Подготовка кромок под сварку — Студопедия
Подготовка кромок металла под сварку делается с целью обеспечения полного провара металла по всей его толщине и получения: доброкачественного сварного соединения.
Различные виды подготовки кромок металла при сварке стыковых швов показаны на фиг. 49. Скос кромок делается для металла толщиной свыше 5 мм. Угол скоса 70—90° выбирают из расчета возможности свободного доступа к вершине шва и ее проварки.
Скос кромок можно производить различными способами. Самым грубым и малопроизводительным из них является срубание кромок ручным или пневматическим зубилом. При этом способе края кромок получаются неровные. Наиболее ровные и чистые кромки получаются при изготовлении их на специальных кромкострогальных или фрезерных станках. Применение кислородной резки, ручной или механизированной, для скоса кромок является самым экономичным. Шлаки и окалина, остающиеся после кислородной резки, должны быть удалены с помощью зубила и стальной щетки.
Следует уделять большое внимание чистоте кромок, так как загрязненная поверхность кромок металла приводит к плохому провару и образованию в сварном шве неметаллических включений. Поэтому перед сваркой кромки, а также соседние с каждой кромкой участки на ширину 20—30 мм должны очищаться до металлического блеска от окалины, ржавчины, масла, краски и других загрязнений. Очистка от окалины, краски и масла может осуществляться непосредственно пламенем сварочной горелки. При этом окалина отстает от металла, а масло и краска сгорают. После нагрева пламенем поверхность зачищается стальной щеткой.
При сборке деталей под сварку нужно следить за тем, чтобы кромки правильно располагались одна относительно другой, чтобы выдерживались установленные зазоры, не было перекосов и т. д.
Для того чтобы в процессе сварки установленные зазоры и положение деталей не изменялись, перед сваркой делают предварительную прихватку деталей, т. е. свариваемые детали соединяют друг с другом в нескольких местах короткими швами. Длину прихваток и расстояние между ними выбирают в зависимости от толщины свариваемого металла и длины шва. При сварке тонкого металла и коротких швах длина прихваток может быть не более 5 мм. При сварке толстого металла и значительных длинах швов длина прихватки может быть 20—30 мм при расстоянии между ними 300—500 мм. Прихватку следует производить на тех же режимах сварки, что и сварку самого шва, тщательно проваривая участок прихватки. В случае сварки деталей значительной толщины прихватка может заполнять разделку примерно на 2/3 ее глубины.
Порядок постановки прихваток имеет важное значение, особенно при сварке длинных швов.
Виды подготовки кромок под сварку:
а —с отбортовкой кромок; б, и, к — без скоса кромок; в —со скосом одной кромки; г — со скосом двух кромок; д — с двухсторонним скосом двух кромок;е—с криво-линейным скосом кромок; ж — с использованием остающейся или съемной подкладки;
– для автоматической сварки под флюсом α = 30° ± 5° и 10° ± 2° при пря-молинейном и криволинейном скосах кромок в случае стыковых и угловых со-единений, тавровые соединения требуют большего угла, который равен соот-ветственно 50° ± 5° и 20 ± 2;
– для сварки в среде защитных газов α = 40° ± 2° и 20° ± 2° при прямолиней-ном скосе одной и двух кромок — в случае криволинейного скоса α = 12° ± 2°.
Детали при стыковом соединении должны иметь, как правило, одинако-вую толщину. Допустимая разность толщины при сварке составляет не более 1, 2, 3 и 4 мм при толщине деталей соответственно до 4, 20, 30 и более мм. Если разность толщины больше, то на детали с большей толщиной делают скос под углом 15° с одной или двух сторон (Рис. 5, л).
При угловом соединении допускается не делать скос кромок а формиро-вание шва производить за счет смещения деталей на величину h (Рис. 5, и, к). Смещение может быть менее 0,5 s или более 0,5 s при толщине деталей до 6 и 30 мм соответственно.
Выбор типа соединения и способа подготовки кромок зависит от условий его работы, толщины соединяемых деталей, конфигурации изделия и условий сварки. Так, наиболее дешевые соединения без подготовки кромок, но их сквозное проплавление ограничено толщиной детали. Скосы двух кромок, осо-
бенно криволинейные, наиболее трудоёмки, но позволяют сократить массу наплавляемого металла и время сварки.
Зазоры между соединяемыми деталями обычно невелики, в противном случае возможны вытекание расплавленного металла и прожог кромок. Это об-стоятельство особенно может проявиться при автоматической сварке.
Для защиты обратной стороны шва от вытекания металла могут быть ис-пользованы ниже перечисленные приёмы:
– Замок,т.е.перекрытие одной детали другой(Рис.5,
дорогой.
– Остающаяся стальная подкладка (Рис.5, ж),толщина которой t1до-
стигает 0,5 толщины детали, но не менее 3 мм, ширина b1 = 10 … 30 мм, а зазор между подкладкой и деталями z не должен быть более 0,5 … 1 мм. Этот способ применяют, в частности, при сварке шаровых резервуаров, сосудов малого диаметра. Такие подкладки соответствуют соединениям С10, С 19 (см. Табл. 1).
– Съёмная технологическая подкладка из меди для стали,из графита длямеди и т. п., которая не приваривается и её удаляют после сварки (С9, С18).
– Предварительная ручная, подварка корня шва (С12,С13,С21, С23,У5,
У10, Т2) является трудоёмкой, её применяют, когда свариваемое изделие не-возможно кантовать или точно собрать перед сваркой.
– Заделка зазора асбестовой набивкой или флюсовой подушкой.
Сварные соединения можно выполнять автоматической, полуавтоматиче-ской или ручной сваркой. Способ сварки выбирают в зависимости от геометри-ческих размеров изделий, свойств материалов, формы сварного шва и серийно-сти производства.
Автоматическая и полуавтоматическая сварка обладает большой произ-водительностью, обеспечивает высокое качество и надёжность соединения, не требует высокой квалификации сварщика, даёт наибольший эффект в серийном и массовом производстве, а также при соединении толстостенныx деталей. Не-достатком этих способов является ограничение по конфигурации и положению шва. Наиболее распространенные автоматы способны сваривать прямо-линейныe горизонтальные швы или соединять цилиндрические детали типа тел вращения.
Форма сварных швов после сварки видна в табл. 3. Так ширина зоны рас-плавленного металла несколько больше, чем исходный зазор между кромками. По высоте сварной шов больше толщины детали, т. е. имеет место так называе-мое усиление шва. Конструктивные элементы швов также регламентированы перечисленными ранее стандартами.
Усиление шва при необходимости снимают строганием, точением или шлифовальными кругами до требуемой шероховатости поверхности.
