Термическая обработка цветных сплавов :: Технология металлов
ТЕРМИЧЕСКАЯ ОБРАБОТКА МЕДИ И ЛАТУНИ
Медь.
Это наиболее распространенный в технике и промышленности цветной металл, обладающий высокой пластичностью, теплопроводностью и электропроводимостью. На основе меди образовывают технические сплавы — латунь и бронзу.
Медь применяют для производства листов, ленты, проволоки методом холодной деформации. В процессе деформации она теряет пластичность и приобретает упругость. Потеря пластичности затрудняет прокалку, протяжку и волочение, а в некоторых случаях делает невозможной дальнейшую обработку металла.
Для снятия иагартовки или наклепа и восстановления пластических свойств меди проводят рекристаллизационный отжиг по режиму: нагрев до температуры 450—500° С со скоростью 200—220° С/ч, выдержка в зависимости от конфигурации и массы изделия от 0,5 до 1,5 ч, охлаждение на спокойном воздухе. Структура металла после отжига состоит из равноосных кристаллов, прочность σв=190 МПа, относительное удлинение δ = 22%.
Латунь.
Сплав меди с цинком называют латунью. Различают двухкомпонентные (простые) латуни, состоящие только из меди, цинка и некоторых примесей, и многокомпонентные (специальные) латуни, в которые вводят еще один или несколько легирующих элементов (свинец, кремний, олово) для придания сплаву тех или иных свойств.
Двухкомпонентныелатуни в зависимости от способа обработки подразделяют на деформируемые и литейные.
деформируемые двухкомпонентные латуни (Л96, Л90, Л80, Л63 и др.) обладают высокой пластичностью и хорошо обрабатываются давлением, их используют для изготовления листов, ленты, полос, труб, проволоки и прутков разного профиля.
Литейные латуни применяют для отливки фасонных деталей. В процессе холодной обработки давлением двухкомпонентные латуни, как и медь, получают наклеп, вследствие которого возрастает прочность и падает пластичность. Поэтому такие латуни подвергают термической обработке — рекристаллизационному отжигу по режиму: нагрев до 450—650° С, со скоростью 180—200° С/ч, выдержка 1,5—2,0 ч и охлаждение на спокойном воздухе. Прочность латуни после отжига σ Β = 240-320 МПа, относительное удлинение δ = 49-52%·
Латунные изделия с большим внутренним напряжением в металле подвержены растрескиванию. При длительном хранении на воздухе на них образуются продольные и поперечные трещины. Чтобы избежать этого, изделия перед длительным хранением подвергают низкотемпературному отжигу при 250—300° С.
Наличие в многокомпонентных (специальных) латунях легирующих элементов (марганца, олова, никеля, свинца и кремния) придает им повышенную прочность, твердость и высокую коррозионную стойкость в атмосферных условиях и морской воде. Наиболее высокой устойчивостью в морской воде обладают латуни, легированные оловом, например ЛО70-1, ЛА77-2 и ЛАН59-3-2, получившие название морской латуни, их применяют в основном для изготовления деталей морских судов.
По способу обработки специальные латуни подразделяют на деформируемые и литейные. Деформируемые латуни используют для получения полуфабрикатов (листов, труб, ленты), пружин, деталей часов и приборов. Литейные многокомпонентные латуни применяют для изготовления полуфабрикатов и фасонных деталей методом литья (гребные винты, лопасти, детали арматуры и т.п.). Требуемые механические свойства специальной латуни обеспечивают термической обработкой их, режимы которой приведены в таблице. Для получения мелкого зерна перед глубокой вытяжкой деформируемые латуни для листов, лент, полос подвергают отжигу при температуре 450—500° С.
Таблица
Режимы термической обработки специальных латуней *
Марка сплава | Назначение обработки | Вид обработки | Темпера тура нагрева, °С | Выдержка, ч |
Деформируемые латуни | ||||
ЛА77-2 | Снятие наклепа | Рекристаллизацион- ный отжиг | 600-650 | 2-3 |
ЛО90-1 | То же | То же | 600-650 | 2-3 |
ЛО80-4 | Снятие напряжений | Низкий отжиг | 350—400 | 1-2 |
Литейные латуни | ||||
ЛА67-2,5 | Снятие напряжений | Рекристаллизацион- лый отжиг | 300-400 | 2-3 |
ЛКС80-3-3 | То же | То же | 250—300 | 1,5-2 |
ЛС59-1Л | » | » | 250—300 | 1-2 |
* Охлаждающая среда — воздух.
ТЕРМИЧЕСКОЕ УПРОЧНЕНИЕ БРОНЗЫ
Бронза — сплав меди с оловом, свинцом, кремнием, алюминием, бериллием и другими элементами. По основному легирующему элементу бронзы разделяют на оловянные и безоловянные (специальные), по механическим свойствам — на деформируемые и литейные.
Деформируемые оловянные бронзы
марок Бр.ОФ8-0,3, Бр.ОЦ4-3, Бр.ОЦС4-4-2,5 выпускают в виде прутков, лент, проволоки для пружин. Структура этих бронз состоит из α-твердого раствора. Основным видом термической обработки бронз является высокий отжиг по режиму: нагрев до 600—650° С, выдержка при этой температуре в течение 1—2 ч и быстрое охлаждение. Прочность после отжига σв — 350-450 МПа, относительное удлинение б= 18—22%, твердость НВ 70—90.
Литейные оловянные бронзы марок Бр.ОЦ5-5-5, Бр.ОСНЗ-7-5-1, Бр.ОЦСЗ,5-7-5 используют для изготовления антифрикционных деталей (втулок, подшипников, вкладышей и др.). Литейные оловянные бронзы подвергают отжигу при 540—550° С в течение 60—90 мин.
Безоловянные бронзы Бр.5, Бр.7, Бр.АМц9-2, Бр.КН1-3 идругие марки имеют высокую прочность, хорошие антикоррозионные и антифрикционные свойства. Из этих бронз изготовляют шестерни, втулки, мембраны и другие детали. Для облегчения обработки давлением бронзы подвергают гомогенизации при 700—750° С с последующим быстрым охлаждением. Отливки, имеющие внутренние напряжения, отжигают при 550° С с выдержкой 90—120 мин.
Наиболее часто в промышленности применяют двойные -алюминиевые бронзы марок Бр.А5, Бр.А7 и бронзы, добавочно легированные никелем, марганцем, железом и другими элементами, например Бр.АЖН10-4-4. Эти бронзы используют для различных втулок, фланцев, направляющих седел, шестерен и других небольших деталей, испытывающих большие нагрузки.
Двойные алюминиевые бронзы подвергают закалке и отпуску по режиму: нагрев под закалку до 880—900° С со скоростью 180—200° С/ч, выдержка при этой температуре 1,5—2 ч, охлаждение в воде; отпуск при 400—450° С в течение 90—120 мин. Структура сплава после закалки состоит из мартенсита, после отпуска—из тонкой механической смеси; прочность бронзы σ в = 550МПа, δ = 5%, твердость НВ 380—400.
Бериллиевая бронза Бр.Б2 — сплав меди с бериллием. Уникальные свойства — высокая прочность и упругость при одновременной химической стойкости, немагнитность и способность к термическому упрочнению — все это делает бериллиевую бронзу незаменимым материалом для изготовления пружин часов и приборов, мембран, пружинистых контактов и других деталей. Высокая твердость и немагнитность позволяют использовать бронзу в качестве ударного инструмента (молотки, зубила), не образующего искр при ударе о камень и металл. Такой инструмент применяют при работах во взрывоопасных средах. Бронзу Бр.Б2 закаливают при 800—820° С с охлаждением в воде, а затем подвергают искусственному старению при 300—350° С. При этом прочность сплава σ
ТЕРМИЧЕСКОЕ УПРОЧНЕНИЕ АЛЮМИНИЕВЫХ СПЛАВОВ
Деформируемые алюминиевые сплавы разделяют на неупрочняемые термической обработкой и упрочняемые. Кнеупрочняемым алюминиевым сплавам относят сплавы марки АМц2, АМг2, АМгЗ, имеющие невысокую прочность и высокую пластичность; их применяют для изделий, получаемых глубокой вытяжкой, упрочняют холодной обработкой давлением (нагартовкой).
Наиболее распространены сплавы, упрочняемые термической обработкой. К ним относят дюралюминий марок Д1, Д16, Д3П, в состав которых входят алюминий, медь, магний и марганец. Основными видами термического упрочнения дюралюминия являются закалка и старение. Закалку проводят при 505—515° С с последующим охлаждением в холодной воде. Старение применяют как естественное, так и искусственное. При естественном старении сплав выдерживают в течение 4—5 сут, при искусственном — 0,8—2,0 ч; температура старения — не ниже 100—150°С; прочность после обработки σ Β = 490 МПа, 6=14%. Сплавы Д1 и Д16 применяют для изготовления деталей и элементов строительных конструкций, а также изделий для летательных аппаратов.
Авиаль (АВ, АВТ, АВТ1)—это деформируемый сплав, обладающий более высокой пластичностью, свариваемостью и коррозионной стойкостью, чем дюралюминиевые; подвергают закалке в воде при 515—525° С и старению: сплавы АВ и АВТ — естественному, сплав АВТ1 — искусственному при 160° С с выдержкой 12—18 ч. Применяют авиаль для производства листов, труб, лопастей винтов вертолетов и т. п.
