Незаделанные кратеры, пористость швов при сварке изделий
Незаделанные кратеры получаются в результате небрежного и неумелого выполнения сварки. В месте кратера толщина шва резко уменьшается, что вызывает понижение прочности сварного соединения. При действии динамической нагрузки разрушение шва почти всегда начинается с кратера, поэтому кратер необходимо обязательно заделывать.
При сварке изделий из низкоуглеродистой стали заделка кратера может осуществляться как на самом шве, так и с выводом его на основной металл. На легированной стали кратеры должны заделываться только непосредственно на швах во избежание возникновения трещин в основном металле.
Как уже отмечалось, при автоматической сварке кратеры выводятся на специальные выводные планки.
Пористость наружного слоя шва и внутренние газовые поры. Пористость в швах образуется при наличии газов, не успевших выделиться из жидкого металла при его быстром остывании.
Причины образования пористости швов следующие:
а) загрязнение свариваемой поверхности или электродной проволоки ржавчиной, маслом, краской, а также повышенная влажность покрытия или флюса.
б) повышенная скорость сварки, при которой ускоряется процесс затвердевания наплавленного металла и одновременно задерживается выделение газов;
в) недостаточная раскисленность, насыщенность газами или окислами основного металла.
Швы с большим количеством пор имеют низкую прочность и подлежат обязательному исправлению путем вырубки и повторной заварки.
Для предупреждения образования пористости швов рекомендуется:
1) сварку производить только по чистым кромкам;
2) наложение шва вести с такой скоростью, чтобы ванна расплавленного металла находилась более продолжительное время в жидком состоянии. Для этого рекомендуется производить кольцеобразные и петлеобразные возвратно-поступательные движения концом электрода;
3) электроды и флюсы перед сваркой необходимо прокаливать.
Кратеры сварочные — — Энциклопедия по машиностроению XXL
Красностойкость 6 — 242 — см. также Победит — Красностойкость Кратеры сварочные — см. Сварочные кратеры Кратчайшее расстояние между двумя прямыми [c.122]Если в конце шва сразу оборвать дугу, то кратер сварочной ванны останется в шве в виде углубления. В нем при усадке металла во время его кристаллизации возникают трещины, раковины, рыхлоты. Поэтому при завершении шва нужно некоторое время не перемещать [c.118]
Сварочная головка установлена на самоходной тележке, перемещающейся по направляющим вдоль свариваемых кромок полос. На этой же тележке размещены флюсоаппарат и катушка с электродной проволокой. Скорость сварки стыкового шва — около 1 м/мин. Сварку стыкового шва производят без технологических планок, так как кратер сварочной дуги выводят на самый край полосы, который в дальнейшем обрезают на дисковых ножницах.
Примером таких электродов может служить электрод марки ЦМ-7С. Так как покрытие из-за меньшей теплопроводности плавится с некоторым запаздыванием по отношению к плавлению электродного стержня, то на конце электрода образуется чехольчик, который при сварке опирают на поверхность изделия. В процессе сварки электрод должен быть наклонен под углом 15—20° к вертикали для лучшего вытеснения металла из кратера. Сварочный ток увеличивается против обычного на 20—40% и, в зависимости от диаметра электрода, выбирается по формуле [c.224]
На схемах 16, Пб, Не, III, IV, V п VI показана техника выполнения сварки начала и конца последующих слоев, которая заключается в том, что поперечные колебания электрода при его подходе к концу стыка, т. е. к торцу накладок, заменяются на круговые движения электрода, осуществляемые по возрастающим концентрическим окружностям с выводом кратера сварочной ванны на участок шва, отстоящий от конца накладок на 10— 15 мм, или на поверхность накладки.
Далее электрод перемещается в направлении сварочной ванны, где скорость сварки несколько замедляется и электроду придают незначительные по амплитуде поперечные колебания. После полной заварки кратера сварочной ванны электрод перемещают вдоль свариваемых кромок с рабочей скоростью сварки. [c.123]
Для автоматической дуговой сварки под флюсом используют непокрытую электродную проволоку и флюс для защиты дуги и сварочной ванны от воздуха. Подача и перемещение электродной проволоки механизированы. Автоматизированы процессы зажигания дуги и заварки кратера в конце шва.
Ручную сварку производят наклонной горелкой углом вперед, угол наклона к поверхности. изделия составляет 70—80°. Присадочную проволоку подают под углом 10—15° (рис. 49). По окончании сварки дугу постепенно обрывают для заварки кратера, при ручной сварке — ее постепенным растяжением, при автоматической — специальным устройством заварки кратера, обеспечивающим постепенное уменьшение сварочного тока. Для защиты охлаждающегося металла подачу газа прекращают через 10—15 с после выключения тока.
[c.82]
Кратер — углубление, образующееся в конце шва при внезапном прекращении сварки. Размеры и форма кратера зависят от величины сварочного тока и способа сварки. Например, при автоматической сварке он имеет удлиненную форму, а при ручной дуговой — круглую. Наличие такого дефекта также резко снижает работоспособность сварных конструкций особенно гфи вибрационных нагрузках (до 20-30%). [c.11]
Сварочные кантователи-башмаки для тавровых балок 8 — 242 Сварочные кантователи-кондукторы для тавровых балок 8 — 243 Сварочные клещи 8 — 261 Сварочные козлы для балок 5 — 462 Сварочные контакторы силовые 5 — 345 Сварочные кратеры 5 — 307 Сварочные манипуляторы 8 — 241, 243 [c.253]
Глубина провара (расплавления) и кратер. Глубина провара должна обеспечить полное сплавление основного металла с наплавленным электродным и нормально колеблется в пределах от 1,5 до 5 мм. Глубина провара зависит от силы сварочного тока, длины дуги, скорости перемещения электрода вдоль шва, чистоты поверхности основного металла, полярности (при сварке постоянным током), размера электрода и характера его покрытия.
В процессе сварки под непосредственным воздействием вольтовой дуги на поверхности расплавленного основного металла образуется углубление (кратер), форма и размеры которого зависят от диаметра и марки электрода, силы сварочного тока, физико-химических свойств основного металла, характера газовой среды, окружающей вольтову дугу, и скорости сварки. [c.307]
Кратеры. В зоне сварочной дуги поверхность жидкой ванны получается вогнутой, поэтому при обрыве дуги в шве остается углубление (кратер). Кратеры понижают прочность шва, так как уменьшают его сечение. Металл кратера сильнее насыщен кислородом и азотом, чем металл остальной части шва, и поэтому обладает пониженными механическими свойствами.
[c. 358]
Для автоматической дуговой сварки под флюсом используют непокрытую электродную проволоку и флюс для защиты дуги и сварочной ванны от воздуха. Подача и перемещение электродной проволоки механизированы. Автоматизированы процессы зажигания дуги и заварки кратера в конце шва. В процессе автоматической сварки под флюсом (рис. 5.8) дуга /О горит между проволокой 3 и основным металлом S. Столб дуги и металлическая ванна жидкого металла Р со всех сторон плотно закрыты слоем флюса 5 толщиной 30. .. 50 мм. Часть флюса расплавляется, в результате чего вокруг дуги образуется газовая полость, а на поверхности расплавленного металла — ванна жидкого шлака Для сварки под флюсом [c.231]
В, причем большее его значение допускается для автоматической сварки. Режим возбуждения дуги характерен наличием во вторичном контуре тока высокой частоты и высокого напряжения, а также высокочастотным искровым разрядом между электродом и изделием. При исправной сварочной цепи и надлежащей настройке осциллятора этот режим длится десятые доли секунды и после возникновения дугового разряда установка переходит, в режим нагрузки.
Техника заварки кратера при окончании шва зависит от конструкции автомата. Если сварка производится на установках с неподвижным автоматом и перемещающимся изделием, то при подходе дуги к концу шва останавливают изделие и, не выключая тока, прекращают подачу электр )дной проволоки до естественного обрыва дуги. На сварочных трактирах при подходе дуги к концу шва останавливают трактор и непродолжительное время продолжают сварку на месте, затем, не выключая тока, останавливают подачу проволоки, дуга растягивается до естественного обрыва.
При определенном значении плотности и достаточной общей мощности электронного луча в сварочной ванне образуется канал-кратер, который может распространяться на всю толщину свариваемого материала, так же как и при сварке лучом лазера. Перемещение свариваемого изделия или электронного луча приводит к периодическому переносу жидкого металла из зоны плавления в зону кристаллизации при непрерывном воздействии электронного пучка на свариваемый материал. Образование кратера на всю глубину проплавления позволяет получить исключительно малый объем сварочной ванны и, сле- [c.247]
Устройство для плавного снижения сварочного тока позволяет предотвратить появление кратера шва при быстром гашении дуги в конце сварки. Это возможно при плавном уменьшении сварочного тока до нуля примерно за 5. .. 6 с. В установках для автоматизированной сварки неплавящимся электродом в среде защитных газов данный процесс осуществляется автоматически с помощью
[c.144]
Газовый клапан используют для экономии защитного газа. Его устанавливают по возможности ближе к сварочной горелке, включают до зажигания дуги и выключают после обрыва дуги и полного затвердевания металла в кратере шва. Наибольшее распространение получили электромагнитные газовые клапаны. [c.167]
Электросхема автомата обеспечивает подъем и опускание электродной проволоки при вспомогательных операциях (закорачивание проволоки перед сваркой, подъем проволоки из шлака после сварки, заправка проволоки в головку), включение сварочного тока, зажигание дуги, подачу электродной проволоки в зону сварки передвижение автомата по свариваемому изделию и заварку кратера. [c.169]
Кристаллизация металла сварочной ванны по мере удаления дуги приводит к образованию шва, соединяющего свариваемые детали. При случайных обрывах дуги или при смене электродов кристаллизация металла сварочной ванны приводит к образованию сварочного кратера (углублению в шве, по форме напоминающему наружную поверхность сварочной ванны). Затвердевающий шлак образует на поверхности шва шлаковую корку.
[c.95]
Основу покрытия составляют криолит, хлористые и фтористые соли натрия и калия. Сила сварочного тока = (50. .. 60)rf,, (Уд = 30. .. 36 В. Ток постоянный обратной полярности. При сварке алюминиевый электрод расплавляется в 2. .. 3 раза быстрее стального. Покрытия электродов имеют значительное электрическое сопротивление. При обрывах дуги кратер и конец электрода покрываются пленкой шлака, препятствующей ее повторному зажиганию. Поэтому сварку рекомендуют выполнять на высоких скоростях, без колебания конца электрода, непрерывно в пределах одного электрода. [c.449]
При ручной сварке применяют «левый» способ. Наклон горелки к оси шва должен быть 45. .. 60° вылет вольфрамового электрода 12. .. 15 мм. Присадочный металл подают под углом 20. .. 30° к оси шва. При многопроходной сварке последующие швы необходимо накладывать после полного охлаждения, зачистки и обезжиривания предыдущих слоев. Швы, обращенные к агрессивной среде, выполняются в последнюю очередь. Начинать и заканчивать сварные швы необходимо на технологических планках. Для предотвращения образования трещин в кратере заканчивают сварку с уменьшением сварочного тока. Режимы сварки никеля приведены в табл. 12.13.
[c.464]
Вертикальные швы (рис. VII.3, е) выполняют сверху вниз при сварке металла толщиной до 3 мм и снизу вверх — при сварке более толстого металла. При сварке сверху вниз расплавленный металл, который стремится стечь вниз, всегда находится под дугой, вследствие чего глубина проплавления незначительна. Из-за стекания металла при сварке сверху вниз невозможно применять поперечные колебания конца электрода для увеличения поперечного сечения сварного шва. При сварке толстого металла в вертикальном положении в направлении снизу вверх кратер сварочной ванны удерживает капли электродного металла. Электрод в этом случае наклоняют вверх от горизонтальной оси (положение / рис. VI 1.3, ж). Сварочный ток для электрода диаметром 4 мм устанавливают не более 160 А, чтобы объем жидкого металла в сварочной ванне не был слишком большим. При выполнении швов больших поперечных сечений с использованием поперечных колебаний конца электрода поверхность сварочной ванны (кратера) должна быть меньшей, чем поперечное сечение шва в процессе сварки жидкий металл ванны должен затвердевать вслед за перемещением дуги. Это обеспечивает провар и цормальное формирование вертикального шва.
[c.429]
Процесс сварки иач1и1ается обычным способом. В конце шва неремощение дор кателя задерживается для заварки кратера, а затем быстрым движением нерсмеп ается на начало следующего шва без выключения сварочного тока и нодачи электродной проволоки. Наиболее удобно этим способом сваривать угловые швы в тавровых соединениях. [c.43]
При разделительной резке изделие устанавливают в положение, в котором наиболее благоприятны условия для вытекания расплавлеппого металла из места реза. При вертикальных резах резку ведут сверху вниз, для того чтобы выплавляемый металл не засорял выполненный разрез. Для отклонения дуги магнитным дутьем в направлении реза второй сварочный кабель присоединяют сверху у начала разреза. Разделительную резку начинают с кромки или с середины листа. В последнем случае вначале прорезают отверстие. Затем, наклонив электрод так, чтобы кратер был расположен на торцовой кромке реза, оплавляют ее (рис, 64). Если
[c.76]
При сварке алюминиевых сплавов больших толщин и с высокой производительностью применяют трехфазную дугу и неплавнщиеся вольфрамовые электроды. Источники питания для такого вида сварки также имеют падающие внен1пие характеристики и позволяют регулировать режим с помощью переключателя ступеней или подмагничиваемых шунтов. Здесь также необходима компенсация постоянной составляющей путем включения батареи конденсаторов в сварочную цепь. Как правило, схему источника питания комплектуют осциллятором и системой заварки кратера.
