Оборудование Димет: Технология
Технология нанесения металлов на поверхность деталей и изделий, реализуемая оборудованием ДИМЕТ®, использует газодинамический (газотермический) метод нанесения покрытий. Метод разработан на основе открытого в 80-х годах прошлого столетия эффекта закрепления твердых частиц, движущихся со сверхзвуковой скоростью, на поверхности при соударении с ней. Технология является новой и ранее в промышленности не использовалось. Оборудование ДИМЕТ® сертифицировано по системе ГОСТ Р. Сертификат соответствия N РОСС RU.ТН02.Н00580.
Основные элементы технологии
Технология нанесения покрытий включает в себя нагрев сжатого газа (воздуха), подачу его в сверхзвуковое сопло и формирование в этом сопле сверхзвукового воздушного потока, подачу в этот поток порошкового материала, ускорение этого материала в сопле сверхзвуковым потоком воздуха и направление его на поверхность обрабатываемого изделия.
В качестве порошковых материалов используются порошки металлов, сплавов или их механические смеси с керамическими порошками.
Особенности технологии
В технологии напыления Димет (которую на практике удобно называть «наращиванием» металла) условие, чтобы падающие на подложку частицы имели высокую температуру, не является обязательным, что обуславливает ее уникальность. В данном случае с твердой подложкой взаимодействуют частицы, находящиеся в нерасплавленном состоянии, но обладающие очень высокой скоростью. Ускорение частиц до нужных скоростей осуществляется сверхзвуковым воздушным потоком с помощью оригинальных установок серии ДИМЕТ®, не имеющих аналогов в традиционных методах нанесения покрытий.
Способ формирования металлических покрытий оборудованием ДИМЕТ® — в газодинамическом (газотермическом) методе, т.е. закрепление твердых металлических частиц, обладающих большой кинетической энергией, на поверхность подложки в процессе высокоскоростного удара.
Привлекательность технологии нанесения металла на поверхность деталей и изделий состоит в том, что оборудование и создаваемые с его помощью покрытия свободны от большинства недостатков, присущих другим методам нанесения металлических покрытий, и обладают рядом технологических, экономических и экологических преимуществ.
Расходные материалы
Для нанесения покрытий с помощью оборудования ДИМЕТ® необходимы специальные порошковые материалы (композиции), которые разрабатываются и производятся из порошков, выпускаемых российской промышленностью. Рекомендации по применению порошковых материалов для различных случаев применения представлены тут.
Расходными элементами при работе оборудования являются также сменные сопловые вставки, которые изнашиваются в процессе нанесения покрытий.
Газодинамическое напыление | Цинкование металлопроката | Компания Мир Металла (Москва, Люберцы)
Газодинамическое напыление металла и других металлических изделий, — это быстрый, эффективный и малозатратный способ защиты металлоизделий от коррозии и воздействия внешней природной среды.
Технология газодинамического цинкования или напыления (ХГН) позволяет напылять цинковые, алюминиевые, медные, никелевые оловянные покрытия, для чего используются соответствующие порошки или смеси данных порошков с керамической крошкой.
Такое покрытие характеризуется высокой прочностью, отличными эксплуатационными свойствами и что очень важно – может наноситься любая требуемая толщина цинкового покрытия.
Данным методом можно производить цинкование, которое аналогично ГОСТ 9.316-2006 нижеперечисленных металлических изделий:
- цинкованых кованых изделий;
- цинкование крупногабаритных изделий;
- цинкование сложных металлических конструкций;
- цинкование мелких металлических деталей;
- цинкование крепежных изделий;
- цинкование метизов;
- цинкование кронштейнов;
- цинкование баков;
- цинкование стальных листов;
- цинкование автобусных остановок;
— для восстановления поврежденных поверхностей и утраченных объемов изделия
— очистки поверхностей металла и бетона
— матирования поверхностей и создание требуемого микрорельефа
— для нанесения цинковых и иных композитных покрытий
— очистки и покраски автомобильных дисков
— восстановление поверхности кованых изделий
— восстановление внутренней и внешней поверхности труб б/у
— узлов гидравлических систем
Напыление металлов.

В процессе напыления поток мелкодисперсных расплавленных или нагретых до кипения частиц направляют на поверхность металла. При взаимодействии с поверхностью распыляемые элементы осаждаются на поверхности заготовки, обеспечивая надёжный неразрушаемый контакт.
В общем виде существует два основных вида напыления: газодинамическое и вакуумное. При вакуумном напылении перенос напыляемых частиц осуществляется при разрежении 10-2 Па, что способствует более плотному прилеганию напыляемого слоя и производится в магнетронных, катодных или ионно-плазменных установках. В этих установках на обрабатываемую поверхность подаётся поток расплавленных мелкодисперсных частиц, поскольку считалось, что для создания устойчивого, малопористого и однородного слоя это условие является обязательным.
Технология газодинамического напыления включает в себя подачу через сверхзвуковое (600-700 м/с) сопло мелкодисперсных частиц металла (0,01-50 мкм) и нагрев сжатого воздуха до 400-600°C. В результате образуется слой металла, который обладает высокой адгезией (40-100 Н/мм2) и низкой пористостью (1-3%).
Напыление металлов — одна из самых современных и перспективных технологий кузовного ремонта.
Напылением решается задача восстановления изношенных поверхностей, геометрии кузова, ремонт легкосплавных деталей и механизмов (устранение трещин, сколов).
Кроме того, напыление цинка или цинкование — лучшая защита металла и сварочных соединений от коррозии.
Если даже не нагревать напыляемые частицы до температуры плавления, а направить поток на обрабатываемую поверхность со сверхзвуковой скоростью 600-700 м/с (скорость звука составляет 331 м/с), то показатели полученного покрытия: на отрыв, микротвёрдость, пористость и однородность, ничем не уступали покрытиям, полученным при высокотемпературном напылении.
Дело в том, что при нагревании давление воздуха в камере в соответствии с законом Шарля повышается, а следовательно, повышается и скорость истечения из сопла.
MIG-пайка кузова
Процесс пайки не разрушает цинковый защитный слой и тем более металл. MIG-Пайка происходит при более низкой температуре плавления припоя — приблизительно 900°C. Кроме того, медная пайка обладает отличными антикоррозийными свойствами.
Ремонт алюминия
Использование алюминия в автомобилестроении снижает вес автотранспорта и при этом это очень прочный металл. Кроме того, алюминий поглощает силу удара — деформации кузова при этом расположены в месте, где был нанесен удар.
Защита металлов от коррозии
Коррозия — это разрушение металла или сплава в результате его окисления под воздействием окружающей среды. В наибольшей степени коррозии подвергаются кузовные элементы автомобиля (особенно сварочные соединения). Коррозия не только ослабляет металл, но и может стать причиной разрушения кузова.
Реставрация авто
Плохое состояние кузова совершенно не говорит о том, что ему вынесен окончательный приговор. Реставрацией называется комплекс ремонтно/изготовительных процессов для восстановления первоначальных форм и функциональных характеристик автомобиля.
Ультразвуковая обработка
Ультразвук позволяет снять напряжения с поверхности металла методом образования «микроребер жесткости», которые возникают под действием акустической энергии. При ультразвуковом поверхностном упрочнении повышаются микротвёрдость и износостойкость металла.
Цинкование кузова
Самым распространённым способом защиты металлов от коррозии является цинкование, дающее наиболее длительную — 25-30 лет защиту. На воздухе цинк покрывается тонкой оксидной или карбонатной плёнкой, которая защищает железо от взаимодействия с окружающей средой.
Напыление цинка
Технологическим прорывом в сфере ремонта и восстановления металла стала технология напыления. Покрытие цинком или цинкование — лучшая защита металла и сварочных соединений от коррозии.
Лужение кузова
Лужение — нанесение на поверхность металла слоя олова или сплава на его основе. Оловянное покрытие применяется для защиты металлических изделий от коррозии. Его основные преимущества — хорошая адгезия и защита от коррозии, а также легкая обрабатываемость.
Please enable JavaScript to view the comments powered by Disqus.
Газодинамическое сверхзвуковое напыление металла | Sur-Face
Отправить запрос
Отправьте нам свое сообщение и в ближайшее время оно будет обработано.
Газодинамическое напыление – это процесс, при котором формируется плотное и качественное покрытие вследствие соударения холодных частиц металла с поверхностью обрабатываемых деталей. При этом металлические песчинки подаются в газовом потоке со скоростью до 1000 м/сек. Во время ударов нерасплавленной частицы металла о поверхность изделий они деформируются, а их кинетическая энергия превращается в тепловую. Вследствие этого и формируется сплошной слой из плотно расположенных друг к другу деформированных песчинок. Основная особенность газодинамического сверхзвукового напыления металлов – формирование покрытий осуществляется в условиях комнатных температур, поэтому устраняется риск окисления материала и поверхности деталей, отсутствует неравновесная кристаллизация и высокие внутренние напряжения в обрабатываемых изделиях.
Наш коллектив занимается газодинамическим напылением металлов в Москве и области. Мы используем проверенные напыляемые материалы, благодаря чему металлические и полимерные покрытия получаются качественными, прочными, плотными и долговечными. Также наши специалисты применяют высокотехнологичное оборудование, что позволяет выполнять напыление металлов в максимально сжатые сроки.
Газодинамическое сверхзвуковое напыление металла
Технология газодинамического сверхзвукового напыления металлов позволяет качественно подготовить любую твёрдую поверхность для дальнейшего нанесения металлического и полимерного покрытия с высокой адгезией. Суть данной методики заключается в следующем: в малогабаритные сверхзвуковые аппараты подаются сжатые воздушные массы и углеродное горючее, которое под действием плазмоэлектрохимических устройств воспламеняется в камерах сгорания. Через реактивную горелку подаётся струя посредством трансформации химической энергии горючего в кинетическую энергию продукта сгорания.
