Литье титана
Наш завод выпускает широкий перечень отливок из титана разнообразной конфигурации и сложности. Титановые отливки широко применяется в машиностроении, нефтяной отрасли, оборонной и авиационной промышленности. Наш цех имеет 10 вакуумных. плавильных печей, специальные печи для подготовки форм к технологическому процессу литья.
Для изготовления титановых отливок имеется участок модельной оснастки, на котором производится вся необходимая оснастка для последующего производства. Наш литейный цех имеет широкие возможности по изготовлению отливок из титановых сплавов разнообразных конфигураций, начиная с изделий массой 20 грамм и заканчивая 2,5 тоннами. Благодаря отработанным технологиям обеспечиваем высокое качество отливаемых изделий с наименьшей толщиной стенок 3 миллиметра.
Мы изготавливаем титановые отливки. которые отвечают современным стандартам. Мощности нашего производства позволяют изготавливать до 1000 тонн титановых отливок в год. Полученные титановые заготовки мы можем обработать механическим путем для получения конечного изделия в соответствии с требованиями заказчика.
Мы занимаемся поставками титанового литья и различных изделий из титановых сплавов. Постоянным клиентам готовы предложить гибкую систему скидок.
Применяемые технологии
Литье титана по выплавляемым моделям ЛВМ
Литье титановых сплавов в стержневые и корковые формы
Центробежное литье
Прессование из порошков
Термообработка под вакуумным нагревом
Главной особенностью титанового литья низкий коэффициент расширения и усадки, немагнитность, жаростойкость и химическая стойкость. Если сравнивать со стальным литьем, то титановые отливки имеют меньшую плотность и вес практически в 2 раза. Однако для нагретого титана необходима защита, которая оградит его от окисления атмосферными газами. Эта особенность несколько затрудняет технологический процесс и требует применения специальных вакуумных печей.
Благодаря отработанной технологии мы получаем отливки, которые могут иметь минимальную толщину 3 мм.
Используемые титановые сплавы
ВТ-5Л, ВТ-6Л, ВТ-20Л, ВТ10Л, ВТ20Л и так далее.
Изделия, получаемые титановым литьем на нашем предприятии
Крыльчатка, улитка, конфузор, теплообмнники, кожуха, фланцы, отводы, ножки, воронки, вставки колонны, шнеки, основание, стабилизаторы, корпуса, титановые изделия для авиакосмической отрасли, компоненты промышленных механизмов, инструменты, изделия для протезирования, шаровые корпуса, тарелки клапанов, крышки, дистилляторы, сушилки, центрифуги, титановый круг, втулки, подпятники и многое другое.
Особенности применения изделий из титана и его сплавов
Титан находит широкое применение в различных отраслях промышленности. Благодаря своим свойствам он намного превосходит обычную сталь и даже нержавейку. Его выделяет легкость, прочность, устойчивость к коррозии, стойкость к высоким температурам и тепловому расширению.
Именно поэтому на многих предприятиях широко применяется именно титановые изделия, их обширно используют в разнообразных устройствах. Изделия из титана пользуются большим спросом в химическом машиностроении, металлургии, судостроении, автомобилестроении, медицине и аэрокосмической промышленности.
Применение титана в медицине
Благодаря инертности к биологическим средам изделия из титана обширно применяются в медицинской отрасли, в частности в виде инструментов, протезов и имплантатов. При небольшом весе он очень прочен. К тому же долговечен, гипоаллергенен и выделяется отличной приживляемостью к тканям человека.
Мехобработка титана
Металл имеет некоторые сложности в металлообработке вследствие высокой твердости и вязкости. Он требует применения инструментов с повышенной твердостью и характеристиками. В результате обычные универсальные станки не всегда способны обеспечить необходимую точность.
На нашем предприятии мы применяем специальные станки с ЧПУ и инструменты, которые позволяют получить требуемую точность согласно чертежам. У нас работают высококвалифицированные специалисты, которые имеют большой опыт работы с титановыми заготовками.
Заказ титанового литья и мехобработки
Для заказа литья и мехобработки титановых изделий нам необходим чертеж изделия с указанием технологических требований и количества изделий. Присылайте его на Этот адрес электронной почты защищён от спам-ботов. У вас должен быть включен JavaScript для просмотра..
Титановое литье
АО «Зеленодольский завод имени А.М. Горького» выпускает широкую номенклатуру титанового литья различной конфигурации, сложности и применения – судостроение, оборонная промышленность, химическая и нефтегазовая отрасль.
Заводской цех титанового литья — один из крупнейших в мире по производству отливок из титановых сплавов. Запущенный в эксплуатацию в 1967 году, цех на сегодняшний день оборудован 9 вакуумными плавильно-заливочными печами, 19 электрическими печами для термопрокалки литейных форм, 5 рентгеновскими камерами, лабораторией капиллярной дефектоскопии, участком модельной оснастки и др.
В 2012 году на заводе была изготовлена миллионная титановая отливка.
Преимущества использования титановых сплавов
Титан обладает высокой коррозионной стойкостью, легкостью, а также сохраняет свои механические свойства при повышенных температурах. Благодаря этому он используется в самых критических и ответственных применениях – там, где другие материалы не обеспечат должной надежности. Кроме того, применение титана часто экономически более выгодно применения нержавеющих сталей и других материалов, поскольку срок службы титановых изделий в разы превышает срок службы изделий из нержавеющих сталей. Вес изделий из титана в среднем в два раза меньше, что позволяет экономить на несущих металлоконструкциях.
Возможности литейного производства
Производственные мощности Зеленодольского завода позволяют производить отливки сложной конфигурации весом от 30 грамм до 2500 килограмм. Геометрические габариты производимых отливок: диаметр до 2.5 метров, высота до 1.5 метров, толщина стенки от 3 мм.
При этом возможно применение любых титановых сплавов, соответствующих Российским и зарубежным стандартам. Мощность титанового производства позволяет производить до 600 тонн титанового литья в год. В цехе эксплуатируется крупнейшая в мире вакуумная печь для плавки и заливки титановых сплавов Нева-5.
Стандарты и сертификаты титанового литья
Зеленодольский завод производит титановое литье в соответствии с Российскими и международными стандартами, а также сертифицирован в соответствии с EN ISO 9001: 2008, для поставок литья на международный рынок имеются квалификации NORSOK M650, PED (97/23/EC), DuPont.
Международные поставки титанового литья
АО «Зеленодольский завод им. А.М. Горького» на протяжении 20 лет специализируется на поставке литья, запорной, регулирующей арматуры, деталей насосного оборудования и т.п. для стран Западной Европы, Азии, Америки, Австралии.
АО «Зеленодольский завод им. А.М. Горького» приглашает Вас к более тесному сотрудничеству и готов рассмотреть Ваши перспективные предложения по освоению и поставке титановых изделий для нужд Вашего производства. По международным поставкам титановых отливок обращаться в управление маркетинга: [email protected], тел. +7 (84371)2-12-11, 2-12-72, контактное лицо зам. начальника УММиЛП Гордеев Евгений Александрович, так же все Ваши отзывы с пожеланиями, замечаниями и предложениями Вы можете направить нам заполнив форму обратной связи.
Ферротитан:
Побочной продукцией титанового производства является производство ферротитана, использующегося в сталеплавильной и литейной промышленности, а также при производстве сварочных электродов.
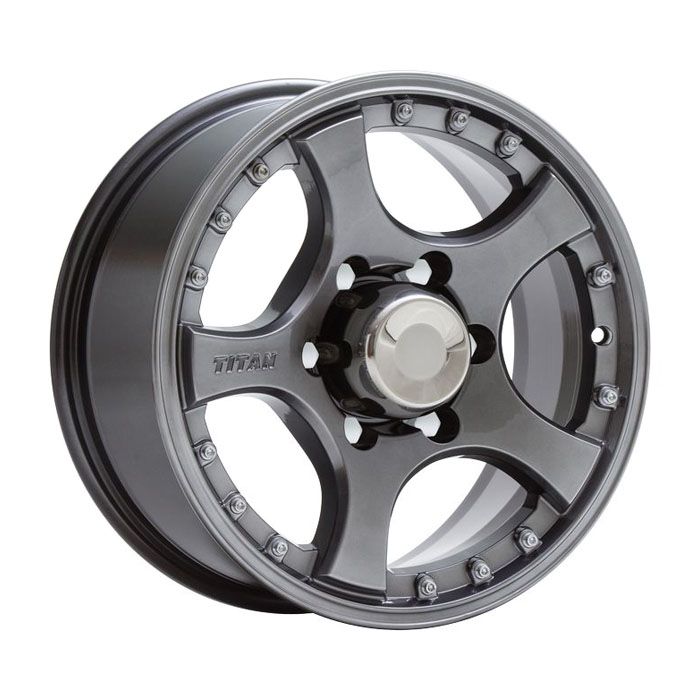
Сертификат соответствия EN ISO 9001: 2008
Сертификат PED (97/23/EC)
Сертификат PED (97/23/EC)
Сертификат PED (97/23/EC)
Особенности плавки и литья титановых сплавов
Высокая реакционная способность титана не позволяет проводить процесс плавления его в атмосфере воздуха, так как в расплавленном состоянии он активно взаимодействует с кислородом и азотам. Первоначально плавку титана и его сплавов вели в атмосфере аргона и гелия, позже появились вакуумные печи, которые в настоящее время являются основным типом плавильного оборудования. Для получения фасонных отливок из титана применяют вакуумные электродуговые гарнисажные плавильно-литейные установки, в которых совмещены процессы плавления металла, приготовления расплава, заливки литейных форм и формирования отливки (см. рис. 8.4).
Рис. 8.4. Схема вакуумно-дуговой печи с расходуемым электродом для плавки титановых сплавов:
1 — вакуумная камера, 2 — электрическим кабель, 3 —шланги водяного охлаждения.
4 — водоохлаждаемый тигель, 5 — гарнисаж, б — соленоид, 7 — расходуемый электрод, 8 — держатель, 9 — вращающийся стол, 10 — литейная форма
Расплавленный титан реагирует практически со всеми известными огнеупорными материалами (оксидами алюминия, магния, кремния и др.), что затрудняет выбор удовлетворительного материала для плавильных тиглей. В гарнисажной печи расплавленный титан находится в контакте со слоем твердого титана толщиной 5—50 мм, называемым гарнисажем и постоянно поддерживаемым на стенках и дне водоохлаждаемого тигля. При вакуумной гарнисажной плавке исключается взаимодействие расплава с атмосферой и материалом тигля, что повышает однородность металла и предупреждает появление в отливке тугоплавких включений.
После расплавления расходуемого электрода печь поворачивают и производят заливку расплава во вращающуюся на столе 9 форму 10, Под действием центробежных сил расплав хорошо заполняет форму, отливка получается плотной, без газовых раковин. Прибыли устанавливают не на верхнюю, а на боковую часть питаемого узла, при этом металл под действием центробежных сил двигается от прибыли к отливке.
Литейные формы, изготовленные из обычно применяемых огнеупорных материалов, не могут быть применены для получения отливок из титана по отмеченным ранее причинам. Широко распространены графитовые формы. Их изготовляют из смесей, в состав которых входят в качестве основы графит, в качестве связующего — смолы, пеки. Смеси уплотняют на встряхивающих или прессовых машинах под давлением 0,2—0,8 МПа. Изготовленные формы после выдержки на воздухе от 8 ч до 3 сут подвергают сушке при температуре 120°С и обжигу в восстановительной атмосфере при 700—980 °С в течение 1—24 ч. При этой температуре связующее коксуется и из формы практически полностью удаляются все летучие вещества.
