Как организовать контроль качества сварных швов и соединений
1980 год. Северное море, Норвегия. Разлом буровой платформы.
2004 год. CША, Хьюстон. Взрыв и сильный пожар на нефтехимическом заводе.
2016 год. Канада. Разлив 63,6 тыс. литров нефти из-за утечки в нефтепроводе.
Причиной всех этих аварий стала некачественная сварка. Там не доглядели, там упустили, там понадеялись на авось. Жертвы, разрушения, убытки.
Предотвратить подобные инциденты призван своевременный и профессиональный контроль качества сварных швов и соединений.
Кто уполномочен проводить контроль качества сварных швов и соединений?
Контроль осуществляет аттестованный специалист. В РФ аттестацию специалистов сварочных технологий проводит Национальное Агентство Контроля Сварки (НАКС), которое ведет соответствующий реестр аттестованного персонала. Кроме того, для целей контроля качества сварных швов необходимо пройти аттестацию по неразрушающему контролю.
Что подлежит контролю?
Сварка бывает ручная, полуавтоматическая и автоматическая.
- Ручная сварка — это процесс создания соединения при помощи электрической дуги. Дуга между поверхностью металла и электродом зажигается и стабильно горит, формируя практически ровный шов. В работе применяются электроды не длиннее 45 см.
- Полуавтоматическая — сварочный процесс, при котором электрод подается в зону сварки с переменной или постоянной скоростью, куда одновременно поступает инертный или активный газ. Это могут быть и смеси, которые защищают нагретые элементы от воздействия окружающей среды. Такая сварка обеспечивает высококачественный шов и удобство работы.
- Автоматическая — это механизированный вид сварки.
Направление и скорость движения электрода выполняется автоматическим способом. Для данного метода требуются ровные поверхности свариваемых элементов.
Как правило, к контролю предъявляется ручная сварка. При ручной сварке в металле и сварных швах часто образуются дефекты, которые влияют на качество изделия. Серьезные изъяны могут привести к непоправимым последствиям — разрыву трубопровода, разрушению металлоконструкций или обрушению из-за некачественно сваренной арматуры.
Где и когда проводится контроль сварных швов и соединений?
Для проведения проверки инспектор выезжает
- на место производства сварочных работ при изготовлении изделия,
- на объект, где сварные изделия будут свариваться между собой, монтироваться и применяться.
Рассмотрим в качестве примера трубы.
- На заводе-изготовителе материал проходит через ультразвуковой автоматический прибор, который способен находить в металле дефекты, возникающие при прокатке, и они устраняются.
- Дальше трубы поступают на сварку. Технологический процесс примерно выглядит так: лист металла сворачивается и делается продольный сварочный шов. Вот в этот момент инспекторы SGS приезжают на производство и смотрят, не нарушается ли технология. Преимущество проведения инспекции на заводе-изготовителей в том, что бракованное изделие не будет отгружено, т.е. заказчик сэкономит время на транспортировку и отбраковку конструкций с дефектом.
- Входной контроль на объекте применения сварных изделий также эффективен, поскольку позволяет не допустить в производство строительных работ дефектные изделия.
- После передачи качественных труб и других материалов в производство сварочно-монтажных работ, производится сборка этих материалов и их сварка в единый технологический или магистральный трубопровод. Контроль качества сварки на этом этапе не менее важен.
Наибольшего эффекта можно добиться, используя комбинацию этих инспекций, то есть проводя как контроль производства трубной продукции, так и её входной контроль на объекте.
О методах и порядке проведения контроля сварных швов читайте в нашей следующей статье.
Группа SGS является мировым лидером на рынке контроля, экспертизы, испытаний и сертификации. Основанная в 1878 году, сегодня SGS признана эталоном качества и деловой этики. Более 94,000 сотрудников работает в сети SGS, насчитывающей свыше 2,600 офисов и лабораторий по всему миру со штаб-квартирой в Женеве, Швейцария.
Сущность метода контроля
Методы неразрушающего контроля сварных соединений
Внешний осмотр и обмеры сварных швов-наиболее простые и широко распространенные способы контроля их качества. Они являются первыми контрольными операциями по приемке готового сварного узла и изделия.
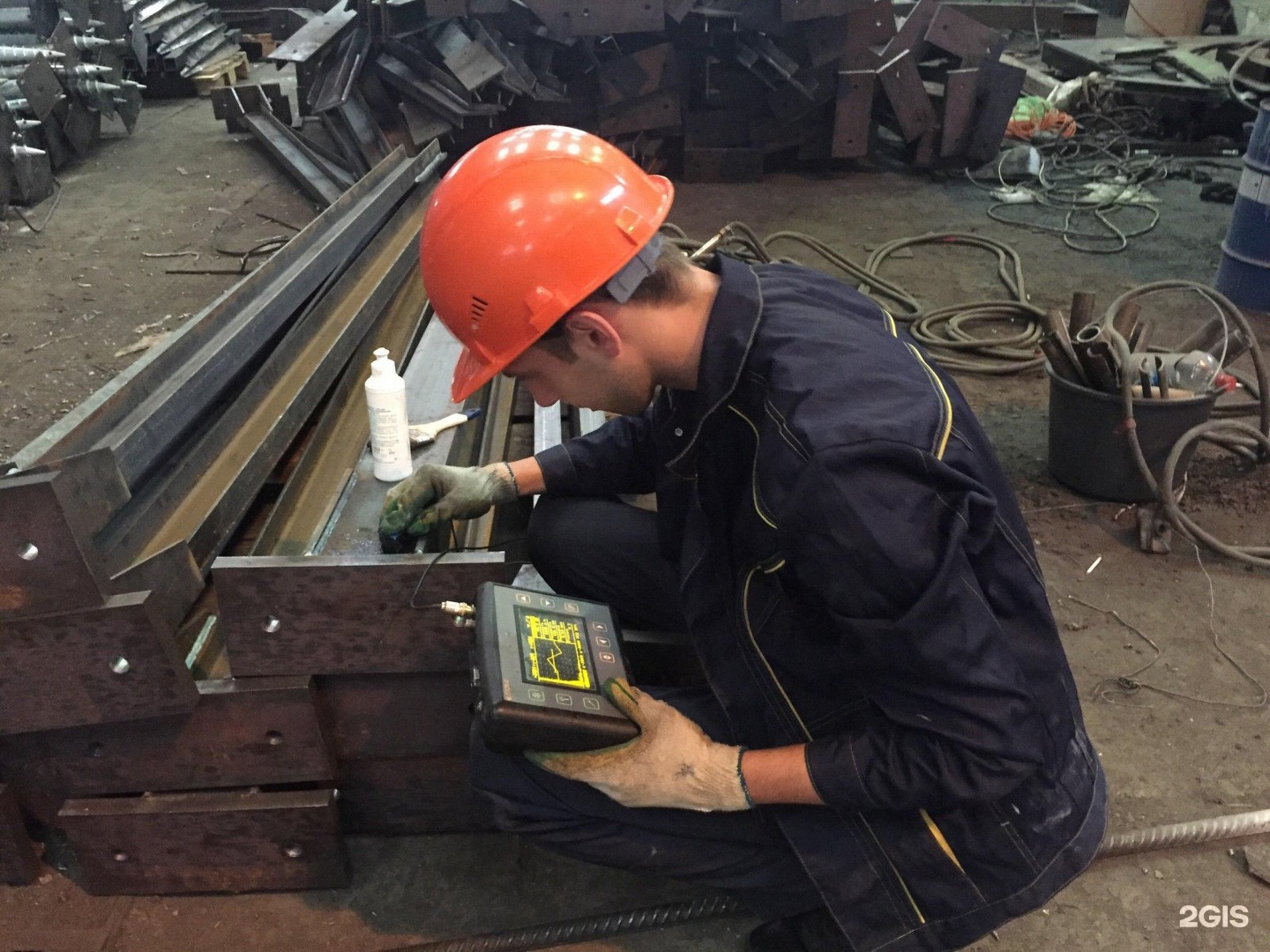
Внешним осмотром сварных швов выявляют наружные дефекты: непровары, наплывы, подрезы, наружные трещины и поры, смещение свариваемых кромок деталей и т.п.
Обмеры сварных швов позволяют судить о качестве сварного соединения: недостаточное сечение шва уменьшает его прочность, слишком большое увеличивает внутренние напряжения и деформации. Размеры сечения шва проверяют по его параметрам в зависимости от типа соединения У стыкового шва проверяют его ширину, высоту, размер выпуклости со стороны корня шва, в угловом-измеряют катет. Замеренные параметры должны соответствовать ТУ или ГОСТам. Размеры сварных швов контролируют измерительными инструментами и специальными шаблонами.
Внешний осмотр и обмеры сварных швов не дают возможности окончательно судить о качестве сварки. Они устанавливают только внешние дефекты шва и позволяют определить их сомнительные участки, которые могут быть проверены более точными способами.

Контроль непроницаемости сварных швов и соединений. Сварные швы и соединения ряда изделий и сооружений должны отвечать требованиям непроницаемости (герметичности) для различных жидкостей и газов. Учитывая это, во многих сварных конструкциях (емкости, трубопроводы, химическая аппаратура и т.д.) сварные швы подвергают контролю на непроницаемость. Этот вид контроля производится после окончания монтажа или изготовления конструкции. Дефекты, выявленные внешним осмотром, устраняют до начала испытаний. Непроницаемость сварных швов контролируют следующими методами: капиллярным (керосином), химическим (аммиаком), пузырьковым (воздушным или гидравлическим давлением), вакуумированием или газоэлектрическим течеискателями.
Для обнаружения скрытых внутренних дефектов применяют следующие методы неразрушающего контроля:
- Магнитные методы контроля основаны на обнаружении полей магнитного рассеяния, образующихся в местах дефектов при намагничивании контролируемых изделий.
- Радиационные методы контроля являются надежным и широко распространенными методами контроля, основанными на способности рентгеновского и гамма-излучения проникать через металл. Выявление дефектов при радиационных методах основано на разном поглощении рентгеновского или гамма-излучения участками металла с дефектами и без них.
- Ультразвуковой метод основан на способности ультразвуковых волн проникать в металл на большую глубину и отражаться от находящихся в нем дефектных участков.
Неразрушающий контроль качества сварных соединений металлоконструкций в Москве
Для того чтобы узнать, можно ли использовать металлические детали строительной конструкции, необходим контроль качества сварных соединений металлоконструкций. Для достоверных результатов выбирают наиболее актуальный метод исследований, после чего выносят официальное заключение. В нем будет указано, соответствуют ли швы требованиям нормативных документов, в частности, ГОСТ 3242-79 и РД 34.
До того как вводить конструкции в эксплуатацию, нужно обязательно проконтролировать качество сварных соединений в независимой лаборатории. Процедура требуется для следующих случаев:
- прокладка технологического трубопровода;
- строительство канализации и водопровода;
- возведение металлических каркасов здания;
- укладка газопровода.
Если тестирование не провести, в эксплуатацию могут ввести некачественные детали. Например, трубу водопровода. При подаче воды жидкость под давлением будет вытекать через бракованный шов, что может вывести из строя большие участки трубопровода. А это, в свою очередь, потребует большого расхода средств на ремонт.
