Как отличить шлак от металла при сварке и как его выгнать | ММА сварка для начинающих
Как отличить шлак от металла при сварке и как его выгнатьВо время сварки новички сталкиваются с большим количеством вопросов, один из которых, как отличить шлак от металла. Шлак отличается от металла не только цветом и плотностью, но и текучестью. Однако когда учишься варить, контролировать полностью процесс сварки, следить за дугой и движением электрода, да ещё и обращать внимание на шлак, не имеющему опыта сварщику очень трудно.
Тем не менее, научившись разжигать дугу и вести электрода, с данным вопросом разобраться все-таки придется, ведь в процессе сварки нужно не просто различать, где металл, а где шлак, но и уметь выгнать его из сварочной ванны. В данной статье сайта про сварку mmasvarka.ru будет рассказано о том, как отличить шлак от металла, и выгнать его во время сварки.
Из-за чего появляется шлак на металле
Наверняка вы не раз замечали, что прямо над сварочным швом и по его краям, сразу после сварки, образуется темная сильнопористая корка, которая легко отлетает от металла при ударе молотком. Это и есть тот самый пресловутый шлак — не что иное, как продукт сгоревшей электродной обмазки и окислившегося металла.
Ни в коем случае не стоит думать, что шлак это зло. Конечно же, нет, ведь главной его задачей, является перекрыть доступ кислорода к сварочной ванне, и защитить тем самым металл от окисления. Однако, если шлак попадёт непосредственно в сам сварочный шов, то, быть беде. При попадании в сварочную ванну, шлак серьезно ослабляет прочность сварного соединения и может стать причиной его разрушения в дальнейшем.
Как отличить шлак от металла при сварке
Чтобы отличить шлак от раскалённого металла в процессе сварки, достаточно запомнить следующее:
- Шлак имеет более темный цвет, чем нагретый металл;
- Текучесть металла намного выше шлака;
- Шлак и металл имеют разную плотность;
- Шлак остывает намного медленнее, чем металл;
- Шлак легче металла.
О чем это все говорит? На самом деле, все очень просто, и в процессе сварки отличить шлак от металла, совсем несложно.
Достаточно лишь приглядеться к самому процессу, и станет понятно, что шлак зачастую стремится сбежать в сварочную ванну, он темного цвета и легко сдувается, если изменить угол движения электродом. Следует помнить всегда о том, что шлак не должен попасть в сварочную ванну, и это самое главное правило при сварке металлов.
Как выгнать шлак во время сварки
Чтобы полностью выгнать шлак при сварке, достаточно выдерживать большой наклон электрода. Кстати, так легче будет распознать этот самый шлак от металла. При этом важно заметить, что большой наклон электрода способен сдуть не только шлак, но и раскалённый металл, поэтому здесь важно найти «золотую середину».
Разрушение сварочного соединения вследствие попадания шлакаДля начинающих сварщиков, которые еще не умеют отличать шлак от металла, держать электрод во время сварки нужно вертикально. Делая небольшие колебательные движения электродом поперёк шва, нужно добиться, тем самым, перекрывания кромки фасок. Также можно попробовать варить углом назад, таким образом, отличить шлак от металла будет намного проще.
Ну и последнее, при сварке электродами с основным покрытием, распознать шлак намного проще. Выгнать его получится как самим электродом (изменив его наклон), так и повышением силы тока или же короткой дугой. Не бойтесь экспериментировать, и у вас, наверняка, все получится!
Почему при сварке образуются раковины и шлак – почему шлакуется сварочный шов?
Много шлака при сварке
Главный побочный эффект от дуговой сварки – это сварочный шлак. Он представляет собой побочный материал неметаллического происхождения, который состоит либо из расплавленного электронного покрытия плавящегося электрода (при ручной дуговой сварке, в том числе при сварке инвертором) либо из расплавленного сварочного флюса (автоматическая сварка под флюсом).
Этот материал является побочным, потому что после непосредственного соединения он подлежит удалению. В случае, когда по каким-то причинам он начинает контактировать с затвердевающей деталью и становится уже частью полученного шва – это является серьезным дефектом. Такой результат называется шлаковыми включениями. Они визуально видны на поверхности изделия. Удалить шлаковые включения, когда они уже полностью находятся в затвердевшей детали можно только путем сверления, чтобы потом сварить его заново.
Главная причина возникновения шлаковых включений – это ситуация, когда небольшой объем металла слишком быстро застывает, в результате чего весь шлак не успевает «выйти» за пределы области сварочной ванны. При наличии этого дефекта эксплуатация соединения по назначению будет невозможна.
Шлаковые включения могут быть макроскопические и микроскопические. Первые появляются в случае плохой зачистки кромок либо вообще её отсутствия. Они представляют собой сферический материал, с удлиненными хвостами. Избежать их появление можно путем тщательного очищения кромок соединяемых деталей. Микроскопические включения могут возникнуть в процессе возникновения химических реакций в процессе сварки, когда металл кристаллизуется.
Полное устранение такого производственного брака невозможно, при незначительных шлаковых включениях соединение может быть признано качественным. Существуют определенные условия и признаки, при которых устанавливается допустимое значение наличия такого вида брака на изделии. Такие допустимости устанавливаются в зависимости от количества, расположения и размера дефектного шва; от процентного соотношения площади всего брака к площади наплавленного металла на изделии; от удельного веса наплавленного металла.
Основные причины появления шлаковых включений.
- Быстрое застывание металла небольших объемов, в результате чего шлак не успевает выйти за границы сварочной ванны.
- Применение электродов и флюса большого удельного веса и/или из тугоплавких материалов.
- Малые показатели раскисления металла. Раскисление подразумевает процесс исключения из уже мягкого металла молекул кислорода.
Кислород для него является вредной составляющей, которая ухудшает качество.
- Высокие показатели силы поверхностного натяжения шлака. При этом, он не всплывает на поверхность.
- Плохо зачищены кромки деталей или валики шва.
- Низкое качество электрода, а точнее его покрытия, плавление которого осуществляется неравномерно, его частицы попадают в сварочную ванну.
- Не соблюдение правил и техники и режимов соединения деталей (выбор неподходящей скорости, угла наклона электрода), изменение длины дуги без причины.
- Непрофессионализм сварщика. Если вам нужно качественное изделие, лучше привлечь к этому нелегкому делу специалиста в этой области. Если вы хотите сделать все сами, то прежде чем браться за ответственную сложную работу, нужно наработать практику с несложными соединениями.
Так выглядит сварочный шлак после удаления со шва
Профессиональные сварщики умеют сразу же отличить шлак от металла при сварке и «выгонять» его в процессе работы, однако, у каждого свои советы, как это сделать.
Чтобы шлак не закрывал сварочную ванну, необходимо регулировать положение электрода. Положение должно быть таким, чтобы направление газа от испарения покрытия электрода выдувало данный дефект на поверхность шва. Сварщику ни в коем случае нельзя оставлять его в сварочной ванне. Сварочный шлак должен оперативно поддаться процессу кристаллизации и без особых усилий удаляться.
Попадание шлака в готовое соединение бывает неизбежно, такой дефект если не невозможно устранить, то зачастую очень сложно. Именно поэтому существуют допустимые нормы наличия «лишних» включений в уже сваренном изделии. Например, в межгосударственном стандарте касательно строительных стальных конструкций (введен в действие в 2001 году). В приложении к этому документу предусмотрены требования к качеству сварных соединений, допустимые дефекты.
Длинные дефекты | He допускаются | ||
Короткие дефекты: | |||
стыковой шов | h ≤ 0,2 S | h ≤ 0,25 S | h ≤ 0,3 S |
угловой шов | h ≤ 0,2 K | h ≤ 0,25 K | h ≤ 0,3 K |
Максимальный размер включения | 2 мм | 3 мм | 4 мм |
Таким образом, чтобы обеспечить правильное появление шлака на поверхности сварочного шва, необходимо знать, как его отличить от металла. В случае, если заметно, что шлак остается в сварочной ванне и не выходит наверх, нужно изменить угол наклона электрода. Перед процессом соединения необходимо позаботиться о надлежащем состоянии кромок, а также о правильном выборе режимов и параметров. Электроды нужно выбирать высокого качества, тогда и сварной шов будет качественный. Если соблюсти все условия, тогда шлак будет не вязкий, низкого удельного веса, с малым поверхностным натяжением.
Источник: https://svarkaed.ru/svarka/obuchenie-svarke/svarochnyj-shlak.html
Как увидеть шлак при сварке и не спутать с металлом
Как увидеть шлак при сварке и не спутать с металломОсновная проблема начинающих сварщиков заключается в том, что они не понимают, что происходит в процессе сварки, и не умеют отличать шлак от расплавленного металла. Всё это доставляет массу проблем и нежелание заниматься электросваркой в дальнейшем.
А ведь от того, насколько быстро новичок начнёт отличать шлак от металла, зависит скорость обучения и качество сварного шва. Научись отличать шлак от металла — и ты поймёшь, как варить! Именно так говорят опытные сварщики, но не дают толком никакого разъяснения.
Как научиться отличать шлак от металла при сварке
На самом деле существует достаточно много советов и способов отличать шлак при сварке. Чем быстрее вы научитесь это делать, тем лучше для вас в плане опыта и дальнейшей практики.
Итак, первое, что нужно знать начинающему сварщику, так это то, что учиться отличать шлак лучше всего при сварке электродами с основным покрытием. Рутиловые электроды хоть и лучше, но шлак рассмотреть при их использовании гораздо сложнее из-за его большей плотности.
При сварке электродами с основным покрытием, шлак выглядит чуть темнее расплавленного металла. Он имеет большую текучесть, и как бы следует за электродом, образуя собой корку для защиты сварочной ванны от кислорода. Это такая себе плёнка, которая после застывания превращается в шлак.
Поэтому, исходя из всего вышеперечисленного, нужно выделить основные моменты, которые связаны вот с чем:
- Цвет шлака темнее, чем металла;
- Шлак более подвижен, чем металл, он как пенка, хорошо растекается;
- Плотность у шлака и металла разная;
- После того, как дуга погасла можно увидеть, что металл быстро остывает и меняет цвет в отличие от шлака;
- Металл тяжелее шлака.
Наиболее просто учиться отличать шлак от металла, если варить основными электродами, в верхнем положении. В таком случае жидкие капли шлака, которые образуются за сварочной ванной, начнут сразу же стекать вниз.
Практический способ определения шлака
Также можно воспользоваться и другим способом, как отличить шлак от металла при сварке. Для этого понадобится целый электрод, на котором нужно счистить покрытие на некотором расстоянии. Берём плоскогубцы и через каждые 5 см сдираем электродное покрытие, оставляя только один металлический стержень.
Для чего это нужно делать? Всё просто, и при дальнейшем обучении сварки используем именно этот электрод. Теперь при сгорании электрода будет отчётливо видно, где шлак, когда электрод начнёт плавиться с покрытым обмазкой участком, а где металл.
Достаточно немного посмотреть под углом, чтобы увидеть, как шлак прирастает к металлу тонкой корочкой. Таким образом, используя все вышеперечисленные советы можно быстро научиться в процессе сварки определять, где шлак, а где жидкий металл.
Как отличать шлак от металла при сварке. Совет начинающему (Видео)
Array ( [TAGS] => Сварка [~TAGS] => Сварка [ID] => 111138 [~ID] => 111138 [NAME] => Как отличать шлак от металла при сварке. Совет начинающему (Видео) [~NAME] => Как отличать шлак от металла при сварке. Совет начинающему (Видео) [IBLOCK_ID] => 1 [~IBLOCK_ID] => 1 [IBLOCK_SECTION_ID] => 2004 [~IBLOCK_SECTION_ID] => 2004 [DETAIL_TEXT] =>Как отличать шлак от металла при сварке.
[~DETAIL_TEXT] =>
youtube.com/embed/AXB-HlYxaps?feature=oembed" frameborder="0" allow="accelerometer; autoplay; clipboard-write; encrypted-media; gyroscope; picture-in-picture" allowfullscreen="">
[DETAIL_TEXT_TYPE] => html [~DETAIL_TEXT_TYPE] => html [PREVIEW_TEXT] => Как отличать шлак от металла при сварке. Совет начинающему (Видео) [~PREVIEW_TEXT] => Как отличать шлак от металла при сварке. Совет начинающему (Видео) [PREVIEW_TEXT_TYPE] => text [~PREVIEW_TEXT_TYPE] => text [DETAIL_PICTURE] => [~DETAIL_PICTURE] => [TIMESTAMP_X] => 20.10.2020 10:48:56 [~TIMESTAMP_X] => 20.10.2020 10:48:56 [ACTIVE_FROM] => 20.10.2020 [~ACTIVE_FROM] => 20.10.2020 [LIST_PAGE_URL] => /news/ [~LIST_PAGE_URL] => /news/ [DETAIL_PAGE_URL] => /news/2004/111138/ [~DETAIL_PAGE_URL] => /news/2004/111138/ [LANG_DIR] => / [~LANG_DIR] => / [CODE] => kak_otlichat_shlak_ot_metalla_pri_svarke_sovet_nachinayushchemu_video [~CODE] => kak_otlichat_shlak_ot_metalla_pri_svarke_sovet_nachinayushchemu_video [EXTERNAL_ID] => 111138 [~EXTERNAL_ID] => 111138 [IBLOCK_TYPE_ID] => news [~IBLOCK_TYPE_ID] => news [IBLOCK_CODE] => news [~IBLOCK_CODE] => news [IBLOCK_EXTERNAL_ID] => clothes_news_s1 [~IBLOCK_EXTERNAL_ID] => clothes_news_s1 [LID] => s1 [~LID] => s1 [NAV_RESULT] => [DISPLAY_ACTIVE_FROM] => 20.10.2020 [IPROPERTY_VALUES] => Array ( [SECTION_META_TITLE] => Как отличать шлак от металла при сварке. Совет начинающему (Видео) [SECTION_META_KEYWORDS] => как отличать шлак от металла при сварке. совет начинающему (видео) [SECTION_META_DESCRIPTION] => Как отличать шлак от металла при сварке. Совет начинающему (Видео) [SECTION_PAGE_TITLE] => Как отличать шлак от металла при сварке. Совет начинающему (Видео) [ELEMENT_META_TITLE] => Как отличать шлак от металла при сварке. Совет начинающему (Видео) [ELEMENT_META_KEYWORDS] => как отличать шлак от металла при сварке. совет начинающему (видео) [ELEMENT_META_DESCRIPTION] => Как отличать шлак от металла при сварке. Совет начинающему (Видео) [ELEMENT_PAGE_TITLE] => Как отличать шлак от металла при сварке. Совет начинающему (Видео) [SECTION_PICTURE_FILE_ALT] => Как отличать шлак от металла при сварке.
