Износостойкие — Центр защитных покрытий — Урал
Центр защитных покрытий — Урал (ЦЗПУ) предлагает нанесение износостойких покрытий. Износостойкое покрытие — это защитное газотермическое покрытие, повышающее сопротивление поверхности различным видам изнашивания. Правильный выбор износостойкого покрытия может продлить жизнь изделия в несколько раз, практически не увеличивая его стоимости, а правильность выбора защитного покрытия зависит от знаний и опыта конструктора, полноты информации об условиях монтажа и эксплуатации. Износостойкие покрытия применяют для повышения износостойкости деталей машин и инструментов, для устранения задирания трущихся поверхностей, восстановления размеров изношенных деталей и исправления деталей, размеры которых оказались заниженными при механической обработке. Износостойкое газотермическое напыление применяются так же и при ремонте оборудования или упрочнении рабочих поверхностей новых деталей. Основные технологические процессы, которые сегодня используются на практике — это плазменное напыление на воздухе с использованием таких плазмообразующих газов, как аргон, азот, гелий, воздух; высокоскоростное напыление; детонационное или газопламенное напыление, а также электродуговая металлизация. В зависимости от назначения покрытия и условий его работы меняются требования к точности соблюдения основных параметров — его состава, плотности, толщины, прочности сцепления с подложкой. Износостойкие покрытия обеспечивают высокую твердость и хорошие антикоррозионные свойства. Мы наносим различные износостойкие покрытия, каждое из которых имеет свои особенности звоните, пишите и уточняйте у наших менеджеров, мы работаем со всеми городами Приволжского федерального округа и Уральского федерального округа.
Изнашивание металлов процесс разрушения поверностных слоев трущихся тел который характеризуется разнообразием условий их нагружения. И, в зависимости от условий нагружения следует выбирать те материалы, которые имеют большее сопротивление изнашиванию. При восстановлении изношенных деталей машин и оборудования применяют износостойкое напыление. Износостойкое газотермическое напыление это получение покрытия из нагретых и ускоренных частиц напыляемого материала с применением высокотемпературной газовой струи, при соударении которых с основой или напыленным материалом происходит их соединение за счет сварки, адгезии и механического сцепления. ЦЗПУ восстанавливает изношенные части деталей машин и оборудования, а так же наносит износостойкие покрытия. Обращайтесь, пишите, звоните — мы всегда поможем Вам.
способ плазменного напыления износостойких покрытий — патент РФ 2462533
Изобретение относится к технологии газотермического напыления, а именно к плазменным способам напыления износостойких покрытий на детали, работающие при одновременном воздействии износа и коррозионных сред, и может быть использовано в машиностроении, металлургии, энергетике и других сферах производства. Согласно способу осуществляют ввод дисперсного керамического порошка через кольцевую щель в воздушно-плазменную струю и последующее его напыление на предварительно обработанную поверхность изделия. При этом используют дисперсные частицы оксида алюминия Al
Изобретение относится к технологии газотермического напыления, а именно к плазменным способам напыления износостойких покрытий на детали, работающие при одновременном воздействии износа и коррозионных сред и используемые в машиностроении, металлургии, энергетике и других сферах производства.
Известен способ получения износостойкого покрытия (Борисов Ю.С., Харламов Ю.А., Сидоренко С.Л. и др. Газотермические покрытия из порошковых материалов. Справочник. Киев: «Наукова думка». 1987. С.544), включающий ввод в плазменную струю порошка оксида алюминия (Al 2O3) дисперсностью менее 80 мкм точечным методом, при мощности плазмотрона 70-100 кВт, плазмообразующим газом является смесь воздуха с природным газом. Относительная износостойкость такого покрытия — 1,5 при среднем значении микротвердости составляющих покрытие фаз 1100 кг/мм2, пористость — 8-15%.
Недостатком способа является неравномерное заполнение порошком плазменной струи по ее поперечному сечению, что приводит к неравномерности плавления частиц и существенному различию их скоростей и, как следствие, к получению низкой воспроизводимости свойств напыляемых покрытий. Микротвердость и износостойкость таких покрытий недостаточно высокие, кроме того, они характеризуются низким качеством.
Широкое применение получил способ нанесения плазменных покрытий, в котором ввод порошка в плазменный поток осуществляется под углом к направлению потока по кольцевой щели, окружающей плазменный поток. Использование кольцевого способа позволяет значительно уменьшить недостатки точечного способа нанесения покрытий и получить более высококачественные покрытия, что подтверждают проведенные эксперименты, представленные в описании предлагаемого изобретения.
Наиболее близким к предлагаемому изобретению является способ плазменной обработки по патенту EP № 0423370 (опубл. 18.10.1990), включающий ввод дисперсного керамического порошка через кольцевую щель в воздушно-плазменную струю и его напыление на предварительно обработанную поверхность изделия.
Основной недостаток — конструктивные особенности не позволяют использовать широкий интервал фракционного состава порошкового материала, что в ряде случаев не позволяет получать покрытия с заданными значениями пористости и микротвердости составляющих покрытие фаз.
Задача предлагаемого технического решения состоит в создании покрытия с низкой пористостью, повышенными значениями микротвердости составляющих покрытие фаз и износостойкости.
Поставленная задача достигается тем, что в предлагаемом способе плазменного напыления износостойких покрытий, включающем ввод дисперсного керамического порошка через кольцевую щель в воздушно-плазменную струю и последующее его напыление на предварительно обработанную поверхность изделия, новым является то, что напыление ведут дисперсными частицами оксида алюминия (Al2O 3) со следующим фракционным составом: 20-40 мкм в количестве 75-85% и остальное — менее 20 мкм. При этом регулируют мощность плазмотрона в пределах 44-54 кВт, а расход воздуха составляет 1-2 г/с. Относительно небольшая мощность плазмотрона исключает перегрев обрабатываемых изделий.
Таким образом, отличительными признаками предлагаемого способа являются следующие: соотношение фракций используемого порошка, мощность плазмотрона и расход плазмообразующего газа.
При осуществлении предлагаемого способа обнаружен положительный эффект, сущность которого заключается в повышении микротвердости составляющих покрытие фаз, что можно объяснить повышением количества межзеренных границ вследствие использования порошков различной дисперсности. Кроме этого, полученные покрытия отличаются высокой износостойкостью, в том числе при работе в коррозионных средах, высоким качеством как по высоте слоя, так и по границе раздела со сталью.
Технический результат достигается при сочетании следующих факторов. Выбранная мощность плазмотрона 44-54 кВт и расход плазмообразующего газа 1-2 г/с, позволяют обеспечить высокое качество покрытий с пористостью не более 2%. Изменение расхода плазмообразующего газа и мощности плазмотрона в сторону их повышения и уменьшения приводит к снижению износостойкости напыленных слоев, микротвердость составляющих покрытие фаз при этом возрастает.
Равномерный кольцевой ввод в поток плазмы композиции оксида алюминия с оптимальным фракционным составом (20-40 мкм в количестве 75-85% и остальное — менее 20 мкм), при описанных характеристиках режима плазменного напыления, позволяет повысить количество межзеренных границ, а это, одновременно с высоким качеством покрытия, обеспечивает увеличение его микротвердости и износостойкости.
При увеличении размера частиц снижается количество межзеренных границ, соответственно, и уровень микротвердости. Частицы меньших фракций используются целенаправленно для повышения количества межзеренных границ.
Покрытия в целом характеризуются композиционной структурой. В матричном материале расположены области скоплений ультрадисперсных включений. В процессе транспортировки порошков мелкие частицы образуют конгломераты в подводящих порошок коммуникациях, которые при напылении дробятся, оплавляются, расплавляются. Все эти моменты и влияют на появление областей скопления ультрадисперсных включений. И, естественно, чем мельче фракция, тем больше будет образовываться областей ультрадисперсных включений. Эти фрагменты структуры покрытий повышают хрупкость напыленных слоев и являются очагами износа. Поскольку задача состояла в повышении микротвердости (износостойкости) и сохранении пластичности покрытий, то это значит, что нужно было обеспечить появление минимального количества вышеописанных областей ультрадисперсных включений и при этом использовать частицы мелких фракций. Исходя из этого были найдены оптимальные соотношения фракций порошка, которые и предлагаются в заявке.
Предлагаемый способ осуществляется следующим образом.
Порошок подают в узел кольцевого ввода плазмотрона для напыления на стальные образцы, предварительно подвергнутые дробеструйной обработке и обезжириванию. Напыление осуществляют электродуговым плазмотроном постоянного тока ПНК — 50 при следующих режимах: мощность плазмотрона 44-54 кВт, плазмообразующий газ — воздух, расход плазмообразующего газа — 1-2 г/с. В качестве исходного порошка для нанесения покрытия используют оксид алюминия (Al 2O3) фракции 20-40 мкм в количестве 75-85% и остальное — менее 20 мкм. Напыляемые частицы порошка после ввода в воздушно-плазменную струю нагреваются до высоких температур, ускоряются и при попадании на поверхность изделия образуют покрытие. Оплавленные и расплавленные частицы, осаждаясь на подложку, легко деформируются, большую роль при этом играет и динамика струи, которая определяется расходом плазмообразующего газа. Такие условия предотвращают образование пустот и зон несплавления. В результате на стальном образце формируется керамическое покрытие. Высокие физико-механические характеристики покрытия обеспечиваются как подобранным экспериментально фракционным составом порошка Al
В результате проведенных экспериментов режим № 2, характеристики которого представлены в таблице, был принят как оптимальный.
Микродюрометрические исследования проводят на приборе ПМТ-3. Пористость покрытий оценивают микроскопическим методом по секущей.
Испытания износостойкости в коррозионной среде выполняют на специальном стенде ПВ-12, разработанном в НИИХИММАШ (г. Москва). Условия испытаний на данном стенде максимально соответствуют таковым для промышленных деталей, например деталей бурового оборудования. Результаты испытаний приведены в таблице.
Пример.
На стальном образце необходимо сформировать плазменное покрытие с микро-твердостью составляющих его фаз не менее 1200 кг/мм2, относительной износостойкостью не менее 2 и с пористостью менее 2% (см. таблицу режим № 2). Для получения покрытия с указанными рабочими характеристиками используют керамический порошок оксида алюминия (Al2 O3) с соотношением фракций: 20-40 мкм в количестве 75-85% и остальное — менее 20 мкм. Ввод частиц порошка в плазменный поток осуществляют через узел кольцевого ввода. В качестве плазмообразующего газа используют воздух, расход которого составляет 1,5 г/с; мощность плазмотрона поддерживают в диапазоне 47-50 кВт. В результате на стальном образце формируется керамическое покрытие с требуемыми рабочими характеристиками.
Режимы напыления и свойства полученных покрытий представлены в таблице, в которой приведены режимные параметры 1-3 при соотношении фракций порошка оксида алюминия: 20-40 мкм в количестве 75-85% и остальное — менее 20 мкм; а в режиме 4 — для фракции порошка 80 мкм.
Результаты реализации предложенных режимов напыления и свойства покрытий, полученных при кольцевом и точечном вводах порошков в плазменный поток, представленные в таблице, показывают, что микротвердость увеличилась на 6,9-19,6% в сравнении с точечным видом подачи частиц; эксплуатационные свойства (стойкость покрытий в условиях одновременного воздействия абразивного изнашивания и коррозионной среды) повышены в 1,2-1,5 раза относительно точечного ввода, пористость снижена в 4-7,5 раза. Кроме того, предлагаемое техническое решение отличается энергосбережением (мощность процесса напыления снижена на 26-56 кВт) и ресурсосбережением (в качестве плазмообразующего газа используется воздух без добавок природного газа).
В процессе проведения экспериментов при кольцевом вводе порошка был подобран оптимальный режим (режим № 2) для напыления керамического порошка в виде оксида алюминия (Al2O3) с приведенными в таблице параметрами.
Таким образом, использование предлагаемого способа позволяет получить покрытия, характеризующиеся высокими физико-механическими и эксплуатационными свойствами, а именно повышенными значениями микротвердости составляющих покрытие фаз и износостойкости покрытий в условиях одновременного воздействия абразивного изнашивания и коррозионной среды, высоким качеством за счет снижения пористости.
