Термообработка сварных швов и соединений: процесс выполнения
Различают три разновидности термической обработки деталей. Первая разновидность — это подготовка деталей перед сваркой. Некоторые конфигурации свариваемых изделий (например, трубы больших диаметров) требуют предварительного подогрева до 110 – 120 С0 непосредственно перед сваркой. К некоторым изделиям применяют определенные методы во время сварки. В этой статье мы расскажем, как проводится термообработка сварных швов уже готовых сваренных изделий.1 / 1
Для чего нужна термообработка
В процессе сварки в металле свариваемых деталей происходят разнообразные процессы. Главные из которых это:
- неравномерный прогрев и охлаждение различных зон;
- фазовые преобразования в металле;
-
химическое взаимодействие с окружающим пространством.
Все эти процессы приводят к появлению местных напряжений, которые могут стать причиной возникновения трещин и, в тяжелых случаях, привести к полному разрушению изделия. От всех этих неприятностей поможет избавиться термообработка сварных соединений.
Виды обработки
Термообработка может производиться разными способами в различных режимах. В зависимости от химического состава и геометрических размеров изделия используют следующие виды термообработки.
Стабилизирующий отжиг
Изделие нагревается до температуры 970 градусов, и эта температура поддерживается в течение полутора часов. Далее происходит естественное охлаждение. Метод получил широкое распространение при термообработке высоколегированных сталей.
Термический отдых
Этот процесс предусматривает нагрев металла до 300 С 0 с последующей выдержкой при этой температуре. Идеальное время выдержки два часа. Кроме снятия напряжения, этот способ снижает количество растворенного водорода в металле шва. Такой метод более всего может пригодиться для обработки изделий с толстыми стенками, где другие методы применить сложно.
Нормализация
Применяется при термической обработке труб малого диаметра. Такие трубы имеют тонкие стенки. В данном случае шов с участком трубы нагревают до 800 градусов и выдерживают около получаса. Таким образом, удается снять только часть напряжений, но это не главное. Главная цель этого вида обработки – придание металлу мелкозернистой однородной структуры.
Высокий отпуск
Подходит для сталей перлитного класса. Время обработки выбирается в пределах нескольких часов. Температуру нагрева доводят до 600 – 700 градусов. Такая обработка решает множество проблем для низколегированных сталей. Остаточное напряжение снимается практически полностью, исчезает закалочная структура.
Аустенизация
Самый высокотемпературный вид. Процессы идут при 1100 градусах в течение 120 – 180 минут. Далее проходит естественное остывание на воздухе. Применяется, в основном, на высоколегированных сталях, придавая им высокую пластичность при незначительных остаточных напряжениях.
Применение различных видов термообработки позволяет повысить прочность сварных швов, увеличить надежность изделий и значительно продлевает срок технической эксплуатации, способствуя повышению коррозионной стойкости металла.
Особенности процесса и применяемое оборудование
Термическая обработка швов требует различных технологий и оборудования. Существует три основных типа оборудования для термической обработки.
Радиационное оборудование — это наиболее простой, а значит, и самый распространенный вид оборудования. Нагрев изделия происходит за счет передачи тепла от нагретой нихромовой проволоки. Между проволокой и изделием прокладывают термостойкий электроизоляционный материал и постепенно увеличивают напряжение на нагревательном элементе (нихромовая проволока). Работа проходит намного быстрее, если нагревательная проволока уже изолирована, и нет необходимости каждый раз изолировать изделие.
Регулировка напряжения может осуществляться различными средствами: от простейших способов переключения отводов на обмотке понижающего трансформатора или устройства гасящих сопротивлений, до высокотехнологичных электронных преобразователей напряжения на тиристорах.
Газопламенное оборудование намного хлопотнее предыдущего вида. Согласитесь, что обеспечить подачу электрического питания намного проще, чем подачу газа. Такие же сложности с регулировкой процесса и контролем параметров. И еще проблематичнее выглядят возможности механизации или автоматизации термообработки сварных швов с применением газопламенного оборудования. Но есть у этого оборудования и одно неоспоримое преимущество – низкая стоимость работ. Это становится понятным при самом приближенном сравнении стоимости электроэнергии и газа.
Индукционные установки
Этот вид термообработки требует специального дорогостоящего оборудования и квалифицированного обслуживания. Промышленность выпускает как переносные индукционные установки, рассчитанные на обработку некрупных деталей в «полевых» условиях, так и многофункциональные гиганты, на основе которых создаются целые производственные участки.
На таких участках используют мощные индукционные установки, вырабатывающие высокочастотное напряжение. Это напряжение подаётся на провода, особым образом расположенные на обрабатываемом изделии. Протекающий в проводах ток, в свою очередь, вызывает появление токов в обрабатываемой детали, которые и разогревают её до нужной температуры.
Индукционные установки используются не только для термообработки сварных швов, но и для разогрева труб в процессе их изгибания. Таким образом, имеется возможность на одной промышленной линии осуществлять разогрев труб перед сваркой, непосредственно сварку труб и термообработку сварных швов. К этому участку обычно примыкает участок приварки фланцев и других деталей.
Необходимо отметить, что все эти процессы легко механизируются и автоматизируются. При наличии необходимого набора датчиков, компьютера и программного обеспечения можно создавать полностью автоматические производственные линии.
Термообработка сварных швов и соединений
Для создания крупных магистральных трубопроводов используют коллекторы с большим внутренним диаметром. Это применяется в теплосетях и системах водоснабжения. Из-за большого веса проходящей жидкости возрастает и давление на стенки коммуникации. Поэтому последние выполняются из материалов достаточной толщины, чтобы выдерживать большие нагрузки. Но это создает новую проблему — сложно качественно сварить стороны с такой толщиной, обеспечив длительную последующую эксплуатацию. При такой массе изделия прогрев достигает сравнительно небольшой зоны, что приводит к ряду физических процессов, неблагоприятно сказывающихся на дальнейшем использовании материала. Для решения этой проблемы разработана и применяется термообработка сварных соединений. Что это такое? В каких случаях необходима термообработка после сварки? Каким оборудованием и как выполняется процесс?
Суть и предназначение процесса
Сварочный шов создается электрической дугой и присадочным материалом с электрода при температуре от 1500 до 5000 градусов. Это приводит к нескольким негативным явлениям на толстом металле. А именно:
- Непосредственно в месте соединения основного и присадочного материалов происходит значительный перегрев. Это содействует кристаллизации металла с крупной зернистой структурой, что снижает его пластичность. Выгорание марганца и кремния тоже подвергает эту область преобразованию в жесткий участок, плохо взаимодействующий, при естественных расширениях, со всей конструкцией.
- Немного дальше от шва образуется зона закалки. Она испытывает значительный, но меньший перегрев, чем предыдущий участок, поэтому в ней происходит закаливание некоторых элементов. Этот участок характеризуется включениями с высокой твердостью и сниженной пластичностью. Ухудшаются показатели металла и по ударной вязкости.
- На удаленном расстоянии от шва появляется зона разупрочнения. Благодаря непродолжительному воздействию умеренной температуры от электрической дуги, данный участок сохраняет высокую пластичность, но снижаются характеристики по прочности.
Общим дефектом после сварки являются остаточные напряжения в металле, которые способны деформировать изделие. Из-за этого возникают трудности при монтаже объемных конструкций, где требуется точность при стыковке новых узлов. Остаточное напряжение вызывает и последующее образование трещин, что недопустимо для швов трубопроводов. В сочетании с высокой температурой, это способствует снижению коррозионной устойчивости, циклической прочности, и способности сопротивляться хрупким разрушениям в условиях холода.
Термообработка сварных швов выполняется при температуре от 700 до 1000 градусов. Это позволяет устранить последствия неравномерного прогрева при дуговой сварке на толстых металлах, чем повышает надежность будущих коллекторов и магистралей трубопроводов. Труба и наложенный шов приобретают более похожую структуру, и лучше взаимодействуют во время естественных физических процессов (расширения и сужения материалов, воздействия влаги и т.д.).
Термообработка сварных соединений трубопроводов происходит в три этапа:
- нагрев околошовной зоны или всего изделия одним из нескольких видов оборудование;
- выдержка материала на заданной температуре в течении определенного времени;
- последующее планомерное охлаждение до нормальных температур.
Это нейтрализует остаточные явления от сварки, выравнивая структуру металла, и снимая напряжение в металле, способствующее деформации. Процесс может выполняться несколькими способами, а технология разнится в зависимости от типа и толщины металла. Не все сварные соединения необходимо подвергать термообработке, но в некоторых случаях она является обязательной.
Что и когда подвергается термической обработке
Нейтрализации остаточных явлений от электродуговой сварки необходимо подвергать все трубопроводы диаметром от 108 мм, имеющими стенку 10 мм и более. Для этого используют индукционный нагрев изделия током с частотой 50 Гц. Термообработка способна воздействовать на металл трубы со стенкой 45-60 мм, для чего применяют гибкие электронагревательные проволоки или муфельные печи. Если толщина стенки конструкции не более 25 мм, то можно использовать газопламенный способ нагрева. Во всех случаях важен фактор равномерности распределения температуры во все стороны от сварочного соединения.
Стыки, выполненные с применением труб из стали 12XIMФ и ее разновидности 15XIMIФ, имеющие толщину стенки магистрали 45 мм должны подвергаться термической обработке сразу после окончания сварочных работ. Охлаждение материала не должно допускаться до температуры 300 градусов. Стыки из аналогичных сталей на трубах с диаметром 600 мм, при стенке 25 мм, обрабатываются в этот же временной период. В случае невозможности выполнить процесс, соединение необходимо укрыть слоем теплоизоляции 15 мм, а при первой же возможности произвести обработку. Максимальный срок на проведение этих работ составляет трое суток.
Термообработке необходимо подвергать не только кольцевые швы на трубопроводе, но и вваренные отводы, краны, заглушки. Крепление под участок трубы, которое присоединялось посредством сварки, тоже необходимо обработать нагревом.
Режимы процесса
Разные виды стали подвергаются термообработке в конкретный временной промежуток. Влияет на режим и толщина стенки изделия. На хромомолибденовых сталях и их сплавах с ванадием применяется нагрев индукционным способом, с частотой тока в 50 Гц и выше, или радиационным методом по следующим показателям:
Толщина стенки, мм | Радиационный способ, минуты | Индукционный способ, минуты |
До 20 | 40 | 25 |
21-25 | 70 | 40 |
26-30 | 100 | 40 |
31-35 | 120 | 60 |
36-45 | 140 | 70 |
46-60 | 160 | 90 |
61-80 | 160 | 110 |
81-100 | 160 | 140 |
Виды оборудования
Термообработка выполняется несколькими видами средств, выбор которых зависит от толщины свариваемых труб и местной доступности оборудования. Выделяются три основные способа нагрева околошовной зоны.
Индукционный
На рабочем месте устанавливается аппарат, вырабатывающий переменное высокочастотное напряжение. К нему подсоединяется нагревательный элемент, которым служит гибкий провод. Последний наматывают на сварочное соединение, предварительно укутанное асбестом для теплоизоляции. Эту технологию можно применять независимо от положения трубы в пространстве (вертикального или горизонтального).
Намотку провода производят вплотную к изолятору, а между витками оставляют зазор в 25 мм. Таким образом должно быть покрыто по 250 мм участка трубы с каждой стороны шва. После правильного наложения витков аппарат включается на время, предназначенное для конкретной толщины стенки трубопровода. Напряжение, проходя через витки провода, создает индукцию и разогревает изделие. Похожим способом выполняется и накладка цельных поясов, содержащих внутри себя ряд проводов, которые сразу покрывают нужную ширину трубы.
Радиационный
Вторым распространенным способом термической обработки сварных соединений является радиационный метод. Здесь тепловой эффект исходит от специальных нихромовых проводов, по которым идет напряжение, и околошовную зону греет непосредственно тепло от провода, а не индукция тока, как в первом способе. Тэн укладывают на основу из теплоизоляции.
Газопламенный
Самым дешевым способом выполнить термическую обработку сварного шва является пламя от горения смеси ацетилена и кислорода. Это подходит для труб с диаметром не более100 мм. На горелку устанавливается мундштук с крупным отверстием. Для равномерности подачи тепла от пламени на сопло одевается асбестовая воронка, распределяющая пламя по ширине в 250 мм. Правильный нагрев производится одновременно двумя горелками, работающими с каждой стороны.
Виды термообработки
Тепловое воздействие на сварочное соединение и прилегающую зону может выполняться по разной технологии для достижения определенных целей. Вот основные процессы и их влияние на изделие:
- Термический отдых. Трубопровод подвергают нагреву до 300 градусов с удержание этой температуры до 120 минут. Это действие способствует снижению содержания водорода в шве, и частичному снятию остаточного напряжения. Метод применяется на особо толстостенных изделиях, где невозможно выполнить другие техники термообработки.
- Высокий отпуск. Трубу и сварной шов нагревают до температуры 600-700 градусов. Выдержка происходит в течении 1-3 часов в зависимости от толщины стенки. Вследствие чего остаточное напряжение снижается до 90%. В низколегированных сталях разрушается закалочная структура, а карбиды становятся крупнее. Это приводит к повышению пластичности и ударной вязкости. Чаще всего этот вид термообработки применяют на сталях перлитного класса.
- Нормализация. Шов и трубу нагревают до 800 градусов, но на короткое время (выдержка от 20 до 40 минут). Это частично убирает напряжение в металле, но главным образом придает однородность и мелкозернистую структуру, что улучшает механические свойства. Такая технология используется на тонкостенных трубах небольшого диаметра.
- Аустенизация. Разогрев материала до 1100 градусов с длительным удержанием температуры (около двух часов) и последующим остыванием на воздухе. Реализуется на высоколегированных сталях для снижения остаточного напряжения и повышения пластичности.
- Стабилизирующий отжиг. Трубопровод с наложенным швом разогревают до 970 градусов с выдержкой до 180 минут. Охлаждение выполняется естественным образом на воздухе. Метод предупреждает возникновение межкристаллической коррозии на высоколегированных сталях.
Применение термообработки на трубопроводах из различных металлов значительно продлевает их срок эксплуатации. Для успешного использования метода важно правильно подбирать температуру, время выдержки и способ нагрева.
Поделись с друзьями
0
0
0
0
Нормализация сварных соединений — Энциклопедия по машиностроению XXL
Термообработка сварных швов. Индукционный нагрев широко используется для термообработки (отпуска или нормализации) сварных соединений. Кольцевые сварные швы на трубах и аппаратах нагревают одновременным способом в кольцевых разъемных или неразъемных индукторах промышленной или средней частоты.
Нормализация сварных соединений не приводит к изменению их предела усталости, изменяется только место разрушения. Это связано с тем, что нормализация повышает прочностные свойства металла, но в то же время снижает упрочнение сварного стыка, полученное при сварке вследствие значительной пластической деформации при высоких температурах.

