Ручной сварочный экструдер сваривания пластмасс
1
Формирования коренных швов, прихваток — 1 500 р.
2
Для сварки стыковых и угловых — 1 500 р.
3
Для сварки эллипсов, окружностей и внешних тупых углов — 1 500 р.
4
Для сварки внешних углов под 90 градусов — 3 500 р.
5
Для сварки внутренних углов под 90 градусов — 3 500 р.
6
Для сварки углов трех плоскостей — 1 500 р.
7
Переходник от экструдера к литьевым формам — 1 500 р.
8
Универсальная насадка — 3 500 р.
9
Фторопластовая насадка — 3 500 р.
10 Для сварки эллипсов, окружностей и внешних тупых углов — 1 500 р.
11
Для формирования швов острых внутренних углов — 1 500 р.
12
Для сварки внешних углов под 90 градусов — 1 500 р.
13
Для сварки внутренних углов под 90 градусов — 1 500 р.
Для щелевых заполнений в «0» с листом — 1 500 р.
15
Насадка к экструдеру для труднодоступных мест по вашим размерам — 3 500 р.
16
Для узких труднодоступных мест с поворотом башмака на 360 градусов — 3 500 р.
17
Фторопластовая насадка — 3 500 р.
Эффективный и мощный экструдер ручной сварки Local After-Sales Service
Alibaba.com предлагает широкий выбор надежных, эффективных и модернизированных. экструдер ручной сварки для различных сварочных целей. Эти. экструдер ручной сварки широко используются в коммерческом и промышленном секторах благодаря своим обширным возможностям и превосходной точности, удовлетворяя самые разные требования. Эти машины сертифицированы и проверены группами строгого контроля качества и уполномоченными регулирующими органами, чтобы гарантировать оптимальную производительность продуктов.Покупайте эти продукты в проверенных и надежных магазинах. экструдер ручной сварки продавцы и поставщики на сайте.
Блестящие и качественные. экструдер ручной сварки, доступные на сайте, сделаны из материалов, которые обладают высокой эффективностью и экологичностью. Эти устройства прочны благодаря своему материалу и могут выдерживать грубое обращение, ежедневное использование или любые другие внешние воздействия. Эти. экструдер ручной сварки доступны как в полуавтоматическом, так и в автоматическом режиме в зависимости от ваших требований и моделей. Объединение основных технологий в один продукт - эти. экструдер ручной сварки предлагают более высокую степень автоматизации.
На Alibaba.com вы можете выбирать из различных разновидностей. экструдер ручной сварки доступны в различных формах, размерах, цветах, функциях и возможностях в зависимости от выбранной модели. Эти выдающиеся. экструдер ручной сварки машины сертифицированы и оснащены мощными ультразвуковыми сигналами.
Компактные размеры и защитные рамы делают это. экструдер ручной сварки отлично подходит для коммерческого использования и предлагает лучшую универсальность.
Alibaba.com предлагает обширную линейку. экструдер ручной сварки варианты, которые могут соответствовать вашим требованиям и бюджету, чтобы сэкономить ваши деньги. Эти продукты имеют сертификаты ISO, CE, SGS для лучшего обеспечения качества. Вы можете размещать OEM-заказы вместе с индивидуальной упаковкой, приобретая их оптом.
что это такое, как и где используется, характеристики
Главная / Приспособления и детали
Назад
Время на чтение: 4 мин
0
1134
Место ручного экструдера для сварки — одно из почётных на полках с оборудованием строительных магазинов.
Его основная работа — соединение полипропиленовых заготовок и деталей из полипропилена, создание конструкций из пластмасс и предметов из плотной плёнки, сварка листов пластика, пайка резервуаров, сооружение предметов детской площадки и тому подобное.
Однако, для пайки поливинилхлоридных деталей этот аппарат не подходит, как и для создания трубопроводных конструкций. Прочность швов, полученных с помощью экструдера, менее 85 процентов, поэтому трубопровод не будет достаточно герметизирован.
- Общая информация
- Виды
- РУЧНОЙ СВАРОЧНЫЙ ЭКСТРУДЕР: СХЕМА РАБОТЫ
- Виды швов
- Подготовительный этап
- Выполнение сварки
- Заключение
Общая информация
Этот аппарат работает по такой системе: нагретая воздушная масса, идущая из сопел экструдера и увеличивает температуру промежутка (канавы или стыка) между соединяющимися деталями, делая последние пластичнее.
Параллельно в рабочую зону аппарата подходит прут. Он плавится и соединяется с диском (его называют также шнек), образуя однородную пластиковую массу.
Через фильерный инструмент или сварочный башмак выходит расплавленная полимерная смесь. Шов получается, когда вся масса остывает до комнатной температуры. Это похоже на выдавливание кетчупа из упаковки.
Поверхности, которые соединяет мастер, должны быть идентичны друг другу. Это подразумевает, что составные элементы, плотность упаковки материала и его текучесть у деталей одинаковы.
Прут для сварки по этим характеристикам также должен быть похож на элементы.
youtube.com/embed/PREsEEoR58U?feature=oembed» frameborder=»0″ allow=»accelerometer; autoplay; encrypted-media; gyroscope; picture-in-picture» allowfullscreen=»»/>
Подведем итоги
Сварка полипропиленовых листов в последнее время находит все больше сфер применения, так как позволяет получить изделия с высокими эксплуатационными характеристиками. Качество производимых работ в большой мере связаны с выбором инструмента и его правильного применения.
Большое распространение при сварочных работах с полипропиленом имеет ручной инструмент, применение которого возможно как в быту, так и в промышленности. Ручной инструмент типа экструдера позволяет получать надежные соединения без потери мобильности монтажа.
youtube.com/embed/-8yCQLiEFmo?feature=oembed» frameborder=»0″ allow=»accelerometer; autoplay; clipboard-write; encrypted-media; gyroscope; picture-in-picture» allowfullscreen=»»/>Виды
- Шнековые. В них проволока для присадки плавится в шнековом резервуаре экструдерного аппарата и выдавливается сквозь стержень с винтовой поверхностью вдоль оси — шнек. Вместо проволоки используют и материал в гранулированном состоянии. Он находится в специальном отделении, где соединяется в однородную расплавленную массу и становится пригодным к подаче.
- Безшнековые. Прут в этих моделях накаляется электронагревателями в участке нагрева. Задний конец проволоки в этом варианте остается твердым и подталкивает нагретый вязкий материал на участок образования шва.
- Скомбинированные. В них совмещаются шнековы и безшнековый типы.
Виды ручного сварочного экструдера
- Шнековые (присадочный материал расплавляется в шнековом (экструзионном) отделении аппарата и выдавливается наружу с помощью шнека).
Присадочный материал – это пруток или специальные гранулы, которые помещаются в шнековое отделение и уже там под воздействием высокой температуры при взаимодействии со шнеком становятся однородной массой, готовой к использования.
- Безшнековые или плунжерного типа. Пруток в таких экструдерах нагревается сначала с помощью электронагревателей вокруг области нагрева, а задняя твердая часть присадочного материала выступает в качестве поршня для передней уже вязкой массы.
- Комбинированные (сочетаются два вышеизложенных вида).
Безшнековые сварочные экструдеры обладают меньшей производительностью по сравнению со шнековыми. Но есть и плюсы: лёгкость и компактность, что позволяет использовать его в труднодоступном месте.
Особенность и приоритетность использования обусловлена следующими факторами.
- Ручной экструдер для сварки может варить изделия с толстыми стенками.
- Быстрая скорость сварки.
- Сведение к минимуму человеческого фактора.
Здесь не требуется следить за состоянием сварочной ванны, как при сварке металла, контролировать правильное выведение сварочного шлака, выводить «ёлочки» и «зигзаги». Использовать это оборудование новичку будет проще всего.
РУЧНОЙ СВАРОЧНЫЙ ЭКСТРУДЕР: СХЕМА РАБОТЫ
Перед тем, как соединять элементы, их нужно нагреть. В корпус сварочного экструдера для этой цели может быть встроен термофен. Он нужен для того, чтобы пластиковые детали нагрелись потоком воздуха перед тем, как на них подастся присадочный материал.
Нагретая воздушная масса может идти не только от термофена, но и от компрессорной установки или организационной пневмосети. Присадочная проволока нагревается благодаря электрическим нагревателям, встроенным по кругу экструзионного отделения.
В устаревших моделях экструдеров шнековая камера подогревается жарким воздухом, который нагревает также и зону сварочной работы. Перед тем, как «дойти до сварки» воздух идёт через отделение с диском и плавит материалы для присадки.
Последний подходит к зоне сварки сквозь башмак в состоянии своеобразной лавы.
Ручной сварочный экструдерный аппарат используют в основном для пайки полиэтилена с низким давлением, полипропиленовых деталей и остальных типов термических пластмасс из первой группы.
У них температура плавления и температура разрушения рознятся на 50 градусов Цельсия. Это уменьшает беспокойство по поводу деструкции, так как даже перенапряжение на 35-45 градусов не повреждает итоговое соединение.
Вторая группа термических пластмасс включает поливинилиденфторид и поливинилхлорид. Они плавятся и разрушаются с очень маленькой температурной разницей, поэтому тут важно жёстко контролировать терморежим сварки.
