Особенности металлургических процессов при сварке под флюсом и в среде углекислого газа
Особенности металлургических процессов при сварке под флюсом и в среде углекислого газа
Категория:
Сварочные работы
Особенности металлургических процессов при сварке под флюсом и в среде углекислого газа
Металлургические процессы при сварке под флюсом характеризуются следующими особенностями (в отличие от металлургических процессов при сварке открытой дугой и покрытыми электродами):
— лучшая защита расплавленного металла от азота и кислорода воздуха;
— большой объем сварочной ванны и достаточно длительное пребывание металла в жидком состоянии, что способствует более полному протеканию химических реакций между шлаком и жидким металлом;
— возможность установить зависимость между режимом сварки и химическим составом металла шва.
При сварке в углекислом газе плавильное пространство закрыто струей углекислого газа, оттесняющего атмосферный воздух от зоны сварки.
Процесс окисления расплавленного металла происходит как при переходе капель с электродной проволоки в сварочную ванну, так и на поверхности последней. Взаимодействие жидкого металла и газа протекает весьма энергично, несмотря на кратковременность их контактирования. Это объясняется высокой температурой в зоне сварки и большой поверхностью соприкосновения жидкого металла с газом.
Чтобы прекратить реакции окисления, а также пополнить выгоревшие примеси, при сварке в углекислом газе применяют электродную проволоку, легированную марганцем и кремнием.
Содержание углерода в электродной проволоке должно быть небольшим, так как в противном случае возможно образование пор и горячих трещин в металле шва. Азот, попавший в зону сварки, взаимодействует с кислородом углекислого газа, образуя нерастворимые в металле окислы азота, уходящие в атмосферу.
Реклама:
Читать далее:
Подготовка металла к сварке и сборке соединений под сварку
Статьи по теме:
Особенности металлургических процессов при сварке в углекислом газе
Оборудование, материаловедение, механика и …
Статьи Чертежи Таблицы О сайте Реклама Особенности металлургических процессов при сварке в углекислом газе. Особенностью сварки в углекислом газе является сравнительно сильное выгорание элементов, обладающих большим химическим сродством к кислороду (А1, Т1, N. g, Мп, 51, С и др.). Выгорание происходит за счет окисляющего действия как углекислого газа, так и атомарного кислорода, который образуется в ре- [c.57]ОСОБЕННОСТИ МЕТАЛЛУРГИЧЕСКИХ ПРОЦЕССОВ ПРИ СВАРКЕ В УГЛЕКИСЛОМ ГАЗЕ [c.47]
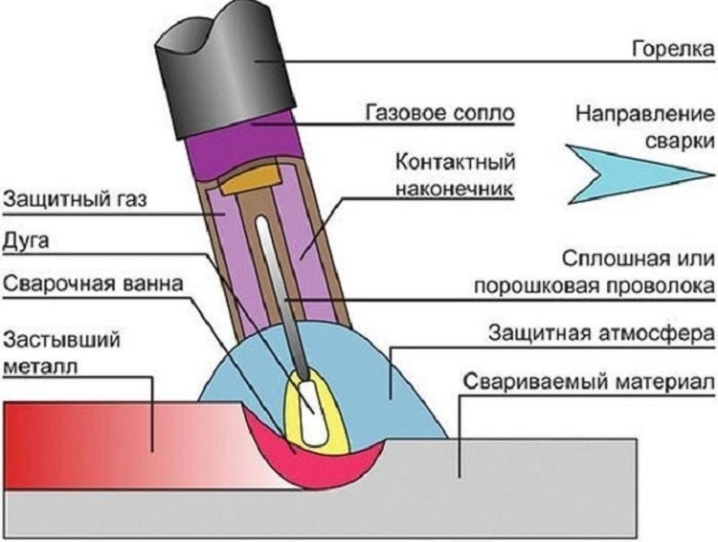
Дуговая сварка в защитных газах. Из активных защитных газов наибольшее распространение получил углекислый газ (СО2), обеспечивающий защиту сварочной ванны от контакта с азотом воздуха. Особенность металлургического процесса в этом случае обусловлена сильным окислительным действием СО2. Дуга, горящая в СО2, оказывает большее оксилительное воздействие на металл (33 % О), чем горящая на воздухе (21 % О). Результатом является сильное окисление сварочной ванны по реакции [c.68]
При сварке легированных сталей необходимо использовать специальные сварочные проволоки, содержащие раскислители (марганец и кремний) — Св08ГС, Св08Г2С, СвО,7ГС, которые предохраняют от окисления легирующие добавки свариваемого металла (защитный газ СО2 — сильный окислитель). Подробно металлургические особенности процесса сварки в углекислом газе рассматриваются в работе [18]. [c.382]
Смотреть главы в:
Оборудование и технология автоматической и полуавтоматической сварки -> Особенности металлургических процессов при сварке в углекислом газе
2. 61 — Особенности процесса
Газы металлургические
Металлургические процессы при сварке
Металлургические процессы при сварке Особенности металлургических процессов при сварке
Металлургический к оке
Особенности металлургических процессов
Особенности металлургических процессов при сварке
Особенности сварки
Особенности сварки в углекислом газе
Процесс сварки
Сварка без в углекислом газе
Углекислый газ
© 2021 Mash-xxl.info Реклама на сайте
Металлургические процессы при сварке — Энциклопедия по машиностроению XXL
из «Полуавтоматическая сварка в среде углекислого газа »
Металлургические процессы, происходящие при сварке в среде углекислого газа, слагаются из окисления, раскисления и легирования металла шва.
В результате разложения образуется смесь из трех различных газов углекислого газа, окиси углерода и кислорода. Встречные стрелки реакции означают, что направление ее может изменяться в зависимости от внешних условий. Одним из таких условий является температура газовой смеси. При повышении температуры реакция идет вправо, в сторону увеличения кислорода и окиси углерода. Понижение температуры обусловливает соединение СО и О2 с образованием углекислого газа. Это изменение состава газовой смеси при сварке показано на фиг. 3. В различных частях сварочной дуги состав смеси неодинаков в центральной части, где температура достигает 6200—6300°, углекислый газ разлагается почти полностью в области, прилегающей к сварочной ванне, количество углекислого газа преобладает над суммарным количеством кислорода и окиси углерода.

Степень окисления элементов, которые входят в состав стали, различна и зависит от химического сродства их к кислороду. В первую очередь окисляется кремний, сродство которого к кислороду больше чем у других элементов. Окисление марганца происходит интенсивнее, чем окисление железа и углерода. Кроме углекислого газа, в окислении участвует кислород воздуха, попавший в зону сварочной дуги, и влага, которая соде,ржится в углекислом газе. Вода при высокой температуре дуги испаряется, разлагаясь на водород и кислород. Окислению способствует также ржавчина на поверхности деталей в месте сварки, так как, во-первых, она представляет собой окисел железа, который при плавлении металла превращается в закись железа с выделением свободного кислорода, и, во-вторых, в ней присутствует влага. [c.27]
Полученные окислы кремния и марганца не растворяются в жидком металле. Они вступают во взаимодействие друг с другом и образуют легкоплавкое соединение, которое в виде шлака всплывает на поверхность сварочной ванны.
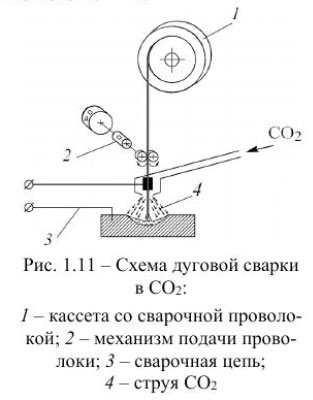
При раскислении кремний и марганец выг( рают, переходя в шлак. Уменьшается их содержание в металле шва. Пол ченное сварное соединение не будет качественным, если химический состав шва по количеству кремния и особенно марганца будет значительно отличаться от основного металла. Чтобы компенсировать частичное выгорание кремния и марганца, применяют сварочную проволоку с таким количеством этих элементов, которого было бы достаточно не только для успешного протекания реакций раскисления, но и для восполнения их потерь. Это избыточное количество кремния и марганца в электродном металле выполняет функции легирования. Поэтому шов сварного соединения из низкоуглеродистой стали, выполненный проволокой с содержанием не ниже 0,60%5 и 0,90%Мп, имеет эти элементы в количестве, не уступающем их содержанию в основном металле.
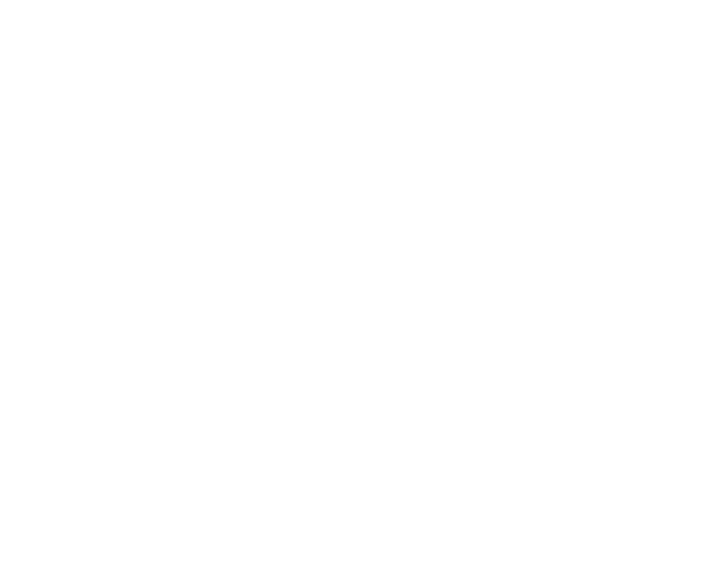
Вернуться к основной статье
Металлургические процессы при сварке сталей в струе СО2
Углекислый газ СО2 обладает молекулярной массой 44 и плотностью 1,96 кг/м3, поэтому он хорошо вытесняет воздух, плотность которого ниже (1,29 кг/м3). Поставляют углекислый газ в баллонах или контейнерах, где он находится в жидком состоянии, так как переход из жидкого в газообразное состояние происходит
при следующих критических параметрах газа: Гкр = 304 К, /?кр = = 7,887 МПа.
Для сварки применяют углекислый газ с пониженным содержанием вредных примесей — кислорода, азота, оксида углерода, влаги — в соответствии с ГОСТ 8050-74, т. е. отличающийся от пищевого СО2.
Углекислый газ в области высоких температур диссоциирует на СО и О2. На этот процесс расходуется часть тепловой энергии Q дугового разряда:
2С02 <=*2СО + О2-0. (10.15)
Рост константы равновесия процесса диссоциации при повышении температуры следует из рис. 9.3.
В условиях высоких и быстроменяющихся температур при
сварке состав продуктов диссоциации СО2 в разных точках дугового разряда будет изменяться.
На рис. 10.12 приведена схематическая диаграмма распределения температуры и концентраций газов вдоль оси сварного шва при движении сварочной головки с постоянной скоростью VCB.
В точке О на оси столба дуги происходят резкое повышение температуры и диссоциация СО2. С каплями электродного металла, проходящими через
дуговой промежуток, будет со — Рис 1012 Изменение
температу-
прикасаться атмосфера, состоя — рЫ и концентрации СО, СО2 и Ог щая из 66,6 % СО и 33,3 % О2. при сварке в углекислом газе
Поэтому СО2 называют активным защитным газом. Он защищает зону дуги от компонентов воздуха и прежде всего от азота и водорода. Но в то же время большая концентрация СО будет тормозить
этот процесс и, кроме того, задерживать окисление углерода стали
(находящегося в соединении РезС), сдвигая реакцию влево:
[Fe3C] + [FeO]<=>4Fe + CC>T. (10.17)
Однако чтобы предотвратить окисление металла значительным количеством кислорода, образующегося в атмосфере дуги, необходим дополнительный ввод в сварочную проволоку раскислителей. Обычно применяют кремний (около 1 %) и марганец (около 2 %). Поэтому для сварки низкоуглеродистых сталей применяют специальные сварочные проволоки (Св-08ГС, Св-08Г2С). При сварке легированных сталей необходимо использовать специальные сварочные проволоки Св-08ХЗГ2СМ, Св-10ХГ2СМА, Св-08Г2СДЮ, также содержащие раскислители (марганец и кремний), которые предохраняют от окисления легирующие элементы, входящие в состав стали и сварочной проволоки. Раскисляющие добавки, содержащиеся в каплях электродного металла, растворяются в жидком
металле сварочной ванны и задерживают окисление железа и рас
творенных в нем элементов. Диссоциация содержащихся в СО2 паров воды
2Н20 <=± 2Н2 + 02 (10.18)
тоже будет тормозиться вследствие высокого парциального давления кислорода, полученного при диссоциации СО2.
На участках, удаленных от оси столба дуги, будет происходить догорание окиси углерода, т. е. рекомбинация молекул СО с большим выделением тепловой энергии, которая раньше расходовалась на диссоциацию газа (около 30 % электрической мощности дуги):
2СО + 02<=> 2С02 + Q. (10.19)
Выделение теплоты при обратном процессе на периферийных участках дугового разряда увеличивает глубину проплавления и
ширину шва. По сравнению с дугой, горящей в аргоне, при дуговой сварке в СО2 проплавление увеличивается, а ширина шва уменьшается, и это приходится учитывать технологам.
Газовая атмосфера на участках, удаленных от оси столба дуги,
будет обогащаться СО2 и водородом, образовавшимся при диссоциации паров воды. Взаимодействуя с СО2, Н2 будет связываться в молекулы Н2О:
Н2 + С02 Н20 + СО. (10.20)
Таким образом, при сварке в струе углекислого газа металл поглощает водород в меньших количествах, чем при других видах сварки. В среднем при сварке низкоуглеродистых, низколегированных сталей в струе СО2 содержание водорода в наплавленном
металле колеблется от 0,5 до 2 • 10 5 м3/кг.
При вводе Si и Мп в сварочную проволоку атмосфера будет по-прежнему окислительной, но эти элементы, попадая в сварочную ванну, будут связывать кислород, растворенный в металле, т. е. раскислять металл шва:
[FeO] + [Мп] +±Fe + (MnO)t; (10.21)
2[FeO] + [Si] <=>2Fe + (Si02)t. (10.22)
В хвостовой части сварочной ванны шлак всплывает на поверхность металла, но обычно его недостаточно, чтобы создать сплошной защитный слой на поверхности шва. Металл, наплавленный при сварке в струе СО2, чище (содержит меньше шлаковых включений), и поэтому его пластические свойства несколько выше, чем при сварке под слоем флюса. Главный недостаток сварки в струе СО2 — разбрызгивание металла электрода (до 12 %). Его
сводят к минимуму, добавляя 3 % кислорода к СО2. Это позволяет перейти к струйному переносу металла электрода. В качестве активного защитного газа в отдельных случаях можно применять также перегретый водяной пар, который вытесняет из зоны столба дуги азот и кислород атмосферы (JI. C. Сапиро). Однако при взаимодействии пара с жидким металлом будет выделяться большое количество водорода:
Н20 + Fe -> [FeO] + h3;
h3 -► 2[Н].
Это приводит к образованию пор, а в легированных сталях — и к образованию холодных трещин.
Металлургические процессы при сварке под слоем флюса и в среде защитных газов
Металлургические процессы при сварке под слоем флюса и в среде защитных газов
Основные металлургические процессы в сварочной ванне
Размеры и время существования сварочной ванны могут сильно изменяться в зависимости от способа и режима сварки; в то же время эти два фактора имеют важнейшее значение с точки зрения полноты проходящих химических реакций, очистки жидкого металла от газов и шлаков, формирования шва. Необходимо учитывать различие в степени участия основного и электродного металла в формировании шва в зависимости от способа сварки
Количество и состав шлаков при ручной сварке и при сварке под флюсом различны. При ручной сварке капли из дугового промежутка, двигаясь с большой скоростью, погружаются в сварочную ванну, перемешиваются в ней с металлом и перемещаются от дугового пятна назад и в стороны. При движении капель в ванне происходит разделение металла и шлака вследствие разрушения шлаковых оболочек из-за значительного газообразования внутри капель и разницы в удельном весе металла и шлака. Весь металл в ванне энергично перемешивается и выделяющиеся нерастворимые газы удаляются в атмосферу. В сварочной ванне продолжаются интенсивные окислительно-восстановительные реакции с образованием легкоплавких шлаков, всплывающих на поверхность шва и создающих шлаковый покров. Кроме того, происходит очищение металла ванны от серы. Основное значение металлургических реакций в сварочной ванне — раскисление металла шва и очищение его от вредных примесей и газов. Указанные процессы в полной мере заисят от состава толстого покрытия электрода, чистоты свариваемых кромок, влажности кромок и покрытия электрода, размеров и времени существования сварочной ванны.
Наилучшим образом раскисляют и очищают металл шва электроды, содержащиe в покрытии большой процент мрамора (СаСО3) и значительный процент ферросплавов. При наличии на кромках окалины в сварочную ванну попадает кислород, что вызывает интенсивное образование FeO, в свою очередь, приводящее к выгоранию углерода и возможному образованию пор в шве. Влажность кромок или покрытия и наличие ржавчины приводят к окислению металла шва и насыщению его водородом по реакции Fe + h3O = FeO + 2H.
