Качество под контролем. Лаборатория неразурушающего контроля
УЗК контроль в Екатеринбурге
Ультразвуковой метод контроля является одним из основных методов неразрушающего контроля.
Ультразвуковой контроль основан на способности высокочастотных колебаний проникать в металл и отражаться от поверхности трещин, пустот и других несплошностей.
Контролируемые объекты:Методы ультразвуковой дефектоскопии позволяют производить контроль сварных соединений, сосудов и аппаратов высокого давления, трубопроводов, поковок, листового проката и другой продукции.
Полезно знать, что ультразвуковой метод контроля, помимо своего прямого назначения, а именно, обнаружения дефектов, также применяется для измерения толщины. Ультразвуковая толщинометрия, в свою очередь, является не менее важной процедурой для контроля качества и безопасности изделий.Преимущества:
- высокая чувствительность к наиболее опасным дефектам типа трещин и непроваров;
- высокая точность и скорость исследования;
- возможность вести контроль непосредственно на рабочих местах без прерывания технологического процесса;
- не требуется выведения контролируемой детали или всего объекта из эксплуатации;
- исследуемый объект не повреждается;
- возможность проводить контроль изделий из разнообразных материалов, как металлов, так и неметаллов.
Трудности при контроле металлов с крупнозернистой структурой из-за большого рассеяния и сильного затухания ультразвука, а также повышенные требования к состоянию поверхности контроля (шероховатости и волнистости)
Применяемое оборудование:- А1214 «Expert»
- Peleng 307
- Уралец А9812
Перед тем, как приступить к УЗК, необходимо подготовить поверхность контролируемого объекта. Подготовка заключается в том, чтобы придать поверхности шероховатость. Если диагностируется сварные соединения, то шероховатостям требуется задать направление, которое расположится перпендикулярно шву. Для устранения воздушного зазора, исследуемый участок обрабатывается контактными жидкостями (водой, маслом, глицерином).Нормативные документы в Екатеринбурге:
РД СТО 02495307-002-2008 Ультразвуковой контроль сварных соединений арматуры в железобетонных конструкциях.
РД ПНАЭ Г-7-030-91 «Ультразвуковой контроль. Часть II. Контроль сварных соединений и наплавки».
РД 34.17.450-98 МЕТОДИЧЕСКИЕ УКАЗАНИЯ ПО УЛЬТРАЗВУКОВОМУ КОНТРОЛЮ БЕЗ РАЗЛОПАЧИВАНИЯ ОБОДА ДИСКА В РАЙОНЕ ВЕРХНИХ КОНЦЕНТРАТОРОВ Т-ОБРАЗНОГО ПАЗА.
РД 34.17.302-97 (ОП-501, ЦД-97) «Котлы паровые и водогрейные. Трубопроводы пара и горячей воды, сосуды. Сварные соединения. Контроль качества. Ультразвуковой контроль. Основные положения».
РД РОСЭК-001-96 «Машины грузоподъемные. Конструкции металлические. Контроль ультразвуковой. Основные положения».
РД СТО 00220256-005-2005 «Швы стыковых, угловых и тавровых сварных соединений сосудов и аппаратов, работающих под давлением. Методика ультразвукового контроля».
РД СНиП 3.05.03-85 (2000) «Тепловые сети».
РД ВСН 012-88 «Строительство магистральных и промысловых трубопроводов. Контроль качества и приемка работ. Часть1».
РД ПБ 03-585-03 «Правила устройства и безопасной эксплуатации технологических трубопроводов».
РД СТО Газпром-2006 «Инструкция по неразрушающим методам контроля качества сварных соединений при строительстве и ремонте промысловых и магистральных газопроводов».
РДИ 38.18.016-94 «Инструкция по УЗК сварных соединений технологического оборудования».
РД ОСТ-32-100-87″Ультразвуковой контроль швов сварных соединений мостов, локомотивов и вагонов».
РДСНиП 3.03.01-87 «Несущие и ограждающие конструкции».
РДПБ 03-576-03 «Правила устройства и безопасной эксплуатации сосудов, работающих под давлением».
РД 153-34.1-003-01 (РТМ-1С) «Сварка, термообработка и контроль трубных систем котлов и трубопроводов при монтаже и ремонте энергетического оборудования».
ГОСТ 17624-87 «Бетоны. Ультразвуковой метод определения прочности бетона».
Методические рекомендации по статистической оценке прочности бетона при испытании неразрушающими методами (МДС 62-1.2000)
УЗК контроль — универсальный метод выявления дефектов
Ультразвуковое исследование объекта возглавляет перечень методов контроля. Ведь его проведение основывается на свойствах высокочастотных колебаний, а значит может применяться как для металлов, так и не металлических материалов. В Екатеринбурге ультразвуковой контроль качества на самых выгодных условиях сотрудничества, выполняет наша лаборатория. Опытные специалисты готовы выполнить исследование любого объекта, не зависимо от размеров и характеристик, ориентируясь на сроки заказчика. Результатом такой работы станет детальное заключение экспертной комиссии установленного законодательством образца.
Проводятся исследования контролируемого объекта с помощью мощное современного оборудования, что позволяет гарантировать заказчику:
- Выявление дефектов любого размера;
- Определение дополнительных параметров;
- Оперативность получения информации.
Высокая чувствительность применяемого оборудования позволяет не только провести дефектовку, но и классифицировать выявленные изъяны.
Инспекционный контроль сварных соединений в мостостроении
Приведена краткая информация о результатах и опыте инспекционного ультразвукового контроля и возможности использования результатов для оценки стабильности и уровня технологического процесса сварки при монтаже пролетных строений мостов.
Об авторах:
Дымкин Григорий Яковлевич
Доктор техн. наук, профессор, заведующий отделом ультразвуковой дефектоскопии на железнодорожном транспорте НИИ мостов ПГУПС, директор НК-Центра, III уровень по акустическому контролю.
Цомук Сергей Роальдович
Кандидат техн. наук, доцент, старший научный сотрудник отдела ультразвуковой дефектоскопии НИИ мостов ПГУПС, III уровень по акустическому контролю.
Шевелев Александр Владимирович
Научный сотрудник отдела ультразвуковой дефектоскопии НИИ мостов ПГУПС, аспирант кафедры «Диагностика и безопасность технических объектов» ПГУПС, II уровень по акустическому контролю.
Этинген Илья Зусевич
Научный сотрудник отдела ультразвуковой дефектоскопии НИИ мостов ПГУПС, аспирант кафедры «Диагностика и безопасность технических объектов» ПГУПС, II уровень по акустическому контролю.
Инспекционный контроль (выборочный повторный контроль продукции) выполняют с целью повышения достоверности неразрушающего контроля.
Впервые обязательный инспекционный ультразвуковой контроль (УЗК) не менее S % от объема приемочного УЗК, выполненного каждым звеном дефектоскопистов, введен в отечественном мостостроении.
Одним из примеров организации и проведения инспекционного УЗК в мостостроении в последнее время являются работы, выполненные НИИ мостов и АО «Дальмостострой» при строительстве автодорожной части мостового перехода через реку Амур у г. Хабаровска (рис. I). Общая протяженность монтажных стыковых сварных швов листов из стали 10ХСНД и 15ХСНД с толщинами 12 мм — 12 мм, 12 мм — 16 мм и 16 мм — 16 мм около 18 км. Технологическая инструкция по УЗК прошла техническую экспертизу в НИИ мостов и утверждена заказчиком (МПС РФ).
Программа инспекционного контроля предусматривала проведение УЗК сварных швов в объеме 5% специально сформированной Группой специалистов НИИ мостов, сертифицированных на II и III уровень квалификации и имеющих опыт контроля аналогичных соединений. Отбор швов производился таким образом, чтобы проверке в равной пропорции подвергались как результаты УЗК швов разных типоразмеров, так и результаты работы всех дефектоскопистов.
В период с июля 1996 г. по октябрь 1998 г. группой инспекционного контроля проверено 906 м сварных швов (рис. 2). Контроль выполнялся при температуре окружающего воздуха от минус 7° С до плюс 30° С.
Рис. 1. Мостовой переход через реку Амур у г. Хабаровска
При инспекционном контроле использовали ультразвуковые дефектоскопы УД2-12 с пьезоэлектрическими преобразователями П121-5-70 (частота 5 МГц, угол ввода 70°) и П121-2,5-65 (частота 25 МГц, угол ввода 65°) и USN-52 (фирмы Krautkramer, Германия) с преобразователем П121-4-70 (частота 4 МГц, угол ввода 70°).
Рис. 2. Инспекционный контроль сварных швов
При обнаружении в ходе инспекционного контроля трех и более случаев неправильной оценки качества швов одним дефектоскопистом на одном пролете моста (1800 м сварных швов) этим же дефектоскопистом производилась полная перепроверка всех сварных швов, проконтролированных им на данном пролете моста.
Отдельные выявленные при инспекционном контроле сомнительные сечения анализировались комиссией и, в случае окончательного решения о недопустимости дефекта, вскрывались. На нулевом этапе инспекционного контроля были обнаружены многочисленные отступления от действующей Инструкции в организации, проведении и оформлении результатов УЗК, а также выявлено большое число недопустимых дефектов (рис. 3). Соответствующее пролетное строение было забраковано, после чего был выполнен повторный сплошной приемочный контроль стыковых соединений с ремонтом дефектных сечений. Количество дефектов, выявленных на последующих пяти этапах инспекции, оказалось существенно меньшим и приблизительно одинаковым. По данным вскрытия 29 дефектных участков видимые дефекты распределились следующим образом: шлаковые включения — 3 шт. (10 %), поры — 10 шт. 35 %), скопления пор — 3 шт. (10 %), несплавления — 10 шт. 35 %), непровар — 1 шт., дефекты сложной формы (непровар со шлаком, две поры, соединенные трещиной ) — 2 шт.
Таким образом, введение инспекционного контроля позволило упорядочить оформление документации по контролю, откорректировать работу операторов штатного контроля, выявить значительное количество пропущенных при штатном контроле недопустимых дефектов, что заметно дисциплинировало работу дефектоско- пистов (рис. 3).
Рис. 3. Количество выявленных дефектов на 1 м сварного шва за 6 этапов инспекционного контроля (июль 1996 — октябрь 1998)
Кроме того, совместный анализ результатов инспекционного контроля привел к улучшению подготовки швов под контроль, позволил усовершенствовать технологию сварки и откорректировать отдельные положения инструкций по сварке и ультразвуковому контролю.
Положительный опыт ультразвукового инспекционного контроля сварных швов моста через реку Амур, проведенного специалистами НИИ мостов, подтверждает необходимость и целесообразность его применения и при строительстве других ответственных сварных металлоконструкций.
Благодарим журнал «В Мире НК» за любезно предоставленную информацию http://www.ndtworld.comДефектоскопия сварных соединений | Испытание и ультразвуковой контроль швов в Ростове-на-Дону
Чем хорош ультразвуковой контроль сварных соединений?
В современном строительстве существует острая необходимость в оперативном контроле сварных соединений и толщинометрии на строительном объекте с выдачей результата контроля. Актуальные госты и своды правил регламентируют виды и методы такого контроля. Одним из них является ультразвуковой контроль сварных соединений прибором УД4-ТМ, стоящий на вооружении в нашей лаборатории. Основной принцип данного прибора основан на прохождении, отражении и трансформации ультразвуковых колебаний на несплошностях и неоднородностях материала (дефектах). Дефектоскоп УД4-ТМ специализирован для неразрушающего контроля сварных соединений, материалов и изделий на присутствие дефектов типа нарушения сплошности, измерение амплитуды от дефектов эхосигналов, определение координат дефектов, измерение времени распространения ультразвуковых колебаний в изделии или материале. У данного прибора существуют функции неразрушающего контроля изделий из ферромагнитных и немагнитных сплавов и металлов на присутствие поверхностных дефектов типа трещин, расслоений, раковин, закатов и неметаллических включений. На наших объектах целиком и полностью используется большая часть этих параметров, позволяющих своевременно оценить изделие или конструкцию и оперативно принять решение по её эксплуатации или же устранению, если это является недопустимым дефектом.
№ п/п | Наименование испытания | Единица измерения | Стоимость, руб без НДС | ||||||||
---|---|---|---|---|---|---|---|---|---|---|---|
7 |
Испытание сварных швов металлоконструкций, стыков арматуры по ГОСТ 23118-2012, 57997-2017, 14098-2014, 23858-79, СП 70.![]() |
||||||||||
7.1 | ВИК и УЗК металлоконструкций и ж/б конструкций: |
|
|
||||||||
7.1.1 | ВИК сварных стыков арматуры | 1 стык | 100 | ||||||||
7.1.2 | ВИК сварных швов с одной стороны (конструкции) | 1 п.м. шва | 100 | ||||||||
7.1.3 | УЗК сварных стыков арматуры | 1 стык | 300 | ||||||||
7.![]() |
УЗК сварных швов металлоконструкций | 1 п.м. шва | 1000 | ||||||||
7.1.5 | Толщинометрия металлоконструкций | 1 точка | 400 | ||||||||
7.2 | ВИК сварных швов трубопроводов: |
|
|
||||||||
7.2.1 | ø трубопроводов до 60 мм | 1 стык | 30 | ||||||||
7.![]() |
ø трубопроводов до 219 мм | 1 стык | 40 | ||||||||
7.2.3 | ø трубопроводов до 377 мм | 1 стык | 60 | ||||||||
7.2.4 | ø трубопроводов до 530 мм | 1 стык | 80 | ||||||||
7.2.5 | ø трубопроводов до 1020 мм | 1 стык | 130 | ||||||||
7.![]() |
УЗК сварных швов трубопроводов: |
|
|
||||||||
7.3.1 | ø трубопроводов от 50 до 114 мм и толщиной стенки 4-12мм | 1 стык | 450 | ||||||||
7.3.2 | ø трубопроводов до 219 мм и толщиной стенки 4-12мм | 1 стык | 550 | ||||||||
7.3.3 | ø трубопроводов до 377 мм и толщиной стенки 4-12мм | 1 стык | 950 | ||||||||
7.![]() |
ø трубопроводов до 530 мм и толщиной стенки 4-12мм | 1 стык | 1150 | ||||||||
7.3.5 | ø трубопроводов до 730 мм и толщиной стенки 4-12мм | 1 стык | 1650 | ||||||||
7.3.6 | ø трубопроводов до 1020 мм и толщиной стенки 4-12мм | 1 стык | 2450 | ||||||||
7.4 | Испытание образцов на растяжение арматуры: |
|
|
||||||||
7.![]() |
ø до 25 | 1 образец | 700 | ||||||||
7.4.2 | ø 28-32 | 1 образец | 800 | ||||||||
7.4.3 | ø 36-40 | 1 образец | 1000 |
Ультразвуковой контроль сварных соединений в Ростове-на-Дону. Позвоните нам, чтобы получить консультацию.