Нормализация сварных соединений и зон термического влия ния осуществляется при температуре 850—900° С в зависимости от марки стали. [c.28]
Высокий отпуск является основным видом термической обработки в монтажных условиях, он позволяет на 70—90 % снизить уровень остаточных сварочных напряжений. При высоком отпуске применяют медленную скорость охлаждения после окончания выдержки (300— 400°С/ч) до 300 °С, что достигается охлаждением сварных соединений под слоем теплоизоляции, после чего допускается охлаждение на воздухе. Основным отличием нормализации сварных соединений от этого вида термической обработки является охлаждение под слоем теплоизоляции после окончания выдержки, что гарантирует высокую пластичность металла сварных соединений. Термический отдых применяют для сварных соединений, металл которых имеет повышенную склонность к образованию трещин. Сварные соединения для этого нагревают до 250—300 °С и затем подвергают выдержке в течение нескольких часов. При термическом отдыхе в сварных соединениях уменьшается содержание водорода и несколько снижается уровень остаточных сварочных напряжений.
[c.206]
Восстановить структуру и механические свойства углеродистых сталей на указанном участке можно только последующей нормализацией сварного соединения. [c.272]
В случае необходимости производится нормализация сварного соединения с нагревом той же горелкой [c.365]
За истекшие годы, казалось бы, вполне устоялись наши представления о возможностях электрошлаковой сварки толстого металла. Немало было сделано в нашей стране и за рубежом, в частности в Великобритании, для устранения основного препятствия на пути этого прогрессивного способа сварки — необходимости нормализации сварного соединения. К сожалению, будучи довольно эффективными в применении к нелегированным сталям, все эти средства оказались недостаточными в случае легированных сталей, для которых неизбежное разупрочнение металла околошовной зоны требует восстановления его свойств высокотемпературной термообработкой.
[c.25]
В последние годы разработаны и находят применение более экономичные, по сравнению с полной нормализацией, приемы повышения ударной вязкости сварного соединения, выполненного электрошлаковой сваркой. К их числу относится сварка с пониженной погонной энергией и сопутствующей нормализацией металла сравнительно небольшой толщины (до 40 мм). Эта нормализация состоит в том, что на участке сварного соединения, остывшем примерно до температуры 500° С, устанавливают дополнительные нагреватели (горелки, индукторы и др.). Перемещаясь со скоростью сварки, они нагревают металл сварного соединения до телшературы нормализации. Находит также применение нормализация сварного соединения в интервале более низких температур (Лсз—АС]). [c.486]
После электрошлаковой сварки низкоуглеродистой стали толщиной более 80—100 мм требуется высокотемпературная термическая обработка — нормализация сварного соединения.

Нормализация сварных соединений может обеспечить некоторое улучшение свойств вследствие перекристаллизации и измельчения зерна, поэтому термообработка рациональна при однослойной сварке под флюсом металла большой толщины, при 174 [c.174]
До —70 при любой толщине и условии нормализации сварных соединений [c.197]
К недостаткам электрошлаковой сварки следует отнести образование крупного зерна в шве и околошовной зоне вследствие замедленного нагрева и охлаждения. После сварки необходима термическая обработка (отжиг или нормализация) для измельчения зерна в металле сварного соединения. [c.202]
Для обеспечения равнопрочности сварного соединения после сварки производят полную термообработку изделия, которая заключается в закалке и последующем высоком отпуске или в нормализации. [c.125]
Термическая обработка для снятия сварочных напряжений — отпуск 630—650° С для получения пластичного сварного соединения и выравнивания «механических свойств — закалка с отпуском для сварных соединений, выполненных ЭШС, — нормализация, а выполненных КТС — отпуск.
[c.139]
Термическая обработка путем нормализации и улучшения не позволяет повысить предел усталости сварных соединений до уровня прочности основного металла в том же состоянии термической обработки. При сварке трением в зоне сварного стыка происходит нарушение волокнистой структуры, которую имеет основной металл. Это нарушение структуры металла снижает его сопротивляемость циклическим нагрузкам. Снижение предела усталости нормализованных и улучшенных сварных соединений по сравнению с основным металлом, имеющим волокнистую структуру и аналогично термообработанным, характеризуется следующим соотношением [c.189]
Механические свойства сварного соединения, выполненного из стали 25Л, 35Л пластинчатыми электродами из стали ЮХСНД (ГОСТ 5058—65) и прошедшего до сварки высокий отпуск, а после сварки нормализацию и высокий отпуск, значительно превышают свойства основного металла. Механические свойства различных зон сварного соединения из стали МСт. 5, выполненного пластинчатыми электродами из стали ЮХСНД после сварки и термической обработки, приведены в табл. 57.
[c.523]
Для получения оптимальных механических свойств сварное соединение должно подвергаться термической обработке, устраняющей перегрев околошовной зоны и измельчение первичной структуры металла шва. Термическая обработка сварного изделия заключается в нормализации или закалке с последующим отпуском по режиму стали. [c.524]
В настоящее время имеется достаточно технических оснований для применения системы унификации и нормализации узлов трубопроводов. С введением межотраслевых нормалей устранены допускавшиеся в трубопроводах излишние запасы прочности, установлен единый ограничительный ассортимент труб для технологических трубопроводов, унифицированы номенклатура, конструкции и нормализованы типоразмеры деталей трубопроводов, марки стали, применяемые для их изготовления, и обеспечено широкое внедрение сварных соединений тру-
[c. 18]
При применении в связи с эксплуатационной необходимостью металлов с пониженной свариваемостью проектировать конструкции следует с учетом этого свойства. Для сведения к минимуму неблагоприятных изменений свойств металла сварного соединения и исключения в нем дефектов необходимо применять виды и режимы сварки, оказывающие минимальное термическое и другие воздействия на металл, и проводить технологические мероприятия (подогрев, искусственное охлаждение и др.), снижающие влияние на него сварочных воздействий. Термическая обработка после сварки (нормализация, закалка с отпуском и др.) может в значительной степени устранять неоднородность свойств в сварных заготовках. Прочность зоны сварного соединения может быть повышена механической обработкой после сварки прокаткой, проковкой и др. [c.288]
Св-ОЗГА ГОСТ 2246—60 16ГС (ЗН) и 16ГТ(ЗЫ) двухслойной стали АН-348А или ОСЦ-45 по ГОСТ 9087—59, или им Для рабочей температуры стенки от —30 до+ 450 С.
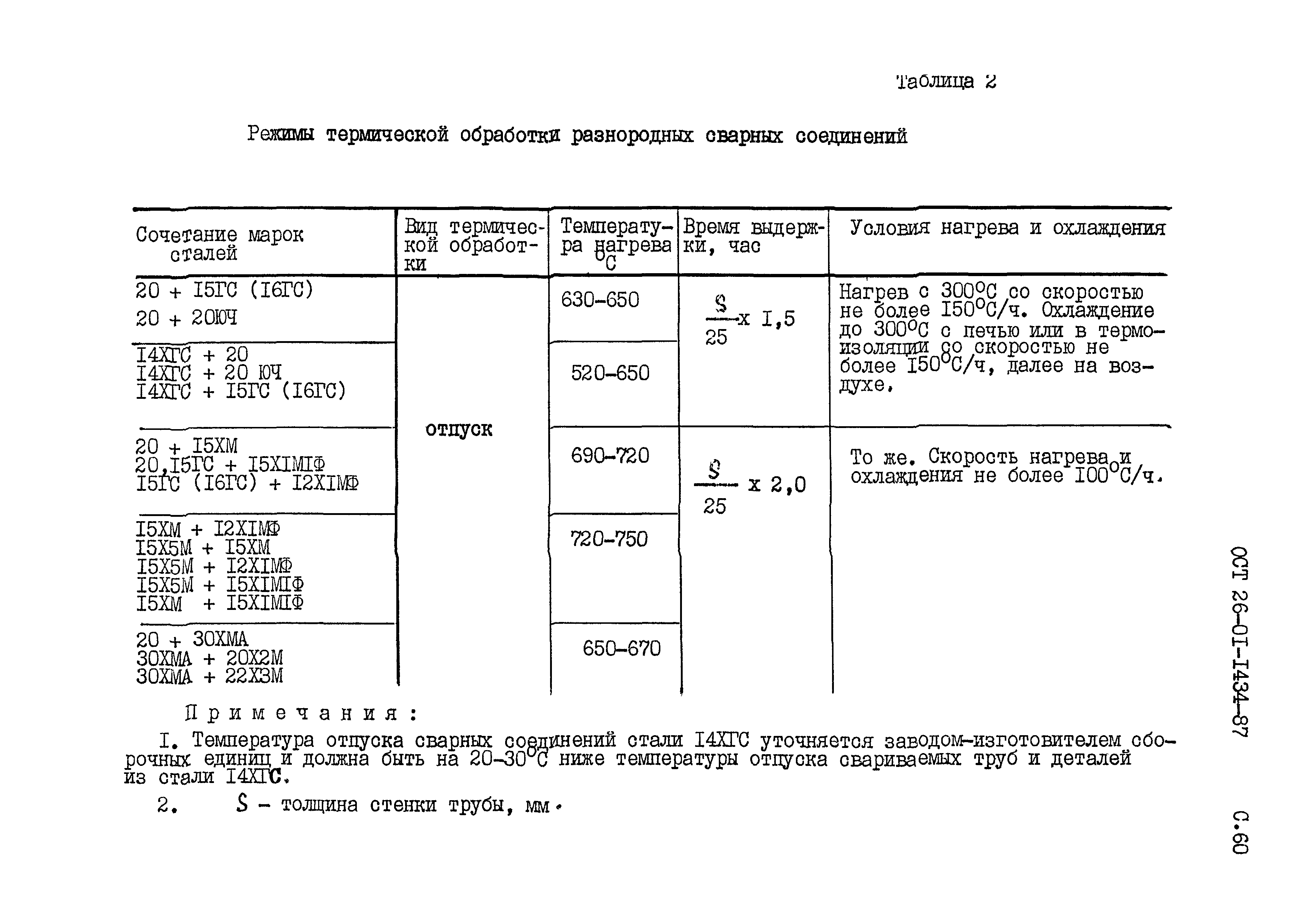
Г2С(М) равноценных Для рабочей температуры стенкп от — 30 до 4- 475 С. Для рабочей температуры стенки от — 31 до — 40 С при толщине металла )ie более 24. ii.ii. Для рабочей температуры стенки от — 31 до — 70 С и любой толщине металла при условии нормализации сварных соединений [c.352]
Г2С1(МК) Для рабочей температуры стенки от — 41 до — 70°С и любой толщине металла при условии нормализации сварных соединений [c.353]
Сталь 20ХМФ сваривается с предварительным и сопутствующим подогревом изделий до температуры 250—300° С. После сварки изделие подвергают высокому отпуску помещают в печь при температуре не более 200° С, нагревают до 700° С со скоростью 40— 50 град/час, выдерживают при 700° С от 2 до 5 час., охлаждают до 200° С со скоростью 40—50 град час. Нормализация сварных соединений при температуре 920—940° С не рекомендуется, так как при этом наблюдается резкое разупрочнение металла шва.
[c.223]
Термической обработке (отжигу или нормализации) сварные соединения подвергают с целью снятия внутренних термических напряжений, предупреждения образования трещин, а также для восстановления нормальной структуры металла. Режимы термообработки зависят от марки свариваемой стали и обычно указыва- [c.425]
В табл. 10-5 приведены типичные режимы сварки низколегированной стали с пониженным содержанием углерода (например 09Г2ДТ). Сварку такой стали на приведенных режимах также можно выполнять без нормализации сварных соединений. [c.523]
Применение стыковой сварки оплавлением заставляет использовать нетехнологичные штамповки с удлиненным хвостовиком, припуск на оплавление составляет 6—7 мм на сторону. При этом наличие видманштетовой структуры в зоне перегрева требует нормализации сварного соединения, а сварочные дес рмации вынуждают применять расточку ушков после сварки. Сварка трением позволяет обходиться без последующей термообработки, припуск на осадку составляет всего 3—4 мм на сторону. Кроме того, сварка трением дает возможность сваривать детали 1, окончательно обработанные в соответствии с чертежом, с деталями 2 и выдерживать указанные выше требования чертежа.
[c.339]
Св.-ОЗГА То же То же 16ГС 09Г2С Для рабочей температуры стенки от —30 до -1-450°. Для рабочей температуры стенки от —31 до —40° прн любой толщине металла при условии нормализации сварных соединений Для рабочей температуры стеики от —30 до -Ь475°. [c.98]
Г2С талла свыше 24 мм при отсутствии нормализации сва 1-ных соединений Для рабочей температуры стенки от —41 до —70 при отсутствии нормализации сварных соединений [c.98]
В сварных соединениях зону перекристаллизации разделяют на два участка зону перегрева с относительно крупным зерном (Гмакс 1273 К) и зону нормализации с мелким зерном (7 тах[c. 513]
Восстановительная термообработка проводилась индукционным способом со ступенчатым перемещением индуктора. Термической обработке подвергались прямые и гнутые трубы и их сварные соединения без демонтажа паропровода. И проводилось по двум режимам одинарная нормализация с отпуском и двойная нормализация с отпуском. Исследование структуры всех труб паропроводов и кратковременных и длительных свойств пробных гибов 0 273×32 мм и 0 325×38 мм после термообработки показало следующее [c.259]
Низкоуглеродистая сталь с содержанием до 0,25%С Среднеуглеродистая сталь с содержанием 0,26 — 0,45%С Высокоуглеродистая сталь с содержанием 0.46 — 0.759Й С 120—150°С — на многослойных швах при сварке больших толшин (40 ММ) 150 — 300°С 300 — 450°С Отпуск при 640 — 670°С для снятия сварочных напряжений, выравнивания структуры и механических свойств. В некоторых случаях (Например, ЭШС) нормализация при 920—940 С с последующим отпуском. Для получения требуемых механических свойств сварного соединения при сварке среднелегированной стали применяется закалка с последующим отпуском
[c. 137]
Прочность сварных соединений стали Х15Н9Ю может быть повышена до а = = ПОн-130 кПмм путем их нормализации при 950—975° С, обработки холодом при —70° С с выдержкой 2 ч или при температурах —50 или —60° С с выдержкой 4 ч и последующей рихтовкой и старением при 400 10° С с выдержкой I ч, охлаждение на воздухе. [c.142]
Нами было исследовано влияние таких видов термической обработки, как отжиг, нормализация и улучшение на усталостную прочность соединений, выполненных сВ аркой трением из сталей 45 и 40Х. Результаты испытаний показали, что отжиг снижает усталостную прочность сварных соединений. По сравнению со сварными соединениями без термической обработки предел усталости снижается на 357о. Разрушение при испытаниях происходит по сварному стыку. Таким образом, отжиг отрицательно влияет на усталостную прочность оварных соединений из-за общего понижения прочностных свойств металла и металла зоны сварки. [c.189]
При автоматической многослойной сварке (больше одного слоя) после наложения каждого слоя поверхность шва тщательно очищают от шлака. Для поддержания устойчивой дуги сварку производят с применением флюса. Сварку выполняют только качественными (толстообмазанными) электродами, состав электродной проволоки подбирают так, чтобы основной металл и металл сварного соединения были бы равнопрочны. В процессе сварки обечайка деформируется. Для придания ей цилиндрической формы обечайку калибруют путем обкатки в листогибочных вальцах в горячем состоянии. Последнее используется также для нормализации, в процессе которой сварные швы и околошовная зона освобождаются от сварочных напряжений. На рис. 15-5 показана электрошлаковая сварка применительно к продольному шву барабана. Для выполнения сварочных работ барабан располагают в вертикальном положении неподвижно. На кромки стыкуемой обечайки накладывают медные ползуны — кристаллизаторы, перемещаемые в процессе сварки снизу вверх, а расстояние между кромками устанавливается дистанционной планкой. В образовавшийся объем, ограниченный кромками обечайки, ползунами н дистанционной планкой, вводят электродную проволоку и возбуждают сварочную дугу под слоем флюса, который при разогреве расплавляется.
