РДИ 38.18.017-94 Инструкция по магнитопорошковому контролю оборудования и сварных соединений, РД от 23 июня 1994 года №38.18.017-94
РДИ 38.18.017-94
СОГЛАСОВАНО с Госгортехнадзором РФ | УТВЕРЖДАЮ |
Директор
ВНИКТИнефтехимоборудование к.т.н., с.н.с. | А.Е.Фолиянц |
Зам. директора
по научной работе, к.т.н., с.н.с. | Н.В.Мартынов |
Руководитель лаборатории НМК, руководитель темы, к.т.н., с.н.с. | Б.П.Пилин |
1. ВВЕДЕНИЕ
1.2. Инструкция
определяет порядок проведения магнитопорошковой дефектоскопии
технологического оборудования нефтехимических, химических и
нефтеперерабатывающих предприятий, в частности, деталей
насосно-компрессорного оборудования, элементов, корпусов сосудов и
аппаратов, сварных швов и околошовной зоны.
1.3. Инструкция
составлена взамен инструкции 18-04-ИК76 на основании исследований
лаборатории неразрушающих методов контроля
ВНИКТИнефтехимоборудование, изучения работ по магнитопорошковому
методу контроля других НИИ и опыта дефектоскопии на предприятиях
отрасли в соответствии с положениями и требованиями ГОСТ
21105-87 «Контроль неразрушающий. Магнитопорошковый метод».
2. ОСНОВНЫЕ ПОЛОЖЕНИЯ
2.1. Магнитопорошковый
метод дефектоскопии предназначен для выявления поверхностных и
подповерхностных нарушений сплошности: трещин различного
происхождения, непроваров сварных соединений, волосовин, флокенов,
закатов, надрывов и т.п.
2.2. Магнитопорошковый
метод основан на намагничивании контролируемого изделия и выявлении
магнитного поля рассеяния, возникающего над дефектом, с помощью
ферромагнитных частиц, играющих роль индикатора.
2.3. Магнитопорошковый
метод применим для контроля объектов только из ферромагнитных
материалов, магнитные свойства которых, формы и размеры дают
возможность создавать в местах нарушения сплошности магнитные поля
рассеяния, достаточные для притяжения частиц магнитного
порошка.
Магнитопорошковый метод
позволяет контролировать изделия с немагнитными покрытиями (краска,
цинк, хром, кадмий, полимерные пленки и т.д.) если толщина покрытия
не превышает 100 мкм.
2.4. Чувствительность и
разрешающая способность магнитопорошкового метода зависят от
качества магнитного порошка, магнитных характеристик материала
объекта контроля, его формы, размеров и шероховатости поверхности,
от напряженности намагничивающего поля и направления
намагничивающего потока к плоскости дефекта, от способа
намагничивания и условий регистрации индикаторного рисунка
(осаждения магнитного порошка в месте расположения дефекта), от
освещенности осматриваемого участка объекта контроля и др.
факторов.
2.5. Предельная
чувствительность магнитопорошкового метода дефектоскопии при
благоприятных условиях контроля соответствует выявлению
несплошностей с раскрытием 1 мкм и более, глубиной 10 мкм и более и
протяженностью 0,5 мм и более. При контроле сварных соединений с
неснятым валиком усиления, выполненных ручной сваркой,
чувствительность снижается на порядок и более.
2.6. Наилучшая
выявляемость дефекта достигается при расположении его плоскости
перпендикулярно направлению магнитного потока. Если дефект наклонен
к поверхности объекта контроля под углом менее 20°, выявление
дефекта не гарантируется.
2.7. Подповерхностные
дефекты обнаруживаются хуже, чем поверхностные. Дефекты, залегающие
на глубине более 2-3 мм от поверхности, могут быть не обнаружены.
Чувствительность к выявлению подповерхностных дефектов ниже
указанной в п.2.5.
2.8. Чистота обработки контролируемых магнитопорошковым методам поверхностей должна соответствовать по параметру шероховатости 10 мкм.
Изделия, имеющие
грубообработанную поверхность (80), грубые риски, забоины, наклеи и другие
повреждения, контролировать нецелесообразно в связи с возможностью
регистрации ложных дефектов.
2.9. В зависимости от
размеров выявляемых поверхностных дефектов согласно ГОСТ 21105-75* устанавливаются три
условных уровня чувствительности, указанных в таблице 1.
* На территории Российской Федерации документ не действует. Действует ГОСТ 21105-87. — Примечание изготовителя базы данных.
Таблица 1
Классификация уровней чувствительности
Условный уровень чувствительности | Чувствительность контроля | Максимально допустимая шероховатость контролируемой поверхности, мкм (по ГОСТ 2789-73) | |
ширина
(раскрытие) условного дефекта, мкм | Глубина
условного дефекта, мкм | ||
А | 2,5 | 25 | 2,5 |
Б | 10 | 100 | 40 |
В | 25 | 250 | 40 |
2.10. При соблюдении всех
требований настоящей инструкции чувствительность при контроле
соответствует уровню Б ГОСТа
21105-87 и позволяет выявлять поверхностные дефекты с
раскрытием 10 мкм, глубиной 100 мкм и протяженностью свыше 0,5
мм.
На практике уровень
чувствительности Б применяют для контроля деталей
насосно-компрессорного оборудования и сварных швов со снятым
валиком усиления и уровень чувствительности В — для сварных швов
при наличии валика усиления.