[c.150]
Гасить дугу следует выключением сварочного тока кнопкой, расположенной на горелке, предварительно заплавив кратер. [c.108]
При автоматической сварке дефекты возникают вследствие колебания напряжения в сети, проскальзывания проволоки в подающих роликах, неравномерной скорости сварки из-за люфтов в механизме передвижения сварочной головки, неправильного угла наклона электрода, протекания жидкого металла в зазор. При ручной и полуавтоматической сварках дефекты могут быть вызваны недостаточной квалификацией сварщика, нарушением технологических режимов, плохим качеством электродов и других сварочных материалов. Нарушение формы и размеров шва нередко свидетельствуют о наличии таких дефектов, как наплывы (натеки), подфезы, прожоги и незаверенные кратеры. [c.135]
Внешнему осмотру и измерению размеров шва подлежат основной металл и все швы по всей.длине. При проверке выявляются поверхностные дефекты и отклонения от заданных размеров.

Сварочная ванна (рис. 124) имеет характерную форму, вытянутую в направлении сварки. В головной части ванны расположен канал (кратер) 3. Это область наиболее яркого свечения. На передней стенке канала существует слой расплавленного металла, испытывающий постоянные возмущения. Здесь наблюдается характерное искривление передней стенки в виде ступеньки, которая периодически перемещается по высоте канала. Удаление расплавленного металла с передней стенки осуществляется при перемещении ступеньки сверху вниз. Перенос расплавленного металла из головной части ванны в хвостовую происходит по боковым стенкам в горизонтальном направлении. В хвостовой части ванны 4 расплавленный металл завихряю-щимися потоками поднимается вверх и частично выносится на поверхность сварочной ванны.
[c.239]
Для ручной сварки алюминиевых сплавов, цветных металлов и легированных сталей при переменном токе выпускают установки УДГУ-302у1 УДГ-501-1. Они обеспечивают компенсацию постоянной составляющей сварочной цепи, плавную регулировку сварочного тока, заварку кратера и комплектуются тремя горелками серии ГР. Для увеличения радиуса действия сварочного аппарата имеется съемный переносной блок поджигания дуги, в котором размещены газовый клапан, возбудитель-стабилизатор дуги и дистанционный регулятор сварочного тока.
[c.165]
Другая схема (рис. 3.47) предусмалривает использование 2 электродов. Обрывать дугу следует постепенным ее удлинением, а при автоматической сварке — уменьшением силы сварочного тока. Для предупреждения окисления вольфрама и защиты расплавленного металла в кратере [c.132]
Повреждения, вызванные несоответствием сварочных материалов, характеризуются образованием и развитием трещин I — IV типов в металле швов сварных соединений. Так, в сварных соединениях эксплуатирующихся паропроводов периодически выявляются кристаллизационные трещины, образовавшиеся при сварке швов 09X1МФ. Причиной их возникновения обычно служит неблагоприятное сочетание химического состава наплавленного металла (например, повышенное содержание серы при пониженном количестве марганца Мп подкладном кольце с плотной посадкой, сварка на повышенных токовых режимах с незаполненными кратерами при обрывах дуги и др.). [c.105]
Что представляет собой дефект называемый кратер шва
Виды дефектов сварочных швов
В силу разных обстоятельств сварочные стыки могут иметь повреждения, влияющие на их прочностные характеристики. Все виды дефектов сварных соединений разделяются на три основные группы:
- наружные дефекты. К данной группе относят неравномерность формы стыкового соединения, наплывы, трещины, прожоги металла, подрезы шва, кратеры и другие изъяны, возникающие на поверхности. Обнаружить их можно при визуальном осмотре;
- внутренние дефекты. Это может быть некачественное сплавление металла, пористость и трещины, сторонние включения (оксидные, шлаковые и неметаллические) и другие, находящиеся внутри шовного соединения;
- сквозные дефекты. Сюда относят трещины, подрезы, прожоги и другие повреждения, которые изнутри проходят на внешнюю поверхность сквозь шовное соединение.
Дефекты любого вида не допускаются в сварных соединениях и подлежат устранению, особенно касается это случаев, когда металлоконструкции выступают составляющими элементами несущих конструкций и должны выдерживать интенсивные нагрузки.
youtube.com/embed/hHXBolW6RnU?feature=oembed» frameborder=»0″ allow=»accelerometer; autoplay; encrypted-media; gyroscope; picture-in-picture» allowfullscreen=»»/>
Причины возникновения дефектов
Есть два типа факторов, влияющих на качество сварочных работ:
- Объективные — имеющие отношение к свойствам свариваемых материалов, поведению металлов в условиях, диктуемых технологическим процессом. Недаром одной из важных характеристик любого сплава является свариваемость. Иногда возникает необходимость сварить материалы с плохой свариваемостью. Такие задачи иногда ставятся в мелкосерийном или единичном производстве. Даже при полном соблюдении требований технологического процесса может сохраняться определенный процент брака, который приходится официально считать допустимым.
- Субъективные — зависящие от исполнителей. Причем к исполнителям следует относить не только рабочих, выполняющих сварку, но и технологов, которые несут ответственность за правильность параметров технологического процесса, верный выбор оборудования и режимов сварки.
Основными субъективными причинами возникновения дефектов сварочных швов являются:
- ошибки при подготовке свариваемых поверхностей;
- применение инструмента, отличного от указанного технологом;
- неисправность сварочного инструмента;
- малый опыт работы и низкая квалификация сварщика;
- отступление от требуемых режимов сварки.
Характеристики и причины основных дефектов сварки
Не в каждом случае качество сварки соответствует установленным требованиям. Классификация дефектов сварных соединений в полном составе изложена в ГОСТ 30242-97. Но среди всех обозначенных в документе изъянов выделяют основные, которые чаще обычного выявляются при контроле и обследовании соединительных стыков.
Трещины
Для сварочных швов наибольшую опасность представляют трещины. Они способны спровоцировать мгновенное разрушение металлических конструкций и привести к трагическим последствиям.
Причинами появления трещин могут быть:
- неправильное расположение стыков;
- резкое охлаждение места сварки;
- неправильный выбор материалов;
- кристаллизация металла вследствие чрезмерно высоких температур.
По размеру различают микро- и макротрещины, по типу образования – поперечные, продольные и радиальные.
Вне зависимости от видов и причин возникновения трещины – это недопустимые дефекты сварных соединений металла.
Подрезы
Это образующиеся на наружной поверхности шовного валика продольные углубления. Если на шве есть подрез, то в месте его появления уменьшается сечение шва, а также образуется очаг концентрации напряжения.
Превышенная величина сварочного тока – основная причина появления таких дефектов. Довольно часто наблюдаются подрезы в горизонтальных швах.
Наплывы
Это натекший на поверхность избыток металла, который не имеет должного сплавления с соединяемой поверхностью. Часто наплыв возникает при сварке стыковых или угловых швов в горизонтальном положении. Образуется при недостаточном прогреве основного металла, избытка присадочного материала, наличия окалин на соединяемых кромках.
Прожоги
Такие дефекты являют собой сквозное отверстие, возникшее вследствие вытекания из сварочной ванны расплавленного металла. В данном случае с другой стороны отверстия как правило образуется натек.
Прожог может быть вызван слишком медленным передвижением электрода по линии сваривания, повышенным сварочным током, неплотным прилеганием к основному металлу прокладки или же недостаточной ее толщиной, большим зазором между соединяемыми кромками.
Непровары
Если на сварочном шве обнаружены локальные несплавления между основным и наплавленным металлом, то дефект такого типа называют непровар. Он существенно понижает прочностные свойства шва и соответственно всей конструкции.
Причины непроваров состоят в следующем: чрезмерно высокая скорость сваривания, некачественная подготовка кромок к сварному процессу, наличие ржавчины, окалин и других загрязнений на соединяемых поверхностях.
Кратеры
Образующиеся вследствие обрыва сварочной дуги углубления в соединительном валике называют кратерами. Такие изъяны существенно уменьшают сечение стыка, что негативно сказывается на прочности. Кратер опасен тем, что внутри него могут находиться усадочные рыхлости, приводящие к появлению трещин.
Свищи
Поверхностные дефекты в виде полости. Понижают прочность соединительного стыка и провоцируют образование трещин. Свищи имеют произвольную форму, могут возникать как на внешней поверхности, так и внутри шва.
Пористость
Поры – это заполненные газами полости, образующиеся при повышенном газообразовании внутри металла. Возникают при наличии разнообразных загрязнений на свариваемых поверхностях, при повышенной скорости сварки, а также повышенной вместительности углерода в используемом присадочном материале.
Посторонние включения
Качество шва существенно ухудшают сторонние включения – оксидные, шлаковые, вольфрамовые, флюсовые и другие включения. Главная ошибка, приводящая к их наличию – неправильный режим сварки. Любое из присутствующих включений понижает прочность и надежность соединения и подлежит устранению.
Дефекты группы 1 — Трещины
Трещины
Трещины (100; Е) — дефект сварного соединения в виде разрыва в сварном шве и (или) прилегающих к нему зонах или — несплошность вызванная местным разрывом шва, который может возникнуть в результате охлаждения или действия нагрузок (ГОСТ 30242)
Трещины являются недопустимыми дефектами, так как являются концентратором напряжения и очагом разрушения. Это самые опасные дефекты сварного соединения, часто приводящие к его разрушению. Проявляются они в виде разрыва в сварном шве или в прилегающих к нему зонах. Сначала трещины образуются с очень малым раскрытием, но под действием напряжений их распространение может быть соизмеримо со скоростью звука, в результате чего происходит разрушение конструкции.
Чаще всего трещины проявляются при сварке высокоуглеродистых и легированных сталей в результате быстрого охлаждения сварочной ванны. Вероятность появления трещин увеличивается при жестком закреплении свариваемых деталей.
Образованию трещин способствует повышенное содержание углерода в расплавленном металле, а также кремния, никеля и особенно вредных примесей серы, фосфора и водорода.
Причинами образования трещин чаще всего является несоблюдение технологии и режимов сварки. Это может проявляться, например, в неправильном расположении швов в сварной конструкции, что приводит к высокой концентрации напряжений. Большие напряжения в сварных конструкциях могут возникнуть также при несоблюдении заданного порядка наложения сварных швов.
Кстати, более подробно об образовании трещин в сталях мы уже писали в статье.
Удаление трещин. Поверхностные трещины в сварных конструкциях устраняются в следующем порядке: сначала засверливают концы трещины, чтобы она не распространялась дальше по шву, затем трещину удаляют механическим путем или строжкой, после чего место удаления дефекта зачищают и заваривают.
Внутренние трещины (как впрочем, и остальные внутренние дефекты) удаляют механическим способом или строжкой с последующей заваркой данного участка.
По происхождению трещины подразделяются на:
- холодные трещины
- горячие трещины
Холодные трещины
Холодные трещины возникают при температурах ниже 300°С, то есть сразу после остывания шва. Кроме того, холодные трещины могут возникнуть и через длительный промежуток времени. Причиной появления холодных трещин являются сварочные напряжения, возникающие во время фазовых превращений, приводящих к снижению прочностных свойств металла. Причиной появления холодных трещин может стать растворенный атомарный водород, не успевший выделиться во время сварки. Причинами попадания водорода могут служить непросушенные швы или сварочные материалы, нарушения защиты сварочной ванны. Холодные трещины на изломе имеют чистый блестящий вид кристаллов.
Горячие трещины
Горячие трещины появляются в процессе кристаллизации металла при температурах 1100 — 1300°С вследствие резкого снижения пластических свойств и развития растягивающих деформаций. Появляются горячие трещины на границах зерен кристаллической решетки. Появлению горячих трещин способствует повышенное содержание в металле шва углерода, кремния, водорода, никеля, серы и фосфора. Горячие трещины могут возникать как в массиве шва, так и в зоне термического влияния. Распространяться горячие трещины могут как вдоль, так и поперек шва. Они могут быть внутренними или выходить на поверхность. Горячие трещины на изломе имеют желтовато — оранжевый оттенок.
По размерам трещины подразделяются на:
- макроскопические
- микроскопические
Макроскопические трещины
Макроскопические трещины или просто трещины (100; Е) — видны невооруженным глазом или через лупу небольшого (2 — 4х — кратного) увеличения при визуальном контроле
Микроскопические трещины
Микроскопические трещины или микротрещина (1001) — трещина микроскопических размеров, которую обнаруживают физическими методами не менее чем при пятидесятикратном увеличении
По расположению трещины подразделяются на:
- продольные
- поперечные
Продольная трещина
Продольная трещина (101; Еа) — трещина сварного соединения, ориентированная вдоль оси сварного шва
Продольная трещина может располагаться :
— в металле сварного шва (1011)
— на границе сплавления (1012)
— в зоне термического влияния (1013)
— в основном металле (1014)
Поперечная трещина
Поперечная трещина (102; Eb) — трещина, ориентированная поперёк оси сварного шва.
Поперечная трещина может располагаться:
— в металле сварного шва (1021)
— в зоне термического влияния (1023)
— в основном металле (1024)
Также согласно ГОСТ 30242 трещины бывают:
- радиальные
- в кратере
- раздельные
- разветвленные
Радиальные трещины
Радиальные трещины (103; Е) — трещины радиально расходящиеся из одной точки. Трещины данного типа известны как звездоподобные трещины.
Радиальные трещины могут располагаться:
- в металле сварного шва (1031)
- в зоне термического влияния (1033)
- в основном металле (1034)
Трещина в кратере
Трещина в кратере (104; Ес) — трещина в кратере сварного шва. Конечно определение звучит абсурдно, но по — другому и мы придумать не можем.
Трещина в кратере бывает:
- продольной (1045)
- поперечной (1046)
- звездоподобной (1047)
Раздельные трещины
Раздельные трещины (105; Е) — группа трещин, которые могут находиться:
- в металле сварного шва (1051)
- в зоне термического влияния (1053)
- в основном металле (1054)
Разветвленные трещины
Разветвленные трещины (106; Е) — группа трещин, возникших из одной трещины.
Разветвленные трещины могут располагаться:
- в металле сварного шва (1061)
- в зоне термического влияния (1063)
- в основном металле (1064)
Причины появления дефектов
Каждый из всех встречающихся дефектов возникает вследствие конкретных факторов. При этом выделяют причины образования дефектов сварных соединений общего характера:
- использование некачественных расходных материалов для сваривания элементов;
- несоблюдение сварочных технологий;
- низкое качество металла, из которого создаются конструкции;
- некачественное или неисправное оборудование;
- неправильный режим сварки;
- технологические ошибки, вызванные низкой квалификацией сварщика.
