Стационарные магнитные дефектоскопы | НТЦ Эксперт
Магнитный дефектоскоп Константа MFL предназначен для обнаружения коррозионных повреждений, расположенных на наружной и внутренней поверхностях днищ цилиндрических резервуаров. Прибор позволяет обнаружить дефекты без удаления защитного покрытия, используя эффект Холла для анализа магнитного поля рассеяния дефекта в соответствии с ГОСТ 24450.
Обнаружение дефекта сопровождается световой сигнализацией, позволяющей оценить его глубину и координаты. При подключении дефектоскопа по каналу USB к компьютеру с использованием программы MFL Client возможно анализировать обнаруженные дефекты в режиме реального времени. Габариты дефектоскопа позволяют проводить сканирование труднодоступных участков резервуаров.
Подробнее…
Магнитоанизотропный сканнер-дефектоскоп Stressvision Expert предназначен для измерения, индикации и визуализации механических (технологических, остаточных) напряжений в основном металле, сварных швах и околошовной зоне с представлением информации о наличии условий развития разрушений в исследуемой зоне.
Оператор пошагово перемещает датчик прибора по поверхности участка изделия, результат записывается в электронном виде. После компьютерной обработки строятся и выводятся на дисплей картограммы распределения механических напряжений, зоны концентрации напряжений и др. Степень опасности и наличие условий разрушения участка исследуемого изделия с выявленными участками КМН (концентрации механических напряжений), КНН и градиентами РГМН (разница главных механических напряжений) оценивается по методике общего пользования (СП, РД и т.п.).
Подробнее…
Магнитопорошковый дефектоскоп NOVOTEST МПД-17П предназначен для проведения качественного неразрушающего контроля различных поверхностных и подповерхностных дефектов, возникающих в металлических (ферромагнитных) конструкциях и изделиях. Прибор позволяет обнаружить такие дефекты, как трещины, раковины, дефекты сварных соединений, волосовины, неоднородности, расслоения.
Магнитопорошковый дефектоскоп МПД-17П применяют на предприятиях железнодорожного транспорта при проведении различного ремонта подвижного состава (контроль качества деталей и узлов). Прибором контролируют качество головной части автосцепки СА-3, СА-ЗМ и боковых рам вагонных тележек. Кроме того, на металлургических, машиностроительных и других промышленных предприятиях с помощью магнитопорошкового дефектоскопа возможен контроль качества различных изделий и конструкций, а также автоматическое размагничивание контролируемых деталей.
Подробнее…
Горизонтальный магнитный дефектоскоп MINIMAG производства чешской компании ATG, предназначен для магнитопорошкового контроля изделий из ферромагнитной стали и чугуна. Принцип действия дефектоскопа основан на создании магнитного поля над дефектами контролируемой детали с последующим выявлением их магнитной суспензией. Наибольшая плотность магнитных силовых линий наблюдается непосредственно над трещиной и уменьшается с удалением от нее.
Магнитный дефектоскоп MINIMAG позволяет намагничивать циркулярной магнитизацией прямым прохождением тока сквозь деталь или с помощью вспомогательного проводника, а так же продольной магнитизацией с помощью катушки. Конструкция оборудования предусматривает подключение источников тока серии MAGMAN типа A (AC ток) или H (HW ток). Настольный вариант рабочей скамьи и переносной вид генератора обеспечивают возможность транспортировки.
Подробнее…
Горизонтальные магнитопорошковые дефектоскопы UNIMAG Basic являются универсальными устройствами, способными подключаться к мобильным или стационарным генераторам тока типа MAGMAN. Призматические держатели могут заменяться роллерами для ручного вращения объектов контроля. Пространство роллеров может быть различным по величине под различные диаметры контролируемых объектов.
Совместимые генераторы тока могут быть одно или двухполупериодные, оптимальной является комбинация скамьи UNIMAG 1200 (или 1800) с генератором MAGMAN 6000 H. Данная конфигурация является преимущественно экономичным решением с очень хорошим соотношением цена/мощность с превосходной выявляющей способностью намагничивающего устройства.
Подробнее…
Горизонтальный дефектоскоп с закрытой магнитной цепью UNIMAG 400 AC/DC производства чешской компании ATG, предназначен для магнитопорошкового контроля изделий из ферромагнитной стали и чугуна. Принцип действия дефектоскопа основан на создании магнитного поля над дефектами контролируемой детали с последующим выявлением их магнитной суспензией. Наибольшая плотность магнитных силовых линий наблюдается непосредственно над трещиной и уменьшается с удалением от нее.
Установка магнитного контроля UNIMAG 400 имеет жесткую конструкцию со стальной рамой и комплектующие с высоким сроком службы, обеспечивающие надежную эксплуатацию прибора в круглосуточном режиме крупносерийных производств. Система управления намагничивания гарантирует проведение контроля в соответствии с установленными параметрами. В случае недопустимого отклонения контрольных параметров (понижение напряжения в сети, окисление на контактах или составляющих) система остановит процесс контроля, о чем оповестит оператора, и не допустит извлечение детали без проведения комплектного контроля.
Подробнее…
Горизонтальный магнитный дефектоскоп UNIMAG 500 AC/AC TWIN производства чешской компании ATG, предназначен для неразрушающего магнитного контроля изделий из ферромагнитной стали и чугуна. Принцип действия дефектоскопа основан на создании магнитного поля над дефектами контролируемой детали с последующим выявлением их магнитной суспензией. Наибольшая плотность магнитных силовых линий наблюдается непосредственно над трещиной и уменьшается с удалением от нее.
Левая головка намагничивания имеет разъемную конструкцию с отдельными пневматическими цилиндрами и возможность подъема на 10 мм. Данная функция предназначена для контроля деталей имеющих U или Y- образную геометрию. Система управления намагничиванием UNIMAG 500 гарантирует проведение контроля в соответствии с установленными параметрами. В случае недопустимых отклонений контрольных параметров (снижение напряжения в сети, окись на контактах или компонентах и тд.) система остановит контрольный процесс, о чем предупредит оператора и не допустит извлечение детали без проведения комплексного контроля.
Подробнее…
Горизонтальный дефектоскоп UNIMAG 1200 AEROTESTER предназначен для неразрушающих испытаний изделий из ферромагнитной стали и чугуна магнитопорошковым методом. Технические параметры дефектоскопа соответствуют условиям применения в авиационной промышленности.
Принцип действия дефектоскопа основан на создании магнитного поля над дефектами контролируемой детали с последующим выявлением их магнитной суспензией. Наибольшая плотность магнитных силовых линий наблюдается непосредственно над трещиной и уменьшается с удалением от нее.
Подробнее…
Большой горизонтальный промышленный дефектоскоп UNIMAG 5600 AC предназначен магнитного контроля изделий из ферромагнитной стали и чугуна. Принцип действия дефектоскопа основан на создании магнитного поля над дефектами контролируемой детали с последующим выявлением их магнитной суспензией. Наибольшая плотность магнитных силовых линий наблюдается непосредственно над трещиной и уменьшается с удалением от нее.
Подробнее…
Модульный переносной магнитопорошковый дефектоскоп МД-М представляет собой революционное решение для ручного магнитопорошкового контроля в авиационной, автомобильной, железнодорожной промышленности и предназначен для замены устаревших дефектоскопов ПМД-70 и ПМД-87 (УНМ 300/2000). Прибор позволяет контролировать различные по форме и размерам изделия, их сварные швы, внутренние поверхности отверстий, а также труднодоступные зоны путем намагничивания отдельных участков или изделия в целом. Контроль осуществляется с помощью набора намагничивающих устройств, питаемых постоянным, переменным или импульсным токами. |
Подробнее…
Импульсный магнитопорошковый дефектоскоп СМ-20 относится к стационарным специализированным средствам и предназначен для проведения магнитопорошкового контроля изделий из ферромагнитных материалов в цеховых условиях. Прибор позволяет контролировать различные по форме и размерам изделия, в том числе крупногабаритные, путем намагничивания отдельных участков или объекта в целом. Контроль осуществляется с помощью гибких кабелей различного сечения, либо специальных электроконтактов, питаемых импульсным током. Автоматическое размагничивание изделий осуществляется с помощью штатного намагничивающего устройства.
Подробнее…
Импульсный магнитопорошковый дефектоскоп СМ-30М относится к стационарным специализированным средствам и предназначен для проведения магнитопорошкового контроля изделий из ферромагнитных материалов в цеховых условиях. Прибор позволяет контролировать различные по форме и размерам изделия, в том числе крупногабаритные, путем намагничивания отдельных участков или объекта в целом. Намагничивание или размагничивание изделий постоянным магнитным полем осуществляется при подключении соленоида (диаметром 600 мм) к модулю СМ-30М и установке контролируемых деталей внутрь соленоида. Размагничивание объектов контроля происходит автоматически.
Подробнее…
KR 650 – новый крестовой электромагнит компании Helling. Магнит KR 650 имеет встроенную подвеску, ножной переключатель, емкость для сбора отработанной суспензии и блок управления. Магнит используется при магнитном неразрушающем контроле всевозможных прутков, отливок, поковок и других ферромагнитных заготовок.