3. АППАРАТУРА И ПОМЕЩЕНИЕ ДЛЯ МАГНИТОПОРОШКОВОГО КОНТРОЛЯ
3.1. Основными средствами
магнитопорошкового метода контроля технологического оборудования
отрасли являются универсальные дефектоскопы типа ПМД-87, МД-50П,
МД-87П, ПМД-70 и др. Краткие технические характеристики и область
применения этих дефектоскопов даны в приложении 2.
Допускается применение
других типов дефектоскопов, которые обеспечивают требуемые режимы
намагничивания контролируемых изделий или их участков.
Дефектоскопы имеют
источники тока намагничивания, устройства для подвода тока к
контролируемому изделию (токовые контакты) и для полюсного
намагничивания (соленоиды, электромагниты, гибкие кабели),
измерители тока (или напряженности магнитного поля), устройства для
нанесения магнитной суспензии на контролируемое изделие и
устройства для размагничивания контролируемого изделия после
контроля.
3.2. Для каждого типа
дефектоскопов на заводе должна быть инструкция по работе на нем.
Она должна быть изучена операторами, работающими на данном
дефектоскопе.
3.3. Электроизмерительные
приборы дефектоскопов (измерители тока, напряженности и др.)
подлежат государственной проверке в установленные сроки при помощи
образцовых приборов.
Электрическая часть
дефектоскопов (заземление, изоляция, устройство для регулировки
тока, сигнальные устройства) должна проверяться не реже одного раза
в квартал.
3.4. Соленоиды для
продольного намагничивания деталей, имеющие отношение длины к
диаметру более 10, должны обеспечивать в центре напряженность поля
не менее 200 А/см (250 э).
Соленоиды для
намагничивания коротких деталей (дисков, шестерен, пальцев
крейцкопфов и т.д.) должны иметь в центре напряженность поля не
менее 400 А/см (500 э).
3.5. В состав средств
магнитопорошкового метода контроля входят также приборы и
устройства для оценки качества магнитного порошка и магнитной
суспензии, осветительные и ультрафиолетовые лампы для осмотра
поверхности изделия, контрольные образцы с дефектами для проверки
чувствительности, устройства для контроля степени размагничивания,
устройства для транспортировки, установки и кантовки на участке
контроля контролируемых изделий.
3.6. Контрольные образцы
для проверки качества магнитной суспензии и чувствительности должны
иметь как видимые, так и невидимые невооруженным глазом
естественные трещины или искусственные, изготовленные путем хорошо
зачеканенных вставок. Участки с дефектами кернят или обводят
электрографом, а сам образец должен иметь номер, клеймо и паспорт
ЦЗЛ (ОТК). В паспорте указываются: материал детали, величина
намагничивающего тока, род тока (постоянный или переменный), способ
намагничивания, количество и длина дефектов, приводится эскиз или
фотография дефектов с осажденным на них порошком.
Примечание: Рекомендуется
в качестве контрольных образцов использовать ранее забракованные
детали с естественными дефектами, изготовленные из сталей,
магнитные характеристики которых позволяют проводить
магнитопорошковый контроль способом остаточной намагниченности.
3.7. Сосуды для хранения
магнитной суспензии, ванны, поддоны должны быть изготовлены из
немагнитного материала (пластмассы, алюминия, стекла). Сосуды
должны плотно закрываться во избежание загрязнения суспензии.
3.8. Помещение для
размещения дефектоскопов и проведения магнитопорошкового контроля
должно быть изолированным, сухим и теплым, защищенным от попадания
пыли и стружки. Оно должно быть обеспечено вентиляцией с 5-ти
кратным обменом, горячей и холодной водой, а для контроля крупных
изделий — механизированными средствами для транспортировки,
установки и кантования изделий.
3.9. При недостаточной
общей освещенности помещения, для усиления местного освещения
контролируемых поверхностей изделий необходимо иметь переносную
лампу напряжением не более 12 B.
Освещенность осматриваемой поверхности изделия, контролируемого с помощью черного магнитного порошка, должна быть не менее 500 лк. Измерение освещенности проводить люксметром.
Примечание: Ориентировочно, косвенным методом освещенность можно проверить так: если при имеющейся освещенности четко видны выявленные на контрольных образцах дефекты, то она достаточна.
4. МАГНИТНЫЕ ПОРОШКИ И СУСПЕНЗИИ
4.1. Магнитные порошки,
используемые в качестве индикаторов дефектов, должны удовлетворять
требованиям ГОСТ
9849-86 и содержать Fe98,5%, C0,08% и минимальное количество
неферромагнитных примесей. Частицы порошка должны быть в основном
одного размера и, желательно, величиной 810 мкм. Наиболее полно удовлетворяет этим
требованиям порошок ПЖВ1.71.26 ГОСТ
9849-86.
4.2. Поступающий на завод
порошок должен быть испытан в заводской лаборатории на содержание
Fe, С и размер частиц. Результаты исследований оформляют актом и
записывают в журнале регистрации анализов магнитного порошка с
указанием его пригодности для дефектоскопии.
4.3. Магнитные порошки
выбирают с учетом цвета контролируемой поверхности; для изделий со
светлой поверхностью используют черный магнитный порошок, для
изделий с темной поверхностью — магнитолюминесцентный порошок или
цветную пасту КМ-К ТУ 6-09-5387-88*.
________________
*
ТУ, упомянутые здесь и далее по тексту, являются авторской
разработкой. За дополнительной информацией обратитесь по ссылке. — Примечание изготовителя базы
данных.
4.4. Магнитные порошки
наносят на контролируемое изделие сухим способом — путем распыления
или мокрым способом — в виде суспензии, путем полива или погружения
изделия в суспензию.
