Дж. Стронг «Практика современной физической лаборотории». Глава XV ФОРМОВКА И ЛИТЬЁ Процесс формовки и отливки металлов очень мало изменился за всё время своего существования. Изменения затронули только обслуживающие аппараты, но сущность процесса осталась той же, какой была во времена доисторического человека. Процесс отливки металла казался удивительным искусством тем, кто никогда им не занимался, а специалисты ревностно охраняли секреты своего ремесла, чтобы другие не узнали, как оно несложно. Цель этой главы — познакомить читателя с деталями процесса отливки
металлов. Только немногие лаборатории имеют оборудование для работы с расплавленным
металлом, так что экспериментатор часто бывает вынужден пользоваться услугами специальных литеен. Однако в большинстве случаев
экспериментатор имеет возможность изготовить в своей лаборатории модель, по
которой будет сделана отливка. Отливка по восковым моделям. Имеется два метода отливки металлических изделий:
отливка по восковым моделям и отливка в песочных формах. Первый метод
заключается в следующем. Восковую модель покрывают песком и огнеупорной глиной
и затем обжигают, освобождая форму от воска. Получается готовая форма для
заливки металла. Таким методом пользуются при отливке скульптур, золотых зубов,
инкрустаций и во всех других случаях, когда требуется только одна отливка; ибо
очевидно, что по олной модели можно отлить таким способом только одно изделие.
Отсюда название метода «потеряный воск». Преимущество метода отливки по восковым моделям состоит в том, что модель можно сделать сколь угодно сложной, независимо от наличия выемок. Елинственно, о чём следует позаботиться, это об устройстве отверстий для заливки металла и выхода воздуха. При отливке пустотелых скульптур внутренний сердечник обычно поддерживается в форме стержнями из того же металла, из какого должна быть отлита статуя. Материал, идущий на изготовление моделей, состоит из смеси пчелиного
воска и парафина. Его можно получить уже приготовленным или
без труда изготовить самому, так как пропорция воска и парафина не является
строгой. Маленькие модели укрепляют на конце небольшого стержня. Чтобы снять модель,
к стержню прикладывают кусок горячего металла; когда стержень достаточно нагреется, воск начнёт таять и модель
соскользнёт с конца стержня. Если требуется отлить изделие из свинца, гарта, баббита, олова и его
сплавов, припоя или других подобных металлов, то форму можно делать из гипса. Если в центре миски над водой осталась небольшая кучка порошка, то нужно подождать, пока она сделается влажной, и
затем осторожно размешать содержимое
миски, чтобы освободить его от пузырьков воздуха. После этого с помощью
мягкой кисти осторожно покрывают модель приготовленной смесью (рис. Дантисты пользуются усечённым конусом
(наклон 5—10°), причём дном служит меньшее основание. Такой конус гарантирует,
что при заливке металла форма останется внутри сосуда и не будет разбита. Это
станет очевидным из следующего абзаца, где описывается процесс заливки металла
в форму. Когда смесь затвердела, прут, поддерживающий модель, вытаскивают и
вокруг оставшейся дыры (литника) делают воронку для приёма жидкого металла
(рис. Форму помещают на металлический диск, в центре которого имеется
отверстие, соединённое трубкой с небольшим резервуаром. На трубку надет зажим,
запирающий её до тех пор, пока металл не будет расплавлен. К резервуару
присоединён маленький ручкой насос, позволяющий уменьшить давление в резервуаре
до половины или четверти атмосферного. так, что жёлоб тигля примыкает к литнику. Остаётся взвести пружину, положить металл в тигель и нarpеть его с помощью ручной горелки. Когда металл расплавится, освобождают тормоз, брусок приводит во вращение и центробежная сила заставляет металл войти в форму. Необходимо, чтобы дно
формы было достаточно прочным, в противном случае оно
может не выдержать, и расплавленный металл будет разбрызган по комнате. Модели для приготовления песочных форм. Обычно
отливка всевозможных деталей независимо от их размеров и металла, из
которого они должны быть отлиты, производится в песочных формах.
Отливка в постоянных формах,
хотя и является существенной, применяется лишь тогда, когда высокая стоимость
металлических форм оправдывается большим количеством отливаемых деталей. Прежде чем приступить к
изготовлению модели, следует в
первую очередь составить точный чертёж отливаемой детали (рис. 403) Затем по этому чертежу изготовляют чертёж модели.
Последний может быть выполнен на
тонкой бумаге (рис. 404). Чтобы было удобно работать с
этим чертежом, следует проставить на нём все необходимые размеры.
Для того чтобы
проиллюстрировать отливку в песочных формах, на рисунках показан
процесс изготовления полярной оси телескопа. Конструкция оси
предусматривает заливку баббитом, так как при этом устраняется
необходимость зажимать всю ось в патроне токарного станка для её
высверливания, — операция, выполнимая лишь на очень большом токарном
станке. Проектируя модель, следует прежде всего выбрать плоскость разъёма формы.
Плоскость эта должна быть выбрана так, чтобы обе части модели можно было
вынуть из песочной формы. Для этого плоскость разъёма должна проходить таким
образом, чтобы все точки отливаемого изделия, будучи нормально спроектированы
на неё, оказались внутри сечения или на нём. Если такой плоскости не имеется,
то выбирают ту, которая лучше всего удовлетворяет выдвинутому требованию;
выступающие же части выполняют с помощью формовочных шишек. Модель также должна разниматься вдоль плоскости разъёма, если только эта
плоскость не совпадает с одной из поверхностей
отливаемого предмета. В последнем случае модель делают из одного куска (рис. 405). Так как при вытаскивании из песочной формы предмета с параллельными сторонами
стенки формы из-за трения разрушаются, то необходимо придавать модели некоторую
конусность относительно плоскости разъёма. Для точных работ конусность эта
может быть уменьшена до 1/2°, в большинстве же случаев её делают равной
3°. Для круглых предметов с плоскостью разъёма, проходящей через ось,
конусность совсем не требуется. Если одна из частей модели имеет выступ, не лежащий в плоскости разъёма, тр между ним и плоскостью разъёма вставляют отдельную
болванку, которую можно вынуть, когда первая половина формы готова. Болванка
эта носит название «фальшивой шишки». Объёму, занимаемому фальшивой шишкой в
первой половине формы, соответствует равный объём песка во второй половине.
Фальшивая шишка также должна иметь конусность. Из приведённого ниже описания
процесса изготовления формы станет ясно, чтв фальшивыми шишками следует
пользоваться только в одной половине формы. Этой половиной должна быть часть
формы, изготовляемая по той половине модели, в которой имеются углубления для
штырей, скрепляющих обе половины модели. Если нужно отлить изделие со сквозным отверстием, то в тех местах, где у
отлитого изделия должно быть отверстие, на модели делают выступы. Эти выступы
образуют в песке во время формовки углубления, куда помещаются концы шишки,
чтобы она не всплыла во время заливки расплавленного металла. Конусность
выступов должна соответствовать остальным частям модели. Для шишек следует
изготовить отдельные чертежи, учитывающие наличие упомянутых выступов (рис. Шишку формуют отдельно из песка или другого формовочного материал и
помещают в форму, для того чтобы получить в отлитом изделии отверстие или
внутреннюю полость. Если отверстие не сквозное, то шишка пересекает поверхность
изделия только в одном месте и лежит в песке формы только одним концом. При
этом необходимо, чтобы выступ на модели, образующий в песке углубление для
конца шишки, был достаточно длинным, так как иначе шишка, заделанная одним
концом, будет укреплена непрочно. Если такая конструкция невыполнима, то можно
сделать у шишки выступы, служащие для неё опорами внутри формы. Такие выступы
образуют внутри отлитого изделия пустоты, которые приходится потом заделывать.
Другой способ заключается в том, что шишку поддерживают металлическими подставками.
Подставки эти, имеющие вид булавок с широкой головкой и изогнутым стержнем,
втыкаются формовщиком в песочную форму и в дальнейшем сплавляются с металлом
отливки. Так как почти все металлы при затвердевании получают усадку, то размеры модели следует несколько увеличить, чтобы компенсировать усадку. Величина усадки зависит от того, из какого металла изготовляется отливка; в табл. I приведены значения усадки для различных металлов. Приведённые в таблице цифры показывают, сколько сантиметров нало прибавить к размерам модели на каждый метр. Удобно пользоваться усадочными масштабами с делениями большими, чем деления обыкновенного метра на величину усадки. Если по одной модели предстоит выполнить большое число отливок, то
обычно, пользуясь деревянной моделью как первичной, отливают рабочую модель из
алюминия или другого металла и уже по этой модели изготовляют формы. Иначе обстоит дело при отливке изделий из сплавов, особенно если
температуры плавления металлов, входящих в состав этих сплавов, сильно
отличаются друг от друга. Если охлаждение сплава идёт медленно, то за время
охлаждения в нём успевают вырасти большие кристаллы. Некоторые металлы,
входящие в состав сплавов, могут выкристаллизовываться, придавая хрупкость
толстым отливкам из сплава и рассыпая в них целые гнёзда кристаллов. Лучше
всего, повидимому, отливать из сплавов детали толщиной от 5 до 8 мм, но
и толщина в 3 мм не является предельной. Деревянные модели изготовляют из белой сосны, сахарной сосны или
красного дерева. Дерево, идущее на изготовление моделей, не должно иметь сучков
и должно быть хорошо высушено. Если модель состоит из двух кусков (не считая
фальшивых шишек), то оба эти куска должны быть скреплены между собой так, чтобы формовщик мог разнять и вновь соединить их.
При изготовлении модели лучше всего сначала обработать плоскость разъёма вместе
со скрепляющими шипами. Для скрепления частей разъёмной модели можно пользоваться
деревянными штырями или специальными штифтами с гнёздами (рис. Изготовление моделей принципиально ничем не отличается от обычной практики деревообделочного производства. Для скрепления отдельных частей модели можно пользоваться клеем и всеми известными приёмами соединения деревянных деталей при условии, что полученная модель будет иметь желаемую форму. Внешние поверхности модели должны быть совершенно гладкими. Любая шероховатость или неровность поверхности приведёт к тому, что формовщик при освобождении модели из формы вынужден будет сильно постукивать по модели. В результате форма и, следовательно, отливка будут иметь большие размеры, что проектировалось. Особенно гладкими должны быть те места, где модели придана конусность. Каждая часть разъёмной модели, а также фальшивые шишки снабжаются специальной
пластинкой, которая вделывается впотай со стороны плоскости разъёма (рис. Установлено, что при изготовлении отливок острые углы, внутренние и образованные внешними поверхностями, являются источником всевозможных неприятностей. Острые края формы могут осыпаться, а если отливку
и удаётся изготовить, то действующие в ней внутренние напряжения могут
разрушить её вдоль этих углов. Чтобы
избавиться от подобных неприятностей, принято углы закруглять. Можно
сразу изготовить модель с закругленными углами, но легче сделать закруглённый
переход из воска. Изготовляемые для закругления углов ленты имеют различный размер, так что радиус закругления можно
выбрать по желанию. Точно так же можно приобрести или изготовить подходящего
размера инструмент для вдавливания ленты. После того как углы модели закруглены,
её вновь покрывают шеллаком. Если модель предназначена для изготовления только
одной формы, то закруглённый переход можно сделать из наиболее твёрдых сортов
пластилина или пластицина. Эги материалы хорошо пристают к покрытий шеллаком модели, а нужный профиль им можно
придать пальцами или с помощью деревянного инструмента, после чего их следует
покрыть шеллаком. Если
при отливке изделия шишки не применяются, то всю модель покрывают чистым шеллаком; если же шишки применяются,
то модель покрывают темночёрной смесью шеллака с сажей (смесь эта хорошо
растворяется в спирту), а выступы, соответствующие концам шишки, покрывают
чистым шеллаком или окрашивают в красный цвет. Такая разноцветная окраска
сразу показывает формовщику, где должна лежать шишка (рис. 410). (В СССР выступы («знаки») принято красить чёрной краской; цвет же
модели по называет, для какой отливки модель предназначена: красный — для
чугуна, синий — для стали, жёлтый — для цветных металлов. Если отливка требует применения шишек, то сразу же возникает вопрос об
изготовлении шишечных ящиков. Последние представляют, по существу, деревянные
формы для формовки шишек. Требования относительно конусности и усадки остаются
для них теми же, что и при изготовлении моделей. Цилиндрические шишки формуют в
разъёмных ящиках, состоящих из двух половин. Плоскость разъёма в этом случае не
имеет никакого отношения к плоскости разъёма модели. Соединять обе части шишечного
ящика не требуется, так как обе половины шишки формуются отдельно и склеиваются
после прокаливания. Если обе половины шишки одинаковы, то изготовляют только
одну часть шишечного ящика. Если же шишки цилиндрические, то изготовлять самим
ящик вообще не ‘нужно, так как большинство литеен имеет запас готовых ящиков
или даже шишек. Отметим ещё один важный момент: так как модель намечает в форме только концы шишки и так как шишка может быть несимметрична, то полезно делать концы шишки разными, чтобы формовщик был вынужден поместить шишку внутрь формы только в нужном положении. Весьма интересен применяемый уже много лет способ изготовления шишечного
ящика для цилиндрических шишек. Отливка в песочных формах. Чтобы изготовить форму, формовщик
поступает следующим образом. Прежде всего он разнимает
модель, укладывает на стол плоскостью разъёма вниз ту часть модели, в которой
нет соединительных штырей, и ставит на место фальшивые шишки. Поверх этой части
накладывается деревянная или металлическая рама — нижняя опока. Когда нижняя опока до половины наполнена, песок осторожно утрамбовывают
вокруг модели с помощью деревянного инструмента, имеющего форму двойной
лопатки, один конец которой — плоский, а другой имеет вид усечённого тупого
клина [рис. 414(b)]. После этого добавляют новые порции песка, пока нижняя опока не будет
заполнена до краёв хорошо утрамбованным песком. Затем песок протыкают во многих
местах тонкой проволочкой, чтобы облегчить выход пара и газов, образующихся при
заливке расплавленного металла в форму [рис.
414 (с)]. Потом нижнюю опоку целиком переворачивают,
кладут на стол плоскостью разъёма кверху и вынимают фальшивые шишки, как
показано на рис. Вторую половину модели накладывают на
первую так, чтобы соединительные штыри .вошли в гнёзда. Чтобы обе половины формы не слиплись, плоскость разъёма формы посыпают сухим песком
[рис. 414(f)]. Затем верхнюю опоку ставят на нижнюю, наполняют её песком и утрамбовывают так же, как
это делали с нижней опокой [рис. 414(g)]. Так же, как и в нижней опоке,
песок протыкают тонкой проволокой, как
показано на рис. 414(h). В том месте, где под слоем находящегося в опоке
песка нет модели, проделывают лить ик, проходящий чуть дальше плоскости
разъёма. Проделывают его с помощью куска тонкостенной латунной трубки,
осторожно втыкая её в песок и удаляя затем вместе со штабиком песка [рис. 414(i)]. Литник диаметром около 25 мм достаточен
для отливок весом от 5 до 50 кг. Удобно проделывать литник не сразу, а вытаскивая за раз слой песка толщиной около 25 мм. Нельзя устраивать литник упирающимся непосредственно в модель, так как в этом случае форма могла бы быть повреждена заливаемым металлом. Вокруг отверстия литника делают углубление для заливки расплавленного металла [рис. 414 (j) и (k)]. Верхнюю опоку осторожно снимают с нижней и кладут рядом, плоскостью разъёма кверху. В отверстие пластинки, вделанной в плоскость разъёма нижней половины модели, вставляют стержень и слегка постукивают по нему со всех сторон, чтобы освободить модель от прилипшего песка [рис. 414(l)]. Затем во второе отверстие пластинки ввинчивают ручку и осторожно вынимают
модель из формы [рис. 414 (m)]. В плоскости разъёма проделывают жёлоб от литника к форме. Из верхней опоки модель вытаскивают таким же способом,
как из нижней [рис. 414 (р)]. Если отливка очень
велика или имеет сложные очертания, то в верхней опоке проделывают один или
несколько выпоров. Единственное отличие выпоров от литника состоит в том, что
выпоры делают в наиболее высоко поднятых частях формы. В формах сложного
очертания выпоры образуют выход для находящегося в форме воздуха. В больших
формах выпоры служат для улавливания подымающегося на
поверхность шлака и резервуарами для непомещающегося в форму металла, который
снова стекает в форму по мере того, как остывает и получает усадку отливка
[рис. 414 (q)]. Теперь можно уложить в форму шишки и составить верхнюю и нижнюю опоки.
Если форма предназначена для тонких отливок из сплавов, то предварительно
следует прогреть обе половины формы с помощью ручной горелки. Процесс изготовления шишки заключается в следующем. Шишечные ящики
наполняют смесью крупного песка со связывающим веществом, утрамбовывают и
снимают излишек песка, проводя по плоскости разъёма ящика краем ровной
пластинки. Перевернув шишечные ящики на лист металла и слегка
постукивая по ним, освобождают обе половины шишки и потом отжигают их в
печи в течение нескольких часов. Затем половинки склеивают между собой смесью,
из которой они сделаны, или клеем и снова отжигают (рис. 415). Для изготовления
шишек применяют чистый кварцевый песок, просеянный через сито № 50, но задержанный
ситом № 70. В качестве связывающих может служить большое количество веществ,
полный список которых читатель найдёт в руководствах по литейному делу. Если
в качестве связывающего вещества взято льняное масло, то шишки отжигают в течение полутора часов при температуре 220°С. Если пользуются другими связывающими веществами, то прокаливание ведётся в течение полутора
часов при 175°С. Наиболее прочные шишки получают, когда пользуются льняным
маслом; смола и дёготь дают наименее прочные шишки. Тонкие, ломкие шишки часто укрепляют железной проволокой. Если шишка
очень велика, то необходимо, чтобы газы, образующиеся в ней при заливке металла,
имели выход, так как в противном случае они могут раздуть отливку. Чтобы этого
не случилось, в песок, идущий на изготовление шишек, вкладывают полоски воска.