Высокопрочные (σв=550-700 МПа) алюминиевые сплавы В95 и В96 имеют меньшую пластичность, чем дюралюминий. Термическая обработка этих сплавов заключается в закалке при 465—475° С с охлаждением в холодной или горячей воде и искусственном старении при 135—145° С в течение 14—16 ч. Применяют сплавы в самолетостроении для нагруженных конструкций, работающих длительное время при 100—200° С.
Ковочные алюминиевые сплавы марок АК1, АК6, АК8 подвергают закалке при 500—575° С с охлаждением в проточной воде и искусственному старению при 150—165° С с выдержкой 6—15 ч; прочность сплава σΒ = 380-460 МПа, относительное удлинение δ = 7-10%.
Литейные алюминиевые сплавы называют силуминами. Наиболее распространены термически упрочняемые сплавы марок АЛ4, АЛ6 и АЛ20 Отливки из сплавов АЛ4 и АЛ6 закаливают при 535—545° С с охлаждением в горячей (60—80° С) воде и подвергают искусственному старению при 175° С в течение 2—3 ч; после термической обработки σв=260 МПа, δ = 4-6%, твердость НВ 75—80. Для снятия внутренних напряжений отливки из этих сплавов отжигают при 300° С в течение 5—Ю ч с охлаждением на воздухе. Жаропрочные сплавы марок АЛ 11 и АЛ20, идущие для изготовления поршней, головок цилиндров, топок котлов, работающих при 200—300° С, подвергают закалке (нагрев до 535—545° С, выдержка при этой температуре в течение 3—6 ч и охлаждение в проточной воде), а также стабилизирующему отпуску при 175—180° С в течение 5—10 ч; после термической обработки σв=300-350 МПа, δ=3-5%.
ТЕРМИЧЕСКАЯ ОБРАБОТКА МАГНИЕВЫХ И ТИТАНОВЫХ СПЛАВОВ
Магниевые сплавы.
Основными элементами в магниевых сплавах (кроме магния) являются алюминий, цинк, марганец и цирконий. Магниевые сплавы делят на деформируемые и литейные.
Деформируемые магниевые сплавы марок МА1, МА8, МА14 подвергают термическому упрочнению по режиму: нагрев под закалку до 410—415° С, выдержка 15—18 ч, охлаждение на воздухе и искусственное старение при 175° С в течение 15—16 ч; после термообработки σΒ = 320~430 МПа, δ = 6-14%. Сплавы МА2, МАЗ и МА5 термической обработке не подвергают; их применяют для изготовления листов, плит, профилей и поковок.
Химический состав литейных магниевых сплавов(МЛ4, МЛ5, МЛ12 и др.) близок к составу деформируемых, но пластичность и прочность литейных сплавов значительно ниже. Это связано с грубой литейной структурой сплавов Термическая обработка отливок с последующим старением способствует растворению избыточных фаз, сконцентрированных по границам зерен и повышению пластичности и прочности сплава.
Особенностью магниевых сплавов является малая скорость диффузионных процессов (фазовые превращения протекают медленно), что требует большой выдержки под закалку и старение. По этой причине закалка сплавов возможна только на воздухе. Старение литейных магниевых сплавов проводят при 200—300° С; под закалку их нагревают до 380—420° С; после закалки и старения σв = 250-270 МПа.
Магниевые сплавы можно применять, как жаропрочные, способные работать при температурах до 400° С. Вследствие высокой удельной прочности магниевые сплавы широко применяют в авиации, ракетостроении, автомобильной и электротехнической промышленности. Большим недостатком магниевых сплавов является низкая стойкость против коррозии во влажной атмосфере.
Титановые сплавы.
Титан является одним изважнейших современных конструкционных материалов; обладает высокой прочностью, повышенной температурой плавления (1665° С), малой плотностью (4500 кг/м3) и высокой коррозионной стойкостью даже в морской воде. На основе титана образовывают сплавы повышенной прочности, широко применяемые в авиации и ракетостроении, энергомашиностроении, судостроении, химической промышленности и других областях промышленности. Основными добавками в титановых сплавах являются алюминий, молибден, ванадий, марганец, хром, олово и железо.
Титановые сплавы марок ВТ5, ВТ6-С, ВТ9 и ВТ16 подвергают отжигу, закалке и старению. Полуфабрикаты (прутки, поковки, трубы) из сплава, дополнительно легированного оловом (ВТ5-1), проходят рекристаллизационный отжиг при 700—800° С в целях снятия наклепа. Листовые титановые сплавы отжигают при 600—650° С. Длительность отжига поковок, прутков и труб составляет 25—30 мин, алистов — 50—70 мин.
Высоконагруженные детали из сплава ВТ14, работающие при температуре 400° С, закаливают с последующим старением по режиму: температура закалки 820—840° С, охлаждение в воде, старение при 480—500° С в течение 12—16 ч; после закалки и старения: σв=1150-1400 МПа, 6 = 6—10%, твердость HRC56—60.
Источник:
Николаев Е.Н., Коротин И.М. Термическая обработка металлов токами высокой частоты М.: Высшая школа, 1984.
Режимы отжига бронз | Всё о цветных металлах и сплавах (бронза, медь, латунь и др)
ООО ВПО ПромМеталл http://bronza555.ru/
[email protected] +7-903-798-09-70 (звоните!)
СКЛАДСКУЮ СПРАВКУ МОЖНО СКАЧАТЬ ЗДЕСЬ
Режимы отжига бронз. Режим закалки и отпуска бронз (БрОФ, ОЦС, БрАЖ9-4, БрАЖН, БрБ2)
отсюда

20.01.2015
В табл. 17 представлены марки и режимы термической обработки основных промышленных дисперсионно твердеющих сплавов на медной основе.
Все эти сплавы претерпевают фазовые превращения в твердом состоянии и подвергаются закалке без полиморфного превращения. Закалка или обработка на твердый раствор преследует две цели: подготовить сплав к старению и добиться максимальной пластичности для дальнейшей деформации.
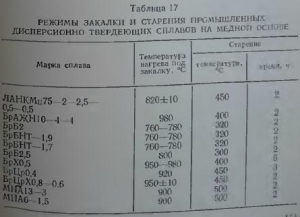
Если закалке подвергают нагартованный материал, то при нагреве под закалку в нем развиваются процессы возврата и рекристализации. Как и при рекристаллизационном отжиге высокая степень деформации (выше 30°) низкая температура и короткое время нагрева дают мелкое зерно Наоборот, малые степени деформации, длительное время нагрева и высокие температуры приводят к грубозернистым структурам. Крупные зерна могут образоваться вследствие нагрева под закалку в материале предварительно пластически деформированном на 5—15%.
Температура нагрева под закалку должна обеспечивать возможно бoлee полное растворение избыточных фаз в матричной фазе и находиться в двойной системе между линиями сольвуса и солидуса. Хотя процессы растворения избыточных фаз значительно ускоряются с повышением температуры, нагрев в непосредственной близости к пинии солидуса технологически нерационален. В этом случае из-за возможного перепада температур в садке и неточности теплового контроля возникает опасность пережога изделия Отсюда вытекает строгое требование контролировать температуру в закалочных печах с точностью +/- 10° С. Заметим, что слишком высокие температуры нагрева под закалку могут привести также к роет\ зерна до недопустимых размеров.
Время выдержки определяется полнотой процессов растворения избыточных фаз. Чем дисперснее избыточная фаза, тем быстрее она растворяется. Деформированные сплавы выдерживают меньшее время, чем литые. Если избыточная фаза полностью не растворена, то получить оптимальные свойства после старения не представляется возможным. Длительные нагревы, помимо задолженности печей, приводят к росту зерна, сильному окалинообразованию и нежелательному увеличению диффузионной зоны, состоящей из окислов легирующего элемента.
Охлаждение при закалке должно быть достаточно резким, чтобы исключить распад пересыщенного матричного раствора в процессе охлаждения. Закалка в воде дает большие остаточные термические напряжения и вызывает поводку и коробление изделия. Поэтому при выборе закалочных сред следует руководствоваться критическими скоростями.
Критические скорости охлаждения при закалке можно оценить из термокинетических диаграмм фазовых превращений. На рис. 50 приведена для примера термокинетическая диаграмма для латуни ЛАНКМц75—2—2,5—0,5—0,5 состава, % (по массе) : 75,6 Cu; 2,0 Al; 2,1 Ni; 0,61 Si, 0,68 Mn На диаграмме четко различаются два кинетических максимума, соответствующие двум стадиям распада:
1) высокотемпературной (выше 520° С) с образованием крупнопластинчатых выделений; 2) низкотемпературной (ниже 520° С) с образованием дисперсных частиц.
Сплавы на основе меди отличаются высокой прокаливаемостью из-за высокой теплопроводности. Например изделия из бериллиевой бронзы, обладающей наименьшей теплопроводностью, закаливаются в сечении 200 мм.
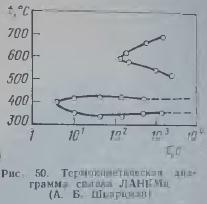
Если полуфабрикат подлежит старению, закалка может быть не очень резкой, так как температура максимального упрочнения при старении находится внутри температурного интервала стадии низкотемпературного распада, протекающего при непрерывном охлаждении. Поэтому важно не допустить высокотемпературного распада, при котором выделяется стабильная фаза крупных размеров, в связи с чем уменьшается вклад низкотемпературного распада в общее упрочнение. Полуфабрикаты, подвергаемые в дальнейшем пластической деформации, необходимо закаливать со скоростями не меньше критической скорости охлаждения.