Презентация к уроку: Подготовка кромок под сварку
Инфоурок › Другое ›Презентации›Презентация к уроку: Подготовка кромок под сваркуОписание презентации по отдельным слайдам:
1 слайд Описание слайда: ГЕОМЕТРИЧЕСКИЕ ХАРАКТЕРИСТИКИ ПОДГОТОВКИ КРОМОК ПОД СВАРКУ Цель: Рассмотреть виды разделок кромок свариваемых деталей и зазоры между ними зависят от толщины свариваемого металла, способов сварки и видов сварных швов (стыковые, угловые). Знания: Разновидности форм, размеров разделок кромок под сварку, которые должны соответствовать действующим стандартам, требованиям чертежа и техническим условиям. Умения: Правильное создание кромок под сварку для получения заданной геометрической формы и удаления дефектного слоя на практических занятиях 2 слайд Описание слайда:ПОДГОТОВКА КРОМОК ПОД СВАРКУ Цель подготовки кромок: Для того, чтобы добиться высокого качества сварного соединения и при этом обеспечить провар металла по всей его толщине, кромки металлических деталей необходимо специальным образом подготовить, то есть, выполнить скос кромок.
ПОДГОТОВКА КРОМОК ПОД СВАРКУ Основные операции до создания формы кромок: Вначале следует уделять внимание чистоте кромок, так как загрязненная поверхность кромок металла приводит к плохому провару и образованию в сварном шве неметаллических включений. Поэтому перед сваркой кромки, а также соседние с каждой кромкой участки на ширину 20—30 мм должны очищаться до металлического блеска от окалины, ржавчины, масла, краски и других загрязнений. Очистка от окалины, краски и масла может осуществляться непосредственно пламенем сварочной горелки. При этом окалина отстает от металла, а масло и краска сгорают. После нагрева пламенем поверхность зачищается стальной щеткой.
4 слайд Описание слайда:РАЗДЕЛКА КРОМОК ДЕТАЛЕЙ Различают разделку кромок: без скоса, односторонний скос, двухсторонний скос, V-образный, Х-образный и К-образный скос кромок при сварке. Выбор каждого конкретного вида скоса зависит от толщины металла и от особых требований к сварному шву. V-образный скос – это односторонний скос одной или двух кромок. V-образный скос кромок выполняется при сварке металлических листов толщиной от 3 до 26 мм. Х-образный скос – это двухсторонний скос обеих кромок металла. О, К-образном скосе кромок речь идет в том случае, если одна из свариваемых кромок имеет двухсторонний скос, а вторая – односторонний. И Х-образный, и К-образный скос кромок делают в том случае, когда сварке подвергаются металлические изделия толщиной от 12 до 40 мм.
5 слайд Описание слайда:РАЗДЕЛКА КРОМОК ДЕТАЛЕЙ
РАЗДЕЛКА КРОМОК ДЕТАЛЕЙ ЗАДАНИЕ: Добавить словосочетание в предложение Если ведется ручная дуговая сварка металлических листов толщиной от 20 до 60 мм, то также применяется и еще один вид скоса кромок – криволинейный U-образный скос. Делается такой скос кромок при сварке … на одной или на обеих кромках свариваемых листов. Предлагаемый ответ Если сварке подвергаются две металлических заготовки разной толщины, то кромка листа с большей толщиной …, чем кромка второго листа. скашивается больше Предлагаемый ответ Форма кромок обеспечивает … сварного шва и может быть различной: под углом с прямолинейным скосом кромок, с притуплением кромок и без него; под углом с криволинейным скосом кромок. правильное формование Предлагаемый ответ
7 слайд Описание слайда:ПОДГОТОВКА КРОМОК ПОД СВАРКУ Скос кромок металлических заготовок может производиться различными способами: Срубание кромок с помощью ручного или пневматического зубила. Это самый грубый и самый неточный способ подготовки кромок к сварке. Его недостатком является то, что при применении зубила края кромок получаются очень неровными. Подготовка кромок на специальном оборудовании – кромкострогательных станках или фрезерных машинах. При применении этого способа подготовки кромок к сварке скос получается более ровным, а края кромок более чистыми. Применение для выполнения скоса кромок кислородной резки. Этот способ считается самым экономичным и производительным. Кислородный резак может быть как ручным, так и механическим. Здесь важно помнить, что после его применения на поверхности металла могут остаться шлаки и окалина – их следует удалить с помощью зубила или металлической щетки. Подготовка кромок абразивным кругом предусматривает зачистку с двух сторон поверхности листа в местах разделки кромок и будущей сварки на ширине 40 мм от торцов. Кромки зачищают до полного удаления окалины и ржавчины, трещин и пр. Операцию выполняют с использованием электрической или пневматической шлифовальной машины с применением шлифовальных кругов.
8 слайд Описание слайда:Инструменты для зачистки кромок
9 слайд Описание слайда:Курс профессиональной переподготовки
Педагог-библиотекарь
Курс профессиональной переподготовки
Специалист в области охраны труда
Курс профессиональной переподготовки
Библиотекарь
Найдите материал к любому уроку,
указав свой предмет (категорию), класс, учебник и тему:
Выберите категорию: Все категорииАлгебраАнглийский языкАстрономияБиологияВнеурочная деятельностьВсеобщая историяГеографияГеометрияДиректору, завучуДоп. образованиеДошкольное образованиеЕстествознаниеИЗО, МХКИностранные языкиИнформатикаИстория РоссииКлассному руководителюКоррекционное обучениеЛитератураЛитературное чтениеЛогопедия, ДефектологияМатематикаМузыкаНачальные классыНемецкий языкОБЖОбществознаниеОкружающий мирПриродоведениеРелигиоведениеРодная литератураРодной языкРусский языкСоциальному педагогуТехнологияУкраинский языкФизикаФизическая культураФилософияФранцузский языкХимияЧерчениеШкольному психологуЭкологияДругое
Выберите класс: Все классыДошкольники1 класс2 класс3 класс4 класс5 класс6 класс7 класс8 класс9 класс10 класс11 класс
Выберите учебник: Все учебники
Выберите тему: Все темы
также Вы можете выбрать тип материала:
Общая информация
Номер материала: ДВ-571053
Похожие материалы
Вам будут интересны эти курсы:
Оставьте свой комментарий
3. Подготовка кромок под сварку
Кромки разделывают в целях полного провара заготовок по сечению, что является одним из условий равнопрочности сварного соединения с основным металлом. Формы подготовки кромок под сварку различают V, K, X – образные
При ручной электродуговой сварке основными видами сварных соединений являются стыковые, угловые, тавровые и соединения внахлестку. Стыковые соединения в зависимости от толщины свариваемых листов делятся на несколько типов. При толщине листов от 1 до 3 мм применяются стыковые соединения с отбортовкой кромок.