Применяются и оболочковые графитовые формы с фенолоформальдегидной смолой в качестве связующего. Мелкие сложные тонкостенные отливки из титановых сплавов получают в неразъемных формах, изготовленных по выплавляемым моделям. В состав суспензии входит высокодисперсный графитовый порошок и связующее на основе фенолоформальдегидных смол, в качестве обсыпочного материала — зернистый графит.
В настоящее время разрабатываются процессы изготовления форм на основе использования обычных огнеупорных материалов (Al2O3, MgO) с применением защитных углеродных, карбидных и металлических покрытий, повышающих инертность форм к расплавленному титану и его сплавам.
Контрольные вопросы
1. Какие печи используют для плавки медных, алюминиевых, магниевых и титановых сплавов?
2. Как предохраняют сплавы цветных металлов от окисления в процессе плавки и литья?
3. С какой целью проводят операцию рафинирования? Назовите способы рафинирования.
4. Что такое модифицирование сплавов? Расскажите о модифицировании алюминиевых и магниевых сплавов.
5. Расскажите об особенностях плавки и литья титановых сплавов.
Плавка и литье титана — Энциклопедия по машиностроению XXL
Плавка и литье титана [c.61]Плавка и литье титана. Плавка титана связана с большими техническими трудностями, так как расплавленный титан реагирует со всеми обычными огнеупорными материалами и горит при высоких температурах даже в азоте. Поэтому дуговую плавку титановой губки осуществляют в вакууме. В качестве тигля используют водоохлаждаемый медный цилиндр. Электрод изготовляют из титановой губки прессованием. Между электродом и дном тигля зажигается дуга. Нижняя часть электрода расплавляется, образуя жидкую ванну и слиток. Для получения достаточно хорошо проплавленного металла полученный слиток переплавляют второй раз, используя его в качестве электрода. Слитки получают массой от 500 кг до 4—5 т, диаметром 800—850 мм. [c.64]
В работе [88] проведен анализ повышения химической однородности металла в плавильных агрегатах в зависимости от способа плавки и литья титана (при дуговой плавке с расходуемым электродом и при использовании независимых источников тепла для плавления сыпучей шихты). [c.69]
Разработаны рациональные технологические процессы плавки и литья цветных металлов, обеспечивающие минимальные потери дефицитных металлов, высокое качество изделий при низкой себестоимости и невысоком браке изделий. Сплавы цветных металлов, применяемые для получения отливок, условно можно разделить на легкие и тяжелые. Алюминиевые, магниевые и тита-
[c.166]
Необходимость разработки принципиально новой технологии изготовления углеродных форм, методов плавки и заливки возникла в связи с освоением производства точных литых заготовок из тугоплавких сплавов на основе титана и других ( -металлов IV—VI групп Периодической системы элементов. Применение литейной технологии из- [c.188]
Плавка специальных сплавов в индукционных вакуумных печах. Наиболее высокими жаропрочными свойствами, необходимыми для производства литых турбинных лопаток, обладают литые сплавы на никелевой основе типа ЖС. Основным методом получения лопаток из этих сплавов является литье по выплавляемым моделям. Однако указанные сплавы из-за большого содержания алюминия и титана легко окисляются и образуют в процессе плавки и разливки плотные окисные плены, которые, попадая в отливки, нарушают сплошность [c.260]
Максимальное сопротивление абразивному изнашиванию стали как в литом, так и в отожженном состоянии получено при содержании 1,10% С, 3,10% Сг и 0,86% Ti (плавка № 202). В литом состоянии сталь имеет структуру аустенита со значительным количеством крупноигольчатого мартенсита, мелкие зернистые карбиды титана и незначительное количество эвтектики, включающей цементитный карбид (Fe, Сг)зС. [c.108]
Минимальные потери массы при изнашивании после отпуска отмечены у образцов стали, содержащей 1,40 /о С, 7,05% Сг и 0,70% Ti (плавка № 311). В литом состоянии сталь имеет структуру мелкозернистого аустенита и включает небольшое количество эвтектики. Карбидная фаза состоит из карбида титана, а также из гексагонального и кубического карбидов, связанных в основном в двойных эвтектиках. С увеличением содержания гексагонального карбида для сталей такого типа во всех случаях отмечено снижение сопротивления изнашиванию.
[c. 108]
С целью получения пластичного литого металла в процессе плавки производится подача специальным дозатором добавок, в частности, для сплава ЦМ-2А—циркония и титана в количествах 0,07—0,15% циркония 0,07—0,3% —титана. [c.79]
Электроды прессуют из губчатого титана или изготовляют литьем либо ковкой. Для электрошлаковой плавки требуется флюс с высокой температурой кипения (не менее 2000° С = =2273°К), чтобы шлак можно было перегреть выше температуры плавления титана. В качестве флюса наиболее подходящим и дешевым оказался фтористый кальций. В результате исследований разработан метод электрошлаковой выплавки титана с хорошими механическими свойствами и поверхностью, не тре- [c.89]
Следовательно, положительное влияние легирующих добавок бериллия, титана и циркония на свойства алюминиевомагниевых сплавов заключается (наряду с уменьшением окисления сплава в процессе плавки, литья и термической обработки, уменьшением газовой пористости и измельчением зерна) также и в том, что эти элементы входят в твердый раствор сплава, способствуя дополнительному повышению его механических свойств в результате термической обработки. [c.368]
Литейные титановые сплавы стали применять в промышленности для фасонного литья. По жидкотекучести титан находится примерно на уровне углеродистой стали, однако в действительности получать крупногабаритные тонкостенные отливки из титана значительно труднее из-за быстрого остывания и затвердевания металла, что объясняется невысокой энтальпией жидкого титана и трудностью получения высокого перегрева при существующих способах плавки титана. [c.30]
Дуговая плавка в высоком вакууме особенно оправдала себя при получении литых молибдена ( 3-3), тантала ( 3-5), циркония 7-1) и титана ( 7-2). Подробнее см. [Л. 5]. [c.473]
На рис. 7.13 показана электронно-лучевая гарниссаж ная промышленная установка для литья тугоплавких металлов, в которой находятся четыре аксиальные пушки мощностью 120 кВт каждая. Емкость тигля для плавки титана 6 л. Печь снабжена системой дистанционного наблюдения и управления процессом.
[c.275]
Литейные титановые спшавы не содержат эвтек-тик, однако небольшой интервал кристаллизации (50-70 °С) обусловливает вполне удовлетворительные литейные свойства. Величина линейной усадки титана близка к величине усадки углеродистой стали и составляет около 1,5 % при литье в керамические формы и около 2 % при литье в металлическую форму. Применение вакуума при плавке и литье титановых сплавов исключает образование газовой пористости, оксидных и шлаковых включений. Высокая химическая активность расплавленного титана предъявляет жесткие требованР1я к [c.712]
Электронно-лучевой переплав на холодном поду. Задача процесса применительно к суперсплавам заключается в дополнительной очистке от примесных химических элементов и снижении загрязненности неметаллическими включениями. Сначала электронно-лучевую плавку под вакуумом применяли при капельном оплавлении и литье тугоплавких металлов. Первые усилия по применению этого метода для производства суперсплавов дали неудовлетворительные результаты, так как в слиток попадали неоплавленные компоненты шихтовых материалов. Процесс электронно-лучевого переплава на холодном поду был разработан с цедью разрешения этих затруднений. Первая крупномасштабная установка построена в начале 1960-х гг., но применяли ее от случая к случаю и главным образом для обработки титана [8]. Позднее построили две новых крупных установки, и хотя их по-прежнему используют при производстве титановых материалов, можно с их помощью рафинировать и суперсплавы. Однако применительно к суперсплавам этот процесс все еще носит характер разработок. [c.147]
Особые случаи полунепрерывного литья имеют место при получении слитков дуговой, электронной и плазменной плавкой, а также электрошлаковым переплавом. В этих процессах плавка и затвсрде-ваине совмещены в одном узле плавильного агрегата — в кристаллизаторе, а литья как такового нет слиток непрерывно наплавляется сверху либо в глухом кристаллизаторе, либо в проходном с непрерывной вытяжкой. Такие способы получения слитков применяются для высококачественных сталей, титана, молибдена, циркония и других тугоплавких редких металлов и их сплавов.
[c.119]
Литейные свойства титана близки к свойствам среднеуглеродистой стали и из него можно изготовлять отливки довольно сложной, формы. Однако высокая химическая активность расплавленного титана затрудняет осуществление нз него фасонного литья. Плавку для литья ведут, главным образом, в дуговых печах в охлаждаемых медных или графитовых тиглях разливку титана производят в графитовые формы, изготовленные механической обработкой. Загрязнение титана углеродом при отливке в графитовые формы незначительно. Механические свойства литого титана (предел прочности и ударная вязкость) не уступают свойствам титана такого же состава, подвергнутого горячей обработке давлением. При нагреве слитка перед горячей деформацией, как известно, кроме образования окалины на поверхности происходит также проникновение газов в поверхностный слой титана, в результате чего он приобретает повышенную твердость и хрупкость. Принимают, что изменение твердости поверхностного слоя титана в пределах 50 единиц по Виккерсу (НУ50) безоласно. В этом шучае толщина слоя металла повышенной твердости в зависимости от температуры и длительности нагрева может быть характеризована данными, представленными в табл. 3. Видно, что при ограничении времени нагрева насыщение титана газами может быть локализовано в тонком поверхностном слое. [c.10]
Технически чистый титан (ВТ1), выплавленный в дуговых печах, позволяет как в лито1М, так и в предварительно деформированном состоянии производить осадку с б0льи1ими скоростями при температурах выше ООО» за один нагрев без разрушения. Титановые сплавы дуговой плавки имеют несколько меньшую пластичность при высоких температурах и высоких скоростях деформирования, чем технически чистый титан. Однако допустимая степень деформации в предварительно кованом состоянии при температурах выше 800°—850° для сплавов ВТЗ, ВТЗ-1, ВТ4, ВТ6 и ВТ8, при температурах выше 1000° для сплава ВТ5 и выше 1100° для сплава типа TI-371 близка к технически чистому титану (фиг.

Несколько иная картина получается при испытании на ударную вязкость сплава ВТ1 (технически чистого титана) дугсзой плавки при тех же температурах в зависимости от длительности нагрева (фиг. 212) ударная вязкость при 1000 и 1100° имеет одинаковые значения как в литом, так и в деформированном металле, причем длительность нагрева в пределах 6 час. при температуре 1000° не оказывает существенного влияния на ударную вязкость. Нагрев же при 1100° более 4 час. приводит к некоторому снижению ударной вязкости кованого металла. [c.284]
Помимо этого производства, второй перопективной областью применения гарниссажной плавки титана является фасонно-заготовительное литье, т. е. литье фасонных заготовок для последующей горячей обработки давлением, например ко пьцевых заготовок для последующей раскатки или штамповок и трубных заготовок для получения труб и бесшовных обечаек. Применение фасоннолитых заготовок может дать существенное удешевление стоимости производства труб и кольцевых деталей и значительно увеличить коэффициент использования металла. [c.66]
Ведутся исследования по совершенствованию гарниссажной плавки титана (замене водяного охлаждения тигля другими хладагентами), а также по изысканию средств, и методов для вторичного охлаждения слитков в процессе литья. [c.68]
Большинство деформируемых алюминиевых сплавов способно воспринимать закалку (без полиморфного превращения) и старение и в результате этого существенно упрочняться. Типичные легирующие компоненты рассматриваемых сплавов, кроме марганца, — медь, магний, кремний, цинк, В специальных жаропрочных сплавах содержатся железо, никель, хром, титан в количестве 0,2—1%. Во всех алюминиевых сплавах введение 0,1 — 0,2% титана вызывает сильное измельчение зериа в литом состоянии. Этот эффект частично сохраняется и после рекристаллизации. В некоторые сплавы вводят бериллий (0,001—0,0027о) для уменьшения окисления при плавке.
