ГОСТ УЗК (ультразвуковой контроль) сварных швов. ГОСТ на ультразвуковую дефектоскопию
- Главная
- Блог
- ГОСТ УЗК (ультразвуковой контроль) сварных швов
Чтобы более полно раскрыть тему, разберемся для начала, что такое ГОСТы. Как следует из официального определения, ГОСТ – государственный стандарт, который отражает требования к качеству изделий, услуг или работ. В ГОСТах отражаются современные достижения технологий и практический опыт.
Для грамотного и правильного выполнения неразрушающего обследования методом ультразвуковой дефектоскопии сварных швов, существует ГОСТ и специальные нормативные документы, которые регламентируют основные требования и правила выполнения работ.
Дефектоскопия методом УЗК хоть и простая в исполнении процедура, однако, она требует внимательности и определенных знаний для получения наиболее достоверных результатов, именно поэтому так важно соблюдать все предписания нормативной документации.
Важным является тот факт, что проведения подобного рода исследования должно производится сертифицированным специалистом по данной услуге.
На данный момент, в России действует нормативный документ, введенный в 2015 году: ГОСТ Р 55724-2013 Контроль неразрушающий. Соединения сварные. Методы ультразвуковые. Данный документ является переработанной редакцией ГОСТ, введенного в 1988 году.
Кроме ГОСТов на сварные работы, при ультразвуковом обследовании руководствуются ГОСТами на работу толщиномеров, методы и средства проверки, общие технические требования и т.д.
Стандарт 2015 года регламентирует соединения угловые, стыковые, тавровые, соединения внахлест. И соединения, выполненные различными видами сварки: электрошлаковой, дуговой, газовой, газопрессовой, электронно-лучевой, лазерной и т.д.
Проводится ультразвуковой контроль сварных соединений согласно ГОСТ для трубопроводов различного назначения (транспортирование газо- и нефтепродуктов, воды и других веществ), резервуаров, строительных конструкций, изделий промышленного и хозяйственного назначения, различных транспортных средств для общего пользования и сельскохозяйственного – перечень очень широкий.
ГОСТы на ультразвуковой контроль
Всего существует около 30 нормативных документов, которые определяют порядок проведения испытаний или обследований, применяемое оборудование и др.
Перечислим некоторые действующие на данный момент ГОСТы по ультразвуковому контролю:
- ГОСТ Р 55724-2013 — Контроль неразрушающий. Соединения сварные. Методы ультразвуковые.
- ГОСТ 8.502-84 — Толщиномеры покрытий. Методы и средства поверки.
- ГОСТ Р 55725-2013 — Контроль неразрушающий. Преобразователи ультразвуковые пьезоэлектрические. Общие технические требования.
- ГОСТ 28702-90 — Контроль неразрушающий. Толщиномеры ультразвуковые. Общие технические требования.
- ГОСТ Р 55809-2013
- ГОСТ 27750-88 — Контроль неразрушающий. Покрытия восстановительные. Методы контроля толщины покрытий.
- ГОСТ 23858-79 — Соединения сварные стыковые и тавровые арматуры железобетонных конструкций. Ультразвуковые методы контроля качества. Правила приемки.
- ГОСТ 17624-87 — Бетоны. Ультразвуковой метод определения прочности.
- ГОСТ 24983-81 — Трубы железобетонные напорные. Ультразвуковой метод контроля и оценки трещиностойкости.
- ГОСТ 26266-90 — Контроль неразрушающий. Преобразователи ультразвуковые. Общие технические требования.
- ГОСТ 12.1.001-89 — Межгосударственный стандарт. Система стандартов безопасности труда. Ультразвук. Общие требования безопасности.
- ГОСТ Р ИСО 10332-99 — Трубы стальные напорные бесшовные и сварные (кроме труб, изготовленных дуговой сваркой под флюсом). Ультразвуковой метод контроля сплошности.
- ГОСТ 24507-80 — Контроль неразрушающий. Поковки из черных и цветных металлов. Методы ультразвуковой дефектоскопии.
- ГОСТ ИСО 4386-1-94 — Подшипники скольжения металлические многослойные. Неразрушающие ультразвуковые испытания соединения слоя подшипникового металла и основы.
- ГОСТ 21397-81 — Контроль неразрушающий. Комплект стандартных образцов для ультразвукового контроля полуфабрикатов и изделий из алюминиевых сплавов. Технические условия.
Проведение ультразвуковой дефектоскопии по ГОСТ
Проведение ультразвукового (эхо-импульского, зеракально-теневого или эхо-теневого) контроля описано в главе 9 Национального Стандарта РФ «Контроль неразрушающий. Соединения сварные.»
В данной главе описываются ультразвуковые методы неразрушающего контроля сварных соединений по ГОСТ. Приведены нормативы по уровням чувствительности (поисковый, опорный, браковочный и т.д.). Определена максимальная скорость сканирования участков – 150 мм/с. Приведены нормы прозвучивания изделий, имеющих различную форму и диаметры. А также имеется пункт, который напоминает, что каждое оборудование следует использовать в соответствии с эго эксплуатационными характеристиками и правилами, которые описаны в руководстве к данному устройству.
Если говорить о последовательности выполнения звуковой дефектоскопии сварных швов, то процесс выглядит так:
- В первую очередь с соединения удаляются старые покрытия (краска, лак, грунтовка и т.п.) и ржавчина.
- Далее того, чтобы звуковые волны беспрепятственно проникали в металл, поверхность его обрабатывается специальными проводящими растворами и веществами (некоторые масла, глицерин).
- После этого производится настройка прибора согласно заданным начальным параметрам обследования.
- После настройки, прибор прикладывается к поверхности и начинает двигаться вдоль и поперек соединения, просматривая внутреннюю поверхность.
- При обнаружении дефектов, они фиксируются в специальный акт, если возможно, определяются и записываются их размеры и конкретное местоположение.
Согласно ГОСТ ультразвуковая дефектоскопия одного соединения должна проводиться в несколько подходов.
Способы контроля, схемы прозвучивания и способы сканирования сварных соединений
Способы контроля
По ГОСТ ультразвук можно проводить различными методами, такими как: зеркально-теневой, эхо-теневой, эхо-импульсный, дифракционный, эхо-зеркальный или дельта метод.
Проведение обследования любым из упомянутых способов не обходится без преобразователей, которые подключены к совмещенной или раздельной схеме.
Эхо-импульсный
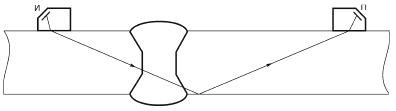
Зеркально-теневой
Эхо-теневой прямым лучом (а) и наклонными лучами (б) ПЭП
Эхо-зеркальный
Дифракционный
Вариации дельта-метода
Способы сканирования
Согласно ГОСТ, ультразвуковой контроль имеет два основных метода сканирования: продольное и поперечное. На практике, оба эти способа совмещают для получения наиболее точных и обширных данных о наличии повреждений в сварном соединении.
Варианты поперечно-продольного сканирования
Наименее популярен способ сканирования качающимся лучом, но он также допускается государственным стандартом к проведению.
Способ качающегося луча
Схемы прозвучивания
Схемы прозвучивания для каждого типа сварного шва разные. Например, согласно ГОСТу на ультразвуковой контроль сварных швов стыковые соединения обследуются прямым, однократно-отраженным или двукратно-отраженным лучом.
Прозвучивания стыкового шва двукратно-отраженным лучом
Согласно ГОСТ по ультразвуковому контролю сварных соединений, исследование можно вести с прямыми и наклонными преобразователями, схемой прямого или однократно-отраженного луча.
Схема прозвучивания углового шва совмещенными наклонными и прямым преобразователями
Стоит отметить, что стандарты допускают применение различных схем прозвучивания в любых видах сварных соединений, которые имеются в нормативных документах для контроля.
Эхо-импульсных контроль пересекающихся сварных швов производят наклонными преобразователями схемой прозвучивания, которая приведена на рисунке:
УЗК точно выявляет поперечные трещины. Такая процедура проводится наклонными преобразователями схемами прозвучивания, которые представлены ниже:
Исследование стыковых сварных соединений на наличие поперечных трещин: а) — со снятым валиком шва; б) – в присутствии валика шва
Требования безопасности
Обязательным пунктом в любой нормативной литературе, является пункт о безопасности. В ГОСТ неразрушающего ультразвукового контроля сварных соединений он также присутствует. В нем отражены правила технической эксплуатации электроустановок потребителей, правила безопасности при работе с этими приборами.
Также в нем имеются ограничения по уровню шума, который создается на рабочем месте специалиста по дефектоскопии. Регламентируются нормы пожарной безопасности.
Документы, упомянутые в данном разделе, применяются не только к УЗК контролю, они имеют широкое распространение на другие виды работ и обследования, соответственно.
Работы, выполненные согласно утвержденным стандартам, являются более качественными, а значит, в их достоверности не стоит сомневаться. ГОСТы ультразвукового контроля сварных швов помогают регулировать качество выпускаемой продукции, правильно проводить обследования, тем самым защищая людей от некачественных изделий, которые могут принести вред их жизни и здоровью.
