Физические методы контроля сварных соединений это
Радиационная дефектоскопия – рентгено- и гаммаграфический метод контроля. Рентгено- и гаммаграфия – это метод получения на рентгеновской, пленке или экране изображения предмета (изделия), просвечиваемого рентгеновским или гамма-излучением. Он основан на способности рентгеновского и гамма-излучения проходить через непрозрачные предметы, в том числе через металлы, и действовать на рентгеновскую пленку и некоторые химические элементы, благодаря чему последние флуоресцируют (светятся).
При этом дефекты, встречающиеся при сварке в теле изделия и чаще всего имеющие характер пустот (непроваров, трещин, раковин, пор и т. д.), на рентгеновской пленке (на рентгенограммах) имеют вид пятен (раковины, поры) или полос (непровары).
Как правило, просвечивают 3-15% общей длины сварного шва, у особо ответственных конструкций просвечивают все швы.
Рентгеновские аппараты, применяемые для контроля изделий, состоят из рентгеновской трубки, источника питания и пульта управления.
Схема просвечивания рентгеновским излучением изделия показана на рис. 137. В зависимости от режима просвечивания (при толщине металла до 50 мм), качества пленки и правильности дальнейшей ее обработки удается выявить дефекты размером 1-3% от толщины контролируемых деталей. В настоящее время широкое применение нашли рентгеновские аппараты ИРА-1Д, ИРА-2Д, РУП-120-5-1, РУП-200-5, РУП-400-5 и др.
Гамма-излучение образуется в результате внутриатомного распада радиоактивных веществ. В качестве источников гамма-излучения применяют следующие радиоактивные вещества: тулий-170, иридий-192, цезий-137, кобальт-60 для просвечивания металла толщиной 1-60 мм.

Чувствительность гамма-снимков, полученных с помощью радиоактивных изотопов – тулия-170, иридия-192 и других, приближается к чувствительности рентгеновских.
Гамма-излучение вредно для здоровья человека, поэтому ампулы с радиоактивным веществом помещают в специальные аппараты – гамма-установки, имеющие дистанционное управление (рис. 138).
Схема панорамного просвечивания сварных стыков трубопроводов с помощью гамма-источника показана на рис. 139.
А – отдельные дефекты, которые по своему расположению не образуют цепочки или скопления;
Б – цепочка дефектов, расположенных на одной линии в количестве более трех с расстоянием между ними, равным трехкратной величине дефектов и менее;
В – скопление дефектов в одном месте с расположением их в количестве более трех с расстоянием между ними, равным трехкратной величине дефектов и менее.
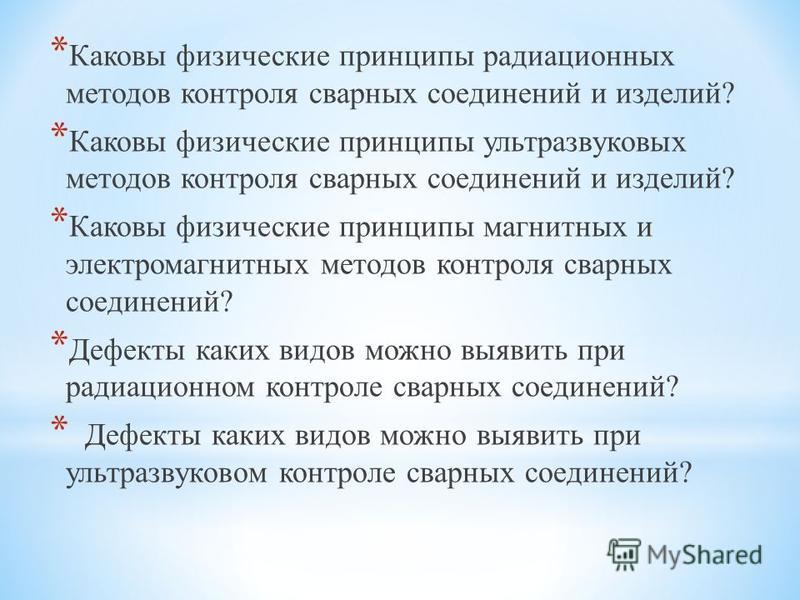
Сварной шов при радиационной дефектоскопии бракуется, если на рентгеновском или гамма-снимке обнаружены следующие дефекты:
шлаковые включения или раковины по группе А и В размером по высоте шва более 10% толщины стенки, если она не превышает 20 мм, а также более 3 мм при толщине стенки более 20 мм;
шлаковые включения, расположенные цепочкой или сплошной линией вдоль шва (группа Б), при суммарной их длине, превышающей 200 мм на 1 м шва;
поры, расположенные в виде сплошной сетки;
скопление на отдельных участках шва свыше пяти пор нa 1 см 2 площади шва.
Ультразвуковой метод контроля. Этот метод основан на способности высокочастотных колебаний частотой около 20000 Гц проникать в металл и отражаться от поверхности дефектов (встретившихся препятствий). Отраженные ультразвуковые колебания имеют ту же скорость, что и прямые, это свойство имеет основное значение в ультразвуковой дефектоскопии.
Узкие направленные пучки ультразвуковых колебаний для целей дефектоскопии получают с помощью пьезоэлектрических пластин кварца или титаната бария (пьезодатчика).

Схема ультразвукового метода контроля сварных соединений показана на рис. 140. Современные ультразвуковые дефектоскопы работают по схеме импульсного излучения, т. е. ультразвуковые колебания от пьезокристалла посылаются не непрерывно, а импульсами; во время пауз отраженные колебания поступают на тот же пьезокристалл, что обеспечивает высокую чистоту приема отраженных волн.

Пьезокристалл ультразвукового дефектоскопа помещается в специальный призматический или плоский щуп. Поверхность, по которой перемещается щуп, должна быть зачищена до металлического блеска. Для обеспечения необходимого акустического контакта между щупом и контролируемым изделием наносится слой минерального масла.
Магнитный метод дефектоскопии. Сварной шов стального или чугунного изделия покрывают смесью из масла и магнитного железного порошка (размер частиц 5-10 мкм). Изделие намагничивают пропусканием тока через обмотку, состоящую из нескольких витков, намотанных вокруг изделия.

Магнитографический метод контроля. При этом методе, разработанном в нашей стране, результаты записываются на магнитную ленту. Сущность этого метода контроля состоит в намагничивании сварного соединения и фиксации магнитного потока на ферромагнитную ленту. Лента накладывается на контролируемое изделие, которое намагничивается импульсным полем. Магнитное поле при наличии дефектов распределяется по поверхности детали по-разному, и соответственно ферромагнитные частицы на ленте намагнитятся в различной степени. Затем ферромагнитная лента снимается с контролируемого изделия и ее «протягивают» через воспроизводящее устройство (рис.

Результаты магнитографического контроля рассматривают на экране 9 осциллографа 7, на котором при наличии дефектов в контролируемом изделии возникают всплески (вертикальные импульсы). По величине и форме отклонения луча на экране осциллографа судят о величине и характере дефекта сварного соединения.
Магнитографический метод применяется для контроля сварных соединений толщиной не более 12 мм. Этим методом можно выявить макротрещины, непровары глубиной 4-5% от толщины контролируемого металла, шлаковые включения и газовые поры.
Магнитографический метод требует высокой квалификации оператора.
Под контролем качества сварки подразумеваются проверка условий и порядок выполнения сварочных работ, а также определение качества выполненных сварных соединений в соответствии с техническими требованиями.
В сварочном производстве применяют следующие виды контроля: входной (предупредительный), текущий (пооперационный) и приемочный (выходной) готовых изделий и узлов.
Цель входного контроля – уменьшить вероятность возникновениябрака при выполнении сварочных работ (контроль документации, качества исходных и сварочных материалов, квалификации сварщиков и т. д.).
Текущий контроль осуществляется в процессе сборочно-сварочных работ.
Приемочный, или выходной контроль, осуществляется для выявления наружных и внутренних дефектов сварки.
Различают разрушающие и неразрушающие методы контроля качества сварных соединений.
Разрушающие методы контроля качества сварных соединений
Разрушающие испытания проводят на образцах-свидетелях, моделях и реже на самих изделиях для получения информации, прямо характеризующей прочность, качество или надежность соединений. К их числу относятся: механические испытания, металлографические исследования, химический анализ и специальные испытания. Эти методы применяют главным образом при разработке технологии изготовления металлических конструкций или для выборочного контроля готовой продукции.
Механические испытания предусматривают статические испытания различных участков сварного соединения на растяжение, изгиб, твердость и динамические испытания на ударный изгиб и усталостную прочность.
Металлографические исследования проводят для установления структуры металла сварного соединения и наличия дефектов.
При макроструктурном методе определяют характер и расположение видимых дефектов в разных зонах сварных соединений путем изучения макрошлифов и изломов металла невооруженным глазом или с помощью лупы.
Химический анализ позволяет установить состав основного и наплавленного металла, электродов и их соответствие ТУ на изготовление сварного соединения.
Специальные испытания проводят для получения характеристик сварных соединений, учитывающих условия эксплуатации (коррозионная стойкость, ползучесть металла при воздействии повышенных температур и др.).
Неразрушающие методы контроля качества сварных соединений
При неразрушающих испытаниях оценивают те или иные физические свойства, косвенно характеризующие прочность или надежность сварного соединения. Неразрушающие методы (ими проверяется более 80 % сварных соединений) применяют, как правило, после изготовления изделия для обнаружения в нем дефектов. К неразрушающим методам контроля качества сварных соединений относятся: внешний осмотр, радиационный, ультразвуковой и магнитный контроль, контроль на непроницаемость и ряд других методов, имеющих ограниченное применение.
Внешнему осмотру подвергается 100 % сварных соединений. Осмотр выполняют невооруженным глазом или с помощью лупы, используя шаблоны и мерительный инструмент. При этом проверяются геометрические размеры швов, наличие подрезов, трещин, непроваров, кратеров и других наружных дефектов.
Контролю на непроницаемость подвергают трубопроводы и емкости, предназначенные для транспортирования и хранения газов и жидкостей и, как правило, работающие при избыточном давлении.
Пневматические испытания основаны на создании с одной стороны шва избыточного давления воздуха (10. 20 кПа) и промазывании другой стороны шва мыльной пеной, образующей пузыри под действием проникающего через неплотности сжатого воздуха. Негерметичность можно также оценить по падению давления воздуха в емкости, снабженной манометром.
Вид гидравлического испытания зависит от конструкции изделия. Налив воды применяют для испытания на прочность и плотность вертикальных резервуаров, газгольдеров и других сосудов с толщиной стенки не более 10 мм. Воду наливают на полную высоту сосуда и выдерживают не менее 2 ч. Поливу из шланга с брандспойтом под давлением не ниже 0,1 МПа подвергают сварные швы открытых сосудов. При испытании с дополнительным гидростатическим давлением последнее создают в наполненном водой и закрытом сосуде с помощью гидравлического насоса. Величину давления определяют по техническим условиям и правилам Котлонадзора. Дефектные места устанавливают по наличию капель, струек воды и отпотеваний.
Внутренние дефекты сварных соединений выявляют просвечиванием рентгеновскими лучами (толщина металла до 60 мм (рис. 1)), или гамма-лучами (толщина металла до 300 мм (рис. 2)). Выявление дефектов основано на различном поглощении рентгеновского или гамма-излучения участками металла с дефектами и без них. Результаты фиксируются на пленке или выводятся на специальный экран. Размеры выявляемых дефектов: при рентгенографии – 1. 3 % от толщины металла, при радиографии – 2. 4 %.
Рис. 1. Рентгенографический контроль сварных соединений: 1 – рентгеновская трубка; 2 – сварное соединение; 3 – кассета; 4 – пленка
При оценке качества швов рекомендуется иметь эталонные снимки характерных дефектов для разных толщин металла. Альбомы эталонных снимков утверждаются инспекцией Ростехнадзора и являются неотъемлемой частью ТУ на приемку изделий.
Рис. 2. Схема просвечивания гамма-лучами: 1 – затвор; 2 – свинцовая капсула; 3 – капсула с веществом; 4 – сварное соединение; 5 – кассета с пленкой
Магнитографический контроль основан на обнаружении полей рассеивания, образующихся в местах расположения дефектов при намагничивании контролируемых сварных соединений (рис. 3). Поля рассеивания фиксируются на эластичной магнитной ленте, плотно прижатой к поверхности шва. Запись производят на дефектоскопе. Магнитографический контроль можно применять только для проверки сварных соединений металлов и сплавов небольшой толщины, обладающих ферромагнитными свойствами. Выявляют поверхностные и подповерхностные макротрещины, непровары, поры и шлаковые включения глубиной 2. 7 % на металле толщиной 4. 12 мм. Менее четко обнаруживаются поры округлой формы, широкие непровары (2,5. 3 мм), поперечные трещины, направление которых совпадает с направлением магнитного потока.
Ультразвуковой контроль основан на способности ультразвуковых колебаний (механические колебания частотой 16. 25 МГц) отражаться от поверхности, разделяющей среды с разными акустическими свойствами. Для получения ультразвуковых колебаний используют свойство титаната бария, кристаллов кварца и некоторых других веществ преобразовывать электрические колебания в механические и наоборот (обратный и прямой пьезоэффекты).
Рис. 3. Схема прохождения магнитного потока в сварном соединении: а – при отсутствии дефекта; б – при наличии дефекта; 1 – поле магнитного рассеяния; 2 – дефекты шва
Ультразвуковой контроль имеет определенные преимущества перед радиационными методами: высокую чувствительность (площадь обнаруживаемого дефекта 0,2. 2,5 мм² при толщине металла до 10 мм и 2. 15 мм² при больших толщинах), возможность контроля при одностороннем доступе к шву, высокую производительность, возможность определения точных координат залегания дефекта, мобильность аппаратуры.
Основным методом УЗ-контроля является эхо-метод. Этим методом контролируют около 90 % всех сварных соединений толщиной более 4 мм.
На рис. 4 представлена принципиальная схема УЗ-контроля эхоимпульсным методом с совмещенной схемой включения искателя и приемника. Импульсный генератор 1 формирует короткие электрические импульсы с длинными паузами. Искатель 5 преобразует эти импульсы в ультразвуковые колебания. При встрече с дефектом волны от него отражаются, снова попадают на искатель и преобразуются в электрические колебания, поступающие на усилитель 2 и дальше на экран прибора 3. Зондирующий импульс генератора 6 размещается в начале развертки, импульс от донной поверхности 8 – в конце развертки, а импульс от дефекта 7 – между ними. В процессе контроля сварного соединения искатель перемещается зигзагообразно по основному металлу вдоль шва 4. Для обеспечения акустического контакта поверхность изделия в месте контроля обильно смазывают маслом (например, компрессорным).
К недостаткам метода следует отнести прежде всего низкую помехоустойчивость к наружным отражателям, резкую зависимость амплитуды сигнала от ориентации дефекта.
Рис. 4. Ультразвуковой контроль сварных соединений: 1 – генератор; 2 – усилитель; 3 – экран прибора; 4 – сварной шов; 5 – искательприемник; 6 – начальный импульс; 7 – импульс от дефекта; 8 – импульс от донной поверхности
Люминесцентная и цветная дефектоскопия относятся к методам капиллярной дефектоскопии. Контролируемую поверхность покрывают слоем флюоресцирующего раствора или ярко-красной проникающей жидкости. Затем раствор или жидкость удаляют, а поверхность облучают ультрафиолетовым светом (люминесцентный метод) или покрывают белой проявляющей краской (цветная дефектоскопия). В первом случае дефекты начинают светиться, а во втором – проявляются на фоне белой краски. С помощью этих методов выявляют поверхностные дефекты, главным образом трещины, в том числе в сварных соединениях из немагнитных сталей, цветных металлов и сплавов.
В каждом конкретном случае способ и объемы контроля качества сварного соединения выбираются в зависимости от назначения и степени ответственности конструкции в соответствии с отраслевыми нормативными документами, специальными техническими условиями или проектом.