Автоматическая сварка и наплавка под слоем флюса
Автоматическая и полуавтоматическая сварка плавящимся электродом, под слоем флюса или в среде защитных газов дает более стабильный шов с повышением производительности в 2.. .8 раз по сравнению с ручной дуговой сваркой.
Основное промышленное применение находит сварка под флюсом одной вертикально расположенной электродной проволокой сплошного сечения . Нагрев и плавление основного и присадочного металлов происходят за счет тепла, получаемого при преобразовании подводимой к дуге электрической энергии. Дуга возникает между электродной проволокой 2 и основным металлом 3, присоединенным к полюсам источника питания. В качестве такого источника используют специальные однофазные или трехфазные сварочные трансформаторы переменного тока с пологопадающей внешней характеристикой, генераторы и выпрямители с пологопадающей или падающей внешней характеристикой. Сварку на постоянном токе преимущественно ведут при обратной полярности. Возможна сварка и при прямой полярности.
Подвод тока к электродной проволоке и ориентацию ее конца по отношению к свариваемым кромкам осуществляют мундштуком 4. Ток к изделию подводят через неподвижные или подвижные контактные устройства (струбцины, щетки и др.). Режим существования дуги при сварке под слоем флюса определяется силой тока, напряжением и длиной дуги. Обычно применяют силу тока 1000. ..1200 А, что при открытой дуге невозможно вследствие разбрызгивания металла шва. Сварку ведут короткой дугой. Некоторые современные автоматы поддерживают отклонение длины дуги в пределах ±0. 2. ..0,3 мм. Напряжение колеблется в пределах 18. ..55 В.
В процессе сварки электрод и основной металл со всех сторон окружены слоем флюса 5, насыпаемым из флюсоалпарата 6, работающего обычно от заводской сети сжатого воздуха (при массовом производстве). Высоту и ширину слоя устанавливают, исходя из условия обеспечения эффективной изоляции зоны сварки от окружающего воздуха и создания плотного формирующего жидкий металл барьера. Обычная высота слоя флюса 20.. .60 мм. При нагреве и плавлении флюс выделяет газы и пары, способствующие стабилизации дугового разряда.
Дуга находится в заполненном парами и газами пузыре, сводом которого является прослойка 7 из жидкого шлака. Таким образом, флюс при этом способе сварки защищает расплавленный металл электрода и ванны от воздуха; концентрирует тепло в зоне сварки; замедляет остывание ванны, позволяя попавшим в нее газам выйти наружу; облегчает ионизацию дугового промежутка, обеспечивая стабильность процесса; легирует металл шва дополнительными элементами; предотвращает выгорание полезных примесей.
Для автоматической сварки применяют плавленые и керамические неплавленые флюсы. Керамические неплавленые флюсы представляют собой крупинки (гранулы) размером 1…3 мм, изготовленные из материалов, входящих в состав обычных покрытий электродов Для электродуговой ручной сварки. По характеру шлака различают кислые и основные флюсы, а по назначению— для сварки низкоуглеродистых сталей, легиро-1анных спецсталей, цветных’металлов для наплавочных работ и т. д.
стабилизации горения дуги
Довольно широко применяют флюсы марок АН-348А, ОСЦ-45, АН-15, АВ-5, 48-ОФ-10, в которых основой служат окислы марганца и кремния. Дополнительно в флюс добавляют компоненты для повышения жидкотекучести шлаков (CaF2), и легирования
металла шва (феррохром, ферротитан и др.).
Для автоматической сварки и наплавки промышленность выпускает аппараты марок АБСК, А1401, А1423, А384МК, А580М, тракторы ТС-17М-1, АДС-1004-04, АДФ-1001, ТС-44, ДТС-38 и др.
При ремонте сельскохозяйственной техники широко используют наплавку под слоем флюса для восстановления геометрических параметров изношенных деталей.
Для защиты металла от воздействия воздуха, кроме шлакового покрытия, применяют газовую защиту вокруг дуги и расплавленного металла. В качестве защитных применяют инертные (аргон, гелий) и активные газы (водород, окись углерода или их смесь с азотом). Наибольшее распространение получили аргонодуговая сварка и сварка в среде углекислого газа. При аргонодуговой сварке наплавящимся электродом через специальную горелку, в которой установлен вольфрамовый электрод 3, пропускают инертный газ (аргон или гелий). Возбуждение дуги происходит между электродом и свариваемым изделием. Для заполнения разделки кромок в зону вводят присадочный материал 2, химический состав которого близок к составу свариваемого материала. Применяют электроды диаметром 2.. .6 мм. Аргон подают в горелку под давлением 0,03.. .0,05 МПа.
Аргонодуговую сварку применяют для сварки легированных сталей, алюминия и его сплавов, титана, магниевых сплавов.
В ряде случаев сварку выполняют и плавящимся электродом. В этом случае применяют проволоку диаметром 0,6.. .3 мм, которую автоматически подают в наконечник 2 горелки. Защитный газ через специальный канал 4 наконечника горелки попадает в пламя дуги .
Сварка в углекислом газе — наиболее дешевый способ по сравнению с другими видами сварки в защитных средах, широко применяется при восстановлении деталей сельскохозяйственных машин, особенно чугунных. Процесс наплавки в среде углекислого газа, по существу, аналогичен процессу сварки.
Для наплавки в среде углекислого газа используют электродные проволоки с повышенным содержанием кремния, марганца и титана (Св. 08ГС, Св. 08Г2С, Св. 10ХГ2С и др.). Для образования износостойкого наплавленного слоя применяют порошковые проволоки (ПП-6ХЗВ10,ПП-сормайт-1, ПП-сормайт-2, ПП-10Х10В4 и др.).
Наплавку тел вращения производят, используя токарно-винторезный станок.
Для восстановления изношенных деталей в ремонтной практике нередко применяют вибродуговую наплавку, в основе которой контактная сварка и электрическая дуга. Наплавку можно вести на воздухе, в среде защитного газа, в жидкости. Процесс состоит из трех этапов: замыкание электрода с деталью, размыкание, холостой ход. В момент короткого замыкания конец электрода оплавляется. При отрыве электрода перемычка взрывообразно разрушается и процесс переходит в дуговой. В этот момент и происходит перенос металла электрода на наплавляемую деталь. Наплавку чаще ведут на постоянном токе, что обеспечивает лучшую стабильность процесса.
Установки для автоматической вибродуговой наплавки обычно монтируют на базе токарно-винторезных станков, на суппорте которых устанавливают вибродуговую головку ЭВГ-2, КУМА-5М, ОКС-1252 и др.
. Сварка в среде аргона. Сущность. Область применения.
Сварка в среде аргона используется в ответственных случаях так как аргон очень дорогой. Аргон идеальный защитный газ он имеет большие атомы которые не растворимы. Аргон тяжелее воздуха он не горюч не ядовит. Применяется в завариваем трещины , пробои картеров КПП на отечественных и иностранных автомобилях в среде аргона. Сварка аргоном позволяет обеспечить высокую производительность сварки, максимально сократить зону термического влияния, появляется возможность производства сварки при повышенной плотности мощности.
Сварка в среде углекислого газа. Сущность. Область применения.
Углекислый газ тяжелее воздуха, не горюч, не ядовит Сущность процесса сварки в углекислом газе заключается в следующем. Поступающий в зону сварки углекислый газ защищает ее от вредного влияния атмосферы воздуха. Причем при высокой температуре сварочной дуги углекислый газ частично диссоциируется на окись углерода и кислород 2С022СО + O2.
В результате в зоне дуги образуется смесь из трех различных газов: углекислого газа, окиси углерода и кислорода. для того что бы О2 нетрилизовать вводят в него окислители Si,Mg,Al и таким образом эта самый распостраненый способ качественной сварки стали. Применяют в самолетостроении, где преобладает сварка металлов малых толщин (1-3 мм), в производстве химической аппаратуры. Важное значение имеет газовая сварка в прокладке и монтаже трубопроводов самых разнообразных назначений, в особенности малых диаметров, до 100 мм. Газовая сварка является незаменимым мощным средством при ремонте и с этой целью широко используется в ремонтных мастерских для всех видов транспорта, в сельском хозяйстве и т. Д
Плазменно-дуговая сварка
Плазменная струя, применяемая для сварки, представляет собой направленный поток частично или полностью ионизированного газа, имеющего температуру 10 000 – 20 000 °С. Плазму получают в плазменных горелках, пропуская газ через столб сжатой дуги. Дуга горит в узком канале сопла горелки, через который продувают газ. При этом столб дуги сжимается, что приводит к повышению в нем плотности энергии и температуры. Газ, проходящий через столб дуги, нагревается, ионизируется и выходит из сопла в виде высокотемпературной плазменной струи. В качестве плазмообразующих газов применяют азот, аргон, водород, гелий и воздух и их смеси.
Сварка в углекислом газе.
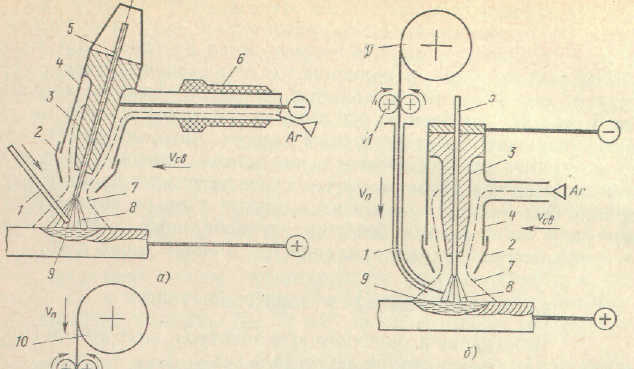
Сварка в углекислом газе
Преимущество сварки в углекислом газе перед сваркой под флюсом состоит в том, что сварщик может наблюдать за ходом горения дуги, не закрытой флюсом. При ее производстве не нужны приспособления для подачи и отсоса флюса, которые усложняют сварочное оборудование. Отпадает необходимость в последующей очистке швов от шлака и остатков флюса, что особенно важно при многослойной сварке.
Сварку в углекислом газе производят почти во всех пространственных положениях. Она осуществляется при питании дуги постоянным током обратной полярности. Во время сварки постоянным током прямой полярности снижается стабильность горения дуги, ухудшается формирование шва, происходит увеличение потери электродного металла на угар и разбрызгивание. Однако коэффициент наплавки в 1,6–1,8 раза выше, чем при обратной полярности. Это качество используют при наплавочных работах. Сварку можно производить и на переменном токе при включении в сварочную цепь осциллятора.
В качестве источников питания дуги постоянным током используют сварочные выпрямители с жесткой внешней или универсальной характеристиками.
В углекислом газе успешно сваривают листовой материал из углеродистых и низколегированных сталей. Листы толщиной 0,6–1,0 мм сваривают с отбортовкой кромок. Допускается также сварка без отбортовки, но с зазором между кромками не более 0,3–0,5 мм. Листы толщиной 1,0–8,0 мм сваривают без разделки кромок, при этом зазор между свариваемыми кромками должен быть не более 1 мм. Листы толщиной 8–12 мм сваривают V-образным швом, а при больших толщинах – Х-образным швом. Перед сваркой кромки изделия должны быть тщательно очищены от грязи, краски, окислов и окалины.
Наилучшие результаты дает сварка при больших плотностях тока, обеспечивающих более устойчивое горение дуги, высокую производительность процесса и снижение потерь металла на разбрызгивание. Для этого при сварке в углекислом газе применяют электродную проволоку диаметром 0,5–2,0 мм и выполняют сварку при плотности тока не менее 80 А/мм2.
Сварочная проволока применяется из низкоуглеродистой стали с повышенным содержанием кремния и марганца марок Св–08ГС, Св–08Г2С. Поверхность проволоки должна быть чистой от смазки, антикоррозионных покрытий, ржавчины и загрязнений, нарушающих устойчивость режима сварки. Режим сварки выбирается в зависимости от толщины свариваемых кромок.
Сварочный ток и скорость сварки в значительной степени зависят от размеров разделки свариваемого шва, т. е. от количества наплавляемого металла. Напряжение устанавливается таким, чтобы получить устойчивый процесс сварки при возможно короткой дуге (1,5–4,0 мм). При большей длине дуги процесс сварки неустойчивый, увеличивается разбрызгивание металла, возрастает возможность окисления и азотирования наплавляемого металла.
Скорость подачи электродной проволоки зависит от сварочного тока и напряжения, чтобы процесс протекал устойчиво при вполне удовлетворительном формировании шва и незначительном разбрызгивании металла. Расход углекислого газа устанавливается так, чтобы обеспечить полную защиту металла шва от воздействия атмосферного воздуха. При сварке толстых изделий сварочными токами 500–1000 А расход газа достигает 15–20 л/мин. Расстояние от торца мундштука горелки до сварного соединения должно быть при сварочных токах до 150 А в пределах 7–15 мм, а при токах до 500 А – в пределах 15–25 мм.
Полуавтоматическую сварку можно вести углом вперед, перемещая горелку справа налево, и углом назад, перемещая горелку слева направо. При сварке углом вперед глубина проплавления меньше, наплавляемый валик получается широкий. Такой метод применяют при сварке тонкостенных изделий и при сварке сталей, склонных к образованию закалочных структур.
При сварке углом назад глубина проплавления больше, а ширина валика несколько уменьшается. Угол наклона горелки относительно вертикальной оси составляет 5–15°. Перед началом сварки следует отрегулировать расход углекислого газа и только спустя 30–40 с возбудить дугу и приступить к сварке. Это необходимо, чтобы газ вытеснил воздух из шлангов и каналов сварочной горелки. Вылет электродной проволоки устанавливается в пределах 8–15 мм при диаметре проволоки 0,5–1,2 мм и 15–35 мм – при диаметре проволоки 1,2–3 мм. В процессе сварки электроду сообщается такое движение, чтобы получилось хорошее заполнение металлом разделки свариваемых кромок и удовлетворительное формирование наплавляемого валика. Эти движения аналогичны движениям электрода при ручной дуговой сварке качественными электродами.
Для снижения опасности образования трещин рекомендуется первый слой сваривать при малом сварочном токе. Заканчивать шов следует заполнением кратера металлом. Затем прекращается подача электродной проволоки и выключается ток. Подача газа на заваренный кратер продолжается до полного затвердевания металла.
При сварке в углекислом газе следует помнить об отравляющих действиях оксида углерода СО, выделяющегося при сварке. Поэтому при сварке в резервуарах и закрытых помещениях необходимо обеспечить хорошую вентиляцию.
Данный текст является ознакомительным фрагментом.
Продолжение на ЛитРесСварка в защитных газах
Лекция 2. Сварка в защитных газах.
Технология автоматической дуговой сварки в защитных газах
2.1. Особенности сварки в защитных газах
Сущностью и отличительной особенностью дуговой сварки в защитных газах является защита расплавленного и нагретого до высокой температуры основного и электродного металла от вредного влияния воздуха защитными газами, обеспечивающими физическую изоляцию металла и зоны сварки от контакта с воздухом и заданную атмосферу в зоне сварки. Используют инертные и активные защитные газы (см. главу 12 «Сварочные материалы»).
При дуговой сварке применяют два основных способа газовой защиты: местная и общая в камерах (сварка в контролируемой среде).
Наиболее распространенной является струйная местная защита в потоке газа, истекающего из сопла сварочной горелки. Качество струйной защиты зависит от конструкции и размеров сопла 1, расхода защитного газа и расстояния L от среза сопла А-А до поверхности свариваемого материала. В строении газового потока различают две области (рис. 2.1): ядро, струи 2 и периферийный участок 3.
Рис. 2.1. Схема газового потока из сопла сварочной горелки:
1 сопло горелки; 2 ядро потока; 3 периферийная область; H длина ядра потока; L расстояние от среза до детали; АА сечение среза сопла; D диаметр сопла
При истечении в окружающую воздушную среду в ядре потока 2 сохраняются скорость и состав газа, имеющиеся в сечении А-А на срезе сопла. Периферийная же часть потока 3 представляет собой область, в которой защитный газ смешивается с окружающим воздухом, а скорость в любом сечении по длине потока изменяется от первоначальной (имеющейся на срезе сопла) до нулевой на внешней границе струи. Поэтому надежная защита металла может осуществляться только в пределах ядра потока. Чем больше высота Н этого участка, тем выше его защитные свойства. Максимальная высота Н наблюдается при ламинарном истечении газа из сопла. При турбулентом характере истечения газа такое строение потока нарушается и защитные свойства его резко падают. Характер истечения зависит от конфигурации проточной части сопла, его размеров и расхода газа. На практике применяют три вида сопл: конические, цилиндрические и профилированные (рис. 2.2).
Рис. 2.2 Формы сопел сварочных горелок: а коническая;б цилиндрическая; в профилированная
Расход защитного газа выбирают оптимальным для обеспечения истечения струи, близкого к ламинарному. Для улучшения струйной защиты на входе в сопло в горелке устанавливают мелкие сетки, пористые материалы и т.п., позволяющие дополнительно выравнивать поток газа на выходе из сопла. При сварке со струйной защитой возможен подсос воздуха в зону сварки. Для улучшения и увеличения области защиты, особенно при сварке активных материалов, к соплу горелки крепят дополнительные колпаки приставки.