Вид контроля | Метод контроля | Характеристика метода | Область применения | Обозначение стандарта на метод контроля | |||
Выявляемые дефекты | Чувствительность | Особенности метода | |||||
Технический осмотр | Внешний осмотр и измерение | Поверхностные дефекты | Выявляются несплошности отклонения размера и формы сварного соединения от заданных величин более 0,1 мм, а также поверхностное окисление сварного соединения | Метод позволяет обнаруживать дефекты минимального выявляемого размера при осмотре и измерении сварного соединения с использованием оптических приборов с увеличением до 10 и измерительных приборов | Не ограничивается | — | |
Капиллярный | Цветной | Дефекты (несплошности), выходящие на поверхность | Условные уровни чувствительности по ГОСТ 18442-80 | Чувствительность и достоверность метода зависят от качества подготовки поверхности соединения к контролю | Не ограничивается | ГОСТ 18442-80 | |
Радиационный | Радиографический | Внутренние и поверхностные дефекты (несплошности), а также дефекты формы соединения | От 0,5 до 5,0% контролируемой толщины металла | Выявляемость дефектов по ГОСТ 7512-82. Чувствительность зависит от характеристик контролируемого сварного соединения и средств контроля | По ГОСТ 20426-82 | ГОСТ 7512-82 | |
Акустический | Ультразвуковой | Внутренние и поверхностные дефекты (несплошности) | Толщина сварного соеинения, мм | Предельная чувствительность, мм | Размер, количество и характер дефектов определяются в условных показателях по ГОСТ 14782-86 | По ГОСТ 14782-86 | ГОСТ 14782-86 |
От 1,5 до 10 включ. | 0,5-2,5 | ||||||
Св. 10 до 50 « | 2,0-7,0 | ||||||
» 50 » 150 « | 3,5-15,0 | ||||||
» 150 » 400 « | 10,0-80,0 | ||||||
» 400 » 2000 « | 35,0-200,0 | ||||||
Магнитный | Магнито- феррозондовый | Поверхностные и подповерхностные несплошности | Условные уровни чувствительности по ГОСТ 21104-80* | Метод обеспечивает выявление: | По ГОСТ 21104-75 | ГОСТ 21104-75 | |
_______________ | |||||||
Магнито- | Поверхностные и подповерхностные несплошности | Условные уровни чувствительности по ГОСТ 21105-87 | Метод обеспечивает выявление внутренних несплошностей, расположенных от поверхности соединения на глубине до 2 мм включительно. Чувствительность и достоверность метода зависят от качества подготовки соединения к контролю | По ГОСТ 21105-87 | ГОСТ 21105-87 | ||
Магнито- | Поверхностные, подповерхностные и внутренние несплошности | От 2 до 7% от толщины контролируемого металла | Достоверность контроля снижается при наличии неровностей на контролируемой поверхности соединения размером более 1 мм. Чувствительность снижается с увеличением глубины залегания несплошности | Сварные стыковые соединения, выполненные дуговой газовой сваркой, конструкции из ферромагнитных материалов. Контролируемая толщина не более 25 мм | — | ||
Течеискание | Радиационный | Сквозные дефекты | По криптону 85 — от 1·10 до 1·10 мм МПа/с | Радиоактивная опасность | Обнаружение мест течей в сварных соединениях, работающих под давлением, замкнутых конструкций ядерной энергетики, а также замкнутых конструкций, когда невозможно применение других методов течеискания. | — | |
Масс- | Сквозные дефекты | По способу: | Условия эксплуатации течеискателей: температура окружающей среды 10-35 °С, наибольшая относительная влажность воздуха 80% | Способ накопления давления — определение суммарной степени утечек замкнутых конструкций. | — | ||
Манометрический | Сквозные дефекты | По способу: | Чувствительность метода снижается при контроле конструкций больших объемов. | Сварные соединения замкнутых конструкций, работающих под давлением: | — | ||
Галоидный | Сквозные дефекты | По фреону 12: | Достоверность и чувствительность контроля снижается, если контролируемая поверхность имеет неровности (наплывы, углубления), препятствующие приближению щупа к контролируемой поверхности | Обнаружение места и величины локальных течей в сварных соединениях замкнутых конструкций, работающих под давлением. | — | ||
Газоаналитический | Сквозные дефекты | По фреону 12 (90%) в смеси с воздухом от 2·10 до 4·10 мм МПа/с | Достоверность контроля снижаются при наличии в окружающей атмосфере различных паров и газов, включая растворители для подготовки поверхности контролируемого соединения, табачный дым и газы, образующиеся при сварке | Обнаружение места локальных течей в сварных соединениях замкнутых конструкций, работающих под давлением. Контролируемая толщина не ограничивается | — | ||
Химический | Сквозные дефекты | По аммиаку — до 6,65·10 мм МПа/с | Требуется соблюдение правил противопожарной безопасности и правил работы с вредными химическими веществами | Обнаружение места локальных течей в сварных соединениях открытых и закрытых конструкций, работающих под давлением или предназначенных для хранения жидкостей. Контролируемая толщина не ограничивается | — | ||
Акустический | Сквозные дефекты | Не менее 1·10 мм МПа/с | Контроль производят при отсутствии шумовых помех. Возможен дистанционный контроль | Обнаружение мест течей в сварных соединениях подземных водо- и газопроводах высокого давления. Контролируемая толщина не ограничивается | — | ||
Капиллярный | Сквозные дефекты | Люминесцентный — от 1·10 до 5·10 мм МПа/с | Требуется тщательная очистка контролируемой поверхности. Чувствительность метода снижается при контроле больших толщин и при контроле сварных соединений, расположенных во всех пространственных положениях, отличных от нижнего. | Обнаружение мест течей в сварных соединениях открытых и закрытых конструкций: | — | ||
Наливом воды под напором | Сквозные дефекты | От 3·10 до 2·10 мм МПа/с | При контроле сварных соединений большой емкости должна быть обеспечена жесткость конструкции | Обнаружение мест локальных течей в сварных соединениях закрытых конструкций, работающих под давлением. Контролируемая толщина, не ограничивается | Нормативно- техническая документация, утвержденная в установленном порядке | ||
Наливом воды без напора | Сквозные дефекты | Не более 1·10 мм МПа/с | При контроле сварных соединений большой емкости должна быть обеспечена жесткость конструкции | Обнаружение мест локальных течей в сварных соединениях открытых конструкций. Контролируемая толщина не ограничивается | Нормативно- техническая документация, утвержденная в установленном порядке | ||
Поливанием струей воды под напором | Сквозные дефекты | Не более 1·10 мм МПа/с | Чувствительность метода повышается при люминесцентно-индика- торном покрытии осматриваемой поверхности. Контроль производят до монтажа оборудования | Обнаружение мест локальных течей в сварных соединениях открытых конструкций. Контролируемая толщина не ограничивается | Нормативно- техническая документация, утвержденная в установленном порядке | ||
Поливанием рассеянной струей воды | Сквозные дефекты | Не более 1·10 мм МПа/с | Чувствительность метода повышается при люминесцентно- индикаторном покрытии осматриваемой поверхности. Контроль производят до монтажа оборудования | Обнаружение мест локальных течей в сварных соединениях открытых конструкций. Контролируемая толщина не ограничивается | Нормативно- техническая документация, утвержденная в установленном порядке | ||
Пузырьковый | Сквозные дефекты | Пневматический: | Контроль производится сжатым воздухом. | Обнаружение мест локальных течей. Пневмогидравлический аквариумный и бароаквариумный способы: | Нормативно- техническая документация, утвержденная в установленном порядке | ||
Вскрытие | Внутренние дефекты | Выявляются макроскопические дефекты | Вскрытие производится вырубкой, сверлением, газовой или воздушно-дуговой строжкой, шлифованием, а также вырезкой участка сварного соединения с последующим изготовлением из него послойных шлифов. После контроля требуется заварка вскрытого участка сварного соединения | Сварные соединения, которые не подвергаются термообработке или недоступны для радиационного и акустического контроля. | — | ||
Технологическая проба | Внутренние и поверхностные дефекты | Выявляются макроскопические и микроскопические дефекты | Контрольная проба выполняется по тому же технологическому процессу и тем же сварщиком (сварщиками), что и контролируемые сварные соединения | Не ограничивается | — |
ГОСТы по неразрушающему контролю
ГОСТы по визуальному контролю
ГОСТ 9378-93 (ИСО 2632-1-85, ИСО 2632-2-85) Образцы шероховатости поверхности (сравнения)
ГОСТ 9038-90 Меры длины концевые плоскопараллельные
ГОСТ 25142-82 «Шероховатость поверхности. Термины и определения».
ГОСТ 2789-73 (СТ СЭВ 638-77) Шероховатость поверхности. Параметры и характеристики
ГОСТ 27964-88 (СТ СЭВ 6134-87, ИСО 4287/2-84) Измерение параметров шероховатости. Термины и определения
ГОСТ 25706-83 — Лупы. Типы, основные параметры. Общие технические требования.
ГОСТ 166-89. Штангенциркули. Технические условия.
ГОСТ 164-90 Штангенрейсмасы. Технические условия.
ГОСТ 162-90 Штангенглубиномеры. Технические условия.
ГОСТ 1643-81 Основные нормы взаимозаменяемости. Передачи зубчатые цилиндрические. Допуски
ГОСТ 10-88 Нутромеры микрометрические
ГОСТ 1198-75 Скобы с отсчетным устройством
ГОСТ 577-68 Часовые индикаторы типа ИЧ
ГОСТ 6507-90 Микрометры. Технические условия
ГОСТ 427-75 Линейки измерительные металлические.
ГОСТ 7502-98 Рулетки измерительные металлические
ГОСТ 7661-67 Глубиномеры индикаторные. Технические условия.
ГОСТ 7470-92 Глубиномеры микрометрические. Технические условия.
ГОСТ 3749-77, Угольники поверочные 90 град. Технические условия
ГОСТ 24521-80 Контроль неразрушающий оптический. Термины и определения
ГОСТ 8.296-2015 «Государственная система обеспечения единства измерений (ГСИ). Государственная поверочная схема для средств измерений параметров шероховатости Rmax, Rz в от 0,001 до 3000 мкм и Ra в от 0,001 до 750 мкм»
ГОСТ 2875-88 Меры плоского угла призматические. Общие технические условия
ГОСТ 5378-88 Угломеры с нониусом. Технические условия
ГОСТ 868-82 Нутромеры индикаторные с ценой деления 0,01 мм. Технические условия (с Изменениями № 1, 2, 3)
ГОСТ 11358-89 Толщиномеры и стенкомеры индикаторные с ценой деления 0,01 и 0,1 мм. Технические условия
ГОСТ 11098-75 Скобы с отсчетным устройством. Технические условия
ГОСТы по ультразвуковому контролю
ГОСТ 8.502-84 Толщиномеры покрытий. Методы и средства поверки.
ГОСТ Р 55809-2013 Контроль неразрушающий. Дефектоскопы ультразвуковые. Методы измерений основных параметров
ГОСТ Р ИСО 16809-2015 Контроль неразрушающий. Контроль ультразвуковой. Измерение толщины
ГОСТ Р 55808-2013 Контроль неразрушающий. Преобразователи ультразвуковые. Методы испытаний
ГОСТ 18061-90 — Толщиномеры радиоизотопные. Общие технические условия
ГОСТ 27750-88 — Контроль неразрушающий. Покрытия восстановительные. Методы контроля толщины покрытий
ГОСТ 28702-90 — Контроль неразрушающий. Толщиномеры ультразвуковые. Общие технические требования
ГОСТ 22238-76 — Контроль неразрушающий. Меры образцовые для поверки толщиномеров неорганических покрытий. Общие положения
ГОСТ Р 55725-2013 Контроль неразрушающий. Преобразователи ультразвуковые пьезоэлектрические. Общие технические требования
ГОСТ 25863-83 Контроль неразрушающий. Толщиномеры ультразвуковые контактные. Общие технические требования
ГОСТ 8.495-83 Толщиномеры ультразвуковые контактные. Методы и средства поверки
ГОСТ 22727-88 Прокат листовой. Методы ультразвукового контроля
ГОСТ 18576-96 Контроль неразрушающий. Рельсы железнодорожные. Методы ультразвуковые
ГОСТ 12.1.001-89 Межгосударственный стандарт. Система стандартов безопасности труда. Ультразвук. Общие требования безопасности.
ГОСТ Р 55724-2013 Контроль неразрушающий. Соединения сварные. Методы ультразвуковые.
ГОСТ 28831-90 Прокат толстолистовой. Методы ультразвукового контроля.
ГОСТ 23858-79 Соединения сварные стыковые и тавровые арматуры железобетонных конструкций. Ультразвуковые методы контроля качества. Правила приемки.
ГОСТ 24507-80 Контроль неразрушающий. Поковки из черных и цветных металлов. Методы ультразвуковой дефектоскопии.
ГОСТ 17410-78 Контроль неразрушающий. Трубы металлические бесшовные цилиндрические. Методы ультразвуковой дефектоскопиии.
ГОСТ Р ИСО 10124-99 Трубы стальные напорные бесшовные и сварные (кроме труб, изготовленных дуговой сваркой под флюсом). Ультразвуковой метод контроля расслоений.
ГОСТ Р ИСО 10332-99 Трубы стальные напорные бесшовные и сварные (кроме труб, изготовленных дуговой сваркой под флюсом). Ультразвуковой метод контроля сплошности.
ГОСТ Р ИСО 10543-99 Трубы стальные напорные бесшовные и сварные горячетянутые. Метод ультразвуковой толщинометрии.
ГОСТ 17624-87 Бетоны. Ультразвуковой метод определения прочности.
ГОСТ ИСО 4386-1-94 Подшипники скольжения металлические многослойные. Неразрушающие ультразвуковые испытания соединения слоя подшипникового металла и основы.
ГОСТ 21120-75 Прутки и заготовки круглого и прямоугольного сечения. Методы ультразвуковой дефектоскопии.
ГОСТ 26126-84 Контроль неразрушающий. Соединения паяные. Ультразвуковые методы контроля качества.
ГОСТ Р 55614-2013 Контроль неразрушающий. Толщиномеры ультразвуковые. Общие технические требования.
ГОСТ 26266-90 Контроль неразрушающий. Преобразователи ультразвуковые. Общие технические требования.
ГОСТ 21397-81 Контроль неразрушающий. Комплект стандартных образцов для ультразвукового контроля полуфабрикатов и изделий из алюминиевых сплавов. Технические условия.
