Дефекты. Виды дефектов изделий, причины возникновения, обнаружение и исправление :: SYL.ru
Обнаружение дефекта какой-либо продукции в наше время – явление весьма распространенное. И если приобретение некачественных галантерейных товаров может обернуться лишь тратой денег, то нарушение технологии изготовления машин и оборудования повлечет куда более серьезные и негативные последствия, вплоть до гибели людей. В данной статье дается общая классификация дефектов, описываются причины их возникновения, а также способы устранения (когда это возможно). Особое внимание уделяется нарушениям внутреннего строения металлов и некачественным сварным соединениям, как дефектам, представляющим наибольшую опасность для общества. Нередко причинами масштабных катастроф становятся дефекты сварных швов.
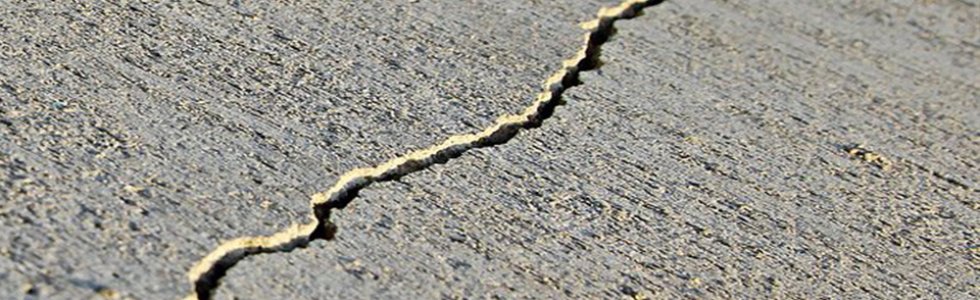
Основные положения
Определений и понятий дефекта существует очень много. В общем случае, дефект – это любое несоответствие конкретного изделия конструкторской документации, отраслевым стандартам и нормам, а также ГОСТу. Они могут быть скрытыми (невозможно обнаружить невооруженным глазом) и явными. Последние еще называются поверхностными дефектами.
Виды дефектов также можно классифицировать по степени влияния на способность изделия выполнять возложенные на него функции: незначительные, значительные, а также критические. Единого рецепта отнесения того или иного дефекта к конкретному классу нет. Это, можно сказать, коллективная экспертиза группы специалистов. Нужно учитывать эпюру нагрузок изделия, наличие (отсутствие) концентраторов напряжений, место возникновения дефекта.
Виды дефектов могут быть совершенно идентичными, а вот влияние на работоспособность заданного конкретного изделия может разниться, причем весьма значительно. Так, скажем, развитие отпускной хрупкости второго рода в стали, из которой изготовлена кочерга, никак не повлияет на ее эксплуатационные характеристики и срок службы. А вот если подобный дефект возникнет в материале высоконагруженного скоростного вала, то он просто разлетится на мелкие осколки, когда накопится значительная усталость от высокочастотных знакопеременных динамических нагрузок.
Профилактика и предупреждение дефектов
Чтобы минимизировать вероятность возникновения дефектов, необходимо очень внимательно и ответственно подходить к этапу подготовки производства, а также соблюдать все требования технологической и конструкторской документации:
- перед тем как приступить к свариванию поверхностей, нужно убедиться в том, что последние имеют правильную геометрию;
- сам процесс должен проходить с соблюдением всех норм режимов обработки; отсутствие должной квалификации у исполнителя является причиной брака в большинстве случаев; решением может стать применение специальных сварочных автоматов и роботов, которые позволяют получать качественный и равномерный шов по всех длине;
- каждый сварной шов после окончания работ в обязательном порядке должен проверяться специалистами отдела ОТК на предмет наличия скрытых и явных дефектов; данная мера позволяет вовремя выявлять и предпринимать меры по устранению брака.
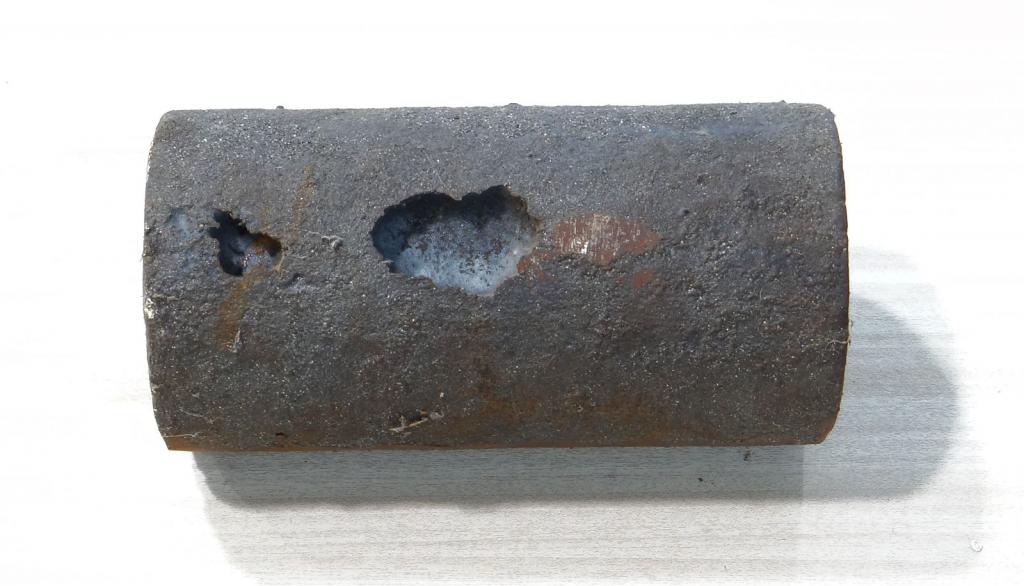
Незначительные дефекты
Данный вид дефекта не может повлиять на эксплуатационные характеристики изделия и стать причиной выхода узла или механизма из строя. Также его наличие нисколько не влияет на обеспечение безопасной эксплуатации машины. К таким видам дефектов можно отнести какие-либо внешние нарушения: пятна, неправильная форма, наличие пустот на поверхности кованой заготовки, которые впоследствии снимутся при обработке резанием и т. д.
Значительные дефекты
К значительным относятся дефекты, наличие которых оказывает существенное влияние на эксплуатацию изделия и срок его полезного действия, но которые не относятся к критическим. Иными словами, при наличии такого вида дефекта, характеристики изделия несколько ухудшаются, но оно все еще может использоваться непосредственно по назначению. Примером такого несоответствия конструкторской документации может служить наличие незначительных пор на поверхности стальных изделий.
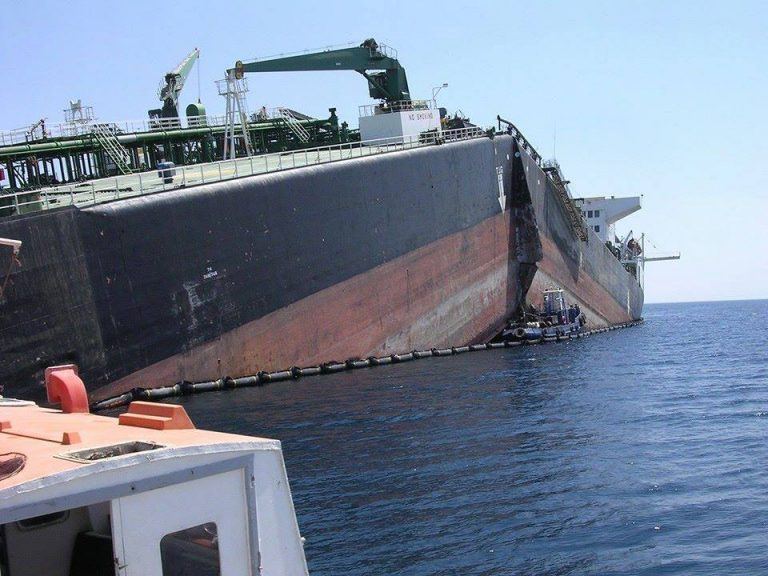
Критические виды дефектов
Дефект, возникновение которого делает невозможным использование конкретного изделия по назначению (из соображений безопасности и ввиду отсутствия физической возможности), называется критическим. Примеры таких дефектов не нужно долго выдумывать. Классическим критическим дефектом является пережег стали (дефект металла, при котором границы зерен в результате значительного превышения допустимой температуры термической обработки окисляются, и материал становится хрупким). Производство комплектующих и изделий из такой стали категорически запрещено. Данный вид дефектов относится к категории неисправимого брака. Существует единственный выход – переплавка стали и получение после отжига равновесной структуры металла с исходными механическими и физическими свойствами.
К критическим относятся также дефекты сварных швов нагруженных элементов. Сварочное дело – это вообще очень серьезное и ответственное занятие, строго регламентируемое множеством законов и подзаконных актов. Контроль качества выполнения сварных соединений осуществляется высококвалифицированными специалистами с применением сложного и очень дорогостоящего узкоспециализированного оборудования по обнаружению скрытых дефектов. Вид дефекта, а также его значимость должны определяться с ювелирной точностью.
