Нож из напильника — плюсы и минусы, изготовление, как закалить
Хороший нож всегда считался атрибутом настоящего мужчины. А самодельный клинок – это повод гордиться перед друзьями. Главное условие – наличие качественного материала. Можно взять любое железо, и закалить. Но лучший результат получается при использовании стали, легированной углеродом.
Что использовать в качестве донора?
- Толстое сверло по металлу. Только нужно учесть особенность – легированный металл только на рабочей половинке, хвостовик – обычная «закалка»
- Шатун от поршневой группы двигателя
- Торцевой ключ
- Рессора. Пожалуй, самая популярная заготовка
- Напильник.
Традиционно, холодное оружие (даже если оно – просто колбаску порезать) изготавливают между молотом и наковальней. Для перечисленных заготовок – это обязательное условие, необходимо придать им новую форму. Даже рессору придется отковать, чтобы убрать серповидность. Исключение составляет самодельный нож из напильника.
Может быть, этот материал покажется необычным? По сути это просто качественная сталь. Хорошие экземпляры, это те, что изготовлены 30-50 лет назад. Советская металлургия соблюдала стандарты легирования стали. Если вам удастся отыскать такую заготовку (пусть и покрытую ржавчиной), можете смело браться за работу.
Ковка ножа из напильника
Если у вас есть навыки кузнечного дела, и оборудованная кузница – нож из напильника можно сделать на профессиональной основе. Для чего нужна ковка, ведь форма заготовки и так подходящая?
- При ковке металл приобретает новые свойства, становится прочнее и эластичнее, даже после закалки
- Все-таки напильник слишком толстый для клинка, вам придется снимать часть металла во время формирования спусков. При ковке металл остается «в массе», вы просто уменьшаете толщину молотом
- Придав грубую форму изделию, вы потратите меньше времени на финальную обработку.
К тому же, вы полностью уберете насечки.
Если у вас нет соответствующего оборудования – можно изготовить нож из напильника без ковки. При этом готовое изделие будет ничуть не хуже. Опять же, при условии качественного «донора».
Пайка медных труб — несколько способов реализации
При таком количестве китайских дешевых инструментов, сложно найти настоящий советский напильник. Дешевые напильники делаются из обычной стали, и сильно закаливаются.
Обратите внимание
Проверить качество металла можно, положив напильник на край стола, и ударив по хвостовику молотком. Закаленный кончик сломается, легированный металл просто погнется.
Или поднесите напильник к точильному станку. Длинные снопы искр говорят об обычной стали. Короткий и пушистый сноп – высоколегированная сталь. Однако сделать нож из напильника без термообработки не выйдет. Как минимум, заготовку придется «отпустить» и снова «закалить».
Кстати, качественные напильники, легированные углеродом, тоже проходят процедуру заводского закаливания. Поэтому обточить такого «донора» с помощью традиционного инструмента не удастся. Наждак будет стачиваться одновременно с заготовкой.
Изготовление ножа из напильника – пошаговая инструкция
Для работы понадобятся:
- Хороший крупный донор-напильник, «Сделано в СССР»
- Ножовка по металлу (пара запасных полотен)
- Напильник для работы с удобной большой рукоятью
- Наждачная бумага и брусок
- Верстак и тиски
- Струбцины (2 шт.)
- Древесный (шашлычный) уголь для горна
- Отработка (старое моторное масло) для закалки.
Хороший нож получится из напильника со сточенными зубьями. Тогда вам не придется удалять их своими руками.
Для начала, металл необходимо отжечь. Для этого изготавливаем «походный» горн. Насыпаем земляной очаг, вставляем в него двухдюймовую трубу (для притока воздуха) и разжигаем древесный уголь. Воздух в трубу подаем с помощью компрессора для надувного матраса.
Когда сталь раскалится до красного цвета, прекращайте подачу воздуха, и оставляйте заготовку медленно остывать вместе с костром. Металл станет податливым и готовым к механической обработке.
По заранее заготовленным лекалам, отрезаем лишний металл с помощью ножовки.
Стараемся максимально точно повторить будущую форму, чтобы меньше работать напильником. Вырезаем хвостовик, длина должна быть равна вашим пальцам.
Затем обрабатываем заготовку наждаком или напильником, до придания формы по лекалу. Прижимаем будущий нож к верстаку с помощью струбцины и обтачиваем спуски.
Как просверлить отверстие в стекле, и что для этого нужно?
Это ответственная часть работ, и выполнять ее «на глазок» не следует. Обе стороны клинка должны быть обработаны симметрично, угол снятия металла одинаковый по всей длине спуска, включая загиб кончика. Для удобства можно изготовить несложное приспособление – металлическая труба с направляющей, на которую крепится длинный напильник.
Поскольку заготовка отожжена, обработка проходит без лишних усилий. Когда грубое придание формы окончено, производим финишную обработку наждачной бумагой. Для этого ее можно обернуть вокруг деревянного бруска.
Клинок готов, однако мягкость отожженного металла не позволит им пользоваться в полную силу.
Как закалить нож из напильника?
При закаливании меняется структура металла, он приобретает твердость и некоторую хрупкость.
Закалка ножа из напильника производится в масле-отработке. Нагреваем клинок то темно-вишневого цвета.
Обратите внимание
Если на улице солнце, и по цвету температуру не определить – проверяем готовность с помощью магнита.
Сталь, нагретая до нужной температуры, не магнитится. Затем резко опускаем нож в банку с отработанным маслом. Для более скорого охлаждения, банку с маслом можно поставить в тазик с холодной водой. Закалка будет эффективней.
Проверить твердость стали можно с помощью стеклянной посуды.
Качественно закаленная сталь оставляет борозды на стекле.
Инструкция, как сделать нож из напильника будет неполной, без технологии изготовления рукоятки. Хвостовик оставлен достаточно длинный, рукоять делаем наборную. Для удержания сегментов рукояти, на хвостовике можно сделать хаотично проточенные насечки.
Изготовление рукояти
Для начала нарисуем внешний вид. Если вытачивать рукоять по месту, нож будет выглядеть некрасиво.
Идеальный материал – береза. Используется само дерево, береста удаляется. Разумеется, можно выточить рукоять из любого материала, с которым удобно работать.
Для изготовления больстера используется кусочек алюминия или обрезки напильника.
Как сделать больстер для ножа рассказано в этом видео
Нож делается не в качестве сувенира, поэтому рукоять должна быть прочной. Нарезаем заготовки на бруски и насаживаем больстер на хвостовик.
Чтобы не повредить лезвие ножа, оборачиваем его плотным материалом.
Мангал из дисков автомобиля — компактное решение для пикника
Набираем рукоять, чередуя бруски разного цвета. Между ними прокладываем листы толстой бересты. Рукоять крепится на эпоксидный клей. Можно использовать полиэфирную смолу, если клинок будет использоваться как ударный инструмент (она более эластичная). Набранную из заготовок рукоятку зажимаем в прессе, для придания монолитности.
После окончательного застывания клея, выравниваем (спиливаем) края до ровной плоскости, и размечаем контуры рукояти по заранее изготовленному эскизу. С помощью ножовки придаем рукояти общие черты дизайна.
Затем обтачиваем заготовку с помощью грубого и мелкого напильника. Набор обрабатывается как цельный кусок дерева. После схватывания клея, он по сути таковым и является. В конце, наждачной бумагой вручную придаем рукояти требуемую форму.
Готовую рукоять можно отполировать, покрыть лаком, использовать различные морилки.
Заточка лезвия производится традиционными способами – данный нож ничем не отличается от промышленных образцов.
Обратите внимание
Правовые моменты: Любой нож, кухонный, туристический, поварской, может быть признан холодным оружием.
Лучший способ обезопасить себя от неприятных моментов общения с полицией – перед изготовлением проконсультироваться у эксперта. Однако есть несколько признаков, которые гарантированно выведут ваш клинок из категории ХО:
- отсутствие упоров для пальцев
- отсутствие кровостоков
- толщина клинка более 6 мм
- длина лезвия менее 90 мм.
Ножик из напильника, плюсы и минусы
Минус, пожалуй, один – кропотливый и трудоемкий процесс изготовления. Еще один недостаток (скорее особенность) – из такого материала, как напильник, нельзя изготовить тонкое и гибкое лезвие.
Достоинства – нож очень прочный и долговечный.
Материал изготовления доступный и фактически бесплатный. К тому же толщина обуха – 6 мм, один из признаков, что нож не является холодным оружием.
Нож из напильника своими руками – смотрите видео. Подробный мануал по изготовлению ножа.
Изготовление ножа из автомобильной рессоры. Ножи из рессорной стали Как сделать нож из пружинной стали
Тем, кто может достать старые автомобильные рессоры, хорошо повезло – для их производства применяли высокоуглеродистую сталь, которая подходит для изготовления отличных ножей. После того, как вы закалите такой нож, его режущая кромка будет отличаться высокой стойкостью, такое лезвие позволит разрезать достаточно твердые предметы.
Как сделать нож из рессоры
Чтобы получить нож из рессоры в домашних условиях, подготовим список таких материалов и инструментов:рессора автомобиля;
кусок древесины для отделки рукояти;
болгарка;
дрель или сверлильный станок;
наждачная бумага с разной зернистостью;
печь для закалки металла, масло;
лобзик или другие инструменты для резки дерева;
струбцины.

Ковка ножа из рессоры проходит в несколько этапов
Этап 1.В первую очередь нужно собрать все материалы для работы, чтобы они были наготове. У автора исходным материалом послужил лист рессоры от старой машины.
Поскольку рессора выполнена в изогнутой форме, то ее необходимо выгнуть. Это делается так: металл нагревается, после чего постепенно остывает. Для нагрева подойдет горелка, также можно просто положить лист рессоры в хорошо разожженный костер.
После того, как заготовка остынет, нужно взять молоток и наковальню, и обработать рессору так, чтобы она стала прямой пластиной. После отпуска металл стал более мягок, он будет легко поддаваться резке, сверлению, и т. д.
Этап 2.
Сначала нужно изготовить шаблон ножа. Автор использовал готовый шаблон из интернета. Если есть желание – его можно улучшить. После распечатки шаблона бумагу нужно наклеить на картон и ножницами вырезать шаблон. Подержав его в руках, мы можем прикинуть, как будет выглядеть нож из рессоры.
После этого нужно приложить шаблон к металлу и обвести маркером.
Этап 3.
Сейчас мы приступаем к самому тяжелому этапу работы – нам нужно вырезать профиль ножа. Это делается с помощью болгарки – орудуя этим инструментом, не рекомендуется перегревать металл. Если в месте резки сталь начинает менять цвет – это значит, что он перегревается. В таком случае металл нужно полить водой. В тех местах, где нельзя вырезать, металл можно просверлить рядом отверстий и потом эту часть обломать.
Этап 4.
Это заключительный этап формировки основного профиля лезвия. Для такой работы очень удобен и прост ленточный шлифовальный станок. Умельцы с большим опытом могут использовать болгарку. Наружную плоскость ножа следует отшлифовать, чтобы она блестела. Для прижатия заготовки к шлифовальной ленте автор воспользовался бруском. Здесь также нужно следить, чтобы металл не перегревался.
Другой ответственный момент шлифовки заключается в изготовлении на ноже скосов.
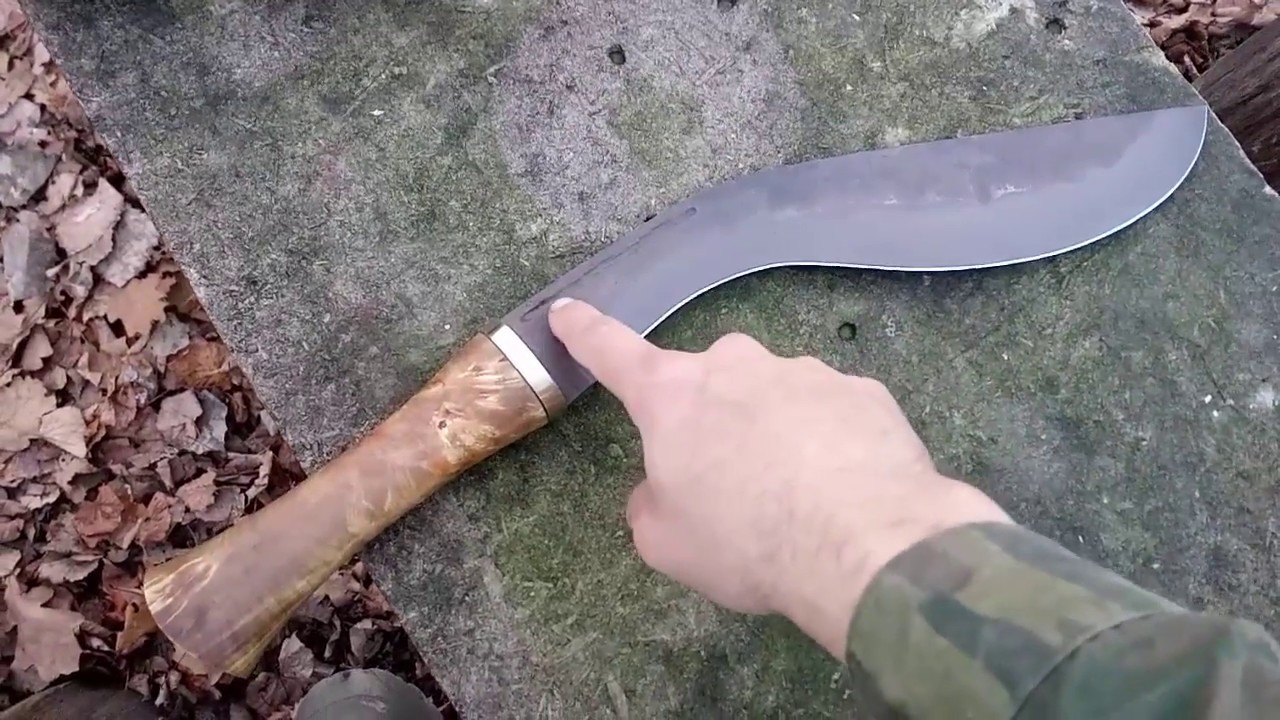
Этап 5.
Чтобы надежно закрепить накладки на рукоятке, в данном ноже используется 4 штифта. Для них нужно просверлить отверстия. Для подбора диаметра ориентируемся на имеющиеся штифты, которыми традиционно служат стержни из латуни. Для этого случая подойдут и обычный стальные гвозди.
Этап 6.
После закалки клинок приобретает твердость и долго не тупится. Чтобы закалить лезвие, нужно взять масло – подойдет моторное или растительное, печка или хороший костер. Металл необходимо нагреть до такого состояния, при котором к нему не будет притягиваться постоянный магнит. Как отмечает автор, во время нагрева металл отличается тусклым красным цветом. После этого нужно опустить заготовку в масло. Следует быть осторожными, поскольку масло часто воспламеняется с дымом и брызгами, летящими в разные стороны. Емкость для закалки нужно брать металлическую.
Случается, что во время закалки металл начинает деформироваться. Такую ситуацию можно исправить. Для решения проблемы нужно нагреть заготовку, выровнять, и затем опять попробовать закалить.
После закалки обязательно следует сделать отпуск металла, в противном случае вы получите очень хрупкий нож. Для этой операции берем бытовую духовку, помещаем в нее заготовку и прогреваем сталь при температуре 200°C на протяжении часа. После этого нужно дать заготовке постепенно остыть, при этом духовку не нужно открывать, сталь должна остыть закрытой внутри.
Этап 7.
Для изготовления накладок на рукоятку, берем две дощечки небольшой толщины. Вырезаем их до требуемого размера и сверлим в них отверстия для штифтов.
Теперь склеиваем заготовки при помощи эпоксидного клея, нанеся по хорошему слою на обе накладки. Затем нужно вставить штифты и хорошо зажать ручку струбциной. Оставляем в таком виде на 24 часа, чтобы клей полностью высох. Сразу для удаления остатков клея берем тряпочку или туалетную бумагу.
После того, как клей высохнет, нож нужно достать и окончательно сформировать форму рукояти. Для этих работ используем ленточный шлифовальный станок.
При выборе ножа очень важно учитывать материал, из которого он изготовлен. Ведь для выполнения различных функций лезвие должно быть не только острым, но и прочным. К тому же, нужно обращать внимание, чтобы клинки не тупились и не гнулись при незначительной нагрузке. Эти свойства зависят от материала, из которых изготовлены ножи . В зависимости от задач, которые нож должен выполнять, будь то нож для разделки, охотничий или туристический , отличаются и характеристики материала.
Ножи из рессоры , несомненно, были самыми популярными среди людей, мало-мальски имеющих отношение к машинам. Их действительно изготавливали из рессор старых автомобилей, поскольку это был один из самых доступных материалов. При этом ножи использовались, как на кухне для резки продуктов , так и для бытовых нужд.
Сейчас рессорная сталь не сдает своих позиций и довольно распространена в производстве ножей.
Почему именно рессора автомобиля?
Во-первых, благодаря «идеальности» наших дорог, этот элемент ходовой часто приходил в негодность, поэтому и славился своей доступностью, и его часто можно было встретить на дорогах и в гаражах простых граждан.
Во-вторых, в конструкции рессоры используется несколько листов углеродистой стали. Вот из этих листов в домашних условиях можно было изготовить множество ножей.
В-третьих, рессорная сталь обладает высокой эластичностью, поэтому ее обработка возможна для всех желающих, имеющих минимальный набор инструментов и приспособлений.
В чем же особенность ножа из рессоры?
Здесь, в первую очередь, нужно упомянуть об особенностях стали, из которой изготовлен клинок. В производстве ее называют конструкционной рессорно-пружинной сталью 65Г, и, как понятно из названия, ее применяют в изготовлении пружин, пружинных рессор, шайб и других деталей, работающих без ударных нагрузок. Она считается одной из самых дешевых марок углеродистой стали, однако она обладает хорошей гибкостью и ударной вязкостью, что облегчает процесс ее обработки. К тому же этому виду материала присуща хорошая твердость, что играет не последнюю роль при выборе ножа .
Наличие в стали кремния, марганца, хрома и никеля обеспечивает высокую упругость и закаливание. В качестве антикоррозийной защиты применяют оцинковку. Однако на практике этого оказывается недостаточно, и самым большим недостатком этого материала остается высокая склонность к коррозии. Все же сталь 65Г обладает большими преимуществами, и получила широкое применение в производстве различных инструментов, для которых важной особенностью является износостойкость.
Применение рессорной стали
Из-за своей универсальности, обусловленной характеристиками стали, нож из рессоры изготавливается как в домашних условиях, так и серийно. Это могут быть кухонные ножи, которые прекрасно режут продукты и разделывают мясо, армейские, туристические и ножи для выживания , способные открыть жестяную банку консервов либо заточить кол.
Из стали 65Г производят также цельнометаллические мачете и топоры, поскольку их клинки отлично подходят для рубки. Из рессорного листа недорого и быстро можно выковать меч, и многие реконструкторы используют эту сталь в своем хобби. К сожалению, рессорная сталь является ржавеющей, поэтому она не подходит для подводного плавания .
Кухонный нож
Широкое использование нож из рессоры получил на кухне. Тогда многие имели доступ к этому материалу и пытались использовать его как можно максимально. Хорошие ножи серийного производства иногда были не по карману обычной семье, но для резки продуктов дорогие приборы и не требовались. Поэтому, из рессор мастерили универсальные ножи и с разнообразными самодельными рукоятями из эпоксидной смолы, дерева или обычной изоленты. Такие ножи не славятся выдающимися характеристиками, но со своей задачей справляются отлично.
Туристический нож
Нож из рессоры прекрасно подойдет для применения в диких условиях. Обычно нагрузка на него невелика. Но, стоит учитывать, что если сталь была недостаточно закалена, клинок затупится на первой же консервной банке. Заточить кол не представляет проблемы для такого ножа, однако следует остерегаться влаги — рессорная сталь подвержена коррозии.
Армейский нож
Прекрасные свойства рессорной стали позволяют создать хорошие тактические ножи . Благодаря прочности этого металла, они без проблем разрезают веревки, ткань, их можно использовать для бытовых целей, а также при спасательных работах. Но все же, в военных условиях предпочтение отдается ножам из нержавеющей стали.
Топор, мачете, меч
Что касается орудий посолидней, то для их изготовления необходима как листовая сталь, так и специально приобретенная на производстве. Сталь 65Г обладает такой прочностью, что используется в ковшах бульдозера, скрепераи другой техники. Понятно, что на прочность материала влияет и толщина, поэтому для изготовления более крупных орудий потребуется рессора от грузовика или специально заказанная на заводе.
При правильной обработке и надлежащем уходе из рессорной стали выходят отличные топоры, которые пригодятся в хозяйстве для рубки небольших предметов. Из длинного листа получится и такое экзотическое орудие как мачете , которое с легкостью справится с ветками или кустарниками. Благодаря хорошей ударной вязкости стали 65Г, в домашних условиях можно изготовить даже самый передовой мачете, прямой, изогнутый или с зазубринами. Таким же образом происходит и изготовление меча.
Изготовление ножа из рессоры дома
Как уже отмечалось, благодаря доступности и простоте обработки, ножи из рессорной стали можно изготавливать в домашних условиях. На первый взгляд, в этом нет ничего сложного, но все же нужно знать некоторые особенности, влияющие на качество выходного продукта. В Интернете можно найти множество видео с описанием процесса ковки, закаливания клинка и изготовления рукояти.
В целом, из рессорной стали можно изготовить как профессиональное холодное оружие с замечательными характеристиками и изящной формы, так и обычные ножи для бытовых нужд, которые не уступают в долговечности и прочности.
Для начала следует определиться, для каких целей, и что именно будет сделано. Если это кухонный нож, то подойдет любой лист. А если вы хотите изготовить мачете, меч или топор, то лучше выбрать рессору от грузовой машины. Конечно, для изготовления ножей с лучшими характеристиками лучше приобрести сталь на производстве. Для бытовых целей пригодитсястарый использованный материал. Рессорный лист может быть толщиной от 5 до 8 мм, в зависимости от автомобиля. Сталь для грузовых машин традиционно крепче, поэтому ее следует использовать для длинных крепких клинков.
Следующим шагом может быть обычная заточка одного или обоих краев рессоры. Если нужно сделать изделие тоньше, для этой задачи подойдет крупный наждак или камень для заточки. Конечно, данная процедура займет немало времени, но результат того стоит.
С помощью ковки создается форма ножа и меняется его ширина. Закалка стали улучшает качество материала, нагревание в масле придает ей черный цвет (воронение), что также дает дополнительную защиту от коррозии. К тому же, ножи из вороненой стали выглядят очень эффектно.
Рессорная сталь для ножа позволяет с легкостью наносить на клинок гравировку или создавать на нем желоба. По желанию можно выполнить клинок с односторонней или двухсторонней заточкой. Также очень важной деталью в ноже является рукоять. Она должна быть удобной для руки и может быть выполнена из эпоксидной смолы, дерева, металла и кости.
Даже с учетом недостатков рессорной стали 65Г, она не потеряла своей популярности и позволяет изготовлять ножи для различных нужд, которые славятся прочностью и долговечностью.
Прочитали 3028 раз(а)
Сегодня, даже при таком большом ассортименте различных ножей прекрасного качества от известных производителей, ножи ручной ковки по-прежнему пользуются особой популярностью. Это и неудивительно, так как такие ножи обладают особой энергетикой и привлекательностью. А если сам клинок сделан из легированной стали и со знанием дела, то такой нож бесценен. Из различных способов собственноручного изготовления ножа наиболее трудоемким является ковка ножа своими руками. Следует отметить тот факт, что ковка ножа позволяет создать наиболее прочный и качественный клинок, который прослужит не один десяток лет и при этом сохранит свои качества. Ковка ножа своими руками — дело, требующее от мастера высокого уровня навыков владения инструментом, знания металлов и их свойств. Для тех, кто решил выковать нож впервые, описанные ниже рекомендации помогут сделать свой первый клинок.
Как выбрать сталь для ножа
Качественный самодельный нож отличает правильный подбор стали для него, от этого будут зависеть режущие и прочностные характеристики самого ножа. Чтобы правильно подобрать сталь, необходимо знать и понимать, какими свойствами обладает сама сталь. Для ковки ножа своими руками нужно ориентироваться на пять основных свойств стали — устойчивость к износу, твердость, прочность, вязкость, красностойкость.
Твердость — это свойство стали, указывающее на её способность сопротивляться проникновению в неё другого более твердого материала. Говоря проще, твердая сталь лучше сопротивляется деформации. Сам показатель твердости измеряется по шкале Роквела и имеет показатель от 20 до 67 HRC.
Устойчивость к износу — сопротивление материала изнашиванию в процессе эксплуатации. Это свойство напрямую зависит от твердости самой стали.
Прочность указывает на способность сохранять целостность под воздействием различных внешних сил. Проверить прочность можно на изгиб или при сильном ударе.
Пластичность — способность стали поглощать и рассеивать кинетическую энергию во время удара и деформации.
Красностойкость — это показатель, отвечающий за устойчивость стали к температурам и сохранению её изначальных качеств при нагреве. От того насколько сталь устойчива к термообработке, зависит минимальный показатель температуры, при котором её можно ковать. Самыми красностойкими сталями являются твердые марки, рабочая температура ковки для которых более 900 °C. При этом необходимо отметить, что температура плавления стали составляет 1450 — 1520 °C.
Все эти свойства связаны между собой и преобладание одного из них ведет к ухудшению другого. При этом то или иное свойство стали зависит от содержания в ней различных легирующих элементов и добавок, таких как кремний, углерод, хром, ванадий, вольфрам, кобальт, никель, молибден.
Наличие тех или иных легирующих элементов и их пропорциональное использование при изготовлении стали, знание свойств, которые придают легирующие элементы и добавки, позволило создавать сталь для определенных целей и нужд. Такие стали имеют каждая свою маркировку. При этом отечественные и зарубежные марки стали обозначаются по-разному. Для удобства в марке стали указан основной состав одного или нескольких легирующих элементов. Например, сталь марки У9 говорит о содержании в ней углерода в десятых долях процента. Аналогом стали марки «У» являются стали 10хх, где «хх» — это содержание углерода. И чем меньше значение, тем меньше его содержание. Или такая сталь как Х12МФ указывает на высокое содержание хрома и молибдена, что говорит о нержавеющих и высокопрочностных свойствах стали.
К отечественным маркам, которые часто используются при ковке ножей в домашних условиях, относятся все стали с маркировкой от У7 до У16 , ШХ15 , 65Г , Р6М5 , Х12МФ . Из зарубежных аналогов можно выделить сталь O-1 , 1095 , 52100 , M-2 , A-2 , 440C , AUS , ATS-34 , D-2 . Каждая их вышеприведенных марок используется в изготовлении ножей, различного инструмента и запчастей. Например, марки стали Р6М5, У7-У13, 65Г применяют для производства сверел, буров, тросов, рессор, подшипников, напильников. Поэтому именно из этих предметов народные умельцы делают ножи ручной ковки.
Конечно, можно найти и другие изделия из той или иной стали. Для этого достаточно будет прочитать полное описание марки стали и её применение в Марочнике Стали и Сплавов, а потом использовать изделие из неё для ковки ножа.
Для ковки ножа потребуется определенный инструмент кузнеца, который можно приобрести в магазине. Но можно использовать и непрофессиональный инструмент:
- молот на 3 — 4 кг и молоток меньшего веса до 1 кг;
- кузнеческие щипцы или обычные пассатижи, но без изоляции на ручках, а также разводной ключ;
- тиски;
- наковальня или её самодельный аналог из двутавра;
- болгарка и сварочный аппарат;
- точильный станок;
- печь.
Если с обычным инструментом все более-менее понятно, то по поводу печи необходимо сделать некоторые пояснения. Все дело в том, что в обычном очаге сложно получить температуру более 900 °С. Да и греться заготовка там будет целую вечность. Поэтому необходимо немного усовершенствовать очаг. Если ранее Вы не занимались хотя бы закалкой металла, то придется сделать с нуля небольшую печь из толстостенного металла. Затем присоединить к ней трубу, по которой будет поступать воздух при помощи вентилятора или старого пылесоса. Таким нехитрым образом можно получить достаточно надежное горнило для доведения заготовок до температуры 900 — 1200 °С. В качестве топлива используется обычный древесный уголь, желательно такой, который дает как можно больше жару и горит подольше.
Прежде чем приступить к самим работам, необходимо сделать эскиз самого ножа.
По сути, нож довольно простой предмет, состоящий из клинка и рукоятки. Но вот каждый из этих элементов имеет целый набор составляющих. На демонстрирующем конструкцию ножа фото можно увидеть все элементы ножа и как они называются.
Также необходимо знать и о некоторых основных профилях клинков, чтобы сделать наиболее подходящий эскиз. На фото ниже приведены профили ножей.
Выбрав наиболее подходящий для Вас профиль, можно смело приниматься за создание эскиза. Конечно, опытные мастера обходятся без зарисовки, но для новичка все же важно сделать эскиз и держать его перед глазами в процессе ковки.
Ковка ножа из сверла
Сверла получили большую популярность при ковке ножей благодаря используемой в них легированной стали Р6М5, которая отличается прочностью, легкостью заточки и износоустойчивостью.
При выборе сверла для ковки следует отметить один важный момент. Большие сверла состоят из рабочей спиралевидной части из Р6М5 и хвостовика из обычной стали. Маленькие сверла обычно полностью из Р6М5. При ковке ножа из большого сверла необходимо сразу определить, где какая сталь и где между ними граница. Сделать это можно достаточно просто, всего лишь немного проточив сверло по всей длине. Там, где обычная сталь, сноп искр будет большой и желто-оранжевого оттенка. А вот там, где легированная сталь, сноп будет реденьким и ближе к красноватому оттенку. Описанная выше процедура необходима для того, чтобы определить, где у ножа будет начинаться клинок, а где хвостовик. Закончив с этим, переходим к самой ковке.
Вначале разводим огонь в печи , подключаем поддув и ждем, когда угли разгорятся достаточно сильно, после чего помещаем сверло в горнило . Но делаем это с помощью клещей и так, чтобы хвостовик большей частью оставался вне огня.