Смотрите также:
Компактная система визуального контроля для выравнивания и отслеживания узких стыковых швов при дуговой сварке в среде защитного газа CO2
«>Na XD, Zhang YM, Liu YS, Walcott B (2010) Нелинейная идентификация процесса лазерной сварки. IEEE Trans Control Syst Technol 18(4):927–934
Статья Google Scholar
Браун Л.Дж., Мейн С.П., Вебер Р.А. (1998) Адаптивная компенсация времени простоя с применением к системе роботизированной сварки. IEEE Trans Control Syst Technol 6(3):335–349
Статья Google Scholar
Dufour M, Cielo P (1984) Оптический контроль для адаптивной сварки.Appl Opt 23(4):1132–1134
Статья Google Scholar
Ван Л.К., Сюй Д., Тан М. (2004) Надежное обнаружение зигзагообразной линии сварного шва. Материалы Международной конференции IEEE по робототехнике и биомиметике, Шэньян, Китай, стр. 721–726
Zhang H, Ding XL, Chen MH, Da BQ, Zou CH (2004) Система отслеживания шва для дуговой сварки под флюсом. Lect Notes Contr Inf Sci 299:144–151
Статья Google Scholar
Сюй Д., Ван Л.К., Тан М. (2004) Метод обработки изображений и визуального контроля для робота для дуговой сварки.Материалы Международной конференции IEEE по робототехнике и биомиметике, Шэньян, Китай, стр. 727–732
Umeagukwu C, McCormick J (1991) Исследование метода массива для роботизированного отслеживания сварных швов. IEEE Trans Ind Elec 38(3):223–229
Статья Google Scholar
Bjorkelund M (1986) Настоящая система отслеживания швов для дуговой сварки. Международный симпозиум по промышленным роботам, Брюссель, стр. 697–706
. Google Scholar
Наяк Н., Томпсон Д., Рэй А., Ваврек А. (1987) Концептуальная разработка адаптивного отслеживания швов в реальном времени для автоматизации сварки. Материалы Международной конференции IEEE по робототехнике и автоматизации, Роли, США, стр. 1019–1024, 1987 г.
Махаджан А., Фигероа Ф. (1997) Интеллектуальное отслеживание шва с использованием ультразвуковых датчиков для роботизированной сварки. Robotica 15(3):275–281
Статья Google Scholar
Shan P, Sun D, Tu WH, Hu SS (2002) Разработка технологии отслеживания шва с помощью ультразвукового датчика при сварке CO2. Trans China Weld Inst 23(5):19–22
Google Scholar
Wilson WJ, Hulls CC, Bell GS (1996) Относительное управление концевым рабочим органом с использованием визуального слежения на основе декартового положения.IEEE Trans Robot Autom 12(5):684–696
Статья Google Scholar
Thuilot B, Martinet P, Cordesses L, Gallice J (2002) Визуальное сопровождение на основе положения: удержание объекта в поле зрения. Материалы Международной конференции IEEE по робототехнике и автоматизации, Вашингтон, округ Колумбия, США, стр. 1624–1629
Мариоттини Г.Л., Ориоло Г., Праттичиццо Д. (2007) Визуальное сопровождение на основе изображений для неголономных мобильных роботов с использованием эпиполярной геометрии.IEEE Trans Robot 23(1):87–100
Статья Google Scholar
Mahony R, Hamel T (2005) Визуальное сервоуправление воздушными роботизированными системами на основе изображений с использованием линейных характеристик изображения. IEEE Trans Robot 21(2):227–239
Статья Google Scholar
Malis E, Chaumette F, Boudet S (1999) 2-1/2-d визуальный сервопривод. IEEE Trans Robot Autom 15(2):238–250
Статья Google Scholar
Malis E, Chaumette F (2000) 2 1/2D визуальное слежение по отношению к неизвестным объектам с помощью новой схемы оценки смещения камеры. Int J Comput Vis 37(1):79–97
МАТЕМАТИКА Статья Google Scholar
Дэн Л., Шарифи Ф.Ф., Уилсон В.Дж. (2005) Гибридное управление движением и стратегии планирования для визуального следования. IEEE Trans Ind Electron 52(4):1024–1040
Статья Google Scholar
Yan ZG, Xu D (2008) Система визуального контроля для сварки узких стыковых швов в производстве контейнеров.Международная конференция UKACC по контролю, Манчестер
Google Scholar
Бингул З., Кук Г.Э. (2006) Модель прогнозирования удлинения электрода в режиме реального времени для GMAW. IEEE/ASME Trans Mechatronics 11(1):47–54
Статья Google Scholar
Бонкович М., Хаце А., Езерник К. (2008) Неоткалиброванное визуальное сопровождение на основе популяции. IEEE/ASME Trans Mechatronics 13(3):393–397
Статья Google Scholar
Fang ZJ, Xu D, Tan M (2010) Система визуального отслеживания шва для стыковой сварки тонкого листа.Int J Adv Manuf Technol 49(5–8):519–526
Статья Google Scholar
Xu D, Yan ZG, Fang ZJ, Tan M (2011) Система визуального отслеживания для узких стыковых швов при дуговой сварке в среде защитного газа CO2. Международная конференция по автоматизации, роботам и приложениям, Веллингтон, Новая Зеландия
(PDF) Предложена надежная система визуального сервоуправления для робота для сварки узких швов с двумя головками
, позволяющая уменьшить влияние различных ошибок шва и повысить качество узких сварных соединений
[6–8].
Датчики играют решающую роль в сварочной роботизированной системе. Итак,
до сих пор в промышленных сварочных роботах
использовались различные типы датчиков, такие как индуктивные датчики, ультразвуковые датчики,
и датчики технического зрения [9–11]. Среди них системы датчиков технического зрения
использовались для захвата и понимания сварных
швов благодаря их бесконтактной атрибуции, высокой точности и
обильной информации. В работах [12–14] исследователи использовали
видеодатчики для проверки и запоминания положения шва
перед сваркой, а затем использовали эту информацию для направления
горелки для выравнивания шва.
Преимущество таких методов состоит в том, что информация датчика изображения заменяет ручное обучение,
и, таким образом, сокращает время обучения и позволяет быстро получить
положение шва надежным и надежным способом.
В случае, когда рассматривается узкий пласт,
вышеупомянутые методы, такие как обучение и воспроизведение или
подход, основанный на видеодатчиках, трудно
достичь желаемой точности, поскольку может быть воспроизведена большая ошибка
термическими искажениями процесса сварки [13].Хотя
обучение в автономном режиме с использованием видеодатчика может облегчить проблему получения точной траектории шва, оно имеет определенные недостатки [4,8,12,13]. Во-первых,
фактическая
геометрическая форма свариваемой детали не может быть точно представлена одной траекторией шва из-за наличия больших допусков при обработке
и ошибки сборки. Во-вторых, с помощью сложного электрического и механического оборудования
, даже если точная сборка может удовлетворить требования к сварке, стоимость
, возможно, слишком высока и невыгодна для малых и средних сварочных установок.В-третьих, фактическая аппаратная конфигурация, включая манипуляторы, концевые зажимы и другое вспомогательное сварочное оборудование, должна быть тщательно откалибрована, а погрешность, вызванная тепловыми искажениями, также трудно учитывать. Таким образом, любое отклонение в роботизированной точности,
геометрических формах сварного шва, размерах детали
и тепловых искажениях приведет к тому, что рассчитанный
путь сварки станет бесполезным.Таким образом, адаптация или интеллект
сварочного робота к различным отклонениям в сварочной среде по-прежнему является ключевым фактором. Это именно мотивация данного исследования. В этой работе
мы разрабатываем эффективный и интеллектуальный промышленный сварочный робот
с двумя головками и датчиками зрения для контроля отслеживания узкого шва
. Сварочная роботизированная система способна
определять мгновенное состояние шва во время процесса сварки
и управлять горелкой для немедленного выравнивания узкого шва.
В настоящее время существует несколько существующих методов, таких как
визуальное слежение на основе положения (PBVS) [14], визуальное слежение на основе изображений (IBVS) [15] и гибридное визуальное слежение (HVS)
.[16], который может осуществлять управление слежением за швом сварочных роботов
под управлением системы технического зрения. Для систем PBVS и
HVS
комплексная калибровка датчика технического зрения завершается путем разработки подходящего алгоритма калибровки.В результате
точность визуального контроля весьма чувствительна к ошибкам
калибровки в системах ПБВС и ВВС. Кроме того, контрольный метод
обычно используется для борьбы с большим смещением. Для задачи управления
небольшим смещением между узким стыковым швом и горелкой
IBVS считается более надежной и эффективной
стратегией при работе с ошибками калибровки камеры и робота
[17–19]. Таким образом, система IBVS использовалась в области
отслеживания узких швов с помощью сварочных роботов, таких как контейнер
и лазерная сварка [18,19].В частности, в [18]
было показано, что предложенный алгоритм отслеживания шва в реальном времени может удовлетворить
требованиям точности роботизированной лазерной сварки. Декартовы положения
(положение и ориентация), измеренные с помощью датчиков зрения
, были добавлены к траектории робота во время движения робота
. Результаты моделирования показали, что процедура отслеживания шва
в реальном времени хорошо подходит для сварки траекторий шва средней кривизны, а точность отслеживания (0. 1–
0,5 мм)canbereached. В работе [20] авторами разработан сварочный манипулятор
для автоматического выполнения операции стыковой сварки цилиндрических листовых металлов, широко применяемых в системах природного газа
и системах отопления. . Однако в процессе сварки
различные помехи и слабые элементы шва, зафиксированные видеодатчиком
, могут привести к нестабильности извлечения элемента шва
и контроля отслеживания. С целью снижения влияния
возмущений в работе [13] была представлена система слежения за плоским стыковым
швом в режиме реального времени с визуальными датчиками для роботов-манипуляторов
.Для описания взаимосвязи между выпрямляющим напряжением и смещением применялась модель авторегрессии с экзогенным входом
. Затем,
, с учетом различных смещений на основе модели ARX, был разработан нечетко-пропорционально-интегральный контроллер слежения за швом
(PID).
Эксперимент [13] показал, что большинство смещений
можно регулировать в диапазоне ±0,3 мм. В [21] авторы
представили метод надежной идентификации и локализации трехмерных (3D) узких сварных швов,
достижения роботизированной сварки с помощью активного лазерного зрения.Результаты [21]
показали, что метод может обеспечить трехмерную декартову точность в пределах 1 мм — диапазон, приемлемый для большинства применений роботизированной дуговой сварки.
В частности, лазерный визуальный датчик может не подходить для отслеживания
узкого шва, потому что деформированную полосу лазерного
узкого шва трудно зафиксировать и распознать во время
сварки. Для решения этой проблемы в статье [22] была представлена роботизированная сварочная система с пассивным зрением, которая может эффективно выполнять функцию отслеживания шва при импульсной сварке MAG.Экспериментальные результаты, представленные в [22]
, продемонстрировали, что можно получить удовлетворительный прямой и криволинейный
линейный шов.