Подробнее…
устройство и применение. Неразрушающий контроль
На производствах и в строительной сфере неразрушающий контроль является одним из самых популярных способов диагностики материалов. С помощью этого метода строители оценивают качество сварных соединений, проверяют плотность на отдельных участках конструкций, выявляя глубинные дефекты и изъяны. Диагностические магнитные дефектоскопы позволяют обнаруживать как поверхностные, так и подповерхностные разрушения с высокой степенью точности.
Устройство прибора
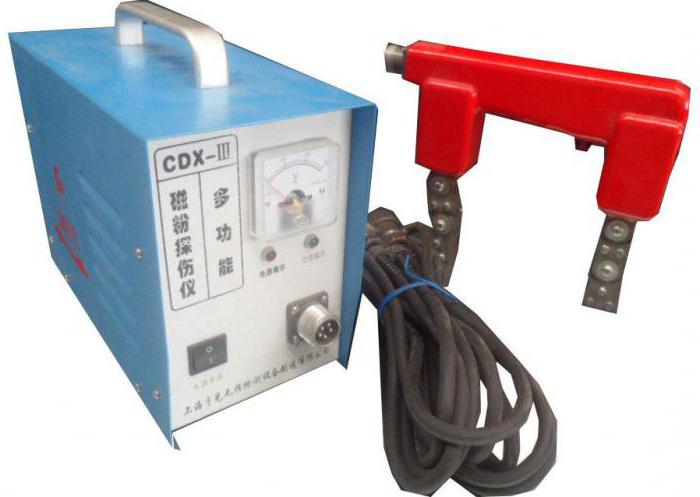
Основу сегмента магнитных толщиномеров и дефектоскопов представляют ручные аппараты, обеспеченные намагничиваемыми рабочими органами – как правило, в виде клещей. Внешне это небольшие приборы, начинку которых составляет электромагнит, регулирующий полюса волнового воздействия. Средний класс позволяет работать с магнитной проницаемостью, коэффициент которой выше 40. Корпус обеспечивается эргономичной рукояткой, благодаря которой устройство можно использовать в труднодоступных местах. Для подачи электротока приборы также обеспечиваются кабелем, подсоединяемым или к генераторной станции (если работы выполняются на улице), или к бытовой электросети на 220 В. Более сложное оборудование неразрушающего контроля имеет стационарную базу, подключенную к компьютеру. Такие средства диагностики чаще применяются для проверки качества выпускаемых деталей на производствах. Они выполняют контроль качества, фиксируя мельчайшие отклонения от нормативных показателей.
Феррозондовые дефектоскопы
Разновидность магнитных приборов, ориентированных на выявление дефектов на глубине до 10 мм. В частности, их используют для фиксации нарушений сплошности структуры конструкций и деталей. Это могут быть закаты, раковины, трещины и волосовины. Применяют феррозондовый метод и для оценки качества сварных швов. После завершения рабочего сеанса магнитные дефектоскопы такого типа могут определять и уровень размагниченности детали в рамках комплексной диагностики. В плане применения к деталям разных форм и размеров устройства практически не имеют ограничений. Но, опять же, следует не забывать о максимальной глубине анализа структуры.
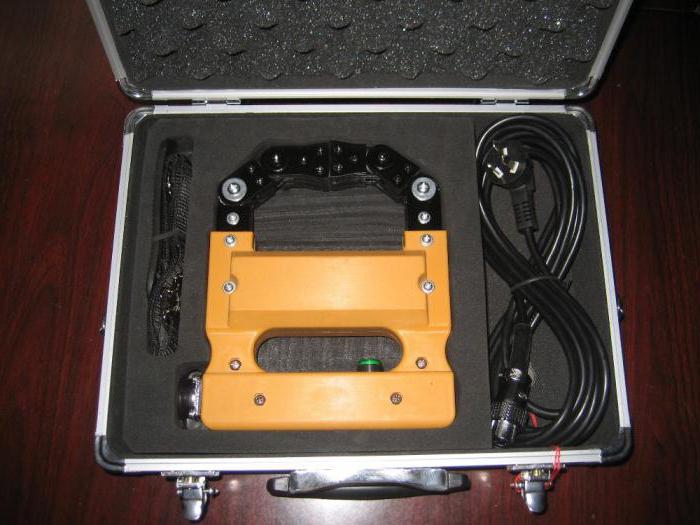
Магнитографические и вихретоковые дефектоскопы
С помощью магнитографических аппаратов оператор может обнаруживать недостатки изделий на глубине от 1 до 18 мм. И вновь целевыми признаками отклонений в структуре выступают нарушения сплошности и дефекты сварных соединений. К особенностям вихретоковой техники контроля можно отнести анализ взаимодействия электромагнитного поля с волнами, образуемыми вихревыми токами, которые подаются на предмет контроля. Чаще всего вихретоковый дефектоскоп применяется для обследования изделий, выполненных из электропроводящих материалов. Приборы такого типа показывают высокоточный результат при анализе деталей с активными электрофизическими свойствами, но важно учитывать, что они работают на небольшой глубине – не более 2 мм. Что касается характера дефектов, то вихретоковой метод позволяет выявлять несплошности и трещины.
Магнитно-порошковые дефектоскопы
Такие устройства тоже ориентируются преимущественно на поверхностные дефекты, которые можно фиксировать на глубине до 1,5-2 мм. При этом допускается возможность исследований на предмет выявления широкого спектра дефектов – от параметров сварного шва до обнаружения признаков расслоения и микротрещин. Принцип работы такого оборудования неразрушающего контроля основывается на активности частиц порошка. Под действием электротока они направляются в сторону неоднородности магнитных колебаний. Это позволяет фиксировать недостатки поверхности целевого объекта исследования.
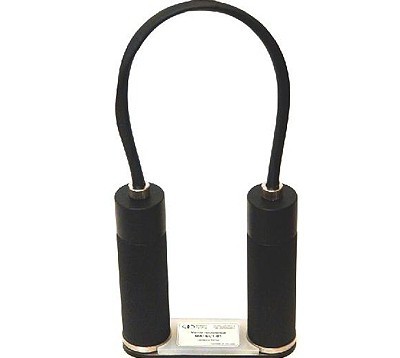
Наибольшая точность определения дефектных зон таким методом будет присутствовать в случае, если плоскость дефектного участка формирует 90-градусный угол с направлением магнитного потока. По мере отклонения от этого угла сокращается и чувствительность прибора. В процессе работы с такими приборами используется и дополнительный инструментарий, позволяющий фиксировать параметры дефектов. Например, магнитный дефектоскоп «Магест 01» в базовой комплектации обеспечивается двукратной лупой и ультрафиолетовым фонарем. То есть непосредственное определение изъяна на поверхности выполняется оператором путем визуальной проверки.
Подготовка к работе
Подготовительные мероприятия можно разделить на две группы. В первую войдет непосредственно подготовка рабочей поверхности, а во вторую – настройка прибора. Что касается первой части, то деталь должна быть очищена от ржавчины, различного рода смазок, масляных пятен, грязи и пыли. Качественный результат можно получить только на чистой и сухой поверхности. Далее выполняется настройка дефектоскопа, в которой ключевым этапом будет калибровка с проверкой по эталонам. Последние представляют собой образцы материалов с дефектами, по которым можно оценивать корректность результатов анализа прибора. Также в зависимости от модели можно фиксировать диапазон рабочей глубины и чувствительность. Эти показатели зависят от задач по выявлению дефектов, характеристик обследуемого материала и возможностей самого аппарата. Современные высокотехнологичные дефектоскопы позволяют выполнять и автоматическую настройку по заданным параметрам.
Намагничивание детали
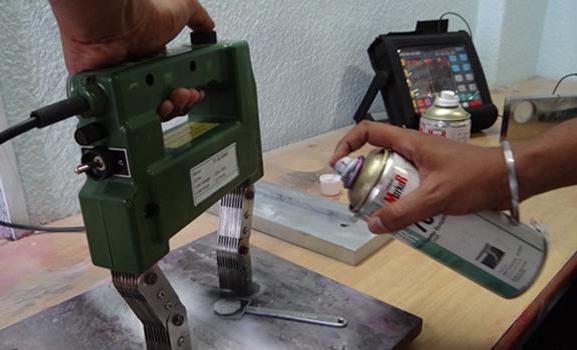
Первая стадия рабочих операций, в ходе которой выполняется намагничивание обследуемого объекта. Изначально важно правильно определить направление потока и тип намагничивания с параметрами чувствительности. К примеру, порошковый метод позволяет выполнять полюсное, циркулярное и комбинированное воздействие на деталь. В частности, циркулярное намагничивание осуществляется посредством пропускания электротока прямо по изделию, по основному проводнику, по обмотке или по отдельному участку элемента с подключением электрических контакторов. В режиме полюсного воздействия магнитные дефектоскопы обеспечивают намагничивание с применением катушек, в среде соленоида, посредством переносного электромагнита или с помощью постоянных магнитов. Соответственно, комбинированный метод позволяет сочетать два способа, подключая дополнительное оснащение в процессе намагничивания заготовки.
