Магнитная дефектоскопия
Магнитная дефектоскопия — это метод выявления внутренних и поверхностных дефектов деталей, которые изготовлены из ферромагнитных материалов, основанный на образовании магнитного потока рассеяния в местах залегания дефектов. Очагами разрушения деталей, подверженных в работе большим напряжениям (детали авиамотора, турбинные лопатки и диски и другие) обычно являются мельчайшие трещины на поверхности, волосовины, включения и прочее.Выявление и отсев дефектных деталей в первой трети 20 века производились, в случае поверхностных дефектов, травлением и осмотром. Методов установления внутренних пороков без разрушения деталей, кроме рентгеновского просвечивания, не существовало. В 30-х годах большое распространение в практике промышленности получила магнитная дефектоскопия.
Основными достоинствами магнитной дефектоскопии являются:
1) Возможность испытания детали без разрушения ее. При этом выявление поверхностных дефектов не сопровождается порчей поверхности, что весьма существенно при массовом испытании полированных деталей, например, ролики и шарики, шарикоподшипниковые кольца, детали авиамотора и другие.
2) Высокая чувствительность и большая скорость испытания магнитной дефектоскопией, основанная на следующем явлении: на поверхности детали, внесенной в магнитное поле или предварительно намагниченной (материалы с достаточно большими значениями коэрцитивной силы и остаточным намагничиванием), в местах залегания дефекта образуется магнитный поток рассеяния индикаторов. Поэтому требуется только отыскать удобный индикатор, легко и быстро обнаруживающий присутствие магнитного потока рассеяния. В качестве таких материалов часто используют мелкие фракции каких-либо металлических порошков. Иногда, используются материалы и методы магнитной дефектоскопии, которые позволяют более точно обнаруживать дефекты при разных типах освещения, например, при ультрафиолетовом.

Магнитная дефектоскопия
Методы магнитной дефектоскопии деталей, порошков и магнитных суспензий. Что такое магнитная дефектоскопия и для чего она нужна.
Магнитная дефектоскопия: что это такое и для чего нужна магнитопорошковая дефектоскопия
Методы порошков и магнитных суспензий используются для выявления поверхностных дефектов (трещины закалочные, шлифовочные, а также волосовины), последние — преимущественно для обнаружения внутренних дефектов. Метод порошков заключается в том, что на поверхности намагниченного испытуемого объекта распыляют слабомагнитный порошок FeO3O4 (окись закиси железа). Магнитные пылинки втягиваются в зоны магнитного потока рассеяния, и вдоль трещины образуются большие скопления порошка, которые и делают ее легко заметной для невооруженного глаза.
Методы неразрушающего контроля к содержанию
Магнитная дефектоскпия — один из методов неразрушающего контроля. Магнитный метод разделяется на 2 вида обследований: магнито-порошковый и магнито-индукционный. Оба метода служат для обнаружения специфических магнитных потоков, возникающих при различных дефектах.
Лучшие результаты получаются, если создать магнитным пылинкам возможность свободно перемещаться вблизи испытуемой поверхности. Последнее достигается с помощью магнитной суспензии, которая представляет собой жидкость — трансформаторное масло со взвешенным в ней порошком FeO3O4. Намагниченная деталь погружается в ванну с магнитной суспензией на две—три минуты.
Магнитные пылинки, свободно перемещаясь в жидкости, образуют большие скопления в местах залегания дефектов. В ванну погружается одновременно большое количество деталей, так что пропускная способность при испытании этим методом мелких деталей весьма велика.
Испытуемые детали намагничиваются продольно, поперечно или циркулярно, сообразно с формой детали, а также характером и расположением дефектов. Намагничивание мелких деталей производится группами в 25—100 штук.
7.4. Магнитная дефектоскопия, магнитопорошковый метод
Магнитная дефектоскопия — это частный случай магнитного неразрушающего контроля, предусматривающий способ обнаружения дефектов в виде нарушения сплошности в объектах из ферромагнитных материалов. Сущность способа — регистрация магнитных полей рассеяния вблизи этих дефектов.
При помещении в однородное магнитное поле объекта контроля, не имеющего дефектов и резкого изменения формы, магнитный поток Фм будет проходить по пути наименьшего сопротивления через материал, практически не выходя за пределы объекта (рис. 7.4, а).
Рис. 7.4. Принцип магнитной дефектоскопии
Некоторая
незначительная часть магнитного потока
Фо может проходить
по воздуху. Это связано с тем, что
магнитное сопротивление
материала (металла) много меньше (в раз) сопротивления воздуха,
поскольку оно обратно пропорционально
магнитной проницаемости.
При
наличии трещины, перпендикулярной
направлению магнитного потока,
возникает препятствие в виде воздушного
промежутка, резко
увеличивающего магнитное сопротивление
на этом участке. Поэтому поток Ф н будет в основном огибать трещину снизу.
Вместе с
тем часть потока будет замыкаться в
воздух над трещиной, т.е. появляется
поток рассеяния над дефектом ФД (рис. 7.4, б).
В
материале с очень большой магнитной
проницаемостью и малым
магнитным сопротивлением весь магнитный
поток пойдет под трещиной
и потока ФД практически не будет. Это означает
весьма низкую
чувствительность магнитной дефектоскопии
при контроле таких
материалов.
Величина зависит не только от вида ферромагнетика,
но и от напряженности
намагничивающего поля (см. рис. 7.1).
Поэтому правильный
выбор оптимальных режимов намагничивания
усиливает
поток
рассеяния
Дефекты оптимально обнаруживаются в случае, когда направление намагничивания контролируемой детали перпендикулярно направлению дефекта. Для создания оптимальных условий контроля применяют три вида намагничивания:
Циркулярное намагничивание предназначено для деталей, имеющих форму тел вращения (при этом что-то вращается: деталь или магнитный поток). Продольное (полюсное) намагничивание осуществляется с помощью электромагнитов, постоянных магнитов или соленоидов. При этом деталь намагничивается обычно вдоль своего наибольшего размера. На ее краях образуются полюсы, создающие поле обратного направления. Комбинированное намагничивание осуществляется при одновременном намагничивании детали двумя или несколькими изменяющимися магнитными полями.
Виды, способы и схемы намагничивания деталей при магнитном неразрушающем контроле приведены в табл. 7.1 [2].
