Железнодорожные пути без стыков — Railway Supply
Бесстыковой или «бархатный» путь на сегодня считается наиболее прогрессивной технологией на железнодорожном транспорте во всем мире. Его главное преимущество — снижение износа колес и верхнего строения пути, которое происходит через стыки между рельсами в традиционных системах.
В настоящее время существует несколько технологий сварки рельсовКроме отсутствия стука колес, он также позволяет повысить скорость движения и комфорт для пассажиров. Украина — одна из передовых стран по внедрению данной технологии.
Основное преимущество «бархатного» пути — полная (или почти полная) ликвидация стыков, которые являются причиной дополнительных ударных динамических воздействий колес на рельсы. Стыки приводят к быстрому накоплению дефектов в рельсах и колесах, и в конечном итоге — к преждевременному износу колес подвижного состава и железнодорожного пути.
Как отмечается в журнале «Наука и инновации», ликвидация стыков «ведет к значительному снижению динамических сил взаимодействия, снижение сопротивления движению поездов (в среднем на 10%), увеличению сроков службы элементов верхнего строения пути (от 10 до 25%), сокращению расходов на ремонт пути и подвижного состава (до 35%), экономии металла на стыковые соединения (5-7 т на 1 км) ».
Считается, что первый сварной путь был использован в Германии в 1924 году. Одними из передовых также были железные США и СССР. Обычным явлением на магистральных линиях «бархатный» путь стал в 1950 — 1960-х годах. К 1990 ее протяженность в масштабах постсоветских государств составляла 29% сети (55,5 тыс. км).
Сейчас доля выросла и процесс перевода путей из обычных на «бархатные» активно продолжается. В частности, на Байкало-Амурской магистрали (БАМ) и Транссибе в России. Такая линия была построена недавно при перепрошивке железной дороги на острове Сахалин на пути 1520 мм. Интересно также, что на Восточно-Сибирской магистрали «РЖД» широко применяла для укладки в «бархатный» путь рельсы японского производства.
Украина всегда была одной из передовых по внедрению этой прогрессивной технологии. В 1995 году таких путей в стране было 14,5 тыс. км или 46,7%. К 2010 году протяженность выросла до 20 тыс. км и их доля составляла 67%.
Данная конструкция, в частности, позволила запустить движение ускоренных пассажирских поездов к Евро-2012. Их скорость на некоторых участках составила 160 км / ч.
В 2000-х годах украинская наука, промышленность и железная дорога сделали большой скачок в плане развития технологии бесстыкового пути. Стоит отметить, что одно из украинских предприятий — Каховский завод электросварочного оборудования ( «КЗЭСО») — вышел на позиции мирового лидера в производстве машин для обустройства «бархатной» колеи.
Мобильный рельсосварочный комплекс украинского производстваПроизведенное в Украине оборудование нашло применение в 78 странах, в том числе, таких железнодорожных государствах, как США, Китай, Индия, Австралия, а также в странах Европейского Союза и СНГ. На экспорт было поставлено более 2 тыс. машин. Украинские производители занимали 60% всего мирового парка стационарных и 95% передвижных рельсосварочных машин. Активное участие в разработках принимал Институт электросварки им. Е.А. Патона Национальной академии наук Украины.
Работа продолжается и сегодня. К 2020 году сварные рельсы уже установлено на 78,1% главных путей, то есть на 20 тыс. 856 км. В 2021-м планируется заменить еще около 350 км звеньевых путей на бесстыковые.
В прошлом году «КЗЭСО» поставило Укрзализныце четыре новых рельсосварочных комплекса КСМ007. Они построены на базе грузовых автомобилей Volvo, способных также передвигаться по рельсам.
Поезд с предварительно сваренными рельсами в СШАВ США технология непрерывных сварных рельсов получила название CWR (Continuous Welded Rail). Иногда такие рельсы еще называют «ленточными».
Заключается технология в том, что рельсы стандартной длины сваривают в состояние непрерывной конструкции, длина которой может достигать нескольких километров.
Несмотря на то, что бесстыковые пути характеризуются меньшими затратами на обслуживание, главная проблема их эксплуатации связана с температурными расширениями. Это грозит выбросами пути. Вопрос решается путем применения вставок или уравнительных пролетов из обычных рельсов, а также пристальным мониторингом состояния пути в наиболее жаркие летние дни.
В Германии также есть опыт покраски рельсов в белый цвет для меньшего их нагрева.