4.5. Магнитные суспензии
готовят либо на водной основе (водные суспензии), либо на основе
масла и керосина (масляные суспензии).
Водная суспензия обладает
большей чувствительностью по сравнению с масляной, ее целесообразно
применять при контроле крупных деталей при недостаточном токе
намагничивания или при контроле деталей с мелкими зубьями или
мелкой резьбой. Однако, водная суспензия может вызывать
корродирование изделий.
Масляная суспензия не
способствует корродированию изделия, не требует предварительного
обезжиривания и последующей сушки изделия.
4.6. Для
магнитопорошковой дефектоскопии рекомендуется применять следующие
составы водных магнитных суспензий:
I | |
Черный магнитный
порошок | 20±5 г |
или магнитолюминесцентный
порошок | 5±1 г |
Бихромат калия (калиевый
хромпик KCrO) | 5±1 г |
Сода кальцинированная
(NaCO) | 10±1 г |
Эмульгатор ОП-7 или
ОП-10 | 5±1 г |
Вода водопроводная | 1 л |
II | |
Черный магнитный
порошок | 20±5 г |
или магнитолюминесцентный
порошок | 5±1 г |
Нитрат натрия (NaNO) | 15±1 г |
Эмульгатор ОП-7 или
ОП-10 | 5±1 г |
Вода водопроводная | 1 л |
Примечание: Детали с
покрытиями из кадмия и цинка могут корродировать в суспензии с
нитритом натрия. | |
III | |
Черный магнитный
порошок | 20±5 г |
или магнитолюминесцентный
порошок | 5±1 г |
Сода кальцинированная
(NaCO) | 12±2 г |
Мыло хозяйственное
кусковое | 1±0,5 г |
Вода водопроводная | 1 л |
Мыльно-содовую водную
суспензию приготавливают следующим образом: растворяют мелко
наструганное мыло в 300 мл горячей (50-70 °С) воды. После
охлаждения мыльный раствор вливают в содовый и добавляют
недостающее количество воды. Магнитный порошок хорошо размешивают
до тестообразного состояния с малым количеством жидкости, а затем
со всей жидкостью суспензии.
Мыльно-содовая суспензия
не вызывает коррозии легированных углеродистых сталей без покрытий,
а также с защитными покрытиями в виде оксидного фосфата, кадмия,
хрома и цинка с пассивацией.
4.7. Водную магнитную
суспензию необходимо тщательно оберегать от масла, которое вызывает
коагуляцию магнитного порошка и снижает четкость выявления
дефектов.
В
случае появления хлопьев суспензию надо заменить свежей,
предварительно вымыв и обезжирив сосуд для суспензии.
4.8. Для контроля
деталей, подверженных корродированию, следует применять масляные
суспензии следующих составов:
I | |
Черный магнитный
порошок | 20±5 г |
Трансформаторное масло (или
масло РМ, МК, МС) | 0,5 л |
Керосин | 0,5 л |
II | |
Магнитный порошок | 20±5 г |
Трансформаторное масло | 0,5 л |
Топливо марки T-1 | 0,5 л |
Кинематическая вязкость
масляной и керосино-масляной суспензии не должна превышать 25 сст
при 20 °С.
4.9. При приготовлении
суспензии вначале магнитный порошок тщательно перемешивают с
небольшим количеством жидкости (основы суспензии) до получения
однородной массы с консистенцией сметаны, а затем размешивают со
всем количеством жидкости.
Примечание: При контроле
деталей в приложенном магнитном поле количество черного магнитного
порошка в суспензии может быть уменьшено на 5-10 г/л.
4.10. Магнитную суспензию
как вновь приготовленную, так и отработавшую, нужно хранить в
закрытом сосуде.
4.11. Перед употреблением
суспензию проверять на контрольном эталоне.
Суспензия считается
годной, если она выявляет на эталоне все отмеченные в его паспорте
дефекты при соблюдении изложенных в нем условий намагничивания.
Если дефекты на эталоне
не проявятся или проявятся нечетко, необходимо установить, чем это
вызвано: неисправностью дефектоскопа или неудовлетворительным
качеством магнитной суспензии.
4.12. Так как при
использовании суспензия обедняется, что приводит к снижению
чувствительности метода контроля, необходимо периодически проверять
концентрацию магнитного порошка в суспензии и добавлять его в
суспензию до оптимального количества. При полной загрузке
магнитного дефектоскопа проверять концентрацию магнитного порошка в
суспензии не реже двух раз в неделю.
Контроль концентрации
магнитного порошка в суспензии проводить лабораторным путем или с
применением приборов МП-10И, АКС-1, выпускаемых заводом
«Контрольприбор» (г.Москва), или другими приборами.
4.13. Если в цехе
универсальный дефектоскоп, на котором производится контроль
разнообразных деталей, то варьировать составом суспензий не
рекомендуется. Следует использовать суспензию, применяемую для
контроля большинства деталей.
Материалы, применяемые
для магнитопорошковой дефектоскопии, даны в Приложении 1.
5. ОСНОВЫ НАМАГНИЧИВАНИЯ ИЗДЕЛИЙ ПРИ МАГНИТОПОРОШКОВОМ МЕТОДЕ КОНТРОЛЯ
5.1. Лучше всего
выявляются дефекты, когда направление магнитного потока
перпендикулярно направлению (плоскости) дефекта. В зависимости от
ориентации возможных дефектов, размеров и формы контролируемого
изделия применяют следующие виды намагничивания: циркулярное,
продольное (полюсное) и комбинированное. Основные способы
намагничивания и схемы их осуществления приведены в табл.2.