Чтобы металлоконструкции получались качественными и выносливыми, следует строго соблюдать нормы сваривания и доверять работы профессиональным сварщикам.
Устранение и предотвращение сварочного дефекта
Устраняя сварочный дефект в виде несплавления, очищают корень в месте изъяна и проводят сварку ещё раз. Во время установок важных конструкций дефектный участок срубают или вырезают, а затем сваривают заново.
Следующие методы помогут предотвратить появление непровара в сварных швах:
Разделка кромок
Метод, когда заранее разделывают кромки под определённым углом. При этом оставляют свободный контакт электрода к корню шва и притупление. В нужном месте очищают грязь, окисел, ржавчину и обезжиривают поверхность. Подготовленные детали ровно помещают в одной плоскости, оставляя между кромками зазор.
Более подробно про подготовку металла под сварку вы можете прочитать тут.
Тепловая подача
Способ, когда скорость проведения сварки устанавливают так, чтобы металл кромок успевал плавиться, поскольку во время быстрого перемещения электрода теплоты хватит лишь для шовного образования. Сваривая неоднократно детали, удаляют шлак после всех проходов, так как он помешает плавлению предшествующего шва.
Поочерёдное следование режимам сварки
Установка среднего или высокого значения тока, которая будет соответствовать толщине и металлу подготовленных деталей. Для избегания непроваров на концах шва и при замене электрода у инверторов регулируют функцию повышения напряжения на недолгое время. Для предотвращения несплавления на старом сварочном устройстве без регулирования параметров дуги выбирают время для того, чтобы выявить минимальные колебания сетевого напряжения.
Правильное положение электрода
При сваривании дугу проводят по оси стыка для одинакового прогревания обеих кромок. Не соблюдая этого, кромка не сплавится со швом. Под углом 5-20 градусов электрод перемещают вперёд. При сварке угловых швов «лодочкой» электрод держат на одинаковом расстоянии от поверхности деталей. Когда заготовки соединяют в несимметричную «лодочку», электрод располагают под углом 30 градусов к одной из плоскостей деталей.
Сваривают детали на высоком токе, имеющим прямую или обратную полярность. Во время сварки током с обратной полярностью используют короткую дугу, из-за чего могут появиться подрезы. А из-за большого диаметра электрода частицы шлака могут попасть в кромочный промежуток.
Тугоплавкие оксиды
Это компоненты, образующиеся при нагреве сплавов и легированной стали. Если неправильно сварить элементы ,то шлак остается внутри шва, образуя дефекты в виде непроваров. Чтобы предотвратить это, нужен кислород для образования оксидов. Пользуясь плавящимся электродом, стоит подобрать устройство с покрытием, которое будет соответствовать виду металла.
Теперь преодоление местного непровара не должно пугать начинающих сварщиков. Главное — не создать причин, способствующих его образованию. В случае, если его избежать не удалось, можно устранить дефект, но лучше попытаться предотвратить возникновение несплавления.
[Всего: 0 Средний: 0/5]
Методы выявления дефектов
Выявление дефектов сварных соединений осуществляется следующими способами:
- визуальный осмотр и обмер стыковочных швов;
- испытания стыков на непроницаемость;
- определение дефекта сварного соединения специальными приборами;
- испытания образцов на прочность в лабораторных условиях.
Осмотр сварочного шва осуществляется только после очистки его от шлака, устранения застывших брызг металла и других типов загрязнений. Проверке подлежат размеры и правильность формы соединений, наличие или отсутствие прожогов, кратеров, трещин, свищей и других погрешностей.
Испытание непроницаемости позволяет выявить дефекты сварных соединений трубопроводов, например, поры, трещины, сквозные непровары. Проверяются конструкции несколькими способами:
- обдуванием или заполнением швов воздухом;
- поливом струей воды или наполнение отсеков водой под давлением;
- смазыванием швов керосином.
Если в ходе проверки обнаружен дефект, то деталь возвращается на дополнительную обработку.
Восемь советов для уменьшения вероятности образования подрезов в сварном шве
Ниже приведены рекомендации, которые помогут уменьшить вероятность образования подрезов при сварке изделий из труб, листов, швеллеров, уголков и т.д.
Правильное тепловложение
Одной из самых главных причин образования подрезов в сварных швах является большая величина нагрева при выполнении сварки вблизи свободных краев детали в результате чего происходит более глубокое проплавление одной из кромок, что приводит к образованию канавки, которая остается после затвердевания металла сварочной ванны. Это может привести к перегреву и расплавлению близлежащего основного металла или ранее наложенного металла шва. Для предотвращения необходимо следить за тепловложением при этом уменьшая сварочный ток при приближении к более тонким участкам детали или к свободному краю изделия.
Правильный угол электрода
Как известно угол электрода играет очень важную роль для предотвращения образования дефектов при сварке. Если выполнить сварку с неправильным углом, который будет направлять больше тепла к свободным кромкам изделия, вероятность образования подреза увеличивается в несколько раз. В связи с чем необходимо использовать правильный угол, чтобы направлять больше тепла на более толстую часть детали.
Правильная скорость сварки
Сварка с большой скоростью является еще одной причиной образования подрезов на сварных швах. При большой скорости некоторая часть основного метала переходит в расплавленный металл сварного шва и в результате быстрой кристаллизации остаются углубления (канавки) по краям. Поэтому рекомендуется производить сварку в умеренном темпе потому что слишком маленькая скорость сварки не дает удовлетворительных результатов. Таким образом, конкретным условиям сварки соответствует определенный диапазон скорости, в пределах которого возможно получение швов без подрезов.
Правильный выбор газовой защиты
При сварке полуавтоматом неправильный выбор защитных газов также является одной из основных причин подрезов при сварке. Сварщик должен быть уверен, что использует правильную сварочную смесь, которая подходит именно для сварки этого металла. Применение смесей углекислоты с инертными газами обеспечивает качественные результаты при сварке углеродистых сталей.
Правильная техника сварки
Причиной образования подрезов при сварке также является попытка сварщика выполнять сварку с чрезмерными поперечными колебаниями электрода. Рекомендуется выполнять сварку с минимальными поперечными колебаниями – так называемым «ниточным швом». Размер колебаний не должен превышать допустимых значений, потому что это значительно увеличивает вероятность образования подреза в сварном шве. Для предотвращения образования данного дефекта сварного шва необходимо либо уменьшить ширину поперечных колебаний электрода, либо выполнять многослойный шов вместо однослойного.
При ручной дуговой сварке покрытыми электродами рекомендуемый размах поперечных колебаний должен составлять не более 2-3 диаметров электрода.
Правильное пространственное положение при сварке
Сварка в горизонтальном или вертикальном положении в свою очередь увеличивает вероятность образования подреза шва. В данном случае, канавка образуется из-за недостаточного заполнения вдоль зоны сплавления шва. Если есть возможность, сварку необходимо выполнять в нижнем положении.
Использовать многослойную сварку
Это самый лучший вариант для предотвращения образования подрезов при сварке. Техника наложения многослойного шва подразумевает выполнение всех вышесказанных рекомендаций и помогает добиться качественных сварных соединений с гарантированными механическими свойствами.
Использование предварительного подогрева
Предварительный подогрев снижает скорость кристаллизации металла и улучшает смачиваемость за счет меньшей разности температур между сильно нагретым металлом сварочной ванны и слабо нагретым основным металлом.
Способы устранения дефектов
Любой сварочный процесс сопровождается образованием дефектов, вне зависимости выполняется он инвертором, полуавтоматом, трансформатором или другим оборудованием. При этом выделяют недопустимые и допустимые дефекты сварных соединений, по сложности которых определяется пригодность или непригодность конструкции к дальнейшей эксплуатации.
Способы устранения дефектов сварных соединений выбираются с учетом типа обнаруженного повреждения:
- прожоги исправляют тщательной зачисткой стыка с последующей его заваркой;
- для устранения подрезов выполняется наплавка тонкого соединения по всей линии дефекта;
- исправление трещины осуществляется методом ее полного рассверливания, вырубкой шва на проблемном участке, очисткой поверхностей и повторным завариванием с соблюдением сварочной технологии и действующих нормативов;
- непровары удаляются путем их вырезания и повторного сваривания;
- свищи и кратеры вырезаются до достижения основного металла, после чего по-новому завариваются;
- наплывы аккуратно срезаются, но при этом обязательно следует проверить срез на предмет наличия непровара;
- деформация при сварке устраняется термическим или термомеханическим способом;
- все типы дефектов с посторонними включениями устраняют вырезкой и завариванием.
Если в ходе обследования обнаружены технологические дефекты сварных соединений труб, то устранять их следует строго в соответствии нормативных требований одним из методов:
- механическим без последующей заварки;
- механическим с завариванием места выборки;
- вырезкой участка трубы, на котором присутствует дефект;
- полным удалением шовного соединения и выполнением нового.
При проверке на прочность и герметичность газораспределительных сетей разрешается исправлять дефекты сварных соединений газопроводов в случае, когда сварочный процесс выполнялся дуговой сваркой и не допускается при сваривании газовой сваркой.
Видовое разнообразие дефектов
Неопытный сварщик в процессе создания сварных стыков полуавтоматом может столкнуться с разными видами дефектов сварки. Они отличаются внешними характеристиками и появляются вследствие нарушения технологии сварки: ТИГ, электродуговая ручная сварка, автомат и т.п.
Причины дефектов сварных швов.
Такие проблемы важно хорошенько изучить, что позволит не допускать порчу свариваемых деталей при ручной дуговой сварке и реализации иных технологий создания соединений металлоконструкций в дальнейшем.
- наружные: трещины, подрезы, наплывы, кратеры, окалины, сварные раковины;
- внутренние: пористая структура, недостаточная провариваемость, посторонние включения;
- сквозные: трещины, прожоги.
Наружные недостатки имеют такое название, так как находятся на лицевой стороне соединения и видимы глазу. Для их обнаружения достаточно провести визуальный осмотр детали. Внутренние дефекты располагаются внутри сварочного соединения, поэтому сразу не заметны.
Определить наличие данной проблемы можно с помощью дефектоскопии сварных швов, включая ультразвуковую, механическую и рентген обработку. Наиболее катастрофичны сквозные изъяны, поскольку их устранение не всегда осуществляется на 100%.
Наружные дефекты
При нарушении технологии сварки и применении расходного материала неважного качества можно получить следующие дефекты сварки: наплывы, подрезы, незаваренные кратеры, поверхностные поры, прожоги, трещины и т. п.
Наплывы являются результатом стекания расплавленного металла сварной проволоки на нерасплавленный основной металл конструкции или предварительно осуществленный валик.
Такие недостатки могут иметь местный характер и проявляться отдельными зонами, а могут приобретать вытянутую форму и занимать приличную площадь на металлоизделии.
Основная причина появления наплывов заключаются в следующем:
- сварщик неверно выставил силу тока при длинной дуге и ошибся с подбором скорости работы оборудования;
- был выбран чрезмерно большой наклон плоскости, на которую накладывался сварной шов;
- электрод неправильно вели, или он изменил свое первоначальное положении при выполнении кольцевых швов под флюсом;
- сварщик имел недостаточный опыт или работал в неудобном пространственном положении: вертикальном или горизонтальном.
Подрезы являются углублениями на поверхности основного металла, идущими по краям сварного шва. Глубина подреза может колебаться в пределах 0,1-1 мм.
Причинами, по которым образуются такие дефекты сварных соединений, являются:
- ток чрезмерно высокой силы;
- напряжение дуги свыше нормы;
- неудобная поза сварщика в пространственном плане;
- небрежно выполненная сварка.
Наличие такой погрешностей опасно, поскольку подрезы способны уменьшить рабочую толщину металла в местах соединения металлических деталей, спровоцировать появление местной концентрации напряжений от рабочих нагрузок и стать причиной деформации сварных швов со временем.
Наименования дефектов сварного шва.
Также отметим, что подрезы стыковых и угловых швов, располагающиеся поперек действующих на них сил, могут вызвать резкое снижение вибрационной прочности соединений.
Кратер ‒ вмятина, появляющаяся в случае резкого обрыва дуги в конце сварки. Очень часто такая проблема возникает при создании коротких швов.
Размер кратера определяется величиной сварного тока:
- при ручном методе сварки его диаметр составляет 3-20 мм;
- при автоматической сварке кратер приобретает форму удлиненной канавки.
Прожоги представляют собой проплавление основного или наплавленного металла, на котором иногда образуются сквозные отверстия.
Причиной возникновения данных дефектов являются:
- недостаточное притупление кромок, большой зазор между ними;
- завышенный сварочный ток или мощность горелки на фоне невысоких скоростей сварки;
- недостаточного поджатия флюсовой подушки, медной подкладки при автоматической сварке;
- при чрезмерно длительной сварке, недостаточном усилии сжатия, при наличии загрязнений на поверхностях сварных деталей, проволоки при точечной и шовной контактной сварке.
Особенно часто можно наблюдать прожоги при сварке тонкого металла, при организации первого прохода многослойного сварного шва. Такие дефекты можно устранить, но даже после этого соединение не приобретает удовлетворительные характеристики и эстетический вид.
Поэтому стоит изначально прилагать все усилия, чтобы не допустить появления подобных дефектов на поверхности сварного шва.
На заметку! Отдельно стоит отметить такой дефект, как трещина сварного соединения. Ответим, что называют трещиной: нарушение плоскости металла, спровоцированное охлаждением, воздействием нагрузок. Она может относиться и к наружным, и к внутренним дефектам сварки.
Обнаружить наружные дефекты на сварных швах можно с помощью визуально-измерительного контроля, капиллярной дефектоскопии, а также иными способами неразрушающего контроля: рентген, ультразвук.
Внутренние дефекты
Разновидности сварных соединений.