Повысить скорость на бесстыковых магистралях позволяют усовершенствованные стрелочные переводы, которые обеспечивают скорость движения до 160-200 км / ч вместо 120 км / ч. Подобные комплекты выпускаются на АО «Днепропетровский стрелочный завод». По состоянию на начало 2021 было изготовлено и установлено в действующую колею более 800 комплектов таких стрелочных переводов.
Современные технологии в металлургии позволяют изготавливать рельсы значительно большей длиныАльтернативной технологией, которая может дополнять сварку, является применение более длинных рельсов, чем предусмотрено стандартной конструкцией (в Украине стандарт — до 25 м).
Например, рельсы длиной 108 м выпускает на заводе во Франции компания TataSteel. По информации производителя, они имеют усиленную прочность и устанавливаются на некоторые линии в горных районах Германии, Швейцарии и странах Скандинавии.
Тарас Рейка
Железнодорожный журнал “Railway Supply”
По теме:
RWS Маркет: Элементы электрообогрева стрелочных переводов
Узнавайте первыми самые свежие новости железнодорожной отрасли в Украине и мире на нашей странице в Facebook, канале в Telegram, читайте журнал Railway Supply онлайн.
Разместите рекламу на портале и в журнале Railway Supply. Подробная информация в Railway Supply media kit
Рельсовые стыки
Рельсовый стык является местом соединения двух примыкающих концов рельсов при наличии специального скрепления и удержания их в соответствии с нормами в отношении плана и профиля пути. Рельсовый стык состоит в основном из двух стыковых накладок, по одной с каждой стороны рельса, удерживающихся на месте с помощью болтов, как правило, с пружинными шайбами или рельсовыми стыковыми пружинами, чтобы препятствовать ослаблению натяжения болтов.
На протяжении ряда лет ни одна деталь пути не причиняла забот работникам по содержанию пути больше, чем рельсовый стык. Представляя самую слабую часть пути, он постоянно изучался, и в результате было создано множество конструкций, каждая из которых предусматривала ликвидацию присущих ему недостатков.
Среди других усовершенствований очень важным является усовершенствование болта.
Первое улучшение в этом направлении привело к применению закаленного болта, с некоторым увеличением предела упругости стали, из которой он был изготовлен. В результате усиленных лабораторных исследований и полевых опытов было предложено витковые или пружинные шайбы и рельсовые стыковые пружины изготовлять из легированной стали с высокой величиной реактивного давления для того, чтобы не допускать снижения натяжения болтов.
Накладки
Стыковые накладки могут быть разбиты на два основных класса: 1) накладки с короткой полкой или без нее (двухголовые) и 2) с длинной полкой, или уголковые.
Каждый из этих видов может быть подразделен на два типа заклинивающиеся и шарнирные. Стыки с накладками зажимающими подошву рельса, такие, как непрерывные системы Ниафи (Niafie) и др., больше не находят применения как стандартные.
Раньше обычные рельсовые стыки с накладками заклинивающегося типа были приняты как стандартные. Опирание рельсовых концов в этом случае сопровождается заклиниванием накладки.
Вертикальная часть накладки предусматривает место для размещения болтов, а верхняя и нижняя поверхности наклонены так, чтобы плотно примыкать к нижней поверхности головки рельса и к верхней поверхности подошвы.
