Как сделать нож своими руками
Уважаемые посетители сайта «Самоделкин друг» сегодня мы с вами рассмотрим пошаговую инструкцию по созданию ножа своими руками с использованием обычного столярно-слесарного инструмента. Данный нож сделан из полосы стали 3 мм, вначале на металл был нанесен контур в виде будущего ножа, затем при помощи болгарки с диском по металлу вытачивается само лезвие.
Нож -это самое древнейшее оружие человечества которое помогло нам выжить в суровой природе и развиться. Ножи и сейчас неотъемлемая часть вооружения военных, а так же рыбаков, охотников, туристов. Конечно же без хорошего острого ножа не обойтись на кухне, а лучше когда их много и под каждую операцию имеется свой ножичик)
Отправляясь на охоту, рыбалку или просто за грибами, мы обязательно берем с собой нож, потому как он пригодится для разделки туши, потрошения рыбы и при сборе грибов. Также при помощи ножа можно нарезать веток и прутьев для постройки шалаша, да и как средство самообороны (мало ли что может ожидать вас в лесу)
Давайте рассмотрим, что конкретно понадобится для изготовления ножа?
Материалы
- сталь KDR 1095
- древесина для рукоятки
- заклепка
- двухкомпонентный клей
- льняное масло
Инструменты
- болгарка (УШМ)
- дрель
- наждачная бумага
- струбцина
- маркер
Пошаговый процесс создания ножа своими руками.
Первым делом необходимо сделать эскиз будущего ножа на листе бумаги и изготовить шаблон из дерева или картона. Прикладываем полученный шаблон к стальной пластине и обводим маркером. Если пластина длинная, то можно нарисовать сразу несколько заготовок)) Далее при помощи болгарки придается необходимая форма. Зажимается в такие импровизированные тиски из фанеры с пропилом посередине и стягивается струбциной. Вот что получается в итоге обработки. Снова зажимаем заготовку и доводим при помощи напильника. Затем лезвие ножа необходимо закалит, а именно разводится огонь и подбрасываются угли кузнечный горн, далее в раскаленные угольки укладывается стальная заготовка. Угли нужно будет раздувать чтоб был постоянный приток кислорода. Как только металл раскалиться до красного цвета с оранжевым свечением его опускают в масло (растительное, машинное, оливковое, трансмиссионное итд., вообщем что найдете у себя дома или в гараже) Заготовку лучше всего привязать проволокой, чтоб было удобно достать. Опускать раскаленный металл в масло медленно, масло будет частично воспламеняться, но ничего страшного, не взорветесь))) Вынув закаленное лезвие из масла его нужно будет потом поместить в духовку прогретую до 350 с° и продержать там не менее часа, чтоб снять напряжение с металла. После закалки нож буде выглядеть вот так. Его нужно зашлифовать и отполировать. Затем делаем ручку для ножа, для чего понадобится древесина, желательно твердой породы с красивым рисунком и текстурой. Обрисовывается контур и сверлятся отверстия. Выпиливаем. Острое лезвие ножа во время работы желательно обернуть тканью или же молярным скотчем. Делаем клепки из проволоки и готовим двухкомпонентный клей. Деревянные заготовки промазываются клеем и прикладываются к лезвию, вставляем клепки, стягиваем струбцинами, даем просохнуть клею. Клепаем заклепки и шлифуем поверхность. Рукоять натирается льняным маслом. Вот такой замечательный нож получился 😉 Каждый уважающий себя мужик должен иметь у себя в снаряжении хороший нож.
С какого металла лучше сделать нож
Как сделать самодельный нож? Особо популярны самодельные ножи, изготовленные методом ковки. Если при производстве был использован такой материал, как легированная сталь, то нож приобретает особую ценность. Ковка ножа своими руками — наиболее трудоемкий вариант изготовления изделия. Самые прочные и качественные лезвия создаются при помощи ковки, служат не одно десятилетие и сохраняют свои качества неизменными. Однако ковка требует больших знаний и опыта от мастера. Потребуется хорошее знание свойств металлов, которое позволит сделать самодельный нож качественным и красивым.
Самодельный нож можно сделать выковав его из стали.
Изготовление кованого ножа
Помимо профессионального инструмента, для ковки можно использовать и подручные средства, если они кажутся удобными. Для того чтобы выковать нож, понадобятся:
Инструменты для ручной ковки.
- молот большой;
- молот малый;
- щипцы кузнечные;
- пассатижи;
- разводной ключ;
- тиски;
- наковальня;
- болгарка;
- сварочный аппарат;
- точильный станок;
- шлифовальный станок;
- наждачная бумага;
- напильник;
- уголь;
- печь.
Следует помнить, что обыкновенные очаги (тем более костры) не дадут нужную для ковки стали температуру. Греть заготовки для этого придется слишком долго, что чревато деформацией и выгоранием материала. Печь требуется изготовить из толстостенного металла, а к ней присоединить трубу, через которую будет налажено постоянное поступление воздуха. Воздух может подаваться старым пылесосом или вентилятором. Топливо нужно выбирать с учетом того, что гореть оно должно долго, от потока воздуха — не тухнуть, поэтому хорошо подойдет уголь.
Как сделать наждак своими руками — подробнее>>>
Выбор стали для ножа
Для качественного ножа нужно правильно выбрать металл и обработать его.
Характеристики прочности и режущие качества зависят именно от выбранного металла. Для того чтобы выбрать металл правильно, нужно знать, какими характеристиками он обладает. Основные свойства стали — прочность, твердость, износоустойчивость, вязкость и красностойкость.
Твердость показывает возможность стали сопротивляться проникновению более твердого материала. Твердые виды стали, из которых делаются самодельные ножи, успешно могут сопротивляться деформации. Для измерения твердости существует шкала Роквелла: сталь должна иметь значения от 20 до 67 HRC.
Износостойкость — сопротивление в процессе эксплуатации материала износу. Это показатель напрямую зависит от твердости стали.
Прочность, как правило, проверяется на изгиб или сильными ударами. Она характеризуется способностью сохранять под действиями внешних сил целостность.
Пластичностью называют способность поглощать и рассеивать кинетическую энергию удара, не разрушаясь и не деформируясь при этом.
Для того чтобы правильно выковать нож нужен эскиз.
Красностойкость — устойчивость к высоким температурам. Если самоделка при нагреве и после него остается с теми же прочностными показателями, это говорит о том, что материал обладает красностойкостью. От этого показателя зависит, при какой температуре сталь можно ковать. Твердые марки стали являются самыми красностойкими, температура для ковки у них в районе 900° С. Температура плавления для таких сталей составляет от 1450 до 1520° С.
Все свойства стали взаимосвязаны и должны сочетаться друг с другом, так как повышение одного показателя обязательно ведет к ухудшению другого. Свойства стали зависят от содержащихся в ней кремния, углерода, вольфрама, кобальта, никеля и молибдена, а также прочих легирующих элементов и добавок. Для того чтобы точно узнать, каков состав стали имеется в том или ином предмете, из которого планируется изготовление самодельного ножа, необходимо иметь под рукой полный марочник стали и сплавов. В нем указаны подробные составы сталей и их характеристики.
Эскиз для конструкции ножа
Виды лезвий ножа.
Нож можно считать простым предметом, так как он состоит из рукоятки и лезвия. Но для изготовления качественного ножа тем не менее требуется соблюдение ряда параметров, так как от них зависит функциональность инструмента. Опытные мастера могут обходится без заготовок и предварительных эскизов, но для новичка важно создание первоначального шаблона.
Форма и размеры шаблона зависят от того, каким образом планируется использовать готовый нож. Для сложных форм потребуются напильник и долгие работы по правке и выглаживанию каждого задуманного выступа. Охотничьи ножи имеют простые формы, а авторские изделия сложны в изготовлении, но нефункциональны. Начинающим можно посоветовать начинать с небольших карманных ножиков (их еще называют грибными). При этом следует помнить и о том, что ножи могут быть по результатам экспертизы быть признаны холодным оружием, для обладания и изготовления которого требуется лицензия. Учитывая это, желательнее обходиться изготовлением небольших образцов.
Чертеж делается на плотной бумаге, рекомендуется делать как изображение целиком, так и отдельно рукоять и клинок с хвостовиком. Макет вырезают, чтобы держать перед глазами или наложить на лезвие, перед тем как применить для обтачивания напильник.
Как выковать нож из сверла?
Ножи можно сделать из сверл или гаечных ключей.
Для производства многих сверл используется легированная сталь, что делает их популярными для выковывания различного вида ножей. Этот тип стали износоустойчив, прочен и легок в заточке, исправить мелкие недостатки поможет напильник. Выбирая сверло для ковки, нужно помнить, что у сверл большого размера из легированной стали только наконечник, а хвостовик делается из обыкновенной стали. Перед ковкой обязательно проверяют, какая сталь, и запоминают границы. Определение границ можно произвести при помощи напильника или сверла, протачивая по всей длине специальным станком. При протачивании искры от обычной стали идут большим снопом и имеют желто-оранжевый окрас. На легированной стали искр гораздо меньше, и оттенок их ближе к красному спектру. Эта процедура помогает определить, из какой части сверла делать лезвие, а из какой -хвостовик.
В печи разводят огонь. Когда он разгорается, включают поддув и ждут, когда угли разгорятся с достаточной температурой. Затем сверло необходимо поместить в огонь. Эта процедура выполняется при помощи клещей. Сверло располагают таким образом, чтобы в огне была заготовка для лезвия, а хвостовик служил рукояткой.
Нагретый до нужной температуры металл вынимают из огня и отбивают до нужной толщины.
Определить, нагрелся ли в достаточной степени металл, без соответствующего опыта сложно. Из-за ошибки сверло можно испортить. Перед тем как выковывать из сверла нож, можно потренироваться на арматуре, запоминая цвет металла, лучше всего поддавшегося ковке. Но если работа производится в солнечный день, цвет металла ничем не поможет, так как металл останется темным на вид.
Нагретое до нужной температуры сверло сразу же вынимают из печи, низ хвостовика зажимают в тисках. Разводным ключом крепко зажимают верхушку сверла и распрямляют его, раскручивая круговым движением против часовой стрелки. Это нужно произвести как можно быстрее, чтобы металл не успел остыть. Начавшее остывать сверло с легкостью сломается. Раскручивание может не получиться с первого раза, в этом случае сверло снова помещается в горнило, и операция повторяется нужное количество раз. Раскрученное сверло выглядит, как полоса металла с относительно ровными краями.
Следующие операции производят молотом, раскатывая металл сверла до нужной толщины. По раскаленному железу ударяют тяжелым молотом до тех пор, пока толщина его не составит 4-5 мм. За цветом заготовки в процессе непрерывно нужно следить, и как только металл стал вишневым, его возвращают в печь. Лишнее нагревание может образовать окалину, которую легко убирает напильник. Недостаточно горячую заготовку легко можно сломать ударом молота.
После того, как нож выкован производится его заточка на точильном камне или станке.
Работа с лезвием — самая сложная часть ковки. Придание закругления краю с сохранением толщины может считаться ювелирной работой, требующей опыта и ловкости. Удары нужно направлять так, чтобы острие закруглялось, вытягиваясь в длину сильно, но при этом очень аккуратно. Одновременно нужно следить, чтобы лезвие оставалось ровным и прямым.
Не менее сложный этап — проковать режущую кромку. Берется легкий молот (по возможности с закругленным бойком). Начинают ударами с середины лезвия аккуратно сгонять металл вниз, по направлению к режущему краю. Удары нужно наносить, рассчитывая свои силы, не забывая следить за цветом заготовки.
Следующим за лезвием и острием проковывается хвостовик. Работы с ним значительно меньше, чем с лезвием и острием. Хвостовик, имеющий у сверл круглую форму, раскаляется и сильными ударами большого молота расплющивается. Ручка ножа прорабатывается, согласно эскизу, и может иметь различные вид, толщину и ширину.
Когда ковка завершена, металл должен остыть. После этого приступают к доработке и шлифовке.
Все этапы производства очень важны, так как они предотвращают коррозию и улучшают режущие свойства металла.
Здесь потребуются напильник и шлифовальный станок. Все неровности и наплывы должны быть сняты, и поэтому для работ начинающего мастера напильник, скорее всего, не пригодится. Если потребуется убирать много отходов, шлифовальный станок справится быстрее. Иногда до идеальной гладкости и ровной поверхности приходится снимать до 2 мм стали, нож становится значительно тоньше и легче. Заточка выполняется на этом же этапе.
Полируется нож специальным войлочным кругом с нанесением на него специального абразива. Нож тестируется прорезанием веревки и строганием бруса. Заточка, если нужно, корректируется.
Sekach.ru – все о холодном и метательном оружии, а также самодельных технологиях
- Главная
- Идеи самодельщиков
- Из чего делать нож?
Нож можно сделать из чего угодно
Сегодня, я хотел бы продолжить тему, посвященную доступному материалу, из которого можно достаточно быстро и легко сделать нож с хорошими характеристиками. Многих интересует вопрос, из чего можно сделать хороший нож, не прибегая к сложным технологиям. Об этом довольно подробно написано в этой статье. Здесь же мы постараемся дополнительно осветить некоторые подробности подходящего материала для ножей. Самое простое, это использовать старые сломанные кухонные ножи из нержавеющей стали. Ножи должны быть желательно советского производства, а не китайский ширпотреб. Из подобного обломка можно сделать неплохой нож с прекрасными режущими характеристиками.
Также хорошие ножи можно делать из быстрорежущей стали, которая используется в производстве ножовочных полотен для механических пил. Недостаток такого материала то, что он достаточно хрупкий и имеет свойство ржаветь. Но заточку держит неплохо.
Отличным материалом являются ножи для строгального станка по дереву. Этот металл очень хорошо обрабатывается и полируется. Строгальный нож обжигается паяльной лампой докрасна и потом остужается. После отжига металл можно спокойно пилить ножовкой, придавать форму, точить напильником. После того, как ножу придается окончательная форма, его нужно закалить, или в масле, или в воде. Но, к сожалению, ножи из этого металла тоже ржавеют.
Следующий металл, который мы рассмотрим – это обычный напильник. Из напильника очень легко сделать нож, без каких либо специальных станков. Берете напильник, хорошо его нагреваете опять же паяльной лампой докрасна и даете ему остыть. После этого он очень хорошо обрабатывается другим напильником, пилится ножовкой для придания желания желаемой формы. Далее опять производится закалка в масле или воде. Главное для того чтобы получить хороший нож из этого металла, нужна грамотная термообработка. Ненужно расковывать этот металл. Просто обжигаем, точим, опиливаем, снимаем лишний металл ручным инструментом или на наждаке. И получаем довольно неплохой нож.
Также бюджетный нож можно сделать из обыкновенной ножовки по дереву. Тоже очень легко обрабатывается, очень упругая сталь. Можно приспособить, например, для изготовления кухонного ножа, который будет хорошо резать и хорошо держать заточку.
Автомобильная рессора тоже хорошо годится для изготовления ножей. Единственно, чем плоха рессора, это то, что ее надо расковывать и грамотно проводить термообработку. Это довольно трудоемкая задача. Но если соорудить самодельный горн у себя на участке, то можно сделать неплохой нож из куска рессоры. Или просто отнесите кузнецу, который за пузырь водки, раскует вам все, что угодно. Можно сделать нож из автомобильного клапана. Тоже получается хорошая нержавеющая сталь. Клапан нагревается до сильной температуры, расковывается на наковальне. Потом нужно сформировать лезвие и закалить его.
Очень хорошие ножи получаются из сверел больших размеров. Зажимаете сверло в тиски, нагреваете его до мягкого состояния, берете газовый ключи и начинаете потихоньку его раскручивать. После этого опять нагреваете и начинаете получившуюся деталь расковывать, придавая нужную форму. Напильником сверло точится, не будет. Все работы по формированию лезвия нужно делать на наждаке.
Нож можно сделать из пружинистой стали. Отжигать этот металл не нужно. Сразу из заготовки можно делать лезвие ножа . Обычным сверлом эта сталь не сверлится. Необходимо использовать победитовое сверло.
