Дефекты и контроль сварных швов
Подробности- Подробности
- Опубликовано 27.05.2012 13:13
- Просмотров: 10377
Основные требования к качеству сварки
Современное состояние сварочной техники позволяет обеспечить высокое качество сварки.
Основные требования к качеству сварки обычно определяются в технических условиях (ТУ) на изготовление данного вида продукции, а для массового производства — в государственных стандартах (ГОСТ). В технических условиях к сварному соединению могут предъявляться такие требования: соблюдение определенной формы и размеров шва, наличие определенных механических свойств, химического состава, плотности и т. д. К сварным соединениям могут предъявляться и специальные требования, например, достаточная коррозионная стойкость в определенной среде, определенная электропроводность и пр.
Если сварные швы или сварные изделия не отвечают техническим условиям, то они бракуются.
При сварке брак бывает исправимый и неисправимый. В большинстве случаев брак при сварке можно исправить. С этой целью чаще всего дефектный шов вырубают и заваривают вновь. Однако исправление брака требует дополнительной затраты времени, рабочей силы и материалов, что вызывает удорожание продукции. Поэтому дешевле и проще своевременно принять меры к предупреждению появления дефектов или выявлению и устранению их в самом начале производственного процесса.
Виды контроля при производстве сварочных работ
Качество сборки и сварки изделий определяется отделом технического контроля завода (ОТК).
При производстве сварочных работ осуществляются три основных вида контроля: предварительный контроль, контроль в процессе сварки, контроль готового изделия или узла. Цель предварительного контроля — предупредить возможность появления брака. Он включает в себя проверку марки и состава основного металла, качества присадочной проволоки, кислорода, карбида, ацетилена, флюсов, проверку качества заготовки и сборки деталей под сварку, проверку состояния и работы контрольно-измерительных приборов и инструментов (манометров, редукторов, горелок), а также квалификации сварщиков.
Контроль в процессе сварки включает систематическую проверку режима сварки, исправности работы сварочной аппаратуры и приспособлений, проверку соблюдения сварщиком установленного технологического процесса сварки, осмотр и обмер шва шаблонами. Данный вид контроля осуществляется мастером и контролером ОТК- Контролем готового изделия или узла определяется качество выполненной сварки. Для этого производится наружный осмотр и обмер швов, испытание на плотность (для швов сосудов, работающих под давлением), металлографические, физические и химические исследования, механические испытания сварных образцов.
Читайте также
Добавить комментарий
Методы контроля качества сварных швов
Методы контроля качества сварных швов
Категория:
Сварочные работы
Методы контроля качества сварных швов
ВНЕШНИИ ОСМОТР. Служит для определения наружных дефектов в сварных швах. Производится невооруженным глазом или с помощью лупы не более 10-кратного увеличения.
ПРОСВЕЧИВАНИЕ СВАРНЫХ СОЕДИНЕНИИ (ГОСТ 7512—75). Основан на способности рентгеновских или гамма-лучей проникать через толщу металла, действуя на чувствительную фотопленку, приложенную к шву с обратной стороны. В местах, где имеются поры, шлаковые включения или непровар, на пленке образуются более темные пятна.
УЛЬТРАЗВУКОВОЙ МЕТОД (ГОСТ 14782—76). Основан на различном отражении направленного пучка высокочастотных звуковых колебаний от металла (сварного шва) и имеющихся в нем дефектов в виде несплошностей.
ЛЮМИНЕСЦЕНТНАЯ И ЦВЕТНАЯ ДЕФЕКТОСКОПИЯ (ГОСТ 3242—69). В полость дефекта вводится флюоресцирующий раствор или ярко-красная проникающая жидкость, которая затем удаляется с поверхности.
КЕРОСИНОВАЯ ПРОБА (ГОСТ 3285—65). Служит для определения плотности сварных швов на металле толщиной до 10 мм. Обнаруживаются дефекты размером 0,1 мм и выше.
ГИДРАВЛИЧЕСКИЕ ИСПЫТАНИЯ (наливом ГОСТ 3845—65: давлением ГОСТ 1999—60). Налив воды применяется для испытания ил прочность и плотность вертикальных резервуаров, газгольдеров и других сосудов.
ТЕХНОЛОГИЧЕСКАЯ ПРОБА. Служит для определения сплавления металла, характера излома соединений (по шву или по основному металлу), наличия непровара и других внутренних дефектов на образцах-.
ОПРЕДЕЛЕНИЕ СКЛОННОСТИ ШВОВ К МЕЖКРИ-СТАЛЛИТНОИ КОРРОЗИИ (ГОСТ 6032—58). Служит для проведения контроля сварных соединений, изготовленных из легированных аустенитных сталей.
МЕТАЛЛОГРАФИЧЕСКОЕ ИССЛЕДОВАНИЕ (ГОСТ 3242—69). Макроструктура контролируется для установления глубины проплавления металла, ширины зоны термического влияния, наличия внутренних дефектов.
МЕХАНИЧЕСКИЕ ИСПЫТАНИЯ (ГОСТ 6996—66). Определяется прочность сварных соединений. Образцы свариваются в тех же условиях, что и изделие, или вырезаются из него. Испытания на разрыв и загиб (сплющивание для труб диаметром до 100 мм) обязательны, а на ударную вязкость — для определенных изделий.
Реклама:
Читать далее:
Дефекты сварных швов
Статьи по теме:
Дефекты сварки и контроль качества сварных соединений
ДЕФЕКТЫ СВАРКИ И КОНТРОЛЬ КАЧЕСТВА СВАРНЫХ СОЕДИНЕНИЙ [c.267]Контроль качества сварных соединений. Для предупреждения дефектов сварных швов нужно тщательно соблюдать термический режим сварки, выбирать соответствующие электроды и следить за исправностью оборудования, кроме того, сварочные операции должны производиться рабочими высокой квалификации. Если в каком-либо шве обнаруживают микро- или макротрещины, шов полностью удаляют, а электроды [c.158]
Подготовка должна проводиться по специальным программам, утвержденным соответствующим министерством (ведомством).

Ультразвуковая дефектоскопия получила распространение при контроле качества сварных соединений, выполненных всеми методами сварки и пайки. Этим методом можно обнаруживать дефекты в деталях большой толщины стальных — до 700 мм. [c.550]
Для повышения эффективности и качества сварочных работ на монтаже на всех этапах производства строительно-монтажных работ следует организовать эффективную систему контроля качества сварки, включающую предупредительный, пооперационный контроль и контроль готовых сварных соединений. В процессе предупредительного контроля проверяют квалификацию сварщиков, термистов, дефектоскопистов и инженерно-технических работников, осуществляющих оперативное руководство сборочно-сварочными работами, термообработкой и контролем качества сварки техническое состояние и соблюдение правил эксплуатации сварочного оборудования, сборочно-сварочной оснастки и приспособлений, аппаратуры и контрольно-измерительных приборов качество сварочных материалов, материалов для дефектоскопии, выполнение требований их хранения, подготовки к использованию проектную и исполнительную техническую документацию на соответствие требованиям всех действующих стандартов и других нормативных документов а также производят учет и анализ причин брака, разработку и осуществление мероприятий по его предупреждению.
Контроль качества сварных соединений и исправление дефектов сварки [c.317]
Контроль качества сварных швов и соединений проводится согласно ГОСТ 3242—69 с целью выявления наружных, внутренних и сквозных дефектов. Контроль качества сварных соединений и конструкций складывается из методов контроля, предупреждающих образование дефектов, и методов контроля, выявляющих сами дефекты.
В работе рассмотрен широкий круг вопросов, связанных с контролем качества сварных соединений из пластмасс и эффективным его применением в строительстве. Описаны свойства и характеристики пластмасс. Изложены основные методы контроля параметров режима сварки и качества сварных соединений. Рассмотрены дефекты сварных соединений, их образование и влияние на прочность шва. Подробно рассмотрены рентгенографический, ультразвуковой, капиллярный и другие методы контроля качества сварных соединений из пластмасс и примеры их практического применения.
Для контроля качества сварных соединений аппаратуры емкостного типа, работающей под давлением, применяют различные методы, основными из которых являются 100%-ный визуальный осмотр швов, выборочный контроль рентгенопросвечиванием и ультразвуком. Готовые изделия проходят испытания внутренним давлением, превышающим в 1,2—1,5 раза рабочее, а также проверку герметичности. Ультразвуковой контроль может быть использован не только для выявления дефектов, но и для контроля толщины антикоррозионного слоя, нанесенного сваркой. При этом используют раздельно-совмещенный искатель, устанавливаемый со стороны основного материала. Он позволяет получать на экране два сигнала, отраженные от наружной поверхности и границы раздела. При толщине наплавленного слоя более 0,5 мм точность определения составляет 1 %.
[c.234]
В книге приведены характеристики свариваемых алюминиевых сплавов, свойства сварных соединений. Описаны дефекты при сварке и способы их выявления и предупреждения, способы подготовки деталей под сварку, технология ручной, полуавтоматической и автоматической сварки, оборудование для сварки и необходимый контроль качества сварных соединений. Рекомендованы режимы сварки алюминиевых сплавов и требуемые при этом марки присадочной проволоки в зависимости от толщины свариваемых элементов и способа сварки.
[c.2]
Перспективные методы контроля качества сварного соединения. В последние годы в ЦНИИТМАШе разработаны методы распознавания формы дефекта на основе использования УЗК и применения ЭВМ. Это может иметь большое практическое значение для техники получения сварного соединения, поскольку в трудах акад. Г. А. Николаева показано, что работоспособность сварных конструкций определяется прежде всего формой дефектов. Одним из новых и перспективных методов для исследования процессов ДС и неразрушающего контроля готовых сварных соединений является метод акустической эмиссии (АЭ), основанный на использовании явления эмиссии упругих волн. Процессы ДС сопровождаются рядом динамических явлений (пластическое деформирование, разрыв внутренних связей и др.), при которых происходит излучение упругих волн, вследствие чего они контролируются акустическими методами. При контроле процесса ДС методом АЭ проявляется его активность дефект как источник сигнала обнаруживается в процессе сварки [3]. Метод АЭ уже получил практическое применение для контроля процесса образования соединения при ДС и оценки его качества. Так, например, при ДС меди с бериллием установлено, что по кинетическим зависимостям интенсивности сигналов АЭ от длительности нагрева и охлаждения можно достаточно эффективно контролировать развитие релаксационных процессов в зоне соединения, образование и разрушение интерметаллидных прослоек [14]. Перспективным методом контроля качества ДС является также голографическая дефектоскопия. Проведенные эксперименты дали положительные результаты при контроле тонкостенных конструкций [13].
[c.253]
Контрольные сварные соединения выполняются на специальных припусках или на приварных контрольных пластинах совместно со сваркой основного изделия либо отдельно от изделия, если совместное их изготовление невыполнимо. Качество сварного шва оценивается по результатам наиболее ответственной из предъявляемых контрольной пробой соединений. При обнаружении неисправимых дефектов все производственные сварные соединения должны быть проверены в полном объеме тем же методом дефектоскопии, которым выявлены дефекты, за исключением случаев, когда производственные сварные соединения подвергаются 100-процентному контролю. Контрольное сварное соединение с дефектом бракуется и должно быть снова выполнено тем же сварщиком для повторного контроля.