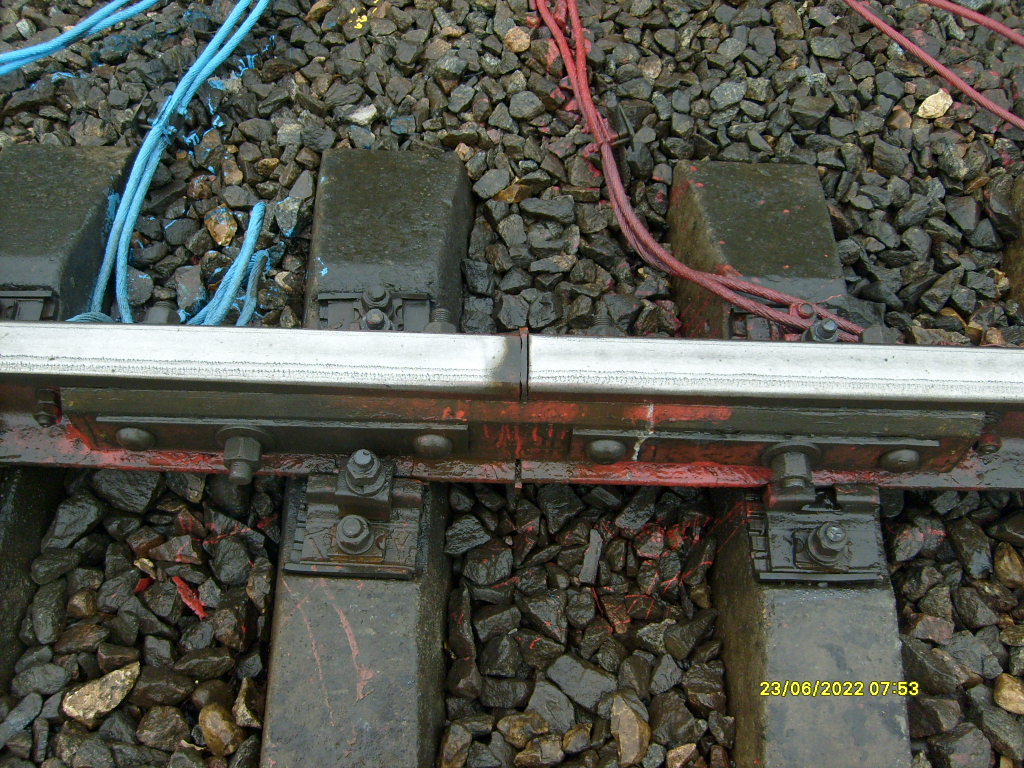
Без отнесения к классу или типу стыковые накладки разделяются на четырехдырные и шестидырные и бывают длиной соответственно 610 или 914 мм, хотя имеются и другие размеры, незначительно отличающиеся от этих величин.
До введения стыков с накладками без полок широко применялись уголковые накладки. Они имели шпунты (пазы) для того, чтобы поместить костыль, прикрепляющий рельс в стыке. Практика применения такой накладки привела к повышенному износу шпал и изломам накладок. Стыки с двухголовыми накладками позволяют забивать костыли без шпунтов в них. Однако применение накладок без выступающих частей (двухголовых) требует при забивке костыля для прикрепления рельса поворота его головки в полевую сторону. Рельсы в стыках с уголковыми накладками могут быть пришиты костылями, опирающимися головкой непосредственно в выступающую часть накладки, что не требует вырезов в накладке и специальных стыковых подкладок.
При выборе класса и типа стыка следует учитывать работу, которую он должен выполнять.

Стык на шпале, как правило, применяется с более длинными накладками; он размещается на трех шпалах: одна в центре и две по концам накладок. Успех этого способа опирания зависит от содержания средней шпалы, а также шпал, находящихся в непосредственной близости от нее.
Стык на весу принято применять с более короткими накладками. Обычно он опирается на две шпалы, по одной с каждой стороны. Чтобы получить удовлетворительные результаты при применении этого стыка, обе шпалы должны работать в одинаковых условиях.
Стык с неопределенным местом опирания работает в благоприятных условиях с накладками 914 мм, потому что эта длина гарантирует, что каждый конец рельса будет опираться, по крайней мере, на одну шпалу, и перемещение шпал на протяжении рельсового звена или в месте стыка не потребуется для того, чтобы создать удовлетворяющее требованиям опирание.

Конструкция. Применение какой-либо конструкции накладки зависит от колесной нагрузки, скорости, тоннажа, профиля рельса, размера и размещения отверстий в рельсах, просвета между верхом накладки и ребордами колес, возможности завертывания гаек, способов прикрепления, запаса на неизбежный износ составных частей.
Работа стыковой накладки под вертикальной нагрузкой соответствует работе простой балки, опертой на две опоры и нагруженной приблизительно в середине. При совершенном закреплении рельсов в стыках нагрузка распределяется по всей длине накладки. Максимальный положительный момент будет под колесом в центре. Точка приложения нагрузки и положения опор зависит от различных условий и в том числе от пригонки рельсов и накладок и сравнительной жесткости их. К конструкции современного стыка должны предъявляться требования, обеспечивающие достаточную прочность его, при которой отдельные рельсовые звенья превращаются в сплошную нить. В стыке прогиб должен быть таким, как и в целом рельсе.