ФОРМУЛА ИЗОБРЕТЕНИЯ
Способ плазменного напыления износостойких покрытий, включающий ввод дисперсного керамического порошка через кольцевую щель в воздушно-плазменную струю и последующее его напыление на предварительно обработанную поверхность изделия, отличающийся тем, что напыление ведут дисперсными частицами оксида алюминия (Al2O 3) со следующим соотношением фракционного состава: 20-40 мкм в количестве 75-85% и менее 20 мкм — остальное, при мощности плазмотрона в пределах 44-54 кВт и расходе воздуха 1-2 г/с.
Электродуговая металлизация износостойких покрытий — ТСЗП
Газотермическое напыление износостойких покрытий широко применимо в различных отраслях промышленности. Рабочие поверхности гидравлических узлов, каландровых валов, формовочные плиты, стенки кристаллизаторов, десятки других номенклатурных наименований серийно изготавливаются и ремонтируются с напылением износостойких покрытий.
Наиболее распространенным техническим решением является высокоскоростное напыление карбидов вольфрама, хрома на никелевой или кобальтовой связке, а также других твердых сплавов на поверхности. Технология хорошо зарекомендовала себя благодаря высокому уровню адгезии, твердости покрытия, низкой пористости.
Процесс высокоскоростного напыление постоянно развивается в направлениях снижения удельной стоимости нанесения покрытий, расширения применимости метода (разработка новых сопел для нанесения, повышение мобильности оборудования).
Помимо высокоскоростного напыления целесообразным является использование и других технологий газотермического напыления для создания толстых слоев твердых износостойких покрытий. Сегодня мы применяем электродуговую металлизацию как более дешевый аналог износостойких покрытий.
Специально производимые по заданию наших инженеров порошковые проволоки полностью совместимы с современными металлизаторами, а преимущества электродуговой металлизации (отсутствие открытого огня, высокая мобильность оборудования, простота использования) перед высокоскоростным напылением позволяют расширять применимость функциональных покрытий.
Энергии установки электродуговой металлизации недостаточно для прогрева большинства твердых материалов. Поэтому мы используем специально разработанную порошковую проволоку, оболочка которой изготовлена из легкоплавких сплавов, а наполнение представляет собой шихтовую смесь Fe-Cr-B-Al-Y.
Рис.1. Нанесение износостойких покрытия электродуговым металлизатором
В процессе электродуговой металлизации начинается трехстадийный процесс: сначала от энергии металлизатора расплавляется оболочка, плавление представляет собой эндотермическую реакцию; выделяющееся при плавлении оболочки тепло проплавляет шихтовую смесь. Продуктом нагрева шихты являются бориды железа.
Свойства покрытий
Типовая микроструктура представляет собой ламеллярно-пористую структуру, где светлые участки – металлическая основа, формируемая из капель расплавленного металла, а темные – прослойки оксидов, образующиеся при окислении капель на дистанции напыления. Покрытия отличаются значительной микрогетерогенностью и неравномерным сплавлением отдельных напыленных частиц друг с другом. Вероятно, микрогетерогенность структуры покрытий обусловлена наличием в ПП тугоплавких борсодержащих компонентов. Покрытия из ПП марки-3 (рис. 15 в) обладают меньшей микрогетерогенностью, их структура более тонкая, оксидных пленок меньше, и они мельче, что, вероятно, связано с меньшей степенью окисления покрытий.
Оксидные пленки могут способствовать отслаиванию металла по механизму внутреннего трения, увеличивая скорость механического износа металлического покрытия. Благоприятная микроструктура покрытия из ПП марки-3 с минимальным количеством оксидных пленок в конечном итоге может обусловливать высокие показатели его физико-механических и служебных свойств, в том числе высокой стойкости к износу.
Рис.2. Структура на поперечных шлифах покрытий
Твердость: 1100-1200HV
Адгезия: до 50 МПа.
Толщина покрытия: 0,4 -3мм
Пористость: от 2,5%
Как уже описывалось, главным предназначением данных покрытий, является придание износостойкости. Сравнительные показатели по ASTM G65 приведены в таблице ниже.
Материал | Технология нанесения | Износ, г | Износ, см3 | Твердость, HRC |
Порошковые проволоки | ЭДМ | 0,0261 | 0,00335 | 58,2-67,2 |
WC | HVOF | 0,0199 | 0,001328 | >70 |
FeCrNiMoSi | HVOF | 0,1073 | 0,01274 | 50-52 |
WC+NiCrBSi (50% WC по массе) | LC | 0,087 | 0,00704 | 48,0-57,1 |
Получаемые электродуговой металлизации покрытия показывают износостойкость на уровне типовых наплавляемых систем, уступая при этом покрытиям, получаемым высокоскоростным методом с применением дорогостоящего карбида вольфрама мелкой фракции.
Применимость.
Основными преимуществами являются:
1. Относительно большие максимальные толщины (до 3 мм)
2. Простота нанесения покрытия
3. Мобильность оборудования
4. Отсутствие открытого пламени
Таким образом, можно говорить о применимости для больших объектов, демонтаж которых является достаточно дорогим процессом, и которые предпочтительно обрабатывать на месте эксплуатации, например, системы транспорта песка на цементных и других производствах, вентиляторы пылеудаления, обечайки компактирующих устройств.
Рис.3.Обечайка компактирующего минеральные удобрения устройства после нанесения покрытия.
Низкая стоимость материала (до 6 раз ниже, чем стоимость порошка карбида вольфрама), производительность при нанесении, позволяют применять данные покрытия для гидравлических систем, где не требуется высокий уровень адгезии, т.е. гидравлика работает вне условий высокой абразивности среды, например, прессовое оборудование, а также в механизмах транспорта абразивных материалов, например, шнеки.
Напыление износостойкими эластомерными покрытиями MetaLine
Износостойкое, не содержащее растворители, двухкомпонентное полиуретановое защитное покрытие для быстрого и простого нанесения посредством картушной системы напыления.
Полиуретановое защитное покрытие
Серия 700 — это наносимый в теплом состоянии термореактивный эластомер. Материал отличается высочайшей устойчивостью к износу и абсолютно гладкой поверхностью покрытия. Вследствие быстрой реакции в течение буквально нескольких минут можно нанести покрытие толщиной от 0,5 до 20 мм. После отвердевания при комнатной температуре (без термической обработки!) образуется полиуретановое покрытие необычайной стабильности формы, износостойкости и долговечности. Полиуретановое защитное покрытие МетаЛайн может использоваться как в сухой, так и во влажной среде. Материал наносится с помощью специального картушного напылительного пистолета, без предварительного взвешивания и смешивания компонентов! (Нанесение напылением или литьем во время одного рабочего хода!)
Полиуретановое защитное покрытие серии МетаЛайн, зарекомендовавшее себя успешным применением в разнообразных отраслях по всему мире, обладает рядом неоспоримых преимуществ:
— Исключительно высокая устойчивость к абразивному износу
— Высокая устойчивость против входной и плоскостной кавитации
— Не требуется инвестиций в дорогостоящую технику нанесения
— Технические параметры и качество превышают полиуретан горячего нанесения
— Легко ремонтируется и восстанавливается
— Используется для ремонта „заводских“ покрытий
— Располагает самым низким удельным весом среди всех известных защитных покрытий, а значит, отсутствуют проблемы балансировки
— Не влияет на вибрационные характеристики
— Неограниченная гибкость наращивания слоя любой толщины
— Нанесение полиуретанового покрытия на поверхности любого контура
— Новая специальная грунтовка обеспечивает великолепную адгезию на бронированных, покрытых сваркой или измененных термическим способом поверхностях
Может применятся не только как покрытие для быстрого ремонта или защиты, но и как самостоятельный тип защиты деталей на производствах машин, оборудования и механизмов.
МетаЛайн 700 позволит значительно снизить финансовые расходы, сократит потерю времени на простои, а поставщикам услуг ремонтно-восстановительного характера позволит выйти в лидеры на любом рынке.
Материал наносится без предварительной или последующей температурной обработки покрываемой области.
Использование специальных праймеров позволяет достичь великолепной прочности адгезии покрытия с поверхностью.
ЛИНЕЙКА ВКЛЮЧАЕТ ТРИ ЭЛАСТОМЕРНЫХ ПОКРЫТИЯ РАЗЛИЧНОЙ ТВЕРДОСТИ:
M 760 — мягкое полиуретановое покрытие (твердость 60 А по Шору)
M 785 — полумягкое полиуретановое покрытие (твердость 85 по Шору)
M 795 — полужесткое полиуретановое покрытие (твердость 95 по Шору)
Основные характеристики:
- Метод нанесения – напыление картушным пистолетом или литье
- Доступные цвета – серый, синий, черный, желтый, темно-зеленый, красный
- Пропорции смешивания – 2:1 по объему
- Твердость – от 72 до 95 по Шору A
- Плотность – 1,05 гмм3
- Адгезия — до 20 Н/мм2
- Прочность на растяжение / разрыв – 20 Нмм2
- Напряжение (при 100% натяжении) – 7 Нмм2
- Сопротивление на раздирание – 55 Нмм2
- Удлинение на разрыве — 380%
- Эластичность по отскоку — 45%
- Термостойкость (сухая влажная среда) — от -50оС до 100оС +80оС
- Износ (по TABER-тесту, Н-22, сухой, 1 кг, 1000 об.) – 8,2 мг
- Износ — 73мм3
- Содержание твердых частиц – 100%
- Время схватывания (при 50оС) – 1 минута
- Полное отвердевание (при 20оС) — > 1 суток (зависит от последующей нагрузки)
- Затраты материала – 1 кгм2 (при толщине слоя – 1 мм)
Примеры наиболее удачных покрытий, получаемых термическим напылением
Содержание страницы
Несмотря на то, что на сегодняшний день существуют многие десятки разнообразных металлических и керамических покрытий, получаемых термическим напылением, понастоящему удачных из них лишь единицы. Ведь что значит хорошее покрытие? Хорошим можно назвать только то покрытие, которое, наряду со своим прямым предназначением, удовлетворяет целому ряду побочных требований и может применяться в разных областях. Любое покрытие, которое предлагает рынок, так или иначе, выполняет ту задачу, для которой оно было создано, однако, для основной массы покрытий на этом все и кончается. Самые неудачные покрытия характеризуются тем, что создают массу технологических и конструктивных трудностей, имеют очень узкую область применения, ненадежны, и даже свою единственную функцию выполняют с минимальным эффектом. Примером таких неудачных покрытий могут служить все твердые, чисто керамические покрытия на основе Al2O3 или Cr2O3, термобарьерные покрытия из ZrO2-Y2O3, коррозионнозащитные покрытия из пористых сталей, инконелей, нихромов, цинка или алюминия, уплотняющие покрытия из алюминиевой бронзы, и многие другие. Причем речь идет не о каких-то редких покрытиях, а о вполне «классических», получивших самое широкое распространение и предлагаемых практически всеми предприятиями, работающими с термическим напылением. На взгляд автора, именно то, что большинство предлагаемых покрытий является неудачными, создает отрасли термического напыления дурную славу среди потребителей и тормозит внедрение действительно хороших покрытий. Автору часто приходилось слышать от потенциальных заказчиков фразы о том, что они уже «обжигались» на технологиях термического напыления. Сегодня мало кто из производственников готов поверить заявлению, что не все покрытия пористые, непрочные, еле держатся на деталях и «чуть что не так» — отваливаются. Именно по этой причине в настоящей главе речь пойдет только о хороших, надежных покрытиях, делающих честь их создателям, и дающих действительно большой эффект.
Покрытия из самофлюсующихся сплавов
Технология покрытий из самофлюсующихся сплавов на основе никеля или кобальта была первой настоящей удачей в истории термического напыления. Как и полагается выдающемуся изобретению, эта технология не потеряла своей актуальности за более чем 70 лет своего существования.
Технология базируется на свойствах стеллитов, то есть, относительно легкоплавких сплавов системы CoCrSi, наплавляемых на стальную подложку, первые из которых были изобретены американским инженером Элвудом Хейнсом в 1907 году. В 1917 году он, совместно с М.Д. О’Брайеном, владельцем канадской золотодобывающей шахты в местечке Делоро (Онтарио), основал компанию Deloro Smelting and Refining Company Ltd, из которой позже возникла фирма Deloro Stellite (из золотоносной породы Делоро с 1868 года добывали помимо золота также и кобальт).