Расплавленный флюс обладает электропроводностью.
[c.171]
После сварки соединение подверглось нормализации при 950° С, затем отпуску при 620° С и охлаждению со скоростью V = 50° С/ч (рис. 16, б). Предел выносливости равен 12,5 кгс/мм . Образцы испытывались со снятым усилением шва. Усталостные изломы, так же как и в сварном соединении стали 0Х12НДЛ со сталью 15Г2ВЛ, происходили по зоне сплавления металла электрода со сталью 0Х12НДЛ. [c.35]
Отпуск после сварки — Режимы
Выбор режима подогрева при сварке или отпуска после сварки определяется требованиями отсутствия трещин и обеспечения необходимого уровня механических свойств сварного соединения. Для сварных конструкций из малоуглеродистой стали или хромомолибденовой относительно небольшой толщины — до 10—15 мм — удается обеспечить указанные требования за счет соответствующего выбора термического режима сварки без применения подогрева или отпуска сваренного изделия.

Рис. 9. Механические свойства наплавленного металла КТИ-10 в зависимости от режима отпуска после сварки [3, 15] |
Местный высокий отпуск применяется для крупных деталей в местах, где непосредственно производилась сварка, с целью снижения уровня сварочных напряжений и повышения пластичности металла.
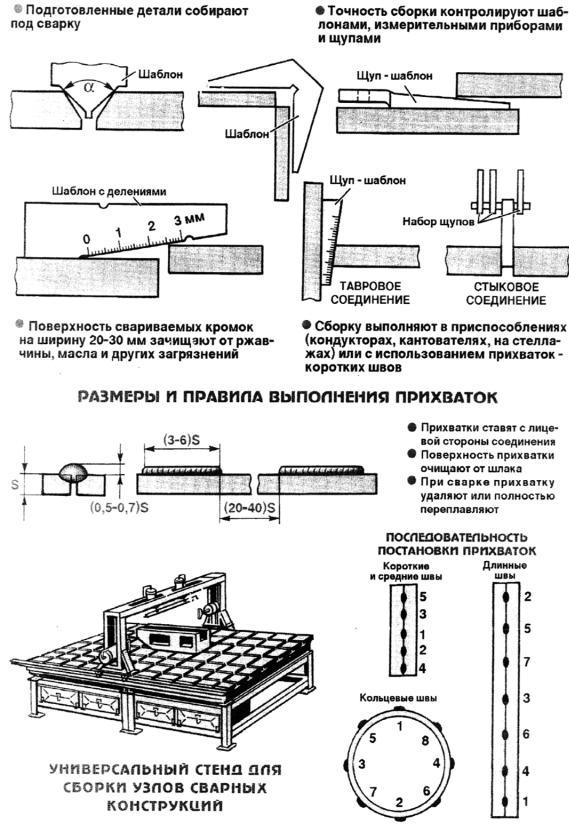
Применение 279 — конструкционная — Износостойкость — Влияние высокочастотной поверхностной закалки 677 — легированная—Механические свойства после цементации, закалки и низкого отпуска 684 — Сварка газовая 202 — малоуглеродистая — Сварка атомно-водородная — Режимы 220 [c.788]
В ряде случаев представляется целесообразным использовать для сварных изделий из перлитных и хромистых сталей режим полной термической обработки закалку с последующим отпуском. При этом обеспечивается наиболее высокая однородность сварного соединения. Данный вид термической обработки может применяться для отливок, подвергаемых крупным заваркам в целях ремонта. На сварку отливка поступает в отожженном состоянии, а после сварки деталь проходит полную термообработку по режиму для основного металла.
[c.92]
После сварки и установки крестовин барабан подвергается отпуску для снятия внутренних напряжений по следующему режиму посадка в печь при температуре 450—500° С, нагрев до температуры 600° С по 80° С в час, выдержка при данной температуре 4—8 ч, охлаждение до температуры цеха на воздухе на выкаченной подине печи. [c.336]
При применении в связи с эксплуатационной необходимостью металлов с пониженной свариваемостью проектировать конструкции следует с учетом этого свойства. Для сведения к минимуму неблагоприятных изменений свойств металла сварного соединения и исключения в нем дефектов необходимо применять виды и режимы сварки, оказывающие минимальное термическое и другие воздействия на металл, и проводить технологические мероприятия (подогрев, искусственное охлаждение и др.), снижающие влияние на него сварочных воздействий. Термическая обработка после сварки (нормализация, закалка с отпуском и др.) может в значительной степени устранять неоднородность свойств в сварных заготовках. Прочность зоны сварного соединения может быть повышена механической обработкой после сварки прокаткой, проковкой и др.
[c.288]
Увеличить стойкость сварного соединения против холодных трещин можно, изменяя параметры режима сварки так, чтобы уменьшить скорость охлаждения металла, уменьшая тем самым опасность возникновения хрупкого закаленного участка в зоне термического влияния. Для этого можно выбирать режим сварки с повышенной энергией, увеличивая мощность источника тепла или уменьшая скорость сварки. Применяют подогрев изделия после сварки или сопутствующий подогрев во время сварки, например газовой горелкой, высокочастотным индуктором, либо второй сварочной дугой. Мелкие детали после сварки можно укладывать в ящик с песком, Детали из сталей с плохой стойкостью против холодных трещин подвергают после сварки общей термообработке (отпуску) в печах.
[c.34]
В зависимости от толщины стенки трубных элементов и класса стали сварка швов выполняется с предварительным и сопутствующим подогревом (табл. 3.32). После сварки проводится термическая обработка по режиму высокого отпуска при температуре 630…750 °С с учетом марки стали и толщины стенки трубных элементов. [c.255]
Рис. 31. Влияние термического режима сварки на длительную прочность и пластичность при температуре 565° С металла шва типа Э-ХМФ (электроды ЦЛ-20М) после сварки отпуск при 720—740° С — 5 ч |
В связи с практической невозможностью полного исключения при изготовлении конструкций различного рода зародышевых дефектов, являющихся в дальнейшем при неблагоприятных обстоятельствах очагами развития эксплуатационных тещин, методы лабораторных и стендовых испытаний должны оценивать также влияние возможных дефектов на прочность изделия.
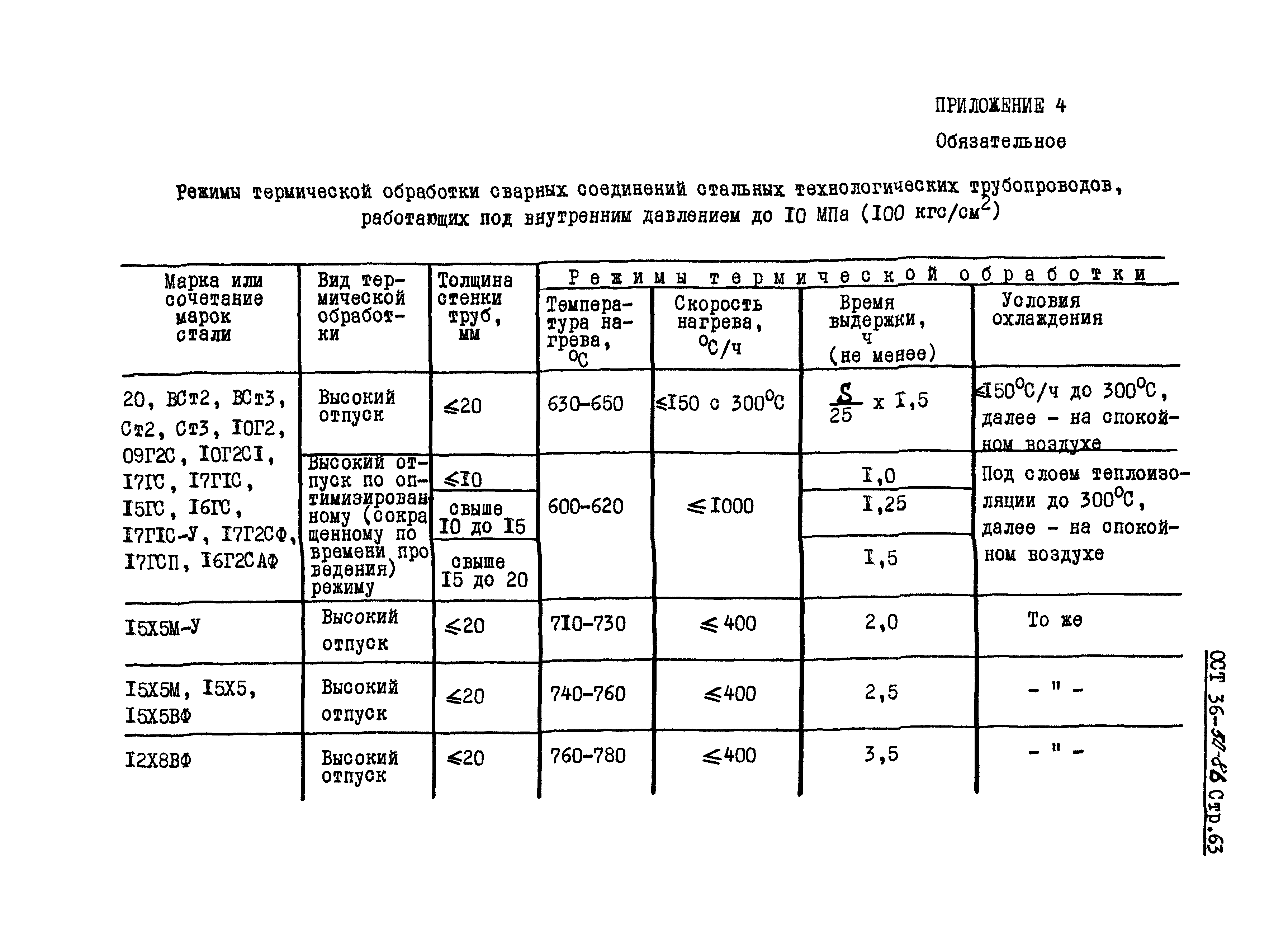
На рис. 101 аналогичные зависимости приведены для швов типов Э-ХМ и Э-ХМФ. Для них также в исходном состоянии после сварки длительная пластичность заметно ниже, чем в отпущенном состоянии. Особо следует обратить внимание на то, что даже при сравнительно небольших отклонениях от оптимального режима отпуска шва типа Э-ХМФ (недоотпуск при 680° С) длительная пластичность шва совсем не повышается, оставаясь на уровне исходного состояния, что наиболее наглядно проявляется при наличии концентратора. Таким образом, для данных составов благоприятное влияние отпуска сказывается лишь при строгом выдерживании установленной температуры отпуска в пределах 730° С.
[c.180]
Образование трещин при высоких температурах в малоуглеродистых и хромомолибденовых швах типа Э-ХМ возможно, как показывает опыт эксплуатации, при наличии в них различного рода дефектов и в первую очередь надрывов в корне шва. В то же время развитие трещин идет относительно медленно и поэтому они обнаруживаются обычно при осмотрах во время капитальных ремонтов. Трещины же в швах типов Э-ХМФ и Э-МФБ даже при сравнительно небольших отклонениях от оптимального режима отпуска (недоотпуске) могут достигать значительного развития, приводя в отдельных случаях к аварийным последствиям. Зародышевые трещины в этих швах могут возникать и непосредственно после сварки в условиях жесткости, при отклонениях от режима подогрева или недоотпуске. Критерием склонности швов к хрупким разрушениям при высоких температурах является величина их длительной пластичности, оцениваемая по результатам испытания образцов на растяжение с постоянной скоростью деформации (и. 14).
[c. 192]
После сварки заготовок из стали 15231 выполняли термическую обработку по режиму закалка с температуры 890° С в воду и отпуск при 550° С (Ов = 97,4 кгс/мм ). Опыты показали, что для высокопрочной стали 15231 предел выносливости образцов с угловым швом (с радиусом галтели в зоне шва / = 10 мм) находится на уровне предела выносливости образцов с поперечным отверстием или шпоночной канавкой. Для стали 11600 (сТв = 60 кгс/мм ) прочность образцов оказалась несколько ниже, чем для образцов со шпоночным пазом или поперечным отверстием. [c.195]
Достаточно высокие значения ударной вязкости у этой стали зависят от режима термической обработки и старения (рис. 272). С понижением температуры испытания она несколько упрочняется, но отпуск при 500° С значительно улучшает ударную вязкость после двойной закалки и после сварки. Сварные изделия после сварки рекомендуется подвергать отпуску для снятия сварочных напряжений и устранения воздействия интервала температур более низкого отпуска (рис. 273) [7091.
[c.467]
После сварки блоков, в зависимости от их габаритов, применяют либо нормализацию с нагревом в печи всего блока по режиму температура нагрева 900— 920° С. охлаждение на воздухе до 250—300° С и последующий отпуск при 630— 650° С в течение 20 ч, либо местную термическую обработку с индукционным нагревом. [c.658]
В соответствии с изменением механических свойств меняются и жаропрочные свойства сварных соединений, оцениваемые по результатам их испытания на длительную прочность. При высокой исходной прочности заготовок и низком отпуске после сварки при 700° С — 5 ч кривые длительной прочности сварных соединений идут выше соответствующих кривых высокоотпущенного состояния (рис. 112, б). По уровню прочности сварные соединения низкоотпущенных вариантов на 10—15% ниже прочности основного металла, обработанного по тому же термическому режиму. При длительности до разрушения в пределах 10 ч изломы проходят пластично при удовлетворительной величине относительного сужения.