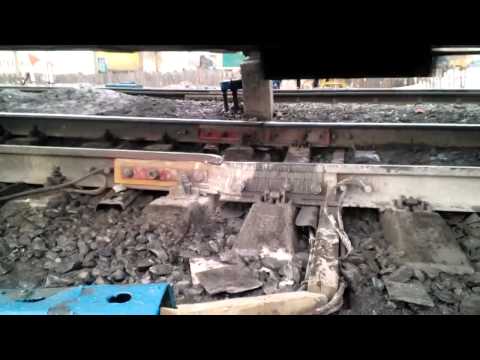
Рельсовый стык согласно условиям AREA должен удовлетворять следующим основным требованиям:
- в стыке не должно быть отступлений по шаблону и уровню;
- прогиб в стыке не должен практически отличаться от прогиба целого рельса;
- стык не должен допускать вертикальных и горизонтальных перемещений концов рельсов один относительно другого, но должен предусматривать возможность продольных перемещений рельсов, связанных с удлинением и сокращением рельса при изменении температуры;
- стык должен быть как можно проще и иметь как можно меньше деталей, чтобы отвечать максимально своему назначению.
Ограничения в промежутках, создаваемых вертикальной плоскостью соприкасания накладки и шейки рельса и между накладкой и ребордами колес в горизонтальной плоскости, делают физически невозможным создать конструкцию стыка такой же прочности, как и рельс. Однако те конструкции, которые повсюду применяются, достаточно прочны, чтобы противостоять осевым нагрузкам, которые на них воздействуют, без большого количества дефектов.
Преобладающее количество дефектов в стыках современной конструкции почти всегда проявляется в виде трещин, начинающихся в верхней части накладки вблизи стыкового зазора. Напряжения в верхней части этого сечения изменяются от сжимающих до растягивающих и в 1,5 раза больше напряжений в нижних волокнах того же сечения.
На нижней поверхности соприкасания с рельсом напряжения изменяются от растягивающих до сжимающих и составляют половину величины напряжения в верхней части. Предполагается, что высокие контактные напряжения в месте опирания концов рельсов на верхнюю поверхность накладки, которые в сочетании с напряжениями изгиба, очевидно, создадут достаточно высокое напряжение на разрыв, могут привести к появлению трещин.
Поскольку середина верхней части накладки считается наиболее уязвимой для трещин, были поставлены опыты на машине под катящейся нагрузкой для выявления возможности уменьшить напряжения в этих местах. Было найдено, что вышлифовывание поверхности в средней части накладки увеличивает сопротивление появлению трещин без заметного укорочения срока службы накладки. В результате некоторые дороги применили новые накладки с вышлифованной поверхностью в середине, изготовленные на сталепрокатных заводах. AREA рекомендует делать такую площадку от 32 до 38 мм длиной и от 0,8 до 1,6 мм глубиной и распространить ее по ширине накладки до места, где накладка при сильном износе может захватить верхнюю выкружку и шейку рельса.
Конструкция AREA.
Надежная конструкция стыковой накладки была предметом изучения Рельсового комитета AREA в течение многих лет, после чего различные конструкции были приняты и опубликованы как стандартные. Поскольку профиль существующего рельса частично был улучшен и введены более тяжелые рельсы, AREA изъяла из употребления некоторые из устаревших стыковых накладок и добавила новые. В настоящее время только восемь стыковых накладок включены в Руководство AREA. Две основные конструкции накладок, применяющиеся с рельсами типов 44,6 RA-A и 49,6 кг/пог. м RE, являются уголковыми накладками заклинивающегося типа.
Другие шесть конструкций все без вырезов и полок — двухголовые накладки шарнирного типа для рельсов типа 57,0 кг/пог. м RE, 65,5 кг/пег. м и 66,0 кг/пог. м RE и заклинивающегося для рельсов 65,5 кг/пог. л RE, 66 кг/пог. м RE и 69,4 кг/пог. м RE.
Все шесть конструкций, исключая одну для рельса 69,4 кг/пог. лг RE. Накладка к рельсам 69,4 кг/пег. м RE была принята.
Стандартизация.
Общие соображения о практичности стыковых накладок на протяжении ряда лет привели к созданию двух направлений.
Первое направление утверждает, что форма поперечного сечения может быть уменьшена до жесткой нормы, что многие непоследовательные различия в разных вариантах, которые не влияют на срок службы накладки, могут быть объединены и что принципиальные особенности конструкции теперь хорошо обоснованы. Оно также поддерживает мнение о том, что различные имеющиеся конструкции накладок являются только разновидностями основного типа. Этот единственный основной тип мог быть пересмотрен для применения с различными профилями рельса, и он должен в равной мере удовлетворять все дороги.
