Диагностика сварных конструкций
Техническая диагностика сварных конструкций – занимается установлением и изучением признаков, характеризующих техническое состояние изделий, для предсказания возможных отклонений контролируемых параметров (например, длина трещины или толщина изделия) за допустимые пределы, вследствие чего возникают внезапные отказы.Техническая диагностика даёт возможность оценить продолжительность эксплуатации изделия, т. е. его долговечность при появлении дефектов.
Основными задачами диагностики технического состояния являются контроль и оценка качества изделия. В задачу контроля качества входят измерение размеров, определение свойств, проверка сплошности и однородности материала и конструктивного элемента с обязательной проверкой соответствия материала и изделия регламентируемым требованиям НТД.
Диагностирование (испытания) при исследовании процессов старения, износа и усталости материалов, выбор параметров конструкций, позволяющих определить их техническое состояние, и оценку фактических значений диагностических параметров, достигнутых при изготовлении, проводят в основном В лабораторных условиях на относительно ограниченном числе образцов.
Диагностирование в процессе эксплуатации осуществляется при рабочих воздействиях либо внешним осмотром конструкций, либо при помощи диагностической аппаратуры, дающей возможность измерять или контролировать нужный параметр с заданной точностью.
Для перехода от измеренных физических величин к искомым параметрам, характеризующим искомые свойства материалов конструкций, используют тарировочные зависимости, то есть производят настройку диагностических средств на образцах с известными и по возможности близкими к контролируемому объекту свойствами.
Цель неразрушающих методов контроля сводится к обнаружению дефектов и к постановке задачи по контролю и оценке качества материала в исходном состоянии. Неразрушающие методы контроля служат инструментом для улучшения качества конструирования и технологических процессов изготовления аппаратов и конструкций.
Диагностика сварных швов
Сварные конструкции должны контролироваться на всех этапах их производства. Кроме того, систематической проверки требует и оборудование, предназначенное для их изготовления. Одним из самых важных моментов является последовательный контроль выполнения сварочных соединений. Диагностику сварных швов сотрудники ООО ЭУЦ «СЕКТОР» проводят в двух направлениях: контроль самого процесса сварки либо диагностика готового элемента или изделия. В процессе диагностики сварного соединения, различают разрушающие и неразрушающие методы. К неразрушающим методам диагностики качества сварных швов относят, как внешний осмотр дефектов, выходящих на поверхность, так и контроль на герметичность металлоконструкцийОбследование сварных швов
Внешнее обследование сварных швов является наиболее простым и широко распространенным способом диагностики их качества. Этот метод является первой контрольной операцией по приемке сварного узла в готовом элементе или изделии.
Следующий способ диагностики сварных швов, который предлагает компания ООО ЭУЦ «СЕКТОР» – это выполнение обмеров сварного соединения, которые позволяют судить о качестве. Например, при недостаточном сечении шва уменьшается прочность соединения, если шов слишком широкий, то это влечет увеличение внутреннего напряжения и деформацию.
Внешнее обследование сварных швов не дает полноценно судить о качестве сварочного соединения. Это лишь позволяет установить внешние дефекты шва и определить сомнительные участки, которые впоследствии можно проверить более точными способами.
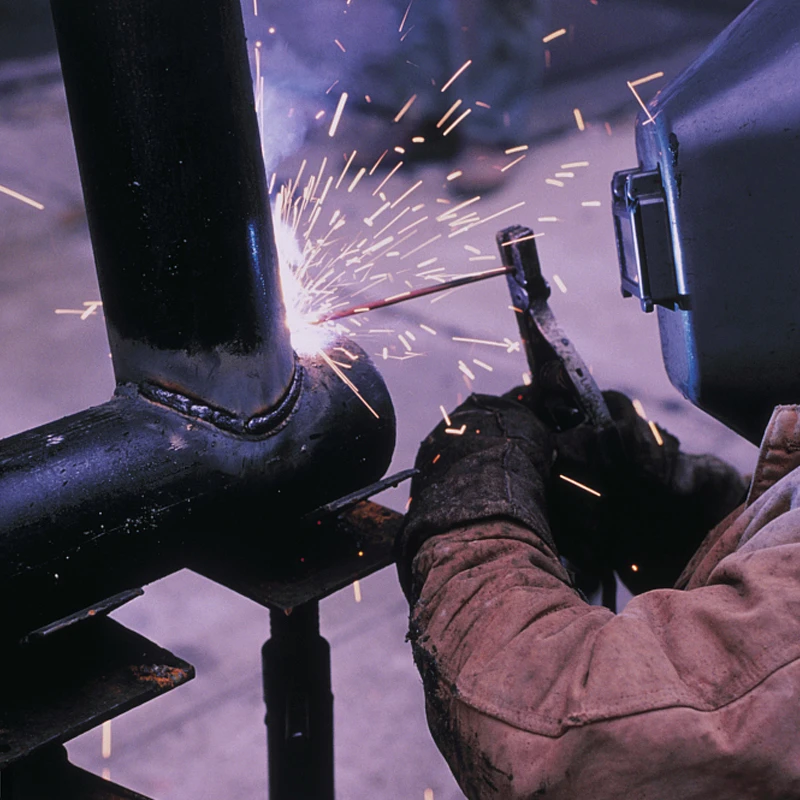
Итак, господа и дамы, обратившись в компанию ООО ЭУЦ «СЕКТОР» по адресу: 105082, г. Москва, ул. Фридриха Энгельса, д. 75, стр. 20, офис 21, по телефонам: +7 (915) 288-92-16, +7 (495) 765-64-31, +7 (915) 288-94-86
Ультраструйная диагностика качества сварных швов Текст научной статьи по специальности «Технологии материалов»
УДК 621.791.75 DOI: 10.18698/0536-1044-2015-12-52-61
Ультраструйная диагностика
*
качества сварных швов
М.И. Абашин1, С.В. Бочкарев2, А.И. Цаплин2, Н.В. Коберник1
1 МГТУ им. Н.Э. Баумана, 105005, Москва, Российская Федерация, 2-я Бауманская ул., д. 5, стр. 1
2 Пермский национальный исследовательский политехнический университет, 614990, Пермь, Пермский край, Российская Федерация, Комсомольский пр., д. 29
Ultra-Jet Diagnostics of the Quality of Welds
M.I. Abashin1, S.V. Bochkarev2, A.I. Tsaplin2, N.V. Kobernik1
1 BMSTU, 105005, Moscow, Russian Federation, 2nd Baumanskaya St., Bldg. 5, Block 1
2 Perm National Research Polytechnic University, 614990, Perm, Perm Region, Russian Federation, Komsomolsky Prospekt, Bldg. 29
e-mail: [email protected], [email protected], [email protected], [email protected]
Предложен новый метод оценки параметров качества сварных соединений, в частности ударной вязкости разрушения, основанный на воздействии высокоскоростной струей воды на поверхность контролируемого объекта (информативными признаками служат геометрические характеристики образовавшейся гидрокаверны).
Ключевые слова: диагностика, ультраструйное воздействие, сварной шов, твердость, ударная вязкость.
A new method of evaluating quality parameters of welded joints is proposed in the article. In particular, the method deals with impact fracture toughness and is based on the impact that a high speed water jet has on the surface of the controlled object.
Keywords: diagnosis, ultra-jet impact, weld, hardness, shock viscosity.
Существующие способы сварки, характеризующиеся наличием развитой научно-методической базы и богатого практического опыта, не дают
ответов на вопросы, связанные с контролем качества сварных соединений и обеспечения их надежности. В стандарте ISO 3834-2 [1] указано,
* Работа выполнена при финансовой поддержке РФФИ (проект № 13-08-96004-р_урал_а).
что сварка является особенным процессом, результат которого не всегда может быть проверен испытанием после его завершения. Качество сварных соединений должно быть обеспечено в процессе производства.
В современных условиях совершенствование технологии сварки, а также методов диагностики ее качества возможно в рамках создания на основе CALS-технологий единого информационного пространства, объединяющего следующие виды работ [2-4]:
• создание и уточнение с учетом механики разрушения научно-обоснованных норм на размеры дефектов;
• разработка новых, более эффективных, методов неразрушающего контроля (НК) изделий, направленных на выявление поверхностных и подповерхностных дефектов, а также на определение качества термической обработки сварных соединений;
• создание методик оперативного выбора оптимальных технологических режимов сварки.
Нахождение оптимальных режимов для различных методов сварки и повышение качества сварного шва неразрывно связаны с созданием методов контроля, которые позволяли бы гарантировать решение поставленной задачи. В первую очередь это относится к методам НК, для которых сварные конструкции — самый распространенный объект [5].
Общий обзор современных методов и средств НК сварных соединений представлен в работах [6, 7]. Закономерности формирования зеренной структуры показаны в работе [8] на примере сварки трением с перемешиванием.
Качество сварных швов обеспечивается оптимальными технологическими режимами, которые можно прогнозировать методами математического моделирования. В работе [9] представлена модель расчета остаточных напряжений в сварных соединениях, где учтено влияние фазовых переходов при предшествующей термической обработке материалов на макроскопические характеристики среды. Моделирование позволяет также прогнозировать амплитудные значения упругих деформаций в сварном соединении при циклическом нагружении [10].
В работе [11] рассчитана глубина воздействия интенсивной пластической деформации на структуру поверхностных слоев при сварке. В работе [12] представлена методика расчетной оценки показателей свариваемости низколегированной стали с помощью компьютерного мо-
делирования. Эффективность моделирования различных акустических схем контроля проанализирована в работе [13] на примере выявления дефектов, локализованных в наименее благоприятных для их обнаружения условиях (модель наихудшей дефектной ситуации).
Мониторинг качества сварных швов эффективен при использовании рекуррентных нейронных сетей [14], методов вейвлет-преоб-разований [15, 16], имитационного моделирования, в том числе с применением метода конечных элементов [17, 18].
Качество сварных швов оценивают механическими испытаниями на растяжение [19, 20] и кручение [21]. Механические испытания образцов, вырезанных из дефектных зон кольцевого сварного соединения, эффективны при использовании ультразвукового сканера-дефектоскопа [22].
Эксплуатационная пригодность конструкций в реальном масштабе времени и местоположение дефектов могут быть оценены с помощью акустико-эмиссионного аппаратно-программного комплекса [23]. Акустико-эмиссионная диагностика позволяет выявить структурное состояние сварного соединения и может служить основой метода оценки его прочностных свойств [24]. В сочетании с кинетическим ин-дентированием для оценки степени поврежден-ности металла сварного соединения акустико-эмиссионную диагностику применяют в условиях эксплуатации при малоцикловой усталости [25] и в процессе сварки [26].
Для обнаружения дефектов сварки, их классификации, оперативной оценки технологического процесса применяют традиционные методы ультразвукового контроля [27-29]. Ультразвуковое воздействие может быть эффективным, если требуется повысить надежность сварных швов [30] и сопротивление сварных соединений усталостному разрушению [31].
Ширографические и спекл-интерферометри-ческие измерительные системы, рассмотренные в работе [32], позволяют оценить напряженно-деформированное состояние и остаточные напряжения сварных конструкций не только при их изготовлении, но и в процессе эксплуатации.
Для определения химического состава металла шва применяют методы металлографических исследований структуры сварных соединений и измерения твердости [33].
Несмотря на разнообразие методов контроля сварки, важнейшей задачей остается выявление наиболее опасных зон сварного шва, к которым могут быть отнесены структурно-механические неоднородности, различные дефекты, конструктивные и технологические концентраторы напряжений [34-36].
Поскольку на качество, а следовательно, и на надежность сварных соединений, влияет множество факторов, актуальным остается вопрос разработки метода контроля, который позволял бы интегрально оценить состояние металла сварного соединения.
В настоящей статье предложен новый метод, основанный на процессе гидроразрушения поверхностного слоя материала высокоскоростной струей жидкости — метод ультраструйной диагностики [37, 38]. Этот метод позволяет создавать имитационные, знакопеременные и нестационарные нагрузки на исследуемое изделие.
Методика проведения исследований. Исследования проводили на сварном соединении пластин из низкоуглеродистой стали Ст3сп по ГОСТ 380-2005 толщиной 10 мм с У-образной разделкой кромок. Угол разделки кромок составлял (35_5притупление кромок 1,8±0,8 мм.
Процесс проводили на подкладной ленте марки ЛМС по ТУ 6-48-00204961-12-90 за один проход автоматической дуговой сваркой под флюсом двумя проволочными электродами. Параметры режима сварки: первая дуга — постоянный ток, обратная полярность, /1 = 550 А, Цд1 = 29 В, угол наклона электрода а1 = 90°; вторая дуга — переменный ток с балансом 75 %, 12 = 550 А, Цд2 = 29 В, угол наклона электрода а2 = 65° (схема углом вперед). Расстояние между электродами составляло 27 мм, скорость сварки 26 м/ч.
а б
Рис. 1. Схема расположение точек замера твердости
на схеме (а) и на образце (б): 1-21 — точки замера твердости (белым цветом показаны значения подачи, сопла гидроструйной установки, мм/с)
В качестве присадочных материалов применяли проволоку сварочную сплошного сечения марки L60 (0,05…0,15 % C; 0,8… 1,25 % Mn; 0,1…0,35 % Si) диаметром 4 мм и флюс марки 761 (производства фирмы Lincoln Electric, США).
Структуру соединений исследовали на оптическом микроскопе Leica MDILM (Германия) с использованием программы Qwin (Германия) для анализа изображений, а также на растровом электронном микроскопе FEI Quanta 3D FEG (США), оснащенном приставкой для микро-рентгеноспектрального анализа.
После сварки измеряли твердость по Вик-керсу (HV 5) сварного шва и околошовной зоны на универсальном приборе Wilson Wolpert 930 N (США) вдавливанием индентора при нагрузке 50 Н.
Качество сварного шва диагностировали ультраструйным воздействием, вызывающим образование гидрокаверны перпендикулярно поверхности сварного шва, при следующих режимах: давление струи воды 380 МПа; диаметр струи 0,2 мм; скорость подачи сопла гидроструйной установки 0,5 и 2 мм/с.
Твердость замеряли по схеме, указанной на рис. 1, согласно ГОСТ 9013-59 (ИСО 6508-86) с помощью портативного твердомера МЕТ-ДУ с применением динамического датчика. В каждой точке делали четыре замера и фиксировали среднее значение, автоматически вычисляемое прибором.
На профилографе-профилометре БВ-7669М производства НИИ «Измерения» (Москва) были сняты профили по трассам (рис. 2). Трассы 1-6 проходили вдоль гидрокаверны, трассы 7.0-7.3 перпендикулярно гидрокаверне.
Рис. 2. Схемы трассирования сварного шва: А и В — зоны, где определяли ударную вязкость (белым цветом показаны значения подачи сопла гидроструйной установки, мм/с)
Рис. 3. Образец сварного шва с гидрокавернами, возникшими в результате ультраструйного воздействия на трех уровнях: верхнем (точки 1,4, 7,10), среднем (точки 2, 5, 8,11,14) и нижнем (точки 3, 6, 9,12,15)
Гидрокаверны присутствовали в поперечном сечении сварного шва на трех уровнях: верхнем, среднем и нижнем (рис. 3).
Ударную вязкость металла шва сварного соединения, полученного сваркой под флюсом, определяли испытаниями по методу Шарпи (КСУ) на образцах типа X по ГОСТ 6996-66 при температуре -20 °С. Ударную вязкость металла сварного шва, полученного дуговой сваркой, определили также по методу Шарпи (КСи) на образцах типа VII по ГОСТ 6996-66 при температуре 20 °С.
Результаты исследований и их обсуждение.
Микроструктуру металла шва можно охарактеризовать как состоящую из лучистых кристаллов бейнита, окруженных полосами феррита и перлита. Кристаллы металла шва имеют строгую столбчатую направленность, характерную для сварного шва. В ней присутствуют бейнит-ная, ферритная и перлитная составляющие (рис. 4). Кристаллы бейнита, декорированные ферритно-перлитной смесью, имеют средний размер 400… 600 мкм, средний размер полиэдрических зерен, из которых состоит феррит, 80.100 мкм.
Таблица 1
Зависимость глубины гидрокаверны от твердости материала
Номер трассы Твердость материала НВ Глубина гидрокаверны, мкм
7.0 225 49,7
7. 1 331 45,4
7.2 283 55,5
7.3 257 100,6
Для всех трасс наблюдается высокая корреляция между твердостью материала (табл. 1) и глубиной образовавшейся гидрокаверны.
Для трасс 7.1-7.3 отмечается монотонная зависимость глубины гидрокаверны от твердости материала. А в трассе 7.0, которая соответствует точке 21 замера твердости (см. рис. 1), наблюдается отступление от монотонности. Это можно объяснить тем, что точка 21 лежит вне зоны наплавляемого металла и зоны термического влияния, что, в свою очередь, позволяет сделать вывод об отсутствии разупрочнения металла в области точки 21.
Ниже представлены результаты механических испытаний и замера твердости в точках согласно выбранной схеме (рис. 1, а).
