Наплавка валиков – технология, оборудование + Видео
Наплавка валиков – эффективный способ восстановления этих деталей. Но из-за их конструкции технология имеет некоторые особенности, которые мы подробно рассмотрим в этой статье.
1 Особенности наплавки и ее виды
Это один из способов нанесения металлического слоя на поверхность детали путем расплавления реставрационного материала ручной, газовой либо автоматической сваркой. Применяется наплавка в различных целях, но главное ее предназначение – восстановление изношенных деталей и их геометрических размеров. Иногда эту операцию проводят и для повышения качества материала, например, когда хотят улучшить коррозионную стойкость, повысить износоустойчивость, твердость, жаростойкость и т. д.
Огромную роль играет качество шва, ведь по сути он и определяет конечный результат. Дефекты в виде пор, трещин и разных включений недопустимы. Также необходимо придерживаться следующих правил:
- Смешивание основного и присадочного материала должно быть минимальным.
- Чем меньше будет сварочная ванна, тем лучше.
- Припуски на последующую обработку должны находиться в строго заданных пределах.
- Следует свести к минимуму напряжения и остаточные деформации в изделии.

Нанесение металлического слоя на поверхность детали
Для восстановления цилиндрических поверхностей допускается использование любого вида наплавки, но большей популярностью пользуется электродуговая и электрошлаковая технология. Первая может осуществляться открытой дугой в среде защитных газов или под слоем флюса. Каждый из этих способов имеет свои плюсы и минусы. Например, при наплавке открытой дугой не нужна специальная защита сварочной ванны. В среде защитных газов или под флюсом получается задавать свойства шва.
Недостатком электродугового метода можно назвать деформацию изделия из-за значительного нагрева. Также после наплавки деталь подвергается закалке, а это может спровоцировать появление горячих трещин. К тому же не обойтись без дополнительной термической обработки. Очень часто износ незначительный, а толщина наплавленного слоя составляет несколько миллиметров, и чтобы изделие соответствовало заданным размерам, потребуется дальнейшая механическая обработка.

Электродуговой метод наплавки
Отдав предпочтение вибродуговой наплавке валков можно рассчитывать на высокую производительность, а поверхность получается достаточно твердой даже без последующей термической обработки. По сути, это один из видов электродуговой сварки. Ее особенность – вибрирующий электрод с частотой от 20 до 100 Гц. Этим способом восстанавливают валы диаметром от 8 и до 200 мм.
Электрошлаковая наплавка (ЭШН) отличается высокой производительностью. Отдав предпочтение этому способу, получится обеспечить химическую однородность плакирующего слоя. Он будет иметь и одинаковую структуру на всей площади, что гарантирует равномерный износ детали. Также появляется возможность варьировать геометрию и химический состав шва в широких пределах. К недостаткам следует отнести такие особенности:
- возможность наплавки валов только в одном положении;
- процесс нельзя прерывать;
- материал шва имеет крупнозернистую структуру;
- необходимость в изготовлении технологической оснастки.
2 Область использования
Наплавка цилиндрических поверхностей весьма востребована, ведь это наиболее выгодный способ восстановления дорогостоящего оборудования. Износу подвержены рабочие валки прокатных и обжимных станов. Валы гидротурбин также нуждаются в реставрационных работах. А что уж говорить о машиностроении, где множество деталей имеют именно цилиндрическую форму.

Наплавка цилиндрических поверхностей
Такие изделия работают в неодинаковых условиях, имеют разные габариты и отличаются по химическому составу. И чтобы подобрать оптимальные режимы, наплавочные материалы и способ восстановления, необходимо учитывать все эти факторы. Например, при восстановлении коленвалов необходимо одновременно решить несколько задач. Во-первых, восстановить размеры шеек. Во-вторых, обеспечить достаточную износостойкость. В-третьих, добиться высоких показателей усталостной прочности. В-четвертых, обеспечить правильную работу всех сопряженных деталей.
3 Способы наплавки цилиндрических изделий
Существует два способа наплавки валов – продольная и круговая. В первом случае валики формируются вдоль оси, а во втором идут по окружности. Продольный метод более целесообразно использовать при работе с длинными деталями, имеющими небольшой диаметр. Поверхность предварительно очищают от ржавчины, грязи, пыли, масляных пятен и влаги, а затем наплавляют первый валик.

Продольный способ формирования изделия
Далее прокручивают деталь на 180° и повторно наносят шов. Третий валик наплавляется уже через 90° относительно второго прохода. А чтобы нанести четвертый слой, необходимо опять развернуть цилиндрическую деталь на 180°. Если наплавка валиков происходила под флюсом, то необходимо хорошенько обить защитную корку и зачистить поверхность шва металлической щеткой. Потом наносится защитное покрытие таким образом, чтобы каждый новый проход перекрывал предыдущий.
Швы должны выходить за пределы восстанавливаемой поверхности поочередно, сначала на полдиаметра вала, потом на целый диаметр. Если есть шпоночный паз, то первым восстанавливают его.

Круговой метод наплавления
При наплавке валов круговым методом деталь постоянно поворачивается вокруг своей оси, поэтому этот способ более сложный в исполнении. Да и понадобится специальное оборудование. Однако этот метод меньше снижает предел усталостной прочности, чем предыдущий. Таким способом обычно наплавляют торец вала, при этом шов накладывают от центра к периферии. Затем следует обработка на токарном станке.
4 Технология наплавки шаг за шагом
Прежде чем приступать непосредственно к наплавочным работам, необходимо подготовить поверхность детали. При повторной наплавке изделия обтачивают на вальцетокарном станке. Если на поверхности детали есть мелкие вмятины, бороздки, растрескивания термического характера, тогда предварительную обточку не проводят. Еще обрабатываемую деталь проверяют на биение, оно не должно превышать 0,3 мм. Все шпоночные пазы необходимо закрыть графитовыми либо медными вставками. Причем последние должны выступать над наплавленным слоем минимум на 1 мм.

Подготовка к наплавочным работам
Далее по технологии наплавки валов следует предварительный подогрев. Температура зависит от ряда факторов, так, при использовании порошковых материалов изделие нагревают до 370 °C. Если осуществляют наплавку проволокой 30ХГСА, достаточно 250 °C. Флюс обязательно просушивают, если он влажный, тогда необходима перезакалка при температуре 300–400 °C.
Затем деталь зажимается в патроне и оборудование вращает ее с постоянной скоростью, а сварочная головка движется прямолинейно вдоль вала. Расплавленный металл подается капельно и формирует довольно плотный слой. Затем к месту наплавки подают охлаждающую жидкость, насыщенную ионизирующими солями, которые благоприятно влияют на горение дуги.

Процесс наплавки вала
При ЭШН технология немного иная. Оплавление присадочного и основного материала происходит в шлаковой ванне. Через нее пропускают сварочный ток, который нагревает соединяемые материалы. При этом жидкий шлак имеет меньшую плотность и постоянно находится сверху шва, тем самым защищая его от воздуха. Кроме того, присадочный материал, проходя в жидком состоянии слой шлака, очищается от всех вредных примесей.
5 Какими должны быть оборудование и материалы?
Теперь пришло самое время поговорить про оборудование, нужное для наплавки валов. Установка для восстановления прокатных валов состоит из люнетов для поддержки изделия; механизма, обеспечивающего вращение вала и сварочной головки АБС; источников питания и электронагревателя. Сварочную головку подвешивают на специальных направляющих и путем перестановки сменных шестерен регулируют скорость ее перемещения. Такое оборудование посредством специального пульта предусматривает управление процессом подачи наплавочного материала, скоростью передвижения головки, вылетом электрода.

Установка для восстановления прокатных валов
А вот изменять угол наклона подачи сварочной проволоки, а также обеспечивать перемещение головки поперек валков оборудование позволяет только вручную. Флюс засыпают в специальный бункер, откуда он и подается. Электронагреватель состоит из двух полукорыт. Очень важно обеспечить свободное перемещение этого узла к любому участку. С этой целью нижнее полукорыто устанавливают на специальную тележку.
Правильно подобрать способ и наплавочный материал можно только после тщательного анализа условий работы и иных особенностей обрабатываемого изделия. Для восстановления стальных валков для станов горячей прокатки нашла свое применение порошковая проволока ПП-Нп-35В9Х3СФ. Этот материал может обеспечить прекрасную износостойкость, однако его стоимость велика, так как в состав входит 10% дорогого вольфрама. А вот для ремонта рабочих элементов обжимных станов и наплавки коленчатых валов прекрасно подойдет и более дешевая проволока Нп-30ХГСА.