[c.201]
Введением присадки 0,2—0,5% Т1 (или 2г) в качестве раскислителя к техническому бериллию [Л. 10] и плавкой в вакуумной печи удалось получить материал, из которого можно при 600—900° С изготовлять жесть толщиной 4—0,1 мм и путем горячей обработки вытягивать колпачки диаметром до 17 мм. Тем не менее, обычно на практике, даже при использовании этого материала, считают более рациональным вырезать тонкие диски для окошек рентгеновских трубок из массивных прокатанных слитков [Л. 46]. Бериллий с присадкой титана в отличие от спеченного чистого бериллия является газонепроницаемым. Поэтому такой материал пригоден для производства окошек специальных рентгеновских трубок вместо линдеманового стекла [Л. 32], Бериллиевые диски толщиной 1 мм, вырезанные из маленьких, полученных центробежным литьем слитков, также газонепроницаемы. Простое устройство для изготовления таких слитков в вакуумной высокочастотной печи показано на рис. 5-5-1А. [c.238]
Титановое литье
Продукция → Металлургия
Титановое литье
Мы предлагаем широкую номенклатуру титанового литья различной конфигурации, сложности и применения – судостроение, оборонная промышленность, химическая и нефтегазовая отрасль.
Титан обладает высокой коррозионной стойкостью, легкостью, а также сохраняет свои механические свойства при повышенных температурах. Благодаря этому он используется там, где другие материалы не обеспечат должной надежности. Кроме того, применение титана часто экономически более выгодно применения нержавеющих сталей и других материалов, поскольку срок службы титановых изделий в разы превышает срок службы изделий из нержавеющих сталей. Вес изделий из титана в среднем в два раза меньше, что позволяет экономить на несущих металлоконструкциях.
Цех титанового литья АО «Зеленодольский завод имени А.М. Горького», входящего в состав АО «Судостроительная Корпорация «Ак Барс», является одним из крупнейших в мире по производству отливок из титановых сплавов. Запущенный в эксплуатацию в 1967 году, цех на сегодняшний день оборудован 9 вакуумными плавильно-заливочными печами, 19 электрическими печами для термопрокалки литейных форм, 5 рентгеновскими камерами, лабораторией капиллярной дефектоскопии, участком модельной оснастки и др. В цеху эксплуатируется вакуумная дуговая гарнисажная печь НЕВА-5, являющаяся крупнейшей из используемых в Российской промышленности и одной из крупнейших в мире печей для производства отливок из титана. В 2012 году в цеху была изготовлена миллионная титановая отливка.
Наши производственные мощности позволяют производить отливки сложной конфигурации весом от 30 грамм до 2500 килограмм. Геометрические габариты производимых отливок: диаметр до 2,5 метров, высота до 1,5 метров, толщина стенки от 3 мм. При этом возможно применение любых титановых сплавов, соответствующих российским и зарубежным стандартам. Мощность титанового производства позволяет производить до 600 тонн титанового литья в год.
Титановое литье производится в соответствии с Российскими и международными стандартами, а также сертифицировано в соответствии с EN ISO 9001: 2008, для поставок литья на международный рынок имеются квалификации NORSOK M650, PED (97/23/EC), DuPont. Имеется многолетний опыт поставки литья, запорной, регулирующей арматуры, деталей насосного оборудования и т.п. для заказчиков из стран Западной Европы, Азии, Америки, Австралии.
Побочной продукцией титанового производства является производство ферротитана, использующегося в сталеплавильной и литейной промышленности, а также при производстве сварочных электродов. Осуществляется выпуск ферротитана всех марок по ГОСТ 4761-91 с максимальным использованием мелкодисперсных отходов (в том числе стружки) и кусковых отходов любых титановых сплавов. Технология защищена патентом Российской Федерации. Мощность ферротитанового производства – до 60 тонн в месяц.
Задайте вопрос нашему специалисту:
Департамент маркетинга и продаж гражданской продукции
- тел.: +7 (84371) 2-11-72
- e-mail:
Также за более подробной информацией Вы можете обратиться на АО «Зеленодольский завод имени А.М. Горького»
Стоматологическое литьё из титановых сплавов
Стоматологическое литьё из титановых сплавов
Стоматологическое литьё из титановых сплавов
Каминский Алексей Ярославович
МОУ «Средняя общеобразовательная
школа поселка Черкизово», 11 класс
Научный руководитель:
Васильев Валерий Алексеевич,
доктор технических наук,
профессор кафедры «Литейные технологии» МГТУ им. Н.Э. Баумана
Введение
В данной работе рассматривается создание стоматологических моделей, плавильно-литейных установок для стоматологического литья, свойства титановых сплавов, а так же возможные дефекты отливок.
В своей работе я исследовал два элемента стоматологических отливок – тонкую пластинку и часть дуги бюгеля. Исследования проходили на приборе ПМТ-3, мерилась микротвердость, данные записывались и обрабатывались в программе статистического анализа Statistica. Проходило изучение отливок под микроскопом на наличие таких дефектов как горячие и холодные трещины, рыхлости, растущие дендриты и наличие альфированного слоя.
1. Создание моделей
Перед созданием восковой модели снимается модель слепка полости рта (рис. 1) с помощью альгинатов или двухкомпонентных силиконовых масс, точно воспроизводящие поверхности слизистой полости рта.
На получившеюся
мастер-модель переносится рисунок с диагностической модели, и по этому рисунку
наносится воск для заливки поднутрений. После того как мастер-модель готова, ее
дублируют гелем или силиконом и на основе получившихся слепков изготавливают
модель из огнеупорного материала (рис. 2). После этого начинается моделирование
протеза воском.
Первым этапом является установка восковых моделей кламмеров и решетчатых моделей ретенций (рис. 3, 4, 5), далее наносится тонкая подкладка из гладкого воска для улучшения литья. Дальше формируется, начиная с центра, дуга бюгеля (рис. 6). Края пластины обрезаются под прямым углом к дуге.
Рис. 1. Модель полости рта Рис. 2. Мастер модель
Рис. 3. Бюгель Рис. 4. Бюгель
Рис. 5. Кламмер
Рис. 6. Формирование дуги бюгеля Рис. 7. Установка литниковой системы
Важно, чтобы все восковые заготовки и пластмассовые шаблоны были плотно и прочно посажены на модель или соединены воском, чтобы паковочная масса не затекала под них во время паковки.
Для ускоренного моделирования применяются различные восковые заготовки, такие как: заготовки для кламмеров, решетчатые ретенции для верхней и нижней челюстей, заготовки основного воска для литья он бывает как гладкий, так и рубчатый, соответственно меняются его свойства. Данные заготовки и шаблоны применяются в различных случаях в зависимости от поставленной задачи или слепка полости рта.
После того как
восковая модель готова, на нее устанавливаю литниковую систему (рис. 7).
Литьё всегда происходит от наиболее массивных частей к наименее массивным. В
процессе охлаждения расплавленный металл вытягивается из литейных каналов и
массивных частей. Более тонкие части модели остывают быстрее, чем более
массивные. Поэтому, литниковые каналы должны устанавливаться на наиболее
массивных участках конструкций, например, на переходе от седловидной части к дуге
протеза.
Массивные части, в которые металл может попасть только через другие тонкие части модели, следует снабдить дополнительным каналонаполнителем. В центре над смоделированным каналом на расстоянии 10 мм фиксируется воронка с литниковыми каналами (рис. 8).
Рис. 8. Установка воронки Рис. 9. Модель помещена в кювету
Очень важно, чтобы металл быстро заполнял опоку. Это условие необходимо всегда соблюдать при установке литейных каналов. Необходимо избегать чрезмерно изогнутых каналов, препятствующих свободному перетеканию металла.
После всю конструкцию помещают в специальную кювету для дальнейшей паковки модели (рис. 9). Когда паковочная масса застыла, из неё выплавляют воск. Далее начинается заливка металла в полученную опоку.
2. Плавильно-литейные установки
2.1. Центробежные установки
Центробежные установки (ЦБПЛУ) (рис. 10, 11) позволяют получать широкую гамму изделий, в том числе самого высокого качества. Наибольшее распространение получили ЦБПЛУ с вертикальной осью вращения центрального вала. Ось опоки горизонтальна, ось тигля наклонена по отношению к оси центрального вала на угол 6-7 градусов для лучшего истечения расплава из тигля. Нагрев, как правило, индукционный (хотя в небольших установках иногда используется и резисторный нагрев). При заливке формы относительное положение тигля и опоки не изменяется. Оси опоки и противовеса совпадают.
Рис. 10. ЦБПЛУ фирмы
Аверон.
Рис. 11 Принципиальная схема установки
Общий вид камеры
Вакуумные центробежные ПЛУ позволяют плавить практически любые типы сплавов, включая Рt, но для них требуется вакуумный насос и надежные вакуумные уплотнения. Часто для устранения окисления расплава и уменьшения его газонасыщенности используют инертный газ, обычно Аr, делая 3-5 промежуточных промывок рабочего пространства литейной установки.
Обязательным условием является применение высокочистого Ar, осушение его перед использованием и удаление следов кислорода (это относится ко всем методам плавки в среде инертного газа). Именно поэтому ЦБПЛУ для плавки в вакууме и в среде инертного газа распространены примерно одинаково. Если закончился инертный газ, то нужно заправлять баллон (а это требует времени), а вакуумная установка входит в комплект поставки. Если рассматривать начальную стоимость при покупке, то литейная установка с вакуумным насосом стоит дороже. Центробежные ПЛУ имеют большое количество подвижных частей, склонность к выплеску металла в процессе заливки, большую трудоемкость в обслуживании. В результате её обслуживание становится дороже. Однако в них можно плавить любые типы сплавов, включая высокотемпературные сплавы Pt и Pd. Они выпускаются как с ручным управлением (РФ, Волгодонск, «Центролит-20», «Центролит-50»), так и полностью автоматизированными (ASEG, GALLONI, OKAY VAC, JELENCO Eagle).
2.2. Стопорные плавильно-литейные установки
Большую конкуренцию ЦБПЛУ составляют СПЛУ (рис. 12, 13). Принцип их
действия заключается в следующем. Металл плавится в тигле с донным отверстием,
перекрытым стопором. Снизу к тиглю подводится, а часто через прокладки и
прижимается, литейная форма. При расплавлении литейного сплава и достижения
температуры заливки стопор поднимается, металл через отверстие сливается в
форму. Как правило, контактная термопара помещается в нижнюю часть стопора, в
ряде случаев дополнительные термопары устанавливаются и вокруг тигля. Если
форма поджата к тиглю, то выплеск металла при заливке исключается.
Рис. 12. СПЛУ “Flowlogic 515” от NTUTEC/USA Рис. 13. Принципиальная схема установки
Общий вид камеры
Для исключения окисления металла и насыщения его газами, плавку и заливку ведут в среде инертного газа, чаще всего — Аr.
Практически не имея подвижных частей, стопорные ПЛУ получают широкое распространение, так как являются простыми в обслуживании и эксплуатации. На ПЛУ можно производить отливки любых сплавов, включая Pt, Pd и другие высокотемпературные сплавы.
2.3. Литейные установки с разрезным тиглем
Заслуживает внимания вакуумная индукционная ПЛУ «Наутилус МС плюс», разработанная фирмой «ВЕGО» (рис. 14, 15). Прежде всего, момент окончания плавки (начала заливки) определяется не по показанию пирометра, а по расчётному количеству энергии, необходимой для плавки и перегрева расплава. Режим плавки записывается в архив и всегда может быть повторен при необходимости.