Результаты механических испытаний сварного соединения пластин из низкоуглеродистой стали Ст3сп
Твердость, НВ. С
Основной металл (области точек 1-4)….. 27,0.30,0
Зона термического влияния
(области точек 5-12)…………………30,0.32,0
Зона шва (области точек 13-20)……….. 32,0.34,0
Таблица 3
Результаты механических испытаний
алюминиевого сварного шва, полученного ручной дуговой сваркой
Таблица 2
Результаты локальных замеров твердости
Номер точки замера твердости Твердость HB Номер точки замера твердости Твердость HB
1 222 11 259
2 313 12 350
3 233 13 282
4 297 14 283
5 265 15 257
6 334 16 228
7 333 17 228
8 295 18 281
9 247 19 282
10 297 20 331
Параметры Область сварного шва
Верх Середина Низ
Предел прочности, МПа 862,0 839,0 855,0
Предел текучести, МПа 828,0 793,0 814,0
КСи, кДж/см2: зона А зона В 525,0 630,0 656,0 909,0 833,0 778,0
Из табл. 2 ясно, что твердость в зоне сварного соединения монотонно возрастает при переходе от основного металла к зонам термического влияния и шва в среднем на 15 %. Результаты измерений в точках показывают, что максимальная твердость отмечается в центре сварного шва, (трассы 7.1, 7.2, точки 6, 8,10,12,20).
Сравниваем также глубину образовавшейся в результате ультраструйной диагностики гидрокаверны и ударную вязкость (КСи). Представленные в табл. 3 результаты показывают, что в середине шва с максимальной твердостью прочность ниже, чем в верхней и нижней частях шва.
Литература
Выводы
1. Ультраструйная диагностика сварных швов является примером перспективной технологии, обладающей широкими функциональными возможностями. Эта технология может стать частью аппарата по обслуживанию элементов оборудования, включающего выбор рациональных режимов сварки на этапе технологической подготовки, оценку состояния действующих и ремонт вышедших из строя изделий.
2. Реализация предложенной идеи поможет создать высокоэффективный аппарат ультраструйной диагностики, позволяющий оперативно решать ряд практически важных вопросов, связанных с оценкой качества сварных швов в материалах конструкций потенциально опасных объектов.
[1] EN ISO 3834-2. Требования к качеству при сварке. Сварка плавлением металлических
материалов. Ч. 2: Более высокие требования к качеству.
[2] Бербасова Н.Ю., Куликов В.П., Основский В.А., Тарапсенко С.И. Управление каче-
ством сварных конструкций на основе системно-процессного моделирования. Сварочное производство, 2008, № 3, с. 12-18.
[3] Стеклов О.И. Сварка начала XXI века. Территория Нефтегаз, 2007, № 12, с. 44-53.
[4] Cullison A., Johnsen M.R. Fifty Years of Welding’s Latest and Best. Welding Journal, 2003,
Mar, pp. 46-54.
[5] Коновалов Н.Н., Щербаков Е.С. Совершенствование электронной базы средств нераз-
рушающего контроля и его методическое обеспечение. Сварочное производство, 2014, № 9, с. 45-47.
[6] Атрощенко В.В., Бычков В.М., Медведев А.Ю., Савичев М.П., Кривалев И.В. Неразру-
шающий контроль сварных соединений блисков, полученных линейной сваркой трением. Сварка и диагностика, 2014, № 4, с. 43-45.
[7] Шаповалов Е.В., Галаган Р.М., Клищар Ф.С., Запара В.И. Современные методы и сред-
ства неразрушающего контроля сварного соединения, выполненного контактной точечной сваркой (обзор). Техническая диагностика и неразрушающий контроль, 2013, № 1, с. 10-22.
8] Миронов С.Ю. Формирование зеренной структуры при сварке трением с перемешива-
нием. Физическаямезомеханика, 2014, т. 17, № 1, с. 103-113.
9] Кректулева Р.А., Черепанов О.И., Черепанов Р.О. Численное решение квазистатиче-
ской задачи расчета остаточных напряжений в сварных швах с учетом фазовых превращений. Физическая мезомеханика, 2013, т. 16, № 6, с. 51-57.
10] Смирнов С.В., Пугачева Н.Б., Мясникова М.В., Смирнова Е.О. Структурная неоднородность сварного соединения алюминиевого сплава и моделирование его упругой деформации. Физическая мезомеханика, 2014, т. 17, № 1, с. 51-56.
11] Батаев И.А., Батаев А. А., Мали В.И., Батаев В.А., Балаганский И.А. Структурные изменения поверхностных слоев стальных пластин в процессе сварки взрывом. Материаловедение и термическая обработка, 2013, № 9, с. 19-24.
12] Макаров Э.Л. Компьютерная оценка свариваемости низколегированной стали. Сварка и диагностика, 2014, № 4, с. 23-29.
13] Бадалян В.Г., Базулин А.Е., Базулин Е.Г., Самарин П.Ф., Тихонов Д.С. Использование моделирования для оптимизации методик УЗК. Сварка и диагностика, 2014, № 6, с. 18-22.
14] Климов В.С., Комиренко А.В. Применение нейросетевых технологий распознавания образов для диагностики контактной сварки в производственной среде. Сварка и диагностика, 2013, № 2, с. 40-44.
15] Бигус Г.А., Травкин А. А., Даниев Ю.Ф. Вейвлет анализ сигналов акустической эмиссии при диагностике конструкций. Сварка и диагностика, 2012, № 4, с. 34-38.
16] Скачков И.О. Мониторинг качества контактной точечной сварки переменным током с применением вейвлет-анализа. Техническая диагностика и неразрушающий контроль, 2012, № 3, с. 43-47.
17] Nonomura S., Hyoma K., Kobayashi K., Yamaoka H., Miyasaka F. Control of the Penetration Shape by Pulsed Current Waveform. Transactions of the Japan welding society. Quarterly Journal of the Japan welding society, 2015, vol. 33, no. 1, pp. 82-88.
18] Okabe T., Yasuda K., Nakata K. Dynamic Observations of Welding Pghenomena and Finite Element Analysis in High Frequency Electric Resistance Welding. Transactions of the Japan welding society. Quarterly Journal of the Japan welding society, 2014, vol. 32, no. 3, pp. 156-163.
19] Процив Ю.В., Сапунов А.Л. Предотвращение трещинообразования при изготовлении сварных кольцевых заготовок из горячекатаных профилей стареющих никелевых сплавов. Материаловедение и термическая обработка, 2011, № 8, c. 19-24.
20] Sadasue T., Igi S., Taniguchi K., Ikeda R., Oi K. Fracture behavior and numerical study of resistance spot welded joints in high strength steel sheet. Transactions of the Japan welding society. Quarterly Journal of the Japan welding society, 2014, vol. 32, no. 2, pp. 64-72.
21] Morisada Y., Tamashiro K., Kamai M., Ueji R., Fujii H. Development of Small sized Friction Stir Welding Equipment for Hand-operated Welding. Transactions of the Japan welding society. Quarterly Journal of the Japan welding society, 2014, vol. 32, no. 2, pp. 52-56.
22] Козлов Д.М., Попович А.Л. Автоматизированный неразрушающий контроль кольцевых соединений трубопроводов, выполненных контактной стыковой сваркой оплавлением. Сварка и диагностика, 2014, № 5, c. 56-57.
23] Попов А.В. Оценка прочности сварных и паяных соединений конструкций ракетно-космической техники методом акустической эмиссии. В мире неразрушающего контроля, 2015, № 1(67), c. 10-13.
24] Сивцев М.Н., Слепцов Г.Н. Исследование структуры сварных соединений при различных технологических параметрах сварки низколегированных сталей. Материаловедение и термическая обработка, 2014, № 2, c. 19-24.
25] Черняева Е.В., Галкин Д.И., Бигус Г.А., Мерсон Д.Л. Применение метода акустической эмиссии для неразрушающего контроля состояния основного металла и сварных соединений трубопроводов, работающих в условиях малоцикловой усталости. Сварка и диагностика, 2010, № 2, c. 50-56.
26] Гуменюк В.А., Казаков Н.А., Сульженко В.А. Акустико-эмиссионный контроль процесса сварки корпуса глубоководного аппарата. В мире неразрушающего контроля, 2007, № 1(35), c. 57-60.
[27] Разыграев Н.П., Разыграев А.Н. Приемочный и эксплуатационный ультразвуковой контроль головными волнами эхо-методом. В мире неразрушающего контроля, 2007, № 4(38), c. 57-60.
[28] Давыдов Д.М. Ультразвуковой контроль. Проблемы и их решения в тепловой и атомной энергетике. Сварка и диагностика, 2010, № 2, c. 57-60.
[29] Бобров В.Т., Самокрутов А.А., Алехин С.Г., Бобров С.В. Исследование эматехнологии ультразвукового контроля контактной точечной сварки в автомобилестроении. Сварка и диагностика, 2014, № 4, c. 55-59.
[30] Зуев Л.Б., Псахье С.Г., Оришич А.М., Ковалев О.Б., Юдина Е.В., Афонин Ю.В., Данилов
В.И., Полетика Т.М. Структура и свойства сварных соединений, выполненных лазерной и точечной сваркой. Физическаямезомеханика, 2005, т. 8, спец. вып., с. 87-90.
[31] Панин В.Е., Сапожников С.В., Каблов Е.Н., Плешанов В.С., Клименов В. А., Иванов Ю.Ф., Почивалов Ю.И., Кибиткин В.В., Напрюшкин А.А., Нехорошков О.Н., Лукин В.И. Влияние ультразвуковой ударной обработки на структуру и сопротивление усталости сварных соединений высокопрочной стали ВКС-12. Физическая мезомеха-ника, 2006, т. 9, № 2, с. 85-96.
[32] Лобанов Л.М., Пивторак В.А. Диагностика конструкций методами электронной ши-рографии и спекл-интерферометрии. Сварка и диагностика, 2014, № 2, с. 27-32.
[33] Гончаров А.Л., Драгунов В.К., Слива А.П., Портнов М.А., Терентьев Е.В., Грибков М.С. Исследование сварных соединений разнородных сталей деталей магнитопрово-да, выполненных ЭЛС. Сварка и диагностика, 2014, № 5, с. 28-32.
[34] Варовин А. Я., Карзов Г.П., Марголин Б.З. Проблемы прогнозирования работоспособности конструкций по данным неразрушающего контроля. Вопросы материаловедения, 2007, № 3, с. 169-186.
[35] Antipov V.S., Vasil’ev V.D., Udralov Yu.I. Radiographic Inspection of the Weld Seams: Test Parameters. Russian Journal of Nondestructive Testing, 2006, vol. 42, no. 2, с. 106-110.
[36] Matzkanin G.A., Yolken H.T. Selecting a Nondestructive Testing Method: Ultrasonic Testing. Welding Journal, 2008, May, pp. 26-32.
[37] Абашин М.И., Барзов А.А., Галиновский А.Л. Анализ физико-технологических особенностей процесса ультраструйной диагностики. Вестник МГТУ им. Н.Э. Баумана. Сер Естественные науки, 2012, спец. вып., с. 7-18.
[38] Абашин М.И., Галиновский А.Л., Бочкарев С.В., Цаплин А.И., Проваторов А.С., Хафизов М. В. Моделирование ультраструйного воздействия для контроля качества покрытий. Физическая мезомеханика, 2015, т. 18, № 1, с. 84-89.
References
[1] EN ISO 3834-2. Trebovaniia k kachestvu pri svarke. Svarka plavleniem metallicheskikh mate-
rialov. Chast’ 2: Bolee vysokie trebovaniia k kachestvu [Quality requirements for welding. Fusion welding of metallic materials. Part 2: Higher quality requirements]. 2005.
[2] Berbasova N.Iu., Kulikov V.P., Osnovskii V.A., Tarapsenko S.I. Upravlenie kachestvom
svarnykh konstruktsii na osnove sistemno-protsessnogo modelirovaniia [Welded construction refinement on the base of the welding engineering system modelling]. Svarochnoe pro-izvodstvo [Welding International]. 2008, no. 3, pp. 12-18.
[3] Steklov O. I. Svarka nachala XXI veka [Welding the beginning of the XXI century]. Territoriia
Neftegaz [Territory Neftegaz]. 2007, no. 12, pp. 44-53.
[4] Cullison A., Johnsen M.R. Fifty Years of Welding’s Latest and Best. Welding Journal, 2003,
Mar, pp. 46-54.
[5] Konovalov N.N., Shcherbakov E.S. Sovershenstvovanie elektronnoi bazy sredstv ne-
razrushaiushchego kontrolia i ego metodicheskoe obespechenie [Electronic base updating of the nondestructive test devices and its methodological support]. Svarochnoe proizvodstvo [Welding International]. 2014, no. 9, pp. 45-47.
[6] Atroshchenko V.V., Bychkov V.M., Medvedev A.Iu., Savichev M.P., Krivalev I.V. Ne-
razrushaiushchii kontrol’ svarnykh soedinenii bliskov, poluchennykh lineinoi svarkoi treniem [Non-destructive testing of welds blisks obtained linear friction welding]. Svarka i diagnostika [Welding and Diagnostics]. 2014, no. 4, pp. 43-45.
[7] Shapovalov E.V., Galagan R.M., Klishchar F.S., Zapara V.I. Sovremennye metody i sredstva
nerazrushaiushchego kontrolia svarnogo soedineniia, vypolnennogo kontaktnoi tochech-noi svarkoi (obzor) [Modern methods and means of nondestructive testing of welded joints made contact spot welding (Review)]. Tekhnicheskaia diagnostika i nerazrushaiushchii kontrol’ [Technical Diagnostics and Nondestructive Testing]. 2013, no. 1, pp. 10-22.
[8] Mironov S.Iu. Formirovanie zerennoi struktury pri svarke treniem s peremeshivaniem
[Grain structure formation in friction stir welding]. Fizicheskaia mezomekhanika [Physical Mesomechanics]. 2014, vol. 17, no. 1, pp. 103-113.
[9] Krektuleva R. A., Cherepanov O.I., Cherepanov R.O. Chislennoe reshenie kvazistaticheskoi
zadachi rascheta ostatochnykh napriazhenii v svarnykh shvakh s uchetom fazovykh prev-rashchenii [Numerical solution of a quasistatic residual stress problem for welds with regard to phase transformations]. Fizicheskaia mezomekhanika [Physical Mesomechanics]. 2013, vol. 16, no. 6, pp. 51-57.
[10] Smirnov S.V., Pugacheva N.B., Miasnikova M.V., Smirnova E.O. Strukturnaia neodnorod-nost’ svarnogo soedineniia aliuminievogo splava i modelirovanie ego uprugoi deformatsii [Heterogeneity of an Al alloy weld and simulation of its elastic deformation]. Fizicheskaia mezomekhanika [Physical Mesomechanics]. 2014, vol. 17, no. 1, pp. 51-56.
[11] Bataev I.A., Bataev A.A., Mali V.I., Bataev V.A., Balaganskii I.A. Strukturnye izmeneniia poverkhnostnykh sloev stal’nykh plastin v protsesse svarki vzryvom [Structural changes in the surface layers of steel plates in explosion welding]. Materialovedenie i termicheskaia obrabotka [Materials and Heat Treatment]. 2013, no. 9, pp. 19-24.
[12] Makarov E.L. Komp’iuternaia otsenka svarivaemosti nizkolegirovannoi stali [Computer assessment of the weldability of low-alloy steel]. Svarka i diagnostika [Welding and Diagnostics]. 2014, no. 4, pp. 23-29.
[13] Badalian V.G., Bazulin A.E., Bazulin E.G., Samarin P.F., Tikhonov D.S. Ispol’zovanie mod-elirovaniia dlia optimizatsii metodik UZK [Using simulation techniques to optimize the ultrasonic testing]. Svarka i diagnostika [Welding and Diagnostics]. 2014, no. 6, pp. 18-22.
[14] Klimov V.S., Komirenko A.V. Primenenie neirosetevykh tekhnologii raspoznavaniia obra-zov dlia diagnostiki kontaktnoi svarki v proizvodstvennoi srede [Application of neural network pattern recognition technology for the diagnosis of resistance welding in the production environment]. Svarka i diagnostika [Welding and Diagnostics]. 2013, no. 2, pp. 40-44.
[15] Bigus G.A., Tpavkin A.A., Daniev Iu.F. Veivlet-analiz signalov akusticheskoi emissii pri di-agnostike konstruktsii [Wavelet analysis of the acoustic emission signals during diagnosis designs]. Svarka i diagnostika [Welding and Diagnostics]. 2012, no. 4, pp. 34-38.
[16] Skachkov I.O. Monitoring kachestva kontaktnoi tochechnoi svarki peremennym tokom s primeneniem veivlet-analiza [Monitoring the quality of resistance spot welding alternating current using wavelet analysis]. Tekhnicheskaia diagnostika i nerazrushaiushchii kontrol’ [Technical Diagnostics and Nondestructive Testing]. 2012, no. 3, pp. 43-47.