Дальнейшее развитие самофлюсующихся сплавов проводилось фирмой Deloro Stellite сначала в Америке, а затем в Германии, где с 1970 года существует фирма Deloro Stellite GmbH.
Первые стеллиты применялись для наплавки на сталь по технологиям сварки. Лишь с появлением в 40-х годах порошков стеллитов, пригодных для газопламенного напыления, появилась современная технология термического напыления самофлюсующихся сплавов с последующим их оплавлением. Составы сплавов для термического напыления обособились от сплавов для сварки в сторону уменьшения их температуры плавления и увеличения флюсующего эффекта. Основная заслуга в разработке и внедрении таких специальных порошковых материалов для термического напыления принадлежит фирме Sulzer Metco, которая в 50-е годы, одновременно совершенствовала порошки самофлюсующихся сплавов и устройства газопламенного напыления для этих порошков. В настоящее время все фирмы, производящие порошки для термического напыления, имеют в ассортименте порошки самофлюсующихся сплавов.
В чем же успех покрытий из самофлюсующихся сплавов? Напомним, что в 50-е годы не существовало еще устройств напыления, сообщающих частицам скорости, достаточные для образования плотных покрытий. Пористые же металлические покрытия, за исключением покрытий анодной защиты из цинка или алюминия, практически бессмысленны, так как не защищают ни от коррозии, ни от механического износа. Использование самофлюсующихся кобальтовых и никелевых сплавов позволило решить эту проблему: грубое пористое покрытие после специальной термической обработки (оплавления) становится газоплотным, а прочность его связи со стальным или чугунным субстратом превышает 250 МПа.
Рассмотрим механизм функционирования самофлюсующихся сплавов:
Современные самофлюсующиеся сплавы имеют следующий состав: хром – 9-15%, бор — 2-4%, кремний – 2-4%, остаток – никель или кобальт (никель применяется чаще из-за его более высокой коррозионной стойкости). Эти сплавы частично плавятся при 1050-1100°C, — дают эвтектические расплавы с высоким содержанием бора и кремния. Эвтектический расплав при температуре > 1050°C активно реагирует с оксидами железа, никеля и кобальта в системе покрытие-субстрат, разрушая их восстановлением, например по реакциям:
2B + Fe2O3 = B2O3 + 2Fe; 3Si + 2Fe2O3 = 3SiO2 + 4Fe; 2B + 3NiO = B2O3 + 3Ni
Легкие оксиды бора и кремния выносятся эвтектическим расплавом на поверхность покрытия, а лишенные оксидных пленок частицы покрытия спекаются через расплав эвтектики между собой и с очищенным от оксидов субстратом.
Таким образом, добавки бора и кремния позволили «убить одним выстрелом двух зайцев»:
- Снизить температуру образования расплава в никелевых или кобальтовых сплавах с 1400°C до 1050°C, то есть, до температуры, приемлемой для многих стальных и чугунных изделий и относительно доступной технически (нагревание можно осуществлять как в печах с защитной атмосферой, так и локально, на воздухе – индуктивно или ацетиленокислородными горелками).
- Полностью очистить поверхности субстрата и частиц от пленок оксидов и обеспечить, тем самым, спекание покрытия и металлургическую связь с субстратом. Флюсующее действие эвтектического расплава, содержащего бор и кремний, настолько сильно, что допускает даже быстрый нагрев субстрата с покрытием до 1050-1100°C на воздухе, а также использования чугуна в качестве субстрата (из-за прослоек графита, получить хорошее покрытие на чугун другими способами очень сложно).
С точки зрения химии, разница между высокотемпературной пайкой под флюсом и оплавлением самофлюсующихся сплавов состоит в том, что расплавленные легкоплавкие оксидные и фторидные флюсы просто растворяют оксидные пленки, не вступая с ними в окислительно-восстановительные реакции.
С практической же точки зрения, процесс оплавления покрытия из самофлюсующихся сплавов идентичен процессам пайки. Разница только в том, что при пайке припой плавится, как правило, полностью, а самофлюсующиеся сплавы плавятся частично. Частичное плавление позволяет получать из самофлюсующихся сплавов покрытия толщиной более 2 мм, тогда как покрытия из припоев обычно имеют толщину менее 100 мкм.
С помощью напыленных покрытий из самофлюсующихся сплавов можно, на самом деле, с большим успехом паять стальные и чугунные изделия: спаиваемые детали ставятся напыленными поверхностями друг на друга, помещаются в печь с защитной атмосферой и нагреваются до 1050-1100°C. При этом получаются газоплотное соединение толщиной 200-300 мкм и прочностью до 300 МПа.
Высокотемпературная пайка самофлюсующимися сплавами имеет важные преимущества перед, гораздо более распространенной, высокотемпературной пайкой чистой медью, особенно для крупных изделий из чугуна:
- Толщина швов, паянных медью, очень мала (менее 10 мкм), так как расплавленная жидкая медь легко вытекает из шва. Такая малая толщина шва предъявляет высокие требования к качеству и точности сопрягаемых поверхностей. Кроме того, тончайшие прослойки меди не могут компенсировать возможные термические напряжения, возникающие при охлаждении паяных изделий. Самофлюсующиеся сплавы дают толстые швы (200-300 мкм), которые легко выдерживают как несовершенства поверхностей сопрягаемых деталей, так и значительные горячие деформации (в интервале температур охлаждения 1000- 700°C).
- Нанесение припоя из самофлюсующихся сплавов методами термического напыления позволяет очень точно поместить его на тех местах, где он нужен, без риска, что он куда-нибудь сместится (медный припой, в виде проволоки, сетки или фольги подготавливать и размещать гораздо сложнее). Кроме того, расход материала припоя и загрязнение изделия избыточным припоем, в случае использования термического напыления, минимальны.
- Медные паяные швы, а также остатки меди на поверхностях стальных и чугунных изделий, представляют собой потенциальный источник коррозии: при наличии электролита (водных растворов солей, кислот или оснований) медь является активным катодом по отношению к стали и чугуну и вызывает их повышенную коррозию. Самофлюсующиеся сплавы в этом смысле гораздо менее опасны в связи с их сильной пассивацией.
- Пайка медью требует температуры в печи около 1100°C. Эта температура является абсолютным пределом для простых ретортных печей с защитной атмосферой и ретортами из печной хромоникелевой стали или инконеля. На практике, пайку медью проводят в очень дорогих вакуумных печах, что, вместе с повышенным расходом электроэнергии, значительно увеличивает стоимость процесса. Недостатком вакуумных печей является также и то, что нагрев и охлаждение крупных изделий происходит гораздо менее равномерно, чем в ретортной печи с инертной газовой атмосферой (газ равномерно распределяет тепло, а стенки ретортной печи равномерно нагревают и охлаждают садку), то есть вакуумная печь становится источником термических напряжений в изделии. Пайка самофлюсующимися сплавами требует около 1050°C (такие порошки, как Metco 12C оплавляются при этой температуре). Разница всего в 50°C позволяет уверенно использовать ретортные печи для работы с самофлюсующимися сплавами.
- 1100°C слишком высокая температура не только для ретортных печей, но и для чугунов, которые начинают плавиться уже при 1137°C, поэтому для высокотемпературной пайки чугунов переход с 1100°C на 1050°C значит очень много также в смысле надежности технологии.
- Использование термически напыленных покрытий из самофлюсующихся сплавов в комбинации с последующей термической обработкой в печи позволяет, в одном процессе, собрать сложное стальное, чугунное или комбинированное изделие из простых частей и надежно защитить его от коррозии, как на наружных, так и на внутренних поверхностях. Примером таких изделий могут служить сложные паяные детали головок цилиндров больших судовых дизелей, которые работают в условиях коррозии кислыми водными растворами (конденсат продуктов сгорания мазутов).
На рисунках 43-46 показаны образцы изделий с покрытиями из самофлюсующихся сплавов, изделий, паянных этими сплавами, а также оптические микрофотографии поперечных сечений (все результаты из работ автора).
Рис. 43. Деталь головки цилиндра (водоохлаждаемый узел клапана) до и после пайки порошком Metco 12C, нанесенным газопламенным напылением.
До напыления и пайки:
после пайки:
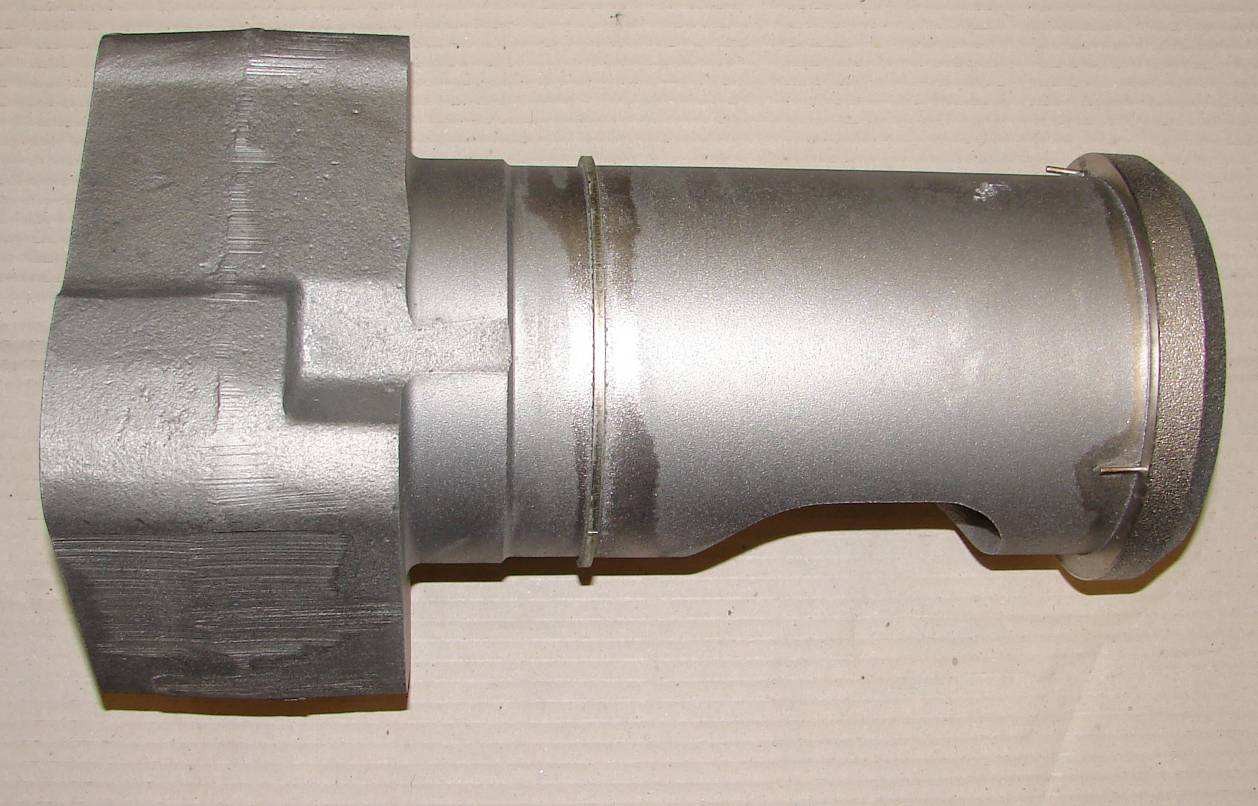
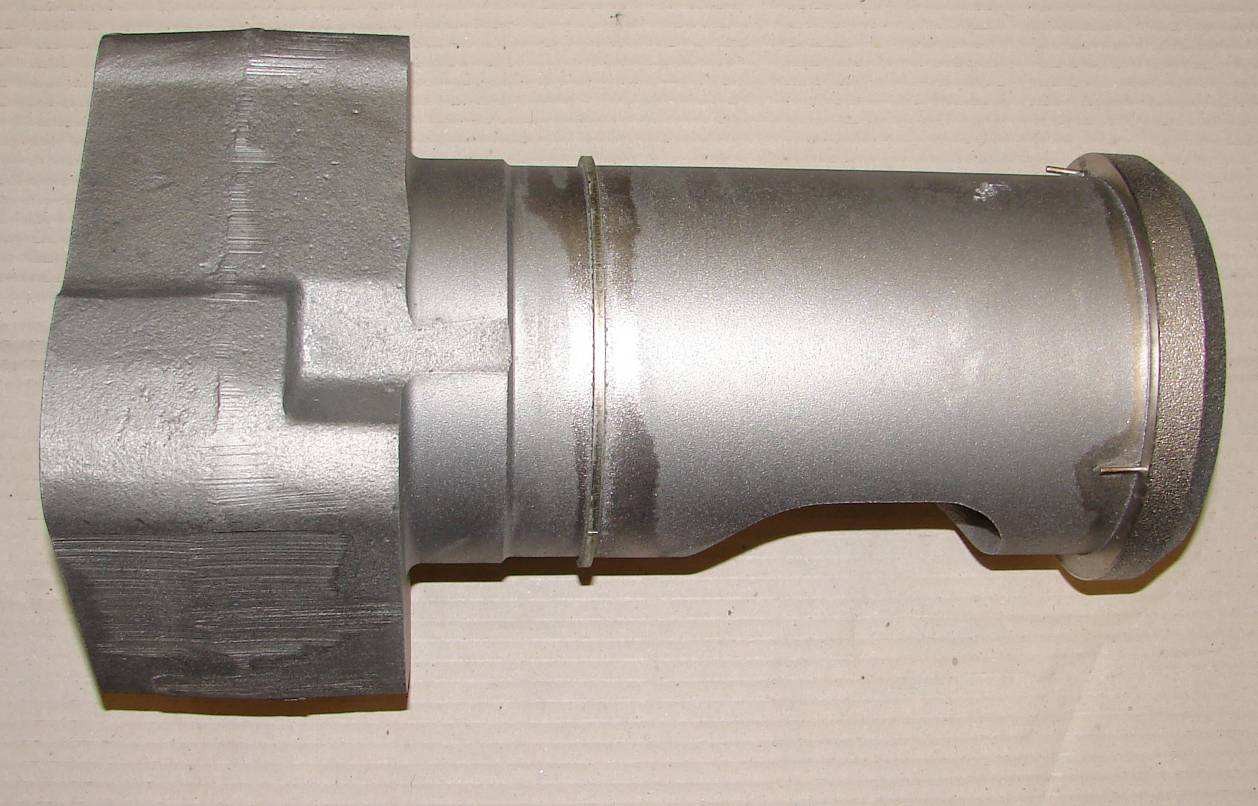
Рис. 44. Поперечный разрез паяного шва — сверху и снизу чугун (травление).
