей, которые называют пенетрантами, проникать по капиллярам в любом материале. Это не обязательно металл. Так можно проверить стекло, пластик, керамику и прочее.
Суть метода дефектоскопии заключается в том, что проникающую жидкость наносят на контролируемый участок трубопровода. Через некоторое время, обычно это 20 минут, ее удаляют, и на этот же участок наносится индикатор, который начинает из дефектов шва вытягивать пенетрант.
Из проникающих жидкостей самый простой – керосин. Для его применения необходимо четко знать технологию нанесения. Это надо делать так:
- с внешней стороны наносится жидкий меловой раствор;
- он должен просохнуть;
- с обратной стороны наносится керосин;
- если со стороны мелового раствора появились мокрые линии или пятна, значит, дефекты в металле присутствуют.
Дефектоскопия соединений на проницаемость
Этот метод используется для контроля качества сварных швов резервуаров и емкостей. Для этого их заполняют жидкостью или газом, а затем создают внутри избыточное давление. Среда начинает искать выход, и если в швах присутствуют трещины или другие изъяны, то она быстро начинает через них просачиваться наружу.
Эффективность способа увеличивается, если по стыкам с внешней стороны распределить мыльный раствор. Особенно, если резервуар заполнить газом.
Пузырьки на стыках покажут, что швы проварены некачественно.
Оборудование для дефектоскопии трубопроводов
Современные технологии дефектоскопии – это, в основном, внутритрубная диагностика. Для этого используется специальное оборудование, которое называется внутритрубные дефектоскопы. Они помещаются внутрь трубопровода и доводятся до требуемых участков, где самостоятельно проводят контроль. Многие из них снабжены камерами: фото и видео.
С их помощью определяют:
- форму поперечного сечения трубы;
- наличие коррозии;
- вмятины;
- произошло ли утончение металла и прочие изъяны.
Некоторые аппараты двигаются по трубопроводу за счет перемещаемого потока. Некоторые за счет установленного электродвигателя. Внутри есть датчики, функция которых – накапливать и сохранять полученную информацию.
Внутритрубная дефектоскопия магистральных трубопроводов – это технология, которая позволяет не использовать аппаратуру, ведущую систематические исследования. При этом скорость контроля выше всех известных методов дефектоскопии. Но используется этот вариант только в трубопроводах большого диаметра.
Исследования трубопроводов этим методом проводится в несколько этапов:
- подготовка, она же диагностика;
- очистительные мероприятия внутреннего пространства трубопровода;
- калибровка – это обеспечение внутренней проходимости труб;
- использование профилемера – так обследуются изгибы, повороты и прочие неровности;
- применение ультразвуковой дефектоскопии и магнитной;
- определение безопасности работы трубопровода.
Итоги
Деградация металла – серьезная проблема, особенно в конструкциях, внутри которых перемещаются различные среды под большим давлением. Со временем прочность соединительных участков падает, что может привести к серьезным последствиям. Решается проблема сегодня просто – контролем, для чего используются различные методы дефектоскопии трубопроводов.
У каждого выше обозначенного способа есть свои плюсы и минусы. Но они гарантируют высокую точность дефектовки, что требуется во время контрольных обследований. Поэтому вновь вводимые трубопроводы обследуются в обязательном порядке. Эксплуатируемые проверяются по строго утвержденному графику планово-предупредительного ремонта. Нарушать сроки проведения дефектоскопии нельзя ни под каким предлогом.
Ультразвуковая дефектоскопия сварного шва: видео.
А как считаете вы, какой способ из предложенных самый информативный? Напишите в комментариях. Сохраните статью в закладках, поделитесь ею в социальных сетях.
Дефектоскопия трубопроводов: разновидности методов- Обзор +Видео
Радиационная
Радиационная дефектоскопия по своему принципу напоминает рентгеновское обследование. Выделившиеся в процессе ядерной реакции гамма-лучи обладают высокой проникающей способностью. Проходя через материал, излучение попадает на фотопластинку. После ее проявления под микроскопом можно исследовать картину распределения дефекта в металле.
Интересующий вопрос о вредности гамма-излучения остается актуальным. Несмотря на предусмотренные средства защиты, организм человека получает повышенную долю облучения. Если добавить дороговизну оборудования, станет ясно, что данный способ не является приоритетным.
Магнитно-порошковые дефектоскопы
Дефектоскоп позволяет контролировать различные по форме детали, сварные швы, внутренние поверхности отверстий путём намагничивания отдельных контролируемых участков или изделия в целом циркулярным или продольным полем, создаваемым с помощью набора намагничивающих устройств, питаемых импульсным или постоянным током, или с помощью постоянных магнитов.
Принцип действия основан на создании поля рассеяния над дефектами контролируемой детали с последующим выявлением их магнитной суспензией. Наибольшая плотность магнитных силовых линий поля рассеяния наблюдается непосредственно над трещиной (или над другой несплошностью) и уменьшается с удалением от неё.
Для обнаружения несплошности на поверхность детали наносят магнитный порошок, взвешенный в воздухе (сухим способом) или в жидкости (мокрым способом). На частицу в поле рассеяния будут действовать силы: магнитного поля, направленная в область наибольшей плотности магнитных силовых линий, то есть к месту расположения трещины; тяжести; выталкивающего действия жидкости; трения; силы электростатического и магнитного взаимодействия, возникающие между частицами.
В магнитном поле частицы намагничиваются и соединяются в цепочки. Под действием результирующей силы частицы притягиваются к трещине и накапливаются над ней, образуя скопление порошка. Ширина полоски (валика) из осевшего порошка значительно больше ширины раскрытия трещины. По этому осаждению — индикаторному рисунку определяют наличие дефектов.
Критерии выбора оборудования
Выбор системы телеинспекции производится с учётом характеристик объектов, на которых они будут применяться, а также особенностей работы оборудования различного вида. Рассмотрим типичные области применения, особенности функционирования, достоинства и недостатки устройств, использующихся для видеодиагностики трубопроводов.
Самоходные роботы – тележки.
Одной из главных технических характеристик таких устройств является минимальный и максимальный пределы диаметров обследуемых труб или коллекторов. Наименьший размер трубы определяется габаритами тележки, наибольший зависит от наличия конструктивных элементов, обеспечивающих позиционирование видеокамеры по высоте вблизи оси трубопровода (колеса большого диаметра, проставочные втулки на колеса для расширения колеи, механизм подъема видеокамеры и т.п.), а также от таких параметров, как яркость источников подсветки, чувствительность и разрешающая способность камеры, наличие функции zoom и других опций. На современном рынке представлены роботы различных типоразмеров и производителей, способные работать в трубах диаметром от 100 до 3000 мм.
Вторая важная характеристика робота – глубина обследования, то есть расстояние, на которое он способен продвинуться в трубе. С одной стороны, расстояние определяется длиной кабеля, то есть, необходимо выбирать барабан нужной ёмкости. С другой стороны, максимальное значение пути робота определяется весом робота, обеспечивающим сцепление колес с поверхностью трубы, материалом и формой колес, наличием протекторов и грунтозацепов, мощностью электродвигателя и удельным весом протаскиваемого кабеля, так как при увеличении пройденного расстояния увеличивается сопротивление трения кабеля о стенки трубы.
Проталкиваемые модули.
Такая система телеинспекции применяется в основном для осмотра трубопроводов диаметром от 100 до 400 мм. Минимальное значение диаметра зависит от размеров камеры. При работе в трубах большого диаметра, направляющий пруток может закручиваться в процессе проталкивания, что делает невозможным дальнейшее продвижение. Максимальная длина проталкивания модуля зависит от упругих свойств прутка, которые определяются материалом прутка и его диаметром. Например, для проталкивания камеры на расстояние 30 – 50 метров, диаметр прутка должен быть не менее 7 мм, если же требуется обследовать 60 – 80 метров внутритрубного пространства, следует воспользоваться прутком от 9 мм толщиной.
Плавающие модули.
Система телеинспекции этого типа оказывается вне конкуренции, когда необходимо провести видеообследование безнапорной трубы или коллектора при уровне их заполнения стоками от 300 мм. Положительным качеством плавающей камеры для телеинспекции является возможность обследования коллекторов большого диаметра без сложных мероприятий по остановке потока. Минусом является узкая сфера применения – только безнапорные, частично наполненные стоки.
Методы ультразвуковой дефектоскопии
Существует несколько методов ультразвукового контроля: эхо-импульсный, эхо-зеркальный,
эхо-сквозной, дельта-метод (разновидность эхо-зеркального), когерентный метод
(разновидность эхо-импульсного), теневой, зеркально теневой. Рассмотрим кратко
наиболее распространенные из них, см. рисунок:
1. Эхо-импульсный метод. Он заключается в направлении акустической волны
на сварное соединение и регистрации отражённой волны от дефекта. При таком методе
источником и приёмником волн выступает один преобразователь (схема а) на рисунке).
2. Теневой метод. Такой метод ультразвуковой дефектоскопии заключается
в использовании двух преобразователей, установленных на разные стороны сварного
соединения. При таком методе один из преобразователей генерирует акустические
волны (излучатель), а второй их регистрирует (приёмник). При этом приёмник должен
быть расположен строго по направлению движения волны, переданной излучателем.
При таком методе признаком дефекта является пропадание ультразвуковых колебаний.
В потоке ультразвука получается “глухая область”, это означает, что
волна на этом участке не преодолела сварной дефект (схема б) на рисунке).
3. Эхо-зеркальный метод. Он также заключается в использовании двух преобразователей,
но располагаются они с одной стороны сварного соединения. Сгенерированные приёмником
ультразвуковые колебания отражаются от дефекта и регистрируются приёмником.
На практике такой метод получил широкое распространение для поиска дефектов,
расположенных перпендикулярно поверхности сварного соединения, например, сварных
трещин (схема в) на рисунке).
4. Зеркально-теневой метод. По своей сути представляет собой теневой
метод, но преобразователи располагаются не на противоположных поверхностях сварного
соединения, а на одной. При этом регистрируются не прямой поток ультразвуковых
волн, а поток, отражённый от второй поверхности сварного соединения. Признаком
дефекта является пропадание отражённых колебаний (схема г) на рисунке).
При ультразвуковой дефектоскопии сварных соединений используется, в основном,
эхо-импульсный метод контроля. Реже применяется теневой метод и другие.
Радиационный метод
Для контроля качества сварки используют радиационные методы и устройства. По сути это тот же рентгеновский аппарат, используемый в больницах, или прибор с источником гамма-излучения, приспособленный для облучения сварных соединений.
Он основан на способности этих лучей, проникать через любые материалы. Интенсивность проникновения зависит от вида исследуемых веществ. Благодаря этому на фотопленке, стоящей за исследуемым изделием, остается изображение, характеризующее состояние данного материала.
Все дефекты сварки в виде неоднородностей выявляются на пленке. Метод контроля очень точный, но дорогой и вредный для людей, требует подготовительных работ по установке защитных экранов и проведения организационных мероприятий.
История
- Жак и Пьер Кюри в 1880—1881 годах обнаружили обратимый пьезоэлектрический эффект, что позволило использовать кварц как преобразователь электрических колебаний в звуковые
- Первый дефектоскоп для обнаружения повреждений в электроцепи был разработан Дмитрием Александровичем Лачиновым в конце 1880-х годов — Дефектоскоп Лачинова
- Лорд Рэлей в 1885—1910 годах разработал теорию распространения звука в твердых веществах
- Эхо-импульсный способ впервые применили Лангвэн и Шиловски с пьезоэлектрическими преобразователями в водной среде в 1915—1917 гг
- В 1922 году запатентован магнитный метод обнаружения дефектов артиллерийских стволов с помощью магнитного порошка, открытый Уильямом Э. Хоуком во время Первой мировой войны
- Первые дефектоскопы, работающие на непрерывном звуке, создали в 1928 С.
Я. Соколов и в 1931 г. Мюльхойзер
- 1937—1938 год — первая в мире установка, использующая переменный ток для контроля конструкций железной дороги и колесных пар (компания MAGNAFLUX, США)
- Эхо-импульсные дефектоскопы (принцип действия и прибор) создали впервые в 1939—1942 г. Файрстон в США, Спрулс в Великобритании и Крузе в Германии
- Первые эхо-импульсные дефектоскопы были выпущены в 1943 г. почти одновременно фирмами «Сперри продактс инк.» (Данберри, США) и «Кельвин энд Хьюз лтд.» (Лондон)
Разновидности методов МК
Чтобы выявлять и фиксировать потоки рассеяния, указывающие на присутствие деформаций и повреждений, применяют несколько методов МК, различающихся в соответствии с ГОСТ 24450-80 по способам получения исходных данных:
- Магнитопорошковый – наиболее распространенный и востребованный метод. Отличающийся простотой применения, высокой сенсетивностью и универсальностью, он используется для обнаружения поверхностных и расположенных на глубине до 2 мм деформаций с помощью магнитного порошка в качестве индикатора
- Индукционный – основан на применении индукционных преобразователей (катушек), улавливающих локальные потоки возмущения поля, образующиеся над повреждениями намагниченного объекта контроля
- Магниторезисторный – использует магниторезистивные преобразователи для выявления и регистрации потоков рассеивания над деформациями намагниченного объекта контроля
- Магнитографический – использование записи магнитного поля исследуемого объекта на соответствующем носителе.
Воспроизведение полученной сигналограммы анализируется для выявления дефектов
- Пондеромоторный – построен на пондеромоторном взаимодействии фиксируемого магнитного поля исследуемого объекта и магнитного поля постоянного магнита, электромагнита или рамки с током
- Феррозондовый – использование феррозондовых преобразователей для обнаружения и регистрации рассеяния магнитных полей сварочных швов и прочих исследуемых объектов
- Метод эффекта Холла – применение одноименных преобразователей для фиксации локальных возмущений полей над объектами контроля
Пенетранты
С английского это слово переводится, как впитывающий. В настоящее время существует более десятка составов пенетрантов (водные или на основе органических жидкостей: керосин, масла и так далее). Все они обладают малым поверхностным натяжением и сильной цветовой контрастностью, что позволяет их легко увидеть. То есть, суть метода такова: наносится пенетрант на поверхность сварочного шва, он проникает внутрь, если есть дефект, окрашивается с этой же стороны после очистки нанесенного слоя.
Сегодня производители предлагают разные проникающие жидкости с разным эффектом обнаружения изъяном.
- Люминесцентные. Из названия понятно, что в их состав входят люминесцентные добавки. После нанесения такой жидкости на шов нужно посветить на стык ультрафиолетовой лампой. Если дефект есть, то люминесцентные вещества будут отсвечивать, и это будет видно.
- Цветные. В состав жидкостей входят специальные светящиеся красители. Чаще всего это красители ярко-красные. Они хорошо видны даже при дневном свете. Наносите такую жидкость на шов, и если с другой стороны появились красные пятнышки, то дефект обнаружен.
Есть разделение пенетрантов по чувствительности. Первый класс – это жидкости, с помощью которых можно определить дефекты с поперечным размером от 0,1 до 1,0 микрона. Второй класс – до 0,5 микрон. При этом учитывается, что глубина изъяна должна превосходить его ширину в десять раз.
Наносить пенетранты можно любым способом, сегодня предлагаются баллончики с этой жидкостью. В комплект к ним прилагаются очистители для зачистки дефектуемой поверхности и проявитель, с помощью которого выявляется проникновение пенетранта и показывается рисунок.
Как это надо делать правильно.
- Шов и околошовные участки необходимо хорошо очистить. Нельзя использовать механические методы, они могут стать причиной занесения грязи в сами трещины и поры. Используют теплую воду или мыльный раствор, последний этап – очистка очистителем.
- Иногда появляется необходимость протравить поверхность шва. Главное после этого кислоту убрать.
- Вся поверхность высушивается.
- Если контроль качества сварных соединений металлоконструкций или трубопроводов проводится при минусовой температуре, то сам шов перед нанесением пенетрантов надо обработать этиловым спиртом.
- Наносится впитывающая жидкость, которую через 5-20 минут надо удалить.
- После чего наносится проявитель (индикатор), который из дефектов сварного шва вытягивает пенетрант. Если дефект небольшой, то придется вооружиться лупой.
Если никаких изменений на поверхности шва нет, то и дефектов нет.
Магнитная дефектоскопия
Явление электромагнетизма используется в магнитных дефектоскопах. Каждый металл имеет свою степень магнитной проницаемости. При прохождении через неоднородные материалы магнитное поле искажается, что говорит о присутствии инородных элементов внутри структуры.
Это используется в приборе для контроля качества сварки. Он вырабатывает магнитное поле, которое проникает в исследуемый металл. Неоднородности фиксируются магнитопорошковым или магнитографическим способом.
В первом случае на сварной шов наносят ферромагнитный порошок. Там где происходит скопление порошка вероятнее всего непровар, нет сплошного соединения. Порошок может быть сухим или влажным, с примесью масла или керосина.
Во втором случае на шов накладывают ферромагнитную ленту. Затем ее пропускают через прибор, где анализируют все аномалии, зафиксированные на ленте, и определяют дефекты сварки.
Магнитный способ контроля качества имеет ограничения, связанные с самим принципом действия прибора. Он может проверять качество сварных соединений только ферромагнетиков, к которым некоторые стали и цветные металлы не относятся. Соответственно, такой способ контроля имеет ограниченное применение.
Неразрушающий контроль качества сварных соединений трубопроводов: методы и их характеристика
Неразрушающий контроль сварных швов трубопровода подразумевает регулярный мониторинг целостности конструкции. Дефектом считаются трещины, коррозии и другие изъяны сварных соединений, приводящих к снижению эксплуатационных свойств, нарушению герметичности и т. д.
Содержание
- 1 Методы системы неразрушающего контроля
- 2 Визуальный осмотр соединения
- 3 Ультразвуковой метод
- 4 Магнитная дефектоскопия сварных соединений
- 5 Рентгеновская дефектоскопия
- 6 Метод исследования гамма-излучением
- 7 Электрический метод
- 8 Тепловая дефектоскопия
- 9 Особенности контроля качества швов трубопроводов
Методы системы неразрушающего контроля
Существует множество способов обнаружения дефектов в местах сварки металлоконструкций. Как правило, специалисты применяют несколько методов одновременно. Ниже перечислены самые распространённые.
Визуальный осмотр соединения
При внешнем осмотре есть возможность обнаружить только явные дефекты, видимые невооружённым взглядом или с помощью увеличительного прибора.
Внешний контроль, как самый первичный, применим ко всем видам соединений вне зависимости от их назначения и степени ответственности за неисправность.
Визуальный осмотр не может выявить скрытых проблем, поэтому далее следует диагностика более точными способами.
Ультразвуковой метод
Дефектоскопия ультразвуком основана на свойствах проникновения волн через толщу металла и отражения их от чужеродных включений.
Ультразвуковые дефектоскопы действуют следующим образом: на пластину из кварца воздействуют высокочастотным электрическим полем, пластина, в свою очередь, начинает транслировать ультразвуковые волны, которые направляются на место соединения.
В точке, где находится дефект, происходит отражение волновых колебаний, которые принимаются второй пластиной. Далее показатели усиливаются и передаются в осциллограф. На экране прибора синхронно отображаются импульс, направленный на шов, и волна, отражённая от изъяна. Таким образом распознаётся величина и координаты неисправности.
Магнитная дефектоскопия сварных соединений
Метод основан на активации диффузного магнитного поля, которое проходит через сварной шов и образует разнонаправленные магнитные потоки на местах локации дефектов. Магнитный метод подразделяется на способы:
- Магнитопорошковый. При проверке таким способом соединение намагничивается, а его поверхность обрабатывается железосодержащим порошком или суспензией.
Далее место шва подвергается воздействию магнитного поля, которое равномерно распределяет нанесённое вещество. В месте неоднородности шва порошок или суспензия скапливается, что и определяет координаты дефекта.
- Магнитографический. Предварительно на место шва накладывают магнитную плёнку, после чего на участок воздействуют магнитным полем. Зафиксированную информацию считывают с плёнки с помощью дефектоскопа и преобразуют её в изображение или звук. Обработанные таким образом данные выводятся на монитор.
Рентгеновская дефектоскопия
Рентгеновские лучи по-разному рассеиваются в веществах, различных по молекулярной структуре. На этом свойстве и основан рентгеновский метод контроля. Для реализации исследования с одной стороны соединения размещают источник излучения, а с другой — детектор. Рентгеновские лучи, проходя через шов, воздействуют на индикатор (фотобумагу или негатив), на котором отображается полная траектория прохождения лучей через место проверки. Затемнения на снимке указывают на места более интенсивного прохождения лучей, а, следовательно, на проблемную зону. Для рентгеновского исследования применяют приборы РУП-120-5 и РУП-200-5.
Метод исследования гамма-излучением
Схема диагностики гамма-лучами идентична рентгеновской, однако, в качестве источника излучения используются радиоактивные изотопы.