Совет начинающему (Видео) [SECTION_PICTURE_FILE_TITLE] => Как отличать шлак от металла при сварке. Совет начинающему (Видео) [SECTION_DETAIL_PICTURE_FILE_ALT] => Как отличать шлак от металла при сварке. Совет начинающему (Видео) [SECTION_DETAIL_PICTURE_FILE_TITLE] => Как отличать шлак от металла при сварке. Совет начинающему (Видео) [ELEMENT_PREVIEW_PICTURE_FILE_ALT] => Как отличать шлак от металла при сварке. Совет начинающему (Видео) [ELEMENT_PREVIEW_PICTURE_FILE_TITLE] => Как отличать шлак от металла при сварке. Совет начинающему (Видео) [ELEMENT_DETAIL_PICTURE_FILE_ALT] => Как отличать шлак от металла при сварке. Совет начинающему (Видео) [ELEMENT_DETAIL_PICTURE_FILE_TITLE] => Как отличать шлак от металла при сварке. Совет начинающему (Видео) ) [FIELDS] => Array ( [TAGS] => Сварка ) [DISPLAY_PROPERTIES] => Array ( ) [IBLOCK] => Array ( [ID] => 1 [~ID] => 1 [TIMESTAMP_X] => 15.
02.2016 17:09:48 [~TIMESTAMP_X] => 15.02.2016 17:09:48 [IBLOCK_TYPE_ID] => news [~IBLOCK_TYPE_ID] => news [LID] => s1 [~LID] => s1 [CODE] => news [~CODE] => news [NAME] => Пресс-центр [~NAME] => Пресс-центр [ACTIVE] => Y [~ACTIVE] => Y [SORT] => 500 [~SORT] => 500 [LIST_PAGE_URL] => /news/ [~LIST_PAGE_URL] => /news/ [DETAIL_PAGE_URL] => #SITE_DIR#/news/#SECTION_ID#/#ELEMENT_ID#/ [~DETAIL_PAGE_URL] => #SITE_DIR#/news/#SECTION_ID#/#ELEMENT_ID#/ [SECTION_PAGE_URL] => #SITE_DIR#/news/#SECTION_ID#/ [~SECTION_PAGE_URL] => #SITE_DIR#/news/#SECTION_ID#/ [PICTURE] => [~PICTURE] => [DESCRIPTION] => [~DESCRIPTION] => [DESCRIPTION_TYPE] => text [~DESCRIPTION_TYPE] => text [RSS_TTL] => 24 [~RSS_TTL] => 24 [RSS_ACTIVE] => Y [~RSS_ACTIVE] => Y [RSS_FILE_ACTIVE] => N [~RSS_FILE_ACTIVE] => N [RSS_FILE_LIMIT] => 0 [~RSS_FILE_LIMIT] => 0 [RSS_FILE_DAYS] => 0 [~RSS_FILE_DAYS] => 0 [RSS_YANDEX_ACTIVE] => N [~RSS_YANDEX_ACTIVE] => N [XML_ID] => clothes_news_s1 [~XML_ID] => clothes_news_s1 [TMP_ID] => c83b747129a532c27a029fc5ccf0d07c [~TMP_ID] => c83b747129a532c27a029fc5ccf0d07c [INDEX_ELEMENT] => Y [~INDEX_ELEMENT] => Y [INDEX_SECTION] => Y [~INDEX_SECTION] => Y [WORKFLOW] => N [~WORKFLOW] => N [BIZPROC] => N [~BIZPROC] => N [SECTION_CHOOSER] => L [~SECTION_CHOOSER] => L [LIST_MODE] => [~LIST_MODE] => [RIGHTS_MODE] => S [~RIGHTS_MODE] => S [SECTION_PROPERTY] => N [~SECTION_PROPERTY] => N [PROPERTY_INDEX] => N [~PROPERTY_INDEX] => N [VERSION] => 1 [~VERSION] => 1 [LAST_CONV_ELEMENT] => 0 [~LAST_CONV_ELEMENT] => 0 [SOCNET_GROUP_ID] => [~SOCNET_GROUP_ID] => [EDIT_FILE_BEFORE] => [~EDIT_FILE_BEFORE] => [EDIT_FILE_AFTER] => [~EDIT_FILE_AFTER] => [SECTIONS_NAME] => Разделы [~SECTIONS_NAME] => Разделы [SECTION_NAME] => Раздел [~SECTION_NAME] => Раздел [ELEMENTS_NAME] => Новости [~ELEMENTS_NAME] => Новости [ELEMENT_NAME] => Новость [~ELEMENT_NAME] => Новость [CANONICAL_PAGE_URL] => [~CANONICAL_PAGE_URL] => [EXTERNAL_ID] => clothes_news_s1 [~EXTERNAL_ID] => clothes_news_s1 [LANG_DIR] => / [~LANG_DIR] => / [SERVER_NAME] => www.
alfa-industry.ru [~SERVER_NAME] => www.alfa-industry.ru ) [SECTION] => Array ( [PATH] => Array ( [0] => Array ( [ID] => 2004 [~ID] => 2004 [TIMESTAMP_X] => 2019-03-15 12:54:37 [~TIMESTAMP_X] => 2019-03-15 12:54:37 [MODIFIED_BY] => 1 [~MODIFIED_BY] => 1 [DATE_CREATE] => 2019-03-15 12:54:37 [~DATE_CREATE] => 2019-03-15 12:54:37 [CREATED_BY] => 1 [~CREATED_BY] => 1 [IBLOCK_ID] => 1 [~IBLOCK_ID] => 1 [IBLOCK_SECTION_ID] => [~IBLOCK_SECTION_ID] => [ACTIVE] => Y [~ACTIVE] => Y [GLOBAL_ACTIVE] => Y [~GLOBAL_ACTIVE] => Y [SORT] => 500 [~SORT] => 500 [NAME] => Видео по сварке [~NAME] => Видео по сварке [PICTURE] => [~PICTURE] => [LEFT_MARGIN] => 13 [~LEFT_MARGIN] => 13 [RIGHT_MARGIN] => 14 [~RIGHT_MARGIN] => 14 [DEPTH_LEVEL] => 1 [~DEPTH_LEVEL] => 1 [DESCRIPTION] => [~DESCRIPTION] => [DESCRIPTION_TYPE] => text [~DESCRIPTION_TYPE] => text [SEARCHABLE_CONTENT] => ВИДЕО ПО СВАРКЕ [~SEARCHABLE_CONTENT] => ВИДЕО ПО СВАРКЕ [CODE] => [~CODE] => [XML_ID] => [~XML_ID] => [TMP_ID] => [~TMP_ID] => [DETAIL_PICTURE] => [~DETAIL_PICTURE] => [SOCNET_GROUP_ID] => [~SOCNET_GROUP_ID] => [LIST_PAGE_URL] => /news/ [~LIST_PAGE_URL] => /news/ [SECTION_PAGE_URL] => /news/2004/ [~SECTION_PAGE_URL] => /news/2004/ [IBLOCK_TYPE_ID] => news [~IBLOCK_TYPE_ID] => news [IBLOCK_CODE] => news [~IBLOCK_CODE] => news [IBLOCK_EXTERNAL_ID] => clothes_news_s1 [~IBLOCK_EXTERNAL_ID] => clothes_news_s1 [EXTERNAL_ID] => [~EXTERNAL_ID] => [IPROPERTY_VALUES] => Array ( [SECTION_META_TITLE] => Видео по сварке [SECTION_META_KEYWORDS] => видео по сварке [SECTION_META_DESCRIPTION] => [SECTION_PAGE_TITLE] => Видео по сварке [ELEMENT_META_TITLE] => Видео по сварке [ELEMENT_META_KEYWORDS] => видео по сварке [ELEMENT_META_DESCRIPTION] => [ELEMENT_PAGE_TITLE] => Видео по сварке [SECTION_PICTURE_FILE_ALT] => Видео по сварке [SECTION_PICTURE_FILE_TITLE] => Видео по сварке [SECTION_DETAIL_PICTURE_FILE_ALT] => Видео по сварке [SECTION_DETAIL_PICTURE_FILE_TITLE] => Видео по сварке [ELEMENT_PREVIEW_PICTURE_FILE_ALT] => Видео по сварке [ELEMENT_PREVIEW_PICTURE_FILE_TITLE] => Видео по сварке [ELEMENT_DETAIL_PICTURE_FILE_ALT] => Видео по сварке [ELEMENT_DETAIL_PICTURE_FILE_TITLE] => Видео по сварке ) ) ) ) [SECTION_URL] => /news/2004/ )

20.10.2020
Просмотров: 808
Сварка металла: подготовка кромок, цветных, как отличить от шлака, толстого, как нагреть электросваркой, детали и изделия из сплавов, индукционная
Сварка металлов изобретена людьми немногим позже, чем сама металлообработка. Уже древние кузнецы умели создать из отдельных железных изделий единое целое. Сегодня сварка составная часть современной цивилизации.
Ее используют на производстве, в быту, при изготовлении строительных конструкций и автомобилей, деталей механизмов, украшений. Выполняют под водой и в космическом пространстве.
Современные технологии позволяют достигать такой прочности полученного изделия, как если бы оно изначально было цельным.
Свариваемость металлов изучают профильные институты разных стран мира, а сварщик одна из самых востребованных сегодня рабочих профессий.
Основные понятия процесса
Задача сварки — создание неразъемного соединения деталей. Чтобы его получить, необходимо сдвинуть атомы, образующие металл настолько близко, чтобы начали действовать межатомные силы сцепления. Почему это происходит, какие при этом протекаю физические процессы, изучено достаточно слабо, но самим свойством пользуются давно.
Добиваются соединения тремя методами:
- Термическим, расплавляя металл самих соединяемых деталей, либо дополнительной присадки. Пример — распространенная дуговая и газовая, лазером, струей плазмы. Сюда относится и пайка.
- Термомеханическим, при котором изделия раскаляют, после чего сжимают либо выполняют проковку. Это самый древний способ, которым владели кузнецы уже пятого тысячелетия до Н.Э. Кроме ковки это диффузионная сварка, контактная, индукционно-прессовая.
- Механическим методом изделия сваривают, подвергая различным воздействиям без специального нагрева. Пример — ультразвуковые методики, соединения взрывом, трением, давлением.
Первый тип наиболее распространен на стройке, в быту. С ее помощью соединяют сталь, чугун, выполняют сварку цветных металлов и сплавов.
Второй и третий методы применяют на промышленных линиях, при серийных выпусках, а также для изготовления уникальных изделий.
Не зависимо от используемой методики, существует всего две разновидности процесса:
- Бесшовный, когда соединяется металл непосредственно самих деталей.
- С образованием шва. При этом применяют вспомогательные присадки. Они могут как точно соответствовать основному металлу, так и отличаться. Пример — соединение стали медным электродом, пайка оловом, все виды сварки с использованием плавкого электрода.
История
До второй половины XIX единственным методом сварных соединений была ковка, а также пайка. Кузнецы раскаляли и накладывали друг на друга заготовки, после чего били молотами. Разумеется, о надежности и точности говорить не приходилось.
Пайка отличается тем, что при ней не происходит расплав кромок соединяемых деталей. Это своего рода «склеивание», где роль клеящего состава играет расплавленный металл.
Настоящая революция сварочных процессов началась с открытием процесса электрической дуги. Для соединения деталей ее сумели применить русские инженеры. Методику дуговой сварки угольными электродами изобрел Н.Н. Бенардос, а спустя буквально несколько месяцев, Н. Г. Славянов сумел выполнить первое соединение металлов плавящимся электродом.
Настоящим сварочным бумом отмечен век XX. Французские инженеры изобрели газовую сварку, в 1956 г. токарь А. И. Чудиков сумел соединить вращающиеся на токарном станке детали трением. К концу 60-х люди узнали, как сварить металл лазером. Примерно тогда же появились промышленные аппараты плазменного напыления, сварка индукционная, диффузионная и пр.
Основные способы
На сегодня насчитывается более 150 различных способов сварных работ. Отличаясь деталями, все они входят в несколько основных категорий, которые мы вкратце рассмотрим.
Электродуговая
Наиболее распространенная на сегодня технология. Ее разделяют на два основных типа: неплавящимся и плавким электродом.
Оба они основаны на температурном воздействии вольтовой дуги. В первом случае задача как нагреть металл электросваркой решается с помощью тугоплавкого электрода из вольфрама. Сам он не плавится, а только образует дугу, формируя сварочную ванну из материала самих деталей либо с добавлением присадки.
Последнюю вносят рукой, как сварочный пруток, либо автоматической подачей, как тонкую проволоку.
Во втором варианте дуга образуется между свариваемым металлом и плавящимся электродом. Последний одновременно служит для формирования шва, который образуется струйным переносом его металла.
Для концентрации дуги, а также образования защитного слоя, металлический стержень покрывают слоем специальной обмазки. К обмазке так же добавляют ряд компонентов, перенос которых улучшает качество шва.
Впервые синтетический рутил, основу обмазки большинства видов электродов, был получен при разработке технологии изготовления белой краски: титановых белил, в 50-х годах прошлого века. Сегодня этот метод является основным источником для электродной промышленности.