Нанесение магнитного индикатора
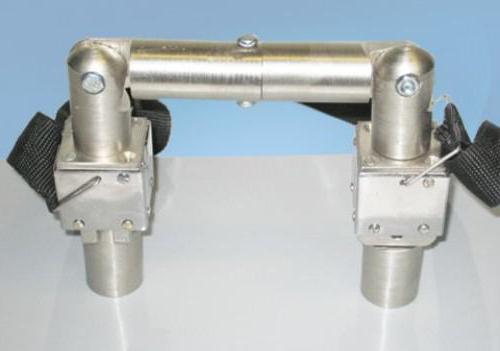
На предварительно подготовленную и намагниченную поверхность наносится индикаторный материал. Он позволяет выявлять недостатки детали под воздействием электромагнитного поля. Уже говорилось, что в этом качестве могут использоваться порошки, но некоторые модели работают также с суспензиями. В обоих случаях перед работой важно учитывать оптимальные условия для применения аппарата. К примеру, дефектоскоп магнитный «МД-6» рекомендуется использовать при температурном режиме от -40 до 50 °С и при влажности воздуха до 98%. Если условия соответствуют требованиям к эксплуатации, то можно начинать нанесение индикатора. Порошок наносят по всей зоне – так, чтобы предусматривался и небольшой охват непредназначенных для исследования зон. Это позволит получить более точную картину дефекта. Суспензия наносится струей при помощи шланга или аэрозоля. Также существуют методы погружения детали в емкость с магнитной индикаторной смесью. Далее можно переходить непосредственно к дефектовке изделия.
Осмотр детали
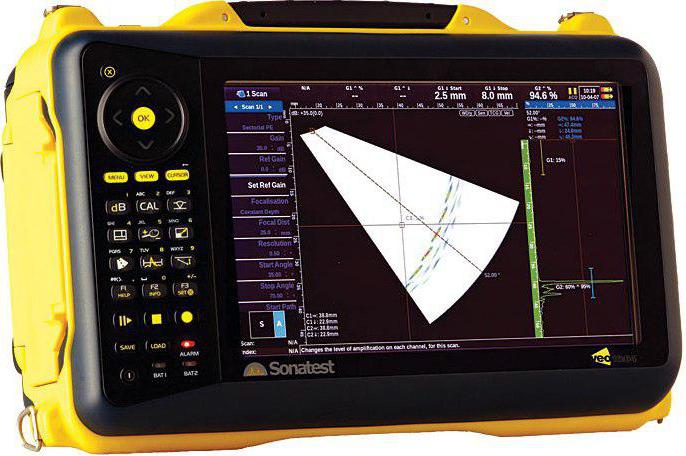
Оператор должен дождаться момента, когда завершится активность индикатора, будь то частицы порошка или суспензия. Изделие проверяется визуальным способом с вышеупомянутыми приспособлениями в виде оптических устройств. При этом увеличительная способность данных приборов не должна превышать х10. Также в зависимости от требований к обследованию оператор может сделать снимки уже для более точного компьютерного анализа. Многофункциональные магнитные дефектоскопы-станции имеют в базовом оснащении аппаратуру для расшифровки реплик с порошковыми отложениями. Полученные в ходе разбраковки рисунки в дальнейшем сверяются с нормативными образцами, что позволяет вынести заключение о качестве изделия и его допустимости к целевому применению.
Заключение
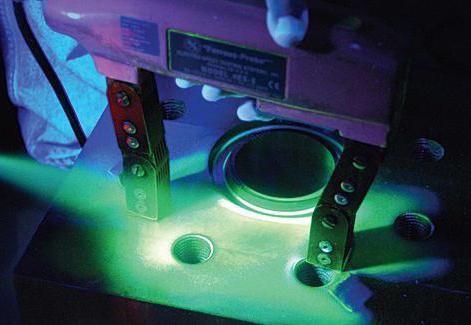
Магнитные приборы для дефектоскопии широко используются в разных областях. Но у них также есть и недостатки, ограничивающие применение. В зависимости от условий эксплуатации к ним можно отнести и требования к температурному режиму, а в некоторых случаях и недостаточную точность. В качестве универсального средства контроля специалисты рекомендуют применять многоканальный магнитный дефектоскоп, который также способен поддерживать функцию ультразвукового анализа. Количество каналов может достигать 32-х. Это значит, что аппарат сможет поддерживать оптимальные параметры дефектоскопии применительно к такому же количеству разноплановых задач. В сущности, под каналами понимается количество режимов работы, ориентированных на определенные характеристики целевого материала и условия окружающей среды. Такие модели стоят недешево, но зато обеспечивают корректность результатов при выявлении дефектов поверхности и внутренней структуры разного рода.
Приборы неразрушающего контроля — Википедия
Прибо́ры неразруша́ющего контро́ля — средства используемые при различных методах неразрушающего контроля для определения свойств и параметров, и оценки надёжности объекта, конструкции или сварного шва.
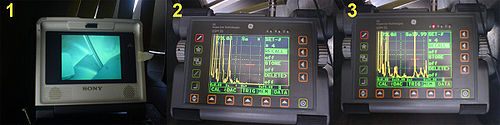
Дефектоскоп — прибор неразрушающего контроля для выявления и оценки внутренних и поверхностных дефектов материалов и изделий. В зависимости от метода неразрушающего контроля, дефектоскопы можно классифицировать на вихретоковые, магнитные, ультразвуковые.
Дефектоскоп — устройство для обнаружения дефектов в изделиях из различных металлических и неметаллических материалов методами неразрушающего контроля. К дефектам относятся нарушения сплошности или однородности структуры, зоны коррозионного поражения, отклонения химического состава и размеров и др. Область техники и технологии, занимается разработкой и использованием дефектоскопов называется дефектоскопией. С дефектоскопами функционально связаны и другие виды средств неразрушающего контроля: течеискатели, толщиномеры, твердомеры, Структуроскопы, интроскопы и Стилоскоп.
Импульсные ультразвуковые дефектоскопы[править | править код]
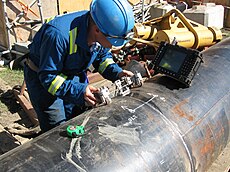
В импульсных дефектоскопах используются эхо-метод, теневой и зеркально-теневой методы контроля. Эхо-метод основан на посылке в изделие коротких импульсов ультразвуковых колебаний и регистрации интенсивности и времени прихода эхо, отраженных от несплошностей (дефектов). Для контроля изделия датчик еходефектоскопа сканирует его поверхность. Метод позволяет обнаруживать поверхностные и глубинные дефекты с различной ориентацией. При теневом методе ультразвуковые колебания, встретив на своем пути дефект, отражаются в обратном направлении. О наличии дефекта судят по уменьшению энергии ультразвуковых колебаний или по изменению фазы ультразвуковых колебаний, огибающих дефект. Метод широко применяют для контроля сварных швов, рельсов и др.
Зеркально-теневой метод используют вместо или в дополнение к эхо-метода для выявления дефектов, дающих слабое отражение ультразвуковых волн в направлении раздельно-совмещенного преобразователя. Дефекты (например, вертикальные трещины), ориентированные перпендикулярно к поверхности, по которой перемещают преобразователь (поверхности ввода), дают очень слабый рассеянный и донный сигналы благодаря тому, что на их поверхности продольная волна трансформируется в главную, которая в свою очередь излучает боковые волны, уносящие энергию. Пример применения зеркально-теневого метода — контроль рельсов на вертикальные трещины в шейке. По чувствительности этот метод обычно в 10-100 раз хуже эхо-метода.
При контроле сварных соединений необходимо обеспечивать тщательное прозвучивание всего шва металла. Ультразвуковые волны вводятся в шов через основной металл с помощью наклонных акустических преобразователей. При поиске дефектов делают продольно-поперечное перемещение (сканирование) преобразователя вдоль шва, одновременно осуществляя его вращательное движение. Чувствительность ультразвукового контроля определяется минимальными размерами выявленных дефектов или эталонных отражателей (моделей дефектов). В качестве эталонных отражателей обычно используют плоскодонные сверления, ориентированные перпендикулярно направлению прозвучивания, а также боковые сверления или зарубки.
Принцип работы основан на определении различия полного механического сопротивления (импеданса) дефектного участка по сравнению с доброкачественным, для чего контролируемая поверхность сканируется с помощью двух пьезоэлементов, один из которых возбуждает колебания в материале, а другой воспринимает колебания. Импедансные дефектоскопы предназначены для выявления дефектов, расслоений, пористости и нарушения целостности композитных материалов и сотовых структур в авиастроении, космической, автомобильной и других отраслях промышленности.
Резонансный метод основан на определении собственных резонансных частот упругих колебаний (частотой 1 — 10 МГц) при возбуждении их в изделии. Этим методом измеряют толщину стенок металлических и некоторых неметаллических изделий. При возможности измерения с одной стороны погрешность измерения — около 1 %. Кроме того, с помощью резонансной дефектоскопии можно выявлять зоны коррозионного поражения. Вариантом резонансного метода является спектрально-акустическая дефектоскопия .

Дефектоскоп позволяет контролировать различные по форме детали, сварные швы, внутренние поверхности отверстий путем намагничивания отдельных контролируемых участков или изделия в целом циркулярным или продольным полем, создаваемым с помощью набора намагничивается устройств, питающихся импульсным или постоянным током, или с помощью постоянных магнитов. Принцип действия основан на создании поля рассеяния над дефектами контролируемой детали с последующим выявлением их магнитной суспензией. Наибольшая плотность магнитных силовых линий поля рассеяния наблюдается непосредственно над трещиной (или над другой несплошное) и уменьшается с удалением от неё[1].