Хотя рассмотренные до сих пор методы или системы отслеживания швов на основе зрения
обеспечили эффективные решения некоторых проблем отслеживания швов, они, безусловно, имеют ограничения. Действительно, они
могут применяться только при некоторых особых условиях или условиях окружающей среды. В этой статье мы сосредоточим наше внимание на ситуации, когда
представлен узкий шов на производственной линии.Мы разрабатываем
интегрированную систему контроля зрения, включающую начальную точку
1850 Int J Adv Manuf Technol (2014) 71:1849–1860
Датчики | Бесплатный полнотекстовый | Распознавание траектории сварного шва для автоматизированной скиповой сварки Наведение пространственно-прерывистого сварного шва на основе датчика лазерного зрения
2.2. Определение углового положения и траектории угловых сварных швов
На рис. 4 показана схема определения положения и траектории сварки. Система координат была установлена с точкой пересечения оси плоского зеркала лазерной сканирующей системы измерения смещения (т.ось вала двигателя) и ось падающего лазера в качестве начала отсчета O. Направление оси плоского зеркала (т.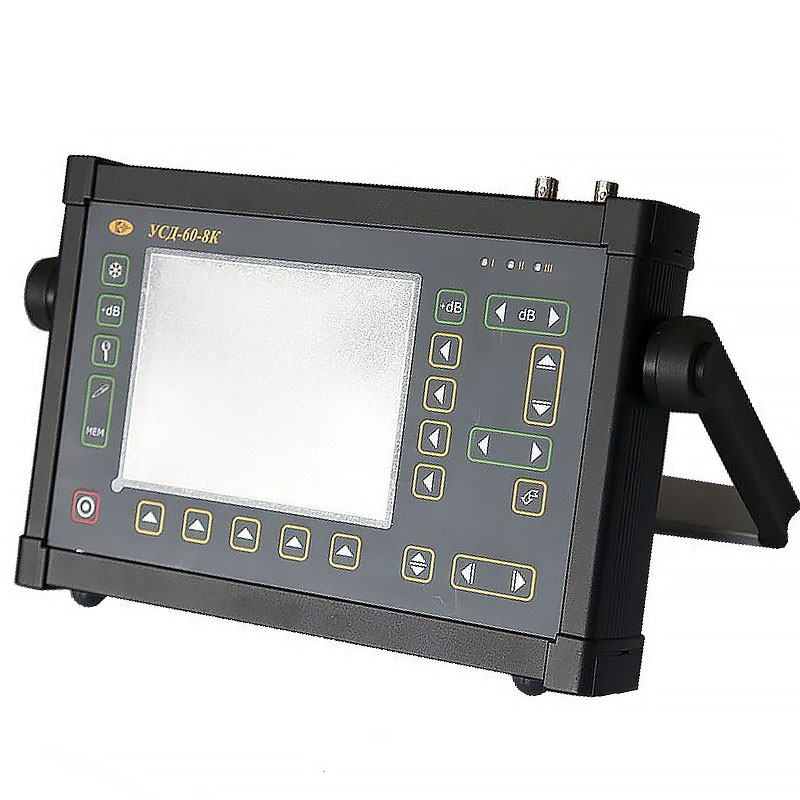
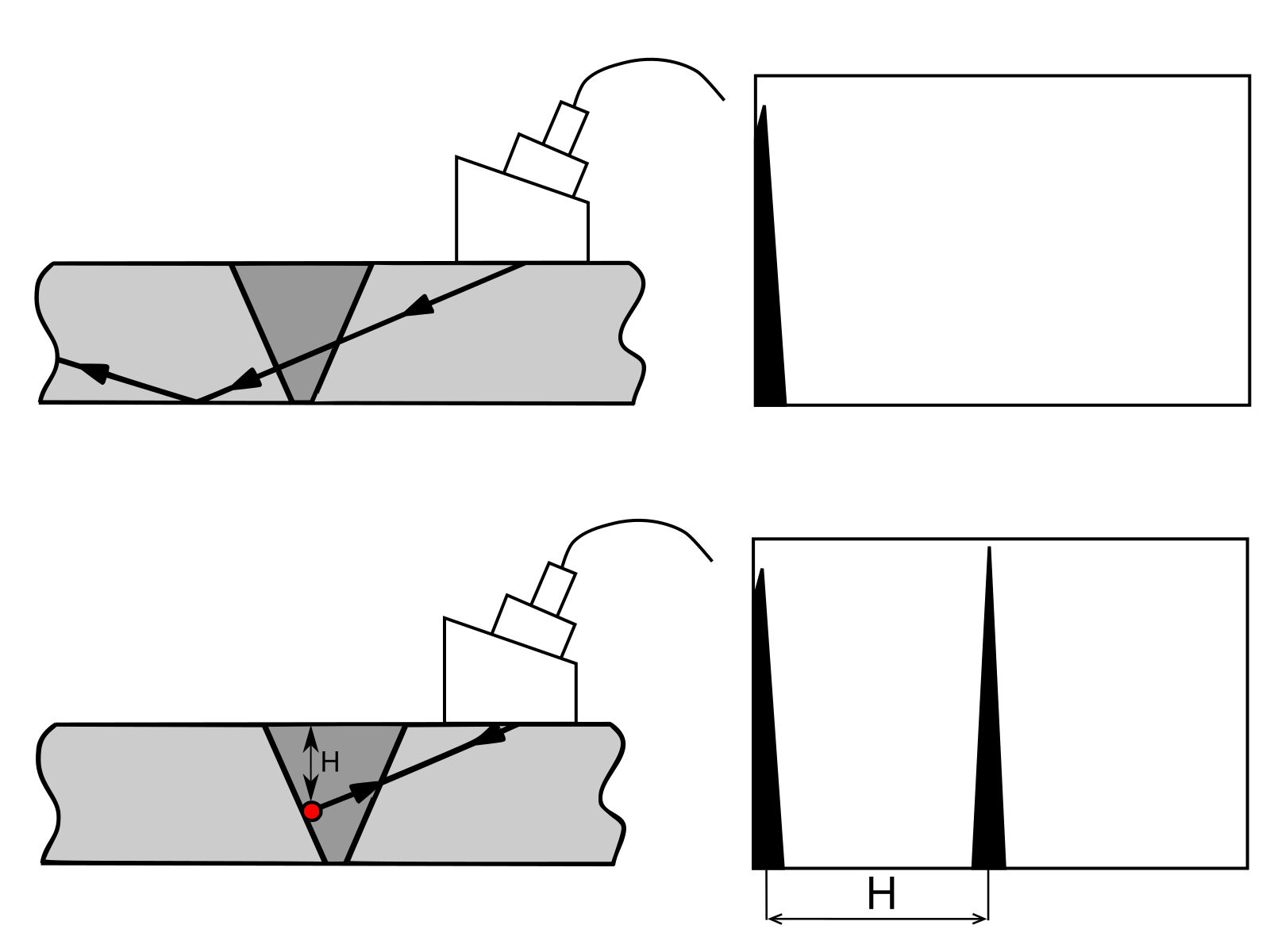
{x0=S y0=Lcos(nθ+α) n=1,2,3,⋯,Nz0=Lsin(nθ+α) n=1,2,3,⋯,NH=H0−z0
(1)
где s — длина перемещения системного устройства, L — расстояние от начала координат О до точки измерения на поверхности разделки сварочного шва (т.т. е. длина падающего лазерного луча), H0 обозначает базовую высоту от начала координат O до уровня земли, n — порядковый номер точки измерения, N — количество измерений в цикле сканирования, θ — угол между соседними измерительными лазерными лучами, α — угол между исходным измерительным лазерным лучом и осью Y.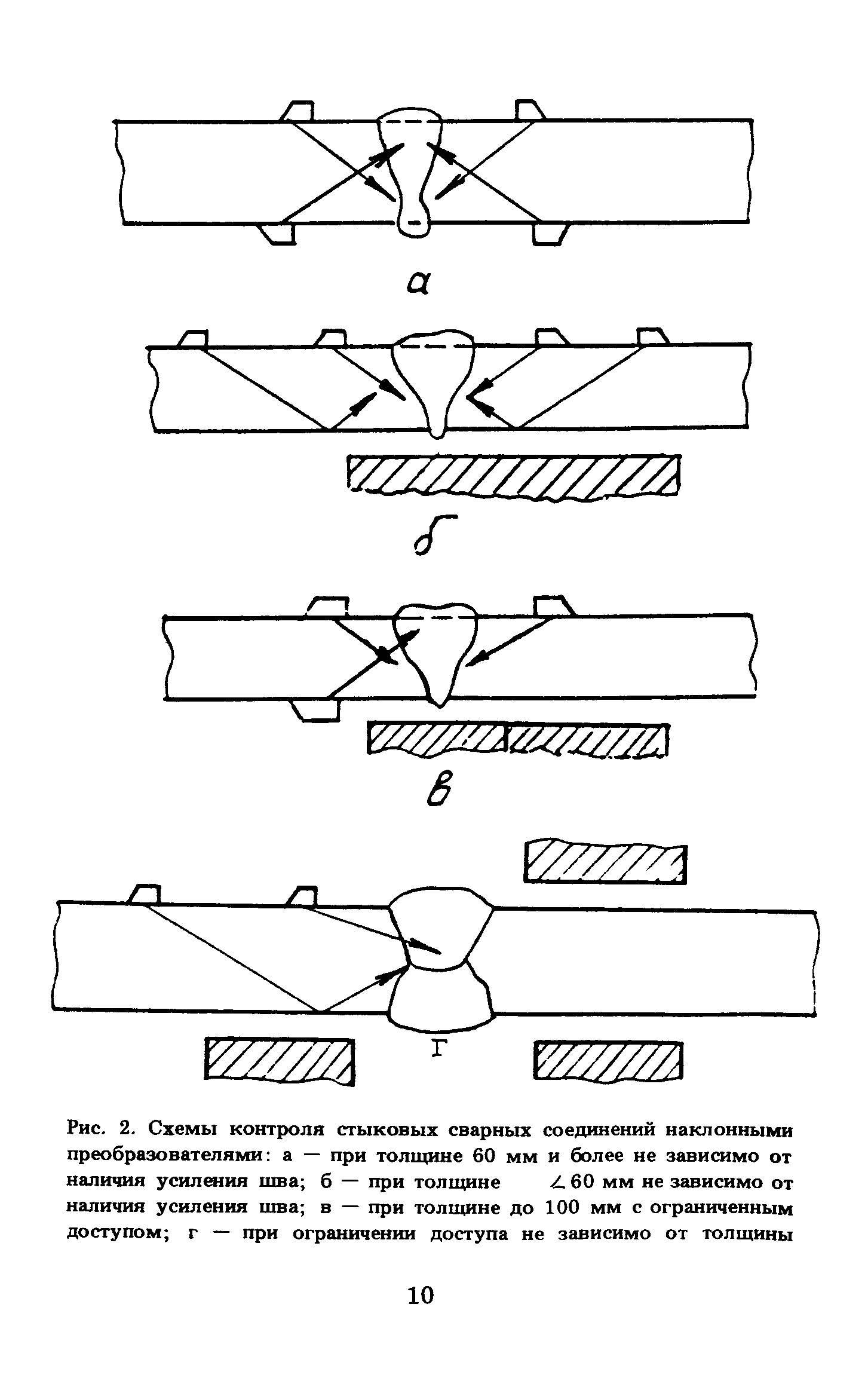
2.3. Извлечение признаков траектории шва
Контурная кривая объекта имеет два элемента формы, т. е. вписанный радиус и вогнуто-выпуклый элемент характеристического треугольника.Характеристический треугольник строился следующим образом: контурная кривая дискретизировалась равномерно. Две точки, т. е. pi′ и pi″, были найдены по часовой стрелке и против часовой стрелки вдоль контурной кривой, при этом случайная точка pi была начальной точкой. l (известная как длина сегментированной дуги) обозначала длину дуг между двумя точками и pi, а характеристический треугольник Δpi′pipi″ был образован описанием точки pi для формы контурной кривой. Как показано на рисунке 5, pi и pk — две случайные точки выборки на контурной кривой, O — центр формы контура, Δpi′pipi″ и Δpk′pkpk″ — характеристические треугольники в точках выборки pi и pk, Oi и Ok представляет собой центр Δpi′pipi″ и Δpk′pkpk″.Li и Lk обозначали расстояния от O до pi и pk, Li′ и Lk′ – расстояния от O до Oi и Ok, LOi и LOk – расстояния от pi и pk до Oi и Ok, Ri и Rk – расстояния от радиусы вписанной окружности Δpi′pipi″ и Δpk′pkpk″.
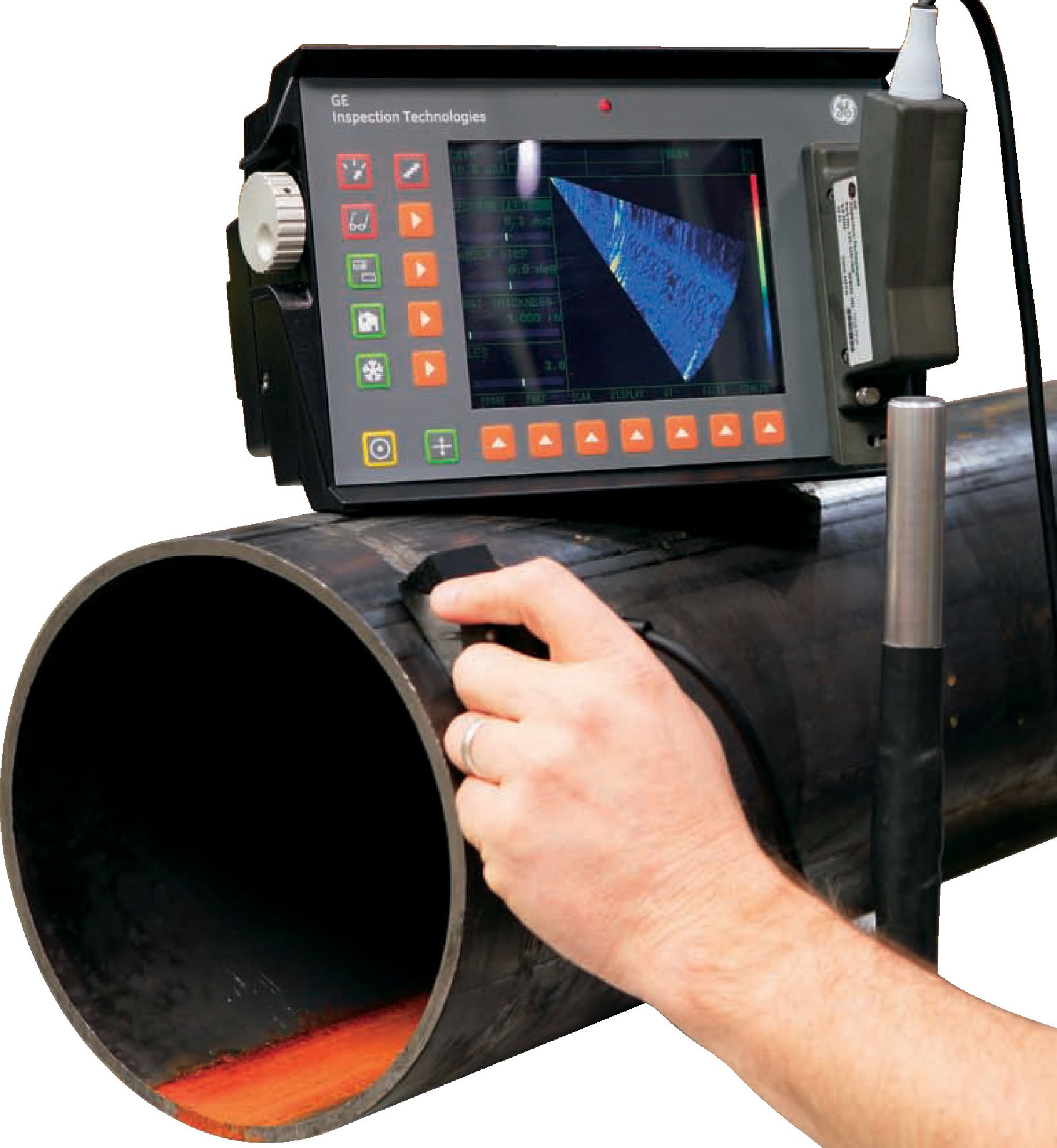
Δi=(Pi+m+⋯+Pi+1−mPi)−(mPi−Pi−m−⋯−Pi−1)m, m≤i≤N−m
(2)
В уравнении Pi+m+⋯+Pi+1−mPi — разность Pi в обратном направлении, mPi−Pi−m−⋯−Pi−1 — разность Pi в прямом направлении, а m — длина данных, пройденных разностный метод. Разумный m может устранить шумовые помехи.
Дифференциальный анализ был выполнен для траектории пространственно прерывистого угла сварного шва на основе уравнения (2), первой крайней точки Pa и последней крайней точки Pb после решения дифференциального анализа. Тогда интервал траектории сварного шва [a,b] находился там, где необходимо было выделить элемент формы.
Ri=ci(ci-li’)(ci-li″)(ci-li‴)ci
(3)
где Ri — вписанный радиус характеристического треугольника Δpi′pipi″ в точке pi, li′, li″ и li‴ относятся к расстоянию от точки pi до точки pi′, расстоянию от точки pi до точки pi″ и расстоянию от точки pi′ до точки pi″ соответственно, а ci обозначает полупериметр треугольника.Вогнуто-выпуклый элемент был произведением вогнутости и выпуклости формы на вогнуто-выпуклую высоту. Как показано на рисунке 5, вогнутость и выпуклость формы определялись следующим образом: когда расстояние Li между центроидом контура O и точкой pi было больше, чем расстояние между центроидом контура O и внутренним центром Oi характеристического треугольника Δpi′pipi″ форма контура в точке pi была выпуклой по отношению к центроиду, причем вогнутость и выпуклость формы были положительными.