Когда шишки прокаливаются, воск вытекает, оставляя отверстия для выхода газов. Расплавленный металл вливают в форму осторожно. Предварительно
следует снять шлак и накипь, образующиеся на поверхности находящегося в ковше
или тигле металла. Если металл имеет достаточно низкую температуру
плавления, позволяющую использовать железный сосуд, то можно воспользоваться
чайником, у которого носик сообщается с нижней частью. В этом случае при
заливке металла в форму плавающий шлак и окислы останутся внутри чайника. Если
форма вмещает большое количество металла, то рабочий, обычно, размешивает в ней метал, погружая в выпор железный прут и двигая его вверх и вниз. Благодаря размешиванию, находящийся в выпоре
металл не затвердевает до тех пор, пока не затвердеют внешние слои отливки. Обычно большие отливки оставляют остывать на всю ночь. Меньшие отливки
можно извлекать из формы немедленно. Иногда, при изготовлении инструментов,
небольшие отливки извлекают из форм ещё нагретыми до
красного каления и погружают их в воду. Образующийся при этом пар сдувает
песок с поверхности отливки и даже выдувает из неё шишки. Полученные таким
образом отливки оказываются совершенно чистыми. Когда отливка вынута из формы [рис. 414 (u)], нужно обрубить литник, выпоры и
жёлоб. Если отливка изготовляется самой лабораторией, то нужно помнить о том,
что литники и выпоры увеличивают количество металла, необходимого для изготовления
отливки. Литейная не включает этот металл в стоимость
отливки, так как литник и выпоры идут снова в дело. Баббиты состоят в основном из сплава свинца и олова с некоторым количеством
сурьмы, достаточным для того, чтобы при застывании металл несколько расширялся. Отливка в формах из раковин. Остаётся ещё один метод отливки изделий, который может оказаться полезным в лабораторных условиях, — отливка в формах из раковин каракатицы. Достоинства этого метода заключаются в его простоте и быстроте изготовления отливки:
изготовление и заливка формы отнимают около получаса. Однако отливаемое изделие
не может иметь толщину более 6 — 7 мм, ширину более 40 мм и длину
более 75 мм. Модель должна быть металлической, так как она подвергается
давлению. Конусность может быть весьма мала или даже совсем отсутствовать. Не
должно быть шишек. Рис. 418 даёт ясное представление об этом методе. Мягкая
известковая поверхность раковины весьма податлива и сохраняет очень чёткий
отпечаток любого вдавленного предмета. Джон Стронг «Практика современной физической лаборотории», ОГИЗ, Ленинград, 1948, стр. 415-437. |
Пустотелое литье металла – технологии и инновации
Пустотелое литье металла применяется в том случае если необходимо получить отливку с большим количеством мелких деталей или отверстий. Обычно пустотелое литье металла используется не только на заводах, но и некоторыми мастерами в домашних условиях.
Для начала нужно изготовить модель будущей детали и форму. Лучше всего брать смесь парафина и стеарина, приблизительно по 50% каждого и из этого материала делать модель. После создания ее покрывают смесью на основе керамики и обжигают.
Парафин внутри плавится и испаряется. Если форму разрезать, то на стенках керамики получится отпечаток модели. Если потом сложить две половинки и налить внутрь полости расплавленный металл, то получится металлическая копия парафиновой модели. Это наиболее простая и доступная технология пустотелого литья металла, которая применяется на литейных заводах.
Преимущества
Этот метод нашел применение в тех случаях, когда необходимо отлить заготовки с четкими формами и размерами. Обычная штамповка или ковка не всегда для этого подходит. Жидкий металл имеет свойство заполнять все пустоты в форме, поэтому это наиболее оптимальный способ добиться желаемого результата. Среди главных достоинств пустотелого литья можно назвать такие, как:
— высокое качество;
— надежность;
— доступность;
— простота;
— разнообразие форм и моделей.
Пустотелое литье набирает популярность благодаря простоте метода и доступности. К тому же с каждым годом растет потребность в отливках с точными линиями и формами. Среди инноваций в этой технологии можно назвать применение вакуума для заливки металла в форму.
Вакуум удаляет всю грязь, воздух и металл полностью заполняет все существующие пустоты. Для этого используют дополнительное оборудование, но отсутствие необходимости обрабатывать готовые отливки делает эту технологию выгодной в производственных масштабах.
Подготовка
Литье из чистого металла или сплавов требует наличия оборудования, модели и формы. В последнее время модель изготавливают также из пенопласта. Во время выгорания внутри керамического слоя пенопласт оставляет на стенках керамики отпечаток своей формы, после чего можно отливать детали.
К тому же, пенопласт дешевый и есть в необходимом количестве.
Изготовить из него модель проще, чем из стеарина или воска.
Время, которое идет на изготовление модели, зависит от сложности будущей детали. Если много мелких элементов, углублений и отверстий, то изготовление займет больше времени. Остатки пенопласта или парафина вымываются водой под сильным давлением.
Применяемая на предприятиях технология пустотелого литья не имеет существенных недостатков. Нужно только следить за состоянием формы. Она должна быть без дефектов и серьезных повреждений. Если все нормально, то заготовка получится высокого качества.
Отливка металлических изделий по 3D-печатным фотополимерным формам
Компания Formlabs, производитель популярных настольных фотополимерных 3D-принтеров линейки Form, опубликовала руководство по литью металлических моделей в формы, напечатанные из фирменной «высокотемпературной» фотополимерной смолы. Само собой, надеяться на возможность отливки деталей из тугоплавких металлов не стоит. Речь идет лишь о работе с относительно легкоплавкими металлами и сплавами, такими как олово, и изготовлении декоративных, а не функциональных моделей. Конечно, ничто не мешает печатать выжигаемые мастер-модели для изготовления гипсовых форм и дальнейшего литья более тугоплавкими металлами, но при работе с оловом можно печатать сами формы, несколько упрощая процесс и повышая качество конечных изделий.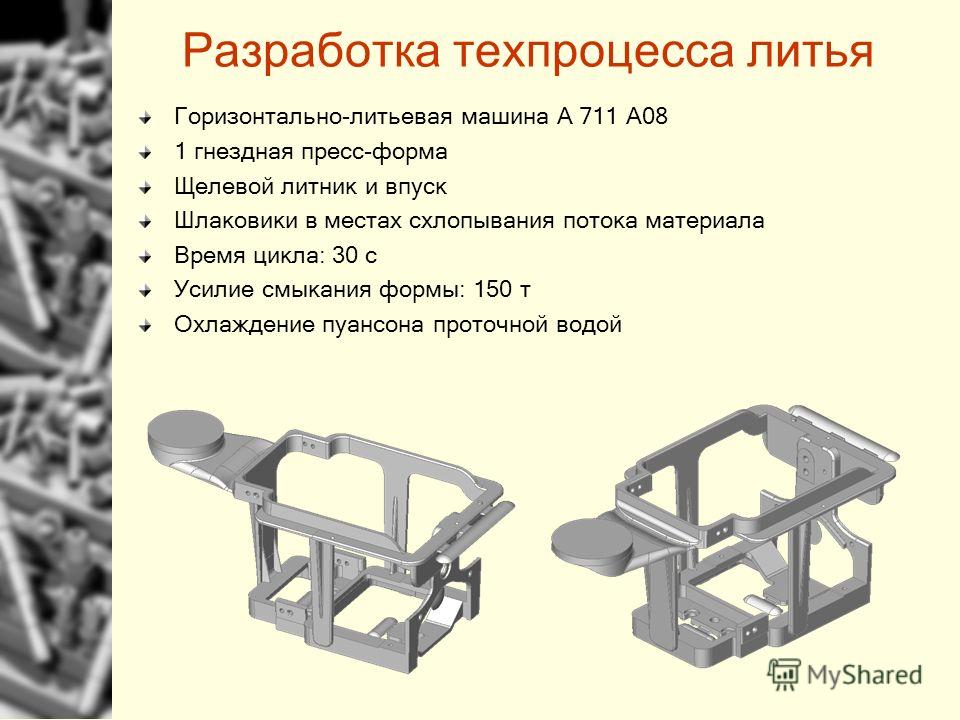
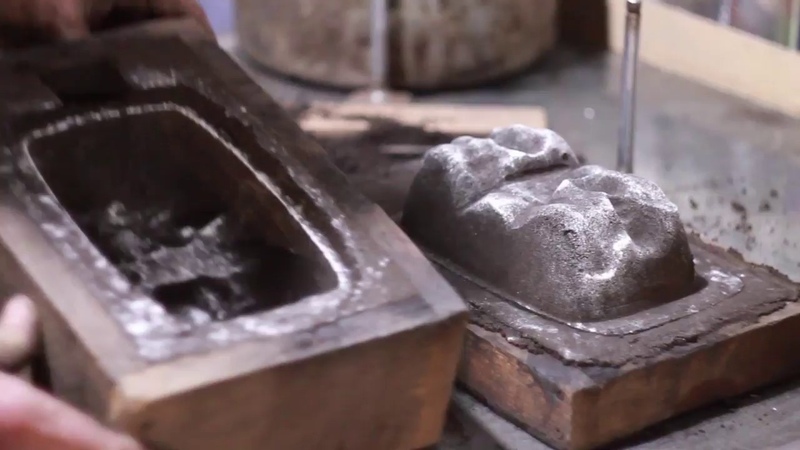

А у вас есть интересные новости? Поделитесь с нами своими разработками, и мы расскажем о них всему миру! Ждем ваши идеи по адресу [email protected].
Литье (металлообработка) — Casting (metalworking)
Заливка жидкого металла в форму
Расплавленный металл перед разливкой Отливка чугуна в песчаной формеВ металлообработке и производстве ювелирных изделий литье — это процесс, при котором жидкий металл доставляется в форму (обычно с помощью тигля ), которая содержит негативное изображение (т. Е. Трехмерное негативное изображение) заданной формы. Металл заливается в форму через полый канал, называемый литником . Затем металл и форма охлаждают, а металлическую часть ( отливку ) извлекают. Литье чаще всего используется для изготовления сложных форм, изготовление которых другими методами было бы затруднительно или неэкономично.
Процессы литья известны тысячи лет и широко используются для изготовления скульптур (особенно из бронзы ), ювелирных изделий из драгоценных металлов , оружия и инструментов. Высокотехнологичные отливки используются в 90 процентах товаров длительного пользования, включая автомобили, грузовики, авиакосмическую промышленность, поезда, горнодобывающее и строительное оборудование, нефтяные скважины, приборы, трубы, гидранты, ветряные турбины, атомные станции, медицинские устройства, оборонные изделия, игрушки и более.
Традиционные методы включают литье по выплавляемым моделям (которое может быть далее разделено на центробежное литье и литье с прямой заливкой с помощью вакуума ), литье в гипсовые формы и литье в песчаные формы .
Современный процесс литья подразделяется на две основные категории: литье одноразового и длительного пользования. Кроме того, он разрушается материалом формы, например песком или металлом, и методом разливки, таким как сила тяжести, вакуум или низкое давление.
Литье в расходные формы
Литье в расходные формы — это общая классификация, которая включает формованные изделия из песка, пластика, ракушечника, гипса и лепные изделия (техника выплавляемого воска). Этот метод литья в формы предполагает использование временных одноразовых форм.
Литье в песок
Литье в песчаные формы — один из самых популярных и простых видов литья, применяемый веками. Литье в песчаные формы позволяет производить меньшие партии, чем постоянное литье в формы, и по очень разумной цене. Этот метод не только позволяет производителям создавать изделия с низкими затратами, но и дает другие преимущества литья в песчаные формы, такие как операции очень малых размеров. Этот процесс позволяет отливки, достаточно маленькие, умещающиеся на ладони, и достаточно большие, только для станины поездов (одна отливка может создать всю станину для одного вагона). Литье в песчаные формы также позволяет разливать большинство металлов в зависимости от типа песка, используемого для форм.
Для литья в песчаные формы требуется несколько дней, а иногда и недель, для производства с высокой производительностью (1–20 штук в час на пресс-форму), и он является непревзойденным для производства крупных деталей. Зеленый (влажный) песок, имеющий черный цвет, почти не имеет ограничения по массе, тогда как для сухого песка практический предел массы составляет 2 300–2 700 кг (5 100–6 000 фунтов). Минимальный вес детали составляет 0,075–0,1 кг (0,17–0,22 фунта). Для связывания песка используются глины, химические связующие или полимеризованные масла (например, моторное масло). В большинстве операций песок можно повторно использовать повторно, и он не требует значительного обслуживания.
Формовка из суглинка
Литье из глины использовалось для изготовления больших симметричных объектов, таких как пушки и церковные колокола. Суглинок — это смесь глины и песка с соломой или навозом. Модель изготовленного изделия сформирована из рыхлого материала (сорочка). Форма формируется вокруг этой сорочки, покрывая ее суглинком. Затем это запекается (обжигается), и сорочка снимается. Затем форму ставят вертикально в яму перед печью для разливки металла. После этого форма отламывается. Таким образом, формы можно использовать только один раз, поэтому для большинства целей предпочтительны другие методы.
Литье по гипсовой форме
Литье из гипса аналогично литью в песчаные формы, за исключением того, что вместо песка в качестве материала формы используется гипс . Как правило, на подготовку формы уходит меньше недели, после чего достигается производительность 1–10 единиц / час формы для изделий массой от 45 кг (99 фунтов) и массой до 30 г (1 унция). с очень хорошей обработкой поверхности и жесткими допусками . Литье из гипса является недорогой альтернативой другим процессам формования сложных деталей из-за низкой стоимости гипса и его способности производить отливки почти чистой формы . Самый большой недостаток заключается в том, что его можно использовать только с цветными материалами с низкой температурой плавления, такими как алюминий, медь, магний и цинк.
Формование корпуса
Формовка раковины аналогична литью в песчаные формы, но полость формовки образована закаленной «скорлупой» из песка, а не колбой, заполненной песком. Используемый песок более мелкий, чем песок для литья под давлением, и смешивается со смолой, так что он может нагреваться посредством рисунка и затвердевать в оболочку вокруг рисунка. Из-за смолы и более мелкого песка он дает гораздо более тонкую поверхность. Процесс легко автоматизируется и более точен, чем литье в песчаные формы. Обычные литые металлы включают чугун , алюминий, магний и медные сплавы. Этот процесс идеально подходит для сложных предметов от малого до среднего.
Литье по выплавляемым моделям
Крышка клапана из литья под давлением
Литье по выплавляемым моделям (известное в искусстве как литье по выплавляемым моделям ) — это процесс, который практикуется на протяжении тысяч лет, причем процесс литья по выплавляемым моделям является одним из старейших известных методов обработки металлов давлением. Начиная с 5000 лет назад, когда пчелиный воск формировал узор, до современных высокотехнологичных восков, огнеупорных материалов и специальных сплавов, отливки обеспечивают производство высококачественных компонентов с ключевыми преимуществами точности, повторяемости, универсальности и целостности.
Литье по выплавляемым моделям получило свое название от того факта, что узор покрыт огнеупорным материалом или окружен им. Восковые модели требуют особой осторожности, поскольку они недостаточно прочные, чтобы выдерживать нагрузки, возникающие при изготовлении формы. Одним из преимуществ литья по выплавляемым моделям является то, что воск можно использовать повторно.
Этот процесс подходит для воспроизводимого производства деталей чистой формы из различных металлов и сплавов с высокими эксплуатационными характеристиками. Хотя этот процесс обычно используется для небольших отливок, этот процесс использовался для производства полных дверных коробок самолетов, со стальными отливками до 300 кг и алюминиевыми отливками до 30 кг. По сравнению с другими процессами литья, такими как литье под давлением или литье в песчаные формы , это может быть дорогостоящий процесс. Однако компоненты, которые могут быть изготовлены с использованием литья по выплавляемым моделям, могут иметь замысловатые контуры, и в большинстве случаев компоненты отливаются по форме, близкой к конечной, поэтому после литья требуется небольшая доработка или не требуется ее вовсе.
Отходы лепки из гипса
Прочный гипсовый промежуточный продукт часто используется в качестве этапа при изготовлении бронзовой скульптуры или в качестве ориентира для создания резного камня. После завершения штукатурки работа становится более долговечной (при хранении в помещении), чем глиняный оригинал, который необходимо поддерживать во влажном состоянии, чтобы избежать трещин. Имея под рукой недорогую штукатурку, дорогостоящие работы по бронзовому литью или резьбе по камню могут быть отложены до тех пор, пока не будет найден покровитель, и, поскольку такая работа считается техническим, а не художественным процессом, ее можно даже отложить на неопределенный срок. художника.
