виды, способы контроля и устранения
Сварные металлоконструкции активно используются в разных сферах жизнедеятельности. Но в процессе сваривания отдельных элементов в цельные конструкции могут возникать дефекты сварных швов и соединений, которые негативно сказываются на прочности и безопасности эксплуатации готовых металлоизделий.
Что такое дефекты сварных соединений
Размерные параметры сварного соединения четко определены государственными стандартами, при этом свой ГОСТ есть у каждого вида сварки. Любые отклонения от установленных нормативно-техническими документами показателей считаются дефектами. Возникают они как при проведении сварочных работ, так и при нарушении требований в процессе подготовки соединяемых элементов и сборке конструкций в единое целое.
Виды дефектов сварочных швов
В силу разных обстоятельств сварочные стыки могут иметь повреждения, влияющие на их прочностные характеристики. Все виды дефектов сварных соединений разделяются на три основные группы:
- внутренние дефекты. Это может быть некачественное сплавление металла, пористость и трещины, сторонние включения (оксидные, шлаковые и неметаллические) и другие, находящиеся внутри шовного соединения;
- сквозные дефекты. Сюда относят трещины, подрезы, прожоги и другие повреждения, которые изнутри проходят на внешнюю поверхность сквозь шовное соединение.
Дефекты любого вида не допускаются в сварных соединениях и подлежат устранению, особенно касается это случаев, когда металлоконструкции выступают составляющими элементами несущих конструкций и должны выдерживать интенсивные нагрузки.
Характеристики и причины основных дефектов сварки
Не в каждом случае качество сварки соответствует установленным требованиям. Классификация дефектов сварных соединений в полном составе изложена в ГОСТ 30242-97. Но среди всех обозначенных в документе изъянов выделяют основные, которые чаще обычного выявляются при контроле и обследовании соединительных стыков.
Трещины
Для сварочных швов наибольшую опасность представляют трещины. Они способны спровоцировать мгновенное разрушение металлических конструкций и привести к трагическим последствиям.
Причинами появления трещин могут быть:
- неправильное расположение стыков;
- резкое охлаждение места сварки;
- неправильный выбор материалов;
- кристаллизация металла вследствие чрезмерно высоких температур.
По размеру различают микро- и макротрещины, по типу образования – поперечные, продольные и радиальные.
Вне зависимости от видов и причин возникновения трещины – это недопустимые дефекты сварных соединений металла.
Подрезы
Превышенная величина сварочного тока – основная причина появления таких дефектов. Довольно часто наблюдаются подрезы в горизонтальных швах.
Наплывы
Это натекший на поверхность избыток металла, который не имеет должного сплавления с соединяемой поверхностью. Часто наплыв возникает при сварке стыковых или угловых швов в горизонтальном положении. Образуется при недостаточном прогреве основного металла, избытка присадочного материала, наличия окалин на соединяемых кромках.
Прожоги
Такие дефекты являют собой сквозное отверстие, возникшее вследствие вытекания из сварочной ванны расплавленного металла. В данном случае с другой стороны отверстия как правило образуется натек.
Прожог может быть вызван слишком медленным передвижением электрода по линии сваривания, повышенным сварочным током, неплотным прилеганием к основному металлу прокладки или же недостаточной ее толщиной, большим зазором между соединяемыми кромками.
Непровары
Если на сварочном шве обнаружены локальные несплавления между основным и наплавленным металлом, то дефект такого типа называют непровар. Он существенно понижает прочностные свойства шва и соответственно всей конструкции.
Причины непроваров состоят в следующем: чрезмерно высокая скорость сваривания, некачественная подготовка кромок к сварному процессу, наличие ржавчины, окалин и других загрязнений на соединяемых поверхностях.
Кратеры
Образующиеся вследствие обрыва сварочной дуги углубления в соединительном валике называют кратерами. Такие изъяны существенно уменьшают сечение стыка, что негативно сказывается на прочности. Кратер опасен тем, что внутри него могут находиться усадочные рыхлости, приводящие к появлению трещин.
Свищи
Поверхностные дефекты в виде полости. Понижают прочность соединительного стыка и провоцируют образование трещин. Свищи имеют произвольную форму, могут возникать как на внешней поверхности, так и внутри шва.
Пористость
Поры – это заполненные газами полости, образующиеся при повышенном газообразовании внутри металла. Возникают при наличии разнообразных загрязнений на свариваемых поверхностях, при повышенной скорости сварки, а также повышенной вместительности углерода в используемом присадочном материале.
Посторонние включения
Качество шва существенно ухудшают сторонние включения – оксидные, шлаковые, вольфрамовые, флюсовые и другие включения. Главная ошибка, приводящая к их наличию – неправильный режим сварки. Любое из присутствующих включений понижает прочность и надежность соединения и подлежит устранению.
Причины появления дефектов
Каждый из всех встречающихся дефектов возникает вследствие конкретных факторов. При этом выделяют причины образования дефектов сварных соединений общего характера:
- использование некачественных расходных материалов для сваривания элементов;
- несоблюдение сварочных технологий;
- низкое качество металла, из которого создаются конструкции;
- некачественное или неисправное оборудование;
- неправильный режим сварки;
- технологические ошибки, вызванные низкой квалификацией сварщика.
Чтобы металлоконструкции получались качественными и выносливыми, следует строго соблюдать нормы сваривания и доверять работы профессиональным сварщикам.
Методы выявления дефектов
Выявление дефектов сварных соединений осуществляется следующими способами:
- визуальный осмотр и обмер стыковочных швов;
- испытания стыков на непроницаемость;
- определение дефекта сварного соединения специальными приборами;
- испытания образцов на прочность в лабораторных условиях.
Осмотр сварочного шва осуществляется только после очистки его от шлака, устранения застывших брызг металла и других типов загрязнений. Проверке подлежат размеры и правильность формы соединений, наличие или отсутствие прожогов, кратеров, трещин, свищей и других погрешностей.
Испытание непроницаемости позволяет выявить дефекты сварных соединений трубопроводов, например, поры, трещины, сквозные непровары. Проверяются конструкции несколькими способами:
- обдуванием или заполнением швов воздухом;
- поливом струей воды или наполнение отсеков водой под давлением;
- смазыванием швов керосином.
Если в ходе проверки обнаружен дефект, то деталь возвращается на дополнительную обработку.
Способы устранения дефектов
Любой сварочный процесс сопровождается образованием дефектов, вне зависимости выполняется он инвертором, полуавтоматом, трансформатором или другим оборудованием. При этом выделяют недопустимые и допустимые дефекты сварных соединений, по сложности которых определяется пригодность или непригодность конструкции к дальнейшей эксплуатации.
Способы устранения дефектов сварных соединений выбираются с учетом типа обнаруженного повреждения:
- прожоги исправляют тщательной зачисткой стыка с последующей его заваркой;
- для устранения подрезов выполняется наплавка тонкого соединения по всей линии дефекта;
- исправление трещины осуществляется методом ее полного рассверливания, вырубкой шва на проблемном участке, очисткой поверхностей и повторным завариванием с соблюдением сварочной технологии и действующих нормативов;
- непровары удаляются путем их вырезания и повторного сваривания;
- свищи и кратеры вырезаются до достижения основного металла, после чего по-новому завариваются;
- наплывы аккуратно срезаются, но при этом обязательно следует проверить срез на предмет наличия непровара;
- деформация при сварке устраняется термическим или термомеханическим способом;
- все типы дефектов с посторонними включениями устраняют вырезкой и завариванием.