Специалисты лаборатории «Строймат и К» оценят сварные швы:
- с помощью специальных приборов;
- визуально (трещины, царапины, сколы).
Мы используем основные виды контроля сварных соединений:
- разрушающий;
- неразрушающий.
Разрушающий контроль сварных соединений
Тестирование можно провести на небольших участках металлоконструкции или взять контрольные образцы. Метод актуален для сварки постоянного типа (чтобы проверить квалификацию сварщика и качество его работы). Также с помощью метода проверяют качество материалов самой конструкции.
Способы разрушающего контроля, которые применяют специалисты нашей лаборатории:
- тестирование статического изгиба;
- исследование места соединения — ударный изгиб и устойчивость при механическом старении;
- испытания статического напряжения;
- определение уровня твердости шва на различных участках.
Неразрушающий контроль сварных соединений
После такого тестирования изделие не разрушается, его можно использовать. Этот метод применяется чаще, чем разрушающий.
Какие способы используют в компании «Строймат и К»:
- капиллярный;
- визуальный;
- магнитный;
- ультразвуковой;
- радиографический.
Чтобы результаты были максимально достоверными, рекомендуем использовать сразу несколько способов тестирования.
Капиллярный
Применим для таких объектов, как трубопроводы и резервуары. Опытные специалисты выявят малейшую негерметичность или механический брак (трещины). Для тестирования необходимо создать поверхностное натяжение, например, с помощью керосина, и оценить результаты с помощью окрашенной жидкости.
Визуальный
Для такого вида контроля сварных соединений приборы не нужно. Но этот метод требует высокой квалификации и опыта лаборанта. Недорогой, но действенный способ неразрушающего контроля металлоконструкций.
Что выявляется:
- подрезы;
- царапины;
- наплывы;
- непроваренные участки;
- смещения.
Производится без использования оборудования. Это наиболее дешевый метод контроля, который не дает нужной точности, но позволяет выявить грубые дефекты — наплывы металла, подрезы, смещения, царапины, непроваренные участки.
Магнитная дефектоскопия
Контролируется качество швов с помощью магнитного поля. Если в изделии есть дефект, то поле изменит конфигурацию в месте брака. Метод делится на два способа:
- магнитографический;
- магнитопорошковый.
Магнитографический
Наклеиваем ферромагнитную ленту на шов. В случае брака дефекты визуально проявляются на ленте.
Магнитопорошковый
Действенный способ для выявления скрытых дефектов. На изделие насыпают специальный магнитный порошок. В местах, где есть скрытый брак, порошка будет больше всего. Можно применять для всех металлов, кроме:
- алюминия;
- хромоникелевой стали;
- меди.
Ультразвуковой
Лаборатория «Строймат и К» оснащена современными ультразвуковыми дефектоскопами для операционного неразрушающего контроля качества сварных соединений металлоконструкций. Отраженная от металла волна фиксируется, после чего специалист определяет наличие дефектов по характеру искажений.
Радиографический
Проверяем швы с помощью специального рентгеновского аппарата. Способ выявляет даже самые мелкие дефекты, которые не смогли обнаружить при других исследованиях. Гамма-лучи проходят через шов, затем результат фиксируется на снимке. В местах, где поглощение лучей меньше, скорее всего, будет скрытый дефект.
Кому необходима услуга контроля сварных соединений
Строительная лаборатория сотрудничает с государственными и частными заказчиками, которым важно убедиться в высоком качестве сварного шва. Испытания можно проводить непосредственно во время сварки, на производстве или исследовать уже готовые и даже введенные в эксплуатацию конструкции.
Мы рекомендуем проводить такие проверки несколько раз, особенно для объектов с повышенной нагрузкой на швы (например, складов или больших торговых центров). Если брак найти вовремя, это поможет починить конструкцию до того, как она сломается.
Оставить заявку
Контроль качества сварных швов
Контроль качества сварных швов
Для своевременного выявления дефектов необходим тщательный и систематический контроль сварных соединений трубопроводов на всех стадиях производства сварки. В зависимости от требований проекта или технических условий контроль сварных соединений технологических трубопроводов осуществляется путем наружного осмотра всех стыков, механических испытаний и физических методов контроля (металлографического исследования, просвечивания рентгеновскими или гамма-лучами, ультразвука, магнитографического способа), а также проверки плотности сварных стыков гидравлическим или пневматическим испытанием. В отдельных случаях в зависимости от материала труб и назначения трубопровода сварные швы проверяют на коррозионную стойкость.
Наружному осмотру подвергают каждый сваренный стык трубопровода. Путем осмотра выявляют внешние дефекты шва: наплывы, подрезы, кратеры, прожоги, трещины, свищи, наружные поры.
Механические испытания сварных соединений производят, чтобы определить их прочность и пластичность. Обязательными, видами механических испытаний являются испытания на растяжение, загиб или сплющивание и на ударную вязкость. Для проведения механических испытаний каждый сварщик одновременно со сваркой трубопровода осуществляет сварку контрольных (пробных) стыков, из которых вырезают образцы. Механические испытания контрольных стыков выполняют только при сварке трубопроводов, подведомственных органам Госгортехнадзора, на газопроводах, подведомственных органам газовой инспекции, а также на внутризаводских трубопроводах, транспортирующих огне- и взрывоопасные или токсичные газообразные и жидкие продукты. Механические испытания производят в соответствии с ГОСТ 6996—54.
Металлографическое исследование осуществляют, чтобы определить структуру металла шва и околошовной зоны, выявить в сварном шве газовые или шлаковые включения, волосяные трещины, непровары. При металлографическом исследовании проверяют излом сварного шва и определяют его макро- и микроструктуру. Эти исследования обязательны только для паропроводов первой и второй категорий, подведомственных Госгортехнадзору, и трубопроводов специального назначения. Исследованию подвергаются образцы, вырезанные из контрольного стыка.
Просвечивание рентгено- и гамма-лучами — наиболее распространенный способ контроля сварных швов без разрушения. Просвечивание позволяет обнаружить внутренние дефекты сварки — трещины, непровар, шлаковые включения и поры. Для просвечивания сварных швов применяют стационарные (РУП-200, РУП-400-5) и переносные (РУП-120-5-1 иИРА-1д) рентгеновские установки. Стационарные установки из-за больших габаритных размеров используют на заводах и в лабораториях; переносные — в монтажных условиях.
Гамма-лучи возникают в результате процессов, происходящих при распаде ядер элементов или изотопов, обладающих искусственной или естественной радиоактивностью. Эти лучи способны проникать через слой металла значительной толщины и действовать на рентгенопленку, приложенную к шву с обратной стороны. В тех местах, где имеются дефекты, поглощение лучей металлом будет меньше, и они окажут более сильное воздействие на эмульсию пленки. В данном месте на пленке появится темное пятно, по форме соответствующее дефекту шва. Для просвечивания пользуются гамма-лучами радиоактивных элементов цезия-137,. туллия-170, кобальта-60, иридия-192, европия-152. Для просвечивания радиоактивные вещества, излучающие гамма-лучи, помещают в специальные ампулы, заключенные в свинцовые кожухи (контейнеры). Рентгеновское и гамма-просвечивание проводят в соответствии с ГОСТ 7512—55. Недостатком способа контроля гамма-лучами является его вредность, требующая особых мер к охране людей от их воздействия.
Магнитографический способ контроля сварных швов основан на принципе изменения магнитного рассеивания, возникающего во время намагничивания контролируемого изделия в местах расположения дефектов. Особенностью этого способа является «запись» обнаруживаемых дефектов на специальную магнитофонную пленку (ленту).
Данный способ контроля применяют для труб толщиной до 20 мм, он позволяет четко выявить такие дефекты сварных швов, как продольные трещины, непровар, шлаковые включения и поры.
Ультразвуковой способ контроля сварных швов основан на различном отражении направленного пучка высокочастотных звуковых колебаний от металла (сварного шва) и имеющихся в нем дефектов.
Ультразвуковой контроль применяют для труб с внутренним диаметром 80 мм и более и стенками толщиной свыше 10 мм. Наибольшее применение для контроля нашли ультразвуковые дефектоскопы УЗД-7Н, НИИМ-5 и УЗД-39.
Недостатком данного способа контроля является то, что он позволяет определить лишь место дефекта, а не его характер.
Контролю физическими методами подвергают наихудшие стыки из отобранных по внешнему осмотру, в количестве:
Для трубопроводов I и II категорий…………………….. 3%
Для трубопроводов III категории ……………………….. 2%
Для трубопроводов IV категории…………………………. 1%
Количество стыков определяется от общего числа сваренных каждым сварщиком стыков, но оно должно быть не менее одного. Контролю необходимо подвергать весь периметр стыка.
При физических методах контроля сварные швы полагается браковать, если в них обнаружены следующие дефекты: трещины любых размеров; непровар глубиной более 15% от толщины стенки трубы, если она не превышает 20 мм, а при толщине стенки свыше 20 мм — более 3 мм; шлаковые включения и поры глубиной более 10% от толщины стенки трубы, если она не превышает 20 мм и 3 мм — при толщине стенки свыше 20 мм; скопления включений и пор в виде сплошной сетки дефектов в шве независимо от их глубины. Шлаковые включения глубиной до 10% от толщины стенки и длиной не более 30 мм, а также скопления пор длиной не более 15 мм не являются признаками брака.
Исправление дефектов сварных стыков трубопроводов допускается, если при условном диаметре трубопровода до 100 мм длина трещин меньше 20 мм и при условном диаметре свыше 100 мм — меньше 50 мм, а также если протяженность участков с недопустимыми дефектами меньше ¼окружности стыка. В процессе исправления необходимо вырубить дефектные места и вновь их заварить. В остальных случаях дефектный стык должен быть удален из трубопровода и на его место вварена катушка. Все подвергавшиеся исправлению участки стыков должны быть проверены физическими методами контроля.
1. Какие применяют способы контроля сварных швов?
2. В чем сущность просвечивания гамма-лучами? Какие радиоактивные элементы используются при этом?
3. Как производится исправление дефектов сварного шва?
Все материалы раздела «Сварка труб» :
● Способы сварки трубопроводов и виды сварных соединений
● Подготовка труб под сварку
● Технология газовой сварки и резки
● Кислородно-флюсовая и дуговая резка
● Технология ручной электродуговой сварки, электроды
● Источники питания сварочной дуги
● Автоматическая и полуавтоматическая сварка под флюсом
● Автоматическая и полуавтоматическая сварка в защитных газах
● Сварка трубопроводов из легированной стали
● Сварка трубопроводов высокого давления, термообработка сварных соединений
● Сварка трубопроводов из алюминия и его сплавов, из меди и ее сплавов
● Пайка трубопроводов, дефекты сварных швов
● Контроль качества сварных швов
● Виды сварки и применяемое оборудование
● Сварка и склеивание винипластовых труб
● Сварка полиэтиленовых трубопроводов
● Правила техники безопасности при резке и сварке трубопроводов
Методы контроля качества сварных соединений и наплавок
Методы контроля качества сварных соединений и наплавок
Внешний осмотр и измерения. Внешний осмотр производят невооруженным глазом, а в сомнительных местах – с помощью лупы четырех-семикратного увеличения. При контроле используется нормальный и специальный мерительный инструмент (шаблоны, линейки и др.). Внешнему осмотру подвергаются все сварные соединения и наплавки. Обнаруженные недопустимые дефекты должны быть исправлены до проведения последующего контроля другими методами.