Вид намагничивания (по форме магнитного потока) | Способ намагничивания | Схема намагничивания |
Продольное (полюсное) | Постноянным магнитом | |
| ||
Соленоидом | | |
Циркулярное | Пропусканием тока по детали | |
С помощью провода с током помещаемого в отверстие детали (вращающейся) | | |
С помощью контактов, устанавливаемых на детали (вращающейся) | | |
Путем индуцирования тока в детали | | |
Комбинированное | Пропусканием тока по детали и электромагнитом | |
Пропусканием (двух или более) сдвинутых по фазе токов по детали во взаимно перпендикулярных направлениях | | |
Путем индуцирования тока в детали и током, проходящем по проводнику помещаемого в отверстие детали | |
Различают магнитомягкие и магнитожесткие материалы. Магни-томягкие размагничиваются при убирании поля (стали СтЗ, Ст10). Магнитожесткие остаются намагниченными при удалении поля (закаленная сталь).
Намагниченные детали из магнитожестких материалов после проведения контроля должны быть размагничены во избежание налипания на них металлических стружек и опилок, которые в последующем могут попасть в подшипники, направляющие, зубчатые передачи и другие узлы и вывести их из строя. Качество размагничивания можно проверить с помощью магнитометра, магнитной стрелки или с помощью бритвенного лезвия, подвешенного на нитке.
Существует три способа размагничивания:
Статическое размагничивание осуществляется при помощи внешнего магнитного поля, которое приводит намагниченность магнитного материала к такому значению, что при удалении поля она становится равной нулю. Для динамического размагничивания деталь помещают в переменное магнитное поле с амплитудой, равномерно уменьшающейся от некоторого максимального значения до нуля. При этом происходит постепенное перемагничивание в соответствии со схемой, приведенной на рис. 7.5. В ряде случаев может быть использован более эффективный способ размагничивания — нагрев изделия до температуры точки Кюри, при которой магнитные свойства материала пропадают. Этот способ имеет весьма ограниченное применение, так как при нагреве могут изменяться механические свойства материала.
Магнитные дефектоскопы состоят из следующих основных узлов: источника тока, устройства для подвода тока к детали и ее по люсного намагничивания, магнитного преобразователя для индикации магнитного поля, осветительного устройства, измерителя тока или напряженности магнитного поля, полюсного намагничивания, магнитного преобразователя для индикации магнитного поля, осветительного устройства, измерителя тока или напряженности магнитного поля.
Рис 7.5. Схема динамического размагничивания
В зависимости от назначения в дефектоскопах могут быть не все из перечисленных узлов, но могут быть и дополнительные узлы (например, узлы для автоматического перемещения детали и механической разбраковки, дефектоотметчики и т.п.).
Для регистрации магнитных полей рассеяния от дефектов наибольшее применение нашли магнитные порошки, обеспечивающие наивысшую чувствительность. При магнитопорошковой дефектоскопии контроль включает следующие основные этапы:
подготовка поверхности деталей;
намагничивание деталей;
обработка сухим порошком или суспензией;
осмотр деталей, оценка имеющихся дефектов и, при необходимости, размагничивание.
Магнитопорошковым методом определяют поверхностные дефекты и дефекты, располагающиеся на небольшой глубине. Чувствительность контроля определяется многими факторами: магнитными характеристиками материала, свойствами применяемого порошка и т.п. Увеличение шероховатости приводит к снижению чувствительности, поскольку магнитный порошок оседает на неровностях поверхности, т. е. поверхность нужно готовить: очистить от окалины, грязи, смазки. Наклеп поверхности часто принимают за дефект. Контроль сварных швов возможен только после их механической зашлифовки. Допускается проведение контроля по немагнитным покрытиям. Наличие таких покрытий при толщине до 20 мкм практически не влияет на чувствительность метода.
Чувствительность магнитопорошкового метода дефектоскопии определяется на контрольных образцах с естественными или искусственными дефектами. Конструктивно образцы с поверхностными искусственными дефектами аналогичны соответствующим образцам, используемым в капиллярном контроле (см. 4.4).
Рис. 7.6. Комплект оборудования для магнитолюминесцентнои дефектоскопии:
а — намагничивающее устройство «МАГУС-М»; б — комплект стандартных образцов; в — ультрафиолетовый осветитель «УФО-9-ЭВ»
Для магнитопорошкового контроля в основном применяют дефектоскопы трех видов:
стационарные универсальные;
передвижные и переносные универсальные;
специализированные (стационарные, передвижные, переносные).
Для решения задач технической диагностики нефтегазового оборудования применяют в основном переносные магнитол орошко вые дефектоскопы. Например, переносный магнитопорошковый дефектоскоп ПМД-70, выпускаемый отечественной промышленностью [17, т. 4 с. 419]. В полевых условиях эффективным средством для контроля локальных участков зарекомендовали себя портативные устройства для полюсного намагничивания в виде электромагнитного ярма (различной мощности) и намагничивающие устройства на постоянных магнитах. Так, на рис. 7.6 приведен выпускаемый предприятием «Энерговест» (г. Екатеринбург) комплект оборудования для магнитолюминесцентнои дефектоскопии на базе намагничивающего устройства «МАГУС-М», состоящего из двух постоянных магнитов. Магниты изготовлены из сплава редкоземельных элементов и соединены друг с другом жестким магнитопроводом. Отличительной особенностью устройства «МАГУС-М» является наличие механизма отключения магнитного потока.
Помимо намагничивающего устройства комплект включает стандартные образцы для контроля чувствительности и портативный ультрафиолетовый облучатель «УФО9-ЭВ». В качестве расходных материалов применяют соответствующие магнитные порошки, поставляемые обычно в аэрозольных упаковках. Особенностью данного комплекта является возможность его применения во взрывопожароопасных помещениях, где использование сетевого электрооборудования запрещено правилами безопасности.
Магнитопорошковая дефектоскопия
22.08.2016Магнитопорошковая дефектоскопия (МПД) — метод неразрушающего контроля для обнаружения и локализации поверхностных и подповерхностных дефектов ферромагнитных материалов (важно — у измеряемых материалов должна быть относительная магнитная проницаемость не менее 40).
Магнитопорошковый метод дефектоскопии основывается на выявлении локальных магнитных полей рассеяния, возникающих над дефектами. К диагностируемым с помощью такого метода дефектам относятся: непровар, поры, трещины, волосовины, флокены и другие (дефекты с шириной раскрытия до нескольких мкм на глубине до 1-2 мм).