Важно! Выполняя ковку ножа впервые, можно не сразу определить, когда металл нагрелся до необходимой температуры. Вследствие чего можно испортить не одно сверло. Поэтому прежде чем браться за ковку сверла, можно немного потренироваться с нагревом и ковкой металла на обычной арматуре. При этом необходимо запоминать, какого цвета был металл и когда он ковался наиболее мягко.
Также стоит помнить о том, что на солнечном свете даже нагретый до 1100 °С металл будет выглядеть темным.
Как только сверло нагреется до необходимой температуры, а это более 1000 °С , его сразу же необходимо вынуть из горнила , и зажать низ хвостовика в тисках. После чего взять разводной ключ, зажать им верхушку сверла и сделать круговое движение, расправляя спираль. Делать все необходимо быстро, чтобы металл не успел остыть, иначе рискуете сломать сверло. Если не получилось сделать это за один раз, ничего страшного. Просто повторно раскалите сверло и повторите процедуру. В результате должна получиться относительно ровная полоска металла.
Следующим шагом будет ковка сверла и раскатка металла до приемлемой толщины . Тут все довольно просто. Раскалив металл до необходимой температуры, берем тяжелый молот и начинаем сильными, но равномерными ударами ровнять металл и придавать ему ровную форму. В результате должна получиться полоска металла толщиной около 4 — 5 мм.
Важно! При ковке металла необходимо постоянно следить за цветом заготовки. Как только она начала тускнеть, приобретая вишневый цвет, её сразу же возвращаем в горн. Лучше лишний раз накалить металл, чем сломать его под ударом молота.
Далее выковывается острие ножа . Тут все несколько сложнее. Дело в том, что необходимо придать заокругленную форму и при этом сохранить необходимую толщину лезвия. Вся работа практически ювелирная и потребует определенной ловкости. Ковка выполняется таким образом, чтобы постепенно заокругливая острие, понемногу оттягивалось лезвие в длину. Удары должны быть сильные, но аккуратные. У новичка может не получиться с первого раза, но немного практики все исправит.
Следующим шагом будет проковка режущей кромки ножа . Это довольно важный и сложный этап. Для этого потребуется более легкий молот и желательно с заокругленным бойком. Начиная с середины лезвия, постепенно сдвигаем металл вниз к режущей кромке. Стараемся сделать режущую кромку как можно тоньше. При этом следим, чтобы само лезвие оставалось прямым и ровным. Удары наносим очень аккуратно и стараемся прилагать лишь столько усилий, сколько требуется для небольшой деформации раскаленного металла. Помним о цвете заготовки и при необходимости отправляем её обратно в горнило.
После того как удалось выковать лезвие и острие, переходим к проковке хвостовика . Сами работы будут намного проще, чем при выковке лезвия. Вначале накаливаем круглый хвостовик сверла и затем раскатываем его сильными ударами молота. В зависимости от эскиза хвостовик может быть как узким, так и широким. Тут уже кому как нравится делать ручку ножа. Кто-то делает простые накладки, а кто-то делает наборную рукоятку.
По завершению ковки даем металлу постепенно остыть и затем переходим к шлифовке . На шлифовальном станке снимаем лишние слои металла и неровности, делая нож идеально ровным и блестящим. При шлифовке может уйти до 2 мм толщины, и нож станет намного легче и тоньше. Также на этом этапе можно выполнить заточку ножа. Напоследок выполняем закалку ножа. О том, как это делается, будет написано ниже.
Ковка ножа из сверла видео-обзор :
Еще одним популярным материалом для ковки ножей является подшипник, а именно его внутренний или внешний обод. Причем внутренний даже предпочтительней. Все работы по ковке ножа из подшипника практически идентичны ковке из сверла. За некоторым исключением.
Во-первых, заготовку из ободка подшипника вырезаем при помощи болгарки. Длину стараемся взять с запасом, так чтобы и на нож хватило и еще 1 — 2 см осталось. Во-вторых, на начальной стадии ковки вырезанную заготовку следует приварить к прутку арматуры. И в таком виде накалять и ковать. В-третьих, если в случае со сверлом заготовку раскатывали из круглой в плоскую, то для обоймы подшипника её необходимо просто выровнять. А дальнейшие действия по ковке самого клинка и хвостовика полностью аналогичны. Единственное, что стоит отметить, — из подшипника все же удобнее делать нож с накладными рукоятками.
Ковка ножа из подшипника видео-обзор :
В поисках подходящей стали для качественного ножа многие используют рессору. Металл этой автомобильной запчасти отличается высокой упругостью и долговечностью, что делает его прекрасным образцом для ножей ручной ковки. Справедливости ради, необходимо отметить, что нож из рессоры можно изготовить и обычным вырезанием профиля ножа с дальнейшей заточкой и закалкой. Но все же, чтобы нож был действительно надежным, его лучше проковать, тем более что толщина рессоры достаточно велика, а для хорошего ножа её следует уменьшить.
Ковку ножа из рессоры начинаем с зачистки болгаркой от ржавчины и разметки пластины. Потребуется лишь небольшая часть рессоры, поэтому отметив её, отрезаем при помощи болгарки. Далее привариваем заготовку к арматуре и накаляем её. После чего постепенно проковываем, доводя до необходимой толщины. Выковываем острие и режущую кромку, как это делать, описано выше на примере ковки ножа из сверла. Добившись желаемого, оставляем нож постепенно остывать и затем шлифуем и затачиваем его.
Ковка ножа из рессоры видео-обзор :
Ковка ножа из напильника
Износостойкую и прочную сталь можно найти в различном слесарном инструменте и напильник тому яркий пример. Изготовление ножей из напильника достаточно популярное занятие. Тем более что клинки получаются на редкость долговечными с прекрасной режущей кромкой. Но ковка ножа из напильника имеет свои особенности.
Прежде всего, потребуется очистить напильник от насечек и возможной ржавчины. Сделать это можно с помощью болгарки. Далее при необходимости отрезаем от напильника заготовку необходимой длины. После чего привариваем её к куску арматуры и засовываем в горнило. Накалив заготовку до нужной температуры, приступаем к раскатке заготовки до необходимой нам толщины. Затем делаем острие и режущую кромку. Хвостовик ножа из напильника лучше всего сделать под накладную ручку.
Ковка ножа из напильника видео-обзор :
Ковка ножа из троса
Изготовление ножа из стального троса довольно редкое явление. Так как в отличие от всех описанных выше заготовок, трос представляет собой разрозненные волокна проволоки, и ковать их довольно сложно. К тому же сталь троса не обладает такими высокими характеристиками, как сталь сверла или напильника. В большинстве своем ножи из троса куют из-за их необычного рисунка на клине, отдаленно напоминающего дамасскую сталь. Для того чтобы сделать такой нож, необходимо приложить несколько больше усилий, чем при ковке из обычного бруска стали.
Ковка ножа из троса начинается, как и обычная ковка. Вот только есть несколько маленьких секретов. Во-первых, это касается хвостовика. Многие мастера делают хвостовик ножа из троса в виде готовой рукоятки. Смотрится это весьма необычно и красиво. И тут есть два подхода в изготовлении рукоятки. Взять толстый трос и затем сварить его конец, сделав монолитным куском. Или сделать рукоятку в форме петли, а из концов выковать клинок. Во-вторых, ковка троса — дело сложное из-за разрозненных проволок, из которых состоит трос. Чтобы сделать нож, потребуется их сварить между собой. А это целое искусство и рассчитывать, что нож из троса получится с первого раза, не стоит. Сварку можно выполнить двумя путями. Первый — проварить электросваркой вдоль больших канавок. Второй — выполнить кузнеческую сварку. Второй вариант сложнее и в то же время предпочтительней.
Итак, выбрав способ создания рукоятки, приступаем к ковке ножа. Для этого раскаливаем трос до ярко-красного цвета. Затем вынимаем его и посыпаем бурой. После чего вновь отправляем в горнило. Таким нехитрым образом выполняется подготовка к кузнеческой сварке. представляет собой соль тетраборной кислоты и применяется мастерами для сварки отдельных слоев стали. По сути это флюс, который облегчает процесс плавки и предохраняет расплавленный металл от попадания кислорода и устраняет оксиды металла. Буру можно найти в свободном доступе без особых проблем.
После того как трос обработали бурой со всех сторон и он раскалился от 900 до 1200°С и более, вынимаем его из горнила и начинаем проковывать. Удары наносим тяжелым молотом, но при этом стараемся сохранить волокна троса вместе. Сложность ковки троса именно в этом. Но потренировавшись можно добиться приемлемых результатов. В конце концов, трос можно накалять и проковывать сколько угодно раз. Но при этом каждый раз, нагревая его в горне, посыпать трос бурой. В результате получится монолитный кусок стали, состоящий из множества слоев, почти как у дамасской стали. После чего остается лишь выковать клинок необходимой формы. На демонстрирующих ковку ножей видео уже не раз было показано, как именно делается раскатка клинка, создание режущей кромки и острия.
Закалка и отпуск клинка
Как уже отмечалось ранее, закалка ножа — это один из самых важных этапов его изготовления. Ведь именно от того насколько правильно была она выполнена, зависят рабочие характеристики ножа. Сам процесс закалки выполняется уже после того, как нож остыл и был отшлифован на точильном станке.
Начинается с его нагрева от светло-красного до оранжевого цвета. После чего нож опускается в воду или масло. При этом в воду добавляется 2 — 3 ложки поваренной соли на 1 л, а температура воды должна быть 18 — 25 °С, масла 25 — 30 °С. Закалка выполняется довольно быстро и чтобы все прошло удачно после закалки клинок необходимо отпустить. Сама закалка стали происходит в диапазоне температур от 750 до 550 °С. Момент закалки можно даже прочувствовать, когда сталь начинает «дрожать и стонать» в жидкости. Как только процесс заканчивается, клинок необходимо достать и дать ему остыть естественный образом.
Отпуск клинка выполняется уже после закалки. Сам процесс подразумевает ослабление внутреннего напряжения стали, что делает его более гибким и устойчивым к различного рода нагрузкам. Перед тем как сделать отпуск, клинок следует очистить от возможной окалины и затем вновь нагреть. Но температура при отпуске значительно меньше. Сам нож нужно уже держать над пламенем и наблюдать за ним. Как только вся поверхность покроется желто-оранжевой пленкой, убираем нож от огня и даем ему остыть естественным образом.
Иногда закалка и отпуск производятся при помощи масла или воды, а иногда через масло в воду. Такая закалка выполняется очень быстро. Сначала клинок опускается в масло на 2 — 3 секунды, а затем в воду. При таком подходе риск сделать закалку неправильно минимален.
Ковка ножа своими руками лишь кажется простой задачей. Кроме того что придется довольно много помахать кузнечным молотом, так еще и без опыта в вопросе ковки металла с первого раза может не получиться выковать нож. Поэтому сначала необходимо набить руку и немного потренироваться, а затем уже приступать к ковке ножа.
Вторичное сырье не позволит сделать клинок высочайшего качества. Но многим нравится ощущение перерождения других материалов в режущие и колющие предметы. Например, ковка ножа из напильника или цепи, рессоры, клапана, подшипника, троса, сверла.
Нож из подшипника
Для ножей используются подшипники от автомобилей, обычно диаметром сантиметров 10-15.
Ножи из троса
Из троса получаются хорошие клинки, но дамасские свойства не высокие из-за крупных рисунков. Ножи из троса содержат небольшое количество углерода, поэтому к их телам нужно приваривать режущую кромку из дамаска.
Ножи из рессоры
Многие предпочитают делать ножи своими руками из рессоры, которая была изготовлена еще в советский период. Тогда использовалась для рессоры высококачественная сталь 65Г. Свойства металла рессоры повышаются за счет правильного соотношения составных частей и технологичной термообработки. Если ножи из рессоры перекалить, то они станут хрупкими.
Ножи из цепи
Широко применяется для ковки такой вторичный материал, как цепи. Чаще это цепи от бензопилы, но бывают и моторные цепи от бензинового двигателя.
Ножи из клапана
Для изготовления ножей своими руками из клапана берутся пустотелые выпускные клапаны. Не каждый умелец знает, как грамотно оттянуть нож из клапана. Поэтому это не лучший вариант.
Ножи из сверла
Хорошие ножи получаются из сверла. Инструментальная сталь, из которой изготовлены сверла, говорит сама за себя. Если правильно закалить клинок, сделанный своими руками из сверла, то он не будет ломаться при ударных нагрузках и сможет противостоять высокой нагрузке на изгиб.
Ножи из напильников
Чтобы изготовить своими руками нужно сначала нарисовать эскиз – форму лезвия и ручки, выбрать способ крепления, как на видео. Металлом для напильника является углеродистая сталь У10. Ее твердость составляет 57 — 58 HRC. Эти свойства металла при ковке сохраняются, и ножи из напильника получаются крепкими, с высокими режущими показателями и выдерживают большую нагрузку.
Ножи из пилы
Альтернативой может быть использование механической пилы для железнодорожного рельса. Их прочность даже выше, чем у напильников. Оба эти изделия как нельзя лучше подходят для ковки ножей в домашних условиях. Так как старый напильник более доступен, то технологию из него и рассмотрим более подробно. Также процесс можно посмотреть на видео.
Этапы переделки напильника в нож
Ковка в домашних условиях должна происходить при строгом соблюдении всех мер предосторожности.
Будем пользоваться:
- Напильником (желательно советским).
- Материалом для изготовления рукоятки (пластик, кость, дерево и др).
- Обувным кремом и воском.
- Газовой плитой или другим нагревательным устройством.
- Станком, тисками и болгаркой.
- Магнитом.
- Наждачной бумагой.
- Материалом для заклепок (желательно латунь).
- Клеем для кожи и металла.
Сначала производим обжиг напильника в печи, как на видео. Накаливаем его на протяжении 6 часов и оставляем там до полного остывания. Это делаем для того, чтобы сталь стала такой, как перед заводской обработкой. Вместо печи можно использовать раскаленные угли костра. В домашних условиях для этого можно использовать газовую конфорку. На нее кладут будущий нож тем местом, где предполагается режущая часть. Сверху ставят металлический тепловой экран так, чтобы он не касался напильника. Заготовку посыпают солью, которая при нагревании должна расплавиться. Время процесса – 6 часов.
Затем отрезают от заготовки все лишнее, чтобы она соответствовала нарисованному эскизу. Теперь нужно просверлить отверстия для клепок и закалить будущий нож. Заготовку равномерно прогревают до накаливания одного цвета. Рукоятку можно не закаливать. Если сталь закалилась, то она не будет магнититься. Это сигнал к дальнейшим действиям. На этой стадии заготовка должна царапать стекло, если все сделано правильно.
Самая ответственная часть дела закончена, можно приступать к отпуску – процессу изменения свойств стали, с целью снижения хрупкости. Для этого нужно прогреть нож в духовке два часа. Затем нож шлифуется, доводится до гладкого состояния поверхности, как на видео.
Следующим этапом будет травление стали хлорным железом. Результатом станет образование оксидной пленки, она защитит металл от коррозии. Если хлорного железа нет, то можно воспользоваться уксусом или лимонным соком.
Завершающий шаг – рукоятка. Она садится на клей и приклепывается. Заточка предполагается ручная, как на видео, так как царапин нож не боится. Во всяком случае, лучше ручная заточка, чем неумелая на станке. Теперь лезвие нужно натереть воском. Затачивать ножи целесообразно до окончательной закалки металла.
Вместо накладной рукоятки можно использовать кожу, которую надо равномерно намотать и с помощью крема для обуви довести до состояния однородности.
Надо заметить, что ножи, сделанные в домашних условиях, очень устойчивы к механическим обработкам и после закалки, править их можно будет только на алмазной заточной машинке. На обычном точиле получиться поправить только ручную заточку.
Наглядное видео:
Очень прочные и надежные ножи получаются из автомобильных рессор – это вам подтвердит любой кузнец. Главное правильно обработать этот качественный стальной материал. Рессора в качестве материала для ножа была выбрана неслучайно, т.к. :
1) её куски можно легко найти
2) обрабатывается она значительно легче, чем полоса «быстрореза»
3) стоимость ножа сравнительно мала
И так, начнём с того, что автомобильная подвеска бывает рессорной и пружинной. Нас будет интересовать рессорная.
Благо в России две беды: дураки и дороги. В результате сочетания первого и второго, мы имеем множество пригодных (для изготовления ножа) кусков рессоры прямо на догоге. Бесплатно и вне очереди.
Более подробные сведения об изготовлении самодельных ножей с наглядными фото смотрите по прямым ссылкам, расположенным справа >>>>>>>>
Рессора изготавливается из горячекатного стального проката, для которого есть ГОСТ. А теперь несколько слов о самой красавице: Рессора — упругий элемент в подвеске автомобилей, троллейбусов, автобусов. Соединяют кузов с мостами.Воспринимают тяговые и тормозные усилия при движении.
Рессора намного старше автомобиля. К примеру, гоголевские персонажи, обсуждавшие «доедет ли колесо…» глядели, скорее всего, на рессорную коляску. Естественно, унаследовали ее и самобеглые экипажи. В разное время ее очень широко, порою почти тотально использовали в подвесках автомобилей. И сегодня на старой технике можно встретить множество просто потрясающих конструкций. Но разбирать их здесь мы не будем, поскольку и практическая ценность этой информации небольшая, да и места для приличного обзора потребуется намного больше, чем есть во всем журнале.
А потому поговорим о том, что выкристаллизовалось в процессе развития к сегодняшнему дню.
Конструкция:
Рессоры бывают много-, мало- и однолистовыми. До недавнего времени во всем мире были, а в нашей стране еще и сегодня наиболее распространены многолистовые рессоры. Поскольку график изменения изгибающего рессору момента имеет форму треугольника с вершиной в точке нагружения (мост), то этот треугольник и «заполняют листами», чтобы получить более равномерные напряжения в каждом из них. В результате удается убить не одного, не двух, а целое стадо зайцев.
Изготовление:
Для изготовления листов обычно используют горячекатаную полосу из углеродистой пружинной стали. Нужный выгиб придается рихтовкой, а в заводских условиях – в штампах. После этого делается термообработка. Нередко поверхность упрочняется дробеструйной обработкой.
Виды сечения рессоры:
Сечение листа до некоторого времени было прямоугольным со скругленными кромками. Но поскольку усталостное разрушение листов почти всегда начинается сверху, нижнюю поверхность сократили скосами или выемками. В результате в сечении листы большинства современных рессор имеют или трапецию, или своеобразное «Т» с очень толстой ножкой.
Какую рессору взять:
Многие ножеделы сходятся во мнении, что лучше брать рессору, сделанную в глубокие совковые времена. Поскольку там сталь 65Г была значительно лучше, чем сейчас.
Само качество металла зависит не только от соотношения добавок, но и от технологии термообработки. Возможно в советские времена «термитчики» были более квалифицированы. Упорно прививается, что многие «секреты стали» утеряны в далёких-далёких временах. И что современные ножи — не ножи вовсе… Думаю, сталь, она как была так и осталась. Просто когда работаешь с куском «советской рессоры», ты создаёшь нож с «историей».
Не стоит забывать, что многие качества ножа из любого металла задаются технологией его производства. Например, можно перекалить полотно «быстрореза» при работе на наждаке и потом всем рассказывать, какие хрупкие ножи из Р6М5.
Для первого ножа, пойдёт любой кусок. Первой особенностью для вас тогда станет вопрос о распрямлении рессоры. Для этого вам нужно будет осилить:
2. и само Выпрямление — наковальня+молот
Отжиг:
Разведите костёр нагрейте рессору до «красна» и очень медленно охлаждайте. Можно оставить прямо в углях.
После отжига на рессоре может появиться желтый, коричневый или голубой «налёт», легко снимаемый наждачкой.
Выпрямление:
Это дело бесхитростное. Нужна наковальня (можно использовать кусок рельс) и молот, что потяжелее.
Самый лучший вариант — расковывать железо пока горячо.
Можно и на «холодную», но велик шанс расколоть.
Материалы:
Единицы измерения в тексте: 1 дюйм — 2,54 см; 1 фут — 30,5 см; 1 фунт — 0,454 кг. (Прим: для вашего удобства я пересчитал импортные величины в привычные)
Если вы горите желанием сделать нож своими руками, и у вас нет дорогого оборудования, то вот небольшой список материалов, которые могут пригодиться. Я понимаю, что это не самые лучшие материалы, но это работает, хотя может вызвать улыбку.
Кусок рессорной стали 5160 из магазина, примерно 800 гр весом, или около этого. Отмерьте 18-20 см длины от куска, или сколько решите, и берите новую пластину, а не старую автомобильную рессору.
Теперь отправляйтесь в магазин для столяров, и купите:
за 4 доллара дубовый брусок размером 3,5 х 5 х 7,5 см (Прим: собсно, это будет рукоять)
в сварочном отделе купите медный пруток толщиной 3 мм за 1.50 доллара
2 сверла 3 мм за 2 доллара и ещё одно 6 мм сверло
2 напильника, один плоский, и один полукруглый — 7.50 доллара
2 куска водостойкой наждачной бумаги номер 120 за 1 доллар
2 куска водостойкой наждачной бумаги номер 240 за 1 доллар
дешевое зубило
достаточно большая струбцина, которой вы будете прижимать нож к столу или скамье (но можно обойтись и без неё)
Когда будете подбирать стальную полосу в магазине, посмотрите, можно ли купить самую тонкую пластину из того, что у них есть. Мой магазин располагает материалом 0,5 см толщиной и 4 см шириной. Это довольно толстовато для маленького клинка, но все равно годится. (Прим: в нашем случае с напильником придётся повозиться — толщина ресооры будет больше. Но, после уроков труда в далёком дестве, это — не проблема)
Еще вам нужна будет ручная электродрель. Возьмите ее у кого-нибудь на время, т.к. с ней ничего не случится — вы только просверлите несколько отверстий. Далее я буду использовать картинки, чтобы объяснять свои действия.
Для своего первого ножа выбирайте дизайн попроще. 7.5 — 9 см будет подходящей длиной для клинка, потому что вам придется использовать напильники при обработке лезвия. Прямой клинок без выкрутасов легче обрабатывать, да и напильником проще работать по прямой плоскости.
Ручку для ножа тоже выбирайте несложную, без большого количества причудливых углублений под пальцы, и без гарды.Силуэт ножа нарисован маркером, затем я сверлом 6 мм насверлил вокруг рисунка кучу дырок. Придется много поработать ножовкой по металлу вокруг всего этого.
Прикрутите нож к скамье, пню, или что у вас там есть, и с помощью ножовки удалите часть металла вокруг ручки. Делайте это так, чтобы потом напильником можно было рукоятке придать нужную форму. Это должно быть выполнено в первую очередь, потому что если удалите металл вокруг клинка, то потом не сможете его прикрепить к скамье. Рукоять обрабатывается в первую очередь! Как только она приобретет форму, удалите ненужный материал, прикрепите нож сквозь отверстия в рукояти, и принимайтесь за клинок.
Итак, я обсверлил весь силуэт ножа — это здорово облегчит работу ножовочному полотну при его опиливании. Затем я открутил заготовку от скамьи, и заново прикрепил ее так, чтобы удалить лишний металл с рукояти. Сверлом 3 мм были сделаны отверстия в рукояти под медные прутки, а сверлом 6 мм — чтобы ее можно было крепить к скамье, когда обрабатывается какая-то часть лезвия.
Потом я опилил ручку, и добавил пару углублений под пальцы, чтобы она крепче держалась в руке. После этого я обработал напильником остальную часть силуэта, и опилил скос — будьте терпеливы, т.к. работа напильником требует времени. Хорошо, теперь у меня есть заготовка ножа, опиленная ножовкой по металлу, и обработанная напильником. Это начинает приобретать форму.
Я отметил режущий край с помощью моего 6 мм сверла. Зачернил клинок маркером, а потом начал передвигать конец сверла по режущей кромке так, что появилась тонкая линия. Переверните нож, и повторите то же самое на другой стороне, получив две линии, на расстоянии примерно 0,6 мм — 0,8 мм друг от друга. Если эти две линии получились слишком близко друг к другу, то снова отметьте нужное место маркером, возьмите сверло, и передвиньте его вверх или соответственно вниз, повторив все заново. Линии будут отстоять друг от друга примерно на 1/2 толщины пенсовой монеты.
Затем, с помощью подходящих шурупов для дерева, прикрутите нож к верху скамьи. Начинайте обрабатывать напильником плоскость клинка. Цель в том, чтобы соединить процарапанные линии и вершину режущей кромки ножа в одно и то же время. Это потребует много тяжелой упорной работы и терпения.
И, может быть, несколько перерывов по дороге. Чтобы помочь себе в обработке плоскости, я использовал маркер, и обтачивал очень медленно, пытаясь удержать напильник плоско. Маркер покажет вам неровности, которые надо сточить.
Попробуйте закрепить полоску наждачной бумаги на какой-нибудь недорогой основе, например, на шпателе для нанесения краски. Вначале я зачищал наждаком область, которую мы назвали углубление, с помощью плоской дощечки и бумаги номер 120. Потом я стал обрабатывать плоскость продольными движениями к концу клинка, пока все грубые царапины от напильника не исчезли. Это так же выравнивает плоскость.
Используйте немного мыла и воды, чтобы уберечь наждачную бумагу от загрязнения, а когда закончите работу, убедитесь, что вытерли нож насухо, иначе до завтра он поржавеет. Начните обрабатывать наждачкой плоскость клинка и рукоять. Не удаляйте все огрехи, а только излишки, пока не получите немного голого металла — такая «суровость» придаст характер уже готовому ножу.
ОК, огонь зажжен. Я занялся этим на заднем дворе, в специально огороженном месте. Огонь пылает за оградой, и дует несильный ветерок, который помогает нашей работе. Нужно будет еще несколько вещей, чтобы работать с ножом дальше. Магнит я достал из игрушечной коробки моих мальчишек, а после борьбы с проблемой надежно/дешево пришел к следующему.
Взяв два куска 12 мм квадратной трубы 90 см длиной, я вставил в них концы рукояток старых плоскогубцев и сплющил металл по краю, чтобы закрепить соединение. И еще одна важная, необычайно секретная вещь, на которую я вам намекну: старые масляные фильтры, остающиеся после замены масла в автомобилях.
Суньте клинок в горячие угли. Ножу следует находиться там примерно 10 — 15 мин, в зависимости от того, как сильно разгорелись угли. Это ваш первый раз, поэтому вытаскивайте нож из огня на пару секунд каждые 2 — 3 минуты, смотрите на его цвет, и проверяйте режущий край магнитом.
Если сталь притягивается, значит нож еще не готов, суйте его обратно в огонь и грейте до вишнево-красного цвета. Постарайтесь не перегревать нож дольше, чем необходимо, поэтому проверяйте клинок каждую минуту — две, когда решите, что момент готовности уже близок.
Пришло время опустить нож в секретное масло. Магнит не притягивается, цвет стали хорош, и слюни текут от предвкушения. Я закалял сталь, опуская в масло только 2/3 ножа. 2/3 клинка со стороны режущей кромки я держал в масле, пока не погасло пламя — около минуты — а потом медленно погрузил остальную часть ножа, пока он не погрузился полностью, и не перестал идти дым. Когда мы вытаскиваем нож, он выглядит черным и противным. Я опустил его в сосуд с водой, пока он не остыл настолько, чтобы можно было взять его в руки. Теперь вы спросите — этот нож действительно твердый? Ну что ж, давайте проверим. Возьмите напильник, и пройдитесь им по клинку, прикладывая под углом 30 градусов и прижимая деликатно, а не жестко. Напильник будет скользить по режущей кромке, пытаясь за нее зацепиться. Если клинок слишком скользкий, вытрите его тряпкой, удаляя масло. Чтобы лучше очистить металл, можно использовать так же мыло и воду.
Если напильник цепляется за нож, значит закалка не удалась, возвращайтесь к огню, и повторяйте все сначала. Предположим, что клинок прошел пробу напильником, и закалился как следует. Теперь надо его отпустить, так как мы не хотим, чтобы лезвие или его кончик крошились. Напильники очень хрупкие, и наш нож сейчас тоже очень твердый и ломкий. Разогрейте кухонную духовку до температуры 375 — 400 градусов. «Пеките» нож в духовке 45 минут, позвольте ему остыть до комнатной температуры, и снова суньте в духовку на 45 минут при той же температуре. Кстати, не забудьте смыть предварительно с ножа все масло, если не хотите закоптить весь дом. После отпуска стали можно очистить клинок. Беритесь снова за наждачную бумагу, и готовьтесь накладывать деревянные рукоятки на этого малыша.
Я поместил нож в тиски, и обрезал два куска для накладок на будущую рукоять. Положите нож ближе к верхнему краю бруска, тогда будет проще «привязаться» хотя бы к одному его краю. У меня есть медные прутки, и я готов сделать следующий шаг. Просверлите для них отверстия в рукояти.
Я вставил все три стержня, и очертил контур ножа на дубовой плашке, определившись, где будет «лицо» бруска, когда я прикреплю эпоксидкой и медными прутьями дерево к стали. Это фото не очень хорошее, но, думаю, вы сможете увидеть нужный вид с черной полосой на ноже. Я отметил на древесине начало и конец этой линии, а потом соединил их дугой.
Левая щечка рукояти будет обработана и прикреплена, когда мы не сможем нарушить форму после того, как дерево приклеится к ножу. Теперь карандашом надо сформировать левую часть рукояти, в основном ее перед.
Проверьте, достаточно ли хорошо подготовлена накладка, как она прилегает к металлу, и если надо, выгладите ее на наждачной бумаге, чтобы плоскость была совершенной.Соедините оба куска медными прутками, опилите их и обработайте наждачной бумагой, пока накладки не станут зеркально подобными. Еще раз напоминаю о переднем крае! Потом проверьте их на ноже.
Теперь, если обе накладки достаточно хороши, и нет пустоты между ними и ножом, можно обрезать лишнюю длину прутьев, так, чтобы они были заподлицо с деревом. Тщательно очистите нож — там, где будет прилегать дерево. Мыло, горячая вода и старая зубная щетка, потом тщательно ополосните его и вытрите досуха. Если хотите, чтобы он был совершенно сухим, воспользуйтесь сушилкой для волос.
