|
| ||||||||
|
| ||||||||
|
| ||||||||
|
| ||||||||
|
| ||||||||
|
| ||||||||
|
| ||||||||
|
| ||||||||
|
| ||||||||
|
| ||||||||
|
|
Шаблоны для сварки по выгодной стоимости — оптовые цены на Шаблоны для сварки в Москве
Шаблоны для сварки применяются для визуального контроля элементов сварки и сварочных соединений. Большинство моделей представляют собой одну или несколько стальных пластин с выемками под определенные размеры.
Каждый шаблон рассчитан на проведение ряда операций:
УШК-1 – Универсальный шаблон Кроссовского, применяется при проведении визуального и измерительного контроля сварных соединений, служит для контроля тавровых и нахлесточных сварных соединений, стыковых сварных соединений, измерения зазора между кромками свариваемых деталей;
УШС-2 – применяется для контроля катетов угловых швов в диапазоне 4-14 мм – от максимального до минимального зазора, размер устанавливается методом подбора. Представляет собой обойму из 3-х пластин с 2-я выемками на каждой пластине.
УШС-3, УШС-4 – применяется для контроля элементов разделки под сварной шов, электродов и элементов сварного шва;
Ушерова-Маршака (КТ-20, WG-3, «Ласточка») – применяется для измерения скоса кромок при подготовке свариваемых соединений, измерения высоты валика усиления и катета углового шва, а также выпуклости корня шва и измерения зазоров при подготовке деталей к сварке;
WG1, WG2 – зарубежные аналоги УШС-4 и частично шаблона Крассовского, применяются для измерения смещения, угла разделки кромки, величины зазора, угла раскрытия Х-шва, высоты шва, размеров углового шва, ширины шва, глубины подреза;
WG6 – применяется для измерения угла раздела кромки, величины зазора, угла раскрытия X-шва, высоты шва, катета углового шва, ширины шва, глубины подреза;
WG7
– применяется для измерения высоты углового шва, высоты стыкового шва, толщины выпуклого и вогнутого углового шва.
WG11 – применяется для измерения высоты заклепок, сварных швов на сосудах высокого давления и трубах, угла кромки, вогнутости и выпуклости поверхности;
WG12 – применяется для контроля параметров угловых и тавровых соединений сваренных под углом больше или меньше 90°;
WG13 – конусный шаблон применяется для измерения размеров отверстий в диапазоне 0-15 мм;
WG14 – представляет собой угломер и применяется для контроля углов в процессе сварки;
Заполнение сварного шва по сечению и длине
Если невнимательно отнестись к сварочному процессу и неграмотно подготовить свариваемые элементы, их прочность будет недолговечной, и в какой-то момент конструкция разрушится. Особого подхода и профессионализма требует сварка тавровых соединений, так как существуют правила исполнения и методы получения подобных соединений.
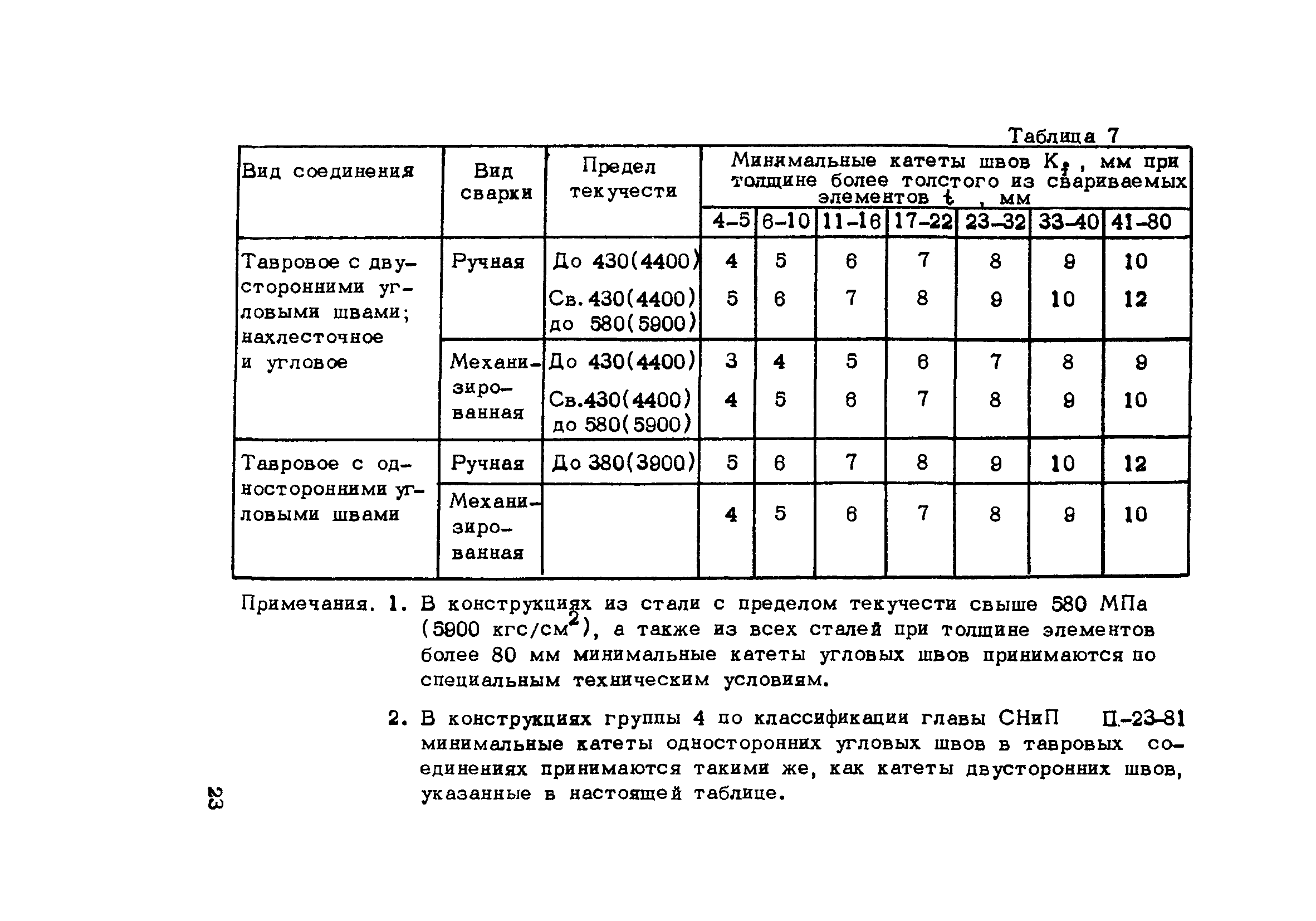
В процессе сварки соединяются:
- Уголки,
- Металлические листы,
- Квадраты,
- Продукция трубопроката,
- Швеллера,
- Рельсы.
При этом используется ручная электродуговая сварка с различным уровнем мощности. Если же подача электрического тока отсутствует, применяется газопламенная ручная, но для ее выполнения нужно транспортировать тяжелое и объемное оборудование.
Типы соединений элементов с помощью сварочных аппаратов
Нередко виды сварных конструкций требуют предварительной обработки поверхностей, которые будут соединяться. Даже в большинстве технологических процессов заложены всевозможные пазы и освобождения, позволяющие обеспечивать надежность сварного шва. Детали необходимо правильно фиксировать и располагать в пространстве, чтобы быстро и качественно сварить между собой.
Подготовка свариваемых поверхностей может происходить при помощи электрического инструмента – шлифовальных кругов, отрезных кругов.