Для выявления несплошности на поверхность детали наносят магнитный порошок, взвешенный в воздухе (сухим способом) или в жидкости (мокрым способом). На долю в поле рассеяния будут действовать силы: магнитного поля, направленная в область наибольшей плотности магнитных силовых линий, то есть до места расположения трещины; тяжести; выталкивающей действия жидкости; трения; силы электростатического и магнитного взаимодействия, возникающих между частицами. В магнитном поле частицы намагничиваются и соединяются в цепочки. Под действием результирующей силы частицы притягиваются к трещине и накапливаются над ней, образуя скопления порошка. Ширина полоски (валика) с оседлой порошка значительно больше ширины раскрытия трещины. По этому осаждению (индикаторному рисунку) определяют наличие дефектов.
Принцип действия основан на методе вихревых токов, который заключается в нарушении вихревых токов в локальной зоне контроля и регистрации изменений электромагнитного поля вихревых токов, обусловленных дефектом и электрофизическими свойствами объекта контроля. Характеризуется небольшой глубиной контроля. Используется для обнаружения трещин и несплошности материала на глубине до 2 мм.
Феррозондовые используют метод магнитной дефектоскопии, основанный на том, что при движении феррозондовые (чувствительного элемента, реагирующего на изменение магнитного поля) вдоль изделия производятся импульсы тока, форма которых зависит от наличия дефектов в изделии. Высокая чувствительность дефектоскопов-градиентометры позволяет выявлять дефекты с шириной раскрытия в несколько микрометров и глубиной от 0,1 мм. Возможно выявление дефектов немагнитным покрытием толщиной до 6 мм. Шероховатость контролируемых поверхностей — до Rz 320 мкм. Дефектоскопы-градиентометры применяются для контроля литых деталей, проката, сварных соединений.
Принцип действия основан на электрическом пробое воздушных промежутков между соприкасающимися поверхностями изоляционного покрытия щупом, подключенным к одному полюсу источника высокого напряжения, и диагностируются объектом, подключенным к другому полюсу источника высокого напряжения непосредственно или через почву с помощью заземления.
Принцип действия термоэлектрических дефектоскопов основан на измерении ЭДС (термо-ЭДС), возникающая в замкнутой цепи при нагреве места контакта двух разнородных материалов. Если один из этих материалов принять за эталон, то при заданной разности температур горячего и холодного контактов величина и знак термо-ЭДС определяться химическим составом второго материала. Этот метод обычно применяют в тех случаях, когда нужно определить марку материала, из которого состоит полуфабрикат или элемент конструкции (в том числе, в готовой конструкции).
В радиационных дефектоскопах осуществляется облучения объектов рентгеновскими, α, β и γ лучами, а также нейтронами. Источники излучений — рентгеновские аппараты, радиоактивные изотопы, линейные ускорители, Бетатрон, Микротрон. Радиационное изображение дефекта превратят в радиографический снимок (радиография), электрический сигнал (радиометрия) или световое изображение на выходном экране радиационно-оптического преобразователя или прибора (радиационная интроскопия, радиоскопия).
Первый радиационный дефектоскоп был внедрен в 1933 году на Балтийском судостроительном заводе изобретателем Л. В. Мысовскую и использовался для выявления дефектов литья в толстых металлических плитах к печам «Мигге-Перроу».
Инфракрасные дефектоскопы используют инфракрасные (тепловые) лучи для обнаружения непрозрачных для видимого света включений. Так называемое инфракрасное изображение дефекта получают в проходящем, отраженном или собственном излучении исследуемого изделия. Дефектные участки в изделии изменяют тепловой поток. Поток инфракрасного излучения пропускают через изделие и регистрируют его распределение теплочувствительным приемником.
Радиодефектоскопия основана на проникающих свойствах радиоволн сантиметрового и миллиметрового диапазонов (микрорадиоволн), позволяет выявлять дефекты главным образом на поверхности изделий обычно из неметаллических материалов. Радиодефектоскопия металлических изделий из-за малой проникающей способностью микрорадиоволн ограничено. Этим методом определяют дефекты в стальных листах, прутьях, проволоке в процессе их изготовления, а также измеряют их толщину или диаметр, толщину диэлектрических покрытий и т. Д. От генератора, работающего в непрерывном или импульсном режиме, микрорадиоволн через рупорные антенны проникают в изделие и, пройдя усилитель принятых сигналов, регистрируются приемным устройством.
ЭОД предназначены для дистанционного контроля высоковольтного энергетического оборудования, находящегося под напряжением. В основе метода диагностики лежит определение характеристик коронных (КР) и поверхностно-частичных разрядов (ПЧР), а также их зависимостей от величины напряжения и степени загрязнения изоляции.
Капиллярный дефектоскоп представляет собой совокупность приборов капиллярного неразрушающего контроля. Капиллярный контроль основан на искусственном повышении световой и цветовой контрастности дефектного участка относительно неповрежденной. Методы капиллярной дефектоскопии позволяют обнаруживать невооруженным глазом тонкие поверхностные трещины и другие несплошности материала, образующиеся при изготовлении и эксплуатации деталей машин. Полости поверхностных трещин заполняют специальными индикаторными веществами (пенетранта), проникающими в них под действием сил капиллярности. Для так называемого люминесцентного метода пенетранты составляют на основе люминофоров (керосин, нориол[2] и др.) На очищенную от избытка пенетранта поверхность наносят тонкий порошок белого проявителя (окись магния, тальк и т. п.), обладает сорбционными свойствами, за счет чего частицы пенетранта извлекаются из полости трещины на поверхность, изображают контуры трещины и ярко светятся в ультрафиолетовых лучах. При так называемом цветном методе контроля пенетранты составляют на основе керосина с добавлением бензола, скипидара и специальных красителей (например, красной краски).
Толщиномер — это измерительный прибор, позволяющий с высокой точностью измерить толщину слоя покрытия металла (такого как краска, лак, грунт, шпаклевка, ржавчина, толщину основной стенки металла, пластмасс, стекла, а также других неметаллических соединений, покрывающих металл). Современные приборы позволяют измерить толщину покрытия без нарушения его целостности.
Применяется в автомобильной, судостроительной промышленности для контроля качества лакокрасочного покрытия транспортных средств, в ремонтных работах, для определения состояния кузова или обшивки по результатам эксплуатации.
В строительстве применяется для определения толщины покрытия металла, имеющего в своем составе противопожарные, антикоррозионные и другие виды компонентов, используемых при создании конструкций зданий.
Толщиномер применяется в работе экспертов-оценщиков, профессиональных полировщиков, контролирующих качество проведения покрасочных работ.
Толщиномеры делятся по принципу их работы, сферы применения, а также способом измерений на:
- механические
- электромагнитные
- ультразвуковые
- магнитные
- вихретоковые
- электромагнитновихретоковые
Течеискатель — прибор предназначен для обнаружения, локализации и количественной оценки величины течи. Работа течеискателей может базироваться на различных физических принципах, ориентированных как на прямые, так и на косвенные измерения параметров. Количественную оценку течи производят, как правило, при использовании тестового газа. Для количественной оценки течи используется отношение произведения величины тестируемого объёма на перепад давления в нём до единицы времени.
Гелиевые масспектрометрические течеискатели[править | править код]
Необходимым условием для использования гелиевых масспектрометрических течеискателей является наличие вакуума в детекторе прибора — в масспектрометр. Согласно течеискатели делят на 2 вида — течеискатели для работы с вакуумированным оборудованием и течеискатели-шнифферы (от англ. Sniffer и нем. Schnüffer — нюхач) с помощью которых фиксируют течи тестового газа с тестируемого объёма в атмосферу. Шнифферы есть дешевле моделями течеискателей и обладают на 4 — 6 порядков более низкой чувствительностью, чем течеискатели на вакууме. Тем не менее большинство течеискателей первого типа комплектуется насадками для защиты входа, которые позволяют им работать в режиме шниффера.
Фреоновые течеискатели используются для поиска протечек на любом оборудовании, но проигрывают 3 — 4 порядка в чувствительности гелиевым масспектрометричним течеискатель. Принцип действия фреоновых течеискателей основан на адсорбции тестового газа на поверхности датчика. В связи с этим при детектировании крупных протечек фреоновые течеискатели могут сорбировать слишком много фреона и потребуются специальные процедуры для релаксации датчика. С другой стороны работа на атмосферном давлении и простота датчика позволяют создавать ручные портативные течеискатели с чувствительностью до 10 — 7 Вт.
- Алешин Н. П., Щербинский В. Г. Радиационная, ультра-звуковая и магнитная дефектоскопии металлоизделий. — М .: Высш.шк., 1991. — 271 с.
- Билокур И. П. Дефектология и неразрушающий контроль .- Киев: Вища шк., 1990. — 207с.
- Адаменко А. А. Современные методы радиационной дефектоскопии. — Киев: Наук. мнение, 1984. — 215 с.
- Герасимов В. Г., Останин Ю. Я., Покровский А. Д. и др. Неразрушающий контроль качества электромагнитными методами. — М .: Энергия, 2008. 215 с.
- Билокур И. П., Коваленко В. А. Дефектоскопия материалов и изделий. — Киев: Техника, 1989. — 192 с.
