Подготовка металла под сварку — подготовительные этапы для сварки полуавтоматом.
Прежде, чем приступить к свариванию металлических изделий, необходимо их подготовить. Непосредственно подготовка металла под сварку состоит из нескольких этапов. Вначале металл подвергается правке, затем осуществляется разметка и резка изделия, его зачистка и подогрев. На заключительной стадии производятся гибка и обработка кромок. Эти процедуры необходимы для того, чтобы добиться качественного соединения элементов конструкции.
Стоит помнить: ржавчина, частички металла, прочие элементы, оставшиеся на поверхности, препятствуют качественной сварке.
Поэтому важна правильная подготовка деталей к сварке, которая позволяет улучшить свариваемость. Количество процедур, которые необходимо выполнить при подготовке деталей под сварку, может различаться в зависимости от конкретной ситуации – степени загрязненности, деформации заготовок, объема работ и прочее. При этом все этапы подготовки регулируются согласно ГОСТ 5264-80.
Содержание статьи
Правка металла – особенности процесса
Металлические заготовки при транспортировке или по иной причине могут деформироваться. В этом случае возникают сложности с их стыковкой в области сваривания, что приводит к снижению качества сварного шва.
Поэтому подготовительно выполняется правка изделия. В зависимости от размеров заготовок и сложности искривленных участков применяется холодная или горячая правка. Она выполняется вручную или специальными приспособлениями. Плиты из чугуна и стали вручную исправляют молотком или кувалдой. При необходимости создать большее давление применяется ручной пресс. Он представляет собой винтовой аппарат с двумя плитами, между которыми укладывают детали с деформированными участками, и выправляют их под высоким давлением.
Если вручную исправить деформацию невозможно, используются специальные приспособления – в частности, листоплавильные станки или прессы различных типов. Данные устройства работают на электродвигателях, вырабатывающих необходимую для работы мощность, для передачи которой используются редукторы. Таким образом удается увеличить давление на искривленные участки.
Особенности разметки заготовок
Подготовка деталей под сварку включает в себя такой важный этап, как разметка заготовок. Необходимость его выполнения связана с несовпадением размеров профилей с параметрами деталей, которые будут использованы в конструкции. Поэтому профиль необходимо подрезать. А перед этим – разметить, задав необходимые размеры.
Выделяют несколько способов разметки: ручная, оптическая, мерная резка. При ручной разметке используются простые инструменты для измерений – например, линейка или штангенциркуль. Если размечается небольшая партия однотипных заготовок, применяются изготовленные из алюминия или профилируемых листов шаблоны. Ручной способ отличается трудоемкостью и низкой скоростью выполнения работы.
При оптическом способе нанесения разметки применяются разметно-маркировочные машины. Их преимущество заключается в высокой скорости – до 10 метров в минуту. Чтобы разметить заготовку, необходимо запрограммировать аппарат под установленные параметры. Для нанесения разметки в данных устройствах используется пневматический крен.
Технология мерной резки не предполагает нанесение разметки на профили – в этом случае в специальные машины закладывается программа с указанием конфигурации и размеров заготовок. В результате аппарат сразу режет изделие под заданную форму.
Резка металла
Это один из важнейших этапов, который предполагает подготовку металла под сварку, поскольку иначе не получится добиться нужного размера заготовок. Выделяют механическую и термическую резку. При механической резке используются ручные и механические инструменты. Процесс термической резки представляет собой плавление металла по предварительно нанесенным отметкам. Этот тип работ также может быть ручным и автоматизированным. Для выполнении операции применяются кислородный резак, дуговая сварка, плазматрон. Также термическая резка осуществляется с применением станков, аппаратов, работающих в полу- или в автоматическом режиме.
Стоит отметить, что термическая резка – это универсальная технология, которая позволяет разрезать изделия в различных направлениях, как прямолинейно, так и криволинейно.
Этапы подготовки кромок
Зачистка изделия
Сварочные работы необходимо проводить на предварительно подготовленных поверхностях – очищенных от механических загрязнений, и химических пленок. Присутствие даже небольших частичек загрязнений может привести к растрескиванию конструкции, пористости, напряжению в металле. В результате сварное соединение утрачивает свои качественные характеристики.
Не стоит забывать об оксидной пленке, которая образуется на поверхности металлов при их контакте с воздухом. Она является жаростойкой, препятствует качественной сварке. Удалить ее можно как болгаркой, так и вручную, щеткой из металла.
На производстве детали зачищаются пескоструйными и дробеструйными аппаратами. Также производится химическая чистка – путем погружения изделий на определенное время в ванну с химическими реагентами. Этот тип очистки в основном используется при подготовке деталей из цветных металлов, а черные, стальные заготовки зачищаются вручную.
Подготовка кромок под сварку
Кромки заготовок, особенно большой толщины, предварительно необходимо зачистить и придать им нужную геометрическую форму. Выделяют плоские, V-образные и Х-образные кромки. Плоские кромки используются при соединении тонких изделий, вторые два вида – при стыковке толстых заготовок.
Важно: кромки не обрабатываются, если толщина детали не более 3 мм.
Подготовка кромок под сварку состоит из обработки ширины зазора, угла разделки, регулировки длины откоса. При подготовке кромок под сварку труб различной толщины их обработка особенно актуальна – в противном случае металл не провариться. Поэтому важно подобрать правильный скос, благодаря которому переход между деталями будет плавным. А это снимет напряжение нагрузки во время использования готового изделия.
Для подрезки кромок при подготовке труб к сварке холодным способом используются станки или ручные инструменты. Термический способ предполагает использование горелок – ручных или автоматических.
Холодная подготовка металла к сварке считается более качественной. В этом случае в разы повышается точность сборки конечного изделия. А после термической обработки фаски зачастую нужно довести до правильных размеров и формы, особенно когда осуществляется подготовка труб под сварку.
Сборка изделий под сварку
Сборка под сварку – это заключительный этап подготовки. В этом случае отдельные детали фиксируются, чтобы они после сварки остались в нужном положении. Зачастую недостаточно просто расположить их рядом или зафиксировать специальным устройством – необходимо выполнить точечную приварку двух деталей. Это обеспечивает надежность конструкции и сохраняет ее форму. Такую заготовку можно расположить так, чтобы было удобно сделать горизонтальный шов.