Изначально в ускоряющие каналы подаются абразивные частицы, которые удаляют коррозию, органические вкрапления и окисные плёнки, делая обрабатываемую поверхность слегка шероховатой. Затем до того момента, пока не образовалась устойчивая окисная плёнка, в ускоряющие каналы подаются напыляемые металлические частицы, которые в дальнейшем и будут составлять защитное покрытие. Очень часто эти процессы объединяют. В качестве напыляемых материалов обычно используют цинковый, медный, алюминиевый, никелевый порошок или любую порошковую краску.
Области применения
Богатый опыт позволяет нашим мастерам выполнять газодинамическое сверхзвуковое напыление металлов в различных отраслях.
Обработка металлических зданий и сооружений, в которых хранят зерновые культуры, содержат крупный и мелкий скот.
Обработка мостовых и дорожных металлических ограждений, защита от негативных воздействий окружающей среды.
Нередко в наш коллектив обращаются клиенты с просьбой нанести защитное металлизированное покрытие на кузов легковых и грузовых автомобилей, фургонов, фур и автобусов. Также мы осуществляем обработку поверхности других видов транспорта (вагоны поездов, баржи и танкеры, портовая и специальная техника).
Наши специалисты применяют газодинамическое напыление для нанесения защитных покрытий на трубопроводы, металлические конструкции, расположенные под открытым небом, системы электростанций и др.
Обработка металлических строительных конструкций, отдельных частей зданий и сооружений.
Практически любая металлическая поверхность после очистки может быть покрыта слоем другого металла, имеющего повышенную стойкость к коррозии и таким образом защищена от воздействий окружающей среды. Пример такой обработки — холодное цинкование, применяющееся после пескоструйной или дробеструйной обработки.
Поделиться этой страницей
Газодинамическое напыление — Компания «АРГОН-СЕРВИС»
Компания «АРГОН-СЕРВИС» осуществит холодное газодинамическое напыление в Пензе, подойдя к своей работе ответственно и профессионально. Сама услуга газодинамического напыления – это новое слово в ремонте металлических запчастей, включая радиаторы охлаждения и кондиционеры, напыление шеек блоков цилиндров и многое другое. При этом мы работаем с абсолютно разными металлами и берёмся даже за самые сложные, на первый взгляд, задачи.
На сегодняшний день газодинамическое напыление с одной стороны ещё новая, но в то же время весьма востребованная услуга, т.к. это один из самых эффективных способов восстановления металла. А иногда и единственный.
В чём основные преимущества газодинамического напыления?
Нет ничего удивительного в том, что газодинамическое напыление в Пензе стало популярным благодаря ремонту автомобилей. Совершенно не важно, говорим ли мы о ремонте кондиционера или повреждении двигателя – порой метод напыления металла является единственным способ спасти запчасть от её полной замены. Но ключевые преимущества такого подхода можно выделить отдельно:
- Мы можем осуществлять покрытие металла в мастерской, не создавая для этого специальных условий;
- Нагревание самой детали не может быть выше 100-150 градусов, благодаря чему исключается риск деформации и излишнего напряжения;
- Полная безопасность – никакой химической реакции, излучения или высокой температуры.
- Поверхность очищается от красок, масел и технических загрязнений, активируется кристаллическая решетка металла. Это становится возможным благодаря напылению путем высокоскоростного потока частиц.
- Возможность обработки локальных участков без попадания на другие детали, поскольку воздействие является узконаправленным и характеризуется малым поперечным пересечением.
- Нанесение различных типов покрытия путем использования всего одной и той же установки.
- Результат способен превзойти любые ожидания, гораздо лучше, чем восстановление металла любым другим методом.
Но что представляет собой газодинамическое напыление в Пензе на практике? Если коротко, то суть технологии заключается в следующем – сжатый воздух нагревается, дальше поступает в соло, где формируется воздушный поток со сверхзвуковой скоростью. После чего металлический порошок подаётся в поток и наносится на поверхность детали. Таким образом и работает один из самых эффективных и доступных методов по восстановлению металлических деталей.
Ремонт каких металлических деталей мы осуществляем?
Как мы уже отмечали ранее, одно из важнейших преимуществ метода нанесения на металлическое покрытие в том, что температура не может быть выше 150 градусов. А это значит мы можем широко применять его в любых авторемонтных работах:
- Осуществляем ремонт радиаторов, генераторов;
- Устраняем коррозию и места прогаров на блоках цилиндров,
- Заделываем повреждения в БЦ, ГБЦ и других механизмах авто,
- Восстанавливаем и герметизируем места утечки в автомобильных кондиционерах,
- Обрабатываем швы и сварные участки для защиты от коррозии (в случаях ремонта кузовов и глушителей) и локальных мест,
- Ремонтируем посадочные места коленвалов и обогреватели задних стекол;
- Герметизируем топливные баки.
Помимо авторемонта газодинамическое напыление применяется для многих других видов ремонтных работ по восстановлению металла:
- Наращивание металла,
- Герметизация агрегатов (для устранения течей)
- Нанесение антифрикционных и теплоизлучающих покрытий, подслоев для пайки, электропроводящих покрытий
- Герметизация сварных швов и стыков
- Защита от коррозии, образующейся при высоких температурах,
- Применение для декоративных и отделочных целей.
И это лишь малая часть тех услуг, что оказывает компания «АРГОН-СЕРВИС». Как правило, мы стараемся подходить к своей работе индивидуально, и заранее консультируем своего клиента по вопросу возможности восстановления его металлической запчасти посредством технологии напыления. Несмотря на доступность метода, существуют и ограничения, которые могут определить специалисты, в том числе и уточнив самые важные детали по телефону.
Газодинамическое напыление в Пензе от «АРГОН-СЕРВИС» доступно каждому!
Помимо высококлассного сервиса, а также тесной работы со своими клиентами, мы делаем всё возможное, чтобы наши цены на услуги были максимально демократическими. Неважно, приходите вы к нам за сваркой аргоном, ремонтом радиаторов или вас интересует газодинамическое напыление в Пензе – вы можете рассчитывать на то, что вас ждут одни из самых низких цен в городе, и в то же время вашей проблемой займутся настоящие профессионалы.
Пишите, звоните – будем рады видеть вас у себя в сервисе и всегда готовы ответить на любые возникшие вопросы.
ГАЗОДИНАМИЧЕСКОЕ НАПЫЛЕНИЕ
Газодинамическое напыление металла
Технология позволяет наносить металлические покрытия не только на металлы, но и на стекло, керамику, камень, бетон. К настоящему времени технология позволяет наносить покрытия из алюминия, цинка, меди, олова, свинца, баббитов, никеля и наносить их не только на металлы, но и на стекло, керамику, камень, бетон.Важно, что температуры при нанесении покрытий не превышают 150 градусов, т.е. температуры работающего двигателя, что позволяет широко применять в авторемонтных работах, а именно:
- Ремонт головки блока цилиндров двигателя;
- Герметизация топливных баков;
- Ремонт радиаторов;
- Ремонт и восстановление кондиционеров автомобиля;
- Ремонт посадочных мест коленвалов и постелей распредвалов;
- Ремонт обогревателей заднего стекла;
- Цинкование, антикоррозийная обработка и многое другое.
Основные элементы технологии холодного газодинамического напыления
Технология газодинамического напыления металлов включает в себя нагрев сжатого газа (воздуха), дальнейшее поступление его в сверхзвуковое сопло с формированием в сопле воздушного потока сверхзвуковой скорости. Далее питатель подает в сверхзвуковой поток металлический порошок (особым образом подготовленный), частицы металла разгоняются и направляются на поверхность детали.
Ремонт ГБЦ, отремонтированный блок цилиндров
В качестве порошковых материалов используются порошки металлов, сплавов или\и их смеси с керамическими порошками. Все составы порошков разработаны специально именно для оборудования. Изменяя режимы работы оборудования можно либо проводить эрозионную (струйно-абразивную) обработку поверхности изделия, либо наносить металлические покрытия требуемых составов.
Преимущества метода газодинамического напыления в следующем:
- Нанесение покрытий при любых значениях температуры и влажности окружающей среды, в обычных условиях мастерской;
- Покрытие не нагреваентся свыше 100-150 градусов, следовательно нет внутренних напряжений деталий, деформаций и окисления материалов покрытия и детали;
- Безопасность — отсутствуют высокие температуры, опасные газы и излучения, нет химически агрессивных отходов, требующих специальной нейтрализации;
- Оборудование используем не только в стационарных условиях, но и в полевых
Газодинамическое напыление металла.
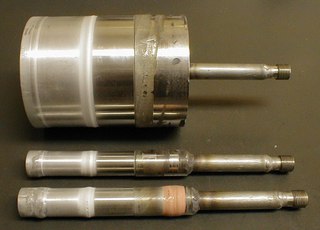
По сути, — более продвинутый вариант давно уже зарекомендовавшего себя газотермического способа восстановления различных металлических деталей и поверхностей. Cold Spray или просто ХГН значительно расширяет возможности «горячего» метода обработки изделий.
В настоящее время, бесспорно, это самая передовая технология восстановления и защиты материалов, получившая широкое распространение как в промышленном секторе, так и гражданской сфере.
Принцип действия, плюсы и минусы ХГН
Имеет два основных отличия от газотермического метода реставрации. Во-первых, напыление защитного или восстановительного покрытия происходит при пониженной температуре, не превышающей 150 °С, что в свою очередь не вызывает напряжения в обрабатываемых деталях и их деформации. Во-вторых, «холодная» технология позволяет создавать слой регулируемой толщины и в точно заданных границах. О других плюсах и минусах расскажем чуть позже, а пока об авторах метода и о том, как он работает.