Чтобы защитить расплав от окисления на сварочную зону через горелку подают поток газа. В зависимости от его свойств различают:
- Сварку в углекислом газе. Как правило ведут полуавтоматическими инверторами. Скорость сварки полуавтоматом в зависимости от толщины металла, диктует и необходимый объем подачи углекислоты. Таким способом сваривают тонколистовой металл, скажем, при ремонтах кузова автомобиля.
- Соединение в среде инертных газов аргона, либо гелия. К примеру, так варят трубопроводы из нержавейки, алюминия, специальных сплавов.
- Сварку в активном газе.
Оборудование, которыми ведут работы отличаются устройством, но как правило это различного типа трансформаторы и генераторы.
Методика дуговой сварки универсальна, позволяет как варить тонкий металл полуавтоматом, так и соединять толстостенные стальные трубы ручным способом.
Автоматическая под флюсом
Сварочный флюс представляет собой порошок из различных веществ. Его задача двойная:
- Защитить расплав металла от окисления.
- Внести в соединение вещества для усиления прочности стыка.
Процесс происходит следующим образом.
Предварительно подготовленные детали фиксируют на специальном стенде. После этого, на место стыка специальной трубкой подают слой флюса, образующего длинный холмик. За ней идет сварочная головка, образующая дугу. Далее может следовать еще одна трубка, засасывающая не использованный порошок флюса.
Работа ведется неплавящимся или плавящимся электродом. Флюс при этом частично расплавляется. Как отличить металл от шлака при сварке задача не ставится: после завершения работы, достаточно простучать шов, чтобы шлаковая корка, образованная расплавом флюса, отскочила.
Электрошлаковая
При сходстве технологии под флюсом, отличие процесса принципиально. Температура тут создается расплавом специального состава, куда помимо металла входит токопроводящий шлак.
Расплав поддерживается проходящим через него электрическим током. При этом, прогрев ведется сразу по всей длине соединения.
Металл образующий соединительный шов одновременно является плавким электродом, подающим ток в расплав. Это может быть проволока, пластина, либо трубчатый мундштук.
Постепенный нагрев и такое же плавное охлаждение исключает перекаливание изделия, не создает дополнительных напряжений.
Метод требует специфического оборудования и выполняется в заводских условиях. Зато, ему доступна сварка толстого металла, сразу на весь массив деталей.
Электронно-лучевая и плазменная, диффузионная и контактная
При различии методов и принципов соединений изделий все эти виды объединяет отсутствие вольтовой дуги (либо ее особая разновидность, как при сварке плазменной). Более того, при контактной технологии дуга нежелательна.
Электронно-лучевое соединение деталей впервые получили еще в 50-е годы. Процесс схож с соединением лазером, но вместо луча фотонов выступает направленный пучок электронов. Таким способом возможно, как соединять крохотные детали, размеры которых измеряются долями миллиметра, так производить сварку листового металла размером в десятки квадратных метров.
Обязательное требование процесса, специфическая особенность электронно-лучевой технологии — помещение соединяемых деталей в вакуум. Поэтому, этому типу сварки ученые пророчат будущее как основной технологии при сборке конструкций космических станций и кораблей.
Сварка плазменная подходит для работы с тугоплавкими металлами. В отличие от электрической дуги, температура которой 6-7 тыс. градусов Цельсия, в потоке плазмы жар достигает 30000ºС. Кроме соединения, процесс позволяет выполнять напыление разнородных металлов.
Диффузная сварка основана на взаимопроникновении атомов металлов плотно сжатых, предварительно нагретых деталей. Этот процесс, называемый диффузией, дал название методу. Эффективен метод в сложных случаях, к примеру с его помощью выполняется сварка цветных металлов.
Сварка контактная также относится к соединению давлением. При сжатии деталей в месте контакта проходит импульс эл. тока, который обеспечивает связь.
Холодное сваривание деталей и индукционный способ
Основа холодной сварки: деформация соединяемых деталей. Иначе — холодная ковка. При всей привлекательности метода (отсутствие эл. тока) с его помощью удается соединять только неокисляющиеся детали.
Индукционный способ является полной противоположностью холодному. Детали греют, причем не пламенем или дугой, а высокочастотным электромагнитным полем. При этом сварные изделия из металла прогреваются на значительную глубину.
Способ технологичен, поэтому применяется, к примеру, на автоматизированных. трубопрокатных линиях.
Особым качеством металлов является такое понятие как свариваемость, то есть способность соединятся сваркой с помощью того, или иного метода. Зависеть она может от многих причин: химический состав, специфические свойства металла либо сплава, методика подготовки деталей под сварку и многое другое.
ГОСТ разделяет это свойство на следующие группы, свариваемые:
- хорошо,
- удовлетворительно,
- ограниченно,
- плохо.
Плохой свариваемостью отличается чугун, алюминий, высоколегированные стали. Основных препятствий два:
- окисная пленка, препятствующая контакту,
- наличие легирующих добавок, в частности углерода делающих шов хрупким и непрочным.
Свариваемость улучшают предварительной специфической подготовкой металла к сварке.
Особенно сложны в отношении свариваемости цветные металлы, каждый со своей спецификой.
Процедура
Хотя технология создания сварных соединений отличается, во всех случаях процесс начинается с подготовительных операций. Для дуговых методов это подготовка кромок под сварку, или как говорят, их разделка. Для холодной ковки — тщательная зачистка (вплоть до полировки) соединяемых деталей и т.п. Подготовка может включать очистку от грязи, обезжиривание.
Еще одно негативное явление, объединяющее все виды сварочных контактов — температурные деформации и напряжения.
Борются с этим по-разному. В некоторых случаях изделия заранее фиксируют струбцинами. Еще один распространенный способ — термическая обработка готового изделия: нагрев с последующим медленным охлаждением (отпуск).
В заключение
Мы рассмотрели далеко не все виды и способы сварки. Кроме того, постоянно развиваются существующие технологии, изобретаются новые.
При этом технологические решения диктуются задачами. В одном случае вопрос стоит как правильно сварить байпас из металла отопительной системы квартиры используя простейший ручной способ, в другом — создать сверхточное изделие для авиапромышленности. Соответственно подход требуется разный.
На смену существующим, неизбежно придут новые методы, более быстрые и надежные.
Загрузка…Шлак на сварных швах — Морской флот
Что такое сварочный шов
Сварочные швы по металлу представляют собой неразъёмное соединение, которое делается при помощи сварки под воздействием высоких температур.
Сварные соединения имеют несколько зон соединения, которые образуются во время самого процесса сварки:
- Сварной шов – этот участок сварного соединения образуется вследствие кристаллизации или в результате какой-либо деформации, которые произошли при сварке. Чаще всего имеют место и кристаллизация, и деформация в месте сварки.
- Металл шва – образуется в результате плавления основного металла.
Как правило, расплавленную или оплавленную часть конструкции соединяют с нужным элементом посредством «прилипания». После остывания металла шва, скрепление полностью завершается.
- Основной металл – это та основная часть, которая подвергается плавлению или сварке.
- Зона сплавления – эта зона обычно находится на границе или между основным или металлом шва.
- Зона термического влияния – это участок основного металла, который не подвергается расплавлению, но структура и свойства которого изменяются в результате нагрева при сварке или наплавке.
Так, сварные швы могут делиться на несколько типов:
Стыковые – этот тип соединения состоит из двух элементов, которые примыкают к друг другу торцевыми поверхностями. Данный тип сварных швов очень лёгкий в техническом построении и используется довольно часто.
Нахлёстанное – это тот тип, в котором все сварные элементы располагаются параллельно друг к другу. Чаще всего они должны дополнительно частично перекрывать друг друга.
Угловое – в этом типе сварного соединения все элементы свариваются между собой под определённым углом.
Тавровое – данный тип соединения схож с угловым, но здесь требуется приваривать исключительно к боковой поверхности.
Торцовое – здесь вам нужно будет приваривать боковые поверхности материала друг к другу.
Основы электросварки
Разобравшись с видами и типа соединений сварных швов, можно переходить к основам электросварки. Если вы планируете обучаться самостоятельно, то вам необходимо будет запастись всеми необходимыми материалами. Так как с первого раза практики вас, скорее всего, ожидает небольшой провал, то лучше запастись большим количеством материала.
Также важно знать некоторые термины и обозначения перед началом работ:
- Сварная дуга – это раскалённый до невероятно высоких температур (порядка 5-7 тысяч) газ, так что обращаться со сваркой нужно предельно аккуратно, иначе вы рискуете нанести себе или окружающим серьёзные ожоги.
- Дуговая сварка – этот вид сварки делается при помощи электрической дуги, которая нагревает газ до невероятно высоких температур. При соприкосновении с поверхностью металлического изделия, металл начинает плавиться вследствие чего образуется так называемая – «сварочная ванна». После остывания металла появляется сварной шов.
- Аргонодуговая сварка – практически, как дуговой вид сварки, только в качестве разогреваемого газа здесь необходимо использовать аргон. Данный вид сварки очень хорошо подходит для различных прутьев арматуры толщиной не более 5 миллиметров.
Подготовительные работы
По причинам, которые были описаны выше, все сварочные работы лучше всего проводить в помещении, где нечему гореть, в противном случае вы рискуете устроить пожар. Найдя пожаро-безопасное помещение, необходимо подготовить все нужные для работ материалы. Прежде всего подумайте о своей защите, приобретите специальную сварочную маску, перчатки для сварки, а также желательно дополнительно приобрести специальный костюм, который сделан из огнеупорного материала.
Когда вы уверены, что обезопасили себя от случайной искры или ожога, вам нужно приобрести все необходимые инструменты для работ. В их число входят:
- Вам в обязательном порядке понадобится сам сварочный аппарат.
- Также нужен будет небольшой комплект электродов, которые будет проводить достаточное количество электричества для нагрева газа до нужной температуры.
- Специальный небольшой молоточек, который понадобится для того, чтобы оббивать ненужный шлак.
- А также щётка с жёсткими ворсинками для удаления различного рода мусора.
- Трансформатор. Благодаря ему обычный переменный электрический ток, который проходит через наши розетки, будет преобразован в постоянный. Большинство сварок на мировом рынке работают только с помощью постоянного тока.
Как правильно варить электросваркой
Когда всё готово для начала сварочного процесса обязательно тщательно проверьте поверхность тех элементов, которые собираетесь сваривать между собой, на наличие на них ржавчины или любых других дефектов. При обнаружении таковых, рекомендуется попытаться их устранить или заменить дефектные элементы на более качественные.
Теперь, когда всё готово к работе можно приступать:
- Сначала требуется прикрепить специальный зажим массы к своей рабочей заготовке и вставить электрод в держатель на сварке. Затем нужно попытаться поджечь дугу. Электрод необходимо устанавливать под углом около 70 градусов относительно заготовке. Для поджигания дуги, необходимо провести по заготовке электродом со скоростью примерно 7-10 см в секунду. Со стороны это будет выглядеть так, как будто вы поджигаете спичку. При появлении характерного треска и искр загорится сама газовая дуга. Если всё это произошло, то значит у вас всё получилось.
- Затем, устанавливаем электрод примерно под таким же углом. После установки вам будет необходимо соприкоснуться с рабочей заготовкой, и тут же немного поднять электрод так, чтобы в итоге получился небольшой зазор в 3-5 миллиметров между поверхностью металла и электродом.
После соприкосновения с металлом дуга начинает гореть. Однако будет плавиться не только металл заготовки, но и самой дуги. Старайтесь поддерживать размеры зазора и одновременно перемещать электрод по горизонтали или вертикали (зависит от того в какую сторону вам нужно).
- Также во время процесса сварки, если вы приблизились слишком близко (также это может быть связано с малым напряжением) к поверхности металла, то ваш электрод может прилипнуть. Для того чтобы он отлип, поводите им из стороны в сторону. Затем обратно зажгите дугу.
- Старайтесь как можно лучше настроить трансформатор. Ведь если тока будет слишком много, то металл расплавится, как масло, а если тока слишком мало, то дуга попросту погаснет.
Как правильно варить шов
Немного разобравшись с работой дуги и самой сварки приступаем к выполнению швов. Швы в нашем случае делятся только на горизонтальные и вертикальные.
Ниже расположена небольшая инструкция для каждого из этих типов:
1.

Делать такой шов проще простого. Достаточно всего лишь постепенно вести дугу по горизонтали, соблюдая зазор в 3-5 миллиметров. Также желательно как можно лучше закрепить материал, на который вам нужно сделать шов.
При сварке нужно вести дугу не сильно быстро, но и не сильно медленно – это нужно для того, чтобы зазор между металлическими материалами постепенно залился оплавившимся металлом и при этом успел остыть.
2. Вертикальный шов
Процесс сварки вертикальных швов довольно сильно схож с процессом сварки горизонтальных швов, только в этом случае вам нужно сваривать под другим углом. Самый главный принцип в сварке вертикальных швов – это соблюдать определённое правило – никогда не вести дугу слишком быстро или слишком медленно. Так как в этом случае если металл будет подвергаться большому нагреву (дуга идёт слишком медленно) он будет понемногу стекать вниз, а при условии, что дуга идёт слишком быстро у вас может получиться некачественный шов.
Ваша задача должна состоять в том, чтобы слить обе кромки, плавя их сварочной дугой, одновременно направляя туда же капли металла из раскаленного до состояния жидкости конца электрода.
Как правильно варить трубы
Процесс сварки труб с помощью электросварки довольно трудоёмок и требует определённого уровня мастерства и аккуратности. Если вы желаете самостоятельно учится сваривать трубы, то лучше всего дня начала попробовать трубы на толстом металле.
Небольшая инструкция:
- Раскладываем все трубы на специальном столе или стенде, на которых вам будет удобно с ними работать.
- В этом способе вам нужно будет сваривать трубу в два шага. Первый шаг свариваем первое полукольцо в одну сторону, затем второе в другую. Здесь следует использовать методику ведения «сверху вниз», используя 4-миллиметровый электрод с органическим напылением.