Я обрезал прутки, и зачистил наждачкой грани, чтобы потом не откалывались щепки. Потом эпоксидной смолой смазал внутренние части деревянных накладок, рукоять ножа и стержни, и соединил все вместе.
Обернув все это четырьмя жирными резиновыми полосами (жирными — чтобы не прилипли), я оставил нож до высыхания, а потом удалил излишки выступившей смолы, и получил готовый нож.
выбор заготовки, набор инструментов, пошаговая инструкция
Хороший нож всегда был атрибутом настоящих мужчин. А если он еще и сделан собственными руками, то это уже повод похвастаться перед друзьями.
Главное условие — иметь качественные материалы для изготовления. Конечно, можно взять любую сталь и провести ее закалку. Но самые качественные изделия получаются при использовании стали, легированной углеродом.
Выбор заготовки
Для самодельного ножа можно использовать следующие заготовки:
- Сверло по металлу большого размера. Но надо учесть, что легированный металл там только на рабочей поверхности, а хвостовик — обычной «закалки».
- Шатун поршневой группы двигателей.
- Торцевой ключ.
- Рессора — чаще всего выступает в роли заготовки.
- Напильник.
Как правило, холодное оружие производят между молотом и наковальней — для практически всех заготовок это обязательный этап, позволяющий придать им другую форму. Исключение — нож из напильника.
На первый взгляд, такой материал может показаться необычным. Нет ничего странного, это просто сталь высокого качества. Хорошие изделия те, что изготавливались 30−50 лет назад. Дело в том, что советские металлурги придерживались стандартов легирования стали. Если сможете найти подобную заготовку (даже ржавую), можете смело приступать к работе.
Ковка металла перед работой
Когда вы знаете кузнечное дело и имеете соответствующее оборудование, сможете сделать профессиональное изделие. Но для чего нужна ковка, если у заготовки и так подходящая форма:
- Металл обретает более высокую прочность и эластичность.
- Напильник немного толстый для клинка, при формировании спусков часть металла придется снять. При ковке металл останется в изделии просто будет уменьшена толщина.
- Потребуется меньше времени для финальной обработки.
Кроме того, можно убрать насечки. Хотя это необязательно, ведь они придают изделиям оригинальность.
Если нет специального оборудования, можно изготовить нож без ковки. При использовании качественных заготовок получится отличный клинок.Так как отечественный рынок заполнили дешевые китайские инструменты, найти настоящие советские инструменты очень непросто. Для недорогих инструментов берут обычную, сильно закаленную сталь.
Проверить металл можно, поставив напильник на краю стола, после чего нанести удар молотком. Закаленный конец сломается, а легированный — немного погнется. Также можно поднести инструмент к точильному станку. Если искры длинные — сталь обычная, если короткие и пушистые — перед вами высоколегированный металл. Но термообработка в любом случае нужна: как минимум заготовки «отпускаются» и повторно «закаляются».
Нож из напильника своими руками
В работе не обойтись без:
- Хорошего крупного напильника советского производства.
- Ножовки по металлу (несколько запасных полотен).
- Рабочего напильника с удобной рукояткой.
- Наждачной бумаги и бруска.
- Верстака и тисков.
- Струбцин (2 шт.).
- Древесного (шашлычного) угля для горна.
- Отработки (старого моторного масла) для проведения закалки.
Хорошие изделия получаются из напильников со сточенными зубьями — в таком случае не придется тратить время на их удаление.
На начальном этапе метал отжигают. Но перед этим следует сделать «походный» горн: насыпают очаг земли, вставляют двухдюймовую трубу (чтобы поступал воздух) и разжигают уголь. Когда сталь станет красной, прекратите подавать воздух и оставьте заготовку медленно остывать. Металл будет податлив, и его с легкостью можно будет поддавать обработке.
Все лишнее отрезается ножовкой по заранее подготовленным лекалам. Постарайтесь по максимуму точно повторить будущую форму, чтобы поменьше работать напильником. Вырежьте хвостовик длиной с собственные пальцы.
Затем обработайте заготовку, используя напильник или наждак, придавая форму по лекалу. Прижмите будущий нож к верстаку и посредством струбцины обточите спуски. Данная часть работы отличается ответственностью, выполнять ее на глаз не стоит. Две стороны должны получиться симметрическими, угол снятия металла — одинаковым по всей длине спуска, включительно с загибом кончика. Для удобности можно соорудить вспомогательное приспособление в виде металлической трубы с направляющей, на ней закрепить длинный напильник.
Так как заготовка отожжена, на ее обработку не уйдет много усилий. После окончания грубого придания формы производится финальная обработка наждачной бумагой. Для максимальной эффективности ее можно намотать на небольшой деревянный брусок.
Клинок готов, но мягкость отожженной стали не позволит пользоваться им вовсю, потому понадобится закаливание.
Процедура закаливания
При проведении данной процедуры изменяется структура металла, он становится твердым и немного хрупким. Закалку проводят в масле-отработке. Следует нагревать готовое изделие до тех пор, пока оно не обретет темно-вишневый оттенок.
Когда на улице солнечная погода, и по цвету сложно определить температуру, готовность можно проверить с помощью магнита: если сталь хорошо прогрелась, она не намагнитится. Потом быстро опустите клинок в емкость с маслом. Чтобы быстрее ее охладить, поставьте под емкость тазик с холодной водой — так можно добиться более эффективного результата.
Проверить твердость поможет стеклянная посуда: при хорошей закалке на нем останутся борозды. Самый главный минус — трудоемкий процесс изготовления. Еще одна особенность — из напильника нельзя сделать тонкое и гибкое лезвие.
Среди бесспорных достоинств — прочность и долговечность таких изделий. Материал для изготовления находится в свободном доступе, практически бесплатный, с толщиной обуха 6 мм, что не позволяет причислить ножи из напильников к холодному оружию.
Дом, дизайн, ремонт, декор. Двор и сад. Своими руками
Нож из рессоры. Ковка ножа из советского вторичного сырья Нож из рессоры в домашних условиях
Нож – это отличная вещь, которая может быть полезна не только в качестве прекрасного инструмента, но и в виде замечательного сувенира. Каждый мальчишка будет рад такому подарку. Если нож изготовлен вручную, то он сразу становится уникальной ценностью в глазах владельца.
Взрослые тоже не всегда используют ножи исключительно в бытовых целях – многие люди их коллекционируют. Критерии выбора у всех разные, но каждый знает, что качественная сталь – это обязательное условие для хорошего ножа. Но и красиво выполненная ручка может произвести не меньшее впечатление, чем прочное лезвие, способное долго держать заточку.
В чем же особенность ножа из рессоры?
Причина популярности такого изделия, как нож из рессоры, заключается в свойствах металла. Высокая износостойкость и прочность в сочетании с высокой пластичностью позволили многим поколениям мастеров пользоваться рессорами как главным источником сырья.
Рессоры изготавливают из рессорно-пружинной стали 65Г, но могут быть применены другие марки: 50ХГСА, 50ХГА, 50ХФА. Это тоже рессорно-пружинные стали – определить какая из них взята в качестве материала для клинка можно только с помощью химического анализа. Либо по нюансам поведения металла при обработке, но с этим справятся только опытные мастера. Для начинающего изготовителя разница между перечисленными материалами будет практически незаметна.
Применение рессорной стали
65Г считается одной из самых дешевых пружинных сталей. При этом она обладает рядом уникальных свойств, делающих ее незаменимой для создания пружин. Рессорная сталь для ножа содержит хром, никель, марганец, кремний. Эти элементы придают свойства, за которые изготовителями выбирается именно этот материал:
- хорошая гибкость;
- высокая ударная вязкость;
- твёрдость;
- износостойкость;
Термообработка играет большую роль в улучшении качеств материала. Сталь становится прочнее, повышается ее твердость. К сожалению, она недостаточно устойчива к коррозии – имеет обыкновение ржаветь. Но достоинства перевешивают недостатки и ее часто используют как материал для клинка.
Такие ножи применяют в самых разных сферах. В первую очередь в качестве кухонных – крепкие, прочные, долговечные – что ещё нужно для ежедневной работы на кухне и, например, для разделки мяса? Те же соображения заставляли охотников, рыбаков и туристов стараться заполучить в свой арсенал эту качественную «самоделку». Поэтому многие мастера делали на продажу туристические и охотничьи ножи.
Благодаря хорошим характеристикам стали, эти ножи были популярны среди военных. Солдаты срочной службы, имевшие доступ к инструментам для металлообработки, в кустарных условиях изготавливали армейские ножи.Со временем, изготовители начали замахиваться на более серьёзные изделия: топоры, мечи, мачете, катаны. Из-за хорошей ударной вязкости рессорные стали прекрасно подходят для ковки. Ковкой можно изготовить клинок любой формы, даже самой причудливой.
Как сделать нож из рессоры
Изготовление ножа из рессоры может отнять много времени и сил, особенно, если человек делает это в первый раз. Но рессорно-пружинная сталь хорошо поддаётся обработке и «стерпит» ошибки новичка, поэтому именно из неё лучше всего создавать свой первый нож.
Обычно, материал находят на открытом воздухе: на улице, на автобазах, рядом с гаражами, на автомобильных свалках и других аналогичных местах. Поэтому рессора может быть покрыта грязью и ржавчиной и перед работой ее надо тщательно отчистить. Если необходимо выпрямить выгнутую рессору, то её нагревают до красна, а затем дают остыть в нормальных условиях – при комнатной температуре.
Как сделать нож из рессоры с помощью ковки
Все рессорно-пружинные стали, в том числе 65Г, объединяет одно качество: они прекрасно поддаются ковке. Ножи из рессорной стали, изготовленные ковкой, будут более надёжными и долговечными, потому что в процессе обработки происходит упрочнение металла за счёт пластической деформации и изменения макроструктуры.
Прежде чем проковать рессору, необходимо вырезать из неё профиль будущего клинка. Затем заготовку надёжно крепят, и нагревают до красна. Ковкой создаётся остриё и лезвие. Этим способом легко придать клинку требуемую форму, а также задать его ширину. Ковкой из рессоры хорошо удается изготавливать топоры и различные экзотические вещи, такие как мачете или меч.
Лезвию дают остыть до температуры окружающей среды после того как работа закончена.
Как выточить нож из рессоры своими руками
Необходимо, в первую очередь, определиться с внешним видом будущего изделия. Форма зависит от назначения ножа: кухонный, охотничий, сувенирный или какой-либо другой. В итоге клинок может быть любой – на это влияют только фантазия и возможности изготовителя. Если выбор сделан, то нужно взять готовый шаблон или выполнить его самостоятельно из картона или плотной бумаги.
Далее, чтобы изготовить нож из рессоры своими руками, надо быть готовым начать работу с металлом. Сначала шаблон необходимо приложить к металлической заготовке и обвести маркером, карандашом, чертилкой (ГОСТ 24473-80) или другим разметочным инструментом. По контуру, полученному посредством шаблона, требуется вырезать профиль изделия. Подойдут следующие инструменты:
- ленточная пила;
- угловая шлифмашинка, она же «болгарка» – важно не перегреть заготовку при отрезании;
- сверлильный станок или дрель – в этом случае вдоль контура сверлят отверстия, затем перегородки между ними ломают или выпиливают;
- можно использовать ручной инструмент;
Сам процесс обработки достаточно прост, хотя и требует определённой концентрации, чтобы вырезать заготовку в соответствии с разметкой. Когда обработка успешно завершена и заготовка стала соответствовать шаблону, то можно приступать к формированию клинка. Основная задача – сделать скосы. Лезвие снова размечают, определяя размеры скосов. При дальнейшей обработке следует строго придерживаться разметки.
Для работы лучше всего использовать электрическое точило. Также подойдут и ленточная шлифмашинка, и «болгарка», но, в случае последней, требуется хорошее владение инструментом. Можно выточить скосы вручную – напильником. На этом работы по металлу должны быть закончены, потому что далее клинок пройдёт термическую обработку, после которой сделать с заготовкой что-либо ещё будет очень сложно.
Закалка лезвия
Основной вид термической обработки – это закалка. Она нужна, чтобы лезвие было прочным, и могло оставаться острым долгое время после заточки. Существуют разные приёмы:
— закалка, с нагревом только режущей кромки;
— закалка режущей кромки нагревом изделия целиком;
— закалка с отпуском;
— полная закалка;
В первом случае только крайняя часть лезвия нагревается до немагнитного состояния, после чего его помещают в масло и выдерживают, пока масло не перестанет пузыриться. Второй способ сложнее: нагревается нож целиком, но погружать его в масло требуется только на треть – чтобы режущий край был покрыт жидкостью.
Закалка с отпуском – это метод, при котором остывание заготовки проводится в два этапа: сначала в при повышенной температуре, но ниже температуры закалки, затем при комнатной температуре.
Самый простой способ закалки – это полная закалка клинка, но при этом способе есть вероятность, что лезвие поведёт. Тогда надо провести рихтовку испорченной заготовки. Это можно сделать как предварительно разогрев лезвие, так и в холодном состоянии.
Изготовление рукоятки
Ручку можно изготовить практически из любого сырья, но особой популярностью пользуются дерево, пластик, кожа, кость. Красиво выглядят наборные ручки с чередующимися слоями, например, кожи и бересты.
Кость – это традиционный материал, для изготовления разнообразных безделушек и предметов быта. Обладая навыком резьбы по кости можно сделать уникальную, красивую ручку. Но проще всего взять две деревянные или пластиковые накладки, поместить их по обе стороны от хвостовика и закрепить между собой заклепками, а для большей прочности ещё и эпоксидным клеем. Иногда для крепления используют винты и гайки, но если важен внешний вид, то лучше их не применять.
Рукоять должна быть удобной, поэтому требуется уделить большое внимание ее обработке. Для этого используются сначала напильники, а затем наждачная бумага. Если накладки деревянные, то их обязательно надо пропитать маслом, чтобы обеспечить долговечность древесины. Пропитка подчеркивает структуру дерева и придает изделию привлекательный внешний облик. После закрепления рукоятки проводят ее окончательную шлифовку.
Работа над ножом из рессоры практически завершена, осталось только заточить его. Для этого используют:
- бруски;
- мусаты;
- точильные станки;
- механические точилки;
- электрические точилки;
Действительно хорошие результаты получают применяя брусок или электрическую точилку. Чтобы хорошо заточить нож с помощью бруска или точильного камня понадобится не мало времени. Если на обычный кухонный нож достаточно потратить около получаса, то выравнивание и заточка длинного кованого ножа может занять несколько дней.
Для лучшего контроля процесса заточки точильный камень помещают на устойчивую горизонтальную поверхность. Оптимальный его размер – примерно в полтора раза длиннее лезвия. Начинать заточку требуется грубым точильным камнем, с крупным зерном. Продолжать надо до тех пор, пока не появится заусенец. После этого берётся мелкозернистый камень, далее процесс продолжается с его помощью. Чтобы самодельный нож из рессоры стал острым, а заточка держалась долго, надо соблюдать следующие правила:
- движение осуществляется путём поступательных перемещений ножа вдоль бруска – режущей частью вперёд;
- конец бруска и конец лезвия должны «встретиться». Нужно синхронизировать смещение ножа поперёк бруска (от ручки к лезвию) и перемещение ножа вдоль бруска;
- плоскость клинка и поверхность бруска должны составлять угол от 20 до 25 градусов – это универсальный угол заточки. В зависимости от назначения ножа, угол может меняться, но важно, чтобы он удерживался постоянным всё время пока происходит затачивание ножа;
В конце необходимо провести шлифовку лезвия, чтобы надолго сохранить нож острым. Для этого берётся точильный камень с самым мелким зерном. Затем аккуратно, чтобы не испортить уже сделанное, снимается заусенец.
Заточка — процесс требующий терпения и внимательности. Навык приходит только с опытом, поэтому все, кто не хочет ждать, могут воспользоваться электрической точилкой. Это сэкономит время, а также позволит сохранить ножи в превосходном состоянии.
Изготовление ножа — это процесс сложный, требующий внимания, концентрации, тщательности, навыков работы с металлом. Но труд не будет напрасным, ведь в итоге получится прекрасное изделие, созданное своими руками. Чем с большей любовью и старанием мастер подходил к делу, тем лучше будет изделие. Даже новичок, если окажется терпелив и настойчив, сможет овладеть навыками и тоже станет гордиться результатами своей работы.
Наглядное видео:
Очень прочные и надежные ножи получаются из автомобильных рессор – это вам подтвердит любой кузнец. Главное правильно обработать этот качественный стальной материал. Рессора в качестве материала для ножа была выбрана неслучайно, т.к. :
1) её куски можно легко найти
2) обрабатывается она значительно легче, чем полоса «быстрореза»
3) стоимость ножа сравнительно мала
И так, начнём с того, что автомобильная подвеска бывает рессорной и пружинной. Нас будет интересовать рессорная.
Благо в России две беды: дураки и дороги. В результате сочетания первого и второго, мы имеем множество пригодных (для изготовления ножа) кусков рессоры прямо на догоге. Бесплатно и вне очереди.
Более подробные сведения об изготовлении самодельных ножей с наглядными фото смотрите по прямым ссылкам, расположенным справа >>>>>>>>
Рессора изготавливается из горячекатного стального проката, для которого есть ГОСТ. А теперь несколько слов о самой красавице: Рессора — упругий элемент в подвеске автомобилей, троллейбусов, автобусов. Соединяют кузов с мостами.Воспринимают тяговые и тормозные усилия при движении.
Рессора намного старше автомобиля. К примеру, гоголевские персонажи, обсуждавшие «доедет ли колесо…» глядели, скорее всего, на рессорную коляску. Естественно, унаследовали ее и самобеглые экипажи. В разное время ее очень широко, порою почти тотально использовали в подвесках автомобилей. И сегодня на старой технике можно встретить множество просто потрясающих конструкций. Но разбирать их здесь мы не будем, поскольку и практическая ценность этой информации небольшая, да и места для приличного обзора потребуется намного больше, чем есть во всем журнале.
А потому поговорим о том, что выкристаллизовалось в процессе развития к сегодняшнему дню.
Конструкция:
Рессоры бывают много-, мало- и однолистовыми. До недавнего времени во всем мире были, а в нашей стране еще и сегодня наиболее распространены многолистовые рессоры. Поскольку график изменения изгибающего рессору момента имеет форму треугольника с вершиной в точке нагружения (мост), то этот треугольник и «заполняют листами», чтобы получить более равномерные напряжения в каждом из них. В результате удается убить не одного, не двух, а целое стадо зайцев.
Изготовление:
Для изготовления листов обычно используют горячекатаную полосу из углеродистой пружинной стали. Нужный выгиб придается рихтовкой, а в заводских условиях – в штампах. После этого делается термообработка. Нередко поверхность упрочняется дробеструйной обработкой.
Виды сечения рессоры:
Сечение листа до некоторого времени было прямоугольным со скругленными кромками. Но поскольку усталостное разрушение листов почти всегда начинается сверху, нижнюю поверхность сократили скосами или выемками. В результате в сечении листы большинства современных рессор имеют или трапецию, или своеобразное «Т» с очень толстой ножкой.
Какую рессору взять:
Многие ножеделы сходятся во мнении, что лучше брать рессору, сделанную в глубокие совковые времена. Поскольку там сталь 65Г была значительно лучше, чем сейчас.
Само качество металла зависит не только от соотношения добавок, но и от технологии термообработки. Возможно в советские времена «термитчики» были более квалифицированы. Упорно прививается, что многие «секреты стали» утеряны в далёких-далёких временах. И что современные ножи — не ножи вовсе… Думаю, сталь, она как была так и осталась. Просто когда работаешь с куском «советской рессоры», ты создаёшь нож с «историей».
Не стоит забывать, что многие качества ножа из любого металла задаются технологией его производства. Например, можно перекалить полотно «быстрореза» при работе на наждаке и потом всем рассказывать, какие хрупкие ножи из Р6М5.
Для первого ножа, пойдёт любой кусок. Первой особенностью для вас тогда станет вопрос о распрямлении рессоры. Для этого вам нужно будет осилить:
2. и само Выпрямление — наковальня+молот
Отжиг:
Разведите костёр нагрейте рессору до «красна» и очень медленно охлаждайте. Можно оставить прямо в углях.
После отжига на рессоре может появиться желтый, коричневый или голубой «налёт», легко снимаемый наждачкой.
Выпрямление:
Это дело бесхитростное. Нужна наковальня (можно использовать кусок рельс) и молот, что потяжелее.
Самый лучший вариант — расковывать железо пока горячо.
Можно и на «холодную», но велик шанс расколоть.
Материалы:
Единицы измерения в тексте: 1 дюйм — 2,54 см; 1 фут — 30,5 см; 1 фунт — 0,454 кг. (Прим: для вашего удобства я пересчитал импортные величины в привычные)
Если вы горите желанием сделать нож своими руками, и у вас нет дорогого оборудования, то вот небольшой список материалов, которые могут пригодиться. Я понимаю, что это не самые лучшие материалы, но это работает, хотя может вызвать улыбку.
Кусок рессорной стали 5160 из магазина, примерно 800 гр весом, или около этого. Отмерьте 18-20 см длины от куска, или сколько решите, и берите новую пластину, а не старую автомобильную рессору.
Теперь отправляйтесь в магазин для столяров, и купите:
за 4 доллара дубовый брусок размером 3,5 х 5 х 7,5 см (Прим: собсно, это будет рукоять)
в сварочном отделе купите медный пруток толщиной 3 мм за 1.50 доллара
2 сверла 3 мм за 2 доллара и ещё одно 6 мм сверло
2 напильника, один плоский, и один полукруглый — 7.50 доллара
2 куска водостойкой наждачной бумаги номер 120 за 1 доллар
2 куска водостойкой наждачной бумаги номер 240 за 1 доллар
дешевое зубило
достаточно большая струбцина, которой вы будете прижимать нож к столу или скамье (но можно обойтись и без неё)
Когда будете подбирать стальную полосу в магазине, посмотрите, можно ли купить самую тонкую пластину из того, что у них есть. Мой магазин располагает материалом 0,5 см толщиной и 4 см шириной. Это довольно толстовато для маленького клинка, но все равно годится. (Прим: в нашем случае с напильником придётся повозиться — толщина ресооры будет больше. Но, после уроков труда в далёком дестве, это — не проблема)
Еще вам нужна будет ручная электродрель. Возьмите ее у кого-нибудь на время, т.к. с ней ничего не случится — вы только просверлите несколько отверстий. Далее я буду использовать картинки, чтобы объяснять свои действия.
Для своего первого ножа выбирайте дизайн попроще. 7.5 — 9 см будет подходящей длиной для клинка, потому что вам придется использовать напильники при обработке лезвия. Прямой клинок без выкрутасов легче обрабатывать, да и напильником проще работать по прямой плоскости.
Ручку для ножа тоже выбирайте несложную, без большого количества причудливых углублений под пальцы, и без гарды.Силуэт ножа нарисован маркером, затем я сверлом 6 мм насверлил вокруг рисунка кучу дырок. Придется много поработать ножовкой по металлу вокруг всего этого.
Прикрутите нож к скамье, пню, или что у вас там есть, и с помощью ножовки удалите часть металла вокруг ручки. Делайте это так, чтобы потом напильником можно было рукоятке придать нужную форму. Это должно быть выполнено в первую очередь, потому что если удалите металл вокруг клинка, то потом не сможете его прикрепить к скамье. Рукоять обрабатывается в первую очередь! Как только она приобретет форму, удалите ненужный материал, прикрепите нож сквозь отверстия в рукояти, и принимайтесь за клинок.
Итак, я обсверлил весь силуэт ножа — это здорово облегчит работу ножовочному полотну при его опиливании. Затем я открутил заготовку от скамьи, и заново прикрепил ее так, чтобы удалить лишний металл с рукояти. Сверлом 3 мм были сделаны отверстия в рукояти под медные прутки, а сверлом 6 мм — чтобы ее можно было крепить к скамье, когда обрабатывается какая-то часть лезвия.
Потом я опилил ручку, и добавил пару углублений под пальцы, чтобы она крепче держалась в руке. После этого я обработал напильником остальную часть силуэта, и опилил скос — будьте терпеливы, т.к. работа напильником требует времени. Хорошо, теперь у меня есть заготовка ножа, опиленная ножовкой по металлу, и обработанная напильником. Это начинает приобретать форму.
Я отметил режущий край с помощью моего 6 мм сверла. Зачернил клинок маркером, а потом начал передвигать конец сверла по режущей кромке так, что появилась тонкая линия. Переверните нож, и повторите то же самое на другой стороне, получив две линии, на расстоянии примерно 0,6 мм — 0,8 мм друг от друга. Если эти две линии получились слишком близко друг к другу, то снова отметьте нужное место маркером, возьмите сверло, и передвиньте его вверх или соответственно вниз, повторив все заново. Линии будут отстоять друг от друга примерно на 1/2 толщины пенсовой монеты.
Затем, с помощью подходящих шурупов для дерева, прикрутите нож к верху скамьи. Начинайте обрабатывать напильником плоскость клинка. Цель в том, чтобы соединить процарапанные линии и вершину режущей кромки ножа в одно и то же время. Это потребует много тяжелой упорной работы и терпения.
И, может быть, несколько перерывов по дороге. Чтобы помочь себе в обработке плоскости, я использовал маркер, и обтачивал очень медленно, пытаясь удержать напильник плоско. Маркер покажет вам неровности, которые надо сточить.
Попробуйте закрепить полоску наждачной бумаги на какой-нибудь недорогой основе, например, на шпателе для нанесения краски. Вначале я зачищал наждаком область, которую мы назвали углубление, с помощью плоской дощечки и бумаги номер 120. Потом я стал обрабатывать плоскость продольными движениями к концу клинка, пока все грубые царапины от напильника не исчезли. Это так же выравнивает плоскость.
Используйте немного мыла и воды, чтобы уберечь наждачную бумагу от загрязнения, а когда закончите работу, убедитесь, что вытерли нож насухо, иначе до завтра он поржавеет. Начните обрабатывать наждачкой плоскость клинка и рукоять. Не удаляйте все огрехи, а только излишки, пока не получите немного голого металла — такая «суровость» придаст характер уже готовому ножу.
ОК, огонь зажжен. Я занялся этим на заднем дворе, в специально огороженном месте. Огонь пылает за оградой, и дует несильный ветерок, который помогает нашей работе. Нужно будет еще несколько вещей, чтобы работать с ножом дальше. Магнит я достал из игрушечной коробки моих мальчишек, а после борьбы с проблемой надежно/дешево пришел к следующему.
Взяв два куска 12 мм квадратной трубы 90 см длиной, я вставил в них концы рукояток старых плоскогубцев и сплющил металл по краю, чтобы закрепить соединение. И еще одна важная, необычайно секретная вещь, на которую я вам намекну: старые масляные фильтры, остающиеся после замены масла в автомобилях.
Суньте клинок в горячие угли. Ножу следует находиться там примерно 10 — 15 мин, в зависимости от того, как сильно разгорелись угли. Это ваш первый раз, поэтому вытаскивайте нож из огня на пару секунд каждые 2 — 3 минуты, смотрите на его цвет, и проверяйте режущий край магнитом.
Если сталь притягивается, значит нож еще не готов, суйте его обратно в огонь и грейте до вишнево-красного цвета. Постарайтесь не перегревать нож дольше, чем необходимо, поэтому проверяйте клинок каждую минуту — две, когда решите, что момент готовности уже близок.
Пришло время опустить нож в секретное масло. Магнит не притягивается, цвет стали хорош, и слюни текут от предвкушения. Я закалял сталь, опуская в масло только 2/3 ножа. 2/3 клинка со стороны режущей кромки я держал в масле, пока не погасло пламя — около минуты — а потом медленно погрузил остальную часть ножа, пока он не погрузился полностью, и не перестал идти дым. Когда мы вытаскиваем нож, он выглядит черным и противным. Я опустил его в сосуд с водой, пока он не остыл настолько, чтобы можно было взять его в руки. Теперь вы спросите — этот нож действительно твердый? Ну что ж, давайте проверим. Возьмите напильник, и пройдитесь им по клинку, прикладывая под углом 30 градусов и прижимая деликатно, а не жестко. Напильник будет скользить по режущей кромке, пытаясь за нее зацепиться. Если клинок слишком скользкий, вытрите его тряпкой, удаляя масло. Чтобы лучше очистить металл, можно использовать так же мыло и воду.
Если напильник цепляется за нож, значит закалка не удалась, возвращайтесь к огню, и повторяйте все сначала. Предположим, что клинок прошел пробу напильником, и закалился как следует. Теперь надо его отпустить, так как мы не хотим, чтобы лезвие или его кончик крошились. Напильники очень хрупкие, и наш нож сейчас тоже очень твердый и ломкий. Разогрейте кухонную духовку до температуры 375 — 400 градусов. «Пеките» нож в духовке 45 минут, позвольте ему остыть до комнатной температуры, и снова суньте в духовку на 45 минут при той же температуре. Кстати, не забудьте смыть предварительно с ножа все масло, если не хотите закоптить весь дом. После отпуска стали можно очистить клинок. Беритесь снова за наждачную бумагу, и готовьтесь накладывать деревянные рукоятки на этого малыша.
Я поместил нож в тиски, и обрезал два куска для накладок на будущую рукоять. Положите нож ближе к верхнему краю бруска, тогда будет проще «привязаться» хотя бы к одному его краю. У меня есть медные прутки, и я готов сделать следующий шаг. Просверлите для них отверстия в рукояти.
Я вставил все три стержня, и очертил контур ножа на дубовой плашке, определившись, где будет «лицо» бруска, когда я прикреплю эпоксидкой и медными прутьями дерево к стали. Это фото не очень хорошее, но, думаю, вы сможете увидеть нужный вид с черной полосой на ноже. Я отметил на древесине начало и конец этой линии, а потом соединил их дугой.
Левая щечка рукояти будет обработана и прикреплена, когда мы не сможем нарушить форму после того, как дерево приклеится к ножу. Теперь карандашом надо сформировать левую часть рукояти, в основном ее перед.