Чтобы работа со 2й группой термопластов протекала «как надо», шнековая деталь должна быть особой: иметь специальную форму, чтобы перемешивание массы было равномерным, а сам полимер не перегревался.
При работе с элементами из этих материалов, экструдер должен долго работать в ожидающем режиме или не выключатся долгое время.
Конструкция и принцип работы
Ручной экструдер выполнен в виде механического приспособления, при использовании которого соединение материалов осуществляется поэтапно: вначале пластик подвергается нагреву для придания ему вязкого состояния, а затем полученная масса выдавливается на поверхность в месте стыка. После охлаждения ПНД, ПВХ и других легкоплавких пластических масс на месте проведенных работ появляется прочный сварочный шов.
Устройство экструдера
Чтобы было удобнее работать с этим прибором, производители выпускают его в виде пистолета с ручкой и верхней насадкой, предназначенной для нагрева рабочей смеси. В конструкции экструдера можно выделить следующие рабочие узлы:
- термонагреватель;
- камера для расплавления пластика;
- дробильный шнековый механизм;
- экструзионная камера;
- система контроля;
- сварочное сопло;
- питатель;
- двигатель.
Принцип действия
Перед работой в экструдер вставляют присадочный пруток, который должен быть выполнен из материала, планирующегося для использования в сварочных работах. Сам рабочий процесс выглядит так: на верхней панели прибора крепят приёмную втулку с отверстием, в которую затем вставляется присадочный пруток. Он должен располагаться в нём таким образом, чтобы свободный конец оказался в области его захвата шнеком.
Когда специалист запускает электродвигатель, подвергаясь воздействию насыщенной струи горячего воздуха, пруток нагревается, и одновременно с этим по прошествии некоторого времени, которое заранее выставлено датчиком прибора, пруток подаётся в область его измельчения. Здесь шнек, совершающий вращательные движения, начинает дробить пруток, который приобретает вид гранулированной массы. В результате нагрева она начинает плавиться и постепенно перемещается в область плавления, где гранулят уже имеет полностью однородный состав.
Испытывая воздействие давления со стороны шнека, гранулят направляется в сварочную зону, а оттуда идёт в сварочное сопло, где в процессе прижима к поверхности соединяемых изделий выходит наружу в виде однородной полосы заданной ширины, определяемой конфигурацией сопла. Учитывая, что температура за пределами свариваемого изделия гораздо ниже создаваемой термонагревателем, материал прутка быстро охлаждается, в результате чего возникает сварочный шов.
youtube.com/embed/KaAFKmtXNc4?feature=oembed» frameborder=»0″ allow=»accelerometer; autoplay; clipboard-write; encrypted-media; gyroscope; picture-in-picture» allowfullscreen=»»/>При использовании более габаритных и производительных моделей экструдеров функцию нагрева присадочного прутка берёт на себя внешний термонагреватель, в который воздух поступает от небольшого компрессора. Экструдеры могут отличаться между собой и способом нагрева присадочного материала. В отдельных моделях для этой цели используются кольцевые нагревательные элементы, установленные в корпусе термонагревателя.
На систему контроля в составе экструдера возложены следующие функции:
- Отключение термонагревателя при продолжающем работу шнеке. Это позволяет предотвратить прилипание частиц гранулята к стенкам сварочной камеры.
- Блокировка «холодного старта». Срабатывает при допущении, что в зоне работы шнека всё ещё находится неоднородный присадочный материал.
- Запуск привода шнекового измельчителя.
- Включение термонагревателя.
- Предварительный выбор температуры нагрева, который зависит от температуры плавления пластика.
Подготовительный этап
Момент подготовки перед экструзионной сварки отличается от такого для других типов. Но, как и в других случаях, поверхности деталей нужно очистить от грязи и пыли, иначе шов получится некачественным.
Также пластмассы легко окисляются из-за воздействия воздуха. Очистить кромки нужно не более чем за двадцать минут до начала пайки.
Если вы сделаете это раньше, детали всё равно придется расчищать заново. Не пробуйте использовать для очистки растворитель, он может деформировать пластмассу.
Краткий обзор моделей
- 1507 СS. Шнековый экструдер со встроенной системой подачи воздуха и воздушным нагревом камеры пластификации. Позволяет сваривать пластиковые детали толщиной до 15 мм. Используется в помещениях.
- 2007 CS. Еще одна шнековая модель со встроенной подачей воздуха. Нагрев камеры пластификации – раздельный.
Температура массы и воздуха отслеживается цифровыми контроллерами. Подходит для работ внутри помещений и под открытым небом. Рекомендована для сварки геомембран.
- 3000 CS. Экструдер, выполненный по шнековой схеме. Нагрев пластификационной камеры – раздельный. Как и предыдущей модификации, имеются цифровые контроллеры для мониторинга температуры воздуха и массы. Используется в помещениях и на открытых площадках, в том числе при сваривании геомембран.
- 1002 С. Шнековый прибор облегченной конструкции. Для нагрева камеры пластификации используется воздушный поток. Управление температурой массы и воздуха – аналоговое. Несмотря на небольшие размеры и вес, модель способна сваривать пластик толщиной до 15 мм.
- 5002 С. Шнековый экструдер со встроенной системой нагнетания воздуха. Нагрев камеры пластификации – раздельный. В устройстве используются цифровые контроллеры, позволяющие прецизионно управлять температурой массы и воздуха. Может применяться внутри и снаружи помещений.
Серия 5002 С рекомендована для сварки деталей толщиной до 45 мм.
- 6002 С. Устройство шнекового типа со встроенной подачей воздуха. Камера пластификации имеет раздельную систему нагрева. Контроллеры – цифровые. Используется как в помещениях, так и в полевых условиях. Особенность – работа на грануляте.
ООО «ЦСП» предлагает все ручные сварочные экструдеры DOHLE, официально представленные на российском рынке. Также в продаже есть аксессуары. Приборы поставляются в оригинальной комплектации, включающей инструкцию по эксплуатации на русском языке. На технику действует гарантия производителя. Сроки поставки ручных экструдеров минимальны благодаря прямому сотрудничеству с заводом.
Cварочный экструдер
Выполнение сварки
Если экструдерный аппарат не новый, и вы уже использовали его раньше, уберите из резервуара остатки присадки, которые вы применяли до этого.
Сделать это нужно, даже если вы использовали тот же материал, что и в этот раз. Если присадка нагреется еще раз, её прочность уменьшится.
Затем нужно снять блокировку с холодного пуска, разогреть устройство и подающие детали до температуры, при которой вы собираетесь работать, установить настройки производительности.
Во время того, как вы будете варить, поддерживайте необходимый наклон экструдера. Он будет зависеть от того, какой тип шва вы выбрали. Если вы проработали долго и нуждаетесь в перерыве, поместите сварочный аппарат на подставку для него.
Если пауза будет долгой, снизьте температуру аппарата примерно на 45 градусов. Нагрев присадки приостановится, но проблем с продолжением процесса не будет.
Выполнение сварки экструдером
Если аппарат используется не впервые, тогда нужно удалить присадочный материал, используемый ранее. Даже если он того же состава. Повторный нагрев присадочного материала снижает его прочность.
Перед непосредственным началом сварки необходимо снять блокировки холодного пуска, нагреть аппарат и сварочный башмак до температуры, необходимой для работы, настроить производительность.
В процессе сварки необходимо поддерживать нужный угол наклона сварочного аппарата в зависимости от вида проделываемого шва. Если вам необходимо сделать перерыв, то экструдер нужно поставить на специальную подставку. Если перерыв планируется длительный – уменьшите температуру примерно на 40-50 градусов. Такое понижение температуры позволит приостановить нагревание присадочного материала и быстро возобновить работу.
Таким образом, сварка ручным сварочным экструдером является одной из самых несложных в применении среди остальных видов сварки и с применением других аппаратов. Совсем не необходимо быть профессионалом. Нужно лишь соблюдать инструкцию по эксплуатации экструдера и соблюдать вышеизложенные правила при работе с аппаратом и свариваемыми материалами.
|
пластиковый PE PP ручной сварочный штрангпресс (HJ-30B) — Купить Пластиковый экструзионный сварочный аппарат в ru.made-in-china.com
Пластиковый PE PP ручной сварочный экструдер (HJ-30B)модель: HJ-30B
Huashida представляет этот ручной экструдер для сварки. Сварочные аппараты экструдера просты в использовании. Все модели отличаются легкостью, компактностью и плавностью хода на этапе сварки.
Это запатентованный продукт нашей компании. Основная машина импортируется из Германии METABO, вентилятор из Швейцарии LEISTER.
Он имеет 7 скоростей A-B-C-D-E-F-G, D и E — нормальные рабочие скорости.
Подает сигнал тревоги при перегреве, необходимости замены угольной щетки или аварийном отключении.
Характеристики:
Многофункциональный дисплей
Двусторонний ввод проволоки без скручивания
Свободно регулируемая поворотная рукоятка
Эргономичная конструкция
Необслуживаемый нагнетатель
Вращающийся на 360 ° сварочный башмак
Низкий уровень шума, высокая передача мощности
Модель | HJ-30B |
Напряжение | 220V |
Мощность экструдера | 1100 Вт |
Мощность вентилятора горячего воздуха | 3400 Вт |
Скорость сварки | 3.0 кг / 4 мм |
Вес | 4,8 кг |
Сварочные стержни | Ø 2,5-4,0 мм |
Сварочный материал | PE |
Qingdao Huashida Machinery Co.