Чувствительность магнитопорошкового метода зависит:
- от магнитных характеристик материала детали
- напряженности намагничивающего поля
- размера, формы и шероховатости поверхности детали
- размера, формы, местоположения и ориентации дефекта
- взаимного направления намагничивающего поля и дефекта
- свойств дефектоскопического материала
- способа нанесения дефектоскопического материала на поверхность детали
- способа и условий регистрации индикаторного рисунка выявляемого дефекта
Этим методом обнаруживаются дефекты:
- поверхностные с шириной раскрытия у поверхности 0,002 мм и более, глубиной 0,01 мм и более
- подповерхностные, лежащие на глубине до 2 мм
- внутренние (больших размеров), лежащие на глубине более 2 мм
- под различного рода покрытиями, но при условии, что толщина немагнитного покрытия не более 0,25 мм
Этапы магнитнопорошкового метода дефектоскопии:
- Подготовка детали к контролю. Заключается в очистке поверхности измеряемой детали от грязи, ржавчины, различных смазочных материалов. В случаях, когда поверхность детали темная (что может затруднять диагностику) — наносят тонким слоем контрастную белую краску.
- Намагничивание детали. Один из основных этапов контроля. От правильного выбора способа, направления и вида намагничивания, а также рода тока во многом зависит чувствительность и возможность обнаружения дефектов.
- Нанесение магнитного индикатора. В зависимости от метода нанесения (сухой или мокрый способ измерения) используют либо сухой порошок, либо суспензию (смеси воды с антикоррозионными веществами, смеси трансформаторного масла с керосином либо в трансформаторном масле).
- Осмотр контролируемого объекта. Изучение индикаторного рисунка. Детали изучаются визуально, в некоторых случаях могут использоваться оптические приборы с увеличением до 10x.
Преимущества магнитопорошковой дефектоскопии:
- Расходные материалы (порошок, суспензия и др.) можно собирать и использовать повторно — низкая стоимость расходных материалов
- Низкие требования к качеству покрытия
- малая трудоемкость и достаточно высокая оперативность измерений
Недостатки магнитопорошковой дефектоскопии:
- Ограничения для получения достоверного результата ( наибольшая вероятность выявления дефектов достигается в случае, когда плоскость дефекта составляет угол 90 градусов с направлением магнитного потока. С уменьшением этого угла чувствительность метода снижается, и при углах, существенно меньших 90 градусов, дефекты могут быть не обнаружены)
- Высокое влияние состояния поверхностного слоя металла измеряемого контролируемого объекта (т.н. «зоны наклепа», где напряжения могут превышать напряжения основного металла в тысячи раз)
- Неравномерность магнитных свойств металла
- Снижение чувствительности метода при толщине покрытия более 100-150 мкм — могут быть выявлены дефекты размером не менее 0,15 мм
- Выявление преимущественно поверхностных дефектов или дефектов с минимальным залеганием под поверхностью.
Основными приборами для магнитопорошкового метода дефектоскопии являются магнитопорошковые дефектоскопы (подразделяются на переносные и стационарные), переносные электромагниты и расходные материалы (аэрозоли, концентраты и суспензии).
Перейти к выбору приборов для магнитопорошкового метода дефектоскопии
К списку статейОСОБЕННОСТИ МАГНИТОПОРОШКОВОГО МЕТОДА МАГНИТНОЙ ДЕФЕКТОСКОПИИ |
Магнитная дефектоскопия и в настоящее время остаётся одним из наиболее популярных методов неразрушающего контроля. Такие достоинства метода, как высокая производительность, хорошая чувствительность к поверхностным дефектам, возможность контроля изделийсложной формы, а также высокая информативность, позволяющая специалисту по картине осаждений порошка определять вид и характер дефектов, обеспечивают преимущества, в ряде случаев недостижимые другими методами контроля.
Магнитная дефектоскопия относится к неразрушающему методу контроля материалов (изделий), предназначена для выявления поверхностных и подповерхностных нарушений сплошности: волосовин, трещин различного происхождения, непроваров сварных соединений, флокенов, закатов, надрывов и тому подобные, а так же для контроля толщины немагнитных покрытий на деталях из ферромагнитных материалов и толщины стенок тонкостенных деталей. Дефектом является каждое несоответствие продукции требованиям, установленным нормативной документацией. Но обнаружить все дефекты невозможно, ведь само понятие дефект является индивидуальным для каждого изделия и детали, именно поэтому главной задачей магнитной дефектоскопии является обнаружение всех недопустимых дефектов, наличие которых может привести к повреждению механизма.
Сущность метода магнитной дефектоскопии заключается в намагничивании изделий из ферромагнитных материалов и в дальнейшей регистрации полей рассеяния в местах дефектов изделий. Ферромагнитные материалы это материалы, которое при температуре ниже точки Кюри, способно обладать намагниченностью в отсутствие внешнего магнитного поля. При этом ферромагнитные материалы способны сами в окружающем пространстве создавать магнитное поле. Точка Кюри характеризуется температурой скачкообразного перехода между ферромагнитным и парамагнитным состоянием, причём для каждого материала температура точки Кюри имеет своё значение. Ферромагнитные материалы условно могут быть разделены на две основные группы: магнитомягкие и магнитотвёрдые. Характерной особенностью магнитомягких материалов являются малая коэрцитивная сила, то есть значение напряженности магнитного поля, необходимое для полного размагничивания ферромагнитного вещества и большая магнитная восприимчивость. Характерной особенностью магнитотвёрдых материалов являются большая коэрцитивная и малая магнитная восприимчивость.
По способу получения информации о полях рассеяния различают магнитопорошковую дефектоскопию, индукционную дефектоскопию, феррозондовую дефектоскопию и магнитографическую дефектоскопию. Все эти методы контроля объединяют два общих признака — объект контроля обладает ярко выраженными характеристиками ферромагнетика и обязательной процедурой контроля является намагничивание.
Наиболее широко распространенным методом магнитной дефектоскопии при проведении экспертизы является метод магнитного порошка. Магнитопорошковый метод неразрушающего контроля, основан на явлении притяжения частиц магнитного порошка магнитными потоками рассеяния, возникающими над дефектами в намагниченных объектах контроля. Наличие и протяженность индикаторных рисунков, вызванных полями рассеяния дефектов, можно регистрировать визуально или автоматическими устройствами обработки изображения. Частицы порошка, попавшие в зоны магнитных полей рассеяния, оседают на поверхности деталей вблизи мест расположения дефектов. Ширина полосы, по которой происходит оседание порошка, значительно больше ширины «раскрытия» дефекта, поэтому невидимые до этого дефекты фиксируют по осевшему около них порошку даже невооруженным глазом. Метод магнитного порошка весьма прост и позволяет определять места и контуры нарушений сплошности материала, расположенные на поверхности деталей, а также подповерхностных дефектов. Магнитопорошковый метод может быть так же использован для контроля объектов с немагнитными покрытиями. Чувствительность магнитопорошкового метода определяется магнитными характеристиками материала объекта контроля, его формой, размерами и шероховатостью поверхности, напряженностью намагничивающего поля, местоположением и ориентацией дефектов, взаимным направлением намагничивающего поля и дефекта, свойствами дефектоскопического материала, способом его нанесения на объект контроля, а также способом и условиями регистрации индикаторного рисунка выявляемых дефектов.