Если в ходе обследования обнаружены технологические дефекты сварных соединений труб, то устранять их следует строго в соответствии нормативных требований одним из методов:
- механическим без последующей заварки;
- механическим с завариванием места выборки;
- вырезкой участка трубы, на котором присутствует дефект;
- полным удалением шовного соединения и выполнением нового.
При проверке на прочность и герметичность газораспределительных сетей разрешается исправлять дефекты сварных соединений газопроводов в случае, когда сварочный процесс выполнялся дуговой сваркой и не допускается при сваривании газовой сваркой.
Методы контроля сварных соединений
Тот факт, что влияние дефектов на качество сварной металлоконструкции максимизирует риски разрушения изделий доказывать не нужно. Чтобы в процессе сваривания получать действительно надежные, прочные и выносливые конструкции, после завершения работ должен проводиться контроль качества сварных соединений.
Осуществляется контроль сварочных швов поэтапно:
- предварительный. Включает проверку марки металла, качества заготовок, кислорода, присадочной проволоки и других расходных материалов;
- контроль в ходе сварочных работ. Подразумевает постоянные проверки режима сварки, исправности оборудования, осмотр швов и измерение их специальными шаблонами. При выявлении отклонений от установленных стандартов сразу же можно провести удаление дефектов сварных соединений;
- контроль готовой конструкции. Внешние дефекты можно увидеть при обычном осмотре. При необходимости стыки проверяются на плотность, а также подвергаются другим испытаниям.
Все методы контроля сварных соединений разделяются на две группы – разрушающие и неразрушающие. Как правило для выявления дефектов применяются неразрушающие методы, к которым принадлежат:
- внешний осмотр:
- ультразвуковая дефектоскопия;
- магнитный контроль;
- цветная дефектоскопия;
- радиационная дефектоскопия;
- капиллярная дефектоскопия;
- контроль стыков на проницаемость и другие методы обнаружения дефектов сварных соединений.
Методы разрушающего контроля подразумевают испытания отобранных образцов и применяются в основном при необходимости получить параметры сварного шва и зоны термического влияния. Контроль осуществляется химическим анализом, механическими и металлографическими испытаниями.
Заключение
Чтобы сварочный шов по всем параметрам соответствовал стандартам качества и заданным требованиям, то начиная с подготовки подлежащих соединению элементов и до окончания сварочного процесса необходимо осуществлять контроль. Это позволит предотвратить основные дефекты сварных соединений или же оперативно их устранить.
обнаружение и способы их устранения
Сварка — один из самых востребованных процессов металлообработки, позволяющий в самых разных конструкциях соединять стальные детали. В связи с химической неоднородностью металлических поверхностей, кристаллизацией металлов при создании сварного шва, взаимодействии образующего в сварочной ванне жидкого металла с твердыми частицами детали и по ряду других причин нередко в процессе сварки возникают дефекты. Наличие их не только понижает качество готовой конструкции, но также делает ее дальнейшую эксплуатацию опасной для жизни.
Если при проведении контроля качества обнаружены изъяны, влияющие на прочность и надежность изделия, то исправление дефектов сварки в таких случаях является обязательным мероприятием.
Какие дефекты возникают при сварочных работах
В зависимости от причин возникновения, размеров, форм и места размещения на шве различают разные виды дефектов. Чтобы понять какие способы устранения дефектов сварных соединений будут наилучшими, вначале нужно определить их вид и почему они возникли.
Согласно классификации по ГОСТу 30242-97 выделяют следующие группы дефектов:
- трещины в сварочных швах, которые могут быть поперечными, продольными, радиальными и другими;
- нарушение формы шва за счет образования натеков, подрезов, прожогов, выпуклостей, смещений и других изъянов;
- наличие в месте сварки пор, полостей, свищей, кратеров. Они могут скопляться на одном участке или же распределяться по всему шву равномерно;
- непроваренные участки и несплавленные кромки;
- наличие твердых (оксидных, металлических, шлаковых) вкраплений и включений в сварном шве.
По месту расположения дефекты разделяются на внутренние, наружные и сквозные. Конкретное цифровое обозначение классификатором установлено на все образующиеся дефекты сварных соединений и способы их устранения выбираются в соответствии проставленных в местах их присутствия номеров.
Методы обнаружения дефектов
После проведения сварочных работ полученный шов должен проверяться на наличие или отсутствие брака. Только так можно понять требуется или нет устранение дефектов сварки.
Способы для выявления бракованных участков применяют разные:
- визуальный осмотр. Результат будет более точным, если осмотр проводить с применением приборов с увеличительным эффектом;
- магнитный метод, при котором брак определяется степенью искажения волн;
- дефектоскопия. На наличие недостатков указывает изменение цвета сварного соединения после контакта поверхностей со специальным идентифицирующим составом, например, керосином;
- исследование ультразвуком. Проводится с помощью дефектоскопа, брак определятся по звуковым волнам посредством измерения их отражения;
- радиационный способ. Сварные соединения просвечиваются рентгеном, в результате все детали дефекта видны на полученном снимке.
Качество полученных в процессе сварки соединений обозначается маркировкой. У каждого профессионального сварщика есть собственное клеймо, которое он ставит на участке выполнения сварки.
Устранение дефектов сварки
Если в ходе контрольных испытаний обнаружен недопустимый для безопасной эксплуатации конструкций брак, то неизбежным процессом является устранение дефектов сварных соединений.
Для ликвидации выявленных недостатков используются следующие методы устранения дефектов сварных швов:
- непровары, сторонние включения, небольшие внутренние трещины подлежат механической вырубке или полной зачистке, после чего проводится повторное сваривание;
- ликвидация крупных и глубоких трещин осуществляется посредством заварки после предварительной их механической зачистки или сверления;
- заварка тонкими слоями или наплавка используется для устранения подрезов и неполных швов;
- наплывы уничтожаются механическим путем с применением абразивного инструмента;
- термической обработкой устраняется перегрев металла.
Это основные способы исправления дефектов сварных соединений, которые используются для ликвидации брака. После исправления конструкции повторно проходят контрольные испытания и только при полном отсутствии изъянов разрешается их дальнейшая эксплуатация.
Особенности исправления дефектов
Если выполненные с применением сварки конструкции не соответствуют техническим условиям по причине наличия брака, то здесь важно не только правильно выбрать способы устранения дефектов сварных швов, но также безошибочно выполнить все необходимые действия.
В стальных изделиях бракованные сварные швы исправлять следует плазменно-дуговой резкой или строжкой, после чего эти участки обрабатываются абразивными кругами. Наплавкой ниточного шва ликвидируются подрезы, при этом выполняется наплавка по всей длине дефекта. При исправлении неровностей и наплывов механическим способом нужно следить за общим сечением и не допускать его занижения.
Перед тем как исправляются свищи в сварном шве необходимо сперва провести вырубку, тщательно зачистить образовавшуюся полость и после этого повторно заварить изделие.
Чтобы качественно ликвидировать дефекты сварных швов и способы их устранения провести эффективно, то следует соблюдать несколько простых правил:
- длина исправляемого участка должна превышать длину дефекта;
- ширина вырубки должна быть такой, чтобы максимальный размер нового шва не превышал более чем в два раза его ширину до ликвидации дефекта;
- на поверхностях выборок не должно присутствовать никаких заусенцев и острых углублений, очертания должны быть плавными и без резких выступов;
- при выполнении заварки на прилегающих к дефекту участках нужно обеспечить перекрытие основного металла.
В конструкциях из титана, алюминия и сплавов этих металлов ликвидацию дефектов разрешается выполнять только механическими методами: резкой или абразивной шлифовкой. В некоторых случаях допускается вырубка.