Таблица
2
Основные способы и схемы намагничивания изделий
Вид
намагничивания (по форме магнитного потока) | Способ
намагничивания | Схема
намагничивания |
Циркулярное | Пропусканием
тока по всему изделию | |
Пропусканием
тока по контролируемой части изделия | ||
С помощью
провода с током, помещаемого в отверстие изделия | ||
Путем
индуцирования тока в изделии | ||
Продольное (полюсное) | Постоянным
магнитом | |
Электромагнитом | ||
Продольное (полюсное) | Намагничивающим соленоидом | |
Пропусканием
через изделие электрического тока и магнитного потока от
электромагнита | ||
Пропусканием
по изделию двух (или более) независимых токов во взаимно
перпендикулярных направлениях | ||
Комбинированное | Путем
индуцирования тока в изделии и током, проходящим по проводнику,
помещенному в отверстии изделия | |
Пропусканием
тока по изделию и при помощи соленоида |
Примечание: Обозначения
на чертежах означают: — изделие; — магнитный поток; — намагничивающий ток.
5.1.1. Циркулярное
намагничивание осуществляют путем пропускания тока через
контролируемое изделие, по стержню или проводнику, помещенному
внутри полой детали или ее отверстии, или путем индуцирования тока
в самом изделии. При циркулярном намагничивании магнитные линии
замыкаются внутри изделия, не образуя в нем магнитных полюсов.
Наиболее эффективно циркулярное намагничивание для тел вращения.
При таком намагничивании лучше обнаруживаются дефекты, совпадающие
по направлению с направлением тока.
Магнитно-порошковая дефектоскопия — Большая Энциклопедия Нефти и Газа, статья, страница 1
Магнитно-порошковая дефектоскопия
Cтраница 1
Магнитно-порошковая дефектоскопия основана на обследовании магнитного сопротивления шва или металла цельной детали. На деталь накладывают сверхчувствительную фотобумагу, на которую насыпают ровный тонкий слой порошка и помещают в поле сильного соленоида постоянного тока, порошок опрыскивают быстросохнущим прозрачным лаком ( цапонлак и др.), затем бумагу освещают сильным светом и проявляют. На бумаге создается картина магнитного поля, на которой определяется наличие или отсутствие дефектов. [1]
Магнитно-порошковая дефектоскопия выявляет поверхностные и подповерхностные дефекты типа нарушения сплошности. Магнитно-порошковую дефектоскопию применяют только для ферромагнитных материалов, которые подвергаются намагничиванию. При помещении изделия ( рис. 3.35) с дефектом в продольное однородное магнитное поле в месте нахождения подповерхностного скрытого дефекта магнитный поток будет рассеиваться в пространство, что создает на поверхности изделия магнитные полюса. [3]
Магнитно-порошковая дефектоскопия позволяет выявлять поверхностные и подповерхностные ( на глубине до 1 — 2 мм) дефекты сварных соединений типа трещин, непроваров, пор, подрезов. [4]
Магнитно-порошковая дефектоскопия осуществляется только в полуавтоматическом режиме. Автоматизации подвергаются процессы намагничивания и размагничивания изделий. Возможности магнитно-порошковой дефектоскопии в значительной мере ограничиваются качеством применяемого магнитного порошка и размерами его зерен. Графики ( рис. 3.36) показывают связь между размерами зерен порошка и степенью выявления различных де-с Ьектов. Магнитные свойства по-рошка влияют при этом на качество контроля в меныг. [6]
Магнитно-порошковую дефектоскопию клепаных барабанов проводят для выявления поверхностных дефектов на обечайках, днищах, трубных и заклепочных отверстиях. Для контроля металла обечаек и днищ барабанов токоподводящие электроды устанавливают на расстоянии 180 — 200 мм. [8]
По окончании магнитно-порошковой дефектоскопии возможные прижоги металла в местах контакта токоподводящих электродов удаляют абразивным инструментом. Дефектные места могут быть выбраны шлифовальной машинкой и повторно проконтролированы магнитно-порошковой дефектоскопией или травлением. [10]
В практике проведения магнитно-порошковой дефектоскопии хорошо зарекомендовали себя намагничивающие устройства в виде портативных электромагнитов переменного тока, отличающиеся простотой конструкции. Эти устройства рекомендуется применять при контроле изделий с толщиной стенки более 20 мм. Магнитопровод набирают из пластин электротехнического железа толщи
Магнитная порошковая дефектоскопия | Контроль и испытание металла элементов котлов
Метод магнитной порошковой дефектоскопии, называемый также методом магнитной суспензии, основан на выявлении нарушения целости металла по скоплению магнитного порошка около дефекта. В этих местах образуются потоки рассеяния и возникают магнитные полюса, притягивающие частички порошка. При небольшой намагниченности выявляются открытые трещины и надрывы, при намагниченности 300—500 Гс * — поверхностные плены и более глубокие волосовины. По мере увеличения намагниченности обнаруживаются более мелкие волосовины, а при намагниченности около 1000 Гс выявляются и неглубокие риски на поверхности. При намагниченности около 1500 Гс обнаруживаются волосовины и другие дефекты, не доходящие до поверхности на 1—3 мм.
Методом магнитной дефектоскопии выявляют трещины в заклепочных и сварных швах, вальцовочных соединениях, трубных решетках и днищах барабанов котлов.