Дефектоскопы. Виды и принципы работы дефектоскопов.
Дефектоскоп — устройство для обнаружения дефектов в изделиях из различных металлических и неметаллических материалов методами неразрушающего контроля. К дефектам относятся нарушения сплошности или однородности структуры, зоны коррозионного поражения, отклонения химического состава и размеров и др. Область техники и технологии, занимающаяся разработкой и использованием дефектоскопов называется дефектоскопия. К дефектоскопам относят также течеискатели (водородные течеискатели и гелиевые течеискатели), толщиномеры, твердомеры, структуроскоп, интроскопы, стилоскопы и др.
Область примененияДефектоскопы используются почти во всех областях промышленности. Некоторые дефектоскопы позволяют проверять изделия, движущиеся со значительной скоростью (например, трубы в процессе прокатки), или сами могут передвигаться с большой скоростью относительно изделия (например, рельсовые дефектоскопы, тележки и вагоны). Существуют дефектоскопы для контроля изделий, нагретых до высокой температуры.
— Импульсные ультразвуковые дефектоскопы
В импульсных дефектоскопах используются эхо-метод, теневой и зеркально-теневой методы контроля. Эхо-метод основан на посылке дефектоскопом в изделие коротких импульсов ультразвуковых колебаний и регистрации интенсивности и времени прихода эхосигналов, отражённых от дефектов. Для контроля изделия датчик эхо-дефектоскопа сканирует его поверхность. Метод позволяет обнаруживать поверхностные и глубинные дефекты с различной ориентировкой. При теневом методе ультразвуковые колебания, встретив на своём пути дефект, отражаются обратно в дефектоскоп. О наличии дефекта судят по уменьшению энергии ультразвуковых колебаний или по изменению фазы ультразвуковых колебаний, огибающих дефект. Метод широко применяют для контроля сварных швов, рельсов и др. Зеркально-теневой метод используют вместо или в дополнение к эхо-методу для выявления дефектов, дающих слабое отражение ультразвуковых волн в направлении раздельно-совмещенного преобразователя. Дефекты (например, вертикальные трещины), ориентированные перпендикулярно поверхности, по которой перемещают преобразователь (поверхности ввода), дают очень слабый рассеянный сигнал и донный сигнал.
Импедансные дефектоскопы
Принцип работы импендансных дефектоскопов основан на различии полного механического сопротивления (импеданса) дефектного участка по сравнению с доброкачественным и заключается в измерении импеданса изделия прибором, сканирующим поверхность и возбуждающим в изделии упругие колебания звуковой частоты. Этим методом можно выявлять дефекты в клеевых, паяных и др. соединениях, между тонкой обшивкой и элементами жёсткости или заполнителями в многослойных конструкциях.
Резонансные дефектоскопы
Основаны на определении собственных резонансных частот упругих колебаний (частотой 1—10 МГц) при возбуждении их в изделии. Этим методом измеряют толщину стенок металлических и некоторых неметаллических изделий. При возможности измерения с одной стороны точность измерения около 1%. Кроме того, этим методом можно выявлять зоны коррозионного поражения.
Другие методы акустической дефектоскопии:
— Акустико-эмиссионный дефектоскоп основан на приеме и анализе волн акустической эмиссии, возникающих в изделии при развитии трещин в процессе его нагружения.
— Велосиметрический дефектоскоп основан на измерении изменения скорости распространения упругих волн в зоне расположения дефектов в многослойных конструкциях, используется для обнаружения зон нарушения сцепления между слоями металла.
— Акустико-топографический дефектоскоп основан на возбуждении в контролируемом изделии мощных изгибных колебаний заданной (в первом варианте метода) или непрерывно меняющейся (во втором варианте) частоты с одновременной визуализацией картины колебаний поверхности изделия, напр. путём нанесения на эту поверхность тонкодисперсного порошка. При достаточно сильных колебаниях поверхности изделия с заданной частотой частицы порошка из мест, не принадлежащих узлам, постепенно смещаются к узлам колебаний, рисуя картину распределения узловых линий на поверхности. Для бездефектного изотропного материала эта картина получается чёткой и непрерывной. В зоне дефекта картина меняется: узловые линии искажаются в месте наличия включений, а также на участках, характеризующихся анизотропией механич. свойств, или прерываются при наличии расслоения. Если используется второй вариант метода то при наличии расслоения находящийся над ним участок верхнего слоя изделия рассматривается как колеблющаяся, закреплённая по краю диафрагма; в момент резонанса, амплитуда её колебаний резко возрастает, и частицы порошка перемещаются к границам дефектной зоны, оконтуривая её с большой точностью. Работа дефектоскопа ведётся на частотах 30—200 кГц. Чувствительность метода весьма высока: в многослойном изделии с толщиной верхнего листа 0,25 мм обнаруживаются дефекты протяжённостью 1 —1,5 мм. Мёртвая зона отсутствует, сканирование не требуется — излучатель прижимается к поверхности изделия в одной точке.
Магнитно-порошковые дефектоскопы
Эти дефектоскопы позволяют контролировать различные по форме детали, сварные швы, внутренние поверхности отверстий, намагничивая отдельные участки или изделия в целом циркулярным или продольным полем, создаваемым с помощью набора намагничивающих устройств, питаемых импульсным или постоянным током, или с помощью постоянных магнитов. Принцип действия магнитно-порошкового дефектоскопа основан на создании поля рассеяния над дефектами с последующим выявлением их магнитной суспензией. Наибольшая плотность магнитных силовых линий поля рассеяния наблюдается непосредственно над дефектом и уменьшается с удалением от нее. Для обнаружения дефекта на поверхность детали наносят магнитный порошок, взвешенный в воздухе (сухим способом) или в жидкости (мокрым способом). В магнитном поле частицы намагничиваются и соединяются в цепочки. Под действием результирующей силы частицы накапливаются над трещиной, образуя скопление порошка. По этому осаждению – индикаторному рисунку — определяют наличие дефектов.
Вихретоковые дефектоскопы
Принцип действия вихретоковых дефектоскопов заключающется в возбуждении вихревых токов в локальной зоне контроля и регистрации изменений их электромагнитного поля, обусловленных дефектом и электрофизическими свойствами объекта контроля.
Феррозондовые дефектоскопы
Используют метод магнитной дефектоскопии, основанный на том, что при движении феррозонда (чувствительного элемента, реагирующего на изменение магнитного поля) вдоль изделия вырабатываются импульсы тока, форма которых зависит от наличия дефектов в изделии. Высокая чувствительность дефектоскопов -градиентометров позволяет выявлять дефекты с шириной раскрытия в несколько микрометров и глубиной от 0,1 мм. Возможно выявление дефектов дефектоскопом под немагнитным покрытием толщиной до 6 мм. Шероховатость контролируемых поверхностей — до Rz 320 мкм. Дефектоскопы -градиентометры применяются для контроля литых деталей, проката, сварных соединений.
Электроискровые дефектоскопы
Принцип действия дефектоскопов основан на электрическом пробое воздушных промежутков между касающимся поверхности изоляционного покрытия щупом, подключенным к одному полюсу источника высокого напряжения, и диагностируемым объектом, подключенным к другому полюсу источника высокого напряжения непосредственно или через грунт при помощи заземлителя.
Термоэлектрические дефектоскопы
Принцип действия дефектоскопов основан на измерении электродвижущей силы, возникающей в замкнутой цепи при нагреве места контакта двух разнородных материалов. Этот метод обычно применяют в тех случаях, когда требуется определить марку материала, из которого состоит полуфабрикат или элемент конструкции (в т.ч. и в готовой конструкции).
Радиационные дефектоскопы
В этих дефектоскопах осуществляется облучение объектов рентгеновскими, α-, β- и γ-лучами, а также нейтронами. Радиационное изображение дефекта преобразуют в радиографический снимок (радиография), электрический сигнал (радиометрия) или световое изображение на выходном экране радиационно-оптического преобразователя или дефектоскопа (радиационная интроскопия, радиоскопия).
Инфракрасные дефектоскопы
Инфракрасные дефектоскопы используют инфракрасные (тепловые) лучи для обнаружения непрозрачных для видимого света включений. Так называемое инфракрасное изображение дефекта получают в проходящем, отражённом или собственном излучении исследуемого изделия.
Радиоволновые дефектоскопы
Радиоволновые дефектоскопы основаны на проникающих свойствах радиоволн сантиметрового и миллиметрового диапазонов (микрорадиоволн), позволяет обнаруживать дефекты главным образом на поверхности изделий обычно из неметаллических материалов. Радиодефектоскопия металлических изделий из-за малой проникающей способности микрорадиоволн ограничена. Этим методом определяют дефекты в стальных изделиях, а также измеряют их толщину или диаметр, толщину диэлектрических покрытий и т.д. От генератора, работающего в непрерывном или импульсном режиме, микрорадиоволны через рупорные антенны дефектоскопа проникают в изделие и, пройдя усилитель принятых сигналов, регистрируются приёмным устройством.
Электронно-оптические дефектоскопы
Электронно-оптические дефектоскопы предназначены для дистанционного контроля высоковольтного энергетического оборудования находящегося под напряжением. В основе метода диагностики лежит определение характеристик коронных (КР) и поверхностно-частичных разрядов (ПЧР), а так же их зависимостей от величины напряжения и степени загрязнения изоляции.