Если при повторном контроле снова будут обнаружены бракованные участки, то такие конструкции опять подлежат исправлению. На одном и том же участке сварного шва количество исправлений не должно превышать трех, в противном случае металлоконструкция выполняется с нуля.
Интересное видео
причины их образования и способы устранения
Вопросы, рассмотренные в материале:
- Что такое дефекты дуговой сварки по ГОСТу
- Какие бывают дефекты ручной дуговой сварки
- Какие дефекты возникают при дуговой сварке изделий из чугуна
- Как исправить дефекты шва, выполненного дуговой сваркой
Сварка, наравне с другими способами обработки металлов, не исключает появления дефектов. На самом деле существует немало причин, которые могут привести к их образованию. Но ключевой из них принято считать химические процессы, протекающие в пограничных областях зоны обработки без контроля со стороны сварщика. Далее разберем основные дефекты дуговой сварки и их особенности.
Дефекты дуговой сварки по ГОСТу
В ГОСТе 30242-97 «Дефекты соединений при сварке металлов плавлением. Классификация, обозначение, определения» перечислены все изъяны, которые могут возникнуть на подобных соединениях. Однако этой информации недостаточно, чтобы понять причины их появления.
Дефектом называется отклонение от норм, установленных ГОСТами, техническими условиями, чертежами проектов.
В п. 2.1. ГОСТа 30242 говорится следующее: «Дефекты при сварке плавлением образуются вследствие нарушения требований нормативных документов к сварочным материалам, подготовке, сборке и сварке соединяемых элементов, термической, механической обработке сварных соединений и конструкции в целом». Иными словами, проблемы возникают, когда в процессе работы не соблюдается технология.
Рекомендовано к прочтению
ГОСТ 30242 предполагает шесть основных разновидностей дефектов:
- трещины;
- полости, поры;
- твердые включения;
- несплавления и непровары;
- нарушение формы шва;
- иные дефекты, не относящиеся к пяти первым группам.
ГОСТ 30242 устанавливает:
1. Трехзначное цифровое обозначение каждого дефекта либо цифровое обозначение его разновидностей, состоящее из четырех знаков.
Например: натек обозначается шифром 509, а натек при работе в горизонтальном положении – 5091.
2. Буквенное обозначение для большинства дефектов, которое используется в сборниках справочных радиограмм Международного института сварки (МИС).
Например: трещина – Е, газовая полость – А.
Основные дефекты ручной дуговой сварки
Качество сварочных швов зависит от трех ключевых факторов:
- качества, способа хранения всех используемых в процессе работы материалов;
- подготовки материалов;
- наличия у сварщика необходимого опыта.
Существует насколько видов дефектов ручной дуговой сварки:
1. Проблемы с нормальным зажиганием дуги.
Некачественное зажигание при дуговом методе обработки представляет собой залипание электрода, сильное увеличение длины дуги. В результате чего наблюдается непровар начала шва, зашлаковка, образование пор.
Если производитель электродов подошел халатно к своему делу и допустил слишком сильное оголение торца в зоне зажигания, в начале работы формируется пучок пор или «стартовые поры». В этом случае важно успеть остановиться, зачистить, произвести выборку либо вырубить зубилом некачественное начало электрода. Только устранив проблему, можно снова приступать к зажиганию дуги.
2. Слишком «выпуклые» валики.
Данный дефект возникает при работе с угловыми и стыковыми соединениями. При дуговой сварке последующих валиков может возникнуть зашлаковка, непровар между кромкой разделки и швом или между глубокими западаниями, образовавшимися между валиками.
Такой дефект дуговой сварки имеет несколько причин образования и ряд способов устранения:
- При недостаточной скорости работы и без манипулирования придется увеличить поступательное движение электрода.
- Если осуществляется манипулирование «дугой назад» при наложении вертикальных, потолочных швов, лучше выбрать метод «лестница» либо «дугой вперед».
- При работе с потолочными швами «углом назад» рекомендуется отдать предпочтение способу «углом вперед» либо действовать под прямым углом к направлению работы.
- Если чувствуется, что установлен малый сварочный ток для нижнего положения, его увеличивают.
- При избыточном сварочном токе во время работы с вертикальными и потолочными швами рекомендуется уменьшить этот показатель до минимального.
Чтобы не допустить появления дефектов дуговой сварки, в процессе работы важно следить за полнотой и геометрией шва, жидкой ванной и управлять всеми показателями за счет изменения скорости и угла наклона электрода. Обязательно нужно делать задержку на кромках, ведь чем сильнее кромка прогрета, тем лучше собирается на ней жидкий металл шва при уходе электрода по направлению другой кромке. Этот прием не позволяет металлу собираться в середине шва.
3. Подрезы.
Они ведут к зашлаковке и непровару и очень опасны подрезы в теле сечения шва, особенно, когда речь идет о работе с нержавеющими сталями. Есть несколько причин, по которым могут образовываться подрезы. В первую очередь, когда допущен ранний уход электрода от кромки, что приводит к незаполнению кратера электродным металлом. Также проблема может крыться в слишком короткой дуге, специалисты называют это «сварка опиранием». В таком случае кристаллизующийся металл шва подрезается «козырьком» обмазки.
Еще одна причина – это резкий уход от кромки, в результате чего жидкотекучий шлак заполняет подрез. При проплавлении другой кромки шлак застывает в подрезе и потом не всегда получается выплавить его.
Можно значительно упростить себе работу, если задерживаться на кромке до тех пор, пока весь кратер не заполнится электродным металлом. К другой кромке переходят плавно, не допуская резких колебаний.
4. Наплывы.
Слишком долгая задержка на кромке тоже приводит к образованию дефектов дуговой сварки – на изделии появляется подтек жидкого металла. Либо такой же результат возможен при сильном сварочном токе, когда сварщик просто не может справиться с жидким металлом шва. Чтобы решить проблемы, наплыв срубают и зачищают пострадавшую зону.
5. Непровары.
Чертежи, техпроцессы и справочники по дуговой сварке устанавливают зазор при сборке в пределах от 0 до 2-3 мм.
Если речь идет о дуговой сварке V-образной разделки (без подварки корня шва с обратной стороны), то сборка с недостаточным зазором или вовсе без него станет причиной непровара и зашлаковки корня шва. Если же допустить подобную ошибку во время двухсторонней дуговой сварки Х-образной и V-образной разделки (с подваркой с обратной стороны), придется потратить время на более глубокую выборку обратной стороны корня шва, частичный скос кромок. Кроме того, не избежать финансовых затрат, так как потребуется дополнительный расход электродов на заполнение глубокой выборки.
6. Свищи.
Свищи в кратере шва возникают после завершения работы, если использовался слишком сильный сварочный ток. Либо причина данного дефекта дуговой сварки может скрываться в отрыве дуги за счет ее удлинения.
7. Усадочная раковина.
Эта проблема обычно появляется, когда производится дуговая сварка корневого валика, металла большой толщины, при наличии большого зазора и во время работы с аустенитными сталями. Кроме того, усадочная раковина может образоваться при использовании слишком сильного тока и чрезмерной величине сварочной ванны.
Усадка в кратере валика иногда приводит к появлению трещины. Этот факт значительно снижает производительность труда, так как после окончания каждого электрода требуется механическая зачистка. Когда производится дуговая сварка сталей перлитного класса с жестким креплением деталей, обычно образуется раковина с трещиной. Тогда как при работе с аустенитными сталями раковины с трещинами появляются в результате низкой теплоотдачи и высокого линейного расширения. Это приводит к тому, что требуется выводить кратер обратно на шов либо на кромку разделки.