Его разработчиком является «Обнинский центр порошкового напыления» (Россия). Производимое ими оборудование получило название ДИМЕТ ® . Оно сертифицировано по системе ГОСТ Р и защищено патентами России, США, Канады и других стран. В основу технологии заложен принцип сверхзвукового воздействия мельчайшими частицами легкоплавких и других материалов на обрабатываемую поверхность. В основном это полимеры или сплавы карбидов с металлами с размером частиц 0,01-0,5 мкм. Смешиваясь с газом они подаются на изделие со скоростью 500-1000 м/с.
В зависимости от состава расходного материала (порошка) и изменения режимов его нанесения можно получить однородное или композиционное покрытие с твердой или пористой структурой и своей функциональной задачей. Это может быть: восстановление геометрии изделия, упрочнение и защита металла от коррозии, повышение тепло- и электропроводности материала, а также образование износостойкого покрытия, выдерживающего воздействие химически активных сред, высоких тепловых нагрузок и т. д.
Кстати, обнинские инженеры разработали уже несколько модификаций установок ДИМЕТ ® . Учитывая широкую востребованность данного оборудования, сейчас серийно выпускаются как ручные, так и автоматизированные аппараты холодного газодинамического напыления, что позволяет использовать их в промышленности, нефтегазовой отрасли, а также в малом бизнесе для обработки небольших деталей. Тем более, что ничего особо сложного в самой технологии нет. Для работы комплекса (помимо материала для напыления) необходим только сжатый воздух (подается под давлением 0,6-1,0 МПа и расходом 0,3-0,4 м3/мин.) и электросеть напряжением 220 В.
Теперь ещё о преимуществах и недостатках метода. Во-первых, в отличие от газотермического способа ХГН может эффективно применяться при обычном давлении, в любом температурном диапазоне и уровне влажности. В-вторых, он экологически абсолютно безопасен. В-третьих, благодаря большой скорости, может применяться и для абразивной чистки поверхности. Ну, а единственным недостатком технологии является возможность нанесения покрытий только из относительно пластичных металлов, таких как медь, алюминий, цинк, никель и др.
Область применения ХГН
Более подробно хотелось бы остановиться на сферах использования технологии холодного газодинамического напыления порошковыми материалами, чтобы наглядно показать насколько она сегодня востребована.
Устранение дефектов, восстановление поверхностей и герметизация
Всё это — работа, которой могут заниматься даже малые предприятия. К примеру, в небольших мастерских можно ремонтировать детали из легких сплавов (части автомобильной конструкции, допустим), прежде всего, алюминиевых и алюминиевомагниевых. Причем, легко устраняются дефекты, возникшие как в процессе производства, так и в процессе эксплуатации. А отсутствие сильного нагрева и низкая энергетика метода позволяют чинить даже тонкостенные изделия.
Отлично подходит ХГН и для восстановления изношенных поверхностей. Например, такой трудоемкий процесс, как «наращивание» металла в посадочных местах подшипников, теперь могут осуществлять даже малые предприятия, не говоря уже о восстановлении герметизации (когда применение жидких герметиков невозможно) в трубопроводах, теплообменниках или сосудах для рабочих газов, жидкостей.
Очень эффективен в ремонте сложных изделий, где требуется точное восстановление геометрических параметров, устранение скрытых дефектов, но при этом с сохранением всех эксплуатационных характеристик, а также товарного вида. Именно поэтому данный метод активно используется в оборонно-промышленном комплексе, железнодорожной и авиационной промышленности, сельском хозяйстве, газоперекачке и пр.
Не обойтись без этой технологии и в создании контактных площадок. Благодаря возможности легкого нанесения покрытий на любые металлические, керамические и стеклянные поверхности ХГН применяется и в производстве электротехнических изделий. Например, в процессах меднения, создании силовых токонесущих сетей, нанесении токовводов, изготовлении подслоев под пайку и т. д.
Антикоррозийная обработка и устранение глубоких дефектов
Напыление так называемого антифрикционного покрытия — высокоэффективный способ избавления от локальных повреждений (глубоких сколов, задиров, царапин). Это позволяет избежать процедуры полной перезаливки или даже замены изделия, что, естественно, экономически не выгодно.
А в антикорроизонной обработке и защите от высокотемпературной коррозии различных коммуникаций данному методу вообще нет равных. К слову, различные модификации оборудования ДИМЕТ ® обеспечивают качественную обработку внутренней поверхности труб диаметром от 100 мм и длиной до 12 м.
Процесс газодинамического напыления представляет собой закрепление частиц металла на металлических, стеклянных, керамических или бетонных изделиях в момент соударения газопорошковой смести с внешней поверхностью-подложкой. Происходит это благодаря предварительному ускорению этих частиц в сопле для сверхзвукового разгона частиц, при этом температура разгоняемых металлических частиц не превышает температуру их плавления. Металлический слой, нанесенный на изделие по методу холодного газодинамического напыления, отличается качественной сцепкой с поверхностью основы и устойчив к механическим повреждениям.
История открытия явления и факты, обнаруженные опытным путем
Тот факт, что для образования металлического покрытия на поверхности-подложке нет необходимости доводить металлические частицы до состояния плавления или близкого к нему, как это обычно происходит при использовании стандартных методик напыления, был обнаружен в конце ХХ века российскими учеными. Результаты ряда экспериментов, проводимых научными сотрудниками РАН, показали, что поверхностное напыление можно получать и при нагреве твердых металлических частиц до температуры, которая гораздо ниже температуры их плавления.
Кроме того, в ходе экспериментов были зафиксированы следующие важные факты:
- главным параметром в технологии холодного газодинамического напыления, от которого зависит качество адгезии, является скорость разгона газопорошковой смеси. Именно этот параметр влияет на степень сцепки напыления с поверхностью, на которую оно наносится, а также на такие характеристики напыляемого слоя, как пористость и механическая прочность.
При скорости твердых частиц выше 500-600 м/с эрозийные процессы трансформируются в прочный слой напыления;
- эмпирическим путем был обнаружен критический предел расхода частиц, при котором металлический слой не образуется при любой длительности воздействия газопорошкового потока на подложку;
- если расход порошка превышает критическую величину, то происходит крепкое и надежное сцепление частиц на напыляемой поверхности, и образуется плотный напыляемый слой;
- из всего объема твердых частиц, разгоняемых сверхзвуковым потоком, только небольшое количество образует слой поверхностного напыления. Основная масса частиц распыляется и не имеет возможности закрепиться на обрабатываемой поверхности. Соответственно, количество металлических частиц, наносимых и фиксирующихся на изделии, напрямую зависит от объема расходуемого порошкового материала;
- поверхность подложки в процессе формирования слоя напыления нагревается незначительно.Температура поверхности, обтекаемой потоком газа и подложки, которая находится в процессе газодинамического напыления, отличается друг от друга примерно на 45 градусов.
Виды холодного газодинамического напыления и их преимущества
Холодное газодинамическое напыление имеет 2 вида:
- Напыление высокого давления, при котором используется гелий, азот или смесь газов. Расход порошкового материала составляет 4,5-13,5 кг/ч.
- Холодное газодинамическое напыление низкого давления, осуществляемое при помощи сжатого воздуха. Объем расходуемого порошка колеблется в пределах 0,3-3 кг/ч.
Оба вида напыления имеют свои преимущества и недостатки:
- при использовании в технологическом процессе высокого давления покрытие получается более качественным, при том, что размер твердых частиц металлического порошка может варьироваться от 5 до 50 мкм, а не в пределах 5-30 мкм, как в технологии со сжатым воздухом;
- в технологическом процессе напыления низкого давления используется менее габаритное оборудование, стоимость которого значительно ниже того, что используется для напыления под высоким давлением.
Технологический процесс напыления высокого и низкого давления
В процессе холодного напыления высокого давления газ нагревается и соединяется с твердыми частицами порошкового материала. Эта газопорошковая смесь поступает в сверхзвуковое сопло, разгоняется там до сверхзвуковой скорости и под давлением 7-40 бар направляется на поверхность изделия, на котором необходимо образовать металлическое покрытие.
Холодное напыление, при котором используется сжатый воздух, технологически отличается от метода напыления под высоким давлением тем, что основные процессы происходят сразу в сопле для разгона частиц до сверхзвуковой скорости: газ нагревается непосредственно в нем, а порошок поступает в сопло перпендикулярно газовому потоку. Кроме того, при использовании метода напыления с низким давлением используются порошки, в которых кроме частиц металла присутствуют керамические частицы. Такие добавки улучшают состояние поверхности изделия, на которое наносится напыление, и повышают качество адгезии материалов. Кроме того, в процессе прохождения потока смеси через оборудование керамические частицы дополнительно очищают стенки и выходное отверстие сопла.
Область применения холодного газодинамического напыления
Холодное газодинамическое покрытие применяется для решения следующих задач:
- реставрация металлических деталей, которые были подвержены сколам, трещинам, истиранию и другим механическим повреждениям;
- покрытие металлических изделий напылением с целью увеличения их антикоррозийных и теплопроводных свойств;
- защита контактных поверхностей наконечников металлических кабелей.
Покупка и продажа оборудования для бизнеса
- Главная
- Информационные статьи
- Технологии
- “Оборонка” поделилась методом реставрации металлических изделий
Кстати, обнинские инженеры разработали уже несколько модификаций установок ДИМЕТ. Учитывая широкую востребованность данного оборудования, сейчас серийно выпускаются как ручные, так и автоматизированные аппараты холодного газодинамического напыления, что позволяет использовать их в промышленности, нефтегазовой отрасли, а также в малом бизнесе для обработки небольших деталей. Тем более, что ничего особо сложного в самой технологии нет. Для работы комплекса (помимо материала для напыления) необходим только сжатый воздух (подается под давлением 0,6-1,0 МПа и расходом 0,3-0,4 м3/мин.) и электросеть напряжением 220 В.