Рис 45. Стальная труба пароперегревателя мусоросжигательной установки с толстым коррозионнозащитным покрытием из Metco 12C.
Рис 46. Поперечное сечение готового (оплавленного) покрытия из Metco 12C; хорошо видна, типичная для этих покрытий, закрытая усадочная пористость.
Покрытия из самофлюсующихся сплавов бывают не только чисто металлическими, но и композиционными – с металлической матрицей и керамическими тугоплавкими частицами, чаще всего из карбидов вольфрама. Технология получения таких покрытий аналогична технологии обычных, чисто металлических, покрытий из самофлюсующихся сплавов, за исключением того, что в порошок для напыления примешивается порошок WC. Покрытия, содержащие карбиды вольфрама, применяются как особо износостойкие, коррозионнозащитные покрытия. Такие покрытия, хотя и уступают спеченным твердым сплавам в твердости и износостойкости (из-за остаточной закрытой пористости и меньшего содержания карбидов вольфрама), но, по своей сути, аналогичны последним.
Область применения покрытий из самофлюсующихся сплавов очень широка:
- защита материалов на основе железа от окисления до температуры около 800°C
- защита от «горячей» коррозии в продуктах сгорания «грязных» топлив
- защита от «мокрой» коррозии в морской воде, растворах кислот, солей и оснований
- защита от абразивного износа
- защита от износа в парах трения
- защита деталей от «пригорания» различных веществ, например раскаленного стекла в пресс-формах выделки стеклотары
- ремонт и восстановление размеров стальных и чугунных изделий
К сожалению, применение оплавляемых покрытий из самофлюсующихся сплавов ограничено необходимой высокой температурой термообработки. Эта температура не дает использовать такие покрытия на деталях, которые уже прошли основную механическую обработку, на особо больших деталях и во многих других случаях, где нагрев до 1050°C попросту невозможен. Кроме того, самофлюсующиеся сплавы «не работают» на высоколегированных хромистых сталях, так как их флюсующее действие не распространяется на оксид хрома.
Покрытия из порошковой смеси: молибден + самофлюсующийся сплав
Наряду с никелем, кобальтом и медью, молибден — один из самых «благодарных» металлов для термического напыления из-за того, что его оксиды восстанавливаются при относительно высоком парциальном давлении кислорода (металл хорошо очищается от оксидов даже в нейтральном ацетиленокислородном пламени). Кроме того, молибден очень пластичен при высоких температурах, что имеет решающее значение для уплотнения покрытия при напылении. Важной особенностью молибдена является его высокая температура плавления (2620°C), которая, с одной стороны требует устройств напыления с высокой температурой пламени, но, с другой стороны, предоставляет расплавленным частицам молибдена очень высокую термическую энергию. Эта энергия выделяется в формирующемся покрытии при остывании частиц и приводит к нагреванию соседних частиц, а также поверхности субстрата, что при разумном использовании, может дать значительную прибавку в прочности связей.
Покрытия из молибдена имеют достоинства при применении для пар трения (прекрасные антизадирные и антифрикционные свойства). В настоящее время в мировой автомобильной промышленности происходит вытеснение хромированных поршневых колец кольцами с плазменно напыленными молибденовыми покрытиями, которые имеют более высокий ресурс службы. Несмотря на несравненно более высокую цену молибденовых покрытий, внедрение их в этой области оказывается экономически выгодным.
Существует два основных вида молибденовых покрытий: покрытия из чистого молибдена (порошок для атмосферного плазменного напыления или проволока для газопламенного напыления) и покрытия из порошковой смеси молибдена и самофлюсующегося никелевого сплава. Газопламенное напыление молибденовой проволокой более старый, дешевый и распространенный процесс, но существенно лучшее качество имеют комбинированные плазменно напыленные покрытия молибден плюс самофлюсующийся сплав.
Рассмотрим механизм функционирования этого комбинированного покрытия:
Как известно, температура плавления самофлюсующихся сплавов лежит около 1050°C, тогда как молибден плавится при 2620°C. При нагревании в пламени такой порошковой смеси до температуры, достаточной для плавления частиц молибдена, автоматически образуются сильно перегретые капельки расплава самофлюсующегося сплава. Когда такие капельки попадают на поверхность субстрата, в них должно хватать энергии на восстановление оксидных пленок, образование металлургической связи с материалом субстрата и на растекание по поверхности до того, как они кристаллизуются. Из-за высокой температуры плавления, частицы молибдена кристаллизуются сразу же,
приходя на субстрат, при этом функция этих застывших частиц не менее важна: остывающие твердые частицы молибдена поддерживают частицы самофлюсующегося сплава дольше в расплавленном состоянии и создают собой механические препятствия для образования сплошной пленки расплава, что абсолютно необходимо для уменьшения усадочных напряжений растяжения в покрытии (см. предыдущую главу).
Таким образом, получается следующее принципиальное преимущество двухфазного покрытия из смеси порошков молибдена и самофлюсующегося сплава:
При термическом напылении на холодный субстрат порошков молибдена или самофлюсующегося сплава по отдельности, нельзя получить плотные покрытия, тогда как из их смеси это возможно!
На рисунках 47 и 48 приведены электронные микрофотографии поперечного шлифа покрытия Mo + NiCrBSi на титановом субстрате, полученного атмосферным плазменным напылением (однокатодный плазматрон А60 фирмы Thermico GmbH).
Светлая фаза – молибден, более темная – самофлюсующийся сплав.
Рис. 47. Покрытие Mo + NiCrBSi на титановом субстрате.
Рис. 48. Увеличенный фрагмент того же покрытия.
Для сравнения пористости и качества связи с субстратом приведем оптическую микрофотографию плазменно напыленного покрытия из чистого молибдена по результатам [3] (рисунок 49):
Рис. 49. Покрытие из чистого молибдена.
Покрытия из карбидов хрома или вольфрама
Покрытия, содержащие карбиды хрома или вольфрама относятся одновременно к износостойким и коррозионнозащитным, так как эти карбиды имеют очень высокую твердость (> 9,5 по Моосу) и стабильны в растворах большинства солей, кислот и оснований. По максимальной температуре применения на воздухе существуют большие различия между карбидами хрома и вольфрама: компактные карбиды хрома могут использоваться до 1000°C, а карбиды вольфрама, — только до 500°C из-за того, что стабильная плотная пленка оксида хрома (Cr2O3) предотвращает дальнейшее окисление карбидов хрома, а легкоплавкий оксид вольфрама (WO3) интенсивно испаряется уже с 600°C и совершенно не защищает карбид от окисления. По твердости и прочности карбиды вольфрама превосходят карбиды хрома.
Получить на металлическом субстрате плотное покрытие из чистых карбидов невозможно никаким способом, поэтому, когда говорят о карбидных покрытиях всегда имеют в ввиду композиции с наполнителем из карбидов на металлической связке. В качестве связки можно, в принципе, использовать любой пластичный металл или сплав, но в широкой промышленной практике традиционно применяются никелевые сплавы для Cr3C2 и кобальтовые сплавы для WC. Наибольшее распространение получили связки из классического нихрома (80Ni20Cr) добавляемые к Cr3C2 в количестве от 10 до 35%, а для WC – чистый кобальт в количестве 10-20%. Для термического напыления применяют как простые смеси порошков карбидов с порошками металлических сплавов, так и спеченные агломерированные порошки. Последние дают покрытия более высокого качества из-за идеального распределения мелких частиц карбидов. На рисунках 50 и 51 изображены типичные сферические частицы агломератов Cr3C2— 80Ni20Cr (порошок Amperit 588 фирмы H.C.Starck) и WC-Co (порошок Amperit 512 фирмы H.C.Starck) .
Рис. 50. Светлая фаза — 80Ni20Cr, серая фаза — Cr3C2, черная фаза – поры.
Рис. 51. Светлая фаза — WC, серая фаза – Co, черная фаза – поры.
Коммерческие агломерированные спеченные порошки, производства компаний H.C. Starck и Sulzer Metco, имеют очень узкое распределение частиц по размерам, так как только такие порошки позволяют, при термическом напылении, сообщить всем частицам примерно одинаковые температуру и скорость. «Одинаковость» частиц в порошке имеет также решающее преимущество при радиальном вводе порошка в пламя и, кроме того, придает даже мелкозернистым порошкам неплохую сыпучесть.
Исторически, первые карбидные покрытия изготавливались атмосферным плазменным напылением из простых смесей порошков карбидов и металлов. С развитием техники HVOF и появлением на мировом рынке агломерированных спеченных порошков происходило постепенное вытеснение плазменного напыления высокоскоростным газопламенным, так как покрытия получались более плотными. В настоящее время, использование агломерированных спеченных порошков в комбинации с технологией HVOF – это «классика», плазменное напыление карбидов – «каменный век», а «последней модой» для карбидных материалов являются технологии HVAF и холодного напыления.
Автор совершенно не согласен с общепринятым мнением, что технология плазменного напыления устарела по отношению к карбидным материалам. Напротив, только эта технология, в комбинации с соответствующими ей порошками, позволяет решить проблемы карбидных покрытий, не устраненные до сих пор никаким другим способом. Общественное же мнение основывается только на факте, что плазменное напыление порошков, «заточенных» под HVOF, дает более пористые покрытия. Этот факт верен, но абсолютно неверен вывод из него о том, что плазменное напыление для карбидных порошков непригодно; просто порошки оптимизированные под плазменное напыление должны быть другими. Детально о таких новых карбидных порошках и покрытиях из них будет рассказано в отдельной главе, а пока продолжим рассмотрение «классических» карбидных покрытий.
В работе [4] приведен доскональный обзор покрытий из Cr3C2-NiCr полученных на разных устройствах высокоскоростного газопламенного напыления. Из всего массива информации этого исследования приведем только сравнение структур (электронная микроскопия) покрытий из одного и того же агломерированного спеченного порошка (75% Cr3C2 + 25% 80Ni20Cr, 5-30 мкм производства WOKA-Sulzer Metco), напыленных с помощью разных устройств (рисунки 52 — 55):
Рис. 52. Покрытие Cr3C2-NiCr, напыленное устройством Aerospray HVAF.