[17] Nonomura S., Hyoma K., Kobayashi K., Yamaoka H., Miyasaka F. Control of the Penetration Shape by Pulsed Current Waveform. Transactions of the Japan welding society. Quarterly Journal of the Japan welding society, 2015, vol. 33, no. 1, pp. 82-88.
[18] Okabe T., Yasuda K., Nakata K. Dynamic Observations of Welding Pghenomena and Finite Element Analysis in High Frequency Electric Resistance Welding. Transactions of the Japan welding society. Quarterly Journal of the Japan welding society, 2014, vol. 32, no. 3, pp. 156-163.
[19] Protsiv Iu.V., Sapunov A.L. Predotvrashchenie treshchinoobrazovaniia pri izgotovlenii svarnykh kol’tsevykh zagotovok iz goriachekatanykh profilei stareiushchikh nikelevykh splavov [Prevention of cracking in the manufacture of welded ring blanks of hot-rolled profiles aging nickel alloys]. Materialovedenie i termicheskaia obrabotka [Materials and Heat Treatment]. 2011, no. 8, pp. 19-24.
[20] Sadasue T., Igi S., Taniguchi K., Ikeda R., Oi K. Fracture behavior and numerical study of resistance spot welded joints in high strength steel sheet. Transactions of the Japan welding society. Quarterly Journal of the Japan welding society, 2014, vol. 32, no. 2, pp. 64-72.
[21] Morisada Y., Tamashiro K., Kamai M., Ueji R., Fujii H. Development of Small sized Friction Stir Welding Equipment for Hand-operated Welding. Transactions of the Japan welding society. Quarterly Journal of the Japan welding society, 2014, vol. 32, no. 2, pp. 52-56.
[22] Kozlov D.M., Popovich A.L. Avtomatizirovannyi nerazrushaiushchii kontrol’ kol’tsevykh soedinenii truboprovodov, vypolnennykh kontaktnoi stykovoi svarkoi oplavleniem [Automated non-destructive testing of annular pipe connections made contact butt welding]. Svarka i diagnostika [Welding and Diagnostics]. 2014, no. 5, pp. 56-57.
[23] Popov A.V. Otsenka prochnosti svarnykh i paianykh soedinenii konstruktsii raketno-kosmicheskoi tekhniki metodom akusticheskoi emissii [Strength Assessment of SpaceRocket Hardware Welded and Soldered Joints by Acoustic Emission Method]. V mire ne-razrushaiushchego kontrolia [In the world of non-destructive testing]. 2015, no. 1(67), pp. 57-60.
[24] Sivtsev M.N., Sleptsov G.N. Issledovanie struktury svarnykh soedinenii pri razlichnykh tekhnologicheskikh parametrakh svarki nizkolegirovannykh stalei [Investigation of the structure of welded joints at different technological parameters welding low alloy steels]. Materialovedenie i termicheskaia obrabotka [Materials and Heat Treatment]. 2014, no. 2, pp. 19-24.
[25] Cherniaeva E.V., Galkin D.I., Bigus G.A., Merson D.L. Primenenie metoda akusticheskoi emissii dlia nerazrushaiushchego kontrolia sostoianiia osnovnogo metalla i svarnykh soedinenii truboprovodov, rabotaiushchikh v usloviiakh malotsiklovoi ustalosti [Application of acoustic emission method for non-destructive monitoring of the base metal and welded joints of pipelines, operating under low-cycle fatigue]. Svarka i diagnostika [Welding and Diagnostics]. 2010, no. 2, pp. 50-56.
[26] Gumeniuk V.A., Kazakov N.A., Sul’zhenko V.A. Akuctiko-emissionnyi kontrol’ protsessa svarki korpusa glubokovodnogo apparata [Akuctiko emission control of the welding process deepwater housing unit]. V mire nerazrushaiushchego kontrolia [In the world of nondestructive testing]. 2007, no. 1(35), pp. 57-60.
[27] Razygraev N.P., Razygraev A.N. Priemochnyi i ekspluatatsionnyi ul’trazvukovoi kontrol’ golovnymi volnami ekho-metodom [Acceptance and operational control of the bow wave ultrasonic echo technique]. V mire nerazrushaiushchego kontrolia [In the world of nondestructive testing]. 2007, no. 4(38), pp. 57-60.
[28] Davydov D.M. Ul’trazvukovoi kontrol’. Problemy i ikh resheniia v teplovoi i atomnoi ener-getike [Ultrasonic testing. Problems and solutions in thermal and nuclear power]. Svarka i diagnostika [Welding and Diagnostics]. 2010, no. 2, pp. 57-60.
[29] Bobrov V.T., Samokrutov A.A., Alekhin S.G., Bobrov S.V. Issledovanie ematekhnologii ul’trazvukovogo kontrolia kontaktnoi tochechnoi svarki v avtomobilestroenii [Research ema technologies ultrasonic testing resistance spot welding in the automotive industry]. Svarka i diagnostika [Welding and Diagnostics]. 2014, no. 4, pp. 55-59.
[30] Zuev L.B., Psakh’e S.G., Orishich A.M., Kovalev O.B., Iudina E.V., Afonin Iu.V., Danilov V.I., Poletika T.M. Struktura i svoistva svarnykh soedinenii, vypolnennykh lazernoi i tochechnoi svarkoi [Structure and properties of laser and spot welds]. Fizicheskaia mezomek-hanika [Physical Mesomechanics]. 2005, vol. 8, no. S, pp. 87-90.
[31] Panin V.E., Sapozhnikov S.V., Kablov E.N., Pleshanov V.S., Klimenov V.A., Ivanov Iu.F., Pochivalov Iu.I., Kibitkin V.V., Napriushkin A.A. , Nekhoroshkov O.N., Lukin V.I. Vliianie ul’trazvukovoi udarnoi obrabotki na strukturu i soprotivlenie ustalosti svarnykh soedinenii vysokoprochnoi stali VKS-12 [Effect of ultrasonic shock treatment on the structure and fatigue strength of welded joints of high-strength steel VKS-12]. Fizicheskaia mezomekhanika [Physical Mesomechanics]. 2006, vol. 9, no. 2, pp. 85-96.
[32] Lobanov L.M., Pivtorak V.A. Diagnostika konstruktsii metodami elektronnoi shirografii i spekl-interferometrii [Diagnosis structures using electron shearography and speckle inter-ferometry]. Svarka i diagnostika [Welding and Diagnostics]. 2014, no. 2, pp. 27-32.
[33] Goncharov A.L., Dragunov V.K., Sliva A.P., Portnov M.A., Terent’ev E.V., Gribkov M.S. Is-sledovanie svarnykh soedinenii raznorodnykh stalei detalei magnitoprovoda, vypolnennykh ELS [Investigation of welded joints of dissimilar steels magnetic parts made ELS]. Svarka i diagnostika [Welding and Diagnostics]. 2014, no. 5, pp. 28-32.
[34] Varovin A.Ia., Karzov G.P., Margolin B.Z. Problemy prognozirovaniia rabotosposobnosti konstruktsii po dannym nerazrushaiushchego kontrolia [Problems of prediction of serviceability of structures from the nondestructive testing data]. Voprosy materialovedeniia [Inorganic Materials: Applied Research]. 2007, no. 3, pp. 169-186.
[35] Antipov V.S., Vasil’ev V.D., Udralov Yu.I. Radiographic inspection of the weld seams: test parameters. Russian Journal of Nondestructive Testing, 2006, vol. 42, no. 2, pp. 106-110.
[36] Matzkanin G.A., Yolken H.T. Selecting a Nondestructive Testing Method: Ultrasonic Testing. Welding Journal, 2008, May, pp. 26-32.
[37] Abashin M.I., Barzov A.A., Galinovskii A.L. Analiz fiziko-tekhnologicheskikh osobennostei protsessa ul’trastruinoi diagnostiki [Analysis of the physical and technological characteristics of the process of diagnosis ultra jet]. Vestnik MGTU im. N.E. Baumana. Ser Estestven-nye nauki [Herald of the Bauman Moscow State Technical University. Series Natural Sciences]. 2012, special is., pp. 7-18.
[38] Abashin M.I., Galinovskii A.L., Bochkarev S.V., Tsaplin A.I., Provatorov A.S., Khafizov M.V. Modelirovanie ul’trastruinogo vozdeistviia dlia kontrolia kachestva pokrytii [Modeling of ultra-jet influence for coating quality control]. Fizicheskaia mezomekhanika [Physical Mesomechanics]. 2015, vol. 18, no. 1, pp. 84-89.
Информация об авторах
АБАШИН Михаил Иванович (Москва) — кандидат технических наук, доцент кафедры «Технология ракетно-космического машиностроения». МГТУ им. Н.Э. Баумана (105005, Москва, Российская Федерация, 2-я Бауманская ул., д. 5, стр.1, e-mail: [email protected]).
БОЧКАРЕВ Сергей Васильевич (Пермь) — доктор технических наук, профессор кафедры «Микропроцессорные средства автоматизации». Пермский национальный исследовательский политехнический университет (614990, Пермь, Пермский край, Российская Федерация, Комсомольский пр., д. 29, e-mail: [email protected]).
ЦАПЛИН Алексей Иванович (Пермь) — доктор технических наук, зав. кафедрой «Общая физика». Пермский национальный исследовательский политехнический университет (614990, Пермь, Пермский край, Российская Федерация, Комсомольский пр., д. 29, e-mail: [email protected]).
КОБЕРНИК Николай Владимирович (Москва) — кандидат технических наук, доцент кафедры «Технология сварки и диагностики». МГТУ им. Н.Э. Баумана (105005, Москва, Российская Федерация, 2-я Бауманская ул., д. 5, стр.1, e-mail: [email protected]).
Статья поступила в редакцию 10.10.2015 Information about the authors
ABASHIN Mikhail Ivanovich (Moscow) — Candidate of Science (Eng. ), Associate Professor, Department of Technologies of Rocket and Aerospace Engineering. Bauman Moscow State Technical University (105005, Moscow, Russian Federation, 2nd Baumanskaya St., Bldg. 5, Block 1, e-mail: [email protected]).
BOCHKAREV Sergey Vasilievich (Perm) — Doctor of Science (Eng.), Professor, Department of Automation Microprocessors. Perm National Research Polytechnic University (614990, Perm, Perm Region, Russian Federation, Komso-molsky Prospekt, Bldg. 29, e-mail: [email protected]).
TSAPLIN Aleksey Ivanovich (Perm) — Doctor of Science (Eng.), Head of Department of General Physics. Perm National Research Polytechnic University (614990, Perm, Perm Region, Russian Federation, Komsomolsky Prospekt, Bldg. 29, e-mail: [email protected]).
KOBERNIK Nikolai Vladimirovich (Moscow) — Candidate of Science (Eng. ), Associate Professor, Department of Welding Technology and Diagnostics. Bauman Moscow State Technical University (105005, Moscow, Russian Federation, 2nd Baumanskaya St., Bldg. 5, Block 1, e-mail: [email protected]).
Диагностика и ремонт сварочного оборудования
Сервисный центр магазина «Сварка» выполняет диагностику и ремонт сварочных аппаратов: Selco, Wallius, Wameta, Сварис, FoxWeld, EWM, Kemppi, ESAB, ПДГ и др. Производим ремонт инверторных сварочных аппаратов или любого другого типа.
Правила проведения диагностики сварочного оборудования
- Оборудование принимается для диагностики только в чистом виде. Очистка от пыли и грязи — платная услуга.
- Стоимость диагностики — БЕСПЛАТНО.
- Срок проведения диагностики: от — до 5‐ти рабочих дней. В случае необходимости отправки оборудования Изготовителю срок диагностики согласовывается дополнительно.
Правила проведения платного ремонта оборудования
- Оборудование принимается в платный ремонт после оплаты диагностики.
- Срок ремонта от 3 до 30 дней согласовывается индивидуально.
- Срок гарантии на проведённый ремонт определяется типом отремонтированного узла.
Вы можете отремонтировать сварочный аппарат в нашем сервисе, для этого обратитесь в магазин сварочного оборудования.
Получите информацию о наличии необходимого сварочного оборудования в Петербурге, а также о возможности купить сварочный аппарат со скидкой по акции, приобретению по акции средств защиты: костюм сварщика, сварочные маски, спецодежду для сварщиков со спилком.
У нас Вы можете купить сварочные электроды всех диаметров, газовую горелку, газовый баллон от 5 до 50 л, а также купить в розницу и оптом профессиональное сварочное оборудование.
Мы ждем Вас в нашем сервисном центре.
Подробная инструкция по ремонту сварочного оборудования.
Внимание! Аппарат принимается на ремонт только в чистом виде и кабелей заземления и электрододержателей.
Гарантийный ремонт аппаратов
- Если аппарат на гарантии, клиент предоставляет гарантийный талон.
- Если аппарат не гарантийный, покупатель оплачивает сумму диагностики.
- Не гарантийные аппараты принимаются в ремонт только после оплаты диагностики.
- Продавец делает скан гарантийного талона. Гарантийный талон остается на руках у клиента. С задней стороны гарантийного талона ставится дата приемки аппарата в ремонт с печатью СЦС.
- Продавец делает два экземпляра акта о приемке на ремонт и помещает их в папку «РЕМОНТ» за файлом «В РАБОТЕ» в отдельном файле, туда же кладется скан гарантийного талона и чека. В акте указываются возникшие неисправности, указывается, что это гарантийный ремонт, а так же модель и серийный номер.
Акт приемки оборудования в ремонт:
- модель и серийный номер аппарата,
- обязательная сумма диагностики, согласованная с покупателем,
- описание дефекта и наличие внешних механических повреждений (следы ударов, вмятины, оплавленные коннекторы и вилки, выдернутые из корпуса кабель и т.д.).
- комплектация (коробка, наличие ремня и т.п.)
- копия гарантийного талона,
— гарантийный или не гарантийный ремонт, - ФИО покупателя или название компании и телефоны для связи,
- подписи сотрудника магазина и покупателя.
- Покупателю сообщается, в течение какого времени ему позвонят и назовут стоимость ремонта.
- При перемещении аппаратов в мастерскую, необходимо приложить к аппарату один экземпляр акта приемки на ремонт, на нее наладчик вносит следующую информацию: проведенные работы и их стоимость, замена деталей, с прилагаемыми кассовыми и товарными чеками и акт перемещения. Если аппаратов передается несколько штук – все они вносятся в один акт перемещения. На актах перемещения ставят свой подписи сотрудники, отгрузившие аппарат и принявшие его. Один из актов остается в магазине, второй – у менеджера по ремонту.
- В мастерской принимает аппарат наладчик и менеджер по ремонту. Последний ведет учет ремонтных аппаратов в реестре.
- После диагностики аппаратов менеджер по ремонту передает информацию по электронной почте о ее итогах (гарантийный случай или нет, стоимость работ, деталей и т.д.). Сотрудник магазина связывается с покупателем и озвучивает стоимость работ, если ремонт не гарантийный. Ремонт начинается только после согласия покупателя с названной суммой. В случае отказа покупателя, аппарат возвращается без возврата суммы диагностики.
- Сотрудник заносит в акт заявки на ремонт полученную информацию от наладчика и итог разговора с клиентом.
- Сотрудник, который забирает аппарат обратно, расписывается в приемке аппарата на двух актах о перемещении аппарата. Акты возвращаются в папку.
- После ремонта аппарата на заявке на ремонт должны быть указаны все исправленные неисправности, стоимость деталей и затраченное на ремонт время.
- При возвращении аппаратов из мастерской, на самом аппарате наклеивается надпись «готово», сотрудники магазина отзваниваются клиенту о готовности аппарата. В актах о перемещении делается пометка о приемке аппарата с мастерской с указанием даты.
- После возвращения аппарата клиенту, в заявках и гарантийном талоне делается отметка «выдано клиенту» с указанием даты и подписями сотрудника, выдавшего аппарат, и печатью СЦС и клиента. Также клиенту выдается заявка о приемке на ремонт с описанием проведенных работ и стоимостью.
- После окончания всех операций документы вкладываются в файл, который перемещается за файл «ОТРАБОТАННЫЕ».
Не гарантийный ремонт аппаратов
- Если аппарат не гарантийный, покупатель оплачивает сумму диагностики.
- Не гарантийные аппараты принимаются в ремонт только после оплаты диагностики.
- В заявке указываются возникшие неисправности, указывается, что это не гарантийный ремонт, а так же модель и серийный номер.
- 3-й экземпляр отдается клиенту. В акте указываются возникшие неисправности, указывается, что это не гарантийный ремонт, а так же модель и серийный номер.
Акт приемки оборудования в ремонт:
- модель и серийный номер аппарата,
- обязательная сумма диагностики, согласованная с покупателем,
- описание дефекта и наличие внешних механических повреждений (следы ударов, вмятины, оплавленные коннекторы и вилки, выдернутые из корпуса кабель и т.д.)
- комплектация (коробка, наличие ремня и т.п.)
— гарантийный или не гарантийный ремонт, - ФИО покупателя или название компании и телефоны для связи,
- подписи сотрудника магазина и покупателя.
- Покупателю сообщается, в течение какого времени ему позвонят и назовут стоимость ремонта.