При контроле магнитопорошковым методом применяют стационарные, передвижные и переносные дефектоскопы. В зависимости от назначения дефектоскопы включают в себя блок питания, блок формирования намагничивающего тока, намагничивающие устройства, устройство для размагничивания, устройство для нанесения дефектоскопических материалов, блок автоматического управления технологическими операциями контроля, исполнительные устройства для осуществления автоматических операций контроля, приборы и устройства для контроля качества дефектоскопических материалов и технологических процессов, устройства для осмотра контролируемой поверхности и регистрации дефектов.
При магнитопорошковом методе контроля применяют магнитные дефектоскопические материалы: порошки, суспензии и магнитогуммированные пасты. В зависимости от состояния контролируемой поверхности (цвета и шероховатости), магнитных свойств материала и требуемой чувствительности контроля, для улучшения видимости порошка применяют порошки контрастного цвета по отношению к цвету контролируемых деталей. Наряду с обычными порошками красно-коричневого и темно-серого цветов, используемых при контроле деталей со светлой поверхностью, применяются порошки светло-серого, жёлтого или зелёного цветов для контроля деталей с темной поверхностью. Значительно ярче вырисовываются дефекты при использовании магнитных порошков, частицы которых покрыты слоем люминофора, такой порошок позволяет выявлять дефекты при условии затемнения невооруженным глазом. Это даёт возможность применять метод в полевых, монтажных условиях для контроля деталей машин и аппаратов, в том числе и сложной конфигурации.
Основными свойствами магнитных порошков, влияющих на выявляемость дефектов, является дисперсность, магнитные и оптические характеристики. Свойства магнитной суспензии, влияющие на выявляемость дефектов, определяются составом, концентрацией и свойствами отдельных её компонентов. При этом магнитная суспензия не должна вызывать коррозии контролируемой поверхности. Магнитогуммированная паста представляет собой смесь магнитного порошка и затвердевающих органических полимерных веществ. Качество готовых дефектоскопических материалов определяют перед проведением контроля на стандартных образцах предприятий, аттестованных в установленном порядке.
Магнитопорошковый метод контроля включает следующе технологические операции: подготовку к контролю, намагничивание объекта контроля, нанесение дефектоскопического материала на объект контроля, осмотр контролируемой поверхности и регистрацию индикаторных рисунков дефектов, оценку результатов контроля, размагничивание.
В зависимости от магнитных свойств материалов объекта и требуемой чувствительности контроля при магнитопорошковом методе контроля применяют способ остаточной намагниченности и способ приложенного поля.
При контроле способом остаточной намагниченности объект контроля предварительно намагничивают, а затем, после снятия намагничивающего поля, на его поверхность наносят дефектоскопический материал. Осмотр контролируемой поверхности проводят после стекания основной массы суспензии. Промежуток времени между указанными выше операциями должен быть не более часа.
При контроле способом приложенного поля операции намагничивания объекта контроля и нанесения суспензии выполняют одновременно. При этом индикаторные рисунки выявляемых дефектов образуются в процессе намагничивания. Намагничивание прекращают после стекания с контролируемой поверхности основной массы суспензии. Осмотр контролируемой поверхности проводят после прекращения намагничивания.
Вид и способ намагничивания выбирают в зависимости от размеров и формы объекта, материала и толщины покрытия, а также от характера и ориентации дефектов, подлежащих выявлению. При этом наилучшее условие выявления дефектов — перпендикулярное направление намагничивающего поля по отношению к направлению ожидаемых дефектов. При необходимости выявления дефектов различной ориентации применяют намагничивание в двух или трех взаимно перпендикулярных направлениях, комбинированное намагничивание, а также намагничивание во вращающемся магнитном поле.
Для нанесения магнитного порошка на поверхность объекта применяют способы магнитной суспензии, сухого магнитного порошка, магнитогуммированной пасты. Магнитную суспензию наносят на контролируемую поверхность поливом или погружением объекта в ванну с суспензией, а также аэрозольным способом. Сухой магнитный порошок наносят на контролируемую поверхность при помощи различных распылителей, погружением объекта в ёмкость с порошком, а также способом воздушной взвеси. Магнитогуммированную пасту готовят непосредственно. Осмотр контролируемой поверхности и регистрацию индикаторных рисунков выявляемых дефектов проводят визуально или с применением автоматизированных систем обработки изображений. При визуальном осмотре могут быть использованы различные оптические устройства (лупы, микроскопы, эндоскопы).
Детали, после проведения магнитопорошковой дефектоскопии признанные годными необходимо, при необходимости, размагничены, так как статочная намагниченность, в ряде случаев может повести к нарушению нормальной работы изделия, в котором будут находиться намагниченные детали. Так, например, намагниченность деталей может вызвать повышенный износ в узлах трения в результате притяжения железных частиц. Поэтому после магнитного контроля и необходимо производить размагничивание деталей, при необходимости.
Способы размагничивания и проверки степени размагничивания, а также допустимую норму остаточной намагниченности каждого изделия устанавливается в отраслевой нормативно-технической документации на контроль изделий.
Магнитно-порошковый метод успешно применяется не только в процессе производства изделий, но и при их эксплуатации, например для обнаружения трещин усталостного происхождения. Переносные дефектоскопы позволяют применять магнитопорошковый метод для контроля деталей, узлов и агрегатов без их разборки.
При эксплуатации машин, работающих в условиях больших нагрузок, предъявляются высокие требования к прочности их отдельных деталей и узлов. Поэтому очень большое значение приобретает своевременное и надёжное выявление поверхностных дефектов, возникающих в процессе изготовления машин и при их эксплуатации. Эти дефекты под действием вибрации, различных нагрузок, термических и других воздействий, могут быстро увеличиваться и приводить к нежелательным простоям, а так же к серьёзным авариям и поломкам машин. В связи с этим большое внимание и по сей день уделяется неразрушающим методам контроля, среди которых видное место принадлежит магнитной дефектоскопии. Ведь главной задачей магнитного метода контроля является необходимость и важность выявления поверхностных дефектов, а значит и предотвращение возможных негативных последствий.
Список литературы:
1.Зацепин Н.Н., Коржова Л.В. Магнитная дефектоскопия. Минск: Наука и техника, 1981. 208 с.
2.Лившиц Б.Г., Крапошин В.С, Линецкий Я.Л. Физические свойства металлов и сплавов. — 2-е изд. — М.: Металлургия, 1980. 318 с.
3.Михеев М.Н., Горкунов Э.С. Магнитные методы структурного анализа и неразрушающего контроля. – М.: Наука, 1993. 252 с.