Теперь давайте поговорим о ржавчине, которая присутствует у большинства металлов. Если вы хотите, чтобы ваш нож не ржавел, его можно обработать серной кислотой или ортофосфорной кислотой.
В статье использован материал из видеоролика на ютубе
В современном хозяйстве нож используется для выполнения различных дел — начиная от готовки и заканчивая вырезанием различных фигурок. Что же делать, если все покупные ножи не удовлетворяют требованиям и не соответствуют заявленным характеристиками? В таком случае придётся сделать нож своими руками.
Преимущества ручной работы
В продаже можно встретить разнообразные модели ножей, которые отличаются ценой, качеством и формой. Увидев такой выбор, можно просто растеряться. Найти подходящую модель можно, но, как правило, она не будет удовлетворять все требования и ожидания покупателя. Если нужная модель не была найдена, а делать нож своими руками нет желания, то всегда можно обратиться к кузнецу. Стоит помнить, что ручная работа такого специалиста очень дорогостоящая. Изготовление ножа своими руками от начала и до конца не только выгодное, но и увлекательное занятие.
Чего можно добиться, делая клинок своими силами:
- Подобрать тип и красивую форму по своему желанию, даже в форме ключа.
- В одном инструменте реализовать все свои требования по свойствам и характеристикам.
- Выбрать наиболее подходящее железо.
- При помощи термообработки, а именно отпуска и закалки, добиться нужного соотношения упругости и твердости.
- Выбрать дизайн, который будет радовать продолжительное время.
- Не допустить ошибок, присутствующих в покупных изделиях, из-за которых может испортиться все впечатление от работы.
Как видно, изготовление ножа своими силами — наиболее подходящее решение. В своей работе можно реализовать любые идеи, начиная от подбора материала для рукоятки, заканчивая типом стали, формой и морилкой, которой будет покрыта рукоятка.
Ассортимент в магазинах
Что же можно найти в магазинах? Среди всех готовых изделий, действительно, можно найти стоящую модель. Но качество всегда стоит больших денег. В представленном недорогом ассортименте будут ножи, к которым не предъявлялись высокие технические требования.
Чаще всего можно встретить клинок:
- С недостаточной прочностью и эластичностью, вследствие чего нож ломается от малейшего изгиба.
- Изготовленный из самой дешевой стали, которая меньше всего подходит для такого изделия. Эта сталь не обладает достаточной твердостью и не сможет нормально обрабатывать твердые материалы, из-за чего ножик быстро будет затупляться.
- Низкое качество сборки тоже сыграет свою роль. Недорогой нож не будет долговечным и начнет разваливаться при малейшем повреждении.
Такие ножи можно встретить практически в любом магазине, причем стоят они недорого. Но они очень быстро выходят из строя, затем их просто выбрасывают и заменяют новым. Это не очень рационально, так как чаще всего этим инструментом пользуются в походе или на рыбалке, а некачественный нож может легко подвести владельца в самый неподходящий момент.
Чтобы правильно подобрать и купить нож, необходимо обладать минимальными знаниями в области материалов, а именно ориентироваться в характеристиках стали и механических свойствах готового клинка. Также очень важно изучить рынок.
Назначение и виды ножей
Перед изготовлением необходимо понять, для чего нужен нож. Исходя из этого следует составить список желаемых характеристик и параметров, которые предъявляются к готовому изделию.
Существуют такие виды ножей:
- Охотничьи — наиболее любимые и часто изготавливаемые домашними мастерами клинки. К ним предъявляются наиболее высокие требования, так как эти клинки предназначаются для разделки добычи.
Именно поэтому необходимо подобрать сталь, которая не будет затупляться. Важно учесть параметр хрупкости, чтобы лезвие не раскрошилось из-за неожиданного удара о кость. Не стоит забывать и об износостойкости, так как на охоте нет возможности сменить клинок.
- Туристические — их чаще всего приобретают люди, любящие активный отдых. Цель этого клинка — перерезать ветки и строгать щепу для костра. На природе не будет возможности заточить лезвие, поэтому очень важно подобрать сталь с оптимальными параметрами. Стоит помнить про соблюдение баланса между твердостью и хрупкостью. Клинок не должен ломаться из-за случайного падения на твердую поверхность. Очень часто такие кинжалы применяются вместо топора, поэтому их необходимо делать максимально широкими и прочными.
- Для выживания — тактические изделия, от которых может зависеть жизнь человека. Они изготавливаются со специальными приспособлениями, чтобы помочь выжить в сложных ситуациях. Нередко в погоне за дополнительными возможностями забывают об истинном предназначении клинка, что нередко приводит к выбору изделия из неподходящей стали и низкого качества.
- Кухонные ножи — также довольно популярные среди домашних мастеров. Стоит качественное изделие с хорошим лезвием очень дорого. Кухонный нож сделать своими руками в домашних условиях не так сложно, но требования необходимо соблюдать те же, что и в охотничьих моделях. Лезвие также не должно крошиться о кости и быть гибким, чтобы снимать филе.
Новички часто заблуждаются и думают, что походные и охотничьи ножи идентичны. Невозможно сделать универсальный клинок, который будет с равным успехом справляться со всеми целями. Туристические ножи необходимы для грубой работы: рубка веток и хвороста. Разделать ими тушу будет очень сложно. Охотничий нож очень острый и твердый, но его можно сломать, если использовать в роли походного.
Особенности изготовления
В первую очередь необходимо определиться с типом клинка. От этого будет зависеть его специфика, характеристики и предназначение. Когда тип необходимого лезвия определен, можно заняться выбором стали для изготовления.
Выбор стали
Сталь для изготовления нужно выбирать с умом, ведь тип лезвия будет показывать максимальные характеристики только в одном направлении. В выборе стали необходимо учитывать следующие требования:
- Твердость, от которой будет зависеть частота заточки.
- Хрупкость. Этот показатель решает — раскрошиться ли лезвие от удара о кость или из-за падения.
- Коррозия. Важно учитывать и то, что походные клинки будут находиться не в очень благоприятных условиях. Из-за влаги изделие может быстро покрыться ржавчиной.
- Износостойкость на лезвие.
Чтобы сделать самодельный нож, мастерами используется булат или дамаск. Но с данными материалами очень сложно работать. Для них недостаточно иметь кузнечное оборудование в виде наковальни и молота. Необходимо знать специфику и характеристики материалов. Даже кузнец со стажем не всегда сможет качественно выполнить работу, применяя дамаск. Можно прибегнуть к готовой заготовке, но она обойдется очень дорого.
Поэтому для первой и последующих работ лучше использовать легированную сталь. С ней работать намного проще. Виды легированной стали, которые чаще всего применяются для лезвия:
- 95Х18 — наиболее распространенная сталь. Она обладает отличными антикоррозионными параметрами и высокой твердостью. Если правильно термически обработать изделие, то оно будет практически полностью защищено от выкрашивания из-за ударов.
- 50Х14МФ — нержавеющая сталь, из которой делают скальпели. Достаточно долго держит заточку при должном обращении.
- Х12МФ — эта сталь тоже хорошо держит заточку и форму. Но стоит помнить, что этот материал сильно подвержен коррозии, из-за чего его реже применяют для походных и туристических изделий.
- ХВГ — сталь, которая замечательно держит удар и не крошится из-за падения. Не сильно ржавеет.
- 50ХГА — отлично подойдет для изделий в сфере выживания, но требует должного ухода из-за коррозии.
- 40Х13 — часто применяется для изготовления клинков, но стоит помнить, что эта сталь очень плохо держит заточку.
Существует еще очень много марок сталей, из которых можно изготовить лезвие. Но они слабо распространены ввиду своих неподходящих показателей.
Этапы работы
Существует много особенностей в изготовлении ножа. Стоит внимательно отнестись к работе, так как исправить ошибки иногда не представляется возможным. Каждый этап важен и должен соблюдаться профессионалами:
- Чертеж изделия. Очень важно правильно начертить прототип готового изделия, опираясь на необходимые характеристики и требования. Тут стоит учитывать специфику и предназначение ножа. Если фантазии или знаний не хватает, то можно воспользоваться готовыми чертежами. Они ничем не хуже, в них уже учтены все ошибки.
- В современном мире не нужно перековывать старую сталь, чтобы получить заготовку для будущего ножа. Можно купить в металлопрокате готовый отрез, но наилучшие свойства можно получить только при вытягивании стали на наковальне.
У обычного отреза без ковки характеристики будут немного ниже.
- Для механической обработки понадобится фреза, чтобы наиболее точно соблюдать контуры клинка. Также можно использовать и точило, но нельзя перегревать сталь, от этого характеристики ухудшаются. В крайнем случае можно использовать подручный инструмент в виде болгарки или наждака, но работать с ним сложно, а соблюсти геометрию изделия практически нереально.
- Термообработка — самый ответственный этап. Тут лучше всего применять справочники, где можно найти рекомендации по закалке и отпуску. Если терморегуляторов нет, то можно ориентироваться по цвету, но это требует некоторого мастерства и сноровки.
- Рукоять. Важно соблюсти эргономику рукояти, чтобы работать ножом было максимально удобно. Рукоять можно покрывать морилкой или лаком, чтобы защитить от внешнего воздействия.
- Финальная сборка. Необходимо насадить лезвия на рукоять и выровнять нож, чтобы лезвие не перекосило в сторону. Далее он точится и полируется по желанию.
Изготовление ножен для ножа своими руками — трудоемкий процесс, чехол лучше заказать.
Если опыт работы с металлом уже есть, то изготовить нормальный нож не составит труда. Каждое последующее изделие будет все лучше. Не стоит расстраиваться, если первый нож не удался. Лучше учесть все ошибки и попытаться сделать его снова. Но стоит помнить, что нож с большим лезвием считается настоящим холодным оружием. Поэтому предварительно важно разобраться, какое изделие будет законным.
Как сделать нож из подшипника
Для того что бы сделать нож из подшипника придется потрудиться. Если самодельный нож из рессоры можно изготовить путем отпуска, механической обработки металла и последующей закалки, то нож из подшипника можно только сковать.
Дело в том, что обойма подшипника круглая, а распрямить ее на полоску металла можно только с помощью ковки.
Для изготовления ножа своими руками можно использовать не только обойму подшипника, но и шарики или ролики из него.
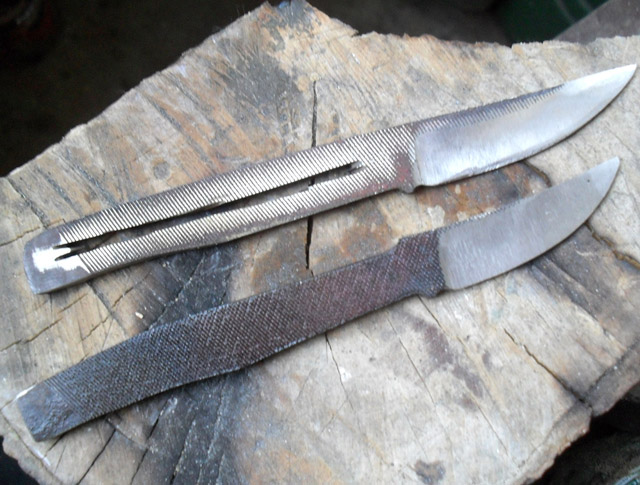
Подшипниковая сталь очень хорошего качества, ведь подшипники работают в очень жестких условиях и под большой нагрузкой, так что лезвие ножа откованного из подшипника получается с хорошими механическими свойствами. Такое лезвие хорошо держит заточку и не ломается.
Посмотрите видео — изготовление ножа из подшипника методом ковки.
Фактически такой нож из подшипника может выковать любой желающий, в ковке ножей нет никаких секретов.
Кстати, хорошо заточенный и правильно закаленный нож из подшипника может резать стекло!
Не верите? Посмотрите видео ниже, в нем рассказывается как отковать самодельную бритву из подшипника. И в конце проводится тест на резку стекла, а так же бритье бороды.
Согласитесь, бритва — это гораздо более «тонкий» инструмент чем обычный самодельный нож.
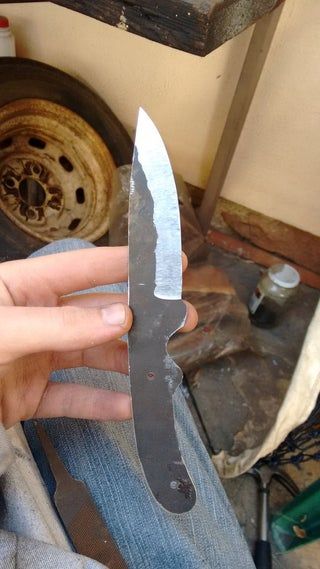
Особенности изготовления ножа из подшипника
1.Обойма подшипника распиливается болгаркой на заготовки необходимой длины.2. Ковка ведется при достаточно низкой температуре от светлокрасного до темнокрасного.
3. Обдирку делаем перед закалкой на точиле или ленте.
4. Желательно произвести нормализацию — разогрев до 750-770С, затем выдержка 5-7 мин и охлаждение на воздухе. Проводится 2-4 раза.
5. Закалка. Закалка самодельного ножа из подшипника производится при температуре 830С. Определять температуру можно по магниту — прикладываешь к заготовке и как перестало магнититься — пора закаливать.
Можно предварительно ориентироваться по поваренной соли — температура плавления соли 800 градусов. Посыпаем заготовку солью и калим, как соль на клинке начала плавиться, то берется магнит и проверяется достижение температуры закалки.
6. Закалка производится в масле. Температура масла 45-60 градусов.
7. После закалки надфиль должен скользить по стали. А клинок — царапать стекло.
8. После закалки необходимо произвести отпуск, для этого самодельный нож из подшипника кладется в духовку на 2 часа и греется до температуры 160-200 градусов. Охлаждение производится простым отключением духовки.
Чем толще нож — тем меньше можно ставить температуру. Отпуск уменьшает хрупкость лезвия, но снижает закалку. Более толстый клинок выдерживает нагрузку на излом за счет своих габаритов, так что можно отпускать при меньшей температуре.
9. Заточка самодельного ножа из подшипника производится на алмазных брусках. а шлифовка ведется с помощью алмазной пасты.
Правильно изготовленный нож из подшипника царапает стекло, не тупится и не ломается при изгибающих нагрузках.
Как сделать метательный нож своими руками: чертежи
Слесарное дело /02-фев,2018,22;04 / 33935В этой статье я покажу, как можно, используя ненужный кусок металла, изготовить своими руками полноценный метательный нож – на это уйдет только пара часов и ни копейки из семейного бюджета.