Если промежуток времени между извлечением из печи и переносом в закалочную ванну относительно большой, то это может вызвать значительные изменения свойств и в пределах одного изделия, и по всей садке. Если конфигурация одиночного изделия проста, а масса большая, то колебания свойств невелики из-за не очень быстрой потерн температуры. Разброс свойств по садке может достигать значительных величин, так как после извлечения садки из печи изделия, лежащие сверху, остывают быстрее и эффект их закалки будет меньше по сравнению с изделиями, лежащими под ними. Поэтому конструкция закалочных агрегатов должна обеспечивать непосредственное погружение изделия из печи в охлаждающую ванну.
Качество закаленного металла контролируют металлографически либо по величине удельной электропроводности.
Температуру и продолжительность старения определяют экспериментально в каждом отдельном случае с учетом требуемых свойств конкретного полуфабриката или изделия. В зависимости от режима, структурных изменений и получаемого комплекса свойств старение подразделяют на полное, неполное и стабилизирующее.
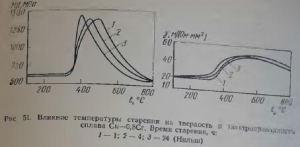
Дополнительное повышение прочности медных сплавов и твердости можно получить холодной деформацией независимо от того, когда ее вести — между закалкой и старением или после них. В обоих случаях при одинаковой степени деформации достигаются одинаковые твердость и прочность. Деформация после старения не представляет затруднений, так как материал достаточно пластичен. При необходимости получения наибольшей электропроводности деформация между закалкой и старением более выгодна.
Рассмотрим более детально принципы выбора упрочняющей термической обработки бериллиевых бронз. Растворимость бериллия в меди при 870° С составляет приблизительно 2,3% (по массе) и падает до 0,2% при комнатной температуре. При закалке с высоких температур в бериллиевых бронзах фиксируется пересыщенный твердый раствор и они приобретают способность к старению. Из-за опасности роста зерна сплавы БрБ2 и БрБ2,5 нагревают под закалку до температуры 770-790° С, а сплавы БНТ1,9 и БНТ1,7 — до 760-780° С. Повышение температуры нагрева под закалку способствует пересыщению твердого раствора бериллием и вакансиями. Оба эти фактора ускоряют распад при последующем старении. Однако пластичность сплавов при старении снижается и ухудшается штампуемость.
Снижение температуры нагрева под закалку интенсифицирует при старении прерывистый распад в сплаве БрБ2, который приводит к образованию грубой двухфазной структуры с некогерентными выделениями. Из за преимущественной локализации прерывистого распада по межзеренным границам сплав охрупчивается. Объемная доля зон приграничного распада в состаренной бронзе БрБ2 составляет 30, 20 и 12% при закалке с температур 760, 780 и 800° С соответственно.
Критическая скорость охлаждения бериллиевых бронз составляет 30—60° С/с Слишком медленное охлаждение при температурах ниже 580°С приводит к образованию по межзеренным границам сетки у’-фазы Замедленное охлаждение между 580 и 260° С обусловливает преждевременное выделение из твердого раствора фазы-упрочнителя и, следовательно, приводит к уменьшению способности к последующему старению Введение в бериллиевую бронзу никеля и кобальта заметно замедляет фазовые превращения, а следовательно, уменьшает критическую скорость охлаждения. Дисперсионное твердение бериллиевых бронз дает возможность получать широкую гамму свойств.
Обычно бериллиевые бронзы подвергают НТМО. Hиже приведены оптимальные режимы старения полосы БрБ2 толщиной 0,5 мм, обжатой после закалки на 40%:
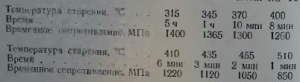
Предварительная холодная прокатка с обжатием 20-40% ускоряет прерывистый распад, но с увеличением обжатия от 50 до 90% он подавляется. Равномерный распад по всему объему обеспечивает получение высоких упругих характеристик в сплаве БрБ2.
Режимы старения выбирают в зависимости от требуемых физико-механических свойств. На рис. 52 показано влияние времени старения бериллиевой бронзы на временное сопротивление при разных температурах старения. Полное искусственное старение, обеспечивающее максимальную прочность, проводится при температуре (320±10)°С в течение двух часов. Режимы неполного искусственного старения, обеспечивающие заданный уровень свойств (пунктир на рис. 52), соответствуют восходящим ветвям кривых 1, 3 и 4 на рис. 52. Его проводят или при сравнительно низких температурах и длительных выдержках (режим 1 — 290° С; 2—3 ч), или при температуре полного старения, но укороченных выдержках (режим 3 — 320°С; 30—50 мин), и, наконец, при повышенных температурах и коротких выдержках (режим 1 — 370°С; 7—10 мин).
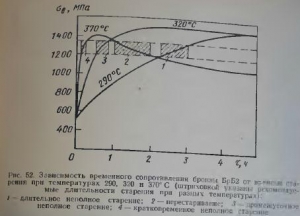
При решении вопроса, какому режиму старения — неполному старению или перестариванию — отдать предпочтение следует руководствоваться темп свойствами, которые являются определяющими в эксплуатации данного изделия. Это может быть повышенная ударная вяз кость удовлетворительная способность к формоизменению после старения, стабильность в работе, повышенная электро- или теплопроводность, минимальное коробление и деформация при старении, высокая коррозионная стойкость и т. д.
Неполное старение приводит к большей пластичности при заданном уровне прочности. Это связано с более быстрым ростом в процессе старения временного сопротивления по сравнению с пределом текучести. Технологическое время при неполном старении относительно невелико, и в ряде случаев требуется тщательный его контроль.
Перестаривание облегчает контроль при длительных выдержках, так как свойства полуфабриката не слишком сильно зависят от времени. Большая полнота выделения упрочняющей фазы обусловливает более высокий уровень электропроводности у, минимальный уровень остаточных напряжении, сравнительно высокий модуль упругости и повышенную пластичность (рис. 53).
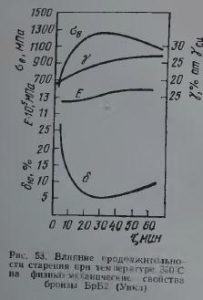
В большинстве случаев термическая обработка продолжительностью более двух часов экономически невыгодна, а менее 10 мин — не позволяет осуществлять эффективный контроль.
Ступенчатое или двойное старение можно проводить по двум схемам: 1) неполное старение с последующим повторным старением. Такой процесс позволяет легко контролировать пластичность, прочность и твердость и заключается в длительном нагреве ниже 320° С или кратковременном выше 320° C с последующим непродолжительным старением выше первоначальной температуры; 2) старение на максимальную прочность при высокой температуре в интервале 320-360° С с последующим длительным старением (8-24 ч) при 260-290° С. При такой обработке выделяется несколько большее количество упрочняющей у-фазы, в результате чего повышают прочность, твердость, электропроводность Скорость охлаждения после старения не лимитируется.
Остаточные напряжения после старения можно уменьшить низкотемпературным отжигом без изменения прочности и твердости. Изделие нагревают до 150-200° С в течение 15-30 мин. Эту обработку часто используют для снятия машинных, правочных или формирующих напряжении и таким образом стабилизируют форму и размер изделия.
Некоторые темы по термообработке бронз с Чипмейкера
Понравилось это:
Нравится Загрузка…
Похожее
Некоторые темы по термообработке бериллиевой бронзы с Чипмейкера
ООО ВПО ПромМеталл http://bronza555.ru/
[email protected] +7-903-798-09-70 (звоните!)
Складскую справку можно скачать здесь
Аналогичная тема по меди, бронзам и латуни здесь
Закалка бериллиевой бронзы
Подскажите, пожалуйста, режимы закалки деталей из бериллиевой бронзы БРБ2
термически упрочняется
закалка+старение (t 800, вода + старение 300-350)
прочность 1200МПа
- Старение при 320-350 градусов, если не изменяет память 2-3ч. Впрочем если деталь не сильно ответственная и тонкостенная, то можно и 1ч. Мы ленту до 0,5 делаем без закалки, сразу старение. После старения и появятся упругие свойства.
Вопрос по БрБ2
какую термообработку надо сделать проволоке БрБ2 ф 3.0мм, если она очень твердая и ломается на изгиб, чтобы она приняла просто твердое состояние соответственно ГОСТ ?
- Ваша проволока находится в нагартованном состоянии. Попробуйте ее нагреть до 760-780*С и закалить в воду, а затем отпустить при 300-350*С. Вообще то эта бронза сильно упрочняется в результате т.о. и даже после выше упомянутой обработки пластичность будет всего 3-5%.
- можно глянув на рисунки взятые из книги «Промышленные цветные металлы и сплавы» (неплохая, кстати, книга по цветным металлам) поиграть с температурой и временем старения, в зависимости от того для чего вам нужна эта бронза.
Пружина из БрБ2
взяли готовую пружину (по чертежу — из БрБ2), закалили 750 градусов — в воду, пружина стала пластичной. Завили по размерам, которые нам нужны. Облагораживаем — 340 градусов 4 часа. Пружина упругих свойств не приобретает. Толщина проволоки — 2,5 мм. Печь муфельная. Что не так?
- Закалите из 780, старение проведите при 320 (плюс минус 5). Твердость должна быть 38-40. Если твердости не даст, значит подмена материала (на берилку очень похожа бронза БрКМЦ, часто путают сдуру), или не правильно показывают температурные датчики. Особенно вреден перегрев, при старении, 340, мне кажется, многовато. Если при старении получается перегрев, материал нужно перекаливать. При 780 выдержите полчаса. Скорость нагрева — любая.