При использовании твердости как критерия качества термической обработки следует иметь в виду, что твердость сварных соединений в значительной мере зависит от условий термообработки [12]. Например, при твердости металла шва типа Э-09ХМФ выше НВ 250 (2500 МПа) можно однозначно констатировать, что отпуск после сварки не проводился или его темле-ратура была заметно ниже регламентированной. В то же время если твердость ниже НВ 250, то это еще не говорит о качественном проведении термообработки, так как при чрезмерно высоком подогреве (450—500 °С) пониженная твердость может быть получена и в исходном состоянии. Твердость нялсе НВ 220 свидетельствует о качественном проведении отпуска по установленному режиму. На основании сказанного регламентированная твердость после отпуска должна быть ниже возможной в исходном состоянии при чрезмерно высоком подогреве, поэтому для наиболее ответственных и нагруженных сварных соединений предпочтительнее твердость не выше НВ 220 [12].
[c.171]
Термообработка после сварки различна для разных марок стали. Для отливок из стали ЗОЛ и 35Л при заварке сквозных трещин и вварке усилительных вкладышей обязателен отжиг или высокий отпуск. Для улучшения механических свойств сварного соединения и его обрабатываемости при заварке мелких дефектов на углеродистой стали, содержащей углерода более 0,35%, термическая обработка рекомендуется по режиму для данной стали. Для других сталей, сваренных в термически обработанном состоянии, обязателен отпуск с нагревом до температуры на 50—100° ниже температуры отпуска стали. Для стали 27ГС, 20ХГС и других сталей, склонных к отпускной хрупкости, температура отпуска после сварки должна быть вне области температуры отпускной хрупкости.

Термообработка после сварки имеет следующие особенности. При заварке крупных дефектов стали ЛХН2 требуется термическая обработка по режиму для данной стали. После заварки мелких дефектов в термически обработанной отливке обязателен повторный отпуск по режиму для данной стали. Для всякой другой стали рассматриваемой группы, сваренной в термически обработанном состоянии, обязателен отпуск для снятия напряжений с нагревом до температуры на 50—100° ниже температуры отпуска стали. Для стали ЗОХГСА и других сталей, склонных к отпускной хрупкости, температура отпуска после сварки должна быть вне области отпускной хрупкости. [c.189]
Отпуск после сварки кованой стали 15Х1М1Ф должен производиться при температуре 720—740°С. Применение местного отпуска является нежелательным и может допускаться в отдельных случаях при строгом соблюдении установленных режимов. [c.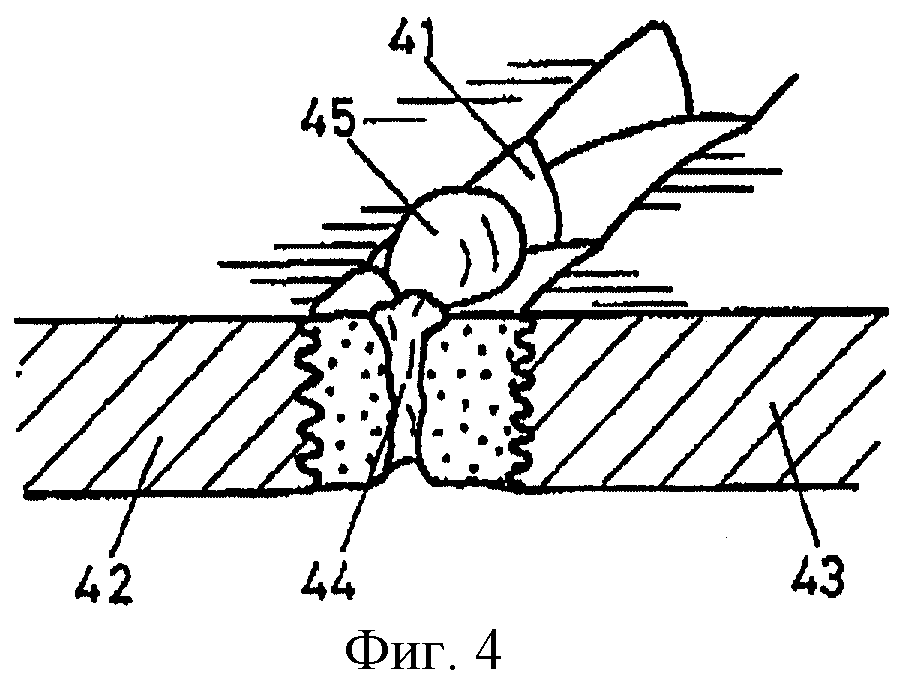
Сравнительно широко применяются композитные соединения при сварке сталей одного класса, близких по своим физическим свойствам, но имеющих различный химический состав и механические свойстйа. Однако и в этом случае, как показали исследовании института электросварки им. Патона [23], в сварочных соединениях из низколегированных сталей в зоне сплавления при определенных соотношениях легирующих элементов может наблюдаться концентрационная неоднородность, приводящая к разрушению по зоне сплавления при вибрационной нагрузке. При сварке композитных Соединений возникают вопросы, связанные с выбором электродов, режима подогрева и отпуска после сварки и обеспечения уровня прочностных и пластических свойств таких соединений. Обычно композитные соединения применяются при изготовлении корпусов цилиндров мощных турбин. Корпуса изготавливаются в виде сварных конструкций, в которых области, подвергающиеся действию высоких температур, выполнены из стали 20ХМФ или 15Х1М1Ф, а области, работающие при низких температурах, изготовляются из углеродистой стали 25Л.
[c.150]
Подогрев при сварке до 300—350°С, отпуск после сварки при температуре 690—710°С. Полуавтоматическая сварка в среде углекислого газа производится проволокой Св-08ХГСМФА диаметром 3 мм. Сила оварочного тока 350—420 а, напряжение дуги 28—32 в скорость подачи проволоки 100—140 м/н-, расход углекислого газа 1000—1400 л1ч. Сварные соединения, полученные при указанных режимах сварки, обладают вполне удовлетворительными свойствами и аналогичны свойствам соединений, выполненных ручной дуговой сваркой. В табл. 79 приведены результаты механических испытаний сварнолитых соединений, выполненных полуавтоматической сваркой в среде углекислого газа после отпуска при температуре ТЮХ. [c.171]
Однако проведение отжига и отпуска требует наличия сложных нагревательных устройств, точного соблюдения режимов, что в усло-9ИЯХ ремонта деталей не всегда осуществимо. Поэтому в некоторых случаях отжиг и отпуск после сварки или наплавки можно заменить предварительным подогревом изделия, тем более, что предваритель- Ный подогрев изделий из металлов, способных подвергаться закалке, необходим с целью устранения явления закалки и образования микротрещин. Такого рода рекомендации оправдываютсл исследованиями и практикой.
[c.41]
С). Однако в ряде случаев, особенно при относительно кратковременной работе установок, обработку заготовок перед сваркой ведут по режиму отпуска при 660—680° С в течение 5 ч. Свойства сварных соединений в этих случаях уступают свойствам основного металла, однако абсолютные значения прочности сохраняются на более высоком уровне, чем для ранее рассмотренных сварных соединений. Так, для сварных соединений стали 15Х12ВМФ (отпуск до сварки по режиму 680″ С — 5 ч, а после сварки по режиму 700° С — 5 ч) предел длительной прочности при 580° С за 10 ч составляет 15 16 кГ1мм . В то же время для сварных соединений, обработанных до и после сварки по режиму высокого от-48 [c.48]
Свойства сварных соединений с точки зрения равнопрочтгости с основным металлом зависят не только от режима термообработки после сваркн, но и от режима термообработки изделия перед сваркой. Так, если отпуск после закалки перед сваркой проводили при температурах ниже тех, которые используют при термообработке
[c. 269]
Исследованиями установлено, что сварка теплоустойчивых сталей больших толщин должна производиться с применением предварительного и сопутствующего подогрева. Для уменьшения величины остаточных напряжений сварное соединение после сварки должно подвергаться отпуску при температуре, не превышающей температуру отпуска стали до сварки. Во избежание значительного укрупнения зерен и падения ударной вязкости по линии сплавления, сварка должна осуществляться на режимах с ограниченными тепловложе-ниями. Для предотвращения развития диффузионных процессов необходимо стремиться максимально приблизить химический состав шва к составу основного металла. Наилучшие результаты по получению заданного (требуемого) химического состава металла шва определены при легировании через сварную проволоку. [c.121]
Примечание. После сварки сталей 12ХМ и 12МХ необходимо проводить отпуск по режиму, предусмотренному нормативной документацией на термическую обработку.
[c. 346]
Как показали исследования, остаточные напряжения в сварных соединениях паропроводов из перлитных сталей непосредственно после сварки могут достигать предела текучести металла шва. Однако они редко приводят к повреждениям сварных стыков, если им не сопутствуют дефекты сварки или грубые нарушения установленных режимов сварки. Остаточные напряжения в стыках перлитных трубопроводов снижаются при высоком отпуске, проводимом после сварки. В процессе эксплуатации при высоких температурах они относительно быстро релаксируют. Так, сразу после сварки электродами ЦЛ-14 в сварных стыках паропровода из стали 12МХ одного из котлов ТП-230, на котором в порядке эксперимента не производился отпуск сварных соединений, среднеквадратичные напряжения на внутренней поверхности стыка достигали 16,3 /сГ/жж . После 5 500 ч эксплуатации сварных стыков, не проходивших термической обработки, величина среднеквадратичных напряжений снизилась до 4,4 кГ1мм . [c.201]
Металл перлитного шва в зависимости от его легированности, термического режима сварки и режима отпуска существенно меняет свои свойства.

На фиг. 10 приведены кривые длительной прочности сварных соединений стали 15ХШ1Ф (электроды ЦЛ-27) при двух уровнях прочности заготовок до сварки. В одном случае сталь перед сваркой термически обрабатывалась на предел текучести при комнатной температуре, равный 40—45 кПмм (нижний уровень прочности для стали) в другом предел текучести заготовки был равен 52—58 кПм.мР. После сварки все образцы прошли отпуск по режиму 720—730 — 5 час.
[c.28]
Режимы дополнительной термообработки после холодной или горячен. реформации (гибки, обжатия, штамповки и др.) и после сварки для разных размеров труб (отпуск, аустениэация, нормализация, время выдержки, зона нагрева) должны устанавливаться совместной инструкцией завода, утвержденной главным инженером и согласованной с основными положениями, разработанными ЦНИИТМАШ. Рекомендуемые режимы дополнительной термообработки указаны в табл. 4.1.3. [c.268]
Для обеспечения пластических свойств металла шва и околошов-ной зоны на уровне свойств основного металла следует выбирать режимы, обеспечивающие получение швов повышенного сечения, применять двухдуговую сварку или производить предварительный подогрев металла до температуры 150…200 °С. Среднеуглеродистые и среднелегированные стали рекомендуется сваривать под флюсом при толщине свариваемого металла не менее 4 мм. Сварку можно вести как на переменном, так и на постоянном токе. Диаметр электродной проволоки выбирают 2. ..5 мм. При сварке с одной стороны не допускается использование медных и медно-флюсовых подкладок из-за возможности попадания в шов меди и образования вследствие этого горячих трещин. Для увеличения сопротивляемости сварных швов горячим трещинам, а также повышения пластичности и ударной вязкости металла шва используют основные флюсы, такие как АН-26, АН-20, 48-ОФ-10, уменьшающие содержание серы и окисных включений в металле шва. Во избежание пористости и наводоражи-вания швов флюсы перед сваркой необходимо прокаливать при температуре 300…350 °С в течение 2…3 ч, чтобы их влажность не превышала 0,1 %. Конструкционные среднеуглеродистые и среднелегированные стали под флюсом сваривают, как правило, без подогрева. Только в случае сварки жестких узлов и узлов из сталей ЗОХГСА и ЗОХГСНА при большой толщине изделий применяют подогрев до температуры 250…300 °С. После сварки во всех случаях необходим общий отпуск при температуре 600 °С или местный послесварочный отпуск при температуре 300 ° С для предупреждения образования холодных трещин.
[c.150]
Свариваемость двухфазных хромоникелевых сталей переходных классов по сравнению с однофазными выше, особенно сопротивляемость образованию трещин и межкристаллитной коррозии. Мартенситно-стареющие коррозионностойкие стали (08Х15Н5Д2Т и др.) могут иметь в зоне сварного соединения ослабленные участки в отношении величины ударной вязкости и стойкости против коррозии. Антикоррозионные свойства сварных соединений восстанавливаются после полной термической обработки. Рекомендуется для этих же целей отпуск перед сваркой при 600—650 °С. Для предотвращения старения металла в зоне сварного соединения в процессе эксплуатации конструкции и последующего снижения его пластических свойств применяют термообработку после сварки (при 600—650 °С). Хромоникелевые стали сваривают практически всеми методами. Режимы стремятся подбирать так, чтобы сварка происходила при малых значениях погонной энергии. Успешно сваривают хромоникелевые стали контактной сваркой.
[c. 511]
Поэтому во избежание саморастрескивания деталей отжиг или высокий отпуск следует проводить немедленно после сварки. Более подробные данные по режимам термической обработки для других хромистых сталей приведены в табл. 28 с указанием получаемой при этом твердости. Ими можно пользоваться при обработке сварных соединений. [c.719]
Термообработка сварных швов: технология, оборудование
При крупномасштабном изготовлении металлических конструкций и соединении трубопроводов проводится дополнительная обработка, про которую забывают начинающие сварщики. К одному из таких технологических процессов относится термообработка сварных швов. Оно позволяет улучшить характеристики готового крепления, продлить срок его эксплуатации.
Термообработка сварных швовСуть и назначение процесса
Термообработка после сварки нужна для того чтобы улучшить ухудшившиеся характеристики материала при скреплении. К ним относятся:
- Изменение параметров металла из-за перегрева.
При использовании сварочного оборудования детали нагреваются до 5000 градусов. Появляются крупные зёрна металла, что приводит к ухудшению показателя пластичности.
- Вокруг готового шва образуется место закалки. Эта область не устойчива для ударов.
- Удалённые области обладают малым показателем прочности. Связано это с кратковременным сильным нагревом.
Главный недостаток, который образуется на соединенной конструкции после сварки — внутренние напряжения. Это приводит к деформации изделия при эксплуатации. Остаточное напряжение становится причиной разрушения соединений из-за чего трубопроводы, металлоконструкции приходят в негодность.
Тепловая обработка проводится при температуре до 1000 градусов по Цельсию. Состоит технологический процесс из трёх этапов:
- С помощью специального оборудования происходит равномерный прогрев в области шва. Это изменяет механические свойства материала.
- Сохранение рабочей температуры на определённый промежуток времени.
Длительность зависит от того, насколько нужно изменить свойства и структуру материала.
- Последним этапом является охлаждение. Температура должна опускаться равномерно, чтобы добиться повышения пластичности и ударной вязкости.
