Принцип работы плазмотронов. Плазматроны и порошковые питатели
Плазматроны и порошковые питатели
курсовая работа
Для работы плазмотрона необходимо к нему подвести электропитание, плазмообразующий газ, охлаждение электродов и подачу порошков. Схематически это представлено на рис.1.
Рис.1. Структурная схема систем питания плазмотрона
Принцип работы плазмотрона для напыления покрытий состоит в том, что электрическая дуга, горящая между вольфрамовым катодом, имеющим форму стержня, и медным анодом, имеющим форму сопла, нагревает подаваемый в плазмотрон газ до температуры образования плазмы, т.е. до состояния, когда газ становится электропроводным. В поток нагретого газа вводится порошок, поступающий из порошкового питателя. Образующиеся расплавленные частицы порошка выносятся потоком плазмы из сопла и наплавляются на поверхность изделия, расположенную перед соплом (рис.1).
Рис.2. Схема плазмотрона в процессе плазменного напыления покрытий
Представленная на рис. 2 схема плазмотрона относится к линейному типу плазмотрона постоянного тока с косвенной дугой. Такая схема плазмотрона нашла наибольшее применение для процесса плазменного напыления порошковых материалов из-за ее простой конструкции и надежной работы. В научных исследованиях и в производстве в настоящее время используется широкая гамма различных конструкций плазмотронов [2].
Сопло — наиболее ответственный элемент плазматрона. Именно конструкция сопла определяет длину дуги и ее стабильность, скорость и характер истечения струи, а следовательно, в значительной мере — тепловой КПД плазматрона и эффективный КПД процесса нагрева распыляемого материала. В плазмотронах с самоустанавливающейся дугой канал сопла гладкий и имеет наибольшую длину (10-30мм). Для некоторой фиксации дуги разрядный канал выполняется с уступом. В плазматронах с фиксированной дугой применяют секционированные сопла с межэлектродными вставками. Наличие секций (5-10) позволяет сначала растянуть дугу, а затем фиксировать анодное пятно на выходе из канала. Для получения ламинарных и сверхзвуковых плазменных струй сопла профилируют.
Рис.3. Конструктивные схемы электродных узлов в плазменных распылителях:
а — цилиндрическое гладкое сопло; б — цилиндрическое сопло с уступом; в — сопло с межэлектродными вставками; г — профилированное сопло; д — вольфрамовый электрод; е — электрод с циркониевой вставкой; 1 — вольфрамовая вставка; 2 — держатель электрода; 3 — циркониевая вставка
На рис.3, а — г приведены конструкции сопел различного назначения. Продолжительность работы сопла невелика и составляет 10-50 ч, поэтому конструкция плазматрона должна обеспечивать легкую и быструю его смену. В этом отношении перспективны так называемые «сухие» сопла, не требующие при смене разгерметизации плазмотрона. Сопла изготавливают в основном из меди, но они быстро изнашиваются из-за того, что на «холодных» электродах опорное пятно дуги перемещается скачкообразно, т.е. в течение некоторого времени остается неподвижным (10-4 — 10-5 с). Это время определяется скоростью смещения приэлектродного участка дуги относительно неподвижною пятна процессом шунтирования промежутка дуга-электрод. Решая дифференциальное уравнение теплопроводности Фурье:
можно вычислить глубину проникновения температурного поля и материал электрода за время t. Здесь а — коэффициент теплопроводности, с — теплоемкость, у — удельный вес, qv — внутреннее тепловыделение.
Глубина проникновения температурного поля для простейшего случая плоского электрода в отсутствие джоулева тепловыделения в электроде qv=0, что справедливо для многих плазмотронов, определяется выражением
Для меди а=112,4*10-6м2/с, при t=10-4c, =3*10-4 м.
Для вольфрама а=60,6*10-6 м2/с, =1,9*10-4 м.
Из расчетов видно, что более подходящим материалом является вольфрам. Однако изготовить сопло из вольфрама очень сложно. Поэтому на практике применяют вставки из вольфрама, что позволяет уменьшить эрозию канала медного сопла, а также позволяет работать плазмотрону в режиме обратной полярности (минус на сопле) [2,4].
Другим ответственным элементом плазматрона является стержневой электрод, который изготавливают из вольфрама (торированного, лантанированного, итерированного) в виде вставки с интенсивным охлаждением водой (рис.2, д). При использовании окислительных газов вольфрам заменяют цирконием или гафнием. Образующаяся на поверхности такого электрода тугоплавкая оксидная пленка препятствует его разрушению. При работе плазмотрона в режиме обратной полярности стержневой электрод (анод) изготавливают из меди. Необходима высокая соосность электрода и сопла.
Эффективность нагрева порошка в плазматроне и равномерность распределения его по пятну напыления зависят от схемы ввода порошка в сопловую часть плазматрона [4].
Делись добром 😉
Асинхронный двигатель с аварийным дизель-генератором
Принцип работы
При подаче к обмотке статора напряжения, в каждой фазе создаётся магнитный поток, который изменяется с частотой подаваемого напряжения. Эти магнитные потоки сдвинуты относительно друг друга на 120°, как во времени, так и в пространстве. ..
Двухколесное транспортное средство с гибридным приводом
3.5 Принцип работы
Во время движения, велосипедист нажимает правую рукоять управления приводом. Благодаря этому, трос управления приводом прижимает привод к шестерне аккумулятора и колесу. В результате этого…
Использование процесса грохочения при переработке строительных материалов
1.4.3 Принцип работы
Конструкция грохота и режим его работы должны обеспечивать вибротранспортирование слоя материала по ситу и передавать ударные импульсы коробу с натянутым в нем ситом, для его очистки, т.е. грохот должен работать с подбрасыванием материала…
Использование современного программного обеспечения для проектировании цепной передачи в металлорежущем станке
5. Принцип работы программы
Программа состоит из одного главного окна. Рисунок1.Главное окно программы В левой стороне содержатся операторы, запоминающие данные вводимые пользователем…
Исследование работы тестоделителя «Suction Dough Divider SD-180» и определение неисправностей, нарушающих его работоспособность
2.
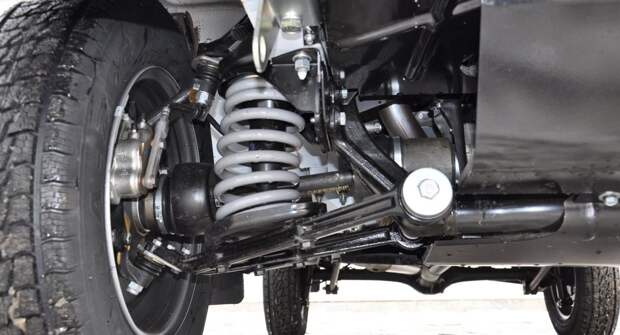
Всасывающий поршень (G) всасывает тесто из бункера (F) в камеру для теста (E) при движении поршня влево (наружу) — «всасывающий ход». Тестовый нож (H) полностью вытягивается и целиком открывает отверстие между бункером и камерой для теста…
МНЭ АСУ вибрационного электрического стенда ВЭДС-10А
4 Устройство и принцип работы
Вибрационный электрический стенд типа ВЭДС-10А состоит из усилителя и пульта управления вибратором СУПВ-0,1А размещенных в одном шкафу, и вибратора ВЭД-10А. Стенки шкафа усилителя и пульта управления имеют вентиляционные жалюзи…
Плазматроны и порошковые питатели
Классификация плазмотронов
На схеме ниже приведена классификация плазматронов Схема.1. Классификация плазмотронов Размещено на http://www.allbest.ru/ Для функционирования всех типов плазмотронов требуются подвод к ним электроэнергии, газовой и плазмообразующей сред…
Приспособление для зенкерования детали
4. Конструкция и принцип работы приспособления.

Разрабатывается приспособление, на котором зенкеруется отверстие радиусом 36 мм. Конструкция спроектированного приспособления представлена на сборочном чертеже ТПЖА. 293224. 203 СБ…
Проектирование маршрутного технологического процесса сборки изделия
1.2 Служебное назначение изделия, принцип работы узла и условия обеспечения нормальной работы
Механический клапан предназначен для автоматических установок, распыляющих смазочно-охлаждающие жидкости. Принцип работы. Клапан состоит из корпуса, разделенного на две полости, в одну из которых подается сжатый воздух…
Проектирование систем централизованного теплоснабжения района города Вологды от газовой котельной и отопления жилого здания
2.1 Принцип работы котельной
Котельная ОАО с/х «Заречье» является газовой котельной с установленными водогрейными котлами…
Расчет конструкторских и технологических параметров сепаратора ОМЕ
1.

Сепаратор ОМЕ — очиститель тарельчатого типа с ручной периодической выгрузкой осадка из барабана. Изготавливается в полузакрытом исполнении. Сепаратор предназначен для непрерывной очистки молока от посторонних примесей…
Системы видеонаблюдения и контроля доступа на предприятие
2.1 Принцип работы
Система контроля доступа — это совокупность технических и организационных средств, с помощью которых решаются задачи управления пропуском людей в помещения и охраняемые зоны, а также задачи учета и контроля. Проходная предприятия…
Техническое обслуживание сетевого адаптера D-Link DGE-560T
4. Принцип работы
Система водяного охлаждения состоит из ватерблоков, их число изменяется в зависимости от количества охлаждаемых объектов, радиатор с вентилятором или несколькими вентиляторами, помпы (помпа — это насос), часто аквариумный или фонтанный…
Турбокомпрессоры в двигателях внутреннего сгорания
2. ПРИНЦИП РАБОТЫ
Принцип работы основан на использовании энергии отработавших газов. Поток выхлопных газов попадает на крыльчатку турбины (закреплённой на валу), тем самым раскручивая её и находящиеся на одном валу с нею лопасти компрессора…
Центробежные компрессоры Березанской КС
3.2 Принцип работы
Перекачиваемый газ по газопроводу через всасывающий патрубок поступает на вход двухступенчатого центробежного нагнетателя, где происходит его сжатие, и выбрасывается через нагнетательный патрубок в магистральный газопровод…
Анахов_Проектир_плазмотронов
%PDF-1.6 % 1 0 obj > endobj 1584 0 obj >stream GPL Ghostscript 9.022018-11-16T15:10:34+05:002018-11-16T15:04:08+05:00PDFCreator Version 1.2.12018-11-16T15:10:34+05:009d7ec90b-ebe2-11e8-0000-40c55d552400uuid:ac0039ed-3298-4766-8b7d-f808be408bc2application/pdf

особенности, принцип работы, преимущества и недостатки
Плазменную резку очень часто используют в таких отраслях промышленности, как судостроение, машиностроение, а также при изготовлении металлоконструкций, коммунальной сфере и т. п. Кроме этого, плазморез довольно часто используется в частной мастерской. С его помощью быстро и качественно разрезают любой материал, проводящий ток, и некоторые нетокопроводящие материалы – дерево, камень и пластик.
Технология плазменной резки позволяет разрезать листовой металл и трубы, выполнять фигурный рез или изготавливать детали. Работа осуществляется при помощи высокотемпературной плазменной дуги. Чтобы ее создать, потребуется только источник тока, воздух и резак. Чтобы работа выполнялась довольно легко, а рез получался ровным и красивым, следует выяснить, как осуществляется принцип работы плазменной резки.
Как устроен плазморез
Этот аппарат состоит из следующих элементов:
- источник питания;
- воздушный компрессор;
- плазменный резак или плазмотрон;
- кабель-шланговый пакет.
Источник питания для аппарата плазменной резки осуществляет подачу на плазмотрон определенной силы тока. Представляет собой инвертор или трансформатор.
Инверторы довольно легкие, в плане энергопотребления экономные, по цене недорогие, однако, способны разрезать заготовки небольшой толщины. Из-за этого их применяют только в частных мастерских и на маленьких производствах. У инверторных плазморезов КПД на 30% больше, чем у трансформаторных и у них лучше горит дуга. Часто используют их для работ в труднодоступных местах.
Трансформаторы гораздо увесистее, тратят много энергии, но при этом имеют меньшую чувствительность к перепадам напряжения, и с их помощью разрезают заготовки большой толщины.
Плазменный резак считается главным элементом плазмореза. Его основными элементами являются:
- сопло;
- охладитель/изолятор;
- канал, необходимый для подачи сжатого воздуха;
- электрод.
Компрессор требуется для подачи воздуха. Принцип работы плазменной резки предусматривает применение защитных и плазмообразующих газов. Для аппаратов, которые рассчитаны на силу тока до 200 А, применяется только сжатый воздух как для охлаждения, так и для создания плазмы. Они способны разрезать заготовки толщиной в 50 мм.
Кабель-шланговый пакет используется для соединения компрессора, источника питания и плазмотрона. По электрическому кабелю от инвертора или трансформатора начинает поступать ток для возбуждения электрической дуги, а по шлангу осуществляется подача сжатого воздуха, который требуется для возникновения внутри плазмотрона плазмы.
Принцип работы
При нажатии на кнопку розжига начинается подача тока высокой частоты от источника питания (инвертора или трансформатора). В результате этого внутри плазмотрона образуется дежурная электрическая дуга, температура которой достигает 8 тыс. градусов. Столб этой дуги начинает заполнять весь канал.
После того как возникла дежурная дуга, в камеру начинает поступать сжатый воздух. Вырываясь из патрубка, он проходит через электрическую дугу, нагревается, при этом увеличиваясь в объеме в 50 или 100 раз. Кроме того, воздух начинает ионизироваться и перестает быть диэлектриком, приобретая свойства проводить ток.
Сопло плазмотрона, суженное книзу, обжимает воздух, создавая из него поток, которое начинает вырываться оттуда со скоростью 2 – 3 м/с. В этом момент температура воздуха часто достигает 30 тыс. градусов. Именно такой раскаленный ионизированный воздух и является плазмой.
В то время, когда плазма начинает вырываться из сопла, происходит ее соприкосновение с поверхностью обрабатываемого металла, дежурная дуга в этот момент гаснет, а зажигается режущая. Она начинает разогревать заготовку в месте реза. Металл в результате этого плавится и появляется рез. На поверхности разрезаемого металла образуются небольшие частички расплавленного металла, сдуваемые с нее потоком воздуха. Таким образом осуществляется работа плазмотрона.
Преимущества плазменной резки
Работы по резке металла часто осуществляются на стройплощадке, в мастерской или цеху. Можно использовать для этого автоген, но не всех это устраивает. Если объем работ, связанный с резкой металла, слишком большой, а требования, предъявляемые к качеству реза, очень высоки, то следует подумать о том, чтобы использовать плазменный резак, имеющим следующие достоинства:
- Если мощность подобрана правильно, то аппарат плазменной резки позволяет в 10 раз повысить производительность. Такой параметр позволяет плазморезу уступить только промышленной лазерной установке, однако, он значительно выигрывает в себестоимости. Целесообразно с экономической точки зрения применять пламенную резку для металла, имеющего толщину до 50 – 60 мм.
- Универсальность. С помощью плазменной резки обрабатываются чугун, медь, сталь, алюминий и прочий металл.
Необходимо просто выбрать оптимальную мощность и выставить конкретное давление воздуха.
- Высокое качество реза. Аппараты плазменной резки способны обеспечить минимальную ширину реза и кромки без перекаливания, наплывов и грата практически без дополнительной обработки. Кроме того, достаточно важен такой момент, что зона нагрева материала в несколько раз меньше, чем при использовании автогена. А так как термическое воздействие минимально на участке реза, то и деформация от этого вырезанных деталей будет незначительной, даже если они имеют небольшую толщину.
- Не происходит существенного загрязнения окружающей среды. С экономической точки зрения, если имеются большие объемы работ, то плазменная резка гораздо выгоднее кислородной или механической. Во всех остальных случаях учитывают не материалы, а трудоемкость использования.
Недостатки плазменной резки
Недостатки в работе плазменной резки тоже имеются. Первый из них – максимально допустимая толщина реза довольно небольшая, и у самых мощных агрегатов она редко бывает больше 80 – 100 мм.