Магнитную суспензию приготовляют путем смешения магнитного порошка и олеинового мыла с водой. Магнитный порошок получают из сухого мелкоразмолотого немагнитного железного сурика (Fe2O3), смешивая его с керосином до тестообразного состояния и прокаливая в металлическом или глиняном тигле с негерметической крышкой на кузнечном горне или в газоходе котла при 650—800° С. Полученный черный порошок магнитной окиси железа (Fe3O4) во избежание повторного окисления охлаждают и хранят без доступа свежего воздуха. Красный или желтый цвет порошка свидетельствует о недостаточном его раскислении. Такой порошок плохо притягивается магнитом; его снова смешивают с керосином и прокаливают вторично. Если нет сухого железного сурика, можно использовать тертый масляный сурик, прокалив его в тигле без добавления керосина. Получающийся порошок загрязнен маслянистой сажей, но вполне пригоден для приготовления магнитной суспензии.
При приготовлении магнитной суспензии на 1 л суспензии берут 15—12 г олеинового мыла и 50—60 г магнитного порошка. Мыло растворяют в небольшом количестве горячей воды, затем добавляют магнитный порошок и тщательно все перемешивают. После этого суспензию разбавляют горячей водой до нужной консистенции. Олеиновое мыло позволяет получить однородную и устойчивую смесь порошка и воды. Иногда применяют хозяйственное мыло хорошего качества, в этом случае смесь получается менее однородной.
Для намагничивания контролируемых участков барабанов используют обычно переменный ток 1400—1700 А напряжением 3—6 В, получаемый от сварочного или испытательного трансформатора. Поверх существующей вторичной (разомкнутой) обмотки сварочного трансформатора накладывают 3—5 витков гибкого кабеля или изолированной шинной красной меди сечением 100—240 мм2, которые образуют вторичную обмотку. К клеммам этой обмотки присоединяют гибкий изолированный кабель такого же сечения для намагничивания элементов барабана.
Первичную обмотку трансформатора присоединяют к сети через предохранители и двухполюсный рубильник закрытого типа. Второй рубильник устанавливают вблизи трансформатора. Монтер, обслуживающий этот рубильник, должен находиться в поле зрения рабочего, стоящего у лаза барабана, или сам должен стоять у лаза.
Сопротивление вторичной цепи должно быть минимальным. Трансформатор устанавливают возможно ближе к барабану. Длина цепи должна быть не больше 10—15 м, а число контактов — не более 4. Мощность трансформатора должна быть 8— 10 кВА. Допускается и меньшая мощность, так как при очень коротких промежутках времени включения перегрузка неопасна. Предохранители в этом случае ставят на ток, составляющий 40— 50% полного рабочего тока. Это предохраняет трансформатор от перегрузки при нахождении его по каким-либо причинам под рабочим током длительное время.
* В системе СИ магнитная индукция измеряется в тесла (Тл). 1 Тл = 104 Гс (гаусс).
Магнитопорошковый контроль
Лаборатория «ПРОконтроль». Мы знаем о магнитной дефектоскопии всё!
В процессе производства детали, начиная от литья и далее, во время обработки (прокатка, ковка, сварка), а также в процессе эксплуатации стальных деталей (сгибание и растягивающие нагрузки), возникают предпосылки для возникновения микротрещин. Чаще всего, образование трещин начинается на поверхности изделия. Затем, трещина распространяется вглубь металла, что обусловлено концентрацией напряжений в вершине трещины. В результате, появление любой незначительной микротрещины, может привести к усталостному разрушению детали. Именно поэтому — трещины, являются важным типом дефектов и должны быть своевременно выявлены и устранены. Наиболее чувствительным методом для обнаружения поверхностных трещин в ферромагнитных деталях — является магнитопорошковая дефектоскопия проводимая специалистами «ПРОконтроль».
Магнитная дефектоскопия и области её применения.
Магнитный неразрушающий контроль — применяется во всех отраслях, где используются детали из:
Стали;
Чугуна;
Металлов и сплавов, обладающих ферромагнитными свойствами.
Метод широко применяется на всех этапах обработки металлов и в их процессе эксплуатации. Методом магнитопорошковой дефектоскопии, производится контроль сварных соединений, контроль готовой продукции и полуфабрикатов. А так же контроль деталей бывших в употреблении.
Магнитопорошковая дефектоскопия — физические принципы.
Магнитопорошковая дефектоскопия — надёжный метод неразрушающего контроля. Магнитная дефектоскопия деталей, используется для обнаружения: трещин, пористости, не провара сварных швов. Востребована при выявлении других дефектов у ферромагнитных материалов. Метод позволяет визуально фиксировать характер и величину поверхностных, и около поверхностных дефектов детали. Метод тестирования, заключается в наведении магнитного поля на компонент, подлежащий контролю, и обработки намагниченной поверхности порошком или раствором оксида железа.
Если деталь не имеет повреждений — магнитное поле распределяется по всей поверхности равномерно, ориентируя слой оксида железа вдоль силовых линий. При наличии разрывов поверхности — силовые линии на границах разрыва имеют большую плотность. Именно это явление вызывает притягивание частиц порошка по краям области разрыва, что позволяет визуально зафиксировать наличие дефекта. Для выявления дефект, а силовые линии магнитного поля должны быть направленны перпендикулярно разрыву, что вызывает большее возмущение потока. Если линия разрыва проходит параллельно магнитным силовым линиям, возмущение незначительно, и выявить такие дефекты затруднительно.
Как это работает?
Намагничивание — достигается путем воздействия на деталь внешним магнитным полем, либо путем пропускания электрического тока через диагностируемый объект. Оба метода могут быть объединены, чтобы дать возможность выявления трещин во всех направлениях:
Намагничивание внешним магнитным полем. В этом случае, объект зажимается в коромысле электромагнита. Таким образом, магнитное поле генерируется в продольном направлении объекта и трещины, которые ориентированы перпендикулярно к полю (т.е. поперечные трещины) вызывают возмущение магнитного потока и концентрацию порошка.
