Подготовка деталей (заготовок) под сварку
Сварка – распространенная операция при монтаже оборудования и трубопроводов. Применяют дуговую ручную, механизированную и автоматическую сварку под флюсом и в среде защитных газов, газовую сварку и резку. Перед образованием сварного соединения выполняют операции по подготовке деталей под сварку и их сборку; после сварки — термическую обработку по необходимости и зачистку сварных швов, контроль сварного соединения. При подготовке и сборке деталей (заготовок) под сварку следует обеспечить заданные зазоры между свариваемыми элементами, разделку кромок под сварку, которую получают механическими способами, газопламенной, плазменной резкой. Свариваемые кромки на ширину 25….30 мм должны быть очищены от окалины, коррозии, масла, краски и прочих загрязнений и высушены. Для ручной дуговой сварки основные типы, конструктивные элементы и размеры сварных соединений принимают в соответствии с ГОСТ 5264–80.
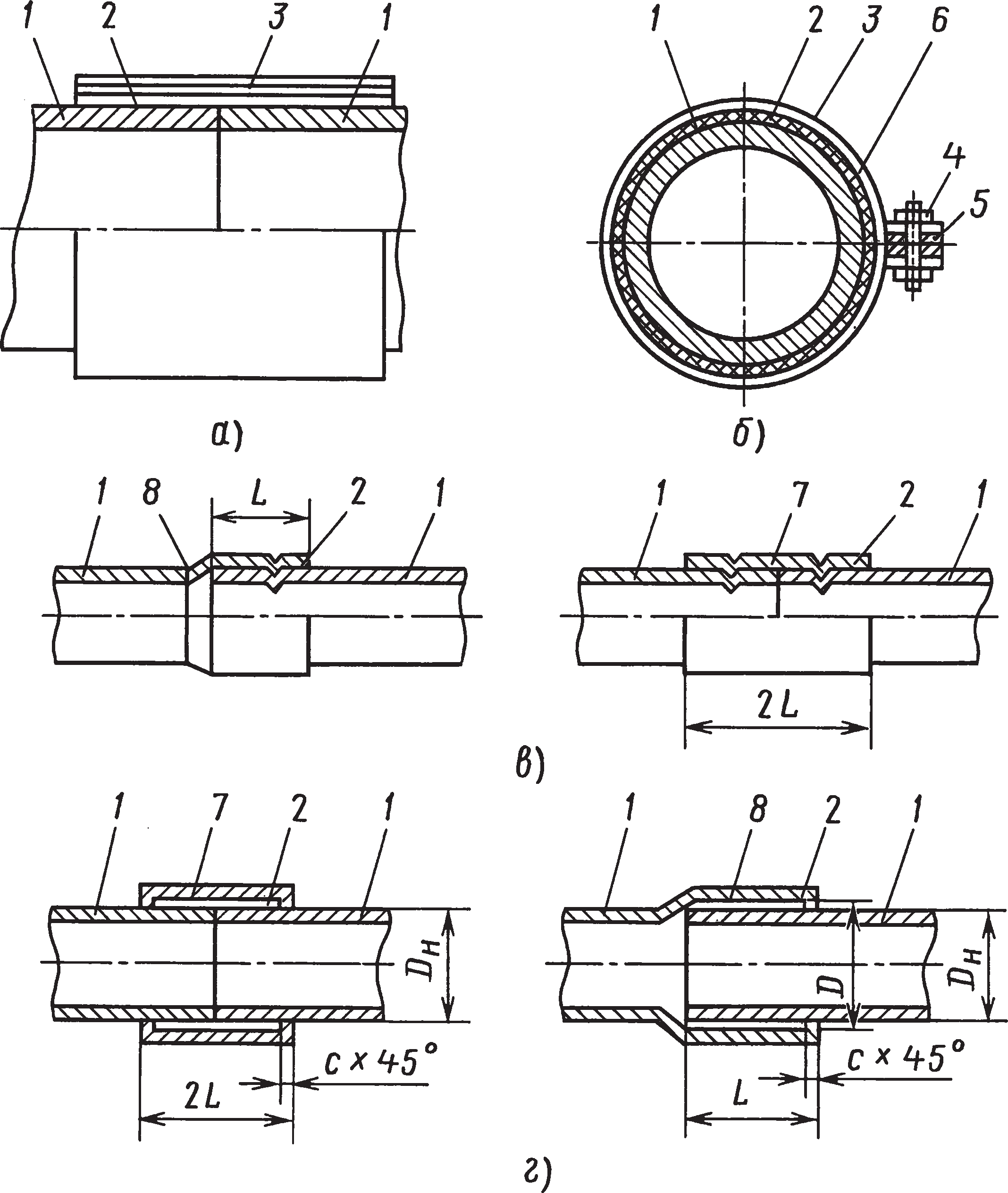
Рис. 2. Схемы клеевых соединений трубопроводов: а — бандажного типа; б — бандаж из металлической ленты; в — клеемеханическое; г — муфтового и раструбного типов; 1 — склеиваемые трубы; 2 — клей; 3 — стеклоткань; 4 — резьбовое соединение; 5 — вкладыши; 6 — бандаж из металлической ленты; 7 — муфта; 8 — раструб