Капиллярные дефектоскопы
Капиллярный дефектоскоп представляет собой совокупность приборов капиллярного неразрушающего контроля. Методы капиллярной дефектоскопии позволяют обнаруживать невооружённым глазом тонкие поверхностные трещины и др. несплошности материала, образующиеся при изготовлении и эксплуатации деталей машин. Полости поверхностных трещин заполняют специальными индикаторными веществами (пенетрантами), проникающими в них под действием сил капиллярности. Для так называемого люминесцентного метода пенетранты составляют на основе люминофоров (керосин, нориол и др.).
История
Первые дефектоскопы, работающие на непрерывном звуке, создали в 1928 г. С. Я. Соколов и в 1931 г. Мюльхойзер. 1937-1938 год — первый в мире дефектоскоп, использующий переменный ток для контроля конструкций железной дороги и колесных пар (компания MAGNAFLUX, США). Эхо-импульсные дефектоскопы (принцип действия и прибор) создали впервые в 1939— 1942 г. Файрстон в США , Спрулс в Великобритании и Крузе в Германии. Первые эхо-импульсные дефектоскопы были выпущены в 1943 г. почти одновременно фирмами «Сперри продактс инк.» (Ден-бери, США) и «Кельвин энд Хьюз лтд.» (Лондон) источник: ru.wikipedia.org
как работают разные типы приборов и где их применяют
Контроль качества производства и строительства должен осуществляться на каждом этапе. Иногда проверить работу объекта нужно уже в процессе эксплуатации. Прибор, который помогает проводить подобного рода экспертизу неразрушающим методом, называется дефектоскоп. Видов дефектоскопов существует огромное множество. Отличаются они по принципу работы и назначению. Изучите самые популярные методы дефектоскопии и полезные рекомендации по выбору устройства, чтобы не ошибиться при выборе и быстро освоить работу.
Содержание
В зависимости от цели дефектоскопии и области его применения, кардинально меняется методика выявления повреждений и брака, на которой основывается работа того или иного дефектоскопа.
Прибор вихретокового типа
Зачем нужна дефектоскопия ↑
Дефектоскопия – мероприятия, которые направлены на выявление всевозможных отклонений от проекта и нормативов во время производства или эксплуатации объекта. Дефектоскопия помогает обнаружить неисправность задолго до того, как она даст о себе знать. Таким образом, можно предотвратить поломки механизмов, разрушение конструкций и аварии на производстве.
Дефектоскоп – прибор, предназначенный для проверки и выявления дефектов на поверхности или в теле всевозможных изделий. Дефекты могут быть самыми разнообразными. Одни приборы нужны для обнаружения следов коррозии, другие – для поиска полостей, утончения, несоответствия размеров и прочих физико-механических изъянов, а третьи могут определить дефекты на уровне молекулярного строения – найти изменения структуры тела, его химического состава.
Дефектоскоп с электронным дисплеем
В каких отраслях применяется дефектоскопия ↑
Дефектоскоп относят к классу приборов под общим названием «средства неразрушающего контроля». В процессе производства изделия часто поддаются всевозможным проверкам. Некоторые детали подвергают испытаниям в лабораториях, где определяют их запас прочности, способность противостоять всевозможным нагрузкам и воздействиям. Недостаток такой методики в том, что она проводится выборочно и не гарантирует 100% качество всей продукции.
Диагностика трубопровода
Неразрушающий контроль, к которому относят и проверку дефектоскопом, позволяет оценить состояние конкретного изделия или элемента конструкции на месте и без проведения испытаний. Инструмент незаменим в таких отраслях:
- строительство;
- машиностроение;
- производство металлопроката;
- энергетика;
- научно-исследовательские работы;
- химия;
- горная промышленность.
Неразрушающий контроль в авиастроении
Дефектоскопом проверяют качество соединения (особенно важно это для сварки трубопроводов высокого давления), состояние конструкции в строительстве (металлической, железобетонной), степень износа механизма, наличие повреждения детали. Практически во всех отраслях промышленности, где важно контролировать состояние и соответствие нормам твердых элементов, применяют разные дефектоскопы.
Классификация дефектоскопов по методу проверки ↑
В зависимости от метода проверки, выделяют такие типы дефектоскопов:
- акустические;
- вихретоковые;
- электролитические;
- искровые;
- магнитно-порошковые;
- рентгеновские аппараты;
- капиллярный;
- импедансный и другие.
Панель управления УЗ дефектоскопа
Сравнивать их сложно, они настолько разные по строению, работе и даже внешнему виду, что объединяет их только назначение. Выделить какой-то из приборов и уверенно сказать, что он лучший, универсальный и заменит все остальные невозможно. Поэтому при выборе важно не принимать опрометчивых решений и не покупать первую попавшуюся модель.
Самые популярные дефектоскопы, которыми можно проводить экспертизу неразрушающим методом: ультразвуковой (акустический), магнитный и вихретоковый. Они компактны, мобильны и просты в эксплуатации и понимании принципа. Другие используются не так широко, но каждый прочно занимает свою нишу среди других средств дефектоскопии.
Виды дефектоскопии
Акустический – работа ультразвука ↑
Акустический дефектоскоп – понятие, объединяющее в себе схожие по общему принципу приборы неразрушающего контроля. Основывается акустическая дефектоскопия на свойствах звуковой волны. Из школьного курса физики известно, что основные параметры волны не изменяются при движении в однородной среде. Однако, если на пути волны возникает новая среда, частота и длина ее изменяются.
Чем выше частота звука, тем точнее результат, поэтому из всего диапазона применяют ультразвуковые волны. Ультразвуковой дефектоскоп излучает звуковые волны, которые проходят сквозь проверяемый объект. Если присутствуют полости, вкрапления других материалов или прочие дефекты, ультразвуковая волна обязательно укажет на них изменением параметров.
Все результаты должны заноситься в журнал
Ультразвуковые дефектоскопы, работающие по принципу эхо-метода, являются наиболее распространенными и доступными. УЗ-волна проникает в объект, если дефектов не обнаружено, отражения не происходит, соответственно, прибор ничего не улавливает и не регистрирует. Если же возникло отражение УЗ, это указывает на наличие изъяна. Генератор ультразвука является так же и приемником, что очень удобно и облегчает проведение дефектоскопии.
Мини-модель ультразвукового типа
Зеркальный метод похож на эхо, но используется два устройства – приемник и передатчик. Преимущество такого метода в том, что оба устройства находятся по одну сторону от объекта, что облегчает процесс установки, настройки и произведения замеров.
Отдельно выделяют методы анализа ультразвука, который прошел через объект насквозь. Используют понятие «звуковая тень». Если внутри объекта присутствует дефект, он способствует резкому затуханию колебаний, то есть, создает тень. На этом принципе основывается теневой метод ультразвуковой дефектоскопии, когда генератор и приемник колебаний располагаются на одной акустической оси с разных сторон.
Проверка ультразвуком
Недостатки такого прибора в том, что предъявляются строгие требования к размерам, конфигурации и даже степени шероховатости поверхности проверяемого элемента, что делает устройство не совсем универсальным.
Вихретоковый – магнитные поля и вихревые токи ↑
Французский физик Жан Фуко посвятил не один год изучению вихревых токов (токов Фуко), которые возникают в проводниках при создании в непосредственной близости к ним переменного магнитного поля. Основываясь на том, что при наличии в теле дефекта, эти самые вихревые токи создают свое – вторичное магнитное поле, осуществляют дефектоскопию вихретоковые устройства.
Вихретоковый дефектоскоп создает исходное переменное магнитное поле, а вот вторичное поле, которое и дает возможность выявить и проанализировать недостаток в объекте, возникает в результате электромагнитной индукции. Дефектоскоп улавливает вторичное поле, регистрирует его параметры и делает вывод о виде и качестве дефекта.
Производительность этого прибора высокая, проверка осуществляется довольно быстро. Однако вихревые токи могут возникать исключительно в тех материалах, которые являются проводниками, поэтому область применения такого девайса значительно уже его аналогов.
Устройство вызывает в материале вихревые токи
Магнитнопорошковый – наглядная картина ↑
Еще один распространенный метод дефектоскопии – магнитно-порошковый. Он применяется для оценки сварных соединений, качества защитного слоя, надежности трубопроводов и так далее. Особо ценят это метод для проверки сложных по форме элементов и труднодоступных для других приборов участков.
Принцип работы магнитного дефектоскопа основан на физических свойствах ферромагнитных материалов. Они имеют способность намагничиваться. При помощи постоянных магнитов или специальных устройств, которые могут создавать продольное или циркулярное магнитное поле.
После воздействия на участок объекта магнитом, на него сухим или мокрым способом наносят так называемый реагент – магнитный порошок. Под действием магнитного поля, которое возникло в результате намагничивания, порошок соединяется в цепочки, структурируется и образует на поверхности четкий рисунок в виде изогнутых линий.
Намагничивание специальным прибором
Этот рисунок наглядно демонстрирует работу магнитного поля. Зная его особенности и основные параметры, при помощи магнитного дефектоскопа можно определить, в каком месте располагается дефект. Как правило, непосредственно над изъяном (трещиной или полостью) наблюдается ярко выраженное скопление порошка. Для определения характеристик дефекта, полученную картинку сверяют с эталоном.