При формовании отходов обычная и тонкая гипсовая форма, армированная сизалем или мешковиной, заливается поверх исходной глиняной смеси. После затвердевания он затем удаляется из влажной глины, попутно разрушая мелкие детали в поднутрениях, присутствующих в глине, но которые теперь удерживаются в форме. Затем форма может быть использована в любое более позднее время (но только один раз) для отливки гипсового позитивного изображения, идентичного исходной глине. Поверхность этой штукатурки может быть дополнительно обработана, окрашена и покрыта воском, чтобы она напоминала законченную бронзовую отливку.
Литье по схеме испарения
Это класс процессов литья, в которых используются материалы шаблона, которые испаряются во время заливки, что означает, что нет необходимости извлекать материал шаблона из формы перед литьем. Двумя основными процессами являются литье по потерянной пены и литье в полную форму.
Литье по потере пены
Литье по выплавляемым моделям — это тип процесса литья по выпариванию, который похож на литье по выплавляемым моделям, за исключением того, что вместо воска используется пена. В этом процессе используется низкая температура кипения пены, чтобы упростить процесс литья по выплавляемым моделям, устраняя необходимость плавить воск из формы.
Литье в полную форму
Литье в полную форму — это процесс литья по схеме испарения, который представляет собой комбинацию литья в песчаные формы и литья по потерянной пене . Он использует пенополистирол образец пенопласта , который затем в окружении песка, так же, как литье в песчаные формы . Затем металл заливается прямо в форму, которая при контакте испаряет пену.
Литье в формы длительного пользования
Постоянный процесс формованияЛитье в формы длительного пользования отличается от процессов одноразового использования тем, что форму не требуется повторно формовать после каждого производственного цикла. Этот метод включает как минимум четыре различных метода: постоянное литье, штамповку, центробежное литье и непрерывное литье. Эта форма литья также приводит к улучшенной повторяемости производимых деталей и обеспечивает результаты, близкие к чистой форме .
Постоянное литье в форму
Литье в постоянные формы — это процесс литья металла, в котором используются формы многократного использования («постоянные формы»), обычно сделанные из металла . Чаще всего для заполнения формы используется сила тяжести. Однако также используются давление газа или вакуум . Разновидность типичного процесса литья под действием силы тяжести, называемого отливкой из шлама , позволяет получать полые отливки. Обычные литейные металлы — это сплавы алюминия , магния и меди . Другие материалы включают сплавы олова , цинка и свинца, а также железо и сталь, которые также разливают в графитовых формах. Постоянные формы, выдерживающие более одного литья, имеют ограниченный срок службы до износа.
Литье под давлением
В процессе литья под давлением расплавленный металл под высоким давлением попадает в полости формы (которые обрабатываются в штампы). Большинство отливок под давлением изготавливается из цветных металлов , особенно из сплавов на основе цинка , меди и алюминия, но возможно литье под давлением из черных металлов . Метод литья под давлением особенно подходит для применений, где требуется много деталей малого и среднего размера с хорошей детализацией, прекрасным качеством поверхности и однородностью размеров.
Полутвердое металлическое литье
Отливка из полутвердого металла (SSM) — это модифицированный процесс литья под давлением, который снижает или устраняет остаточную пористость, присутствующую в большинстве отливок под давлением. Вместо использования жидкого металла в качестве исходного материала, при литье SSM используется исходный материал с более высокой вязкостью, который является частично твердым и частично жидким. Модифицированная машина для литья под давлением используется для впрыскивания полутвердой суспензии в многократно используемые штампы из закаленной стали. Высокая вязкость полутвердого металла, наряду с использованием контролируемых условий заполнения фильеры, гарантирует, что полутвердый металл заполняет матрицу нетурбулентным образом, так что вредная пористость может быть практически устранена.
Отливки из SSM, используемые в промышленных масштабах в основном для алюминиевых и магниевых сплавов, могут подвергаться термообработке до состояния T4, T5 или T6. Комбинация термообработки, высоких скоростей охлаждения (за счет использования стальных штампов без покрытия) и минимальной пористости обеспечивает отличное сочетание прочности и пластичности. К другим преимуществам литья из SSM относятся способность создавать детали сложной формы, герметичность, жесткие допуски на размеры и возможность отливать тонкие стенки.
Центробежное литье
В этом процессе расплавленный металл заливается в форму и дает возможность затвердеть, пока форма вращается. Металл заливается в центр формы по ее оси вращения. За счет силы инерции жидкий металл выбрасывается к периферии.
Центробежное литье не зависит как от силы тяжести, так и от давления, поскольку оно создает собственную подачу силы с помощью временной песчаной формы, удерживаемой в прядильной камере. Время выполнения зависит от приложения. Полу- и истинно центробежная обработка позволяет изготавливать пресс-форму со скоростью 30–50 штук в час с практическим пределом для серийной обработки примерно 9000 кг общей массы с типичным пределом на единицу 2,3–4,5 кг.
В промышленном отношении центробежное литье железнодорожных колес было одним из первых применений метода, разработанного немецкой промышленной компанией Krupp, и эта возможность способствовала быстрому росту предприятия.
Небольшие предметы искусства, такие как ювелирные изделия, часто отливаются этим методом с использованием процесса выплавляемого воска, поскольку силы позволяют довольно вязким жидким металлам проходить через очень маленькие проходы и превращаться в мелкие детали, такие как листья и лепестки. Этот эффект аналогичен преимуществам вакуумного литья, а также применяется к литью ювелирных изделий.
Непрерывное литье
Непрерывное литье — это усовершенствованный процесс литья для непрерывного крупносерийного производства металлических профилей с постоянным поперечным сечением. Расплавленный металл заливается в форму с открытым концом и водяным охлаждением, что позволяет сформировать «пленку» твердого металла над все еще жидким центром, постепенно затвердевая снаружи внутри. После затвердевания нить по мере ее иногда называется, непрерывно извлекается из формы. Пряди заданной длины можно отрезать механическими ножницами или перемещающимися кислородно-ацетиленовыми горелками и передать на дальнейшие процессы формования или на склад. Размеры отливок могут варьироваться от полосы (толщиной несколько миллиметров и шириной около пяти метров) до заготовок (квадрат от 90 до 160 мм) до плит (шириной 1,25 м и толщиной 230 мм). Иногда перед резкой прядь может пройти первоначальный процесс горячей прокатки .
Непрерывное литье используется из-за более низких затрат, связанных с непрерывным производством стандартного продукта, а также повышения качества конечного продукта. Такие металлы, как сталь, медь, алюминий и свинец, разливаются непрерывно, причем сталь является металлом с наибольшей массой, отлитой с использованием этого метода.
Терминология
В процессах литья металлов используется следующая терминология:
- Шаблон : приблизительный дубликат окончательной отливки, использованной для формирования полости формы.
- Формовочный материал: материал, который упаковывается вокруг шаблона, а затем шаблон удаляется, чтобы оставить полость, в которую будет заливаться литейный материал.
- Колба : жесткий деревянный или металлический каркас, удерживающий формовочный материал.
- Cope : верхняя половина выкройки, колбы, формы или стержня.
- Перетащите : нижнюю половину выкройки, колбы, формы или стержня.
- Сердечник : вставка в литейную форму, которая создает внутренние элементы в отливке, например отверстия.
- Отпечаток сердцевины: область, добавленная к узору, сердцевине или форме, используемая для определения местонахождения и поддержки сердцевины.
- Полость пресс-формы: объединенная открытая зона формовочного материала и сердечника, где металл заливается для производства отливки.
- Подъемник : дополнительная пустота в форме, которая заполняется расплавленным материалом для компенсации усадки во время затвердевания.
- Система вентиляции: сеть соединенных каналов, по которым расплавленный материал поступает в полости формы.
- Разливочная чашка или сливной резервуар: часть литниковой системы, которая принимает расплавленный материал из разливочной емкости.
- Литник : Разливочная чашка прикрепляется к литнику, который является вертикальной частью литниковой системы. Другой конец литника прикрепляется к направляющим.
- Направляющие: горизонтальная часть литниковой системы, которая соединяет литники с воротами.
- Ворота: Контролируемый вход бегунов в полости формы.
- Вентиляционные отверстия: дополнительные каналы, обеспечивающие отвод газов, образующихся во время заливки.
- Линия разъема или поверхность разъема: граница раздела между половиной выступа и половинками формы, опоки или шаблона.
- Осадка : конус на отливке или шаблоне, позволяющий извлекать ее из формы.
- Ящик для стержней: пресс-форма или матрица, используемая для производства стержней.
- Венчик: Длинный вертикальный удерживающий стержень для сердечника, который после литья становится неотъемлемой частью литья, обеспечивает поддержку сердечника.
Некоторые специализированные процессы, такие как литье под давлением, используют дополнительную терминологию.
Теория
Литье — это процесс затвердевания , что означает, что явление затвердевания контролирует большинство свойств отливки. Более того, большинство дефектов литья возникает во время затвердевания, например, газовая пористость и усадка при затвердевании .
Отверждение происходит в два этапа: зарождение и рост кристаллов . На стадии зародышеобразования в жидкости образуются твердые частицы. Когда эти частицы образуются, их внутренняя энергия ниже, чем у окружающей жидкости, что создает энергетическую границу между ними. Формирование поверхности на этой границе раздела требует энергии, поэтому, когда происходит зародышеобразование, материал фактически переохлаждается, то есть охлаждается ниже температуры затвердевания из-за дополнительной энергии, необходимой для образования поверхностей раздела. Затем он восстанавливается или снова нагревается до температуры затвердевания для стадии роста кристаллов. Зарождение происходит на уже существующей твердой поверхности, потому что для частичной поверхности раздела требуется не так много энергии, как для полной сферической поверхности раздела. Это может быть выгодно, поскольку мелкозернистые отливки обладают лучшими свойствами, чем крупнозернистые отливки. Мелкозернистая структура может быть вызвана измельчением зерна или инокуляцией , которая представляет собой процесс добавления примесей, чтобы вызвать зародышеобразование.
Все зародыши представляют собой кристалл, который растет по мере извлечения теплоты плавления из жидкости до тех пор, пока жидкость не перестанет существовать. Направление, скорость и тип роста можно контролировать, чтобы максимизировать свойства отливки. Направленное затвердевание — это когда материал затвердевает на одном конце и продолжает затвердевать на другом конце; это наиболее идеальный тип роста зерна, поскольку он позволяет жидкому материалу компенсировать усадку.
Кривые охлаждения
Промежуточные скорости охлаждения из расплава приводят к дендритной микроструктуре. На этом изображении можно увидеть первичные и вторичные дендриты.Кривые охлаждения важны для контроля качества отливки. Самая важная часть кривой охлаждения — это скорость охлаждения, которая влияет на микроструктуру и свойства. Вообще говоря, быстро охлаждаемая область отливки будет иметь мелкозернистую структуру, а область, которая медленно охлаждается, будет иметь крупнозернистую структуру. Ниже приведен пример кривой охлаждения чистого металла или эвтектического сплава с определяющей терминологией.
Обратите внимание, что до термической остановки материал был жидким, а после него — твердым; во время термической остановки материал превращается из жидкости в твердое тело. Также обратите внимание, что чем больше перегрев, тем больше времени у жидкого материала для того, чтобы превратиться в сложные детали.
Приведенная выше кривая охлаждения отображает основную ситуацию с чистым металлом, однако большинство отливок изготовлено из сплавов, кривая охлаждения которых имеет форму, показанную ниже. {n}}
Где t — время затвердевания, V — объем отливки, A — площадь поверхности отливки, которая контактирует с формой , n — постоянная величина, а B — постоянная формы. Это наиболее полезно для определения затвердевания стояка перед отливкой, потому что, если стояк сначала затвердеет, он бесполезен.
Система ворот
Простая система ворот для горизонтальной разделительной формы. Вентиляционная система служит многим целям, наиболее важной из которых является транспортировка жидкого материала к форме, а также контроль усадки, скорости жидкости, турбулентности и улавливания окалины . Затворы обычно прикрепляются к самой толстой части отливки, чтобы помочь контролировать усадку. В особенно больших отливках может потребоваться несколько заслонок или направляющих для ввода металла более чем в одну точку в полости кристаллизатора. Скорость материала важна, потому что, если материал движется слишком медленно, он может остыть перед полным заполнением, что приведет к неправильному прохождению и холодному закрытию. Если материал движется слишком быстро, жидкий материал может разрушить форму и загрязнить окончательную отливку. Форма и длина литниковой системы также могут контролировать скорость охлаждения материала; короткие круглые или квадратные каналы минимизируют потери тепла.
Система ворот может быть спроектирована так, чтобы минимизировать турбулентность, в зависимости от отливаемого материала. Например, сталь, чугун и большинство медных сплавов нечувствительны к турбулентности, но сплавы алюминия и магния чувствительны к турбулентности. Нечувствительные к турбулентности материалы обычно имеют короткую и открытую литниковую систему, чтобы заполнить форму как можно быстрее. Однако для материалов, чувствительных к турбулентности, используются короткие литники, чтобы минимизировать расстояние, на которое материал должен упасть при входе в форму. Прямоугольные разливочные стаканы и конические литники используются для предотвращения образования завихрений при попадании материала в форму; эти вихри имеют тенденцию засасывать газ и оксиды в форму. Большой литник используется для рассеивания кинетической энергии жидкого материала, когда он падает вниз по литнику, что снижает турбулентность. Дроссель , который является самой маленькой площадью поперечного сечения в литниковой системе , используемой для управления потоком, может быть размещен вблизи литника хорошо , чтобы замедлить и сгладить поток. Обратите внимание, что на некоторых формах штуцер по-прежнему размещается на воротах, чтобы облегчить разделение детали, но вызывает сильную турбулентность. Затворы обычно прикрепляются к нижней части отливки, чтобы минимизировать турбулентность и разбрызгивание.
Вентиляционная система также может быть разработана для улавливания окалины. Один из методов состоит в том, чтобы воспользоваться тем фактом, что часть шлака имеет более низкую плотность, чем основной материал, поэтому он всплывает в верхнюю часть литниковой системы. Следовательно, длинные плоские полозья с воротами, выходящими из нижней части полозьев, могут задерживать шлаки в полозьях; Учтите, что длинные плоские полозья охлаждают материал быстрее, чем круглые или квадратные полозья. Для материалов, у которых плотность окалины аналогична плотности основного материала, таких как алюминий, могут быть предпочтительными удлинители рабочего стола и желоба . В них используется преимущество того факта, что окалина обычно находится в начале заливки, поэтому желоб проходит за последние затворы, и загрязнения содержатся в колодцах. Сетки или фильтры также могут использоваться для улавливания загрязнений.
Важно, чтобы размер литниковой системы был небольшим, потому что все это необходимо вырезать из отливки и переплавить для повторного использования. Эффективность или производительность литейной системы можно рассчитать, разделив вес отливки на вес залитого металла. Следовательно, чем выше число, тем эффективнее система затворов / стояки.
Усадка
Есть три типа сжатия: сжатие жидкости , усадки при затвердевании и усадке модельщика в . Усадка жидкости редко является проблемой, потому что в форму за ней течет больше материала. Усадка при затвердевании происходит из-за того, что металлы менее плотны как жидкость, чем твердое тело, поэтому во время затвердевания плотность металла резко увеличивается. Усадка Patternmaker относится к усадке, которая возникает при охлаждении материала от температуры затвердевания до комнатной температуры, что происходит из-за теплового сжатия .
Усадка при затвердевании
Металл | Процент |
---|---|
Алюминий | 6,6 |
Медь | 4.9 |
Магний | 4.0 или 4.2 |
Цинк | 3,7 или 6,5 |
Низкоуглеродистая сталь | 2,5–3,0 |
Высокая углеродистая сталь | 4.0 |
Белый чугун | 4,0–5,5 |
серый чугун | −2,5–1,6 |
Ковкий чугун | −4,5–2,7 |
Большинство материалов сжимаются по мере затвердевания, но, как показано в соседней таблице, некоторые материалы, например серый чугун, этого не делают . Для материалов, которые дают усадку при затвердевании, тип усадки зависит от того, насколько широк диапазон замерзания материала. Для материалов с узким диапазоном замерзания, менее 50 ° C (122 ° F), полость, известная как труба , образуется в центре отливки, потому что внешняя оболочка сначала замерзает и постепенно затвердевает к центру. Чистые и эвтектические металлы обычно имеют узкие интервалы кристаллизации. Эти материалы имеют тенденцию образовывать пленку в формах на открытом воздухе, поэтому они известны как сплавы, образующие пленку . Для материалов с широким диапазоном замерзания, превышающим 110 ° C (230 ° F), гораздо большая часть отливки занимает мягкую или слякотную зону (диапазон температур между солидусом и ликвидусом), что приводит к образованию небольших карманов жидкости. во всем и в конечном итоге пористость. Эти отливки обычно имеют низкую пластичность , вязкость и сопротивление усталости . Более того, чтобы эти типы материалов были непроницаемыми для жидкости, требуется вторичная операция по пропитке отливки металлом или смолой с более низкой точкой плавления.
Для материалов, которые имеют узкие диапазоны затвердевания, трубы могут быть преодолены путем разработки отливки, способствующей направленной кристаллизации, что означает, что отливка сначала замерзает в точке, наиболее удаленной от затвора, а затем постепенно затвердевает к затвору. Это позволяет непрерывно подавать жидкий материал в точке затвердевания, чтобы компенсировать усадку. Обратите внимание, что в месте затвердевания окончательного материала все еще остается усадочная пустота, но при правильной конструкции она будет в литниковой системе или стояке.