К сборке изделий предъявляются следующие требования:
Сборка осуществляется после того, как полностью завершена подготовка поверхности металла под сварку. К местам соединения деталей нужно обеспечить свободный доступ. Все заготовки должны быть надежно скреплены, чтобы избежать деформации при сварке.
Особенности подготовки труб к сварке
Подготовка труб к сварке требует ответственного отношения. Так, трубы, изготовленные из низколегированной и углеродистой стали обрабатываются только вручную холодным способом. Марка стали влияет на глубину снятия металла. При подготовке труб к сварке нужно обязательно проверять толщину стенок: по всей окружности торцов в месте соединения она должна быть одинаковой. А сами торцы – перпендикулярными.
После того, как изделия подготовлены, можно переходить к сварочным работам. Для этого может использоваться полуавтоматический инвертор. И подготовка к работе сварочного полуавтомата – не менее важный аспект работы. Необходимо выставить силу тока, скорость подачи сварочной проволоки, расход защитного газа.
Таким образом, подготовка металла под сварку – один из важнейших этапов работы. Времени она занимает много, однако при соблюдении всех правил гарантирует высокое качество конечного результата.
Подробнее с подготовкой металла можно ознакомиться на видео:
[Всего голосов: 2 Средний: 3.5/5]Подготовка металла под сварку
Содержание
Введение……………………………………………………
Подготовка металла под сварку…
Сборка деталей под сварку.…………
Сборочно-сварочные
Основные требования безопасности труда…………………………10
Литература……………………………………………………
Введение.
Сваркой называется процесс получения неразъемных соединений по средствам установления межатомных связей между свариваемыми частями при их местном или общем нагреве или пластическом деформировании, или совместным действием того и другого.
В 1802г. впервые в мире профессор физики Санкт-Петербургской медико-хирургической академии В.В. Петров (1761-1834) открыл электрическую дугу и описал явление, происходящее в ней, а также указал на возможность ее практического применения.
В 1881г. русский изобретатель Н.Н. Бенардос (1842-1905) применил электрическую дугу для соединения и разъединение сталей. Дуга Н.Н. Бенардоса горела между угольным электродом и свариваемым металлом. Присадочным прутком для образования шва служила стальная проволока, В качестве источника электрической энергии использовались аккумуляторные батареи. Сварка, предложенная Н.Н. Бенардосом, применялась в России в мастерских Риго-Орловской железной дороги при ремонте подвижного состава. Н.Н. Бенардосом были открыты и другие виды сварки: контактно-точечная сварка несколькими электродами в защитном газе, а также механизированная подача электрода в дугу.
В 1888г. русский инженер Н.Г. Славянов (1854-1997) предложил дуговую сварку плавящимся металлическим электродом. Он разработал научные основы дуговой сварки, применил флюс для защиты металла сварочной ванны от воздействия воздуха, предложил наплавку и сварку чугуна. Н.Г.Славянов изготовил сварочный генератор своей конструкции и организовал первый в мире электросварочный цех в Пермских пушечных мастерских, где работал с 1883 по 1897г. Н.Н. Бенардос и Н.Г. Славянов положил начало автоматизации сварочных процессов. Однако в условиях царской России их изобретения не нашли большого применения. Только после Октябрьской революции сварка получает распространение в нашей стране. Уже в начале 20-х годов под руководством профессора В.П. Вологдина на Дальнем Востоке производили ремонт судов дуговой сваркой, а также изготовление сварных котлов, а несколько позже — сварку судов и ответственных конструкций.
Развитие и промышленное применение сварки требовало разработки и изготовления надежных источников питания, обеспечивающих устойчивое горение дуги. Такое оборудование — сварочный генератор СМ-1 и сварочный трансформатор с нормальным, магнитным рассеянием СТ-2 было изготовлено впервые в 1924 году ленинградским заводом «Электрик». В том же году, ученый В.П.Никитин разработал принципиально новую схему сварочного трансформатора типа СТН.
В 1928 году Д.А. Дульчевский изобрел автоматическую сварку под флюсом.
Новый этап в развитии сварки относится к концу 30-х годов, когда коллективом института электросварки, АН УССР под руководством академика АН УССР Е.О. Патона был разработан промышленный способ, автоматической сварки под флюсом. Внедрение его в производство началось в 1940 году. Позже был разработан способ полуавтоматической сварки под флюсом
В конце 40-х годов получила промышленное применение сварка в защитном газе. Коллективами Центрального научно-исследовательского института технологии машиностроения (ЦНИИТМаш) и Института электросварки им. Е.О. Патона (ИЭС) разработана и в 1952 году внедрена полуавтоматическая сварка в углекислом газе. Огромным достижением сварочной техники явилась разработка коллективом ИЭС с 1949 года электрошлаковой сварки, позволяющей сваривать металлы практически любой толщины.
Впервые в мире космонавтики К.С. Шониным и Б.Н. Кубасовым была произведена сварка в космосе (сварка в вакууме).
В 1932 году К.К. Хренов разработал подводную электрическую сварку металлов, покрыв электрод специальной обмазкой (добился устойчивости газового пузырька).
Авторы сварки в углекислом газе плавящимся электродом и электрошлаковой сварки — К.М. Новожилов, Г.З. Волошкевич, К.В.Любавский удостоены Ленинской премии.
В последние годы в стране стали применяться: сварка ультразвуком, электронно-лучевая, плазменная, диффузионная, колодная сварка, сварка трением и т.д.
Большой вклад в развитие сварки внесли ученые : В.П Вологдин, В.П. Никитин, Д.А Дульчевский, Е.О. Патон, а также коллективы: ИЭС им. Е.О. Патона, ЦНИИТМаш, Московского Высшего технического училища (МВТУ)» им. Н.Баумана, Всесоюзного научно-исследовательского, проектно-конструкторского и технологического института электросварочного оборудования (ВНИИЭСО), Всесоюзного научно-исследовательского и конструкторского института автогенного машиностроения (ВНИИавтогенмаш) и др.
В промышленности
Республики Беларусь эффективно применяются
современные сварочные
В машиностроении, строительстве, энергетике и других отраслях работают тысячи квалифицированных рабочих, техников и инженеров-сварщиков, которые вносят значительный вклад в развитие сварочного производства и подготовку кадров для промышленности Беларуси.
В Республике Беларусь в 1992 году в составе НПО порошковой металлургии создан Научно-исследовательский и конструкторско-технологический Институт сварки и защитных покрытий (НИИ СП). Основными направлениями деятельности НИИ СП являются руководство государственными программами в области сварки и покрытий, проведение фундаментальных и прикладных исследований, оказание практической помощи промышленным предприятиям и организациям по сварке.