Намагничивание электрическим током. Применяется для выявления продольных трещин. При подключении источника тока к детали, перпендикулярно направлению тока — формируется кольцевое магнитное поле. Продольные трещины — вызывают возмущение потока и концентрацию порошка на краях продольных трещин.
Комбинированное намагничивание. Часто, трещины не имеют преобладающее направление. Массовые продукты, например, в автомобильной промышленности, как правило, проверяются в стационарных лабораториях, проводящих магнитный неразрушающий контроль. В этом случае — метод намагничивания магнитным полем, чередуют с методом намагничивания электрическим током. Комбинированный метод позволяет выявить трещины любой ориентации.
«ПРОконтроль» — в наличие всё необходимое!
Средства визуализации дефекта: Для визуальной фиксации места магнитного возмущения, вызванного дефектом диагностируемой детали, используется жидкая суспензия на основе очень мелкого ферромагнитного порошка железа, или оксида железа.
Для того, что бы добиться повышения контраста частиц оксида — порошок железа окрашивают, с помощью флуоресцентных пигментов. При освещении ультрафиолетовым светом (УФ-излучение) в лабораторных условиях и на объектах, трещины проявляются ярким желто-зелёным цветом с высокой контрастностью. Это позволяет, с высокой точностью фиксировать микротрещины.
Неоспоримые преимущества магнитопорошковой дефектоскопии «ПРОконтроль»:
Порошковая дефектоскопия обеспечивает самую высокую чувствительность, для обнаружения поверхностных трещин;
Выявляет четкие и воспроизводимые признаки трещин;
Короткое время тестирования;
Магнитно порошковая дефектоскопия не потребует специальной подготовки поверхности;
Возможность обнаружения скрытых трещин;
Не предъявляет повышенных требований в отношение объектов исследований.
Специалисты Научно-производственной лаборатории «ПРОконтроль» — выполнят работы любой сложности.
Минимально возможные цены на наши Услуги, обусловлены маркетинговой политикой «ПРОконтроль» и оптимизацией расходов. «ПРОконтроль» — это минимально возможные сроки проведения магнитно порошковой дефектоскопии, личная ответственность каждого специалиста, гарантированный результат!
Магнитно-порошковая дефектоскопия — Большая Энциклопедия Нефти и Газа, статья, страница 3
Магнитно-порошковая дефектоскопия
Cтраница 3
Перечисленные выше методы применяются в следующей последовательности: визуальный послойный контроль в процессе сварки, цветная или магнитно-порошковая дефектоскопия, гидравлический метод с люминесцентным индикаторным покрытием. Вскрытие шва осуществляется в качестве дополнительного метода контроля по усмотрению завода-изготовителя. [31]
Для оценки качества сварных соединений, контроль которых невозможно осуществить методами гамма -, рентгено — или ультразвуковой дефектоскопии, применяют магнитно-порошковую дефектоскопию, цветную дефектоскопию, контроль сварных соединений методом вскрытия, визуальный послойный контроль, контроль гидравлическим методом с люминесцентным индикаторным покры-тием. Перечисленные методы контроля применяются в следующей последовательности: визуальный послойный контроль в процессе сварки, цветная или магнитно-порошковая дефектоскопия, контроль вскрытием шва, контроль гидравлическим методом с люминесцентным индикаторным покрытием. Вскрытие шва применяется в качестве дополнительного метода контроля, назначаемого, например, при невозможности проведения визуального послойного контроля сварного шва в процессе сварки. [32]
Для оценки качества сварных соединений, контроль которых невозможно осуществить методами гамма -, рентгено — или ультразвуковой дефектоскопии, применяют магнитно-порошковую дефектоскопию, цветную дефектоскопию, контроль сварных соединений методом вскрытия, визуальный послойный контроль, контроль гидравлическим методом с люминесцентным индикаторным покрытием. Перечисленные методы контроля осуществляют в следующей последовательности: визуальный послойный контроль в процессе сварки, цветная или магнитно-порошковая дефектоскопия, контроль вскрытием шва, контроль гидравлическим методом. [33]
Контроль поверхности барабана, трубных отверстий, штуцеров и сварных соединений при обследовании матал-ла и выборке дефектов осуществляют внешним осмотром, магнитно-порошковой дефектоскопией и ультразвуковым методом. [34]
Контроль поверхности барабана, трубных отверстий, штуцеров и сварных соединений при обследовании металла и выборке дефектов проводят внешним осмотром и при помощи магнитно-порошковой дефектоскопии. Поверхность металла барабана и его сварные швы проверяют ультразвуковым дефектоскопом. Если при выборочном контроле поверхностей барабана обнаружены дефекты, проверяют магнитно-порошковой дефектоскопией поверхности всех гнезд. В случае обнаружения при выборочном ультразвуковом контроле швов дефектов, по размерам, больше допустимых нормами Госгортехнадзора СССР для котельных барабанов, такие швы подвергают 100 % — ному контролю. [35]
В соответствии с [29] основные электросварные продольные и поперечные швы барабанов с околошовной зоной по 60 — 80 мм на сторону подвергают визуальному осмотру, магнитно-порошковой дефектоскопии и ультразвуковому контролю в объеме 100 % каждые 50 тыс. ч эксплуатации. Корпуса обечаек с внутренней поверхности контролируют визуальным осмотром и магнитной дефектоскопией через каждые 25 тыс. ч эксплуатации. При этом для контроля на внутренней поверхности в водном объеме вблизи трубных отверстий подготавливают контрольные участки размером 200X200 мм, по одному на каждом листе обечайки. Днища проверяют каждые 50 тыс. ч эксплуатации визуальным осмотром. При выявлении дефектов на контрольных участках величина этих участков удваивается. [36]
Остаточная намагниченность деталей турбины повышается при нарушении изоляции подшипников генератора и возбудителя, она может также возрасти при ремонтных работах в результате сварки, электроотпуска, магнитно-порошковой дефектоскопии. [38]
Для подтверждения достоверности ультразвукового контроля проводят выборочную магнитно-порошковую дефектоскопию заклепочных или трубных отверстий, для чего удаляют пять — семь заклепок ( и труб) из числа забракованных и проводят магнитно-порошковую дефектоскопию. [39]
С; притирка и сушка; наплавка твердым сплавом при равномер
Магнитопорошковая дефектоскопия, магнитопорошковый метод неразрушающего контроля
Магнитопорошковая дефектоскопия (МПД) – это метод неразрушающего контроля предназначенный для определения мелких дефектов в поверхностной и подповерхностной структуре металла, проходящих внутрь изделия. Данный метод эффективен в определении трещин, надрывов, волосовин, непроваров, пор и других дефектов.