Рис. 53. Покрытие Cr3C2-NiCr, напыленное устройством Microjet HVOF.
Рис. 54. Покрытие Cr3C2-NiCr, напыленное устройством Jet Kote HVOF.
Рис. 55. Покрытие Cr3C2-NiCr, напыленное устройством JP-5000 HVOF.
Анализ приведенных структур показывает следующие общие аспекты:
- Все покрытия имеют примерно одинаковую пористость величиной 1-3% в виде сетки микротрещин и дефектов связей между частицами, то есть, все они не газоплотные.
- Во всех шлифах наблюдается значительное выкрашивание зерен, свидетельствующее, совместно с сеткой трещин, о высоких остаточных напряжениях растяжения в покрытиях.
- Во всех покрытиях имеется минимум три фазы: белая (NiCr), светло-серая (твердый раствор хрома и его низших карбидов, — CrxC, где x > 2, например, Cr7C3 или Cr23C6) и темно-серая (исходные зерна высшего карбида Cr3C2).
Несмотря на то, что был использован один и тот же порошок, разница в структурах весьма значительна, особенно в отношении содержания карбидной фазы Cr3C2, самой темной после пор и трещин: наибольшее содержание в покрытии высшей карбидной фазы Cr3C2 дает устройство Aerospray HVAF, а наименьшее – устройство Microjet HVOF. Тем самым, на первый взгляд, подтверждается мнение о том, что устройства HVAF дают покрытия лучшего качества, — содержание исходного Cr3C2 в них больше, чем в остальных покрытиях, напыленных устройствами HVOF.
Автор работы [4] S.J.Matthews рассматривает все возможные механизмы превращения карбидной фазы во время напыления, в том числе и утверждение некоторых исследователей, что уменьшение содержания карбидной фазы связано с ее разложением на хром и углерод под действием высокой температуры пламени и из-за дополнительного разогрева при ударе. Если принять эту гипотезу за истину, то получается, что «холодное» пламя HVAF предпочтительнее «горячего» пламени HVOF. Такой вывод прекрасно оправдывает современную «моду» на эти устройства .
Однако, гораздо более реалистично мнение других ученых, четко доказывающих, что, уменьшение содержания фазы Cr3C2 (образование из нее более светлой, деформированной фазы) связано с окислением Cr3C2 до низших карбидов (например, раствора Cr7C3 в хроме) во время напыления и формирования покрытия. В отличие от зерен Cr3C2, хром и его низшие карбиды пластически деформируются и образуют прослойки при температурах, далеких от температуры плавления.
Иначе говоря, проблема не в слишком высокой температуре частиц в пламени устройств HVOF, а в окислительной среде пламени, которая, при более высоких температурах, приводит к более сильному окислению карбидных частиц.
Что же касается температуры частиц, то она явно слишком низкая в «холодном» пламени HVAF, что проявляется в плохой связи между частицами в покрытии (сетка трещин вокруг частиц и поры между ними). На это же указывает тот «парадоксальный» факт, что твердость покрытий HVAF часто меньше, чем покрытий HVOF, при том, что покрытия HVAF содержат больше твердой фазы Cr3C2. «Парадокс» объясняется очень просто, — слабые связи между зернами в покрытии HVAF легко рвутся при нажиме пирамидки индентора, и от него остается больший отпечаток (рассчитывается меньшая твердость).
Из вышеизложенного можно сделать несложный вывод: для уменьшения окисления карбидов, было бы правильным не уменьшать температуру частиц, а заменить окислительное пламя на восстановительное, другими словами, использовать устройства плазменного напыления.
Само собой, что решить такую задачу «в лоб», то есть, используя стандартные HVOF порошки для устройств плазменного напыления, не получится. Это видно уже на примере самого «горячего» HVOF-устройства Microjet HVOF (рисунок 53): при остывании матрицы хрома с низшими карбидами от температуры, близкой к температуре плавления, в ней образуется сетка трещин из-за критических напряжений растяжения.
Необходимо изменить состав порошка таким образом, чтобы никакая непрерывная матрица не могла бы образовываться даже в случае плавления всех частиц, то есть, разработать карбидное покрытие, оптимизированное для «супер горячего» плазменного напыления.
Просмотров: 403
Напыление Износостойких Покрытий на металл в Санкт-Петербурге (СПб)
Работы по нанесению двухкомпонентного полиуретанового покрытия Hi Chem (или Tuff Stuff/ Durabond) фирмы Rhino Linings (США) включают в себя подготовку поверхности и собственно нанесение покрытия.
Все работы по нанесение грунта, шпатлеванию, нанесение полиуретанового покрытия производятся на тщательно просушенной поверхности при температуре окружающего воздуха не ниже +15 ºС и относительной влажности не выше 70 %. Температура обрабатываемой поверхности должна быть не ниже 15-20 ºС, а температура исходных материалов к началу использования – 20-30 ºС.
Контроль параметров окружающей среды и температуры поверхности осуществляется с помощью соответствующих датчиков в составе прибора «Константа К 5»
Готовое полиуретановое покрытие подвергать воздействию жидкостей не ранее чем через 24 часа после его нанесения (при условии, что его отверждение происходило при температуре не ниже 20 ºС).
Срок эксплуатации покрытия не менее 10 лет.
Порядок выполнения работ по нанесению покрытия на металлическую поверхность:
- Устройство лесов для обработки стен и потолка емкостей.
- Удаление старого покрытия ручным способом с помощью игольчатых пистолетов, шлифмашин, шпателей, стамесок, молотков.
- Дробеструйная очистка металлических поверхностей до степени Sa=2,5 в помещениях с использованием абразивного порошка, а вне помещений – кварцевого песка.
- Уборка песка.
- Обеспыливание поверхностей с помощью промышленного пылесоса.
- Обезжиривание поверхности уайт-спиритом. Поскольку уайт-спирит поглощает влагу и смешивается с водой в любых соотношениях, то при работе держать тару с уайт-спиритом плотно закрытой и следить за качественной просушкой поверхности после ее обработки. Наиболее ответственные места рекомендуется обрабатывать уайт-спиритом из только что распечатанной тары.
- В случае необходимости на стадии подготовительных работ применяются ремонтные материалы «Бельзона» согласно инструкции по применению данного состава. Расход данного материала 20 — 50 гр. на 1 кв. м.
- Устройство защитных укрытий необрабатываемых поверхностей (укрытие пола, люков, обмотка труб и т.д.) с помощью ПЭ пленки и строительного скотча.
- Нанесение Праймера 251 фирмы Rhino Linings (США) на поверхности металлоконструкций (потолок, нижняя часть стен). Рекомендуется наносить в два слоя толщиной 50 100 мкм. Время сушки грунта при комнатной температуре от 2 до 8 часов. При необходимости допускается разведение грунта (праймер 251) добавлением в него до 10 % ацетона. Расход данного материала 150-200 гр. на 1 кв. м.
- Напыление двухкомпонентного полиуретанового покрытия «Hi Chem» толщиной 2 мм методом воздушного распыления под давлением 10 атм. Требуемая толщина покрытия достигается его нанесением в несколько проходов. Время полного отверждения покрытия 24 часа.Расход данного материала 2,3 — 2,6 л. на 1 кв. м.
- Контроль толщины покрытия осуществляется электромагнитным датчиком в составе прибора «Константа К-5»
- Снятие и уборка защитных укрытий, удаление излишков материала, демонтаж лесов.
Порядок выполнения работ по нанесению покрытия на бетонную поверхность:
- Удаление старого покрытия ручным способом с помощью игольчатых пистолетов, шлифмашин, шпателей, стамесок, молотков.
- Дробеструйная очистка бетонных поверхностей в помещениях с использованием абразивного порошка, а вне помещений – кварцевого песка.
- Уборка песка.
- Обеспыливание поверхностей с помощью промышленного пылесоса.
- Обезжиривание поверхности уайт-спиритом. Поскольку уайт-спирит поглощает влагу и смешивается с водой в любых соотношениях, то при работе держать тару с уайт-спиритом плотно закрытой и следить за качественной просушкой поверхности после ее обработки. Наиболее ответственные места рекомендуется обрабатывать уайт-спиритом из только что распечатанной тары.
- Монтаж защитных укрытий необрабатываемых поверхностей.
- Нанесение на бетонную поверхность одного-двух слоев грунта «Флореп». Рекомендуемая толщина 50-100 мкм. Время сушки каждого слоя не менее 12 часов.
- Заделка дефектов (трещины, выбоины и т.д.) с помощью шпатлевки «Флореп». Использование данного материала согласно инструкции производителя.
- Напыление двухкомпонентного полиуретанового покрытия «Hi Chem» толщиной 2 мм методом воздушного распыления под давлением 10 атм. Требуемая толщина покрытия достигается его нанесением в несколько проходов. Время полного отверждения покрытия 24 часа.
- Снятие и уборка защитных укрытий, удаление излишков материала.