К внутренним дефектам сварки причисляют:
- Холодные трещины. Появляются исключительно после остывания и затвердевания сварного соединения вследствие его несоответствия действующим нагрузкам.
- Горячие трещины. Проявляются в момент нахождения металла сварного соединения в состоянии между температурой плавления и отвердевания ввиду применения низкокачественной присадки, неверной технологии заварки кратера, из-за резкой остановки сварочного процесса, вследствие прожогов при сварке.
Такие дефекты могут иметь несколько типов расположения: вдоль и поперек соединения металлических деталей.
- Поры. Могут возникнуть при любой технологии сварки из-за наличия загрязнений на поверхности соединяемых деталей, неважной защиты сварной ванны потоком газа, маслом, краской, сварки несовместимых сплавов, ржавчины и окисления металла. Поры различаются по размерам и, зачастую, имеют хаотичное распределение по сварному шву: располагаются как внутри соединения, так и на его поверхности.
Устранение выявленных дефектов сварочных швов, незаметных глазу, необходимо осуществлять после определения основных причин, спровоцировавших появление дефекта, вне зависимости от того факта, осуществлялась технология лазерной сварки или применялся иной вид выполнения сварочных операций.
Это позволит подобрать наиболее эффективный метод борьбы с проблемой и не допустить таких ошибок в будущем.
Сквозные
Сквозные дефекты представляют собой отверстия в металлической детали, которое образуется вследствие неправильной сварки. Мастер выбирает неверный режим работы сварочного аппарата и прожигает металл насквозь.
Дефекты контактной сварки сквозного типа – это:
- подрез при выполнении сварки;
- трещина;
- прожог.
Методы контроля сварных соединений
Тот факт, что влияние дефектов на качество сварной металлоконструкции максимизирует риски разрушения изделий доказывать не нужно. Чтобы в процессе сваривания получать действительно надежные, прочные и выносливые конструкции, после завершения работ должен проводиться контроль качества сварных соединений.
Осуществляется контроль сварочных швов поэтапно:
- предварительный. Включает проверку марки металла, качества заготовок, кислорода, присадочной проволоки и других расходных материалов;
- контроль в ходе сварочных работ. Подразумевает постоянные проверки режима сварки, исправности оборудования, осмотр швов и измерение их специальными шаблонами. При выявлении отклонений от установленных стандартов сразу же можно провести удаление дефектов сварных соединений;
- контроль готовой конструкции. Внешние дефекты можно увидеть при обычном осмотре. При необходимости стыки проверяются на плотность, а также подвергаются другим испытаниям.
Все методы контроля сварных соединений разделяются на две группы – разрушающие и неразрушающие. Как правило для выявления дефектов применяются неразрушающие методы, к которым принадлежат:
- внешний осмотр:
- ультразвуковая дефектоскопия;
- магнитный контроль;
- цветная дефектоскопия;
- радиационная дефектоскопия;
- капиллярная дефектоскопия;
- контроль стыков на проницаемость и другие методы обнаружения дефектов сварных соединений.
Методы разрушающего контроля подразумевают испытания отобранных образцов и применяются в основном при необходимости получить параметры сварного шва и зоны термического влияния. Контроль осуществляется химическим анализом, механическими и металлографическими испытаниями.
Подведем итоги
Дефекты сварочных швов возникают при нарушении технологии сварки и ставят под угрозу стабильность сварочного шва и функциональность всей металлоконструкции.
По этой причине уважающему себя мастеру важно выучить основные дефекты швов ‒ появления пор, наплывов, прогаров и т.п ‒ и причины их образования при сварочном процессе.
Это позволит подобрать максимально эффективное решение для устранения недостатков соединений при точечной сварке, использовании лазера, электрической дуги, аргона и т.п.
youtube.com/embed/qupoowu67vk?feature=oembed» frameborder=»0″ allow=»accelerometer; autoplay; clipboard-write; encrypted-media; gyroscope; picture-in-picture» allowfullscreen=»»/>Функции пуска и остановки
X8 MIG Welder Руководство 1902370, ред. 2020
Функции пуска и остановки
Touch Sense Ignition
Функция Touch Sense Ignition сводит к минимуму разбрызгивание и стабилизирует дугу непосредственно после зажигания.
Для включения или выключения функции Touch Sense Ignition с помощью панели Control Pad выберите Настройки > Логика пуска и останова > Touch Sense Ignition.
Нарастание тока
Функция мощности постепенно повышает мощность сварки / скорость подачи проволоки до необходимого уровня. Пользователь включает или выключает функцию и устанавливает начальное значение мощности / скорость подачи проволоки для функции нарастания мощности.
Для регулировки функции нарастания мощности с помощью панели Control Pad выберите Настройки > Логика пуска и останова > Нарастание мощности. При выборе ВКЛ. на экране появляются опции для регулировки Время и Уровень.
Горячий старт
При использовании функции горячего старта сварка начинается со значениями параметров, отличающимися от значений, которые используются для остальной части сварочной работы. По истечении установленного периода времени значения параметров функции горячего старта автоматически устанавливаются равными значениям обычной сварки. Эту функцию можно использовать, например, при сварке материалов большой толщины, когда использование более высокой мощность (тепловложение) в начале сварки помогает обеспечить высокое качество сварного шва.
При использовании логики 2T кнопки сварочной горелки функция горячего старта применяется в течение установленного периода времени.
Рисунок: Горячий старт в режиме 2T
1. | Кнопка нажата. |
2.![]() | Кнопка отпущена. |
При использовании логики 4T или WP Switch функция горячего старта включается при нажатии кнопки и выключается при отпускании кнопки.
Рисунок: Горячий старт в режиме 4T/WP Switch
1. | Кнопка нажата.![]() |
2. | Кнопка отпущена. |
3. | Кнопка нажата. |
4.![]() | Кнопка отпущена. |
Для регулировки функции горячего старта с помощью панели Control Pad выберите Настройки > Логика пуска и останова > Горячий старт. При выборе ВКЛ. на экране появляются опции для регулировки Время и Уровень. По умолчанию функция горячего старта выключена.
Заварка кратера
При сварке с высокой мощностью в конце сварного шва обычно образуется кратер. Функция заварки кратера постепенно снижает мощность сварки / скорость подачи проволоки в конце выполнения сварочной работы, чтобы кратер можно было заполнять при пониженном уровне мощности.
При использовании логики 2T кнопки сварочной горелки отпускание кнопки запускает последовательность заварки кратера.
Рисунок: Заварка кратера в режиме 2T
1. | Кнопка нажата. |
2. | Кнопка отпущена. |
При использовании логики 4T или WP Switch кнопки сварочной горелки нажатие кнопки во время сварки (в случае использования WP Switch нажатие продолжительностью > 0,5 с) запускает последовательность заварки кратера. Система поддерживает конечный уровень мощности заварки кратера до отпускания кнопки горелки. Отпускание кнопки немедленно останавливает последовательность заварки кратера.
Рисунок: Заварка кратера в режиме 4T/WP Switch
1. | Кнопка нажата. |
2.![]() | Кнопка отпущена. |
3. | Кнопка нажата. |
4. | Кнопка отпущена. |
Для регулировки функции заварки кратера с помощью панели Control Pad выберите Настройки > Логика пуска и останова > Заварка кратера. При выборе ВКЛ. на экране появляются опции для регулировки Время и Начальный уровень и Конечный уровень.
• | Время: Для режима 2T этот параметр определяет период времени действия последовательности заварки кратера. Для режима 4T/WP Switch этот параметр определяет время перехода от начального уровня для конечного уровня. |
• | Начальный уровень: уровень мощности на момент начала заварки кратера.![]() |
• | Конечный уровень: уровень мощности на момент окончания заварки кратера. |
При использовании 4T Timer нажатие кнопки сварочной горелки (в случае использования WP Switch нажатие продолжительностью > 0,5 с) запускает последовательность заварки кратера, которая выполняется не менее периода времени, установленного для таймера 4T Timer, даже если кнопка сварочной горелки будет отпущена до истечения этого периода.
Подача газа перед сваркой
Функция подачи газа перед сваркой обеспечивает защиту заготовки защитным газом в момент зажигания дуги, чтобы расплавленный металл не контактировал с воздухом. Это очень важно для таких материалов, требующих хорошей газовой защиты, как нержавеющая сталь, алюминий и титан.
При использовании логики 2T кнопки сварочной горелки функция подачи газа перед сваркой применяется в течение установленного периода времени. При использовании логики 4T или WP Switch функция подачи газа перед сваркой выключается при отпускании кнопки.
Для регулировки подачи газа перед сваркой с помощью панели Control Pad выберите Настройки > Логика пуска и останова > Время подачи газа перед сваркой.
Подача газа после сварки
Функция подачи газа после сварки обеспечивает защиту заготовки защитным газом после гашения дуги, чтобы расплавленный металл не контактировал с воздухом. Заготовка будет защищена защитным газом до остывания до приемлемой температуры. Это особенно важно для таких материалов, требующих хорошей газовой защиты, как нержавеющая сталь, алюминий и титан.
При использовании логики 2T кнопки сварочной горелки функция подачи газа после сварки применяется в течение установленного периода времени. При использовании логики 4T или WP Switch функция подачи газа после сварки выключается при отпускании кнопки, но не менее установленного периода времени.
Для регулировки функции подачи газа после сварки выберите Настройки > Логика пуска и останова > Подача газа после сварки. Выберите Установить время > Время подачи газа после сварки, чтобы установить время работы функции подачи газа после сварки, или Установить по умолчанию, чтобы выбрать предварительно установленное время.
Замедленный старт
Функция замедленного старта устанавливает скорость подачи проволоки до зажигания сварочной дуги, т. е. до того, как присадочная проволока коснется заготовки. После зажигания дуги скорость подачи проволоки автоматически переключается на обычную установленную пользователем скорость. Функция замедленного старта всегда включена.
Для регулировки уровня замедленного старта с помощью панели Control Pad выберите Настройки > Логика пуска и останова > Уровень замедленного старта. Диапазон регулировки составляет 10 %…90 %.
Рисунок: Замедленный старт
Конечный шаг МПП
Непосредственно после гашения дуги механизм подачи проволоки подает несколько миллиметров присадочной проволоки, чтобы проволока не прилипала к контактному наконечнику.
Для включения или выключения функции завершения подачи проволоки с помощью панели Control Pad выберите Настройки > Логика пуска и останова > Завершение подачи проволоки.
Окончание сварки — Cварочные работы
Окончание сварки
Правильная заварка кратера при обрыве дуги — окончание сварки — играет важную роль в сварочном процессе. В зоне кратера скапливается наибольшее количество вредных примесей, образовавшихся в процессе кристаллизация металла. В этой зоне трещины образуются наиболее часто. Если сварка закончена, то при обрыве дуги не рекомендуется резко отводить электрод от изделия. Перемещения электрода следует прекратить и до обрыва медленно удлинять дугу. Такой прием способствует заполнению кратера электродным металлом. В некоторых случаях, например при сварке низкоуглеродистой стали, кратер выводят на основной металл, в сторону от шва. Если понадобилась смена электродов или произошел случайный обрыв дуги, то ее можно возбудить на еще нерасплавленном основном металле переД кратером. Металл проплавляют на кратере. Если ведется сварка стали, которая образует закалочные структуры, т0 вывод кратера в сторону недопустим из-за возможности образования трещин.
Рис. 112. Сварка на весу
Рис. 113. Сварка на медной съемной подкладке
Рис. 114. Сварка на остающейся стальной подкладке
Рис. 115. Сварка с предварительным подварочным швом
Читать далее:
Сварочные флюсы
Сварочные электроды
Общие сведения о сварке арматуры
Противопожарные мероприятия при сварке
Безопасность труда при сварке технологических трубопроводов
Безопасность труда при сварке строительных металлических и железобетонных конструкций
Защита от поражения электрическим током при сварке
Техника безопасности и производственная санитария при сварке
Управление качеством сварки
Статистический метод контроля
Ваш отзыв
Имя | Помнить |
Сообщение | |
Обнаружение и идентификация дефектов стали во время подготовки поверхности
Покрытия сжимаются по мере отверждения, что приводит к небольшой толщине пленки на острых кромках и сварных швах, и это является классической причиной разрушения покрытий.
Ремонт дефектов, как правило, не входит в рабочие обязанности оператора установки абразивоструйной обработки, но, когда вам поручается подготовка поверхности, необходимо, чтобы обеспечивалась надлежащая адгезия покрытия и предотвращались дефекты поверхности. Оператор установки абразивоструйной обработки — единственный человек на рабочем участке, который смотрит на каждый квадратный сантиметр стальной поверхности, становясь таким образом последней линией защиты по обнаружению дефектов.
Поиск и сообщение о дефектах не только важно, но и приветствуется. Предоставление такой дополнительной услуги является хорошим способом произвести впечатление и выделиться на фоне конкурентов. Но сначала необходимо знать, что искать.
ISO 8501-3, «Подготовка стальной поверхности перед нанесением лакокрасочных материалов и относящихся к ним продуктов», сортирует дефекты на три категории:
• Сварные швы
• Кромки
• Стальные поверхности в целом
При проверке на наличие дефектов обратите особое внимание на сварные соединения, разрезы, проколы и задиры. Проведите рукой в перчатке по проблемным местам, ищите участки, за которые она может зацепиться, чтобы определить выступы. Некоторые выступы, например, брызги при сварке, могут быть удалены с помощью абразивоструйной обработки. Другие потребуют шлифовки.
Если вы оказались в таком положении, когда вас просят шлифовать выступ с помощью электроинструмента, важно не оставлять шероховатостей, заусенцев или дошлифовки на поверхности. Важно также отметить, что при шлифовании дефектов не следует уменьшать массу подложки до меньшей, чем окружающий металл, или выполнять шлифование таким образом, чтобы создавался избыточный нагрев — в обоих случаях сталь будет ослабевать. Кроме того, дефекты шлифования должны быть впоследствии проверены в ходе испытания в перчатках, чтобы убедиться в том, что в процессе работы не было создано более острых краев.