4.Шелихов Г.С., Глазков Ю.А., Сапунов М.В. Магнитопорошковый контроль с применением переносных дефектоскопов. М.: ИД Спектр, 2010. 192 с.
5.Щербинин В.Е., Горкунов Э.С. Магнитный контроль качества металлов. – Екатеринбург: УрО РАН, 1996. – 265 с.
6.ГОСТ 21105-87 Контроль неразрушающий. Магнитопорошковый метод. М.: Издательствово стандартов, 2005. – 12 с.
ОСОБЕННОСТИ МАГНИТОПОРОШКОВОГО МЕТОДА МАГНИТНОЙ ДЕФЕКТОСКОПИИ
Written by: Антипов Сергей Михайлович, Смышляев Сергей Александрович, Вылцан Станислав Сергеевич
Published by: БАСАРАНОВИЧ ЕКАТЕРИНА
Date Published: 03/27/2017
Edition: ЕВРАЗИЙСКИЙ СОЮЗ УЧЕНЫХ_30.04.2015_4(13)
Available in: Ebook
Что такое магнитопорошковая дефектоскопия сварных швов?
Самым первым методом контроля качества сварных соединений было простейшее сравнение готового шва с так называемым эталоном. Профессионалы варили, по их мнению, качественный шов, который и называли эталонным. С ним в последствии сравнивали все остальные швы. С тех пор технологии шагнули вперед и появились более совершенные методы контроля.


Современные методы контроля качества предполагают использование приборов, которые позволяют обнаружить скрытые от глаз дефекты. Один из таких приборов — дефектоскоп для проверки сварных швов. При этом дефектоскоп может применяться при самых различных методах контроля: от радиографического до акустического. В этой статье мы расскажем, что такое магнитопорошковая дефектоскопия сварных швов и каковы особенности данного метода контроля качества.
Содержание статьи
Общая информация
Магнитопорошковая дефектоскопия сварных соединений (она же магнитно-порошковая дефектоскопия) — метод контроля качества, суть которого заключается в обнаружении магнитных полей вокруг дефекта с применением ферримагнитных веществ.
Если у детали есть какой-либо дефект, то над ним обязательно образуется магнитное поле, которое будет искажаться. Деталь изначально намагничена и магнитные линии просто огибают дефекты, встречающиеся на пути. В результате происходит искажение магнитного поля. К тому же, по краям заготовки могут образовываться магнитные полюсы, которые в свою очередь создают локальные магнитный поля. На рисунке ниже схематично изображено магнитное поле.


Вся информация об изменении магнитного поля фиксируется с помощью дефектоскопа. Чем дефект больше, тем больше рассеивание, а значит и вероятность обнаружения дефекта. А если магнитные линии располагаются под прямым углом относительно дефекта, то вероятность его обнаружения повышается.
Технология
Теперь подробнее о том, как происходит магнитопорошковая дефектоскопия сварных швов. Чтобы обнаружить дефект недостаточно иметь правильное оборудование. Нужно также использовать специальное ферримагнитное вещество. Проще говоря, магнитный порошок. Его наносят на сварное соединение с помощью сухого или мокрого метода.
При сухом методе используется обычное порошкообразное магнитное вещество. А при мокром — специальная магнитная суспензия. В данном случае суспензия — это смесь магнитного порошка и жидкости. В качестве жидкости можно использовать трансформаторное масло, его смесь с керосином, а также смесь воды с веществами, препятствующими образованию коррозии.


Нельзя однозначно сказать, какой метод лучше: сухой или мокрый. В разных ситуациях приходится выбирать разные методы, а порой и вовсе комбинировать их между собой. В любом случае, вы сможете обнаружить даже мелкие дефекты, вне зависимости от того, какое магнитное вещество будете использовать. При применении порошка или суспензии вещество просто «собирается» вокруг дефекта, образуя замысловатые рисунки, если дефектов много. Таким образом удается точно определить не только местоположение, но и размер дефекта.
Пару слов об оборудовании. Оно может быть самым разнообразным: производители предлагают компактные бюджетные модели с минимумов функций, но вы также можете купить высокотехнологичные приборы с жидкокристаллическим дисплеем и множеством настроек. Обычно дефектоскоп приобретают исходя из сферы его применения. Если контроль качества будет проводиться на выездном объекте, то важнее компактность, нежели большой функционал. А если контроль будет проводиться стационарно в цеху, то размер прибора не играет никакой роли. В таких случаях можно сделать ставку на функционал и приобрести более технологичное устройство.
Особенности
Магнитопорошковый контроль, как и любой другой метод контроля сварных швов, имеет свои особенности, которые нужно знать и учитывать. Так главная особенность — это невозможность проведения контроля, если деталь изготовлена не из ферримагнитных металлов. Это нужно учитывать, если вы собираетесь проводить контроль деталей из цинка или меди. Ведь такие металлы являются диамагнетиками, а значит вы просто не сможете провести качественный контроль.
Также нужно учитывать, что у данного метода контроля есть так называемый параметр чувствительности. Т.е., степень того, насколько точно будет выявлен дефект. И чувствительность зависит от многих факторов. На чувствительность влияют магнитные характеристики металла, напряженность магнитного поля, количество дефектов, их размер. Также влияет размер самой детали и ее форма. В некоторых случаях на чувствительность влияет выбранный метод нанесения ферримагнитного вещества (сухой или мокрый). Все это нужно учитывать, чтобы понять, насколько качественно пройдет контроль.
Читайте также: СНИП и контроль качества
Также учтите, что с помощью магнитно-порошкового метода можно обнаружить не все дефекты. Например, вы не сможете обнаружить дефект, глубина которого менее 0,01 миллиметра. Зато вы без проблем обнаружите большие внутренние дефекты, располагающиеся на глубине более 2 миллиметров. Словом, магнитопорошковая дефектоскопия сварных швов не может использоваться как полноценный метод контроля качества, заменяющий все остальные методы. Магнитопорошковую дефектоскопию нужно использовать в связке с другими способами контроля, чтобы получить объективную картину.
Уровни чувствительности
Выше мы упомянули чувствительность. Давайте подробнее остановимся на этой теме, поскольку понимание всей сути позволит вам лучше разобраться в теме.
Итак, согласно ГОСТу №21105-87 мы знаем, что существует всего три уровня чувствительности. Каждому уровню соответствует своя буква (уровень А, Б, В) и все они зависят от размеров дефектов.
Уровень А самый высокий, чувствительность большая. Есть возможность обнаружить дефекты размером от 2,5 микрометра. Ниже вы можете видеть более подробную таблицу с информацией о других уровнях чувствительности.