Наиболее эффективной является общая защита в камерах с контролируемой средой. Камеры заполняют инертным газом высокой чистоты под небольшим избыточным давлением (0,0050,01 МПа), в камере располагаются свариваемое изделие и сварочное оборудование (автомат). Сварку производят внутри камеры изолированно от воздушной среды. Такой способ защиты обычно используют при сварке изделий из химически активных металлов (титан, цирконий, тантал, молибден и др.). Достоинства сварки в защитных газах высокая производительность, высокое качество защиты, доступность наблюдения за процессом горения дуги, простота механизации и автоматизации, возможность сварки в различных пространственных положениях. Сварка в защитных газах может выполняться неплавящимся и плавящимся электродами. На рисунке 2.3 приведены схемы постов для различных вариантов дуговой сварки в защитных газах.
Рис. 2.3. Схемы постов для сварки в защитных газах: а неплавящимся электродом в инертных газах на постоянном токе прямой полярности; б тоже, на переменном токе; в плавящимся электродом на постоянном токе обратной полярности
2. 2. Классификация методов снижения разбрызгивания при сварке в углекислом газе
Разбрызгивание электродного металла при сварке в СО2 является одним из основных недостатков этого способа сварки. Разбрызгивание сопровождается увеличением расхода электродной проволоки и защитного газа, забрызгиванием поверхности свариваемых деталей и деталей сварочной горелки. Все это приводит к увеличению себестоимости сварочных работ за счет увеличения затрат на материалы и повышению трудоемкости вследствие затрат труда на зачистку от брызг.
Основными причинами разбрызгивания является:
1. увеличение размера капель электродного металла при повышении напряжения;
2. недостаточная стабильность процесса сварки;
3. реактивные силы, выталкивающие каплю металла из зоны сварки в начале короткого замыкания;
4. интенсивное газовыделение в объеме жидкого металла капли и сварочной ванны, сопровождающееся взрывообразными выбросами расплавленного металла из сварочной ванны;
5. газодинамический удар при разрушении перемычки между электродом и переходящей в сварочную ванну каплей при сварке с короткими замыканиями.
В настоящее время проблема снижения разбрызгивания является актуальной и работы направленные на ее решение ведутся в различных направлениях.
Все известные методы снижения разбрызгивания можно разделить на два направления:
1 Химические методы:
— использование газовых смесей для защиты зоны сварки;
— двухслойная защита;
— использование активированных и порошковых проволок.
2 Энергетические методы (методы, влияющие на энергетические процессы сварки):
— подбор режимов;
— импульсно-дуговая сварка;
— сварка пульсирующей дугой;
— сварка с принудительными короткими замыканиями;
— синергетические системы управления параметрами режима;
— импульсная подача сварочной проволоки.
Сварка в смесях защитных газов. Сущность способа состоит в том, что при изменении химического состава защитного газа в существенной степени изменяются физические и металлургические процессы сварки. Это проявляется, во-первых, через окислительную способность защитной среды, во-вторых, через ее теплофизические свойства, влияющие на дугу.
Инертные газы обладают рядом особенностей: отсутствием диссоциации и отрицательных ионов, низким напряжением горения дуги благодаря наличию метастабильных уровней возбуждения и ступенчатой ионизации. В зависимости от применяемого инертного газа изменяются поверхностное натяжение и размер капель электродного металла. А также коэффициент расплавления электрода.
Для дуги в углекислом газе характерны высокие значения теплопроводности и градиента потенциала в столбе дуги. Применение СО2 связано с нестабильностью горения дуги, вызванной силой, отталкивающей каплю вверх и в сторону, действующей против направления переноса металла и создаваемой высоким давлением газа внутри столба струями пара с поверхности сварочной ванны, ударяющими в каплю.
Рассмотрим влияние компонентов газовой среды на примере смеси для высокого производительного процесса TIME. Обычно используют 65 % Аг + 26,5 % Не + 8 % С02 + 0,5 % 02.
Добавка гелия увеличивает потенциал ионизации и градиент потенциала в столбе дуги. За счет этого возрастают напряжение и энергия дуги. Плазменный поток становится более мощным и стабилизирует дугу.
Добавка О2 к аргону повышает стабильность горения дуги и улучшает перенос металла, уменьшая разбрызгивание. Добавка кислорода к углекислому газу улучшает отделение брызг от основного металла, улучшает внешний вид шва и снижает склонность к образованию пор при сварке металла, покрытого ржавчиной.
Предлагается рассматривать действие парамагнитных сил и положительной магнитной восприимчивости кислорода и других газов на критическое значение тока перехода к струйному переносу.
Предполагается, что наличие парамагнитного газа усиливает действие электродинамической силы, что приводит к уменьшению критического значения тока. Кроме того, существует возможность сепарации компонентов газовой смеси и концентрация кислорода вблизи расплавленной капли под воздействием магнитного поля, что снижает поверхностное натяжение металла.
Преимущества данного способа:
1 Снижение уровня разбрызгивания.
2 Переход к струйному переносу.
3 Снижение уровня критического тока.
4 Меньшая восприимчивость к качеству поверхности свариваемых изделий.
Недостатками же сварки в смесях защитных газов являются:
1 Смеси на основе аргона дорогостоящие.
2 Невозможность длительного хранения готовых смесей газов [21].
3 Повышенная окислительная способность атмосферы.
4 Отсутствие управляемости процесса (отсутствие управляемого переноса).
Двухслойная защита. Сущность заключается в использовании двух потоков защитного газа: внутреннего, по которому подают аргон, для улучшения защиты и уменьшения сжатия столба дуги; и наружного, по которому подают углекислый газ. Подобная защита сварочной дуги обеспечивает стабильность горения дуги с минимальным разбрызгиванием.
Использование активированных и порошковых проволок.
Сущность процесса состоит в том, что в зону сварки посредством проволоки вносятся некоторые химические элементы, влияющие на теплофизические свойства сварочной дуги.
При сварке проволоками различных систем легирования наибольшее влияние на характеристики переноса электродного металла оказывает кремний. Другие элементы: алюминий, титан, молибден, марганец, хром, никель и др. располагаются в соответствии с их способность изменять поверхностное натяжение расплавленного металла.
При нанесении на поверхность проволоки покрытий, состоящих из тонкого слоя солей щелочных и щелочноземельных металлов (соли цезия + соли калия: соли цезия + соли натрия; растворов углекислого калия, а также оксиды других металлов Fe304, CeО2) расширяются технологические возможности процесса сварки, за счет повышения стабильности горения дуги и снижения разбрызгивания.
Наличие в сварочной дуге легкоионизируемых щелочных металлов резко уменьшает диаметр столба дуги, а площадь активных пятен расширяется. Электромагнитная сила способствует отрыву капель электродного металла.
Введение в электродную проволоку шихты, состоящей из 10% К2С03; 10% Nа2СО3; 5% CaF2 остальное двуокись титана благоприятно сказывается на стабильности горения дуги и характере переноса металла. Применение активаторов на основе титана снижает разбрызгивание до 50%.
К недостаткам активированных покрытий можно отнести его осыпание с поверхности проволоки. Эта проблема решается нанесением покрытия в процессе сварки при помощи специального устройства, устанавливаемого на сварочную горелку.
Существуют технологии изготовления проволок, поверхность которых насыщена кислородом, который увеличивает стабильность горения дуги и уменьшает разбрызгивание до 3% за счет снижения силы поверхностного натяжения.
С целью повышения стойкости против атмосферной коррозии, на проволоку наносят покрытие — черный хром. Данное покрытие не только защищает проволоку от коррозии, но и снижает разбрызгивание и потери электродного металла.
Порошковые проволоки широко применяются для производства сварных изделий, благодаря хорошим технологическим свойствам. Это направление сварочной техники широко развивается как в нашей стране так и за рубежом. Флюс, входящий в состав порошковых проволок позволяет вводить в зону сварки компоненты, улучшающие стабильность горения дуги, улучшающие формирование шва, обеспечивающие минимальные потери металла на угар и разбрызгивание и, позволяет применять различные системы легирования.
Подбор режимов. Стабильность процесса, качество формирования шва и разбрызгивание электродного металла зависят от правильного выбора параметров режима сварки. При правильно подобранных режимах, когда скорость подачи равна скорости плавления, разбрызгивание не превышает 6 -10%.
Для каждого диаметра проволоки имеется диапазон так называемого критического тока, при котором разбрызгивание увеличивается примерно в два раза. Эти режимы применять нерационально.
Импульсно-дуговая сварка. Способ заключается в наложении на дежурную дугу импульсов большого тока. Применяется два основных способа управления переносом металла при импульсно-дуговой сварке плавящимся электродом. В первом случае расплавление конца электрода и формирование на его торце капли необходимого размера происходят во время протекания, так называемого, базового тока. При наложении тока на дугу он только отрывает образовавшуюся ранее каплю от электрода. Во втором случае плавление и отрыв капли осуществляются одним и тем же импульсом тока. Базовый ток в этом случае служит только для поддержания горения дуги в промежутках между импульсами тока и практически не расплавляет проволоку. Само наложение импульсов, представляющих собой управляющие воздействия, существенно стабилизирует процесс сварки, так как компенсирует действие возмущений, вызываемых капельным переносом металла, блужданием активного пятна (особенно при малых токах) вследствие электромагнитных, тепловых и других влияний газовыми потоками в дуге. Однако, наблюдаются колебания основных энергетических параметров процесса: средних значений напряжения на дуге и сварочного тока. Эти изменения происходят при действии на дугу как внешних возмущений (колебания напряжения питающей сети, скорости подачи электродной проволоки из-за несовершенства подающих механизмов, неравномерность движения руки сварщика), так и закономерно возникающие в зоне сварки во время плавления электродной проволоки. В результате могут нарушаться стабильность процесса и геометрические размеры шва.
Это, в конечном счете, ухудшает качество и уменьшает производительность сварки, а также не дает возможности вести процесс во всех пространственных положениях.
Сварка пульсирующей дугой. Сущность процесса заключается в том, что скорость и количество вводимой в изделие энергии определяется не только режимом сварки, но и периодичностью пульсации сварочного тока.
Последний, в свою очередь, задается в зависимости от теплофизических характеристик металла, типа соединения, геометрии и пространственного положения шва. При этом сварочный ток может изменяться от максимальной величины до минимальной или до нуля, а частота пульсации — от десятых долей до нескольких секунд. Это обуславливает следующие преимущества данного способа сварки:
а) возможность реализации на стандартном оборудовании;
б) электрические параметры дуги изменяются плавно по показательной функции, что способствует более рациональной отдаче тепла изделию;
в) плавная пульсация мощности дуги обуславливает плавное изменение ее давления; чем больше объем сварочной ванны, тем медленнее нарастает давление на жидкий металл, что предотвращает выплески его, прожоги, снижает разбрызгивание;
г) благодаря периодическому снижению мощности дуги и кристаллизации в этот период ванны облегчается сварка в различных пространственных положениях;
д) специфические условия структурообразования сварных соединений при сварке пульсирующей дугой обеспечивают высокие пластические свойства сварных соединений.
Но так, же можно выделить следующие недостатки:
1. Процесс сварки пульсирующей дугой протекает с многократными повторами нагревов и охлаждений в интервале температур превращений аустенита, которые усугубляют химическую и структурную неоднородность металла ЗТВ. Усиление неоднородности происходит за счет того, что в условиях многократных охлаждений периодически образуются и растворяются сложные агрегаты, включающие различные структурные составляющие. В общем случае могут образовываться феррит с различной степенью перенасыщения углеродом, карбиды, выделяющиеся как из феррита, так и из аустенита.
2. При сварке с пульсирующей дугой воздействие в основном ориентировано на сварную ванну. Процесс не управляет переносом металла. Снижение разбрызгивания является косвенным следствием.
Сварка плавящимся электродом с принудительными короткими замыканиями. Сущность данного способа заключается в том, что на интервале горения дуги в импульсе происходит интенсивное расплавление торца электрода и свариваемой детали. При этом вследствие силового воздействия дуги металл сварочной ванны вытесняется в хвостовую часть и удерживается там в течении всей стадии плавления. По истечении заданного времени горения дуги в импульсе производят ступенчатое уменьшение сварочного тока до значения тока паузы. Это приводит к соответствующему снижению скорости плавления электрода и ослаблению силового воздействия дуги на сварочную ванну, которая стремится в этот момент заполнить кратер, образовавшийся под торцом электрода на стадии действия импульса тока. Одновременно с этим капля под действием сил тяжести и поверхностного натяжения стремится занять соосное с проволокой положение.
В результате этих встречных взаимонаправленных движений происходит принудительное короткое замыкание, в начальный момент которого в сварочной цепи производят увеличение тока, что позволит значительно повысить скорость нарастания тока короткого замыкания и тем самым ускорить образование и разрушение жидкой перемычки. Причем на протяжении всей стадии короткого замыкания.
К преимуществам данного способа можно отнести:
1. Данный способ реализует управляемый перенос металла, что позволит управлять параметрами определяющими его.
2. Снижение объема сварочной ванны, а, значит, облегчение сварки в различных пространственных положениях.
3. Стабилизируется процесс горения дуги.
4.Снижается перегрев капли, что снижает выгорание элементов из металла. Снижаются сварочные деформации. Ширина зоны разупрочнения снижается в ряде случаев 3.. .4 раза.
К недостаткам можно отнести то, что:
1 Необходимость использования в комплекте сварочного образования специальных сильноточных импульсных регуляторов сварочного тока с малой инерцией.
2 Необходимость использования большого количества обратных связей для управления каплеобразованием.
Имульсно-дуговая сварка с синергетическим управлением параметрами режимов. Выбор оптимальных параметров импульсов тока при сварке с синергетическим управлением базируется на следующих трех основных требованиях:
— для любой скорости подачи электродной проволоки параметры являются целью поддержания постоянной длины дуги;
— базовый ток должен обеспечивать стабильное горение дуги в паузе;
— для заданной скорости подачи электродной проволоки амплитуда, длительность и частота следования импульсов тока, а также значение базового тока автоматически устанавливаются таким образом, чтобы за каждый импульс тока отделялась одна капля электродного материала.
Таким образом, можно сказать, что сущность данного процесса заключается в том, что для любой скорости подачи электродной проволоки параметры импульсов тока, а также значения базового тока и длительность паузы строго соответствуют скорости плавления электрода. При этом обеспечивается мелкокапельный перенос металла по принципу один импульс — одна капля электродного металла.
Применение синергетического управления обеспечивает:
— простоту выбора и переналадки оптимальных параметров режима сварки;
— стабильность горения дуги при изменении скорости подачи проволоки, вылета электрода и напряжения сети;
— облегчение формирования шва во всех пространственных положениях;
— качественную заварку кратера и благоприятное начало шва;
— меньшую чувствительность сварных соединений к термическому разупрочнению металла околошовной зоны;
— возможность использования проволок увеличенного диаметра;
— меньший расход электродной проволоки на единицу длины шва.
К недостаткам импульсно-дуговой сварки с синергетическими системами управления параметрами режимов можно отнести:
— использование относительно низкой погонной энергии;
— необходимость в тщательной зачистке кромок от ржавчины, окалины, масла и краски во избежание образования дефектов сварного соединения;
— более высокая стоимость оборудования и затрат на его эксплуатацию и ремонт.
Импульсная подача сварочной проволоки. Сущность процесса сварки с импульсной подачей сварочной проволоки заключается в программировании скорости подачи электродной проволоки по законам, обеспечивающим контролируемый перенос капли расплавленного электродного металла в жидкую сварочную ванну.
В основу процесса дуговой сварки с импульсной подачей электродной проволоки положено использование дополнительной силы, которая прикладываясь к капле, резко изменяет характер плавления и переноса электродного металла аналогично импульсу электродинамической силы при импульсно — дуговом процессе. В данном случае дополнительной силой выступает сила инерции, действующая в период торможения электрода.
Дозирование переносимого металла происходит за счет установки оптимальных значений шага подачи и частоты следования импульсов.
Данный способ имеет ряд преимуществ по сравнению с постоянной подачей электродной проволоки:
1. Осуществляется управляемый перенос металла;
2. Меньше выгорание элементов из расплавленного металла, за счет уменьшения времени пребывания капли на торце электрода;
3. Снижение разбрызгивания. Происходит за счет совместного действия силы поверхностного натяжения действующей со стороны сварочной ванны и остатков кинетической энергии капли, которая способствует увеличению скорости втягивания капли и одновременно утонению перемычки, вследствие чего при ее взрыве, вместо брызг образуются искры.
Вследствие вышесказанного можно сделать вывод, что наиболее перспективными методами снижения разбрызгивания, в настоящее время, являются методы, обеспечивающие управляемый перенос расплавленного металла, а именно импульсно-дуговые процессы и процесс сварки с импульсной подачей сварочной проволоки.
2.3. Подготовка деталей и режимы сварки в защитных газах
Требования на подготовку деталей под сварку в защитных газах в основном аналогичны, как и для сварки под флюсом.
