Дефекты сварных соединений — НПК Сибирь
Система контроля качества, создаваемая с целью обследования объекта на наличие отклонений от технических требований, призвана выявлять дефекты, несущие угрозу для конструкции. Сварные соединения — один из главных объектов контроля.
Сварка плавлением — сложный процесс физико-химических преобразований. Качество сварного шва зависит от множества факторов, которые приходится учитывать при разработке сварочной технологии и выборе оборудования.
Основные дефекты швов сварных соединений
В идеале металл в зоне соединения не должен уступать по механическим свойствам материалу соединяемых деталей. На практике неизбежно возникают отклонения, влияющие на состав и структуру металла шва. Те из них, которые по своим параметрам выходят за рамки отработанной технологии, признаются дефектами.
Дефекты сварки перечислены и систематизированы ГОСТ 30242-97.
По своей локализации дефекты шва разделяют на наружные (внешние) и внутренние.
Основные типы дефектов, описываемые стандартом это:
- трещины (продольные, поперечные, радиальные и пр.), т.е. дефекты материала в виде разрыва;
- поры или полости (цепочки и скопления пор, свищи и др.), образуемые выделяющимися газами;
- твердые включения (флюсовые, оксидные, металлические — попадание инородных частиц в материал шва;
- несплавления, непровары, представляющие собой зоны, не заполненные металлом;
- отклонения формы шва (подрезы, искажения профиля, смещения кромок, прожоги и т.п.) как в поперечном сечении, так и вдоль линии соединения;
- прочие дефекты.
Чем грозит дефект сварного шва
С точки зрения прочности дефекты сварки опасны ослаблением сечения несущей детали в местах, не заполненных металлом шва и зонах измененной кристаллической структуры, возникновением точек концентрации напряжения и разрушениями при ударных и циклических нагрузках.
Последствия отклонения параметров шва от предписанных техническими требованиями зависят от задачи, выполняемой конструкцией. В зависимости от оценки последствий разрушения, устанавливается допустимость каждого вида дефектов. Для недопустимых дефектов сварных соединений определяется возможность и способы их устранения.
Устранение дефектов сварки
Причины дефектов сварных соединений известны. Также как и способы борьбы с ними: совершенствование технологии, строгое выполнение требований по подготовке кромок и проведению сварки, обучение сварщиков, повышение квалификации.
Возможность исправления выявленных дефектов шва определяется в каждой отрасли и даже для отдельного объекта, изделия по-своему. В общем случае можно, например, срезать излишек металла в случае наплыва или натека, «доварить», добавить металл в полость трещины или раковины, но точечная, не предусмотренная отработанной технологией, плавка материала может повлиять на структуру шва нежелательным образом. Для объектов повышенной опасности более надёжной признается полная переделка.
В любом случае после устранения дефекта необходимо тщательное обследование зоны доработки с использованием неразрушающего контроля.
Дефекты сварки: виды и причины
Дефекты сварных швов при соединении металлических деталей методом плавления возникают из-за нарушения норм сварки, правил использования аппарата, его неисправности или неверного подбора оснастки. В результате страдает либо внешний вид готового изделия, либо его эксплуатационные характеристики.
Дефекты сварки классифицируются в соответствии с государственным стандартом ГОСТ 30242-97 и делятся на шесть групп:
- трещины на поверхности металла;
- полости, кратеры и поры;
- твёрдые посторонние включения внутри шва;
- непровары;
- изменения формы шва или самого изделия;
- прочие дефекты.
Трещины образуются в результате нарушения межкристаллических связей в структуре металла, быстро распространяются по поверхности, приводя к её разрушению. Причинами появления трещин могут быть другие дефекты шва, из-за которых возникает повышенное напряжение поверхности, а также сварки при слишком низкой температуре, повышенное содержание в металле серы или фосфора, сосредоточение большого количества швов на малой площади.
Поры представляют собой пузырьки газа в толще металла и образуются в результате реакции углерода с закисью железа. Другой причиной появления пор может стать то, что газы, содержащиеся в металле, не успевают полностью выделиться в процессе сварки.
К схожим дефектам относятся полости и кратеры. Они образуются в том случае, если варка производится отсыревшим электродом, либо если на поверхности самого металла или сварочной проволоки осталась ржавчина.
Твёрдые включения внутри шва — это шлак, который не успел всплыть на поверхность сварочной ванны. Такое случается, если варка выполняется слишком быстро или поверхности и кромки были плохо очищены. При многослойной сварке шлак образуется при некачественной зачистке швов между слоями.
Непроварами называют такие дефекты, в результате которых детали соединяются между собой не по всей длине шва. Непроваренные участки обладают высоким показателем напряжения, что ведёт к постепенному разрушению изделия. Такой дефект считается одним из самых опасных. Причинами непровара могут стать слишком малые показатели сварочного тока, большая скорость сварки, излишняя длина дуги, смещение кромок или неправильно выбранная полярность сварочного аппарата.
К нарушениям формы сварочного шва относятся:
- подрезы — локальные уменьшения толщины свариваемого металла, вызванные чрезмерным напряжением сварочной дуги или неправильным ведением электрода;
- прожоги, образующиеся при несоответствии толщины металла диаметру электрода и мощности аппарата, слишком медленном ведении электрода или чрезмерной силе тока;
-
наплавы металла на поверхности шва, возникающие при неправильном положении детали и сварочного элемента.
Под исправлением дефектов обычно понимается подварка шва в нужном месте. Исправлять шов более двух раз не рекомендуется, поскольку это приводит к истончению поверхности металла и образованию прожогов.
Дефекты сварных швов и соединений
ОСНОВНЫЕ ВИДЫ ДЕФЕКТОВ ПРИ СВАРКЕ
КРИТЕРИИ ОЦЕНКИ ТЕХНОЛОГИЧЕСКИХ ДЕФЕКТОВ В СВАРНЫХ КОНСТРУКЦИЯХ
Существующие нормы допустимых дефектов составлены главным образом из технологических возможностей производства, а в ряде случаев и волевым порядком, с ссылкой на опыт эксплуатации.
По вопросу влияния дефектов сварки (непроваров, пор, включений и т. д.) выполнено большое количество работ, однако до настоящего» времени не удалось выработать единый подход к оценке влияния технологических дефектов на служебные характеристики сварных конструкций, что сдерживает разработку и внедрение научно обоснованных норм по допустимым отклонениям.
1. Чувствительность сварных соединений к концентрации напряжений в зоне дефекта.
2. Концентрацию напряжений, вызванную формой шва и дефектом.
3. Характер действующих нагрузок.
Критериями чувствительности сварных соединений к дефектам являются: при переменных (вибрационных) нагрузках- предел выносливости, а при статических нагрузках — предел прочности.
Сварные соединения низкоуглеродистой стали (автоматическая и ручная сварка), стали Х18Н10Т (сварка в аргоне) не чувствительны к концентрации напряжений при статических нагрузках. Сварные соединения низколегированных сталей, сплавов АМг-6, Д16Т- чувствительны к концентрации напряжений при статических нагрузках.
При вибрационных нагрузках все сварные соединения чувствительны к дефектам-концентраторам.
В сварных соединениях, чувствительных к концентрации напряжений, при определении допустимости оставления в конструкции выявленных дефектов необходимо предварительно оценить влияние формы шва на механические характеристики сварных соединений, которая может значительно превысить влияние дефекта. Для разбраковки сварных соединений по результатам неразрушающего контроля предлагается метод, предусматривающий сопоставление теоретических коэффициентов концентрации напряжений формы сварного шва и выявленного по снимку или ультразвуком дефекта.

Для определения теоретического коэффициента концентрации напряжений выявленного дефекта необходимо знать параметры дефекта. Для сферических пор концентрация напряжений и прочность зависит не от величины поры, а от расположения пор в сечении шва и расстояния между ними.
Метод сопоставления коэффициента концентрации напряжений применим к дефектам, имеющим конечный радиус (поры, включения) и не распространяется на такие дефекты, как непровар_и окисные пленки.
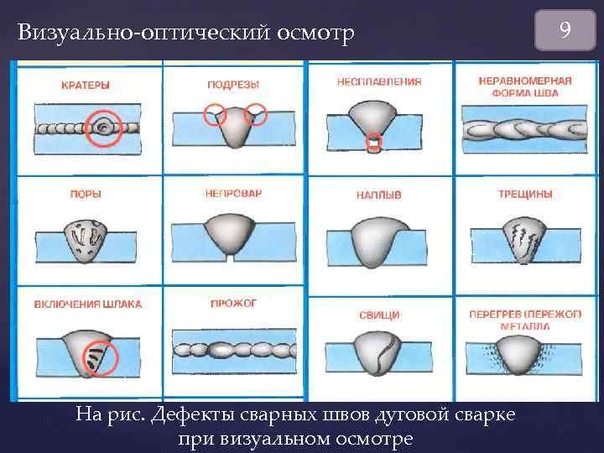
Необходимость учета характера действующих нагрузок и формы шва при назначении норм допустимости дефектов в сварных конструкциях подтверждается полученными экспериментальными данными по влиянию смещения кромок, шлаковых включений, пористости и других дефектов на прочность и выносливость сварных соединений.
Внутренние дефекты сварных соединений, часть 1 — МашПром-Эксперт (Санкт-Петербург)
Высокое качество сварных соединений металлоконструкций – это показатель правильности выбранной технологии сварки металлоконструкций, пригодности сварочных материалов и основного металла, квалификации сварщиков, качества организации рабочего места сварщика, а так же технического состояния оборудования и оснастки.
Работы, необходимые для устранения дефектов сварных соединений металлоконструкций оказывают значительное влияние на стоимость выпускаемой продукции, поэтому дешевле организовать мероприятия по снижению вероятности образования дефектов в сварных соединениях.
В предыдущей статье мы говорили о дефектах сварных соединений металлоконструкций относящихся к наружным, сейчас — о внутренних. К внутренним дефектам сварных соединений металлоконструкций относят горячие и холодные трещины, поры, шлаковые включения и внутренние непровары.
Горячие трещины сварного шва.
Горячие трещины сварного шва – это межкристаллитные разрушения возникающие в твердожидком состоянии при завершении процесса кристаллизации при сварке металлоконструкций. Потенциальную склонность к образованию горячих трещин имеют все конструкционные сплавы при любых видах сварки плавлением.
Чистые металлы без примесей кристаллизуются и плавятся при одной и той же температуре. С присутствием легирующего элемента или примеси это будут уже две разных температуры. В интервале температур (интервале кристаллизации) расплав находится в двухфазном состоянии, в нем присутствуют и жидкие и твердые частицы.
Кроме того при переходе металла из жидкого состояния в твердое резко сокращается его объем, происходит усадка. Усадка шва при сварке металлоконструкций, как правило, происходит в стесненных условиях и возникают растягивающие напряжения и деформации.
Выделим три главных причины зарождения кристаллизационных трещин:
- величина интервала кристаллизации сплава, которая зависти от его химического состава;
- величина минимальной пластичности сплава в интервале кристаллизации, которая зависит от его химического состава, размеров кристаллитов и направления их роста;
- темпа нарастания упругопластических деформаций в процессе кристаллизации и последующего охлаждения сварного соединения и зависти от скорости охлаждения.
Варьируя эти факторы, можно найти оптимальные конструктивные и технологические решения, стойкие против горячих трещин при сварке металлоконструкций.
Интервал кристаллизации сплава
Все химические элементы, входящие в состав металла шва, делим на три группы. Первая — вредные примеси, увеличивающие интервал кристаллизации и снижающие стойкость металла шва против кристаллизационных трещин (сера, фосфор) при сварке металлоконструкций.
Вторая — элементы, влияние которых может быть как положительным, так и отрицательным, в зависимости от их концентрации и сочетания. Третья группа — элементы, присутствие которых не влияет на образование горячих трещин при сварке металлоконструкций.
Для уменьшения вероятности образования горячих трещин при сварке металлоконструкций требуется использование материалов (электродов, проволоки, флюса) с минимальным содержанием вредных веществ. Так же для снижения концентрации вредных примесей связывают их в тугоплавкие прочные соединения, например с марганцем.
Так же на вероятность возникновения горячих трещин при сварке металлоконструкций оказывает влияние формы сварочной ванны. Кристаллиты в сварочном шве растут противоположном теплоотводу направлении. Если шов слишком узкий, а провар глубокий, кристаллиты растут навстречу друг другу. Трещины могут возникать в зоне срастания кристаллитов.
С другой стороны, при наплавке, когда укладываются широкие швы с малой глубиной проплавления кристаллиты растут снизу вверх, вытесняя легкоплавкие составляющие на поверхность шва, где и возможно возникновение горячих трещин.
Анализ зависимости критического содержания углерода в стали, выше которого при сварке металлоконструкций в сварочном шве возникают горячие трещины, от формы шва показывает, что наиболее благоприятная его форма — чашеобразный шов.
Темп деформации при кристализации.
Как уже говорилось на темп деформации при сварке металлоконструкций оказывает влияние главным образом скорость охлаждения металла шва.
Согласно проведенным исследованиям скорость охлаждения, при сварке листов встык за один проход, в свою очередь, зависит от коэффициента теплопроводности, теплоемкости, удельного веса свариваемого металла, толщина свариваемых листов и температуры.
Важным параметром здесь является температура сопутствующего подогрева, которую следует увеличивать для уменьшение скорости охлаждения. Предварительный или сопутствующий подогрев деталей сварного соединения при сварке металлоконструкций является эффективной мерой, обеспечения уменьшения темпа деформации кристаллизующегося металла.
Требуемая для исключения образования горячих трещин температура подогрева, зависит от химического состава металла шва. Чем больше углерода содержится в металле шва, тем выше температура подогрева. На практике свариваемые детали металлоконструкций можно подогреть в печах или в газовом пламени.
Кроме изменения температурного режима, величину растягивающих напряжений и темп деформации металла в интервале кристаллизации можно уменьшить за счет рационализации конструкций узлов и элементов металлоконструкций подлежащих сварке. Это уменьшение количества и сосредоточенности швов, оптимальной разделки кромок, устранения излишней жесткости сварных узлов.
Размер первичных кристаллов шва.
Размер первичных кристаллов шва так же оказывает влияние на темп деформации. Деформация металла шва при высоких температурах в процессе его кристаллизации и последующего остывания осуществляется, в основном, путем скольжения и поворота кристаллитов друг относительно друга.
Следовательно, чем меньше размеры кристалликов в шве, тем больше плоскостей скольжения, тем более пластичен металл, тем больше значение величины минимальной пластичности сплава в интервале кристаллизации.
Кроме того, измельчение кристаллитов в шве в процессе кристаллизации способствует уменьшению степени химической неоднородности шва, то есть уменьшению концентрации вредных примесей на границе кристаллитов. Поэтому швы с мелкозернистой структурой обладают более высокой стойкостью против кристаллизационных трещин.
Дефекты сварного соединения и их причины. Дефекты сварных соединений. Классификация дефектов сварных швов
Сегодня сварка используется повсеместно для соединения различных металлических деталей. Она успешно используется как в промышленности, так и в частных бытовых условиях. называется неразъемное соединение деталей посредством сварки. В результате этого формируются различные участки, которые характеризуются определенным набором свойств. Все зависит от степени нагрева. Они могут различаться по физическим, химическим и механическим свойствам. Основные дефекты сварных соединений известны достаточно давно. Их следует избегать в процессе выполнения работы.
Сварка используется для соединения металлических деталей в промышленности и бытовых условиях.
Характеристика и виды сварных соединений
Перед тем как начать разговор о дефектах сварных соединений, стоит подробнее поговорить об их основных видах и характеристиках. Принцип сварки достаточно прост. Расплавленный металл образует шов, который кристаллизуется. Тот материал, который частично оплавляется, составляет зону сплавления. Рядом с этой зоной образуется та, в которой нагретый металл испытывает дополнительные напряжения. Ее называют зоной термического влияния. После этого идет основной металл. Его структура и свойства в процессе проведения работ никак не изменяются.