Термообработка после сварки позволяет снять остаточные напряжения, выровнять металлическую структуру, избавиться от крупных зёрен.
Виды термообработки
Термообработка сварных соединений может проводиться несколькими способами. К наиболее эффективным относятся:
- Нагревание деталей до сваривания. Применяется при работе с низкоуглеродистыми сталями. Сварщик нагревает рабочие поверхности до 200 градусов. После сваривания конструкция должна остыть при комнатной температуре.
- Отпуск металла. Подразумевает под собой нагрев деталей до критических температур. Заготовки выдерживаются в таком режиме до 5 часов.
Затем материал медленно охлаждается.
- Термический отдых. Заготовки разогреваются до 300 градусов. При такой температуре они выдерживается до трех часов. Постепенно остаточные нагрузки исчезают, шов становится прочнее.
- Нормализация. Проводится для уменьшения крупных зёрен структуры материала, увеличения показателей прочности.
- Аустенизация. Перед сваркой детали разогревают до 1100 градусов. Выдержка при такой температуре составляет 90 минут. Процесс охлаждения происходит на свежем воздухе. Механические свойства улучшаются, остаточное напряжение исчезает.
- Стабилизирующий отжиг. Готовый шов нагревают до 800 градусов. На протяжении трех часов температура поддерживается на одном уровне. Снижается риск образования ржавчины.
Метод термической обработки зависит от используемого материала.
Применение нагревательных элементовВиды оборудования
Для проведения термической обработки используют определённое оборудование. Его выбор зависит от металла, толщины заготовок, возможностей сварщика. К нему относятся:
- Индукционные установки. Представляют собой аппараты, которые вырабатывают высокочастотное напряжение. Дополнительно на установке закрепляется нагревательный провод. Его другой конец обматывается вокруг шва. Важно оставлять между витками по 2,5 см.
- Радиационное оборудование. Для разогревания области вокруг креплений и самого соединения используются нихромовые провода. На них подаётся напряжение, которое способствует нагреванию рабочей поверхности.
- Газопламенное оборудование. Простой способ нагрева рабочих поверхностей. Для этого применяются газовые горелки, к которым подключается ацетилен, кислород. Чтобы увеличить зону прогрева, на горелку закрепляется широкий мундштук.
Прежде чем начинать использовать то или иное оборудование нужно изучить особенности работы с ним. Применение нагревательных машин требует определённых навыков.
Технология термообработки
Помимо изучения технологии сварки, нужно знать способы обработки швов. Этапы проведения термической обработки зависят от выбранного оборудования, используемого для соединения материала, его толщины. Сварщику необходимо равномерно прогреть область соединения.
Пошаговая термическая обработка соединений
Термическая обработка сварных швов должна происходить в определённой последовательности. Проведение работ:
- Нагреваемое место покрывается теплоизолирующим материалом.
- Сверху закрепляются нихромовые провода, через которые будет идти ток.
- С помощью напряжения задаётся температура нагрева.
Нагревательные элементы снимаются с места соединения. Поверхность освобождается от лишнего материала.
Термообработка сварных швов считается необходимым технологическим процессом для улучшения механических показателей соединённой конструкции. Без дополнительного нагревания остается внутреннее напряжение, которое может привести к разрушению соединения.
Термообработка сварных изделий, металлоконструкций и сварных швов
Д. А. Чичиндаев, А.С. Степанов. / 12.12.2019
Для чего нужна термообработка сварных стыков (швов, соединений, металлоконструкций, изделий и трубопроводов)?
Давайте сперва определим понятие термообработки применимо к сварным изделиям и сварным швам.
Термообработка сварных изделий – это совокупность операций нагрева, выдержки и охлаждения зон сварки (околошовных зон (ОШВ), сварных швов (СВ)) для достижения требуемых параметров и физико-механических свойств сварных швов и, как следствие, сварных изделий.
Для чего проводится термообработка:
Термообработка, как правило, проводится для повышения эксплуатационных характеристик сварных изделий. Она снимает поверхностные и внутренние напряжения в металле, образовавшиеся после сварки.
Показатели качественной термообработки в монтажных условиях:
Сварной шов после сварки имеет, более высокие показатели твердости нежели основной металл. После проведения качественной термообработки показатели твердости сварного шва снижаются до требуемых НТД РФ величин. В монтажных условиях дефектоскописты лаборатории Неразрушающего Контроля при помощи твердомеров производят проверку показателей твердости и контроль соблюдения требуемого НТД РФ диапазона твердости сварного шва.
Основные способы проведения термообработки сварных соединений:
Термообработка после сварки проводится как в заводских условиях, так и на монтаже. В монтажных условиях термообработка сварных стыков и соединений проводится в основном по программе отжига для снятия напряжений (низкотемпературный отжиг или высокий отпуск) двумя способами: радиационный (нагрев производится керамическими ковриками) и индукционный (нагрев производится индуктором, обмотанным вокруг изделия). Оба способа позволяют произвести с заданными параметрами контролируемый подъем температуры до требуемой, провести выдержку температуры и последующее контролируемое охлаждение. В заводских условиях возможно еще использовать печной способ термообработки и иные программы термообработки.
Диапазоны использования радиационного и индукционного методов
Согласно требованиям РТМ-1С, действующим в тепловой энергетике (при выполнении термообработки в других отраслях следует руководствоваться соответствующей Нормативной Документацией) для термообработки трубопроводов со стенками до 50 мм возможно использование как радиационного метода так и индукционного. Для стенок 50 мм и выше – рекомендовано использование индуктивного способа.
Компания ООО «ТЭК-Консалтинг» специализируется на проведении термообработки сварных стыков различного диаметра и толщин стенок.
Основные этапы взаимодействия ООО «ТЭК-Консалтинг» с Заказчиком по запросу на проведение операций предварительного подогрева и термообработки:
· Выяснение технических требований Заказчика, заполнение опросного листа, который вы можете скачать по ссылке:
СКАЧАТЬ ОПРОСНЫЙ ЛИСТ на ПРОВЕДЕНИЕ ТЕРМООБРАБОТКИ СВАРНЫХ СОЕДИНЕНИЙ
· Расчет и передача технико-коммерческого предложения в требуемые Заказчиком сроки
· Оперативное согласование и подписание договора с Заказчиком
· При необходимости и по требованию Заказчика – разработка технологии термообработки
· Срочная доукомплектация необходимыми расходными материалами под конкретный проект
· Выезд с оборудованием и аттестованным персоналом Исполнителя на площадку Заказчика
· Исполнение Договора – проведение термообработки сварных стыков в сменном режиме 24/7
· Проведение контроля показателей твердости твердомерами до термообработки и после, протоколирование показателей, ведение журналов термообработки, температура термообработки фиксируется аттестованными регистраторами автоматически с записью на диаграммную ленту
· Подготовка сдаточной документации по требованиям Заказчика, передача Заказчику
ООО «ТЭК-Консалтинг» — строительно-монтажная компания с длительным опытом работ на рынке энергетики в России. Обладая собственным парком оборудования и аттестованными специалистами – операторами термистами, мы в кратчайшие сроки проведем термообработку сварных стыков различного объема и диаметра.
Обработка сварного шва после сварки: термическая, механическая, антикоррозийная
Сварка — самый надежный, быстрый и экономичный способ создания неразъемных соединений металлов и их сплавов. В ходе сварочного процесса металл нагревается до температуры плавления. Это вызывает в нем внутренние напряжения. Кроме того, на поверхности сварочного шва остается шлак. Для удаления шлака и снятия внутренних напряжений в металле применяются различные способы обработки сварного шва.
Обработка сварного шваОсновные способы обработки сварных соединений
Наиболее распространенными стали следующие методы обработки сварного шва:
- Термическая. Применяется для ликвидации внутренних остаточных напряжений. Проводится путем локального или общего прогрева.
- Механическая.
Зачистка сварных швов после сварки удаляет шлаки и окалину с поверхности соединения.
- Химическая. Состоит из обезжиривания и покрытия защитным слоем. Препятствует возникновению коррозионных очагов. Метод используют для обработки материалов, подверженных коррозии, которым предстоит работать в активных средах.
Способ воздействия выбирают, применяясь к техническим требованиям к конструкции и условиям ее эксплуатации. Часто применяют последовательно все три метода.
Термообработка
Термическая обработка сварных соединений обязательно проводится после сварки тонкостенных изделий, особо подверженных деформациям под воздействием внутренних напряжений. К таким конструкциям относятся трубопроводы, различные емкости, сосуды давления.
Термическая обработка сварного шва
Проводится термообработка и для большинства ответственных конструкций, таких, как корпуса атомных и химических реакторов.
Заключается термообработка в нагреве детали и ее последующем охлаждении по строго заданному температурному графику.
Зачем нужна
В ходе сварки нагревается небольшая область детали в районе шва. Неравномерный прогрев и приводит к возникновению внутренних напряжений, способных деформировать или даже разрушить деталь. Кроме того, в зоне неравномерного нагрева изменяется структура кристаллической решетки металла, что приводит к ухудшению его физико-механических и химических свойств.
Рядом со сварным швом зона закалки, в которой прочность повышена, а упругость, наоборот, понижена. Ее окружает зона разупрочнения, в которой пластичность сохраняется, а прочность становится ниже, чем была до сваривания.
Термическая обработка сварных соединений призвана восстановить внутреннее строение металла и его свойства, вернуть характеристики прочности, пластичности и коррозионной устойчивости к проектным значениям.
Особенности проведения
Обработка осуществляется при высоких температурных значениях, в диапазоне 600- 1000 °С. Это позволяет преодолеть негативные последствия неравномерного нагрева и приблизить структуру шва и околошовной зоны к структуре самой детали.
Обработка проходит в три стадии:
- Нагревается область рядом со швом.
- Конструкция выдерживается некоторое время в нагретом состоянии.
- Изделие охлаждается в соответствии с графиком обработки.
Процесс термообработки швов на трубопроводе
Существует несколько видов обработки сварного шва. Выбор зависит от конфигурации конструкции, толщины детали и цели, которую собираются достигнуть.
Для каждого вида обработки применяется свой специфический график нагрева, выдержки и охлаждения.
Достоинства и недостатки
К достоинствам обработки нагревом относят:
- Восстановление целевых характеристик прочности и пластичности;
- Снятие внутренних напряжений, обеспечение долговечности шва и всей конструкции;
- Улучшение, при необходимости, этих показателей.
Отрицательные моменты при проведении обработки нагревом следующие:
- Высокие требования к квалификации работников.
- Необратимость процессов. В случае несоблюдения графика термообработки сварных швов исправить брак практически невозможно.
- Требуется дорогостоящее и громоздкое оборудование
- Высокое энергопотребление, низкая экологичность.
В большинстве случаев преимущества перевешивают недостатки.
Что подвергают обработке
Термообработке подвергают сварные швы в ответственных конструкциях. Сюда входят
- магистральные трубопроводы
- сварные конструкции различных механизмов и станков, испытывающих высокие нагрузки
- изделия, которым предстоит работать в сложных условиях эксплуатации.
При термообработке сравнительно небольших изделий используют муфельные печи.
Самодельная муфельная печь
Для обработки нагревом габаритных конструкций применяют нагрев пламенем газовых горелок или индукционный способ. В отдельных случаях применяют радиационный метод.
Термообработку для повышения коррозионной стойкости следует проводить по возможности скорее по окончании сварки.
Параметры проведения процесса
Продолжительность процесса во многом определяется маркой сплава и толщиной заготовки. Для хром-молибденовых сплавов применяют индукционный или радиационный способы нагрева. С увеличением толщины типовая продолжительность нагрева (в минутах) растет:
Толщина детали, см | Радиационный | Индукционный |
2,0 | 40 | 25 |
2,0-2,5 | 70 | 40 |
2,5-3,0 | 100 | 40 |
3,0-3,5 | 120 | 60 |
3,5-4,5 | 140 | 70 |
4,5-6,0 | 150 | 90 |
6,0-8,0 | 160 | 110 |
Индукционный способ требует меньшего времени на обработку, но отличается большими энергозатратами. Перед обработкой следует обязательно выполнить зачистку сварочного шва.
Используемое оборудование
Термообработка сварных швов выполняется с использованием нескольких основных способов, каждый требует своего набора оборудования:
- Индукционный. Требует генератора высокочастотного переменного тока большой мощности. Нагревательным элементом является катушка индуктивности, намотанная поверх участка детали, подлежащего нагреву.
- Радиационный. Используется инфракрасное излучение от нагретой нихромовой проволоки, через которую пропускается сильный электрический ток. Требует мощных источников тока. Может применяться для прогрева материалов со слабыми электромагнитными свойствами.
- Газовый. Наиболее экономичный по энергозатратам способ. Используется специальная горелка. Факел пламени формируется так, чтобы равномерно прогневать зону термообработки.
Выбор метода нагрева проводят, сопоставляя цель обработки, толщину конструкций, характеристики материала и экономические соображения.
Виды термической обработки
Виды термообработки сварных швов различаются по своей цели. Специалисты отличают следующие процессы:
- Отдых. Конструкцию доводят до 300 °С и выдерживают полтора — два часа. Снижает механические напряжения и снижает содержание водорода в материале шва.
- Отпуск. Состоит в нагреве до 700 °С и трехчасовой выдержке. Практически полностью снимает напряжения, дает возможность повысить пластичность.
- Нормализация. Всю конструкцию, включая шов, нагревают до 800 °С и выдерживают 30-40 минут. Позволяет достичь однородности и мелкозернистости структуры металла. Используется на изделиях малой толщины.
- Аустенизация. Изделие нагревают до 1100 °С и выдерживают 120 минут. Охлаждение проводят при комнатной температуре. Повышает пластичность высоколегированных сплавов за счет преобразования их кристаллической структуры.
- Отжиг. Нагрев до 960 °С, трехчасовая выдержка и остывание при комнатной температуре. Используется для высоколегированных сплавов для повышения коррозионной стойкости.
- Индукционный отпуск сварного шва
- Подготовка труб к нормализации сварного шва
Как правило, перед термообработкой проводится зачистка сварного соединения.
Контроль температуры
При проведении термообработки ключевое значение имеет температура нагрева конструкции. Для контроля температуры применяют:
- Термокарандаш и термокраска. Представляют собой химическое соединение, меняющее цвет по мере изменения температуры. Наносятся на поверхность изделия.
- Тепловизоры и пирометры. Электронные устройства, дистанционно измеряющие температуру.
Термокарандаши и термокраска – традиционные средства, достаточно трудоемкие в применения и требующие постоянного визуального контроля со стороны оператора и его оперативного вмешательства в случае выхода параметров за пределы допустимых значений.
Пирометр
Тепловизоры и пирометры обладают большей точностью и могут быть встроены в автоматическую систему поддержания постоянной температуры.
Другие виды обработки
Кроме термообработки, широко используются также механические и химические виды очистки сварных швов.