ГОСТ 24830-81 Изделия огнеупорные бетонные. Ультразвуковой метод контроля качества
ГОСТ 24332-88 Кирпич и камни силикатные. Ультразвуковой метод определения прочности при сжатии
ГОСТ 26134-84 Бетоны. Ультразвуковой метод определения морозостойкости
ГОСТ 24983-81 Трубы железобетонные напорные. Ультразвуковой метод контроля и оценки трещиностойкости
ГОСТ Р 55808-2013 Контроль неразрушающий. Преобразователи ультразвуковые. Методы испытаний
ГОСТ 23667-85 Контроль неразрушающий. Дефектоскопы ультразвуковые. Методы определения основных параметров. (утратил силу с 01 июля 2015)
ГОСТ 23702-90 Контроль неразрушающий. Преобразователи ультразвуковые. Методы испытаний (утратил силу с 01 июля 2015)
ГОСТ 26266-90 — Контроль неразрушающий. Преобразователи ультразвуковые. Общие технические требования (утратил силу с 01 июля 2015)
ГОСТ 14782-86 Контроль неразрушающий. Соединения сварные. Методы ультразвуковые (утратил силу с 01 июля 2015)
ГОСТы по акустическому контролю
ГОСТ 27655-88 Акустическая эмиссия. Термины, определения и обозначения
ГОСТ 23829-85 Контроль неразрушающий акустический. Термины и определения
ГОСТ 20415-82 Контроль неразрушающий. Методы акустические. Общие положения.
ГОСТ Р 52731-2007 Контроль неразрушающий. Акустический метод контроля механических напряжений. Общие требования.
ГОСТ 25714-83 Акустический звуковой метод определения открытой пористости, кажущейся плотности, плотности и предела прочности при сжатии огнеупорных изделий.
ГОСТы по радиографическому контролю
ГОСТ 29074-91 Аппаратура контроля радиационной обстановки.
ГОСТ 26114-84 — Контроль неразрушающий. Дефектоскопы на базе ускорителей заряженных частиц. Основные параметры и общие технические требования
ГОСТ 29025-91 — Дефектоскопы рентгенотелевизионные с рентгеновскими электронно-оптическими преобразователями и электрорентгенографические. Общие технические требования
ГОСТ 8.452-82 — Государственная система обеспечения единства измерений. Приборы рентгенорадиометрические. Методы и средства поверки
ГОСТ 7512-82 Контроль неразрушающий. Соединения сварные. Радиографический метод
ГОСТ 27947-88 Контроль неразрушающий. Рентгенотелевизионный метод. Общие требования
Гост 25113-86 Контроль неразрушающий. Аппараты рентгеновские для промышленной дефектоскопии. Общие технические условия
ГОСТ 24034-80 Контроль неразрушающий радиационный. Термины и определения
Гост 23764-79 Гамма-дефектоскопы. Общие технические условия
Гост 22091.9-86 Приборы рентгеновские. Методы измерения размеров эффективного фокусного пятна
Гост 22091.5-86 Приборы рентгеновские. Методы измерения тока рентгеновской трубки
ГОСТ 15843-79 Принадлежности для промышленной радиографии. Основные размеры
Гост 20337-74 Приборы рентгеновские. Термины и определения
Гост 17064-71 Основные функциональные узлы, принадлежности и вспомогательные устройства гамма-аппаратов. Термины и определения
Гост 16950-81 Техника радиационно-защитная. Термины и определения
Гост 22091.14-86 Приборы рентгеновские. Методы измерения напряжения рентгеновской трубки
ГОСТ 23055-78 Контроль неразрушающий. Сварка металлов плавлением. Классификация сварных соединений по результатам радиографического контроля
ГОСТ 20426-82 Контроль неразрушающий. Методы дефектоскопии радиационные. Область применения
Гост 15484-81 Излучения ионизирующие и их измерения. Термины и определения
ГОСТ 17209-89 Средства измерений объемной активности радионуклидов в жидкости.Общие технические требования и методы испытаний
ГОСТ 23923-89 Средства измерений удельной активности радионуклида. Общие технические требования и методы испытаний
ГОСТ 27451-87 Средства измерений ионизирующих излучений. Общие технические условия
ГОСТ 23480-79 Контроль неразрушающий. Методы радиоволнового вида. Общие требования (с Изменениями N 1, 2)
ГОСТ 7512-82 Контроль неразрушающий. Соединения сварные. Радиографический метод
ГОСТ 23764-79 Гамма-дефектоскопы. Общие технические условия
ГОСТы по капиллярному контролю
ГОСТ 24522-80 Контроль неразрушающий капиллярный. Термины и определения
ГОСТ 28369-89 Контроль неразрушающий. УФ-облучатели. Общие технологические требования.
ГОСТ 18442-80* Контроль неразрушающий. Капиллярные методы. Общие требования
ГОСТ 23349–84 Контроль неразрушающий. Дефектоскопы капиллярные. Общие технологические требования.
ГОСТы по магнитному контролю
ГОСТ Р 50649-94, Совместимость технических средств электромагнитная. Устойчивость к импульсному магнитному полю.
ГОСТ Р 50648—94. Совместимость технических средств электромагнитная. Устойчивость к магнитному полю промышленной частоты.
ГОСТ Р 51317.4.2-99 Совместимость технических средств электромагнитная. Устойчивость к электростатическим разрядам. Требования и методы.
ГОСТ Р 51317.4.3-99 Совместимость технических средств электромагнитная. Устойчивость к радиочастотному электромагнитному полю.
ГОСТ Р 56512-2015 Контроль неразрушающий. Магнитопорошковый метод. Типовые технологические процессы.
ГОСТ 30415-96 Сталь. Неразрушающий контроль механических свойств и микроструктуры металлопродукции магнитным методом Steel
ГОСТ 25225-82 Контроль неразрущающий. Швы сварных соединений трубопроводов. Магнитографический метод
ГОСТ 24450-80 Контроль неразрушающий магнитный. Термины и определения
ГОСТ ISO 17638-2018 Неразрушающий контроль сварных соединений. Магнитопорошковый контроль
ГОСТ 21105-87 Контроль неразрушающий. Магнитопорошковый метод (утратил силу с 01 июня 2016)
ГОСТ 26697-85 Контроль неразрушающий. Дефектоскопы магнитные и вихретоковые. Общие технические требования.
ГОСТы по тепловому контролю
ГОСТ Р 8.619-2006 Приборы тепловизионные измерительные. Методика поверки
ГОСТ Р 54852-2011 Здания и сооружения. Метод тепловизионного контроля качества теплоизоляции ограждающих конструкций
ГОСТ 7076-99 Измерение теплопроводности
ГОСТ 25380-82 Метод измерения плотности тепловых потоков
ГОСТ 25314-82 Контроль неразрушающий тепловой. Термины и определения
ГОСТ 23483-79 Контроль неразрушающий. Методы теплового вида. Общие требования
ГОСТы по контролю герметичности
ГОСТ Р 51780-2001 Методы и средства испытаний на герметичность
ГОСТ 24054-80 Изделия машиностроения и приборостроения. Методы испытаний на герметичность. Общие требования
ГОСТ 28517-90 Контроль неразрушающий. Масс-спектрометрический метод течеискания. Общие требования
ГОСТы по контролю твердости
ГОСТ 9013-59 Металлы. Метод измерения твердости по Роквеллу
ГОСТ 8.426-81 Приборы для измерения твердости металлов методом упругого отскока бойка (по Шору)
ГОСТ 2999-75 Металлы и сплавы. Метод измерения твердости по Виккерсу
ГОСТ 24621-91 (ИСО 868-85) Пластмассы и эбонит. Определение твердости при вдавливании с помощью дюрометра (твердость по Шору)
ГОСТ 263-75 Резина. Метод определения твердости по Шору A.
ГОСТ 9031-75 Меры твердости образцовые. Технические условия
ГОСТ 23273-78 Металлы и сплавы. Измерение твердости методом упругого отскока бойка (по Шору)
ГОСТ 22690-88 БЕТОНЫ. Определение прочности механическими методами неразрушающего контроля
Металлы и сплавы. Метод измерения твердости по Роквеллу при малых нагрузках (по Супер-Роквеллу)
ГОСТ 8.335-2004 Государственная система обеспечения единства измерений (ГСИ). Меры твердости эталонные. Методика поверки
Спектральный анализ
ГОСТ 22536.0-87. Сталь углеродистая и чугун нелегированный. Методы анализа.
ГОСТ Р 54153-2010. Сталь. Метод атомно-эмиссионного спектрального анализа.
ГОСТ 27809-95. Чугун и сталь. Метод спектрографического анализа.
ГОСТ 27611-88. Чугун. Методы фотоэлектрического спектрального анализа.
ГОСТ 24231-80. Цветные металлы и сплавы. Общие требования к отбору и подготовки проб для химического анализа.
ГОСТ 9717.1-82. Медь. Методы спектрального анализа.
ГОСТ 9716.2-79. Сплавы медно-цинковые. Метод спектрального анализа по металлическим стандартным образцам с фотоэлектрической регистрацией спектра.
ГОСТ 6012-98. Никель. Методы химико-атомно-эмиссионного спектрального анализа.
ГОСТ 15483.10-2004. Олово. Методы атомно-эмиссионного спектрального анализа.
ГОСТ 8857-77. Свинец. Метод спектрального анализа.
ГОСТ 13348-74. Сплавы свинцово-сурьмянистые. Метод спектрального анализа.
ГОСТ 17261-77. Цинк. Спектральный метод анализа.
ГОСТ 23328-95. Сплавы цинковые. Методы спектрального анализа.
ГОСТ 9519.1-77. Баббиты кальциевые. Методы спектрального анализа.
ГОСТ 9519.2-77. Баббиты кальциевые. Метод спектрального анализа.
ГОСТ 23902-79. Сплавы титановые. Методы спектрального анализа.
ГОСТ 12223.0-76. Иридий. Метод спектрального анализа.
ГОСТ 12227.0-76. Родий. Метод спектрального анализа.
ГОСТ 3221-85. Алюминий первичный. Методы спектрального анализа.
ГОСТ 7727-81. Алюминий литейный деформируемый. Методы спектрального анализа.
ГОСТ ИСО 7347-94. Ферросплавы. Экспериментальные методы контроля систематической погрешности отбора и подготовки проб.
ГОСТ 30975-2002. Ферросплавы. Экспериментальные методы оценки вариации качества и методы контроля точности отбора проб.
ГОСТ 16321.2-70. Серебряно-медные сплавы. Метод спектрального анализа.
ГОСТ 12563.2-83. Золото-палладиевые сплавы. Метод спектрального анализа.
ГОСТ 12551.2-82. Платино-медные сплавы. Методы спектрального анализа.
ГОСТ 12553.2-77. Платино-палладиевые сплавы. Метод спектрального анализа.
ГОСТ 12556.2-82. Платино-родиевые сплавы. Методы спектрального анализа.
ГОСТ 12559.2-82. Платино-иридиевые сплавы. Методы спектрального анализа.
ГОСТ 17234-71. Золотые сплавы. Метод определения содержание золота и серебра.
ГОСТ 27973.1-88. Золото. Методы атомно-эмиссионного спектрального анализа.