Порошковая проволока
Наплавка валиков со сложными калибрами производится специальными материалами из дисперсионно-твердеющих или мартенситно-стареющих сталей, тогда слой прекрасно поддается механической обработке. Это обусловлено их твердостью, которая составляет 28–35 HRC. После закалки это значение возрастает почти в два раза.
Наплавка валов — Полуавтоматическая сварка — MIG/MAG
Для ремонта валов энергетического оборудовани у нас есть такая инструкция. Может и Вам пригодится.
Если требуется обеспечить конкретные размеры посадочных мест, а глубина дефектов не превышает 1 мм от номинального диаметра, предпочтительно применять метод газопламенного напыления в следующей последовательности:
— посадочные места протачиваются с полным удалением коррозии и обеспечением шероховатости Rz 120 и более;
– при вращении вала от 5 до 15 об/мин на обработанные посадочные места производится равномерное газопламенное напыление слоя металла толщиной до 2,5 мм;
– не менее чем через 4 часа после напыления, посадочные места протачиваются и шлифуются шкуркой с обеспечением требуемых диаметров, шероховатости и цилиндричности.
Если требуется обеспечить конкретные размеры посадочных мест, а глубина дефектов превышает 1 мм от номинального диаметра, применяется метод электродуговой наплавки в следующей последовательности:
– проточить поверхности, нуждающиеся в восстановлении до устранения видимых дефектов, но на глубину не менее 3 мм
– произвести визуальный контроль и МПД подготовленных поверхностей и всех мест — концентраторов напряжений (галтельных переходов, уступов и т.п.)
– при обнаружении скрытых ранее дефектов, составить дополнительный акт дефектации, сообщить Заказчику;
– в шпоночный паз установить фальш-шпонку или укрепить стенки паза медными пластинами;
– произвести предварительный подогрев до температуры от 150 до 200 °С в печи с выкатным подом;
– соседние поверхности защитить от брызг расплавленного металла асбестовым шнуром, или съемными металлическими кожухами;
– произвести наплавку до диаметра превышающего номинальный от 3 до 6 мм полуавтоматом в среде углекислого газа сварочной проволокой Св-08Г2С ГОСТ 2246-70 током величиной от 100 до 130 А, кольцевыми валиками, не допуская длительных перерывов в работе;
– для равномерного охлаждения вал загрузить в подогретую печь или укрыть изоляционным материалом до полного остывания;
– установить вал на токарный станок, выставить по базовым поверхностям;
– перецентровать вал, при необходимости;
– провести предварительную токарную обработку поверхностей согласно чертежу с припусками от 0,2 до 0,3 мм на сторону;
– произвести визуальный контроль и МПД наплавленных поверхностей и всех мест — концентраторов напряжений (галтельных переходов, уступов и т.п.), при обнаружении дефектов, повторить наплавку и предварительную токарную обработку;
— окончательно точить и шлифовать шкуркой поверхности согласно чертежу;
– не снимая вал со станка произвести контроль качества восстановления посадочных мест.
Для наплавки кольцевых валиков используется специальный вращатель. Думаю, добитый токарный станок тоже подойдёт.
Изменено пользователем ZHANНаплавка валов — Справочник химика 21
из «Ремонт центробежных и поршневых насосов нефтеперерабатывающих и нефтехимических предприятий»
Выработка и выход из стрюя подшипников скольжения или качения, а также коррозионные оспины, появление рисок и надиров при попадании мелких посторонних частиц во вкладыши подшипников вместе со смазкой приводят к износу шеек валов. [c.48]Шейки вала, работающего в подшипниках скольжения, обычно вырабатываются неравномерно и в продольном сечении принимают форму конуса, в поперечном — эллипса. Шейки вала, работающего в подшипниках качения, изнашиваются при протачивании внутренней обоймы подшипника на валу вследствие прослабления при изготовлении или выработке посадочных мест в процессе эксплуатации насоса [7]. [c.49]
В зависимости от износа посадочных мест валов применяют следующие методы восстановления хромирование при износе посадочных мест до 0,3 мм осталивание (железнение) с последующим шлифованием при износе посадочных мест до 0,8 мм наплавку при износе посадочных мест более 0,8 мм [5]. [c.49]
Восстановление и упрочнение валов наплавкой значительно увеличивают срок их службы, обеспечивают большую экономию запасных частей, сокращение затрат на ремонт оборудования. Известны различные способы наплавки — электродуговая, элек-трошлаковая, газовая, термитная, трением, электронно-лучевая и др. Валы восстанавливают обычно электродуговой наплавкой, не вызывающей деформации обрабатываемых изделий. Для восстановления изношенных валов можно также использовать наплавку трением. Этот процесс по затратам электроэнергии значительно экономичнее электродугового. [c.49]
В ремонтном производстве для восстановления валов часто применяют электродуговую наплавку под слоем флюса, в ср еде диоксида углерода, в струе охлаждающей жидкости, с комбинированной защитой дуги, порошковой лентой и др. Автоматическую электродуговую наплавку под слоем флюса широко применяют для наплавки валов, изготовленных из нормализованных и закаленных среднеуглерюдистых и низколегированных сталей, а также из малоуглеродистых сталей, не подвергающихся термической обработке, имеющих износ от 0,3 до 4,0 мм при однослойной наплавке и свыше 4 мм — при многослойной. Производительность процесса очень высока. Валы диаметром до 50 мм этим способом восстанавливать сложно, так как шлак, не успев затвердеть, стекает с наплавляемого изделия. [c.49]
Электродуговая наплавка в среде диоксида углерода широко распространена в ремонтном производстве для восстановления валов диаметром до 40 мм. [c.49]
Автоматическая наплавка порошковой проволокой, которая позволяет наносить слой металла любого химического состава и получать закалочные структуры различной твердости [8], получила широкое распространение в последнее время. Автоматическая наплавка ленточным электродом и порошковой лентой в 2-3 раза производительнее, чем обычной электродной проволокой, и дает возможность за один ход аппарата наносить слой металла шириной до 100 мм, толщиной 2-8 мм. Этим способом нельзя наплавлять валы малого диаметра. Тугоплавкие сплавы наплавляют плазменным способом, который производительнее других способов. [c.50]
В последние годы разработаны новые способы наплавки с комбинированной зашитой дуги и сварочной ванны для устранения отдельных недостатков того или иного способа восстановления. [c.50]
При восстановлении посадочных мест вала ручной электродуговой наплавкой поврежденное место вала протачивают на станке на величину наиболее глубоких повреждений. Затем наплавляют вал до нужных размеров с учетом последующей проточки и шлифовки. Наиболее ответственная операция — наплавка вала. На Уфимском заводе синтетического спирта разработано приспособление, позволяющее качественно провести наплавку. Приспособление, показанное на рис. 2.16,а, состоит из рамы 4, на которую крепят неподвижную 7 и передвижную 3 стойки, что позволяет наплавлять валы различной длины. Вал 1 помешается между четырьмя роликами 5 и может свободно вращаться вокруг своей оси. Расстояние между роликами в зависимости от диаметра вала регулируют пазом 8 и гайкой 6. [c.50]
В стерлитамакском производственном объединении Каустик разработано и внедрено приспособление для наплавки валов аналогичной конструкции, показанное на рис. 2.16,6. В этом приспособлении вал 2 устанавливают в опорные подшипники 1. Рабочий может одновременно наплавлять вал и вращать его. [c.50]
На Омском заводе синтетического спирта разработано приспособление для наплавки валов с охлаждением, показанное на рис. 2.18. Большую часть вала 3 пофужают в воду, заполняющую ванну /, а на выступающую над водой часть вала накладывают один-два валика сварного шва. [c.52]
Кроме ручной применяют автоматическую электродуговую наплавку вибрирующим электродом. Головки для наплавки ГВМК-1 выпускают с вылетом мундштука до 50 мм. Иногда наплавку вала целесообразно проводить без снятия рабочих колес. В этих случаях для головки изготовляют мундштук длиной 250 — 300 мм. Восстановление валов вибродуговой наплавкой показано на рис. 2.19. [c.52]
При наплавке лентой от проплавления основного металла зависит степень его перемешивания с наплавленным. Благодаря постоянному перемещению дуги глубина проплавления основного металла при наплавке лентой меньше, чем при наплавке проволокой. Наибольшее влияние на глубину проплавления и перемешивания основного металла с наплавленным оказывает скорость наплавки. С ее ростом увеличивается гл бина проплавления, уменьшаются ширина и толщина наплавляемого валика. При малых скоростях наплавки снижается проплавление основного металла. [c.52]
Восстановление деталей контактным злектроимпульсным покрытием заключается в приварке металлической ленты под воздействием сварочных импульсов. Чтобы исключить нафев детали и улучшить условия закалки приварного слоя, в зону сварки подают охлаждающую жидкость. [c.53]
При приварке ленты толщиной 0,3 — 0,4 мм рекомендуемая емкость батареи конденсаторов 6400 мкФ. Напряжение заряда конденсаторов регулируют в пределах 260 — 425 В. Ленту приваривают при напряжении 325 — 380 В. Чем больше диамеф восстанавливаемой
Наплавка валов ручной дуговой сваркой
Наплавка металла электродом ручная дуговая и прочая: зубев шестерни, рельсовых концов, порошки, расход
Главная страница » О сварке » Как правильно варить » Наплавка металла: электродом и другие
Наплавка представляет собой нанесение дополнительного слоя металла на поверхность различных изделий и деталей посредством сварки. Данная процедура не только восстанавливает первоначальные свойства детали, но и придает ей дополнительные ценные характеристики. Является одним из самых простых и эффективных способов возвращать элементам работоспособность.