Если нужно обеспечить определенный угол, как раз отрезным кругом можно выполнить подобную работу.
Шлифовальные процедуры позволяют получить гладкие и ровные поверхности на соединяемых элементах.
Обработка может коснуться одной детали, а другая сохраниться в первоначальном виде, и тогда несколько экономится металл. Существует и односторонняя и двусторонняя сварка, и поэтому нужно подбирать виды обработки поверхностей. Сварщики обычно работают с угловыми, тавровыми или сваривают встык.
Процессы, происходящие в структуре соединения при сварке
Процесс кристаллизации шва начинается сразу после отвода дуги от свариваемого участка. Застывание металла происходит в направлении, обратном отводу тепла в структуру основной поверхности, начиная от краев сварочной ванны к ее центру. Средняя скорость кристаллизации и скорость сварки равны. По границам шва формируются кристаллиты наплавляемого и основного металла, обеспечивающие монолитность строения слоев и прочность соединения.
Образование шва и околошовной зоны.
Остановка начального процесса кристаллизации происходит достаточно быстро, при остывании шва на 20-30° С, то есть до температуры 1450-1500° С. После его завершения в структуре металла не происходит никаких изменений до его остывания до 850° С, когда металл начинает выходить из аустенитной формы.
Затем происходит процесс вторичной кристаллизации в структуре строения шва и прилегающем к нему основном металле. Он также протекает в коротком температурном диапазоне. Структура сварного шва становится стабильной по достижении им температуры в 720° С.
Кристаллиты сварочного шва имеют столбчатое строение структуры, характерное для процесса литья металла. Этот вид кристаллизации способствует вытеснению газовых и шлаковых фракций.
Разделка швов для достижения качества
Наиболее распространенным вариантом разделки является обработка торцов, когда выполняется скос под определенным углом, и полученное пространство заполняется расплавленным металлом во время сваривания.
Металлические могут иметь толщину от 4 до 25 миллиметров, и для них используется торцевой скос определенной формы. Если же деталь имеет толщину от 12 миллиметров, тогда может потребоваться предварительная двусторонняя разделка.
При использовании разделки уменьшается расход сварных материалов, поэтому данный способ полезен не только для надежности, но и для увеличения экономических показателей.
И сварка тавровых соединений требует дополнительной разделки швов, поэтому нужно предусмотреть предварительную обработку деталей.
Кромка одного элемента должна перпендикулярно прилегать к плоскости другой детали, так что объединение нужно выполнять с обеспечением максимальной прочности и с соблюдением перпендикулярности.
Если толщина металлических элементов меньше или равна 10 миллиметров, разделку применять не обязательно и сварка производится с двух сторон. Кромка металлической детали не обрабатывается, и только контролируется качество поверхности.
Но когда элемент, располагаемый перпендикулярно, обладает меньшей толщиной, чем вторая часть таврового соединения, тогда необходимо выбирать угол расположения электрода.
Строение сварных соединений
В процессе дуговой сварки происходит расплавление основного и присадочного материала, образуется жидкая сварочная ванна, при затвердевании которой формируется сварное соединение. Рассмотрим более детально особенности процесса плавления и кристаллизации при сварке. В отличие от большой металлургии, размеры сварочной ванны небольшие, время нахождения металла в жидком состоянии мало, одновременно происходят процессы нагрева и кристаллизации металла, в результате неравномерности нагрева и охлаждения возникают значительные внутренние напряжения. Сварочную ванну условно можно разделить на две части (см. рисунок ниже): головная (АВ и САД), в которой происходит нагрев и плавление основного металла и хвостовая (ВК и СКД), в которой идут процессы охлаждения, кристаллизации и формирования сварного шва. Фронтом кристаллизации служат стенки сварочной ванны, форма которой происходит по нормали к поверхности фронта.
Скорость роста кристаллов на разных участках ванны — разная. В точках В, С и Д Vкр = 0, а в точке К Vкр = Vсв. Во всех других точках хвостовой части ванны она будет меняться от 0 до Vcв. При этом растущие столбчатые или дендритные кристаллы будут изгибаться в сторону движения дуги. Вследствие избирательности процесса кристаллизации перед фронтом будет накапливаться примесь и центральные части шва будут обогащены примесью. В зависимости от формы сварочной ванны (глубокая и узкая) кристаллы будут расти навстречу друг другу, образовывая транскристаллитную структуру, которая крайне не желательна, поскольку может вызвать образование трещин в середине шва. Для измельчения крупно дендритной литой структуры сварных швов применяют:
— модифицирование — введение в сварочную ванну готовых центров кристаллизации, в виде порошков тугоплавких металлов;
— применение в процессе сварки механических колебаний ванны, или электромагнитного перемешивания жидкого металла;
— применение, по возможности многопроходных швов. термическая или термомеханическая обработка сварного шва.
Кроме расплавления металла сварочный источник воздействует также на основной металл. Количество вносимого тепла определяется погонной энергией источника: отношение мощности к скорости сварки (q/v) Процесс распространения тепла описывается температурными полями. Температурным полем называют совокупность значений температуры в данный момент во всех точках пространства (тела). Температурное поле удобно характеризовать изотермами. Изотермические поверхности являются геометрическими местами точек тела, имеющими одинаковую температуру. Геометрические места точек пересечения изотермической поверхности с какой-либо поверхностью является изотермой. В частном случае нагрева металлического листа каким-либо неподвижным сосредоточенным сварочным источником тепла (дугой, газовым пламенем, электронным лучом) изотермы на наружной поверхности будут представляться окружностями. При этом каждая точка основного металла, находящаяся на некотором расстоянии от оси шва, будет вначале нагреваться, а затем охлаждаться. Кривая, описывающая изменения температуры точки во времени называется термическим циклом. Основными характеристиками термического цикла есть: максимальная температура, время нагрева, время охлаждения Особенно важными параметрами является максимальная температура, так как она определяет возможность протекания структурных превращений в металле и время охлаждения, которое связано со скоростью охлаждения — одним из основных факторов вероятности получения закалочных структур.
Металл однопроходного шва имеет структуру литой стали. При многослойном сваривании последний шов имеет крупнозернистую структуру литой стали, а предыдущие швы, вследствие термического действия — структуру с мелкими зернами феррита и перлита. После процесса кристаллизации и перитектического преобразова-ния шов имеет структуру аустенита, зерна которого образовываются на границах первичных столбчатых кристаллов. При снижении температуры структурных изменений не будет до температуры Аr3. Потом начнутся преобразования в твердой фазе — вторичная кристаллизация. Будет выделяться феррит, а аустенит будет обогащаться углеродом и при температуре 727°С произойдет эвтектоидное преобразование As → Фр + Цк. Высокие скорости охлаждения металла сварного шва влияют на характер преобразований, которые рассматривались для равновесных условий. Необходимо следующие особенности вторичных преобразований:
1. Феррит, что выделяется при переходе через температуру, что характеризуется линией GS не успевает весь выделиться и потому аустенит в момент эвтектоидного преобразования будет иметь меньше углерода чем 0,8%.
2. В результате эвтектоидного преобразования образовывается большее количество перлита с меньшим содержимым углерода, чем при равновесных превращениях (за счет смещения точки S вниз и влево).
3. Образовывается перлит, который имеет более тонкое строение. Скорость охлаждения металла шва изменяется в очень широких границах. В начальный момент она составляет 200 — 300 град/с, а затем быстро снижается.