Теперь еще о преимуществах и недостатках метода. Оборудование для напыления металлов из китая? Во-первых, в отличие от газотермического способа ХГН может эффективно применяться при обычном давлении, в любом температурном диапазоне и уровне влажности.
В-вторых, он экологически абсолютно безопасен. В-третьих, благодаря большой скорости, может применяться и для абразивной чистки поверхности. Ну, а единственным недостатком технологии является возможность нанесения покрытий только из относительно пластичных металлов, таких как медь, алюминий, цинк, никель и др.
Область применения ХГН
Более подробно хотелось бы остановиться на сферах использования технологии холодного газодинамического напыления порошковыми материалами, чтобы наглядно показать насколько она сегодня востребована.
Устранение дефектов, восстановление поверхностей и герметизация
Все это – работа, которой могут заниматься даже малые предприятия. К примеру, в небольших мастерских можно ремонтировать детали из легких сплавов (части автомобильной конструкции, допустим), прежде всего, алюминиевых и алюминиевомагниевых. Причем, легко устраняются дефекты, возникшие как в процессе производства, так и в процессе эксплуатации.
А отсутствие сильного нагрева и низкая энергетика метода позволяют чинить даже тонкостенные изделия.
Отлично подходит ХГН и для восстановления изношенных поверхностей. Например, такой трудоемкий процесс, как “наращивание” металла в посадочных местах подшипников, теперь могут осуществлять даже малые предприятия, не говоря уже о восстановлении герметизации (когда применение жидких герметиков невозможно) в трубопроводах, теплообменниках или сосудах для рабочих газов, жидкостей.
Высокоточное восстановление деталей различных механизмов, токопроведение
ХГН очень эффективен в ремонте сложных изделий, где требуется точное восстановление геометрических параметров, устранение скрытых дефектов, но при этом с сохранением всех эксплуатационных характеристик, а также товарного вида. Именно поэтому данный метод активно используется в оборонно-промышленном комплексе, железнодорожной и авиационной промышленности, сельском хозяйстве, газоперекачке и пр.
Не обойтись без этой технологии и в создании контактных площадок. Цены на оборудование для напыления металлов? Благодаря возможности легкого нанесения покрытий на любые металлические, керамические и стеклянные поверхности ХГН применяется и в производстве электротехнических изделий. Например, в процессах меднения, создании силовых токонесущих сетей, нанесении токовводов, изготовлении подслоев под пайку и т. д.
Антикоррозийная обработка и устранение глубоких дефектов
Напыление так называемого антифрикционного покрытия – высокоэффективный способ избавления от локальных повреждений (глубоких сколов, задиров, царапин). Это позволяет избежать процедуры полной перезаливки или даже замены изделия, что, естественно, экономически не выгодно.
А в антикорроизонной обработке и защите от высокотемпературной коррозии различных коммуникаций данному методу вообще нет равных. К слову, различные модификации оборудования ДИМЕТ ® обеспечивают качественную обработку внутренней поверхности труб диаметром от 100 мм и длиной до 12 м.
Дополнительная информация:
Газодинамическим методом наносятся жаростойкие покрытия, которые обеспечивают защиту вплоть до 1000-1100 градусов Цельсия. Электропроводность в среднем составляет 80-90 % электропроводности объемного материала. Коррозионная стойкость зависит от характеристик агрессивной среды.
Работа оборудования ДИМЕТ, разработанного и серийно выпускаемого ” Обнинским центром порошкового напыления” (ООО “ОЦПН “), основана на эффекте закрепления частиц металла, если они движутся со сверхзвуковой скоростью, на поверхности при соударении с ней, газодинамическое напыление металлов ДИМЕТ. Технология позволяет наносить металлические покрытия не только на металлы, но и на стекло, керамику, камень, бетон. К настоящему времени технология ДИМЕТ позволяет наносить покрытия из алюминия, цинка, меди, олова, свинца, баббитов, никеля и наносить их не только на металлы, но и на стекло, керамику, камень, бетон.
Специалисты Плакарта производят покрытия газодинамическим способом для промышленного оборудования (например, на фото – антикоррозионное покрытие теплообменника без демонтажа). Кроме того, мы поставляем установки холодного газодинамического напыления под ключ (наладка, сервис, обучение).
В зависимости от состава расходного материала (порошка) и изменения режимов его нанесения можно получить однородное или композиционное покрытие с твердой или пористой структурой и своей функциональной задачей. Это может быть: восстановление геометрии изделия, упрочнение и защита металла от коррозии, повышение тепло- и электропроводности материала, а также образование износостойкого покрытия, выдерживающего воздействие химически активных сред, высоких тепловых нагрузок и т. д.
В описании изобретения Браунинга данные проблемы оговариваются, но не разрешаются. Выход из данного положения открывает метод напыления, в котором порошок не нагревается до расплавленного состояния. Идея о возможности “холодной сварки” мелких металлических частиц при высокоскоростном соударении их с твердой поверхностью высказана в изобретении Шестакова еще в 1967 году Предложение о холодной сварке частиц в динамическом режиме в свое время не получило развития.
Оборудование для холодного газодинамического напыления металлов? Т.к. для реализации режима холодного напыления необходимы были новые предложения по устройству соплового узла.
Холодное газодинамическое напыление — новейший метод в области термического напыления. По сравнению с обычными процессами термического напыления холодное газодинамическое напыление имеет особые преимущества, поскольку распыляемый материал не расплавляется и не плавится во время процесса. Таким образом, тепловое воздействие на покрытие и материал подложки остается низким.
Высокая кинетическая энергия частиц и высокая степень деформации при воздействии на подложку, которая связана с ней, позволяет изготавливать однородные и очень плотные покрытия. Диапазон толщины покрытия варьируется от нескольких сотых долей миллиметра до нескольких сантиметров.
В получаемых металлических покрытиях, физические и химические свойства практически не отличаются от свойств базового материала.
Согласно новейшей системной технологии компании «Impact Innovations GmbH» инертный газ — предпочтительно азот или гелий — подается в пистолет-распылитель под давлением до 50 бар (725 фунтов на кв. дюйм) и нагревается до максимальной температуры 1100 °C (2012 °F) в корпусе пистолета.
Последующее расширение нагретого и находящегося под высоким давлением газа в сужающемся-расширяющемся сопле до давления окружающей среды приводит к ускорению технологического инертного газа до сверхзвуковой скорости и в то же время к охлаждению газа до температуры ниже 100 °C (373 °F).
Распыляемые порошки впрыскиваются в сужающуюся часть сопла с помощью устройства подачи порошка и газа-носителя и ускоряются до скорости частиц 1200 м/с в основном газовом потоке.
В сильно суженом сопле распылителя частицы ударяются о необработанные, в большинстве случаев, поверхности компонентов, деформируются и превращаются в сильно адгезионное/когезионное и низкооксидное покрытие.
Воздействие скорости частиц на качество и эффективность покрытия
- Частица покрытия достигла минимальной скорости удара, которая необходима для возбуждения механизма взаимодействия с поверхностью подложки (обрабатываемого образца). Эта так называемая «критическая скорость» влияет на свойства материала покрытия.
- Поскольку скорость удара выше критической скорости, деформация и качество сцепления частиц возрастают.
- Если скорость удара слишком высока («скорость эрозии»), происходит больше разрушения материала, чем его добавления. Покрытие не образуется.
- Чтобы образовалось плотное и хорошо сформированное покрытие, значение скорости удара частиц должно быть между значениями критической скорости и скорости эрозии.
Что может быть покрыто методом холодного газодинамического напыления?
Материалы для покрытия
Металлы: например, магний, алюминий, титан, никель, медь, тантал, ниобий, серебро, золото и др.
Сплавы: например, никель-хром, бронза, алюминиевые сплавы, латунь, титановые сплавы, порошки из MCrAlY (сплавы на основе базового металла (Co, Ni, Cr, Fe) с добавлением хрома, алюминия и иттрия) и др.
Смешанные материалы (металлическая матрица в сочетании с твердыми фазами): например, металл и керамика, композиты.
Материалы основы
Металлические изделия и образцы, пластмасса, а также стекло и керамика.
Индивидуальная обработка
Каждый отдельный материал обрабатывается индивидуально.
Обработка материалов требует индивидуальной регулировки температуры и давления газа. Комбинация этих двух физических параметров определяет скорость частиц и качество покрытия. Диапазон оптимальной скорости распыления, ограниченный критической скоростью и скоростью эрозии, называется диапазоном осаждения. В рамках этого диапазона на качество нанесения покрытий влияют параметры.
(PDF) Сравнительный обзор процессов и технологий холодного газодинамического напыления
43. Д.-Ю. Ким, Ж.-Дж. Парк, Ж.-Г. Ли, Д. Ким, С.Дж. Тарк, С. Ан
и др., Осаждение медных электродов холодным напылением на кремниевые и стеклянные подложки
, J. Therm. Спрей Технол. 22
(2013) 1092–1102
44. H.Y. Ли, Ю. Ю, Ю. Ли, Ю. Хонг, К. Ko,
Межфазные исследования между пленками WO3, Y2O3
, нанесенными холодным напылением, и подложкой Si, Appl. Серфинг. Sci. 227 (2004)
244–249
45. И. Бурлаков, Й. Йирковский, Л. Каван, Р. Боллхорн, РБ
Хайман, Холодное газодинамическое напыление (CGDS) TiO
2
(анатаз) на полисульфоновые подложки: микро-
структурная характеристика и фотокаталитическая эффективность, J.