Вы можете видеть, что в таблице указана графа о максимально допустимой шероховатости. Все дело в том, что магнитопорошковая дефектоскопия сварных соединений и успешность ее проведения во многом зависят именно от параметра шероховатости поверхности детали. Есть шероховатость будет превышать допустимые значения, контроль будет менее объективным и точным. Но эту проблему можно частично исправить, если использовать порошок крупной фракции. Его нужно наносить сухим способом. Тогда появится возможность обнаружить глубокие дефекты при повышенной шероховатости поверхности детали.
Выше мы указывали, от чего зависит чувствительность данного метода контроля. Но мы не упомянули, что большое влияние оказывает подвижность частиц магнитного порошка. Важно, чтобы подвижность была высокой или выше среднего. Чтобы этого добиться нужно применять порошок с частицами разной формы. Такой порошок не будет прилипать к детали и позволит проводить более качественный контроль.
Также на чувствительность может влиять род тока, с помощью которого вы намагничиваете деталь при контроле. Мы рекомендуем устанавливать постоянный ток. Он формирует магнитное поле, способное проникать вглубь заготовки, а значит лучше обнаруживать дефекты. На изображении ниже более подробно изображен этот принцип.


Отдельно поговорим о применении сухого и мокрого метода. В своей практике мы обнаружили, что при сухом методе чувствительность существенно повышается. Это значит, что при применении сухого порошка контроль более объективен, чем при использовании суспензии. Кстати, есть свои секреты, как можно повысить чувствительность при применении сухого порошка. Профессионалы рекомендуют распылять порошок в специальном устройстве, которое затем будет подать вещество по шлангу прямо на сварное соединение.
Есть и более продвинутые способы нанесения порошка. Можно поместить деталь в специальную герметичную камеру, где порошок будет находиться во взвешенном состоянии. В таком случае саму деталь нужно погрузить в рыхлое вещество, после чего медленно и аккуратно извлечь. Чувствительность при этом будет очень высокой. Но, в силу трудоемкости этот метод применяется нечасто, хотя все же имеет право на жизнь. Особенно, если нужно провести контроль детали, изготовленной из металла, имеющего немагнитное покрытие.
Вместо заключения
Дефектоскоп — прибор, который можно применять в связке с многими методами контроля. Существует цветная дефектоскопия сварных швов, акустическая, вихретоковая, термоэлектрическая и многие другие. Но среди них всех особняком стоит магнитно-порошковая дефектоскопия, поскольку это мобильный и простой в применении метод.
С помощью магнитного дефектоскопа можно провести контроль в труднодоступных местах (в том числе на внутренней стороне детали, например, трубы), можно проводить контроль на высоте, поскольку оборудование очень компактное и легкое. Словом, преимуществ много. А вы когда-нибудь сталкивались с магнитно-порошковой дефектоскопией? Расскажите о своем опыте в комментариях. Желаем удачи в работе!
[Всего голосов: 1 Средний: 5/5]Магнитная дефектоскопия: эффективная и недорогая технология
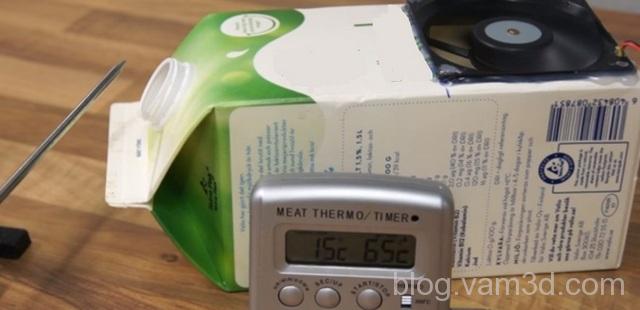
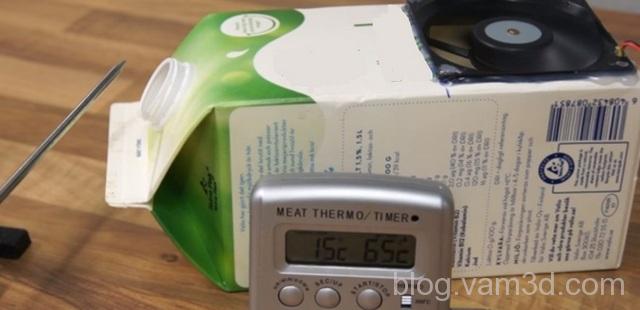
Магнитная дефектоскопия представляет собой метод неразрушающей диагностики и контроля полученного сварного шва. Заключается данная технология контроля в определении рассеянных потоков, которые образуются в соединениях при наличии внешних и внутренних скрытых дефектов. Сегодня данная технология дефектоскопии благодаря своей простоте и эффективности широко используется в различных отраслях промышленности.
Метод магнитной дефектоскопии
Для определения скрытых внутренних дефектов необходимо создать направленный магнитный поток, для чего через изделие пропускают электрический ток. Это позволяет создать электрическое и магнитное поле с определённым показателем плотности. Такое магнитное поле может отклоняться только в том случае, если, проходя через соединение, поток встречает внутренние дефекты. Специальное оборудование улавливает такие изменения направления магнитного потока, что и позволяет определить наличие дефектов и их размер.