Таким образом, зоны металла, которые имели большую скорость охлаждения, будут иметь мелкозернистую перлитную структуру, причем количество перлита будет больше чем при равновесных условиях. По химическом составу металл шва обычно отличается от основного металла, так как имеет литую структуру, которая имеет худшие механические свойства, чем основный металл, и для обеспечения условия равнопрочности металл шва легируют специальными элементами, которые повышают его механические свойства. Кроме этого, как правило, металл шва всегда имеет меньшее содержание углерода, чем основный металл, благодаря особым условиям, которые имеют место при сварке.
Зона основного металла, в которой за счет нагрева и охлаждения происходят изменения структуры и свойств, называется зоной термического влияния (ЗТВ). Ширина зоны заканчивается температурой около 100°С. и, при сварке может изменяться в зависимости от режима и способа сварки от десятых долей миллиметра до 40 — 50 мм.
При сварке низкоуглеродных сталей (0,1 — 0,25% С) ЗТВ в основном состоит из таких участков:
1. Участок неполного расплавления — это зона металла, который нагревался до температур, которые лежат между линиями солидус и ликвидус. При дуговых методах сварки участок небольшой и крайне трудно различим.
2. Участок перегрева — включает металл, который нагревался от 1100 – 1200°С до температуры солидус, характеризуется крупным зерном и низкими механическими свойствами. Часто в перлите наблюдаются пластинки феррита, которые выделились под углом 120° (такая структура носит название видмандштеттова). Участок сплавления и участок перегрева вместе называются еще околошовной зоной (ОШЗ). В ОШЗ структура и свойства резко отличаются от основного металла: снижается пластичность и ударная вязкость, образовываются горячие и холодные трещины.
3. Участок нормализации — включает металл, который был нагрет выше температуры (Ас3) до – 1100 — 1200°С. Процессы перекристаллизации дают мелкие зерна аустенита, которые не успевают вырасти и при превращении дают мелкие зерна феррита и перлита. Эта структура и участок имеет очень хорошие механические свойства.
4. Участок неполной перекристаллизации — зона металла, который был нагрет между температурами 727°С (Aс1) и Ас3. На этом участке могут быть крупные зерна феррита, который не прошел перекристаллизацию, а также мелкие зерна перлита, которые образовались с аустенита, поэтому этот участок имеет относительно невысокие механические свойства.
5. Участок рекристаллизации — металл нагрет выше температуры рекристаллизации (для железа Трек = 0,4 Тпл = 450°С) и до 727°С. Если металл не имел холодной пластической деформации перед сваркой, то этого участка не существует, а если такая деформация имела место, то получим крупные зерна, феррита и перлита, причем размер зерен будет определятся степенью пластической деформации.
6. Участок синеломкости — металл нагрет от 100°С до 500°С. Этот участок не имеет видимого изменения структуры, тем не менее характеризуется снижением пластических свойств, которое вызвано выделением с твердого раствора феррита субмикроскопических частичек различных примесей, которые располагаются по границам зерен.
В ЗТВ проходят также диффузные процессы. В зависимости от температуры и времени выдержки можно наблюдать диффузию углерода и иных элементов с ОШЗ и наоборот. Примером такого процесса есть проникновение меди в основный металл при наплавке меди на сталь, снижение содержания углерода в ОШЗ при наплавке швами, которые содержат элементы, с которыми углерод образовывает нерастворимые соединения (карбиды).
Требования к сварным швам таврового соединения
Но если сварка тавровых соединений требует высокой степени прочности и это предписано в технологическом процессе, тогда в обязательном порядке исполняется разделка.
Толстая, располагаемая перпендикулярно, должна дополнительно обрабатываться, чтобы сварка позволила добиться качественного совмещения. Пользуются односторонней или двусторонней разделкой, при этом кромка срезается под углом 45 градусов.
Свариваемые элементы, которые превышают своей толщиной 10 миллиметров, свариваются в несколько слоев, таким образом, происходит заполнение всех имеющихся пустот.
Все предварительные виды обработки на производственных предприятиях всегда описываются в технологических процессах, и если в чертеже имеется тавровое соединение, технолог должен подробно расписать методы разделки.
Перед тем, как попасть к сварщику на участок, детали могут обрабатываться слесарями для получения поверхностей, которые впоследствии будут соединяться посредством сварки.
В бытовых условиях все несколько упрощено, и человеку, пытающемуся сварить две детали перпендикулярно, придется самостоятельно принимать решение о предварительной обработке и использовать специальный инструмент.
Еще по этой теме на нашем сайте:
- Сколько стоит сантиметр аргонной сварки — используем сварочный аппарат, сваривая алюминий Аргонная сварка, цена за сантиметр которой варьируется, достаточно популярна среди используемых видов сварки сегодня. В основном, используется в работе сварка аргоном алюминия. Видео можно увидеть…
- Сварка чугуна электродом — видео процесса Чугун представляет собой железоуглеродистый специальный сплав, который отличается высоким содержанием углерода (2,14%).
Благодаря этому в сравнении с другими сталями он находится в свободном состоянии. К…
- Ручная сварка для начинающих — самоучитель по сварке дома В данный момент необходимость сварочных работ имеется практически в любой отрасли промышленности. И сложно вспомнить хотя бы одну отрасль, где не применялся бы труд сварщика….
- Mig Mag сварка — что это и какой выбрать сварочный полуавтомат Mig для сварки Отвечая на вопрос: «Mig Mag сварка: что это и как работает?», в первую очередь, необходимо рассказать о принципе действия этого метода сварки. Данный метод основан…
Поделитесь со своими друзьями в соцсетях ссылкой на этот материал (нажмите на иконки):
Способы заполнения шва по сечению и длине
Для заполнения швов по длине применяются метод «напроход» и обратноступенчатый метод. Метод сварки «напроход» заключается в том, что сварной шов выполняется от начала до конца в одном направлении.
При обратноступенчатом методе длинный шов подразделяют на сравнительно короткие участки.
Но методы заполнения швов по сечению различают (рис. 45):
— однослойные швы;
Рис. 45. Сварные швы:
а— однослойный и однопроходной, б— многослойный и многопроходной. в — многослойный
— многослойные швы;
• — многослойные многопроходные ШВЫ.
Многослойные многопроходные швы отличаются от многослойных тем, что некоторые слои выполняются за несколько проходов, тогда как в многослойных обычных швах каждый шов выполняется за один проход.
Многослойные швы чаще применяют при сварке стыковых соединений, а многопроходные — при сварке угловых и тавровых соединений.
Чтобы нагрев металла Шва был более равномерным по всей его длине, используют также способы двойного слоя, способы заполнения секциями, каскадом и горкой. В основе всех этих — способов — метод обратноступенчатой сварки.
Способ двойного слоя заключается в том, что налоясе — ние второго слоя ведется по еще неостывшему первому слою (после удаления Шлака). Сварка производится на длине 200-400 мм в противоположных направлениях для предотвращения появления горячих трещин.
При сварке толстых стальных листов (20 мм и более) применяют сварку каскадом и горкой. Как показано на рис. 46, заполнение многослойного шва при сварке секциями и каскадом производится по всей толщине свари-
ваемого металла на определенной длине ступени. Длина ступени подбирается так, чтобы металл в корне шва омел температуру не менее 200 ‘С в процессе выполнения сварного шва по всей толщине. При этом условии металл обладает достаточной пластичностью, и трещины не образуются. Сварка горкой выполняется проходами по всей толщине металла.