Прочие ГОСТы
ГОСТ 14254-96 Степени защиты, обеспечиваемые оболочками (код IP)
ГОСТ Р 8.736-2011 Измерения прямые многократные. Методы обработки результатов измерений. Основные положения
ГОСТ 18353-79. Контроль неразрушающий. Классификация видов и методов
ГОСТы по неразрушающему контролю и их зарубежные аналоги
ГОСТ 8.283-78 Дефектоскопы электромагнитные. Методы и средства поверки
ГОСТ 8.062-85 Государственный специальный эталон и государственная поверочная схема для средств измерений твердости по шкалам Бринелля
ГОСТ 7122-81 Швы сварные и металл наплавленный. Методы отбора проб для определения химического состава
ГОСТ 6996-66 (СТ СЭВ 3521-82 — СТ СЭВ 3524-82, СТ СЭВ 6732-89) Сварные соединения. Методы определения механических свойств
ГОСТ 3242-79 Соединения сварные. Методы контроля качества
ГОСТ 30242-97 Дефекты соединений при сварке металлов плавлением. Классификация, обозначение и определения
ГОСТ 10243-75, Сталь. Методы испытаний и оценки макроструктуры
ГОСТ 2601-84 Сварка металлов. Термины и определения основных понятий
ГОСТ 25820-2000 Бетоны легкие. Технические условия
ГОСТ 21104-75 Контроль неразрушающий. Феррозондовый метод
ГОСТ 16504-81 Испытания и контроль качества продукции. Основные термины и определения.
ГОСТ Р 52079-2003 Трубы стальные сварные для магистральных газопроводов, нефтепроводов и нефтепродуктовпроводов. Технические условия.
ГОСТ 8.315-97 ГСИ. Стандартные образцы состава и свойств веществ и материалов.
ГОСТ 25812-83 Трубопроводы стальные магистральные. Общие требования к защите от коррозии.
ГОСТ 27333-87 Контроль неразрушающий. Измерение удельной электрической проводимости цветных металлов вихретоковым методом.
ГОСТ Р 50599-93 Сосуды и аппараты стальные сварные высокого давления. Контроль неразрушающий при изготовлении и эксплуатации.
ГОСТ 15467-79 Управление качеством продукции. Основные понятия. Термины и определения.
ГОСТ Р 50779.11-2000 Статистические методы. Статистическое управление качеством. Термины и определения
РМГ 52-2002 Общие методические рекомендации по применению положений ГОСТ 8.315-97 при разработке и применении стандартных образцов
Об утверждении правил аттестации сварщиков и специалистов сварочного производства
Об утверждении правил аттестации персонала в области неразрушающего контроля
Об утверждении «инструкции по визуальному и измерительному контролю»
Об утверждении федерального государственного образовательного стандарта среднего профессионального образования по профессии 15.01.36 Дефектоскопист
ГОСТ Р 51694-2000 Материалы лакокрасочные. Определение толщины покрытия
ГОСТ 9.402-2004 Покрытия лакокрасочные. Подготовка металлических поверхностей к окрашиванию
ГОСТ Р 50.05.16-2018 Оценка соответствия в форме контроля. Неразрушающий контроль. Метрологическое обеспечение.
ГОСТ 31937-2011 Здания и сооружения. Правила обследования и мониторинга технического состояния
ГОСТ 8.520-84 Государственная система обеспечения единства измерений (ГСИ). Весы лабораторные образцовые и общего назначения. Методика поверки (с Поправкой)
ГОСТ 3242-79. Соединения сварные. Методы контроля качества
На главную | База 1 | База 2 | База 3 |
Поиск по реквизитамПоиск по номеру документаПоиск по названию документаПоиск по тексту документа |
Искать все виды документовДокументы неопределённого видаISOАвиационные правилаАльбомАпелляционное определениеАТКАТК-РЭАТПЭАТРВИВМРВМУВНВНиРВНКРВНМДВНПВНПБВНТМ/МЧМ СССРВНТПВНТП/МПСВНЭВОМВПНРМВППБВРДВРДСВременное положениеВременное руководствоВременные методические рекомендацииВременные нормативыВременные рекомендацииВременные указанияВременный порядокВрТЕРВрТЕРрВрТЭСНВрТЭСНрВСНВСН АСВСН ВКВСН-АПКВСПВСТПВТУВТУ МММПВТУ НКММПВУП СНЭВУППВУТПВыпускГКИНПГКИНП (ОНТА)ГНГОСТГОСТ CEN/TRГОСТ CISPRГОСТ ENГОСТ EN ISOГОСТ EN/TSГОСТ IECГОСТ IEC/PASГОСТ IEC/TRГОСТ IEC/TSГОСТ ISOГОСТ ISO GuideГОСТ ISO/DISГОСТ ISO/HL7ГОСТ ISO/IECГОСТ ISO/IEC GuideГОСТ ISO/TRГОСТ ISO/TSГОСТ OIML RГОСТ ЕНГОСТ ИСОГОСТ ИСО/МЭКГОСТ ИСО/ТОГОСТ ИСО/ТСГОСТ МЭКГОСТ РГОСТ Р ЕНГОСТ Р ЕН ИСОГОСТ Р ИСОГОСТ Р ИСО/HL7ГОСТ Р ИСО/АСТМГОСТ Р ИСО/МЭКГОСТ Р ИСО/МЭК МФСГОСТ Р ИСО/МЭК ТОГОСТ Р ИСО/ТОГОСТ Р ИСО/ТСГОСТ Р ИСО/ТУГОСТ Р МЭКГОСТ Р МЭК/ТОГОСТ Р МЭК/ТСГОСТ ЭД1ГСНГСНрГСССДГЭСНГЭСНмГЭСНмрГЭСНмтГЭСНпГЭСНПиТЕРГЭСНПиТЕРрГЭСНрГЭСНсДИДиОРДирективное письмоДоговорДополнение к ВСНДополнение к РНиПДСЕКЕНВиРЕНВиР-ПЕНиРЕСДЗемЕТКСЖНМЗаключениеЗаконЗаконопроектЗональный типовой проектИИБТВИДИКИМИНИнструктивное письмоИнструкцияИнструкция НСАМИнформационно-методическое письмоИнформационно-технический сборникИнформационное письмоИнформацияИОТИРИСОИСО/TRИТНИТОсИТПИТСИЭСНИЭСНиЕР Республика КарелияККарта трудового процессаКарта-нарядКаталогКаталог-справочникККТКОКодексКОТКПОКСИКТКТПММ-МВИМВИМВНМВРМГСНМДМДКМДСМеждународные стандартыМетодикаМетодика НСАММетодические рекомендацииМетодические рекомендации к СПМетодические указанияМетодический документМетодическое пособиеМетодическое руководствоМИМИ БГЕИМИ УЯВИМИГКМММНМОДНМонтажные чертежиМос МУМосМРМосСанПинМППБМРМРДСМРОМРРМРТУМСанПиНМСНМСПМТМУМУ ОТ РММУКМЭКННАС ГАНБ ЖТНВННГЭАНДНДПНиТУНКНормыНормы времениНПНПБНПРМНРНРБНСПНТПНТП АПКНТП ЭППНТПДНТПСНТСНЦКРНЦСОДМОДНОЕРЖОЕРЖкрОЕРЖмОЕРЖмрОЕРЖпОЕРЖрОКОМТРМОНОНДОНКОНТПОПВОПКП АЭСОПНРМСОРДОСГиСППиНОСНОСН-АПКОСПОССПЖОССЦЖОСТОСТ 1ОСТ 2ОСТ 34ОСТ 4ОСТ 5ОСТ ВКСОСТ КЗ СНКОСТ НКЗагОСТ НКЛесОСТ НКМОСТ НКММПОСТ НКППОСТ НКПП и НКВТОСТ НКСМОСТ НКТПОСТ5ОСТНОСЭМЖОТРОТТПП ССФЖТПБПБПРВПБЭ НППБЯПВ НППВКМПВСРПГВУПереченьПиН АЭПисьмоПМГПНАЭПНД ФПНД Ф СБПНД Ф ТПНСТПОПоложениеПорядокПособиеПособие в развитие СНиППособие к ВНТППособие к ВСНПособие к МГСНПособие к МРПособие к РДПособие к РТМПособие к СНПособие к СНиППособие к СППособие к СТОПособие по применению СППостановлениеПОТ РПОЭСНрППБППБ-АСППБ-СППБВППБОППРПРПР РСКПР СМНПравилаПрактическое пособие к СППРБ АСПрейскурантПриказПротоколПСРр Калининградской областиПТБПТЭПУГПУЭПЦСНПЭУРР ГазпромР НОПРИЗР НОСТРОЙР НОСТРОЙ/НОПР РСКР СМНР-НП СРО ССКРазъяснениеРаспоряжениеРАФРБРГРДРД БГЕИРД БТРД ГМРД НИИКраностроенияРД РОСЭКРД РСКРД РТМРД СМАРД СМНРД ЭОРД-АПКРДИРДМРДМУРДПРДСРДТПРегламентРекомендацииРекомендацияРешениеРешение коллегииРКРМРМГРМДРМКРНДРНиПРПРРТОП ТЭРС ГАРСНРСТ РСФСРРСТ РСФСР ЭД1РТРТМРТПРУРуководствоРУЭСТОП ГАРЭГА РФРЭСНрСАСанитарные нормыСанитарные правилаСанПиНСборникСборник НТД к СНиПСборники ПВРСборники РСН МОСборники РСН ПНРСборники РСН ССРСборники ценСБЦПСДАСДАЭСДОССерияСЗКСНСН-РФСНиПСНиРСНККСНОРСНПСОСоглашениеСПСП АССП АЭССправочникСправочное пособие к ВСНСправочное пособие к СНиПСправочное пособие к СПСправочное пособие к ТЕРСправочное пособие к ТЕРрСРПССНССЦСТ ССФЖТСТ СЭВСТ ЦКБАСТ-НП СРОСТАСТКСТМСТНСТН ЦЭСТОСТО 030 НОСТРОЙСТО АСЧМСТО БДПСТО ВНИИСТСТО ГазпромСТО Газпром РДСТО ГГИСТО ГУ ГГИСТО ДД ХМАОСТО ДОКТОР БЕТОНСТО МАДИСТО МВИСТО МИСТО НААГСТО НАКССТО НКССТО НОПСТО НОСТРОЙСТО НОСТРОЙ/НОПСТО РЖДСТО РосГеоСТО РОСТЕХЭКСПЕРТИЗАСТО САСТО СМКСТО ФЦССТО ЦКТИСТО-ГК «Трансстрой»СТО-НСОПБСТПСТП ВНИИГСТП НИИЭССтП РМПСУПСССУРСУСНСЦНПРТВТЕТелеграммаТелетайпограммаТематическая подборкаТЕРТЕР Алтайский крайТЕР Белгородская областьТЕР Калининградской областиТЕР Карачаево-Черкесская РеспубликаТЕР Краснодарского краяТЕР Мурманская областьТЕР Новосибирской областиТЕР Орловской областиТЕР Республика ДагестанТЕР Республика КарелияТЕР Ростовской областиТЕР Самарской областиТЕР Смоленской обл.ТЕР Ямало-Ненецкий автономный округТЕР Ярославской областиТЕРмТЕРм Алтайский крайТЕРм Белгородская областьТЕРм Воронежской областиТЕРм Калининградской областиТЕРм Карачаево-Черкесская РеспубликаТЕРм Мурманская областьТЕРм Республика ДагестанТЕРм Республика КарелияТЕРм Ямало-Ненецкий автономный округТЕРмрТЕРмр Алтайский крайТЕРмр Белгородская областьТЕРмр Карачаево-Черкесская РеспубликаТЕРмр Краснодарского краяТЕРмр Республика ДагестанТЕРмр Республика КарелияТЕРмр Ямало-Ненецкий автономный округТЕРпТЕРп Алтайский крайТЕРп Белгородская областьТЕРп Калининградской областиТЕРп Карачаево-Черкесская РеспубликаТЕРп Краснодарского краяТЕРп Республика КарелияТЕРп Ямало-Ненецкий автономный округТЕРп Ярославской областиТЕРрТЕРр Алтайский крайТЕРр Белгородская областьТЕРр Калининградской областиТЕРр Карачаево-Черкесская РеспубликаТЕРр Краснодарского краяТЕРр Новосибирской областиТЕРр Омской областиТЕРр Орловской областиТЕРр Республика ДагестанТЕРр Республика КарелияТЕРр Ростовской областиТЕРр Рязанской областиТЕРр Самарской областиТЕРр Смоленской областиТЕРр Удмуртской РеспубликиТЕРр Ульяновской областиТЕРр Ямало-Ненецкий автономный округТЕРррТЕРрр Ямало-Ненецкий автономный округТЕРс Ямало-Ненецкий автономный округТЕРтр Ямало-Ненецкий автономный округТехнический каталогТехнический регламентТехнический регламент Таможенного союзаТехнический циркулярТехнологическая инструкцияТехнологическая картаТехнологические картыТехнологический регламентТИТИ РТИ РОТиповая инструкцияТиповая технологическая инструкцияТиповое положениеТиповой проектТиповые конструкцииТиповые материалы для проектированияТиповые проектные решенияТКТКБЯТМД Санкт-ПетербургТНПБТОИТОИ-РДТПТПРТРТР АВОКТР ЕАЭСТР ТСТРДТСНТСН МУТСН ПМСТСН РКТСН ЭКТСН ЭОТСНэ и ТЕРэТССЦТССЦ Алтайский крайТССЦ Белгородская областьТССЦ Воронежской областиТССЦ Карачаево-Черкесская РеспубликаТССЦ Ямало-Ненецкий автономный округТССЦпгТССЦпг Белгородская областьТСЦТСЦ Белгородская областьТСЦ Краснодарского краяТСЦ Орловской областиТСЦ Республика ДагестанТСЦ Республика КарелияТСЦ Ростовской областиТСЦ Ульяновской областиТСЦмТСЦО Ямало-Ненецкий автономный округТСЦп Калининградской областиТСЦПГ Ямало-Ненецкий автономный округТСЦэ Калининградской областиТСЭМТСЭМ Алтайский крайТСЭМ Белгородская областьТСЭМ Карачаево-Черкесская РеспубликаТСЭМ Ямало-Ненецкий автономный округТТТТКТТПТУТУ-газТУКТЭСНиЕР Воронежской областиТЭСНиЕРм Воронежской областиТЭСНиЕРрТЭСНиТЕРэУУ-СТУказУказаниеУказанияУКНУНУОУРврУРкрУРррУРСНУСНУТП БГЕИФАПФедеральный законФедеральный стандарт оценкиФЕРФЕРмФЕРмрФЕРпФЕРрФормаФорма ИГАСНФРФСНФССЦФССЦпгФСЭМФТС ЖТЦВЦенникЦИРВЦиркулярЦПИШифрЭксплуатационный циркулярЭРД |
Показать все найденныеПоказать действующиеПоказать частично действующиеПоказать не действующиеПоказать проектыПоказать документы с неизвестным статусом |
Упорядочить по номеру документаУпорядочить по дате введения |
РДИ 38.18.016-94 Инструкция по ультразвуковому контролю сварных соединений технологического оборудования, РД от 23 июня 1994 года №38.18.016-94
РДИ 38.18.016-94
УТВЕРЖДАЮ
Зам. руководителя
Департамента нефтепереработки Минтопэнерго РФ В.П.Белов 23.06.1994
г.