Классификация сварных швов по положению в пространстве.
Существует несколько основных видов сварных соединений. Наиболее распространенными среди них являются встык, внахлест, тавровые и угловые. Все они различаются между собой установкой основных материалов, расположением шва. На качества шва напрямую влияет множество самых разнообразных факторов. Могут образовываться и внутренние дефекты, и наружные. На качество швов напрямую влияет степень загрязненности металлов, которые подлежат соединению.
Здесь могут присутствовать самые разнообразные окислы, жировые пленки и так далее. Именно поэтому свариваемые поверхности обязательно нужно очищать перед проведением работ. Кстати, в процессе их проведения нужно бороться с окислами, образующимися на поверхности. В любом случае прочность конечного соединения напрямую зависит от отсутствия дефектов. Шов иногда может иметь точно такую же прочность, что и основной материал, но этого достаточно сложно достичь.
О дефектах сварных соединений
Как уже отмечалось ранее, дефекты сварных соединений могут носить самый разнообразный характер. О них обязательно нужно помнить в процессе проведения работ. Если человек имеет багаж знаний по ним, то он сможет сваривать детали, у которых будут идеальные швы. Именно к этому и нужно стремиться.
Таблица основных видов сварных соединений.
- Подрез. Это один из видов дефектов сварных соединений.
Представляет собой канавку, которая образуется в месте сплавления основного металла и шва. Чаще всего такие дефекты появляются тогда, когда есть большие сварочные ванны. Имеется в виду, что расплавляется большое количество металла вследствие использования больших показателей тока.
- Наплав. Этот дефект характеризуется тем, что происходит натекание материала шва на основной металл. Очень неприятный недостаток.
- Непровар. Такой дефект сварных соединений может иметь место в тех случаях, когда образуется недостаточная расплавленность основного металла в местах соединений конструктивных элементов. Это место чаще всего заполняется шлаком, который, ввиду своей структуры, образует пористости и пустоты во швах. Это недопустимо. Конструкция сразу теряет свои свойства. Когда используется дуговая сварка, то непровар может образоваться из-за использования недостаточной силы тока. Это один из самых опасных дефектов. Связано это прежде всего с тем что в этом месте начинают образовываться дополнительные напряжения в ходе последующей эксплуатации конструкции.
Это очень часто приводит к скорому ее разрушению. От этого дефекта можно избавиться. Для этого непровар выявляют, а затем производят наплавку в сложных участках.
- Трещины. Это частичное разрушение материала на шве или в зоне, которая расположена около него. Они могут образовываться по нескольким причинам. Если говорить о процессе, когда металл еще горячий, то трещины появляются в результате кристаллизации металла. В твердом состоянии с ним могут также происходить самые разнообразные структурные превращения. Это вторая причина появления подобных дефектов.
Дефекты сварных швов: несплавления, неравномерная форма, наплыв, трещины, свищи, перегрев.
Механизм образования горячих трещин достаточно прост. В ходе выполнения сварочных работ происходит нагрев металла. После того как источник тепла устраняется, он начинает постепенно охлаждаться. Разумеется, начинают образовываться и зоны кристаллизации. Они начинают плавать среди еще расплавленного металла. Если бы не было микрозон, которые позволяют осуществлять взаимодействие горячего и холодного материала, то все сварные соединения содержали бы дефекты. Однако этого не происходит. Таким образом, можно считать, что чем выше интервал кристаллизации, тем более возможно появление горячих трещин. Углерод напрямую влияет на этот показатель. Здесь прямая зависимость. Чем больше в стали углерода, тем шире становится интервал кристаллизации.
Холодные трещины могут образовываться в месте шва. Они появляются при охлаждении материала до температуры приблизительно в 200-300 градусов по Цельсию. Они могут появляться не сразу, что делает их более опасными. Связано появление холодных трещин с тем, что в материале начинают возникать различные структурные превращения вследствие тех или иных химических превращений. Здесь существует прямая зависимость от количества в материале углерода. Чем его больше, тем больше вероятность того, что появятся холодные трещины. Эта склонность к образованию холодных и горячих трещин определяет такой параметр, как свариваемость металлов. Этот параметр характеризует способность получения свариваемого соединения, ничем не отличающегося от основных материалов.
Поры и неметаллические включения
Дефекты сварных швов: кратеры, подрезы, поры, непровар, шлак, прожог.
Поры. Эти дефекты сварных соединений встречаются достаточно часто. Поры представляют собой пустоты, которые заполняются газом. Они могут иметь микроскопические размеры, а могут образовывать в структуре дефекты размером в несколько миллиметров. При этом образуются они чаще всего в местах соединения шва с основным материалом. На этот дефект оказывает влияние множество самых разнообразных параметров.
Самым главным из них является концентрация газа в варочной ванне. Газ выделяется из металла в процессе его плавления. Этот процесс никак нельзя предотвратить. Угарный газ не способен растворяться в железе, соответственно, он выделяется в виде пузырьков.
Неметаллические включения. Эти дефекты самих сварных соединений связаны с попаданием инородных включений в структуру шва в результате проведения работ.
Трещины в сварном соединении.
Существует огромное разнообразие таких включений. Шлаковые, к примеру, могут образовываться в результате недостаточной очистки материалов, которые подлежат соединению.
Их причиной может стать недостаточно полное удаление шлака при многослойной сварке. При работе, которая производится за счет плавления, образуется во шве материал, который по физическим и химическим свойствам отличается от основного металла. В связи с этим также могут образовываться подобные дефекты. Инородные включения могут носить самый разнообразный характер.
Изучение дефектов
Дефект сварки – поры, это заполнение пустот газами.
Разумеется, если есть дефекты различных сварных соединений, то их обязательно нужно изучать. Для этого достаточно часто используется макроанализ. Он заключается в том, что структура металла изучается с помощью невооруженного глаза или лупы. В отличие от микроскопического анализа, макроанализ не позволяет в должной мере изучить структуру материала. Его основная задача – это контроль качества соединяемых деталей в процессе сварки. Он позволяет определить тип излома, волокнистое строение, нарушения сплошной структуры и так далее. Для того чтобы провести такой анализ, необходимо изучаемую часть подвергнуть травлению специальными элементами и обработке на шлифовальных машинах. Этот образец носит название макрошлифа. На его поверхности не должно быть никаких неровностей или инородных включений, в том числе и масляных.
Все те дефекты, которые были описаны выше, вполне могут изучаться и выявляться с помощью макроанализа.
Чтобы выявить структуру материала, чаще всего используются методы поверхностного травления.
Виды наплывов в швах.
Такой подход самым лучшим образом подходит для низкоуглеродистых и среднеуглеродистых сталей. Макрошлиф, который подготовлен заранее, нужно погрузить в реактив той частью, которая подвергается анализу. При этом его поверхность обязательно должна быть зачищена с помощью спирта. В результате взаимодействия элементов происходит химическая реакция. Она позволяет вытеснять медь из раствора. Происходит замещение материалов. Медь в результате осаждается на поверхности пробника. Те места, где на основной материал медь легла не полностью, подвергаются травлению. Эти места и содержат какие-либо дефекты. После этого образец изымается из водного раствора, сушится и очищается. Все эти действия нужно проделывать максимально быстро, чтобы не произошло реакции окисления. В результате этого можно выявить те участки, где присутствует большое количество углерода, серы и других материалов.
Травление участков, которые содержат эти материалы происходит не одинаково. Там, где присутствует большая концентрация углерода и фосфора, медь на поверхности выделяется неинтенсивно. Здесь минимальная степень защиты металла. Вследствие этого данные места подвергаются самому большому травлению. В результате проведения реакции эти участки окрашиваются в более темный цвет. Лучше использовать этот метод для сталей, которые содержат минимальное количество углерода. Если его будет очень много, то медь с поверхности образца будет весьма проблематично удалить.
Виды подрезов в швах.
Есть и другие методы макроанализа структуры материалов при сварном соединении. К примеру, часто для определения количества серы используется метод фотоотпечатков. Фотобумагу при этом смачивают и держат на свету какое-то время. После этого она просушивается между листами фольгированной бумаги. Раствор, в который она изначально помещается, содержит определенное количество серной кислоты. Затем, разумеется, эта бумага ровным слоем укладывается на макрошлиф.
Она должна разглаживаться с помощью валика, чтобы полностью были исключены все ее деформации. Все пузырьки воздуха, которые могут оставаться между фотобумагой и металлом, должны быть полностью удалены. Только в этом случае исследование будет носить объективный характер. Ее нужно удерживать в таком положении приблизительно 3-10 минут. Время зависит от того, какова изначальная толщина пробника, а также от других факторов.
Виды непроваров.
Включения серы, которые располагаются в наплавленном металле, обязательно вступят в реакцию с кислотой, которая была нанесена на поверхность фотобумаги. В очагах выделения сероводорода будет образовываться такое вещество, которое носит название фотоэмульсия. Участки сернистого серебра, которые будут образовываться в результате реакции, наглядно показывают распределение серы в металле.
Разумеется, эти участки будут наблюдаться на бумаге. Фотобумага, которая была использована для проведения опыта, подлежит мытью, а затем выдерживанию в растворе гипосульфита. После этого ее еще раз промывают в жидкости и сушат. В том случае если в сварном шве будут присутствовать фтористые включения, они обязательно выделятся наружу в виде участков темного цвета.
Подведение итогов
Таким образом, в настоящее время существует множество методов выявления дефектов сварных соединений. Все они имеют определенную цель. Каждый способ позволяет выяснить, сколько в структуре шва содержится того или иного материала, который может пагубно влиять на его структуру.
Помимо методов макроанализа, в последнее время достаточно часто внедряются методы микроанализа. Они имеют то же самое предназначение, что и предыдущие. Однако дополнительно позволяют изучить структуру материала. Здесь работа ведется на молекулярном уровне строения кристаллической решетки.
Что такое дефекты сварных соединений? По сути, это отклонения от требований к техническим характеристикам сварного шва, а соответственно и всей конструкции. Именно дефекты сварки снижают прочность шва и надежность сварочных стыков. Их можно разделить на несколько видов.
Виды дефектов сварных швов:
- отклонения от размеров и формы шва;
- изъяны микро- и макроструктуры;
- коробление и деформация конструкций.
Отклонения от размеров шва и его формы
Размерные показатели сварочного шва определяются государственными стандартами. И у каждого вида сварки есть свой ГОСТ. К примеру, при сварке, где задействован способ плавления, дефекты сварного шва определяет неравномерная наполненность свариваемой канавки, плюс разница ширины и высоты шва на всем его протяжении. Что касается формы, то она неровная, имеются так называемые седла (впадины), бугры, структура его чешуйчатая.
Причины из возникновения при сварке ручной – это низкое качество электродов, низкая квалификация сварщика, нарушение технологии сваривания. Причины при автоматической сварке – это скачки напряжения, угол наклона подачи электрода неправильно выбран, присадочная проволока проскакивает в механизме подачи и так далее.
Если говорить о сварке давлением, то ее дефектами сварных швов выступают вмятины глубокого типа, неравномерное распределение точек вдоль сварочного шва, может произойти смещение заготовок относительно друг друга.
К дефектам нарушения формы относятся прожоги, подрезы, наплывы и незаверенные кратеры.
Наплывы
Обычно такие дефекты сварочных швов образуются, когда производится сварка заготовок, лежащих в горизонтальной плоскости. А сам сварочный процесс производится сверху. Наплыв – это затвердевший жидкий металл в виде бугорков, которые образуются в момент соприкосновения горячего расплавленного металла электрода с холодной поверхностью заготовки. Наплывы могут быть разных размеров: от маленьких капель до больших рядов, протяженных на приличную длину сварочного шва.
Причинами появления наплывов могут выступать большой ток, подающийся на электрод, длинная электрическая дуга, наклон заготовки, неправильно выбранный угол установки электрода. Как результат – трещины в сварочном шве, непровары и прочие изъяны.
Подрезы
Этот дефект представляет собой канавку (углубление) в сварочном шве, которая часто образуется при сварке около металла заготовки. Причинами могут быть большой ток и длинная дуга, которые создают перегрев самого металла, а также сварочного наполнителя. Именно состояние большой температуры становятся причиной оплавления кромки двух заготовок. Если производится сварка угловых соединений, то чаще всего причинами подреза являются неправильно устанавливаемый электрод, особенно, когда произошло смещение в сторону вертикально установленной заготовки. При этом перегрев происходит именно на вертикальной стенке стыка, здесь и образуется подрез. А вот на горизонтальной в это время образуется наплыв, потому что металл начинает стекать вниз.
При газовой сварке подрезы могут возникать только по одной причине – увеличенная мощность горелки. Необходимо отметить, что подрезы – достаточно серьезный дефект сварочного шва. Он приводит к ослаблению заготовки по толщине, а это наипервейшая причина разрушения стыка, а соответственно всей сварной конструкции.
Прожоги
Само название уже говорит за себя. На месте сварки и в свариваемых металлах по кромкам образуются отверстия. Причины:
- большое расстояние между заготовками;
- большой ток и мощная горелка при быстрой сварке;
- неправильная форма кромок, очень заостренная;
- большая продолжительность процесса на одном месте.
Чаще всего этот вид дефектов получается, когда свариваются между собой тонкие листы металлов, или когда ведется многослойная сварка и наносится первый слой.
Кратеры
Это углубления в сварном шве. Обычно этот дефект образуется при обрыве дуги. Поэтому его опытные сварщики пытаются сразу же оплавить. Это самое простое устранение дефектов сварки. Когда сварка ведется автоматическим способом, то кратер обычно появляется на выходе из шва, то есть, на выходной планке.
Есть подвид кратеров, который называется усадочной раковиной. Она образуется под воздействием усадки металла в шве. Все дело в том, что металл при остывании уменьшается в объеме.
Дефекты макроструктуры
Эти виды дефектов сварных соединений можно выявить, если увеличить структуру сварного шва в 10 раз. К этому типу изъянов относятся трещины, непровары, газовые поры, шлаковые вкрапления.
Поры образуются, когда шов быстро остывает. При этом находящиеся в его теле газообразующие элементы не успевают выйти наружу. Так происходит, когда кромки заготовок покрыты ржавчиной, пятнами масла или краски, используется флюс с повышенной влажностью, был неправильно настроен сварочный аппарат по току или газу, большое содержание углерода в свариваемых металлах и так далее.
Поры могут быть большими и маленькими, располагаться могут кучно или равномерно вдоль шва, есть поры сквозные, называемые свищами. В общем, их количество и размеры зависят от времени, за которое ванна находится в жидком состоянии. Чем дольше сварочная ванна жидкая, тем меньше пор, потому что газы успевают покинуть жидкий металл.
Шлаковые включения – это, по сути, небрежность со стороны сварщика при сварке. Значит, он плохо подготовил два соединяемых металла к сварке. На них осталась грязь, ржавчина. Если данный вид дефектов появился при многослойной сварке, то значит, сварщик плохо провел удаление шлака с предыдущих слоев.
Эти дефекты могут иметь размеры в несколько микрон или d несколько миллиметров, форма разная: от сферы до тонкой линии. Расположение – по всему телу шва.
Непровар – дефект серьезный. Получается так, что металл заготовки несплавился с металлом электрода (электросварка) или присадочной проволоки (газовая сварка). Могут несплавится между собой и слой наплавляемого металла. Причин непровара немало:
- слишком большой ток при сварке был использован;
- загрязнение кромок;
- неправильно был поднесен электрод к оси шва;
- очень маленький зазор между двумя заготовками;
- кромки имеют слишком заостренные концы;
- вынужденный перерыв, в процессе которого металлы остывают;
- увеличенная скорость сварки.