[c.213]
При изготовлении рабочих колес необходимо учитывать высокие требования к качеству сварного соединения. Как показал опыт их эксплуатации, непровары, шлаковые включения и другие дефекты размываются потоком, что приводит в конечном счете к образованию сквозных свищей, больших промывов, ухудшению гидравлических показателей колеса и выходу его из строя. Затрудненный доступ к швам при сварке вместе с необходимостью введения высокого подогрева затрудняют получение качественных швов и требуют использования высококвалифицированных сварщиков. В то же время имеющийся опыт изготовления высоконапряженных колес на ЛМЗ показал, что при соблюдении заданного технологического режима сварки и тщательном контроле могут быть получены рабочие колеса, обладающие высокой эксплуатационной надежностью. [c.137]
Качество сварных соединений считается неудовлетворительным, если в них при любом виде контроля будут обнаружены внутренние или наружные дефекты, выходящие за пределы норм, установленных настоящими Правилами, ТУ на изготовление изделия и инструкциями по сварке и контролю сварных соединений.
[c.38]
По видам дефектов, не указанным в настоящих Правилах , качество сварных соединений должно оцениваться в соответствии с нормами, установленными техническими условиями на изготовление изделия и производственными инструкциями по сварке и контролю сварных соединений. [c.570]
Качество сварных, соединений контролируют в три этапа предварительный контроль (проверка качества основного металла, сварочных материалов, деталей, поступающих на сборку, сборки деталей под сварку и т.д.) контроль за исполнением технологического процесса контроль качества сварки в готовом изделии (внешний осмотр, испытание на плотность, методы дефекте- и рентгеноскопии). [c.921]
Повышению производительности, уменьшению дефектов в сварном шве, снижению уровня сварочных деформаций и остаточных напряжений, а значит и улучшению геометрической формы шаровой оболочки способствует применение при автоматической сварке под флюсом дополнительного порошкообразного присадочного металла (ППМ). Однако и при этом способе сварки могут появляться присущие ему дефекты в виде несплавлений по кромке. Они связаны с тем, что применение ППМ позволяет максимально использовать тепло перегрева сварочной ванны для целей плавления присадочного металла. Вследствие этого уменьшается количество расплавляемого основного металла и увеличивается вероятность появления несплавлений при отклонениях от технологии сварки. Понятно, что высокое качество сварных соединений может быть обеспечено только при надлежащем контроле за соблюдением режимов сварки.
[c.207]
Цветной контроль. Для обнаружения самых различных поверхностных трещин цветной контроль незаменим. Особенно он ценен при сварке ответственных изделий. Контроль выполняется следующим образом. На предварительно очищенную контролируемую поверХ ность наносится смачивающая жидкость. При проверке небольшой поверхности жидкость наносится кистью. При больших размерах поверхности изделия (если это возможно) его окунают в жидкость. Смачивающая жидкость наносится на поверхность два раза. Перед нанесением второго слоя деталь должна быть просушена на воздухе в течение 1—2 минут. Под действием капиллярных сил нанесенная таким способом жидкость проникает в полости дефектов. После этого ее удаляют с поверхности изделия, и контролируемую поверхность покрывают белой проявляющей краской. Белую краску наносят сразу же после удаления проникающей жидкости. Через 5—6 минут в месте дефекта на белом фоне проявляется красный рисунок, соответствующий форме дефекта. Контролируемую поверхность рекомендуется осматривать при хорошем освещении невооруженным глазом или с помощью лупы. Цветной дефектоскопией можно проверять качество сварных соединений у изделий из магнитных и немагнитных материалов, черных и цветных металлов, пластмасс. Простота контроля, отсутствие необходимости в электроэнергии дает цветной дефектоскопии большие преимущества перед другими методами контроля.
[c.180]
Основным технологическим процессом, применяющимся при изготовлении строительных конструкций, является сварка, от которой во многом зависят качество и надежность конструкций в целом. Несмотря на прогресс в развитии сварочной техники и технологии, в сварных соединениях по ряду причин возникают дефекты различного вида и размеров, приводящие к снижению работоспособности и долговечности конструкций, а иногда к аварийным ситуациям. Для того чтобы исключить поступление в эксплуатацию сварных соединений с недопустимыми дефектами, необходимо применять эффективные методы неразрушающего контроля.
[c.3]
Дефекты сварки и их влияние на прочность сварных соединений. При сварке плавлением в сварных швах могут образовываться дефекты различного вида. По правилам контроля и техническим условиям на прием готовой продукции оценку качества сварного соединения производят по внешнему осмотру и результатам физических методов контроля. Внешним осмотром определяют наружные дефекты, а физическими методами контроля — внутренние и невидимые поверхностные и подповерхностные дефекты. С этой точки зрения образующиеся при сварке дефекты целесообразно разделить на наружные и внутренние. В предлагаемой книге рассмотрены внутренние дефекты, которые подлежат выявлению ультразвуком (рис. 1.1).
[c.8]
Качество сварных соединений металлоконструкций считается удовлетворительным, если в них при любом методе контроля не обнаружены внутренние или наружные дефекты, выходящие за пределы норм, установленных техническими условиями на ремонт или сварку, инструкциями по контролю сварных соединений и Правилами устройства и безопасной эксплуатации [c.89]
Дефекты сварных соединений и контроль качества сварки [c.120]
При изготовлении и монтаже ответственных трубопроводов и конструкций применяются дорогостоящие материалы операции подготовки и сварки весьма трудоемки. Брак сварки в готовой конструкции требует огромных затрат на его исправление. Еще опаснее снижение надежности конструкции, вызванное невыявленными дефектами. Поэтому контроль качества сварки должен быть в основном профилактическим и максимально гарантировать высокое качество сварных соединений.
[c.168]
Качество сварного соединения определяют испытанием обработанной детали на изгиб, причем наибольшее напряжение берется 0,75—0,80 от предела текучести материала, иа которого изготовлена деталь, с последующим контролем места сварки магнитным дефектоскопом. При газопрессовой сварке дефекты редки и если встречаются, то, как правило, расположены в поверхностных слоях изделия. [c.319]
Существенный вклад сделан советскими учеными в области контроля качества сварных соединений. В 1929—1930 гг. в СССР С. Я. Соколовым впервые был разработан ультразвуковой метод контроля металлов. В довоенный и, особенно, в послевоенный периоды разработаны эффективные методы контроля с использованием рентгеновских лучей, излучений радиоактивных изотопов, магнитографии и т. д. (С. Т. Назаров, С. В. Румянцев, Н. В. Хим-ченко и др.). В последние годы советскими исследователями проводится разработка активных методов контроля, которые дают возможность не только обнаруживать, но и предотвращать возникновение дефектов в сварных соединениях непосредственно в процессе сварки.
[c.141]
Контроль качества сварных соединений из нержавеющих сталей осложняется невозможностью обнаружения микротрещин гамма- и рентгенографированием. Ультразвуковой контроль свар—ных соединений аустенитных сталей также недостаточно надежен, поэтому особое значение приобретает пооперационный контроль. Подлежащие сварке крод и и прилегающие участки зоны основного металла зачищают по ширине не менее чем на 20 мм, обезжиривают и подвергают осмотру. Тщательному осмотру снаружи и изнутри подвергаются корневые проходы в швах. Контроль сварки аустенитных сталей осуществляется травлением наружной поверхности швов. Крупные дефекты сварки (непровары, зашлаковка, макротрещины и т. д.) обнаруживаются гамма- и рентгенографией. [c.159]
Контроль качества сварных соединений просвечиванием или ультразвуковой дефектоскопией выполняется дефекто-скопистами с отражением параметров и результатов контроля соответственно в журнале сварных соединений просвечиванием или в журнале ультразвукового контроля сварных соединений. Оценки качества стыков в баллах заносят в таблицу сведений по сварке и контролю сварных соединений ремонтного формуляра. Журналы по контролю являются первичными документами, их оформляют в одном экземпляре и хранят в делах ремонтной организации. Гамма- или рентгеноснимки также хранят в делах ремонтной организации. При необходимости по требованию заказчика ремонтная организация должна представить с ремонтной документацией заключения по результатам контроля просвечиванием или ультразвуковой дефектоскопией, оформленные в соответствии с требованиями ГОСТ 7512—82 и ГОСТ 14782—76. Такие заключения в обязательном порядке выдают на стыки, оцененные баллом 1 ( неудовлетворительно ). На основании заключений производят вырезку стыка, а в сварочном журнале после устранения дефекта делают отметку о вырезке и переварке стыка. В таблицу сведений по сварке и контролю ремонтного формуляра заносят сведения только по сварным соединениям, оцененным баллами 2 и 3. На оцененные баллом 2 стыки также составляют заключение в двух экземплярах, один из которых передают с ремонтной документацией, другой хранят в делах ремонтной организации.
Исправление дефектов сварных соединений производят с оформлением всей документации, предусмотренной на сварочные работы при ремонте.
[c.454]
На достоверность выявления наружных и внутренних дефектов сварки влияют свойства свариваемых сталей, конструкция сварного соединения, отработанность методики контроля и ее стандартизация, качество дефектоскопической аппаратуры. Поэтому при назначении методор контроля качества сварных соединений, исходя из установленных [c.573]
Современные методы сварки позволяют получать сварные соединения, не уступающие по своим механическим свойствам ooHOBiHOMy металлу. Однако выход установок из строя часто происходит из-за дефектов в сварных швах. Поэтому контроль качества сварных соединений — непременная и важная операция в процессе монтажа. В зависимости от условий работы конструкции (температуры, давления), и возможности ремонта готового изделия устанавливается несколько категорий сварных соединений. Объем контрольных операций определяется категорией соединений.
[c.109]
Конструкция должна обеспечить свободный доступ при выполиенни сварки возможность всесторонней защиты металла шва инертным газом и доступность контроля качества сварного соединения (визуальным осмотром, рентгеновским просвечиванием, методом красок и др.). Наиболее эффективным методом контроля окончательно готовых деталей для выявления поверхностных дефектов является ЛЮМ-А (люминесцентный контроль). [c.327]
Правильньи выбор метода и аппаратуры для контроля качества сварных соединений связан с особенностями различных видов сварки и сварных соединений со спецификой возникающих при этом дефектов. Название видов сварки и их классификация даются в ГОСТ 2601 — 74 и 19521—74.19232—73. [c.5]
Контроль качества сварных соединений производится КСЛ управления по заявкам монтажных участков. Успех работы зависит от своевременности выполнения контроля как физическими методами без разрушения, так и проведением механических испытаний. Работа лаборатории контролируется руководством управления, а в техническом плане — центральной сварочной лабораторией треста. Результаты контроля физическими методами дают возможность установить характер наиболее часто встречающихся дефектов, выявить и исключить причины их появления. Поэтому обратная связь от контроля к сварочному процессу наиболее эффективна, если контроль во времени не отстает от проведения сварочных работ. При установившемся уровне технологии имеется возможность осуществлять обработку инфор—мации о браке статистическими методами (гл. X), что по. вышает эффективность контроля и улучшает качество сварки.
[c.220]
Приведены основные сведения по сварочным материалам, характеристики и правила эксплуатации современного оборудования и аппаратуры для производства газосварочных работ, изложены практв ческие рекомендации по технологии газовой сварки металлов, спла-ВО.В и пластмасс. Рассмотрены основные дефекты сварных соединений причины их появления, способы контроля качества сварных соединений, а также вопросы техники безопасности.