Директор института, канд.
техн. наук, ст. науч. сотр. А.Е.Фолиянц
Зам. директора института
по научной работе, канд. техн. наук, ст. науч. сотр.
Н.В.Мартынов
Зав. лабораторией
неразрушающих методов контроля, канд. техн. наук, ст. науч. сотр.
Б.П.Пилин
Ответственные
исполнители:
Старший научный сотрудник
З.И.Ролдугина
Старший научный сотрудник
И.А.Митрофанова
1. ОБЩИЕ ПОЛОЖЕНИЯ
1.1. Настоящая инструкция
распространяется на ультразвуковой контроль стыковых, угловых и
тавровых сварных соединений из сталей перлитного и
мартенситно-ферритного классов, выполняемый в условиях монтажа,
ремонта и эксплуатации сосудов, аппаратов, трубопроводов на
предприятиях химической и нефтехимической промышленности.
1.2. Настоящая инструкция
устанавливает порядок, методику проведения ручного ультразвукового
контроля следующих видов сварных соединений, выполненных
электрошлаковой и дуговой сваркой:
—
стыковых кольцевых сварных соединений трубопроводов, сосудов и
аппаратов с толщиной свариваемых элементов не менее 8 мм и с
номинальным наружным диаметром не менее 200 мм;
—
стыковых продольных сварных соединений трубопроводов, сосудов и
аппаратов с толщиной свариваемых элементов не менее 8 мм и с
номинальным наружным диаметром не менее 400 мм;
—
угловых и тавровых сварных соединений, выполненных из плоских и
цилиндрических (трубных) элементов с толщиной элементов не менее 8
мм и номинальным наружным диаметром корпуса (при вварке штуцеров в
корпус) не менее 800 мм, диаметром штуцера не менее 100 мм при
отношении диаметра ввариваемого штуцера к диаметру корпуса не более
0,5;
—
тавровых сварных соединений с толщиной стенки свариваемых элементов
не менее 8 мм;
—
нахлесточных сварных соединений с толщиной свариваемых элементов не
менее 8 мм.
1.3. В соответствии с
настоящей инструкцией разрешается проводить ультразвуковой контроль
сварных швов в любом пространственном положении. Допустимая
температура окружающего воздуха в зоне контроля определяется типом
используемого дефектоскопа и указывается в инструкции по его
эксплуатации.
1.4. Инструкция учитывает
требования ГОСТ
14782-86, ГОСТ 20415-75*,
ГОСТ 23829-79**, ОСТ 2044-83, ОСТ
26.291-87, СНиП
3.05.05-84.
________________
*
На территории Российской Федерации действует ГОСТ
20415-82;
** На территории
Российской Федерации действует ГОСТ
23829-85. — Примечание изготовителя базы данных.
1.5. Контроль по
настоящей инструкции обеспечивает выявление дефектов типа трещин,
непроваров, пор, неметаллических и металлических включений без
расшифровки характера этих дефектов и без определения их
действительных размеров, но с регистрацией координат, расположения
и количества дефектов.
1.6. Положения настоящей
инструкции распространяются на ультразвуковой контроль сварных
соединений при температуре поверхности до 70 °С.
1.7. Настоящая инструкция
не распространяется на ультразвуковой контроль антикоррозионной
наплавки и контроль сварных соединений с неполным проплавлением
свариваемых элементов (т.е. при наличии конструктивного
зазора).
1.8. Контроль по
настоящей инструкции не гарантирует выявление:
—
вольфрамовых включений;
—
дефектов, расположенных в мертвой зоне преобразователя;
—
дефектов, размеры которых меньше длины поперечной ультразвуковой
волны;
—
плоских дефектов, ориентированных относительно акустической оси
искателя под углом менее 70°.
1.9. С введением в
действие настоящей инструкции отменяется действующая в отрасли
«Инструкция по ультразвуковому контролю сварных соединений
технологического оборудования, РДИ 38.18.002-83».
1.10. Для проведения
работ по ультразвуковому контролю на предприятии должна быть
организована лаборатория неразрушающих методов контроля.
1.11. Лаборатория должна
быть укомплектована аппаратурой из рекомендуемого перечня приборов,
приведенного в приложении 2. Качественный состав и необходимое
количество приборов определяются на основании характера и объема
выполняемых работ по ультразвуковому контролю на каждом конкретном
предприятии.
1.12. Для организации
работ по ультразвуковому контролю лаборатория должна иметь
нормативно-техническую документацию, приведенную в конце основного
текста настоящей инструкции.
1.13. Ультразвуковой
контроль осуществляется по заявке, форма которой устанавливается
предприятием. В заявке следует указывать название установки, объект
контроля, тип сварного соединения, его расположение на объекте
контроля, марку стали, толщину и диаметр сварных элементов и другие
необходимые сведения.
1.14. Ответственность за
результаты ультразвукового контроля несет специалист, подписавший
заключение о результатах контроля.
2. ТРЕБОВАНИЯ К СПЕЦИАЛИСТАМ
2.1. К проведению работ
по ультразвуковому контролю допускаются лица, прошедшие обучение и
аттестацию в соответствии с «Правилами
аттестации специалистов неразрушающего контроля»* и имеющие I,
II или III уровень квалификации.
________________
*
На территории Российской Федерации действуют ПБ
03-440-02, здесь и далее по тексту. — Примечание изготовителя
базы данных.
Обучение специалистов
проводится по типовым программам (приложение 4 «Правил
аттестации специалистов неразрушающего контроля»).
К
аттестации по акустическому (ультразвуковому) методу контроля
допускаются специалисты, имеющие после специальной подготовки стаж
работы по указанному методу не менее:
для I уровня квалификации
— 6 месяцев
для II уровня
квалификации — 12 месяцев.
Минимальный стаж работы
после специальной подготовки, необходимый для аттестации кандидата
на III уровень, указан в приведенной ниже таблице.
Общее
образование и специальная подготовка | Стаж
работы | |
II
уровень | неаттестованного | |
ВУЗ или ИПК по
неразрушающему контролю | 12 | 24 |
Техникум по
неразрушающему контролю | 24 | 48 |
Технический
ВУЗ или техникум | 48 | 72 |
Аттестацию проводят
специализированные организации, имеющие лицензию Госгортехнадзора
России. В приложении 3 приведен перечень организаций, которые могут
проводить аттестацию специалистов на I, II и III уровни
квалификации.
2.2. Специалисты I уровня
квалификации ведут работу по контролю конкретной продукции без
выдачи заключения о качестве объекта. Специалист I уровня не несет
ответственности за выбор метода контроля, аппаратуры и режимов ее
работы.
2.3. Специалисты II
уровня квалификации:
—
выполняют контроль и оценку качества продукции;
—
руководят работой специалиста I уровня квалификации;
—
дают заключение о качестве объекта по результатам контроля,
выполненного специалистом I уровня квалификации;
—
ведут подготовку специалистов I уровня квалификации;
—
разрабатывают технологические карты контроля в соответствии с
действующими нормативно-техническими документами по контролю
конкретной продукции в рамках своей квалификации;
—
проводят инспекционный контроль продукции, проконтролированной
специалистами I и II уровней квалификации.
2.4. Специалисты III
уровня квалификации:
—
выполняют контроль и оценку качества продукции;
—
руководят работой специалистов I и II уровней квалификации;
—
дают заключение о качестве продукции по результатам контроля,
выполненного специалистом I уровня квалификации;
—
ведут подготовку специалистов I, II и III уровней квалификации;
—
разрабатывают методики и технологические карты контроля в
соответствии с действующими нормативно-техническими документами по
контролю конкретной продукции в рамках своей квалификации;
—
согласовывают технологические карты, разработанные специалистами II
уровня;
—
проводят инспекционный контроль продукции, проконтролированной
специалистами I и II уровней квалификации.
2.5. Согласно «Правилам
аттестации специалистов неразрушающего контроля» срок действия
квалификационного удостоверения специалистов I и II уровней — 3
года, III уровня — 5 лет.
2.6. В случае изменения
места работы специалиста I и II уровней квалификации, перерыва в
работе по ультразвуковому контролю более одного года и истечения
срока действия квалификационного удостоверения, оно теряет
силу.
2.7. По истечении первого
срока действия квалификационное удостоверение может быть продлено
соответствующим аттестационным органом при условиях:
—
ходатайства с места работы;
—
отсутствия перерыва в работе по УЗ контролю более одного года.
При отсутствии этих
документов специалист должен пройти повторную аттестацию в одной из
организаций, приведенных в приложении 3.
2.8. По истечении двух
сроков действия квалификационного удостоверения проводится
повторная аттестация в одной из организаций, приведенных в
приложении 3.
3. СРЕДСТВА КОНТРОЛЯ
3.1. При контроле сварных
соединений следует применять ультразвуковые эхо-импульсные
отечественные дефектоскопы УД2-12, УД11ПУ и импортные USK-6, USK-7
и др.