- Если вы свариваете трубы с маленьким диаметром, старайтесь их сваривать непрерывной дугой, если же диаметр трубы крупный, то сваривайте её с помощью способа, приведённого во 2-м пункте.
Как удалить шлак
Во время проведения работ у вас может образоваться различного рода дефекты в местах сплава – шлак. Перед тем как приступить к уборке шлака, необходимо дать шву остыть. Когда вы убедились, что шов остыл, постучите по нему небольшим молотком (лучше всего приобретите специальный для удаления шлака).
После постукивания шлак основной слой шлака отлетит сам, оставшиеся слои можно убрать при помощи наждачки.
Итак, если Вы новичок в сварке и благодаря ТД «Дока» только что приобрели отличный сварочный аппарат инверторного типа и замечательную маску «хамелеон», тогда это статья для Вас.
Прежде чем приступать к выполнению сварочных работ, хотелось бы поговорить о правилах безопасности при работе со сварочным оборудованием. Не стоит игнорировать данный момент. Настоятельно рекомендуем изучить ПУЭ (Правила эксплуатации электроустановок) глава 7.6 «Электросварочные установки». Будьте уверены, что из этого документа Вы почерпнете много полезной информации не только о правилах безопасности при обращении со сварочным оборудованием, но и о электробезопасности всего Вашего загородного дома, дачи.
Далее Вам определенно потребуется качественные перчатки сварщика (краги) и одежда из негорючего материала. Многие пытаются варить в хозяйственных (садовых) перчатках и иногда даже в одежде без рукавов. Поверьте – ожоги от брызг сварки весьма болезненны и заживают очень долго. Также обязательно застегивайтесь на все пуговицы и одевайте качественную обувь. Особенно памятные случаи были с залетанием раскаленного металла и шлака за шиворот и в сапоги с заправленными в них штанами. Крики, танцы, чудеса ловкости начинающих сварщиков.
Старайтесь избегать по возможности использование длинных переносок, так как это ведет к существенным потерям мощности сварочных аппаратов. Если вы все же используете такую переноску, разматывайте кабель с катушки до конца.
Электроды обязательно должны быть просушены, при необходимости прокалены. Вам как новичку и так возможно будет непросто разжигать сварочную дугу, делать это непрокаленными электродами в разы труднее. Режимы (температура и время) прокалки указываются на упаковке электродов. В нашем магазине найдется все для сварки, поэтому если Вы решите купить печь или пенал для прокалки электродов то мы будем рады Вам помочь в выборе.
Маска «хамелеон» должна быть настроена под конкретный вид работы и величину сварочного тока. Обязательно внимательно прочтите паспорт или инструкцию по эксплуатации к сварочной маске. Не начинайте сварку, не убедившись в том, что светофильтр исправен. Некоторые забывают перевести его из положения Grind (зачистка) – получают приличного «зайца».
Сварочный ток должен быть подобран в соответствии с типом выполняемого сварочного соединения, не забывайте что в нижнем положении он всегда выше на 20-30% чем в потолочном и на 10-20% чем в вертикальном. Ориентировочная сила тока указывается на коробке с электродами.
Для новичков желательно начинать варить с рутиловых электродов типа МР3-С.
Не рекомендую использовать электроды УОНИ или дедовские запасы «лохматых годов», на первый раз возьмите свежие МР3-С или АНО-21.
Не стоит сразу пытаться варить изделие: бак для бани, либо ставить забор и т. д., несмотря на то, что это в общем-то не очень и трудно. Помните, что главным оружием солдата-новобранца является лопата, а начинающего сварщика – угловая шлифовальная машинка, она же «болгарка». Поэтому для того, чтобы свести использование главного орудия к минимуму в дальнейшем, начинать нужно с наложения (наплавки) пробных валиков, чтобы «почувствовать сварку».
Желательно для первых тренировок найти толстую пластину металла достаточного размера. Зачистите болгаркой до металлического блеска поверхность металла и наложите пробный валик в нижнем положении углом вперед без колебаний электрода слева направо если вы правша и справа налево если левша.
Поэкспериментируйте с величиной сварочного тока и манипуляциями электродом.
Далее наплавляйте валики, производя колебательные поперечные движения. Обычно геометрия манипуляций электродом представляет собой варианты, представленные на рисунке ниже. Валик должен получаться ровным с равномерными чешуйками. Общее правило у профессионалов: сварочный ток должен быть максимально возможным для качественного провара и внешнего вида.
Старайтесь держать короткую дугу, т.е. электрод должен быть постоянно в 2-3 мм от сварочной ванны, для этого его нужно постепенно плавно подавать в зону сварки, исходя из скорости и величины тока. Это тоже надо прочувствовать.
Клемму заземления или «массу» старайтесь крепить как можно ближе к месту сварки. Электрод зажимайте в держаке плотно. Следите за тем, чтобы огарок был не менее 10 см, не стоит дальше жечь электрод.
Наблюдайте за сварочной ванной. Научитесь отличать металл от шлака. Шлак через сварочную маску, выглядит как темные пятна на солнце.
После окончания сварки аккуратно обстучите специальным молоточком шлак. Подчеркиваю аккуратно, не стоит долбить со всей дури, случаев попадания не остывшего шлака на открытые участки кожи и в глаза предостаточно, причем, как правило, страдают именно новички. Если у Вас маска «хамелеон» тогда желательно ее вообще не поднимать при данной операции.
Зажигайте сварочный электрод либо легким постукиванием, либо «чирком» как спичку.
Если электрод прилип и после того как вы его оторвали, не зажигается, то необходимо потихоньку обломать обмазку руками, так как в таких случаях обычно сгорает стержень электрода. Если вы будете стучать электродом, что есть мочи, то наоборот обмазка отлетит больше, чем надо и останется голый стержень, и снова вероятность залипания увеличится в геометрической прогрессии.
Также рекомендуем поэкспериментировать с крутилкой Arc Force (форсаж дуги) на сварочном аппарате. Она предназначена для регулировки «жесткости дуги». «Мягкая дуга» обеспечивает малое разбрызгивание при мелкокапельном переносе, а «жесткая» позволяет получить глубокое проплавление сварного шва. Также регулировку Arc Force многие сварщики «в теме» используют для предотвращения залипания электрода. Обычно в таких случаях при начале сварки выкручивают ее на полную, а после розжига дуги возвращают в требуемое положение.
Следующий этап курса молодого бойца – вертикальные валики.
Прихватываем пластину, например к заборному столбу, и пробуем положить вертикальный шов. Направление сварки снизу вверх. Если электроды рутиловые, то сварка производится в «отрыв», иначе сварочная ванна «потечет».
В принципе если Вы успешно выполнили наплавку в вертикальном положении, то можно потихоньку приступать к «заборостроению». Для начинающих любителей этого будет достаточно, а остальному научитесь «в бою».
Но для особо пытливых можно попрактиковаться в горизонтальных и потолочных положениях.
Конечно, мало у кого сразу получится хорошо наплавить валик в потолочном положении, однако это даст Вам пищу для размышлений как формируется сварной шов, как себя ведет металл при сварке и т.д.
Для успешного «заборостроения» необходимо не только владение сваркой, но правильной подгонкой, подготовкой под сварку.
Учтите что при сварке металл всегда «сжимается», также его ведет в ту сторону, с которой вы варите. Учитывайте поводки и стягивание при сварке, так как это может сильно сказаться на размерах Ваших конструкций. Рекомендуем по возможности собирать конструкцию на прихватках, применять специальные приспособления (струбцины и т. д.), далее после этого как следует еще раз проверить размеры и геометрию, а обваривать «намертво» конструкцию в самом конце. Если шов длинный, то настоятельно советую варить его от центра к концам короткими швами «в разбежку», в шахматном порядке, если шов двусторонний. Принцип «семь раз отмерь, один отрежь» – в случае сварочных работ актуален как никогда. Это поможет избежать проблем описанных выше.
Если что-то не получается, не отчаивайтесь – обязательно получится позже. Сварка любит терпеливых и настойчивых, учит быть таковыми. В любом случае, ТД «ДОКА» желает Вам удачи!
Копирование контента без указания ссылки на первоисточник ЗАПРЕЩЕНО.
Корневые дефекты шва
При наплавлении первого валика вдоль корня стыкового шва проникновение металла в корень может быть недостаточным в силу недостаточной силы сварочного тока или чрезмерной скорости сварки. Причина может также заключаться в слишком большом диаметре электрода для данной канавки. При слишком большой силе сварочного тока может произойти прожог корня шва.
Дефекты сплавления
Если сила тока недостаточная или слишком высокая скорость сварки, могут произойти несплавления между наплавленным и основным металлом.
Несплавления могут иметь место и в том случае, если используется слишком маленький электрод при сварке на большом участке холодного основного металла. В этом случае следует использовать электрод большего диаметра и подогревать основной металл.
Дефекты кромок шва
Дефекты кромок могут произойти в силу чрезмерной силы сварочного тока. Однако такие дефекты могут возникнуть и при правильном токе, если дуга будет слишком длинной или если неправильно перемещается электрод. При сварке снизу вверх в вертикальном положении при колебательном движении электрода последний нужно на мгновение прижимать к каждой стороне валика, чтобы металл хорошо проник в шов и чтобы избежать дефектов кромки шва. Дефекты кромки могут быть индикаторами разрыва в сварном соединении.
Поры в сварном шве
Поры в шве могут образоваться из-за содержания влаги в покрытии электрода, особенно при сварке электродами с основным покрытием. Кроме того, причиной образования пор может быть мокрый или влажный основной металл свариваемого изделия. Такой шов ухудшает прочность соединения.
Тепловые трещины
Тепловые трещины могут образоваться во время и сразу после периода охлаждения шва по двум основным причинам:
Из-за включений в основном металле, которые имеют тенденцию к сегрегации и могут образовать слой в середине шва. Этот слой препятствует сращиванию кристаллов. К таким веществам прежде всего относятся углерод и сера. В случаях, когда тепловые трещины вызваны такими веществами, перейдите на электрод с основным покрытием. Если же трещины появились при сварке электродом с основным покрытием, значит данный металл является несвариваемым.
Напряжение через шов может вызвать появление тепловых трещин, даже если основной металл не сегрегирует в шве В определенный промежуток критической температуры, сразу же после коагуляции валика шов имеет очень слабую способность к деформации и, если усадка металла больше, чем растяжение шва, образуется трещина. Этого можно избежать, зажав свариваемую деталь специальным зажимным приспособлением, которое ограничивает усадку металла.
Тепловые трещины появляются в середине валика и представляют собой прямую трещину на поверхности.
Усадочные трещины
Усадочные трещины образуются тогда, когда способность шва к деформации (вязкость) меньше, чем реальная усадка. Такие трещины обычно бывают поперечными и вызываются значительной продольной усадкой. Чтобы избежать образования таких трещин, лучше всего использовать электроды с основным покрытием.
Водородные трещины
Трещины в металле шва образуются под воздействием водорода и могут образоваться в стали любого типа, которая прошла закалку или закаляется во время сварки. Сталь с высоким пределом текучести будет содержать определенное количество упроченной структуры, обычно это мартензит. Чем выше точка плавления, тем выше риск образования водородных трещин, они образуются в основном металле,, который непосредственно прилегает к зоне плавления, и, сочетаясь со сварочным напряжением, образуют трещины в металле шва.
Для сварки закаленной стали можно использовать только сухие электроды с основным покрытием, т. к. в этом случае выделяется очень мало водорода. Влажные электроды выделяют очень много водорода. Другими источниками водорода являются ржавчина, масло, краска или конденсация вдоль сварочной канавки. Подогрев канавки, скажем, до 50°С значительно снизит количество водорода.
Включения шлака в шов
Шлак состоит из неметаллических частиц с покрытия электрода. После каждого валика необходимо тщательно удалять весь шлак. Для этого используйте обрубочный молоток и проволочную щетку. Частицы шлака, попавшие в шов, серьезно снизят прочность соединения. Старайтесь избегать выжигания выемок, т. к. попавший туда шлак трудно удалить.
При подготовке сварочной канавки убедитесь, что она имеет достаточный зазор для обеспечения хорошего сплавления и облегчения удаления шлака. Удалите окалины и ржавчину со свариваемой поверхности и проверьте, правильно ли вы выбрали электрод для данной сварочной позиций.
Электроды с толстым или качественным покрытием
Электроды с толстым или качественным покрытием
Категория:
Сварка металлов
Электроды с толстым или качественным покрытием
Эти электроды называют также качественными. Их легко отличить по внешнему виду: слой покрытия имеет значительную толщину, 1—3 мм; вес покрытия 15—60% и более от веса электродного стержня. Покрытия, помимо стабилизации дуги, защищают сварочную ванну от вредного влияния атмосферного воздуха, улучшают химический состав, структуру и механические свойства наплавленного металла, обеспечивают достаточно устойчивое горение дуги.
Основой металлургического процесса при сварке, как и в сталеплавильных печах, является взаимодействие между шлаком и металлом. Шлак при сварке образуется главным образом из расплавленного покрытия электрода, в которое вводят в тонкоразмо-лотом виде различные минеральные вещества, руды, горные породы и т. п. Шлак, образующийся вместе с расплавленным металлом при плавлении электрода, защищает ванну от доступа воздуха; при затвердевании ванны шлак замедляет охлаждение. При замедленном охлаждении разлагаются нестойкие соединения азота с яшлезом, причем освободившийся азот удаляется из металла, и содержание азота в металле снижается до допустимой нормы 0,01 — 0,03%. Содержание вредных примесей, в особенности серы и фосфора, в материалах для изготовления покрытий доводится до возможного минимума. Все материалы должны строго контролироваться по содержанию фосфора и серы.
Существующие разнообразные качественные электродные покрытия могут быть классифицированы по различным признакам, например по характеру шлака. По химическому составу шлаки, получаемые при расплавлении электродных покрытий, могут быть разделены на кислые и основные. Важнейшими кислотными окислами в электродных обмазках являются: двуокись кремния Si02 и двуокись титана ТЮ2. Основными окислами являются Na20, CaO, MgO, MnO, FeO и др. Окислы А1203, Fe203, Сг203 являются промежуточными, нейтральными или амфогерными. Преобладание кислотных или основных окислов делает шлак соответственно кислым или основным.