Вогнуто-выпуклая высота определялась следующим образом: LOi — расстояние между точкой отбора проб pi и внутренним центром Oi в характеристическом треугольнике Δpi′pipi″.Чем больше был LOi, тем круче был наклон формы. Чем меньше был LOi, тем более пологим был наклон формы.
Следовательно, уравнение для решения степени вогнуто-выпуклого элемента (CCH) былоCCHi={LOi , Li-Li’>00 , Li-Li’=0-LOi , Li-Li’<0, i=1,2,3,⋯,N
(4)
Для упорядоченной выборки контурной кривой необходимо выбрать соответствующую начальную точку. Когда начальная точка набора точек дискретизации изменялась, набор точек дискретизации претерпевал сдвиг, и соответственно изменялась только фаза соответствующего коэффициента преобразования Фурье, при этом значение его амплитуды оставалось постоянным. Таким образом, при использовании только амплитуды коэффициента Фурье для описания конечного признака формы было устранено влияние положения начальной точки на дескриптор формы Фурье. Поэтому вписанный радиус Ri, нормированный во всех точках выборки, был объединен с вогнуто-выпуклым признаком CCHi в виде комплексного числа zi=Ri+CCHij, чтобы окончательно получить набор комплексных чисел (далее именуемый признаком формы сложная функция), соответствующая набору точек выборки контура, которые могут характеризовать особенности формы.Действительная часть комплексной функции представляла точки выборки, описание общей характеристики формы контурной кривой, а мнимая часть характеризовала детализированные особенности формы контурной кривой в точках выборки.
Zk=1N∑i=1N(Ri+CCHij)exp(−j2πkiN), i=1,2,3,⋯,N
(5)
где Zk обозначает коэффициент преобразования Фурье комплексной функции признаков формы, N представляет количество точек выборки, а k представляет собой переменную частотной области.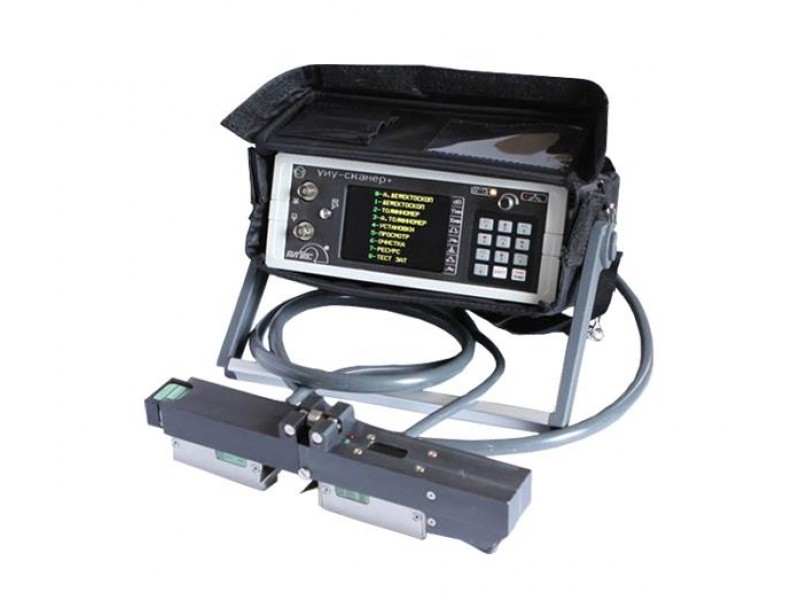
W=[ |Z1| |Z2| |Z3|⋯|Zk| ]
(6)
где k — переменная частотной области, |Zk| — модуль коэффициента преобразования Фурье с k в качестве переменной частотной области, а W — дескриптор формы Фурье.Датчик слежения за швом TH6D | ABICOR BINZEL
Датчик слежения за швом TH6D | АБИКОР БИНЗЕЛЬСША | английский
Повышение производительности и сокращение брака деталей.TH6x надежно находит сварной шов в режиме реального времени и направляет робота так быстро, как вы можете сварить деталь. Надежный и уникальный, TH6x сканирует соединение по оси XYZ, чтобы увеличить время безотказной работы робота и общее качество сварки.

Особенности и преимущества отслеживания швов TH6x:
- Трехлинейный лазерный контроль обеспечивает надежное отслеживание сварного соединения в режиме реального времени
- Дорожки на отражающих поверхностях, таких как алюминий и нержавеющая сталь
- Бесконтактный и независимый как от системы, так и от процесса
- Подключается к роботу или жесткой системе автоматизации с помощью Ethernet или аналогового соединения
- Предварительно нагруженные сварные соединения позволяют легко программировать и работать с помощью всего нескольких настроек
- Для использования в процессах MIG, TIG и субдуговых сварках
- Работает в приложениях, не связанных со сваркой, таких как склеивание и резка
Краткий обзор функций отслеживания швов TH6x:
Лазерная триангуляция для большей точности
TH6x оценивает текущее положение шва, информацию о зазоре, смещение кромки и положение сварочного инструмента относительно поверхности.
Эти значения измеряются и записываются в режиме реального времени, а затем передаются в систему управления роботом, которая направляет сварочную горелку через соединение, добавляя к процессу всего миллисекунды.
Предварительно нагруженные сварные соединения
Бесконтактное отслеживание TH6x позволяет отслеживать швы практически любой формы. Все часто используемые сварочные соединения предварительно загружены в программное обеспечение с графическим интерфейсом пользователя TH6x для быстрого поиска и простого программирования с минимальными затратами.
Интерфейсы через Ethernet, последовательные или аналоговые для всех основных OEM-производителей роботов или систем аппаратной автоматизации.
Отслеживание шва «Узкощелевые» сварные швы
Единственный оптический датчик слежения за швом, способный отслеживать швы в узкощелевых стыковых сварных швах с помощью TH6i с помощью нашей уникальной камеры в оттенках серого. Эта функция в сочетании с зеленым светом выше позволяет распознавать стыковые соединения, обнаруживать контраст яркости на краю и точно сканировать стыки — даже на отражающих поверхностях.
Устройство отслеживания швов TH6x Видео о продукции:
TH6x Seam Tracker Обзор продукта
TH6i Отслеживание узкощелевого шва
Сравнение отслеживания шва TH6D
Круглые формы для отслеживания швов TH6D
Параметры отслеживания швов для каждого типа шва и поля обзора:
TH6D поставляется в трех вариантах: GF, CF и KF.Каждая модель отличается разрешением и диапазоном измерения, чтобы точно соответствовать вашему сварному соединению.
TH6D-GF — наиболее универсальная модель, способная выполнять сварку как толстых, так и тонких листов с большим полем зрения. Для небольших и особенно больших швов лучше всего подходят модели CF и KF соответственно. См. технические характеристики для получения дополнительной информации.
Крепления для роботизированных сварочных горелок BINZEL всех марок и стилей.
Для узкощелевых стыковых швов с зазорами до . 02 миллиметра, TH6i — это уникальное решение для отслеживания шва в режиме реального времени, которое помогает роботу управлять процессом.
TH6i в оттенках серого сочетается с зеленым светом, который уменьшает яркость краев.
Затем камера в оттенках серого обнаруживает освещенную поверхность с видимой контрастной линией, распознает и передает роботу ход стыкового сварного шва.
Технические характеристики:
Измерительные линии: | 3 |
Рабочее расстояние: | 150 мм |
Скорость измерения: | 60–240 Гц |
Размеры: | Зависит от модели |
Рабочая температура: | от 10°C до 45°C |
TH6D-GF Технические характеристики:
Разрешение (ШхВ) | .![]() |
Поле зрения: | 35 мм x 60 мм |
Размеры (ДхВхШ): | 70 х 121 х 40 мм |
TH6D-CF Технические характеристики:
Разрешение (ШхВ) | 0,030 x 0,070 мм |
Поле зрения: | 16 мм x 24 мм |
Размеры (ДхВхШ): | 70 х 121 х 40 мм |
Технические характеристики TH6D-KF:
Разрешение (ШхВ) | .080 x 0,120 мм |
Поле зрения: | 40 мм x 80 мм |
Размеры (ДхВхШ): | 70 х 121 х 40 мм |
Технические характеристики TH6i:
Разрешение (ШхВ) | 0,030 x 0,070 мм |
Поле зрения: | 16 мм x 24 мм |
Размеры (ДхВхШ): | 70 х 191 х 40 мм |
Камера в оттенках серого: | Обнаруживает стыковые соединения от .![]() |
Сенсорные головки | Процессорный блок EPC | Кабельный процессор | Силовые кабели Соединительные кабели | Ethernet-кабели | Удлинительные кабели | Аксессуары для машинного интерфейса | |
Головки датчиков | |
ОПИСАНИЕ | НОМЕР ДЕТАЛИ |
Головка датчика TH6D 150-CF | 514.5042 |
Головка датчика TH6D 150-GF | 514,5154 |
Головка датчика TH6D 150-KF | 514.5043 |
Защитный блок TH6D в сборе | 514.5044 |
Головка датчика TH6i 150-CF | 514,5082 |
Защитный блок TH6i | 514.5084 |
Вернуться к началу | |
Блок обработки EPC | |
ОПИСАНИЕ | НОМЕР ДЕТАЛИ |
Блок обработки EPC для TH6D-CF | 514.![]() |
Блок обработки EPC для TH6D-GF | 514,5155 |
Блок обработки EPC для TH6D-KF | 514.5047 |
Блок обработки EPC для TH6i-CF | 514.5083 |
Вернуться к началу | |
Кабельный процессор | |
ОПИСАНИЕ | НОМЕР ДЕТАЛИ |
Кабель питания TH6x Процессор | 514.5041 |
Вернуться к началу | |
Силовые кабели | |
ОПИСАНИЕ | НОМЕР ДЕТАЛИ |
Датчик кабеля питания TH6x, 10 м | 514.5031 |
Датчик кабеля питания TH6x, 15 м | 514.5032 |
Датчик кабеля питания TH6x, 25 м | 514.![]() |
Датчик кабеля питания TH6x 35 м | 514.5104 |
Датчик кабеля питания TH6x 50 м | 514,5133 |
Вернуться к началу | |
Соединительные кабели | |
ОПИСАНИЕ | НОМЕР ДЕТАЛИ |
Соединительный кабель TH6x CAT6A, красный, 1 метр | 514.5037 |
Соединительный кабель TH6x CAT6A, красный, 2 метра | 514.5038 |
Соединительный кабель TH6x CAT6A, красный, 5 м | 514.5039 |
Соединительный кабель TH6x CAT6A, красный, 10 м | 514.5040 |
Вернуться к началу | |
Кабели Ethernet | |
ОПИСАНИЕ | НОМЕР ДЕТАЛИ |
Кабельный датчик TH6x Ethernet, 10 м | 514.![]() |
Кабель Ethernet TH6x Датчик 15 м | 514.5035 |
Датчик кабеля Ethernet TH6x, 25 м | 514.5036 |
Датчик кабеля Ethernet TH6x, 35 м | 514.5103 |
Датчик кабеля Ethernet TH6x, 50 м | 514,5132 |
Вернуться к началу | |
Удлинительные кабели | |
ОПИСАНИЕ | НОМЕР ДЕТАЛИ |
Кабель-удлинитель Датчик Ethernet 2 метра | 514.5102 |
Кабель-удлинитель Датчик Ethernet 5 метров | 514,5134 |
Кабель-удлинитель Датчик Ethernet 8 метров | 514,5135 |
Кабель-удлинитель Датчик Ethernet 10 м | 514,5136 |
Кабель-удлинитель Датчик Ethernet 20 метров | 514,5137 |
Удлинительный кабель Датчик мощности 2 метра | 514.![]() |
Удлинительный кабель Датчик мощности 5 метров | 514,5124 |
Удлинительный кабель Датчик мощности 8 метров | 514,5139 |
Удлинительный кабель Датчик мощности 10 м | 514.5140 |
Удлинительный кабель Датчик мощности 20 метров | 514,5141 |
Вернуться к началу | |
Аксессуары для машинного интерфейса | |
ОПИСАНИЕ | НОМЕР ДЕТАЛИ |
Калибровочный блок в сборе (ABB и KUKA) включает точку и перекрестную линию для калибровочной пластины | 514.5062 |
Калибровочная пластина (ABB или KUKA) | 514.5051 |
Наконечник для калибровочной пластины (ABB или KUKA) | 514.5049 |
Crossline для калибровочной пластины (ABB или KUKA) | 514.![]() |
Блок калибровки (FANUC или Yaskawa) | 514.0237 |
Цифровой/аналоговый интерфейс WAGO | 514.5050 |
Вернуться к началу |
Начните сегодня и узнайте, что может дать вам система отслеживания швов TH6D уже сегодня, и начните достигать своих производственных целей.
Мы будем рады лично продемонстрировать вам, как трехстрочная выборка TH6D, сканирование соединений в реальном времени и мощная программа с графическим интерфейсом пользователя помогают вашей сварочной ячейке производить больше продукции быстрее с меньшим количеством переделок.
Хотите немедленно поговорить с кем-нибудь? Позвоните нам по телефону 800-542-4867.
ABICOR BINZEL USA, Inc. 650 Medimmune Ct., Suite 110Frederick, MD 21703Google Maps001-301-846-4196 Канал ABICOR BINZEL на YouTubeПосетите канал нашей компании на YouTube и узнайте больше о ABICOR BINZEL.

Нам нужно ваше согласие на загрузку сервиса Youtube!
Мы используем Youtube для встраивания контента, который может собирать данные о вашей активности.Пожалуйста, ознакомьтесь с деталями и примите услугу, чтобы увидеть этот контент.Предотвращение дугового разряда
Дуга дуги может вызвать ряд проблем при сварке, в том числе чрезмерное разбрызгивание, непровар, пористость и низкое качество. Что это такое и как это можно предотвратить? В этой статье мы рассмотрим дуновение дуги и обсудим способы устранения неполадок и устранения этого явления для создания лучшего сварного шва. Дуговой удар возникает при дуговой сварке постоянным током, когда поток дуги не следует по кратчайшему пути между электродом и заготовкой и отклоняется вперед или назад от направления движения или, реже, в одну сторону.
Во-первых, давайте рассмотрим некоторые термины, связанные с дуговым разрядом. Обратный удар возникает при сварке в направлении соединения заготовки, конца соединения или в угол. Удар вперед возникает при сварке вдали от места соединения заготовки или на начальном конце соединения. Поступательный удар может быть особенно проблематичным с электродами из порошка железа SMAW или другими электродами, которые образуют большие шлаковые покрытия, когда тяжелый шлак или кратер затягиваются вперед и под дугу.