Просмотров: 40089 Создан: 2012-10-20 Источник: Трубные технологии
7.5.1. Объем контроля сварных соединений резервуаров физическими методами определяется в рабочей документации КМ в зависимости от:
класса резервуара по степени опасности;
категории сварного шва;
уровня расчетных напряжений в сварном соединении;
условий и режима эксплуатации резервуара, включая температуру эксплуатации, цикличность нагружения, сейсмичность района и т.д.
7.5.2. Контроль радиографический
7.5.2.1. Контроль радиографический (рентгенографированием или гаммаграфированием) должен производиться в соответствии с нормативными документами, утвержденными в установленном порядке, для всех резервуаров объемом 1000 м и более.
Наряду с радиографическим контролем может применяться рентгенотелевизионный контроль согласно установленным нормативным документам.
Радиографический контроль выполняется только после приемки сварных соединений по визуальному контролю.
При контроле пересечений швов рентгеновские пленки должны размещаться Т-образно или крестообразно – по две пленки на каждое пересечение швов.
Снимки должны иметь длину не менее 240 мм, а ширину – согласно соответствующим стандартам. Чувствительность снимков должна соответствовать 3-му классу согласно этому стандарту.
Маркировочные знаки должны устанавливаться согласно стандарту и содержать идентификационные номера резервуара и контролируемого конструктивного элемента, а также номер рентгенограммы, указанный на развертке контролируемого элемента.
Для соединений из деталей толщиной 8 мм и более допускается вместо радиографического контроля применять контроль ультразвуковой дефектоскопией.
7.5.2.2. Оценка внутренних дефектов сварных швов при радиографическом контроле должна производиться по соответствующим стандартам и должна соответствовать:
для резервуаров III класса – 6-му классу;
для резервуаров II класса – 5-му классу;
для резервуаров I класса – 4-му классу.
Допускаемые виды и размеры дефектов в сварных соединениях в зависимости от их класса регламентируются соответствующими стандартами.
7.5.2.3. Радиографический контроль применяется для контроля стыковых сварных швов стенки и стыковых швов окраек днищ в зоне сопряжения со стенкой резервуаров.
Количество и размещение рентгенограмм устанавливается следующим образом: полотнища стенок резервуаров должны контролироваться в соответствии с табл. 7.3;
Таблица 7.3
Объем контроля сварных соединений рулонных полотнищ стенки резервуара физическими методами, %
Зона контроля | РВС III класса объемом 1000 м и более | РВС II класса | РВС I класса |
Вертикальные сварные соединения в поясах: | |||
1, 2 | |||
3, 4 | |||
остальных | – | ||
Горизонтальные сварные соединения между поясами: | |||
1-3 | |||
3-5 | |||
остальными | – |
Примечания: 1. Участки всех вертикальных сварных соединений в зонах примыкания к днищу длиной не менее 240 мм на резервуарах объемом более 1000 м подлежат обязательному контролю.
2. При выборе зон контроля вертикальных и горизонтальных соединений преимущественное внимание следует уделять проверке качества мест пересечения швов.
монтажные стыки полотнищ стенок должны контролироваться в объеме 100 % вертикальных швов и всех пересечений вертикальных и горизонтальных швов;
стенки резервуаров полистовой сборки должны контролироваться в соответствии с табл. 7.4;
все радиальные швы кольцевых окраек днищ должны контролироваться в зоне примыкания нижнего пояса стенки (один снимок на каждый радиальный шов).
Таблица 7.4
Объем контроля сварных соединений рулонных полотнищ стенки резервуара физическими методами, %
Зона контроля | РВС III класса объемом 1000 м и более | РВС II класса | РВС I класса |
Вертикальные соединения стенки по поясам: | |||
1, 2 | |||
3, 4 | |||
5, 6 | |||
остальные | – | ||
Горизонтальные соединения между поясами стенки: | |||
1-2 | |||
2-3 | |||
3-4 | – | ||
остальные | – |
Примечание. При выборе зон контроля преимущественное внимание уделять контролю качества мест пересечения швов.
7.5.2.4. При обнаружении недопустимых дефектов сварного шва должны быть определены границы дефектного участка. Кроме того, должен быть сделан дополнительный снимок (не считая снимков, необходимых для определения границ дефекта) в любом месте этого же или другого шва, выполненного тем же сварщиком, который допустил дефект. На схемах расположения рентгенограмм должны быть указаны места, где были обнаружены недопустимые дефекты и проводилось исправление. Если в сварном соединении установлен уровень дефектности более 10 %, то объем контроля таких швов удваивается.
7.5.3. Ультразвуковая дефектоскопия
7.5.3.1. Ультразвуковая дефектоскопия производится для выявления внутренних дефектов (трещин, непроваров, шлаковых включений, газовых пор) с указанием количества дефектов, их эквивалентной площади, условной протяженности и координат расположения.
7.5.3.2. Ультразвуковая дефектоскопия должна производиться в соответствии со стандартом.
7.5.4. Магнитопорошковая или цветная дефектоскопия
7.5.4.1. Контроль магнитопорошковой или цветной дефектоскопией производится в целях выявления поверхностных дефектов основного металла и сварных швов, невидимых невооруженным глазом. Магнитопорошковой или цветной дефектоскопии подлежат:
все вертикальные сварные швы стенки и швы соединения стенки с днищем резервуаров, эксплуатируемых при температуре хранимого продукта свыше 120 °С;
сварные швы приварки люков и патрубков к стенке резервуаров после их термической обработки;
места на поверхности листов стенок резервуаров с пределом текучести свыше 345 МПа, где производилось удаление технологических приспособлений.
7.5.5. Контроль при гидравлических испытаниях резервуара
7.5.5.1. При гидравлических испытаниях резервуара фиксируются и бракуются все места, где появляются течи и отпотины. После опорожнения резервуара в этих местах производятся необходимый ремонт и контроль.
7.5.5.2. Дефектные места в настиле стационарной крыши и в зоне ее примыкания к стенке, выявленные в процессе пневматических испытаний резервуара, фиксируются по появлению пузырьков на соединениях, покрытых пенообразующим раствором.
VIII. Оборудование для безопасной эксплуатации резервуаров
Общие требования
Настоящие Правила предусматривают обязательное оснащение резервуаров следующими устройствами и оборудованием для безопасной эксплуатации:
приборами контроля уровня;
устройствами пожарной безопасности;
Полный комплект устанавливаемых на резервуаре устройств и оборудования с его привязкой к проекту КМ должен быть разработан в проекте «Оборудование резервуара», выполненном специализированной (технологической) проектной организацией.
Дыхательная аппаратура
8.2.1. Дыхательная аппаратура должна устанавливаться на стационарной крыше резервуаров и должна обеспечивать проектные величины внутреннего давления и вакуума или их отсутствие (для атмосферных резервуаров и резервуаров с понтоном). В первом случае дыхательная аппаратура выполняется в виде совмещенных дыхательных клапанов (клапанов давления и вакуума) и предохранительных клапанов, во втором случае – в виде вентиляционных патрубков.
8.2.2. Минимальная пропускная способность дыхательных клапанов, предохранительных клапанов и вентиляционных патрубков определяется в зависимости от максимальной производительности приемораздаточных операций (включая аварийные условия) по следующим формулам:
пропускная способность клапана по внутреннему давлению, м /ч,
= 2,71M + 0,026V;
пропускная способность клапана по вакууму, м /ч,
= M + 0,22V;
пропускная способность вентиляционного патрубка, м /ч,
= M + 0,02V
= M + 0,22V, что больше,
где М – производительность залива продукта в резервуар, м /ч;
М – производительность слива продукта из резервуара, м /ч;
V – полный объем резервуара, включая объем газового пространства под стационарной крышей, м .
Не допускается изменение производительности приемораздаточных операций после введения резервуара в эксплуатацию без пересчета пропускной способности дыхательной аппаратуры, а также увеличение производительности слива продукта в аварийных условиях.
Минимальное количество вентиляционных патрубков резервуаров с понтоном указано в п. 3.9.16.
Предохранительные клапаны должны быть отрегулированы на повышенные (на 5-10 %) величины внутреннего давления и вакуума, чтобы предохранительные клапаны поработали вместе с дыхательными.
8.2.3. Дыхательные и предохранительные клапаны должны устанавливаться совместно с огневыми предохранителями, обеспечивающими защиту от проникновения пламени в резервуар в течение заданного промежутка времени.
8.2.4. Для уменьшения потерь от испарения продукта под дыхательным клапаном рекомендуется устанавливать диск-отражатель, входящий в комплект клапана.
Приборы контроля уровня
8.3.1. Приборы контроля уровня должны обеспечивать оперативный контроль уровня продукта (местный или дистанционный). Максимальный уровень продукта должен контролироваться сигнализаторами уровня (минимум два), передающими сигнал на отключение насосного оборудования. В резервуарах с плавающей крышей или понтоном следует устанавливать на равных расстояниях не менее трех сигнализаторов уровня, работающих параллельно.
8.3.2. При отсутствии сигнализаторов максимального уровня должны быть предусмотрены переливные устройства, соединенные с резервной емкостью или сливным трубопроводом, исключающие превышение уровня залива продукта сверх проектного.
Дата добавления: 2016-11-02 ; просмотров: 261 | Нарушение авторских прав
Физические методы контроля — Справочник химика 21
Неразрушающие физические методы контроля металлических покрытий [c.274]Методы диагностики технического состояния можно разделить на разрушающие и неразрушающие. К методам разрушающего контроля можно отнести предпусковое или периодическое гидравлическое испытание, а также механические испытания образцов, вырезанных из элементов. Неразрушающие методы предполагают применение физических методов контроля качества без нарушения работоспособности конструкции. [c.4]
Наиболее эффективно применение для этой цели различных физических методов контроля ультразвукового, магнитного, гамма-лучевого, рентгеновского, цветного и др. Основным преимуществом физических методов дефектоскопии является проведение контроля без разрушения или повреждения изделий, что позволяет вместо выборочного производить 100%-ный контроль ответственных деталей. [c.3]
Актуальной задачей остается определение качества микроэлементов, в том числе изделий микроэлектроники и вычислительной техники. Для ее решения необходимо искать новые физические методы контроля и совершенствовать те приборы, пока очень малочисленные, которые применяются сейчас, — рентгеновские аппараты с высокочувствительной рентгеновской пленкой, рентгенотелевизионные микроскопы с 800-кратным увеличением и микрофокусными трубками 0,ЗХ1,4 мм, точечные инфракрасные пирометры, тепловизионные микроскопы с разрешением до 0,01° по температуре и некоторые другие. [c.60]
Трубопроводы, проходящие под железнодорожными путями или шоссейными дорогами, укладывают в защитные патроны, диаметр которых на 50—100 мм больше диаметра изолированного трубопровода. Укладываемые в патронах секции трубопроводов должны быть заранее испытаны, а их стыки прове-. репы физическими методами контроля. [c.364]
Выявленные дефектные места и повреждения изоляции должны быть исправлены методами, обеспечивающими монолитность и однородность покрытия. После исправления дефектов ремонтируемые места должны подвергаться вторичной проверке физическими методами контроля. (Наносить второй слой битумного покрытия по оберточной бумаге запрещается.) [c.101]
Особенно удобны физические методы контроля, поскольку они не нарушают течения реакции. Например, контроль за ходом процесса можно проводить по поглощению света определенной длины волны, по вращению плоскости поляризации, по электропроводности. Если реакция идет в газовой фазе и сопровождается изменением числа молей реагентов, то необходимые сведения можно получить из измерений давления выделившихся газов. [c.207]
Низкотемпературный метод позволяет снижать скорость многих реакций до тех пор, пока не будет найдена температура, при которой их удобно измерять. Кроме того, можно использовать широкий температурный интервал. В случае сложных реакций можно изолировать параллельные или последовательные реакции и изучать их при различных температурах. Удобны физические методы контроля за кинетикой. Основное ограничение накладывает точка замерзания растворителя, что лимитирует применимость таких методов к водным растворам. [c.340]
Если испытывается газопровод низкого или среднего давлений, то стыки не изолируются и не засыпаются, кроме случая, когда стыки проверяются физическими методами контроля. При испытании на прочность время испытания не ограничено, оно проводится до тех пор, пока не будут выявлены дефекты (но не менее 1 ч). [c.79]
Большой интерес представляет своевременное обнаружение начальных стадий межкристаллитной коррозии металла аппаратуры непосредственно в эксплуатационных условиях на заводах химической, нефтяной и других отраслей промышленности, когда отсутствует доступ к внутренним стенкам аппаратов и обследовать их невозможно без остановки и демонтажа. Стремление к более объективной оценке поражения металла МКК выдвигает необходимость использования неразрушающих физических методов контроля. [c.103]
Переход к сварным конструкциям объясняется достижениями науки в области теории и практики сварочных процессов, физических методов контроля швов, электросварочного машиностроения. Применение сварочных конструкций до 1936 г. ограничивалось недостаточным развитием процессов сварки защищенной дугой. При сварке голыми электродами или электродами с ионизирующими покрытиями наплавленный металл представляет собой сплав системы Ге—N3 (0,15—0,20% N3) или Ре—О2 (0,1—0,2% [c.9]
Рентгеноустановка. Камера для физических методов контроля [c.448]
В качестве вспомогательных способов контроля температурного режима термической стерилизации могут быть также использованы химические и биологические индикаторы. Однако они не могут заменять физических методов контроля, а только служат подтверждающим доказательством фактической температуры стерилизации. [c.382]
Из данных табл. 12 и 13 следует, что различные физические методы контроля — ультразвуковой, токовихревой и цветной — дают хорошо согласующиеся результаты при определении начальных стадий межкристаллитной коррозии тонколистовой нержавеющей стали, обеспечивая достаточную для практики чувствительность контроля. Вместе с тем рекомендуемый ГОСТ 6032—75 метод загиба образцов после их кипячения в стандартном растворе можно применять для испытания тонколистового материала только при значительном поражении металла межкристаллитной коррозией (свыше 30—50 мкм). [c.106]
НИИхиммашем разработана и внедрена в производство комплексная дефектоскопия деталей машин и аппаратов, которая предусматривает наиболее рациональное сочетание различных физических методов контроля в зависимости от формы, размеров и материалов изделия [ 103, 104, 115]. Обычно дефектоскопию деталей проводят по следующей схеме. Поверхностные дефекты выявляют магнитным или цветным методами, реже — люминесцентным, а внутренние — ультразвуковым. Рентгеновский и гамма-лучевой методы применяют при контроле сварных соединений, а также используют как дополнительные средства контроля в тех случаях, когда остальные не дают достаточно надежных результатов. [c.174]
Опыт показал, что комплексное применение физических методов контроля позволяет не только обнаружить дефекты на поверхности или в толще изделия, но и во многих случаях решает более сложную задачу, определяя их форму и размеры, а также пространственное расположение. Это дает возможность оценивать влияние дефектов на прочность контролируемых изделий, определять степень их опасности и устанавливать соответствие качества изделий техническим условиям. Ниже рассмотрены примеры применения комплексной дефектоскопии для оценки качества сварных соединений и деталей некоторых машин и аппаратов химических производств. [c.174]
Склонность стали к коррозионному растрескиванию может быть оценена по электрохимическим характеристикам напряженного и ненапряженного металла, а также путем физических исследований и прямых коррозионных испытаний. К физическим методам контроля относятся акустический и ультразвуковой методы, рентгеноструктурный анализ, оценка электросопротивления материала, магнитометрические методы. Общим во всех этих методах является то, что в их основу положен поиск поверхностной трещины, причина возникновения которой может быть как следствием коррози- [c.118]
Следует отметить, что для изменения меняющейся во времени концентрации сахарозы Л. Вильгельми впервые использовал физический метод контроля — изменение угла вращения плоскости поляризации светового луча, проходящего через кислотный раствор сахарозы.) [c.11]