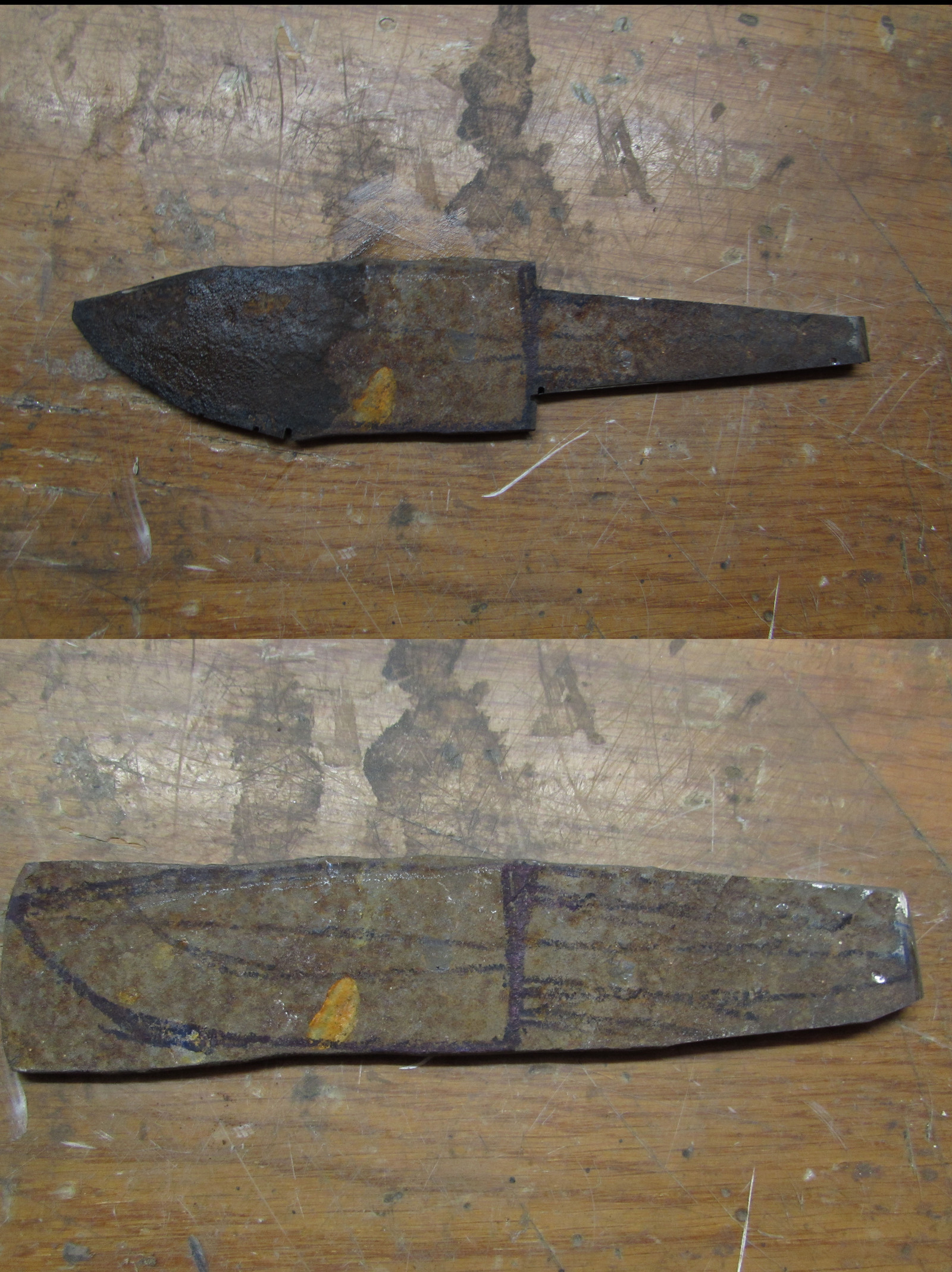
Ранее на сейте было много тем, как сделать отличные ножи для охоты и рыбалки: пример здесь.
В Интернете несложно найти метательные ножи по разной стоимости. Но для того, чтобы научиться их метать, нужно купить по крайней мере пять штук. Такая сумма вряд ли кого-нибудь обрадует. Если не хочешь ее платить – изготовь метательные ножи самостоятельно! Это делается весьма просто. Здесь я указал для тебя наиболее популярные модели со всеми замерами. Сохрани эти чертежи у себя, а я опишу, как их правильно использовать.
Чертежи метательного ножа: «Кобра»
Чертеж с основными размерами модели ножа «Кобра». Толщина клинка: 5,0 мм. Вес: 145 г.
Чертежи метательного ножа: «Овод»
Чертеж с основными размерами модели ножа «Овод». Толщина клинка: 5,0 мм. Вес: 210 г.
Чертежи метательного ножа: «Удар»
Чертеж с основными размерами модели ножа «Удар». Толщина клинка: 5,0 мм. Вес: 272 г.
Как изготовить метательный нож в домашних условиях
Перечень необходимых для этого инструментов:
• стальной лист, толщина – от 2 мм и больше;
• ножовка по металлу;
• тиски;
• бумага, ножницы, карандаш;
• напильник, наждачная бумага.
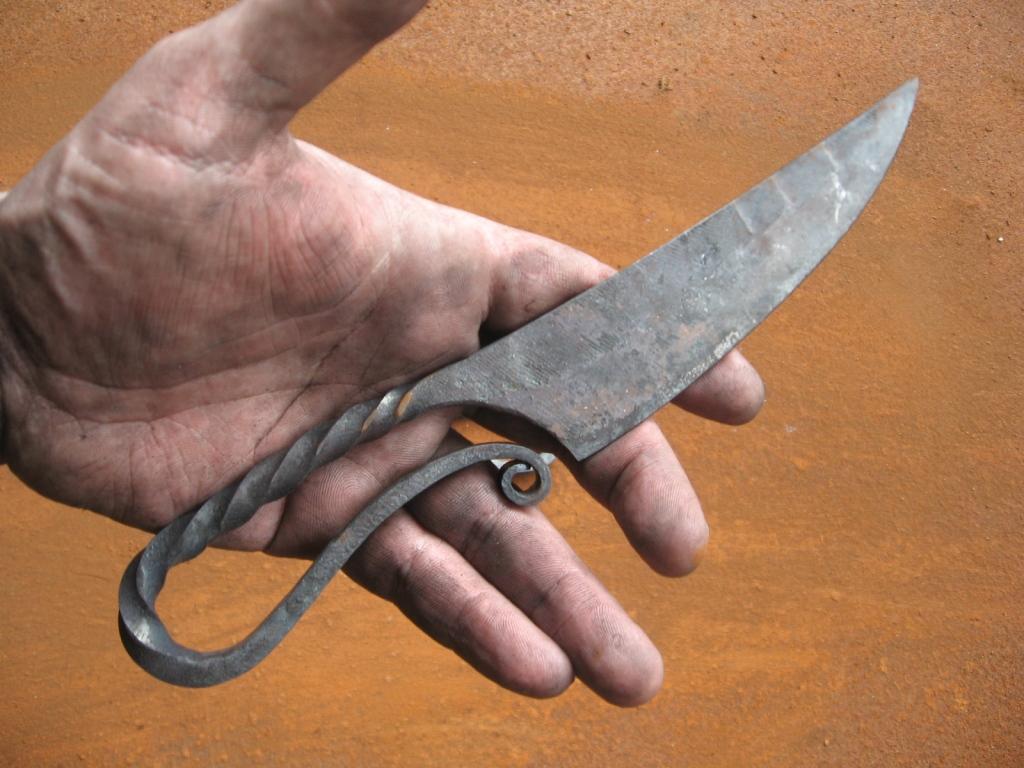
Шаг первый.
Нужно взять лист бумаги, нарисовать эскиз метательного ножа, который мы собираемся изготавливать, и вырезать.
Шаг второй.
Следует перенести эскиз на подготовленный стальной лист. Чтобы создать качественный метательный нож, рекомендуется брать нержавеющую сталь – именно нержавейка показана на рисунке.
Шаг третий.
Необходимо зажать металлическую пластину в тисках и ровно вырезать заготовку по контуру.
Шаг четвертый.
Используя напильник, нужно сформировать на клинке режущую кромку.
Шаг пятый.
Взяв наждачную бумагу, следует отполировать всю поверхность клинка.
В результате всех правильных действий у вас получится данный тип метательного ножа:
Во время метания такой нож держите за рукоять, потому что из-за особой балансировки метательного ножа этого типа клинок отличается большим весом, в отличие от рукоятки. Для проверки балансировки ножа следует положить нож на палец в месте, где соединяется клинок и рукоять – так будет видно, в какую сторону идет перевес.
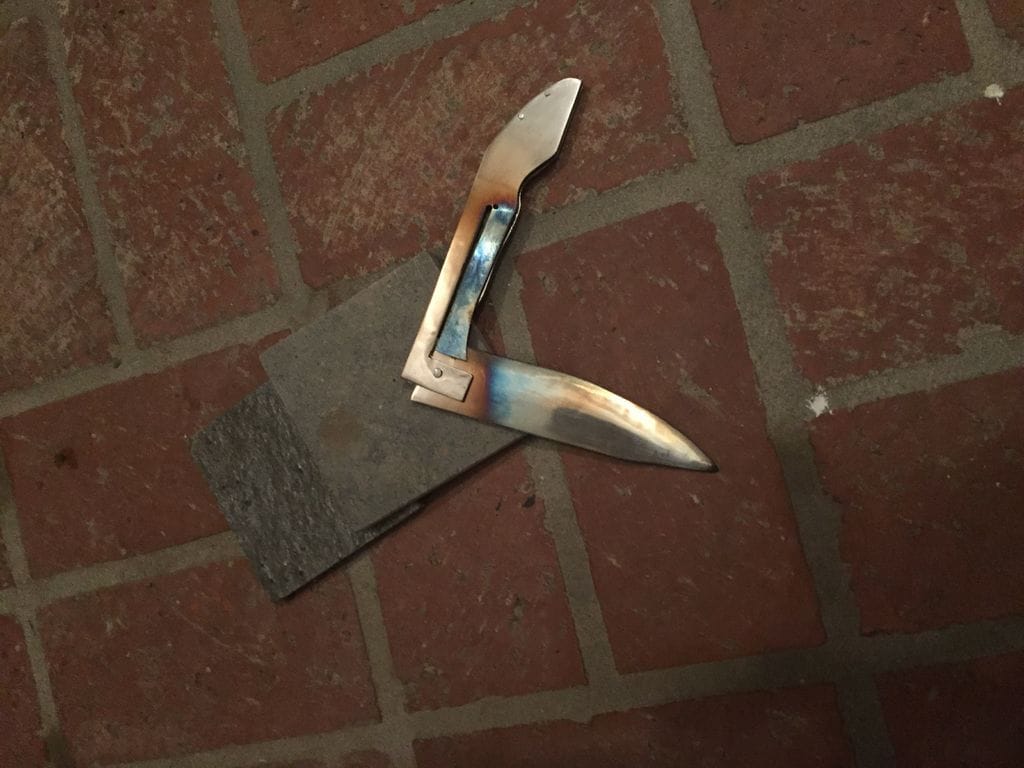
Регулярные тренировки позволят вам уверенно чувствовать себя в метании ножей на средних дистанциях. Эти навыки могут пригодиться не только в соревнованиях и развлечениях с друзьями, но и в сложных ситуациях, где нужно проявить себя в самообороне.
Как сделать нож из напильника
Стальной материал, из которого сделан напильник, имеет высокое качество, из него можно сделать хороший нож. Эту работу можно выполнить самостоятельно, правильно обрабатывая металл. В статье подробно описывается, как сделать нож из напильника.Какие нужны материалы, и заготовки?
При изготовлении ножа, лезвие необходимо закалить, это не является сложным делом. Если напильник изготовлен из стали углеродистого вида, можно сделать резак или клинок, который будет отличаться высоким качеством.
Чтобы закалить лезвие, нужно заранее приготовить все требуемые предметы, и инструменты.
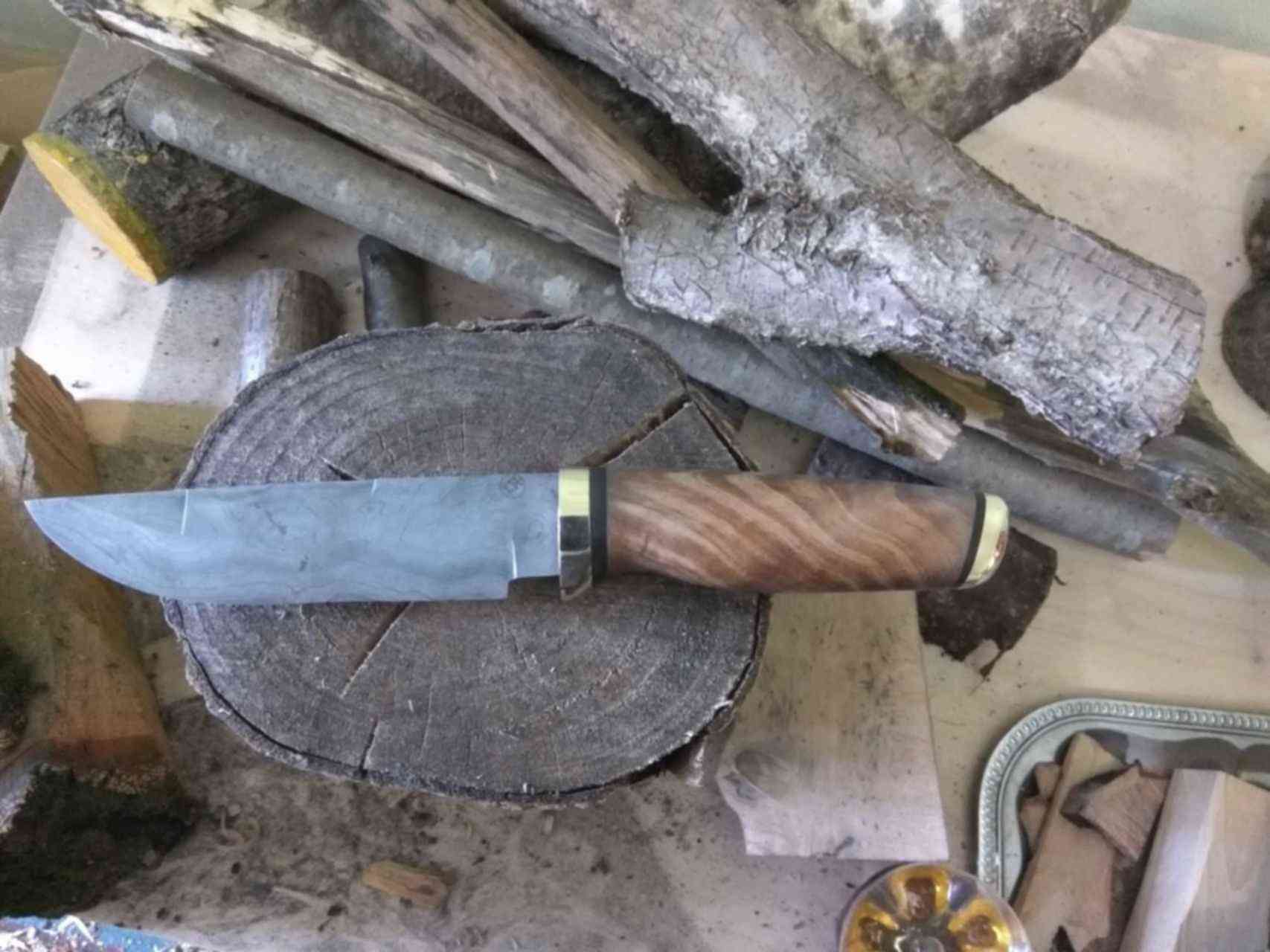
- Заранее продумывают рукоятку для будущего изделия.
- Латунные заклепки, и хлорное железо, также эпоксидную смолу.
- Затем нужно приготовить магнит, тиски, брусок для заточки ножа, болгарку, и наждачную бумагу.
Перед тем как приступить к работе, необходимо выполнить чертеж, нарисовать на бумаге, выбранную форму лезвия, и рукоятки. Также в чертеже нужно указать вариант прикрепления рукоятки к лезвию. Затем можно сделать выкройку из бумаги готового изделия, и выполнять работу по ней.
Как выполнить обжиг стального напильника?
Вначале выполняют обжиг приготовленного предмета для лезвия ножа, то есть напильника. Заготовку помещают в раскаленную плиту, и оставляют до 5 часов, затем напильник должен постепенно остывать, вместе с печкой. Основной целью является прокалить инструмент при высокой температуре, около 700 градусов, охлаждают напильник постепенно. Обжигают только тот участок напильника, который будет применяться для изготовления лезвия.
Если обжиг выполняют в газовой плите, то нужно учитывать, что для качественного обжига нужно создать тепловой экран, так как температура не будет слишком высокой. Для этого над напильником укладывают крупные предметы из металла, а на самый верх помещают металлическую пластину. Это позволяет удерживать, и направлять тепло на заготовку, а не рассеиваться по всей комнате. Что определить, правильно ли нагревается сталь, на неё насыпают обычную соль. При слишком высокой температуре, соль будет плавиться, это говорит о том, что обжиг проходит правильно.
При нагревании, напильник должен стать одного раскаленного цвета, его нужно сохранить в течение 4 часов, путем обжига. По истечению времени закала, заготовку постепенно охлаждают, вначале температуру снижают на четверть, после 30 минут, ещё настолько же градусов. Используя такой постепенный метод, необходимо охладить напильник. Этот этап нельзя пропускать, так как впоследствии металл может раскрошиться, и не получится выполнить из него высококачественное изделие.