Наплавление может производится с различными целями:
- восстановление геометрии изделия;
- придание конструкции новой формы;
- образование слоя, обладающего конкретными физико-механическими свойствами;
- повышение износостойкости, антикоррозийности, прочности, твердости и других свойств основного материала.
Суть процесса состоит во взаимопроникновении раскаленных материалов друг в друга, происходящем на молекулярном уровне. Для этого поверхностный слой основного изделия нагревается до расплавления на небольшую глубину, а присадка — до жидкого состояния. Получившееся соединение отличается высоким уровнем надежности. Основным достоинством технологии является возможность регулировать толщину данного слоя в значительных пределах и нанесения присадки на элементы различной формы.
Ниже вы найдете подробный обзор всех видов наплавки, а далее рассмотрение в деталях наплавки электродами.
В настоящее время в промышленной и производственных сферах используется большое количество способов наплавки. Далее мы рассмотрим различные виды наплавления в зависимости от типа используемого наплавочного материала.
Ручная дуговая наплавка покрытыми электродами
Наплавка электродами с покрытием является наиболее универсальным методом, может осуществляться во всех пространственных положениях. Применяется как в промышленной отрасли, так и в бытовой сфере.
- Популярность данного способа обусловлена несколькими причинами: простота, удобство, гибкость, отсутствие необходимости в специальном оснащении.
- Основные недостатки: низкая производительность, тяжелые условия для исполнителя, нестабильность качества полученного слоя, большое проплавление основного материала.
Наплавление требует от исполнителя наличия определенных навыков. Необходимо при минимальном токе оплавить оба компонента.
С помощью определения состава металла подбирается тип электрода, а толщина и форма заготовок влияет на диаметр сварочного стержня. Если толщина наплавленного материала составляет менее 1,5 мм. — то диаметр прутка должен быть 3 мм. При толщине более 1,5 мм. — 4-6 мм.
Поверхность детали нужно очистить от различного рода загрязнений.
Необходимость предварительного подогрева и последующей термообработки также зависит от марки используемых электродов.
Наплавка изделий из стали осуществляется на постоянном токе обратной полярности.
Данный метод подразумевает применение различных схем наплавочных швов.
При работе с плоскими изделиями выделяют два основных вида:
- использование узких валиков (на картинке), каждый последующий валик должен перекрывать другой на 0,3-0,4 своей ширины;
- применение широких валиков, которые получаются при увеличенных поперечных движениях электрода.
Ещё одним видом является накладка узких валиков на некотором расстоянии друг от друга. Шлаковая корка удаляется после наложения нескольких валиков. Затем промежутки также заполняются валиками.
Наплавка изделий цилиндрической формы производится тремя способами:
- валиками вдоль образующей цилиндра;
- валиками по замкнутым окружностям;
- по винтовой линии.
Подробнее наплавка цилиндров будет проанализирована далее.
Производители и продавцы предлагают обширный ассортимент наплавочных электродов с покрытием. Наиболее популярными являются следующие марки:
ОЗН-6 используются для наплавки деталей оборудования различного назначения, эксплуатирующееся в условиях значительных ударных нагрузок и интенсивного изнашивания. Металл, наплавленный с помощью электродов данной марки, обладает повышенной стойкостью к образованию трещин.
Электроды ОЗИ-5 применяются для наплавления металлорежущего инструмента и штампов. Наплавленный металл обладает высокой стойкостью к смятию и истиранию при значительных ударных нагрузках.
Ручная дуговая наплавка также может проводиться угольными, графитовыми или вольфрамовыми электродами. Наплавление данными сварочными материалами имеет ограниченное применение, поэтому используется редко.
Вибродуговая наплавка выполняется путем вибрации электрода, амплитуда которой составляет 0,75-1,0 диаметра стержня. Процедура осуществляется на токе обратной полярности силой в 80-300 А. В моменты соприкосновения основного изделия и проволоки электрода происходит короткое замыкание, которое разогревает обе поверхности до температуры плавления.
Данный способ позволяет получить прочный и тонкий слой. При этом небольшой нагрев исключает деформацию детали.
Вибродуговой способ применяются для наплавления наружных и внутренних цилиндрических, наружных конических и плоских поверхностей. Также данный метод используется для восстановления следующих конструкций: шейки валов, штоки буровых насосов, замки бурильных труб и других.
Электрошлаковая наплавка основана на применении тепла, образующегося при прохождении тока через расплавленный шлак. Главная особенность данного метода — высокая производительность. За час работы исполнитель может получить сотни килограммов наплавленного металла. Другие характерные черты ЭШН: отсутствие разбрызгивания, экономичность расхода присадочных материалов и электроэнергии, низкие скорости нагрева и охлаждения отрицательно сказываются на структуре наплавленного слоя, небольшая склонность металла к образованию пор.
К сведению! Для получения стабильного процесса необходимо, чтобы глубина шлаковой ванны составляла не менее 30 мм. Несоблюдение этого правила приводит к неустойчивости процесса.
В качестве присадочного материала могут применяются электроды различного сечения: прутки, пластины и т.п.
Основные достоинства: процесс остается устойчивым в обширном диапазоне плотностей тока: 0,2-300 А/мм2, возможность наплавки слоев большой толщины за один проход, данный способ может применяться для работы с материалами, склонными к образованию трещин, возможность придавать наплавленному металлу нужную форму.
Главные недостатки: перегрев основного изделия в зоне термического влияния из-за большой погонной энергии процесса, необходимость сложного и уникального оборудования, невозможность получения тонких слоев, значительная длительность подготовки.
Автоматический комплекс плазменной наплавки SBI (Австрия)
В настоящее время активно используется метод плазменной наплавки. В качестве источника тепла выступает высокотемпературная сжатая дуга, получаемая в специальных горелках. Присадочным материалом может быть наплавочный порошок, лента, проволока, электрод и пр.
Плазменная наплавка с подачей в ванну двух плавящихся электродов обеспечивает высокую производительность.
Универсальным подвидом плазменной наплавки является наплавление с вдуванием порошка в дугу. При выполнении подобных работ применяется горелка комбинированного типа, которая выдает два вида дуги: прямая и косвенная. Наплавочные порошки при помощи транспортирующего газа подаются из питателя в горелку и там вдуваются в дугу. За время пребывания в дуге большая часть порошка расплавляется, и на поверхность основного изделия он попадает в виде капелек.
Рабочую поверхность перед началом наплавления следует зачистить от различных загрязнений: ржавчина, влага, окалина и масло.
При наложении первого наплавочного слоя каждый предыдущий валик нужно перекрывать на 20-30% его ширины.
- Основные преимущества: высокое качество наплавленного слоя, небольшая глубина проплавления основного металла, высокая прочность сцепления, возможность получения слоев малой толщины.
- Недостатки: сравнитель
Наплавка валов в Санкт-Петербурге
В процессе эксплуатации механизмов, машин и различного оборудования отдельные узлы и агрегаты периодически ломаются или приходят в негодность. При этом работа целого производственного участка или техники может быть остановлена на неопределенное время до устранения неисправностей. Для скорейшего ремонта и ввода в строй понадобится выполнить определенный вид ремонта, включая и наплавку валов.
Работы по наплавке валов выполняют на участке, который расположен в закрытом помещении с температурой воздуха более +15ºС. Успешное завершение необходимых технологических операций зависит от выбранного оборудования под наплавку и дальнейшую механическую обработку, а также опыта специалистов. Все работы проводят автоматическими сварочными аппаратами с выпрямителем для дуговой сварки в качестве источника питания. После наплавки валы обрабатывают на токарных станках.