Допускается применение
других дефектоскопов, обеспечивающих проведение контроля в
соответствии с требованиями настоящей инструкции.
3.2. Каждый дефектоскоп
должен иметь паспорт, техническое описание и инструкцию по
эксплуатации.
3.3. Дефектоскопы
подлежат обязательной поверке 1 раз в год, а также после каждого
ремонта, в организациях, имеющих право на поверку.
3.4. Приказом по
предприятию назначаются ответственные за состояние аппаратуры лица
из числа ИТР или высококвалифицированных дефектоскопистов, имеющих
уровень квалификации не ниже II-го, которые должны 1 раз в квартал
и непосредственно после ремонта проверять исправность
дефектоскопической аппаратуры, находящейся в распоряжении службы
контроля.
3.5. Для контроля сварных
соединений следует применять прямые, раздельно-совмещенные и
наклонные преобразователи с рабочей частотой в диапазоне 1,8-10 МГц
и углами ввода 40°, 45°; 50°; 60°, 65°; 70°. Преобразователи должны
удовлетворять требованиям ГОСТа
23702-79.
3.6. Для обеспечения
достоверности результатов контроля следует регулярно проверять
следующие параметры:
—
условную чувствительность;
—
стрелу преобразователя;
—
точку ввода;
—
угол ввода;
—
величину мертвой зоны;
—
разрешающую способность.
3.7. Проверка основных
параметров контроля при работе с отечественными дефектоскопами
проводится в соответствии с ГОСТ
14782-86 по стандартным образцам, входящим в «Комплект
контрольных образцов и вспомогательных устройств КОУ-2» (ПО «Волна,
г.Кишинев).
3.8. При работе с
импортными дефектоскопами проверка основных параметров контроля
проводится по образцам Международного института сварки V1 и V2 в
соответствии с методическими рекомендациями по использованию
дефектоскопа или инструкцией по его эксплуатации.
3.9. Для настройки
дефектоскопа и оценки измеряемых характеристик, обнаруженных
дефектов необходимо иметь испытательные образцы с искусственными
отражателями заданных размеров и местоположения.
3.10. Испытательные
образцы и искусственные отражатели в них должны быть изготовлены в
соответствии с требованиями ГОСТа
14782-86.
3.11. Рекомендуемые
размеры испытательных образцов в зависимости от толщины
контролируемого изделия приведены в табл.1.
Таблица 1
Рекомендуемые размеры испытательных образцов
Толщина
контролируемого изделия, , мм | Ширина,
мм | Длина,
мм |
До 10 вкл. | 20 | 80 |
Св. 10 до 20 вкл. | 30 | 100 |
Св. 20 до 30 вкл. | 40 | 5+30 |
Св. 30 до 60 вкл. | 60 | 4+30 |
Отклонение толщины
образца от номинальной толщины контролируемого изделия не должно
превышать ±3 мм.
3.12. Искусственные
отражатели в испытательных образцах могут быть изготовлены в виде
плоскодонных, боковых цилиндрических или плоских угловых
отражателей (зарубок). Размеры отражающей поверхности искусственных
отражателей определяются предельно-допустимыми размерами для
конкретной толщины изделия (рис.1).
Рис.1. — Испытательные образцы
Испытательные образцы
Рис.1
3.13. При изготовлении в
испытательных образцах искусственных отражателей в виде плоских
угловых отражателей (зарубок) следует использовать инструмент,
входящий в КЭУ-I (ТУ-25-08-468-69).
3.14. Соотношение между
площадью вертикальной грани плоского углового отражателя (зарубки)
и площадью плоскодонного отражателя
, дающими сигнал одинаковой амплитуды,
определяется выражением:
;
значение коэффициента зависит от угла ввода ультразвукового луча
в металл и определяется по табл.2.
Таблица 2
Значения коэффициента
Угол ввода,
град. | 40 | 45 | 50 | 60 | 65 | 70 |
2,4 | 1,75 | 1,3 | 0,6 | 0,5 | 0,75 |
4. ПОДГОТОВКА К КОНТРОЛЮ
4.1. Перед проведением
контроля дефектоскопист должен:
—
изучить объект контроля;
—
произвести его внешний осмотр;
—
определить способ контроля;
—
определить угол ввода и выбрать преобразователь;
—
определить пределы перемещения преобразователя и зону зачистки;
—
настроить дефектоскоп.
4.2. Изучение объекта
контроля предусматривает изучение технической документации на
контролируемый объект, особенностей конструкции и технологии
изготовления сварного соединения, анализ результатов предыдущего
контроля, а также определение необходимого объема контроля и норм
отбраковки.
4.3. По результатам
внешнего осмотра устанавливается пригодность изделия к контролю,
при этом определяется:
—
соответствие ширины валика усиления требованиям
нормативно-технической документации на контролируемое изделие;
—
наличие недоступных для контроля участков изделия;
—
отсутствие недопустимых внешних дефектов.
4.4. Контроль
ультразвуковым методом следует проводить только после устранения
всех обнаруженных при внешнем осмотре дефектов.
4.5. Выбор способа
контроля и угла ввода преобразователя определяется возможностью
прозвучивания всего сечения сварного шва.
При контроле сварных швов
применяют следующие способы контроля:
—
прямым или раздельно-совмещенным преобразователем;
—
наклонным преобразователем;
—
прямым лучом;
—
однократно отраженным лучом;
—
двукратно или многократно отраженным лучом.
4.6. Контроль прямым или
раздельно-совмещенным преобразователем проводят на стыковых сварных
швах со снятым валиком усиления (как правило, на сварных
соединениях большой толщины, выполненных автоматической сваркой), а
также на угловых и тавровых сварных соединениях с плоскими
стенками, при двустороннем доступе к изделию.
Способ контроля прямым
лучом наклонными преобразователями применяют для выявления дефектов
в корне шва (в стыковых швах с V-образной разделкой) или в нижней
части шва (в стыковых швах с Х-образной разделкой).
Способ контроля
однократно-отраженным лучом наклонными преобразователями применяют
для контроля середины и верхней части шва.
Способ контроля двукратно
и многократно отраженным лучом используют в тех случаях, когда
сварное соединение имеет малую толщину и/или большую ширину валика
усиления или размера катета углового шва, что препятствует вводу
прямого ультразвукового луча в наплавленный металл шва.
Все применяемые схемы
контроля приведены в методиках контроля каждого типа сварного
соединения в настоящей инструкции.
Значения углов ввода и
способы контроля сварных соединений различных толщин и типов
приведены в табл.3.
Таблица 3
Параметры контроля сварных соединений
Тип сварного
соединения | Толщина
сваренных элементов | Ширина валика
усиления или катет сварного шва | Рабочая
частота | Угол ввода, не
менее град. | Ширина зоны
зачистки с одной стороны шва |
1 | 2 | 3 | 4 | 5 | 6 |
Стыковые
сварные соединения | |||||
— с односторонним швом (V-образная разделка кромок) | 8 | 21 | 4,0-5,0 | 70 | 85 |
10 | 23 | 4,0-5,0 | 70 | 95 | |
12 | 26 | 4,0-5,0 | 65 | 90 | |
14 | 26 | 2,0-2,5 | 65 | 100 | |
16 | 28 | 2,0-2,5 | 65 | 110 | |
18 | 28 | 2,0-2,5 | 65 | 115 | |
20 | 28 | 2,0-2,5 | 65 | 125 | |
22 | 31 | 2,0-2,5 | 65 | 135 | |
24 | 31 | 2,0-2,5 | 65 | 145 | |
— с двухсторонним швом (Х-образная разделка кромок) | 26 | 28 | 2,0-2,5 | 65 | 150 |
28 | 28 | 2,0-2,5 | 65 | 160 | |
30 | 34 | 2,0-2,5 | 65 | 170 | |
32 | 34 | 2,0-2,5 | 65 | 175 | |
34 | 34 | 2,0-2,5 | 65 | 185 | |
36 | 34 | 2,0-2,5 | 65 | 195 | |
38 | 34 | 2,0-2,5 | 65 | 205 | |
40 | 37 | 2,0-2,5 | 65 | 210 | |
42 | 37 | 2,0-2,5 | 65 | 220 | |
44 | 37 | 2,0-2,5 | 65 | 230 | |
46 | 37 | 2,0-2,5 | 65 | 240 | |
48 | 37 | 2,0-2,5 | 50 | 155 | |
50 | 41 | 2,0-2,5 | 50 | 160 | |
52 | 41 | 2,0-2,5 | 50 | 165 | |
54 | 41 | 2,0-2,5 | 50 | 170 | |
56 | 44 | 2,0-2,5 | 50 | 175 | |
58 | 44 | 2,0-2,5 | 50 | 180 | |
60 | 44 | 2,0-2,5 | 50 | 185 | |
65 | 47 | 2,0-2,5 | 40 | 150 | |
70 | 47 | 2,0-2,5 | 40 | 160 | |
75 | 50 | 2,0-2,5 | 40 | 165 | |
80 | 50 | 2,0-2,5 | 40 | 175 | |
85 | 53 | 2,0-2,5 | 40 | 180 | |
90 | 53 | 2,0-2,5 | 40 | 190 | |
Угловые
сварные соединения | |||||
— с V-образной разделкой кромок | 8 | 13 | 4,0-5,0 | 70 | 85 |
10 | 18 | 4,0-5,0 | 70 | 95 | |
12 | 18 | 4,0-5,0 | 70 | 105 | |
14 | 23 | 2,0-2,5 | 70 | 115 | |
16 | 29 | 2,0-2,5 | 70 | 130 | |
18 | 29 | 2,0-2,5 | 70 | 140 | |
— с K-образной разделкой кромок | 20 | 17 | 2,0-2,5 | 65 | 150 |
22 | 20 | 2,0-2,5 | 65 | 135 | |
24 | 23 | 2,0-2,5 | 65 | 140 | |
26 | 25 | 2,0-2,5 | 65 | 150 |
ГОСТ 23055-78 Контроль неразрушающий. Сварка металлов плавлением. Классификация сварных соединений по результатам радиографического контроля (с Изменениями N 1, 2), ГОСТ от 07 апреля 1978 года №23055-78
ГОСТ 23055-78
Группа В09
МКС 25.160.40
Дата введения 1979-07-01
1. УТВЕРЖДЕН И ВВЕДЕН В ДЕЙСТВИЕ Постановлением Государственного комитета СССР по стандартам от 07.04.78 N 960
2. ВВЕДЕН ВПЕРВЫЕ
3. ССЫЛОЧНЫЕ НОРМАТИВНО-ТЕХНИЧЕСКИЕ ДОКУМЕНТЫ
4. Ограничение срока действия снято по протоколу N 3-93 Межгосударственного совета по стандартизации, метрологии и сертификации (ИУС 5-6-93)
5. ИЗДАНИЕ (декабрь 2004 г.) с Изменениями N 1, 2, утвержденными в декабре 1983 г., декабре 1988 г. (ИУС 3-84, 3-89)
1. Настоящий стандарт распространяется на сварные соединения, выполненные сваркой плавлением изделий из металлов и их сплавов с толщиной свариваемых элементов от 1 до 400 мм и устанавливает семь классов сварных соединений по максимальным допустимым размерам пор, шлаковых, вольфрамовых и окисных включений, выявляемых при радиографическом контроле.
Стандарт не распространяется на сварные соединения изделий, подведомственных Госатомэнергонадзору СССР и Госгортехнадзору СССР.
В стандарте учтены требования ГОСТ 6636, ГОСТ 2601, ГОСТ 7512, ГОСТ 15467 и рекомендации по стандартизации РС 2192-72.
(Измененная редакция, Изм. N 2).
2. ПОРЫ И ВКЛЮЧЕНИЯ
2.1. За размеры пор, шлаковых и вольфрамовых включений принимаются размеры их изображений на радиограммах:
диаметр — для сферических пор и включений;
длина и ширина — для удлиненных пор и включений.