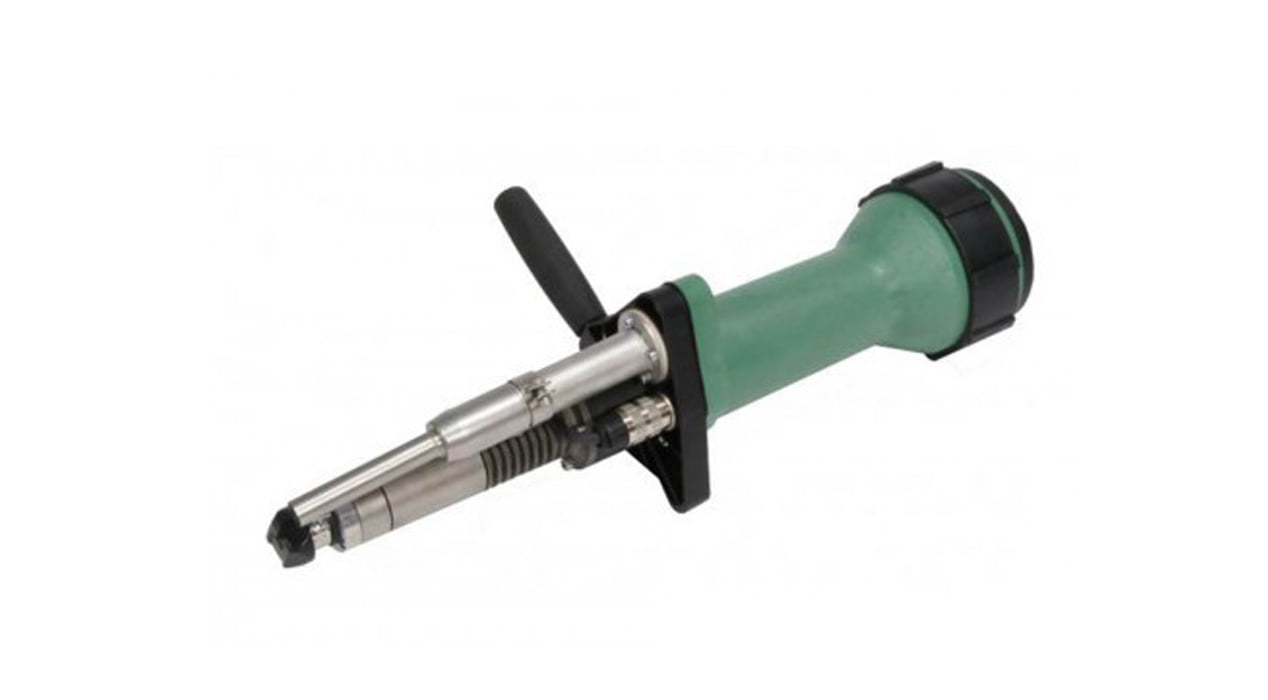
Наш завод находится в промышленной зоне Чэн Ян, Циндао, провинция Шаньдун. мы были одобрены и получили сертификат ISO: 2008 от SGS. Приглашаем всех клиентов посетить завод.
Наша продукция в основном включает одношнековый экструдер
и конический экструдер с двойным конусом
Вакуумная калибровка предварительно изолированной трубы за пределами оболочки из полиэтилена высокого давления Экструзионная линия
20-630 мм Экструзионная линия для производства однослойных / многослойных труб из полиэтилена высокой плотности
Экструзионная линия для производства спирально-гофрированных труб из полиэтилена высокой плотности 200-3000 мм
Линия для совместной экструзии труб из полипропилена, армированных стекловолокном )
Закрытие швов для кольцевой сварки электролитическим плавлением и лента для электросварки
Использование экструдера для оригинальной нити Filabot ™
Введение
Это недорогой экструдер пластиковой нити для любителей, которые хотят попробовать экструдируют собственный термопласт для использования в некоторых 3D-принтерах.
Большая часть информации на этой странице основана на Руководство по эксплуатации предоставлено производителем по адресу:
.http://cdn.shopify.com/s/files/1/0236/7897/files/
FilabotOriginalOperationalManualV2.pdf? 2997Пожалуйста, прочтите это руководство по мере необходимости и посмотрите видео на с помощью устройства, например:
https: // www.youtube.com/watch?v=H6tbZVsGuFk&feature=player_embedded
A. Безопасность
A1. Убедитесь, что вы получили инструкцию по использованию этот экструдер перед началом. Если у вас есть вопросы, обратитесь к рекомендации и спросите у инструктора.
A2. Обеспечить, что материал, загружаемый в экструдер, представляет собой чистый сухой полимер известного типа, и что вы заранее определили наилучшие начальные настройки экструдера.
A3. Перед тем, как начать, прочтите все инструкции здесь.
A4. Обязательно наденьте на защитные очки. и надлежащим образом. одежда (запрещается свободная одежда и волосы, только обувь с закрытыми носками.
А5. Для операций с горячими металлическими поверхностями износ перчатки хлопковые . Горячие и холодные металлы могут выглядеть одинаково, поэтому будьте осторожны.
А6. Не оставляйте экструдер без присмотра, если питание включен или экструдер горячий.
A7. Ничего не кладите на экструдер.
А8. Не касайтесь кожей горячего пластика.
А9. Никогда не оставляйте экструдер без присмотра, если он включен.
A10. Не кладите пальцы в бункер, если машина включена.
A11. В случае аварийной ситуации или аварии определите немедленно начальник лаборатории или инструктор и следуйте их указаниям.
А12. Прочтите, пожалуйста, о конкретном полимере, которым вы являетесь используя, либо с www.
matweb.com, на сайте производителя или в других авторитетных местах. Например, у DuPont есть информация о Surlyn 1601 на http://www.dupont.com/content/dam/dupont/products-and-services/packaging-materials-and-solutions/packaging-materials-and-solutions-landing/documents/surlyn_1601.pdf и хорошее руководство по экструзии Surlyn на http://www.dupont.com/content/dam/dupont/products-and-services/packaging-materials-and-solutions/packaging-materials-and-solutions-landing/documents/surlyn_extrusion_guide_.pdf
Примечание
Температуры ствола относятся к рекомендуемым диапазон «температур обработки». Если у вас нет значений для каждого зон, начните с установки сопла около нижнего конца указан диапазон температур обработки.
Производитель Filabot предоставил следующие диапазон общих температур обработки для некоторых распространенных пластмасс:
Также могут быть полезны следующие:

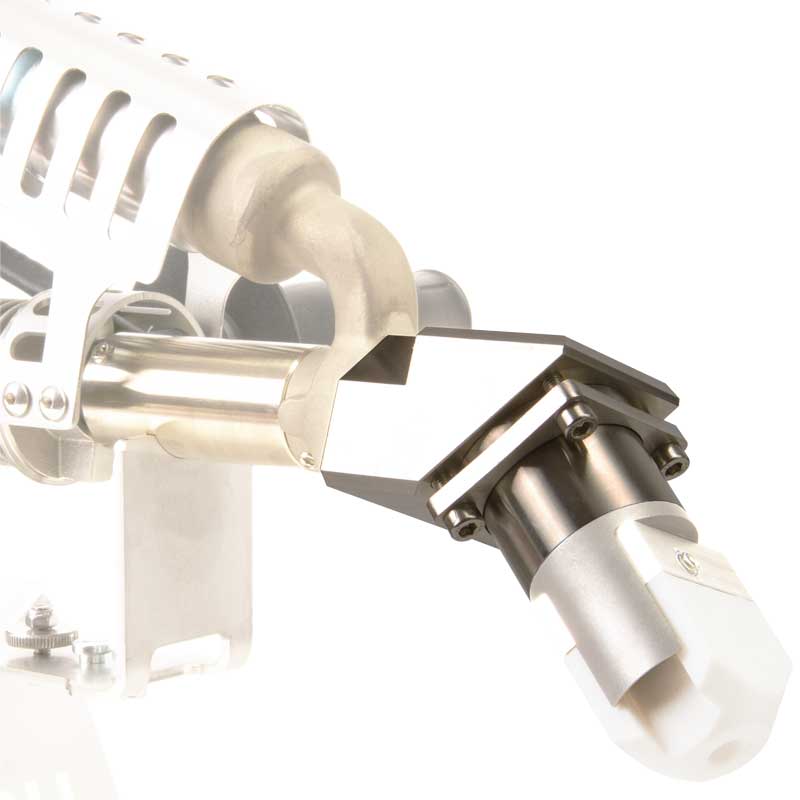

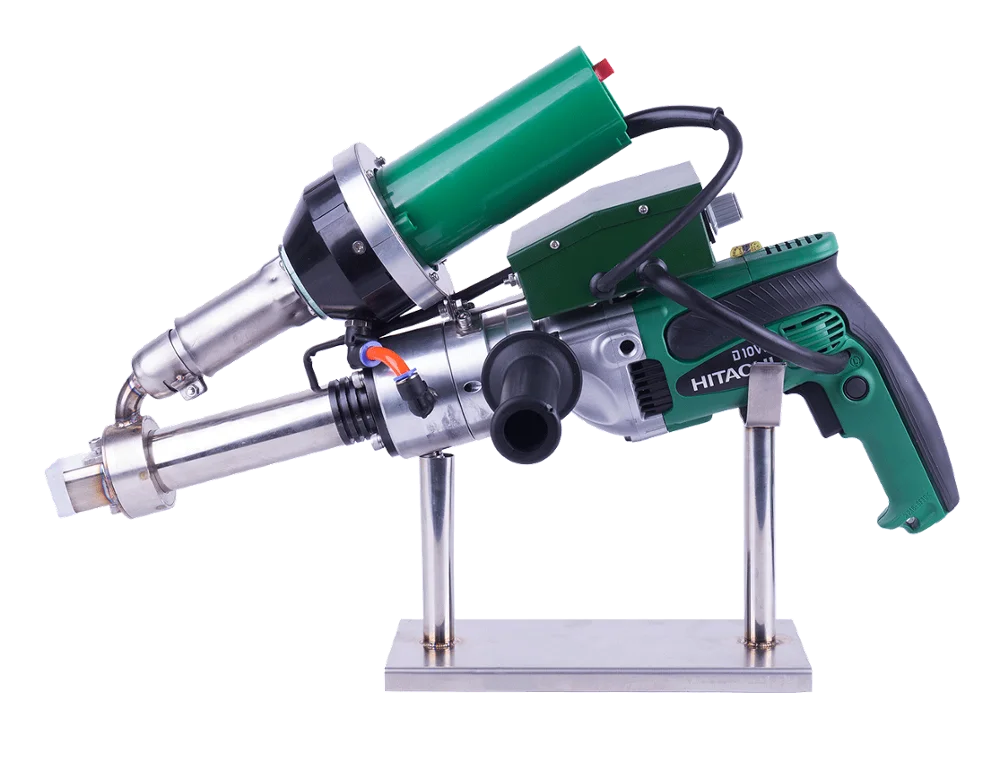
** Температура экструзии
Эта таблица цитируется с
Ричардсон, Т.