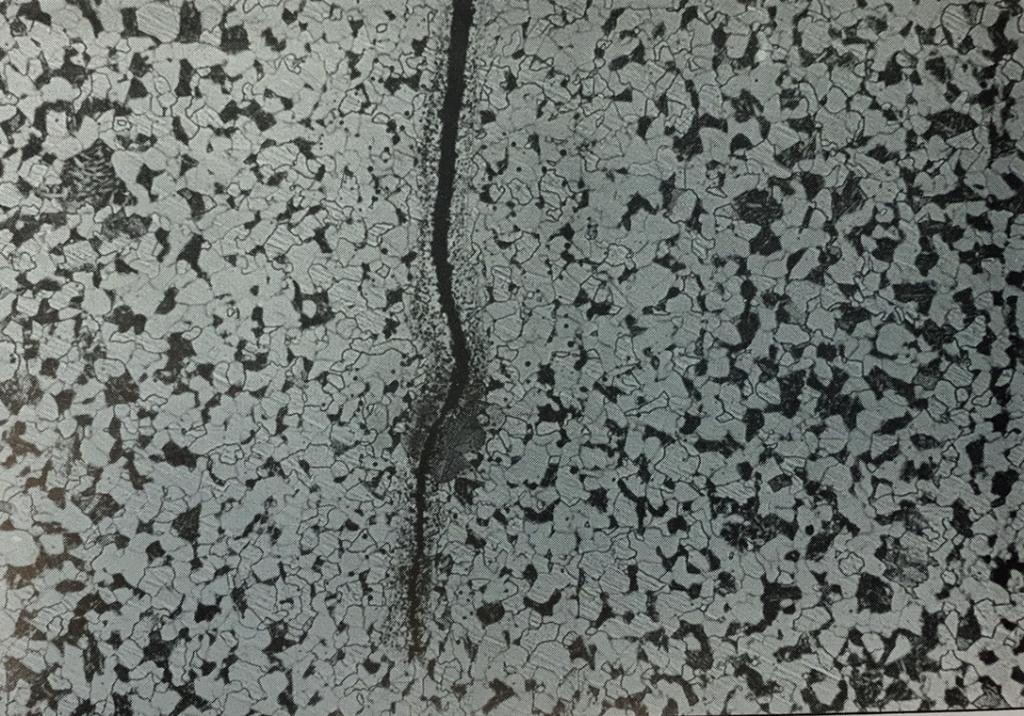
Методы обнаружения дефектов
Наличие дефектов свидетельствует о серьезных нарушениях технологического процесса. И чем раньше они обнаружены, тем быстрее будут приняты меры к их устранению. Это напрямую влияет на экономические показатели работы промышленного предприятия, а в некоторых случаях может предотвратить катастрофу и гибель людей.
Основные способы выявления дефектов следующие: визуальные (увеличение до 30 крат, возможно применение лупы), проверка механических свойств (ударная вязкость, сопротивление растяжению, хладноломкость, красноломкость и другие), контроль с использованием микроанализа (с применением оптического и электронного металлографических микроскопов), контроль с использованием рентгеновского излучения, контроль ультразвуком, проведение испытаний на коррозионную стойкость (как правило, используется специальное оборудование – ванны соляного тумана).
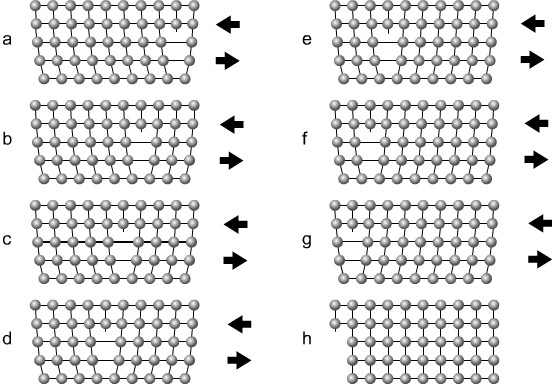
Внутренние дефекты в зоне сварного шва
Дефекты сварных швов в большинстве случаев являются скрытыми, и их можно увидеть лишь при помощи специальной аппаратуры. Поэтому такой вид брака особенно опасен. Процесс сваривания изделий является очень сложным. В некоторых случаях зона сваривания предварительно подогревается до определенной температуры, чтобы обеспечить максимальное качество сварного шва.
В сварном шве могут возникать следующие виды внутренних дефектов: поры, окислы металлов и неметаллические включения, непровар шва, растрескивание, перегрев, пережог.
Поры – это полости, в которых под большим давлением скапливаются газы (водород, углекислый газ и другие). Такие дефекты могут спровоцировать хрупкий излом в зоне сварного шва. Причина возникновения дефектов такого типа – некачественные и отсыревшие сварочные электроды, наличие на свариваемой поверхности окислов металла.
Если возникает такой дефект, как внутренний непровар, то всю вину можно возлагать на сварщика. Скорее всего, работы проводил малоопытный рабочий, который только недавно получил профессию. Непровар представляет собой отсутствие сварного шва на определенном (как правило, небольшом) участке. Помимо низкой квалификации персонала, данный дефект может возникнуть при маленьком зазоре между свариваемыми поверхностями, ускоренной рабочей подаче, наличие в зоне плавки электрода окислов и других посторонних неметаллических включений. В случае электродуговой сварки вызвать непровар могут неправильно подобранные режимы (прежде всего – сила тока).
Трещины могут возникать как в продольном, так и в поперечном сечении. Данный дефект является особенно опасным, так как распространение трещин не ограничивается лишь зоной наплавки, но зачастую затрагивает и свариваемые изделия.
Перегрев возникает вследствие протекания вторичной рекристаллизации металла (ускоренного роста зерен за счет поглощения соседних зерен). Такая структура приводит к тому, что зона сварного шва охрупчивается. Внешне такой дефект не дает о себе знать. Чтобы получить возможность сравнить балл металла с эталонной шкалой, нужно вырезать контрольный образец, отшлифовать, отполировать, а затем протравить гладкую поверхность специальным реактивом (4-6 % раствор азотной кислоты на спирту) с целью выявить границы зерен. И только после этого комплекса мероприятий в объективе металлографического микроскопа будет просматриваться структура стали. Если разрушение конструкции недопустимо, то можно отполировать и протравить участок сварного шва, а затем прикрепить к конструкции специальный мобильный микроскоп.
Устранение дефектов внутренних
Классификация дефектов может производиться также по принципу возможности устранения негативных последствий дефекта и восстановления работоспособности механизма. Сварные дефекты, в большинстве своем, являются неисправимыми. И это накладывает на исполнителей работ и инженеров, разрабатывающих технологический процесс, большую ответственность.
Но некоторые виды несоответствий технологическому процессу все же можно при желании устранить. В частности, исправление дефектов возможно осуществить при возникновении так называемого перегрева. Для этого вся конструкция помещается в печь, выдерживается в ней некоторое время при заданной температуре (выше линии ПСК на диаграмме железо-углерод), а затем остывает вместе с печью. Понятно, что далеко не все конструкции могут поместиться в небольшое печное пространство. Таким образом, восстановление нормальных размеров зерна не всегда возможно ввиду отсутствия необходимой материально-технической базы.
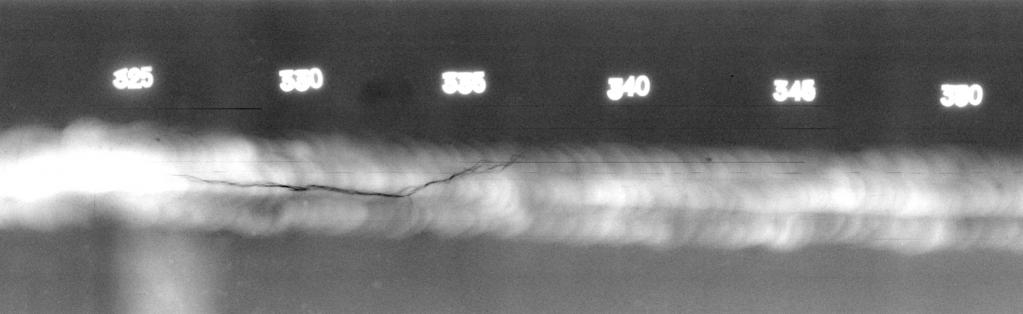
Внешние дефекты в зоне сварных швов и способы их устранения
Такие дефекты обнаруживаются при визуальном осмотре сварного шва. К основным видам дефектов такого рода можно отнести отклонение от заданных геометрических размеров, возникновение так называемых наплывов и подрезов, непровары и прожоги.
Нарушение геометрических размеров сварного шва возникает, как правило, по вине неопытного сварщика. Помимо чисто внешней стороны, наличие такого дефекта негативно сказывается и на механических свойствах всех сварной конструкции. Устранить подобный дефект практически невозможно. Да и работы будут стоить очень дорого. Поэтому не рекомендуется поручать сварку ответственных изделий новичкам в профессии.
Наплывы – также являются «болезнью» многих неопытных сварщиков. Возникают в результате чрезмерного оплавления металла электродов при замедленной рабочей подаче. Подобные дефекты относятся к категории незначительных и оказывают влияние лишь на внешний вид сварного шва. Устраняется механической обработкой резанием шва (фрезерование, шлифование, строгание, долбление и т. д.).
В отличие от наплывов, так называемые подрезы характеризуются недостаточным оплавлением материала. Дефект заключается в образовании незаполненных участков на стыке свариваемых изделий. Подрез, в зависимости от конкретных технических условий, можно отнести как к исправимому, так и к неисправимому дефекту. Так, если подобный брак был допущен при сваривании очень ответственных поверхностей (реакторы атомных станций, корпус подводной лодки и т. д.), то он не подлежит исправлению. Любое вмешательство в данном случае с целью исправить сварной шов – грубейшее нарушение, которое может повлечь очень серьезные последствия. А вот если будущая конструкция не является составной частью очень ответственного узла или механизма, то допускается исправление подреза повторным сварным швом.
Внешний непровар, как и внутренний, характеризуется отсутствием сплавления между материалом электрода и свариваемыми поверхностями. Устранение подобного дефекта является экономически нецелесообразным, так как требует удаления материала расплавленного электрода из зазора между свариваемыми поверхностями.
Трещины на поверхности сварного шва относятся к категории дефектов поверхности. Могут образовываться вдоль сварного шва по линии контакта свариваемых изделий, так и в поперечном сечении. Чаще всего такие дефекты возникают как результат неравномерного прогрева участков свариваемых изделий в зоне оплавления металла. Поэтому при проведении работ с ответственными изделиями осуществляется предварительный термический нагрев изделий в зоне сварного оплавления.
Прожог возникает в результате значительного локального перегрева металла и образования сквозного отверстия, через которое вытекает жидкий расплав. Устранить подобный дефект можно лишь латкой, приваренной непосредственно над таким отверстием. Но, по понятным причинам, такое решение подойдет далеко не для каждого случая.