Кислые шлаки могут уменьшать содержание кислорода в наплавленном металле, что объясняется следующим образом. Кислород содержится в расплавленном железе в форме закиси железа FeO, имеющей ясно выраженный основной характер и реагирующей с кислотными окислами шлака, если они имеются в избытке; образуемые силикаты или титанаты закиси железа 2Fe0-Si02 и 2FeO -Ti02 в ванне металла практически нерастворимы. В результате происходит непрерывный переход закиси железа из металла в шлак, т. е. экстрагирование закиси железа из металла шлаком. Подобный процесс раскисления металла кислым шлаком называется диффузионным раскислением.
Большое распространение имеют покрытия, дающие шлаки сильно основного характера с большим содержанием окиси кальция СаО; эти шлаки обеспечивают получение наплавленного металла особенно высокого качества. Шлаки основного характера не производят диффузионного раскисления металла, и для уменьшения содержания кислорода в ванне в обмазки приходится вводить сильные раскислители (кремний, титан) в форме ферросплавов.
По характеру металлургических реакций, протекающих в сварочной ванне, качественные электроды можно разделить на две группы.
Для быстрого и энергичного проведения подобной реакции в обмазку вводят в большом количестве окислы железа в форме железных руд либо железной окалины или же другие окислы, легко отдающие кислород и способные интенсивно окислять металл ванны, например двуокись марганца Мп02 в виде минерала пиролюзита. Дополнительным источником углерода, сверх содержащегося в основном металле, служит обычно ферромарганец, вводимый в значительном количестве в подобные обмазки. Протекающие в ванне экзотермические реакции освобождают значительное количество тепла и дополнительно разогревают ванну.
Весьма важны физические свойства шлака. Температура плавления шлака, как показывает опыт, должна находиться в пределах 1100—1200 °С. При температуре плавления стали 1400— 1500 °С шлак должен обладать малой вязкостью, большой подвижностью и жидкотекучестью, что важно для правильного формирования сварного шва. Существенное значение имеет характер затвердевания расплавленного шлака. Шлаки не имеют строго определенной температуры плавления. При повышении температуры вязкость шлака постепенно падает, а при понижении возрастает. Переход от жидкого состояния к твердому может быть
растянут на значительный температурный интервал, такие шлаки называются длинными. Если же переход от твердого состояния к жидкому происходит в небольшом температурном интервале, то шлаки называются короткими (рис. 43). Опыт показывает, что при сварке лучшие результаты при прочих равных условиях обычно дают короткие шлаки.
Одной шлаковой защиты недостаточно, как бы ни была она совершенна. Для получения высококачественного наплавленного металла необходимо легирование, т. е. введение в металл таких элементов, как марганец, хром, никель и т. д. Наиболее важное значение имеет легирование марганцем, которое в практике применяется чаще всего. Легирующие элементы вводят в обмазку в виде тонкоизмельчен-ных ферросплавов, ферромарганца, ферросилиция, феррохрома и т. п. Ферросплавы, кроме того, являются сильными раскис-лителями и уменьшают содержание кислорода в ванне, восстанавливая закись железа.
Помимо минеральных веществ для образования шлаков и ферросплавов для восстановления и легирования в обмазки часто вводят органические вещества: целлюлозу, крахмал, декстрин, сахар, пищевую муку, древесную муку и т. п. Органические вещества под воздействием высокой температуры при сварке разлагаются с образованием смеси газов, имеющих восстановительные свойства, устраняющие доступ кислорода к ванне; соединения железа с азотом в присутствии водорода или газов, богатых водородом, как показывает опыт, при сварке вообще не образуются. Введение органических веществ, в особенности целлюлозы, позволяет уменьшить количество обмазки на электроде, что особенно важно для электродов, предназначенных для сварки в вертикальном и потолочном положениях. Для качественной обмазки важен не только ее состав, но и количество, наносимое на электрод, так как ход и конечный результат металлургической реакции зависят от количества шлака, взаимодействующего с металлом.
Рис. 1. Диаграмма затвердевания шлаков
Реклама:
Читать далее:
Классификация покрытых электродов
Статьи по теме:
На поверхности — Производительность сварки
На формирование надлежащего конверсионного покрытия предварительной обработки и адгезию последующих покрытий к сварным швам влияет чистота зоны сварки. В процессе сварки могут образовываться различные неорганические загрязнения в зависимости от используемого метода сварки.
Эти неорганические загрязнения необходимо удалить, чтобы обеспечить успех последующих операций по предварительной обработке и нанесению покрытия. В этой статье представлена информация о сварочных брызгах и загрязнениях от сварочного шлака, образовавшихся в процессе сварки, и представлен рекомендуемый метод их удаления для каждого из них.
Определение сварочных загрязнений Зона термического влияния (ЗТВ). Неорганические загрязнения, образующиеся в процессе сварки, локализуются в области, прилегающей к сварному шву, и включают сварочные брызги, сварочный шлак, окалину и различные элементы, которые можно найти в присадочном металле сварного шва. Область, в которой отображаются эффекты процесса сварки, называется зоной термического влияния (ЗТВ).
ЗТВ — это участок основного материала, который не плавится, и его микроструктура и механические свойства были изменены в результате сварки.Тепло от процесса сварки и последующего повторного охлаждения вызывает изменения в ЗТВ. Степень изменения свойств зависит в первую очередь от основного материала, присадочного металла сварного шва, а также количества и концентрации тепла, выделяемого в процессе сварки. Различные области ЗТВ показаны на Рисунке 1.
Сварочные брызги Брызги металла при сварке определяются как мелкие частицы расплавленного металла, выходящие из сварочной ванны, которые прилипают к поверхности основного металла. Основной причиной образования сварочных брызг является нарушение расплавленной сварочной ванны во время переноса проволоки в сварной шов.Помехи обычно возникают из-за недостаточного количества защитного газа, грязного основного металла, слишком высоких скоростей движения, слишком длинной проволоки или зависимости между силой тока и напряжением. Обычно это наблюдается, когда сварочное напряжение слишком высокое или низкое или сила тока слишком высока для данной комбинации проволоки и газа.
Брызги могут также возникать в результате использования газа или газовой смеси, выбранных для защиты. Брызги сварки необходимо удалить с поверхности детали, подлежащей окраске.Очень сложно нанести равномерное покрытие, если на детали остаются брызги, а покрытие часто плохо прилипает.
Оба фактора приводят к преждевременному разрушению покрытия либо из-за коррозии, образующейся вокруг участков с плохим покрытием, либо из-за того, что брызги отбивают деталь, обнажая основной металл без покрытия. Пример сварочных брызг показан на Рисунке 2.
Сварочный шлак Сварочный шлак образуется, когда флюс, твердый защитный материал, используемый в процессе сварки, плавится в зоне сварного шва или поверх нее.Шлак — это затвердевший остающийся флюс, который образуется на сварном шве по мере охлаждения области сварного шва.
Дуговая сварка защитным металлом (SMAW или сварка стержнем) и дуговая сварка порошковой проволокой (FCAW) используют флюсовые материалы для образования шлака, который защищает или помогает защитить сварной шов во время затвердевания сварочной ванны. Газы, образующиеся из шлаковых систем для любого процесса, такие же, как и те, которые обычно поступают извне при других методах сварки. Обычно при обоих этих сварочных процессах также образуется большее количество брызг.
Затем шлак должен быть удален механически, чтобы подготовить сварной шов к последующей обработке, так как он слабо прилегает к сварному шву и не имеет поверхности, восприимчивой к покрытию. Удаляемый шлак также содержит многие элементы, присутствующие в присадочном металле сварного шва, которые всплыли на поверхность сварного шва и могут вызвать проблемы с покрытием, если их не удалить. Пример сварочного шлака показан на рисунке 3.
Как упоминалось ранее, существуют сварочные процессы, в которых не используется флюс и используются защитные газы, подаваемые извне. В газовой дуговой сварке (GMAW или MIG) и газовой вольфрамовой сварке (GTAW или TIG) используется смесь инертного или полуинертного газа для защиты сварных швов от загрязнения, поэтому на сварном шве не образуется слой шлака.
Загрязнения при сварке должны быть удалены, чтобы обеспечить восприимчивую поверхность для последующего нанесения конверсионных покрытий и покрытий. Есть два метода удаления: механический и химический.Механические методы состоят из ручного или автоматического истирания. В химическом методе обычно используется кислотный травильный раствор, хотя нейтральные органические соединения использовались в особых случаях.
Удаление брызг при сварке Брызги сварочного шва удаляются механическими методами. Обычно используются следующие методы: шлифование, шлифование, пескоструйная очистка или соскабливание. Шлифование и шлифование можно производить с помощью абразивных кругов или лент, а также ручных или механических абразивных щеток (проволочных щеток).
Пескоструйная очистка обычно выполняется на сборках с несколькими открытыми поверхностями сварных швов, которые легко контактируют с материалами для струйной очистки. Пескоструйная очистка включает абразивоструйную очистку с использованием пневматических носителей или абразивоструйную очистку с использованием механических носителей.
Царапины или сколы часто используются для легко удаляемых брызг. В качестве инструмента обычно выбирают отбойный молоток или долото.
Использование химических материалов, предотвращающих разбрызгивание, также можно использовать для минимизации или устранения прилипания брызг к основному металлу.Антибрызгивание наносится на свариваемую поверхность и оставляет на металле защитную пленку, которая предотвращает прилипание брызг после затвердевания.
Удаление сварочного шлака Сварочный шлак также удаляется с использованием тех же механических методов. Для удаления шлака соскабливание или скалывание часто выполняется молотком или зубилом, поскольку он обычно плохо прилипает и легко удаляется. Шлифовка и шлифовка также могут выполняться с использованием абразивных кругов или лент, а также ручных или механических абразивных щеток (проволочных щеток).Пескоструйная очистка обычно выполняется с использованием абразивно-струйной очистки или струйной очистки с использованием абразивных материалов.
Удаление шлака химическими методами часто предпринимается и очень редко бывает успешным. Шлак очень трудно или невозможно удалить с помощью большинства доступных продуктов кислотного травления. Шлак имеет щелочную природу и обычно присутствует в виде толстого слоя. Кислотный рассол воздействует на шлак, начиная с внешней поверхности, удаляя его слоями.
Поскольку шлак является щелочным, он также частично нейтрализует кислоту во время травления.Время выдержки процесса обычно составляет от 60 до 120 секунд для кислотного травления, что обычно не позволяет кислоте полностью удалить шлак.
Chemetall U.S. Inc.
Основные сведения о порошковой проволоке
При правильной сварке порошковая проволока может минимизировать затраты, улучшить качество и повысить производительность. Как и любой присадочный металл, он имеет уникальные характеристики, преимущества, ограничения и области применения, в которых он лучше всего работает. Знание того, когда и как использовать порошковую проволоку, может помочь вам добиться успеха.
Порошковая проволока — это трубчатая проволока, наполненная металлическими порошками, небольшими количествами стабилизаторов дуги, которые обеспечивают определенные преимущества. К ним относятся более широкие профили проплавления, более высокая устойчивость к загрязненному или горячекатаному основному металлу и меньшее количество островков кремния в окончательном сварном шве. Порошковая проволока обеспечивает более высокую скорость наплавки, чем сплошная проволока при заданном тепловложении. Проволока с металлическим сердечником не дает шлака, как порошковая проволока.Отсутствие шлака делает порошковую проволоку более эффективной, поскольку больше проволоки откладывается в стыках, как металл шва. Отсутствие шлака также снижает очистку между проходами и после сварки.
Порошковая проволока с металлическим сердечником легко легируется и доступна во многих различных химикатах, поэтому с ее помощью можно сваривать самые разные недрагоценные металлы. Вы можете использовать проволоку с металлическим сердечником во многих случаях, таких же, как сплошная проволока, но она лучше всего подходит для сварных швов длиной шесть дюймов и более, в плоском или горизонтальном положении с использованием переноса распылением или импульсной газовой дуговой сваркой (GMAW).Перенос распылением максимизирует преимущества металлопорошковой проволоки двумя ключевыми способами: 1) вы можете сваривать быстрее и 2) при этом практически не образуются брызги, поэтому вы можете уменьшить объем очистки после сварки. Порошковая проволока хорошо подходит для других областей применения: проволоки, склонные к прожогу; компоненты с плохой сборкой; и рабочие места, где важна эстетика.
сочетание трубчатой структуры порошковой проволоки и использования распылителя
передача создает широкую конусообразную дугу и широкий профиль проплавления. Этот
форма дуги создает постоянный профиль валика, который легко перекрывает зазоры и
точно без прожога. Другие ключевые преимущества металлопорошковой проволоки
включают:
- Он производит более мелкие капли жидкого металла через дуга, которая снижает турбулентность в сварочной ванне.
- Он обеспечивает высокую скорость перемещения и высокую производительность наплавки (по сравнению с к сплошной проволоке), чтобы повысить производительность.
- Он может минимизировать дефекты сварных швов, такие как отсутствие плавления и подрез, позволяющий сократить переделки.
- Он может сваривать прокатную окалину и ржавчину и при этом производить очень мало брызг, что снижает потребность в шлифовке перед сваркой, шлифовать пескоструйная очистка или нанесение состава против разбрызгивания.
с металлическим сердечником
проволока дороже за единицу, чем сплошная проволока. Вам нужно будет учесть
может ли ваше приложение компенсировать эти дополнительные расходы за счет выполнения сварочных работ
работа более эффективна. Если вы часто свариваете в режиме короткого замыкания,
положение или в течение небольшого процента времени порошковая проволока может не
экономически эффективным.Порошковая проволока — наиболее производительная сварка в положении для
на более длительные периоды времени и обеспечивает здесь лучшую долгосрочную экономию.