Следующий недостаток – достаточно жесткие требования, предъявляемые к отклонению от перпендикулярности реза. Угол отклонения не должен быть больше 10 – 50 градусов и зависит это от толщины детали. Если случается выход за эти пределы, то возникает довольно существенное расширение реза, что в результате влечет за собой быстрый износ расходных материалов.
Кроме того, рабочее оборудование довольно сложное, что делает совершенно невозможным использование двух резаков одновременно, которые подключаются к одному аппарату.
Заключение
Принцип работы плазменной резки довольно прост. Кроме того, аппарат, который используется для этого, имеет большое количество преимуществ, в несколько раз превосходящие имеющиеся недостатки. Если его правильно эксплуатировать, то можно существенно сэкономить время и получить качественный результат.
- Автор: Николай Иванович Матвеев
- Распечатать
Оцените статью:
(3 голоса, среднее: 3. 7 из 5)
Поделитесь с друзьями!
вид и устройство плазмотрона, принцип работы резака и советы по выбору
Первые плазменные станки были изобретены в 50-х годах XX века. Оборудование было громоздким и дорогостоящим, использовалось оно только в некоторых отраслях промышленности. Но уже к концу двадцатого столетия плазменная резка металла стала доступной, и спрос на неё вырос.
Сегодня этот вид резки занимает одно из лидирующих мест в металлообрабатывающей отрасли. Оборудование, применяемое в технологии плазменной резки металла, постоянно модернизируется, становясь всё более практичным и удобным.
Виды и способы плазменной резки
Плазменной называется резка металла под большим потоком плазмы, которая образуется за счёт обдува газом электрической дуги. Нагреваясь, газ ионизируется на положительные и отрицательные частицы. Температура потока плазмы достигает нескольких тысяч градусов.
По видам плазменная резка бывает:
- разделительная;
- поверхностная.
При разделительной резке электрод утопает в разрезе металла. Угол между поверхностью металла и электродом должен быть от 60° до 90°, а при поверхностной он не может быть более 30°.
Существует два способа резки:
- при помощи плазменной дуги;
- при помощи плазменной струи.
При первом способе дуга горит между неплавящимся электродом и разрезаемым металлом. При втором — между формирующимся наконечником плазматрона и электродом. Изделие не включается в электрическую цепь при плазменной струе.
Для обработки металлов широко применяется плазменно-дуговая резка, а для обработки неметаллических заготовок — обработка плазменной струёй.
com/embed/jHLvelXARpM?feature=oembed» frameborder=»0″ allow=»accelerometer; autoplay; encrypted-media; gyroscope; picture-in-picture» allowfullscreen=»»/>Элементы прибора
Устройство плазмотрона представлено таким образом, чтобы обеспечивать резку металлов, относящихся к классу тугоплавких. Электрод (катод) имеет специальную циркониевую или гафниевую вставку. Использование указанных металлов при высоких температурах позволяет добиться эффекта выбивания электронов с их поверхности (термоэлектронная эмиссия).
Сопло – еще один расходный элемент плазмотрона, который всегда изолируется от катода.
Прибор также оснащен механизмом для закручивания газа, образующего плазму.
Расходники способны функционировать в течение одной 8-часовой рабочей смены, если речь идет об обработке металла толщиной до 1 см. Далее они подлежат замене, причем последнюю желательно проводить одновременно для катода и сопла.
При несоблюдении сроков замены качество получаемого реза значительно ухудшается, могут появиться волны или дать о себе знать эффект реза под углом. Если гафниевая или циркониевая вставка выгорят более чем на 2 мм, то электрод пригорит. Следствием станет значительный перегрев устройства.
Чтобы расплавленный обрабатываемый материал не повредил элементы плазмотрона, его оснащают защитным кожухом. Регулярный демонтаж и чистка кожуха – залог долгой и качественной работы всего прибора. При несоблюдении элементарных условий эксплуатации можно в скором времени добиться серьезной поломки плазмореза. Не менее важно чистить и другие элементы.
Классификация плазмотронов
Плазмотроны для резки металла делятся на электродуговые, высокочастотные и комбинированные.
По виду образования дуги:
- С дугой прямого действия, которая горит между металлическим изделием и неплавящимся электродом. Источник питания — постоянный ток.
- С дугой косвенного действия. Не связанная с изделием, она возбуждается и горит между анодом-соплом и катодом-электродом.
Питание осуществляется переменным током.
По виду охлаждения:
- воздушное;
- водяное.
Более популярным является водяное охлаждение плазмотрона, так как теплоёмкость воздуха ниже, чем воды. Водяное охлаждение позволяет устанавливать на сопло и электрод высокие тепловые нагрузки, что увеличивает производительность плазменной сварки. Недостаток этого вида охлаждения состоит в усложнении конструкции самого устройства и необходимости постоянной подачи чистой воды.
По способу стабилизации дуги:
- водяной;
- вихревой;
- двойной;
- аксиальный одинарный;
- магнитный.
Водяной способ стабилизации дуги сложен по конструкции, имеет ненадёжную систему автоматической подачи и регулирования электрода.
Наиболее простыми и распространёнными являются вихревой, двойной и аксиальный одинарный виды стабилизации дуги. Магнитный способ стабилизации дуги не очень эффективен. Он создаёт малый сжимающий столб дуги, устройство сложное в эксплуатации.
По виду электрода для работы с металлом:
- газозащищённые;
- расходуемые;
- плёнкозащищённые.
Чаще других используются газозащищенные катоды с вольфрамовым стержнем. Расходуемые — это графитовые катоды. Из циркония, запрессованного в медной обойме, изготавливаются плёнкозащищенные электроды.
Разновидности плазмотронов
Весь спектр современных технических приборов для резки металлов можно поделить на три класса:
- плазмотроны на электрической дуге;
- высокочастотные плазморезы;
- комбинированные устройства.
Чтобы понять особенности работы каждого вида плазмотрона из обозначенных классов, следует рассмотреть их по отдельности.
Устройство аппарата для резки плазмой
По своей сущности плазмотрон представляет собой генератор плазмы. Это надёжное и компактное устройство, в котором легко регулируется пуск, мощность и остановка рабочих режимов.
Плазмотрон состоит из конструктивных элементов:
- Кожух.
- Корпус фторопластовый.
- Электродный узел.
- Механизм закрутки воздушного потока.
- Втулка изоляционная.
- Электрод.
- Гайка сопла.
- Сопло.
Основными расходными материалами прибора являются сопло и электрод. Они изнашиваются с одинаковой интенсивностью, поэтому менять их следует одновременно. Несвоевременная замена повлияет на качество реза и приведёт к износу остальных элементов устройства.
Кожух применяется для защиты прибора от металлической пыли и брызг металла. Кожух и плазмотрон периодически необходимо чистить от загрязнений.
Плазмотрон «Мультиплаз-3500»
Это оборудование широко используется для резки металлопроката и по своим эксплуатационным качествам и функциональности ничуть не уступает другим моделям. Плазматрон «Мультиплаз-3500» обладает массой достоинств, среди которых одними из ключевых являются размер и вес данного прибора. Этот аппарат при своих девяти килограммах (вместе с горелкой) достаточно компактен, поэтому его легко можно переносить в руке с одного места на другое. Значительно снизить вес плазматрона удалось благодаря смекалке производителей, которые сделали прибор таким, чтобы для его функционирования не требовалось газового баллона. Здесь в качестве так называемой рабочей жидкости используется обыкновенная вода или раствор спирта.
Принцип работы устройства
Перед работой нужно убедиться, что у компрессора достаточный показатель давления, а у водяных устройств жидкость разогрета до необходимой температуры.
- От источника питания после нажатия на кнопку «розжиг» подаётся ток высокой частоты. Внутри прибора образуется дежурная электрическая дуга, весь канал заполняет столб дуги.
- Сжатый воздух начинает поступать в камеру устройства. Проходя через электрическую дугу, он нагревается и увеличивается в объёме, перестаёт быть диэлектриком и проводит ток.
- Со скоростью от 2 до 3 м/с из сопла прибора начинает вырываться поток воздуха, температура которого может достигать 30 тысяч градусов. Этот раскалённый воздух и является плазмой.
- Вместо дежурной зажигается режущая дуга, которая, соприкасаясь с заготовкой металла, разогревает её в месте реза. В зоне плавки появляется рез, а образующиеся на заготовке частички расплавленного металла от потока воздуха разлетаются.
- Отпустив кнопку «розжиг», горение дуги прекращается.
- По краям реза отбивается шлак, при необходимости изделие зачищается от него.
Базовое знание принципа работы плазмотрона не только поможет понять, как управлять процессом резки, но и сделает работу лёгкой, а рез — ровным и красивым.
Высокочастотные плазморезы
Особенностью приборов данного класса является отсутствие электродов, поскольку связь с питающим источником осуществляется благодаря индуктивному (или емкостному) принципу. Соответственно, плазматроны делятся на индукционные и емкостные.
Принцип работы плазмотронов, принадлежащих к классу высокочастотных устройств, подразумевает выполнение камеры, где происходит разряд, из не проводящих ток материалов.
Зачастую применяется стекло или керамика.
Изоляция стенок осуществляется по газодинамическому принципу, поэтому приборы застрахованы от перегрева и могут охлаждаться за счет воздуха.
Типы плазмотронов
На предприятиях широко применяется автоматическая и ручная резка плазмой.
Резать металл можно различными типами приборов.
- Плазменные резаки для резки металлов. В эту группу входит воздушно-плазменный и газоплазменный резак. Воздушно-плазменный резак выделяется простой конструкцией и применяется для резки чёрных металлов. Он может работать как от однофазной, так и трёхфазной сети. Газоплазменный аппарат работает на водяном паре, для образования плазмы применяется водород, аргон, кислород, азот.
- Индукционный резак. Это высокочастотное устройство, работающее по принципу индуктивно-связанной плазмы с температурой до 6000 К и высокой плотностью электронов.
- Комбинированные аппараты. Представлены симбиозом токов высокой частоты и электрической дуги.
Электрический разряд сжимается под воздействием магнитного поля.
- Газовые устройства, работающее за счёт сжатия столба дуги плазмообразующим газом.
- Водяные устройства, рабочим телом которых является паровой газ. Высокотемпературный водяной пар способствует ускоренному сгоранию углерода.
- Магнитные резаки. Такие приборы малоэффективны и не пользуются популярностью. Их основное преимущество в том, что регулировка сжатия электрической дуги осуществляется без потери газа.
В зависимости от типа плазмотрона можно без труда обрабатывать сталь любых видов, в том числе металлы с высоким тепловым расширением, а также материалы, которые электрический ток не проводят.
Система стабилизации дуги в процессе работы плазмотрона
В зависимости от способа стабилизации дуги, все плазмотроны делятся на газовые, водяные и магнитные. Надо сказать, что система стабилизации дуги является очень важной для процесса функционирования плазмотрона, ведь именно она обеспечивает сжатие столба и его фиксацию по оси электрода и сопла.
Самая простая и распространённая система стабилизации дуги – газовая. Её принцип работы заключается в охлаждении и сжимании стенок столба дуги внешним, более холодным плазмообразующим газом. Водяная система даёт возможность достичь большей степени сжатия и поднять температуру столба дуги до 50000 градусов.
Плазмотроны такого типа используют графитовый электрод, подающийся в меру его сгорания, поскольку пары воды вблизи электрода обеспечивают повышенную скорость этого процесса. По сравнению с этими двумя системами стабилизации, магнитная стабилизация дуги считается менее эффективной, однако её преимущество заключается в возможности регулировки степени сжатия без потерь плазмообразующего газа.
Преимущества и недостатки технологии резки
Эта технология по сравнению с прочими способами обработки имеет свои преимущества.
- Высокая производительность, лёгкость освоения.
- Плазменная резка обладает высокой точностью и разнообразием линий реза.
- Обрабатываемая поверхность не требует дополнительной шлифовки.
- В процессе работы загрязнение окружающей среды минимальное.
- Используемое ручное оборудование мобильно, имеет малый вес и габариты.
К недостаткам этого метода можно отнести небольшую, до 100 мм, толщину среза. Нельзя работать одновременно двумя приборами, а также отклоняться от перпендикулярности среза.
Наиболее популярные в России аппараты плазменной сварки
Это генератор электродуговой низкотемпературной плазмы, получаемой посредством разогрева паров рабочей жидкости к состоянию ионизации и предназначается для металлов Источник севпроект.рф
МППК (многофункциональный портативный плазменный комплекс) Горыныч рассчитан на выработку плазм из жидкости – воды или водно-спиртовой смеси, где пар выполняет защитную функцию. Такие агрегаты производят с силой тока 8,10 и 12 A и при этом они универсальны, то есть, Горыныч может, как резать, так и варить разные детали, но это не все. Задав необходимую мощность, аппарат можно использовать в качестве паяльной лампы, кузнечного горна и даже огнетушителя, если в качестве жидкости используется вода. МППК достаточно легок – масса плазмотрона с кабелем и шлангом не превышает 5,4 кг, а для его питания нужна обычная розетка ≈220±22 V и 50 A. Агрегат создает дугу прямой полярности с КПД не менее 80%.
Являясь аппаратами нового поколения, обладая повышенным качеством, он более чем в 2,5 раза экономичней и в 5 раз легче используемых плазмотронов Источник eduard-romanov.uaprom.net
Если говорить о деньгах, Мультиплаз-15000 является самым выгодным плазменным сварочным аппаратом среди своих аналогов. Кроме того, такой агрегат можно назвать самым легким среди подобных, так, масса источника питания составляет 33 кг а вес плазмотрона вместе с кабелем и шлангом на 9 метров – 5 кг. Потребляемая мощность составляет 15 kW при входном напряжении 380±38 V, с частотой сети 50 A. Сварка функционирует в диапазоне тока от 20 до 100 A, расходует 480 л/мин сжатого воздуха и ее КПД составляет 85% — это позволяет разрезать лист стали толщиной до 50 мм. Безусловно, Мультиплаз-15000 больше подходит для промышленных предприятий и автомастерских, но его также покупают для бытового применения.
Выбор плазмотрона
Чтобы правильно выбрать аппарат для плазменной резки металла, нужно определиться, какими характеристиками должен обладать прибор. Исходными данными могут быть:
- автоматизированный или ручной способ резки;
- продолжительность работы;
- расход электрической энергии;
- толщина металла;
- тип металла;
- с какой частотой осуществляется замена расходных материалов;
- отзывы пользователей об оборудовании и производителях.
Хорошим вариантом оптимальной цены и мощности является модель Сварог CUN 40 B (R 34). Это лёгкий и компактный прибор, который применяется в раскрое тонколистовых металлов менее 0,12 см. Он прост в управлении, неприхотлив в эксплуатации, расход сжатого воздуха минимальный.
К аппаратам с наилучшими показателями энергосбережения можно отнести модель AURORA PRO AIRFORCE 60 IGBT. Он подойдёт для резки материала, проводящего ток. Принцип работы основан на бесконтактном поджиге дуги. Результатом проведения резки является качественная работа без деформации металла.
Для резки толстого металла подойдёт модель BRIMA CUT 120. Устройство используется при резке цветного, углеродистого, нержавеющего металла и меди. Толщина металла может доходить до 35 мм. Он имеет встроенную регулировку дуги и плавно изменяет рабочие параметры устройства.
Как самостоятельно собрать плазменный резак из инвертора читайте в этой статье.
Как самостоятельно собрать плазменный резак из инвертора читайте в этой статье.
Резак CP PT 31
CP PT 31 получил широкое распространение благодаря своей простоте и доступной цене. Большинство бюджетных аппаратов плазменной резки комплектуются именно такими резаками, чем объясняется популярность данной модели. Как правило, такие аппараты без центрального евро разъема, а подключение резака к аппарату происходит через гайку M16х1,5 и 2PIN разъем.
Шарнирное соединение на стыке рукава и рукоятки не нагружает руку резчика, а легкий вес резака позволит производить длительный рез без напряжения руки. Резак оснащен плавным курком, а рукав укрыт в джинсовую ткань по всей длине, что минимизирует риски случайно повредить шланг-пакет плазматрона. Максимальный рез резака — 14 мм.