Чтобы избежать подобного дефекта дуговой сварки, необходимо выбрать среди таких способов работы, как:
- обратно-ступенчатый метод;
- непрерывный, осуществляемый двумя сварщиками, с перехватом дуги;
- метод «дуга в дугу».
8. Поры.
Поры могут появиться в сварном шве сразу по ряду причин:
- Некачественная подготовка кромок. В результате на них остаются грязь, окалина, ржавчина – кромки необходимо зачистить.
- Высокое содержание влаги. Требуется сделать предварительный подогрев свариваемых кромок и прокалку электродов.
- Сквозняки в зоне работы.
- Некачественные электроды. Ржавый металлический стержень, эксцентричное покрытие вызывает появление «козырька» и увеличение длины дуги.
- Сильное магнитное дутье. В данном случае длина дуги сильно увеличивается из-за большого отклонения дуги.
- Несовпадение химического состава основного и присадочного материала.
Существует и ряд других причин, требующих отдельной подготовки заготовок.
Поры могут образовываться по вине сварщика, а точнее – из-за его недостаточной квалификации. В этом случае возможны две причины:
- нечеткое зажигание дуги (залипание, подъем электрода после зажигания на очень высокую длину дуги) и попытка переплавить такое зажигание;
- работа длинной дугой.
Чтобы повысить качество сварочных операций при дуговой обработке, сварщики должны детально изучать практические рекомендации, отрабатывать приемы и использовать их на практике. Дело в том, что нередко им приходится изготавливать и осуществлять монтаж продукции на АЭС, ТЭЦ, химическом и других видах оборудования. Во всех перечисленных случаях к соединениям предъявляются особенно высокие требования.
Дефекты дуговой сварки изделий из чугуна
Главными показателями качества сварного соединения чугунных изделий, полученных дуговым способом, считаются структура, механические свойства и сплошность. Структуру оценивают, исходя из количества твердых структурных составляющих. Так, если в сварном соединении присутствует большая доля карбидов, это говорит о низком качестве дуговой сварки. Одним из основных показателей качества считается равнопрочность сварного соединения чугуна.
В равной степени оцениваются механические свойства металла шва и ЗТВ (зона термического влияния). Если в сварном соединении присутствуют трещины, его качество считается неудовлетворительным. Поры в шве и зоне сплавления приводят к ослаблению соединения, а значит, оно не может использоваться под давлением.
Все названные показатели качества сварного соединения зависят от свариваемости чугуна, особенностей сварочного материала, режимов и конкретной техники дуговой сварки. Если специалист учитывает сразу все факторы, в результате удается получить надежное сварное соединение.
Рассмотрим основные дефекты дуговой сварки изделий из чугуна. При несоблюдении технологии в процессе работы с чугуном и однотипным металлом первые трещины появляются на шве или наплавке, откуда расходятся по основному металлу. Если дуговая сварка ведется разнородным материалом, то трещины образуются на самой детали в непосредственной близости от шва. Отметим, что они располагаются поперек или вдоль швов. Нередко происходит отрыв стальной наплавки в месте сплавления с чугуном.
При использовании электродов на базе никеля при дуговой сварке чугуна в швах могут появляться горячие трещины. Кроме того, в соединениях чугуна можно обнаружить поры, несплавления, спель.
В некоторых отливках повышение твердости материала шва и ЗТВ по сравнению с основным металлом приравнивается к дефектам, поскольку осложняет обработку поверхностей и даже не позволяет эксплуатировать изделие. Например, это актуально, когда речь идет о направляющих и необходимости скольжения по плоскости сопряженных деталей.
Оценка качества соединения и допустимость выявленного дефекта производятся в соответствии с назначением изделия и требованиями к нему.
Исправление дефектов шва, выполненного дуговой сваркой
Вне зависимости от типа сварки, дефекты не во всех случаях приводят к выбраковке продукции. Ряд нарушений технологии либо отклонений от нормы может быть исправлен сразу после завершения работы.
Проще и эффективнее всего можно устранить сварочный дефект, вырубив забракованный участок и еще раз его заварив. При этом обязательно нужно учитывать возможные дефекты дуговой сварки стальных изделий и пользоваться известными способами их предупреждения и устранения. На самом деле, чтобы убрать некоторые дефекты либо вовсе избежать их появления, нужно только сменить положение рабочего инструмента с электродом.
Не стоит забывать, что дуговая сварка методом «на подъем» вызывает перераспределение жидкого металла в зоне ванны, а за счет принципа «углом вперед» сокращается глубина проплавления.
Нужно понимать, что на исправление брака расходуются лишние средства. Поэтому рекомендуется организовать сварочный процесс так, чтобы не пришлось сталкиваться с такими работами.
Легче всего избежать дефектов при дуговой сварке, добавив один из компонентов при работе в защитной среде. В результате повышается коэффициент заполняемости шва, предотвращаются возможные подрезы.
Чтобы сделать расплавленный металл, заполняющий корневую часть шва, более жидким, предварительно нагревают место обработки до определенной температуры при помощи специальных добавок, то есть флюсов.
Кроме того, добиться желаемого эффекта позволяет повышение силы тока. Снизить вероятность нарушения режима можно за счет тщательной зачистки сварных кромок и удаления с их поверхности окисных пленок.
Почему следует обращаться именно к нам
Мы с уважением относимся ко всем клиентам и одинаково скрупулезно выполняем задания любого объема.
Наши производственные мощности позволяют обрабатывать различные материалы:
- цветные металлы;
- чугун;
- нержавеющую сталь.
При выполнении заказа наши специалисты применяют все известные способы механической обработки металла. Современное оборудование последнего поколения дает возможность добиваться максимального соответствия изначальным чертежам.
Для того чтобы приблизить заготовку к предъявленному заказчиком эскизу, наши специалисты используют универсальное оборудование, предназначенное для ювелирной заточки инструмента для особо сложных операций. В наших производственных цехах металл становится пластичным материалом, из которого можно выполнить любую заготовку.
Преимуществом обращения к нашим специалистам является соблюдение ими ГОСТа и всех технологических нормативов. На каждом этапе работы ведется жесткий контроль качества, поэтому мы гарантируем клиентам добросовестно выполненный продукт.
Благодаря опыту наших мастеров на выходе получается образцовое изделие, отвечающее самым взыскательным требованиям. При этом мы отталкиваемся от мощной материальной базы и ориентируемся на инновационные технологические наработки.
Мы работаем с заказчиками со всех регионов России. Если вы хотите сделать заказ на металлообработку, наши менеджеры готовы выслушать все условия. В случае необходимости клиенту предоставляется бесплатная профильная консультация.
виды, причины, основные, внутренние, сквозные, внешние, методы контроля
Дефектами сварных швов и соединений называют различные отклонения от требований чертежа и условий выполнения сварочных работ, ухудшающих качество соединения (его эксплуатационные свойства, герметичность, сплошность и др.). От возникновения брака не застрахован никто, поэтому сварщик должен знать возможные дефекты, причины их возникновения, а также методы устранения, о чем дальше и пойдет речь.