Листы толщиною от 1 до 8 мм свариваются в стык без подготовки кромок. Для листов толщиною от 1 до 6 мм применяется односторонняя сварка иногда с остающимися или съемными подкладками; листы толщиною от 3—3,5 мм до 8 мм свариваются с двух сторон. Предельная толщина металла в этом случае определяется возможностью проплавления всего сечения с одной или с двух сторон. Для обеспечения провара всего сечения при сварке листов большей толщины делается скос кромок, называемый разделкой кромок.
Для металла толщиной от 3 до 26 мм предусматривается так называемый V-образный односторонний или двусторонний скос кромок. При этих соединениях также могут применяться остающиеся или съемные подкладки. Металл толщиною от 12 до 40 мм может свариваться К-образным соединением, при котором производится двусторонний скос одной только кромки. Для толщин от 20 до 60 мм с целью экономии наплавленного металла может применяться U-образное соединение с криволинейным скосом одной или двух кромок.
Для металла толщиной от 12 до 60 мм делается Х-образная подготовка крсмок, при которой производится двусторонний скос каждой кромки. При Х-образном стыковом соединении для толщин металла от 30 до 60 мм может применяться также двусторонний криволинейный скос двух кромок. Основными конструктивными элементами разделки являются: угол разделки кромок, притупление и зазор в стыке. Угол разделки кромок для V- и Х-образных соединений берут равным 60°, а для V-образного соединения со скосом одной кромки так же, как и для К-образного соединения, равным 50°.
Величина нескошениой части или так называемое притупление составляет 1—2 мм, а величина зазора принимается равной 2 мм. Угловые соединения при толщине металла не более 3 мм могут выполняться с отбортовкой кромок. При больших толщинах, в зависимости от вида углового соединения и толщины свариваемых листов, сварка производится без скоса, а также с односторонним или двусторонним скосом кромок вертикального листа.
Тавровые соединения, применяемые для толщин металла от 2 до 60 мм, также выполняются без скоса или со скосом кромок вертикального листа. Соединения без скоса кромок применяются для толщин от 2 до 30 мм. Такие соединения свариваются как односторонними, так и двусторонними швами. При этом величина зазора может составлять от 0 до 4 мм. Величина катета выбирается в зависимости от толщины листов и условий работы.
Соединения с односторонним скосом кромок выполняются при толщине листов от 4 до 26 мм и двусторонним скосом для толщин металла от 12 до 60 мм. Угол разделки кромок берут равным 50°, а притупление от 1 до 2 мм, величина зазора обычно составляет около 2 мм. Соединения внахлестку выполняются одно- или двусторонние. Швы накладываются сплошные или прерывистые. Соединения внахлестку могут выполняться также с круглыми или удлиненными отверстиям.
Подготовка под сварку кромок и поверхностей свариваемых деталей
Вырезку деталей и выполнение скосов кромок под сварку следует производить термической или механической резкой в соответствии с требованиями СНиП III-18-75. Разделка кромок под сварку должна соответствовать способу и технологии сварки, толщине свариваемых элементов и положению швов в пространстве. Конструктивные элементы кромок должны соответствовать требованиям ГОСТ 5264—80, ГОСТ 11534—75, ГОСТ 11533—75, ГОСТ 14771—76, ГОСТ 14776—79, ГОСТ 15164—78, ГОСТ 23518—79.
Кромки деталей из низколегированной стали классов до С60/45 включительно, не подлежащие сварке или не полностью проплавляемые при сварке, после ручной кислородной резки, а также кромки аналогичных деталей из сталей всех классов после воздушно-дуговой резки подлежат механической обработке (строжке, фрезеровке, обработке абразивным инструментом).
Механическая обработка производится на глубину, обеспечивающую удаление дефектов поверхности, при этом после воздушно-дуговой резки не менее 2 мм. Поверхности кромок не должны иметь надрывов и трещин.
Кромки деталей из углеродистой стали класса С38/23 после ручной кислородной резки должны быть очищены и не иметь шероховатостей, превышающих 1 мм, а для конструкций, возводимых или эксплуатируемых в районах с расчетной температурой ниже минус 40° и до минус 65 °С включительно, не более 0,5 мм.
Кромки деталей после машинной кислородной и плазменно-дуговой резки, не подлежащие сварке или не полностью проплавляемые при сварке, не должны иметь неровностей, превышающих 0,3 мм.
Точность деталей и заготовок и качество поверхности реза при газовой и плазменно-дуговой резке сталей должны соответствовать ГОСТ 14792—80.
Кромки работающих на растяжение деталей из низколегированных сталей класса до С60/45 включительно всех толщин и из углеродистой стали толщиной свыше 10 мм, фасонок из низколегированной стали класса до С60/45 включительно, всех расчетных деталей в конструкциях, воспринимающих динамические нагрузки, либо возводимых и эксплуатируемых в районах с расчетной температурой ниже минус 65 °С, после резки с помощью ножниц подлежат механической обработке с тем, чтобы удалить дефекты поверхности. Шероховатость кромок должна быть не грубее третьего класса чистоты поверхности по ГОСТ 2789—73.
Остальные кромки после резки на ножницах не должны иметь неровностей, заусенцев и завалов, превышающих 0,3 мм, и трещин.
При подготовке кромок под сварку допускается применение (без последующей обработки) резки способами, обеспечивающими требуемую форму кромок и соблюдение допусков по размерам. При этом отклонения прямолинейности кромок от проектного очертания определяются допусками на зазоры, установленными ГОСТ 5264— 80, ГОСТ 8713—79 и ГОСТ 14771—76.
После воздушно-дуговой резки стали классов С52/40 и С60/45 и после кислородной резки стали класса С60/45 необходима зачистка кромок абразивным инструментом.
Скосы по толщине на концах растянутых деталей (при сопряжении деталей разной толщины) в конструкциях, воспринимающих динамическую нагрузку, должны выполняться машинной кислородной резкой или механической обработкой и не должны иметь ступенек. Неровности и риски в детали должны быть сглажены абразивным инструментом вдоль усилия.
На подготовленных под сварку кромках и поверхностях не допускается наличие влаги, ржавчины, окалины, масла, краски и других загрязнений.
При использовании металлопроката, не подвергнутого консервации, проплавляемые поверхности и прилегающие к ним зоны металла шириной не менее 20 мм, а также кромки листов в местах примыкания выводных планок перед сборкой должны быть очищены до чистого металла. Продукты очистки не должны оставаться в зазорах между собранными деталями.