, & Локенсгард, Э., (1997). Промышленные пластмассы: теория и применение . Олбани, Нью-Йорк: Delmar
Б. Установка
Положение
Примечание
Данный экструдер является настольной моделью, и обычно его кладут на стол, выдавливая нить горизонтально.Поскольку любители вряд ли будут иметь охладители и намотчики нити накала, один из методов использования Filabot — дать экструдату упасть на чистый участок пола. Однако расстояние между Филаботом и пол определяет натяжение мягкой нити на выходе насадка. Чем больше расстояние, тем больше тянет нить. новая нить опускается вниз, и в результате получается более тонкая нить; сокращение расстояние, вероятно, приведет к немного более толстой нити.В Производитель Filabot предлагает столы высотой от 24 до 40 дюймов. над полом.
![]()
B1. Поставьте Filabot на стол так, чтобы нить выдавливалась. от края стола и приземлиться на пол. Если это расстояние слишком велико или слишком маленький, вам может потребоваться отрегулировать его с помощью платформы.
БИ 2. Очистите место, где будет собираться нить. Попробуйте использовать чистое ведро а не пол.
B3. Если вы экструдируете нить для использования в MakerBot Replicator 2, Replicator 2X или Stratasys FDM 1650, затем матрица или сопло для Следует использовать 1,75 мм, а не сопло для 3,0 мм.
Примечание
Если штамп нужно отремонтировать или заменить, он будет обслуживаться, когда машина полностью нагрета. Никогда не пытайтесь удалить штамп из холодной машины.
Температура
B4.Убедитесь, что все три переключателя (Extrude, Temperature Контроллер и основное питание): ВЫКЛ.
, затем подключите Шнур питания Filabot перед включением основного питания и температуры Контроллер. Не включайте вытягивание сейчас .
B5. Нажмите кнопку с двойной стрелкой вверх или вниз, и вы увидите мигающую точку. справа от зеленого параметра заданного значения (SV).
B6. Затем вы можете использовать кнопку <<, чтобы переместить десятичный разряд в положение, которое вы хотите изменить.
B7. Для изменения уставки используйте кнопку с двойной стрелкой вверх или вниз. температуру до желаемого значения. Помните, что это в C.
B8. Нажмите кнопку Set, чтобы записать эту настройку. Зеленый на дисплее теперь должно отображаться A100.
B9. Нажмите кнопку Set еще раз, и вы увидите измеренная температура отображается красным изменением (текущее значение, PV).
B10.
Следите за температурой по мере ее повышения. Это может занять 15 до 30 минут.
Модель Журнал учета
B11. Запишите свою работу в журнал для этой машины.
В12. Когда вы это сделаете, посмотрите, какой была предыдущая работа и сравните цвет пластика, который может еще быть в форсунках, с листинг. Обратите внимание на использованные температуры. Вполне возможно, что вы собираются выдавить ваш материал при гораздо более низкой температуре, но материал в стволе требует большей температуры.Если это так, проконсультируйтесь с инструктором. Скорее всего, вам придется выдавить какой-то материал во время переналадки при более высокой температуре, чем ваша материал требует.
С. Экструзионная нить
C1. Как только экструдер прогреется до заданной температуры, добавьте материал до половины заполнения. бункер. Пожалуйста, не добавляйте ничего, кроме чистой смолы известных типа в бункер.
C2.Включите переключатель Extrude. Это приведет к вращению винта. Если бочка пуста, может потребоваться момент, когда материал начнет выходить из сопла. Потерпи.
C3. Направьте нить в чистое место на полу или чистое ведро, в котором оно будет образовывать неплотные катушки.
Примечание
Первая нить может быть смесью ваших полимер и полимер предыдущего пользователя, и его следует собрать и утилизировать надлежащим образом.При первом использовании нового экструдера, вполне вероятно, что первая нить будет содержать металлические загрязнения от винт и цилиндр, как показано серым цветом справа. Загрязненная нить накала, подобная этой, не должна использоваться в 3D. принтер, потому что металлическая стружка может быстро забить сопло 3D-принтера.
C4. В качестве альтернативы Filabot можно использовать с Filawinder для автоматической намотки. Если вы хотите это сделать, позиция Filabot рядом с Filawinder и переместите датчик между ними так, чтобы петля из нити проходит через датчик.
Для получения конкретных инструкций по используя Filawinder, см .:
http://techweb.bsu.edu/jcflowers1/rlo/filastruder.htm#Filawinder
C5. Следите за толщиной нити и сделайте отрегулируйте высоту падения по мере необходимости.
Примечание
Легко забыть, что есть драгоценное, чистое нить на полу.Все, что нужно, — это неосторожно наступить на него, чтобы загрязнение нити. Не сорить, поддерживайте чистоту, содержите это в чистоте.
C6. При необходимости добавьте гранулы в бункер.
монитор.
D. Завершение цикла экструзии и Уборка
Примечание
Завершение экструзии, потому что вам нужно будет удалить смолу из бункера и выдавить весь пластик из ствола
D1.
Когда вы будете готовы прекратить выдавливание, оставьте Filabot включенным, пока вы аккуратно сливаете содержимое бункера в емкость и возвращаете Филабот к столу, все еще выдавливая все, что осталось в бочке.
D2. Дайте Filabot поработать одновременно с нагревателем и экструдер, пока материал не перестанет выходить из цилиндра.
D3. Когда материал не выходит из ствола, выключите Экструдер, регулятор температуры и выключатели основного питания.
D4. Отключите Filabot.
D5. это еще горячим, поэтому избегайте ожогов, когда перемещаете Filabot в то место, где он должен храниться.
D6. Закончите делать заметки в машине При необходимости войдите и сделайте свои собственные заметки.
D7. Внимательно и плотно намотайте пригодную нить для использования в 3D-печати.
D8. Поместите нить в герметичные пакеты, чтобы сохранить влагу. и пыль подальше от них.
D9. Тщательно и полностью маркируйте результаты своей работы.
![]()
D10. Хорошо очистите область. Уберите смолу. Отказаться загрязненная нить.
D11. Проконсультируйтесь с руководителем лаборатории или инструктором, чтобы убедитесь, что вы не пропустили задачу.
Wegener Welding LLC — Оборудование для производства пластмасс, экструдер для пластмасс
В Wegener Welding сварка пластмасс — единственный наш бизнес. Wegener Welding — международный поставщик высококачественного сварочного, технологического и испытательного оборудования.Обслуживая многие сегменты индустрии сварки пластмасс, мы предлагаем сварочные аппараты горячим воздухом, аппараты для экструзии пластмассы, аппараты для сварки пластмассовых листов, аппараты для гибки пластмассовых листов, аппараты для стыковой сварки пластмассовых труб, ленточные пилы для пластмассовых труб, аппараты для сварки плавлением пластиковых труб, аппараты для сварки пенопластом и многочисленные специализированные сварщики. для рынка термопластов. Линейки продуктов наших партнеров Wegener International, Hürner и Buckleys образуют всеобъемлющий источник уникального в отрасли оборудования для сварки и испытаний пластмасс.