У последнего метода имеются преимущества:
- гамма-лучи имеют более выраженную способность к прониканию в толщи металла, что позволяет использовать метод на громоздких конструкциях;
- экономически метод контроля гамма-лучами более выгоден ввиду низкой себестоимости.
Существенным недостатком способа является его радиоактивная токсичность. Малейшие нарушения в технике безопасности при его применении могут привести к серьёзным последствиям для здоровья специалистов, осуществляющих диагностику.
Для диагностики гамма-лучами используют дефектоскопы ГУП-Со-0,5-1, ГУП-Со-5-1, ГУП-Со-50, РИД-21-Г.
Электрический метод
Метод основан на взаимодействии электрического поля с поверхностью шва и внутреннего содержимого исследуемого объекта. Например, при воздействии электрического тока на шов в местах несоответствий констатируется более низкое напряжение. Таким образом выявляется место и размер повреждения.
Тепловая дефектоскопия
При данном способе место соединения шва подвергают термическому излучению, данные которого передаются на регистрирующее устройство. Различная температура в определённых участках шва указывает на наличие изъянов. Метод широко применяется для диагностики изменения сплошности в месте соединения, выявлении шлаковых включений, пор, расслоений.
В комплексе с вышеперечисленными способами прочность швов проверяют с помощью:
- обработки керосином;
- аммиаком;
- газовым и гидравлическим давлением;
- вакуум-камерой.
Особенности контроля качества швов трубопроводов
Способы мониторинга качества швов трубопроводов описаны в ГОСТ 3242-79.
Непрерывный контроль сварных соединений трубопроводов рентгеновским или ультразвуковым способом следует осуществлять после исправления дефектов, выявленных визуальным осмотром, а трубопроводов РY свыше 10 МПа (100кгс/см2) — после диагностики магнитопорошковым методом. На соединениях должны отсутствовать трещины, прожоги, грубая шероховатость, подрезы глубиной более 0,5 миллиметров.
Преимущественными методами диагностики швов для данной категории металлоконструкций являются:
- ультразвуковой;
- рентгенографический.
Диагностика должна производиться по всему периметру соединения.
Дефектоскопия сварных соединений | Испытание и ультразвуковой контроль швов в Ростове-на-Дону
Чем хорош ультразвуковой контроль сварных соединений?
В современном строительстве существует острая необходимость в оперативном контроле сварных соединений и толщинометрии на строительном объекте с выдачей результата контроля. Актуальные госты и своды правил регламентируют виды и методы такого контроля. Одним из них является ультразвуковой контроль сварных соединений прибором УД4-ТМ, стоящий на вооружении в нашей лаборатории. Основной принцип данного прибора основан на прохождении, отражении и трансформации ультразвуковых колебаний на несплошностях и неоднородностях материала (дефектах). Дефектоскоп УД4-ТМ специализирован для неразрушающего контроля сварных соединений, материалов и изделий на присутствие дефектов типа нарушения сплошности, измерение амплитуды от дефектов эхосигналов, определение координат дефектов, измерение времени распространения ультразвуковых колебаний в изделии или материале. У данного прибора существуют функции неразрушающего контроля изделий из ферромагнитных и немагнитных сплавов и металлов на присутствие поверхностных дефектов типа трещин, расслоений, раковин, закатов и неметаллических включений. На наших объектах целиком и полностью используется большая часть этих параметров, позволяющих своевременно оценить изделие или конструкцию и оперативно принять решение по её эксплуатации или же устранению, если это является недопустимым дефектом.
№ п/п | Наименование испытания | Единица измерения | Стоимость, руб без НДС | ||||||||
---|---|---|---|---|---|---|---|---|---|---|---|
7 |
Испытание сварных швов металлоконструкций, стыков арматуры по ГОСТ 23118-2012, 57997-2017, 14098-2014, 23858-79, СП 70.![]() |
||||||||||
7.1 | ВИК и УЗК металлоконструкций и ж/б конструкций: |
|
|
||||||||
7.1.1 | ВИК сварных стыков арматуры | 1 стык | |||||||||
7.1.2 | ВИК сварных швов с одной стороны (конструкции) | 1 п.м. шва | 100 | ||||||||
7.1.3 | УЗК сварных стыков арматуры | 1 стык | 300 | ||||||||
7.![]() |
УЗК сварных швов металлоконструкций | 1 п.м. шва | 1000 | ||||||||
7.1.5 | Толщинометрия металлоконструкций | 1 точка | 400 | ||||||||
7.2 | ВИК сварных швов трубопроводов: |
|
|
||||||||
7.2.1 | ø трубопроводов до 60 мм | 1 стык | 50 | ||||||||
7.![]() |
ø трубопроводов до 219 мм | 1 стык | 60 | ||||||||
7.2.3 | ø трубопроводов до 377 мм | 1 стык | 80 | ||||||||
7.2.4 | ø трубопроводов до 530 мм | 1 стык | 100 | ||||||||
7.2.5 | ø трубопроводов до 1020 мм | 1 стык | 150 | ||||||||
7.![]() |
УЗК сварных швов трубопроводов: |
|
|
||||||||
7.3.1 | ø трубопроводов от 50 до 114 мм и толщиной стенки 4-12мм | 1 стык | 500 | ||||||||
7.3.2 | ø трубопроводов до 219 мм и толщиной стенки 4-12мм | 1 стык | 600 | ||||||||
7.3.3 | ø трубопроводов до 377 мм и толщиной стенки 4-12мм | 1 стык | 1000 | ||||||||
7.![]() |
ø трубопроводов до 530 мм и толщиной стенки 4-12мм | 1 стык | 1200 | ||||||||
7.3.5 | ø трубопроводов до 730 мм и толщиной стенки 4-12мм | 1 стык | 17000 | ||||||||
7.3.6 | ø трубопроводов до 1020 мм и толщиной стенки 4-12мм | 1 стык | 2500 | ||||||||
7.4 | Испытание образцов на растяжение арматуры: |
|
|
||||||||
7.![]() |
ø до 25 | 1 образец | 900 | ||||||||
7.4.2 | ø 28-32 | 1 образец | 1100 | ||||||||
7.4.3 | ø 36-40 | 1 образец | 1300 |
Ультразвуковой контроль сварных соединений в Ростове-на-Дону. Позвоните нам, чтобы получить консультацию.
Смотрите также:
- Испытание строительных материалов
- Сейсмоакустический контроль свай
- Обследование зданий и сооружений
Возврат к списку
Поделиться:
распространена ультразвуковая дефектоскопия сварных швов и соединений
Содержание
- Получение и свойства ультразвуковых колебаний
- Углы направления ультразвуковых колебаний
- Методы ультразвуковой дефектоскопии
- Сущность процесса ультразвуковой дефектоскопии
- Принцип ультразвукового контроля
- Параметры оценки дефектов при ультразвуковом контроле
Критические углы
При выполнении ультразвукового контроля оператору нужно выбрать тип преобразователя, выполнить калибровку и настройку прибора на предполагаемые дефекты объекта. Критические углы падения (продольные и поперечные) необходимо учитывать в том случае, когда ультразвук проходит через твердые поверхности материалов.
Первый критический угол — это наименьший угол падения продольной волны, при котором преломленный луч не пересекает границу второй твердой среды. Например, для границы оргстекло-сталь он равен 27,5º.
Вторым критическим углом считают наименьший угол падения продольного луча, при котором преломление не проникает через границу во вторую твердую среду и при этом не обнаруживаются внутренние повреждения. Для оргстекла-стали он составляет 57,5º.
Третий критический угол — наименьший угол падения поперечного луча, при котором отсутствует отраженная продольная волна. Луч идет по поверхности объекта, не распознавая дефектов внутри него. Для пересечения границы сталь-воздух угол равен 33,3º.
Получение и свойства ультразвуковых колебаний
Ультразвуковые колебания, называемые также акустическими волнами с частотой, превышающей 20кГц. Они представляют собой механические колебания, которые способны распространяться в упругих средах. В дефектоскопии используется диапазон частот 0,5-10МГц.
При распространении упругих волн в металле частицы металла колеблются относительно точки равновесия. Расстояние между двумя частицами металла, колеблющимися в одинаковой фазе, будет являться длиной ультразвуковой волны. Длина волны L связана со скоростью её распространения c и с частотой колебаний f. Эта зависимость выражается формулой: L=c/f.
Скорость распространения акустической волны зависит от физических свойств среды и от типа волны. Скорость продольной волны примерно в 2 раза выше, чем скорость поперечной.
Углы направления ультразвуковых колебаний
При наклонном падении продольной акустической волны на границу раздела двух сред 1 и 2 (см. рисунок ниже), вместе с отражением возникает явление преломления и трансформации ультразвуковой волны. Проявляются преломлённые и отражённые продольные волны, а также сдвиговые поперечные волны.
На схеме а) показано, что падающая под углом β волна Сl1 разделяется на преломлённую Сl2 и сдвиговую Сt2, которые распространяются в металле. Отражённая волна на рисунке не показана. При определённом критическом значении угла падения β= βкр1, преломлённая продольная волна перестанет проникать вглубь металла и будет распространяться только по её поверхности (схема б) на рисунке выше). Дальнейшее увеличение угла падения до βкр2. приведёт к тому, что сдвиговая волна будет распространяться только на поверхности металла (схема в) на рисунке). Такое явление широко используется на практике при ультразвуковой дефектоскопии сварных соединений для генерирования в контролируемых сварных швах акустических волн определённого типа.
Ультразвуковой метод и его технология
Технология ультразвукового контроля используется производством, промышленностью с момента развития радиотехнического процесса. Эффект и устройство технологии в том, что ультразвуковые волны акустического типа не меняют прямолинейную траекторию движения при прохождении однородной среды. Ультразвуковой метод используется также при проверке металлов и соединений, имеющих различную структуру. Такие случаи подразумевают, что происходит частичный процесс отражения волн, зависит от химических свойств металлов, чем больше сопротивление звуковых волн, тем сильнее воздействует эффект отражения.
Дефектоскопия или ультразвуковой контроль не разрушают соединения по структуре. Технология проведения ультразвуковой диагностики включает поиск структур, не отвечающих по химическим или физическим свойствам показателям, любые отклонения считаются дефектом. Показания колебаний рассчитываются по формуле L=c/f, где L описывает длину волны, Скорость перемещения ультразвуковых колебаний, f частоту колебаний. Определение дефекта происходит по амплитуде отраженной волны, тем самым возможно вычислить размер недочета.
Процесс ультразвукового метода
Сварные соединения подразумевают работу с наличием газовых ванн, испарения которых не всегда успевают удалиться в окружающую среду. Ультразвуковой метод контроля позволяет выявить газообразные вещества в сварных соединениях, за счет сопротивления волн. Газообразная среда веществ обладает сопротивлением в пять раз меньшим по отношению к кристаллической решетке металлических материалов. Ультразвуковой контроль металла позволяет вывить среды за счет отражения колебаний.
Методы ультразвуковой дефектоскопии
Существует несколько методов ультразвукового контроля: эхо-импульсный, эхо-зеркальный, эхо-сквозной, дельта-метод (разновидность эхо-зеркального), когерентный метод (разновидность эхо-импульсного), теневой, зеркально теневой. Рассмотрим кратко наиболее распространенные из них, см. рисунок:
1. Эхо-импульсный метод
. Он заключается в направлении акустической волны на сварное соединение и регистрации отражённой волны от дефекта. При таком методе источником и приёмником волн выступает один преобразователь (схема а) на рисунке).
2. Теневой метод
. Такой метод ультразвуковой дефектоскопии заключается в использовании двух преобразователей, установленных на разные стороны сварного соединения. При таком методе один из преобразователей генерирует акустические волны (излучатель), а второй их регистрирует (приёмник). При этом приёмник должен быть расположен строго по направлению движения волны, переданной излучателем. При таком методе признаком дефекта является пропадание ультразвуковых колебаний. В потоке ультразвука получается «глухая область», это означает, что волна на этом участке не преодолела сварной дефект (схема б) на рисунке).
3. Эхо-зеркальный метод
. Он также заключается в использовании двух преобразователей, но располагаются они с одной стороны сварного соединения. Сгенерированные приёмником ультразвуковые колебания отражаются от дефекта и регистрируются приёмником. На практике такой метод получил широкое распространение для поиска дефектов, расположенных перпендикулярно поверхности сварного соединения, например, сварных трещин (схема в) на рисунке).
4. Зеркально-теневой метод
. По своей сути представляет собой теневой метод, но преобразователи располагаются не на противоположных поверхностях сварного соединения, а на одной. При этом регистрируются не прямой поток ультразвуковых волн, а поток, отражённый от второй поверхности сварного соединения. Признаком дефекта является пропадание отражённых колебаний (схема г) на рисунке).
При ультразвуковой дефектоскопии сварных соединений используется, в основном, эхо-импульсный метод контроля. Реже применяется теневой метод и другие.
Виды и методы ультразвукового контроля сварных соединений
Для диагностирования стыков ультразвуком используют разные методики:
- прямой луч;
- отражение однократное;
- отражение двукратное;
- отражение многократное.
Касательно направления луча, то его подбирают по нормали, где опасность дефектов особенно высока. Наиболее распространенные варианты измерений:
- эхо-импульсная диагностика. Прибор генерирует волну и настроен на прием оклика. Если его нет, то это значит, что дефекты не обнаружены. Если же результат обратный, то в исследуемой массе есть разделение сред;
- эхо-зеркальный.
Подразумевает использование генерирующего волну датчика и приемника-улавливателя. Размещение приборов – под углом к оси стыка. Приемник ловит все ультразвуковые излучения и по ним диагностируются трещины или их отсутствие;
- теневая диагностика. Волны проходят по всей площади стыка. Приемник располагается позади сварного соединения. В случае, когда излучение отражается и не попадает на приемник, фиксируется теневой участок;
- зеркально-теневая дефектоскопия. Технология сочетает теневой и зеркальный методы исследований. Используется комплект датчиков, которые улавливают отраженные звуковые колебания. Если идет чистая волна, то это значит, что шов не имеет дефектов;
- дельта-метод подразумевает воздействие на объект направленным лучом. По отражению звукового сигнала определяются изъяны стыка. Когда возникает необходимость в получении точных результатов, то можно воспользоваться к тонкой настройке диагностического оборудования.
На практике чаще всего определяют проблемные участки сварки при помощи эхо-импульсной и теневой диагностики. Метод неразрушающего контроля дает возможность выявить бракованный отрезок, который со временем может привести к разгерметизации сварочного шва. Это отличный метод профилактики аварийных ситуаций. Особенное, если речь идет о магистралях высокого давления.
Сущность процесса ультразвуковой дефектоскопии
Принцип ультразвукового контроля
Ультразвуковой контроль сварных соединений относится к неразрушающим методам контроля варки и является одним из наиболее применяемых методов. Акустические ультразвуковые волны способны распространяться внутри твёрдого тела на значительную глубину. Волны отражаются от границ или от нарушений сплошности, т.к. они обладают другими акустическими свойствами.
Направляя ультразвуковые волны на сварное соединение с помощью специальных приборов — ультразвуковых дефектоскопов и улавливая отражённые сигналы, на экране дефектоскопа отображаются импульсы излученной и отражённой волн. По расположению этих импульсов и по их интенсивности, можно судить о расположении дефектов, их величине и определить характер сварного дефекта.
При контроле сварных швов необходимо тщательно выполнить прозвучивание всего металла сварного шва. Существуют способы прозвучивания прямой и отражённой волной. Прямой волной прозвучивают нижнюю часть шва, а отражённой волной — верхнюю, как это показано на рисунке справа.
Параметры оценки дефектов при ультразвуковом контроле
Чувствительность ультразвукового контроля определяется наименьшим размером дефекта (или эталонного отражателя), который возможно выявить. Роль эталонных отражателей часто играют плоскодонные отверстия, расположенные перпендикулярно направлению прозвучивания, а также боковые отверстия или зарубки, см. рисунок:
Разрешающая способность эхо-метода определяется минимальным расстоянием между двумя дефектами, при котором их можно определить, как раздельные дефекты, а не как один.
При ультразвуковом контроле, выявленный дефект оценивают, исходя из следующих параметров: амплитуды ультразвуковой волны, условной протяжённости, высоты и ширины дефекта, и его формы.
Условную длину сварного дефекта определяют длиной перемещения излучателя вдоль соединения, на протяжении которой фиксируется эхо-сигнал, исходящий от дефекта. Таким же образом, при перемещении излучателя по нормали к сварному соединению, можно определить условную ширину дефекта.
Условную высоту оценивают, исходя из разности интервалов времени между излучённой и отражённой от дефекта волной при крайних положениях излучателя.
Определить истинную величину сварного дефекта при ультразвуковом контроле очень часто оказывается затруднительно. Поэтому, чаще всего стремятся вычислить его эквивалентные величины (площадь или диаметр). Эквивалентной площадью сварного дефекта принято считать, к примеру, площадь плоскодонного отверстия в образце, амплитуда отражённой волны от которого равна амплитуде отражённой волны в проверяемом шве. Почти во всех случаях вычисленная эквивалентная площадь дефекта меньше его настоящей площади.
Форму сварного дефекта (плоскостной или объёмный) устанавливают, используя специальную методику, исходя из формы эхо-сигнала, отображаемого на экране дефектоскопа.
На точность данных, полученных при ультразвуковом контроле, влияют несколько факторов. Основные из них — это:
1. Уровень квалификации оператора 2. Внимательность оператора при работе и тщательность проведения контроля 3. Соответствие измеряемых показателей тем, которые предусмотрены инструкцией
Магнитострикционные преобразователи ультразвуковых дефектоскопов
Магнитоскрикция заключается в деформации ферромагнитной детали, которая размещена в силовом магнитном поле. Длина этой детали изменяется в зависимости от вида силовых линий магнитного поля, её материала, температуры и степени намагниченности. В ультразвуковых дефектоскопах используются ферромагнетики, относительное изменение длины которых – не менее 10-5.
Работают такие преобразователи следующим образом. В приборе создаётся переменное электромагнитное поле, при этом ферромагнитный стержень начинает совершать колебания удвоенной амплитуды. Поскольку линейная деформация магнитостриктора не зависит от направления силовых линий магнитного поля, то подмагничивания такого элемента не требуется.
Как и пьезоэффект, магнитострикция обратима. В качестве излучателей применяются химически чистый никель, а также его сплавы с медью или железом. Минимальная частота, при которой обнаружение дефектов сварных конструкций окажется эффективным, составляет 60 Гц, хотя в приборах обычно реализуются частоты от 300 Гц.
Магнитострикционные преобразователи конструктивно проще, однако уступают пьезогенераторам по параметрам минимальной площади диагностируемой зоны: она должна быть достаточно большой. Кроме того, такие ультразвуковые дефектоскопы теряют свою чувствительность при обследовании только что полученных сварных швов. Ещё одним ограничением магнитострикционных источников получения ультразвуковых волн считается их повышенная энергоёмкость. Зато они более компактны, а потому применимы в стеснённых для диагностики условиях.
Технология проведения ультразвукового контроля
Технология акустического контроля сварки зависит от типа сварного соединения и от требований, предъявляемых к качеству изделия.
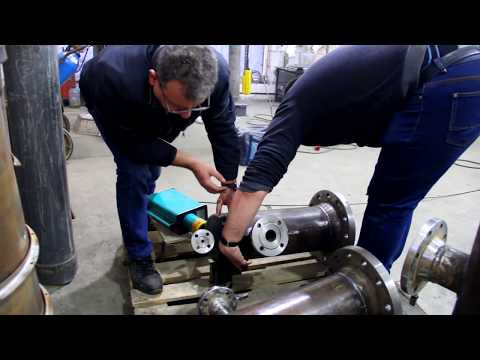
1. Контроль сварного соединения внешним осмотром 2. Выбор метода контроля и типа преобразователя 3. Определение границ перемещения преобразователя 4. Подготовка поверхности сварного соединения для контроля 5. Размещение, включение, проверку работоспособности приборов и оборудования для контроля, их настройка 6. Прозвучивание металла сварного шва и зоны термического влияния 7. Оформление данных, полученных при контроле 8. Определение качества сварки, исходя из результатов контроля 9. Оценка качества сварки на соответствие требованиям, предъявляемым к металлоконструкции.
При внешнем осмотре сварного соединения устанавливают толщину свариваемого металла, тип соединения, размеры сварного шва (величину усиления или размер катета) и устанавливают наличие или отсутствие внешних сварных дефектов. Недопустимые дефекты необходимо устранить.
Контролируя сварное соединение, преобразователем совершают продольно-поперечные движения вдоль сварного шва, а также, одновременно с этим, вращательные движения, см. рисунок слева.
Анализ сварных швов
Дефектоскопия сварных швов трубопроводов является обязательной процедурой перед запуском в эксплуатацию магистральных коммуникаций, особенно проходящих под землей.