Перед наплавкой валов проводят подготовительные работы, в результате которых поверхности очищают от смазки, загрязнений, коррозии. Затем оценивают степень износа и при необходимости проводят токарную обработку для устранения глубоких вырывов или неравномерного износа. Допускается износ до 0,5 мм на сторону. При наличии трещин наплавку не выполняют.
Для наплавки используют такие материалы, как порошковые проволоки. В результате получают нелегированный или низколегированный наплавленный металл с определенной твердостью. Процесс наплавки происходит в защитной среде из марганцевых флюсов или защитных газов (аргон, углекислота). Валы диаметром до 100 мм наплавляют с использованием самозащитной порошковой проволоки.
Применение флюсов позволяет добиться хорошего формирования наплавленного металла и минимальных припусков под дальнейшую обработку. В некоторых случаях при наплавке валов большого диаметра применяют подогрев газовым пламенем.
Заказ наплавки валов в ТМЕ Cooperation
Обращаясь в ТМЕ Cooperation, можно разместить заказ на наплавку валов. Для этого достаточно найти в базе данных компании исполнителя с приемлемыми ценами.
Преимущества работы с ТМЕ Cooperation:
- минимальное время обработки запросов;
- прием нестандартных заказов;
- выбор предприятий в Санкт-Петербурге и по регионам;
- при необходимости исполнителям оказывается соответствующая помощь для завершения работ в указанные сроки.
Восстановление отверстий наплавкой и расточкой
30.05.2019
Продолжительная эксплуатация машин и механизмов приводит к износу посадочных мест подшипников, валов, втулок, пальцев – как и любые детали они со временем потребуют восстановления. Замена корпусов или крышек, в которых расположены отверстия, обходится слишком дорого и занимает продолжительное время. Повреждения приводят к тому, что техника и оборудование надолго выходят из строя. Компания производитель работ и заказчик несут значительные убытки в результате простоя.
Поэтому изготовители металлообрабатывающего оборудования разработали и представили на рынок специализированные мобильные комплексы для обновления геометрии радиальных проемов в металлических деталях. Это позволило отказаться от полного демонтажа изношенных деталей и ремонтировать, не снимая их с техники и оборудования.
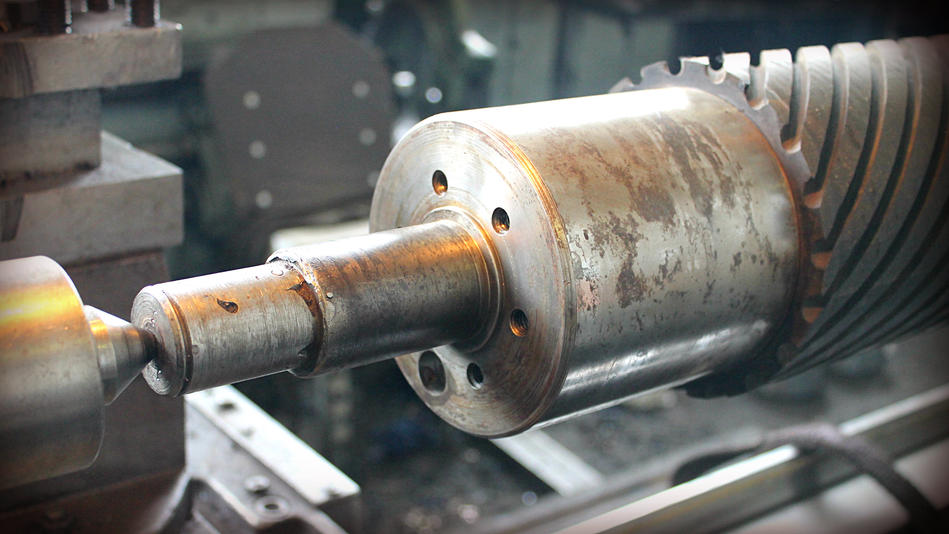
Что такое восстановление отверстий
Под реставрацией посадочных мест вращающихся, опорных и фиксирующих элементов цилиндрической формы подразумевают исправление нарушений размеров радиальной геометрии путем:
- предварительной подготовки;
- проточки для устранения эллипсности;
- наплавки металла на поверхность;
- черновой и финишной механической обработки.
Для выполнения восстановительного комплекса работ применяют специализированное оборудование, совмещающее в себе применение современных сварочных технологий и возможность металлообработки с высокой точностью фрезерования. Процесс реставрационных мероприятий предусматривает возможность обработки одного отверстия или одновременно нескольких, расположенных на одной оси.
Реставрация посадочных мест позволяет значительно сэкономить время и деньги за счёт отказа от приобретения от приобретения нового оборудования или дорогих запасных частей. При этом мобильная конструкция наплавочного восстановительного оборудования позволяет производить работы как в стационарных, так и в полевых условиях.
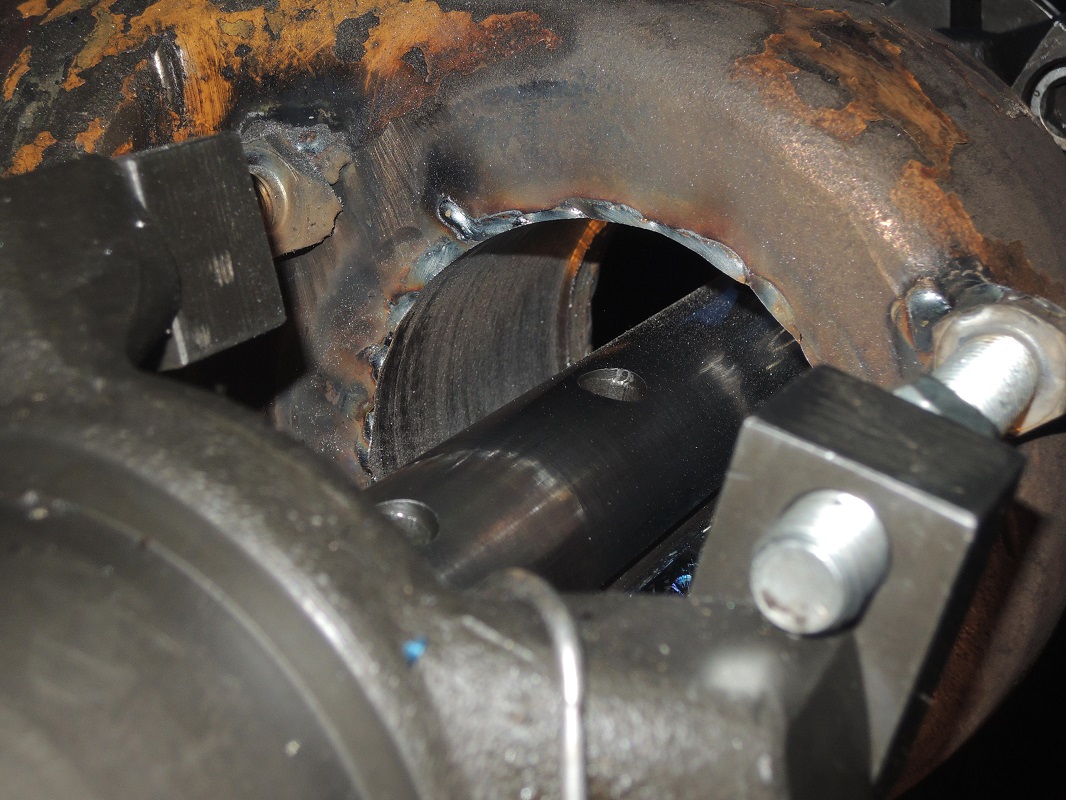
В каких случаях применяется
Применение расточно-наплавочных комплексов необходимо для приведения в рабочее состояние дорожной и строительной техники, погрузчиков и подъемных кранов, прокатных станов, конвейеров, электродвигателей, металлообрабатывающих станков и другого оборудования. Современный инструмент для реставрации узлов с радиальными проемами позволяет выполнять:
- наплавление металлического слоя;
- радиальную расточку отверстий в металле с точностью обработки 0,01 мм;
- снятие фасок и торцевание;
- проточку канавок для установки стопорных колец;
- сверление;
- нарезание резьбы.
Отремонтированные таким образом детали и компоненты приобретают не только первоначальные геометрические размеры в соединениях и сочленениях, но и механические свойства обновленных поверхностей: твердость, прочность, износостойкость и т.п.
Мобильная расточка и наплавка отверстий очень удобна для выполнения реставрационных работ в полевых условиях. Владельцу машин и механизмов не нужно решать вопрос демонтажа изношенного узла и транспортировки его в ремонтную мастерскую или на завод. Ремонтно-восстановительные мероприятия организуют и проводят на месте.