(Измененная редакция, Изм. N 2).
2.2, 2.2.1. (Исключены, Изм. N 1).
2.3. За размер скопления пор, шлаковых или вольфрамовых включений принимается его длина, измеренная по наиболее удаленным друг от друга краям изображений пор или включений в скоплении.
2.3.1. Скоплением называется три или более расположенных беспорядочно пор, шлаковых или вольфрамовых включений с расстоянием между любыми двумя близлежащими краями изображений пор или включений более одной, но не более трех их максимальных ширин или диаметров.
2.3, 2.3.1. (Измененная редакция, Изм. N 2).
2.4. За размеры окисных включений, непроваров и трещин принимается их длина.
2.5. Поры или включения с расстоянием между ними не более их максимальной ширины или диаметра, независимо от их числа и взаимного расположения, рассматриваются как одна пора или одно включение, размеры которых определяются в соответствии с п.2.1.
(Измененная редакция, Изм. N 2).
2.5а. (Исключен, Изм. N 2).
3. Максимальные допустимые длина, ширина и суммарная длина пор, шлаковых, вольфрамовых и окисных включений для любого участка радиограммы длиной 100 мм для классов 1-7 приведены в табл.1-7. Длина скоплений не должна превышать 1,5 максимальных допустимых длин отдельных дефектов, приведенных в табл.1-7.
Таблица 1
Класс 1
мм
Толщина свариваемых элементов | Поры или включения | Суммарная длина | |
Ширина (диаметр) | Длина | ||
До 3 | 0,2 | 0,2 | 2,0 |
Св. 3 до 5 | 0,3 | 0,3 | 3,0 |
» 5 » 8 | 0,4 | 0,4 | 4,0 |
» 8 » 11 | 0,5 | 0,5 | 5,0 |
» 11 » 14 | 0,6 | 0,6 | 6,0 |
» 14 » 20 | 0,8 | 0,8 | 8,0 |
» 20 » 26 | 1,0 | 1,0 | 10,0 |
» 26 » 34 | 1,2 | 1,2 | 12,0 |
» 34 » 45 | 1,5 | 1,5 | 15,0 |
» 45 » 67 | 2,0 | 2,0 | 20,0 |
» 67 » 90 | 2,5 | 2,5 | 25,0 |
» 90 » 120 | 3,0 | 3,0 | 30,0 |
» 120 » 200 | 4,0 | 4,0 | 40,0 |
» 200 » 400 | 5,0 | 5,0 | 50,0 |
Таблица 2
Класс 2
мм
Толщина свариваемых элементов | Поры или включения | Суммарная длина | |
Ширина (диаметр) | Длина | ||
До 3 | 0,3 | 0,6 | 3,0 |
Св. 3 до 5 | 0,4 | 0,8 | 4,0 |
» 5 » 8 | 0,5 | 1,0 | 5,0 |
» 8 » 11 | 0,6 | 1,2 | 6,0 |
» 11 » 14 | 0,8 | 1,5 | 8,0 |
» 14 » 20 | 1,0 | 2,0 | 10,0 |
» 20 » 26 | 1,2 | 2,5 | 12,0 |
» 26 » 34 | 1,5 | 3,0 | 15,0 |
» 34 » 45 | 2,0 | 4,0 | 20,0 |
» 45 » 67 | 2,5 | 5,0 | 25,0 |
» 67 » 90 | 3,0 | 6,0 | 30,0 |
» 90 » 120 | 4,0 | 8,0 | 40,0 |
» 120 » 200 | 5,0 | 10,0 | 50,0 |
» 200 » 400 | 5,0 | 10,0 | 60,0 |
Примечание к табл.1 и 2. Поры и включения с расстояниями между ними не более трех максимальных ширин или диаметров в классах 1 и 2 не допускаются.
Таблица 3
Класс 3
мм
Толщина свариваемых элементов | Поры или включения | Суммарная длина | |
Ширина (диаметр) | Длина | ||
До 3 | 0,4 | 1,2 | 4,0 |
Св. 3 до 5 | 0,5 | 1,5 | 5,0 |
» 5 » 8 | 0,6 | 2,0 | 6,0 |
» 8 » 11 | 0,8 | 2,5 | 8,0 |
» 11 » 14 | 1,0 | 3,0 | 10,0 |
» 14 » 20 | 1,2 | 3,5 | 12,0 |
» 20 » 26 | 1,5 | 5,0 | 15,0 |
» 26 » 34 | 2,0 | 6,0 | 20,0 |
» 34 » 45 | 2,5 | 8,0 | 25,0 |
» 45 » 67 | 3,0 | 9,0 | 30,0 |
» 67 » 90 | 4,0 | 10,0 | 40,0 |
» 90 » 120 | 5,0 | 10,0 | 50,0 |
» 120 » 200 | 5,0 | 10,0 | 60,0 |
» 200 » 400 | 5,0 | 10,0 | 70,0 |
Таблица 4
Класс 4
мм
Толщина свариваемых элементов | Поры или включения | Суммарная длина | |
Ширина (диаметр) | Длина | ||
До 3 | 0,5 | 1,5 | 5,0 |
Св. 3 до 5 | 0,6 | 2,0 | 6,0 |
» 5 » 8 | 0,8 | 2,5 | 8,0 |
» 8 » 11 | 1,0 | 3,0 | 10,0 |
» 11 » 14 | 1,2 | 3,5 | 12,0 |
» 14 » 20 | 1,5 | 5,0 | 15,0 |
» 20 » 26 | 2,0 | 6,0 | 20,0 |
» 26 » 34 | 2,5 | 8,0 | 25,0 |
» 34 » 45 | 3,0 | 9,0 | 30,0 |
» 45 » 67 | 4,0 | 12,0 | 40,0 |
» 67 » 90 | 5,0 | 12,0 | 50,0 |
» 90 » 120 | 5,0 | 12,0 | 60,0 |
» 120 » 200 | 5,0 | 12,0 | 70,0 |
» 200 » 400 | 5,0 | 12,0 | 80,0 |
Таблица 5
Класс 5
мм
Толщина свариваемых элементов | Поры или включения | Суммарная длина | |
Ширина (диаметр) | Длина | ||
До 3 | 0,6 | 2,0 | 6,0 |
Св. 3 до 5 | 0,8 | 2,5 | 8,0 |
» 5 » 8 | 1,0 | 3,0 | 10,0 |
» 8 » 11 | 1,2 | 3,5 | 12,0 |
» 11 » 14 | 1,5 | 5,0 | 15,0 |
» 14 » 20 | 2,0 | 6,0 | 20,0 |
» 20 » 26 | 2,5 | 8,0 | 25,0 |
» 26 » 34 | 3,0 | 10,0 | 30,0 |
» 34 » 45 | 4,0 | 12,0 | 40,0 |
» 45 » 67 | 5,0 | 15,0 | 50,0 |
» 67 » 90 | 5,0 | 15,0 | 60,0 |
» 90 » 120 | 5,0 | 15,0 | 70,0 |
» 120 » 200 | 5,0 | 15,0 | 80,0 |
» 200 » 400 | 5,0 | 15,0 | 90,0 |
Таблица 6
Класс 6
мм
Толщина свариваемых элементов | Поры или включения | Суммарная длина | |
Ширина (диаметр) | Длина | ||
До 3 | 0,8 | 3,0 | 8,0 |
Св. 3 до 5 | 1,0 | 4,0 | 10,0 |
» 5 » 8 | 1,2 | 5,0 | 12,0 |
» 8 » 11 | 1,5 | 6,0 | 15,0 |
» 11 » 14 | 2,0 | 8,0 | 20,0 |
» 14 » 20 | 2,5 | 10,0 | 25,0 |
» 20 » 26 | 3,0 | 12,0 | 30,0 |
» 26 » 34 | 4,0 | 15,0 | 40,0 |
» 34 » 45 | 5,0 | 20,0 | 50,0 |
» 45 » 67 | 5,0 | 20,0 | 60,0 |
» 67 » 90 | 5,0 | 20,0 | 70,0 |
» 90 » 120 | 5,0 | 20,0 | 80,0 |
» 120 » 200 | 5,0 | 20,0 | 90,0 |
Таблица 7
Класс 7
мм
Толщина свариваемых элементов | Поры или включения | Суммарная длина | |
Ширина (диаметр) | Длина | ||
До 3 | 1,0 | 5,0 | 10,0 |
Св. 3 до 5 | 1,2 | 6,0 | 12,0 |
» 5 » 8 | 1,5 | 8,0 | 15,0 |
» 8 » 11 | 2,0 | 10,0 | 20,0 |
» 11 » 14 | 2,5 | 12,0 | 25,0 |
» 14 » 20 | 3,0 | 15,0 | 30,0 |
» 20 » 26 | 4,0 | 20,0 | 40,0 |
» 26 » 34 | 5,0 | 25,0 | 50,0 |
» 34 » 45 | 5,0 | 25,0 | 60,0 |
» 45 » 67 | 5,0 | 25,0 | 70,0 |
» 67 » 90 | 5,0 | 25,0 | 80,0 |
» 90 » 120 | 5,0 | 25,0 | 90,0 |
Примечания к табл.1-7:
1. Поры для включения с длиной изображения менее 0,2 мм при расшифровке радиограмм не учитываются.
2. При различной толщине свариваемых элементов максимальный допустимый размер пор или включений выбирается по меньшей толщине.
3.1. Класс сварного соединения, максимальные допустимые размеры непроваров (в случаях, когда непровары допускаются конструкцией или условиями эксплуатации сварных coeдинений), а также дополнительные ограничения по числу и длине пор и включений, их суммарной длине и расстоянию между ними должны быть приведены в нормативно-технической документации на cварные изделия.
3, 3.1. (Измененная редакция, Изм. N 2).
3.1.1. Непровары в классах 1-3 не допускаются.
3.1.2. Трещины в классах 1-7 не допускаются.
3.2. При длине радиограмм менее 100 мм приведенная в табл.1-7 максимальная допустимая суммарная длина пор и включений (для любого участка радиограмм длиной 100 мм) уменьшается пропорционально длине радиограмм, но не должна быть менее соответствующей максимальной допустимой длины отдельных пор и включений.
3.2.1. При наличии смежных радиограмм с длиной менее 100 мм каждая, а также в случаях, когда наибольшее число пор и включений выявлено на смежных краях двух радиограмм (при любой длине этих радиограмм), при определении максимальной суммарной длины пор и включений эти радиограммы должны рассматриваться как одна радиограмма.
3.2, 3.2.1. (Измененная редакция, Изм. N 2).
4. Для стыковых и угловых соединений могут выбираться классы 1-7.
Для нахлесточных и тавровых сварных соединений в зависимости от отношения меньшей толщины свариваемых элементов к большей могут выбираться:
при отношении толщин свариваемых элементов не менее 0,8 — классы 4-7;
при отношении толщин свариваемых элементов менее 0,8, но не менее 0,6 — классы 5-7;
при отношении толщин свариваемых элементов менее 0,6, но не менее 0,4 — классы 6-7;
при отношении толщин свариваемых элементов менее 0,4, но не менее 0,2 — класс 7.
4.1. Нахлесточные и тавровые сварные соединения с отношением толщин свариваемых элементов менее 0,2 радиографическим методом не контролируются.
5. Чувствительность контроля — по ГОСТ 7512. При этом значения чувствительности не должны превышать:
для сварных соединений 1-го класса — значений, приведенных для 1-го класса чувствительности по ГОСТ 7512;
для сварных соединений 2-4 классов — значений, приведенных для 2-го класса чувствительности по ГОСТ 7512;
для сварных соединений 5-7 классов — значений, приведенных для 3-го класса чувствительности по ГОСТ 7512.
(Измененная редакция, Изм. N 1).