Что касается трещин, то их можно разделить в зависимости от температуры их появления. То есть, холодные или горячие. Горячие появляются, когда происходит затвердевание металла, а кристаллизация начинается при температуре 1100-1300С. При этом внутри шовного металла появляются усадочные напряжения, начинают образовываться прослойки полужидкого вида. Они и становятся впоследствии трещинами. Если в наплавляемом металле содержится много водорода, углерода или кремния, то это также причина возникновения горячих трещин.
Холодные трещины образуются при температуре 100-300С. Причинами являются все те же напряжения, возникающие в теле наплавляемого металла, когда он начинает остывать. К тому же внутри сварочного шва остается водород (газ), который стремится выйти наружу. И это дополнительные напряжения. Кстати, горячие трещины на лицевой части шва не видны, они считаются внутренними. А вот холодные тут же появляются на внешней стороне шва, их хорошо видно невооруженным глазом. Это наружные дефекты сварных швов и соединений.
Есть еще два вида трещин: отпускные и ламелярные. Первые образуются уже тогда, когда сварка закончена и производятся операции по следующей обработке металлом. Вторые имеют очень интересную технологию появления. Они образуются еще при высоких температурах, но свое дальнейшее развитие получают уже в остывшем металле. Кстати, чаще всего этот вид дефекта образуется из микроскопических трещин. Оба варианта относятся к категории – внешний дефект.
Дефекты микроструктуры
К дефектам микроструктуры нужно отнести микроскопические трещины и поры, включения неметаллического типа (кислородные, нитридные), крупная зернистость структуры наплавленного металла с элементами перегревов и пережогов.
Самый опасный из всех перечисленных дефектов – пережог. При нем внутри шва появляются в большом количестве крупные зерна структуры металла, которые имеют минимальные прочностные связи между собой. Отсюда высокая хрупкость стыка. Причинами пережога являются присутствие кислорода в зоне сварки, а значит, изоляция ванны была плохой. Сюда же можно добавить высокую температуру сварочного процесса.
Допустимые и недопустимые дефекты
Понятно, что все дефекты сварных соединений негативно влияют на качество сварной конструкции. Но есть такие, при которых конструкция может эксплуатироваться без проблем, а есть те, при которых эксплуатировать ее строго запрещено.
Поэтому перед тем как определить, можно или нельзя эксплуатировать сварную конструкцию, необходимо принять во внимание все обстоятельства и факторы, влияющие на выбор.
- Необходимо определить соответствует ли конструкция всем геометрическим и габаритным параметрам строго по проекту или чертежу.
- Тип дефекта, его размеры и место в соединении.
- Каким механическим нагрузкам будет подвергаться строение или сооружение. Выдержат ли их сварочные соединения.
- Характер окружающей среды. Природные нагрузки негативно влияют на состояние сварного шва.
- Функции, возложенные на конструкцию. То есть, один дефект может выдержать определенные нагрузки, а другие ему противопоказаны.
Определить допустимость дефектов можно только специальной аппаратурой. Поэтому рекомендуется использовать оборудование, которое по степени проверки дефекта была выше, чем номинальная допустимая величина самого изъяна. К примеру, трещину размером 3 мм нельзя измерять прибором, который определяет минимальные трещины длиною 5 мм.
Кстати, на допустимость влияют не только размеры и форма дефектов, не последнее слово за их количеством и частотой расположения.
Заключение по теме
Дефекты сварных соединений влияют на качество стыка между элементами собираемой конструкции, а значит, и на всю конструкцию в целом. Поэтому исправлению дефектов сварки придается особое внимание. Устраняться сами они не могут. Есть изъяны, которые можно легко устранить, есть, которые устранить можно, но непросто. Способы их устранения известны. А есть дефекты, которые не подлежат исправлению. Так что лучше проводить процесс грамотно. Поэтому изучайте процессы появления швов и причины их образования.
Надежность конструкции зависит от качества выполненных работ. Дефекты сварных креплений не допускаются, иначе изделие может выйти из строя в самый неподходящий момент. Халатность при работе, невысокая квалификация мастера, могут повлечь за собой различные проблемы, технологии работ и оборудование должны применяться в соответствие с ГОСТами. Значения сварных швов могут быть в допуске или напротив, в последнем случае, необходимо заново проделывать работу до достижения требуемого результата.
При воздействии различных факторов при работе образуются некоторые недопустимые несоответствия шва. Дефекты сварки подразделяются на несколько групп, допуски которых находят подробное описание в ГОСТе:
- Наружные дефекты имеют неравномерную форму конструкции, следствием не соблюдения технологии формирования.
- Согласно ГОСТ-23055, к внутренним бракованным частям принимаются неметаллические либо шлаковые отложения, несплавления и непровары металлических изделий. К выявлению данной категории брака применяются приборы контроля сварочного производства.
Исправление производится рассверливанием по всей полости, в целях исключения развития, брак удаляется и наваривается новое соединение.
Полости
Произвольная форма, появившееся при результате воздействия газов, называется полостью. Возникает при расплавлении металла, не полном цикле оттеснения излишних газов, не правильного формирования сварочной ванны. Несплошности образовываются к форме продолговатых полостей, к категории относятся кратеры и раковины. Основной разновидностью браковки сварки, являются свищи, появившиеся обстоятельствами:
- пластичность металла не соответствует требованиям;
- закалочные структуры;
- неравномерный нагрев.
Дефекты отличаются по форме, глубине и расположению, которое может находится как на внутри, так и на внешней части шва. Свищи имеют продолговатую трубчатую форму, причиной появления являются газы. Не соблюдение технического регламента, а именно наличие на участке сварки масла, окисления и прочих загрязнений ведут к дефекту конструкции.
Некачественный инструмент может организовать непоправимые разрушения, так же как и использование вспомогательных материалов в виде флюсов. Повышенная скорость изготовления, нестандартный ход защитных газов неблагоприятно воздействуют на характеристики шва. Поры образуются вследствие применения неисправного инструмента, проволоки, чрезмерно проветриваемого помещения.
При обрыве дуги, либо не верного способа выполнения конечного участка, образуются кратеры. Внешний вид обуславливается видом воронки, которую нужно заварить по обнаружению. Современные агрегаты, изготавливающие сварочный шов, способны устранить несоответсвие путем снижения тока по окончанию соединения.
Твердые включения
Инородные вещества любого происхождения являются серьезной проблемой в процессе сварки. Основные ошибки — большая скорость сварки, ток малой силы, загрязненность кромок. Дефекты сварного шва производятся из-за:
- флюсовых остатков;
- шлаковых либо оксидных включений.
Оксидные, образовываются результатом отсутствия зачистки металла, химического воздействия. Шлак, при соблюдении технологии, всплывает на поверхность, однако при некоторых ситуациях остается внутри шва. Защитными газами создается среда, при которой невозможно включения инородного тела. Металлические включения могут быть опасны, т.к. имеют размеры до нескольких десятков миллиметров.
Условия возникновения зависят на тип образования:
- разобщенным;
- линейным;
- прочим образованием.
Участок производимых действий по сварки, на котором превышается содержание шлаковых добавок, переваривается. Зачастую включения проявляются на местах стыковки статичного и добавляемого шва, при исполнении многослойных изделий.
Несплавления и непровары
Отсутствие стыковки основного металла, или между отдельными элементами называется несплавлением. Различаются на поверхностные, состоящие между вилками, расположенные при основании шва. Основными причинами несплавлений определяют:
- увеличенная длина дуги;
- несоответствующая зачистка кромок;
- уменьшенный сварочный ток;
- повышенная скорость сварки.
Наличие дефекта статическими соединениями может быть восполнено дополнительным наплавом. В результате, происходит снижение прочности, возникает концентрация напряжений зоной несплавления.
Недостаточное сплавление стыка при зоне сварки именуется непровар. Основными причинами является остатки ржавчины, окисления, окалины, других неблагоприятных воздействий. В следствие уменьшения концентрации, возрастает возможность появления напряжений, отрицательно сказывающихся на конструкции в целом. При отклонениях от допусков, зоны с непроваренным швом зачищаются до основания, операция по сварке происходит заново.
Отклонение от заданных параметров формы поверхности шва, геометрического состояния соединения, обуславливается нарушением формы.
Существуют различные нарушения, каждый из которых возникает вследствие определенных условий.
- Подрезы – по краям сварного шва образуется дефект в виде углублений при продольном расположении. Образуется зачастую при повышенной скорости сварки, результатом чего сварочная ванная затвердевает быстрее, чем положено. Увеличенное расстояние дуги способствует распространению ширины шва по металлу, т.к. при такой схеме теплоотдача дуги остается на прежнем уровне, мощности не хватает для расплавления всей полости металла.
- Избыток наплавленного материала, обнаруженный на внутренней стороне сварного шва – превышение проплава. Дефектами линейного смещения называют состояние, при котором соединяемые детали располагаются на разном уровне, между стыками существует разница в высоте. Существует угловой тип брака, при ситуациях, когда угол асимметричен стыковому элементу.
- Наплав – избыточное количество материала, образованное при процессе стыковки шва. Дефект образуется вследствие излишне длинной дуги, неверного наклона электрода, повышенного сварочного тока.
- Прожог – сквозное отверстие, образованное в результате вытекания металлической составляющей сварочной ванны. Брак образуется результатом использования большого тока при малой скорости движения электродом, плохая подкладка или неверный зазор кромок.
Также существуют прочие неприятности, связанные с формой, к примеру, вогнутые края шва, образованные со стороны корня соединения. К прочим несоответствиям приравниваются задиры поверхностного типа, случайная дуга, брызги металла, и другие.
Методы обнаружения и контроля
Качественный шов имеет соответствующие показатели маркировки. На крупных предприятиях каждый специалист устанавливает определенное клеймо на стыкуемый участок. Для обнаружения дефектов применяются следующие способы:
- визуальный осмотр;
- цветная дефектоскопия;
- ультразвуковой метод определения бракованных участков;
- радиационный;
- магнитный метод.
После того, как обнаружен дефект, сотрудником отдела качества определяется дальнейшая судьба детали, в большинстве случаев они отправляются на доработку. Наплывы удаляются с помощью абразивного инструмента, путем механических воздействий. Заварка применяется при дефектоскопии крупных трещин, с предварительным зачищенным местом остаточной сварки.
Приступим к подробному рассмотрению дефектов согласно классификации.
Дефекты группы 1 — Трещины
Трещины (100; Е) — дефект сварного соединения в виде разрыва в сварном шве и (или) прилегающих к нему зонах
или
— несплошность вызванная местным разрывом шва, который может возникнуть в результате охлаждения или действия нагрузок ()
Трещины являются недопустимыми дефектами, так как являются концентратором напряжения и очагом разрушения. Это самые опасные дефекты сварного соединения, часто приводящие к его разрушению. Проявляются они в виде разрыва в сварном шве или в прилегающих к нему зонах. Сначала трещины образуются с очень малым раскрытием, но под действием напряжений их распространение может быть соизмеримо со скоростью звука, в результате чего происходит разрушение конструкции.
Чаще всего трещины проявляются при сварке высокоуглеродистых и легированных сталей в результате быстрого охлаждения сварочной ванны. Вероятность появления трещин увеличивается при жестком закреплении свариваемых деталей.
Образованию трещин способствует повышенное содержание углерода в расплавленном металле, а также кремния, никеля и особенно вредных примесей серы, фосфора и водорода.
Причинами образования трещин чаще всего является несоблюдение технологии и режимов сварки. Это может проявляться, например, в неправильном расположении швов в сварной конструкции, что приводит к высокой концентрации напряжений. Большие напряжения в сварных конструкциях могут возникнуть также при несоблюдении заданного порядка наложения сварных швов.
Удаление трещин. Поверхностные трещины в сварных конструкциях устраняются в следующем порядке: сначала засверливают концы трещины, чтобы она не распространялась дальше по шву, затем трещину удаляют механическим путем или строжкой, после чего место удаления дефекта зачищают и заваривают.
Внутренние трещины (как впрочем, и остальные внутренние дефекты) удаляют механическим способом или строжкой с последующей заваркой данного участка.
По происхождению трещины подразделяются на:
— холодные трещины
— горячие трещины
Холодные трещины возникают при температурах ниже 300°С, то есть сразу после остывания шва. Кроме того, холодные трещины могут возникнуть и через длительный промежуток времени. Причиной появления холодных трещин являются сварочные напряжения, возникающие во время фазовых превращений, приводящих к снижению прочностных свойств металла. Причиной появления холодных трещин может стать растворенный атомарный водород, не успевший выделиться во время сварки. Причинами попадания водорода могут служить непросушенные швы или сварочные материалы, нарушения защиты сварочной ванны. Холодные трещины на изломе имеют чистый блестящий вид кристаллов.
Горячие трещины появляются в процессе кристаллизации металла при температурах 1100 — 1300°С вследствие резкого снижения пластических свойств и развития растягивающих деформаций. Появляются горячие трещины на границах зерен кристаллической решетки. Появлению горячих трещин способствует повышенное содержание в металле шва углерода, кремния, водорода, никеля, серы и фосфора. Горячие трещины могут возникать как в массиве шва, так и в зоне термического влияния. Распространяться горячие трещины могут как вдоль, так и поперек шва. Они могут быть внутренними или выходить на поверхность. Горячие трещины на изломе имеют желтовато — оранжевый оттенок.
По размерам трещины подразделяются на:
- макроскопические
- микроскопические
Макроскопические трещины или просто трещины (100; Е) — видны невооруженным глазом или через лупу небольшого (2 — 4х — кратного) увеличения при визуальном контроле
Микроскопические трещины или микротрещина (1001) — трещина микроскопических размеров, которую обнаруживают физическими методами не менее чем при пятидесятикратном увеличении
По расположению трещины подразделяются на:
- продольные
- поперечные
Продольная трещина (101; Еа) — трещина сварного соединения, ориентированная вдоль оси сварного шва
Продольная трещина может располагаться :
В металле сварного шва (1011)
На границе сплавления (1012)
В зоне термического влияния (1013)
В основном металле (1014)
Поперечная трещина (102; Eb) — трещина, ориентированная поперёк оси сварного шва.
Поперечная трещина может располагаться:
В металле сварного шва (1021)
В зоне термического влияния (1023)
В основном металле (1024)
Газовая полость (200;А) — полость произвольной формы, без углов, образованная газами, задержанными в расплавленном металле
или
— полость произвольной формы, без углов, образованная газами, задержанными в расплавленном металле
Газовые полости образуются в сварочной ванне в виде пузырьков газа (водород, азот, окиси углерода и др.) которые застывают в металле при кристаллизации металла во время сварки.
Отличие газовой полости от газовой поры в форме т.е. пора имеет практически правильную шаровидную форму, а газовая полость имеет форму как указано на рисунке выше.
Газовая пора (2011; Аа) — несплошность, образованная газами, задержанными в расплавленном металле. Имеет, как правило, сферическую форму
или
— газовая полость обычно сферической формы ( — 97)
Равномерно распределенная пористость (2012) — группа газовых пор, распределенных равномерно в металле сварного шва. Следует отличать от цепочки пор (2014)
Скопление пор (2013) — группа газовых полостей (три или более), расположенных кучно с расстоянием между ними менее трех максимальных размеров большей из полостей
Цепочка пор (2014) — ряд газовых пор, расположенных в линию, обычно параллельно оси сварного шва, с расстоянием между ними менее трех максимальных размеров большей из пор
Продолговатая полость (2015; Ab) — несплошность, вытянутая вдоль оси сварного шва. Длина несплошности не менее чем в два раза превышает высоту.
Свищ (2016; Ab) — трубчатая полость в металле сварного шва, вызванная выделением газа. Форма и положение свища определяются режимом затвердевания и источником газа. Обычно свищи группируются в скопления и распределяются елочкой.