Однако такой кинетический способ установления последовательного характера реакции возможен лишь при соизмеримости значений [X] и [А]. Если же [X] с [А], последовательная реакция кинетически будет имитировать простую одностадийную. Установить образование промежуточного вешества в этом случае удается лишь физическими методами контроля — оптической и ЭПР-спектроскопии, резонансной флюоресценции и др. [c.79]
В случае катализа ферментами, как показали физические методы контроля, механизм процесса включает последовательные стадии превращения первичного комплекса А с Е, С, [c.175]
ПБ 03-440-02. Типовая программа подготовки по ТК и список экзаменационных вопросов приведены в Приложении. Существенной частью аттестации является практический экзамен, который сдают с использованием экзаменационных образцов, соответствующих объектам контро-лям. При разработке программ практического экзамена можно использовать лабораторные работы по ТК, созданные в ряде российских вузов в рамках учебных курсов по специальности «Неразрушающие физические методы контроля». [c.361]
В связи с указанной разработкой обратим внимание на возможность создания с ее помощью многопараметрового диагностического портрета объекта достаточно доступными средствами. В данном случае каждый канал содержит информацию, полученную разными физическими методами. Учитывая, что каждый из сигналов содержит разную информацию в различных частотных диапазонах, целесообразное число которых достигает 8… 10 (см. главу 10), можно видеть, сколь информативным является данный простейший двухканальный (по физическим методам контроля) анализ. Это тем более ценно, что диагностический портрет объекта может быть получен дешевыми средствами. [c.285]
Сравнительный анализ выявляемости несплошностей в зависимости от физического метода контроля проводили в работах 49—53 и др.]. На рис. 89 приведены результаты экспериментального исследования выявляемости несплошностей тремя методами контроля в зависимости от их линейного размера а [53 Наилучшей выявляемостью обладает УЗК, наихудшей — РГ. [c.188]
Ниже обсуждена выявляемость несплошностей в зависимости от физических методов контроля, типа и ориентации дефекта, методики контроля, материала, типа сварного соединения, человеческого фактора. [c.146]
Физическим методом контроля долншо быть проверено отсутствие трещин в нарезанной части кованого (штампованного) крюка, отсутствие трещнн в нарезанной части вилки пластинчатого крюка и в оси соединення пластинчатого крюка с вилкой или траверсой. Такая проверка производится не реже одного раза в 12 месяцев. Необходимость и периодичность проверки других деталей подвески устанавлнвается администрацией предприятия [c.101]
В литературе указывается, что физические методы контроля, основанные на капиллярных явлениях, ненадежно выявляют дефекты типа волосовин [631. Характер индикаторного следа при выявлении волосовины приведен в табл. 24 и на рис. 122 (болт из нержавеющей стали). Как известно, волосовины представляют собою вытянутые вдоль прокатки газовые или неметаллические включения в поперечном сечении они часто имеют округлую форму. В НИИхиммаше проведена работа по сопоставлению данных магнитной и цветной дефектоскопии при выявлении волосовин на крепежных шпильках из углеродистой стали. [c.169]
Вводимый в дополнение к 0,55 по СНиП коэффициент надежности (запаса) по материалу свидетельствует о фактическом использовании предельного состояния наступления разрушения для угловьгх швов, так же как и коэффициент 0,85 для неконтролируемых физическими методами стыковых швов в табл.З СНиП, который вводит понижение расчетного сопротивления металла сварных стыковых соединений, назначаемого по пределу текучести металла. Так как физические методы контроля обнаруживают лишь несплошности и не дают сведений о механических свойствах металла по Оц2, то коэффи- [c.291]
Химченко Н. В., Шварц Г. А. и др. Физические методы контроля межкристаллитной коррозии тонколистовой нержавеющей стали. Труды НИИхиммаша , 1973, вып. 57, с. 161 — 197. [c.261]
Для газопроводов с давлением до 6 кГ/с.ч на отдельных участках трассы, а также при прокладке вводов между зданиями и под арками зданий указанные расстояния до зданий и подземных сооружений июгут быть уменьшены при условии применения бесшовных труб и гнутых отводов, проверки всех сварных стыков физическими методами контроля, наложения иа трубы весьма усиленной изоляции. [c.318]
Слежение за развитием разрупсения упрощается при использовании физических методов контроля. Так как при испьггании на коррозионное растрескивание практически отсутствуют посторонние шумы, сигналы акустической эмиссии позволяют достаточно четко фиксировать начало растрескивания и момент окончания роста трещины. При испьггании пассивирующихся металлов колебания электродного-потенциала также сигнализируют о продвижении трещины. Количественную оценку длины трещины можно получить, фиксируя изменение податливости [c.492]
В программе PIS также делали попытки выделить влияние на достоверность таких факторов как физический метод контроля, методики контроля, перебраковка и недобраковка, человеческий фактор, тип дефекта, материал. [c.188]
В табл. 26 даны обобщенные ориентировочные оценки выявляемости несплощностей в зависимости от применяемого физического метода контроля и типа дефекта. [c.192]
сварных швов, соединений трубопроводов и металлоконструкций
На чтение 5 мин. Просмотров 36 Опубликовано
При создании металлоконструкцию с использованием сварки очень важно контролировать надежность и четкость выполнения сварных соединений.
Внимание! Если изначально не выявить и не исправить дефекты, то велика вероятность, что прочность шва будет понижена, что скажется на качестве всей конструкции.
Что такое контроль качества сварных соединений
Контроль подразделяется на первичный и на окончательный. При первичном происходит профилактика возникновения дефектов. Контроль качества сварных соединений заключается в проверке электродов, флюсов, соблюдении технологического процесса и режимов работы. Окончательный контроль осуществляется уже на самих швах.
Визуальный осмотрФизический контроль сварочных швов
Среди множества методов контроля качества сварных швов отдельное место занимают физические, среди которых:
- Радиационный метод контроля. Он включает в себя рентгено-и гаммо-графический метод, основан на способности рентгеновских лучей проходить сквозь непрозрачные предметы. В таком случае дефекты, которые чаще всего бывают пустотами, на рентгеновском снимке выглядят в виде пятен или полос. Гамма-излучение действует по такой же системе, но имеет более низкую чувствительность. Бракуется изделие при выявлении следующих дефектов: шлаковые включения единичные и цепочкой, а также поры.
- Ультразвуковой метод. Основан на возможности ультразвука проникать внутрь конструкции и отражаться от дефектов.
- Магнитный метод дефектоскопии. Проверяемый шов смазывают составом из масла и специального намагнимагниченного порошка само изделие также намагничивают с использованием тока, который пропускают через обмотку. Под влиянием магнитного поля частицы железного порошка больше распространяются вокруг дефектов.
- Гидравлические испытания. Сосуд наполняется водой и создается повышенное давление. Такой метод используется при испытании паровых и водяных котлов.
- Пневматические испытания – испытания сжатым воздухом.
Все детали испытательных процессов зависят от технических условий для каждого испытуемого объекта.
Контроль с помощью рентгенаКонтроль качества сварных швов
Сварные швы могут стать самым ненадежным местом всей металлоконструкции, если они выполнены с нарушением технических условий и правил, поэтому важно производить полноценную оценку, начиная от визуального осмотра и заканчивая самыми современными физическими и химическими способами. Выбранный метод проверки зависит еще и от конкретной конструкции, где есть сварные швы, а также от функций, которые она будет выполнять.
Соединений металлоконструкций
Различные металлоконструкции после сварки также нуждаются в проверке качества, поскольку сварные швы влияют на надежность и общий срок службы таких конструкций. К основным методам проверки и контроля качества сварных соединений металлоконструкций относят:
- визуально измерительный;
- ультразвуковой;
- капиллярный;
- оценка проницаемости;
- радиационный контроль.
На проницаемость швы можно проверять с использованием керосина, вакуум-аппаратом, а также гелиевым или галлоидными течеискателями.
Оценка с помощью специальных жидкостей.Соединений трубопроводов
Любые сварные швы трубопроводов не должны иметь: трещин, кратеров, прожогов.
Важно! Недопустимы любые ошибки некачественной сварки.
Среди основных методов контроля при проверке трубопроводов используют:
- Магнитографический контроль, который позволяет обнаружить поля рассеяния. Отражается на радиограмме в виде графиков. Позволяет выявить непровары, цепочки шлака, микротрещины.
- Рентгеновское излучение.
- Проверка проницаемости с использованием гидравлики, пневматики, а также пузырькового метода.
Для пневматических испытаний в трубопровод запускают в больших количествах воду или газ, а на поверхность наносят пенообразующий состав, который при проникновении жидкости или газа будет пузыриться, что укажет на наличие недостатка.
Вакуумный метод контроля сварных соединений
Вакуумный метод контроля используются в ситуациях, когда другие варианты проверки по каким-либо вариантам исключены. Используется чаще всего для проверки качества сварных швов в:
- резервуарных днищах;
- газгольдеров;
- емкостей типа цистерн и бочек.
При таком методе вакуум создается при помощи специальной камеры на наиболее доступной стороне проверяемого участка шва. Сам шов обрабатывается мыльным растворов. В результате разности давлений с двух сторон шва воздух будет проникать в камеру, если есть огрехи в проверяемом шве. Если есть дефекты, то появятся мыльные пузыри, которые отлично видны в камере, поскольку у нее прозрачная поверхность.
Методы контроля сварных соединений
К наиболее часто применяемым методам оценки сварных соединений относят:
- Капиллярный метод. Он основан на том, что некоторые жидкости имеют свойство проникать даже в трещины, незаметные глазу. Такие жидкости называются капиллярами. Он прост в применении и не требует наличия дорогостоящего оборудования. Капиллярный метод
- Радиационный контроль. Это уменьшенная версия стандартного рентгена. Также известен под названием «гаммаграфический контроль». В таком случае гамма лучи проникают через металл и на специальной пленке фиксируют найденные дефекты.
- С использованием аммиака. Один из способов пневматических испытаний. Аммиак закачивается под давлением под давлением так, чтобы его количество было равно сотой доли от всего объема воздуха, а проверяемые швы перед оклеивают лентой из бумаги или медицинским бинтом, который пропитан фенолфталеином. Там, где будет проходит аммиак, на ленте останутся красные пятна.
- Оценка на непроницаемость с помощью керосина. Метод контроля простой и при этом эффективный, не требует крупных материальных затрат. Керосин способен проникать сквозь мельчайшие трещины и обнаруживать так дефекты.
Важно! На каждом производстве применяются свои методы контроля сварных швов. Это могут быть более дорогие или менее дорогие способы, важно, чтобы они были максимально эффективны для конкретных металлоконструкций.
Что проверяют при контроле сварочных материалов
Это предварительная форма проверки, при которой оценивают все необходимое для проведения качественных сварочных работ. В такую форму проверки входит:
- внешний осмотр и проверка механических свойств электродов;
- погружение электродов в воду температурой от 15 до 25 градусов на сутки, бракованные начнут разрушаться;
- проверка флюса и сравнение его характеристик с ГОСТом;
- проверка защитных газов – баллон должен обязательно иметь сертификат;
- проверка сварочной проволоки и оценка сертификата качества.
Если при сварке используется качественный материал, а также соблюдены все технические условия, то дефекты в швах возникают крайне редко, а значит, конструкции будут служить длительное время и отличаться надежностью.
Лекция 15. Контроль сварных соединений (продолжение) наплавочные работы
15.1. Визуальный контроль
Визуальный контроль сварных швов проводят по всей их протяженности с двух сторон невооруженным глазом или с применением лупы 4–7 кратного увеличения. Перед контролем сварной шой и прилегающие к нему поверхности основного металла должны быть очищены от шлака, брызг и других загрязнений. Измерительный контроль проводят не менее, чем в трех местах, расположенных равномерно по длине сварного шва. Для этой цели используют шаблоны и измерительные инструменты.
15.2. Физические методы контроля
Физические методы контроля выполняют после удовлетворительных результатов визуального и измерительного контроля. Они проводятся для выявления в сварных соединениях скрытых внутренних дефектов. Метод контроля зависит от типа производства, технических требований к изделию, возможности производства. Многие из методов – аналогичны тем, которые применяют для контроля качества литых заготовок. Основные физические методы контроля сварных соединений:
ультразвуковой контроль;
рентгенодефектоскопия;
магнитные методы;
люминисцентный метод;
испытания на герметичность.
15.2.1. Ультразвуковой контроль
Ультрозвуковой контроль (рис. 15.1.) основан на способности ультразвуковых колебаний проникать в толщину металла и отражаться от неметаллических включений, пор и других дефектов. Частота колебаний ультразвуковой волны –0,5–10 МГц. Для возбуждения ультразвуковой волны используют пьезоэлемент из кварца, титаната бария и др., который размещают в специальном преобразователе – датчике. При прохождении волны через границу раздела двух сред (дефекта) волна отражается и луч попадает в приемник и усилитель, откуда попадает на экран дефектоскопа. Возможен контроль деталей толщиной до 300 мм. Недостатки способа: трудность определения харктера дефекта; невозможность контроля заготовок толщной менее 10 мм; низкая производительность; необходимость в высокой квалификации оператора.
15.2.2. Рентгеноскопический контроль
Этот способ контроля (рис. 15.2. б) основан на различном поглощении рентгеновских лучей различными веществами. Лучи напрвляют на сварной шов, а с обратной стороны подкладывают фотопленку. Дефектные места пропускают лучи с меньшим поглощением, чем сплошной металл. После проявления на фотопленке хорошо видны очертания дефектов шва в виде темных пятен и линий. Более плотные, чем металл, включения, например вольфрам, имеют на снимке светлый цвет.
Определяемые дефекты: поры, трещины, непровары, шлаковые включения. Рентгеноскопический контроль применяют для просвечивания ответственных крупногабаритных изделий толщиной более 20 мм, трубопроводов и резервуаров. Главные недостатки способа – высокая стоимость и опасность для персонала.
15.2.3. Магнитные методы контроля
Магнитные методы контроля основаны на исследовании магнитных полей рассеяния на намагниченном контролируемом изделии.Имеется несколько методов магнитного контроля сварных швов: магнитно-порошковый, магнитнографический, индукционный и др.
Магнитно-порошковый контроль состоит в том, что после намагничивания изделия сварной шов посыпают магнитным порошком (из железной окалины) или покрывают суспензией (смесь магнитного порошка с керосином, маслом). В зоне дефекта порошок распределяется неравномерно: скапливается по краям трещин, пор, включений. Это и указывает на налчие и месторасположение дефекта. Однако вид дефекта определить затруднительно.
Магнитографический контроль состоит в том, что на сварной шов накладывают ферромагнитную пленку, а затем шов намагничивают соленоидом или магнитом. В зависимости от вида и величины дефекта в соответствующих местах пленки будет разная степень намагничивания. Магнитные сигналы преобразуют в звуковые или наблюдают на экране осциллографа. Аппараты отличаются большой точностью, простотой, невысокой стоимостью используемых материалов, возможностью контроля в любых протранственных положениях, безопасностью персонала.
15.2.4.Люминисцентный метод контроля
Основан на использовании свойств некоторых жидкостей хорошо смачивать поверхности металла и проникать в трещины, поры, и другие дефекты сварного шва. А при добавлении в них флюоресцирующих веществ – светиться в ультрафиолетовых лучах. Состав жидкости: керосин – 50%, бензин –25%, трансформаторное масло –25%, флюоресцирующее вещество – до 0,03% сверх 100% (состоит из концентрата углеводородов). На контролируемую поверхность наносят слой жидкости (поверхность очищена от шлака, брызг, масел) и выдерживают в течение 10–15 мин. Затем изделия промывают и просушивают, после чего на его поверхность наносят тонкий слой талька. Оставшаяся в местах дефектов жидкость пропитывает порошок. Через 30–50 мин сухой порошок сдувают и контролируемую поверхность освещают ультрофиолетовыми лучами от ртутно-кварцевых ламп. В местах дефектов возникает яркое желто-зеленое свечение.