Механическая
Проводится с использование проволочных щеток или абразивных дисков. В промышленных условиях щетка, диск или лепестковая абразивная насадка закрепляет в угловой шлифовальной машинке (в быту называемой «болгарка»)
Способом механической зачистки с поверхности соединения удаляют шлаки, окалину, брызги застывшего металла и оксидную пленку.
Механическая обработка сварного шва
Зачистка сварного шва после сварки применяется перед термообработкой или покраской.
Химическая
Призвана удалить с поверхности шва следы жира, смазки, оксидные пленки и другие загрязнения. Проводится перед нанесением на конструкцию покрытий, предохраняющих от коррозии.
Травление — обработка сильнодействующими кислотами — проводится перед механической обработкой. После нее проводят пассивацию — нанесение вещества, образующего на поверхности защитную пленку.
Химическая обработка сварного шва
Химическая обработка металла проводится химически активными веществами, многие из которых пожароопасны и могут причинить серьезный вред здоровью. Поэтому следует строго соблюдать правила техники безопасности.
Термическая обработка сварных соединений
Хотя термическая обработка является своевременной и дорогостоящей операцией, она является обязательной во многих прикладных кодексах и стандартах.
Существует множество терминов, которые используются для описания диапазона термообработок, которые могут применяться к сварному соединению, каждый из которых имеет очень специфическое значение…
Обработка раствора
Предназначен для приема в раствор элементов и соединений, которые затем удерживаются в растворе за счет быстрого охлаждения от высокой температуры обработки раствора.Повышает коррозионную стойкость, а также может снижать прочность соединения. Может сопровождаться термообработкой при более низкой температуре для контролируемого преобразования выделений (старение или дисперсионное твердение) в некоторых сплавах.
Отжиг
Включает нагрев металла до высокой температуры, при котором происходит рекристаллизация и / или фазовое превращение, а затем его медленно охлаждают, часто в печи для термообработки. Этот процесс выполняется для размягчения металла после того, как он был закален, на примере холодной обработки, когда полный отжиг дает очень мягкую микроструктуру.Часто отмечается снижение текучести и прочности на разрыв, а в случае ферритных сталей — обычно снижение ударной вязкости.
Нормализация
Выполняется только на ферритных сталях и включает нагрев стали на 30-50 ° C выше верхней температуры превращения, а затем охлаждение на неподвижном воздухе. Этот процесс термообработки приводит к уменьшению размера зерна с улучшением прочности и ударной вязкости.
Закалка
Эта термообработка требует быстрого охлаждения от высокой температуры.Ферритная сталь должна быть нагрета до температуры выше верхней температуры превращения, а затем закаляться в воде, масле или воздушной струе. Получение очень прочного мелкозернистого мартенсита. Стали всегда подвергаются отпуску после процесса закалки и никогда не используются в закаленном состоянии.
Закалка
Выполняется при относительно низкой температуре, ниже нижней температуры превращения ферритных сталей. Этот процесс снижает твердость, снижает предел прочности и улучшает ударную вязкость и пластичность.Большинство нормализованных сталей подвергаются отпуску перед сваркой, при этом все закаленные стали используются в закаленном и отпущенном состоянии.
Отверждение от старения или осаждения
Еще одна низкотемпературная термообработка, предназначенная для получения выделений правильного размера и распределения, что увеличивает текучесть и предел прочности. Эта термообработка обычно следует за термообработкой на твердый раствор. Более продолжительное время и / или высокие температуры приводят к увеличению размера осадка, и как твердость, так и прочность снижаются.
Снятие напряжения
Как следует из названия, этот процесс предназначен для уменьшения остаточных напряжений, возникающих при усадке сварного шва. При повышении температуры металла предел текучести уменьшается, что позволяет перераспределить остаточные напряжения за счет ползучести сварного шва и основного металла. Охлаждение от температуры снятия напряжения контролируется, чтобы предотвратить возникновение вредных температурных градиентов.
Пост-нагрев
Осуществляется сразу после завершения сварки. Это низкотемпературная термообработка, при которой предварительный нагрев увеличивается на 100 ° C и поддерживается в течение примерно 3 или 4 часов.Таким образом, содействие диффузии любого водорода в сварном шве или HAZ (зона термического воздействия) из соединения снижает риск образования холодных трещин, вызванных водородом. Используется только там, где водородное холодное растрескивание является серьезной проблемой — ферритные стали, которые очень чувствительны к трещинам, очень толстые соединения и т. Д.
Термическая обработка после сварки
Существует три основных причины, по которым проводится термообработка после сварки:
- Для достижения стабильности размеров с целью сохранения допусков во время операций механической обработки или во время перетряски
- Для изготовления специальных металлургических конструкций с целью достижения требуемых механических свойств
- Для снижения риска возникновения проблем в процессе эксплуатации, таких как коррозия под напряжением или хрупкое разрушение, за счет снижения остаточного напряжения в свариваемом компоненте.
Снятие напряжений — одна из основных термических обработок для достижения вышеуказанных целей.
Это дорогостоящая операция, требующая, чтобы вся или часть свариваемой детали была нагрета до высокой температуры. Это может вызвать нежелательные эффекты в некоторых сплавах.
Однако высокое остаточное напряжение, зафиксированное в сварном соединении, может вызвать деформацию, выходящую за рамки допустимых параметров, когда элемент подвергается механической обработке или когда он вводится в эксплуатацию. Высокие остаточные напряжения в углеродистых и низколегированных сталях могут увеличить риск хрупкого разрушения, создавая движущую силу для распространения трещин.Остаточные напряжения вызовут коррозионное растрескивание под напряжением в правильной среде.
Чтобы снизить этот уровень остаточного напряжения, компонент повторно нагревают до достаточно высокой температуры. При повышении температуры предел текучести падает, позволяя возникать деформации и уменьшаться остаточному напряжению до тех пор, пока не будет достигнут приемлемый уровень. Компонент будет выдерживаться при этой температуре, известной как замачивание, в течение определенного периода времени, пока не будет достигнуто стабильное состояние, а затем снова охладиться до комнатной температуры.Остаточное напряжение, остающееся в соединении, равно пределу текучести при температуре выдержки.
Для получения дополнительной информации см. Полную статью TWI здесь или узнайте больше о применении и управлении термообработкой от TWI.
Westermans имеет на складе широкий ассортимент продукции для термообработки и снятия напряжения, нажмите здесь, чтобы увидеть машины от AEC и Cooperheat, в качестве альтернативы, если у вас есть оборудование для термообработки, которое вам больше не требуется, мы всегда заинтересованы в покупке для наших клиентов по всему миру, отправьте подробности Питеру Вестерману здесь или по электронной почте peter @ westermans.com.
Термическая обработка сварных соединений — Часть 2
Часть 1 этой серии статей дает определения некоторых термических обработок, которые могут применяться к сварному соединению, и касается операции снятия напряжений в сборке из ферритной стали.
Закалка
Отпуск — это термообработка, которая применима только к сталям и проводится для размягчения любых твердых микроструктур, которые могли образоваться во время предыдущих термообработок, улучшения пластичности и вязкости.Отпуск также позволяет образовывать выделения и контролировать их размер для обеспечения требуемых механических свойств. Это особенно важно для хромомолибденовых сталей, устойчивых к ползучести. Отпуск включает нагрев стали до температуры ниже нижней критической температуры; на эту температуру влияют любые легирующие элементы, которые были добавлены в сталь, так что для углеродисто-марганцевой стали температура составляет около 650 ° C, для стали 2¼CrMo — 760 ° C. Закаленные стали всегда отпускаются.Нормализованные стали также обычно поставляются в отпущенном состоянии, хотя иногда низкоуглеродистую углеродисто-марганцевую сталь можно сваривать только в нормализованном состоянии, отпуск достигается во время PWHT. Отожженные стали в отпущенном состоянии не поставляются.
Отпуск инструментальных сталей может проводиться при температуре до 150 ° C, но для конструкционных сталей, которыми занимается инженер-сварщик, температура отпуска обычно находится в пределах 550-760 ° C, в зависимости от состава стали. .
Термическая обработка после сварки (PWHT)
Как упоминалось в Части 1, PWHT — это особый термин, который охватывает как снятие напряжений, так и отпуск, и его не следует путать с термообработкой после сварки. Такая обработка может включать старение алюминиевых сплавов, обработку аустенитной нержавеющей стали на твердый раствор, выделение водорода и т. Д. PWHT является обязательным требованием во многих нормах и спецификациях при соблюдении определенных критериев. Он снижает риск хрупкого разрушения за счет уменьшения остаточного напряжения и повышения ударной вязкости, а также снижает риск коррозионного растрескивания под напряжением.Однако он оказывает незначительное положительное влияние на усталостные характеристики, если только напряжения не являются в основном сжимающими.
Это важная переменная во всех квалификационных спецификациях процедуры сварки, таких как ISO 15614 Часть 1 и ASME IX. Добавление или исключение PWHT или термообработки вне установленных временных и / или температурных диапазонов требует повторной аттестации процедур сварки. Температуры PWHT для сварных швов, выполненных в соответствии с требованиями EN 13445, ASME VIII и BS PD 5500, приведены ниже в таблице 1.
Таблица 1: Температуры PWHT из технических характеристик сосудов под давлением
Марка стали | BS EN 13445 | ASME VIII | BS PD 5500 |
---|---|---|---|
| Нормальная температура выдержки ° C | Диапазон температур ° C | |
C Сталь | 550-600 | 593 | 580-620 |
C 1/2 Mo | 550-620 | 593 | 630-670 |
1Cr 1/2 Mo | 630-680 | 593 | 630-700 |
2 1/4 Cr / Mo | 670-720 | 677 | 630-750 |
5CrMo | 700-750 | 677 | 710-750 |
3 1/2 Ni | 530-580 | 593 | 580-620 |
Обратите внимание на таблицу 1, что ASME VIII определяет минимальную температуру выдержки, а не диапазон температур, как в спецификациях BS и EN.
Как упоминалось выше, PWHT является обязательным требованием при соблюдении определенных критериев, главным из которых является толщина. BS EN 13445 и BSPD 5500 требуют, чтобы швы толщиной более 35 мм были PWHT, а ASME VII — более 19 мм. Однако, если сосуд должен быть введен в эксплуатацию, где возможна коррозия под напряжением, PWHT является обязательной, независимо от толщины. Время выдержки также зависит от толщины. Как правило, это один час на каждые 25 мм толщины; для обеспечения точности следует ссылаться на соответствующую спецификацию.
Эти различные требования в рамках спецификаций означают, что необходимо проявлять большую осторожность, если необходимо провести квалификационное испытание процедуры, которое предназначено для соответствия более чем одной спецификации. Еще одним важным моментом является то, что температура PWHT не должна быть выше исходной температуры отпуска, поскольку существует риск снижения прочности ниже указанного минимума для стали. Термоструйная термообработка при температуре выше отпускной температуры возможна только в том случае, если проводятся механические испытания, чтобы показать, что сталь имеет адекватные механические свойства. Очевидно, что испытания должны проводиться на реальном материале в новых условиях термообработки.
Максимальная и минимальная скорости нагрева и охлаждения выше 350-400 ° C также указаны в кодах приложений. Слишком высокая скорость нагрева или охлаждения может привести к неприемлемой деформации из-за неравномерного нагрева или охлаждения, а в компонентах с очень жесткими ограничениями может вызвать образование трещин под напряжением во время нагрева.
Применение PWHT
Метод PWHT зависит от ряда факторов; какое оборудование имеется, каковы размеры и конфигурация компонента, какая температура выдержки должна быть достигнута, может ли оборудование обеспечить равномерный нагрев при требуемой скорости нагрева? Лучше всего использовать печь.Это может быть постоянная стационарная печь или временная печь, возведенная вокруг компонента, последняя особенно полезна для больших громоздких конструкций или для термообработки больших компонентов на месте. Постоянные печи могут быть загружены тележкой со станиной печи на колесах, на которой размещается компонент, или топкой с цилиндрической головкой, в которой используется неподвижный под и съемная крышка. Обычно печь, предназначенная для термической обработки сосуда высокого давления на 150 тонн, имеет размеры около 20 м в длину, дверцу 5×5 м и потребляет около 900 кубических метров газа в час.
Печи можно обогревать электричеством, резистивным или индукционным нагревом, природным газом или маслом. При использовании ископаемого топлива следует позаботиться о том, чтобы топливо не содержало таких элементов, как сера, которые могут вызвать проблемы с растрескиванием некоторых сплавов, особенно если это аустенитные стали или никелевые стали — например, коррозионно-стойкая оболочка. Какое бы топливо ни использовалось, атмосферу в печи следует тщательно контролировать, чтобы не происходило чрезмерного окисления, образования накипи или науглероживания из-за несгоревшего углерода в атмосфере печи.Если печь работает на газе или жидком топливе, пламя не должно касаться компонента или термопар для контроля температуры; это приведет либо к локальному перегреву, либо к недостижению температуры PWHT.
Очень важно следить за температурой компонентов во время термообработки. В большинстве современных печей используется зонное управление с помощью термопар, измеряющих и контролирующих температуру областей внутри печи, причем управление осуществляется автоматически с помощью компьютерного программного обеспечения. Зональный контроль особенно полезен для управления скоростью нагрева при PWHT-обработке деталей из стали различной толщины.Однако не рекомендуется использовать мониторинг температуры печи, поскольку это доказывает, что в компоненте достигнуты правильные температуры. Поэтому термопары обычно прикрепляются к поверхности компонента через определенные промежутки времени, и именно они используются для автоматического регулирования скорости нагрева и охлаждения, а также температуры выдержки для достижения однородной температуры. Нет никаких жестких правил относительно количества и расположения термопар, каждый элемент нужно оценивать отдельно.
Как упоминалось ранее, предел текучести уменьшается при повышении температуры, и компонент может быть неспособен выдерживать свой собственный вес при температуре PWHT. Таким образом, существует реальная возможность чрезмерного искажения. Важно, чтобы компонент имел надлежащую опору во время термообработки, а козлы, форма которых подходила для компонента, должны быть размещены через равные промежутки времени. Расстояние между ними будет зависеть от формы, диаметра и толщины предмета. Внутренние опоры могут потребоваться внутри цилиндра, такого как сосуд высокого давления; в таком случае опоры должны быть из аналогичного материала, чтобы коэффициенты теплового расширения были согласованы.