- При перемещении аппаратов в мастерскую, необходимо приложить к аппарату один экземпляр акта приемки на ремонт, на нее наладчик вносит следующую информацию: проведенные работы и их стоимость, замена деталей, с прилагаемыми кассовыми и товарными чеками и акт перемещения. Если аппаратов передается несколько штук – все они вносятся в один акт перемещения. На актах перемещения ставят свой подписи сотрудники, отгрузившие аппарат и принявшие его. Один из актов остается в магазине, второй – у менеджера по ремонту.
- В мастерской принимает аппарат наладчик и менеджер по ремонту. Последний ведет учет ремонтных аппаратов в реестре.
- После диагностики аппаратов менеджер по ремонту передает информацию по электронной почте о ее итогах (гарантийный случай или нет, стоимость работ, деталей и т.д.). Сотрудник магазина связывается с покупателем и озвучивает стоимость работ. Ремонт начинается только после согласия покупателя с названной суммой. В случае отказа покупателя, аппарат возвращается без возврата суммы диагностики.
- Сотрудник заносит в акт заявки на ремонт полученную информацию от наладчика и итог разговора с клиентом.
- Сотрудник, который забирает аппарат обратно, расписывается в приемке аппарата на двух актах о перемещении аппарата.
- После ремонта аппарата на заявке на ремонт должны быть указаны все исправленные неисправности, стоимость деталей и затраченное на ремонт время.
- При возвращении аппаратов из мастерской, на самом аппарате наклеивается надпись «готово», сотрудники магазина отзваниваются клиенту о готовности аппарата. В актах о перемещении делается пометка о приемке аппарата с мастерской с указанием даты.
- После возвращения аппарата клиенту, в заявках делается отметка «выдано клиенту» с указанием даты и подписями сотрудника, выдавшего аппарат, и печатью СЦС и клиента. Также клиенту выдается заявка о приемке на ремонт с описанием проведенных работ и стоимостью.
Стоимость диагностики – БЕСПЛАТНО. Чек прикрепляется к гарантийному талону или акту о приемке в случае не гарантийного ремонта. Взимается с клиента при приемке аппарата на ремонт. Если по каким-либо причинам оплата не была принята, то об этом делается пометка в заявке на ремонт, как и при оплате по безналичному расчету.
При выдаче аппарата клиенту пробивается чек на сумму ремонта, указанную в акте на ремонт или выставляется счет, если оплата по безналичному расчету.
Все продаваемое в магазине сварочное оборудование имеет необходимые сертификаты государственного образца.
На оборудование всех производителей предоставляется гарантийное обслуживание. Также все производители силами своих сервисных центров осуществляют и послегарантийное обслуживание.
Наш магазин «Сварка» работает только с теми производителями, качество оборудования и уровень обслуживания которых находятся на высоком уровне.
Гарантийные сроки и адреса сервисных центров:
- Сварог — Гарантия 5 лет распространяется на аппараты серии ARC и MIG с максимальным током сварки до 200 А (модели аппаратов уточняйте у менеджеров) и все аппараты серий PRO и EASY. На остальные аппараты, включая промышленные модели гарантия — 24 месяцев.
- KEMPPI — гарантийный срок 24 месяца.
- GYSMI — гарантийный срок 12 месяцев.
- EWM — гарантийный срок 36 месяцев
- ESAB — гарантийный срок 24 месяца.
- Lincoln Electric — гарантийный срок от 24-х до 36-и месяцев в зависимости от модели сварочного аппарата.
- Fubag — 12 месяцев
- Aurora — гаантийный срок 24 месяцев
- Ресанта — 12 месяцев
- 3M — гарантийный срок 24 месяца.
- FoxWeld — гарантийный срок 12 месяцев.
- Trafimet — гарантийный срок 6 месяцев.
курсы центра «Контроль и диагностика» в Москве
«НУЦ «Контроль и диагностика» проводит обучение и квалификацию специалистов сварочного производства в соответствии с программами обучения Международного института сварки для следующих категорий персонала:
- Международный инженер по сварке
- Международный технолог по сварке
- Международный специалист по сварке
- Международный инспектор по сварке
- Международный сварщик
В Европе и мире есть ассоциации, имеющие общественно-профессиональный характер. Именно эти профессиональные неправительственные ассоциации разрабатывают политику и правила проведения обучения персонала и присвоения квалификации.
В настоящее время существуют две международные инженерные ассоциации, объединяющие мировую сварочную общественность. Это Международный институт сварки (МИС), основанный в 1948 г., в состав которого входят более 50 развитых стран мира, и Европейская федерация по сварке (EФС), основанная в 1971 г. и включающая 28 стран Европы.
В рамках МИСа и ЕФС создана во взаимодействии с ISO глобальная гармонизированная система обучения, квалификации и сертификации персонала сварочных производств, основанная на соблюдении требований стандартов серии ISO 9000, ISO 14000, ISO 3834/EN 729 и ISO 14731/EN 719 при производстве ответственных сварных конструкций и сертификации сварочных производств в части квалификации персонала.
Для внедрения и обеспечения деятельности в каждой стране член МИСа учреждает Уполномоченный национальный орган (ANB).
В России Российским научно-техническим сварочным обществом (РНТСО) был учрежден в 2001 г. и признан Международным институтом сварки Уполномоченный Национальный Орган по квалификации сварочного персонала — НОУДПО «Научно-учебный центр «Контроль и диагностика» — с правом выдачи дипломов международного образца, признаваемых во всех промышленно развитых странах мира.
Для обучения по программам Международного института сварки необходимо направить заявку в адрес «НУЦ «Контроль и диагностика»
Реестр владельцев международных дипломов.
Более детальную информацию можно получить у наших специалистов.
Кафедра сварки, мониторинга и диагностики конструкций
Кафедра «Сварка, диагностика и мониторинг конструкций» была создана в 2001 году при участии ИФТПС СО РАН, Института нефти и газа имени Губкина и ЯТЕК, является выпускающей кафедрой, осуществляет подготовку по направлению 15.03.01 «Машиностроение».
На базе кафедры есть лаборатории: «Физика твердого тела», «Материаловедение», «Технология сварки в региональных условиях» и «Диагностика и производство сварных конструкций».
Отдельным направлением идет организация летней учебной и производственной практик студентов, где они осваивают профессиональные навыки и набирают материал для будущего дипломного проекта.
В 2011 году кафедра с работодателями разработала учебный план по направлению подготовки 150700.62 Машиностроение, в вариативной части были введены дисциплины, которые, по опыту работы предыдущих лет с предприятиями, была необходимость ввести. Были созданы базовые кафедры на предприятиях судостроения и сварки металлических конструкций, что позволило готовить по специальности с 1 курса.
Выпускники кафедры работают в различных областях промышленности: ООО «Якутгазстрой», ООО «Сибстроймонтаж», ИФТПС ЯНЦ СО РАН, Жатайский судоремонтный завод, Жатайский завод металлоконструкций, Министерство ЖКХ и энергетики, ООО «Газсервис», ОАО «Саханефтегазсбыт», ООО «Стройкон», ООО «Судовая компания «Якутск», Сахатранснефтегаз, ООО «Сибинкон», ООО «Газэкспертсервис», ООО «СПК Новый город», ОАО РПИИ Якутпроект.
В настоящее время подана заявка на открытие магистратуры «Машиностроение».
Создается инжиринговый центр по ремонту судовых конструкций, с участием ЛОРПа и Санкт-Петербургского Политехнического Института. 2 выпускника из группы МС-12 подали заявки на поступление магистратуры в Красноярский политехнический институт, а 1 выпускник пройдет повышение квалификации в Финляндии.
Кафедра «Сварка, диагностика и мониторинг конструкций» была создана в 2001 году при участии ИФТПС СО РАН, Института нефти и газа имени Губкина и ЯТЕК, является выпускающей кафедрой, осуществляет подготовку по направлению 15.03.01 «Машиностроение».
В 2013 году приказом №101-ОД от 08 февраля 2013 года кафедре присвоена имя академика В.И. ЛАРИОНОВА.
На базе кафедры есть лаборатории: «Физика твердого тела», «Материаловедение», «Технология сварки в региональных условиях» и «Диагностика и производство сварных конструкций».
Отдельным направлением идет организация летней учебной и производственной практик студентов, где они осваивают профессиональные навыки и набирают материал для будущего дипломного проекта.
В 2011 году кафедра с работодателями разработала учебный план по направлению подготовки 150700.62 Машиностроение, в вариативной части были введены дисциплины, которые, по опыту работы предыдущих лет с предприятиями, была необходимость ввести. Были созданы базовые кафедры на предприятиях судостроения и сварки металлических конструкций, что позволило готовить по специальности с 1 курса.
Выпускники кафедры работают в различных областях промышленности: ООО «Якутгазстрой», ООО «Сибстроймонтаж», ИФТПС ЯНЦ СО РАН, Жатайский судоремонтный завод, Жатайский завод металлоконструкций, Министерство ЖКХ и энергетики, ООО «Газсервис», ОАО «Саханефтегазсбыт», ООО «Стройкон», ООО «Судовая компания «Якутск», Сахатранснефтегаз, ООО «Сибинкон», ООО «Газэкспертсервис», ООО «СПК Новый город», ОАО РПИИ Якутпроект.
В настоящее время подана заявка на открытие магистратуры «Машиностроение».
Создается инжиринговый центр по ремонту судовых конструкций, с участием ЛОРПа и Санкт-Петербургского Политехнического Института. 2 выпускника из группы МС-12 подали заявки на поступление магистратуры в Красноярский политехнический институт, а 1 выпускник пройдет повышение квалификации в Финляндии.
УЗК-контроль сварных швов. Рассматриваем во всех подробностях
В отраслях машиностроения, строительства и других разделах промышленности без сварочных процессов не обойтись. Сварка, как элемент прочного и надежного соединения деталей и узлов, занимает ведущее место в хозяйственной деятельности человека. Без нее невозможно благоустроить быт, проложить коммуникации, дать воду, газ. Главным условием длительной эксплуатации сварных элементов является качество сварки. Определить визуально это почти невозможно, но способ есть.
Ультразвуковая дефектоскопия
В начале 30-х годов прошлого века ученые разработали новый метод контроля сварных швов ультразвуком – ультразвуковая дефектоскопия. Он основан на свойстве высокочастотных колебаний проникать в структуру металлического изделия и отражаться от неровностей и пустот с разной звуковой проницаемостью. Эта особенность акустических волн положена в основу метода ультразвуковой дефектоскопии. Акустические волны представлены упругими колебаниями материальных частиц в диапазоне от 20 кГц до 500 мГц.
Технология проведения узк-контроля сварных швов заключается в следующем. Специальным устройством искусственно создается ультразвуковая волна, затем она направляется в точку исследования. Попадая в проверяемый шов она отражается. В случае неудовлетворительной сварки ультразвуковая волна преломляется и отклоняется от обычного вектора. Оператор узк-оборудования видит на мониторе отклонение и дает определение дефекту. Этот способ дефектоскопии получил название «узк метод неразрушающего контроля». Суть отражения, преломления волн и другой специфики разберет лишь оператор-дефектоскопист. Все измерения производятся согласно установленному ГОСТу.
Применять способ диагностики сварных швов ультразвуком можно для различных типов металлов:
- высоколегированные стали;
- чугун;
- алюминий, медь, бронза, латунь и другие сплавы;
- слабо проводящие ультразвук металлы.
Узк-контроль и области его использования
Узк-контроль металла применяется в большинстве областей промышленности и народного хозяйства. Незаменима дефектоскопия на объектах, связанных с повышенной опасностью: газопроводы, нефтепроводы, теплосети. Контроль и диагностика сварных соединений ультразвуком применяется:
- в энергетике;
- в химической и нефтегазовой отраслях;
- для определения износа труб в магистральных трубопроводных сетях;
- для обнаружения изъянов сварных швов в изделиях, подверженных воздействию повышенных температур и давления;
- в изделиях, эксплуатация которых проходит в активных средах.
- в гидравлических и водопроводных системах;
- узк-контроль деталей с нестандартной геометрической формой;
- в индивидуальных случаях при реконструкции зданий и помещений.
В большинстве отраслях машиностроения не обойтись без ультразвукового контроля узлов и агрегатов. Компактность оборудования позволяет проводить узк-контроль труб и других изделий в полевых условиях.
Положительные стороны узк-контроля
Работы по ультразвуковому контролю сварных швов имеют ряд преимуществ:
- высокая точность проверки качества швов за малый промежуток времени;
- диагностика в полевых условиях;
- при выполнении работ по узк-контролю изделие не подвергается деформации;
- при проведении диагностики не требуется выведение объекта из эксплуатации;
- работы безопасны для окружающих;
- приемлемая стоимость.
Положительным аспектом являются параметры проведения работ по ультразвуковому контролю. Оператор-дефектоскопист, используя специальное оборудование, осуществляет диагностику сварных швов изделия на глубине до 10 метров. Практика доказывает, что узк-контроль деталей может быть одинаково эффективен для проверки любых типов сварных соединений, имеющих толщину шва от 4 до 800 мм.
Какие дефекты можно выявить, используя метод узк-диагностики?
Основанный на методе ультразвуковой дефектоскопии, данный способ позволяет четко определить брак в сварном шве. Правильно проведенная диагностика места сварки дает полное представление о специфике дефекта. Специфическими задачами метода служит выявление следующих недостатков:
- определение трещин в зоне около сварных швов;
- выявление пор и зон объекта, пораженных коррозией;
- поиск участков сварного шва с дефектами;
- шовные расслоения металла;
- определение участков объекта с несоответствующим химическим составом, искаженным геометрическим размером;
- провисание наплавленного метала в нижней части шва.
Услуги по узк-контролю сварных швов от компании «ДСН»
Многие организации в целях экономии средств или своей некомпетентности обходят стороной работы по выполнению узк-контроля или обращают на него внимание непосредственно перед вводом промышленного объекта в эксплуатацию. Это приводит к дополнительным расходам, а иногда и к аварийным ситуациям и техногенным катастрофам в процессе использования. Для исключения подобных моментов важно вовремя проводить ультразвуковую дефектоскопию.
Узк-контроль сварных швов выполняется согласно ГОСТ 24507-80 и ГОСТ 21120-75. Компания «ДСН» предоставляет полный спектр услуг по ультразвуковой диагностике сварных швов с полной классификацией выявленных дефектов по типам и размерам. В список работ предприятия включена ультразвуковая толщинометрия, необходимая при экспертизе промышленной безопасности, главной задачей которой является распознавание соответствия толщины металла согласно входящим паспортным данным.
Цена услуг узк-контроля зависит от габаритных размеров и геометрии объекта, шероховатости, количества и других факторов. Менеджеры помогут рассчитать стоимость диагностики любого изделия, а специалисты компании «ДСН» выполнят работы по узк-контролю качественно и быстро в соответствии с требованиями и нормами.
Диагностика сварки посредством оптимизации скопления частиц и выбора функций
В предыдущем докладе был представлен подход к диагностике сварки, основанный на оптической спектроскопии плазмы. Он заключался в использовании алгоритмов оптимизации и синтетических спектров для получения профилей участия видов, участвующих в плазме. Здесь обсуждается модификация модели: с одной стороны, алгоритм управляемого случайного поиска был заменен реализацией оптимизации роя частиц.С другой стороны, был включен этап выбора признаков для определения тех спектральных окон, в которых будет происходить процесс оптимизации. Будут показаны как экспериментальные, так и полевые испытания, чтобы проиллюстрировать производительность решения, которое улучшает результаты предыдущей работы.
1. Введение
Сварочные процессы играют важную роль в современной промышленности, поскольку они используются в широком спектре промышленных сценариев. Следует упомянуть некоторые типичные примеры: изготовление тяжелых компонентов для атомных электростанций (например,g., парогенераторы), автомобили, двигатели для аэронавтики и трубки для различных применений энергии или гражданского строительства. В некоторых из этих применений требования к качеству сварки очень жесткие: пористость, возникающая в процессе сварки трубы с трубной решеткой парогенератора, является хорошим примером в этом отношении.
Одной из основных проблем, с которыми сталкиваются инженеры на ранних этапах определения конкретной процедуры сварки, является сложность физических характеристик процесса [1, 2].Хотя были предприняты как теоретические, так и экспериментальные работы, опыт показывает, что определение оптимальных параметров для данного сценария требует выполнения предыдущих исследований в лаборатории, а затем проведения испытаний сварки купонов для проверки прогнозируемого поведения. Несмотря на все эти усилия, дефекты будут появляться в процессе, даже если все переменные будут тщательно контролироваться. Это подразумевает использование как разрушающих, так и неразрушающих методов оценки для исследования полученных швов и проверки их соответствия требуемым стандартам.