Старение брб2
занимаемся изготовлением контактов из брб2, ее рекомендуют старить в защитной среде во избежания окисных пленок. Может кто посоветовать печь?
- Бр.Б2 калят от 750° в воде и здесь, как ни крути, получишь диэлектрическую плёнку (оксид CuO+гидрооксид Cu(OH)2+шпинель CuBeO2 ИМХО). Старение ~300°С около 4-6 часов (на максимальную упругость).Выводы:1) при закалке образуется «оксидная» плёнка и её нужно удалять;
2) старение усиливает толщину плёнки, но не существенно, следовательно, удалять плёнку лучше после старения;
3) зачем нужна защитная атмосфера, если в любом случае нужно выполнять зачистку контакта?
4) если даже небольшой окисел от закалки допустим, а значит допустимо значительное снижение эл. проводимости, то не понятно почему используется медный сплав?
Опять Старение БрБ2
Отжиг и закалка бериллиевой бронзы(2,5%Be)
Есть задача сделать из бериллиевой бронзы(содержание бериллия 2,5%) упругие контакты.
Как можно в домашних условиях сначала сделать мягкой бронзу(отжечь), а потом придать нужную форму и закалить?
У меня никак не получается закалить, туфта какая то выходит, нету никакой упругости.
- Отжига как такового нет, есть старение Из букваря «Бронзу Бр.Б2 закаливают при 800—820° С с охлаждением в воде, а затем подвергают искусственному старению при 300—350° С. При этом прочность сплава σΒ=1300 МПа, твердость HRC37—40.«
- Немного дополню. После закалки на воду бронза становится мягенькой и пластичной, а вот остальное получают после старения. Если нужна сложная форма, то в стальной оснастке повторяющую форму. Гнут частенько после закалки.
Закалка Брб2
Посоветуйте хорошую литературу по закалке бериллевой бронзы Брб2, интересует конкретный вопрос которого не нашел в литературе, а именно время выдержки на температуре дисперсионного твердения в зависимости от толщины материала из которого изготавливают пружины (0,5 ,1,2,3 мм и т.д. )
- Почитайте ГОСТ 1789-70. По конк. вопросу — рекомендуемое время старения 3 часа многократно превышает время прогрева садки, так что не заморачивайтесь…Тут другие подводные камни. Б. бронзой занимался 5 лет, работая на приборном заводе, правда пружины были не толще 1 мм — контакты
Закалка бериллиевой бронзы
Подскажите, пожалуйста, режимы закалки деталей из бериллиевой бронзы БРБ2
- закалка+старение (t 800, вода + старение 300-350). прочность 1200МПа
- Старение при 320-350 градусов, если не изменяет память 2-3ч. Впрочем если деталь не сильно ответственная и тонкостенная, то можно и 1ч. Мы ленту до 0,5 делаем без закалки, сразу старение. После старения и появятся упругие свойства.
Фиксация угла пластины из БрБ2
Делаем контактны пластины из ленты ДПРНМ 0,3 НД БрБ2. Их вырубаем и гнем на угол 4-60. После гибки угол соответствует 5-60. Далее проводим дисперсионное твердение в заневоленном состоянии. После т.о. пластина разгибается на 3015`-3040`. В приспособлении сделали высвобождение под углом, ничего не изменилось. Посоветуйте пожалуйста варианты фиксации угла.
- Можно попробовать после старения, охлдить и не разбирая, в той же приспособе отпустить еще на 250, пару часов. А ваще, трудно сказать какое там состояние поставки. Я бы сам закалил, но уже в согнутом состоянии (в приспособе, например), потом состарил, не разбирая с приспособления. Твердость закаленной и состаренной берилки должна быть 37 — 39 ед.
БрБ2 проблемы
Понравилось это:
Нравится Загрузка…
Похожее
Бериллиевые бронзы: состав, свойства, обработка
Бериллиевые бронзы — это сплавы меди с бериллием. Они применяются в промышленности для изготовления упругих элементов ответственного назначения (плоских и витых пружин, упругих элементов в виде гофрированных мембран, токопроводящих упругих деталей электрооборудования, пружинящих деталей электронных приборов и устройств и т.д.). Их отличают высокие: прочностные свойства, предел упругости и релаксационная стойкость, электро- и теплопроводность, сопротивление коррозии и коррозионной усталости. Они не магнитны, не дают искры при ударе, технологичны, т.е. хорошо штампуются, свариваются. Из бериллиевой бронзы изготавливают инструменты стойкие к образованию искры для работы на пожароопасных производствах. Бериллиевые бронзы мало склонны к хладоломкости и могут работать в интервале температур от -200°С до +250°С. К недостаткам этих сплавов относятся высокая стоимость и дефицитность бериллия, а также его токсичность.
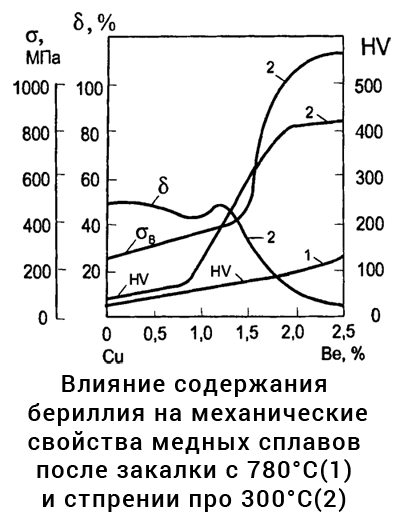
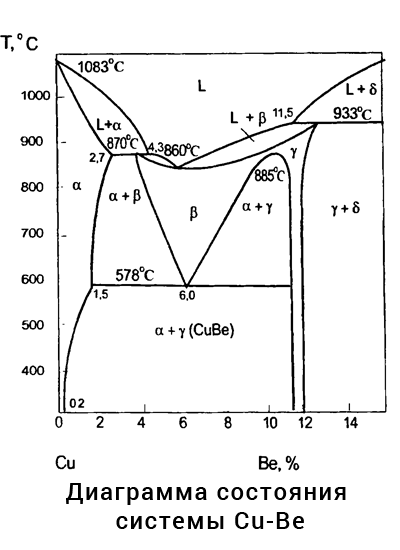
Оптимальными свойствами обладают сплавы, содержащие около 2—2,5 % Be. При дальнейшем увеличении содержания бериллия прочностные свойства повышаются незначительно, а пластичность становиться чрезмерно малой.
Согласно диаграмме состояния Cu-Be, в равновесии с α-твердым раствором бериллия в меди в твердом состоянии могут находиться фазы β и γ. Равновесная γ(CuBe)-фаза — твердый раствор на основе соединения CuBe — имеет упорядоченную ОЦК решетку. Такую же решетку, но неупорядоченную имеет β-фаза. Фаза β устойчива только до температуры 578°С, при которой она претерпевает эвтектоидный распад β → α+γ (CuBe).
Марка бронзы | Be | Ni | Ti | Mg | Примеси | Примерное назначение |
БрБ 2 | 1,8–2,1 | 0,2-0,5 | – | – | 0,15Al; 0,15Fe; 0,15Si; 0,005Pb; в сумме не более 0,5 | Прутки, проволока, листы, лента, полосы. Пружины и пружинящие детали ответственного назначения, мембраны, износостойкие детали всех видов, детали часовых механизмов, неискрящии инструмент |
БрБ 2,5 | 2,3–2,6 | 0,2–0,5 | – | – | 0,1Al; 0,15Fe; 0,15Si; 0,005Pb; в сумме не более 0,5 | |
БрБНТ 1,7 | 1,60–1,85 | 0,2–0,4 | 0,1–0,25 | – | 0,1Al; 0,15Fe; 0,15Si; 0,005Pb; в сумме не более 0,5 | |
БрБНТ 1,9 | 1,85–2,10 | 0,2–0,4 | 0,10–0,25 | – | 0,1Al; 0,15Fe; 0,15Si; 0,005Pb; в сумме не более 0,5 | |
БрБНТ 1,9Мг | 1,85–2,10 | 0,2–0,4 | 0,10–0,25 | 0,07–0,13 | 0,1Al; 0,15Fe; 0,15Si; 0,005Pb; в сумме не более 0,5 | |
БрБНТ | 0,4–0,7 | 1,4–1,6 | 0,05–0,15 | – | 0,1Al; 0,15Fe; 0,15Si; 0,005Pb; в сумме не более 0,5 | Листы, полосы, прутки. Детали машин стыковой сварки, электроды для сварки коррозионностойких сталей и жаропрочных сплавов |
Бериллиевые бронзы широко применяются за рубежом в промышленно развитых странах. Из них изготовляют плиты, листы, ленты, горячепрессованные прутки, сварные и бесшовные трубы, прессованные профили и другие полуфабрикаты. Для улучшения свойств бериллиевые бронзы дополнительно легируют небольшими добавками металлов VIIIA группы — кобальтом, никелем и железом. В марочном составе обычно оценивают суммарное содержание этих металлов.