В целом многослойная сварка имеет ряд преимуществ перед однослойной сваркой:
— объем сварочной ванны уменьшается, в результате чего увеличивается скорость остывания металла и уменьшается размер зерен;
— небольшая сила сварочного тока при многослойной сварке вызывает расплавление небольшого количества основного металла; вследствие чего химический
Рис. 46. Схемы заполнения многослойного шаа с малым интервалом времени: о — секциями, б — кеск&дом, в — горкой |
состав наплавленного металла близок к составу основного металла;
— каждый последующий слой шва термически влияет на металл предыдущего слоя, в результате чего он и око — лошовный металл имеют мелкозернистую структуру с повышенной вязкостью и пластичностью.
Виды сварных швов.
Сварной шов – это место сплава разных элементов одной конструкции. Во время сварки металл в этом месте расплавляется, а впоследствии, остывая, кристаллизуется, что обеспечивает прочность и герметичность шва.
Сварные швы могут иметь различную форму сечения. По этому параметру сварные швы подразделяются на
- стыковые, отличительной особенностью которых является то, что отдельные элементы изделия перед сваркой прикладываются друг к другу на одной плоскости методом «встык».
- угловые, в которых составные части конструкции присоединяются друг к другу под определенным углом.
- прорезные или электрозаклепочные – здесь отдельные элементы конструкции присоединяются друг к другу в одной части с помощью установки специальной сварной заклепки. При этом верхняя деталь проплавляется полностью, а нижняя – частично
Максимальный катет сварного шва гост
Скачать максимальный катет сварного шва гост doc
Минимальные катеты швов k f min , мм,.
Нагрузка на балку настила собирается с соответствующей грузовой площади рис. Определение нормативной и расчетной нагрузок. Нормативная нагрузка на балку при опирании на нее сплошного стального настила принимается равномерно распределенной:. Определение усилий и компоновка сечения. Расчетный пролет балки настила l равен шагу колонн В.
Требуемый момент сопротивления поперечного сечения балки в этом случае определяется:. Уточнение коэффициента с 1 , М и Q c учетом собственного веса балки настила. Равномерно распределенная нагрузка от собственного веса балки настила длиной 1 м. Проверка несущей способности балки. Проверка прочности по нормальным напряжениям в середине балки:.
Общую устойчивость балок настила проверять не надо, поскольку их сжатые пояса надежно закреплены в горизонтальном направлении приваренным к ним стальным сплошным настилом.
Проверка местной устойчивости поясов и стенки прокатных балок не требуется, так как она обеспечивается большой их толщиной, обусловленной технологическими условиями проката. Прогибы, определяемые от нормативных нагрузок, не должны превышать их предельных значений, установленных нормами проектирования.
Для однопролетной балки, нагруженной равномерно распределенной нагрузкой, проверка прогиба производится по формуле.
Подскажите пожалуйста какой максимальный катет может быть у сварного шва Т3 прикрепления пластины в тавр к пластине? Вопрос возникает потому что в толстых Гостах , даны только рисунки а размеры катетов не регламентируются. Вообще очень много путаницы в обозначении сварных швов. Как за границей используя стандартные средства AutoCAD обозначают сварку по всем правилам. По моему мнению при обозначении сварки надо просто ставить толщину катета и номер Госта ещё наверное. Хотя просто толщины катета должно хватать всегда.
Дополнительные данные о сварных швах можно написать в примечаниях.
Похожее:
Угловой шов для стальных соединений | Рекомендации по угловым сварным швам
Если грани двух элементов наклонены под углом, используется угловой шов. Угловые швы обычно имеют треугольное сечение. Для угловой сварки угол между соединяемыми поверхностями должен находиться в диапазоне от 60 до 120 градусов. Калибр углового шва
от компании GAL GAGE Важными факторами, определяющими производительность углового шва, являются марка электрода, используемого для сварки, длина сварного шва и толщина сварного шва, которая зависит от длины участка.Длина ветви (S) и толщина горловины (St) сварного шва представлены на изображении ниже.
Толщина горловины зависит от угла наклона между поверхностями, максимум 70% длины ножки при угле от 60 до 90 градусов. Что уменьшается до 50% при увеличении угла до 120 градусов. Значения толщины горловины для различных углов приведены в таблице ниже.
Значения толщины горловины для различных углов углового шваУгол между свариваемыми поверхностями | Отношение эффективной толщины горловины к длине участка углового шва (St / S) |
60 — 90 град. | 0,70 |
91-100 град. | 0,65 |
101-106 град. | 0.60 |
107 — 113 град. | 0,55 |
114-120 град. | 0,50 |
Рекомендации по использованию угловых швов в стальных конструкциях
- Минимальный возврат конца , необходимый для завершения угловых сварных швов на концах, должен быть спроектирован вокруг углов на минимальную длину 2 x длина плеча.
- При использовании угловых швов для стыков внахлест , расстояние притирки должно быть в четыре раза (4t) толщины более тонкого элемента.
- Угловые сварные швы , заканчивающиеся на концах соединяемых частей, следует возвращать вокруг углов на расстояние, по крайней мере, в два раза превышающее длину ветви.
Когда элементы подвергаются воздействию изгибающих моментов вокруг длинной оси, одинарные угловые сварные швы не используются.
В некоторых случаях, когда используются прерывистые угловые швы , расстояние между сварными швами не должно превышать 16 (16 т) толщины элемента или 300 мм для стального соединения сжимаемых элементов и в 24 раза минимальной толщины для сварного шва при растяжении.Не рекомендуется использовать прерывистый сварной шов, если надлежащий контроль коррозии невозможен.
Полная пропускная способность углового шва достигается только тогда, когда толщина шва St, превышает половину толщины элемента. Эффективная длина углового сварного шва для расчета рассчитывается как
(Фактическая длина — 2 x длина плеча)> = 4 x длина плеча
Общий обзор дефектов геометрической формы — угловые швы
До сих пор в этой статье, посвященной опыту сварки, мы рассмотрели недостатки сварки, такие как трещины, отсутствие плавления, неполное заполнение канавок и вогнутость корней, а также другие недостатки.
Эта третья и последняя статья посвящена дефектам, возникающим при угловых сварных швах, и способам их устранения.
В этой статье особое внимание будет уделено:
- Чрезмерная выпуклость
- Угловые швы большого диаметра
- Угловые швы меньшего размера
- Асимметричные угловые швы
- Плохая установка
Рис. 1. Чрезмерная выпуклость
Эта особенность также подпадает под определение избыточного металла шва (см. Часть 1) и может быть описана как металл шва, лежащий за пределами плоскости, соединяющей пальцы шва. Обратите внимание, что термин «армирование», хотя он широко используется в спецификациях ASME / AWS, в Европе избегается, поскольку он подразумевает, что избыток металла способствует прочности сварного соединения. Так бывает редко.
Общие причины
Плохая техника и наплавка больших объемов металла «холодного» шва.
Приемка
Требование к идеальной конструкции углового шва «под углом» часто бывает труднодостижимым, особенно при ручной сварке.Принятие
BS EN ISO 5817 основано на форме углового сварного шва под углом с определенным расчетным сечением, и любой излишек металла шва измеряется по отношению к этой угловой поверхности. Пределы этого дефекта связаны с высотой излишка металла и шириной валика с максимальными значениями от 3 мм для строгого уровня качества до 5 мм для среднего уровня качества. Удивительно, но нет никакого упоминания о «плавном переходе», необходимом на носках сварного шва для такой формы сварного шва.