Проверьте, достаточно ли хорошо подготовлена накладка, как она прилегает к металлу, и если надо, выгладите ее на наждачной бумаге, чтобы плоскость была совершенной.Соедините оба куска медными прутками, опилите их и обработайте наждачной бумагой, пока накладки не станут зеркально подобными. Еще раз напоминаю о переднем крае! Потом проверьте их на ноже.
Теперь, если обе накладки достаточно хороши, и нет пустоты между ними и ножом, можно обрезать лишнюю длину прутьев, так, чтобы они были заподлицо с деревом. Тщательно очистите нож — там, где будет прилегать дерево. Мыло, горячая вода и старая зубная щетка, потом тщательно ополосните его и вытрите досуха. Если хотите, чтобы он был совершенно сухим, воспользуйтесь сушилкой для волос.
Я обрезал прутки, и зачистил наждачкой грани, чтобы потом не откалывались щепки. Потом эпоксидной смолой смазал внутренние части деревянных накладок, рукоять ножа и стержни, и соединил все вместе.
Обернув все это четырьмя жирными резиновыми полосами (жирными — чтобы не прилипли), я оставил нож до высыхания, а потом удалил излишки выступившей смолы, и получил готовый нож.
Фотоотчёт о том, как я изготовил нож своими руками из автомобильной рессоры. Было это уже давно, я только сейчас откопал эти фото. Я в тот момент работал электриком в больнице, и у меня было много свободного времени. Вот я и тратил его на изготовление различных предметов. Точнее, я учился этому, поскольку я совсем не профессионал, а лишь любитель. Очень люблю ножи, и всегда хотел сделать нож себе сам. Думаю, многие из вас разделяют мои мысли, что, каким бы ни был ваш нож — главное, что вы его сделали сами, своими руками!
На вид мой нож из рессоры от грузового автомобиля получился не очень подходящим под различные шаблоны и критерии, но зато он имеет весьма оригинальную форму. Думаю, многим из вас приходили в голову мысли, как изготовить нож своими руками. Так что, возможно, этот отчёт будет полезен для вас, а если не полезен — так, во всяком случае, интересен!
Материал для клинка я тупо нашёл на улице. Это автомобильная рессора, предположительно от КамАЗа, которая, видимо, отлетела у него на кочке. Я взял и притащил её к себе на работу. Взял болгарку и распилил её на 3 части. Рессора имеет закруглённую форму и неравную толщину. Поэтому я выбрал подходящий кусок и отпилил его. Получились две равные заготовки для двух моих будущих клинков.
Заготовка для одного из клинков. Сталь 65г.
После работы с болгаркой идёт муторная и весьма кропотливая работа с наждаком. Нужно вывести форму клинка, снять ненужное. А ненужного оказалось довольно много. Толщина рессоры была около 8 мм. Ну где вы видели нож с такой толщиной в обухе? Так что я снял около 2-3 мм, потом плюнул — и решил оставить такую толщину. Пускай мой нож и будет слегка толстоватым.
Затем пошла работа с мелкими брусками. Так как у меня не было возможности поставить на наждак другие бруски (их просто не было), то пришлось работать вручную и скоблить клинок камнем. На фото видна разница после работы с крупнозернистым бруском и более мелким.
Затем снял немного лишнего с хвостовика.
Получилась вот такая форма. Причём полировать весь клинок я не стал и оставил на спусках следы от крупного бруска. На электрическом наждаке можно было бы, но руками — это очень муторно. Кто когда-нибудь делал это, тот поймёт! Скажете, а почему ты просто не купил мелкозернистый камень и не поставил на наждак? Просто как-то не доходили руки до этого. Сидел на работе и неспеша скоблил его бруском. Другие в карты играют, а я сижу и наяриваю! Кому что)) Размеры: длина клинка без хвостовика 13.5 см ширина 3.5 см, толщина в обухе 6 мм.
Затем я взял кусок войлока, пасту ГОИ и начал полировать клинок, приблизительно до зеркального блеска. На фото клинок до обработки ГОИ.
Затем я в одном из своих походов заготовил бересту для рукояти. Но, правда, слегка разошёлся и заготовил чуть больше, чем требовалось.
Добрые люди подогнали мне своих обрезков кожи толщиной 3 мм. Кожа пошла на рукоять и на ножны. Вырезал из кожи вот такие квадратики, проделывал отверстия для хвостовика. Кожа толстая — режется очень трудно. Использовал только шило и нож.
Тем, кто может достать старые автомобильные рессоры, хорошо повезло – для их производства применяли высокоуглеродистую сталь, которая подходит для изготовления отличных ножей. После того, как вы закалите такой нож, его режущая кромка будет отличаться высокой стойкостью, такое лезвие позволит разрезать достаточно твердые предметы.
Как сделать нож из рессоры
Чтобы получить нож из рессоры в домашних условиях, подготовим список таких материалов и инструментов:рессора автомобиля;
кусок древесины для отделки рукояти;
эпоксидный клей;
болгарка;
дрель или сверлильный станок;
наждачная бумага с разной зернистостью;
печь для закалки металла, масло;
лобзик или другие инструменты для резки дерева;
струбцины.
Ковка ножа из рессоры проходит в несколько этапов
Этап 1.В первую очередь нужно собрать все материалы для работы, чтобы они были наготове. У автора исходным материалом послужил лист рессоры от старой машины.
Поскольку рессора выполнена в изогнутой форме, то ее необходимо выгнуть. Это делается так: металл нагревается, после чего постепенно остывает. Для нагрева подойдет горелка, также можно просто положить лист рессоры в хорошо разожженный костер.
После того, как заготовка остынет, нужно взять молоток и наковальню, и обработать рессору так, чтобы она стала прямой пластиной. После отпуска металл стал более мягок, он будет легко поддаваться резке, сверлению, и т. д.
Этап 2.
Сначала нужно изготовить шаблон ножа. Автор использовал готовый шаблон из интернета. Если есть желание – его можно улучшить. После распечатки шаблона бумагу нужно наклеить на картон и ножницами вырезать шаблон. Подержав его в руках, мы можем прикинуть, как будет выглядеть нож из рессоры.
После этого нужно приложить шаблон к металлу и обвести маркером.
Этап 3.
Сейчас мы приступаем к самому тяжелому этапу работы – нам нужно вырезать профиль ножа. Это делается с помощью болгарки – орудуя этим инструментом, не рекомендуется перегревать металл. Если в месте резки сталь начинает менять цвет – это значит, что он перегревается. В таком случае металл нужно полить водой. В тех местах, где нельзя вырезать, металл можно просверлить рядом отверстий и потом эту часть обломать.
Этап 4.
Это заключительный этап формировки основного профиля лезвия. Для такой работы очень удобен и прост ленточный шлифовальный станок. Умельцы с большим опытом могут использовать болгарку. Наружную плоскость ножа следует отшлифовать, чтобы она блестела. Для прижатия заготовки к шлифовальной ленте автор воспользовался бруском. Здесь также нужно следить, чтобы металл не перегревался.
Другой ответственный момент шлифовки заключается в изготовлении на ноже скосов.
Этап 5.
Чтобы надежно закрепить накладки на рукоятке, в данном ноже используется 4 штифта. Для них нужно просверлить отверстия. Для подбора диаметра ориентируемся на имеющиеся штифты, которыми традиционно служат стержни из латуни. Для этого случая подойдут и обычный стальные гвозди.
Этап 6.
После закалки клинок приобретает твердость и долго не тупится. Чтобы закалить лезвие, нужно взять масло – подойдет моторное или растительное, печка или хороший костер. Металл необходимо нагреть до такого состояния, при котором к нему не будет притягиваться постоянный магнит. Как отмечает автор, во время нагрева металл отличается тусклым красным цветом. После этого нужно опустить заготовку в масло. Следует быть осторожными, поскольку масло часто воспламеняется с дымом и брызгами, летящими в разные стороны. Емкость для закалки нужно брать металлическую.
Случается, что во время закалки металл начинает деформироваться. Такую ситуацию можно исправить. Для решения проблемы нужно нагреть заготовку, выровнять, и затем опять попробовать закалить.
После закалки обязательно следует сделать отпуск металла, в противном случае вы получите очень хрупкий нож. Для этой операции берем бытовую духовку, помещаем в нее заготовку и прогреваем сталь при температуре 200°C на протяжении часа. После этого нужно дать заготовке постепенно остыть, при этом духовку не нужно открывать, сталь должна остыть закрытой внутри.
Этап 7.
Для изготовления накладок на рукоятку, берем две дощечки небольшой толщины. Вырезаем их до требуемого размера и сверлим в них отверстия для штифтов.
Теперь склеиваем заготовки при помощи эпоксидного клея, нанеся по хорошему слою на обе накладки. Затем нужно вставить штифты и хорошо зажать ручку струбциной. Оставляем в таком виде на 24 часа, чтобы клей полностью высох. Сразу для удаления остатков клея берем тряпочку или туалетную бумагу.
После того, как клей высохнет, нож нужно достать и окончательно сформировать форму рукояти. Для этих работ используем ленточный шлифовальный станок.
Если есть немного свободного времени и ненужная рессора от грузовика или другого автомобиля, то можно своими руками сделать достаточно красивый и уникальный нож. Возможно, с первого раза он не будет совсем идеальным, но главное – сделан своими руками. Главной прелестью этой самоделки является то, что нож может быть практически любой формы, необходимо просто включить немного фантазии.
Материалы и инструменты для самоделки:
болгарка;
рессора от грузовика;
надфиль;
эпоксидная смола;
льняное масло.
Процесс изготовления ножа
Материал для клинка можно достать на любом авторынке, иногда автомобили могут потерять рессору прямо посреди дороги. В данном случае используется рессора от Камаза. Можно взять и от другого автомобиля, в таком случае толщина клинка будет меньше, и ее ненужно будет уменьшать вручную.
Шаг 1. Подготовка материала
При помощи болгарки автор разрезал ее на три части, так как деталь имеет разную толщину и закругленную форму, необходимо выбрать оптимальную часть для данного типа ножа. Та часть рессоры, которая идеально подошла для клинка распиливается еще пополам, в итоге имеется две одинаковых заготовки.
Шаг 2. Форма ножа
Нужно взять заготовку и примерно разделить ее на две части пополам, из одной половины будет изготовлено само лезвие ножа, вторая половина будет входить внутрь ручки. Ту часть, которая будет находиться в ручке, необходимо немного обрезать с двух сторон, чтобы она стала меньше и могла поместиться в рукоятке.
Так как рессора имеет толщину примерно в 8 мм, а таких ножей практически не бывает, то нужно наждаком длительное время убирать толщину до желаемой. Затем на станке нужно придать форму лезвия, желательно, чтобы был мелкозернистый камень, в противном случае, нож будет выглядеть шероховатым и немного не аккуратным.
Шаг 3. Создание рукояти
Необходимо взять небольшой деревянный брусок (уделите особое внимание выбору дерева для рукояти) и выточить рукоять нужной формы, в данном случае нужно воспользоваться фантазией и представить, каким вы хотите видеть свой будущий нож. При помощи дрели и надфиля подготавливается место под ту часть клинка, которая должна находиться в рукояти. Для лучшего крепления можно воспользоваться эпоксидной смолой.
Автор решил сделать ручку комбинированную, используя резину, бересту и березовый кап.
Отрезаем лишнее и шлифуем…
После проведения всех процедур нужно обработать ручку. Понадобится льняное масло, подогретое на водяной бане до температуры 70-75 градусов. Нож при этом предварительно нужно спрятать в морозильную камеру на 30 – 40 минут. При соединении холодного ножа и теплого масла, по рукояти начинают бежать пузырьки, таким образом, воздух из дерева выходит, а это место заполняется льняным маслом. Такую процедуру нужно проделать несколько раз. После этого ручка ножа помещается в масло минимум на сутки.
Шаг 4. Изготовление ножен
Потребуется небольшой кусок кожи, по форме ножа нужно сделать выкройку. При помощи шила делаются отверстия (так как кожа весьма жесткий материал), а потом части сшиваются обычной крепкой ниткой.
Как отжечь подшипник. Делаем нож из обоймы подшипника своими руками
Русские умельцы ножевого дела, никогда не ищут лёгких путей. Потому что это – для многих хобби и увлечение. Бывает, что из простого занятия, получается настоящий небольшой бизнес. Но в большинстве своём, для людей это всё же, это отдых и отвлечение от повседневной жизни. Каждый человек, определяет свой досуг сам. Любители ковать, довольно часто изготавливают свои изделия из необычных вещей, например: нож из подшипника. Очень интересный и непростой процесс.
Самодельный нож из подшипника.
Плюсы и минусы ножа из подшипника
Многие обыватели скажут, что зачем этим заниматься, когда можно пойти в магазин и прикупить себе парочку замечательных клинков. Но мы же, им не указываем, как проводить своё время. Так что если неинтересно, идём на другой ресурс, а здесь будет статья, содержащая в себе немало полезной информации особенно для новичков. Потому что изложение планируется в пошаговом ракурсе.
Мы уже писали о том, что «идеального ножа» на всё случаи жизни, не существует. И это правда, но стремиться к идеалу нужно всегда. Поэтому попробуем выделить положительные и отрицательные стороны клинка из подшипника. Чтобы знать, что получится в результате правильной обработки металла.
Сталь подшипника изначально предназначена для высоких нагрузок, по этой причине она отличается пластичностью и однородностью при нагреве. А в итоге получается изделие с жёсткостью от 61 до 64 единиц по шкале Роквелла. И главное – высочайшая износостойкость клинка. Единственным минусом можно назвать, хрупкость во время обработки. Очень важно, правильно выполнить закалку, а ковку «на холодную», вообще, исключить.
Как сделать нож из подшипника своими руками
Понятно, что в данном деле без ковки никак не обойтись. Нужно обязательно распрямить обойму изделия. Знатоки таких вещей, разделяются на два лагеря, какую часть лучше выбрать для работы: внутреннюю или внешнюю. Однозначного ответа нет, но многие утверждают, что внутреннее кольцо состоит из лучшей стали. Подкрепляя свои слова, тем, что эта часть несёт на себе большую нагрузку.
Но, как бы там ни было, новичку однозначно без разницы. Для начала нужно, чтобы хоть что-то получилось и не треснуло во время закалки. Для нормальной работы потребуется свой, определённый набор инструментов. Ну и главное – кузница.
Требующиеся материалы и инструменты
У совсем «зелёного» новичка вряд ли есть необходимый инструмент, поэтому им нужно обзавестись. Что-то можно изготовить самостоятельно, а другое только купить. Но опять же, покупной инструмент позволительно заменить аналогичным более простым, но увеличится время изготовления. Если нет в планах, заниматься кузнечным и ножевым делом, покупать что-либо, конечно, бессмысленно, если только мелочи. Материалы потребуются следующие:
- подшипник, желательно в разобранном состоянии;
- деревянный брусок, для изготовления рукояти;
- стержни для заклёпок, лучше из латуни;
- эпоксидный клей или похожий по свойствам заменитель;
- масло или воск для пропитки рукояти;
- малярный скотч, листок бумаги, карандаш, маркер.
Кухонный нож из подшипника.
С материалами не очень сложно и всё доступно. А вот что касаемо инструмента, обратите внимание, как уже говорилось выше, если не найдётся профессионального, пробуйте заменить на более доступные варианты. Их мы также укажем для ясности:
- металлические тиски, зажимы, струбцины;
- УШМ (болгарка) с набором различных дисков;
- горн или муфельную печь, которую можно изготовить самостоятельно;
- сверлильный станок или дрель с набором свёрл;
- бумага наждачная разной зернистости;
- полировальная машина, можно УШМ с полировочным кругом;
- духовой шкаф газовой плиты, для отпуска металла;
- наковальня и два молота разного веса, один – 6 кг, второй – 1,5-2 кг;
- ленточная шлифмашина или опять УШМ с абразивным кругом;
- электролобзик или просто ножовка с мелкими зубцами;
- сварочный аппарат;
- комплект для травления или гравёр (это по желанию).
Большинство этих предметов можно заменить аналогами. Что касается муфельной печи и горна, эти хитрые конструкции можно изготовить своими руками (читайте в статье «Закалка ножа в домашних условиях»).
Подготовка детали к ковке и обработка подшипника
Допустимы к изготовлению ножа из подшипника, любые экземпляры с рабочих машин и двигателей. Если он достался вам в собранном состоянии, самым лучшим способом получить из него заготовку, будет распил «болгаркой». Для этого зажимаем изделие в тиски и при помощи УШМ делаем разрез под углом.
Это делается для одной простой цели, в будущем будет проще ковать остриё и носик клинка. Затем при помощи слесарных инструментов, требуется разогнуть, насколько получится верхнюю обойму. Внимание! Ни в коем случае не стучать молотком, иначе загубите деталь, не начав с ней работать. Вынуть все ненужные части и можно приступать к следующему этапу.
Для полноценной работы, тем более для новичков, обязательно надо сделать эскиз на бумаге будущего клинка. Учесть толщину заготовки и её длину, вернее, то что в результате должно получиться. Чертёж должен содержать в себе всю информацию по размерам, в том числе и рукояти. Для клинков из такого материала лучше использовать накладной метод монтажа рукояти из двух половинок дерева, закреплённых с помощью заклёпок. Чертёж упростит задачу во много раз.
Отжиг и ковка обоймы подшипника
В верхней обойме подшипника чаще всего используется сталь ШХ15, но для точных характеристик, можно воспользоваться справочниками. Маркировка металла иногда присутствует на самих изделиях. Соответственно каждая марка стали ведёт себя по-разному во время ковки и закалки. В наш эксперимент попал экземпляр именно тот, что указан выше.
Подшипник для изготовления ножа.
Такую сталь, нужно подвергать обязательному отжигу, процесс происходит таким образом. В соответствии со справочником, буквы «ШХ», обозначают – подшипниковую сталь с легированием хромом. Отжиг её производится при температуре 800 °С, со снижением её со скоростью 10-20 град/час. Вся эта информация свободно доступна в интернете, пользуйтесь обязательно.
Многим людям, плохо знакомым с ковкой, будет сложно работать с кузнечными клещами. Для упрощения этой задачи к заготовке приваривается пруток. Деталь укладывается в печь и разогревается до 900-1100 °С, выглядеть она будет темно-жёлтой. Но лучше пользоваться лазерным термометром. Если его нет, пробуем сталь магнитом, заготовка не магнитится – значит, разогрев достиг определённой точки Кюри.
При достижении этого значения можно постепенно начинать ковку. Для начала маленьким молотом аккуратно выпрямляем деталь. Всегда контролируйте температуру, лучше подстраховаться и нагреть её, чем на холодную просто разрушить. Следующим приступает к работе большой молот. Проковку нужно выполнять по всем правилам:
- несильными ударами молота, с середины детали «сгоняем» метал в сторону, формируя, таким образом, спуски;
- работа над остриём, немного отличается от общего принципа, носик клинка аккуратно подгоняем к острию;
- обязательна оттяжка заготовки по длине для хвостовика;
- выполнив всё верно, обух будет не более 2 мм.
Вдруг вам вообще не захочется ковать, достаточно просто выпрямить деталь, и остальное можно сточить на шлифовальной машине. Но учтите, потеря в ширине и длине клинка, и сам процесс ковки придаёт металлу дополнительную жёсткость.
По окончании ковочного процесса обязательно требуется провести «нормализацию» стали. Нагреваем заготовку до 900 °С, вынимаем из печи и оставляем на воздухе остывать.
Обдирочные и шлифовальные работы с заготовкой
Всё, что было выполнено в процессе ковки, можно назвать «черновой» работой. Теперь предстоит привести деталь в соответствующий вид. Срежьте при помощи УШМ пруток. На шлифовальном станке, или ленточной машине не сильно прижимая, аккуратно нужно снять весь нагар с металла.
Таким образом, уйдут все неровности и поверхность станет блестящей. Не увлекайтесь этим процессом, дабы не снять лишнего с заготовки. Хотя после этой процедуры, в руках у вас уже будет практически клинок.
Перенос контуров с шаблона на клинок
Дошло дело и до эскиза, который мы выполняли в самом начале. Может случиться так, что чертёж не совпадёт с реальностью. Грустить, тут нет смысла, ведь это черновой вариант. Его надо вырезать и приложить на клинок, а есть смысл, даже приклеить на время любым бумажным клеем.
Чертеж ножа для изготовления из подшипника.
Теперь деталь можно закрепить в тиски, и при помощи «болгарки», абразивным кругом доводим клинок до нужного вам вида, попутно, срезая все задиры и неровности. Единственным минусом может быть, металл нагреется, и бумага сгорит. Поэтому прежде чем её приклеивать, надо процарапать все контуры с эскиза. Задача не из лёгких, но это просто необходимо.
Во время вырезания образа клинка нельзя допускать перегревания детали, даже небольших участков. Поливайте водой заготовку. По окончании работ можно переходить к следующему этапу.
Заточка и шлифовка
В самом начале изготовления ножа вы должны были задуматься: для каких целей он создаётся. Так как заточка для каждого типа изделия абсолютно разная. Но первым делом нужно вывести спуски.
Заострять внимание на них не будем, но запомните: главное в спусках – это симметричность. Только после их выведения, можно приниматься за заточку клинка, но сначала шлифовка. Её можно производить на шлифмашине или при помощи УШМ со специальным кругом. Затем в хвостовике просверливаются два-три несквозных отверстия для крепления рукояти. Во время закалки может случиться неприятность, если просверлить отверстия полностью.
Закалка и отпуск клинка
Очень важный момент, особенно для новичков. Согласно справочнику, температура закалки стали — 830 °С. Разогреть печь, до заданной отметки поможет термометр. Если его нет в наличии, следует воспользоваться одним из способов:
- самый простой и распространённый, проверять магнитом, как только не «прилипает» клинок к нему – цель достигнута;
- следующий очень интересный, посыпать деталь солью, её отметка плавления в 800 °С, значит осталось ещё немного;
- и способ для «прожжённых» профессионалов – цвет заготовки становится светло-красный.
Все способы действенны, но точнее термометра нет ничего. А в данном случае очень важна точность. Нагрев до нужной точки, клинок вынимается и опускается в масло с выдержкой 1 минута на 1 мм толщины изделия. Масло можно использовать практически любое: растительное, минеральное, машинное отработанное или трансформаторное.
Закалка лезвия ножа.
Предварительно его нужно подогреть до 50 °С, это необходимо для хорошего обволакивания погружаемого изделия. Производя такие работы, будьте аккуратны, наденьте защитные очки и перчатки, есть вероятность разбрызгивания масла. Не нужно шевелить клинком, когда он находится в погружении.
После охлаждения заготовки пришёл момент для отпуска стали. Процедура ослабит напряжение в структуре кристаллической решётки металла, возникшее при ковке и закалке. В справочнике указанна температура в 150 °С и время 1,5 часа. Разогрев духовой шкаф кухонной газовой плиты, помещаем туда клин на нужное время.
Очистка клинка
После всех проведённых манипуляций, грубой очистки на гриндере, на клинке останутся тонкие, мелкие царапины. Убирать их надо вручную используя наждачную бумагу. Обрабатывать нужно начиная с зерна 400 перпендикулярно царапинам.
Затем переходим к 600-ому зерну и заканчиваем 800-ым. Добиться зеркального блеска, можно использовав пасту ГОИ или специальные шлифовальные смеси.
Подготовка накладок и сборка ножа
Материалов для изготовления рукояти, довольно широкий выбор: различные металлы, пластмассы, кожа, обмотка бечёвкой и прочие варианты. Но многие мастера любят работать именно с древесиной, она часто подчёркивает уникальность клинка и его красоту.
Подготовка накладок для ножа.
Принцип накладной рукояти довольно прост, и надёжнее, чем другие способы крепления. После отпуска металла можно насверлить отверстия в хвостовике окончательно. А также приготовить брусок:
- Примерить к хвостовику, разметить и придать форму близкую к его размерам.
- Зажав деталь в тиски, разрезать вдоль, строго пополам;
- Для устранения зазоров внутренние части половинок ошкуривают наждачкой.
- Делается разметка в соответствии с отверстиями на хвостовике, и насверливаются в дереве.
- Следующим этапом, можно поступить по-разному, проще всего заклепать ручку клёпками.
- На точильном станке или гриндере обработать рукоять окончательно, под нужную форму вместе с хвостовиком.
- В заключении дерево обрабатывают наждачкой с мелким зерном и пропитывают специальными масляными растворами или покрывают лаком. Зависит от сорта древесины.
Для доведения дела до окончательного варианта можно смастерить ещё и ножны. Но это уже другая и довольно обширная тема. Весь описанный процесс, для новичка может показаться очень сложным. Но люди, занимающиеся этим постоянно, изготавливают такие ножи, словно на конвейере. Так что не расстраиваться при случайных ошибках, продолжать работать, пробовать. И результат не заставит себя долго ждать. Удачи в начинаниях!
Сегодня, даже при таком большом ассортименте различных ножей прекрасного качества от известных производителей, ножи ручной ковки по-прежнему пользуются особой популярностью. Это и неудивительно, так как такие ножи обладают особой энергетикой и привлекательностью. А если сам клинок сделан из легированной стали и со знанием дела, то такой нож бесценен. Из различных способов собственноручного изготовления ножа наиболее трудоемким является ковка ножа своими руками. Следует отметить тот факт, что ковка ножа позволяет создать наиболее прочный и качественный клинок, который прослужит не один десяток лет и при этом сохранит свои качества. Ковка ножа своими руками — дело, требующее от мастера высокого уровня навыков владения инструментом, знания металлов и их свойств. Для тех, кто решил выковать нож впервые, описанные ниже рекомендации помогут сделать свой первый клинок.
Как выбрать сталь для ножа
Качественный самодельный нож отличает правильный подбор стали для него, от этого будут зависеть режущие и прочностные характеристики самого ножа. Чтобы правильно подобрать сталь, необходимо знать и понимать, какими свойствами обладает сама сталь. Для ковки ножа своими руками нужно ориентироваться на пять основных свойств стали — устойчивость к износу, твердость, прочность, вязкость, красностойкость.
Твердость — это свойство стали, указывающее на её способность сопротивляться проникновению в неё другого более твердого материала. Говоря проще, твердая сталь лучше сопротивляется деформации. Сам показатель твердости измеряется по шкале Роквела и имеет показатель от 20 до 67 HRC.
Устойчивость к износу — сопротивление материала изнашиванию в процессе эксплуатации. Это свойство напрямую зависит от твердости самой стали.
Прочность указывает на способность сохранять целостность под воздействием различных внешних сил. Проверить прочность можно на изгиб или при сильном ударе.
Пластичность — способность стали поглощать и рассеивать кинетическую энергию во время удара и деформации.
Красностойкость — это показатель, отвечающий за устойчивость стали к температурам и сохранению её изначальных качеств при нагреве. От того насколько сталь устойчива к термообработке, зависит минимальный показатель температуры, при котором её можно ковать. Самыми красностойкими сталями являются твердые марки, рабочая температура ковки для которых более 900 °C. При этом необходимо отметить, что температура плавления стали составляет 1450 — 1520 °C.
Все эти свойства связаны между собой и преобладание одного из них ведет к ухудшению другого. При этом то или иное свойство стали зависит от содержания в ней различных легирующих элементов и добавок, таких как кремний, углерод, хром, ванадий, вольфрам, кобальт, никель, молибден.
Наличие тех или иных легирующих элементов и их пропорциональное использование при изготовлении стали, знание свойств, которые придают легирующие элементы и добавки, позволило создавать сталь для определенных целей и нужд. Такие стали имеют каждая свою маркировку. При этом отечественные и зарубежные марки стали обозначаются по-разному. Для удобства в марке стали указан основной состав одного или нескольких легирующих элементов. Например, сталь марки У9 говорит о содержании в ней углерода в десятых долях процента. Аналогом стали марки «У» являются стали 10хх, где «хх» — это содержание углерода. И чем меньше значение, тем меньше его содержание. Или такая сталь как Х12МФ указывает на высокое содержание хрома и молибдена, что говорит о нержавеющих и высокопрочностных свойствах стали.
К отечественным маркам, которые часто используются при ковке ножей в домашних условиях, относятся все стали с маркировкой от У7 до У16 , ШХ15 , 65Г , Р6М5 , Х12МФ . Из зарубежных аналогов можно выделить сталь O-1 , 1095 , 52100 , M-2 , A-2 , 440C , AUS , ATS-34 , D-2 . Каждая их вышеприведенных марок используется в изготовлении ножей, различного инструмента и запчастей. Например, марки стали Р6М5, У7-У13, 65Г применяют для производства сверел, буров, тросов, рессор, подшипников, напильников. Поэтому именно из этих предметов народные умельцы делают ножи ручной ковки.
Конечно, можно найти и другие изделия из той или иной стали. Для этого достаточно будет прочитать полное описание марки стали и её применение в Марочнике Стали и Сплавов, а потом использовать изделие из неё для ковки ножа.
Для ковки ножа потребуется определенный инструмент кузнеца, который можно приобрести в магазине. Но можно использовать и непрофессиональный инструмент:
- молот на 3 — 4 кг и молоток меньшего веса до 1 кг;
- кузнеческие щипцы или обычные пассатижи, но без изоляции на ручках, а также разводной ключ;
- тиски;
- наковальня или её самодельный аналог из двутавра;
- болгарка и сварочный аппарат;
- точильный станок;
- печь.
Если с обычным инструментом все более-менее понятно, то по поводу печи необходимо сделать некоторые пояснения. Все дело в том, что в обычном очаге сложно получить температуру более 900 °С. Да и греться заготовка там будет целую вечность. Поэтому необходимо немного усовершенствовать очаг. Если ранее Вы не занимались хотя бы закалкой металла, то придется сделать с нуля небольшую печь из толстостенного металла. Затем присоединить к ней трубу, по которой будет поступать воздух при помощи вентилятора или старого пылесоса. Таким нехитрым образом можно получить достаточно надежное горнило для доведения заготовок до температуры 900 — 1200 °С. В качестве топлива используется обычный древесный уголь, желательно такой, который дает как можно больше жару и горит подольше.
Прежде чем приступить к самим работам, необходимо сделать эскиз самого ножа.
По сути, нож довольно простой предмет, состоящий из клинка и рукоятки. Но вот каждый из этих элементов имеет целый набор составляющих. На демонстрирующем конструкцию ножа фото можно увидеть все элементы ножа и как они называются.