Подступенки и подступенки
Различные типы стояков Подъемники, также известные как питатели , являются наиболее распространенным способом обеспечения направленного затвердевания. Он подает жидкий металл в застывающую отливку, чтобы компенсировать усадку при затвердевании. Для правильной работы стояка он должен затвердеть после отливки, иначе он не сможет подавать жидкий металл на усадку внутри отливки. Подступенки увеличивают стоимость отливки, потому что они снижают выход каждой отливки; т.е. больше металла теряется в виде лома при каждой отливке. Другой способ способствовать направленному отверждению — это добавление в пресс-форму холода. Холод — это любой материал, который будет отводить тепло от отливки быстрее, чем материал, используемый для формования.
Подступенки классифицируются по трем критериям. Во-первых, если стояк открыт для атмосферы, тогда он называется открытым стояком, в противном случае он известен как слепой тип. Второй критерий — где находится стояк; если он расположен на отливке, он называется верхним подступенком, а если он расположен рядом с отливкой, он известен как боковой подступенок . Наконец, если стояк расположен на литниковой системе так, что он заполняется после формовочной полости, он известен как активный стояк или горячий стояк , но если стояк заполняется материалами, которые уже прошли через формовочную полость, он известен как мертвый стояк или холодный стояк .
Вспомогательные приспособления для стояков — это элементы, используемые для помощи стоякам в создании направленного затвердевания или уменьшения количества требуемых стояков. Одним из таких элементов является озноб, который ускоряет охлаждение определенной части формы. Выделяют два типа: внешний и внутренний озноб. Наружные холодки представляют собой массы из материала с высокой теплоемкостью и высокой теплопроводностью, которые помещаются на край формовочной полости. Внутренние коконы представляют собой куски того же самого металла, который заливается, которые помещаются внутрь полости формы и становятся частью отливки. Изоляционные втулки и покрытия могут быть также установлены вокруг полости стояка для замедления затвердевания стояка. Змеевики нагревателя также могут быть установлены вокруг или над полостью стояка для замедления затвердевания.
Термоусадочная машина
Металл | Процент | дюйм / фут |
---|---|---|
Алюминий | 1,0–1,3 | 1 / 8 — 5 / 32 |
Латунь | 1.![]() | 3 ⁄ 16 |
Магний | 1,0–1,3 | 1 / 8 — 5 / 32 |
Чугун | 0,8–1,0 | 1 / 10 — 1 / 8 |
Стали | 1,5–2,0 | 3 / 16 — 1 / 4 |
Усадку после затвердевания можно устранить с помощью шаблона увеличенного размера, разработанного специально для используемого сплава. Сужение правило s , или сжиматься правилами S , которые используются , чтобы сделать образцы негабаритного для компенсации этого типа усадки. Эти линейки имеют превышение размера до 2,5% в зависимости от отливаемого материала. Эти правители в основном упоминаются по их процентному изменению. Шаблон, соответствующий существующей детали, будет выполнен следующим образом: сначала существующая деталь будет измерена с помощью стандартной линейки, затем при построении шаблона изготовитель шаблона будет использовать правило сжатия, гарантирующее, что отливка будет сжиматься с правильный размер.
Обратите внимание, что усадка создателя выкройки не учитывает преобразования фазового перехода. Например, эвтектические реакции, мартенситные реакции и графитизация могут вызывать расширение или сжатие.
Полость формы
Полость формы отливки не соответствует точным размерам готовой детали по ряду причин. Эти модификации полости пресс-формы известны как допуски и учитывают усадку, тягу, механическую обработку и деформацию изготовителя модели . В процессах многоразового использования эти припуски передаются непосредственно в постоянную форму, но в процессах одноразовой формы они передаются в шаблоны, которые позже образуют полость формы. Обратите внимание, что для форм длительного пользования требуется допуск на изменение размеров формы из-за нагрева до рабочих температур.
Для поверхностей отливки, перпендикулярных линии разъема формы, необходимо предусмотреть тягу. Это сделано для того, чтобы отливку можно было выпускать в процессах длительного пользования или выкройку можно было извлечь из формы без разрушения формы в процессах одноразового использования. Требуемый угол наклона зависит от размера и формы элемента, глубины полости пресс-формы, способа удаления детали или рисунка из пресс-формы, материала рисунка или детали, материала пресс-формы и типа процесса. Обычно осадка составляет не менее 1%.
Припуск на обработку сильно варьируется от одного процесса к другому. Отливки в песчаные формы обычно имеют шероховатую поверхность, поэтому требуют большего припуска на механическую обработку, тогда как литье под давлением имеет очень чистую поверхность, которая может не требовать каких-либо допусков на обработку. Кроме того, в чертеже может быть достаточно припуска на механическую обработку для начала.
Допуск на искажение необходим только для определенных геометрических форм. Например, U-образные отливки будут иметь тенденцию к деформации, при этом ножки раскладываются наружу, потому что основание формы может сжиматься, когда ножки ограничены формой. Этого можно избежать, спроектировав полость формы для начала с наклоном ноги внутрь. Кроме того, длинные горизонтальные секции имеют тенденцию провисать в середине, если ребра не включены, поэтому может потребоваться поправка на деформацию.
Сердечники могут использоваться в процессах одноразовых форм для изготовления внутренних элементов. Сердцевина может быть металлической, но обычно это песок.
Заполнение
Схема процесса разливки постоянной формы под низким давлениемСуществует несколько распространенных методов заполнения полости формы: гравитация , низкое давление , высокое давление и вакуум .
Вакуумное наполнение, также известное как наполнение противодавлением , более эффективно по металлу, чем заливка самотеком, поскольку меньше материала затвердевает в литниковой системе. Разливка под действием силы тяжести дает выход металла только от 15 до 50% по сравнению с 60-95% при разливке под вакуумом. Также имеется меньшая турбулентность, поэтому систему вентиляции можно упростить, поскольку она не должна контролировать турбулентность. Кроме того, поскольку металл вытягивается из-под верхней части ванны, металл не содержит окалины и шлака, так как они имеют меньшую плотность (легче) и всплывают в верхнюю часть ванны. Перепад давления помогает металлу течь во все детали пресс-формы. Наконец, можно использовать более низкие температуры, что улучшает структуру зерна. Первая запатентованная машина и процесс для вакуумного литья датируются 1879 годом.
Для заполнения под низким давлением используется давление воздуха от 5 до 15 фунтов на квадратный дюйм (от 35 до 100 кПа изб.), Чтобы нагнетать жидкий металл по подающей трубе в полость формы. Это устраняет турбулентность, присущую гравитационному литью, и увеличивает плотность, повторяемость, допуски и однородность зерна. После затвердевания отливки давление сбрасывается, и оставшаяся жидкость возвращается в тигель, что увеличивает выход.
Наклонное наполнение
Заполнение под наклоном , также известное как литье под наклоном , представляет собой необычный метод заполнения, при котором тигель прикрепляется к литниковой системе, и оба они медленно вращаются, так что металл входит в полость формы с небольшой турбулентностью. Целью является уменьшение пористости и включений за счет ограничения турбулентности. Для большинства применений заполнение под наклоном невозможно из-за следующей проблемы: если система вращается достаточно медленно, чтобы не вызывать турбулентность, передняя часть потока металла начинает затвердевать, что приводит к неправильному ходу. Если система вращается быстрее, это вызывает турбулентность, которая не дает цели. Дюрвиль из Франции был первым, кто попробовал использовать наклонный заброс в 1800-х годах. Он попытался использовать его для уменьшения дефектов поверхности при отливке чеканки из алюминиевой бронзы .
Макроструктура
Макроструктура зерен в слитках и большинстве отливок имеет три отдельные области или зоны: зону охлаждения, столбчатую зону и равноосную зону. На изображении ниже изображены эти зоны.
Зона охлаждения названа так потому, что она возникает у стенок формы, где стена охлаждает материал. Здесь происходит фаза зародышеобразования в процессе затвердевания. Чем больше тепла удаляется, тем больше зерна увеличиваются к центру отливки. Это тонкие длинные колонны , расположенные перпендикулярно поверхности отливки, что нежелательно, поскольку они обладают анизотропными свойствами. Наконец, в центре равноосной зоны расположены сферические беспорядочно ориентированные кристаллы. Это желательно, поскольку они обладают изотропными свойствами. Созданию этой зоны можно способствовать, используя низкую температуру разливки, включения сплава или модификаторы .
Осмотр
Обычными методами контроля стальных отливок являются испытания на магнитные частицы и испытания на проникающую способность . Распространенными методами контроля алюминиевых отливок являются радиография , ультразвуковой контроль и проникающий контроль .
Дефекты
Есть ряд проблем, с которыми можно столкнуться в процессе литья. Основными типами являются: газовая пористость , усадочные дефекты , плесень дефектов материала , заливки металла дефектов , а также металлургические дефекты .
Моделирование процесса литья
Высокопроизводительное программное обеспечение для моделирования процессов литья предоставляет возможности для интерактивной или автоматизированной оценки результатов (например, заполнения формы и затвердевания, пористости и характеристик текучести). Фото: Componenta BV, Нидерланды)При моделировании процесса литья используются численные методы для расчета качества литых деталей с учетом заполнения литейной формы, затвердевания и охлаждения, а также обеспечивается количественный прогноз механических свойств отливки, термических напряжений и деформации. Моделирование точно описывает качество литого компонента до начала производства. Литую оснастку можно спроектировать с учетом требуемых свойств компонентов. Это дает преимущества, помимо сокращения количества проб перед производством, поскольку точная компоновка всей системы литья также приводит к экономии энергии, материалов и инструментов.
Программное обеспечение поддерживает пользователя в проектировании компонентов, определении практики плавления и методах литья, вплоть до изготовления моделей и форм, термообработки и чистовой обработки. Это экономит затраты на всем процессе изготовления отливок.
Моделирование процесса литья изначально разрабатывалось в университетах с начала 70-х годов, в основном в Европе и США, и считается наиболее важной инновацией в технологии литья за последние 50 лет. С конца 80-х годов доступны коммерческие программы, которые позволяют литейным предприятиям по-новому взглянуть на то, что происходит внутри формы или штампа в процессе литья.
Смотрите также
Рекомендации
Примечания
Библиография
- Блэр, Малькольм; Стивенс, Томас Л. (1995), Справочник по стальному литью (6-е изд.), ASM International, ISBN 978-0-87170-556-3 .
- Дегармо, Э. Пол; Black, J T .; Козер, Рональд А. (2003), Материалы и процессы в производстве (9-е изд.), Wiley, ISBN 0-471-65653-4 .
- Калпакджян, Серопе; Шмид, Стивен (2006), Производство и технология (5-е изд.
), Пирсон, ISBN 0-13-148965-8 .
- Киссел, Дж. Рэндольф; Ферри, Роберт Л. (2002), Алюминиевые конструкции: руководство по их спецификациям и дизайну (2-е изд.), John Wiley and Sons, ISBN 978-0-471-01965-7 .
- Schleg, Frederick P .; Kohloff, Frederick H .; Сильвия, Дж. Герин; Американское литейное общество (2003), Технология литья металлов , Американское литейное общество, ISBN 978-0-87433-257-5 .
- Стефанеску, Дору Майкл (2008), Наука и техника затвердевания отливок (2-е изд.), Springer, ISBN 978-0-387-74609-8 .
- Рави, Б. (2010), Металлическое литье: компьютерное проектирование и анализ (1-е изд.), PHI, ISBN 978-81-203-2726-9 .
внешняя ссылка
Викискладе есть медиафайлы по теме кастинга .![]() |
Как сделать форму для литья
Изготовление литейных форм, на фрезерном станке Roland Modela
Студент ФабЛаба рассказывает, как она сделала форму для литья на фрезерном станке Roland Modela, и отлила в форму металл и пластик.
Задача: Разработать произвольную фигурку или изделие, которое мы могли бы повторить несколько раз, сделав для него форму для литья.
Я решила скачать модель фигуры с Thingiverse и по-своему персонализировать её в Rhinoceros. Мне хотелось попробовать поработать с твёрдыми материалами такими как металл или жесткий пластик, поэтому сама форма для литья должна была быть мягкой. Контрформу мы делали из воска для моделирования с помощью фрезерного станка Roland Modela, а для самой формы мы использовали термостойкий силикон.
Скачать файл модели формы можно здесь:
Rhino 3D модель Формы для литья [.3dm]
Общие рекомендации при изготовлении формы и контрформы:
1) Рассчитайте диаметр используемой фрезы. Убедитесь, что вы оставляете достаточно места между вашим изделием и стенкой контрформы.
2) Оставьте отверстие достаточного размера для заливания материала, а также дополнительное вентиляционное отверстия для выхода воздуха.
3) Стенки контрформы должны быть немного наклонены.
4) Если вы делаете форму из двух частей, не забудьте сделать шипы и пазы для точного соединения половинок.
5) Помните, что для отливки твердых изделий нужны мягкие формы.
6) Обратите внимание на соотношение смешиваемых материалов отливки.
Процесс изготовления
Изменить форму черепа я пробовала двумя разными способами, чтобы получить двустороннюю форму для отливки. Так как отливать я буду из металла, и изделие будет твердым, то сама форма должна быть мягкой. Я подготовила 3D-модель контрформы в Rhinoceros, которую буду вырезать из бруска воска для моделирования размером 7,0 X 14,1 X 3,5 см. Также я учла и оставила необходимые отверстия для заливки металла и вентиляционные отверстия.
После того, как я закончила делать 3D-модель, я стала вырезать из бруска модельного воска контрформу, на фрезерном станке Roland Modela. Для черновой обработки я использовала концевую 2-зубую фрезу диаметром 3 мм, для чистовой — сферическую фрезу диаметром 1,5 мм. Я прошлась по чистовой только в одном направлении (ху), так как на мой взгляд и этого было вполне достаточно, и дополнительная обработка была ни к чему, а время — сэкономилось. На черновую и чистовую обработку в общей сложности ушло примерно 3 часа и 20 минут.
Когда контрформа была вырезана, я начала делать собственно саму форму из термостойкого силикона. Как я упоминала ранее, форма должна была быть не только мягкой, но и очень термостойкой, поэтому я использовала силикон повышенной термостойкости Mold MAX® 60.
Порядок действий изготовления нашей формы для литья:
1) Нанести некоторое количество универсальной разделительной смазки-спрея и дать ей подсохнуть в течение 3 минут.
2) Сделать смесь для силикона: компоненты A и B смешиваются в массовой пропорции 100A:3B (или согласно инструкции к тому силикону, который вы используете).
3) Вылить смесь в контрформу, убедившись, что внутрь не попали пузырьки воздуха.
4) На всякий случай тщательно простучать форму, пока все пузырьки воздуха не выйдут на поверхность.
5) Дать силикону застыть в течение суток.
К сожалению, в моём случае получилось так, что через сутки силикон был всё ещё незастывшим. Оказалось, что весы были испорчены, показывали неверный результат, и я смешала в неправильной пропорции! После очистки контрформы с помощью воды и мыла я постаралась сделать всё правильно.
Хоть и со второго раза, но получилось же!
Теперь всё готово к долгожданной отливке.
Для того, чтобы отлить металлические изделия я сделала следующие шаги:
1) Добавить тальк в форму.
2) Нагреть печку или сосуд, в котором будете плавить металл, подождать пока ваши заготовки расплавятся. Соблюдайте технику безопасности и работайте в перчатках!
3) Сложить обе части формы и выровняв сжать их каким-нибудь удобным для вас способом. Части формы должны быть хорошо сжаты, чтобы не допустить протечек.
4) Аккуратно и неспешно залить расплавленный металл.
5) Сразу же окунуть форму в холодную воду для охлаждения. Оставить форму в воде до тех пор, пока она достаточно хорошо не остынет и можно будет её трогать.
6) Снять форму и достать ваше изделие.
Черепа вышли очень неплохими, с хорошей детализацией. Один из них я отполировала, а второй оставила без обработки (см. рисунки).
После завершения работ с металлом, я попробовала сделать то же самое из пластика.
Процесс был проще, так как пропорция смеси для материала составляет 1:1.
Также пластиком легче оперировать, он не горячий и отливать из него проще.
Результат на картинке:
Мелкое литье цветных металлов с нуля — Литье в домашних условиях
Ну вот, добрались до формовки. Решил не гнуть пальцы, быть ближе к народу (Ленин на субботнике бревно таскал — а чем я хуже? 🙂 ). В смысле, что отливка будет проходить в самодельные формовочные массы, рецепты которых буду менять на ходу и тут же выкладывать вместе с результатами.
—————-
Небольшое лирическое отступление о формовочных массах.
На использование фирменных я перешел не оттого, что они гарантируют какой-то результат или удобнее в работе. Банальное стечение обстоятельств — нужно лить, кончился огнеупор, а где его срочно найти — ХЗ, к тому же уже знал, где и почем можно купить фирменную. Купил, попробовал — ничотак, сойдет. А потом уже, естественно — зачем что-то мудрить самому, когда все есть готовое.