Учтите также плюсы и минусы защитного газа. Вам потребуется высокий уровень аргона (90 процентов аргона / 10 процентов CO 2 или от 75 до 95 процентов аргона с остатком CO 2 ), чтобы получить максимальную пользу от порошковой проволоки в режиме распыления. Аргон — более дорогой газ, поэтому решите, снизит ли ваша производительность и качество ваши затраты.Обратитесь к проверенному дистрибьютору сварочного оборудования или производителю присадочного металла, чтобы провести испытание на время и определить вашу потенциальную экономию.
Помните также, что сварка — это только один этап производства. процесс. Если вы увеличите производительность с помощью порошковой проволоки, сможет ли ваша послесварочная сварка такие операции, как покраска, не отстают? Это важно для определения общей стоимости экономия.
Советы и приемыСварка порошковой проволокой аналогична сварке сплошной проволокой, за некоторыми исключениями.
- Используйте приводные ролики с V-образной насечкой. Порошковая проволока может легко сломаться при слишком сильном натяжении. Приводные ролики с V-образной насечкой имеют мелкие зубья для захвата и направления проволоки; вам нужно меньшее натяжение для подачи проволоки по лайнеру.
- Более длинный вылет не приведет к беспорядочной передаче. Расстояние между контактным наконечником и рабочей поверхностью — зазор между сварочной горелкой и основным материалом — может быть немного больше при использовании порошковой проволоки.
Лучше всего подходит зазор от 1/2 дюйма до 1 дюйма (в зависимости от диаметра проволоки и рабочей точки).Обычно рекомендуется увеличивать расстояние от наконечника до обрабатываемой детали по мере увеличения скорости подачи и диаметра проволоки.
- Можно использовать проволоку большего диаметра. При переходе на порошковую проволоку с сплошной проволоки обычно можно использовать проволоку на один диаметр больше. Поскольку порошковая проволока имеет более широкий конус дуги, она меньше концентрирует тепло и снижает вероятность прожога. Проволока также лучше перекрывает зазоры и обеспечивает стабильное сплавление боковых стенок.
- Меньше манипуляций со сварочным пистолетом и лужей. Более широкий металлический переходник / дуговый конус с порошковой проволокой позволяет изготавливать сварные швы большего размера без плетения.
Более высокие уровни аргона, необходимые для порошковой проволоки, влияют на рабочий цикл пистолета. Производители пистолетов оценивают пистолеты по определенному типу газа. Обычно 100-процентный рабочий цикл при определенной силе тока относится к использованию пистолета со 100-процентным CO 2 . Поскольку CO 2 лучше охлаждает пистолет, чем аргон, вы можете получить от 30 до 50 процентов снижения охлаждения с высоким содержанием аргона.Выберите пистолет с достаточной силой тока для работы.
Сочетание высокого уровня аргона и распыления приводит к меньшему образованию видимого дыма, что приводит к заметно большему лучистому свету от дуги, поскольку меньше дыма его фильтрует. Возможность сварки с металлическими сердечниками при более высоких силах тока также увеличивает излучаемый свет. Будьте особенно осторожны, чтобы закрыть открытые участки кожи, увеличьте оттенок сварочной линзы и, при необходимости, поместите экраны вокруг сварочной ячейки.
Сделайте правильный выбор Помните, что выбор правильного присадочного металла для работы — важная составляющая успеха вашей сварочной операции. Знание того, когда целесообразно использовать порошковую проволоку, может помочь повысить производительность и сэкономить деньги — вы сможете выполнять сварку более эффективно, наплавить больше металла, уменьшить проблемы с качеством и тратить меньше времени на очистку сварных швов в нужных областях.
4,7 3 голоса
Рейтинг статьи
Сварка против. Пайка — в чем разница?
Сварка включает в себя несколько основных процессов, некоторые из которых особенно важны в промышленности.Это дуговая сварка, газовая сварка, пайка и контактная сварка. Все используются для плавления металла; часто используется наполнитель. В этой статье кратко описаны эти сварочные процессы и некоторые примеры их использования.
Дуговая и газовая сварка
Дуговая и газовая сварка — это то, что обычно приходит на ум, когда мы слышим слово «сварка». Они используют высокую температуру от электрической дуги или кислородно-ацетиленовых горелок для плавления металла. При соединении деталей в стык добавляется присадочный материал, образуя сварной шов.Правильно выполненный сварной шов может быть таким же прочным, как и основной металл. Сваркой можно соединить практически любой металл, хотя для некоторых материалов требуются более сложные процессы. Он может соединять похожие и, в некоторой степени, разнородные металлы.
Три основных метода дуговой сварки — это дуговая сварка металлическим электродом в защитных оболочках (SMAW или электродная сварка), дуговая сварка металлическим электродом в среде защитного газа (GMAW или MIG) и дуговая сварка вольфрамовым электродом в среде защитного газа (GTAW или TIG). Во всех случаях расплавленный металл требует защиты от воздуха для обеспечения надлежащего плавления. При сварке штангой эта защита обеспечивается флюсом, нанесенным на сам присадочный стержень.Сварка MIG использует тот же подход в процессах с сердечником из флюса или использует инертный защитный газ при подаче сварочной проволоки без покрытия из катушки в расплавленную сварочную ванну. Как для сварки штангой, так и для сварки методом MIG, штанга или проволока обеспечивает электрический путь, который создает дугу на заготовке. Сварка TIG сочетает в себе элементы двух других процессов: в ней используются отдельные присадочные стержни и защитный газ. Его основное отличие — электрод: он изготовлен из вольфрама и не плавится.
Сварка палкой — это простой, но довольно сложный процесс.Покрытие стержня флюсом производит много дыма, а иногда и брызг. Шлак покрывает сварной шов, и его необходимо удалить щеткой или сколами. Тем не менее, это надежный метод сплавления металла в реальном мире. Доступны электроды, которые могут прожечь ржавчину и окалину, что обеспечивает надежность процесса. Он широко используется на открытом воздухе, где потеря защитного газа от ветра не вызывает беспокойства.
Сварка Mig решает эту проблему за счет использования проволоки с флюсовым сердечником, которая пропускает защитный флюс через центр сварочной проволоки.Подобно сварке штучной сваркой в отношении дыма, брызг и шлака, ее преимущество состоит в том, что сварочная проволока подается на катушках, что позволяет сварщику наносить длинные валики без необходимости заменять сварочный стержень после стольких дюймов. Но реальное применение МиГ находится в закрытых помещениях, где используется защитный газ. Этот газ обеспечивает четкую видимость соединения во время сварки, устраняет дым, удаляя покрытие из флюса, и создает готовое соединение без шлака.
Tig идет еще дальше и почти всегда выполняется в чистых помещениях.Вольфрамовым электродом можно управлять с помощью ножного или ручного управления, что позволяет сварщику TIG точно определять количество тепла, попадающего в металл. Его можно использовать для соединения тонких металлов и очень хрупких деталей.
Другие процессы дуги включают сварку под флюсом, при которой используется гранулированный флюс, который помещается перед движущимся электродом для получения больших и длинных сварных швов, и плазменная сварка, при которой используется поток ионизированного газа для получения высококачественных и точных сварных швов.
В газовой сварке используются горелки и присадочные стержни, аналогичные тем, которые используются для сварки вольфрамовым электродом. Ацетилен в сочетании с кислородом дает очень горячее пламя, которое быстро и легко плавит металл на небольшой площади. Газовая сварка несколько уступила по популярности дуговой сварке, но те же горелки, которые используются для газовой сварки, все еще широко используются для резки черных металлов и для предварительного нагрева металлов перед дуговой сваркой.
Хотя большая часть приведенного выше обсуждения относится к ручной сварке, автоматическая сварка является обычным явлением.Это устраняет переменную квалификацию при производстве качественных сварных швов, не говоря уже о многих опасностях, связанных с самой сваркой.
Пайка
Горелка — это основной метод ручной пайки с использованием пропана или оксиацетиленовых смесей. Пайка также выполняется в печах и с помощью индукционных процессов.
Пайка происходит при температуре выше 800 ° F, но ниже температуры плавления основных металлов. Именно это отличает пайку от газовой или дуговой сварки, при которой присадочный металл и основной металл обычно имеют схожие точки плавления. Он также различает пайку как сварочный процесс, а не как процесс склеивания, такой как пайка.
Как и при сварке, паяное соединение может развить свою полную прочность только при отсутствии воздуха. Таким образом, прутки для пайки иногда покрываются флюсом, как и прутки для сварки. Паяльные печи обычно заполнены атмосферой инертного газа. Типичные присадочные материалы включают медные, серебряные или никелевые сплавы.
Пайка применяется там, где деформация основного металла недопустима.Его часто используют для ремонта, не влияя на металлургические свойства сломанных деталей. Бронза обычно используется в качестве наполнителя для пайки литого и кованого железа, стали, меди, латуни и т. Д. Пайка может использоваться для соединения разнородных металлов. Сложные изделия могут быть изготовлены с использованием наполнителей, температура плавления которых становится все ниже. Для таких изделий доступны предварительно отформованные формы наполнителя, такие как кольца для пайки.
Иногда различают термины «пайка» и «сварка твердым припоем». В первом случае капиллярное действие используется для втягивания наполнителя в промежуток между сопрягаемыми частями, такими как трубка и гнездо или плотно прилегающее стыковое соединение. Зазоры в этих узлах обычно составляют 0,025-0,05 мм, но используются специальные присадочные стержни с более широкими зазорами. Сварка пайкой часто дает более толстый валик, как дуговая сварка, но не зависит от капиллярного действия.
Основное различие между пайкой и дуговой сваркой состоит в том, что при пайке присадочный материал втягивается в соединение сразу.Когда основной металл становится достаточно горячим, чтобы расплавить присадочный металл, вступает в действие капиллярное действие, создавая чистое соединение, не требующее отделки. Это делает его пригодным для производства в печах. По этой причине пайку часто сравнивают с пайкой. Фраза «серебряная пайка» на самом деле описывает процесс пайки.
Сварка сопротивлением
Сварка сопротивлением — это термин, применяемый к точечной сварке, шовной сварке, выступающей сварке, сварке разрядом конденсаторов и т. Д., Когда сопротивление потоку электричества вызывает тепло, а для завершения сварки применяется давление.Точечная сварка широко используется при производстве автомобилей, а шовная сварка — распространенный метод изготовления труб и подобных изделий.
Другие способы сварки
Электронно-лучевая сварка и сварка трением — это специальные процессы. Электронно-лучевая сварка и лазерная сварка используются в крупносерийном или дорогостоящем производстве сложных деталей для таких отраслей, как аэрокосмическая и автомобильная. Сварка трением — это твердотельный процесс (то есть без внешнего источника тепла), используемый для соединения труб, приводных валов и т. Д.Тепло создается вращением соединяемых предметов друг против друга. По мере того, как металлы пластифицируются, они сдвигаются вместе под высоким давлением. Сварка также используется для соединения пластмасс, для чего используется собственное специализированное оборудование, такое как аппараты для ультразвуковой сварки.
Сводка
В этой статье представлено краткое обсуждение нескольких различных сварочных процессов с целью противопоставления сварки и пайки. Для получения дополнительной информации о сопутствующих продуктах обратитесь к другим нашим руководствам или посетите платформу Thomas Supplier Discovery Platform, чтобы найти потенциальные источники поставок или просмотреть подробную информацию о конкретных продуктах.Более подробную информацию об образовательных возможностях, сертификатах, стандартах и других ресурсах, касающихся сварки, можно найти на веб-сайте Американского общества сварщиков.
Больше от Custom Manufacturing & Fabricating
Сварка и изготовление металлов — Staub Manufacturing Solutions
Что такое сварка MIG?
Сварка в среде инертного газа (MIG) — это процесс газовой дуговой сварки (GMAW), в котором используется сплошной проволочный электрод, который нагревается и подается в сварочную ванну от сварочного пистолета (или горелки). Затем два основных материала плавятся вместе, в результате чего они соединяются. Сварочная горелка также подает инертный защитный газ вдоль проволочного электрода, что помогает защитить процесс от загрязнений, переносимых по воздуху.
MIG обеспечивает однородный, свободный от шлака сварной шов и может использоваться в любом положении. Она требует меньшего мастерства оператора, чем сварка TIG, и требует минимальной очистки.
СваркаMIG — это высокопроизводительный сварочный процесс, поскольку проволока (электрод / присадочный металл) подается непрерывно, что позволяет выполнять длинные сварные швы без пусков и остановок.Это можно сделать вручную или автоматически с помощью робототехники.
СваркаMIG может использоваться для алюминия, нержавеющей и углеродистой стали, от листового металла 24-го калибра до сверхпрочных конструкционных плит и профилей. Staub часто использует сварку MIG для изготовления рам, опор, кронштейнов, кронштейнов и тележек.
Что такое сварка TIG?
Сварка вольфрамовым электродом в среде инертного газа (TIG) — это процесс дуговой сварки вольфрамовым электродом (GTAW), в котором используется неплавящийся вольфрамовый электрод, который подводит ток к сварочной дуге. При сварке TIG дуга образуется между неплавящимся вольфрамовым электродом и свариваемым металлом. Газ подается через горелку для защиты электрода и расплавленной сварочной ванны. Если используется присадочная проволока, она добавляется в сварочную ванну отдельно.
Сварка TIG обеспечивает прочный шов без шлака. Он обеспечивает большой контроль, что делает его хорошим процессом сварки для высокодетализированных проектов. Благодаря относительно небольшой дуге он хорошо подходит для сварки тонких листов, обеспечивая низкие искажения и отсутствие брызг.
СваркуTIG можно применять для алюминия, нержавеющей стали и углеродистой стали, от листового металла толщиной до 1/8 дюйма и конструкций. Компания Staub обычно использует сварку TIG для кронштейнов из тонкого листового металла, индивидуальных электрических шкафов и сложных сварных узлов.
Что такое контактная сварка?