Также необходимо знать и о некоторых основных профилях клинков, чтобы сделать наиболее подходящий эскиз. На фото ниже приведены профили ножей.
Выбрав наиболее подходящий для Вас профиль, можно смело приниматься за создание эскиза. Конечно, опытные мастера обходятся без зарисовки, но для новичка все же важно сделать эскиз и держать его перед глазами в процессе ковки.
Ковка ножа из сверла
Сверла получили большую популярность при ковке ножей благодаря используемой в них легированной стали Р6М5, которая отличается прочностью, легкостью заточки и износоустойчивостью.
При выборе сверла для ковки следует отметить один важный момент. Большие сверла состоят из рабочей спиралевидной части из Р6М5 и хвостовика из обычной стали. Маленькие сверла обычно полностью из Р6М5. При ковке ножа из большого сверла необходимо сразу определить, где какая сталь и где между ними граница. Сделать это можно достаточно просто, всего лишь немного проточив сверло по всей длине. Там, где обычная сталь, сноп искр будет большой и желто-оранжевого оттенка. А вот там, где легированная сталь, сноп будет реденьким и ближе к красноватому оттенку. Описанная выше процедура необходима для того, чтобы определить, где у ножа будет начинаться клинок, а где хвостовик. Закончив с этим, переходим к самой ковке.
Вначале разводим огонь в печи , подключаем поддув и ждем, когда угли разгорятся достаточно сильно, после чего помещаем сверло в горнило . Но делаем это с помощью клещей и так, чтобы хвостовик большей частью оставался вне огня.
Важно! Выполняя ковку ножа впервые, можно не сразу определить, когда металл нагрелся до необходимой температуры. Вследствие чего можно испортить не одно сверло. Поэтому прежде чем браться за ковку сверла, можно немного потренироваться с нагревом и ковкой металла на обычной арматуре. При этом необходимо запоминать, какого цвета был металл и когда он ковался наиболее мягко. Также стоит помнить о том, что на солнечном свете даже нагретый до 1100 °С металл будет выглядеть темным.
Как только сверло нагреется до необходимой температуры, а это более 1000 °С , его сразу же необходимо вынуть из горнила , и зажать низ хвостовика в тисках. После чего взять разводной ключ, зажать им верхушку сверла и сделать круговое движение, расправляя спираль. Делать все необходимо быстро, чтобы металл не успел остыть, иначе рискуете сломать сверло. Если не получилось сделать это за один раз, ничего страшного. Просто повторно раскалите сверло и повторите процедуру. В результате должна получиться относительно ровная полоска металла.
Следующим шагом будет ковка сверла и раскатка металла до приемлемой толщины . Тут все довольно просто. Раскалив металл до необходимой температуры, берем тяжелый молот и начинаем сильными, но равномерными ударами ровнять металл и придавать ему ровную форму. В результате должна получиться полоска металла толщиной около 4 — 5 мм.
Важно! При ковке металла необходимо постоянно следить за цветом заготовки. Как только она начала тускнеть, приобретая вишневый цвет, её сразу же возвращаем в горн. Лучше лишний раз накалить металл, чем сломать его под ударом молота.
Далее выковывается острие ножа . Тут все несколько сложнее. Дело в том, что необходимо придать заокругленную форму и при этом сохранить необходимую толщину лезвия. Вся работа практически ювелирная и потребует определенной ловкости. Ковка выполняется таким образом, чтобы постепенно заокругливая острие, понемногу оттягивалось лезвие в длину. Удары должны быть сильные, но аккуратные. У новичка может не получиться с первого раза, но немного практики все исправит.
Следующим шагом будет проковка режущей кромки ножа . Это довольно важный и сложный этап. Для этого потребуется более легкий молот и желательно с заокругленным бойком. Начиная с середины лезвия, постепенно сдвигаем металл вниз к режущей кромке. Стараемся сделать режущую кромку как можно тоньше. При этом следим, чтобы само лезвие оставалось прямым и ровным. Удары наносим очень аккуратно и стараемся прилагать лишь столько усилий, сколько требуется для небольшой деформации раскаленного металла. Помним о цвете заготовки и при необходимости отправляем её обратно в горнило.
После того как удалось выковать лезвие и острие, переходим к проковке хвостовика . Сами работы будут намного проще, чем при выковке лезвия. Вначале накаливаем круглый хвостовик сверла и затем раскатываем его сильными ударами молота. В зависимости от эскиза хвостовик может быть как узким, так и широким. Тут уже кому как нравится делать ручку ножа. Кто-то делает простые накладки, а кто-то делает наборную рукоятку.
По завершению ковки даем металлу постепенно остыть и затем переходим к шлифовке . На шлифовальном станке снимаем лишние слои металла и неровности, делая нож идеально ровным и блестящим. При шлифовке может уйти до 2 мм толщины, и нож станет намного легче и тоньше. Также на этом этапе можно выполнить заточку ножа. Напоследок выполняем закалку ножа. О том, как это делается, будет написано ниже.
Ковка ножа из сверла видео-обзор :
Еще одним популярным материалом для ковки ножей является подшипник, а именно его внутренний или внешний обод. Причем внутренний даже предпочтительней. Все работы по ковке ножа из подшипника практически идентичны ковке из сверла. За некоторым исключением.
Во-первых, заготовку из ободка подшипника вырезаем при помощи болгарки. Длину стараемся взять с запасом, так чтобы и на нож хватило и еще 1 — 2 см осталось. Во-вторых, на начальной стадии ковки вырезанную заготовку следует приварить к прутку арматуры. И в таком виде накалять и ковать. В-третьих, если в случае со сверлом заготовку раскатывали из круглой в плоскую, то для обоймы подшипника её необходимо просто выровнять. А дальнейшие действия по ковке самого клинка и хвостовика полностью аналогичны. Единственное, что стоит отметить, — из подшипника все же удобнее делать нож с накладными рукоятками.
Ковка ножа из подшипника видео-обзор :
В поисках подходящей стали для качественного ножа многие используют рессору. Металл этой автомобильной запчасти отличается высокой упругостью и долговечностью, что делает его прекрасным образцом для ножей ручной ковки. Справедливости ради, необходимо отметить, что нож из рессоры можно изготовить и обычным вырезанием профиля ножа с дальнейшей заточкой и закалкой. Но все же, чтобы нож был действительно надежным, его лучше проковать, тем более что толщина рессоры достаточно велика, а для хорошего ножа её следует уменьшить.
Ковку ножа из рессоры начинаем с зачистки болгаркой от ржавчины и разметки пластины. Потребуется лишь небольшая часть рессоры, поэтому отметив её, отрезаем при помощи болгарки. Далее привариваем заготовку к арматуре и накаляем её. После чего постепенно проковываем, доводя до необходимой толщины. Выковываем острие и режущую кромку, как это делать, описано выше на примере ковки ножа из сверла. Добившись желаемого, оставляем нож постепенно остывать и затем шлифуем и затачиваем его.
Ковка ножа из рессоры видео-обзор :
Ковка ножа из напильника
Износостойкую и прочную сталь можно найти в различном слесарном инструменте и напильник тому яркий пример. Изготовление ножей из напильника достаточно популярное занятие. Тем более что клинки получаются на редкость долговечными с прекрасной режущей кромкой. Но ковка ножа из напильника имеет свои особенности.
Прежде всего, потребуется очистить напильник от насечек и возможной ржавчины. Сделать это можно с помощью болгарки. Далее при необходимости отрезаем от напильника заготовку необходимой длины. После чего привариваем её к куску арматуры и засовываем в горнило. Накалив заготовку до нужной температуры, приступаем к раскатке заготовки до необходимой нам толщины. Затем делаем острие и режущую кромку. Хвостовик ножа из напильника лучше всего сделать под накладную ручку.
Ковка ножа из напильника видео-обзор :
Ковка ножа из троса
Изготовление ножа из стального троса довольно редкое явление. Так как в отличие от всех описанных выше заготовок, трос представляет собой разрозненные волокна проволоки, и ковать их довольно сложно. К тому же сталь троса не обладает такими высокими характеристиками, как сталь сверла или напильника. В большинстве своем ножи из троса куют из-за их необычного рисунка на клине, отдаленно напоминающего дамасскую сталь. Для того чтобы сделать такой нож, необходимо приложить несколько больше усилий, чем при ковке из обычного бруска стали.
Ковка ножа из троса начинается, как и обычная ковка. Вот только есть несколько маленьких секретов. Во-первых, это касается хвостовика. Многие мастера делают хвостовик ножа из троса в виде готовой рукоятки. Смотрится это весьма необычно и красиво. И тут есть два подхода в изготовлении рукоятки. Взять толстый трос и затем сварить его конец, сделав монолитным куском. Или сделать рукоятку в форме петли, а из концов выковать клинок. Во-вторых, ковка троса — дело сложное из-за разрозненных проволок, из которых состоит трос. Чтобы сделать нож, потребуется их сварить между собой. А это целое искусство и рассчитывать, что нож из троса получится с первого раза, не стоит. Сварку можно выполнить двумя путями. Первый — проварить электросваркой вдоль больших канавок. Второй — выполнить кузнеческую сварку. Второй вариант сложнее и в то же время предпочтительней.
Итак, выбрав способ создания рукоятки, приступаем к ковке ножа. Для этого раскаливаем трос до ярко-красного цвета. Затем вынимаем его и посыпаем бурой. После чего вновь отправляем в горнило. Таким нехитрым образом выполняется подготовка к кузнеческой сварке. представляет собой соль тетраборной кислоты и применяется мастерами для сварки отдельных слоев стали. По сути это флюс, который облегчает процесс плавки и предохраняет расплавленный металл от попадания кислорода и устраняет оксиды металла. Буру можно найти в свободном доступе без особых проблем.
После того как трос обработали бурой со всех сторон и он раскалился от 900 до 1200°С и более, вынимаем его из горнила и начинаем проковывать. Удары наносим тяжелым молотом, но при этом стараемся сохранить волокна троса вместе. Сложность ковки троса именно в этом. Но потренировавшись можно добиться приемлемых результатов. В конце концов, трос можно накалять и проковывать сколько угодно раз. Но при этом каждый раз, нагревая его в горне, посыпать трос бурой. В результате получится монолитный кусок стали, состоящий из множества слоев, почти как у дамасской стали. После чего остается лишь выковать клинок необходимой формы. На демонстрирующих ковку ножей видео уже не раз было показано, как именно делается раскатка клинка, создание режущей кромки и острия.
Закалка и отпуск клинка
Как уже отмечалось ранее, закалка ножа — это один из самых важных этапов его изготовления. Ведь именно от того насколько правильно была она выполнена, зависят рабочие характеристики ножа. Сам процесс закалки выполняется уже после того, как нож остыл и был отшлифован на точильном станке.
Начинается с его нагрева от светло-красного до оранжевого цвета. После чего нож опускается в воду или масло. При этом в воду добавляется 2 — 3 ложки поваренной соли на 1 л, а температура воды должна быть 18 — 25 °С, масла 25 — 30 °С. Закалка выполняется довольно быстро и чтобы все прошло удачно после закалки клинок необходимо отпустить. Сама закалка стали происходит в диапазоне температур от 750 до 550 °С. Момент закалки можно даже прочувствовать, когда сталь начинает «дрожать и стонать» в жидкости. Как только процесс заканчивается, клинок необходимо достать и дать ему остыть естественный образом.
Отпуск клинка выполняется уже после закалки. Сам процесс подразумевает ослабление внутреннего напряжения стали, что делает его более гибким и устойчивым к различного рода нагрузкам. Перед тем как сделать отпуск, клинок следует очистить от возможной окалины и затем вновь нагреть. Но температура при отпуске значительно меньше. Сам нож нужно уже держать над пламенем и наблюдать за ним. Как только вся поверхность покроется желто-оранжевой пленкой, убираем нож от огня и даем ему остыть естественным образом.
Иногда закалка и отпуск производятся при помощи масла или воды, а иногда через масло в воду. Такая закалка выполняется очень быстро. Сначала клинок опускается в масло на 2 — 3 секунды, а затем в воду. При таком подходе риск сделать закалку неправильно минимален.
Ковка ножа своими руками лишь кажется простой задачей. Кроме того что придется довольно много помахать кузнечным молотом, так еще и без опыта в вопросе ковки металла с первого раза может не получиться выковать нож. Поэтому сначала необходимо набить руку и немного потренироваться, а затем уже приступать к ковке ножа.
Закалка.
Проблема.
Поскольку я делаю ножи в основном из подшипников от автомобилей, по размеру обычно это диаметр сантиметров 10-15, и начинал полным дятлом, после чисто интуитивных попыток возникли следующие проблемы:
После закалки в воде сталь хрупкая настолько, что разлетается как стекло при сильном ударе
Собственно, все. Остальное все меня устраивало. Но мне хотелось, чтобы «не ржавело», «хорошо резало», «держало заточку», «не раскалывалось».
Болометра у меня нет, «все на глазок», и когда я читаю рекомендации «выдержать два часа при температуре 453 градуса» — это не для меня. В конце концов, плюс-минус твердости или вязкости мне фиолетово. Меня вполне устроит «более-менее» приличное качество по перечисленным параметрам.
Поэтому.
Решение проблемы:
1. Отковываю, обязательно соблюдая следующие условия:
При нагреве я лучше недогрею, чем перегрею. Стараюсь не накалять до белого свечения, работаю в диапазоне красного-желтого. Лучше я почаще буду совать-вынимать, чем пережгу.
Внимательно следим за деталью, когда лежит в горне: попытка сэкономить и делать одновременно две детали приводит к тому, что или пережжешь, или что-то испортишь.
Нагрелось до красного яркого с кусками желтого свечения – вынимаем
Периодически пшикаем-брызгаем из бутылочки пластиковой (как на шашлык) – лучше видно температуру, где что нагрето, да и угли экономит
Особенно внимательно, когда есть тонкие детали (лезвие, например) – не пережечь!
2. НИ В КОЕМ СЛУЧАЕ НЕ БИТЬ ПО ХОЛОДНОМУ МЕТАЛЛУ!
Когда куешь, металл пластичен. И по свечению видно, если он начинает остывать. Конечно, хочется за один раз отковать «побольше». Надо бороться с этим искушением.
Как только при ударе молотом (а я все вручную, нет механики) – чувствуешь, что пластичность уменьшается – останавливаемся, греем дальше.
Пояснение: насколько я понял, объясняется все просто. Как только я треснул молотом по подостывшему металлу, возникают микро-трещины, которые плохо «залечиваются» даже хорошим нагревом, и потом по ним все ломается. Вот и все.
3. Собственно, закалка.
Я пробовал в воду. При любых (почти) вариантах – хрупкая сталь получается. Поэтому взял, слил в канистру отработанного машинного (не проблема достать). Читал картинки и про то, какие температуры для каких марок стали… Разбирался в свечениях и цвете металла. Сухой остаток:
Когда форма детали скована – я стараюсь максимально близко к финальной форме, чтобы поменьше точить, — приступаю к закалке
Нагреваю до (в среднем) цвета-свечения между красным и желтым (на глазок) – но для этого есть обоснования теоретические, скажу ниже, — и опускаю ВЕРТИКАЛЬНО ЗА ХВОСТИК кончиком лезвия вниз быстро-быстро в масло. Держу несколько минут, чтобы полностью остыло.
Нагреваю до темно-красного цвета и закаляю еще раз
Если «ведет» нож, что бывает, — просто искривляется он – нагреваю до темно-красного цвета (минимальная пластичность) и подправляю, если надо, закаляю еще раз.
Кладу рядом с углями на поддон, вырубаю горн – пусть остывает все вместе.
Результат – шикарно все, и без заморочек. Могу подвести длинную базу, но такой повтор закалок с понижением верхней температуры нагрева на опыте дает отличный результат в среднем, независимо от взятого подшипника (японских экзотик не пробовал, брать не буду – в основном наш Автоваз, Уралаз, Камаз, Газ, и пр. Совецкие заводы.)
Теперь теория.
Если мы возьмем картинку переходов разных аустентитов в мартенситы и прочие цементиты,
… то обратим внимание, что В СРЕДНЕМ диапазон правильного нагрева выше 850, но ниже 900 градусов. Поэтому нагревать надо примерно до диапазона цветов как на картинке ниже.
Повтор ХУЖЕ не делает, а ЛУЧШЕ делает. Вот и все.
Поскольку подход этот «крестьянский» я его излагаю просто и все.
Вопрос задает Валерий, Московская область:
Недавно услышал от знакомого, что из подшипника можно изготовить отличный нож. Меня очень заинтересовало это, поскольку люблю все мастерить своими руками. Хотелось бы подробнее узнать об этой технологии.
Предоставляем слово нашему эксперту:
Подшипники изготовляют из стали высокого качества, поскольку они работают в трудных условиях и не теряют своих характеристик при значительных нагрузках. Если выковать из него нож, можно получить отличный инструмент. Он не потеряет остроты в самых трудных условиях эксплуатации.
Для ковки ножа из подшипника необходимо следовать представленной инструкции:
- При помощи болгарки необходимо отрезать заготовку нужной длины, используя обойму подшипника. Нужно учитывать запас в 1-2 см.
- Полученную заготовку необходимо приварить к прутку арматуры, исполняющей роль рукоятки.
- Ковка осуществляется при достаточно низких температурах, чтобы материал изменился от светло-красного до более темного оттенка.
- Перед закалкой осуществляется обдирка на точиле или при помощи напильника.
- Для улучшения характеристик ножа рекомендуется произвести нормализацию металла. Для этого его разогревают до 750°С, ждут 5 минут и охлаждают на воздухе. Такие манипуляции повторяют 2-4 раза.
- Производится закалка. Чаще всего это осуществляется при температуре 830°С. Для определения подходящего момента для закалки используют магнит. Когда сталь перестала магнититься, можно приступать к данному процессу. Температура плавления поваренной соли составляет 800°С. Поэтому ею посыпают заготовку, чтобы примерно определить момент достижения оптимальных характеристик для закалки.
- Закалка происходит в масле, температура которого достигает 50-60°С. Заготовку помещают в емкость с подготовленным веществом на 1 час. Все это время ее нельзя шевелить и прислонять к стенкам резервуара.
- После закалки проводят отпуск. Нож помещают в духовку при температуре 160-200°С на 2 часа. Для охлаждения просто гасят огонь.
- Для заточки ножа используется алмазные бруски, для шлифовки – алмазная паста. В процессе данной обработки может утратиться до 2 мм толщины заготовки, что вполне нормально.
Если следовать все правильно и в точности следовать инструкции, полученный нож сможет поцарапать стекло. В процессе эксплуатации он не тупится и не разрушается при нагрузках изгибающего характера. Представленным способом легче всего делать нож с накладными рукоятками.
Сейчас в продаже имеется достаточно большой ассортимент разнообразных ножиков хорошего качества. Однако большой популярностью пользуются ножи ручной ковки. Такие изделия имеют особую энергетику. Ножи своими руками могут изготавливаться по-разному. Самым сложным способом является вариант ручной ковки. Стоит понимать, что ковка дает возможность сделать прочный клинок отменного качества, который сможет прослужить достаточно большое количество времени, не потеряв при этом свои качества.
Нож, выкованный из прочного материала, способен прослужить долгие годы, не сломавшись и не потеряв свои качества.
Для того чтобы ковать нож, понадобится иметь некоторые знания касательно металлов и их свойств. Помимо того, нужно досконально владеть инструментом для ковки. Людям, которые решили сделать данное изделие своими руками впервые, важно ознакомиться с некоторыми рекомендациями.
Как правильно выбирать материал для изготовления ножа?
Рисунок 1. Конструкция кованого ножа.
Чтобы сделать качественный клинок, нужно подобрать подходящую для него сталь. От выбора материала будут зависеть режущие характеристики ножика и его прочность. Для правильного подбора металла важно знать, какие свойства имеет такой материал. Понадобится ориентироваться на 5 главных свойств стали:
- Устойчивость к износу — сопротивление стали изнашиванию при использовании. Данное свойство будет зависеть от твердости материала.
- Твердость — свойство материала, которое указывает на его способность сопротивляться попаданию в нее твердых материалов. Стоит знать, что твердый материал меньше подвергается деформации. Показатель прочности можно измерить по шкале Роквела.
- Прочность — возможность сохранять целостность при воздействии атмосферных сил.
- Пластичность — возможность материала впитывать и распределять кинетическую энергию при ударе и деформации.
- Красностойкость — устойчивость металла к высокой температуре и способность сохранять свойства в процессе нагрева. Минимальная температура ковки стали будет зависеть от устойчивости материала к термической обработке. Рекомендуется выбирать твердые марки, рабочая температура ковки для которых больше 900°С. Стоит знать, что температура плавления данного материала составляет приблизительно 1500°С.
Все данные характеристики связаны между собой. Преобладание одного из них приводит к ухудшению остальных. Каждое свойство материала будет зависеть от содержания в нем легирующих элементов и добавок, к которым можно отнести кремний, вольфрам, молибден и другие.
Рисунок 2. Виды профилей ножа.
Наличие всех легирующих элементов и применение их в необходимой пропорции в процессе изготовления стали, а также знание их свойств позволяет создать сталь для необходимых целей. Каждая из подобных сталей имеет свою маркировку. Стоит отметить, что российские и европейские марки имеют разные обозначения.
К российским производителям, которые достаточно часто применяются в процессе ковки клинков своими руками, можно отнести стали с маркировкой У7-У16, Р6М5, Х12МФ и другие. Из европейских марок можно отметить стали 1095, М-2, А-2 и другие.
Подробное описание марки металла можно найти в «Марочнике стали и сплавов».
Вернуться к оглавлению
Какие инструменты необходимы для ковки ножика своими руками?
Чтобы выполнить ковку клинка, понадобится иметь специальный инструмент кузнеца, однако можно воспользоваться и любительскими инструментами:
- Молот на 4 кг.
- Молоток до 1 кг.
- Тиски.
- Станок для точки.
- Печка.
- Наковальня.
- Аппарат для сварки.
- Болгарка.
- Щипцы кузнеца или обыкновенные пассатижи.
- Разводной ключ.
Инструменты для ковки: молоток, тиски, разводной ключ, щипцы кузнеца, зубило, подбойка.
Следует знать некоторые нюансы касательно печки. Понадобится достичь температуры приблизительно 1000-1200°С, чего сделать в обыкновенной печи не получится. В связи с этим надо будет усовершенствовать печку. Конструкция изготавливается из металла с толстыми стенками, после чего присоединяется труба, в которую будет подаваться воздух из пылесоса. В качестве топлива подойдет уголь.
Перед изготовлением ножа понадобится сделать эскиз. Нож является простым предметом, который состоит из клинка и рукоятки, но данные элементы имеют множество составляющих. На рис. 1 можно увидеть эскиз конструкции со всеми ее составляющими. Существующие виды профилей можно увидеть на рис. 2. После того как будет выбран подходящий профиль, можно будет перейти к созданию эскиза. Профессионалы не всегда используют чертежи, однако новичкам они будут необходимы.
Вернуться к оглавлению
Как сделать кованые ножи из напильника или троса?
Напильник изготавливается из износостойкой стали, в связи с чем достаточно часто из данного инструмента изготавливаются ножики. Такие клинки будут иметь хорошую режущую кромку.
Нож, выкованный из троса, уступает по своим характеристикам другим, но клинок обладает необыкновенно красивым рисунком, напоминающим дамасскую сталь.
Первым делом нужно будет выполнить очистку инструмента от насечек и ржавчины. Данное действие можно сделать, используя болгарку. Если есть необходимость, от напильника надо будет отрезать заготовку нужной длины. После этого изделие приваривается к арматурному пруту и засовывается в печку. Изделие надо нагреть до необходимой температуры, после чего можно будет приступить к раскатке изделия до нужной толщины. Далее делается острие и кромка для резки. Хвостовик ножика из данного инструмента рекомендуется делать под накладную рукоятку.
Трос нужно расколоть до красного цвета, после чего вынуть его из печки и посыпать бурой. После этого трос нужно раскалить до 1000°С, снова вынуть из печки и начать проковывать. Удары наносятся молотком, при этом важно стараться сохранить все волокна вместе.
В конечном итоге может получиться полоса стали, которая состоит из нескольких слоев. Из нее можно будет ковать нож необходимой формы.
Вернуться к оглавлению
Куем нож из сверла сами
Для ковки ножиков достаточно часто используются сверла. Связано это с тем, что данные изделия изготавливаются из стали Р6М5, которая подходит для клинков. Она имеет хороший уровень прочности и проста в заточке.
Следует знать, что сверла больших размеров состоят из рабочей части из стали Р6М5 и хвостовика из обыкновенной стали. Сверла небольших размеров в большинстве случаев изготавливаются из Р6М5.
Нож из напильника обладает отличными режущими свойствами.
Если планируется ковать ножик из сверла больших размеров, нужно сразу определить, где располагается каждый вид стали. Для этого нужно проточить сверло по длине. В местах, где присутствует обыкновенная сталь, будет образовываться большое количество искр. При точке сверла из легированной стали искр будет мало. Данную процедуру понадобится выполнить для того, чтобы определиться, где у ножика будет клинок, а где хвостовик.
Ковка выполняется следующим образом:
Прежде всего разводится огонь в печке, после чего подключается поддув. Далее нужно подождать, когда топливо начнет сильно гореть. После этого сверло помещается в печь. Сделать это нужно при помощи клещей так, чтобы хвостовик располагался вне огня. Если ковка выполняется впервые, достаточно сложно определить с первого раза, нагрелся ли металл до нужной температуры. В связи с этим будет испорчено не одно сверло. Чтобы не испортить большое количество материала, рекомендуется первым делом потренироваться с нагревом и ковкой на арматурных прутьях.
Нужно будет запомнить, какой цвет имел металл и когда его было легко ковать. Стоит учитывать и то, что при солнечном свете даже нагретый до 1000°С металл не будет светлым.
После того как сверло раскалится до температуры больше 1000°С, его понадобится вынуть из печки, после чего закрепить в тисках нижнюю часть хвостовика. После этого надо будет взять разводной ключ, прижать им верхнюю часть сверла и расправить спираль с помощью круговых движений. Все действия понадобится производить быстро, чтобы металл не успевал остывать, иначе сверло сломается. Если выполнить все действия за один подход не получилось, нужно будет повторно нагреть сверло и повторить процесс. В конечном итоге получится сравнительно ровная полоса металла.
На следующем этапе нужно будет выполнить ковку сверла и раскатать металл до нужной толщины. Для этого понадобится нагреть металл до нужной температуры, взять тяжелый молоток, после чего сильными ударами выровнять сталь, придавая необходимую форму. В конечном итоге получится стальная полоса толщиной приблизительно 3-5 мм. В процессе ковки материала надо будет постоянно следить за цветом изделия. Как только появится тусклый цвет, заготовку нужно будет вернуть в горн.
Далее понадобится выковать острие ножика. Стоит знать, что изделию нужно будет придать круглую форму, сохранив при этом нужную толщину конструкции. Ковка должна выполняться так, чтобы в процессе проделывания отверстия слегка оттягивалось лезвие по длине. Бить нужно аккуратно.
Следующим шагом выполняется проковка кромки для резки. Для этого нужно использовать легкий молоток. Металл сдвигается вниз к кромке, при этом начинать нужно со середины лезвия. Режущая кромка должна получиться тонкой, а лезвие должно остаться прямым. Все удары нужно наносить аккуратно. Важно следить за цветом изделия.
Далее выполняется проковка хвостовика. Прежде всего накаливается хвостовик сверла круглой формы, после чего изделие раскатывается сильными ударами молотка. Хвостовик может быть узким или широким. Все будет зависеть от составленного эскиза.
После того как металл остынет, можно будет производить шлифовку. Понадобится снять излишки металла, чтобы сделать ножик ровным и придать ему блеска. После шлифовки изделие может стать на 2 мм тоньше, в результате чего нож будет иметь меньший вес. На данном этапе может быть выполнена заточка и закалка клинка.
Ковка ножа кукри из рессоры
Внимание!!! Данная самоделка размещена исключительно в ознакомительных целях.
Запрещено создание и применение в качестве холодного оружия, согласно ст223.4 УК РФ грозит лишение свободы до двух лет!
Здравствуйте все. Как всегда, гулял в сети и случайно наткнулся на статью, где автор рассказывал про ковку интересного на вид ножа под названием кукри. Не стал особенно искать историю такого вида ножа так поверхностно почитал и ничего особенно не понял про происхождение ножа кукри. В основном этот нож используется для хозяйственных нужд для рубки кустов небольших деревцев типов нож для выживания. На видео обзорах вроде бы интересный нож его используют как заменитель мачете кстати в нашей стране не является холодным оружием даже при длине 40 см длиной, так как им почти не реально произвести калящий удар.
Мне стало интересно как реально работает, как им пользоваться и я решил ковать себе нож кукри. В этой статье об этом и пойдет речь кому не интересно просто пролистайте фото в статье все не особо профессиональные выводы и действия. Все кто сейчас дальше читает эту статью большое спасибо. И так нож кукри куют из разных доступных сталей самую подходящий я выбрал 65г в народе рессора. Не в первый раз работаю с такой сталью очень нравится ковка 65г, а так же результат лишь один существенный минус стали 65г это то что очень быстро ржавеет. В этом случае есть выход это зачернить или нанести патину я так и сделал так клинок будет менее подвержен коррозии. И так вроде бы предисловие написал теперь приступаю к ковке.