Photochem. Photobiol. A: Chem. 187 (2007) 285–292
46. А. Ганесан, Дж. Аффи, М. Ямада, М. Фукумото, Bonding
, исследования поведения холодного напыления меди на полимерной подложке из ПВХ
, Surf.Покрытия Технол. 207 (2012) 262–
269
47. D. Zhang, P.H. Шипвей, Д. Маккартни, Холодный газ
динамическое напыление алюминия: роль подложки
Характеристикив образовании отложений, J. Therm. Спрей
Технол. 14 (2005) 109–116
48. P.C. Кинг, С. Захири, М. Джахеди, Дж. Френд, Aluminium
покрытие из цирконата титаната свинца — исследование холодного напыления
переменных, Surf. Покрытия Технол. 205 (2010) 2016–2222
49. ПК. Кинг, А.Дж. Пул, С. Хорн, Р. де Нис, С. Гулиция, М.З.
Джахеди, Встраивание частиц меди в полимеры
холодным напылением, Surf. Покрытия Технол. 216 (2013) 60–67
50. A.S. Алхулайфи, Г.А. Бак, В.Дж. Арбегаст, Численное и экспериментальное исследование
газодинамических эффектов холодного напыления
для полимерных покрытий, J. Therm. Спрей Технол. 21
(2012) 852–862
51. Ю. Сюй, И. М. Хатчингс, Осаждение термопластичного порошка
холодным распылением, Surf.Покрытия Технол. 201 (2006)
3044–3050
52. L. Zhu, T.-C. Джен, Ю.-Т. Пан, Х.-С. Chen, Particle
Механизм связывания в холодном газодинамическом напылении: трехмерный подход
, J. Therm. Спрей Технол. 26
(2017) 1859–1873
53. Y. Kim, S. Yang, J.-W. Ли, Ж.-О. Чой, С.-Х. Ahn, C.S. Lee,
Фотоэлектрические характеристики сенсибилизированного красителем солнечного элемента
(DSSC), изготовленного с помощью системы осаждения наночастиц
(NPDS), Mater. Пер. 54 (2013) 2064–2068
54. Д.-М. Чун, С.-Х. Ан, Механизм осаждения керамических частиц
, нанесенных методом сухого напыления, при комнатной температуре с использованием системы осаждения наночастиц
, Acta Mater. 59 (2011) 2693–2703
55. H.Y. Ли, Ю. Ю, Ю. Ли, Ю. Хонг, К. Ko, Тонкопленочные покрытия
из WO
3
с помощью динамического распыления холодного газа: техническое примечание,
J. Therm. Спрей Технол. 14 (2005) 183–186
56. S.-Q. Фан, К.-J. Ли, Г.-Дж. Ян, Л.-З. Чжан, Ж.-К. Гао,
Y.-X. Xi, Изготовление нано-TiO
2
покрытия для сенсибилизированного красителем-
солнечного элемента путем вакуумного холодного напыления при комнатной температуре
, J. Therm. Спрей Технол. 16 (2007) 893–897
57. М. Ямада, Х. Исаго, Х. Накано, М. Фукумото, Холод
напыление TiO
2
Покрытие фотокатализатора азотом
технологический газ, J. Therm . Спрей Технол. 19 (2010) 1218–1223
58.S.-Q. Fan, G.-J. Ян, К.-Дж. Ли, Г.-Дж. Лю, К.-Х. Ли, Л.-З.
Чжан, Характеристика микроструктуры покрытия Nano-TiO2
, нанесенного методом холодного вакуумного напыления, J. Therm. Спрей
Технол. 15 (2006) 513–517
59. Р.Н. Раоэлисон, К. Верди, Х. Ляо, Динамическое распыление холодного газа
Аддитивное производство сегодня: возможности депозита, технологии
Технологические решения и жизнеспособные приложения, Mater. Des. 133
(2017) 266–287
60.Х. Ассади, Т. Шмидт, Х. Рихтер, Ж.-О. Kliemann, K.
Binder, F. Gärtner et al., О выборе параметров при холодном распылении
, J. Therm. Спрей Технол. 20 (2011) 1161–1176
61. М. Фукумото, Х. Терада, М. Машико, К. Сато, М. Ямада,
Э. Ямагути, Осаждение мелких частиц меди с помощью процессов холодного распыления
, Mater . Пер. 50 (2009) 1482–1488
62. G.-J. Ян, К.-Дж. Ли, С.-К. Фан, Ю.-Й. Ван, К.-Х. Li,
Влияние отжига на фотокаталитические характеристики и адгезию
наноструктурированного TiO, нанесенного методом холодного напыления в вакууме
2
покрытия, J. Therm. Спрей Технол. 16 (2007) 873–880
63. Я.-Ю. Ван, Л. И, К.-Х. Ли, Г.-Дж. Ян, Ю. Лю, К.-Дж. Li
и др., Электрические и механические свойства наноразмерных покрытий
структурированного TiN, нанесенных методом холодного вакуумного напыления
Контроль микроструктуры покрытия вид проект механизма растрескивания
термически напыленных покрытий проект
электрические и механические свойства наноразмерных покрытий -, Vaccum 86
(2012) 953–959
64.Д.-М. Чун, К.-С. Ким, Ж.-О. Цой, Г.-Ю. Ли, К.С.Ли,
S.-H. Ан, Многослойное осаждение керамики и металла при комнатной температуре
с использованием системы осаждения наночастиц
(NPDS) и процесса планаризации, Int. J. Adv. Manuf.
Technol. 72 (2014) 41–46
65. Д.М. Чун, М. Ким, J.C. Lee, S.H. Ahn, TiO
2
нанесение покрытия на металлические и полимерные подложки
методом осаждения наночастиц
system (NPDS), CIRP Ann. 57 (2008) 551–554
66. Д.-М. Чун, Ж.-О. Чой, К.С. Ли, И. Канно, Х. Котера, С.-Х.
Ahn, Система осаждения наночастиц (NPDS): низкоэнергетическая
Процессы сухого напыления без растворителей для прямого нанесения рисунка на
металлов и керамики при комнатной температуре, Int. J. Precis.
англ. Manuf. 13 (2012) 1107–1112
67. S.-Q. Fan, C.-J. Ли, Г.-Дж. Ян, Л.-З. Чжан, Ж.-К. Гао,
Y.-X. Xi, Изготовление покрытия nano-TiO 2 для сенсибилизированного красителем солнечного элемента
методом холодного вакуумного напыления при комнатной температуре
, J.Therm. Спрей Технол. 16 (2007) 892–897
68. R. Kromer, R.N. Раоэлисон, К. Ланглад, Ю. Се, М.П.
Planche, T. Sapanathan et al., Динамическое распыление холодного газа
Технология: всесторонний обзор условий обработки
для различных технологических разработок на сегодняшний день, Addit.
Производитель. 19 (2017) 134–159
69. Дж. Картикеян, Технология холодного напыления: International
Статус и усилия США (2004) 1–14
70. C.-J. Ли, Х.-Т. Ван, К. Чжан, Г.-Дж. Ян, В.-Й. Ли, Х.Л.
Ляо, Влияние напыляемых материалов и их поверхностного окисления
на критическую скорость при холодном напылении, J. Therm. Спрей
Технол. 19 (2010) 95–101
71. C.-J. Ли, В.-Й. Li, Характеристики нанесения покрытия из титана
при холодном напылении, Surf. Покрытия Технол. 167 (2003)
278–283
72. C.-J. Ли, В.-Й. Ли, Ю.-Й. Ван, Г.-Дж. Ян, Х. Фуканума,
Теоретическая модель для прогнозирования эффективности осаждения при холодном напылении
, Thin Solid Films 489 (2005) 79–85
73.К.-Дж. Ли, В.-Й. Ли, Х. Ляо, Исследование критической скорости
для осаждения частиц при холодном напылении, J.
Therm. Спрей Технол. 15 (2006) 212–222
74. J.-G. Legoux, E. Irissou, S. Desaulniers, J. Bobyn, B.
Harvey, W. Wong, E. Gagnon, S. Yue, Характеристика и оценка
производительности системы извлечения гелия
, предназначенной для холодного распыления NRC Publ Arch (NPArC)
2010, 1-22
75. CJ Sutcliffe, A.Папворт, К. Галлахер, П. Фокс, Р. Х.
Морган, У. О’Нил и др., Производство в холодном газе
— новый подход к изготовлению металлических компонентов почти чистой формы
, Mater. Res. Soc. Proc. 758 (2003) 73–84
S.T. Ойинбо и Т.-К. Jen: Manufacturing Rev.6, 25 (2019) 17
Производство в холодном газе в динамике | Департамент инженерии
Производство холодного газа в динамике
Центр инновационных производственных исследований (IMRC) Департамент инженерии
Для производства компонентов или для целей модификации и ремонта многие отрасли промышленности заинтересованы в создании компонентов аддитивно, путем нанесения плотных слоев порошковых металлов.Однако высокие температуры, применяемые в настоящее время для плавления металлических частиц, могут подорвать целостность и стабильность получаемого материала. «Холодное газодинамическое напыление» предлагает альтернативный подход «без плавления».
Недостатки существующих процессов
Добавление одного металла к другому представляет собой проблему, для решения которой существующие методы не подходят. Обычное напыление порошковых металлов требует высоких температур и обеспечивает недостаточный контроль, в то время как сварка вызывает высокую степень термической деформации.Плакировка одного металла другим с помощью лазеров связана с высокой степенью искажения, растрескивания (в некоторых системах материалов) и потерей контроля над геометрией и микроструктурой наплавленного материала. Несмотря на это, в настоящее время это метод выбора в коммерческих системах аддитивного производства. Многие проблемы, связанные с существующими технологиями, вызваны высокими температурами, необходимыми для плавления сырья — до 2000 ° C. Технология, способная соединять слои различных типов металлов и других материалов при низких температурах, дает значительные преимущества.