Сборка сварных соединений заключается в последовательном расположении собираемых деталей по чертежу и предварительном скреплении их между собой с помощью различных приспособлений (рис. 3) с последующим наложением коротких сварных швов, располагаемых равномерно по периметру стыка (прихваток). Прихватки выполняют длиной до 60 мм на расстоянии не более 500 мм. Детали, элементы и узлы трубопроводов собирают под сварку также на прихватках. Число и длина прихваток зависят от диаметра трубопровода. Соединяемые концы труб, деталей и элементов трубопроводов перед сборкой и сваркой должны быть очищены от коррозии и загрязнений по кромкам и прилегающим к ним наружной и внутренней поверхностям на ширину 10…15 мм.
Смещение кромок при сборке стыка контролируют линейками, а отклонение от перпендикулярности подготовленных под сварку торцов — угольниками по двум взаимно-перпендикулярным направлениям. Размеры снятой фаски проверяют по шаблону.
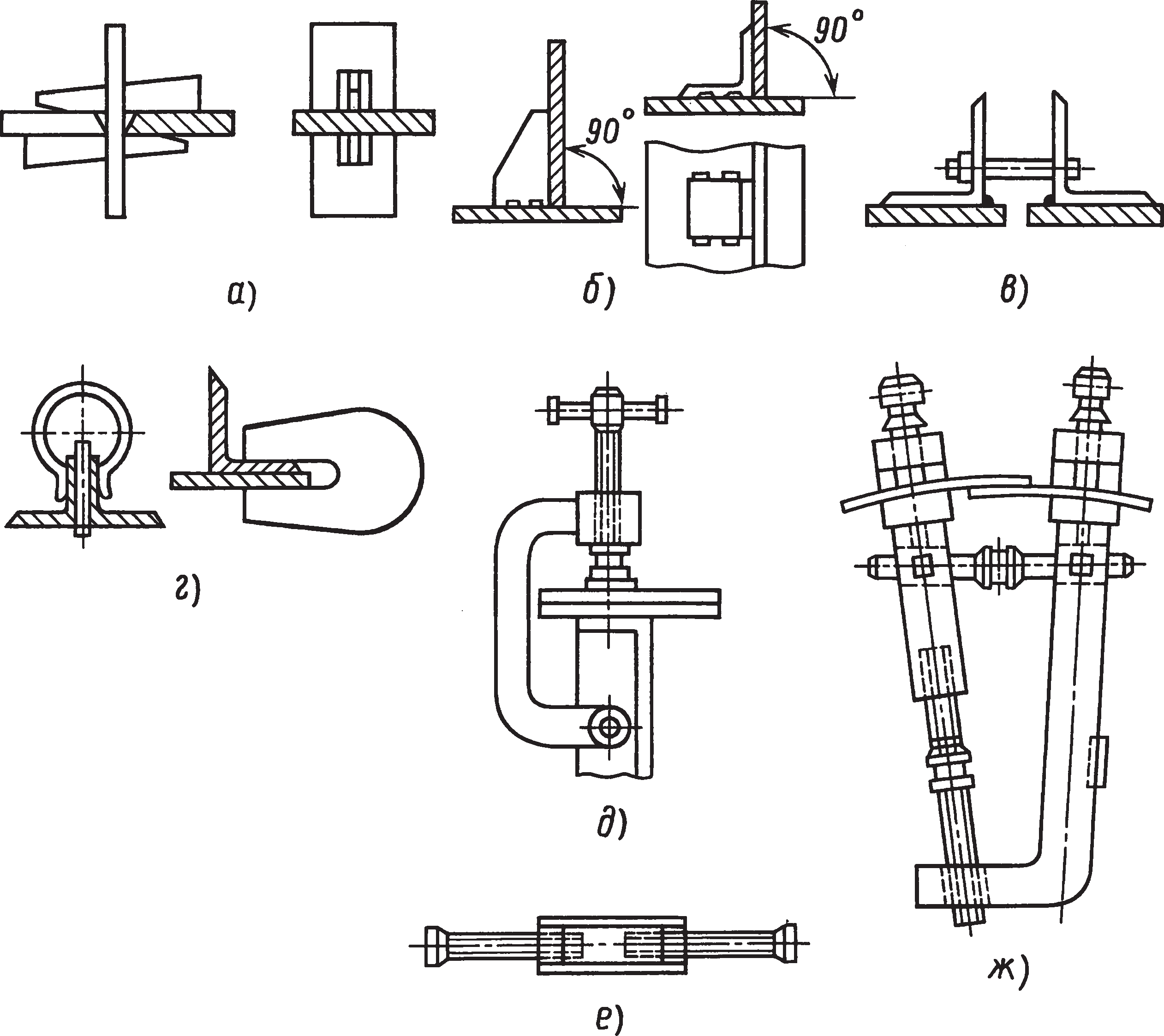
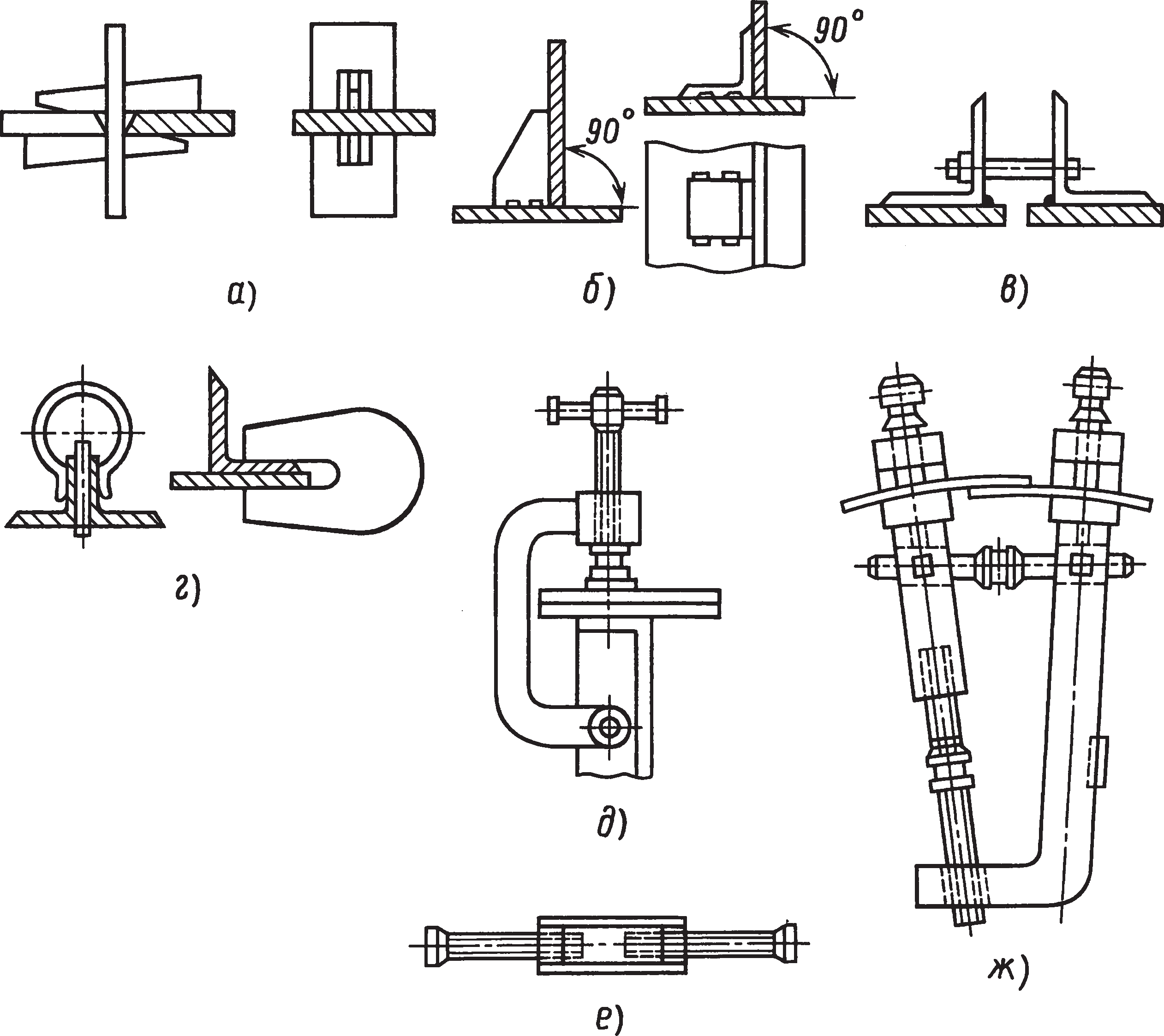