Поскольку я не ювелир, озабоченный каждодневной гонкой объемов, то могу спокойно сравнить свой опыт использования самопальных масс с фирменными. Так вот, никакого облегчения при переходе на фирменную массу я не получил. Плюс единственный — я точно знаю ее в работе, что и как с ней делать, работать могу на автопилоте. Остальное — минусы. По технологии производителя, опоки с массой нужно прокаливать при t 730-750″С три-четыре часа, причем поднимать температуру тоже по их графику. Нарушать или сокращать режим прокалки нельзя, потому, что (по словам дистибьютора формомасс) за этот период происходит спекание керамических компонентов массы. Поскольку прокалочной печи с электронным управлением у меня нет (у меня и термопары-то в ней нет), то температуру, ессно, поддерживаю на глаз, по цвету металлической опоки. В принципе, все мои неудачи и брак можно списать на нарушение технологии. Однако, почитав жалобы народа на ювелирных форумах, понял, что те же проблемы и у тех, кто обладает дорогущими печами с управлением от компа. Цена формомассы на количество проблем с ней не влияет, у пользователей дорогих масс все то же самое.
Возникает вопрос — а нафига мне их керамика в опоке? Единственный ответ — формомасса расчитана на использование вакуумных литейных машин, и от нее требуется соответствующая газопроницаемость. Я никогда вакуумом при литье не пользовался и не собираюсь (почему — расскажу потом, когда до литья дойдем), и смысла для меня в этих волшебных качествах микрокерамики никакого.
В общем-то, и без такой прокалки качество формомасс меня устраивает, благо лить ёлки по полкило весом мне не нужно. Точнее — до сих пор устраивало. А теперь пришла мысль — а не сварить ли мне свой «лак Страдивари», в смысле, свою формомассу, которую не нужно прокаливать часами и прочее? Работал же раньще, и ничего — получалось не хуже.
Почитав на тех же форумах про брак при литье, сравнил со своими результатами. У некоторых ювелиров брак доходит до 40%, у везунчиков — 10-15%. У меня в среднем 20%, то есть из 5 заформованных опок одна идет в брак. То ли дуракам везет, то ли «тут не без водолаза…». И это при том, что только литейные машины у ювелиров стоят от 3000 до 40000 $! Плюс прокалочная печь за 2000-5000, плюс еще по мелочи…
Итог: как сказал в детстве все тот же т. Ленин — «Мы пойдем другим путем!», то есть — будем экспериментировать, до полной победы коммунизма… тьфу…самопальной формомассы. Если же эксперименты все-таки окончатся провалом — тогда честно признаюсь «Ребята, не мучьте мозг, покупайте готовое». А пока — будем посмотреть. Жаль только, что опробованные когда-то рецепты позабывал…
——————
Долго чесал репу, что покупать — ехать в магазин медтехники (полтора часа туда-обратно)и купить 1 кг супергипса за 220р., или дойти 300 метров от дома до строительного рынка и взять 40 кг. скульптурного гипса Г-16. Победила лень — купил Г-16. Теперь буду пихать его куда только можно, потому что 40 кг мне нафиг не нужны.
Составляю первую смесь для полнотелой формовки (то есть, когда формовочной массой заливается весь объем опоки). Смеси на основе жидкого стекла или этилсиликата буду называть оболочечными.
Рецепт №1 (в объемных частях):
Гипс скульптурный Г16 — 35%
Песок мелкий — 10%
Песок крупный — 10%
Шамотный порошок — 35%
Асбест молотый — 10%
Что откуда взялось:
Песок — с ближайшей стройки. Хорошо было бы найти белый, он лучше всего подходит, но не нашел, набрал обыкновенного (потом обязательно найду белый). Просеял через сито с ячейкой 2 мм, все, что крупнее — выбросил. Оставшееся с помощью бытового сита (на фото) разделил на две фракции — ту, что осталась в сите, назвал крупной, а ту, что просеялась — мелкой.
Обе долго мыл в проточной воде, особенно мелкий, пока не пошла чистая вода.
Шамотный порошок — у приятеля на даче нашел огнеупорный кирпич (писал о нем на форуме).
В итоге он был идентифицирован как легковесный магнезиальный шамот — чтобы знать в следующий раз, где и что искать. Самое ближайшее (для меня) место — Подольский завод огнеупоров, хотя этот кирпич приятелю привезли на дачу вместе с другими огнеупорными кирпичами с рынка.
Кирпич очень легкий, обрабатывается всем, даже ногтем. За пять минут драчевым напильником напилил кучку на полстакана и смолол в электрокофемолке.
Перед тем, как в ней молоть, нужно наточить ножи. Если вы думаете, что от кофе ножи не тупятся, то сильно ошибаетесь. После помола ножи опять нужно подточить — увидите сами, как они притупились. Острые ножи лучше мелят, и меньше нагрузка на двигатель.
Молол около минуты, получился пылевидный порошок.
Асбест — купил листовой асбест на том же строительном рынке, отломил кусочек, накрошил помельче, смолол в той же кофемолке.
Для тех, кто боится асбеста — поищите на форуме в «Разговорах» тему Arty про асбест, я там высказывал свое мнение о нем и свои меры безопасности при работе. Кто уж совсем боится — ну упс, ничем помочь не могу…
Чем для нас хорош асбест: даже при самом мелком помоле он все равно сохраняет свою волокнистую структуру, и кроме огнеупорных функций будет выполнять и функции микроармирования — а это очень важно для прочности формы.
Если будете молоть — имейте в виду, что при помоле асбест многократно увеличивается в объеме. На фото — перемолотый 1 куб.см асбеста (специально по линейке отрезал), рядом монетка в 5 копеек — кучка получилась приличная. Поэтому, говоря об объемных частях асбеста, я имею в виду уже перемолотый и плотно смятый пальцами в комок.
Смешивать компоненты заранее нежелательно — при хранении от перетряхивания и прочего мелкие и тяжелые фракции окажутся на дне, крупные и легкие вверху. Гипс в любом случае добавлять в последнюю очередь, перед формовкой. Я, чтоб не путаться, всегда смешиваю непосредственно все компоненты перед формовкой.
Если будете пробовать какие-то свои смеси, то обязательно записывайте точные пропорции, чтобы при удачной отливке можно было повторить.
Компоненты готовы, теперь перейдем к формовочному оборудованию.
Важнейший компонент оборудования для формовки — вакуумный насос. У меня насоса нет никакого, покупать фирменный не буду, сделаю самодельный из автомобильного ножного (надеюсь, народ на форуме поможет советами). Когда сделаю — расскажу в подробностях. До недавних пор пользовался смешной с виду приспособой для домашнего консервирования, пока не сломалась. Вот нашел ее в инете:
Вы будете смеяться, но в паре с вибростоликом эта приспособа делала то, что от нее требовалось — убирала из смеси пузырьки воздуха. Во всяком случае, т.н. корольки на отливках встречались редко, не чаще, чем у ювелиров.
Приналичии хорошего вакуумника вибростол вроде бы и не нужен, но раз хорошего нет, то — нужен.
К сожелению, с вибростолом произошла авария. Когда вытащил его из шкафа и включил попробовать, моторчик задымил и сгорел. Жаль, но придется делать другой. Думаю, в течении недели сделаю и заодно подробно расскажу, как его делать. А пока буду пользоваться своей старой приспособой из китайской стригальной машинки.
Стригла она никак, но в качестве ручного вибратора работает прекрасно. Опоки всех размеров, какие я лил, вибрировала без проблем. Переделка простейшая — выкинул все, что стрижет, оставив только металлический язычок, который и вибрирует. К нему прикрепил кусок резины. Конечно, неудобно в работе, третьей руки не хватает, да и с вакуумом ее не совместишь, но это лучше, чем ничего. Попытка прикрепить ее к вибростолику не удалась — не хватает мощности вибрации.
Теперь нужно сделать силиконовую основу под опоки, чтобы при заливке формомассы из-под них не вытекало на стол. (Специально для съемки делать не буду, слеплю из пластилина).
Замешиваем столовую ложку гипса, ставим опоку на кусочек полиэтилена (низ опоки там, где сделаны пупырышки) и заливаем на дно слой гипса около 1 см. Он нам нужен временно, поэтому ждем 20 минут и продолжаем.
Кладем на стол кусок плотного полиэтилена, выдавливаем на него силиконовый строительный герметик, разравниваем, чтобы получилась лепешка толщиной 3-4 мм и диаметром немного больше опоки. Оставляем ее на несколько минут. Смазывем нижнюю часть опоки вместе с дном маслом или кремом погуще, и осторожно ставим в центр лепешки. Потом добавляем герметика вокруг дна опоки, чтобы получился кольцевой бортик высотой 5-7 мм. Если чувствуете, что опока провалилась до самого полиэтилена, то приподнимаете ее и добавляете силикона под нее. Зубочисткой примазываете силикон к стенкам опоки и оставляете на несколько часов, пока силикон не высохнет.
После высыхания отделяете опоку и получаете силиконовую подставку точно под опоку. Для эстетики можете обрезать излишки лепешки до самого бортика.
Последнее, что осталось (как-то забыл об этом сказать при изготовлении опок) — сантиметровый отрезок той же трубы, из который сделана опока. Для чего он нужен — расскажу во время формовки.
—————
Ну вот, вроде бы для формовки все готово. А формовать будем завтра, потому что хочу спать… 🙂
Как изготавливать пресс-формы для литья под давлением, отливки и термоформования с помощью 3D-печати
Изготовление форм для литья используется в различных отраслях такими специалистами, как проектировщики, производственники и преподаватели при создании коротких производственных циклов, прототипов сложных пресс-форм, испытания изделий из пластмасс для дальнейшего использования на практике и, главным образом, в тех случаях, когда необходимо сделать несколько экземпляров детали без особых затрат и усилий. Это позволяет быстро изготавливать небольшие партии от 150 до 600 деталей или проверить конструкцию пресс-формы, прежде чем приступать к изготовлению дорогостоящей оснастки.
Изготовление формы с помощью настольной 3D-печати позволяет инженерам и проектировщикам расширить сферу использования материалов и возможности своего 3D-принтера за границы быстрого прототипирования в область промышленного производства. Изготовленные 3D-печатью модели для процессов формования, как правило, получаются быстрее и дешевле, чем модели, изготавливаемые фрезерованием на станках ЧПУ, и проще, чем изготовленные с помощью силиконовых форм.
Формы для небольших партий, напечатанные на 3D-принтере, как правило, не такие дорогие и более просты в изготовлении по сравнению с формами, изготавливаемыми на станках с ЧПУ или с помощью силиконовых форм.
В этой статье мы рассмотрим три технологии изготовления пресс-форм, которые легко дополняются 3D-печатью: литье под давлением, отливка и термоформование. Для более углубленного ознакомления с этими технологиями, а также для с рекомендациями по изготовлению форм и 3D-печати см. наш последний вебинар.
Литье под давлением было изобретено в 1872 году Джоном Уэсли Хайатом и вначале действовало по тому же принципу, что и шприц для подкожных инъекций. Современная установка для литья под давлением была окончательно создана в 1956 году в результате изобретения плавающего шнека.
В современном технологическом процессе литья под давлением плавающий шнек подает гранулы пластичного полимера из загрузочного бункера в обогреваемый цилиндр экструдера. По мере приближения к нагревателю гранулы плавятся и выталкиваются в полость формы, находящейся под давлением. После формования и остывания детали внутри формы она выталкивается, и форма используется повторно.
Небольшая пластиковая деталь, изготовленная с помощью формы для литья под давлением, полученной методом 3D-печати непосредственно из высокотемпературного полимера Formlabs High Temp Resin.
Полимеры, используемые для процессов литья под давлением, сравнительно дешевы и могут использоваться для достижения самых разнообразных свойств, поэтому литье под давлением широко применяется для создания упаковок и товаров массового потребления (любопытный факт: элементы LEGO, для которых важны как прочность, так и точность, изготавливаются литьем под давлением).
Благодаря доступным по цене настольным 3D-принтерам, термостойким материалам для 3D-печати и установкам для литья под давлением можно самим создавать формы для производства функциональных прототипов и небольших деталей из пластмасс. В случае малосерийного производства (примерно 10-100 деталей) созданные 3D-печатью формы для литья под давлением, в сравнении с дорогими металлическим формами, позволяют сэкономить время и деньги. Они также дают более гибкий подход к производству, позволяя инженерам и проектировщикам путем незначительных затрат времени и денег создавать прототипы литьевых форм и тестировать их конфигурации или легко изменять формы, продолжая работу над своими проектами.
Формы могут непосредственно печататься на 3D-принтере с использованием различных материалов, таких как стандартные или High Temp Resin Formlabs. Испытания для нашего технического доклада по литью под давлением проводились с использованием литьевой установки Galomb Model-B100 Injection Molder, стоимость которой составляет около 3500 долларов США.
Технический докладЗагрузите наш технический доклад, чтобы получить пошаговое описание методов, использовавшихся для тестирования работоспособности напечатанных на 3D-принтере форм для литья под давлением, а также узнать о примерах передового опыта и рекомендациях при проектировании форм для 3D-печати.
Скачать технический докладЛитье — популярная технология во многих отраслях, в частности, ювелирной промышленности, стоматологии и машиностроении. Оно может использоваться для изготовления как мелких, так и крупных деталей из самых различных металлов. Изобретенное свыше 5000 лет назад, литье позволяет работать с самыми разнообразными материалами и представляет собой один из самых простых способов изготовления деталей из металла.
При литье пустая форма создается по мастер-форме, которая может быть изготовлена вручную или напечатана на 3D-принтере (как это показано в видео-учебнике BJB Enterprises в разделе как изготовить силиконовую форму с помощью 3D-принтера Formlabs SLA). Мастер-форма погружается в материал литейной формы, например, песок, глину, бетон, эпоксидную смолу, гипс или силикон. Материал литейной формы затвердевает, пластик или металл заливается внутрь формы, и мастер-форма либо удаляется, либо сгорает, в результате чего образуется готовая деталь.
Можно напечатать точную мастер-форму для литья, используя. например, полимер Formlabs Castable Resin, который сгорает, образуя литейную форму многократного использования.
Технический докладИз этого технического доклада вы узнаете, как отливать ювелирные узоры по 3D-моделям, и как прямое литье по выплавляемым или по восковым моделям работает, как метод изготовления форм.
Скачать технический докладОтливки из вулканизированной резины могут использоваться для изготовления восковых моделей в количествах, необходимых для литья по выплавляемым моделям металлических деталей, таких как ювелирные изделия, мелкие детали промышленного назначения и игрушки.
3D-принтеры могут изготавливать мастер-модели, которые используются для формования отливок с вулканизацией при комнатной температуре (RTV) и даже отливок из жаростойкой вулканизированной резины.
Печатаемые непосредственно на 3D-принтере образцы ювелирных изделий могут использоваться для изготовления отливок из резины, вулканизируемой при комнатной температуре (RTV), или из природного каучука, вулканизируемого под действием высокой температуры.
При проектировании и производстве изготовление металлических отливок является наиболее экономичным и производительным технологическим процессом изготовления деталей с мелкими элементами и сложной геометрией. Производственники и проектировщики используют литье для изготовления критически важных деталей авиационной, автомобильной отрасли и здравоохранения.
Стереолитографические 3D-принтеры (SLA) идеально подходят для процессов литья при изготовлении металлических частей с меньшими затратами, большей гибкостью проектирования и за меньшее время, чем традиционные методы, без затрат, присущих 3D-принтерам прямой печати металлом.
Из этого технического доклада вы узнаете, как можно использовать скорость и гибкость 3D-печати без затрат, характерных для принтеров прямого спекания металла, используя рабочие процессы литья металла, а также подробные пошаговые руководства по литью в песчаные формы; узнаете об инвестициях в процессы литья с использованием 3D-принтеров и полимеров Formlabs.
Скачать технический докладДва этих процесса: термоформования и вакуумного формирования похожи на литье под давлением тем, что используют нагрев и давление для создания готовых изделий из пластмассы. Эти методы были созданы в 40-е годы для производства безукоризненных фонарей кабин летательных аппаратов и рельефных армейских карт.
Сегодня их обычно используют для производства упаковки для автомобильных запчастей, где точность размеров может быть не столь критичной, а неравномерность толщины приемлема.
Упаковка для этой бритвы была сделана вакуумным формованием.
При термоформовании нагретый лист пластика сжимается между двух половинок формы для получения детали. При вакуумном формовании используется только одна половина формы, а для прижатия пластика к форме используется вакуум. Установки, используемые в этих технологических процессах, очень дешевы, их даже можно сделать своими руками.
На этой схеме А обозначает давление на обратной стороне формы, В — давление со стороны пластика, накладываемого на форму, и С обозначает тепло самого пластика.
Печать формы для термоформования на 3D-принтере SLA — быстрый и эффективный метод создания высококачественных вакуум-формованных деталей для мелкосерийного производства. Напечатанные формы для термоформания можно использовать для изготовления прототипов упаковки, прозрачных ортодонтических ретейнеров и безопасных для пищевых продуктов форм для шоколадных кондитерских изделий.
При моделировании деталей для изготовления пресс-форм, необходимо учитывать такие факторы, как давление, отвод газов, различия в охлаждении и нагреве.
Посмотрите наш вебинар , чтобы изучить различные технологии изготовления пресс-форм и узнать, как изготавливать формы для литья под давлением, формы для термоформования и литьевые формы.
Объяснение процесса литья металла
Что такое литье металла?