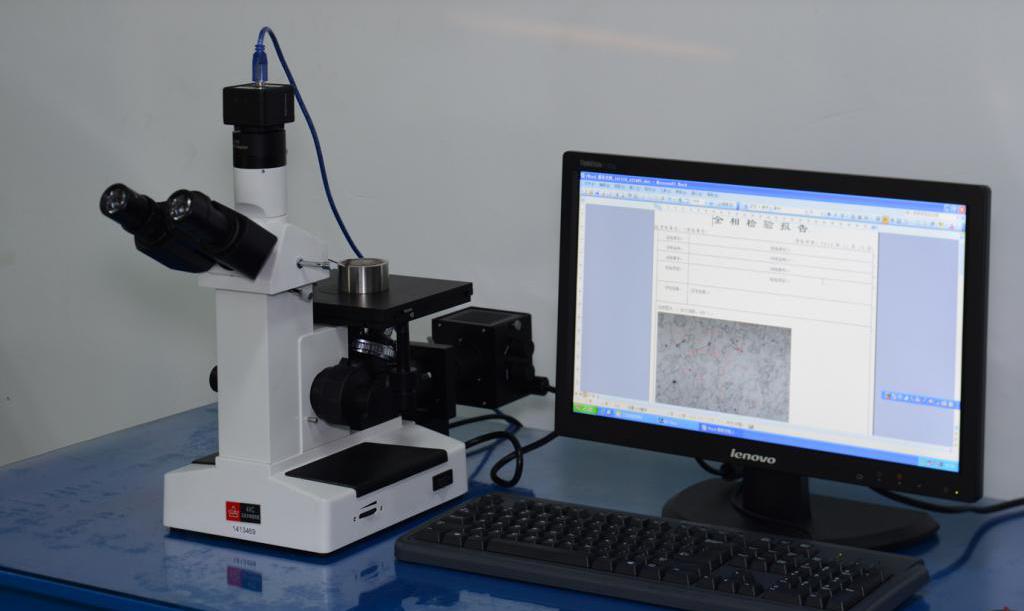
Основные методы профилактики появления дефектов
После проведения операций по исправлению дефектов необходимо еще более тщательно проводить контроль качества сварного шва. Ведь зачастую попытки устранить брак лишь усугубляют ситуацию. Если дефекты будут выявлены повторно, то рекомендуется больше не отправлять такие изделия на доработку, а списывать их как производственный брак. Дело в том, что многократный нагрев и охлаждение металлов могут привести к нежелательным структурным изменениям в стали, а также возникновению множества дефектов кристаллического строения металла.
Ни технологии, ни хорошая заработная плата инженерного и рабочего персонала не может полностью гарантировать отсутствие брака. Хороший и опытный сварщик способен даже на старом и далеко не самом лучшем оборудовании выдавать поразительный результат. Поэтому главным направлением в деле профилактики брака сварочных работ является постоянное повышение квалификации и мотивации рабочего персонала. Необходимо всеми возможными способами повышать культуру производства, увеличивать коллективную ответственность бригады рабочих, устанавливать хорошие отношения в коллективе.
Виды дефектов и их характеристика
Дефект — это отдельное несоответствие продукции установленным требованиям.
Повреждение — событие, заключающееся в нарушении исправного состояния объекта при сохранении работоспособного состояния.
По своим последствиям дефекты подразделяют на:
- критические
- значительные
- малозначительные
По месту расположения дефекты делят на:
- наружные
- внутренние
По возможности устранения выделяют:
- исправимые
- неисправимые
По отражению в нормативной документации выделяют:
- явные
- скрытые
Критический дефект такой, при наличии которого использование детали невозможно. Значительный дефект существенно влияет на использование детали и (или) на ее долговечность, а малозначительный — не оказывает такого влияния. Наружные дефекты выявляются осмотром или путем измерений. Внутренние дефекты выявляются способами структуроскопии или проникающими способами. Устранение исправимого дефекта технически возможно и экономически целесообразно, а неисправимого — невозможно или нецелесообразно. Если для выявления дефекта в технической документации предусмотрены соответствующие правила и средства, то дефект считается явным, в противном случае дефект признают скрытым.
В зависимости от того, какая стадия жизненного цикла автомобиля повлияла на возникновение дефектов, они бывают:
- конструктивные
- производственные
- эксплуатационные
Конструктивные дефекты возникают в результате ошибок и просчетов конструирования, производственные — в результате нарушения технологического процесса изготовления или восстановления деталей, а эксплуатационные — в результате использования автомобиля.
Состояние деталей определяется значениями параметров, в качестве которых применяют размеры (линейные и угловые) элементов детали, их форму и взаимное расположение, наличие трещин, размеры трещин и пробоин, расход пробного вещества (воды, воздуха) сквозь течи, механические характеристики. Эти значения могут быть допустимыми и предельными. Детали с допустимыми значениями параметров используют в дальнейшем без восстановительных работ, а с предельными — выбраковывают. Если значения параметров находятся в отрезке значений между допустимым и предельным, то деталь подлежит восстановлению. У деталей измеряют те параметры, которые изменяются при их использовании.
Техническое состояние деталей в основном определяется эксплуатационными дефектами в виде износов, усталостных изменений, деформаций, изломов, трещин, пробоин, коррозии и старения материала.
Дефекты. Виды дефектов изделий. Виды сварных дефектов. Виды дефектов товаров и ткани
Дефект, он же производственный брак, может быть практически у всех изделий. Если говорить вкратце, то это продукция, которая не допускается к потребителю из-за несоответствия выдвигаемым требованиям. К примеру, негерметичная упаковка, недостаточная прочность сварного шва и так далее. Давайте же более подробно поговорим о том, что такое дефекты, а также рассмотрим виды дефектов различных материалов.
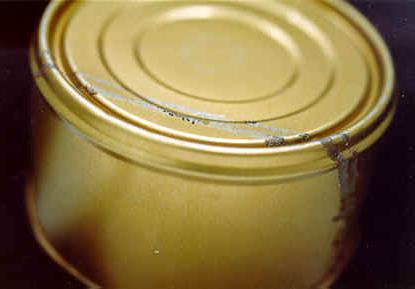
Общие сведения
Любая промышленность в той или иной степени выпускает бракованные изделия, то есть дефективные. Как правило, брак определяется уже после отправки на склад или к потребителю. В этом случае производитель может как отозвать свою продукцию, так и оставить ее. К примеру, дефект упаковок для бытовых губок нельзя считать критическим, а вот брак в тормозной системе автомобиля может привести к гибели водителя. Поэтому нужно понимать, что дефекты бывают разные: одни допустимы, другие – нет. Можно говорить о том, что любая продукция, которая имеет хотя бы одно отклонение от установленных норм, считается дефективной, остальная же относится к категории годной. И тут совершенно не важно, о какой отрасли промышленности идет речь. Как вы уже поняли, любое производство имеет свои дефекты. Виды дефектов разделяются на исправимые и неисправимые. Продукцию, относящуюся к первой группе, можно сделать годной (если это экономически целесообразно), ко второй – нельзя.
Виды дефектов в строительстве
Иногда по новостям мы слышим информацию, что где-то рухнул дом, обвалилась кирпичная кладка и т. п. Нередко всему виной становится какой-либо дефект, который не был выявлен во время контрольной проверки. Так, в строительной отрасли любое несовпадение с техническим заданием (ТЗ) или установленными правилами называется конструктивным дефектом. Если же речь идет о несоответствии технической документации на изготовление продукции, это называется производственным дефектом. Но это еще далеко не весь список. Дело в том, что в строительстве встречаются и другие дефекты. Виды дефектов тут классифицируются следующим образом:
- явный дефект определяется при внешнем осмотре, то есть визуально;
- скрытый дефект не предусматривает нормы контроля. Он обычно выявляется после отправки товара потребителю.
Можно говорить о том, что явный дефект менее опасен для потребителя, так как его значительно проще обнаружить и устранить. Однако далеко не всегда явные дефекты устраняются производителем. Часто можно купить продукцию, которая визуально не соответствует норме, к примеру, имеющую сколы на своей поверхности, негерметичную упаковку и т. п.
Критический, значительный и малозначительный дефект
Все эти виды брака условно можно поместить в одну группу, так как они взаимосвязаны. Дело в том, что такие несоответствия, так или иначе, влияют на эффективность использования продукции, но в разной мере. Например, критический брак говорит о том, что эффективность товара, в зависимости от сферы применения, будет гораздо ниже. Обычно использование продукции по назначению в данном случае невозможно или запрещено. В качестве примера можно привести сломанный кухонный нож, негерметичный компрессор для подачи сжатого воздуха и т. п.
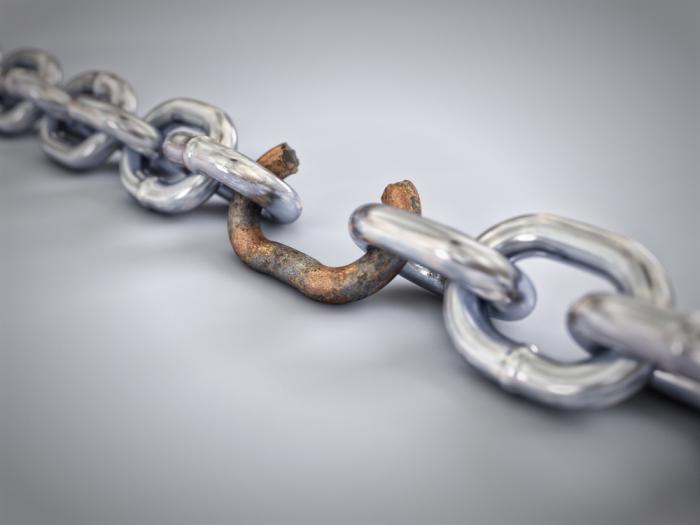
Значительный дефект – это тот, который не является критическим, но оказывает существенное воздействие на долговечность и эффективность использования продукции по назначению. К примеру, микротрещина в металлическом листе считается значительным дефектом. Такого рода бракованная продукция может использоваться, но уже не так долго и не под такой большой нагрузкой. Малозначительный дефект – тот, который практически не влияет на долговечность и эффективность использования продукции. К примеру, потертая краска на радиаторе отопления считается незначительным дефектом.
Виды сварных дефектов
Сложно недооценить важность сварных соединений. Согласитесь, они определяют качество изделия в целом. К примеру, хорошо сваренный корпус твердотопливного котла смотрится куда лучше, нежели тот, на котором выявлены дефекты. Виды дефектов сварочных работ делятся на внутренние и наружные браки. Первый определяется визуально, а второй можно обнаружить лишь при проведении дефектоскопии.
Кроме того, в данном случае можно говорить о допустимых и недопустимых дефектах. Группа товаров с допустимым браком может использоваться с эффективностью менее 100%, вторая группа к потребителю не допускается. Однако сам по себе дефект – это уже что-то ненормальное, требующее устранения. Сегодня дефекты сварных швов устраняют, используя современные технологии сварки и допуская к работе только квалифицированных мастеров. Помимо этого, добавляют специальные присадочные материалы, используют сварочное оборудование и многое другое. Давайте более подробно рассмотрим виды дефектов изделия (сварного) и то, как они влияют на эффективность использования продукции и безопасность для потребителя.
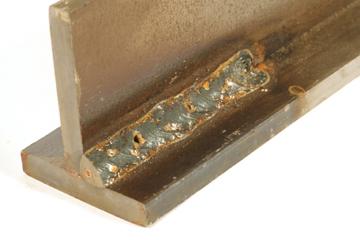
Наружный брак
Любое нарушение геометрии конструкции называется наружным дефектом. К таким стоит отнести наплыв, непровар, подрез и др. Практически все это определяется на глаз. К примеру, основной причиной непровара служит малое проникновение в металл дуги. Это бывает из-за недостаточного тока. Исправляется такой дефект крайне просто: стараются увеличить динамику и уменьшить длину сварочной дуги. Кроме того, данный брак нередко встречается из-за слишком быстрого выполнения работ, поэтому иногда имеет смысл делать сварной шов более размеренно.
Еще один типичный и часто встречаемый дефект – подрез. Это брак, который представляет собой канавку (углубление) в основном металле около сварного соединения. Обычно образуется из-за неправильно выбранного тока и скорости сварки. В принципе, тут многое зависит от человеческого фактора.
Прожог тоже встречается довольно часто. Данный дефект представляет собой сквозное отверстие в сварном шве. Случается брак из-за слишком медленной сварки и большого тока. В итоге происходит утечка сварочной ванны.
Наплыв возникает в результате появления окалины на поверхности при неправильно выбранном режиме сварки. Такой брак представляет собой натекание присадки на основной металл без сплавления.
Внутренние дефекты
Такого рода брак выявляется несколько реже, так как обнаружить его невооруженным глазом сможет далеко не каждый. Именно поэтому нередко возникает поломка сварной конструкции, что может быть очень опасно для человека. Один из самых распространенных и опасных дефектов – горячие трещины. Они могут быть как продольными, так и поперечными. Возникают в промежуточный период плавления и затвердевания металла, а также из-за ошибки при выборе присадочного материала и его химического состава. Ответственность за такой дефект полностью ложится на плечи сварщика. Существуют еще и холодные трещины. Они возникают уже после затвердевания металла и остывания шва. Обычно появляются из-за превышения нагрузок на шов.
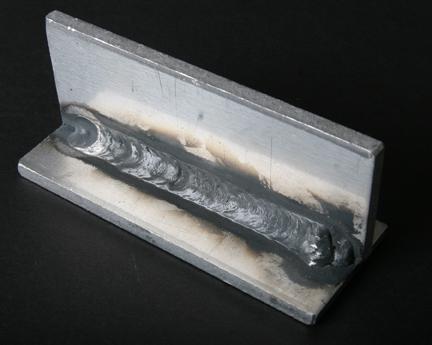
Поры – дефект, появляющийся при всех видах сварочный работ. Можно с уверенностью говорить о том, что с такими проблемами сталкивался каждый сварщик. Если перечислять все основные виды дефектов сварных соединений, то данный будет на первом месте. Возникает он из-за недостаточной защиты ванны сварочным газом. В результате образуются поры, которые отличаются между собой размерами и хаотичностью распределения.
О пороках ткани
В процессе изготовления какой-либо продукции возникает брак. Ткачество не исключение. Существуют самые различные виды дефектов ткани, которые мы сейчас постараемся рассмотреть. Самый распространенный брак – близка. Он подразумевает под собой отсутствие одной или нескольких нитей на определенном протяжении. Зачастую данный дефект появляется из-за обрыва нити в процессе выполнения работ. Это бывает по причине неисправного ламельного устройства или в результате ошибки оператора, который остановил станок позже, чем нужно. Интересно то, что такого рода дефект не учитывается, если он находится на закрытых частях изделия. При этом в продажу не допускается продукция с близками 10-20 см в две нити.
Нередко встречается и подплетина. Такой порок представляет собой обрыв одной или двух нитей и заделку их в ткань. В результате изделие в месте заделки приобретает неправильную форму. Такой дефект недопустим в изделиях 1-го и 2-го сорта. Дефект под названием «неподработка нитей» влияет на качество изделия так же, как и подплетина. Заключается порок в том, что основные нити не переплетаются с нитями утка, в результате чего оказываются на поверхности ткани, изменяя ее форму. Брак, связанный исключительно с неправильной работой ткацкого агрегата, называется недосек. Заключается он в наличии по утку разрешенных полос.
Другие дефекты тканей
Существуют и иные виды дефектов товаров, изготовленных из ткани. Но прежде стоит отметить, что порок бывает местный (локальный) и распространенный. Первый обычно небольшой и находится лишь на определенном участке изделия. К таким дефектам можно отнести близны, подплетины. А вот пороки, распространяющиеся по всей длине куска ткани, называются распространенными. К таким обычно относят засоренность, полосатость и др. Еще один интересный момент заключается в том, что все эти пороки могут возникать на разных этапах производства. Так, дефект может появиться еще при прядении из-за недостаточного качества исходного сырья или же уже при отделке. Все это говорит о том, что требуется тщательный контроль на всех этапах. Помимо этого, необходимо закупать только качественное сырье. Это же касается и ткацкого оборудования и, собственно, квалификации сотрудников.
К примеру, наличие загрязнений и маслянистых пятен зависит от обильности смазки станка. А так как современное оборудование смазывается автоматически, то винить оператора смысла нет. Это же касается и дыр, просечек, а также пробоин на изделии, которые появляются вследствие некорректной работы станка. Такие товары не проходят контроль качества и сразу же бракуются. Стоит обратить ваше внимание на то, что в ткацком деле есть устраняемые дефекты. Местные пороки в любом случае снижают сортность, однако при раскрое ткани их можно обходить, осуществляя поставку продукции высшего сорта.
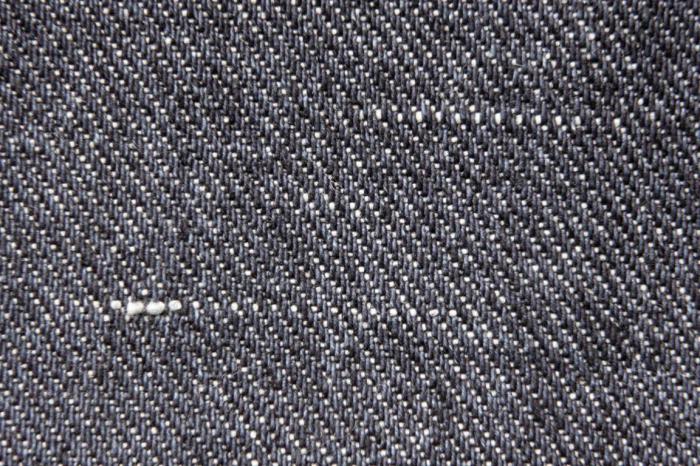
Дефекты металла и металлических изделий
На сегодняшний день не существует бездефектных металлических образцов. Это говорит о том, что в той или иной степени брак присутствует. Но интересно то, что в результате протекания некоторых процессов и выполнения механических операций, качество металла может значительно понизиться, вследствие чего наступит полная непригодность изделия к дальнейшей эксплуатации.
Наиболее часто встречаются дефекты, возникающие при деформации металла, находящегося в твердом состоянии. Чем меньше деформация, тем меньшее количество дефектов появится. Некоторые марки стали обладают хорошей упругостью, это позволяет после небольшого деформирования принимать свою прежнюю форму. Однако если постоянно повышать нагрузку, то наступит переломный момент, когда восстановить металл будет невозможно. В любом случае имеет смысл говорить о том, что тут, как и в ткачестве, некоторые виды дефектов металла возникают еще при отливке, а другие уже при конечной обработке изделия.
К примеру, литейные дефекты встречаются очень часто. В металлургической промышленности с ними стараются постоянно бороться, разрабатывая все новые способы отливки. Неравномерность остывания и затвердевания жидкого металла приводит к тому, что образуются поры и сдвиги внутренних слоев. Также существуют различные виды дефектов деталей, проходящих вторичную механическую и термическую обработку. Имеет место и брак, возникающий при перевозке или хранении металлического изделия.
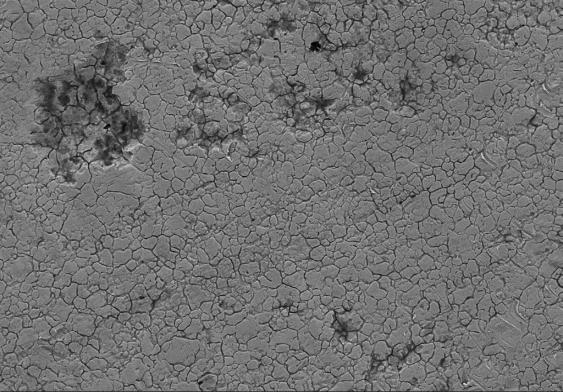
Заключение
Как вы видите, есть самые различные дефекты. Виды дефектов металлов, сварных соединений и тканей мы с вами рассмотрели. Но вы должны понимать, что брак присутствует как в пищевой, так и в химической промышленности. Тут даже нельзя говорить о человеческом факторе, так как машины тоже иногда дают сбой, что приводит к аналогичному результату. Тем не менее некоторые виды дефектов продукции можно исключить частичной или полной автоматизацией технологического процесса, что в настоящее время и производится.
Что же касается покупателя как конечного потребителя, то не стоит покупать бракованные изделия. Нередко их предлагают со скидкой и другими заманчивыми предложениями. Это имеет смысл только тогда, когда назначение изделия не носит ответственного характера, в остальных же случаях любые дефекты могут привести к самым неожиданным и даже печальным последствиям. Поэтому прежде чем что-то приобретать, убедитесь в качестве товара, а также в его исправности. Ведь даже незначительная погрешность в процессе производства может стоить вам здоровья, а нередко и жизни.
Дефекты. Виды дефектов изделий, причины возникновения, обнаружение и исправление
Обнаружение дефекта какой-либо продукции в наше время – явление весьма распространенное. И если приобретение некачественных галантерейных товаров может обернуться лишь тратой денег, то нарушение технологии изготовления машин и оборудования повлечет куда более серьезные и негативные последствия, вплоть до гибели людей. В данной статье дается общая классификация дефектов, описываются причины их возникновения, а также способы устранения (когда это возможно). Особое внимание уделяется нарушениям внутреннего строения металлов и некачественным сварным соединениям, как дефектам, представляющим наибольшую опасность для общества. Нередко причинами масштабных катастроф становятся дефекты сварных швов.

Основные положения
Определений и понятий дефекта существует очень много. В общем случае, дефект – это любое несоответствие конкретного изделия конструкторской документации, отраслевым стандартам и нормам, а также ГОСТу. Они могут быть скрытыми (невозможно обнаружить невооруженным глазом) и явными. Последние еще называются поверхностными дефектами.
Виды дефектов также можно классифицировать по степени влияния на способность изделия выполнять возложенные на него функции: незначительные, значительные, а также критические. Единого рецепта отнесения того или иного дефекта к конкретному классу нет. Это, можно сказать, коллективная экспертиза группы специалистов. Нужно учитывать эпюру нагрузок изделия, наличие (отсутствие) концентраторов напряжений, место возникновения дефекта.
Виды дефектов могут быть совершенно идентичными, а вот влияние на работоспособность заданного конкретного изделия может разниться, причем весьма значительно. Так, скажем, развитие отпускной хрупкости второго рода в стали, из которой изготовлена кочерга, никак не повлияет на ее эксплуатационные характеристики и срок службы. А вот если подобный дефект возникнет в материале высоконагруженного скоростного вала, то он просто разлетится на мелкие осколки, когда накопится значительная усталость от высокочастотных знакопеременных динамических нагрузок.
Профилактика и предупреждение дефектов
Чтобы минимизировать вероятность возникновения дефектов, необходимо очень внимательно и ответственно подходить к этапу подготовки производства, а также соблюдать все требования технологической и конструкторской документации:
- перед тем как приступить к свариванию поверхностей, нужно убедиться в том, что последние имеют правильную геометрию;
- сам процесс должен проходить с соблюдением всех норм режимов обработки; отсутствие должной квалификации у исполнителя является причиной брака в большинстве случаев; решением может стать применение специальных сварочных автоматов и роботов, которые позволяют получать качественный и равномерный шов по всех длине;
- каждый сварной шов после окончания работ в обязательном порядке должен проверяться специалистами отдела ОТК на предмет наличия скрытых и явных дефектов; данная мера позволяет вовремя выявлять и предпринимать меры по устранению брака.

Незначительные дефекты
Данный вид дефекта не может повлиять на эксплуатационные характеристики изделия и стать причиной выхода узла или механизма из строя. Также его наличие нисколько не влияет на обеспечение безопасной эксплуатации машины. К таким видам дефектов можно отнести какие-либо внешние нарушения: пятна, неправильная форма, наличие пустот на поверхности кованой заготовки, которые впоследствии снимутся при обработке резанием и т. д.
Значительные дефекты
К значительным относятся дефекты, наличие которых оказывает существенное влияние на эксплуатацию изделия и срок его полезного действия, но которые не относятся к критическим. Иными словами, при наличии такого вида дефекта, характеристики изделия несколько ухудшаются, но оно все еще может использоваться непосредственно по назначению. Примером такого несоответствия конструкторской документации может служить наличие незначительных пор на поверхности стальных изделий.

Критические виды дефектов
Дефект, возникновение которого делает невозможным использование конкретного изделия по назначению (из соображений безопасности и ввиду отсутствия физической возможности), называется критическим. Примеры таких дефектов не нужно долго выдумывать. Классическим критическим дефектом является пережег стали (дефект металла, при котором границы зерен в результате значительного превышения допустимой температуры термической обработки окисляются, и материал становится хрупким). Производство комплектующих и изделий из такой стали категорически запрещено. Данный вид дефектов относится к категории неисправимого брака. Существует единственный выход – переплавка стали и получение после отжига равновесной структуры металла с исходными механическими и физическими свойствами.
К критическим относятся также дефекты сварных швов нагруженных элементов. Сварочное дело – это вообще очень серьезное и ответственное занятие, строго регламентируемое множеством законов и подзаконных актов. Контроль качества выполнения сварных соединений осуществляется высококвалифицированными специалистами с применением сложного и очень дорогостоящего узкоспециализированного оборудования по обнаружению скрытых дефектов. Вид дефекта, а также его значимость должны определяться с ювелирной точностью.

Методы обнаружения дефектов
Наличие дефектов свидетельствует о серьезных нарушениях технологического процесса. И чем раньше они обнаружены, тем быстрее будут приняты меры к их устранению. Это напрямую влияет на экономические показатели работы промышленного предприятия, а в некоторых случаях может предотвратить катастрофу и гибель людей.
Основные способы выявления дефектов следующие: визуальные (увеличение до 30 крат, возможно применение лупы), проверка механических свойств (ударная вязкость, сопротивление растяжению, хладноломкость, красноломкость и другие), контроль с использованием микроанализа (с применением оптического и электронного металлографических микроскопов), контроль с использованием рентгеновского излучения, контроль ультразвуком, проведение испытаний на коррозионную стойкость (как правило, используется специальное оборудование – ванны соляного тумана).

Внутренние дефекты в зоне сварного шва
Дефекты сварных швов в большинстве случаев являются скрытыми, и их можно увидеть лишь при помощи специальной аппаратуры. Поэтому такой вид брака особенно опасен. Процесс сваривания изделий является очень сложным. В некоторых случаях зона сваривания предварительно подогревается до определенной температуры, чтобы обеспечить максимальное качество сварного шва.
В сварном шве могут возникать следующие виды внутренних дефектов: поры, окислы металлов и неметаллические включения, непровар шва, растрескивание, перегрев, пережог.
Поры – это полости, в которых под большим давлением скапливаются газы (водород, углекислый газ и другие). Такие дефекты могут спровоцировать хрупкий излом в зоне сварного шва. Причина возникновения дефектов такого типа – некачественные и отсыревшие сварочные электроды, наличие на свариваемой поверхности окислов металла.
Если возникает такой дефект, как внутренний непровар, то всю вину можно возлагать на сварщика. Скорее всего, работы проводил малоопытный рабочий, который только недавно получил профессию. Непровар представляет собой отсутствие сварного шва на определенном (как правило, небольшом) участке. Помимо низкой квалификации персонала, данный дефект может возникнуть при маленьком зазоре между свариваемыми поверхностями, ускоренной рабочей подаче, наличие в зоне плавки электрода окислов и других посторонних неметаллических включений. В случае электродуговой сварки вызвать непровар могут неправильно подобранные режимы (прежде всего – сила тока).
Трещины могут возникать как в продольном, так и в поперечном сечении. Данный дефект является особенно опасным, так как распространение трещин не ограничивается лишь зоной наплавки, но зачастую затрагивает и свариваемые изделия.
Перегрев возникает вследствие протекания вторичной рекристаллизации металла (ускоренного роста зерен за счет поглощения соседних зерен). Такая структура приводит к тому, что зона сварного шва охрупчивается. Внешне такой дефект не дает о себе знать. Чтобы получить возможность сравнить балл металла с эталонной шкалой, нужно вырезать контрольный образец, отшлифовать, отполировать, а затем протравить гладкую поверхность специальным реактивом (4-6 % раствор азотной кислоты на спирту) с целью выявить границы зерен. И только после этого комплекса мероприятий в объективе металлографического микроскопа будет просматриваться структура стали. Если разрушение конструкции недопустимо, то можно отполировать и протравить участок сварного шва, а затем прикрепить к конструкции специальный мобильный микроскоп.
Устранение дефектов внутренних
Классификация дефектов может производиться также по принципу возможности устранения негативных последствий дефекта и восстановления работоспособности механизма. Сварные дефекты, в большинстве своем, являются неисправимыми. И это накладывает на исполнителей работ и инженеров, разрабатывающих технологический процесс, большую ответственность.
Но некоторые виды несоответствий технологическому процессу все же можно при желании устранить. В частности, исправление дефектов возможно осуществить при возникновении так называемого перегрева. Для этого вся конструкция помещается в печь, выдерживается в ней некоторое время при заданной температуре (выше линии ПСК на диаграмме железо-углерод), а затем остывает вместе с печью. Понятно, что далеко не все конструкции могут поместиться в небольшое печное пространство. Таким образом, восстановление нормальных размеров зерна не всегда возможно ввиду отсутствия необходимой материально-технической базы.

Внешние дефекты в зоне сварных швов и способы их устранения
Такие дефекты обнаруживаются при визуальном осмотре сварного шва. К основным видам дефектов такого рода можно отнести отклонение от заданных геометрических размеров, возникновение так называемых наплывов и подрезов, непровары и прожоги.
Нарушение геометрических размеров сварного шва возникает, как правило, по вине неопытного сварщика. Помимо чисто внешней стороны, наличие такого дефекта негативно сказывается и на механических свойствах всех сварной конструкции. Устранить подобный дефект практически невозможно. Да и работы будут стоить очень дорого. Поэтому не рекомендуется поручать сварку ответственных изделий новичкам в профессии.
Наплывы – также являются «болезнью» многих неопытных сварщиков. Возникают в результате чрезмерного оплавления металла электродов при замедленной рабочей подаче. Подобные дефекты относятся к категории незначительных и оказывают влияние лишь на внешний вид сварного шва. Устраняется механической обработкой резанием шва (фрезерование, шлифование, строгание, долбление и т. д.).
В отличие от наплывов, так называемые подрезы характеризуются недостаточным оплавлением материала. Дефект заключается в образовании незаполненных участков на стыке свариваемых изделий. Подрез, в зависимости от конкретных технических условий, можно отнести как к исправимому, так и к неисправимому дефекту. Так, если подобный брак был допущен при сваривании очень ответственных поверхностей (реакторы атомных станций, корпус подводной лодки и т. д.), то он не подлежит исправлению. Любое вмешательство в данном случае с целью исправить сварной шов – грубейшее нарушение, которое может повлечь очень серьезные последствия. А вот если будущая конструкция не является составной частью очень ответственного узла или механизма, то допускается исправление подреза повторным сварным швом.
Внешний непровар, как и внутренний, характеризуется отсутствием сплавления между материалом электрода и свариваемыми поверхностями. Устранение подобного дефекта является экономически нецелесообразным, так как требует удаления материала расплавленного электрода из зазора между свариваемыми поверхностями.
Трещины на поверхности сварного шва относятся к категории дефектов поверхности. Могут образовываться вдоль сварного шва по линии контакта свариваемых изделий, так и в поперечном сечении. Чаще всего такие дефекты возникают как результат неравномерного прогрева участков свариваемых изделий в зоне оплавления металла. Поэтому при проведении работ с ответственными изделиями осуществляется предварительный термический нагрев изделий в зоне сварного оплавления.
Прожог возникает в результате значительного локального перегрева металла и образования сквозного отверстия, через которое вытекает жидкий расплав. Устранить подобный дефект можно лишь латкой, приваренной непосредственно над таким отверстием. Но, по понятным причинам, такое решение подойдет далеко не для каждого случая.

Основные методы профилактики появления дефектов
После проведения операций по исправлению дефектов необходимо еще более тщательно проводить контроль качества сварного шва. Ведь зачастую попытки устранить брак лишь усугубляют ситуацию. Если дефекты будут выявлены повторно, то рекомендуется больше не отправлять такие изделия на доработку, а списывать их как производственный брак. Дело в том, что многократный нагрев и охлаждение металлов могут привести к нежелательным структурным изменениям в стали, а также возникновению множества дефектов кристаллического строения металла.
Ни технологии, ни хорошая заработная плата инженерного и рабочего персонала не может полностью гарантировать отсутствие брака. Хороший и опытный сварщик способен даже на старом и далеко не самом лучшем оборудовании выдавать поразительный результат. Поэтому главным направлением в деле профилактики брака сварочных работ является постоянное повышение квалификации и мотивации рабочего персонала. Необходимо всеми возможными способами повышать культуру производства, увеличивать коллективную ответственность бригады рабочих, устанавливать хорошие отношения в коллективе.
Дефекты изделий — ООО «Судебно-экспертная коллегия»
Дефектом называется каждое отдельное несоответствие продукции установленным требованиям.
К дефектам производственного характера можно отнести конструктивные дефекты, вносимые в изделие на стадии его проектирования, и технологические дефекты
Конструктивные дефекты обусловлены неоптимальным выбором структуры изделия, ошибками в выборе конструктивных форм и размеров деталей, ошибками в выборе материалов деталей и подборе комплектующих элементов, заданием ошибочных требований к качеству изготовления узлов и деталей, неполным или некачественным проведением всех расчетов, необходимых для определения требований к конструктивным единицам изделия с учетом действующих нагрузок и подтверждения надежности изделия.
Технологические дефекты формируются в процессе изготовления деталей, сборки конструктивных единиц, сборки и отладки станка или всей автоматической линии. К технологическим можно отнести дефекты, обусловленные несоответствием используемого сырья требованиям технологической документации, нарушением технологии производства продукции, неквалифицированными действиями персонала. По характеру проявления технологические дефекты можно разделить на механические дефекты, несоответствия геометрической формы и шероховатости, несоответствия свойств материалов, несоответствия электрических, магнитных, пневматических и оптических характеристик.
Дефекты эксплуатационного характера обусловлены нарушением правил эксплуатации изделия, условий хранения и транспортировки, интенсивным использованием изделия, естественным износом. К данным дефектам относятся механические повреждения в виде трещин, сколов, царапин, пластических деформаций и разрыва материала, коррозия, оплавление, окалины и т.д. Дефекты из-за нарушения правил эксплуатации изделия возникают из-за его использования не по функциональному назначению, нарушения процедур предварительной подготовки или работы промышленного оборудования, использования несоответствующих вспомогательных инструментов, оснастки и расходных материалов, интенсивном использовании оборудования при превышении его допустимой календарной производительности, несоблюдения условий внешней среды при функционировании оборудования, воздействия агрессивных сред. Дефекты вследствие естественного износа могут проявляться в виде износа основных деталей в результате трения, коробления ответственных деталей из-за перераспределения внутренних напряжений в процессе эксплуатации, коррозии, старения пластмасс, резины, рабочей жидкости, смазочных масел, электронной аппаратуры и др. Дефекты вследствие естественного износа возникают в результате медленно протекающих процессов, которые приводят к прогрессивному ухудшению технических характеристик изделий производственно-технического назначения, называемому физическим старением.
По уровню значимости дефекты подразделяются на малозначительные, значительные и критические.
Малозначительным дефектом называется дефект, который существенно не влияет на использование продукции по назначению и ее долговечность. В результате малозначительного дефекта изделие теряет некоторую рыночную привлекательность, но сохраняет все исходные технические характеристики.
Значительным дефектом называется дефект, который существенно влияет на использование продукции по назначению и (или) на ее долговечность, но не является критическим.
Критическим дефектом называется дефект, при наличии которого использование продукции по назначению практически невозможно или недопустимо.
По уровню степени выявления дефекты подразделяются на скрытые и явные.
Явным дефектом называется дефект, для выявления которого в нормативной документации, обязательной для данного вида контроля, предусмотрены соответствующие правила, методы и средства.
Скрытым дефектом называется дефект, для выявления которого в нормативной документации, обязательной для данного вида контроля, не предусмотрены соответствующие правила, методы и средства.
Таким образом, критерием для дифференциации дефекта по данной классификации является наличие формализованных нормированных процедур выявления данного дефекта.
По уровню экономической целесообразности дефекты подразделяются на устранимые и неустранимые.
Устранимым дефектом называется дефект, устранение которого технически возможно и экономически целесообразно.
Неустранимым дефектом называется дефект,устранение которого технически невозможно или экономически нецелесообразно.
Следует отметить, что при современном развитии уровня техники существует техническая возможность устранения преимущественного большинства дефектов, поэтому критерием для дифференциации дефекта по данной классификации является отношение приращения стоимости изделия в результате ремонта к стоимости самого ремонта.
Проконсультироваться по вопросам назначения судебной технической (механико-технологической) экспертизы в Судебно-экспертной коллегии Вы можете по адресу: г. Минск, ул. Жуковского, д. 11А, 4-й этажили по телефонам +375 (17) 317 04 71; +375 (17) 317 04 72; +375 (17) 317 04 73; +375 (17) 317 04 74; +375 (17) 317 04 75; +375 (17) 317 04 76; +375 (44) 588 60 11.
© К.И.Дадьков
Дефекты сварных соединений — Википедия
Дефе́кты сварны́х соедине́ний — любые отклонения от заданных нормативными документами параметров соединений при сварке, образовавшиеся вследствие нарушения требований к сварочным материалам, подготовке, сборке и сварке соединяемых элементов, термической и механической обработке сварных соединений и конструкции в целом.
По данным американского общества инженеров-механиков (ASME) причины дефектов сварки распределены следующим образом: 45 % — ошибки выбора технологии сварки, 32 % — ошибки сварщика, 12 % — сбои в работе сварочного оборудования, 10 % — неподходящие сварочные материалы, 1 % — прочее
Классификация дефектов изложена в ГОСТ 30242-97 «Дефекты соединений при сварке металлов плавлением. Классификация, обозначение и определения»[2], а также в ГОСТ Р ИСО 6520-1-2012 «Классификация дефектов геометрии и сплошности в металлических материалах. Часть 1. Сварка плавлением»[3], которые соответствуют стандарту ISO 6520[4].
Дефекты соединений при сварке разделяются на шесть групп:
- Трещины — несплошности, вызванная местным разрывом шва, который может возникнуть в результате охлаждения или действия нагрузок.
- Полости и поры — несплошность произвольной формы, образованная газами, задержанными в расплавленном металле, которая не имеет углов.
- Твёрдые включения — твёрдые инородные вещества металлического или неметаллического происхождения в металле сварного шва.
- Несплавления и непровары — отсутствие соединения между металлом сварного шва и основным металлом или между отдельными валиками сварного шва.
- Нарушение формы шва — отклонение формы наружных поверхностей сварного шва или геометрии соединения от установленного значения.
- Прочие дефекты — все дефекты, которые не могут быть включены в перечисленные выше группы.
Трещины[править | править код]
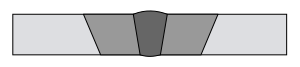
Основной металл — светло серый
Зона термического влияния — серый
Металл сварного шва — тёмно серый
Трещины возникающие в соединениях при сварке могут располагаться в металле сварного шва, в зоне термического влияния, в основном металле.
В зависимости от ориентации трещины делятся на:
- продольные (ориентированные параллельно оси сварного шва). Преимущественно обуславливаются высокими усадочными напряжениями[5].
- поперечные (ориентированные поперек оси сварного шва). Как правило, образуются в результате продольной усадки металла с низкой пластичностью и, обычно, неглубоки.
- радиальные (радиально расходящиеся из одной точки)
Кроме того, отдельно выделяют следующие виды трещин:
- размещённые в кратере сварного шва
- групповые и раздельные
- групповые разветвлённые
- микротрещины, обнаруживаемые физическими методами при не менее чем 50-кратном увеличении.