Для процессов лазерной и дуговой сварки были предложены различные подходы к мониторингу, основанные на использовании электрических [3–5], акустических [6, 7] и оптических датчиков [8, 9]. Также использовались промышленные камеры видимого диапазона, обычно с помощью фильтров и источников освещения [10, 11], и инфракрасная термография также использовалась как для онлайн-контроля, так и для офлайн-контроля [12, 13]. Среди всех этих альтернатив только первая была серьезно коммерциализирована, поскольку она позволяет установить надежное окно процесса.Однако некоторые дефекты, такие как выявление ложных материалов в стыке, невозможно обнаружить с помощью этого подхода. Помимо выбранной сенсорной технологии, большие усилия были предприняты в стратегиях обработки, предназначенных для обнаружения дефектов [14, 15] и классификации [16–18].
Оптическая спектроскопия плазмы также изучалась на предмет ее применения в диагностике сварки [19, 20], и в настоящее время она является одним из наиболее перспективных решений в этой области. Невосприимчивость оптического волокна к сильным электромагнитным помехам, возникающим во время процесса, надежность спектроскопических анализов различных частиц, обнаруживаемых в плазме, и возможность выявления паразитных материалов в сварочной ванне являются одними из наиболее важных. преимущества.Типичным подходом при использовании плазменной спектроскопии в этом контексте было определение электронной температуры плазмы с помощью двух или более линий излучения одного и того же вида [19–22]. Однако он имеет свои ограничения, такие как неопределенность в идентификации линий излучения плазмы, что привело к исследованию других параметров мониторинга [23–25].
Недавно были предложены новые альтернативы анализа: например, Sibillano et al. [26] представили так называемую методику картирования ковариаций для анализа динамики плазмы при лазерной сварке, а Грослиер и др.[27] изучали применение анализа шага к сигналам напряжения и тока при сварке внахлест (MIG-MAG). Другой метод основан на генерации синтетических спектров для согласования с реальными экспериментальными данными с помощью алгоритмов оптимизации [28]. Таким образом, полученные профили участия выбранных видов показали четкую корреляцию с событиями качества. Однако некоторые проблемы привели к пересмотру и улучшению предыдущей модели. С одной стороны, ранее выбранный алгоритм оптимизации CRS6 (Controlled Random Search-6) был заменен простой реализацией PSO (оптимизация роя частиц) [29].С другой стороны, примечательно, что профили Ar II продемонстрировали недостаточную чувствительность к некоторым дефектам в некоторых экспериментальных результатах, обсуждаемых в [28], что, как предполагалось, было связано с использованием относительных интенсивностей из NIST [30] локальная база данных для генерации синтетических спектров. Для решения этой проблемы в модели был рассмотрен алгоритм выбора признаков, обеспечивающий выбор более узкого спектрального диапазона, в котором будет происходить оптимизация.
2. Параметры спектроскопического мониторинга для онлайн-контроля сварки
Электронная температура плазмы 𝑇𝑒 — это спектроскопический параметр, обычно используемый в качестве параметра мониторинга в этой структуре.Хотя более точную оценку этой температуры можно получить с помощью графика Больцмана [31], это решение, которое подразумевает рассмотрение нескольких эмиссионных линий и дополнительного процесса регрессии, обычно заменяется упрощенным выражением [19]: 𝑇𝑒 = 𝐸𝑚 (2) −𝐸𝑚 (1) 𝐼𝑘ln (1) 𝐴 (2) 𝑔𝑚 / 𝐼 (2) 𝜆 (1) (2) 𝐴 (1) 𝑔𝑚, (1) 𝜆 (2) (1) где — энергия верхнего уровня, постоянная Больцмана, интенсивность линии излучения, вероятность перехода, 𝑔 статистический вес, и 𝜆 длина волны, связанная с соответствующей линией излучения.Для частного случая дуговой сварки (1) варьируется, включая в логарифме знаменателя частное между энергиями верхнего уровня линии излучения [32].
Появление дефектов связано с возникновением возмущений на профиле 𝑇𝑒, но, хотя корреляция между этим спектроскопическим параметром и качеством швов доказана [19–22], есть некоторые проблемы, такие как выбор эмиссионных линий для участия в оценке 𝑇𝑒, что привело к исследованию альтернативных подходов.
Анализ длины волны, связанной с максимальной интенсивностью излучения плазменного континуума [23], среднеквадратичным сигналом плазмы [25], а также методом от линии к континууму, используемым с алгоритмом выбора признаков [24], являются некоторыми решениями, которые были недавно исследованы. Совершенно другой подход был предложен в [28], где модель, основанная на определении так называемых профилей участия плазменных частиц, была построена путем генерации синтетических спектров и, впоследствии, с использованием алгоритмов оптимизации, чтобы попытаться сопоставить реальные сварочные спектры. .Синтетические спектры создаются после идентификации наиболее значимых видов, участвующих в процессе, и с использованием локальной копии базы данных со спектроскопической информацией о необходимых элементах. В этом процессе используются как центральные длины волн, так и относительные интенсивности, но последние приводят к проблемам сходимости этапа оптимизации, если рассматривать широкий спектральный диапазон. Эта проблема была идентифицирована в [28], поскольку Ar II, преобладающий компонент в нашем сценарии в анализируемом диапазоне длин волн (195–535 нм), не показал ожидаемой реакции на некоторые дефекты, в то время как другие профили (Fe I, Mn I, Ar I) позволили правильно выявить дефекты.
Возможное решение этой проблемы заключается в определении более узких спектральных окон, в которых будет выполняться процесс оптимизации и, как следствие, генерация профилей участия. Очевидно, это порождает неопределенность в выборе наиболее подходящих спектральных диапазонов с точки зрения обнаружения дефектов. Подобная проблема изучалась в [24], где алгоритм выбора признаков (SFFS) [33] использовался для определения тех эмиссионных линий, которые наиболее различаются с точки зрения обнаружения дефектов.Результаты показали высокую зависимость между выбранным спектральным диапазоном и соответствующим профилем мониторинга выходного сигнала. Помимо этой модификации, простая реализация алгоритма PSO (оптимизация роя частиц) будет использоваться вместо исходного CRS6, поскольку будет продемонстрировано, что первый демонстрирует улучшенные вычислительные характеристики.
3. Модификации оригинальной модели
3.1. Алгоритм оптимизации: PSO
В исходной реализации (см. Рисунок 1) для выполнения этапа оптимизации использовался управляемый алгоритм случайного поиска CRS6.Естественная эволюция модели заключается во включении лучшего алгоритма с точки зрения вычислительной производительности всего решения. В этой связи стоит упомянуть, что эта модель изначально не предназначена для использования в сценарии анализа в реальном времени, а предназначена для лучшего понимания динамики различных частиц в плазме и их поведения при появлении различных дефектов в процессе сварки. . Однако его можно использовать в качестве поддержки для других спектроскопических подходов для онлайн-мониторинга (например,g., в технико-экономических обоснованиях), что оправдывает поиск более эффективных реализаций.
После некоторых начальных исследований PSO был выбран в качестве хорошего кандидата, учитывая его простоту и широкое распространение в нескольких сценариях. В области сварки некоторые авторы выбрали алгоритмы PSO для решения оптимизации ключевых параметров сварки [34] или для этапа обучения нейронных сетей [35]. PSO был первоначально предложен в 1995 году [29], и он вдохновлен социальным поведением стай птиц и стайками рыб, претерпев много изменений по сравнению с его первоначальной формулировкой, с новыми версиями и приложениями.Помимо уже упомянутых, типичными областями применения PSO являются анализ изображений и видео, проектирование антенн или выработка электроэнергии и системы, просто чтобы упомянуть некоторые примеры.
Исходный алгоритм PSO можно резюмировать следующим образом. (1) Инициализировать совокупность частиц со случайным положением и скоростями по измерениям D в пространстве поиска. (2) Оценить предопределенную функцию соответствия оптимизации для каждой частицы. (3) Сравните последнюю оценку пригодности текущей частицы с ее «предыдущим лучшим» 𝑝 лучшим.Если текущее значение лучше, то best будет обновлено, а 𝑝𝑖 (предыдущее лучшее положение) будет обновлено до текущего местоположения 𝑥𝑖. (4) Определите частицу в рое с наибольшим успехом на данный момент (best) и назначьте ее местоположение на. (5) Приступайте к изменению скорости и положения каждой частицы в рое в соответствии со следующим выражением: 𝑣id (𝑡 + 1) = 𝑤𝑣id (𝑡) + 𝑐1𝑟1𝑝id (𝑡) −𝑥id (𝑡) + 𝑐2𝑟2𝑝gd (𝑡) −𝑥id, 𝑥 (𝑡) id (𝑡 + 1) = 𝑥id (𝑡) + 𝑣id (𝑡 + 1). (2) (6) Если условие остановки выполнено, то выйти с наилучшим на данный момент результатом; в противном случае повторите с пункта 2.Каждая частица внутри роя определяется своим положением 𝑋𝑖 и скоростью 𝑉𝑖 в 𝐷-мерном пространстве поиска, где 𝑋𝑖 = 𝑥𝑖1, 𝑥𝑖2,…, 𝑥𝑖𝐷𝑉, (3) 𝑖 = 𝑣𝑖1, 𝑣𝑖2,…, 𝑣𝑖𝐷. (4)
В (2) 𝑤 — инерционный вес, 𝑐1 и 𝑐2 — положительные постоянные , обычно определяемые как скорость обучения, а 𝑟1 и 𝑟2 — случайные функции в диапазоне [0,1]. Уравнение (2) описывает базовый алгоритм PSO, где значения параметров 𝑤, 𝑐1 и 𝑐2 могут существенно повлиять на поведение алгоритма [15], даже сделав его нестабильным.Вес инерции можно интерпретировать как текучесть среды, в которой движутся частицы роя, и типичные значения могут быть между 0,4 и 0,9. Параметрам 𝑐1 и 𝑐2 обычно присваивается значение 2, хотя они могут иметь значительное влияние на результаты поиска. Кроме того, рекомендуется поддерживать скорости частиц в диапазоне [−𝑉max, + 𝑉max], но оптимальное значение 𝑉max зависит от конкретной анализируемой задачи. Альтернативой (2) является использование так называемого метода сужения [36]: 𝑣id𝑣 (𝑡 + 1) = 𝜒id (𝑡) + 𝑐1𝑟1𝑝id (𝑡) −𝑥id (𝑡) + 𝑐2𝑟2𝑝gd (𝑡) −𝑥id, 𝑥 (𝑡) id (𝑡 + 1) = 𝑥id (𝑡) + 𝑣id (𝑡 + 1), (5) куда 2𝜒 = √𝜙 − 2 + 𝜙2−4𝜙, 𝜙 = 𝜙1 + 𝜙2> 4.(6)
Типичные значения этих параметров: = 4,1, 𝜙1 = 𝜙2 и 𝜒 = 0,7298. Хотя в этом нет необходимости, рекомендуется установить 𝑉max = 𝑋max.
После того, как решение, описанное в (5), было реализовано, были выполнены некоторые тесты для сравнения производительности PSO с результатами, предлагаемыми CRS6, которые суммированы в таблице 1, где Условие — это условие остановки 𝜀 алгоритма: || 𝑓 ∗ − 𝑓̂𝑥 ∗ || ≤𝜀, (7) где 𝑓 (𝑥) — функция, которую необходимо минимизировать, 𝑓 ∗ — минимум, 𝑥 ∗ — значение, которое необходимо найти в процессе оптимизации, а ̂𝑥 ∗ — приближение к 𝑥 ∗.
|
Использование спектра сварочной плазмы, полученного во время эксперимента При лабораторных испытаниях время сходимости и время обработки PSO определялись при различных условиях, описанных в таблице 2. Частиц — количество частиц, учитываемых в рое для процесса оптимизации, Итераций — количество итераций, учитываемых при каждом поиске, Участие — относительная концентрация частиц (нейтральных атомов и ионов), участвующих в плазме, и Время обработки общее расчетное время вычислений для процесса оптимизации. Были рассчитаны как среднее значение, так и стандартное отклонение (std) участия Ar I и Ar II, что указывает на способность PSO сходиться к ожидаемому решению.Следует отметить, что процесс оптимизации проводился по набору из 150 идентичных спектров, таким образом имитируя идеальный шов без каких-либо дефектов.
|
С точки зрения вычислительной производительности , можно заметить, что PSO предлагает в этом случае время обработки от 0.От 035 до 0,248 с (с использованием 20 частиц), тогда как результаты для CRS6 в таблице 1 варьировались от 0,11 до 0,79. Также стоит отметить, что значения сходимости как для Ar I, так и для Ar II довольно похожи, но стандартное отклонение (std) явно выше для CRS6, и, хотя параметры, подлежащие корректировке в обоих случаях, различны, кажется очевидным, что Вычислительная производительность PSO превосходит производительность CRS6, что оправдывает включение первого в анализируемую модель.
3.2. Использование алгоритма SFFS для выбора спектрального диапазона
В искусстве распознавания образов, то есть в автоматическом распознавании, описании, классификации и группировке образов в различных дисциплинах, от биологии и психологии до компьютерного зрения или дистанционного зондирования [37 ], методы уменьшения размерности используются до распознавания / классификации. Эти попытки найти минимальное количество измерений, в которых может быть выражен набор данных без значительной потери информации, сокращают количество переменных представления шаблона (т.е.е. количество функций), необходимое для анализа. Есть две основные причины, по которым количество функций должно быть как можно меньше: стоимость измерения и точность классификации. Небольшое количество функций может облегчить проклятие размерности [38], если количество обучающих выборок ограничено, но, что более важно, коэффициент попадания классификации может быть значительно увеличен, если разделимость классов или расстояние между шаблонами, принадлежащими разным кластерам, одновременно максимально. Существует множество методов описания [37], которые достигают этих целей двумя разными способами.Алгоритмы выбора функций выбирают (надеюсь) лучшее подмножество входного набора функций, в то время как методы, которые создают новые функции на основе преобразований или комбинации исходного набора функций, называются алгоритмами извлечения признаков. Хотя обе альтернативы нацелены на максимальное разделение классов, выбор признаков предпочтительнее при работе со спектральными данными, поскольку он также обеспечивает физическое понимание проблемы [39]. Более того, уменьшение размерности может быть выполнено обратно или заранее, чтобы идентифицировать спектральные полосы, которые лучше всего разделяют классы (исправить швы и дефекты), и использовать их для построения сигнала мониторинга.Таким образом, отношение сигнал / шум последнего и, как следствие, повышается чувствительность к дефектам. Реализуемость этого подхода была продемонстрирована в предыдущей работе [24], где метод от линии к континууму (т.е. отношения между линиями интенсивности и соседним с ними фоновым излучением) использовался для создания выходных профилей мониторинга и расстояния Бхаттачарьи [40 ] использовался в качестве критерия для измерения разделимости классов для выбора длины волны. Это вероятностное расстояние очень удобно для оценки разделимости классов для нормальных распределений, но даже для ненормальных случаев оно кажется разумным уравнением [41].Расстояние Махаланобиса, заданное формулой (8), является частным случаем расстояния Бхаттачарьи, которое предполагает равные ковариации классов: 𝐽𝑀 = 𝜇2 − 𝜇1𝑇Σ − 1𝜇2 − 𝜇1, (8) где 𝜇𝑖 — среднее значение класса, а Σ — ковариационная матрица. Он также широко используется как мера несходства, потому что для многомерного признака, характеризующегося его средним вектором 𝜇∈𝑅𝑝 и ковариационной матрицей Σ∈𝑅𝑝 ×, требуется около 2 флопов, в то время как вычисление расстояния Бхаттачарьи включает 𝑝3 / 3 + 2𝑝2 флопа [ 42].
Учитывая вышеупомянутую необходимость ограничения процесса оптимизации спектральными диапазонами, более узкими, чем тот, который предоставляется спектрометром, использование алгоритма SFFS для определения подходящих спектральных областей кажется интересным в этом сценарии, поскольку он представляет собой автоматическую процедуру вместо того, чтобы для выполнения конкретных исследований для новых процессов или спектрометров. В этом случае здесь будет оцениваться эффективность использования расстояния Махаланобиса для извлечения наиболее подходящих длин волн, которые будут составлять выходной контрольный сигнал.Пусть 𝑋 — количество спектральных областей, в которых будет выполняться процесс оптимизации и, следовательно, генерация профилей участия, то есть 𝑋 — количество полос, которые необходимо выбрать. В определенный момент процесса выбора 𝑆 — это текущий набор ранее выбранных диапазонов, а 𝑅 — набор оставшихся или невыбранных диапазонов. Процесс выбора начинается с 𝑆 = ∅. Псевдокод, описывающий процедуру выбора, выглядит следующим образом: , а | 𝑆 | <𝑋 do select band 𝑆inc = argmax [𝐽𝑀 (𝑆𝑈𝑆inc)] 𝑆 = 𝑆𝑈𝑆inc 𝑅 = 𝑅⧵𝑆inc while | 𝑆 |> 2 выберите диапазон 𝑆exc = argmax [𝐽𝑀 (𝑆⧵𝑆exc)] if 𝐽𝑀 (𝑆⧵𝑆exc)> 𝐽𝑀 (𝑆) 𝑆 = 𝑆⧵𝑆exc 𝑅 = 𝑅𝑈𝑆exc else break end end конец , где «𝑆𝑈𝑆inc» означает, что полоса 𝑆inc включена в набор 𝑆, «𝑆⧵𝑆exc» означает, что полоса exc исключена из набора 𝑆, а 𝜙 — это пустой набор.