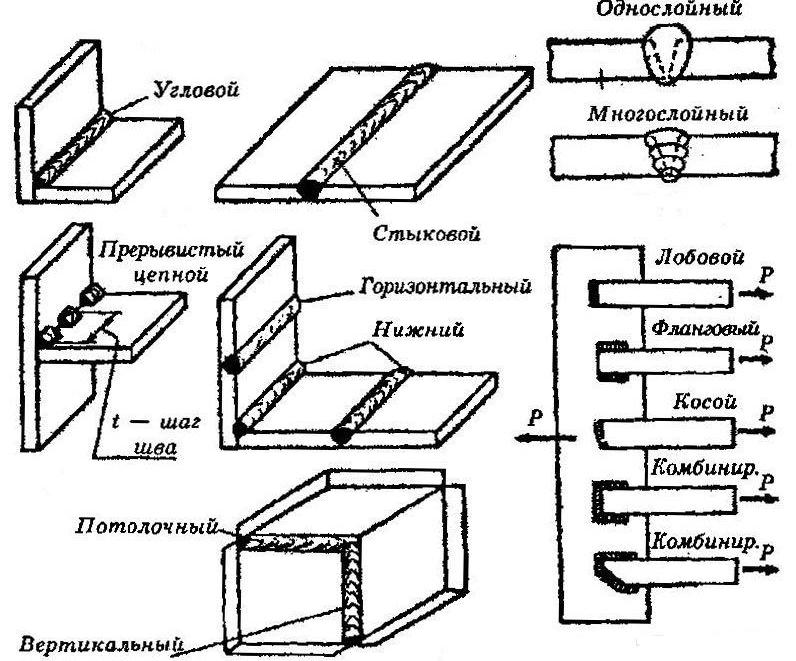
Классификация сварочных швов.
Причины возникновения дефектов сварочных соединений
Сварочный процесс осложняется многими факторами, к которым можно отнести как объективные (свойства соединяемых материалов), так и субъективные (точное соблюдение технологичности процесса, правильность выбора технологии). Оправдать возникновение брака у профессионального сварщика можно только объективными причинами, да и то лишь в какой-то мере.
Основными причинами, которые приводят к образованию дефектов сварочных швов, являются:
- неправильная подготовка свариваемых поверхностей;
- несоответствие или неисправность сварочного инструмента;
- неправильный выбор защитных флюсов или газов и нарушение технологии их использования;
- недостаточная квалификация сварщика;
- несоблюдение в полной мере требуемых режимов сварки (мощность рабочего тока, длина дуги и др.).
Читайте также:
Как правильно варить легированные стали.
В чем особенности сварки алюминия аргоном.
Все сварочные технологии сморите здесь.
Разновидности дефектов сварочных швов
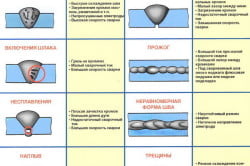
Таблица дефектов сварочных швов.
Все дефекты таких соединений можно разделить на 2 основных типа:
- Внешние, которые можно обнаружить невооруженным глазом. Они могут проявляться в виде прожога, непровара и других признаков.
- Внутренние, которые проявляются в виде трещин, пор и других нежелательных образований.
Далее будут рассмотрены обе категории более подробно.
Внешние дефекты сварочных соединений
К данным дефектам относятся нарушения геометрических размеров сварных соединений (наплывы, подрезы), а также прожоги, непровары и незаваренные кратеры.
Наплывы (натеки) наиболее часто появляются при горизонтальной сварке вертикальных поверхностей. Это приводит к натеканию расплавленного металла на кромки основного металла, имеющего намного меньшую температуру (рис. 1). Они могут возникать на небольшом участке или же иметь большую протяженность вдоль сварной зоны.
Причинами возникновения наплывов являются:
- длинная дуга;
- большая величина сварного тока;
- неправильное положение электрода.
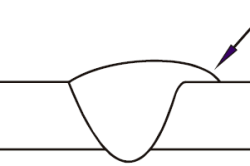
Рисунок 1. Наплывы чаще выявляются при горизонтальной сварке.
При кольцевом соединении наплывы могут появляться при большом или недостаточном смещении электрода с зенита. В местах наплывов достаточно часто могут возникать и другие дефекты. Не допустить образование наплывов можно подбором правильного режима сварки и качественной подготовкой свариваемой поверхности (удаление окалины и др.).
Подрез – дефект в виде канавки в основном металле по краям сварочного шва (рис. 2). Данный дефект является самым распространенным при сварке нахлесточных или тавровых соединений, но иногда возникает при создании стыковых соединений. В большинстве случаев он возникает из-за неправильно подобранных параметров сварочного процесса.
При угловой сварке подрезы могут возникать из-за того, что дуга направляется больше на вертикальную поверхность, чем на горизонтальную. Это приводит к тому, что расплавленный металл стекает на нижнюю кромку и его не хватает для полного заполнения ванны. При слишком большой скорости сварки и большом напряжении сварочные швы могут выйти горбатыми. Из-за быстрого затвердевания сварочной ванны также могут образовываться подрезы. Снижение скорости сварки позволяет устранить этот дефект.
На возникновение подрезов влияет и длина дуги. При увеличении величины дуги возрастает и размер шва, что приводит к увеличению количества расплавленного основного металла. Так как при увеличении длины дуги тепловложение остается прежним, его не хватает на весь шов, кромки быстро остывают, в результате чего образуются подрезы. Уменьшение длины дуги не только может избавить от подрезов, но и увеличивает проплавление.
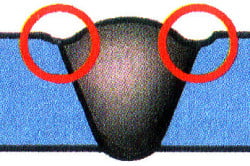
Рисунок 2. Подрез представляет собой дефект, проявляющийся в виде канавки по краям сварочного шва.
Прожогами называются дефекты сварки, которые проявляются в сквозном проплавлении и вытекании жидкого металла через сквозное отверстие в шве. При этом с другой стороны места соединения может образоваться натек. Прожоги возникают из-за слишком большого значения рабочего тока, большого зазора между кромками металла, недостаточной скорости перемещения электрода, недостаточной толщины подкладки или ее неплотного прилегания к основному металлу. Устранение данного дефекта выполняется снижением рабочего тока и увеличением скорости перемещения электрода. При этом особое внимание следует обратить на качество подгонки кромок детали, чтобы расплавленный металл не выливался из сварной ванны.
Непровары – это локальные несплавления наплавленного металла с основным металлом или слоев шва между собой. К этому дефекту можно отнести и незаполнение сечения шва (рис. 3).
Непровары существенно уменьшают качество состыковки и могут привести к тому, что сварочное соединение со временем разрушится.
Этот дефект возникает из-за недостаточной величины рабочего тока, высокой скорости сварки, плохой подготовки свариваемых поверхностей, присутствия на кромках детали посторонних веществ (шлака, ржавчины и др.) и загрязнений. Не допустить возникновение непроваров можно выбором требуемого значения сварочного тока.
Внутренние дефекты сварочных соединений
К самым распространенным внутренним дефектам относятся горячие, холодные трещины и поры.
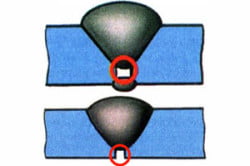
Рисунок 3. Непровары значительно уменьшают качество состыковки и приводят к разрушению сварочного соединения.
Горячие трещины появляются при нагреве металла до температуры более 1200 °С, в результате чего происходит быстрое уменьшение пластических свойств металла (кристаллизация). Горячие трещины возникают на границах зерен кристаллической решетки. Их возникновению способствует наличие большого количества в металле различных примесей. Распространяться такие трещины могут как поперек, так и вдоль шва.
Холодные трещины появляются при температуре металла ниже 130°С. Иногда такие дефекты могут возникать и со временем. Причинами их появления могут быть сварочные напряжения, образующиеся во время фазовых превращений, или растворенный атомарный водород, который не успел выделиться при сварке.