Допускается производить сварку без предварительной зачистки при отсутствии на кромках и поверхностях свариваемых деталей загрязнений, а также при наличии покрытия — защитного грунта, слоя цинка или алюминия и т. п., если металл шва и сварное соединение по своим свойствам отвечают требованиям строительных норм, а выделение вредных газов и аэрозолей при сварке не превышает санитарных норм.
Подготовка кромок и конструкция стыков
Сварка алюминия и его сплавов
Есть несколько более важных решений, влияющих на успех сварки, чем правильная конструкция соединения. Проблемы с качеством или производительностью сварного шва часто можно объяснить неправильной подготовкой кромок. Конструкция соединения определяется требованиями к прочности, сплавом, толщиной материала, типом и расположением соединения, доступом для сварки и используемым процессом сварки.
Существует три основных вида сварного шва: стыковой, угловой и краевой, показанные на рис. 5.3, из которых можно разработать шесть основных типов соединений. Это стыковое, тройниковое, угловое, крестообразное, краевое и нахлесточное соединения, показанные на рис. 5.4.
Статическая прочность на растяжение этих типов сварных швов определяется толщиной шва (рис. 5.5). Размер стыкового сварного шва с полным проплавлением определяется толщиной наплавленного металла шва в плоскости листа или
.5.3 Стыковые, угловые и кромочные швы. |
5.4 Типы стыков, полученные при стыковой, угловой и торцевой сварке. |
(в)
5.6 Толщина горловины углового шва: (а) угловой шов; (б) угловой шов под углом и выпуклый. |
5.5 Толщина стыкового шва при стыковом шве: (a) стыковой сварной шов полностью; (б) частичный стыковой сварной шов; (c) Т-образный стыковой шов.
труба, 12 на рис. 5.5. При расчете допустимого статического расчетного напряжения стыкового или углового шва для избыточного металла сварного шва кредит не принимается, т.е. е. что над поверхностью основного металла для стыка или за пределами равнобедренного треугольника углового шва, как указано в (t2 — t2).
■ Равная длина колена 45 °, выпуклая поверхность правильного равнобедренного треугольника Избыток металла сварного шва не влияет на прочность.Плоский носок
Филе неравной длины ноги |
вогнутая поверхность уменьшенная толщина горловины, если судить по длине ноги |
1,7 Наклон под углом, выпуклый, вогнутый и неравной длины ножек.
Для углового шва форма сварного шва и степень проникновения в корень будут влиять на толщину шва.На рис. 5.6 эффективная толщина горловины равна tj. Размер углового шва должен быть определен проектировщиком и должен быть достаточным, чтобы выдерживать нагрузку. Поэтому горловина может полностью отличаться от толщины материала.
Угловой шов также может быть описан как угловой, вогнутый или выпуклый. Кроме того, угловой сварной шов может иметь неодинаковые отрезки длины. Эти четыре типа углового шва показаны на рис. 5.7.
5.5.1 Сварка встык
Стыковой шов, типичные формы которого показаны на рис.5.8, представляет собой простой и легко спроектированный стык, в котором используется минимальное количество материала. На рис. 5.8 также приведены определения некоторых характеристик подготовки под сварку, таких как «поверхность основания», «угол скоса» и «прилегающий угол». Стыковые швы, как показано на рис. 5.5, также можно классифицировать как полный провар или частичный провар.
При обычных процессах сварки плавлением, таких как TIG и MIG, проникновение металла шва в поверхность плоской пластины из прохода валика по пластине обычно составляет 3 мм и 6 мм соответственно.Для получения стыкового сварного шва с полным проплавлением при толщинах, превышающих эти, необходимо, чтобы две близко расположенные стыковые кромки были скошены, хотя оставление небольшого зазора между кромками увеличивает проплавление. Типичные приготовления к сварке для различных процессов можно найти в соответствующей главе о процессах. Стыковые соединения могут быть односторонними или двухсторонними — если они двусторонние, часто необходимо зарезать или зашлифовать первую свариваемую сторону, чтобы получить соединение без каких-либо непроваров.
Одноместный — V
Двойной — V
Одинарный скос
Двухместный — V
Одноместный — V
1,8 Различные формы стыкового шва.
5.9 Предлагаемая конструкция для соединения листов разной толщины. |
Эффективный размер стыкового сварного шва с полным проплавлением равен расчетной толщине горловины, по сути, толщине пластины / трубы более тонкого компонента.Как упоминалось в другом месте, не учитывается высота наплавленного металлического шва или глубина проплавления корня. Хотя это не часто используется в производстве алюминия из-за необходимости согласования прочности соединения и прочности основного металла, в слабо нагруженных соединениях соединение с частичным проваром (рис. 5.5b) может быть приемлемым. Частичное проплавление может быть достигнуто за счет использования стыкового стыка с закрытым квадратным сечением или толстой корневой поверхности. Соединение с частичным проплавлением дает рентабельность, так как подготовка кромок практически отсутствует, она экономична по присадочному металлу и ее легко собрать, поскольку не нужно контролировать корневой зазор.Ограничения заключаются в том, что интерпретация рентгенограмм затруднена из-за отсутствия проникновения, снижается усталостная долговечность и снижается статическая механическая прочность. Эффективный размер в случае шва с частичным проплавлением — это ширина сварного шва за вычетом высоты крышки.
Если необходимо сварить две секции неравной толщины, задача сварщика будет облегчена, и лучшие свойства, в частности усталостные, будут достигнуты, если более толстая из двух частей будет иметь фаску или конус для соответствия более тонкой.Для достижения этого конус на более толстом компоненте должен быть в диапазоне от 4 до 1, чтобы уменьшить эффект повышения напряжения при резком изменении толщины (рис. 5.9).
Форма подготовки сварного шва может быть выбрана так, чтобы обеспечить проплавление корня и прочное основание, чтобы обеспечить требуемую последовательность проходов или контролировать разбавление металла сварного шва от основного металла. Процесс MIG может, но с трудом, использоваться для получения прочного, бездефектного проплавленного валика — для прочного соединения необходимо использовать либо подкладную планку, либо полосу, либо сварной шов необходимо обрезать и сделать второй боковой сварной шов. .Эти методы более подробно рассматриваются в другом месте. Процесс TIG можно использовать для получения прочного, полностью пропитанного корневого валика без обрезки или подкладки. «Спущенный» конический шов (рис. 5.10) разработан для того, чтобы обеспечить высочайшее качество корневого прохода с использованием процесса TIG. Это используется в таких случаях, как стыковая сварка труб, когда сварные швы должны быть односторонними и иметь гладкий корневой валик, который не будет препятствовать потоку в трубе.