Последователи второго направления стоят против жестких размеров конструкций накладок, но признают, что значительное увеличение конструкций нежелательно. Однако, по их мнению, основные принципы конструкции теперь лучше поняты (выражены), чем прежде, но последнее слово в этой области еще не сказано, и жесткая стандартизация будет замедлять и, возможно, остановит дальнейшее развитие. Они обращают внимание на тот факт, что изготовители сделали многое в области развития конструкции стыков, и это прогрессивное движение со стороны изготовителей было бы задержано и, возможно, устранено совсем введением жесткой стандартизации, и важный фактор, который вел к улучшению конструкции, был бы закрыт.
И в настоящее время некоторые накладки частных конструкций испытываются Рельсовым комитетом AREA попутно с накладками конструкции AREA, и хотя опыты не закончены, накладки частных конструкций показывают превосходные результаты.
Переходные накладки и рельсы, изменяющиеся по высоте.

Когда необходимо соединить рельсы с разной высотой и разных профилей, прибегают к помощи стыков специальной конструкции для того, чтобы выравнить рельсы по высоте и по боковой грани с внутренней стороны. Эти специальные стыки названы переходными и представлены в виде различных конструкций накладок, начиная от обычного профиля стыковой накладки и до поперечного сечения, представляющего единое целое с подкладкой, изготовленных из прокатной или литой стали. Для соединения рельсов разных весов применяются также изменяющиеся по высоте рельсы. Их обычно делают из более тяжелого рельса длиной от 2,4 до 5,5 м со скосом всех поверхностей, за исключением стороны рельса, обращенной внутрь колеи, чтобы подогнать его по размерам к профилю меньшего рельса и, таким образом, допуская использование стандартных накладок для обоих профилей рельсов.
Изолирующие стыки.
Изолирующие стыки служат для того, чтобы задерживать идущий от рельса к рельсу электрический ток с помощью изоляторов, разделяющих рельсовые концы и другие металлические детали стыка. Чтобы сохранить прочность стыка и в то же время изолировать части стыка один от другого так, как это требуется, изолятор должен быть приспособлен к формам стыковых деталей, быть по возможности тонким и хорошо сопротивляться истиранию.
Изолятор представляет фибровый материал толщиной 3,2 и 4,8 мм; изготовленный из хлопкового волокна, обработанный химически. Ему может быть придана любая форма для возможности применять между подошвой рельса и подкладкой, стыковой накладкой и шейкой рельса, в качестве изолирующих прокладок между торцами рельсов, для изоляции гаек и болтов. Фибровое волокно обладает высокой прочностью, податливостью и высокими изолирующими качествами, так что при применении оно обеспечивает надежную работу путевой цепи, поскольку хорошо сопротивляется впитыванию воды и противостоит ударам, которые могут иметь место при проходе поезда. Работа стыков с такими прокладками не нарушалась в течение четырех лет, и прокладки после этого срока остались еще пригодными для дальнейшей службы.
Особая тщательность должна быть соблюдена при сборке изолирующих стыков для удлинения срока их службы. Концы рельсов, которые примыкают к фибре, должны быть ровными и обрезанными под прямым углом так, чтобы можно было поместить между ними изолирующую прокладку.
Другими мерами, применяемыми для безотказной работы изолирующего стыка, является удаление пыли и ржавчины со всех элементов стыка, применение чистой смазки для покрытия поверхности рельсовых концов; обеспечение правильного стыкового зазора между концами рельсов для изолирующей прокладки, которая должна быть на одном уровне с рельсами, правильной сборки стыка и затяжки болтов ручным гаечным ключом.
Стыки на разводных мостах.
На концах подвижных пролетов предусматриваются стыки, которые надежно соединяют концы рельсов, когда мост закрыт, и обеспечивают быстрое разъединение концов, когда мост должен быть открыт. Рельсы в этих случаях могут быть обрезаны под прямым углом или скошены по возможности на большом протяжении, чтобы дать возможность стыку максимально удлиняться.
Вследствие неустойчивости примыкающих насыпей к мостам многие железные дороги не делают стыков в пределах 1,8 м от обратной стенки устоя моста; в случае необходимости применяются укороченные рельсы. Некоторые дороги не применяют противоугонов на металлических мостах, где шпалы уложены прямо на металлические балки; для удлинения и сокращения рельсов на концах мостов обычно предусматриваются температурные компенсаторы. Они представляют стрелочные остряки с пружинами или другими приспособлениями, чтобы возвращать их на место. Более тщательно разработанные конструкции имеют специальную плиту (лафет) для перемещения остряков.