4. Подтверждение экспериментальных и полевых испытаний
Первые исследования были направлены на улучшение результатов, полученных для частиц Ar II в [28], учитывая уже отмеченное отсутствие реакции на некоторые дефекты. После первоначального анализа с помощью SFFS некоторые спектральные полосы были выбраны алгоритмом как наиболее подходящие с точки зрения различения спектров, связанных с правильными швами и с дефектами, соответственно. Детали экспериментальных испытаний описаны в предыдущей работе, но следует упомянуть, что процесс GTAW (газовая дуговая сварка вольфрамом) использовался для сварки листов из нержавеющей стали AISI-304.Дефекты были спровоцированы преднамеренным воздействием на расход защитного газа (аргона). Первые спектральные полосы, выбранные алгоритмом SFFS с использованием расстояния Махаланобиса, представлены в таблице 3.
|
Из этих длин волн те, что находятся в диапазоне от 460 до 490 нм, относятся к линиям излучения Ar II, что предполагает пригодность выбора этого спектрального окна для процесса оптимизации.На рисунке 2 показан результат использования окон между 470 и 483 нм и 470 и 480 нм, соответственно, в сравнении с исходным профилем участия Ar II, полученным при использовании всего спектрального диапазона спектрометра ( Ocean Optics USB2000: От 195 до 535 нм). Можно заметить, что корреляция между дефектом в шве (вызванным возмущением скорости потока защитного газа) и результирующим профилем участия Ar II значительно усиливается, если спектральный диапазон процесса оптимизации сокращается.Результат лучше для более узкого спектрального диапазона, что можно объяснить плохим совпадением, полученным в процессе оптимизации, между синтетическим и реальным спектрами для линии излучения Ar II, расположенной на 480,5 нм.
Аналогичное сравнение показано на рисунке 3, где можно увидеть еще один шов с двумя несплошностями. Опять же, дефекты at≈4,5 и 6,5 см не обнаруживаются четко во всем спектральном диапазоне, но использование окна от 470 до 480 нм дает более чувствительный контрольный сигнал.
Чтобы распространить анализ на другие процессы и материалы, было проведено несколько исследований по данным полевых испытаний [25]. В данном случае свариваемыми материалами были инконель-718 и титан 6Al-4V толщиной 2 и 1,6 мм соответственно. Для первого использовалась присадочная проволока, а в качестве защитного газа (10 л / мин) — аргон, который также направляется к нижней стороне пластин (30 л / мин). Оптическая установка в основном состояла из оптического волокна с диаметром сердцевины 600 мкм и м, соединяющего спектрометр (снова USB2000), и конец волокна, действующий как входная оптика, расположенный примерно в 10 см от конца электрода.Помимо правильных швов, во время анализа были выявлены различные дефекты для получения желаемых спектроскопических данных.
На рис. 4 показан шов Inconel-718, внесенный в каталог как правильный после визуального и рентгеновского контроля. Изображенные профили участия Ar II не показывают каких-либо явных возмущений, хотя оба сигнала демонстрируют значительный уровень шума. Стоит отметить, что другие спектроскопические параметры, такие как RMS-профиль плазмы [25], также демонстрируют такое поведение. Возможное объяснение этому можно найти в возмущениях, влияющих на процесс, которые не вызывают дефектов.Соответствующий профиль тепловложения (полученный Tecnalia [43] с помощью системы электрических датчиков) также является постоянным (рис. 4 (c)), как и ожидалось для шва без дефектов.
Дефектный шов проанализирован на Рисунке 5, где траектория движения сварочной горелки над швом была отклонена (Рисунок 5 (а)). Можно понять, что сигнал подводимого тепла указывает на дефект при 𝑥 ≈ 25–30 с, в то время как остальная часть профиля почти постоянна. На рис. 5 (b) изображены два разных профиля участия, соответствующие двум спектральным диапазонам: от 340 до 350 нм и от 470 до 480 нм.Первая полоса была выбрана с учетом того, что алгоритм выбора признаков указывает полосу 344,15, являющуюся в этом случае разновидностью Fe I, выбранной для процесса. Это окно генерирует контрольный сигнал с сильным возмущением, коррелированным с наблюдаемым в сигнале подводимого тепла, хотя другие области также указывают на возникновение дефектов. Для сравнения, профиль Ar I в этом случае не демонстрирует столь явных возмущений.
Шов, показанный на Рисунке 6, был выполнен для соединения двух пластин Inconel-718 с смещением приблизительно 1 мм, что в данном случае является максимально допустимым 0.3 мм (15% толщины листа). Сигнал подводимого тепла, изображенный на рисунке 6 (c), не проявляет никаких возмущений и остается постоянным в течение всего процесса. Почти такая же ситуация может наблюдаться в профиле presented, представленном на рисунке 6 (d), рассчитанном с использованием эмиссионных линий Ar II, расположенных при 460,96 и 487,99 нм соответственно. Однако профиль участия в этом случае несколько более шумный, что говорит о том, что возникла некорректная ситуация.
Дефекты, вызванные недостаточной чистотой, также были исследованы на пластинах Ti6Al-4V, моделируя эту ситуацию путем нанесения масла на стык перед процессом сварки.В испытании, описанном на Рисунке 7, присутствие масла приводит к явному дефекту при ≈30 с, о чем свидетельствует профиль тепловложения. Уменьшение спектрального диапазона для генерации профиля участия Ar II (рисунок 7 (b)) дает ответ, аналогичный тому, который получен для всего диапазона спектрометра, хотя чувствительность последнего оказывается несколько хуже, особенно около = 40-е годы. Следует отметить изменение сигнала Ar II при ≈18 с, что может быть связано с нанесением масла в середине сварочного тракта.Интерпретация появления дефекта позже в шве может быть объяснена перетягиванием масла сварочной дугой к месту дефекта.
Тот же дефект пытались повторить для шва, изображенного на Рисунке 8, но после визуального осмотра дефектов в этом случае не наблюдалось. Опять же, сигнал подводимого тепла остается постоянным в течение всего процесса, в то время как профиль 𝑇𝑒 имеет четкий наклон и некоторые незначительные возмущения. Сигнал, исходящий от частиц Ar II (470–480 нм), четко указывает на наличие дефектов, что, по-видимому, хорошо согласуется с анализируемым сценарием.
5. Заключение
Эволюция спектроскопической модели, предложенной в предыдущем документе для диагностики сварки, была представлена и обсуждена в этой статье. Первоначальное предложение было основано на создании синтетических спектров и использовании алгоритмов оптимизации для создания профилей участия тех видов, которые вносят вклад в сварочную плазму. Показано, что между этими профилями и качеством шва, то есть появлением дефектов, существует прямая зависимость.Однако экспериментальные тесты показали, что Ar II, преобладающий вид в анализируемом спектральном диапазоне, не проявляет такой же ответ, связанный с некоторыми дефектами, правильно сигнализируемыми другими видами. Пересмотр предложенной модели показал, что проблема могла быть мотивирована использованием относительных интенсивностей из спектроскопической базы данных NIST для создания синтетических спектров. В частности, использование широких спектральных диапазонов с такими интенсивностями, по-видимому, привело к упомянутому отсутствию чувствительности, которое можно найти в профилях участия Ar II.Возможное решение этой проблемы заключается в уменьшении спектрального окна, в котором происходит процесс оптимизации, что было реализовано в этой статье с помощью алгоритма выбора характеристик, который помогает указать подходящие спектральные диапазоны, которые будут использоваться. Было продемонстрировано, что этот новый подход значительно улучшил результаты, полученные в исходной работе, учитывая, что теперь сигнал участия Ar II показывает хорошую корреляцию с дефектами, изученными в экспериментальных испытаниях.Кроме того, чтобы продлить срок действия модели, в анализ были включены полевые испытания образцов Inconel-718 и Ti6Al-4V, которые также позволяют обнаруживать различные дефекты сварных швов: отклонение траектории, несоосность и отсутствие чистоты.
Помимо использования алгоритма SFFS с расстоянием Махалонобиса для уменьшения спектрального диапазона в процессе оптимизации, алгоритм CRS6, использованный для выполнения этой задачи в исходном вкладе, также был заменен простой реализацией PSO, улучшающей таким образом вычислительная производительность схемы обработки.
Некоторые вопросы остаются нерешенными, и их необходимо решить в будущем для улучшения предложенной модели. С одной стороны, следует избегать использования относительных интенсивностей при генерации синтетических спектров: решение, которое необходимо изучить, может быть основано на схеме обратной связи, в которой интенсивности выбранных эмиссионных линий могут быть рассчитаны на основе оценки спектроскопических данных. параметр, такой как температура плазмы 𝑇𝑒, с использованием различных компонентов в процессе. Также может быть интересно попытаться связать профили относительного участия последовательных стадий ионизации для данного элемента через уравнение Саха, хотя следует изучить, будет ли этот подход чрезмерно дорогостоящим с точки зрения вычислительной производительности модели.Применение этого метода может лежать в рамках LIBS (Laser Induced Breakdown Spectroscopy), где он может быть использован для количественной оценки состава образцов.
Благодарности
Работа поддержана проектами TEC2010-20224-C02-02 и OPENAER CENIT 2007–2010. Авторы хотят поблагодарить Хосе Дж. Валдианде (Photonics Engineering Group), Хуана М. Этайо (Tecnalia) за данные о подводимой теплоте, а также Марту Давилу и Рауля Льоренте (ITP) за его помощь и поддержку во время полевых испытаний.Кроме того, авторы благодарят ITP за предоставленную возможность опубликовать данные полевых испытаний, полученные в рамках проекта OPENAER CENIT 2007–2010.
(PDF) Сегментация изображений сварочной дуги для диагностики сварки
ДИАГНОСТИКА, Том. 14, № 1 (2013)
FIDALI, JAMROZIK, BZYMEK, TIMOFIEJCZUK, Сегментация сварки…
18
методы сегментации дали правильные и приемлемые результаты
. Исключением был подход Watershed.
В целом все достигнутые результаты были лучше, чем
в случае инфракрасных изображений.
Подводя итог, можно констатировать, что для определения
соответствующей ROI методы сегментации, основанные на
, активный поиск контура объекта кажется лучшим решением
. В настоящее время применение
этих подходов к анализу изображений, перекодированных в
видимом диапазоне электромагнитного излучения, рассматривается авторами
.
СПИСОК ЛИТЕРАТУРЫ
[1] Рокингер О.: Слияние последовательностей изображений с использованием инвариантного вейвлет-преобразования
. Труды
Международной конференции по обработке изображений
, том 3, стр. 288-291, 1997.
[2] Саджади Ф .: Сравнительный анализ слияния изображений,
Proc. конференции 2005 IEEE Computer Society
по компьютерному зрению и шаблонам
Распознавание (CVPR’05) — семинары, Vol.03,
стр.8, 2005.
[3] Информация о
http://www.ishotimaging.com/weldi-home.html,
Серия Weld-i, Контроль сварочных швов
Системы.
[4] Камиллери Д., Грей Т. и Комлекчи Т.: Использование термографии
для калибровки сварки плавлением
Процедуры в приложениях виртуального производства.
Proc. Информационной конференции 2004, т. 5 с.
121-131, 2004.
[5] Бзымек А., Фидали М., Ямрозик В.,
Тимофейчук А.: Система диагностического зрения для оценки сварных швов
и процесса сварки.
Проблемы обслуживания, 4/2008, стр. 39-52.
[6] Ямрозик В .: Метод диагностики промышленных
процессов с использованием слияния данных, кандидатская диссертация,
Гливице, 2012.
[7] Фидали М., Ямрозик В .: Обработка слитых
инфракрасных и визуальных изображений сварочной дуги для
обнаружения неисправностей, Труды 11-го количественного исследования
InfraRed Thermography, 11-14 июня 2012 г.,
Неаполь, Италия.
[8] [8] Бзымек А., Тимофейчук А.: Оценка стабильности сварочного процесса
на основе анализа и распознавания изображения
, Диагностика 4 (52) /
2009, стр 41-44.
[9] Чжан, Ю.М., Ковачевич, Р., Руан, С.: Определение
и управление геометрией сварочной ванны для
Автоматическая сварка GTA, Транзакции
ASME, 1995, т. 117, стр.210-222.
[10] Гонсалес Р. К., Вудс Р.Э., Эддинс С. Л .:
Цифровая обработка изображений с использованием Matlab, Pearson,
Prentice Hall, London, 2004.
[11] Зува Т., Олугбара О. О., Оджо С. О. и Нгвира
С. М .: Сегментация изображений, Доступные
Методы, разработки и открытые выпуски,
Canadian Journal on Image Processing и
Computer Vision Vol. 2, № 3, март 2011.
[12] Ходжатолеслами С.А., Киттлер Дж .: Регион
рост: новый подход, Обработка изображений,
IEEE Transactions on, vol.7, номер 7, стр. 1079-
1084, июль 1998 г. DOI: 10.1109 / 83.701170.
[13] Информация о
http://homepages.inf.ed.ac.uk/rbf/CVonline/LO
CAL_COPIES / MORSE / region.pdf.
[14] Reyad YA, El-Zaart A., Mathkour H., Al-
Zuair M .: Пороговое значение изображения с использованием разделения и
Методы слиянияс логнормальным распределением
, Canadian Journal on Image
Processing и компьютерное зрение, Vol. 1, вып.
3, июль 2010 г.
[15] Татираджу С., Мехта А. Сегментация изображений
с использованием кластеризации k-средних, EM и нормализованных
Cuts, doi = 10.1.1.187.6371.
[16] Чан, Т.Ф., Весе Л.А.: Активные контуры
без краев, транзакции IEEE на изображении
Обработка том 10, № 2, стр. 266-277, февраль 2001 г.,
doi: 10.1109 / 83.
Марек ФИДАЛИ, PhD,
доцент кафедры
Институт основ машиностроения
Машиностроение.Основное направление
: техническая
диагностика, инфракрасная
термография, модальная
анализ сигналов и изображений
обработка
Войцех ЯМРОЗИК,
PhD, доцент
Институт основ проектирования машинного оборудования
. Его основные области интересов— это
методов технической диагностики
, приложения
термовизона, обработка и анализ изображений
, а также
, а также слияние неопределенной
и противоречивой информации.
Анна БЗЫМЕК, кандидат технических наук,
доцент кафедры
Институт основ машиностроения
Машиностроение. Основное направление исследований
:
методы обработки изображений,
обработки, анализа и распознавания
, системы технического зрения
в технической диагностике,
обработки сигналов.
Анна ТИМОФЕЙЧУК,
профессор института
Основы машиностроения
Проектирование.Основное направление исследований
: частотно-временной анализ
сигналов, диагностика
вывод, обработка изображений,
анализ и распознавание.
Мониторинг профиля и диагностика неисправностей с помощью Sensor Fusion для ультразвуковой сварки | Журнал производственной науки и техники
Случай А фокусируется на выявлении неисправностей в неконтролируемых сценариях (a) — (e). Создайте в общей сложности 1200 образцов профиля по 200 образцов в каждом классе, как показано на рис.6. Пять сценариев OOC задаются следующим образом: (a) средний сдвиг опорных сигналов «блока»: x1 → x1 + 0,1σx11K × 1, в результате чего χ ~ 1, ⋅, m = b1, m (x1 + 0,1σx11K × 1) + b2, mx2 + ε1, m, χ ~ 2, ⋅, m = b3, m (x1 + 0,1σx11K × 1) 2 + 0,1σx11K × 1) 2 + b4, mx3 + ε2, m , А χ ~ 4, ⋅, m = b7, m (x1 + 0,1σx11K × 1) + ε4, m; (b) наложение синусоидального члена на «блочный» сигнал: x1 → x1 + 0.1σx1ys, y s — синусоидальная функция, в результате чего χ ~ 1, ⋅, m = b1, m (x1 + 0.1σx1ys) + b2, mx2 + ε1, m, χ ~ 2, ⋅, m = b3, m (x1 + σx1ys) 2 + b4, mx3 + ε2, m и χ ∼ 4, ⋅ , m = b7, m (x1 + 0.1σx1ys) + ε4, m; (c) увеличение стандартного отклонения члена ошибки e 1 : σε1.m → 3σε1.m, что приводит к χ ~ 1, ⋅, m = b1, mx1 + b2, mx2 + ε ~ 1, m, где ε ~ 1, m∼N (0, (3 × 0,5) 2) ; (г) средний сдвиг параметра модели b 1 : μb1 → μb1 + 5σb1, что дает χ ~ 1, ⋅, m = b ~ 1, mx1 + b2, mx2 + ε1, m, где b ~ 1, m∼N (μb1 + 5σb1, σb12) ; и (e) увеличение стандартного отклонения параметра модели b 1 : σb1 → 4σb1, что дает χ ~ 1, ⋅, m = b ~ 1, mx1 + b2, mx2 + ε1, m, где b ~ 1, m∼N (μb1, (4σb1) 2) .