Свищ образуется при случайных коротких замыканиях вольфрамового электрода или резком обрыве дуги, а также в результате неправильного гашения дуги при ручной и автоматической сварке.
Возможной причиной развития свища чаще всего является некачественная подготовка поверхности и присадочной проволоки под сварку.
Дефект обнаруживается визуально и подлежит переварке.
Исправить такой дефект можно только после полного удаления металла шва на этом участке.
Поверхностная пора (2017) — газовая пора, которая нарушает сплошность поверхности сварного шва
Усадочная раковина (202; R) — полость, образующаяся вследствие усадки во время затвердевания
Кратер (2024; К) — усадочная раковина в конце валика сварного шва, не заваренная до или во время выполнения последующих проходов
или
— дефект сварного шва, который образуется в виде углублений в местах резкого отрыва дуги в конце сварки. В углублениях кратера могут появляться усадочные рыхлости, часто переходящие в трещины.
Кратеры обычно появляются в результате неправильных действий сварщика. При автоматической сварке кратер может появляться в местах выводных планок, где обрывается сварочный шов. Кратеры уменьшают рабочее сечение сварочного шва, то есть снижают его прочность. Кроме того, в кратерах могут возникать усадочные рыхлости, которые способствуют образованию трещин. Кратеры вырубают до основного металла, зачищают и заваривают.
Дефекты группы 3 — Твердые включения
Подобные включения ослабляют сечение шва, снижают его прочность и становятся зонами концентрации напряжений.
Места швов с твердыми включениями вырубают до здорового металла или удаляют строжкой и впоследствии заваривают.
Твердое включение (300) — твердые инородные вещества металлического или неметаллического происхождения в металле сварного шва. Включения, имеющие хотя бы один острый угол, называются остроугольными включениями
Шлаковое включение (301; Ва) — шлак, попавший в металл сварного шва.
В зависимости от условий образования такие включения могут быть:
— линейными (3011)
— разобщенными (3012
— прочими (3013)
Шлак, образующийся при плавлении электродного покрытия или флюса, всегда всплывает на поверхность сварочной ванны. Шлак может оставаться внутри металла только при нарушении техники и технологии процесса (большим скорость сварки, неправильный наклон электрода, плохая зачистка ранее выполненного валика). Чаще всего шлаковые включения остаются в шве в результате подтекания шлака при выполнении корневых валиков и глубоких разделках. Сварка под флюсом кольцевых швов сопровождается шлаковыми включениями из-за несоблюдения рекомендуемой величины смещения электрода (зенита).
При сварке в защитных газах шлаковые включения встречаются редко. Шлаковые включения могут иметь размер до нескольких десятков миллиметров и поэтому являются очень опасными. Они уменьшают сечение шва и приводят к концентрации напряжений в нем.
Участок шва, на котором шлаковые включения превышают допустимые нормы, подлежит вырубке и переварке.
Флюсовое включение (302; G) — флюс, попавший в металл сварного шва
В зависимости от условий образования флюсовые включения могут быть:
— линейными (3021)
— разобщенными (3022)
— прочими (3023)
Флюсовые включения образуются из-за флюса, не вступившего в реакцию с расплавленным металлом шва и не всплывшего на поверхность сварного шва. Причиной образования флюсовых включений является использование флюса с большой грануляцией, завышение скорости сварки, случайном попадании гранул флюса в сварочную ванну.
Оксидное включение (303; J) — оксид металла, попавший в металл сварного шва во время затвердевания.
Оксидные включения получаются в результате образования труднорастворимых тугоплавких пленок. Чаше всего они возникают вследствие значительных поверхностных загрязнений или при нарушениях защиты сварочной ванны. Также окисные включения, могут возникать в металле шва из-за слабой их растворимости и слишком быстрого охлаждения.
Являясь прослойкой в массиве шва, оксидные включения резко снижают прочность сварного соединения и могут привести к. его разрушению под приложенной в процессе эксплуатации нагрузкой.
Металлическое включение (304, Н) — частица инородного металла, попавшая в металл сварного шва
Различают металлические включения из:
— вольфрама (3041)
— меди (3042)
— другого металла (3043)
Вольфрамовые включения возникают при нарушении зашиты сварочной ванны при сварке неплавящимся вольфрамовым электродом. Кроме этого, вольфрамовые включения возникают при коротких замыканиях или завышенной плотности тока. Особенно часто встречаются вольфрамовые включения при сварке алюминия и его сплавов, в которых вольфрам нерастворим.
Характерные признаки образования вольфрамовых включений — замыкания треск и резкая вспышка дуги. Расплавленный конец электрода при этом разбрызгивается и попадает в расплавленным металл в виде мелких (или одного крупного) включения. Если в момент замыкания металл шва был достаточно затвердевшим, вольфрамовое включение останется на его поверхности. Чаще всего электрод замыкается при отделении капли присадочного металла во время сварки стыков в различных (неудобных для сварки) пространственных положениях шва. Отделившийся от электрода кусок вольфрама увлекается расплавленным присадочным металлом внутрь шва.
Дефекты группы 4 — Несплавления и непровар
Несплавление (401) — отсутствие соединения между металлом сварного шва и основным металлом или между отдельными валками сварного шва.
Различают несплавления:
— по боковой стороне (4011)
— между валиками (4012)
— в корне сварного шва (4013)
Несплавления образуются при дуговой сварке из-за того, что дуга не расплавила часть кромки стыка и не сформировала шов с ее участием.
Чаще всего несплавления образуются из-за неправильного выбора формы угла и разделки, плохо зачищенной поверхности кромок, из-за плохой зачистки шва между проходами, химической неоднородности металла, неправильных режимов сварки (маленькая сила тока, завышенная скорость сварки).
Непровар (неполный провар) (402; D) — несплавление основного металла по всей длине шва или на участке, возникающее вследствие неспособности расплавленного металла проникнуть в корень соединения
или
местное нарушение сплавления между свариваемыми элементами, между металлом шва и основным металлом или между отдельными слоями шва при многослойной сварке.
Неполное проплавление (непровар) в стыковых соединениях может возникать в середине сечения при двусторонней сварке или в корне шва при односторонней сварке, как без подкладки, так и на формирующей подкладке, за счет неравномерного ее прилегания.
Характерной особенностью непровара являются его окончания, имеющие вид трещины, размеры которых, например для сплава АМг6, соизмеримы с межзеренными расстояниями. Непровар может также сопровождаться присутствием пор и оксидных включений.
В сварных соединениях, не чувствительных к непровару при статическом нагружении, ослабление сечения шва может быть скомпенсировано усилением или проплавом. Например, усиление шва в стыках труб из низкоуглеродистой стали с кольцевым непроваром по всей длине в корне шва при статических нагрузках полностью компенсирует ослабление сечения, создаваемое непроваром до 20 % от толщины стенки трубы. Сварные соединения, не чувствительные к непровару при статических нагрузках, могут снижать статическую прочность при секционной или многослойной сварке при низких температурах (- 60 — 70 °С). Это связано с повторным нагревом, который создает местную термопластическую деформацию и старение металла. В местах непровара снижается запас пластичности — охрупчивание, что ведет к резкому снижению прочности.
В результате непровара снижается сечение шва и возникает местная концентрация напряжений, что в конечном итоге снижает прочность сварного соединения. При вибрационных нагрузках даже мелкие непровары могут снижать прочность соединения до 40%. Большие непровары корня шва могут снизить прочность до 70%.
Непровар в корне шва происходит при недостаточной силе тока или при повышенной скорости сварки, непровар кромки шва — при смещении электрода с оси стыка, непровар между слоями — при плохой очистке предыдущих слоев, большом объеме наплавленного металла. Также причина образования непровара — плохая зачистка металла от окалины, ржавчины и загрязнений, малый зазор при сборке, большое притупление, малый угол скоса кромок, недостаточный сварочный ток, большая скорость сварки, смещение электрода от центра стыка.
Участки с непроварами приходится вырубать до основного металла, зачищать и вновь заваривать.
Группа 5. Нарушение формы шва
Нарушение формы (500) — отклонение формы наружных поверхностей сварного шва или геометрии соединения от установленного значения
Дефекты формы и размеров сварных швов снижают прочность и ухудшают внешний вид шва. Причины их возникновения при механизированных способах сварки — колебания напряжения в сети, проскальзывание проволоки в подающих роликах, неравномерная скорость сварки из-за люфтов в механизме перемещения сварочного автомата, неправильный угол наклона электрода, протекание жидкого металла в зазоры, их неравномерность по длине стыка и т.п. Дефекты формы и размеров швов косвенно указывают на возможность образования внутренних дефектов в шве.
Подрез непрерывный протяженный (5011; F) — углубление продольное на наружной поверхности валика сварного шва, образовавшееся при сварке
Подрез перемежающийся локальный (5012; F) — углубление продольное отдельными участками на наружной поверхности валика сварного шва
Подрезы приводят к ослаблению сечения основного металла и местной концентрации напряжений под влиянием рабочих нагрузок. При электродуговой сварке подрезы возникают при повышенном токе и напряжении дуги, а при газовой сварке — из-за повышенной мощности сварного пламени.
Подрезы часто образуются при сваривании горизонтальных швов на вертикальной плоскости. При ручной дуговом сварке угловых соединении причиной возникновения подрезов часто является неправильная техника выполнения швов, в частности неправильное положение электрода по отношению к оси шва, особенно при работе в стесненных условиях. Иногда подрезы образуются на внутренних валиках швов, выполненных аргонодуговой сваркой. Причиной их образования могут быть плохая сборка (смешение кромок), неточное ведение электрода по разделке.
Этот дефект обнаруживается визуально и при отклонениях выше установленной нормы полежит заварке тонким (ниточным) швов электродами малого диаметра.
Усадочная канавка (5013) — подрез со стороны корня одностороннего сварного шва, вызванный усадкой по границе сплавления
При сварке внутреннем валике иногда образуется усадочная канавка, расположенная по оси шва. Устранить ее можно уменьшением объема сварочной ванны. Для этого необходимо уменьшить притупление или изменить режим сварки увеличить ее скорость или уменьшить силу сварочного тока.
Превышение выпуклости стыкового шва (502) — избыток наплавленного металла на лицевой стороне стыкового шва сверх установленного значения
Превышение выпуклости углового шва (503) — избыток наплавленного металла на лицевой стороне углового шва (на всей длине или на участке) сверх установленного значения
В процессе сварки из-за неправильных режимов сварки, а также по ряду других причин (низкая скорость сварки, неудобное пространственное положение, однопроходная сварка в узкую разделку) при формировании шва избыток металла кристаллизуется в центре сварочной ванны в виде выпуклости, превышающей допустимые значения. Чрезмерную выпуклость другими словами называют превышением усиления шва.
Превышение выпуклости удаляют механическим способом — шлифовальным инструментом.
Превышение проплава (504) — избыток наплавленного металла на обратной стороне стыкового шва сверх установленного значения
Местное превышение проплава (5041) — местный избыточный проплав сверх установленного значения
Превышение проплава чаще всего возникает из-за плохой подготовки сварочных кромок (неодинаковый зазор в стыке, разной толщины металла по длине шва) и химической неоднородности свариваемого металла.
Неправильный профиль сварного шва (505) — угол α между поверхностью основного металла и плоскостью, касательной к поверхности сварного шва, менее установленного значения
Причины образования неправильного профиля сварного шва тождественны причинам превышения проплава.
Наплав (506) (он же наплыв) — избыток наплавленного металла сварного шва, натекший на поверхность основного металла, но не сплавленный с ним
Они могут быть местными — в виде отдельных застывших капель, а также иметь значительную протяженность вдоль шва. Причины образования наплывов — большой сварочный ток, слишком длинная дуга, неправильный наклон электрода, большой угол наклона изделия при сварке на спуск, плохая очистка свариваемых кромок. При выполнении кольцевых швов наплывы образуются при недостаточном или излишнем смещении электрода с зенита. В местах наплывов часто могут выявляться непровары, трещины и др.
Наплывы удаляют механическим способом, проверяя, нет ли в этих местах непровара.
Линейное смещение (507) — смещение между двумя свариваемыми элементами, при котором их поверхности располагаются параллельно, но не на требуемом уровне
Угловое смещение (508) — смещение между двумя свариваемыми элементами, при котором их поверхности располагаются под углом, отличающимся от требуемого
Натек (509) — металл сварного шва, осевший вследствие действия силы тяжести и не имеющий сплавления с соединяемой поверхностью.
В зависимости от условий это может быть:
— 5091 натек при горизонтальном положении сварки ;
— 5092 натек в нижнем или потолочном положении сварки;
— 5093 натек в угловом сварном шве;
— 5094 натекание в шве нахлесточного соединения
Чаще всего натеки образуются при выполнении горизонтальных сварных швов на вертикальной плоскости. Причины образования натеков и методы их устранения одинаковы с наплавами (наплывами).
Прожог (510) — вытекание металла сварочной ванны, в результате которого образуется сквозное отверстие в сварном шве
Прожоги чаще всего образуются на тонкостенных соединениях или соединениях с подкладными полосами, кольцами, когда сварку выполняют на повышенном режиме или при увеличенном зазоре между кромками. В местах прожога металл окисляется и становится рыхлым, непрочным, неплотным. По возможности такие участки тщательно зачищают до полного удаления некачественного металла. В недоступных для зачистки местах, где могут появиться прожоги, при сварке первого слоя следует обдувать обратную сторону шва защитным газом. Прожог может образоваться при внезапной остановке подачи защитного газа. При сварке поворотных кольцевых стыков прожоги вызываются неправильным расположением электрода относительно зенита.
Прожоги являются характерным дефектом сварки тонкостенных изделий: обечаек сильфонных компенсаторов, труб гибких металлических шлангов, арматуры с трубами. В процессе сборки этих деталей особенно важно соблюдать требования по точности обработки сопрягаемых поверхностей и качеству сборки. Размеры ванны здесь настолько малы, что малейшее нарушение в обработке или сборке приводит к изменению теплоотвода, а значит, к резкому изменению нагрева. В результате чрезмерного нагрева свариваемых кромок ванна мгновенно разрывается, каждая кромка оплавляется самостоятельно и образуется прожог.
Прожоги исправляют путем их вырубки, зачистки дефектных мест и заваривания.
Неполное заполнение разделки кромок (511) — продольная непрерывная или прерывистая канавка на поверхности сварного шва из-за недостаточности присадочного металла при сварке
Неполное заполнение разделки кромок возникает при неправильно выбранных режимов сварки (силы сварочного тока, скорости сварки), а также при неправильном выборе разделки кромок. Устранить данный дефект можно после зачистки и заварки дефектного места.
Чрезмерная асимметрия углового шва (512) — чрезмерное превышение размеров одного катета над другим
Чрезмерная асимметрия углового шва характерна при сварке металлов с различной теплопроводностью и неудобных пространственным положением сварки.
Нижеследующие дефекты в объяснениях не нуждаются т.к. причины возникновения неравномерной ширины шва, неровной поверхности, вогнутость корня шва заключается чаще всего в неправильно подобранных режимах сварки, неудобном положении при сварке, неправильным выбором разделки кромок.
Причины возникновения и методы устранения пор в корне шва идентичны газовым порам, а про дефект возобновление — все понятно из определения.
Неравномерная ширина шва (513) — отклонение ширины от установленного значения вдоль сварного шва
Неровная поверхность (514) — грубая неравномерность формы поверхности усиления шва по длине
Вогнутость корня шва (515) — неглубокая канавка со стороны корня одностороннего сварного шва, образовавшаяся вследствие усадки
Пористость в корне сварного шва (516) — наличие пор в корне сварного шва вследствие возникновения пузырьков во время затвердевания металла
Возобновление (517) — местная неровность поверхности в месте возобновления сварки
Группа 6.