[c.2]
Контроль качества сварных соединений корпуса цементной печи. Перед сваркой проверяют качество обработки кромок, зазо ро,в, притуплений, углов раскрытия и чистоты поверхности. Сварные соединения корпуса цементной неч И контролируют как в процессе сварки, так после ее окончания. В процессе сварочных работ кантролируют последовательность наложения слоев (И режимы сварки, а также отсутствие в наплавленном металле трещин, пор и друпих дефектов. После сварки производят внешний осмотр сварных швов. и исправляют обнаруженные дефекты 5% длины швов подвергают физическим методам контроля. Результаты контроля оформляют актом. [c.212]
В более общем случае, применительно к новым материалам повьпыенной прочности, своеобразие их реакции на присутствие дефектов, а также многообразие конструктивных форм и условий эксплуатации сварных изделий требует не только более индивидуального подхода к каждому случаю, но и большей оперативности в выдаче рекомендаций по размерам дефектов, которые можно считать допустимыми. Поскольку одновременно эти два требования удовлетворить не удастся, то на практике нормы допустимых дефектов применительно к изделиям новой техники нередко устанавливают волевым порядком на основе инженерной интуиции с учетом накопленного опьгга регламентации дефектов, а также того, что может обеспечить достигнутый уровень технологии сварки и контроля качества. Такие нормы обычно оказываются достаточно жесткими, чтобы обеспечить работоспособность изделия, однако коэффициент запаса при этом остается неизвестным. Когда в готовом изделии обнаружен дефект, по размеру несколько выходящий за пределы норм, то нередко возникает сомнение, обосновано ли требование об его исправлении, если это трудно осуществимо или невозможно. Для решения подобных вопросов необходима расчетно-экспериментальная методика, позволяющая оперативно оценивать вероятность нарушения работоспособности конкретного соединения с дефектами в пределах заданного ресурса. С учетом изложенного вьпие анализа состояния вопроса основные положения такой методики можно сформулировать следующим образом.
[c.393]
В соответствии с Правилами аттестации сварщико качество контрольных сварных соединений считается неудовлетворительным, если при любом виде контроля будут обнаружены внутренние и наружные дефекты, выходящие яч пределы норм, установленных Правилами, соответствующими стандартами, техническими условиями на изготовление изделия и инструкциями по сварке и контролю сварных соединений. [c.48]
Изложены основные сведения о видах сварки и сварных соединений, о возможных дефектах и способах их устранения. Рассмотрены вопросы контроля качесчва сварных соединений металлических конструкций и трубопроводов неразрушающнми (внешним осмотром, тече-исканием, капиллярным, магнитным, ультразвуковым и радиационным) и разрушающими (механическими) методами. Даны основы управления качеством сварки конструкций и организации контроля. [c.2]
Качество сварных соединений оценивают по результатам разрушающего и неразрущающего контроля. Каждый вид контроля позволяет установить снижение показателей надежности сварного соединения, так называемую потерю качества. Предложена схема-модель формирования качества (надежности) сварных соединений, согласно которой потеря качества происходит на двух ступенях при изменении свойств материала за счет сварки — технологическая потеря и при эксплуатации из-за влияния сварочных дефектов — производственная потеря. На практике обычно преобладает одна из ступеней. Технологическая потеря может быть оценена
[c.221]
При организации контроля сварочных работ необходимо исходить из того, что проверка качества сварных конструкций состоит из следующих этапов предупредительный контроль, выявление дефектов в сварных соединениях и контроль сварной конструкции в целом. Предупредительный контроль и контроль сварных соединений должны быть организованы так, чтобы время между сваркой и контролем было сокращено до минимума. Тогда при обнаружении дефектов можно оперативно установить причины, вызвавшие брак, и принять срочные меры к предотвращению брака при последующей сварке. Не менее важна для получения сварных соединений необходимого качества организация статистического контроля, позволяющего предугадывать возможность появления брака и огаределять вероятные причины его возникновения.
[c.260]
Внешний осмотр производят с помощью лупы с 4—10-кратным увеличением. При этом проверяют расположение сварных точек или швов в соответствии с чертежом форму и размеры вмятины от электродов (роликов) наличие наружных дефектов зазоры между деталями после сварки. Отпечатки точек должны пметь форму окружности (допускается овальность не более 3 2). Отпечатки роликового шва должны иметь равномерную чешуйчатость. Размеры отпечатков от электродов (роликов) не являются критерием оценки качества сварного соединения. Однако изменение размеров отпечатков при постановке ряда точек плп участка шва с неизменной настройкой машины свидетельствует о нарушении условий сварки и возможном ухудшении качества. В этом случае сварку следует прекратить п произвестп контроль технологической пробой и исследованием макроструктуры. Зазоры между деталями после сварки (раскрытие нахлестки) должны быть не более 20% толщины листа для деталей толщиной до 2,0 мм включительно и 15%— для деталей толщиной свыше 2,0 мм.
[c.315]
На основе полученных результатов Н. Б. Бабкиным было разработано несколько конструкций специальных металлических искательных головок 1) головка с постоянным углом ввода поляризованных сдвиговых колебаний для контроля стыковых сварных соединений, а также для обнаружения дефектов в массивных металлических изделиях, обладающих повышенным уровнем структурной реверберации 2) головка для контроля качества сварки при точечной и роликовой сварке и 3) головка с регулируемым углом ввода поляризованных сдвиговых УЗК при постоянном положении точки ввода их. Опробование этих головок полностью подтвердило целесообразность использования поляризованных сдвиговых волн для решения сложных задач ультразвуковой эходефектоскопии и навело на мысль о возможности использования этих волн и для других целей, в частности для получения поверхностных УЗК-
[c. 74]
Основные дефекты сварных швов и методы контроля качества сварки
Все дефекты сварных швов можно разделить на внешние и внутренние. К внешним дефектам относятся завышение размеров швов, наплывы, подрезы, кратеры, прожоги; к внутренним — непровары, газовые поры, шлаковые включения, трещины (рис. 5.9).
Рис. 5.9. Дефекты сварных швов.
Завышение размеров швов вызывает увеличение сварочных деформаций конструкций, излишний расход сварочных материалов, увеличение массы конструкции, а также времени выполнения сварки. Снижение размеров швов уменьшает прочность соединения.
Наплывами называют излишне наплавленный металл около кромок шва, натекший во время сварки на непрогретый основной металл и не сплавившийся с ним. Наплывы образуются из-за неправильного режима сварки и смещения конца электрода к одной из кромок, особенно часто при вертикальной сварке. Наплывы часто сопровождаются непроварами или подрезами основного металла.
Подрезами называют выемки в основном металле вдоль края шва, выплавляемые в процессе сварки. Подрезы появляются из-за неправильного отложения наплавленного металла при сварке на повышенном режиме или при пространственном положении шва, отличном от нижнего. Подрезы ослабляют сечение основного металла и вызывают резкую местную концентрацию напряжений, т. е. появление больших напряжений на отдельных небольших участках.
В зоне сварочной дуги поверхность жидкой ванны получается вогнутой, поэтому при обрыве дуги в шве остается углубление — кратер. Кратеры снижают прочность шва, так как уменьшают его сечение.
Прожоги обычно образуются на тонком металле в виде сквозных отверстий в шве или основном металле. Причины их возникновения — излишняя сила тока и малая скорость сварки.
Непровары — это местное отсутствие сплавления между наплавленным и основным металлом или между смежными валиками при многослойной сварке. Непровары уменьшают рабочее сечение шва и являются очагами концентрации напряжений. Причины непроваров: неправильный режим сварки и подготовка кромок, наличие загрязнений в шве.
Газовые поры образуются в наплавленном металле вследствие выделения газов, растворенных в жидком металле. При охлаждении растворимость газов в металле уменьшается и часть их стремится удалиться в атмосферу. Встречая сопротивление кристаллизующегося металла, газы не могут полностью выйти наружу и остаются в нем, образуя внутренние поры, раковины или выходящие на поверхность свищи. Газовые поры нарушают сплошность и однородность металла. Пористость шва появляется вследствие загрязнения свариваемых кромок ржавчиной, маслом, краской; влажности кромок, электродов или флюсов; неправильного состава электродной обмазки или флюса и т. п.
Шлаковые включения в металле шва нарушают его сплошность и однородность, снижая этим прочность соединения. Шлаковые включения образуются вследствие применения несоответствующих марок электродов, а также при неправильном режиме сварки и плохой обработке корня шва (при двусторонней сварке).
Трещины возникают как в шве, так и в основном металле. Они могут быть сквозными, внутренними и поверхностными. Трещины уменьшают прочность соединения и могут нарушить его непроницаемость. Причины образования трещин разнообразны: неправильный режим сварки, неправильное (жесткое) закрепление свариваемых деталей и т. п.
Большинство выявленных дефектов сварных швов устраняют путем удаления дефектных участков шва и последующей повторной заварки.
При изготовлении корпусных конструкций, а также при формировании корпуса судна на построечном месте сварные швы принимают на основе результатов контроля: квалификации сварщиков, качества свариваемых и сварочных материалов, сварочного оборудования, инструмента, оснастки; качества сборки под сварку и технологии выполнения сварных швов; качества сварных швов.
При контроле качества сборки под сварку проверяют: соответствие собранных деталей требованиям чертежа, правильность их сборки и расположения в конструкции; правильность разделки кромок деталей под сварку, зазор между стыкуемыми деталями; положение кромки одной детали относительно кромки другой; угол между деталями; чистоту поверхности свариваемых кромок и плоскостей; правильность расположения, размеры и количество сборочных прихваток, гребенок и других временных сборочных приспособлений.
Контроль технологии выполнения сварных швов предусматривает проверку соблюдения последовательности и правильности выполнения швов, предусмотренных схемой сварки; соответствие применяемых режимов сварки и марок сварочных материалов указанным в технологических процессах на сварку, соответствие качества и состояния сварочных материалов техническим условиям на эти материалы.
Непосредственно качество сварных швов проверяют: внешним осмотром и измерением, рентгено- и гаммаграфированием, ультразвуком, вскрытием швов, испытанием на непроницаемость. Метод контроля качества сварных швов выбирают в зависимости от назначения конструкции, наличия на заводе соответствующей аппаратуры и т. п.
Внешнему осмотру подвергают все швы независимо от их категории на всей протяженности с двух сторон. Перед осмотром сварной шов и прилегающая к нему поверхность металла должны быть очищены от шлака, брызг и других загрязнений. При внешнем осмотре можно обнаружить подрезы, наплывы, смещения шва, прожоги, кратеры, трещины и поры на поверхности шва. В некоторых случаях при осмотре сварных швов ответственных конструкций применяют лупы.
При контроле сварных швов измерением устанавливают соответствие размеров швов требованиям чертежа или другой проектной документации. При этом измеряют ширину, высоту усиления шва, катеты шва и др. Измерения проводят не реже чем через 1 м шва, но не менее одного измерения на каждом отдельном шве.
Контроль швов рентгено- или гаммаграфированием проводят в целях выявления внутренних дефектов: трещин, непроваров, газовых и шлаковых включений. Рентгено- и гаммаграфирование швов осуществляют в выборочном порядке. При этом в зависимости от категории швов должно быть просвечено 2— 20 % протяженности швов. Метод контроля (рентгено- или гаммаграфирование) выбирают исходя из технических возможностей и целесообразности их применения. При этом во всех случаях, когда это возможно, следует применять рентгенографирование.
Рентгенографирование основано на свойствах рентгеновских лучей проходить сквозь металл и воздействовать на фотопластинку или пленку, помещенную в кассете с противоположной стороны просвечиваемого соединения. Интенсивность рентгеновских лучей при прохождении через металл уменьшается и зависит от толщины материала, его плотности и ряда других факторов. Так как сварной шов толще основного металла, интенсивность лучей, прошедших через шов, меньше интенсивности лучей, прошедших через основной металл. Шов получается на пленке в виде светлой полосы на фоне темного изображения основного металла. Трещины, поры, шлаковые включения и непровары сварного шва в меньшей степени задерживают рентгеновские лучи и на светлом фоне выделяются в виде темных полос, пятен и точек.