AWS D1. 1 также имеет следующие ограничения ширины и допустимого превышения:
Избегание
Техника сварщика является основной причиной этой проблемы, и может потребоваться обучение. Также важно обеспечить соблюдение параметров, указанных в спецификации процедур сварки.
Рис. 2. Угловой шов увеличенного диаметра
Как обсуждалось ранее, угловые швы с увеличенным размером могут привести к значительным дополнительным затратам и снижению производительности.
Общие причины
Существуют некоторые причины, связанные со сваркой, например, высокий сварочный ток, низкая скорость перемещения, а также некоторые меры, связанные с контролем (например, «в целях безопасности увеличьте угол наклона на x мм»).
Приемка
BS EN ISO 5817 имеет ограничения, относящиеся к фактическому диаметру сварного шва (например, для строгих уровней качества фактический сварной шов [a] может превышать номинальное (расчетное) значение сварного шва [h] на 1 + 0,15a, но не более чем на 3 мм. средний уровень качества (D) чрезмерная толщина горловины не ограничена.
Избегание
Соблюдайте указанные процедуру и параметры сварки и не увеличивайте размер сварного шва. По возможности механизируйте сварочные работы.
Угловые швы меньшего размера (угловые швы меньшего размера, чем указано в спецификации)
Рис.3. Угловой шов меньшего размера
Общие причины
Причины, связанные со сваркой, связаны с высокими скоростями сварки и низкими сварочными токами.
Приемка
Таким образом, обычно предполагается, что угловые швы будут иметь, по крайней мере, указанный размер.BS EN SIO 5817 утверждает, что ограничения недостаточной толщины горловины не применимы к процессам с доказательством большей глубины проплавления, поэтому угловой шов с кажущейся толщиной горловины меньше предписанной не следует рассматривать как несовершенную, если фактическая толщина горловины с компенсирующая большая глубина проникновения соответствует номинальному значению. То есть, если мы можем быть уверены, что есть хорошее проникновение, меньшее галтели может быть приемлемым, однако это следует обсудить с проектировщиком изготовления.Пределы, установленные стандартом.
Трудно оправдать то, что глубокое проникновение обеспечивает требуемую минимальную расчетную толщину горловины. Проникновение — это характеристика сварного шва, которую трудно измерить напрямую, и необходимо полагаться на строгий контроль как процесса сварки, так и сварщика. На ручную сварку редко можно положиться для обеспечения требуемой прочности, но это вариант с механизированными сварочными системами.
Избегание
Соблюдайте указанные процедуру и параметры сварки.Используйте достаточный ток и соответствующую скорость движения. По возможности механизируйте сварочные работы.
Рис. 4. Асимметричный угловой шов (угловой шов, при котором ветви имеют неравную длину)
Общие причины
Из-за неправильного расположения электродов или из-за силы тяжести, вытягивающей ванну расплава к одной стороне соединения. В основном это проблема угловых сварных швов, выполненных в горизонтальном / вертикальном (PB) положении.
Приемка
Есть случаи, когда может быть указана асимметрия (например, чтобы поместить концентрацию напряжения пальца в конкретную область).
BS EN ISO 5817 для углового шва длиной 10 мм (т. Е. С горлом 7,1 мм) допускает разницу в длине ножек примерно на 2,5 мм при строгом уровне качества и 3,4 мм на среднем уровне качества. Принятие зависит от толщины горла.
Следствием этого недостатка является значительное увеличение объема сварного шва. При соблюдении требований к длине ног потери силы не будет. Возможно, именно поэтому в других стандартах требование не указывается, и его приемлемость предоставляется инспекционному персоналу для вынесения «инженерного решения».
Рис. 5. Плохая установка
Самый распространенный дефект — это чрезмерный зазор между сопрягаемыми поверхностями материалов.
Общие причины
Плохая практика в мастерской, плохие размеры и допуски размеров на чертежах.
Приемка
Основной проблемой угловых сварных швов является обеспечение зазора между компонентами в определенных пределах. BS EN ISO 5817 определяет следующие критерии приемлемости:
Где h = посадочный зазор и a = расчетное отверстие углового шва
На рис. 5 показано, что зазор приводит к уменьшению длины ножки на вертикальной пластине, а это, в свою очередь, приводит к уменьшению толщины горловины соединения.Закругление ножки длиной 10 мм с корневым зазором 3 мм дает эффективную ножку 7 мм (горловина 4,9 мм вместо ожидаемых 7 мм).
Если применение BS EN ISO 5817 не требуется, можно следовать руководству BS EN 1011-2, которое рекомендует максимальный зазор 3 мм. В этом стандарте также указано, что размер углового сварного шва может быть увеличен для компенсации большого зазора.
Это несоответствие устранено в AWS D1.1. что обеспечивает корневой зазор до 5 мм для материала толщиной до 75 мм.Однако «если расстояние (стыка) превышает 2 мм, участок углового сварного шва должен быть увеличен на величину корневого отверстия, или подрядчик должен продемонстрировать, что эффективное горло было получено».
Эта статья была первоначально опубликована в Connect, январь 2004 г. С тех пор она была обновлена, и эта веб-страница больше не отражает в точности печатную версию.
Сосредоточьтесь на правильном размере сварного шва при разработке диапазонов параметров WPS
Изготовитель и монтажник должны определить наиболее подходящий диапазон скоростей движения для конкретного применения, а не слепо полагаться на опубликованные сертификаты продукта.Однако следование методологии, представленной здесь, дает еще один возможный план того, как этого можно достичь.
Компания по производству металлоконструкций готовится к проекту, который должен быть сварен в соответствии с Приложением по сейсмическим воздействиям D1.8 Американского общества сварщиков, и хотела бы использовать сварку 0,045 в газозащитной порошковой проволоке E71T-1 (FCAW-G ) провод. У этого производителя есть возможность расположить сталь так, чтобы она могла свариваться в нижнем положении.
Они хотели бы использовать провод определенного производителя, но скорость движения, при которой проводилось тестирование огибающей с высоким / низким тепловложением, не указана на их D1.8 сертификатов. Им необходимо это, чтобы указать диапазон скорости движения в своих технических требованиях к процедуре сварки (WPS). Есть ли причина, по которой скорости движения не указаны?
Хотя было бы намного проще передать эти скорости движения непосредственно в WPS, вскоре будет показано, что это может быть не такой уж и хорошей идеей. Конечно, требуется несколько простых и систематических расчетов, но нет причин бояться чисел или уравнений в области сварки.
Самый последний D1.8 сертификат для электрода E71T-1 показан ниже в Таблица 1 . Хотя это не показано здесь, как высокие тепловыделения, так и низкотемпературные отложения соответствовали требованиям к механическим свойствам AWS D1.8, включая предел прочности на разрыв, предел текучести, удлинение и ударную вязкость с V-образным надрезом по Шарпи при 70 ° F. скорость движения можно легко определить, изменив формулу подводимого тепла при сварке, представленную на рис. 1 , рис. В целях иллюстрации результирующие скорости движения для испытаний как с высоким, так и с низким тепловложением показаны на рис. , рис. 2 .
Исходя из поставленного выше вопроса, можно предположить, что теперь уместно использовать вычисления из , рис. 2 , и, следовательно, отображать «диапазон скорости движения» на их WPS от 2,9 до 10,8 дюймов в минуту. Кроме того, изготовитель или монтажник может также захотеть получить диапазон тока от 160 до 215 ампер из сертификата D1.8. Теперь мы обсудим, почему здесь нужно проявлять осторожность.