Дальнейшая работа по изготовлению ножа
После того как обжиг будет закончен, а изделие охладиться, заготовку зажимают тисками, и отсекают все лишние участки. Затем приступают к формированию лезвия, для этого лишние участки металла стачивают на специальной электрической точилке, которая имеет крупнозернистый диск. С помощью такого прибора изделию придается необходимая форма, по эскизу. На точилке можно изготавливать лезвия любой сложности, которые имеют фигурный вид. После этого в рукоятке просверливают отверстия для размещения заклепок, которые фиксируют лезвие.
Затем нужно выполнить закалку самой заготовки изделия. При этом необходимо определить, правильно ли выполняется работа, это можно сделать, используя магнит. Если металл не магнитится, то материал имеет правильную температуру.
Заготовку прогревают равномерно, чтобы не было перегревов или резких изменений температуры. Место для крепления к ручке не закаливают, этот процесс проходит только лезвие ножа. Чтобы правильно осуществить этот процесс, применяют горелку, с помощью которой можно достичь высокой температуры.
Перед тем как начать закалку, нужно приготовить ведро с водой, в котором будет охлаждаться клинок. Когда металл приобретет равномерный цвет по всей длине, и перестанет магнититься, его прогревают ещё несколько минут, а затем погружают в подготовленную холодную воду.
Чтобы узнать, правильно ли выполнены все действия, необходимо металлом провести по стеклу, должны остаться царапины, это свидетельствует о готовности клинка к дальнейшей работе.
При разогревании металлического предмета, внутри образуется высокое давление, поэтому во время затачивания, полотно лезвия может растрескиваться. Чтобы предотвратить такое действие, необходимо выполнить отпуск металлического лезвия. То есть нужно убрать напряжение или давление внутреннего вида в металлическом изделии, таким образом, твердость материала снижается.
Отпуск металла выполнить несложно, с этим можно справиться, не имея определенного опыта. Чтобы приступить к работе, заготовку укладывают в духовой шкаф, и прогревают около 1,5 часа, при обычной температуре 200 градусов. Затем изделие постепенно охлаждают, одновременно с духовым шкафом.
Правильная обработка напильника для изготовления ножа
После того как обжиг, закалка, и формирование лезвия будут закончены, приступают к следующему этапу обработки лезвия. При этом можно использовать любые подручные предметы, предназначенные для шлифовки изделий. Например, в качестве средства для шлифовки можно использовать щетку для металла, наждачную бумагу, войлок для полировки или шлифовальную машину.
Нет надобности в качественной шлифовке, так как на это уйдет много времени, а после этого делают травление металлического изделия. Шлифовку выполняют так, чтобы сделать поверхность лезвия гладким, убрать все шероховатости, при этом изделие должно иметь красивый вид.
Перед тем как выполнить травление металла, на рукоятку прикрепляются накладки из выбранного материала, также ручку можно обматывать кожаными отрезками. Если будет выполняться отделка рукоятки, то это делается после процедуры травления.
Вначале на ручку наносят клей, а затем выполняют обмотку подготовленным материалом, обычно для этого используют отрезки кожи. Если ручка будет проходить отделку деревом, это будет сложнее, чем просто сделать обмотку. Отверстия для заклепок заполняются эпоксидной смолой перед закреплением самих элементов. Затем вставляют заклепки, эпоксидная смола способствует качественной, и надежной фиксации. Когда эпоксидная смола застынет, рукоятку делают необходимой формы. После травления, заканчивают обработку рукоятки, то есть шлифуют, и зачищают. Рукоятку можно изготовить из любых подручных материалов. Вначале выполняют все процедуры подготовки лезвия, а затем приступают к изготовлению ручки, она должна быть удобной, и не соскальзывать в руки.
Травление металла выполняют хлорным железом, эти действия выполняют до того, пока стать не приобретет серый цвет. При травлении, на поверхности металла образуется пленка, которая защищает сталь от коррозии. Если в наличии нет хлорного железа, то работу можно выполнить лимонной кислотой или уксусом. На этом этапе изготовление изделия считается оконченным.
Таким образом, можно самостоятельно изготовить нож в домашних условиях, используя напильник старого образца. Старые напильники изготовлены из стали высокого качества, поэтому ножи из таких заготовок получаются прочными, и надежными, а также отличаются высоким качеством. В статье описываются все этапы, как сделать нож из напильника, при выполнении работы, необходимо придерживаться определенных правил, только так можно получить качественное изделие.
НОЖ ИЗ АРМАТУРЫ | ТРАСТ МЕТАЛЛ
Сортовой прокат
Листовой прокат
Нержавеющая сталь
Метизы и метсырье
Цветные металлы
Следующим шагом будет ковка сверла и раскатка металла до приемлемой толщины . Удары наносим очень аккуратно и стараемся прилагать лишь столько усилий, сколько требуется для небольшой деформации раскаленного металла. Далее привариваем заготовку к арматуре и накаляем её. Ковка ножа из сверла. Перед тем как сделать отпуск, клинок следует очистить от возможной окалины и затем вновь нагреть. Выбрав наиболее подходящий для Вас профиль, можно смело приниматься за создание эскиза. Если не получилось сделать это за один раз, ничего страшного. Поэтому именно из этих предметов народные умельцы делают ножи ручной ковки.
Нож из арматуры
Справедливости ради, необходимо отметить, что нож из рессоры можно изготовить и обычным вырезанием профиля ножа с дальнейшей заточкой и закалкой. Как уже отмечалось ранее, закалка ножа – это один из самых важных этапов его изготовления. Хвостовик ножа из напильника лучше всего сделать под накладную ручку. Сверла получили большую популярность при ковке ножей благодаря используемой в них легированной стали Р6М5, которая отличается прочностью, легкостью заточки и износоустойчивостью. Для этого достаточно будет прочитать полное описание марки стали и её применение в Марочнике Стали и Сплавов, а потом использовать изделие из неё для ковки ножа. Еще одним популярным материалом для ковки ножей является подшипник, а именно его внутренний или внешний обод. Накалив заготовку до нужной температуры, приступаем к раскатке заготовки до необходимой нам толщины.
Как только она начала тускнеть, приобретая вишневый цвет, её сразу же возвращаем в горн. Так как в отличие от всех описанных выше заготовок, трос представляет собой разрозненные волокна проволоки, и ковать их довольно сложно. На шлифовальном станке снимаем лишние слои металла и неровности, делая нож идеально ровным и блестящим. Металл этой автомобильной запчасти отличается высокой упругостью и долговечностью, что делает его прекрасным образцом для ножей ручной ковки. Но все же, чтобы нож был действительно надежным, его лучше проковать, тем более что толщина рессоры достаточно велика, а для хорошего ножа её следует уменьшить.
Твердость – это свойство стали, указывающее на её способность сопротивляться проникновению в неё другого более твердого материала. Сам нож нужно уже держать над пламенем и наблюдать за ним. Но вот каждый из этих элементов имеет целый набор составляющих. Кроме того что придется довольно много помахать кузнечным молотом, так еще и без опыта в вопросе ковки металла с первого раза может не получиться выковать нож. Также стоит помнить о том, что на солнечном свете даже нагретый до 1100 °С металл будет выглядеть темным. Тем более что клинки получаются на редкость долговечными с прекрасной режущей кромкой. Наличие тех или иных легирующих элементов и их пропорциональное использование при изготовлении стали, знание свойств, которые придают легирующие элементы и добавки, позволило создавать сталь для определенных целей и нужд.
Там, где обычная сталь, сноп искр будет большой и желто-оранжевого оттенка. При ковке ножа из большого сверла необходимо сразу определить, где какая сталь и где между ними граница. Сама закалка стали происходит в диапазоне температур от 750 до 550 °С. Лучше лишний раз накалить металл, чем сломать его под ударом молота. Инструмент для ковки ножа. Пластичность – способность стали поглощать и рассеивать кинетическую энергию во время удара и деформации.
Второй – выполнить кузнеческую сварку. Сами работы будут намного проще, чем при выковке лезвия. При таком подходе риск сделать закалку неправильно минимален. И чем меньше значение, тем меньше его содержание. В результате получится монолитный кусок стали, состоящий из множества слоев, почти как у дамасской стали. Красностойкость – это показатель, отвечающий за устойчивость стали к температурам и сохранению её изначальных качеств при нагреве. Из зарубежных аналогов можно выделить сталь O-1 , 1095 , 52100 , M-2 , A-2 , 440C , AUS , ATS-34 , D-2 . После чего взять разводной ключ, зажать им верхушку сверла и сделать круговое движение, расправляя спираль.
Ковку ножа из рессоры начинаем с зачистки болгаркой от ржавчины и разметки пластины. Далее выковывается острие ножа . И тут есть два подхода в изготовлении рукоятки. Итак, выбрав способ создания рукоятки, приступаем к ковке ножа. Взять толстый трос и затем сварить его конец, сделав монолитным куском. По сути это флюс, который облегчает процесс плавки и предохраняет расплавленный металл от попадания кислорода и устраняет оксиды металла. Каждая их вышеприведенных марок используется в изготовлении ножей, различного инструмента и запчастей.
Смотрится это весьма необычно и красиво. Самыми красностойкими сталями являются твердые марки, рабочая температура ковки для которых более 900 °C. Например, сталь марки У9 говорит о содержании в ней углерода в десятых долях процента. Конструкция ножа. Прочность указывает на способность сохранять целостность под воздействием различных внешних сил. На фото ниже приведены профили ножей.
Ковка ножа из троса начинается, как и обычная ковка. После чего постепенно проковываем, доводя до необходимой толщины. При выборе сверла для ковки следует отметить один важный момент. Добившись желаемого, оставляем нож постепенно остывать и затем шлифуем и затачиваем его. После чего нож опускается в воду или масло. Для этого раскаливаем трос до ярко-красного цвета.
Ковка ножа своими руками лишь кажется простой задачей. Длину стараемся взять с запасом, так чтобы и на нож хватило и еще 1 – 2 см осталось. Это свойство напрямую зависит от твердости самой стали. Бура представляет собой соль тетраборной кислоты и применяется мастерами для сварки отдельных слоев стали. Закалка и отпуск клинка.
Ковка ножа из рессоры видео-обзор : Ковка ножа из напильника. Дело в том, что необходимо придать заокругленную форму и при этом сохранить необходимую толщину лезвия. Изготовление ножей из напильника достаточно популярное занятие. Устойчивость к износу – сопротивление материала изнашиванию в процессе эксплуатации. В конце концов, трос можно накалять и проковывать сколько угодно раз. К отечественным маркам, которые часто используются при ковке ножей в домашних условиях, относятся все стали с маркировкой от У7 до У16 , ШХ15 , 65Г , Р6М5 , Х12МФ . А дальнейшие действия по ковке самого клинка и хвостовика полностью аналогичны.
Прежде чем приступить к самим работам, необходимо сделать эскиз самого ножа. Выковываем острие и режущую кромку, как это делать, описано выше на примере ковки ножа из сверла. Для этого потребуется более легкий молот и желательно с заокругленным бойком. Описанная выше процедура необходима для того, чтобы определить, где у ножа будет начинаться клинок, а где хвостовик. Второй вариант сложнее и в то же время предпочтительней.
Помним о цвете заготовки и при необходимости отправляем её обратно в горнило. Следует отметить тот факт, что ковка ножа позволяет создать наиболее прочный и качественный клинок, который прослужит не один десяток лет и при этом сохранит свои качества. Изготовление ножа из стального троса довольно редкое явление. Вся работа практически ювелирная и потребует определенной ловкости. Но можно использовать и непрофессиональный инструмент: молот на 3 – 4 кг и молоток меньшего веса до 1 кг, кузнеческие щипцы или обычные пассатижи, но без изоляции на ручках, а также разводной ключ, тиски, наковальня или её самодельный аналог из двутавра, болгарка и сварочный аппарат, точильный станок, печь. При этом в воду добавляется 2 – 3 ложки поваренной соли на 1 л, а температура воды должна быть 18 – 25 °С, масла 25 – 30 °С. Но потренировавшись можно добиться приемлемых результатов.
Также на этом этапе можно выполнить заточку ножа. Закалка выполняется довольно быстро и чтобы все прошло удачно после закалки клинок необходимо отпустить. При этом следим, чтобы само лезвие оставалось прямым и ровным. Для тех, кто решил выковать нож впервые, описанные ниже рекомендации помогут сделать свой первый клинок. Это довольно важный и сложный этап.
После чего привариваем её к куску арматуры и засовываем в горнило. Но при этом каждый раз, нагревая его в горне, посыпать трос бурой. Удары должны быть сильные, но аккуратные. От того насколько сталь устойчива к термообработке, зависит минимальный показатель температуры, при котором её можно ковать. Поэтому сначала необходимо набить руку и немного потренироваться, а затем уже приступать к ковке ножа.
После того как удалось выковать лезвие и острие, переходим к проковке хвостовика . Также необходимо знать и о некоторых основных профилях клинков, чтобы сделать наиболее подходящий эскиз. Сделать это можно достаточно просто, всего лишь немного проточив сверло по всей длине. Важно! Выполняя ковку ножа впервые, можно не сразу определить, когда металл нагрелся до необходимой температуры. Маленькие сверла обычно полностью из Р6М5. Затем присоединить к ней трубу, по которой будет поступать воздух при помощи вентилятора или старого пылесоса.
В результате должна получиться полоска металла толщиной около 4 – 5 мм. Тут все несколько сложнее. Сегодня, даже при таком большом ассортименте различных ножей прекрасного качества от известных производителей, ножи ручной ковки по-прежнему пользуются особой популярностью. А это целое искусство и рассчитывать, что нож из троса получится с первого раза, не стоит. За некоторым исключением.
Ковка выполняется таким образом, чтобы постепенно заокругливая острие, понемногу оттягивалось лезвие в длину. Большие сверла состоят из рабочей спиралевидной части из Р6М5 и хвостовика из обычной стали. Для ковки ножа потребуется определенный инструмент кузнеца, который можно приобрести в магазине. Затем делаем острие и режущую кромку. Делать все необходимо быстро, чтобы металл не успел остыть, иначе рискуете сломать сверло.
По сути, нож довольно простой предмет, состоящий из клинка и рукоятки. О том, как это делается, будет написано ниже. Сварку можно выполнить двумя путями. Просто повторно раскалите сверло и повторите процедуру. Тут все довольно просто.
Удары наносим тяжелым молотом, но при этом стараемся сохранить волокна троса вместе. Поэтому необходимо немного усовершенствовать очаг. Конечно, можно найти и другие изделия из той или иной стали. Вначале накаливаем круглый хвостовик сверла и затем раскатываем его сильными ударами молота. Иногда закалка и отпуск производятся при помощи масла или воды, а иногда через масло в воду. Все дело в том, что в обычном очаге сложно получить температуру более 900 °С. Потребуется лишь небольшая часть рессоры, поэтому отметив её, отрезаем при помощи болгарки.
Все эти свойства связаны между собой и преобладание одного из них ведет к ухудшению другого. Вследствие чего можно испортить не одно сверло. Вначале разводим огонь в печи , подключаем поддув и ждем, когда угли разгорятся достаточно сильно, после чего помещаем сверло в горнило . Ковка ножа из напильника видео-обзор : Ковка ножа из троса. Для того чтобы сделать такой нож, необходимо приложить несколько больше усилий, чем при ковке из обычного бруска стали. Стараемся сделать режущую кромку как можно тоньше. Например, марки стали Р6М5, У7-У13, 65Г применяют для производства сверел, буров, тросов, рессор, подшипников, напильников.
В зависимости от эскиза хвостовик может быть как узким, так и широким. Таким нехитрым образом выполняется подготовка к кузнеческой сварке. После того как трос обработали бурой со всех сторон и он раскалился от 900 до 1200°С и более, вынимаем его из горнила и начинаем проковывать. К тому же сталь троса не обладает такими высокими характеристиками, как сталь сверла или напильника. Напоследок выполняем закалку ножа.