Литье металла — это современный процесс с древними корнями. В процессе литья металла металлические формы формируются путем заливки расплавленного металла в полость формы, где он охлаждается, а затем извлекается из формы. Литье металла, возможно, является самым ранним и самым влиятельным промышленным процессом в истории. Из него изготавливают многие металлические предметы, используемые в нашей повседневной жизни: автомобильные детали, колеса поездов, фонарные столбы, педали школьного автобуса и многое другое.Кроме того, литейные заводы полагаются на вторичную переработку металла как на экономичный источник сырья, значительно сокращая отходы металлолома, который может оказаться на свалках.
История литья металлов
Самая старая известная металлическая отливка — это отливка медной лягушки, которая, как полагают, была произведена в 3200 году до нашей эры в Месопотамии, когда медь была широко используемым материалом. Позже, примерно в 2000 году до нашей эры, было обнаружено железо. Но только примерно в 700 г. до н.э. в Китае было освоено первое производство чугуна.Примечательно, что процесс литья металлов из песка также был изобретен в Китае в 645 году до нашей эры.
Тигельный процесс, метод, используемый для производства тонкой или инструментальной стали, появлялся и исчезал в различных местах по всему миру с начала 1-го тысячелетия нашей эры. Эта техника впервые появилась в Индии и Центральной Азии, пока не появилась в Северной Европе около 800 г. н.э., где ее использовали для изготовления мечей викингов. Эта техника не использовалась до 1750 года, когда Бенджамин Хантсман заново изобрел ее в Англии.Хантсман нагревает небольшие кусочки углеродистой стали в закрытом тигле, который представляет собой керамический горшок с огнеупорными свойствами, который может выдерживать высокую степень нагрева. Хантсман впервые достиг температуры, достаточной для плавления стали.
За последние тысячи лет отливка металлов в пригодные для использования объекты эволюционировала и стала более точной и автоматизированной, но процесс, по сути, остался прежним. Инновации в автоматизации литейных процессов, такие как кондиционер для литья в песчаные формы VIBRA-DRUM® компании General Kinematics, упростили обработку больших объемов отливок, а также улучшили качество отливок.Эта машина является революционной в области обработки больших объемов пресс-формы и песка для литейного производства.
Процесс литья металла
- Изготовление выкройки — Выкройка является точной копией внешнего вида отливки. Выкройки обычно изготавливаются из дерева, металла, пластика или гипса. Изготовление лекал невероятно важно для промышленного изготовления деталей, где необходимы точные расчеты, чтобы детали подходили друг другу и работали вместе.
- Изготовление стержней — Если отливка является полой, дополнительный кусок песка или металла (так называемый стержень) придает внутренней форме форму, чтобы сделать ее полой.Сердечники обычно прочные, но разборные, поэтому их можно легко удалить из готовой отливки.
- Отливка — Чтобы представить себе процесс литья металла, представьте, что вы идете по пляжу в сторону океана. Посмотрите на след, который вы оставляете на мокром песке. Ваша ступня будет стержнем, а отпечаток, оставленный на песке, — это слепок вашей ступни. Формование — это многоэтапный процесс, при котором формируется слепок вокруг шаблона с использованием формовочного песка. При литье форма помещается в раму, называемую колбой.Зеленый песок или формовочный песок набивается в колбу вокруг выкройки. Это называется литьем металла в песчаные формы. Когда песок плотно набит, узор можно удалить, а гипс останется. В качестве альтернативы можно создать неразрушаемую металлическую форму, состоящую из двух частей, чтобы форму можно было многократно использовать для отливки идентичных деталей для промышленного применения.
- Плавка и разливка расплавленного металла — После расплавления металл выливается в полость формы и оставляется для застывания.
После затвердевания начинается процесс вытяжки: формы подвергаются вибрации для удаления песка из отливки. В промышленных применениях такое оборудование, как наши двухмассовые встряски, поддерживает высокую производительность благодаря своей эффективной и бесперебойной работе. Удаленный песок обычно собирается, охлаждается и восстанавливается для повторного использования в будущих отливках. Кондиционер для литья песка VIBRA-DRUM® улучшает этот процесс отделения песка от отливок, удаляя и охлаждая песок и отливки и испаряя влагу, одновременно уменьшая повреждения отливок, которые являются обычным явлением на этом этапе процесса.Конечным результатом является чистая отливка и песок, готовый к процессу рекультивации.
- Очистка — На этом последнем этапе отлитый металлический объект извлекается из формы и затем очищается. Во время зачистки предмет очищается от формовочного материала, удаляются неровности.
Современные отливки
Сегодня почти все механические устройства, которые мы используем, от автомобилей до стиральных машин, изготавливаются из металлических деталей, созданных с помощью процесса литья. Разница между сегодняшними изделиями из литого металла и изделиями, которые были изготовлены даже 100 лет назад, заключается в точности и допусках, которые могут быть достигнуты с помощью компьютеризированного автоматизированного процесса проектирования, а также современных методов изготовления детализированных стержней и форм. Современное литье металла представляет собой инновации в действии.
На протяжении веков были разработаны различные комбинации сырья для производства различных типов металлов. Некоторые литые изделия используются в двигателях, требующих высокой устойчивости к жаре и холоду.Чугунные трубы должны противостоять коррозии и высокому давлению. Остальные литые детали должны быть легкими, но прочными. Во многих приложениях детали конструируются с учетом точных допусков между расширением и сжатием.
Другие процессы литья включают гипсовое литье, литье под давлением и литье по выплавляемым моделям. Литье из гипса просто заменяет песок гипсовой формой.
Для литья под давлением требуются две большие движущиеся детали из цветных металлов, которые зажимаются вместе под высоким давлением. Расплавленный металл вводится в матрицу, и после затвердевания металлические части разделяются.
Процесс литья по выплавляемым моделям начинается с заполнения формы воском. После того как воск затвердеет, на него несколько раз наносят керамический материал. Его нагревают до тех пор, пока воск не расплавится и не останется керамическая форма. Форма заполняется расплавленным металлом, охлаждается, после чего керамический материал отламывается.
Горжусь тем, что служу литейной промышленности
General Kinematics гордится тем, что является ведущим производителем оборудования для автоматизированной вибрационной обработки, который внедряет инновации вместе с литейной промышленностью на протяжении почти 60 лет.Чтобы получить больше информации обо всем литейном оборудовании General Kinematics, свяжитесь с нами сегодня!
Металлические литейные формы на заказ — Детали, изготовленные на заказ, кованые, литые и плакированные — Bunty LLC
Сегодня высок спрос на качественные металлические детали на заказ. Металлические литейные формы по индивидуальному заказу позволяют клиентам получить широкий спектр индивидуальных деталей, отлитых из желаемых металлов и металлических сплавов. Самым большим преимуществом наличия нестандартных форм является то, что они позволяют многократно использовать их.Они позволяют изготавливать большое количество различных деталей за небольшую плату.
Мы можем помочь вашему предприятию с минимальными затратами изготовить высококачественные металлические детали с помощью литья по индивидуальному заказу. Наши возможности включают в себя широкий выбор металлов и металлических сплавов, и мы предоставим отличные формы для литья металлов на заказ в соответствии с вашими требованиями.
Индивидуальные типы литейных форм Для литья металла по индивидуальному заказу используются временные или постоянные формы.В большинстве случаев наши клиенты выбирают постоянные формы, чтобы повторно использовать их всякий раз, когда им нужно создать несколько копий индивидуального изделия. Основное отличие временных форм от постоянных — возможность их повторного использования.
- Временные формы : Временные формы обычно не выдерживают процесса литья в условиях, допускающих повторное использование. Формы из песка иллюстрируют один из популярных типов временных форм.
- Постоянные формы : Производители обычно создают постоянные формы для получения отливок многократного использования.Графит, нержавеющая сталь и сталь иллюстрируют три популярных сегодня материала для изготовления постоянных форм. Хотя эти формы со временем изнашиваются, конечно, они служат дольше, чем временные формы. Клиенты, которым нужны индивидуальные формы, часто предпочитают вкладывать средства в высококачественные постоянные формы, чтобы производить несколько копий идентичных деталей.
Процесс литья в постоянную металлическую форму обычно включает не менее шести отдельных этапов:
- Сначала производитель тщательно изготавливает постоянную форму из материала, выбранного клиентом .
Природа металлических сплавов, используемых в отливке, обычно определяет тип материала, используемого при изготовлении формы.
- В процессе изготовления формы производитель должен тщательно измерить и обработать детали постоянной формы , чтобы убедиться, что они плотно прилегают друг к другу. Команда разработчиков создает ворота, позволяющие проникать расплавленному металлу; он также создает «литник», отверстие, позволяющее попадать горячему металлу через затвор. Постоянная форма обычно также имеет каналы для отвода газов.
- Во многих случаях постоянным формам требуется сила тяжести, чтобы расплавленный металл мог заполнить форму. Производитель должен предоставить способ плавки металлических сплавов , а затем безопасно загрузить этот расплавленный материал в форму .
- За счет предварительного нагрева и смазки постоянной металлической формы производитель способствует более плавному заполнению. Производитель также плотно скрепляет детали пресс-формы вместе (часто с помощью оборудования).
Эта операция происходит в высокотемпературной среде, поэтому автоматизация помогает закрепить нагретые компоненты формы.После сборки формы производитель заливает расплавленный металл через литник в литник. В некоторых случаях автоматизированные центробежные силы помогают более полно распределять металл через форму; в других случаях этому процессу заполнения формы способствует только сила тяжести. После завершения операции заполнения производитель позволяет металлу частично остыть и затвердеть внутри формы.
- В конце концов, производитель отстегивает пресс-форму (обычно с помощью выталкивающих штифтов).
- Окончательное охлаждение происходит перед началом чистовых операций.
Для процесса литья металла по индивидуальному заказу, как минимум, требуется форма, адаптированная к требованиям клиента, а также возможность плавления и заливки металлических сплавов в такую форму. Команда дизайнеров тщательно изготавливает временные или постоянные формы в соответствии с указаниями клиента. В то время как производители иногда используют временные формы, такие как формы из песка или пластика, индивидуальное формование чаще включает создание постоянных и, следовательно, многоразовых форм.Литье металла по индивидуальному заказу обычно происходит при сравнительно высоких температурах.
Металлы, используемые в любом проекте по отливке металла на заказ, в значительной степени определяют типы материалов, необходимых для использования в формах для постоянного литья. Часто производители отливают промышленные компоненты в формы из графита, керамики или нержавеющей стали. Постоянная форма многократного использования должна, как правило, оставаться способной выдерживать тепло, выделяемое расплавленным металлом, без изменения своей формы, разрушения, изгиба или растворения.Предполагаемый метод литья, например Независимо от того, использует ли производитель литье под давлением или литье под действием силы тяжести, он также может принимать участие в выборе материалов, необходимых при изготовлении формы.
Использование нестандартных литых компонентов, созданных с помощью специальных металлических литейных форм, безусловно, дает множество преимуществ:
- Все компоненты будут созданы согласно спецификации
- Размер более точен, чем при традиционных процессах ковки и сварки
- В процессе меньше стресса
- Конечный продукт более высокого качества
- Сокращение сроков изготовления
- Меньше энергопотребление
- Эффективно используемые материалы (без обрезки и падений)
- Возможности автоматизированного производства
- Вы можете выбрать создание индивидуальных металлических форм, которые можно использовать повторно, если вам понадобится больше компонентов.
Технология литья под давлением, используемая ООО «Банти», дает клиентам ряд важных преимуществ.
- Использование нестандартной постоянной формы позволяет нам создавать самые разнообразные формы и надежно воспроизводить объекты.
- Использование этого процесса литья помогает создавать металлические изделия с более прочной и однородной внутренней структурой.
- Отливка из металла по индивидуальному заказу позволяет изготавливать изделия с декоративными деталями поверхности.
- Этот производственный процесс имеет экономические преимущества. Хотя постоянные формы со временем изнашиваются, они обычно служат намного дольше, чем многие другие производственные инструменты.Использование постоянных нестандартных форм позволяет вам со временем оптимизировать вложения в высококачественные формы.
КОНТАКТЫ BUNTY LLC СЕГОДНЯ
Для получения дополнительной информации о наших формах для литья под давлением и других возможностях свяжитесь с нами напрямую через удобную форму на веб-сайте или запросите ценовое предложение здесь. Мы приветствуем ваши запросы.
Что такое металлическое литье? | Типы литья металла
Отливка металла определяется как процесс, при котором расплавленный металл заливается в форму, содержащую полую полость желаемой геометрической формы, и ему дают остыть для образования затвердевшей детали.Термин « литье » также используется для описания детали, изготовленной в процессе литья, возраст которого составляет 6000 лет. Исторически он использовался для изготовления сложных и / или больших деталей, которые было бы сложно или дорого производить с использованием других производственных процессов.
Рисунок 1. Отливка металла В первую очередь, отливка дает слитков и формы . Слиток представляет собой отливку простой формы, предназначенную для дальнейшей обработки, такой как прессование металла, ковка и т. Д. Фигурное литье предназначено для отливок, близких к конечной или конечной, для получения сложных геометрических форм, которые ближе к конечной детали.
Металлическое литье можно разделить на две группы по основному характеру конструкции кристаллизатора. то есть одноразовая форма и постоянная форма отливки . В дальнейшем их можно разделить на группы в зависимости от материала выкройки.
- Расходная форма
- Постоянный узор
- Литье в песчаные формы
- Гипсовая лепнина
- Форма корпуса
- Керамическая форма
- Выкройка расходная
- Потеря пены
- Литье по выплавляемым моделям
- Постоянный узор
- Перманентная форма
- Литье самотеком
- Низкое давление / вакуум
- Литье под давлением
Перед выбором подходящей металлической отливки для данной конструкции инженерного изделия необходимо учесть следующие факторы.
- Форма и размер детали
- Необходимое количество
- Требуемый допуск
- Материал
Отливка сменной формы
Отливка в сменную форму, как следует из названия, использует временную форму одноразового использования для производства окончательной отливки, так как форма будет сломана, чтобы вывести отливку. Эти формы обычно изготавливаются из таких материалов, как песок, керамика и гипс. Обычно их склеивают с помощью связующего, называемого связующим, для улучшения его свойств.Сложные и сложные геометрические формы можно отливать с использованием одноразовых литейных форм.
Отливка в постоянную форму
Иногда называемое отливкой в формы длительного пользования, для непрерывного литья в формы используются постоянные формы, которые повторно используются после каждого производственного цикла. Хотя постоянное литье в форму позволяет получать повторяемые детали из-за повторного использования одной и той же формы, она позволяет производить только простые отливки, поскольку для удаления отливок необходимо открывать форму.
Рисунок 3. Отливка в неразъемную форму (кредит — Alibaba)Отливка в композитную форму
Как следует из названия, для изготовления отливок используются как одноразовые, так и многоразовые литейные формы. Обычно к ним относятся такие материалы, как песок, дерево, графит и металл.
Ступени литья металла
- Изготовление выкройки — Копия отливаемой детали изготавливается из подходящего материала, такого как дерево, металлопластик или гипс.
- Изготовление пресс-форм — Изготовление пресс-форм — это многоступенчатый процесс, в котором шаблоны и стержни используются для создания пресс-формы. Тип и способ изготовления форм будут различаться в зависимости от типа отливки металла. Например, при литье в песчаные формы для создания форм используется песок внутри опоки, а для литья под давлением используются формы из закаленной инструментальной стали.
- Плавление и разливка металла — Затем жидкость плавится и заливается в полость формы под действием силы тяжести или под высоким давлением. Затем отливке дают затвердеть, прежде чем отливки будут извлечены из формы.
Опять же, удаление литой детали будет зависеть от типа металлической отливки.
- Последующая обработка — На этом последнем этапе отлитый металлический объект извлекается из формы и затем очищается. Во время зачистки предмет очищается от формовочного материала, удаляются неровности.
Элементы литниковой системы
Одним из наиболее распространенных способов литья металла является литье в песчаные формы, форма которого состоит из двух половин. Содержащаяся внутри коробки, называемой колбой, верхняя половина называется колпачком, а нижняя половина — сопротивлением.Как показано на изображении (Рисунок 5) ниже, колба также разделена на две половины. Линия, разделяющая две половинки, называется линией разделения.
Рис. 5 Система вентилей для литья металла (источник: Groover (2010)) Система вентилей — это канал или путь, по которому расплавленный металл течет в полость. Как показано выше, литниковая система состоит из разливочной чашки и нижнего литника, через который металл попадает в желоб, ведущий в основную полость. Разливочная чашка сводит к минимуму разбрызгивание и турбулентность, когда металл течет через литник, который сужается для облегчения потока.Большая часть отливки страдает от усадки во время охлаждения, и чтобы свести к минимуму проблему усадки, используется стояк. Подъемник — это простой резервуар в форме, который подает расплавленный материал к участкам усадки для компенсации его затвердевания. Есть четыре различных типа стояков, а именно. верхний подступенок, боковой подступенок, жалюзи и открытый подступенок.
Пригодность материала
Хотя можно использовать почти все металлы, наиболее распространенными являются железо, сталь, алюминий, магний и сплавы на основе меди, такие как бронза.
Цинк, алюминий, магний и латунь широко используются при литье под давлением, тогда как алюминиевый сплав, латунный сплав, чугун и литая сталь являются очень популярными материалами для литья под давлением.