Стыковые накладки для крепления остряка в корне.
Применение стандартной прямой накладки для крепления остряка в корне затрудняло бы его отвод. Поэтому применяется специальное крепление, состоящее из корневого вкладыша из литой стали, изогнутой накладки, специальной накладки с приспособлением, не допускающим проворачивания болта при его закреплении, и корневых болтов. Изогнутая накладка находится с внутренней стороны колеи и отогнута под углом отвода остряка, когда он находится в отведенном положении. Один из болтов корневого вкладыша сделан с утолщением, которое соответствует отверстию корневого болта ближайшего к острию остряка и допускает перемещение остряка в поперечном направлении, но не в продольном.
Как изготавливаются стальные рельсы
29 сентября 2017 г.
Стальной рельс, который мы также называем рельсами, гусеницами, является важным элементом рельсовой системы. Стальной рельс используется с рельсовым стыком и железнодорожными крепежными элементами, такими как рельсовые зажимы, рельсовые стяжки, стрелочные переводы, чтобы поезд двигался быстро и устойчиво без рулевого управления.
Как известно, рельсовая система состоит из двух параллельных рельсов и шпал. На шпалах закреплены стальные рельсы, а под шпалой находится балласт железнодорожного пути. Стальной рельс может выдерживать гораздо больший вес по сравнению с рельсами из других материалов. Из-за огромного давления для изготовления стального рельса требуется высококачественная сталь.
В настоящее время мы хотели бы сделать часть стального рельса китайским иероглифом «工». И стальные рельсы имеют свою судьбу в зависимости от использования. Некоторые стальные рельсы используются для контакта с колесами, которые называются головками рельсов. Некоторые стальные рельсы в середине пути, которые называются решеткой рельсов, и некоторые стальные рельсы внизу, которые называются фланцами рельсов. Различные способы предъявляют разные требования к прочности, стабильности и стойкости к истиранию стального рельса. Таким образом, существует множество стандартов стальных рельсов.
Типы железнодорожных путей выражаются в километрах на метр. Чем тяжелее стальной рельс на метр, тем больший вес может выдержать рельс.
Что касается размеров железнодорожных путей, то между странами существуют некоторые различия. Общие стандарты в Европе: 40 кг/м, 50 кг/м и 60 кг/м. Стандарты Common Rail в Китае: 43 кг, 50 кг, 60 кг и 75 кг. Как правило, наиболее распространенными стандартами рельсов являются 43 кг, 60 кг/м и 75 кг/м . Соединенные Штаты предпочитают более тяжелые рельсы. Например, угольная линия применялась к рельсам 75 кг/м в США. Конечно, упомянутые рельсы относятся к категории тяжелых стальных рельсов. Где можно купить железнодорожный рельс? Если вы хотите найти производителей легкорельсового транспорта, вы можете выбрать AGICO Rail.
Процесс производства стальных рельсов прост. Самое главное прокатка стали. После выбора подходящей стальной заготовки следующим шагом является прокатка стали.
Утилизация стальной заготовки
Принять блюм непрерывного литья для улучшения макроструктуры стальной заготовки. Кроме того, применяется технология вакуумной дегазации и вторичного рафинирования для обеспечения внутреннего качества стальной заготовки. Эта технология может контролировать содержание остаточного элемента и газа и обеспечивать чистоту стали.
Прокат
Как известно, стальную заготовку путем прокатки, охлаждения и правки можно превратить в рельсы. Во время процесса жизненно важная часть катится. Существует два метода прокатки: калибровочная прокатка и универсальная прокатка .
Накатка желобков проще, чем универсальная прокатка. Деформация металла устойчивая. Прокатка в канавках подходит для черновой деформации из-за простой системы управления. Но рисунок отверстий имеет асимметричный дизайн, поэтому симметрия стальной секции рельса не очень хорошая. Кроме того, точность контроля не является жесткой, поэтому качество поверхности нельзя контролировать должным образом.
В мире популярна универсальная прокатка, которая является лучшей технологией производства стального рельса. Универсальная система прокатки состоит из пары активных горизонтальных валков и пары пассивных горизонтальных валков. Эти четыре ролика работают на одном уровне.
Плоский валок обрабатывает полотно рельса. Вертикальный валок и плоский валок вместе обрабатывают головку рельса и гребень рельса. Направляющая балка прокатного стана установлена непосредственно на опоре подшипника, которая может двигаться как целая система, а процесс прокатки полностью автоматизирован.