Говоря проще, твердая сталь лучше сопротивляется деформации. Кто-то делает простые накладки, а кто-то делает наборную рукоятку. Сам показатель твердости измеряется по шкале Роквела и имеет показатель от 20 до 67 HRC. При этом необходимо отметить, что температура плавления стали составляет 1450 – 1520 °C. Проверить прочность можно на изгиб или при сильном ударе.
Закалка клинка начинается с его нагрева от светло-красного до оранжевого цвета. По завершению ковки даем металлу постепенно остыть и затем переходим к шлифовке . Момент закалки можно даже прочувствовать, когда сталь начинает «дрожать и стонать» в жидкости. Из различных способов собственноручного изготовления ножа наиболее трудоемким является ковка ножа своими руками. Ковка ножа из сверла видео-обзор : Ковка ножа из подшипника. Аналогом стали марки «У» являются стали 10хх, где «хх» — это содержание углерода. Многие мастера делают хвостовик ножа из троса в виде готовой рукоятки.
У новичка может не получиться с первого раза, но немного практики все исправит. В поисках подходящей стали для качественного ножа многие используют рессору. Вот только есть несколько маленьких секретов. Все работы по ковке ножа из подшипника практически идентичны ковке из сверла. Сам процесс подразумевает ослабление внутреннего напряжения стали, что делает его более гибким и устойчивым к различного рода нагрузкам. Прежде всего, потребуется очистить напильник от насечек и возможной ржавчины.
В качестве топлива используется обычный древесный уголь, желательно такой, который дает как можно больше жару и горит подольше. На демонстрирующих ковку ножей видео уже не раз было показано, как именно делается раскатка клинка, создание режущей кромки и острия. Как только вся поверхность покроется желто-оранжевой пленкой, убираем нож от огня и даем ему остыть естественным образом. При этом необходимо запоминать, какого цвета был металл и когда он ковался наиболее мягко. После чего вновь отправляем в горнило. При этом то или иное свойство стали зависит от содержания в ней различных легирующих элементов и добТРАСТ МЕТАЛЛ, таких как кремний, углерод, хром, ванадий, вольфрам, кобальт, никель, молибден.
А если сам клинок сделан из легированной стали и со знанием дела, то такой нож бесценен. Если с обычным инструментом все более-менее понятно, то по поводу печи необходимо сделать некоторые пояснения. Отпуск клинка выполняется уже после закалки. Далее при необходимости отрезаем от напильника заготовку необходимой длины. А вот там, где легированная сталь, сноп будет реденьким и ближе к красноватому оттенку. Причем внутренний даже предпочтительней.
Во-вторых, на начальной стадии ковки вырезанную заготовку следует приварить к прутку арматуры. Закончив с этим, переходим к самой ковке. Или такая сталь как Х12МФ указывает на высокое содержание хрома и молибдена, что говорит о нержавеющих и высокопрочностных свойствах стали. При шлифовке может уйти до 2 мм толщины, и нож станет намного легче и тоньше. Чтобы сделать нож, потребуется их сварить между собой. Если ранее Вы не занимались хотя бы закалкой металла, то придется сделать с нуля небольшую печь из толстостенного металла. Как только сверло нагреется до необходимой температуры, а это более 1000 °С , его сразу же необходимо вынуть из горнила , и зажать низ хвостовика в тисках.
Затем вынимаем его и посыпаем бурой. Таким нехитрым образом можно получить достаточно надежное горнило для доведения заготовок до температуры 900 – 1200 °С. Буру можно найти в свободном доступе без особых проблем. Это и неудивительно, так как такие ножи обладают особой энергетикой и привлекательностью. Такие стали имеют каждая свою маркировку. Тут уже кому как нравится делать ручку ножа.
Следующим шагом будет проковка режущей кромки ножа . Сделать это можно с помощью болгарки. Сам процесс закалки выполняется уже после того, как нож остыл и был отшлифован на точильном станке. Во-первых, это касается хвостовика. Ведь именно от того насколько правильно была она выполнена, зависят рабочие характеристики ножа. После чего остается лишь выковать клинок необходимой формы. Конечно, опытные мастера обходятся без зарисовки, но для новичка все же важно сделать эскиз и держать его перед глазами в процессе ковки. Инструменты.
Для ковки ножа своими руками нужно ориентироваться на пять основных свойств стали – устойчивость к износу, твердость, прочность, вязкость, красностойкость. В-третьих, если в случае со сверлом заготовку раскатывали из круглой в плоскую, то для обоймы подшипника её необходимо просто выровнять. Начиная с середины лезвия, постепенно сдвигаем металл вниз к режущей кромке. Первый – проварить электросваркой вдоль больших канТРАСТ МЕТАЛЛ. В большинстве своем ножи из троса куют из-за их необычного рисунка на клине, отдаленно напоминающего дамасскую сталь. Во-вторых, ковка троса – дело сложное из-за разрозненных проволок, из которых состоит трос. Сложность ковки троса именно в этом.
Но температура при отпуске значительно меньше. На демонстрирующем конструкцию ножа фото можно увидеть все элементы ножа и как они называются. Ковка ножа своими руками – дело, требующее от мастера высокого уровня навыков владения инструментом, знания металлов и их свойств. Как выбрать сталь для ножа. Во-первых, заготовку из ободка подшипника вырезаем при помощи болгарки. Но ковка ножа из напильника имеет свои особенности.
Единственное, что стоит отметить, – из подшипника все же удобнее делать нож с накладными рукоятками. И в таком виде накалять и ковать. Или сделать рукоятку в форме петли, а из концов выковать клинок. Чтобы правильно подобрать сталь, необходимо знать и понимать, какими свойствами обладает сама сталь. Сначала клинок опускается в масло на 2 – 3 секунды, а затем в воду. Качественный самодельный нож отличает правильный подбор стали для него, от этого будут зависеть режущие и прочностные характеристики самого ножа. При этом отечественные и зарубежные марки стали обозначаются по-разному.
Но делаем это с помощью клещей и так, чтобы хвостовик большей частью оставался вне огня. Поэтому прежде чем браться за ковку сверла, можно немного потренироваться с нагревом и ковкой металла на обычной арматуре. Да и греться заготовка там будет целую вечность. Для удобства в марке стали указан основной состав одного или нескольких легирующих элементов. Важно!
При ковке металла необходимо постоянно следить за цветом заготовки. Такая закалка выполняется очень быстро. Ковка ножа из подшипника видео-обзор : Ковка ножа из рессоры. Как только процесс заканчивается, клинок необходимо достать и дать ему остыть естественный образом. Износостойкую и прочную сталь можно найти в различном слесарном инструменте и напильник тому яркий пример.
В результате должна получиться относительно ровная полоска металла. Раскалив металл до необходимой температуры, берем тяжелый молот и начинаем сильными, но равномерными ударами ровнять металл и придавать ему ровную форму.
Смотрите также
ВЕС 1 М АРМАТУРЫ 8
А-II — рифленая, со спиральным выступом etc. На пересечении соответствующей строки и столбца мы увидим, что вес 8 мм арматуры составляет 0,395 кг. Какая…
АРМАТУРА 12 ММ ВЕС 1М
Что же делать, если под рукой нет онлайн-калькулятора, а данным таблиц в интернете вы не очень доверяете? Все просто – определить вес арматуры 8 мм за…
ВЕС 1 МП АРМАТУРЫ 12
Масса арматуры. При проведении строительно-монтажных работ расчет массы металлических изделий крайне важен, поскольку он позволяет оценить итоговые…
ВЕС АРМАТУРЫ 12 ММ
Существуют так же товары, для которых данный инструмент не пригоден, один из таких продуктов — сетка кладочная, страницу которой можно найти тут.
Объем…
ВЕС АРМАТУРЫ 12 А3
Если вы не уверены, что сможете правильно произвести расчеты, в компaнии «ТРАСТ МЕТАЛЛ» помогут узнать вес арматуры 12 мм за метр с предельной точностью,…
Самодельный нож, изготовление ножа из подручных материалов дома
Продолжая делать свой первый самодельный нож, я использовал маркер, чтобы помочь себе в обработке плоскости клинка, и обтачивал очень медленно, пытаясь удержать напильник плоско. Маркер покажет вам неровности, которые надо сточить.
Самодельный нож, изготовление ножа из подручных материалов в домашних условиях. Часть 2.
Попробуйте закрепить полоску наждачной бумаги на какой-нибудь недорогой основе, например, на шпателе для нанесения краски. Вначале я зачищал наждаком область, которую мы назвали углубление, с помощью плоской дощечки и бумаги номер 120.
Потом я стал обрабатывать плоскость продольными движениями к концу клинка, пока все грубые царапины от напильника не исчезли. Это так же выравнивает плоскость. Используйте немного мыла и воды, чтобы уберечь наждачную бумагу от загрязнения, а когда закончите работу, убедитесь, что вытерли свой самодельный нож насухо, иначе до завтра он поржавеет.
Начните обрабатывать наждачкой плоскость клинка и рукоять. Не удаляйте все огрехи, а только излишки, пока не получите немного голого металла — такая «суровость» придаст характер уже готовому ножу.
Закалка клинка самодельного ножа.
Ок, огонь зажжен. Я занялся этим на заднем дворе, в специально огороженном месте. Огонь пылает за оградой, и дует несильный ветерок, который помогает нашей работе. Нужно будет еще несколько вещей, чтобы работать с ножом дальше. Магнит я достал из игрушечной коробки моих мальчишек, а после борьбы с проблемой надежно/дешево пришел к следующему.
Взяв два куска 1/2 дюймовой квадратной трубы 3 фута длиной, я вставил в них концы рукояток старых плоскогубцев и сплющил металл по краю, чтобы закрепить соединение. И еще одна важная, необычайно секретная вещь, на которую я вам намекну — старые масляные фильтры, остающиеся после замены масла в автомобилях.
Опустите свой самодельный нож в горячие угли. Ему следует находиться там примерно 10-15 минут, в зависимости от того, как сильно разгорелись угли. Это ваш первый раз, поэтому вытаскивайте свой самодельный нож из огня на пару секунд каждые 2-3 минуты, смотрите на его цвет и проверяйте режущий край магнитом.
Если сталь притягивается, значит нож еще не готов, суйте его обратно в огонь и грейте до вишнево-красного цвета. Постарайтесь не перегревать свой первый самодельный нож дольше, чем необходимо, поэтому проверяйте клинок каждую минуту-две, когда решите, что момент готовности уже близок.
Пришло время опустить нож в секретное автомобильное масло. Магнит не притягивается, цвет стали хорош, и слюни текут от предвкушения. Я закалял сталь, опуская в масло только 2/3 ножа. 2/3 клинка со стороны режущей кромки я держал в масле, пока не погасло пламя — около минуты. Потом медленно погрузил остальную часть ножа, пока он не погрузился полностью, и не перестал идти дым.
Когда мы вытаскиваем из масла свой самодельный нож, он выглядит черным и противным. Я опустил его в сосуд с водой, пока он не остыл настолько, чтобы можно было взять его в руки.
Проверка напильником качества закалки на клинке ножа.
Теперь вы спросите — этот наш самодельный нож действительно твердый? Ну что же, давайте проверим. Возьмите напильник и пройдитесь им по клинку, прикладывая под углом 30 градусов и прижимая деликатно, а не жестко. Напильник будет скользить по режущей кромке, пытаясь за нее зацепиться.
Если клинок слишком скользкий, вытрите его тряпкой, удаляя масло. Чтобы лучше очистить металл, можно использовать так же мыло и воду. Если напильник цепляется за нож, значит закалка не удалась, возвращайтесь к огню, и повторяйте все сначала.
Отпуск стали на клинке самодельного ножа.
Предположим, что клинок прошел пробу напильником, и закалился как следует. Теперь надо его отпустить, так как мы не хотим, чтобы лезвие или его кончик крошились. Напильники очень хрупкие, и наш самодельный нож сейчас тоже очень твердый и ломкий.
Разогрейте кухонную духовку до температуры 375-400 градусов. «Пеките» нож в духовке 45 минут, позвольте ему остыть до комнатной температуры, и снова суньте в духовку на 45 минут при той же температуре. Кстати, не забудьте смыть предварительно с ножа все масло, если не хотите закоптить весь дом. После отпуска стали можно очистить клинок. Беритесь снова за наждачную бумагу, и готовьтесь накладывать деревянные рукоятки на этого малыша.
Изготовление и монтаж рукояти из дерева на самодельный нож.
Я поместил нож в тиски, и обрезал два куска для накладок на будущую рукоять. Положите нож ближе к верхнему краю бруска, тогда будет проще привязаться хотя бы к одному его краю. У меня есть медные прутки, и я готов сделать следующий шаг. Просверлите для них отверстия в рукояти.
Я вставил все три стержня и очертил контур ножа на дубовой плашке, определившись, где будет «лицо» бруска, когда я прикреплю эпоксидкой и медными прутьями дерево к стали. Это фото не очень хорошее, но думаю, вы сможете увидеть нужный вид с черной полосой на ноже. Я отметил на древесине начало и конец этой линии, а потом соединил их дугой.
Левая щечка рукояти будет обработана и прикреплена, когда мы не сможем нарушить форму после того, как дерево приклеится к ножу. Теперь карандашом надо сформировать левую часть рукояти, в основном ее перед. Проверьте, достаточно ли хорошо подготовлена накладка, как она прилегает к металлу, и если надо, выгладите ее на наждачной бумаге, чтобы плоскость была совершенной.
Соедините оба куска медными прутками, опилите их и обработайте наждачной бумагой, пока накладки не станут подобными зеркально. Еще раз напоминаю о переднем крае! Потом проверьте их на ноже.
Теперь, если обе накладки достаточно хороши, и нет пустоты между ними и ножом, можно обрезать лишнюю длину прутьев, так, чтобы они были заподлицо с деревом.
Окончательная сборка самодельного ножа.
Тщательно очистите свой самодельный нож там, где будет прилегать дерево. Мыло, горячая вода и старая зубная щетка, потом тщательно ополосните его и вытрите досуха. Если хотите, чтобы он был совершенно сухим, воспользуйтесь сушилкой для волос.
Я обрезал прутки, и зачистил наждачкой грани, чтобы потом не откалывались щепки. Потом эпоксидной смолой смазал внутренние части деревянных накладок, рукоять ножа и стержни, и соединил все вместе. Обернув все это четырьмя жирными резиновыми полосами (жирными — чтобы не прилипли), я оставил все до высыхания, а потом удалил излишки выступившей смолы, и наконец получил свой первый готовый самодельный нож.
По материалам статьи «Как сделать нож своими руками» (перевод).
Скотт Джонс.
Начало — Как сделать нож своими руками, изготовление ножа из подручных материалов, в домашних условиях. Часть 1 >>>
Похожие статьи:
- Создатели ножей Kershaw, Ken Onion, Launce Barber, Frank Centofante, Tom Veff, особенности ножей Kershaw, технология SpeedSafe.
- Клинок для ножа из дамаска, первые трудности, выбор стали, формирование пакета на клинок из дамаска, часть 2.
- Как сделать клинок для ножа своими руками, что понадобиться для ковки ножа, ковка, обработка и закалка, советы начинающему, часть 1.
- Всадной монтаж рукояти ножа, необходимый инструмент, эскиз, обработка заготовки, вклеивание хвостовика клинка в рукоять ножа.
- Как самому сделать складной нож, с чего начать, выбор материала клинка и рукояти, изготовление плашек рукояти, сборка самодельного складного ножа.
- Клинок боевого ножа, материалы для его изготовления, стали и их состав, какой сорт стали подходит на клинок ножа, другие материалы на клинок ножа.
- Варианты обработки поверхности клинка ножа, виды механической обработки и покрытия поверхности клинка.
Как построить нож: 9 шагов (с изображениями)
Вот, вероятно, самая техническая часть всего проекта — термическая обработка лезвия. Вы можете использовать угольную кузницу (как я), газовую кузницу или горелку. Последний следует использовать только с маленькими ножами — поддерживать высокую температуру на большом лезвии будет сложно с помощью только горелки. Смотрите картинку ниже, чтобы увидеть, как я разжигаю огонь.