Технология метода магнитопорошковой дефектоскопии
Основой метода является притяжение магнитного порошка выходящим на поверхность объекта магнитным потоком. Наличие дефектов в ферромагнитном объекте вызывает отклонение силовых линий магнитного поля, создание местных магнитных полей рассеяния и локальных магнитных полюсов и, соответственно, изменения в движении порошка.
Магнитопорошковая дефектоскопия состоит из следующих этапов:
- Предварительная подготовка поверхности, очистка от ржавчины и загрязнений.
- Намагничивание исследуемой поверхности.
- Нанесение на поверхность мелкодисперсного ферромагнитного порошка.
- Визуальное изучение поверхности и фиксация образованных индикаторных рисунков.
- Размагничивание поверхности.
Мелкодисперсный магнитный порошок вовлекается в сферу действия образованных локальных магнитных полюсов и растекается по поверхности изделия, образуя валики по форме трещин и иных дефектов. В магнитопорошковой дефектоскопии используется сухой и мокрый способы нанесения порошка. Как правило, для грубообработанных или необработанных поверхностей используется сухой метод. Контроль изделий с высоким классом шероховатости производится посредством суспензии из мелкодисперсного порошка на основе масла или керосина.
Для улучшения видимости при магнитопорошковом методе неразрушающего контроля в порошок добавляется двуокись титана или окись цинка для придания ему серого цвета. Также применяется контроль с помощью ультрафиолетового излучения, для чего используется специальный люминесцентный магнитный порошок.
Преимущества магнитопорошковой дефектоскопии
Магнитопорошковый метод неразрушающего контроля относится к наиболее перспективным и эффективным направлениям анализа и измерений в металлургии, машиностроении, нефте- и газовой промышленности. Он широко применяется при контроле состояния трубопроводов горячей и холодной воды, газо- и нефтепроводов, позволяет производить оценку и диагностику структуры материалов.
К основным преимуществам магнитопорошковой дефектоскопии можно отнести:
- Сравнительно небольшие трудоемкость и временные затраты на проведение диагностики.
- Высокая точность метода, возможность обнаружения поверхностных и подповерхностных дефектов.
- Одинаковая эффективность в выявлении как полых дефектов, так и несплошностей заполненных другими веществами, например водой, нефтью или пылью.
- Возможность эффективного поиска усталостных трещин, возникающих в ходе эксплуатации объекта.
По данному направлению компания «Полиинформ» предлагает проведение полного комплекса исследований различных объектов как с применением МПД, так и в комплексе с другими технологиями неразрушающего контроля.
Магнитопорошковая дефектоскопия — один из самых безопасных методов состояния трубопроводов в рамках, которые требует порядок экспертизы промышленной безопасности.
Магнитно-порошковая дефектоскопия
Самым первым методом контроля качества сварных соединений было простейшее сравнение готового шва с так называемым эталоном. Профессионалы варили, по их мнению, качественный шов, который и называли эталонным. С ним в последствии сравнивали все остальные швы. С тех пор технологии шагнули вперед и появились более совершенные методы контроля.
Современные методы контроля качества предполагают использование приборов, которые позволяют обнаружить скрытые от глаз дефекты. Один из таких приборов — дефектоскоп для проверки сварных швов. При этом дефектоскоп может применяться при самых различных методах контроля: от радиографического до акустического. В этой статье мы расскажем, что такое магнитопорошковая дефектоскопия сварных швов и каковы особенности данного метода контроля качества.
Магнитопорошковая дефектоскопия сварных соединений (она же магнитно-порошковая дефектоскопия) — метод контроля качества, суть которого заключается в обнаружении магнитных полей вокруг дефекта с применением ферримагнитных веществ.
Если у детали есть какой-либо дефект, то над ним обязательно образуется магнитное поле, которое будет искажаться. Деталь изначально намагничена и магнитные линии просто огибают дефекты, встречающиеся на пути. В результате происходит искажение магнитного поля. К тому же, по краям заготовки могут образовываться магнитные полюсы, которые в свою очередь создают локальные магнитный поля. На рисунке ниже схематично изображено магнитное поле.