Контроль сварных швов на непроницаемость:
— керосиновая проба,
— цветная дефектоскопия,
— контроль гелиевыми и галоидными течеискателями.
При керосиновой пробе сварные соединения с одной стороны окрашивают меловым раствором, а с другой – смачивают керосином. В местах неплотностей на поверхности, покрытой мелом, через несколько часов выступают темные пятна. Контроль возможен при двустороннем доступе к сварным соединениям.
При цветной дефектоскопии на отполированную поверхность сварного шва наносят вначале специальный окрашивающий раствор, который проникает в дефекты шва. После выдержки окрашивающий раствор смывают с поверхности. Далее после просушки на эту же поверхность наносят тонкий слой мелового покрытия.
При вакуумном методе участки испытываемого сварного шва смачивают мыльным раствором. Затем на них накладывают специальную вакуум-камеру, представляющую собой металлическую раму с прозрачным верхом из органического стекла и уплотнением из мягкой губчатой резины, благодаря которой камера присасывается к стыку при создании в ней вакуума вакуумным насосом. Данные рамы можно доставить на предприятие, воспользовавшись услугами транспортной компании. Рекомендации по тарифам вы можете узнать на этой странице http://www.nsvlog.ru/tarify/. В местах расположения сквозных дефектов появляются пузырьки, хорошо заметные через оргстекло камеры. Вакуумный метод контроля применяется в тех случаях, когда невозможен двусторонний доступ к сварным швам.
При контроле с помощью гелиевых или голоидных течеискателей испытываемое изделие наполняется гелием или смесью воздуха с фреоном. При наличии неплотностей гелий или фреон проникает через них и улавливается щупом течеискателя. Расположение дефектов фиксируется в момент подачи течеискателем звукового сигнала.
При радиографическом контроле используются рентгеновские или гамма-установки, излучающие соответственно рентгеновские и гамма-лучи, способные приникать через толщу металла и действовать на рентгеновскую пленку, приложенную с обратной стороны шва. В местах расположения дефектов степень засвечивания пленки больше, а после обработки на пленке видны потемнения, соответствующие по форме дефектами.
При ультразвуковом контроле сварное соединение «прощупывает» специальный искатель, который оператор перемещает параллельно шву. Дефекты сварного шва видны на экране ультразвукового дефектоскопа в виде соответствующих импульсов.
Контроль лабораторными методами производится на образцах, вырезанных из контрольных сварных соединений. Сварку контрольных соединений производят в условиях, аналогичных сварке производственных соединений. При этом должны применяться те же основные и сварочные материалы, способы и режимы сварки, что и при сварке изделия.
Для проведения механических испытаний изготавливают специальные образцы установленных стандартов формы и размеров. Эти образцы испытывают в лаборатории на испытательных машинах для определения временного сопротивления разрыву, угла загиба (сплющивания), ударной вязкости.
Вырезанный из сварного соединения образец шлифуют, затем полируют и травят специальным раствором. Осмотр шлифов производят с помощью микроскопов, обеспечивающих увеличение в 50-100 раз и более.
Испытание на межкристаллитную коррозию подвергают сварные соединения из аустенитных сталей. Для проведения испытаний специальные из аустенитных сталей. Для проведения испытаний специальные образцы кипятят в растворе серной кислоты и медного купороса в течение 24 часов. Далее их промывают и загибают на угол 90 градусов. Качество сварного соединения считается удовлетворительным, если на образцах не возникли трещины или надрывы коррозионного характера.
Читайте также:
Современные условия труда
Методы контроля качества сварных соединений и наплавок
Автоматический светофильтр Optrel
Процесс кислородной резки
Техника кислородной резки
Контроль качества сварных швов засверловкой
Механические испытания сварных соединений. Механические испытания выявляют качество наплавленного металла и сварного соединения в целом и широко применяются при определении качества сварки ответственных конструкций (подъемно-транспортных машин, котлов, трубопроводов и т. д.). Механические испытания сварных соединений регламентированы ГОСТ 6996. Однако число вырезаемых образцов ограничивается трудностями заделки мест выреза, а ограниченное количество образцов не может отразить полного состояния всех швов. Поэтому этот вид испытаний является дополнительным.
Контроль с помощью засверловок. Этим способом могут выявляться: 1) непровары по границе шва и между отдельными слоями; 2) газовые и шлаковые включения; 3) трещины в шве и в местах сплавления.
Фиг.113.Контроль качества швов засверловкой.
Засверловка швов производится ручной пневматической или электрической дрелью, сверлом с углом заточки 90° (фиг. 113). Сверло следует подбирать так, чтобы было вскрыто все сечение шва и захвачен основной металл по 1,5—3,0 мм на сторону. При швах шире 20 мм сверление отверстий производится на части шва с обязательным захватом зоны сплавления. Сверление производится до вскрытия вершины шва. Стенки засверленного отверстия должны иметь гладкую поверхность.
Для выявления границ сплавления засверленное место протравляют химическим реактивом (хорошие результаты дает реактив: двойная соль хлорной меди и аммония 10 г на 100 см3 воды). Осмотр засверленной лунки после травления производится невооруженным глазом или с помощью лупы. При обнаружении непровара или иных пороков шва в одной лунке производят дополнительное сверление для определения их границ. Участки шва, имеющие пороки, должны вырубаться и завариваться вновь.
Места и количество отверстий устанавливаются в соответствии с размерами конструкций и длиной швов, но не менее трех на конструкцию. Засверленные отверстия в швах ответственных конструкций (котлах, трубопроводах и др.) подлежат заварке; в строительных конструкциях они часто остаются незаваренными.
Контроль качества | gacmrnaks
Контроль качества сварных соединений необходим для:
Своевременного выявления и устранения дефектов швов
Получения сварного соединения высокого качества
Определения соответствия изделия требованиям заказчика
Под качеством продукции понимается совокупность ее свойств, которые обеспечивают пригодность этой продукции удовлетворять определенные потребности, в соответствии с назначением этой продукции. Одним из главных свойств этой совокупности, является надежность. Под надежностью понимают свойство продукции (изделия, машины) выполнять заданные функции, сохраняя во времени установленные эксплуатационные параметры в пределах конкретных значений, установленных разработчиками этой продукции.
Контроль качества сварных соединений начинается с проверки качества подготовки шва, и заканчивается проверкой полученного соединения.
Проверка качества сварочных соединений включает в себя:
К разрушающим видам проверки относятся:
Металлографические исследования
Физико-химические исследования
Механические испытания
Контроль исходных материалов, заготовок и качества сборки
Контроль оборудования, оснастки и приборов
Контроль режимов сварки, пайки, склеивания
Контроль квалификации производственного персонала
Неразрушающие виды включают в себя:
Контроль внешнего вида сварных швов
Радиационные виды неразрушающего контроля
Акустические виды неразрушающего контроля
Магнитные виды неразрушающего контроля
Электромагнитные методы
Капиллярные методы
Методы контроля сплошности сварных швов течеисканием
Тепловые методы контроля
Качество сварного шва — обзор
6.

Харрис и Смит исследовали применение факторного метода для прогнозирования качества сварного шва для процесса наплавки дугой с переносом плазмы (PTA) на низкоуглеродистую сталь. ( 36 ). В качестве переменных процесса учитывались ток, скорость подачи порошка, скорость перемещения резака, ширина колебаний и расстояние от резака. Были измерены четыре характеристики качества наплавки, а именно: высота, ширина, твердость и разбавление наплавки.Было подтверждено, что все параметры процесса действовали как основные параметры процесса при контроле качества отложений. Также сообщалось, что процесс PTA является отличным выбором для нанесения высококачественных твердых покрытий при низком контролируемом разбавлении.
Оптимизация сварки трением разнородных материалов с использованием факторного расчета была изучена Мурти и Сундаресан ( 37 ). Они изучили сварку трением трех разнородных материалов, используемых в промышленности: низколегированной стали с аустенитной нержавеющей сталью, среднеуглеродистой стали с быстрорежущей сталью и алюминия с нержавеющей сталью. Основная цель заключалась в определении металлургических и механических характеристик сварных соединений трением, полученных при оптимальных режимах сварки. Были разработаны три математические модели для связи прочности на разрыв с надрезом (NTS) и энергии сдвига с параметрами процесса, а именно: давление трения, время трения и давление ковки с разными уровнями в зависимости от двух материалов, из которых образовано соединение. Сообщалось, что статистический экспериментальный план был полезен для сокращения количества испытаний, необходимых для оптимизации условий сварки трением.Кроме того, прочность соединения, созданного с использованием оптимизированных условий, вполне соответствовала прогнозируемым результатам. Более того, во всех случаях прочность соединения была по крайней мере такой же высокой, как у более мягкого из двух материалов, из которых образовывалось соединение.
Контроль искажений в роботизированной CO 2 -экранированной FCAW исследовали Арья и Пармар ( 38 ). Метод трехуровневого дробного факторного анализа был использован для разработки математических моделей для прогнозирования угловой деформации в низкоуглеродистой стали толщиной 10 мм.Влияние напряжения дуги, скорости подачи проволоки, скорости сварки и угла канавки на угловую деформацию в одинарных V-образных стыковых сварных швах было исследовано с запечатыванием и без него. Был сделан вывод, что разработанные модели были достаточно точными и могут быть с успехом использованы для контроля угловой деформации в автоматических сварочных линиях с использованием процесса FCAW.
Zhou et al. ( 39 ) использовали факторные эксперименты для исследования влияния параметров соединения (скорости вращения, времени трения и давления) на NTS фрикционных соединений из разнородных композиционных материалов на основе алюминия и нержавеющей стали MMC / AISI304.Было замечено, что давление трения и скорость вращения имеют статистически значимое влияние на значения NTS. Более того, они сообщили, что самый высокий НТС наблюдается в соединениях, изготовленных при высоком давлении трения 120 МПа.
Усталостная износостойкость крестообразных соединений FCAW, содержащих непровар, с использованием схемы эксперимента была исследована Баласубраманианом и Гуха ( 40 ). Цель заключалась в оптимизации некоторых размерных факторов, влияющих на усталостную долговечность крестообразных соединений, изготовленных из закаленной и отпущенной стали (класс ASTM 517 F).Было упомянуто, что методы, описанные в этой работе, были довольно простыми и экономичными для оптимизации длительных испытаний на усталость. Также сообщалось, что некоторые факторы, влияющие на усталостную выносливость, были оптимизированы для достижения максимальной усталостной долговечности, но валидность процедуры ограничена областью факторов, рассматриваемой для исследования. Было отмечено, что метод дисперсионного анализа (ANOVA) является наиболее удобным для определения значимости основных эффектов и эффектов взаимодействия совместных размеров.Те же авторы ( 41 ) продолжили свои исследования, разработав математические модели с использованием плана эксперимента для прогнозирования усталостной долговечности дуговой сварки экранированным металлом (SMAW) и крестообразных соединений FCAW, выходящих из строя в области корня и пальца ноги. Используя разработанные модели, усталостную долговечность крестообразного соединения SMAW и FCAW можно спрогнозировать с уровнем достоверности 95%, однако достоверность моделей ограничена областью факторов. Было обнаружено, что метод факторного экспериментирования при планировании эксперимента более экономичен для прогнозирования влияния различных факторов на усталостную долговечность за счет проведения минимального количества экспериментов.