Станки
Машины для стыковой сварки, Сварка на гибочных машинах, Машины для специальной продукции
Оборудование
Экструзионные сварщики, сварщики горячим газом, клиновые сварщики, испытатели для проверки качества
Машины специальные
Машины специальные
Индивидуально и в зависимости от продукта
решений
Специализированное обучение
Индивидуальный тренинг по сварке термопластов
Сервис
Поддержка США / Канады
ввод в эксплуатацию на месте
Служба запасных частей
Наши проверенные временем аппараты для сварки фильтров и фильтрующих материалов уникальны во всем мире. Полный спектр тестеров искры переменного тока, детекторов точечных отверстий и выходных отверстий постоянного тока, а также кабельных тестеров дополняет наши предложения продукции. Последние дополнения к нашей линейке испытательного оборудования — это электронные детекторы утечек для проверки целостности и векторного картирования непроводящей гидроизоляции и кровельных мембран.
Наряду с разнообразной сварочной продукцией мы предлагаем нашим клиентам отличный сервис. Благодаря круглосуточной готовности к выполнению работ, отгрузке в тот же день по заказам деталей, обученным на заводе техническим специалистам и экстренным арендодателям Wegener стремится удовлетворить все ваши потребности.
Понимание потребностей клиентов и их правильное выполнение
Мы чувствуем себя обязанными соблюдать этот девиз, от первоначальных переговоров до послепродажного обслуживания.
услуга.
Просто сообщите нам, что вам нужно, мы с нетерпением ждем вашего запроса!
Ваша команда в WEGENER Welding
Extrusion — обзор | Темы ScienceDirect
Введение
Экструзия — это процесс нагревания практически только ТП, которые могут иметь форму порошков, шариков, хлопьев, гранул или комбинаций этих форм. Этот пластик попадает в бункер экструдера. В экструдере используется пластификатор [спиральный винт, который вращается внутри нагретого цилиндра (цилиндра)] для плавления пластика (глава 3). Затем расплавленный пластик продавливают через фильеру, чтобы получить желаемую непрерывную форму продукта. На рис. 5.1 показана очень упрощенная схема процесса экструзии. Информация о фильерах (однослойных и соэкструдированных), используемых при экструзии, приведена в главе 17.
Рисунок 5.1. Упрощенный пример одношнекового экструдера
Экструзия — самый популярный процесс формования ТП.Он перерабатывает более 36 мас.% Всех пластмасс, потребляемых во всем мире, в такие продукты, как довольно простые пленки, листы, стержни, покрытия до очень сложных профилей, используемых в оконных профилях и т. Д. Большинство используемых пластиков — это полиэтилен (PE) (Глава 2) . 451 Используются другие пластмассы (таблица 5.1). В отличие от литья под давлением, второго основного процесса, в котором потребляются пластмассы (32 мас. %), Экструзия обычно приводит к полуфабрикату или промежуточному продукту. Для производства годных к употреблению продуктов требуется дальнейшая обработка.
Таблица 5.1. Пример экструдированных термопластов (любезно предоставлен Spirex)
Смола dala b | Удельный вес (г · см −1 ) | Плотность (фунт-фут −1 ) | Удельный объем 1 фунтов −1 | Удельный объем (см 1 г −1 ) | Температура экструзии (° of) | Удельная теплоемкость (БТЕ фунт −1 ° F −1 | Вода абсорбция за 24 часа (%) | Максимально допустимое содержание воды | |||||||||
---|---|---|---|---|---|---|---|---|---|---|---|---|---|---|---|---|---|
ABS, экструзия | 1.02 | 64,0 | 27,0 | 0,980 | 435 | 0,34 | 0,25 | ||||||||||
АБС, впрыск | 1,05 | 65,0 | 26,0 | 0,952 | 0,40 | 0,40 | 0,20 900 | ||||||||||
Ацеталь, литье под давлением | 1,41 | 88,0 | 19,7 | 0,709 | 0,35 | 0,25 | |||||||||||
Акрил, экструзия | 1.![]() | 74,3 | 23,3 | 0,839 | 375 | 0,35 | 0,30 | ||||||||||
Акрил, инжекционный | 1,16 | 72,0 | 24,1 | 0,868 | 380 | 0,35 | 1,50 | 900 0,15||||||||||
CAB | 1,20 | 74,6 | 23,1 | 0,833 | 380 | 0,35 | 1,50 | 0,15 | |||||||||
Ацетат целлюлозы, экструзия | 1.28 | 80,2 | 21,6 | 0,781 | 380 | 0,40 | 2,50 | ||||||||||
Ацетат целлюлозы, инъекция | 1,26 | 79,0 | 21,9 | 0,794 | 0 | 0,36 | 2,40 | ||||||||||
Пропионат целлюлозы, экструзия | 1,22 | 76,1 | 22,7 | 0,821 | 380 | 0,40 | 1,70 | ||||||||||
Пропионат целлюлозы, инъекция | 1.22 | 75,5 | 22,9 | 0,828 | 0,40 | 2,00 | 0,25 | ||||||||||
CTFE | 2,11 | 134,0 | 13,1 | 0,473 | 0,22 | 0,01 | 2,11 | 134,0 | 12,9 | 0,465 | 600 | 0,28 | <0,01 | ||||
иономер, экструзия | 0.![]() | 59,6 | 29,0 | 1,050 | 500 | 0,54 | 0,07 | ||||||||||
Иономер, инжекционный | 0,95 | 59,1 | 29,2 | 1.060 | 0,54 | 0,2030 | Нейлон-6 | 1,13 | 70,5 | 24,5 | 0,886 | 520 | 0,40 | 1,60 | 0,15 | ||
Нион-6,6 | 1.14 | 71,2 | 24,3 | 0,878 | 510 | 0,40 | 1,50 | ||||||||||
Нейлон-6,10 | 1,08 | 67,4 | 25,6 | 0,927 | 0,40 | 0,40 | 0,40 | 0,40 | 900 0,15|||||||||
Нейлон-6,12 | 1,07 | 66,8 | 25,9 | 0,935 | 475 | 0,40 | 0,40 | 0,20 | |||||||||
Нейлон-11 | 1.04 | 64,9 | 26,6 | 0,962 | 460 | 0,47 | 0,30 | 0,10 | |||||||||
Нейлон-12 | 1,02 | 63,7 | 27,1 | 0,980 | 450 | 0,25 | 900 0,10|||||||||||
на основе фениленоксида | 1,08 | 67,5 | 25,6 | 0,926 | 480 | 0,32 | 0,07 | ||||||||||
Полиалломер | 0.![]() | 56,2 | 30,7 | 1,110 | 405 | 0,50 | 0,01 | ||||||||||
Полиариленовый эфир | 1,06 | 66,2 | 30,7 | 0,940 | 460 | 900 Поликарбонат | 1,20 | 74,9 | 23,1 | 0,832 | 550 | 0,30 | 0,20 | 0,02 | |||
Полиэстер PBT | 1.34 | 83,6 | 20,7 | 0,746 | 0,08 | 0,04 | |||||||||||
Полиэстер ПЭТ | 1,31 | 8,18 | 21,1 | 0,746 | 480 | 0,40 | 0,10 | 0,005 900 | |||||||||
Полиэтилен HD, экструзия | 0,96 | 59,9 | 28,8 | 1.040 | 410 | & lt; 0,01 | |||||||||||
Полиэтилен HD, инжекция | 0.95 | 59,9 | 29,1 | 1,050 | 480 | & lt; 0,01 | |||||||||||
HD полиэтилен, выдувное формование | 0,95 | 56,9 | 28,8 | 1,040 | 410 | 0,01 | & lt | ||||||||||
Полиэтилен LD, пленка | 0,92 | 57,44 | 30,1 | 1,090 | 350 | & lt; 0,01 | |||||||||||
Полиэтилен LD, инъекция | 0.![]() | 57,4 | 30,1 | 1,09 | 400 | <0,01 | |||||||||||
Полиэтилен LD, проволока | 0,92 | 57,4 | 30,1 | 1,090 | 400 | & lt; 0,01 | |||||||||||
Полиэтилен ЛД, доб. покрытие | 0,92 | 57,1 | 30,0 | 1,090 | 600 | & lt; 0,01 | |||||||||||
Полиэтилен LLD, экструзия | 0.92 | 57,4 | 30,1 | 1,087 | 500 | ||||||||||||
Полиэтилен LLD, инжекционный | 0,93 | 58,0 | 29,8 | 1,075 | 425 | Экструзионный полипропилен | 0,92 | 56,8 | 30,4 | 1,100 | 450 | 0,10 | |||||
Полипропилен для инъекций | 0.90 | 56,2 | 30,7 | 1,110 | 490 | & lt; 0,10 | |||||||||||
Полистирол, ударопрочный лист | 1,04 | 64,9 | 26,6 | 0,963 | 450 | 0,1030 | |||||||||||
Полистирол, кристалл gp | 1,05 | 65,5 | 26,2 | 0,968 | 440 | 0,10 | |||||||||||
Полистирол, инъекционный удар | 1.![]() | 64,9 | 26,6 | 0,968 | 440 | 0,30 | |||||||||||
Полисульфон | 1,25 | 77,4 | 22,3 | 0,807 | 650 | 680 | 0,30 | 0,025 | |||||||||
Полиуретан | 1,20 | 74,9 | 23,1 | 0,834 | 400 | 400 | 0,10 | 0,03 | |||||||||
ПВХ, жесткие профили | 1.39 | 86,6 | 19,9 | 0,720 | 365 | 0,02 | |||||||||||
ПВХ, труба | 1,44 | 87,5 | 19,7 | 0,714 | 380 | 0,10 | |||||||||||
ПВХ , жесткий впрыск | 1,29 | 83,6 | 21,0 | 0,756 | 380 | 0,10 | 0,07 | ||||||||||
ПВХ, гибкий провод | 1.37 | 85,5 | 20,2 | 0,731 | 365 | ||||||||||||
ПВХ, гибкие экструдированные формы | 1,23 | 76,8 | 22,5 | 0,814 | 350 | ||||||||||||
ПВХ, гибкий впрыск | 1,29 | 80,5 | 21,4 | 0,776 | 300 | ||||||||||||
PTFE | 2,16 | 134,8 | 12.![]() | 0,464 | & lt; 0,01 | ||||||||||||
SAN | 1,08 | 67,4 | 25,6 | 0,927 | 420 | 470 | 0,03 | 0,02 | |||||||||
TFE | 106,1 | 16,3 | 0,589 | 610 | 0,01 | ||||||||||||
Уретановые эластомеры | 0,83 | 51,6 | 33,5 | 1.210 | 390 | 400 | 0,07 | 0,03 |
a Конкретная информация обо всех настройках машины и пластических свойствах изначально получается путем использования технических данных поставщика смолы на используемый состав или смолу.