Понадобится инструмент
- Дрель
- Болгарка
- Грин дер с набором лент
- Кузнечный горн
- Молот разного веса для ковки
Понадобится материалы
- Кусок рессоры от грузового авто
- Дерево для рукояти сухое
- Клей
- Наждачная бумага разная
- Диски на болгарку отрезной и шлифовочный
- Масло для пропитки рукояти
Ковка клинка
1. Для дальнейшей ковки нагреваю до желтого цвета рессору и даю ей остыть процедуру повторил два раза второй раз нагревал сильнее чем первый. Так произошел отпуск металл теперь ковать будет проще. Нагреваю полосу до желтого цвета, и наношу удары бойком молотка вытягивая немного по длине. При достижении необходимой длинны и толщены начинаю формировать острие. От кончика начинаю ковать спуски одновременно формируя примерный вид лезвия. Отковав 15 см от кончика ставлю на край наковальни обух и произвожу изгиб лезвия характерный для ножа кукри. При сгибании клинка в месте сгибания проковал лезвие чтобы не было утолщения. От места изгиба продолжаю проковать лезвие, но уже стараясь сделать уже чем кончик клинка. Спуски отковал приступать к хвостовику сильно не мучился все равно болгаркой отрезать лишнее придется. Толщина на обухе 4 мм спуску до 1.5 мм чтобы при закалке не сжечь режущею кромку. Вот и все с ковкой выключаю горн он еще с углями ложу клинок на угли, и оставляю до полного остывания вместе с горном иначе нож будет твердым при шлифовке так как структура металла очень мелкая напряжена и клинок может даже лопнуть при ударе или при закалках, а это обидно после пару часов труда случайно сломать клинок было у меня такое и не раз. После полного остывания зажимаю в тески и отрезаю все ненужное и приступаю к шлифовке.
Шлифовка клинка и нарезка дола
2. После обрезки всего лишнего зажимаю хвостовик в тески обдирочным диском шлифую поверхность в черновую до толщены 1.2 мм. С обеих сторон отшлифовав спуски делаю разметку дола он там необязателен, но все делают, и я сделал так нож брутальный смотрится. Дол прорезал тонким отрезным диском потом шоркал про наждачной бумагой. Напильником сделал шип у рукояти не помню как его называют и не знаю зачем он там как я понял этот шип как печать или знак мастера кузнеца, а люди раздули типа увеличивает прочность клинка по моему это бред. После всего этого на Гриндере шлифую разной наждачной бумагой, но не в блеск самая мелкая бумага 120. Металл хоть и не калил еще, но бумага ест его бедно. Спустя два часа наконец то закончил мучиться на Грин дере попив кофе приступил к розжигу горна для закалки клинка горн буду топить древесным углем не знаю почему, но на древесном угле закалка происходит лучше, чем на каменном угле. Параллельно поставил рядом с огневом емкость с маслом для нагрева иначе закалка будет некачественная или вообще не закалится клинок.
После полного прогрева углей нагреваю клинок до состояния когда клинок не прилипает к магниту держу еще секунд 30ть. Окунаю в подогретое заранее масло до шестидесяти градусов вот и все. Сталь 65г не закалится до 60 единиц, но 40-45 единиц получить можно. После закалки произвожу отпуск по-простому просто нагреваю клинок до цвета побежалости почти темно золотого цвета, и как побежалость меняет цвет на синий со стороны обуха перестаю нагревать и даю остынуть зажав хвостовик в тесках. Стаю смотрю на клинок и думаю может оставить клинок таким цветным все равно его хотел травить. В общем так и оставил красивый хамелеон. По качеству закалки клинок прочный упругий точится так себе кромка не крошиться в общем закалка произошла успешно.
Рукоять
Для рукояти взял кусок сухой древесины не знаю что за дерево валялся среди кучи кусков выбрал подходящей формы и без трещин сучков. Дата закладки на сушку 17 год октябрь есть и еще старше не стал брать оставлю для лучших времен. Стругаю немного дерева ножом формируя примерную форму чтобы на Гриндере не трудится долго. Делаю разметку для хвостовика просверливаю отверстие в дереве, и делаю насечки на хвостовике для более хорошего удержание рукояти. Приклеиваю все на двух составной клей и оставляю сохнуть на пару часов. После высыхания приступаю к шлифовке ручки на Гриндере сначала грубой лентой, а потом и мелкой. Форму формировал на глаз просто примерял к руке и шлифовал что мешало в общем подогнал под свою руку и шлифовал мелкой наждачной вручную. Для декора пропитал на паровой бане натуральным воском в течение двух часов пока пузырись не перестала ручка чтобы не портилась ручка от влаги, и для декора обжог немного газовой горелкой и шлифовал немного на войлочном диске чтобы не марало руки, а также для блеска да и эстетичней выглядеть стала.
Вот и все ковка ножа кукри из стали 65г завершена. Нож решил проверить на зимней рыбалке немного порыбачил, подмерз, взял свой кукри и пошел в лес с первого удара нож мне понравился рубить хорошо щепу колит на ура классный нож для приготовления дровишек для костра, а так мне кажется бесполезная игрушка. В целом нож очень крепкий ручка крепкая лезвие держит заточку так что сходил я на рыбалку и все приехал и положил свой кукри на пыльную полку. Вывод такой не все что на картинке незаменимое и функциональное как кажется на вид. Но как говорится пока сам не споткнётся не поймешь. Всем спасибо за внимание спасибо за то что хватило сил дочитать до конца. Всем удачи и добра и до новых Самоделок друзья.
Источник
Мачете из рессоры своими руками
Автор На чтение 16 мин. Опубликовано
Изготовлено по мотивам видео на Ютубе (с Соколовым Григорием в главной роли))
Для начала повторил его конструкцию. Но полотна пилы от 63 рамы не нашёл.
А покупать посчитал нецелесообразным. К тому же, по отзывам, с 63 рамы б.у. пилы часто бывают подожжёные, и не держат лезвие. С термообработкой связываться тоже не хотелось.
Добыл диск от круглопильного станка диаметром 710 мм, толщина 3мм.
Сделал контур будующего мачете из картона, по своей руке.
Как нарисовать и процесс изготовления, подробно расписан в видео у Григория. Ручку намотал шнуром 6мм.
Заточил лезвие болгаркой и шлифмашинкой … И немедленно побежал рубить кусты. Гммм… А рукоятка то из шнура не очень.
Если свалить несколько деревцев, ещё куда не шло. Но я то планировал более интенсивную работу. Надысь взял земельный участок, обильно заросший кустами. Их там сотни.
Рукоятка со шнуром тонкая и неудобная, даже с прокладками из верёвок.
В общем я мгновенно намял руку, и заработал 3 заслуженные боевые мозоли. Ладонь стала красная, как клешня у варёного рака.
Ручку сразу переделал. 2 накладки из бука.
Как оказалось полотно пилы сверлится (но сверло должно быть качественым, не китайским).
К тому же выявился ещё один недостаток – большой вес. У Григория лезвие из полотна 2 мм. У меня при тех же габаритах 3 мм. Плоскости я немного шлифанул, но полотно тоньше делать не стал.
Лезвия у меня вышло 870 граммов. С новой могучей ручкой — 1100 грамм. Одной рукой долго не поработаешь. Посмотел в инете, многие мечи имели вес от 1 кг до 1.5. Отдельные экземпляры двуручных 2.7. Однако! ! Решил уменьшить ширину и срезать лишнее.
После облегчия лезвие вышло 715 грамм, рукоятка 102 грамма.
Общий вес 817 грамм. Общая длина 565 мм. Рукоятка 190мм.
Такой вес понравился. Сила удара не уменьшилась. Работать стало легче и сподручнее.
Впечатления.
Самые сильные удары – в области лезвия на расстоянии 15 см от рукоятки, очень мощно заглубляется в древесину и совершенно нет отдачи в руку. Тонкие ветки можно рубить как угодно. Сразу заметил, что не стоит рубить под 90 градусов. Под углом гораздо легче и глубже. Для обычных ударов хват рукой у лезвия, для акцентированных у основания ручки. Для совсем зверских — двумя руками. Лучше всего рубятся зелёные ветки и живые деревца. Хуже всего сухостой.
Двуручная рукоятка удобна. Акцентированные удары можно наносить двумя руками.
Рукоять из двух половинок бука. Форма прямая. Изогнутая на мой взгляд не катит.
Это не сабля для ударов с оттягом. Проверено практикой. Слишком широкая рукоять – плохо, как и узкая.
Сечение – овал. Пальцы не должны смыкаться. У меня сечение 38х28 мм. Но тут надо по руке ориентироваться. В ручке несколько отверстий для крепления темляка. На мой взгляд темляк в работе, мешает. Но для переноски удобен. Ну или если есть риск безвозвратно выронить инструмент (река, горы.) Вообще на ручке всё должно быть плавно, и никаких выступающих деталей – руку мгновенно смозолишь при интенсивной работе. Я покрыл рукоять воском.
Покупал для полировки машины. Карнуба какая то). С льняным маслом заморачиваться пока не стал. Лезвие попробую заворонить в кока коле. Хотя это и не обязательно. Вроде бы не ржавеет. Практика покажет.
Не решил из чего делать ножны. У Григория шина от бензопилы. Я пока взял полоски толстого картона от коробки и смотал скотчем. Перевозить в машине и носить в сумке можно.
Лезвие в верхней части затачивать не стал. Только прямой участок. Когда рубишь деревца у земли
, их часто срубаешь с одного удара и лезвие касается земли ( как раз тупой закруглённой частью).
Впрочем заточу немного, как лопату. Копать можно будет и корни рубить.
Общий вывод.
Задумка удалась. Тонкие сучья, ветки и деревья толщиной 5-6 см срубаются на раз. И делать это гораздо удобнее чем топором. В разы. Бензопила для тонких кустов неудобна.
Для толстых деревьев удобнее бензопила или лучковая пила. Мачете очень удобно для своей ниши – кустарник, сучки, тонкие деревья.
На мой взгляд вес более 800 грамм делать не надо – много не намахаешь. Тонкое лезвие (2-3мм), при достаточной массе и скорости, мощно врубается в древесину. При ударе у рукояти, лезвие входит сантиметров на 5 с одного маха. Возможно инструмент пригодится при рубке мяса или отрубать бошки курицам. Не пробовал. За несколько дней работы, на лезвии, ни одной зазубрины. Хотя вру, появилось пара маленьких.
Пила была сделана в СССР. Сталь добрая.
В целом .
Да я в восторге ваще!). Этакий ножик для реального мужика. Фотка с рукой прилагается).
Срубать деревья с одного удара – это что то. Этакий мачетный ваншот). Когда орудуешь двумя руками, чувствуешь себя самураем и реальным мужиком одновременно. Получилась практичная и интересная штука. В чём то стильная. Кусты рубить – одно удовольствие. И игра и полезное дело.
Нож – это отличная вещь, которая может быть полезна не только в качестве прекрасного инструмента, но и в виде замечательного сувенира. Каждый мальчишка будет рад такому подарку. Если нож изготовлен вручную, то он сразу становится уникальной ценностью в глазах владельца.
Взрослые тоже не всегда используют ножи исключительно в бытовых целях – многие люди их коллекционируют. Критерии выбора у всех разные, но каждый знает, что качественная сталь – это обязательное условие для хорошего ножа. Но и красиво выполненная ручка может произвести не меньшее впечатление, чем прочное лезвие, способное долго держать заточку.
В чем же особенность ножа из рессоры?
Причина популярности такого изделия, как нож из рессоры, заключается в свойствах металла. Высокая износостойкость и прочность в сочетании с высокой пластичностью позволили многим поколениям мастеров пользоваться рессорами как главным источником сырья.
Характеристики рессорно-пружинной стали
Рессоры изготавливают из рессорно-пружинной стали 65Г, но могут быть применены другие марки: 50ХГСА, 50ХГА, 50ХФА. Это тоже рессорно-пружинные стали – определить какая из них взята в качестве материала для клинка можно только с помощью химического анализа. Либо по нюансам поведения металла при обработке, но с этим справятся только опытные мастера. Для начинающего изготовителя разница между перечисленными материалами будет практически незаметна.
Применение рессорной стали
65Г считается одной из самых дешевых пружинных сталей. При этом она обладает рядом уникальных свойств, делающих ее незаменимой для создания пружин. Рессорная сталь для ножа содержит хром, никель, марганец, кремний. Эти элементы придают свойства, за которые изготовителями выбирается именно этот материал:
- хорошая гибкость;
- высокая ударная вязкость;
- твёрдость;
- износостойкость;
Термообработка играет большую роль в улучшении качеств материала. Сталь становится прочнее, повышается ее твердость. К сожалению, она недостаточно устойчива к коррозии – имеет обыкновение ржаветь. Но достоинства перевешивают недостатки и ее часто используют как материал для клинка.
Такие ножи применяют в самых разных сферах. В первую очередь в качестве кухонных – крепкие, прочные, долговечные – что ещё нужно для ежедневной работы на кухне и, например, для разделки мяса? Те же соображения заставляли охотников, рыбаков и туристов стараться заполучить в свой арсенал эту качественную «самоделку». Поэтому многие мастера делали на продажу туристические и охотничьи ножи.
Благодаря хорошим характеристикам стали, эти ножи были популярны среди военных. Солдаты срочной службы, имевшие доступ к инструментам для металлообработки, в кустарных условиях изготавливали армейские ножи.Со временем, изготовители начали замахиваться на более серьёзные изделия: топоры, мечи, мачете, катаны. Из-за хорошей ударной вязкости рессорные стали прекрасно подходят для ковки. Ковкой можно изготовить клинок любой формы, даже самой причудливой.
Как сделать нож из рессоры
Изготовление ножа из рессоры может отнять много времени и сил, особенно, если человек делает это в первый раз. Но рессорно-пружинная сталь хорошо поддаётся обработке и «стерпит» ошибки новичка, поэтому именно из неё лучше всего создавать свой первый нож.
Обычно, материал находят на открытом воздухе: на улице, на автобазах, рядом с гаражами, на автомобильных свалках и других аналогичных местах. Поэтому рессора может быть покрыта грязью и ржавчиной и перед работой ее надо тщательно отчистить. Если необходимо выпрямить выгнутую рессору, то её нагревают до красна, а затем дают остыть в нормальных условиях – при комнатной температуре.
Как сделать нож из рессоры с помощью ковки
Все рессорно-пружинные стали, в том числе 65Г, объединяет одно качество: они прекрасно поддаются ковке. Ножи из рессорной стали, изготовленные ковкой, будут более надёжными и долговечными, потому что в процессе обработки происходит упрочнение металла за счёт пластической деформации и изменения макроструктуры.
Прежде чем проковать рессору, необходимо вырезать из неё профиль будущего клинка. Затем заготовку надёжно крепят, и нагревают до красна. Ковкой создаётся остриё и лезвие. Этим способом легко придать клинку требуемую форму, а также задать его ширину. Ковкой из рессоры хорошо удается изготавливать топоры и различные экзотические вещи, такие как мачете или меч.
Лезвию дают остыть до температуры окружающей среды после того как работа закончена.
Как выточить нож из рессоры своими руками
Необходимо, в первую очередь, определиться с внешним видом будущего изделия. Форма зависит от назначения ножа: кухонный, охотничий, сувенирный или какой-либо другой. В итоге клинок может быть любой – на это влияют только фантазия и возможности изготовителя. Если выбор сделан, то нужно взять готовый шаблон или выполнить его самостоятельно из картона или плотной бумаги.
Далее, чтобы изготовить нож из рессоры своими руками, надо быть готовым начать работу с металлом. Сначала шаблон необходимо приложить к металлической заготовке и обвести маркером, карандашом, чертилкой (ГОСТ 24473-80) или другим разметочным инструментом. По контуру, полученному посредством шаблона, требуется вырезать профиль изделия. Подойдут следующие инструменты:
- ленточная пила;
- угловая шлифмашинка, она же «болгарка» – важно не перегреть заготовку при отрезании;
- сверлильный станок или дрель – в этом случае вдоль контура сверлят отверстия, затем перегородки между ними ломают или выпиливают;
- можно использовать ручной инструмент;
Сам процесс обработки достаточно прост, хотя и требует определённой концентрации, чтобы вырезать заготовку в соответствии с разметкой. Когда обработка успешно завершена и заготовка стала соответствовать шаблону, то можно приступать к формированию клинка. Основная задача – сделать скосы. Лезвие снова размечают, определяя размеры скосов. При дальнейшей обработке следует строго придерживаться разметки.
Для работы лучше всего использовать электрическое точило. Также подойдут и ленточная шлифмашинка, и «болгарка», но, в случае последней, требуется хорошее владение инструментом. Можно выточить скосы вручную – напильником. На этом работы по металлу должны быть закончены, потому что далее клинок пройдёт термическую обработку, после которой сделать с заготовкой что-либо ещё будет очень сложно.
Закалка лезвия
Основной вид термической обработки – это закалка. Она нужна, чтобы лезвие было прочным, и могло оставаться острым долгое время после заточки. Существуют разные приёмы:
— закалка, с нагревом только режущей кромки;
— закалка режущей кромки нагревом изделия целиком;
— закалка с отпуском;
В первом случае только крайняя часть лезвия нагревается до немагнитного состояния, после чего его помещают в масло и выдерживают, пока масло не перестанет пузыриться. Второй способ сложнее: нагревается нож целиком, но погружать его в масло требуется только на треть – чтобы режущий край был покрыт жидкостью.
Закалка с отпуском – это метод, при котором остывание заготовки проводится в два этапа: сначала в при повышенной температуре, но ниже температуры закалки, затем при комнатной температуре.
Самый простой способ закалки – это полная закалка клинка, но при этом способе есть вероятность, что лезвие поведёт. Тогда надо провести рихтовку испорченной заготовки. Это можно сделать как предварительно разогрев лезвие, так и в холодном состоянии.
Изготовление рукоятки
Ручку можно изготовить практически из любого сырья, но особой популярностью пользуются дерево, пластик, кожа, кость. Красиво выглядят наборные ручки с чередующимися слоями, например, кожи и бересты.
Кость – это традиционный материал, для изготовления разнообразных безделушек и предметов быта. Обладая навыком резьбы по кости можно сделать уникальную, красивую ручку. Но проще всего взять две деревянные или пластиковые накладки, поместить их по обе стороны от хвостовика и закрепить между собой заклепками, а для большей прочности ещё и эпоксидным клеем. Иногда для крепления используют винты и гайки, но если важен внешний вид, то лучше их не применять.
Рукоять должна быть удобной, поэтому требуется уделить большое внимание ее обработке. Для этого используются сначала напильники, а затем наждачная бумага. Если накладки деревянные, то их обязательно надо пропитать маслом, чтобы обеспечить долговечность древесины. Пропитка подчеркивает структуру дерева и придает изделию привлекательный внешний облик. После закрепления рукоятки проводят ее окончательную шлифовку.
Заточка ножа
Работа над ножом из рессоры практически завершена, осталось только заточить его. Для этого используют:
- бруски;
- мусаты;
- точильные станки;
- механические точилки;
- электрические точилки;
Действительно хорошие результаты получают применяя брусок или электрическую точилку. Чтобы хорошо заточить нож с помощью бруска или точильного камня понадобится не мало времени. Если на обычный кухонный нож достаточно потратить около получаса, то выравнивание и заточка длинного кованого ножа может занять несколько дней.
Для лучшего контроля процесса заточки точильный камень помещают на устойчивую горизонтальную поверхность. Оптимальный его размер – примерно в полтора раза длиннее лезвия. Начинать заточку требуется грубым точильным камнем, с крупным зерном. Продолжать надо до тех пор, пока не появится заусенец. После этого берётся мелкозернистый камень, далее процесс продолжается с его помощью. Чтобы самодельный нож из рессоры стал острым, а заточка держалась долго, надо соблюдать следующие правила:
- движение осуществляется путём поступательных перемещений ножа вдоль бруска – режущей частью вперёд;
- конец бруска и конец лезвия должны «встретиться». Нужно синхронизировать смещение ножа поперёк бруска (от ручки к лезвию) и перемещение ножа вдоль бруска;
- плоскость клинка и поверхность бруска должны составлять угол от 20 до 25 градусов – это универсальный угол заточки. В зависимости от назначения ножа, угол может меняться, но важно, чтобы он удерживался постоянным всё время пока происходит затачивание ножа;
В конце необходимо провести шлифовку лезвия, чтобы надолго сохранить нож острым. Для этого берётся точильный камень с самым мелким зерном. Затем аккуратно, чтобы не испортить уже сделанное, снимается заусенец.
Заточка — процесс требующий терпения и внимательности. Навык приходит только с опытом, поэтому все, кто не хочет ждать, могут воспользоваться электрической точилкой. Это сэкономит время, а также позволит сохранить ножи в превосходном состоянии.
Изготовление ножа — это процесс сложный, требующий внимания, концентрации, тщательности, навыков работы с металлом. Но труд не будет напрасным, ведь в итоге получится прекрасное изделие, созданное своими руками. Чем с большей любовью и старанием мастер подходил к делу, тем лучше будет изделие. Даже новичок, если окажется терпелив и настойчив, сможет овладеть навыками и тоже станет гордиться результатами своей работы.
Если вы нашли ошибку, пожалуйста, выделите фрагмент текста и нажмите Ctrl+Enter.
Как сделать нож из рессоры
Чтобы получить нож из рессоры в домашних условиях, подготовим список таких материалов и инструментов:
• рессора автомобиля;
• кусок древесины для отделки рукояти;
• эпоксидный клей;
• болгарка;
• дрель или сверлильный станок;
• наждачная бумага с разной зернистостью;
• печь для закалки металла, масло;
• лобзик или другие инструменты для резки дерева;
• струбцины.
Ковка ножа из рессоры проходит в несколько этапов
Этап 1.
В первую очередь нужно собрать все материалы для работы, чтобы они были наготове. У автора исходным материалом послужил лист рессоры от старой машины.
Поскольку рессора выполнена в изогнутой форме, то ее необходимо выгнуть. Это делается так: металл нагревается, после чего постепенно остывает. Для нагрева подойдет горелка, также можно просто положить лист рессоры в хорошо разожженный костер.
После того, как заготовка остынет, нужно взять молоток и наковальню, и обработать рессору так, чтобы она стала прямой пластиной. После отпуска металл стал более мягок, он будет легко поддаваться резке, сверлению, и т. д.
Этап 2.
Сначала нужно изготовить шаблон ножа. Автор использовал готовый шаблон из интернета. Если есть желание – его можно улучшить. После распечатки шаблона бумагу нужно наклеить на картон и ножницами вырезать шаблон. Подержав его в руках, мы можем прикинуть, как будет выглядеть нож из рессоры.
После этого нужно приложить шаблон к металлу и обвести маркером.
Этап 3.
Сейчас мы приступаем к самому тяжелому этапу работы – нам нужно вырезать профиль ножа. Это делается с помощью болгарки – орудуя этим инструментом, не рекомендуется перегревать металл. Если в месте резки сталь начинает менять цвет – это значит, что он перегревается. В таком случае металл нужно полить водой. В тех местах, где нельзя вырезать, металл можно просверлить рядом отверстий и потом эту часть обломать.
Этап 4.
Это заключительный этап формировки основного профиля лезвия. Для такой работы очень удобен и прост ленточный шлифовальный станок. Умельцы с большим опытом могут использовать болгарку. Наружную плоскость ножа следует отшлифовать, чтобы она блестела. Для прижатия заготовки к шлифовальной ленте автор воспользовался бруском. Здесь также нужно следить, чтобы металл не перегревался.
Другой ответственный момент шлифовки заключается в изготовлении на ноже скосов.
Этап 5.
Чтобы надежно закрепить накладки на рукоятке, в данном ноже используется 4 штифта. Для них нужно просверлить отверстия. Для подбора диаметра ориентируемся на имеющиеся штифты, которыми традиционно служат стержни из латуни. Для этого случая подойдут и обычный стальные гвозди.
Этап 6.
После закалки клинок приобретает твердость и долго не тупится. Чтобы закалить лезвие, нужно взять масло – подойдет моторное или растительное, печка или хороший костер. Металл необходимо нагреть до такого состояния, при котором к нему не будет притягиваться постоянный магнит. Как отмечает автор, во время нагрева металл отличается тусклым красным цветом. После этого нужно опустить заготовку в масло. Следует быть осторожными, поскольку масло часто воспламеняется с дымом и брызгами, летящими в разные стороны. Емкость для закалки нужно брать металлическую.
Случается, что во время закалки металл начинает деформироваться. Такую ситуацию можно исправить. Для решения проблемы нужно нагреть заготовку, выровнять, и затем опять попробовать закалить.
Этап 7.
Для изготовления накладок на рукоятку, берем две дощечки небольшой толщины. Вырезаем их до требуемого размера и сверлим в них отверстия для штифтов.
Теперь склеиваем заготовки при помощи эпоксидного клея, нанеся по хорошему слою на обе накладки. Затем нужно вставить штифты и хорошо зажать ручку струбциной. Оставляем в таком виде на 24 часа, чтобы клей полностью высох. Сразу для удаления остатков клея берем тряпочку или туалетную бумагу.
После того, как клей высохнет, нож нужно достать и окончательно сформировать форму рукояти. Для этих работ используем ленточный шлифовальный станок.
На завершающем этапе нож полируем, если нужно – делаем поверхность клинка зеркальной. Можно отполировать и рукоятку, так она станет гладкой.
Деревянные накладки в обязательном порядке пропитываем льняным маслом или другими пропитками. Иногда для этого нагревают пчелиный воск и смешивают его со льняным маслом.
В конце работы наш нож нож из рессоры своими руками следует хорошо наточить. Самым доступным вариантом является мелкозернистая наждачная бумага.
Нож ручной ковки: Введение в изготовление лезвий
Этот класс ограничен 8 студентами, и нет никаких возмещений или переводов за обучение.
ДАННЫЙ КЛАСС ПРОДАН!
Это вводный курс, который научит студентов, как сделать нож за два дня и как использовать восстановленные материалы из листовых рессор, роликовых подшипников и других квалифицированных стальных деталей для изготовления лезвий.
О классе:
Этот 2-дневный курс разработан, чтобы служить базовым практическим введением в ремесло изготовления клинков.Инструкция будет включать информацию об инструментах и оборудовании, выборе материалов, механике корпуса, конструктивных соображениях, методах ковки, основных принципах термообработки и методах отделки. Это будет довольно активный класс с большим упором на участие учеников, который будет включать в себя достаточное количество тепла, шума, пота и физических нагрузок. Каждый ученик начнет с сегмента 1/4 ″ x3 / 4 ″ x6 ″ из высокоуглеродистой пружинной стали и, выполнив ковку, профилирование, снятие фаски, термообработку и отделку, создаст собственное собственное лезвие ручной ковки.
Этот класс в первую очередь будет посвящен основам кузнечного дела. Это не просто урок изготовления ножей. Вы не просто шлифуете узор, а затем подвергаете его термообработке. Не то чтобы в таком способе изготовления ножей что-то не так, но изучение кузнечного дела дает вам совершенно другой набор навыков и огромный диапазон возможностей в работе с металлоломом (как в пост-катастрофической или постапокалиптической ситуации). вы не можете достичь, просто отшлифуя узор лезвия.
Ножи будут кузнечно-обработанными, и если у вас все будет хорошо, вы пойдете домой с готовым ножом с ручкой из паракорда. Кроме того, вы получите пару защитных очков, беруши, файл и карточку для файлов, которые можно использовать в классе и взять с собой.
Вы фактически научитесь нагревать, толкать и формировать из пружинной стали лезвие. Будьте готовы к большому количеству молотков.
Студенты познакомятся с металлами, нагревом, ковкой, ковкой, ковкой, правкой, шлифованием, формованием, изготовлением ножей и ручек.
Не возлагайте больших надежд на качество вашего первого лезвия. 🙂 Сделать приличный клинок в самый первый раз, когда вы когда-либо взмахнете молотком, довольно амбициозно, но вы сделаете его и узнаете достаточно, чтобы сделать это самостоятельно, или, конечно, сделаете это снова в более продвинутом классе с больше информации и техники в следующий раз.
span { цвет фона: # 111111! important; } .fusion-content-box-1 .fusion-content-box-hover .link-area-box-hover.заголовок .icon> span { цвет границы: # 111111! важно; }]]>
Информация о классе
ИНФОРМАЦИЯ О КУРСЕ
Даты: 23-24 февраля, 9.00 — 16.00.
Расположение: Указания будут отправлены всем зарегистрированным студентам заранее по электронной почте.
Жилье: Размещение в лагере бесплатно для любого зарегистрированного студента в нашем кампусе площадью 50 акров. Есть также отели в 10 минутах езды от кампуса с почтовым индексом 78260.
ИНФОРМАЦИЯ ОБ ОБУЧЕНИИ
ЭТО КЛАСС ПРОДАН!
Чтобы попасть в список ожидания следующего занятия, отправьте нам электронное письмо по адресу:
Вы можете ознакомиться с нашей политикой оплаты обучения здесь: https://thehumanpath.net/about/payment-policies/
Нож ручной ковки: Введение в изготовление лезвий — январь 2020
Этот класс ограничен 8 студентами, и нет никаких возмещений или переводов за обучение.
НАЖМИТЕ ЗДЕСЬ ДЛЯ РЕГИСТРАЦИИ
Это вводный курс, который научит студентов, как сделать нож за два дня и как использовать восстановленные материалы из листовых рессор, роликовых подшипников и других квалифицированных стальных деталей для изготовления лезвий.
О классе:
Этот 2-дневный курс разработан, чтобы служить базовым практическим введением в ремесло изготовления клинков. Инструкция будет включать информацию об инструментах и оборудовании, выборе материалов, механике корпуса, конструктивных соображениях, методах ковки, основных принципах термообработки и методах отделки.Это будет довольно активный класс с большим упором на участие учеников, который будет включать в себя достаточное количество тепла, шума, пота и физических нагрузок. Каждый ученик начнет с сегмента 1/4 ″ x3 / 4 ″ x6 ″ из высокоуглеродистой пружинной стали и, выполнив ковку, профилирование, снятие фаски, термообработку и отделку, создаст собственное собственное лезвие ручной ковки.
Этот класс в первую очередь будет посвящен основам кузнечного дела. Это не просто урок изготовления ножей. Вы не просто шлифуете узор, а затем подвергаете его термообработке.Не то чтобы в таком способе изготовления ножей что-то не так, но изучение кузнечного дела дает вам совершенно другой набор навыков и огромный диапазон возможностей в работе с металлоломом (как в пост-катастрофической или постапокалиптической ситуации). вы не можете достичь, просто отшлифуя узор лезвия.
Ножи будут кузнечно-обработанными, и если у вас все будет хорошо, вы пойдете домой с готовым ножом с ручкой из паракорда. Кроме того, вы получите пару защитных очков, беруши, файл и карточку для файлов, которые можно использовать в классе и взять с собой.
Студенты научатся нагревать, колотить и придавать форму из пружинной стали лезвия.