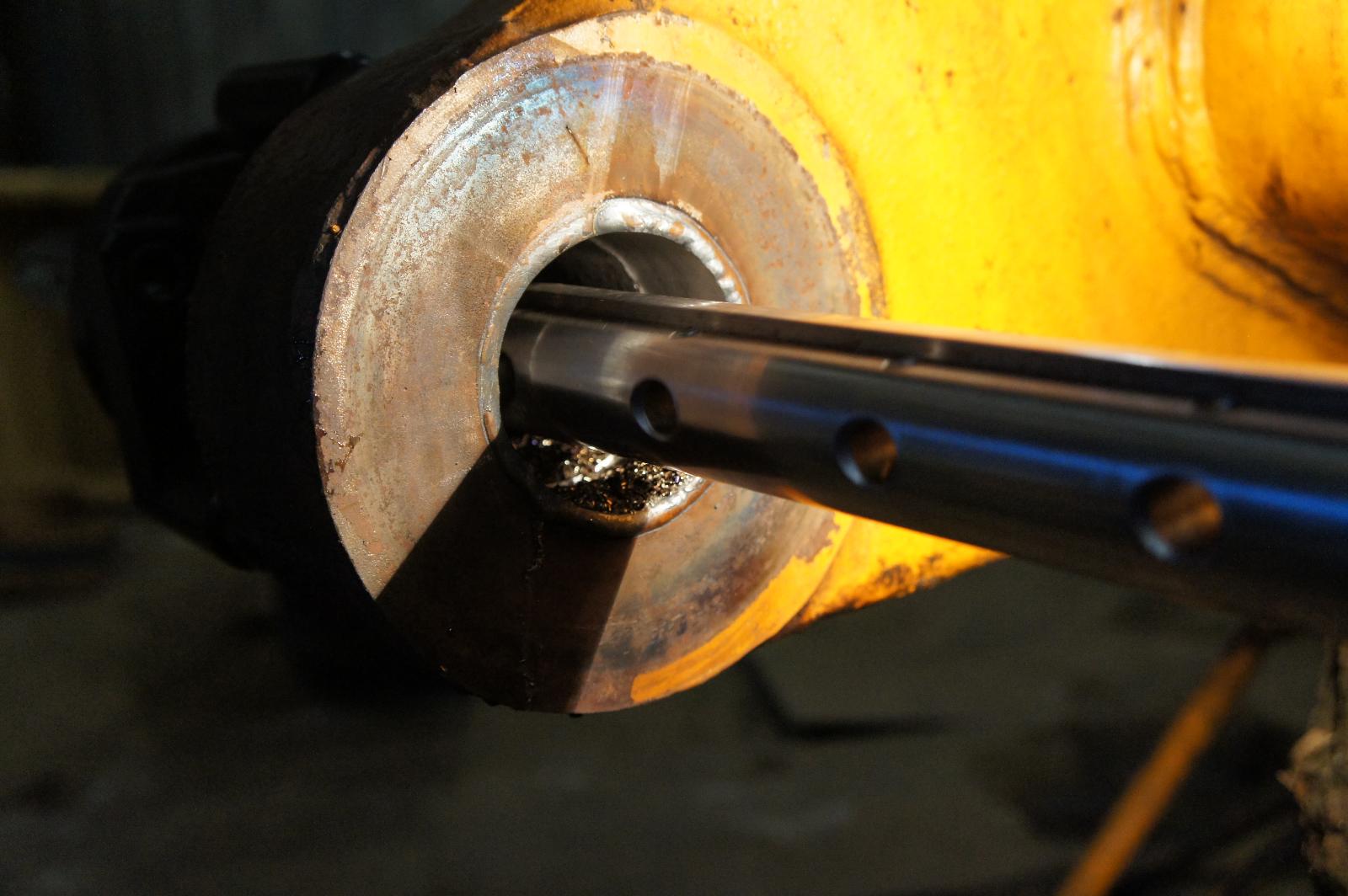
Такое оборудование широко используют:
- в судостроении и ремонте судов;
- при восстановлении энергетического и горнодобывающего оборудования;
- для ремонта дорожно-строительной техники;
- в тяжелой индустрии и сельском хозяйстве;
- для наплавки и расточки отверстий экскаватора;
- при обслуживании подвижного железнодорожного состава;
- для реставрации коммунального и лифтового оборудования;
- для ремонта подъемно-транспортных механизмов, землеройной и дорожной техники;
- на конвейерах и прокатных станах и на предприятиях тяжелой промышленности.
Специфика реставрируемых элементов такова, что они требуют предельно точно соблюдать все размеры и соотношения, учитывать особенности соединения, а также характер механического воздействия в работе детали, узла и всей системы в целом.
Станки для восстановления отверстий деталей с наплавкой и расточкой применяют для различных видов работ в труднодоступных местах. С их помощью:
- обеспечивают работоспособность оборудования и трубчатых деталей длиной до 4 метра;
- нарезают резьбу;
- приводят в норму диаметральные размеры;
- обрабатывают снаружи параллельные поверхности;
- производят шлифование и сверление.
Наплавка с последующей фрезерной обработкой признана на сегодняшний день лучшей технологией для возвращения работоспособности дорогостоящим узлам и механизмам. Поэтому приобретение специализированного станка при наличии нескольких единиц рабочей техники всегда экономически оправдано. В том случае, если количество механизмов невелико, можно обратиться за оказанием подобной услуги.
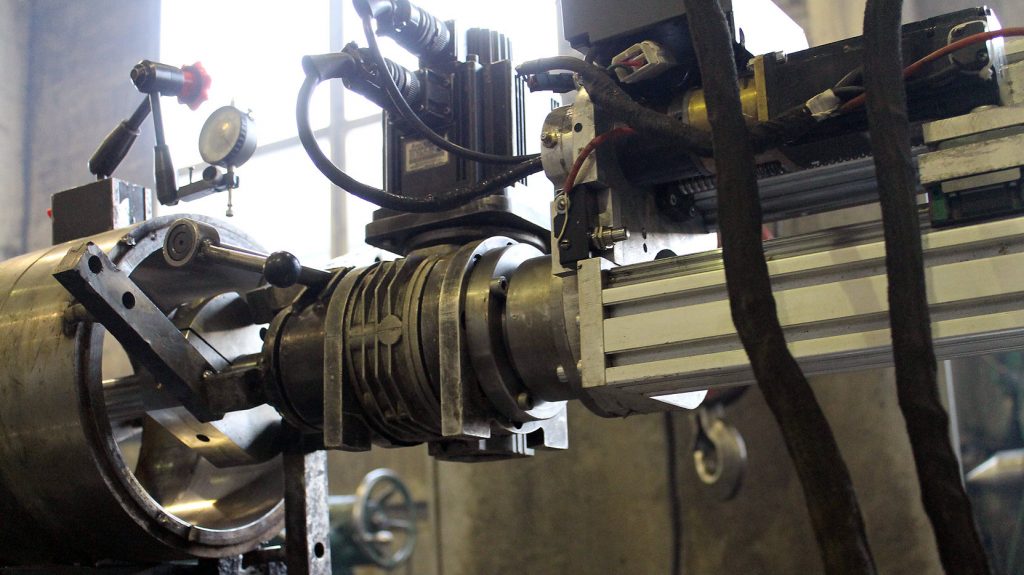
Этапы проведения работ
Наплавочный способ восстановления изношенных деталей включает 6 последовательных этапов:
- подготовка, осмотр и измерения;
- установка и центровка рабочего вала;
- первая расточка отверстий в металле для устранения эллипсности и других дефектов;
- нанесение металла на поверхность;
- окончательное фрезерование под номинальный размер;
- финишная обработка поверхности.
Первичная расточка необходима даже при отсутствии дефектов, поскольку толщина обновленного слоя не может быть менее 2 мм. Завершающая (финальная) – производится в случаях повышенных требований к качеству поверхности.
Перед тем как восстановить разбитое отверстие в металле, расточно-наплавочный станок закрепляют на корпусе детали при помощи сварки или другим доступным способом. После выполнения центровки возможна простая проточка под калиброванный ремонтный размер или восстановление размеров в прежний номинал. В этом случае комплексная обработка предусматривает проработку всех технологических этапов, перечисленных выше.