Для максимального увеличения производительности или, по крайней мере, удовлетворения требований к характеристикам экструдированных пластиков, а также для минимизации затрат на экструзию продуктов важно понимать технологические свойства различных пластмасс. При производстве различных экструдированных продуктов могут использоваться определенные пластмассы. Понимание таких факторов, как их реологическое поведение по отношению к разложению, а также проблемы, которые могут возникнуть, дает информацию, которая облегчит экструдирование продуктов (главы 1,2,3 и другие главы).
После фильеры экструдат (расплав) калибруется, охлаждается и упаковывается множеством вспомогательных устройств, включая калибраторы вакуума, резервуары для воды, охлаждающие валки, тянущие устройства, резаки и намоточные устройства (Глава 18).Перед головкой между экструдером и головкой может быть установлен насос для расплава для получения более однородного экструдата. Точный выбор и расположение этих составных частей экструзионной системы будет зависеть от конечного продукта и требований допусков, которые необходимо соблюдать. 25, 27, 33, 143 196, 476
На выходе из экструдера экструдат (расплав) вытягивается с помощью вытягивающего действия или другого устройства, на котором он подвергается воздействию для охлаждения, обычно с помощью устройства с водой и / или продувкой воздухом. Это важный аспект последующего контроля, если существуют жесткие требования к размерам или требуется консервация пластмасс. Целью процессора является определение допуска, необходимого для скорости извлечения, и проверка того, что оборудование, расположенное ниже по потоку, соответствует общим требованиям к линии. Даже если жесткие требования к размерам не требуются, есть вероятность, что лучший контроль скорости вытягивания позволит более жесткие допуски, так что произойдет снижение выхода материала, что приведет к снижению стоимости продукта.
Безусловно, практически все экструдеры используют винты в пластиках для плавления пластмасс. Однако плунжер, популярная более века система плавления, используется для обработки пластмасс, которые нельзя расплавить шнеком. Плунжерные устройства, по сути, являются устройствами периодического действия, и, хотя можно добиться постоянной производительности путем последовательной работы двух или более плунжеров, этот метод практически не имеет значения практически для всех TP. Плунжер используется для обработки пластмасс, которые почти не плавятся.Другой возможностью является ротационный экструдер, устройство, в котором вращающиеся диски или роторы используются для создания сдвига. Однако экструзия TPs почти полностью зависит от вращающегося шнека как устройства доставки расплава. 143, 476
ТП характеризуются низкой теплопроводностью, высокой удельной теплоемкостью и высокой вязкостью расплава. Приготовление однородного гомогенного расплава и его доставка при соответствующем давлении и постоянной скорости может создать значительные проблемы, если не будет обработано должным образом (Глава 3).Основными вариантами экструдера являются одношнековый и двухшнековый. Из них одношнековый экструдер на сегодняшний день является наиболее универсальным и популярным в использовании.
Одношнековый экструдер состоит по существу из шнека, который вращается в аксиально фиксированном положении внутри плотно прилегающего канала ствола. Размеры экструдера идентифицируются по внутреннему диаметру цилиндра. Диапазон размеров от до 24 дюймов в диаметре с обычным диаметром от 1 до 6 дюймов (размеры в Европе и Азии варьируются от 20 до 600 мм с обычным диаметром от 25 до 159 мм.). Винт имеет электрический привод от различных устройств, таких как зубчато-редукторный механизм или ремень, для удовлетворения различных требований к производительности и стоимости. Эти редукторы рассчитаны на механическую и тепловую мощность в соответствии с определением Американских производителей оборудования (AGMA). Рейтинговая система AGMA основана на понимании того, что не все редукторы используются одинаково. Существуют также системы безредукторных приводов, в которых используется высокомоментный двигатель Siemens с необычным полым валом с низким моментом инерции. 476
Производительность экструдера зависит от скорости вращения шнека, геометрии шнека и вязкости расплава. Давление, развиваемое в системе экструдера, в значительной степени зависит от сопротивления фильеры и зависит от геометрии фильеры и вязкости расплава. Давление экструзии ниже, чем при литье под давлением. Обычно они составляют от 500 до 5000 фунтов на квадратный дюйм (от 3,5 до 35 МПа). В крайних случаях давление экструзии может возрасти до 10 000 фунтов на квадратный дюйм (69 МПа). Варианты одиночного шнека включают барьерный шнек или шнек для извлечения расплава и шнек с удалением воздуха (Глава 3).
Двухшнековый экструдер может иметь параллельные или конические шнеки, и эти шнеки могут вращаться в одном направлении (вращение в одном направлении) или в противоположных направлениях (в противоположном направлении). Экструдеры с более чем двумя шнеками известны как многошнековые экструдеры. Эти экструдеры обычно используются, когда смешивание и гомогенизация расплава очень важны, в частности, когда в пластик должны быть включены добавки, наполнители и / или армирующие элементы.
Они широко используются для компаундирования пластмасс, включая термочувствительные материалы, такие как ПВХ, обработки материалов, которые трудно подавать (например, некоторых порошков), реактивной обработки, 197 и для удаления летучих веществ из пластика. В частности, двухшнековые экструдеры предлагают широкие возможности обработки. Их можно использовать с голоданием, так что время пребывания, величину сдвига и контроль температуры расплава можно контролировать с помощью их сегментной модульной конструкции.
Биаксиально ориентированный полипропилен — обзор
8.2.1 Литературные исследования процессов обработки поверхности
В открытой литературе проводились исследования различных процессов обработки, в частности, в том, что касается биаксиально ориентированного полипропилена (БОПП).Например, Зенкевич 9 изучал влияние уровня энергии обработки коронным разрядом на поверхностную энергию пленки БОПП. В диапазоне энергии обработки коронным разрядом до 1,2 кДж / м 2 наблюдается быстрое увеличение поверхностной энергии с увеличением энергии обработки. Выше этого значения свободная энергия поверхности возрастает относительно медленно. Кроме того, степень окисления поверхностного слоя прямо пропорциональна энергии обработки коронным разрядом.
В другом исследовании, связанном с обработкой коронным разрядом, Guimond et al. 10 сравнили обработку БОПП воздушным коронным разрядом с атмосферным тлеющим разрядом азота (APGD). В этой работе было показано, что обработка азотом APGD приводит к более высокой поверхностной энергии, чем обработка воздушным коронным разрядом, и приводит к образованию на поверхности полипропилена в основном амино, амидных и гидроксильных функциональных групп. Кроме того, для обоих типов обработки обнаружено, что повышенная поверхностная энергия спадает аналогичным образом с увеличением времени после обработки.
Strobel et al. 11 сравнили обработанные коронным разрядом и обработанные пламенем полипропиленовые пленки с целью дать представление о механизме этих двух процессов. Атомно-силовая микроскопия (АСМ) и рентгеновская фотоэлектронная спектроскопия (XPS) были использованы для характеристики обработанной биаксиально ориентированной полипропиленовой пленки. В то время как оба процесса окисляют поверхность полипропилена, обработка коронным разрядом приводит к образованию водорастворимых низкомолекулярных окисленных материалов, тогда как обработка пламенем — нет. Результаты компьютерного моделирования показывают, что отношение кислорода к гидроксилу в коронном разряде намного выше, чем в пламени.Разрыв цепи и образование окисленных материалов с низким молекулярным весом связаны с реакциями с участием атомов O. Более высокие отношения O к OH в короне в большей степени способствуют образованию окисленных продуктов с низким молекулярным весом. Поверхностный окисленный полипропилен демонстрирует значительный термодинамический гистерезис краевого угла, который в первую очередь вызван микроскопической химической неоднородностью.
Эта статья является примером из открытой литературы, в котором указывается, что существуют различия в поверхностях, которые создаются с помощью различных процессов обработки.Значительно более ранняя статья Подгайного 12 содержала резюме исследований самого процесса обработки коронным разрядом. Были идентифицированы химические функциональные группы, которые образуются коронным разрядом на пленках, и обсуждено их влияние на смачиваемость и адгезию пленки.