Поры – это полости внутри шва, заполненные газом, который не успел выделиться в процессе сварки. Они могут иметь различную форму и размеры, которые зависят от размеров пузырьков газа. Основными причинами возникновения такого дефекта являются:
- наличие примесей в присадочном или основном металле;
- некачественная обработка свариваемых поверхностей;
- повышенное содержание углерода;
- нарушения защиты сварочной ванны.
Одиночные поры не несут большой опасности, но их цепочка снижает механические характеристики изделия. Участок сварочного шва, на котором обнаружены поры, подлежит переварке с предварительной механической зачисткой.
Способы выявления дефектов сварочных соединений
Дефекты сварных швов можно выявить такими способами:
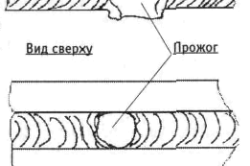
Схема прожога сварного шва.
- внешним осмотром и обмером швов;
- испытанием непроницаемости;
- специальными приборами.
Внешний осмотр проводится только после качественной очистки соединения от шлака, брызг металла и других загрязнений. При этом проверке подлежат правильность размеров и формы швов и отсутствие каких-либо дефектов. Размеры швов можно проверить с помощью специальных шаблонов.
Испытание непроницаемости позволяет выявить поры, сквозные непровары и трещины. Контроль качества сварных швов с использованием специальных приборов позволяет обнаружить внутренние дефекты соединений. Такой контроль может осуществляться следующими способами:
- просвечиванием рентгеновскими лучами или гамма-лучами радиоактивных изотопов;
- намагничиванием, то есть нахождением внутренних дефектов с помощью магнитного поля;
- прозвучиванием, то есть обнаружением дефектов с помощью ультразвуковых колебаний;
- засверливанием с частичным разрушением шва в месте контроля.
Следует отметить, что выполнить ряд сварочных соединений без дефектов практически невозможно. При этом следует обеспечить в шве минимум допустимых дефектов. При осуществлении сварочных работ необходимо помнить, что правильный выбор оборудования и технологии сварки имеет большое влияние на весь процесс сварки.
Виды дефектов сварных швов и методы их устранения
Отклонения от утвержденных стандартов, технических условий и требований, возникшие при изготовлении различных изделий или соединении конструкций при помощи сварки, называют дефектами сварного шва (соединения). Они классифицируются по ряду признаков: степени воздействия на качество соединения, характеру проявления, местоположения и т.д.
Основные причины появления дефектов сварных соединений:
- Низкое качество соединяемых материалов.
- Некачественное или неисправное сварочное оборудование.
- Нарушение технологии ведения сварки и неверно выбранные параметры.
- Неправильно подобранные расходные материалы для сварки.
- Недостаточно высокая квалификация специалиста, осуществляющего сварку.
Если дефекты сварного шва не оказывают заметного влияния на эксплуатационные качества изделий или прочность конструкций и укладываются в установленные нормы, то их называют допустимыми. Дефекты, наличие которых может привести к разрушению конструкции или детали при воздействии нормативных нагрузок, считаются недопустимыми и требуют устранения. Причем по техническим требованиям допускается не более двух попыток, так как последующие в любом случае ухудшают качество соединения.
В зависимости от местоположения дефекты сварного соединения делят на 3 группы: наружные, внутренние и сквозные. К первым относятся поверхностные трещины, подрезы, наплывы и кратеры, ко вторым – непровары, поры, свищи и посторонние твердые включения, к третьим – сквозные трещины и прожоги.
Несплавление или непровар – дефект сварного шва, при котором отсутствует прочное соединение между основным и наплавляемым металлом из-за недостаточного взаимного проникновения. Непроваром считается и неполное заполнение полости между соединяемыми поверхностями наплавляемым металлом, или наличие просвета между наплавленными слоями при двусторонней сварке. В любом из этих случаев дефект считается недопустимым и требует устранения путем дополнительного наплавления металла.
Основными причинами непровара являются недостаточно высокий для работы с рабочими поверхностями данной толщины сварочный ток, а также чрезмерно быстрое перемещение электрода. В ряде случаев он является следствием неправильного подбора диаметра электрода или полярности подключения кабелей, а также недостаточного зазора между соединяемыми кромками или их перекос. Иногда данный дефект проявляется при попадании шлака между кромками.
Трещины – достаточно опасные дефекты сварного шва, часто приводящие к полному разрушению соединения. Выражаются образованием видимых разрывов в наплавленном или основном металле, а также на стыке между ними. Могут быть продольными, поперечными и продольно-поперечными (звездообразными). Различают горячие и холодные трещины. Первые образуются во время перехода металла из жидкого состояния в твердое и обычно являются результатом неправильного выбора типа присадочных материалов. Холодные трещины проявляются после полного остывания металла, а в некоторых случаях уже после воздействия нагрузок.
Основные причины проявления этого дефекта – превышение допустимых нагрузок при эксплуатации, резкие перепады температур, неправильное расположение швов.
Устранение данного дефекта осуществляется путем сверления отверстий на концах трещины для предупреждения распространения, срезом поврежденной части шва и повторной сваркой с учетом причин появления брака.
Подрезы – дефекты сварного соединения, выражающиеся в образовании продольных углублений в основном металле по одну или обе стороны от шва. Как правило, односторонний подрез встречается при сварке поверхностей, расположенных под углом друг к другу, например, тавровых соединений. В данном случае его причиной является стекание расплава на горизонтальную поверхность (на последней в результате образуется наплав), ввиду того что дуга в большей степени направлена на вертикальную. Двусторонний подрез образуется при излишне высоком сварочном токе, длине дуги или скорости перемещения электрода или горелки.
Подрез уменьшает прочность сварочного соединения пропорционально глубине канавок. Устраняется этот дефект достаточно легко – путем наплавления небольшого количества металла в сами углубления.
Наплывы – достаточно распространенные дефекты, выражающиеся в образовании излишков наплавляемого металла, не соединившегося с основным. Причинами этого явления могут быть некачественная предварительная подготовка кромок или недостаточный прогрев основного металла из-за малого тока.
Сами по себе наплавы не ухудшают прочности сварного соединения, однако чаще всего свидетельствуют о наличии иных дефектов – подрезов или непроваров. В связи с этим их устраняют путем среза для проверки качества шва.
Прожоги – дефекты сварочного шва, выражающиеся в образовании сквозного отверстия в наплавляемом металле в результате его утечки из сварочной ванны. Прожог обычно является итогом превышения сварочного тока или низкой скорости перемещения горелки или электрода, а также недопустимо большое расстояние между кромками соединяемых поверхностей. Обычно проявляется при сварке алюминия.
Так как сквозные отверстия снижают прочность сварного соединения, прожоги требуют устранения, которое осуществляется путем их заваривания.
Кратеры – конические углубления в шве, причиной появления которых является резкий обрыв сварочной дуги. Основная опасность данных дефектов заключается в увеличении риска образования трещин, поэтому кратеры подлежат заварке. В качественных современных сварочных аппаратах образование подобных дефектов предотвращается специальными системами, автоматически снижающими ток при обрыве дуги.
Поры, раковины и свищи – дефекты сварного соединения, выражающиеся в образовании внутри наплавленного металла в виде наполненных газом полостей. Бывают внутренними и поверхностными, различными по размеру, форме и природе появления. Обычно возникают в результате чрезмерно интенсивного процесса образования газа в металле, связанного с неправильной подготовкой соединяемых поверхностей, низким качеством присадок или нарушением условий хранения электродов, а также наличием посторонних примесей в основном и наплавляемом металле.
Наличие пор делает соединение хрупким и неустойчивым к различным видам нагрузок. Устраняется данная проблема путем вырезания части шва и последующим его завариванием с соблюдением требований и технологии.