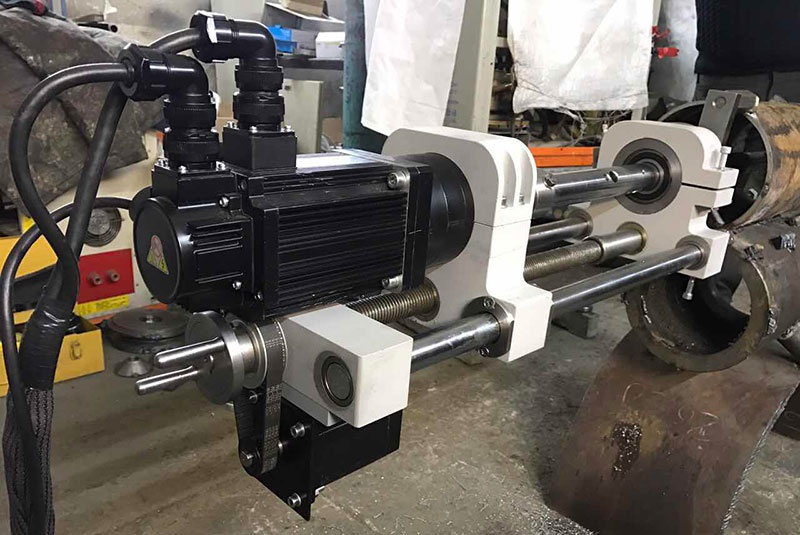
Важной технической особенностью мобильных расточно-наплавочных комплексов является возможность одновременной проработки двух и более мест, расположенных на одной оси. При этом диаметры обработки разных поверхностей могут быть различны.
Подготовка поверхности
На этапе подготовки к восстановлению деталей сваркой и наплавкой выполняют осмотр осмотр ремонтируемой детали, производят необходимые измерения, проверяют совпадение осей, определяют способ закрепления центровочного комплекта. В зависимости от типа и конструкции детали центровочный блок может быть зафиксирован с двух сторон, а для обработки нескольких разнесенных поверхностей, на крайних торцах.
Рабочий агрегат жестко закрепляют на корпусе детали с помощью электросварки или другим возможным способом. В результате вес обрабатывающего инструмента не будет влиять на точность выполнения операций.

Установка и центровка вала
Особая конструкция центровочного комплекта позволяет установить любое положение борштанги, чтобы обеспечить необходимое направление оси места восстановления или точное осевое совпадение двух обрабатываемых диаметров. В этом случае центровка борштанги производится после выполнения комплекса измерений по менее изношенному узлу.
На предварительно отцентрированную борштангу закрепляют фиксирующие суппорты, которые при помощи сварки окончательно фиксируют станок в нужном положении. Для крепления станка допускается вместо сварки применять метизы соответствующих диаметров, а при малой толщине детали — зажимные элементы типа струбцин.
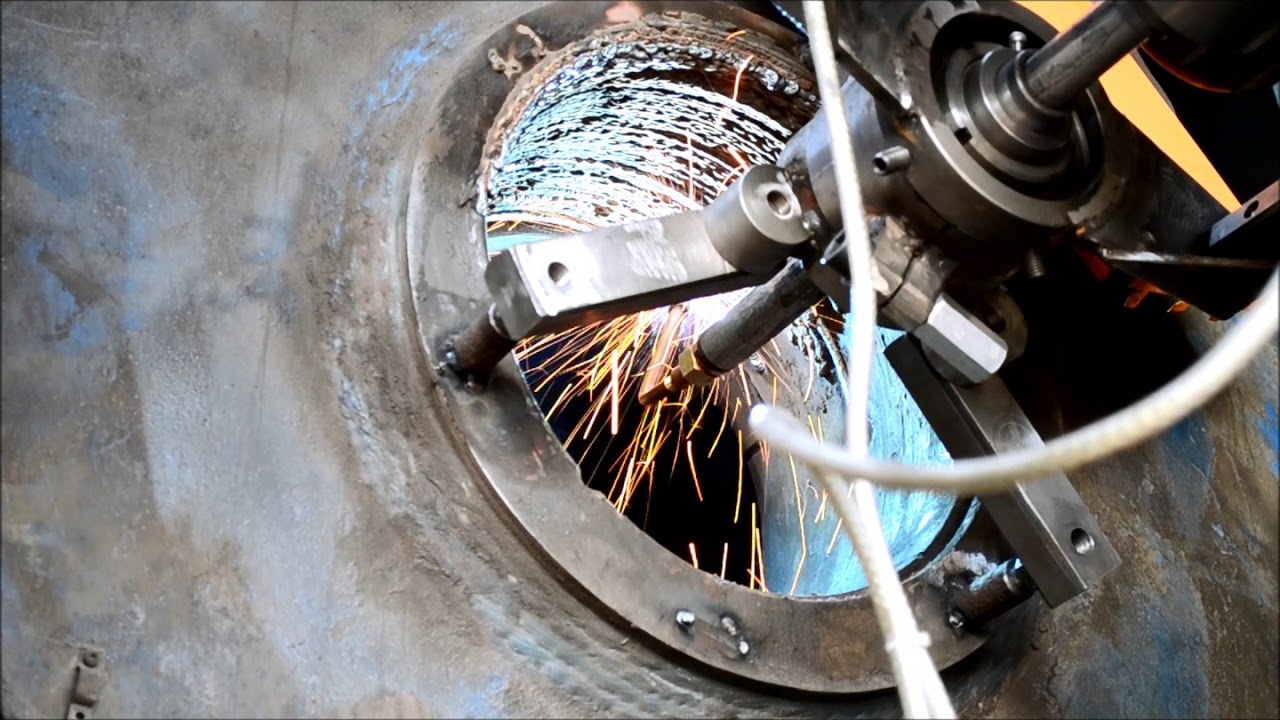
Фрезерование и устранение эллипсности
После окончательной фиксации станка центровочный комплект удаляют, и на борштангу устанавливают резец, с помощью которого будет производиться первая расточка. Она необходима для устранения эллипсности, которая возникает в результате износа при работе машин и механизмов. Кроме этого, проведенные ранее измерения могли показать нарушение соосности двух противоположных посадочных мест.
После первой фрезеровки поверхностей оба отверстия будут располагаться на одной оси, и геометрическая конфигурация станет точно радиальной, без эллипсоидных отклонений. Однако размер после завершения работы уже не будет соответствовать заводскому номиналу. В этом случае возможны два технических решения по восстановлению диаметра:
- повторное фрезерование под расчетный ремонтный размер с высокой точность обработки и горячая установка металлической гильзы;
- нанесение металла на поверхность и расточка под заводской номинал.
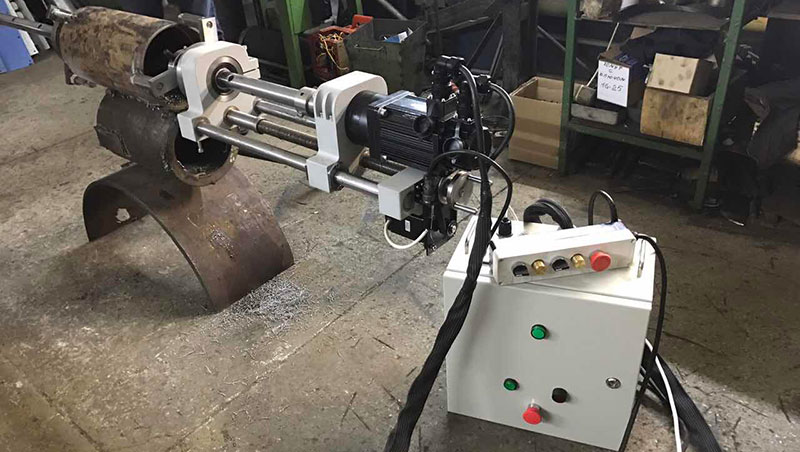
Работа мобильного расточно-наплавочного комплекса предусматривает второй вариант восстановления и ремонта отверстий. Это проще, быстрее и намного дешевле, чем изготовить и установить ремонтную гильзу. Кроме того, подобная технология обновляет тело металла и исключает возможность смещения нового покрытия, в отличие от запрессованной гильзы.
Наплавка
Для наплавления слоя металла на радиальную поверхность используется электросварочный аппарат инверторного типа с автоматической подачей проволоки к месту обработки. В зависимости от марки сплава восстановление деталей вибродуговой наплавкой может осуществляться в обычных атмосферных условиях или защитной инертной среде. Обычно она представляет собой смесь из 80% аргона и 20% углекислого газа.
Расточная борштанга заменяется на наплавочную, к которой подключается сварочный инверторный аппарат и газовый баллон. При отсутствии готовой смеси аргона и углекислого газа подключаются 2 баллона через специальный редукторный смеситель.
Наплавка предусматривает нанесение одного или нескольких слоев металла и осуществляется в автоматическом режиме. Работа станка обеспечивает самостоятельное вращение сварочной насадки и ее продольное перемещение без участия оператора.