В последние годы ученые-сварщики Беларусии работают над созданием ресурсосберегающих технологий, которые позволяют снизить потребление электроэнергии, уменьшить расход материалов, рационально использовать труд сварщиков при изготовлении различных конструкций, машин и изделий.
В настоящее
время сваривают материалы
Существенно расширились условия проведения сварочных работ: сварку осуществляют в условиях высоких температур, радиации, под водой, в космосе. Сварные швы выполняют в любых пространственных положениях.
Сварка во многих случаях заменила такие трудоемкие процессы изготовления конструкций, как клепка, литье, соединение на резьбе, ковка.
Преимущества сварки над этими процессами:
— экономия металла — 10…30% и более в зависимости от сложности конструкции;
— сокращение сроков работы и
уменьшение стоимости
— возможность механизации и автоматизации сварочного производства;
— возможность использования
— герметичность сварочных соединений выше, чем клепаных и резьбовых;
— уменьшение производственного
шума и улучшение условий
Подготовка металла под сварку.
Если металл, идущий на изготовление сварных конструкций, загрязнен или деформирован, то его нужно предварительно очистить и выправить. Очистка может производиться ручными и механическими проволочными щетками, пескоструем, пламенем специальной горелки, промывкой горячей водой или раствором щелочи, травлением в растворах различных кислот и другими способами.
Для правки
металла применяются
Рис. Листоправильный станок
Уголки правят на углоправильных вальцах.
Рис. Углоправильный станок
Правка
швеллерного и двутаврового
Рис. правильно-гибочный пресс
При очень
малых объемах производства и
отсутствии правильного
После правки металл подвергается разметке, при которой на нем мелом, кернами и чертилкой наносятся размеры заготовки детали, подвергаемой затем сварке. При серийном производстве однотипных изделий для разметки широко применяются шаблоны из картона, фанеры или тонколистового металла, соответствующие по своей форме и размерам заготовляемой детали.
Режут металл на гильотинных и дисковых ножницах, дисковых пилах и прессах или ручными газокислородными резаками и машинами для газокислородной резки. Механическая резка применяется обычно для металла толщиной до 10—12 мм, а в отдельных случаях —до 25—30 мм. Более толстый металл, а также детали сложной формы, как правило, режут с помощью газокислородной резки.
Перед сваркой кромки деталей, если это является необходимым, подвергают обрезке, скосу и очистке. Скос кромок выполняется в соответствии с типом сварного соединения. Для получения ровной и чистой поверхности кромок их прострагивают на кромкострогальных станках, длина строгания на которых достигает нескольких метров.
На многих заводах громоздкие и дорогие кромкострогальные станки заменяют специальными машинами для кислородной резки, обеспечивающими чистую поверхность разреза, необходимую точность и высокую производительность резки.
Машинная кислородная резка является распространенным способом подготовки кромок листов под сварку, особенно при большой толщине свариваемого металла (деталей станин, листов, котельных барабанов и др.). Машинная кислородная резка должна применяться во всех случаях, когда это допустимо по техническим условиям на изготовление данного изделия. Для ускорения процесс резки и скоса кромок выполняют одновременно несколькими резаками, установленными на одной машине под соответствующими углами наклона.
Нельзя сваривать детали, кромки которых покрыты ржавчиной, маслом, краской и другими загрязнениями, так как это ухудшает условия горения дуги, вызывает пористость наплавленного металла и понижает прочность сварного соединения.
От загрязнений кромки очищают проволочными щетками, наждачным камнем, пескоструем, травлением. Для механической очистки применяют ручные переносные машинки с гибким валом, на конце которого укрепляется проволочная щетка или наждачный камень. Другой конец вала соединяется с электродвигателем, смонтированным на легкой передвижной тележке.
На кромках не должно быть зарезов глубиной более 1,5 мм, прямолинейность кромок должна быть проверена с помощью рейки ч измерительной линейки, а углы скоса кромок — шаблонами.
Литые заготовки перед сваркой должны быть тщательно очищены от остатков формовочной земли, а имеющаяся на поверхности литейная корка — снята наждачным камнем в тех местах, где будут накладываться сварные швы.
При изготовлении различных резервуаров, котлов и сосудов из листового металла последний подвергается вальцовке и штамповке. Для вальцовки применяются гибочные вальцы, а для штамповки — механические и гидравлические прессы. Гибке и вальцовке может подвергаться также и профильный прокат металла — полосы, уголки, швеллеры, двутавры и трубы. В зависимости от толщины и требуемой формы заготовки вальцовка и гибка металла производятся в холодном или горячем состоянии.
Сборка деталей под сварку.
Предварительно заготовленные и подготовленные к сварке детали затем поступают на сборку отдельных узлов и изделий в целом.
Сборка является весьма ответственной операцией в общем технологическом процессе изготовления сварных конструкций. При сборке важно обеспечивать требуемую точность пригонки и совпадения кромок свариваемых элементов.
Сварные конструкции собирают различными способами. В некоторых случаях собирают всю конструкцию, а затем ее сваривают. Но при этом цикл сварочных работ удлиняется, а сварка собранной конструкции в ряде случаев бывает затруднена, так как сварщикам не всегда приходится выполнять швы в наиболее удобном для сварки положении.
Поэтому широко распространен способ сборки и сварки крупных конструкций из предварительно сваренных узлов. В этом случае процесс изготовления ускоряется и улучшается качество выполнения сварочных работ, так как сварку узлов осуществляют в приспособлениях. Данный способ применяется при изготовлении, например, судов, вагонов, цистерн и резервуаров, мостов, каркасов зданий и др.
Использование приспособлений обеспечивает точность взаимного расположения собираемых и свариваемых частей, облегчает трудоемкость сборочных работ, сокращает продолжительность процесса сборки, облегчает труд сварщика при установке, прихватке и поворотах изделия. Некоторые приспособления препятствуют короблению деталей при сварке, так как обеспечивают жесткое закрепление свариваемых частей.
Точность сборки изделий под сварку зависит от их конструкции и назначения, а также способа сварки. Обычно она указывается на чертежах и в технических условиях на изготовление изделия.
Для проверки точности сборки деталей под сварку используются шаблоны, измерительные линейки и щупы, а также универсальные измерители швов.
ПРОЕКТ на тему «Подготовка металла к сварке».