6. (Исключен, Изм. N 1).
ПРИЛОЖЕНИЯ 1, 2. (Исключены, Изм. N 1).
Электронный текст документа
подготовлен АО «Кодекс» и сверен по:
официальное издание
М.: ИПК Издательство стандартов, 2005
ГОСТ Р 50608-93
ГОСТ Р 50608-93
Г87
ОКП 36 4400
Дата введения 1994-07-01
1 РАЗРАБОТАН И ВНЕСЕН Техническим комитетом по стандартизации ТК 271 «Установки холодильные холодопроизводительностью свыше 2,5 тыс. станд. ккал/ч (3,0 кВт)»
2 УТВЕРЖДЕН И ВВЕДЕН В ДЕЙСТВИЕ Постановлением Госстандарта России от 12.11.93 N 240
3 ВВЕДЕН ВПЕРВЫЕ
1 ОБЛАСТЬ ПРИМЕНЕНИЯ
Настоящий стандарт распространяется на стальные теплообменные, емкостные и вспомогательные аппараты, предназначенные для работы в составе аммиачных, углеводородных и хладоновых холодильных машин и установок (далее — аппараты), и устанавливает требования к конструкции сварных швов аппаратов и методы контроля их качества в развитие ГОСТ 5264, ГОСТ 8713, ГОСТ 14771 и ГОСТ 16037.
Стандарт не распространяется на фильтры, смесители, сепараторы, смотровые и другие подобные устройства, встраиваемые в трубопроводы, а также на аппараты и сосуды из труб внутренним диаметром не более 150 мм.
Обязательные требования к качеству сварных швов аппаратов, обеспечивающие их безопасность для жизни, здоровья и имущества населения, изложены в разделе 6 и пунктах 5.1-5.5, 5.8, 5.11-5.17.
Термины и определения — по ГОСТ 2601.
2 НОРМАТИВНЫЕ ССЫЛКИ
В настоящем стандарте использованы ссылки на следующие стандарты:
ГОСТ 2601-84 Сварка металлов. Термины и определения основных понятий
ГОСТ 5264-80 Ручная дуговая сварка. Соединения сварные. Основные типы, конструктивные элементы и размеры
ГОСТ 6996-66 Сварные соединения. Методы определения механических свойств
ГОСТ 8713-79 Сварка под флюсом. Соединения сварные. Основные типы, конструктивные элементы и размеры
ГОСТ 14771-76 Дуговая сварка в защитном газе. Соединения сварные. Основные типы, конструктивные элементы и размеры
ГОСТ 16037-80 Соединения сварные стальных трубопроводов. Основные типы, конструктивные элементы и размеры
ГОСТ 23055-78 Контроль неразрушающий. Сварка металлов плавлением. Классификация сварных соединений по результатам радиографического контроля
3 ОБОЗНАЧЕНИЯ
Приняты следующие обозначения конструктивных элементов свариваемых деталей и сварных швов:
— толщина обечайки;
— толщина патрубка;
— толщина шва;
— глубина разделки под сварку;
— высота шва;
— ширина шва;
— расстояние от поверхности фланца или трубной решетки до сварного шва.
4 КЛАССИФИКАЦИЯ
4.1 Сварные швы аппаратов должны быть отнесены к одной из четырех категорий (рисунок 1).
Рисунок 1
Категория А. Продольные сварные швы обечаек корпуса, распределительной камеры, переходников, патрубков, сварные швы штампованных или плоских днищ, изготовленных из нескольких частей.
Категория В. Кольцевые сварные швы обечаек корпуса, патрубков, кольцевые сварные швы, соединяющие штампованные эллиптические днища с обечайками корпуса, распределительной камеры, отстойников.
Категория С. Сварные швы, присоединяющие фланцы, трубные доски, плоские днища к обечайкам, а также фланцы к эллиптическим и сферическим днищам.
Категория D. Сварные швы, соединяющие патрубки и штуцера с обечайками и днищами.
5 ТЕХНИЧЕСКИЕ ТРЕБОВАНИЯ
5.1 Сварные швы категории А должны быть стыковыми двусторонними или односторонними, выполненными по технологии, обеспечивающей проплавление на всю глубину по ГОСТ 5264, ГОСТ 8713 и ГОСТ 14771.
5.2 Сварные швы категории В должны быть стыковыми двусторонними или односторонними с применением подкладки (остающейся или удаляемой после сварки) по ГОСТ 5264, ГОСТ 8713, ГОСТ 14771 и ГОСТ 16037.
5.3 Сварные швы категории С должны быть:
5.3.1 Для аммиачных и углеводородных аппаратов — стыковыми двусторонними (рисунки 2 и 3) или односторонними, выполненными по технологии, обеспечивающей проплавление на всю глубину, или односторонними с применением подкладки (остающейся или удаляемой после сварки) (рисунки 4 и 5).
Рисунок 2
Рисунок 3
Рисунок 4
Рисунок 5
5.3.2 Для хладоновых аппаратов — угловыми или тавровыми швами (рисунки 6, 7, 8, 9 и 10).
Рисунок 6
Рисунок 7
Рисунок 8
Рисунок 9
Рисунок 10
5.4 Сварные швы категории D должны быть угловыми или тавровыми швами (рисунки 11, 12, 13, 14, 15, 16 и 17).
Рисунок 11
Рисунок 12
Рисунок 13
Рисунок 14
Рисунок 15
Рисунок 16
Рисунок 17
5.5 Стыковые, угловые и тавровые швы полостей, содержащих холодильный агент, должны быть швами с полным проплавлением.
5.6 Допускается применять швы с неполным проплавлением (конструктивным зазором) по типу У5 или У7 ГОСТ 16037, соединяющие фланцы с патрубками хладоновых аппаратов, эксплуатируемых при температуре не ниже минус 28 °С, а также соединяющие фланцы с днищами крышек, не находящихся под давлением холодильного агента.
5.7. Допускается применять швы с неполным проплавлением для соединений гильза — обечайка (рисунок 18), бобышка — обечайка (рисунок 19) для аппаратов, эксплуатируемых при температуре не ниже минус 28 °С.
Рисунок 18
Рисунок 19
5.8 Остающиеся подкладные кольца должны быть изготовлены из стали той же марки, из которой изготовлены свариваемые детали.
5.9 В качестве удаляемых подкладных колец следует применять медные, керамические или флюсовые кольца.
5.10 Приведенные на рисунках 1-19 примеры конструкции сварных швов являются рекомендуемыми.
5.11 Продольные швы смежных обечаек должны быть смещены относительно друг друга на расстояние, равное пятикратной толщине наиболее толстого элемента, но не менее чем на 100 мм между осями швов.
5.12 На всех свариваемых деталях должна быть сохранена маркировка предприятия — поставщика металла. В состав маркировки должны входить:
— марка материала;
— номер плавки.
5.13 В сборочном чертеже сварного узла или на специальном эскизе должны быть указаны схема маркировки деталей, места простановки клейм сварщиков и клейм представителей ОТК, осуществляющих входной контроль материалов и контроль качества сварки на промежуточных операциях.
5.14 Если конструкторской или технологической документацией предусмотрена послесварочная термическая обработка, то окончательный контроль качества сварных швов проводят после нее.
5.15 Кромки подготовленных под сварку деталей и прилегающие к ним поверхности должны быть зачищены с двух сторон до полного удаления окалины, ржавчины, грата и брызг после термической резки, краски, масел и других загрязнений.
5.16 При сварке необходимо защищать внутреннюю поверхность защитным газом (углекислым газом или аргоном).
5.17 Качество и контроль сварных соединений должны обеспечивать прочность и герметичность аппаратов в соответствии с требованиями, установленными в конструкторской документации.
6 МЕТОДЫ КОНТРОЛЯ КАЧЕСТВА СВАРНЫХ ШВОВ
6.1 Технология сварки, а также сварщики и операторы установок для автоматической сварки должны быть аттестованы в соответствии с требованиями отраслевых нормативных документов.
6.2 Методы контроля качества сварных швов различных категорий указаны в таблице 6.1.
Таблица 6.1 — Методы контроля качества сварных швов
Категория сварного шва | Внешний осмотр | Радиографический контроль или ультразвуковая дефектоскопия | Цветная |
А | + | + | |
В | + | + | |
С | + | + | |
D | + | + |
6.3 Объем контроля сварных швов радиографическим или ультразвуковым методами должен быть не менее указанного в Правилах устройства и безопасной эксплуатации холодильных систем, утвержденных Госпроматомнадзором СССР 01.11.91 г.
6.4 При объеме контроля радиографическим или ультразвуковым методами менее 100% общей длины сварных швов обязательному контролю подлежат места пересечений сварных швов категорий А и В для фреоновых аппаратов и сварных швов категорий А, В, С для углеводородных и аммиачных аппаратов, а также участки сварных швов, перекрываемые укрепляющими кольцами.
6.5 По требованию заказчика сварные швы категорий А, В и С аммиачных и углеводородных аппаратов и сварные швы категорий А и В хладоновых аппаратов должны быть проверены радиографическим методом при выполнении следующих условий:
6.5.1 Объем контроля сварных швов аммиачных и углеводородных аппаратов должен составлять 100% независимо от рабочей температуры хладагента в аппарате.
6.5.2 Допускается ультразвуковая дефектоскопия взамен радиографического контроля для замыкающего сварного шва аппарата, если конструкция аппарата не позволяет применить радиографический метод.
6.6 Проверка ударной вязкости
6.6.1 Для аппаратов, изготовленных из углеродистой и низколегированной стали, предназначенных для эксплуатации при температуре ниже минус 28 °С, должны быть подвергнуты испытаниям на ударный изгиб образцы типов IX, Х или XI по ГОСТ 6996 (Шарпи). Испытания следует проводить при минимальной рабочей температуре аппарата.
6.6.2 Минимальное значение ударной вязкости составляет 20 Дж/см (2 кгс·м/см).
6.6.3 Образцы должны быть вырезаны из контрольного стыкового сварного соединения.
6.6.4 При сварке контрольных соединений пластины следует прихватить к свариваемым элементам так, чтобы шов контрольных пластин являлся продолжением шва свариваемого изделия.
6.6.5 Если прихватка пластин невозможна (кольцевые швы и т.д.), то сварку пластин следует проводить отдельно, но с обязательным соблюдением всех условий сварки контролируемых стыковых соединений.
6.6.6 Из каждого контрольного сварного соединения должны быть вырезаны по три образца для испытания наплавленного металла и по три образца для испытания металла околошовной зоны. При этом канавка должна быть расположена перпендикулярно к поверхности пластины.
6.6.7 При получении неудовлетворительных результатов хотя бы одного из видов испытания испытание этого вида должно быть повторено на удвоенном количестве образцов, вырезанных из того же контрольного соединения.
6.6.8 Если при повторном испытании хотя бы на одном из образцов получен неудовлетворительный результат, качество контролируемого сварного соединения сосуда следует считать неудовлетворительным.
6.7 В сварных соединениях не допускаются следующие наружные дефекты:
— несоответствие их форм и размеров требованиям стандартов и чертежей;
— трещины;
— свищи и пористость наружной поверхности шва;
— подрезы;
— наплывы, прожоги и незаплавленные кратеры;
— смещение кромок свариваемых элементов выше максимально допустимого, указанного в таблице 6.2.
Таблица 6.2
В миллиметрах
Толщина свариваемых листов | Максимально допустимое смещение кромок | |
Категория сварного шва | ||
А | В, С | |
До 12 | ||
Св. 12 до 20 | 3,2 |
6.8 В сварных соединениях не допускаются следующие внутренние дефекты:
— трещины, непровары и несплавления;
— поры и включения, количество которых выходит за пределы норм, установленных ГОСТ 23055 для 4-го класса дефектности сварного шва.
Текст документа сверен по:
официальное издание
М.: Издательство стандартов, 1994