Контактная сварка — это процесс соединения металлов путем приложения давления и пропускания тока через соединяемые материалы. Эта процедура очень рентабельна, поскольку она быстра и не требует дополнительных материалов (наполнителей) для создания склеивания.
Компания Staub Manufacturing предлагает два типа контактной сварки:
Точечная сварка: Точечная сварка использует поверхности противоположных электродов (обычно из медного сплава) для приложения силы к перекрывающимся поверхностям листового металла и фокусировки тока в желаемом месте сварки. После создания достаточного сопротивления (тепла) и соединения материалов образуется сварной шов. Точечная сварка — это быстрый и надежный способ изготовления изделий из листового металла, таких как электрические шкафы, рамы, крепления и различные составные части.
Проекционная сварка: Как и точечная сварка, проекционная сварка также использует тепло, выделяемое сопротивлением. Вместо того, чтобы фокусировать ток в одном месте, проекционная сварка сваривает в заранее определенных точках, используя выступы, рельефы или пересечения, наряду с выделением тепла в точке контакта. Когда выделяется достаточное количество тепла, выступы разрушаются, образуя сварной шов. Этот процесс используется компанией Staub для эффективного прикрепления сварных крепежей, таких как гайки, болты, штифты и шпильки, к различным изделиям из листового металла.
Свяжитесь с Staub Manufacturing Solutions по всем вопросам, связанным с производственной сваркой MIG, TIG и контактной сваркой в средних и крупных объемах. Staub производит высококачественные сварные изделия для OEM-производителей, обслуживающих различные отрасли промышленности, включая сельское хозяйство, грузовые автомобили, электронику на заказ, пищевое оборудование и многое другое.
Завод Инжиниринг | Сварка низкоуглеродистой стали: найдите подходящий присадочный материал
Низкоуглеродистые сталиобладают многочисленными преимуществами — от легкой свариваемости до способности сгибать и формовать материал — что делает их хорошо подходящими для широкого спектра сварочных работ.При наличии множества вариантов низкоуглеродистой стали, как в ходе операции определить, какой присадочный металл является правильным выбором для конкретного применения?
Что такое низкоуглеродистая сталь?
Базовые материалы, которые считаются низкоуглеродистой сталью, обычно не содержат легирующих элементов. Низкоуглеродистые стали имеют предел содержания углерода 0,25% и также называются низкоуглеродистыми сталями. Две распространенные мягкие стали, используемые во многих сферах производства и производства, — это ASTM A36 и AISI 1018.
Характеристики низкоуглеродистой стали различаются в зависимости от типа материала, но, как правило, низкоуглеродистые стали имеют более низкий предел прочности и предел текучести, чем низколегированные стали.Предел прочности на разрыв обычно составляет 70 кг на квадратный дюйм (тыс. Фунтов на квадратный дюйм) или ниже, а предел текучести может составлять всего 30 фунтов на квадратный дюйм.
Более низкие пределы прочности и текучести означают, что материал не такой твердый, поэтому его можно сгибать или раскатывать в разные формы. В случаях, когда требуются более высокие показатели текучести и прочности на разрыв, материал может быть разделен на более толстые и тяжелые секции, чтобы компенсировать более низкие значения прочности.
В целом, мягкие стали обладают очень хорошей свариваемостью, и отсутствие дополнительных легирующих элементов в мягких сталях также делает их экономически выгодным вариантом для многих сварочных работ.
Варианты присадочного металла
Присадочные металлы из низкоуглеродистой стали обычно имеют более высокие характеристики, чем базовые материалы, с более высоким пределом прочности и прочности.
Известно, что стандартные присадочные металлы из низкоуглеродистой стали обладают хорошей свариваемостью. Присадочные металлы из низкоуглеродистой стали для сварки проволокой доступны в вариантах сплошной, порошковой и порошковой проволоки для производства и изготовления.
Основные материалы из низкоуглеродистой стали и присадочные металлы обладают многочисленными преимуществами — от легкой свариваемости до способности сгибать и формовать материалы, что делает их подходящими для широкого спектра сварочных работ.Предоставлено: Хобарт
.Жесткие провода
Жесткие провода универсальны для многих приложений, потому что они могут использоваться при очень низких или очень высоких токах. При сварке более толстых материалов сплошной проволокой рекомендуется использовать процесс переноса распылением; для более тонких материалов лучше всего работает процесс переноса короткого замыкания. Сплошная проволока обеспечивает хорошую скорость перемещения и внешний вид валика, а также возможность глубокого проплавления при сварке более плотных стыков или углов из-за более узкого профиля проплавления.Обычные присадочные металлы для сплошной проволоки из мягкой стали включают такие классификации Американского сварочного общества (AWS), как ER70S-3 и ER70S-6.
Сплошная проволока обычно используется в автомобильной и роботизированной сварке. Поскольку сплошные проволоки имеют высокую прочность колонны и часто имеют медное покрытие, они немного жестче, чем другие проволоки, и обеспечивают хорошую подачу. Однако имейте в виду, что сплошная проволока может иметь более высокие тепловложения, чем проволока с металлическим сердечником, поэтому глубокая движущая дуга сплошной проволоки может иногда приводить к чрезмерному проникновению или прожогу.
Также имейте в виду, что сплошная проволока не смачивает поверхности с прокатной окалиной. Поскольку в сплошную проволоку добавлено меньше раскислителей, она не справляется с поверхностными загрязнениями, как это могут делать другие присадочные металлы, что требует от сварщиков более низких скоростей перемещения материалов с прокатной окалиной или ржавчиной.
Металлопорошковая проволока
Порошковая проволока может использоваться практически в любом сварочном аппарате для низкоуглеродистой стали, в котором используется сплошная проволока. Если сплошная проволока имеет более узкий, пальцевидный профиль проникновения, то проволока с металлическим сердечником имеет более широкий и более широкий профиль проникновения, который не такой глубокий.В результате проволока с металлическим сердечником лучше смачивается и крепится к боковым стенкам, и, как правило, ее можно использовать при меньших тепловыделениях при сохранении того же внешнего вида валика. Более широкий профиль проникновения и дополнительное смачивание также могут сделать размещение проволоки более щадящим.
Поскольку проволока с металлическим сердечником имеет порошковую сердцевину, в ее состав может входить больше раскислителей, чем в проволоке сплошного сечения. Благодаря этому они могут лучше справляться с прокатной окалиной и грязными основными материалами и с более высокими скоростями движения. Их более высокая производительность наплавки приводит к более высокой производительности.Хотя порошковая проволока обычно дороже, чем сплошная проволока, повышение производительности может обеспечить быструю окупаемость инвестиций. Из-за этих факторов порошковую проволоку часто рекомендуют при выполнении сварных швов от 6 дюймов и более, а также для операций, направленных на увеличение скорости движения. Один из наиболее распространенных вариантов с металлическим сердечником для низкоуглеродистой стали — E70C-6M.
Порошковая проволока в газовой среде
При сварке низкоуглеродистой стали используются два распространенных варианта порошковой проволоки в среде защитных газов: E70T-1 для плоских и горизонтальных швов и E71T-1 для сварки во всех положениях.
Предлагая аналогичные или более высокие скорости наплавки, чем у металлической порошковой проволоки, присадочные металлы E70T-1 хорошо подходят для толстых и тяжелых сварных соединений, требующих большого количества сварочного металла. Эта проволока также является хорошим вариантом для материалов с тяжелой прокатной окалиной или ржавчиной и может обеспечить хороший внешний вид валика и более высокую скорость движения даже на этих материалах.
Поскольку при использовании проволоки с металлическим сердечником и сплошной проволокой может быть труднее выполнить большие сварные швы, которые не провисают, плоская и горизонтальная порошковая проволока подходят для этих целей, поскольку шлак помогает удерживать сварной шов на месте при его охлаждении.Однако шлак требует больше времени на очистку после сварки.
Если приложение не позволяет выполнять сварку в плоском или горизонтальном положении, порошковая проволока E71T-1 предлагает вариант во всех положениях. Эта проволока хорошо подходит для сварки вертикально вверх или над головой, обеспечивает более высокую скорость перемещения и более плоский профиль валика. Как и присадочные материалы E70T-1, проволока для установки во всех положениях действительно образует шлак, который необходимо удалить после сварки. Рекомендуется использовать технику перетаскивания для проволоки, образующей шлак, и технику проталкивания для проволоки, которая не образует шлак.
Низкоуглеродистые стали можно сваривать сплошной, порошковой или порошковой проволокой. Выбор подходящего присадочного металла для области применения требует учета свойств материала и желаемой производительности. Предоставлено: Хобарт
.Советы по выбору присадочных материалов из низкоуглеродистой стали
При выборе подходящего присадочного металла для сварки низкоуглеродистой стали следует учитывать некоторые дополнительные факторы.
Состояние основного материала является важным фактором при выборе присадочного металла.Некоторые мягкие стали A36 и 1018 бывают горячекатаные или холоднокатаные. Горячекатаная низкоуглеродистая сталь может привести к образованию прокатной окалины на поверхности материала, которую труднее правильно сварить. Низкоуглеродистые стали, подвергнутые холодной прокатке, имеют чистую отделку, но иногда на поверхности есть легкое масло.
Если на основном материале есть легкая прокатная окалина или ржавчина, рекомендуется ее удалить. Если это невозможно, выберите металлическую или порошковую проволоку, которая, как правило, дает лучшие результаты в таких ситуациях.Для деталей, подвергнутых холодной прокатке или имеющих легкое масло на поверхности, допустимы наплавочные металлы из твердой проволоки, такие как ER70S-6.
Конструкция свариваемого соединения также имеет значение. Сварное соединение с узкой V-образной канавкой может потребовать более глубокого проникновения в более узкое место и лучше всего подходит для сплошной проволоки. Порошковая проволока, устанавливаемая во всех положениях, не обеспечивает глубокого, похожего на пальцы проплавления, как у сплошной проволоки, и больше подходит для сварки более мелких конструкций стыков.
Материалы из низкоуглеродистой стали обеспечивают легкую свариваемость и гибкость во многих сварочных операциях.Понимание характеристик типа основного материала из низкоуглеродистой стали, целей применения сварки и конструкции сварного шва, а также его согласование с подходящим присадочным металлом из низкоуглеродистой стали помогает повысить производительность, производительность и качество сварки.
Tig против Mig | Какая разница? — Trimantec
Можете ли вы вспомнить многие объекты, которые сделаны не из сварных частей или не сварены сами по себе? Это сложная задача. Мы знаем, что сварка является неотъемлемой частью производственного процесса, но при таком большом количестве различных методов может быть трудно понять разницу или определить, какой метод лучше.Большинство промышленных компаний следят за достижениями и изменениями в стилях и технологиях сварки, но некоторые не знают, с чего начать. Если вы незнакомы или просто нуждаетесь в переподготовке, прочтите информацию о различиях между наиболее распространенными методами сварки, используемыми на производстве.
Сварка 101
Концепция сварки восходит к средневековому периоду, когда процесс нагрева и молотка известен как «кузнечная сварка». Перенесемся в последние 100 лет, и мы можем увидеть развитие почти всех современных инноваций в области сварки, которые у нас есть сегодня. Сейчас мы сталкиваемся с множеством методов сварки, у каждого из которых есть свои плюсы и минусы. Два основных метода сварки, связанных с нашей отраслью, — это MIG и TIG, но мы также рассмотрим другой основной метод — сварку палкой. Выбранный метод должен зависеть от металла, окружающей среды, области применения, скорости и т. Д.
Сварка МИГ
Также известная как газовая дуговая сварка металла (GMAW), сварка MIG является наиболее распространенным типом сварки, используемым профессионалами в области автоматизации и производства.
Присадочная проволока и поток защитного газа через сварочную горелку во время сварки MIG
Металлы:- Нержавеющая сталь
- Мягкая сталь
- Алюминиевый сплав
- Скорость
- Гибкость
- Минимальная очистка
MIG используют проволочный сварочный электрод, который автоматически подает катушку с постоянной скоростью. Электрический ток между проволокой и металлической поверхностью создает дугу, которая плавит проволоку и помогает создать высокопрочный сварной шов с минимальной очисткой. Инертный защитный газ проходит через сварочный пистолет вместе с электродом и защищает сварной шов от загрязнения. Сварку MIG можно использовать для нержавеющей стали, низкоуглеродистой стали и алюминия толщиной до 26-го калибра, а также для более толстых деталей. Вероятно, это самый простой метод для изучения, позволяющий получать красивые и прочные сварные швы. Требуется минимальная очистка, что означает практически полное отсутствие шлифовки или шлифовки.Это стандартный метод для наших сварочных служб.
Дуговая сварка под флюсом (FCAW) — это разновидность сварки MIG, которая очень похожа, но не требует защитного газа. Вместо этого он питает порошковую проволоку для защиты дуги, что является простым подходом, который хорошо работает в условиях сильного ветра или на грязных металлах. Его можно использовать на одинаковых металлах и различной толщины. Хотя этот процесс широко не используется в производстве, он в основном используется в строительстве из-за его скорости и портативности.
Сварка TIG
СваркаTIG, также известная как газо-вольфрамовая дуговая сварка (GTAW), представляет собой другой процесс дуговой сварки, в котором для создания сварного шва используется неплавящийся вольфрамовый электрод. В отличие от MIG, присадочная проволока наносится вручную.
Обратите внимание на ручную присадочную проволоку, используемую при сварке TIG
Металлы:- Нержавеющая сталь
- Мягкая сталь
- Алюминиевые сплавы
- Титан *
- хромомолибден *
- Медь *
- Латунь *
- И более
* Указывает на металлы, используемые исключительно в этом методе.
Выбрано для:- Высокое качество
- Лучшая отделка
- Без очистки
- Самый широкий выбор типов и размеров металла
- Разбавитель металлов
Как следует из более длинного названия, в этом методе также используется защитный газ (часто аргон) и присадочный металл для защиты зоны сварки от загрязнения. Сварку TIG намного сложнее освоить и она значительно медленнее, чем другие методы, но она обеспечивает максимальную управляемость, позволяющую получать более прочные и качественные сварные швы.Дополнительным преимуществом является то, что это наиболее чистый метод, часто не требующий чрезмерной очистки.