Зная, какие виды дефектов следует искать, давайте посмотрим на различные степени подготовки поверхности.
Существуют три степени для стальных поверхностей с видимыми дефектами, как указано в стандарте ISO 8501-3:
P1 Легкая подготовка: перед нанесением краски не требуется никакой подготовки или требуется только подготовка в минимальном объеме. ;
P2 Тщательная подготовка: большинство дефектов устраняется.;
P3 Очень тщательная подготовка: поверхность не имеет значительных видимых дефектов.
При принятии решения о степени подготовки убедитесь, что вы готовите поверхность в соответствии со спецификациями, особенно с учетом того, что для одного изготовления могут потребоваться различные степени подготовки, например: P1 на внутренней стороне и P3 на внешней стене.
Достижение консенсуса между всеми соответствующими сторонами относительно оценок подготовки и конкретных видимых недостатков до начала работы может сэкономить время и усилия.
Системы автоматизированного проектирования — САПР Работа в AutoCADСамоучитель Теперь мы рассмотрим пример создания этого же чертежа, но уже в относительных
полярных координатах. Однако сначала нужно удалить ранее созданные объекты
чертежа. 1. Выберите из системы меню команду Изменить? Стереть . Указатель изменит форму с перекрестия на маленький квадратик, который называется отмечающим указателем . Когда он появляется на экране, это означает, что указатель можно использовать для выбора объектов чертежа. Обратите также внимание на командное окно: в нем появился запрос на выбор объектов. 2. Поместите отмечающий указатель на одну из линий и щелкните мышью – линия превратится из сплошной в пунктирную. Этот процесс называется выделением объектов чертежа. Примечание. Для того чтобы вам было проще понять,
на какой линии находится
отмечающий указатель, AutoCAD временно выделяет ее утолщенным контуром.
В нашем случае это не существенно, однако на сложных чертежах это значительно
упрощает задачу выбора нужных объектов. 3. Проделайте то же самое с остальными линиями. 4. Нажмите Enter для завершения выделения и применения к выделенным объектам команды Стереть . Созданный вами четырехугольник будет удален с чертежа, а выполнение команды Стереть завершится. |
%PDF-1.4 % 364 0 объект > эндообъект внешняя ссылка 364 136 0000000016 00000 н 0000003918 00000 н 0000004153 00000 н 0000004180 00000 н 0000004229 00000 н 0000004265 00000 н 0000004888 00000 н 0000005001 00000 н 0000005115 00000 н 0000005228 00000 н 0000005342 00000 н 0000005455 00000 н 0000005569 00000 н 0000005683 00000 н 0000005797 00000 н 0000005911 00000 н 0000006024 00000 н 0000006199 00000 н 0000006343 00000 н 0000006516 00000 н 0000006670 00000 н 0000006750 00000 н 0000006830 00000 н 0000006911 00000 н 0000006991 00000 н 0000007071 00000 н 0000007149 00000 н 0000007229 00000 н 0000007308 00000 н 0000007388 00000 н 0000007467 00000 н 0000007547 00000 н 0000007627 00000 н 0000007706 00000 н 0000007785 00000 н 0000007865 00000 н 0000007944 00000 н 0000008024 00000 н 0000008103 00000 н 0000008182 00000 н 0000008261 00000 н 0000008341 00000 н 0000008420 00000 н 0000008499 00000 н 0000008579 00000 н 0000008659 00000 н 0000008739 00000 н 0000008817 00000 н 0000008896 00000 н 0000008975 00000 н 0000009054 00000 н 0000009133 00000 н 0000009211 00000 н 0000009290 00000 н 0000009369 00000 н 0000009448 00000 н 0000009527 00000 н 0000009606 00000 н 0000009684 00000 н 0000009762 00000 н 0000009842 00000 н 0000009921 00000 н 0000010001 00000 н 0000010082 00000 н 0000010162 00000 н 0000010723 00000 н 0000010882 00000 н 0000011390 00000 н 0000011620 00000 н 0000011698 00000 н 0000017867 00000 н 0000018412 00000 н 0000018790 00000 н 0000019202 00000 н 0000024807 00000 н 0000025217 00000 н 0000025603 00000 н 0000025888 00000 н 0000026745 00000 н 0000027694 00000 н 0000027848 00000 н 0000028240 00000 н 0000028564 00000 н 0000031835 00000 н 0000032399 00000 н 0000032771 00000 н 0000032970 00000 н 0000033196 00000 н 0000033262 00000 н 0000034221 00000 н 0000035134 00000 н 0000036073 00000 н 0000036947 00000 н 0000037298 00000 н 0000038283 00000 н 0000039159 00000 н 0000051358 00000 н 0000054875 00000 н 0000055320 00000 н 0000055543 00000 н 0000056769 00000 н 0000057004 00000 н 0000057339 00000 н 0000057435 00000 н 0000058961 00000 н 0000059235 00000 н 0000059767 00000 н 0000059881 00000 н 0000099230 00000 н 0000099269 00000 н 0000099327 00000 н 0000099492 00000 н 0000099595 00000 н 0000099696 00000 н 0000099811 00000 н 0000099972 00000 н 0000100074 00000 н 0000100179 00000 н 0000100328 00000 н 0000100436 00000 н 0000100604 00000 н 0000100761 00000 н 0000100870 00000 н 0000100994 00000 н 0000101122 00000 н 0000101246 00000 н 0000101404 00000 н 0000101527 00000 н 0000101631 00000 н 0000101760 00000 н 0000101884 00000 н 0000101998 00000 н 0000102138 00000 н 0000102247 00000 н 0000102369 00000 н 0000003016 00000 н трейлер ]>> startxref 0 %%EOF 499 0 объект >поток xڤ[HTaζYh^VvL]ky6D374k/ںۺv3@*z+EK4gζZ7|3|9
ПРИВАРНОЙ ШПИНДЕЛЬ РУЛЕВОГО РЫЧАГА — Metallurgical Technologies, Inc.
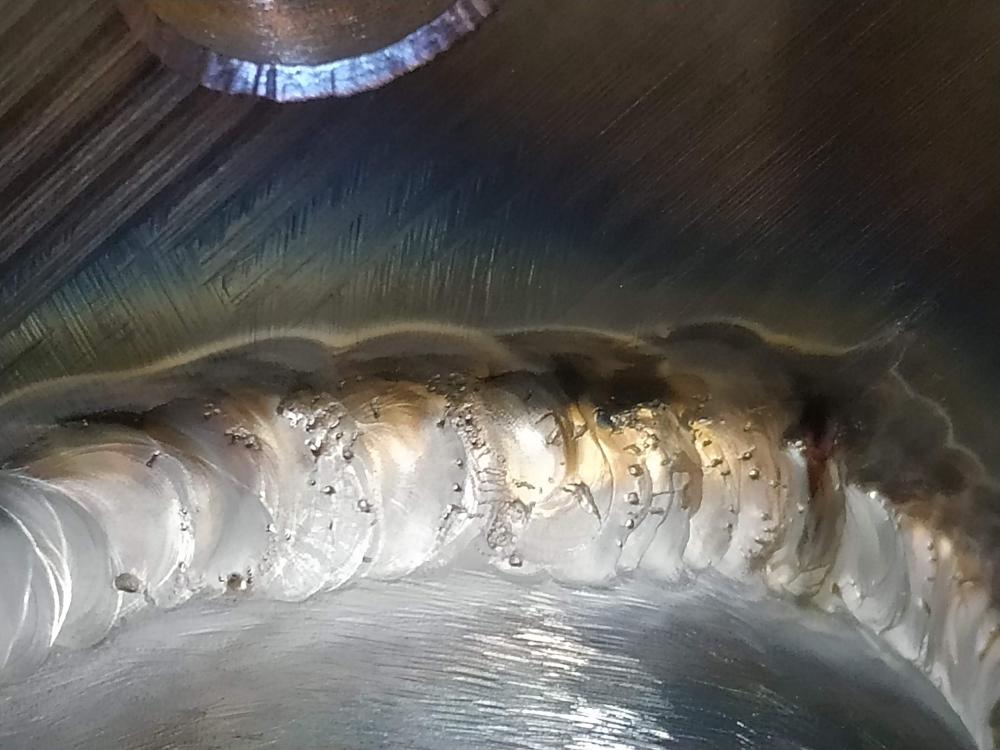
АНАЛИЗ УДАРНОГО РАЗЛОМА, СВАРНЫЙ ШПИНДЕЛЬ РУЛЕВОГО РЫЧАГА В СБОРЕ
Сводка:
Сварной левый передний шпиндель/рулевой рычаг в сборе с трещиной в месте углового сварного шва между рулевым рычагом и внутренней тормозной втулкой был получен для анализа с целью определения характера отказа. Для сравнения был представлен неповрежденный правый передний шпиндель/рулевой рычаг. Результаты показывают, что разрушение сварного соединения произошло из-за приложения одиночной ударной нагрузки. Исследование поверхности излома сварного шва выявило сочетание вязкой и хрупкой перегрузки (разрыв в виде углублений и раскол), что соответствует ударной нагрузке.Признаков прогрессирующего роста трещин вследствие усталости нет.
Местом зарождения разрушения была ранее существовавшая кратерная трещина, образовавшаяся во время сварки. Кратерные трещины возникают при высокой температуре, когда металл сварного шва затвердевает в конце сварочного прохода. Подобные кратерные трещины были обнаружены на других угловых сварных соединениях узла шпинделя/рулевого рычага, а также в угловых сварных соединениях представленного для сравнения правого переднего узла шпинделя/рулевого рычага.
Наличие дендритной структуры с сильным окислением в трещинах указывает на растрескивание затвердевания.Наличие никелированного покрытия вдоль поверхности излома трещины сварного шва контрольного образца подтверждает, что трещины присутствовали до нанесения покрытия.
Химический анализ основного металла рулевого рычага показал, что это низколегированная сталь SAE 4140. Микроанализ основного металла рулевого рычага и присадочного металла определил, что присадочный металл представляет собой низколегированную сталь SAE 4140 или аналогичную марку. Первоначальный проход сварного шва на угловом соединении контрольного образца был идентифицирован как марка аустенитной нержавеющей стали.Этот начальный проход с использованием наполнителя из нержавеющей стали не был отмечен в сварном соединении вышедшего из строя узла.
Измерения твердости сварного шва в поперечном сечении показали, что твердость металла шва составляет 27 HRC. Твердость зоны термического влияния сварного шва (ЗТВ) варьировалась от высокой 29 HRC до низкой 19 HRC в основном металле. Шпиндель не подвергался термической обработке (не подвергался аустенизации, закалке и отпуску), однако после сварки был снят стресс.
АНАЛИЗ:
Две сварные стальные (левая и правая передняя) оси/рулевой рычаг были получены на анализ.Левый шпиндель/рулевой рычаг сломался вдоль углового сварного шва между рулевым рычагом и внутренней тормозной колодкой. Для сравнения был представлен правый передний шпиндель/рулевой рычаг. Предполагается, что перелом произошел в результате бокового удара другого транспортного средства во время гонки xxxxxxxxx на xxxxxxxxx.
На рис. 1 представлен общий вид вышедшего из строя узла в том состоянии, в котором он был получен. Более близкий вид поверхности разрушения рулевого рычага представлен на рис. 2. Разрушение произошло по всему сварному шву по окружности и поперек соседнего рулевого рычага.На изломе сварного шва видна ранее существовавшая горячая трещина (кратерная трещина), увеличенная на рис. 3. Трещина распространяется по ширине сварного шва и находится в конце сварочного прохода. Поверхность трещины окислена с обильным скоплением ржавчины. Разрушение сварного соединения началось по ранее существовавшей трещине, а затем нарастало в направлениях, указанных стрелками на рис. 3.
Также были проверены другие сварные детали шпинделя и рулевого рычага. Подобные кратерные трещины были обнаружены в угловом сварном соединении внешней тормозной втулки и опорного рычага (рис. 4 и 5).При осмотре сварных швов контрольного шпинделя/рулевого рычага были обнаружены аналогичные лункообразные трещины в угловом сварном соединении рулевого рычага/внутренней тормозной бобышки. Пример показан на рисунках 6 и 7. (Трещины в виде лунок также наблюдались на угловом сварном соединении внешней тормозной бобышки/углового сварного шва опорного рычага.) Трещины расположены там, где процесс сварки прекратился.
Участок излома, содержащий ранее существовавшую кратерную трещину в месте зарождения на рулевом рычаге, был отрезан и подготовлен для дальнейшего анализа.Поверхность излома очищали ультразвуком с моющим средством на водной основе (Alconox) и подвергали исследованию с увеличением с помощью сканирующего электронного микроскопа (СЭМ).
На рис. 8 представлена микрофотография SEM с малым увеличением ранее существовавшей области горячей трещины/кратерной трещины и окружающей поверхности излома сварного шва. Были нанесены на карту различные участки поверхности разлома, которые подробно показаны при большем увеличении на следующих рисунках. Обратите внимание, что ранее существовавшая трещина в кратере имела глубину примерно 0,125 (1/8) дюйма.
На рисунках 9 и 10 показаны увеличенные изображения поверхности разрушения кратерной трещины вдоль внешней поверхности сварного шва. Изображение с большим увеличением на Рисунке 10 показывает, что поверхность излома сильно окислена, что указывает на то, что она вскрылась во время высокотемпературной сварки.
На рисунках 11 и 12 показаны увеличенные изображения поверхности кратера/горячей трещины рядом с обработанным пазом внутренней тормозной бобышки (нижняя область горячей трещины на рисунке 8). Поверхность имеет дендритную структуру, свидетельствующую о горячей трещине затвердевания. Область вязкой перегрузки также присутствует между этой областью горячей трещины и остальной частью трещины кратера. Пластическая перегрузка является результатом изменения плоскостей излома при ударном разрушении.
На рисунках 13 и 14 представлены микрофотографии СЭМ с большим увеличением поверхности излома сварного шва с каждой стороны кратерной трещины. На обоих рисунках показаны поверхности излома под действием вязкой перегрузки. Признаков усталостного разрушения вокруг трещины не обнаружено. При дополнительном осмотре поверхности излома сварного шва были обнаружены углубления, которые являются признаками вязкой перегрузки, подтверждая, что разрушение произошло из-за перегрузки, а не из-за усталости.