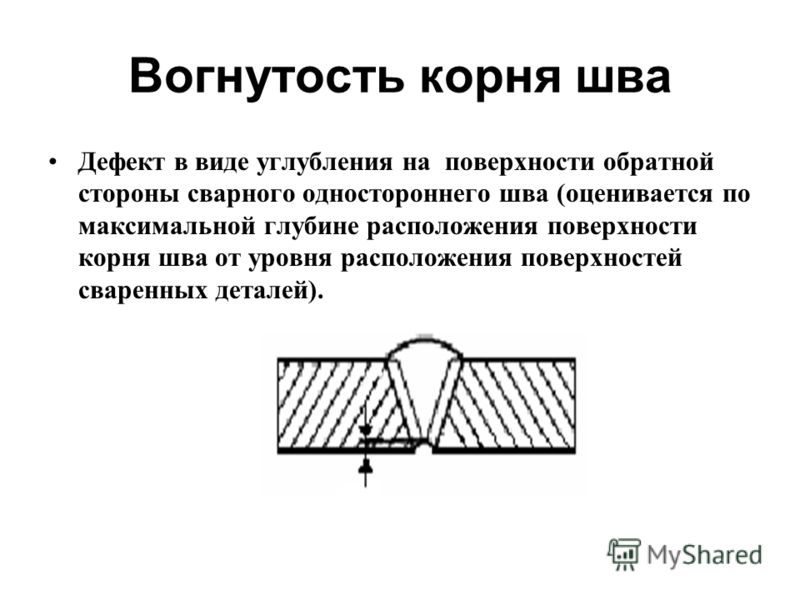
Прочие дефекты (600) — все дефекты, которые не могут быть включены в группы 1 — 5
Случайная дуга (601) — местное повреждение поверхности основного металла, примыкающего к сварному шву, возникшее в результате случайного горения дуги.
Случайная дуга особенна, опасна для нержавеющих сталей т.к. может быть причиной начала коррозии. При сварке закаливающихся сталей случайная дуга может стать причиной образования трещин.
Брызги металла (602) — капли наплавленного или присадочного металла, образовавшиеся во время сварки и прилипшие к поверхности затвердевшего металла сварного шва или околошовной зоны основного металла.
Да, да, да брызги металла тоже является дефектом (особенно в это трудно вериться начинающим сварщикам). Брызги на сваренном металле не только портят внешний (товарный) вид шва, но и являются очагами образования коррозии для нержавеющих сталей и местом образования трещин для закаливающихся сталей.
Вольфрамовые брызги (6021) — частицы вольфрама, выброшенные из расплавленной зоны электрода на поверхность основного металла или затвердевшего металла сварного шва
Поверхностные задиры (603) — повреждение поверхности, вызванное удалением временно приваренного приспособления
Вышеуказанные дефекты 6 группы достаточно легко исправимы необходимо просто удалить шлифованием данные места до «здорового» металла.
Утонение металла (606) — уменьшение толщины металла до значения менее допустимого при механической обработке
Если вы перестарались с удалением дефектов и неожиданно обнаружили утонение металла, сильно не расстраивайтесь — просто выполните наплавку в данном месте с последующей механической обработкой.
В ходе сварных работ, как и при любых других способах обработки металлов не исключены дефекты сварочных швов, образующихся по целому ряду причин.
Перечень факторов, влияющих на качество сварного соединения очень обширен, однако основной причиной дефектов являются неуправляемые химические процессы, происходящие в пограничных областях зоны сварки.
Причиной деффектов может быть кристаллизация металла, его химическая неоднородность, а также взаимодействие расплавленной массы с твердым материалом заготовок или с окружающими газами и шлаками. Ещё одной нуждающейся в учёте причиной появления дефектов (трещин, в частности) являются нежелательные напряжения в зоне сварки.
Характер отклонений сварных соединений от нормы (дефектов) зависит от . Это объясняется технологическими особенностями того или иного процесса.
Различие достаточно отчётливо проявляется во всех основных её видах, а именно – при электродуговой обработке металлов, контактном сваривании листовых заготовок и, наконец, в газовой сварке.
Электродуговой метод
К основным причинам образования дефектов при можно отнести два основных фактора. Это химические реакции, приводящие к нарушению структуры швов, а также серьёзные отклонения от существующих технологий.
Сварочные дефекты, возникающие во втором случае, чаще всего проявляются в виде прожогов, непроваров и нарушений геометрических размеров шва или трещин, возникающих после остывания материала.
Процесс образования холодных трещин при сварке объясняется недопустимыми механическими нагрузками на шовное соединение. Такие отклонения от нормальной структуры шва чаще всего наблюдаются при сваривании углеродистых (легированных) сталей, а также большинства чугунных изделий.
Вообще же в теории электродуговой сварки рассматриваются самые различные нарушения структуры сварного соединения. Помимо так называемого «холодного» растрескивания к таким дефектам причисляют «горячие», макроскопические и микротрещины.
Все перечисленные отклонения от нормы со временем приводят к расширению зоны действия дефекта и аварийным разрушениям некачественно проваренной конструкции. По этой причине исследованию качества образующихся при дуговой сварке швов уделяется повышенное внимание.
Газосварка
Основные причины дефектов, проявляющихся при газовой сварке, чаще всего те же, что и в перечисленных ранее случаях, касающихся других категорий сварочных работ.
Это те же нарушения в технологии подготовки заготовок перед сплавлением и ошибки, допущенные во время формирования шва (по причине использования нестандартных расходных материалов, например).
Вот почему с целью предупреждения дефектов газосварки особое внимание уделяется грамотному выбору правильного режима сваривания, а также уровню квалификации самого исполнителя работ.
По доступности выявления нарушений при газосварке все известные дефекты делятся на поверхностные и скрытые. К первой категории относятся типовые непровары, значительные по размеру наплывы, а также вогнутости, прорезы, кратеры, образующиеся на основании (в корне шва).
Сюда же следует отнести недопустимое смещение линии стыка (неправильная их разделка), резкие перепады по толщине и поверхностные трещины.
К скрытым и, как правило, трудно выявляемым дефектам газовой сварки относятся внутренние пористые образования, микроскопические газовые каналы, а также шлаковые и оксидные вкрапления.
Этот список может быть продолжен такими нередко возникающими нарушениями структуры свариваемых заготовок, как малозаметные непровары между слоями и внутренние микротрещины.
Точечный контактный метод
К дефектам контактного сваривания принято относить следующие визуально различимые (наружные) нарушения в структуре соединений:
- наблюдаемые невооружённым глазом трещины;
- точечные прожоги;
- наружные выплески;
- разрывы металла с поверхностным проявлением структуры;
- нарушения формы контакта и многие другие.
Основными причинами появления таких отклонений в структуре контакта являются неправильное выставление параметров (амплитуды или длительности) импульсного тока, недостаточное усилие при сжатии электродов.
К дефектам приводит некачественная подготовка обрабатываемых поверхностей перед сваркой, близкое расположение контактной точки к краю точечного соединения.
Среди других причин – недостаточная величина нахлеста заготовок, недопустимый перекос сочленяемых деталей, износ электродов и многое другое.
Основным скрытым дефектом при сварке контактными методами является «слипание» листовых заготовок, при котором между ними образуется лишь кажущийся, чисто внешний контакт. Данный дефект может проявляться не только при сварке под давлением, но и при других известных видах точечного сваривания.
Обнаружить визуально этот вид дефектного образования обычными методами физического контроля практически невозможно
. Предупредить его удаётся только путём строгого соблюдения технологии и поддержания в норме основных параметров сварочного процесса (амплитуды и длительности импульсного тока, а также необходимого усилия сжатия).
Исправление и предотвращение
Наличие дефектов при любом типе сварки не всегда приводит к непоправимому результату и выбраковке заготовки. Существует определённый набор нарушений техпроцесса или отклонений от нормы, которые могут быть исправлены сразу же по завершении процесса.
Простейшим и кардинальным способом исправления любого огреха при сварке является вырубка забракованного участка и повторное его заваривание (с учётом обнаруженной неисправности, конечно). Для исключения или исправления ряда дефектов вполне достаточно скорректировать положение рабочего инструмента с электродом.
При использовании этого приёма следует помнить о том, что сварка методом «на подъём» способствует перераспределению расплавленного металла в зоне ванны, а работа по способу «углом вперед» позволяет снизить глубину проплавления.
Поскольку на исправление брака потребуются дополнительные расходы – желательно так организовать сварочный процесс, чтобы исключить необходимость повторных работ.
Один из наиболее эффективных способов предотвращения дефектов – это добавление одного из компонентов при сварке в защитной среде, что позволяет увеличить коэффициент заполняемости шва и предотвращает возможные подрезы.
Для повышения текучести жидкого металла, обеспечивающей заполнение корневой части шва, достаточно нагреть предварительно место сварки до определённой температуры посредством специальных добавок (флюсов).
Достичь требуемого эффекта нередко удаётся и за счёт увеличением силы тока. При этом тщательная зачистка сварных кромок и удаление с их поверхности окисных плёнок также снижают вероятность нарушения режима сварки.
Разделка трещин
Для устранения холодных трещин применяется способ их повторной сварки с ограничением расширения области дефекта по обе стороны (подготовку специальных «уловителей»).
Такие уловители выполняются в виде небольших отверстий, просверленных на удалении порядка 1,5 см от краёв образования, способных замедлить или полностью прекратить его рост.
Ремонт трещин предполагает определенный порядок операций, учитывающий необходимость тщательной подготовки к повторному свариванию. На этом этапе подготавливаемые к восстановлению кромки сначала разделываются под углом 60 °.
Для проведения этой операции используется либо обычное зубило, либо специальный разделочный электрод, посредством которого края реза полностью очищают от всех мешающих сплавлению образований и неровностей.
Просверленные ранее ограничивающие отверстия-ловушки удалять совсем необязательно.
Наличие дефектов сварки, как правило, приводит к снижению прочностных показателей подготавливаемого соединения, и, как следствие – к нарушению работоспособности конструкции (её повышенной аварийности). Именно поэтому вопросу обнаружения и исправления дефектов всегда уделяется особое внимание.
Виды дефектов сварных швов
Дефекты, возникающие в сварных соединениях, разделяются на внешние и внутренние.
К внешним порокам швов, выполненных сваркой плавлением, относятся: неравномерность поперечного сечения, несоответствие размеров шва заданным по проекту, подрезы основного металла, наружные трещины в шве или рядом с ним, незаваренные кратеры и открытые поры.
Внутренними пороками являются непровары, загрязнение металла шва шлаковыми включениями, внутренние поры и трещины, перегрев металла шва и изменение свойств основного металла в зоне теплового влияния.
При контактной стыковой сварке возможны такие внешние дефекты, как смещение или перекос осей деталей в стыке. Внутренними дефектами являются непровары, расслоения, рыхлость, трещины, неметаллические включения и структурные изменения.
Рис. 1. Внешние дефекты сварных швов:
а — неравномерность сечения швов; б, в — несоответствие размеров (к) шва заданным; г, д — подрезы основного металла; е—трещины или поры
При точечной или роликовой сварке нахлесточных соединений могут быть следующие внешние дефекты: выплески, глубокие вмятины, подплавление поверхности деталей и трещины. Внутренними дефектами являются непровары, рыхлость, трещины в ядре и структурные изменения.
Рис. 2. Внутренние дефекты сварных швов: a,б, в — непровары; г, д — шлаковые включения; е — поры
Помимо перечисленных дефектов, возникающих в отдельных сварных соединениях в результате неправильных приемов работы, доброкачественных материалов или неисправности аппаратуры, инструментов и приспособлений, а также вследствие неправильно установленных режимов сварки, имеют место дефекты сварных изделий (конструкций) в целом.
К таким дефектам относятся деформации конструкций, вызываемые действием усадки швов, и отклонения от проектных размеров.
Классификация видов и способов контроля
Для обеспечения высокого качества сварных соединений необходим постоянный и тщательный контроль их производства, начиная от контроля исходных материалов и заготовок и кончая испытанием готовой продукции.
Борьбу за качество продукции, выпускаемой сварочными цехами, ведут как по линии разработки методов обнаружения и исправления дефектов, так и по линии изучения причин возникновения брака. На основе анализа причин появления дефектов разрабатывают мероприятия для предупреждения брака продукции.
Различные профилактические мероприятия имеют особую ценность для производства, так как обеспечивают нормальный ход производства, гарантируют своевременное выполнение производственного плана и способствуют снижению себестоимости выпускаемой продукции.
Разнообразие дефектов в сварных швах и особенно возможность появления скрытых дефектов затрудняет технику выполнения контрольных операций и приводит к необходимости разработки специальных методов контроля.
Все контрольные операции, применяемые в сварочном производстве, можно разделить в хронологическом порядке на следующие группы: предварительный контроль, контроль в процессе сварки (текущий контроль) и заключительный контроль (приемо-сдаточные испытания).
Элементы, входящие в каждую из этих групп, показаны на классификационной схеме 2.
Классификация способов контроля процесса изготовления сварных конструкций.
Разбираем сварку в деталях. Основные дефекты сварных швов и их устранения.
Разбираем сварку в деталях!
В процессе работы в силу разных причин каждый сварщик сталкивается с разными дефектами сварного шва. О том какими бывают эти дефекты, в чем их основная причина и как их устранять, наши советы от профессионалов. Все виды образующихся дефектов швов делятся на три группы:
Наружные, к ним относятся: трещины, подрезы, наплывы, кратеры Внутрение, чаще всего бывают: пористость, непровары и посторонние включения Сквозные — трещины, прожоги
1. Наплывы. Они образуются в процессе натекания жидкого металла на кромки основного шва, который был недостаточно прогрет. Чаще всего наплывы образуются при сварке горизонтальных швов.
Устранение. Наплывы необходимо срубать и проверять нет ли на их месте непровар
2. Подрезы. Это места уменьшения основного металла на месте его перехода к усилению шва. Они приводят к ослаблению сечения основного металла и могут стать причиной разрушения сварного соединения.
Устранение. Подрезы следует устранять подваркой ниточного шва. Для предотвращения данного дефекта следует более точно подбирать сварочный режим.
3. Прожоги. Это сквозное проплавление основного металла с натеками на обратную сторону свариемого металла. Прожог возникает в случаи большого зазора между свариваемыми кромками, при недостаточном притуплении кромок, при завышенной мощности сварного пламени и при недостаточной скорости сварки.
Устранение. Прожоги устраняются вырубкой дефектных мест с последующей их заваркой.
4. Незаваренные кратеры. Образуются в результате резкого обрыва пламени в конце сварки. Они уменьшают сечения сварочного шва, снижают его прочность и могут стать причиной образования трещин.
Устранение. Устраняются вырубкой основного металла с последующей заваркой.
5. Непровар. Это местное несплавление оновного металла с наплавлением, а также несплавление между собой слоев шва при многослойной сварке. Образуется из-за неправильной подготовке кромок под сварку, недостаточной мощности сварочного пламени, большой скорости сварки, присутствием шлака и ржавчины.
Устранение. Участки вырубают и затем заваривают. 6. Шлаковые включения в сварном шве. Образуется при зачистке свариваемого металла и присадочной проволоки, а также при неправильном выборе сварочных режимов. Шлаковые включения ослабляют сечения шва снижают прочность и являются концентрации зонами напряжения.
Устранение. Места швов со шлаковыми включениями необходимо вырубать и заваривать. 7. Трещины. Это наиболее опасные дефекты сварных швов. Трещины могут возникать в сварочном шве и в околошовной зоне. Они могут образовываются во время и после сварки. Причиной их может являться как несоблюдения режимов сварки, так и неправильное расположения сварных швов в конкретной конструкции. Это вызывает высокое напряжение приводящая, часто к полному разрушению конструкции.