Твердые (шлаковые, флюсовые, оксидные, металлические и др.) включения в металле шва являются одними самых сложных дефектов, ввиду сложности их обнаружения. Визуально снаружи они незаметны, поэтому могут быть выявлены только при помощи различных инструментальных методов оценки качества соединения.
Основные причины появления посторонних включений в металле – низкое качество расходных материалов и недостаточно качественная подготовка кромок. Устраняются вырезкой шва и повторной сваркой.
различных типов сварных соединений
Сварное соединение — это край или точка, в которой две или более металлических или пластмассовых детали соединяются вместе. Две или более детали (металлические или пластмассовые) соединяются с помощью подходящего процесса сварки для образования прочного соединения. По данным Американского общества сварщиков, существует пять основных типов сварных соединений: стыковые, угловые, внахлестку, тройники и кромочные соединения.
5 основных сварных швов:
1. Стыковое соединение
2.Угловой шарнир
3. Соединение внахлест
4. Тройник и
5. Торцевое соединение
Давайте подробно обсудим каждую из них
1. Стыковое соединение:
Соединение, образованное соединением концов двух частей, называется стыковым соединением. В стыковом соединении две части лежат в одной плоскости или бок о бок. Это самый простой тип соединения, используемый для соединения металлических или пластиковых деталей.
Различные типы сварных швов при стыковой сварке:
(i) Квадратный стыковой шов
(ii) Сварной шов с канавкой под углом
(iii) Сварной шов с V-образной канавкой
(iv) Сварной шов с J-образной канавкой
(v) Сварной шов с U-образной канавкой
(vi) Сварной шов с развальцовкой и V-образной канавкой
( vii) Стыковой сварной шов с развальцовкой, скосом и канавкой
Также читают:
2.Угловой шарнир
Соединение, образованное путем размещения угла двух частей под прямым углом, называется угловым соединением (см. Рис. Выше). Две части, которые будут свариваться угловым соединением, образуют форму L.
Различные типы сварных швов в угловых соединениях:
(i) Угловой сварной шов
(ii) Точечный сварной шов
(iii) Сварной шов с квадратной канавкой или стыковой сварной шов
(iv) Сварной шов с V-образной канавкой
(v) Сварной шов с канавкой под углом
(vi) Шов с U-образной канавкой
(vii ) Сварной шов с J-образной канавкой
(viii) Сварной шов с развальцовкой и V-образной канавкой
(ix) Краевой шов
(x) Сварной шов с угловым фланцем
3.Тройник
Соединение, выполненное путем пересечения двух частей под прямым углом (т. Е. Под углом 90 градусов), при этом одна часть находится в центре другой. Он называется Т-образным соединением, так как две сварные части выглядят как английская буква «Т».
Типы сварных швов в тройнике следующие
(i) Угловой сварной шов
(ii) Вставной сварной шов
(iii) Щелевой сварной шов
(iv) Скос-канавка
(v) J-образный шов
(vi) Конический сварной шов
(vii) Сквозной расплав
4.Внахлестку
Соединение внахлест образуется, когда две части кладут друг на друга и затем сваривают (см. Рис. Выше). Он может быть односторонним или двусторонним. Эти типы сварных соединений чаще всего используются для соединения двух деталей разной толщины.
Различные типы сварных швов внахлестку:
(i) Угловой сварной шов
(ii) Сварной шов со скосом и канавкой
(iii) Сварной шов с J-образной канавкой
(iv) Вставной шов
(v) Щелевой сварной шов
(vi) Точечный сварной шов
(vii) Сварной шов с конусом и канавкой под развальцовку
5.Кромочный стык
Соединение, образованное сваркой краев двух частей вместе, называется краевым соединением. Это соединение используется там, где края двух листов прилегают друг к другу и в точке сварки находятся примерно в параллельных плоскостях. В этом соединении сварной шов не полностью проникает через толщину соединения, поэтому его нельзя использовать при приложении напряжения и давления.
Различные типы сварных швов в этом сварном шве:
(i) Сварной шов с квадратной канавкой или стыковой сварной шов
(ii) Сварной шов с канавкой под углом
(iii) Сварной шов с V-образной канавкой
(iv) Сварной шов с J-образной канавкой
(v) Сварной шов с U-образной канавкой
(vi) Торцевой фланец Сварной шов
(vii) Угловой шов
В этой статье мы узнали о различных типах сварных соединений, используемых для соединения металлических или пластиковых деталей.Если вы найдете эту информацию ценной, не забудьте поставить лайк и поделиться ею.
,Сварка контактным швом (RSEW) Преимущества и недостатки
Принцип работы
для сварки контактным швом (RSEW) Сварка сопротивлением (RSEW) очень похожа на точечную сварку (RSW), но здесь используются круглые вращающиеся электроды. И здесь мы получаем непрерывный сварной шов, герметичный (если процесс идеальный). Шовно-сварочная форма сопротивления Процесс представляет собой серию сварных швов внахлест. Два или более листа основного металла обычно проходит между роликами электродов, как показано на следующем рисунке, который передавать ток, а также механическое давление, необходимое для создания сварной шов, который обычно является газонепроницаемым или непроницаемым для жидкости.См. Этапы RSEW
Прочтите:
Сварка контактным швом (RSEW): преимущества и недостатки
Преимущества
- Могут быть выполнены газонепроницаемые и водонепроницаемые соединения.
- Перекрытие меньше, чем при точечной или выступающей сварке.
- Возможно одновременное изготовление одинарных и параллельных швов.
Недостатки
- Сварочный процесс ограничивается прямой или равномерно изогнутой линией.
- Металлические листы толщиной более 3 мм могут вызывать проблемы при сварке.
- Может потребоваться изменить конструкцию электродов для сварки металлических листов с препятствиями.
Приложения RSEW
- Кольцевой шов может иметь прямоугольную, квадратную или даже круглую форму.
- Большинство металлов можно сваривать (кроме меди и некоторых медных сплавов с высоким содержанием меди).
- Стыковая сварка возможна.
Прочтите:
,
Дефекты / несовершенства сварных швов — включения шлака
Описаны характерные особенности и основные причины дефектов шлака.
Идентификационный номер
Шлак обычно представляет собой удлиненные линии, непрерывные или прерывистые по длине сварного шва. Это легко определить на рентгенограмме, Рис. 1. Включения шлака обычно связаны с процессами флюса, то есть MMA, FCA и дугой под флюсом, но они также могут возникать при сварке MIG.
Причины
Поскольку шлак является остатком покрытия из флюса при сварке стержневым электродом, он в основном является продуктом раскисления в результате реакции между флюсом, воздухом и поверхностным оксидом. Шлак захватывается сварным швом, когда два соседних сварных валика осаждаются с недостаточным перекрытием и образуется пустота. При нанесении следующего слоя уловленный шлак не расплавляется. Шлак также может попадать в полости в многоходовых сварных швах из-за чрезмерного подреза в носке шва или неровного профиля поверхности предыдущих прогонов сварного шва, Рис.
Поскольку оба они влияют на легкость удаления шлака, на риск дефектов шлака влияет
- Тип покрытия флюса
- Сварочная техника
Тип и конфигурация соединения, положение сварки и ограничения доступа — все это влияет на риск образования дефектов шлака.