Гаммаграфирование основано на том, что при радиоактивном распаде некоторых элементов одновременно с излучением альфа- и бета-частиц имеет место излучение гамма-лучей. Последние по своей природе близки к рентгеновским. Гамма-лучи, так же как и рентгеновские, способны проходить через металлы и воздействовать на фотопластинку. При прохождении через различные среды гамма-лучи поглощаются в различной степени и по-разному воздействуют на фотопластинку. Для гаммаграфирования сварных швов судовых корпусных конструкций применяют в основном переносные контейнеры различной конструкции.
В последние годы взамен рентгено- и гаммаграфирования все чаще применяют ультразвуковой метод контроля качества сварных швов. Этот метод основан на свойстве ультразвуковых волн отражаться от границ двух сред, обладающих различными акустическими свойствами. Большинство ультразвуковых дефектоскопов состоит из следующих основных частей: щупа — излучателя ультразвуковых колебаний,- в котором обычно используются пьезокристаллы, превращающие электрическую энергию в механические колебания; генератора кратковременных высокочастотных электрических импульсов и приемника — усилителя электрических сигналов, возникающих в щупе при попадании на него отраженных от дефектов ультразвуковых колебаний. При контроле качества сварного шва ультразвуковым методом щуп-излучатель перемещают вдоль шва. Для обеспечения надежной передачи ультразвуковых колебаний от щупа к изделию и обратно необходимо наносить на изделие специальную контактирующую жидкость с малым поглощением ультразвуковых колебаний (например, трансформаторное масло и т. п.).
Контроль сварных швов вскрытием применяют для установления характера, размеров и глубины залегания дефектов, выявленных другими методами, если подобная расшифровка необходима и не может быть сделана без вскрытия шва. Вскрытие шва может производиться вырубкой, газовой или воздушно-дуговой строжкой, сверлением и другими способами.
Методы контроля сварных соединений металлоконструкций
Это последствия прорыва нефтепровода, а причина — чаще всего в некачественных соединениях.
В предыдущей статье мы рассказали о том, кем и где проводится контроль сварных швов и соединений. Теперь давайте рассмотрим подробнее, как именно должен проводиться этот контроль.
Как проводят контроль качества при изготовлении металлоконструкций, трубной продукции, емкостного и прочего оборудования?
Начинается контроль за сваркой с визуального осмотра и измерений. Для этого используются специальные инструментальные наборы ВИК.
Справочная информация: Наборы, применяемые cпециалистами SGS, соответствуют необходимым инструкциям и методике ПНАЭ. Входящие в комплект средства отвечают требованиям ГОСТ и ТУ. Комплектация:
- штангенциркуль и стальная линейка;
- угольник и шаблоны;
- щупы;
- измерительный инструмент;
- лупы просмотровые;
- лупа измерительная;
- фонарик и маркеры;
- паспорт и инструкция.
Контролю качества подлежит не только материал, но также сборка и сварка продукции. Обращается внимание на наружные дефекты: подрезы, микротрещины, чешуйки, непровары.
Если такие недостатки выявлены при осмотре и измерениях, то остальные виды контроля не проводятся вплоть до момента устранения обнаруженных дефектов.
Михаил Бондарь, операционный менеджер департамента услуг для промышленного сектора, SGS
При визуально-измерительном контроле используется, в том числе, шаблон сварщика. Это универсальный инструмент, который не только подтверждает геометрию сварного шва, но и позволяет проверить его на соответствие ГОСТам.
Однако внутренние недостатки обнаружить визуально невозможно. Они возникают, когда нарушен технологический процесс сварки и/или применены материалы низкого качества. Трещины, непровары, шлаковые включения, газовые поры — чрезвычайно опасны, потому что со временем швы с такими дефектами могут разойтись.
При рентгенографическом и ультразвуковом контроле выявляют внутренние повреждения и определяют превышают ли эти несоответствия допустимые нормы.
Когда образуется напряжение, от скрытого дефекта может пойти трещина и произойти разрыв трубопровода или сварного шва металлоконструкций.
Василий Артюшенко, эксперт департамента услуг для промышленного сектора, SGSПодумайте, что произойдет, если разорвется газопровод или нефтепровод. Может пострадать не только экология, но и люди.
Этими методами проверяется не только результат сварки (сварные соединения), но и процесс производства.
Для надлежащего контроля производства могут применяться различные технологии. Если рентгеном мы можем выявлять дефекты, которые распределены на максимальной площади, то посредством ультразвукового контроля хорошо просматриваются боковые несоответствия.
Цветная или капиллярная дефектоскопия используется для выявления микротрещин на поверхностях. Для ее проведения сначала зачищаются околошовная зона и сам шов, затем на всю поверхность наносится специальным краситель и дается время выдержки. Затем смывается и наносится следующий раствор. При такой технологии микротрещины окрашиваются и становятся видны на белом фоне.
Суть магнитопорошковой дефектоскопии — в выявлении магнитного поля в зоне дефекта. Для этой цели применяются ферромагнетики. Если в сварном шве присутствует несоответсвие, то вокруг него формируются искажения. Такие изменения фиксируются при помощи дефектоскопа. При большом дефекте происходит большее рассеивание, а значит растет вероятность обнаружения.
О компании SGS
Группа SGS является мировым лидером на рынке контроля, экспертизы, испытаний и сертификации. Основанная в 1878 году, сегодня SGS признана эталоном качества и деловой этики. Более 94,000 сотрудников работает в сети SGS, насчитывающей свыше 2,600 офисов и лабораторий по всему миру со штаб-квартирой в Женеве, Швейцария.
Контроль качества сварных соединений и швов
Контроль качества труб, кроме оценки и контроля качества отливок, должен включать в себя также контроль качества сварных швов, который проводится непосредственно при выполнении сварного соединения. Дефекты здесь могут быть как внешними, так и внутренними, и если первые можно обнаружить при визуальном анализе, в крайнем случае вооружившись увеличительным прибором, например, лупой, то для поиска вторых применяют различные методы неразрушающего контроля качества, среди которых присутствует радиационный (радиографический) метод.
При неразрушающих методах контроля качества сварных соединений следует исследовать их на следующие изъяны, которые находятся внутри сварного шва и потому не имеют внешние признаки:
- скрытые трещины и раковины,
- газовые полости и поры,
- непровары,
- несплавления,
- твердые включения (шлаковые, оксидные, металлические и др.),
- вогнутости и выпуклости корня шва,
- прожоги и подрезы,
- превышения проплавов и прочие дефекты сварки.
Оборудование для контроля качества сварных швов и соединений
Контроль качества сварки и сварных конструкций при радиографическом методе может осуществляться при помощи рентгеновского оборудования, широкий спектр которого представлен на рынке. При этом дефекты сварных швов на полученных рентгеновских снимках проявляются в виде темных пятен за счет того, что, проходя через них, рентгеновские лучи теряют первоначальную интенсивность.
Часто визуальный анализ снимков недостаточно эффективен и удобен, поэтому снимки обрабатывают и исследуют на компьютере, для чего помимо рентгеновского аппарата используют систему визуализации — камеру, подключенную к ПК с установленной на нем программой для ее контроля, а также для анализа и обработки изображений.
Программные продукты для контроля качества сварных соединений и швов
Программное обеспечение, разрабатываемое специалистами компании «Альтами», применяется для анализа и форматирования изображений, в том числе — рентгеновских снимков, и проведения измерений. Приложение Altami Studio предоставляет все необходимые инструменты для повышения качества снимков (настройка яркости и контраста, гамма-коррекция, разработанный специально для обработки рентгенов фильтр Псевдоцвета и многое другое), а также для измерений — длины, периметра, площади объектов. В программе существует функция автоматического поиска требуемых объектов с последующим выводом статистики (периметра и площади).
Кроме того, используя наработки в области автоматизации контроля качества, отдел разработок «Альтами», может обеспечить автоматизацию контроля качества сварных соединений и швов программным продуктом на основе Altami Studio.
Смотрите также:
Автоматизация поиска резисторов на электронной плате и определение их номинала с помощью программного продукта Altami.
Подробнее
Читать другие материалы по теме:
Контроль качестваАвтоматизация контроля качества
Сканер поверхности
Программа для микроскопа
Захват видео
Кроссплатформенное программное обеспечение Altami для Windows, Linux, Mac
Контроль качества продукции
Дефекты и контроль качества сварных швов
При неправильной технологии сварных работ сварной шов может иметь дефекты. Неко горые из них, такие, как подрез, чрезмерное или малое усиление шва, нар>окная трещина, пористость и зашлакованность шва, могут быть обнаружены в результате внешнего осмотра.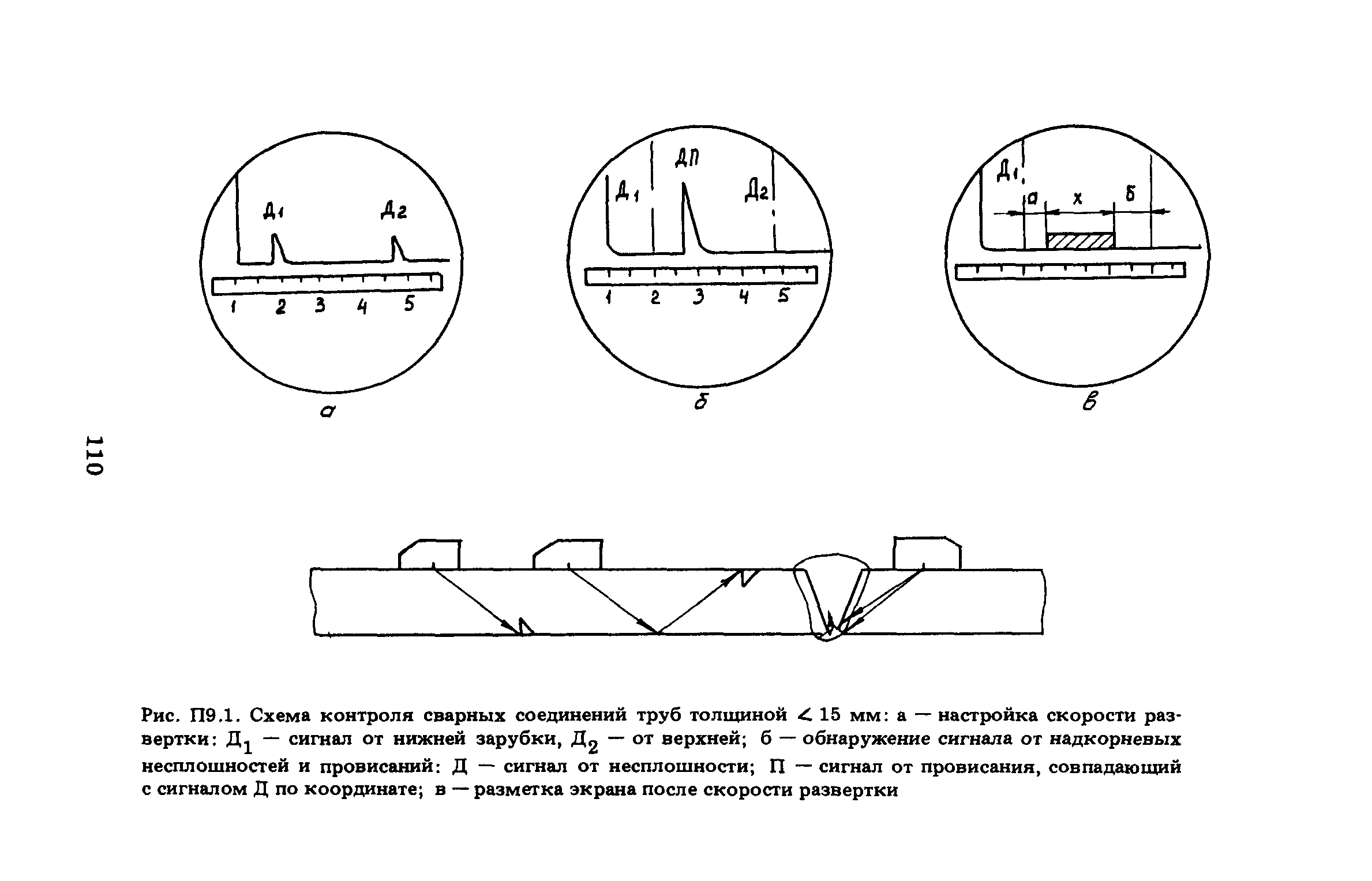
Предварительный контроль предусматривает проверку качества сварочных материалов, состояния сварочного оборудования. Пооперационный контроль включает проверку качества подготовки и сборки деталей под сварку, соблюдения режимов предварительного подогрева, режимов сварки и порядка выполнения многослойных швов, проведения термообработки после сварки. Контролю внешним осмотром подвергают сварной шов и прилегающую к нему зону шириной 20 мм по обе стороны от шва по всей протяженности сварного соединения. При внешнем осмотре проверяют качество поверхности сварных соединений.