Основные типы и конструктивные элементы выполняемых дуговой сваркой в защитных газах швов сварных соединений из сталей, а также сплавов на никелевой и железоникелевой основах регламентированы ГОСТ 14771-76, которым предусмотрено четыре типа соединений при сварке металла толщиной от 0,5 до 100 мм и более. В зависимости от формы подготовки кромок и толщины свариваемых деталей швы выполняются в соединениях: с отбортовкой кромок, без скоса кромок, со скосом кромок одной или двух кромок как с одной, так и с двух сторон. По характеру выполнения швов они могут быть одно- и двусторонними. Односторонние швы могут выполняться как на весу, так и на различного рода съемных и остающихся подкладках.
Стандартом установлены следующие обозначения способов сварки в защитных газах: ИН в инертных газах неплавящимся электродом без присадочного материала, ИНП в инертных газах неплавящимся электродом с присадочным металлом, ИП в инертных газах и их смесях с углекислым газом и кислородом плавящимся электродом, УП в углекислом газе и его смеси с кислородом плавящимся электродом.
К основным параметрам сварочных режимов сварки в защитных газах относятся диаметр электрода или электродной проволоки, сварочный ток, напряжение дуги, скорость подачи электродной проволоки, скорость сварки, вылет электрода, расход защитного газа, наклон электрода вдоль оси шва, род тока и полярность.
Диаметр электродной проволоки. Выбирается в пределах 0,53 мм в зависимости от толщины свариваемого металла и положения шва в пространстве. С уменьшением диаметра проволоки при прочих равных условиях повышается устойчивость горения дуги, увеличиваются глубина проплавления и коэффициент наплавки, уменьшается разбрызгивание жидкого металла.
С увеличением диаметра проволоки должна быть увеличена сила тока.
Сварочный ток. С увеличением сварочного тока повышается глубина проплавления. Это приводит к увеличению доли основного металла в шве. Ширина шва сначала несколько увеличивается, а затем уменьшается. Сварочный ток устанавливают в зависимости от диаметра электрода и толщины свариваемого металла.
Напряжение дуги. С увеличением напряжения дуги глубина проплавления уменьшается, а ширина шва увеличивается. Чрезмерное увеличение напряжения дуги сопровождается повышенным разбрызгиванием жидкого металла, ухудшением газовой защиты и образованием пор в наплавленном металле. Напряжение дуги устанавливается в зависимости от выбранного сварочного тока.
Скорость подачи электродной проволоки. Скорость подачи связана со сварочным током. Ее устанавливают с таким расчетом, чтобы в процессе сварки не происходило коротких замыканий и обрывов дуги, а протекал устойчивый процесс плавления электрода.
Скорость сварки. С увеличением скорости сварки уменьшаются все геометрические размеры шва. Она устанавливается в зависимости от толщины свариваемого металла и с учетом обеспечения хорошего формирования шва. Сварку металла большой толщины лучше выполнять более узкими валиками на большей скорости. При слишком большой скорости сварки конец электрода может выйти из зоны защиты и окислиться на воздухе. Медленная скорость сварки вызывает чрезмерное увеличение сварочной ванны и повышает вероятность образования пор в металле шва.
Вылет электрода. С увеличением вылета электрода ухудшаются устойчивость горения дуги и формирование шва, а также увеличивается разбрызгивание жидкого металла. Очень малый вылет затрудняет наблюдение за процессом сварки, вызывает частое подгорание газового сопла и токоподводящего контактного наконечника. Кроме вылета электрода необходимо выдерживать определенное расстояние от сопла горелки до поверхности свариваемого металла, так как с увеличением этого расстояния ухудшается газовая защита зоны сварки и возможно попадание кислорода и азота воздуха в расплавленном металле.
Величину вылета электрода, а также расстояние от сопла горелки до поверхности металла устанавливают в зависимости от выбранного диаметра электродной проволоки. Некоторые значения параметров при сварке в углекислом газе приведены в таблице 2.1:
Таблица 2. 1
Параметры сварки в углекислом газе
Расход защитного газа определяют в основном в зависимости отвыбранного диаметра электродной проволоки и тепловой мощности дуги, зависящей от силы тока. Но на него оказывают также влияние скорость сварки, конфигурация изделия и наличие движения воздуха в цехе, ветра и т.п. Для улучшения газовой защиты в этих случаях приходится увеличивать расход защитного газа, уменьшать скорость сварки, приближать сопло к поверхности металла или пользоваться защитными щитами и другими устройствами.
Наклон электрода вдоль оси шва оказывает влияние на глубину проплавления и качество шва. При сварке углом вперед труднее вести наблюдение за формированием шва, но лучше видны свариваемые кромки и легче управлять электродом. Ширина шва при этом возрастает, а глубина проплавления уменьшается. Сварку углом вперед рекомендуется применять при небольших толщинах металла, когда существует опасность появления сквозных прожогов. При сварке углом назад улучшается видимость зоны сварки, повышается глубина проплавления и наплавленный металл получается более плотным.
2.4. Сварка неплавящимся электродом
Для неплавящихся электродов при сварке в защитных газах могут применяться стержни вольфрама или графита. В основном сварку производят вольфрамовым электродом. Высокая стойкость его наблюдается при использовании защитных газов, не взаимодействующих с вольфрамом. Основным защитным газом является аргон, а процесс называют аргонодуговой сваркой вольфрамовым электродом.
Горение дуги в гелии происходит при более высоком напряжении (в 1,41,7 раза выше, чем в аргоне). Это требует применения для питания дуги специализированных источников с повышенным напряжением холостого хода. Поэтому, учитывая дефицитность гелия, этот процесс применяется гораздо реже. Чаще гелий используют как добавку к аргону. Применение аргоногелиевых смесей целесообразно в тех случаях, когда требуется повысить проплавляющую способность дуги без увеличения сварочного тока. Наряду с инертными газами для сварки вольфрамовым электродом используют и некоторые активные газы, например азот и водород или их смеси с аргоном.
Аргонодуговая сварка вольфрамовым электродом может выполняться с местной или общей защитой, без подачи или с подачей присадочной проволоки, на постоянном или переменном токе.
Большинство металлов сваривают на постоянном токе прямой полярности. Сварку алюминия, магния и бериллия ведут на переменном токе.
При сварке на постоянном токе при прямой полярности обеспечиваются лучшие условия для термоэлектронной эмиссии с электрода, выше его стойкость и допускаемый предел силы тока.
Например, предельная сила тока для вольфрамового электрода диаметром 3 мм ориентировочно составляет при прямой полярности 240280 А, а при обратной лишь 2042 А, при переменном токе промежуточное значение 140160 А. Дуга на прямой полярности легко возбуждается и горит при напряжении 1015 В в широком диапазоне плотностей тока. При обратной полярности возрастает напряжение дуги, уменьшается устойчивость горения, резко снижается стойкость электрода, повышаются его нагрев и расход. Эти особенности дуги обратной полярности делают ее непригодной для непосредственного применения в сварочном процессе. Однако дуга обратной полярности обладает важным технологическим свойством: при ее воздействии на поверхность свариваемого металла происходит удаление поверхностных оксидов. Происходит очистка поверхности металла. Это явление объясняется тем, что при обратной полярности поверхность металла бомбардируется тяжелыми положительными ионами аргона, которые, перемещаясь под действием электрического поля от анода (электрод) к катоду (изделие), разрушают оксидные пленки на поверхности металла, а выходящие с катода (поверхности изделия) электроды способствуют их удалению. Этот процесс удаления поверхностных оксидов получил название процесса катодного распыления (катодной очистки).
Указанное свойство используют при сварке алюминия, магния, бериллия и их сплавов, имеющих на поверхности прочные оксидные пленки. Поскольку же при постоянном токе обратной полярности стойкость вольфрамового электрода низка, то для этой цели используют переменный ток. При этом удаление пленки, т.е. катодная очистка, происходит в полярность сварочного тока, когда свариваемое изделие является катодом. Таким образом, при сварке вольфрамовым электродом на переменном токе в определенной степени реализуются преимущества дуги прямой и обратной полярностей, т.е. обеспечиваются устойчивость электрода и разрушение поверхностных оксидов на изделии.
Аргонодуговая сварка может выполняться вручную или автоматически. На рисунке 2.4 показаны циклограммы процессов для различных вариантов сварки.
а б
Рис. 2.4. Циклограмма процесса сварки в защитном газе:
а неплавящимся вольфрамовым электродом; б плавящимся электродом;
I сварочный ток; Uд напряжение дуги; Vсв скорость сварки; Q расход защитного газа; Vпп подача проволоки; Uосц напряжение осциллятора
Защитный газ подают за 1015с до начала горения дуги. Дуга возбуждается кратковременным разрядом осциллятора или замыканием электрода и основного металла угольным стержнем. Ручную сварку производят наклонной горелкой углом вперед, угол наклона к поверхности изделия составляет 7080º. Присадочную проволоку подают с передней стороны сварочной ванны под углом 1015º к поверхности изделия. По окончании сварки дугу обрывают постепенно подъемом электрода для заварки кратера. Для защиты охлаждающегося металла подачу газа прекращают через 1015 с после выключения тока.
Примерный режим ручной аргонодуговой сварки вольфрамовым электродом стыкового соединения из высоколегированной стали толщиной 3 мм: диаметр вольфрамового электрода 34 мм, диаметр присадочной проволоки 1,62 мм, сварочный ток 120160 А, напряжение дуги 1216 В, расход аргона 67 дм3/мин. Ручную аргонодуговую сварку вольфрамовым электродом применяют главным образом для соединения металла относительно небольшой толщины (до 3 мм), при небольшой протяженности швов, имеющих сложную форму или расположенных в труднодоступных местах. Конструкции, имеющие протяженные швы, изготовляют автоматической сваркой неплавяшимся вольфрамовым электродом с подачей присадочной проволоки, выбранной в зависимости от мощности дуги или диаметра вольфрамового электрода.
dп=(0,5…0,7)×d. (2.1)
При сварке вольфрамовым электродом используют источники питания с крутопадающими вольтамперными характеристиками.
14.5. Разновидности аргонодуговой сварки вольфрамовым электродом
Основным недостатком способов сварки со свободногорящей дугой является их невысокая производительность. Разработано несколько разновидностей сварки вольфрамовым электродом, основанных на увеличении проплавляющей способности дуги за счет увеличения интенсивности теплового и силового воздействия дуги на свариваемый металл. К этим разновидностям относятся сварка погруженной дугой, с применением флюса, при повышенном давлении защитной среды, импульсно-дуговая, плазменная сварка.
Сварка погруженной дугой. С увеличением диаметра электрода и силы тока увеличиваются давление дуги и удельное количество вводимой в металл теплоты. Под давлением дуги происходит оттеснение под электродом жидкого металла. Дуга при этом погружается в сварочную ванну, а поддержание заданного напряжения (длины дуги) достигается опусканием электрода ниже поверхности свариваемого металла. Глубина проплавления достигает 1012 мм и выше, расход аргона составляет 1520 л/мин.
Сварка с применением флюса. Нанесение на поверхность свариваемых кромок слоя флюса небольшой толщины (0,20,5 мм), состоящего из соединений фтора, хлора и некоторых оксидов, способствует повышению сосредоточенности теплового потока в пятне нагрева и увеличению проплавляющей способности дуги. При этом благодаря высокой концентрации тепловой энергии повышается эффективность проплавления и снижается погонная энергия при сварке.
Сварка при повышенном давлении защитной среды. Мощность дуги возрастает с увеличением давления окружающей зону сварки защитной атмосферы при неизменной силе тока и длине дуги. Дуга при этом сжимается, благодаря чему увеличивается еe проплавляющая способность примерно на 2560%. Этот способ может использоваться при сварке в камерах с контролируемой средой, с применением общей защиты.
Импульсно-дуговая сварка вольфрамовым электродом.
Заключается в применении в качестве источника теплоты импульсной дуги с целью концентрации во времени теплового и силового воздействия дуги на основной и электродный металл. При стесненном теплоотводе полнее используется теплота дуги на расплавление основного металла, чем при сварке постоянной дугой. Проплавляющая способность импульсной дуги наиболее эффективно проявляется при сварке тонколистового металла толщиной до 23 мм. Дуга пульсирует с заданным соотношением импульса подачи тока и паузы (рис. 2.5).
а б
Рис. 2.5. Изменение силы тока и напряжения дуги при импульсной аргонодуговой сварке вольфрамовым электродом и формирования шва:
а изменение параметров режима; б формирование шва
Сплошной шов получается расплавлением отдельных точек с определенным перекрытием (рис 14.5, б). Повторные возбуждения и устойчивость дуги обеспечиваются благодаря горению маломощной дежурной дуги (1015 % от силы тока в импульсе). Основной сварочный ток подается в виде отдельных импульсов (рисунок 14.5,а) большой силы. Наряду с силой тока, напряжением, скоростью сварки к основным параметрам импульсно-дуговой сварки относятся длительность импульса tсв и паузы tП длительность цикла сварки:
Т=tCВ+tП, (1.2)
и шаг точек:
S=V(tCB+tП), (1.3)
где VСВ скорость сварки.
Отношение tП/tСВ=G называют жесткостью режим а. Жесткость режима при заданной энергии импульса и длительности цикла характеризует проплавляющую способность дуги. Изменяя параметры режима импульсно-дуговой сварки, можно в широких пределах изменять кристаллизацию металла шва и таким образом влиять на свойства сварных соединений. Технологические преимущества сварки импульсной дугой вольфрамовым электродом в наибольшей степени проявляются при сварке тонкого материала отсутствуют дефекты формирования шва, провисания и подрезы, улучшаются условия формирования шва в различных пространственных положениях, снижаются требования к квалификации сварщика. Так, при сварке металла определенной толщины требуется значительно меньшая погонная энергия, существенно снижаются деформации и прожоги тонколистовых деталей.
Сварка сжатой дугой. Сварка сжатой дугой отличается от обычной дуговой сварки вольфрамовым электродом сжатием дуги в канале сопла горелки потоком плазмообразующего газа. Основные преимущества сжатой дуги более высокая стабильность ее горения и повышенная концентрация энергии в пятне нагрева (10105 Вт/см2).
Сварка сжатой дугой осуществляется переменным или постоянным током прямой полярности. Возбуждают дугу с помощью осциллятора. Для облегчения возбуждения дуги прямого действия используют дежурную дугу, горящую между соплом горелки и электродом. Для питания плазмообразующей дуги требуются источники питания сварочного тока с рабочим напряжением до 126 В и более.
Сжатой дугой можно сваривать практически все металлы в нижнем и вертикальном положениях. В качестве плазмообразующего газа используют аргон и гелий, которые также могут быть и защитными, расход их составляет 0,21,5 л/мин. Плазменная сварка обладает высокой производительностью, малой чувствительностью к колебаниям длины дуги. Без скоса кромок можно сваривать за один проход металл толщиной до 15 мм. Сжатой дугой сваривают стыковые и угловые швы.
Стыковые соединения на металле толщиной до 2 мм можно сваривать с отбортовкой кромок, при толщине деталей свыше 10 мм рекомендуется делать скос кромок. При необходимости можно использовать присадочный металл.
14.6. Сварка в защитных газах плавящимся электродом
Основными разновидностями сварки плавящимся электродом в защитных газах являются аргонодуговая сварка и сварка в углекислом газе.
Сварка в защитных газах плавящимся электродом имеет ряд особенностей. Так, устойчивое горение дуги обеспечивается при высокой плотности тока в электроде (100 А/мм2 и выше) при возрастающей вольтамперной статической характеристике.
Стабильность параметров сварного шва (глубина проплавления и ширина) зависит от постоянства длины дуги, которая обеспечивается за счет процесса саморегулирования дуги при постоянной скорости подачи электродной проволоки. При этом соблюдается условие равенства скорости плавления электрода и его подачи. Так как процесс ведется на режимах с высокими плотностями сварочного тока, то обычно применяют электродную проволоку небольшого диаметра (d ≈ 0,8…2,5 мм), с большими скоростями ее подачи. В этих условиях процесс саморегулирования не может обеспечиваться при использовании источников питания с падающими характеристиками.
Поэтому применяют источники питания с жесткой или возрастающей вольтамперной характеристикой. Сварку обычно ведут на постоянном токе обратной полярности. При прямой полярности скорость расплавления в 1,41,6 раза выше, чем при обратной, однако дуга горит менее стабильно с интенсивным разбрызгиванием.
К основным параметрам сварочного режима относятся сила тока, напряжение дуги, скорость сварки, диаметр и скорость подачи электродной проволоки, расход защитных газов. Сварочный ток зависит от диаметра и состава электрода, его устанавливают в соответствии со скоростью подачи электродной проволоки. Скорость сварки обычно 1580 м/ч, ее выбирают с учетом производительности и качества формирования шва. Выбор параметров режима обычно производят по экспериментальным табличным данным. Для улучшения формирования шва сварку проводят на медной подкладке с формирующей канавкой или на остающейся подкладке из основного металла. Для сварки тонколистового металла используют проволоку диаметром 0,51,2 мм.
Металл толщиной до 4 мм сваривают без разделки кромок. При сварке с двух сторон можно сваривать без разделки кромок металл толщиной до 12 мм. При больших толщинах применяют разделку кромок.
Аргонодуговая сварка плавящимся электродом в основном применяется для сварки цветных металлов (алюминий, магний, медь, титан и их сплавы) и легированных сталей. Сварка производится на режимах с мелкокапельным и струйным переносом электродного металла. При струйном переносе глубина проплавления увеличивается.