Государственное автономное профессиональное
образовательное учреждение московской области
«профессиональный КОЛЛЕДЖ «московия»
ПРОЕКТ
на тему «Подготовка металла к сварке»
Исполнитель:
Студент СВ-16 гр.
Крутилин Д.Е.
Кашира, 2018 год

Содержание:
1. Введение
2. Ручная механическая подготовка металла к сварке
2.1. Правка металлических заготовок
2.2. Разметка заготовок
2.3. Резка металла
2.4. Подготовка кромок под сварку
2.5. Сборка деталей
3. Заключение
Литература и источники информации

1. ВВЕДЕНИЕ
Основанием выбора такой темы, как « Подготовка металла под сварку» обусловлено тем, что это один из главных этапов сварочного процесса при любом методе сварки. Тщательная подготовка изделий в итоге поможет получить качественный, прочный и надежный шов.
Подготовка металла под сварку очень актуальный в настоящее время вопрос.
Обработка металла в настоящее время классифицируется по видам и методам. Причем, в основе большинства видов лежит механический метод (точение, растачивание, фрезерование, сверление, шлифование, полирование и пр.). Главным их недостатком является большое количество образующейся металлической стружки, угара, опилок, что очень неблагоприятно сказывается на здоровье человека при производстве работ, требует значительных трудозатрат.
Цель проекта: рассмотреть существующие методы и способы подготовки металла под сварку.