Отопление
Нагрев лучше для резкого улучшения механических свойств. Наиболее распространенными технологиями нагрева являются закалка и отпуск, термическая обработка и медленная закалка. Между тем, используйте печь с шагающими балками для нагрева стальных заготовок, которая может контролировать газофракционирование и предотвращать обезуглероживание и неравномерную температуру.
Выпрямление
Мы хотели бы использовать длинный стержень для прокатки, охлаждения и правки. Эта технология лучше подходит для увеличения выхода продукции, снижения остаточного напряжения и увеличения срока службы стального рельса.
Проверка
Через онлайн-центр проверки качества используйте ультразвуковые волны, вихревые и лазерные волны для проверки внутреннего качества стали, качества поверхности рельса и размеров железнодорожного пути.
Резка
Обычно для сверления и обработки головки рельса используют твердосплавный станок, чтобы обеспечить высокую точность.
С развитием общества высокоскоростная железная дорога, железная дорога с тяжелыми грузами и системы автоматического управления железной дорогой становятся мейнстримом. С 1980-х годов Китай изучил эту часть и теперь принимает новые технологии.
Помимо передовой технологии производства, AGICO RAIL предлагает железнодорожные пути различных стандартов и различных размеров железнодорожных путей. Как производитель железнодорожных компонентов, мы также предоставляем услуги по индивидуальному заказу соединительных стержней, рельсовых зажимов, железнодорожных костылей и т. д.
Как железные дороги справляются с тепловым расширением?
С развитием современных бесстыковых рельсов (CWR) железнодорожным сетям во всем мире приходится справляться с тепловым расширением или напряжением рельсов. Короче говоря, рельсы сжимаются при низких температурах и испытывают растягивающие напряжения, при высоких температурах рельсы расширяются и сжимаются под нагрузкой. Это может привести к тепловым перегибам, которые выведут рельсы за пределы ширины колеи и могут привести к сходу с рельсов, если не будут приняты превентивные меры.
Как железные дороги справляются с тепловым расширением? Железные дороги борются с тепловым расширением, нагревая рельс перед установкой. Поэтому рельс нагревается до нейтральной температуры рельса, нагревается, а затем охлаждается по мере укладки рельса. Кроме того, для обнаружения неисправностей рельсов внедряются различные технологии с использованием придорожных устройств.
Предыстория
Когда в 19 веке впервые были построены железные дороги, каждый рельс скреплялся накладкой (Великобритания) или шарнирным стержнем (США), которые издавали классический щелкающий звук, когда поезд проезжал мимо. Однако техническое обслуживание соединений было утомительным, так как их нужно было правильно смазывать и обслуживать, чтобы предотвратить нежелательный износ концов рельсов. Это была утомительная задача, которую выполняли путевые бригады, поскольку им приходилось осматривать каждый шарнир, чтобы убедиться, что он поддерживается в соответствии с приемлемыми стандартами.
Соединяемый рельс соединялся с помощью соединительной планки по обеим сторонам рельса с помощью болтов, удерживающих его на месте. Однако распространенной проблемой было то, что болты часто ломали соединительную планку, особенно под нагрузкой тяжелого поезда. Кроме того, стыки часто приходилось изолировать при наличии сигнальных цепей, когда между рельсами заливали эпоксидное вещество, укрепляющее стыки.
Последствия постоянного удара колес поезда о стыках рельсов.Джефф Хэмптон
Сочлененный рельс дополнительно обеспечивал пассажирам ухабистую езду, так как каждое колесо ударялось о шарнир при прохождении. По мере развития железнодорожных технологий и появления высокоскоростных поездов возникла необходимость в альтернативе старой практике. Хотя на горизонте маячила замена сочлененных рельсов, она давала различные преимущества.
Несмотря на то, что сочлененные рельсы были более тяжелыми как для поездов, так и для железнодорожной инфраструктуры, они доказали свое преимущество, когда рельсы реагировали на интенсивные температуры. При правильной установке между направляющими на соединительной планке должен быть крошечный смазанный зазор, чтобы справиться с тепловым расширением. Однако случай, когда сустав не двигается, будет иметь аналогичные реакции на CWR.
Начиная с пятидесятых годов сварные рельсы были установлены на различных железнодорожных сетях и начали доказывать свою эффективность. Это обеспечило гораздо более плавную езду для пассажиров и меньше головной боли при обслуживании. Кроме того, сварной рельс снижает трение и износ как рельсовой инфраструктуры, так и ходовой части поезда. Однако из-за отсутствия соединительных стержней, когда рельс расширялся из-за чрезмерного нагрева, рельсы не имели люфта, поэтому они расширялись и деформировались под давлением. Тем не менее, принимаются различные меры предосторожности, чтобы уменьшить вероятность повреждения рельса из-за теплового расширения.