Хотя термическая обработка сосуда высокого давления за одну операцию в печи, достаточно большой, чтобы вместить весь сосуд, является предпочтительным методом, это не всегда возможно. В этом случае нормы применения сосуда высокого давления разрешают термическую обработку готового сосуда по частям в печи. Необходимо перекрывать нагретые участки — ширина перекрытия обычно зависит от толщины сосуда. BS EN 13445, например, определяет перекрытие 5√Re, где R = внутренний диаметр и e = толщина; ASME VIII определяет перекрытие 1. 5 метров. Следует помнить, что если это будет сделано, в резервуаре будет область (которая может содержать сварные швы), которая испытала два цикла PWHT, и это необходимо учитывать при квалификационных испытаниях процедуры сварки. Также вызывает беспокойство область между нагретой зоной внутри печи и холодной зоной вне печи. Температурный градиент должен контролироваться путем соответствующей изоляции емкости теплоизолирующими одеялами, а требования приведены в прикладных кодах.
Конечно, возможно собрать и послать сосуд по частям, а затем провести локальную термообработку на окончательном закрывающем шве. Местная PWHT будет обсуждаться в следующей части этой серии, посвященной термообработке.
В следующей статье будет представлена дополнительная информация о других сплавах и методах применения и контроля термообработки.
Для получения дополнительной информации свяжитесь с нами.
Линия термообработки сварных швов труб
Правильная нормализация сварного шва восстанавливает свойства растяжения ЗТВ.
Мировой спрос на энергию рос более или менее стабильно в течение многих лет, и конца этому не видно. По данным Международного энергетического агентства, поставки нефти увеличились с 76,76 миллиона баррелей в сутки в сентябре 2001 года до 88,7 миллиона в июле 2011 года, т.е. на 16 процентов. 1 Аналогичным образом, количество эксплуатируемых нефтяных вышек увеличилось с 2242 в 2001 году до 3397 в 2011 году, т.е. 52 процента. 2
Резкий рост спроса на энергию, в свою очередь, стимулировал спрос на трубы с продольным швом, производимые на непрерывных сварочных линиях — трубах, используемых для транспортировки нефти и газа под высоким давлением.Такая труба должна соответствовать строгим стандартам, в том числе установленным API. Чтобы соответствовать этим стандартам, важно понимать динамику нормализации шва. Также необходимо понимать тепло
процессы обработки, использующие промежуточную закалку. Это связано с тем, что металлы и толстые стенки, используемые в трубопроводе, усложняют термообработку сварных швов. Параметры процесса, такие как время нагрева, частота и конструкция змеевика, также влияют на конечный результат. Хороший способ увидеть и понять эти влияния — использовать численное моделирование.
Зачем нужно термически обрабатывать сварные швы?
При высокочастотной сварке внешняя и внутренняя стороны стенки трубы подвергаются самым высоким температурам. Это создает зону термического влияния (HAZ) с характерной формой песочных часов. Нагрев также изменяет свойства растяжения ЗТВ, снижая ее ударную вязкость (ее способность поглощать удары без разрушения). Термическая обработка сварного шва восстанавливает свойства прочности на растяжение. HAZ, возвращая их к уровням, равным уровням основного материала.
Однако современные высокопрочные низколегированные стали (HSLA) получают свою прочность отчасти из-за небольшого размера зерна — единственного механизма прочности, который положительно влияет на прочность и вязкость . Таким образом, эти стали имеют меньший размер зерна, чем те, которые можно получить при нормализующей термообработке, поэтому для труб более высоких марок может потребоваться более сложная термообработка. процессы.
Важно понимать, что во время термической обработки шва на линии более холодная часть трубы действует как теплоотвод.Соответственно, скорость охлаждения в основном является результатом внутренней теплопроводности в трубе. Правильно выполненная термообработка сварного шва обеспечивает зону нагрева с правильными нормализующими температурами; то есть при достаточно малой разнице температур между стенками интерьер и экстерьер. Кроме того, он должен покрывать всю ЗТВ на внутренней стене.
Численный анализ 2D
Единственный способ понять, что происходит внутри стальной стены, — это использовать инструменты численного моделирования для исследования процесса отжига шва.Процесс можно представить в виде двухмерной модели поперечного сечения. Электромагнитные и тепловые вычисления должны быть коррелированы для анализа процесса. 3
Несколько факторов влияют на разницу температур между внешней и внутренней стороной стенки трубы при увеличении толщины стенки. Текущая глубина проникновения мала, пока температура остается ниже точки Кюри. Независимо от глубины проникновения, напряженность магнитного поля от индукционной катушки уменьшается с расстоянием.Поэтому удельная мощность выше снаружи.
трубы, чем внутри, даже при температурах выше точки Кюри.
На рисунке 1 показано, как тепло проводится в стенке трубы на поздней стадии процесса нагрева. Труба действует как теплоотвод для нагретой зоны, а фазовое превращение происходит в разное время снаружи и внутри стены из-за разницы температур. Энергия, необходимая для преобразования, задерживает выравнивание температуры.
Потери тепла с внутренней поверхности трубы из-за излучения и конвекции способствуют разнице температур между внутренней и внешней поверхностями стенок. Это вызывает стационарную разницу температур, которую невозможно уравновесить за счет теплопроводности, и которая может стать значительной в толстостенных трубах.
Разметка линий и отслеживание швов
Результат термообработки сварного шва также зависит от расположения линии. Поскольку пространство на мельницах часто ограничено, очень важно рассчитать длину рулонов и расстояния между ними, чтобы достичь оптимальных результатов.Двухмерное моделирование процесса нормализации может проверить схему, а также рассчитать охлаждающую часть процесса.
Рис. 1: На этом изотемпературном графике стрелки указывают направление теплопроводного теплового потока в стенке трубы.
Часто непрерывно сварная труба скручивается после сварки. Следовательно, сварной шов перемещается из положения «12 часов», когда он попадает в секцию нормализатора шва.Отслеживание шва требуется для удержания катушек нормализатора шва в правильном положении. Есть два типа слежения: горизонтальное и орбитальное.
Система горизонтального слежения имеет катушку с фиксированным минимальным расстоянием до положения трубы на 12 часов и перемещается только горизонтально из этого положения. Когда сварной шов перемещается из положения «12 часов», расстояние соединения между сварным швом и катушкой увеличивается, что снижает эффективность катушки. Кроме того, катушка больше не расположена симметрично относительно трубки.По горизонтали Системы слежения не подходят для больших отклонений или для толстых стенок, обычно используемых в трубопроводе.
Орбитальные системы слежения удерживают катушки в одном и том же положении относительно сварного шва, когда шов отклоняется от положения на 12 часов. Это означает, что на схему нагрева не влияет перекручивание трубки или трубки. Нагрев оптимизируется в любом положении в диапазоне слежения. Нет необходимости в увеличении размера зоны нагрева (что также требует увеличения длины охлаждения).Если все сделано правильно, Орбитальное слежение обеспечивает правильную нормализацию сварного шва независимо от его положения.
Имитационная проверка
Результаты бегущей строки показывают, что двумерное моделирование полезно при разработке компоновки линий. Конечно, окончательные параметры процесса должны быть точно настроены на линии для достижения наилучших возможных результатов для различных размеров и марок материалов. Хорошо спроектированная линия необходима для производства труб с желаемой скоростью и качеством.
Артикул:
- Отчет о рынке нефти , Международное энергетическое агентство, республика.iea.org
- Мировое количество буровых установок, текущее и историческое значение , Baker Hughes Inc., www.bakerhughes.com
- Джон Инге Аспергейм и Леф Маркегард, «Оптимизация процесса отжига швов с помощью двухмерного моделирования», статья размещена на сайте www.efd-induction.com
Джон Инге Асперхейм и Лейф Маркегард — инженеры-исследователи и инженеры-конструкторы в EFD Induction, Bøleveien 10, P.O. Box 363 Sentrum, 3701 Skien, Norway, [email protected] , jia @ no.efdgroup.net , www.efd-induction.com
Термическая обработка сварных соединений — часть 1
Термическая обработка — это трудоемкая и дорогостоящая операция. Это может повлиять на прочность и ударную вязкость сварного соединения, его коррозионную стойкость и уровень остаточного напряжения, но также является обязательной операцией, указанной во многих прикладных нормах и стандартах. Кроме того, это важный параметр в квалификационных требованиях к процедуре сварки.
Прежде чем обсуждать диапазон термических обработок, которым может подвергаться металл, необходимо четко определить, что подразумевается под различными терминами, используемыми для описания диапазона термических обработок, которые могут применяться к сварному соединению. Такие термины часто используются неправильно, особенно неспециалистами; для металлурга они имеют очень точное значение.
Рис.1 Термическая обработка сварных соединений
РастворВыполняется при высокой температуре и предназначен для приема в раствор элементов и соединений, которые затем удерживаются в растворе за счет быстрого охлаждения от температуры обработки в растворе.Это может быть сделано для уменьшения прочности соединения или повышения его коррозионной стойкости.
Для некоторых сплавов за ней может следовать термообработка при более низкой температуре для контролируемого преобразования выделений (старение или дисперсионное твердение).
ОтжигОн заключается в нагреве металла до высокой температуры, при котором происходит рекристаллизация и / или фазовое превращение, а затем в медленном охлаждении, часто в печи для термообработки.Это часто выполняется для смягчения металла после его закалки, например, путем холодной обработки; полный отжиг, дающий самую мягкую микроструктуру. Это также приводит к снижению как текучести, так и предела прочности на разрыв, а в случае ферритных сталей, как правило, к снижению ударной вязкости.
НормализацияЭто термическая обработка, проводимая только для ферритных сталей. Он включает нагрев стали примерно на 30-50 ° C выше верхней температуры превращения (для 0.20% углеродистой стали (это будет около 910 ° C) и охлаждение на неподвижном воздухе. Это приводит к уменьшению размера зерна и повышению прочности и ударной вязкости.
ЗакалкаЭто быстрое охлаждение от высокой температуры. Ферритная сталь должна быть нагрета до температуры выше верхней температуры превращения и закалена в воде, масле или воздушной струе для получения очень высокопрочного мелкозернистого мартенсита. Стали никогда не используются в закаленном состоянии, они всегда отпускаются после операции закалки.
ЗакалкаТермическая обработка ферритных сталей при относительно низкой температуре, ниже более низкой температуры превращения; в обычной конструкционной углеродистой стали это значение будет в диапазоне 600-650 ° C.
Снижает твердость, снижает предел прочности и улучшает пластичность и ударную вязкость. Большинство нормализованных сталей подвергаются отпуску перед сваркой, все закаленные стали используются в закаленном и отпущенном состоянии.
Отверждение от старения или осадковНизкотемпературная термообработка, предназначенная для получения осадков правильного размера и распределения, тем самым увеличивая текучесть и предел прочности.Обычно этому предшествует термообработка на твердый раствор. Для стали температура может быть где-то между 450-740 ° C, алюминиевый сплав будет выдерживаться при температуре 100-200 ° C. Более продолжительное время и / или более высокие температуры приводят к увеличению размера осадка и снижению как твердости, так и прочности.
Снятие напряженийКак следует из названия, это термообработка, предназначенная для снижения остаточных напряжений, возникающих при усадке сварного шва. Он основан на том факте, что с повышением температуры металла предел текучести уменьшается, что позволяет перераспределить остаточные напряжения за счет ползучести сварного шва и основного металла.Охлаждение от температуры снятия напряжения контролируется, чтобы не возникало вредных температурных градиентов.
Пост-нагревНизкотемпературная термообработка, проводимая сразу после завершения сварки путем увеличения предварительного нагрева примерно на 100 ° C и поддержания этой температуры в течение 3 или 4 часов. Это способствует диффузии водорода в зонах сварного шва или термического влияния из стыка и снижает риск образования холодных трещин, вызванных водородом. Он используется только для ферритных сталей, где водородное холодное растрескивание является серьезной проблемой. I.е. стали с очень высокой чувствительностью к трещинам, очень толстыми соединениями и т. д.
Термическая обработка после сварки (PWHT)Итак, что означает термин «термообработка после сварки»? Для некоторых инженеров это довольно расплывчатый термин, который используется для описания любой термической обработки, проводимой после завершения сварки. Однако для других, особенно тех, кто работает в соответствии с нормами для сосудов высокого давления, такими как ASME VIII, он имеет очень точное значение.
Поэтому рекомендуется, когда инженер говорит о термообработке, отжиге, отпуске или снятии напряжений после сварки.
Термическая обработка после сварки может проводиться по одной или нескольким из трех основных причин:
- для достижения стабильности размеров с целью сохранения допусков во время операций механической обработки или во время встряхивания при эксплуатации
- для изготовления специальных металлургических конструкций с целью достижения требуемых механических свойств
- для снижения риска возникновения проблем в процессе эксплуатации, таких как коррозия под напряжением или хрупкое разрушение, за счет снижения остаточного напряжения в сварном элементе.
Диапазон термообработок для достижения одной или нескольких из этих трех целей в диапазоне свариваемых черных и цветных металлов и сплавов, очевидно, слишком обширен, чтобы подробно описать их в этих кратких статьях с практическими знаниями.Акцент в следующем разделе будет сделан на PWHT углеродистых и низколегированных сталей в соответствии с требованиями стандартов, хотя кратко будут упомянуты другие формы термообработки, с которыми инженер-сварщик может столкнуться в ферросплавных сплавах. Здесь задействованы два основных механизма: во-первых, снятие напряжения и, во-вторых, микроструктурные модификации или отпуск.
Как термическая обработка может повлиять на сварные соединения
Хотя инженеры и хотят обратного, термообработка может ослабить сварные соединения.Поскольку сварочное оборудование использует тепловую энергию для сплавления деталей и добавления наполняющих металлов, применение большего количества тепла может еще больше изменить свойства соединения сварного шва. Действительно досадный факт, особенно с учетом того, что термическая обработка требует чрезмерного количества производственных ресурсов.
Тепло в печи может вызвать проблемы со связностью сварного шва
Это не значит, что руководитель проекта может пропустить обязательную операцию термообработки, даже если задействованные детали были сварены.В то же время бригадир печи не может без разбора послать несколько сварных компонентов, не без принятия нескольких важных для процесса контрмер. Без этих мер идеально расположенный сварной шов может состариться и ослабнуть. Преобразовательная энергия сплава может даже вызвать коррозионный эффект, который разъедает поверхность сварного шва. Чтобы устранить такие опасения по поводу подрыва соединения, специалисты по обеспечению качества часто используют инструменты оптической микроскопии для проверки образцов сварных швов.
Помещение зерна сварного шва под микроскоп
Допустим, это проект по производству оборудования.Этап термообработки может быть выполнен только после того, как детали будут сварены. Аппарат для дуговой сварки, независимо от того, использует ли он технологию TIG или MIG или какой-либо другой вариант процесса, создает идеальное стыковое соединение с одинаково идеальной скошенной кромкой. Собранные детали прочные и прочные. После термообработки детали соединенного материала становятся еще более устойчивыми к коррозии и тверже. Это все хорошо, но как насчет того шва? После того, как побывали в печи, все еще так же жестко? Или это сустав, ослабленный переутомлением? Что ж, вернемся к оптическому прицелу, содержание углерода и основные металлы в сварном шве создают сложную смесь твердых ферритно-карбидных тел.Ввиду этого сварные детали могут стать такими же сложными для термической обработки, как и цельнометаллические заготовки.