Магнитный порошок в спрее
Остальные виды и их принцип действия ↑
Методы дефектоскопии совершенствуются с каждым годом. Появляются новые методики, другие постепенно изживают себя. Многие дефектоскопы имеют довольно узкоспециализированное назначение и применяются только в определенных отраслях промышленности.
Принцип работы феррозондового дефектоскопа основывается на оценке импульсов, возникающих при движении устройства вдоль объекта. Применяется в металлургии, при производстве металлопроката и диагностики сварных соединений.
Радиационный дефектоскоп облучает объект рентгеновскими лучами, альфа-, бета-, гамма-излучением или нейтронами. В результате получают подробный снимок элемента со всеми присутствующими дефектами и неоднородностями. Метод дорогой, но очень информативный.
Капиллярный дефектоскоп выявляет поверхностные трещины и несплошности в результате воздействия на объект специальным проявляющим веществом. Оценка результата производится визуальным методом. Применяется капиллярная дефектоскопия по большей части в машиностроении, авиации, судостроении.
В энергетике для анализа работы и выявления несовершенства элементов, находящихся под высоким напряжением, применяют электронно-оптический дефектоскоп. Он способен уловить малейшие изменения коронных и поверхностно-частичных разрядов, что дает возможность оценить работу оборудования без его остановки – дистанционно.
Снимки радиационной дефектоскопии
Основные параметры, на которые следует обратить внимание при выборе дефектоскопа любого типа:
- диапазон;
- назначение;
- производительность;
- сложность монтажа;
- диапазон температур;
- надежность.
Магнитопорошковый прибор МД-М
Разные модели отличаются по диапазону измерения. Это значит, что одни способны выявить дефекты в 1 мкм, а предел для других – 10 мм, например. Если в машиностроении микротрещины в детали играют существенную роль, то для дефектоскопии в строительстве нет смысла покупать сверхточный прибор.
Также производитель обязательно указывает, для каких материалов предназначен конкретный дефектоскоп, недочеты какого характера он должен выявлять. Могут предъявляться требования к характеру поверхности элемента, наличию защитного слоя, размерам и форме объекта.
Под параметром «производительность» подразумевается скорость сканирования и объем работы, который можно выполнить за единицу времени при помощи определенного дефектоскопа. Так, вихретоковый и феррозондовый способы обеспечивают высокую скорость, в то время как процесс намагничивания и обработки каждого отдельного участка магнитным инструментом может занять довольно продолжительное время.
Важная деталь – установка. Выбирая модель дефектоскопа имеет смысл задуматься, как долго и насколько сложно его устанавливать. Ручные мобильные приспособления, которые можно достать из сумки в любой момент, предпочтительней для дежурной дефектоскопии в процессе производства или монтажа. Более сложное и точное оборудование требует длительной установки и наладки.
Ультразвуковой прибор требует наладки перед началом работы
Поскольку неразрушающий контроль может производиться как в помещении, так и на улице, в том числе в зимнее время, заранее уточните, можно ли работать выбранным устройством при отрицательных температурах. Также обязательно выяснить, допустимо ли выполнять диагностику в условиях агрессивной среды, если это необходимо.
Зная, как работает дефектоскоп того или иного типа, вы легко сможете определиться с главным – способом дефектоскопии. А определиться с моделью поможет опытный консультант.
Магнитная дефектоскопия
СВАРКА, РЕЗКА МЕТАЛЛОВ
Физические основы магнитной дефектоскопии. Магнитные методы контроля основаны на обнаружении магнитных потоков рассеяния, возникающих при наличии различных дефектов, в намагниченных изделиях из ферромагнитных материалов (железа, никеля, кобальта и некоторых сплавов).
Намагничивание осуществляется пропусканием тока по детали, созданием магнитного поля вокруг детали магнитом или электромагнитом.
Простым способом создания магнитного потока является пропускание тока плотностью 15—20 А/мм по виткам сварочного провода, наматываемого тремя — шестью витками на изделие. Для намагничивания лучше применять постоянный ток.
Магнитный поток, распространяясь по изделию и встречая на своем пути дефект, огибает его вследствие того, что магнитная проницаемость дефекта значительно ниже магнитной проницаемости основного металла. В результате этого часть магнитно-силовых линий вытесняется дефектом на поверхность, образуя местный магнитный поток рассеяния (рис. 51).
В зависимости от способа регистрации магнитного потока рассеяния магнитные методы контроля подразделяют на магнитопорошковый и магнитографический. В первом случае потоки рассеяния выявляются с помощью магнитного порошка, во втором — регистрируются на магнитную ленту.
Магнитопорошковый метод. Применяют два способа контроля с помощью магнитного порошка: сухой и мокрый. В первом
Рис. 51. Распределение магнитного потока по сечению качественного (а) и дефектного (б) шва |
случае на поверхность намагниченной детали наносят магнитный порошок (железные опилки, окалина и др.) в сухом виде, во втором — в виде суспензии с керосином, маслом, мыльным раствором. Под действием втягивающей силы магнитных полей рассеянью частицы порошка перемещаются по поверхности детали и скапливаются в виде валиков над дефектами. Форма этих скоплений соответствует очертаниям выявляемых дефектов.
Методика магнитопорошкового контроля включает следующие операции: подготовку поверхностей перед контролем и очистку их от загрязнений, окалины, следов шлака после сварки; подготовку суспензии, заключающуюся в интенсивном перемешивании магнитного порошка с транспортируемой жидкостью; намагничивание контролируемого изделия; нанесение суспензии или порошка на поверхность контролируемого изделия; осмотр поверхности изделия и выявление мест, покрытых отложениями порошка; размагничивание.
Метод отличается высокой чувствительностью к тонким и мелким трещинам, простотой выполнения, оперативностью и наглядностью результатов.
Чувствительность магнитопорошкового метода зависит от ряда факторов: размера частиц порошка и способа его нанесения, напряженности приложенного намагничивающего поля, вида приложенного тока (переменный или постоянный), формы, размера и глубины залегания дефектов, а также от их ориентации относительно поверхности изделия и направления намагничивания, состояния и формы поверхностей, способа намагничивания.
При контроле магнитными методами наиболее уверенно выявляются плоскостные дефекты: трещины, непровары и несплав — ления, наибольший размер которых ориентирован под прямым или близким к нему углом относительно направления магнитного потока. Дефекты округлой формы (поры, шлаковые включения, раковины) не могут создавать достаточного потока рассеяния и, как правило, при контроле обнаруживаются удовлетворительно.
Дефектоскопы для магнитопорошкового метода контроля включают источники тока, устройства для подвода тока к детали, устройства для полюсного намагничивания (соленоиды, электромагниты), устройства для нанесения на контролируемую деталь порошка или суспензии, измерители тока (или напряженности поля).
Стационарные универсальные дефектоскопы (УМДЭ-2500, ХМД-10П, МД-5 и др.) широко распространены на предприятиях с крупносерийным выпуском разнотипных деталей. На таких установках можно контролировать детали различной конфигурации с производительностью от десятков до многих сотен деталей в час.
Из группы переносных и передвижных дефектоскопов серийно выпускаются дефектоскопы ПМД-70 и МД-50П. Переносной магнитный дефектоскоп ПМД-70 предназначен для магнитного контроля сварных швов в полевых условиях. Передвижной дефектоскоп МД-50П применяется для контроля крупногабаритных массивных изделий по участкам.
Магнитографический метод. Сущность этого метода (рис. 52) заключается в намагничивании контролируемого участка сварного шва и околошовной зоны с одновременной записью магнитного поля на магнитную ленту и последующем считывании полученной информации с нее специальными устройствами магнитографических дефектоскопов.
Технология магнитографического контроля включает следующие операции: очистку контролируемых соединений от шлака, налипших брызг металла и различных загрязнений;
наложение на шов отрезка размагниченной магнитной ленты и ее прижим эластичной резиновой лентой;
намагничивание контролируемого изделия при оптимальных режимах в зависимости от типа намагничивающего устройства,
far Рис. 52. Схема магнитографического контроля. /— сварной шов; 2—дефект; 3 — магнитная пленка; 4— намагничивающее устройство |
толщины сварного шва и его магнитных свойств;
расшифровку результатов контроля, для чего магнитную ленту устанавливают в считывающее устройство дефектоскопа и по сигналам на экранах дефектоскопа выявляют дефекты.
Магнитографический метод в основном применяют для контроля стыковых швов, выполненный сваркой плавлением, и в первую очередь при дефектоскопии швов магистральных трубопроводов. Этим методом можно контролировать сварные изделия и конструкции толщиной до 20—25 мм.
Чувствительность магнитографического контроля примерно такая же, как и магнитопорошкового. Она зависит от размеров, формы, глубины и ориентации дефектов, параметров считывающей головки дефектоскопа и типа магнитной ленты. Магнитогра — фией наиболее уверенно выявляются плоскостные дефекты (трещины, непровары, несплавления), а также протяженные дефекты в виде цепочек шлака, преимущественно ориентированные поперек направления магнитного потока. Значительно хуже выявляются округлые дефекты (поры, шлаковые включения). Практикой установлено, что этим методом уверенно обнаруживаются внутренние
плоскостные дефекты, когда их вертикальный размер составляет 8—10% толщины сварного шва.