Для сварки AC-TIG земля должна быть 4.Мин. 5 мм, для сварки TIG и MIG на постоянном токе земля должна быть мин. 2 мм |
Прочность прочного стыкового шва без дефектов обычно соответствует прочности присадочного металла или прочности основного металла после отжига, как описано в главе 2. Стыковое соединение является наилучшим в условиях динамической нагрузки, особенно если превышение металл шва зачищается заподлицо. Для достижения наилучших свойств две составные части требуют точного совмещения, что подразумевает соответствующие прихваты, сборку и фиксацию.
5.5.2 Опорные стержни и опорные полосы
Несмотря на то, что на обратной стороне стыкового сварного шва можно нанести герметизирующий слой без задних канавок, нельзя полагаться на то, что он даст прочный, бездефектный сварной шов. Односторонние соединения можно сваривать методом TIG для получения надежного корневого прохода, но для обычного (неимпульсного) процесса MIG часто требуется постоянная или временная подкладка для нанесения корневого прохода MIG. Назначение подкладки или полосы — поддерживать корневой проход в тех местах, где условия затрудняют управление бортом.Обычно несущий стержень является временным и может быть снят, как только сварка будет завершена, а поддерживающая полоса является постоянной частью соединения. Несущий стержень или планка могут значительно упростить задачу установки соединения — например, легко справляются с изменениями корневого зазора, и соединения могут быть самозажимными, может быть достигнут хороший внешний вид корневого валика, а затраты могут быть снижены.
Рифленая временная опорная планка обеспечивает хорошую форму проплавленного валика, причем канавка используется в качестве формы для расплавленного металла сварного шва.Это обеспечит лучшие динамические характеристики, чем постоянная подкладка. Резервное пруткового материала может быть недорогой мягкой стали, но более длительный срок службы может быть получена из бара с меньшим риском загрязнения, если используется нержавеющая сталь. Также можно использовать керамическую основу в виде гибкой полосы плитки или клейкой ленты. Следует избегать использования меди или медных сплавов, потому что
5.11 Типичные самовыжимные экструзии. Предоставлено ALCAN. |
риска заражения.Несущий стержень без канавок потребует, чтобы корневой проход был заземлен и, возможно, был нанесен герметизирующий проход для создания прочного шва. При сварке TIG с использованием подкладного стержня сварной шов следует выполнять без корневого зазора. Это необходимо для предотвращения прямого воздействия дуги TIG на материал основы и, возможно, его плавления.
Несъемная несущая полоса вплавляется в корневой проход, и необходимо тщательно выбирать сплав, совместимый с основным металлом и наполнителем. Полоса должна быть примерно 4-6 мм толщиной и закреплена на месте.Однако многие профили из алюминия могут изготавливаться со встроенной подкладной полосой, и таким образом упрощается сборка стыков. Можно спроектировать выдавленных как с опорной полосы и построенной в такой форме, что соединение само-отсадки, как показано на рис. 5.11.
Щели, связанные с постоянными подкладными полосами, приводят к локальной концентрации напряжений. Это может снизить сопротивление удару и усталости, если корень находится в зоне сильной нагрузки. Щель также может вызвать локальную коррозию, хотя даже в морской среде это не было зарегистрировано как серьезная проблема при выборе правильного сплава.Несмотря на эти потенциальные недостатки, постоянные подкладочные полосы являются обычным явлением во многих конструкциях, используемых в сложных условиях.
Основа из инертного газа может использоваться для критических применений, таких как пищевая или фармацевтическая промышленность, трубопроводы или сосуды, и очень полезна, когда нет доступа к задней части сварного шва для создания задней строжки и уплотнения. Продувка аргоном предотвратит окисление корневого валика и оксидных пленок, вплавленных в стык, обеспечивая гладкую, ровную корневую валику TIG.Типовые конструкции опорных стержней и полос приведены на рис. 5.12.
Временная опорная планка для листа толщиной более 3 мм (TIG) или 6 мм (MIG) |
Сварка алюминия и его сплавов Толщина t »- |
Похожего дизайн временной подложки бара для пластины или труб менее 6 мм толщины |
Корневой зазор заданный | Г л | |
А | ||
А 4 | Ø | illWv |
Конструкция с постоянной подкладкой для толстых и тонких листов |
Предлагаемая подготовка к сварке и подкладка для горизонтально-вертикального (ПК) положения сварки |
5.5.3 Тройник Как следует из названия, Т-образное соединение (рис. 5.4b) — это соединение, в котором один элемент расположен примерно под прямым углом к своему партнеру, при этом наиболее распространенными применениями являются соединения пластины с пластиной или ответвления. Стойка Т-образной формы может быть соединена стыковым сварным швом, угловым сварным швом или сварными швами или комбинацией |
два типа сварного шва (рис. 5.5c). Тройник — это простой сварной шов, который легко спроектировать, который, за исключением Т-образного стыка, практически не требует подготовки кромок.Точность подгонки в большой степени зависит от точности, с которой подготовлен край стойки T. Неправильный разрез даст переменный зазор, что может привести к недостаточной толщине горловины, как показано на рис. 5.13.
Угловой сварной шов может вызвать трудности при достижении полного проплавления в корне, в результате чего в углу образуется пустота. Это считается нежелательным, особенно в критических случаях, поскольку отсутствие плавления приводит к увеличению напряжения в корне, а также уменьшает толщину горловины.Сварщик должен знать об этой проблеме, так как основная причина — неправильная техника сварки.
Если Т-образный стык представляет собой фланцевое соединение, необходимо оставить достаточно металла, чтобы сварной шов не расплавил угол фланца и не допустил изменений в подгонке. Как показывает практика, достаточной считается длина ветви углового сварного шва в 2,5–3 раза (рис. 5.14). Это не может предотвратить коробление кромки фланца из-за деформации под воздействием тепла сварки, особенно когда размер галтеля велик по сравнению с толщиной фланца.
Прочность углового сварного тройника определяется прочностью на сдвиг углового сварного шва или сварных швов, прочность стыкового тройника — прочностью металла сварного шва или ЗТВ. Если соединение подвергается поперечным сдвигающим нагрузкам, изгибающие напряжения в соединении могут привести к преждевременному выходу из строя, особенно если соединение выполнено угловой сваркой только с одной стороны. Угловые сварные швы с обеих сторон или Т-образное стыковое соединение с полным проплавлением позволяют значительно увеличить нагрузки до разрушения (рис.5.15). Плохие динамические характеристики тройников: изменение сечения с горизонтального на вертикальное
5.15 Модернизация угловых сварных швов с боковой нагрузкой для повышения производительности. |
вызывает высокие напряжения на носках сварных швов, резко сокращая усталостный ресурс.
5.5.4 Угловой шарнир
Угловое соединение можно рассматривать как стыковое соединение и используется для соединения двух пластин под прямым углом друг к другу (рис.5.4f). Может быть сложно собрать и поддерживать правильное выравнивание, особенно в тонких гибких листах. Корень одностороннего сварного шва при растягивающей нагрузке очень слаб, и для достижения максимальной прочности угловое соединение необходимо сваривать с обеих сторон. Односторонний сварной шов может также иметь складку, содержащую оксиды, вдоль центральной линии проплавленного валика, что дополнительно снижает прочность сварного шва. Было обнаружено, что импульсная сварка на переменном токе AC-TIG эффективна для уменьшения вероятности появления этой особенности.Угловое соединение чаще всего встречается в приложениях с низкой нагрузкой и при обработке листового металла.
5.5.5 Кромочный стык
Краевое соединение (рис. 5.4e) легко собрать и удерживать во время сварки. Как и угловой сварной шов, он является слабым в ситуациях нагружения, которые вызывают растяжение корня, и редко используется в конструкциях, ограничиваясь ненесущими приложениями в тонких листах. Оплавление углов соединяемых кромок может быть проблемой и может привести к неглубокому сварному шву с небольшой толщиной шва.
5.5.6 Внахлестку
Соединение внахлестку, пожалуй, самое простое в сборке соединение. Он состоит из двух перекрывающихся пластин, соединенных угловым швом (рис. 5.4c). Различия в размерах компонентов легко адаптируются, и подготовка кромок не требуется, хотя скос, как на рис. 5.16, можно использовать для гарантии полного сращивания корня.
Соединение неэкономично с точки зрения материала, так как материал перекрытия является ненужным. Перекрытие должно быть как минимум в три раза больше толщины более тонкой пластины.Также необходимо следить за тем, чтобы сварной шов не расплавил угол верхней пластины, поскольку это приводит к уменьшению эффективной толщины горловины галтеля.
Прочность соединения определяется прочностью на сдвиг углового шва. Размеры и длина сварных швов должны быть указаны проектировщиком, чтобы гарантировать соответствующую несущую способность.
5.5.7 Точечная, электрозаклепочная и щелевая сварка
Скошенная кромка пластины, как указано выше, помогает достичь полного проникновения в корень |
Квадратный край, как показано выше, может затруднить полное проникновение в корень, что приведет к отсутствию дефекта плавления и уменьшению толщины горловины. |
5.16 Срезание кромки листа внахлест для улучшения проплавления. |
Электродуговая сварка и точечная сварка показаны на рис. 5.17. Как TIG, так и MIG процессы способны полностью проплавить 2-3 мм через верхний лист соединения внахлест, чтобы обеспечить приемлемый сварной шов. Лазер и
5.17 Электрозаклепка и точечная сварка с использованием сварки TIG или MIG. |
может выполнять точечную сварку и сварку «штырями» на листах значительной толщины, в случае электронно-лучевой сварки до 200 мм.
СваркаTIG обычно ограничивается тонкими листами толщиной менее 2 мм и находит лишь очень ограниченное применение в производстве. Основная часть точечной сварки выполняется с использованием сварки MIG и более подробно рассматривается в главе 7. Однако проектировщик должен знать о переменном качестве точечной сварки, что приводит к низкой прочности и плохим усталостным характеристикам. Высокая сдержанность, присущая этой форме сварного шва, почти всегда приводит к деформации, особенно когда сварные швы имеют небольшой шаг, и может привести к образованию горячих трещин в ЗТВ.Эти особенности ограничивают возможности точечной сварки.
Электрозаклепка похожа на точечную сварку, за исключением того, что верхняя пластина разрезается, образуя отверстие, которое либо полностью заполняется металлом сварного шва, либо сваривается угловой сваркой вокруг обода. Этот тип сварки страдает теми же проблемами, что и точечная сварка, с переменным качеством и недостаточной прочностью. Их обоих обычно избегают, когда требуется структурная целостность.
Щелевой сварной шов гораздо более полезен в конструкционных целях, чем точечная сварка или сварка электрозаклепкой, поскольку требуется наплавка достаточной длины сварного шва.Это позволяет создать стабильную сварочную ванну и выполнить прочный шов. Сварной шов может быть однопроходным, полностью заполняя щель, или угловым швом с обеих сторон. Для обеспечения наилучшего качества позиции запуска и остановки должны находиться на верхней пластине, вне паза. Пазы под угловую сварку предпочтительнее, если толщина листа превышает 5 мм. Прочность щелевого шва определяется сопротивлением сдвигу наплавленного металла.
Таблица A.4 BS EN BS EN Старый BS / DTD Температура (° C) числовое химическое число обозначение обозначение Liquidus Solidus IVIdUng диапазон Al 99.99 1 660 660 0 AW-1080A Al 99,8 1A AW-1070A…
Таблица A.3 Цифровое обозначение BS EN Химическое обозначение BS EN Старый номер BS Обозначение ANSI Температура (° C) Ликвидус Солидус Диапазон плавления Al 99,5 LM0 640 658 18 AC -46100 Al Si10Cu2Fe…
Таблица A.2 Свойства Алюминий Железо Никель Медь Титан Кристаллическая структура FCC BCC FCC FCC HCP Плотность (г / см3) 2,7 7,85 8,9 8,93 4,5 Точка плавления (° C) 660 1536 1455 1083 1670…
.Документ не найден — PTC.com
PTC.com- Магазин
- EN
- Войти
- Почему PTC
- Преимущества PTC
- Что мы делаем
- Истории клиентов
- Информация о компании
- История
- Быстрые факты
- Управленческая команда
- Карьера
- Корпоративная ответственность
- Офисы по всему миру
- Свяжитесь с нами
- Пресса и СМИ
- Новости
- Связи с инвесторами
- Каталог социальных сетей
- Преимущества PTC
- Решения
- Общие проблемы
- Интернет вещей
- корпоративных приложений
- Управление жизненным циклом продукта
- Компьютерное проектирование
- Управление жизненным циклом услуг
- Общие проблемы
- Продукты
- Семейства продуктов
- PTC Creo
- PTC Windchill
- PTC Arbortext
- PTC Mathcad
- Целостность PTC
- PTC Servigistics
- ThingWorx
- Все товары
- Ключевые темы
- Работа в среде с несколькими САПР
- 3D CAD
- Визуализация
- PLM для розничной торговли
- Управление производственными процессами
- Глобальная разработка продуктов
- Качество продукции в мире
- Гибкое моделирование
- Ресурсы для продукта
- Бесплатные загрузки
- Как купить
- Обучение
- Академическая программа PTC
- Истории клиентов PTC Creo
- Бесплатная 30-дневная пробная версия PTC Creo
- Справочные центры PTC
- Семейства продуктов
- Услуги
- Услуги
- Услуги обучения
- Стратегические услуги
- Услуги по развертыванию
- Обучение и усыновление
- Услуги по оптимизации
- Облачные службы
- Услуги по обновлению Windchill 11
- Услуги
- Сообщества
- Сети
- Сообщество PTC
- Партнеры
- Академическая программа PTC
- Каталог социальных сетей
- Блоги
- Истории жизненного цикла продукта
- PTC Creo
- PTC Mathcad
- Руководитель службы
- События
- LiveWorx
- Интернет-трансляции и семинары
- Сети
Подготовка кромок и выравнивание для сварки труб »Мир трубопроводной техники
Теги: #piping_engineering #piping_welding #edge_preparation #piping_fabrication
Подготовка кромки
Кромки, подлежащие сварке, должны быть подготовлены в соответствии с требованиями к конструкции соединения любым из следующих рекомендуемых методов:
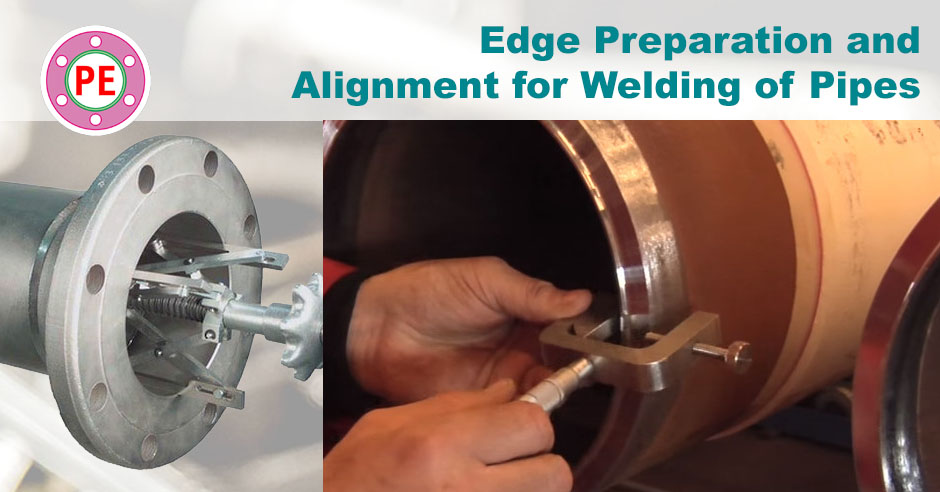
Подготовка и выравнивание кромок
- Углеродистая сталь: Должны использоваться методы газовой резки, механической обработки или шлифования.После газовой резки оксиды следует удалить путем скалывания или шлифования.
- Низколегированные стали (содержащие до 5% хрома): Должны использоваться методы газовой резки, механической обработки или шлифования. После газовой резки
следует произвести механическую обработку или шлифование поверхности среза. - Высоколегированная сталь (> 5% хрома) и нержавеющая сталь, никелевые сплавы: Должны использоваться методы плазменной резки, механической обработки или шлифования. После плазменной резки поверхности среза должны быть обработаны или отшлифованы до гладкости.
Очистка
Свариваемые концы должны быть тщательно очищены от краски, масла, жира, ржавчины, оксидов, песка, земли и других посторонних веществ. Перед началом сварки концы должны быть полностью сухими.
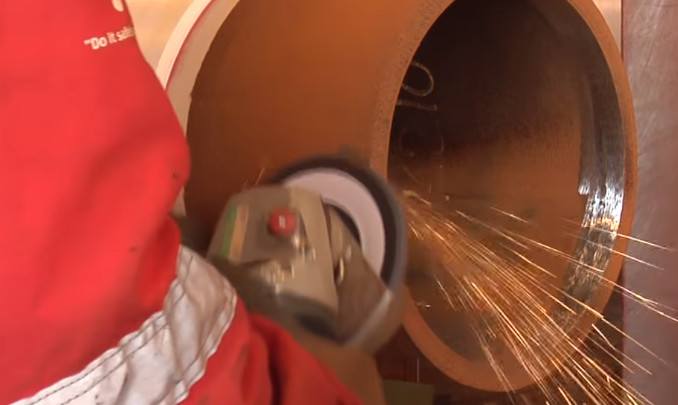
Использование шлифовальных машин для очистки кромок
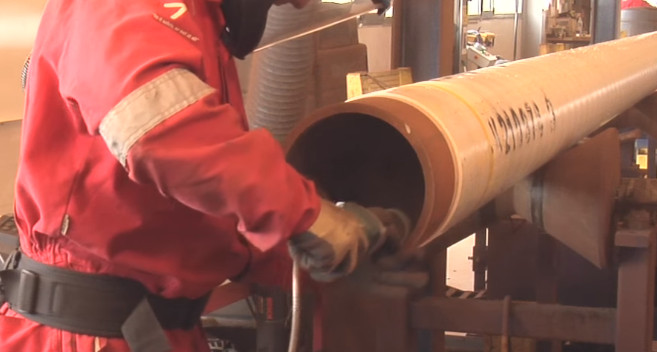
Использование шлифовального станка для очистки внутренних кромок
Снятие фаски с конца трубы
Конец трубы должен быть скошен в соответствии с действующим стандартом с помощью станка для снятия фаски. Размеры фаски должны быть правильно измерены.
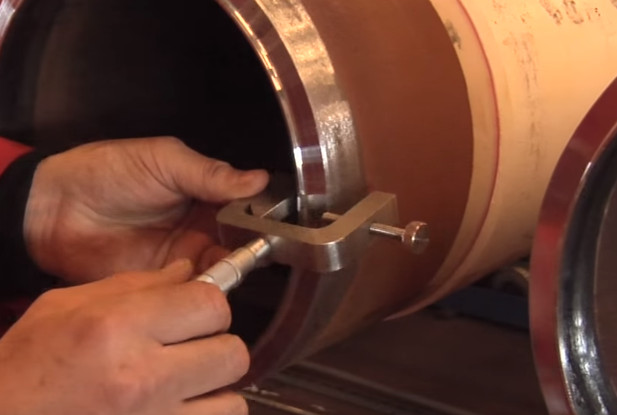
Измерение размеров скоса
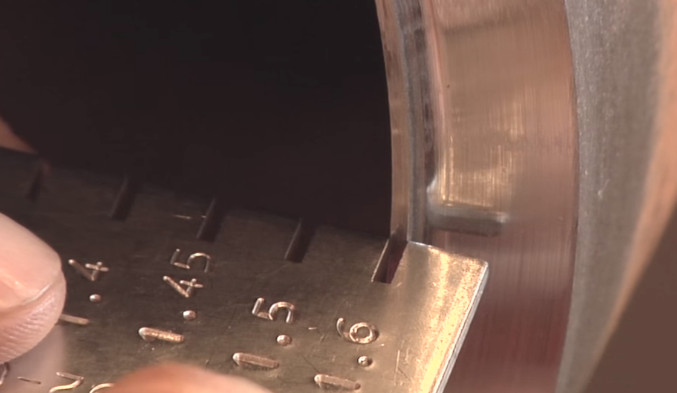
Измерение толщины фаски
Проверить магнетизм конца трубы
Магнетизм может отрицательно сказаться на качестве сварного шва трубы. После снятия фаски на конце трубы необходимо проверить наличие остаточного магнетизма на конце трубы. При обнаружении трубу необходимо размагнитить.
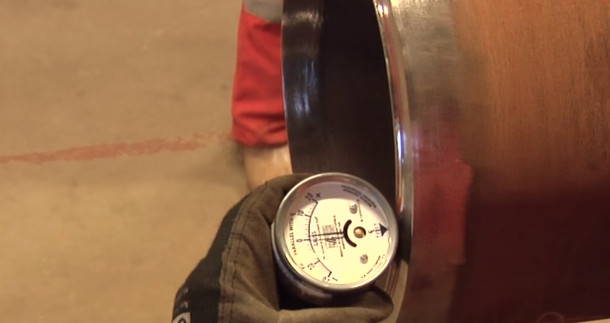
Проверить магнетизм конца трубы
Выравнивание и расстояние
Свариваемые компоненты должны быть выровнены и разнесены в соответствии с требованиями, изложенными в применимых нормах.Особое внимание следует уделить обеспечению надлежащей подгонки и центровки, когда сварка выполняется методом GT AW. Нагревание пламенем для регулировки и исправления концов не допускается, если иное не одобрено ответственным инженером.
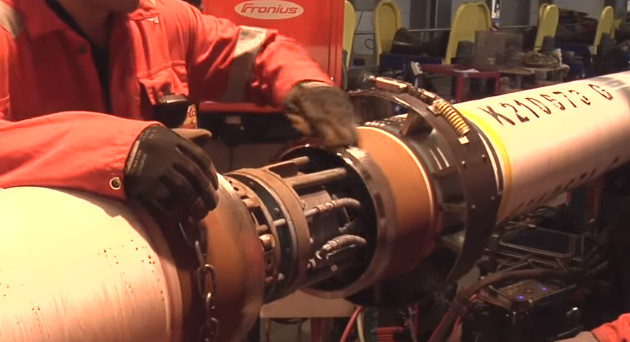
Внутренние зажимы для выравнивания труб
Проволочную распорку подходящего диаметра можно использовать для сохранения отверстия в корне шва во время прихватывания, но ее необходимо удалить после прихваточной сварки и перед укладкой корневого валика.
Для труб с толщиной стенки 5 мм и более свариваемые концы должны быть закреплены на месте с помощью муфт, хомутов и С-образных хомутов для обеспечения идеального совмещения.Хомуты должны быть отсоединены после завершения сварки, не вызывая неровностей поверхности. Любые неровности на поверхности трубы должны быть отремонтированы надлежащим образом, согласно требованиям ответственного инженера.
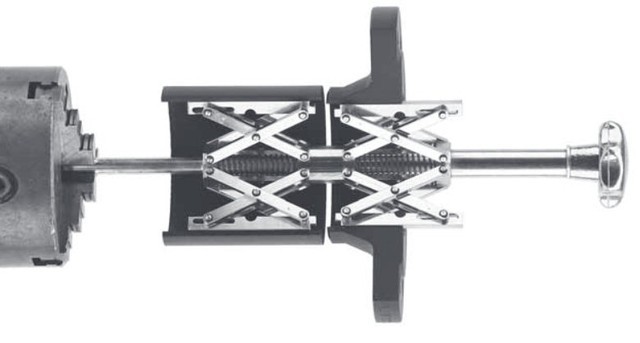
Инструмент для внутреннего выравнивания фланца
Прихватка
Прихваточные швы для сохранения соосности трубных соединений должны выполняться только квалифицированными сварщиками с использованием утвержденных Технических условий на процедуру сварки. Поскольку прихваточные швы входят в состав конструкции f
.Документ не найден — PTC.com
PTC.com- Магазин
- EN
- Войти
- Почему PTC
- Преимущества PTC
- Что мы делаем
- Истории клиентов
- Информация о компании
- История
- Быстрые факты
- Управленческая команда
- Карьера
- Корпоративная ответственность
- Офисы по всему миру
- Свяжитесь с нами
- Пресса и СМИ
- Новости
- Связи с инвесторами
- Каталог социальных сетей
- Преимущества PTC
- Решения
- Общие проблемы
- Интернет вещей
- корпоративных приложений
- Управление жизненным циклом продукта
- Компьютерное проектирование
- Управление жизненным циклом услуг
- Общие проблемы
- Продукты
- Семейства продуктов
- PTC Creo
- PTC Windchill
- PTC Arbortext
- PTC Mathcad
- Целостность PTC
- PTC Servigistics
- ThingWorx
- Все товары
- Ключевые темы
- Работа в среде с несколькими САПР
- 3D CAD
- Визуализация
- PLM для розничной торговли
- Управление производственными процессами
- Глобальная разработка продуктов
- Качество продукции в мире
- Гибкое моделирование
- Ресурсы для продукта
- Бесплатные загрузки
- Как купить
- Обучение
- Академическая программа PTC
- Истории клиентов PTC Creo
- Бесплатная 30-дневная пробная версия PTC Creo
- Справочные центры PTC
- Семейства продуктов
- Услуги
- Услуги
- Услуги обучения
- Стратегические услуги
- Услуги по развертыванию
- Обучение и усыновление
- Услуги по оптимизации
- Облачные службы
- Услуги по обновлению Windchill 11
- Услуги
- Сообщества
- Сети
- Сообщество PTC
- Партнеры
- Академическая программа PTC
- Каталог социальных сетей
- Блоги
- Истории жизненного цикла продукта
- PTC Creo
- PTC Mathcad
- Руководитель службы
- События
- LiveWorx
- Интернет-трансляции и семинары
- Сети