Недостатки способа – высокая трудоемкость и длительность процесса контроля, возможность выявления только поверхностных дефектов.
15.2.5. Испытания на герметичность
Основные способы испытания на герметичность: испытания керосином, пневматические, вакуум-аппаратом, гидравлические.
Испытания керосином проводят на изделиях толщиной до 10 мм. С одной стороны изделие обильно смачивают керосином, а с другой стороны сварные швы покрывают водным меловым раствором. При наличии даже мельчайших пор, трещин или непроваров керосин просачивается и на окрашенных мелом поверхностях появляются керосиновые пятна.
Пневматические испытания проводят нагнетанием в испытываемый резервуар сжатого воздуха до рабочего давления, а швы покрывают мыльной эмульсией. При наличии дефектов появляются мыльные пузыри. Вариант способа – погружение испытуемого сосуда в ванну с водой. В этом случае дефекты определяются по пузырькам воздуха.
Вакуумным аппаратом контолируют сварные швы, имеющие односторонний доступ, когда невозможно использовать предыдущие способы. Контролируемый сварной шов смачивают мыльным раствором и затем на него устанавливают вакуумный аппарат с резиновым уплотнением. При откачивании воздуха и образовании вакуума в камере аппарата в местах дефектов появляются мыльные пузыри.
Гидравлические испытания проводят с целью испытания сварных швов не только на герметичность, но и на прочность. Этим испытаниям подвергают сосуды или изделия, работающие под давлением. Перед испытанием все отверстия изделия закрывают заглушками, а изделие заполняют водой. Давление воды внутри изделия создают с помощью гидравлического пресса. Оно обычно в 1,5 раза выше рабочего давления. Время выдержки под давлением оговаривается техническими условиями. Затем давление снижают до рабочего и проверяют наличие дефектов по пропуску воды в швах.
Предварительный и заводской контроль сварных соединений
Предварительный и заводской контроль сварных соединений
Категория:
Сварка металлов
Предварительный и заводской контроль сварных соединений
Контроль качества сварки имеет важное значение. Обеспечить постоянное высокое качество сварных изделий возможно лишь при надлежащей организации контроля качества во всех стадиях производства.
Контроль исходных материалов производится при помощи химического анализа, металлографических исследований, механических испытаний, пробы на свариваемость, сварки пробных образцов и т. д. Контролю подлежат основной металл, присадочный металл, проволока, прутки, электроды, обмазки, флюсы. Контролируются также газы, ацетилен и кислород для газовой сварки.
Основной металл должен удовлетворять требованиям соответствующих стандартов и технических условий. Для сварки стали существенное зцачепие имеет химический состав основного металла, в особенности содержание углерода, затем серы и фосфора. Часто достаточно изменения содержания углерода на несколько сотых долей процента, чтобы заметно изменились сварочные свойства металла, появилась склонность к образованию трещин, закалке и т. д.
В отношении серы важно не только среднее содержание, но и равномерность ее распределения по объему металла. Сера, равномерно распределенная по сечению металла, менее опасна, чем местные ее скопления, образующиеся вследствие ликвации. Нередко наблюдается, что при общем допустимом содержании серы порядка 0,04—0,05% имеются скопления ее в отдельных прослойках с повышением содержания в них до 0,12—0,15%. Такие местные скопления серы опасны и могут служить причиной образования трещин при сварке. Поэтому не всегда достаточно знать общее содержание серы в металле, часто необходимо выяснить и равномерность ее распределения; лучше всего об этом можно судить, получив отпечаток шлифа металла по способу Баумана, на котором места с повышенным содержанием серы приобретают темную окраску. Такой металл может оказаться мало пригодным для сварки даже при общем содержании серы в нем, не превышающем допустимых норм.
Существенное значение для последующей сварки может иметь процесс изготовления металла. Например, мартеновская сталь для сварки лучше бессемеровской. Спокойная мартеновская сталь лучше кипящей, так как последняя обладает повышенной склон ностью к образованию пор и трещин. В сталях, чувствительных к термообработке, часто существенное значение имеет структура и предшествующая термическая обработка металла, нередко результаты сварки могут быть улучшены надлежащей термической обработкой основного металла, нормализацией, высоким отпуском, отжигом и т. д.
Рис. 1. Отпечаток по Бауману
Пригодность специальных сталей к сварке часто требует проверки их посредством одной из проб на свариваемость. Электроды и присадочная проволока должны иметь соответствующие сертификаты. В сомнительных случаях должна быть проведена сварка с наблюдением за процессом и последующим всесторонним испытанием образцов. Контроль подготовки под сварку заключается в проверке правильности сборки, подготовки под сварку, правильности постановки прихваток, состояния поверхности кромок. Проверяются размеры заготовок и чистота поверхности кромок под сварку.
Контроль в процессе производства сварочных работ заключается в проверке квалификации сварщиков, исправности оборудования, наличия исправных контрольно-измерительных приборов, строгого соблюдения установленного технологического процесса. Особенно важна проверка квалификации сварщиков для газовой и дуговой сварки, выполняемых вручную. Квалификация проверяется периодически, на сварке соответствующих проб. К ответственным работам, например подлежащим приемке инспек-цией Госгортехнадзора, допускаются лишь сварщики, имеющие особое удостоверение (паспорт) на право выполнения ответственных сварочных работ.
Весьма важными являются контроль и приемка готовых сварных изделий. Контроль и приемка готовых сварных изделий часто производятся в отдельном помещении или на отдельных рабочих местах специальным персоналом; требования к сварным изделиям определяются техническими условиями.
Внешний осмотр и обмер изделий и сварных швов. Достаточно опытный контролер может выявить ряд дефектов внешним осмотром сварных швов изделия. Этим способом на поверхности сварных швов выявляются трещины, подрезы, раковины, порй, кратеры, неравномерное распределение наплавленного металла, слишком неровная, гру-бочешуйчатая его поверхность и т. д. Осмотр производится невооруженным глазом; места, сомнительные по трещинам, просматриваются в лупу. Осмотр вша производится по возможности сразу после сварки и во всяком случае до окраски изделия. мелом поверхности керосин выступает в виде темных пятен. Наблюдать появление пятен и отмечать дефектные места нужно немедленно после смачивания керосином, иначе керосин, просочившийся через сварной шов, быстро растечется по меловой окраске и затруднит установление точного местоположения дефекта. В зависимости от толщины металла и формы шва выдержка под керосином продолжается от 15 мин до 2 ч. Выявленные дефекты вырубают и подваривают.
Рис. 2. Шаблоны для обмера швов
Часто применяется испытание на плотность воздухом. Для проверки плотности швов сварное изделие заполняют воздухом под давлением, установленным техническими условиями на данное изделие. Неплотность шва определяют по пузырькам, образующимся на поверхности шва при смачивании ее мыльной водой. Мелкие изделия можно погружать в бак с водой так, чтобы сварные швы, подлежащие контролю, находились на глубине 2—5 см от поверхности воды; неплотности обнаруживают по появлению воздушных пузырьков. Во избежание опасного взрыва испытание воздухом должно производиться при давлениях, совершенно безопасных для прочности изделий.
Рис. 3. Проверка плотности сварных швов: а — воздухом; б — керосином
При подходящей форме сварных соединений, например нахлес-точных, испытание воздухом может быть произведено при малом расходе воздуха и повышенных давлениях без опасности повреждения изделия повышенным давлением по способу, показанному рис. 228, а и б. Кромку изделия засверливают, и в полость зазора нахлестки по шлангу 1 подают воздух под давлением. Места неплотности выявляют осмотром швов 2, смоченных мыльной водой. По окончании испытания просверленное контрольное отверстие заваривают. В этом случае можно производить испытание не воздухом, а накачивая по шлангу керосин 3 под давлением, наблюдая при этом за появлением керосиновых пятен на закрашенной поверхности швов.
Плотность швов можно проверять также, продувая их струей сжатого воздуха под давлением не менее 4 am. Насадку шланга передвигают по поверхности шва, противоположная сторона которого смочена мыльной водой; неплотности обнаруживают по появлению пузырьков. При испытании изделий воздухом под давлением необходимо соблюдать следующие правила техники безопасности.
1. Испытания производить обязательно в изолированном помещении или на огражденном участке.
2. Применять проверенные и достаточно точные манометры.
3. На магистрали, подающей воздух к изделию, обязательно устанавливать промежуточный бачок с предохранительными клапанами, отрегулированными на испытательное давление.
С. Т. Назаров предложил оригинальный химический способ проверки плотности сварных швов. Газообразный аммиак Nh4 подают в количестве около 1% объема изделия; затем нагнетают воздух под давлением, предписанным условиями приемки. На сварные швы предварительно накладывают бумажную ленту, пропитанную раствором азотнокислой ртути или фенолфталеина. Дефектные места определяют по пятнам на ленте. Лента-химо-грамма служит документом, характеризующим плотность сварного шва.
Гидравлическое испытание. Плотность сварных швов можно проверять также и гидравлическим испытанием, производимым для испытания на прочность. Гидравлически испытывают, просто наливая в емкость жидкость (воду, керосин и т. п.) или же создавая дополнительно гидростатическое давление. Последнее создается заполнением изделия водой и нагнетанием ее до давления, предписанного правилами приемки данного изделия и проверяемого по контрольному манометру.
Вода должна заполнять весь объем изделия, без воздушных мешков, опасных при возможном разрушении изделия в процессе испытания. Время выдержки изделий под давлением также определяется правилами приемки. Осмотр швов для проверки плотности производят при испытательном давлении с обстукиванием сварных швов молотком, вес и длина ручки которого устанавливаются правилами приемки.
Засверливание сварных швов. Эта операция позволяет контролировать сварные швы на изделии и служит ценным подспорьем при внешнем осмотре и других методах испытаний. Засверливание производится электрическими, пневматическими или ручными сверлильными машинками со спиральными сверлами или специальными коническими фрезами диаметром 6—25 мм с углом заточки 90°. Засверливание следует вести с расчетом вскрытия всего сечения шва и захвата основного металла по 1—2 мм на сторону (рис. 4).
Засверловка должна иметь возможно гладкую поверхность. Для оценки шва поверхность засверловки шлифуют и травят реактивом для выявления макроструктуры, после чего осматривают в лупу.
Рис. 4. Засверливание сварного шва
Это дает возможность обнаружить непровары, трещины, включения и т. д.
По окончании контроля отверстия заваривают; количество за-сверловок определяется условиями приемки.
Технические условия часто предусматривают вырезку образцов из сварных изделий и их лабораторные испытания.
Металлографические исследования образцов. При этом изучают макро- и микроструктуру металла, а иногда и структуру излома образца. Образцы для металлографического исследования вырезают из изделия таким образом, чтобы поверхность шлифа включала полное сечение сварного шва, зону влияния и не подверженный изменениям основной металл. Обработка вырезанных образцов, их шлифование, полирование и травление производят обычными приемами, применяемыми при металлографическом исследовании металла. Помимо металлографического исследования в необходимых случаях проводят химический анализ металла сварного соединения.
Физические методы контроля сварных соединений. Под физическими методами контроля подразумеваются способы определения качества металла или сварного соединения по изменению каких-либо физических свойств, например проницаемости для коротковолновых электромагнитных излучений, звуковых колебаний, магнитной проницаемости, электропроводности и т. д. Физические методы контроля могут применяться не только для образцов сварки, но и для целых сварных изделий. Физические методы позволяют проверить качество сварного шва на всем его протяжении без повреждения изделия. Физические методы находятся в настоящее время в стадии разработки и промышленного освоения.
Реклама:
Читать далее:
Контроль сварных соединений рентгеновскими и гамма-лучами
Статьи по теме:
Капиллярный метод контроля сварных швов
Контроль сварных швов является основным способом определить их качества.
Существует несколько технологических контрольных методов, которые сегодня применяются при проверке сварочных швов, основной из них – капиллярный контроль. Он является неразрушающим и включает в себя несколько вариантов проведения данного процесса с использование разных расходных материалов. С его помощью определяются наружные поверхностные и внутренние дефекты или их отсутствие, а также изменения в зоне нагрева двух соединяемых заготовок.
Капиллярным контролем сварных соединений можно выявить практически все дефекты шва: поры, трещины, раковины, прожоги и непровары. Можно определить, как расположен дефект в плане его ориентации к поверхности сварного шва, можно определить размеры изъянов. Капиллярный метод контроля используется при сварке любых металлов (черных и цветных), пластмасс, стекла, керамики и так далее. То есть, это контроль имеет обширную область применения при определении дефектов в сварочных швах.
Суть всего контрольного процесса заключается в том, что, используя специальные жидкости (индикаторы), которые имеют свойство глубоко проникать в любые материалы, если в них есть пустоты, просачиваться сквозь него и появляться на противоположной стороне от места их нанесения. То есть, проникая в тело металла, индикаторные жидкости оставляют следы, по которым и определяются дефекты. Такие следы можно обнаружить визуально, а можно использовать для их определения специальные приборы преобразователи. Все современные методы контроля сварных швов капиллярным способом регламентируются ГОСТами.
Содержание
Классификация капиллярного контроля
Существует две категории капиллярного контроля сварных швов: основные и комбинированные. Первый подразумевает под собой чисто капиллярный контроль, второй – это объединение нескольких неразрушающих способов контроля, в состав которых входит и капиллярный.
К основным методам можно отнести:
- В зависимости от того, какой проникающий раствор для этого используется: это растворы и фильтрующие суспензии.
- В зависимости от того, каким способом считывать получаемую информацию: цветовой (он же хроматический), яркостный (он же ахроматический), люминесцентный и люминесцентно-хроматический.
К комбинированным: электростатический, магнитный, электроиндукционный, радиационная технология поглощения или излучения. Во всех них используются проникающие индикаторные жидкости, то есть, применяется капиллярный вариант, но считывание информации происходит по-разному. В основном же на группы эта категория делится по характеру воздействия на поверхность сварного шва.
Как применяется технология капиллярной дефектоскопии
В принцип метод достаточно прост. Необходимо поверхность сварочного шва очистить и хорошо высушить. После этого на нее наносится проникающая жидкость, остатки которой через некоторое время надо полностью удалить. Остальная же часть проникнет внутрь тела металла. Далее на обработанную поверхность наносится проявитель, который просто вытянет из дефектов оставшуюся в металле жидкость. Она проявится на поверхности в виде рисунков, которые и обозначат количество, форму и вид изъяна. Но это просто всего лишь на словах. Сам же процесс – достаточно серьезное мероприятия, поэтому к нему надо относиться со всем внимание и точно следовать технологически этапам, принимая во внимание нюансы.
Подготовка сварного шва к контролю
Как и в случае со сваркой, металл соединения необходимо очистить от всех загрязнений. Для этого можно использовать химический способ или механический, обычно, как показывает практика, специалисты применяют комбинацию из двух вариантов. То есть, зачищают металлическую поверхность наждачкой или железной щеткой, а после обрабатывают растворителем или спиртом.
Правда, механическую чистку рекомендуется применять лишь в том случае, если валик имеет пористую поверхность, или она имеет перепады и глубокие подрезы. Все дело в том, что поверхностные дефекты сварного шва при обработке жесткими материалами затираются, поэтому и не проявляются после их обработки проникающими жидкостями.
Что касается химикатов, которые используются для чистки поверхности шва, то их необходимо обязательно после окончания чистящего процесса удалять тепловой водой или другими реагентами. Просто они могут вступать в реакцию с жидкостями для контроля, тем самым выдавая неверные показатели. И последнее – это хорошо просушить поверхность металла. Таким образом, достигается полное отсутствие воды и растворителей.
Нанесение индикатора
Существует несколько способов нанесения индикаторной жидкости.
- Обычный капиллярный метод – это когда жидкость наносится на проверяемую поверхность, и она сама по капиллярам металла проникает внутрь валика. Нанесение может производиться обычным смачивание, капельным распылением или струей, погружением сваренных заготовок в индикаторную жидкость.