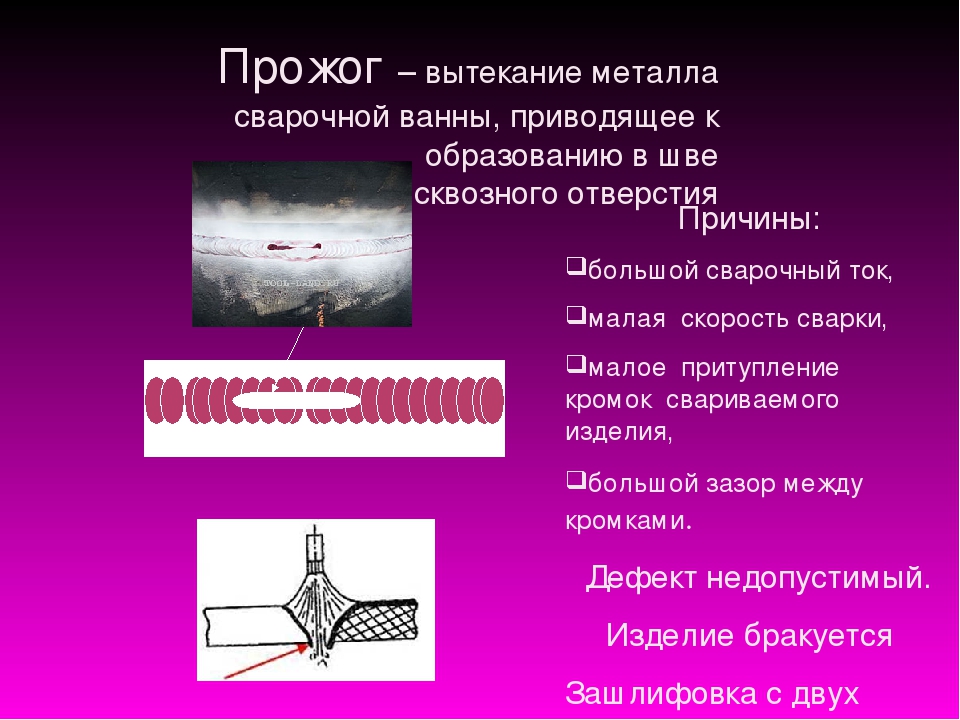
Намагничивание стыков производят либо подвижными магнитами, перемещаемыми вдоль намагничиваемого шва, либо неподвижными, охватывающими часть или весь периметр контролируемого сварного шва. В качестве магнитоноси- Геля используют двухслойные магнитные ленты, аналогичные применяемым в звукозаписи. Магнитная лента перед проведением контроля накладывается внатяг магнитным слоем на контролируемый шов так, чтобы ось шва совпадала с осью ленты, и плотно к нему прижимается. На свободном конце ленты со стороны условного начала записывают карандашом номер шва и клеймо сварщика, а также выявленные наружным осмотром дефекты сварного соединения. [c.316]
Ультразвуковой метод контроля сварных соединений основан на способности упругих колебаний высокой частоты, невоспринимае-мых ухом человека, проникать в металл и отражаться от поверхности трещин, пустот, шлаковых включений и других дефектов швов благодаря различной звуковой проводимости металла и воздуха. Импульсы, идущие от щупа дефектоскопа, которым исследуется шов, свидетельствующие о его качестве и наличии дефектов, отражаются на экране электроннолучевой трубки. Так как магнитографический и ультразвуковой методы контроля дают возможность быстро определить наличие дефекта в шве, но не выявляют характера самого дефекта, то этими методами рекомендуется проверять все подлежащие контролю швы и те из них, в которых будут обнаружены дефекты, подвергать гамма- или рентгеновскому излучению для определения точного характера дефекта и способов его устранения. [c.40]
Контроль и обеспечение качества при изготовлении сварных конструкций, подверженных усталостным нагрузкам
Сталь является основным материалом для многих типов несущих конструкций и компонентов строительной техники, кранов-манипуляторов, лесозаготовительных машин, горнодобывающего оборудования, транспортных средств и сельскохозяйственного оборудования. Обычно 60–80% веса автомобиля составляют стальные листы и стальные отливки толщиной 6–70 мм с использованием сварки в качестве основной технологии соединения. Конструкционные детали грузовиков, автобусов и поездов также часто изготавливаются с использованием различных технологий сварки.Таким образом, большая часть продукции, используемой в глобальной транспортной системе, часто состоит из тяжелых стальных конструкций, в которых сварка является доминирующей технологией соединения. Конструктивные детали и компоненты многих из этих продуктов постоянно подвергаются переменным нагрузкам во время работы. Обычно диапазон нагрузок для многих типов транспортных средств и механизмов составляет 1000–20 000 циклов в час. Это означает, что в течение срока службы 10 000–25 000 часов работы компоненты выдержат 10–500 миллионов диапазонов нагрузок.Таким образом, усталостная нагрузка является наиболее частым видом отказа для вышеупомянутых изделий.
Материалы и технологии изготовления сварных конструкций постоянно развиваются. Конечные пользователи также продолжают расширять границы конструкций, используемых в автомобилестроении, строительстве, на море, в производстве энергии и во многих других областях. Попытки снизить вес и стоимость, повысить энергоэффективность, улучшить характеристики и уменьшить воздействие на окружающую среду по-прежнему создают проблемы при расчетах на усталость сварных конструкций.Конструкции, в которых используется сварка высокопрочных материалов, также требуют фундаментального понимания возможных режимов и механизмов разрушения. Чтобы сделать возможным производство более легких конструкций, использование высокопрочных материалов быстро увеличивается. Однако при проектировании сварной конструкции из высокопрочной стали проектировщику необходимо учитывать несколько важных факторов, чтобы учесть потенциал облегчения, т. Е. Уменьшить разброс качества при производстве и в то же время повысить качество сварки.
Усталостные разрушения сварных конструкций часто начинаются в сварном шве, где усталостная прочность обычно ниже, чем у основного материала и компонентов с надрезом, см. Рис. 1а. Усталостная долговечность основного материала и компонентов с надрезами определяется фазой зарождения трещины; однако в сварных конструкциях большая часть фазы распространения расходуется из-за дефектов и изъянов, которые возникают в процессе сварки. Существует большой разброс значений усталостной долговечности сварных соединений, который в основном связан с изменением локальной геометрии, размера и расположения дефектов и остаточных напряжений, возникающих в процессе сварки.Это подтверждено многочисленными исследованиями и включено в стандарты качества сварных швов и рекомендации по расчету на усталость сварных соединений [1, 2]. Поскольку дефекты, дефекты и другие виды неровностей являются обычным явлением в сварных швах, становится важным иметь правила и критерии приемки для них. Эти дефекты сварного шва определяют усталостную долговечность, что подтверждается диаграммой Китагавы, рис. 1b, на которой показана зависимость усталостной прочности от размера дефекта в различных местах сварного соединения [6].Система классов сварных швов описывает многие виды дефектов и устанавливает допустимые пределы для различных уровней качества, например, ISO 5817 [3], имеющий классы D, C и B, где B имеет наивысшее качество сварки, а D — самое низкое.
Однако действующие правила, приведенные в этой системе, показывают недельную связь с утомлением, что было доказано в нескольких исследованиях [4, 5]. Следовательно, если конструкторы используют эту систему для уменьшения веса несущей конструкции и оптимизации толщины листа наряду с геометрией сварного шва с учетом усталости, они сталкиваются с проблемой выбора подходящего качества, выраженного как уровень качества сварки.
a Схематическое изображение усталостной прочности основного материала, а также деталей с надрезом и сваркой. b Диаграмма Китагавы, зависимость усталостной прочности от размера дефекта, с указанными положениями сварных швов [6]
Проектирование и изготовление сварных конструкций — важные задачи, требующие точности, особенно при роботизированной сварке в серийном производстве. Однако для легких сварных конструкций, где используются более тонкие и высокопрочные стали, повышенные уровни номинальных напряжений требуют учета других аспектов проектирования, таких как изгиб, пластическое смятие и усталостная прочность. Высокопрочные стали страдают повышенной чувствительностью к зазубринам и дефектам по сравнению с мягкими сталями. Для сварных компонентов усталостная прочность будет одинаковой для высокопрочной и низкоуглеродистой стали, если не будет достигнуто улучшение качества сварки [6]. Таким образом, улучшение конструкции сварной конструкции за счет использования высокопрочной стали требует улучшенного качества сварки, что, в свою очередь, требует улучшенного обеспечения качества. Сегодня большая часть контроля качества сварных компонентов осуществляется в процессе аудита отдельно от производственной линии с использованием стандартных портативных измерительных приборов.Хаммерсберг и Олссон [7] пришли к выводу, что основные стандартные калибры и методы обеспечения качества сварных швов устарели, если не будут приняты меры для исследования и улучшения используемых систем измерения относительно реальных изменений, происходящих в процессе производства. Таким образом, для полного достижения облегчения конструкции сварных конструкций производственные компании, использующие серийное производство, столкнутся с проблемами в обеспечении качества при использовании высокопрочной стали в своей продукции.
Другими методами и инструментами, которые могут использоваться для оценки геометрии поверхности сварного шва, являются лазерные профильные датчики или системы технического зрения, в которых сканирующее устройство используется для определения поверхности, а затем алгоритм вычисляет определенные характеристики поверхности измеряемого сварного соединения [8, 9,10].
В данном исследовании дается краткое описание того, как определять качество сварного шва, различные системы качества сварки для контроля качества сварных швов и гарантии для сварных конструкций, подверженных усталостным нагрузкам. Кроме того, он проливает свет на аспекты, которые важны для обеспечения качества сварных конструкций, а также на то, как сварные швы могут быть спроектированы и изготовлены для определенной цели. Наконец, представлен новый онлайн-метод беспристрастного контроля качества геометрических сварных швов, который успешно подтверждается испытаниями.Основное внимание в этом исследовании уделяется аспектам внешней формы геометрии сварного шва; следовательно, внутренние аспекты, такие как проникновение и отсутствие плавления, не рассматриваются.