Для резака CP PT 31 подходят только свои уникальные расходные части, не совместимые с другими резаками — это сопла, катоды, диффузоры, насадка и головка плазмотрона. Подробно ознакомиться с комплектующими и технической информацией вы можете на нашем сайте в карточке товаров.
Резак плазменный CP PT 31
Артикул: 073.310.106 Резак плазменный CP PT 31 5м (M16х1,5; 2pin) PLA3105 Плазмотрон CP PT 31 подключается к аппаратам воздушно-плазменной резки через гайку M16х1,5. Обратная связь между резаком и аппаратом происходит с помощью 2 PIN разъема. Толщина чистого реза 14 мм.
Цена: 4 256 р
Резак CP SG-55
Резак плазменный CP SG-55 также, как и резак CP PT 31 часто входит в комплектацию аппаратов бытового сегмента. Подключение осуществляется через гайку M16х1,5 и 2PIN разъем. Отличается дизайном рукоятки, которая не уступает в удобстве и комфортной эксплуатации. Резак с шарнирным соединением, шланг-пакет защищен тканевым чехлом.
SG-55 имеет уникальные комплектующие, которые совместимы только с этим плазмотроном (катод, сопло и защитная насадка). Самое важное, что конструктивная особенность головки резака не требует газового диффузора. Максимальная толщина разрезаемого металла составляет 15 мм.
Резак плазменный CP SG-55
Артикул: 073.055.105 Резак плазменный CP SG-55 5м (M16х1,5; 2pin) PLA5505
Плазмотрон CP SG-55 подключается к аппаратам воздушно-плазменной резки через гайку M16х1,5. Обратная связь между резаком и аппаратом происходит с помощью 2 PIN разъема. Толщина чистого реза 15 мм.
Цена: 3 882 р
Резак CP 50
Плазменный резак CP 50 сочетает в себе улучшенные технические характеристики и особую конструкцию, что, безусловно, подойдет для профессиональной эксплуатации. Плазмотрон подключается к аппаратам воздушно-плазменной резки через центральный евро адаптер. Также, центральный адаптер можно демонтировать и заменить на разъем 1/4G, установив дополнительные переходники.
На стыке силового кабеля и рукоятки установлен шарнир, который помогает комфортно эксплуатировать резак. Безопасную эксплуатацию гарантирует специальный предохранитель на кнопке, который исключает случайное нажатие. Толщина реза – 15 мм. Все комплектующие к резаку доступны в ассортименте фирменной продукции — это головка плазмотрона, диффузор, катод, сопло и защитная насадка.
Резак плазменный CP 50
Артикул: 073.500.106 Резак плазменный CP 50 Евро адаптер 6м PLA5006
Плазмотрон CP 50 подключается к аппаратам воздушно-плазменной резки через центральный евро адаптер. Толщина чистого реза 15 мм.
Цена: 13 424 р
Резак CP P80
Плазменный резак CP P80 уже можно отнести к промышленному классу, но все же он входит в группу популярных плазмотронов, т.к. им комплектуют большинство аппаратов воздушно-плазменной резки, с током реза до 80 А. Это переходная модель резака, которая мало чем отличается от резака CP 81, о котором мы расскажем чуть позже.
В резаке предусмотрен предохранитель от случайного нажатия на курок и появилась возможность подсоединения роликовой насадки, для удобства раскроя металла. Еще на резак можно установить специальную защитную насадку. В ассортименте фирменной продукции также есть сопла, катод и головка плазмотрона с внутренней резьбой присоединения 1/8G.
В ассортименте фирменной продукции доступны два варианта подключения — с накидной гайкой M16х1,5 и 2PIN разъемом, и с классическим евро адапетром. Максимальная толщина реза составляет 23 мм.
Резаки плазменные CP P80
Артикул: 073.800.106 Резак плазменный CP P80 5м (M16х1,5; 2pin) PLA1615
Плазмотрон CP P80 подключается к аппаратам воздушно-плазменной резки через M16х1,5 и 2pin. Толщина чистого реза 23 мм. Можно укомплектовать роликовой насадкой для удобного раскроя металла.
Цена: 9 564 р
Артикул: 073.800.105 Резак плазменный CP P80 Евро адаптер 5м PLA8005
Плазмотрон CP P80 подключается к аппаратам воздушно-плазменной резки через центральный евро адаптер. Толщина чистого реза 23 мм. Можно укомплектовать роликовой насадкой для удобного раскроя металла.
Цена: 10 615 р
Резаки серии СР 81, СР 101 и СР 141
Плазменные резаки СР 81, СР 101 и СР 141 имеют стандартный евроразъем подключения, с предустановленными 4PIN коннекторами. PIN коннекторы установлены в ячейки евроадаптера 9/1/6/3. Мы настоятельно рекомендуем перед установкой убедиться в том, что пины на плазменном резаке совпадают с пинами на аппарате воздушно-плазменной резки CUT, несовпадение пинов приведет к поломке как оборудования, так и резака. Если необходимо, то евро адаптер на плазменном резаке можно разобрать и подсоединить к аппарату, который не имеет евро разъем.
Резаки серии CP имеют свои конструктивные особенности, а именно: защита курка от случайного нажатия, гибкое шарнирное соединение, прорезиненный кожух, укрывающий шланг-пакеты. Защитная насадка резаков оснащена медным кольцом, которое замыкает цепь на плазмотроне. Таким образом реализована система безопасной смены расходных частей, которая предотвратит замыкание или внезапное включение плазмотрона.
Резак CP 81 рассчитан на рез до 23 мм, CP 101 до 28 мм, и резак 141 серии на рез до 35 мм. Когда мы говорим о резе, мы подразумеваем чистый рез, а не грязный рез.
Чистый рез — это максимально качественный рез материала, который не требует серьёзной финишной обработки. Грязный рез — это рез, выше заявленных значений резака, но возможно при резе будет образовываться грат, застывшие капли металла на изделии. Крупный грат необходимо будет срезать болгаркой, а не большой можно будет отбить молотком.
Кроме того, на качество реза помимо качества самого плазменного резака, влияют еще такие факторы как: качество сжатого воздуха, достаточное давление на выходе из компрессора, качество самого плазменного источника и стабильность сетевого напряжения, а также своевременная замена сопел и катодов. Соблюдая все эти параметры — вы добьетесь идеального реза.
В ассортименте фирменной продукции к данным резам есть специальные наборы балеринок, которые используются для резки окружностей, геометрических форм из листового металла.
Артикул: 073.810.007 Набор балеринок CP 81 BAL5700
Набор для резки окружностей, геометрических форм из листового металла. Используется совместно с резаком плазменным CP 81.
Цена: 5 599 р
Артикул: 073.101.077 Набор балеринок CP 101-141-151 BAL7700
Набор для резки окружностей, геометрических форм из листового металла. Используется совместно с резаком плазменным CP 101, CP 141 и CP 151.
Цена: 5 636 р
Резаки плазменные серии СР 81, СР 101 и СР 141
Артикул: 073.141.112 Резак плазменный CP 141 Евро адаптер 12м PLA1412
Плазмотрон CP 141 подключается к аппаратам воздушно-плазменной резки через центральный Евро адаптер. Толщина чистого реза 35 мм. Резак можно использовать совместно с набором балеринок из ассортимента фирменной продукции.
Цена: 25 332 р
Артикул: 073.141.106 Резак плазменный CP 141 Евро адаптер 6м PLA1416
Плазмотрон CP 141 подключается к аппаратам воздушно-плазменной резки через центральный Евро адаптер. Толщина чистого реза 35 мм. Резак можно использовать совместно с набором балеринок из ассортимента фирменной продукции.
Цена: 18 845 р
Артикул: 073.101.106 Резак плазменный CP 101 Евро адаптер 6м PLA1016
Плазмотрон CP 101 подключается к аппаратам воздушно-плазменной резки через центральный Евро адаптер. Толщина чистого реза 28 мм. Резак можно использовать совместно с набором балеринок из ассортимента фирменной продукции.
Цена: 18 117 р
Артикул: 073.810.106 Резак плазменный CP 81 Евро адаптер 6м PLA8106
Плазмотрон CP 81 подключается к аппаратам воздушно-плазменной резки через центральный Евро адаптер. Толщина чистого реза 23 мм. Резак можно использовать совместно с набором балеринок из ассортимента фирменной продукции.
Цена: 14 087 р
Плазматроны с маркировкой ACP
Резаки с обозначением ACP предназначены для подключения к ЧПУ станкам. Из-за своей формы их часто называют «карандашами». Резак ACP 80 подключается к плазменному источнику гайкой M16x1,5, а команда старта и остановки реза проходит посредством 2PIN разъема. Максимальный чистый рез составляем 23 мм.
Плазмотрон ACP 81 и ACP 141 подключаются к источнику через центральный евро адаптер, который можно разобрать и подключить к любому плазменному источнику. Максимальный рез 81 модели — 23 мм, а 141 плазмотрон режет до 35 мм. Большинство комплектующих к автоматическим резакам схоже с комплектующими стандартных плазмотронов, за исключением сменного элемента горелки CUT — головки плазмотрона.
Автоматические плазменные резаки к ЧПУ станкам
Артикул: 073.810.206 Резак плазменный автоматический ACP 81 (M16x1,5; 2pin) 6м PLA0681
Автоматический плазмотрон ACP 81 подключается к аппаратам воздушно-плазменной резки через M16х1,5. Обратная связь между резаком и аппаратом происходит с помощью 2 PIN разъема. Толщина чистого реза 23 мм.
Цена: 23 912 р
Артикул: 073.800.210 Резак плазменный автоматический ACP 80 (M16x1,5; 2pin) 10м PLA1080
Автоматический плазмотрон ACP 80 подключается к аппаратам воздушно-плазменной резки через M16х1,5. Обратная связь между резаком и аппаратом происходит с помощью 2 PIN разъема. Толщина чистого реза 23 мм.
Цена: 21 641 р
Артикул: 073.141.212 Резак плазменный автоматический ACP 141 Евро адаптер 12м PLA1412-1
Автоматический плазмотрон ACP 141 подключается к аппаратам воздушно-плазменной резки через центральный Евро адаптер. Толщина чистого реза 35 мм.
Цена: 43 999 р
Артикул: 073.141.206 Резак плазменный автоматический ACP 141 Евро адаптер 6м PLA1416-1
Автоматический плазмотрон ACP 141 подключается к аппаратам воздушно-плазменной резки через центральный Евро адаптер. Толщина чистого реза 35 мм.
Цена: 34 794 р
Плазменные резаки доступны различной длины, подробную техническую информацию вы можете найти в карточке товара на сайте ПТК или на сайтах наших дилеров по России, Казахстане, и республике Беларусь.
Безопасность эксплуатации прибора
Перед работой с устройством необходимо изучить паспорт производителя и нормативную документацию по технике безопасности ГОСТ 12 . 3.003−86.
- Обслуживание оборудования и ремонт должны осуществляться с отключённой сетью.
- На рабочем месте не должно быть легковоспламеняющихся жидкостей и горючих материалов.
- Рабочее место необходимо обеспечить средствами пожаротушения, хорошо проветривать, а при необходимости следует установить искусственную вентиляцию.
- Специалист должен использовать при работе специальную одеждой, обувьюи другие средства защиты.
- При резке лучше использовать специальные столы, которые оснащены системой для удаления газов и пара.
- Если работы проводятся на открытом воздухе, необходим навес.
- Нельзя оставлять плазматрон долгое время включённым.
Соблюдение безопасности при эксплуатации прибора поможет избежать профессиональных заболеваний и травм.
Технология сварки и резки металлов плазмой
Принцип плазменно-дуговой технологии сварки заключается в мощном прогреве обрабатываемых металлов плазмой, которая в данном случае является ионизированным газом, полученным при работе электрической дуги под повышенным давлением. Горелка, которую используют в таких агрегатах, называется плазмотроном – с ее помощью можно варить и резать любые металлы, отображенные в периодической таблице Менделеева. Также плазмотроном можно варить и резать неметаллы, если этому не препятствуют физические или химические свойства материала, как то, отсутствие адгезии, различные особенности вступления в реакцию и т.п.
Основные особенности плазменной сварки
Плазмотрон позволяет резать и сваривать любые известные в природе металлы и неметаллы, если только для этого нет серьезных фундаментальных физических или химических препятствий Источник proinstrumentinfo.ru
Рассмотрим существенные особенности, которыми обладает плазменно-дуговая сварка. В рабочую зону из плазмотрона выбрасывается струя плазмы, но иногда при необходимости также используется дополнительный инертный газ для создания защитного облака, которое создает оптимальные рабочие условия для химически нейтральной среды. В результате получается, что вся термическая энергия через плазменную струю передается на сварочную ванну, но при этом лишь частично (в малом количестве) попадает на близлежащие области. Для корпуса плазменной горелки используется сталь, а для анода – медь. При этом у медного электрода имеется специальная полость, по которой поступает вода для охлаждения, а между ним и катодом с давлением от 2-х до 5-ти атмосфер поступает рабочий газ для подпитки дуги.
Применение плазмотронов:
Плазмотроны могут применяться:
– при сварке, резке и обработке металлов, а также различных твердотельных материалов,
– для расплавления и рафинирования (очистки) металлических сплавов,
– при нанесении защитных покрытий на металлические поверхности (керамики, электроизоляции и т.д.),
– для упрочнения дешевых материалов металлическим наплавом,
– для подогрева металлического расплава в мартеновских и плавильных печах,
– для термического обезвреживания высокотоксичной органики,
– для получения нанодисперсных порошков и соединений,
– при плазменной горной и шахтной проходке,
– при безмазутной растопке угольных котельных на электростанциях,
– и пр.
Плазменный «стелс» — наш ответ американским «невидимкам»
Внизу мелькали костистые гребни цепей великого хребта Гиндукуш, «убийцы индуса». Шеренги скалистых безлесных гор строго параллельно главному хребту. Арцыбашев вгляделся в горизонт. Там, впереди, должна вздыматься главная гряда сияющих вершин, и бортовой радар, светясь зеленым, показывал эту великую стену.
«Ганнибал у ворот!» Это означало, что группа уже на месте, и объект находится в поле зрения. Арцыбашев двинул рычажок на пульте, и только чутье подсказало ему, что заработал стокилограммовый плазмогенератор в носу машины. Через несколько секунд МиГ окутала голубоватая дымка.
В этот момент его отметка исчезла с экранов радиолокаторов Кабульского аэроузла и даже с индикаторов мощного А-50. Четыре самолета разом растаяли в пространстве, словно исчезнув в очередном «Бермудском треугольнике»…
Трудно сказать, кто является автором идеи о плазменных стелсах-генераторах, но Максим Калашников (чей отрывок стал эпиграфом к статье) был далеко не первый. Идея быстро проникла в массы и накрепко завладела умами.
Чтобы понять, как работает “плазменный стелс”, необходимо перенестись на сто лет в прошлое.
1919 год. Дж. Хеттингер получает патент на плазменную антенну. Устройство для излучения и приема радиоволн, в котором вместо металлических проводников используется ионизированный газ. Изобретение Хеттингера нашло применение не сразу. Лишь в наши дни, с появлением плазменных твердотельных антенн, появилась возможность создания высокоскоростных сетей обмена данными (WiGig).
Военных, наоборот, заинтересовала возможность формирования плазменных антенн в открытом пространстве. Основной задачей ставится повышение скрытности боевой техники. Такая система обладает лучшей помехозащищенностью и способна к безынерционному изменению её параметров.
Что мы имеем в итоге?
Как и любой металл, содержащий свободные электроны, ионизированный газ (плазма) обладает великолепной электропроводностью.
Теперь обратимся к основам радиолокации. Здесь все определяет принцип изменения направления движения радиоволн при прохождении сквозь неоднородную среду. И чем выше электропроводность отражающей среды, тем сильнее отражение радиоволн от границы раздела двух сред.
Подтверждением высокой отражающей способности плазмы служит отражение радиоволн от ионосферы Земли.
Кого-то может смутить упоминание о снижении заметности военной техники. Но заметность снижается не за счет каких-то эффектов при работе плазменной антенны, а в момент её отключения. В отличие от металлических конструкций, плазменная антенна существует лишь во время работы генератора. А потом она бесследно исчезает.