Коганти и др. ( 42 ) использовали полный факторный расчет для определения оптимальных параметров процесса сварки MIG для необработанных алюминиевых сплавов 5754. Исследовано влияние параметров процесса сварки на разрушающую нагрузку соединения внахлест (прочность на сдвиг) и проплавление шва. Параметры процесса: потребляемая мощность, скорость горелки, напряжение, ток, скорость подачи проволоки, частота импульсов и расход газа. Прочность соединений и проплавление шва были измерены для различных рабочих диапазонов коэффициентов сварки. Было указано, что потребляемая мощность и скорость потока газа были двумя важными факторами, основанными на данных от сдвиговой нагрузки до разрушения и проплавления сварного шва. Также сообщалось, что чем ниже потребляемая мощность, тем ниже нагрузка сдвига до разрушения и глубина проникновения, и наоборот. Оптимальными настройками коэффициента для более высокой прочности соединения были высокая потребляемая мощность и высокий расход газа.
Sampath ( 43 ) представил инновационный подход, основанный на ограничениях, который оказался весьма эффективным при разработке спецификации расходуемых сплошных проволочных электродов для GMAW из сталей HSLA-80 и HSLA-100, которые соответствуют или превосходят требования ВМС США.Первоначально он преобразовал требования ВМС США в набор ограничений, которые связывали химический состав стали с определенными металлургическими характеристиками. Впоследствии факторный план 2 3 был использован для разработки партии сварочных электродов с целью оценки их характеристик. Было показано, что среди восьми использованных электродов два электрода соответствовали требованиям ER-100 или превосходили их, а один электрод соответствовал требованиям ER-120 или превосходил их. Был сделан вывод, что использование этого подхода значительно снижает риск, связанный с разработкой технических характеристик электродов.
Pine et al. ( 44 ) представили экспериментальное и численное исследование для определения жесткости на кручение, предела упругости и предела прочности сваренных точечной сваркой, клеевых и сварных коробчатых секций. Они исследовали множество факторов, а именно: технику соединения, толщину листа, прочность стали, площадь сечения, конструкцию сечения и торцевой шов, используя методы факторного проектирования, чтобы определить их влияние на крутильные свойства коробчатых сечений. Авторы пришли к выводу, что технология соединения, площадь сечения и толщина сечения были основными факторами, которые имеют наибольшее влияние на жесткость коробчатых секций на кручение. Было обнаружено, что жесткость на кручение можно улучшить без существенного увеличения веса, изменив технику соединения с точечной сварки с шагом 50 мм на клеевое соединение, увеличив площадь сечения и, в меньшей степени, изменив конструкцию сечения. Кроме того, прочность стали была наиболее важным фактором при определении предела упругости и предела прочности.
Хан и др. ( 45 ) использовали полное факторное проектирование для оптимизации процесса лазерной сварки, чтобы получить наиболее желаемое качество сварки с точки зрения геометрии сварного шва и механической прочности, а также определить соответствующие оптимальные настройки параметров сварки.Мощность лазера и скорость сварки были указаны как наиболее важные факторы, влияющие на геометрию сварного шва, а также на силу сдвига сварного шва. Максимально достижимая длина сопротивления сварного шва и, следовательно, усилие сдвига сварного шва были ограничены по энергии в зависимости от условий сварки, конфигурации соединения и используемых материалов. Оптимальные результаты были представлены в числовом и графическом виде, что позволяет быстрее находить оптимальные настройки для лазерной сварки.
Контроль качества
Обеспечение соблюдения сварщиками определенных процедур — важный шаг в общей системе качества сварки.
Существует ряд причин для проверки сварного шва, самая важная из которых — определить, достаточно ли его качество для предполагаемого применения. Чтобы оценить качество сварного шва, необходимо иметь форму измерения для сравнения его характеристик и квалифицированного специалиста для выполнения оценки. Нецелесообразно оценивать качество без определенной формы критерии приемки. Это также непрактично для человека, который не разбирается в необходимых процедурах для выполнения этой задачи.
Оценка характеристик сварного шва включает размер сварного шва и наличие несплошностей. Размер сварного шва может быть чрезвычайно важным, поскольку он часто напрямую зависит от прочности и связанных с этим характеристик. Сварные швы меньшего размера могут не выдерживать нагрузки, возникающие во время эксплуатации, а сварные швы большего размера могут создавать концентрацию напряжений или способствовать потенциальной деформации сварного шва.
сварная деталь.
Выявление неоднородностей сварного шва также важно, потому что дефекты внутри сварного шва или рядом с ним, в зависимости от их размера или расположения, могут помешать сварному шву выполнять свои функции.Когда несплошности имеют неприемлемый размер или находятся в неприемлемом месте, они называются дефектами сварки, и они могут вызвать преждевременный выход из строя сварного шва из-за снижения прочности или создания напряжения. концентрации в свариваемом элементе.
Определение качества сварного шва
Критерии приемки качества сварного шва могут быть получены из ряда источников. На чертеже или чертеже сварочного производства указаны размеры сварных швов и другие требования к размерам сварки, такие как длина и расположение. Эти требования к размерам устанавливаются путем расчетов или взяты из проверенных конструкций, которые соответствуют требованиям к характеристикам сварного соединения.
Число допустимых и неприемлемых несплошностей сварного шва для контроля сварки обычно получают из правил и стандартов по сварке. Сварочные нормы и стандарты были разработаны для многих типов сварочных работ. Важно выбрать стандарт сварки, предназначенный для использования в конкретной отрасли или области применения, в которой вы работаете.
Обязанности инспектора сварки
Проверка сварки требует знания чертежей сварных швов, символов, конструкции стыков, процедур, норм и стандартов, а также методов проверки и испытаний. По этой причине многие правила и стандарты в области сварки требуют, чтобы инспектор по сварке имел официальную квалификацию или обладал необходимыми знаниями и опытом для проведения проверки.
Контроль сварных швов настолько хорош, насколько хорош человек, проводящий испытания. Вот несколько вещей, которые должен знать инспектор по сварке, и задачи, которые он должен уметь выполнять:
- Квалификация работы сварщика и технологии сварки. Необходимо соблюдать специальные процедуры для аттестации сварщиков и процедур сварки. Процесс аттестации является неотъемлемой частью общей системы качества сварки, и от инспектора сварки часто требуется координировать и проверять эти типы квалификационных испытаний.
Эти квалификации обычно включают изготовление сварных образцов, представляющих сварные швы, которые будут использоваться при производственной сварке. Эти сварные образцы обычно требуется испытать после завершения. Рентгенография, микротравление, направляемые изгибы, поперечное растяжение и трещинообразование — вот некоторые из используемых тестов.Результаты испытаний должны соответствовать минимальным требованиям или превышать их. оговаривается в правилах сварки или стандарте, прежде чем процедура может быть аттестована.
- Визуальный осмотр.
При правильном выполнении это часто самый простой, наименее затратный и самый эффективный метод контроля сварки для многих областей применения. Инспектор по сварке должен уметь идентифицировать все различные дефекты сварки во время визуального осмотра. Он также должен быть в состоянии оценить, с точки зрения соответствующих правил или стандартов сварки, значимость выявленных разрывов для определения того, принимать или отклонять их во время тестирования и производства.
Инспектор сварки с хорошим зрением может быть сравнительно быстро обучен компетентным инструктором и может оказаться важным активом для системы качества сварки (хорошее зрение, очевидно, необходимо для визуального контроля).
- Обнаружение поверхностных трещин. Инспектор по сварке иногда требуется для проведения испытаний сварных швов методами обнаружения поверхностных трещин. Ему также, возможно, придется оценить результаты тестирования этих методов тестирования. Инспектор должен понимать методы тестирования, такие как проникающая жидкость и магнитопорошковая проверка.
Кроме того, он должен знать, как используются тесты и что они будут найти.
- Радиографический и ультразвуковой контроль сварных швов. Эти два метода контроля входят в группу, известную как неразрушающий контроль (NDT). Эти методы контроля используются для проверки внутренней структуры сварного шва с целью установления целостности сварного шва без разрушения сварного компонента. От инспектора сварки может потребоваться понимание этого типа испытаний и компетентность в
интерпретация результатов.Радиографический и ультразвуковой контроль сварных швов — два наиболее распространенных метода неразрушающего контроля, используемых для обнаружения неоднородностей во внутренней структуре сварных швов. Очевидным преимуществом обоих методов является их способность помочь установить внутреннюю целостность сварного шва без разрушения сварного компонента.
При радиографическом контроле используются рентгеновские лучи, произведенные рентгеновской трубкой, или гамма-лучи, произведенные радиоактивным изотопом.
Основной принцип рентгенологического обследования такой же, как и для медицинской радиографии.Проникающее излучение проходит через твердый объект, в данном случае сварной шов, на фотопленку, в результате чего создается изображение внутренней структуры объекта. Количество энергии поглощение объекта зависит от его толщины и плотности. Энергия, не поглощаемая объектом, приведет к обнажению рентгеновской пленки. Когда пленка проявится, эти области будут темными. Области пленки, подвергшиеся воздействию меньшего количества энергии, остаются более светлыми.
Дефекты внутри сварного шва или рядом с ним могут помешать сварному шву выполнять свои функции.
Таким образом, области сварного шва, толщина которых была изменена из-за неоднородностей, таких как пористость или трещины, будут отображаться на пленке в виде темных контуров. Включения низкой плотности, такие как шлак, будут отображаться как темные области на пленке, а включения высокой плотности, такие как вольфрам, появятся как светлые области.
Все неоднородности обнаруживаются путем просмотра формы и изменения плотности обработанная пленка.
При ультразвуковом контроле используются механические колебания, похожие на звуковые волны, но более высокой частоты.Луч ультразвуковой энергии направляется в проверяемый сварной шов. Этот луч проходит через сварной шов с незначительными потерями, за исключением случаев, когда он перехватывается и отражается неоднородностью. Используется метод отражения ультразвукового контактного импульса. В этой системе используется датчик, который превращает электрическую энергию в механическую. Преобразователь возбуждается высокочастотным напряжением, которое заставляет кристалл механически вибрировать. Кристаллический зонд становится источником ультразвуковой механической вибрации.
Эти колебания передаются на испытуемый образец через связующую жидкость, обычно масляную пленку, называемую связующим веществом. Когда импульс ультразвуковых волн попадает в разрыв в образце для испытаний, он отражается обратно в исходную точку.
Таким образом, энергия возвращается к преобразователю. Преобразователь теперь служит приемником отраженной энергии. Первоначальный сигнал или главный удар, отраженные эхо-сигналы от неоднородностей и эхо-сигналы от задней поверхности испытательного образца отображаются в виде кривой на экране электронно-лучевого осциллографа.