Типовое применение
Почти все технические изделия, которые мы используем, от стиральных машин до сверл для колонн, от автомобилей до велосипедов, производятся из металлических деталей, которые, скорее всего, будут изготовлены с использованием одного из процессов литья металла. Этот старинный производственный процесс со временем повысил точность и допуски.
Как правило, отливки используются для изготовления блоков двигателей автомобилей, коленчатых валов, корпусов электроинструментов, таких как сверлильные станки, детали водопровода, лопатки турбин, металлические статуи, некоторые шестерни и корпуса коробок передач.
Как и в случае с любыми другими производственными процессами, базовое понимание процесса, лежащих в его основе научных данных, его плюсов и минусов имеет важное значение для производства недорогих качественных инженерных продуктов.
Преимущества литья металла
- Металлическое литье позволяет производить сложные формы
- Такие детали, как внутренние полости или полые профили, легко достигаются
- Крупногабаритные детали можно изготавливать из цельного литья
- Материалы, которые сложно или дорого производить с использованием другого производственного процесса, можно отливать
- По сравнению с другими производственными процессами, литье для средних и крупных партий дешевле
- Почти все металлы можно отливать
- Форма, близкая к конечной, часто без постобработки или с очень незначительной постобработкой
По указанным выше причинам литье металла является одной из важных технологий изготовления формы сетки. Другие включают ковку чистой формы, штамповку листового металла, аддитивное производство и литье металла под давлением.
Недостатки металлического литья
- Относительно грубая обработка поверхности и, следовательно, более широкий допуск должен быть разрешен и не подходит для стыковки интерфейсов
- Металлическое литье, такое как отливка корпуса, имеет ограничения по размеру и рисунку
- Изготовление выкроек требует много времени и средств, хотя в последнее время для изготовления пресс-форм используются такие процессы аддитивного производства, как струйное распыление связующего.
- Литье под давлением для малых и средних партий может быть очень дорогим из-за высокой стоимости штампа
- Размер детали и выбор материала зависят от выбранного процесса литья.Например, для непрерывного литья в формы можно использовать только цветные металлы
- Били П. (2001). Литейное производство (второе издание). Оксфорд: Баттерворт Хайнеманн.
- Калпакчян, С., и Шмид, С. Р. (2009). Производство и технология (шестое издание). Лондон: Пирсон.
Способы литья металла: срок службы отливки
Что такое литье металла?
Литье металла — это процесс изготовления предметов путем заливки расплавленного металла в пустое пространство.Затем металл охлаждается и затвердевает, принимая форму, приданную ему этой формованной формой. Литье часто является менее дорогим способом изготовления детали по сравнению с механической обработкой детали из цельного металла. Есть много способов литья металла на выбор. Какой тип отливки наиболее эффективен, зависит от используемых металлов, размера партии и сложности отливки.
Перед запуском производственного цикла полезно узнать некоторые термины и методы в литейном цехе.
Справиться и перетянуть или «Таран и качели» — это слова, обозначающие движущиеся и неподвижные части зеленой песчаной формы.Терминология для литья
Литейная форма
Форма — это полость в материале, которая принимает жидкий металл и производит охлажденный объект в форме этой полости. Формы могут быть простыми. Формы, используемые для создания металлических слитков, похожи на формы для выпечки хлеба, где металл просто заливают внутрь и оставляют охлаждаться. Большинство форм предназначены для более сложных форм и основаны на узоре.Рисунок отпечатан на разрезной форме. Половина рисунка отпечатывается на одной стороне формы, а половина — на другой, а затем половинки зажимаются вместе перед заполнением формы. Сделав форму из двух частей, шаблон можно вынуть перед заполнением. Эти формы могут изготавливаться с горизонтальным разделением
Угловая пластина
При горизонтальном формовании верхняя половина формы называется опорой , а нижняя половина называется опорой .
Качели и толкатель
При вертикальном формовании передняя половина пресс-формы называется качанием , а задняя половина называется цилиндром .
Формовочные стержни
Если в пресс-форме должны быть внутренние пространства или отверстия, часто делают стержень . Эти ядра имеют форму внутреннего пространства. Сердечники обычно удерживаются на месте, выступая за отливку и удерживаясь на месте посредством отпечатков сердцевины , которые подвешивают сердцевину как мост между двумя банками. Пустые пространства вокруг сердечника заполнятся металлом, и ядро будет удалено из окончательной отливки, оставив отверстие там, где оно было раньше.Если ядро очень длинное, оно может поддерживаться венцами , чтобы поддерживать его. Обычно они изготавливаются из того же металла, что и окончательная отливка, поскольку они располагаются в пространстве, которое будет затоплено материалом и станет частью окончательной отливки.
Допуск на размер
Одним из важных факторов при выборе метода литья является допуск на размер . Допуск на размер — это допустимое отклонение размера конечного продукта. Металл дает усадку при охлаждении, и на сколько влияет тип отливки.Если продукт должен быть точным, клиенту может потребоваться метод литья, который позволяет производить литье почти сеткой . Это означает, что продукт очень близок к нужному размеру, когда его вытряхивают из формы.
Обработка поверхности
Еще одно соображение — Обработка поверхности . Насколько зернистой, неровной или шероховатой может быть поверхность отливки? То, что приемлемо для чугунной сковороды, не приемлемо для обручального кольца. Очень гладкие металлические поверхности обычно создаются с помощью механической обработки, что требует дополнительных затрат: если желаемый результат является блестящим и гладким, выбор метода литья с более тонкой обработкой может снизить затраты на обработку.
Чистота поверхности означает, насколько мелкой или зернистой является поверхность отливки перед обработкой.Способы литья металлов
Металлическое литье подразделяется на две основные категории: процессы с использованием многоразовых форм и процессы с использованием одноразовых форм.
Многоразовые или постоянные формы создают множество предметов, тогда как одноразовые формы разрушаются в процессе литья. Хотя с точки зрения непрофессионала может показаться, что многоразовые формы должны быть более рентабельными для большого производственного цикла, это не всегда так.Большинство изделий из чугуна и стали изготавливаются методом одноразового литья.
Низкотемпературные формовочные материалы (смолы, шоколад, воск и т. Д.) Почти всегда используют многоразовые формы. Что отличает металлургию, так это высокие температуры. Это создает большую нагрузку на форму. Поэтому неудивительно, что сплавы с более низкой температурой плавления, такие как цинк, алюминий, магний, олово или медь, чаще подходят для процессов многократного использования.
Однако в некоторых случаях даже черные металлы разливают в формы многократного использования.Сложность конструкции, выбор металла и требования к допускам на размеры и отделке поверхности — все это влияет на то, подходят ли многоразовые формы.
Постоянные формы могут быть простыми, как эта форма, или более сложными, состоящими из двух частей.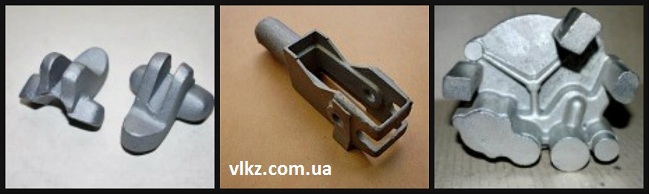
Многоразовые формы
Постоянные формы
Постоянные формы обычно изготавливаются из металла, который имеет более высокую температуру плавления, чем металл, которым они заполнены. Жидкий металл заливается без какого-либо внешнего давления. Постоянные стержни должны быть простыми, чтобы их можно было извлечь для повторного использования из готовой отливки.
Эти формы иногда используются для литья чугуна, а также для низкотемпературных сплавов. Поворотные столы, а не сборочные линии, являются наиболее распространенным производственным процессом. Отдельные операции, такие как нанесение покрытия на форму, размещение стержней, закрытие формы, заливка, открытие формы и выталкивание отливки, выполняются по мере прохождения каждой формы через следующие станции.
Формы предварительно нагреваются перед заливкой первой отливки, чтобы они не растрескались из-за разницы температур.
Отливки, полученные этим методом, не могут иметь столь же тонкие стенки, как у отливок при использовании других методов многократного использования, таких как литье под давлением. Однако отливки производятся с «жесткими допусками», что означает, что размер окончательной отливки можно более точно спрогнозировать. Изготовленные таким образом отливки бывают плотными и мелкозернистыми. Они имеют более гладкую поверхность и позволяют избежать нескольких типов дефектов.
Эта форма молдинга достаточно прочна для использования с железом, но не является предпочтительным для желтых латуней.Желтые латуни с высоким содержанием цинка загрязняют плесень или умирают.
Полупостоянные формы
Единственное изменение в литье в полупостоянные формы состоит в том, что стержни, используемые в процессе литья, могут быть одноразовыми песчаными стержнями. Более сложные формы стержней возможны с песчаными стержнями, потому что их не нужно извлекать неповрежденными из окончательной отливки. Если в отливке оставить отверстие для удаления стержней, их можно «вытрясти» на вибростоле, чтобы они стекали, как песок через песочные часы. Преимущества допусков, плотности и внешнего вида при отливке в неразъемную форму существуют только в секции, отлитой относительно металлической формы.
Слякотное литье
Этот красочно названный стиль литья позволяет создавать полые отливки без стержней, просто покрывая внутреннюю часть формы небольшим количеством металла, создавая металлическую «пленку». Есть разные способы подойти к литью из слякоти в зависимости от того, как быстро схватывается металл или другой материал. В одном методе основатель может налить небольшое количество жидкости в форму и вращать, чтобы покрыть внутреннюю часть металлом. В другом случае основатель может полностью заполнить форму, а затем вылить лишний материал по истечении заданного времени охлаждения.Цинк, алюминий и олово — это металлы, которые обычно отливают из слякоти.
Центробежное литье
При истинном центробежном литье кристаллизатор с водяным охлаждением вращается вокруг своей центральной оси с высокой скоростью при подаче жидкого металла. Центробежная сила вытягивает жидкий металл по поверхности формы ровным слоем. Чтобы этот метод работал, финальная отливка должна иметь ровную геометрию вокруг оси вращения. Таким образом, эта форма отливки лучше всего подходит для форм, которые имеют примерно цилиндрическую или круглую форму, например, трубы или кольца.
Объекты, отлитые этим методом, обычно имеют очень низкий процент дефектов. Загрязнения попадают близко к отверстию или внутренней поверхности отливки и могут быть удалены механической обработкой. Большинство труб или фитингов, которые будут использоваться под давлением, отлиты центробежным способом из-за прочности их бесшовной конструкции.
Некоторые небольшие металлические отливки, например ювелирные изделия, изготавливаются с помощью центрифуги, которая вращает всю форму вокруг центральной точки, вытягивая металл из тигля по мере его вращения. Это не центробежное литье, а форма литья под давлением.
Центробежное литье не имеет швов, и загрязнения могут удаляться из отверстия.Литье под давлением
Методы литья под давлением используют силы, отличные от силы тяжести, для управления потоком металла в постоянную изложницу. При литье под давлением используются воздух или газ, вакуум, механические или центробежные силы. Эти методы позволяют литейным предприятиям точно контролировать скорость заполнения формы: гравитация всегда действует с одной и той же силой, но искусственные силы могут варьироваться.
Вакуумное литье втягивает металл в форму, когда в ней разгерметизировано давление, а создаваемый вакуум вытягивает жидкий металл из резервуара внизу.Вакуум должен оставаться, пока металл остывает, поэтому этот метод в основном используется для тонкостенных отливок. Обеспечивает отличную чистоту поверхности. Отливки под низким давлением меняют этот процесс, создавая давление в печи, в которой находится жидкий металл, вместо создания вакуума в форме. Металл проталкивается через стояки в полость формы.
Все машины для литья под давлением (см. Ниже) также используют ту или иную форму давления для создания отливок.
Литье под давлением
Машины для литья под давлением состоят из резервуара с расплавленным металлом, металлической формы или штампа на двух пластинах и системы впрыска, которая втягивает материал и нагнетает его под давлением в штамп.
Процесс литья под давлением начинается с открытой формы. Форсунки распыляют на форму смазку, чтобы предотвратить прилипание детали. Две половины пресс-формы, затем закрывают и закрытую пресс-форму впрыскивают с помощью nossle давления. Перед открытием кубика новой отливке дается время остыть. Штифты выталкивателя выталкивают новую отливку из матрицы, и затем процесс начинается снова.
Есть две формы впрыска металла при литье под давлением. Литье под давлением с холодной камерой работает как шприц: перед отливкой каждой формы камеру впрыска необходимо заполнить расплавленным металлом, а затем поршень выталкивает содержимое форсунки в матрицу.Литье под давлением с горячей камерой или гусиной шеей работает за счет погружения камеры системы впрыска в расплавленный металл, причем форма системы означает, что инжектор сам заполняется. Литье в горячей камере под давлением выталкивает этот материал в форму либо поршнем, либо давлением воздуха.
Системы «гибкая шея» более подвержены коррозии, поскольку они находятся в ванне из расплавленного металла. По этой причине они обычно используются с алюминием или алюминиево-цинковыми сплавами, которые имеют более низкую температуру плавления. Форсунка для литья под давлением с поршневой или холодной камерой может использоваться для более высоких температур, необходимых для плавления латуни и бронзы, поскольку инжектор не подвергается постоянному воздействию тепла.
Непрерывное литье
Даже металлические детали, которые мы считаем полностью обработанными, прокатанными или обработанными иным образом, часто начинались с литейных цехов. Непрерывное литье создает блюмы, заготовки и плиты, которые представляют собой простые металлические формы разных размеров, путем экструзии их через постоянную форму. Этот процесс литья создает сырье для обработанной стали.
Процесс непрерывной разливки начинается высоко над цехом.Расплавленный металл подается в воронку, контролирующую скорость разливки. Воронка заполняет форму под ней, которая представляет собой простую форму, обычно длиной 20-80 дюймов, а по ширине имеет форму квадрата, круга или прямоугольника. Стенки кристаллизатора охлаждаются, так что внешняя часть отливки замерзает при ее прохождении. Когда металл покидает форму, он затвердевает, но остается податливым. Это позволяет машине непрерывного литья изгибать его так, чтобы готовая продукция выходила горизонтально. Ряд колес направляет плиту к конвейерной ленте, а охлаждающие спреи укрепляют поверхность.Газовые форсунки на горизонтальной поверхности разрезают цельнометаллический кусок на нужную длину, чтобы их можно было поднимать и штабелировать.
Раздвижные формы
Методы сменных форм — явные победители, когда дело доходит до литья черных металлов. Они экономичны, потому что не обязательно должны быть устойчивыми к воздействию высоких температур.
Литье в песчаные формы
Литье в песчаные формы является наиболее распространенным методом литья металлов. Этому производственному процессу не менее трех тысяч лет: первые свидетельства литья из глины пришли из Китая во времена династии Шан (ок.С 1600 по 1046 год до нашей эры).
Неудивительно, что этот процесс до сих пор так популярен: песок дешев, много, податлив и хорошо переносит тепло.
Керны, созданные из песка, легко удалить: их можно вытряхнуть с помощью вибростола. Бегунки и ворота, используемые для направления металла в полость формы, либо вырезаются вручную опытным формовщиком, либо создаются как часть рисунка.
Поверхность изделий, отлитых в песчаные формы, часто шероховатая, а допуски по размерам неточны, поэтому отливка в песчаные формы отлично подходит для изготовления крупных и прочных изделий, от декоративных ограждений до чугунных поддонов и деталей двигателей автомобилей.
Подробнее о литье в песчаные формы читайте в нашей предыдущей статье этой серии.
Облицовка корпуса
Отливка корпуса — это форма литья в песчаные формы, обеспечивающая более жесткие допуски на размеры. Это очень похоже на лепку из песка, только песок смешан со смолой. Смесь песка и смолы заливают каждую половину модели горячего металла. Эта смесь тает и остывает, образуя оболочку. «Оболочки» формы собираются вместе и обычно поддерживаются колбой, полной песка. Благодаря смоле, обеспечивающей дополнительную поддержку внутренних поверхностей, эти оболочки образуют очень точную форму.
Часто корпусное формование используется для изготовления стержней для традиционного литья в песчаные формы. Смола придает песчаным сердцевинам прочность, позволяющую сохранять форму, даже когда их помещают в пустоту, которая станет отливкой. Эти сердечники оболочки могут быть полыми, создаваемыми в горячей металлической форме в процессе, подобном литью шламов. Две половины стержневой формы зажимаются и нагреваются, а затем заполняются песком, покрытым смолой. Форма запекается до тех пор, пока толщина оболочки не станет достаточно толстой, чтобы выдержать размер сердцевины, а затем излишек неотвержденного смолистого песка выливается обратно. Когда две половины формы разделяются, они открывают прочную сердцевину, готовую к установке в форму для литья в песчаные формы, что создает пространство в отливке.
Литье по выплавляемым моделям (литье по выплавляемым моделям)
Литье в песчаные формы на сегодняшний день является наиболее распространенной формой литья металлов, и все же есть один аспект литья в песчаные формы, который делает его непригодным для некоторых проектов. Образцы для литья в песчаные формы необходимо удалить из формы, которую они создают, что может означать создание сложной конструкции.Требования к чертежу, размещение линий разъема, ворот, подступенков и стержней требуют, чтобы изготовитель выкройки внимательно рассмотрел потребности выкройки на каждой стадии процесса литья.