Тип покрытия флюсом
Одна из основных функций флюсового покрытия при сварке — это образование шлака, который будет свободно течь по поверхности сварочной ванны, защищая его от окисления.Поскольку шлак влияет на рабочие характеристики ММА-электрода, его поверхностное натяжение и скорость замерзания могут быть не менее важными свойствами. Для сварки в плоском и горизонтальном / вертикальном положениях предпочтительным является относительно вязкий шлак, поскольку он дает гладкий профиль сварного шва, с меньшей вероятностью захватывается и при затвердевании обычно легче удаляется. При вертикальной сварке шлак должен быть более текучим, чтобы вытекать к поверхности сварочной ванны, но иметь более высокое поверхностное натяжение, чтобы обеспечивать поддержку сварочной ванне и быстро замерзать.
Состав флюсового покрытия также играет важную роль в риске образования шлаковых включений из-за его влияния на форму сварного шва и легкости удаления шлака. Сварочная ванна с низким содержанием кислорода будет иметь высокое поверхностное натяжение, приводящее к выпуклому сварному шву с плохим смачиванием основного металла. Таким образом, окисляющий флюс, содержащий, например, оксид железа, создает сварочную ванну с низким поверхностным натяжением с более вогнутым профилем валика сварного шва и способствует смачиванию основного металла.Высокосиликатный флюс дает стекловидный шлак, часто саморазлагающийся. Флюсы с содержанием извести образуют налипший шлак, который трудно удалить.
Простота удаления шлака для основных типов флюсов:
- Рутиловые или кислотные флюсы — большие количества оксида титана (рутила) с некоторыми силикатами. Уровень кислорода в сварочной ванне достаточно высок, чтобы получить плоский или слегка выпуклый сварной шов. Текучесть шлака определяется содержанием фторида кальция. Покрытия без фтора, предназначенные для сварки в плоском положении, создают гладкие профили валика и легко удаляются шлаки.Более жидкий фторидный шлак, предназначенный для позиционной сварки, удалить труднее.
- Основные флюсы — высокая доля карбоната кальция (известняк) и фторида кальция (флюсодержащего пара) в флюсе снижает содержание кислорода в сварочной ванне и, следовательно, его поверхностное натяжение. Шлак более текучий, чем шлак с рутиловым покрытием. Быстрое замерзание также способствует сварке в вертикальном и верхнем положениях, но шлаковое покрытие удалить сложнее.
Следовательно, риск включения шлака значительно выше при использовании основных флюсов из-за присущего им выпуклого профиля сварного шва и трудности удаления шлака с подошв сварного шва, особенно при многопроходных сварных швах.
Сварочная техника
Сварочная техника играет важную роль в предотвращении образования шлаковых включений. Манипуляции с электродами должны обеспечивать соответствующую форму и степень перекрытия сварных швов, чтобы избежать образования карманов, в которых может скапливаться шлак. Таким образом, правильный размер электрода для подготовки шва, правильный угол к заготовке для хорошего проплавления и гладкий профиль сварного шва — все это важно для предотвращения уноса шлака.
При многопроходной вертикальной сварке, особенно с использованием основных электродов, необходимо позаботиться о расплавлении любых оставшихся мелких шлаковых карманов и минимизации подрезов.При использовании переплетения небольшая задержка на крайних краях переплетения будет способствовать сплавлению боковых стенок и созданию более плоского профиля сварного шва.
Слишком высокий ток в сочетании с высокой скоростью сварки также приведет к подрезу боковой стенки, что затрудняет удаление шлака.
Крайне важно удалить весь шлак перед нанесением следующего цикла. Это можно сделать между прогонами шлифованием, легким скалыванием или щеткой. Инструменты для очистки должны быть идентифицированы для различных материалов, например, стали или нержавеющей стали, и разделены.
При сварке сложными электродами, в стыковых соединениях с узкими клиновыми швами или когда шлак задерживается из-за подрезов, может потребоваться шлифовка поверхности шва между слоями, чтобы обеспечить полное удаление шлака.
Лучшая практика
Для предотвращения шлаковых включений можно использовать следующие методы:
- Используйте методы сварки для получения гладких сварных швов и соответствующей сварки между прогонами, чтобы избежать образования карманов для захвата шлака
- Используйте правильный ток и скорость движения, чтобы избежать подрезания боковой стенки, что затруднит удаление шлака
- Удаляйте шлак между прогонами, уделяя особое внимание удалению шлака, застрявшего в щелях.
- Используйте шлифование при сварке сложных стыковых соединений, в противном случае для удаления шлака может быть достаточно обработки проволочной щеткой или небольшого скола.
Стандарты приемки
Включения шлака и флюса являются линейными дефектами, но поскольку они не имеют острых краев по сравнению с трещинами, они могут быть разрешены специальными стандартами и правилами. Пределы для стали указаны в BE EN ISO 5817: 2007 для трех уровней качества.
Статья подготовлена Биллом Лукасом с помощью Джин Мазерс и Колин Эйлинс.
Эта статья Job Knowledge изначально была опубликована в Connect, сентябрь / октябрь 1999 г.Он был обновлен, поэтому веб-страница больше не отражает в точности печатную версию.
,Сварочные дефекты и разрывы — онлайн-видео скачать на ppt
Презентация на тему: «Сварочные дефекты и несплошности» — стенограмма презентации:
1 Сварочные дефекты и несплошности
2 Что означает дефект сварного шва?
Любой дефект, снижающий пригодность сварного изделия (сварного шва).
3 Что означает несплошность сварного шва?
Прерывание типичной структуры материала.Нарушение непрерывности не обязательно является дефектом.
4 Нарушения сплошности сварного соединения
Несоосность (высокое-низкое) Поднутрение Недостаточное заполнение Вогнутость или выпуклость Чрезмерное армирование Неправильное усиление Недостаточное заполнение Перекрытие Прожиг Неполное или недостаточное проникновение Неполное сплавление Неравномерность поверхности Удары дуги Включения Трещины от трещин Поперечные трещины вольфрама Корень Underbead и околошовной зоны Горячая холодная или несвоевременное основного металла Разрывы Клееный разрывая слоистость и отслоений Laps и швах Пористость равномерно Рассеянный Кластер Линейные трубопроводы Молоток Marks зоны термического влияния микроструктуры изменения в несущем каркасе ламинаций Размер или размеры
5 Нарушения сплошности сварного соединения
Несоосность (высокое-низкое) Поднутрение Недостаточное заполнение Вогнутость или выпуклость Чрезмерное армирование Неправильное усиление Недостаточное заполнение Перекрытие Прожиг Неполное или недостаточное проникновение Неполное сплавление Неравномерность поверхности Удары дуги Включения Трещины от трещин Поперечные трещины вольфрама Корень Underbead и околошовной зоны Горячая холодная или несвоевременное основного металла Разрывы Клееный разрывая слоистость и отслоений Laps и швах Пористость равномерно Рассеянный Кластер Линейные трубопроводы Молоток Marks зоны термического влияния микроструктуры изменения в несущем каркасе ламинаций Размер или размеры
6 Несоосность (высокий-низкий) Определение: соединение не совмещено в корне
Причина: небрежность
7
Поднутрение Определение: канавка, вырезанная на носке сварного шва и оставленная незаполненной.Причина: высокий ток, угол наклона электрода, большая длина дуги или ржавчина.
8
Недостаточное заполнение Определение: поверхность шва находится ниже прилегающих поверхностей основного металла Причина: неправильная техника сварки
9
Определение прожига: когда отверстие полностью проплавлено в основном металле.Причина: чрезмерное тепловложение.
10 Неполное или недостаточное проникновение
Определение: Когда металл сварного шва не проникает на требуемую глубину в корень шва Причина: низкая сила тока, низкий предварительный нагрев, плотное раскрытие корня, высокая скорость перемещения, короткая длина дуги.
11 Arc Strike Определение: Локализованное слияние вне зоны сварного шва.
Причина: Невнимательность