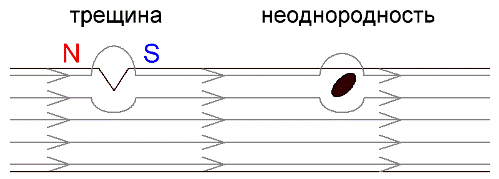
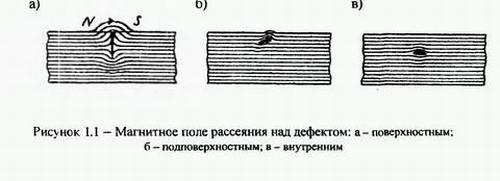
Техлоголия. Чтобы обнаружить дефект недостаточно иметь правильное оборудование. Нужно также использовать специальное ферримагнитное вещество. Проще говоря, магнитный порошок. Его наносят на сварное соединение с помощью сухого или мокрого метода.
При сухом методе используется обычное порошкообразное магнитное вещество. А при мокром — специальная магнитная суспензия. В данном случае суспензия — это смесь магнитного порошка и жидкости. В качестве жидкости можно использовать трансформаторное масло, его смесь с керосином, а также смесь воды с веществами, препятствующими образованию коррозии.
Дефектоскопия называется порошковой, поскольку для фиксации магнитного поля рассеяния применяют ферромагнитный порошок (зернистостью 5-10 мкм) с высокой магнитной проницаемостью. Для проверки деталей, поверхность которых по цвету темная, применяют буро-красный порошок оксида железа (Fe2О3), а для светлых деталей – черный или темно-коричневый порошок магнетита (Fe3О4). 30 -50 г магнитного порошка смешивают с 1 литром трансформаторного масла, керосина или смеси из них, получая в результате магнитную суспензию, которой и поливают деталь в процессе дефектоскопии.
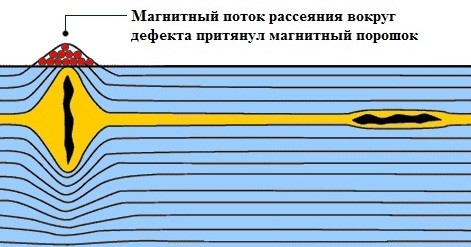
Согласно ГОСТу №21105-87 существует всего три уровня чувствительности. Каждому уровню соответствует своя буква (уровень А, Б, В) и все они зависят от размеров дефектов.
Уровень А самый высокий, чувствительность большая. Есть возможность обнаружить дефекты размером от 2,5 микрометра. Ниже вы можете видеть более подробную таблицу с информацией о других уровнях чувствительности.
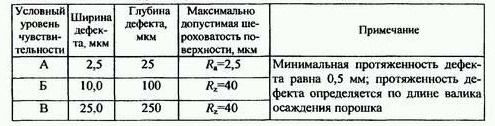
В таблице указана графа о максимально допустимой шероховатости. Все дело в том, что магнитопорошковая дефектоскопия сварных соединений и успешность ее проведения во многом зависят именно от параметра шероховатости поверхности детали. Есть шероховатость будет превышать допустимые значения, контроль будет менее объективным и точным. Но эту проблему можно частично исправить, если использовать порошок крупной фракции. Его нужно наносить сухим способом. Тогда появится возможность обнаружить глубокие дефекты при повышенной шероховатости поверхности детали.
Большое влияние оказывает подвижность частиц магнитного порошка. Важно, чтобы подвижность была высокой или выше среднего. Чтобы этого добиться нужно применять порошок с частицами разной формы. Такой порошок не будет прилипать к детали и позволит проводить более качественный контроль.
Также на чувствительность может влиять род тока, с помощью которого вы намагничиваете деталь при контроле. Рекомендуем устанавливать постоянный ток. Он формирует магнитное поле, способное проникать вглубь заготовки, а значит лучше обнаруживать дефекты. На изображении ниже более подробно изображен этот принцип.
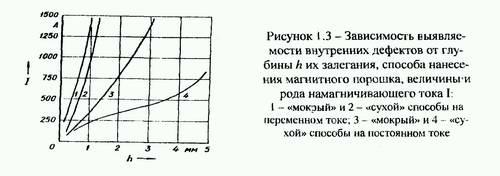
Отдельно поговорим о применении сухого и мокрого метода. В своей практике мы обнаружили, что при сухом методе чувствительность существенно повышается. Это значит, что при применении сухого порошка контроль более объективен, чем при использовании суспензии. Кстати, есть свои секреты, как можно повысить чувствительность при применении сухого порошка. Профессионалы рекомендуют распылять порошок в специальном устройстве, которое затем будет подать вещество по шлангу прямо на сварное соединение.
Есть и более продвинутые способы нанесения порошка. Можно поместить деталь в специальную герметичную камеру, где порошок будет находиться во взвешенном состоянии. В таком случае саму деталь нужно погрузить в рыхлое вещество, после чего медленно и аккуратно извлечь. Чувствительность при этом будет очень высокой. Но, в силу трудоемкости этот метод применяется нечасто, хотя все же имеет право на жизнь. Особенно, если нужно провести контроль детали, изготовленной из металла, имеющего немагнитное покрытие.
Дефектоскоп — это прибор, который можно применять в связке с многими методами контроля. Существует цветная дефектоскопия сварных швов, акустическая, вихретоковая, термоэлектрическая и многие другие. Но среди них всех особняком стоит магнитно-порошковая дефектоскопия, поскольку это мобильный и простой в применении метод.
С помощью магнитного дефектоскопа можно провести контроль в труднодоступных местах (в том числе на внутренней стороне детали, например, трубы), можно проводить контроль на высоте, поскольку оборудование очень компактное и легкое.