В любой конструкции сварной шов являлся слабым местом, по этим причинам их качество всегда должно быть под контролем. На сварных швах лежит важная ответственность – они определяют герметичность и качество готового сооружения в целом.
Суть различных подходов для анализа таких стыков состоит в оценке тех или других физических свойств, характеризующих надежность и прочность трубопровода. Дефектоскопия определяет не только размер дефектов, но и оценивает качественное состояние швов. В эту оценку входит:
- показатель прочности;
- возможность противостоять коррозийным образованиям;
- степень пластичности;
- структура металла шовного соединения и области возле него;
- количество о габариты дефекта.
Способ ультразвукового исследования – это один из основных методов выявления дефектов на сварных швах.
Видео: Обзор дефектоскопа магнитопорошкового
Дефектоскопия сварных соединений трубопроводов имеет следующие преимущества.
- Быстрое проведение ревизии.
- Высокая точность исследования.
- Небольшая стоимость.
- Абсолютная безвредность для человека.
- Мобильность используемых для проверки устройств.
- Возможность выполнять проверку качества функционирующего трубопровода.
Самая простая процедура дефектоскопии – это визуальный осмотр. Визуально – измерительный способ позволяет на основе первых полученных результатов при внешнем осмотре определить наличие многих дефектов.
С помощью данного осмотра проверяют уровень качества готовых сварных стыков. Этот вид исследования применяют независимо от других типов контроля. Чаще всего он является очень информативным, и кроме этого, он самый дешевый.
Этим методом выявляют отклонения от номинальных размеров. При этом поверхность трубопровода тщательно очищают от грязи, металлических брызг, ржавых образований, окалины, масла и прочих загрязнений.
В зону внимания попадают сварные швы и прилегающая к ним зона. Все найденные на этом этапе недостатки устраняют до выполнения иных способов дефектоскопии.
Например, заметно выраженные различия в высоте сварного шва свидетельствуют о том, что дуга во время сварочных работ прерывалась.
На период проверочных мероприятий такие стыки рекомендуют обработать 10% раствором азотной кислоты. Если будут заметны грубые геометрические нарушения, то это свидетельствует о нарушении качества сварного шва.
Видео: В видео представлен краткий обзор ультразвуковых приборовTG 110-DL, Avenger EZ
Преимущества данного метода исследования следующие:
- Чаще всего на такую операцию нужно немного времени.
- Небольшая стоимость проверки.
- Безопасность данной процедуры для человеческого здоровья.
- Можно проверить действующий трубопровод.
Ну и куда же без недостатков:
- Возможность разрушающего действия.
- Потребность в спецреактивах и иных расходных материалах.
- Опытные образцы после этого процесса не всегда подлежали восстановлению.
Дефектоскопия стыков трубопроводов
Дефектоскопия соединений трубопроводов – это довольно ответственный процесс, который начинают только после того, как сварной шов готовый. Место состыковки должно остыть и его необходимо очистить от загрязнений.
Еще одним методом проверки является цветная дефектоскопия трубопроводов, ее по-другому называют капиллярный контроль. В основе данной проверке лежит капиллярная активность жидкости. Поры и потрескавшиеся образования создают сетку в стыке.
Когда они контактируют с жидкостью, то они просто пропускают ее сквозь себя. Такой способ дает возможность обнаружить скрытие проблемные образования. Проводят такую процедуру в соответствии к ГОСТу 1844-80.
Часто для этого вида поверки применяют магнитную дефектоскопию. В ее основу положили такое явление, как электромагнетизм. Возле проверяемой зоны механизм создает магнитное поле. Его линии свободно проходят сквозь металл, но когда присутствует повреждение, то линии теряют ровность.
Видео: Проведение внутритрубной диагностики магистральных трубопроводов
Чтобы зафиксировать полученное изображение, используют магнитографическую или магнитопорошковую дефектоскопию. Если применяют порошок, то его накладывают сухим или в виде влажной массы (в нее добавляют масло). Порошок станет скапливаться только в проблемных местах.
Преимущества и недостатки ультразвуковой дефектоскопии
Преимуществами данного метода контроля являются:
1. Высокая чувствительность приборов 2. Компактность оборудования и приборов 3. Информацию о качестве сварного соединения можно получить достаточно быстро 4. Возможность контроля соединений большой толщины 5. Низкая стоимость дефектоскопии, т.к. затраты при её проведении минимальны 6. Безопасен для здоровья человека (по сравнению, например, с методом рентгеновской дефектоскопии, или методом радиационной дефектоскопии) 7. Этим методом можно выявить почти все известные сварные дефекты 8. Данный метод контроля не разрушает сварное соединение 9. Возможность проводить проверку в «полевых» условиях, благодаря наличию переносных дефектоскопов.
К недостаткам ультразвуковой дефектоскопии можно отнести:
1. Необходима подготовка поверхности соединения 2. Если дефект расположен перпендикулярно движению волны, его можно пропустить при проверке 3. Если размер дефекта меньше длины волны, то дефект остаётся «невидимым», т.к. он не отражает волну. А если увеличивать длину волны, то глубина проверки снижается. 4. Данные о дефекте часто оказывается ограниченными. Могут возникнуть трудности с определением вида сварного дефекта и его формы. 5. Сложность контроля сварки материалов с крупнозернистой структурой. Например, при сварке чугунов, или сварке высоколегированных сталей с крупнозернистой структурой шва (аустенитной, или перлитной), т.к. акустические волны в такой структуре быстро затухают.
Контроль сварных швов трубопроводов: полное руководство по методам визуального контроля и контроля методом неразрушающего контроля
- Домашняя страница
- Контроль сварных швов трубопроводов: полное руководство по методам визуального контроля и контроля методом неразрушающего контроля
Контроль сварных швов трубопроводов: полное руководство по методам визуального и неразрушающего контроля
Только в Соединенных Штатах с 2010 по 2018 год было зарегистрировано почти 5 512 инцидентов с трубопроводами. Эти данные многое говорят о необходимости проверки такой важной инфраструктуры по всему миру. Отказ трубопровода может быть чрезвычайно разрушительным; таким образом, риск для жизни людей, окружающей среды, а также ущерб и затраты на ремонт могут быть огромными. Болезненные точки, такие как сварные швы, являются факторами, способствующими такому отказу. Для выявления таких областей риска и повышения безопасности эксплуатации необходимо изучить передовые методы проверки.
Изучение методов контроля сварных швов трубопроводов
Сварка трубопроводов на объектах разведки, добычи и переработки нефти и газа должна быть высокого качества, если ожидается, что они будут работать в течение длительного времени. Экстремальная температура, давление и химическое взаимодействие являются другими причинами, по которым желательна надежная сварка. Но учитывая проблемы, связанные со сваркой трубопроводов, т. е. потенциальные дефекты сварки, сложную настройку сварки для труб разных размеров и неправильную сварку вокруг сложных геометрических участков, необходимость контроля становится настоятельной.
За прошедшие годы в различных отраслях промышленности были внедрены различные методы контроля, чтобы удовлетворить широкий спектр потребностей в контроле сварных швов трубопроводов. Основываясь на их эффективности, некоторые из этих типов методов контроля обсуждаются ниже:
- Разрушающие испытания : Разрушающие испытания сосредоточены на проверке целостности самого материала трубы и сварного соединения с помощью различных испытаний для проверки металлов. устойчивость до точки отказа. Обнаружение точки отказа позволяет техническим специалистам анализировать качество сварки и изучать влияние нагрузки и напряжения на соединение. Сварной шов, сертифицированный разрушающими испытаниями, может быть установлен в качестве стандарта для сварки трубопроводов и точно воссоздан для будущих операций.
Основным недостатком этой системы контроля является ее неспособность представить все условия нагрузки во время испытания образца. Используемый образец сварного шва полностью разрушается, что увеличивает количество отходов, затраты на изготовление и контроль. Тест в основном используется для целей сертификации; таким образом, качество сварки не может быть точно гарантировано каждый раз в разных рабочих условиях.
- Визуальный осмотр : Визуальный осмотр является основным методом контроля, который используют все технические специалисты, чтобы сделать предположение о качестве сварных швов в трубопроводах. Это самый простой и недорогой метод проверки, а также эффективный способ выявления любых серьезных проблем со сваркой по мере их возникновения. Визуальный контроль может выполняться до, во время или после сварки, что предотвращает распространение дефекта на следующую фазу процесса. Более заметные дефекты, такие как трещины, брызги сварки, деформация, неполное сплавление и более крупные поры, могут быть легко обнаружены. Основной подход к проверке на наличие утечек в сварных швах трубопровода заключается в создании давления в трубопроводе и использовании такой среды, как мыльная вода, которая может визуализировать выход воздуха в виде пузырьков.
Недостатком этого метода контроля является невозможность зафиксировать все мелкие и глубинные дефекты на поверхности сварного шва. Тем не менее, его можно использовать как способ предотвращения появления значительных дефектов, уменьшая потребность в обширном анализе неразрушающего контроля (НК).
- Капиллярный контроль : Капиллярный контроль часто считается передовым методом визуального контроля. Поскольку видимый проникающий краситель наносится на поверхность сварного шва, любые трещины или точечные отверстия, которые трудно обнаружить во время визуального осмотра, могут отображаться контрастным цветом. Несмотря на то, что это быстро, портативно и подходит для всех видов геометрии, можно определить только поверхностные дефекты на гладких поверхностях, что может быть проблемой, особенно для критических конструкций, таких как трубопроводы.
- Неразрушающий контроль : Неразрушающий контроль был выбран промышленностью благодаря его эффективности и способности проверять трубопроводы, не вызывая их повреждения.
Усовершенствованные приборы и датчики неразрушающего контроля доказали свою эффективность при контроле сварных швов трубопроводов. Неразрушающий контроль может облегчить точную идентификацию всех крупных и мелких дефектов на поверхности и под поверхностью сварного шва, чтобы дать полное представление о качестве сварного шва. Этому способствует гибкость и портативность передовых приборов неразрушающего контроля, которые дополнительно обеспечивают преимущества контроля в сложных зонах, контроля на месте и контроля в режиме реального времени, необходимых для контроля сварных швов трубопроводов.
Основными проблемами, связанными с разрушающим и визуальным контролем, являются их неспособность обнаружить все дефекты и неоднородности в сварном шве, что вызывает серьезные проблемы с эффективностью. Преимущество точности, аккуратности и гибкости, которые обеспечивает неразрушающий контроль, является причиной того, что его преимущество перед другими методами контроля растет.
Повышение эффективности контроля за счет усовершенствования методов неразрушающего контроля
Когда мы обсуждаем эффективность неразрушающего контроля для контроля сварных швов трубопроводов по сравнению с другими методами контроля, возникает вопрос, как неразрушающий контроль делает это возможным. Вот несколько причин, почему:
- Полный контроль : С помощью усовершенствованных приборов для вихретокового (EC) и ультразвукового контроля (UT) можно выявить широкий спектр дефектов сварного шва. Гибкие датчики и сканеры позволяют проводить проверку даже сложных геометрий, таких как изгибы труб. Полное сканирование позволяет эффективно анализировать данные.
- Портативное сканирование : Благодаря портативным решениям для неразрушающего контроля возможен простой и быстрый контроль. Возможность проверки инструментов на месте сокращает время в пути и время между сканированиями, а более широкий охват датчиков повышает эффективность проверки. Мобильность также повышает эффективность инспекции на участках трубопровода с малым просветом или в труднодоступных местах, устраняя необходимость создавать доступ или подвергаться потенциальной опасности.
- Масштабируемость : С помощью инструментов, настраиваемых в соответствии с масштабом, и возможности комбинировать несколько инструментов для очень сложных объемных проверок можно сократить время, необходимое для полной проверки сварных швов трубопровода.
- Улучшенный анализ данных : Усовершенствованные сканеры и датчики неразрушающего контроля могут быстро сканировать и регистрировать большие объемы данных. Более быстрый анализ с использованием передовых приборов и программного обеспечения улучшает связь и сокращает время простоя при проверке. С помощью анализа в реальном времени можно еще больше ускорить процесс. Улучшенные возможности отображения A и C-скана повышают точность при обнаружении дефектов и характеризации.
Контроль сварных швов трубопроводов упрощается для нефтегазовой промышленности благодаря расширенным функциям приборов неразрушающего контроля, программного обеспечения, сканеров и датчиков. Предоставив техническим специалистам доступ и охват для проверки, можно улучшить обнаружение дефектов и анализ качества сварки.
Инспекция сварных швов трубопроводов упрощается благодаря решениям NDT
Фактор риска, связанный с нефтегазопроводами и сварными швами, огромен, поэтому требуются точные технологии контроля. Благодаря технологиям ультразвукового сканирования, таким как сканер Weld Crawler и ElbowFlex от Zetec, можно достичь портативных и гибких возможностей контроля. Кроме того, качество сварки, обеспечиваемое передовыми приборами, датчиками и программным обеспечением для неразрушающего контроля, может позволить нефтяной и газовой промышленности свести к минимуму опасности и потребности в ремонте и рассчитывать на более прибыльную работу.
Zetec специализируется на передовых решениях для вихретокового и ультразвукового контроля, которые могут соответствовать вашим потребностям в контроле сварных швов трубопроводов. Наши портативные сканеры и гусеничные сканеры для неразрушающего контроля могут помочь сократить время простоя при проверке и повысить производительность. Чтобы узнать больше, свяжитесь с нами сегодня !
Отдел продуктов для неразрушающего контроля
Разработчики Zetec являются ведущими экспертами в области ультразвуковых и вихретоковых технологий, и мы можем помочь вам сориентироваться в любом из наших решений или устройств для неразрушающего контроля.
Определение размеров дефектов с помощью механизированного ультразвукового контроля кольцевых сварных швов трубопроводов
Определение размеров дефектов с использованием механизированного ультразвука контроль кольцевых сварных швов трубопроводаNDT.net — июль 2001 г., Том. 6 № 7 |
Томас С Коннелли. ООО «Альянс Пайплайн»
Хенк ван Дейк. Weldsonix International Inc
Алан Гилрой-Скотт. Целостность Менеджмент Инк
Автор, ответственный за переписку:
Эл. почта: [email protected], Web: http://www.pipelinetech.com/
1.0 Аннотация
Чтобы избежать ненужного ремонта кольцевых сварных швов при строительстве трубопровода, точный размер дефекта
становится все более важным. В этом документе обсуждается проверка и оценка газовых
Металлические дуговые кольцевые сварные швы с механизированным ультразвуковым контролем с использованием альтернативного кольцевого шва
критерии приемлемости.
Методы определения размера дефекта были применены из национальных стандартов, которые используют сигнал амплитуда для определения размера дефекта и сигнатуры сигнала для установления взаимодействия через стенку дефекты сварного шва, расположенные рядом друг с другом по вертикали.
1.1 Сокращения и ключевые словаGMAW | Дуговая сварка металлическим газом |
Дефект | Неоднородность сварного шва |
Суммарные дефекты | Дефекты, лежащие друг над другом вдоль одной стороны скоса сварного шва |
ФШ | Полная высота экрана |
Стопка Отсканированная презентация | Представление ультразвуковых данных с использованием цвета для амплитуды изображения |
ТОФД | Времяпролетная дифракция |
ЛКП | Отсутствие поперечного проникновения |
ЭКА | Инженерно-критическая оценка |
ID | Внутренний диаметр |
ОД | Внешний диаметр |
Оверлей | Обнаружение плоскостных дефектов в смежных зонах контроля |
Сигнал Подпись | Эхо-динамическая трасса, традиционно просматриваемая на дефектоскопе |
Сфокусированный зонд | Ультразвуковой датчик с точно контролируемым размером луча в его рабочий диапазон |
Стандартный зонд | Ультразвуковой датчик без особых изменений размера луча |

Большинство дефектов, возникающих при дуговой сварке металлическим электродом в среде защитного газа (GMAW), плоские по своей природе и ориентируется по первоначальному профилю скоса сварного шва. Такие дефекты легко обнаруживаются с помощью ультразвука. осмотра, рис. 1. Относительный размер таких дефектов можно оценить путем сравнения отраженный ультразвуковой сигнал от калибровочных отверстий с плоским дном, выточенных в той же ориентации, что и скос сварного шва.
Рис. 1. Конструкция сварного шва. |
В начале 1980-х годов были разработаны механизированные ультразвуковые системы для контроля объемов производства.
Производительность до 100 сварок в сутки. Первые системы использовали обычные ультразвуковые преобразователи для
обеспечить полное покрытие объема сварного шва. Результаты были многообещающими, но лучшее различение
дефекты в пределах фаски сварного шва вызывали беспокойство.
NOVA, газотранспортная компания Канады и RTD BV из Нидерландов, разработали концепция использования сфокусированных датчиков, ориентированных на осмотр отдельных участков сварного шва. Транзит было введено измерение времени, чтобы определить местонахождение дефекта в пределах определенных «временных ворот», которые можно напрямую связан с данным местом в объеме сварного шва, рис. 2. Это устранило случайные ложные вызовы, когда отражения геометрии сварного шва были ошибочно истолкованы как дефекты сварного шва.
Рис. 2: Геометрия и время прохождения. |
Прогрессивные разработки ультразвукового контроля перешли на обнаружение неплоских
объемные дефекты в теле шва. Исторически сложилось так, что такие недостатки, как пористость,
трудно обнаружить и различить с помощью ультразвукового контроля. Техника, известная как «наложение А». сканирование» или представление «необработанных данных» было разработано для выявления таких дефектов, рис. 3. Совсем недавно
Времяпролетная дифракция (TOFD) применялась для улучшения контроля сфокусированного зонда.
Рис. 3: Суммарное сканирование «А», показывающее пористость и геометрию. |
В настоящее время метод TOFD, рисунок 4, используется в механизированных ультразвуковых системах на трубопроводах. в качестве подстраховки. Это помогает оператору обнаружить наличие трещин по центральной линии, дефектов, а в случае измерения амплитуды дает информацию о степени серьезности дефекта. размера. Кроме того, он действует как инструмент подтверждения дефектов, обнаруженных при сканировании «А».
A = боковая волна, B = дифракция дефекта на верхнем конце, C = дифракция на нижнем конце дефекта, D = отражение волны сжатия внутри трубы,
E = отражение поперечной волны внутри трубы Рис. ![]() |
Метод контроля сфокусированными зондами, который стал известен как «зональный контроль». Массив сфокусированные датчики были организованы таким образом, чтобы контролировать все зоны сварного шва GMAW за один раз. пропуск осмотра. Вообще говоря, зоны контроля отражали проходы сварки, необходимые для завершить сварку. Типичная матрица датчиков показана на рис. 5.9.0015
Рис. 5: Пример массива датчиков. |
Зональный контроль позволяет применять альтернативные критерии приемлемости дефектов на основе
Инженерно-критическая оценка (ECA). ECA дает возможность кольцевому сварному шву
компенсировать дефекты, которые должны быть определены на основе прочности и ударной вязкости сварного шва вместе
с полным знанием нагрузок, которые будут применяться. Эта техника опирается на
метод контроля, который может определить размер или, по крайней мере, классифицировать дефекты сварного шва по различным группам размеров. Зональный
Контроль позволяет классифицировать дефекты на основе размера фокусного пятна зонда. Типичный
зона контроля может быть порядка 3 мм с соответствующим размером фокусного пятна 2 мм.
При зональном контроле дефект считается существующим, если он производит ультразвуковой сигнал выше заданного
пороговая амплитуда, например 40% полной высоты экрана (FSH). Однажды выше этого порога
Амплитуда дефекта консервативно принимается за всю зону контроля по высоте.
длина окружности дефекта, при этом выдается сигнал выше пороговой амплитуды
измерено. Решение о ремонте сварного шва принимается путем сравнения этой окружной длины.
с рассчитанной допустимой длиной из расчетов ECA. Если датчики от двух соседних
зоны контроля обнаруживают дефект в одном и том же месте по окружности, дефект, как правило,
считается комплексным дефектом и оценивается как имеющий сквозную высоту стенки как контрольного
зоны.
Традиционный метод зональной инспекции имеет три недостатка:
- Слишком консервативен. Любой дефект, дающий ультразвуковой сигнал выше определенного пороговое значение классифицируется как полная зона контроля по высоте.
- Многие дефекты возникают между проходами сварки и обнаруживаются в двух зонах контроля. Их часто классифицируют как многослойные дефекты и оценивают слишком консервативно.
- Строительные спецификации могут потребовать тщательного определения сквозного дефекта стены высота и сквозное взаимодействие смежных по вертикали дефектов. Зональная инспекция имеет трудно удовлетворить такие требования, кроме как в консервативной манере.
Таким образом, возможно, что дефекты будут меньше, чем размеры с помощью механизированного ультразвукового метода.