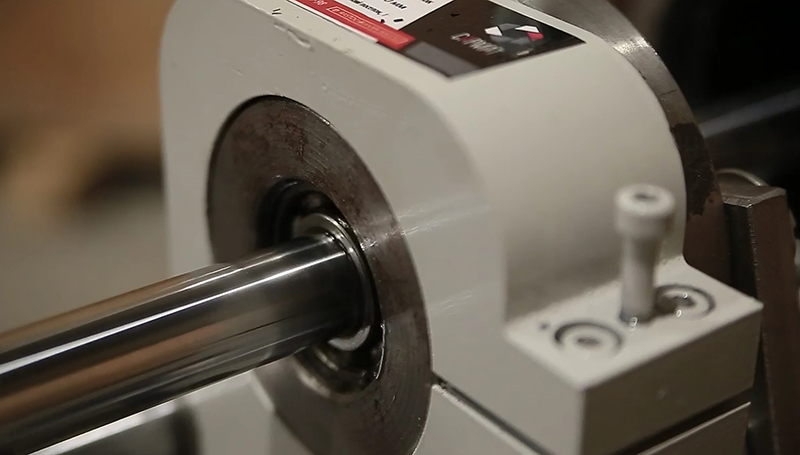
Физико-механические свойства наплавляемого слоя полностью соответствуют или даже превышают характеристики основного металла обрабатываемой детали. В зависимости от марки сварочной проволоки, силы тока и скорости прохождения твердость слоя находится в пределах 20-30 HRC.
Фрезерование под номинал
После наплавки металла и его полного остывания наплавочную штангу снимают и на ее место снова устанавливают фрезеровальный инструмент. Механические способы восстановления отверстий предусматривают проточку поверхности за два раза. Сначала выполняется черновая проточка для максимального приближения к номинальному размеру с обязательным плюсовым допуском. При этом величина допуска не превышает 0,5 мм, обычно 0,2-0,3 мм.
Первая обработка не обеспечивает высокой точности, поскольку производится с другой целью. Во время фрезерования под номинал устраняют весь поверхностный сварочный шлак и грубые неровности после наложения слоев. В результате геометрия отверстия приобретает ровную поверхность, максимально приближенную к номинальному размеру.
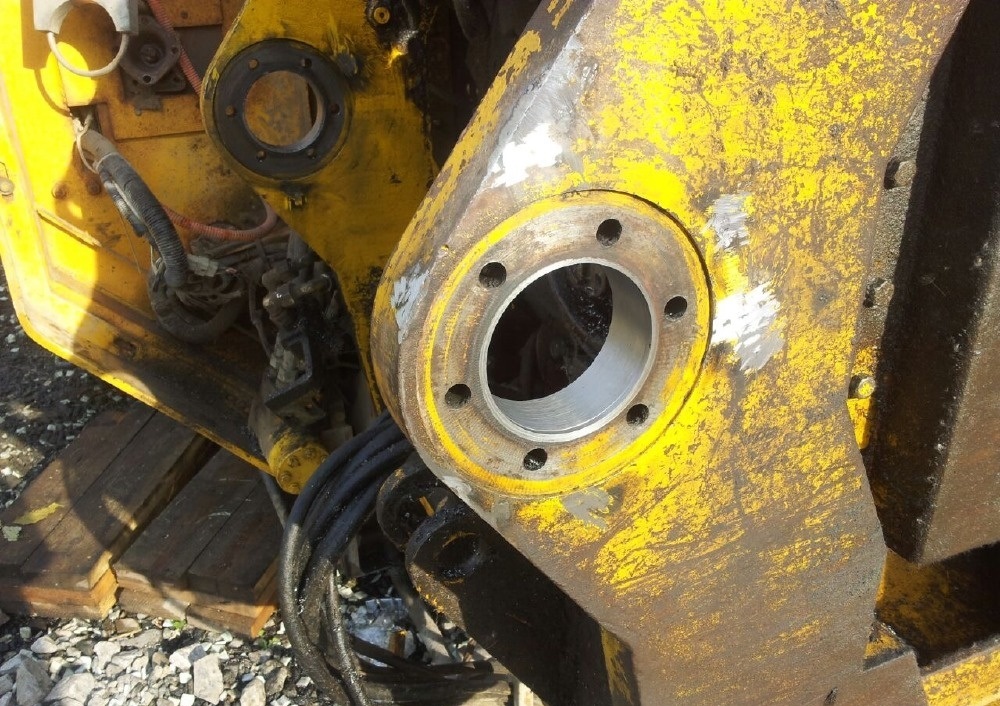
Финишная обработка поверхности
На следующем этапе работ выполняют чистовое фрезерование с обеспечением точности в пределах 0,01 мм. Для этого снижают скорость прохождения резца и постоянно контролируют проточки с помощью выносных цифровых индикаторов.
Окончанием работ является проведение контрольных замеров, определяющих качество работы, демонтаж станка с корпуса и механическая зачистка следов сварки, которая применялась для фиксации суппортов. Расточно-наплавочная технология предусматривает возможность немедленной сборки отреставрированного узла и начало работы механизма.
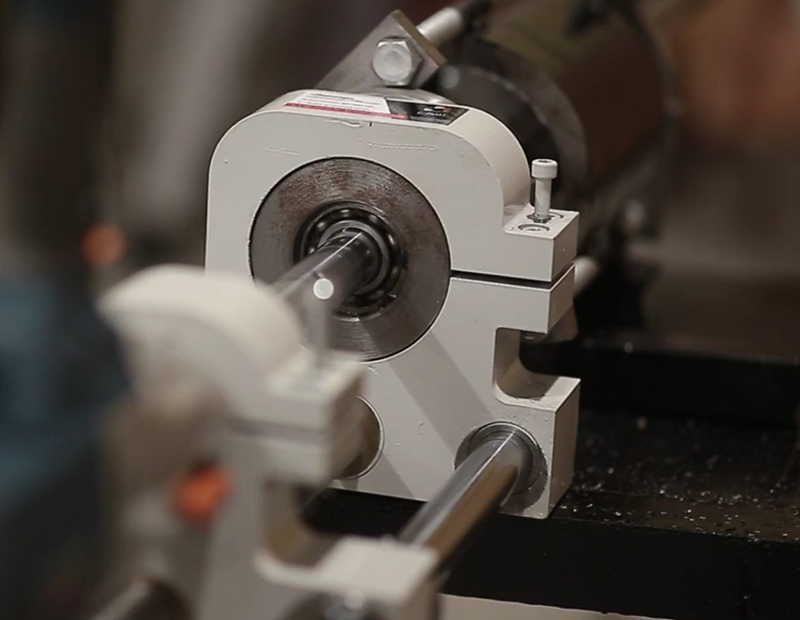
Необходимое оборудование
Самые мощные мобильные комплексы оборудования позволяют реставрировать радиальные элементы диаметром от 25 мм до 1,5-2,0 метра при длине обработанной поверхности до 4-х и более метров.
Одним из известных торговых брендов для восстановления и ремонта отверстий наплавкой являются американские расточные комплексы Climax. Их конструкция допускает точную обработку диаметров от 35 до 2030 мм с точностью и скоростью стационарного станка. Движение рабочих органов осуществляется при помощи электрического и гидравлического привода. Управление оборудованием полностью автоматизировано. Наличие специальных запатентованных кронштейнов позволяет отказаться от применения сварки для фиксации на корпусе реставрируемого узла или детали. Однако стоимость таких комплексов предусматривает их приобретение только в случае большого парка ремонтируемой и обслуживаемой техники.
Более доступное по цене оборудование для восстановления отверстий это станки модельного ряда WS, выпускаемые европейской компанией Sir Meccanica. Модели WS компактны и предусматривают мобильное применение. В качестве режущего инструмента используются стандартные токарные резцы из быстрорежущей стали. Электропривод отличается низким уровнем энергопотребления.