На рисунках 15 и 16 показаны увеличенные изображения переходной области между ЗТВ сварного шва и основным металлом. Топография поверхности излома меняется от вязкой перегрузки в ЗТВ до скола в основном металле. Наличие сколов на поверхности излома основного металла указывает на разрушение из-за высокой ударной нагрузки и перлитной (незакаленной и отпущенной) микроструктуры.
Образец поверхности излома, исследованный с помощью СЭМ, был разрезан в осевом направлении через трещину кратера и подготовлен для металлографического исследования в соответствии со стандартом ASTM E3-01.Полированная поверхность подвергалась микротравлению (2% нитала), чтобы выявить микроструктуру поперечного сечения. Это было сделано в соответствии с рекомендациями ASTM E407-99.
Рисунок 17 представляет собой монтаж двух оптических микрофотографий, демонстрирующих полное поперечное сечение разрушения сварного шва. Идентифицируется место инициации и области кратеров/горячих трещин.
На рисунках 18 и 19 показаны увеличенные изображения места инициации. Отмечено никелирование по внешней поверхности шва. На поверхности излома не наблюдается никелирования, что позволяет предположить, что кратерная трещина была закрыта на поверхности или, возможно, заполнена тонкой оксидной пленкой во время никелирования.
Рис. 20 представляет собой увеличенное изображение окисленной облицовки стенок пустот в металле сварного шва. Это также указывает на горячую трещину затвердевания.
На рис. 21 представлена микрофотография с большим увеличением микроструктуры рулевого рычага вдали от ЗТВ. Структура в основном перлитная, что указывает на то, что основной металл изначально находился в отожженном или нормализованном состоянии (не аустенитизированный, закаленный и отпущенный).
Влияние тепловложения во время сварки было исследовано с помощью испытаний на микротвердость сварного соединения.Профиль твердости сварного шва/ЗТВ/основного металла был создан путем испытаний с небольшими приращениями по сварному шву и основному металлу рулевого рычага. Измерения проводились с использованием индентора Knoop (HK) с нагрузкой 300 грамм в соответствии с рекомендациями ASTM E384-99є1. Значения HK были преобразованы приблизительно в шкалу Роквелла «C» (HRC) с использованием соответствующей формулы в ASTM E140-02.
Созданный профиль представлен на рис. 22. Твердость металла шва составила 27 HRC на внутренней кромке шва.Твердость металла ЗТВ варьировалась от высокой 29 HRC до низкой 20 HRC. Основной металл имел твердость 19 HRC. Твердость 20 HRC примерно соответствует пределу прочности при растяжении 110 ksi. Твердость ЗТВ указывала на то, что после сварки сварное соединение было снято с напряжения и отпущено.
Химический состав корпуса рулевого рычага определяли с помощью оптико-эмиссионного спектрометра (ОЭС) в соответствии со стандартом ASTM E415-99a. Анализ показал, что металл соответствует требованиям низколегированной стали SAE 4140 (таблица 1).
Из-за ограничений по размеру образца присадочный металл сварного шва был проанализирован с использованием энергодисперсионного рентгеновского спектрометра (EDS) в сочетании с SEM. Анализ проводили в общем в соответствии со стандартом ASTM E1508-98 (03). Результаты показывают, что присадочный металл представляет собой низколегированную сталь, подобную SAE 4140. Спектры ЭДС присадочного металла сварного шва и корпуса рулевого рычага представлены на рисунках 23 и 24 соответственно. Отображаемые спектры практически идентичны.
Угловой сварной шов сравнительного шпинделя/рулевого рычага, в котором также имелась трещина в форме кратера, был разрезан в осевом направлении через трещину, подготовлен металлографически и подвергнут микротравлению.На рис. 25 показан монтаж поперечного сечения сравнительного углового шва с кратерной трещиной. Эта кратерная трещина имеет глубину приблизительно 0,08 дюйма, что несколько меньше, чем глубина 0,125 дюйма в вышедшей из строя сборке. Начальный проход сварки (внутренний проход) не подвергается травлению и был выполнен с присадочным металлом из нержавеющей стали. Анализ ЭДС (рис. 26) определил, что это хромоникелевая (аустенитная) нержавеющая сталь.
На рисунках 27 и 28 показаны увеличенные изображения поверхностей трещин кратера. На рис. 28 видно, что никелирование присутствует как на внешней поверхности шва, так и по обеим поверхностям кратерной трещины вблизи раскрытия.Наличие никелирования свидетельствует о том, что трещина образовалась и была открыта до процесса покрытия.
На рисунках 29 и 30 показаны увеличенные изображения вершины трещины сварного шва и прилегающих междендритных затвердевших или «горячих» трещин. Поверхности трещин выстилает слой окисления, что является дополнительным подтверждением горячекристаллитного растрескивания.
ХИМИЧЕСКИЙ АНАЛИЗ
Таблица 1
Химический состав (мас. %)
Элемент | Рулевой рычаг | Технические характеристики SAE 4140 |
Углерод | 0.39 | 0,38-0,43 |
Марганец | 0,84 | 0,75-1,00 |
Фосфор | 0,013 | 0,030 макс. |
Сера | 0,033 | 0,040 макс. |
Кремний | 0,32 | 0,15-0,35 |
Хром | 0.87 | 0,80-1,10 |
Молибден | 0,16 | 0,15-0,25 |
Рулевой рычаг соответствует требованиям к химическому составу низколегированной стали SAE 4140
.
-2 | 27 | 290 |
0 | 28 | 294 |
2 | 29 | 304 |
5 | 29 | 307 |
10 | 26 | 287 |
15 | 28 | 296 |
20 | 28 | 296 |
25 | 25 | 280 |
30 | 23 | 265 |
40 | 25 | 280 |
50 | 20 | 249 |
75 | 20 | 253 |
100 | 19 | 247 |
150 | 20 | 253 |
200 | 20 | 253 |
ВЫВОДЫ:
Разрушение углового сварного шва рулевого рычага/внутреннего тормозного выступа произошло в результате однократной ударной нагрузки.Разрушение, инициированное вдоль сварного шва, в кратерной трещине глубиной 1/8 дюйма, образовавшейся при охлаждении в конце сварочного прохода. Аналогичные трещины были отмечены и на других угловых сварных соединениях как на неисправном, так и на образце сравнения.
Поверхности вязкого и скалывающего разрушения (без признаков прогрессирующего растрескивания из-за усталости) определяют ударную перегрузку как вид разрушения. Наличие дендритной структуры с окислением в кратерной трещине и междендритных трещинах блока сравнения, а также никелирование поверхности излома блока сравнения подтверждает горячее кристаллическое растрескивание как источник инициирования разрушения.
ИЗОБРАЖЕНИЙ:
Рис. 1: Общий вид левого переднего шпинделя/рулевого рычага в сборе. Рулевой рычаг отломился от остальной части корпуса рулевого рычага вдоль углового сварного шва между рулевым рычагом и внутренней тормозной колодкой. (Фото PA9332)
Рис. 2: Приближенный вид сварного шва с трещиной на рулевом рычаге. Вдоль верхней части поверхности разрушения сварного шва видна ранее существовавшая трещина в виде кратера с ржавой/окисленной поверхностью.Предварительная трещина находится там, где процесс сварки остановился. (Фото PA9336)
Рис. 3. Приближенный вид трещины в виде кратера, показанной на рис. 2. На поверхности трещины до ультразвуковой очистки имелись сильные отложения ржавчины. Разрушение сварного шва произошло от кратерной трещины. Трещина росла в направлениях, указанных стрелками. (Фото PA9337)
Рис. 4: Фотография крупным планом другой кратерной трещины (стрелка) в угловом сварном соединении внешней втулки тормоза и опорного рычага.(Фото PA9341)
Рис. 5. Приближенный вид трещины в виде кратера (стрелка), показанной на рис. 4. Трещина расположена в конце прохода сварки. (Фото PA9342)
Рис. 6: Крупный план сравнительного рулевого рычага и внутренней тормозной колодки. Еще две лункообразные трещины (стрелки) едва заметны в угловом сварном соединении. На рис. 7 показан более крупный вид трещин. (Фото PA9339)
Рис. 7: Крупный план двух лункообразных трещин (стрелки) в угловом сварном соединении рулевого рычага/внутреннего тормозного выступа, показанных на Рис. 6.Кратерные трещины также были отмечены в угловом сварном соединении внешней тормозной бобышки и опорного рычага сравнительной сборки. (Фото PA9340)
Рис. 8: СЭМ-фотография с малым увеличением поверхности излома сварного шва рулевого рычага на месте ранее существовавшей кратерной трещины после ультразвуковой очистки. Поверхность излома закартирована. Микрофотографии различных областей с большим увеличением представлены на следующих рисунках. (РЭМ-фото 2S4895, Mag: 14X)
Рис. 9: СЭМ-микрофотография с повышенным увеличением ранее существовавшей кратерной трещины на поверхности излома вдоль внешней поверхности сварного шва.Изображение с большим увеличением представлено на рис. 10. (SEM Photo 2S4896, Mag: 50X)
Рис. 10: СЭМ-микрофотография ранее существовавшей кратерной трещины на внешней поверхности сварного шва, сделанная с большим увеличением. Поверхность излома сильно окислена, что указывает на то, что она образовалась при высокотемпературной сварке. (РЭМ-фото 2S4897, Mag: 500X)
Рис. 11: СЭМ-микрофотография области пластичных и горячих трещин, примыкающей к обработанной прорези внутренней тормозной бобышки.Рельеф поверхности состоит из «ямочек» (пластическая перегрузка) и дендритных (горячие трещины) структур. Изображение с большим увеличением представлено на рис. 12. (SEM Photo 2S4898, Mag: 50X)
Рисунок 12: СЭМ-изображение с большим увеличением перехода от пластической перегрузки к дендритной структуре горячей трещины, представленной на рисунке 11. (SEM Photo 2S4900, Mag: 500X)
Рис. 13: СЭМ-микрофотография с большим увеличением поверхности излома, вызванного вязкой перегрузкой, вдоль одной стороны ранее существовавшей трещины (правая верхняя часть Рис. 8).Между вязкой перегрузкой и кратером/горячей трещиной не было отмечено никаких признаков усталостного разрушения. (SEM Photo 2S4903, Mag: 3000X)
Рис. 14. Снимок с большим увеличением, сделанный с помощью СЭМ, на котором показана поверхность разрушения из-за вязкой перегрузки вдоль середины сварного шва вдоль другой стороны ранее существовавшей горячей трещины (левая сторона кратера/горячей трещины на Рис. 8). Между вязкой перегрузкой и кратером/горячей трещиной не было отмечено никаких признаков усталостного разрушения. (SEM Photo 2S4906, Mag: 1000X)
Рис. 15: СЭМ-микрофотография перехода излома от ЗТВ сварного шва к основному металлу.Топография поверхности разрушения изменяется от вязкой перегрузки до хрупкого скола. Изображение с большим увеличением представлено на рис. 16. (SEM Photo 2S4910, Mag: 50X)
Рис. 16: Микрофотография СЭМ с большим увеличением, на которой видно переход от вязкого разрушения под нагрузкой (ямки) ЗТВ сварного шва к хрупкому разрушению под нагрузкой (отколу) основного металла. Наличие расщепления указывает на то, что разрушение произошло из-за ударной нагрузки, и указывает на перлитную (незакаленную и отпущенную) микроструктуру.(РЭМ-фото 2S4911, Mag: 300X)
Рис. 17: Монтаж оптических микрофотографий поперечного сечения несостоявшегося сварного соединения в области кратерной трещины и горячей трещины. (Фото C9258 и C9259, Mag: 15X)
Рис. 18: Оптическая микрофотография с большим увеличением места зарождения трещины в кратере. По внешней поверхности шва наблюдается тонкий слой никелирования. (Фото C9260, Mag: 100X)
Рис. 19: Оптическая микрофотография с большим увеличением места зарождения трещины в кратере.Слой никелирования легко растворяется. На изломе отсутствует никелирование. (Фото C9261 Mag: 500X)
Рис. 20: Оптическая микрофотография с большим увеличением заполненных оксидом пустот вдоль излома в области горячей трещины. (Фото C9262, Mag: 500X)
Рис. 21: Оптическая микрофотография основного металла рулевого рычага вдали от ЗТВ. Микроструктура перлитная, что свидетельствует о том, что деталь не подвергалась термообработке (аустенитизации, закалке и отпуску).(Фото C9274, Mag: 100X)
Рисунок 22: Профиль твердости поперечного сечения сварного шва/ЗТВ/основного металла
Рис. 23: Спектр EDS присадочного металла углового сварного шва рулевого рычага/тормоза. Сходство между этим спектром и следующим за рулевым рычагом указывает на совместимый низколегированный наполнитель. (СПТ6017)
Рисунок 24: Спектр ЭДС основного металла рулевого рычага. Химический анализ OES идентифицировал металл как низколегированную сталь SAE 4140.Обратите внимание на сходство между этим спектром и наполнителем сварного шва на рисунке 23. (SPT6018)
Рисунок 25: Монтаж оптических фотомикрографов поперечного сечения, критерия трещины в филе сварно из сравнительного шпинделя наружного тормоза / опорной руки. Обратите внимание на белый внутренний проход из нержавеющей стали. (Фото C9263 и C9264, Mag: 15X)
Рис. 26: Спектр ЭДС присадочного металла внутреннего шва из нержавеющей стали, показанного на Рис. 25.Элементный состав указывает на хромоникелевую (аустенитную) нержавеющую сталь. (СПТ6021)
Рис. 27: Оптическая микрофотография с большим увеличением поперечного сечения сварного шва внешней тормозной бобышки/опорного рычага сравнительного шпинделя с трещинами. Изображение зарождения трещины (область в рамке) с большим увеличением представлено на рис. 28. (Фото C9265, Mag: 50X)
Рис. 28: Оптическая микрофотография раскрытия трещины с большим увеличением, представленная на Рис. 27.Никелевое покрытие покрывает поверхность излома, указывая на то, что трещина присутствовала до нанесения покрытия. (Фото C9266, Mag: 200X)
Рисунок 29: Оптическая микрофотография междендритных горячих трещин, покрытых окислением. Наличие междендритных трещин, выстланных окислением, указывает на горячее затвердевание/кратерное растрескивание. (Фото C9269, Mag: 100X)
Рисунок 30: Оптическая микрофотография с большим увеличением окисления в сварном шве и междендритных трещинах.(Фото C9270, Mag: 500X)
Предотвращение образования концевых кратерных дефектов при сварке мощным лазерным лучом закрытых кольцевых швов
Буназив И., Аксельсен О.М., Фростеварг Дж., Каплан А.Ф. (2018) Гибридная оптоволоконная лазерно-дуговая сварка толстостенной стали HSLA с глубоким проплавлением. J Mater Process Technol 256: 216–228
CAS Статья Google Scholar
Чуриаке С., Хлудзинский М., Порруа-Лара М., Домингес-Абесия А., Абад-Фрага Ф., Санчес-Амая Дж. М. (2019) Лазерная гибридная стыковая сварка морской стали большой толщины.Металлы 9(1):100
CAS Статья Google Scholar
Lutz W (2013) Laser-Schweißanlage wird Kernstück für mehr Wettbewerbsfähigkeit, https://cloos.de/shop/media/import/CuReport-303616_Manitowoc-DE.pdf
Jasnau U, Gaede R (2008) Hochleistungfaserlaser im Schiffbau. Laser Technik J 5(2):30–33
Артикул Google Scholar
Turner C, Reisgen U (2016) Verfahren aus dem Schiffbau.Laser-MSG-Hybridschweißen auf dem Weg in die Baumaschinenbranche, VDBUM-Info: Forum für Baufachleute 44(4):18–19
Google Scholar
Юстюндаг О., Авилов В., Гуменюк А., Ретмайер М. (2018) Гибридная лазерная дуговая сварка с полным проплавлением листов S355 толщиной до 28 мм с использованием электромагнитной поддержки сварочной ванны. В: Журнал физики: Серия конференций (Том 1109, № 1, стр. 012015). IOP Publishing
Буназив И., Аксельсен О.М., Рен Х, Салминен А. (2015) Возможности гибридной сварки толстых профилей для арктических условий.Phys Procedia 78:74–83
CAS Статья Google Scholar
Вахба М., Мизутани М., Катаяма С. (2016) Однопроходная гибридная лазерно-дуговая сварка стыковых соединений с квадратной канавкой толщиной 25 мм. Mater Des 97:1–6
CAS Статья Google Scholar
Гук С., Гуменюк А., Ретмайер М. (2010) Формирование сварного шва и механические свойства кольцевых сварных швов, выполненных с помощью лазерно-GMA-гибридного процесса на трубах марки X65.В Международном конгрессе по применению лазеров и электрооптики (том 2010 г., № 1, 62–69, LIA.