Дуга магнитного поля
Дуга магнитного поля возникает из-за несбалансированного состояния магнитного поля, окружающего дугу. Это несбалансированное состояние возникает из-за того, что в большинстве случаев дуга будет дальше от одного конца соединения, чем от другого, и будет находиться на разных расстояниях от соединения заготовки. Дисбаланс также существует из-за изменения направления тока при его протекании от электрода через дугу, в заготовку и через нее.
Визуализация магнитного поля
Чтобы понять, как горит дуга, полезно визуализировать магнитное поле. На рис. 3-37 показан постоянный ток, проходящий через проводник (который может быть электродом или потоком плазмы между электродом и сварным соединением). Вокруг проводника создается магнитное поле, или поток, с силовыми линиями, которые могут быть представлены концентрическими окружностями в плоскостях под прямым углом к направлению тока. Эти круговые силовые линии уменьшаются по интенсивности по мере удаления от электрического проводника.
Поля концентрических потоков останутся круглыми, если они смогут оставаться в одной среде, достаточно обширной, чтобы содержать их, пока они не уменьшатся практически до нуля. Но если среда меняется (например, со стальной пластины на воздух), круговые силовые линии искажаются и имеют тенденцию концентрироваться в стали, где они встречают меньшее сопротивление. На границе между кромками стальной пластины и воздухом происходит сдавливание силовых линий магнитного поля, вызывающее деформацию круговых силовых линий. Это сжатие может привести к сильной концентрации флюса позади или впереди сварочной дуги. Затем дуга имеет тенденцию двигаться в направлении, которое уменьшит сдавливание и восстановит баланс магнитного поля. Он отклоняется в сторону концентрации магнитного потока. Это отклонение наблюдается как удар дуги.
На рис. 3-38 показано сжатие и искажение полей флюса в начале и в конце сварного шва.В начале линии магнитного потока сосредоточены за электродом. Дуга пытается компенсировать этот дисбаланс, двигаясь вперед, что создает прямой удар дуги. По мере приближения электрода к концу шва сжатие происходит впереди дуги, что приводит к смещению дуги назад и развитию обратного удара. В середине шва в двух элементах одинаковой ширины магнитное поле было бы симметричным, и не было бы ни обратного, ни прямого удара дуги. Но если один элемент должен быть широким, а другой узким, в середине сварного шва может произойти боковой удар.
Понимание эффекта возврата сварочного тока через заготовку
Еще одно явление «сдавливания» возникает из-за возврата тока обратно к соединению заготовки внутри заготовки. Как показано на рис. 3-39 , магнитный поток также создается электрическим током, проходящим через заготовку к проводнику заготовки. Жирная линия представляет собой путь сварочного тока, а светлые линии представляют собой магнитное поле, создаваемое током.Когда ток меняет направление или поворачивает угол от дуги к заготовке, в точке х происходит концентрация потока, что заставляет дугу, как указано, дуть в сторону от соединения с заготовкой.
Движение дуги из-за этого эффекта будет сочетаться с движением, возникающим в результате концентрации, описанной ранее, чтобы дать наблюдаемое дуновение дуги. Эффект обратного тока может уменьшать или увеличивать дуновение дуги, вызванное магнитным потоком дуги. Фактически, управление направлением обратного тока является одним из способов управления дуновением дуги, что особенно полезно при автоматической сварке.
В Рисунок 3-40(a) , кабель заготовки подсоединяется к начальному концу шва, а флюс, возникающий в результате возврата сварочного тока в процессе работы, находится за дугой. Результирующее дуговое движение будет вперед. Однако ближе к концу шва движение дуги вперед уменьшит общий удар дуги, компенсируя часть обратного удара, возникающего из-за концентрации потока от дуги на конце заготовки, см. рис. 3-41 (a). ). В Рисунок 3-40(b) , рабочий трос присоединяется к концу шва, что приводит к обратному удару. Здесь это увеличит обратный удар дугового флюса на конце сварного шва.
Комбинация «сжатых» магнитных потоков проиллюстрирована на Рис. 3-41(b) . Соединение заготовки в конце сварного шва, однако, может быть тем, что необходимо сварщику для уменьшения чрезмерного прямого удара в начале сварного шва.
Поскольку эффект возврата сварочного тока через заготовку менее силен, чем концентрация магнитного потока дуги на концах заготовок, позиционирование соединения заготовки лишь умеренно эффективно для контроля дуновения дуги. Необходимо также использовать другие меры, чтобы уменьшить трудности, вызванные дугой при сварке.
Другие проблемные области
Угловые и стыковые соединения с глубокими V-образными канавками
Где еще возникает проблема с дуговым разрядом? Он также встречается в углах угловых швов и в сварных швах с глубокой подваркой.Причина точно такая же, как и при сварке прямого шва — скопления линий магнитного потока и движение дуги для снятия таких скоплений. Рисунки 3-42 и 3-43 иллюстрируют ситуации, в которых зажигание дуги постоянным током может быть проблемой.
Высокие токи
При слабом токе дует меньше дуги, чем при сильном.Почему? Потому что напряженность магнитного поля на данном расстоянии от проводника электрического тока пропорциональна квадрату сварочного тока. Обычно серьезных проблем с дуновением дуги не возникает при сварке штучными электродами на постоянном токе приблизительно до 250 ампер (но это не точный параметр, так как большое влияние могут оказывать подгонка стыка и геометрия).
Постоянный ток
Использование переменного тока заметно снижает дуговой разряд. Быстрое изменение направления тока вызывает вихревые токи в основном металле, а поля, создаваемые вихревыми токами, значительно снижают силу магнитных полей, вызывающих дуговой разряд.
Магниточувствительные материалы
Некоторые материалы, такие как 9-процентная никелевая сталь, обладают очень высокой магнитной проницаемостью и очень легко намагничиваются внешними магнитными полями, такими как поля линий электропередач и т. д. Эти материалы очень трудно сваривать из-за к удару дуги, вызванному магнитными полями в материале. Такие поля легко обнаруживаются и измеряются недорогими ручными измерителями Гаусса. Полей выше 20 Гаусс обычно достаточно, чтобы вызвать проблемы со сваркой.
Продувка термической дугой
Мы уже рассмотрели наиболее распространенную форму продувки дуги, продувку магнитной дугой, но с какими другими формами может столкнуться сварщик? Второй тип – это термическая дуга. Физика электрической дуги требует наличия горячей точки как на электроде, так и на пластине, чтобы поддерживать непрерывный поток тока в потоке дуги. По мере продвижения электрода вдоль изделия дуга будет иметь тенденцию отставать. Это естественное отставание дуги вызвано нежеланием дуги двигаться к более холодной пластине.Пространство между концом электрода и горячей поверхностью расплавленного кратера ионизировано и, следовательно, представляет собой более проводящий путь, чем от электрода к более холодной пластине. Когда сварка выполняется вручную, небольшое количество «теплового обратного удара» из-за запаздывания дуги не является вредным, но может стать проблемой при более высоких скоростях автоматической сварки или когда термический обратный удар добавляется к магнитному обратному удару. .
Дуговая продувка несколькими дугами
Некоторые последние достижения в области сварки включают использование нескольких сварочных дуг для повышения скорости и производительности.Но этот тип сварки также может вызвать проблемы с дугой. В частности, когда две дуги расположены близко друг к другу, их магнитные поля реагируют, вызывая дуговой разряд на обеих дугах.
Когда две дуги расположены близко друг к другу и имеют противоположную полярность, как в Рис. 3-44(a) , , магнитные поля между дугами заставляют их сдуваться друг от друга. Если дуги имеют одинаковую полярность, как в , то магнитные поля между дугами противодействуют друг другу. Это приводит к более слабому полю между дугами, из-за чего дуги дуют навстречу друг другу.
Обычно при использовании двух дуг предлагается, чтобы одна была постоянного тока, а другая переменного тока, как показано на рис. 3-44(c) . В этом случае поле потока дуги переменного тока полностью меняется на противоположное для каждого цикла, а влияние на поле постоянного тока мало. В результате происходит очень небольшое дуновение дуги.
Другим часто используемым устройством являются две дуги переменного тока. Помехи от дугового разряда здесь в значительной степени избегают за счет фазового сдвига тока одной дуги на 80–90 градусов относительно тока другой дуги.Так называемое соединение «Скотт» выполняет это автоматически. При фазовом сдвиге ток и магнитное поле одной дуги достигают максимума, когда ток и магнитное поле другой дуги находятся на минимальном уровне или близки к нему. В результате дуновение дуги очень мало.
Как снизить риск возникновения дугового разряда
Не все дуговые разряды вредны. На самом деле, небольшое количество иногда можно использовать с пользой, чтобы помочь сформировать форму валика, контролировать расплавленный шлак и контролировать проникновение. Если дуговой разряд вызывает или способствует возникновению таких дефектов, как подрезы, неравномерное проплавление, искривленные валики, валики неправильной ширины, пористость, волнистые валики и чрезмерное разбрызгивание, его необходимо контролировать.
Возможные корректирующие меры включают следующее:
Если в процессе экранированной дуговой сварки используется постоянный ток, особенно при силе тока выше 250 ампер, переход на переменный ток может устранить проблемы
Удерживайте как можно более короткую дугу, чтобы сила дуги противодействовала удару дуги
Уменьшите сварочный ток, что может потребовать снижения скорости дуги
Наклоните электрод с заготовкой в направлении, противоположном направлению дутья дуги, как показано на рис. 3-45
Сделайте толстые прихватки на обоих концах шва; применять частые прихваточные швы вдоль шва, особенно если посадка неплотная
Приварка к толстой прихватке или к уже сделанному сварному шву
Используйте технику обратной ступенчатой сварки, как показано на рис. 3-46
Сварка вдали от соединения с заготовкой для уменьшения обратного удара; приваривать к соединению заготовки, чтобы уменьшить прямой удар
В процессах с тяжелым шлаком может быть желательна небольшая обратная продувка; чтобы получить это, приварите к соединению заготовки
Оберните рабочий кабель вокруг заготовки так, чтобы ток, возвращающийся к источнику питания, проходил через него в таком направлении, чтобы установленное магнитное поле
было стремится нейтрализовать магнитное поле, вызывающее дуговой разряд
Направление удара дуги можно наблюдать при открытом дуговом процессе, но при процессе под флюсом его сложнее диагностировать, и он должен определяться типом дефекта сварного шва.
Обратный удар обозначается следующим:
Брызги
Подрез, непрерывный или прерывистый
Узкий, высокий валик, обычно с подрезом
Увеличение проникновения
Поверхностная пористость на конце сварных швов на листовом металле
Удар вперед обозначается:
Широкий валик неправильной ширины
Волнистый валик
Подрез, обычно прерывистый
Уменьшение проникновения
Влияние крепления на дуновение дуги
Еще одна предосторожность, о которой оператор сварки должен знать при дуновении дуги, касается его связи с креплением. Стальные приспособления для удержания заготовок могут влиять на магнитное поле вокруг дуги и на дуновение дуги и со временем могут намагничиться. Обычно крепление не вызывает проблем при сварке штучными электродами, когда сила тока не превышает 250 ампер. Приспособления для использования с более высокими токами и при механизированной сварке должны быть спроектированы с учетом мер предосторожности, чтобы в приспособлении не создавалась ситуация, способствующая выдуванию дуги. Для каждого крепежного устройства может потребоваться специальное исследование, чтобы определить наилучший способ предотвращения помех от магнитных полей.
Обратите внимание на следующие моменты:
Приспособления для сварки продольного шва цилиндров (см. Рисунок 3-47 ) должны быть рассчитаны на зазор не менее 1 дюйма между опорной балкой
и изделием. Зажимные пальцы или стержни, удерживающие изделие, должны быть немагнитными. Не присоединяйте кабель заготовки к медному опорному стержню; если возможно, сделайте рабочее соединение
непосредственно с заготовкой
Изготовьте приспособление из низкоуглеродистой стали. Это необходимо для предотвращения накопления постоянного магнетизма в приспособлении
Приварка к закрытому концу креплений «рупорного типа» уменьшает обратный удар
Конструкция приспособления должна быть достаточно длинной, чтобы при необходимости можно было использовать концевые выступы
Не используйте медную полосу, вставленную в стальной стержень, в качестве подложки, как в Рисунок 3-48 . Стальная часть опорного стержня усилит дуновение дуги
Обеспечьте непрерывный или тесный зажим деталей, подлежащих шовной сварке. Широкий, прерывистый зажим может привести к разрыву швов между точками зажима, что
приведет к продувке дугой зазоров
Не встраивайте в приспособление большие массы стали только с одной стороны шва.Противовес с аналогичной массой на другой стороне
Понимая механику дугового разряда и то, как правильно диагностировать его в сварном шве, операторы должны быть в состоянии исключить его из своих приложений и иметь возможность создавать сварные швы без проблем, обычно связанных с дуговым разрядом.
Промышленные швейные изделия — Производство сварных изделий в РФ
В SealWerks мы обычно комбинируем промышленный пошив со сваркой или герметизацией изделий.Швейно-сварочные услуги включают полный комплекс услуг по резке в дополнение к высокочастотной сварке и прошивке швов, кромок и областей усиления на изделии. Много раз при изготовлении продукта на заказ требуется трубчатая или цилиндрическая конструкция для свойств надувания, которые лучше всего достигаются с помощью сварных швов. Промышленное шитье используется для прикрепления вспомогательных приспособлений, таких как липучки, ремни и другое вспомогательное оборудование. Сшитые швы могут располагаться рядом, поверх или пересекать сварные швы.
В надувной сумке используется высокочастотная сварка для воздухонепроницаемых швов и коммерческое шитье для добавления других необходимых функций, таких как молнии.
Объедините промышленное шитье с радиочастотной сваркой, чтобы сделать продукцию более гибкой.
Используйте промышленное шитье в сочетании с процессами запайки, чтобы придать изделию большую гибкость. Во многих случаях лучший способ добиться гибкости формы или конфигурации на тяжелых материалах — это включить тяжелое шитье с использованием различных вариантов стежков.SealWerks имеет множество коммерческих швейных рабочих мест, которые могут работать с тяжелыми материалами, такими как ПВХ, резина, холст и многое другое. Наши швейные операторы и промышленные швейные машины могут управлять многими конфигурациями, большими и малыми, для получения высококачественных результатов. Чтобы удовлетворить ваши конкретные потребности и производить качественную и долговечную продукцию, мы обычно используем усиленные углы для обеспечения долговечности.