Отличительной особенностью данной установки является разрезной (вдоль оси) тигель. По расплавлении металлической шихты части тигля смещаются, и расплав в доли секунды заполняет литейную форму. Подобная конструкция тигля не обеспечивает точности попадания струи расплава в стояк, что приводит к неоднородности отливок в разных частях литейной формы. Кроме того, величина вакуума в полостях тигля и литейной формы одинакова. Следовательно, заливка осуществляется только под действием гравитационных сил, что не всегда обеспечивает максимальную плотность отливок.
2.4. Дуговые плавилъно-литейные установки
Перспективным
для стоматологического литья являются установки вакуумно-дуговой плавки с
последующей заливкой металлического расплава по схеме «сверху давление — снизу
вакуум», что характерно для стопорных ПЛУ. Подобные установки выпускаются
фирмами «Dentaurum» (только для плавки титана) и «Dor-a-matic» (рис. 16, 17) (для литья Ti, XK, ХКМ, драгоценным металлов и сплавов). Данные установки позволяют
добиться очень высокого, стабильного качества литья.
Рис. 14. Установка «Наутилус МС плюс» Рис. 15. Принципиальная схема установки
фирмы Bego. Общий вид камеры
Рис. 16. Дуговая ПЛУ Dor-a-matic. Общий вид камеры
Данные литейные установки основаны на принципе плавки титана в защитной среде аргона на медном тигле посредством вольтовой дуги, точно также в промышленности сплавляют титановую губку для получения чистого титана. Заливка металла в кювету происходит при помощи вакуума в литейной камере и повышенного давления аргона в плавильной камере во время опрокидывания тигля.
В начале процесса обе камеры плавильная (вверху) и литейная (в низу) промываются аргоном, затем из обеих камер эвакуируется смесь воздуха и аргона, после чего плавильная камера заполняется аргоном, а в литейной образуется вакуум. Включается вольтовая дуга и начинается процесс плавления титана. После прохождения определенного времени резко опрокидывается плавильный тигель и металл заполняет находящуюся в вакууме форму, собственный вес, а также повышающееся давление аргона на этот момент также способствуют его заливке. Этот принцип даёт возможность получать хорошие, плотные отливки из чистого титана.
Но какой бы не была литейная установка и способ литья, существует определенный процент брака отливок и одним из браков будет незаполнение до конца формы. Причина тому то, что с самого начала заливки металла начинается остановка его потока.
Рис. 17. Принципиальная схема установки
3. Механизм остановки потока
При изучении жидкотекучести металлов и сплавов важно иметь представление о механизме остановки потока в канале литейной формы.
Е. Липс и Г. Ниппер методом аналогии изучали механизм течения и остановки жидкости, кристаллизующейся в интервале температур. Они предложили схему, по которой остановка потока сплава происходит из-за накопления твердых кристаллов на его конце, в связи с понижением температуры ниже ликвидуса. Если в расплавленном металле появляется твердая фаза, происходит резкое повышение его вязкости. С накоплением твердой фазы увеличивается также сила внутреннего трения, что оказывает большое влияние на процесс течения металла.
При поступлении металла в канал литейной формы на его стенках образуется твердая корочка, так как обычно между жидким металлом и формой существует очень большой перепад температур, обуславливающий высокую интенсивность охлаждения металла в начальные моменты. С течением времени, по мере прогрева формы, интенсивность теплоотвода уменьшается. Но приход тепла к корочке за счет поступления новых порций металла остаётся постоянным, и она начинает оплавляться и уменьшаться.
Уменьшению размеров корочки также способствует частичный смыв кристаллов движущимся потоком. Накопление обломков кристаллов на конце потока приводит к постепенному нарастанию сил внутреннего трения. Условия течения металла заметно ухудшаются. Наконец в определенный момент количество скопившихся обломков становиться настолько большим, а сопротивление внутреннему трению на столько значительным, что поток останавливается.
Макроструктура спиральной пробы из сплава ВТ1Л позволяет проследить за отдельными стадиями формирования потока металла (рис. 18).
Для начального и последующих участков
спирали характерно транскристаллическое строение металла. При литье титана
корочка на начальных участках литейного канала, по-видимому, полностью не
расплавляется. У самой поверхности спирали имеется тонкий слой равноосных,
мелких кристаллов. Имеющиеся готовые центры кристаллизации (корочка), а также незначительное
количество обломков перед фронтом растущих кристаллов создают благоприятные
условия для роста столбчатых дендритов вплоть до середины спирали (участок I и II). По мере
приближения к концу спирали длина столбчатых дендритов начинает сокращаться.
Снятие перегрева металла создаёт условия для устойчивого существования
кристаллических обломков внутри жидкости и препятствует дальнейшему росту
дендритов (участок III).
Наконец для самого конца пробы характерна мелкокристаллическая структура (участок IV). Наличие большого количества готовых кристаллических зародышей и отсутствие перегрева металла полностью подавляет развитие дендритов, несмотря на относительно высокую интенсивность теплоотвода на этом участке спирали.
Рис. 18: Схема остановки потока металла по О.Н.Магницкому [1]
а) – макроструктура спиральной пробы и отдельных ее участков;
б) – строение потока к моменту остановки
4. Химические свойства титановых сплавов
Химические свойства титана определяются внешними электронами, расположенными в 3d- и 4s-оболочках, соотношением размеров атомов и кристаллическим его строением. По способности отдавать внешние электроны при реакциях титан занимает среднее положение в ряду наиболее электроположительных металлов групп I—III (подгруппа А) и наиболее электроотрицательных металлов групп I—V (подгруппа Б). По величине атомного радиуса титан занимает среднее положение между металлами групп I и II с наибольшими радиусами и металлоидами (бор, углерод, азот, кислород и водород) с наименьшими атомными радиусами.
При
температурах выше 700 °С и особенно в расплавленном состоянии титан обладает
чрезвычайно высокой химической активностью. Он энергично взаимодействует
практически со всеми материалами, с которыми находится в контакте на различных
стадиях изготовления отливок (атмосфера печи, огнеупоры и т. п.). Особенно
активно взаимодействует титан с газами: кислородом, азотом, водородом, окисью
углерода, двуокисью углерода, водяным паром, аммиаком и др.
Азот, кислород и углерод, растворяясь в титане, занимают октаэдральные поры гексагональной решетки, которые по размерам больше, чем поры решетки объемно-центрированного куба. Поэтому растворимость указанных элементов в β-фазе вызывает большое искажение кристаллической решетки, чем при растворении в α-фазе. Это является причиной большей растворимости азота, кислорода и углерода в α-фазе.
Первой стадией взаимодействия титана с кислородом является внедрение атомов кислорода в кристаллическую решетку металла. Но как показали многочисленные исследования кинетики поглощения кислорода титаном, образование окалины на поверхности образца определяется не скоростью поглощения газа, а диффузионными процессами.
Максимальная растворимость кислорода в α-титане составляет примерно 14,5% вес., а в β-титане — около 1,8% вес. Кислород является энергичным α-стабилизатором. При содержании кислорода выше предела растворимости в системе титан-кислород появляется фаза на основе закиси титана TiO, которая имеет золотисто-желтый цвет с металлическим блеском. Далее может образовываться фаза на основе окиси титана Ti2O3 темно-фиолетового цвета и, наконец, на основе двуокиси титана TiO2 — белого цвета.
Титан начинает взаимодействовать с кислородом уже при довольно низких температурах. При комнатной температуре на титане, находящемся в атмосфере кислорода, уже образуется окисная пленка, которая защищает его от дальнейшего окисления. Но при температуре 450…500 °С эта пленка начинает растворяться в металле. Особенно интенсивно процесс диффузии кислорода в титане происходит при температурах выше 700…800 °С. При достижении определенной толщины окисная пленка начинает растрескиваться и диффузия в глубь металла значительно усиливается. При высоких температурах окисная пленка уже не является защитной, т. е. поглощение титаном кислорода является необратимым процессом.
Сродство титана к азоту также очень велико. Титан является единственным элементом, который горит в среде азота. Заметное поглощение азота начинается уже при температурах 500…550 °С, при температуре выше 600 °С скорость поглощения резко увеличивается. Азот, так же как и кислород, является весьма сильным α-стабилизатором. При взаимодействии титана с азотом первоначально образуются твердые растворы внедрения. Максимальная растворимость азота в α-титане составляет около 7% вес., растворимость в В-титане значительно меньше и не превышает 2% вес.
При нагреве титана в атмосфере азота до температуры 800…1000 °С его поверхность тускнеет в результате образования пленки нитрида титана. Эта весьма тонкая пленка прочно связана с металлической основой. Процесс поглощения азота титаном мало зависит от давления газа и является, так же как в случае с кислородом, необратимым процессом. Скорость поглощения азота титаном значительно меньше скорости поглощения кислорода. Поэтому при взаимодействии титана с воздухом основную роль играет кислород, хотя воздух на 4/5 состоит из азота. Заметное поглощение водорода титаном начинается при температуре 250…300 °С. Сначала этот процесс протекает сравнительно медленно, но при температурах 300…350 °С скорость его увеличивается. В противоположность реакции титана с кислородом и азотом при взаимодействии с водородом на поверхности металла пленки не образуется. Это можно объяснить малыми размерами атомов водорода, которые сразу диффундируют в глубь кристаллической решетки титана
Водород, так же как кислород и азот, образует с титаном твердые растворы внедрения. Предел растворимости водорода в α-титане достигает максимума при температуре около 300 °С и составляет примерно 0,2% вес. Растворимость водорода уменьшается как при повышении, так и при понижении температуры. Наиболее резкое уменьшение растворимости наблюдается при температурах 500…600 °С. Растворимость при комнатной температуре составляет не более 0,002% вес. В В-титане растворимость водорода значительно выше. Ее максимальное значение — около 2% вес. достигается при температуре 600 °С. С повышением давления водорода его растворимость в титане увеличивается. Водород является β-стабилизатором. Большую растворимость водорода в β-фазе, чем в α-фазе, объясняют следующим образом. Кристаллическая решетка α-фазы имеет два типа пор, в которых могли бы разместиться атомы водорода — тетраэдральные поры с радиусом 3,4 нм и октаэдральные поры с радиусом 6,2 нм. Радиус атома водорода равен 4,1 нм. Тетраэдральные поры малы, октаэдральные же слишком велики и размещение в них атомов водорода сопровождается повышением свободной энергии системы за счет большей свободы колебания атомов. Поры в решетке объемно-центрированного куба имеют радиус 4,4 нм, что обеспечивает благоприятные геометрические соотношения при растворении водорода в β-титане.
Скорость поглощения водорода титаном зависит не только от температуры, но и от наличия поверхностных пленок и загрязнений. Если на поверхности металла имеются окисные пленки, скорость поглощения водорода заметно понижается. Водород, в отличие от кислорода и азота, можно практически полностью удалить из титана путем нагрева металла в вакууме. Вакуумный отжиг при температуре 750…800 °С снижает содержание водорода в титане до 0,002%. Наличие окисной пленки затрудняет удаление водорода.
Титан энергично взаимодействует с углеродом. Углерод является α-стабилизатором. Максимальная растворимость углерода при температуре 920 °С составляет 0,48% вес. С понижением температуры растворимость углерода резко падает. Растворимость углерода в В-титане достигает максимального значения — 0,8% вес. при 1750 °С. Вследствие малой растворимости углерода в α- и β-фазах присутствие его в сплавах титана выше 0,1% обусловливает появление в структуре свободных карбидов. Линия ликвидуса системы титан-углерод при увеличении содержания углерода непрерывно увеличивается от перитектической температуры (1750 °С) до температуры плавления карбида титана (3400…3500 °C). В этой системе образуется единственный карбид TiC. Однако карбид титана, как и большинство других фаз внедрения (TiO, TiN), является веществом переменного состава с широкой областью гомогенности.