Марка | Страна | Стандарт | Ве | Другие элементы и примеси |
С17000 | США | ASTM B194 | 1,60–1,79 | 0,20 Аl; 0,20 Si; (Niі+Co) > 0,20; (Ni+Со+Fе) = 0,6 |
С17200 | США | ASTM B194, В570 | 1,8–2,0 | (Ni+Со) > 0,20; (Ni+Со+Fе) = 0,6 сумма примесей не более 0,5 |
CuBe1,7 (2.1245) |
Германия | DIN 17666 | 1,6–1.8 | (Ni+Со) > 0,20; (Ni+Со+Fe) = 0,6 |
CuВе2 | Германия | DIN 17666 | 1,8–2,1 | (Ni+Со) > 0,20; (Ni+Со+Fе) = 0,6 сумма примесей не более 0,5 |
CuВе2РЬ (2.1248) | Германия | DIN 17666 | 1,8–2,1 | 0,20–0,6 РЬ; (Ni+Со) > 0,20; (Ni+Со+Fе) = 0,6 сумма примесей не более 0,5 |
С1700 | Япония | JIS130 | 1,6–1,79 | (Cu+Ве+Nі+Со+Fе)>99,5; (Ni+Со) > 0,2; (Ni+Со+Fе) > 0,6 |
С1720 | Японии | JIS Н3130 | 1,8–2,0 | (Cu+Ве+Nі+Со+Fе)>99,5; (Ni+Со) > 0,2; (Ni+Со+Fе) > 0,6 |
Сu-Ве 250 | Англия | — | 1,8–2,0 | 0,25 (Со+Ni) |
Сu-Ве 275 | Англия | — | 2,13–2,8 | 0,3–0,6 (Со+Ni) |
V Ве | Франция | — | 1,6–1,9 | 0,15–0,35(Со+Ni) |
Термическая обработка бериллиевой бронзы
Предельная растворимость бериллия в меди в двойной системе Cu-Be при 870°С составляет 2,7% (по массе), и она резко уменьшается с понижением температуры. Это указывает на возможность применения упрочняющей термообработки к меднобериллиевым сплавам. Бериллиевые бронзы являются дисперсионно-твердеющими сплавами, причем эффект упрочнения при термической обработке у них максимальный среди всех сплавов на медной основе. Они подвергаются закалке и последующему старению.
Марка | Температура, °С | Обрабатываемость резанием, % (ЛС63-3 — 100%) |
Линейная усадка, % |
Коэффициент трения | |||||
литья | горячей обработки | отжига | закалки | старения | со смазкой | без смазки | |||
1) Низкотемпературный отжиг для повышения упругих характеристик, рекристаллизационный отжиг проводят при температурах 600–700°С. | |||||||||
БрБ2 | 1030‑1060 | 700‑800 | 760‑780 | 320 | 20 | 1,8 | 0,016 | 0,35 | |
БрБ 2,51) | 1030‑1060 | 700‑800 | — | 770‑790 | 300 | — | — | — | — |
БрБНТ 1,7 | 1030‑1060 | 700‑800 | — | 755‑775 | 300 | — | — | — | — |
БрБНТ1,9 | 1030‑1060 | 700‑800 | — | 760‑780 | 320 | — | — | — | — |
При термической обработке бериллиевых бронз существенным является выбор температуры нагрева под закалку (Tзак). Ее значение определяет полноту перевода легирующих элементов в твердый раствор и возможность его гомогонизации. С точки зрения указанных факторов, предпочтительно повышение температуры закалки.
Нагрев под закалку выше оптимальной температуры способствует дополнительному пересыщению твердого раствора бериллием (особенно для сплава БрБ2,5) и вакансиями. Оба эти фактора ускоряют распад твердого раствора при последующем старении, но повышение температуры закалки приводит к росту зерен α-твердого раствора, что приводит к понижению пластичности и упругих свойств и ухудшает штампуемость. Для получения мелкого зерна при нагреве до температуры закалки в структуре бронзы должно сохраняться некоторое количество равномерно распределенных включений избыточной β-фазы, которые препятствуют собирательной рекристаллизации α-твердого раствора. Получению мелкозернистой сгруктуры способствует также никель: дисперсные частицы фазы NiBe не растворяются полностью при нагреве под закалку и сдерживают рост зерен α-раствора.
Диапазон температур нагрева под закалку бериллиевых бронз составляет 760—800°С. Выше указанных температур бронзы нагревать не следует из-за опасности роста зерен и ухудшения служебных характеристик сплава. Нагрев под закалку ниже оптимальной температуры уменьшает пересыщение α-твердого раствора бериллием в закаленном сплаве и интенсифицирует прерывистый распад при старении с образованием грубой двухфазной структуры с некогерентным выделением γ-частиц в приграничных участках. Закалка с низких температур стимулирует прерывистый распад особенно сильно при высокотемпературном старении (выше 350°С). Локализованный в приграничных участках прерывистый распад твердого раствора приводит к охрупчиванию сплава.
Скорость охлаждения
Важным параметром закалки бериллиевых бронз является скорость охлаждения, которое должно быть достаточно резким, чтобы исключить распад пересыщенного твердого раствора. При выборе закалочных сред руководствуются критическими скоростями (vKp), оцениваемыми с помощью термокинетических диаграмм или диаграмм изотермического превращения переохлажденного α-твердого раствора. Эти диаграммы строят по микроструктурным исследованиям или по изменению свойств в процессе распада α-раствора по сравнению со свойствами после старения на максиматьную прочность.
Данные показывают, что при закалке бронзы наибольшие скорости охлаждения должны быть в интервале температур 550— 250°С. Замедленное охлаждение в этом интервале может вызвать преждевременное выделение из α-твердого раствора фазы-упрочнителя и, следовательно, привести к уменьшению способности к последующему старению. Критическая скорость закалочного охлаждения, позволяющая получить необходимое сочетание физико-механических свойств составляет 60°С/с для бронзы с 2,46% Ве и 0,27% Со.
Критическая скорость охлаждения у бериллиевых бронз достаточно высока и составляет 30— 60°С/с, поэтому их обычно закаливают в воде. Для уменьшения критической скорости в бериллиевые бронзы вводят никель или кобальт. Добавки этих металлов приводят к повышению устойчивости переохлажденного α-твердого раствора в области температуры его наименьшей стабильности (~ 500°С). Примерно так же на устойчивость твердого раствора влияют небольшие добавки магния. Важным достоинством бериллиевых бронз является их высокая пластичность при умеренной прочности в закаленном состоянии: σв = 400—500 МПа. δ = 30—45%. В этом состоянии они легко переносят операции гибки, вытяжки и другие виды деформации.
Температурный режим старения и фазовые переходы при старении
Температурный режим старения зависит от необходимого сочетания свойств изделия и находится в интервале температур 300—350°С. При старении бериллиевых бронз распад α-раствора характеризуется сложностью форм фазовых переходов. Превращение проходит через ряд метастабильных состояний, последовательность которых зависит от температуры изотермической выдержки. При температурах ниже 430°С распад начинается с образования зон Гинье-Престона (ЗГП), представляющих собой дискообразные монослои атомов бериллия, расположенные паралельно плоскостям {100} матрицы. Их диаметр оценивается пределами 2— 10 нм, а толщина — 0,2—1,0 нм. Монослои окружены полями искажений решетки матрицы.
После образования ЗГП при температурах ниже 300—350°С появляются частицы метастабильной γ»-фазы, имеющей моноклинную решетку: а = b = 0,254 нм, с = 0,324 нм, Р — 85°25′.
Метастабильная γ’-фаза образуется из γ»-фазы при температурах ниже 350°С, либо непосредственно из ЗГП при более высоких температурах. Она имеет объемноцентрированную тетрагональную решетку с периодом а = 0,279 нм и с — 0,254 нм и плоскостью габитуса {112}α. По мере развития процесса старения размеры выделений γ’-фазы увеличиваются а тетрогональность ее решетки уменьшается.
После длительного старения и особенно выше температуры 400 °С γ’-фаза теряет когерентность с матрицей, степень тетрагональности ее решетки приближается к единице, и она превращается в стабильную γ(CuBe)-фазу. Возможно образование γ-фазы из метастабильной γ’-фазы и непосредственно из α-твердого раствора. Таким образом, в бериллиевых бронзах при различных температурах старения наблюдается следующая последовательность превращений:
300°C : αCu-Be→ ЗГП → γ» → γ’ → γ(CuBe)
350‑400°C : αCu-Be→ ЗГП → γ’ → γ(CuBe)
После дисперсионного твердения при старении готовые детали приобретают высокиеупругие свойства: предел упругости достигает 750—770 МПа, предел выносливости 250—290 МПа (на базе 1⋅108 циклов), твердость 350—400 HV. Температуроустойчивость упругих элементов из бериллиевых бронз значительно выше по сравнению с другими сплавами на медной основе, электропроводность составляет 25—30 % от электропроводности меди. Бериллиевые бронзы хорошо свариваются и паяются. Обработка резанием даже после дисперсионного твердения затруднений не вызывает.