Еще одной сложностью является сообщение о «сложенных» дефектах. Совокупные дефекты — это дефекты, возникающие в
два последовательных прохода сварки или зоны контроля, но в одном и том же месте по окружности. Приемлемая длина таких дефектов всегда значительно меньше однозонных дефектов, поэтому сварной шов
обычно требуется ремонт. Редко дефекты стопки подтверждаются после изготовления поперечных сечений.
области, хотя ультразвуковые сигналы, полученные от инспекционных датчиков, явно затрагивали
предполагают, что рассматриваемый дефект действительно находится в двух зонах контроля.
В этом документе рассматривается работа по разработке ультразвукового оборудования, которая проводилась в Канаде в
подготовка к проекту Alliance Pipeline членами команды Alliance Pipeline Ltd.
техническая группа и Weldsonix International Inc. Работа была направлена на устранение
метод определения размера, который измеряет высоту дефекта более точно, но, тем не менее, основан на длительном
установленные национальные стандарты. Концепция измерения амплитуды использовалась в ядерной,
изготовление, первичная ковка и литейное производство в Европе в течение примерно 30 лет. Этот
работа также вводит понятие сигнатуры сигнала для характеристики дефекта. Эта характеристика
используется для различения пакетных и межзональных дефектов.
- 3.1 Предпосылки и принципы проекта
- Точно оценить можно только те дефекты, которые лежат на заранее заданной подготовке под сварку. Такой
дефекты возникают в течение относительно небольшого заранее определенного временного интервала.
- Дефекты, лежащие за пределами этого временного интервала, можно оценить с помощью вспомогательного метода TOFD.
- Для измерения высоты дефекта ультразвуковым лучом этот луч должен быть больше, чем высота дефекта и обеспечить «перекрытие» по обе стороны от дефекта.
- Для измерения дефектов, которые могут возникнуть в любом месте при подготовке к сварке, набор датчиков требуется полное и перекрывающееся покрытие по всей толщине стенки.
- Сравнение амплитуды ультразвука с калибровочными отражателями, обработанными при калибровке. блок, представляющий плоские дефекты сварного шва.
- Интерпретация сигнатур сигналов.
- Разработка и изготовление эталонных блоков, точно отображающих дефекты производственных сварных швов.
- Выполнение двух кольцевых сварных швов GMAW, содержащих полную серию дефектов производственных сварных швов разной высоты и длины.
- Разработка оптимизированной процедуры ультразвукового контроля.
- Сканирование двух сварных швов и определение размеров дефектов на основе ответов как традиционных калибровочные блоки и недавно разработанный эталонный блок.
- Вскрытие тестовых сварных швов для сравнения фактических и расчетных размеров дефектов.
Работа по определению размеров дефектов применялась для контроля механизированных кольцевых сварных швов GMAW с использованием модифицированный J-образный скос. В частности, методы калибровки, обсуждаемые в этой статье, нацелены на заполнение и заглушка проходит только потому, что модифицированный J-образный скос обеспечивает очень стабильную корневую и посадочную зоны. Габаритные размеры. Дефекты, возникающие в этих областях, могут быть точно определены из-за плотного прилегания. размерные допуски, применяемые к этому участку в процессе обработки, рис. 1.
Работа основывалась на следующих принципах:
Размер дефекта был основан на двух методах:
Вышеуказанные методы определения размеров дефектов не распространяются на объемные дефекты.
3.2 Экспериментальная программаРабота состояла из:
Традиционно калибровка ультразвуковой системы основана на откликах плоскодонных
отверстия (FBH). Обзор типичных дефектов кольцевых швов показал, что плоскодонные надрезы (FBN)
с высотой 1, 2 или 3 мм и длиной, превышающей ширину луча, обеспечили бы гораздо большую
реалистичное представление дефектов сварки. Были изготовлены эталонные блоки, которые содержали оба
отверстия и пазы, чтобы можно было сравнить ультразвуковые отклики.
Три калибровочных образца были изготовлены с использованием проектной трубы NPS 42 x 16 мм (0,56 дюйма) WT от трубопроводная система Альянса. Отверстия с плоским дном и надрезы были подготовлены с помощью электроразряда. механическая обработка. Калибровочные отражатели были основаны на препарате скоса соединения J. используется американским методом механизированной сварки CRC-Evans и канадским RMS, рис. 1. Детали компоновки эталонных блоков приведены ниже.
Подготовка под сварку GMAW с типовыми положениями эталонного отражателя.![]() |
Схематический вид подготовки к сварке GMAW с типичным положением эталонного отражателя. |
Следующие отклики были получены от отверстий с плоским дном и пазов с плоским дном с использованием эталонный отклик 80% от полной высоты экрана, установленный на 2-мм FBH. Ответы были то же самое с использованием методов импульс-эхо и шаг-улов:
1 мм fbh | паз 1 мм | 2 мм внутр. | паз 2 мм | 3 мм внутр. | паз 3 мм |
20% | 80% | 80% | >100% | >100% | >100% |
Этот первый тест, описанный выше, дал три отклика, превышающие 100% высоты экрана. А
Таким образом, второе сканирование было проведено после снижения калибровочного отклика на 12 дБ:
1 мм fbh | паз 1 мм | 2 мм fbh | паз 2 мм | 3 мм внутр. | паз 3 мм |
5% | 20% | 20% | 40% | 45% | 65% |
Эти результаты показывают, что выемки обеспечивают гораздо более высокую реакцию, чем традиционные плоскодонные отверстия.
4.1 Расчет отклика плоскодонных отражателей.Различия в ультразвуковом отклике между плоскодонными отражателями разных площадей могут быть объясняется следующей формулой:
DV 1,2 =40 log D1/D2
Где:
DV 1,2 = Амплитуда или разность усиления от двух отражателей 1 и 2
D 1 = Зона 1
D 2 = Зона 2
Ультразвуковые отклики можно рассчитать для FBH различного диаметра следующим образом:
0,5 мм fbh | 1 мм внутр.![]() | 1,5 мм внутр. | 2 мм внутр. | 3 мм внутр. | 4 мм внутр. |
-24 дБ | -12 дБ | -5 дБ | 0 дБ | 7 дБ | 12 дБ |
Удвоение диаметра приводит к увеличению ультразвукового отклика на 12 дБ. Эти ответы могут быть по сравнению со значениями, полученными для надрезов с плоским дном с высотой надреза, сравнимой с плоской диаметр нижнего отверстия:
Выемка 0,5 мм | паз 1 мм | паз 1,5 мм | паз 2 мм | паз 3 мм | Выемка 4 мм |
-6 дБ | 0 дБ | 3 дБ | 6 дБ | 9 дБ | 12 дБ |
Из этих результатов видно, что 2 мм FBH и 1 мм паз с плоским дном обеспечат
такой же отклик при опорном уровне 0 дБ.
Применение этих рассчитанных откликов к диапазону высот дефектов, обнаруженных в дуговой сварке металлическим электродом в среде защитного газа.
приводит к соотношению амплитуды и высоты дефекта, подробно описанному в
таблице 1.
Диапазон амплитуд | Высота дефекта | Диапазон амплитуд | Высота дефекта |
0-5% | 0,2 мм | 50%-55% | 2,6 мм |
5%-10% | 0,5 мм | 55%-60% | 2,8 мм |
10%-15% | 0,7 мм | 60%-65% | 3,0 мм |
15%-20% | 1,0 мм | 65%-70% | 3,3 мм |
20%-25% | 1,2 мм | 70%-75% | 3,6 мм |
25%-30% | 1,5 мм | 75%-80% | 4,0 мм |
30%-35% | 1,7 мм | 80%-85% | 4,2 мм |
35%-40% | 2,0 мм | 85%-90% | 4,4 мм |
40%-45% | 2,2 мм | 90%-95% | 4,6 мм |
45%-50% | 2,4 мм | 95%-100% | 4,8 мм |
Таблица 1: Зависимость амплитуды от высоты дефекта на основе расчетной амплитудной характеристики.![]() |
- 0,5 мм и 1,5 мм
- >1,5 мм и 3,0 мм
- >3,0 мм и 6,0 мм
- > 6,0 мм
Две процедуры ультразвукового контроля были оценены для определения наилучшего сквозного
охват доступен как с «фокусированными», так и со «стандартными» инспекционными датчиками. Цель процедуры
разработка заключалась в том, чтобы произвести измеримое и однородное ультразвуковое покрытие по всей
толщина сварного шва, чтобы гарантировать возможность обнаружения и количественной оценки дефектов независимо от положения на сварном шве
скос Подробная информация о двух наборах датчиков, обозначенных как «A» и «B», приведена в таблице 2. Датчики
используемые для работы, отражают текущие производственные контрольные датчики от Krautkramer, используемые
Weldsonix. Стандартные датчики имеют размер фокусного пятна примерно 3 мм по сравнению с
сфокусированные зонды с размером фокусного пятна около 2 мм. Углы осмотра были
получено при установке зондов на Polypenco ТМ материал клина необходимого угла.
Зона досмотра | Блок датчиков «А» | Блок датчиков «B» | |
Заливка 3, крышка | 55° 5 МГц, стандартный зонд 3/8 дюйма работает в импульсно-эхо-режиме. | 55° 5МГц, 3/8″ стандартный рабочий датчик в режиме импульс/эхо | |
Заполнение 2 | Стандартный датчик 45 и 55°5 МГц 3/8 дюйма работа в режиме тангаж/кэтч | 45 и 55°5 МГц 1/2-дюймовый сфокусированный датчик работа в режиме тангаж/кэтч | |
Заполнение 1 | Стандартный датчик 45 и 55°5 МГц 3/8 дюйма работа в режиме тангаж/кэтч | 45 и 55°5 МГц 1/2″ фокусированные датчики работа в режиме тангаж/кэтч | |
Горячий проход 2 | 50° 5 МГц 3/8″ стандартный датчик работа в импульсно-эхо-режиме | 50°5MHz 3/8″ стандартный рабочий датчик в режиме импульс/эхо | |
Горячий проход 1 | Стандартный датчик 50°5 МГц 3/8 дюйма работа в импульсно-эхо-режиме | 50°5MHz 3/8″ стандартный рабочий датчик в режиме импульс/эхо | |
Таблица 2: Подробная информация о наборе датчиков для двух процедур проверки, оцененных в исследовании.![]() |
Две матрицы зондов, A и B, были откалиброваны на отверстиях с плоским дном диаметром 2 мм, чтобы обеспечить 80% ответа от полной высоты экрана (FSH). Затем сфокусированные зонды и стандартные зонды были по сравнению с определением амплитуды прослеживания, доступной в соседних зонах контроля.
Сканирование эталонных блоков двумя наборами датчиков дало значительные результаты. «Стандартные» датчики давали 40% превышения полной шкалы (-6 дБ) в соседних зонах в той же плоскости. Однако «сфокусированные» датчики давали только 20 % FSH (-12 дБ) при тех же параметрах. условия.
Эталонный блок был отсканирован двумя наборами датчиков. Стандартные датчики обеспечили 80%
ФСГ для отражателей, расположенных между зонами контроля, с фокусированными преобразователями, обеспечивающими 55%
ФСГ в тех же условиях. На основании этих результатов было установлено, что стандарт
зонды, а не сфокусированные зонды обеспечивали необходимое однородное покрытие.
Трубопроводная система Alliance состоит из 24-, 36- и 42-дюймовых магистральных труб, работающих при давлении до до 1740 фунтов на квадратный дюйм. Процедура ультразвукового контроля, описанная в этом документе, касается проверки трубы диаметром 36 дюймов с толщиной стенки 14,2 мм, для выполнения которой требуется шесть проходов сварки, Таблица 3. Процедуры проверки были разработаны в соответствии с требованиями CSA Z662, Oil and Gas Трубопроводные системы. Кроме того, в проекте использовались альтернативные критерии приемки, приведенные в Приложение K Z662, требующее возможности определения размера дефекта.
Описание прохода | Номинальная высота, мм | ||
Корневой проход (включая землю) | 3* | ||
Горячий проход | 2,8* | ||
Заполнение проходов 1, 2 и 3 | 2,8*, 2,8*, 2,8* | ||
Колпачок проходной | 1,5* | ||
Таблица 3: Максимальная высота сквозной стенки сварных швов, измеренная на скосе сварного шва для получения
сварной шов с номинальной толщиной стенки 14,2 мм.![]() |
5.2 Установка сквозного покрытия стены
В трубопроводной системе Alliance каждый сварочный проход в зоне заполнения имеет высоту примерно 3 мм. Таким образом, луч преобразователя должен быть больше 3 мм, чтобы идентифицировать дефекты, возникающие между заполняющие проходы, между горячим проходом и первым заполняющим проходом или между закрывающим проходом и последним заполняющим проходом. Обсуждавшиеся ранее «стандартные» пробники обеспечивают размер луча -6 дБ, равный 3 мм. Когда такое пучок проецируется с углом преломления 45 градусов на подготовку скоса заполняющего прохода 5 градусов это обеспечивает покрытие приблизительно 4 мм.
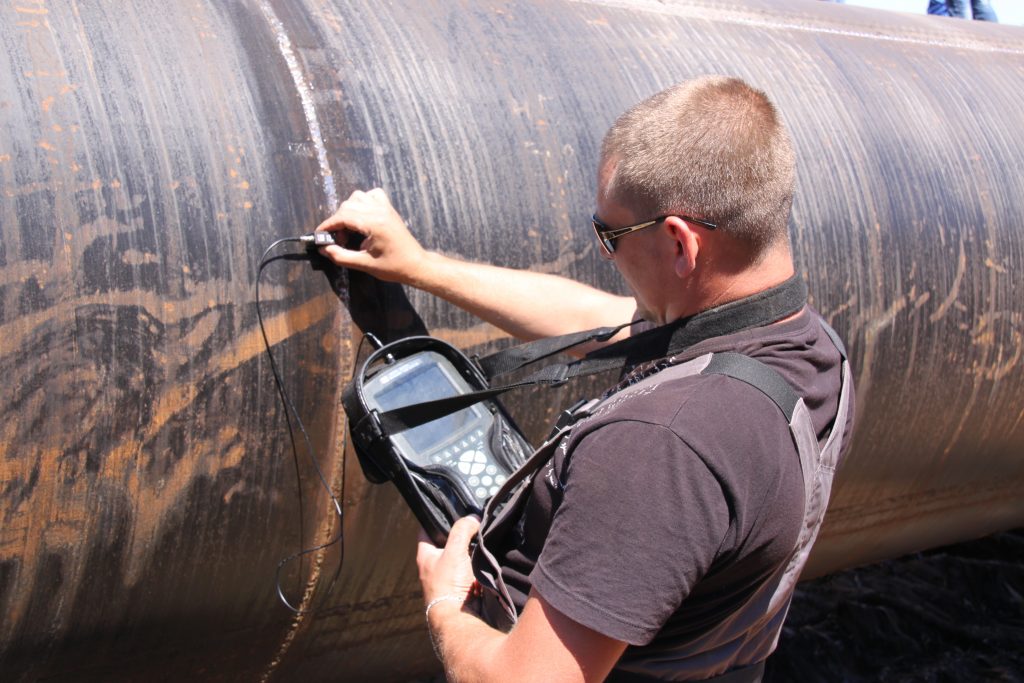
5.3 Размер зоны
Для обеспечения полного осмотра и необходимого обхода третьей зоны наполнения и крышки. Традиционно требуются зоны контроля ~3 мм. При применении зональной проверки к этому сварному шву, любой дефект, вызывающий отражение ультразвука выше пороговой амплитуды оценивается как дефект высотой 2,8 мм. Дефекты, возникающие в 2 или 3 соседних зонах насыпи, будут оценивается как 5,6 или 8,4 мм в высоту соответственно. Это приведет к довольно консервативному подходу к размеру дефектов сварки и может привести к ненужному ремонту сварки.
5.4 Определение амплитуды и сигнатуры
Установив полное покрытие инспекции с помощью подходящего набора датчиков, следующим шагом было улучшить возможности измерения амплитуды.

Для этого соотношение между высотой дефекта и откликом на ультразвуковой сигнал представленный в Таблице 1, был использован для четырех групп. Группы отражают категории высоты дефекта используется в расчетах ECA.
«сложенные» дефекты, возникающие в двух соседних зонах контроля, и дефекты, возникающие просто между
два прохода сварки. Дефекты в двух зонах контроля выявляются двумя и более датчиками
в результате чего можно сделать вывод, что такие дефекты возникли в двух последовательных проходах сварки и
поэтому большой. В действительности такие дефекты, как правило, возникают на границе раздела сварных швов, и их не так много.
большой, как показывает результат проверки.
Рис. 6: Различие между пакетными и межзональными дефектами. |
Следующей задачей было разработать методологию, позволяющую различать такие дефекты и избегать ненужного ремонта. Решение заключалось в использовании амплитудной «сигнатуры» или «эхо динамическое». Каждое ультразвуковое отражение имеет уникальную подпись, которую можно увидеть по букве «А». скан презентации. Однако, когда отражение превышает 100% полной высоты экрана, эта сигнатура часто теряется, рис. 6.
В связи с этим в систему был включен логарифмический усилитель для обеспечения высокой амплитуды
отраженные данные подлежат повторной обработке. Амплитуды, превышающие 100% полной высоты экрана, могут быть повторно обработаны
без повторного осмотра сварного шва. Эта повторная обработка позволяет оператору определить
форму или «характеристику» отраженного сигнала независимо от начальной амплитуды. Поскольку
ультразвуковой сигнал от данного дефекта уникален, ультразвуковой техник может определить, является ли дефект
действительно собраны путем изучения и сравнения сигнатур отклика от двух преобразователей
вовлеченный. Если сигнатуры одинаковые, дефект просто улавливается обоими датчиками.
и может рассматриваться как межзональный дефект. Дефекты, имеющие разные сигнатуры, можно рассматривать
как сложенный. Этот метод обеспечивает точную дифференциацию таких дефектов
особенно когда учитывается и амплитуда дефектов.
Шаг 1. Просмотрите амплитудные характеристики всех трех зон контроля.

Шаг 2. Если менее 100% во всех зонах, результирующая высота дефекта составляет от 0,5 мм до 1,5 мм; если больше, чем 100% в любой зоне контроля переходите к шагу 3.
Шаг 3. С помощью логарифмического усилителя уменьшите все амплитуды на -12 дБ и определите результирующий амплитуды во всех трех зонах.
Шаг 4. Рассчитайте исходные максимальные амплитуды, умножив амплитуду -12 дБ на 4.
Шаг 5. На основе амплитуд -12 дБ интерпретируйте сигнатуры сигнала, если уровень ниже 100% FSH.
Шаг 6. Рассчитайте высоту дефекта.
Общие примеры этой методологии определения размеров приведены в таблице 4.
Тип дефекта | Шаг 1 | Этап 2 | Этап 3 | Этап 4 | Этап 5 | Шаг 6 | ||||||
Амплитудный отклик | Размер дефекта | Амплитуда — 12 дБ | Расчетный % ФСГ | Та же подпись | Размер дефекта, мм | |||||||
Зона 1 | Зона 2 | Зона 3 | Зона 1 | Зона 2 | Зона 3 | Зона 1 | Зона 2 | Зона 3 | ||||
LOF | 0-40% | ~40% | 0-40% | ~0,5 мм | ~0,5 мм | |||||||
LOF | 0-40% | 0-40% | 0-40% | ~120% | 0-40% | н/д | 0,5 — 1,5 | |||||
LOF | 0-40% | > 100 % | 0-40% | _ | 0-10% | ~30% | 0-10% | 0-40% | ~120% | 0-40% | н/д | 0,5 — 1,5 |
LOF | 0-40% | > 100 % | > 100 % | _ | 0-10% | ~30% | ~30% | 0-40% | ~120% | ~120% | да | 0,5 — 1,5 |
LOF | 0-40% | > 100 % | > 100 % | _ | 0-10% | ~30% | ~30% | 0-40% | ~120% | ~120% | нет | 1,5 — 3,0 |
LOF | 0-40% | > 100 % | 0-40% | _ | 0-10% | ~65% | 0-10% | 0-40% | ~260% | 0-40% | н/д | 1,5 — 3,0 |
LOF | > 100 % | > 100 % | 0-40% | _ | ~65% | ~65% | 0-10% | ~260% | ~260% | 0-40% | да | 1,5 — 3,0 |
LOF | > 100 % | > 100 % | 0-40% | _ | ~75% | ~65% | 0-10% | ~300% | ~260% | 0-40% | да или нет | 3,0–6,0 |
LOF | > 100 % | > 100 % | 0-40% | _ | ~65% | ~65% | 0-10% | ~260% | ~260% | 0-40% | нет | 3,0 — 6,0 |
LOF | > 100 % | > 100 % | > 100 % | _ | ~65% | ~65% | ~65% | ~260% | ~260% | ~260% | да или нет | >6,0 |
Таблица 4: Инструкции по классификации ультразвуковых операторов.![]() |
- Тип дефекта LOF = непровар на скосе 5 градусов.