Из пяти описанных выше сценариев OOC, все профили в потоках 1, 2 и 4 затронуты в (a) и (b), а в (c), (d) и (e) только профили в потоке 1 имеют неконтролируемые шаблоны. Так как большое количество ε ~ 1, m, сгенерированных при неисправности (c), будет перекрываться с контролирующими ε1, m′s, и что b ~ 1, m′s, генерируемые b ~ 1, m ∼N (μb1, (4σb1) 2) в неисправности (e) будет сильно перекрываться с контролируемым b1, m′s, неисправности (c) и (e) будет очень трудно отделить от контролируемого класса .
Половина из этих 1200 выборок используется в качестве обучающих. Перед моделированием UMLDA сгенерированные данные нормализуются путем удаления общего среднего всех обучающих выборок из исходных данных. Используя процедуры, описанные в разд. 2 и 3.1, к нормализованным данным применяется регуляризованный UMLDA. В UMLDA собственные тензоры, соответствующие p th EMP, Up∈R4 × 128, p = 1, 2, 3, 4, получаются с помощью up (1) ∘up (2) , где up ( 1) ∈R4 × 1 и выше (2) ∈R128 × 1.На рисунке 7 показано значение Up, полученное из набора обучающих данных в одном прогоне моделирования для случая A. Как видно из рисунка 7, собственные векторы, соответствующие первому EMP, показывают эффективное различение потоков 1 и 4, тогда как соответствующие второму ЭМИ демонстрируют сильную дискриминацию по отношению к потоку 2. Собственные векторы, соответствующие третьему и четвертому ЭМИ, показывают слабую дискриминацию по отношению к потоку 4, тогда как ограниченная полезная информация извлекается из потока 3 для дискриминантного анализа.Эти результаты полностью совместимы с моделью генерации данных, таким образом подразумевая, что R-UMLDA может эффективно извлекать информацию для дискриминантного анализа многопоточных профилей.
Используя первые p EMP ( p = 1, 2, 3, 4), многопоточные профили можно проецировать на p некоррелированных объектов, которые затем передаются в NNC. Производительность классификации в тестовом наборе данных показана на рис.m> 0, cm> 0) / Mtest. Как видно на рис. 8, первые два признака, извлеченные R-UMLDA, являются наиболее мощными признаками для классификации. Добавление третьего и четвертого признаков немного улучшает правильность классификации.
Более подробные результаты классификации в отношении количества функций, введенных в классификатор, показаны в матрицах путаницы в таблице 1. Из таблицы 1 мы можем легко заметить улучшение точности классификации, когда используются два или более EMP вместо использования только одного. первый.Мы также замечаем, что при использовании двух или более функций большинство ошибок классификации возникает из-за разделения классов управления, сбоя (c) и сбоя (e) друг от друга. Это наблюдение полностью совместимо с моделью генерации данных, на основе которой мы ожидали, что сбои (c) и (e) являются наиболее сложными классами для отделения от контролируемого класса.
Применяя методы конкурента, описанные в гл. 3.1, рис.9 (a) показывает классификационную эффективность NNC для различных методов извлечения признаков в случае тестового набора данных. Представленные на графике результаты представляют собой средние значения правильной классификации за 100 прогонов моделирования. На рис. 9 (a) кривые с треугольными маркерами соответствуют характеристикам классификации для функций UMPCA и MPCA. Очевидно, что эти результаты значительно хуже, чем у методов на основе LDA, независимо от количества используемых функций. Это согласуется с нашим пониманием экстракторов признаков на основе PCA, которые не используют информацию о классах и ищут только прогнозы, чтобы максимизировать захваченную изменчивость, а не классовую дискриминацию.
Кривые с крестиками, звездочками и звездочками на рис. 9 (а) соответствуют векторизованным методам LDA (включая LDA, ULDA и RLDA), тогда как кривые с квадратными и круговыми маркерами соответствуют методам UMLDA. Из рис. 9 (а) видно, что первые два признака, извлеченные R-UMLDA, являются наиболее мощными признаками в классификации. Помимо первых двух функций, производительность R-UMLDA улучшается очень медленно с увеличением количества используемых функций.Первые три функции, извлеченные с помощью векторизованных методов LDA, также являются мощными, но улучшение от использования первых двух функций R-UMLDA незначительно.
Наилучший коэффициент правильной классификации достигается при использовании R-UMLDA-A. Рисунок 9 (a) показывает, что R-UMLDA-A превосходит все другие алгоритмы. Это демонстрирует, что агрегирование является эффективной процедурой, и действительно существует дополнительная различительная информация от различных регуляризованных экстракторов признаков R-UMLDA.
Проблемы с MIG и способы их устранения
GMAW: Общие проблемы MIG и способы их устраненияПерепечатано с разрешения журнала Practical Welding Today за сентябрь / октябрь 1997 г., авторское право 1997 г. принадлежит The Croydon Group, Ltd., Рокфорд, Иллинойс.
Во многом так же, как автоматическая коробка передач упростила процесс вождения, газовая дуговая сварка (GMAW) упростила процесс сварки. Из всех методов сварки GMAW считается одним из самых простых в освоении и применении.Основная причина в том, что источник питания выполняет практически всю работу, регулируя параметры сварки для работы в различных условиях; очень похоже на сложную электронику автоматической коробки передач.
Поскольку требуются меньшие навыки, многие операторы могут выполнять сварку GMA на приемлемом уровне с ограниченным обучением. Однако эти же операторы сталкиваются с проблемами, когда начинают создавать сварные швы низкого качества и не могут диагностировать и устранять свои собственные проблемы. Приведенные ниже рекомендации помогут даже неопытным операторам в создании высококачественных сварных швов, а также дадут советы тем, кто использует процесс GMAW в течение нескольких лет.
Наиболее распространенные проблемы при сварке делятся на четыре категории:
- Пористость сварного шва
- Неправильный профиль сварного шва
- Отсутствие слияния
- Неправильная доставка проводов, связанных с настройкой и обслуживанием оборудования.
1. Пористость металла сварного шва
Наиболее частой причиной пористости сварного шва является неправильное состояние поверхности металла.Например, масло, ржавчина, краска или смазка на основном металле могут препятствовать правильному провару сварного шва и, следовательно, вызывать пористость. Сварочные процессы, при которых образуется шлак, такие как дуговая сварка защищенным металлом (SMAW) или дуговая сварка порошковой проволокой (FCAW), как правило, переносят поверхностные загрязнения лучше, чем GMAW, поскольку компоненты, обнаруженные в шлаке, помогают очистить поверхность металла. В GMAW единственная защита от загрязнения обеспечивается элементами, встроенными в проволоку.
Средства правовой защиты
Чтобы контролировать пористость, используйте раскислитель внутри проволоки, например кремний, марганец или следовые количества алюминия, циркония или титана.Химический состав проволоки можно определить, обратившись к системе классификации проволоки Американского сварочного общества (AWS).
Протестируйте различные типы проводов, чтобы подобрать правильный химический состав для конкретного применения. Для начала попробуйте самый распространенный тип провода ER70S-3 (Lincoln L50), который содержит 0,9–1,4% марганца и 0,45–0,75% кремния. Если пористость в готовом сварном шве все еще присутствует, увеличьте количество кремния и марганца в проволоке, переключившись на ER70S-4 (Lincoln L54) или ER70S-6 с самым высоким уровнем кремния (0.8-1,15 процента) и марганца (1,4-1,8 процента). Некоторые операторы предпочитают использовать тройной раскислитель, такой как ER70S-2 (Lincoln L52), который помимо кремния и марганца содержит алюминий, цирконий или титан.
В дополнение к замене проволоки, дополнительно предотвратите образование пористости, очистив поверхность металла шлифовальным станком или химическими растворителями (например, обезжиривающим средством). Небольшое предостережение, однако при использовании растворителей не используйте хлорированные обезжириватели, такие как трихлорэтилен рядом со сварочной дугой — дым может вступить в реакцию с дугой с образованием токсичных газов.
Проблема пористости № 2: Газовое покрытие
Вторая ведущая причина пористости в сварных швах — проблема с защитным газом. В процессе GMAW используется защитный газ, который физически защищает сварочную ванну от воздуха и действует как стабилизатор дуги. При нарушении подачи защитного газа существует вероятность того, что воздух может загрязнить сварочную ванну и вызвать пористость.
Средства правовой защиты
Расход защитного газа зависит от размера провода, силы тока, режима передачи и скорости ветра.Типичный расход газа должен составлять примерно 30-40 кубических футов в час. С помощью расходомера проверьте правильность настройки расхода защитного газа. Сегодня на рынке представлено множество расходомеров, от простых стрелочных индикаторов до шариковых расходомеров и заканчивая сложными компьютеризированными моделями. Некоторые операторы ошибочно думают, что регулятор давления — это все, что нужно, но измеритель давления не будет устанавливать расход.
Чистый защитный газ из двуокиси углерода требует использования специальных расходомеров, разработанных специально для двуокиси углерода.На эти специальные расходомеры не влияет обледенение, которое может возникнуть при переходе диоксида углерода из жидкой формы в газообразную.
Если сильный ветер уносит защитный газ от лужи, может потребоваться установка ветрозащитных экранов. Согласно нормам AWS по сварке конструкций, не рекомендуется выполнять сварку GMA при скорости ветра более 5 миль в час. Внутри помещений системы вентиляции могут препятствовать проникновению газа. В этом случае перенаправьте поток воздуха в сторону от лужи. Если требуется удаление дыма, используйте оборудование, разработанное специально для этой цели, например, экстракционные пистолеты MAGNUM ™ от Lincoln Electric — они удаляют дым, но не нарушают работу защитного газа.
Турбулентный поток газа на выходе из пистолета также может привести к проблемам с пористостью. В идеале газ должен лежать над сварочной лужей, как одеяло. Турбулентный поток газа может быть вызван слишком сильным потоком, чрезмерным количеством брызг внутри сопла пистолета или скоплением брызг в газовом диффузоре.
Другими возможными причинами недостаточного потока газа могут быть повреждение пистолетов, кабелей, газовых линий, шлангов или ослабленных газовых фитингов. Эти поврежденные аксессуары могут создавать так называемый «эффект Вентури», когда воздух всасывается через эти отверстия и поток уменьшается.
Наконец, сварка методом сопротивления или обратной стороны может привести к проблемам с газовым покрытием. Попробуйте выполнять сварку толчковыми или передовыми методами, при которых газовая оболочка располагается впереди дуги и позволяет газу оседать в стыке.
Проблема пористости № 3: Свойства основного металла
Другая причина пористости сварного шва может быть связана просто с химическим составом основного металла. Например, основной металл может иметь чрезвычайно высокое содержание серы.
Средство устранения
К сожалению, если проблема с пористостью связана со свойствами основного металла, мало что можно сделать.Лучшее решение — использовать сталь другой марки или перейти на шлакообразующий процесс сварки.
2. Неправильный профиль сварного шва
Если операторы сталкиваются с выпуклой или вогнутой формой валика, это может указывать на проблему с подводом тепла или технологией.
Неправильный шов Проблема № 1: Недостаточная подача тепла
Выпуклый или «вязаный» валик указывает на то, что используемые настройки слишком низкие для толщины свариваемого материала.Другими словами, в сварном шве недостаточно тепла, чтобы он мог проникнуть в основной металл.
Средства правовой защиты
Чтобы решить проблему, связанную с работой «слишком холодно», оператор должен сначала определить, соответствует ли сила тока толщине материала. Таблицы доступны у основных производителей, включая Lincoln Electric, и содержат рекомендации по использованию силы тока в различных условиях.
Если сила тока определена как достаточно высокая, проверьте напряжение.Слишком низкое напряжение обычно сопровождается еще одним явным признаком проблемы: большим количеством брызг. С другой стороны, если напряжение будет слишком высоким, у оператора возникнут проблемы с управлением процессом, и сварной шов будет иметь тенденцию к подрезанию.
Один из способов проверить, правильно ли установлено напряжение, — это проверить его путем прослушивания. Правильно работающая дуга будет издавать определенный звук. Например, при передаче короткой дуги при низких значениях тока дуга должна иметь устойчивое гудение. При высокой силе тока с переносом дуги струйным переносом дуга будет издавать потрескивающий звук.Звук дуги также может указывать на проблемы — устойчивое шипение указывает на то, что напряжение слишком высокое и оператор склонен к подрезанию; а громкий скрипучий звук может указывать на слишком низкое напряжение.
Неправильный шов Проблема № 2: Методика
Вогнутый или выпуклый валик также может быть вызван использованием неправильной техники сварки. Например, техника толчка или форхенда имеет тенденцию создавать более плоскую форму бусинки, чем техника тяги или бэкхенда.
Средство правовой защиты
Для получения оптимальной формы валика рекомендуется использовать угол проталкивания 5-10 градусов.
Неправильный борт. Проблема № 3: Несоответствующий рабочий кабель
Проблемы с рабочим кабелем могут привести к недостаточному напряжению на дуге. Свидетельством проблемы с рабочим кабелем может быть неправильная форма борта или поврежденный рабочий кабель.
Средство устранения
Рабочие кабели имеют тенденцию к перегреву, если они слишком малы или чрезмерно изношены. При замене кабеля обратитесь к таблице, чтобы определить размер в зависимости от длины и тока. Чем выше ток и чем больше расстояние, тем больше потребуется кабель.
3. Отсутствие сплавления
Если расходный материал неправильно приклеился к основному металлу, может возникнуть нарушение плавления. Неправильная сварка создает слабый сварной шов низкого качества и в конечном итоге может привести к структурным проблемам в готовом изделии.
Проблема отсутствия сплавления: холодная притирка в процессе переноса короткой дуги
При переносе короткой дуги проволока непосредственно касается сварочной ванны, и короткое замыкание в системе приводит к расплавлению конца проволоки и отрыву капли .Это происходит от 40 до 200 раз в секунду. Проблемы Fusion может произойти, когда металл в сварочной ванне расплавлен, но там не осталось сплавить его к опорной плите достаточно энергии. В этих случаях сварной шов будет иметь хороший внешний вид, но на самом деле ни один металл не был соединен вместе. Поскольку отсутствие плавления трудно обнаружить визуально, его необходимо проверить с помощью пенетранта красителя, ультразвукового исследования или испытания на изгиб.
Способы устранения
Чтобы гарантировать правильное соединение, убедитесь, что напряжение и сила тока установлены правильно.Если после выполнения этих регулировок у оператора все еще возникают проблемы, возможно, потребуется изменить технику сварки. Например, переход на порошковую проволоку или использование вместо этого метода переноса дуги со струйным переносом. При переносе дуги распылением дуга никогда не гаснет, поэтому холодная притирка и отсутствие плавления не являются проблемой. Дуговая сварка распылением происходит при силе тока, достаточной для расплавления конца проволоки и продвижения капли через дугу в сварочную ванну.
4.Неисправная подача проволоки
Если проволока подается неравномерно или оператор слышит дребезжащий звук внутри кабеля пистолета, возможно, проблема связана с системой подачи проволоки. Большинство проблем, связанных с доставкой проводов, связано с настройкой и обслуживанием оборудования.
Неисправная подача проволоки Проблема № 1: Контактный наконечник
Операторы склонны использовать наконечники слишком большого размера, что может привести к проблемам с контактами, нестабильности дуги, пористости и плохой форме валика.
Средство устранения
Убедитесь, что контактный наконечник пистолета находится в рабочем состоянии и имеет размер, соответствующий используемому проводу. Визуально осмотрите наконечник, и если он изнашивается (приобретает форму яйца), его необходимо заменить.
Неисправная подача проволоки Проблема № 2: вкладыш пистолета
Вкладыш пистолета, как и контактный наконечник, должен соответствовать размеру проволоки, проходящей через него. Его также необходимо очистить или заменить, если проволока подается не плавно.
Средство устранения
Чтобы очистить гильзу, продуйте ее сжатым воздухом низкого давления со стороны контактного наконечника или замените гильзу.
Неправильная подача проволоки Проблема № 3: Изношенный пистолет
Внутри пистолета находятся очень тонкие жилы медной проволоки, которые со временем порвутся и изнашиваются.
Средство устранения
Если пистолет сильно нагревается во время использования в одной конкретной области, это означает, что имеется внутреннее повреждение и его необходимо заменить.Кроме того, убедитесь, что размер пистолета достаточно велик для применения. Операторам нравится использовать небольшие пистолеты, так как они легки в руке, но если пистолет слишком мал для применения, он перегреется.
Неисправная подача проволоки Проблема № 4: Приводной ролик
Приводные ролики механизма подачи проволоки периодически изнашиваются и требуют замены.
Способы устранения
Обычно есть визуальные признаки износа канавок валков, если требуется замена.Также убедитесь, что натяжение приводного ролика установлено правильно. Чтобы проверить натяжение, отсоедините сварочный входной кабель от устройства подачи или переключитесь на опцию холодной подачи. Протяните проволоку и зажмите ее большим и указательным пальцами на выходе из пистолета. Если проволоку можно остановить защемлением, необходимо большее натяжение приводного ролика. Оптимальное натяжение будет указано при подаче, которая не прекращается во время защемления проволоки. Если натяжение приводного ролика слишком велико, это может деформировать проволоку, что приведет к запутыванию (запутыванию) и обратному ожогу (когда дуга поднимается по проволоке и приваривает проволоку к контактному наконечнику).