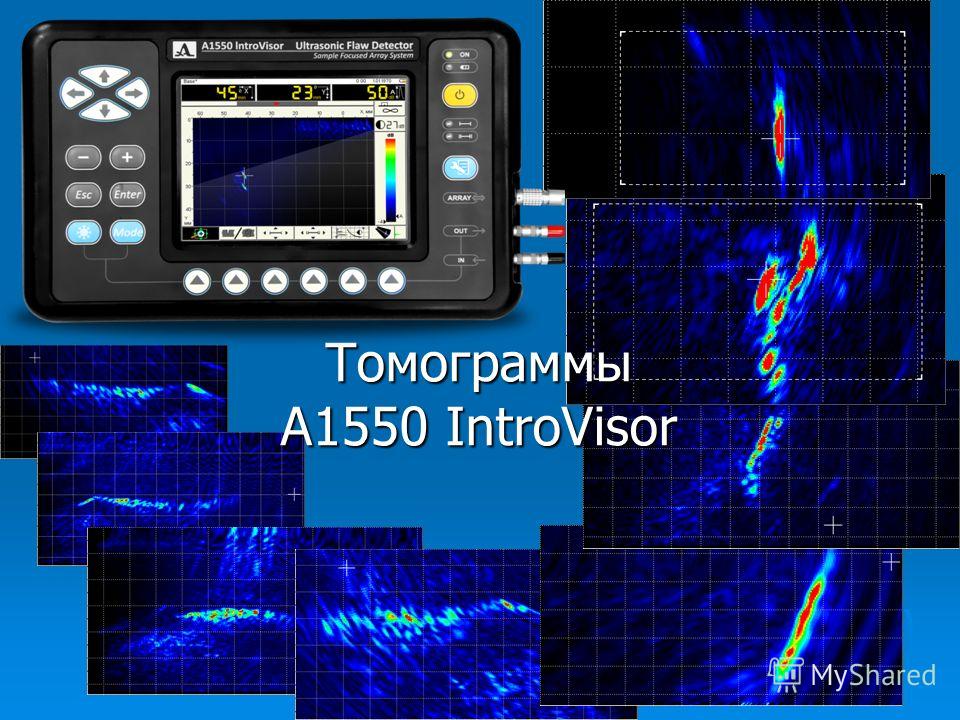
В зависимости от типа используемого оборудования для изменения направления магнитного потока принято выделять два вида такой дефектоскопии:
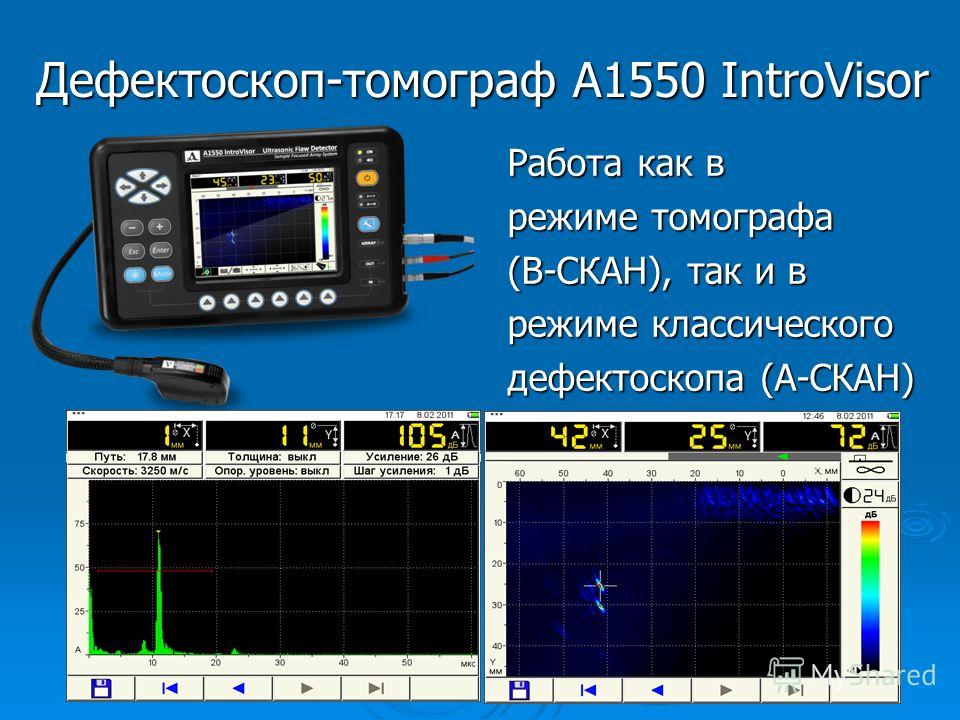
- Магнитопорошковый.
- Магнитографический.
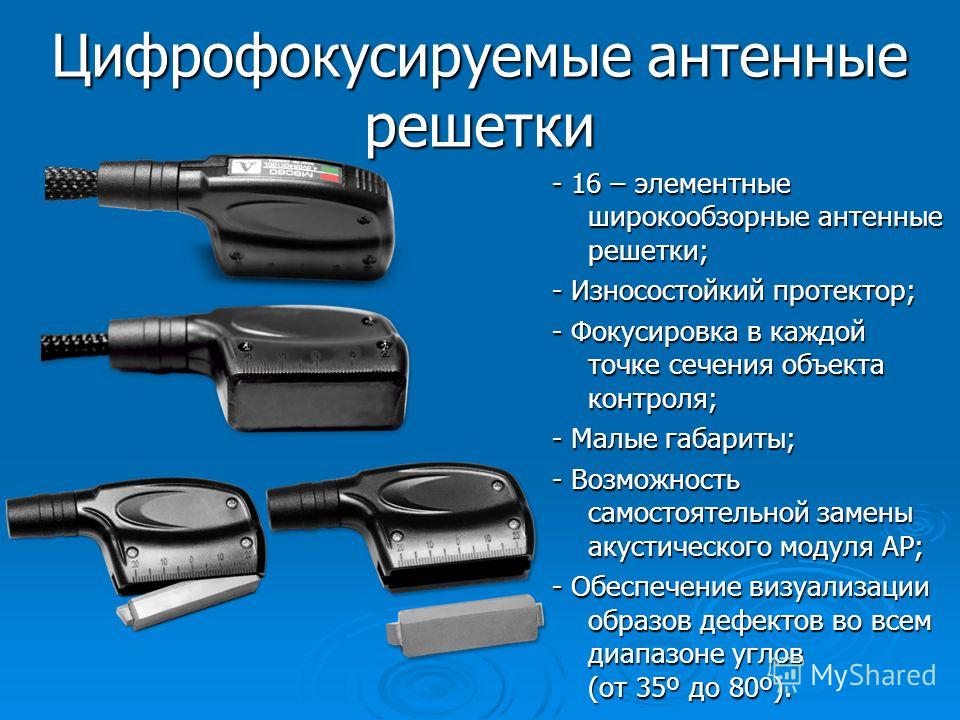
Поговорим поподробнее о каждом из таких способов определение дефектов в сварном шве.
Выбираем магнитный порошок
Особенностью данного метода дефектоскопии является использование специального магнитного порошка. Такой порошок может использоваться сухим или суспензией. Если используется сухой материал, на поверхность имеющегося сварного соединения наносят тонкий слой магнитного порошка. В данном случае можно использовать мелкодисперсные окалины или железные опилки. Если же используется мокрый порошок, то наносят соответствующую суспензию.
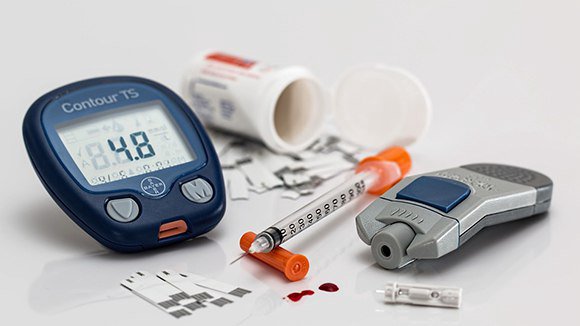
На сварное соединение, с нанесенным на него порошком, подается электрический ток, после чего частицы порошка перемещаются равномерно по плоскости сварного шва. При наличии скрытых дефектов используемый магнитный порошок будет скапливаться валиками именно над такими внутренними дефектами. По форме такого уплотнения можно судить о характере и размерах выявленного повреждения.