- Зоны 1, 2 и 3 — это три зоны проверки. Рисунок 7.
- При появлении дефекта в трех и более каналах должны пройти все три амплитудные характеристики 100 % для дефекта, подлежащего суммированию, т. е. более 6 мм в высоту.
- «Старт/стоп» сварки, лежащие в одной вертикальной плоскости, могут быть перетрассированы максимум в шести зонах. две зоны с наибольшей амплитудой используются для определения размеров дефектов и определения сквозных стенок разделение. Отклик TOFD также подвергается тщательной проверке для обнаружения сквозных дефектов.
- Примечания:
Два механизированных сварных шва GMA были выполнены на проектной трубе диаметром 36 дюймов (914 мм) и
Толщина стенки 0,56 дюйма (14,2 мм) при использовании процесса сварки CRC-Evans. Во время сварки
процесса различные дефекты непровара боковых стенок были созданы в заполняющих проходах путем регулировки сварного шва
слежение во время сварки. Плохое отслеживание сварного шва является частой причиной зонального и межзонального отсутствия сварки.
дефекты сплавления боковых стенок и являются типичными дефектами, возникающими во время сварки. В целом
было создано девять подходящих дефектов.
Размеры девяти дефектов, образовавшихся в двух сварных швах с затравкой, были определены с использованием шестиэтапного метода определения размеров. обсуждается в разделе 6, а также в дополнение к традиционному методу определения размеров зон.
После сканирования, ультразвуковой оценки и определения размера дефекты были удалены из
засеянные кольцевые сварные швы. Участки окружности, содержащие дефект плюс 10 мм прочного сварного шва
обе стороны были вырезаны. Срезы были надрезаны вокруг места дефекта и сломаны. открываются после охлаждения ниже температуры вязко-хрупкого перехода погружением в жидкий азот.
Эта методика представляла полную длину, форму и высоту дефектов, образующихся при сварке.
Этот метод ломки в холодном состоянии был принят после консультаций с Гентским университетом, Ссылка 8, которая определила, что многократное поперечное сечение сварных швов с дефектами может привести к неполному сварному шву. неточная оценка формы дефекта. Подробная информация о девяти дефектах двух сварных швов приведена ниже. представлено в Приложении A к J [Pdf 390 КБ]. Результаты контроля двух сварных швов приведены в таблице 5.
Дефект № | Сварной шов № 2 | ||
1 | 2 | 3 | |
Расположение окружности в мм (12 час), | 1438-1495 | 1443-2900 | 1928-1950 |
Макс.![]() | 3,0-6,0 | 3,0-6,0 | 3,0-6,0 |
Максимальная высота при зональной проклейке, мм | 5,6 | 8.4 | 7,6 |
Максимальная измеряемая высота, мм | ~6,4 | ~ 5,8 | ~3,5 |
Положение дефекта | Заполнение 1 и 2 | Заполнение 1 и 2 | Между заливкой 1 и 2 |
Дефект № | Сварной шов № 8 | ||
1 | 2 | 3 | |
Расположение окружности в мм (12 час), | 2620-2730 | 2640-2750 | 2165-2226 |
Макс. высота с учетом амплитуды, мм | 2.2 | 2,6 | 3,0-6,0 |
Максимальная высота при зональной проклейке, мм | 2,8 | 5,6 | 5,6 |
Максимальная измеряемая высота, мм | не видно | ~ 2,8 | ~4,3 |
Положение дефекта | Заполнение 1 | Заполнение 1 | Между заливкой 1 и 2 |
Дефект № | 4 | 5 | 6 |
Расположение окружности в мм (12 час), | 1670-1740 | 1115-1240 | 309-560 |
Макс.![]() | 2,6 | 2.4 | 3,0-6,0 |
Максимальная высота при зональной проклейке, мм | 5,6 | 5,6 | 5,6 |
Максимальная измеряемая высота, мм | ~ 2,7 | ~ 2,3 | ~3,4 |
Положение дефекта | Заполнение 1 | Заполнение 2 | Между заливкой 1 и 2 |
Таблица 5: Результаты ультразвукового и измеренного контроля двух тестовых сварных швов |
A Обзор поверхностей разрушения девяти плоских дефектов в Приложении A к J [Pdf of 390 КБ] показывает, что они
неправильной формы, но имеют значительно большую длину, чем высоту. Следовательно, калибровочная насечка, как
в отличие от калибровочного отверстия, по-видимому, обеспечивает лучшую основу для эталонной калибровки.
Результаты двух сканирований показывают, что зональный размер имеет тенденцию завышать дефекты сварки. Этот проявляется на зональных и межзональных дефектах и является результатом самой методики зональной проклейки и нерегулярный характер плоских дефектов. Амплитуды превышения трассы выше порогового уровня считается занимающим всю зону контроля в методе зональной калибровки и приводит к консервативная оценка. Повышение порогового уровня устранит такое чрезмерное отслеживание, но риск отсутствие межзональных дефектов, которые производят относительно небольшие ультразвуковые амплитуды.
С другой стороны, измерение амплитуды обеспечивает гораздо более точное определение высоты дефекта.
Однако есть два результата, которые требуют дальнейшего объяснения; недостаток 1 и недостаток 7. В этих двух
Примеры фактическая измеренная высота дефекта немного больше, чем определенная высота с
размер амплитуды. На первый взгляд может показаться, что это нарушает основное правило, требующее ультразвукового контроля. решимость быть консерватором. Обзор фактических поверхностей разрушения в Приложении A к J [Pdf of 390 КБ]
показывает, что максимальная высота возникает на очень коротком расстоянии и является результатом
нестандартный характер дефекта. Таким образом, это измерение не является критическим, которое следует использовать в
определение допустимой длины таких дефектов. Действительно, режим отказа всех текущих GMAW
кольцевые сварные швы будут пластичным разрушением, а не хрупким разрушением. При таких обстоятельствах
площадь или средняя высота дефекта будет более точной оценкой критического
Габаритные размеры. По средним высотам дефектов 1 и 7 видно, что размер амплитуды
по-прежнему дает консервативную оценку.
Определение размера амплитуды и анализ характеристик сигнала позволяют техническому специалисту определить разницу
между межзональными дефектами и пакетными дефектами. Использование стандартных несфокусированных преобразователей
обеспечивает однородное ультразвуковое покрытие по всей толщине стенки сварного шва. В частности,
Для обнаружения межзональных дефектов доступно 80% отклика FSH. Этот высокий уровень отклика
помогает выездному специалисту в оценке сигнальной сигнатуры межзональных дефектов в сочетании с
возможность уменьшить отклик сигнала на 12 дБ для тех, кто превышает 100% полной высоты экрана. Сигнал
сигнатуры независимо от исходной амплитуды теперь можно интерпретировать и использовать для определения того,
дефекты являются межзональными или явно занимают две зоны и должны рассматриваться как таковые. Размер
Точность таких многослойных дефектов обычно относится к категории от 3 до 6 мм. Дальше
уточнение возможности определения размеров очевидно доступно, но становится все более трудоемким для
выездной техник, который должен проверять и оценивать до 130 сварных швов в день при типичной
Канадская механизированная бригада магистральных сварщиков.
В настоящее время три основных подрядчика по сварке строят трубопроводную систему Alliance в
В Канаде самый низкий уровень ремонта (менее 1%) и самый высокий уровень производства (до
290 сварок/день) любого наземного проекта строительства газопровода с механизированной дуговой сваркой
построено на сегодняшний день.
В некоторых случаях было выполнено до 900 последовательных сварных швов без одного бракуемого дефекта. В не менее 80% дефектов, обнаруженных на 600 км трубопровода, построенного на сегодняшний день, относятся к 0,5 мм и 3,0 мм в высоту. Стекированные вызовы дефектов практически исключены, а конвейер подрядчики в настоящее время согласны с размерами заявленных дефектов.
- Ультразвуковой контроль материалов 4 издание — J Krautkrämer, H. Krautkrämer
- DIN 54 127 часть 1 — Калибровка ультразвукового дефектоскопического оборудования и высоты эха оценка
- BS 3923 часть 1 1986 Ультразвуковой контроль сварных швов. Методы ручного обследования сварка плавлением ферритной стали.
- BS 3923 часть 1 1972 Ультразвуковой контроль сварных швов. Автоматическая проверка сварных швов плавлением стыковые соединения из ферритной стали.
- ASTM 1961 1998 Стандартная практика механизированного ультразвукового контроля кольцевых сварных швов
использование Зональной Дискриминации с Целевыми Поисковыми Единицами.
- BS 7706 1993 Калибровка и настройка метода ультразвуковой времяпролетной дифракции для обнаружение, локализация и определение размеров дефектов. Критические оценки подхода TOFD к ультразвуковому контролю сварных швов А. Эрхард, Э. Шульц, Г. Бреков, Х. Вюстенберг Bundesanstalt für Materialforschung und -prüfung П. Крайер Innotest AG, Эшликон CH
- Надежность механизированных систем УЗК для контроля кольцевых сварных швов на трубопроводе Строительство Р. ван Агтовен. Дж.А. де Раад Röntgen Technische Dienst BV, P.O. Box 10065, 3004 AB, РОТТЕРДАМ, НИДЕРЛАНДЫ
- Гентский университет, Бельгия, конференция и материалы IPLOCA, Лондон, март 1999 г.
- API 1104, восемнадцатое издание, «Стандарт для сварки трубопроводов и связанных с ними объектов».
Обзор эталонных дефектов, обнаруженных в нефтепроводной промышленности
Обзор эталонных дефектов, обнаруженных в нефтепроводной промышленности Международный журнал научных и инженерных исследований, том 6, выпуск 2, февраль 2015 г. 844
ISSN 2229-5518
Обзор эталонных дефектов, обнаруженных в нефтепроводной промышленности
Wissam Alobaidi, Eric Sandgren, Hussain Al-Rizzo
Аннотация. Нефть и природный газ транспортируются по трубопроводам более века, что дает большое количество информации о дефектах производства и эксплуатации. Исследования направлены на раннее выявление дефектов корпуса и сварных швов труб в процессе производства. Наиболее часто дефекты возникают в сварных швах, и их можно разделить на 7 основных типов: пористость, шлаковые включения, непровары, непровары, трещины, прожоги и неправильной формы. Любая из них может встречаться в пяти наиболее распространенных конфигурациях сварки, используемых в производстве. Пять распространенных типов соединений: сварное соединение встык, тройниковое соединение, угловое сварное соединение, соединение внахлест и кромочное соединение. Цель состоит в том, чтобы помочь в устранении проблем в производственном процессе, которые приводят к производственным дефектам, тем самым повышая качество продукции. Взаимосвязь между типом дефекта и методами неразрушающего контроля (НК), которые лучше всего выявляют каждый тип, представлены в табличной форме. В таблице также указано расположение дефекта (поверхностный, подповерхностный или и то, и другое) с методами неразрушающего контроля. Иллюстрации каждого типа дефекта представлены для справки. Отношение типа и местоположения дефекта к затратам и трудозатратам, необходимым для обнаружения каждого типа, представлено в графической форме. Поверхностные дефекты легко обнаруживаются при визуальном контроле, в то время как подповерхностные дефекты могут быть обнаружены при радиографическом контроле при проведении рекомендованной скорости 50 мм/с, но если они пропущены, их можно обнаружить при помощи ультразвукового контроля, который является более трудоемким, и что должно быть проверено с помощью второго метода неразрушающего контроля, цифрового рентгеновского контроля. Чтобы повысить эффективность производства и ряд станций неразрушающего контроля, необходимых для производства нефте- и газопроводов, мы должны определить, как внедрить новые методы, чтобы скрыть недостатки существующих методов обнаружения дефектов.
Это позволит сократить трудозатраты и увеличить производительность при сохранении качества готовой продукции.
Термины индекса — Нефтепровод, Трубопровод природного газа, Дефект трубы, Осмотр трубы, Непрерывность сварного шва, Обнаружение дефекта сварного шва, Металлическая труба, Сварной шов , Неразрушающий контроль.
————————— ——————————
1 ВВЕДЕНИЕ
HE Наиболее эффективной системой транспортировки нефти и газа на большие расстояния является трубопровод. Существующая трубопроводная инфраструктура устаревает, что вызывает серьезную озабоченность по поводу оставшегося срока полезного использования существующих трубопроводов. Для защиты как окружающей среды, так и населения районов, обслуживаемых этими трубопроводами, становится все более важным разработать способы контроля целостности этих сооружений. Операторы обеспокоены мониторингом утечек и обнаружением потенциальных неисправностей на старых участках трубопроводной системы [1]. Нефть и природный газ транспортируются по трубопроводам с начала 20 века. Обладая более чем столетним опытом работы с этой технологией, в отрасли ведется тщательный учет неблагоприятных результатов из-за дефектов сварных швов и материалов. Помимо угрозы общественной безопасности и окружающей среде, отказы трубопроводов могут привести к травмам. Записи показывают, что в период с 1996 и 2003
[2].
Неразрушающая оценка (NDE) для обнаружения и выявления разрывов в самих трубах как во время производства, так и во время эксплуатации представляет собой эффективную методологию для обеспечения целостности существующей сети [3-16]. Ультразвуковой датчик с наклонным лучом пример для исследования участка тела трубы, как показано на рис. 1.
____________________________________
Виссам Алобаиди, автор-корреспондент, кандидат инженерных наук и систем, машиностроения и материаловедения, Арканзасский университет в Литл-Роке, США, E-Mail: [email protected]
Эрик Сандгрен, профессор инженерных наук и систем, машиностроения и материаловедения, Арканзасский университет в Литл-Роке, США, E-mail: exsandgren@ualr. edu
Хусейн Аль-Риццо, профессор инженерных наук и систем, телекоммуникации и сетевой инженерии, Арканзасский университет в Литл-Роке, США, электронная почта: [email protected]
Рис. 1. Схема ультразвукового датчика с наклонным лучом, используемого для трубопровода.
Где θR — угол отражения волны, T — толщина трубы, 1-я ветвь, 2-я ветвь и 3-я ветвь показывают конфигурацию звуковых путей. Отметим, что дефекты в теле трубы обычно представляют собой расслоения или включения [17], как показано на рис. 1.
За столетие, прошедшее с тех пор, как впервые были введены в эксплуатацию трубопроводы для нефти и природного газа, методы изготовления и сварки значительно усовершенствовались. Сегодняшняя сталь содержит меньше примесных включений, а сварка — более точный процесс [2], [18]. Труба испытывается под давлением производителем
перед отправкой с завода. Новые сварные швы оцениваются с помощью неразрушающего контроля.0015
ISSN 2229-5518
, чтобы убедиться, что они не имеют разрывов. При производстве труб необходимы хорошо зарекомендовавшие себя и проверенные стандарты, чтобы обеспечить постоянную целостность трубопроводной сети в будущем [18]. Государственные учреждения, заинтересованные стороны и землевладельцы требуют, чтобы установленные трубопроводы были максимально свободны от дефектов [1],[2],[18]. Отрезки труб должны быть доставлены с завода в поле. Несмотря на осторожность при изготовлении и монтаже, многократное изгибание секций трубы при транспортировке иногда может привести к появлению трещин в стенке трубы. Это транзитное усталостное растрескивание обычно выявляется при испытании установленного трубопровода под давлением перед вводом в эксплуатацию. Тем не менее, некоторая усталость при транспортировке остается незамеченной при этом предварительном испытании и может ухудшиться, когда труба неоднократно подвергается воздействию давления во время нормальной эксплуатации. В конце концов, эти необнаруженные разрывы могут привести к отказу [2]. Из-за свойств материалов на некоторых участках труб в течение срока службы образуются более крупные разрывы.
Такая секция должна быть индивидуально проверена на структурную целостность, и должна быть сделана оценка ее постоянной пригодности к эксплуатации. За последние несколько десятилетий был разработан растущий арсенал методов тестирования для точного определения величины таких разрывов [18].
В последнее время исследования перешли к раннему выявлению дефектов корпуса и сварных швов трубопровода в процессе изготовления. Большая часть исследований сосредоточена на обнаружении дефектов уменьшения толщины стенки трубы и согласовании этого обнаружения с существующими технологиями неразрушающего контроля.
Отсутствие информации о других типах дефектов, которые могут возникнуть при изготовлении нефте- и газопроводов, побудило нас исследовать ряд поверхностных и подземных несплошностей и представить информацию в одном месте. Источником большей части представленной здесь информации являются технические веб-сайты. Часть информации исходит из личного опыта работы автора в трубном производстве.
Со всей этой информацией, собранной в одном документе, исследователям будет легче
воспользоваться неиспользованными областями исследования и найти решения различных проблем, имеющихся в этой области. Более того, в этой статье мы представляем подробный обзор типов несплошностей сварных швов и их положения относительно сварного шва. В работе представлен весь спектр несплошностей сварных швов и корпусов, которые могут возникнуть в процессе изготовления как до формовки трубы, так и после формовки. Мы также обсуждаем разрывы, которые могут образовываться внутри самого сварного шва.
Нашей основной целью является выявление всех потенциальных дефектов, которые могут возникнуть в процессе производства
, и предоставление широкого пространства для исследований способов уменьшения этих дефектов за счет дальнейшего развития
существующих технологий неразрушающего контроля, доступных на заводе по производству труб
.
2 ОБЗОР ТИПОВ СВАРНЫХ СОЕДИНЕНИЙ
Сварка – это способ соединения компонентов путем плавления присадочного материала для сплавления составных частей [19]. В сварке используются пять основных типов соединений:
Во-первых, сварка встык. Так делают трубы. Куски имеют одинаковую толщину и соединены по краям V-образными двойными и одинарными заполнениями, U-образными двойными и одинарными заполнениями и квадратными соединениями с заполнением, как показано на рис. 2, [20], [21].
Рис. 2. Схема пяти типов заполнения стыкового шва.
Во-вторых, тройниковый сварной шов. Тройниковые соединения выполняются с перекрещиванием деталей под углом 90°, при этом соединение происходит посередине одной части конструкции. Швы бывают скошенными, одинарными или двойными, J-образными, одинарными или двойными, и квадратными, как показано на рис. 3, [20], [21].
Рис. 3. Схема заполнения пяти тройниковых сварных швов.
IJSER © 2015 http://www.ijser.org
Международный журнал научных и инженерных исследований, том 6, выпуск 2, февраль 2015 г. 846
ISSN 2229-5518
В-третьих, угловой сварной шов. Углы формируются с помощью угловой сварки, еще одного соединения, компоненты которого соединяются под углом
90°. Сварной шов расположен на внешней кромке и может
используйте V-образное одинарное или двойное заполнение, U-образное одинарное или двойное заполнение или квадратные заделки, как показано на рис. 4, [20], [21].
Рис. 4. Схема трех типов заполнения угловых швов.
Четвертый, сварной шов внахлестку. Для создания сварного шва внахлест одна деталь размещается так, чтобы одна часть перекрывала другую на определенном расстоянии. Они соединены в параллельном интерфейсе. Бортик может быть спущен только с одной стороны или с обеих сторон нахлеста, как показано на рис. 5, [20], [21].
Рис. 5. Схема заполнения нахлесточных швов.
В-пятых, кромочное сварное соединение. Краевой сварной шов — это еще один тип сварного шва, в котором компоненты параллельны сварному шву. Два листа кладутся вместе, а бортик укладывается по совмещенным кромкам деталей. Это можно использовать для соединения J-образной детали с плоским листом или двумя плоскими листами, как показано на рис. 6, [20], [21].
Рис. 6. Схема заполнения кромочного шва.
3 ДЕФЕКТЫ
В процессе производства стали могут оставаться примеси в готовой стали. Эти включения могут привести к тому, что кристаллическая структура стали будет связана в более слабом состоянии, что приведет к несплошностям. Более современные методы производства стали значительно снизили вероятность включения, создавая сталь гораздо более высокого качества. Тем не менее, даже более низкая частота включений может привести к отказу [2]. На рис. 7 показано идеальное формирование сварочного валика в поперечном сечении трубы.
Рис. 7. Поперечное сечение идеального контура для сварного шва для нефте- и газопровода.
3.1 Пористость
Дефекты пористости возникают из-за пузырьков газа, попавших в металлический наполнитель при его затвердевании. Источников образования этих пузырьков в процессе сварки много, но пористости чаще всего можно избежать, если перед сваркой детали полностью очистить. Пористость также может быть уменьшена, если сварочный ток поддерживается ниже чрезмерного уровня. Более высокая скорость производства с большей вероятностью приведет к образованию дефектов пористости [17], [22].
Три распространенных типа дефектов пористости показаны на рис. 8.
Рис. 8. Поперечное сечение кластерных, линейных и червячных несплошностей пористости в сварном шве трубопровода.
IJSER © 2015 http://www.ijser.org
Международный журнал научных и инженерных исследований, том 6, выпуск 2, февраль 2015 г. 847
ISSN 2229-5518
3.2 Включения
Неметаллические вещества, застрявшие в металле сварного шва или между валиком и основанием, называются шлаковыми включениями [17], [22], как показано на рис. 9.