Бегг Д., Бейнон Г., Хансен Э., Дефалко Дж., Лайт К. (2009) Разработка система гибридной лазерной дуговой сварки для строительства трубопроводов В: 7-я Международная конференция по трубопроводам, 2008 г. Цифровая коллекция Американского общества инженеров-механиков, стр. 429–435
Кейтель С., Нойберт Дж., Шеллер В., Лидтке М., Цезарь С. (2013) Патент США № 8 373 083. Вашингтон, округ Колумбия: U.С. Ведомство по патентам и товарным знакам.
Артинов А., Кархин В., Бахманн М., Ретмайер М. (2019) Математическое моделирование геометрических различий между кратером на конце сварного шва и стационарной сварочной ванной, Конференция: Международный конгресс по применению лазеров и электрооптики ( ICALEO®), в: Орландо, Флорида, США, Том: ISBN: 978–1–940168-1-42
Гебхардт М.О., Гуменюк А., Ретмайер М. (2013) Численный анализ горячих трещин в трубах, сваренных методом лазерной гибридной сварки .Adv Mater Sci Eng:1–8
Статья Google Scholar
Кироз В., Гуменюк А., Ретмайер М. (2012) Исследование склонности лазерных сварных швов к образованию горячих трещин с контролируемым испытанием на свариваемость при растяжении. J Strain Anal Eng Des 47(8):587–599
Статья Google Scholar
Кироз В., Гебхардт М., Гук С., Гуменюк А., Ретмайер М. (2010) Горячее растрескивание при сварке мощным лазерным лучом толстых высокопрочных конструкционных сталей в условиях ограничения.На Международном конгрессе по применению лазеров и электрооптики (том 2010 г., № 1, стр. 225–232). ЛИА.
Эфтимиадис П., Нор К. (2018) Лазерная сварка разнородных высокопрочных стальных сплавов со сложной геометрией. Металлы 8(10):792
CAS Статья Google Scholar
Патент DE 102016204556A1, Способ лазерной сварки, сварка и аппарат для лазерной сварки
Патент DE 102005004787 B4, Использование листа и способ получения лазерной сварки с уменьшенным кратером
90 102005004787 A1, Лазерный сварной шов с минимальной концевой воронкой, в конечной точке шва расположен избыток материалаDebRoy T, David SA (1995) Физические процессы при сварке плавлением.Версия Mod Phys 67 (1): 85
CAS Статья Google Scholar
Дэвид С.А., ДебРой Т. (1992) Текущие вопросы и проблемы науки о сварке. Science 257(5069):497–502
CAS Статья Google Scholar
Сохаил М., Хан С.В., На С.Дж., Гуменюк А., Ретмайер М. (2014) Характеристики поведения сварочной ванны при лазерной сварке с различной потребляемой мощностью. Welding World 58(3):269–277
Статья Google Scholar
Наиболее распространенные дефекты сварки MIG на алюминии и стали и как их избежать
В этой статье описываются некоторые из наиболее распространенных дефектов сварки MIG, такие как пористость, непровар и прожог, а также способы их выявления по внешнему виду валика сварного шва.
Некоторыми из наиболее распространенных дефектов сварки являются пористость, несплавление и прожоги, при этом алюминий представляет несколько больше проблем при сварке, чем сталь. Алюминий проводит тепло примерно в шесть раз быстрее, чем сталь, плюс он обладает отличной теплопроводностью в сочетании с низкой температурой плавления, что делает его чрезвычайно восприимчивым к деформации и прожогу. Кроме того, алюминиевая проволока имеет меньшую прочность на растяжение, что может вызвать проблемы с подачей проволоки и привести к дефектам сварки, если не используется правильное оборудование.Мы выделим различия здесь.
Пористость:
Защитный газ защищает расплавленную сварочную ванну от окружающей атмосферы, которая в противном случае загрязнила бы сварной шов. На рис. 1 показано, как отсутствие защитного газа на стали может вызвать пористость (отверстия) в валике сварного шва, которые образуются на лицевой и внутренней поверхности сварного шва в отсутствие защитного газа. Отсутствие защитного газа может быть вызвано неправильной настройкой оборудования, пробоиной в гильзе пистолета или ветром, сдувающим защитный газ.
РИС. 1. Отсутствие защитного газа на стали — Отсутствие или недостаточное количество защитного газа легко определить по пористости и (отверстиям) на лицевой и внутренней поверхности сварного шва.
РИС. 2
На алюминии сварной шов, выглядящий как копоть (РИС. 2), может быть вызван использованием метода перетаскивания, а не толкания (РИС. 3, ниже). Копоть можно удалить, но при вскрытии сварного шва будут обнаружены точечные отверстия, в которых застрявшие в сварном шве примеси.Алюминий образует оксид, который необходимо удалить перед сваркой. Проволочная щетка является наиболее распространенным методом очистки алюминия, но ее необходимо выполнять щеткой из нержавеющей стали, чтобы избежать загрязнения сварного шва примесями стальной щетки.
РИС. 3.
Техника толкания против сопротивления. При сварке стали приемлем либо толкание, либо волочение пистолета, но при работе с алюминием метод волочения приведет к дефектам сварки.
Непровар
Отсутствие сварки может произойти, если напряжение или скорость подачи проволоки установлены слишком низко, или когда скорость перемещения оператора слишком высока.Поскольку алюминий проводит тепло намного быстрее, чем сталь, он склонен к неплавлению в начале сварки, пока в сварку не будет вложено достаточно энергии. Некоторое сварочное оборудование решает эту проблему, автоматически увеличивая ток в начале сварки, а затем уменьшая его, чтобы избежать чрезмерного нагрева.
Кратеры
При сварке алюминия на конце сварного шва могут образовываться кратеры. Если они не заполнены, они создают точку напряжения, которая может привести к растрескиванию. Это требует, чтобы пользователь снова быстро спустил курок, чтобы заполнить кратер, хотя некоторые сварочные аппараты предлагают таймер кратера, который заполнит кратер при отпускании курка пистолета.
Прожечь
Слишком большое тепловложение может быть вызвано слишком высокими значениями напряжения или скорости подачи проволоки или слишком низкой скоростью перемещения. Это может привести к деформации или прогоранию, особенно на более тонких материалах, используемых в индустрии вывесок, алюминий более подвержен этому воздействию, чем сталь. Как правило, для алюминия требуется более высокая скорость перемещения, чем для стали, чтобы избежать накопления тепла.
Подача алюминия
Из-за низкой столбчатой прочности подачу алюминиевой проволоки можно сравнить с проталкиванием мокрой лапши через соломинку.«Птичье гнездо», или запутывание проволоки между приводным роликом и вкладышем, является распространенной, трудоемкой и дорогостоящей проблемой. Чтобы очистить его, оператор должен остановить сварку, обрезать проволоку, выбросить проволоку из горелки и заново подать новую проволоку через направляющий канал. Также может потребоваться очистка или замена контактного наконечника из-за прогорания, возникающего при прекращении подачи проволоки. • Существует несколько способов подачи алюминиевой проволоки: только проталкивание, катушкодержатель, система проталкивания и система непрерывной подачи проталкивания.
Только проталкивание: Подача алюминиевой проволоки через систему проталкивания может быть затруднена, но в ограниченных случаях это возможно. Требуются приводные ролики с U-образной канавкой для обеспечения большего поверхностного контакта с проволокой, тефлоновая футеровка, достаточное давление приводного ролика, способность удерживать кабель пистолета прямо и высокая устойчивость к боли.
Пистолет для катушки: Пистолет для катушки, такой как Spoolmatic® 15A или 30A, устраняет возможность застревания птиц, помещая 4-дюймовую (1 фунт.) на пистолете, поэтому проволока подается только на несколько дюймов. Катушки могут работать с алюминиевой проволокой диаметром от 0,023 до 1/16 дюйма и позволяют оператору использовать более длинные кабели (15–50 футов).
Катушка катушки требует замены ролика после каждого фунта проволоки, по сравнению с катушкой на 8 или 15 фунтов в двухтактной системе.
Пушпульный пистолет: В двухтактном пистолете двигатель в пистолете протягивает проволоку через направляющий канал, а двигатель в блоке управления сваркой или механизмом подачи становится вспомогательным двигателем.Поддерживая постоянное натяжение троса, двухтактная система помогает избежать застревания птиц. Он более эргономичен, чем шпульный пистолет, так как вес шпули не находится в руках оператора.
Кроме того, шпульку нужно менять реже, чем на шпульном пистолете, что позволяет покупать шпули большего размера. Однако помните, что алюминий образует оксидный слой после того, как какое-то время находился на воздухе. Если вы используете всего один или два фунта алюминия в неделю, лучшим выбором может быть шпуля меньшего размера.
Выбор подходящего оборудования
Правильный выбор оборудования может решить многие из этих проблем до того, как они возникнут. Технология AutoSetTM, используемая во многих сварочных аппаратах Millermatic компании Miller, избавляет оператора от необходимости вводить параметры при сварке стали. С Auto-Set оператор просто выбирает толщину стали и диаметр используемой проволоки, а машина устанавливает оптимальное напряжение и скорость подачи проволоки.
Для точной настройки или для сварки алюминия аппарат, оснащенный бесступенчатой регулировкой напряжения, такой как Millermatic 212 AutoSet или Millermatic 252, позволяет оператору точно настраивать параметры, чтобы избежать слишком сильного или слишком слабого нагрева сварного шва.В более старом оборудовании могут использоваться настройки с резьбой, что затрудняет настройку, особенно при сварке тонкого материала.
Кроме того, как Millermatic 212, так и Millermatic 252 могут использовать шпульные пистолеты, что упрощает настройку для сварки как стали, так и алюминия. Millermatic 252 также имеет функцию Auto Gun DetectTM, поэтому оператору нужно только взять MIG-пистолет или пистолет с катушкой и нажать на курок, чтобы начать сварку.
Для более специализированной сварки алюминия такие аппараты, как Millermatic 350P, оснащены импульсной сваркой MIG, которая помогает исключить прожоги тонких материалов.Кроме того, он оснащен двухтактным пистолетом XR-Aluma-ProTM, который помогает устранить проблемы с подачей проволоки. Дополнительная технология, такая как Aluminium Pulse Hot StartTM, обеспечивает большую мощность в начале сварки, чтобы избежать «холодного старта», которому подвержена сварка алюминия.
Поиск и устранение неисправностей
На фото выше показан пример хорошего сварного шва на стали. Ниже приведены фотографии некоторых плохих сварных швов, которые могут возникнуть в результате различных потенциальных проблем, в том числе следующих:
Слишком низкое напряжение — Слишком низкое Слишком низкое напряжение приводит к плохому началу дуги, плохому контролю и провару.Это также вызывает чрезмерное разбрызгивание, выпуклый профиль валика и плохую врезку на концах сварного шва.
Слишком высокая скорость подачи проволоки/сила тока — Установка слишком высокой скорости подачи проволоки или силы тока (в зависимости от типа используемого аппарата) может вызвать плохой запуск дуги и привести к чрезмерно широкому валику сварного шва, прожогу и искажение.