- Компрессионный – это когда жидкость подается на поверхность сварного шва под давлением. Таким образом, она быстрее проникает внутрь дефектов, вытесняя из них воздух.
- Вакуумный – это противоположность компрессионному. В данном случае заготовки помещаются в вакуумную установку, вследствие чего из пор, раковин и трещин отсасывается воздух. Далее наносится жидкий индикатор, который заполняет их, потому что внутри полостей давление намного меньше, чем атмосферное.
- Деформационный. На индикатор воздействуют, к примеру, звуковыми волнами, под действием которых он и проникает внутрь металла. При этом размер изъяна немного увеличивается, то есть, происходит его деформация.
- Ультразвуковой – это когда заполнение производится под действием ультразвука.
Все данные способы проникновения жидкости в тело металла должны производиться при температуре 10-50С.
Очистка от индикатора
Проводя очистку поверхности валика, необходимо понимать, что нельзя удалять жидкость с поверхностных дефектов. Чем можно чистить.
- Теплой водой, температура которой не превышает +50С. Это можно проводить при помощи тряпки или губки.
- Растворителем. Сначала поверхность высушивают, а затем тряпкой, смоченной в растворителе, производится протирание поверхности.
- Эмульгаторами: на водной или масляной основе. Сначала удаляется с поверхности проникающая жидкость, и сразу наносятся эмульгаторы, которые снимаются тряпкой.
- Комбинированный вариант. Сначала поверхность омывается водой, после используется растворитель.
Обязательно поверхность сварочного шва после чистки индикаторной жидкости высушивается. Здесь можно использовать разные методы, главное – не повышать температуру валика выше +50С. К примеру, можно просто протереть поверхность неворсистой тряпочкой, можно просто нагреть заготовки, или использовать фен для удаления влаги.
Нанесение проявителя
Этот процесс в технологии капиллярного контроля сварных соединений должен проводиться сразу же после окончания сушки металла после очищения его поверхности. Для этого можно использовать разные проявители.
- Сухой. Его наносят на поверхность равномерным слоем без утолщений или снижения толщины. Для этого обычно используется обычное напыление. Важно – данный вид проявителя применяется только в сочетании флуоресцентными индикаторами.
- Жидкий на основе водной суспензии. Его наносят или методом распыления, или замачиванием валика, путем утопления свариваемых заготовок в жидкий проявитель. Важно – утопление производится в самые короткие сроки, после чего вся жидкость удаляется методом принудительной просушки.
- Жидкий на основе растворителя. Наносится обычным распылением так, чтобы слой проявителя на поверхности остался равномерным.
- Жидкий в виде водного раствора. Все то же самое, что и в случае проявителя на основе суспензии.
Обычно процесс проявления длиться 10-30 минут в зависимости от выбранного материала. Если появляется необходимость, то время можно увеличить.
Способы выявления дефектов сварного шва
Процесс выявления можно начинать сразу после нанесения проявителя. Но лучше, если после того как полностью закончится процесс проявления. Для этого можно использовать увеличительные стекла (лупы) или специальные очки.
Если капиллярная дефектоскопия сварного шва проводилась с помощью флуоресцентных индикаторов, то использовать для контроля специальные очки фотохроматического типа не надо. Просто оператор должен проводить контроль в темном помещении. Он должен в него войти и в течение 5 минут привыкнуть к темноте. После чего и начать процесс выявления дефектов. Сам контроль проводится под действием ультрафиолетового освещения. Оно может быть общим или зонированным (освещается только участок, где лежит сваренная конструкция). Самое важное, чтобы в поле зрения оператора не попадали отсвечивающие предметы, их просто не должно быть в помещении.
Если используются цветные индикаторы, то их проявление можно наблюдать и при дневном, и при искусственном свете. Главное, чтобы на поверхности контролируемого металла не было бликов, а мощность светового потока составляло не менее 500 лк.
Повторный контроль
Если по каким-то причинам итоги капиллярного контроля оказались неудовлетворительными, то можно провести повторный контроль. Он проводится точно так же, как и первый, с использованием все тех же технологий и индикаторов. Нельзя использовать индикаторные жидкости другой марки от другого производителя. Самое важное – это очистить металлическую поверхность от старых материалов (проявителя и индикатора). Все остальные действия от очистки до проявления проводятся точно также.
Контроль капиллярный керосином
Керосин является полярно-активной жидкостью с низкой вязкостью, отсюда и большая его проникающая способность. Обычно с его помощью выискиваются дефекты сварных швов диаметром 0,1 мм при толщине стыка в 25 мм. И раньше, и сейчас керосин используется для контроля сварки резервуаров, которые работают под давлением. Сам процесс достаточно простой.
Для этого понадобиться керосин и меловой раствор, который наносится на обратную сторону сварного шва. По сути, раствор будет выполнять функции индикатора, на котором проявятся керосиновые пятна. Саму жидкость можно распылить на поверхность, смочить ею валик или просто уложить по стыку смоченную в керосине ленты или тряпку. После определенного времени с обратной стороны начнут проявляться масляные пятна, хорошо видимые на меловой поверхности. Нередко в керосин добавляют яркие пигменты, чтобы увеличить чувствительность контроля.
Как и все капиллярные способы контроля с использование индикаторных жидкостей, керосин наносится на испытуемые поверхности сварных валиков разными способами.
- Вакуумным, для чего используются специальные вакуумные установки переносного типа. Их устанавливают со стороны нанесенной меловой смеси.
- Пневматический. Поверхность валика, смоченную керосином, обдувают потоком сжатого воздуха при давлении 0,3-0,4 МПа.
- Вибрационный. Проникновение материала проходит под действием ультразвуковых колебаний.
Используя керосин при капиллярном контроле сварочных швов, необходимо применять материал с большой чистотой. Ведь примеси только увеличивают вязкость керосина, что делает его проникающие свойства низкими. А это может привести к неопределению самых маленьких дефектов, что отразиться на искаженной информации о качестве сварочного шва.
Капиллярные способы контроля на сегодняшний день считаются самыми простыми, но в то же время самыми дешевыми и эффективными. Именно поэтому они чаще других способов сегодня используются при проверке сварочных конструкций
Проверка физических сварных швов: Руководство 2020
Вы новичок в сварке? Вы ветеран, который хочет освежиться? Или вы тот, кто собирается стать квалифицированным сварщиком? К какой бы категории вы ни относились, важно, чтобы вы знали все, что нужно знать о тестировании своих моделей.
Прежде всего следует отметить, что в существует два основных типа физических испытаний сварных швов: разрушающий и неразрушающий . Но это все, что мы собираемся вам рассказать, а пока вам нужно прочитать, чтобы узнать больше!
Методы разрушающих физических испытаний сварных швов
Разрушающие методы испытаний сварных швов относятся к методам разрушения исследуемой детали. Они подвергаются сильному стрессу до тех пор, пока не могут больше его терпеть.
Как правило, любые микроскопические, коррозионные и химические испытания проводятся в лаборатории. Остальное можно сделать в вашей мастерской.
Испытание кислотным травлением
Испытание кислотным травлением считается довольно распространенным явлением большинством инспекторов сварки. Хотя это может быть не ваш любимый способ проверки сварных соединений. Почему? Потому что вы имеете дело с едкими веществами. Plus , вы должны обеспечить их безопасное хранение.
В наши дни, однако, используемые кислоты созданы специально для растворения шлаковых включений, чтобы проверить границы между сварными швами и краями основного металла. Проще говоря, он проверяет топографическую анатомию вашего сварного шва. Это было бы невозможно определить на основе визуальных тестов.
Сварщиков отталкивает процесс. Это скорее… попытка.
Вы должны осторожно нанести раствор азотной кислоты или соляной раствор на сварной образец. Затем вы отрежете образец поперечного сечения и погрузите его в кислоту. Поскольку он настолько коррозионный, раствор по существу «впитается» в образец для испытаний. Тогда границы вашего изделия будут выделены, включения шлака растворятся, и появятся газовые карманы. Короче говоря, любые дефекты становятся суперузнаваемыми.
Этот тип тестирования отлично подходит для определения прочности и целостности ваших суставов. Любые границы сварных швов, которые появляются при испытании кислотным травлением, подчеркивают, насколько быстро ваша деталь будет треснуть в «реальном мире».Не говоря уже о том, что любые проблемы с пористостью, трещины на волосах, плохое сплавление и другое ухудшение также будут обнаружены в этих тестах.
Управляемый тест на изгиб
Управляемый тест на изгиб прекрасен и прост. Кроме того, их выполнение относительно недорого. Обычно они используются для определения прочности и пластичности сварной детали. Поскольку лучше всего, если образцы и будут простыми, управляемый изгиб все же обычно используется для стыковых сварных соединений.
Все испытания на изгиб (включая свободный изгиб и изгиб назад) требуют изгиба объекта в трех местах под определенным углом.Чрезмерное растяжение соединения гарантирует, что любые дефекты в детали будут обнаружены невероятно быстро.
А пока мы сосредоточимся на управляемых испытаниях на изгиб, прежде чем перейдем к двум другим.
При этом типе гибки необходимо обернуть деталь вокруг каркаса. Диаметр должен быть указан до начала исследования, чтобы вы точно знали , что вы ищете.
Конечно, здесь используется приспособление, чтобы помочь вам в этом начинании. Обычно у них есть мужчина и женщина, но некоторые представляют собой трубогиба сантехника.
После того, как вы правильно прикрепите образец к зажимному приспособлению, к вашему предмету будет приложена деформация. Удельная сила, используемая здесь, определяется диаметром первого и толщиной объекта. Иногда вам нужно будет согнуть кусок под углом 180 градусов, но в других случаях это будет 90 или 120 градусов.
По окончании испытания вам нужно осмотреть сварную деталь. Гарантированно обнаруживаются любые дефекты на натяжной поверхности. Во многих руководствах указано, что любое повреждение более 3 мм является основанием для отказа.
Бесплатный тест на изгиб
Хотя вы не найдете бесплатных тестов на изгиб, необходимых для квалификации сварщика, его все же можно провести в мастерской. Это простой способ определить пластичность металла, вставляемого в сварное соединение.
Итак, как это делается? Отличный вопрос, давайте перейдем к нему!
Во-первых, вам нужно будет зажать испытательный образец в тисках и измерить его в продольном направлении, делая отметки по ходу движения. Затем вы должны взять молоток и ударить им до «начального изгиба».Теперь осталось сделать последний изгиб . Для этого просто полностью поместите весь образец в тиски, и ваш последний изгиб будет сформирован. Следует отметить, что эти тиски должны обладать большей силой, чем та, которая необходима для первоначального изгиба.
Когда все это будет выполнено, вам нужно измерить расстояние между отметками, которые вы сделали ранее. Но вы еще не закончили. Чтобы испытание было полностью завершено, вам нужно найти процент удлинения.Для этого нужно вычесть исходное расстояние от конечного. Разделите сумму на первое расстояние и умножьте это на 100.
Как мы уже говорили ранее, это , а не , необходимое для квалификации сварщика. Вам может быть интересно, почему. Что ж, параметры этих тестов невероятно сложно контролировать. С точки зрения непрофессионала, вы не можете сделать его честным тестом, потому что многие переменные неизвестны. Это то, что предпочтительнее проводить обследования на изгиб с гидом.
Испытание на обратный изгиб
Заключительное испытание на изгиб — это версия для обратного изгиба.Он используется для определения качества металла и его проникновения в основание сварного стыкового соединения.
Вы можете использовать тест на изгиб назад, чтобы проверить детали, аналогичные тесту на свободный изгиб, который мы только что обсудили. Однако вам нужно манипулировать ими так, чтобы корень сварного шва находился на стороне натяжения.
Независимо от типа соединения, с которым вы работаете, каждый испытанный образец должен изгибаться под углом 90 градусов без раскалывания, трещин или разломов.
Честно говоря, тест на изгиб назад почти полностью заменен разновидностью управляемого изгиба (во многом как тест на свободный изгиб). Почему это? Что ж, даже если вы знаете, что он должен изгибаться на 90 градусов, больше ничего нельзя измерить (поскольку вы ничего не зажимаете в определенных точках).
Nick Break Test
Этот метод испытания сварных швов (часто называемый испытанием на излом) удобен для определения внутреннего качества металла, который вы использовали. Это позволит выявить такие дефекты, как включения шлака, расплав, окисленный металл, газовые карманы и обгоревший металл.Если вы не видите ничего из этого по окончании теста, поздравляем! Вы, друг мой, сварщик на уровне A-plus. Изображение предоставлено: Welpedia
Имейте в виду, что в зависимости от типа соединения, приведенный ниже метод может немного измениться.
Однако, прежде чем вы сможете приступить к экзамену на разрыв зарубки, вам необходимо разрезать испытательный образец пламенем. Обычно это образец стыкового или углового сварного шва, так как они лучше всего подходят для испытаний на разрыв.
После того, как вы это сделаете, отпилите ¼ дюйма в центре каждого среднего края.Затем поместите изделие на две опоры. Убедитесь, что они стальные, иначе вы их повредите! Затем возьмите молоток и сломайте образец. Вам нужно будет нанести удар прямо в то место, где вы разрезали металл.
При разрушении открытый металл шва не должен иметь газовых карманов размером больше шестнадцатой дюйма, быть сплавленным и не содержать шлаковых включений. . Еще один важный аспект, о котором следует помнить при осмотре изделия, — это то, что на квадратном дюйме не должно быть более шести пор.Если на больше, ваш образец выйдет из строя.
Испытание на прочность на растяжение
Для того, чтобы ваша техника стыковой сварки была одобрена, вам, как правило, необходимо пройти испытание на прочность на растяжение. Считайте это методом управляемой проверки на изгиб для богатых людей.
Обычно они используют образец поперечного, квадратного или прямоугольного поперечного сечения вашего изделия. Это гарантирует, что каждая часть вашего образца будет исследована. Вы спросите, что мы подразумеваем под через каждую часть ? Ну, мы говорим о основных металлах, металле сварного шва, и HAZ (зоны термического влияния).Изображение предоставлено: Arcraft Plasma
. Если вы используете этот метод для проверки стыкового шва плоской пластины, у вас не возникнет много проблем. Однако, если вы тестируете образец стыкового соединения трубы, изогнутая структура может испортить результаты.
Для проведения этой процедуры необходимо заранее измерить толщину и площадь поперечного сечения. Затем надежно поместите его в устройство, которое помещает на него лот тяги — да, достаточно, чтобы сломать ваш образец. Здесь калибр машины покажет вам нагрузку в фунтах (сохраняется только нагрузка на разрыв).
Последним этапом является расчет «прочности на разрыв», иначе называемого напряжением в фунтах на квадратный дюйм. Поверьте, это не так сложно, как кажется. Просто разделите разрывную нагрузку на начальную площадь поперечного сечения. Обычно ваш образец должен выдерживать более 90% прочности основного металла.
Методы неразрушающего контроля сварных швов
Целью этого типа испытаний является проверка качества сварного шва без повреждения детали .Иногда сварщики называют это NDT, NDE (неразрушающий контроль) или NDI (неразрушающий контроль).
Гидростатическое испытание
В основном гидростатическое испытание используется для определения целостности новых или недавно измененных систем трубопроводов. Это невероятно важно, поскольку это, как правило, последний экзамен перед внедрением в реальные приложения.
Поскольку гидростатические испытания очень важны, процедура выполняется до , буквы .
Давайте выделим это маркером, чтобы было легче понять:
- Испытательные образцы подвергаются давлению, в 1,5 раза превышающему давление, которое они должны выдерживать
- Все стыки должны быть доступны (без краски, изоляции или засыпки)
- Все вентиляционные отверстия будут открыты перед испытанием, поэтому воздух будет удален перед приложением давления
- Любое оборудование, которое не требуется испытывать, будет отсоединено или заблокировано
- Пружинные опоры будут удалены или ограничены
- Испытание выполнено после завершения горячих работ
- Любые рентгеновские испытания выполнены до гидростатические исследования
- Ваш тестовый пакет будет передан вам перед проведением экзамена
- Все испытательное оборудование должно иметь необходимые сертификаты
- Регулирующие клапаны удалено
- Вращающиеся детали не подвергаются испытаниям давлением
- Манометры должны устанавливаться в нижних и верхних точках в больших системах 9 0159 Он будет заполнен от нижней точки
- После этого система будет полностью вентилирована
- Давление во время теста будет применяться в течение 10 минут и постоянно увеличиваться в течение
- Вам необходимо проверить всю систему на предмет утечек
- После утечек были исправлены, гидростатические испытания необходимо будет провести снова.