- Испытания разрушающих сварных швов. Разрушающие методы для проверки целостности или рабочих характеристик сварного шва включают разрезание, изгиб или разрыв сварного компонента, а также оценку различных механических или физических характеристик. Некоторые из этих испытаний — это испытание на управляемый изгиб, испытание на макротравление, испытание на растяжение с уменьшенным сечением, испытание на излом и испытание на удар по Шарпи с V-образным надрезом. Эти тесты используются
во время процедуры сварки или аттестационных испытаний сварщика.Инспектор по сварке часто требуется для проведения, контроля или оценки этих методов испытаний.
- Интерпретация деталей сварки и обозначений сварных швов. Инспектор по сварке должен уметь читать инженерные и производственные чертежи, а также уметь интерпретировать все детали и символы, которые предоставляют информацию о требованиях к сварке.
Глядя только на некоторые функции инспектора сварки, легко увидеть, что у инспектора сварки может быть много обязанностей.Эти обязанности обычно меняются от одной инженерной или производственной среды к другой. Однако основная задача инспектора по сварке — помогать координировать операции по контролю качества сварки в организации.
Одним из основных компонентов успешной системы контроля качества сварки является создание, внедрение и контроль правильной программы контроля качества сварки. Программа может быть создана только после завершения оценки требований к качеству сварного шва или критериев приемки, приобретения знаний о методах контроля и испытаний и использования должным образом квалифицированных и опытных сварщиков. инспекторы.
Контроль гладких сварных швов Сотрудничество между людьми и роботами — Новости метрологии и качества
Роботы используются во все большем количестве ситуаций, многие из которых связаны с сотрудничеством между людьми и роботами. В совместном проекте с Volkswagen AG Институт телекоммуникаций им. Фраунгофера, Институт Генриха Герца, HHI, продемонстрирует преимущества, которые может принести использование взаимодействия человека и робота (HRC) для проверки сварных швов в автомобильной промышленности.
Безупречные сварные швы — важнейший критерий качества в автомобилестроении. В будущем сварные швы будут проверяться командой человек-робот, каждый из которых будет вкладывать свои навыки и знания. Управляемый жестами и голосовыми командами, робот будет удерживать и перемещать определенные компоненты в нужное положение, в то время как сотрудник отмечает и записывает любые дефекты качества сварки.
Совместный исследовательский проект EASY COHMO (Системы помощи в эргономике для бесконтактной работы человека и машины) основан на многолетнем опыте Fraunhofer HHI в области 3D-захвата, обработки 3D-информации и 3D-визуализации. Эта система для визуального контроля сварных швов на ключевых компонентах автомобильного производства является прекрасным примером того, как HRC может работать в промышленности. В ближайшие годы эта технология будет оказывать конкретную помощь в процедурах проверки в Volkswagen.
От ручного контроля к стандартам Индустрии 4.0
Робот представляет заготовку в эргономичном положении для облегчения проверки.Процесс проверки остается неизменным на протяжении десятилетий.Прежде всего, каждый компонент должен быть вручную закреплен на поворотном позиционере, чтобы его можно было проверять со всех сторон. Это неизбежно приводит к тому, что служащему приходится занимать неэргономичные позиции, что может привести к повторяющимся травмам от растяжения. Кроме того, на эту сложную процедуру отводится очень мало времени, что может отрицательно сказаться на качестве проверки.
В настоящее время сотрудники могут проводить проверку по своему усмотрению. Это неизбежно приводит к нестандартизированной процедуре, которая затрудняет выявление систематических дефектов на основе наблюдений различных инспекторов. Кроме того, любые такие дефекты часто не регистрируются или их приходится вносить в отдельную систему с помощью клавиатуры и мыши.
В будущем этот процесс проверки будет интерактивным, при этом роботы будут использовать для удержания тяжелых компонентов и маневрирования их в положение, в котором сотрудники смогут проверять их эргономично. Такие роботы будут иметь как минимум шесть осей и, следовательно, смогут перемещать, поворачивать и наклонять компонент во всех возможных направлениях. Робот автоматически удалит компонент с линии и представит его для проверки.Сотрудник будет взаимодействовать с роботом с помощью явных и неявных жестов, тем самым направляя компонент в желаемое положение. Сотрудники могут сосредоточить свое внимание на выявлении дефектов и, как следствие, упускать из виду меньшее количество дефектов.
Мультимодальный контроль
Расширенный пользовательский интерфейс на основе жестов руки проецируется на компонент и рабочее место, где он служит для управления роботом и процедурой проверки.
Промежуточное программное обеспечение, разработанное Fraunhofer HHI, координирует работу различных датчиков, которые служат для регистрации общей рабочей ситуации.Основываясь на положении и жестах сотрудника, программное обеспечение рассчитывает необходимое движение манипулятора. Это также обеспечивает безопасность пользователя. Например, всякий раз, когда сотрудник перестает смотреть прямо на компонент, программное обеспечение останавливает роботизированную руку в качестве меры предосторожности.
«Робот также можно настроить так, чтобы он отвечал на персонализированные инструкции», — объясняет Пол Хойецки, менеджер проекта Fraunhofer HHI. « Наш новый интерфейс восприятия способен обрабатывать индивидуальные жесты и голосовые команды пользователя.Это означает, что систему можно быстро настроить в соответствии с конкретными требованиями рабочей станции ».
Жесты используются для обозначения, классификации и подтверждения дефектов компонента. Посредством точного отслеживания объектов и дополнений на основе проектора сотрудникам предоставляется интерфейс непосредственно на компоненте в зоне их рабочего пространства. Это обеспечивает эффективный и интуитивно понятный способ создания цифровой 3D-записи любых дефектов сварных швов. Напротив, в нынешней процедуре проверки отсутствует какой-либо систематический учет дефектов, потому что существует очень мало формализованного обмена информацией между различными сотрудниками.С помощью новой процедуры любые дефекты могут быть немедленно внесены в систему, а затем статистически оценены. Это означает, что систематические дефекты выявляются быстрее и, таким образом, могут быть устранены на этапе сварки.
Возможность расширения на все рабочие станции человек-робот
Положение дефектов сварных швов, идентифицированных пользователем, может быть определено комбинацией отслеживания пальцев и трехмерного отслеживания шва и точно задокументировано. Система включает большое количество датчиков в сочетании с мультимодальным управлением на основе улучшенного промежуточного программного обеспечения, а также настраиваемых инструкций по эксплуатации и машинного обучения. Это подход, который вполне может стать прорывом для дальнейших приложений HRC, а также расширить возможности для сотрудничества и взаимодействия между людьми и роботами.
Совместный проект EASY COHMO является частью исследовательского альянса 3Dsensation и финансируется Федеральным министерством образования и исследований Германии (BMBF) в рамках программы государственного финансирования.
Дополнительная информация: www.fraunhofer.de
ССЫЛКА НА ГЛАВНУЮ
Последние заголовки новостей
Вам также могут понравиться эти «Последние новости»… щелкните изображение, чтобы прочитать статьи
Verisurf Peel Back Value с решением для 3D-сканирования на основе MBD
Verisurf Software объявила о дистрибьюторском соглашении с peel 3d присвоение Verisurf статуса всемирного дистрибьютора всей линейки продуктов для ручного 3D сканирования.
Параллельно у Verisurf Software есть
Скорость лазерного сканирования 3D Переоборудование суперяхты
Испанская группа Bravo Yacht Design Group (BYD) недавно завершила свое 200-е 3D-сканирование яхты. 73-метровый Lürssen Coral Ocean только что прошел подробное внешнее сканирование, прежде чем получить обширную модернизацию.
Датчик Smart Profile для встроенного многомерного управления
Эффективное встроенное тестирование является необходимым условием во многих производственных процессах, помогая для сокращения времени простоя, сведения к минимуму количества брака, снижения производственных затрат и улучшения контроля качества.Ключевой компонент
NIST объявил о программе финансирования НИОКР на 2021 год
Национальный институт стандартов и технологий (NIST) Министерства торговли США объявил о проведении фазы I исследований инноваций малого бизнеса (SBIR) в 2021 финансовом году темы.
Программа NIST SBIR поощряет
Поставщик аэрокосмической отрасли получает первый сертификат качества PPAP
Компания Hanwha Aerospace объявила, что недавно получила первую в мире сертификацию процесса утверждения деталей продукта (PPAP) от Rolls-Royce. один из трех ведущих мировых авиадвигателей
Renishaw Technology Aids INEOS TEAM UK Прогресс в финале PRADA Cup
Глобальная инженерная компания Renishaw рада, что сэр Бен Эйнсли и INEOS TEAM UK получили удалось выиграть место в финале Мировой серии PRADA America’s Cup
Высотомер повышает точность проверок обрабатываемых компонентов
Поскольку допуски на компоненты ужесточаются, а требования заказчиков ужесточаются, Chelburn Precision стремилась улучшить их измерительные способности.
Компания со штаб-квартирой в Рочдейле, Великобритания, нашла решение в
Обнаружение ошибок машинного обучения для доставки на производственной линии Smart Factory для аэрокосмических креплений
LISI Aerospace (BAI UK) и Университета Шеффилдских перспективных производственных исследований Центр (AMRC) совместно получил финансирование в размере 975 000 фунтов стерлингов (1365 000 долларов США) от Института аэрокосмических технологий (ATI) для повышения производительности
Компоненты технического зрения представляют самую маленькую встроенную систему технического зрения
Роботизированный 3D-принтер Ai Build завершил новый раунд финансирования
Британская компания Ai Build, занимающаяся разработкой искусственного интеллекта (AI) и роботизированных технологий для крупномасштабного аддитивного производства (AM), привлек 1 млн долларов (0,74 млн фунтов стерлингов) в рамках нового раунда финансирования.
Выбор редакции… щелкните изображение, чтобы прочитать полные статьи
Автоматическое измерение зазора активизирует критический компонент ИТЭР
Команда инженеров из Research Instruments (RI), Германия, завершили этап проектирования прототипа внутренней вертикальной мишени (IVT) ИТЭР.Осуществленная в рекордно короткие сроки и с тоннами железа,
AI Deep Learning Inspection «взлетает» в авиационной промышленности
Искусственный интеллект (AI) может использоваться разными способами: для данных обработка, аналитика, комбинаторные методы… ИИ — это концепция, которая распространяется на любую возможную область применения.