Также существует эффект временного пропадания радиосвязи во время спуска космических аппаратов с орбиты. Но ведь связь пропадает не из-за невидимости КА. Это банальные помехи, создаваемые в антенных устройствах самого спускаемого аппарата, вызванные сильными электромагнитными полями. С Земли спускаемую капсулу видно, а вот связаться с сидящими внутри космонавтами невозможно. При необходимости, данную проблему можно решить оригинальным способом. Инженеры предлагают использовать в качестве антенны… само облако плазмы, окутавшее спускаемый аппарат.
Урок физики. 9-й класс. Тема: “Плазма”
Четвертое агрегатное состояние вещества — частично или полностью ионизированный газ. Согласно современным расчетам, плазма является фазовым состоянием 99,9% барионного вещества во Вселенной.
Различают низкотемпературную (меньше миллиона К) и высокотемпературную (свыше миллиона К) плазму.
1 000 000 К = 999 727 °С.
Представить такое сложно.
Предположим, создатели “стелс-генератора” выбрали низкотемпературную плазму, подобную той, что используется в плазменных резаках (температура факела ~ от 5000 до 30 000 °C).
ДЛЯ СЛУЖЕБНОГО ПОЛЬЗОВАНИЯ Первый (и последний) полет сверхсекретного “стелс-самолета” с установленным на его борту плазмагенератором
Светимость и ИК-сигнатура “плазменного облака” будут подобны метеориту, а сам “стелс” заметен на расстоянии в тысячи километров.
Наконец, простой и известный факт. Врывающиеся в атмосферу Земли на скорости 11…72 км/с метеориты (как и боеголовки МБР) хорошо обнаруживаются с помощью РЛС, несмотря на окутавшее их облако плазмы.
Не меньший интерес вызывают способы создания и удержания “плазменного экрана” вокруг летательного аппарата. Чем создавать плазму? Как подавать на обшивку? Как, при этом, защитить обшивку ЛА от нагрева?
Проблемы эти столь велики, что здесь не отделаться “100-кг генератором под носовым обтекателем” (привет М. Калашникову).
Наконец, никто из сторонников плазменных “стелс-экранов” не задумывается над тем, откуда черпать энергию для облака плазмы размером с самолет!
Современным боевым самолетам с трудом хватает электроэнергии для обеспечения работы БРЭО, систем радиоэлектронной борьбы и ЭДСУ.
Система электроснабжения истребителей Су-27 состоит из двух систем постоянного и переменного тока. В качестве источников питания используются два интегральных привода-генератора ГП-21 (2 х 30 кВт) и два бесколлекторных генератора постоянного тока (2 х 12 кВт).
В качестве примера типовой нагрузки — мощный радар Н035 “Ирбис” (Су-35). Средняя мощность излучения — 5 кВт, макс. пиковая мощность — 20 кВт.
Для сравнения: простейшая плазменная мусоросжигательная установка (плазменный факел в ограниченном объеме плавильной камеры, t = 1500…2000°С, производительность 250 кг/ч) имеет установленную мощность плазмотрона 150 кВт!
В итоге для создания плазменного экрана размером с самолет придется поднимать в небо целую АЭС.
Потом еще возникнет вопрос о сохранности аппаратуры ЛА и об угрозе жизни пилота вследствие воздействия электромагнитных полей высокой напряженности. Впрочем, тепловой нагрев гораздо быстрее поставит точку в данном вопросе.
Вывод
Прежде чем бросаться сверлить тысячи отверстий в обшивке и ставить на крыло ядерный реактор, необходимо ответить на вопрос: ДЛЯ ЧЕГО?
Все попытки найти хоть какие-то сведения о разработке и создании “плазменных стелсов”, как правило, приводят к одному и тому же вымышленному интервью со специалистами Исследовательского центра им. Келдыша.
«Мы приняли решение делать «невидимки» по технологиям, основанным на принципиально иных физических принципах», — рассказал директор Исследовательского центра им. Келдыша Анатолий Коротеев. По его словам, если создать вблизи летательного аппарата экран из плазмы, то самолет становится невидимым для радаров. Простой пример: если бросить в стену теннисный мячик, он отскочит и вернётся обратно. Так же и сигнал РЛС отражается от самолёта и возвращается на приёмную антенну. Самолет обнаружен. Если у стенки угловатые грани и наклонены они в разные стороны, то мячик отскочит куда угодно, но назад не вернется. Сигнал потерян. На этом принципе основаны американские «стелс». Если же обложить стенку мягкими матами и кинуть в них мяч, то он просто шлепнется об нее, потеряет энергию и упадет рядом со стенкой. Так же и плазменное образование поглощает энергию радиоволн.”
— Легенда из Интернета, 2010 год.
Уважаемый ученый, д.т.н. Анатолий Сазонович Коротеев, вряд ли бы стал рассказывать подобное о свойствах плазмы. Очевидно, что “утку” про стелс-генератор придумал какой-то безграмотный журналист. Плазменное образование в силу своей природы не способно поглощать радиоволны, так, как это описано в цитируемом “интервью”.
В силу своей высочайшей электропроводности плазма не может способствовать снижению радиолокационной заметности. При включении такое “облако” засияет ярчайшей отметкой на экранах всех радаров, а его заметность станет еще выше, чем у цельнометаллического самолета. Во всех без исключения спектрах!
Утверждать обратное — все равно, что заявлять о том, что Земля плоская.
И вызывает немалую тревогу, что обитатели самой читающей в мире страны с поголовным 10-классным образованием с такой легкостью верят в разную чепуху.
Ну, а пока — угловатость форм, параллельность граней, использование радиопоглощающих красок и композитов. “Сухой” Т-50 с технологией “стелс”. Будущее отечественной авиации без плазма-генераторов.
По мотивам спора на сайте «ВО» и комментариев от посетителя opus.
Плазменная резка металла. Принцип работы
- > О компании
- > Опросные листы
- > Монтаж
- > Информация
- > Контакты
Для осуществления плазменной резки используется такой аппарат, как плазморез. С его помощью формируется поток ионизированного воздуха с высокой температурой (плазма), который и разрезает предмет. Основной принцип плазменной резки заключатся в том, что ионизированный воздух может быть проводников электрического тока.
Как устроен плазморез и от чего питается
Аппарат складывается с нескольких частей:
- плазмотрон;
- источник питания;
- компрессор;
- кабель-шланги.
Для аппарата в качестве источника питания может быть использован:
- Трансформатор. Его главным преимуществом является то, что он нечувствительный к перепадам напряжения и может резать предметы любой толщины.
Среди недостатков – большой вес и низкий КПД.
- Инвертор. С его помощью невозможно резать заготовки большой толщины. Однако, положительных моментов в его использовании значительно больше.
У инвертора КПД на треть выше, чем у трансформатора. Он легче, компактнее и работает стабильнее. кроме того, инвертор стоит дешевле, нежели трансформатор. Его намного проще применять на труднодоступных участках.
Плазмотрон и компрессор
Эта часть аппарата представляет собой плазменный резак, который непосредственно используют для разрезания заготовки. Плазмотрон является основной частью плазмореза.
Для подачи воздуха в аппарате используется компрессор. Его работа направлена на вихревую подачу воздуха, которая способствует расположению катодного пятна дуги идеально по центру. Если этого не произойдет, плазморез не будет работать эффективно.
Принцип работы и технология
После включения плазмореза, образуется поток ионизированного воздуха под высокой температурой. Одновременно формируется электрическая дуга, которая локально разогревает заготовку – метал плавиться, после чего образуется рез. В этот период температура плазмы составляет до 30 градусов по Цельсию. Частички расплавленного металла сдуваются с поверхности предмета потоком воздуха, который исходит из сопла.
При помощи плазменной резки может быть обработан любой тип металла, если его толщина не превышает 220 мм.
Аппарат начинает действовать после зажигания плазмообразующего газа (от искры в контуре электрической дуги). Искра воспламеняет газ, он ионизируется и преобразовывается в плазму. У нее очень высокая скорость выхода – от 800 до 1500 м/с.
Виды
Есть три вида плазменной резки, которые отличаются в зависимости от среды применения:
- Простой. Используется исключительно воздух и электрический ток.
- С защитным газом. Кроме плазмообразующего, применяется еще и защитный газ, который отгораживает зону реза от воздействия окружающей среды.
- С водой.
Вместо защитного газа используется вода, которая выполняет те же функции. Она также охлаждает плазмотрон и вбирает в себя опасные вещества.
Помимо высокой эффективности, плазменная резка обладает еще и безопасностью. Все компоненты и материалы абсолютно пожаробезопасные.
Плазменная резка может осуществляться двумя основными способами:
- Плазменно-дуговой. Обрабатываемая поверхность замыкается в проводящий контур.
- Резка плазменной струей. Металл не включается в проводящий контур. Такой способ можно использовать при наличии стороннего образования с высокой температурой. Его применяют для резки металлов, которые не проводят электрический ток.
Плазменная резка является довольно универсальным инструментом, поэтому у нее очень широкая сфера применения. Ее используют на разных отраслях промышленности для обработки таких предметов и материалов, как трубы, чугун, сталь, бетон и пр.
Владельцы собственных гаражей мечтают иметь на руках лазерный резак по металлу. Универсальный инструмент активно используют во время работы с металлическими изделиями. Смастерить полезный агрегат можно своими руками. Ниже представлены некоторые рекомендации для самостоятельного изготовления лазерного резака.
Виды резака по металлу
Существует три разновидности универсального инструмента: газовые, твердотельные и волоконные.
Читать далее >>>
Декоративная резка металла – процесс создания четких металлических предметов и деталей. Он приобрел быструю популярность среди людей. Это вызвало стремительное развитие оформления декора в различных жизненных аспектах. К примеру, благодаря компьютерным технологиям, станок резки по металлу способен с повышенной четкостью и точностью создать настоящее произведение искусства. Данные изделия из металла применяют при постройке предметов и объектов: заборы, лестницы, уличные таблички, магазинные вывески. Изделия применяют в машиностроении и строительстве.
Читать далее >>>
Компания Красноярский крановый завод предлагает услуги плазменной резки металла в Красноярске. Наше оборудование способно резать самые разные металлы различной толщины. Резка металла является популярной услугой в работе с металлом.
С помощью плазмы резать металл можно любой формы и по любым чертежам.
Плазменная резка металла с ЧПУ позволяет выполнять раскрой любой сложности.
Наши операторы очень ЧПУ – профессионалы своего дела, всегда добиваются высокого качества резки. На выходе вы получаете готовые детали с ровными кромками. Никакая дополнительная обработка торцов больше не требуется.
Читать далее >>>
Опубликовать в социальных сетях
Плазменная сварка — принцип работы и ТОП-3 аппарата © Геостарт
Рубрика: Полезно
Для соединения деталей из вольфрама (W), молибдена (Mo), различных структур нержавеющих сталей и никелевых сплавов (авиа и приборостроение) применяется сварка плазморезом, где поток плазмы является источником энергии. Температура плазменной дуги порой достигает 30000°C, тогда как привычная всем электрическая дуга имеет только 5000-7-000°C – разница довольно-таки существенная. Практика показала, что данный способ оказался гораздо эффективнее по многим параметрам, по сравнению с классической газовой и электрической сваркой.
Технология сварки и резки металлов плазмой
Принцип плазменно-дуговой технологии сварки заключается в мощном прогреве обрабатываемых металлов плазмой, которая в данном случае является ионизированным газом, полученным при работе электрической дуги под повышенным давлением. Горелка, которую используют в таких агрегатах, называется плазмотроном – с ее помощью можно варить и резать любые металлы, отображенные в периодической таблице Менделеева. Также плазмотроном можно варить и резать неметаллы, если этому не препятствуют физические или химические свойства материала, как то, отсутствие адгезии, различные особенности вступления в реакцию и т.п.
Основные особенности плазменной сварки
Рассмотрим существенные особенности, которыми обладает плазменно-дуговая сварка. В рабочую зону из плазмотрона выбрасывается струя плазмы, но иногда при необходимости также используется дополнительный инертный газ для создания защитного облака, которое создает оптимальные рабочие условия для химически нейтральной среды. В результате получается, что вся термическая энергия через плазменную струю передается на сварочную ванну, но при этом лишь частично (в малом количестве) попадает на близлежащие области. Для корпуса плазменной горелки используется сталь, а для анода – медь. При этом у медного электрода имеется специальная полость, по которой поступает вода для охлаждения, а между ним и катодом с давлением от 2-х до 5-ти атмосфер поступает рабочий газ для подпитки дуги.
Итак, газ в плазмотроне нагревается от плазменной дуги, что приводит к его ионизации. Объем горячего газа за счет свойства теплового расширения увеличивается от 50-ти до 100-а раз, что способствует скоростному выбросу из сопла. Получается, что кинетическая и тепловая энергия являются главной причинно появления мощного энергетического потока у плазменной сварки. Следует еще отметить, что в плазмотроне обычно применяются горелки постоянного тока.
Существует несколько разновидностей таких агрегатов:
- дуга находится между плавящимся электродом и сварочной ванной;
- дуга находится между НЕ плавящимся электродом и сварочной ванной, а плазма выбрасывается струей газа.
Примечание: для образования плазмы используются такие газы, как аргон (Ar), азот (N2), кислород (O2) или обычный воздух.
Также все сварки такого типа различаются по величине силы тока:
- малые (микроплазменные) – 0,1-50 А;
- средние – 50-150 А;
- большие от 150 А и выше.
Если микроплазменный вариант позволяет избежать прожогов в свариваемых деталях, то агрегаты, работающие на больших токах, проплавляет металл толщиной до 8 мм за один проход без кромочной разделки, что позволяет без особых затруднений резать заготовки. Вполне естественно, что на средних токах вы сможете как варить, так и резать металл.
Выбор плазменного сварочного аппарата
По большому счету плазменный сварочный аппарат состоит из двух основных модулей – это источник электропитания с интегрированным инвертором и сварочная горелка, а все остальное можно назвать дополнениями. При помощи такого агрегата можно варить, резать или даже паять самые разные металлы, невзирая на их повышенную толщину, так как плазменный поток разогревает материал гораздо лучше, нежели обычная газовая или электрическая сварка.
История развития плазменной сварки
Плазменную сварку можно отнести к разряду новых технологий, хотя ее стали применять еще в прошлом столетии, но давайте сделаем короткий экскурс в историю. В конце 50-х годов XX века инженеры-конструкторы американской компании Union Carbide Corp сделали первый аппарат плазменной резки, хотя при этом питались идеями физика из Соединенных Штатов И. Ленгмура. Несмотря на то, что данный метод начали применять 70 лет назад, его можно назвать всего лишь прообразом современной технологии. Все методы защиты сварочной ванны с применением инертных газов, а также разработку портативных аппаратов придумали в период с 1963 по 2006 годы.
Безусловно, плазменная резка, которая увидела свет в 1963 году, значительно увеличила скорость производства, но при этом была одна существенная проблема – на металлическую поверхность сильно воздействовало окисление. В 1965 году начали впрыскивать воду, и это снизило процент окалины, но инженеры-конструкторы на этом не собирались останавливаться. В результате исследований в 1987 году появляется резак с контактным пуском, а в 1990 с плазмой начали работать под водой на глубине до 5 (пяти!) метров. В 1999 мир услышал о создании коаксиальной технологии (газ поступает по общей оси), а в 2006 году начали использовать портативные полуавтоматы.
Популярность и назначение плазменной сварки
На сегодняшний день плазменные агрегаты претендуют на завоевание основной ниши на рынке сварочных аппаратов, причем популярность таких моделей стала расти и не только в промышленном секторе, но и среди бытовых потребителей. Если быть более точным, то можно обратиться к цифрам: сейчас 65% работ, которые раньше выполнялись при помощи электросварки, отошли в сферу деятельности плазмы, то есть, уже больше половины и это явный и стремительный прогресс.
При помощи плазменного оборудования монтируют трубопроводы разного назначения, ее используют в машино- и самолетостроении, строительстве, ремонте различных механизмов, но это лишь часть всей сферы применения. Кроме того, способность плазмотрона обрабатывать неметаллы может заменять гидроизоляцию, например, оплавление стыков железобетонных блоков, плит и перекрытий.