Рис. 12. Поперечное сечение несплошностей типа трещин в сварном шве трубопровода.
Рис. 9. Поперечное сечение шлаковых включений в сварном шве трубопровода.
3.3 Непровар (LOF)
Загрязненные поверхности могут привести к дефектам непровара (LOF) в сварных швах. Название объясняет, как возникает дефект: наплавленный валик не прилипает к основному металлу, не сплавляется с ним, оставляя слабое соединение [17], [22], как показано на рис. 10.
Рис. 10. Поперечное сечение несплошности LOF в сварном шве трубопровода.
3.4 Непровар (LOP)
Непровар (LOP) описывает тип дефекта, при котором металл сварного шва не полностью заполняет соединение. Заполнение меньше, чем должно быть, что приводит к точке напряжения, которая может легко привести к трещине [17], [22], как показано на рис. 11.
Рис. 11. Поперечное сечение несплошности LOP в сварном шве трубопровода.
3.5 Трещины
Если металл сварного шва дает усадку по мере затвердевания, внутри валика могут образоваться трещины. Это ослабляет сварной шов, поскольку металл шва перестает быть сплошным [17], [22], как показано на рис. 12.
3.6 Прожог
Дефект прожога возникает из-за чрезмерного нагрева, который фактически прожигает металл сварного шва, часто образуя комки металла на обратной стороне сварного шва [17], как показано на рис. 13.
Рис. 13. Поперечное сечение прожога несплошности сварного шва трубопровода.
3.7 Неправильные формы
Любое отклонение от идеального контура сварного шва называется дефектом неправильной формы. Каждый тип неправильной формы имеет свою особую причину, но все они приводят к чувствительным к нагрузкам суставам, которые подвержены раннему выходу из строя [17], [22]. Различные типы дефектов неправильной формы показаны на рис. 14.
Рис. 14. Поперечное сечение дефектов подреза, недолива, высокого сварного шва и дефектов внахлест в сварных швах трубопровода.
IJSER © 2015 http://www.ijser.org
Международный журнал научных и инженерных исследований, том 6, выпуск 2, февраль 2015 г. 848
ISSN 2229-5518
характеристик эталонных дефектов и соответствующих методов обнаружения неразрушающего контроля, используемых в производстве нефтяных труб, показаны в таблице 1 ниже.
Таблица 1: Сводка эталонных дефектов и методов обнаружения неразрушающего контроля, используемых в производстве нефтяных труб.

Pipe Section shape | Defect Typ | Surface | Sub-Surface | NDT Techniques | |
Defects including in the weld only | Тип дефекта | Поверхность | Sub-Surface | NDT Techniques | |
Cluster Porosity | UT | Strongly Detectable | |||
Кластер Пористость | RT | 015 | |||
Cluster Porosity | DXR | ||||
Linear Porosity | UT | Сильно Обнаруживаемый | |||
Линейный Пористость | RT | Detectable | |||
Linear Porosity | DXR | ||||
Worm Porosity | UT | Сильно Обнаруживаемый | |||
0015 | Worm Porosity | RT | Detectable | ||
Worm Porosity | DXR | ||||
Шлак | UT | 4 Сильно обнаруживаемый 150015 | |||
Slag | RT | Detectable | |||
Slag | DXR | ||||
Непровар | UT | 14 Сильно50014 Detectable | |||
Lack of fusion | RT | Weakly Detectable | |||
Lack of fusion | DXR | ||||
Отсутствие проходки | 31 | 310131 | UT | Strongly Detectable | |
Lack of penetration | RT | Weakly Detectable | |||
Отсутствие проходки | DXR | UT | Сильно Обнаруживаемый | ||
Crack | RT | Detectable | |||
Crack | DXR | ||||
Прожигание насквозь | VI | Сильно Обнаруживаемый | |||
Burn Through | RT | Strongly Detectable | |||
Burn Through | |||||
Подрез | VI | Сильно Обнаруживаемый | |||
Undercut | RT | Strongly Detectable | |||
Undercut | |||||
Недостаточное заполнение | VI | Сильно Обнаруживаемый | |||
Underfill | RT | Strongly Detectable | |||
Underfill | |||||
Сильный шов | VI | Сильно Обнаруживаемый | |||
High Weld | |||||
Overlap | VI | Strongly Detectable | |||
Перекрытие |
Методы неразрушающего контроля, используемые для контроля качества при производстве труб. Ультразвуковой контроль (UT), радиографический контроль (RT), цифровой рентгеновский контроль (DXR), электромагнитный контроль (ET), магнитопорошковый контроль (MPT) и визуальный контроль (VI) являются распространенными методами неразрушающего контроля, используемыми при производстве труб.
Дефекты, рассмотренные в обзоре, обобщены в Таблице 1 выше. Фиолетовый цвет означает, что дефект может появиться на поверхности, желтый означает, что дефект может появиться под поверхностью. Обратите внимание, что большинство дефектов в таблице имеют оба цвета, а это означает, что они могут появляться в любом положении, хотя примеры поперечных сечений показывают только один тип или другой. Зеленый цвет указывает на необходимость проверки обнаружения того или иного типа дефекта с помощью УЗК, с вторичным
DXR-инспекция.
IJSER © 2015 http://www.ijser.org
Международный журнал научных и инженерных исследований, том 6, выпуск 2, февраль 2015 г. 850
ISSN 2229-5518
инженеры-технологи и те, кто отвечает за проектирование или кто должен исследовать проблему с производственными процессами трубопроводов, часто обращаются к таким веб-сайтам, как Американское общество инженеров-механиков (ASME), Американское общество неразрушающего контроля (ASNT), Ресурсный центр по неразрушающему контролю, Американский институт нефти (API) и другие технические сайты при исследовании проблемы или ссылке на источник.
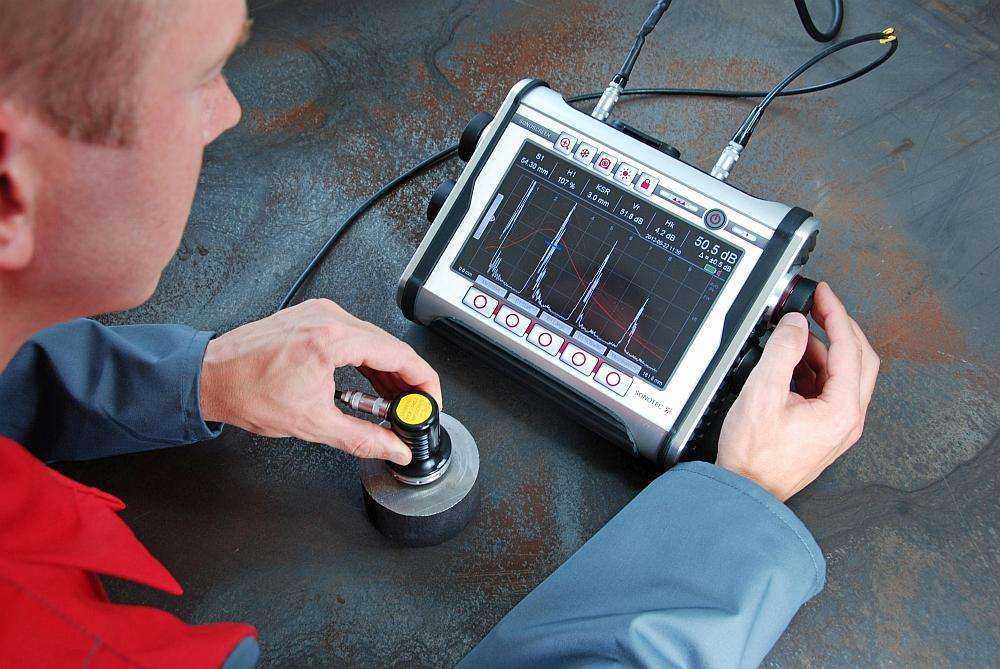
Следует отметить, что Резюме обследования, которое
приводится в Таблице 1, показывает нам широкий спектр типов дефектов, которые появляются в сварных швах, используемых при производстве труб. Многие из этих дефектов могут быть как поверхностными, так и подповерхностными, в частности пористость, трещины и включения.
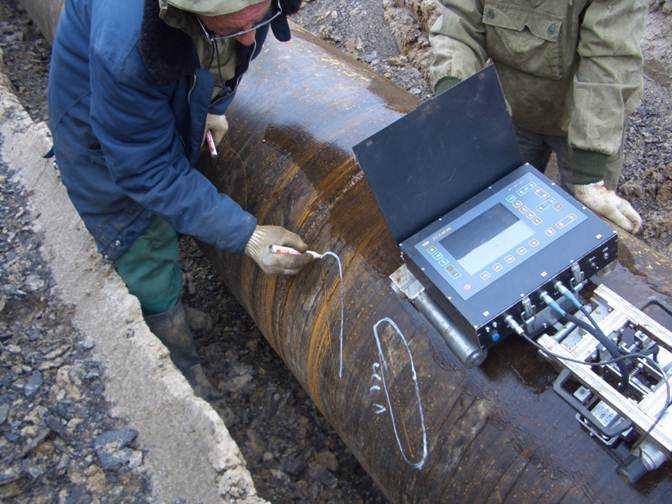
Большинство поверхностных дефектов улавливаются VI, но способность обнаруживать дефекты таким образом зависит от размера дефекта; некоторые слишком малы, чтобы их увидеть. Дефекты меньшего размера могут быть обнаружены с помощью RT, но это все же обычно зависит от размера дефекта. Способ испытания трубы на станциях РТ — поступательное, винтовое движение со скоростью, равной технологической скорости, которая зависит от потребностей заказчика, по опыту автора. Обычно рекомендуемая скорость составляет 50 мм/с, что дает хорошие возможности для обнаружения небольших дефектов с помощью RT. Но многократно используется производственная скорость, и в этом случае станция РТ пропустит более мелкие дефекты (например, из-за моргания глаз при переходе дефекта на экран монитора).
По этой причине приведенная выше сводная таблица основана на рекомендованной для
скорости 50 мм/с [23].

дефекты, а затем проверьте их с помощью DXR.
Когда мы разрабатываем новый способ изготовления труб, возникают новые проблемы либо в теле трубы, либо в сварном шве. Поэтому нам необходимо дополнить новый проект исследованием возможных дефектов, которые могут возникнуть в модифицированном производственном процессе, а также определить методы неразрушающего контроля, наилучшие для обнаружения этих дефектов, чтобы обеспечить безопасность и долгий срок службы продуктов и сохранить их. окружающая среда безопасна.
6 ЗАКЛЮЧЕНИЕ
◊ Шесть наиболее распространенных методов (VI, UT, RT, ET, MPT и DXR) технологии неразрушающего контроля широко применяются в производстве нефтяных труб. Хотя эти методы невыгодно использовать для труб малого диаметра, от 254 мм до 762 мм, поскольку они требуют слишком много времени и труда для этих меньших труб. Подповерхностные дефекты сначала обнаруживаются с помощью УЗК, а затем проверяются с помощью DXR.
◊ V-образные, U-образные и квадратные сварные швы используются в нефтепроводной промышленности.
◊ Большинство дефектов труб возникает в результате сварочных работ.
◊ Перед сваркой поверхность испытуемого объекта должна быть абсолютно чистой (без каких-либо веществ, препятствующих плавлению в процессе сварки, таких как ржавчина, жир и т. д.).
◊ Если дефекты прожога в сварном шве не будут обнаружены до испытания гидравлической системы, это приведет к значительной задержке производства.
◊ Дефекты прожога, низкого давления, недоливки и подрезки, если они не обнаружены во время изготовления, сокращают срок службы трубопровода и, скорее всего, приведут к будущим утечкам в трубе во время эксплуатации. А вот прожог, если он возникает при монтаже трубы в полевых условиях, вызывает немедленную течь, если ее не обнаружить.
◊ Множественные трещины вызовут ослабление конструкции
сварного шва.
IJSER © 2015 http://www.ijser.org
International Journal of Scientific & Engineering Research, Volume 6, Issue 2, February-2015 851
ISSN 2229-5518
На рис. дефект и его расположение, поверхностное или подповерхностное. Линия представляет относительную стоимость и трудозатраты, необходимые для обнаружения типа дефекта, показывая, что подповерхностные несплошности требуют гораздо больше времени и затрат по сравнению с поверхностными дефектами.
Поскольку для обнаружения поверхностных дефектов требуется время, оно должно быть больше нуля по оси Y, а большинство поверхностных дефектов
обнаруживаются VI. Для выявления подповерхностных дефектов требуется гораздо больше времени. Обычно их можно обнаружить с помощью RT на рекомендуемой скорости; в противном случае они должны быть перехвачены UT и проверены DXR.
Стоимость и трудозатраты для подповерхностного слоя Вверх
Стоимость и трудозатраты для наземного Вниз
Подземный
Поверхность
0
Рисунок 15. Взаимосвязь между поверхностными и подповерхностными дефектами и количеством труда и времени,
необходимых для обнаружения, по типу дефекта.
IJSER © 2015 http://www.ijser.org
Международный журнал научных и инженерных исследований, том 6, выпуск 2, февраль 2015 г.0009
[1] A. A. Carvalho, JMA Rebello, LVS Sagrilo, C.
S. Camerini и IVJ Miranda, «Сигналы MFL и искусственные нейронные сети, применяемые для обнаружения и классификации дефектов сварки труб», NDT E Int. , том. 39, стр. 661–667, 2006.
[2] «U.S. Департамент транспорта / Управление безопасности трубопроводов и опасных материалов». [Онлайн]. Доступно: http://primis.phmsa.dot.gov/comm/FactSheets/FSMaterialWeldFailure.htm. [Доступ: 02 февраля 2015 г.].
[3] Дж. Коллар и К. Лагер, «Неразрушающий оптический метод для электрического тестирования интегральных схем с изолированным затвором», Electron. лат. , том. 7, нет. 15, стр.
432–433, 1971.
[4] Дж. Р. Уэйт, «Обзор электромагнитных методов неразрушающего контроля», Proc. IEEE , том. 67, нет. 6, pp. 892–903, 1979.
[5] H. Hoshikawa, H. Saiton, J. Koido, and Y. Ishibashi, «Поток энергии в удаленном поле, вихретоковый неразрушающий контроль», IEEE Trans. Магниты , вып.
26, нет. 2, pp. 885–888, 1990.
[6] X.W. Dai, R. Ludwig, and R. Palanisamy, «Численное моделирование импульсных вихретоковых явлений неразрушающего контроля», IEEE Trans. Магн. , том. 26, нет. 6, pp. 3089–3096, 1990.
[7] О. Михелссон и Ф. Х. Ульманн, «Об использовании 3D H-&-формулировки для прямого решения для вихретокового неразрушающего контроля», IEEE Trans. Магн. , том. 34, нет. 5, pp. 2672–2675, 1998.
[8] Р. В. Сабариего и П. Дулар, «Подход возмущения для моделирования задач вихретокового неразрушающего контроля с дифференциальными датчиками», IEEE Trans. Магн. , том. 43, нет. 4, стр. 1289–
1292, 2007.
[9] С. Каорси, А. Масса и М. Пасторино, «Микроволновая процедура идентификации трещин, основанная на генетическом алгоритме для неразрушающего контроля», IEEE Trans. Антенны Распространение. , том. 49, нет. 12, pp.
1812–1820, 2001.
[10] Э. Кербрат, К. Прада, Д. Кассеро, М. Финк, «Ультразвуковой неразрушающий контроль рассеивающих сред с использованием разложения оператора обращения времени », IEEE Trans. Ультрасон. Ферроэлектр. Частота Контроль , том. 49, нет. 8, pp. 1103–1113, 2002.
[11] Дж. Р. Клейкомб, А. Браздейкис, М. Ле, Р. А.
Ярбро, Г. Гогошин и Дж. Х. Миллер, «Неразрушающий контроль топливных элементов PEM», IEEE Trans. заявл. Суперконд. , том. 13, нет. 2, стр. 211–214,
2003.
[12] А. Берньери, Г. Бетта, Л. Ферриньо и М. Ларакка, «Двухосный датчик для неразрушающего контроля проводящих материалов», IEEE Trans. Инструм. Изм. , том. 53, нет. 3, стр. 678–684, 2004.
[13] Д. Васич, В. Билас и Д. Амбруш, «Импульсный вихретоковый неразрушающий контроль ферромагнитных труб», IEEE Trans. Инструм. Изм. , том. 53, нет. 4, стр. 1289–1294, 2004.
[14] Х.-К. Ву, Н. Гупта и П. С. Милаварапу, «Слепое обнаружение мультигребней для автоматического неразрушающего контроля с использованием ультразвуковых сигналов», IEEE Trans. Ультрасон. Ферроэлектр. Частота Контроль , том. 53, нет. 10, pp.
1902–1911, 2006.
. IEEE Trans. Инструм. Изм. , том.
56, нет. 5, стр. 1961–1966, 2007.
[16] К. Хуанг, Ю. Ву, Дж. Барух, П. Цзян и Ю. Пэн, «Шаблонная модель для моделирования дефектов для оценки неразрушающего контроля в X- Рентгенография», IEEE Trans. Сист. Мужик, Киберн. ASystems Humans , том. 39, нет. 2, стр. 466–475, 2009.
[17] «Интерпретация рентгенограмм — сварные швы». [Онлайн].
Доступно: https://www.ndeed.org/EducationResources/CommunityCollege/R adiography/TechCalibrations/RadiographInterp.ht m. [Доступ: 02 февраля 2015 г.].
[18] А. Кошэм и П. Хопкинс, «Влияние вмятин на трубопроводах — рекомендации в Руководстве по оценке дефектов трубопроводов», Int. Дж. Пресс. Судно. Пип. , том.
81, стр. 127–139, 2004.
[19] «ОЛИМП». [Онлайн]. Доступно:
http://www.olympus-ims.com/en/ndt-tutorials
/flaw-detection/weld-overview/. [Доступ: 02-
, февраль 2015 г.].
[20] «ATELIERS B.G.INC.» [Онлайн]. Доступно: http://www.ateliersbg.com/news/the-5-types-of-basic-welding-joints.aspx. [Доступ: 02 февраля 2015 г.].
IJSER © 2015 http://www.ijser.org
Международный журнал научных и инженерных исследований, том 6, выпуск 2, февраль 2015 г. ” [Онлайн]. Доступно: http://www.globalspec.com/learnmore/manufact uring_process_equipment/welding_equipment_supplies/welding_brazing_soldering_equipment. [Доступ: 02 февраля 2015 г.].
[22] «Дефекты сварки». [Онлайн]. Доступно: http://nptel.ac.in/courses/112107144/welding/lecture13.htm. [Доступ: 02 февраля 2015 г.].
[23] R. Drai, A. Benchaala, M. Zergoug, A. Badidi Bouda, Y. Kabir, and J. Hadj Djilani, Разработка протоколов для оценки коррозии и отложений в трубах с помощью рентгенографии , №. Апреля. 2005, стр. 1–33.
IJSER © 2015 http://www.ijser.org
Контроль корневых дефектов кольцевых сварных швов райзера
Надежность осмотра на недостатки корней в сварных швах с обхват 20-25 июня 2004 г.Бумага 51523
Реферат
Усталостная нагрузка на глубоководные стояки приводит к необходимости обнаружения мелких корневых дефектов во время производственного контроля. Механизированные сварные швы для морских трубопроводов также подвергаются экстремальным нагрузкам во время укладки, что приводит к аналогичным требованиям. Автоматизированный ультразвуковой контроль с использованием зональных методов был принят в качестве метода выбора для этих проверок, но в открытом доступе мало информации об ожидаемой надежности различных доступных систем. Для каждой установки проводится обширная индивидуальная аттестация. Их масштабы могут быть уменьшены за счет наличия такой справочной информации.
В этом документе рассматриваются данные совместных отраслевых проектов в области, осуществляемых TWI, и сравниваются их результаты с такими данными, которые доступны в открытом доступе. Также дан анализ будущих требований и возможностей имеющихся в настоящее время теоретических моделей для расширения диапазона квалификаций.