В поле
Applied Automation Technologies присоединяется к Andretti Autosport в качестве официального метрологического решения команды
Andretti Autosport объявила, что Applied Automation Technologies (AAT3D) будет выступать в качестве официального метрологического решения команды.AAT3D начался в 1987 году как программное обеспечение для измерения размеров на основе САПР и был разработан в
Цифровой отпечаток пальца обеспечивает цифровой двойник для каждой производимой детали
Идентификатор FeaturePrint от Alitheon является универсальным идентификатором практически любого продукта. Благодаря развитому машинному зрению и статистическим методам, даже самые стойкие объекты теперь могут быть снова надежно идентифицированы
Прецизионная гранитная основа может улучшить производительность станков
Требования к машиностроению в целом и в других отраслях постоянно растут. в частности, в станкостроении.Достижение максимальной точности и производительности без увеличения затрат — постоянная задача:
ASTM D7177 | EPI The Liner Company
Испытание воздушного канала ASTM D 7177 исключает испытание водного баланса в поверхностных осадках с геомембранным покрытием из ПВХ
1 пенсионер, Environmental Protection, Inc., 9939 US-131 South, Mancelona, MI 49659; pvcliner @ geomembrane.com www.geomembrane.com
2 Президент и главный исполнительный директор, Environmental Protection, Inc., 9939 US-131 South, Mancelona, MI 49659; [email protected]
Нажмите здесь, чтобы просмотреть PDF-версию
РЕФЕРАТ : В этом документе будет представлено подробное описание программ контроля качества установки и обеспечения качества инженерных работ, реализованных на геомембранной лагуне площадью 73000 квадратных метров (787 800 футов2), установленной в проекте улучшения лагуны для очистки сточных вод в деревне Мантон в Мантоне, Мичиган, США. Испытания на прочность в воздушном канале двухканальных термических сварных швов геомембран ПВХ были разработаны для обеспечения контроля качества полевых сварных швов геомембран ПВХ по всей длине. Этот метод позволяет эффективно проверять на отслаивание каждый дюйм сварного шва и устраняет необходимость вырезать отверстия в футеровке для удаления образцов, чтобы выполнить испытание на отслаивание только на небольшой части шва. Этот метод испытаний был принят как Стандартные технические условия ASTM D 7177 для оценки геомембран с двойным швом из поливинилхлорида (ПВХ) в июне 2005 года и впервые широко использовался в строительном сезоне 2006 года.Дизайнеры Fleis & Vandenbrink Engineers работали с Департаментом качества окружающей среды штата Мичиган над устранением устаревшего и устаревшего теста водного баланса, потребовав тестирования воздушного канала для полевых швов геомембраны ПВХ. Успех этого проекта стал основой для внедрения этой новой технологии испытаний вместо проверки водного баланса, что позволило сэкономить драгоценное время клиентов и, в конечном итоге, драгоценное финансирование для строительства поверхностных водохранилищ с покрытием из ПВХ.
ВВЕДЕНИЕ
Есть старое клише о том, что изначально трать больше на качественный продукт и экономить деньги в долгосрочной перспективе.В этом документе содержится информация о том, как качественная сварка и испытания геомембраны из ПВХ могут обеспечить немедленную экономию средств для владельцев, операторов и местных жителей.
Термическая сварка ПВХ-материала — не новая разработка. Этот процесс уже много лет используется при производстве всех видов ПВХ. Однако за последние 5 лет или около того произошли новые разработки и усовершенствования в оборудовании и технологиях термической сварки тонких гибких пленок ПВХ, используемых в качестве геомембран.В процессе разработки этих новых методов и бесчисленных часов работы в полевых условиях с новым оборудованием, авторам стало совершенно очевидно, что испытание двухканальных сварных швов ПВХ с воздушным каналом также является напряженным испытанием прочности и качества всей длины. каждого сварного шва. В то время как термическая сварка любой термопластической геомембраны сегодня относительно проста, сварка швов большой длины без малейших дефектов прочности на отслаивание по-прежнему является сложной задачей. Это стало известно о некоторых из первых проектов при разработке этих методов тестирования воздушных каналов из ПВХ.Например, полевой шов, из которого был удален разрушающий образец (и этот образец прошел независимые лабораторные испытания на отслаивание), не прошел при испытании воздушного канала по всей его длине. Большая часть того же испытанного шва не была соединена полностью, прошла испытания с воздушным наконечником, но начала раскалываться при испытании воздушного канала. Именно тогда авторы были более чем когда-либо убеждены в том, что испытания геомембран из ПВХ в воздушном канале действительно могут измерить прочность и, следовательно, качество всей длины сварного шва.
Авторы также обнаружили, что термическая сварка швов большой длины (> 60-100 м) (200-300 футов), которые легко проходят испытание с воздушным наконечником, неизменно проваливает испытание воздушного канала на небольшой площади, если оператор не был тщательно обучен. сварочный аппарат правильно настроен. Температура, скорость и контактное давление имеют решающее значение для получения однородного сварного шва любой геомембраны. Слишком горячая сварка и слишком быстрое перемещение являются основными препятствиями для успешной и стабильной сварки ПВХ.Они также обнаружили, что слишком высокое давление воздуха при очень высоких температурах листа может привести к повреждению сварного шва ПВХ, проходящего иначе. Это не относится к испытаниям геомембран HDPE.
Уверенность в том, что испытание воздушного канала может обеспечить испытание сварных швов ПВХ на прочность в реальном времени, подтолкнула других к этому исследованию и, в конечном итоге, к разработке Стандартных технических условий ASTM D 7177 для оценки воздушного канала двухслойных геомембран из поливинилхлорида (ПВХ). Эта процедура применяется только к испытаниям прочности воздушного канала сварных швов геомембраны ПВХ.Несмотря на то, что предпринимались серьезные попытки разработать аналогичную процедуру для испытания по всей длине других термопластичных геомембранных сварных швов (например, полиэтилена высокой плотности), ни одна из них не была успешной или стандартизированной.
В проекте Manton было признано, что превосходное испытание геомембранных швов ПВХ путем проверки целостности и прочности сделает ненужным дорогостоящее и трудоемкое испытание водного баланса. (Не говоря уже о том, что тест водного баланса не определяет дефект, он только говорит вам, что лагуна протекает, но не где.) Спецификации проекта требовали проведения теста водного баланса штата Миннесота, если все требования тестирования воздушного канала не были выполнены к удовлетворению владельца. Тест водного баланса по существу состоит из наполнения каждой лагуны чистой водой и измерения любых изменений за 30-дневный период. Любые изменения уровня воды сравниваются с контрольными данными, чтобы определить целостность системы вкладыша лагуны. Орган управления обычно представляет собой ствол, расположенный в зоне облицовки или рядом с ней, или на метеостанции.Измерения проводятся в течение четырех недель и сравниваются с атмосферными приростами и потерями для определения скорости утечки в лагуне. Обратной стороной теста водного баланса является стоимость времени, а также стоимость откачки чистой воды, чтобы заполнить лагуны на глубину до шести футов, а затем снова слить ее.
ПРАКТИЧЕСКИЙ ПРИМЕР
В деревне Мантон на северо-западе Нижнего Мичигана есть очистные сооружения с использованием трех прудов.Первоначально пруды были построены с использованием глинистой почвы в качестве облицовки. В 2006 г. возникла необходимость в реабилитации лагун и уменьшении утечек из прудов. Компания Elmer’s Crane & Dozer, Inc. из Траверс-Сити, штат Мичиган, США, была выбрана в качестве генерального подрядчика проекта. Они выполнили все земляные работы на участке.
Компания Elmer выбрала Environmental Protection, Inc. (EPI) из Манселоны, штат Мичиган, США, для изготовления и установки системы геомембранного покрытия из ПВХ. STS Consultants, Inc.была привлечена в качестве независимой третьей стороны по обеспечению качества строительства (CQA) для наблюдения за установкой и испытаниями футеровки. Чтобы полностью выстлать лагуны, потребовалось 73 000 м2 геомембраны из ПВХ толщиной 40 мил. EPI изготовила из ПВХ толщиной 40 мил панелей размером 1400 м2 (15 000 квадратных футов — 75 футов в ширину и 200 футов в длину). Эти большие панели нестандартного размера использовались для уменьшения количества требуемых полевых швов.
Существующая система лагун состояла из трех больших прудов.Новый дизайн потребует ремонта двух из существующих лагун, чтобы они включали две отстойные лагуны (лагуны номер два и четыре) и один бассейн аэрации (лагуна 1а). Третья существующая лагуна будет выведена из эксплуатации, но оставлена нетронутой для будущего расширения.
Последовательно каждую лагуну осушали, обезвоживали и удаляли ил, а затем выкапывали грунт до первоначального глиняного покрытия. Поскольку этот проект представлял собой реконструкцию существующих лагун, инженер также спроектировал систему отвода газа в земляное полотно, которая позволила бы любым газам от разложения органических веществ выходить за пределы хвостовика и не задерживаться под системой хвостовика. Затем на глиняное земляное полотно был помещен слой песчаной подушки для подготовки геомембраны из ПВХ.
Последовательность действий была практически одинаковой для каждой лагуны. После того, как геомембрана из ПВХ была установлена и все испытания были завершены, подрядчик по земляным работам начал укладывать один фут покровного грунта на всю систему футеровки, используя тяжелое оборудование и бульдозеры с GPS-наведением для окончательной профилирования. Боковые откосы также были покрыты каменной наброской для сохранения покровного слоя почвы и минимизации эрозии.После завершения этапа раскопок, укладки футеровки и покрытия почвы каждая отдельная лагуна была снова введена в эксплуатацию до начала работ на следующей лагуне. Использование теста прочности воздушного канала вместо 30-дневного теста водного баланса также позволило сэкономить минимум один месяц между завершением одной лагуны и началом осушения следующей. Эта последовательность позволила Деревне Мантон продолжить бесперебойную работу в процессе реабилитации.
СВАРКА
После того, как земляное полотно лагуны было завершено, геомембранные панели из ПВХ были развернуты и сваривались с использованием аппаратов для сварки горячим воздухом Leister Twinny, которые производили двухпутный сварной шов с незакрепленным воздушным каналом между сварными швами.На рис. 1 показан увеличенный вид прижимных роликов и сопла горячего воздуха, которые образуют два параллельных сварных шва с воздушным каналом между ними.
Перед производственной сваркой каждая машина была настроена и выполнены пробные сварные швы. Минимальная требуемая прочность на отрыв составляла 2,6 кН / м (15 фунтов / дюйм ширины) образца, а требование прочности на сдвиг составляло 14 кН / м (77,6 фунта / дюйм). Все пробные сварные швы и разрушающие образцы были испытаны в соответствии со стандартным методом испытаний ASTM D 6392 для определения целостности неармированных геомембранных швов.На этом проекте было произведено примерно 3700 погонных метров (12000 футов) полевого пласта. Инженер CQA удалил 26 разрушающих образцов (> 1 образец на 150 м шва). Все разрушающие образцы были протестированы в лаборатории EPI, и 50% образцов (13) также были отправлены в независимую лабораторию (TRI / Environmental, Inc., Остин, Техас). Все образцы соответствуют требованиям спецификации при испытании в соответствии с ASTM D 6392.
РИС.1.) Двухканальный сварочный аппарат горячим воздухом
ТЕСТИРОВАНИЕ ВОЗДУШНОГО КАНАЛА
Испытания воздушных каналов в швах двойных направляющих проводились сразу после завершения сварки и охлаждения материала до температуры окружающей среды. Спецификации для этого проекта требовали, чтобы все швы были испытаны воздушным каналом в соответствии с методом испытаний GRI GM6. Требования к испытаниям ASTM D 7177 определяют минимальное давление для каждой конкретной температуры геомембранного листа.В этом проекте требования ASTM коррелировали с требованиями испытаний GRI GM6 (GM6 был фактически немного ниже требований ASTM). Кроме того, метод испытаний ASTM D 7177 позволит проверить прочность шва на отслаивание, а также целостность. EPI использовала минимальные требования метода ASTM D 7177, поскольку они были более специфичны для геомембраны из ПВХ, чем требования GM6, и обеспечили большее доверие CQA.