Такой метод имеет ряд неоспоримых преимуществ:
- высокая температура плазмы при резке и сваривании материалов:
- повышенный уровень КПД;
- низкий расход инертных газов;
- малая площадь прогрева, что практически исключает деформацию и существенно понижает усадку шва;
- применение технологии не только для металлов, но также для неметаллов;
- отпадает потребность в периодическом приобретении баллонов с газом или их заправке;
- агрегат легко перемещать с место на место;
- повышенный диапазон по толщине металлических заготовок для обработки;
- улучшенная система безопасности;
- доступная стоимость.
Наиболее популярные в России аппараты плазменной сварки
МППК (многофункциональный портативный плазменный комплекс) Горыныч рассчитан на выработку плазм из жидкости – воды или водно-спиртовой смеси, где пар выполняет защитную функцию. Такие агрегаты производят с силой тока 8,10 и 12 A и при этом они универсальны, то есть, Горыныч может, как резать, так и варить разные детали, но это не все. Задав необходимую мощность, аппарат можно использовать в качестве паяльной лампы, кузнечного горна и даже огнетушителя, если в качестве жидкости используется вода. МППК достаточно легок – масса плазмотрона с кабелем и шлангом не превышает 5,4 кг, а для его питания нужна обычная розетка ≈220±22 V и 50 A. Агрегат создает дугу прямой полярности с КПД не менее 80%.
Если говорить о деньгах, Мультиплаз-15000 является самым выгодным плазменным сварочным аппаратом среди своих аналогов. Кроме того, такой агрегат можно назвать самым легким среди подобных, так, масса источника питания составляет 33 кг а вес плазмотрона вместе с кабелем и шлангом на 9 метров – 5 кг. Потребляемая мощность составляет 15 kW при входном напряжении 380±38 V, с частотой сети 50 A. Сварка функционирует в диапазоне тока от 20 до 100 A, расходует 480 л/мин сжатого воздуха и ее КПД составляет 85% — это позволяет разрезать лист стали толщиной до 50 мм. Безусловно, Мультиплаз-15000 больше подходит для промышленных предприятий и автомастерских, но его также покупают для бытового применения.
В Российской Федерации достаточно популярной является модель плазменной сварки Плазариум SP3, представляющая собой компактный и надежный в работе электроприбор. Агрегат работает от сети ≈220±22 V с частотой 50 A и потребляет 2,64 kW, имеет ступенчатую программируемую регулировку от 1 до 12 A. Плазариум SP3 предназначен в основном для резки и сварки металлических деталей малой толщины и пользуется достаточной популярностью. Примечательно, что масса горелки нетто составляет всего 600 г, а длина кабеля 2 м, и это очень удобно для тех же автомастерских или любых станций техобслуживания. Еще можно отметить, что данное устройство соответствует всем нынешним требованиям правил техники безопасности, включая пожарную защиту.
Заключение
В заключение можно отметить, что аппараты плазменной сварки отличаются друг от друга по мощности и силе тока, поэтому, при выборе прибора на эти характеристики следует обращать первостепенное внимание. Далеко не последнее значение имеют масса и габариты прибора, но опять-таки все зависит от вида выполняемых работ – они могут быть стационарными, где блок питания не нужно переносить или мобильными, когда сварка постоянно нужна в разных местах.
автор Воронина Соня |
Плазменно-дуговая резка. Вопросы процесса и оборудования
Процесс плазменной дуги всегда рассматривался как альтернатива кислородно-топливному процессу. В этой части серии описываются основы процесса с акцентом на рабочие характеристики и преимущества многих вариантов процесса.
Щелкните здесь , чтобы посмотреть наши последние технические подкасты на YouTube .
Основы процесса
Процесс плазменной резки показан на Рис. 1 . Основной принцип заключается в том, что дуга, образующаяся между электродом и заготовкой, сужается медным соплом с мелким отверстием. Это увеличивает температуру и скорость плазмы, выходящей из сопла. Температура плазмы превышает 20 000°C, а скорость может приближаться к скорости звука. При резке поток плазмообразующего газа увеличивается так, что глубоко проникающая плазменная струя прорезает материал, а расплавленный материал удаляется в вытекающей плазме.
Процесс отличается от кислородно-топливного процесса тем, что в плазменном процессе используется дуга для плавления металла, тогда как в кислородно-топливном процессе кислород окисляет металл, а тепло экзотермической реакции плавит металл. . Таким образом, в отличие от кислородно-топливного процесса, плазменный процесс можно применять для резки металлов, образующих тугоплавкие оксиды, таких как нержавеющая сталь, алюминий, чугун и сплавы цветных металлов.
Источник питания
Источник питания, необходимый для плазменно-дугового процесса, должен иметь падающую характеристику и высокое напряжение. Хотя рабочее напряжение для поддержания плазмы обычно составляет от 50 до 60 В, напряжение холостого хода, необходимое для зажигания дуги, может достигать 400 В постоянного тока.
При инициировании вспомогательная дуга формируется внутри корпуса горелки между электродом и соплом. Для резки дуга должна быть перенесена на заготовку в так называемом «перенесенном» режиме дуги. Электрод имеет отрицательную полярность, а заготовка – положительную, так что большая часть энергии дуги (примерно две трети) используется для резки.
Состав газа
В традиционной системе с использованием вольфрамового электрода плазма является инертной, образованной с использованием либо аргона, либо аргона-H 2 или азот. Однако, как описано в Варианты процесса , можно использовать окисляющие газы, такие как воздух или кислород, но электрод должен быть из меди с гафнием.
Поток плазмообразующего газа имеет решающее значение и должен быть установлен в соответствии с текущим уровнем и диаметром отверстия сопла. Если расход газа слишком мал для текущего уровня или уровень тока слишком высок для диаметра отверстия сопла, дуга сломается, образуя две последовательные дуги: электрод к соплу и сопло к заготовке. Эффект «двойной дуги» обычно катастрофичен при плавлении сопла.
Качество резки
Качество кромки плазменной резки такое же, как и при кислородно-топливном процессе. Однако, поскольку плазменный процесс режет плавлением, характерной чертой является более высокая степень плавления по направлению к верхней части металла, что приводит к закруглению верхней кромки, плохой прямоугольности кромки или скосу кромки реза. Поскольку эти ограничения связаны со степенью сужения дуги, доступно несколько конструкций горелок, улучшающих сужение дуги и обеспечивающих более равномерный нагрев в верхней и нижней части реза.
Варианты процесса
Варианты процесса, Рис. 2а-2е , в основном были разработаны для улучшения качества резки и стабильности дуги, снижения шума и образования дыма или увеличения скорости резки.
Двойной газ
Процесс работает в основном так же, как и обычная система, но вокруг сопла вводится вторичный газовый экран, Рис. 2a . Положительные эффекты вторичного газа заключаются в усилении сужения дуги и более эффективном «выдувании» окалины. Плазмообразующий газ обычно представляет собой аргон, аргон-H 2 или азот, а вторичный газ выбирается в зависимости от разрезаемого металла.
Сталь
воздух, кислород, азот
Нержавеющая сталь
азот, аргон-H 2 , CO 2
- Алюминий
аргон-H 2 , азот/CO 2
Преимущества по сравнению с обычной плазмой:
- Снижение риска «двойного искрения»
- Более высокие скорости резания
- Уменьшение закругления верхней кромки
Впрыск воды
В качестве плазмообразующего газа обычно используется азот. Вода впрыскивается радиально в плазменную дугу, Рис. 2b , чтобы вызвать большую степень сжатия. Температура также значительно повышается, достигая 30 000°C.
Преимущества по сравнению с обычной плазмой:
- Улучшение качества и прямоугольности резки
- Повышенная скорость резания
- Меньший риск «двойного искрения»
- Уменьшение эрозии сопла
Водяной кожух
Плазма может работать либо с водяным кожухом, Рис. 2c , либо даже с заготовкой, погруженной на глубину от 50 до 75 мм ниже поверхности воды. По сравнению с обычной плазмой вода действует как барьер, обеспечивая следующие преимущества:
Удаление дыма
- Снижение уровня шума
- Увеличенный срок службы сопла
В типичном примере уровня шума при высоком токе 115 дБ для обычной плазмы водяной экран эффективно снижает уровень шума примерно до 96 дБ, а под водой — до 52–85 дБ.
Поскольку водяной экран не увеличивает степень сужения, прямоугольность режущей кромки и скорость резания заметно не улучшаются.
Воздушная плазма
Инертный или нереакционноспособный плазмообразующий газ (аргон или азот) можно заменить воздухом, но для этого требуется специальный электрод из гафния или циркония, закрепленный в медном держателе, Рис. 2d . Воздух также может заменить воду для охлаждения горелки. Преимущество воздушно-плазменной горелки в том, что в ней вместо дорогостоящих газов используется воздух.
Следует отметить, что хотя электрод и сопло являются единственными расходными материалами, электроды с гафниевым наконечником могут быть дороже по сравнению с вольфрамовыми электродами.
Плазменная резка с высоким допуском
В попытке улучшить качество резки и конкурировать с превосходным качеством резки лазерных систем, доступны системы плазменной дуговой резки с высоким допуском (HTPAC), которые работают с сильно сжатой плазмой. Фокусировка плазмы осуществляется за счет закручивания плазмы, генерируемой кислородом, когда она входит в отверстие для плазмы, а вторичный поток газа впрыскивается ниже по потоку от плазменного сопла, Рис. 2e . Некоторые системы имеют отдельное магнитное поле, окружающее дугу. Это стабилизирует струю плазмы за счет поддержания вращения, вызванного закрученным газом. Преимущества систем HTPAC:
- Качество резки находится между обычной плазменной дугой и лазерной резкой
- Узкий пропил
- Меньшая деформация благодаря меньшей зоне термического влияния
HTPAC — это механизированная техника, требующая точного и высокоскоростного оборудования. Основные недостатки заключаются в том, что максимальная толщина ограничена примерно 6 мм, а скорость резки обычно ниже, чем у обычных плазменных процессов, и составляет примерно 60-80% скорости лазерной резки.
Эта статья была подготовлена Биллом Лукасом в сотрудничестве с Дерриком Хилтоном, BOC.
Процесс заключается в нагревании газа до температуры, при которой он ионизируется или проводит электричество. Газ находится под давлением и выстреливается над вольфрамовым электродом.
Станок плазменной резки добавляет электричество, которое образует цепь с металлом, подлежащим резке.
В процессе выделяется тепло, превращающее газ в плазму, которая может резать металл.
Этот процесс можно использовать как для резки, так и для строжки металла. При строжке этот процесс предлагает более низкую стоимость, более низкий уровень дыма и шума по сравнению со строжкой угольной дугой.
Машина относительно проста в использовании… Проверьте газовые линии и соединения, включите воздушный компрессор (для моделей с воздушным охлаждением), а затем включите питание.
Легко!
Обзор
В процессе плазменно-дуговой резки металл разрезается путем плавления секции металла сжатой дугой. Высокоскоростной струйный поток горячего ионизированного газа плавит металл, а затем удаляет расплавленный материал, образуя пропил. Базовая компоновка горелки для плазменной дуговой резки, аналогичной горелке для плазменной дуговой сварки, показана на рис. 10-71.
Существуют три варианта процесса:
- низкоточная плазменная резка
- сильноточная плазменная резка
- резка с добавлением воды
Слаботочная дуговая резка, обеспечивающая высококачественную резку тонких материалов, использует максимальный ток 100 ампер и гораздо меньшую горелку, чем сильноточная версия. Были разработаны модификации процессов и оборудования, позволяющие использовать кислород в дроссельном газе для эффективной резки стали.
Все плазменные резаки сужают дугу, пропуская ее через отверстие, когда она движется от электрода к заготовке. По мере того, как дроссельный газ проходит через дугу, он быстро нагревается до высокой температуры, расширяется и ускоряется при прохождении через сужающее отверстие. Интенсивность и скорость дугового плазменного газа определяются такими переменными, как тип дросселирующего газа и его давление на входе, форма и диаметр сужающего отверстия, а также плотность энергии плазмы на работе.
Сужение сопла фокусирует дугу. Поток газа регулирует скорость плазмы.Преимущества и недостатки
Преимущества
Процесс плазменной резки имеет множество преимуществ:
- Небольшой риск изменения формы металла (так называемая деформация)
- Точная резка
- Резка без шлака при работе с алюминием, нержавеющей и углеродистой сталью
- Работает во всех положениях
- Быстрый процесс
- Работает со многими типами металлов
- Не требуются газовые баллоны
Недостатки
Некоторые недостатки плазменной резки:
- Создает небольшой скос (7 градусов – приблизительно)
- Риск поражения электрическим током при небезопасной эксплуатации
- Требуется источник чистого воздуха — некоторые теперь поставляются с компрессорами, построенными в
- Для работы требуется электричество, поэтому он не полностью портативный
- Нерентабельно для очень толстой стали
Плазменно-дуговая резка
Основная схема плазменно-дуговой резки показана на рис. 10-72. Процесс работает на постоянном токе, прямой полярности (dcsp), отрицательном электроде, с ограниченной переносимой дугой.
В режиме переносной дуги дуга зажигается между электродом горелки и заготовкой. Дуга инициируется вспомогательной дугой между электродом и сужающим соплом. Форсунка подключается к земле (плюс) через токоограничивающий резистор и контакт реле вспомогательной дуги.
Вспомогательная дуга инициируется высокочастотным генератором, соединенным с электродом и соплом. Затем источник сварочного тока поддерживает эту слаботочную дугу внутри горелки. Ионизированный газ от вспомогательной дуги продувается через сужающее отверстие сопла.
Образует путь с низким сопротивлением для зажигания основной дуги между электродом и заготовкой.
При зажигании основной дуги реле вспомогательной дуги может автоматически размыкаться во избежание ненужного нагрева сужающего сопла.
Принципы работы
Расходные материалы для плазменной резки: качество и скорость резки снижаются при повреждении электрода или наконечника сопла Основная схема плазменной резки показана на рис. 10-72. Процесс работает на постоянном токе, прямой полярности (dcsp), отрицательном электроде, с ограниченной переносимой дугой. В режиме переносной дуги дуга зажигается между электродом горелки и заготовкой. Дуга инициируется вспомогательной дугой между электродом и сужающим соплом. Форсунка подключается к земле (плюс) через токоограничивающий резистор и контакт реле вспомогательной дуги. Дежурная дуга инициируется высокочастотным генератором, соединенным с электродом и соплом.
Затем источник сварочного тока поддерживает эту дугу слабого тока внутри горелки. Ионизированный газ от вспомогательной дуги продувается через сужающее отверстие сопла. Это формирует путь с низким сопротивлением для зажигания основной дуги между электродом и заготовкой. Когда загорается основная дуга, реле вспомогательной дуги может автоматически размыкаться во избежание ненужного нагрева сужающего сопла.
Поскольку сужающее плазму сопло подвергается воздействию высоких температур факела плазмы (примерно от 18 032 до 25 232 °F (от 10 000 до 14 000 °C)), сопло должно быть изготовлено из меди с водяным охлаждением. Кроме того, горелка должна быть рассчитана на создание пограничного слоя газа между плазмой и соплом.
См. также : Газы для плазменной резки – Руководство по выбору
Горелки
Плазменная горелка для запуска дугиГорелки для плазменной резки подходят к держателям резака в автоматических машинах для газовой резки.
Как правило, при запуске плазменно-дугового резака поместите наконечник на 1/4″ над пластиной. Не прикасайтесь к пластине (следуйте указаниям производителя).
Всегда начинайте с края с небольшим количеством металла под наконечником.
Сильноточная резка
Узкий разрез, оставшийся после процесса плазменной резки Для резки на сильном токе резак устанавливается на механическую каретку. Автоматическая фигурная резка может быть выполнена на том же оборудовании, что и кислородная резка, если достижима достаточно высокая скорость перемещения. Вокруг плазмы используется водяная струя для уменьшения дыма и шума. Рабочие столы, содержащие воду, контактирующую с нижней стороной разрезаемого металла, также снижают уровень шума и дыма.