Тест на магнитные частицы
Люди, которые проработали в отрасли в течение многих лет, обычно называют испытания на магнитные частицы как MT или MPI (контроль магнитных частиц).Это позволяет вам обнаружить любые изъяны на поверхности ферромагнитных материалов. По сути, он просто проверяет наличие поверхностных ошибок.
Удивительно эффективен для проверки разрыва поверхности, растрескивания, холодного нахлеста, наличия проплавления боковин и т.д. . Однако он работает только с магнитными материалами (отсюда и название).
Несмотря на то, что здесь существует множество методов, наиболее часто используется ручной электромагнитный магнит ярма. Также используется другое оборудование, включая белую краску (разновидность удаляемой) и магнитные чернила.
Как это делается? Ответ, вероятно, проще, чем вы думаете.
После того, как вы разместите кусок на белом фоне, вы готовы приступить к работе. Сначала вы намагнитите деталь с помощью магнита. Если здесь есть какие-либо поверхностные дефекты, силовые линии магнитного поля будут колебаться вокруг них. В принципе, любые отклонения от нормы будут ясны как день. Затем чернила наносятся, чтобы дать вам еще более четкое представление о том, что происходит на поверхностном уровне.
Это может быть фантастика для людей с ограниченным бюджетом.Несмотря на то, что это может показаться дорогим, вы можете найти относительно дешевые решения, которые позволят вам безупречно выполнять MPI. Не говоря уже о том, что это дает невероятно быстрые результаты. Plus , вы можете изучить материалы довольно странной формы!
Обратной стороной здесь является то, что вы должны работать с ферромагнитными материалами, чтобы они работали. Возможно, вы этого не делаете. В этом случае вам придется согласиться на другой метод испытания сварных швов. Не волнуйтесь, вы можете найти их все здесь!
Тестирование магнитными частицами >> Посмотрите видео ниже:
Рентгеновский тест
Возможно, Рентгеновский контроль (или радиографический контроль) является лучшим, универсальным и широко используемым процедура неразрушающего контроля.В основном он используется для определения прочности сварных швов. И нет, мы имеем в виду не внешнее, а внутреннее.
Он основан на прохождении рентгеновских лучей через металл для получения фотографических свидетельств переданной лучистой энергии. Они легко отображают аномалии в сварных швах, поскольку все материалы поглощают определенное количество вышеупомянутой лучистой энергии.
Но ясно, что эти лучи не приходят из воздуха. Что-то должно произойти, чтобы они были произведены, верно? Абсолютно!
Генераторы излучают экстремальные напряжения на рентгеновскую трубку.Это приводит к сокращению длины волны рентгеновского излучения и испусканию безумного количества энергии, которое, в конечном итоге, проникает сквозь металл. Когда это произойдет, не , а все этой энергии перейдут на другую сторону материала. Количество, которое делает , , зависит от множества факторов (таких как атомный номер, толщина и т. Д.). Вообще говоря, толстые участки поглощают гораздо больше лучистой энергии. Поэтому их рентгенограммы будут светлее.
Этот процесс позволяет вам «заглянуть внутрь» материала, с которым вы работаете.
Это кажется надежным упражнением, не так ли? Что ж, если изображение нечеткое и нечеткое, вы не сможете его хорошо прочитать. Тем самым испортил весь тест. Итак, для борьбы с этим используется устройство, известное как IQI (индикатор качества изображения). Этот удобный маленький парень гарантирует, что вы получите качественное рентгеновское изображение!
Гамма-тест
Честно говоря, этот метод неразрушающего контроля сварных швов очень похож на рентгеновскую версию, о которой мы только что говорили.Несмотря на это, мы поговорим об этом.
Это может быть сделано мобильными специалистами или в специальной лаборатории. Но пока мы сосредоточимся на возможностях мобильных гамма-тестеров. Почему? Потому что это потрясающе!
Эти ребята прошли годы обучения, чтобы научить вас методам гамма-исследования на месте. Это замечательно продуманный процесс. Каждый техник-испытатель управляет грузовиком для фотолаборатории, который используется для воплощения ваших мечтаний о гамма-луче в жизнь.
Они поместят ваш тестовый образец в свой украшенный фургон. И после этого начинается волшебство.
Здесь капсула, полная сульфата радия, будет излучать гамма-лучи в вашу деталь. Преимущество этого метода перед рентгеновскими лучами в том, что они на намного короче на , что позволяет им тестировать до смешного толстые образцы. Как вы можете догадаться, изучение материалов с высокой плотностью займет гораздо больше времени.
В конце дня обычно используют рентгеновские лучи.Они дешевле, и больше людей умеют их проводить. Но ничто не может быть таким портативным и удобным, как тестирование гамма-излучения.
Флуоресцентный тест на пенетрант
Обычно люди называют это просто «тестом на краситель» (он гораздо интереснее, правда?). В любом случае, это фантастический метод, который можно использовать, если вы хотите выявить протечки, трещины, поры и другие дефекты.
В этой процедуре исследования используются флуоресцентные краски или красители, обладающие высокой проникающей способностью.И хотя его можно использовать для любого материала, лучше оставить его тем, которые не являются магнитными.
Есть три метода, которые вы можете использовать для нанесения красителя на поверхность вашего образца (после того, как вы его очистили и высушили). Окуните, распылите или нанесите кистью. Не забудьте удалить излишки материала мокрой скалой или пескоструйным аппаратом.
Как только вы преодолеете это препятствие, вы должны нанести сухой проявитель поверх. Затем поместите обработанный образец под черный свет, чтобы наблюдать, как любые дефекты освещаются яркими флуоресцентными цветами.
В качестве альтернативы вы можете использовать неоновый краситель, который появляется при обычном свете, чтобы сделать его даже менее сложным. Мы полагаем, что бы ни плавало на вашей лодке! Лично это один из наших любимых. Но есть недостатков метода исследования красителя, включая тот факт, что вы можете пропустить дефекты, которые находятся под поверхностью. Кроме того, вы не сможете проводить испытания красок или красок на пористых материалах.
При всем вышесказанном, мы считаем, что плюсы в значительной степени перевешивают минусы.Почему? Поскольку обучение практически не требуется, оно несложно и дешево. О чем еще ты можешь попросить?
Испытания на твердость
При испытаниях сварных швов термин твердость относится к способности материала сопротивляться вдавливанию. Это , как правило, выполняется как неразрушающий тип теста в лаборатории. Однако вы не найдете экзаменов на твердость, проводимых в мастерских.
Целью таких тестов является контроль качества предметов, используемых по определенным причинам в «реальном мире». Но есть не только , одно испытание на твердость . Существует множество методов, поэтому мы рассмотрим каждый по очереди.
Готовы?
File Test
Безусловно, это самый простой тест на твердость, который вы можете выполнить. Все, что вам нужно, это немного смазки для локтей и напильник. Просто запустите файл поверх тестового образца (потрите его как следует). Таким образом, вы можете определить, мягче или тверже напильник для металла, который вы только что напилили.
Машины для испытания на твердость
Помимо проверки файлов, вы можете приобрести машину, которая автоматически выполняет испытания на твердость. Каждый тип устройства был разработан для выполнения одной функции, но вы можете легко использовать более одного вида на металле.
Поскольку существует очень много типов, , мы рассмотрим только самые распространенные. Обычно приборы Роквелла и Бринелля используются в лабораториях учеными, определяющими твердость металла.
Давайте углубимся в детали.
Твердомер по Бринеллю
Здесь вы должны закрепить образец для испытаний на опоре станка. Вы быстро поймете, что прикреплен стальной шарик. Это будет действовать как фактор локального давления при испытании, потому что на мяч автоматически будет приложено 3003 кг (6620 фунтов), а значит, и на ваш образец для испытаний. Он остается в таком состоянии примерно 30 секунд, прежде чем будет выпущен.
После всего этого довольно долгого процесса вам нужно измерить диаметр сделанной вмятины.Это звучит странно, учитывая, что вашей первой мыслью было, вероятно, измерить глубину вмятины. Однако, если вы хотите использовать числа Бринелля, вы должны измерить диаметр.
Есть довольно запутанная формула, которую можно использовать для получения чисел. Но вам лучше найти диаграмму в Интернете, чтобы преобразовать ваши результаты для вас.
Твердомер по Роквеллу
Этот прибор похож на версию по Бринеллю, о которой мы только что говорили. Разница в том, что он прикладывает меньшую силу к меньшему мячу.
Вам будет приятно узнать, что вы do измеряете глубину с этим. Не говоря уже о том, что вам не нужно блуждать в поисках диаграмм конверсии. Почему? Потому что к устройству прикреплен циферблат! Как и в случае с машиной Бринелля, данные отображаются в виде «чисел Роквелла», которые используются во многих нормах и правилах по сварке.
Magnaflux Test
Судя по названию, можно предположить, что этот метод неразрушающего контроля быстр. И ты был бы прав! Он использует намагниченность и ферромагнитные частицы для выделения поверхностных и приповерхностных дефектов на стали и связанных сплавах.
По сути, это похоже на использование очень мощной лупы для проверки качества сварных швов. Сказав это, здесь задействовано стекло ноль , так что… зеркало без стекла?
Ладно, вперед!
Использует магнитное поле, а также различные ферромагнитные порошки. Как только вышеупомянутые ферромагнитные частицы попадают в намагниченное поле, они притягиваются к полюсам. Там все они будут держаться очень крепко. Это позволяет вам точно увидеть, где и какие дефекты есть у вашего изделия.
Электромагнитные испытания
Как ни странно, электромагнитные испытания часто называют вихретоковыми испытаниями. Не спрашивайте нас, почему мы думаем, что это очаровательно, просто так! Очевидно, у названия есть причина, но, честно говоря, мы не знаем причину.
Принцип, лежащий в основе этой техники обследования, заключается в том, что электрический ток проходит через проводник. Вы не увидите, что это используется во всей сварочной промышленности, но он отлично подходит для стержней, угловых соединений и сварных труб.
Для этого вам необходимо произвести электрический заряд, который проникнет в материал. После этого вам нужно будет не забыть измерить текущие изменения и физические различия, которые произошли во время экзамена.
Конечно, с помощью этого теста вы можете определить, сколько разрывов в вашей детали. Но более того, вы сможете увидеть, как соответственно изменяются размеры и удельное сопротивление. Честно говоря, удельное сопротивление зависит от многих факторов (чистота, ориентация кристаллов, тепло, твердость и т. Д.), Что будет чрезвычайно сложно отследить, какое свойство материала способствовало этому.
Ладно, круто, а как работает? Вас ждет угощение, потому что мы собираемся вам рассказать.
Один из способов измерения вихревых токов у испытуемого — это сделать образец центром индукционной катушки. Затем вам нужно измерить резистивную или индуктивную составляющую. Но не волнуйтесь, в настоящее время есть электронные устройства, которые делают это за вас. Вы не ошибетесь, правда?
Прежде чем мы продолжим, давайте перечислим шаги, которые вы должны предпринять для проведения этого типа теста.Иметь дело? Вот они:
- Ваш образец будет помещен в поле катушки, в котором находится переменный ток
- Катушка может иметь форму «катушки» , но она также может быть прямоугольной, зондовой или даже трубчатой
- . вихревой ток создает свое собственное поле (он противостоит первому магнитному полю, создаваемому катушкой)
- На магнитные поля влияет присутствие вихревого тока
- Если в вашей работе есть дефекты или повреждения, вихревой ток будет искажать
- Чтобы получить результаты, вам необходимо измерить это изменение.
Тестирование акустической эмиссии
Тестирование акустической эмиссии, обычно называемое AE-тестированием, ищет и отслеживает ультразвуковые волны напряжения.Это делается, когда материал находится под нагрузкой и из-за этого деформируется или меняет форму.
Самое интересное — это то, как это работает.
В первую очередь вам необходимо разместить крошечные датчики на вашем образце. После этого все сводится к датчикам и цифровому учету. Но, конечно, мы все это объясним.
Эти маленькие устройства преобразуют волны напряжения в электрические импульсы. Сигналы сразу же отправляются на компьютер для считывания данных.Помните, что волны стресса будут только тогда, когда есть что-то, что будет стимулировать его. Вот почему вам нужно приложить усилие, повысить температуру или сложить еще больше груза.
Наступит момент, когда вы заметите, что высвобождение энергии чрезвычайно велико. Почему? Потому что внешний раздражитель добавляет к ситуации все больше и больше давления и напряжения.
Думайте об испытании акустической эмиссии как о небольшой ряби, возникающей внутри вашего образца. Он измеряет указанную рябь.
Тестирование феррита
Последний метод тестирования сварных швов, о котором мы должны поговорить с вами сегодня, — это тестирование феррита. Ты слышал об этом? Возможно, вы это сделали, но сейчас мы подробно рассмотрим это для вас.
Этот метод известен своей невероятной скоростью и почти 100% точностью при попытке определить количество феррита в определенных металлах. О, и мы упоминали, что это тоже довольно рентабельно?
Он позволяет узнать, насколько лучше обработан металл для выполняемой работы.Однако вы не можете провести этот тест в своей мастерской, вам нужно попросить специалиста сделать это за вас — но это то же самое для многих вещей.
Plus, он позволяет узнать, есть ли внутри ваших материалов какие-либо повреждающие компоненты. Обычно это мешает детали работать так хорошо, как могло бы.
Часто задаваемые вопросы
Вот несколько общих вопросов, которые часто возникают у людей о физических испытаниях сварных швов:
Почему требуется неразрушающий контроль (неразрушающий контроль)?
Почему требуется неразрушающий контроль? Простая причина, по которой требуется неразрушающий контроль, — это проверить сварной шов вашего объекта, не повредив его.Сварка должна выдерживать большую силу и нагрузки, поэтому жизненно важно, чтобы сварной шов был достаточно прочным, чтобы выдерживать его содержимое. Важно, чтобы сварной шов был наилучшего качества, чтобы он соответствовал минимальным стандартам.
Ваш сварной шов должен выдерживать и выдерживать несколько сил, в зависимости от того, что вы свариваете, будет определять, какой метод неразрушающего контроля потребуется. Например, если вы выполняете сварку топливного бака, вы должны использовать «Жидкостный пенетрант»; это позволяет вам проверять наличие зазоров или ошибок без какого-либо повреждения или разрушения сварного шва.Изображение предоставлено: detectstar
Когда дело доходит до сварки, когда расплавленные лужи начинают остывать и затвердевать, сварной шов может частично потерять свое качество. Это может быть вызвано неправильной настройкой, ошибкой оборудования, влажностью, но чаще всего из-за человеческой ошибки.
Таким образом, сварной шов мог быть высшего качества, но когда он остынет, он может достичь этого качества, поэтому очень важно проверить сварной шов, как только он затвердеет. Неразрушающий контроль — наиболее используемый метод по сравнению с разрушающим контролем.
NDT лучше всего, потому что сварной шов не будет поврежден в процессе испытания, но он по-прежнему так же надежен, как и разрушающий контроль. Таким образом, качество тестирования не будет нарушено, и ваш сварной шов не пострадает во время тестирования.
Необходимо проверить сварной шов, чтобы подтвердить качество вашей работы; это связано с тем, что сварка сильно зависит от факторов, контролируемых людьми. Проверка вашего сварного шва позволит убедиться в том, что качество соответствует условиям эксплуатации и выдерживает любые элементы с выдающимся качеством.