Когда воздушный канал накачан (фиг. 2) до испытательного давления, соответствующего температуре материала, напряжение отслаивания равно 2.6 кН / м (15 фунтов / дюйм в ширину) приложено к внутренней части ОБЕИХ сторон двухколейного сварного шва. Таким образом, оба сварных шва испытываются одновременно. Напряжение отслаивания изнутри сварного шва аналогично напряжению, приложенному к испытательному образцу в тензиометре, когда он испытывается на отслаивание с внешней стороны сварочного канала.
РИС. 2.) Увеличенный вид надутого двойного шва геомембраны ПВХ, полученного термической сваркой горячим воздухом Leister Twinny.
Значительное исследование было проведено по этому методу испытаний по сравнению давления отслаивания в воздушном канале с фактическими результатами лабораторных испытаний образца на отслаивание. «Испытания в воздушном канале термосваренных ПВХ-швов» Томаса и др. (2003) описывает испытания, использованные для установления взаимосвязи между давлением воздуха в канале из ПВХ и температурой материала ПВХ во время испытания. Эти результаты полевых испытаний были затем сопоставлены с результатами лабораторных испытаний, чтобы установить взаимосвязь между давлением в воздушном канале и прочностью сварного шва на отслаивание.Дальнейшие усовершенствования включали испытания при низких температурах с очень жестким материалом и испытания при очень высоких температурах материала. Полученная информация дает следующую таблицу 1, которая упоминается в ASTM D 7177:
.
Таблица 1. Давление, необходимое для проверки прочности на отрыв 2,6 кН / м (15 фунтов / дюйм) для ПВХ
Лист | Лист | Давление воздуха | Давление воздуха | Время удержания |
4. | 40 | 345 | 50 | 30 |
7 | 45 | 324 | 47 | 30 |
10 | 50 | 310 | 45 | 30 |
13 | 55 | 290 | 42 | 30 |
15.5 | 60 | 276 | 40 | 30 |
18 | 65 | 262 | 38 | 30 |
21 | 70 | 241 | 35 | 30 |
24 | 75 | 228 | 33 | 30 |
26. | 80 | 214 | 31 | 30 |
29,5 | 85 | 193 | 28 | 30 |
32 | 90 | 179 | 26 | 30 |
35 | 95 | 165 | 24 | 30 |
37.5 | 100 | 152 | 22 | 30 |
40,5 | 105 | 138 | 20 | 30 |
43.5 | 110 | 131 | 19 | 30 |
Давление в воздушном канале, используемое для этого проекта, составляло от 138 до 214 кПа (от 20 до 31 фунта на квадратный дюйм) и, как правило, на верхнем пределе от 165 до 193 кПа (от 24 до 28 фунтов на квадратный дюйм). Учитывая температуру листа во время испытаний, использованное давление обеспечило бы прочность шва по всей длине шва в соответствии с ASTM D 7177. Любой шов, который не выдерживал требуемого давления, исследовали для поиска точки утечки, а затем испытывали. в каждом направлении от утечки. Затем место утечки закрывали ремонтной накладкой после завершения испытания воздушного канала. Затем этот ремонтный патч был протестирован с использованием метода воздушной пики согласно ASTM D 4437.
Понимание взаимосвязи между давлением воздуха и температурой листа материала имеет решающее значение при испытании гибких геомембран из ПВХ.Если давление недостаточно высокое, единственная проверка — целостность, поэтому давление должно быть достаточно высоким, чтобы нагружать сварной шов в режиме отслаивания. И наоборот, если давление слишком высокое (что часто бывает при очень высоких температурах материала, то есть выше 32 ° C), проходящий шов может быть нарушен. Из-за чрезмерного давления воздуха в канале из ПВХ при очень высокой температуре листа мы ожидаем, что сварной шов будет иметь гораздо более высокую прочность на отслаивание, чем требует стандартная спецификация, и мы приводим к тому, что шов не проходит испытание воздушного канала, когда он обычно проходит разрушающее отслаивание. тест.При испытании прочности на отрыв геомембраны из ПВХ наблюдается обратная зависимость температуры листа материала от давления в воздушном канале.
В идеальном случае перед испытанием каждый шов должен быть герметичным и без дефектов более 100% его длины. Однако идеал сложно реализовать в полевых условиях. Дождь, грязь, ветер, ошибка оператора, выгорание — все это усугубляет проблемы при сварке идеального шва. В этом проекте 71% швов были сварены и испытаны по всей длине без ошибок, без отверстий.По мере улучшения операторов и оборудования этот показатель также будет улучшаться.
ТЕСТИРОВАНИЕ ТРОЙНИКОВ КАНАЛА ВОЗДУХА
ВСЕ полевые швы должны быть проверены, и Т-образные швы могут быть трудными, если не сваривать должным образом. Т-образные швы определяются как точка в шве, в которой три слоя материала перекрывают друг друга. Это происходит в том месте, где сварной шов с двойным рельсовым полем пересекает заводской шов, обычно под углом 90 градусов. Заводские сварные панели из ПВХ-геомембраны в рамках этого проекта состояли из полос ПВХ-материала шириной 193 см (76 дюймов).
РИС. 3.) Схема панели на чертеже Lagoon 2
Как показано на рисунке 3, каждая панель состоит из 12 полос ПВХ шириной 193 см (76 дюймов), каждая длиной 61 м (200 футов). Заводские швы на рис.3 вертикальные. В каждой панели одиннадцать заводских швов. Линии, показанные на рис. 3, представляют собой полевые швы. В этой лагуне имеется примерно 1200 м (4000 футов) простого двухпанельного полевого шва внахлест (показаны вертикальные полевые швы).Приблизительно 400 м (1225 футов) шва (горизонтальные швы, показанные на рис. 3) представляют собой типичные Т-образные швы, когда конец одной заводской панели перекрывает конец другой заводской панели. Поскольку заводские швы обычно не совпадают точно от конца одной панели до конца следующей панели, потенциал одного из этих горизонтальных швов может составлять 146 Тс. В конце каждого полевого шва создается дополнительный Т-образный шов. Полевой Т-образный шов должен быть специально подготовлен так, чтобы не было незакрепленной кромки в месте пересечения сварщиком ранее сваренного полевого шва.
РИС. 4.) Образец из ПВХ геомембраны Т-шов
Испытание воздушного канала через каждую букву «Т» требует большой осторожности при сварке (фиг. 4), чтобы исключить утечки и иметь возможность квалифицированно выполнить испытание воздушного канала. На каждой «Т» есть возможность иметь крошечное отверстие на стыке трех слоев материала. Это еще одна ключевая причина, почему испытание каждого шва по воздушному каналу имеет решающее значение для целостности системы лайнера, обнаруживая и устраняя эти отверстия.Специалисты по сварке проявляют особую осторожность при настройке сварочного аппарата, чтобы убедиться, что этот тип перекрытия полностью герметизирован, поэтому испытание воздушного канала можно использовать для проверки прочности и непрерывности этих швов.
В этом проекте заводские швы не имели рыхлых кромок, поэтому процесс сварки Т-образных швов в ПВХ был относительно простым. Снижение скорости движения сварочного аппарата позволило расплавленному ПВХ-материалу стекать вместе в стыке трех слоев материала, обеспечивая необходимую герметичность и прочность сварного шва.Если на заводских швах есть свободные края, то каждый свободный край необходимо будет обрезать, аналогично процессу, применяемому для сварных швов в полевых условиях, которые пересекают другие швы. В этом проекте все заводские торцевые швы панелей были испытаны по всей длине.
ВЫВОДЫ
Обратной стороной теста водного баланса является стоимость времени, а также стоимость откачки чистой воды для заполнения лагун с последующим ее сливом.Если тест показывает, что водоем протекает, нет никакого способа узнать, где может быть утечка. На проекте Manton устранение проверки водного баланса каждой лагуны позволило сэкономить не менее 90 дней на графике строительства и перекачивании миллионов галлонов воды.
Испытания воздушных каналов на непрерывность и сопротивление отслаиванию всех сварных швов ПВХ в полевых условиях дают регулирующим органам, инженерам и владельцу уверенность в том, что каждый дюйм полевого шва превышает минимальные установленные требования к прочности.Инвестиции в превосходную систему сварки и испытаний сварных швов сэкономили сообществу Manton значительное время строительства и значительные реальные деньги.
ССЫЛКИ
ASTM D 7177. Стандартные технические условия для оценки воздушного канала поливинилхлоридных (ПВХ) двухслойных геомембран со швом, Американское общество испытаний и материалов, Вест Коншохокен, Пенсильвания, США.
ASTM D 4437, Стандартная практика для определения целостности полевых швов, используемых при соединении гибких полимерных листовых геомембран, Американское общество испытаний и материалов, Вест Коншохокен, Пенсильвания, США.
ASTM D 6392. Стандартный метод испытаний для определения целостности неармированных геомембранных швов, полученных с использованием методов термоядерного синтеза, Американское общество испытаний и материалов, Вест Коншохокен, Пенсильвания, США.
Метод испытаний GRI GM6. Стандартная практика испытания двухслойных геомембран в воздушном канале под давлением, Институт геосинтетических исследований, Фолсом, Пенсильвания, США.
Томас Р. У. и Старк Т. Д., Испытания в воздушном канале термически склеенных швов ПВХ, 4 сентября 2002 г.
Томас, Р.У., Старк, Т. Д., и Чой, Х., Испытания в воздушном канале термоскрепленных ПВХ-швов, Международный журнал Geosynthetics, Международная ассоциация промышленных тканей (IFAI), том 10, № 3, октябрь 2003 г., стр. 645-659.
Томас Р.В. и Старк Т.Д., Испытания в воздушном канале термоскрепленных геомембранных швов ПВХ, Отчет о геотехнических тканях, Международная ассоциация промышленных тканей, том 20, № 8, октябрь 2003 г., стр. 10.
Старк, Т.Д., Чой, Х., и Томас, Р.W., Испытание термоскрепленных ПВХ-швов при низких температурах в воздушном канале, Международная ассоциация геосинтетических монтажников, Международная ассоциация промышленных тканей (IFAI), том 4, выпуск 1, зима 2004 г. , стр. 5-7.
Для получения дополнительной информации звоните 800-OK-LINER уже сегодня!
Использование сварочной камеры для обнаружения несоосности шва
В автоматизированных сварочных процессах правильное отслеживание сварочной головки относительно сварного шва критически важно для обеспечения оптимального качества сварки.
Это часто достигается с помощью автоматизированного устройства отслеживания шва в процессе производства, такого как механические щупы или лазерные устройства отслеживания шва. Совсем недавно лазерные устройства отслеживания шва стали популярным способом автоматического отслеживания совмещения шва, особенно в сложных процессах, таких как продольная сварка трубы SAW. Механические щупы встречаются реже, но все еще используются некоторыми системными интеграторами для специальных приложений.