2. РУЧНАЯ МЕХАНИЧЕСКАЯ ПОДГОТОВКА
МЕТАЛЛА К СВАРКЕ
Прежде, чем приступить к свариванию металлических изделий, необходимо их подготовить. Непосредственно подготовка металла под сварку состоит из нескольких этапов. Вначале металл подвергается правке, затем осуществляется разметка и резка изделия, его зачистка и подогрев. На заключительной стадии производятся гибка и обработка кромок. Эти процедуры необходимы для того, чтобы добиться качественного соединения элементов конструкции.
Стоит помнить: ржавчина, частички металла, прочие элементы, оставшиеся на поверхности, препятствуют качественной сварке.
Поэтому важна правильная подготовка деталей к сварке, которая позволяет улучшить свариваемость. Количество процедур, которые необходимо выполнить при подготовке деталей под сварку, может различаться в зависимости от конкретной ситуации – степени загрязненности, деформации заготовок, объема работ и прочее. При этом все этапы подготовки регулируются согласно ГОСТ 5264-80.
2.1. ПРАВКА МЕТАЛЛИЧЕСКИХ ЗАГОТОВОК
Металлические заготовки при транспортировке или по иной причине могут деформироваться. В этом случае возникают сложности с их стыковкой в области сваривания, что приводит к снижению качества сварного шва.
Поэтому подготовительно выполняется правка изделия. В зависимости от размеров заготовок и сложности искривленных участков применяется холодная или горячая правка. Она выполняется вручную или специальными приспособлениями. Плиты из чугуна и стали вручную исправляют молотком или кувалдой. При необходимости создать большее давление применяется ручной пресс. Он представляет собой винтовой аппарат с двумя плитами, между которыми укладывают детали с деформированными участками, и выправляют их под высоким давлением.
Если вручную исправить деформацию невозможно, используются специальные приспособления – в частности, листоплавильные станки или прессы различных типов. Данные устройства работают на электродвигателях, вырабатывающих необходимую для работы мощность, для передачи которой используются редукторы. Таким образом удается увеличить давление на искривленные участки.