Проектирование и изготовление сварных конструкций — важные задачи, требующие точности, особенно при роботизированной сварке в серийном производстве. Однако для легких сварных конструкций, где используются более тонкие и высокопрочные стали, повышенные уровни номинальных напряжений требуют учета других аспектов проектирования, таких как изгиб, пластическое смятие и усталостная прочность.Высокопрочные стали страдают повышенной чувствительностью к зазубринам и дефектам по сравнению с мягкими сталями. Для сварных компонентов усталостная прочность будет одинаковой для высокопрочной и низкоуглеродистой стали, если не будет достигнуто улучшение качества сварки [6]. Таким образом, улучшение конструкции сварной конструкции за счет использования высокопрочной стали требует улучшенного качества сварки, что, в свою очередь, требует улучшенного обеспечения качества. Сегодня большая часть контроля качества сварных компонентов осуществляется путем аудита отдельно от производственной линии с использованием стандартных калибров. Хаммерсберг и Олссон [7] пришли к выводу, что основные стандартные приборы и методы для обеспечения качества сварных швов устарели, если не будут приняты меры для исследования и улучшения используемых систем измерения относительно реальных изменений, происходящих в процессе производства. Таким образом, для полного достижения облегчения конструкции сварных конструкций производственные компании, использующие серийное производство, столкнутся с проблемами в обеспечении качества при использовании высокопрочной стали в своей продукции.
В данном исследовании дается краткое описание различных систем качества сварных швов для контроля и обеспечения качества сварных конструкций, подвергающихся усталостным нагрузкам.Кроме того, он проливает свет на аспекты, которые важны для обеспечения качества сварных конструкций, а также на то, как сварные швы могут быть спроектированы и изготовлены для определенной цели. Наконец, представлен новый онлайн-метод объективного контроля качества геометрических сварных швов, который успешно подтверждается испытаниями и внедрением в среду производства сварных швов.
Контроль качества сварки: визуальный, физический и неразрушающий
Для обеспечения удовлетворительных характеристик сварной конструкции качество сварных швов должно определяться соответствующими процедурами испытаний.Поэтому они проходят контрольные испытания в таких же или более суровых условиях, чем те, с которыми сталкиваются сварные конструкции в полевых условиях.
Эта страница содержит советы по визуальному осмотру. На следующих страницах описаны методы контроля GMAW и физических испытаний сварных швов.
Эти тесты выявляют слабые или дефектные участки, которые можно исправить до того, как оборудование будет выпущено для использования в полевых условиях. Испытания также определяют правильность конструкции сварки для боеприпасов и предотвращают травмы и неудобства для персонала.
NDT относится к неразрушающему контролю. Это подход к испытаниям, который включает оценку сварного шва без повреждения. Это экономит время и деньги, включая использование дистанционного визуального осмотра (RVI), рентгеновских лучей, ультразвуковых испытаний и испытаний на проникновение жидкости.
Качество большинства сварных швов проверяется в зависимости от функции, для которой оно предназначено. Если вы фиксируете деталь на станке, если машина работает правильно, сварной шов часто считается правильным. Есть несколько способов определить правильность сварного шва:
- Распределение : сварочный материал равномерно распределяется между двумя соединенными материалами.
- Отходы : Сварной шов не содержит отходов, таких как шлак. Шлак после остывания должен отслаиваться от проекта. Он должен легко сниматься. При сварке MIG любые остатки защитного газа также должны удаляться без особых проблем. TIG, будучи самым чистым процессом, также должен быть безотходным. В Tig если вы видите отходы, это обычно означает, что свариваемый материал не был тщательно очищен.
- Пористость : Поверхность сварного шва не должна иметь неровностей или пористых отверстий (так называемая пористость).Отверстия способствуют слабости. Если вы видите дыры, это обычно означает, что основной металл был загрязнен или имел оксидное покрытие.
Если вы используете Mig или Tig, пористость указывает на то, что при сварке требуется больше защитного газа. Пористость сварных швов алюминия — ключевой показатель недостаточного использования газа.
- Герметичность : Если соединение не плотное, это указывает на проблему со сваркой. При кислородно-ацетиленовой сварке, если используется автогенная сварка, где нет присадочного материала, сварной шов должен быть плотным.То же самое для автогенной сварки TIG. Зазор не так важен для других типов сварных швов, поскольку любой зазор заполняется присадочным материалом. Тем не менее, пробелы, как правило, указывают на потенциальную проблему качества.
- Герметичность : Если вы ремонтируете предмет, содержащий жидкость, утечка — это верный (и очевидный) способ обнаружить проблему. То же самое для чего-то, что будет содержать газ. Один из методов тестирования — использовать мыльные пузыри для проверки наличия проблем (можно легко нанести с помощью шприца.
- Прочность : Большинство сварных швов должны демонстрировать требуемую прочность. Один из способов обеспечить надлежащую прочность — начать с присадочного металла и электродов, превышающих требования к прочности.
Другие проверки с использованием визуальных методов включают проверки до (поверхность корня, зазор, угол скоса, подгонка стыка), во время (скорость расхода электрода, поток металла, звук дуги и свет) и после сварки (поднутрение, проблема проплавления корня, точечные отверстия, чрезмерное разбрызгивание, размеры сварного шва), как описано ниже.
Общие ошибки сварки
Неполное проникновение
Этот термин используется для описания неспособности присадочного металла и основного металла сплавиться вместе в основании соединения. Заливка возникает в сварных швах с разделкой кромок, когда наплавленный металл и основной металл не сплавлены в основании соединения. Частая причина неполного проплавления — это конструкция стыка, не подходящая для процесса сварки или условий строительства. Когда канавка приваривается только с одной стороны, неполное проплавление может возникнуть при следующих условиях.
- Размер поверхности корня слишком велик, хотя отверстие в корне достаточное.
- Корневое отверстие слишком маленькое.
- Угол наклона V-образной канавки слишком мал.
- Электрод слишком большой.
- Скорость движения слишком высока.
- Слишком низкий сварочный ток.
Отсутствие Fusion
Отсутствие сплавления — это неспособность сварочного процесса соединить вместе слои металла шва или металла сварного шва и основного металла.Металл шва просто катится по поверхности пластины. Обычно это называют перекрытием. Отсутствие сварки вызвано следующими причинами:
- Невозможность повысить до точки плавления температуру основного металла или ранее наплавленного металла шва.
- Неправильное флюсование, при котором оксид и другие инородные материалы не растворяются с поверхностей, с которыми должен плавиться наплавленный металл.
- Грязные поверхности тарелок.
- Неправильный размер или тип электрода.
- Неправильная регулировка тока.
Подрезка
Поднутрение — это выгорание основного металла на носке сварного шва. Подрезание может быть вызвано следующими причинами:
- Регулировка тока слишком велика.
- Слишком большой дуговый зазор.
- Неполное заполнение кратера металлом сварного шва.
Включения шлака
Шлаковые включения представляют собой продолговатые или шаровидные карманы оксидов металлов и других твердых соединений.Они вызывают пористость металла шва. При дуговой сварке включения шлака обычно состоят из материалов покрытия электродов или флюсов. При многослойных сварочных операциях отсутствие шлака между слоями приводит к появлению шлаковых включений. Большую часть шлаков можно предотвратить с помощью:
- Подготовка канавки и сварка перед нанесением каждого валика.
- Удаление всего шлака.
- Убедиться, что шлак поднимается на поверхность сварочной ванны.
- Позаботьтесь о том, чтобы не оставлять контуров, которые будет трудно полностью пропустить дугой.
Пористость
Пористость — это наличие карманов, не содержащих твердого материала. Они отличаются от шлаковых включений тем, что в карманах содержится не твердое вещество, а газ.
Газы, образующие пустоты, имеют вид:
- Газ, выделяемый при охлаждении сварного шва из-за пониженных перепадов температуры растворимости.
- Газы, образующиеся в результате химических реакций в сварном шве.
Пористость лучше всего предотвратить, избегая:
- Перегрев и подрез металла шва.
- Слишком большое значение тока.
- Слишком длинная дуга.
Визуальный осмотр (VT)
Визуальный контроль — это процесс контроля качества сварных швов неразрушающим контролем (NDT), при котором сварной шов проверяется на глаз для определения неоднородностей поверхности. Это наиболее распространенный метод проверки качества сварных швов.
Преимущества неразрушающего контроля качества сварных швов:
- Недорого (обычно только трудозатраты)
- Недорогое оборудование
- Электропитание отсутствует
- Быстрое выявление дефектов и затрат на последующий ремонт из-за проблем, которые не были обнаружены в начале
Недостатки:
- Требуется подготовка инспекторов
- Требуется хорошее зрение или зрение исправлено до 20/40
- Может пропустить внутренние дефекты
- Отчет должен быть оформлен инспектором
- Возможна человеческая ошибка
Этапы визуального контроля качества сварки
- Практика и разработка процедур последовательного применения подхода
- Проверить материалы перед сваркой
- Контроль качества сварки при сварке
- Контроль после завершения сварки
- Отметить проблемы и отремонтировать сварной шов
Оборудование для визуальной сварки
Калибр углового шва
Калибр углового шва — важный инструмент для проверки качества сварного шва.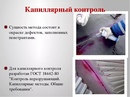
. Показано: Набор для угловой сварки Estone из 7 частей Калибр Калибр Проверка сварки Ульнар MM и дюйм MG11
Для визуального контроля качества сварного шва требуется несколько единиц оборудования:
- Переносной калибр углового калибра при сварке:
- Плоскостность сварного шва
- Выпуклость (внешний вид сварного шва)
- Вогнутость (как сварной шов закругляется внутрь)
- Защитные линзы с карманом для просмотра и затемненными линзами для использования при наблюдении за процессом сварки
- Увеличительное стекло по коду в вашем районе
- Фонарик
- Зубило и / или сварочный молоток для удаления брызг и шлака перед проверкой сварного шва
- Температурный прибор (Tempelstick, Pyrometer) для определения температуры предварительного, промежуточного и последующего нагрева.
- Магнит для обозначения типа свариваемого материала
- Рулетка
- Суппорт
Визуальный осмотр перед сваркой
- Контрольные чертежи
- Посмотрите на положение сварного шва и его соответствие спецификации.
Следите за вертикальным направлением движения
- Контрольные символы угловой сварки
- Соответствует ли процедура местным нормам и правилам сварки.
Проверка сварочного материала
- Соответствуют ли приобретенные материалы спецификациям для размера и типа основного металла? Проверьте размер электрода, выбор газа и марку.
- Проверить материалы на предмет дефектов. Ищите загрязняющие вещества, такие как ржавчина, окалина, мельница, ламинация и т. Д.
- Подготовлены ли материалы для правильных углов
Осмотр сборки
Для проверки сборки выполните следующие действия по проверке качества сварки:
- Проверить на соответствие
- Центровка приспособлений и приспособлений. Проверить чистоту (поищите брызги от предыдущих работ)
- Проверить качество, если используются прихваточные швы. Прихваточный шов должен выполняться тем же электродом, что и основной шов.
- Проверьте использование предварительного нагрева, чтобы снизить скорость охлаждения и минимизировать искажения
Осмотр оборудования
- Проверить на наличие повреждений (кабели, зажимы заземления, электрододержатель).