Для титанового литья в качестве формовочных материалов применяются: магнезит, электрокорунд, двуокись циркония, графит. Принципиальная возможность осуществления химических реакций между титаном и огнеупорными веществами в заданных условиях может быть установлена путем сопоставления величин изобарно-изотермического потенциала. Наименее прочным огнеупором является кремнезем, а наиболее прочным — двуокись тория. Низшие окислы титана термодинамически более прочны по сравнению с высшими.
5. Диаграммы плавкости
Химический состав поверхностного слоя отливок изменяется главным образом в результате его насыщения продуктами взаимодействия между металлом и формой. Большое значение имеют также газы, адсорбированные на поверхности формы.
Одной из характерных особенностей титановых сплавов является склонность к химическому взаимодействию с формовочными материалами и образование поверхностного, так называемого альфированного слоя.
Величина поверхностного слоя измененного химического состава, часто называемого альфированным слоем, определяется по резко отличающемуся виду микроструктуры и по значительно повышенной микротвердости. Наиболее вредной примесью является кислород, образующийся в результате химических реакций с окисными огнеупорами и десорбируемый с поверхности формы. Кислород диффундирует в металл при температурах до 800 °С (рис. 19). То, что загрязнение металла происходит в основном за счет взаимодействия с формой, было подтверждено спектральным анализом. На поверхности отливок установлено повышенное содержание элементов, входящих в огнеупорный окисел формовочного материала: было обнаружено до 22% Al (рис. 20) при заливке в корундовые формы, до 9% Zn при заливке в формы из двуокиси циркония. Металл, залитый в магнезитовые формы, содержит очень небольшие количества магния, так как его растворимость в титане мала. При заливке металла в графитовые формы наблюдается повышенное содержание углерода — до 1,0%.
На степень насыщения поверхностного слоя продуктами взаимодействия оказывают также влияние размеры отливки.
Большое влияние на развитие реакций между отливкой и формой оказывает температура формы. При заливке металла в формы, которые были на греты до температуры выше 600 ºС, отливки были сильно поражены газовыми дефектами. Литая поверхность была недопустимо низкого качества.
Характер формирования микронеровностей поверхности титановых отливок подчиняется тем же законам, что и формирование поверхности других литейных сплавов. Титановые сплавы склонны к образованию спаев на поверхности отливок. Для предупреждения этого дефекта необходимо обеспечить равномерное спокойное заполнение металла без разделения его на отдельные потоки.
Рис. 19. Диаграмма состояния системы Ti – O Рис. 20. Диаграмма состояния системы Ti – Al
6. Трещины
Трещиноустойчивостъ характеризует способность металлов и сплавов к релаксации напряжений, возникающих в отливке при затвердевании и охлаждении, в результате усадки, фазовых превращений или температурного перепада.
В практике литья обычно различают два вида трещин: горячие и холодные. Это деление весьма условно. Считается, что горячие трещины образуются в области, близкой к температуре солидуса. По внешнему виду такие трещины отличаются окисленной поверхностью. Холодные трещины имеют блестящую поверхность и образуются в области упругих деформаций при температуре значительно ниже температуры кристаллизации.
6.1. Горячие трещины
Отличительной особенностью титана и большинства сплавов на его основе является высокая устойчивость против образования горячих трещин.
Большинство двойных сплавов на основе титана при введении до 10% легирующего элемента также не склонно к образованию трещин при затрудненной усадке.
Характерное для литейных сплавов на основе титана сочетание физико-механических свойств — малые значения модуля упругости и коэффициента линейного расширения, склонность к вязкому разрушению и повышенная прочность при высоких температурах — обусловливает их высокую трещиноустойчивость. Это упрощает решение многих технологических вопросов и дает возможность технологам-литейщикам при разработке конструкции отливки и выборе материала для формы руководствоваться главным образом экономическими соображениями и удобствами осуществления технологического процесса.
6.2. Холодные трещины
Специфической особенностью титановых отливок является наличие в большинстве из них поверхностного альфированного слоя измененного химического состава, образующегося в результате взаимодействия отливки с формой или с атмосферой при плохой защите мест, подвергающихся сварке. В этом слое, обладающем очень низкими пластическими свойствами и повышенной твердостью, трещины могут возникать при весьма малых нагрузках.
Считается, что границы зерен в сплавах обладают пониженной сопротивляемостью сдвигу по сравнению с телом зерна. Это свойство поликристаллических агрегатов обусловлено несопряженностью кристаллической решетки на поверхностях раздела зерен, вследствие чего там создается высокая концентрация искажений и дефектов кристаллического строения.
Известно, что одним из основных факторов, влияющих на образование холодных трещин, является напряжение, производимое на поверхности. В титановых отливках, полученных в керамических формах, это влияние усугубляется наличием альфированного слоя. С течением времени микротрещина, возникающая в альфированном слое, может увеличиваться в размерах и стать причиной разрушения изделия.
7. Исследовательская часть
В своей исследовательской части работы мне пришлось провести исследования на тонкой пластине отлитой, из титана в Московском Государственном Стоматологическом Университете при помощи ординатора Д.М. Кривенко на СПЛУ Dor-a-matic. Предназначением данной отливки был эксперимент, при котором на пластинку наносился слой эмали, применяющейся в стоматологии, для выяснения причин, влияющих на адгезию между металлом и эмалью. Во время данного эксперимента пластинку сгибали, и чем больше был угол, на котором отлетала эмаль от пластики, тем сильней была адгезия. Моей задачей было изучение данной пластины на наличие дефектов, таких как дефекты, появившиеся во время заливки, а так же механические дефекты. Проходило исследование остановки потока, поверхности отливки на наличие вздутий, рыхлостей, дендритов, горячих и холодных трещин, наличия или отсутствия альфированного слоя — причин, всячески ухудшающих адгезию между металлом и эмалью.
Первые исследования проходили на приборе для изучения микротвёрдости различных отливок и материалов — ПМТ-3 (рис. 21). Главными элементами данного прибора были: рабочий стол, увеличительное устройство и алмазная пирамидка, с углом при вершине в 136°, которая вдавливалась в отливку под массой груза. Первым этапом был выбор области на объекте, где нужно было измерить микротвёрдость. После этого алмазная пирамида вдавливалась под массой груза в данную область. Следующим этапом было измерение диаметра отпечатка пирамиды и получение по табличным данным, зависящим от значений массы груза и диаметра полученного отпечатка пирамиды, значения микротвердости данного участка отливки. В процессе исследований были проведены замеры микротвёрдостей на двух различных видах отливок: широкой дуги бюгеля и тонкой пластинки. Полученные данные были занесены и обработаны с помощью программы статистического анализа Statistica 6.0, разработанной фирмой StataSoft. Данные полученные с дуги бюгеля очень отличаются от данных тонкой пластинки. Этим отличием был отчетливо выраженный α-слой, характеризующийся большой микротвердостью на дуге бюгеля и его полное отсутствие на пластинке. Таким образом, на адгезию между металлом и эмалью альфированный слой никак не влияет.
Рис. 21. Работа за прибором ПМТ-3
Так в чем же причина отсутствия α-слоя? При рассмотрении пластинки и отрезка дуги бюгеля под микроскопом можно сделать вывод: при остановки потока на тонкой отливки α-слой просто не успевает образоваться. Это видно, как при малом увеличении (рис. 22…25),так и при сильном (рис. 26…29). Альтернативная ситуация происходит при рассмотрении дуги бюгеля — виден отчетливо выраженный α-слой с повышенной микротвердостью (рис. 30).
Если альфированный слой отсутствует, а значит, существуют другие причины, которые способствуют отколу эмали от металлической пластинки. При изучении поверхности отлитой пластинки выявляются такие технические браки, как горячие (рис. 31) и холодные (рис. 32) трещины. Присутствуют и причины появления горячих трещин — это обширные дендриты и рыхлости на поверхности (рис. 33).
Рис. 22. Остановка потока. Голова потока Рис. 23. Остановка потока. Голова потока
Рис. 24. Остановка потока. Голова потока Рис. 25. Остановка потока. Начало потока
Рис. 26. Замеры микротвердости Рис. 27. Замеры микротвердости
Рис. 28. Замеры микротвердости Рис. 29. Замеры микротвердости
Рис. 30. Бюгель Рис. 31а. Горячие трещины
Рис. 31б. Горячие трещины Рис. 32. Холодные трещины
а б
Рис. 33. Дендриты и рыхлости
8. Обработка экспериментальных данных в программе Statistica
На приборе для измерения микротвердости поверхности материалов ПМТ-3 я получил значения микротвердости (табл. 1…4) на отливки бюгеля и тонкой пластинки.
Таблица 1.
Замер на пластине №3 (Голова потока)
| Глубина, мм | Микротвёрдость, Hμ | 239,3571-22,1085*log10(x) | Остатки |
1 | 0,025 | 277 | 274,776243 | 2,22375668 |
2 | 0,075 | 286 | 264,227808 | 21,7721919 |
3 | 0,125 | 244 | 259,323065 | -15,323065 |
4 | 0,175 | 216 | 256,092393 | -40,0923933 |
5 | 0,225 | 259 | 253,679373 | 5,3206272 |
6 | 0,275 | 251 | 251,752613 | -0,752613138 |
7 | 0,325 | 277 | 250,148627 | 26,8513733 |
Таблица 2.
Замер на пластине №4 (Голова потока)
| Глубина, мм | Микротвёрдость, Hμ | 216,8289-8,4156*log10(x) | Остатки |
1 | 0,025 | 216 | 230,311196 | -14,3111961 |
2 | 0,075 | 244 | 226,295934 | 17,7040656 |
3 | 0,125 | 251 | 224,428944 | 26,5710559 |
4 | 0,175 | 193 | 223,199189 | -30,199189 |
5 | 0,225 | 244 | 222,280673 | 21,7193272 |
6 | 0,275 | 198 | 221,547252 | -23,5472518 |
7 | 0,325 | 223 | 220,936694 | 2,06330561 |
Таблица 3.
Замер на пластине №4 (Поперечное сечение)
| Глубина, мм | Микротвёрдость, Hμ | 222,7969-13,5088*log10(x) | Остатки |
1 | 0,025 | 236 | 244,438808 | -8,43880801 |
2 | 0,125 | 229 | 234,996562 | -5,99656202 |
3 | 0,175 | 229 | 233,022548 | -4,02254761 |
4 | 0,225 | 229 | 231,548137 | -2,5481368 |
Таблица 4.
Бюгель
| Глубина, мм | Микротвёрдость, Hμ | 136,195-188,7965*LOG10(x) | Остатки |
1 | 0,005 | 583 | 570,62141 | 12,3785904 |
2 | 0,03 | 447 | 423,709177 | 23,290823 |
3 | 0,055 | 353 | 374,010115 | -21,0101155 |
4 | 0,11 | 268 | 317,176706 | -49,1767059 |
5 | 0,16 | 251 | 286,454362 | -35,4543617 |
6 | 0,21 | 268 | 264,157625 | 3,84237508 |
7 | 0,26 | 268 | 246,645984 | 21,3540157 |
8 | 0,31 | 277 | 232,224132 | 44,775868 |
На основе данных таблиц были построены графики рассеяния (scatterplots), рассеяния с гистограммами (scatterplots with histograms) и вероятность-вероятность (probability-probability) (рис. 34…43). На основе данных анализировался коэффициент корреляции – r, p – значение, так же на графике показано уравнение прямой и доверительный интервал.
Рис. 34.
Рис. 35.
Рис. 36.
Рис. 37.
Рис. 38.
Рис. 39.
Рис. 40.
Рис. 41.
Рис. 42.
Рис. 43.