Студенты познакомятся с металлами, нагревом, ковкой, ковкой, ковкой, правкой, шлифованием, формованием, изготовлением ножей и ручек.
ИНФОРМАЦИЯ О КУРСЕ
Даты: 11–12 января 2020 г. с 9:00 до 16:00.
Расположение: Указания будут отправлены всем зарегистрированным студентам заранее по электронной почте.
Жилье: Размещение в лагере бесплатно для любого зарегистрированного студента в нашем кампусе площадью 50 акров.Есть также отели в 10 минутах езды от кампуса с почтовым индексом 78260.
охватывать { цвет фона: # 111111! important; } .fusion-content-box-1 .fusion-content-box-hover .link-area-box-hover .heading .icon> span { цвет границы: # 111111! важно; }]]>Информация об обучении
Обычная стоимость обучения: 220 долларов США (взимается плата за онлайн-обработку)
Скидка на чек / денежный перевод: 220 долларов США (Без комиссии онлайн)
Наличными: $ 200
Чтобы зарегистрироваться с помощью наличных денег, денежного перевода или чека, отправьте нам электронное письмо по адресу:
Вы можете ознакомиться с нашей политикой оплаты обучения здесь: https: // herbalmedics.академия / о нас / политика обучения /
Нож ручной ковки: Введение в изготовление лезвий — май 2021 г.
Это вводный курс, который научит студентов, как сделать нож за два дня и как использовать вторичные материалы из листовых рессор, роликовых подшипников и других квалифицированных стальных деталей для сделать лезвия.
О классе:
Этот 2-дневный курс разработан, чтобы служить базовым практическим введением в ремесло изготовления клинков.Инструкция будет включать информацию об инструментах и оборудовании, выборе материалов, механике корпуса, конструктивных соображениях, методах ковки, основных принципах термообработки и методах отделки. Это будет довольно активный класс с большим упором на участие учеников, который будет включать в себя достаточное количество тепла, шума, пота и физических нагрузок. Каждый ученик начнет с сегмента 1/4 ″ x3 / 4 ″ x6 ″ из высокоуглеродистой пружинной стали и, выполнив ковку, профилирование, снятие фаски, термообработку и отделку, создаст собственное собственное лезвие ручной ковки.
Этот курс в первую очередь посвящен ознакомлению с основами кузнечного дела — студенты научатся кузнечному делу своими ножами с нуля, что даст студентам отличную основу и знания по работе с металлоломом.
Ножи будут выкованы, и студенты пойдут домой с готовым ножом с рукояткой из паракорда. Кроме того, вы получите пару защитных очков, беруши, файл и карточку для файлов, чтобы использовать их в классе и забрать домой.
Студенты научатся нагревать, колотить и придавать форму из пружинной стали лезвия.
Студенты познакомятся с металлами, нагревом, ковкой, методами обработки молотком, правкой, шлифованием, формованием, изготовлением ножей и ручек.
Bladesmithing имеет глубокие корни в Арканзасе
Популярность серии Forged in Fire от History Channel показывает высокий интерес к изучению исторического ремесла изготовления клинков. Арканзас имеет много связей с этой формой искусства, и штат является домом для многих талантливых мастеров-клинков, некоторые из которых были представлены и выиграли соревнования в этой серии.
« Forged in Fire был хорош для кузнецов клинка», — сказал Джерри Фиск, известный мастер по изготовлению клинков из Нэшвилла, штат Арканзас. «Иногда мастера могут использовать всю возможную помощь, чтобы рассказать людям о том, что они делают. Это шоу дало толчок всей индустрии, и это хорошо. Приятно видеть, что ребята из Арканзаса хорошо проводят время в эфире, ведь у нас здесь есть несколько выдающихся мастеров-мастеров клинка ».
Фиск сказал, что слово «кузнец» происходит от старого слова «поразить», или нанести удар, поэтому так много людей по имени Смит.«Итак, кузнец работает с клинками, ювелир — с золотом и т. Д.», — сказал он. «Нужно взять стальной пруток, который вы сделали или купили, и долбить его до тех пор, пока не будет сформирована желаемая форма. Затем формируется ручка из желаемых материалов, от простых до очень экзотических, и в моем случае все это можно выгравировать и декорировать ».
По словам Фиска, 10 процентов всемирно признанных мастеров-клинков — арканзанцы. «Первая школа изготовления клинков [Школа кузнечного дела Билла Морана] была открыта здесь в 1987 году», — сказал он.«Люди со всего мира приезжали сюда, чтобы изучить основы и вдохновиться, как они делают по сей день».
Школа, которая работает вместе с колледжем Тексаркана, обучает ремеслу и сертифицирует производителей ножей на уровне подмастерья и мастера клинка. В Вашингтоне, штат Арканзас, в течение всего года предлагается серия интенсивных курсов, которая является одной из главных исторических деревень страны и одновременно представляет собой парк штата и город. Курсы преподаются в реплике однокомнатной школы, которая гармонирует с атмосферой Исторического парка штата Вашингтон, а инструкторами являются мастера клинка мирового класса, одобренные Американским обществом кузнецов (ABS).Долгие годы школа была единственной в стране. Он назван в честь Билла Морана, первого кузнеца этого века, успешно выплавившего дамасскую сталь.
«Арканзас, с момента основания ABS, был рассадником кузнечного дела», — сказал Джим Кроуэлл, мастер по изготовлению лезвий и бывший кузнец из фольклорного центра Озарк в Маунтин-Вью. «Возможно, потому что Б. Хьюз, отец-основатель организации, был деканом студентов колледжа Тексаркана и уважаемым автором публикаций на открытом воздухе и ножевых изданий.Он также историк и знал, что оригинальный нож Боуи был изготовлен в Вашингтоне, штат Арканзас, который сейчас является парком штата Арканзас ».
Одна из многих структур, которые люди могут совершить сейчас, когда они посещают Исторический парк штата Вашингтон, — это кузнечная мастерская. В магазине, построенном в 1960 году Фондом реставрации Pioneer Washington Restoration Foundation, есть рабочие кузницы. Самому известному кузнецу Вашингтона, Джеймсу Блэку, приписывают создание одного из оригинальных ножей Боуи для Джеймса «Джима» Боуи в начале 1830-х годов.В течение года в государственном парке проходят кузнечные мастерские, где можно научиться ремеслу. Другие государственные парки по всему штату также проводят вводные программы кузнечного дела, в том числе Народный центр Озарк в Маунтин-Вью. Историю кузнечного дела можно узнать в таких торговых точках, как Исторический музей Арканзаса в Литл-Роке, в котором есть постоянная галерея ножей и выставка с антикварными и современными кованными лезвиями, Зал славы АБС и мастерская кузнечного дела на территории, где проходят демонстрации кузнецов и кузнецов. кузнецы.
Тем, кто заинтересован в обучении этому ремеслу, Кроуэлл, который в настоящее время преподает в Школе клинкового мастерства Билла Морана и на семинарах по всей стране, предлагает присоединиться к ABS. «Это самая большая группа такого типа в мире», — сказал он. «У них есть информативный веб-сайт с большим количеством информации, книг, статей и DVD. Интернет также предоставляет доступ к большому количеству информации, видео практически по всем аспектам этого ремесла. Найдите аккредитованную школу рядом с вами, которая предлагает уроки кузнечного дела и / или кузнечного дела.В общинных колледжах иногда проводятся продолжительные и вечерние курсы. ABS предлагает несколько классов в нескольких местах здесь и за рубежом. Получите как можно больше знаний. Читайте, переходите к Hammer-ins [это мероприятия, на которых демонстрируются демонстрации и мастера, у которых можно учиться.] Независимо от того, сколько вы читаете, все сводится к применению того, что вы прочитали и узнали в классе. На мой взгляд, как минимум нужна кузница, болгарка, сверлильный станок и ленточная пила. Получите хорошую надежную инструкцию, это бесценно.
Фиск добавил, что каждый февраль в штате Литл-Рок также проводится выставка нестандартных ножей. «Люди могут пойти туда, посмотреть ножи и спросить, сколько часов это может занять или что этот мастер по лезвиям сделал с ножом, на который вы смотрите», — сказал он. «Я потратил до 120 часов на то, чтобы просто гравировать нож, а не делать его, а просто гравировать. На то, чтобы сделать то, чем вы и клиент будете гордиться, уходит много времени. Как производитель, то, что вы делаете хорошо, может быть передано в этой семье из поколения в поколение.История ножа этого производителя также будет передана ».
Фиск отметил, что материал, из которого изготовлены эти ножи, также выделяется. «Некоторые используют высокоуглеродистую сталь или автомобильную пружину, или они делают свою собственную дамасскую сталь, выкованную в собственных мастерских», — сказал он. «Количество слоев может варьироваться от трех до миллиона и более. Я сделал ножей на сумму до 320 миллионов. Прямо сейчас у меня есть проверенная сталь 250-го года, сделанная из сломанного меча. Клиент просит меня выковать из него сталь в его собственный нож.Я сначала проанализирую его, чтобы увидеть, над чем я работаю, а затем начну работу над этим в следующем году. У меня есть древесина с единственного дерева, которое лично посадил Томас Джефферсон, древесина с дерева, которое посадил Джордж Вашингтон, и т. Д. У меня есть много исторических материалов, некоторым из которых тысячи лет ».
Кроуэлл сказал, что есть много причин, по которым его привлекает историческое ремесло, которое имеет такие давние корни в Арканзасе. «Создание чего-то красивого и полезного собственными руками и навыками кажется мне самым достойным делом… Что-то цельное, что прослужит много поколений», — сказал он.«Мне также нравится, что это можно сделать без электричества и современных удобств. То, что мы делаем, реально, а не где-то на электронной машине. Я делаю ножи вот уже 36 лет и 31 из них я был мастером-кузнецом ABS и сертифицированным инструктором. Я никогда не ожидал, что это станет делом моей жизни много лет назад. Я считаю, что эта работа стоит того, и ей нет конца. Всегда есть чему поучиться у стольких людей, которые так щедро тратят свое время и знания ».
Испытательный стальной лом для изготовления ножей
Большая часть истории была выкована из стали, у которой не было определенного номера или определенного списка ингредиентов.Исторические кузнецы интерпретировали качество и свойства стали исключительно на основе тщательного наблюдения и простых процедур тестирования.
По сей день японские кузнецы мечей работают исключительно с ненумерованной сталью, изготовленной из древесного угля и железного песка в традиционных плавильных печах. Их обучают и практикуют в искусстве понимания стали, внимательно изучая ее в различных условиях. В этой статье мы обсудим несколько основных методов, которые можно использовать для определения пригодности куска неизвестной вторичной стали для изготовления ножей.
Обзор стали
Исторический тест
Тест файла
Искровой тест
Испытание на разрыв
Forge Test
Yaki-Ire Test
Blade Test
Сталь Обзор
Простая сталь — это сплав, состоящий в основном из железа с очень небольшим количеством углерода (обычно менее 1%) и часто других легирующих металлов в небольших количествах. Стали с большим содержанием других ингредиентов будут вести себя совсем иначе, чем простые стали, и могут затруднить получение достоверных результатов с использованием традиционных методов.
Современная простая высокоуглеродистая сталь для изготовления ножей обычно содержит 0,5% -1,0% углерода, а подавляющее большинство остального составляет железо. Часто присутствует некоторое количество марганца, которое способствует повышению прочности, но слишком большое его количество может увеличить глубину затвердевания и затруднить контроль над хамоном.
Первоначальной целью описанных здесь испытаний является удаление нежелательных сплавов из кучи металлолома. Сталь с содержанием углерода около 0,3% или менее является конструкционной или мягкой сталью и не затвердевает до образования надлежащего хамона или прочной режущей кромки (хотя это полезный практический материал для обучения ковке).Кованое железо почти не содержит углерода и не твердеет. Чугун хрупкий, и его нельзя ковать без раскалывания. Инструментальные стали и специальные стали с большим количеством других легирующих ингредиентов могут вести себя как простая углеродистая сталь в одном испытании, но не в других.
Второстепенная цель — установить характеристики подходящей стали путем тестирования различных подходов к термообработке и отпуску. В относительно контролируемых условиях и повторных испытаниях некоторые аспекты температуры или размещения глины могут быть уточнены и адаптированы к каждой конкретной части стали.
Исторический тест
Исторический тест — это, безусловно, самый простой способ удалить большинство нежелательных материалов из потенциального лома. Идея теста состоит в том, чтобы начать с определения характеристик предметов на основе их первоначального дизайна и использования в прошлом. В большинстве случаев четкая идентификация в историческом тесте позволяет сразу перейти к кузнечному тесту.
Если предмет раньше использовался как пружина, режущий инструмент или износостойкая деталь, он может иметь правильную долю углерода, чтобы сделать полезное лезвие.Пружины могут иметь форму подвесных листов или спиралей, а также сельскохозяйственных частей, которые необходимо изгибать и возвращать, например, грабли для сена. Режущие инструменты включают напильники, рашпили, долота, пилы и газонокосилки. Износостойкие детали часто связаны с сельским хозяйством и могут включать зубья бороны, лемехи, зубья культиватора и подшипники. Обратите внимание, что чрезвычайно износостойкие стали, такие как пластины грейдера, бесполезны, так как их очень трудно подпиливать и полировать.
Лезвия косилки, пилы, вилы и несколько лемехов ржавеют в куче хлама в прерии.Тест файла
Тест файла дает представление об относительной твердости. Используя напильник на незащищенном от ржавчины углу образца, степень прикуса может указывать на содержание углерода в закаленном куске стали. Если файл может легко вгрызаться и изменять форму материала, возможно, используется мягкая сталь, но в той степени, в которой файл скользит или скользит по поверхности и не может врезаться, материал будет твердым и, вероятно, с более высоким содержанием углерода.
Как и в случае с другими тестами, практика и последовательность важны для достижения надежных результатов.Сравнение неизвестного образца с известными образцами — эффективный способ сузить возможный диапазон твердости. Обратите внимание, что твердость является показателем содержания углерода только тогда, когда сталь находится в закаленном состоянии, и испытание напильником дает наилучшие результаты в сочетании с испытанием на разрыв.
Использование напильника для проверки твердости кромки и корешка другого напильника, выкованного в лезвие.Искровой тест
В других местах много написано о методе, известном как искровое испытание, поэтому в этой статье он упоминается лишь вскользь.В большинстве случаев этот тест часто можно обойти, используя тест истории или файл, а затем переходя непосредственно к тесту на разрыв для более точного подтверждения количества углерода в образце.
Этот метод используется не столько для обработки стального лома, сколько для блюминга и плавки, но могут быть случаи, когда необычный предмет из черных металлов не может быть четко дифференцирован между чугуном, углеродистой сталью или мягкой сталью, и этот быстрый тест может оказаться полезным. .
Идея искрового теста состоит в том, чтобы определить приблизительное количество углерода, наблюдая за цветом, формой, длиной и типом искры, выбрасываемой шлифовальным кругом.Эффективное и последовательное использование этого теста требует практики и повторения.
Типичная диаграмма искрового испытания, длина, форма, цвет, интенсивность и стиль — все это подсказки.Испытание на разрыв
Если исторический тест не дал результатов или количество углерода все еще остается под вопросом, следующим шагом является тест на разрыв. Испытание на разрыв можно проводить без ковки для тонких изделий, разрезав наполовину абразивным кругом (аналогично испытанию на разрыв), но лучше всего сначала выполнить ковку.
Небольшой уголок, образец или конец материала выковывают до толщины примерно 2-3 мм, ширины примерно 1 см и длины 3 см. Вся зона испытания нагревается до немагнитного состояния и закаливается в воде для придания ей максимально возможной жесткости. Испытуемый участок зажимают в тисках и сгибают или ударяют молотком до тех пор, пока он не сломается или не загнется под углом 90 градусов.
Если деталь отломилась, не погнувшись, она может считаться высокоуглеродистой. Если он изгибается, не ломаясь, его можно рассматривать как низкоуглеродистый, а если он ломается через некоторое время после частичного изгиба, это, вероятно, что-то среднее.Изучение характера разрыва может дать дополнительные сведения о размере зерна, а разрыв волокна может указывать на некоторую форму стали, работающей на сдвиг. В большинстве случаев изготовления ножей только сталь, которая легко отламывается, будет достаточно твердой, чтобы получить хорошую режущую кромку.
Испытание на холодный разрыв проводится в центре срезной стальной листовой рессоры (две нижние части) для определения собственной зернистой структуры перед ковкой. Сравните размер зерна с обрезанными кончиками хвостовиков (две верхние части) после ковки.Кузнечный тест
Если кусок стали уже прошел испытания, следующим этапом является изготовление из него небольшого испытательного лезвия или его части. Цель этого испытания — увидеть, как сталь движется под действием молотка и реагирует на формование. Этот тест может помочь устранить странные стальные сплавы, такие как закалка на воздухе и быстрорежущие стали, к которым сложно применять традиционные методы.
Следует помнить о жесткости, трещинах, коротких замыканиях и линейных включениях, а также о сильной точечной коррозии и ограничениях исходных размеров.Охлаждение на воздухе или отжиг с последующей опилкой также может выявить некоторые стали, закаленные на воздухе или чрезвычайно износостойкие. Если материал проходит испытание на разрыв, но имеет линейные трещины или наслоения, как у кованого железа, это может быть форма стали, работающей на сдвиг.
Ковка небольшого испытательного лезвия для определения пригодности стали перед попыткой более крупного проекта.Тест Яки-Ире
Следующим этапом является испытание на пригодность стального образца для дифференциального упрочнения с использованием небольшой испытательной лопатки или секции, созданной в ходе кузнечного испытания.Некоторая грубая форма и очистка выполняются напильником, затем наносится глиняная смесь и дается высохнуть. Тщательный нагрев и закалка стали в контролируемых условиях поможет определить, выдерживает ли сплав традиционную закалку в воде.
Если лезвие выдерживает закалку и испытание напильником указывает на соответствующую твердость, следующий пункт, который необходимо проверить, — это внешний вид и расположение линии хамона с использованием грубого водяного камня. Если хамон хорошо виден рядом или ниже места размещения глины, эта сталь хорошо чувствительна к яки-гневу.Если она мутная, отсутствует или находится намного выше места размещения глины, с этой сталью будет труднее работать.
Сталь с более высоким содержанием марганца затвердеет глубже, и хамон окажется на лезвии намного выше, чем глина. Это может быть компенсировано до некоторой степени, перемещая пластилин вниз, но это может привести к потере деталей и качества возврата.
В качестве дополнительного шага файлы испытаний на твердость могут дать приблизительное представление о разнице между позвоночником и кромкой и помочь определить, нуждается ли процесс закалки в модификации для рассматриваемой стали.Повторение теста яки-ире при разных температурах и с разным темпом отпуска может помочь выбрать лучшую комбинацию для определенного куска стали.
Закалка небольшого тестового лезвия. В идеале расположение хамона должно быть рядом с местом размещения глины, а не высоко на лезвии.Тест лезвия
Заключительный этап — изготовление лезвия из стали от начала до конца, применяя информацию, полученную в предыдущих тестах. Лезвие можно использовать для испытаний и эксплуатационных испытаний в реальных условиях, чтобы определить пригодность стали для определенных целей.Некоторые области, о которых следует знать, могут включать в себя заточку, удержание кромки, геометрию, твердость, ударную вязкость и устойчивость, а также эффективность для различных типов задач резания.
Затраты времени, необходимого на этапах тестирования, в частности, на ковку, яки-ire и испытания лезвия, могут сэкономить время, материалы и нервы в долгосрочной перспективе. Повторные испытания также могут помочь в определении наилучшего сочетания температур и методов для получения наилучшего возможного лезвия из каждого сырья.
Правильно выкованное, закаленное и обработанное лезвие будет работать так, как задумано, а полная полировка, наконец, раскроет все уникальные внутренние механизмы каждого переработанного куска стали.С помощью нескольких простых методов, внимательного наблюдения и прилежной последовательности можно оценить характер и качество неизвестного куска стали для целей исторического изготовления ножей.
Часто задаваемые вопросы — Все о Laguiole.
Многих из вас интересуют одни и те же вещи:
Как выбрать нож Laguiole?
Какую ручку выбрать для Laguiole?
Какой тип лезвия мне выбрать?
Итак, чтобы ответить на все ваши вопросы, мы попросили наших мастеров-производителей столовых приборов внести свой вклад, чтобы мы могли предоставить вам все необходимые ответы!
Выбор ножа.
Выбор ножа — общие замечания.
Как выбрать Laguiole? Какой карманный нож выбрать? Если вы хотите купить складной нож, при принятии решения следует учитывать несколько критериев. Во-первых, его размер, который обычно колеблется от 7 до 13 сантиметров. Размер ладони — решающий фактор. В зависимости от использования складного ножа, вы можете выбрать из нескольких типов лезвий, например, карбоновое лезвие, практичное и дешевое.Отвал Sandvik — самый распространенный и самый прочный. Лезвие должно быть твердым и прочным. Наконец, ручка придаст вашему ножу форму и дизайн.
Рукоять может быть изготовлена из палисандрового дерева, морского ушка (моллюсков), палисандра или оливкового дерева в зависимости от вашего бюджета и ваших пожеланий.
Если нож используется для еды или приготовления пищи, стоит отметить, что, помимо ручки и лезвия, нож состоит из других частей, таких как чешуя. Это внешние части ручки.Чешуйки сделаны из дерева, прочности, смолы, кости… Они прикрепляются к ножу и придают ему неповторимый вид и неповторимый стиль.
Как выбрать размер ножа Laguiole?
Для карманного или сумочного ножа рекомендуется использовать нож диаметром 9 см.
Размер в сложенном виде: 9 см.
Размер в разложенном виде: 17 см.
Нож длиной 10 см поместится в любую руку.
Размер в сложенном виде: 10 см.
Размер в разложенном виде: 20 см.
Нож длиной 11 см поместится в любую руку.
Размер в сложенном виде: 11 см.
Размер в разложенном виде: 20 см.
Для больших мужских рук рекомендуется нож длиной 12 см.
Размер в сложенном виде: 12 см.
Размер в разложенном виде: 22 см.
Все, что нужно знать о ручках.
Существует два типа ручек из рога:
Древесина обычно лучше справляется с изменениями температуры и течением времени. Даже если оба материала могут получить новую жизнь, если их аккуратно отшлифовать и позаботиться о них.
Мы используем несколько типов рожков:
Коровий рог и бараний рог.
Выходит из твердой верхней части рупора. Он может быть белым (рог коровы или барана) и переходить от полностью белого к темно-бежевому («пламенный рог»).Он может быть темным (рог буйвола) от темно-бежевого до сплошного черного.
Рога ручки.
Рога оленя, косули, лося или вапити издавна использовались для изготовления инструментов и оружия.
Олени ежегодно отращивают рога и теряют рога, а это значит, что животному не причиняется никакого вреда. Панты — прочный, красивый и недорогой материал. Рога прочные и простые в использовании, поэтому они популярны в утилитарных конструкциях.
Для ножей Laguiole доступно множество материалов рукоятки:
Stamina изготовлена из цветного дерева, внутрь которого была введена полностью тонированная смола. Stamina — это сверхпрочный материал: он способен выдерживать испытание временем и суровыми условиями (грязь, влажность, удары …) намного лучше, чем стандартная деревянная ручка. Прежде всего, выносливость сохраняет свою форму, несмотря ни на что, и в то же время предлагает вам безупречный внешний вид и превосходные цвета. Это идеальный вариант, если вы хотите деревянную ручку без недостатков.
Все, что нужно знать о лезвиях.
Все зависит от предполагаемого использования и того, сколько усилий вы готовы приложить, чтобы ухаживать за своим ножом.
Карбон подвержен ржавчине, поэтому после использования его необходимо тщательно протереть. С другой стороны, сталь не ржавеет и требует меньшего ухода.
Чаще всего мы используем сталь и нержавеющую сталь.
К сожалению, карбон со временем ржавеет и темнеет. Поэтому такие лезвия требуют тщательного ухода.Их нельзя оставлять в контакте с влажностью. Однако по сравнению с нержавеющей сталью углерод затачивается намного лучше.
Если вы хорошо ухаживаете за своим ножом и тщательно протираете его после каждого использования, то предпочтительнее выбрать карбоновое лезвие для гниды.
Если вы дарите нож тому, кто не разбирается в ножах, то лучше выбрать стандартное лезвие из нержавеющей стали.
Выбор угольного лезвия происходит на этапе 4 нашего модуля настройки.
85% ножей, которые мы продаем, имеют лезвие из нержавеющей стали, а 15% — из карбона. Эти цифры легко объяснимы: за ножами из нержавеющей стали проще ухаживать: это выгодная покупка!
Углеродное лезвие по цене точно так же, как лезвие из нержавеющей стали. Фактически, вы можете заказать один на все наши ножи. Мы собираем ножи с угольным лезвием только по специальному запросу. Единственное изменение касается времени обработки, которое увеличилось примерно на 2 недели, так как это особый производственный процесс.
Самая известная сталь для лезвий ножей — это сталь 440 , которую любители Opinel и Laguiole из числа наших дедов хорошо знали и любили. Этот сплав очень легко затачивался с помощью любого точильного камня или прута. Но классическое лезвие из стали 440 со временем темнеет, и его следует полировать, полировать, никогда не мыть под водой и регулярно протирать тканью, чтобы избежать ржавчины.
В те времена потемнение лезвия могло испачкать пищу людей и придать ей металлический привкус, но в то время на это никто не обращал внимания, и люди обходились.
С тех пор стали развиваться сплавы, и металлообрабатывающая промышленность создала сталь, которая лучше подходит для повседневного использования. Все это говорит о том, что сталь 440, которая теперь называется 440 нержавеющая сталь л, является современной версией стали наших предков. В настоящее время это также самый распространенный сплав. Лезвие из нержавеющей стали белого цвета не темнеет, его не так просто затачивать, но по сравнению с полученным качеством этот недостаток минимален.
Затем появилась сталь 12С7 .Он очень популярен прямо сейчас, поскольку предлагает лучшее из обоих миров без недостатков (прост в обслуживании и не нужно беспокоиться о ржавчине)
Примечание: Что касается карманных ножей Laguiole, стальное лезвие 440C по-прежнему гарантирует высокое качество для частого повседневного использования.
Шкала Rockwell HRC: испытание, которое заключается в измерении глубины проникновения стальной нагрузки для измерения твердости металлов
53-54 HRC и выше считаются приемлемыми значениями твердости для лезвия ножа
Выше 58 -60 HRC, это очень качественное лезвие
Однако имейте в виду, что очень твердое лезвие будет труднее затачивать.
Несмотря на то, что в былые времена характерный щелчок, который сопровождал складывание ножей Laguiole, остался в прошлом.
На самом деле, в те времена ножи Laguiole не оснащались стопорными штифтами. В результате, лезвие держал удар механизм блокировки слишком сильно и быстро стал тупым. Лезвие лезвия необходимо регулярно затачивать.
Для того, чтобы не допустить этого, современные Laguioles снабжены механизмом стопорного штифта блокировки.
Стопорный штифт — это небольшой металлический элемент, вставленный в механизм блокировки возле пятки, который предохраняет лезвие от щелчка.Таким образом, лезвие лезвия больше не задевает фиксирующий механизм, когда вы складываете нож. Щелкающий звук все еще слышен (для тех, кто испытывает ностальгию), но лезвие теперь защищено.
Нож Laguiole должен также «понсетер», то есть показывать правильное натяжение в запирающем механизме. Проверить это несложно: все, что вам нужно сделать, это аккуратно надавить на сложенное лезвие. Вы должны почувствовать легкую эластичность, свидетельствующую о правильно сбалансированном натяжении между лезвием и запорным механизмом.Если вы посмотрите на другую сторону ножа, вы увидите, что лезвие идеально отцентрировано / между двумя вкладышами. Настоящее произведение искусства !
Вопросы по дамасской стали.
Это выражение относится к мерцающим муаровым кускам ткани, сотканным в городе Дамаск, а не к лезвиям, которые там выковывались.
Поковка из дамасской стали — это способ рафинирования чугуна посредством чередования операций штамповки, складывания и вытягивания.Эти шаги направлены на избавление от примесей в металле. Таким образом, композитный материал создается с последовательностью более или менее однородных слоев, обычно комбинаций железа, стали или никеля.
Неоднородная текстура обеспечивает исключительные механические качества, потому что дамасская сталь может быть только частично закалена (ни железо, ни никель). В результате металл сопротивляется разрушению за счет дифрагирующих ударных волн.
Есть несколько методов ковки дамасской стали:
Западная техника или техника Меровингов.
Его использовали кузнецы Меровингов, этот процесс, который заключался в изменении формы металла, по необъяснимым причинам был утерян к концу 11 века.
Восточная дамасская сталь или плавленая Дамасская сталь является воплощением дамасской стали.
Wootz для кузнецов то же самое, что Философский камень для алхимиков, но, несмотря на продолжающиеся усилия, кажется, что до сих пор никому не удавалось воссоздать этот чрезвычайно сложный процесс изготовления.
Японский Дамаск — это тип, который встречается в наши дни.
Ковка путем штамповки и вытягивания.
Первоначально тысячи слоев, составляющих лезвия мечей, постепенно уменьшились до нескольких сотен. Действительно, если больше, текстура становится слишком плотной, и кислотное травление больше не дает эстетически приятных результатов.
Помимо бесспорных механических свойств лезвий из дамасской стали, важно подчеркнуть их красивый внешний вид.
За композитным качеством материала скрываются многочисленные анаморфные возможности, которые зависят как от сгибания и вытягивания, так и от глубокой обработки (например, лепки) металла.
Как только элемент из дамасской стали приобрел желаемую форму, все, что остается сделать, это погрузить его в кислоту, которая чернеет только углерод и, таким образом, раскрывает структуру металла.
Нержавеющая дамасская сталь, тем не менее, с высоким содержанием углерода, изготавливается из порошковой стали (очень мелкое зерно, прочная кромка), поскольку внутреннее механическое качество металла позволяет проводить очень жесткую закалку (до 63-4 Роквелла) после криогенизации.
Объективно говоря, дамасское лезвие тверже (63-4 Rockwell), чем стандартное лезвие (58-60 HRC), но всегда имейте в виду, что чем тверже лезвие, тем сложнее его заточить.