Критическое значение сварочного тока, при котором капельный перенос сменяется струйным, для каждого металла различно и зависит от диаметра проволоки. Так, при сварке сталей это происходит при плотности тока от 60 до 120 А на 1 мм2 сечения электрода, при сварке алюминия 70 А. Например, для электродной проволоки из стали марки Св-12Х18Н9Т для разных диаметров при горении дуги в среде аргона критический ток имеет следующие значения:
При сварке сталей в качестве защитного газа в основном используют аргон с добавками углекислого газа или кислорода (15% по объему). Введение активных газов стабилизирует горение дуги, снижает разбрызгивание. Наряду с этим окислительная среда повышает стойкость швов против водородной пористости.
При импульсном питании дуги сварочным током появляется дополнительная возможность управления процессом плавления и переноса электродного металла. В этом случае используют тот же принцип питания дуги, что и при сварке вольфрамовым электродом при импульсно-дуговой сварке. От источника небольшой мощности питается дуга, формирующая каплю жидкого металла на электроде, которая сбрасывается в момент подачи импульса тока большого значения. За счет возникающих электродинамических сил капле придается строгая направленность перемещения в сварочную ванну, чем предотвращается разбрызгивание и обеспечивается возможность сварки швов в различных пространственных положениях.
При аргонодуговой сварке плавящимся электродом предъявляются более жесткие требования к качеству сборки деталей, чем при сварке вольфрамовым электродом. Перед сваркой необходима тщательная очистка кромок свариваемых деталей и электродной проволоки.
Сварка плавящимся электродом в углекислом газе. Этим способом можно сваривать большинство сталей, удовлетворительно сваривающихся другими видами сварки. В первую очередь сваривают углеродистые и низколегированные стали толщиной более 3 мм проволокой диаметром 0,82 мм. Некоторое применение этот способ находит при сварке конструкций из высоколегированных сталей.
Наряду с другими преимуществами, характерными для сварки в защитных газах, сварка в углекислом газе характеризуется высокой производительностью и низкой стоимостью. Процесс экономичен, защитный газ не дефицитен, обеспечивает достаточно высокое качество металла швов. Механизированная сварка в углекислом газе, как более производительный процесс, успешно конкурирует с ручной дуговой сваркой покрытыми электродами по своей универсальности. К недостаткам ее следует отнести повышенное разбрызгивание и более грубое формирование швов.
При сварке в углекислом газе происходит окисление металла и потеря легирующих элементов. Поэтому основной особенностью этого способа является необходимость применения электродных проволок с повышенным содержанием элементов раскислителей (кремния, марганца), компенсирующих их выгорание в зоне сварки, предотвращающих окисление металла в ванне и образование пор. Для углеродистых сталей в основном используют сварочные проволоки сплошного сечения СВ-10ГС, Св-08Г2С, а также порошковые проволоки, содержащие в наполнителе порошки ферросплавов кремния и марганца.
Автоматическая и механизированная сварка в углекислом газе ведется на постоянном токе обратной полярности. Устойчивый процесс обеспечивается при высоких плотностях тока, поэтому используют проволоки малых диаметров 0,82,5 мм, а питание дуги производят от источников с жесткой внешней характеристикой. При сварке в углекислом газе, даже на высоких плотностях сварочного тока, практически не удается добиться струйного переноса металла электрода. Сварочный ток устанавливают и определяют скоростью подачи проволоки. Напряжение дуги должно быть не больше 3234 В, так как с увеличением напряжения и длины дуги увеличивается разбрызгивание и окисление. Обычно UД=20…30 В скорость сварки от 20 до 80 м/ч, расход газа 625 л/мин. Например, при механизированной сварке низкоуглеродистой стали толщиной 8 мм сварку можно выполнять проволокой диаметром 2 мм, на силе тока 260280 А, при напряжении 2830 В, расходе газа 1620 л/мин за один проход без разделки кромок. Наряду с СО2 также используют защитные смеси газов СО2+Аr, СО2+О2 и др. При этом улучшается капельный перенос, уменьшается разбрызгивание, улучшается формирование швов.
2.7. Сварка с импульсной подачей электродной проволокой в смеси защитных газов
Одним из способов осуществления управляемого переноса электродного металла, является использование устройства с импульсной подачей сварочной проволоки.
В основу процесса дуговой сварки с импульсной подачей сварочной проволоки, положено использование дополнительной силы (силы инерции, действующей в период торможения электрода), которая прикладываясь к капле, резко изменяет характер плавления и переноса электродного металла аналогично импульсу электродинамической силы при импульсно — дуговом процессе.
Одним из путей повышения эффективности применения сварки с импульсной подачей сварочной проволоки является использование смеси (Ar+CO2). Это позволит обеспечить лучшее формирование шва и меньшую величину разбрызгивания электродного металла, чем при сварке в чистом углекислом газе.
Наименьшая величина разбрызгивания (ψразб.) достигается при содержании Ar(70%±3%)+СО2(30%±3%). При величине тока в пределах от 100А до 140А осуществляется управляемый перенос. С увеличением сварочного тока свыше 140А для указанного механизма, перенос неуправляемый.
Рис. 2.6. График зависимости величины разбрызгивания (ψразб.) от величины сварочного тока.
Процесс сварки с импульсной подачей электродной проволоки в смеси газов протекает в четыре этапа:
— этап формирования капли (рис. 2.7): происходит формирование капли за счет плавления электродной проволоки.
Рис. 14.7. Этап формирования капли
— этап движения электродной проволоки (рис. 2.8): под действием упругих сил за счет использования механизма импульсной подачи, происходит перемещение электродной проволоки с находящейся на ее торце жидкой каплей в направлении металлической ванны.
18 19 20
Рис. 2.8. Этап движения электродной проволоки — этап торможения капли: происходит торможение подачи сварочной проволоки в результате достижения штоком конца угла опускания. При этом, в силу определенной инерционности жидкого металла, капля, находящаяся на торце электрода продолжает движение (рис. 2.9).
Рис. 2.9. Этап торможения капли — этап короткого замыкания: происходит cоприкосновение жидкой капли, находящейся на торце электрода и металлической ванны, образование перемычки и переход металла капли в сварочную ванну (рис. 2.10).
Рис.2.10. Этап короткого замыкания, утончения и разрыва перемычки
Синхронизированный график скорости подачи электродной проволоки представлен на рисунке 2.11.
Рис. 2.11. График скорости подачи электродной проволоки:
1 — этап формирования капли; 2 — этап движения электродной проволоки; 3 этап торможения капли; 4 — этап короткого замыкания.
Во время первых трех этапов дуговой промежуток большую часть времени горит при токе меньше действующего значения.
И только во время короткого замыкания ток повышается до максимального значения. Так как время короткого замыкания и перехода капли электродного металла в сварочную ванну меньше других этапов каплепереноса, то соответственно и время действия максимального тока значительно меньше.
В связи с этим при рассмотрении процессов сварки с постоянной и импульсной подачей даже при одинаковой производительности процесса тепловложения в основной металл будет различным (рис. 2.12, а,б).
Для достижения одинаковых значений геометрических размеров шва необходимо уменьшить значение энергетических параметров для сварки с импульсной подачей электродной проволоки в СО2 на 20-30% по сравнению с постоянной подачей в СО2. В свою очередь для сварки в смеси газов значение величины тока и напряжения необходимо уменьшить на 10-15 %.
Газовая среда в свою очередь влияет на значение эффективного КПД нагрева изделия сварочной дуги:
— для дуговой сварки и наплавки в углекислом газе, 0,72-0,92;
— для дуговой сварки и наплавки в аргоне, 0,7-0,8.
Изменение эффективного КПД нагрева изделия сварочной дуги влечет за собой изменение эффективной тепловой мощности сварочной дуги (рис. 2.12, б,в).
а б
в
Рис. 2.12 Температурные поля: а) сварка с постоянной подачей
сварочной проволоки в среде защитных газов СО2; б) сварка с импульсной подачейсварочной проволоки в среде защитных газов СО2; в) сварка с импульсной подачей сварочной проволоки в среде защитных газов 70%Ar+30%СО2
Также при сварке с импульсной подачей электродной проволоки с использованием инертных газов имеют место процессы окисления, азотирования, наводороживания, а также растворения газов и вредных примесей в сварочной ванне. Это связано с несовершенством газовой защитной зоны сварки и проникновением в нее атмосферного воздуха.
Кроме того, неизбежное присутствие даже небольших концентраций вредных примесей в инертных газах, наличие окисленных поверхностных слоев на кромках металла и сварочной проволоки способствуют образованию оксидов, нитридов и других веществ, заметно ухудшающих физико-механические свойства сварных соединений. В свою очередь кремний, растворяясь в феррите. Повышает предел текучести и уменьшает склонность к хладноломкости, марганец же образует твердый раствор с железом и немного повышает твердость и прочность.
Как видно из гистограмм (рис. 14.13 а,б,в) содержание легирующих элементов (марганца и кремния), с повышением величины тока, превышает содержание относительно основного металла на 40-60% для всех способов сварки. Это объясняется тем, что при сварке, элементы Mn и Si, участвующие в раскисление, при их достаточной концентрации в электродном металле, также частично усваиваются, переходя в сварной шов. Однако стоит отметить, что только при использовании сварки с ИПЭП в смеси газов химический состав сварного шва одинаков на всем диапазоне токов.
Так же при сварке с ИПЭП происходит меньшее выгорание Mn и Si относительно сварки с постоянной подачей на 10-20%, что приводит к повышению механических свойств из-за меньшего тепловложения в каплю электродного металла. Это объясняется тем, что эффективная тепловая мощность сварочной дуги различна, как из режимов сварки (силы тока и напряжения), так и из-за значения эффективного нагрева изделий.
При использовании сварки с ИПЭП в смеси газов позволяет предотвратить выгорание углерода, что позволяет сделать вывод о том, что металл шва и основной металл схожи по твердости и пластичности (равнопрочное сварное соединение).
Содержание хрома в свою очередь для всех способ сварки относительно основного металла снижается на 30-40%.
Рисунок 2.13 Содержание химических элементов в сварном шве: а)I=100A; б) а)I=120A; в)I=140A;
ВОПРОСЫ
1. Каковы особенности и способы защиты металла с использованием защитных газов?
2. Расскажите о подготовке деталей и выборе технологических параметров режима, определяющих условия сварки в защитных газах.
3. Охарактеризуйте особенности технологии сварки вольфрамовым электродом в защитных газах.
4. Какие существуют разновидности сварки вольфрамовым электродом в защитном газе? Их особенности.
5. Расскажите об особенностях процесса и технологии сварки плавящимся электродом в среде аргона.
6. Расскажите об особенностях процесса и технологии сварки плавящимся электродом в углекислом газе.
7. При аргонодуговой сварке на постоянном токе плавящимся электродом для тонких деталей какую полярность лучше использовать?
PAGE 15
Урок 2 — Общие процессы электродуговой сварки
Урок 2 — Общие процессы электродуговой сварки © АВТОРСКОЕ ПРАВО 1998 ГРУППА ESAB, INC.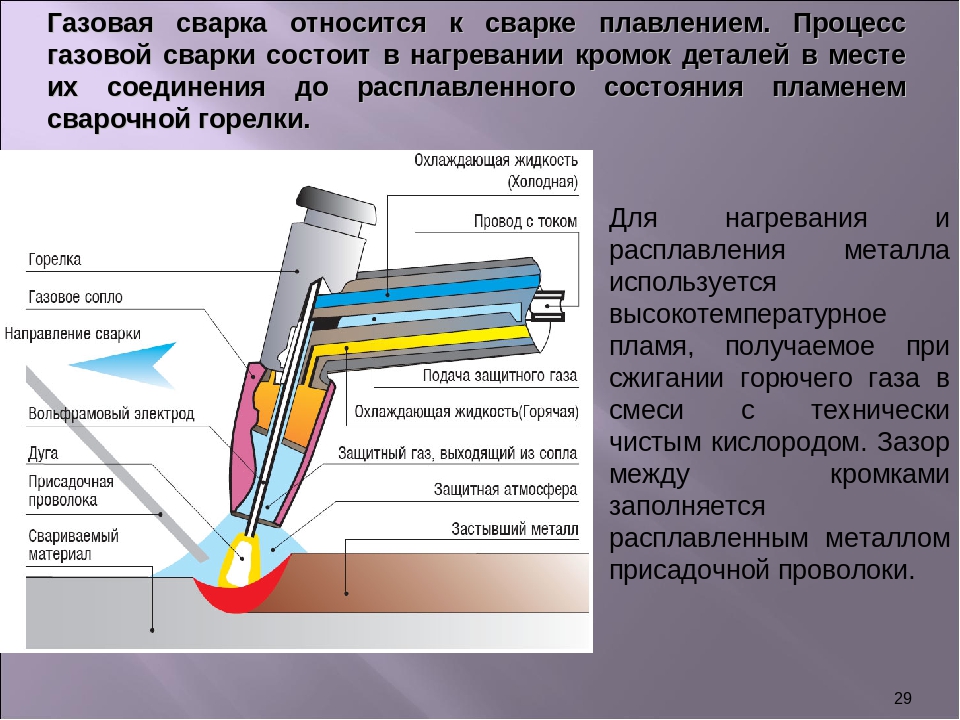
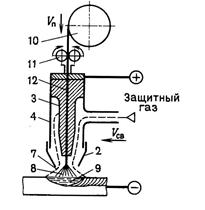
Сварка | Металлургия для чайников
Сварка — это производственный или скульптурный процесс, который соединяет материалы, обычно металлы или термопласты, вызывая коалесценцию. Это часто делается путем расплавления заготовок и добавления присадочного материала для формирования ванны расплавленного материала (сварочная ванна), которая охлаждается и становится прочным соединением, при этом давление иногда используется в сочетании с теплом или само по себе для создания сварного шва. .
Сварочная обработка
Это отличается от пайки и пайки, которые включают плавление материала с более низкой температурой плавления между заготовками для образования связи между ними без плавления заготовок.
Сварка, технология, используемая для соединения металлических деталей, обычно с применением тепла.Этот метод был открыт во время попыток придать железу полезную форму. Сварные клинки были разработаны в первом тысячелетии нашей эры, самые известные из них производились арабскими оружейниками в Дамаске, Сирия. В то время был известен процесс науглероживания железа для производства твердой стали, но полученная сталь была очень хрупкой. Техника сварки, которая включала прослойку относительно мягкого и прочного железа с высокоуглеродистым материалом с последующей ковкой в молоте, позволила получить прочное и прочное лезвие.
Сварка, технология, используемая для соединения металлических деталей, обычно с применением тепла.
Для сварки можно использовать множество различных источников энергии, включая газовое пламя, электрическую дугу, лазер, электронный луч, трение и ультразвук. Хотя сварка часто является промышленным процессом, сварка может выполняться во многих различных средах, включая открытый воздух, под водой и в открытом космосе. Сварка является потенциально опасным мероприятием, и необходимо соблюдать меры предосторожности, чтобы избежать ожогов, поражения электрическим током, повреждения зрения, вдыхания ядовитых газов и паров, а также воздействия интенсивного ультрафиолетового излучения.
Сварка под водой
Сварной шов можно определить как слияние металлов, полученное путем нагревания до подходящей температуры с приложением давления или без него, а также с использованием или без использования присадочного материала. При сварке плавлением источник тепла выделяет достаточное количество тепла для создания и поддержания ванну расплавленного металла необходимого размера. Тепло может подаваться электричеством или газовым пламенем. Сварку электрическим сопротивлением можно рассматривать как сварку плавлением, потому что образуется некоторое количество расплавленного металла.Твердофазные процессы производят сварные швы без плавления основного материала и без добавления присадочного металла. Всегда используется давление, и обычно обеспечивается некоторое количество тепла. Теплота трения выделяется при ультразвуковом соединении и соединении трением, а нагрев в печи обычно используется при диффузионном соединении.
Лазерная сварка
До конца 19 века единственным сварочным процессом была кузнечная сварка, которую кузнецы веками использовали для соединения железа и стали путем нагревания и ковки.Дуговая сварка и кислородно-кислородная сварка были одними из первых процессов, разработанных в конце века, а вскоре за ними последовала сварка электрическим сопротивлением. Сварочные технологии быстро развивались в начале 20 века, поскольку Первая и Вторая мировые войны вызвали спрос на надежные и недорогие методы соединения. После войн было разработано несколько современных методов сварки, в том числе ручные методы, такие как дуговая сварка защищенным металлом, которая в настоящее время является одним из самых популярных методов сварки, а также полуавтоматические и автоматические процессы, такие как дуговая сварка металлическим газом, дуговая сварка под флюсом, сварка под флюсом. дуговая и электрошлаковая сварка.
Лазерная сварка
Развитие продолжилось изобретением лазерной сварки, электронно-лучевой сварки, электромагнитной импульсной сварки и сварки трением с перемешиванием во второй половине века. Сегодня наука продолжает развиваться. Роботизированная сварка является обычным явлением в промышленных условиях, и исследователи продолжают разрабатывать новые методы сварки и лучше понимать качество и свойства сварки.