Если сварщик или сварщик хотел (или был заинтересован) максимизировать свою производительность, он может захотеть уменьшить скорость своего движения.Это было бы логично с точки зрения сварщика, поскольку уменьшило бы количество проходов, необходимых для заполнения стыка. И поэтому, полагает он, это сэкономит компании деньги (или принесет ему больше денег), так как время на очистку и настройку сократится. Таким образом, в соответствии с диапазоном скорости движения, указанным на его WPS, он может использовать скорость движения всего 2,9 дюйма в минуту.
Наконец, пока он оставался в пределах диапазона тока от 160 до 215 ампер и диапазона напряжения от 24 В до 26 В, указанного в WPS, тогда у него, по-видимому, было некоторое оправдание для использования этой скорости движения.Однако проблема возникает с этой логикой, когда используются самые верхние значения 215 ампер и 26 вольт. Опять же, более высокая скорость подачи проволоки приведет к более высокой производительности.
На рис. 3 показаны результирующие тепловложения при сварке в этом сценарии. Очевидно, 116 кДж / дюйм — это слишком много тепла для использования с порошковой проволокой. Некоторые проблемы, которые могут возникнуть при использовании подводимой теплоты 116 кДж / дюйм, включают снижение ударных свойств по Шарпи с V-образным надрезом в сварном шве, размягчение основного материала в зоне термического влияния (HAZ) или отсутствие проплавления и / или сплавление (потому что дуга едет по лужам). Кроме того, это тепловложение превышает максимальное тепловложение «конверта», установленное на сертификате D1.8.
Рассмотрим противоположную ситуацию. Что, если во время изготовления или монтажа используются самые высокие значения скорости движения (10,8 дюймов в минуту) и самые низкие значения тока (160 ампер) и напряжения (24 В)? Очевидно, это приведет к более низкому тепловложению при сварке, чем значение 30 кДж / дюйм, указанное в сертификате D1.8. Но почему это важно?
Ответ на этот вопрос сводится к обеспечению того, чтобы размер сварного шва был достаточно большим (и, следовательно, подводимое при сварке тепло) относительно толщины свариваемой пластины.Слишком мелкие сварные швы могут способствовать растрескиванию зоны термического влияния или растрескивания под валиком. Тогда было бы полезно посмотреть, насколько велики будут сварные швы при таких процедурах сверхнизкого тепловложения.
Процесс анализа размера сварного шва начинается с определения скорости наплавки. Беглый взгляд на литературу по этой проволоке E71T-1 показывает, что при скорости подачи проволоки 275 дюймов в минуту достигается производительность наплавки 5,5 фунтов в час. Это, в сочетании со скоростью перемещения 10,8 дюймов в минуту, дает 0 сварных швов.102 фунта на фут, как показано на рис. 4 .
На этом этапе нам следует вернуться к предыдущей колонке («Предварительный расчет скорости подачи проволоки, скорости хода и напряжения», Welding Tips , ноябрь-декабрь 2010 г.), где мой коллега Кевин Бердсли обсуждал предварительный расчет скорость перемещения, когда известны скорость наплавки и желаемый размер сварного шва. Из таблицы 2 (выдержка из этого столбца) видно, что сварной шов весом 0,102 фунта на фут эквивалентен угловому сварному шву с размером ноги менее ¼.
Кроме того, предположим, что вы свариваете лист из низкоуглеродистой стали толщиной дюйма. Согласно Таблице 5.8 Свода правил по сварке конструкций AWS D1. 1-2010 — сталь , минимальный требуемый размер ветви углового сварного шва составляет дюйма. .Даже если вы выполняете не угловые швы, а швы с полным проплавлением (CJP), концепция остается той же — «сварной шов» должен быть эквивалентен угловому шву дюйма, чтобы гарантировать скорость охлаждения достаточно низкая, чтобы предотвратить растрескивание под валиком или другие дефекты сварного шва, такие как отсутствие плавления.Следовательно, в соответствии с таблицей 2 , угловой шов на 3/4 дюйма с плоской поверхностью (с 10-процентным перекрытием, как это принято в производственной практике) будет иметь сварной стержень 0,128 фунта на фут.
Итак, если мы решим, что нам действительно нравится, как электрод E71T-1 работает при скорости подачи проволоки 275 дюймов в минуту, 160 А и 24 В, каков предел скорости, с которой мы можем двигаться, и при этом сварочный проход будет больше, чем эквивалентный ¼ в филе? Это вопрос простой перестановки формулы, показанной на рис. 4 .Чтобы гарантировать наплавку, эквивалентную минимальной углового сварного шва, скорость перемещения не может быть на больше, чем на , чем 8,6 дюймов в минуту, как показано на , рис. 5, . Сравните этот результат с 10,8 изобр. / Мин, полученным в ходе сертификационного тестирования D1.8.
Теперь, когда мы определили верхний предел скорости движения, каков процесс определения нижнего предела скорости движения? Насколько медленно слишком медленно? Выше был упомянут неприемлемый сценарий, при котором тепловложение 116 кДж / дюйм было получено, когда использовались самые высокие настройки тока и напряжения и самая низкая скорость перемещения на основе «диапазонов», извлеченных непосредственно из D1.8 сертификатов.
Для получения рекомендаций по самому большому сварному шву, который может быть выполнен, можно обратиться к кодексу AWS D1.1, который никогда не требует, чтобы размер ветви однопроходного углового шва превышал 5/16 дюйма. С практической точки зрения довольно сложно нанесите (с помощью одного электрода) однопроходный угловой сварной шов в нижнем положении более 5/16 дюйма без обнаружения таких дефектов, как захваченный шлак, перекрытие или отсутствие проплавления и / или плавления (поскольку дуга движется по лужице) . Исходя из этого, мы начнем расчет минимальной скорости перемещения с углового шва 5/16 дюйма в качестве целевой.Снова обращаясь к Таблица 2 выше, для плоского углового шва 5/16 дюйма потребуется сварной стержень 0,201 фунта на фут.
Кроме того, сварщик может предпочесть сваривать его горячим — используя скорость подачи проволоки 325 дюймов в минуту (что соответствует скорости наплавки 6,5 фунтов в час) и настройку 26 В, указанную в сертификате D1.8. Чтобы гарантировать наплавку, эквивалентную максимуму 5/16 углового сварного шва, скорость перемещения не может быть на меньше, чем на 6,5 дюймов в минуту, как показано на , рис. 6, .Сравните этот результат с 2,9 изобр. / Мин, полученным в ходе сертификационного тестирования D1.8.
Мы достигли нашей конечной цели, построив «консервативный» диапазон скорости перемещения от 6,5 до 8,6 дюймов в минуту, что увеличивает шансы наложения прочного сварного шва. Диапазон от 2,9 до 10,8 изобр. / Мин, который может быть извлечен из сертификатов D1.8, может быть применен неправильно в худшем случае. Это основная причина того, что скорости движения не указаны в сертификатах D1.8 этого производителя.
В конце концов, производитель и монтажник должны определить наиболее подходящий диапазон скоростей движения для конкретного применения, а не слепо полагаться на опубликованные сертификаты продукта.Следование методологии, представленной выше, дает один из возможных вариантов того, как этого можно достичь.