Убедитесь, что ведущие ролики и направляющая трубка расположены как можно ближе друг к другу. Затем проверьте путь от места выхода проволоки с катушки до места, где она входит в приводные ролики. Проволока должна совпадать с входящими направляющими трубками, чтобы не было обрезков проволоки при ее прохождении через трубку. На некоторых механизмах подачи проволоки положение катушки с проволокой можно регулировать — выровняйте ее так, чтобы путь в трубку был прямым.
Неправильная подача проволоки Проблема № 5: Проволока выходит из бобины и запутывается
Некоторые проблемы подачи проволоки возникают из-за того, что инерция катушки с проволокой заставляет ее двигаться по инерции после отпускания курка горелки.
Способ устранения
Если катушка продолжает двигаться по инерции, проволока на катушке ослабнет, и проволока может оторваться или запутаться. Большинство систем подачи проволоки имеют регулируемый тормоз на барабане с проволокой. Натяжение тормоза должно быть установлено таким образом, чтобы катушка не двигалась по инерции.
Следуя этим четырем руководящим принципам, оператор GMAW, плохо знакомый с миром сварки, или даже более опытный специалист сможет легче диагностировать проблемы, прежде чем они повлияют на качество работы.
Ультразвуковая сварка сервоприводасобирает диагностические тест-полоски
Ведущий производитель медицинского оборудования использует серво-ультразвуковую сварочную систему Dukane серии iQ для получения высококачественных результатов при сборке небольших и тонких тест-полосок. Эти тест-полоски используются для измерения общего холестерина, ЛПВП, глюкозы и триглицеридов человека. Сборка небольших медицинских устройств, таких как эти тест-полоски, требует точного, повторяемого и последовательного контроля процесса. Тест-полоски состоят из двух тонких слоев полиэтилентерефталатной (ПЭТ) пленки.Между двумя слоями ПЭТ находится сетчатая мембрана, пропитанная диагностическим химическим веществом.
До инвестирования в технологию серво-ультразвуковой сварки Dukane iQ самой большой проблемой для этого производителя было несоосность тонких пленок ПЭТ в процессе сборки. Доля брака составила более 30%. Серво-ультразвуковая сварочная система серии iQ с запатентованной технологией Melt-Match® решила проблемы центровки сборки и обеспечила точный, воспроизводимый и надежный процесс. Используя цифровое управление процессом от серво-ультразвуковых сварочных аппаратов серии iQ, они изготовили более 20 миллионов тестовых полосок менее чем за три года, снизив при этом процент брака до менее 5%.
Система ультразвуковой сварки сервоприводов серии iQ |
Для определения последовательности цикла сварки для сервосистем iQ доступны несколько параметров. Для этого приложения сервосистема iQ запрограммирована на запуск цикла сварки с минимальным усилием. При запуске каждого цикла сварки ультразвуковой рупор опускается к сборке с высокой скоростью. Затем, примерно на 1,0 мм выше узла, рог замедляется до запрограммированной контролируемой скорости, прежде чем вступит в контакт с тест-полоской.Это когда запускается функция Servo Melt-Match® серии iQ. Лучше всего это описать так: когда система достигает запрограммированного значения усилия срабатывания на тест-полоске, движение рожка вниз прекращается, и ультразвуковые устройства начинают вибрировать рожок для размягчения материала ПЭТ. Затем датчик веса системы обнаруживает запрограммированное падение силы, указывающее на то, что детали начали плавиться. В этот момент снова запускается нисходящее движение сварочного цикла для дальнейшего сжатия деталей. Сварка детали продолжается на запрограммированном расстоянии или значении энергии с определенной скоростью разрушения.Благодаря точному контролю скорости сварки в дополнение к использованию Melt-Detect ™, на тонкую пленку снижается ненужное усилие, которое в противном случае могло бы ее деформировать. Это, в свою очередь, улучшает качество сварки.
На заключительном этапе цикла сварки сервосистема iQ также дает возможность программировать динамическое и / или статическое удержание. Dynamic Hold заставит рупор еще больше сжимать детали после выключения ультразвука. Static Hold позволяет сварочному рупору удерживать свое окончательное положение в конце сварного шва в течение заданного времени.В этом приложении запрограммировано статическое удержание. Это дает материалам достаточно времени для затвердевания без перекоса. По истечении времени статического удержания звуковой сигнал возвращается в исходное (или верхнее положение) положение, готовое к следующему циклу сварки. Это была самая полезная функция для этих тонких тест-полосок из ПЭТ.
Еще одним важным преимуществом использования сервосистемы iQ является возможность дублирования известного процесса на нескольких сервосистемах iQ без каких-либо изменений в результатах сварки.В этом приложении эта функция была основным преимуществом для компании-производителя. Они смогли установить несколько сервосистем iQ для удовлетворения своих растущих потребностей, не вкладывая лишнего времени или усилий в точную настройку процесса для каждого сварщика.
Обширная линейка продуктовDukane, включающая сервоприводы, и наша профессиональная команда продаж и инженеров будут совместно работать с клиентами, чтобы предоставить лучшее решение для их конкретного применения. Для получения дополнительной информации о серво ультразвуковом сварочном аппарате серии iQ и других устройствах для ультразвуковой сварки посетите https: // www.dukane.com или по телефону 630-797-4900.
Ben’s Ремонт и сварка автомобилей
Прибл. Время: 60 минут | Диапазон цен: Получить предложение по цене
Основы диагностики двигателя Услуги по ремонту и сварке автомобилей Ben’s
Система OBD, или бортовая система диагностики, изначально была установлена для контроля выбросов транспортных средств, но она также обнаруживает проблемы в двигателе.Существуют как системы OBD I, так и системы OBD II, причем системы OBD II становятся стандартом для автомобилей, выпущенных после 1996 года. OBD подключается к блоку управления двигателем (ECU), который помогает вашему двигателю работать эффективно, сохраняя при этом низкий уровень выбросов. OBD может идентифицировать и предупреждать водителя о неисправности двигателя, отправляя уведомления об ошибках в систему ECU. ЭБУ отвечает за несколько процессов в двигателе, включая смесь воздуха и топлива, выбросы и синхронизацию двигателя. ЭБУ использует датчики, чтобы контролировать их или вносить корректировки.Если ЭБУ обнаруживает неисправности, он включает световой индикатор «проверьте двигатель» на приборной панели. Затем система OBD записывает код, относящийся к проблеме. К коду может получить доступ обученный техник через диагностическое оборудование двигателя, чтобы правильно диагностировать проблему.
Почему услуги по диагностике двигателя должны выполняться в Ben’s Automotive Repair & Welding?
Диагностика двигателя помогает поддерживать его эффективную работу. Система OBD способна обнаруживать неисправности до того, как они снизят производительность двигателя или вызовут серьезные повреждения.Благодаря обязательной системе OBD, ваш автомобиль способен контролировать и диагностировать свои собственные характеристики. Вы должны выполнить диагностику двигателя, когда загорится индикатор «проверьте двигатель». Диагностика двигателя поможет обнаружить проблемы на раннем этапе, чтобы мелкие проблемы никогда не перерастали в серьезные. Диагностика двигателя также помогает снизить уровень выбросов, а если ваш двигатель неисправен, ваш автомобиль может не пройти тест на выбросы. Когда загорится индикатор «Проверьте двигатель», вам пора связаться с нами для диагностики двигателя.Наши опытные сотрудники приложат все усилия, чтобы ваш двигатель снова заработал должным образом в кратчайшие сроки.
Мы с гордостью обслуживаем потребности клиентов в диагностике двигателя в Маренго, Айова, Сидар-Рапидс, Айова, Айова-Сити, Айова, и прилегающих районах.
Обслуживаемых областей: Маренго, ИА | Сидар-Рапидс, ИА | Айова-Сити, Айова | и прилегающие районы
Основы: устранение неисправностей MIG — Трегаскисс и Бернард
Как и любой сварочный процесс, сварка MIG имеет свои сложности.Даже в этом случае нет причин позволять общим проблемам тормозить вас. Обладая небольшими знаниями и некоторыми прочными навыками поиска и устранения неисправностей, вы легко сможете найти правильное решение, чтобы вернуться к сварке — раньше, чем позже. Придерживайтесь следующих рекомендаций, которые помогут вам на этом пути.
Keep Covered
Дефекты сварки MIG могут вызвать простои и потерю производительности из-за переделок. Воспользуйтесь этими советами, чтобы свести к минимуму эти затраты за счет быстрого выявления и решения проблем сварки MIG.Пористость возникает, когда газовый карман попадает в металл шва.Эта неоднородность может появиться в любой конкретной точке сварного шва или по всей его длине, и / или на поверхности или внутри сварного шва. Результат, независимо от местоположения, всегда один: более слабый сварной шов.
Недостаточное покрытие защитным газом — одна из наиболее частых причин пористости. Чтобы решить эту проблему, сначала проверьте регулятор или расходомер на предмет достаточного расхода газа, при необходимости увеличив его, а также проверьте газовые шланги и пистолет на герметичность. Независимо от того, выполняете ли вы сварку внутри или снаружи, защитите дугу и сварочную лужу от сквозняков с помощью сварочного экрана.
Затем убедитесь, что сопло пистолета MIG достаточно велико для применения, поскольку слишком маленькое сопло может помешать правильному потоку защитного газа. Держите сопло на расстоянии от одной четверти до половины дюйма от обрабатываемой детали, убедитесь, что на нем нет брызг, и всегда используйте правильную выемку для контактного наконечника. Уменьшите скорость движения и держите пистолет MIG рядом с валиком в конце сварного шва, пока расплавленный металл не затвердеет; слишком быстрое извлечение пистолета может нарушить газовую защиту и сделать сварной шов уязвимым для атмосферы.
Дополнительные причины пористости включают: использование неправильного газа (всегда используйте защитный газ для сварки, подходящий для основного металла и присадочного металла), использование слишком большого количества или неправильного типа антибрызгивания (используйте правильное количество и тип для вашего применения) и слишком далеко выдвигать сварочную проволоку из сопла (выходить не более чем на полдюйма за сопло).
Примеси в основном металле, такие как сера и фосфор в стали, или грязный основной металл могут быть дополнительными причинами пористости.Если позволяют спецификации, подумайте о переходе на другой состав основного металла и всегда удаляйте ржавчину, жир, краску, покрытия, масло, влагу и грязь перед сваркой. Присадочные металлы с добавлением раскислителей могут помочь «очистить» сварной шов, но никогда не следует полагаться исключительно на минимизацию пористости. Наконец, немедленно замените все влажные или загрязненные защитные цилиндры.
Не подрезайте
Поднутрение происходит, когда канавка плавится в основном металле рядом с носком сварного шва, и металл шва не может заполнить эту область.Эта неоднородность ослабляет кромку сварного шва, увеличивая вероятность появления трещин. Устранить проблему относительно просто: уменьшите сварочный ток, уменьшите напряжение сварочной дуги и отрегулируйте угол наклона горелки MIG к стыку. Уменьшите скорость движения, чтобы металл шва полностью заполнял расплавленные участки основного металла. При использовании техники плетения сделайте небольшую паузу с каждой стороны сварного шва.
Когда сварочный металл не может полностью сплавить металл шва с основным металлом или с предыдущим наплавленным валиком в многопроходных приложениях, может произойти неполное сплавление.Некоторые называют эту проблему недостатком плавления. Как правило, причиной является неправильный угол наклона пистолета MIG, и вам следует его соответствующим образом отрегулировать. Выполните следующие шаги:
- Поместите борт стрингера рядом с правильной точкой на соединении, отрегулировав рабочий угол или расширив канавку по мере необходимости для полного доступа к ней.
- Удерживайте дугу на передней кромке сварочной ванны, поддерживая угол от нуля до 15 градусов.
- При использовании техники плетения на мгновение удерживайте дугу на боковой стенке канавки.
Если корректировка угла горелки MIG не устраняет неполное плавление, посмотрите, не слишком ли далеко от сварочной лужи идет проволока. В таком случае увеличьте скорость движения и / или сварочный ток, чтобы устранить проблему. И наоборот, если вы подозреваете, что недостаточное количество тепла привело к неполному сварке, выберите более высокий диапазон напряжения и / или при необходимости отрегулируйте скорость подачи проволоки. Наконец, всегда очищайте поверхность основного металла перед сваркой, чтобы удалить загрязнения, которые могут помешать сплаву металла.
Правильные рабочие углы важны для предотвращения ошибок сварки GMA, таких как неполное сплавление.Другая распространенная проблема сварки MIG — разбрызгивание — возникает, когда сварочная ванна выталкивает расплавленный металл и разбрасывает его вдоль сварного валика; этот расплавленный металл затем охлаждается и образует твердую массу на заготовке. Чрезмерное разбрызгивание не только ухудшает внешний вид сварного шва, но также может привести к неполному сплавлению при выполнении нескольких сварочных проходов. Слишком высокая скорость подачи проволоки, слишком высокое значение напряжения и слишком длинное удлинение или вылет сварочной проволоки могут вызвать разбрызгивание.Может помочь уменьшение заданных значений и более короткий вылет.
Как и пористость, недостаточный защитный газ и / или грязные основные материалы могут вызвать разбрызгивание. При необходимости увеличьте поток защитного газа на регуляторе и минимизируйте сквозняки возле сварочной дуги, очистите и высушите сварочную проволоку и удалите всю смазку, грязь и другие загрязнения с основного металла.
К другим факторам, которые могут привести к разбрызгиванию, относятся: контактный наконечник неправильного размера, изношенный контактный наконечник или неправильный наконечник к выемке сопла.Убедитесь, что у вас есть подходящие контактные наконечники, сопла и параметры выемки для конкретного применения.
Следите за жарой
Чрезмерное проплавление происходит, когда металл сварного шва плавится через основной металл и зависает под сварным швом. Обычно причиной проблемы является чрезмерное тепловложение. Чтобы исправить это, выберите более низкий диапазон напряжения, уменьшите скорость подачи проволоки и увеличьте скорость движения.
И наоборот, недостаточный подвод тепла может вызвать непровар или неглубокое сплавление металла шва с основным металлом.Выбор более высокой скорости подачи проволоки, более высокого диапазона напряжения и / или уменьшения скорости движения — все это жизнеспособные решения. Правильная подготовка стыка также помогает предотвратить проплавление — подготовка и конструкция должны обеспечивать доступ ко дну канавки и позволять поддерживать надлежащий вылет и характеристики дуги.
Недостаточное проникновение и чрезмерное проникновение можно исправить путем настройки таких факторов, как напряжение, скорость подачи проволоки и скорость движения.Все о проводе
Прекращение подачи проволоки и неисправность системы подачи проволоки могут отрицательно повлиять на сварочную дугу и создать неровности, которые могут ослабить сварной шов.Расплывчатое скопление проволоки, мешающее ее подаче, является распространенной проблемой. Вы можете решить проблему гнездования птиц, перевернув приводной ролик и вытащив проволоку из пистолета. Затем обрежьте пораженную проволоку и снова пропустите ее через устройство подачи и обратно в пистолет. Если характеристики сварки позволяют, уменьшите натяжение приводного ролика, используйте проволоку большего диаметра и / или уменьшите расстояние подачи проволоки (используйте более короткие кабели), чтобы минимизировать вероятность гнездования птиц.
Если проволока снова плавится и соединяется с контактным наконечником, как показано, наконечник следует заменить, а ведущие ролики проверить на наличие птичьего гнезда, прежде чем продолжить сварку.Burnback также очень распространен. Это происходит, когда в контактном наконечнике образуется сварной шов, и обычно это происходит из-за слишком низкой скорости подачи проволоки и / или из-за слишком близкого удержания горелки MIG к основному металлу во время сварки. Чтобы исправить обратный ожог, увеличьте скорость подачи проволоки и увеличьте расстояние между горелкой MIG от заготовки (сопло должно находиться на расстоянии не более половины дюйма от металла). Замените поврежденные от ожога контактные наконечники, сняв сопло и контактный наконечник (который может оплавиться на проволоку), отрезать провод, установить новый контактный наконечник и заменить сопло на сопло, имеющее соответствующую выемку для наконечника.
Другие причины проблем с подачей проволоки включают засорение лайнера, неправильно обрезанные лайнеры (слишком короткие / заусенцы / защемления) или лайнер неправильного размера. Чтобы устранить эти проблемы, замените любой лайнер, если вы обнаружите засор, всегда обрезайте лайнер в соответствии с указаниями производителя и убедитесь, что вы используете лайнер правильного размера для диаметра сварочной проволоки.
Нет лекарства от всех
Помните, что качественные сварочные швы MIG являются результатом не только хорошей техники сварки, но и вашей способности быстро выявлять и решать проблемы, если они все же возникают.Продолжайте вооружаться некоторой базовой информацией, и вы сможете решать самые распространенные проблемы, связанные со сваркой MIG, без ущерба для времени или качества.