Дуговая сварка
Дуговая сварка — это тип сварки, при котором используется сварочный источник питания для создания электрической дуги между электродом и основным материалом для расплавления металлов в точке сварки. Они могут использовать как постоянный (DC), так и переменный (AC) ток, а также плавящиеся или неплавящиеся электроды.
Дуговая сварка
Зона сварки иногда защищается каким-либо инертным или полуинертным газом, известным как защитный газ, и/или испаряющимся присадочным материалом. Процесс дуговой сварки широко используется из-за его низких капитальных и эксплуатационных затрат. Зажигание дуги называется зажиганием дуги. Дуга может загореться либо легким постукиванием электрода по металлу, либо царапанием электрода по металлу на высокой скорости.
СМАВ
Одним из наиболее распространенных видов дуговой сварки является дуговая сварка в среде защитного газа (SMAW), она также известна как ручная дуговая сварка металлическим электродом (MMA) или сварка электродом. Электрический ток используется для зажигания дуги между основным материалом и расходуемым стержнем электрода, который изготовлен из стали и покрыт флюсом, который защищает зону сварки от окисления и загрязнения за счет выделения углекислого газа (CO2) в процессе сварки. Сердечник электрода сам по себе действует как наполнитель, что делает ненужным отдельный наполнитель.
Сварка ВИГ
Газовая вольфрамовая дуговая сварка (GTAW) часто упоминается как сварка TIG. Сварка TIG является широко используемым процессом высококачественной сварки. Сварка TIG стала популярным выбором сварочных процессов, когда требуется высококачественная и точная сварка. При сварке TIG дуга образуется между неплавящимся вольфрамовым электродом и свариваемым металлом. Газ подается через горелку для защиты электрода и расплавленной сварочной ванны. Если используется присадочная проволока, она добавляется в сварочную ванну отдельно.
Сварка ВИГ
Сварка МИГ
Дуговая сварка металлическим электродом в среде защитного газа (GMAW), также известная как сварка в среде инертного газа или сварка MIG, представляет собой полуавтоматический или автоматический процесс, в котором в качестве электрода используется непрерывная подача проволоки и смесь инертных или полуинертных газов для защиты сварного шва от загрязнение. Поскольку электрод сплошной, скорость сварки GMAW выше, чем для SMAW.
Сварка МИГ
Дуговая сварка металлическим газом (GMAW) часто упоминается как сварка MIG.Сварка MIG является широко используемым процессом сварки с высокой скоростью наплавки. Проволока непрерывно подается с катушки. Поэтому сварку MIG называют полуавтоматической сваркой.
Сварка порошковой проволокой
Родственный процесс, дуговая сварка с флюсовой проволокой (FCAW), использует аналогичное оборудование, но использует проволоку, состоящую из стального электрода, окружающего порошковый наполнитель. Эта порошковая проволока дороже, чем стандартная сплошная проволока, и может образовывать дым и/или шлак, но она обеспечивает еще более высокую скорость сварки и большее проникновение металла.
Дуговая сварка под флюсом
Дуговая сварка под флюсом (SAW) — это высокопроизводительный метод сварки, при котором дуга зажигается под покрывающим слоем флюса. Это повышает качество дуги, поскольку загрязняющие вещества в атмосфере блокируются флюсом. Шлак, образующийся на сварном шве, обычно отделяется сам по себе, а в сочетании с использованием непрерывной подачи проволоки скорость наплавки высока.
Условия работы значительно улучшены по сравнению с другими процессами дуговой сварки, поскольку флюс скрывает дугу и почти не образуется дым.Этот процесс широко используется в промышленности, особенно для крупногабаритных изделий и при производстве сварных сосудов под давлением. Другие процессы дуговой сварки включают сварку атомарным водородом, электрошлаковую сварку, электрогазовую сварку и дуговую сварку.
Газовая сварка
Наиболее распространенным процессом газовой сварки является кислородно-кислородная сварка, также известная как кислородно-ацетиленовая сварка. Это один из старейших и наиболее универсальных сварочных процессов, но в последние годы он стал менее популярным в промышленности.Он до сих пор широко используется для сварки труб и труб, а также ремонтных работ.
Аппарат для газовой сварки
Это относительно недорогое и простое оборудование, обычно использующее сжигание ацетилена в кислороде для получения температуры сварочного пламени около 3100 °C. Пламя, поскольку оно менее концентрировано, чем электрическая дуга, вызывает более медленное охлаждение сварного шва, что может привести к большим остаточным напряжениям и искривлению сварного шва, хотя и облегчает сварку высоколегированных сталей.Аналогичный процесс, обычно называемый газокислородной резкой, используется для резки металлов.
Сварка сопротивлением
Точечная сварка сопротивлением (RSW), шовная сварка сопротивлением (RSEW) и сварка с выступом (PW) являются широко используемыми процессами контактной сварки. Сварка сопротивлением использует приложение электрического тока и механического давления для создания сварного шва между двумя кусками металла. Сварочные электроды проводят электрический ток к двум кускам металла, когда они соединяются вместе.
Схема точечной сварки
Сварка сопротивлением включает выделение тепла за счет пропускания тока через сопротивление, вызванное контактом между двумя или более металлическими поверхностями.Небольшие лужицы расплавленного металла образуются в зоне сварки при пропускании через металл высокого тока (1000–100 000 А). В целом, методы контактной сварки эффективны и не загрязняют окружающую среду, но их применение несколько ограничено, а стоимость оборудования может быть высокой.
Аппарат для точечной сварки
В цикле сварки сначала должно выделяться достаточное количество тепла, чтобы перевести небольшой объем металла в расплавленное состояние. Затем этот металл охлаждается под давлением до тех пор, пока он не обретет достаточную прочность, чтобы удерживать детали вместе.Плотность тока и давление должны быть достаточными для образования очага сварки, но не настолько высокими, чтобы вытеснить расплавленный металл из зоны сварки.
Электронно-лучевая сварка
Электронно-лучевая сварка (ЭЛС) — это процесс соединения плавлением, при котором сварной шов создается за счет воздействия пучка электронов высокой энергии для нагрева сварного соединения. Электроны — элементарные атомарные частицы, характеризующиеся отрицательным зарядом и чрезвычайно малой массой. Поднятие электронов до высокоэнергетического состояния путем их ускорения примерно до 30–70 процентов скорости света обеспечивает энергию для нагрева сварного шва.
Электронно-лучевая сварка «Вспышка»
ЭЛС-пистолет работает аналогично телевизионному кинескопу. Основное отличие состоит в том, что кинескоп телевизора непрерывно сканирует поверхность люминесцентного экрана, используя электронный луч низкой интенсивности для создания изображения. Пистолет EBW использует электронный луч высокой интенсивности для нацеливания на сварной шов. Сварной шов преобразует электронный пучок в тепло, необходимое для сварки плавлением.
Роботизированная сварка
Существует два популярных типа промышленных сварочных роботов.Это роботы с артикуляцией и прямолинейные роботы. Робототехника управляет движением вращающегося запястья в пространстве. Прямолинейные роботы движутся в линию по любой из трех осей (X, Y, Z). В дополнение к линейному движению робота вдоль осей к роботу прикреплено запястье, обеспечивающее вращательное движение.
Роботизированная сварка
Создает роботизированную рабочую зону коробчатой формы. Шарнирные роботы используют руки и вращающиеся суставы. Эти роботы двигаются как человеческая рука с вращающимся запястьем на конце.Это создает роботизированную рабочую зону неправильной формы.
Пайка и пайка
Пайка и пайка — это процессы соединения, при которых детали соединяются без расплавления основных металлов. Припойные металлы плавятся при температуре ниже 840 °F. Твердые присадочные металлы плавятся при температуре выше 840 °F.
Пайка
Пайка обычно используется для электрических соединений или механических соединений, но пайка используется только для механических соединений из-за высоких температур.
Вам также может понравиться
Случайные сообщения
- Анализ сбоев
Анализ сбоев — это процесс сбора и анализа данных для определения причины сбоя.…
- Алюминиевый сплав
Алюминий – универсальный металл, который можно отливать в любой известной форме. Его можно катать, штамповать, волочить, вращать, формовать в рулонах… - Характеристика материалов
Характеристика, когда она используется в материаловедении, относится к использованию внешних методов для исследования внутренней ул… - Гальваника
Гальванизация, процесс покрытия металлического предмета тонким слоем другого металла посредством электролиза. Э… - Фазовые диаграммы Fe-Mn, Fe-Co, Fe-Mo
В чистом железе превращения A4 (1394 °C) и A3 (912 °C) происходят при постоянных температурах. Если элемент входит…
Сварка Basic | Металлургия для чайников
Краткое описание процесса сварки
Сварка — это процесс соединения, при котором соединение может быть достигнуто с использованием высоких температур, высокого давления или того и другого. В этой лекции обсуждается только использование высоких температур для изготовления соединения, поскольку это, безусловно, самый распространенный метод сварки конструкционных сталей.
Сварка
По сути, это процесс, при котором интенсивный источник тепла воздействует на соединяемые поверхности для достижения локального плавления. Обычно в расплавленную сварочную ванну добавляют дополнительный «присадочный металл», чтобы перекрыть зазор между поверхностями и получить требуемую форму и размеры сварного шва при охлаждении.В наиболее распространенных процессах сварки стальных конструкций используется электрическая дуга, поддерживаемая между стержнем присадочного металла и заготовкой, чтобы обеспечить интенсивный источник тепла.
При отсутствии защиты расплавленный металл в сварочной ванне может легко поглощать кислород и азот из атмосферы. Это поглощение может привести к пористости и хрупкости затвердевшего металла сварного шва. Методы, используемые для предотвращения поглощения газа в сварочной ванне, различаются в зависимости от процесса сварки. Ниже более подробно рассмотрены основные процессы сварки, применяемые для соединения конструкционных сталей.
Основные сварочные процессы
а. Ручная дуговая сварка металлическим электродом (MMA)
В этом процессе сварщик использует металлический стержневой электрод с плавким минеральным покрытием в держателе, подключенном к источнику электропитания. Между электродом и зоной сварки зажигается дуга, которая замыкает цепь возврата к источнику электроэнергии. Дуга плавит как электрод, так и область поверхности заготовки. Электромагнитные силы, создаваемые в дуге, помогают выбрасывать капли расплавленного электрода на расплавленную область заготовки, где два металла сплавляются, образуя сварочную ванну.
Покрытие электрода из флюса вносит свой вклад в содержание сварочной ванны за счет прямого добавления металла и металлургических реакций, которые очищают расплавленный металл. Флюс также создает локальную газообразную атмосферу, которая предотвращает поглощение атмосферных газов металлом сварного шва.
Существует много типов электродов. Основные отличия между ними заключаются во флюсовом покрытии. Три основных класса электродов показаны ниже:
1. Рутил: электроды общего назначения для применений, не требующих строгого контроля механических свойств.Эти электроды содержат большое количество оксида титана в флюсовом покрытии.
2. Основной: Эти электроды обеспечивают сварку с большей прочностью и ударной вязкостью, чем рутиловые. Электроды имеют покрытие, содержащее карбонат кальция и другие карбонаты и плавиковый шпат.
3. Целлюлозный: дуга, создаваемая этим типом электрода, очень проникающая. Эти электроды имеют высокую долю горючих органических материалов в своем покрытии.
б. Дуговая сварка под флюсом (SAW)
В этом процессе используется электрод из неизолированной проволоки и флюс, добавляемый отдельно в виде гранул или порошка поверх дуги и сварочной ванны.Флюс защищает расплавленный металл, образуя слой шлака, а также стабилизирует дугу. Этот процесс используется в основном в механической системе, подающей непрерывный отрезок проволоки из катушки, в то время как сварочный провод перемещается вдоль соединения. Машина SAW может подавать несколько проволок, одну за другой, так что может быть выполнен многопроходный сварной шов. Дуговая сварка под флюсом обеспечивает более прочные соединения, чем ручная сварка, но она не подходит для труднодоступных мест.
в. Сварка в среде защитных газов
В этом процессе используется электрод из неизолированной проволоки, а вокруг дуги и сварочной ванны подается защитный газ.Этот газ предотвращает загрязнение электрода и сварочной ванны воздухом. Существует три основных варианта этого процесса, как показано ниже:
1. Сварка MIG (металл-инертный газ) — в качестве защиты используется аргон или гелий. Этот процесс обычно используется для цветных металлов.
2. Сварка MAG (металл-активный газ) — двуокись углерода (обычно в смеси с аргоном) используется для защиты. Этот процесс обычно используется для углеродистых и углеродисто-марганцевых сталей.
3. TIG (вольфрамовый инертный газ) – аргон или гелий используется для защиты и зажигания дуги между заготовкой и неплавящимся вольфрамовым электродом.Этот процесс обычно используется для тонколистовой обработки и точной сварки.
Проектирование и подготовка сварных соединений
Существует два основных типа сварных соединений, известных как стыковые и угловые швы. Схематические изображения этих двух типов сварных швов показаны на рис. 1. Фактическая форма сварного шва определяется подготовкой соединяемой области. Тип подготовки под сварку зависит от процесса сварки и технологии изготовления.
Примеры различных видов подготовки под сварку показаны на рис. 2.Сварной шов должен быть расположен и сформирован таким образом, чтобы он был легко доступен с точки зрения как процесса сварки, так и положения сварки. Детализированная форма сварного шва спроектирована таким образом, чтобы адекватно распределять имеющееся тепло и помогать контролировать проникновение металла сварного шва и, таким образом, создавать прочное соединение. Трудно избежать дефектов, вызванных оператором, таких как непровар и непровар, если подготовка и конструкция шва препятствуют хорошему доступу для сварки.
Влияние термического цикла сварки на микроструктуру
Интенсивное выделение тепла в процессе сварки влияет на микроструктуру как металла шва, так и основного металла вблизи границы плавления (граница между твердым и жидким металлом).Таким образом, цикл сварки влияет на механические свойства соединения.
Расплавленная сварочная ванна быстро охлаждается, так как соединяемые металлы действуют как эффективный теплоотвод. Это охлаждение приводит к тому, что металл шва имеет микроструктуру кокильного литья. При сварке конструкционных сталей присадочный металл обычно не имеет того же состава, что и основной металл. Если бы составы были одинаковыми, быстрое охлаждение могло бы привести к образованию твердых и хрупких фаз, т.е. мартенсита, в микроструктуре металла шва.Этой проблемы можно избежать, используя присадочные металлы с более низким содержанием углерода, чем основная сталь.
Основной металл вблизи расплавленной сварочной ванны быстро нагревается до температуры, зависящей от расстояния до границы сплавления. Близко к границе плавления достигаются пиковые температуры вблизи точки плавления, в то время как материал, находящийся всего в нескольких миллиметрах от него, может достигать лишь нескольких сотен градусов по Цельсию. Исходный материал вблизи границы плавления нагревается в поле аустенитной фазы.При охлаждении эта область трансформируется в микроструктуру, отличную от остального исходного материала. В этой области скорость охлаждения обычно высока, и, следовательно, существует тенденция к образованию структур низкотемпературного превращения, таких как бейнит и мартенсит, которые более твердые и более хрупкие, чем основная масса основного металла. Эта область известна как зона термического влияния (ЗТВ).
На микроструктуру ЗТВ влияют три фактора:
- Химический состав основного металла.
- Скорость подвода тепла при сварке.
- Скорость охлаждения в ЗТВ после сварки.
Химический состав основного металла важен, поскольку он определяет прокаливаемость ЗТВ. Скорость подвода тепла имеет большое значение, поскольку она напрямую влияет на размер зерна в ЗТВ. Чем дольше время нахождения выше температуры укрупнения зерна основного металла при сварке, тем грубее структура в ЗТВ. Как правило, высокая скорость подвода тепла приводит к более длительному термическому циклу и, следовательно, к более грубой микроструктуре ЗТВ.
Следует отметить, что скорость тепловложения также влияет на скорость охлаждения в ЗТВ. Как правило, чем выше скорость подвода тепла, тем ниже скорость охлаждения. Величина подводимого тепла зависит от параметров процесса сварки: напряжения дуги, тока дуги и скорости сварки. Помимо скорости подводимого тепла, на скорость охлаждения в ЗТВ влияют еще два фактора. Во-первых, важны конструкция и толщина шва, поскольку они определяют скорость отвода тепла от сварного шва во время охлаждения. Во-вторых, температура соединяемых деталей, т. е. любой предварительный нагрев, имеет большое значение, поскольку определяет температурный градиент, существующий между сварным швом и основным металлом.
Остаточные сварочные напряжения и деформация
Интенсивное тепло, связанное со сваркой, вызывает расширение зоны сварки. При охлаждении происходит сокращение. Окружающий холодный материал сопротивляется этому расширению и последующему сжатию, что приводит к возникновению поля остаточных напряжений вблизи сварного шва.В металле сварного шва остаточное напряжение носит преимущественно растягивающий характер. Это остаточное растягивающее напряжение уравновешивается сжимающим напряжением, возникающим в основном металле.