Ищете дополнительную информацию о добавлении портов для надувания на сшитых и сварных изделиях? Посетите нашу страницу на Уплотнение трубной оправки
В промышленных и медицинских изделиях используется как шитье, так и радиочастотная сварка на изделиях
.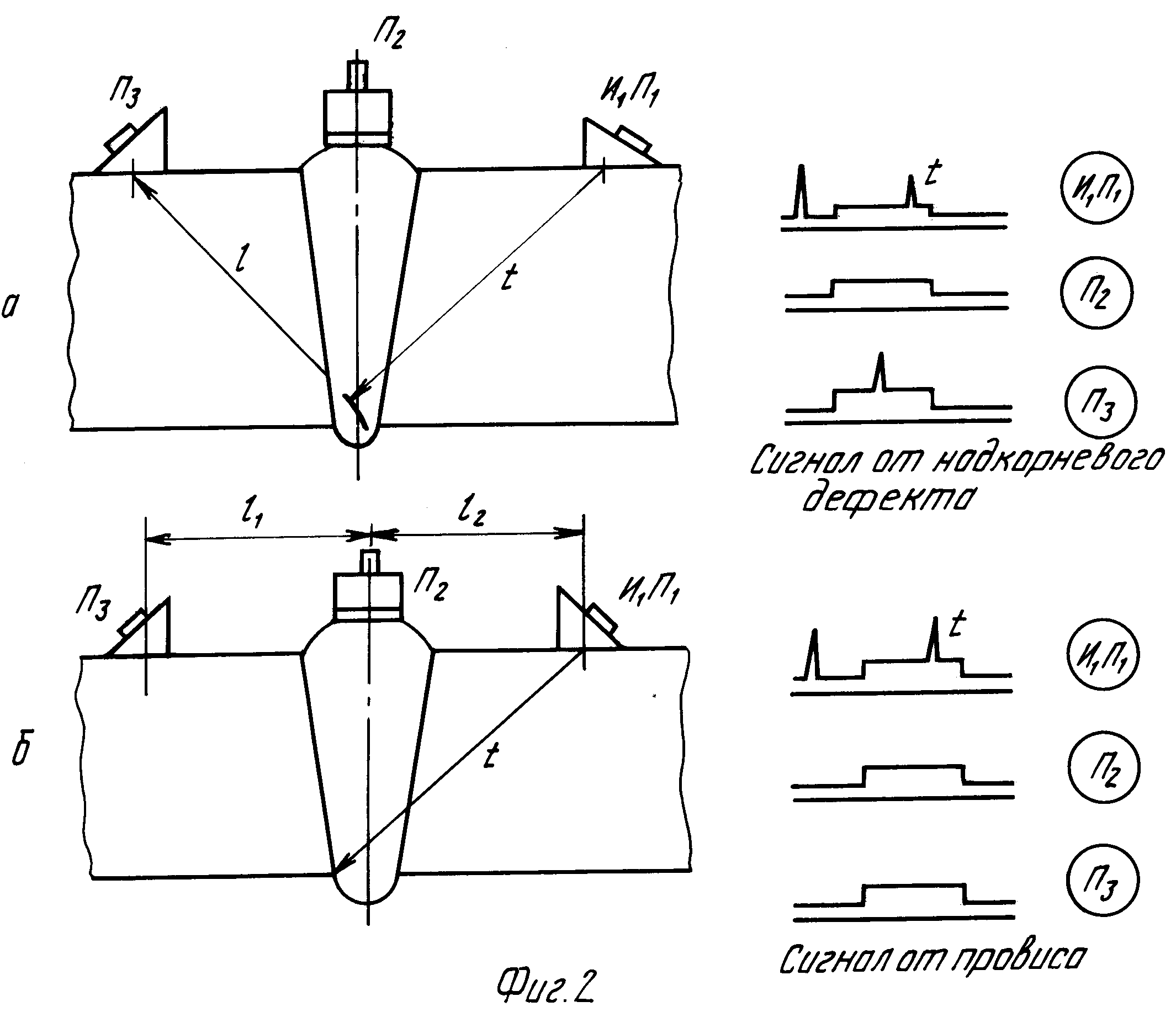
Многие продукты в промышленной и медицинской промышленности требуют использования промышленного шитья и сварки для достижения наилучшей интеграции нескольких материалов, герметичности и добавления дополнительных приспособлений.Шитье позволяет добавлять ремешки, пряжки, кнопки и карманы к корпусу изделия. Этот внешний слой, сваренный радиочастотой со сварными швами, используется для герметизации внутренней прокладки или других материалов, чтобы он не намокал, помогал контролировать воздействие загрязняющих элементов и предотвращал личный контакт с пациентами.
Некоторые другие продукты, которые мы производим, которые требуют шитья и сварки:
- Предварительно подготовленные воздушные шланги (канал PCA)
- Чехлы для сидений в аэропортах
- Обертки для контроля давления и температуры
- Терапевтические сапоги
- Непромокаемые грузовые сумки
- Медицинские подушки
- Надувные изделия
- Торговые стенды и баннеры
- Звукоизолирующие шторы
- И многое другое!
Чтобы быть долговечными, коммерческие чехлы для сидений требуют сшивания и сварки на тяжелых материалах.
PCA требуются прочные сварные швы, способные выдерживать различные внешние факторы. Коммерческое шитье используется для прикрепления концов манжет.
Ищете дополнительную информацию о шлангах PCA? Посетите наш веб-сайт по адресу PCA Rigid Duct
.Свяжитесь с SealWerks, чтобы обсудить ваши потребности в продукте и узнать, как приступить к созданию индивидуального дизайна и прототипа продукта, или определить оптимальный производственный процесс для существующего продукта.Мы здесь, чтобы помочь вам лучше понять варианты процесса, чтобы вы могли начать работу!
Методы сварки и использование лазерного освещения при визуализации сварки
Автор и авторское право: Cavitar Ltd
Сварка относится к процессу, в котором материалы, обычно металлы или термопласты, соединяются друг с другом с использованием высоких температур для расплавления материалов и образования соединения. Обычно на стык также наплавляют наполнитель, чтобы сделать его прочнее. Успех процесса сварки и прочность конечного продукта зависят от ряда факторов, таких как профиль сварного шва на стыке и постоянный равномерный поток защитного газа во избежание окисления расплавленных металлов или присадочного материала. .Многие из этих факторов можно визуализировать для изучения или отслеживания процесса сварки. В этой статье представлены некоторые методы визуализации сварки, которые можно использовать для сбора информации о процессах сварки, изучения их возможных применений и обсуждения исследований, проведенных по этой теме.
Раздел 2 знакомит с наиболее распространенными промышленными процессами сварки, тогда как Раздел 3 посвящен методам визуализации, которые можно использовать для визуализации сварки. В разделе 4 обсуждаются особенности, которые можно отобразить при сварке, и почему собранная информация представляет интерес, а также, где это возможно, обобщаются результаты предыдущих исследований по этой теме.
Помимо сварки, большинство этих принципов визуализации применимы к визуализации лазерного, дугового и плазменного аддитивного производства.
Рис. 1. Типичная установка для исследований в области сварки и аддитивного производства: высокоскоростная камера
справа и лазерная подсветка слева.
2.1 Дуговая сварка металлическим электродом в среде защитного газа (GMAW)
При дуговой сварке металлическим электродом в среде защитного газа (GMAW), также известной как сварка металлическим электродом в среде инертного газа (MIG) и сварка металлическим активным газом (MAG), сварочная горелка используется для создания электрической дуги между расходуемым проволочным электродом, подаваемым через горелку, и сварочной горелкой. металлы, которые свариваются.Тепло дуги расплавляет металлы. Защитный газ проходит через сварочную горелку, защищая расплавленные металлы от контакта с воздухом. Источником питания, используемым в GMAW, обычно является постоянное напряжение и постоянный ток, хотя возможен и переменный ток. Методы переноса металла, обычно используемые в GMAW, включают шаровидный, короткозамкнутый, распыление и импульсное распыление. Выбор метода зависит от цели сварки. В промышленной сварке GMAW является наиболее часто используемым процессом, поскольку он может быть автоматизирован, а также быстр и универсален.Процесс наиболее подходит для помещений из-за использования защитного газа.
Несмотря на распространенность GMAW, исследования этого процесса ограничены. Во многом это связано с трудностями получения достоверных изображений процесса. Яркость электрической дуги легко нарушает процесс визуализации и не позволяет камерам увидеть процесс сварки. Однако это препятствие можно преодолеть с помощью правильной техники визуализации, источника света и фильтра, которые рассматриваются в разделах 3 и 4.
Рис. 2. GMAW: принцип работы. (1) Направление движения, (2) Заготовка, (3) Затвердевший металл сварного шва,
(4) Контактная трубка, (5) Электрод (присадочная проволока), (6) Защитный газ, (7) Ванна расплава.
2.1.1 Холодный перенос металла (CMT)
Холодный перенос металла (CMT) отличается от обычного GMAW главным образом с точки зрения тепловложения и стабильности дуги. В CMT обнаруживается каждое короткое замыкание, и каждый сигнал обнаружения заставляет присадочную проволоку отводиться от сварного шва, давая ей время остыть перед введением следующей капли присадочного материала.Этот метод сводит к минимуму количество брызг и обеспечивает более гладкий и прочный шов, чем традиционный метод GMAW. Было обнаружено, что CMT превосходит обычный GMAW, особенно при сварке стали и алюминия (Selvi et al. 2018).
2.2 Дуговая сварка вольфрамовым электродом в среде защитного газа (GTAW)
Дуговая сварка вольфрамовым электродом (GTAW), также называемая сваркой вольфрамовым электродом в среде инертного газа (TIG), использует сварочную горелку вместо сварочного пистолета для образования электрической дуги между неплавящимся вольфрамовым электродом и металлом заготовки. Подобно GMAW, защитный газ защищает сварной шов от загрязнения. Присадочный металл обычно используется для соединения металлов заготовки вместе, но это не всегда требуется. Источником питания, используемым в GTAW, является постоянный ток.
GTAW наиболее подходит для сварки магниевых, медных и алюминиевых сплавов и других цветных металлов, а также тонких профилей из нержавеющей стали. По сравнению с GMAW, GTAW обеспечивает сварку с большей прочностью и более высоким качеством благодаря тому, что оператор имеет больший контроль над сваркой.Взамен это медленнее и сложнее. С точки зрения визуализации GTAW легче визуализировать, чем GMAW, из-за различий в тепле и количестве брызг.
Рис. 3. GTAW: принцип работы. (1) Направление движения, (2) Заготовка, (3) Сварной шов,
(4) Контактная трубка, (5) Электрод, (6) Защитный газ, (7) Ванна расплава, (8) Присадочный стержень.
2.3 Плазменная дуговая сварка (PAW)
Установка плазменно-дуговой сварки (PAW) очень похожа на GTAW в том смысле, что PAW также использует электрод, который часто изготавливается из спеченного вольфрама. Однако в PAW электрод расположен внутри сварочной горелки, что позволяет отделить плазменную дугу от оболочки защитного газа. По мере того как плазма проталкивается через маленькое отверстие сопла горелки, тепло и скорость дуги увеличиваются, улучшая свойства теплопередачи, стабильность и форму дуги. PAW можно использовать для соединения заготовок как с присадочным материалом, так и без него.
Рисунок 4. PAW: принцип работы. (1) Направление движения, (2) Заготовка, (3) Сварной шов, (4) Электрод, (5) Плазменный газ,
(6) Корпус горелки с водяным охлаждением, (7) Защитный газ, (8) Защитный газ сопло, (9) плазменная дуга, (10) расплавленная ванна, (11) опциональный присадочный стержень.
2.4 Лазерная сварка (LBW)
При лазерной сварке (LBW) вместо электрической дуги используется лазер для плавления свариваемых материалов. Самые большие преимущества LBW заключаются в том, что его можно легко автоматизировать (как и большинство процессов LBW), а источник тепла имеет высокую концентрацию, что позволяет успешно выполнять глубокие и узкие сварные швы. Для тонких заготовок можно использовать импульсный лазерный луч. Поскольку тепло может быть сосредоточено на небольшой площади, нагревание и охлаждение поверхности заготовки происходит быстро.Однако это может создать проблемы при сварке сталей с высоким содержанием углерода, так как поверхность может растрескиваться из-за быстрого охлаждения. LBW можно использовать для сварки различных материалов, например. нержавеющая сталь, углеродистая сталь и алюминий, так как мощность сварки лазерного луча легко контролируется.
Исходя из опыта, мы обнаружили, что LBW менее сложно изобразить, чем процессы дуговой сварки. Узкий известный спектр длин волн LBW легче отфильтровать, чем свет, возникающий при дуговой сварке.
Рис. 5. LBW: принцип работы. (1) Направление движения, (2) Заготовка, (3) Сварной шов,
(4) Лазерный луч, (5) Защитный газ, (6) Сопло защитного газа, (7) Ванна расплава.
2.5 Другие сварочные процессы
Другие методы сварки, которые потенциально выигрывают от использования лазерного освещения, включают, например, газовая сварка и сварка давлением, которая далее подразделяется, например, на взрывом, контактной сваркой и сваркой трением. Сварка взрывом изучалась с помощью лазера CAVILUX (см. Pabst 2017, https://www.cavitar.com/library/high-speed-visualization-of-electromagic-pulse-welding/). Дуговая сварка под флюсом, с другой стороны, не выигрывает от лазерного освещения, так как область сварки покрыта гранулированным твердым флюсом.
Как уже упоминалось, визуализация сварочных процессов затруднена из-за яркости электрической дуги, ослепляющей камеру. В этом разделе представлены несколько методов визуализации сварочных процессов с объяснением сильных и слабых сторон каждого из них.
3.1 Общие рекомендации по получению высококачественных изображений сварочных процессов
3.1.1 Фильтрация и освещение
Одним из способов визуализации сварочных процессов является использование технологического освещения в качестве единственного источника света для камеры без включения активного освещения. В этом случае освещение в основном обеспечивается электрической дугой сварочного процесса, температура которой в зависимости от процесса колеблется от 6 000 до 20 000°С. Проблема с использованием только технологического света заключается в том, что он часто слишком яркий для сенсора камеры, что приводит к насыщенным изображениям, которые мало что говорят о процессе.
Рисунок 6а. Тепловое технологическое излучение. Рисунок 6б. Пики излучения технологических элементов.
Количество технологического света, попадающего на датчик камеры, можно уменьшить, используя, например, фильтры нейтральной плотности. Минус такого подхода в том, что области, которые изначально были плохо освещены, становятся еще темнее. Это означает, что не все функции можно визуализировать, просто используя фильтры. Одновременное видение «горячих» и «холодных» областей требует использования как фильтра, предотвращающего насыщение изображения за счет уменьшения количества технологического света, попадающего на датчик камеры, так и дополнительного освещения, освещающего объект по желанию и функционирующего с пропусканием фильтра. группа.Отправная точка не идеальна, так как для получения детализированных высококачественных изображений требуется дополнительный источник света, более мощный, чем чрезвычайно сильная электрическая дуга.