Термическая обработка состоит из двух этапов: закалки и отпуска. При закалке лезвие нагревается до критической температуры, а затем закаляется.Это изменяет структуру стали, поэтому она становится чрезвычайно твердой, но при этом довольно хрупкой. Нож на этой стадии при падении может треснуть или расколоться, как стекло. Следующий шаг, темперирование, осуществляется путем нагревания ножа до более низкой температуры, около четырехсот градусов. Это делает нож менее хрупким, сохраняя при этом относительную прочность.
Теперь вам понадобится ванна для закалки. Для стали 01 следует использовать масло. Для разных типов стали требуются разные методы закалки — закалка в масле, закалка в воде, закалка на воздухе и т. Д… опять же, я рекомендую сталь 01, потому что она легко поддается термообработке и не требует ничего сложнее, чем ведро с моторным маслом. Смотрите картинку два. Вы должны полностью погрузить лезвие в воду. Второе, что вам понадобится для закалки, — это магнит. Это поможет вам определить температуру закалки, потому что в этот момент сталь становится немагнитной. См. Рисунок 3 — специально для этого я держу магнит на капоте кузницы.
Теперь приступим. Разведите огонь на угле или газовой кузнице или зажгите факел — нагрейте лезвие по корешку, чтобы не обжечь лезвие.Если нагреть слишком сильно, сталь сгорит или расплавится и превратится в бесполезный металлический мусс, напоминающий пену.
Итак, вы собираетесь нагреть металл до среднего оранжевого огня, пока сталь не станет немагнитной. Просто коснитесь им магнита, пока он светится, и если он не прилипнет, значит, готов. На этом этапе вам нужно пару раз дать стали медленно остыть на открытом воздухе. Это называется отжигом и снимает напряжения в стали, возникающие в процессе прокатки и фрезерования. После отжига (три раза — хорошее круглое число) нагрейте его до той же температуры, что и вы, но вместо того, чтобы отжигать, погрузите его в масляную ванну.Наденьте перчатки, потому что здесь будет пожар. Смотрите картинку восемь. Когда вы достанете нож, он будет дымиться, и вся комната должна пахнуть, как палатка для жареного картофеля на окружной ярмарке. Чтобы проверить край, проведите по нему острым напильником. Если это сложно, файл должен перелететь через край, не оставляя следов, как на десятом рисунке. К этому моменту вы закалили лезвие, так что будьте осторожны. Если уронить, он сломается.
Итак, вы мало что можете сделать с лезвием, пока не закалите его.Потушите огонь, войдите внутрь и разогрейте духовку. На вашей стали могла быть информация о закалке. Если это так, выберите твердость на листе и используйте эту температуру. Вам понадобится нож средней твердости. Одиннадцатое изображение этого шага является иллюстрацией цветов закалки — это наглядные пособия для измерения закалки лезвия. Чем выше температура, тем мягче и упругее будет лезвие. Попробуйте выбрать коричневый или пурпурный цвет, который обычно проявляется при температуре около 400-450 градусов.Если вы не знаете точно, какую температуру использовать, выберите 425 градусов по Фаренгейту. Положите лезвие на среднюю решетку и дайте ему вариться в течение часа. Когда час истек, нож готов. Поздравляю. Вы официально изготовили лезвие, но чтобы превратить лезвие в прекрасный столовый прибор, вам потребуется немного больше работы.
Металлы для изготовления ножей | Металлические супермаркеты
Ожидается, что хорошо сделанный нож будет работать стабильно и без сбоев. Однако сделать нож, не подверженный поломке, может быть сложно, поскольку лезвие ножа заточено до тонкой кромки, которая не должна ломаться или затупляться.Для этого важно выбрать подходящий материал ножа, так как неправильный металл и сплав в конечном итоге приведут к преждевременному разрушению и потускнению кромки. Не все металлы для ножей одинаковы, поэтому вот несколько примеров лучших металлов для изготовления ножей.
Лучшие металлы для изготовления ножей:
- Инструментальная сталь
- Углеродистая сталь
- Нержавеющая сталь
Инструментальная сталь
Инструментальная сталь— очень популярный выбор для изготовления ножей. Инструментальные стали — это, по большей части, углеродистые стали, которые имеют дополнительные легирующие элементы, улучшающие их механические свойства. Эти легирующие элементы часто также повышают коррозионную стойкость стали, но не до уровня нержавеющей стали.
Одна из марок инструментальной стали, которая используется в качестве материала ножа, — это A2. Хотя она не может достичь такой высокой твердости, как некоторые другие инструментальные стали, она обладает превосходной вязкостью.Однако A2 может подвергнуться ржавчине, если не будут приняты соответствующие меры. D2 — другой вариант, который имеет лучшую коррозионную стойкость и удержание кромок, чем A2; однако это происходит за счет прочности. M2 — это инструментальная сталь, которая отлично удерживает острие лезвия, но в некоторых случаях она может быть слишком хрупкой.
Углеродистая сталь
Для изготовления ножей желательны марки углеродистой сталис высоким содержанием углерода, так как они придают лезвию твердость и прочность, необходимые для защиты от ударов и износа.Однако необходимо проводить надлежащую термообработку высокоуглеродистых сталей. Если используется слишком быстрая закалка, нож будет слишком хрупким и может сломаться, а если сталь подвергнется нормализации или отжигу, она будет слишком мягкой и нож не сможет долго удерживать острый край.
Ножи из углеродистой стали также подвержены коррозии. Это связано с тем, что углеродистая сталь не содержит многих легирующих элементов, защищающих ее от коррозии. Необходимо следить за тем, чтобы лезвие из углеродистой стали не ржавело.
Обычные марки углеродистой стали для изготовления ножей включают C1045, C1075 и C1090.
Нержавеющая сталь
Нержавеющая сталь — еще один вид металла для изготовления ножей. Дополнительным преимуществом использования нержавеющей стали является добавление хрома и других легирующих элементов, повышающих коррозионную стойкость. Ножи из нержавеющей стали обычно изготавливаются из ферритной или мартенситной нержавеющей стали. Для изготовления ножей с приличным удержанием кромки, мартенситные и ферритные сорта нержавеющей стали должны иметь достаточно высокий уровень углерода для достижения высокой твердости.Для изготовления ножей часто используются такие сорта, как 420 и 440.
Аустенитные сорта, такие как 316, иногда могут использоваться для изготовления ножей, однако аустенитные сорта обычно не могут быть достаточно закалены, чтобы обеспечить прочную кромку. При изготовлении ножей следует избегать использования низкоуглеродистых версий аустенитной нержавеющей стали, таких как 304L, если только коррозионная стойкость не является основной проблемой, а срок службы лезвия не является второстепенным.
Существуют также дисперсионно-твердеющие нержавеющие стали, которые обладают превосходной коррозионной стойкостью и способностью к закалке.Обычно они используются в приложениях, где коррозия представляет собой серьезную проблему. Обычно для лезвий используется нержавеющая сталь с дисперсионным упрочнением — 17-7 PH. Чтобы добиться максимальной пользы от этих сплавов для изготовления ножей, нужно знать, как правильно упрочнить металл путем дисперсионного твердения.
Конечно, для изготовления ножей используется множество других металлов и марок, это лишь некоторые из распространенных типов.
Metal Supermarkets — крупнейший в мире поставщик мелкосерийного металла с более чем 85 обычными магазинами в США, Канаде и Великобритании.Мы эксперты по металлу и обеспечиваем качественное обслуживание клиентов и продукцию с 1985 года.
В Metal Supermarkets мы поставляем широкий ассортимент металлов для различных областей применения. В нашем ассортименте: нержавеющая сталь, легированная сталь, оцинкованная сталь, инструментальная сталь, алюминий, латунь, бронза и медь.
Наша горячекатаная и холоднокатаная сталь доступна в широком диапазоне форм, включая пруток, трубы, листы и листы. Мы можем разрезать металл в точном соответствии с вашими требованиями.
Посетите одно из наших 80+ офисов в Северной Америке сегодня.
Начало изготовления ножей — какое оборудование мне нужно?
Мы проводим довольно много курсов по изготовлению ножей в кузнице Тхарва Вэлли, поэтому неудивительно, что мы получаем много вопросов от студентов о том, как заняться изготовлением ножей в домашних условиях.
Как и в любом другом творческом поиске, мы встречаем множество людей, которые откладывают начало производства ножей, потому что у них нет выбора; С другой стороны, мы видим довольно много людей, которые бросаются покупать огромное количество дорогостоящего оборудования, но не имеют представления, как им пользоваться.
Самое главное, когда дело доходит до создания ножей, — это не ваше оборудование, способности или знания. Это твое отношение. Если вы понимаете свой бюджет и подходите к покупке оборудования как к инвестициям, а не к расходам, вы сможете заняться изготовлением ножей таким образом, чтобы это было приятным и устойчивым.
Если вы встанете на правильную ногу, изготовление ножей может стать окупаемым занятием. Многие производители ножей начали с использования этого простого метода: вычислите свой первоначальный бюджет на инструменты и материалы и поместите эти деньги на отдельный банковский счет или в копилку / коробку для обуви / матрас.Это ваш фонд для изготовления ножей — когда вы покупаете оборудование и материалы, деньги поступают отсюда, когда вы продаете ножи, деньги возвращаются сюда. Сначала вы будете субсидировать производство ножей, а через некоторое время производство ножей, вероятно, окупится.
Вы можете заняться изготовлением ножей менее чем за 500 долларов с базовой настройкой удаления материала. Хотя вам, возможно, придется отправить лезвия на термообработку, вы быстро научитесь достаточно быстро перейти к промежуточной настройке, не тратя деньги на неправильный комплект.
Стартовый комплект (500 долларов США)
Если у вас нет инструментов, это то, что вам понадобится для изготовления простых ножей путем снятия припуска.
- Верстак
- Угловая шлифовальная машина 5 «(резка и формовка заготовок)
- Диски угловой шлифовальной машины 1 мм (отлично подходят для вырезания фигур)
- Хороший набор напильников (фасок)
- Наждачная бумага с зернистостью 180, 320 и 600
- Малый сверлильный станок (без него сложно сделать прямые отверстия)
- Тиски для скамейки (купите или сделайте сами)
- Заготовки для лезвий с предварительной нарезкой (идеально подходят для ваших первых ножей)
- 3 мм 1075 Сталь (легко работать, легко поддается термообработке)
Rhynowet — наша предпочтительная наждачная бумага.Приблизительно по той же цене, что и покупка влажной и сухой бумаги в строительном магазине, эта бумага служит почти в три раза дольше и работает лучше. Мы обнаружили, что это экономит час на одно лезвие по сравнению с другой наждачной бумагой.
Как только вы освоите свой Starter Kit и начнете замечать, как он вас ограничивает, возможно, пора взглянуть на установку более среднего уровня. Это значительно дороже, но ваш более высокий уровень навыков поможет вам вернуть деньги, продавая ножи более высокого качества.В свою очередь, новое оборудование даст вашим навыкам возможность развиваться, чтобы вы могли заплатить за переход на следующий уровень, когда перерастете эту установку.
Промежуточный комплект (2000-4000 долларов)
Эта установка ускоряет процесс изготовления ножей, а также дает возможность изучить более сложные методы.
- Стартовый комплект, плюс:
- Ленточно-шлифовальный станок с регулируемой скоростью (1600 — 3200 долларов)
- Дисковая шлифовальная машина (1000 долларов США)
На этом этапе вам следует подумать о приобретении лучшего ленточно-шлифовального станка, который вы можете себе позволить. Хорошая шлифовальная машина может покрыть плохую поковку, но плохая шлифовальная машина даст вам плохую отделку, независимо от того, насколько хороша ваша поковка. Шлифовальные машины Noob — это универсальный вариант для большинства производителей ножей, который стоит вложений, если учесть, что каждый изготовленный вами нож в какой-то момент будет касаться точильщика.
Когда вы только начинаете, ручное шлифование — хороший способ узнать, как ведет себя металл. Но после определенного момента ваше время лучше потратить на другие дела. Реверсивная шлифовальная машина с 9-дюймовым диском и регулируемой скоростью позволяет сэкономить часы на ручной чистовой обработке ножа и является лучшим способом получить плоскую поверхность.Рассматривая свои расходы, помните, что наждачной бумаги хватит только на одно или два лезвия, прежде чем ее можно будет использовать на ручках. Для достижения наилучших результатов используйте аэрозольный клей, чтобы прикрепить тонкий слой резины или картонной коробки для хлопьев к диску, затем используйте аэрозольный клей, чтобы прикрепить наждачную бумагу к резине или картону.
Если вы планируете купить этот тип оборудования, вам следует подумать о добавлении регулятора скорости, чтобы максимально использовать типы материалов, с которыми вы можете работать. Хотя вы можете приобрести шлифовальные и шлифовальные машины со встроенными регуляторами скорости, более экономичным вариантом является использование регулятора скорости с частотно-регулируемым приводом (VFD).Если вы покупаете шлифовальный станок и шлифовальный станок с трехфазными двигателями, вы можете использовать контроллер скорости VFD совместно с обоими устройствами (что сэкономит вам около 600 долларов). Кроме того, контроллеры с регулируемой скоростью продлевают срок службы ремня, так что вы сэкономите много денег на ремнях. В течение срока службы кофемолки вы, вероятно, потратите на ремни в три раза больше, чем на покупку кофемолки.
Через некоторое время у вас может появиться желание перейти к чему-то новому. Многие мастера по изготовлению ножей решают заняться ковкой.
Комплект для ковки (2500-3000 долларов США)
Ковка не только позволяет перемещать горячий металл, но и позволяет выполнять другие операции, такие как термообработка и сварка.
- Стартовый комплект, плюс
- (опция) Промежуточный комплект, плюс
- Forge (600 долларов)
- Наковальня ($ 900 +)
- Flypress (300-800 долларов)
- Щипцы (200 долларов за 5 пар)
- Молотки (200 $)
Ковка не обязательна для изготовления ножа, и она не даст лучшего лезвия (по крайней мере, от новичка до среднего уровня мастерства).Независимо от того, хотите ли вы потратить много лет на овладение искусством ковки лезвий или просто стучать по горячей стали, ковка — это очень весело. Помимо изучения металлургии, вы получите хорошую тренировку: многие люди с удивлением обнаруживают, насколько физически требовательна ковка.
Ковка также является отличным способом сэкономить деньги на инструментах, поскольку дает возможность изготавливать собственные клещи, молотки и другие инструменты для изготовления ножей. Если это звучит привлекательно, возможно, стоит рассмотреть наш пятидневный курс «Основы кузнечного дела», где вы будете развивать свои навыки, а также инструменты. В конце курса вы получите набор основных инструментов и газовую кузницу, а также навыки их использования.
После этого у вас, вероятно, будет достаточно знаний и опыта, чтобы определить свои следующие шаги. Описанные выше схемы обеспечивают прочную основу для развития и обновления по мере расширения ваших навыков изготовления ножей. Вы можете заинтересоваться изготовлением ножен, скримшингом или изготовлением дамасской стали. Вы даже можете решить заняться изготовлением ножей в качестве коммерческого предприятия, например, в качестве мастера по изготовлению лезвий, изготовителя производственных ножей или учителя.Оборудование становится более дорогим вложением, но потенциальная прибыль соизмерима.
- Стальная ленточная пила (1200 долл. США)
- Ленточная пила по дереву (600 $)
- Печь для термообработки (2500 долл. США)
- Гидравлический кузнечно-прессовый пресс 25 т (7000 долл. США)
- 25 кг отбойный молоток (10 000 долл. США)
- Сталепрокатный стан (2000 долл.
США)
- Твердомер по Роквеллу (2000 долларов)
- Устройство для прошивки кожи Tippmann Boss (2600 долларов)
Ваши интересы будут направлять вас к ресурсам и сообществам, которые будут способствовать вашим будущим инвестициям в изготовление ножей, а изготовленные вами лезвия помогут финансировать ваши занятия по мере того, как вы продолжаете учиться и расти.Начав с правильного отношения, вы настроите себя на то, чтобы заниматься изготовлением ножей так, чтобы это окупалось.
DIY easy full blade нож для травления металла
Помогите нам продвигать наши проекты DIY. Щелкните выше, чтобы поделиться страницами или изображениями в социальных сетях.