Корреляция является мерой силы взаимосвязи. Подобно всем статистическим характеристикам, корреляция одновременно и полезна, и ограничена. Если диаграмма рассеяния показывает, например, ярко выраженную линейную взаимосвязь или отсутствие какой-либо взаимосвязи, то корреляция превосходно это отражает. Но если данные содержат определенные проблемы, такие как нелинейная взаимосвязь, неодинаковая изменчивость,
наличие групп или выбросов, корреляция может вводить в заблуждение. Сама по себе корреляция носит ограниченный характер, поскольку ее интерпретация зависит от типа взаимосвязи в данных. Вот почему столь большое значение придается диаграмме рассеяния: она либо подтверждает обычную интерпретацию корреляции, либо показывает наличие в данных определенных проблем, которые приводят к тому, что корреляция лишь вводит нас в заблуждение.
Корреляция, или коэффициент корреляции, обозначаемый r, является числом в диапазоне от -1 до 1, характеризующем силу взаимосвязи в данных. Корреляция, равная 1, указывает на идеальную взаимосвязь в виде прямой линии, причем более высокие значения одной переменной соответствуют идеально предсказуемым более высоким значениям другой переменной. Корреляция, равная -1, указывает на идеальную отрицательную взаимосвязь в виде прямой линии, причем одна переменная уменьшается с ростом другой. Корреляция, равна 0, указывает на то, что взаимосвязь полностью отсутствует. Знак корреляции, положительный или отрицательный, указывает на наклон линии.
P-значение свидетельствует о том, насколько неожиданным является факт, что данные соответствуют нулевой гипотезе. Малые р-значения обозначают большую неожиданность такого факта и приводят к отказу от нулевой гипотезы . Принято отвергать когда р-значения меньше чем 0,05.
Нулевая гипотеза, обозначается и представляет собой такое утверждение, которое принимается тогда, когда нет убедительных аргументов для его отклонения. Из двух гипотез нулевая часто является более определенной.
:μ=μ
Доверительным интервалом называют такой вычисленный на данных интервалах, который с известной вероятностью содержит интересующий нас не известный параметр генеральной совокупности, и эта вероятность определяется с учет случайного эксперимента, который начинается с извлечения случайной выборки.
Остаток – ошибка прогнозирования для каждой из точек данных; указывает на то, насколько далеко от линии находится соответствующая тачка.
9. Выводы
При исследовании выявились основные дефекты отливки – это дендриты, рыхлости, горячие и холодные трещины. Присутствие альфированного слоя на толстой дуге бюгеля и его отсутствие на тонкой пластине. Соответственно следует:
1. Усилить контроль качества отливок.
2. Улучшить среду плавки титана – это снизит количество рыхлостей на поверхности.
3. Не деформировать отливки бюгеля при комнатной температуре, так как альфированный слой очень хрупкий и как следствие этого возникают холодные трещины.
Список используемых источников
1. Магницкий О.Н. Литейные свойства титановых сплавов. — М.: Машиностроение, 1968. — 120 с.
2. Маркскорс Р. Цельнолитые съемные протезы. / «Новое в стамотологии». — 2000. — 80 с.
3. Васильев В.А., Васильев Н.В. Плавильно-литейные установки для изготовления стоматологических и ювелирных изделий. — Литейщик России. — №4 — 2003. — С 23-36.
4. Сигел Э.Ф. Практическая бизнес – статистика, четвёртое издание. – «Вильямс», 2002. — 1056 c.
5. www.bego.com
6. www.manfredi.com
7. www.dor-a-matic.de
8. www.zubtech.ru
В НИТУ «МИСиС» создали новую технологию литья для авиационной промышленности
Ученые из Национального исследовательского технологического университета «МИСиС» разработали безмодельную технологию изготовления деталей из титановых сплавов для российской авиационной промышленности. Новая технология, которая будет использоваться в производстве двигателей для самолетов МС-21, более дешевая, экологически безопасная и позволяет получать более точные детали.
Специалисты Инжинирингового центра «Литейные технологии и материалы» НИТУ «МИСиС» отказались от классической технологии литья титановых сплавов по выплавляемым моделям и предложили безмодельную технологию.
Как отметила ректор НИТУ «МИСиС» Алевтина Черникова, «ученые НИТУ „МИСиС“ разработали уникальную, импортозамещающую технологию, которая позволяет использовать только отечественное сырье и оборудование. Профессор Владимир Белов и возглавляемый им научный коллектив за последние годы представили несколько разработок для авиакосмического комплекса, которые были удостоены государственных премий и самых высоких наград на престижных международных выставках. Только в 2016 году эти изобретения были отмечены золотой медалью выставки Inventions Geneva и премией Правительства Москвы для молодых ученых».
Секрет новой технологии заключается в использовании графитовых заготовок сложной конфигурации, изготавливаемых фрезерованием на станках с числовым программным управлением. Графит почти не взаимодействует с титановым расплавом, поэтому отливки получаются тонкостенными, без загрязнённого альфированного слоя, который снижает пластичность титана. При классической технологии создаются отливки с более толстыми стенками — на изделии присутствует альфированный слой, который необходимо удалять.
Созданная технология позволит не только делать формы полностью из отечественного сырья (сейчас применяются керамические формы, компоненты для которых поставляются из-за рубежа), но и получать детали с большей размерной точностью, чем при традиционных методах литья по выплавляемым моделям. Еще одним преимуществом безмодельной технологии является её дешевизна и экологическая безопасность, в сравнении с западными аналогами.
«Главное достоинство нашей технологии заключается в том, что мы смогли сделать отливку, толщина стенок которой составляет 3-4 мм. В мировой практике подобная технология не известна. При изготовлении отливок по другим технологиям толщина стенки достигает 10 мм, и требуется проведение экологически вредной процедуры травления — удаления лишнего материала химической кислотой. Для данной процедуры выстраивается целая линия экологически вредного производства. Безмодельное литье вообще не требует травления — отливку обдувают дробью, уменьшая толщину стенок. Кроме того, новая технология позволяет минимизировать затраты на механическую обработку изделия», — рассказал руководитель исследовательской группы, заведующий кафедрой «Литейные технологии и художественная обработка материалов» НИТУ «МИСиС», директор Инжинирингового центра «Литейные технологии и материалы» НИТУ «МИСиС», профессор Владимир Белов.
Такая технология идеально подходит для передовых российских проектов в авиационной промышленности, таких как ближне-среднемагистральный пассажирский самолет МС-21. По новой технологии специалисты уже отлили деталь для двигателя ПД-14, который будет использоваться в новом самолете. Деталь — литосварная конструкция внутреннего разделительного корпуса турбины — состоит из семи стоек, внутреннего корпуса и раскатного кольца.
Согласно планам, самолет МС-21 сможет успешно конкурировать как с китайским COMAC C919, так и с Boeing-737 MAX и Airbus A320neo. Самолет планируется поставлять в Малайзию, Египет и Азербайджан: компании из первых двух стран уже подписали соглашения о закупках, подписание соглашения с Азербайджаном состоится в феврале 2017 г.
Как отметил Алексей Ионов, заместитель завкафедрой «Технологии производства двигатели летательных аппаратов» МАИ, «совершенствование воздушно-реактивных двигателей всегда идет по пути повышения тяговой отдачи с одного килограмма конструкции. Условия современной конкуренции таковы, что рынок завоевывает тот, кто может добиться топливной эффективности выше, чем у конкурентов. Усложнение конструкций и технологий их создания требует новых технологических решений. Сейчас линейные технологии в авиадвигателестроении получают новое развитие и работа НИТУ „МИСИС“ в области тонкостенного титанового литья несомненно актуальна и требует дальнейшего развития».
На создание технологии у разработчиков ушло 3 года. Сейчас специалисты продолжают совершенствовать технологию — они ищут способ сделать графитовые формы многоразовыми. В настоящее время проведено опытно-промышленное опробование и ведутся работы по изготовлению нового комплекта отливок для штатного внедрения технологии в производство.
литой титан — как это сделано?
Почему лить титан так сложно?
Знаете ли вы, что литой титан настолько нестабилен, что невосприимчив к морской воде и химической коррозии? Однако свойства титана, предотвращающие химическую коррозию, — это те самые свойства, которые мешают распространенным технологиям литья.
В чистом виде титан настолько нестабилен, что самопроизвольно вступает в реакцию с кислородом с образованием защитного слоя оксида титана. Подобные реакции происходят со многими легированными формами титана, включая «хлеб с маслом» аэрокосмической промышленности: Ti6Al4V класса 5.
При нагревании реакция титана с кислородом настолько интенсивна, что создает большие проблемы в процессе литья. Во время этого процесса расплавленный титан вступает в реакцию даже с наименьшим количеством остаточного кислорода, присутствующего в большинстве тугоплавких соединений. Огнеупоры — это материалы, которые обычно используются для изготовления литейных форм по выплавляемым моделям. Чрезвычайная реакционная способность титана в сочетании с повсеместным присутствием кислорода в окружающей среде ставит перед производителями задачу по эффективному литью титана.Ниже мы обсудим три распространенных метода производства литых титановых деталей: утрамбованный графит, литье металла под давлением и литье по выплавляемым моделям.
Набивной графит для литья титана
Одним из методов управления реактивными свойствами титана является изготовление литейных форм из графита, химически инертного материала. Этот конкретный процесс минимизации реакции литейной формы с титаном известен как литье из утрамбованного графита . Графитовый «песок» сначала смешивается с водой и смоляным сиропом — среди других связующих веществ — а затем утрамбовывается — или утрамбовывается — по рисунку для создания формы.Затем графитовая форма сушится и обжигается для сжигания связующих материалов, оставляя после себя оболочку из чистого графита. Эта оболочка формы затем помещается в вакуумную среду, где расплавленный титан затем заливается в оболочку. После чего он затвердевает и ему дают остыть. Затем графитовая оболочка отламывается, и остается окончательный литой титановый продукт.
Из-за относительно крупной текстуры графитового песка процесс набивного графита имеет тенденцию производить титановые отливки с более шероховатой поверхностью.Хотя процесс набивного графита относительно экономичен для больших объемных отливок, он позволяет получать отливки с низкой детализацией и точностью. Компромисс между допусками на точность и стоимостью делает набивной графит экономически выгодным вариантом для многих отраслей, где не требуется точный контроль размеров.
Литье металла под давлением для литья титана
На другом конце спектра метода набивного графита находится Metal Injection Molding , или MIM. Тонко измельченный титановый порошок смешивают с соответствующими легирующими порошками и смешивают с термопластичным связующим при повышенной температуре.Связующее придает смеси пластичность, позволяя впрыскивать ее в прецизионно обработанную форму.Этот процесс впрыска позволяет получить высокоточную форму с жесткими допусками и мелкими деталями. Затем формованная деталь подвергается воздействию растворителей и катализаторов для удаления связующих термопластов. После удаления связующего деталь становится хрупкой, пористой и до 40% пустует. Затем деталь спекается, чтобы удалить это пустое пространство путем нагревания почти до точки плавления и приложения давления. В процессе спекания удаляется объем пор, происходит существенная усадка детали и отформованная деталь превращается в твердый титановый сплав с ее окончательной формой.
Процесс MIM предлагает отличный контроль размеров и очень подробные функции. Эти преимущества в сочетании с превосходной обработкой поверхности делают MIM идеальным процессом для отливок небольших сетчатых форм, где точность и внешний вид имеют первостепенное значение. Однако многоступенчатый процесс MIM сопряжен с высокими затратами и требует значительных начальных вложений для изготовления форм для литья под давлением.
Титановое литье по выплавляемым моделям
Мы определили две крайности, связанные с процессами производства литого титана: набивной графит с относительно низкой стоимостью и точностью; и литье металла под давлением с более высокой точностью, но более высокими затратами.