Устранение. Поверхностные трещины в сварных швах следует вырубать полностью и заваривать. Что бы во время вырубки трещина не распространялись дальше по шву, края ее следует засверлить.
8. Перегрев металла. Он возникает при большой мощности сварочного пламени и малой скорости сварки. При этом увеличиваются размеры зерен в металле шва и в околошовной зоне, что снижает механические свойства сварного соединения, в особенности ударную вязкость.
Устранение. Перегрев металла можно исправить, только последующей термической обработкой
9. Пористость в сварных швах. Появляется в следствии возникновения большого количества газов в жидком металле сварной ванны, которые не успевают выйти до затвердевания сварного шва. Иногда поры выходя на поверхность образуют свищи, которые бывают внутренними, наружными и сквозными.
Устранение. Участки сварных швов с порами, следует вырубать и заваривать.
10. Пережог металла. Наиболее опасный дефект. При пережоге металла шва появляются окисленные зерна, обладающие малым взаимным сцеплением из за наличия на них оксидной пленки. Пережженный металл хрупок и не поддается исправлению.
Устранение. Участки с переженным металлом следует вырубать до основания металла и заваривать.
03 ноября 2014 г.
Типы, причины и способы устранения (с PDF и викториной)
Здравствуйте, это Амрит, в сегодняшней статье я расскажу о сварочных дефектах .
Как мы уже знаем, сварка — обширная тема, по сварке написано бесчисленное множество книг, так что представьте, насколько важна эта тема!
Не волнуйтесь, я разделил дефекты сварки на несколько основных частей, и этого достаточно для вашего диплома или любого бакалавриата.
Ниже приводится статья, в которой я упомянул типов сварочных дефектов, их причины и способы устранения. Я написал эту тему на очень понятном языке, а также прилагаю PDF-файл этой статьи, чтобы после прочтения вы могли загрузить PD F для автономных занятий.
Что такое дефекты сварки?
Дефекты сварки возникают при сварке из-за неисправной или некачественной техники , использованной неопытным или неквалифицированным сварщиком, или из-за фундаментальных трудностей при сварке .
Идеальный сварной шов или хороший сварной шов должен быть таким, чтобы имелся адекватное сплавление между присадочным металлом и подготовкой кромки вместе с хорошим проплавлением.
Виды дефектов сварки:
Сварочные дефекты в целом подразделяются на две категории:
- Наружные дефекты сварки (Дефекты возникают на верхней поверхности сварного изделия).
- Внутренние сварочные дефекты (Дефекты возникают под поверхностью сварных работ).
Теперь Дефекты внешней сварки подразделяются на следующие типы:
- Неправильный профиль (сварка выполнена неправильно).
- Кратер (большая полость возникает, когда искры электрода непрерывно попадают в одну точку).
- Трещины.
- Брызги и поверхностная пористость (на свариваемых деталях появляются капли).
- Канавка заполнена не полностью (заполнена не полностью).
- Деформация (возникает при неправильной сварке).
и Внутренние сварочные дефекты относятся к следующей категории:
- Волны и внутренняя пористость.
- Трещины.
- Включения.
- Отсутствие плавления.
- Неполный сплав.
Вот несколько причин дефектов сварки и способы их устранения:
Ниже я упомянул дефекты сварки и способы их устранения.
Неполное проникновение:
Неполный провар возникает, когда глубина сварного шва недостаточна.
Проникновение определяется как расстояние от верхней поверхности опорной плиты до максимальной степени самородка шва.
Причины неполного проникновения:
- Неправильные соединения.
- Слишком большая поверхность корня, зазор корня и коническая шестерня.
- Неправильное удерживающее положение электрода.
- Слишком большой диаметр электрода и большая длина дуги.
- Меньший ток дуги и более высокая скорость хода дуги.
- Неправильная полярность при сварке на постоянном токе.
Средства от неполного проникновения:
- Увеличение тепловложения.
- Снижение скорости движения во время сварки.
- Обеспечение правильного прилегания соединяемой поверхности.
- Изменение конструкции шарнира.
Включение:
Это может быть шлак или любой другой посторонний материал, который не имеет возможности плавать на поверхности затвердевающего металла шва и, таким образом, попадает внутрь него.
Инклюзия снижает прочность соединения и делает его более слабым.
Причины включения:
- Слишком большой или слишком низкий ток дуги.
- Длинная дуга и слишком большой диаметр электрода.
- Слишком маленький угол наклона шарнира.
- Недостаточное выкрашивание и очистка предыдущих проходов при многопроходной сварке.
- Неправильно расположенные прихваточные швы.
Средства от включения:
- Очистка поверхности сварочного стана перед нанесением следующего слоя проволочной щеткой.
- Обеспечение достаточного количества защитных газов.
- Изменение конструкции соединения таким образом, чтобы оставалось достаточно места для правильного обращения с лужей расплавленных металлов сварного шва.
Пористость и раковины:
Пористость представляет собой группу небольших пустот, а газовые пузыри представляют собой изолированные отверстия или полости сравнительно большего размера.
В основном они образуются из-за захваченных газов.
Причины пористости и раковин:
- Использование неподходящего электрода и более длинная дуга
- Более высокая скорость распространения дуги.
- Слишком малый и слишком большой ток дуги.
- Из-за захвата газа при затвердевании сварного шва.
- Грязная рабочая поверхность, т.е. наличие окалины, ржавчины, масла, жира и т. Д. На поверхности работы.
Средство от пористости и пузырей:
- Правильный выбор электродных и присадочных материалов.
- Усовершенствуйте методы сварки, такие как предварительный нагрев области сварного шва или увеличение количества подводимого тепла.
- Уменьшение скорости сварки, чтобы дать время для выхода газа.
- Правильная очистка и предотвращение попадания загрязнений в зону сварного шва.
Брызги:
Брызги — это мелкие частицы металла, которые выбрасываются из дуги во время сварки и осаждаются на основном металле вокруг сварного шва по всей его длине.
Причины разбрызгивания:
- Чрезмерный ток дуги.
- Использование более длинной дуги, влажных электродов.
- Электрод покрыт неправильными ингредиентами флюса.
- Из-за расширения пузырьков газа, захваченных в расплавленных глобулах металла.
Средства от брызг:
- Используйте правильный ток дуги для сварки, длину дуги, свежие электроды.
- Использование переменного тока для уменьшения дуги.
Искажения:
Деформация — это изменение формы и разница между положением двух пластин до и после сварки из-за температурного градиента, присутствующего в различных точках на стыках.
В целом, можно сказать, что деформация возникает из-за неравномерного расширения и сжатия металла шва, и все виды деформации увеличиваются с увеличением объема наплавленного металла.
Деформацию сварного шва можно разделить на три типа:
- Продольная усадка (происходит параллельно линиям сварного шва).
- Поперечная усадка (перпендикулярная).
- Угловая усадка (вращение вокруг линий сварки).
Причины искажений:
- Большое количество проходов электродами малого диаметра.
- Низкая скорость перемещения дуги.
- Высокие остаточные напряжения в свариваемом листе.
- Использование неправильной последовательности сварки.
Средства от искажения:
- Используйте необходимое количество сварочного металла в соответствии с требованиями к стыку. Это уменьшит силы сжатия.
- Используйте соответствующее количество сварочных проходов.
- Поместите сварной шов около нейтральной оси.
- Соблюдайте правильную последовательность сварки.
Кроме того, существуют другие средства для предотвращения искажений, а именно:
- Сократите время сварки, чтобы не было возможности расширения слишком большого объема металла.
- Пока большие сварные детали в узлы.
- Упрочнение должно выполняться для снятия усадки во время или после сварки.
- При необходимости вы можете часто использовать штангенциркуль для точного измерения, чтобы обеспечить точность размеров.
Поднутрение Сварочные дефекты:
Поднутрение — это своего рода дефект сварного шва, который образует бороздку в основном металле вместе со сторонами сварного валика.
Канавка уменьшает толщину листа, а также снижает прочность сварного шва.
Под катомПричины поднутрения:
Неправильная манипуляция и наклон электрода и чрезмерное плетение.
- Слишком большой диаметр электрода.
- Более длинная дуга.
- Более высокая скорость перемещения дуги.
- Магнитная дуга.
- Более высокий ток.
Средства устранения поднутрения:
- Используйте электроды соответствующего тока дуги.
- Ткачество должно быть правильным и соответствовать требованиям.
- Используйте правильную скорость хода дуги.
Дефекты сварки горячим отрывом:
В этом дефекте сварки в горячем наплавленном металле начинает образовываться трещина с ближайшего края, так что после его затвердевания трещина увеличивается.
Горячий разрыв также известен как растрескивание при затвердевании из-за разрыва границ зерен металла шва до того, как произойдет полное затвердевание, и металл все еще находится в пластическом состоянии.
Причины горячей слезы:
- Неправильный выбор материалов.
- Неправильный сварочный ток.
- Неправильная толщина электрода.
Средство от горячей слезы:
- Выберите подходящий материал электрода.
- Сварочный ток должен быть оптимальным согласно требованиям.
- Толщина электрода должна быть оптимальной и соответствовать свариваемому основному металлу.
Возможно, вам будет интересно прочитать эти статьи о сварке:
Аппарат для дуговой сварки: типы и детали
Газовая сварка: определение, типы и оборудование
Сварка TIG: детали и принцип работы
Сварка сопротивлением: детали и Рабочий
Плазменная сварка Аппарат для дуговой сварки
Сварка под флюсом
Вот видео о реальных дефектах сварки:
Источник видео: Weld.com Источник видео: Weld.comКраткое описание:
Что такое дефекты сварки?
Дефекты сварки возникают при сварке из-за неисправной или некачественной техники , использованной неопытным или неквалифицированным сварщиком, или из-за фундаментальных трудностей при сварке .
Какие бывают типы сварочных дефектов?
Дефекты сварки подразделяются на следующие типы : неправильный профиль, кратер, трещины, разбрызгивание и поверхностная пористость, неполная заполненная канавка, деформация, раковины и внутренняя пористость, трещины, включения, отсутствие сплавления, неполное сплавление.
Вывод:
В области машиностроения о сварке можно слышать довольно часто. Это один из неразъемных соединений , которые мы используем.
Сегодня мы рассмотрели сварочных дефектов и причин сварки, а также знаем, как предотвратить сварочные дефекты .
Теперь я хочу услышать от вас. Если вам нравится моя статья, поделитесь с друзьями, а также в социальных сетях.И . Если у вас есть какие-либо сомнения, вы можете прокомментировать ниже свои сомнения или все, что вы хотите мне сказать. Я люблю слышать ваше мнение и предложения.
У нас также есть специального сообщества Facebook для вас, ребята, если вы хотите, вы можете присоединиться к нашему сообществу, вот ссылка на нашу группу Facebook . Итак, ура, и наслаждайтесь остатком дня.
Кроме того, я написал статью о деталях, типах и операциях токарного станка, а также о деталях, типах и работе Shaper Machine, возможно, вам будет интересно ее прочитать.
Артикул:
Сообщите нам, понравился ли вам пост. Это единственный способ стать лучше.
Дефект сварки — обзор
12.2 Влияние дефектов сварки на коррозию металла шва
Дефекты сварки, такие как шлак и другие захваты, трещины, микротрещины, пористость, включения, непровар и сплавление и т. Д., Оксиды и другие отложения и т. д. ухудшают коррозионные свойства металла шва. Эти дефекты обычно вызывают ранние точечные образования и трещины в металле шва [3, 4].Сульфидные включения являются наиболее уязвимыми участками для точечной коррозии и щелевой атаки; однако другие неметаллические включения также могут вызывать образование ямок. Кроме того, эти дефекты действуют как области концентрации напряжений, которые способствуют более быстрому инициированию SCC. Неметаллические включения, такие как сульфиды, нежелательны с точки зрения SCC. Влияние неметаллических включений на сокращение срока службы SCC напрямую связано с легким инициированием питтинговой коррозии на участках включения [5]. В кислых растворах и, следовательно, в закупоренных ячейках сульфидные включения растворяются с образованием H 2 S, который ускоряет коррозию стали [6].Сообщается, что H 2 S ускоряет как анодные, так и катодные процессы [5]. Во многих приложениях SCC инициируется из ям, которые действуют как сборщики стресса [7, 8]. В этих случаях время индукции для SCC было больше, чем для питтинга [7]. По-видимому, неметаллические включения не принимают непосредственного участия в зарождении трещин, но их присутствие нежелательно, так как они вызывают точечную коррозию. Кларк и Гордон [9] сообщили, что трещины возникли в результате щелевой коррозии вокруг включенной частицы.Неметаллические включения также играют роль в водородном охрупчивании (ВВ) сварных швов нержавеющей стали. Поверхностные включения облегчают попадание водорода в сварной шов и тем самым вызывают растрескивание [5]. Объемные включения могут действовать как места захвата водорода и, таким образом, способствовать зарождению и развитию внутренних щелей и трещин [5]. Форма сульфидного включения влияет на время зарождения трещины. Удлиненные частицы сульфида могут увеличивать проникновение водорода в металл в шесть раз по сравнению со сферическими включениями [5].Неметаллические включения также вызывают концентрацию напряжений в материале. Степень концентрации напряжений будет зависеть от формы включения [5]. Включения с острыми краями действуют как более эффективные выемки, чем включения сферической или эллиптической формы. Помимо формы, отношение коэффициентов теплового расширения и модуля упругости включения к матрице также в меньшей степени влияет на определение величины концентрации напряжений [5]. Помимо сульфидных включений, металлы сварного шва могут содержать другие включения, возникающие в результате реакций окисления и раскисления в расплавленном металле сварного шва.Они также могут содержать включения шлака, которые могут возникать в результате захвата шлака затвердевшим валиком сварного шва. Степень улавливания шлака определяется покрытием флюсом сварочного материала. Рутиловые покрытия обеспечивают легкость отделения шлака и хорошую форму валика. Сварка в неправильном положении также может вызвать улавливание шлака.
При разработке сварочных материалов обычно корректируют состав металла сварного шва, добавляя легирующие элементы во флюс. Во время сварки эти элементы могут плохо перемешиваться в ванне расплава, в результате чего остаются области, богатые этими элементами, которые могут действовать как центры зародышеобразования для локального коррозионного воздействия.Например, в морских установках покрытие электрода содержит частицы ферромагнезита, которые, если они не смешиваются равномерно в металле сварного шва, оставляют участки более твердые, чем прилегающая матрица [10]. Эти жесткие области предоставляют площадки для инициации SCC в кислой среде. Определенные меры во время сварки, такие как увеличение сварочного тока, уменьшение скорости движения или ширины переплетения, могут помочь в решении проблемы.
Пористость может привести к более быстрому инициированию язвенной коррозии или SCC, поскольку они действуют как места для концентрации напряжения [11].Соответствующий выбор подводимого тепла может уменьшить пористость металла шва. Трещины и микротрещины также способствуют снижению локальной коррозионной стойкости металла шва. Сварной элемент может растрескиваться во время сварки, или сразу после сварки, или во время эксплуатации, или во время термообработки после сварки (PWHT) затвердевшего металла шва, HAZ основного металла или HAZ металла сварного шва. Эти трещины могут действовать как места возникновения трещин или как трещины. В нержавеющих сталях и сплавах на основе никеля микротрещины и горячие трещины представляют собой серьезную проблему.C-Mn-стали и низколегированные стали обычно подвергаются холодному растрескиванию и растрескиванию при повторном нагреве. Подрезы, неплавление и непровар — предпочтительные места для коррозии. Разумный выбор конструкции сварного соединения, параметров сварки, расходных материалов и процесса сварки может помочь избежать проблем с коррозией, связанных с такими неисправными соединениями. Определенные конструкции соединений, такие как соединения внахлестку и колышки, могут привести к атаке щелевой коррозии, и их следует избегать; вместо этого предпочтительны стыковые соединения с полным проплавлением [12].В некоторых приложениях обычной практикой является использование сварочных вставок, которые могут не плавиться должным образом в металле шва и оставлять участки, которые могут стать склонными к разрушению щелей. В дополнение к проблемам щелевой коррозии образованные таким образом щели будут действовать как концентраторы напряжения и вызывать SCC. При сварке сталей, если электроды обожжены, количество водорода, которое увеличивает проплавление валика, уменьшается, что приводит к отсутствию дефектов проникновения в металл шва.