Методы нанесения износостойких покрытий — Энциклопедия по машиностроению XXL
К методам упрочняющей технологии могут быть отнесены и методы нанесения износостойких покрытий, и методы механического упрочнения поверхностного слоя деталей [c.80]В настоящее время щироко используются различные методы обработки поверхностей деталей узлов трения машин и механизмов с целью придания им необходимых триботехнических свойств. В табл. 9.15 приведена классификация современных методов нанесения износостойких покрытий. [c.357]
Методы нанесения износостойких покрытий и упрочнения поверхности трения [c.357]
Нанесение износостойких покрытий — наиболее распространенный и хорошо разработанный метод улучшения триботехнических свойств материалов. На его базе успешно реализованы различные технологические решения, позволяющие существенно улучшить качество поверхностного слоя и повысить прочность сцепления покрытия с подложкой. Конструирование многослойных покрытий является перспективным направлением поверхностной модификации, позволяющим плавно изменять свойство композиции по глубине и исключить отрицательное влияние хрупкого переходного слоя. Материал подслоя выбирают из соображений химической совместимости с основой, а также в целях исключения образующихся в граничной области хрупких интерметаллидных соединений. Идея создания многослойных покрытий реализована для повышения прочности поверхностных слоев, релаксации остаточных напряжений в модифицированных слоях, а также для увеличения вязкости и трещиностойкости. [c.262]
Расширение области применения режущего инструмента связано с разработкой методов модифицирования, сочетающих преимущества пучков заряженных частиц различных энергий и интенсивности, а также традиционных методов упрочнения, таких, как нанесение износостойких покрытий и термическая обработка. В связи с этим можно выделить два основных направления разработки. Это комбинированное модифицирование и комплексная обработка. К первому виду обработки относятся 1) комбинированная обработка на основе использования слабо-точных ионных пучков 2) комбинированная обработка на основе использования слаботочных и сильноточных ионных пучков. Второй вид модификации включает 1) комплексную обработку с использованием воздействия сильноточных ионных и электронных пучков с последующей термической обработкой 2) комплексную обработку с использованием термического, энергетического воздействия и нанесения на инструментальный материал износостойких покрытий. [c.263]
Известны различные методы нанесения карбидных покрытий. Примером наиболее простого способа нанесения карбидного покрытия является обмазка графитовых нагревателей пятиокисью ниобия с превращением последней в процессе нагрева в карбид ниобия [4]. Образование сплошного карбидного покрытия (оболочки) из карбида ниобия на графитовых нагревателях позволило значительно повысить рабочую температуру индукционных вакуумных печей. Перспективными являются покрытия карбидами методом электроискрового осаждения для повышения износостойкости штампов прессового инструмента, металлорежущих станков и т, д. [c.425]
Наиболее часто на производстве встречаются случаи, когда изменение конструкции из-за применения прогрессивных технологических процессов носит более узкий, частный характер. Тем не менее они могут дать весьма существенный эффект. В это направление, в первую очередь, следует включить практически все методы так называемой упрочняющей технологии термомеханическая обработка, виброгалтовка, обдувка дробью, обработка роликами, упрочнение взрывом, химикотермическая обработка поверхностных слоев, нанесение износостойких покрытий гальваническим путем, напылением, наплавкой и т. д. Применение указанных методов вызывает либо изменение химического состава детали или ее поверхностных слоев, либо изменение физико-механических свойств материала. Обычно эти изменения в той или иной мере регламентируются чертежом детали или ТУ. Перечисленные выше направления не охватывают, конечно, все стороны воздействия технологии на показатели надежности и долговечности изделий. Однако проведенный анализ, по-видимому, может быть полезным при оценке возможностей отдельных методов повышения качества продукции. [c.189]
Этот метод наиболее перспективен для нанесения износостойких покрытий на титановые и алюминиевые сплавы. Оптимальная толщина покрытия в этом случае составляет около i мм, а содержание в нем карбида титана может изменяться от 15 до 65 % (объемн.). [c.164]
Все большее распространение получают ионно-плазменные методы нанесения износостойких и декоративных покрытий. [c.524]
Ведутся работы по повышению работоспособности инструментов за счет специальной упрочняющей обработки его режущей части. Среди этих методов наиболее перспективно нанесение износостойких покрытий различных составов, композиций и методов нанесения, которые позволяют повысить стойкость инструментов в 2 —5 раз. [c.297]
Нанесенные описанным методом антифрикционные износостойкие покрытия проходили испытания в различных условиях, показавшие исключительно высокие антифрикционные свойства и износостойкость полученных покрытий. Коэффициент трения покрытия по стали без смазки не превышает 0,08, износостойкость в 3—5 раз выше, чем износостойкость покрытий, нанесенных по известному методу. [c.129]
Большое внимание в книге уделено хромированию — перспективному методу нанесения износостойких и антикоррозионных покрытий, а также непрерывным линиям осаждения покрытий, поскольку со временем рассматриваемый метод найдет широкое применение для осаждения покрытий на стальную полосу. Что касается осаждения металлов в вакууме на полимеры, то этот метод уже сравнительно давно применяется в промышленности. [c.3]
Алюминиевые сплавы имеют ценные эксплуатационные качества малую плотность, высокие прочностные свойства, хорошую обрабатываемость, относительно низкую стоимость и находят все более широкое применение в технике. Целесообразность нанесения металлических покрытий на сплавы диктуется необходимостью улучшения декоративного вида поверхности, придания ей твердости и износостойкости, а также создания специальных свойств (способности к пайке, отражательной способности и т. п.). Наиболее распространенным методом нанесения металлических покрытий на алюминиевые сплавы является электролитическое осаждение. Получение качественных гальванических покрытий с хорошей адгезией на алюминиевых сплавах сопряжено со значительными трудностями и достигается лишь с применением довольно сложных и капризных методов подготовки поверхности (цинкатная обработка, электролитическое осаждение тончайшего слоя цинка и латуни, станнатная обработка, предварительное анодирование и т. п.). Среди литейных алюминиевых сплавов все более широкое применение находят силумины — сплавы, содержащие 81, например, силумин АЛ2, содержащий около 12% 51. [c.106]
Материал рабочей части инструмента назначают исходя из конкретных условий работы. Для повышения работоспособности инструмента применяют технологические методы улучшения его режущих свойств, термохимическую обработку, нанесение износостойких покрытий и другие способы. Материал режущей части влияет на конструктивное исполнение инструмента. Материал крепежной части должен обеспечивать прочность, жесткость и износостойкость. [c.22]
Эффективно нанесение износостойких покрытий TiN методом КИБ с использованием установок типа Булат на цельные головки и резцы к сборным головкам, обеспечивающих повышение их стойкости до двух раз. [c.656]
Основные характеристики установок для нанесения износостойких покрытий методом КИБ [c.826]
Твердые износостойкие тугоплавкие соединения дороги и обладают, как правило, большой хрупкостью. Поэтому их выгодно использовать в качестве покрытий. Способов нанесения износостойких покрытий достаточно много. За последние годы получают все большее распространение лазерные методы модифицирования и легирования поверхностных слоев, электроискровые покрытия, детонационные и полученные нанесением порошков при сверхзвуковой скорости. [c.53]
В настоящей работе рассматривается задача повышения ресурса поршневых колец дизельных двигателей путем нанесения износостойких покрытий на рабочие трущиеся поверхности методом плазменного напыления. [c.100]
Как уже отмечалось, в последние годы наблюдается исключительно бурное развитие технологий нанесения защитных и износостойких покрытий. Результатом можно считать несомненные успехи в увеличении конструктивной прочности изделий, достигнутые за счет напыления покрытий детонационно-газовым, струйно-плазменным, ионно-плазменным и другими прогрессивными методами. Повышение надежности и долговечности деталей обусловлено не только технологиями, но и совершенством методик, используемых для изучения структуры и свойств покрытий и материалов с покрытиями. [c.192]
Для защитно-декоративных целей, а также для повышения износостойкости используют хромовые или никель-хромовые гальванические покрытия. Применение оксидных пленок, полученных химическим или электрохимическим методом, является одним из основных способов защиты от коррозии алюминиевых сплавов. Оксидные пленки обладают также хорошими адгезионными свойствами, и поэтому их применяют как основу при нанесении лакокрасочных покрытий. [c.74]
Поверхностные свойства обеспечиваются как нанесением защитного слоя или покрытия, так и преобразованием поверхностного слоя металла при помощи химических, физических, механических методов, диффузионным насыщением, методов химико-термической обработки. Активно развиваются методы электронно-лучевой и лазерной закалки, вакуумное физическое и химическое напыление износостойких покрытий, ионное азотирование и др. [c.199]
Отмечена высокая прочность сцепления электроискровых покрытий, в том числе и карбидных с основным материалом. При этом значительно возрастают твердость поверхностных слоев, сопротивление схватыванию, что в конечном счете приводит к повышению износостойкости сопряженных пар. Достоинством электроискрового метода нанесения покрытий является также возможность использования различных металлов и их тугоплавких соединений в качестве основы многослойных покрытий. [c.48]
Нанесение высокопрочных износостойких покрытий в вакууме— один из наиболее перспективных методов упрочняющей поверхностной обработки. Особенно широко применяются высокопрочные покрытия на основе соединений переходных металлов. К сожалению, структура и свойства покрытий далеко не всегда соответствуют требованиям, предъявляемым к износостойким поверхностям (см. гл. 1). Твердость покрытий сама по себе не обеспечивает высокой износостойкости, особенно для покрытий толщиной 10″ —10 нм, когда несущая способность поверхности определяется эффективной твердостью деформируемого при трении слоя. Механические свойства этого слоя определяются в значительной мере свойствами подложки. Совершенно очевидно, что покрытия должны иметь высокую пластичность, чтобы выдерживать деформацию поверхностных неровностей при трении, а получаемые методами физического вакуумного осаждения покрытия, как правило, отличаются высокой хрупкостью. [c.145]
Рекомендуемые составы износостойких покрытий для нанесения на твердосплавный инструмент методами VD [c.94]
Для нанесения коррозионно-износостойких покрытий на технологическое оборудование мясокомбинатов используется метод химического никелирования. [c.15]
В книге подробно описаны способы подготовки поверхности изделий к покрытию, а также технологические процессы, составы растворов и режимы работ при получении гальванических, химических, термодиффузионных и других защитно-декоративных и износостойких покрытий. Значительное внимание уделено также возможным неполадкам при нанесении покрытий, методам устранения и контролю качества различных покрытий. Приведенные в справочнике технологические процессы проверены на передовых предприятиях СССР. [c.4]
Диффузионный метод нанесения покрытий в настоящее время наиболее распространен в связи с простотой технологического осуществления, а также возможностью направленного регулирования фазового состава и структуры поверхностных слоев. Самое широкое техническое использование находят покрытия, содержащие карбиды, бориды, силициды, нитриды и другие тугоплавкие и износостойкие соединения, обеспечивающие высокие физико-технические свойства поверхности. [c.132]
Химическое никелирование дает возможность наносить металл на детали самого сложного профиля во все места, доступные для электролита. В этом заключается преимущество его перед гальваническим методом нанесения покрытий. Покрытия получают толщиной до 25 мк. После полуторачасовой термообработки при 600° С износостойкость покрытий становится близкой к хромистым. [c.190]
Химико-термические методы упрочнения поверхности для повышения износостойкости за счет увеличения поверхностной твердости (цементация, азотирование, цианирование, борирование и др. процессы) весьма эффективны для повышения сопротивления абразивному изнашиванию. Для улучшения противозадирных свойств создаются (посредством сульфиди-рования, сульфо-цианирования, селенирования, азотирования) тонкие поверхностные слои, обогащенные химическими соединениями, предотвращающими схватывание и задир при трении.. Большой эффект получается при использовании метода карбонитрации. Широко применяются электрохимические методы нанесения покрытий А1, РЬ, Sn, Ag, Au и др. При восстановлении деталей (в ремонте) используется электролитическое хромирование, никелирование, железнение и др. Значительная часть технологических задач, связанных с необходимостью повышения износостойкости, коррозионной стойкости, жаропрочности, восстановительного ремонта и др. решается при использовании методов металлизации напылением, включающих газоплазменную металлизацию, электродуговую, плазменную, высокочастотную индукционную металлизацию и детонационное напыление покрытий — наносятся металлы и сплавы, оксиды, карбиды, бориды, стекло, фосфор, органические материалы. Плазменное напыление используют для нанесения тугоплавких покрытий окиси алюминия, вольфрама, молибдена, ниобия, интерметаллидов, силицидов, карбидов, боридов и др. Детонационное напыление имеет преимущество в связи с незначительным нагревом покрываемой детали и распыляемых частиц. В последнее время активно развиваются методы нанесения износостойких покрытий в вакууме катодное распыление, термическое напыление, ионное осаждение. В зависимости от реакционной способности газовой среды методы напыления [c.199]
Наиболее освоенным и широко применяемым методом нанесения износостойкого покрытия на инструмент из быстрорежущих сталей является диффузионное насыщение. Преимущество этого способа — возможность оптимизащш строения и фазового состава покрытия. Особый интерес представляют диффузионные покрытия на конструкционных сталях, так как по своим антифрикционным свойствам они не уступают карбидам, изготовленным методом прессования и спекания порошков. [c.173]
Износостойкость повышают методами объемной пли поверхностной термообработки, термохимической обработкой (цементация, азотирование, циани-рованпе, диффузионное хромирование), нанесением износостойких покрытий (электролитическое хромирование), наплавкой износостойких материалов (твердых сплавов, высокомарганцовистых и высокохромистых сплавов). [c.25]
Выбор способа химико-термической обработки обусловлен не только требованиями, предъявляемыми к поверхностному слою, но и температурой, прн которой выполняется эта обработка, и теплостойкостью стали. Наиболее универсальными и эффективными методами упрочнения поверхностного слоя инструментов из быстрорежущих сталей является жидкое цианирование, карбонитрация, ионное азотирование и вакуумно-плазменное нанесение износостойких покрытий. Основные способы химико-термической обработки, применяемые в качестве заключительной операции для повышения стойкости инструментов из быстрорежущих сталей, приведены в табл. 18. [c.613]
Вакуумноплазменное нанесение износостойких покрытий После ионной очистки на поверхность инструмента методом ионной бомбардировки наносят слон нитридов титана или других металлов Для повышения износостойкости рабочей поверхности инструмента вследствие высокой твердости этих соединений (HV 25—45 ГПа, толщина слоя 5—20 мкм) [c.614]