Однако во многих случаях применения литья титана требуется баланс между этими двумя крайними вариантами. Литье по выплавляемым моделям, также известное как метод выплавляемого воска, обеспечивает идеальный баланс между точностью и стоимостью. Процесс литья по выплавляемым моделям начинается с изготовления точной восковой модели — или шаблона — конечного продукта. Этот узор обычно изготавливается методом литья под давлением или с помощью 3D-печати. Затем узор покрывается керамическим материалом, чтобы создать «оболочку» или форму. Форма помещается в печь, где воск плавится и сливается из корпуса, оставляя после себя пустую полость в форме окончательной отливки.
Затем оболочка помещается в вакуумную камеру, где концентрация кислорода практически равна нулю. Затем расплавленный титан заливается в керамическую форму, которая заполняет освободившуюся полость оболочки. Титану дают затвердеть и охладиться, затем керамическую форму разрушают и удаляют из отливки компонента, обнажая окончательную отлитую титановую деталь.
Хотя это менее затратный процесс по сравнению с MIM, литье по выплавляемым моделям позволяет производить титановые отливки с достаточно жесткими допусками для сложных и сложных деталей и элементов.Литье по выплавляемым моделям также может обеспечить относительно гладкую поверхность.
Литье по выплавляемым моделям — это очень рентабельный процесс производства литых титановых компонентов почти чистой и нетто-формы. Благодаря относительно высокой точности его можно использовать для ограничения ненужных операций обработки и отходов материала. Это делает литье по выплавляемым моделям идеальным процессом, который компания FS Precision совершенствует уже более 50 лет! Наши отливки из титана по выплавляемым моделям, соответствующие стандартам ITAR и NADCAP, отражают приверженность нашей компании созданию высококачественных и экономичных компонентов из титанового сплава.
Если вы хотите узнать больше, посмотрите наше видео по литью по выплавляемым моделям. Или, если вы хотите узнать, как мы можем помочь вам с вашими потребностями в литом титане, нажмите кнопку Get A Quote в нижнем левом углу и отправьте нам информацию о своем проекте. Мы отправим вам оценку стоимости и времени выполнения заказа, чтобы помочь вам в процессе разработки вашей программы.
Вкратце
Производство литых титановых компонентов является очень сложной задачей из-за его чрезвычайно нестабильной природы в элементарной форме.В присутствии кислорода элементарный титан самопроизвольно реагирует с образованием более стабильных соединений оксида титана. Эта реакция становится особенно бурной при повышенных температурах.
Несмотря на эти проблемы, преимущества титана для критически важных применений в аэрокосмической, оборонной, подводной и других областях привели к развитию множества методов формирования сложных форм в титановых сплавах.
- Литье металла под давлением (MIM) — хороший метод для небольших форм с замысловатыми деталями, высокой точностью и гладкой поверхностью, например ювелирных изделий.MIM включает в себя дорогостоящий многоступенчатый процесс с относительно высокими начальными вложениями в инструментальную оснастку.
- Литье из утрамбованного графита имеет относительно низкую стоимость по сравнению с MIM, поскольку не требует дорогостоящих первоначальных вложений в инструмент. Однако набивной графит не дает мелких деталей, высокой точности или гладкой поверхности.
- Титан, отлитый по выплавляемым моделям, является идеальным компромиссом для большинства применений в аэрокосмической, оборонной и подводной промышленности. Литье по выплавляемым моделям обеспечивает достаточно мелкие детали и допуски по разумной цене.
FS Precision — один из крупнейших поставщиков титанового литья в мире и растущий мировой лидер в области литья по выплавляемым моделям для неподвижного крыла, поворотного крыла, космических запусков и систем защиты. Наши литейные цеха по выплавляемым моделям, сертифицированные AS9100D, расположены в США и на Тайване. Наши заводы в США зарегистрированы в ITAR и FFL, а наши заводы на Тайване активно поддерживают выполнение обязательств перед правительством Тайваня по зачету с клиентами.
Подробнее о титановых отливках FS Precision AS9100D для аэрокосмической промышленности.
Титановые отливки | Castings Technology International
Cti может поставлять полностью сертифицированные титановые отливки пользователям по всему миру, что не имеет аналогов в Великобритании.
Наши возможности были разработаны для поддержки статического или центробежного литья с использованием графита или методов литья по выплавляемым моделям.
Они включают обширные знания в области проектирования и моделирования для производства с использованием программных пакетов Magmasoft® и ProCast®.
Мы можем изготавливать компоненты, используя методы литья по выплавляемым моделям на основе традиционной восковой оснастки или наши технологии прототипирования, которые особенно подходят для единичных компонентов и компонентов небольшого объема.
Приложения
Cti имеет обширный опыт изготовления титановых отливок для химической, нефтегазовой и морской отраслей, где металл и его сплавы используются для обеспечения их коррозионной стойкости.
Мы также поставляли продукцию для аэрокосмической и оборонной отраслей, где высокое соотношение прочности к массе является ключевым преимуществом, мы производим небольшие лопасти и компоненты для зондов для дозаправки самолетов, а также детали для европейского истребителя Joint Strike Fighter и гаубицы M777.
Мы также поставили в автомобильный сектор титановые турбины для турбонагнетателя и компоненты выхлопных систем для высокопроизводительных автомобилей, в медицинский сектор — с небольшими имплантатами и в сектор безопасности — с форсунками для систем пожаротушения, установленных в агрессивных средах.
Заглядывая в будущее, мы увеличиваем наши мощности, чтобы иметь возможность производить крупномасштабные титановые компоненты, вплоть до кожухов авиационных двигателей.
Объекты
Наша первая титановая печь была введена в эксплуатацию в 2001 году и способна плавить до 30 кг металла.
Позже мы добавили вторую печь, способную плавить до 90 кг, используя тот же процесс индукционной плавки черепа (ISM), и недавно обнародовали планы по вложению 15 миллионов фунтов стерлингов в печь вакуумно-дугового переплава (VAR).
Эта печь будет способна производить отливки весом от 150 кг до 1000 кг и станет одной из самых больших в Европе для производства титановых компонентов для авиакосмической промышленности.
Новая печь позволит нам заливать от 12 кг до 1000 кг расплавленного титана и его сплавов в формы размером до двух.5 метров в диаметре и 2,5 метра в высоту.
Наши плавильно-литейные предприятия поддерживаются отделочным цехом, инспекционным отделом и металлургическими службами с возможностью проведения процессов после литья, включая термообработку в вакууме, и полной сертификации производимых отливок.
Качество
Система управления качествомCti сертифицирована по AS9100C (EN 9100: 2009), что означает, что мы можем изготавливать отливки, соответствующие аэрокосмическим стандартам.
Мы сертифицированы в соответствии со стандартом NORSOK M-650 Rev 4, установленным норвежской нефтяной промышленностью, и можем поставлять отливки из технически чистого титанового сплава в соответствии с NORSOK MDS-T02 Rev5.
Мы также имеем несколько аккредитаций от Nadcap, глобальной программы аккредитации для аэрокосмической, оборонной и смежных отраслей, в том числе аккредитации для вакуумной термообработки (AC7102), сварки (AC7110), проникновения красителей и рентгеновского контроля (AC7114 / 1 и AC7114 / 4. ).
Материалы
Cti имеет многолетний опыт производства сертифицированных отливок из технически чистого титана (ASTM B367 C-2) и его обычного сплава 6Al-4V (ASTM B367 C-5) для изготовления как серийных изделий, так и единичных или небольших прототипов.
У нас также есть опыт изготовления прототипов и отливок из других реактивных сплавов, включая Ti-1.5Al, TiXT, Ti 6-2-4-2, Ti 6-2-4-6, Ti 10-2-4, Нитинол, гамма-алюминид титана и циркониевые сплавы.
Услуги компаний по литью по выплавляемым моделям
Литье по выплавляемым моделям из титана — Ferralloy Inc.В процессе литья по выплавляемым моделям могут использоваться различные сплавы металлов, включая титан, алюминий, медь и нержавеющую сталь, которые являются одними из наиболее распространенных материалов.Поскольку восковая модель создается в точном размере и форме, а деталь, литье по выплавляемым моделям или восковое литье обеспечивает высокую точность размеров.
Титановое литье по выплавляемым моделям дорого по сравнению с другими методами, такими как литье под давлением, хотя требует меньших затрат на оборудование и меньших затрат на чистовую обработку. Литье по выплавляемым моделям может производиться вручную единичными или небольшими партиями или может быть полуавтоматическим и производить сотни деталей одновременно.
Титановое литье по выплавляемым моделям — Ferralloy Inc. Отливкимогут иметь толщину от долей дюйма до 1000 фунтов, хотя большинство деталей весит 15 фунтов или меньше.Титановые отливки очень прочные и легкие и используются для компонентов турбокомпрессоров, промышленных инструментов и инструментов, а также для других применений в оборонной, аэрокосмической, транспортной, энергетической, морской и медицинской отраслях.
Процесс литья по выплавляемым моделям начинается с восковой копии детали, которая была вырезана вручную или на станке или изготовлена методом литья под давлением. Восковой узор прикрепляется к литнику или восковому стержню. В зависимости от размера и формы детали к одному литнику может быть прикреплено несколько сотен шаблонов, в результате чего получается сборка, называемая деревом.
Дерево окунают в керамическую суспензию, называемую паковочной массой. Его несколько раз окунают в смеси, которые становятся все более крупными. Когда паковочная масса на восковом шаблоне станет достаточно толстой, ее оставляют для высыхания. Другой способ — поместить дерево в колбу и залить паковочную массу в емкость, пока дерево полностью не покроется.
Использование низкотемпературной печи или вакуума может ускорить процесс. Когда дерево высохнет, его помещают в духовку или печь вверх дном, чтобы тающий воск стекал.Во время фазы выгорания паковочная масса нагревается еще больше, чтобы полностью удалить остаточную влагу или воск.
Расплав титана заливается в пространство и может быть втянут с использованием вакуума, избыточного давления воздуха или центробежного литья. После охлаждения и затвердевания титановой детали паковочная масса удаляется с помощью различных методов, включая вибрацию, молотки, растворяющий агент или струйную очистку.
TITAL — Аэрокосмические технологии
TITAL — ведущая компания по литью по выплавляемым моделям из титана и алюминиевых сплавов, расположенная в Германии.Используя запатентованный процесс HERO Premium Casting®, TITAL поставляет легкие, высокопрочные отливки по выплавляемым моделям, которые могут поставляться «готовыми к интеграции» и обеспечивать значительную экономию средств и многие другие преимущества для заказчика.
Основные области применения находятся в следующих отраслях: аэрокосмическая, оборонная, электронная, оптическая, медицинская, Формула-1, машиностроение и гражданское строительство.
Все процессы одобрены PRI NADCAP и AS 9100. Проверка качества проводится в соответствии со всеми стандартными спецификациями.Отливки подвергаются радиоскопическому, рентгено-металлургическому и УФ-проникающему исследованию для выявления любых внутренних или внешних дефектов.
РуководствоTITAL по обеспечению качества соответствует требованиям Немецкой ассоциации аэрокосмической промышленности и NADCAP. TITAL обладает сильным потенциалом исследований и разработок для ведущих / будущих приложений.
Отливки по выплавляемым моделям, готовые к интеграции
Большинство отливок поставляются «готовыми к интеграции», что позволяет избежать дорогостоящих и трудоемких операций по обработке и обработке со стороны заказчика.
Объединение многих элементов дизайна в одну отливку приводит к потенциальной экономии затрат для заказчика.
Проектирование по себестоимости
TITAL обеспечивает консультационную поддержку при проектировании деталей и выборе материалов, а также обеспечивает тесный контакт между заказчиком и TITAL на протяжении всего процесса (т. Е. Параллельного проектирования). На территории TITAL регулярно проводятся семинары для дизайнеров-заказчиков с целью оптимизации затрат на проектирование.