2.2 РАЗМЕТКА ЗАГОТОВОК
Подготовка деталей под сварку включает в себя такой важный этап, как разметка заготовок. Необходимость его выполнения связана с несовпадением размеров профилей с параметрами деталей, которые будут использованы в конструкции. Поэтому профиль необходимо подрезать. А перед этим – разметить, задав необходимые размеры.
Выделяют несколько способов разметки: ручная, оптическая, мерная резка. При ручной разметке используются простые инструменты для измерений – например, линейка или штангенциркуль. Если размечается небольшая партия однотипных заготовок, применяются изготовленные из алюминия или профилируемых листов шаблоны. Ручной способ отличается трудоемкостью и низкой скоростью выполнения работы.

При оптическом способе нанесения разметки применяются разметно-маркировочные машины. Их преимущество заключается в высокой скорости – до 10 метров в минуту. Чтобы разметить заготовку, необходимо запрограммировать аппарат под установленные параметры. Для нанесения разметки в данных устройствах используется пневматический крен.
Технология мерной резки не предполагает нанесение разметки на профили – в этом случае в специальные машины закладывается программа с указанием конфигурации и размеров заготовок. В результате аппарат сразу режет изделие под заданную форму.

2.3. РЕЗКА МЕТАЛЛА
Это один из важнейших этапов, который предполагает подготовку металла под сварку, поскольку иначе не получится добиться нужного размера заготовок. Выделяют механическую и термическую резку .
При механической резке используются ручные и механические инструменты.

Процесс термической резки представляет собой плавление металла по предварительно нанесенным отметкам. Этот тип работ также может быть ручным и автоматизированным. Для выполнении операции применяются кислородный резак, дуговая сварка, плазматрон. Также термическая резка осуществляется с применением станков, аппаратов, работающих в полу- или в автоматическом режиме.
Стоит отметить, что термическая резка – это универсальная технология, которая позволяет разрезать изделия в различных направлениях, как прямолинейно, так и криволинейно.