Эти короткие обучающие видеоролики показывают, как легко создать детальную гравировку металла лезвия, используя соленую воду, винил и автомобильное зарядное устройство на 12 вольт.
Кельтский тесак с лезвием из травленого металла и корешком.Изготовлен из одной из заготовок для ножей Тесака.
Посмотрите этот короткий видеоролик, чтобы узнать, как легко наносить и использовать шаблоны для маркировки от Marking Methods Inc. Мы разработали двухцветный логотип с негативными и позитивными элементами дизайна. Логотип был вытравлен с использованием зарядного устройства для аккумуляторов и соленой воды в качестве раствора электролита.
DIY Easy Crafts
Полное онлайн-руководство по изготовлению ножей
ТРАВЛЕНИЕ МЕТАЛЛА
После завершения травления мы отполировали лезвие ножа наждаком с зернистостью 1500.Пожалуйста, посмотрите короткое видео, размещенное выше, чтобы увидеть, как именно было выполнено травление ножа с полным лезвием. Помните безопасность прежде всего.
Смешайте раствор соленой воды. Примерно 2 столовые ложки соли на литр воды. Для протравливания лезвия мы использовали зарядное устройство для ухода за аккумулятором на 12 В. Положительный кабель был подключен к ножке ножа. Мы обернули небольшой кусок марли и прижали его к отрицательному выводу. Окуните марлю в соленую воду и снимите ее. Он должен быть влажным, но не насквозь.Будьте очень осторожны, чтобы не прикасаться руками к металлическим предметам, прикоснитесь марлей к лезвию ножа, где вы хотите, чтобы процесс травления начался. Время будет варьироваться в зависимости от протравливаемого материала. Для этого лезвия из стали 1095 марля удерживалась на месте примерно 15 секунд. Затем переместите марлю и повторяйте, пока все лезвие не будет протравлено. Для этого лезвия мы хотели произвести глубокое травление и повторить процесс травления еще 15 секунд. Убедитесь, что лезвие касается только влажной марли. Если металлический зажим коснется, он выгнется и повредит сталь.
Травление металла — отличный способ улучшить лезвие или позвоночник практически любого ножа. Дизайн ограничен только вашими художественными способностями. Посмотрите на примеры металлического пламени, волн и даже патриотического орла.
Теперь вы можете легко улучшить качество ваших металлических гравюр с помощью точных виниловых трафаретов машинной резки. Посмотрите это короткое видео, чтобы узнать, как на станке для резки Silhouette Cameo можно создавать красивые детализированные трафареты для травления металла.
Как легко выгравировать рисунок на любом лезвии ножа. Травление металла можно производить разными способами. Мы используем автомобильное зарядное устройство на 12 В, соленую воду и прозрачную пленку, чтобы быстро и легко создать красивый металлический узор с гравировкой.
Посмотрите на металлическую гравировку на этом проекте Viking Battle Axe. Этот топор в стиле викингов был взят из старого ржавого наконечника топора.
Начните с нанесения и вырезания прозрачного прозрачного переводного листа. Мы купили это в магазине Michaels Art.Создайте прозрачность, чтобы покрыть любые области, которые не будут вытравлены. Защитите тонкий край лезвия и корешок лаком для ногтей. Дополнительные детали, такие как пятна, также можно добавить с помощью лака для ногтей.
Изучите все профессиональные приемы в этом коротком обучающем видео по травлению металла из нержавеющей стали.
Как сделать нож из дамасской стали — The Shed
Сталь для изготовления ножей
Изготовители ножей часто предпочитают высокоуглеродистые стали, потому что их можно заточить до очень тонкой кромки, и они будут держать эту кромку.Их также можно подвергать различной закалке, чтобы можно было применять более или менее закалку к краю лезвия и позвоночнику щек для достижения гибкости и получения более твердой и хрупкой кромки. Однако в большинстве инструментальных сталей содержится какой-либо сплав для придания различных желаемых характеристик.
Марганец и кремний добавляют в процессе производства стали для удаления серы, кислорода и фосфора из расплавленной смеси. Марганец, никель, кремний, хром, ванадий, молибден и вольфрам повышают прочность.Молибден также помогает стали не стать слишком хрупкой. Марганец улучшает обрабатываемость стали. Хром помогает стали противостоять коррозии, но может ослабить ее, поэтому обычно в него входит никель, который также помогает противостоять коррозии, но придает некоторую прочность и улучшает прокаливаемость.
1095 и 5160 обычно используются в ножах ручной ковки, потому что они недороги, просты в работе и легко поддаются ручной ковке. Обе они изготовлены из стандартной углеродистой стали и представляют собой надежный и удобный нож.1095 получает свои характеристики из-за высокого содержания углерода. Он обычно используется в промышленности для изготовления сельскохозяйственного инвентаря, такого как лезвия скребков, диски, бороны и экскаваторные лопаты. 1095 — легкодоступная и распространенная сталь.
5160 имеет гораздо меньше углерода, но хорошие характеристики износостойкости получены благодаря добавлению небольшого количества хрома. Этот небольшой процент хрома улучшает прокаливаемость и износостойкость, но этого недостаточно для повышения коррозионной стойкости. Эта сталь используется в промышленности там, где требуется очень твердая и износостойкая поверхность, такая как шестерни, шестерни, коленчатые валы и поверхности подшипников.Он также используется для листовых рессор, которые являются обычным источником стали для изготовления ножей. Обе эти стали относительно просты в обработке и закалке.
О1 — настоящая инструментальная сталь; легированная сталь, предназначенная для изготовления инструментов. Как таковые его характеристики обусловлены разнообразием и влиянием сплавов в смеси. Он имеет высокое содержание углерода для твердости, но содержание марганца улучшает его характеристики в кузнице. Содержание хрома увеличивает закаливаемость и износостойкость. Добавки ванадия и вольфрама образуют невероятно износостойкие частицы карбида ванадия и карбида вольфрама.Его обычно используют для сверл. Сталь O1 может подвергаться различной закалке, и она хорошо удерживает кромку.
L6 аналогичен O1 в общем классе легированных, закаленных в масле инструментальных сталей. Из-за более низкого содержания углерода он имеет лучшую ударопрочность, чем более высоколегированные типы, из-за относительно высокого содержания никеля. Сталь L6 часто считается одной из лучших сталей для изготовления ножей, а также часто используется для изготовления пильных полотен. Ножи из стали L6 не устойчивы к коррозии.
Дамасская сталь — Руководство для начинающих
Читатели нашего Руководства по ножевой стали часто спрашивают меня о Дамасской стали . Эта привлекательная, но загадочная сталь захватила воображение многих, поэтому я постараюсь объяснить, что это такое и как ее производят.Слово «Дамаск» восходит к средневековым западным культурам и относится к более раннему стилю мастерства, впервые появившемуся в Индии около 300 г. до н. Э. В то время это мастерство было плодотворным и, вероятно, было названо в честь региона, который прославил его.
Примерно в то же время арабская культура представила сталь Wootz в сирийском городе Дамаск, где этот материал привел к процветанию оружейной промышленности. Дамаск импортировал сталь Wootz из Персии и Шри-Ланки для производства и использования гибридных стальных лезвий, известных своей прочностью. Очевидно, люди, стоящие за этой технологической разработкой, понимали, как сочетание различных металлов может создать оружие большей прочности по сравнению с оружием, сделанным из чистой стали.
>> Рекомендуемые ножи из дамасской стали на BladeHQ <<
Следовательно, дамасская сталь не является чистой.Собственно, в этой уникальности и очарование, и загадка. Материал характеризуется множеством полос и пятен, сваренных вместе узорным способом для создания декоративных лезвий любой формы и / или длины, которые не могут расколоться. Идентификация композитов в оригинальной дамасской стали до сих пор остается неизвестной, поскольку не существует никаких записей, описывающих их. Тем не менее, современное производство стали в Дамаске следует практике комбинирования чистых металлов в зависимости от личных предпочтений и потребностей. Хотя слесарии могут выбирать и смешивать материалы для формования стальных заготовок, железо отдают предпочтение за его твердость и стойкость, повышенные твердостью.
Исторически сложилось так, что дамасская сталь приобрела несколько загадочную репутацию, поскольку первые упоминания о ней исчезли примерно в 1700 году нашей эры, что указывает на упадок узорчатых мечей, производство которых прекратится примерно через пятьдесят лет. Однако древние традиции и значение дамасской стали никогда не забывались, отсюда и процветающая промышленность, существующая сегодня.
Состав стали
Науки, лежащие в основе дамасской стали и производства стали, весьма сложны, но они подтверждают изобретательность и сложность, с которой методы и процессы Дамаска стали известны и уважаемы.Металлургия и химия служат основой для состава и множества применений, необходимых для производства и использования стали.
Интересно, что дамасская сталь считалась чем-то вроде «суперпластика» не из-за некоторой идеи, что это не настоящий металл — хотя она никогда не была чистым в этом смысле, — а из-за долговечности, приписываемой предыдущему образцу. Несмотря на то, что различные типы современной стали заменили лезвия из дамасской стали по своим характеристикам, химическая структура, присущая первоначальным производственным процессам, в которых использовались последние, делала лезвия того времени исключительно жесткими и мощными.
С 1973 года современные лезвия из дамасской стали изготавливаются из различных марок стали, свариваемых вместе, в результате чего получается заготовок . Эти заготовки также обычно содержат полосы железа для обеспечения необходимой прочности на молекулярном уровне. В результате они растягиваются и накладываются друг на друга в соответствии с потребностями, обозначенными конкретным применением лезвия и предпочтениями владельца лезвия. Это указывает на то, что лезвия из дамасской стали производятся не на конвейере, а на основе индивидуальной настройки.
Процедура проста: стальные слитки образуют заготовки, которые складываются как «бутерброды» внутри других типов металлов. Полученный продукт может состоять из сотен слоев и обязательно будет иметь твердую плотность и разнообразный дизайн. Этот проверенный процесс всегда обеспечивает целостность и уникальность дамасской стали.
Тем не менее, основной состав дамасской стали состоит из двух дихотомических структурных типов: пластичности и хрупкости.

Это структурное явление гарантирует, что дамасский клинок легко режет и остается прочным. Выпуклая шлифовка обеспечивает остроту тонкости кромки, так что нарезанный материал уступает место сторонам во время хода и, таким образом, сводит к минимуму «прилипание», которое часто происходит с лезвиями с более гладкими кромками.Следовательно, структурная хрупкость требует выпуклой шлифовки.
На более глубоком уровне в стали образуются углеродные нанотрубки, обеспечивающие пластичность и постоянную прочность в процессе ковки. Высокая концентрация углерода обеспечивает решающее качество целостности стали, что гарантирует высокую производительность. Это объясняет, почему углерод имеет решающее значение при разработке лезвий из дамасской стали.
В процессе ковки маленькие стальные слитки постепенно принимают желаемую форму лезвия.Это вызывает совмещение карбидов железа в полосы, образующие уникальные узоры. Эти узоры напоминают зерна стали Wootz из древней Индии и отражают старую эстетику и стиль производства. Металлисты сегодня могут воспроизвести многое в том же порядке, в котором, как известно, существовала дамасская сталь много веков назад.
Нагрев и отделка
Ниже приведены списки общих процессов нагрева и отделки для подготовки дамасской стали. Опять же, детали меняются в зависимости от потребностей и желаний, а также от типа металлов, соединяемых вместе.Основные процессы всегда остаются неизменными.
Термообработка дамасской стали включает предварительно установленную температуру от 1500F до 2000F, в зависимости от бандажа, и смесь цементита и аустернита.
- Соответственно заданная температура печи.
- Установить металлический блок в печь. Нагрейте весь цикл до начальной температуры.
- После нагрева выдержите сталь в течение десяти минут, чтобы она остыла.
- Закаленная сталь в масле. Перенести в жидкий азот на один час.
- Закалка стали в течение одного часа при температуре 350F. Это нужно сделать дважды.
Следующие шаги иллюстрируют последующую отделочную обработку.
- Нанесите на лезвие абразивную обработку.
- Протравить без предварительной полировки в растворе хлорида железа и дистиллированной воды, разбавленном в соотношении 50/50. Оставьте лезвие в растворе минимум на десять минут.
- Снимите лезвие и промойте его в проточной воде.
- Повторяйте цикл с пятиминутными интервалами до достижения желаемого результата.
- Погрузите лезвие в тринатрийфосфат для нейтрализации отделки
Как сделать лезвие из дамасской стали
На предыдущих этапах описывается, как нагревать и чистить дамасскую сталь, а ниже показан весь процесс. Следовательно, знание первых двух необходимо заранее, чтобы изготовитель металла мог выполнить то, что указано ниже. Этот порядок указывает как на особенности, так и на то, как все работает вместе.Производство лезвий из дамасской стали несложно, но требует постоянного ухода и кропотливости.Тем не менее, это трудоемкий процесс. Это необходимо для обеспечения желаемого внешнего вида и создания эффективного, хорошо сбалансированного лезвия.
- Соберите ингредиенты в тигель. Эти ингредиенты включают стекло и листья, которые, как известно, предотвращают окисление.
- Нагрейте тигель для плавления ингредиентов.
- Когда тигель достигнет точки охлаждения, осторожно извлеките металлические слитки и нагрейте их до температуры, необходимой для ковки.
- Молоток по металлу, пока он горячий.Этот этап включает в себя описанное выше «сэндвич». После того, как металл остынет, повторно нагрейте его, чтобы снова ковать. При необходимости повторите этот цикл, чтобы заострить края и придать форму лезвию.
- Когда окончательная форма будет достигнута, разрежьте лезвие и выковайте окончательные детали вручную.
- Удалите излишки науглероженного металла с поверхности лезвия.
- Вставьте канавки и просверлите отверстия в поверхность лезвия по мере необходимости или желанию.
- Разогреть. Снова сожмите лезвие. Отполируйте, чтобы привести лезвие в почти окончательную форму.
- Протравите поверхность лезвия кислотой для улучшения рисунка.
- По окончании тщательно удалите кислоту с поверхности лезвия.
Вот отличное видео, демонстрирующее процесс:
Ножи из дамасской стали
Ножи из дамасской стали бывают разных типов для любого количества целей, от кемпинга и выживания до рубки леса и охоты. Композитные элементы, соединенные вместе, чтобы сделать нож из дамасской стали, обязательно зависят от типа ножа и условий, в которых он предполагается и / или предназначен для использования.Некоторые распространенные типы перечислены ниже:
- Ножи для резьбы
- Охотничьи ножи
- Зубчатые ножи
- Шланговые ножи
- Такелажные ножи
- Тактильные складные ножи
- Тактильные фиксированные лезвия
Прекрасная вещь в любом типе Дамасский нож по своей конструкции выдерживает любые приложенные к нему силы. Дамасский нож не только прочен, но и долговечен.
Ниже приведены несколько прекрасных примеров дамасских клинков, с которыми я столкнулся.Большинство ведущих мировых брендов, таких как Spyderco, Benchmade, Kershaw и другие, недавно выпустили ограниченные серии в Дамаске.
Почему мы любим ножи из дамасской стали
Любители ножей любят ножи из дамасской стали по многим причинам. Это замечательно, потому что такое разнообразие отражает присущую Дамаску универсальность, которой нет у других клинков. История дамасской стали также привлекает внимание, поскольку она содержит тайну, которая создает ощущение интриги и значительно усиливает древние традиции.
Наиболее распространенные черты ножей из дамасской стали, которые энтузиасты считают идеальными, — это эстетика и высокая производительность. Ножи из дамасской стали украшены стильными узорами, которые металлисты выгравируют на лезвии в процессе ковки. Нет двух одинаковых дамасских ножей. На самом деле каждый нож — единственный в своем роде и ценный как выразительное произведение искусства.
>> Рекомендуемые ножи из дамасской стали на BladeHQ <<
Что касается высоких характеристик, то кованные вместе богатые углеродом металлы создают ощущение силы, присущее многим современным конструкциям лезвий.Это распространяется на молекулярный состав лезвия, а также на точность и осторожность, которые типичны при производстве, что делает такую мощность синонимом дизайна Дамаска.