Дефекты сварки — классификация, причины и способы устранения
Любая неоднородность (или неравномерность) в металле сварного шва, превышающая допустимый предел кода, называется ДЕФЕКТ СВАРКИ (или Дефект сварки). Обратите внимание, что разрыв может быть назван дефектом только тогда, когда , если он превышает указанный предел кода , следовательно, мы можем сказать, что каждый дефект, присутствующий в металле сварного шва, является разрывом, но каждый разрыв, присутствующий в металле сварного шва, не может обязательно будет дефект. Дефект может быть макроскопическим или микроскопическим.
(Примечание: несплошность также обозначается как «отражатель » в некоторых кодах и текстах)
Дефекты могут возникать по следующим причинам; 1.Неправильные параметры сварки
2. Несоответствующие процедуры сварки
3. Плохое состояние процесса
4. Неправильный выбор присадочного металла и основного металла
5. Неквалифицированный сварщик или сварщик
6. Неправильная подготовка к работе
Дефекты можно классифицировать как внешний дефект (также известный как визуальный дефект или поверхностный дефект) или внутренний дефект (также известный как скрытый дефект или внутренний дефект). Внешние дефекты — это дефекты, которые обнаруживаются на самой поверхности. Внутренние дефекты — это те, которые существуют в материале на некоторой глубине. Можно сказать, что дефекты, которых нет на поверхности, — это внутренние дефекты. См. Следующую таблицу;
Различные типы сварочных дефектов, а также их причины и способы устранения описаны ниже; 1. ТРЕЩИНЫ:Это самый опасный дефект.Трещины могут быть любого размера и формы; он может быть микроскопическим или макроскопическим. Трещины могут появиться где угодно, то есть на поверхности, под поверхностью, на любой глубине или в корне. Трещина возникает, когда локализованное напряжение превышает предельное растягивающее напряжение (UTS) материала. Он может размножаться внутри материала.
Трещины бывают двух типов; ГОРЯЧИЕ ТРЕЩИНЫ:Горячие трещины возникают во время сварки или вскоре после ее завершения. Наиболее вероятно, что они возникнут во время затвердевания расплавленной сварочной ванны.Горячие трещины в основном возникают в металле сварного шва, но могут возникать и в зоне термического влияния (ЗТВ).
Когда на металле сварного шва возникает горячая трещина, это называется трещиной затвердевания, а если она возникает в ЗТВ, то трещиной ликвации.
Причины возникновения горячих трещин:
1. Высокая концентрация остаточного напряжения
2. Быстрое охлаждение сварочной ванны
3.Большая толщина основного материала
4. Плохая пластичность свариваемого материала
5. Большой сварочный ток
6. Недостаточная термообработка
Профилактика:
1. Предварительный нагрев и последующий нагрев во избежание быстрого охлаждения
2. Использование правильного присадочного металла
Холодные трещины возникают после затвердевания металла шва; он может развиться даже через несколько дней после завершения сварки.Чаще всего он развивается в ЗТВ, но может встречаться и на металле сварного шва. Часто это связано с неметаллическими включениями.
Причины холодных трещин:
1. Диффузия атомов водорода: Атомы водорода вызывают холодное растрескивание. Эти атомы водорода могут быть индуцированы в металле сварного шва из окружающей среды, электрода, основного металла или любого загрязнения, присутствующего на поверхности основания.
2. Отсутствие предварительного нагрева: Из-за недостаточного предварительного нагрева могут иметь место изменения микроструктуры.Микроструктурные кристаллы могут перестраиваться с образованием мартенсита. Мартенсит очень склонен к образованию трещин. Предварительный нагрев также помогает уменьшить диффузию атомов водорода и гарантирует отсутствие влаги на стыке перед сваркой.
Профилактика:
1. Предварительный нагрев и последующая сварка металла шва
2. Использование электрода с низким содержанием водорода
Звездчатая трещина представляет собой трещину. тип горячей трещины, которая развивается в кратере на металле шва.Кратер — это углубление, образовавшееся на сварном шве в месте разрыва дуги или при замене электрода.
Он возникает, когда центр сварочной ванны затвердевает раньше, чем ее окружает, и из-за этого центр растягивает внешний сварной шов и, таким образом, образуются звездообразные трещины.
Пористость представляет собой неоднородность в виде полостей и возникает из-за улавливания газов в расплавленной сварочной ванне. У этих захваченных газов нет шанса выйти из расплавленной сварочной ванны и, следовательно, вызвать пористость или образование пузырей.Пористость в основном представляет собой небольшую пору или пустоту, тогда как газовые раковины представляют собой сравнительно большие отверстия или полости.
Пористость может присутствовать на поверхности или внутри металла шва. Пористость может возникать индивидуально или также в группах (в основном), группа пористости известна как кластерная пористость.
Пористость бывает пяти основных типов, это;
- Рассеянная пористость
- Кластерная пористость
- Пористость труб
- Линейная пористость2
3
0
26 Улавливаемые газы, вызывающие пористость, в основном представляют собой водород, монооксид углерода, диоксид углерода, азот и кислород.Эти газы образуются из-за флюсов, присутствующих на сварочном электроде, влаги, масла, смазки и других посторонних загрязняющих веществ, присутствующих на стыке, сварочном электроде или присадочной проволоке. Недостаточный поток защитного газа также вызывает пористость при сварке GMAW, FCAW, GTAW и PAW.Профилактика:
- Используйте электрод с низким содержанием водорода
- Обжиг электродов перед сваркой в соответствии с рекомендуемой процедурой
- Тщательная очистка поверхности стыка и прилегающей поверхности область перед сваркой
- Предварительно нагрейте соединение перед сваркой
- Обеспечьте достаточный поток защитных газов при использовании сварки TIG или MIG
Поднутрение выглядит как узкая канавка на основном металле рядом с металлом сварного шва вдоль кромки. Выточка всегда проходит параллельно металлу шва. Он действует как фактор, повышающий напряжение при усталостной нагрузке.
Причины подрезов:
4. НЕЗАЛИВКА:
1. Высокий сварочный ток и напряжение дуги
2. Большой диаметр электрода
3. Неправильный угол электрода
4 .Более длинная дугаКогда поверхность металла шва остается ниже прилегающей поверхности основного металла, это называется недозаполнением. В основном Underfill — это сварка заниженных размеров.
5. ОТСУТСТВИЕ ПРОНИКАНИЯ (НЕПОЛНОЕ ПРОНИКАНИЕ):Когда металл сварного шва не полностью проникает в соединение, это называется Недостаточным проникновением или неполным проникновением.Это один из самых опасных дефектов, поскольку он увеличивает напряжение, и, следовательно, трещина может возникать или распространяться оттуда.
Причины непроницаемости:
1. Слишком маленький корневой зазор
2. Высокая скорость перемещения
3. Низкое тепловложение 4
Слишком большой диаметр электродаПрофилактика:
1.Правильная подготовка швов, т.е. обеспечение подходящего корневого зазора.
2. Правильный подвод тепла
3. Правильная скорость движения
4. Использование электрода подходящего размераОтсутствие проплавления можно устранить путем правильной строжки.
6. ОТСУТСТВИЕ ПЛАВЛЕНИЯ (НЕПОЛНАЯ ПЛАВЛЕНИЕ):Это отсутствие надлежащего плавления (или надлежащего плавления) либо между металлом шва с основным металлом, либо между одним слоем сварного шва с другим. слой.Отсутствие сварки также называется холодной притиркой или холодным швом. Одна из наиболее очевидных причин отсутствия плавления — плохая техника сварки. Отсутствие сплавления является внутренним дефектом, но оно может возникать и на внешней поверхности, если боковая стенка основного металла не сплавляется должным образом с основным металлом, как показано на рисунке ниже, и в этом случае отсутствие плавления также может быть называется «отсутствие плавления боковин».
Причины отсутствия слияния:
7. БРЫЗГИ:
1.Низкий сварочный ток
2. Высокая или слишком низкая скорость движения
3. Неблагоприятное тепловложениеБрызги — это маленькие глобусные металлические капли (из металл шва), выплеснувшийся на основной металл во время сварки. Брызги налипают на основной металл, поэтому их можно удалить металлической щеткой или полировкой.
Причины брызг:
Нахлест:
1.Чрезмерный ток дуги
2. Чрезмерно длинная дуга
3. Неправильный защитный газ
4. Электрод с неправильным потоком
5. Демпфирующие электродыНахлест возникает из-за перетекания металла шва на поверхность основного металла. Во время сварки расплавленный металл перетекает на основной металл без сплавления с основным металлом.
Причины перекрытия:
9. ЧРЕЗМЕРНОЕ ПРОБИВАНИЕ:
1. Слишком низкий ток
2. Большое осаждение за один проход
3. Более длинная дуга
4. Медленная скорость прохождения дугиКогда проплавление металла шва через соединения слишком велико, это называется чрезмерным проваром.Он действует как выемка, где происходит концентрация напряжения. Кроме того, это приводит к экономическим потерям.
Причины чрезмерного проникновения:
1. Слишком большой зазор корня
2. Большой сварочный ток
3. Медленная скорость хода10. ВКЛЮЧЕНИЕ:
Любой захваченный твердый материал (металлический или неметаллический) в металле сварного шва называется включением.Вольфрам, оксиды, шлак и флюс — некоторые из распространенных посторонних материалов, которые захватываются расплавленной сварочной ванной и образуют включения.
Включение может происходить в большинстве процессов сварки плавлением, но очень часто встречается в процессах дуговой сварки в защитном флюсе, таких как дуговая сварка в защитном металлическом корпусе (SMAW), дуговая сварка под флюсом (FCAW) и сварка под флюсом (SAW).
Включение вольфрама происходит в тех сварочных процессах, которые используют «вольфрам» в качестве электродов, таких как сварка TIG и плазменная дуговая сварка (PAW)
Включения бывают четырех типов:- Включение вольфрама
- Включение оксида
- Включение шлака
- Включение флюса
Когда шлак попадает в состав ускользнуть из расплавленной сварочной ванны, то такое включение называется включением шлака.Аналогичным образом, иногда капли вольфрама захватываются металлом сварного шва, что приводит к включению вольфрама (при сварке TIG или плазменно-дуговой сварке — PAW). Поверхностные оксиды также захватываются, что приводит к включению оксидов. Слова «флюс» и «шлак» часто используются как синонимы, но они разные. Флюс — это покрытие электрода (твердый материал, покрывающий электрод), тогда как шлак — это побочный продукт, образующийся в результате реакции между флюсом и расплавленным металлом сварочной ванны.
Включение действует как усилитель стресса, поэтому его следует избегать.
11. ДОРОЖКИ ВАГОНА:Линейные включения шлака вдоль оси сварного шва называются путями вагона. Во время корневого прохода из-за неправильной техники сварки на носке образуется канавка, и эта канавка заполняется шлаком (особенно водородом, захваченным затвердевшим шлаком), и, таким образом, образуются пути вагонов. Он также известен как следы червя.
12. УДАР ДУГИ:Когда электрод или электрододержатель непреднамеренно или случайно попадает в заготовку, возникает нежелательная дуга, вызывающая зажигание дуги.Разряды дуги могут вызвать отказ при изгибе и циклическом нагружении. Помимо этого, это также влияет на эстетику заготовки.
13. ПОЛОСТЬ УСАДКИ:Во время затвердевания расплавленной сварочной ванны происходит усадка металла. Из-за усадки металла сварного шва образуется полость, известная как полость усадки.
Щелкните здесь, чтобы ознакомиться с критериями приемки / отклонения дефектов сварных швов. Пожалуйста, посмотрите эту видеолекцию (приведенную ниже), чтобы лучше понять дефекты сварки:Справочник — Дефекты сварного шва
Справочник — Дефекты сварного шва 3 Продолжение на следующей странице… ОТСУТСТВИЕ СЛИЯНИЯ Отсутствие плавления, также называемое холодной притиркой или холодный шов, когда нет плавления металла шва и поверхности опорной плиты. Этот дефект можно увидеть на рис. 10-2. Самая частая причина нехватки сварки — это плохая техника сварки. Либо сварочная ванна слишком велика (слишком низкая скорость движения), либо металл сварного шва был допущен к прокатке перед дугой. Опять же, дугу нужно держать на передней кромке лужа.Когда это будет сделано, сварочная ванна не будет слишком большой и не сможет погасить дугу. Другая причина — использование очень широкий сварной шов. Если дуга направлена вниз по центру стыка, расплавленный металл шва будет только течь и литой против боковых стенок опорной плиты без их плавления. В тепло дуги необходимо использовать для плавления опорная плита. Это достигается за счет сужения стыка или за счет направляя дугу в сторону стенка опорной плиты.При многопроходной сварке толстого материала расслоение валика по возможности следует использовать технику после прохождения рута. Большие сварные швы перекрывают весь следует избегать разрыва. Отсутствие плавления может также произойти в форма закрученной бусиной короны. Опять же, это обычно вызвано очень низкая скорость движения и попытки сделайте слишком большой сварной шов за один проход. Однако также очень часто вызвано слишком низким сварочным напряжением. В результате смачивание борта будет плохим.Когда сварка алюминия, частая причина дефекта такого типа — наличие алюминия окись. Этот оксид огнеупор с температурой плавления приблизительно 3500 0 F (1927 0 С). Он также не растворяется в расплаве. алюминий. Если этот оксид присутствует на свариваемых поверхностях сплавление с металлом шва будет затруднено.Наиболее распространенные дефекты сварки — OMS
Что вызывает дефекты сварки?
Дефекты сварного шва возникают по нескольким причинам: использование неподходящих материалов для работы, применение неправильного процесса, сварка в сложных условиях или неопытный или неквалифицированный сварщик.
Общие дефекты сварного шва
Несоосность (HiLo)
Несоосность или HiLo — это разница между внутренней и / или внешней высотой двух труб. Плохая центровка приводит к более слабому сварному шву, который хуже справляется с условиями высокой усталости. Улучшение посадки труб — лучший способ уменьшить HiLo перед сваркой.
Чрезмерное проплавление
Чрезмерное проплавление возникает, когда излишек металла шва выступает из корня шва. Обычно это вызвано слишком большим зазором стыка, слишком малыми поверхностями корня или слишком большим тепловложением, которое может вызвать эрозию и / или коррозию.Лучшая подгонка труб и обеспечение правильной техники сварки снизят риски чрезмерного провара.
Корневая вогнутость / вогнутость / обратное всасывание
Корневая вогнутость, вогнутость и обратное всасывание приводят к появлению неглубокой канавки в корне сварного шва, которая возникает при усадке ванны внутри сварного шва.
Трещины
Трещины — наиболее серьезный дефект сварного шва. В конечном итоге они приведут к выходу сварного шва из строя, и подрядчики по сварке делают все возможное, чтобы их избежать. Сварные швы испытывают постоянное внутреннее напряжение в результате усталости, изгиба, изгиба и расширения / сжатия, и растрескивание возникает, когда внутренние напряжения превышают либо основной металл, либо металл сварного шва, либо и то, и другое.Горячие трещины возникают при температурах выше 1000 ° C и обычно возникают из-за загрязнения или проблем с материалом, холодные трещины возникают после охлаждения сварного шва, обычно из-за диффузии водорода, а кратерные трещины появляются из-за недостаточного объема сварочной ванны. Тщательная подготовка сварных швов, выбор правильных материалов и их безопасное хранение помогут предотвратить образование трещин.