Слишком низкая скорость подачи проволоки/сила тока — A n стрелка, часто выпуклый валик с плохой врезкой на концах сварного шва указывает на недостаточную силу тока.
Слишком высокая скорость перемещения — Узкий выпуклый валик с неадекватной врезкой на концах сварного шва, недостаточное проплавление и непостоянный сварной валик вызваны слишком быстрым перемещением.
Слишком низкая скорость перемещения — Слишком медленное перемещение может привести к образованию большого сварного шва с чрезмерным подводом тепла, что приведет к тепловой деформации и возможному прожогу. В большинстве случаев надлежащая скорость движения достигается, когда дуга находится на переднем крае ванны.
Слишком высокое напряжение: Слишком высокое напряжение характеризуется плохим контролем дуги, непостоянным проплавлением и турбулентной сварочной ванной, которая не может последовательно проникнуть в основной материал.
Эта статья была первоначально подготовлена и опубликована в Sign Media Canada (www.signmedia.ca).
Почему трескаются сварные швы | СВАРОЧНЫЕ ОТВЕТЫ
Неудачный сварной шов никогда не бывает хорошим. Независимо от того, лопнул ли сварной шов на оси грузовика или на столбе, удерживающем забор вашего дома, всегда есть последствия.Надеюсь, последствия ограничены временем и деньгами. К сожалению, дефекты сварки могут привести к травмам. Сварные швы могут выйти из строя из-за конструктивных недостатков, но большинство отказов сварных швов происходит по причинам, которые мы, как сварщики, можем предотвратить.
Вероятно, единственным и наиболее важным инструментом для предотвращения трещин является Спецификация процедуры сварки (WPS). WPS используется не только для выполнения внутренних требований или требований заказчика, но и для обеспечения качества. При этом мы не должны слепо следовать WPS, если есть что-то, что мы считаем неправильным, мы должны довести это до сведения нашего руководителя.
Давайте рассмотрим наиболее распространенные типы трещин, их возможные причины и способы их предотвращения.
1. Трещина в зоне термического влияния
Зона теплового воздействия (ЗТВ) сварного шва не ограничивается самим сварным швом, а непосредственной областью основного материала, окружающей сварной шов. Трещина ЗТВ может возникать на концах сварного шва или в нескольких миллиметрах от сварного шва. Наиболее распространенными причинами этого типа трещин являются: избыток водорода, высокие уровни остаточных напряжений в сварном шве и высокое содержание углерода в основном материале.
Трещина в зоне термического влияния
Протравленное сечение сварного шва с трещиной ЗТВ
Чтобы свести к минимуму восприимчивость или предотвратить образование трещин в ЗТВ, необходимо учитывать:
- с использованием электродов с низким содержанием водорода
- предварительный нагрев основного материала
- медленное охлаждение основного материала после сварки
2. Осевая трещина
Трещина по центральной линии, также известная как продольная трещина, обычно проходит по всей длине сварного шва.Этот тип трещины чаще всего вызван неправильным соотношением ширины и глубины, низкой температурой плавления случайных элементов в основном материале и вогнутой поверхностью сварного шва. Хотя один из них может быть корнем проблемы, чаще всего именно их комбинация приводит к растрескиванию сварного шва.
Осевая (продольная) трещина
Чтобы уменьшить вероятность трещины по центральной линии, учтите:
- отношение ширины к глубине от 1:1 до 1,3:1
- запустите более низкий ток, чтобы уменьшить избыточное проникновение
- уменьшите сварочное напряжение или скорость перемещения, чтобы получить поверхность сварного шва от плоской до выпуклой
3.Кратерные трещины
Чаще всего в сварных швах алюминия кратерная трещина возникает из-за отсутствия заполнения на конце сварного шва. Сварные швы из углеродистой и нержавеющей стали менее подвержены образованию кратерных трещин, но при сварке этих материалов необходимо соблюдать осторожность.
Кратерные трещины на концах алюминиевых сварных швов
Чтобы устранить трещины в кратерах, обеспечьте надлежащее заполнение кратеров:
- отступ в конце сварного шва (дойти до конца, а затем снова приварить валик от 1/2 до 1 дюйма
- использовать опцию заполнения кратера сварочного оборудования (если доступно)
4.Поперечные трещины
Поперечные трещины не очень распространены за пределами сварных швов. Однако они возникают из-за высокого остаточного напряжения, чрезмерной прочности сварного шва и избытка водорода.
Поперечные и продольные трещины
Для сведения к минимуму подверженности поперечным трещинам дополнительно:
- предварительный нагрев основного материала
- с использованием расходных материалов меньшей прочности
- медленное охлаждение после сварки
Как упоминалось выше, наиболее важным средством предотвращения трещин является спецификация процедуры сварки, которая была подтверждена испытаниями.Некоторые производители должны следовать определенным кодам, таким как AWS D1.1, AWS D1.2, API 1104 или раздел IX ASME, для квалификации процедур сварки и сварщиков. Коды используются для обеспечения качества и предотвращения сбоев. Хотя наиболее часто используемые нормы сварки различаются в определенных отношениях, все они требуют, чтобы как процедуры сварки, так и сварщики были квалифицированы путем испытаний. Некоторые коды иногда позволяют использовать предварительные процедуры сварки, которые могут сэкономить время и деньги. Если вы не уверены, можно ли использовать прошедший предварительную проверку WPS, всегда следует проявлять осторожность и пройти квалификацию путем тестирования.
Вам нужна дополнительная информация о том, как вы можете выполнить свою собственную процедуру и получить квалификацию сварщика?
«Квалификационные процедуры сварки, сварщики и операторы сварки» — это руководство, разработанное, чтобы помочь вам пройти квалификацию в полном соответствии с Кодексом сварки конструкций AWS D1.1 — сталь.
Неровности сварных швов – Часть 3 Трещины
Трещины в сварном соединении, вероятно, являются наиболее опасными из всех несплошностей сварного шва. Из-за широкого спектра применений и множества типов свариваемых материалов растрескивание является чрезвычайно сложной проблемой.Мы рассмотрим некоторые основные теории и характеристики различных типов трещин в сварных соединениях.
Трещины возникают в металле сварного шва, когда локальные напряжения превышают предел прочности металла. По этой причине нам необходимо учитывать некоторые важные переменные при разработке процедуры сварки, чтобы лучше всего противостоять растрескиванию. Чувствительность основного материала к растрескиванию может быть связана с его химическим составом и/или склонностью к образованию элементов, снижающих его пластичность.Приложение чрезмерных напряжений к сварному соединению, особенно в сочетании с материалом, чувствительным к растрескиванию, может вызвать растрескивание. Напряжения в сварном шве и вокруг него характерны для операции сварки, которая часто вызывает экстремальный локальный нагрев, а также расширение и сжатие в процессе сварки. Растрескивание часто связано с концентрацией напряжений вблизи несплошностей в сварных швах и основном металле, а также вблизи механических надрезов, связанных с конструкцией сварного соединения.Водородное охрупчивание, которое вызывает потерю пластичности и существует в металле шва из-за поглощения водорода, может способствовать образованию трещин в некоторых материалах.
Трещины обычно подразделяются на два типа: горячие трещины и холодные трещины.
Горячие трещины развиваются при повышенных температурах, распространяются между зернами материала и обычно образуются при затвердевании металла шва.
Холодные трещины развиваются после затвердевания сварного шва в результате напряжений и распространяются как между зернами, так и сквозь зерна.Холодные трещины в стали иногда называют замедленными трещинами и часто связаны с водородным охрупчиванием.
Трещины можно разделить еще на два типа: трещины в основном материале и трещины в металле сварного шва.
Трещины в основном материале
Растрескивание в зоне термического влияния (ЗТВ) чаще всего связано с упрочняемым основным материалом. Высокая твердость и низкая пластичность в околошовной зоне часто являются результатом металлургической реакции на термические циклы сварки.В ферритных сталях твердость увеличивается, а пластичность снижается с увеличением содержания углерода и увеличением скорости охлаждения от температуры сварки. Твердость зоны термического влияния связана с прокаливаемостью основного материала, которая, в свою очередь, зависит от химического состава основного материала. Углерод оказывает преобладающее влияние на прокаливаемость стали. Возможно, крайним примером этой прокаливаемости и ее влияния на растрескивание основного металла является сварка чугуна.Этот материал содержит от 2% до 4,5% углерода, что придает сплаву большую твердость и низкую пластичность. Если мы попытаемся сварить этот материал без серьезного учета скорости охлаждения и остаточных напряжений, мы неизбежно столкнемся с растрескиванием основного материала.
Трещины в металле сварного шва
Трещины в металле сварного шва можно разделить на три типа: поперечные, продольные и лункообразные трещины.
Поперечные трещины металла шва перпендикулярны направлению шва.Этот тип трещин чаще встречается в сварных швах, имеющих высокую степень стеснения.
Продольные трещины в сварном шве распространяются в том же направлении, что и шов, и часто ограничиваются центром шва. Этот тип трещины может быть продолжением трещины, которая первоначально возникла в конце сварного шва.
Кратерные трещины могут образовываться в результате резкого обрыва сварного шва, если кратер остается незаполненным металлом сварного шва. Эти трещины обычно имеют звездообразную форму и первоначально простираются только до края кратера.Однако эти трещины могут переходить в продольные трещины сварного шва.
Влияние трещин на целостность сварного шва
Трещины в любой форме обычно являются недопустимыми дефектами и считаются наиболее вредными для рабочих характеристик сварного шва. Трещина по своей природе имеет острые края и, следовательно, действует как концентрация напряжения. Эффект концентрации напряжения трещины больше, чем у большинства других несплошностей. Трещины имеют тенденцию к распространению и могут способствовать разрушению сварного шва, если они подвергаются нагрузкам в процессе эксплуатации.Трещины, независимо от размера, обычно не допускаются в сварных конструкциях, регулируемых большинством производственных норм. Их необходимо удалить, как правило, путем шлифовки или выдалбливания, а выемку заполнить прочным металлом сварного шва.
Заключение
Успешная процедура сварки включает в себя требования контроля, необходимые для преодоления склонности к образованию трещин. Такими средствами контроля, в зависимости от типа материала, могут быть температура предварительного нагрева, температура между проходами, подготовка и тип сварочных материалов, а также термическая обработка после сварки.Инспектор по сварке несет ответственность за оценку этих процедур контроля сварки во время своих проверок, тем самым гарантируя, что сварка выполняется в соответствии с процедурами сварки, которые были разработаны для сведения к минимуму вероятности растрескивания сварного шва.Червоточины / Кратерная труба — Вопросы CSWIP
Удлиненные поры или червоточины
Характерно, что червоточины представляют собой продолговатые поры (рис. 3), которые на рентгенограмме выглядят как елочные косточки.
Рис.3 |
Причина
Червоточины указывают на образование большого количества газа, который затем задерживается в затвердевающем металле сварного шва. Чрезмерный газ будет образовываться из-за сильного загрязнения поверхности или очень толстого слоя краски или грунтовки. Захват более вероятен в щелях, таких как зазор под вертикальным элементом горизонтально-вертикального Т-образного соединения, сваренного угловым швом с обеих сторон.
При сварке Т-образных стыков в загрунтованных листах важно, чтобы толщина покрытия на кромке вертикального элемента не превышала рекомендованный производителем максимум, обычно 20 мкм, из-за избыточного напыления.
Профилактика
Устранение газа и полостей предотвращает появление червоточин.
Генерация газа
— очистить поверхности заготовки
— удалить любые покрытия с зоны стыка
— убедитесь, что толщина грунтовки ниже максимальной, указанной производителем
Геометрия соединения
— избегать геометрии соединения, которая создает полость
Кратерная труба
Во время окончательного затвердевания сварочной ванны образуется кратерная труба, которая часто связана с некоторой газовой пористостью.
Причина
Этот дефект возникает из-за усадки при затвердевании сварочной ванны. Следовательно, условия, преувеличивающие изменение объема жидкости в твердое, будут способствовать ее образованию. Отключение сварочного тока приведет к быстрому затвердеванию большой сварочной ванны.
При сварке TIG автогенные методы или останов проволоки перед отключением сварочного тока могут привести к образованию кратера и дефектам трубы.
Профилактика
Несовершенство трубы кратера можно предотвратить, сняв стопор или используя технику сварки.
Снятие упора
— использовать бирку стекания в стыковых соединениях
— отшлифовать упор, прежде чем переходить к следующему электроду или наплавке последующего сварочного прохода
Сварочная техника
— постепенно уменьшайте сварочный ток, чтобы уменьшить размер сварочной ванны
— добавить наполнитель (TIG) для компенсации усадки сварочной ванны
Пористость материалов
Газы, которые могут вызвать пористость в обычно используемом диапазоне материалов, перечислены в таблице.
Основные газы, вызывающие пористость, и рекомендуемые методы очистки
C-Mn сталь | Водород, азот и кислород | Шлифовка для удаления накипи |
Нержавеющая сталь | Водород | Обезжиривание + проволочная щетка + обезжиривание |
Алюминий и сплавы | Водород | Химическая очистка + проволочная щетка + обезжиривание + соскоблить |
Медь и сплавы | Водород, Азот | Обезжиривание + проволочная щетка + обезжиривание |
Никель и сплавы | Азот | Обезжиривание + проволочная щетка + обезжиривание |
Обнаружение и меры по исправлению положения
Если дефекты являются нарушением поверхности, их можно обнаружить с помощью пенетрантной или магнитопорошковой дефектоскопии.Подповерхностные дефекты обнаруживаются с помощью рентгенографии или ультразвукового контроля. Рентгенография обычно более эффективна для обнаружения и характеристики дефектов пористости. Однако обнаружение мелких пор затруднено, особенно в толстых срезах.
Для исправления обычно требуется удаление путем локальной выдалбливания или шлифовки, но если пористость широко распространена, следует удалить весь сварной шов. Соединение должно быть повторно подготовлено и повторно сварено, как указано в согласованной процедуре.
.