Аналогичное исследование химических групп, полученных при обработке пламенем, было проведено Sutherland et al. 13 В этом исследовании было обнаружено, что около 30% включенного кислорода на обработанных пламенем поверхностях полипропилена присутствует в виде гидроксильных групп.Также наблюдалась переориентация или миграция поверхностных функциональных групп, которые были включены в процессе обработки пламенем. Кроме того, сканирующая электронная микроскопия (SEM) показала определенные изменения в топографии поверхности, вызванные интенсивной обработкой пламенем.
Другие субстраты, кроме БОПП, также были изучены при сравнении обработки пламенем и коронным разрядом. Компания NatureWorks LLC опубликовала технический бюллетень 14 о влиянии обоих типов обработки на биаксиально ориентированную полимолочную кислоту (BOPLA). Представленное исследование было выполнено с заявленной целью получения наилучших настроек оборудования для получения максимального увеличения поверхностной энергии. Кроме того, образцы пленок BOPLA хранили и тестировали с течением времени, чтобы определить, как долго пленка сохраняет свой высокий уровень поверхностной энергии.
В этом исследовании было показано, что соотношение топлива и кислорода 1: 1 при обработке пламенем приводит к наивысшему уровню поверхностной энергии (> 70 дин / см) для пленки BOPLA. С другой стороны, большинство упаковочных пленок, используемых для гибкой упаковки, достигают максимальной поверхностной энергии при обработке 0.5% избыток кислорода в топливной смеси. Когда скорость линии пленки увеличивается, поверхностная энергия падает при использовании фиксированной мощности горелки и зазора горелки. Следовательно, мощность горелки должна увеличиваться по мере увеличения линейной скорости для поддержания высокой поверхностной энергии, а также должен быть увеличен зазор горелки, чтобы предотвратить деформацию пленки из-за тепла пламени.
В части обработки коронным разрядом этого исследования, как пленка BOPLA, которая была обработана коронным разрядом во время производства, так и пленка BOPLA, которая не подвергалась предварительной обработке, оценивались на предмет энергии разряда в зависимости от полученной поверхностной энергии и продолжительности времени в днях, в течение которого пленка удерживалась. поверхностная энергия.К обработанной пленке BOPLA необходимо приложить очень небольшую ваттную плотность, чтобы эффективно «выпрямить» поверхностную энергию до уровня 48 дин или выше. В отличие от пленки BOPP, обсуждавшейся ранее, пленка BOPLA, которая не была обработана коронным разрядом во время производства пленки, может быть эффективно обработана позже. Однако необработанная пленка BOPLA требует большей плотности ватт для эффективного увеличения поверхностной энергии по сравнению с обработкой «выпуклостью», но не требует необоснованного уровня плотности ватт, чтобы быть эффективной.
Как уже упоминалось ранее в этой главе, одной из основных причин обработки полимеров, особенно полиолефинов, является улучшение адгезии с чернилами и другими покрытиями. Следует отметить, что в широкий диапазон термина «покрытие» также входит понятие металлизации пленок. Кроме того, необходимо понимать, что требуемый уровень обработки весьма специфичен для каждого приложения. Что касается процесса печати, проблема еще больше усугубляется тем, что в настоящее время промышленность в целом отходит от чернил на основе растворителей в пользу чернил на водной основе или УФ-отверждаемых чернил.
Кроме того, степень обработки пленочных подложек имеет тенденцию изменяться со временем. Кроме того, добавки, такие как добавки, снижающие скольжение, имеют тенденцию мигрировать на поверхность пленки по мере старения пленки, оказывая общий эффект маскировки уровня обработки. Помимо добавок, улучшающих скольжение, на степень обработки может влиять физическое обращение с пленкой, а также температура хранения. Все эти факторы необходимо учитывать при принятии решения о том, какой тип лечебной процедуры, а также какой уровень лечения необходим для достижения желаемого результата.
Растворение гелей в тонких пленках, экструзия трубок
Признак того, что образование гелей вызвано загрязнением или термическим разложением материала, — это точка или «рыбий глаз» в центре. Гели без пятен могут быть образованы HMW или сшитой смолой.
Предыдущий СледующийГели — обычная проблема качества при экструзии прозрачных пленок и трубок менее 0.005 дюймов толщиной. Гели — это в первую очередь визуальные дефекты, вызванные небольшими частями материала с более высокой молекулярной массой или загрязнениями, которые отражают и пропускают свет иначе, чем остальной материал. Они не являются проблемой в непрозрачных или толстостенных продуктах (более 0,02 дюйма), где они не видны.
Гели могут поступать из нескольких источников: хвосты HMW в бимодальной смоле, сшитый материал, вызванный перегревом, добавки с плохой термической стабильностью, мелочь от измельчения, остатки катализатора, такие как диоксид кремния, и другие органические или неорганические загрязнения.
В результате действия сил сдвига в экструдерах гели обычно имеют форму вытянутых эллипсов. Те, что вызваны загрязнением, обычно имеют точку или «рыбий глаз» в центре; гели, вызванные HMW материалом, нет. Когда гели состоят из капель HMW, это в первую очередь косметическая проблема. Однако гели, вызванные загрязнением, могут образовывать слабые места в трубке или даже образовывать дырки в пленке.
Если у вас есть гели в экструдированном продукте, важно знать, возникли ли они в поступающем сырье или были созданы во время экструзии.Гели, образующиеся при полимеризации, называются P-гелями. Они образуются в застойных зонах реактора, где смола перегревается. Они также могут быть фракциями с высокой молекулярной массой, полученными бимодальным способом, или смолой, полученной, когда реактор нуждается в обслуживании.
P-гели — обычная проблема для полиолефинов. Некоторые неолефины также имеют проблемы с высоким гелеобразованием. PVDF может вызвать серьезные проблемы с гелем у производителя, особенно если он изготовлен незадолго до ремонта. Таким образом, переработчики, использующие материал, склонный к гелеобразованию, должны знать графики технического обслуживания реактора.
Гели также могут образовываться во время экструзии. Они называются E-гелями и имеют тенденцию образовываться в результате высоких температур или длительного времени пребывания. Электронные гели могут быть образованы мертвыми зонами в экструдере, например застойными участками в шнеке. Например, секции смешивания Maddock могут создавать мертвые зоны.
Предотвращение п-гелей
Лучшая защита от P-гелей — это проверить поступающий материал на их наличие и четко сообщить поставщикам смол, что вы это делаете. Когда поставщики смолы понимают, что имеют дело с опытным пользователем, чей продукт требует низкого содержания геля, они попытаются отправить хороший материал.Подача контроля качества для гелей особенно важна при работе с многослойной пленкой, потому что у вас есть больше материалов и экструдеров для проверки гелей.
Для тестирования P-гелей требуется тонкий налет материала. Пластины можно приготовить несколькими способами, например, прессованием нескольких гранул смолы. Важно контролировать температуру прессования, чтобы в процессе теста не образовалось больше гелей. Количество гелей на единицу площади бляшки можно подсчитать с помощью диапроектора и поляризованного света для проецирования изображения на экран.Убедитесь, что вы стандартизировали процедуры гель-тестирования в своей компании. Их следует записывать и последовательно выполнять.
Если уровень геля в поступающем материале низкий или, по крайней мере, стабильный, вы можете предпринять шаги по уменьшению гелеобразования во время экструзии, хотя это непросто. Сетчатый фильтр, который обычно используется перед пластиной прерывателя, не захватывает достаточно гелей, чтобы их значительно уменьшить. Добавление дисперсионных смесительных элементов в шнек может уменьшить гелеобразование, но обычно не устраняет их полностью. Новые дисперсионные смесители, которые генерируют удлиненный поток, такие как смеситель CRD, продаваемый Rauwendaal Extrusion Engineering и Madison Group в Мэдисоне, штат Висконсин. , диспергируют больше гелей, чем предыдущие модели. Кроме того, фторполимерные добавки, улучшающие технологичность, обычно используемые для уменьшения разрушения расплава, могут уменьшить количество гелей в полиэтиленовых пленках.
Одним из лучших доступных инструментов для удаления гелей является среда «глубинной фильтрации», такая как диск из пористого спеченного металла или войлочная прокладка из случайных стальных волокон в трехмерном расположении. Эти глубинные фильтры имеют заданные характеристики и десятилетиями используются для экструзии высококачественной пленки и волокна, требующих минимально возможного уровня геля.Однако эти фильтры дороги и требуют регулярной замены.
Предотвращение появления «электронных гелей»
Чтобы избежать образования гелей во время экструзии, убедитесь, что шнек и матрица имеют обтекаемую форму. Кроме того, на поверхностях винта, цилиндра и матрицы не должно быть канавок, царапин или вмятин, которые могут собирать расплав и вызывать разрушение.
Также важно проверить трубки подачи смолы, смесители, питатели, бункеры и другое оборудование для обработки сыпучих материалов на предмет мелких частиц, стримеров или загрязнений другими пластиками.При замене смол оборудование для обработки сыпучих материалов необходимо полностью продуть и очистить.
Другой способ уменьшить количество гелей — запустить экструдер с высокостабилизированной версией пластика или даже с другим, более стабильным пластиком, чтобы покрыть критические поверхности устойчивым к деградации слоем.