Методами снижения трещинообразования при сварке являются:
- прокаливание флюсов перед сваркой;
- предварительный подогрев заготовок от 250 до 450 °С;
- сваривание в режиме с оптимальными параметрами;
- медленное охлаждение металла после сварки;
- проведение после сварки мягкого отжига для снятия остаточных напряжений.
Полости и поры[править | править код]
Возникновение этих дефектов преимущественно обуславливается газами, задержанными в расплавленном металле. По расположению они подразделяться на:
- равномерно распределённые по сварному шву;
- расположенные скоплением;
- расположенные цепочкой.
К полостям также относятся свищи — продолговатые трубчатые полости, вызванные выделением газа, и усадочные раковины — полости, которые образуются вследствие усадки при затвердевании. Частным случаем усадочной раковины является кратер — не заваренная усадочная раковина в конце валика сварного шва.
Твёрдые включения[править | править код]
Выделяют следующие виды твёрдых включений:
- шлаковые включения — линейные, разобщённые, прочие;
- флюсовые включения — линейные, разобщённые, прочие;
- оксидные включения;
- металлические включения — вольфрамовые, медные, из другого металла.
Несплавления и непровары[править | править код]
Выделяют следующие типы несплавлений или отсутствий соединения между металлом шва и основным металлом либо между отдельными валиками сварного шва[6]:
- по боковой поверхности;
- между валиками;
- в корне сварного шва.
Термином непровар или неполный провар, называют несплавление основного металла на участке или по всей длине шва, появляющееся из-за неспособности расплавленного металла проникнуть в корень соединения, заполняя зазор между деталями.
Нарушение формы шва[править | править код]
К нарушениям формы шва по ГОСТ 30242-97 относятся:
- подрезы — продольные углубления на наружной поверхности валика шва.
- усадочные канавки — подрезы со стороны корня одностороннего шва из-за усадки вдоль его границы.
- превышения выпуклости стыкового и углового швов.
- превышение проплава — избыток наплавленного металла на обратной стороне стыкового сварного шва.
- неправильный профиль шва — угол между поверхностью основного металла и плоскостью, касательной к поверхности шва, меньше нормального значения.
- наплав — избыток наплавленного металла шва, натёкший на поверхность основного металла.
- линейное и угловое смещения свариваемых элементов — смещение между свариваемыми элементами при их параллельном расположении на разном уровне (линейное) или расположение кромок элементов под углом (угловое).
- натёк — металл шва, не имеющий сплавления с соединяемой поверхностью и образовавшийся в результате перераспределения наплавленного металла шва под действием силы тяжести. Натёки часто возникают при сварке угловых швов или стыковых швов в горизонтальном положении.
- прожог — вытекание металла сварочной ванны, приводящее к образованию в шве сквозного отверстия.
- не полностью заполненная разделка кромок.
- чрезмерная асимметрия углового шва — значительное превышение размеров одного катета над другим.
- неравномерная ширина шва.
- неровная поверхность.
- вогнутость корня сварного шва — неглубокая канавка со стороны корня шва, возникшая из-за усадки.
-
Поперечная усадка
-
Продольная усадка
-
Угловое смещение
-
Угловое смещение
-
Искажение формы
Прочие дефекты[править | править код]
К прочим, в соответствии с ГОСТ 30242-97, относятся все дефекты, не включенные в вышеперечисленные группы. Например:
- местное повреждение металла из-за случайного зажигания дуги
- брызги металла
- поверхностные задиры — повреждения поверхности из-за удаления временно приваренного приспособления
- утонение металла
Классификация по механизму образования[править | править код]
Холодные трещины[править | править код]
Остаточные напряжения могут уменьшить прочность основного металла и привести к его разрыву с образованием холодных трещин. Для снижения появления подобных дефектов используют различные технологические приёмы, например, сварка прерывистым швом, многопроходная сварка[7].
К основным причинам склонности к холодным трещинам относят следующее:
- естественная склонность структуры металла, например, мартенситной
- присутствие в структуре металла водорода (водородное охрупчивание)
- значительный (−100 до +100 °С) диапазон рабочих температур
- высокая жёсткость конструкции соединений
- ошибки в выборе технологии сварки
Горячие трещины[править | править код]
Горячие трещины представляют собой хрупкие межкристаллические разрушения металла шва и околошовной зоны. Они возникают в твердо-жидком состоянии в процессе кристаллизации и при высоких температурах в твёрдом состоянии. Располагаются по границам зёрен.
Горячие трещины в основном обусловлены действием двух факторов: наличием жидких прослоек между зёрнами металла в процессе кристаллизации и усадочными деформациями. В процессе затвердевания происходит перемещение примесей и шлаков в межзёренные пространства, что снижает деформационную способность шва и околошовной зоны. Неравномерность усадки шва и основного металла при охлаждении вызывает внутренние напряжения и, как следствие, появление микро- и макроскопических трещин.
К снижению образования горячих трещин приводят следующие технологические приёмы:
- снижение объёма провоцирующих примесей (сера, фосфор и др.) в металле свариваемых заготовок.
- снижение в металле шва элементов, образующих химические соединения с низкой температурой затвердевания (хром, молибден, ванадий, вольфрам, титан), нарушающих связь между зёрнами.
- снижение жёсткости закрепления свариваемых заготовок и конструктивной жёсткости сварного узла, препятствующих деформации элементов при остывании[7][8].
- ↑ Matthews, Clifford (2001), ASME engineer’s data book, ASME Press, с. 211, ISBN 978-0-7918-0155-0, <https://books.google.com/books?id=7nIqrfROowQC&pg=PA211>
- ↑ ГОСТ 30242-97 «Дефекты соединений при сварке металлов плавлением. Классификация, обозначение и определения»
- ↑ ГОСТ Р ИСО 6520-1-2012 Сварка и родственные процессы. Классификация дефектов геометрии и сплошности в металлических материалах. Часть 1. Сварка плавлением
- ↑ BS EN ISO 6520-1: «Welding and allied processes — Classification of geometric imperfections in metallic materials — Part 1: Fusion welding»(2007)
- ↑ Raj, Jayakumar & Thavasimuthu, 2002, p. 128.
- ↑ Rampaul, 2003, p. 216.
- ↑ 1 2 Cary & Helzer, 2005, pp. 404–405
- ↑ Bull, Steve (2000-03-16), Factors promoting hot cracking, University of Newcastle upon Tyne, <http://www.staff.ncl.ac.uk/s.j.bull/mmm373/WFAULT/sld013.htm>. Проверено 6 декабря 2009.
Библиография[править | править код]
- Cary, Howard B. & Helzer, Scott C. (2005), Modern Welding Technology, Upper Saddle River, New Jersey: Pearson Education, ISBN 0-13-113029-3
- Raj, Baldev; Jayakumar, T. & Thavasimuthu, M. (2002), Practical non-destructive testing (2nd ed.), Woodhead Publishing, ISBN 978-1-85573-600-9, <https://books.google.com/books?id=qXcCKsL2IMUC>
- Rampaul, Hoobasar (2003), Pipe welding procedures (2nd ed.), Industrial Press, ISBN 978-0-8311-3141-8, <https://books.google.com/books?id=cie00sSLFqoC>
- Moreno, Preto (2013), Welding Defects (1st ed.), Aracne, ISBN 978-88-548-5854-1
- Weman, Klas (2003), Welding processes handbook, New York, NY: CRC Press, ISBN 0-8493-1773-8
Стиль ведения дефектов / Habr
Как тестировщик, видел много дефектов, воспроизведение которых вызывало у меня затруднение. Хочется поделиться некоторыми практиками оформления дефектов – надеюсь, что это поможет немного улучшить чью-то жизнь.Предисловие
Участвуя в разработке программного обеспечения, видел, что при написании кода программисты обычно задают стандарт оформления кода (codestyle) — следование определённым практикам, призванным улучшить жизнь программистов. Моя роль в разработке программного обеспечения заключалась в тестировании. В качестве одной из своих обязанностей, как тестировщик, я видел производство информации о качестве программного обеспечения. В качестве одной из классификаций, эту информацию можно было поделить на позитивную и негативную. Позитивная информация обычно заключалась в том, что ожидаемое поведение совпадало с действительным, и результаты тестирования можно было предоставить в виде данных в отчете о тестировании (фича 1- работает, сценарий 2 – работает, и т.д.). А вот негативная информация чаще всего производилась и оформлялась в виде дефектов. (конечно же, бывали и другие рабочие элементы, такие, как риски, запросы на изменение, и др.)
Встречал внутри проектов ведение базы знаний (не только дефектов), ориентированное на то, чтоб его «раз-раз и в продакшн». Прямо как у дорожных рабочих – сдать объект, а потом будь что будет.
Хочется, чтоб процессы по обеспечению качества велись с расчетом на то, что после передачи продукта в релиз его можно было сопровождать, сохраняя о команде разработки хорошие воспоминания.
Обычно дефект включает в себя:
1. Название
2. Критичность
3. Описание: Информация о стенде, шагах воспроизведения, фактическом и ожидаемом результате.
В зависимости от багтрекиговой системы могут быть и другие поля.
О том, из чего состоит дефект и и базовых правилах оформления, таких, как задавать наименование дефекта, отвечающее на вопросы «Что, где, когда?» на просторах интернета и в том числе на самом хабре встречал много статей. Здесь хочу поделиться опытом, полученным собственноручно.
1. Название должно отражать суть проявления дефекта на прикладном уровне
На дефекты могут смотреть не только программисты и тестировщики, но и другие люди, которые заинтересованы в выпуске и продаже продукта. Например: директор центра разработки, руководитель отдела продаж, проектировщик пользовательских интерфейсов, участники команды, разрабатывающей другой продукт, интегрированный с тестируемым. И у них нет времени изучать подробности и анализировать влияние дефекта на область их ответственности. Они вовсе не обязаны быть знакомы со всеми техническими деталями вашего продукта.
Стоит ориентироваться на то, чтоб по названию дефекта можно было понять к какому функционалу он относится, пользуясь поиском по документации или по базе знаний.
Следует учитывать, что при внесении изменений в продукт, техническое описание может измениться, но дефект обычно продолжает проявляться.