При правильной термообработке сварной металлический каркас сохраняет прочность соединения и твердость шва. Однако, если применяется неправильно примененный метод нагрева или охлаждения, соединение может принять технологические напряжения или усталость материала. Из-за проблем с напряжением возникают проблемы с распространением трещин, а с проблемами усталости материала, возможно, из-за изменения содержания углерода или трансформации ферритовых пластин, поверхность сварного шва и корень ослабевают.В зависимости от используемого метода закалки и отпуска присадочный металл в сварном шве может либо размягчиться, либо стать хрупким. Ни одно из состояний сварки под дуговым предохранителем нежелательно. Некоторый интерес представляет технология PWHT (послесварочная термообработка), которая может быть использована для выравнивания сложной ферритно-карбидной смеси присадочного металла. При разумном использовании напряжение в сварном шве и проблемы диффузии водорода могут быть значительно сведены к минимуму.
Термическая обработка после сварки — обзор
Аустенитные стали
Термическая обработка аустенитных сталей после сварки необходима для обеспечения удовлетворительной работы в некоторых условиях, но может также вызвать другие проблемы.Сводка ситуаций, требующих термической обработки, и проблем, связанных с этим, приведена в таблице 3.1.
Таблица 3.1. Проблемы, требующие термообработки аустенитных нержавеющих сталей
Тип материала | Стабильность обработки | Растрескивание при повторном нагреве | Трансгранулярная коррозия под напряжением | Межкристаллитная коррозия под напряжением | Распад сварного шва | Сигма-осаждение | Повреждение линии ножа |
---|---|---|---|---|---|---|---|
304 | ✓ | ✓ | ✓ | ✓ | & gt; 0.06% C | ✗ | ✗ |
304L | ✓ | ✓ | ✓ | ✗ | ✗ | ✗ | ✗ | 316 г | ✓ | ✓ | & gt; 0,06% C | ✗ | ✗ |
316L | ✓ | > 0,1% Nb | ✓ | ||||
321, 347 | ✓ | ✗ # | ✓ | ✗ | ✗ | ✗ | ✓ |
309, 310 | ✓ | ✓ | ✗ | Литой,> 0.1% C | ✗ | ||
18/37 (литье) | ✓ | ✗ | ✓ | ✓ | ✗ | ✗ | ✗ |
✗ | ✓ | ✗ | ✗ | ✗ | ✗ | ||
Применимо HT | 400–450 ° C 550–650 ° C 850–950 ° C 950–1050 ° C Медленное охлаждение 9502 | –1050 ° C Быстрое охлаждение | 850–1050 ° C Медленное охлаждение | 950–1050 ° C Быстрое охлаждение | 950–1050 ° C Быстрое охлаждение | 950–1050 ° C Быстрое охлаждение |
Из-за Чем выше коэффициент теплового расширения аустенитной стали по сравнению с ферритной сталью, проблемы деформации могут быть более серьезными в аустенитных сварных деталях.В тех случаях, когда после сварки должна выполняться обработка с узкими допусками, может потребоваться обработка для частичного снятия напряжения, например, при 550–650 ° C или даже 400–450 ° C, чтобы предотвратить деформацию во время обработки, как обсуждается ниже. Выбор температур для послесварочной термообработки конструкций из аустенитной нержавеющей стали для снятия остаточных напряжений не так прост, как для ферритных сталей, в правилах дается мало рекомендаций.
Основными причинами термической обработки аустенитных нержавеющих сталей являются (i) снятие напряжений и (ii) повторное растворение вредных осадков.Степень снятия напряжения зависит от применяемой температуры, например, большая часть напряжения может сниматься при температуре выше 950 ° C, тогда как около 35% снимается при температуре 550–650 ° C. 17 Снятие напряжения должно сопровождаться медленным охлаждением, но следует отметить, что в диапазоне температур 850–550 ° C это приведет к некоторой форме выпадения осадков. Для повторного растворения осадков требуется температура выше 1000 ° C с последующим быстрым охлаждением, которое приводит к повторному возникновению остаточного напряжения. Следовательно, большая часть снятия напряжения аустенитных сталей — это компромисс.Кроме того, использование самых высоких температур приводит к провисанию неподдерживаемых конструкций, что является дополнительным осложнением.
Проблема растрескивания при повторном нагреве может возникать в некоторых аустенитных сталях. 18 Это может произойти, если закрепленные сварные детали из чувствительных сталей нагреваются, например, до 850 ° C в течение коротких периодов (возможно, менее одного часа) или до более низких температур в течение длительного времени, например, до 500 ° C в течение примерно 1000 час. Склонность к растрескиванию увеличивается с ограничением соединений и, следовательно, становится больше для толстых сварных деталей, чем для тонких.Было обнаружено, что все обычные аустенитные стали подвержены этой форме растрескивания после сварки, за исключением стали типа 316 с содержанием Nb <0,1%. Сталь типа 347 особенно восприимчива. Эту проблему можно предотвратить путем термообработки сварного шва при температуре 950–1050 ° C, чтобы уменьшить выпадение осадков, способствующих растрескиванию. Требуется быстрый нагрев через области более низких критических температур.
Наличие остаточных напряжений при сварке приводит к повышенному риску коррозионного растрескивания аустенитных сварных соединений в определенных средах, 9 см. Рис.3.8. Все обычные относительно низколегированные аустенитные нержавеющие стали страдают от межкристаллитного коррозионного растрескивания под напряжением в хлоридных или гидроксидных средах.
3.8. Коррозионное растрескивание под напряжением в сварных деталях из аустенитной нержавеющей стали.
Концентрация хлорид-ионов, достаточная для того, чтобы вызвать растрескивание, может составлять всего одну часть на миллион в насыщенной кислородом воде, тогда как в случае гидроксильных ионов необходимы концентрации около 40%. Следовательно, во время производства следует принимать меры предосторожности, чтобы исключить контакт с веществами, несущими хлорид-ионы, даже в том, что касается контроля типа растворителя, используемого в маркерах.Коррозионное растрескивание под напряжением происходит только при наличии растягивающего напряжения, поэтому, если общие напряжения уменьшаются за счет снятия остаточных напряжений, склонность к растрескиванию может быть значительно снижена или устранена. Это требует термической обработки для снятия основной части остаточных напряжений и требует температур 800–1050 ° C с последующим медленным охлаждением.
Вторая форма коррозионного растрескивания может возникать в некоторых аустенитных сталях в умеренно / умеренно окислительных средах. Эта форма атаки ускоряется под действием напряжения и возникает по межзерновому механизму, когда на границах зерен происходит выделение богатого хромом (Fe, Cr) 23 C 6 . 19 Обычно это происходит при воздействии температур в диапазоне 500–850 ° C в процессе эксплуатации или во время сварки. Сталь, в которой возникло это состояние, считается «сенсибилизированной» к межкристаллитной атаке. Чувствительность является результатом обеднения хрома вблизи границ зерен. Этого можно избежать, проводя термообработку при температуре около 950 ° C или выше, так что осадки возвращаются в твердый раствор с последующим быстрым охлаждением для предотвращения повторного осаждения на границах зерен.Необходима осторожность при локальной термообработке нержавеющих сталей, поскольку температурный градиент по обе стороны от нагретой ленты будет подвергать материал воздействию температур в критическом диапазоне для осаждения.
Связанная с этим проблема, которая может возникнуть в аустенитных изделиях после сварки в средах с незначительным / умеренным окислением, — это «распад сварного шва». Это форма преимущественной межкристаллитной атаки в ЗТВ сварного шва. Это также вызвано выделением на границах зерен карбидов с высоким содержанием хрома в области ЗТВ, нагретой до температур от 500 до 850 ° C.Чувствительные материалы следует подвергнуть послесварочной термообработке до температуры выше 950 ° C, чтобы карбиды перешли в раствор.
Проблемы осаждения карбидов в стабилизированных марках, например, типов 321 и 347, в значительной степени решаются путем добавления элементов (Ti и Nb), которые образуют карбиды преимущественно по сравнению с хромом. Однако на установках нефтепереработки, где могут образовываться политионовые кислоты, иногда требуется стабилизационная термообработка (например, при 850–920 ° C для типа 347) для устойчивости к межкристаллитному воздействию. 19
Вторым средством преодоления сенсибилизации является снижение уровня углерода в стали. Широко доступны низкоуглеродистые аустенитные марки (304L, 316L) с содержанием углерода, равным или менее 0,03% C, что в значительной степени устраняет проблемы коррозии / коррозии под напряжением, связанной с выделением карбидов. Фактически, при современной практике производства стали уровни углерода в деформируемых аустенитных нержавеющих сталях, как правило, значительно ниже, чем в предыдущие годы, и проблемы, связанные с выделением карбидов, особенно во время сварки, встречаются гораздо реже, чем, скажем, 30 лет назад.
Еще одна трудность, которая может возникнуть в результате термообработки после сварки, связана с «повреждением ножевой линии». Это происходит предпочтительно в области границы плавления сварных деталей из стабилизированных сталей, например типов 321 и 347, после термообработки в диапазоне температур 550–750 ° C в течение более одного часа. Эта атака требует очень специфической окислительной среды, такой как кипящая азотная кислота, и не является широко распространенной проблемой. Этого не происходит, если уровень углерода ниже 0,03%.Для восприимчивых материалов и подходящей среды термообработку при необходимости следует проводить при температуре выше 750 ° C.
При длительной эксплуатации при высоких температурах (около 500–850 ° C) возможно образование хрупкой интерметаллической фазы, известной как сигма-фаза. 20 Время и температура, при которых это происходит, различаются для разных марок аустенитной стали, но в целом это происходит во время эксплуатации при 650–850 ° C в течение периодов от 10 часов для стали марки 304 до 1000 часов для стали типа 310.
Сигма-фаза, как правило, не присутствует в ЗТВ или металле сварных швов непосредственно в сварных конструкциях, а также маловероятна при кратковременной термообработке после сварки полностью аустенитного материала, поскольку это время обычно слишком короткое. Однако его можно обнаружить во время термообработки металлов сварных швов, содержащих заметные количества остаточного δ-феррита (например, металлов сварных швов типов 308, 309), поскольку образование сигмы из феррита происходит значительно быстрее, чем из аустенита. Последние разработки аустенитных нержавеющих сталей 18Cr – 8Ni показывают, что образование сигма-фазы можно замедлить, изменив химический состав.Сигма-фаза, вероятно, мало повлияет на свойства при повышенных температурах, но может вызвать заметное охрупчивание, когда сварная деталь остыла после работы до температуры окружающей среды. Тепловой удар из-за быстрого охлаждения может вызвать растрескивание хрупких конструкций.
Подобные проблемы могут возникать при высокотемпературной эксплуатации высокоуглеродистых литых аустенитных материалов основных составов 25/20 или 18/37. В этих материалах возможно обширное выделение карбидов и сигма-фазы при температурах в диапазоне 500–850 ° C в течение времени менее 1 часа, что делает материал хрупким от комнатной температуры до примерно 750 ° C.
Это наиболее тяжелая ситуация при высоком содержании углерода около 0,4% и становится менее серьезной при содержании углерода порядка 0,1%. Обработка раствором при 1250 ° C может быть использована для возврата карбидов в раствор для восстановления исходного состояния материала, но повторное осаждение быстро произойдет во время эксплуатации в диапазоне 500–850 ° C. Кованые материалы аналогичного состава по отношению к хрому и никелю обычно имеют более низкое содержание углерода, и этой проблемы не возникает.За исключением случаев, когда требуется высокий уровень углерода для высокотемпературной прочности, наиболее подходящим подходом к использованию аустенитных нержавеющих сталей, где требуется термообработка, является выбор одной из марок с низким содержанием углерода.
Термическая обработка после сварки (PWHT)
Сварка является неотъемлемой частью эксплуатации и технического обслуживания активов в нефтяной (добывающей, промежуточной, перерабатывающей) и химической промышленности.Хотя он имеет множество полезных применений, процесс сварки может непреднамеренно ослабить оборудование, создавая остаточные напряжения в материале, что приведет к ухудшению свойств материала.
Чтобы гарантировать сохранение прочности материала детали после сварки, регулярно выполняется процесс, известный как Термическая обработка после сварки (PWHT) . PWHT может использоваться для снижения остаточных напряжений, как метод контроля твердости или даже для повышения прочности материала.
Если PWHT выполняется неправильно или вообще игнорируется, остаточные напряжения могут в сочетании с нагрузочными напряжениями превысить конструктивные ограничения материала.Это может привести к разрушениям сварных швов, более высокому потенциалу растрескивания и повышенной восприимчивости к хрупкому разрушению .
PWHT включает в себя множество различных типов потенциальных обработок; два наиболее распространенных типа — последующий нагрев и снятие напряжения:
- Пост-нагрев:
- Растрескивание, вызванное водородом (HIC) , часто возникает, когда во время сварки в материал попадает много водорода из окружающей среды. Нагревая материал после сварки, можно рассеивать водород из зоны сварки, предотвращая таким образом HIC.Этот процесс известен как пост-нагрев и должен начинаться сразу после завершения сварки. Вместо того, чтобы дать возможность остыть, материал необходимо нагреть до определенной температуры в зависимости от типа и толщины материала. Его следует выдержать при этой температуре в течение нескольких часов в зависимости от толщины материала.
- Снятие напряжения:
- К моменту завершения сварочный процесс может вызвать большое количество остаточных напряжений в материале, что может привести к повышенному потенциалу коррозии под напряжением и растрескивания, вызванного водородом.PWHT может использоваться для снятия этих остаточных напряжений и снижения этого потенциала. Этот процесс включает нагревание материала до определенной температуры с последующим его постепенным охлаждением.
Должен ли материал подвергаться PWHT, зависит от ряда факторов, включая такие вещи, как его система легирования или подвергалась ли он ранее термообработке. Некоторые материалы действительно могут быть повреждены PWHT, в то время как другие почти всегда требуют этого.
Как правило, чем выше содержание углерода в материале, тем больше вероятность, что после проведения сварочных работ потребуется PWHT.Точно так же, чем выше содержание сплава и чем выше толщина поперечного сечения, тем больше вероятность, что материал потребует PWHT.
Список литературы- Фундерберк, Р. Скотт, 1998. «Ключевые концепции: термообработка после сварки». Инновации в сварке Том XV, № 2.
- Ахмед Халил, Кришан Дж., 2002. «Термическая обработка после сварки — примеры из практики», Информационный бюллетень BARC, специальный выпуск ко Дню основателя, стр. 111-115.
Связанные темы
Инструменты темы
Поделиться темой
Внести свой вклад в определение
Мы приветствуем обновления этого определения Integripedia от Inspectioneering сообщество.