В настоящее время предъявляются повышенные требования к режуш им свойствам инструментов, в особенности инструментов для сзанков с ЧПУ и гибких производственных комплексов. Традиционные методы повьииения стойкости инструментов путем сложного легирования почти исчерпали свои возможности. В этой связи разработаны и внедрены методы повышения износостойкости, основанные на создании на рабочих гранях инструментов тонких поверхностных слоев с заданными свойствами. Наибольшее распространение среди них получили химико-термическая обработка и нанесение износостойких покрытий. [c.21]
Применяя низкотемпературную плазму, можно наносить покрытия практически из всех материалов, которые в плазменной струе не сублимируют и не претерпевают интенсивного разложения. Нанесение износостойких, антифрикционных, коррознонно- и жаростойких покрытий плазменным напылением значительно расширяет круг применяемых материалов и улучшает качество покрытий, получаемых газотермическим напылением. Следует отметить, что некоторые тугоплавкие металлы и керамические материалы можно нанести только плазменным методом. Этот метод получает все большее развитие и применение в промышленности. [c.139]
В настоящее время для повышения износостойкости и коррозионной стойкости получили применение пленочные покрытия (толщиной 2—10 мкм) из нитридов (TiN, Ti (N ), ZrN), карбидов (Ti ), оксидов (AI2O3 и др.), обладающих высокой твердостью. Существует много методов создания адгезионных пленочных покрытий. Нанесение покрытий осуществляется осаждением продуктов химических реакций между компонентами газовой среды (например, хлорида титана и метана) на поверхности детали (инструмента) при 1000—1200 °С (метод VD). Другие методы предполагают реактивное или конденсационное осаждение в вакууме при более низкой температуре 450—500 °С, Формирование покрытия в вакууме осуществляется в три стадии I) получение материала покрытия в парообразном состоянии 2) перенос материала покрытия от испарителя к детали 3) осаждение (конденсация) молекул (ионов) материала покрытия на поверхности детали. Чаще применяют следующие методы нанесения покрытия конденсацию из плазменной фазы в условиях ионной бомбардировки (КИБ) реактивное электронно-лучевое плазменное осаждение (РЭП) активированное реактивное напыление (ARE). Не- [c.347]
Суш,ествует много традиционных способов создания поверхностных слоев с повышенной износостойкостью [15, 27, 65. 68]. Наиболее широко применяются методы поверхностной закалки, поверхностного наклепа, различные химикотермические способы обработки (в первую очередь цементация и азотирование) и т. д. Все шире применяются методы, основанные на воздействии на поверхностные слои деталей потоков частиц (ионов, атомов, кластеров) и квантов с высокой энергией. К ним следует отнести в первую очередь вакуумные ионно-плазменные методы [26, 33, 34, 45, 71, 104] и лазерную обработку [16, 23, 38, 104]. Суш,ест-венио развились также способы осаждения покрытий из газовой фазы при атмосферном давлении и в разряженной атмосфере [1, 42, 54, 105]. Мош,ный импульс получило применение газо-термических методов нанесення покрытий в связи с развитием плазменных- [c.152]
Многообразны современные принципы и методы защиты металлов от коррозионного разрушения. В машиностроении наиболее распространена защита металлов путем нанесения разнообразных покрытий — металлических, неметаллических, конверсионных, и комбинированных и т. п., а также использования ингибиторов. Во многих случаях покрытия несут не только антикоррозионную роль, а служат-в качестве слоев, повышающих прираба-тываемость и износостойкость деталей, работающих сопряженно, являются электроизоляторами, носителями определенных магнитных, оптических, каталитических и других свойств (функциональные, декоративные и другие покрытия). Развитие электронной, вычислительной, космической и других новых отраслей техники выдвигает все болеё новые и разнообразные требования к покрытиям, что обусловливает как увеличение видов материалов, так и усложнение технологии нанесения покрытий. [c.100]
Перспективным является создание на рабочих поверхностях деталей тонких пленок материалов с повышенными физикохимическими и механическими характеристиками. Нанесение на материалы однослойных и многослойных тонкопленочных покрытий из металлов и их соединений позволяет создать изделия с уникальными электрофизическими, теплофизическими и физико-механическими свойствами. Выбирая материал покрытия и технологические режимы его нанесения, можно изменять в широких пределах основные поверхностные свойства твердость, коэффициент трения, теплопроводность и электрическую проводимость, коэффициент отражения, износостойкость и коррозионную стойкость, при этом сохраняя выро-кие свойства материала основы. С этой точки зрения ши] о-кие возможности связаны с использованием физических методов упрочнения и нанесения тонкопленочных покрытий в вакууме, находящих широкое применение в нашей стране и за рубежом. [c.109]
Другим методом нанесения тонких износостойких покрытий является метод катодного напыления и ионной бомбардировки. Сущность этого метода заключается в том, что с помощью электро-дугового испарителя наносимый на поверхность инструментов материал (титан, молибден) в вакуумной камере переводится в парообразное состояние (вакуум 1,33-10 —1,33-10 Па). При наличии напряжения на катоде (анодом служит обрабатываемое изделие, а катодом — металл-испаритель) и подачи в камеру азота или другого газа, содержащего азот, ионы испарившегося металла, взаимодействуя с ионами азота, образуют нитриды испарившегося металла (молибдена или титана) и осаждаются на поверхности инструментов, создавая тонкую пленку (0,004— 0,008 мм). Для равномерного нанесения пленок на режущие кромки многозубых инструментов последние загружаются в специальный барабан камеры и вращаются относительно катодов. В настоящее время для упрочнения твердосплавных пластинок износостойкой пленкой выпускаются установки моделей Бу-лат-2м и Вулат-Зм . Основные технические характеристики установки Булат-2м приведены ниже. [c.369]
Износостойкость
Износостойкость
Износ
Потеря материала с поверхности в результате механического воздействия.
Абразивный износ
Износ из-за твердых частиц или твердых выступов, которые прижимаются к твердой поверхности и движутся по ней.
Адгезионный износ
Износ из-за локального склеивания между контактирующими твердыми поверхностями, приводящего к переносу материала между двумя поверхностями или потерям с любой из поверхностей.
Эрозия
Износ из-за механического взаимодействия между этой поверхностью и жидкостью, многокомпонентной жидкостью или падающими жидкими или твердыми частицами
Кавитационная эрозия
Форма эрозии, вызывающая износ материала под действием пузырьков пара в очень турбулентной жидкости.
Усталостный износ
Износ твердой поверхности из-за разрушения материала
усталость.
Фреттинг-износ
Износ, возникающий в результате фреттинга (колебательный
движение, обычно касательное, между двумя соприкасающимися твердыми поверхностями).
Снижение износа за счет термического напыления покрытий
Термораспылительные покрытия для мягких поверхностей подшипников
Термораспылительные покрытия для твердых поверхностей подшипников
Покрытия с термическим напылением для устойчивости к истиранию
Покрытия с термическим напылением для сопротивления истиранию
Покрытия для защиты от эрозии термическим напылением
Покрытия с низким трением и антипригарными свойствами
Износ
Механизм износа очень сложен и теоретическая обработка без использования довольно радикальных упрощений (как показано ниже) не возможно.Следует понимать, что реальная площадь контакта между две твердые поверхности по сравнению с видимой площадью контакта неизменно очень маленькие, ограничиваясь точками контакта между неровности поверхности. Нагрузка на поверхности будет через эти точки соприкосновения и локализованные силы может быть очень большим. Собственные свойства поверхности материала, такие как твердость, прочность, пластичность, наклеп и т. д. очень важны факторы износостойкости, но другие факторы, такие как качество поверхности, смазка, нагрузка, скорость, коррозия, температура и свойства противоположная поверхность и т. д.одинаково важны.
Абразивный износ


Двухкорпусный абразивный износ
Трехкорпусный абразивный износ
Механизм абразивного износа в основном такой же, как обработка, шлифование, полировка или доводка, которые мы используем для придания формы материалы. Абразивный износ двух корпусов возникает, когда одна поверхность (обычно тяжелее второго) отрезает материал от второго, хотя этот механизм очень часто меняется на трёхчастное истирание по мере износа Затем мусор действует как абразив между двумя поверхностями.Абразивы могут действуют как при шлифовании, где абразив закреплен относительно одной поверхности или как при притирке, когда абразивные барабаны производят серию вмятины, а не царапины.
Клейкий износ
Адгезионный износ возникает при формировании и последующий срез сварных стыков между двумя поверхностями скольжения. Для возникновения адгезионного износа необходимо, чтобы поверхности были в интимный контакт друг с другом. Поверхности, которые разделяются смазочные пленки, оксидные пленки и т. д.уменьшить склонность к прилипанию к происходят.
Эрозия
Эрозия вызывается газом или жидкостью, которая может или может не переносить увлеченные твердые частицы, падающие на поверхность. Когда угол столкновения небольшой, износ практически аналогичен к истиранию. Когда угол падения нормален к поверхности, материал перемещается пластическим потоком или смещается хрупким неудача.
Кавитационная эрозия
Кавитация — это образование и обрушение в пределах жидкость, полостей или пузырьков, содержащих пар или газ.Как обычно, кавитация возникает из-за изменений давления в жидкости, приносимой турбулентным потоком или вибрацией, но также может возникать из-за перепады температуры (кипение). Кавитационная эрозия возникает при пузырьки или полости схлопываются на или в непосредственной близости от эродированной поверхности. В механический удар, вызванный кавитацией, похож на удар жидкости ударная эрозия, вызывающая прямое локальное повреждение поверхности или вызывая усталость.
Фреттинг-износ
Фреттинг — колебательное движение малой амплитуды,
обычно по касательной, между двумя соприкасающимися твердыми поверхностями.Раздражение
износ возникает, когда повторная загрузка и разгрузка вызывают циклические напряжения
которые вызывают поверхностное или подповерхностное разрушение и потерю материала.
Вибрация — частая причина фреттинг-износа.
Снижение износа за счет термического напыления покрытий
Покрытия с термическим напылением имеют и используются в очень широкий спектр износостойких поверхностей и для ремонта износа сопротивляющиеся поверхности. Основным преимуществом является то, что покрытие термическим напылением может обеспечить свойства поверхности и материал основы компонента может быть выбран из основных требований, будь то прочность, вес или стоимость без необходимости учитывать его внутреннюю износостойкость или другие свойства поверхности.
Выбор лучшего покрытия для нанесения не часто прямолинейно. Выбор по твердости или от стандарта Испытания на износ покажут такие покрытия, как карбид вольфрама / кобальт HVOF, керамические или плавленые покрытия с плазменным напылением, обеспечивающие максимальная производительность. Действительно, эти покрытия действительно обеспечивают лучшее решение для многих приложений, но они, конечно, не всегда подходит для всех приложений. Необходимо учитывать и другие факторы:
- Стоимость
- Ожидаемый срок службы
- Коррозия
- Контрповерхность
- Влияние процесса на материал подложки
- Обработка поверхности или профиль
- Температура
- Смазка
- Абразивы
- Нагрузки и скорости
- Удары, удары или усталость
- Способность к деформационному отверждению
- Жесткость и угол атаки
- Коэффициент трения
- Пористость
- Могут потребоваться другие особые свойства покрытия
- Термобарьер или проводник
- Электрический изолятор или проводник
- Немагнитный
- Специальные профили поверхности
- Абразивный (требуется эрозионная стойкость, но жертвенный для встречной поверхности)
- Абразивный (требуется для шлифования или захвата контрповерхности)
- Очень низкий коэффициент трения или антипригарные свойства
Покрытия для мягких поверхностей подшипников с помощью термического напыления
Покрытия из мягкого несущего материала допускают заделку абразивных частиц и допускают деформацию для компенсации некоторых перекос опорных поверхностей.Эти поверхности требуют соответствующего смазки и должны быть недорогими, поскольку они изнашиваются, а не сопрягаемая поверхность (обычно намного тверже). Некоторые из этих покрытий довольно пористые с тем преимуществом, что они действуют как резервуары для смазочные материалы. Обычно используются следующие покрытия:
- Алюминиевая бронза
- Фосфорная бронза
- Белый металл или баббит
- Алюминиевая бронза / полимерные композиты
Покрытия для твердых поверхностей подшипников с помощью термического напыления
Покрытия из твердого материала подшипников с высокой износостойкостью сопротивление.Жесткие подшипниковые материалы используются там, где заделка абразивные частицы и самоцентрирование не требуются и где смазка может быть незначительной. Природа термического спрея покрытия, кажется, обеспечивают дополнительные преимущества по сравнению с сопоставимыми коваными или литые материалы из-за пористости, действующей как резервуар для смазки и сложный характер включенных оксидов и аморфных фаз повышение износостойкости. Некоторые покрытия показывают относительно низкую макротвердость твердость по сравнению с их относительной деформируемой или литой материалы, но очень часто демонстрируют повышенную износостойкость.Последующий покрытия обычно используются:
- Керметные покрытия, такие как карбид вольфрама / кобальт и хром карбид / хром никель
- Оксидная керамика, такая как оксид хрома и оксид алюминия
- молибден
- Различные твердые сплавы железа, никеля, хрома или кобальта
Покрытия для стойкости к истиранию с помощью термического напыления
В идеале, материал должен иметь твердость, превышающую сопрягаемой поверхности или абразивных частиц.Последующий покрытия обычно используются:
- Керметные покрытия, такие как карбид вольфрама / кобальт
- Карбид хрома / никель-хром (особенно для высоких температур выше 540 ° C)
- Оксидная керамика, такая как оксид хрома и оксид алюминия
- Плавленые самофлюсующиеся сплавы (NiCrSiB)
- Различные твердые сплавы железа, никеля, хрома или кобальта
Покрытия с термическим напылением для сопротивления истиранию и поверхности Усталость
Покрытия, устойчивые к износу при многократном скольжении, качении, удары или вибрация.Обычно покрытия с хорошей вязкостью и низким остаточное напряжение растяжения лучше всего. Следующие покрытия обычно используемый:
- Керметные покрытия, такие как карбид вольфрама / кобальт
- Карбид хрома / никель-хром (особенно для высоких температур выше 540 ° C)
- Самофлюсующиеся сплавы плавленые
- Алюминиевая бронза
- медь никель индий
- Различные сплавы железа, никеля, хрома или кобальта
Покрытия для защиты от эрозии термическим напылением
Выбор покрытия для защиты от эрозионного износа зависит от степень выраженности и тип эрозии.Для твердой ударной эрозии на малый угол атаки, при котором износ аналогичен истиранию, требуются покрытия высокой твердости. Для твердых углов столкновения около 90 становится более важной вязкость покрытия. Для кавитации и жидкости столкновение, как правило, покрытие с хорошим сопротивлением поверхностной усталости нужно. Обычно используются следующие покрытия:
- Керметные покрытия, такие как карбид вольфрама / кобальт
- Карбид хрома / никель-хром (особенно для высоких температур выше 540 ° C)
- Самофлюсующиеся сплавы плавленые
- Цветные сплавы, алюминиевая бронза, монель
- Оксидная керамика, такая как оксид хрома и оксид алюминия
- Различные сплавы железа, никеля, хрома или кобальта
Покрытия с низким коэффициентом трения и антипригарным покрытием
Материалы полимерного типа PTFE имеют чрезвычайно низкую коэффициент трения и не прилипают к большинству материалов.Эти определенные свойства очень полезны, но эти материалы очень низкая прочность и очень плохая износостойкость. Комбинированные покрытия, где покрытия с термическим напылением используются для обеспечения механической поддержки и шпонки для полимера и обеспечения износостойкости, делают для чрезвычайно эффективный компромисс.