2. Стоит ориентироваться на то, чтоб при воспроизведении дефекта коллеги не тратили впустую время, занимаясь додумыванием вместо своей работы
И чтоб не отвлекали вас от текущих дел. Отвлечение от текущих дел порой требует достаточно много усилий. И выгоднее затратить небольшое количество своего времени на предотвращение отвлечений, чем потом постоянно отвлекаться.
Когда проект маленький и вы являетесь единственным тестировщиком (возможно, сочетая и другие обязанности, например, программиста), дефекты можно оформлять как заблагорассудится. Но когда вы работаете в команде – требуется иной подход. Когда живете один в доме — можно не мыть посуду, не укладывать вещи на свои места и т.д. А когда живете в большой семье – стоит относиться с уважением к тому, что другие члены семьи захотят видеть чистоту и порядок.
Касаемо стенда:
Не стоит так оформлять | Лучше оформить | Примечание |
---|---|---|
На компьютере у моего дедушки в деревне | Машина: CPU: AMD A4-6300, RAM: 2 GB DDR3, HDD: 500GB, экран 1024×768, ОС: Windows 7 x64 | Стоит поточнее указывать где именно проявился дефект. |
На стенде тестирования Хамелеонова и Бабочкиной | Машина1: Windows 10, GCr 20.1 Машина2: Windows 10, FF 30.1 | На стендах часто что-то меняется, и стоит это учитывать. |
Стоит учитывать, что изредка дефекты исправляются в условиях жесткого дедлайна, когда множество людей с нетерпением жаждет их исправления или перепроверки, каждая минута идет на счет золота — и стоит сделать так, чтоб время не утекало впустую из-за небрежного оформления.
3. Описание дефекта не должно содержать не относящейся к нему информации
Не стоит так оформлять | Лучше оформить | Примечание |
---|---|---|
1. Попить кофе 2. Открыть страницу логона 3. Принять ванну 4. Попытаться залогиниться под пользователем user1 |
1. Открыть страницу логона 2. Попытаться залогиниться под пользователем user1 |
Все, что не относится к дефекту, не должно в нем упоминаться. |
Перед тем, как заводить дефект, желательно его воспроизвести, локализовать условия его воспроизведения и отбросить лишнее. Если есть предположение о том, что какой-то фактор не влияет на воспроизведение, то лучше прямо это прописать и не рассчитывать на то, что эта информация будет передана телепатически.
4. Описание дефекта должно содержать достаточное для воспроизведения количество информации
Подобно тому, как инструкция к любому прибору должна иметь достаточное количество информации с учетом того, чтобы им можно было воспользоваться кому-то помимо производителя этих приборов.
Следует учитывать, что члены команды в проекте периодически меняются. По моим наблюдениям люди работают над одним и тем же проектом, не меняя его и не переключаясь на другие, порядка 2-х лет. Следует учитывать эффект грузовичка. Еще бывает так, что в компании несколько тестировщиков, и стоит предусмотреть, чтоб при уходе в отпуск другие тестировщики могли перепроверить этот дефект.
5. Базу дефектов в багтрекере стоит вести с расчетом на перспективу
В идеале описание дефекта можно делать ориентированным на тех, кто работает с продуктом в первый раз и имеет в распоряжении лишь документацию.
Стоит учитывать, что даже после закрытия дефекта он может кому-то понадобиться. Ориентировочная цифра перспективы– 2 года.(ориентировочный расчет).
Например, когда рабочие меняют окна в подъезде, бывает так, что они экономят время и усилия на выносе мусора. Вроде мусор проходу не препятствует, жители спокойно ходят. И ресурсы сэкономлены. НО: через некоторое время наступает момент, когда мусор начинает мешать. А если случится пожар (релиз или еще какое мероприятие), то начинаются неприятности.
Например, какой-то старый дефект всплывает у пользователей (или будет новый, симптомы которого будут совпадать со старым), из-за этого у компании возникает ущерб. Начинают выяснять детали. И если дефект был оформлен как попало, то владельцы явно не будут в восторге от работы тестировщика.
Много раз замечал, что тестировщики при описании дефекта ориентируются на то, что он будет исправлен командой в тот же день. Примерно с 80% дефектов так и происходит –они исправляются на ходу и становятся мало кому нужны. Но вот порядка 20% дефектов продолжают существовать, причем порядка половины оставшихся — в течение достаточно большого промежутка времени. За это время состав команды, работающей над продуктом, претерпевает изменения. И когда новые члены команды начинают работать, то разбор и воспроизведение существующих дефектов начинает занимать очень много времени. На актуализацию каждого дефекта без адекватного описания, даже зная продукт на уровне документации, может уходить уйма времени.
Приведу грубый расчет. Помню, что за 8-часовой рабочий день мне удавалось актуализировать около 5 дефектов без описания. Если бы тестировщики при заведении дефектов тратили дополнительно по 5 минут на каждый заведенный дефект, делая описание подробнее, то на заведение 100 дефектов ушло бы дополнительно 500 минут = порядка 1 рабочего дня. Из этих 100 дефектов порядка 20 останутся незакрытыми в течение достаточно большого количества времени. На их актуализацию при расчете 5 дефектов/день может уйти порядка 4 рабочих дней.
6. Описание дефектов должно учитывать, что программисты, которым предстоит исправлять дефект, могут не быть знакомы с используемым при воспроизведении функционалом
Когда над проектом работает 1-2 программиста, обычно каждый полностью знает весь функционал. Но когда над проектом работает, скажем, 10 программистов – то каждый хорошо знает лишь тот функционал, в который он вносил изменения. И не стоит заставлять программистов изучать поведение незнакомого для них функционала. У них с лихвой достаточно задач по реализации нового функционала.
7. По мере получения информации о дефекте стоит актуализировать шаги воспроизведения
Часто бывает, что важные детали дефекта выявляются уже после его оформления. Их добавляют где-то в комментариях к дефекту. Выгодно актуализировать информацию о шагах воспроизведения в описании дефекта. Особенно если дефект имеет отношение к нескольким командам. Не стоит заставлять всех перечитывать комментарии и вникать в них.
8. Если к дефекту требуется прикрепить много файлов, то перед этим удобно задавать им имена, начинающиеся с цифр
Например:
1 -скриншот окна входа в систему.jpg
2 — скриншот ошибки в консоли.jpg
3 — архив с загружаемыми файлами.zip
Впоследствии, при обсуждении, вложения могут добавляться, их количество может вырастать до десятков. Удобно оперировать указанием на вложения, например: на скриншоте 15… использовать скрипт из вложения 7… см. сообщение в логе архива 25.
9. Стоит отмечать в описании дефекта информацию о частичных исправлениях
Если в одном дефекте собрана информация о нескольких схожих ошибках, например, в описании присутствует:
Ошибка выводится в браузерах:
1. Firefox
2. Google Chrome
3. Internet Explorer
4. Safari
После работы над дефектом выявляется, что дефект исправлен лишь частично, то выгодно актуализировать в нем информацию, не удаляя старое, а используя перечеркнутый шрифт:
Ошибка после исправления 0.1.01.2018 выводится в браузерах:
1. Firefox2. Google Chrome
3. Internet Explorer4. Safari
10. В компании стоит определиться со стандартом критичности дефектов
«Что для русского хорошо, то немцу-смерть». Стоит задать единые критерии определения критичности дефектов для тестировщиков в компании. Может оказаться так, что каждый будет считать, что его дефекты должны быть исправлены в первую очередь и не осознавать, что при этом на исправление более критичных дефектов не будут выделены ресурсы.
11. Дефекты следует заводить как можно быстрее
Своевременность заведения дефектов – немаловажное дело. Чем быстрее они будут заведены – тем скорее и лучше будут исправлены. И тем меньше вероятность пропустить что-то критичное в продакшн. После просмотра заведенного дефекта другими участниками команды может выявиться, что критичность выше, чем кажется на первый взгляд.
Как один из вариантов – если дефект обнаружен во время совещания или иных работ, отвлечься от которых не представляется возможным – можно делать заметку о нем на бумажке, и завести его в конце дня.
12. Не следует игнорировать мелкие дефекты, стоит оформлять их в багтрекере
Вы наверняка не игнорируете мелкий мусор при уборке дома, даже если он не сильно мешает. (Есть, конечно, те, кто не поддерживает в доме чистоту и порядок, но не стоит на них ориентироваться). Подобно этому, не стоит игнорировать мелкие дефекты. Если внутренние договоренности не позволяют заносить их в багтрекер, то можно их фиксировать как-то иначе, например, на какой-нибудь странице или в письмах по почте.
Когда продукт маленький – мелкие дефекты не очень сильно заметны. Но когда продукт становится большим — сценарии более емкими – наличие мелких дефектов начинает донимать.
Можно привести такую аналогию: представим небольшой населенный пункт, например, деревню из двух улиц, на перекрестке которых одна маленькая ямка с грязью. Вроде на каждом (единственном) перекрестке яма, но передвигаться по деревне легко, просто объезжая всякий раз эту яму. И она мало кому мешает. Проходит время. Населенный пункт увеличивается до города-милионника. На каждом перекрестке по ямке с грязью. Если ездить по такому городу на работу через часть-города – то передвигаться, объезжая по одной ямке на каждом перекрестке, станет уже далеко не так комфортно. И возникнет большое желание перебраться в другой город или переизбрать администрацию города. Аналогично с программными продуктами – следует способствовать тому, чтоб у пользователей было желание в них работать, вместо желания удалять.
13. Если дефект был заведен кем-то помимо тестировщика, то при необходимости стоит его подкорректировать
Другие члены команды тоже заводят дефекты. И они вовсе не обязаны быть знакомы с деятельностью тестировщика, у них может быть дополна своих дел. База дефектов – одно из владений тестировщика, подобно тому, как система хранения кода – владения программистов.
Если вы, будучи тестировщиком, видите, что дефект на ваш продукт заведен не совсем корректно, то стоит подкорректировать его. Подобно тому, как стоит поддерживать порядок у себя в доме, складывая вещи на свои места, если гости поставили что-то не туда.
P.S. Недавно начал работать в компании «Модульбанк» и планирую добавить эти практики к имеющимся.