С другой стороны, если используется другой тип фильтра, высокоэффективный узкополосный фильтр, объект изображения может освещаться практически монохроматическим лазерным источником света. Узкополосный фильтр блокирует попадание почти всего технологического света на датчик камеры, за исключением света, излучаемого в узкой полосе пропускания фильтра.В результате активная лазерная подсветка должна быть только более мощной, чем технологический свет в пределах узкой полосы пропускания фильтра. На практике для этого требуется мощность лазера в несколько сотен ватт. Такая установка позволяет одновременно визуализировать как «горячие», так и «холодные» области. Сравнение различных настроек освещения показано на рис. 6.
Рис. 7. Сравнение трех различных установок освещения для визуализации сварочных процессов.
3.1.2 Свойства камеры
В промышленных условиях часто требуется непрерывный мониторинг сварочных процессов в режиме реального времени, что означает использование низкой частоты кадров. С другой стороны, в исследованиях и разработках часто можно использовать высокоскоростные камеры для записи сварочных процессов. Основное преимущество высокоскоростной камеры заключается в том, что она способна фиксировать быстрые явления, которые можно пропустить при использовании обычной камеры с более низкой частотой кадров.
Независимо от частоты кадров камера должна иметь короткое время экспозиции и монохромный датчик, если она будет использоваться с (монохроматическим) лазерным освещением.Короткое время экспозиции помогает уменьшить количество технологического света, проходящего через узкополосный фильтр. Не менее важным является освещение процесса коротким лазерным импульсом (предпочтительно в микросекундном масштабе) вместо, например, источника непрерывного излучения. Короткие лазерные импульсы не вызывают теплового воздействия на объект и упрощают управление безопасностью лазера. По сравнению с цветной камерой монохромная камера обеспечивает улучшенную чувствительность и качество изображения.
3.1.3 Свойства оптики камеры
Основными критериями выбора оптики камеры являются поле зрения и рабочее расстояние. Также необходимо учитывать физические размеры оптики камеры. Регулируемая диафрагма часто оказывается полезной, так как позволяет регулировать общую яркость изображения. Кроме того, меньшая диафрагма обеспечивает большую глубину обзора.
3.1.4 Расположение камеры и освещение
Изменяя относительный угол между камерой и освещением, можно выделить различные особенности процесса сварки.Кроме того, расположение камеры и освещение также играют роль во избежание зеркального отражения от металлических поверхностей заготовки (деталей).
Общие геометрии визуализации включают:
- Камера и освещение направлены на процесс практически с одного направления. Поверхность заготовки и проволоки, среди прочего, хорошо видны. Однако зеркальные отражения могут вызывать помехи в изображениях.
- Боковое освещение: угол между камерой и освещением составляет около 90 градусов.
Эта установка часто уменьшает зеркальные отражения и может улучшить видимость расплавленной ванны.
- Прямая задняя подсветка: объект находится между камерой и подсветкой. Эта установка создает четкие изображения силуэтов, которые подходят, например, для изучения образования капель.
- Непрямая задняя подсветка: подсветка не направлена прямо на камеру. Эта установка улучшает видимость ванны расплава по сравнению с прямым задним освещением.
- Применение рассеивающих элементов или нескольких источников освещения: распределенное освещение, например доставка света по нескольким световым волокнам.Эта настройка уменьшает количество зеркальных отражений.
- Комбинация методов, описанных выше.
Обычно наилучшую конфигурацию для каждой цели можно найти, протестировав различные углы между камерой и источником света. На изображениях ниже показаны две установки прямого освещения и установка непрямого освещения с использованием отражающей пластины.
Рис. 8. Слева: одновременное прямое и контровое освещение дуговой сварки. Справа: прямое освещение лазерной сварки.
Рис. 9. Непрямое освещение с использованием отражающей пластины для выделения динамики расплавленной ванны.
3.2 Сравнение машинного зрения и высокоскоростной визуализации
Машинное зрение относится к непрерывному мониторингу промышленных процессов с помощью решений на основе камер. В сварочных процессах машинное зрение можно использовать для контроля процесса и качества. Параметры процесса можно настроить на основе изображения в реальном времени или результатов, полученных в результате анализа изображения.Машинное зрение в сочетании с передовыми алгоритмами анализа изображений обеспечивает автоматизированное управление процессами и, таким образом, снижает нагрузку на персонал.
Высокоскоростная визуализация определяется как захват нескольких последовательных кадров с высокой скоростью. В сварочной промышленности он в основном используется для исследований и разработок. Высокоскоростная визуализация позволяет увидеть быстрые и сверхбыстрые явления в замедленном темпе, а это означает, что их можно тщательно проанализировать и понять их внутреннюю работу.Выбранное решение определяет скорость формирования изображения: ПЗС-система для хранения данных на месте может записывать 103 изображения со скоростью 10 млн кадров в секунду, тогда как ПЗС-система со стробируемым усилением позволяет записывать 4-12 изображений со скоростью 200 млн кадров в секунду. Подобные скорости могут быть достигнуты с решениями CMOS.
Сочетание машинного зрения и высокоскоростной визуализации также можно использовать для мониторинга промышленных сварочных процессов. Программное обеспечение для анализа можно запрограммировать на запуск высокоскоростной визуализации, когда алгоритмы обнаруживают определенные изменения или особенности в процессе, которые могут представлять интерес для дальнейшего анализа. В настоящее время в обрабатывающей промышленности наблюдается тенденция к такого рода автоматизированному управлению технологическими процессами.
3.3 Лазерная подсветка
Основное преимущество лазерной подсветки при визуализации сварочных процессов заключается в том, что она позволяет использовать высокоэффективный узкополосный фильтр. Таким образом, лазер должен быть только более мощным, чем технологический свет в этой узкой полосе пропускания. На практике для этого требуется мощность лазера в несколько сотен ватт. С другой стороны, фильтрация технологического света означает, что яркость процесса может быть снижена, а на снятых изображениях видно больше информации.
Лазерное освещение позволяет высокой мощности света проходить через апертуру всего в несколько миллиметров, что обеспечивает высокий уровень яркости. Подачу света можно регулировать с шагом 10 нс и точно синхронизировать. По сравнению со светодиодным освещением, лазеры обеспечивают монохроматический свет без пятен и высокую энергетическую освещенность. Лазеры обычно имеют небольшие размеры, что означает, что они подходят для множества установок. Оптоволоконная связь означает, что лазер не обязательно должен располагаться в непосредственной близости от цели.Возможность использования коротких импульсов означает, что быстрые явления могут быть записаны без размытия движения.
Другие преимущества лазерного освещения при визуализации сварочных процессов включают:
- Четкий обзор сквозь тепло
- Возможна высокоскоростная визуализация
- Нет проблем, связанных с размытием движения
- Высококачественные изображения, обеспечивающие одновременный анализ изображений и мониторинг в реальном времени, например. размеры, форма, положение, топография и дефекты поверхности
- Возможны измерения на больших расстояниях
- Поляризованный свет (линейный или круговой)
Методы освещения, ставшие возможными благодаря использованию лазеров, универсальны и включают в себя прямое освещение, освещение с оптоволоконным соединением, освещение со структурированным рисунком и освещение на большом расстоянии. Для особо быстрых явлений, например ударных волн, в лазерной подсветке предусмотрена возможность использования двойных импульсов, что позволяет улавливать скорость распространения ударной волны.
3.4 Фильтры и другие оптические компоненты
Основная функция фильтров — улучшение качества изображения. Фильтры — это мощный инструмент для управления количеством и типом света, попадающего на датчик камеры. Это очень важно, особенно в GMAW и GTAW, где электрическая дуга очень яркая.В зависимости от настройки и наличия дополнительных компонентов, фильтры, которые можно использовать, включают, например, фильтры нейтральной плотности и узкополосные фильтры. (См. Раздел 3.1.1.)
3.5 Шлирен и теневая графика
Шлирен-визуализация используется для изучения явлений, которые не обязательно видны невооруженным глазом, но которые способны изменять направление света. Метод основан на визуализации различий показателей преломления прозрачных сред, таких как воздух или вода. Пример шлирен-установки показан на рисунке 10.
Рис. 10. Z-образная шлирен-установка Cavitar со складкой. (1) камера, (2) маска, (3) вспомогательное зеркало, (4) зеркало,
(5) тестовая область, (6) щель, (7) лазер CAVILUX и (8) дополнительное переднее освещение.
Теневая графика, с другой стороны, представляет собой метод визуализации, при котором изображения захватываются с той же настройкой, что и шлирен-изображения, но без маски. Техника теневой графики создает теневые диаграммы, которые, как выразился Сеттлз (2001: 29), «представляют собой не сфокусированное оптическое изображение», а «простую тень».Теневая графика менее чувствительна, чем шлирен, но подходит для визуализации ударных волн и турбулентных потоков. Эти два метода могут дополнять друг друга с точки зрения информации, которую они дают о явлении. Хотя теневая фотография отображает изменения плотности, она не показывает направление.
В дополнение к использованию маски основное различие между методами состоит в том, что «шлирен-изображение отображает угол отклонения», тогда как «теневая фотография отображает смещение луча в результате отклонения» (Settles 2001: 29). Систему теней значительно проще настроить, поскольку наиболее утомительной задачей шлирен-визуализации обычно является поиск правильного положения маски и достижение нужного уровня чувствительности. Однако преимущества, достигаемые с помощью шлирена, часто перевешивают трудности в настройке: шлирен «подчеркивает, даже преувеличивает детали в шлирен-объекте, тогда как теневая графика обычно их преуменьшает» (Settles 2001: 29). Более того, «его однозначное соответствие изображения 1:1 объекту исследования часто является решающим преимуществом» (Settles 2001: 29).
Чтобы узнать больше о шлирен-визуализации, см. нашу полную статью по этой теме здесь: https://www.cavitar.com/library/schlieren-imaging/
Процессы сварки содержат ряд компонентов и явлений, которые можно изобразить с помощью методов, представленных выше. При визуализации сварочных процессов основное внимание, естественно, уделяется видимым элементам. Создавая изображения и изучая такие особенности, можно обнаруживать и предотвращать дефекты, а также контролировать и оптимизировать процесс. В этом разделе описываются компоненты и явления, которые можно визуализировать, и приводятся примеры некоторых их особенностей, которые могут представлять интерес для изучения.
4.1 Канавка и соединение
Канавка относится к пространству между заготовками, которые должны быть соединены вместе, или к каналу на поверхности одной заготовки. Канавка – это пространство, в которое направляется расплавленный металл и где образуется шов. При разделочной сварке обычно необходима некоторая подготовка соединения. Примеры различных типов канавок показаны на рисунке 11.
Рис. 11. Примеры различных типов канавок.
Некоторые свойства разделки имеют решающее значение для получения качественного сварного шва. К этим свойствам относятся форма кромок соединяемых вместе заготовок, форма паза между заготовками, высота заготовок относительно друг друга и выравнивание заготовок. Все эти свойства можно визуализировать и отслеживать на протяжении всего процесса.
относится к соединению двух или более заготовок, что означает, что оно часто является синонимом канавки .Однако бороздки встречаются и на поверхностях отдельных заготовок. При сварке расположение стыка по отношению к сварочной горелке имеет решающее значение для образования прочного гладкого шва: точное направление тепла улучшает качество сварки. Это особенно важно при LBW, где швы часто бывают узкими, и любое отклонение может привести к отсутствию сращения боковых стенок (см., например, Nilsen et al. 2017). Комбинируя визуализацию процесса сварки с мощными алгоритмами анализа, можно отслеживать, а также автоматически корректировать положение сварочной горелки относительно соединения.
Рис. 12. Пример соединения при плазменной сварке.
4.2 Присадочная проволока
GMAW и SMAW используют расходуемую проволоку, которая подается через сварочный пистолет с равномерной скоростью. Электрическая дуга образуется между проволочным электродом и деталью(ами). Материал проволоки зависит от материала заготовки (деталей), а также от других особенностей процесса сварки и влияет на качество сварного шва.
В режимах GTAW и PAW присадочная проволока подается в зону сварки снаружи сварочной горелки, поскольку для формирования дуги используется неплавящийся электрод (см. ниже).
Рис. 13. Плавучая проволока с флюсовым покрытием для сварки SMAW.
Подробнее в соответствующих примечаниях по применению:
https://www.cavitar.com/library/high-speed-visualization-flux-coated-electrode-hand-welding/
4.2.1 Капли
По мере плавления присадочной проволоки капли присадочного металла переносятся на заготовку, образуя сварной шов. Основная причина для изображения и изучения капель — выявить проблемы с регулярным образованием капель и оптимизировать процесс, чтобы избавиться от любых проблем. Положение присадочной проволоки по отношению к канавке также имеет решающее значение для получения качественного шва.
Рис. 14. Присадочная проволока при сварке GMAW.
4.2.2 Брызги
Брызги состоят из капель сварочного материала, которые разбрызгиваются по рабочему столу или деталям в процессе сварки. Из-за высокой температуры брызги могут повредить рабочую зону, если они не подготовлены, и могут оставить нежелательные круглые следы на готовом изделии.Помимо визуальных дефектов, следы от брызг могут вызвать коррозию. Брызги могут исходить либо от присадочной проволоки, либо от ванны расплава, что особенно характерно для GMAW. Факторы, которые могут вызвать разбрызгивание, включают загрязнения на поверхности заготовки, некоторые защитные газы, определенные свойства дуги, угол сварки и скорость присадочной проволоки.
Гунентирам и др. (2018) показали в своем исследовании, что выбросы брызг можно успешно изучать, сочетая высокоскоростную визуализацию, лазерное освещение и последующий анализ изображения.Они пришли к выводу, что в LBW с порошковым слоем материал порошка влияет на количество образующихся брызг, и визуализацию можно использовать в качестве инструмента анализа для сведения к минимуму разбрызгивания.
Рис. 15. Образование брызг при лазерной сварке.*
4.3 Электрод
В режимах GTAW и PAW неплавящийся вольфрамовый электрод помещается в середину сварочной горелки.Электрическая или плазменная дуга образуется между этим электродом и заготовкой(ями). Визуализированные и изучаемые свойства электрода включают состояние электрода и его положение по отношению к заготовке (заготовкам).
youtube.com/embed/vHa2uaVnoBk» frameborder=»0″ allowfullscreen=»allowfullscreen»/> Рис. 16. Наконечник сварки TIG.