Отсутствие проплавления / неполное сплавление / поднутрение
Неполное проплавление корня шва происходит, когда сварной шов не приваривается к одной стороне корня.Недостаток проплавления возникает, когда обе стороны корня не могут соединиться со сварным швом. Поднутрение — это канавка, которая появляется в основном металле возле корня шва. Правильная подготовка поверхностей стыка и основного металла, а также использование правильных материалов и методов сварки может помочь предотвратить эти дефекты, которые могут привести к плохому качеству, слабым сварным швам и возможному растрескиванию.
Стандарты сварки
Даже если сварка самого высокого качества будет выполняться в оптимальных условиях хорошо подготовленными сварщиками, дефекты будут.Существуют различные национальные и международные стандарты, определяющие приемлемый уровень несовершенства. Вы можете узнать больше о них в BSI и ISO
Устранение дефектов сварных швов
Практически все дефекты сварных швов можно исправить путем более тщательной подготовки, улучшения подгонки труб, использования правильных материалов и техники и надлежащим образом обученных / квалифицированных сварщиков.
Предотвращение проблем с контролем сварных швов
Дефекты обычно обнаруживаются, когда сварные швы подвергаются рентгеновскому или автоматизированному ультразвуковому контролю (AUT), но это происходит на поздней стадии процесса укладки труб на борту трубоукладочного судна.Если обнаружен дефект, то единственным решением является вырезание сварного шва, ведущее к потере времени и значительным затратам. Такие дефекты, как окраска сварных швов из коррозионно-стойких сплавов (CRA), HiLo и пористость, трудно или даже невозможно обнаружить с помощью этих методов.
Ранняя проверка сварного шва на предмет определенных типов поверхностных дефектов снижает риск потери времени, повышает эффективность проекта и снижает затраты. OMS предлагает широкий спектр инструментов и услуг для контроля сварных швов. Чтобы узнать больше об этом, нажмите здесь.
Сварочные дефекты и несплошности — SOMEinSHORT
Что такое дефекты и нарушение целостности?
Дефекты : Дефект или изъяны, которые по своей природе или совокупному эффекту делают деталь или продукт неспособными соответствовать минимальным применимым стандартам или спецификациям приемки. Термин обозначает отклоняемость.
Нарушение сплошности : Нарушение типичной структуры материала, например отсутствие однородности его механических, металлургических или физических характеристик.Нарушение непрерывности не обязательно является дефектом.
Обрыв сварного соединения
- Несоосность (высокое-низкое)
- Недостаточное заполнение
- Вогнутость или выпуклость
- Поднутрение
- Чрезмерное усиление
- Неправильное усиление
- Перекрытие
- Прожиг
- Неполное или недостаточное проникновение
- Неполное сплавление Неровность поверхности Перекрытие
- Брызги
- Трещины
- Пористость
ГАБАРИТНЫЕ ДЕФЕКТЫ
A Дефекты размеров — это любые дефекты, вызывающие появление металла шва.Основной металл, заготовка не соответствуют спецификации или допуску. Узнайте больше о сварке и видах сварочных процессов.
Дефекты размеров в основном вызваны неправильной настройкой или деформацией. Это необходимо сделать до начала процесса сварки.
Несоосность
Определение
Величина смещения стыка у корня
Причина
Невнимательность. Также Также из-за соединения разной толщины (толщина перехода)
Профилактика
Профилактика: Качество изготовления.Углы перехода не должны превышать 2,5 — 1.
Ремонт
Шлифовка. Будьте осторожны с обработкой поверхности и направлением следов заточки. Внутри трубы / трубки сложно.
ПОДЕРКУТ
Определение
Канавка, вырезанная на носке сварного шва и оставленная незаполненной.
Причина
Большой ток, угол электрода, большая длина дуги, ржавчина
Профилактика
Установить станок на металлолом. Перед сваркой очистите металл.
Ремонт
Сварка электродом меньшего размера, иногда с низким содержанием водорода с предварительным нагревом.
Подрезка обычно имеет допустимый предел. Разные нормы и стандарты сильно различаются по допустимой сумме.
НЕДОСТАТОЧНОЕ СМЕЩЕНИЕ ЗАПОЛНЕНИЯ / СВАРКИ
Определение
Поверхность шва ниже прилегающих поверхностей основного металла
Причина
Неправильная техника сварки
Профилактика
Применяйте методы сварки, соответствующие типу и положению сварного шва.
Ремонт
Просто сварить, чтобы заполнить.Может потребоваться подготовка путем измельчения.
Вогнутые и выпуклые сварные профили
ОпределениеВогнутость или выпуклость углового шва, превышающая указанные допустимые пределы
ПОДБОРОЧНЫЙ СВАРНЫЙ
Из-за вогнутого дефекта сварной шов становится слабым по ширине сварного шва (в центре).
Причины
- Слишком высокая скорость движения
- Слишком высокий ток
- Плохое обращение с электродом
ВЫПУСКНОЙ СВАРНЫЙ
Из-за выпуклого дефекта сварной шов становится слабым на концах сварного шва (внешние кромки).
Причины
- Это вызвано следующими причинами:
- Скорость движения слишком низкая
- Ампер до низкого
- Плохое обращение с электродом.
Профилактика: Соблюдайте соответствующие параметры и методы.
Ремонт: Отшлифовать или приварить. Должен плавно переходить в основной металл.
ПРОГНОЗ
Определение:
Когда нежелательное открытое отверстие полностью проплавлено через основной металл.Отверстие может оставаться открытым, а может и не оставаться.
Причина
Чрезмерное тепловложение.
Профилактика
Уменьшите тепловложение за счет увеличения скорости движения, использования радиатора или уменьшения параметров сварки.
Ремонт
Будет определено стандартами. Заполнения может хватить. В противном случае может потребоваться снятие и повторная сварка. Некоторые стандарты могут требовать специального присадочного металла.
НЕПОЛНАЯ СПОСОБНОСТЬ И ПРОНИКНОВЕНИЕ
Неполное проплавление корня — это когда сварным швом не удается соединить одну сторону соединения в корне, а неполное проплавление происходит, когда не соединяются обе стороны соединения.
Некоторые из причин: —
Чрезмерно толстый корневой промежуток. Слишком маленький зазор корня Несоосные сварные швы Потребляемая мощность слишком низкая Слишком низкая подача дуги (тепла)Эти дефекты можно уменьшить при сварке, используя правильные параметры сварки и размер электрода. Это даст правильный ввод энергии дуги.
Неполное или недостаточное проникновение
Определение
Когда металл сварного шва не достигает требуемой глубины в корне стыка
Причина
Низкая сила тока, низкий предварительный нагрев, плотное раскрытие корня, высокая скорость перемещения, короткая длина дуги.
Профилактика
Исправьте способствующие факторы.
Ремонт
Задняя строжка и обратная сварка или снятие и повторная сварка.
Неполное слияние
Определение
Если металл сварного шва не образует когезионной связи с основным металлом.
Причина
Низкая сила тока, крутые углы наклона электродов, высокая скорость перемещения, короткий дуговый зазор, отсутствие предварительного нагрева, слишком маленький электрод, грязный основной металл.
Профилактика
Устраните потенциальные причины.
Ремонт
Снимите и снова приварите, стараясь полностью удалить дефектный участок. Иногда это очень сложно найти.
БРЫЗГИ
Определение
Мелкие частицы металла сварного шва, выброшенные из сварочной операции, прилипающие к поверхности основного металла.
Причина
Большая длина дуги, большие углы наклона электродов, большие силы тока. Неправильные условия сварки и / или загрязненные расходные материалы или препараты, вызывающие взрывы в дуге и сварочной ванне
Профилактика
Устраните причину.Основной металл можно защитить с помощью покрытий или высокотемпературных красок.
Ремонт
Удалить шлифованием или шлифованием. Иногда необходимо испытывать, как если бы это был сварной шов.
Трещина
Растрескивание при затвердевании
Причины: — Большое отношение глубины к ширине сварного шва — Высокая энергия дуги и / или предварительный нагрев — Захват серы, фосфора или ниобия из основного металла
Водородный крекинг
Причины:- Закаленная ЗТВ в сочетании с присутствием водорода, диффундирующего из металла шва.
- Восприимчивость увеличивается с увеличением толщины профиля, особенно у сталей с составом с высоким углеродным эквивалентом.
- Может также встречаться в металле сварного шва
- Повышение нагрева при сварке полезно
- Иногда требуется предварительный нагрев
- Требуется контроль влажности расходных материалов и чистота подготовки сварного шва
Предотвращение
- Предварительный нагрев снижает скорость охлаждения; это может помочь избежать образования мартенсита и обеспечить теплом для диффузии водорода из материала
- Процедура сварки с низким содержанием водорода
Пластинчатый разрыв
Причины: — Низкая пластичность в поперечном направлении в прокатанном листе из-за неметаллических включений — Возникает в основном в соединениях с наплавленным металлом на поверхности пластин — Предварительное нанесение масла на поверхность полезно для восприимчивого листа
Пористость поверхности
• Причины: — Чрезмерное загрязнение из-за жира, сырости или уноса из атмосферы — Иногда вызвано чрезмерным содержанием серы в расходных материалах или основном металле
Арматура
Длина сварного шва с разделкой кромок, выходящего за пределы поверхности пластины
- Чрезмерно
- Недостаточно
- Неправильный контур
Чрезмерное усиление
Определение
Специально определено стандартом.Как правило, арматура должна быть заподлицо до 1/16 дюйма (труба) или заподлицо до 1/8 дюйма (пластина или структурные профили).
Причина
Слишком низкая скорость движения, слишком низкая сила тока
Профилактика
Установите силу тока и скорость движения на пластине для отходов.
Ремонт
Удалить чрезмерное усиление и перо сварных пальцев к плавному переходу к опорной плите.
Недостаточное усиление
Определение
Специально определено стандартом.Как правило, недозаполнение может составлять до 5% толщины металла, но не более 1/32 дюйма, пока толщина покрывается противоположной арматурой.
Причина
Слишком высокая скорость движения.
Профилактика
Используйте соответствующую технику сварки. Используйте подкладку или расходные вставки. Используйте обратный шов или подкладку.
Ремонт
Можно просто увеличить лицевое усиление. Если обратная сварка невозможна, необходимо удалить и повторно заварить.
Неправильный контур сварного шва
Определение
Когда сварной шов имеет угол перехода меньше 135 0 на носке сварного шва.
Причина
Плохая техника сварки
Профилактика
Используйте правильные методы. Часто проблему можно решить с помощью плетения или хлыста.
Ремонт
Поверхность шва должна входить в пластину основания.
Перекрытие
Определение
Когда поверхность сварного шва выходит за пределы носка сварного шва.
Причина
Неправильная техника сварки. Обычно углы электродов и скорость перемещения.
Профилактика
Перекрытие — проблема контура. Правильная техника сварки предотвратит эту проблему.
Ремонт
Перекрытие необходимо удалить, чтобы он плавно переходил в основной металл. Остерегайтесь глубоких следов заточки, идущих поперек груза. Также будьте осторожны с нарушениями плавления, скрытыми шлифовкой. Используйте NDT, чтобы быть уверенным.
Поделиться этой записью: в Твиттере на Фейсбуке в LinkedIn
Разрывы сварных швов — Часть 1 Пористость — Неполное сплавление
Как инспектор по сварке, для того, чтобы вы могли успешно выполнять свою профессиональную деятельность, важно понимать неоднородности сварного шва.Чтобы полностью понять неоднородность сварного шва, мы должны сначала изучить терминологию сварки. Термин прерывистость определяется как нарушение типичной структуры материала, например, отсутствие однородности его механических, металлургических или физических характеристик. Нарушение непрерывности не обязательно является дефектом. С другой стороны, дефект определяется как несплошность или неоднородности, которые по своей природе или накопленному эффекту (например, общей длине трещины) делают деталь или продукт неспособными соответствовать минимальным применимым стандартам или спецификациям приемки.Термин «дефект» обозначает отклоняемость. Поскольку в этой статье мы исследуем эти явления, выходящие за рамки требований какого-либо конкретного сварочного кодекса или стандарта, и мы не будем обсуждать их ограничения в терминах этих документов, мы будем использовать термин разрывы.
Пористость
Пористость определяется как неоднородности полого типа, образованные захватом газа во время затвердевания. Пористость вызывается газами, которые присутствуют в расплавленном сварном шве.Эти газы могут задерживаться и образовывать пузыри или газовые карманы по мере затвердевания сварного шва. Основная причина наличия газов, вызывающих пористость, — это грязный основной материал, влажность на поверхности соединения или электрода, недостаточная или неправильная защита во время процесса сварки, или неправильные условия или методы сварки. Основной материал, загрязненный углеводородами, такими как масло, жир или краска, будет восприимчив к пористости во время процесса сварки. Влага в виде воды или гидратированных оксидов на основном материале и / или сварочных электродах, или утечки воды из плохо обслуживаемых систем охлаждения оборудования, могут ввести водород в процесс сварки и вызвать серьезные проблемы с пористостью во время сварки.Использование защитного газа, который имеет недостаточную скорость потока, загрязнен из его источника или внутри его системы подачи, или не может обеспечить адекватную защиту расплавленного металла сварного шва за счет его удаления ветром или сквозняком, может серьезно повлиять на уровни пористости.
Пористость часто классифицируют по типам в зависимости от ее формы и распределения в сварном шве. Такие описания, как равномерно или случайно рассеянная пористость, кластерная пористость и линейная пористость, или аналогичные термины, используются для описания его распределения.Каждое из этих распределений пористости может предусматривать разные уровни приемлемости в рамках правил сварки или стандарта. Например, наличие линейной пористости обычно имеет более серьезные ограничения, чем те, которые применяются к рассеянной пористости, поскольку линейная пористость часто связана с проблемами плавления в сварном шве. Наиболее практичными методами контроля или устранения пористости являются использование чистых основных материалов, надлежащим образом хранимых и незагрязненных сварочных материалов, сварочного оборудования в надлежащем техническом обслуживании, приемлемых условий окружающей среды и проверенных процедур сварки.
Неполное сплавление и неполное проникновение в стык
Поскольку эти термины иногда используются неправильно, важно понимать разницу между этими двумя неоднородностями сварного шва.
Неполный сплав — это несплошность сварного шва, при которой сплавление металла сварного шва и поверхностей сплавления или прилегающих валиков сварного шва не происходит. Это отсутствие плавления может иметь место в любом месте сварного шва и может присутствовать в угловых сварных швах и / или сварных швах с разделкой кромок. Неполное плавление может быть вызвано неспособностью во время процесса сварки поднять основной материал или ранее наплавленный металл сварного шва до его температуры плавления.Это часто встречается на одном участке углового сварного шва и вызвано неправильным углом сварки, что приводит к дисбалансу тепла между обеими сторонами соединения. Это также может быть вызвано неспособностью удалить оксиды или другой посторонний материал с поверхности основного материала, с которым должен плавиться наплавленный металл шва.
Неполный провар соединения описывается как состояние корня соединения в сварном шве с канавкой, при котором металл сварного шва не выходит на толщину соединения. Это неспособность присадочного металла или основного металла полностью заполнить основание сварного шва.Некоторые распространенные причины неполного проплавления шва связаны с конструкцией шва с разделкой кромок или настройкой, не подходящей для условий сварки. Эти проблемы возникают в ситуациях, когда размеры поверхности корня слишком велики, отверстие корня слишком мало или угол наклона сварного шва с V-образной канавкой слишком мал. Все эти конструктивные особенности соединения ограничивают способность сварного шва проникать через толщину соединения.