Процесс литья по выплавляемым моделям, выплавляемый или прецизионное литье является альтернативой литью в песчаные формы, который может работать с большинством марок металлов, даже с высокоплавкими ферросплавами, и при этом позволяет избежать некоторых из этих проблем, связанных с формированием моделей при литье в песчаные формы.
Конструктор по литью по выплавляемым моделям изготавливает точную металлическую матрицу, в которую отливают восковые или пластмассовые модели.Эти шаблоны собираются на литнике, также сделанном из этого материала: литейщик использует горелку, чтобы расплавить литник, чтобы прикрепить к нему каждый узор.
Эта сборка затем используется для создания оболочки, которая будет использоваться в качестве пресс-формы. Это распыляется, щеткой или погружают в суспензию мелкозернистого, высокой огнеупорного агрегата, а также запатентованный связующий агент, состоящий главным образом из смеси силиката. Затем смеси дают застыть. На узор повторно наносят более крупную суспензию, пока не образуется оболочка из заполнителя вокруг узора.Формы выдерживают до тех пор, пока покрытие не застынет, после чего их нагревают в печи в перевернутом положении, чтобы воск вытек и был собран для повторного использования. После удаления воска формы запекаются в предварительно разогретой печи. Затем формы можно поддерживать с помощью рыхлого песка и заливать любым обычным способом.
Когда отливки остынут, оболочка вокруг отливки по выплавляемым моделям разрушается и стряхивается с помощью вибростола.
Литье по выплавляемым моделям обеспечивает превосходную чистоту поверхности и высокую точность размеров. Здесь нет разделительных линий, как при литье в песчаные формы.
Процесс литья в полную форму или пенопласт
Процесс литья в полную форму или пену представляет собой комбинацию процессов литья в песчаные формы и литья по выплавляемым моделям. Используется рисунок из пенополистирола. Действительно, вспененный узор может быть выполнен в комплекте с системой литников и направляющих, и он может включать устранение допуска тяги. Иногда узор удаляют перед заливкой, но с некоторыми пенами узор можно оставить на месте в форме, чтобы мгновенно испаряться при заливке горячего металла.
Этот процесс идеально подходит для отливок одной или нескольких частей, но иногда литейные заводы производят модели из пенопласта серийно для создания объемов производства. Есть дополнительные расходы на оборудование для изготовления разрушаемых рисунков из пеноматериала, но часто экономические показатели всего процесса литья могут быть благоприятными, если рисунок очень сложный.
Сравнение процессов литья
Консультации с производителями помогают найти наиболее рентабельный способ отливки проекта. Как правило, черные металлы будут отливаться с использованием одноразовых форм, тогда как цветные металлы имеют более широкий диапазон возможностей, но даже из этого простого правила есть исключения.
Вступление в процесс с четким пониманием потребностей проекта поможет выбрать лучший процесс для литья. Нужен ли дизайн точного размера? Насколько тонкими должны быть стены? Какого размера и веса будет отливка в итоге? А как насчет отделки поверхности? Заранее зная ответы на все эти вопросы, опытный дизайнер поможет понять и направить свой продукт через процесс литья, найдя лучший и наименее затратный процесс для выполнения своей работы.
Типы форм для литья алюминия • Bernier Metals
Существует множество типов форм для литья алюминия, которые используются при литье расплавленного алюминия в различные формы и формы. Некоторые формы являются временными, а другие — постоянными и могут использоваться повторно. Эти же типы форм также используются для многих различных металлов и сплавов, помимо алюминия.
Форма для литья в песчаные формы
Самыми старыми типами форм для литья алюминия являются формы, которые использовались со времен Египта.Эти типы форм создаются, когда в песке создается полость, которая находится в ящике или «колбе». Обычно оригинальный «узор» делается из дерева, металла или другого твердого материала. В песчаной полости также есть стержень, который образует центр отливки. Из различных форм для литья алюминия именно эта используется, прежде всего, для блоков двигателей, коллекторов двигателей и других крупных и тяжелых отливок.
Керамическая форма
Другой тип литейной формы, используемый с алюминием и другими расплавленными металлами, — это керамическая форма.Керамическая форма, наиболее часто используемая для процесса литья по выплавляемым моделям, создается вокруг пластика или воска, который плавится при обжиге формы во время ее создания. После того, как воск «потерян», форма готова для приема расплавленного металла. Этот тип процесса литья также называется «прецизионное литье» из-за того, что с его помощью можно получить точные отливки.
Отливка в постоянные формы
Постоянные формы для литья алюминия изготавливаются из таких металлов, как сталь и железо.Расплавленный алюминий под действием силы тяжести или вакуума попадает в постоянную полость формы. Одним из преимуществ отливок этих типов является то, что форма является постоянной; в отличие от форм для литья в песчаные формы, которые обычно разрушаются при извлечении отливок после их охлаждения. Кроме того, он дешевле при использовании для большого количества отливок.
Формы для литья под давлением
В формах для литья под давлением используются стальные штампы или формы для производства большого количества идентичных отливок. В случае алюминия, как и других металлов, расплавленный металл под высоким давлением нагнетается в формы для литья алюминия этого типа. Это универсальный процесс, который позволяет производить большое количество отливок малых и средних размеров.
Форма для раковины
Форма для раковины — это форма для литья в песок, в которой используется смола для связывания песка в тонкую оболочку толщиной от 10 до 20 мм. Хотя использование этих типов форм для литья алюминия обеспечивает лучшую отделку поверхности с более точными размерами, этот процесс определенно более дорогостоящий.
Гипсовые формы
Гипсовые формы создаются с использованием гипсовой суспензии, которую заливают вокруг воска.По мере запекания гипсовой формы узор плавится, оставляя идеальное представление узора. Затем в полость гипсовых форм заливают расплавленный металл. Это еще одна форма «литья по выплавляемым моделям».
Графитовые литейные формы
Графитовые формы и стержни часто используются при центробежном литье алюминия. Этот процесс нагнетает металл в форму и использует быстрое охлаждение для получения качества отливки, невозможного с помощью других методов.
Это семь типов форм для литья алюминия, которые наиболее часто используются для производства алюминиевых отливок.Каждая литейная форма используется для получения определенного качества и различных типов литейных свойств.
Подробнее
Способы литья в формы длительного пользования. постоянное, штамповочное, центробежное, непрерывное литье.
Отливка в формы длительного пользования отличается от процессов одноразового использования тем, что не требуется повторная формовка формы после каждого производственного цикла. Этот метод включает как минимум четыре разных метода: постоянный, штамповочное, центробежное и непрерывное литье.
Литье в постоянную форму — это процесс литья металла, в котором используются формы многократного использования («постоянные формы»), обычно изготавливаемые из металла. Самый распространенный процесс использует гравитацию для заполнения формы, однако газ
также используется давление или вакуум. Разновидность типичного процесса литья под действием силы тяжести, называемого отливкой из слякоти, дает полые отливки. Обычные литейные металлы — это алюминий, магний и
медные сплавы. Другие материалы включают сплавы олова, цинка и свинца, а также железо и сталь, которые также разливают в графитовых формах.Постоянные формы, выдерживающие более одного литья, имеют ограниченный срок службы
до износа.
В процессе литья под давлением расплавленный металл под высоким давлением помещается в полости формы (которые превращаются в штампы). Большинство отливок изготавливаются из цветных металлов, в частности из цинка, сплавы на основе меди и алюминия, но возможно литье под давлением черных металлов. Метод литья под давлением особенно подходит для приложений, где требуется много деталей малого и среднего размера. с хорошей детализацией, прекрасным качеством поверхности и стабильностью размеров..
Центробежное литье не зависит как от силы тяжести, так и от давления, поскольку оно создает собственную подачу силы с помощью временной песчаной формы, удерживаемой в прядильной камере при давлении до 900 Н. Время выполнения зависит от
приложение. Полу- и истинно центробежная обработка позволяет изготавливать пресс-форму со скоростью 30-50 штук в час с практическим пределом для периодической обработки приблизительно 9000 кг общей массой при типичной
Лимит на единицу товара 2,3-4,5 кг.
В промышленности центробежное литье железнодорожных колес было ранним применением метода, разработанного немецкой промышленной компанией Krupp, и эта возможность позволила предприятию быстро развиваться.
Небольшие предметы искусства, такие как ювелирные изделия, часто отливают этим методом с использованием процесса выплавляемого воска, поскольку силы позволяют довольно вязким жидким металлам проходить через очень маленькие каналы и превращаться в мелкие частицы. такие детали, как листья и лепестки. Этот эффект аналогичен преимуществам вакуумного литья, а также применяется к литью ювелирных изделий. .
Непрерывное литье — это усовершенствованный процесс литья для непрерывного крупносерийного производства металлических профилей с постоянным поперечным сечением. Расплавленный металл заливается в открытый,
медная форма с водяным охлаждением, которая позволяет формировать «пленку» из твердого металла над все еще жидким центром. Нить, как ее теперь называют, вынимается из формы и проходит в камеру роликов.
и водные спреи; ролики поддерживают тонкую оболочку пряди, в то время как спреи отводят тепло от пряди, постепенно затвердевая снаружи внутри. После затвердевания,
Пряди заданной длины отрезаются либо механическими ножницами, либо перемещающимися кислородно-ацетиленовыми горелками и передаются на дальнейшие процессы формования или на склад.Размеры литья могут
варьируются от полосы (толщиной несколько миллиметров и шириной около пяти метров) до заготовок (квадрат от 90 до 160 мм) до плит (шириной 1,25 м и толщиной 230 мм). Иногда прядь может сначала нагреться.
процесс прокатки перед резкой.
Непрерывное литье используется из-за более низких затрат, связанных с непрерывным производством стандартного продукта, а также повышает качество конечного продукта. Металлы, такие как сталь, медь
и алюминий отливаются непрерывным способом, причем сталь является металлом с наибольшей массой, отлитой с использованием этого метода.
Дополнительная информация:
металлургия | Определение и история
Использование металлов в настоящее время является кульминацией долгого пути развития, продолжающегося примерно 6 500 лет. Принято считать, что первыми известными металлами были золото, серебро и медь, которые находились в самородном или металлическом состоянии, причем самыми ранними из них, по всей вероятности, были самородки золота, найденные в песках и гравии русел рек. Такие самородные металлы стали известны и ценились за их декоративные и утилитарные ценности во второй половине каменного века.
Ранняя разработка
Золото можно агломерировать в более крупные куски холодным молотком, а самородная медь — нет, и важным шагом к эпохе металлов стало открытие, что металлам, таким как медь, можно придавать форму путем плавления и литья в формах; Среди самых ранних известных изделий этого типа — медные топоры, отлитые на Балканах в IV тысячелетии до нашей эры. Следующим шагом стало открытие возможности извлечения металлов из металлосодержащих минералов. Они были собраны, и их можно было отличить по цвету, текстуре, весу, цвету пламени и запаху при нагревании.Заметно больший выход, полученный при нагревании самородной меди с соответствующими оксидными минералами, мог привести к процессу плавки, поскольку эти оксиды легко восстанавливаются до металла в угольном слое при температурах, превышающих 700 ° C (1300 ° F), в качестве восстановителя. , окись углерода, становится все более стабильной. Чтобы осуществить агломерацию и отделение расплавленной или плавленной меди от связанных с ней минералов, необходимо было ввести оксид железа в качестве флюса. Этот дальнейший шаг вперед можно объяснить присутствием госсановых минералов оксида железа в выветрившихся верхних зонах месторождений сульфида меди.
Во многих регионах в следующий период начали производить медно-мышьяковые сплавы, превосходящие медь по свойствам как в литой, так и в деформируемой форме. Сначала это могло быть случайным из-за сходства цвета и цвета пламени между ярко-зеленым минералом карбоната меди малахитом и продуктами выветривания таких минералов сульфида меди и мышьяка, как энаргит, и, возможно, позже за этим последовал целенаправленный отбор соединений мышьяка из-за запаха чеснока при нагревании.
Содержание мышьяка варьировалось от 1 до 7 процентов, с оловом до 3 процентов. Медные сплавы, в основном не содержащие мышьяка, с более высоким содержанием олова — другими словами, настоящая бронза — появились между 3000 и 2500 годами до нашей эры, начиная с дельты Тигра и Евфрата. Открытие ценности олова могло произойти благодаря использованию станнита, смешанного сульфида меди, железа и олова, хотя этот минерал не так широко доступен, как основной минерал олова, касситерит, который, должно быть, был конечным источником металла.Касситерит поразительно плотный и встречается в виде гальки в аллювиальных отложениях вместе с арсенопиритом и золотом; в определенной степени это также встречается в упомянутых выше госсанах из оксида железа.
Несмотря на то, что бронза могла развиваться независимо в разных местах, наиболее вероятно, что культура бронзы распространилась через торговлю и миграцию народов с Ближнего Востока в Египет, Европу и, возможно, Китай. Во многих цивилизациях производство меди, мышьяковистой меди и оловянной бронзы продолжалось некоторое время вместе.Возможное исчезновение медно-мышьяковых сплавов трудно объяснить. Производство могло быть основано на минералах, которые не были широко доступны и стали дефицитными, но относительный дефицит оловянных минералов не препятствовал существенной торговле этим металлом на значительных расстояниях. Возможно, в конечном итоге предпочтение было отдано оловянной бронзе из-за вероятности отравления мышьяком от паров, образующихся при окислении содержащих мышьяк минералов.
По мере того, как выветрившиеся медные руды в данных местах разрабатывались, более твердые сульфидные руды под ними добывались и плавились.Используемые минералы, такие как халькопирит, сульфид меди и железа, нуждались в окислительном обжиге для удаления серы в виде диоксида серы и получения оксида меди. Это потребовало не только более высокого металлургического мастерства, но и окисления тесно связанного железа, что в сочетании с использованием флюсов оксида железа и более жесткими восстановительными условиями, создаваемыми улучшенными плавильными печами, привело к более высокому содержанию железа в бронзе.
Невозможно провести резкую границу между бронзовым и железным веками.Небольшие куски железа могли быть произведены в медеплавильных печах, поскольку использовались флюсы оксида железа и железосодержащие сульфидные руды меди. Кроме того, более высокие температуры печи могли бы создать более сильные восстановительные условия (то есть более высокое содержание оксида углерода в топочных газах). Первый кусок железа, найденный на железнодорожных путях в провинции Дренте, Нидерланды, был датирован 1350 годом до нашей эры, датой, обычно считающейся средним бронзовым веком для этой местности. В Анатолии, с другой стороны, железо использовалось еще в 2000 году до нашей эры.Иногда встречаются упоминания о железе и в более ранние периоды, но этот материал был метеорного происхождения.
После того, как была установлена связь между новым металлом, обнаруженным в медных расплавах, и рудой, добавленной в качестве флюса, естественно последовала работа печей для производства одного железа. Конечно, к 1400 г. до н. Э. В Анатолии железо приобрело большое значение, а к 1200–1000 гг. До н. Э. Оно в довольно больших масштабах превращалось в оружие, первоначально лезвия кинжалов.По этой причине 1200 г. до н.э. был принят за начало железного века. Свидетельства раскопок указывают на то, что искусство производства железа зародилось в горной стране к югу от Черного моря, в районе, где преобладали хетты. Позже это искусство, по-видимому, распространилось среди филистимлян, поскольку в Гераре были обнаружены неочищенные печи, датируемые 1200 годом до н. Э., Вместе с рядом железных предметов.
Плавка оксида железа с углем требовала высокой температуры, и, поскольку температура плавления железа 1540 ° C (2800 ° F) была недостижима, продукт представлял собой просто губчатую массу пастообразных шариков металла, смешанных с полужидкостью. шлак.Этот продукт, позже известный как блюм, вряд ли можно было использовать в том виде, в каком он стоял, но повторный нагрев и обработка горячим молотком удалили большую часть шлака, создав кованое железо, гораздо более качественный продукт.
На свойства железа сильно влияет присутствие небольшого количества углерода, при этом значительное увеличение прочности связано с содержанием менее 0,5%. При достижимых в то время температурах — около 1200 ° C (2200 ° F) — восстановление с помощью древесного угля дает почти чистое железо, которое было мягким и имело ограниченное применение для оружия и инструментов, но когда соотношение топлива к руде было увеличено и вытяжка печи с изобретением более совершенного сильфона, железо поглотило больше углерода.Это привело к появлению блюмов и продуктов из железа с различным содержанием углерода, что затрудняет определение периода, в течение которого железо могло быть намеренно упрочнено за счет науглероживания или повторного нагрева металла в контакте с избытком древесного угля.
Углеродсодержащее железо имело еще одно большое преимущество: в отличие от бронзы и безуглеродистого железа его можно было сделать еще более твердым путем закалки, то есть быстрого охлаждения путем погружения в воду. Нет никаких доказательств использования этого процесса закалки в раннем железном веке, так что он, должно быть, был либо неизвестен тогда, либо не считался выгодным, поскольку закалка делает железо очень хрупким и должно сопровождаться отпуском или повторным нагревом в более низкая температура для восстановления прочности.То, что, кажется, было установлено на раннем этапе, было практикой многократной холодной ковки и отжига при 600–700 ° C (1100–1300 ° F) — температуре, которая достигается естественным путем при простом огне. Эта практика распространена в некоторых частях Африки даже сегодня.
К 1000 г. до н.э. железо стало известно в Центральной Европе. Его использование медленно распространилось на запад. Производство железа было довольно широко распространено в Великобритании во время римского вторжения в 55 г.