Динамическое напыление холодным газом
В принципе, эти возможности должны иметь динамическое напыление холодным газом (CGDS). CGDS включает газ под высоким давлением с высокой скоростью потока, нагретый до относительно низких температур (150–300 ° C). Используя сужающееся / расширяющееся сопло, поток газа — и любой порошок в нем — ускоряется до скоростей, превышающих 500-1000 м / с. Когда частицы ударяются о поверхность мишени, они сталкиваются и консолидируются, создавая локализованное кузнечное соединение. Получаемые металлические покрытия имеют очень низкую пористость и не подвержены фазовым изменениям, связанным с высокими температурами.CGDS имеет много других преимуществ. Он может обрабатывать широкий спектр металлов — например, медь, алюминий, алюминий MMC, титановые сплавы и нержавеющие стали, и можно изменять толщину слоев от нескольких микрон до нескольких тысяч микрон в зависимости от используемых скоростей перемещения. В то время как скорость осаждения для обычных процессов составляет 0,5–2,0 кг в час, ожидается, что CGDS достигнет скорости осаждения 5–30 кг в час, в зависимости от используемых материалов и имеющихся запасов газа.
Преимущества CGDM:
- Высокая плотность материала
- Минимальная тепловая нагрузка на подложку
- Низкое содержание оксидов
- Сильно деформированная микроструктура
- Фазовая и композиционная стабильность
- Низкое остаточное напряжение
- Хорошая обработка поверхности
- Высокая эффективность наплавки
- Минимальный рост зерен (возможно сохранение нанокристаллических структур)
- Низкие капитальные и эксплуатационные расходы (по сравнению с лазером)
- Управляемый сфокусированный «луч» из материала
- Порошковое сырье можно смешивать и сортировать до функционально классифицированных материалов.
- Осаждение и / или нанесение на разнородные материалы и сплавы.
Из этого можно понять, что CGDS может быть идеальной основой для процесса производства компонентов и, таким образом, для динамического производства холодного газа (CGDM).
Цель исследования
Целью является разработка системы для производства металлических деталей путем сверхзвукового холодного осаждения полимерных, металлических и керамических порошков.
График проекта
- Установите возможность «холодного распыления».
- Переход на твердую свободную форму, системная интеграция.
- Продемонстрировать промышленную применимость и развивать совместные партнерские отношения.
Экспериментальное устройство CGDM, которое было разработано собственными силами, могло работать с гелием, азотом или даже сухим воздухом, но IMRC выбрала работу с гелием, поскольку скорость звука в два раза выше и, таким образом, увеличивает кинетическую энергию частиц, что приводит к большей пластичности. деформация при ударе и улучшенное уплотнение материала.
Исследование
Основным исследуемым материалом является алюминий, так как его особенно трудно обрабатывать лазером. Цель состоит в том, чтобы развить хорошее понимание механики процесса осаждения и оценить качество и особенности обращения с производимыми материалами, сравнивая их с сыпучим материалом в его деформируемой и литой формах. Кроме того, IMRC определит ряд труднообрабатываемых сплавов, например суперсплавы на основе никеля, и подвергнет их одинаковому анализу.Цель состоит в том, чтобы изучить потенциал для производства на месте ряда компонентов на основе металлов.
Завод по переработке гелия
Наилучшие результаты в CGDM достигаются при использовании гелия в качестве технологического газа, однако стоимость гелия делает его использование непомерно высоким с коммерческой точки зрения. В Кембридже мы работаем с BOC над разработкой и оценкой потенциала извлечения и рециркуляции гелия для этого процесса. Компания BOC разработала и установила систему, которая может улавливать, очищать и сжимать поток технологического газа, готовый к повторному распылению.Система является полностью гибкой и настраиваемой, а рабочий процесс не зависит от уровней чистоты газа на входе. Ожидается, что при производстве компонентов будет достигнута эффективность извлечения, превышающая 85%, что сделает использование гелия рентабельной альтернативой азоту. Мы считаем, что это единственный объект такого типа в мире.
Приложения
ПокрытияCGDS успешно применяются в промышленных масштабах для крепления радиаторов и конденсаторов, а также алюминиевых заземляющих лент.В настоящее время д-р Билл О’Нил создает специальную группу по интересам для производителей из ряда секторов, которые могут извлечь выгоду из этой новой технологии. CGDM очень интересен: он потенциально может решить проблемы совместимости материалов, связанные с производством структур из градиентных сплавов. Это также могло бы произвести революцию в индустрии модификации и ремонта пресс-форм, а также в индустрии ремонта компонентов турбин. Команда IMRC в настоящее время разрабатывает ряд приложений для автомобильной, аэрокосмической и биомедицинской отраслей.
Контакты:
Д-р Билл О’Нил
Кембриджский университет
Производственный институт
Технический факультет
Милл-Лейн, Кембридж CB2 1RX, Великобритания
Телефон: +44 (0) 1223 766880
Факс: +44 (0) 1223 766400
E- почта: [email protected]
НАША УНИКАЛЬНАЯ ТЕХНОЛОГИЯ ДИНАМИКИ ХОЛОДНОГО ГАЗА. Мы единственные
производитель холодного спрея в мире, который может напылять твердые сплавы
с чистым воздухом в качестве газа-носителя. Другие производители заявляют
для распыления твердых сплавов, но для этого требуется гелий или другой экзотический
и дорогой газ в качестве их авиаперевозчика. Прочие производители
утверждают, что разработали оборудование для холодного распыления, но они могут
распыляйте только мягкие металлы.Третьи утверждают, что могут продавать
их оборудование для холодного распыления на коммерческом рынке, но мы
являются единственным производителем, который в настоящее время может массово производить наши
оборудование и предоставить переносное оборудование для поля. К
нам известно, что все другие производители холодного спрея должны опрыскивать
внутри закрытой камеры, что дает практическое применение
почти невозможно.
УНИКАЛЬНЫЕ ХАРАКТЕРИСТИКИ. Традиционное покрытие термическим напылением методы (плазменный, электродуговый, HVOF) требуют высокой температуры частиц материала прилипать к поверхности.Обычно это температура превышает температуру плавления материала, создавая тем самым проблемы, присущие термическому спрею. В холодной газодинамической струе — не требуются высокие температуры. Это то, что делает технология уникальна. Эта технология использует поверхностное взаимодействие частиц, движущихся со сверхзвуковой скоростью между машинами 2-3 (требуемая скорость зависит от области применения и газа перевозчик ).Поскольку в холодную погоду высокие температуры не требуются газодинамическое распыление, адгезия и пористость превосходят термические спрей. Традиционные термические методы — по определению — создают нежелательные химические изменения и связанные с ними стрессы во время с дефектом, вызывающим окисление. Холодный газодинамический распылитель использует сверхзвуковая скорость, чтобы распылять материал так быстро на поверхность что образуется прочная связь без нежелательной стороны эффекты, присущие обычным термическим методам.Эта технология имеет существенные преимущества по сравнению с традиционными методами нанесения покрытий из-за низких температур, низкой пористости и превосходной адгезии. Привлекательность метода динамического напыления холодным газом что оборудование для нанесения и нанесенные покрытия имеют отсутствие ограничений, присущих другим методам термического покрытия. Качество покрытия и адгезия превосходны без сложность методов детонации или осаждения экзотических газов.Технология динамического напыления холодным газом обеспечивает гибкость и экономичность для широкого спектра применений во множестве отраслей. Преимущества
Технические характеристики
|
Холодное газодинамическое напыление титановых покрытий
Прайс, Тимоти Саймон (2008) Холодное газодинамическое напыление титановых покрытий. Кандидатская диссертация, Ноттингемский университет.
Аннотация
Динамическое напыление холодным газом, CGDS, является относительно новым методом, используемым для нанесения материалов на поверхность подложки. Он отличается от большинства других методов термического напыления, поскольку субстрат и частицы не подвергаются воздействию высоких температур во время процесса напыления. Это делает CGDS особенно выгодным для распыления материалов, таких как титан, которые вступают в реакцию при высокой температуре.Целью этого проекта было исследование возможности использования титановых покрытий с помощью CGDS в качестве поверхностной обработки медицинских протезов. Порошок титана наносился на подложку Ti6A14V с использованием газообразного гелия при комнатной температуре. Титановые покрытия также были произведены с помощью конкурирующей техники напыления — напыления с закрытой дугой, чтобы можно было провести сравнение двух методов. Были измерены механические свойства титановых покрытий, а также исследовано влияние последующей термообработки на механические свойства.Покрытия были охарактеризованы путем исследования таких свойств, как прочность сцепления, остаточное напряжение и жесткость, а также влияние титанового покрытия, нанесенного методом холодного напыления, на усталостную долговечность напыляемой подложки. Для характеристики отложений также использовались методы сканирующей электронной микроскопии и оптической микроскопии. Для дальнейшего развития и оптимизации процесса CGDS были также нанесены алюминиевые и медные покрытия, и их механические свойства были сопоставлены с таковыми у отложений титана.Кроме того, велосиметрия изображения частиц, PIV, была использована для улучшения общего понимания процесса холодного распыления и влияния параметров распыления на скорость удара частиц.