2.4. ПОДГОТОВКА КРОМОК ПОД СВАРКУ
Сварочные работы необходимо проводить на предварительно подготовленных поверхностях – очищенных от механических загрязнений, и химических пленок. Присутствие даже небольших частичек загрязнений может привести к растрескиванию конструкции, пористости, напряжению в металле. В результате сварное соединение утрачивает свои качественные характеристики.

Не стоит забывать об оксидной пленке, которая образуется на поверхности металлов при их контакте с воздухом. Она является жаростойкой, препятствует качественной сварке. Удалить ее можно как болгаркой, так и вручную, щеткой из металла.
На производстве детали зачищаются пескоструйными и дробеструйными аппаратами. Также производится химическая чистка – путем погружения изделий на определенное время в ванну с химическими реагентами. Этот тип очистки в основном используется при подготовке деталей из цветных металлов, а черные, стальные заготовки зачищаются вручную.
Кромки заготовок, особенно большой толщины, предварительно необходимо зачистить и придать им нужную геометрическую форму. Выделяют плоские, V-образные и Х-образные кромки. Плоские кромки используются при соединении тонких изделий, вторые два вида – при стыковке толстых заготовок.
Важно: кромки не обрабатываются, если толщина детали не более 3 мм.


Подготовка кромок под сварку состоит из обработки ширины зазора, угла разделки, регулировки длины откоса. При подготовке кромок под сварку труб различной толщины их обработка особенно актуальна – в противном случае металл не провариться. Поэтому важно подобрать правильный скос, благодаря которому переход между деталями будет плавным. А это снимет напряжение нагрузки во время использования готового изделия.
Для подрезки кромок при подготовке труб к сварке холодным способом используются станки или ручные инструменты. Термический способ предполагает использование горелок – ручных или автоматических.
Холодная подготовка металла к сварке считается более качественной. В этом случае в разы повышается точность сборки конечного изделия. А после термической обработки фаски зачастую нужно довести до правильных размеров и формы, особенно когда осуществляется подготовка труб под сварку.

2.5 СБОРКА ДЕТАЛЕЙ
Сборка под сварку – это заключительный этап подготовки. В этом случае отдельные детали фиксируются, чтобы они после сварки остались в нужном положении. Зачастую недостаточно просто расположить их рядом или зафиксировать специальным устройством – необходимо выполнить точечную приварку двух деталей. Это обеспечивает надежность конструкции и сохраняет ее форму. Такую заготовку можно расположить так, чтобы было удобно сделать горизонтальный шов.
Сборка осуществляется после того, как полностью завершена подготовка поверхности металла под сварку. К местам соединения деталей нужно обеспечить свободный доступ. Все заготовки должны быть надежно скреплены, чтобы избежать деформации при сварке.

3. ЗАКЛЮЧЕНИЕ
Раскрой металла – это технологический процесс, позволяющий получить металлические заготовки или детали необходимой формы и размеров.
На сегодняшний день существует несколько методов раскроя металлических листов.
Среди них заметное место занимают плазменная резка для раскроя металла.
Данные способы дают возможность выполнять обработку любых типов металла и получать высококачественный результат в самые короткие сроки. При этом процедура является безопасной, экономичной и не наносит вред экологической среде.

Литература и источники информации :
Лупачев В. Г. Сварочные работы. Мн.: Высшая школа, 1997
Лупачев В. Г. Ручная дуговая сварка. Мн.: Высшая школа,2006.
Справочник сварщика / под ред. В. В. Степанова. – М.: машиностроение, 1983
Опорный конспект по предмету.
ГОСТ 5264-80. Ручная дуговая сварка. Соединения сварные.
Основные типы, конструктивные элементы и размеры».
Интернет сайт: https://svarkalegko.com/

Спасибо за внимание!
Подготовка металла к процессу сварки — Моя ковка
Качество сварных соединений во многом зависит от обработки и подготовки металла. Существует несколько разновидностей металла и к каждому из них нужен индивидуальный подход. Подготовка металла к сварке включает в себя несколько операций, и это займет какое-то время.