Ссылки по теме: 5 типов сварных соединений и их использование
Какой метод неразрушающего контроля лучше всего?
Когда дело доходит до методов неразрушающего контроля, сделать вывод о том, какой метод в целом является лучшим, довольно сложно. Какой метод лучше всего зависит от того, какой сварной шов вы хотите проверить.
Еще одним фактором, влияющим на выбор метода, является квалификация лица, выполняющего неразрушающий контроль. Достоверность результатов зависит от знаний и способностей инспекторов. Чтобы получить хорошие и заслуживающие доверия результаты неразрушающего контроля, человек, проверяющий сварной шов, должен быть компетентным, хорошо обученным и иметь опыт работы с методом неразрушающего контроля, который он использует.
Существует множество методов неразрушающего контроля, поэтому свести их к одному методу как лучшему невозможно. Даже сравнивать методы сложно, потому что каждый метод неразрушающего контроля был создан исключительно для своей цели .Все методы неразрушающего контроля уникальны и различны, поэтому маловероятно, что вы сможете использовать только один тип неразрушающего контроля для всех испытаний сварки.
Когда вы пытаетесь решить, какой метод неразрушающего контроля использовать, вы должны принять во внимание все факторы. Для чего используется ваш сварной шов? Что ему нужно будет держать? Где будет сварной шов: внутри, снаружи или в воде? Все эти вопросы вам необходимо задать, прежде чем выбирать метод неразрушающего контроля. В мире неразрушающего контроля не существует универсального решения.
Может быть не сразу очевидно, какой неразрушающий метод лучше всего подойдет для вашего шва. В этом случае вам следует сложить все факторы и рассмотреть каждую динамику того, для чего ваш сварной шов используется. Затем просмотрите различные методы неразрушающего контроля и выберите, какой из них лучше всего подходит для вашего объекта.
Вам необходимо обладать достаточными знаниями о методе неразрушающего контроля, чтобы убедиться, что вы можете проверить свой сварной шов на предмет соответствия минимальным требуемым стандартам.
Какова цель контроля при сварке?
Какова цель контроля при сварке? Что ж, если во время использования сварной шов оказывается неисправным, в зависимости от того, для чего он используется, это может привести к серьезным повреждениям, задержке работы, влияющей на временные рамки, и потенциально может нанести травму другим людям. Очень важно, чтобы ваше сварное изделие было осмотрено после его завершения. Это связано с тем, что объект необходимо сварить по определенной спецификации.
Сварные изделия должны выдерживать большое количество силы и противостоять многочисленным природным элементам, включая жару, дождь и ветер, в зависимости от того, для чего они используются.
Чтобы убедиться, что сварная конструкция безопасна, надежна и может работать до удовлетворительных характеристик, она должна пройти испытание, также известное как инспекция.Испытание должно проводиться кем-то, кто знает, что он делает, обеспечивая соблюдение надлежащей процедуры проверки и высокое качество сварки.
Сварка должна выдерживать большие конструкции, поэтому качество сварки должно быть абсолютно безупречным и выдерживать большое давление. Будь то давление со стороны природных элементов, механизмов или взаимодействия человека, сварная конструкция должна быть достаточно надежной, чтобы служить долго.
Есть два способа проверки и проверки сварки: неразрушающий контроль и разрушающий контроль.Неразрушающий контроль — это когда сварка проверяется, но не вызывает повреждений или разрушений. В отличие от этого, Разрушительное испытание противоположно.
Итак, цель контрольной сварки состоит в том, чтобы гарантировать, что свариваемый объект или конструкция сварены с наилучшим, самым превосходным и выдающимся качеством. Осмотр дает гарантию максимальной безопасности сварки. Это гарантирует уверенность и уверенность в том, что сварка будет надежной и достаточно прочной, чтобы делать то, для чего она предназначена.
Как я могу проверить сварной шов дома?
Как я могу проверить сварной шов дома? При проверке сварки всегда лучше, чтобы ее проверил квалифицированный и опытный в сварке профессионал. Однако, если вы выполняете сварку для собственных нужд, есть несколько способов проверить это дома:
- Метод визуального контроля
- Посмотрите на распределение сварного шва
- Без шлака
- Без примесей или дефектов
- Сверхплотный сварной шов
- Испытание на утечку
- Испытание прочности сварного шва
Для проверки сварного шва требуется определенное оборудование, чтобы гарантировать удовлетворительное качество сварного шва.Итак, если вы проверяете свою сварку из дома, вам следует использовать визуальный контроль , чтобы определить качество вашего сварного шва.
Чтобы проверить сварной шов в домашних условиях, вам нужно будет выполнить несколько простых шагов. Для начала вам нужно посмотреть на распределение сварного шва ; вам нужно будет убедиться, что сварочный материал равномерно распределен между обеими частями материала.
Вам необходимо убедиться, что не содержит отходов, таких как шлак ; когда сварной шов затвердеет, шлак должен легко отслоиться от объекта.Любые другие отходы необходимо удалить и очистить, а на сварном шве не должно быть никаких остатков.
Поверхность сварного шва не должна иметь загрязнений или дефектов; если да, то он может быть не таким сильным, как должен быть . Если на поверхности сварного шва есть пористые отверстия, это приведет к ослаблению. Пористость указывает на то, что свариваемая металлическая основа была грязной или металл имел оксидное покрытие.
Ваш сварной шов должен быть сверхплотным ; не должно быть никаких зазоров, если ваш сварной шов имеет зазоры или не выглядит плотным, это означает, что возникла проблема со сварным швом.Если сварной шов недостаточно плотный или имеет зазор, это может привести к проблемам в будущем и указывать на то, что сварной шов невысокого качества.
Если вы свариваете конструкцию или изделие, требующееся для удержания жидкости , крайне важно, чтобы не было утечек. Если есть, значит, проблема серьезная. Способ проверки на утечку заключается в том, чтобы заполнить конструкцию водой, и если есть утечка, это означает, что есть проблема со сваркой, и она недостаточно надежна, чтобы удерживать воду.
Чтобы проверить прочность сварного шва , вы должны приложить давление, которое он должен выдерживать, с помощью грузов или чего-то подобного, прежде чем вводить свою конструкцию в эксплуатацию. Лучше всего проверить вес перед использованием сварного шва, чтобы убедиться в отсутствии повреждений, если сварной шов недостаточно прочный.
Шлифовка сварного шва ослабляет его?
Шлифовка сварного шва ослабляет его? Если сварной шов был выполнен в соответствии с высокими стандартами и отличным качеством, шлифовка шва не ослабит его.Тем не менее, если вы можете избежать шлифования сварного шва, вы должны это сделать, особенно если сварной шов не был сварен с высочайшим качеством.
Если сварная конструкция должна быть эстетичной, чистой и требует шлифовки сварного шва, это не повредит вашей конструкции. Такие, как ювелирные изделия или автомобильная панель, они должны быть гладкими и плоскими, поэтому шлифовка сварного шва необходима, и она не ослабит сварной шов при правильной шлифовке с использованием правильного оборудования и навыков.
При шлифовании сварного шва следует проявлять особую осторожность, чтобы не повредить основной материал. Это связано с тем, что при чрезмерной шлифовке основного материала и сварного шва сварная конструкция может потерять часть своей прочности и со временем ослабнуть.
Итог
Испытания сварных швов являются ключевыми. Вы, вероятно, уже поняли это, но теперь вы точно знаете, как это сделать, с помощью метода, который подходит для .
Ссылки :
https://www.twi-global.com/technical-knowledge/job-knowledge/bend-testing-073
http: // armyordnance.tpub.com/od16518/od165180101.htm
http://constructionmanuals.tpub.com/14250/css/Nick-Break-Test-172.htm
https://www.twi-global.com/technical- knowledge / job-knowledge / механические-испытания-испытания на растяжение-часть-2-070
http://www.wermac.org/others/ndt_mpi.html
https://www.lincolnelectric.com/en- us / support / process-and-theory / Pages / nondestructivie-weld-detail.aspx? utm_referrer = direct / not + provided
https://www.shawcor.com/integrity-management-solutions/ndt-and-inspection -услуги / береговые-инспекционные-услуги / гамма-радиография- (RT)
https: // www.magnaflux.com/Magnaflux/Resources/Blog/Fluorescent-Penetrant-Infographic
http://www.wermac.org/others/ndt_pressure_testing_practice.html
https://www.magnaflux.com/Magnaflux/Magnaflux/ Particle-Inspection / Equipment.htm
https://www.twi-global.com/technical-knowledge/faqs/acoustic-emission-testing
Методы контроля | Сварка | Сварочное оборудование
Щелкните изображение, чтобы увеличить
Как известно любому, кто занимается производством и сваркой, контроль процессов и деталей является критически важным компонентом успешного бизнеса.Построить и сварить некачественную деталь просто гарантирует выход из строя.
Сегодня ассоциации сварщиков, такие как Канадское бюро сварки, предлагают курсы сертификации, чтобы помочь сварщикам изучить все тонкости надлежащих процессов контроля, но перед тем, как пройти этот курс, вы должны понять некоторые основы контроля сварки.
Ниже приводится руководство, составленное отраслевыми экспертами и отраслевыми онлайн-источниками.
«Проверка сварки часто требует от инспектора сварки самых разных знаний», — отмечает Тони Андерсон из ESAB в онлайн-статье на веб-сайте компании.«Понимание сварочных чертежей, символов сварки, конструкции сварных швов, процедур сварки, норм и стандартов, а также методов контроля и испытаний, и это лишь некоторые из них. По этой причине многие правила и стандарты в области сварки требуют, чтобы инспектор по сварке обладал формальной квалификацией или необходимыми знаниями и опытом для проведения инспекционных услуг ».
Для начала следует признать, что существует множество различных методов контроля сварки. Они включают в себя визуальное, сравнительное, радиографическое и ультразвуковое обнаружение поверхностных трещин (также известное как дефектоскопический контроль красителя и контроль магнитных частиц), использование воды и газа под давлением, а также разрушающие методы.
Самый распространенный метод — и наименее затратный, если все сделано правильно — визуальный. Сварщики ищут трещины, плохое сплавление, перекрытие, оплавленные края и другие несоответствия, которые являются визуальными индикаторами плохого сварного шва.
Другой относительно недорогой метод — это простое сравнение рассматриваемой сварочной инспекции с другими аналогичными сварочными работами. Инспектор по сварке может спросить сварщиков, как они создали конструкцию, чтобы понять, соблюдают ли они надлежащие процедуры сварки, согласно данным ESAB Welding & Cutting.Инспектор также может сравнить сварочную работу с чертежом, предоставленным сварщику.
Радиографические и ультразвуковые методы — два наиболее распространенных метода неразрушающего контроля. Очевидным преимуществом неразрушающего контроля является то, что сварщики могут обнаруживать проблемы со сваркой, не разрушая свариваемую деталь. Согласно заявлению ESAB, радиографический контроль — проникающее излучение проходит через твердый объект на фотопленку — обеспечивает «постоянную запись качества сварного шва, которую относительно легко интерпретировать обученным персоналом.«Это медленный и дорогостоящий метод, но он является хорошим методом для обнаружения пористости, включений, трещин и пустот внутри сварных швов.
Ультразвуковой контроль — механические колебания с помощью луча ультразвуковой энергии направляются в объект — дает сварщикам возможность определить точное положение проблемы в сварном шве. Хотя это хороший метод, ЭСАБ советует сварщикам, использующим этот процесс, иметь высокий уровень подготовки и компетентности операторов. Метод подходит для черных и цветных металлов.
Испытание жидким красителем пенетрантом — это распространенный метод неразрушающего обнаружения трещин в сварных швах. Процесс заключается в нанесении проникающей жидкости на поверхность сварного шва, позволяющей ей впитаться в течение заданного периода времени, а затем удалении излишков жидкости для проверки наличия трещин на поверхности. Обратите внимание, что этот метод полезен только для обнаружения трещин на поверхности; он не обнаружит каких-либо трещин или проблем сварки (пористость или дефекты плавления) в основной части сварного шва.
Для обнаружения более широкого диапазона несоответствий сварного шва лучшим выбором является испытание магнитными частицами.Он может обнаруживать трещины, а также пористость, швы, включения и плохое сплавление. Этот метод работает путем создания магнитного поля в проверяемой детали — магнит притягивает магнитные частицы к своим концам, и магнитные линии проходят между полюсами магнита. Если испытываемая деталь не имеет трещин или других проблем со сваркой, магнитные частицы не будут притягиваться. Этим методом можно тестировать только ферромагнитные материалы.
Методы контроля воды или газа под давлением используются для сварных конструкций, предназначенных для транспортировки жидкости, таких как трубопроводы.В этом методе вода или азот под давлением пропускаются через трубу для обнаружения любых утечек.
Как следует из названия, методы контроля с помощью разрушающей сварки включают в себя физическое разрушение свариваемой детали для оценки детали. Применения включают аттестацию процедуры сварки и аттестационные испытания сварщика, выборочный контроль производственных сварных швов, исследовательский контроль и работы по анализу отказов. По данным ESAB, методы контроля обычно включают разрезание или разрыв сварного компонента для оценки механических и физических характеристик.
Информация основана на онлайн-исследовании по телефону:
Американское общество сварки
Канадское сварочное бюро
ЭСАБ
Welding-advisors.com
испытаний сварного шва: 5 испытаний (со схемой)
Эта статья проливает свет на пять основных испытаний сварного шва. Испытания: 1. Микроскопический тест 2. Макроскопический тест 3. Химические испытания в лаборатории 4. Механические испытания 5. Испытание на растяжение.
1. Микроскопический тест :Использование микроскопа очень важно для определения фактической структуры сварного шва и основного металла. Полированный участок металла шва будет выглядеть полностью однородным, если нет раковин и шлака. С другой стороны, если сварной участок сломан, можно обнаружить определенную кристаллическую структуру.
Однако этот тип секции мог быть поврежден в самой слабой линии.Итак, в качестве образца для исследования берется любая желаемая часть сварного шва. Образцы для микроскопического исследования лучше всего вырезать ножовкой. Любое приложение тепла, например, при газовой резке, может разрушить часть образца. Если исследовать под микроскопом, то окажется, что он покрыт множеством царапин.
2. Макроскопический тест :Этот метод заключается в подготовке поперечного сечения Т-образного углового шва. Его исследуют либо в маломощный микроскоп с увеличением 3-20 диаметров, либо с помощью лупы.Это покажет любые трещины, застрявший шлак, газовые карманы размером с иглу и т. Д. Макрографическое исследование сварных швов может быть легко выполнено в мастерской с помощью мощной ручной лупы.
Конечно, микроскоп детально выявит дефекты сварного шва.
3. Химические испытания в лаборатории :После сварки в сварном металле происходят некоторые химические реакции. Аналитические испытания используются для определения химического состава свариваемого металла.По его составу можно оценить физические свойства металла шва. Добавление марганца увеличивает ударную вязкость стали, уран увеличивает ее прочность на разрыв.
Следует отметить, что действие кислот и щелочей, присутствующих в атмосфере больших промышленных зон, может повлиять на срок службы сварных соединений, поскольку имеет место коррозия. Точно так же на морском побережье коррозия металлических частей происходит из-за воздействия брызг соленой воды и соленой атмосферы.
Площадка для приземления, перила и другие конструкции подвергаются воздействию морских брызг и подвержены ранней ржавчине.В химической промышленности резервуары необходимы для хранения агрессивных химикатов. Химические испытания необходимы в лаборатории, чтобы избежать коррозии сварных соединений.
4. Механические испытания :Механические испытания могут быть классифицированы как:
(1) растяжение;
(2) Гибка;
(3) Изод или Шарпи;
(4) твердость;
(5) Растрескивание и т. Д.
5. Испытание на растяжение :Типичный образец для испытаний на растяжение показан на рис.8.1:
Для испытания сварного соединения на растяжение некоторые образцы вырезают из сварного шва, а один — из самой пластины. Образцы обрабатываются так, чтобы все края были скруглены, а поверхность можно оставить с наплавленным швом или обработать плоской в зависимости от требуемого испытания.