После того, как дамасскому элементу была придана его предполагаемая форма, все, что остается сделать, это погрузить его в кислоту, которая только чернит углерод и, таким образом, раскрывает структуру металла. И кислоты, и сама техника требуют мастерства и специальных ноу-хау, что также объясняет цену лезвий из дамасской стали.
Несомненно, есть фальшивомонетчики, которые продают лезвия с лазерной гравировкой как лезвия из дамасской стали, но они прилагают много усилий, чтобы добиться успеха. Однако да, действительно, существуют лезвия с декоративной лазерной или кислотной обработкой поверхности.
Во время полировки нормально, что рельефы и узоры, образовавшиеся во время первоначального кислотного травления (которое показывает структуру различных слоев в зависимости от их состава), несколько тускнеют.
Ванна с перхлоратом железа позволяет выполнять травление без особого риска.Мы настоятельно не советуем играть с кислотами, перхлорат гораздо менее опасен.
Для идентификации дамасского ножа хорошим показателем является цена. Если ваш «дамасский» нож стоит в районе 20-30 евро, не более (в зависимости от честности продавца), это явно не настоящий дамасский нож.
Подставки, пчелы и пружины.
Муха — это технический термин, обозначающий часть пружины, которая упирается в лезвие, когда нож разложен.
Форма пчелы на Laguiole — отличительная и традиционная особенность ножа Laguiole.
До 1935 года пчелу всегда выковывали, а это означало, что пружина и пчела были сделаны из одного и того же куска металла. Этот результат был получен горячим прессованием куска металла.
С развитием промышленного производства столовых приборов во Франции появились спаянные пчелы — результат более простого и быстрого процесса.
Кованая пчела всегда более устойчива, чем паянная, учитывая, что технические качества цельного куска металла намного превосходят характеристики двух спаянных вместе элементов.
В результате спаянные пчелы присутствуют в стандартном ассортименте складных ножей. Кованые пчелы украшают высококачественные ножи с изысканной отделкой.
Муха — это технический термин, обозначающий часть пружины, которая упирается в лезвие, когда нож разложен.
Существует также легенда, согласно которой Наполеон дал авейронским мастерам столовых приборов использовать пчел в знак их храбрости в бою. На самом деле причина больше связана с эстетическими и риторическими соображениями.
Даже если у пчелы лучшая репутация, чем у мух, «муха» — это, прежде всего, техническое слово при изготовлении столовых приборов, относящееся к сплющенной части пружины. Это передний конец пружины. Он может изображать не только пчелу, но и подкову, клевер, гребешок, лилий или вашу собственную эмблему (мы также можем настроить этот элемент по запросу).
Теперь вы знаете, что вас не угостят!
Пружина в центральной части рукоятки позволяет складывать и раскладывать лезвие. Стальной элемент складного ножа напротив лезвия.
Самыми известными являются скользящие соединения: пружина помещается в верхней части рукоятки между двумя вкладышами и давит на пятку лезвия, чтобы оно оставалось открытым или сложенным.
Пружины могут быть коваными, выточенными и закаленными, что придает им твердость и гибкость. Пружина регулируется мастером по изготовлению столовых приборов, чтобы лезвие не ударялось по ней в сложенном состоянии.
Не все складные ножи оснащены пружинами, удерживающими лезвия на месте.Capucin, очень простая конструкция, имеет только два гвоздя, в то время как Piemont имеет систему трения, поддерживаемую положением большого пальца пользователя на пятке лезвия. Что касается знаменитого Opinel, скользящее кольцо обеспечивает фиксацию лезвия на месте.
Общая анатомия ножа Laguiole.
Настройка ножей Laguiole.
Настройка может принимать различные формы.
Вы можете заказать нож на заказ и выбрать все составляющие его элементы: размер, со штопором или без него, рукоять из дерева разновидностей, рог, морское ушко, камень, пружинный тип (тыльная сторона ножа), гравировка на лезвии.Этот процесс настройки доступен на нашей странице «складной нож по индивидуальному заказу». Время обработки дается вам, как только вы закончите выбирать свои варианты.
Вы также можете выбрать нож в магазине Actiforge и получить на лезвии гравировку с надписью или изображением по вашему желанию.
Общие вопросы по гравировке.
Чтобы сделать ваш Laguiole поистине уникальным, вы можете настроить его индивидуально. Мы предлагаем множество вариантов гравировки и рисунков, чтобы сделать ваши лезвия уникальными.
Это естественно, что вам нужен уникальный нож, поэтому наши производители столовых приборов предлагают широкий выбор вариантов индивидуальной настройки.
На клинке можно выгравировать инициалы, имя, особую дату или выбрать один из доступных символов: знаки зодиака, музыкальные инструменты, спорт… Выбор за вами.
Помимо лезвия, вы также можете выгравировать пружину (на задней части ножа) с вашим именем, фамилией или названием вашей компании и передать их своим сотрудникам.
Знаете ли вы: мы также можем изготовить ножи для сомелье по индивидуальному заказу. Идеально, если вы производитель вина или торговец вином: ваш профессиональный инструмент выгравирован вашим брендом!
На любой вкус, однако вы можете попросить нашего совета, и мы дадим вам свое честное мнение о окончательном виде вашего индивидуального дизайна.
Есть несколько способов гравировки вашего изделия Laguiole.
Мы можем нанести на нож имя, дату или фотографию с помощью лазерной гравировки на лезвии.Он не исчезнет. Это делается на лезвии вашего ножа или на стороне рычага на ножах Laguiole sommelier.
У нас также может быть ваш нож с выгравированными символами:
Знаки зодиака.
Символы любви: сердце — амур — переплетенные сердца — инь / янь.
Эмблемы регионов: Бретань, Эльзас, Корсика, Овернь.
Спортивная символика: теннис — парусный спорт — гольф …
Музыкальные мотивы: скрипка — музыкальная нота…
Фантастические символы: улыбка — бабочка — счастливый клевер.
Вы можете выбрать оба варианта. Нож будет индивидуализирован с именем и символом.
Время гравировки зависит от того, что вы выбрали.
Время гравировки имени или короткого сообщения, выгравированного лазером на лезвии (максимум 2 строки): до 24 часов после размещения заказа.
Время гравировки для взаимосвязанных инициалов, выгравированных лазером на лезвии (максимум 3 буквы): до 24 часов после размещения заказа
Время гравировки для весенней гравировки (задней части ножа): 15 дней
Вы также можете пришлите нам изображение, которое вы хотите выгравировать.Все, что вам нужно сделать, это отправить его нам в электронном виде в формате JPG. Наилучшие результаты достигаются при использовании стилизованного изображения без фона. Для этого варианта гравировки требуется 5 дней.
Вопросы по гравировке лезвия.
Если я выберу гравировку лезвия с именем — оно будет на правой или левой стороне лезвия?
По умолчанию гравировка выполняется на левой стороне, ближе всего к ручке.
Да, на наших лезвиях возможна гравировка на обеих сторонах, но на одной стороне уже есть упоминание «Laguiole».Поэтому мы рекомендуем наносить гравировку на пустую сторону лезвия.
Можно выгравировать лезвие из дамасской стали, но мы не рекомендуем этого делать. Действительно, дамасский узор уже украшает клинок — добавление гравировки только умалит его красоту.
Технически возможно, но не очень хорошо.
Вопросы по гравировке пружин.
Возможна индивидуальная настройка ножа на пружине (спине).
Как я могу выгравировать пружину (верх) моего ножа?
Буквы вытравливаются вручную на пружине, по запросу, перед закалкой. Затем ваш нож собирается из выбранных вами компонентов.
Заказать гравировку пружины ножа можно на странице «Настройка ножа».
Можно ли выгравировать строчные буквы на пружине или можно только прописные?
Можно выгравировать строчные буквы, но мы не рекомендуем это делать.Действительно, финальный вид слишком мал, на наш взгляд. Однако вы можете запросить его, если хотите.
Уход за Laguiole
Правильный уход за ножом важен для того, чтобы продлить ему жизнь. Вообще говоря, ручку складного ножа следует протирать, потому что деревянные ручки не любят воду.
Что касается чистки лезвия, его необходимо мыть тканью и влажной губкой после каждого использования. После того, как вы вымыли лезвие, тщательно вытрите его насухо.
Заточить лезвие — нелегкая задача для людей, которые к этому не привыкли. На самом деле, наиболее удобное решение — затачивать с помощью точильного стержня, соблюдая при этом некоторые правила, например:
Сталь вашего точильного стержня должна быть не меньше длины лезвия вашего ножа.
Во избежание травм держите пальцы за ограждением удилища.
Положите основу лезвия ножа на сталь.
Продвиньте лезвие вдоль стержня до конца и поочередно заточите лезвие с обеих сторон.
C — наконечники для ручек
Как ухаживать за ручкой Laguiole?
Для того, чтобы поддерживать вашу ручку в хорошем состоянии , независимо от их типа, вам следует избегать значительных колебаний температуры и влажности. Кроме того, не следует мыть их водой или, что еще хуже, замачивать их в любой жидкости. Для повседневного ухода достаточно влажной ткани.
Есть несколько типов ручек, которые сделаны животными:
Рога оленя
Рога (кончики или)
Кости (берцовая кость жирафа)
Зубы (бородавочник).
Рог — это деликатный материал, который требует особой осторожности при формовании. Кроме того, он очень быстро высыхает при температуре окружающей среды. Его следует увлажнить маслом для чистых стоп или каким-либо средством для ухода за кожей (светлого или темного цвета в зависимости от типа рога).Это предотвратит растрескивание и втягивание, особенно летом.
Ручки из рога, кости или слоновой кости можно очистить, втирая в них немного очищенного мела.
Ухаживайте за рукоятками из ценных пород дерева, натерев их льняным маслом для приклада. Вы также можете увлажнить их, чтобы придать им блеск: просто налейте немного оливкового масла на мягкую ткань и осторожно протрите ручку.
Знаете ли вы? Если ножом регулярно пользуетесь, пот на ладони — лучшее средство для ухода за ним.
Вы можете исправить трещины, приготовив древесный порошок того же цвета, что и ручка, которую вы хотите отремонтировать (из той же породы дерева или путем ее тонирования). Затем все, что вам нужно сделать, это смешать этот порошок с прозрачным клеем и заполнить трещины. Дайте ему высохнуть и нанесите немного воска, чтобы он сиял.
Если бы нужно было помнить только об одном уходе за нашим карманом и его обслуживании: никогда не помещайте их в посудомоечную машину и храните в сухом месте.
Советы по обслуживанию лезвий.
Никогда не оставляйте нож в контакте с другими предметами: ключами, столовыми приборами… и не храните его в сумке без защиты. Так вы повредите ручку и металлические детали.
Купите нож в ножнах, чтобы защитить его от ударов и возможных брызг. Если вы любите следить за своими лучшими лезвиями, храните их в закрытой витрине — они будут в безопасности от ударов и несчастных случаев в семье.
Для эффективной очистки достаточно просто протереть лезвие влажной тканью.
В зависимости от типа лезвия может потребоваться более специфический уход.
Карбоновые лезвия: эти лезвия могут окисляться со временем. Чтобы вернуть ему былую красоту, натрите лезвие влажной пробкой, смоченной холодным пеплом, и полюбуйтесь результатом: теперь лезвие идеально чистое. Пока вы не нарежете следующую кислую пищу…
Лезвия Damascus: В случае длительного неиспользования вы можете смазать лезвие маслом, чтобы предотвратить потерю контраста (используя некислотную смазку, такую как силиконовая смазка для сантехников или белая смазка.)
С точки зрения надлежащего ухода, мы настоятельно рекомендуем НЕ использовать посудомоечную машину для НИКАКИХ наших ножей Laguiole.
Однако, если вы твердо настроены на это, некоторые из них могут выдержать мытье в посудомоечной машине: ножи с ручкой из пластмассы или картона — но они не будут оставаться красивыми надолго. Использование посудомоечных машин с горячей водой неизбежно приведет к повреждению ваших ножей. Забудьте о подобном лечении, если вы любите свой нож.
➫ Закрыв в Lockback Laguiole нож.
Традиционной системой фиксации является обратный замок: когда лезвие открывается, оно выталкивает позвоночник наружу до тех пор, пока выемка на позвоночнике и лезвие не встанут на место.
С ножами, оснащенными системой блокировки насоса, нет смысла использовать силу для закрытия лезвия. Осторожно нажмите левой рукой, а правой рукой опустите лезвие (для правшей).
➫ Закрытие фиксатора вкладыша Laguiole
Чтобы закрыть нож Laguiole, просто слегка нажмите на насос на задней части ножа, чтобы освободить лезвие, которое затем аккуратно сложится.
Ножи плохо справляются с пылью из карманов или мешков. Фактически, вам нужно избавиться от мелких загрязнений в системе поворота вашего ножа с помощью минерального спирта (скипидара) и сжатого воздуха (например, очистителя клавиатуры). Затем вы можете добавить каплю масла в систему блокировки, чтобы она стала как новенькая.
Все остальные металлические части вашего ножа — сталь, мельхиор и латунь — вернутся к своему первоначальному сиянию с помощью полировальной пасты и хлопчатобумажной ткани! Просто и аккуратно!
Ремонт ножа Laguiole.
Если вы сами не являетесь производителем столовых приборов или хорошо разбираетесь в восстановлении ножей, не пытайтесь починить нож. Попытка может нанести непоправимый ущерб.
У нас есть гарантия на производство на наши ножи, но мы можем отремонтировать нож Laguiole, который попал в аварию (сломанная пружина или лезвие, поврежденная ручка и т. Д.)
Мы не ремонтируем поддельные ножи Laguioles.
Мы начинаем восстановление после оплаты квоты.
Время ожидания перед возвратом ножа: от 15 дней до 1 месяца.
Мы предоставляем услуги по ремонту и восстановлению ваших ножей. Чтобы наши производители столовых приборов могли:
Наши разнообразные навыки позволяют нам ремонтировать и затачивать ваши ножи Laguiole и даже некоторые другие ножи, которые могут быть у вас. Например, вы можете попросить нас восстановить нож вашего дедушки, чтобы вы могли подарить его своему сыну. Не стесняйтесь обращаться к нам, чтобы получить расценки.
➫ Что касается клинков Damascus , то процесс восстановления обычно заключается в удалении слоя окисления. Цель состоит в том, чтобы придать лезвию его первоначальный вид, например, в случаях, когда узор исчез. Избавиться от ржавчины на лезвии из дамасской стали можно с помощью химических средств, таких как использование кислот, которые могут удалить ржавчину, даже самую стойкую. Однако важно использовать мягкие кислоты, чтобы не разъедать часть металла на лезвии. Кислоты, такие как фосфорная или азотная кислоты, очень агрессивны для лезвий.В любом случае для столь тонкого дела лучше обратиться за помощью к профессионалам.
Все о заточке.
Используйте точильный камень с грубым зерном для грубого или сильно поврежденного края, затем мелкий камень для завершающего штриха или для драгоценного ножа (меньший риск, если что-то пойдет не так).
Важно: ВСЕГДА используйте воду, даже на масляном камне. Камень из Арканзаса, продаваемый вместе с бутылкой с маслом, прекрасно справится с водой, намного лучше, чем с маслом … если … если ваш камень не использовался в прошлом с маслом, вам придется продолжать использовать масло, потому что поры камня будет пропитан маслом, и я буду непригоден для использования с водой.
➫ Арканзасский камень, очень прочный камень, который существует в «твердом» (сером) и «мягком» (белом, немного более мягком) вариантах. Идеально подходит для универсального использования, если ваша кромка не слишком повреждена (в противном случае это займет много времени). Помните: используйте воду, а не масло.
➫ Камень Вильсальм: Вильсальм — небольшой город в Бельгии, где можно найти этот уникальный камень: очень тонкий, состоящий из мельчайших зерен граната, встроенных в сланец. Его используют с водой, и он не работает очень долго (крошится), но крошечные гранатовые зерна могут точить даже самую прочную нержавеющую сталь.Это также позволяет получить острую кромку без кожи, но это довольно дорого. Вы можете снова разгладить его, потерев им другой кусок камня Вильсальма, конечно, используя воду.
➫ Алмазный камень или камень DMT: очень удобен, поскольку он небьющийся, его можно использовать без воды (в экстренных случаях) и практически в любом месте (обычно помещается в карман). Его самый большой недостаток — это цена, но его можно использовать с самой прочной сталью.
➫ Камень-коса, он же синтетический камень или камень 1,50 EUR.Практичный для грубой обработки, он дает полосатую и шероховатую кромку, которая на самом деле ничего не прорезает и держится недолго.
Полезно знать: Большой камень будет проще в использовании, но к тому же будет дороже купить (который может быстро превратиться в недоступный в случае камня Вильсалм).
Короче говоря, если вы можете купить только один точильный камень, купите…. два !
➩ Один арканзасский камень, который довольно легко найти и который даст вам безупречные или даже острые лезвия, если это то, что вам нужно.
➩ Камень стоимостью 1,50 евро из местного супермаркета для необработанных алмазов или больших работ. Если вы его повредите или сломаете, вы легко с этим справитесь.
Как заточить лезвие точильным камнем?
Точильный камень должен быть влажным. Погрузите его в воду до тех пор, пока он полностью не пропитается водой и из него больше не будут выходить пузыри. Это должно занять от 5 до 10 минут.
Чтобы использовать его, держите нож под углом 20 ° к точильному камню и медленно сдвиньте каждую сторону ножа по камню несколько раз.У большинства точильных камней есть шероховатая сторона и тонкая сторона — начните с шероховатой стороны, если ваш нож особенно тупой, затем повторите процесс с тонкой стороной. Если во время работы точильный камень выглядит так, как будто он сохнет, просто налейте еще воды и продолжайте.
Посмотрите, как работают наши производители столовых приборов, в этом видео.
Другие техники заточки с использованием камня.
Еще один аксессуар, хорошо известный знатокам тонких лезвий, он также очень эффективен для заточки ножей, которые потеряли свою первоначальную кромку.
Узнайте, как использовать стержень для заточки, из видео ниже.
Карманные твердосплавные точилки невероятно прочные, поэтому они лучшие карманные точилки.
Твердосплавная точилка обрабатывает все кромки, не требуя ни масла, ни воды. Компактный, вы всегда можете иметь его под рукой, работаете ли вы, на рыбалке или в походе.
Laguiole, автор Actiforge.
Действительно ли ваши ножи сделаны во Франции? Они настоящие Laguiole?
Да и да.Наши ножи производятся в Оверни мастерами по изготовлению столовых приборов из Тьера. Их мастерство исходит от длинной линии производителей столовых приборов из Оверни, и они продолжают передавать свою страсть следующим поколениям. Конечно, некоторые производственные технологии со временем эволюционировали, но вера в то, что стоит делать, стоит того, чтобы делать это хорошо, и внимание к деталям осталось неизменным.
Какие гарантии вы предлагаете?
На все ножи Actiforge распространяется гарантия.
На складные ножи действует пожизненная гарантия.
На столовые ножи действует гарантия 2 года.
Наши ножи отправляются вам с сертификатом происхождения, так что вы можете с уверенностью знать, откуда пришел ваш нож: он был произведен во Франции!
Полезно знать: 85% наших ножей производятся в Тьере, а 15% — в Лагиоле, Аверон.
Законы и подделка.
С юридической точки зрения названия городов никому не принадлежат, поэтому они принадлежат всем. Во времена первых Laguioles никто не думал о регистрации бренда, и он стал частью повседневного языка, даже больше, чем бренд.
Изобретенные в 1829 году Пьером Кальмелсом в Лагиоле, они были изготовлены местными мастерами, которые отметили их своими именами, каждый из которых был известен своей преданностью делу. Тогда никто и представить себе не мог, что слава этого ножа будет расти веками!
Нас часто спрашивают: «Как я могу проверить подлинность ножа Laguiole?»…
Можно так много сказать… Это видео резюмирует все эффективно и кратко.
Торговая марка Laguiole не подпадает под IGPIA (французский лейбл, который означает промышленное и кустарное защищенное географическое указание).Действительно, бренд «Laguiole» никогда не создавался, потому что владелец бренда Laguiole должен был иметь возможность продемонстрировать, что потребители знают эти ножи исключительно благодаря ему или ей. Очевидно, это невозможно.
Поэтому китайский нож можно назвать Laguiole. Потребители, желающие покупать качественные ножи, должны быть очень осторожны.
Юридические аспекты Actiforge Laguiole.
Хотите знать, действительно ли наши Laguiole французские? Мы не стали ждать запуска стандарта IGPIA в 2014 году, чтобы подтвердить происхождение нашего производства столовых приборов.
Мы не стали ждать, пока PGI подтвердят подлинность наших ножей .
Каждый год Bureau Veritas инспектирует нашу компанию , чтобы гарантировать, что наши ножи Laguiole качественно и действительно произведены во Франции, в Тьере. Так мы получили , этикетку Origine France Garantie .
Что такое IGPIA?
IGPIA (французское сокращение от Industrial and Artisanal products Geographic Protected Indications) позволяет потребителям знать, поступает ли не агропродовольственный продукт из определенной географической области, когда качество, репутация, мастерство или другие характеристики продукта могут существенно отличаться. связано с указанным географическим происхождением.IGPIA также сертифицирует область производства или обработки: все должно быть спроектировано и произведено в одном и том же географическом районе.
Вопросы о настоящих или поддельных Laguioles?
В настоящее время некоторые ножи действительно производятся в Laguiole, но следует отметить, что большинство лезвий Laguiole производится в Thiers. Так что нет, настоящие французские ножи Laguiole производятся не только в Laguiole.
Нет, это просто украшение. К сожалению, даже некоторые ножи из Азии имеют пастуший крест.Муха, пчела или любой другой орнамент не может гарантировать качество или происхождение вашего Laguiole. Именно поэтому необходимо тщательно проверить все элементы ножа, чтобы определить его качество и надежность.
Знаете ли вы? — Крест пастыря…
В нашем регионе, находящемся под сильным влиянием католической религии, когда пастухи отправлялись перегонять свои стада на летние пастбища, они вонзали лезвия своих ножей в хлеб. Крестный знак затем служил «молебен» для их молитв (иногда его также называют пастушьими четками).Вот почему это украшение находится только на одной стороне ручки.
Французское законодательство о ношении ножа.
Во Франции закон запрещает ношение любого вида ножа, который считается холодным оружием 6-й категории. Этот запрет не учитывает длину лезвия или присутствие блокирующего механизма.
Однако судебная практика французских судов считает, что ношение ножа Laguiole или ножа Opinel или швейцарского армейского ножа типичного размера не должно толковаться как ношение холодного оружия. В таких случаях ношение ножа считается частью французской традиции и разрешено. Но в зависимости от использования его можно повысить до статуса оружия.
В зависимости от обстоятельств полиция допускает, чтобы у вас был традиционный нож, если вы ведете себя нормально.
Наконец, План Vigipirate разрешает выборочные проверки в общественных местах, таких как метро и вокзалы. По соображениям безопасности в таких местах, как аэропорты, правила более строгие, и полиция может конфисковать ножи.
Общие вопросы по ножу Laguiole.
Чтобы дать вам краткую и ясную информацию, команда Actiforge составила видео, в котором рассказывается история ножа Laguiole и его эволюции на протяжении веков.
Ножи Laguiole можно производить в любой точке земного шара, однако только мастера-производители столовых приборов могут подтвердить происхождение своей продукции.
Ножи Actiforge Laguiole поставляются с сертификатом французского происхождения и пожизненной гарантией.Вы не найдете Laguiole, произведенного в Азии, с таким типом отслеживания или гарантией.
Во-первых, важно проводить различие между «производителями ножей» (наши производители столовых приборов производят различные элементы, которые вместе образуют готовый нож) и «сборщиком ножей» (некоторые люди просто собирают запасные части, изготовленные в других местах).
Итак, есть производители и сборщики, а также импортеры, но это совсем другой тип…
Ничто не мешает компании производить или собирать ножи, что объясняет, почему в популярных туристических местах продается множество ножей, иногда менее впечатляющих. качество.Будьте очень осторожны и покупайте ножи только у производителя ножей. Их легко идентифицировать, поскольку только они имеют сертификат происхождения и многолетнюю гарантию (или даже пожизненную гарантию, как у Actiforge).
Как и любой другой продукт, предназначенный для широкой публики, существует широкий ассортимент Laguioles и, следовательно, широкий диапазон цен.
Дизайн ножа Laguiole и его название унаследованы от наших предков. К сожалению, они вовремя забыли их надлежащим образом запатентовать.Через 20 лет любой продукт становится общедоступным. Срок правовой защиты истек. Его также нельзя защитить этикеткой с контролируемым обозначением происхождения, поскольку они относятся только к продуктам питания. В результате любой может называть что угодно Laguiole.
Как мне найти дорогу среди такого количества ножей?
Остерегайтесь исключительно выгодных сделок. Если вы найдете очень дешевый нож Laguiole, скорее всего, он был изготовлен очень далеко. У качества есть цена, и работу производителя столовых приборов нельзя сравнивать с работой станка: вы получаете то, за что платите.
Конечно, цена ножа может варьироваться в зависимости от его различных составляющих. Таким образом, нож с алюминиевой рукояткой будет дешевле, чем нож с рукоятью из морского ушка, а лезвие из дамасского сплава будет стоить дороже, чем простое.
Знаете ли вы: Все товары, проданные на нашем сайте, были , 100% произведены во Франции.
Сертификационный офис Veritas ежегодно проводит аудит нашей компании, поэтому наш нож Laguiole получает этикетку ORIGINE FRANCE GARANTIE.
В интернет-магазине Actiforge или в магазине столовых приборов — в Тьере или Лагиоле, конечно же !
Как узнать Laguiole? Как узнать, что нож настоящий Laguiole? Нам часто задают эти вопросы!
Не существует настоящих или поддельных Laguiole, поскольку Laguiole не является брендом.
Laguiole — это название деревни, отсылающей к традиционному дизайну ножей.
Слово Laguiole не подлежит правовой защите.
Laguiole получил статус «общего слова» апелляционным судом Риома в ходе судебного иска, поданного производителями столовых приборов в защиту имени.
Некоторые недобросовестные торговцы воспользовались этой правовой лазейкой, чтобы использовать репутацию высокого качества, приписываемую этому ножу, для продажи посредственных импортных товаров или даже предметов, не имеющих ничего общего с производством столовых приборов!
Это видео дает вам больше информации о том, как проверить происхождение и качество ножа. В нем перечислены различные предметы, которые необходимо проверить перед покупкой ножа Laguiole.
Сыр Laguiole производится из цельного сырого молока на плато Обрак в южной части Центрального массива.
Как и любой уважающий себя сыр, Laguiole лучше всего подавать в конце еды. Местное красное вино, например, крепкое AOC Marcillac, VDQS ENtraygues, гладкое и шелковистое Le Fel, или даже свежий фруктовый Estaing, сотворит чудеса. Если вы предпочитаете вина Роны, прекрасный сыр Сен-Жозеф или Бруийи должен превосходно дополнить этот сыр Овернь.
Дизайн ножа Laguiole и его название унаследованы от наших предков. К сожалению, они вовремя забыли их надлежащим образом запатентовать.
Через 20 лет любой продукт становится общедоступным. Срок правовой защиты истек. В результате любой может называть что угодно Laguiole.
Он также не может быть защищен этикеткой с контролируемым указанием происхождения, поскольку они применяются только к пищевым продуктам.
Краткое изложение судебной саги о Лагиоле .
В 1993 году Гилберт Шайнер, проницательный бизнесмен из Валь-де-Марн, регистрирует торговую марку Laguiole. Это касается не только столовых приборов, но и множества других предметов: белья, одежды, зажигалок, барбекю…
Деревня Лагиоле отказывается допускать использование своего названия и возбуждает судебный процесс.В 2012 году , несмотря на многочисленные процедуры, поданные городом Лагиоле, суд поддержал позицию Гилберта Шайнера, поскольку «Laguiole» — это существительное, используемое для обозначения ножа, который теперь является частью повседневного языка и без любая очевидная и прямая ссылка на город Лагиоле ‘Затем деревня подает другой, более широкий иск по поводу своего названия — люди Оверни никогда не сдаются!
В постановлении, вынесенном 4 апреля 2014 года, апелляционный суд Парижа отклонил требования города Лагиоле , который хотел, чтобы судебная система признала, что имела место «вводящая в заблуждение коммерческая практика» и нанесение ущерба его названию, имиджу и репутации ».
М. Шайнер может продолжать распространять в обмен на деньги лицензий французским или иностранным компаниям, которые затем могут продавать импортные товары под названием «Laguiole».
Однако жители Laguiole не могут использовать свое имя. деревня больше не будет производить промышленные товары с этикеткой «Laguiole», за исключением пчелиного ножа, который уже производится за пределами деревни.В 2018 году началась новая битва, в которой противостоят сторонники Laguiole PGI
Laguiole Knife Guidelines — Laguiole Imports
Выгравированная на ноже торговая марка не является гарантией качества и не является дорогой на вид упаковкой! Внимательно изучите свою покупку и спросите продавца о ее качествах.Если ваш продавец знает свое дело, вы узнаете все, что вам нужно знать.
Самые настоящие ножи Laguiole, конечно же, производятся из Laguiole , и ручная обработка каждого ножа занимает много времени. Если вы видите, что Laguiole продается по низкой цене, это означает, что он «массово производится» во Франции или, к сожалению, в некоторых других странах. На рынке больше подделок, чем настоящих французских ножей ручной работы Laguiole.
Если нож имеет приятный эстетический вид (без каких-либо пластиковых украшений!), Он «весит». рука и приятный на ощупь захват, вы на пути к покупке достойного продукта.Обратите внимание на толщину и прочность всех металлических компонентов, включая массивные, а не полые валики на концах ручки. Затем убедитесь, что лезвие легко открывается и расположено перпендикулярно пружине (держите его перед собой и прищуривайте вверх по длине — вы должны увидеть прямую линию).
Когда вы снова закроете лезвие, оно не должно стучать или зацепляться за основание пружины и должно легко возвращаться на место.
Пластины, закрывающие гильзу ножа, должны быть хорошо подогнаны.