Позиции резки
Горелка для плазменной резки может использоваться во всех положениях. Его также можно использовать для прокалывания отверстий и выдалбливания. Резак имеет специальную конструкцию для резки и не используется для сварки.
При использовании в неплоских положениях используйте маломощные плазменные машины с током менее 100 ампер. Машины большей мощности могут быть опасны, когда они находятся вне горизонтального положения.
Процедуры
Процедуры плазменной дуговой резки следующие (см. инструкции производителя для вашего конкретного устройства, это общие рекомендации):
- Проверьте давление воздуха (должно быть около 70 фунтов на квадратный дюйм).
- Прикрепил зажим заземления к разрезаемому металлу
- Включите резку
- Отрегулируйте силу тока в соответствии со спецификацией производителя для металла и толщины металла
- Позиционный экран, вырезанный по металлу
- Нажмите кнопку зажигания и установите дугу
- Переместите дугу над линией разреза и выполните разрез.
При необходимости используйте направляющую планку, которая поможет сделать более ровный срез. Держите защитный колпачок и сужающую насадку на расстоянии от 1/8″ до 1/4″ над разрезаемой поверхностью. Не тяните защитную чашку и сужающую насадку по металлу, если только они не предназначены для такого использования. Совет. Сделайте разрез на обратной стороне линии разреза.
- Используйте меньшую скорость перемещения для более толстого металла. Направление резака (вбок, назад, вперед) по выбору резака.
- Переместите резак как можно быстрее.
- При использовании сжатого воздуха убедитесь, что в нем нет влаги. Для линии доступен воздушный фильтр, который может кондиционировать воздух для повышения качества плазменной резки.
Металлы
Металлы, которые обычно режут с помощью этого процесса, это алюминий и нержавеющая сталь. Этот процесс также можно использовать для резки большинства металлов, не содержащих железа (цветных), а также:
- алюминий
- латунь
- углеродистая сталь
- чугун
- медные сплавы
- медь
- высокое содержание никеля
- магний
- мягкая сталь
- сплавы никеля
- нержавеющая сталь
Элементы управления
Для регулировки потока плазмы и вторичного газа требуются специальные элементы управления. Требуется вода для охлаждения горелки, которая контролируется датчиками давления или расхода для защиты горелки. Система охлаждения должна быть автономной, включающей циркуляционный насос и теплообменник.
Варианты процесса
Несколько вариантов процесса используются для улучшения качества PAC для конкретных приложений. Как правило, они применимы к материалам толщиной от 1/8 до 1-1/2 дюйма (от 3 до 38 мм). Вспомогательная защита в виде газа или воды используется для улучшения качества резки.
Двухпоточная плазменная резка
Двухпоточная плазменная резка обеспечивает вторичную газовую подушку вокруг дуговой плазмы, как показано на рис. 10-73. Обычный дроссельный газ — азот. Защитный газ подбирается в зависимости от разрезаемого материала. Для мягкой стали это может быть углекислый газ (CO2) или воздух; для нержавеющих сталей, CO2; и смесь аргона с водородом для алюминия. Для низкоуглеродистой стали скорость резки несколько выше, чем при обычной плазменно-дуговой резке, но качество резки во многих случаях неудовлетворительное.
Плазменная резка с водяным экраном
Этот метод аналогичен плазменной резке с двойным потоком. Вместо вспомогательного защитного газа используется вода. Внешний вид среза и срок службы сопла улучшаются за счет использования воды вместо газа в качестве дополнительной защиты. Прямоугольность реза и скорость реза существенно не улучшаются по сравнению с обычным PAC.
Плазменная резка с впрыском воды
В этой модификации процесса PAC используется симметричная падающая струя воды возле сужающего отверстия сопла для дальнейшего сужения плазменного пламени. Расположение показано на рис. 10-74. Струя воды также защищает плазму от смешивания с окружающей атмосферой. Конец сопла может быть изготовлен из керамики, что помогает предотвратить двойное искрение. Плазма, сжатая водой, производит узкий, четко очерченный разрез на скоростях, превышающих скорости обычного PAC. Поскольку большая часть воды выходит из сопла в виде жидкой струи, она охлаждает кромку пропила, создавая острый угол. Прорез чистый. Когда дроссельный газ и вода впрыскиваются по касательной, плазменный газ закручивается, выходя из сопла и водяной струи. Это может создать высококачественную перпендикулярную поверхность на одной стороне пропила. Другая сторона пропила скошена. При фигурной резке направление движения должно быть выбрано для получения перпендикулярного разреза на детали и косого разреза на ломе.
Вентиляция
Количество образующихся газов и зубцов требует использования местной вытяжки для надлежащей вентиляции. Резку следует производить над водоемом, чтобы удаляемые из среза частицы попадали в воду. Это поможет уменьшить количество паров, выбрасываемых в воздух.
При резке объекта, который может отбросить шлейф, например бочки, соблюдайте осторожность или полностью избегайте такой ситуации.
Области применения
Пример плазменной резки Плазменная дуговая резка может использоваться для резки любого металла. Большинство приложений для:
- углеродистой стали
- алюминий
- нержавеющая сталь
Может использоваться для резки пакета, снятия фаски с листа, фигурной резки и прокалывания.
Меры предосторожности
При работе с мощным оборудованием необходимо носить средства защиты органов слуха. Уровень шума, создаваемого мощным оборудованием, некомфортный. Резчик должен носить защитные наушники.
Также необходимо носить обычную защитную одежду для защиты резака от дуги. Это касается защитной одежды, перчаток и шлема.
Маска пассивного сварщика должна быть оснащена затемнением №. 9-фильтровая стеклянная линза. В качестве альтернативы вы должны носить шлем с автоматическим затемнением.
Существует множество применений слаботочной плазменной резки, включая резку нержавеющей стали и алюминия для производства и обслуживания. Плазменная резка также может использоваться для пакетной резки, и она более эффективна, чем пакетная резка с помощью кислородно-ацетиленовой горелки. Плазменная строжка с низким током также может использоваться для повышения качества отливок.
Избегайте резки во влажных или влажных местах, так как это повышает риск поражения электрическим током.
Используйте машины большей мощности (более 100 ампер) в горизонтальном положении. Точные характеристики уточняйте у производителя.
Поиск и устранение неисправностей
Качество процесса плазменной резки может ухудшиться, если:
- необходимо заменить электрод (двухкратный срок службы электродов сужающего сопла)
- изношена сужающая насадка
Как работает плазменная резка?
Главная » Блог » Как работает плазменная резка?
Процесс плазменной резки, применяемый при резке электропроводящих металлов, использует этот электропроводный газ для передачи энергии от источника электроэнергии через плазменный резак к разрезаемому материалу.
Базовая система плазменной дуговой резки состоит из источника питания, цепи зажигания дуги и горелки. Эти компоненты системы обеспечивают подачу электроэнергии, возможность ионизации и управление технологическим процессом, необходимые для получения высококачественной и высокопроизводительной резки различных материалов.
Блок питания представляет собой источник постоянного тока постоянного тока. Напряжение холостого хода обычно находится в диапазоне от 240 до 400 В постоянного тока. Выходной ток (сила тока) источника питания определяет скорость и толщину резки системы. Основной функцией источника питания является подача необходимой энергии для поддержания плазменной дуги после ионизации.
Цепь зажигания дуги может иметь конструкцию со обратным клапаном, которая используется в устройствах серии Hypertherm Powermax, или цепь высокочастотного генератора, вырабатывающего переменное напряжение от 5000 до 10 000 вольт с частотой приблизительно 2 мегагерца. Это напряжение используется для создания высокоинтенсивной дуги внутри горелки для ионизации газа и образования плазмы.
Горелка служит держателем расходуемого сопла и электрода и обеспечивает охлаждение этих деталей (газом или водой). Сопло и электрод сужают и поддерживают струю плазмы.
Последовательность работы с плазменным резаком
Источник питания и цепь зажигания дуги подключаются к горелке с помощью соединительных проводов и кабелей. Эти провода и кабели обеспечивают надлежащий поток газа, электрический ток и высокую частоту к горелке для запуска и поддержания процесса.
ШАГ 1: Входной сигнал запуска отправляется на источник питания. Это одновременно активирует напряжение холостого хода и подачу газа к горелке (см. рис. 2). Напряжение холостого хода можно измерить от электрода (-) до сопла (+). Обратите внимание, что сопло подключается к плюсу источника питания через резистор и реле (реле вспомогательной дуги), а разрезаемый металл (заготовка) подключается напрямую к плюсу. Газ проходит через сопло и выходит из отверстия. В это время дуги нет, так как нет пути тока для постоянного напряжения.
ЭТАП 2: После стабилизации потока газа активируется высокочастотный контур. Высокая частота прерывается между электродом и соплом внутри горелки таким образом, что газ должен пройти через эту дугу, прежде чем выйти из сопла. Энергия, передаваемая от высокочастотной дуги газу, вызывает ионизацию газа и, следовательно, его электропроводность. Этот электропроводящий газ создает путь тока между электродом и соплом, в результате чего образуется плазменная дуга. Поток газа выталкивает эту дугу через отверстие сопла, создавая вспомогательную дугу.
ШАГ 3: Предполагая, что сопло находится в непосредственной близости от заготовки, вспомогательная дуга будет прикреплена к заготовке, так как путь тока к плюсу (в источнике питания) не ограничен сопротивлением, поскольку положительный форсунка соединение есть. Ток, подаваемый на заготовку, измеряется электроникой в источнике питания. При обнаружении этого тока высокая частота отключается и реле вспомогательной дуги размыкается. Ионизация газа поддерживается за счет энергии основной дуги постоянного тока.
ЭТАП 4: Температура плазменной дуги расплавляет металл, прокалывает заготовку, и высокоскоростной газовый поток удаляет расплавленный материал с нижней части разреза. В это время инициируется движение резака и начинается процесс резки.
Варианты процесса плазменной резки
Обычная плазменная резкаВ этом процессе обычно используется один газ (обычно воздух или азот), который охлаждает и производит плазму. Большинство этих систем рассчитаны на ток менее 100 ампер для резки материалов толщиной менее 5/8 дюйма. В основном используется в ручных приложениях.
Двухгазовая плазменная резка В процессе двухгазовой (кислородно-топливной) плазменной резки используются два газа; один для плазмы и один в качестве защитного газа. Защитный газ используется для защиты области реза от атмосферы, обеспечивая более чистую кромку реза. Это, вероятно, самый популярный вариант, так как можно использовать множество различных комбинаций газов для получения наилучшего качества резки данного материала.
Плазменная резка с водяной защитой представляет собой вариант процесса с использованием двух газов, при котором защитный газ заменяется водой. Он обеспечивает улучшенное охлаждение сопла и заготовки, а также лучшее качество резки нержавеющей стали. Этот процесс предназначен только для механизированных приложений.
Плазменная резка с впрыском водыПлазменная резка с впрыском воды использует один газ для плазмы и использует воду, впрыскиваемую радиально или вихревым способом непосредственно в дугу, что значительно улучшает сужение дуги, поэтому плотность дуги и температура увеличиваются. Этот процесс используется от 260 до 750 ампер для высококачественной резки многих материалов и толщин. Этот процесс предназначен только для механизированных приложений.
Прецизионная плазменная резка Прецизионная плазменная резка обеспечивает превосходное качество резки более тонких материалов (менее 1/2″) на более низких скоростях. Это улучшенное качество является результатом использования новейших технологий для сверхсжатия дуги, что значительно увеличивает плотность энергии. Более медленные скорости необходимы для более точного контурирования устройства движения. Этот процесс предназначен только для механизированных приложений.
Как работает машина плазменной резки?
Вудворд Фаб
Плазменная резка, представляющая собой метод термической резки, широко используется для резки или гравировки на таких материалах, как металлы. Это один из самых быстрых доступных методов резки, который обеспечивает высокое качество и точность резки, не вызывая ухудшения качества материала. Несмотря на то, что это популярный метод резки металла, большинство из нас не знает о плазменной резке. Вам интересно узнать больше об этой технике резки металла? Этот пост предназначен для предоставления вам подробной информации о плазменной резке. Следите за обновлениями.
Чтобы понять, как работает плазменный резак, важно знать, что такое плазма. Существуют три основные формы материи – твердая, жидкая и газообразная. Но есть и четвертый — плазменный. В повседневной жизни плазма может встречаться в нескольких продуктах, таких как люминесцентные лампы, телевизоры и, конечно же, плазменные резаки. Плазму часто называют ионизированным газом, потому что она может быть получена путем нагревания природного газа до экстремальных температур или воздействия на него электромагнитного поля, при котором элемент ионизированного газа становится электропроводящим. В результате плазменные резаки могут без сопротивления проходить через такие металлы, как латунь, алюминий, сталь и медь.
Как работает машина плазменной резки? Машина плазменной резки, также называемая методом термической резки, может резать металлы, которые являются хорошими проводниками электричества. Это делается с помощью ускоренной струи горячей плазмы вместо ее механической резки. Это достигается за счет сжатого воздуха или других газов, в зависимости от разрезаемого материала. По сути, сжатые газы создают нарастание давления на электроде, и плазменный пар выталкивается к режущей головке. В плазменных резаках используется медное сопло для сужения пара плазмы, который затем воздействует на заготовку. Когда ток от резака проходит через плазму, выделяется достаточно тепла, чтобы проплавить заготовку. При этом сжатые газы выдувают расплавленный металл.
Плазменная резка — один из эффективных методов резки тонких и толстых материалов. Благодаря высокой скорости и точности резки этот метод широко используется в ремонте и реставрации автомобилей, промышленном строительстве, производстве, утилизации и утилизации.
Как эффективно использовать машину плазменной резки? До сих пор предыдущий раздел касался работы плазменных резаков. Теперь давайте сосредоточимся на том, как наилучшим образом использовать инструмент.
- Использование в полевых условиях: Существует множество плазменных резаков, от недорогих до моделей известных брендов. Большинство из них ориентированы на производительность и могут точно соответствовать вашим потребностям. Для использования в полевых условиях вам понадобится машина примерно с пятнадцатью-двадцатью проводами. Таким образом, вы можете удовлетворить свои потребности и при этом сэкономить на воздухе и электроэнергии.
- Использование в магазине: Плазменные резаки легко найти в магазинах. Их можно использовать со станками с числовым программным управлением (ЧПУ), и вы будете поражены результатами. Вы можете превратить необработанный стальной лист в заготовку невероятного дизайна. С помощью плазменных резаков вы можете многократно выполнять точные разрезы; вручную, это может быть обыденным и подвержено ошибкам.
- Другое использование: Другие варианты использования этого инструмента зависят от разных проектов.
Это могут быть арт-инсталляции, ремонт квартир и многое другое. Кроме того, плазменный резак также упрощает задачу ремонта, разрезая небольшой кусок металла, не отправляя вас в мастерскую.
Чтобы получить ожидаемое качество и точность резки, важно правильно выбрать машину плазменной резки от ведущего поставщика, такого как Woodward Fab. Просмотрите высококачественную машину плазменной резки PL320 для резки низкоуглеродистой стали толщиной до 5/16″. Компания является ведущим поставщиком инструментов и оборудования для обработки листового металла.
Просмотрите самые продаваемые машины для плазменной резки Ассортимент продукции:
Связанный пост:
- Знайте о 5 основных типах сварочных процессов
- 8 важных советов по повышению безопасности сварки
- Разница между сваркой и изготовлением листового металла
- Распространенные ошибки, которых следует избегать при выборе сварочного аппарата
- Все, что вам нужно знать о сварочных позиционерах
Общие сведения о плазменной дуговой резке
Станок плазменной резки для резки внутренних частей металлической детали.
Изображение предоставлено: Portrait Images Asia by Nonwarit/Shutterstock.com
Плазменно-дуговая резка, также называемая плазменной резкой плавлением или плазменной резкой, представляет собой производственный процесс, в котором используется перегретый ионизированный газ, пропускаемый через плазменную горелку для нагрева, расплавления и, в конечном счете, резки электропроводящего материала в нестандартные формы и конструкции. Этот процесс подходит для широкого спектра металлических материалов, включая конструкционную сталь, легированную сталь, алюминий и медь, и может резать материалы толщиной от 0,5 мм до 180 мм.