Есть несколько методов подсчета гелей в пленке. Существует малоиспользуемый стандарт для ручного подсчета проб в автономном режиме. Автоматические методы, основанные на лазерах или камерах CCD, используются для контроля гелей в производстве.Для автоматического определения геля была предложена процедура ASTM, но некоторые вопросы до сих пор не решены, например, как сообщать результаты и гели какого размера нужно подсчитывать.
Дело гелевого детектива
Иногда стирается грань между P- и E-гелями. В реальном случае процессор, производящий однослойную литьевую пленку из природного гомополимера ПП, имел серьезные проблемы с внешним видом гелей. Первым шагом процессора было определение природы гелей, поэтому область вокруг пятен была исследована под микроскопом.Пленку разрезали через гель для исследования поперечного сечения. Затем образец был залит эпоксидной смолой и отполирован после отверждения эпоксидной смолы. Микрофотография была сделана при 200-кратном увеличении с помощью оптического микроскопа Leica (Laborlux 12 Pol S), оснащенного функциями полировки и микротома.
Образец освещали поляризованным светом и фотографировали проходящий свет. На фотографии процессор мог видеть, что в центре геля было черное пятнышко, что указывало на то, что причиной была деградация или другое загрязнение.Таким образом, следующим шагом была проверка работы экструдера — полностью оснащенной 7,8-дюймовой одношнековой машины с фильерой для литья под давлением и устройствами ориентации в продольном направлении. Тщательный поиск и устранение неисправностей означает, что нельзя ничего воспринимать как должное. Итак, следующим шагом была проверка точности датчиков температуры расплава.
Это было достигнуто с помощью программного обеспечения моделирования экструзии для прогнозирования условий в экструдере с учетом используемой смолы, скорости шнека, ограничения фильеры и заданных температур цилиндра-нагревателя.Компьютерное моделирование поставило под сомнение точность датчиков расплава, предсказав гораздо более высокие температуры расплава, чем показывали датчики. Температура расплава была оценена на уровне 547 F, что является очень высоким показателем для гомополимерной полипропиленовой пленки. Рекомендуемая температура плавления будет около 500 F.
Таким образом, температура цилиндра была понижена, чтобы достичь температуры плавления на матрице 500 F. Однако эта температура вызвала слишком большое противодавление. Наименьшая возможная температура плавления составляла 518 F, при которой гели были менее заметны, но все еще присутствовали.
Конструкция шнека, которая включала 4D-дисперсионный смеситель с барьером, была сочтена подходящей для полипропилена. Настройка машины также была проверена на наличие проблем, но не обнаружена.
Затем был исследован сам полимер. Образец полимера без добавок был отправлен на термогравиметрический анализ, который показал потерю веса 1% при 685 F. Это исключило разрушение полипропилена.
Это оставило пакет присадок, маточную смесь агентов скольжения и антиблокировки, как вероятного виновника.С поставщиком добавки связались и заменили материал-носитель на менее чувствительный к нагреванию и сдвигу. Когда это изменение было внесено, проблема с гелем полностью исчезла.
Крис Раувендал работает в области экструзии почти 30 лет. Он возглавляет собственную консалтинговую фирму в Лос-Альтос-Хиллз, Калифорния, которая занимается проектированием винтов и штампов, а также услугами по поиску и устранению неисправностей. Автор приветствует вопросы и комментарии читателей по электронной почте: chris@rauwendaal. com. Предыдущие статьи этой серии можно найти на сайте www.ptonline.com.
Экструзионная сварка термопластов — TWI
Введение
Экструзионная сварка используется при производстве изделий из толстого сечения, таких как резервуары и трубы, где необходимо производить однородные швы большого объема за один проход, в отличие от сварки горячим газом, где необходимо выполнить шов с использованием несколько прогонов.
При изготовлении резервуаров в основном экструзионная сварка используется для сварки оснований и крышек, хотя в некоторых случаях панели корпуса также свариваются с использованием этой техники.При изготовлении труб большого сечения его можно использовать там, где требуется ручная сварка. Еще одно применение экструзионной сварки — это применение в окружающей среде, где она используется для соединения облицовочного материала при строительстве свалок, отстойников и кровельных покрытий. Он также все чаще используется в сельском хозяйстве и водном хозяйстве, например, при изготовлении систем дренажа земель, отстойников и люков.
Оборудование
Аппараты для экструзионной сварки доступны в различных размерах, от компактных устройств со встроенной подачей воздуха и весом всего 2 штуки.Машины от 8 кг до 13 кг, используемые для сварки облицовочного материала на свалках. Они могут поставляться в конфигурации как на 110 В, так и на 240 В.
Экструзионная сварка исторически использовалась в основном для сварки PP и HDPE, хотя некоторые современные типы экструдеров также были разработаны для сварки PVC и PVDF. В случае ПВХ, из-за его узкого технологического «окна», экструдер необходимо продуть с помощью сварочного прутка из полипропилена или полиэтилена, чтобы гарантировать, что ПВХ-материал не разлагается в цилиндре.
Аппараты для экструзионной сваркипредназначены для обеспечения точного определения определенных параметров для максимального повышения качества сварки, а именно:
- Температура свариваемого материала — экструдат
- Массовый расход сварочного материала
- Температура горячего газа для предварительного нагрева подложки
- Количество горячего газа
Достигаемая скорость сварки зависит от расхода экструдата, толщины материала, площади поперечного сечения шва, а также размера и конструкции сварочного башмака из ПТФЭ.
Препарат
Что касается сварки горячим газом, то хорошее качество сварных швов экструзией можно получить только в том случае, если свариваемые детали правильно подготовлены. Их необходимо соскоблить, чтобы удалить любые загрязнения и оксидный слой на поверхности материала, а затем полностью скрепить вместе, чтобы обеспечить идеальное совмещение для нанесения начального корневого шва 3 мм горячим газом. Корневой проход обеспечивает полное проплавление сварного шва, что увеличивает прочность сварного шва, а также гарантирует, что детали остаются вместе во время процесса экструзии.Из-за большого количества воздуха, используемого для предварительного нагрева (обычно 300 л / мин в соответствии с директивами DVS), стандартный прихваточный шов горячим газом может разрушиться из-за расширения.
Угол экструдера по отношению к заготовке также чрезвычайно важен для обеспечения равномерного предварительного нагрева подложки и равномерного потока экструдата ( Рис. 2a и 2b ). Если используются неверные параметры, например, , т.е. слишком холодный, поверхность сварного шва будет очень шероховатой и неровной на вид, а полученный сварной шов будет иметь низкую прочность.Если сварной шов будет слишком горячим, поверхность будет выглядеть влажной, и сварной шов снова будет иметь низкую прочность.
Современный экструзионный сварочный аппарат имеет возможность отдельно контролировать температуру расплава и предварительный нагрев воздуха с дисплеем на блоке управления для упрощения работы и контроля. Электронное управление плавильной камерой не позволяет приводному двигателю работать, пока материал не достигнет нужной температуры. Это предотвращает нагрузку на двигатель и винтовой привод.
Описание
Приводной двигатель (1) представляет собой электродрель с улучшенным зацеплением, приводящий в движение вал винта в нагретой бочке.Это также подает сварочный стержень (2) в точку ввода стержня (3) через пару прижимных роликов, а затем в экструдер (4). Современные экструдеры имеют специальную подачу сварочного прутка, которая предотвращает скручивание сварочного прутка и обеспечивает постоянную подачу прутка. Это улучшает однородное качество сварного шва, поскольку отклонения на входе из-за скручивания и перегиба сварочного стержня могут привести к отклонениям на выходе. Шнек экструдера измельчает сварочный стержень в гранулы. Полученный гранулят затем подается в плавильную камеру (5), где он плавится.Затем масса проходит через цилиндр к предварительно сформированному сменному башмаку из ПТФЭ (6), где ему придается форма требуемого шва.
В некоторые машины также можно подавать гранулят напрямую, а не сварочный пруток. Эти экструдеры в основном используются на свалках, где есть вероятность образования длинных швов и неблагоприятных погодных условий. Бункеры можно накрыть, чтобы снизить вероятность попадания влаги и загрязнений на сварочный стержень.
Сварочный башмак правильной конструкции, необходимый для данного типа свариваемого шва, размещается на конце экструдера. Основной материал нагревается (пластифицируется) нагревательным соплом (7), при этом воздух подается (в данной конкретной конструкции) через встроенный воздухонагреватель (8).
Экструзионная сварка — это ручной процесс сварки, который зависит от навыков оператора. Поэтому для получения высококачественного шва рекомендуется пройти качественную программу обучения и сертификации.Как и в случае сварки горячим газом, европейский стандарт (BS EN 13067) устанавливает требования к допуску сварщиков пластмасс к экструзионной сварке. Схема сертификации CSWIP PW-6-96 доступна для аттестации персонала, занимающегося сваркой пластмасс, для проведения как теоретического, так и практического экзамена по экструзионной сварке PP и HDPE. Сертификат действителен в течение двух лет с последующим продлением на два года, если сварщик продолжал использовать процесс на регулярной основе в течение этого периода времени.По истечении четырехлетнего периода сварщик должен будет пройти полную повторную проверку.