Разрывы сварного шва — Часть 2
Профиль завершенного сварного шва может существенно повлиять на характеристики этого сварного шва в процессе эксплуатации. Функция инспектора сварки заключается в выявлении этих неоднородностей путем визуального осмотра и часто в оценке их приемлемости или отклонения с помощью применимых правил сварки или стандартных критериев приемки. Неприемлемые профили сварного шва могут вызвать проблемы, связанные с уменьшением толщины основного материала, уменьшением рабочего размера сварного шва или обеспечить концентрацию напряжений на поверхности сварного шва или листа. Эти типы несплошностей сварного шва часто могут серьезно ухудшить общие характеристики сварного компонента, находящегося в эксплуатации. Мы рассмотрим некоторые нарушения сплошности, связанные с профилями сварных швов: поднутрение, перекрытие, недостаточное горло и чрезмерная выпуклость.
Выточка — Эта неоднородность определяется как канавка, проплавленная в основном металле рядом с носком сварного шва или корнем сварного шва и оставленная незаполненной металлом сварного шва . Термин поднутрение используется для описания любого из двух условий.Первый — это плавление основного материала на боковой стенке сварного шва с разделкой кромок на краю валика, в результате чего в боковой стенке в области, где должен быть нанесен следующий валик, образуется острая выемка. Этот тип поднутрения может способствовать улавливанию включений, которые могут быть закрыты последующим валиком сварного шва. При необходимости это состояние можно исправить, обычно шлифуя углубление перед нанесением следующего валика. Однако, если подрез небольшой, опытному сварщику, который знает, на какую глубину проникнет дуга, возможно, нет необходимости удалять подрез.Подрез боковой стенки шва с разделкой кромок никоим образом не повлияет на готовый шов, если условие исправлено до нанесения следующего валика. Второе условие — это уменьшение толщины основного металла на линии, где сварной валик на последнем слое металла шва сцепляется с поверхностью основного металла. Это положение известно как основание сварного шва. Это может произойти на угловом шве или стыковом шве. Величина поднутрения, допустимая на поверхности готового сварного шва, обычно указывается в используемых правилах сварки или стандарте.Необходимо строго соблюдать требования к максимально допустимым подрезам для завершенных сварных швов, поскольку чрезмерные подрезы могут серьезно повлиять на характеристики сварного шва, особенно в условиях эксплуатации, подверженных усталостным нагрузкам. Оба типа поднутрения обычно возникают из-за используемой при сварке техники сварки, неправильного позиционирования электродов и / или неправильной скорости движения.
Высокий ток и большая длина дуги могут увеличить вероятность подреза.
Перекрытие — Эта неоднородность определяется как выступ металла сварного шва за выступ или основание сварного шва.Это состояние может возникать в угловых сварных швах и стыковых соединениях и может приводить к образованию надрезов на носке сварного шва, которые нежелательны из-за концентрации возникающих в них напряжений под нагрузкой. Это нарушение непрерывности может быть вызвано неправильной техникой сварки или недостаточными настройками тока.
Недостаточная горловина — Это условие описывает профиль сварного шва, который обычно имеет вогнутую форму и из-за своей вогнутости обеспечивает недостаточную толщину горловины. Избыточная вогнутость, которая может привести к непреднамеренному уменьшению толщины горловины, может возникать в угловых швах и стыковых соединениях.Проблема, связанная с этой неоднородностью, заключается в ее способности значительно уменьшить ту часть сварного шва, которая контролирует прочность сварного шва, а именно толщину шва. Это состояние обычно вызвано чрезмерным сварочным током или длиной дуги.
Чрезмерная выпуклость –Эта неоднородность может вызвать эффект надреза в зоне сварки и, как следствие, концентрацию напряжений под нагрузкой. По этой причине в некоторых нормах и стандартах указывается максимальная выпуклость сварного профиля.Это состояние обычно вызвано недостаточным током или неправильной сваркой.
Заключение — С внешним профилем или формой завершенного сварного шва связан ряд неоднородностей. Эти неоднородности обычно обнаруживаются при визуальном осмотре сварного шва, однако некоторые из них можно обнаружить с помощью других методов контроля, таких как рентгенография, проникающая жидкость и контроль магнитных частиц. Максимально допустимые ограничения, связанные с этими неоднородностями, зависят от требований к характеристикам сварного компонента и обычно указываются в соответствующих правилах сварки, стандарте или спецификации.Инспектор по сварке часто требуется для определения степени этих неоднородностей и установления их приемлемости или отклонения на основе соответствующих критериев приемки.
46 CFR § 56.30-10 — Фланцевые соединения (изменяет 104.5.1 (a)). | CFR | Закон США
§ 56.30-10 Фланцевые соединения (изменяет 104.5.1 (а)).
(a) Фланцевые или стыковые соединения требуются для трубопроводов классов I и I-L для номинальных диаметров, превышающих 2 дюйма, если иное не указано в данном подразделе.
(b) Фланцы могут быть прикреплены любым способом, показанным на Рисунке 56.30-10 (b), или любыми дополнительными средствами, которые могут быть одобрены Центром морской безопасности. Запрещается превышать номинальные значения давления и температуры соответствующего стандарта ANSI / ASME.
(1) Рисунок 56.30-10 (b), Метод 1. Можно использовать фланцы с резьбой в соответствии с 46 CFR 56.30-20, таблица 56.30-20 (c).
(2) Рисунок 56.30-10 (b), Метод 2. ASME B16.5 (включен посредством ссылки; см. 46 CFR 56.01-2) Фланцы с низкой ступицей класса 150 и 300 с резьбовой резьбой, плюс дополнительная прочность Угловой шов указанного размера может использоваться в системах класса I, не превышающих 750 ° F или 4 NPS, в системах класса II без ограничений по диаметру и в системах класса II-L, не превышающих 1 NPS. Если в соответствии с 46 CFR 56.95-10 требуется 100-процентная радиография для класса, диаметра, толщины стенки и материала соединяемой трубы, использование фланцев с резьбой не допускается, и необходимо обеспечить фланцы для стыковой сварки. Для трубопроводных систем класса II размер галтели прочности может быть ограничен максимум 0,525 дюйма вместо 1,4T.
(3) Рисунок 56.30-10 (b), Метод 3. Надвижные фланцы, соответствующие ASME B16.5, могут использоваться в системах трубопроводов Класса I, Класса II или Класса II-L, чтобы не превышать рабочее давление-температура. номинальные характеристики фланцев класса 300 и ниже, в пределах температурных ограничений материала, выбранного для использования, и не должны превышать 4-дюймовый номинальный размер трубы (NPS) в системах класса I и класса II-L.Если в соответствии с 46 CFR 56.95-10 требуется 100-процентная радиография для класса, диаметра, толщины стенки и материала соединяемой трубы, то надвижные фланцы не допускаются, и требуются фланцы, приваренные встык. Конфигурация на рисунке 127.4.4B (b) стандарта ASME B31.1 (включена посредством ссылки; см. 46 CFR 56.01-2), использующая торцевую сварку и обратную сварку, может быть предпочтительнее, когда желательно устранение пустот. Для систем класса II размер галтели прочности может быть ограничен максимум 0,525 дюйма вместо 1.4T, а расстояние от торца фланца до конца трубы может составлять максимум три восьмых дюйма. Ограничения на использование накладных фланцев содержатся в 46 CFR 56.50-105 для низкотемпературных трубопроводных систем.