Процесс плазменной резки часто представляют как альтернативу лазерной, гидроабразивной и кислородно-топливной резке, и он предлагает определенные преимущества по сравнению с этими вариантами, включая более быстрое время резки и более низкие первоначальные капиталовложения и эксплуатационные расходы. Хотя плазменная резка демонстрирует некоторые преимущества по сравнению с другими процессами резки, ее использование в некоторых производственных приложениях может быть проблематичным, например, при резке непроводящего материала.
Несмотря на то, что у каждого процесса резки есть свои преимущества и недостатки, в этой статье основное внимание уделяется плазменной резке с описанием основ процесса плазменной резки, а также необходимых компонентов и механики машины плазменной резки. Кроме того, в статье рассматриваются различные варианты плазменной резки и предлагаются альтернативы процессам плазменной резки.
Что такое плазма?
Три наиболее часто упоминаемых агрегатных состояния вещества — твердое, жидкое и газообразное. Плазму, однако, часто называют четвертым состоянием материи, и технически это наиболее часто встречающееся состояние — по объему и массе — поскольку оно встречается по всей галактике и за ее пределами (например, в центрах звезд и в форме молния).
Плазма возникает, когда к газу добавляется дополнительная энергия, что позволяет молекулам газа двигаться быстрее и сталкиваться с большей силой. Столкновения между молекулами позволяют молекулам разделяться на составляющие их атомы, а эти отдельные атомы отделяться от электронов внешней оболочки, образуя ионы. По мере того, как все больше атомов теряют свои электроны, газ достигает критической точки, когда количество атомов, теряющих электроны, и количество атомов, принимающих свободные электроны, уравновешиваются. В этот момент ионизированный газ становится плазмой.
Обычно встречающаяся в астрофизической сфере плазма естественным образом встречается в звездах и в межпланетной, межзвездной и межгалактической среде. В земном царстве это происходит только в виде редких явлений, таких как молнии или полярные сияния. Однако его можно создать искусственно путем перегрева газа или воздействия на него сильного электромагнитного поля до тех пор, пока газ не станет ионизированным и не приобретет высокую электропроводность. Этот искусственно созданный ионизированный газ используется в машинах плазменной резки и в процессе плазменно-дуговой резки для разрезания электропроводящего материала.
Пример земной плазмы: множественные удары молнии по мосту. Изображение предоставлено: John Wollwerth/Shutterstock. com
Процесс плазменной резки
Процесс плазменно-дуговой резки представляет собой термический производственный процесс, в котором используется суженная плазменная дуга с переносом для резки широкого спектра металлов, включая конструкционную сталь, легированную сталь, алюминий и медь. Хотя доступно несколько вариантов, основные принципы процесса и необходимые компоненты остаются одинаковыми во всех них. Процесс первичной плазменно-дуговой резки включает следующие этапы:
- Запуск вспомогательной дуги
- Генерация основной дуги
- локальный нагрев и плавка
- выброс материала
- дуговое движение
Запуск пилотной дуги
Процесс начинается с команды пуска, которая побуждает источник питания генерировать напряжение холостого хода до 400 В постоянного тока, т. е. напряжение холостого хода, и инициирует подачу сжатого плазмообразующего газа в узел плазменной горелки, который содержит электрод и плазменное сопло. Как показано на Запуск дежурной дуги на рис. 1 выше, источник питания также подает отрицательное напряжение на электрод, устанавливая его в качестве катода в цепи дежурной дуги, и замыкает нормально разомкнутые контакты цепи сопла, размещая временный положительный контакт. напряжение на сопле, которое затем служит анодом цепи вспомогательной дуги. Затем консоль запуска дуги (ACS) создает высокочастотный потенциал высокого напряжения между электродом и соплом, который генерирует высокочастотную искру. Искра ионизирует плазменный газ, делая его электропроводным и создавая путь тока с низким сопротивлением между электродом и соплом. Вдоль этого пути тока формируется начальная низкоэнергетическая дуга, т. е. вспомогательная дуга, по мере того как энергия течет и разряжается между двумя компонентами.
Генерация основной дуги
После запуска вспомогательная дуга вытекает вместе с плазменным газом через отверстие сопла в направлении заземленной электропроводной заготовки, которая частично ионизирует область между ними и образует новый путь тока с низким сопротивлением. Поскольку поток газа вынуждает вспомогательную дугу выступать дальше через отверстие, дуга в конечном итоге входит в контакт с заготовкой и переходит на нее. Как показано на диаграмме Main Arc Generation на рис. 1 выше, этот перенос дуги создает основную дугу, т. е. плазменную дугу, которая выполняет фактическую операцию резки, и устанавливает заготовку как часть вновь созданной цепи основной дуги. вместе с электродом. Перенос дуги также побуждает источник питания повторно размыкать нормально разомкнутые контакты сопла, удаляя сопло из цепи вспомогательной дуги, а основная дуга увеличивается до оптимальной силы тока резки.
Локальный нагрев и плавление
Сопло сужает ионизированный газ и основную дугу, когда они проходят через отверстие сопла, увеличивая плотность энергии и скорость плазмы. Станки плазменной резки производят плазму с температурой до 20 000°C, которая движется к заготовке со скоростью, в три раза превышающей скорость звука. Эта тепловая и кинетическая энергия используется для операции резки.
В процессе плазменно-дуговой резки используется метод резки плавлением и выдуванием, при котором происходит нагрев, расплавление и испарение локализованной области заготовки. Когда плазма попадает на поверхность заготовки, материал заготовки поглощает тепловую энергию дуги и плазменного газа, увеличивая внутреннюю энергию и выделяя тепло, что ослабляет материал и позволяет его удалять для получения желаемых разрезов.
Выброс материала
Ослабленный материал заготовки выталкивается из пропила — на ширину удаляемого материала и разрезаемого продукта — за счет кинетической энергии используемого плазмообразующего газа. Оптимальный поток плазмообразующего газа определяется током и соплом, при этом слишком низкий или слишком высокий уровень потока плазмы приводит к менее точным разрезам и выходу компонентов из строя.
Дуговое движение
После начала локализованного нагрева, плавления и испарения заготовки плазменная дуга вручную или автоматически перемещается по поверхности заготовки для выполнения полной резки. В случае ручных систем плазменной дуговой резки оператор вручную инициирует процесс и перемещает резак по поверхности, чтобы создать желаемые разрезы. Для автоматизированных систем плазменной дуговой резки машина запрограммирована на перемещение головки резака с оптимальной скоростью для обеспечения точной и аккуратной резки.
Изображение предоставлено: Игорь В. Подкопаев/Shutterstock.com
Варианты процесса плазменной резки
Основные принципы процесса плазменно-дуговой резки остаются одинаковыми для различных доступных вариантов. Тем не менее, каждый вариант процесса обеспечивает определенные преимущества в отношении производственных приложений в зависимости от разрезаемого материала и его свойств, выходной мощности и конкретных требований приложения. Варианты обычно различаются в зависимости от их системы охлаждения, типа плазмообразующего газа, конструкции электрода и типа используемой плазмы.
Некоторые из доступных вариантов плазменной резки включают:
- Стандартная (или обычная) плазменно-дуговая резка
- Плазменно-дуговая резка с использованием вторичной среды
- Плазменная дуговая резка с впрыском воды
Стандартная (или обычная) плазменно-дуговая резка
При обычной плазменной дуговой резке оборудование для плазменной резки включает узел плазменной горелки, в котором используется один плазменный газ, служащий одновременно газом зажигания и газом для резки. Как правило, в стандартном процессе используется азот, кислород или смесь водорода и аргона. Сжатие плазменной дуги и газа осуществляется только соплом без помощи какой-либо вторичной среды. В качестве охлаждающей жидкости для плазмотрона может использоваться вода или воздух.
Плазменно-дуговая резка с вторичной средой
Для плазменно-дуговой резки, в которой используется вторичная среда, дополнительная среда, т. е. вода или газ, перекачивается в плазменную горелку для дальнейшего сужения плазменной дуги и получения специфических характеристик для конкретного применения резки.
Использование вторичного газа в процессе плазменно-дуговой резки может повысить удельную мощность, качество и скорость резки. Кроме того, вторичный газ может уменьшить повреждение системы и риск возникновения двойной дуги, а также продлить срок службы расходных деталей резака. Этот тип плазменной резки подходит для металлических листов толщиной до 75 мм.
Некоторые из наиболее распространенных комбинаций вторичного газа включают:
- воздух, кислород и азот для резки стали
- азот, аргон-H 2 и CO 2 для резки нержавеющей стали
- аргон-H 2 , азот и CO 2 для резки алюминия
Добавление воды в процесс плазменной резки может привести к получению поверхности заготовки с более высокой отражательной способностью. Вода действует как барьер или щит во время процесса резки, поскольку она перекачивается в плазменную горелку, выбрасывается и испаряется плазменной дугой. Этот тип плазменной резки подходит для алюминия и высоколегированных сталей толщиной до 50 мм.
Плазменная дуговая резка с впрыском воды
При плазменной дуговой резке с впрыском воды в процессе резки также используется вода. В плазмотрон впрыскивается вода, которая дополнительно сужает плазменную дугу. В отличие от плазменно-дуговой резки со вторичной средой, большая часть воды остается неиспаренной и вместо этого действует как охлаждающая жидкость для компонентов плазменной горелки и заготовки. Охлаждающий эффект воды обеспечивает меньшую деформацию материала, более высокое качество резки и более длительный срок службы расходных деталей резака. Этот тип плазменно-дуговой резки подходит для подводной плазменной резки металлов толщиной от 3 мм до 75 мм.
Другие варианты
Другие варианты плазменной резки включают:
- Плазменная дуговая резка с повышенным сужением
- Резка плазменной дугой под водой
- Плазменная строжка
- Плазменная маркировка
В отличие от ранее упомянутых вариантов, увеличенное сужение плазменной дуги достигается за счет использования специальных сопел, которые обеспечивают определенные возможности, такие как вращение плазмообразующего газа или регулировка сопла в процессе резки.
Подводная плазменная дуговая резка выполняется на глубине от 60 до 100 мм под водой, что позволяет уменьшить шум, пыль и загрязнение воздуха, но требует больше энергии и больше времени для резки, чем атмосферная плазменная дуговая резка.
Плазменная строжка и плазменная маркировка — это процессы, которые обычно не прорезают заготовку; плазменная строжка удаляет только поверхностный материал заготовки, чтобы получить более гладкую поверхность, в то время как плазменная маркировка создает поверхностные метки на готовых компонентах.
Процесс плазменно-дуговой резки предлагает множество вариантов, которые подходят для широкого спектра производственных применений. Пригодность каждого варианта зависит от спецификаций и требований резания.
Станок плазменно-дуговой резки
В то время как в процессе лазерной резки используются станки для лазерной резки, а в процессе/услуге гидроабразивной резки используется оборудование для гидроабразивной резки с водой под давлением и абразивами, в процессе плазменно-дуговой резки используется оборудование плазменной резки для получения желаемых разрезов на заготовке. Станки плазменной резки варьируются от модели к модели, а также от приложения и приложения с настройками от простых (например, ручные резаки, подключенные к источнику питания) до сложных (например, программируемое и автоматизированное оборудование с ЧПУ). Базовая комплектация оборудования для этих машин плазменной резки включает в себя источник питания плазмы, консоль зажигания дуги, блок горелки, систему подачи газа, систему охлаждения и электропроводящую заготовку.
Источник питания: Источник питания обеспечивает энергию для запуска вспомогательной дуги и поддержания основной дуги на протяжении всего процесса плазменной резки. Как правило, они имеют высокое напряжение без нагрузки (т. е. напряжение холостого хода) в диапазоне от 240 до 400 В постоянного тока для создания вспомогательной дуги, но требуют только от 50 до 60 В постоянного тока для поддержания основной дуги после ее возникновения.
Консоль зажигания дуги (ACS): ACS создает начальную искру, которая инициирует цепь вспомогательной дуги.
Используемые газы и среды: Плазменные газы подразделяются на воспламеняющие газы (зажигают плазменную дугу), режущие газы (используются с плазменной дугой в процессе резки) и вторичные газы (сжимают и охлаждают плазменную дугу). Используемые газы могут быть инертными, реакционноспособными или смесью двух предыдущих типов. Вода также используется в качестве вторичной среды в процессе резки.
Горелка в сборе: Горелка в сборе и детали включают электрод и сопло, подключены к источнику питания и используют плазму и режущие газы для инициирования и выполнения операции плазменной резки.
Система охлаждения: Система охлаждения охлаждает компоненты узла резака и заготовку, продлевая срок службы расходных деталей. Система может быть как с водяным, так и с газовым охлаждением.
Заготовка: Заготовка — это разрезаемый материал. Материал должен быть электропроводным для плазменной резки, поскольку заготовка служит компонентом основной цепи дуги.
Другие варианты установки для плазменно-дуговой резки включают столы для резки, оборудование для контроля загрязнения воздуха и подвесные направляющие системы. Раскройный стол служит рабочей поверхностью для резки заготовки, а контрольно-измерительное оборудование средством удаления выбросов, образующихся в процессе резки. На автоматических станках резак резак подвешивается над головой на системе направляющих, что позволяет перемещаться по поверхности заготовки.
Расходуемые сопла плазмотрона.Изображение предоставлено: Nordroden/Shutterstock.com
Вопросы материалов
Поскольку в процессе плазменной резки используются переносные плазменные дуги, его использование ограничивается резкой только материалов, обладающих электропроводностью. Однако он подходит для широкого спектра металлов, в том числе:
- Конструкционная сталь
- Нелегированная, низколегированная и высоколегированная сталь
- Алюминий
- Плакированные металлические пластины
Плазменно-дуговая резка также может использоваться для таких материалов, как медь, латунь, титан и чугун, хотя некоторые из их температур плавления могут оказаться проблематичными для получения высококачественной резки кромок. В зависимости от технических характеристик машины плазменной дуговой резки и материала заготовки этот процесс позволяет резать материалы толщиной от 0,5 мм до 180 мм.
Альтернативные процессы резки
Среди продемонстрированных преимуществ плазменно-дуговой резки по сравнению с другими методами резки можно отметить следующие:
- Более быстрое время выполнения работ
- Нарезка более высокого качества
- Возможность работы с более толстыми материалами
- Минимальный риск деформации материала
- Более низкие затраты на оборудование и эксплуатационные расходы
Однако, несмотря на эти преимущества, он может не подходить для каждого производственного применения, и другие процессы резки могут оказаться более подходящими и экономически эффективными. Альтернативы плазменной резке включают газокислородную резку, гидроабразивную резку и лазерную резку.
Резюме
Выше изложены основы машины и процесса плазменной дуговой резки, различные варианты плазменной резки, а также некоторые соображения, которые могут приниматься во внимание производителями и механическими мастерскими при принятии решения о том, является ли плазменная резка наиболее оптимальным решением для их конкретной резки. заявление.
Чтобы найти более подробную информацию о местных коммерческих и промышленных поставщиках услуг и оборудования для производства на заказ, посетите платформу поиска поставщиков Thomas, где вы найдете информацию о более чем 500 000 коммерческих и промышленных поставщиков.
Источники
- http://www.techno-isel.com
- http://www.boc-gas.co.nz/en/legacy/attachment?files=tcm:y435-68107,tcm:435-68107,tcm:35-68107
- https://www.esabna.com/us/en/education/blog/the-basics-of-plasma-cutting.cfm
- https://www.researchgate.net
- https://www.lincolnelectric.com/en-us/equipment/plasma-cutter/process-and-theory/Pages/how-a-plasma-cutter-works.aspx
- https://www.twi-global.com/technical-knowledge/job-knowledge/cutting-processes-plasma-arc-cutting-process-and-equipment-considerations-051
- http://www.esabna.com/us/en/education/blog/what-is-plasma-cutting.cfm
- https://weldguru.com/plasma-arc-cutting/
- https://www.
gemathis.com/laser-cutting-vs-plasma-cutting/
Прочие режущие изделия
- Механическая резка, лазерная резка, фрезерование
- Общие сведения о ротационной высечке
- Типы операций высечки
- Инструменты для формовки высечки
- Ведущие поставщики услуг лазерной резки в США
- Типы режущих инструментов
- Ведущие поставщики услуг по высечке и оборудования для высечки в США
- Введение в планшетную высечку
- Различия между гидроабразивным резаком и станком для лазерной резки
- Общие сведения о высечке
- Общие сведения о лазерной резке
- Лазерная резка стали и алюминия
Еще от Изготовление и изготовление на заказ
Как работает плазменная резка и что такое плазменная резка
В этом посте могут быть партнерские ссылки. Покупка через них может принести нам небольшую комиссию бесплатно для вас. Это покрывает нашу заработную плату и позволяет бесплатно использовать наши ресурсы.