- Проверить напряжение дуги
- Проверить амперметр на соответствие спецификации
Визуальный контроль во время сварки
- Проверить электроды на размер, тип и хранение (электроды с низким содержанием водорода хранятся в стабилизирующей печи)
- Проверить корневой проход на склонность к растрескиванию
- Проверьте каждый сварочный проход.Ищите поднутрение и требуемый контур. Убедитесь, что сварной шов должным образом очищен между каждым проходом.
- Проверить наличие кратеров, которые необходимо заполнить
- Проверить последовательность и размер сварных швов. Калибры используются для проверки размера.
Контроль после сварки
- Проверить сварной шов на соответствие нормам и стандартам
- Размер чека с калибрами и оттисками
- Проверить отделку и контур
- Проверить на наличие трещин по стандартам
- Ищите перекрытие
- Проверить поднутрение
- Определить, находится ли разбрызгивание на приемлемом уровне
Испытания газовой сварки
Критерии контроля качества контрольных сварных швов для газовых швов:
- Сварной шов должен иметь одинаковую ширину по всей длине.
Два края должны образовывать прямые параллельные линии.
- Лицевая сторона сварного шва должна быть слегка выпуклой с усилением не более чем на 1,6 мм (1/16 дюйма) над поверхностью пластины. Выпуклость должна быть равномерной по всей длине сварного шва. Он не должен быть высоким в одном месте и низким в другом.
- Поверхность сварного шва должна иметь мелкую равномерно распределенную рябь. На нем не должно быть чрезмерных брызг, окалины и точечной коррозии.
- Края сварного шва не должны иметь подрезов или перекрытий.
- Пуски и остановки должны сливаться воедино, чтобы было трудно там, где они произошли.
- Кратер в конце сварного шва должен быть заполнен и не иметь отверстий или трещин.
Для стыковых соединений:
Если соединение является стыковым, проверьте обратную сторону на предмет полного проникновения через основание соединения. С обратной стороны должна образоваться небольшая бусинка.
Для испытаний на сплавление внахлестку и тройниковое соединение:
Проникновение корня и соединение внахлестку и тройника можно проверить, надавив на верхнюю пластину, пока она не согнется вдвое. Если сварной шов не прошел через корень, пластина расколется в месте стыка при изгибе. Если он сломается, понаблюдайте за степенью проникновения и расплавления у корня. Вероятно, ему не хватит слияния и проникновения.
Контроль качества сварных соединений.
(рис. 63.1 — Операционный контроль
сварных соединений)
Операционный контроль — контроль качества во время технологической операции и после ее завершения. При подготовке к работе и сварке стальных газопроводов на соответствие стандартам необходимо доработать следующие моменты: расположение труб, повторная подгонка концов труб, зачистка, форма и размер швов, количество и положение прихваток, порядок слои.
После дуговой или газовой сварки соединения следует визуально осмотреть. Обязательно выполнение следующих условий:
- Сварной шов и участок с обеих сторон от шва (≥ 20 мм) не должны иметь брызг металла, окалины, шлака и других загрязнений.
- Отсутствие прожога, трещин, поверхностных пор, кратеров и глубоких подрезов.
- Легкая выпуклость металла шва по всему шву, плавный переход к металлу труб;
- Соблюдение норм СНиП относительно смещения швов, ширины шва и размеров зазора.
Сварные соединения проверяют выборочно механическими и физическими методами.
Проведены механические испытания сварных соединений кусков труб. Механические испытания позволяют контролировать квалификацию сварщиков стыков, стыков внутренних, наземных газопроводов и стыков подземных газопроводов (соединенных газовой сваркой).
Стыки, соединяемые дуговой или газовой сваркой, испытывают статическим выравниванием, изгибом или растяжением. Следующие результаты считаются недостаточными:
- Степень предела текучести (среднее арифметическое значение испытаний для одного типа соединений) ниже нижнего предела предела прочности основного металла трубопровода.
- Угол изгиба (среднее арифметическое): для дуговой сварки — менее 120º, для газовой сварки — менее 100º.
- Предел прочности на разрыв или угол изгиба минимум одного из трех выбранных образцов на 10% меньше требуемого значения.
Трубы диаметром ≤ 50 мм подвергаются механическим испытаниям на растяжение (50% образца) и растяжение (остальные 50%).
Сварное соединение не считается хорошо испытанным на растяжение, если предел текучести ниже низкого предела прочности основного металла трубы.При испытании на леску трубу сжимают до появления первой трещины на шве. Затем измеряется величина зазора между рабочими поверхностями пресса. Он не должен превышать показатель стенки трубы, умноженный на 5 (5S).
К физическим относятся следующие методы: рентгенографический и ультразвуковой. Первый метод используется для проверки квалификации сварщика стыка. Оба метода используются для проверки стыков внутренних и внешних газопроводов.
(рис.63.2 — Ультразвуковой контроль
сварных швов)
Ультразвуковой метод обязательно должен быть дважды проверен радиографическим методом: ≥ 10% выбранных для проверки стыков проходят гарантированный контроль. В случае если только один стык, проверенный рентгенологическим методом, дает неудовлетворительный результат, объем рентгенологического исследования увеличивается до 50%. При обнаружении дефектов полностью все стыки, сваренные сварщиком за последний месяц, должны быть проверены радиографическим методом и пройти ультразвуковой контроль.
Проверяемые сварные соединения выбираются из числа с наихудшим внешним видом.
После рентгенологического исследования сортируются стыки со следующими дефектами:
- Трещины, кратеры, прожог
- Шлаковые включения и газовые пустоты
- Отсутствие плавления при разрезании
- Отсутствие плавления между валиками и неправильное сращение корня.
Ультразвуковой метод применяется во избежание эксплуатации труб со сварными швами, имеющими дефекты длиной> 25 мм, при размере шва 300 мм (при длине шва <300 мм размер дефект не должен превышать 10% периметра).
Результаты обследования рентгенологическим и ультразвуковым методами должны быть подтверждены протоколом.
Швы, выполненные газовой сваркой, в которых обнаружен дефект, ремонту не подлежат!
Швы, выполненные дуговой сваркой и имеющие дефекты, можно отремонтировать путем приваривания снятой части (менее 30% шва), не прошедшей испытания. После устранения дефекта все стыки необходимо проверить рентгенографическим методом. Подрезы удаляются приваркой буртиков.Превышение высоты сварного шва снимается механической обработкой.
Запрещается: производить повторный ремонт и исправлять дефекты стыков путем повторного обсуждения.
В случае, если проверка механическими испытаниями и физическими методами дала неудовлетворительный результат, проводится проверка двойного количества стыков.
В случае выявления хотя бы одного дефекта после повторного физического осмотра, все стыки, выполненные сварщиком за последний месяц на объекте, должны пройти радиографический контроль.
В случае выявления хотя бы одного дефектного стыка после механического осмотра, все стыки, выполненные сварщиком за последний месяц на объекте, следует удалить (в случае газовой сварки) или проверить радиографическим методом. (при дуговой сварке).
Подобные статьи:
- СНиП 3.05.02-88 Газоснабжение
- ГОСТ 16037-80 Соединение стальных труб сварное.
- СНиП III-42-80 Магистральные трубопроводы.
- СНиП 42-01-2002 Газораспределительные системы
- Сварка стальных газопроводов: методы и общие условия
- Сварка стальных газопроводов: подготовительные работы и монтаж
- Сварка стальных газопроводов: контроль качества сварных соединений
Каковы методы контроля сварных труб с прямым швом ERW?
В целях защиты качества производимых нами сварных труб ERW мы будем проводить контроль качества каждой сваренной трубы.Итак, каковы методы контроля сварных труб? Сегодня мы проследим за редактором компании Permanent Steel Manufacturing Co., Ltd, производящей сварные трубы, чтобы немного разобраться.
1. Основные требования к внешнему виду швов стальных труб с прямым швом ВПВ.
Перед неразрушающим контролем стальных труб с прямым швом (трубы ERW) внешний вид сварных швов должен соответствовать требованиям. Общие требования к внешнему виду прямошовных сварных швов стальных труб и качеству поверхности сварных соединений следующие:
Внешний вид сварного шва должен быть хорошо сформирован, а ширина должна быть на 2 мм выше края канавки с каждой стороны.Высота приварных лапок угловых швов должна соответствовать проектным требованиям, а форма должна плавно переходить.
Поверхность сварного шва:
(1) Трещины, нерасплавленные, воздушные прослойки, шлаковые включения и брызги не допускаются.
(2) На сварной поверхности труб с расчетной температурой ниже -29 градусов, труб из нержавеющей и легированной стали с большей склонностью к упрочнению не должно быть подрезов. Глубина подреза сварочного шва из других материалов должна быть больше 0.5 мм, длина непрерывной выточки не должна превышать 100 мм, а общая длина выточки с обеих сторон сварного шва не должна превышать 10% от общей длины сварного шва.
(3) Поверхность сварного шва не должна быть ниже поверхности трубопровода. Остаточная высота сварного шва не более 3 мм (максимальная ширина группы сварных швов до заднего паза).
(4) Неправильный край сварного шва не должен превышать 10% толщины стенки и не более 2 мм.
2. Неразрушающий контроль поверхности.
Принцип выбора метода неразрушающего контроля поверхности для стальных труб с прямым швом: для стальных труб из ферромагнитных материалов следует использовать контроль магнитными частицами; для стальных труб из неферромагнитных материалов следует выбирать испытания на проникновение.
Для сварных соединений, которые имеют тенденцию к задержке образования трещин, неразрушающий контроль поверхности следует проводить после охлаждения сварного шва в течение определенного периода времени; для сварных соединений, склонных к повторному нагреву трещин, неразрушающий контроль поверхности следует проводить один раз после сварки и после термообработки.
Применение неразрушающего контроля поверхности проводится в соответствии с требованиями стандарта. Объекты обнаружения и приложения обычно следующие:
(1) Проверка качества наружной поверхности материала трубы.
(2) Обнаружение поверхностных дефектов важных стыковых швов.
(3) Обнаружение поверхностных дефектов важных угловых швов.
(4) Обнаружение поверхностных дефектов приварных муфт ответственных раструбов и перемычек трехходовых патрубков.
(5) Обнаружение дефектов поверхности после гибки труб.
(6) Определение угла наклона сварных соединений с большей склонностью к закалке материала.
(7) Обнаружение канавок в трубах из неаустенитной нержавеющей стали, расчетная температура которых ниже или равна минус 29 градусов Цельсия.
(8) Сварочный шов двухстороннего сварного шва с заданным укоренением, контроль после укоренения
(9) При использовании кислородно-ацетиленового пламени для резки сварочных приспособлений на трубах из сплава, которые имеют тенденцию к затвердеванию, обнаруживаются дефекты отремонтированных деталей.
3. Обнаружение лучей и ультразвуковое обнаружение
Основными объектами радиографического контроля и ультразвукового контроля являются стыковые соединения прямошовных стальных труб и стыковые соединения трубных фитингов, сваренных встык.
Выбор методов неразрушающего контроля должен соответствовать проектной документации. Для обнаружения сварных соединений титана, алюминия и алюминиевых сплавов, меди и медных сплавов, никеля и никелевых сплавов следует выбирать метод лучевого обнаружения.
Для сварных швов, склонных к задержке образования трещин, радиографические и ультразвуковые испытания следует проводить после того, как сварной шов остынет в течение определенного периода времени.
Если основная труба в рубашке имеет кольцевой сварной шов, сварной шов должен быть подвергнут 100% рентгенографическому контролю, и скрытая операция может быть выполнена после прохождения испытания под давлением.