Номенклатура
АВТ: | Автоматизированный ультразвуковой контроль методом зональной дискриминации |
СЕА: | Комиссариат по атомной энергии |
СИВА: | Запатентованное наименование программного обеспечения CEA (Франция) |
ЕСА: | Критическая инженерная оценка |
ФБХ: | Отверстие с плоским дном |
IPLOCA: | Международная ассоциация трубопроводных и морских подрядчиков |
JIP: | Совместный отраслевой проект |
P-скан: | Патентованное название системы ультразвукового сканирования производства Force Technology, Дания |
ПАНИ: | Программа оценки неразрушающего контроля в промышленности (Исследовательский проект UK Health and Safety Executive Research) |
ТС: | Rontgen Technische Dienst b.![]() |
ТОФД: | Времяпролетная дифракция |
UT: | Ультразвуковой контроль |
Введение
Райзеры представляют собой конструкции, чувствительные к динамической усталости, которые обычно считаются наиболее сложной частью глубоководной разработки. Они подвергаются усталостным нагрузкам, создаваемым движением судна, воздействием волн и течений. Сварные швы в стояках более критичны, чем сварные швы в обычных конструкциях кожуха, поскольку кольцевые сварные швы стояков не имеют избыточности, а выход из строя одного сварного шва представляет собой выход из строя всего стояка, что имеет серьезные последствия для окружающей среды и затрат. Ограничение односторонней сваркой в сочетании с менее строгим контролем, присущим производству бесшовных труб, делает сварку стояков более сложной и менее надежной. TWI провела серию экспериментов по программе усталостной прочности (TWI JIP 5680 Усталостные характеристики кольцевых сварных швов, выполненных с одной стороны), которая началась в 1996. Первоначальные результаты этого проекта показали, что разрушение райзеров в режиме усталости, скорее всего, связано с возникновением трещины в корне сварного шва. Это произойдет гораздо раньше, если будут присутствовать производственные дефекты. Поэтому обнаружение дефектов в корне шва является важной частью обеспечения целостности райзера. Поскольку прямой доступ к корню сварного шва невозможен, осмотр необходимо проводить снаружи. Автоматизированный ультразвуковой контроль с зональной дискриминацией (AUT) был разработан как высокоскоростной метод контроля сварных швов трубопроводов и был предложен в качестве достаточно чувствительного средства контроля односторонних кольцевых сварных швов.
В этом документе описывается работа, проведенная TWI для исследования способности AUT выполнять эту задачу.
Общий обзор ультразвуковых методов контроля сварных швов
Ультразвуковой контроль (УЗК) как метод обнаружения дефектов в сварных конструкциях существует уже около 40 лет. Технология развилась от простой ручной техники к более сложным автоматизированным методам. В 1970-х годах были внедрены автоматизированные методы сканирования сварного шва и отображения данных, а к концу того же десятилетия был введен новый метод определения размеров, называемый дифракцией по времени пролета. Многозондовые системы AUT были представлены в 1919 году.80-х, а системы с фазированными решетками — в конце 1990-х. Принцип работы каждой из этих систем более подробно описан ниже.
Ручной ультразвуковой контроль
На рис. 1 показаны основные принципы ручного ультразвукового контроля стыкового сварного шва. Дисплей, известный как А-скан, представляет собой график зависимости амплитуды сигнала от времени. Процедура требует, чтобы оператор использовал ультразвуковые лучи под разными углами к поверхности, чтобы создать картину любых дефектов внутри сварного шва. Использование множества различных углов считается необходимым для обнаружения плохо ориентированных дефектов. Ручной УЗК обладает значительной гибкостью для различных геометрий, но его надежность ограничена возможностью того, что оператор не сможет сканировать 100% площади или не сможет удовлетворительно интерпретировать сигналы А-скана. Определение размеров дефектов обычно осуществляется путем измерения перемещения зонда на наличие сигнала до тех пор, пока он не упадет на фиксированную величину (обычно 6 дБ или 20 дБ), когда зонд проходит через дефект. Другой метод называется методом максимальной амплитуды («Max Amp»). В этом случае датчик перемещается, чтобы максимизировать амплитуду первого и последнего пиковых сигналов А-скана. Это должно улавливать дифрагированные сигналы от концов дефектов.
Рис. 1. Основной принцип ручного ультразвукового контроля — датчики сканируют весь объем сварного шва под разными углами двусторонними кольцевыми швами, он очень медленный и может страдать от проблем с надежностью из-за отсутствия контроля сканирования и усталости оператора.
Автоматизированный ультразвуковой контроль
Автоматизация процесса ручного УЗК осуществляется с помощью сканирующих кадров, которые перемещают одиночный преобразователь по поверхности по фиксированному растровому шаблону. Угол датчика изменяется с помощью различных датчиков, каждый из которых должен заполнить полный растр, чтобы получить все необходимые углы для проверки. Использование этого фиксированного растра позволяет построить полный график положения отражений. Это приводит к серии проекций сварного шва, показывающих положения дефектов, называемых B-сканом (вид с конца сварного шва или поперечного сечения), C-сканом (вид через сварной шов со стороны крышки или вид сверху) и D-сканом. (вид сбоку, показывающий длину и высоту шва). На рис. 2 показаны эти различные виды, возможные при автоматизированной проверке.
Рис. 2. Виды автоматизированной инспекции
Результаты датчиков под разными углами снова используются для построения картины обнаруженного дефекта. Калибровка дефекта осуществляется аналогично ручному УЗК (перемещением щупа).
Возможным ограничением для анализа дефектов является тот факт, что датчики нельзя наклонять для оптимизации сигнала дефекта, как это возможно при ручном контроле.
Этот метод контроля, как правило, более надежен, чем ручной УЗК, но все же слишком медленный для производственного применения.
Времяпролетная дифракция
Метод времяпролетной дифракции (TOFD) ( Рис. 3 ) контроля был введен в качестве улучшенного средства определения размеров дефектов. Два зонда с широкими лучами размещаются по обе стороны от сварного шва, один действует как передатчик, другой как приемник. Время пролета любого отражения от одного зонда к другому контролируется. Показано, что ультразвуковой пучок, как правило, дает не только отраженный, но и дифрагированный сигнал от оконечностей дефекта. Таким образом, дифрагированные сигналы от конечностей выглядят как сигналы, поступающие в приемник в разное время. Проведя геометрические расчеты, можно получить оценку сквозного размера дефекта по толщине.
Рис. 3. Времяпролетный ультразвук
Полученные данные отображаются в виде сканирования по длине сварного шва с указанием его толщины (аналогично приведенному выше D-скану). Сильный отраженный донный сигнал показывает толщину стенки, а вдоль поверхности проходит «боковая» волна, которую также можно увидеть.
TOFD — это очень быстрый метод проверки целых объемов. Он ограничен там, где разница во времени мала и разные сигналы не могут быть разрешены во времени (например, для небольших дефектов, дефектов, близких к задней стенке и дефектов, близких к контролируемой поверхности). Амплитуда дифрагированных сигналов также может быть достаточно низкой и зависеть от геометрии вершины дефекта.
AUT
AUT в настоящее время является широко используемой аббревиатурой для автоматизированного ультразвукового контроля с использованием метода, описанного ниже. На рис. 4 показан принцип работы систем AUT. Концепция AUT была введена как средство очень быстрого контроля стыковых сварных швов труб. Это отличается от автоматизированной ультразвуковой системы. В этом случае ультразвуковые лучи ограничены (сфокусированы) для исследования только небольшого участка сварного шва, и используется множество датчиков, каждый из которых направлен на отдельные части (зоны) сварного шва. Зоны будут включать в себя зоны, специально сфокусированные и расположенные под углом для обнаружения несплавления боковой стенки и корня, а также другие широкоугольные лучи для обнаружения дефектов в объеме сварного шва. При использовании этого метода для полного покрытия необходимо только одно круговое сканирование сварного шва.
Рис. 4. Контроль сварного шва одиночными датчиками, контролирующими отдельные зоны сварки (показаны только три зоны)
Длина дефекта вдоль сварного шва оценивается по перемещению датчика. Существует ряд стратегий для работы с измерением сквозной толщины. Некоторые операторы определяют сигнал, обнаруженный в зоне, как равный размеру зоны, но другие делают оценки в зависимости от степени перекрытия сигналов между зонами. TOFD часто добавляется к системе сканирования, и это доступно одновременно.
Использование остро направленных лучей означает, что калибровка систем AUT должна выполняться на материале, в точности похожем на тот, который будет использоваться на практике. Метод AUT более подробно описан в ASTM E 1961 [1]
Системы с фазированной решеткой
Ультразвуковые системы с фазированной решеткой были доступны для медицинского ультразвука в течение некоторого времени, но являются недавним введением в промышленный контроль. Датчики с фазированной решеткой имеют возможность электронной фокусировки и направления луча. На рис. 5 показано, как датчик с фазированной решеткой формирует луч, который можно сфокусировать и направить.
Рис. 5. Как датчик с фазированной решеткой формирует фокус
Это означает, что один датчик с фазированной решеткой может заменить несколько обычных датчиков с сфокусированным лучом за счет соответствующего электронного переключения. Таким образом, при использовании так же, как и в AUT, рама, содержащая датчик, намного компактнее, чем упомянутая выше система с несколькими датчиками. Методы оценки дефектов те же, что и при АУЗИ.
Следует, однако, отметить, что АУТ с фазированной решеткой имеет ультразвуковые лучи, которые электронно фокусируются с помощью решетки только в плоскости по толщине (хотя в поперечной плоскости может присутствовать некоторая механическая фокусировка). Вероятно, это означает, что разрешение по длине меньше, чем возможно для луча, который также сфокусирован в окружном направлении.
Автоматический ультразвуковой информационный дисплей
На рис. 6 показана основная идея дисплея систем AUT. Информация организована таким образом, чтобы отображаться на электронной ленточной диаграмме, чтобы показать:
- Каждый канал в виде амплитудного сигнала с маркером, когда он превышает определенный порог.
- Индикация (обычно с цветовой кодировкой) синхронизации сигнала в пределах заданного времени стробирования. Это позволяет более точно позиционировать дефект.
- Дополнительные каналы, которые могут включать TOFD или сканирование тела сварного шва.
Предыдущая литература по инспекционной надежности UT
Было проведено несколько исследований по инспекционной надежности ультразвукового контроля. В первую очередь они были направлены на атомную промышленность. Краткое изложение возможностей обычного UT было дано Чепменом и Боукером. [2] Как правило, они определяются путем моделирования и экспериментальных исследований и связаны с толстыми срезами и методами определения размеров с перемещением зонда. Чепмен и Боукер заявляют, что для расстояний менее 150 мм надежно обнаруживается дефект длиной 15 мм и высотой 3 мм при условии, что наклон менее 20° и перекос менее 3°.
Рис. 6. Показания типичного зонального контроля AUT (различные системы могут отличаться) меньше реального размера.
Проект PANI [4] был выполнен для Руководителя по охране труда и технике безопасности компанией AEA Technology и управлялся промышленным руководящим комитетом, включающим представителей TWI, BP, BG Technology, Innogy, Esso, SaFed, Shell и Mitsui Babcock. .
Эти испытания состояли из ручного ультразвукового контроля сварных швов 16 инспекторами и контроля TOFD. Были включены два набора искусственно созданных корневых дефектов.
Результаты показали, во-первых, что обнаруживаемость корневых дефектов значительно улучшается, если корень сошлифован заподлицо. Если корень остается на месте, то надежно определяемый размер превышает 3 мм через стенку (но это основано только на 2 дефектах). В отчете PANI показано, что сигнал от этих дефектов ниже порога сообщения.
Результаты этих проектов, выполненных с помощью ручного ультразвукового контроля, показывают, что обнаружение корневых дефектов становится надежным при глубине около 3 мм через стенку, хотя это не было определено количественно с точки зрения вероятности обнаружения. Следует отметить, что ни в одном из этих исследований специально не использовались сфокусированные зонды или системы с фазированной решеткой. Поэтому общедоступная информация о производительности этих последних технологий очень ограничена.
Для систем AUT некоторые предварительные работы были выполнены TWI для Министерства энергетики Великобритании, [5] , которые сравнили производительность автоматизированного УЗК P-Scan, RTD Rotoscan и рентгенографии. Их инспекции, по-видимому, проводились на слишком высоком уровне чувствительности (для P-Scan он был установлен с использованием ручного стандарта API), а для Rotoscan он был установлен на 12 дБ выше 1/10 толщины стенки через прорезь в стене. Сообщалось о многих показаниях, которые не были подтверждены секционированием (, таблицы 9-13, в Ref [5] ).
Организация IPLOCA (Международная ассоциация подрядчиков по трубопроводам и шельфовым работам) спонсировала некоторые испытания через Гентский университет, и о результатах некоторых из них сообщил Førli. [6] Эти результаты показали, что вероятность обнаружения 90 % была достигнута при толщине стенки 1,2 мм при пороговой установке 40 % полной высоты экрана (FSH). Это было с сигналом от 3-миллиметрового плоскодонного отверстия (FBH), установленным на 50% FSH. В этом случае не делается различий между различными типами дефектов или их расположением. Сообщалось, что TOFD имеет возможность определения размера лучше, чем ± 0,9 мм (с достоверностью 95%). Меньшие дефекты оказались лучше по размеру (хотя неясно, как определялись дефекты размером менее 2 мм через стенку).
Bowers and Warren [7] предоставили некоторые дополнительные результаты тех же экспериментов ( рис. 9 в Ref [7] ) и показали значительное превышение размеров в дополнение к приведенному Фёрли результату. Еще один результат был получен для тестирования импульсного эха с калибровкой, установленной на 80% полной высоты экрана от FBH диаметром 3 мм. Если бы использовался отчетный уровень 40%, то самый большой пропущенный дефект составил бы 2,9 мм сквозь стенку. При такой чувствительности один дефект толщиной 2,1 мм в стенке давал 10%-ную высоту сигнала, о которой, вероятно, не сообщалось даже при более высоких уровнях чувствительности.
Копп и др. [8] заявили, что точность определения размера дефекта вблизи внутренней и внешней поверхности сварного шва составляет «0,2–3 мм» (из статьи неясно, означает ли это «0,2–0,3 мм»). ‘ или ‘0,2-3,0 мм’, но текст предполагает первое). Также они заявляют, что возможность измерения встроенных дефектов была порядка ± 0,8 мм по высоте стенки.
Ginzel [9] предположил, что точность определения размера, заявленная для амплитудных методов, была преувеличена, и улучшенный метод определения размера дефекта может заключаться в использовании большего количества зон. Тот же автор [10] также сообщается, что сигнал от корневых дефектов от датчиков с большим углом наклона, скорее всего, будет отраженным сигналом, а не прямым сигналом. Это влияет на настройку фокусного расстояния, хотя он указал, что это не влияет на надежность проверки.
В более поздней статье Gross et al [11] сравнили размеры сигналов от различных надрезов и плоскодонных отверстий и в итоге решили, что дефекты можно сгруппировать по амплитуде в 4 категории: наименьшая имела размеры от 0,5 до 1,5 мм. Это соответствовало диапазону амплитуд от 5 до 30% FSH по сравнению с ответом от FBH диаметром 2 мм.
Совсем недавно Морган и др. [12] сообщили о результатах существенного квалификационного упражнения с участием семи команд, использующих AUT. Он пришел к выводу, что результат Коппа (выше) был оптимистичным, но недооценка максимального размера на 1,5 мм ограничивает большинство точек данных.
Причины изменчивости в ультразвуковом контроле
Хотя ультразвуковые системы могут быть очень точно настроены и откалиброваны, они никогда не смогут достичь ожидаемых результатов из-за изменчивости дефектов и частотного состава ультразвуковых сигналов. Предположим, например, что дефект представляет собой плоский отражатель, перпендикулярный лучу, но размером, близким к небольшому числу длин волн (при частотном составе 2-8 МГц длина волны будет 1,6-0,4 мм для поперечных волн в стали). . Дефект не будет отражать луч согласованным образом из-за интерференции между отраженным и дифрагированным сигналами. [13] Даже если только части дефекта (например, концы) имеют размеры этого порядка, сигналы могут стать нерегулярными. Разрешение размера дефекта не может быть лучше длины волны даже в идеальных условиях. Использование движения зонда для определения размера ограничено профилем на разных частотах в пределах луча. С помощью этого метода даже точечный дефект может иметь ширину луча.
Разориентация дефекта по отношению к лучу в любом направлении уменьшит отраженный сигнал, как и кривизна дефекта.
Другие возможные эффекты, которые могут вызвать непостоянство, возникают из-за изменений муфты или незначительных изменений из-за зазора в механической системе, возможно, из-за изменений поверхности трубы, изменений толщины стенки трубы и состояния поверхности.
Особые проблемы при контроле корней сварных швов
Корень сварных швов имеет особые трудности для ультразвукового контроля. В первую очередь это связано с тем, что сама геометрия корня может быть источником ультразвуковых сигналов. Наклонный ультразвуковой пучок при попадании в корень типичного шва будет отражаться от поверхности валика сварного шва, особенно со стороны, противоположной приложенному лучу. Сигнал от этой поверхности легко может быть больше, чем сигнал от небольшого дефекта, и последний может быть затенен. Системы AUT пытаются свести к минимуму его влияние, стробируя сигналы по времени, чтобы уловить только сигналы от части корня сварного шва, прилегающей к дефекту. падающий луч, но это может быть затруднительно, особенно если корень сварного шва мал.
Также существует проблема определения размеров поверхностных дефектов разрушения с помощью ультразвукового контроля. Один из самых сильных сигналов, получаемых при ультразвуковом контроле, — сигнал из-за угла. После захвата луча амплитуда сигнала не будет значительно увеличиваться с высотой дефекта. Эти эффекты показаны на Рис.7 .
Еще одна проблема возникает, когда между трубами есть высокий/низкий уровень (из-за разной толщины и несоосности. Это может означать, что небольшие дефекты скрыты или существует вероятность ложных вызовов.
Рис. 7. (Верхний) Полное отражение луча от угла. Увеличение размера угла не влияет на амплитуду возвращаемого сигнала.
(нижний) Частичное отражение. Амплитуда размера отражения зависит от размера дефекта, но это осложняется дифрагированными сигналами. Часть луча продолжается за углом.
Испытания AUT, проведенные TWI
TWI провела ряд испытаний AUT, а также провела анализ и квалификационные упражнения. Подробная информация о них приведена ниже.
Совместный промышленный проект TWI
Образцы
Для JIP использовались две группы образцов труб. В первую группу вошли 10 образцов диаметром 24 дюйма с толщиной стенки 31 мм. Эти образцы включали 40 умышленных дефектов непровара, полученных таким же образом, как и дефекты, возникающие при изготовлении. Длины дефектов были получены путем сравнения рентгенографии и визуального контроля, высоты дефектов методом падения потенциала переменного тока (ACPD) и путем повторения.
Вторая группа состояла из тридцати пяти образцов диаметром 12 дюймов, некоторые из которых содержали усталостные трещины. Первоначально они были оценены с помощью ACPD и магнитопорошковой дефектоскопии (MPI). Некоторые образцы были изготовлены из вышедших из строя усталостных образцов и использовали усталостные трещины, образовавшиеся во время усталостных испытаний. Причина разрушения образца была устранена, поэтому необходимо было сделать полную окружность, чтобы можно было применить системы АУТ. Это было сделано путем сначала просеивания образцов, чтобы избежать разрезания области трещин, затем разрезания соответствующих пар для завершения окружности и, наконец, сварки деталей вместе прихваточным швом.
Использование усталостных трещин было согласовано с руководящим комитетом проекта на том основании, что, хотя они не являются типичными дефектами, которые могут быть обнаружены во время производства, они, вероятно, являются наиболее сложным типом дефектов для обнаружения. Кроме того, они могут предоставить ценные данные для любой будущей попытки проведения проверки в процессе эксплуатации.
Испытания
Четыре инспекционные компании проводили испытания, которые проводились в TWI. Образцы диаметром 24 дюйма проверялись горизонтально, как показано на рисунке 9.2853 Рис.8 . Образцы диаметром 12 дюймов были установлены вертикально, как показано на рис.9 . Испытываемый образец был установлен между двумя «детскими» частями, одна из которых служила основанием для удерживания образца, а другая обеспечивала достаточную дополнительную длину для ленты сканера каретки зонда.
Рис. 8. Многозондовое оборудование, установленное горизонтально на образце диаметром 24 дюйма
Рис. 9. Устройство для контроля труб диаметром 12 дюймов (показано оборудование с фазированной решеткой)
Команды решили работать из своих автомобилей, чтобы не перемещать электронное оборудование. Обеспечено электроснабжение оборудования и подача воды для контактной жидкости. Последний собирали в лотках под образцами.
Калибровка
Было признано, что калибровочные образцы должны соответствовать каждому типу образцов, используемых в испытаниях. Было решено, что TWI должна предоставить калибровочные образцы. Это было сделано для трех компаний, которые предоставили информацию о необходимых отражателях в трубах. Другая компания предпочла изготавливать собственные рефлекторы, для чего им была поставлена труба.
Разрез
Считается, что метод повторения в сочетании с съемкой ACPD обеспечивает достаточную точность при отсутствии дефектов проникновения. Были проведены разрезы всех известных усталостных трещин, которые были пропущены инспекционными группами. Разделение также проводилось в тех случаях, когда три или более инспекционных групп сообщали об отсутствии известных дефектов (предполагаемые ложные вызовы). Никаких дополнительных недостатков в этом процессе обнаружено не было. Однако следует отметить, что у каждого оператора были ложные вызовы в разной степени.