Литье по выплавляемым моделям Hero Premium (алюминий)
Процесс HERO Premium Casting® сочетает в себе инновационный, интеллектуальный и надежный технологический процесс с высокой воспроизводимостью алюминиевых отливок по выплавляемым моделям.В результате получаются легкие, высокопрочные и сложные отливки, отвечающие требованиям завтрашнего дня.
TITAL сертифицирован Airbus как единственная в мире компания по литью по выплавляемым моделям, которая отливает критически важные детали с коэффициентом литья (CF) 1.0 в соответствии с FAR-AC-25.621.
Запатентованный процесс литья HERO Premium Casting отличается от традиционных процессов литья за счет контролируемого компьютерного затвердевания детали. Преимущества этого процесса литья по выплавляемым моделям включают экономию затрат, превосходную прочность материала, автоматизацию процесса, высокие механические свойства и снижение риска возникновения дефектов.Дополнительные преимущества:
- Меньший вес за счет коэффициента литья 1,0
- Толщина тонких стенок (до 1,5 мм, местами до 1 мм)
- Сложная геометрия отливок (задние тяги)
- Воспроизводимость и точность размеров
- Полный контроль процессов по всей цепочке создания стоимости (SAP)
- Полностью обработанная и обработанная поверхность; готов к интеграции
- Надежная профилактическая гарантия качества
- Сокращение времени и стоимости тестирования
- Размер компонента для алюминиевых деталей диаметром примерно 1800 мм x 1800 мм x 600 мм
- Вес: до 80 кг
- Сплавы, эл.грамм. A357, A356
Процесс вакуумного литья по выплавляемым моделям (титан)
- Холодные формы обеспечивают более быстрое затвердевание и более высокие механические свойства
- Атмосфера аргона для меньшего количества α-Case
- Сложная геометрия отливок (задние тяги)
- Высокие механические свойства
- Превосходная прочность материала
- Воспроизводимость и точность размеров
- Размер компонента для титановых деталей диаметром приблизительно 1000 мм x 1000 мм x 600 мм
- Сплавы: TiAl6V4, Ti6242
- Масса: до 300 кг
Быстрое прототипирование при литье по выплавляемым моделям из титана и алюминия
Отливки по выплавляемым моделям на основе моделей быстрого прототипирования сокращают время разработки и обеспечивают гибкость в отделе исследований и разработок заказчиков.Достоинства:
- Те же механические свойства, что и при серийном производстве
- Отдельная производственная линия для коротких сроков поставки
- Экономия затрат на разработку
- Высокая гибкость
- Габаритные размеры почти такие же, как у серийного производства
О компании TITAL
TITAL поставляет ведущим компаниям по всему миру в области аэрокосмической, оборонной, автомобильной промышленности и промышленных систем сложные изделия для литья по выплавляемым моделям из алюминия и титана с использованием процесса литья по выплавляемым моделям.
TITAL была основана в 1974 году, а в 2006 году ее руководство перешло к управлению. Сегодня в компании работает более 500 человек, а выручка за 2011 год составила 53 миллиона евро.
Титановое литье
Титан и его сплавы — эффективные конструкционные материалы, обеспечивающие создание многих видов современного оборудования. БЛМЗ — один из пионеров российского производства фасонного литья титановых сплавов. За последние десятилетия мы доказали, что являемся лидером в исследованиях и разработках новых титановых сплавов и оборудования для фасонного литья.
БЛМЗ — ведущий массовый производитель титановых фасонных отливок, используемых в авиационных двигателях, самолетах, химическом и пищевом машиностроении, судостроении, нефтедобыче, транспортировке и переработке нефти, а также в медицине. Завод поставляет отливки, в том числе после механической обработки, крупнейшим предприятиям России, стран ближнего и дальнего зарубежья. Мы готовы сотрудничать с разработчиками оборудования и комплектующих на стадии проектирования, чтобы реализовать лучшие титановые сплавы и заменить стальные комплектующие на комплектующие из этих сплавов.
Литейные титановые сплавы | |
Отечественный по ОСТ 1-81 | ВТ5Л, ВТ6Л, ВТ20Л, ВТ21Л, ТЛЗ, ТЛ5 |
Зарубежные согласно ASTM 8367 | марка С2, марка С3, марка С5 |
Основные производственные операции:
- автоматические процессы изготовления чугуна и разливки в формы в вакуумных черепных печах, отвечающие лучшим мировым стандартам;
- собственная технология производства опалубок для каждого метода литья, осуществляемого с помощью специального оборудования;
- возможно горячее изостатическое прессование (ГИП) отливок и сварка в среде аргона;
- термическая обработка и чистовая обработка отливок;
- механическая обработка на высокотехнологичном оборудовании.
БЛМЗ осваивает наиболее популярные методы литья титановых сплавов:
- литье по выплавляемым моделям;
- (утрамбованная) отливка из прессованного графита; croning;
- отливка в оболочку; кокильное литье;
- Литье по выкройке из полистирола;
- Процесс бесформенного литья с использованием 3D-формованных графитовых блоков.
Производственная серия | штук / год | до 10 000 |
Размер отливки | мм | мин. 10х10х10, макс. 800 |
Вес отливки | кг | мин 0.005, макс 200 |
толщина стен | мм | мин 2 ± 0,5 |
Точность | мм | до ± 1,5 при самом большом размере |
Мы поставляем покрытие без альфа-слоя с эффективным припуском, что значительно снижает затраты на механическую обработку.
Титановое литье по выплавляемым моделям: что вам нужно знать — производитель компонентов для прецизионного литья и механической обработки
Титан — это металл, который ценится за высокое отношение прочности к плотности, коррозионную стойкость и термостойкость.Несмотря на то, что титан является одним из наиболее распространенных природных элементов на планете, отделить его от других элементов до его основной металлической формы — дорого. Титан легко связывается с кислородом, что создает окисленный слой для улучшенной защиты готовой продукции от коррозии; однако эта же характеристика затрудняет изготовление металлических изделий. Фактически, должны использоваться определенные процессы, чтобы предотвратить его воздействие и связывание с другими элементами.
Благодаря своим уникальным свойствам, титан часто используется для создания деталей авиакосмической, медицинской и промышленной отраслей, а также товаров народного потребления и спортивных товаров. Один из самых распространенных методов создания изделий из титана — литье по выплавляемым моделям. Литье по выплавляемым моделям из титана позволяет изготавливать детали высокой детализации и сложности с гладкой поверхностью и минимальной необходимостью отделочных работ. В этом блоге рассматривается процесс литья титана по выплавляемым моделям, свойства титановых отливок и их широкий спектр применения.
Что такое литье по выплавляемым моделям?
Литье по выплавляемым моделям — это универсальный процесс, который используется с различными материалами для создания сложных компонентов с гладкой поверхностью. Из-за высокой реакционной способности титана литье по выплавляемым моделям с этим металлом требует модификации всего процесса. Литье по выплавляемым моделям из титана следует за этими основными этапами:
- Образец желаемой детали создается из легко плавящегося воска или смолы.
- Рисунок покрыт несколькими слоями термостойкой керамики.из термостойкого материала, обычно керамики. Для литья титана по выплавляемым моделям стандартные керамические формы неприменимы, так как расплавленный титан вступает в реакцию с керамикой. Поэтому форма, используемая для изготовления титана, должна быть изготовлена из специальной керамики, такой как оксид циркония или оксид иттрия.
- По завершении изготовления керамической оболочки воск плавится и сливается, в результате остается полая форма.
- Титан плавится с использованием процессов индукционной или дуговой плавки в медном тигле с водяным охлаждением в специализированном нагревательном аппарате, который предотвращает воздействие других элементов, особенно азота и кислорода.
- Расплав титана заливают в керамическую форму. Центробежные процессы помогают заполнить тонкие стенки.
- Титан замерзает в твердом состоянии при контакте с керамической формой, тем самым создавая желаемый компонент.
Свойства и преимущества титановых отливок
Титан имеет множество явных преимуществ по сравнению с другими металлами, в том числе:
- Легкость Прочность: Он демонстрирует самое высокое отношение прочности к плотности среди всех металлов, что обеспечивает легкую прочность и долговечность.
- Коррозионная стойкость: При воздействии кислорода титан вступает в реакцию, образуя тонкий слой оксида титана на поверхности металла. Этот слой защищает титановую поверхность от коррозии и ржавчины, которые могут повлиять на другие металлы, такие как сталь и алюминий.
- Долговечность: Титан чрезвычайно прочен, поэтому он более устойчив к износу и увеличивает срок службы оборудования, в котором он используется.
- Термостойкость: Титан имеет чрезвычайно высокую температуру плавления и проявляет минимальную ползучесть при колебаниях температуры.Это делает его особенно ценным для аэрокосмических и промышленных компонентов, которые требуют воздействия экстремальных температур.
Титановое литье
(Щелкните, чтобы развернуть)
Уникальные свойства титановых деталей, отлитых по выплавляемым моделям, делают их особенно полезными в широком диапазоне отраслей и сфер применения. К наиболее распространенным относятся:
- Аэрокосмическая промышленность: Титан присутствует во вращающихся и статических компонентах авиационных двигателей, включая лопасти компрессора, роторы и гондолы, а также в конструкциях, рамах, шасси и гидравлических компонентах.
- Военный и оборонный секторы: Титан может выдерживать экстремальные нагрузки и устойчив к коррозии, что делает его идеальным для военных и оборонных приложений, включая самолеты и подводные лодки, бронетанковое вооружение, ракеты, танковую броню и боевые танки.
- Медицинская промышленность: Благодаря высокому соотношению прочности и веса и биосовместимости с человеческим телом, титан является металлом номер один для использования в биомедицине и используется в реконструктивных штифтах, имплантатах бедра и колена, футлярах для кардиостимуляторов, стоматологии. имплантаты и протезирование.Он также используется для хирургических инструментов, инвалидных колясок и костылей.
Другие отрасли и области применения, в которых применяется титановое литье, включают фармацевтическое и химическое производство, нефтегазовую, морскую, автомобильную, транспортную, строительную, потребительскую и спортивные товары.
Хотя титан универсален, процессы очистки и производства делают его более дорогим в производстве, чем производство некоторых других металлов, таких как алюминий и сталь.
Услуги литья по выплавляемым моделям из титана в Impro
Обладая более чем двадцатилетним опытом в области специального литья по выплавляемым моделям, Impro предлагает услуги высочайшего качества литья по выплавляемым моделям для множества отраслей и сфер применения.Наши установки для литья по выплавляемым моделям из титана специально разработаны для производства титановых отливок высочайшего качества по конкурентоспособным ценам. У вас есть дополнительные вопросы или вы хотите начать литье по выплавляемым моделям из титана? Свяжитесь с нами сегодня.
Отливка из чистого титана в формы для выплавляемых форм на основе магнезии, модифицированной диоксидом циркония
Задача: Расплавленный титан обладает высокой реакционной способностью по отношению к обычным материалам форм при повышенных температурах.Целью этого исследования было повышение точности литья из чистого титана путем добавления инертного диоксида циркония в паковочную массу на основе магнезии.
Методы: Автоматическая лазерная записывающая машина теплового расширения (TEM-1000 / Pantos, Nippon Co.) использовалась для измерения теплового расширения паковочных масс. Автоматическая машина для литья аргона (Castmatic-S, Iwatani Co.) использовался для литья образцов из чистого титана. Стереомикроскоп (Nikon SM-2T, Япония) использовался для измерения предельного несоответствия на металлической матрице. Индентор микротвердости по Виккерсу (MXT-50, Matsuzawa Seiki Co.) определял твердость по Виккерсу (VH) титановых образцов. Межфазную реакционную способность титана оценивали с помощью рентгеновского дифрактометра (Rigaku D / max VIII, Токио, Япония). Для исследования внутренней пористости отливок использовался стоматологический рентгеновский аппарат.