Телефон: +44 (0) 1252 405186
Электронная почта: [email protected]
Знакомство с
Природа термораспылительных покрытий
Инженерия поверхностей в двух словах
9000
Форум по проектированию поверхностей Услуги по ремонту пистолетов-распылителей
Расходные материалы для плазмы
Порошковые расходные материалы для термического напыления
Области применения:
Нанесение покрытий на полимеры, армированные углеродным и стекловолокном,
Покрытие HVOF на рулонах для изготовления бумаги
AbradableПроцессы термического напыления:
Процесс термического напыления проволоки сгорания
Процесс термического напыления горючего порошка
Процесс термического напыления дуговой проволоки
Процесс термического напыления плазмы
HVOF4 9000 Процесс термического напыления
Детонационный терм al Spray Process
Theory Plasma Flame Theory
Процесс нанесения покрытия холодным распылением
Износ и использование покрытий термическим напылением
Коррозия и использование покрытий термическим напылением
Глоссарий терминов термического напыления и инженерии поверхностей
Справочник изображений для покрытий термическим напылением
Информация о потоке плазменного газа
Калькулятор коррекции расхода плазменного газа
Контактная форма
Ссылки на другие интересные сайты, связанные с термическим напылением и инженерией поверхностей
Взаимные ссылки
Периодическая таблица элементов
Единицы СИ
Калькуляторы для Преобразование единиц измерения
Испытания на твердость
Архив доски объявлений по проектированию поверхностей
Индекс архива доски сообщений по проектированию поверхностей
Фотогалерея2
Фотогалерея3
© Copyright Gordon England
.Износостойкие покрытия, Услуги термического напыления, Покрытие распылением Hovf, Покрытие плазменным напылением, Нанесение порошковых покрытий
износостойкие покрытия, услуги термического напыления
(напыление HOVF, услуги плазменного напыления, порошковое покрытие)
Покрытия деталей машин с использованием оборудования для термического напыления, такого как HVOF, плазменное напыление, вакуумно-плазменное напыление
Покрытия для:
- Износостойкость
- Коррозионная стойкость
- Термо / электрическая проводимость
- Тепло / электрическая изоляция
- Hard F
3 acing Surface Твердость
Мы выполняем покрытия из
- металлов и сплавов
- Алюминий
- Бронза
- Белый Баббитовый металл 4
- Белый Баббитовый металл 4
- 9000
- Алюминиевая бронза
- Никель Алюминий
- Кобальт-никелевый сплав
- Нержавеющая сталь
- Стеллит
- Молибден
- Керамический оксид хрома
- Глинозем Титания
- Оксид алюминия
- Оксид циркония
0
03
- Карбиды
- Карбид вольфрама
04
03
03 Карбид хрома
04 Никель-хромовый карбид
- Карбид вольфрама
- Ceremets
** Мы также выполняем проекты по нанесению покрытий, в которых материал для покрытия поставляется с вашей стороны.
Оборудование для термического напыления:
- HVOF
- Плазменное распыление (с помощью робота)
- Дуговое распыление
- Дуговое распыление
Порошковое распыление - Wire Flame Spray
- Сварка PTA
Другое основное оборудование для термического напыления и услуги:
(1) HVOF оборудование 9000 Arc5
(Оборудование для распыления Arc5 )
(3) Услуги по нанесению покрытий термическим напылением
(4) Вакуумный плазменный распылитель
(5) Промышленные охладители воды
(6) Вакуумное оборудование для нанесения покрытий на драгоценные металлы
(7) Магнетизм плиты и Линия по производству теплопроводящего покрытия
(8) Оборудование и технологии для производства мишеней
(9) Оборудование для электрощеточного нанесения
(10) Оборудование для пламенного напыления высокой мощности
9000
…
.Износостойкие аэрозольные покрытия из полимочевины гибридного типа Китайский производитель
Описание продукта
Износостойкие аэрозольные покрытия из полимочевины гибридного типа Китайский производитель
Описание: Система покрытия состоит из полиэфирной смолы с аминовыми концевыми группами и аминовой цепи наполнитель и форполимер MDI, относится к самоотверждающейся эластичной полимочевине, обладающей высокой прочностью и устойчивостью к разрыву, а также придает покрытию высокую стойкость к истиранию.
Физико-химические свойства
Свойство | Результат |
Содержание твердого вещества | 10040 |
≤1000 мПа.с | |
Плотность (25 ℃) | 0,95 ~ 1,05 г / см 3 |
Коэффициент смешивания объема | A : R = 1: 1 |
Срок годности | 1 год |
Время гелеобразования | > 5 с |
Предел прочности на разрыв | 19 МПа |
Удлинение | ≥450% |
Hardnes с | ≥90A |
Прочность на разрыв | 50 кН / м |
Адгезия | 11 МПа |
Информация о компании Стойкие покрытия из полимочевины гибридного типа Китайский производитель
Dongying Aonuo International Trade Co.Ltd., специализируется на производстве следующих продуктов:
1. Водонепроницаемое покрытие из полимочевины.
2. Распылители полиуретана.
3. Удлинитель цепи из полиуретана и полимочевины (отверждающие сшивающие агенты) — DMTDA и DETDA.
Упаковка и хранение
Износостойкие аэрозольные покрытия из полимочевины гибридного типа Китайский производитель
1.Упаковка: Часть A: 220 кг / бочка
Часть B: 200 кг / бочка
И 4 бочки упаковываться как поддон.
2. Хранение: Хранить штабелями в прохладном / сухом / вентилируемом месте, беречь от тепла / огня, для предотвращения попадания прямых солнечных лучей, во избежание высокой температуры, не допускать повреждений при столкновении с острыми предметами. Лучшая температура хранения — 15 ~ 40 ℃. И часть A должна быть заполнена азотом, если таковая имеется.
Доставка (время выполнения)
Износостойкие спрей-полимочевинные покрытия гибридного типа Китайский производитель
Срок доставки / выполнения: 5 дней после получения оплаты.
Применение
Износостойкие спрей-полимочевинные покрытия Гибридный тип Китайский производитель
Нефть, нефтехимическая промышленность, химическая промышленность, большие резервуары для хранения химикатов, резервуар, гальваническая ванна, башня карбонизации, резервуар для рассола, антикоррозийное средство бассейна испарения или ремонта, водонепроницаемая изоляция резервуара, объединительная панель, защита сварочного шва, защита основания, зона химической промышленности, лестница, противоскользящая забальзамированная, канал, бассейн и коррозия окружающих объектов.
FAQ
1.Q: Вы фабрика или торговая компания?
A: Мы на заводе.
2. Q: Где вы находитесь? Какой у вас порт доставки?
A: Мы находимся в городе Дунъин, провинция Шаньдун, к северу от Китая. Обычно мы отправляем товар из порта Шанхай.
3 .Q: Каковы условия оплаты?
A: 30% улучшенное и сбалансированное по сравнению с копией BL.Или аккредитив по предъявлении.
4 .Q: Как я могу получить образцы?
A: Образец предоставляется по запросу.
Hvof Покрытие машины для опрыскивания износостойкое для расширения мостов, затвора шлюза
Оборудование для нанесения покрытия из карбида вольфрама, SX-5000/8000 Конфигурация оборудования для распыления HVOF оборудования для термического распыления HVOF
Состоит из пистолета-распылителя, устройства подачи порошка, системы управления, водоохладителя и трубопровода система. Это компактное оборудование, отличающееся простотой эксплуатации, стабильной производительностью, низким расходом топлива и качественным покрытием.
♦ Пистолет-распылитель
♦ Устройство подачи порошка
♦ Система управления
♦ Охладитель воды
Материал покрытия
Распылительное оборудование HVOF может распылять многие виды металлического порошка, такие как карбид вольфрама (WC-Co) и другие твердые металл, Cr3C2-NiCr, MCrAlY, Cr C, Cr Co, Cr и т.д.
Преимущества
(1) Износостойкое покрытие
(2) Антикоррозийное покрытие
(3) Термобарьерное покрытие
(4) Прочие функции покрытие
(5) Восстановите изделия (Отремонтируйте изношенные детали)
(6) Продлите срок службы изделия
(7) Восстановите деталь
A.SX-5000/8000 Шкаф управления термическим напылением высокоскоростного кислородного топлива Шкаф управления при проектировании эквивалентен передовой зарубежной системе управления. Он прост в эксплуатации, с функцией автоматизации во время процесса распыления. Вы можете контролировать систему и управлять пистолетом-распылителем в режиме реального времени и немедленно реагировать на неисправность системы.
Параметры SX-5000 c
Номер | Элементы | Базовый параметр | |||
1 | 60 Одиночный источник питания 220 В переменного тока, 50 Гц | ||||
2 | Входная мощность | 300 Вт | |||
3 | Режим управления | Управление ПЛК | ПЛК Топливный газ и давление | Пропан 0.65 МПа | |
5 | Давление кислорода | 1,1 МПа | |||
6 | Давление воздуха | 0,8 МПа | 0,8 МПа 0 | 1,2 МПа | |
8 | Давление водорода | 0,3 — 0,4 МПа | |||
9 | Размер | 600 × 1760 мм | |||
10 | Вес | 130 кг |
B.SX-5000/8000 машина для подачи порошка высокоскоростного кислородного топлива для термического напыления покрытия
Машина для подачи порошка используется для сохранения распыляемого порошка и отправки его в пистолет-распылитель в соответствии с технологическими требованиями. Он использует азот в качестве подаваемого газа, а порошок распыляется в порошок. Затем измельченный порошок и газообразный азот вместе отправляются в пистолет-распылитель из порошковой трубки. Вы можете использовать потенциометр на панели шкафа управления, чтобы регулировать скорость подачи порошка.
Система охлаждения C.SX-5000/8000 с термическим напылением высокоскоростного кислородного топлива
Spray smaples:
Наши клиенты:
Служба предпродажной поддержки.
* Пример поддержки тестирования.
* Посмотреть наш завод.
Послепродажное обслуживание
* Обучение установке машины, обучение ее использованию.
* Доступны инженеры для обслуживания машин за рубежом.
Если вы заинтересованы в наших продуктах, мы будем рады связаться с нами, моя контактная информация следующая:
.