Схематическое изображение поля остаточных напряжений, полученное для продольной усадки сварного шва, показано на рис. 3. Растягивающие остаточные напряжения имеют величину до предела текучести в металле шва и ЗТВ. Важно отметить, что остаточные напряжения возникают из-за локальных пластических деформаций материала. Эта деформация может привести к растрескиванию металла шва и ЗТВ при сварке, деформации соединяемых деталей или способствовать хрупкому разрушению в процессе эксплуатации.
Поперечные и продольные сжатия в результате сварки могут привести к деформации, если горячий металл сварного шва не является симметричным относительно нейтральной оси изготовления. Типичный угловой поворот в одинарном V-образном стыковом шве показан на рис. 4а. Вращение происходит из-за того, что большая часть сварного шва находится на одной стороне нейтральной оси пластины, что вызывает большее сжимающее напряжение на этой стороне.
Это приводит к искривлению, известному как перекос при изготовлении пластины, как показано на рис. 4b. Деформацию сварного шва можно контролировать путем предварительной настройки или предварительного изгиба узла соединения, чтобы компенсировать деформацию, или путем сдерживания сварного шва, чтобы противостоять деформации. Примеры обоих этих методов показаны на рисунке 5.
Проблем с деформацией легче всего избежать, используя правильную подготовку сварного шва. Использование несимметричных двусторонних сварных швов, таких как показанные на рис. 2e и 2i, компенсирует деформации.Деформация с меньшей стороны сварного шва (созданная первой) устраняется, когда больший шов накладывается на другую сторону. Этот метод известен как сбалансированная сварка.
Невозможно точно предсказать искажение геометрически сложной конструкции, но следует придерживаться одного основного правила. Это правило заключается в том, что сварку желательно начинать в центре изделия, а все последующие сварные швы выполнять от центра к краям, что способствует возникновению усадок в свободном состоянии.
Если искажение не контролируется, есть два метода его исправления: сила и тепло. Искажение световых сечений можно устранить простым применением силы, т.е. применение гидравлических домкратов и прессов. В случае более тяжелых секций требуется локальный нагрев и охлаждение, чтобы вызвать термические напряжения, противодействующие уже существующим.
Устройство для снятия остаточного напряжения
Наиболее распространенным и эффективным способом снятия остаточных напряжений является нагрев. Повышение температуры приводит к снижению предела текучести и способствует ползучести.Ползучесть снимает остаточные напряжения за счет пластической деформации. Стальные сварные детали обычно нагревают до слабого красного каления (600°C) во время обработки для снятия напряжений.
Скорости нагрева и охлаждения во время этого снятия термического напряжения должны тщательно контролироваться, иначе в сварном компоненте могут возникнуть дальнейшие схемы остаточных напряжений. Существует ограничение по размеру конструкций, с которых может быть снято термическое напряжение, как из-за размера необходимых печей, так и из-за возможности деформации конструкции под собственным весом.Однако возможна термическая обработка отдельных стыков в большой конструкции путем размещения вокруг стыков небольших печей или использования электрических нагревательных элементов.
Другие методы снятия напряжения основаны на тепловом расширении, создающем механические силы, способные противодействовать первоначальным остаточным напряжениям. Этот метод может применяться на месте, но точное знание местоположения остаточных сжимающих напряжений жизненно важно, иначе уровень остаточных напряжений может увеличиться, а не уменьшиться.Чисто механическое снятие напряжения также может быть применено при условии, что оно достаточно для компенсации необходимой пластической деформации.
Далее: Свариваемость конструкционной стали
Вам также может понравиться
Случайные сообщения
- Металлография
Металлография — это исследование микроструктуры материалов. Анализ металлографической микроструктуры материала помогает в… - Оптимальное сочетание ПРОЧНОСТИ и ВЯЗКОСТИ
В предыдущих разделах описывалось влияние микроструктуры на прочность и ударную вязкость с использованием металлургических мех...
- Что такое нанотехнологии?
Нанотехнология — это инженерный метод, при котором полностью функционирующие устройства производятся на молекулярном уровне. … - Технология производства стали
Технология производства стали сильно изменилась за последние два десятилетия под давлением возросшего спроса, новых специ… - Технология формовки и термообработки
готовые изделия, в том числе горячая штамповка, горячая и холодная прокатка, бесшовные…
металлургия | Определение и история
Современное использование металлов является кульминацией долгого пути развития, растянувшегося примерно на 6500 лет. Принято считать, что первыми известными металлами были золото, серебро и медь, находившиеся в самородном или металлическом состоянии, из которых самыми ранними, по всей вероятности, были самородки золота, найденные в песках и гравии в руслах рек. Такие самородные металлы стали известны и ценились за их декоративную и утилитарную ценность во второй половине каменного века.
Самая ранняя разработка
Золото может быть агломерировано в более крупные куски путем холодной ковки, но самородная медь не может, и важным шагом на пути к Веку металлов стало открытие того, что такие металлы, как медь, могут быть преобразованы в формы путем плавления и отливки в формы; среди самых ранних известных изделий этого типа — медные топоры, отлитые на Балканах в 4-м тысячелетии до н. э. Еще одним шагом стало открытие того, что металлы можно извлекать из металлосодержащих минералов. Они были собраны, и их можно было отличить по цвету, текстуре, весу, цвету пламени и запаху при нагревании.Заметно больший выход, полученный при нагревании самородной меди с сопутствующими оксидными минералами, мог привести к процессу плавки, поскольку эти оксиды легко восстанавливаются до металла в слое древесного угля при температурах выше 700 ° C (1300 ° F) в качестве восстановителя. , угарный газ, становится все более стабильным. Чтобы осуществить агломерацию и отделение расплавленной или выплавленной меди от сопутствующих минералов, необходимо было ввести оксид железа в качестве флюса. Этот дальнейший шаг вперед можно объяснить наличием минералов оксида железа госсан в выветрелых верхних зонах месторождений сульфидов меди.
Во многих регионах в последующий период производились медно-мышьяковые сплавы, обладающие превосходными свойствами по сравнению с медью как в литом, так и в деформируемом виде. Сначала это могло быть случайным из-за сходства по цвету и цвету пламени между ярко-зеленым медно-карбонатным минералом малахитом и продуктами выветривания таких медно-мышьяковых сульфидных минералов, как энаргит, а позже за этим мог последовать целенаправленный отбор соединений мышьяка на основе их чесночного запаха при нагревании.
Содержание мышьяка варьировалось от 1 до 7 процентов, олова до 3 процентов. Практически не содержащие мышьяка медные сплавы с более высоким содержанием олова — другими словами, настоящая бронза — по-видимому, появились между 3000 и 2500 годами до нашей эры, начиная с дельты Тигра и Евфрата. Открытие значения олова могло произойти благодаря использованию станнита, смешанного сульфида меди, железа и олова, хотя этот минерал не так широко доступен, как основной минерал олова, касситерит, который, должно быть, был конечным источником. металла.Касситерит поразительно плотный и встречается в виде гальки в аллювиальных отложениях вместе с арсенопиритом и золотом; это также происходит в определенной степени в госсанах оксида железа, упомянутых выше.
Хотя бронза могла развиваться независимо в разных местах, наиболее вероятно, что бронзовая культура распространилась через торговлю и миграцию народов с Ближнего Востока в Египет, Европу и, возможно, Китай. Во многих цивилизациях производство меди, мышьяковой меди и оловянной бронзы какое-то время продолжалось вместе.Возможное исчезновение медно-мышьяковых сплавов трудно объяснить. Производство могло быть основано на полезных ископаемых, которые не были широко доступны и стали дефицитными, но относительная нехватка минералов олова не мешала значительной торговле этим металлом на значительных расстояниях. Возможно, оловянные бронзы в конечном итоге стали предпочитаться из-за возможности отравления мышьяком от паров, образующихся при окислении мышьякосодержащих минералов.
По мере разработки выветрелых медных руд в данных местах добывались и плавились более твердые сульфидные руды под ними.Используемые минералы, такие как халькопирит, сульфид меди и железа, нуждались в окислительном обжиге для удаления серы в виде диоксида серы и получения оксида меди. Это не только требовало больших металлургических навыков, но также окисляло тесно связанное железо, что в сочетании с использованием флюсов из оксида железа и более сильными восстановительными условиями, создаваемыми усовершенствованными плавильными печами, приводило к более высокому содержанию железа в бронзе.
Невозможно провести резкое разделение между бронзовым веком и железным веком.Небольшие куски железа должны были производиться в медеплавильных печах, поскольку использовались флюсы оксида железа и железосодержащие сульфидные руды меди. Кроме того, более высокие температуры печи создали бы условия для более сильного восстановления (то есть более высокое содержание монооксида углерода в газах печи). Ранний кусок железа с дороги в провинции Дренте, Нидерланды, был датирован 1350 годом до нашей эры, датой, которую обычно принимают за средний бронзовый век для этой области. С другой стороны, в Анатолии железо использовалось уже в 2000 г. до н. э.Есть также случайные ссылки на железо и в более ранние периоды, но этот материал имел метеоритное происхождение.
Как только была установлена взаимосвязь между новым металлом, обнаруженным в медных плавках, и рудой, добавленной в качестве флюса, естественным образом последовала работа печей для производства только железа. Несомненно, к 1400 г. до н. э. в Анатолии большое значение приобрело железо, а к 1200–1000 гг. до н. э. из него в больших масштабах изготавливали оружие, первоначально лезвия кинжалов.По этой причине 1200 г. до н.э. был принят за начало железного века. Данные раскопок указывают на то, что искусство изготовления железа зародилось в гористой местности к югу от Черного моря, где доминировали хетты. Позже это искусство, по-видимому, распространилось среди филистимлян, поскольку в Гераре были обнаружены грубые печи, датируемые 1200 г. до н. э., вместе с рядом железных предметов.
Плавка оксида железа с древесным углем требовала высокой температуры, и, поскольку температура плавления железа 1540 °C (2800 °F) тогда была недостижима, продукт представлял собой просто губчатую массу пастообразных глобул металла, смешанных с полужидкий шлак.Этот продукт, позже известный как блюм, вряд ли можно было использовать в том виде, в каком он был, но повторный нагрев и горячая ковка устранили большую часть шлака, создав кованое железо, продукт гораздо лучшего качества.
На свойства железа сильно влияет присутствие небольшого количества углерода, при этом значительное увеличение прочности связано с содержанием менее 0,5 процента. При достижимых в то время температурах — около 1200 ° C (2200 ° F) — восстановление древесным углем давало почти чистое железо, которое было мягким и имело ограниченное применение для оружия и инструментов, но когда отношение топлива к руде было увеличено и вытяжка печи с изобретением лучших мехов железо поглощало больше углерода. Это привело к цветению и железным изделиям с различным содержанием углерода, что затрудняло определение периода, в течение которого железо могло быть преднамеренно упрочнено путем науглероживания или повторного нагревания металла в контакте с избытком древесного угля.
Углеродосодержащее железо имело еще одно большое преимущество, заключавшееся в том, что, в отличие от бронзы и безуглеродистого железа, его можно было сделать еще более твердым путем закалки, т. е. быстрого охлаждения путем погружения в воду. Нет никаких свидетельств использования этого процесса закалки в раннем железном веке, так что он должен был быть либо неизвестен тогда, либо не считался выгодным, поскольку закалка делает железо очень хрупким и должна сопровождаться отпуском или повторным нагревом при более низкая температура, чтобы восстановить ударную вязкость.То, что, по-видимому, было установлено на раннем этапе, было практикой многократной холодной ковки и отжига при 600–700 ° C (1100–1300 ° F), температура, естественно достигаемая при простом огне. Эта практика распространена в некоторых частях Африки даже сегодня.
К 1000 г. до н. э. железо стало известно в Центральной Европе. Его использование медленно распространялось на запад. Производство железа было широко распространено в Великобритании во время римского вторжения в 55 г. до н. э. В Азии железо также было известно в древности, в Китае около 700 г. до н.э.
Сварка и марганец | NIOSH
Обзор
Сварочные дымы состоят из металлов, и большинство дымов содержат небольшой процент марганца. Рабочие, работодатели и медицинские работники обеспокоены потенциальными неврологическими последствиями, связанными с воздействием марганца в сварочных дымах. NIOSH проводит исследования и анализирует опубликованную научную литературу для оценки этой проблемы.
Марганец является важным питательным веществом. Здоровый человек с нормальной функцией печени и почек может выделять избыток марганца с пищей.Вдыхание марганца вызывает большую озабоченность, поскольку он обходит нормальные защитные механизмы организма. Это может привести к накоплению марганца и неблагоприятным последствиям для здоровья, включая повреждение легких, печени, почек и центральной нервной системы. Работники-мужчины, подвергающиеся воздействию марганца, также имеют более высокий риск проблем с фертильностью. Длительное воздействие высоких концентраций марганца (> 1 мг/м 3 ) в воздухе может привести к паркинсоническому синдрому, известному как «марганизм». Также сообщается, что хроническое воздействие марганцевого пестицида манеба вызывает симптомы, подобные болезни Паркинсона.Паркинсоноподобные симптомы могут включать тремор, замедленность движений, мышечную ригидность и нарушение равновесия.
Недавние исследования показывают, что неврологические и нейроповеденческие расстройства могут возникать, когда рабочие подвергаются воздействию низких концентраций марганца (<0,2 мг/м 3 ) в сварочном дыму. Эти эффекты включают изменения настроения и кратковременной памяти, изменение времени реакции и снижение зрительно-моторной координации. У пострадавших рабочих часто обнаруживаются аномальные скопления марганца в области мозга, известной как бледный шар.Бледный шар играет важную роль в регуляции движений. NIOSH в настоящее время пересматривает рекомендуемый предел воздействия (REL) для марганца в результате этих исследований. Оценка доступной научной литературы по воздействию марганца при сварке затруднена рядом факторов. Эти факторы включают противоречивые выводы, ограниченные данные о биологических процессах, которые могут привести к определенным последствиям для здоровья, и сложные смеси сварочного дыма. Всеобъемлющий обзор имеющейся научной литературы находится в разработке и будет доступен для публичного ознакомления.В ожидании выпуска окончательного документа существующие ресурсы NIOSH, перечисленные ниже, предлагаются для оказания помощи в оценке и контроле воздействия сварочного дыма на рабочем месте.
Профессиональное воздействие марганца
Воздействие марганцевой пыли происходит главным образом при добыче полезных ископаемых, дроблении руды и металлургических операциях по производству железа, стали, черных и цветных сплавов. Производство сухих батарей, антидетонационных присадок к бензину, пестицидов (например, манеб), пигментов, красителей, чернил и зажигательных устройств также может привести к воздействию марганца на рабочем месте.Пары марганца образуются при металлургических операциях и некоторых видах сварочных работ. Воздействие может значительно варьироваться в зависимости от количества марганца в сварочной проволоке, стержнях, флюсе и основном металле. Сварка в замкнутом пространстве может значительно увеличить воздействие паров марганца. Информацию об оценке профессионального воздействия марганца см. на тематической странице NIOSH, посвященной марганцу.
Неврологические и нейроповеденческие эффекты
Многочисленные исследования показывают, что сварщики могут подвергаться повышенному риску неврологических и нейроповеденческих нарушений здоровья при контакте с такими металлами, как свинец, железо и марганец.Угарный газ, жара и стресс также могут способствовать неврологическим нарушениям у сварщиков. Некоторые исследования показывают, что сварщики, подвергшиеся воздействию низких концентраций марганца (<0,2 мг/м 3 ), хуже справляются с тестами функций мозга и двигательных навыков. Эти эффекты включают изменения настроения и кратковременной памяти, изменение времени реакции и снижение зрительно-моторной координации. Неизвестно, имеют ли эти данные клиническое значение.
Пределы воздействия на рабочем месте для марганца
Агентство | Предел воздействия на рабочем месте |
---|---|
NIOSH REL | 1 мг/м 3 (TWA) и 3 мг/м 3 (STEL) |
НИОСХ ИДЛХ | 500 мг/м 3 |
OSHA PEL | 5 мг/м 3 (потолок) |
ACGIH TLV | 0.02 мг/м 3 (СВЗ) |
IDLH: концентрация, непосредственно опасная для жизни и здоровья
PEL: допустимый предел воздействия
REL: рекомендуемый предел воздействия
STEL: предел кратковременного воздействия
TLV: пороговое предельное значение
TWA: средневзвешенное по времени
Ресурсы NIOSH
Публикация NIOSH № 88-110: Критерии рекомендуемого стандарта: сварка, пайка и термическая резка
Представлены критерии и стандарты для предотвращения профессиональных заболеваний, возникающих в результате воздействия сварки, пайки и термической резки.
Публикация NIOSH № 2005-151: Карманный справочник NIOSH по химическим опасностям — сварочные дымы
Карманный справочник NIOSH по химическим опасностям — соединения марганца и пары (в виде Mn)
NIOSH: IDLH – Соединения марганца (как Mn)
Избранные цитаты из журналов
Ниже приведены избранные журнальные статьи о влиянии сварочного дыма на здоровье с соавторами NIOSH:
Антонини Дж. М., О’Каллаган Дж. П., Миллер Д. Б. [2006]. Разработка модели на животных для изучения потенциальных нейротоксических эффектов, связанных с вдыханием сварочного дыма.Нейротоксикология, сентябрь; 27(5): 745-751.