Магнитопорошковый способ контроля подразумевает выполнение следующих операций:
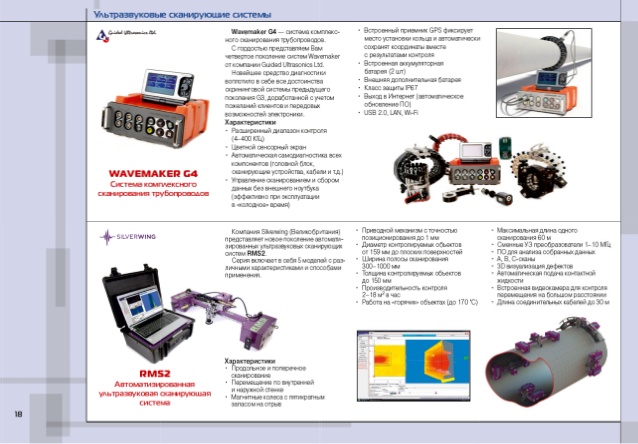
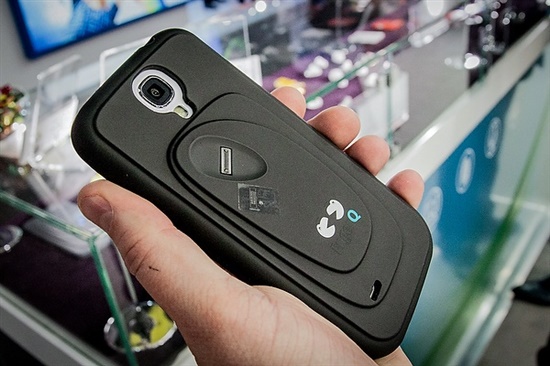
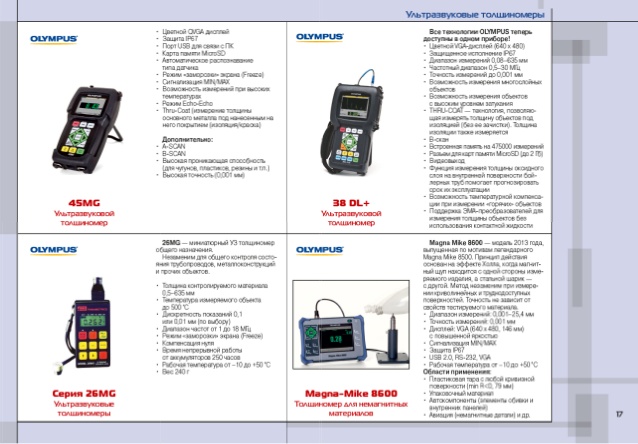
- Проводится подготовка поверхности.
- Готовится суспензия или используемый порошок.
- Выполняется намагничивание.
- Изделие покрывается суспензией.
- Осмотр и определение скрытых дефектов, над которыми будут присутствовать отложения суспензии.
- Размагничивание металлического изделия.
Преимущества магнитопорошковой технологии
Из преимуществ данного способа контроля можем отметить ее отличную эффективность, чувствительность к микроскопическим сварным дефектам. При этом чувствительность данной технологии дефектоскопии зависит от фракции используемого порошка, способа нанесения материала, показателей напряжения магнитного тока, размеров и глубины расположения повреждений.
Подмечено, что данная технология дефектоскопии позволяет лучше всего обнаруживать непровары, трещины и другие плоскостные дефекты. А вот дефекты округлой формы, которые не создают качественного рассеивания намагниченного потока, при таком способе контроля обнаружить зачастую проблематично.
Магнитографическая технология
Сущность данного способа контроля соединений состоит в качественном намагничивании сварного шва, а также расположенной поблизости зоны термического влияния. Специальное оборудование позволяет выполнять запись данных магнитного поля, после чего полученные записи считывают соответствующими устройствами и расшифровывают. Все это и позволяет получить максимально точную картину качества выполненного соединения. Подобная технология отличается производительностью, точностью определения дефектов и максимально возможной степенью автоматизации.
При таком магнитографическом способе контроля выполняются операции:
- Поверхность очищается от загрязнений.
- На сварочный шов накладывают магнитную ленту, после чего ее прижимают резиновой эластичной лентой.
- Проводят намагничивание соединения. Выбор того или иного режима намагничивания зависит от показателя толщины металла, типа используемых приборов и свойств конкретного металлического элемента.
- Производится запись и последующая расшифровка дефектоскопии. Полученные результаты выводятся на экран монитора или же на дисплей устройства для дефектоскопии.
Подобная технология нашла широкое распространение в промышленном производстве, где требуется выполнять сварку оплавлением и в последующем проверяют качество выполненных соединений. Достаточно часто магнитографический способ контроля используется при выполнении магистральных трубопроводов, где от качества соединения зависит безопасность и долговечность использования выполненных металлоконструкций. Отметим, что современные установки для магнитографического контроля позволяют контролировать сварку с толщиной металла до 25 миллиметров.
Точность магнитографического контроля практически идентична магнитопорошковой технологии. На точность выявления дефектов напрямую влияет толщина металлических изделий, глубина и ориентация расположения таких сварочных дефектов. Использование современного оборудования позволяет несколько повысить эффективность данной технологии, поэтому в последние годы магнитографический контроль получает все большее распространение в различных отраслях промышленности. Одним из преимуществ данной технологии является высокая производительность, а также полная автоматизация такого контроля качества выполненных соединений.
Индукционная магнитная дефектоскопия
Данная технология контроля за сварными соединениями появилась относительно недавно и сегодня с успехом используется в различных сферах промышленности. Данная технология основывается на использовании соответствующих рассеянных потоков, движение которых управляется соответствующими индукционными катушками. На исследуемое сварное соединение укладываются индукционные катушки, к которым подключаются соответствующие регистрирующие приборы. На металлическое изделие подают соответствующий электроток, что в свою очередь генерирует магнитное поле. Такое магнитное поле рассеивается индукционными катушками и одновременно выполняется считывание данных по рассеиванию магнитного направленного потока. Следует сказать, что данная технология обладает как определенными преимуществами, в том числе и ее полной автоматизацией работы с максимальной производительностью, так и определенными недостатками. К последним можно отнести низкую чувствительность индукционного метода контроля к мельчайшим дефектам, располагающимся у самой поверхности сварного соединения.