По данным Progressive Railroading, если сила расширяющегося рельса не будет устранена своевременно, у рельса больше не будет места для расширения, таким образом, рельс начнет изгибаться, что приведет к выходу за пределы колеи. Если рельс был смещен далеко за пределы ширины колеи, поезду будет трудно двигаться, что приведет к сходу с рельсов. Это подчеркивает важность превентивных мер для обнаружения неисправностей до того, как они станут серьезной проблемой.
Установка непрерывного сварного рельса (CWR)
Чтобы предотвратить тепловое расширение, сварные рельсы устанавливаются при температуре без напряжений (SFT), которая обычно составляет от 90 до 110 градусов по Фаренгейту в США и 27 градусов по Цельсию (81 по Фаренгейту) в Соединенном Королевстве. Если температура рельса превышает эти температуры, рельс может начать изгибаться под высоким напряжением. Согласно Progressive Railroading, рельс должен быть установлен на нейтральную температуру, однако при укладке рельса невозможно определить нейтральную температуру рельса, поэтому температура устанавливается железной дорогой в зависимости от местоположения и ее климата.
Перед установкой секции непрерывного сварного рельса необходимо измерить температуру рельса, чтобы убедиться, что он соответствует температуре без напряжения. Если температура рельса ниже желаемой, рельс будет нагреваться, что приведет к его расширению. постепенно. Рельс нагревается либо газовой горелкой, либо натяжителем. Натяжитель предпочтительнее, поскольку он равномерно расширяет рельс, в отличие от газовой горелки, где тепло распределяется неравномерно. Однако натяжитель можно использовать только на определенных участках рельса. Ричард Дайк
Для повышения прочности рельса вместо стандартных шипов в железобетонных шпалах используются эластичные крепления. Эти крепления способны предотвращать вертикальные и боковые перемещения рельсов на шпалах и предотвращают отрыв рельса от шпалы в случае расширения, тем самым предотвращая сход рельсов. Тем не менее, железнодорожные костыли и деревянные шпалы широко используются с CWR и столь же эффективны.
Устранение напряжения рельса
В случае теплового расширения неисправность должна быть устранена немедленно, прежде чем произойдет сход рельсов. Для ремонта рельса, подвергшегося термическому расширению, рельс необходимо разрезать, нагреть и сварить. Если обнаруживается, что рельс превышает свой уровень напряжения или имеет излом, рельс повторно нагревают для расширения стали. Как и при установке рельса, при ремонте рельс необходимо нагреть, чтобы достичь уровня отсутствия напряжения. Если рельс не подлежит ремонту, часть рельса заменяют полностью.
Профилактическое техническое обслуживание
Согласно прогрессивным железнодорожным технологиям, существуют различные механизмы для борьбы с тепловым расширением и напряжением рельсов. Одно устройство под названием Railstress Montior сообщает об уровне напряжения и температуре рельса. Устройство прикрепляется к рельсу и использует различные технологии в своем анализе, а также предоставляет подробный отчет о своем обнаружении, который затем отправляется на придорожное устройство. Затем устройство отправляет предупреждения через сигнал тревоги, если это указывает на проблему с целостностью рельса. В дополнение к Railstress Monitor существуют различные устройства с аналогичной технологией. Николя Тавено/Public Domain
Компенсаторы на французском TGV.
В дополнение к этому технологически совершенному оборудованию Федеральное управление железных дорог (FRA) выпустило различные инструкции, предписывающие железным дорогам с CWR иметь обширную программу обучения для путевых бригад и инженеров. Эти программы выявляют проблему напряжения рельсов и знакомят железнодорожный персонал с анатомией теплового расширения, с тем, как ремонтировать расширенные или перегнутые пути, а также с профилактическим обслуживанием, проводимым для предотвращения этих проблем.
Кроме того, компенсационные швы размещаются между длинными участками CWR, чтобы позволить пути расширяться, и часто присутствуют рядом с некоторыми элементами инфраструктуры, такими как мосты, поскольку эти области имеют тенденцию к расширению иначе, чем остальная часть непрерывного сварного шва. рельс. В отличие от сочлененного рельса, эти стыки сужены по диагонали.