Марка | Состояние материала | σB, МПа |
σ0,2 МПа |
δ % |
HV (НВ) | σ0,005 МПа |
E ГПа |
KCU, МДж/м2 | σ-1 на базе 1⋅108 циклов, МПа |
БрБ2 | Закаленное | 500 | 250 | 40 | 90 | 130 | 117 | 0,7 | — |
Состаренное | 1250 | 1000 | 3 | 370 | 770 | 131 | 0,125 | 245 | |
Состаренное после закалки и деформации на 40% | 1350 | 1200 | 2 | 400 | 960 | 135 | 294 | ||
БрБ 2,5 | Закаленное | 550 | 300 | 30 | 115 | 160 | 120,5 | — | — |
Состаренное | 1300 | 1100 | 2 | 380 | 790 | 133 | — | — | |
Состаренное после закалки и деформации на 40% | 1400 | 1300 | 1,5 | 410 | 970 | 138 | 294 | ||
БрБНТ 1,7 | Закаленное | 420 | 220 | 50 | 85 | 120 | 107 | — | — |
Состаренное | 1150 | 930 | 7 | 320 | 700 | 128 | — | 245 | |
Состаренное после закалки и деформации на 40% | 1250 | 1150 | 3 | 360 | 890 | 131,5 | 275 | ||
БрБНТ 1,9 | Закаленное | 480 | 250 | 50 | 90 | 130 | 110 | — | — |
Состаренное | 1250 | 1000 | 6 | 360 | 77 | 130 | — | 245 | |
Состаренное после закалки и деформации на 40% | 1350 | 1180 | 2 | 400 | 960 | 134 | 294 |
Марка | Закалка | Старение по оптимальному режиму | |||
σB, МПа | δ,% | σB, МПа | σ0,02, МПа | δ,% | |
БРБНТ 1,9 | 400 — 500 | 38 — 45 | 1150 — 1250 | 700 | 4 — 6 |
БрБ2 | 400 — 500 | 38 — 45 | 1150 — 1250 | 600 | 4..6 |
БрБ 2,5 | 400 — 500 | 30 — 38 | 1250 — 1350 | 650 | 3 — 5 |
БрБНТ 1,7 | 300 — 400 | 45 — 50 | 1000 — 1100 | 400 | 5 — 7 |
Легирование бериллиевых бронз
Легирование бериллиевых бронз направлено на улучшение их свойств. В качестве легирующих элементов используют Ni, Co и Ti. Эти элементы подавляют прерывистый распад и замедляют непрерывный. Такое влияние никеля и кобальта связывают с тем, что эти элементы, имеющие меньший атомный радиус, чем медь, уменьшают период решетки α-раствора, что приводит к сохранению когерентности матрицы и выделений, т.е. к отностильной стабилизации γ’-фазы. Кроме того, Ni и Ti могут образовывать соединения типа NiВе, Cu3Тi, которые обеспечивают дополнительное упрочнение.
Бериллиевые бронзы отличаются высоким сопротивлением малым пластическим деформациям из-за сильного торможения дислокаций дисперсными частицами, выделившимися из твердого раствора при старении, а следовательно, они имеют высокий предел упругости. С увеличением этого сопротивления уменьшаются микропластические деформации при заданном напряжении и. следовательно, уменьшается релаксация напряжений. Все это приводит к повышению релаксационной стойкости сплавов — основной характеристики, определяющей свойства упругих элементов.
Бериллиевые бронзы часто подвергают низкотемпературной термомеханической обработке (НТМО), заключающейся в применении пластической деформации между операциями закалки и старения. В этом случае деформация закаленного сплава обеспечивает равномерный распад по всему объему твердого раствора при старении и получение высоких упругих характеристик.
способ выбора режимов термической обработки упругих элементов из бериллиевой бронзы бр.б2 — патент РФ 2263156
Изобретение относится к области металлургии, а именно к выбору режимов термической обработки упругих элементов из бериллиевой бронзы Бр.Б2. Предложен способ выбора режимов термической обработки упругих элементов из бериллиевой бронзы Бр.Б2, при этом режим термической обработки выбирают в зависимости от требуемых значений модуля нормальной упругости или модуля сдвига по разработанным диаграммам, описывающим зависимость изменения модуля нормальной упругости или модуля сдвига от режима дисперсионного твердения и исходного состояния материала упругого элемента, закаленного или закаленного и продеформированного, при этом исходное состояние материала упругого элемента выбирают в зависимости от типа упругого элемента. Технический результат — выбор режимов термической обработки для упругих элементов из бериллиевой бронзы Бр.Б2 для достижения необходимых физико-механических характеристик с максимальной точностью. 3 ил.
Рисунки к патенту РФ 2263156
Изобретение относится к металлургии, в частности к термической обработке упругих элементов из бериллиевой бронзы марки Бр.Б2.
Бериллиевая бронза обладает оптимальными электрическими, антикоррозионными, прочностными и упругими характеристиками, в связи с чем данный материал находит большое применение в приборостроении, компьютерной технике, в автомобильной и электронной промышленности для изготовления контактных упругих элементов. С целью получения оптимального сочетания прочностных, пластических и упругих характеристик упругие элементы, изготовленные из бериллиевой бронзы (Бр.Б2), подвергаются термической обработке. Основными видами термообработки являются закалка (приведение в мягкое состояние), как промежуточная операция, и дисперсионное твердение или старение (придание материалу прочностных и упругих свойств).
По использованию режимов проведения операции термической обработки существует несколько рекомендаций:
1. Температура нагрева под закалку — 780±10°С, выдержка при данной температуре в течение 10-20 мин, затем быстрое охлаждение в воде. Температура старения (дисперсионного твердения) — 320±10°С в течение 3 часов [1].
2. 3акалка с 760-780°С в воде и старение при температуре 300-350°С в течение 2 часов [2].
3. Закалка с 770-790°С в воде, старение 310-340°С в течение — 60-240 мин [3].
Вышеприведенные режимы термообработки имеют некоторые недостатки. Во-первых, нет общих, четко установленных температурных и временных режимов дисперсионного твердения, а именно, температура старения колеблется в интервале 300-350°С, а время процесса термообработки — от одного до четырех часов. Во-вторых, контроль качества термообработанных деталей производится путем замера их твердости на образцах-свидетелях. Партия термически обработанных деталей считается качественной, если их твердость составляет не менее 320 HV [3]. Как показала практика, если соблюдать вышеприведенные режимы старения, то значение твердости может достигать 440 HV. Так как твердость служит характеристикой прочности детали, то такой расширенный разброс этого параметра нежелателен, потому что и пределы параметров прочности будут также увеличиваться. Выходит, что одну партию деталей можно получить значительно менее прочную, чем другую, но обе партии будут считаться качественными. Согласно утверждению А.Г. Рахштадта и его коллег [4], измерение твердости является всего лишь методом определения качества процесса термообработки, а не качества детали. Кроме того, для пружин наиболее информативными показателями являются показатели упругости, так как именно они в основном участвуют в расчетах на стадии проектирования и в большей степени характеризуют качество упругих элементов.
В настоящее время на стадии проектирования пружин значения показателей модуля нормальной упругости (Е, ГПа) и модуля сдвига (G,ГПа) берутся из справочных материалов или ГОСТ 15834-77. Эти показатели имеют постоянное установленное значение.
Бериллиевая бронза может эксплуатироваться при повышенных температурах, в слабоагрессивных срезах и под действием токов высокой частоты. Поэтому, учитывая условия работы упругих элементов, важно просчитывать их физико-механические свойства с высокой степенью точности. Для определения жесткости пружин используются формулы [5], в которые подставляются только линейные размеры пружин и значение модуля нормальной упругости или модуля сдвига, в зависимости от типа пружины. Если расчетная жесткость упругих элементов имеет неудовлетворительный результат, то для получения необходимого ее значения, так как значения модулей упругости считаются постоянными величинами, приходится изменять размеры пружин. Подобный метод получения необходимого значения жесткости может вызвать определенные конструктивные трудности, так как изменение размеров пружины в некоторых случаях приводит к изменению размеров контактирующих деталей. Кроме того, пружины обладают частотой собственных колебаний, и если в процессе эксплуатации собственная частота колебаний детали совпадает с частотой вынужденных колебаний, то происходит резонанс, при этом резко сокращается срок службы упругого элемента. Во избежание эффекта резонанса изменяют частоту собственных колебаний пружины, которая также определяется жесткостью, изменение которой опять же создает определенные конструктивные трудности. Из вышесказанного следует, что достоверность максимально точного расчета пружины во многом определяется значением упругих модулей.
Согласно ГОСТ 15834-77 бериллиевая бронза поставляется либо в мягком (закаленном при температуре 770-790°С) состоянии, либо в твердом (закаленном при температуре 770-790°С и деформированном на 30-40% волочением). Значения модуля нормальной упругости бериллиевой бронзы в этих состояниях считаются одинаковыми [1].
Однако при измерении модуля нормальной упругости акустическим методом, он будет определяться формулой:
где — плотность материала, кг/м3, — коэффициент Пуассона, равный
а vl и v — соответственно скорости продольных и поперечных волн, проходящих через материал, м/с, [5], и, как видно из уравнения 1, модуль нормальной упругости прямопропорционален плотности металла. Значения плотности бериллиевой бронзы в мягком и твердом (закаленном и продеформированном) состояниях будут различными. Кроме того, скорости акустических волн, проходящих через материал, также будут разными, так как они являются структурно чувствительными показателями. Отсюда следует, что значение модуля нормальной упругости бронзы Бр.Б2 в мягком и твердом состояниях не может быть одинаковым.
Была проведена работа по определению значений упругих модулей бронзы при различных температурных и временных режимах дисперсионного твердения. Для выявления связи между физическими свойствами бериллиевой бронзы и механическими проводились испытания образцов на растяжение и замер твердости. Образцы подвергались старению при температурах 320±2°С и 340±2°С от 0 до 4 часов с шагом 0,5 часа с мягкого и твердого исходных состояний.
Определение модулей упругости проводилось в два этапа: определение скорости продольных и поперечных волн, проходящих через образец, и определение плотности данных образцов, которая измерялась гидростатическим методом [6]. Максимальная относительная погрешность измерений составляла 0,015%. Известно, что плотность материала зависит от его структурного состояния, так как она определяется межатомным расстоянием кристаллической решетки, которое, в свою очередь, изменяется с изменением структуры материала. Для бериллиевой бронзы марки Бр.Б2 плотность с увеличением времени старения повышается с 8210 кг/м3 до 8310 кг/м 3. В металлургической промышленности изменением плотности пренебрегают, так как во время выплавки и изготовления проката, в процессе термической и пластической обработки она изменяется в пределах 0,1-1,2%. Непостоянство значений плотности можно объяснить наличием металлургических дефектов (пористость, неметаллические включения и т.д.), а также вследствие изменения микроструктуры сплава при проведении операции термообработки. В проведенных исследованиях изменение плотности измерялось с целью снижения погрешности полученных значений упругих модулей. Максимальная относительная погрешность измерения упругих модулей составила 0,3%.
Твердость образцов измерялась на микротвердомере типа ПМТ-3 по ГОСТ 2999-75 «Метод измерения твердости по Виккерсу».
Механические свойства бериллиевой бронзы определялись испытанием термически обработанных образцов на растяжение. Тип образцов, методика проведения испытаний и методика расчетов соответствовали требованиям ГОСТ 1497-84 «Методы испытаний на растяжение».
Исследования показали, что:
1. Так как большой разброс температуры оказывает заметное влияние на изменение скорости фазовых превращений, в результате чего повышается разброс значений механических и физических характеристик изделий из бериллиевой бронзы, то температурная погрешность дисперсионного твердения не должна превышать ±4°С (при разнице температуры старения в 20°С время фазовых превращений изменяется примерно на 30 минут).
2. Для определения режимов дисперсионного твердения необходимо руководствоваться не столько достижением определенных значений твердости, сколько значениями модулей упругости, поскольку они являются более информативными и важными для упругих элементов.
3. Возможны несколько вариантов достижения необходимых значений упругих модулей: с помощью повышения температуры старения или увеличением продолжительности времени старения. Поэтому при выборе оптимальных режимов термообработки следует учитывать как экономический, так и технологический факторы.
4. Значения упругих модулей носят переменный характер и зависят от степени деформации и режимов термообработки, а это означает, что определенные показатели упругих модулей можно получать не за счет изменения размеров детали, а в большинстве случаев за счет правильно подобранного исходного состояния материала (твердого или мягкого) и режимов термообработки.
Сущность изобретения заключается в том, что при расчетах упругих элементов в большинстве случаев можно манипулировать не размерами элементов, а конкретным значением упругих модулей, достигаемым определенным режимом термообработки, выбираемым по разработанным диаграммам зависимости изменения упругих модулей от режимов термообработки.
Техническим результатом заявляемого способа является обоснованный выбор режимов термической обработки, в частности, режимов дисперсионного твердения упругих элементов из Бр.Б2 для достижения необходимых физико-механических характеристик с максимальной точностью.
Для получения вышеуказанного технического результата на стадии разработки упругих элементов при расчете, в зависимости от типа детали, выбирается определенное, требуемое значение модуля нормальной упругости или модуля упругости при сдвиге. Это значение отражается в конструкторской документации вместо требования по твердости. В дальнейшем, по разработанным диаграммам (фигуры 1, 2) для получения требуемых свойств разрабатываемых элементов выбираются исходное состояние материала (мягкое или твердое) и режимы дисперсионного твердения.
Например, (фиг.3) в конструкторской документации предъявляется требование по модулю нормальной упругости Е=(129,5-130) ГПа. Согласно диаграмме на фигуре 1 заложенное значение модуля упругости можно получить несколькими способами:
1. Состояние поставки (твердое), старение при температуре 340±4°С с выдержкой 40-45 мин.
2. Состояние поставки (твердое), старение при температуре 320±4°С с выдержкой 70-80 мин.
3. Закалка 780±4°С, охлаждение в воде или состояние поставки (мягкое), старение при температуре 340±4°С с выдержкой 70-80 мин.
4. Закалка 780±4°С, охлаждение в воде или состояние поставки мягкое, старение при температуре 320±4°С с выдержкой 120-150 мин.
Исходное состояние материала определяется типом упругого элемента, так, если элемент имеет сложную форму, подвергается в процессе изготовления значительным пластическим деформациям, то необходимо применять бронзу в мягком (закаленном) состоянии, так как бронза в твердом состоянии уже деформирована на 30-40% [1] и дальнейшая деформация может привести к образованию микротрещин в структуре материала, что резко понизит ее физико-механические свойства и сократит срок эксплуатации детали. В связи с этим наилучшим режимом термообработки (упрочнением бронзы) является режим способов по пунктам 3 и 4, но, исходя из экономических соображений, оптимальным вариантом будет способ пункта 3, так как процесс старения по нему сокращается примерно на один час, по сравнению со способом пункта 4.
В случае, если деталь на стадии изготовления не подвергается значительным пластическим деформациям, то оптимальными являются способы упрочнения пунктов 1 и 2. Однако способ по п.1 наиболее целесообразен в экономическом и технологическом планах.
Аналогично выбираются исходное состояние бронзы и режимы ее упрочнения (термообработки) для других заданных значений упругих модулей.
Таким образом, с помощью предлагаемого способа можно получать значения упругих модулей деталей из бериллиевой бронзы в пределах 127-133 ГПа для модуля нормальной упругости и 47,5-49,5 ГПа для модуля сдвига. Манипулируя этими значениями, можно варьировать в определенных пределах значениями жесткости и частотами собственных колебаний. При изменении значений упругих модулей в вышеуказанных интервалах твердость детали будет составлять не менее 320 HV, а предел прочности — не менее 1060 МПа. Это означает, что при использовании заявляемого способа выбора режимов термообработки упругих элементов из бериллиевой бронзы марки Бр.Б2 существующие требования к качеству изготавливаемых деталей удовлетворяются.
Контролировать качество упругих элементов рекомендуется ультразвуковым методом. Этот метод является неразрушающим, наиболее технологичным, поэтому его можно использовать как после операции термообработки, так и после нанесения гальванического покрытия (в конечной стадии изготовления пружины), которое влияет на упругие и прочностные характеристики пружин [3].
Список использованной литературы
1. ГОСТ 15834-77. Проволока из бериллиевой бронзы. Технические условия.
2. Ю.М. Лахтин. «Металловедение и термическая обработка металлов». Изд. 2-е, перераб. и доп.: М., «Металлургия», 1979.
3. Р4. 054. 035 — 89 «Рекомендации. Элементы пружинные из сплавов черных и цветных металлов. Термическая обработка».
4. Ж.П. Пастухова, А.Г. Рахштадт. «Пружинные сплавы цветных металлов»: М., «Металлургия», 1983.
5. ОСТ4 Г0.838.200 «Пружины. Методика расчета и указания по проектированию».
6. «Испытание материалов». Справ. изд. под ред. X. Блюменауэра: М., «Металлургия», 1979.
ФОРМУЛА ИЗОБРЕТЕНИЯ
Способ выбора режимов термической обработки упругих элементов из бериллиевой бронзы Бр.Б2, отличающийся тем, что режим термической обработки выбирают в зависимости от требуемых значений модуля нормальной упругости или модуля сдвига по разработанным диаграммам, описывающим зависимость изменения модуля нормальной упругости или модуля сдвига от режима дисперсионного твердения и исходного состояния материала упругого элемента, закаленного или закаленного и продеформированного, при этом исходное состояние материала упругого элемента выбирают в зависимости от типа упругого элемента.
Термическая обработка металлов. Отжиг | Всё о цветных металлах и сплавах (бронза, медь, латунь и др)
Отжиг меди
Термической обработке подвергают и медь. При этом медь можно сделать либо более мягкой, либо более твердой. Однако в отличие от стали закалка меди происходит при медленном остывании на воздухе, а мягкость медь приобретает при быстром охлаждении в воде. Если медную проволоку или трубку нагреть докрасна (600° С) на огне и затем быстро погрузить в воду, то медь станет очень мягкой. После придания нужной формы изделие вновь можно нагреть на огне до 400° С и дать ему остыть на воздухе. Проволока или трубка после этого станет твердой. Если необходимо выгнуть трубку, ее плотно заполняют песком, чтобы избежать сплющивания и образования трещин.
Отжиг латуни позволяет повысить ее пластичность. После отжига латунь становится мягкой, легко гнется, выколачивается и хорошо вытягивается. Для отжига ее нагревают до 600° С и дают, остыть на воздухе при комнатной температуре.
Отжиг и закаливание дюралюминия
Отжиг дюралюминия производят для снижения его твердости. Деталь или заготовку нагревают примерно до 360°С, как и при закалке, выдерживают некоторое время, после чего охлаждают на воздухе. Твердость отожженного дюралюминия почти вдвое ниже, чем закаленного.
Приближенно температуру нагрева дюралюминиевой детали можно определить так: При температуре 350—360°С деревянная лучина, которой проводят по раскаленной поверхности детали, обугливается и оставляет темный след. Достаточно точно температуру детали можно определить с помощью небольшого (со спичечную головку) кусочка медной фольги, который кладут на ее поверхность. При температуре 400°С над фольгой появляется небольшое зеленоватое пламя.
Отожженный дюралюминий обладает небольшой твердостью, его можно штамповать и изгибать вдвое, не опасаясь появления трещин.
Закаливание. Дюралюминий можно подвергать закаливанию. При закаливании детали из этого металла нагревают до 360—400°С, выдерживают некоторое время, затем погружают в воду комнатной температуры и оставляют там до полного охлаждения. Сразу после этого дюралюминий становится мягким и пластичным, легко гнется и куется. Повышенную же твердость он приобретает спустя три-четыре дня. Его твердость (и одновременно хрупкость) увеличивается настолько, что он не выдерживает изгиба на небольшой угол.
Насчет оловянной бронзы
Varnas
Возможно ли повысить ее твердость закалкой и последующийм старением? искал информацию про ето, но пока все время выдает только термообработку берилевых бронз.
HarryA
Может ошибаюсь но вроде, когда железо не знали, это делали наклепом. Как сделать отпуск слышал, а чтоб закалку…
А для чего?
Varnas
закалка — ето резкое охлаждение с высокий температур. В случии части бронз и меди уменьшает твердость. Многие бронзы после етого может подвергатса старению — выдерживанию несколько при температуре несколько сот градусов. Выделяет интерметалидыи сплав упрочняетса. Таким способом увеличиваетса прочность многих спдавов, в том числе и мартенситно стареющих сталей. Закалка быстрорезов на вторичную твердость также можно рассматривать как старение — выделяет в основном карбиды из твердого раствора, но механизм тотже.
Наклеп применяли и у железа — даже в 20 веке (у лезвий кос). У берилевой бронзы применяет закалку, тогда наклеп, потом старение.
begy
термоцикл бр9-бр12 заключается в медленном охлаждении отливки (сверхмассивные опоки), ничего более путного нет.
наклеп не даст сформировать кромку, будет выкрашиваться (мы же о бронзовом ноже?)
в принципе, литой и правильно заточенный (45-50градусов) нож из бр9-бр12 неплохо справляется с разделкой мяса (хуже, чем кремневый или обсидиановый на первых резах, но гораздо дольше не требует правки) ну и править его проще
вообще бронзовый клевец железный доспех прорубает, так что не надо считать оловянные бронзы мягкими
antonioMsk
begy, я конечно понимаю, что Вы бр9-бр12 называете aлюминежелезные бронзы БрАЖ9-4 и БрАЖ12, но для полной ясности учточняйте.
А вопрос у ТС звучал про оловянистые бронзы.
Varnas, посмотрю в старых справочниках.
Оловянистые бронзы использовались в парах трения, и там иногда требуется поднять твердость.
На chipmaker.ru в термическом разделе посмотрите темы или задайте свою.
Varnas
термоцикл бр9-бр12 заключается в медленном охлаждении отливки (сверхмассивные опоки), ничего более путного нет.Как уже заметили — вы говорите про алюминевые бронзы, да имедленное охлаждение тоже можно рассматривать как старение.
наклеп не даст сформировать кромку, будет выкрашиватьсяРазве? У кос чтото невыкрашиваетса кромка.
(мы же о бронзовом ноже?)Пока о бронзовых болстерах, чтоб меньше царапались. Если всеж окажетса возможным поднять твердость по роквелу до примерно 40, то может и о бронзовым топорике.
Varnas, посмотрю в старых справочниках.Было бы неплохо — а то в инете либо про берилевую/алюминевую, либо вобще только упминаняние что можно старить.
Оловянистые бронзы использовались в парах трения,Так и есьт — 6 процентов олова.
На chipmaker.ru в термическом разделе посмотрите темы или задайте свою.Там уже задавали — рекомендаций небыло.
begy
нда… бр, это оловянные бронзы, я говорю о них
begy
Пока о бронзовых болстерах, чтоб меньше царапалисьвас интересует патинирование бронзы
Разве? У кос чтото невыкрашиваетса кромка.никогда не слышал о бронзовых косах
Varnas
вас интересует патинирование бронзыДа???? И где ето я писал?
никогда не слышал о бронзовых косахА по твердости что низкоуглеродистая сталь, незакаленная, что бронза — примерно равные…
Слесарь Кесарев
Если ты закалишь бронзу получишь нобелевскую премию!
Varnas
Идиотов — в топку.
begy
Да???? И где ето я писал?если задача стоит в создании на поверхности бронзы устойчивой к царапинам пленки, то это химическое патинирование
как заберу из литейки бронзу, сделаю видео
Varnas
ну с патинированием то проблем нет — даже в магазине продаетса готовые патины черно зелены, коричневый, зеленый, красный. Есть и амиак наконец. Однако чем бронза тверже, тем царапины будет меньше, особенно если при заточке шоркнуть камнем.
Вот только возникает вопрос — достаточно ли 6 процентов олова для странеия? Если скажем при температурах 400-300 град растворимость олова в меди больше 6 процентов, то выпадения интерметалидов небудет и такая бронза незакаливаетса в принципе.
Пока пробовал на газовой плите греть по несколько часов при разной интенсивности пламени — без толку.
begy
вообще у меня сложилось впечатление, что 12% олова в бронзе, это гораздо лучше, чем 6, в плане твердости, но хрупкость и прочие радости…
а самая твердая, кмк, 20%
лигатура варится при 1100 градусах, в бескислородной, откуда 300-400?
бронза оловянная не закаливается вообще, нагрев с быстрым охлаждением придаст пластичности, немного и не на долго, долгий нагрев без резкого охлаждения ни к чему хорошему не приведет
патинировать лучше долго, не мазью, а парами аммиака, до оливкового (пара недель)пленка толще и равномернее, или марганцовка и купорос, но результат не всегда предсказуем
basp07
begyМожно с 10-й минуты начать:
вообще у меня сложилось впечатление, что 12% олова в бронзе
begy
Можно с 10-й минуты начать:естественно я был на этом мероприятии, что-то из сказанного противоречит написанному мной?
и да, в этом видео есть оговорки
Varnas
вообще у меня сложилось впечатление, что 12% олова в бронзе, это гораздо лучше, чем 6, в плане твердости,Да ктож спорит. Вот только такую бронзу врядли проковаеш. например бронза с 27 процентов олова самая тверда, но под молотком крошитса как стекло.
лигатура варится при 1100 градусах, в бескислородной, откуда 300-400?Вы спутали твердый раствор и расплав…
патинировать лучше долго, не мазью,Серная мазь имхо вобще хрень для ленивых. Медь можно просто серой натирать — получает неплохо, особенно если потом подогревать. А если нагретую медь подсыпать мелкими кристаликами серы, то и текстура само сабой получаетса…
а парами аммиака, до оливкового (пара недель)пленка толще и равномернее,Пробовал сутки — парами както слабо очень получилось, а вот часть которая балы ниже раствора амиака стала черной. И 2000 шкуркой ее оттирать надо ДОЛГО.Жаль только 50 милилитров амиака пару евров стоит…
begy
Да ктож спорит. Вот только такую бронзу врядли проковаеш.видимо упустил, ковать бр12 нельзя
Вы спутали твердый раствор и расплав…я с литьем работаю, так что в твердые растворы не лезу
горячее изделие(80-90градусов) на пару минут в крепкий раствор медного купороса, потом в пары аммиака на пару недель, сколько-нибудь заметное появление пленки на третьи-пятые сутки наблюдается
Пробовал сутки — парами както слабо очень получилось
50 милилитров амиака пару евров стоит…какое страшное место… (хотя мне казалось, вы из Латвии)
у нас полтора евро за литр 25%
Varnas
я с литьем работаю, так что в твердые растворы не лезупечи с регулируемой температурой у вас нет?
горячее изделие(80-90градусов) на пару минут в крепкий раствор медного купороса, потом в пары аммиака на пару недель, сколько-нибудь заметное появление пленки на третьи-пятые сутки наблюдаетсяпатина черная или с оттенками?
какое страшное место… (хотя мне казалось, вы из Латвии)Дык у нас аптечный, 10 процентный, алхимической чистоты 😀.
у нас полтора евро за литр 25%
mara2107
А в моче (простите) амиака много ?
——————
когда воротимся мы в Портленд …
begy
печи с регулируемой температурой у вас нет?муфель прокалочный, литье в мастерскую стараюсь сдавать
Дык у нас аптечный, 10 процентный, алхимической чистоты .в личку написал 😊
А в моче (простите) амиака много ?вообще нет, есть мочевая кислота и мочевина, которые можно разложить с получением оного
очень очень мало, иначе порох изобрел бы третий человек, заливший костер 😊
Varnas
муфель прокалочный, литье в мастерскую стараюсь сдаватьно прокалить чтото с температуро 300-400 град у вас возможности нет?
в личку написалСайт красивый, современный и тд. Беда только что без звонка нельзя узнать ни асортимент, ни цены на реагенты. А так ничего.
basp07
begy
естественно я был на этом мероприятии, что-то из сказанного противоречит написанному мной?
и да, в этом видео есть оговорки
Я этим видео подтвердил ваше мнение. Склоняюсь к тому, что для того чтобы нож из бронзы резал не обязательно его закаливать- та же сталь, если ее проковывать при определенных температурах, упрочняется и рубит-режет. Должно быть, проковывая медь, постепенно добавляли олово, наблюдая за результатом. Не спец в этом, поэтому в догадках.)
begy
но прокалить чтото с температуро 300-400 град у вас возможности нет?есть, только я в Москве, в Риге теперь набегами пару раз в год
Сайт красивый, современный и тд. Беда только что без звонка нельзя узнать ни асортимент, ни цены на реагенты. А так ничего.а без заезда с паспортом и не продадут ничего, зато цены
Varnas
есть, только я в Москве, в Риге теперь набегами пару раз в годВы немогли бы кусок бронзы нагреть до 700-800 охладит в воде и пдогреть при 330 на пару часов? ПОпадалсь когда то статья про термоупрочнение таким способом мышяковистой бронзы, а она очень похоже на оловянную.
begy
Вы немогли бы кусок бронзы нагреть до 700-800 охладит в воде и пдогреть при 330 на пару часов? ПОпадалсь когда то статья про термоупрочнение таким способом мышяковистой бронзы, а она очень похоже на оловянную.
гм… попробую с литниками поиграть, при следующей партии литья
или на неделе, если сколь-нибудь внятный кусок бронзы найду
Varnas
Было бы отлично.