Подробнее в соответствующем примечании по применению:
https://www.cavitar.com/library/modern-variants-of-classical-arc-welding-technologies-with-high-speed-videography/
4.4 Дуга
Электрическая дуга образуется между присадочной проволокой или электродом и изделием при дуговой сварке.Дуга возникает в результате электрического разряда и нагревает металл при сварке. Из-за высокого уровня яркости дугу трудно визуализировать. Лазерное освещение практически необходимо для захвата свойств дуги, так как большую часть яркости можно отфильтровать. Шлирен-установки с мощными источниками света можно использовать для изучения взаимодействия дуги с заготовкой (см., например, Siewert et al. 2014).
Рис. 17. Создание дуги в GMAW – спиновая дуга.
Подробнее в соответствующем примечании по применению:
https://www.cavitar.com/library/modern-variants-of-classical-arc-welding-technologies-with-high-speed-videography/
4.5 Защитный газ
Защитный газ представляет собой газовую смесь, непрерывно вытекающую из сварочного пистолета или горелки во время сварки. Защитный газ защищает расплавленный материал от окисления, обеспечивая прочность соединения. Защитный газ является важным элементом сварки, так как непрерывный и оптимальный поток газа гарантирует, что сварной шов не соприкасается с загрязняющими веществами в воздухе.Согласно Siewert et al. (2014: 1) загрязнение может привести к «нестабильности дуги, окислению, пористости и разбрызгиванию». Кроме того, на плазму и пятна дуги может отрицательно повлиять контакт с кислородом или другими атмосферными газами. Информация о расходе и функциях защитных газов важна, например, при разработке новых сварочных горелок и горелок. Наиболее важной особенностью сварочных пистолетов и горелок с точки зрения защитного газа является функциональное сопло, которое позволяет газу течь без отрыва или турбулентности (Siewert et al.2014).
Защитный газ является одним из наиболее изученных компонентов сварки. Сиверт и др. (2014: 1) сообщают, что для анализа потоков защитного газа были протестированы как лазерная доплеровская анемометрия (LDA), так и велосиметрия изображения частиц (PIV). PIV был более эффективным из этих двух, поскольку он сделал возможным «ненавязчивое обнаружение двумерного поля газового потока с временным разрешением» как в GMAW, так и в GTAW. Однако недостатком этих двух методов анализа является то, что затраты высоки, а освоение техники измерения требует самоотверженности.
Более рентабельным и простым способом изучения потоков защитного газа является метод шлирен-визуализации, хотя проблема, особенно с GMAW, заключается в яркости дуги, которая вызывает искажения изображений. Таким образом, GMAW обычно считается трудным для визуализации процессом. Однако, регулируя ключевые компоненты, то есть источник света и маску, можно получать высококачественные шлирен-изображения защитного газа. В качестве маски Siewert et al. (2014) считают идеальной маску с острым краем, перпендикулярную заготовке, но оптимальными для визуализации различных явлений являются маски разных форм и размеров.Идеальная маска также зависит от формы источника света, так как в оптимальном случае форма маски соответствует форме источника света. Двухцветные фильтры можно дополнительно использовать для улучшения видимости турбулентности, поскольку они повышают контрастность, но, с другой стороны, уменьшают интенсивность света. Чтобы полностью заблокировать яркость дуги, источник лазерного излучения можно комбинировать с «нейтральным серым фильтром с коэффициентом пропускания 1 %» (Siewert et al. 2014: 4).
Кроме того, Siewert et al.(2014: 4) в своем исследовании обнаружили, что консистенция защитного газа влияет на видимость газа на шлирен-изображениях: «особенно хорош переход технологической безгазовой струи в атмосферу. визуализировать использование аргона с заметным процентным содержанием гелия (50%) в качестве защитного газа. Однако следует исходить из того, что гелий оказывает существенное влияние на геометрию дуги и, прежде всего, на газовый поток». Битарас и др. (2018), с другой стороны, успешно использовали шлирен-метод для исследования потоков защитного газа, состоящего из 80 % аргона и 20 % CO 2 и 86 % аргона, 12 % CO 2 и 2 % O 2 .
Дреер и др. (2009) протестировали использование шлирен-визуализации для визуализации защитного газа при наличии дуги и добились хороших результатов с помощью шлирен-установки Z-типа с использованием специальных зеркал, линз, апертур и фильтров. Полученные изображения использовались для изучения свойств потока защитного газа с дугой и без нее, уделяя особое внимание турбулентности и ее влиянию на заготовку. Такая информация может быть использована, например, для разработки новой сварочной горелки с лучшими свойствами потока защитного газа.
Рис. 18. Поток защитного газа при сварке GMAW, снятый шлирен-методом. Видна ударная волна дуги.
В другом исследовании Dreher et al. (2013) продолжили аналогичную работу, используя PIV и шлирен-изображения, чтобы проанализировать, как различные сопла для защитного газа влияют на поток защитного газа. Они также рассмотрели выравнивание горелки и тип соединения как факторы, которые могут повлиять на свойства потока. Для визуализации защитного газа с помощью PIV Dreher et al.(2013) комбинированное импульсное лазерное облучение CAVILUX с использованием трассерных частиц. Основным преимуществом PIV является простота транспортировки измерительных компонентов и возможность использования с любым химическим составом защитного газа. PIV подходит для анализа поля течения в струе без защитного газа и вблизи дуги. С помощью шлирен-метода эффекты турбулентного потока защитного газа могут быть визуализированы более эффективно, но однородность газа имеет решающее значение, поскольку этот метод основан на различиях в плотности.
В дополнение к PIV и шлирену, потоки защитного газа были успешно отображены и проанализированы с помощью теней. Бейер и др. (2013), например, изучали оптимальные скорости потока защитного газа и влияние поперечной тяги и размера сопла на расход защитного газа при сварке металлов в среде инертного газа с использованием портативной системы теневой съемки с лазерным освещением. Их мнение заключалось в том, что скорость потока защитного газа иногда неоправданно увеличивается сварщиками, что приводит к затратам, которых можно было избежать. Они обнаружили, что скорость потока защитного газа должна основываться на ожидаемой максимальной поперечной тяге и размере используемого сопла.Анализ показал, что в некоторых сварочных процессах даже 50-процентное снижение расхода защитного газа не влияет на качество сварки, а это означает, что изучение процесса и определение оптимальных параметров может привести к существенной годовой экономии.
Для получения дополнительной информации о визуализации защитного газа см., например, Bitharas et al. (2016), Siewert et al. (2014) и Schnick et al. (2013).
Рис. 19. Пример формирования дуги при сварке GMAW. Установка включала световую пластину для изучения потока защитного газа методом PIV.
Подробнее в соответствующем примечании по применению:
https://www.cavitar.com/library/piv-measurements-shielding-gas-flow-gas-metal-arc-welding-gmaw-cavilux-hf-diode-laser/
4.6 Ванна расплава
Ванна расплава относится к расплавленному металлу сварного шва, который еще не затвердел, что означает, что он находится в месте сварки в данный момент. Факторы, влияющие на форму и поведение ванны расплава, включают скорость сварки, используемую мощность и точку фокусировки. Понимание свойств ванны расплава важно для оптимизации включения капель присадочного материала в ванну расплава и, как следствие, минимизации количества брызг (см. г. Гунентирам и др. 2018 по различным сварочным материалам, вязкости в ванне расплава и разбрызгиванию и Fabbro 2010 по поведению ванны расплава при LBW).
Салминен и др. (2008) удалось визуализировать форму и окисление ванн расплава с помощью шлирен-визуализации с использованием лазерного освещения. Они заявляют, что в предыдущих исследованиях высокоскоростная визуализация показала, что более узкие сварные швы и более сильные потоки расплава вблизи поверхности сварного шва могут быть достигнуты с увеличением скорости сварки. Однако, когда скорость превышает определенный предел, качество шва ухудшается из-за повышенного разбрызгивания.В собственных исследованиях им не удалось отследить поведение ванны расплава на протяжении всего процесса из-за недостатков используемого оборудования, но, несмотря на это, они обнаружили, что за замочной скважиной ванна расплава обычно расширяется. Кроме того, ванна расплава имеет сходные характеристики по всей глубине проникновения.
Конильо и др. (2014), с другой стороны, используют методологию формы из поляризации для топографической характеристики ванн расплава. Этот метод основан на тепловом излучении, испускаемом ванной расплава, и использует фоново-ориентированный шлирен, чтобы помочь в реконструкции поверхности ванны расплава.Этот метод лучше всего работает при низкой силе тока. Такие топографические измерения дают важную информацию о вогнутости и выпуклости ванны расплава, что, в свою очередь, указывает либо на недостаток, либо на избыток наполнителя.
Рис. 20. Наблюдение ванны расплава при аддитивном производстве CMT в сочетании с шлирен-визуализацией.
4,7 Замочная скважина
В центре ванны расплава образуется замочная скважина, когда дуга нагревает материал и его части испаряются.Замочные скважины особенно важны в LBW, где лазерный луч эффективно испаряет сварочный материал, образуя замочную скважину, через которую энергия передается в окружающие области. Важнейшими характеристиками замочной скважины являются ее размер, форма и поведение, которые влияют на качество сварного шва. Замочная скважина тесно связана с лужей расплава.
Согласно Salminen et al. (2008) взаимосвязь между замочной скважиной и фокальной точкой важна для получения высококачественных сварных швов: предыдущие исследования показывают, что фокальная точка должна быть ниже поверхности заготовки, а замочная скважина должна составлять примерно 85 % размера фокальной точки.Однако в своем собственном исследовании Salminen et al. (2008) обнаружили, что размер замочной скважины зависит от скорости сварки: более высокая скорость приводит к более длинной замочной скважине овальной формы по сравнению с более округлой замочной скважиной при низких скоростях сварки. Кроме того, низкая погонная энергия привела к нестабильности замочной скважины. Они использовали шлирен-установку с лазерным освещением для получения изображений процесса сварки, и, хотя изображение было успешным, они пришли к выводу, что высокоскоростная камера (более 10 000 кадров в секунду) идеально подходит для фиксации быстрых изменений в замочной скважине.
Fabbro (2010) также изучил взаимосвязь замочной скважины и скорости сварки в LBW. Он обнаружил, что помимо скорости сварки, влияющей на форму и размер замочной скважины, важную роль играет и используемый лазер. Новые, высококачественные лазерные лучи имеют меньшее фокусное пятно, и в результате этой повышенной интенсивности форма замочной скважины становится более стабильной (например, выше порог наклона передней стенки замочной скважины).
Рис. 21. Замочная скважина в процессе лазерной сварки NdYAG.
Allemand, C.D., Schoeder, R., Ries, D.E. и Eagar, T.W. 1985. «Метод съемки переноса металла в сварочных дугах». Сварочный журнал 64 (1): 45-47.
Бейер, В., Кэмпбелл, С.В., Рэмси, Г.М., Галлоуэй, А.М., Мур, А.Дж. и Макферсон, Н.А. 2013. «Систематическое исследование влияния поперечной тяги и диаметра сопла на покрытие защитным газом при сварке МИГ». Наука и техника сварки и соединения 18 (8): 652-660.
Битарас, И., Кэмпбелл, С. В., Галлоуэй, А. М., Макферсон, Н. А. и Мур, А. Дж. 2016. «Визуализация переменного потока защитного газа в GTAW». Материалы и дизайн 91: 424-431.
Битарас, И., Макферсон, Н. А., Макги, В., Рой, Д. и Мур, А. Дж. 2018. «Визуализация и оптимизация покрытия защитным газом во время дуговой сварки в среде защитного газа». Журнал технологии обработки материалов 255: 451-462.
Конильо, Н., Матье, А., Обретон, О. и Штольц, К. 2014.«Влияние плазмы на реконструкцию поверхности сварочной ванны с помощью анализа формы по поляризации». Письма по прикладной физике 104, 131603. https://aip.scitation.org/doi/10.1063/1.4870505
Дреер М., Фюссель У., Роуз С., Хэсслер М., Хертель М. и Шник М. 2013. «Методы и результаты, касающиеся потока защитного газа в GMAW». Weld World 57: 391-410.
Дреер, М., Фюссель, У., Шник, М. и Хертель, М. 2009. «Численное моделирование потока защитного газа с помощью сварки GMA и варианты проверки с помощью диагностики.” https://tu-dresden.de/ing/maschinenwesen/if/fue/ressourcen/dateien/lichtbogenprozesse/veroeffentlichungen_Dokumente/DR552B1.pdf?lang=en
Фаббро, Р. 2010. «Анализ поведения ванны расплава и замочной скважины для лазерной сварки с глубоким проплавлением». Journal of Physics D: Applied Physics 43 (44): 445501.
Гунентирам, В., Пейре, П., Шнайдер, М., Дал, М., Косте, Ф., Кутири, И. и Фаббро, Р. 2018. «Экспериментальный анализ образования брызг и поведения ванны расплава во время процесс плавления лазерным лучом в порошковом слое. Journal of Materials Processing Technology 251: 376-386.
McClure, JC, Garcia, G., Hou, H. and Nunes, A.C. 1993. «Наблюдение за потоком газа во время сварки VPPA с использованием метода теневого изображения». НАСА CR-204347.
Нильсен. М., Сикстрём Ф., Кристианссон А.-К. и Анкона, А. 2017. «Визуальное и спектроскопическое зондирование для отслеживания соединений при лазерной стыковой сварке с узким зазором». Оптика и лазерная техника 96: 107-116.
Pabst, C. 2017. «Высокоскоростная визуализация электромагнитно-импульсной сварки.https://www.cavitar.com/library/high-speed-visualization-of-electromagnetic-pulse-welding/
Салминен, А., Лехтинен, Дж. и Харкко, П. 2008. «Влияние параметров сварки на поведение замочной скважины и сварочной ванны при лазерной сварке мощным волоконным лазером». Материалы 27 — й Международной конференции по применению лазеров и электрооптики . Лазерный институт Америки, стр. 354-363.
Шник М., Дреер М., Зшецше Дж., Фюссель У.и Спилле-Кохофф, А. 2013. «Визуализация и оптимизация потоков защитного газа при дуговой сварке». Сварка в мире 56 (1-2): 54-61.
Селви, С., Вишваксенан, А. и Раджасекар, Э. 2018. «Технология холодного переноса металла (CMT) — обзор». Оборонные технологии 14 (1): 28-44. https://doi.org/10.1016/j.dt.2017.08.002
Settles, GS 2001. Методы шлирена и теневой графики: визуализация явлений в прозрачных средах.