Одно из решений, которое иногда внедряется, заключается в том, чтобы управлять процессом сварки вслепую, не имея процесса отслеживания шва, а вместо этого используя технологию контроля после сварки, такую как вихретоковый или ультразвуковой контроль для проверки целостности сварного шва. Но каждая из этих технологий имеет свои ограничения при испытании сварки:
- Вихретоковый контроль использует электромагнитную индукцию для обнаружения дефектов в проводящем сварочном материале и может обнаруживать только внезапные изменения сварного шва. Он плохо обнаруживает постепенные изменения.
- Инструменты для ультразвукового контроля должны быть связаны со средой, которая будет передавать звуковые волны в зону сварного шва, что ограничивает применимость и эффективность технологии.
Следовательно, надежность большинства технологий контроля после сварки невысока, плюс, он выполняется после процесса, а не в течение .
Вот почему это лучшее решение — реализовать какой-либо тип отслеживания сварного шва прямо в процессе сварки. Но, несмотря на комбинацию многократного дублирования измерений, даже лучший метод автоматического отслеживания шва может столкнуться с ситуацией, когда автоматический процесс выходит за пределы шва. Более надежный подход состоит в том, чтобы использовать навыки суждения оператора в сочетании с высококачественным изображением сварного шва, которое может быть получено с помощью сварочной камеры, оснащенной технологией визуализации с расширенным динамическим диапазоном.Сама по себе система автоматического слежения не может сопоставить сочетание хорошего качества изображения сварного шва и оценки и опыта оператора, принимающего решение о размещении сварочной головки.
Изображение сварного шва с камеры сварки
Развитие сварочных камер
Во многом из-за необходимости удаления операторов из сварочной среды в связи с необходимостью обеспечения безопасности и здоровья, использование камер для предоставления операторам удаленных изображений сварочной среды существует уже много лет.При правильной реализации операторы могли видеть, что происходит в сварочной камере, не подвергаясь физическому риску или дискомфорту, находясь в непосредственной близости от сварочного процесса.
Однако до недавнего времени использование камер для удаленного мониторинга сварных швов было лишь частично эффективным из-за трудности одновременного получения изображений как экстремальной яркости дуги, так и темного окружающего фона. Чтобы получить изображения с обоими крайними значениями яркости, операторы должны были остановить процесс и изменить диафрагму камеры или фильтры для получения желаемого изображения.
Но благодаря улучшениям в технологии обработки изображений в сочетании с передовыми технологиями камеры теперь стало возможным получать изображения с расширенным динамическим диапазоном. Сварочная камера, способная создавать изображения с расширенным динамическим диапазоном, может создавать изображения с четкими деталями как области дуги, так и области фона без необходимости останавливать процесс сварки. А благодаря высокому качеству изображения, достигаемому с помощью передовых технологий визуализации, сварочная камера может обеспечить улучшенную видимость совмещения сварного шва со сварочной головкой.
Дополнительной особенностью качественной сварочной камеры являются встроенные дополнительные источники света, позволяющие визуализировать сварочную среду, когда дуга выключена, например, при первоначальном расположении наконечника дуги к сварному шву. Это сокращает время настройки, поскольку нет необходимости менять освещение каждый раз при выключении дуги.
В результате сварочная камера с расширенным динамическим диапазоном позволяет оператору получать более качественные изображения процесса сварки, что обеспечивает лучшее совмещение шва и, в конечном итоге, лучшее качество сварки.
Заключение
Лучшее решение для отслеживания шва — это промышленно упрочненная сварочная камера с расширенным динамическим диапазоном, такая как сварочная камера Xiris XVC-O.
Улучшение качества лазерных сварных швов технических тканей — Международная ассоциация промышленных тканей
Новые абсорбирующие системы улучшают качество лазерной сварки швов на техническом текстиле В рамках исследовательского проекта «Абсорбирующие системы для лазерной сварки текстильных материалов» ученые из Института Хоэнштейна (Бённигхайм) и DWI Leibnitz Institute for Interactive Materials (Аахен) разработали новые абсорбирующие системы для лазерной сварки технического текстиля в инфракрасном диапазоне. спектр.Исследователи уже использовали их для сварки самых разных текстильных материалов.
Результаты своих исследований позволили ученым преодолеть одну из основных проблем лазерной сварки: лишь некоторые ткани поглощают лазерное излучение в ближнем инфракрасном спектре и поэтому по своей природе подходят для лазерной сварки. Чтобы успешно соединить другие ткани, вы должны нанести абсорбирующие материалы на предполагаемые места швов, которые поглощают ближний инфракрасный свет, плавятся и, таким образом, соединяются вместе.Однако абсорберы, которые до сих пор были коммерчески доступны, вызвали обесцвечивание вокруг швов на светлых материалах, и поэтому их потенциальное применение было ограничено.
Новые поглотители обеспечивают технически качественное соединение текстильных материалов. Швы устойчивы к воздействию жидкостей, механически прочны, гибки и не обесцвечиваются, что открывает путь для использования лазерной сварки в качестве альтернативной, высокоэффективной и многообещающей технологии склеивания текстильных изделий. Лазерная сварка имеет ряд преимуществ по сравнению с традиционными методами соединения. Герметизировать швы можно за один раз. Это означает, что, в отличие от традиционных швов, больше нет необходимости в последующем «заклеивании» швов, когда специальные ленты накладываются на отверстия
, образовавшиеся в текстильном материале иглами для сшивания. Швы, созданные лазерной сваркой, также плоские, эластичные, гибкие и устойчивы к воздействию жидкостей
и газов, а также обладают впечатляюще высокой прочностью на растяжение.
Благодаря автоматическому контролю процесса сварки на линии, качество соединения
измеряется автоматически, что позволяет избежать разрыва шва. Стоимость проверки качества шва сводится к минимуму, что особенно важно при производстве высококачественной продукции, такой как медицинский текстиль, защитная одежда, уличное оборудование и текстиль, используемый в производстве автомобилей и мебели.
В ходе проекта параметры настройки лазерной сварки, такие как температура, скорость и давление, были отрегулированы для соответствия различным поглотителям и тканям. Это позволит компаниям-производителям использовать процесс непосредственно для собственных материалов и ассортимента продукции.
Поглотители новой формулы просты в использовании, экономичны и совместимы с различными тканями (тканые, трикотажные и основовязаные, нетканые материалы, ламинат и т. Д.) И аксессуарами (молнии, отражатели и т. Д.). Особенно на легких и прозрачных тканях они обеспечивают визуально и механически идеальные швы с превосходными эксплуатационными характеристиками. Лазерная сварка подходит как для единичного производства, так и для производства с высокой степенью автоматизации.Сведение к минимуму количества стадий процесса и повышение качества вместе с высокой гибкостью процесса помогут малым и средним компаниям увеличить свой оборот и обеспечат конкурентные преимущества.
Источник: www.hohenstein.deКурс самообучения по инспекции и контролю качества сварки
В этом курсе рассматриваются все аспекты, которые имеют решающее значение для понимания этой сложной области; он содержит техническую информацию, которую персонал в этой области должен знать для надлежащего выполнения своей работы. Он также имеет практическое применение в качестве фундаментального курса для нового персонала и для использования в качестве современного курса повышения квалификации для более опытных сотрудников, и это ценный инструмент, который помогает руководству понять обязанности людей, которых они контролируют. Он предназначен для отраслей, где сварка должна выполняться в соответствии со строгими правилами и стандартами.
Целевая аудитория
- Менеджеры по сварке / Супервайзеры / Техники
- Инженеры-проектировщики
- Металлурги
- Специалисты по контролю качества
- Персонал по обеспечению качества
- Специалисты по продажам
- Агенты по закупкам
- Руководители проектов / Супервайзеры 9025
- Использовать признанную терминологию контроля сварки
- Интерпретировать символы сварки и неразрушающего контроля
- Распознавать элементы контроля качества сварки до, во время и после сварки
- Выявить нарушения непрерывности сварки и их причины
- Сообщать требования к процедуре сварки и квалификации работы
- Выявить преимущества и ограничения методов разрушающего и неразрушающего контроля
- Инспектор по сварке : кто инспектор по сварке ?; квалификации; моральный кодекс; коммуникации; обязанности
- Метрические системы, термины и символы сварки : SI Международная система единиц; основные метрические единицы; термины и определения сварки; позиции сварки; элементы и конструкция сварочного обозначения
- Сварка Металлургия : железоуглеродистая система; диаграмма железо-карбид железа; диффузия; влияние скорости охлаждения и добавления сплава на трансформацию
- Подготовка сварного шва и контроль температуры : проверки перед подготовкой сварного шва; совместная проверка подготовки; подогрев и промежуточный обогрев; послесварочный нагрев; отопительные процессы; изоляция нагретых стыков
- Сварка и резка I : выбор способа сварки; несовершенства и неоднородности; кислородно-ацетиленовая сварка; пайка; процессы дуговой сварки, SMAW, GMAW, FCAW, GTAW, SAW, приварка шпилек, термическая и механическая резка
- Процессы сварки и резки II : электрогазовая сварка; плазменная сварка; контактная сварка; вспышка; расстроен; склеивание; перкуссия; твердотельный электронный и лазерный луч; термический; сварка пластиков; пайка
- Методика сварки и квалификация сварщика : технические условия на сварку; совместные конструкции; позиции сварки; тепловложение; температуры предварительного нагрева и промежуточного прохода; снятие участка сварного шва в ремонт; пост термообработка
- Коды, регулирующие контроль сварки : нормативы по сварке конструкций; Код ASME для котлов и сосудов высокого давления; точечный осмотр сварных соединений; обязанности инспектора; Стандарты ASTM; Стандарты API
- Дефекты сварного шва и неоднородности : классификация несплошностей; несплошности основного металла; методы тестирования; глоссарий дефектов сварных швов
- Химические, металлургические и механические испытания сварных швов : сравнение разрушающих и неразрушающих испытаний; химические тесты; формы коррозии; испытания на коррозионную стойкость; металлографический тест
- Визуальный и жидкостный контроль : выбор метода неразрушающего контроля; взаимосвязь сварочных процессов; несплошности и методы контроля; визуальный контроль до, во время и после сварки
- Магнитопорошковый и радиографический контроль : магнитопорошковый контроль; вид намагничивающего тока; размагничивание; интерпретация узоров; не относящиеся к делу показания; радиографические источники; обнаруживаемые дефекты
- Ультразвуковой контроль : преимущества; ограничения; критерии успешной проверки; испытательное оборудование; методы
- Вихретоковый контроль, акустическая эмиссия, контрольные испытания и испытания на герметичность : вихретоковый контроль; основы; осмотр сварных труб и насосно-компрессорных труб; Приложения; акустическая эмиссия; виды выбросов; проверка сосудов под давлением
Цели обучения
По завершении этого курса вы сможете:
Единицы дополнительного образования: 3. 0
Политика отмены
Политика возврата средств за онлайн-курсы (включая самообучение и DVD)
Для всех покупок онлайн, самообучения и DVD продажи считаются окончательными.