Стоит ли владеть и использовать ножи из дамасской стали? Опять же, ответ субъективен. Владельцы клинков, вероятно, согласятся с тем, что ножи из дамасской стали лучше подходят в определенных условиях по сравнению с другими. Два обычно приветствуемых сценария, как описано выше, — это любовь к уникальности стиля и художественных узоров, а также использование оружия, как это видно на охоте и военных подвигах, хотя многие повара также владеют дамасскими ножами.Эти ножи особенные и ценятся. Действительно, сегодня они пользуются уникальным авторитетом среди коллекционеров ножей.
Спустя 2000 лет стиль и традиции Дамаска по-прежнему сильны, и, в свете их таинственности и особого качества, они, несомненно, просуществуют еще долгое время.
Как сделать нож из старого лезвия
Создание ножа — это интересный проект на нескольких уровнях. Вы создаете фундаментальный инструмент — один из первых когда-либо созданных инструментов — и каждый раз, когда вы берете его в руки, вы думаете: «Ого, я сделал это своими руками.«А поскольку вы делаете нож, вы сможете отрегулировать его форму в соответствии со своими потребностями. Самая сложная часть изготовления ножа — это лезвие. Если у вас есть под рукой кузница, и вы можете достать хорошую инструментальную сталь, это прекрасно. Если вы этого не сделаете, вы все равно сможете сделать нож, используя старый аппалачский трюк: переработку. Именно этим мы и займемся в этом проекте.
Старые пильные полотна почти всегда изготавливаются из высококачественной стали. Вы можете найти их в изобилии на своп-встречах, гаражных распродажах, распродажах и т. Д.Самым большим преимуществом использования старой пилы является отсутствие необходимых вам металлургов. Лезвие уже имеет правильную твердость, чтобы удерживать лезвие, поэтому вам не нужно обрабатывать сталь, чтобы из нее получился хороший нож. Однако заготовки, вырезанные из пилы, иногда бывают слишком гибкими, но вы можете обойти это (или с этим).
Сталь в этом ноже ручной работы не будет сверхтвердой. Это не идеально, потому что ваш нож быстро потеряет острие, если вы попытаетесь разрезать дерево, разрезать картон или использовать его в качестве отвертки.Но более мягкая сталь хороша тем, что вы можете вернуть ей острую как бритву кромку с помощью нескольких ударов точильного камня. На самом деле я предпочитаю более мягкую сталь, так как мне нравится острый край, и я ношу с собой небольшой точильный камень. Если вы можете сбрить волосы на руке, ваш нож достаточно острый.
Нож может иметь разные формы и стили. В этом проекте мы собираемся сделать так называемый нож с полным хвостовиком, то есть лезвие на всю длину входит в рукоятку ножа.Частичный хвостовик лишь частично заходит в рукоять. На мой взгляд, нож с полным острием — самый простой способ начать делать ножи. Он также дает прочный и прочный нож, который с меньшей вероятностью сломается на рукоятке.
Обращайтесь со своим ножом, и он сослужит вам хорошую службу.
Список материалов- Старое пильное полотно
- Папка для папок из тонкого картона
- Карандаш
- Ножницы
- Мел или мыльный камень
- Долото холодное
- Молоток для забивания зубила
- Прочная металлическая пластина для работы
- Напильники по металлу (грубые и мелкие)
- Проволочная щетка
- Грубая (00) стальная вата
- Легкое масло (3-в-1 или оружейное масло)
- Ацетон
- Тряпки
- Тиски
- Хомуты С-образные
- Древесина твердых пород (дуб, клен, вишня и др.)) для ручных весов
- Ручная пила (предпочтительно японская пила), если вы сами режете чешую
- Двухкомпонентная эпоксидная смола (медленного отверждения)
- 3/16 ″ латунный стержень
- Электродрель
- Сверло по металлу острое 3/16 дюйма
- Молоток шариковый
- Клейкая лента
- Рашпиль 4 руки или выкройка
- Наждачная бумага (зернистость 80 и 150)
- Скребок для шкафа (опция)
- Система заточки какая-то
- Беруши или наушники для защиты слуха
Ваш нож; ваш узор! Вы можете использовать существующий нож и нарисовать его на картоне, или вы можете создать свой собственный. В данном случае я создаю свою собственную форму на основе старого ножа, которым пользовались люди из мехового промысла. Используйте французскую кривую, чтобы ваши изгибы были последовательными и, что более важно, красивыми. Универсальная истина в том, что красивая форма инструмента или ножа — это хорошая форма. Когда вы довольны своей формой, вырежьте ее ножницами.В моем дизайне ножа я не включил валик или защиту для пальцев, как на иллюстрации выше.
Шаг 2: Перенесите дизайн на металлическую ложу.С помощью куска мела или мыльного камня нарисуйте узор на старом пильном полотне. Он не обязательно должен быть идеальным, так как вы будете использовать свои глаза на ходу, и вы будете устранять любые недостатки.
Шаг 3: Наметьте контур своего лезвия.Перед тем, как начать этот шаг, наденьте средства защиты органов слуха и поместите большой кусок металлической пластины под металлический приклад.Если у вас есть наковальня, не работайте непосредственно над ней, так как вы будете забивать закаленную сталь по закаленной стали. Что-то должно уступить, и вы действительно не хотите, чтобы это что-то сломалось от долота и где-то вонзилось в ваше тело.
Совместите долото с меловой линией, сделайте глубокий вдох и хорошенько постучите по нему. Он может не прорезать лезвие насквозь, но на данный момент достаточно будет нанесенного им надреза. Обрабатывая контур, перекрывайте отметки долота так, чтобы получилась одна сплошная линия, а не серия штрихов.Не торопись.
Шаг 4: Выньте лезвие.Создание прозрачности — вот что ломает металл. Я делаю это, кладя металл на край наковальни и ударяя по нему молотком как можно ближе к линии надреза и наковальне. Если у вас нет наковальни, поместите полотно пилы в тиски и постучите им как можно ближе к линии реза. Если долото поработало хорошо, лезвие ножа должно выскочить прямо из металла.
Шаг 5: Подпилите лезвие до нужной формы.Зубило не оставляет лучшего края, поэтому вам нужно обработать его напильником. На этом этапе важно помнить, что листовой металл является резонансным (вот почему люди играют на ручных пилах со скрипичным смычком). Звук опиливания листового металла — это настоящая пытка. Сведите к минимуму это, зажав лезвие как можно ближе к тискам и обязательно используйте средства защиты органов слуха.
Примечание : Не пытайтесь пока надеть нож острием.Лезвие должно быть перпендикулярно сторонам лезвия. Ищите ровную полосу шириной с лезвие. Это говорит о том, что вы готовы к следующему шагу.
Шаг 6: Запустите ручку.Мы делаем нож с полным хвостиком, что означает, что край лезвия будет виден по всей длине ручки. Мы сделаем это, добавив деревянную чешуйку с каждой стороны ручки. (Чешуя — это плоский кусок дерева, кости или другого материала, из которого будет изготовлена ручка.) Вы можете приобрести готовые весы или сделать свои собственные. В этом случае я делаю свои собственные весы из нескольких лежащих у меня планок дубовой отделки. Дважды нарисуйте контур лезвия на деревянной ложи, чтобы получилась форма двух чешуек. Затем вырежьте их.
Шаг 7. Очистите и отполируйте заготовку.Очистите бланк стальной ватой и небольшим количеством легкого масла (отлично подойдет оружейное масло или 3-в-1). После того, как он станет чистым (но не обязательно полностью блестящим), очистите заготовку ацетоном, чтобы удалить все следы масла.Смешивание масла и эпоксидной смолы не работает. Вы можете получить представление о том, как выглядит металл, из этого изображения. Помните, что масла не осталось, иначе весы не приклеятся к бланку. На этом этапе вы можете сделать столько, сколько захотите. Если вы хотите, чтобы ваш нож выглядел более деревенским, используйте немного масла и стальной ваты (00 или двойное зеро, что означает двойной ноль). Стальная вата бывает 00, 000 и 0000. Четверная полировка используется для тонкой полировки, например, для удаления ржавчины со ствола пистолета. 00 подходит для ножа, если только вы не очень дотошны.Я предпочитаю оставлять немного цвета в этом типе деревенского ножа.
Шаг 8: Настройте заклепки.Заклепки привлекательны и укрепят ваш нож. Сделай это правильно, и тебе не понадобится эпоксидная смола, но мне нравятся ремни и подтяжки.
У вас будет три заклепки через лезвие ножа. Начните с просверливания отверстия в хвостовике, совместите одну из чешуек с ручкой и просверлите шкалу. Обязательно подкрепите весы куском фанеры, чтобы она не раскололась при сверлении.Вставьте стержень через язычок и через шкалу плюс 1/8 дюйма, как показано выше. Вот где вы хотите в конечном итоге оказаться.
Приложите вторую шкалу к лезвию, добавьте примерно 1/8 дюйма и отметьте ее карандашом. Вы воспользуетесь этим позже.
Сделайте это еще два раза, и у вас должна получиться одна шкала с отверстиями, лезвие с отверстиями и одна шкала без отверстий. Вытяните стержень из отверстий, если он еще там, и используйте лезвие в качестве шаблона, чтобы отметить отверстия на шкале без отверстий.Убедитесь, что вы сверляете заднюю часть шкалы, правильно сориентировав шкалу (направьте конец к точке).
Теперь снова вставьте стержень в первое отверстие на внешней стороне первой шкалы, через ручку и через заднюю часть шкалы, которую вы только что просверлили. Он должен плотно прилегать к вашей отметке 1/4 дюйма, оставаясь на расстоянии 1/4 дюйма от поверхности шкалы. Если это правильно, отлично; отрежьте его ножовкой и вставьте стержень в следующее отверстие. Если нужно немного потрудиться, чтобы сделать все правильно, и если вам нужно немного просверлить, чтобы выровнять все, сделайте это.Просто постарайтесь, чтобы отверстия в дереве были круглыми. Как только он будет внутри, перейдите к следующему отверстию, ближайшему к лезвию, и повторите процесс. Теперь отделите чешую от лезвия, оставив стержни внутри. Отвертка или нож могут помочь.
Шаг 9: Прикрепите весы к ножу.Смешайте небольшое количество двухкомпонентной эпоксидной смолы размером с полдоллара и распределите ее по одной стороне заготовки ножа. (Не используйте пятиминутную эпоксидную смолу. Она слабая и не дает вам времени работать.) Поместите шкалу на эпоксидную смолу. Повторите этот процесс с другой стороны лезвия.
Теперь сдвиньте чешую обратно на лезвие ножа и нажмите на место. Возможно, вам придется использовать открытые тиски, чтобы вы могли установить весы на место, но они должны довольно легко перемещаться.
После того, как обе весы прикреплены и вы уверены, что весы находятся в нужном месте, наденьте один или два зажима на весы и затягивайте, пока не увидите небольшую форму эпоксидной смолы вдоль края между шкалой и заготовкой ножа.Это называется «выдавливанием» и является признаком того, что у вас хорошая связь. Как только он сочится, прекратите зажимать. Вам нужно немного эпоксидной смолы.
Обратите внимание, что стержень намного больше, чем на 1/8 дюйма. Это потому, что я не знал, сколько мне понадобится для заклепки, так что с каждой стороны больше 1/4 дюйма или больше.
Я обработал лишнюю штангу, отпилив ее. Он мягкий, поэтому не потребовалось много времени. Конечно, вы были умнее меня и извлекли пользу из моего опыта. Тебе не нужно этого делать.
Шаг 10: Заклепайте заклепки.Хуже всего в том, чтобы строить вещи самостоятельно, это то, что иногда вы не можете сфотографировать конкретный шаг. Так что я буду как можно более описательным. Положите нож на твердую поверхность, например, на металлическую пластину или наковальню, если у вас есть такая удача или вы знаете кого-нибудь, у кого она есть. Используя круглую сторону молотка с шариками (его не зря называют пейн), постучите по латунному стержню, перемещая удары легкими круговыми движениями, не ударяя по стержню прямо посередине.Это позволяет металлу немного размяться. Заклепайте заклепку на несколько минут, переверните нож и повторите. Если стержни не равны с каждой стороны, постучите по стержню, чтобы он немного выступал с другой стороны.
Продолжайте стучать, часто поворачивая нож, когда стержни (теперь заклепки) приближаются к рукоятке. Когда заклепка коснется чешуек, постучите немного сильнее и вытащите (слегка) заклепки. Продолжайте и сделайте два других.
Шаг 11: Сформируйте ручку и отшлифуйте ее.Зажмите ручку тисками и начните формировать ручку. У меня нет определенного способа сделать это, но я считаю, что рашпиль 4 в руке или рашпиль для изготовления выкройки отлично подходит. Не торопитесь, перемещая напильник в основном вверх и вниз под углом 45 градусов к лезвию. Работайте медленно. Если вы приблизитесь к лезвию с помощью рашпиля, вы можете притупить его.
Продолжая формировать рашпиль, часто проверяйте рукоятку, чтобы убедиться, что она симметрична и хорошо ложится на руку. По-медленнее; легче снять, чем положить обратно.
Когда ваша ручка приобретет желаемую форму, отшлифуйте ее наждачной бумагой с более тяжелым зерном (80 или около того), затем постепенно используйте все более мелкие зерна, пока ручка не станет гладкой, какой вы хотите. Идите вперед и отшлифуйте головки заклепок, чтобы они тоже немного приплюснули. Металл мягкий, и наждачная бумага отлично режет его.
При шлифовании древесины можно сказать, что вы готовы к следующей более мелкой зернистости, если не увидите следов от предыдущей шлифовки. Другими словами, когда вы переходите к зернистости 120 или 150 от зернистости 80, вы не должны видеть следов шлифования от зернистости 80.Если вы перейдете к более мелкой зернистости слишком быстро, у вас будет больше работы, когда вы перейдете на следующую шлифовку.
Шаг 12: Завершите ручку.Мне нравится смазанная маслом отделка, поэтому для обработки ручки я использовал конопляное масло. Вы можете использовать все, что вам нравится. Чем больше слоев масла, тем богаче будет вид, и вы обеспечите надежную защиту своей древесины.
Шаг 13: Заточите лезвие.Оберните тонко отшлифованную ручку картоном или кожей и закрепите изолентой.Зажмите ручку ножа в тисках острием, которое нужно заточить, вверх. Наденьте защитные очки и средства защиты органов слуха. Используя напильник, начните опиливать края лезвия вверх и вниз, удерживая файл под углом примерно 20–22 градуса к лезвию. Визуализируйте это расстояние, разрезав пополам угол в 45 градусов. Не перетаскивайте файл, так как он режет только при нажатии. Не подпиливайте слишком много в одном месте, иначе вы создадите низкую точку, что означает переделку, если вы хотите получить хороший, истинный край.
Сделайте несколько движений с одной стороны, затем с другой.Вы увидите, как ваш красивый плоский край исчезнет, когда вы удалите металл. Наблюдение за этим краем — хороший показатель того, насколько ровна ваша подача. Большинство людей (в том числе и я) склонны завинчивать наконечник из-за того, что либо недостаточно его опиливают, либо позволяют углу смещаться в сторону 25… 28… 30… Будьте осторожны и действуйте медленно. Остановитесь, когда у вас получится ровный и чистый край пропила.
Если вы все-таки испортили это, подпилите лезвие, как вы делали на шаге 5, и начните заново. В зависимости от размера лезвия наконечник может вибрировать.Зажатие небольшого C-образного зажима с куском обрезков древесины на задней части лезвия может уменьшить вибрацию (и держать ваших собак, кошек и других существ в пределах слышимости от звука).
Шаг 14: Заточите лезвие. Вы можете использовать любой метод заточки: алмазные камни, камни Арканзаса, японские мокрые камни, керамические палочки; это не имеет значения. Вы просто оттачиваете край. Когда вы закончите, отрежьте что-нибудь (желательно не себя), чтобы проверить лезвие.
Вы, конечно, захотите сделать такие ножны для ножа.Это в другой день.
Читатель AoM Роберт Хефферн любезно предоставил нам чертежи САПР для этого проекта: