Влияние легирующих элементов на свариваемость металлов
Влияние легирующих элементов на свариваемость металлов
При сварке металлов, имеющих различные легирующие элементы (Молибден, Кремний, Хром и др.) могут возникать различные проблемы, влияющие непосредственно на качество полученного сварного соединения (трещины, поры, непровары и т.д.). Для того, чтобы избежать трудностей и проблем, необходимо очень хорошо знать, как влияет тот или иной легирующий элемент на свариваемость изделия.
Знание влияния легирующих элементов на свариваемость различных сталей поспособствует лучшему пониманию процессов сварки.
Углерод
Один из самых значительных химических элементов в сталях.
Содержание углерода в сталях влияет на прочность, закаливаемость, вязкость, свариваемость.
У низкоуглеродистых сталей (углерода менее 0,25%) свариваемость практически не ухудшается.
При увеличении содержания углерода свариваемость резко ухудшается, так как в зонах ЗТВ (зонах термического влияния) возникает большое количество закалочных структур, которые вызывают трещины.

При высоком содержании углерода в присадочном материале увеличивается вероятность образования пор.
Марганец
Марганец является хорошим раскислителем. Электроды или проволоку необходимо применять при сварке в среде СО2. При содержании марганца в металле до 0,8 %, процесс сварки не усложняется. При увеличении содержания стали в металле (1,8%-2,5%) появляется опасность возникновения ХТ (холодных трещин), т.к. марганец способствует появлению хрупких структур (закалочных). При повышенном содержании марганца (11-16%) во время сварки происходит интенсивное выгорание данного вещества. Следовательно, необходимо применять специальные меры, например, использовать сварочные материалы с бОльшим содержанием марганца.
Кремний
Так же как и марганец является хорошим раскислителем. При малом количестве кремний (до 0,03%) на свариваемость не влияет. При содержании кремния 0,8-1,5% свариваемость ухудшается из-за повышенной жидкотекучести кремнистой стали и образования тугоплавких оксидов кремния.

Хром
Содержание хрома в сталях способствует увеличению коррозионной стойкости. Но, при сварке сталей образуются карбиды хрома, которые увеличивают твердость в ЗТВ (зоне термического влияния). Также образуются тугоплавкие окислы, которые затрудняют процесс сварки, а значит ухудшают свариваемость.
Никель
Содержание никеля в сталях способствует увеличению ударной вязкости, которая особенно важная при работе сталей при низких температурах. Также никель способствует увеличению пластичности, прочности стали и измельчению зерна. При этом свариваемость стали не ухудшается. Но, из-за высокой цены данного легирующего элемента, применение ограничено экономическими соображениями.
Молибден
Содержание молибдена в сталях увеличивает несущую способность при высоких температурах и ударных нагрузках, измельчает зерно.
С другой стороны, молибден способствует образованию трещин в ЗТВ и наплавленном металле шва.
Во время сварке окисляется и выгорает. Следовательно, необходимо использовать специальные меры.
Вольфрам
Содержание вольфрама в сталях резко увеличивает твердость стали и ее работоспособность при высоких температурах (красностойкость).
С другой стороны, вольфрам затрудняет процесс сварки и активно окисляется.
Ванадий
Содержание ванадия в сталях резко увеличивает закаливаемость стали. Из-за закаливаемости, а также из-за окисления ванадия и его выгорания, ухудшается свариваемость сталей.
Титан
Использование титана как легирующий элемент обусловлено его высокой коррозионной стойкостью.
Ниобий
Использование ниобия, аналогично титану, обусловлено его высокой коррозионной стойкостью. При сварке сталей ниобий способствует образованию горячих трещин.
Влияние химических элементов на свойства стали.
Условные обозначения химических элементов:
хром ( Cr ) — Х никель ( Ni ) — Н молибден ( Mo ) — М титан ( Ti ) — Т медь ( Cu ) — Д ванадий ( V ) — Ф вольфрам ( W ) — В | азот ( N ) — А алюминий ( Аl ) — Ю бериллий ( Be ) — Л бор ( B ) — Р висмут ( Вi ) — Ви галлий ( Ga ) — Гл | иридий ( Ir ) — И кадмий ( Cd ) — Кд кобальт ( Co ) — К кремний ( Si ) — C магний ( Mg ) — Ш марганец ( Mn ) — Г | свинец ( Pb ) — АС ниобий ( Nb) — Б селен ( Se ) — Е углерод ( C ) — У фосфор ( P ) — П цирконий ( Zr ) — Ц |
ВЛИЯНИЕ ПРИМЕСЕЙ НА СТАЛЬ И ЕЕ СВОЙСТВА
Углерод — находится в стали обычно в виде химического соединения Fe3C, называемого цементитом. С увеличением содержания углерода до 1,2% твердость, прочность и упругость стали увеличиваются, но пластичность и сопротивление удару понижаются, а обрабатываемость ухудшается, ухудшается и свариваемость.
Кремний — если он содержится в стали в небольшом количестве, особого влияния на ее свойства не оказывает.(Полезная примесь; вводят в качестве активного раскислителя и остается в стали в кол-ве 0,4%)
Марганец — как и кремний, содержится в обыкновенной углеродистой стали в небольшом количестве и особого влияния на ее свойства также не оказывает. (Полезная примесь; вводят в сталь для раскисления и остается в ней в кол-ве 0,3-0,8%. Марганец уменьшает вредное влияние кислорода и серы.
Сера — является вредной примесью. Она находится в стали главным образом в виде FeS. Это соединение сообщает стали хрупкость при высоких температурах, например при ковке, — свойство, которое называется красноломкостью. Сера увеличивает истираемость стали, понижает сопротивление усталости и уменьшает коррозионную стойкость.
Фосфор — также является вредной примесью. Снижает вязкость при пониженных температурах, то есть вызывает хладноломкость. Обрабатываемость стали фосфор несколько улучшает, так как способствует отделению стружки.
ЛЕГИРУЮЩИЕ ЭЛЕМЕНТЫ И ИХ ВЛИЯНИЕ НА СВОЙСТВА СТАЛИ
Хром (Х) — наиболее дешевый и распространенный элемент. Он повышает твердость и прочность, незначительно уменьшая пластичность, увеличивает коррозионную стойкость; содержание больших количеств хрома делает сталь нержавеющей и обеспечивает устойчивость магнитных сил.
Никель (Н) — сообщает стали коррозионную стойкость
, высокую прочность и пластичность, увеличивает прокаливаемость, оказывает влияние на изменение коэффициента теплового расширения. Никель – дорогой металл, его стараются заменить более дешевым.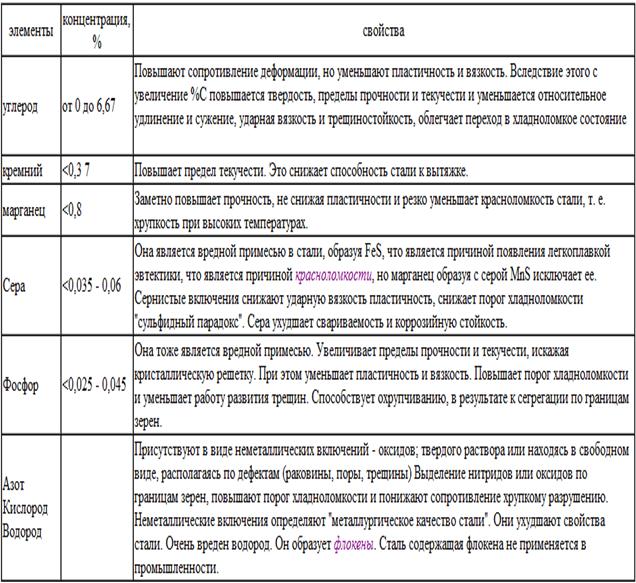
Вольфрам (В) — образует в стали очень твердые химические соединения – карбиды, резко увеличивающие твердость и красностойкость. Вольфрам препятствует росту зерен при нагреве, способствует устранению хрупкости при отпуске. Это дорогой и дефицитный металл.
Ванадий (Ф) — повышает твердость и прочность, измельчает зерно. Увеличивает плотность стали, так как является хорошим раскислителем, он дорог и дефицитен.
Кремний (С)- в количестве свыше 1% оказывает особое влияние на свойства стали: содержание 1-1,5% Si увеличивает прочность, при этом вязкость сохраняется. При большем содержании кремния увеличивается электросопротивление и магнитопроницаемость. Кремний увеличивает также упругость, кислостойкость, окалиностойкость.
Марганец (Г) — при содержании свыше 1% увеличивает твердость, износоустойчивость, стойкость против ударных нагрузок, не уменьшая пластичности.
Кобальт (К) — повышает жаропрочность, магнитные свойства, увеличивает сопротивление удару.
Молибден (М) — увеличивает красностойкость, упругость, предел прочности на растяжение, антикоррозионные свойства и сопротивление окислению при высоких температурах.
Титан (Т) — повышает прочность и плотность стали, способствует измельчению зерна, является хорошим раскислителем, улучшает обрабатываемость и сопротивление коррозии.
Ниобий (Б) — улучшает кислостойкость и способствует уменьшению коррозии в сварных конструкциях.
Алюминий (Ю) — повышает жаростойкость и окалиностойкость.
Медь (Д) — увеличивает антикоррозионные свойства, она вводится главным образом в строительную сталь.
Церий — повышает прочность и особенно пластичность.
Цирконий (Ц) — оказывает особое влияние на величину и рост зерна в стали, измельчает зерно и позволяет получать сталь с заранее заданной зернистостью.
Лантан, цезий, неодим — уменьшают пористость, способствуют уменьшению содержания серы в стали, улучшают качество поверхности, измельчают зерно.
Влияние примесей и лигирующих элементов на свойства сталей и сплавов
Справочная информация
В компании ГП Стальмаш Вы можете купить круг, шестигранник, лист из наличия на складе (отгрузка от 1-3 рабочих дней в зависимости от вида металлопродукции и необходимости подготовки металла)
Сталь конструкционная, легированная, инструментальная, пружинная, подшипниковая, автоматная, нержавеющая, жаропрочная – более 260 марок стали в наличии | Круг. Лист. Полоса. Проволока. Шестигранник.
Оперативная и полная информация о наличии, ценах, условиях и сроках отгрузки по телефонам ГП Стальмаш:
+7 (343) 268-7815, +7 (950) 208-1282, +7 (904) 178-4756, +7 (902) 255-6262 WhatsApp и Viber, +7 (343) 213-1014
ЧАСЫ РАБОТЫ: Пн — Пт: с 06:00 до 16:00, время Московское, во внерабочее время отправляйте запрос на E-mail: 2687815@mail. ru или через форму «Обратная связь»
Влияние примесей на стали и ее свойства
Углерод (( C ) — У) находится в стали обычно в виде химического соединения Fe3C, называемого цементитом.
С увеличением содержания углерода до 1,2% увеличивается твердость, прочность и упругость стали, понижается пластичность и сопротивление удару, ухудшается обрабатываемость и свариваемость.
Кремний (( Si ) — C), если он содержится в стали в небольшом количестве, особого влияния на ее свойства не оказывает.
При повышении содержания кремния значительно улучшаются упругие свойства, магнитопроницаемость, сопротивление коррозии и стойкость против окисления при высоких температурах.
Марганец (( Mn ) — Г), как и кремний, содержится в обыкновенной углеродистой стали в небольшом количестве и особого влияния на ее свойства также не оказывает. Однако марганец образует с железом твердый раствор и несколько повышает твердость и прочность стали, незначительно уменьшая ее пластичность. Марганец связывает серу в соединение MnS, препятствуя образованию вредного соединения FeS. Кроме того, марганец раскисляет сталь. При высоком содержании марганца сталь приобретает исключительно большую твердость и сопротивление износу.
Сера ((S)) является вредной примесью. Она находится в стали главным образом в виде FeS. Это соединение придает стали хрупкость при высоких температурах, например при ковке, — свойство, которое называется красноломкостью. Сера увеличивает истираемость стали, понижает сопротивление усталости и уменьшает коррозионную стойкость.
В углеродистой стали допускается серы не более 0,06-0,07%.
Увеличение хрупкости стали при повышенном содержании серы используется иногда для улучшения обрабатываемости на станках, благодаря чему повышается производительность при обработке.
Фосфор (( P ) — П) также является вредной примесью. Он образует с железом соединение Fe3P, которое растворяется в железе. Кристаллы этого химического соединения очень хрупки. Обычно они располагаются по границам зерен стали, резко ослабляя связь между ними, вследствие чего сталь приобретает очень высокую хрупкость в холодном состоянии (хладноломкость). Особенно сказывается отрицательное влияние фосфора при высоком содержании углерода. Обрабатываемость стали фосфор несколько улучшает, так как способствует отделению стружки.
Легирующие элементы и их влияние на свойства стали
Хром (( Cr ) — Х) – наиболее дешевый и распространенный элемент. Хром повышает твердость и прочность, незначительно уменьшая пластичность, увеличивает коррозионную стойкость; содержание больших количеств хрома делает сталь нержавеющей и обеспечивает устойчивость магнитных сил.
Никель (( Ni ) — Н) придает стали коррозионную стойкость, высокую прочность и пластичность, увеличивает прокаливаемость, оказывает влияние на изменение коэффициента теплового расширения.
Вольфрам (( W ) — В) образует в стали очень твердые химические соединения – карбиды, резко увеличивающие твердость и красностойкость. Вольфрам препятствует росту зерен при нагреве, способствует устранению хрупкости при отпуске.
Ванадий (( V ) — Ф) повышает твердость и прочность, измельчает зерно. Увеличивает плотность стали, так как является хорошим раскислителем.
Кремний (( Si ) — C) в количестве свыше 1% оказывает особое влияние на свойства стали: содержание 1-1,5% увеличивает прочность, при этом вязкость сохраняется. При большем содержании кремния увеличивается электросопротивление и магнитопроницаемость. Кремний увеличивает также упругость, кислостойкость, окалиностойкость.
Марганец (( Mn ) — Г) при содержании свыше 1% увеличивает твердость, износоустойчивость, стойкость против ударных нагрузок, не уменьшая пластичности.
Кобальт (( Co ) — К) повышает жаропрочность, магнитные свойства, увеличивает сопротивление удару.
Молибден (( Mo ) — М) увеличивает красностойкость, упругость, предел прочности на растяжение, антикоррозионные свойства и сопротивление окислению при высоких температурах.
Титан (( Ti ) — Т) повышает прочность и плотность стали, способствует измельчению зерна, является хорошим раскислителем, улучшает обрабатываемость и сопротивление коррозии.
Ниобий (( Nb) — Б) улучшает кислостойкость и способствует уменьшению коррозии в сварных конструкциях.
Алюминий (( Аl ) — Ю) повышает жаростойкость и окалиностойкость.
Медь (( Cu ) — Д) увеличивает антикоррозионные свойства, она вводится главным образом в строительную сталь.
Цирконий (( Zr ) — Ц) оказывает особое влияние на величину и рост зерна в стали, измельчает зерно и позволяет получать сталь с заранее заданной зернистостью.
Легирование — добавление в состав материалов примесей для изменения (улучшения) физических и химических свойств основного материала. Легирование является обобщающим понятием ряда технологических процедур.
В разных отраслях применяются разные технологии легирования.
В металлургии легирование производится введением в расплав или шихту дополнительных элементов (например, в сталь — хрома, никеля, молибдена, вольфрама, ванадия, ниобия, титана), улучшающих механические, физические и химические свойства сплава. Легирование проводится на различных этапах получения металлического материала с целями повышения качества металлургической продукции.
Влияние состава стали на ее свойства:
Углерод — неотъемлемая часть любой стали, так как сталь это сплав углерода с железом. Процентное содержание углерода определяет механические свойства стали. С увеличением содержания углерода в составе стали, твердость, прочность и упругость стали увеличиваются, но пластичность и сопротивление удару понижаются, а обрабатываемость и свариваемость ухудшается.
Кремний — незначительное его содержание в составе стали особого влияния на ее свойства не оказывает. При повышении содержания кремния значительно улучшаются упругие свойства, магнитопроницаемость, сопротивление коррозии и стойкость к окислению при высоких температурах.
Марганец — в углеродистой стали содержится в небольшом количестве и особого влияния на ее свойства не оказывает. Однако он образует с железом твердое соединение повышающее твердость и прочность стали, несколько уменьшая ее пластичность. Марганец связывает серу в соединение MnS, препятствуя образованию вредного соединения FeS. Кроме того, марганец раскисляет сталь. Сталь в состав которой входит большое количество марганца приобретает существенную твердость и сопротивление износу.
Сера — является вредной примесью в составе стали, где она находится преимущественно в виде FeS. Это соединение придает стали хрупкость при высоких температурах — красноломкость. Сера увеличивает истираемость стали, понижает сопротивление усталости и уменьшает коррозионную стойкость.
В углеродистой стали допустимое содержание серы — не более 0,07%.
Фосфор — также является вредной примесью в составе стали. Он образует с железом соединение Fe3P. Кристаллы этого соединения очень хрупки, вследствие чего сталь приобретает высокую хрупкость в холодном состоянии — хладноломкость. Отрицательное влияние фосфора наибольшим образом сказывается при высоком содержании углерода.
Легирующие компоненты в составе стали и их влияние на свойства:
Алюминий — сталь, состав которой дополнен этим элементом, приобретает повышенную жаростойкость и окалиностойкость.
Кремний — увеличивает упругость, кислостойкость, окалиностойкость стали.
Марганец — увеличивает твердость, износоустойчивость, стойкость против ударных нагрузок при этом не уменьшает пластичности.
Медь — улучшает коррозионностойкие свойства стали.
Хром — повышает твердость и прочность стали, незначительно уменьшая пластичность, увеличивает коррозионностойкость. Содержание больших количеств хрома в составе стали придает ей нержавеющие свойства.
Никель — также как и хром придает стали коррозионную стойкость, а также увеличивает прочность и пластичность.
Вольфрам — входя в состав стали, образует очень твердые химические соединения — карбиды, резко увеличивающие твердость и красностойкость. Вольфрам препятствует расширению стали при нагреве, способствует устранению хрупкости при отпуске.
Ванадий — повышает твердость и прочность стали, увеличивает плотность стали. Ванадий является хорошим раскислителем.
Кобальт — повышает жаропрочность, магнитные свойства, увеличивает стойкость против ударных нагрузок.
Молибден — увеличивает красностойкость, упругость, предел прочности на растяжение, улучшает антикоррозионные свойства стали и сопротивление окислению при высоких температурах.
Титан — повышает прочность и плотность стали, является хорошим раскислителем, улучшает обрабатываемость и увеличивает коррозионностойкость.
На нашей металлобазе Вы можете купить самые разнообразные виды металлопроката по оптовым ценам: арматуру, катанку, круг, листы г/к, листы х/к, листы рифленые, листы оцинкованные (оцинковка), листы с полимерным покрытием (полимер), проволоку Вр, проволоку ОК, проволоку оцинкованную, проволоку колючую, гвозди, канаты, метизы, угловой прокат, швеллер, двутавры, электроды, трубы профильные квадратные, трубы профильные прямоугольные, трубы круглые водогазопроводные и др.
www.pm.kg
Свариваемость сталей: классификация, характеристики, определение
Основные критерии, устанавливающие свариваемость
Оценивая свариваемость сталей, всегда уделяют внимание химическому составу металла. Некоторые химические элементы могут повысить этот показатель или снизить его. Углерод считается самым важным элементов, который определяет прочность и пластичность, степень закаливаемости и плавкость. Проведенные исследования указывают на то, что при концентрации этого элемента до 0,25% степень обрабатываемости не снижается. Увеличение количества углерода в составе приводит к образованию закалочных структур и появлению трещин.
Понятие свариваемости
К другим особенностям, которые касаются рассматриваемого вопроса, можно отнести нижеприведенные моменты:
- Практически во всех металлах содержатся вредные примеси, которые могут снижать или повышать обрабатываемость сваркой.
- Фосфор считается вредным веществом, при повышении концентрации появляется хладноломкость.
- Сера становится причиной появления горячих трещин и появлению красноломкости.
- Кремний присутствует практически во всех сталях, при концентрации 0,3% степень обрабатываемости не снижается. Однако, если увеличить его до 1% могут появится тугоплавкие оксиды, которые и снижают рассматриваемый показатель.
- Процесс сварки не затрудняется в случае, если количество марганца не более 1%. Уже при 1,5% есть вероятность появления закалочной структуры и серьезных деформационных трещин в структуре.
- Основным легирующим элементом считается хром. Он добавляется в состав для повышения коррозионной стойкости. При концентрации около 3,5% показатель свариваемости остается практически неизменным, но в легированных составах составляет 12%. При нагреве хром приводит к появлению карбида, который существенно снижает коррозионную стойкость и затрудняет процесс соединения материалов.
- Никель также является основным легирующим элементом, концентрация которого достигает 35%. Это вещество способно повысить пластичность и прочность.
Никель становится причиной улучшения основных свойств материала.
- Молибден включается в состав в небольшом количестве. Он способствует повышению прочности за счет уменьшения зернистости структуры. Однако, на момент воздействия высокой температуры вещество начинает выгорать, за счет чего появляются трещины и другие дефекты.
- В состав часто в качестве легирующего элемента добавляется медь. Ее концентрация составляет около 1%, за счет чего немного повышается коррозионная стойкость. Важной особенностью назовем то, что медь не ухудшает обработку сваркой.
Критерии свариваемости
В зависимости от особенностей структуры и химического состава материала все сплавы делятся на несколько групп. Только при учете подобной классификации можно выбрать наиболее подходящий сплав.
Среднелегированные стали
Среднелегированные стали содержат углерод в количестве от 0,4% и более. Они легированы в основном Ni, Mo, Cr, V, W. Оптимальное сочетание прочности, вязкости и пластичности достигается после закалки и низкого отпуска. Такие среднелегированные стали, как ХВГ, ХВСГ, 9ХС, пользуются большим спросом за счет своих легирующих добавок при изготовлении сверл, разверток и протяжек.
Эти стали выплавляют из чистых шихтовых материалов для повышения пластичности и вязкости. Также их тщательным образом очищают от фосфора, серы, газов и различных неметаллических включений. В этом случае стали могут подвергаться электрошлаковому или вакуумно-дуговому переплаву, рафинированию в ковше жидкими синтетическими шлаками. Хорошее сочетание прочности, вязкости и пластичности среднелегированных сталей достигается термомеханической обработкой.
Технология сварки среднелегированных металлов
Чтобы обеспечить эксплуатационную надежность сварных соединений, нужно при выборе сварочных материалов стремиться к получению швов такого химического состава, при котором их механические свойства имели бы требуемые значения. Степень изменения этих свойств зависит от доли участия основного металла в формировании шва. Поэтому следует выбирать такие сварочные материалы, которые содержат легирующих элементов меньше, чем основной металл. Легирование металла шва за счет основного металла позволяет повысить свойства шва до необходимого уровня.
При сварке среднелегированных глубокопрокаливающихся высокопрочных сталей нужно выбирать такие сварочные материалы, которые обеспечат получение швов, обладающих высокой деформационной способностью при минимально возможном количестве водорода в сварочной ванне. Это достигается применением низколегированных сварочных электродов, не содержащих в покрытии органических веществ и подвергнутых высокотемпературной прокалке. Одновременно при выполнении сварочных работ следует исключить другие источники насыщения сварочной ванны водородом (влага, ржавчина и другие).
Для сварки среднелегированных сталей широко применяются аустенитные сварочные материалы. Для механизированной сварки и изготовления стержней электродов в ГОСТ 2246-70 предусмотрены проволоки марок Св-08Х20Н9Г7Т и Св-08Х21Н10Г6, а в ГОСТ 10052-75 — электроды типа ЭА-1Г6 и др.
Электродные покрытия применяются вида Ф, а для механизированной сварки — основные флюсы. Для сварки среднелегированных высокопрочных сталей используют электроды типов Э-13Х25Н18, Э-08Х21Н10Г6 и другие по ГОСТ 10052-75 и ГОСТ 9467-75.
Высокое качество сварных соединений толщиной 3…5 мм достигается при аргонодуговой сварке неплавящимся электродом. При этом для увеличения проплавляющей способности дуги применяют активирующие флюсы (АФ). Сварка с АФ эффективна при механизированных способах для получения равномерной глубины проплавления. Неплавящийся электрод при сварке с АФ выбирают из наиболее стойких в эксплуатации марок активированного вольфрама.
Газовая сварка легированных сталей осуществляется ацетиленокислородом, который обеспечивает качественный сварной шов. Газы-заменители в данном случае применять не рекомендуется. Но даже ацетиленокислород не может стопроцентно гарантировать получение качественного шва. Этого можно достичь только путем применения дуговой сварки.
Двери из металла своими руками — идеальное решение, если вы хотите сэкономить. Закалка стали — обязательный этап в машиностроении, так как от правильности его выполнения зависит качество продукции. Подробнее читайте в этой статье.
Из металла можно делать очень красивые изделия. Интересные идеи вы найдете по https://elsvarkin.ru/prakticheskoe-primenenie/suveniry-i-ukrasheniya-iz-metalla-svoimi-rukami/ ссылке.
Классификация сталей по свариваемости
Хорошей обрабатываемостью обладают сплавы, в которых при нагреве не образуются трещины. По данной характеристике выделяют четыре основных группы:
- Хорошая обрабатываемость сваркой определяет то, что сталь после термической обработки остается прочным и надежным. При этом создаваемый шов может выдерживать существенное механическое воздействие.
- Удовлетворительная степень позволяет проводить обработку без предварительного подогрева. За счет этого существенно ускоряется процесс, а также снижаются затраты.
- Ограниченно свариваемые стали сложны в обработке, сварку можно провести только при применении специального оборудования.
Именно поэтому повышается себестоимость самого процесса.
- Плохая податливость сварке не позволяет проводить рассматриваемую обработку, так как после получения шва могут появится трещины. Именно поэтому подобные материалы не могут использоваться для получения ответственных элементов.
Классификация сталей по свариваемости
Каждая группа характеризуется своими определенными особенностями, которые нужно учитывать. Сталь 20 относится к первой группе, в то время как распространенная сталь 45 обладает низкой податливостью к сварке.
Металлургические процессы при газовой сварке, кристаллизация металла шва
В процессе газовой сварки расплавленный металл сварочной ванны взаимодействует со сварочным пламенем. Это взаимодействие определяется свойствами свариваемого металла и составом сварочного пламени. Сваривают восстановительной зоной пламени, состоящей в основном из оксида углерода и водорода. Сварочная ванна характеризуется малым объемом расплавленного металла, высокой температурой в месте сварки и большой скоростью расплавления и кристаллизации металла.
Расплавленный металл ванны вступает во взаимодействие с газами сварочного пламени, в результате чего происходят реакции окисления и восстановления. Взаимодействие газов с различными металлами различно. Наиболее легко окисляются металлы, обладающие большим сродством к кислороду. Окисление расплавленного металла происходит как за счет оксидов, находящихся на поверхности свариваемого металла и присадочной проволоки, так и за счет кислорода окружающего воздуха. С увеличением содержания кислорода в свариваемом металле ухудшаются механические свойства сварного соединения. Поэтому при газовой сварке для большинства металлов и сплавов для устранения окислительных процессов в присадочные материалы и флюсы вводят специальные раскислители.
Группы свариваемости
Все группы свариваемости сталей характеризуются своими определенными особенностями. Среди них можно отметить следующие моменты:
- Первая группа, которая характеризуется хорошей свариваемостью, может применяться при сварке без предварительного подогрева и последующей термической обработки шва.
Отпуск выполняется для снижения напряжения в металле. Как правило, подобное свойство связано с низкой концентрацией углерода.
- Вторая характеризуется тем, что склонна к образованию трещин и дефектов на швах. Именно поэтому рекомендуется проводить предварительный подогрев материала, а также последующую термическую обработку для снижения напряжений.
- При ограниченном показателе сталь склонна к образованию трещин. Для того чтобы исключить вероятность появления трещин следует материал предварительно разогреть, после сварки в обязательном порядке проводится термообработка.
- Последняя группа характеризуется тем, что в большинстве случаев на швах образуются трещины. При этом предварительный разогрев структуры не во многом решает проблему. После сварки обязательно проводится многоступенчатое улучшение.
Группы свариваемости
Каждый сплав и металл относится к определенной группе. Кроме этого, степень свариваемости меняется после улучшения материала, к примеру, путем азотирования или закалки.
Как влияют на свариваемость легирующие примеси
Как ранее было отмечено, включение в состав большого количества легирующих элементов приводит к изменению основных характеристик. При этом отметим следующие моменты:
- При низком показателе концентрации сталь лучше поддается сварке.
- Некоторые химические вещества могут повысить рассматриваемый показатель, другие ухудшить.
Именно поэтому при выборе легированного сплава уделяется внимание не только типу легирующих элементов, но и их концентрации. Принятые стандарты ГОСТ определяют то, что при маркировке могут указывать основные химические вещества и их количество в составе.
Влияние содержания углерода на свариваемость стали
Во многом именно углерод определяет основные эксплуатационные характеристики сплава. Слишком высокая концентрация подобного химического вещества приводит к повышению твердости и прочности, но также и хрупкости. Кроме этого, в несколько раз снижается степень свариваемости. К другим особенностям отнесем следующие моменты:
- Если в составе углерода не более 0,25%, то рассматриваемый показатель остается на достаточно высоком уровне.
- Слишком большое количество углерода в составе приводит к тому, что металл после термического воздействия начинает менять свою структуру, за счет чего появляются трещины.
Стоит учитывать, что проводимая химикотермическая процедура может привести к снижению податливости к рассматриваемому способу соединения. Именно поэтому улучшение сплава проводится после создания конструкции путем обработки шва.
Свариваемость низкоуглеродистых сталей
Низкоуглеродистые сплавы хорошо подаются свариванию. При этом можно отметить следующие моменты:
- В подобных сплава концентрация углерода менее 0,25%. Этот показатель свойственен сплавам, которые имеют повышенную гибкость и относительно невысокую твердость поверхностного слоя. Кроме этого, снижается значение хрупкости. Поэтому низкоуглеродистые стали часто используют при создании листовых заготовок.
При добавлении небольшого количество легирующих элементов может быть повышена коррозионная стойкость.
- Для повышения основных характеристик в состав могут добавлять различные легированные элементы, но в небольшом количестве. Примером можно назвать марганец и никель, а также титан.
Низкоуглеродистая сталь
Как правило, подобные металлы не нужно перед обработкой подвергать подогреву, а после проведения процедура закалка или отпуск выполняется только для при необходимости.
Высоколегированные стали
Высоколегированные стали имеют повышенно содержание легирующих элементов — Cr и Ni (обычно не ниже 16% и 7% соответственно). Они придают таким металлам соответствующую структуру и необходимые свойства. Высоколегированные стали по сравнению с менее легированными обладают высокой хладостойкостью, коррозионностойкостью, жаропрочностью и жаростойкостью. Несмотря на высокие свойства этих сталей, их основное служебное назначение определяет соответствующий подбор состава легирования. В соответствии с этим их можно разделить на три группы: жаростойкие, жаропрочные и коррозионностойкие.
После соответствующей термообработки высоколегированные стали обладают высокими прочностными и пластическими свойствами. В отличие от углеродистых при закалке эти материалы приобретают повышенные пластические свойства.
Структуры высоколегированных сталей очень разнообразны и зависят в основном от их химического состава, то есть от содержания основных элементов: хрома (ферритизатора) и никеля (аустенитизатора). Также на структуру влияет содержание других легирующих элементов-ферритизаторов (Mo, Ti, Si, Al, W, V) и аустенизаторов (Co, Cu, C, B).
Легирующие элементы. Сварка
Легирующие элементы
Легированными называют стали, содержащие специально введенный элемент для придания стали определенных свойств и структуры. В зависимости от содержания легирующих элементов стали подразделяют на низколегированные (с содержанием легирующих компонентов, кроме углерода, не более 2,5 %), среднелегированные (с содержанием легирующих компонентов, кроме углерода, 2,5–10 %) и высоколегированные (с содержанием легирующих компонентов, кроме углерода, свыше 10 %).
Свариваемость легированных сталей оценивается не только возможностью получения сварного соединения с физико-механическими свойствами, близкими к свойствам основного металла, но и возможностью сохранения специальных свойств: коррозионной стойкости, жаропрочности, химической стойкости, стойкости против образования закалочных структур и др. Большое влияние на свариваемость стали оказывает наличие в ней различных легирующих примесей: марганца, кремния, хрома, никеля, молибдена и др. Влияние кремния и марганца на свариваемость стали уже рассматривалось, остановимся на других элементах.
Хром содержится в низколегированных сталях до 0,9 %. При таком содержании он не оказывает существенного влияния на свариваемость стали. В конструкционных сталях хрома содержится 0,7–3,5 %, в хромистых – 12–18, в хромоникелевых – 9–35 %. С повышением содержания хрома свариваемость стали ухудшается, так как, окисляясь, хром образует тугоплавкие оксиды Cr2О3, резко повышает твердость стали в зоне термического влияния, образуя карбиды хрома, а также способствует возникновению закалочных структур.
Никель содержится в низколегированных сталях до 0,6 %, в конструкционных сталях – 1,0–5 %; в легированных сталях – 8–35 %. Никель способствует измельчению кристаллических зерен, повышению пластичности и прочностных качеств стали и не снижает свариваемости.
Молибдена в теплоустойчивых сталях содержится от 0,15 до 0,8 %, в сталях, работающих при высоких температурах и ударных нагрузках, – 3,5 %. Молибден способствует измельчению кристаллических зерен, повышению прочности и ударной вязкости стали, но ухудшает свариваемость стали, так как способствует образованию трещин в металле шва и зоне термического влияния. В процессе сварки легко окисляется и выгорает, поэтому требует специальных мер для надежной защиты от выгорания при сварке.
Ванадий содержится в сталях до 1,5 %. Он придает стали высокую прочность, повышает ее вязкость и упругость, но при этом ухудшает свариваемость, так как способствует образованию закалочных структур в металле шва и околошовной зоны. При сварке легко окисляется и выгорает.
Вольфрам содержится в сталях от 0,8 до 18 %. Значительно повышает твердость стали и теплостойкость. Снижает свариваемость стали, в процессе сварки легко окисляется и выгорает.
Титан и ниобий содержатся в нержавеющих и жаропрочных сталях в пределах 0,5–1,0 %. Они являются хорошими карбидообразователями и препятствуют образованию карбидов хрома. При сварке нержавеющих сталей ниобий способствует образованию горячих трещин.
Данный текст является ознакомительным фрагментом.
Продолжение на ЛитРесВольфрам Содержание в стали и влияние
Глубина борирования с увеличением содержания углерода и легирующих элементов в стали снижается, причем наиболее сильно при введении молибдена и вольфрама. Никель, марганец и кобальт мало влияют на глубину слоя.
Наиболее существенное влияние на полиморфизм железа оказывают хром, вольфрам, ванадий, молибден, ниобий, марганец, никель, медь и другие металлы. Они расширяют или сужают область существования у-железа. Например, введение в сталь никеля, марганца и меди понижает температуру точки и повышает температуру точки А , что (при определенном их содержании) расширяет область у-железа от температуры плавления до комнатной (рис. 5.2, а). Такие сплавы представляют собой твердый раствор легирующего элемента в у-же-лезе и относятся к сталям аустенитного класса. [c.79]
Установлено, что фосфор, медь, молибден (0,61%), вольфрам (2,7%), ниобий (0,62—1,6%), азот (0,3—0,35%), введенные в сталь раздельно, снижают склонность металла к коррозионному растрескиванию. Меньшие количества азота (0,061%), бора (0,005%) и кремния (0,81%), а также углерода после 1500-[c.630]
Плохо влияют на свариваемость элементы, дающие в стали устойчивые карбиды. Молибден и вольфрам без значительного ухудшения свариваемости вводят в низкоуглеродистую сталь в количествах до 0,5 %. Ванадий и ниобий ухудшают свариваемость при содержании более 0,2 %. Влияние активных карбидообразователей на свариваемость низколегированных, низкоуглеродистых сталей связано с трудностями растворения устойчивых карбидов при нагреве, трудностями гомогенизации аустенита и вследствие этого с образованием в ЗТВ участков с хрупкими неравновесными структурами. [c.314]
Вольфрам оказывает незначительное влияние на ток пассивации и потенциал пассивации, но заметно снижает ток в пассивном состоянии при содержании его, равном 5—G%, в стали 18% Сг — 8% № [123].
[c. 76]
В состав применяемых в настоящее время нержавеющих сталей и сплавов наряду с хромом, алюминием и никелем входят в различном сочетании марганец, кремний, вольфрам, кобальт и другие элементы. Такие стали и сплавы в различной степени чувствительны к термическому воздействию при нагреве, что в значительной мере затрудняет установление технологического режима резки. Это обусловливается следующими свойствами сталей. Теплопроводность, как правило, уменьшается с увеличением степени легирования стали и числа легирующих элементов. С повышением содержания углерода теплопроводность понижается. Аналогичное влияние оказывает кремний и марганец. Особенно сильно снижают теплопроводность хром и никель. Кроме того, в некоторые марки сталей входят два и более легирующих элемента, суммарное действие их сильнее, чем одного из них в таком же количестве. Так, например, теплопроводность аустенитных сталей при 540° колеблется в пределах 0,01984—0,02025 кал/см- сек- град. Значения коэффициента теплопроводности для мартенситных и ферритных нержавеющих сталей колеблется в пределах 0,02187— 0,02284 кал[см сек град, причем эти значения уменьшаются с увеличением содержания хрома от 12 до 26%. С другой стороны, теплопроводность обычной углеродистой стали составляет более 0,0405 кал/см сек град, а теплопроводность низколегированных сталей, содержащих до 5% Сг, немного ниже.
[c.23]
Элементы второй группы (хром, кремний, молибден, ванадий, вольфрам, титан и алюминий) уменьшают устойчивость аустенита и повышают устойчивость феррита. Они снижают критическую точку Л4 и повышают А3. Тем самым они способствуют сокращению аустенитной области. Влияние этих элементов на полиморфные превращения характеризует диаграмма состояния, представленная на рис. 88, б. По оси абсцисс на диаграмме состояния показано содержание элемента, повышающего устойчивость феррита (возрастает слева направо). Если содержание этих элементов в стали превышает определенный процент, то сталь от комнатных температур до линии солидуса будет иметь структуру феррита. Такая сталь называется ферритной. [c.157]
Следует учитывать также, что целесообразность применения в производстве инструментальных сталей определенных марок должна характеризоваться, помимо режущих свойств, их способностью к восприятию закалки, глубиной прокаливаемости, шлифуемостью, влиянием ковки на структуру стали и пр. , а также расходом легирующих элементов на единицу обрабатываемого изделия, так как наличие низкого содержания легирующих элементов в стали (вольфрам, ванадий и др.) может привести не к экономии, а к перерасходу легирующих элементов за счет снижения стойкости инструмента и увеличению брака в процессе изготовления инструмента.
[c.786]
Легирующие элементы изменяют водородопроницаемость и скорость диффузии. Легирующие элементы, такие, как хром или вольфрам, при увеличении их содержания сверх некоторого предела уменьшают скорость диффузии и водородопроницаемость до такой степени, что диффузионные процессы водорода почти полностью затормаживаются, и сталь вследствие этого или частично, или даже полностью теряет флокеночувствительность. Сильное снижение флокеночувствительности или полная ее потеря происходит и в том случае, когда сталь под влиянием легирующих элементов сохраняет после охлаждения более плотную упаковку атомов (аустенитную структуру) и при комнатной температуре.
[c.79]
Влияние хрома на жаростойкость аустенитной стали, содержащей никель и вольфрам, показано на фиг. И, из которой видно, что при содержании в этой [c.22]
Влияние химического состава. Поверхностное натяжение металла зависит не только от его состава, но и состава контактирующей с ним среды. К поверхностно активным элементам, снижающим поверхностное натяжение сталей, относятся сера, марганец, кремний, углерод, хром, фосфор. Никель, титан, молибден, вольфрам повышают поверхностное натяжение сплавов на основе железа. Количественное влияние отдельных элементов зависит от их содержания и содержания в сплаве других добавок [1, 4]. Поверхностное натяжение металлов обычно определяют в инертном газе — аргоне. [c.26]
Химические элементы, входящие в состав современных конструкционных материалов, по степени их влияния на обрабатываемость можно условно разделить на три группы [68]. Для сталей на ферритной основе в первую, наиболее сильно влияющую группу, входят углерод и кремний. Сильнее всего изменяет обрабатываемость увеличение содержания углерода до 0,5%. Если применить сфероидизирующий отпуск, обеспечивающий структуру зернистого перлита и предотвращающий образование цементитной сетки, то дальнейшее увеличение содержания углерода на обрабатываемость не влияет. Во вторую группу, оказывающую значительно меньшее влияние на ухудшение обрабатываемости, входят в порядке уменьшения степени влияния хром, вольфрам, ванадий и молибден. В третью группу, практически не влияющую на обрабатываемость, входят марганец и никель. Для сталей и сплавов, имеющих аустенитную и хромоникелевую основу, в первую группу входит углерод, увеличение содержания которого непрерывно ухудшает обрабатываемость, алюминий, титан и кремний во вторую — молибден, кобальт, марганец, хром и вольфрам в третью — никель, ниобий и ванадий.
[c.285]
Такие элементы, как тантал, титан и цирконий, не подвергались коррозии и при более высокой концентрации кислорода. Концентрация металла в жидком сплаве после испытания (вследствие влияния окиси) могла увеличиваться примерно в десять раз. Нержавеющие стали, особенно типа нимоник, довольно стойки при более высокой концентрации кислорода, причем содержание металла в теплоносителе оставалось неизменным. На никель, молибден и вольфрам кислород действует так же, как на титан. С добавлением урана даже при повышенной концентрации кислорода стойкость конструкционных материалов не понижалась. Влияние урана на совместимость свойств натрия с другими металлами заключается в том, что являясь геттером он полностью ликвидирует кислород в теплоносителе. В результате наблюдалось, что любая окись, присутствующая вна-
[c.320]
Влияние легирования на сопротивление термической усталости теплоустойчивых перлитных сталей в области максимальной температуры 550° С в первом приближении похоже на влияние на жаропрочность [2]. Это положение подтверждено экспериментальными данными, показывающими, что лучшие характеристики по числу циклов до разрушения у сталей с повышенным до 0,8% содержанием молибдена и легированных сильными карбидообразующими элементами, такими как ванадий или вольфрам.
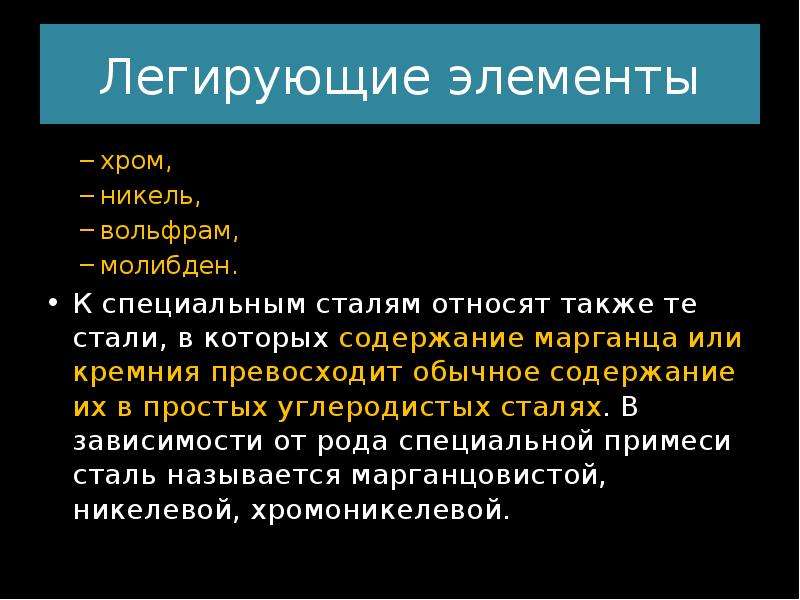
Влияние элементов и структура. Вольфрам обеспечивает красностойкость быстрорежущей стали. Хром способствует большей прокаливаемости быстрорежущей стали. Ванадий в нормальном количестве способствует стойкости карбидов и повышает производительность режущего инструмента, однако повышение содержания [c.377]
Подавить отпускную хрупкость II рода можно быстрым охлаждением при отпуске (например, в масле) или дополнительным легированием стали молибденом или вольфрамом в количестве 0,5%. Молибден и вольфрам сдерживают выделение карбидов по границам зерен и обогащение их фосфором. Однако если содержание молибдена и вольфрама больше чем 0,5%, то их благоприятное влияние исчезает, так как они при больших концентрациях образуют собственные карбиды.
[c.129]
Обеспечение жаростойкости сварных соединений. Способность сталей, сплавов и сварных швов противостоять образованию окалины под действием высоких температур определяется их химическим составом и прежде всего содержанием хрома (см. табл. 10-17 и 10-18). При выборе системы легирования металла шва необходимо иметь в виду, что кремний и алюминий также энергично повышают жаростойкость металла, а ванадий и бор ее снижают. Вольфрам и молибден несколько ослабляют способность металла шва сопротивляться окалинообразованию. Марганец в пределах до 4—6% не оказывает заметного влияния на жаростойкость металла шва. [c.601]
Кремний вводится для повышения предела текучести и сопротивления стали отпуску. Однако в связи с отрицательным влиянием на технологичность при выплавке, разливке и ковке содержание кремния должно быть ограничено [99]. Снижение содержания кремния в стали 9Х2СВФ с 1,4—1,6 до 0,8% способствует повышению технологичности при сохранении высокой теплостойкости [99]. Вольфрам в количестве 0,4—0,6% необходим для повышения прокаливаемости и твердости карбидной фазы. Увеличение концентрации вольфрама до 1,5—2,0% значительно повышает устойчивость против перегрева и отпуска [99].
[c.80]
При дальнейшем нагреве выше критических точек и происходит рост аустенитных зерен. Рост зерна аус-тенита при нагреве стали оказывает большое влияние на результаты термообработки, главным образом закалки. Размер зерна при комнатной температуре, который получен в стали в результате того или иного вида термической обработки, называют действительным зерном. Размер действительного зерна зависит от размера зерна аустенита. Обычно чем крупнее зерно аустенита, тем крупнее действительное зерно. Сталь с крупным действительным зерном имеет пониженный предел прочности, пониженную ударную вязкость и склонность к образованию трещин, поэтому при термообработке всегда стремятся к получению мелкого зерна. По склонности к росту аустенитного зерца при нагреве все стали делят на наследственно мелкозернистые и наследственно крупнозернистые. В наследственно крупнозернистых сталях размер зерна быстро увеличивается даже при небольшом нагреве выше критических точек. В наследственно мелкозернистых сталях при значительном нагреве сохраняется мелкое зерно. На процесс роста зерен в углеродистой стали оказывают влияние температура и продолжительность нагрева, содержание углерода в стали, способы раскисления, применяемые при выплавке стали. Кипящие стали являются, как правило, наследственно крупнозернистыми, а спокойные — наследственно мелкозернистыми. Введение легирующих элементов, за исключением марганца, тормозит рост зерен аустенита при нагревании. Наиболее энергично тормозят рост зерна карбидообразующие элементы титан, ванадий, вольфрам, молибден и хром. Наследственно мелкозернистые стали позволяют использовать расширенный интервал закалочных температур и облегченные условия нагрева стали.
[c.113]
Так, на основании литературных данных и ГОСТ 12348—66 в 1976 г. в отраслевую систему были внесены четыре серии СО высшей точности с аттестованным содержанием марганца в сталях для учета влияния на результаты измерений таких элементов, как хром, вольфрам и кобальт. Впоследствии было показано, что фотометрическая методика определения массового содержания марганца в сталях может использоваться без предварительного отделения мешающих компонентов в диапазоне 0,05 — 15 % Мп и, следовательно, для дифференциальной аттестации содержания марганца в государственных СО для химического и спектрального анализа достаточно одной серии СО вьюшей точности.
[c.97]
Целью легирования инструментальных сталей, принадлежащих к этой группе, в первую очередь является увеличение толщины прокаливаемого слоя, так как твердость обеспечивается большим содержанием углерода в мартенсите. Чем разнообразнее добавки содержит сталь, тем больше диаметр прокаливаемости или расстояние, измеренное от охлаждаемого торца на образце Джомини (рис. 161). Наиболее значительно увеличивает прокаливаемость легирование марганцем, молибденом, хромом и кремнием. С помощью легирования кремнием можно увеличить пределы упругости и текучести. Однако под влиянием добавок кремния растет твердость стали в отожженном состоянии и значительно увеличивается ее склонность к обезуглероживанию. У сталей, легированных, кремнием, температура эвтектоидных превращений выше, чем у нелегированных. Таким образом, для растворения карбидов требуется также большая температура. Сильные карбидообразующие элементы (ванадий, вольфрам, молибден, хром) в небольших количествах растворяются в цементите, уменьшая при этом его растворимость и склонность к коагуляции. Благодаря этому увеличивается устойчивость стали против отпуска и уменьшается чувствительность к образованию крупнозернистой структуры. Однако при наличии легирующих компонентов в количестве более 1—1,5% образуются карбиды уже больших размеров и возникает неоднородность в распределений карбидной фазы главным образом в продольном сечении. Влияние
[c.173]
Как показано в большом количестве работ (см. гл. I, II), таким элементом является молибден, введение которого в сталь в количестве 0,3—0,6 % значительно тормозит развитие отпускной хрупкости.

Определим величину которая равняется следующей алгебраической сумме 15/с = 1ё с +18/с —легирующий элемент (Сг, N1, Мп и т, д.). Легирующие элементы, влияющие на активность углерода в аустените, могут быть разделены на две группы 1) повыщающие активность углероданикель, кобальт, кремний 2) снижающие — марганец, молибден, вольфрам, ванадий, ниобий, Можно ожидать, что элементы первой группы будут способствовать развитию межкристаллитной коррозии (их влияние равносильно повышению содержания углерода в стали), а элементы второй группы уменьшат склонность к межкристаллитной коррозии (их влияние равносильно снижению содержания углерода), что в основном подтверждается экспериментальными данными [17],
[c. 13]
Влияние химического состава весьма значительно. Фосфор, марганец, кремний, хром, алюминий, ванадий (а также никель и медь в присутствии хрома и марганца) увеличивают склонность стали к обратимой хрупкости. Титан, цирконий, азот (а также никель и медь — в отсутствие других легирующих элементов) не влияют на нее. Молибден и вольфрам уменьшают склонность к обратимой хрупкости. Наиболее сильно влияет на развитие обратимой хрупкости фосфор, даже при небольшом содержании его в стали [116, 120, 109, 117, ПО]. При 1ВЫС01КОМ содержании фосфора (0,1—0,2 /о) сталь, вязкая после закалки и высокого отпуска, становится хрупкой после вылеживания в течение нескольких часов на воздухе. Описанное явление обратимо [118, 119, 109]. Сталь с предельно низким содержанием фосфора и марганца практически нечувствительна к хрупкости [109]. Марганец в количестве выше 0,5% придает углеродистой стали чувствительность к обратимой хрупкости [109], однако содержание этого элемента, вызывающее хрупкость, зависит от содержания фосфора [120, ПО].
[c.704]
Влияние карбидов на свойства легированных сталей. Карбиды являются наиболее важной второй фазой большинства сталей. Содержание углерода в большинстве конструкционных сталей в 10 — 100 раз превышает содержание азота. При N s 0,008 % азот либо связьшается алюминием, образуя нитрид A1N, либо вместе с углеродом образует карбонитри-ды. Карбидообразующими элементами в сталях являются железо, марганец, хром, молибден, вольфрам, ванадий, ниобий, титан, цирконий. Они приведены в порядке возрастания их активности при образовании карбидов. Они являются переходными металлами с незаполненной полностью -электронной оболочкой атомов и поэтому активно взаимо- [c.27]
Вольфрам. При обычном содержании в специальных сталях вольфрам на процесс резки влияния не оказывает, однако, так же, как и молибден, увеличивает прокаливаемость стали и твердость вблизи разрезанных кромок. Некоторое замедлепне процесса резки наблюдается при содержании вольфрама около 10%.
[c.312]
Существует несколько методов борирования. Исследования [28] показали, что при абразивном износе максимальной износостойкостью обладают слои, полученные при электролизном борировании, несколько меньшей — слои, полученные в расплавах буры с карбидом бора или силикокальцием, и наименьшей (однако очень высокой) —однофазные боридные слои. Такие результаты авторы объясняют тем,.что при трении скольжения износостойкость боридных слоев в основном определяется глубиной борированного слоя и соотношения в нем боридных фаз РеВ и РегВ чем больше относительное содержание в слое фазы РеВ, тем при прочих равных условиях выше его износостойкость. Легирующие элементы, повышающие относительное процентное содержание высокобористой фазы (марганец, хром, молибден, вольфрам), увеличивают износостойкость борированных слоев, а алюминий и медь уменьшают. Однако влияние легирующих элементов незначительно, и легирование сталей с целью повышения износостойкости борированных слоев нецелесообразно.
[c.56]
Алюминий, присаживаемый к никелю и никельхромовым сплавам, повышает сопротивление окислению. Наиболее высокую окалиностойкость имеет сплав (ЭИ652) с 27% Сг и 3% А1 (см. рис. 27). Вольфрам и молибден несколько ухудшают жаростойкость никеля и нихрома, но их отрицательное влияние в этих сплавах значительно меньше, чем в сплавах с железом. Весьма характерной особенностью является то, что при окислении сплавов с высоким содержанием Мо не обнаружено летучей окиси молибдена, как это имеет место у никельхромистых сталей. [c.222]
Содержание углерода в этих сталях ограничивают обычно длительной прочности Влияние легирующих элементов на время до разрушения сплава на железоникелевой основе типа Х14Н35ВТЮ (ЭИ787) показано на рис 191 [c.321]
Упрочнение при отпуске стали, легированной только ванадием, сопровождается практически полным выделением ванадия из аустенита в составе карбида V . Эффективность влияния карбидов ванадия выше, чем интер-металлидов типа NiAl или Н1з(А1 Ti)2, а-фазы типа Fe— Сг и карбида СггзСе [9]. Легирование стали несколькими элементами, обеспечивающими получение в структуре нескольких карбидных фаз, открывает новые возможности повышения прочности. При одновременном легировании ванадием и вольфрамом наблюдается более интенсивное упрочнение не только после отпуска, но уже и в закаленном состоянии. Механизм влияния вольфрама может быть различным. Так как атомные радиусы ванадия и вольфрама близки, то монокарбид вольфрама (W ) может растворяться в карбиде ванадия (V ), но при дисперсионном твердении, если этот процесс и происходит, то количественно он незначителен [2]. При дисперсионном твердении одновременно протекают два процесса образование участков карбидной фазы, когерентно связанной с аусте-нитом, и обособление карбидов, их коагуляция. При содержании вольфрама до 4% коагулированных карбидов почти нет,— вольфрам, не уменьшая общего количества карбидов V , задерживает их обособление и повышает прочность. При содержании вольфрама 6—8% количество образующихся при отпуске карбидов V уменьшается и прочность падает.
При этом увеличивается количество карбидов FesWs , которые не растворяясь в аустените, связывают углерод и уменьшают количество вольфрама, участвующего в дисперсионном твердении. Обеднение аустенита углеродом при отпуске приводит к образованию е-фазы, что в свою очередь вызывает дополнительное упрочнение [2].
[c.296]
Вольфрамомолибденовые стали типа Р6М5 (Р6АМ5), Р8МЗ содержат 5—8% вольфрама и не более 5% молибдена. По влиянию на теплостойкость молибден замещает вольфрам в соотношении примерно Mo W = 1 1,5. С учетом пересчета по приведенному соотношению при условном содержании вольфрама 12—13% обеспечивается благоприятное влияние молибдена на прочность и вязкость без ухудшения теплостойкости. Поэтому стали вольфрамомолибденовой группы имеют повышенные прочностные характеристики, превосходящие по этому показателю практически все остальные быстрорежущие стали (табл. 1). Указанные в таблице марки являются лучшими для изготовления мелкого концевого инструмента (метчики, развертки диаметром менее 1,5 мм), работающего без повышенных температур в зоне резания. Для резания же труднообрабатываемых материалов инструментом больших размеров эти стали практически непригодны, кроме того, введение молибдена ухудшает технологические свойства сталей, 6
[c.6]
Роль карбидообразующих элементов сводится к повышению устойчивости стали при отпуске и к получению в ряде сталей вторичной твердости. В низколегированных сталях основную роль должны играть такие карбидообразующие элементы, которые могут входить в раствор цементита, а в выфколегированных сталях такие, которые вызывают процесс дисперсионного твердения и обусловлен ное им получение вторичной твердости. К числу таких карбидообразующих элементов относятся хром и вольфрам, которые, обогащая цементит, затрудняют диссоциацию карбидов, а следовательно, замедляют процессы диффузии и коагуляции, способствуя сохранению твердости до более высоких температур нагрева. При больших содержаниях хром и вольфрам образуют специальные дисперсные карбиды, вызывая при повышенных температурах отпуска даже возрастание твердости (явление вторичной твердости) В качестве примера на фиг. 118 приведены кривые изменения твер дости при отпуске хромистых сталей с различным содержанием хрома. Наиболее достоверное объяснение вторичной твердости за ключается в образовании специальными карбидами частиц критической степени дисперсности, после того как железные карбиды под влиянием температуры отпуска значительно укрупнились. Максимальный эффект вторичной твердости в вольфрамовых сталях достигается при более высокой температуре, нежели в хромистых сталях, что находится в прямой связи с переходом значительного количества легирующего элемента в карбиды (хром при температуре 400—450°, вольфрам при температуре 550°). Преимущество ле
[c.230]
5 распространенных легирующих элементов — металлические супермаркеты
Легирующие элементы используются для изменения механических и химических свойств стали, чтобы дать ей преимущества по сравнению со стандартной углеродистой сталью. Хотя существует множество легирующих элементов, используемых для достижения различных улучшенных свойств, некоторые элементы встречаются гораздо чаще, чем другие. Это 5 общих легирующих элементов:
- Хром
- Молибден
- Ванадий
- Марганец
- Никель
Хром
ХромХром, добавляемый в углеродистую сталь в процентах, обычно превышающих 11%, создает нержавеющую сталь.При этом процентном содержании и выше коррозионная стойкость стали значительно возрастает, а окисление железа предотвращается во многих условиях. Железо не окисляется, потому что хром окисляется первым и образует защитный слой на стали. Хром также помогает улучшить механические свойства, даже в меньших количествах. Это повысит прочность стали, твердость и способность к термообработке.
Обычные стали с высоким содержанием хрома включают нержавеющие стали марок 439, 309, 2205.Инструментальная сталь марки Д2 также имеет значительное количество хрома.
Молибден
Молибден Молибден, как и хром, влияет на коррозионную стойкость стали. Молибден также может повысить прокаливаемость, ударную вязкость и прочность на растяжение стали. Он повышает прокаливаемость за счет снижения требуемой скорости закалки в процессе термообработки для получения прочной и твердой стали. Молибден также может снизить риск образования точечной коррозии в стали, поскольку он повышает устойчивость к коррозии, вызванной хлоридами.Эквивалент сопротивления точечной коррозии, или PRE, фактически рассчитывается путем умножения количества молибдена, хрома и никеля на коэффициенты, а затем суммирования значений.
Распространенными марками стали с высоким содержанием молибдена являются группа «А» инструментальных сталей, мартенситностареющие стали, такие как марка 250, и многие нержавеющие стали.
Ванадий
Ванадий Ванадий используется для контроля размера зерна стали, сохраняя его малым. Размер зерна остается небольшим, поскольку карбиды ванадия, образующиеся при добавлении ванадия в сталь, блокируют образование зерен.Эта блокировка предотвращает рост зерен до таких размеров, какими они были бы без добавления ванадия. Эта более мелкозернистая структура помогает повысить пластичность. В некоторых сталях карбиды, образованные ванадием, могут повышать твердость и прочность стали.
Сплавы стали с высоким содержанием ванадия включают инструментальные стали A3, A9, O1 и D2. Стали для лезвий, такие как M390 и VG 10, также содержат относительно большое количество ванадия.
Марганец
МарганецМарганец часто используется в сталях для облегчения процесса термообработки.Когда стали нагревают и закаливают для повышения твердости и прочности, закалку необходимо проводить с высокой скоростью. Чем выше эта скорость, тем более нестабильным становится процесс. Марганец позволяет увеличить твердость и прочность на ту же величину, но с более медленной скоростью закалки. Это помогает снизить риск образования дефектов в процессе нагрева и закалки.
Стали с высоким содержанием марганца включают инструментальные стали A10, A4 и O2. Нержавеющая сталь 201 также содержит относительно большое количество марганца.
Никель
Никель Никель используется для производства аустенитных нержавеющих сталей, поскольку он является активатором аустенита. Когда используется количество хрома около 18% или более, а состав никеля превышает 8%, создается аустенитная нержавеющая сталь. Эта комбинация чрезвычайно устойчива к коррозии, а аустенитные марки являются одними из наиболее широко используемых нержавеющих сталей. Никель также используется для улучшения механических свойств стали. Он используется для повышения ударной вязкости и ударной вязкости даже при более низких температурах.
Стали с высоким содержанием никеля включают все аустенитные нержавеющие стали. Легированные стали, такие как группы 23XX и 25XX, также содержат большое количество никеля.
Металлические супермаркеты
Metal Supermarkets — крупнейший в мире поставщик мелких партий металла с более чем 100 обычными магазинами в США, Канаде и Великобритании. Мы являемся экспертами в области металлов и предоставляем качественное обслуживание клиентов и продукцию с 1985 года.
В супермаркетах металлов мы поставляем широкий ассортимент металлов для различных применений. Наш склад включает в себя: мягкую сталь, нержавеющую сталь, алюминий, инструментальную сталь, легированную сталь, латунь, бронзу и медь.
У нас есть широкий ассортимент форм, включая стержни, трубы, листы, пластины и многое другое. И мы можем порезать металл по вашим точным спецификациям.
Посетите сегодня один из наших более чем 100 офисов в Северной Америке.
Влияние химических элементов на сталь
Вы когда-нибудь задумывались, что на самом деле означают все эти элементы, перечисленные в отчете об испытаниях материалов? Читать дальше!
Углерод
Углерод обычно считается наиболее важным легирующим элементом в стали и может присутствовать в количестве до 2% (хотя в большинстве свариваемых сталей его содержание составляет менее 0.5%). Повышенное количество углерода повышает твердость и прочность на растяжение, а также реакцию на термическую обработку (прокаливаемость). Повышенное количество углерода снижает свариваемость.
Сера
Сера обычно является нежелательной примесью в стали, а не легирующим элементом. В количествах, превышающих 0,05%, он вызывает хрупкость и ухудшает свариваемость. Легирующие добавки серы в количестве от 0,10% до 0,30% улучшают обрабатываемость стали. Такие типы могут называться «ресульфурированными» или «свободнообрабатываемыми».Легкообрабатываемые сплавы не предназначены для использования там, где требуется сварка.
Фосфор
Фосфор обычно считается нежелательной примесью в сталях. Он обычно содержится в количестве до 0,04% в большинстве углеродистых сталей. В закаленных сталях это может привести к охрупчиванию. В низколегированные высокопрочные стали фосфор может добавляться в количестве до 0,10 % для повышения прочности и коррозионной стойкости.
Кремний
Обычно только небольшие суммы (0.20%) кремния присутствует в прокате при его использовании в качестве раскислителя. Однако в стальных отливках обычно присутствует от 0,35 до 1,00%. Кремний растворяется в железе и имеет тенденцию упрочнять его. Наплавленный металл обычно содержит примерно 0,50% кремния в качестве раскислителя. Некоторые присадочные металлы могут содержать до 1% для обеспечения улучшенной очистки и раскисления при сварке на загрязненных поверхностях. Когда эти присадочные металлы используются для сварки на чистых поверхностях, прочность полученного металла сварного шва будет заметно увеличена.Возникающее в результате снижение пластичности может вызвать проблемы с растрескиванием.
Марганец
Стали обычно содержат не менее 0,30% марганца, потому что он способствует раскислению стали, предотвращает образование сульфида железа и включений и способствует большей прочности за счет повышения прокаливаемости стали. В некоторых углеродистых сталях можно найти количества до 1,5%.
Хром
Хром является мощным легирующим элементом стали. Сильно повышает прокаливаемость стали, заметно повышает коррозионную стойкость сплавов в окислительных средах. Его присутствие в некоторых сталях может вызвать чрезмерную твердость и растрескивание в сварных швах и рядом с ними. Нержавеющие стали могут содержать более 12% хрома.
Молибден
Молибден является сильным карбидообразователем и обычно присутствует в легированных сталях в количествах менее 1%. Повышает прокаливаемость и прочность при повышенных температурах. В аустенитных нержавеющих сталях улучшает стойкость к точечной коррозии.
Никель
Никельдобавляется в стали для повышения прокаливаемости.Он часто улучшает ударную вязкость и пластичность стали, даже при повышенной прочности и твердости. Он часто используется для повышения ударной вязкости при низких температурах.
Алюминий
Алюминий добавляется в сталь в очень небольших количествах в качестве раскислителя. Это также измельчитель зерна для повышения прочности; стали с умеренными добавками алюминия были изготовлены с «мелкозернистой практикой».
Ванадий
Добавление ванадия приводит к увеличению прокаливаемости стали. Он очень эффективен, поэтому его добавляют в незначительных количествах. При содержании выше 0,05% сталь может становиться хрупкой во время обработки для снятия термических напряжений.
Общие определения стали
Слиток железа
Максимум 0,03% углерода, используется для эмалирования, цинкования, глубокой вытяжки листов и полос, отличная свариваемость.
Низкоуглеродистый
Максимум 0,15% углерода, используется для электродов, пластин и профилей, листов, полос, отличная свариваемость.
Мягкая сталь
Максимум 0,15-0,30% углерода, используется для конструкционных профилей, пластин и стержней, хорошая свариваемость.
Средний углерод
Максимум 0,30-0,50% углерода, используется для деталей машин, удовлетворительная свариваемость — может потребоваться предварительный и последующий нагрев.
Высокоуглеродистый
Максимум 0,50-1,00% углерода, используется для пружин, штампов, рельсов, плохая свариваемость — трудно сваривать без предварительного и последующего нагрева.
Спасибо Американскому обществу сварщиков за предоставление некоторой информации, используемой в этом ресурсе.
Легированная сталь – обзор
13.5 Легированная сталь
Легированные стали, используемые в гидравлических стальных конструкциях, обычно также изготавливаются литыми или коваными. Таким образом, обсуждение в предыдущем разделе также относится к этим сталям. Примерами элементов из легированной стали в гидравлических затворах являются поршневые и нижние штифты в косых затворах, цапфы в радиальных затворах и ролики в затворах с вертикальным подъемом. Кроме того, в таблице 13 приведены некоторые типичные примеры применения легированной стали.4 в разделе 13.2.3. В гидравлических воротах легированные стали обычно используются из-за их механических свойств, а не из-за коррозионной стойкости или других причин.
Инженеры обычно избегают сварки углеродистой стали с легированной, поэтому свариваемость редко вызывает беспокойство. Это также относится к ремонту несплошностей литья или повреждений, вызванных эксплуатационными нагрузками. Обычной процедурой в таких случаях является дисквалификация отливки или поковки в целом, а не попытка ремонта с помощью сварки.В тех случаях, когда такого ремонта нельзя избежать, следует обратить внимание на свариваемость. Затем рекомендуется ознакомиться с соответствующими результатами расследования. Хороший обзор возможностей сварки в таких случаях представлен, например, в Ref. [33].
Важно правильно определить механические и другие свойства конкретной легированной стали, прежде чем выбрать ее для применения в конструкции гидравлического затвора. Примером такой важности является безуспешное широкомасштабное применение марганцовистой стали в подшипниках цапфы европейских ворот под углом, как описано в Разделе 7.5.4 и 8.4.2.2. В данном случае разрушению способствовало так называемое деформационное упрочнение сплава марганцовистой стали. Примечательным наблюдением является то, что такое же поведение оказалось очень желательным и желательным в других тяжелых условиях эксплуатации, например, в горнодобывающей и карьерной технике.
Поскольку элементы из легированной стали обычно используются для облегчения движения ворот, смазка этих элементов часто является важной проблемой. Подробное обсуждение этого вопроса представлено в Разделе 11.6. Однако важно не только выбрать адекватные и экологически приемлемые смазочные материалы для изделий из легированной стали, но и обеспечить удобный способ их применения. С этой точки зрения болезненным уроком стал отказ подъемной цепи из легированной стали ворот Lith Weir в Маасе, Нидерланды, упомянутый в разделе 12.5.2. Непосредственной причиной этого отказа была перегрузка и разрыв цепи подъемного механизма, в основном из-за недостаточной смазки. Цепь была заменена в 2009 году роликовой цепью из высоколегированной стали с тройными боковыми звеньями, как показано на рис.13.11. Основным улучшением стало устранение неэффективной и загрязняющей окружающую среду смазки цепи из кабины крана и обеспечение сервисных столов для обслуживания цепей на подъемных башнях. Работа этих столов обслуживания представлена на чертежах рис. 13.12.
Рис. 13.11. Новые цепи из высоколегированной стали для Lith Weir на реке Маас, Нидерланды.
Фото Hollandia B.V.Рис. 13.12. Стол обслуживания цепи ворот в плотине Лит на Маасе.
Предоставлено Hollandia B.В. и Рейксватерштат Лимбург.Очевидно, что таблица технического обслуживания, показанная на рис. 13.12, позволила не только обеспечить экологически чистую и эффективную смазку цепей, но и тщательный осмотр, более качественное техническое обслуживание и, как следствие, более низкий риск повторного отказа.
Текущие взгляды Инженерного корпуса армии США немного отличаются в отношении применения легированных сталей в роликовых цепях для гидравлических подъемников ворот. Корпус обычно рекомендует роликовые цепи с боковыми стержнями из алюминиевой бронзы и штифтами из нержавеющей стали.Детали таких цепочек можно увидеть на рис. 3.94 и 11.29 ранее в этой книге. См. также обсуждение цепных материалов в Разделе 11.3.11.
Первичное влияние легирующих элементов на свойства металлов
Очень часто к определенным металлам добавляют легирующие элементы для достижения определенных характеристик, необходимых для конкретного применения. Включение определенных веществ может изменить многие свойства, от прочности до цвета и теплопроводности.Это может сделать изготовление деталей намного проще и часто увеличивает срок службы продукта. Тем не менее, важно иметь некоторое представление о том, как это работает, поскольку добавление различных элементов может повлиять на множество различных свойств. Давайте посмотрим поближе.
Хром
Мы только что увеличили содержание хрома в вашем сплаве. Также повысилась коррозионная стойкость. Большинство нержавеющих сталей содержат около 18 процентов хрома, что обеспечивает хорошую начальную коррозионную стойкость.Увеличение содержания хрома будет постоянно повышать коррозионную стойкость сплава, особенно при высоких температурах.
Никель
Теперь давайте начнем рецепт заново и добавим немного никеля. Никель может иметь множество эффектов на сплав, таких как незначительное повышение коррозионной стойкости (не так сильно, как у хрома) и повышение прочности при высоких температурах. Однако наиболее значительным результатом является повышенная формуемость в результате повышенного содержания никеля.Большинство нержавеющих сталей имеют процентное содержание никеля в диапазоне 8-10 процентов. По мере увеличения этого процента будет увеличиваться и формуемость материала.
Углерод
По сравнению с некоторыми другими элементами содержание углерода в нержавеющей стали относительно низкое, обычно менее 0,2 процента. Увеличение содержания углерода будет иметь много эффектов на свойства. Повышает твердость и прочность, а также улучшает прокаливаемость. Тем не менее, это также может иметь некоторые эффекты, которые производители деталей не ищут.Это повысит хрупкость и может снизить как свариваемость, так и коррозию из-за склонности к образованию мартенсита.
Азот
Азот прибыл на место происшествия. Добавление этого элемента будет иметь много эффектов на сплав. Он также повышает коррозионную стойкость, но на более локальном уровне, чем хром. Это значительно улучшает стойкость к точечной и щелевой коррозии, а также к межкристаллитной коррозии. Азот также может повышать прочность, и его типичное содержание в нержавеющей стали составляет менее 0.1 процент.
Молибден
Добавление молибдена в нержавеющую сталь улучшит стойкость к точечной коррозии и коррозионной стойкости. Нержавеющая сталь 316 обычно имеет повышенное содержание этого элемента и известна своей коррозионной стойкостью. Кроме того, молибден улучшает прочность при повышенных температурах, что делает его часто используемым компонентом в аэрокосмических устройствах, таких как теплообменники или выхлопные системы.
Марганец
Марганец — еще один легирующий элемент, используемый для достижения определенных свойств.Помимо повышения стабильности азота в металле, этот элемент увеличивает прокаливаемость и прочность на разрыв, но не в такой степени, как углерод.
Кремний
Кремний, помимо улучшения прочности и твердости, может быть ключевым фактором в улучшении стойкости к окислению при увеличении его содержания в нержавеющей стали. Будучи стабилизатором феррита, кремний является отличным раскислителем, а также может повысить коррозионную стойкость.
Медь
В нержавеющей стали обычно присутствует остаточное количество меди, но в некоторых случаях ее специально добавляют, т.е.д: 304Cu. Целью этих марок является повышение коррозионной стойкости, особенно в условиях океана, а также обеспечение свойств дисперсионного твердения.
Алюминий
Алюминий, обладающий высокой стойкостью к окислению и коррозии благодаря своему пассивирующему слою, обычно присутствует в ферритных нержавеющих сталях (серия 400) по другой причине. Добавленное содержание алюминия в серии 400 приводит к повышенной пластичности, а также устойчивости к коррозионному растрескиванию под напряжением.
Титан
Титан — это элемент, который в первую очередь добавляется для связывания углерода, также известного как стабилизация карбида. Это улучшает свариваемость, поскольку комбинация углерода и титана (карбиды титана) стабильна и трудно растворяется в стали. Это сводит к минимуму возникновение межкристаллитной коррозии.
Кобальт
Кобальт, как и титан, помогает стабилизировать карбид и улучшить сварку. Однако в ядерных приложениях ограничения по кобальту необходимы, поскольку этот элемент может стать высокорадиоактивным при воздействии радиации.
Все эти элементы могут играть решающую роль в приложении. И производство, и жизненный цикл продукта зависят от того, с какими элементами легирован металл. Как видите, существует множество вариантов легирования и влияние этих легирующих элементов на свойства. Имея все различные марки нержавеющей стали и специальных металлов, обычно можно найти идеальный вариант для вашего продукта.
Все еще сомневаетесь, что лучше использовать для следующего проекта: 304L или 316L? Есть другие вопросы по металлургии? Свяжитесь со специалистом, и мы будем рады помочь.
Ключевой компонент прочности и долговечности нержавеющей стали
| |
Нержавеющая сталь использовалась во многих знаковых сооружениях, как старых, так и новых.![]() | |
|
Тим Ауттеридж, Генеральный секретарь, Международная молибденовая ассоциация (IMOA)
Молибден извлекается из минерала молибденита, открытого Питером Джейкобом Хьельмом в 1782 году.Это оставалось лабораторным любопытством, пока извлечение коммерческих количеств не стало практичным. Сегодня он используется во многих отраслях промышленности, в том числе в строительстве, где он является ключевым компонентом нержавеющей стали.
Эксперименты после Первой мировой войны показали, что молибден может эффективно заменить вольфрам во многих стальных сплавах, и к концу года молибден стал широко распространенным техническим материалом. 1930-х годов. Окончание Второй мировой войны в 1945 году снова привело к увеличению инвестиций в исследования для разработки новых гражданских применений, а послевоенная реконструкция предоставила дополнительные рынки для конструкционных сталей, содержащих молибден.
Сегодня стали и чугун составляют самый большой рыночный сегмент спроса на молибден, однако молибден также имеет неоценимое значение в суперсплавах, сплавах на основе никеля, смазочных материалах, химикатах, электронике и во многих других областях.
Небольшое количество молибдена может существенно повлиять на характеристики металла. При использовании в качестве легирующего элемента молибден может повышать прочность сталей при нормальных и повышенных температурах без ущерба для ударной вязкости. Он также придает исключительную коррозионную стойкость нержавеющим сталям и никелевым сплавам.
Важным, но скрытым применением молибденсодержащей нержавеющей стали является арматура для бетонных конструкций. Федеральное управление автомобильных дорог США заказало испытания на коррозию, чтобы помочь им выбрать материалы арматуры, способные продлить срок службы железобетонных мостов до 75-100 лет, когда бетон был загрязнен хлоридами. Исследование пришло к выводу, что молибденсодержащая нержавеющая сталь типа 316 сможет обеспечить требуемый срок службы.
На противоположном конце спектра, архитектура, возможно, является наиболее заметным из всех применений нержавеющей стали, содержащей молибден. В течение почти 100 лет нержавеющая сталь была предпочтительным материалом для достижения высоких эксплуатационных характеристик в сочетании с современной прогрессивной эстетикой. Уже очень прочный архитектурный материал, когда добавляется молибден, еще больше повышается устойчивость к коррозии, вызванной хлоридами (от прибрежных или противогололедных солей) и загрязнениям. Это делает молибденсодержащие нержавеющие стали идеальным выбором для зданий, мостов, транспортных средств, городской мебели, скульптур и многих других применений.Мало того, что это может продолжаться в течение расчетного срока службы конструкции, при правильном выборе внешний вид соответствующей комбинации молибденсодержащей нержавеющей стали и отделки останется практически неизменным, сводя к минимуму требования к техническому обслуживанию.
IMOA разработала руководство по выбору нержавеющей стали, исходя из предположения, что коррозионное окрашивание эстетически неприемлемо. Система оценки нержавеющей стали предназначена для использования архитекторами, подрядчиками и другими лицами, участвующими в выборе нержавеющей стали, и перечисляет факторы, которые необходимо учитывать при выборе нержавеющей стали для наружных работ, используя простую систему оценки.Он состоит из программного обеспечения и брошюры с описанием системы, тематических исследований со всего мира и ссылок на данные, необходимые для оценки объекта (карты загрязнения, коррозии, климата и т. д.). Программное обеспечение и множество тематических исследований, посвященных использованию молибденсодержащей нержавеющей стали в строительстве, можно найти в Интернете на веб-сайте IMOA.
Примеры впечатляющей архитектуры из нержавеющей стали, содержащей молибден, можно найти по всему миру, от лондонской площади One Canada Square до моста Harbour Drive в Сан-Диего, а также во многих строящихся проектах, включая новое здание кондоминиума на West 57 th St. а также фасад и шпиль 1 Всемирного торгового центра в Нью-Йорке.
Сталь, легированная молибденом, также вносит значительный вклад в устойчивое строительство с точки зрения энергоэффективности и ресурсосбережения. Кондиционирование воздуха является крупнейшим источником потребления энергии во многих современных зданиях, и солнцезащитные средства все чаще используются для уменьшения пассивного поступления солнечного тепла. Федеральное здание в Сан-Франциско, штат Калифорния, включает в себя сложный солнцезащитный крем с компьютерным управлением, изготовленный из содержащей молибден нержавеющей стали типа 316. В сочетании с естественной вентиляцией это значительно снижает потребность в кондиционировании воздуха, сокращая потребление энергии зданием на две трети.Молибден в нержавеющей стали значительно повышает ее устойчивость к коррозии в городской прибрежной среде и, следовательно, помогает гарантировать расчетный срок службы в 100 лет.
Американский институт стальных конструкций (AISC) в прошлом году опубликовал Руководство по проектированию № 27 для конструкционной нержавеющей стали, отвечающее требованиям рекомендаций США по проектированию для больших секций из нержавеющей стали. Более легкие секции из нержавеющей стали уже были включены в спецификацию проектирования США, но для более тяжелых секций не существовало руководства, а это означало, что должностные лица по строительству должны были индивидуально утверждать каждую заявку.Новое руководство написано в форме спецификации, что позволяет проектировщикам ссылаться на него в качестве обоснования, устраняя огромный объем работы и создавая новый потенциал роста в таких приложениях, как пешеходные мосты, здания и другие несущие конструкции.
Молибден вносит дополнительный вклад в более экологичные здания благодаря своей роли в производстве высокопрочной стали (HSS). Хотя предел текучести стали можно увеличить за счет добавления большего количества углерода, это может отрицательно сказаться как на пластичности, так и на свариваемости.Однако с добавлением молибдена возможен повышенный предел текучести без ухудшения свариваемости. Добавление молибдена также поддерживает прочность и улучшает прокаливаемость.
Быстрорежущая сталь позволяет создавать более прочные и легкие конструкции, чем обычная сталь, тем самым экономя ресурсы, а также затраты и энергию при производстве и транспортировке. Хотя выбросы CO 2 в результате производства быстрорежущей стали немного выше, чем при производстве обычной стали, экономия веса за счет использования быстрорежущей стали обычно составляет от 20% до 40%, что приводит к значительному общему сокращению выбросов CO 2 .
Быстрорежущая сталь, используемая при строительстве длиннопролетных конструкций, может заменить обычную сталь, обеспечивая значительную экономию средств и защиту окружающей среды. Крыша стадиона Friends Arena в Стокгольме, Швеция, была построена из быстрорежущей стали с содержанием 750 кг молибдена более высокой прочности. Замена обычной стали на быстрорежущую сталь в отдельных частях крыши позволила сократить общий расход стали на 17 % и общие затраты на 14,5 %, а также сократить выбросы парниковых газов на 17 % по сравнению с обычной сталью в течение жизненного цикла стадиона.
Для получения дополнительной информации о применении молибдена в проектировании и строительстве посетите сайт www.imoa.info, напишите по электронной почте [email protected] или позвоните по телефону +44 20 8747 6120.
О IMOA
Международная молибденовая ассоциация — некоммерческая торговая ассоциация, представляющая интересы большинства мировых производителей и переработчиков молибдена, а также торговцев и конечных пользователей. Молибден добавляют в стали и чугуны для улучшения прочности, ударной вязкости, прокаливаемости и свариваемости для многочисленных применений в автомобильной, судостроительной, строительной, горнодобывающей, химической, нефтегазовой и энергетической отраслях.В нержавеющих сталях и суперсплавах он улучшает коррозионную стойкость и высокотемпературные характеристики и находит применение во многих отраслях промышленности. Он также используется в различных продуктах, от катализаторов и смазочных материалов до пигментов и красок. Чтобы узнать больше, посетите www.imoa.info.
Классификация углеродистых и низколегированных сталей
Американский институт чугуна и стали (AISI) определяет углеродистую сталь следующим образом: Сталь считается углеродистой сталью, если не указано или не требуется минимальное содержание хрома, кобальта, колумбия [ниобия], молибдена, никеля, титана, вольфрама, ванадия или цирконий или любой другой элемент, добавляемый для получения желаемого эффекта сплавления; когда указанный минимум для меди не превышает 0.40 процентов; или когда максимальное содержание, указанное для любого из следующих элементов, не превышает указанных процентов: марганец 1,65, кремний 0,60, медь 0,60.
Стали можно классифицировать по различным системам в зависимости от:
- Состав, например, из углеродистой, низколегированной или нержавеющей стали.
- Методы производства, такие как мартеновский, основной кислородный процесс или методы электропечи.
- Метод отделки, такой как горячая или холодная прокатка
- Форма продукта, такая как стержневая пластина, лист, полоса, труба или структурный профиль
- Практика раскисления, такая как раскисленная, полуспокойная сталь, сталь с крышкой или кромкой
- Микроструктура, такая как ферритная, перлитная и мартенситная
- Требуемый уровень прочности, указанный в стандартах ASTM .
- Термическая обработка, такая как отжиг, закалка и отпуск, а также термомеханическая обработка
- Дескрипторы качества, такие как качество ковки и товарное качество.
Углеродистая сталь
Американский институт чугуна и стали (AISI) определяет углеродистую сталь следующим образом:
Сталь считается углеродистой, если не указано или не требуется минимальное содержание хрома, кобальта, колумбия [ниобия], молибдена, никеля, титана, вольфрама, ванадия или циркония или любого другого элемента, добавляемого для получения желаемого эффекта легирования. ; когда установленный минимум по меди не превышает 0,40 процента; или когда максимальное содержание, указанное для любого из следующих элементов, не превышает указанного процентного содержания: марганец 1.65, кремний 0,60, медь 0,60.
Углеродистая сталь может быть классифицирована в соответствии с различными методами раскисления как сталь с каймой, с крышкой, полуспокойная или спокойно. Практика раскисления и процесс производства стали будут влиять на свойства стали. Однако изменения в углероде оказывают наибольшее влияние на механические свойства, при этом увеличение содержания углерода приводит к увеличению твердости и прочности. Таким образом, углеродистые стали обычно классифицируют в зависимости от содержания углерода.Вообще говоря, углеродистые стали содержат до 2% всех легирующих элементов и могут быть подразделены на низкоуглеродистые стали, среднеуглеродистые стали, высокоуглеродистые стали и сверхвысокоуглеродистые стали; каждое из этих обозначений обсуждается ниже.
Как группа, углеродистые стали являются наиболее часто используемыми сталями. Более 85% стали, производимой и поставляемой в США, составляет углеродистая сталь.
Низкоуглеродистые стали содержат до 0,30 % С. Самой большой категорией стали этого класса является плоский прокат (листовой или полосовой), обычно в холоднокатаном и отожженном состоянии.Содержание углерода в этих сталях с высокой формуемостью очень низкое, менее 0,10% C и до 0,4% Mn. Типичное использование — в панелях кузова автомобиля, белой жести и изделиях из проволоки.
Для стальных конструкционных листов и профилей содержание углерода может быть увеличено примерно до 0,30 %, а более высокое содержание марганца — до 1,5 %. Эти материалы могут быть использованы для штамповок, поковок, бесшовных труб и котельных плит.
Среднеуглеродистые стали аналогичны низкоуглеродистым сталям, за исключением того, что содержание углерода находится в диапазоне от 0.30 до 0,60% и марганца от 0,60 до 1,65%. Увеличение содержания углерода примерно до 0,5 % с сопутствующим увеличением содержания марганца позволяет использовать среднеуглеродистые стали в закаленном и отпущенном состоянии. Использование среднеуглеродистых марганцевых сталей включает валы, оси, шестерни, коленчатые валы, муфты и поковки. Стали с содержанием углерода от 0,40 до 0,60% также используются для изготовления рельсов, железнодорожных колес и железнодорожных осей.
Высокоуглеродистые стали содержат от 0,60 до 1,00% С с содержанием марганца от 0.от 30 до 0,90%. Высокоуглеродистые стали используются для пружинных материалов и высокопрочной проволоки.
Сверхвысокоуглеродистые стали представляют собой экспериментальные сплавы, содержащие от 1,25 до 2,0% С. Эти стали подвергаются термомеханической обработке для получения микроструктуры, состоящей из сверхмелких равноосных зерен сферических, прерывистых доэвтектоидных карбидных частиц.
Высокопрочные низколегированные стали
Высокопрочные низколегированные (HSLA) стали или микролегированные стали предназначены для обеспечения лучших механических свойств и/или большей устойчивости к атмосферной коррозии, чем обычные углеродистые стали в обычном смысле, поскольку они предназначены для удовлетворения конкретных механических свойств, а не химический состав.
Стали HSLA имеют низкое содержание углерода (0,05-0,25% C) для обеспечения адекватной формуемости и свариваемости, а также содержание марганца до 2,0%. Небольшие количества хрома, никеля, молибдена, меди, азота, ванадия, ниобия, титана и циркония используются в различных комбинациях.
Классификация HSLA:
- Атмосферостойкие стали , предназначенные для обеспечения превосходной стойкости к атмосферной коррозии
- Стали контрольного проката , горячекатаные по заданному графику прокатки, предназначенные для образования сильно деформированной аустенитной структуры, которая при охлаждении превращается в очень тонкую равноосную ферритную структуру
- Стали с пониженным содержанием перлита , упрочненные очень мелкозернистым ферритом и дисперсионным твердением, но с низким содержанием углерода и, следовательно, с небольшим содержанием перлита или без него в микроструктуре
- Микролегированные стали с очень небольшими добавками таких элементов, как ниобий, ванадий и/или титан для уменьшения размера зерна и/или дисперсионного твердения
- Сталь с игольчатым ферритом , очень низкоуглеродистая сталь с достаточной прокаливаемостью для превращения при охлаждении в очень мелкую высокопрочную структуру игольчатого феррита, а не в обычную структуру полигонального феррита
- Двухфазные стали , обработанные до микроструктуры феррита, содержащей небольшие равномерно распределенные области высокоуглеродистого мартенсита, в результате чего получается продукт с низким пределом текучести и высокой скоростью деформационного упрочнения, что обеспечивает получение высокопрочной стали превосходной формуемости.
Различные типы сталей HSLA могут также иметь небольшие добавки кальция, редкоземельных элементов или циркония для контроля формы сульфидных включений.
Стали низколегированные
Низколегированные стали представляют собой категорию черных металлов, которые обладают механическими свойствами, превосходящими простые углеродистые стали в результате добавок легирующих элементов, таких как никель, хром и молибден. Общее содержание сплава может колебаться от 2,07% до уровней чуть ниже, чем у нержавеющих сталей, которые содержат не менее 10% Cr .
Для многих низколегированных сталей основной функцией легирующих элементов является повышение прокаливаемости с целью оптимизации механических свойств и ударной вязкости после термической обработки. Однако в некоторых случаях добавки к сплаву используются для уменьшения ухудшения состояния окружающей среды при определенных условиях эксплуатации.
Как и стали в целом, низколегированные стали можно классифицировать в соответствии с:
- Химический состав , например, никелевые стали, никель-хромовые стали, молибденовые стали, хромомолибденовые стали
- Термическая обработка , такая как закалка и отпуск, нормализация и отпуск, отжиг.
Из-за большого разнообразия возможных химических составов и того факта, что некоторые стали используются более чем в одном термообработанном состоянии, среди классификаций легированных сталей существует некоторое совпадение. В этой статье рассматриваются четыре основные группы легированных сталей: (1) низкоуглеродистые закаленные и отпущенные (QT) стали, (2) среднеуглеродистые сверхвысокопрочные стали, (3) подшипниковые стали и (4) жаропрочные стали. стойкие хромомолибденовые стали.
Низкоуглеродистые закаленные и отпущенные стали сочетают в себе высокий предел текучести (от 350 до 1035 МПа) и высокую прочность на растяжение с хорошей ударной вязкостью, пластичностью, коррозионной стойкостью или свариваемостью.Различные стали имеют разные комбинации этих характеристик в зависимости от их предполагаемого применения. Однако некоторые стали, такие как HY-80 и HY-100, подпадают под действие военных спецификаций. Перечисленные стали используются в основном как толстолистовые. Некоторые из этих сталей, а также другие подобные стали производятся в виде поковок или отливок.
Среднеуглеродистые сверхвысокопрочные стали — это конструкционные стали с пределом текучести, который может превышать 1380 МПа. Многие из этих сталей имеют обозначения SAE/AISI или представляют собой запатентованные составы.Формы продукции включают заготовки, прутки, стержни, поковки, листы, трубы и сварочную проволоку.
Подшипниковые стали , используемые для шариковых и роликовых подшипников, состоят из низкоуглеродистых (от 0,10 до 0,20% C ) цементируемых сталей и высокоуглеродистых (-1,0% C) сталей со сквозной закалкой. Многие из этих сталей имеют обозначения SAE/AISI.
Хромолибденовые жаростойкие стали содержат от 0,5 до 9% Cr и от 0,5 до 1.0% Мо . Содержание углерода обычно ниже 0,2%. Хром обеспечивает улучшенную стойкость к окислению и коррозии, а молибден повышает прочность при повышенных температурах. Как правило, они поставляются в нормализованном и отпущенном, закаленном и отпущенном состоянии или в отожженном состоянии. Хромомолибденовые стали широко используются в нефтяной и газовой промышленности, а также на ископаемом топливе и на атомных электростанциях.
Влияние Mn, P, S, Si и V на механические свойства стали
Влияние Mn, P, S, Si и V на механические свойства сталиВлияние Mn, P, S, Si и V на механические свойства стали
Общий символ химический элемент представлен:
А З Н
, где А — это атомный номер, указывающий количество протонов, существующих в ядре атома; N — атомная единица массы, определяемая как отношение средней массы на атом к 1 / 12 атомной массы углерода-12 в его ядерном и электронном основном состоянии; и Z — химический символ элемента.
Марганец, 25 Mn 54,938049
Марганец
повышает прокаливаемость и предел прочности стали, но в меньшей степени
чем углерод. Он также способен снизить критическую скорость охлаждения во время
закалки, тем самым повышая прокаливаемость сталей намного эффективнее, чем любой
другие легирующие элементы. Марганец также имеет тенденцию увеличивать скорость углерода.
проникает во время науглероживания и действует как мягкий раскислитель.тем не мение
когда слишком высокое содержание углерода и слишком высокое содержание марганца сопровождают друг друга, охрупчивание
Марганец способен образовывать сульфид марганца (MnS) с серой,
что выгодно для механической обработки. В то же время он противостоит ломкости
от серы и благоприятно влияет на качество поверхности углеродистой стали.
Для сварки целей соотношение марганца к сере должно быть не менее 10 к 1. Содержание марганца менее 0,30% может способствовать внутренней пористости и растрескиванию. в сварном шве растрескивание также может произойти, если содержание выше 0.80%. Стали с низким содержанием сульфида марганца может содержать серу в форме железа Сульфид (FeS), который может вызвать растрескивание (горяче-короткое состояние) в сварка
Фосфор, 15 P 30,973761
Фосфор
повышает прочность и твердость, но за счет пластичности и ударопрочности
ударная вязкость, особенно в высокоуглеродистых сталях, подвергаемых закалке и отпуску. В виде
такое его содержание в большинстве сталей ограничивается максимум 0.05%. Фосфор
предотвращает прилипание тонколистовых листов при использовании в качестве сплава в стали.
В определенной степени упрочняет низкоуглеродистую сталь, повышает устойчивость к коррозии.
и улучшает обрабатываемость сталей, получаемых автоматическим резанием. Что касается сварки,
содержание фосфора более 0,04 % делает сварной шов хрупким и повышает склонность
взломать. Поверхностное натяжение расплавленного металла шва снижается, что делает его
сложно контролировать.
Сера, 16 S 32.065
Сера улучшает
обрабатываемость, но снижает поперечную пластичность и ударную вязкость с надрезом и
мало влияет на продольные механические свойства.Его содержание
ограничивается до 0,05% в сталях, но добавляется к сталям, предназначенным для механической резки, в количестве до
0,35% с повышенным содержанием марганца для противодействия любым вредным воздействиям
так как сера полезна для механической обработки. При сварке снижается свариваемость
с увеличением содержания серы. Сера ухудшает качество поверхности в
малоуглеродистых и маломарганцевых сталей и способствует короткому замыканию при сварке
с тенденцией к увеличению с увеличением содержания серы.
Кремний, 14 Кремний 28.0855
Кремний увеличивает прочность и твердость, но в меньшей степени, чем у марганца. Это один из основные раскислители, используемые при производстве сталей для улучшения прочности, т.е. быть без дефектов, ветхости или повреждений. Кремний присутствует во всех сталях в определенной степени. Его содержание может составлять до 4% для электролистов, которые широко распространены. используется в магнитных цепях переменного тока.
В сварке,
кремний ухудшает качество поверхности, особенно низкоуглеродистой,
ресульфированные сорта.Это усугубляет тенденцию к растрескиванию, когда содержание углерода
довольно высок. Для наилучших условий сварки содержание кремния не должно превышать
0,10%. Однако количества до 0,30% не так опасны, как высокое содержание серы или
содержание фосфора.
Для цинкования целей стали, содержащие более 0,04% кремния, могут сильно повлиять на толщина и внешний вид оцинкованного покрытия. Это приведет к густоте покрытия, состоящие в основном из цинково-железных сплавов, а поверхность имеет темный и матовый финиш.Но он обеспечивает такую же защиту от коррозии, как и блестящее оцинкованное покрытие. покрытие, внешний слой которого состоит из чистого цинка.
Ванадий, 23 В 50,9415s
Ванадий используется
для уточнения размера зерна. Стали, содержащие ванадий, имеют гораздо более мелкое зерно.
структуры, чем у сталей аналогичного состава без ванадия. Это уменьшает
скорость роста зерна во время процессов термообработки и повышает температуру
при котором происходит укрупнение зерна, что повышает прочность и ударную вязкость
закаленные и отпущенные стали.Содержание до 0,05% увеличивает прокаливаемость, в то время как
большие количества имеют тенденцию к снижению прокаливаемости из-за образования карбида. Ванадий уменьшает разупрочнение при отпуске и вызывает вторичную твердость при высоких температурах.
скоростные стали.
Ванадий используется в азотированных, жаропрочных, инструментальных и пружинных сталях вместе с другими легирующие элементы. Он также используется в микросплавах феррита/перлита. сталей для повышения твердости за счет карбонитридного дисперсионного упрочнения матрица.
Ссылки
1. Automotive Handbook, Bosch, 1 st , английское издание, 1978 г., стр. 154-158
2. Лоуренс Х. Ван Влак, Элементы материаловедения и инженерии, 4 th Издание, Addison-Wesley, 1980, стр. 31–32
.3. http://www.webelements.com
4. http://www.macsteel.com/mdb/general_information/glossary_of_metallurgical_terms.htm
5. http://www.weldind.com/wl4.html
6. http://www.summitsteel.com/term.htm
7. http://www.metals.about.com/library/bl-glossary-m.htm
8.
http://www.