Образец нагружают в машине для испытаний на растяжение, причем нагрузка при разрыве является мерой прочности сварного шва. Нагрузка в килограммах делится на площадь поперечного сечения образца в квадратных миллиметрах, и, таким образом, получается предел прочности образца на растяжение.
Итак, предел прочности при растяжении T = L (нагрузка в кг) / A (площадь в мм)
Стандарт контроля качества спиральных стальных труб перед поставкой
Спиральные стальные трубы (SSAW) перед отправкой с завода должны пройти испытание на механические характеристики, испытание на сплющивание и развальцовку, и они должны соответствовать требованиям стандарта. Метод контроля качества спиральных стальных труб следующий:
1. Судя по поверхности, то есть по внешнему виду. Контроль внешнего вида сварных соединений — простой и широко используемый метод контроля.Это важная часть проверки готовой продукции, в основном для обнаружения дефектов и отклонений размеров на поверхности сварного шва. Обычно его проверяют невооруженным глазом с помощью таких инструментов, как стандартные шаблоны, датчики и увеличительные стекла. Если на поверхности сварного шва есть дефекты, это может означать наличие дефектов внутри сварного шва.
2. Проверка физическими методами.
Физические методы контроля — это методы, в которых для измерения или проверки используются некоторые физические явления. Для проверки внутренних дефектов материалов или деталей обычно используются методы неразрушающего контроля.Неразрушающий контроль включает ультразвуковой контроль, радиографический контроль, проникающий контроль, магнитный контроль и т. Д.
3. Проверка на прочность сосуда высокого давления.
В дополнение к испытанию на герметичность сосуд высокого давления должен быть подвергнут испытанию на прочность. Есть два распространенных типа: гидравлическое испытание и пневматическое испытание. Они могут проверить герметичность сварных швов сосудов и труб, работающих под давлением. Испытание давлением воздуха более чувствительно и быстрее, чем испытание давлением воды, и продукт после испытания не нужно сливать, что особенно подходит для продуктов с затрудненным сливом.Но риск испытания больше, чем риск гидравлического испытания. При проведении испытания необходимо соблюдать соответствующие технические меры безопасности, чтобы предотвратить несчастные случаи во время испытания.
4. Проверка плотности
Для сварных контейнеров, в которых хранятся жидкости или газы, дефекты сварных швов, такие как сквозные трещины, поры, включения шлака, непровар и рыхлая структура, могут быть обнаружены с помощью теста на компактность. Методы испытания на герметичность включают: керосиновое испытание, испытание на водонепроницаемость, испытание на промывку водой и т. Д.
5. Гидростатические испытания
Каждая стальная труба должна быть подвергнута испытанию гидростатическим давлением без утечки. Испытательное давление рассчитывается путем прессования P = 2ST / D, где S — испытательное напряжение гидростатического испытания МПа, а испытательное напряжение гидростатического испытания должно соответствовать соответствующему стандарту на стальную полосу. Выбрано 60% минимальной доходности (235 кв. Время стабилизации: D <508 время выдержки испытательного давления не менее 5 секунд; D≥508 время выдержки испытательного давления не менее 10 секунд
6.Неразрушающий контроль
Рентгеновский или ультразвуковой контроль проводится при ремонте сварных швов стальных труб, стыковых швов стальных полос и кольцевых швов. 100% S-рентгеновский или ультразвуковой контроль должен выполняться для спиральных сварных швов в направлении стали, используемых для транспортировки горючих обычных жидкостей, и спиральных сварных швов стальных труб, используемых для транспортировки воды, сточных вод, воздуха, греющего пара и другие обычные жидкости должны пройти выборочную проверку с помощью рентгеновского или ультразвукового контроля (20%).
Согласно результатам контроля качества спиральных стальных труб, спиральные стальные трубы обычно делятся на три категории: квалифицированная продукция, отремонтированная продукция и лом. Квалифицированная продукция относится к спиральным стальным трубам, внешний вид и внутреннее качество которых соответствуют соответствующим стандартам или техническим требованиям для поставки и приемки; отремонтированные изделия относятся к внешнему виду и внутреннему качеству, которые не полностью соответствуют стандартам и критериям приемки, но допускаются к ремонту и могут соответствовать стандартам и условиям приемки после ремонта Спиральные стальные трубы; Под ломом понимаются спиральные стальные трубы, которые не соответствуют требованиям по внешнему виду и внутреннему качеству и не подлежат ремонту или не соответствуют стандартам и условиям приемки после ремонта.
Отходы делятся на внутренние и внешние. Внутренние отходы — это стальные спиральные стальные трубы, используемые в литейном или литейном производстве; Под внешними отходами понимаются отходы, обнаруженные после доставки спиральной стальной трубы, которые обычно обнажаются во время механической обработки, термообработки или использования, и вызванные этим экономические потери намного больше, чем внутренние отходы. Чтобы уменьшить внешние отходы, спиральные стальные трубы, производимые партиями, должны быть отобраны для экспериментальной термообработки и грубой обработки, прежде чем они покинут завод.Возможные дефекты спиральных стальных труб следует выявлять в максимально возможной степени на заводе по производству спиральных стальных труб, чтобы можно было как можно скорее принять необходимые меры по их устранению.
https://www.nan-steel.com/carbon-steel-pipe/ssaw-steel-pipe.html Контроль и тестирование лазерной сварки| Контроль и испытания электронно-лучевой сварки
Контроль сварных швов деталей, сваренных с помощью лазерной и электронно-лучевой сварки, обычно осуществляется по трем различным направлениям: визуальный контроль; разрушающее испытание; и неразрушающий контроль (NDT).
Визуальный осмотр включает осмотр сварного шва невооруженным глазом и / или с некоторым увеличением. Обычно наши инспекторы проверяют наличие трещин, ямок, пор на поверхности, поднутрений, недозаливок, пропущенных стыков и других аспектов сварного шва.
Визуальный осмотр ограничивается площадью поверхности сварного шва, видимой инспектору, что означает, что нечто вроде глубины проплавления не может быть определено, если сварной шов не является сварным швом с полным проплавлением и вы не можете просмотреть его изнутри сборки.Следовательно, для дальнейшего изучения качества сварного шва часто требуется разрушающее испытание.
Разрушающий контроль включает физическую резку и разрезание детали для определения внутренних характеристик сварного шва. Как правило, либо вырезается производственная деталь, либо изготавливается репрезентативный образец, отражающий точные характеристики соединения. Разрушающие образцы обычно берутся в начале работы, чтобы убедиться, что параметры сварки соответствуют партии.Образцы также можно брать через определенные промежутки времени во время производственного процесса или в конце цикла.
Образцы для разрушающих испытаний точно вырезаны, обработаны, отшлифованы и отполированы до зеркального блеска. Затем применяется кислотное травление, чтобы визуально выделить сварной шов, и затем образец исследуется под микроскопом. Этот осмотр может определить глубину проплавления, ширину сварного шва, а также выявить трещины, поры и другие аномалии внутри сварного шва.
Неразрушающий контроль , как следует из названия, не разрушает деталь, поэтому теоретически каждая деталь может быть исследована таким образом, и это обычно так, если неразрушающий контроль требуется спецификацией.
NDT обычно состоит из проникающего контроля красителя и / или рентгеновского контроля.
При проверке проникающим методом красителя на деталь наносится специальный краситель для выявления трещин и других поверхностных аномалий. Этот метод ограничен тем, что позволяет выявить проблемы только на поверхности сварного шва.
Рентгеновский контроль дает наиболее полное представление о том, что происходит внутри сварного шва. В частности, пористость хорошо видна на рентгеновском снимке.
К каждой сборке предъявляются разные требования, и важно понимать нюансы каждого типа проверки, чтобы разработать режим проверки, который последовательно приведет к высококачественным деталям в рамках требований. Например, деталь с низким риском выхода из строя может просто нуждаться в визуальном осмотре, в то время как деталь, предназначенная для использования в космосе, где отказ может быть катастрофическим, требует гораздо более высокого уровня осмотра.
Метод контроля качества стальной спиральной трубы
Спиральная стальная труба перед отправкой с завода должна пройти механические испытания, испытание на сплющивание и испытание на развальцовку, и должна соответствовать требованиям, указанным в стандарте.Метод контроля качества спиральных стальных труб следующий:
1. Проверка по поверхности, то есть по внешнему видуПроверка внешнего вида сварных соединений является простым и широко используемым методом контроля, который является важным часть контроля готовой продукции, в основном для обнаружения дефектов и отклонений размеров на поверхности сварного шва. Обычно его проверяют невооруженным глазом и с помощью таких инструментов, как стандартные шаблоны, калибры и лупы.Если есть дефект на поверхности сварного шва, есть вероятность дефектов внутри сварного шва.
2. Физический метод проверкиФизический метод проверки — это метод измерения или тестирования с использованием некоторых физических явлений. Проверка внутренних дефектов материалов или деталей обычно проводится с помощью неразрушающего контроля. Неразрушающий контроль включает ультразвуковое дефектоскопирование, радиографический контроль, дефектоскопию и магнитную дефектоскопию.
3. Испытание на прочность сосуда высокого давленияВ дополнение к испытанию на герметичность сосуд высокого давления должен быть подвергнут испытанию на прочность. Существует два типа гидравлического испытания под давлением и испытания под давлением воздуха. Оба они проверяют плотность сварного шва контейнеров и труб, работающих под давлением.
Испытание давлением воздуха более чувствительное и быстрое, чем испытание давлением воды, и испытываемый продукт не требует слива, что особенно подходит для продуктов с затрудненным дренажем.Однако риск испытания больше, чем гидравлического испытания. При проведении испытаний необходимо соблюдать соответствующие технические меры безопасности, чтобы предотвратить несчастные случаи во время испытания.
4. Испытание на плотностьДля сварочных емкостей, в которых хранится жидкость или газ, сварные швы не являются плотными, такими как сквозные трещины, поры, включения шлака, непровар и неплотные структуры, которые могут быть обнаружены с помощью теста на компактность. Методы испытания на компактность включают: испытание на керосин, испытание на водонепроницаемость, испытание на промывку водой и т. Д.
5. Гидростатическое испытаниеКаждая стальная труба должна быть подвергнута гидростатическому испытанию без утечки. Испытательное давление рассчитывается по результатам испытания. Испытательное напряжение Mpa для S-гидростатического испытания в формуле P = 2ST / D и испытательное напряжение при гидростатическом испытании.
Соответствующий стандарт на стальную полосу определяет 60% минимального выхода (Q235 составляет 235 МПа).
6. Время регулированияD <50 Время выдержки испытательного давления не менее 5 секунд; D≥508 время выдержки испытательного давления составляет не менее 10 секунд 4, неразрушающий контроль сварного шва ремонта стальных труб, стыкового шва стальной ленты и кольцевого шва Выполните рентгеновский или ультразвуковой контроль.
Для спирального сварного шва стального направления для транспортировки горючих обычных жидкостей необходимо выполнить 100% рентгеновский или ультразвуковой контроль. Рентгеновские лучи должны применяться к спиральным сварным швам стальных труб, используемых для транспортировки обычных жидкостей, таких как вода, сточные воды, воздух и греющий пар. Выборочная проверка ультразвуковым контролем (20%).
Согласно результатам проверки качества спиральных стальных труб, спиральные стальные трубы обычно делятся на три категории: квалифицированная продукция, отремонтированная продукция и отходы.
Квалифицированная продукция — это спиральные стальные трубы, внешний вид и внутреннее качество которых соответствуют требованиям соответствующих стандартов или технических условий приемки поставки; Отремонтированные изделия относятся к качеству внешнего вида и внутреннего качества, которые не полностью соответствуют стандартам и приемочным полосам, но допускаются к ремонту, а стандартные и приемочные условия могут быть соблюдены после переделки.
Труба стальная спиральная; Под ломом понимается спиральная стальная труба, не отвечающая требованиям по внешнему виду и внутреннему качеству и не требующая стандартных или приемочных условий после ремонта или ремонта.
Исследование точечных сварных соединений с помощью активной термографии
ISO 10447: Контактная сварка — испытание контактных точечных и выступающих сварных швов отслаиванием и долотом
Фастрицкий В.С., Вингрис Л.Т., Ардентов В.В., Флоринский , Ю.Б., Плотников, В.И., Родневский, Л.А.: Аппарат для неразрушающего контроля точечных сварных швов с использованием электромагнитного поля, Рижский политехнический институт (Рига, SU), Патент США 4503392, Дата подачи: 21.07.1981
Polrolniczak, H .: Ультразвуковой контроль как средство обеспечения качества при контактной точечной сварке. Krautkramer — Sonderdruck Nr. SD 297 (1999)
Рой У. Ультразвуковой контроль точечной сварки в автомобильной промышленности. Krautkramer — Sonderdruck Nr. SD 298 (1999)
Денисов, А.А., Шакарджи, К.М., Маев, Р.Г., Пай, Дж. М., Лоуфорд, Б.Б .: Анализ точечных сварных швов с помощью двумерных ультразвуковых решеток. NIST, J. Res. Natl. Inst. Стоять. Technol. 109 , 233–244 (2004)
Артикул Google Scholar
Mac Lauchlan, DT, Latham, WM: EMATS для проверки точечной сварки, Патент США 6250163, дата подачи 9 марта 1999 г.
Карлофф, AC, Чертов, AM, Maev, RG: Ультразвуковое обнаружение и измерение вдавливания в точечной сварке сопротивлением. AIP Conf. Proc. 1211 , 1609 (2010)
Амброзяк, А., Маев, Р.Г., Корзеневский, М., Кустрон, П., Чертов, А.М .: Ультразвуковой контроль сварных стыков стали в режиме реального времени. Сварка. Int. 25 (6), 419–423 (2011)
General Motors Corporation: Ультразвуковой метод и устройство для контроля точечной сварки, Патент США 4711984, дата подачи 9 марта 2987 г.
Kustron, P. , Коцимски, Дж., Чертов, А., Титов, С., Корзеневский, М., Амброзяк, А .: Ультразвуковое исследование качества точечной сварки в режиме реального времени с использованием установки с несколькими датчиками. AIP Conf. Proc. 1211 , 1615 (2010)
Артикул Google Scholar
Мальдаг, X .: Теория и практика инфракрасной технологии неразрушающего контроля. Уайли, Нью-Йорк (2001)
Google Scholar
Алмонд, Д.П., Патель, П.: Фототермическая наука и методы. Спрингер, Нью-Йорк (1966)
Google Scholar
Lockheed Corporation, Адамс, М.Дж., Крисман, Е.М.: Метод и устройство для термографической оценки точечной сварки, Патент США 4854724, дата подачи 5 марта 2986 г.
Шепард С.М., Чаудри Б.Б., Предмески Р.Л., Залузец М.Дж .: Импульсный термографический контроль точечной сварки. SPIE Proc. 3361 , 320–324 (1998)
Артикул Google Scholar
Shepard, SM: Автоматизированный метод и устройство для неразрушающей оценки сварных швов, Патент США 6585146 B2, дата подачи 6 января 2000 г.
Türler, D., Hopkins, D., Reverdy, F. : Неразрушающий контроль точечных сварных швов с использованием акустических и термографических методов.SAE Trans. 112 (5), 572–591 (2003)
Google Scholar
Симер У.: Моделирование и оценка новых термографических методов для использования в автомобильной промышленности. В: Материалы Европейской конференции по неразрушающему контролю, ECNDT (2006)
Siemer, U .: Einsatz der Thermografie als zerstörungsfreies Prüfverfahren in der Automobilindustrie: Entwicklung einer Ingenieurplattform ».Докторская диссертация в Саарландском университете, 8 октября 2010 г.
Schlichting, J., Brauser, S., Pepker, L., Maierhofer, C., Rethmeier, M., Kreutzbruck, M .: Термографические испытания точечная сварка. NDT & E Int. 48 , 23 (2012)
Артикул Google Scholar