, в нашей отрасли есть несколько вещей, более привлекательных для внешнего вида, чем качественные сварные швы TIG нержавеющей или алюминиевой стали. Опытные сварщики, которые часто называют «укладкой» или «укладкой десятицентовиков», создают сварные швы, которые выглядят столь же эстетично, как и конструктивно.
«Укладка кубиков» с использованием сварки TIG на нержавеющей стали
Ручная сварка
Также известная как дуговая сварка или дуговая сварка защищенного металла (SMAW), сварка палкой — это самый простой вид сварки, но не обязательно самый простой для понимания.Его легко освоить и он очень распространен как в тяжелом строительстве, так и в домашних условиях.
При сварке штангой используется электрод «палочка», а не пистолет.
Металлы:- Нержавеющая сталь
- Сталь
- Чугун *
* Обозначает металл, используемый исключительно в этом методе.
Выбрано для:- Более толстые металлы
- На улице / в ветреную погоду
- Прощение грязными или ржавыми металлами
Для сварки штангой не требуется газа, но используется «стержень» плавящегося электрода, который пропускает электрический ток между ним и металлической поверхностью.В некоторых случаях наиболее распространенный электрод диаметром 1/8 дюйма можно использовать всего за одну минуту. Он до сих пор считается самым экономичным методом. Вероятно, вы видели, как этот тип используется в тяжелых условиях на судах, тракторах и т. Д. Это связано с тем, что сварка штучной сваркой лучше всего подходит для более толстого металла, обычно с толщиной 18 и более. В отличие от других методов, при сварке штучной сваркой образуется много шлака — избыточные брызги, которые вы, вероятно, наблюдали во время процесса сварки, — и требуется значительная очистка.Это наименее распространенный метод, используемый в общем производстве, но он подходит для применений, не требующих чистой отделки.
Сварочные ресурсы
Сварка — это разнообразный и постоянно развивающийся процесс. Есть еще много других методов и вариаций, которые здесь не обсуждаются. Эта статья была создана с целью предоставить обзор наиболее распространенных методов сварки, используемых в индивидуальной автоматизации и производстве, при поддержке Miller. Если вы хотите узнать больше, мы рекомендуем посетить MillerWelds.com. С 1927 года они являются лидером отрасли в области сварщиков и сварочных знаний.
Наша группа инженерных решений включает обширный механический цех с командой опытных производителей, вооруженных сварщиками Miller. Если вам нужен продукт под ключ или просто изготовление изделий из металла, позвольте нам предоставить наши сварочные услуги, чтобы они работали на вас. Мы всегда готовы поддержать американское производство.
И НАКОНЕЦ…
Не стесняйтесь обращаться к нам с любыми конкретными вопросами, которые могут у вас возникнуть относительно сварки или любого другого изготовления по индивидуальному заказу.
BONUS В центре внимания опытных профессионалов: научитесь экономно использовать собственные сварочные операции
А если вы похожи на нас и у вас мало сварочных фотографий, вот еще несколько.
тестов металлов: как определить металлы для сварки: Maine Welding Company
Испытания металлов позволяют нам идентифицировать металлы для сварки Необходимо знать состав свариваемого металла, чтобы произвести качественный сварной шов.Сварщики и слесари должны уметь идентифицировать различные металлические изделия, чтобы можно было применять правильные методы работы. Для оборудования должны быть доступны чертежи (MWO). Их необходимо осмотреть, чтобы определить, какой металл будет использоваться, и при необходимости определить его термическую обработку. После некоторой практики сварщик узнает, что определенные части машин или оборудования всегда из чугуна, другие части обычно из поковки и т. Д.
Испытания металлов. В магазине можно провести семь тестов металла для идентификации металлов.Шесть различных тестов приведены в таблице 7-4. Эти тесты следующие:
Проверка внешнего вида. Проверка внешнего вида включает такие параметры, как цвет и внешний вид обработанных и необработанных поверхностей. Форма и форма дают четкие подсказки относительно идентичности металла. Форма может быть описательной; например, форма включает в себя такие элементы, как литые блоки цилиндров, автомобильные бамперы, арматурные стержни, двутавровые балки или уголки, трубы и фитинги. Следует учитывать форму, которая может показать, как деталь была подвергнута катанию, например, отливка с ее очевидным внешним видом и линиями формы разъема, или горячекатаный деформируемый материал, экструдированный или холоднокатаный с гладкой поверхностью.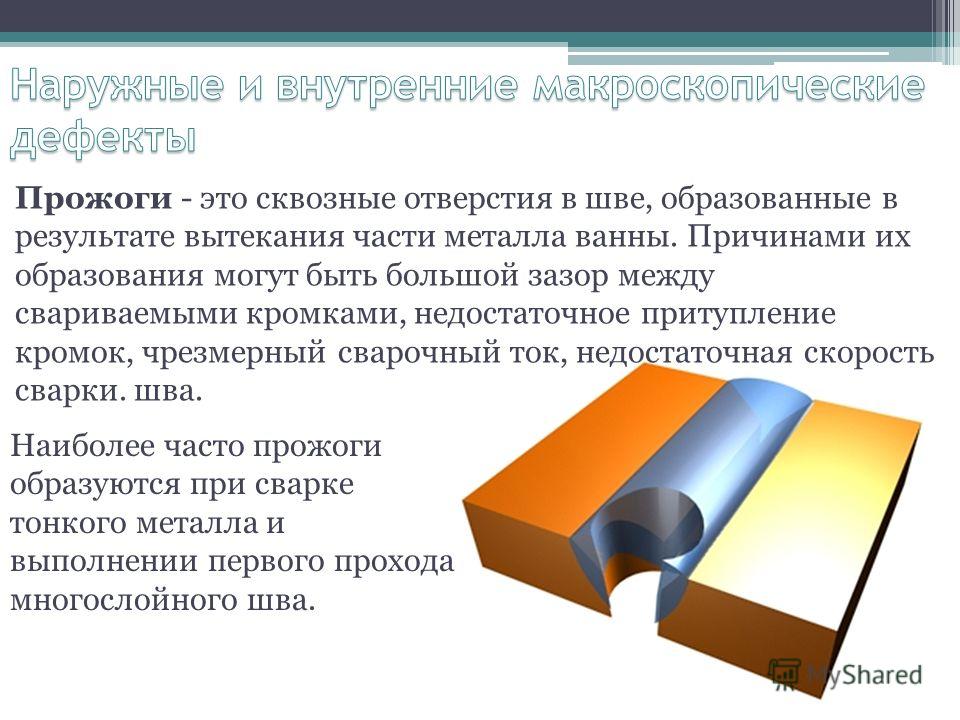
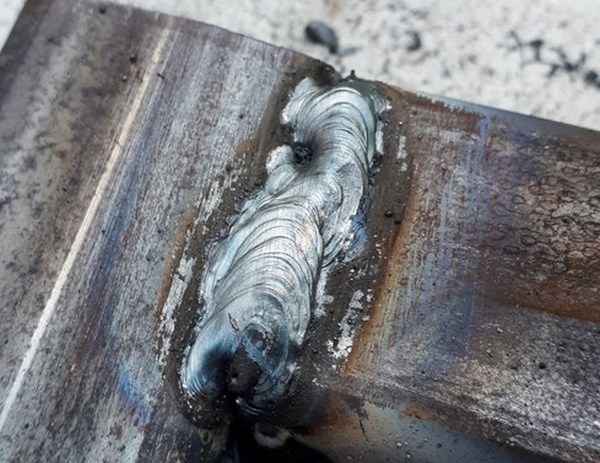
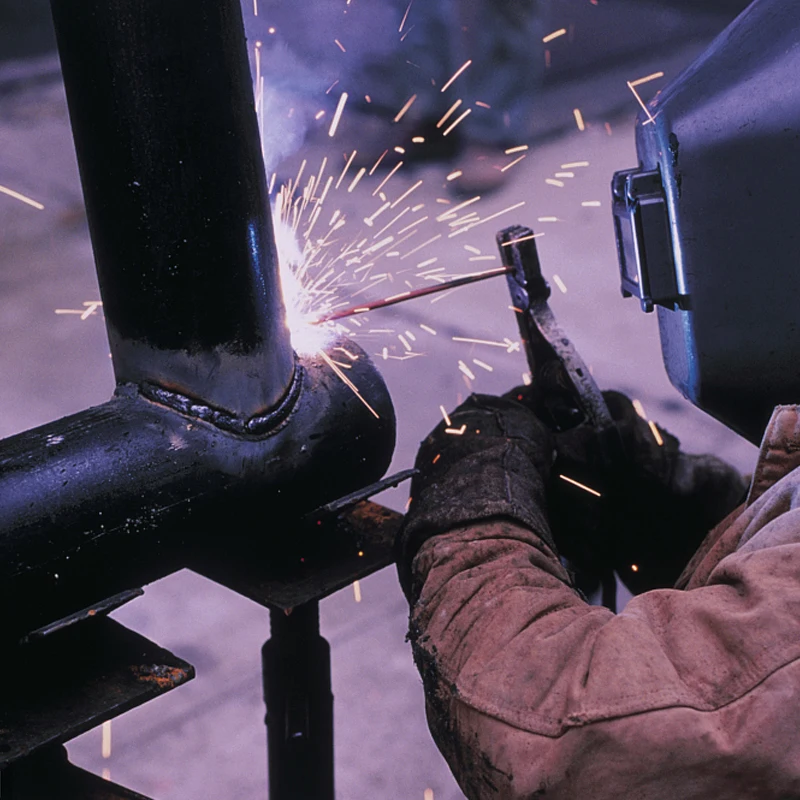


Тест факела. С помощью кислородно-ацетиленовой горелки сварщик может идентифицировать различные металлы, изучая скорость плавления металла и внешний вид лужи расплавленного металла и шлака, а также изменение цвета во время нагрева.Испытание резака следует проводить осторожно, поскольку оно может повредить проверяемую деталь. Кроме того, магний может воспламениться при нагревании на открытом воздухе.


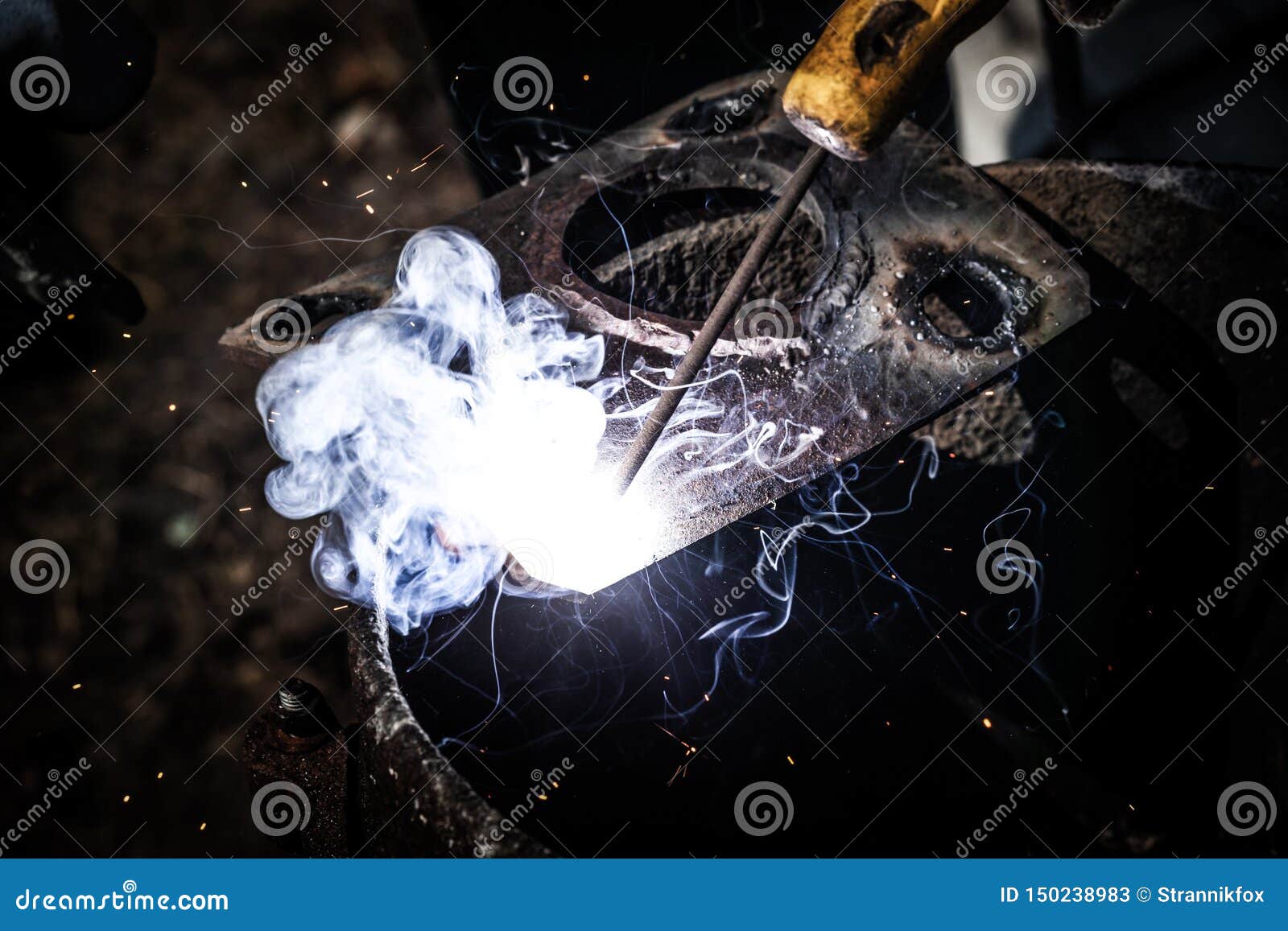