В случае предела усталостной выносливости и несмотря на состояние остаточного напряжения сжатия, измеренное в титановых покрытиях CGDS, после нанесения титанового покрытия CGDS на полученную подложку наблюдалось снижение предела усталостной выносливости на 15%, но не значительного уменьшение наблюдалось при его нанесении на обработанную пескоструйной очисткой основу.При испытании на четырехточечный изгиб было обнаружено, что отношение модуля титанового осадка к модулю соответствующего объемного материала (отношение модулей) составляло 0,17, что значительно ниже единицы. Для меди и алюминия, также нанесенных методом холодного напыления, наблюдалось соотношение модулей 0,41 и 0,16. Объемная доля и соотношение сторон пористости в каждом осадке измеряли с помощью SEM. Однако эквивалентная модель однородного включения Эшелби, снабженная этими данными, не смогла предсказать наблюдаемые низкие отношения модулей.Вместо этого несовершенное связывание между частицами в осадке (подобное трещинам по всей толщине) является источником низких соотношений модулей упругости, при этом прочный оксид на частицах порошка титана и алюминия более эффективен для предотвращения разрушения оксида и образования металлургических связей. между частицами при ударе, отсюда более низкий коэффициент модуля упругости для этих типов материалов.
Метод был разработан, чтобы визуально показать несовершенное межчастичное сцепление, которое, как ожидается, будет обнаружено в отложениях CGDS.Хотя уровни пористости в отложениях холодным напылением низкие, обнаружено, что отдельные частицы плохо связаны друг с другом, что приводит к низким модулям покрытия. При увеличении давления первичного газа в процессе холодного распыления происходит увеличение степени образования межчастичных связей.
Было обнаружено, что термообработка титанового покрытия при 1150 ° C улучшает прочность сцепления покрытия, но резко снижает предел усталостной прочности. Было обнаружено, что та же самая температура термообработки увеличивает коэффициент модуля упругости покрытия до 0.36, и это объясняется более высоким уровнем межчастичного связывания внутри титанового покрытия, происходящего за счет диффузионного связывания. Однако наблюдалось снижение предела усталостной выносливости. Скорее всего, это связано с фазовыми изменениями подложки Ti6A14V, природой релаксации напряжений при термообработке и кислородным охрупчиванием, несмотря на используемую аргоновую печь.
Диагностические инструменты, такие как измерения скорости частиц, также используются для дальнейшего общего понимания процесса CGDS.Измерения скорости частиц проводились для порошков титана и меди с использованием газообразного гелия и азота и ряда параметров распыления. Было обнаружено, что частицы диаметром менее 9 мкм имеют самые низкие скорости частиц как для порошков меди, так и для порошков титана. Для порошка титана была обнаружена разница между частицами самого маленького и самого большого размера до 200 м / с. Эти знания могут быть использованы в будущем для оптимизации гранулометрического состава исходного порошкового материала перед его использованием для нанесения методом холодного напыления.В целом титановый порошок давал самые высокие скорости частиц по сравнению с медным порошком из-за его более низкой плотности и, следовательно, его легче ускорять потоком газа. Модель частиц использовалась для предсказания скоростей частиц. Как правило, модель предсказывала более высокие скорости частиц, чем максимальные измеренные скорости частиц, и это связано с тем, что модель не принимает во внимание частицы, взаимодействующие друг с другом, внешние стенки сопла или внешнюю атмосферу.Все эти факторы могут привести к замедлению движения частиц.
По сравнению с титановыми покрытиями, полученными методом закрытой дуги, титановые покрытия CGDS работают превосходно. Покрытия с защитной дугой имели значительно более низкий предел усталостной прочности из-за остаточных напряжений при растяжении внутри покрытия, образующихся при охлаждении частиц при ударе. Однако покрытия с защитной дугой показали более высокий коэффициент модуля упругости, составляющий примерно 1/3, что сопоставимо с покрытиями, полученными другими методами термического напыления.
Действия (только сотрудники архива)
Изменить вид |
Splashdown: Сверхзвуковое соединение холодного металла в 3-D
ИЗОБРАЖЕНИЕ: Процесс холодного газодинамического напыления (CGDS) уже используется при производстве деталей самолетов и других деликатных поверхностей. Однако весь процесс CGDS от зоны полета до осаждения частиц … посмотреть еще
Кредит: Хонг-Шен Чен, Йоханнесбургский университет.
Когда хрупкая поверхность требует твердого, сверхтонкого металлического покрытия, обычные производственные процессы не работают. Тем не менее, динамическое напыление холодным газом (CGDS) может сделать именно это — с большой оговоркой. CGDS чрезвычайно универсален, но также очень трудно предсказать ключевые аспекты всего процесса. Теперь трехмерная модель на основе температуры, созданная профессором Тьен-Чиен Джен из Йоханнесбургского университета, открывает тайны процесса выращивания пленки CGDS в зоне осаждения частиц.
Модель является первой, которая связывает точки между скоростью столкновения частиц, преобразованием энергии и повышением температуры в зоне столкновения частиц в трех измерениях.
CGDS уже широко используется для производства или ремонта металлических деталей для больших пассажирских авиалайнеров, а также мобильной техники и военной техники.
В этом процессе сопло де Лаваля распыляет металлические частицы микронного размера на короткое расстояние, обычно 25 мм, на поверхность металла или полимера.Частицы ударяются о поверхность со скоростью от 300 до 800 метров в секунду. Для начала скорость звука составляет 343 метра в секунду.
CGDS имеет лучший температурный диапазон среди всех промышленных процессов распыления, используемых сегодня, и экономит энергию, поскольку не требует дополнительного нагрева.
Тайна производства
Однако на заводе начинается тайна. Если у вас есть медная частица размером 5 микрон, как быстро она должна прибыть в зону осаждения на алюминии, если вы раньше не использовали эту комбинацию? Или вы выбираете новый металл для частиц и новый металл для поверхности: как вы вообще начинаете угадывать, какого размера должны быть частицы и с какой скоростью они должны ударить по поверхности, чтобы дать вам хорошо связанное покрытие?
Имейте в виду, что связанное покрытие CGDS не должно иметь испарения, кристаллизации, остаточных напряжений или других термических повреждений — некоторые из основных причин, по которым CGDS используется в первую очередь.Эти вопросы могут иметь огромные финансовые последствия для производственного оборудования в производственном цехе.Физика еще не завершена
Почему CGDS связывает металлические частицы с поверхностью подложки, не поддается пониманию с момента ее изобретения в 1980-х годах военными, говорит Джен, профессор кафедры машиностроения в Университете Йоханнесбурга.
«Сначала военные использовали CGDS для ремонта запчастей в глуши. Затем другие отрасли промышленности поняли, что вы можете использовать его и на очень хрупких поверхностях.Вы можете создать новую склеенную поверхность толщиной всего несколько микрон или продолжать распыление, пока не получите 10-миллиметровое покрытие. После того, как вы заполнили трещины или отверстия, вы можете обработать деталь, чтобы снова получить ее точные размеры, потому что связанное покрытие GDS может быть тверже, чем титан или ванадий, из которого сделана деталь ».
Покрытие CGDS может быть таким твердым из-за сжимающих напряжений, возникающих при ударе частиц о поверхность. По его словам, напряжения увеличивают усталостную долговечность металла. Это похоже на то, что происходит при дробеструйной обработке, промышленном процессе, аналогичном CGDS, но с использованием «шариков» диаметром несколько миллиметров для удара о поверхность.
«CGDS используется для очень дорогостоящего производства и ремонта, но нет всеобъемлющей, реалистичной модели, описывающей физику всего процесса», — говорит Джен.
3D с разбрызгиванием
В CGDS инженеры говорят о двух зонах. Первый — это зона полета между распылительным соплом и обрабатываемой поверхностью. Эта зона была смоделирована Джен в исследовательской статье 2005 года в журнале International Journal of Heat and Mass Transfer .
Вторая зона — это зона осаждения, где распыляемые изделия ударяются о поверхность.Новая 3D-модель описывает эту зону.
Предыдущие двухмерные модели пытались решить загадку, связанную со склеиванием CGDS, но у них есть серьезное ограничение. Когда вы расширяете 2D-модель до 3D, вы получаете «горизонтальный цилиндр», спускающийся к обрабатываемой поверхности.
«К сожалению, опускающийся цилиндр не может достаточно реалистично моделировать то, что происходит с дискретными шариковыми частицами,« разбивающимися »о поверхность подложки», — говорит Джен.
Промышленность знает, что скорость (скорость) приближения частицы к подложке имеет решающее значение.Слишком медленно, и он просто отскочит. Слишком быстро, и он может пройти, как пуля, сквозь тонкий субстрат.
Новая модель представляет собой трехмерную анимацию одиночной сферической частицы, «падающей» в металлическую подложку. Подложка «разбрызгивается», а затем частица и подложка соединяются. «Брызги» субстрата похожи на брызги молока, когда что-то падает в миску кошки. В промышленности это называется струйным режимом », — говорит Джен.
.Холодный металл, повышение температуры
Модель использует несколько параметров, описывающих природу частицы и поверхности: плотность, теплопроводность, удельная теплоемкость, температура плавления, модуль упругости, коэффициент Пуассона, пластичность Джонсона-Кука и повреждение Джонсона-Кука.
Это первая система, которая предсказывает в 3D, как средняя температура в зоне удара частицы будет расти и понижаться в зависимости от размера и скорости удара частицы. Модель была опубликована в журнале Journal of Thermal Spray Technology .
Достаточно быстро, чтобы плавиться
«В этой 3D-модели мы исходили из гипотезы о том, что металлическая частица должна связываться с подложкой при температуре плавления 60%, чтобы создать прочную новую поверхность, не повреждая подложку», — говорит профессор Джен.
Например, медь (Cu) имеет температуру плавления 1083 градуса Цельсия, 60% от которой составляет 650 градусов Цельсия. Таким образом, гипотеза гласит, что медная частица размером 5 микрон, ударяющаяся о поверхность алюминиевой подложки, должна быть достаточно быстрой, чтобы средняя температура зоны удара поднялась как минимум до 650 градусов Цельсия и не намного больше, чтобы произошло хорошее сцепление. Согласно модели, этот критический диапазон скорости удара составляет от 700 до 800 метров в секунду.