Антонини Дж. М., Сантамария А. Б., Дженкинс Н. Т., Альбини Э., Луккини Р. [2006]. Судьба марганца, связанная с вдыханием сварочного дыма: потенциальные неврологические эффекты. Нейротоксикология, май; 27(3): 304-310.
Bowler RM, Roels HA, Nakagawa S, Drezgic M, Diamond E, Park R, Koller W, Bowler RP, Mergler D, Bouchard M, Smith D, Gwiazda R, Doty RL [2007]. Взаимосвязь доза-эффект между воздействием марганца и неврологической, нейропсихологической и легочной функцией у сварщиков мостов в ограниченном пространстве.Occup Environ Med, март; 64(3): 167-177.
Bowler RM, Nakagawa S, Drezgic M, Roels HA, Park RM, Diamond E, Mergler D, Bouchard M, Bowler RP, Kollerg W [2007]. Последствия воздействия дыма при сварке в замкнутом пространстве: серия неврологических и нейропсихологических случаев. Нейротоксикология, март; 28(2): 298-311.
Парк Р.М., Боулер Р.М., Эггерт Д.Э., Даймонд Э., Спенсер К.Дж., Смит Д., Гвязда Р. [2005]. Вопросы оценки неврологического риска профессионального облучения: сварщики моста через залив. Нейротоксикология, май; 27(3): 373-84.
Сантамария А.Б., Кушинг К.А., Антонини Дж.М., Финли Б.Л., Моват Ф.С. [2007]. Обзор состояния науки: представляет ли воздействие марганца во время сварки неврологический риск?, J Toxicol Environ Health. Б сент.; 10(6): 417-465.
Оценка опасности для здоровья NIOSH
Отчет об оценке опасности для здоровья, HETA-2006-0156-3031, Harley-Davidson Motor Company, York, Pennsylvania
Отчет об оценке опасности для здоровья, HETA-2000-0185-2808, Thyssen-Dover Elevator, Middleton, Tennessee
Отчет об оценке опасности для здоровья, HETA-91-0109-2426, Duracell Battery Company, Кливленд, Теннесси
Отчет об оценке опасности для здоровья, HETA-90-0214-2523, Ralston Purina Company, Eveready Battery Company, Marietta, Ohio
НИОШТИК-2
NIOSHTIC-2 — это доступная для поиска библиографическая база данных публикаций по безопасности и гигиене труда, документов, отчетов о грантах и журнальных статей, полностью или частично поддерживаемых NIOSH.
«Марганец» Результаты поиска
Сварка Результаты поиска
Другие государственные ресурсы
Управление по безопасности и гигиене труда (OSHA): Вопросы безопасности и охраны здоровья — сварка, резка и пайкаВнешний значок
OSHA: Вопросы безопасности и охраны здоровья — соединения марганца (как Mn) внешний значок
OSHA: Темы безопасности и здоровья – Токсичные металлы – Марганецвнешний значок
Агентство по регистрации токсичных веществ и заболеваний (ATSDR): токсикологический профиль марганца [проект 2008 г.]
Агентство по охране окружающей среды (EPA): Интегрированная система информации о рисках — марганец (CASRN 7439-96-5) внешний значок
Mine Safety and Health Administration (MSHA): Программа предотвращения профессиональных заболеваний и травм Тема здравоохранения – Отбор проб сварочного дымаexternal icon
En Españolexternal icon
Дополнительные ресурсы
ВОЗ: Краткий документ Международной химической оценки № 12 – Марганец и его соединения. pdf iconexternal icon
eLCOSH: недорогой и легкий блок снижает риск образования сварочного дымаexternal icon
eLCOSH: Предупреждение об опасности – сварочные дымы и газы, внешний значок
En Español, внешний значок
eLCOSH: Welding & Marganese Poisoningexternal icon
En Españolexternal icon
IRJET-Запрашиваемая вами страница не найдена на нашем сайте Январь 2022 г. Выполняется публикация…
Browse Papers
IRJET Получил «Импакт-фактор научного журнала: 7,529» за 2020 год.
Подтвердить здесь
IRJET приглашает к публикации том 9, выпуск 1 (январь 2022 г.) из различных инженерных и технологических дисциплин,
Отправить сейчас..
Browse Papers
IRJET Получил «Импакт-фактор научного журнала: 7,529» за 2020 год.
Подтвердить здесь
IRJET приглашает к публикации том 9, выпуск 1 (январь 2022 г.) из различных инженерных и технологических дисциплин,
Отправить сейчас. .
Browse Papers
IRJET Получил «Импакт-фактор научного журнала: 7,529» за 2020 год.
Подтвердить здесь
IRJET приглашает к публикации том 9, выпуск 1 (январь 2022 г.) из различных инженерных и технологических дисциплин,
Отправить сейчас..
Browse Papers
IRJET Получил «Импакт-фактор научного журнала: 7,529» за 2020 год.
Подтвердить здесь
IRJET приглашает к публикации том 9, выпуск 1 (январь 2022 г.) из различных инженерных и технологических дисциплин,
Отправить сейчас..
Browse Papers
IRJET Получил «Импакт-фактор научного журнала: 7,529» за 2020 год.
Подтвердить здесь
IRJET приглашает к публикации том 9, выпуск 1 (январь 2022 г.) из различных инженерных и технологических дисциплин,
Отправить сейчас..
Browse Papers
IRJET Получил «Импакт-фактор научного журнала: 7,529» за 2020 год.
Подтвердить здесь
IRJET приглашает к публикации том 9, выпуск 1 (январь 2022 г.) из различных инженерных и технологических дисциплин,
Отправить сейчас..
Browse Papers
IRJET Получил «Импакт-фактор научного журнала: 7,529» за 2020 год.
Подтвердить здесь
IRJET приглашает к публикации том 9, выпуск 1 (январь 2022 г.) из различных инженерных и технологических дисциплин,
Отправить сейчас..
Browse Papers
IRJET Получил «Импакт-фактор научного журнала: 7,529» за 2020 год.
Подтвердить здесь
Онлайн-курсы PDH. PDH для профессиональных инженеров. ПДХ Инжиниринг.
«Мне нравится широта ваших курсов HVAC; не только экологичность или энергосбережение
курсы.»
Рассел Бейли, П.Е.
Нью-Йорк
«Это укрепило мои текущие знания и научило меня еще нескольким новым вещам
для раскрытия мне новых источников
информации. »
Стивен Дедак, ЧП
Нью-Джерси
«Материал был очень информативным и организованным. Я многому научился, и они были
очень быстро отвечают на вопросы.
Это было на высшем уровне. Буду использовать
снова. Спасибо.»
Блэр Хейворд, ЧП
Альберта, Канада
«Веб-сайт прост в использовании. Хорошо организован. Я обязательно воспользуюсь вашими услугами снова.
Я передам вашу компанию
имя другим на работе.»
Рой Пфлейдерер, ЧП
Нью-Йорк
«Справочный материал был превосходным, и курс был очень информативным, тем более что я думал, что уже знаком с
с деталями Канзас
Авария в городе Хаятт.»
Майкл Морган, ЧП
Техас
«Мне очень нравится ваша бизнес-модель. Мне нравится возможность просмотреть текст перед покупкой. Я нашел класс
информативный и полезный
на моей работе.»
Уильям Сенкевич, Ч.Е.
Флорида
«У вас отличный выбор курсов и очень информативные статьи.Вы
— лучшее, что я нашел.»
Рассел Смит, ЧП
Пенсильвания
«Я считаю, что такой подход позволяет работающему инженеру легко зарабатывать PDH, предоставляя время для просмотра
материал.»
Хесус Сьерра, ЧП
Калифорния
«Спасибо, что разрешили мне просмотреть неправильные ответы.На самом деле
человек узнает больше
от сбоев.»
Джон Скондрас, ЧП
Пенсильвания
«Курс был хорошо составлен, и использование тематических исследований является эффективным
способ обучения. »
Джек Лундберг, ЧП
Висконсин
«Я очень впечатлен тем, как вы представляете курсы; т.э., что позволяет
студент для ознакомления с курсом
материал перед оплатой и
получение викторины.»
Арвин Свангер, ЧП
Вирджиния
«Спасибо, что предлагаете все эти замечательные курсы. Я, конечно, выучил и
очень понравилось.»
Мехди Рахими, ЧП
Нью-Йорк
«Я очень доволен предлагаемыми курсами, качеством материалов и простотой поиска и
подключение к Интернету
курсы.»
Уильям Валериоти, ЧП
Техас
«Этот материал в значительной степени оправдал мои ожидания. Курс был легким для понимания. Фотографии в основном давали хорошее представление о
обсуждаемые темы.»
Майкл Райан, ЧП
Пенсильвания
«Именно то, что я искал. Нужен 1 балл по этике, и я нашел его здесь.»
Джеральд Нотт, ЧП
Нью-Джерси
«Это был мой первый онлайн-опыт получения необходимых кредитов PDH. Это был
.информативно, выгодно и экономично.
Очень рекомендую
всем инженерам.»
Джеймс Шурелл, ЧП
Огайо
«Я ценю, что вопросы «реального мира» и имеют отношение к моей практике, и
не основано на каком-то непонятном разделе
законов, которые не применяются
— «обычная» практика.»
Марк Каноник, ЧП
Нью-Йорк
«Отличный опыт! Я многому научился, чтобы использовать его в своем медицинском устройстве
организация. »
Иван Харлан, ЧП
Теннесси
«Материал курса имеет хорошее содержание, не слишком математический, с хорошим акцентом на практическое применение технологии.»
Юджин Бойл, П.Е.
Калифорния
«Это был очень приятный опыт. Тема была интересной и хорошо представлена,
а онлайн формат был очень
доступно и просто
использовать. Большое спасибо.»
Патрисия Адамс, ЧП
Канзас
«Отличный способ добиться соответствия непрерывному обучению PE в рамках временных ограничений лицензиата.»
Джозеф Фриссора, ЧП
Нью-Джерси
«Должен признаться, я действительно многому научился. Распечатанная викторина помогает во время
просмотр текстового материала. я
также оценил просмотр
фактические случаи предоставлены.»
Жаклин Брукс, ЧП
Флорида
«Документ Общие ошибки ADA в проектировании помещений очень полезен.
тест действительно требовал исследований в
документ но ответы были
всегда в наличии.»
Гарольд Катлер, ЧП
Массачусетс
«Это было эффективное использование моего времени. Спасибо за разнообразие выбора
в дорожной технике, который мне нужен
для выполнения требований
Сертификация PTOE.»
Джозеф Гилрой, ЧП
Иллинойс
«Очень удобный и доступный способ заработать CEU для выполнения моих требований в штате Делавэр.»
Ричард Роадс, ЧП
Мэриленд
«Узнал много нового о защитном заземлении. До сих пор все курсы, которые я проходил, были отличными.
Надеюсь увидеть больше 40%
курсы со скидкой.»
Кристина Николас, ЧП
Нью-Йорк
«Только что сдал экзамен по радиологическим стандартам и с нетерпением жду дополнительных
курсы. Процесс прост, и
намного эффективнее, чем
необходимость путешествовать.»
Деннис Мейер, ЧП
Айдахо
«Услуги, предоставляемые CEDengineering, очень полезны для профессионалов
Инженеры для приобретения блоков PDH
в любое время.Очень удобно.»
Пол Абелла, ЧП
Аризона
«Пока все было отлично! Поскольку я постоянно работаю матерью двоих детей, у меня не так много
пора искать куда
получить мои кредиты от. »
Кристен Фаррелл, ЧП
Висконсин
«Это было очень информативно и поучительно.Легко понять с иллюстрациями
и графики; определенно делает его
проще впитать все
теорий.»
Виктор Окампо, инженер.
Альберта, Канада
«Хороший обзор принципов полупроводников. Мне понравилось проходить курс по телефону
.мой собственный темп во время моего утра
на метро
на работу.»
Клиффорд Гринблатт, ЧП
Мэриленд
«Просто найти интересные курсы, скачать документы и получить
викторина. Я бы очень рекомендую
вам в любой PE нуждающийся
Единицы CE. »
Марк Хардкасл, ЧП
Миссури
«Очень хороший выбор тем во многих областях техники.»
Рэндалл Дрейлинг, ЧП
Миссури
«Я заново узнал то, что забыл. Я также рад помочь финансово
по ваш рекламный адрес электронной почты который
сниженная цена
на 40%.»
Конрадо Касем, П.Е.
Теннесси
«Отличный курс по разумной цене. Буду пользоваться вашими услугами в будущем.»
Чарльз Флейшер, ЧП
Нью-Йорк
«Это был хороший тест, и он фактически показал, что я прочитал профессиональную этику
Кодыи Нью-Мексико
правил.»
Брун Гильберт, П. Е.
Калифорния
«Мне очень понравились занятия. Они стоили времени и усилий.»
Дэвид Рейнольдс, ЧП
Канзас
«Очень доволен качеством тестовых документов. Буду использовать CEDengineerng
при необходимости дополнительного
Сертификация.»
Томас Каппеллин, П.Е.
Иллинойс
«У меня истек срок действия курса, но вы все равно выполнили обязательство и дали
мне то, за что я заплатил — много
с благодарностью!»
Джефф Ханслик, ЧП
Оклахома
«CEDengineering предлагает удобные, экономичные и актуальные курсы
для инженера.»
Майк Зайдл, П.Е.
Небраска
«Курс был по разумной цене, а материал был кратким и
в хорошем состоянии. »
Глен Шварц, ЧП
Нью-Джерси
«Вопросы соответствовали урокам, а материал урока
хороший справочный материал
для дизайна под дерево.»
Брайан Адамс, П.Е.
Миннесота
«Отлично, удалось получить полезную информацию с помощью простого телефонного звонка.»
Роберт Велнер, ЧП
Нью-Йорк
«У меня был большой опыт прохождения курса «Строительство прибрежных районов — Проектирование»
Корпус Курс и
очень рекомендую.»
Денис Солано, ЧП
Флорида
«Очень понятный, хорошо организованный веб-сайт. Материалы курса этики штата Нью-Джерси были очень
прекрасно приготовлено. »
Юджин Брэкбилл, ЧП
Коннектикут
«Очень хороший опыт. Мне нравится возможность загружать учебные материалы на
обзор везде и
когда угодно.»
Тим Чиддикс, ЧП
Колорадо
«Отлично! Поддерживайте широкий выбор тем на выбор.»
Уильям Бараттино, ЧП
Вирджиния
«Процесс прямой, никакой чепухи. Хороший опыт.»
Тайрон Бааш, П.Е.
Иллинойс
«Вопросы на экзамене были пробными и демонстрировали понимание
материала. Тщательный
и полный.»
Майкл Тобин, ЧП
Аризона
«Это мой второй курс, и мне понравилось то, что курс предложил мне, что
поможет в моей линии
работы. »
Рики Хефлин, ЧП
Оклахома
«Очень быстрая и простая навигация. Я определенно воспользуюсь этим сайтом снова.»
Анджела Уотсон, ЧП
Монтана
«Прост в исполнении. Никаких недоразумений при подходе к сдаче теста или записи сертификата.»
Кеннет Пейдж, П.Е.
Мэриленд
«Это был отличный источник информации о нагревании воды с помощью солнечной энергии. Информативный
и отличное освежение.»
Луан Мане, ЧП
Коннетикут
«Мне нравится подход к подписке и возможности читать материалы в автономном режиме, а затем
вернись, чтобы пройти тест.»
Алекс Млсна, П. Е.
Индиана
«Я оценил количество информации, предоставленной для класса. Я знаю
это вся информация, которую я могу
использование в реальных жизненных ситуациях.»
Натали Дерингер, ЧП
Южная Дакота
«Материалы обзора и образец теста были достаточно подробными, чтобы я мог
успешно завершено
курс.»
Ира Бродская, ЧП
Нью-Джерси
«Веб-сайт прост в использовании, вы можете скачать материал для изучения, а затем вернуться
и пройти тест. Очень
удобный а на моем
собственное расписание .»
Майкл Гладд, ЧП
Грузия
«Спасибо за хорошие курсы на протяжении многих лет. »
Деннис Фундзак, ЧП
Огайо
«Очень легко зарегистрироваться, получить доступ к курсу, пройти тест и распечатать PDH
Сертификат. Спасибо за создание
процесс простой.»
Фред Шайбе, ЧП
Висконсин
«Положительный опыт.Быстро нашел подходящий мне курс и закончил
PDH за один час в
один час.»
Стив Торкилдсон, ЧП
Южная Каролина
«Мне понравилась возможность загрузки документов для ознакомления с содержанием
и пригодность до
наличие для оплаты
материал .»
Ричард Ваймеленберг, ЧП
Мэриленд
«Это хорошее пособие по ЭЭ для инженеров, не являющихся электриками. »
Дуглас Стаффорд, ЧП
Техас
«Всегда есть место для улучшения, но я ничего не могу придумать в вашем
процесс, которому требуется
улучшение.»
Томас Сталкап, ЧП
Арканзас
«Мне очень нравится удобство прохождения викторины онлайн и получения немедленного
Сертификат.»
Марлен Делани, ЧП
Иллинойс
«Обучающие модули CEDengineering — очень удобный способ доступа к информации по
многие различные технические области снаружи
по собственной специализации без
необходимость путешествовать.»
Гектор Герреро, ЧП
Грузия
.