На чувствительность магнитографического метода сильно влияют высота и форма усиления шва, а также состояние его поверхности. При снятом усилении шва максимальная чувствительность контроля к указанным дефектам достигает 5%. Округлые внутренние дефекты обнаруживаются, когда их размер по высоте не меньше 20% толщины изделия.
Для записи магнитных полей при магнитографическом контроле применяют магнитную ленту. Лента выполняется на триацетатной или лавсановой основе с нанесением на нее мельчайших ферромагнитных частиц. В настоящее время серийно выпускаются ленты типа МК-1 (на триацетатной основе) и МК-2 (на лавсановой основе) шириной 35 мм. Лента МК-2 обладает более высокими физико-механическими свойствами, чем лента МК-1, и может применяться при температурах окружающего воздуха от +70 до —70°С; лента МК-1 при температурах ниже —30°С теряет эластичность.
Считывание результагов контроля с магнитной ленты производится магнитографическими дефектоскопами. Промышленностью выпускаются дефектоскопы, имеющие два вида индикации: импульсную и телевизионную. При импульсной индикации на экране электронно-лучевой трубки возникают импульсы, амплитуда которых характеризует величину дефекта в вертикальном направлении, а при видеоиндикации магнитный потенциальный рельеф полей рассеяния от дефектов переносится на экран ЭЛТ. в виде телевизионного изображения магнитограммы отдельных участков шва.
Известны дефектоскопы типа МД-9 с импульсной индикацией и МД-11 с видимым изображением. Наиболее совершенные дефектоскопы МДУ-2У, МД-10ИМ и МГК-1 имеют двойную индикацию.
ПРИЛОЖЕНИЕ
Табл. 1. Применение покрытых электродов при сварке сталей
|
1 | 2 | 3 | 4 | 5 | 6 |
Сварка низкоуглеродистых сталей | |||||
ОММ-5 | 2 | 60-70 | 50-60 | 60-70 | Постоянный |
3 | 100-130 | 80-110 | 90-120 | ||
4 | 160-190 | 130-150 | 140—160 | ||
5 | 200-220 | 150-170 | — | ||
ЦМ-7 | 4 | 160-190 | 130-150 | 140-160 | Постоянный, переменный |
5 | 210-250 | 140-160 | — | ||
б | 260-320 | — | — | ||
ОМА-2 | 2 | 25-45′ | 20-45 | 20-45 | Постоянный, переменный |
3 | 50-80 | 40—80 | 50-80 | ||
УОПИ-13/45 | 2 | 45-65 | 30—40 | 30-45 | Постоянный |
3 | 80-100 | 60-80 | 70-90 | ||
4 | 130-160 | 100-130 | 120-140 | ||
5 | 170-200 | 140-160 | 150-170 | ||
СМ-11 | 4 | 160-220 | 140-180 | 140-180 | Постоятый, переменный |
5 | 200-250 | 160-200 | — |
Табл. 2. Сварка вольфрамовыми электродами стыковых швов
|
Табл. 3. Сварка тонколистовых конструкций (без присадочных материалов с обязательным оплавлением кромок)
|
1 | 2 | 3 | |
Сварка стыковых труб | •ь=І | f=V | Применяется для стыков труб, когда требуется сохранить точный внутренний диаметр трубы и для соединения труб из вязкого металла до 3 мм, позволяющего отбортовыватъ кромки |
Сварка листов встык без отбортовки кромок на подкладке | Применяется в конструкциях, где допускаются ослабленные швы. Листы толщиной до 3 мм собираются встык без зазора на прокладке. После разделки кромок образуется сварное соединение тоньше основного металла | ||
Табл. 4. Сварка трубопроводов |
Вид соединения |
Области применения и технология
1
Стыковое без разделки кромок |
Сварка тонкостенных труб с толщиной стенки до 3 мм, стык собирается с зазором от О до 1,5 мм, заваривается с применением присадочного металла
Стыковое без скоса кромок п с вставным кольцом
Сварка тонкостенных труб с толщиной стенки до 3 мм, обеспечивается полный гарантированный провар всего сечения
Стыковое без скоса кромок с отбор ТОЕНЫМ и вставным кольцом
Сварка тонкостенных труб с гарантированным проваром сечения, когда уменьшение внутреннего диаметра недопустимо
Стыковое с нормальной разделкой кромок |
Сварка стыков труб с толщиной стенок более 3 мм; наиболее распространенный вид соединения
Стыковое с внутренней расточкой для постановки опорного кольца |
Магнитопорошковый дефектоскоп NOVOTEST МПД-DC
Дефектоскоп NOVOTEST МПД-DC на постоянных магнитах предназначен для намагничивания участков сварных соединений и поверхностей изделий из ферромагнитных материалов приложенным магнитным полем при обнаружении поверхностных и подповерхностных дефектов в процессе проведения неразрушающего контроля магнитопорошковым методом. Наличие в конструкции прибора постоянных магнитов и гибкого магнитопровода позволяет проводить оперативный магнитопорошковый контроль объектов сложной формы, в труднодоступных местах и в случае, когда электрическое питание контролирующего оборудования запрещено по нормативным документам или невозможно.
Магнитопорошковый дефектоскоп МПД-DC состоит из двух разнополюсных постоянных магнитов, находящихся в цилиндрических корпусах и соединенных между собой гибким магнитопроводом.Такой магнитопровод позволяет проводить контроль в труднодоступных местах и использовать прибор для контроля угловых сварных соединений. Прибор обеспечивает полюсное намагничивание участков изделий. При контроле полюса такого устройства располагаются поочередно в одной плоскости к поверхности изделия или в двух взаимоперпендикулярных плоскостях, создавая намагничивающее поле в соответствующем направлении. Намагничивающее устройство может эксплуатироваться в цеховых, лабораторных и полевых условиях.
С помощью NOVOTEST МПД-DC осуществляется магнитопорошковый контроль в конструкциях из ферромагнитных материалов с целью выявления поверхностных и подповерхностных нарушений сплошности материала: трещин, флокен, волосовин, непроваров сварных соединений, различных надрывов и многого другого в соответствии с ГОСТ 21105-87. Магнитопорошковый дефектоскоп МПД-DC незаменим в случаях, когда нет возможности эксплуатации электромагнитов, подача электроэнергии затруднена или ограничена по правилам техники безопасности. Например, при осуществлении высотных работ, в полевых условиях, при контроле качества внутренней поверхности котлов и емкостей с температурой окружающей среды от -30 °С до +50 °С и относительной влажностью до 95% при 35°С.
Отличительные особенности магнитопорошкового дефектоскопа МПД-DC:
- возможность проводить оперативный контроль изделий сложной формы и в труднодоступных местах;
- простота применения;
- не требуется подача электричества;
- гибкий магнитопровод;
- возможность изготовления устройств с нестандартной длинной магнитопровода;
- небольшой размер и вес изделия.
Технические характеристики дефектоскопа МПД-DC приведены в таблице:
Параметр | Характеристика* |
Напряженность магнитного поля в центре воздушного зазора между полюсами | 200 кА/м |
Напряжённость магнитного поля, в воздухе в средней области между рабочими торцами магнита, не менее | 65 кА/м |
Магнитная индукция на поверхности магнитов | — 450 мТл – максимальная — 150 мТл – минимальная |
Стандартное межполюсное расстояние | 350 мм |
Условия эксплуатации: — температура — относительная влажность |
от -30 °С до +50 °С до 95 % при температуре 35 °С |
Габаритные размеры, не более | Ø31 х 600 |
Вес, не более | 0,6 кг |
Комплект поставки:
- Намагничивающее устройство
- Паспорт
Дополнительные опции для заказа:
- Магнитопровод нестандартной длины
- Свидетельство о калибровке
- Суспензии и грунт для магнитопорошкового контроля
- Контрольный образец для МПД
Магнитопорошковый дефектоскоп NOVOTEST МПД-DC в наличии на складе. Прибор можно купить с доставкой до двери или до терминалов транспортной компании в следующих городах: Москва, Санкт-Петербург, Екатеринбург, Саратов. Амурск, Ангарск, Архангельск, Астрахань, Барнаул, Белгород, Бийск, Брянск, Воронеж, Великий Новгород, Владивосток, Владикавказ, Владимир, Волгоград, Волгодонск, Вологда, Иваново, Ижевск, Йошкар-Ола, Казань, Калининград, Калуга, Кемерово, Киров, Кострома, Краснодар, Красноярск, Курск, Липецк, Магадан, Магнитогорск, Мурманск, Муром, Набережные Челны, Нальчик, Новокузнецк, Нарьян-Мар, Новороссийск, Новосибирск, Нефтекамск, Нефтеюганск, Новочеркасск, Нижнекамск, Норильск, Нижний Новгород, Обнинск, Омск, Орёл, Оренбург, Оха, Пенза, Пермь, Петрозаводск, Петропавловск-Камчатский, Псков, Ржев, Ростов, Рязань, Самара, Саранск, Смоленск, Сочи, Сыктывкар, Таганрог, Тамбов, Тверь, Тобольск, Тольятти, Томск, Тула, Тюмень, Ульяновск, Уфа, Ханты-Мансийск, Чебоксары, Челябинск, Череповец, Элиста, Ярославль и другие города. А так же Республики Казахстан, Белоруссия и другие страны СНГ.