Рис. 3. Универсальные сборочные приспособления для сварки: а — клинья; б — упоры для листов и угловых профилей; в — уголки на прихватах с бортом; г — скобы; д — струбцины; е и ж — винтовые стяжки
В зависимости от наружного диаметра трубы Dн отклонение от перпендикулярности при контроле угольником с длиной полки 100 мм не должно превышать следующих величин:
Для уменьшения отклонений от соосности и овальности стыкуемых концов труб применяют наружные и внутренние центраторы различных конструкций.
Наружный диаметр, мм | До 133 | 159…219 | 273…325 | 377…630 | Св. 630 |
Отклонение от перпендикулярности торцов к оси трубы, ° | 1 | 2 | 2,5 | 3 | 5 |
Просмотров: 145
Подготовка деталей и материалов под сварку
Сварное соединение высокого качества может быть получено только при условии выполнения всех мероприятий по предотвращению попадания в зону сварки каких-либо загрязнений, помещение или участок для проведения газоэлектричрхкой сварки алюминия должны быть чистыми, сухими, не пыльными, скорость движения воздуха не должна превышать 0,2 м/сек; свариваемые детали и присадочная проволока должны быть подвергнуты специальной обработке по их очистке; в качестве защитных газов можно применять лишь аргон чистый марки А по ГОСТу 10157—62 и гелий ВЧ (высокой чистоты) по МРТУ 51-04-23-64; газоподводящую арматуру, шланги и сварочную горелку следует тщательно промывать спиртом перед началом сварочных работ и регулярно очищать и промывать в процессе работы.
Очистка сварочной проволоки заключается в удалении консервационной смазки растворителем (бензином) или горячей (80— 90° С) водой и в химической обработке для удаления окисной пленки с поверхности проволоки. Расконсервацию и химическую обработку следует проводить на специальном участке вне помещения, выделенного для проведения сварочных работ. Химическая обработка сварочной проволоки может быть осуществлена несколькими способами, однако на практике наиболее часто применяют обработку по следующей технологии:
1) травление в 5%-ном растворе каустической соды NOH при температуре 60—65° С в течение 2—3 мин;
2) промывка в горячей (45—50° С) воде, а затем в холодной проточной воде;
3) осветление в 15—30%-ном растворе азотной кислоты HN03 при температуре 60—65° С в течение 2—3 мин;
4) промывка в горячей (45—50° С) воде, а затем в холодной проточной воде;
5) сушка при температуре, не ниже 60° С до полного удаления влаги.
Если химически обработанная и высушенная сварочная проволока не может быть сразу же использована для сварки, то хранить ее необходимо в специальном плотно закрывающемся шкафу или — ящике. Обычно считают, что срок хранения обработанной проволоки не должен превышать 12 ч. Опыт работы показывает, однако, что такое требование справедливо; лишь при сварке неплавящимся электродом с присадочной проволокой малых диаметров (1—1,6 мм) на малых токах (до 100 а). При сварке же плавящимся электродом на токах свыше 400 а проволокой диаметром 4—5 мм этот срок может быть увеличен до 1—1,5 суток без ущерба для качества сварного соединения при условии соблюдения правил хранения обработанной проволоки. Очищенную проволоку можно брать только в чистых перчатках или рукавицах, чтобы не загрязнить и не нанести на поверхность проволоки жировых остатков.
Свариваемые детали или их кромки также нуждаются в тщательной обработке. Предпочтительно очистку деталей под сварку производить также химической обработкой по приведенному выше режиму, причем небольшие детали желательно обрабатывать целиком, а детали большого размера подавать на сварку целиком обезжиренными и с химически обработанными на расстоянии до 100 мм от стыка сварочными кромками.
По наблюдениям авторов и других исследователей на сварных соединениях небольших размеров целесообразно проводить зачистку кромок шабером непосредственно перед сваркой. Помимо зачистки стыка, необходимо еще удалять окисную пленку шабером или стальной проволочной щеткой в месте токоподвода. При невозможности проведения химической обработки крупногабаритных деталей в некоторых случаях после предварительной экспериментальной проверки можно зачищать кромки стальными проволочными щетками с предварительной и последующей протиркой зачищаемой поверхности спиртом или ацетоном. Желательно, чтобы проволока щеток была из нержавеющей стали диаметром не более 0,2 мм, так как более толстая проволока делает глубокие царапины, являющиеся источниками дефектов. В процессе работы щетки необходимо периодически промывать в каком-либо растворителе.
Допустимые сроки хранения деталей, подготовленных под сварку, те же, что и для обработанной присадочной проволоки, но при условии хранения деталей в сухом и теплом помещении с закрытыми чистыми чехлами сварочными кромками. В случае, когда длительность промежуточных технологических операций (монтаж, контрольные операции и т. д.) превышает допустимые сроки между зачисткой деталей и их сваркой, следует применять сварку плавящимся электродом большого диаметра и принимать все меры по предотвращению загрязнения кромок свариваемых деталей на промежуточных операциях.
При многопроходной сварке перед наложением каждого доследующего валика следует тщательно зачищать поверхности шва и разделки проволочными щетками и протирать их спиртом или ацетоном.
Также по теме:
Подготовка под сварку. — Студопедия
Подготовка металла под сварку заключается в правке, разметке, резке, обработке кромок, гибке и очистки металла, а также сборке деталей.
Правка производится для устранения деформаций прокатных материалов. Листовой и сортовой металл правят в холодном состоянии на листоправильных вальцах и прессах. Сильно деформированный металл правят в горячем состоянии.
Разметка – нанесение размеров детали на металл. Она может быть выполнена индивидуально, по шаблонам, а также оптическим и машинным методом. Индивидуальная разметка – очень трудоемкий процесс. Шаблоны обычно изготовляют из алюминиевого листа. Для разметки используют линейку, угольник, рулетку и чертилку.
Оптическим называют метод разметки по чертежу, проектируемому на размечаемую поверхность металла. Разметочно-маркировачные машины с пневмокерном выполняют разметку со скоростью до 8-10 м/мин при погрешности ± 1мм. В этих машинах применяют программное управление.
Использование приспособления для мерной резки проката, а также машин для тепловой резки с масштабной фотокопировальной или программной системой управления позволяет обходиться без разметки.
Резка металла бывает механической и термической. Механическая резка выполняется с применением различного механического оборудования: ножниц, отрезных станков и прессов. Термическая разделительная резка металла менее производительна, чем резка ножницами, но более универсальна и применяется для получения заготовок разной толщины как прямолинейного, так и криволинейного профиля.
Обработка кромок производится для улучшения условий сварки. Кромки подготавливают термическим и механическим способами. Кромки с односторонним или двусторонним скосом можно получить, используя одновременно два или три резака, расположенных под соответствующими углами. Механическая обработка кромок на станках выполняется для обеспечения требуемой точности сборки, для образования фасок, имеющих заданное очертание, в случаях, когда по техническим условиям необходимо удаление металла с поверхности кромок после резки.
В соединении с разделкой (односторонней и двусторонней) кромки выполняют притупление. При односторонней разделке притупление расположено внизу соединения, при двусторонней – в середине соединения. Притупление необходимо для того, чтобы при прихватке и сварке быстро расплавляющиеся острые кромки не создавали широкую щель, которую трудно заваривать. Отсутствие притупления вызывает образование прожогов при сварке по стыку соединения.
Форма разделки кромок характеризуется углом их скоса, размером притупления и зазором между свариваемыми кромками. Она зависит от типа сварного соединения, толщины свариваемых элементов и применяемого способа сварки.
При толщине свариваемых элементов до 6мм скоса кромок не требуется. В элементах толщиной 5–30мм и более применяют V-образную разделку с суммарным углом скоса 60–80о. Притупление при этом составляет 2–8мм. Если толщина свариваемых элементов 20мм и более, в стыковых соединениях применяют криволинейный скос кромок (U-образную разделку).
Свариваемые кромки устанавливаются с зазором 2–4мм (в зависимости от толщины свариваемых элементов). Сварные соединения ответственного назначения с V-образной разделкой свариваются с двух сторон (с подваркой). В тех случаях, когда не удается сделать подварку, например, в сварных стыках труб малого диаметра, применяют остающиеся подкладки.
Элементы толщиной более 12мм сваривают встык с двух сторон, применяя Х-образную разделку. Соединения такого типа сваривают только в тех случаях, когда имеется доступ с обеих сторон. Х-образную разделку используют, например, в стыковых сварных соединениях сосудов высокого давления, толщина свариваемых элементов которых 50–100мм и более.
Соединения с плоскими наклонными кромками(V-образная разделка) трудно провариваются в вершине и имеют большую ширину на наружной поверхности. Соединения с U-образной разделкой свободны от этих недостатков. Недостаток соединений с U- и V-образными разделками заключается в том, что при одинаковой толщине свариваемых элементов для их заполнения требуется больше электродов, чем для заполнения Х-образной разделки. Объем направленного метала в V-образном шве примерно в два раза больше, чем в Х- образном. Следовательно, соединения с Х- образной разделкой более экономичны, чем соединения с V- образной разделкой.
Гибка металла производится на листогибочных вальцах для изготовления цилиндрических и конических поверхностей. Для получения заготовки с поверхностью сложной формы широко используют холодную штамповку из листового материала толщиной до 10мм.
Очистка металла под сварку – это удаление с его поверхности средств консервации, загрязнений, смазочно-охлаждающих жидкостей, ржавчины, окалины, заусенцев, грата и шлака. Для очистки проката, деталей и заготовок используют механические и химические методы.
К механическим методам относятся дробеструйная и дробеметная обработки, зачистка металлическими щетками, иглофрезами, шлифовальными кругами и лентами.
Химическими методами очистки обезжиривают и травят поверхности свариваемых деталей. Различают ванный и струйный методы. В первом случае детали опускают в ванны с различными растворами и выдерживают их там определенное время. Во втором случае поверхность деталей обрабатывается струями раствора, в результате чего происходит непрерывный процесс очистки. Химические методы достаточно эффективны, однако в производстве сварных конструкций используются главным образом для очистки цветных металлов.
Сборка деталей под сварку выполняется с целью установления взаимного пространственного положения элементов сварной конструкции. Для уменьшения времени сборки, а также повышения её точности применяют различные приспособления: установочные детали, прижимные механизмы, стенды, кондукторы и др.
Точность сборки контролируют шаблонами, щупами (рис.1), а также измерительными приборами.
Сварные узлы и конструкции часто собирают с помощью сварочных прихваток.
Для фиксации подлежащих сварке деталей сечение прихваток должно составлять примерно 1/3 сечения основного шва. Протяжённость прихваток составляет 15–50мм в зависимости от толщины свариваемых элементов и длины шва. Расстояние между прихватками обычно от 100мм до 1м.
Последовательность постановки прихваток для коротких, длинных и кольцевых швов показана на рис.3.
Прихватки ставят с лицевой стороны соединения. Поверхность прихватки очищают от шлака. При сварке прихватку удаляют или полностью переплавляют.
Подготовка деталей под сварку и наплавку
Качество ремонта деталей сваркой и наплавкой в значительной степени зависит от качества их подготовки.
Подготовку деталей разделяют на подготовку поверхностей, подготовку кромок и отверстий, термическую подготовку.
Поверхности деталей перед сваркой или наплавкой должны быть очищены от грязи, жиров и ржавчины, так как наличие на поверхности различных загрязнений ухудшает свариваемость основного и наплавленного металлов, загрязняет сварочный шов и способствует образованию пористости в наплавленном металле.
Очистку поверхностей производят стальными щетками, шабером, напильником, наждачным полотном или обточкой на токарном станке. На деталях из стального литья должна быть удалена литейная корка, а на кованых и штампованных деталях—окалина.
Рисунок 91 Подготовка трещины под заварку Рисунок 92 Подготовка отверстия под заварку | Лучшим способом подготовки поверхностей к сварке и наплавке является пескоструйная очистка. Деталь с трещиной перед заваркой должна быть подготовлена следующим образом. Если трещина будет обнаружена на сварном шве, то его необходимо вырубить по всей длине трещины. Если трещина обнаружена на металле, то необходимо во избежание распространения трещин засверлить по ее концам отверстия диаметром 4—6 мм, а трещину разделать на V-образную канавку с одной или двух сторон в зависимости от толщины стенки. Разделку трещины с двух сторон необходимо производить обязательно при толщине детали более 12 мм. Подготовка под заварку отверстий. С двух сторон отверстия зенкуются при толщине материала больше диаметра отверстия. Для отверстия диаметром от 6 до 20 мм при толщине материала или глубине отверстия менее 0,6 его диаметра под готовку отверстия под заварку можно не производить. Если отверстие имеет резьбу, то перед заваркой она должна быть удалена. Следует иметь в виду, что разделка отверстий должна быть выполнена так, чтобы обеспечить при заварке свободное движение электрода в отверстие. При сварке деталей встык, при постановке вставок или накладок кромки свариваемых деталей должны быть разделаны по общепринятым правилам на сварочные соединения. |
Выбор диаметра электрода и величины сварочного тока при ремонте деталей производят в зависимости от сечения детали, толщины свариваемых частей детали и количества металла, необходимого для наплавки. В таблице даны рекомендуемые диаметры электродов в зависимости от толщины свариваемых частей деталей.
Толщина свариваемых частей детали, мм | Диаметр электродной проволоки, мм |
До 3 | 2—3 |
От 3 до 4 | 3—4 |
От 6 до 10 | 4—5 |
Свыше | 6 |
При наплавке изношенных поверхностей де талей с малой поверхностью наплавки необходимо выбирать электрод диаметром 2—3 мм, в остальных случаях — диаметром 4 мм. Величину сварочного тока устанавливают в соответствии с выбранным диаметром электрода, типом электродного покрытия и положением шва в пространстве. При применении качественных электродов величину сварочного тока следует назначать по данным паспорта или сертификата на эти электроды.
В таблице приведена рекомендуемая сила тока при сварке и наплавке в зависимости от диаметра электрода.
Диаметр электрода, мм | Сила тока, а |
2 | 50—70 |
3 | 80—130 |
4 | 80—130 |
5 | 140—200 |
6 | 220—280 |
I == 45d,
где I—сила тока в а; d—диаметр электрода в мм.
При нанесении швов или валиков в вертикальном или потолочном положении величину сварочного тока назначают на 10—20% меньше, чем при сварке в нижнем положении.
Сварка и подготовка поверхности
Ассортимент Unitor ™ позволяет найти эффективное решение для каждой сварочной системы. Мы считаем, что безопасная сварка — это эффективная сварка, а эффективная сварка ведет к большему контролю над расходами, сводя простои на ремонт к абсолютному минимуму и уменьшая риски для экипажа, груза и судна.
Все оборудование Unitor ™ спроектировано в полном соответствии с действующими правилами техники безопасности на море, и мы делаем техническую информацию доступной для конечных пользователей, помогая обеспечить правильное и безопасное использование оборудования.
Разработано специально для морского судоходства
Это единственные сварочные аппараты на рынке, разработанные специально для морской промышленности. Некоторые из его новаторских функций включают функцию полной защиты (TP), которая автоматически отключает машину, чтобы предотвратить повреждение, вызванное скачками напряжения или сбоями электроснабжения. Кроме того, функция устройства снижения напряжения (VRD) ограничивает напряжение холостого хода в диапазоне 9-13 В, предотвращая несчастные случаи из-за поражения электрическим током.Оба этих новых усовершенствования способствуют безопасной сварке на судне.
Полностью соответствует допускам основных классификационных обществ
Произведено в полном соответствии с действующими нормативами для использования на море, мы постоянно следим за изменениями в правилах, чтобы гарантировать, что наше оборудование всегда будет соответствовать требованиям. Ассортимент расходных материалов Unitor ™ обширен, и производство осуществляется в соответствии с требованиями четырех крупных обществ (DNV GL, ABS, LR, BV).
Глобальная доступность через 2200 портов
Невозможно предсказать, когда и где возникнет необходимость в обслуживании или ремонте.Но одно можно сказать наверняка: когда это произойдет, вам понадобится подходящее оборудование под рукой, чтобы выполнять работу эффективно с минимальным временем простоя. Наши стандартизированные сварочные изделия могут быть доставлены через один из 2200 портов, которые мы обслуживаем через нашу глобальную сеть.
Структурированные программы обучения экипажа
Бортовая сварка происходит в разнообразных, сложных и даже непредсказуемых условиях, а диапазон основных материалов, требующих резки или сварки, обычно очень широк.Мы помогаем вам подготовиться к этому ряду проблем с помощью наших специальных программ обучения в сотрудничестве с нашими партнерами по всему миру, обеспечивая наилучшее качество обучения для вашей команды.
Документация — необходимое условие безопасной сварки.
При каждой возможности мы предлагаем поддержку ascertai
.Процесс резки металлического профиля на электрической угловой шлифовальной машине. Подготовка деталей к сварке металлоконструкции. Люди в Wo Stock Image
Мы жертвуем 10% дополнительных гонораров нашим вкладчикам в качестве стимула для борьбы с COVID-19
Похожие изображения
Промышленная обработка металлов процессом нарезки фрезой
Промышленная обработка металла Процесс резки автомобильных деталей b
Человек, работающий руками, использует ремесленный нож, Процесс ручной резки виниловых наклеек нага, змея в тайском мифе, Создание виниловых наклеек
Процесс раскроя кусков ткани в форме шестиугольников для создания квилта Процесс раскроя кусков ткани в s
Обработка металлических заготовок на токарном станке с режущим инструментом
Токарный станок с ЧПУ в процессе металлообработки, формирующий резку металлических частей вала в голубой сцене.
Процесс распиловки дерева тесаком. Мужчина держит топор
Процесс формования, нарезки, формования сладких булочек и рулетов из теста
Процесс шитья на этапе раскроя ткани
Процесс сварки робота крупным планом Лазерная резка металла на манипуляторе с искрами
Фрезерная обработка металлов.Прецизионная промышленная обработка металлических деталей с ЧПУ на фрезерном стане
Токарь управляет процессом металлообработки механической резки на токарном станке
Процесс резки широкого листа металла на узкие полосы на станке
Процесс стрижки волос крупным планом
.