(4) Рисунок 56.30-10 (b), Метод 4. Фланцы для сварки муфт ASME B16.5 могут использоваться в системах класса I или II-L, не превышающих 3 NPS для фланцев класса 600 и ниже и 21 / 2NPS для класса. Фланцы 900 и 1500 в пределах допустимого рабочего давления и температуры, указанного в стандарте.Если в соответствии с 46 CFR 56.95-10 требуется полная рентгенография для класса, диаметра и толщины стенки соединяемой трубы, использование фланцев для приварки муфт не допускается, и необходимо обеспечить соединение под сварку встык. Для трубопроводов класса II можно использовать фланцы, сваренные с раструбом, без ограничения диаметра, а размер углового сварного шва может быть ограничен максимум 0,525 дюйма вместо 1,4T. Ограничения на использование раструбных швов содержатся в 46 CFR 56.50-105 для низкотемпературных трубопроводных систем.
(5) Рисунок 56.30-10 (b), Метод 5. Фланцы, изготовленные из стального листа, отвечающие требованиям части 54 настоящей главы, могут использоваться для трубопроводов класса II при давлениях, не превышающих 150 фунтов на квадратный дюйм, и температурах, не превышающих 450. ° F. Пластинчатый материал, указанный в UCS-6 (b) раздела VIII Кодекса ASME по котлам и сосудам под давлением (включен посредством ссылки; см. 46 CFR 56.01-2), не может использоваться в этой заявке, за исключением материала, соответствующего ASTM A 36 (включен см. 46 CFR 56.01-2) можно использовать. Изготовленные фланцы должны соответствовать по крайней мере размерам фланца класса 150 ASME B16.5. Размер прочного углового сварного шва может быть ограничен максимум 0,525 дюйма вместо 1,4T, а расстояние от торца фланца до конца трубы может составлять максимум три восьмых дюйма.
(6) Рисунок 56.30-10 (b), Метод 6. Фланцы из листовой стали, отвечающие требованиям к материалам и конструкции, перечисленным в параграфе (b) (5) данного раздела, могут использоваться для трубопроводов класса II для давления, не превышающего 150 фунтов на дюйм. квадратный дюйм или температуры, не превышающие 650 ° F.Фланец должен быть прикреплен к трубе, как показано на Рисунке 56.30-10 (b). Метод 6. Давление не должно превышать номинальное давление и температуру, установленное в соответствии с американскими стандартами. Размер прочного углового сварного шва может быть ограничен максимум 0,525 дюйма вместо 1,4T, а расстояние от торца фланца до конца трубы может составлять максимум три восьмых дюйма.
(7) Рисунок 56.30-10 (b), Метод 7. Фланцы с соединением внахлест (Van Stone) могут использоваться для трубопроводов класса I и класса II.Оборудование Van Stone должно обслуживаться компетентным персоналом. Концы трубы должны быть нагреты от 1650 ° до 1900 ° F. в зависимости от размера трубы до отбортовки. Вышеуказанные температуры необходимо строго соблюдать, чтобы предотвратить чрезмерное образование накипи на трубе. Излишняя толщина металла, образовавшаяся на конце трубы во время операции формовки, должна быть обработана для восстановления первоначального диаметра трубы. На обработанной поверхности не должно быть дефектов поверхности, а задняя часть притира Ван Стоуна должна быть обработана до чистовой обработки, чтобы обеспечить линейный контакт с сопрягаемой поверхностью на фланце по всей окружности как можно ближе к галтелю фланца. фланец.Количество плавок, используемых при формировании фланца, должно определяться размером трубы, и допускается не более двух отжимов на плавку. Ширина фланца внахлестку должна быть как минимум в три раза больше толщины стенки трубы, а конец трубы должен быть должным образом снят с напряжений после завершения операции отбортовки. Производители, желающие произвести этот тип соединения, должны продемонстрировать морскому инспектору, что у них есть необходимое оборудование и персонал для изготовления приемлемого соединения.
(8) Рисунок 56.30-10 (b), Метод 8. Фланцы с приварной шейкой могут использоваться на любом трубопроводе при условии, что фланцы приварены к трубе встык. Соединение должно быть сварено, как показано на Рисунке 56.30-10 (b), Метод 8, с использованием подкладного кольца, которое обеспечит полное проплавление металла шва. Если подкладное кольцо не используется, см. Требования в 46 CFR 56.30-5 (b).
(9) Рисунок 56.30-10 (b), Метод 9. Фланцы приварной шейки также могут быть прикреплены к трубе с помощью двойного стыкового сварного соединения, как показано на Рисунке 56.30-10 (б), Метод 9.
(10) Рисунок 56.30-10 (b), Метод 10. Фланцы могут быть прикреплены путем усадки фланца на конец трубы и развальцовки конца трубы до угла не менее 20 °. Для крепления ступицы к трубе необходимо использовать угловой сварной шов размера, показанного на Рисунке 56.30-10 (b), метод 10. Этот тип фланца ограничен максимальным давлением 300 фунтов на квадратный дюйм при температуре не выше 500 ° F.
(11) Рисунок 56.30-10 (b), Метод 11. Фланец того типа, который описан и проиллюстрирован на Рисунке 56.30-10 (b), метод 10, за исключением исключения углового сварного шва, может использоваться для трубопроводов класса II для давлений, не превышающих 150 фунтов на квадратный дюйм, и температур, не превышающих 450 ° F.
(12) Рисунок 56.30-10 (b), Метод 12. Бронзовые фланцы с высокой ступицей могут использоваться при температурах, не превышающих 425 ° F. Ступица фланца должна быть просверлена на глубину не меньше, чем требуется для резьбового соединения того же диаметра, оставляя буртик для стыковки трубы. Предварительно вставленное кольцо из серебряного припоя с температурой плавления не менее 1000 ° F и достаточным количеством для заполнения кольцевого зазора между фланцем и трубой должно быть вставлено в канавку.Затем труба должна быть вставлена во фланец и снаружи приложено достаточно тепла, чтобы расплавить припой, пока он полностью не заполнит зазор между ступицей и фланцем трубы. На соединяемые поверхности необходимо нанести подходящий флюс для получения удовлетворительного соединения.
(13) Рисунок 56.30-10 (b), Метод 13. Тип фланца, как описано для Рисунка 56.30-10 (b), Метод 12, может использоваться вместо кольцевой канавки, обрабатываемой во втулке ступицы. фланец для предварительно вставленного кольца из серебряного припоя, фаска может быть обработана на конце ступицы, а серебряный припой вводится с конца ступицы для прикрепления трубы к фланцу.
(14) Рис. 56.30-10 (b), Метод 14. Фланцы могут быть прикреплены к трубе из цветных металлов, вставив трубу во фланец и отбортовав конец трубы в выемку, обработанную на лицевой стороне фланца для его установки. Ширина фланца должна быть не менее трехкратной толщины стенки трубы. Кроме того, трубу необходимо надежно припаять к стенке фланца.
(15) Рисунок 56.30-10 (b), Метод 15. Фланец типа, описанного и проиллюстрированного на Рисунке 56.30-10 (b), Метод 14, за исключением случаев, когда пайка пропущена, может использоваться для трубопроводов класса II и если температура не превышает 250 ° F.
Примечание к рис. 56.30-10 (b):
«T» — это номинальная толщина стенки трубы. Обратитесь к тексту параграфа (b) относительно модификаций трубопроводных систем класса II. Размер ноги углового сварного шва не должен превышать толщину соответствующей ступицы ASME.
[CGFR 68-82, 33 FR 18843, 18 декабря 1968 г., с поправками, внесенными CGFR 69-127, 35 FR 9978, 17 июня 1970 г .; CGD 77-140, 54 FR 40605, 2 октября 1989 г .; USCG-2000-7790, 65 FR 58460, 29 сентября 2000 г .; USCG-2003-16630, 73 FR 65177, 31 октября 2008 г .; 73 FR 76247, декабрь.16, 2008] .