Квалификационные упражнения
Компания TWI провела ряд квалификационных упражнений для различных клиентов, и, хотя подробности должны оставаться конфиденциальными, было дано разрешение на использование этих данных неавторизованным образом.
Образцы
Третья группа содержит квалификационные упражнения, в которых учитывались корневые дефекты. Это были ручные швы, содержащие в основном несплавления, изготовленные на TWI мостовым методом, [14] но они также включали несколько недостатков непроницаемости.
Диаметр труб варьировался от 12 до 18 дюймов, а толщина от 14 до 25 мм.
В четвертой группе результатов TWI провела статистическую оценку результатов квалификации, где проверка и разрезание были выполнены другими.
Инспекционные группы
В третьей группе использовались две инспекционные группы. В четвертой группе каждый комплект образцов проверялся одной или двумя бригадами.
Калибровка
Для обеих групп каждая компания производила собственные калибровочные образцы и использовала собственную процедуру проверки и метод анализа для испытаний.
Испытания
В третьей группе испытания проводились в помещениях инспекционных групп в присутствии наблюдателя TWI.
Срезы
Образцы третьей группы были разрезаны методом замораживания. В четвертой группе в основном использовалось секционирование салями.
Результаты и обсуждение
Schneider и Rudlin [15] описали методы построения кривых вероятности обнаружения (POD). Существует два основных варианта: (1) вычислить POD с использованием данных «попадание/промах» и (2) использовать данные об амплитуде сигнала по сравнению с известным порогом (метод зависимости отклика от размера). В приведенном ниже результате метод «попадания/промаха» был использован для данных из проекта, спонсируемого группой (первые две группы) и третьей группы, описанной выше, тогда как метод «отклик против размера» был использован для четвертой группы. Решение о том, какой метод использовать, основано на имеющихся данных.
Существуют различные способы представления кривой POD. Это в значительной степени вопрос выбора с учетом имеющихся данных; мы решили использовать метод, описанный в MIL-HDBK 1823, так как этот документ наиболее близок к стандарту для этих целей. [16] В этом случае как данные совпадения/промаха, так и данные «отклика по сравнению с размером» подгоняются к кумулятивной логарифмически нормальной модели для POD. Было показано, что это хорошо соответствует данным.
Данные POD существенно зависят от процедуры, образцов и операторов. Кроме того, следует признать, что процедура квалификации также может влиять на результаты (например, разрез может быть выполнен только в одном месте дефекта, что создает риск получения оптимистичных результатов, поскольку максимальный размер дефекта был пропущен).
Однако есть основные сходства между проведенными испытаниями, включая метод калибровки (обычно прорезь в корне), которые в целом соответствуют рекомендациям ASTM E 1961.
POD также является статистической величиной, и ее значение усиливается количеством данных (то есть количеством недостатков). Статистические тесты можно использовать для проверки того, являются ли различные наборы данных статистически однородными, т. е. кажутся ли они взятыми из одной и той же совокупности. Эти тесты не показали признаков статистической неоднородности (на уровне значимости 5%) между первыми тремя группами. Таким образом, среднее POD для этих трех групп считается репрезентативным для каждой отдельной группы. Кроме того, предположение о статистической однородности между тремя группами позволяет оценить доверительные интервалы для POD (см. 9).2853 Рис.10 ).
В четвертой группе количество промахов снова было небольшим, но были доступны данные об амплитуде, которые предоставили дополнительную информацию, на которой можно было бы основывать кривые POD. В этих тестах, как правило, квалификация выходила за рамки закона, и поэтому было относительно мало основных недостатков. Однако, как оказалось, между результатами отдельных испытаний в этой группе данных были значительные различия (на уровне 5%), которые могли быть связаны с конкретными недостатками или используемыми процедурами. Для простоты среднее POD для этой группы дано в Рис.10 . Но строить доверительные границы в этом случае нецелесообразно из-за предполагаемой неоднородности внутри этой группы.
Рис. 10. Полученные кривые POD
На рис. 10 показано, что для групп 1-3 90% POD достигается при сквозной толщине около 1 мм. Эта оценка основана на 90 недостатках. Нижний 95% доверительный интервал достигает POD 90% при сквозной толщине около 1,5 мм. Для четвертой группы среднее значение POD равно 9.0% достигается при сквозной толщине около 1,3 мм на основе 31 дефекта в 5 различных испытаниях.
Можно видеть, что метод AUT оказывается значительно более надежным для обнаружения корневых дефектов, чем ручные методы, при которых надежное обнаружение, как упоминалось выше, достигается при размере сквозного отверстия около 3 мм. Это может иметь значение, например, когда выполняется ремонт, а ручное УЗК указано как метод последующего неразрушающего контроля.
Очевидно, что сводная кривая, такая как Рис. 10 не совсем подходит для использования в качестве индикатора производительности систем в отдельных приложениях. Актуальность этой кривой ограничена следующими факторами:
- Отдельный участок дефекта не обязательно может проходить через наибольшую сквозную толщину. Однако во многих случаях делалось три или более срезов, и они были нацелены на максимальную амплитуду ультразвука.
- Не учитывались разные системы калибровки, разные критерии отчетности или другое используемое оборудование или зонды. Использование ASTM E19Однако стандарт 61 ограничивает наблюдаемую изменчивость.
- Форма и длина дефекта не учитывались.
- Диапазон толщины ограничен (всего от 12 мм до 32 мм).
Можно также предположить, что операторы AUT, которые проводят квалификационные испытания для инспекционных компаний, являются лучшими операторами, и это может повлиять на результаты. Система сертификации (помимо тех, которые действуют внутри компаний) для проверки работы оператора позволила бы повысить степень доверия к полученным результатам.
Частота ложных вызовов, отмеченная в TWI JIP, могла возникнуть из-за пробной ситуации и ожиданий операторов. Ложные вызовы операторов на месте вскоре привели бы к недоверию к технике, а этого, похоже, не произошло. Однако неизвестно, приводит ли очевидная разница между ситуациями в испытании и на месте к снижению POD.
Использование данных
Квалификация инспекции для систем AUT
Текущая практика квалификации AUT представляет собой отдельное испытание для каждой новой задачи. Предполагается, что представленную здесь кривую POD можно использовать в качестве общего доказательства возможности обнаружения корневых недостатков в квалификационных упражнениях. Конечно, там, где требуется более высокая надежность контроля, потребуются дополнительные испытания. Использование моделирования должно позволять изучать отдельные эффекты, которые трудно контролировать экспериментально, что обеспечивает более экономичную квалификацию.
Использование POD и данных о размерах в ECA
Расчеты ECA минимальных размеров дефектов, допустимых в данной трубе, обычно основаны на прямоугольной или полуэллиптической форме дефекта. Кривые POD обычно основаны на фактических формах дефектов и используют размер пика по толщине. В большинстве случаев представляется разумным предположить, что данные POD, полученные в ходе этих испытаний для проверки возможности обнаружения дефектов требуемого размера, являются консервативными.
Возможности моделирования
Моделирование AUT было бы полезно при применении метода для квалификации новых ситуаций. Утвержденные модели взаимодействия ультразвуковых лучей с дефектами не распространены и в основном разработаны для атомной промышленности. Эти модели обычно не учитывают две ключевые особенности AUT-тестирования, а именно сфокусированные датчики (включая датчики с фазированной решеткой) и отклик от дефектов, размер которых меньше длины волны ультразвука. Две недавние разработки в определенной степени восполнили этот пробел, хотя ни одна из них еще не была полностью подтверждена:
- Компания CEA выпустила пакет моделирования CIVA, который включает модели для фазированных решеток, а также для пучков с фиксированным фокусом.
[16]
- TWI показал в первоначальных испытаниях, что конечно-элементная модель, разработанная для волноводного контроля, где дефекты обычно меньше длины волны, может быть адаптирована к обычному УЗК.
Будущая работа
TWI в настоящее время участвует в проекте, который предоставит дополнительные данные для приведенной выше общей кривой POD, хотя его основной целью является создание критериев приемлемости, и поэтому усилия сосредоточены на определении размеров трещин. Этот проект будет завершен в 2004 г.
Следует отметить, что существует огромное количество данных многих квалификационных испытаний, доступных в различных компаниях, которые, конечно, не могут быть здесь рассмотрены. Было бы полезно собрать больше этих данных, чтобы повысить точность доступных кривых POD.
TWI участвует в финансируемой Европейской комиссией оценке времяпролетного ультразвука для обнаружения дефектов при производстве сварных швов. Отчет должен быть представлен в 2004 году.
Проверка использования нового программного обеспечения для моделирования (в частности, CIVA) также проводится в рамках основной исследовательской программы TWI. Упомянутые выше модели конечных элементов TWI также будут дорабатываться и проверяться. Разработка этих моделей может привести к лучшему пониманию методов и результатов.
Разработка технологий для плакированных и дуплексных труб представляет собой особую проблему, не охваченную вышеуказанной работой, и в настоящее время находится в стадии реализации в TWI.
Выводы
Две кривые вероятности обнаружения корневых дефектов в сварных швах стояков были построены на основе серии квалификационных испытаний, в которых участвовала компания TWI.
90% POD было достигнуто при высоте дефекта 1 мм для одного набора данных, проанализированных методом «попадание/промах». Нижний 95% доверительный интервал достигает POD 90% при сквозной толщине около 1,5 мм. Среднее значение POD 90% было достигнуто при высоте дефекта 1,3 мм для другого набора данных, проанализированных методом «отклик в зависимости от размера».
Метод УЗК представляется гораздо более надежным, чем ручное УЗК, для контроля кольцевых сварных швов, рассматриваемых в данной статье.
Благодарности
Авторы хотели бы поблагодарить спонсоров JIP за их поддержку. Сюда входили BP Exploration, Marathon Oil, Health and Safety Executive, Statoil, Saipem SpA, Stolt Comex, Coflexip Stena Offshore, Drilquip, Shaw Pipeline Services, RTD, Oceaneering и OIS.
Ссылки
- «Стандартная практика механизированного ультразвукового контроля кольцевых сварных швов с использованием зональной дискриминации с помощью сфокусированных поисковых устройств». Документ ASTM E 1961, 1998.
- Чепмен Р. К. и Боукер К. Дж.: «Подготовка заявлений о возможностях для стандартных процедур неразрушающего контроля». Insight , 43, январь 2001 г., стр. 36–38.
- Заключительный отчет «Характеристика и измерение размеров дефектов сварки в ферритной стали с помощью ультразвукового контроля: Часть 1: Неплоские дефекты», отчет TWI 3537/4/77.
- Заключительный отчет по проекту PANI (1999 г.) от Serco Assurance Ltd, Рисли, Уоррингтон, Чешир, Великобритания.
- Mudge P J: «Кольцевые сварные швы морских трубопроводов». Отчет Министерства энергетики США по неразрушающему контролю OTI 88 530 HMSO (1988).
- Førli O: «Автоматизированный ультразвуковой контроль во время морской укладки трубопровода: критерии приемлемости и квалификация». Документ IIW V-1144-99.
- Бауэрс Дж. и Уоррен Э.: «Применение автоматизированного ультразвукового контроля подводных трубопроводов». 24-я конференция по технологиям морских трубопроводов, Амстердам, февраль 2001 г.
- Копп Ф., Перкинс Г., Стивенс Д. и Прентис Г.: «Возможности определения размеров с высоким разрешением для автоматизированного ультразвукового контроля морских райзеров». Pipes and Pipelines International, май-июнь 2001 г., стр. 12-21.
- Ginzel EA: «Амплитудный контроль и механизированный ультразвуковой контроль с использованием линейного сканирования».
NDT.net 5 (4) . апрель 2000 г.
- Ginzel EA: «Неправильные представления об интерпретации сигналов от околоповерхностных целей при механизированном УЗК кольцевых сварных швов трубопровода». NDT.net, 4, октябрь 1999 г.
- Гросс Б., Коннелли Т., ван Дейк Х. и Гилрой-Скотт А.: «Определение размеров дефектов с помощью механизированного ультразвукового контроля кольцевых сварных швов трубопровода». NDT.net, 6 (7) июль 2001 г.
- Морган Л., Нолан П., Киркхэм А. и Уилкинсон Р.: «Использование автоматизированного ультразвукового контроля (AUT) при строительстве трубопроводов». Insight, 45 (11) , ноябрь 2003 г., стр. 746-753.
- Коффи Дж. М. и Чепмен Р. К.: «Применение теории упругого рассеяния для гладких плоских трещин к количественному прогнозированию ультразвукового обнаружения дефектов и их размеров». Нукл. Energy 22, № 5, октябрь 1983 г., стр. 319-333.
- Лукас В.: «Выполнение дефектных сварных швов для Sizewell B: «Сварка и изготовление металлов», март 1992 г., стр. 81-86 .
- Schneider CRA и Rudlin JR: «Обзор статистических методов, используемых для количественной оценки надежности неразрушающего контроля». Insight, 46 (2) , февраль 2004 г., стр. 77-79.
- Лемери А., Кальмон П., Лексур-Таиби И., Райлон Р. и Паради Л.: «Инструменты моделирования для ультразвукового контроля сварных швов». NDT&E International, 33 (2000), стр. 49.9-213.
jpg»> | |||||||||||||||||||||||||||||||||||||||||||||||||||||||||||||||||||||||||||||||||||||||||||||||||||||||||||||||||||||||||||||||||||||||||||||||||
| |||||||||||||||||||||||||||||||||||||||||||||||||||||||||||||||||||||||||||||||||||||||||||||||||||||||||||||||||||||||||||||||||||||||||||||||||
| jpg»> | ||||||||||||||||||||||||||||||||||||||||||||||||||||||||||||||||||||||||||||||||||||||||||||||||||||||||||||||||||||||||||||||||||||||||||||||||
|
Оценка ультразвуковых методов обнаружения коррозионных трещин в трубопроводах из нержавеющей стали. Отчет о ключевом этапе (Технический отчет)
Оценка ультразвуковых методов обнаружения трещин, вызванных коррозией под напряжением, в трубопроводах из нержавеющей стали.
перейти к основному содержанию
- Полная запись
- Другое связанное исследование
Оцениваются ультразвуковые эхо-импульсные методы обнаружения межкристаллитного коррозионного растрескивания в трубопроводах диаметром 102, 254 и 660 мм из нержавеющей стали типа 304 сортамента 80. Сравнивается эффективность различных ультразвуковых преобразователей. Использовались преобразователи с различной частотой, размером и углом луча. Также были протестированы сфокусированные, несфокусированные и одно- и двухлучевые преобразователи. Кроме того, сравнивались изогнутые и плоские клинья преобразователя. Искусственные отражатели различного размера и ориентации использовались как в сварных, так и в несварных трубах, чтобы обеспечить надежность и чувствительность дефектоскопии. Также представлены данные по сварным участкам труб с межкристаллитными трещинами лабораторного и техногенного происхождения. Приведены некоторые статистические данные для установления вероятности обнаружения малых отражателей для искусственных отражателей в трубах диаметром 102 мм и мелких трещин стресс-коррозии в трубах диаметром 254 мм. Обсуждаются проблемы, связанные с ложными ультразвуковыми сигналами, возникающими из-за геометрии сварного шва.
- Авторов:
- Купперман, Д.С.; Рейманн, К.Дж.; Эллингсон, В. А.
- Дата публикации:
- Исследовательская организация:
- Аргоннская национальная лаборатория, Иллинойс (США)
- Идентификатор ОСТИ:
- 6698180
- Номер(а) отчета:
- ЭПРИ-НП-761
РНН: 78-017383
- Номер контракта с Министерством энергетики:
- W-31-109-ENG-38
- Тип ресурса:
- Технический отчет
- Страна публикации:
- США
- Язык:
- английский
- Тема:
- 42 МАШИНОСТРОЕНИЕ; 36 МАТЕРИАЛОВЕДЕНИЕ; 21 СПЕЦИАЛЬНЫЕ ЯДЕРНЫЕ РЕАКТОРЫ И СВЯЗАННЫЕ С ними УСТАНОВКИ; РЕАКТОРЫ ТИПА BWR; ТРУБЫ; РЕАКТОРНЫЕ МАТЕРИАЛЫ; УЛЬТРАЗВУКОВОЙ КОНТРОЛЬ; НАПРЯЖЕННАЯ КОРРОЗИЯ; НЕРЖАВЕЮЩАЯ СТАЛЬ-304; ОЦЕНКА; ТРЕЩИНЫ; ЭФФЕКТИВНОСТЬ; ПРЕОБРАЗОВАТЕЛИ; СВАРНЫЕ СОЕДИНЕНИЯ; АКУСТИЧЕСКИЕ ИСПЫТАНИЯ; СПЛАВЫ; ХИМИЧЕСКИЕ РЕАКЦИИ; ХРОМОВЫЕ СПЛАВЫ; ХРОМОВЫЕ СТАЛИ; ХРОМО-НИКЕЛЕВЫЕ СТАЛИ; КОРРОЗИЯ; КОРРОЗИОННОСТОЙКИЕ СПЛАВЫ; ТЕРМОСТОЙКИЕ МАТЕРИАЛЫ; ЖАРОСТОЙКИЕ СПЛАВЫ; ЖЕЛЕЗНЫЕ СПЛАВЫ; ЖЕЛЕЗНЫЕ СПЛАВЫ; СУСТАВЫ; МАТЕРИАЛЫ; ИСПЫТАНИЯ МАТЕРИАЛОВ; НИКЕЛЕВЫЕ СПЛАВЫ; НЕРАЗРУШАЮЩИЙ КОНТРОЛЬ; РЕАКТОРЫ; НЕРЖАВЕЮЩИЕ СТАЛИ; СТАЛИ; ТЕСТИРОВАНИЕ; ВОДЯНЫЕ РЕАКТОРЫ; ВОДЯНЫЕ РЕАКТОРЫ; 420500* — Инженерно-технические испытания материалов; 360105 — Металлы и сплавы — коррозия и эрозия; 210100 — Реакторы энергетические, невоспроизводящие, с легководным замедлителем, с кипящим водяным охлаждением
Форматы цитирования
- MLA
- АПА
- Чикаго
- БибТекс
Купперман Д.
С., Рейманн К.Дж. и Эллингсон В.А. Оценка ультразвуковых методов обнаружения трещин, вызванных коррозией под напряжением, в трубопроводах из нержавеющей стали. Отчет о ключевой фазе . США: Н. П., 1978.
Веб. дои: 10.2172/6698180.
Копировать в буфер обмена
Купперман Д.С., Рейманн К.Дж. и Эллингсон В.А. Оценка ультразвуковых методов обнаружения трещин, вызванных коррозией под напряжением, в трубопроводах из нержавеющей стали. Отчет о ключевой фазе . Соединенные Штаты. https://doi.org/10.2172/6698180
Копировать в буфер обмена
Купперман Д. С., Райманн К. Дж. и Эллингсон В. А. 1978.
«Оценка ультразвуковых методов обнаружения трещин от коррозии под напряжением в трубопроводах из нержавеющей стали. Отчет о ключевом этапе». Соединенные Штаты. https://doi.
org/10.2172/6698180. https://www.osti.gov/servlets/purl/6698180.
Копировать в буфер обмена
@статья{osti_6698180,
title = {Оценка ультразвуковых методов обнаружения трещин, вызванных коррозией под напряжением, в трубопроводах из нержавеющей стали. Отчет о ключевой фазе},
автор = {Купперман, Д.С. и Райманн, К.Дж. и Эллингсон, В.А.},
abstractNote = {Исследуются методы ультразвукового эхо-импульса для обнаружения межкристаллитного растрескивания под напряжением в трубопроводах из нержавеющей стали типа 304 сортамента 80 диаметром 102, 254 и 660 мм. Сравнивается эффективность различных ультразвуковых преобразователей. Использовались преобразователи с различной частотой, размером и углом луча. Также были протестированы сфокусированные, несфокусированные и одно- и двухлучевые преобразователи. Кроме того, сравнивались изогнутые и плоские клинья преобразователя. Искусственные отражатели различного размера и ориентации использовались как в сварных, так и в несварных трубах, чтобы обеспечить надежность и чувствительность дефектоскопии. Также представлены данные по сварным участкам труб с межкристаллитными трещинами лабораторного и техногенного происхождения. Приведены некоторые статистические данные для установления вероятности обнаружения малых отражателей для искусственных отражателей в трубах диаметром 102 мм и мелких трещин стресс-коррозии в трубах диаметром 254 мм. Обсуждаются проблемы, связанные с ложными ультразвуковыми сигналами, возникающими из-за геометрии сварного шва.},
дои = {10,2172/6698180},
URL = {https://www.osti.gov/biblio/6698180},
журнал = {},
номер =,
объем = ,
место = {США},
год = {1978},
месяц = {6}
}
Копировать в буфер обмена
Посмотреть технический отчет (6,66 МБ)
https://doi.