Последнее обновление:
Вы чувствуете себя подавленным, пытаясь понять, что такое плазменная резка? Мы знаем, что это может показаться очень сложной областью работы, когда вы впервые смотрите на нее.
Даже терминология может показаться странной, например, что такое «вихревое кольцо», когда оно дома?
К счастью, стоит немного погрузиться под поверхность — все не так сложно, как кажется на первый взгляд. Хотя используемая технология очень впечатляет, а выходная температура невероятна, практическое применение плазменной резки довольно простое.
Итак, , мы составили для вас супер-путеводитель по всему, что вам нужно знать о плазменной резке. Познакомит вас с основами раздела «Что такое плазма?» а затем проведет вас через все тонкости работы плазменной резки, а затем ответит на некоторые вопросы, которые часто возникают у людей по поводу этой работы.
Обещаем, что к концу все станет ясно, и вы сможете объяснять плазменную резку как знатоки.
Быстрый переход
- Что такое плазма?
- Что такое плазменный резак и как он работает?
- Ручная операция
- Прецизионная плазменная операция
- Компоненты плазменной системы
- Материалы
- Процесс плазменной дуговой резки
- Инициирование
- Основная дуга0093
- Местное отопление
- Выброс материала
- Движение
- Варианты процесса резания дуги плазмы
- Преимущества и недостатки плазменной резки
- Часто задаваемые вопросы (FAQS)
- .
- Вам нужна сварочная маска для плазменной резки?
- Может ли плазменный резак резать дерево?
- Будет ли плазменный резак резать ржавый металл?
- Опасны ли плазменные резаки?
- Какой толщины может резать плазменный резак?
Что такое плазма?
Прежде чем говорить о том, как работает плазменная резка, нам сначала нужно ответить на вопрос: «Что такое плазма?»
В школе вы, возможно, слышали о трех состояниях материи: твердом, жидком и газообразном. Ну, их больше трех, а плазма — это четвертое состояние вещества.
Материя переходит из одного состояния в другое, когда вы добавляете энергию к молекулам или атомам материала. Так, например, если вы нагреете лед, он растает и станет водой.
Затем, если вы нагреете его еще немного, он станет газом или паром, как мы обычно называем водяной пар. Наконец, если вы нагреете его еще больше, газ разделится на ионы, и в этот момент начнет проводить электричество и станет плазмой.
Что такое плазменный резак и как он работает?
Проще говоря, плазменные резаки проталкивают вспомогательную электрическую дугу через узкое отверстие, заполненное газом. Плазменным газом может быть любой кислород, аргон, цеховой воздух, азот и т. д.
Этот процесс нагревает газ до температуры, достаточной для его перехода в плазму, четвертое состояние вещества.
В качестве электрического проводника плазма может образовывать цепь с металлом (или другим материалом), который разрезается, и это позволяет плазменной дуге прорезать материал.
Подпишитесь: Получите БЕСПЛАТНО 30-страничную таблицу символов сварки в формате PDF с примерами применения каждого символа!
Ограниченное отверстие известно как сопло. Это узкое отверстие пропускает газ с очень высокой скоростью, и очень высокотемпературный газ, проходящий через сопло на металл, позволяет ему разрезать металл почти так же, как нож проходит через масло.
Вспомогательная дуга, которая создается в большинстве высококачественных плазменных резаков, воздействует между электродом и соплом для ионизации газа перед началом передачи дуги.
В меньших моделях плазменного резака вы можете обнаружить, что создание плазмы начинается, когда наконечник резака используется для создания искры путем прикосновения к металлической поверхности, или может использоваться пусковая схема (высокочастотная конструкция, которая очень похоже на свечу зажигания в двигателе автомобиля). Стоит отметить, что вы можете использовать только плазменный резак, использующий вспомогательную дугу, для запуска станков с ЧПУ.
Ручное управление
Если вы хотите использовать портативную плазменную систему (машины плазменной резки 110 В/220 В), рекомендуется знать, что когда система находится в выключенном состоянии, сопло и электрод соприкасаются внутри факела.
Как только вы нажимаете на курок, вы создаете постоянный ток из источника питания, который затем проходит через соединение, и в то же время начинает поступать плазмообразующий газ.
Затем плазмообразующий газ создает давление внутри сопла до тех пор, пока его не станет достаточно, чтобы отодвинуть сопло от электрода. Это создает вспомогательную дугу, которая позволяет газу превращаться в струю плазмы.
На изображении рабочий режет металл плазменным резаком. Автор изображения Jbolles на Flicker. Как только это происходит, поток постоянного тока переключается с электрода и сопла и образует путь между электродом и разрезаемой заготовкой. Это будет оставаться на месте до тех пор, пока триггер не будет отпущен, после чего он вернется в состояние OFF.
Precision Plasma Operation
Видео выше демонстрирует одну из систем прецизионной плазменной резки на примере ESAB.
В прецизионном плазменном резаке все по-другому. Электрод и сопло разделены за счет использования завихрителя. Это кольцо с крошечными вентиляционными отверстиями, которые выталкивают предварительный поток плазменного газа в вихрь.
Когда блок питания запускается, он создает до 400 В постоянного тока напряжения холостого хода. Затем плазмообразующий газ поступает в горелку. В этот момент сопло временно подключается к положительному потенциалу источника питания и образует цепь дежурной дуги. Электрод, конечно, в этот момент принудительно находится под отрицательным потенциалом. Затем искра высокой частоты (опять же, как в свече зажигания) создается консолью запуска дуги.
Эта искра позволяет плазменному газу ионизироваться, и он приобретает способность проводить электричество, образуя полную вспомогательную дугу. Как только эта дуга соприкасается с заготовкой, то ток смещается, чтобы соединить электрод с разрезаемым металлом. Заготовка всегда кладется на стол для резки, который полностью заземлен, чтобы предотвратить протекание тока в другое место во время работы.
Это изменяет постоянный ток для получения правильной силы тока, выбранной пользователем плазменной резки, и переключает предварительную подачу газа на оптимальную смесь газа для материала, который вы режете. Затем через сопло подается вторичный защитный газ, чтобы еще больше сфокусировать плазменную дугу, что позволяет получить сверхчистый рез, сохраняя углы скоса как можно более низкими и уменьшая пропил.
Компоненты плазменной системы
Плазменная система состоит из 5 основных компонентов:
Блок питания
Блок питания – преобразует однофазное или трехфазное сетевое напряжение переменного тока в полезное постоянное напряжение до 400 В постоянного тока. Это гарантирует, что плазменная дуга остается стабильной на протяжении всего процесса дуговой резки.
Консоль зажигания дуги
Консоль зажигания дуги – это простая схема, предназначенная для подачи переменного напряжения около 5000 В переменного тока на частоте 2 МГц (что является очень высокой частотой) для создания искры, запускающей плазменную дугу
Газ
Газы – поток газа имеет важное значение, и плазменные системы могут использовать практически любой газ, но, как правило, азот, цеховой воздух, кислород, аргон и т. д. Они могут служить двум целям: 1. формировать основу плазменной дуги или 2.
Охлаждение
Система охлаждения – плазменные резаки нагреваются настолько, что без системы охлаждения сопло или электрод могут загореться, поэтому для поддержания температура всегда под контролем
Резак
Плазменный резак — плазменный резак обеспечивает правильное выравнивание плазменной дуги и эффективную работу системы охлаждения. Расходные материалы для плазменной резки включают сопла, электрод и завихрители.
Материалы
С помощью плазменного резака можно резать только электропроводящие предметы. Это связано с тем, что материал является частью цепи плазменной дуги. Если он не электропроводящий – нет ни замыкания, ни резки.
Это означает, что он подходит для большинства металлов, включая:
- Конструкционную сталь, нержавеющую сталь, нелегированную, высоколегированную и низколегированную сталь
- Плакированные металлические пластины
- Алюминий
Вы также можете использовать плазменную резка латуни, чугуна, меди и титана, но температура плавления этих материалов может помешать получению качественной режущей кромки.
Вы можете использовать плазменные резаки для резки материала толщиной от 0,5 мм до 180 мм, хотя это зависит от машины плазменной резки и материала.
Процесс плазменно-дуговой резки
Существует множество вариантов процесса плазменно-дуговой резки, но основные принципы этого процесса остаются неизменными, независимо от того, режете ли вы нержавеющую сталь, конструкционную сталь, легированную сталь, медь или любой другой материал или листовой металл. .
Этот процесс состоит из пяти отдельных фаз:
Инициирование
Инициирование пилотной дуги – это момент, когда дается команда пуска и когда генерируется первоначальная дуга, вызывающая приток газа к электроду и вытесняющий его через газовое сопло.
Генерация основной дуги
Генерация основной дуги — следующим шагом является зажигание дуги и обеспечение образования электрической дуги между электродом в машине плазменной резки и самой заготовкой, и в этот момент начинается резка и одновременно время, если требуются два плазменных газа, защитный газ начнет поступать, чтобы заточить режущее пламя.
Локальный нагрев
Локальный нагрев и плавление – затем, когда плазма начинает работать, температура повышается, что вызывает локальный нагрев и плавление заготовки, но это также может вызвать проблемы внутри сопла, поэтому требуется система охлаждения эта точка.
Эжекция материала
Эжекция материала – ослабленный материал заготовки выбрасывается из пропила с помощью кинетической энергии, обеспечиваемой газовым потоком плазменной струи.
Движение
Движение дуги – затем, после выброса материала, плазменная дуга перемещается по поверхности материала до завершения процесса резки.
Варианты процесса плазменной резки
Как правило, процесс плазменной резки одинаков независимо от варианта. Тем не менее, каждый вариант резки дает определенное преимущество в зависимости от области применения, для которой он используется.0003
Вариантами считаются различные способы использования плазмы для резки в зависимости от системы охлаждения, конструкции электрода в плазменной горелке, используемого плазмообразующего газа или окончательного типа используемой плазмы для резки.
Некоторые из доступных опций:
Стандартный
Стандартная/традиционная плазменная резка – отверстие сопла является единственным элементом, используемым для сужения плазменной дуги, при этом не используется вторичная среда (хладагентом обычно является вода или воздух) .
Со вторичной средой
Плазменно-дуговая резка со вторичной средой – это когда вторичная среда (то есть другая среда) втягивается в плазменную горелку для дальнейшего сужения плазменной дуги и обеспечения определенных характеристик, которые зависят от применения для которой используется плазменная струя.
С впрыском воды
Плазменно-дуговая резка с впрыском воды – при этой форме плазменно-дуговой резки вода впрыскивается в плазменную дугу, обеспечивая значительное повышение температуры через газовое сопло примерно до 30 000 градусов по Цельсию, что может улучшить качество резки. разрез предусмотрен.
Преимущества и недостатки плазменной резки
Преимущества плазменной резки:
- Зависит от серии машины плазменной резки, но часто можно использовать одну или несколько горелок одновременно
- Вы можете резать любой материал который обеспечивает электрическую проводимость
- Вы можете легко обрабатывать высоколегированную сталь, алюминий и подобные материалы средней или большой толщины
- Вы получаете превосходную производительность при работе с малой и средней мягкой сталью любой толщины
- Вы можете прорезать высокопрочную конструкционную сталь без такого большого нагрева, как при других методах резки
- Скорость плазменной резки примерно в 10 раз выше, чем при кислородной резке
- Позволяет эффективно обрабатывать высококачественную заготовку для толстой и средних листов металла
- Плазменная дуговая резка идеально подходит для автоматизации процесса резки
- При плазменной резке под водой – очень низкий уровень шума и очень низкое тепловое воздействие

К недостаткам плазменной резки относятся:
- Максимальная длина реза по-прежнему составляет 180 мм при сухой плазменно-дуговой резке и только 120 мм при работе под водой
- Энергопотребление для плазменной резки высокое
- Она не обеспечивает такое же качество резки, как лазерная резка
- Эксплуатация намного дороже, чем кислородно-ацетиленовая система
- Вы можете обнаружить, что сухая резка производит больше шума, чем вам хотелось бы
Часто задаваемые вопросы (FAQ)
Опасны ли пары плазменной резки?
Хотя технически дым от плазменной резки не опасен, дым от разрезаемого металла опасен. Большинство металлов при сгорании в воздухе образуют токсичные отложения, которые не следует вдыхать, даже оксид железа (ржавчина) при вдыхании может накапливаться в легких и со временем нанести реальный вред вашему здоровью.
Нужна ли вам сварочная маска для плазменной резки?
Официально? Нет. Вы можете просто носить защитные очки для плазменной резки, но мы рекомендуем, чтобы для плазменной резки обязательно надевались защитные очки и сварочная маска. Это обеспечивает максимальную защиту ваших глаз независимо от используемого метода резки.
Может ли плазменный резак резать дерево?
Что такое плазменная резка? Это использование плазменной дуговой резки для резки материалов, и для того, чтобы это происходило эффективно, необходимо, чтобы разрезаемый материал был электропроводным. Если он не является электропроводным, дуга выйдет из строя — древесина не является электропроводной, и поэтому плазменный резак не может резать древесину.
Будет ли плазменный резак резать ржавый металл?
Да, потому что ржавчина проводит электричество так же хорошо, как и любой другой тип металла, поэтому процесс плазменно-дуговой резки совершенно не затруднен из-за ржавчины. Он будет резать грязную сталь, ржавую сталь и даже окрашенную сталь с таким же качеством, как и нержавеющую сталь.
Опасны ли плазменные резаки?
Да. Тепло, выделяемое при плазменной резке, невероятно сильное. Есть риски для ваших глаз (всегда следует носить очки с боковым щитком и сварочный шлем), вашей одежды (необходимо использовать огнестойкие костюмы) и даже ног и рук (требуются специальные перчатки и обувь).
Несмотря на все это, существует риск возгорания искр или расплавленного металла на рабочем месте или на режущем столе.
Какой толщины может резать плазменный резак?
В некоторой степени это зависит от машины и используемого материала. Тем не менее, ваш обычный ручной плазменный резак с радостью создаст плазменную дугу, прорезающую лист из стали или нержавеющей стали толщиной до 38 мм.
Однако, если вы используете плазменный резак с компьютерным управлением, он может выполнять плазменно-дуговую резку толщиной до 180 мм.
Что ждет плазменную резку в будущем?
В наши дни вы можете использовать высокотехнологичные плазменные резаки, чтобы прорезать невероятные 200 дюймов металлической пластины за одну минуту. При этом они выделяют 40 000 градусов тепла.
Ничего. Ученые уже показали, что можно производить режущую плазму с температурой до 10 триллионов градусов. Конечно, крайне маловероятно, что такой режущий плазменный инструмент когда-либо понадобится для резки металла, но это показывает, что у этой технологии есть огромный потенциал в будущем.
Текущая проблема с плазменным резаком — беспорядок, который он оставляет после себя — окалина, если быть точным. Это своего рода осадок расплавленного металла, который прилипает к углам металла и существенно снижает качество резки.
Качество резки оборудования для лазерной резки или гидроабразивной резки, напротив, намного выше, чем при плазменной резке. Это означает, что после резки не требуется никаких отделочных работ.
Если бы вы спросили мастерскую: «Что такое плазменная резка?» они ответят, что это генератор отделочных работ. Они предпочли бы использовать в своей работе оборудование для лазерной резки или оборудование для гидроабразивной резки, но эти машины дороги, как правило, не доступны в переносных диапазонах, и для выполнения работы требуется в 100 раз больше времени, чем для плазменной резки.