Преобразование сверхзвуковой энергии
Когда медная частица движется со сверхзвуковой скоростью и ударяется о поверхность алюминия, ее движущаяся (кинетическая) энергия преобразуется в тепловую (тепловую) энергию, говорит профессор Джен.Это зависит от скорости удара частицы.
«Тепло делает частицу и зону удара« мягкими и липкими », как плавленый сыр. Частица превращается в« мягкую каплю », которая заполняет« кратер от удара »на поверхности подложки. В то же время трение «возникает между каплей и поверхностью кратера, что имеет решающее значение для процесса соединения», — говорит он.
«Трение« захватывает »каплю, и она погружается в поверхность подложки. Когда капля опускается вниз, расплавленная подложка вокруг частицы« разбрызгивается »в типичном режиме струи.Когда струя успокаивается, связь между частицей и поверхностью завершается », — говорит Джен.
Модель и реальный мир
Модель, хотя и ограниченная, соответствует экспериментальным результатам с частицами меди, напыленными на алюминиевую поверхность.
«Когда скорость удара находится в пределах диапазона, предсказанного моделью для размера частиц, достигается достаточная температура связывания и создается прочное покрытие CGDS. В качестве примера мы установили наше оборудование CGDS в лаборатории для частиц меди с средний размер 5 микрон, переносимый азотом, и скорость удара в диапазоне от 700 до 800 метров в секунду, нанесенный вниз на алюминий.
«Модель предсказывает, что при скорости удара около 750 метров в секунду в зоне столкновения частиц будет достигнута критическая температура склеивания 650 градусов Цельсия. В соответствии с этим предсказанием мы получили отличные покрытия со связующим CGDS», — говорит он.
«Однако, как также предсказано моделью, с помощью нашей лабораторной установки мы обнаружили, что, когда скорость удара частицы выходит за пределы критического диапазона, достигается недостаточная температура связывания. Это может привести к плохому покрытию поверхности из-за разрыхленных порошков и отслаивания поверхности, которые не соответствуют производственным стандартам качества », — говорит Джен.
Большой вызов остается
Одночастичная однослойная трехмерная модель будет расширена до многочастичной многослойной модели в последующих проектах.
Джен говорит: «Эта трехмерная модель — первая, описывающая, как температура зоны воздействия влияет на осаждение частиц. Однако реалистичное моделирование зоны осаждения в CGDS остается сложной задачей. одинакового размера или формы и перемещаются с разными скоростями и углами.Таким образом, более полная модель должна будет учитывать диапазоны или распределения всех этих параметров ».
###
Автор-корреспондент Профессор Тьен-Чиен Джен благодарит за финансовую поддержку Национального исследовательского фонда Южной Африки (грант № 105908).
Инновационный метод производства металлической пены с использованием процесса динамического напыления холодным газом с помощью смешения прекурсоров в псевдоожиженном слое
[1] Дж.Банхарт, Производство, характеристика и применение ячеистых металлов и металлических пен, Progress in Materials Science, 46 6 (2001) 559-632.
DOI: 10.1016 / s0079-6425 (00) 00002-5
[2] П.Карлоне, Г.С. Палаццо, Характеристики сварок TIG и FSW в литом магниевом сплаве ZE41A, J Mater Process Tech 215 (2015), 87-94.
DOI: 10.1016 / j.jmatprotec.2014.07.026
[3] П.Карлоне, Г.С. Палаццо, Влияние параметров процесса на микроструктуру и механические свойства при сварке трением с перемешиванием AA2024-T3. Металлография Microstruct Anal 2 (2013), 213–222.
DOI: 10.1007 / s13632-013-0078-4
[4] Л.П. Лефевр, Дж. Банхарт, Пористые металлы и металлические пены: текущее состояние и последние разработки, Современные инженерные материалы 9 10 (2008).
DOI: 10.1002 / adem.200800241
[5] Дж.Банхарт, Маршруты производства металлических пен, JOM 0012 (2000) 22-27.
[6] Дж.Banhart, Патент Германии, 100 15 (2000).
[7] Дж. Банхарт, Дж.Баумейстер, Деформационная характеристика пенопласта, J. Mater Sci. 33 (1998) 1431-40.
[8] Б.Матиясевич, Дж. Банхарт, С. Фихтер, О. Гёрке, Н. Вандерка, Модификация гидрида титана для улучшенного производства алюминиевой пены, Acta Mater., 54 1887- (1900).
DOI: 10.1016 / j.actamat.2005.12.012
[9] Б.Матиясевич, Дж. Банхарт, Совершенствование технологии производства алюминиевой пены путем подбора вспенивающего агента, Scr. Матер., 54 (2006) 503-8.
DOI: 10.1016 / j.scriptamat.2005.10.045
[10] А.Папирин, Технология холодного распыления, Adv. Матер. Процесс. 159 (2001) 49-51.
[11] Дж.Картикеян, Технология холодного напыления, Adv. Матер. Процесс. 163 (2005) 33-35.
[12] Э.Ириссу, Дж. Дж. Легу, А. Н. Рябинин, Б. Йодоин и К. Моро, Обзор процесса и технологии холодного напыления: Часть I — Интеллектуальная собственность, Журнал технологии термального напыления, Том 17 (4) декабрь 2008 г., 495-516.
DOI: 10.1007 / s11666-008-9203-3
[13] Д.Вей, Р. Дэйв, Р. Пфеффер, Смешивание и определение характеристик наноразмерных порошков: оценка различных методов, Journal of Nanoparticle Research 4 (2002) 21–41.
[14] П.Аммендола, Р. Чироне, Ф. Раганати, Псевдоожижение бинарных смесей наночастиц под действием акустических полей, Advanced Powder Technology 22 (2) (2011) 174–183.
DOI: 10.1016 / j.apt.2010.10.002
[15] П.Аммендола, Р. Чироне, Ф. Раганати, Влияние состава смеси, плотности наночастиц и интенсивности звука на качество смешивания нанопорошков, Химическая инженерия и обработка: интенсификация процесса 50 (8) (2011) 885–891.
DOI: 10.1016 / j.cep.2011.05.001
[16] К.Дж. Ходдер, Дж. А. Нычка, А.Г. Макдональд, Сравнение 10 мкм и 20 нм покрытий из металлической матрицы Al-Al2O3, полученных методом динамического напыления холодным газом при низком давлении, Journal of Thermal Spray Technology 23 (5) (2014) 839-848.
DOI: 10.1007 / s11666-014-0094-1
[17] Дж.Лазаро, Э. Солорзано, Х. А. де Саха, М. А. Родригес-Перес, Раннее анизотропное расширение предшественников алюминиевой пены, J Mater Sci 48 (2013) 5036–5046.
DOI: 10.1007 / s10853-013-7291-z
[18] Дж.Лазаро, Э. Лагуна-Гутьеррес, Э. Солорзано, М. А. Родригес-Перес, Влияние микроструктурной анизотропии прекурсоров ТЧ на характеристическое расширение алюминиевой пены, Металлургические операции и транзакции с материалами B том 44B (2013) 984-991.
DOI: 10.1007 / s11663-013-9852-6
[19] Ф.Гарсиа-Морено, Э. Солорзано, Дж. Банхарт, Кинекты коалесценции в жидких алюминиевых пенах, Soft Matter 7 (2011) 9216-9223.
DOI: 10.1039 / c1sm05831b
[20] Дж.Банхарт, И. Дуарте, Исследование кинектов и микроструктуры образования пены алюминия, Acta Mater. 48 (2000) 2349-2362.
DOI: 10.1016 / s1359-6454 (00) 00020-3
Исследование метода холодного газодинамического напыления для нескольких систем материалов (Конференция)
МакКьюн, Р. К., Папирин, А. Н., Холл, Дж. Н., Риггс, II, В. Л., и Зайховски, П. Х. Исследование метода холодного газодинамического напыления для нескольких систем материалов . США: Н. П., 1995.
Интернет.
МакКьюн, Р. К., Папирин, А. Н., Холл, Дж. Н., Риггс, II, В. Л., и Зайховски, П. Х. Исследование метода холодного газодинамического напыления для нескольких систем материалов . Соединенные Штаты.
МакКьюн, Р. К., Папирин, А. Н., Холл, Дж. Н., Риггс, II, В. Л., и Зайховски, П. Х.Солнце .
«Исследование метода холодного газодинамического напыления для нескольких систем материалов». Соединенные Штаты.
@article {osti_377729,
title = {Исследование метода холодного газодинамического напыления для нескольких систем материалов},
author = {МакКьюн, Р. К. и Папирин, А. Н. и Холл, Д. Н. и Риггс, II, В. Л. и Зайховски, П. Н.},
abstractNote = {В этом документе рассказывается о деятельности консорциума компаний, сформированного под эгидой Национального центра производственных наук (NCMS) для изучения метода холодного газодинамического распыления (CGSM), разработанного в России Алхимовым, Папыриным и его коллегами.В этом процессе распыления частицы металлического порошка превращаются в покрытие в результате баллистического удара о подходящую подложку. В некоторых случаях подготовка поверхности основы с использованием таких традиционных методов, как пескоструйная очистка, не требуется. Распылительная форсунка, используемая в этом процессе, была спроектирована таким образом, чтобы обеспечить возможность введения частиц порошка в предварительно нагретый газовый поток, который затем становится сверхзвуковым за счет расширения через сходящееся-расширяющееся горло с сопутствующим понижением температуры.Таким образом, температура газового потока всегда ниже точки плавления материала в виде частиц, обеспечивая покрытие, образованное в основном из частиц в твердом состоянии. Рассмотрены основы CGSM и представлены результаты нескольких комбинаций материалов, изученных на первом этапе исследовательской программы. Были получены экспериментальные покрытия, в том числе медь на глиноземной керамике, сталь на литом алюминии и композит карбида хрома на титане.