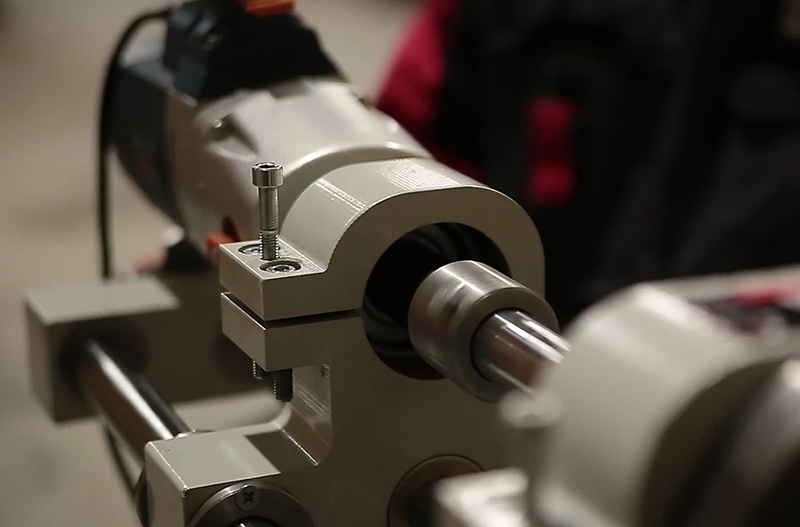
Одними из лучших моделей от отечественных производителей по стоимости и по качеству можно назвать станки серии «Пионер». Это оборудование для мобильной расточки и наплавки отверстий является мощным устройством, позволяет эффективно решать большинство задач, связанных с ремонтом техники и механизмов. Вкладывая относительно небольшие средства в приобретение этого оборудования, вы сможете обеспечить высокое качество ремонтных работ для своей техники и организовать выездные услуги для других компаний.
По желанию заказчика специалисты компании «Сармат» изготовят борштанги любых необходимых размеров и внесут другие конструктивные изменения для выполнения конкретно поставленных задач.
Наплавка под слоем флюса – описание технологии и ее тонкостей + Видео
Наплавка под слоем флюса, будучи механизированным процессом, как правило, выполняется для восстановления цилиндрических и плоских поверхностей.
1 Дуговая наплавка под флюсом – что она собой представляет?
Под наплавкой понимают операцию нанесения восстановительного или защитного металлического слоя на поверхность обрабатываемой детали (конструкции), осуществляемую посредством сварочного оборудования. По характеру процесса такая процедура восстановления деталей бывает прерывистой и непрерывной, по уровню механизации – автоматической, механизированной, ручной и автоматизированной.
Также наплавку различают по варианту защиты металла при ее выполнении:
- под расплавленным (предварительно) покрытием сварочного стержня;
- под слоем флюса.
Нас в рамках данной статьи интересует второй способ защиты металлических деталей.
Наплавка под флюсом вала или какого-либо иного изделия – это операция, в ходе которой сварочная дуга, горящая между деталью из металла и электродом, предохраняется от внешних воздействий составом, прошедшим процедуру расплавления.
Наплавка под флюсом осуществляется посредством совмещения двух движений сварочных стержней. Они, во-первых, передвигаются вдоль получаемого шва, а во-вторых, подаются ближе к детали по мере оплавления. Заметим, что расплавление флюса производится сварочной дугой, а его толщина варьируется в пределах 2–4 сантиметров.
Описываемый метод защиты дает гарантию на то, что воздух из окружающей среды не сможет влиять на металл. Следовательно, негативного процесса окисления вала или плоской конструкции наблюдаться не будет. Применение флюса также обеспечивает сохранность тепла в зоне проведения наплавки и исключает вероятность разбрызгивания металла.
В большинстве случаев обработка деталей по такой технологии ведется проволокой без покрытия, которая выполняет функцию электрода. Выбор сечения используемой сварочной проволоки обуславливается конкретными задачами, ставящимися перед процедурой наплавки. Разрешается применять проволоку диаметром 1–6 миллиметров.
Увеличения производительности и эффективности операции можно добиться двумя путями:
- подачей посредством двух сварочных приспособлений, работающих в полуавтоматическом режиме, в область наплавки одновременно двух проволок;
- применением электродов ленточного типа.
Наплавление вала, других цилиндрических деталей либо изделий с плоской поверхностью в большинстве случаев ведется на обратном по полярности токе:
- на обрабатываемую конструкцию идет «минус»;
- на проволоку для сварки подается «плюс».
2 Наплавка под слоем флюса – достоинства и недостатки методики
На сегодняшний день операция с использованием расплавленного флюса считается самым широко распространенным вариантом наплавки деталей. Причин тому множество. Мы хотим выделить ключевые достоинства этой методики:
- Процесс характеризуется простотой выполнения всех необходимых работ. С наплавкой легко справляются сварщики с достаточно низкой профессиональной подготовкой.
- Производительность труда находится на очень высоком уровне. Это преимущество полностью проявляет себя при обработке простых по конфигурации деталей, поверхность коих описывается сравнительно большими размерами (обработка вала с применением флюса, правда, не будет столь высокопроизводительной).
- Гарантия максимальной безопасности для специалиста, выполняющего наплавку. Сварщик практически полностью защищен от риска получения ожога из-за отсутствия горячих брызг во время процесса.
- Качество наплавочных работ очень высокое. Эстетические показатели обработанных изделий безупречны, а главное, наплавленный металлический валик характеризуется отличной надежностью и прочностью. Эксплуатационный потенциал деталей, прошедших процедуру восстановления, по-настоящему безупречен.
Явных «минусов» рассматриваемой методики не так уж и много. Но они все же есть. Специалисты выделяют несколько недостатков применения флюса:
- Увеличенная зона нагрева. Она не позволяет производить наплавку изделий с малыми геометрическими размерами (например, небольшого вала), а также конструкций очень сложной формы.
- Оборудование имеет высокую стоимость. Намного дешевле использовать стандартное оборудование, предусматривающее выполнение работ покрытыми электродами для ручной дуговой сварки (наплавки).
- Снижение показателя прочности обработанных изделий (иногда их прочностные характеристики уменьшаются на 30–40 процентов).
Кроме того, в наплавленном металле могут формироваться поры и крупные по размерам трещины, что, конечно же, ухудшает эксплуатационные показатели вала либо другой детали после наплавки.
3 Оборудование для автоматической наплавки и особенности его эксплуатации
При обработке цилиндрической поверхности (например, вала) изделие монтируется на центрах либо в патроне обычного токарного станка, который определенным образом модифицируют так, чтобы на его суппорте можно было разместить устройство для наплавки. Наплавочный аппарат располагает специальной кассетой, из которой к электродуге подается сварочная проволока. Подача становится возможной за счет наличия подающего механизма.
При вращении вала проволока начинает перемещаться вдоль шва, а суппорт, передвигаясь в продольном направлении, перемещает электрод по длине детали. Мелкий сыпучий флюс при этом подается из бункера в область горения, где происходит плавление некоторой его части, что приводит к созданию эластичной оболочки вокруг сварочной дуги. Для того чтобы жидкий металл не отекал, проволоку слегка смещают в сторону, которая является по отношению к вращению вала противоположной.
Для выполнения процесса обычно применяется наплавочное оборудование (установки) УД209 и СН2, а также наплавочные специальные головки ОКС5523, А580М, А765. Рекомендуется использовать для наплавки следующие виды проволоки:
- для изделий из высокоуглеродистых сталей – Нп40Х13, Нп80, Нп65Г;
- для деталей из кремниймарганцовистых и марганцовистых сплавов – Св15Г, Св08Г, Св12ГС, Св08ГС, Св08ГА;
- для изделий из низколегированных сталей и сплавов с небольшим содержанием углерода – Св08А и Св08.
Применяемые в наши дни составы для автоматической наплавки под флюсом подразделяют на:
- Комбинированные (спецсмеси). Они включают в себя жидкое стекло, графитовый и феррохромовый порошок и какой-либо плавленый стандартный флюс.
- Керамические. В них обязательно имеются шлакоформирующие и особые стабилизирующие добавки, а также легирующие компоненты. Такой состав керамических флюсов обеспечивает наплавленному слою повышенную стойкость против износа и хорошие показатели твердости. Известные флюсы данной группы – ЖСН1, АНК30, АНК18, КСХ14Р.
- Плавленые. Данные составы используются наиболее часто. В них нет легирующих компонентов. Чаще всего наплавка ведется флюсами АН28, ОСу45, АН348А, АН20.
4 Использование электродной ленты для выполнения наплавки под флюсом
В Советском Союзе в середине прошлого столетия создали уникальный метод восстановления деталей при помощи электродов ленточного типа, которые представляют собой стальную широкую ленту. Ее к основному металлу при наплавке размещают почти под прямым углом, что приводит к повышению производительности выполнения наплавочных мероприятий.
Ленточные электроды обеспечивают возможность:
- увеличивать силу тока для осуществления процесса, а также его скорость;
- наносить за несколько проходов (а иногда и за один) необходимый по толщине наплавочный слой;
- получать большой по ширине и при этом абсолютно плоский наплавленный валик.
Чаще всего описываемые электроды применяются для обработки коррозионностойких металлов и сплавов. Ширина таких сварочных ленточных стержней может достигать 18 сантиметров. Теоретически можно использовать и более широкие электроды, но тогда возрастает вероятность того, что наплавляемый валик просто-напросто потеряет свою форму.