Сварные швы, покрытые усиливающего кольца или опорного вкладыша на трубопроводе должно быть 100% рентгенологически проверены, и должны быть покрыты после прохождения теста.
Для сварных швов, необходимых для промежуточного контроля сварки, неразрушающий контроль должен проводиться после аттестации внешнего вида, радиографический и ультразвуковой контроль должен проводиться после неразрушающего контроля поверхности, а проверенные сварные швы могут продолжать сварку после того, как они будут квалифицированы.
Дефекты / несовершенства сварных швов — неполное сращивание или проплавление корней
Описаны характерные особенности и основные причины неполного сращивания и проплавления корней. Даются общие рекомендации по «передовой практике», чтобы сварщики могли свести к минимуму риск появления дефектов во время изготовления.
Нажмите здесь, чтобы увидеть наши последние подкасты по технической инженерии на YouTube .Заводские и эксплуатационные дефекты и дефекты
Поскольку наличие дефектов в сварном соединении не может сделать компонент неисправным в смысле непригодности для предполагаемого применения, предпочтительным термином является дефект, а не дефект. По этой причине качество производства компонента определяется в терминах уровня качества, на котором четко определены пределы дефектов, например, уровень B, C или D в соответствии с требованиями BS EN ISO 5817.Для американских стандартов ASME IX и AWS D1.1 уровни приемлемости указаны в стандартах.
В коде приложения будут указаны уровни качества, которые должны быть достигнуты для различных соединений.
В целом дефекты можно разделить на те, которые возникают при изготовлении компонента или конструкции, и на те, которые образовались в результате неблагоприятных условий во время эксплуатации. Основные виды дефектов:
производство:
- отсутствие плавления
- Отсутствие или неполное проникновение
- трещины
- пористость
- включений
- неправильная форма и размер шва
сервис:
- хрупкое разрушение
- коррозионное растрескивание под напряжением
- Усталостное разрушение
Процедура сварки, особенности соединения, доступ и техника сварки будут иметь прямое влияние на дефекты изготовления. Неправильная процедура или плохая техника могут вызвать дефекты, ведущие к преждевременному отказу в обслуживании.
Неполное сращение корня или проникновение
Идентификация
Неполное сращивание корня — это когда сварной шов не сваривается одна сторона соединения в корне. Неполное проникновение корня происходит, когда корневая область сустава с обеих сторон не спаяна. Типичные недостатки могут возникнуть в следующих ситуациях:
- чрезмерно толстая поверхность корня в стыковом шве (рис.1а)
- слишком маленький зазор корня (рис. 1b)
- сварных швов с ошибкой (рис. 1c)
- Невозможность удаления достаточного количества металла при резке до прочного металла при двухстороннем сварном шве (рис. 1d)
- Неполное оплавление корня при слишком низком подводе энергии (тепла) дуги (рис. 1e)
- слишком маленький угол скоса,
- Электрод слишком большого диаметра при сварке стержневыми электродами (рис. 2)
Рис. 1 Причины неполного сращения корня
Фиг.2 Влияние диаметра электрода на проплавление и проплавление корня
Причины
Эти типы дефектов более вероятны в процессах с плавящимся электродом (MIG, MAG, FCAW, MMA и SAW), когда металл шва «автоматически» осаждается, когда дуга поглощает электродную проволоку или стержень. Сварщик имеет ограниченный контроль проплавления сварочной ванны независимо от наплавки металла шва. Таким образом, процесс TIG с неплавящимся электродом, в котором сварщик контролирует количество удаляемого присадочного материала независимо от проплавления, менее подвержен этому типу дефекта.
При сварке стержневыми электродами риск неполного оплавления корня и провара корня может быть снижен за счет использования правильных параметров сварки и диаметра электрода, обеспечивающих адекватный подвод энергии дуги и удовлетворительное проплавление. Диаметр электрода также важен, поскольку он должен быть достаточно маленьким, чтобы обеспечить адекватный доступ к корню, особенно при использовании небольшого вогнутого клиновидного угла (рис. 2). Обычно для корневого прохода используют электрод диаметром 2,5 мм или 3,25 мм, чтобы сварщик мог управлять сварочной ванной и контролировать степень проплавления.Однако для проходов заполнения, где требования к проникновению менее критичны, можно использовать электрод диаметром 4 или 5 мм для достижения более высоких скоростей осаждения.
При сварке MIG правильные параметры сварки, соответствующие толщине материала и короткой длине дуги, должны обеспечивать адекватное проплавление сварного шва. Слишком низкий уровень тока для размера поверхности корня приведет к недостаточному провару сварного шва. Слишком высокий уровень, из-за которого сварщик будет двигаться слишком быстро, приведет к тому, что сварочная ванна заткнет корень без достижения адекватного проплавления.
Также важно использовать правильный размер поверхности корня и углы скоса, а также точно установить зазор между корнем. Для предотвращения закрытия корневого зазора потребуется соответствующая закрепка.
Лучшие методы профилактики
Для предотвращения отсутствия сращивания корней можно использовать следующие методы:
- При сварке TIG не используйте слишком большую поверхность впадины или слишком маленький зазор впадины и убедитесь, что сварочный ток достаточен для того, чтобы сварочная ванна полностью прошла через корень.
- При сварке стержневыми электродами используйте правильный уровень тока и не слишком большой диаметр электрода для корневого прохода.
- При сварке MIG / MAG используйте достаточно высокий уровень сварочного тока, который поддерживается соответствующим напряжением дуги для применения.
- При использовании конфигурации шва с корневым зазором убедитесь, что он имеет соответствующую ширину и не смыкается во время прихватывания и последующей сварки.
- Не используйте слишком низкий уровень тока, из-за которого сварочная ванна перекрывает корневой зазор без полного проникновения в корень.
Стандарты приемки
Пределы отсутствия или неполного проникновения указаны в BS EN ISO 5817 для трех уровней качества.
Отсутствие или неполное проникновение корней не допускается для Уровня качества B (строгое) и Уровня C (промежуточного). Однако уровень C делает исключение для стыковых швов с частичным проплавлением, сваренных с обеих сторон.
Для Уровня качества D (умеренного) допускается кратковременное отсутствие или неполное проникновение дефектов.
Неполное корневое проникновение не допускается при производстве сосудов под давлением, но допускается при производстве трубопроводов в зависимости от материала и толщины стенок.
Меры по устранению
Если корень не может быть осмотрен напрямую, например, с использованием метода проникающего или магнитопорошкового контроля, обнаружение осуществляется с помощью радиографии или ультразвукового контроля. Для устранения проблемы обычно требуется удаление путем строжки или шлифовки до прочного металла с последующей повторной сваркой, как правило, в соответствии с первоначальной процедурой сварки.
Соответствующие стандарты
BS EN ISO 5817: 2007 Сварка — сварные соединения плавлением стали, никеля, титана и их сплавов (за исключением лучевой сварки) — Уровни качества для дефектов.
BS EN ISO 10042: 2005 Сварка. Соединения, полученные дуговой сваркой алюминия и его сплавов. Уровни качества для дефектов.
Копии других статей из серии «Рабочие знания для сварщиков» можно найти в разделе «Практические знания по соединению» или с помощью поисковой системы.
Эта статья о вакансиях изначально была опубликована в Connect, март / апрель 1999 г.Он был обновлен, поэтому веб-страница больше не отражает в точности печатную версию.
Порядок контроля качества сварных труб из конструкционной стали
Благодаря соответствующей толщине стенок, хорошему материалу, технологии обработки и стабильности, конструкционная сталь стала лучшим выбором для крупных отечественных и зарубежных проектов трубопроводов для нефти и природного газа. В большой конструкции соединения стальных труб с прямым швом зона сварного шва и термического влияния является наиболее легким местом для образования разнообразных дефектов, подрезов сварного шва, пор, шлака, неплавления и непровара.
Меры по контролю качества конструкционной стали, как указано ниже:
Контроль качества сварки:
► Сделайте высококачественное сырье, затем пройдите инспекцию, прежде чем официально попасть на строительную площадку, и решительно положите конец использование стандартной стали.
► Управление сварочными материалами. Проверить, подходят ли сварочные материалы; достигается ли система хранения и выпечки; чиста ли поверхность сварочного материала без ржавчины; завершено ли неповрежденное покрытие электрода без формы.
► Чистое управление сварочной зоной. Контроль качества зоны сварки без воды, масла, ржавчины и окисной пленки грязи. Это важный фактор для качества очистки, чтобы предотвратить внешние дефекты сварки.
► Выберите правильный метод сварки. Метод должен быть реализован испытательной сваркой и принципами сварки.
Контроль качества в процессе сварки
◆ В соответствии со спецификациями процесса сварки проверка проволоки и флюса является правильной, чтобы предотвратить неправильное использование проволоки и флюса из-за нарушения качества сварки.
◆ Надзор за сварочной средой. После сварки примите соответствующие меры. При неблагоприятных условиях сварки (температура ниже 0 ℃, относительная влажность выше 90%) должно быть.
◆ Перед ожидаемой первой пробной сваркой размеры канавки, включая зазор, тупое пространство, тупой край, угол и неправильное отверстие, должны соответствовать технологическим требованиям.
◆ Убедитесь, что сварочный ток, сварочное напряжение, скорость сварки и другие параметры выбраны правильно как внутри, так и снаружи процесса дуговой сварки под флюсом.
◆ Позвольте персоналу полностью использовать длину стальных труб и листов внутри и снаружи во время процесса сварки под флюсом, а прямой шов повысит эффективность сварочной дуги для внутренних и внешних листов. Это поможет улучшить качество сварки концов труб.
◆ Дайте сварщику сначала проверить чистоту сварочного шлака; если стык обработан полностью; очищена ли канавка от масла, ржавчины, шлака водной краски и других загрязнений.
Контроль качества сварных швов
Методы анализа и оценки сварных швов
Применяемые стандарты
- VT ISO17637
- PT ISO3452
- RT EN16016
Возможные процедуры:
Сварные швы должны соответствовать определенным критериям качества или качественные функции, чтобы объединить компоненты для выполнения требований в течение ожидаемого срока службы.
HTV анализирует и оценивает сварные швы с использованием различных методов и процедур (разрушающих / неразрушающих) для обнаружения дефектов, таких как трещины, раковины, дефекты соединения, включения или поры, которые отрицательно влияют на прочность сварного шва.
Трещина сварного шва из-за SEM Корневой дефект сварного шва под микроскопом Детальный визуальный микроскопический контроль позволяет, например, оценить внешний вид сварного шва. Внешне видимые дефекты поверхности, такие как трещины, бороздки, поры, коррозия , и т. Д., Могут быть обнаружены неразрушающим способом и задокументированы.
Методы металлографического анализа Подготовка микрошлифов и подготовка расширенной тонкой структуры (химические / физические методы тонкой подготовки) делают зернистые структуры видимыми в микрометровом диапазоне. Последующее высокоточное исследование с использованием микроскопа или XRF и SEM / EDX анализы обеспечивает четкую идентификацию дефектов, например, в структуре шва или в формировании зоны термического влияния.
Профиль твердости сварного шва исследуется с помощью прибора для испытания на проплавление (наноиндентирование) . Основной материал, зона термического влияния и фактический сварной шов анализируются в поперечном сечении образца с локальной точностью.
Благодаря множеству других методов, таких как 2D / 3D рентгеновское обследование , которое особенно подходит для выявления раковин и дефектов заедания, HTV обеспечивает комплексный и надежный контроль качества сварных швов .