С помощью станка гибка металла осуществляется быстро и точно.
Если более точно, то краткое описание действий следующее:
- производят правку металла;
- очищают от жиров и ржавчины;
- размечают;
- подвергают рубке;
- производят установку и прихватку.
Правка и гибка металла: особенности
При подготовке металла под сварку устраняются какие-либо неровности, кривизна или другие дефекты, и это называется правкой металла. Эти действия совершаются путем давления на металл при помощи пресса или вручную — ударом молотка.
Правке подвергаются как черные, так и цветные металлы.

Схема правки листового металла: а — деревянным молотком (киянкой), б — деревянным или металлическим бруском.
Помимо того, полосы из стали, прутья, проволока, любой вид труб, стальные круги и даже сварные конструкции.
Существует два метода правки:
- ручная правка — основой являются стальные или чугунные правильные плиты или различные наковальни, выполняется работа молотком;
- машинная правка — осуществляется на правильных машинах.
При правке металла материал может быть как холодным, так и горячим.
Также к подготовке относится и гибка металла. Это работа слесарная, во время которой заготовку изгибают под нужным углом и радиусом и придают ей требующуюся форму. Гибка тоже выполняется вручную, при помощи гибочных станков и прессов. Гибку можно производить как на глаз, так и по разметкам, шаблонам и по образцам.
Вернуться к оглавлению
Очистка от жиров и ржавчины
Очистка выполняется двумя способами:
- Механический. Применяя этот способ, ржавчина и жиры удаляют наждачкой или применяют зачистные машины. Если требуется шероховатая поверхность металла, тогда его подвергают гидроабразивной обработке. Используя этот метод, создают микрорельеф поверхности, благоприятно влияющий на сварочные работы.
- Химический. Металл подвергается очистке химическими растворами, а именно щелочными кислотами.
Вернуться к оглавлению
Разметка металла

Инструменты для разметки металла.
Перед выполнением дальнейших работ на металле производятся разметки или наметки. Размечая листовой металл, на нем вычерчивают контуры деталей с пометкой мест сгибов, намечают центр отверстия и все тонкости будущих деталей. Когда выполняется разметка, необходимо быть очень внимательным, так как малейшая неточность может привести к браку уже готовых деталей.
После проведения работ по нанесению разметочных линий наносятся при помощи кернера углубления, чтобы в процессе дальнейшей обработки сохранились следы наметок. Размечая детали из нержавейки, рекомендуется не использовать кернер.
Вернуться к оглавлению
Рубка металла перед сваркой
Когда производится подготовка металла под сварку, снимают слой металла, а именно фаску, задействовав кромкострогательный станок или газорезательный автомат. В некоторых случаях рубку изготавливают зубилом, которое бывает ручное или пневматическое.

Схема рубки металла
Кромки рубят по рискам, которые нанесены с применением никерного разметчика, они представляют собой две параллельные линии. Внутренняя обозначает верхнее ребро фаски, внешняя находится в нижней части фаски. При отсутствии рисок мастер использует при рубке линейку.
Чтобы при рубке фасок не ошибиться, необходимо к работе относиться с большим вниманием и нажимать на инструмент нужно равномерно. При выполнении рубки фасок края листа должны быть надежно закреплены. Листы, которые не установлены на место, подлежат обрубке прямо на стеллаже или после укладки на пол, но в любом случае материал требуется зажать, чтобы не допустить сдвигов при ударе.
Вернуться к оглавлению
Прихватка перед сваркой
Использование прихватки в сварочных работах — это наилучший способ фиксации расположенных деталей по отношению друг к другу. Сварочными прихватками являются короткие сварные швы. Используя прихватку, избегают смещения свариваемых деталей всей конструкции при проведении работ сварки, уменьшают зазор по отношению к другим деталям, увеличивают жесткость и понижают деформацию.
Чаще всего заранее собранные детали в конструкцию прихватываются точечной сваркой, для которой используют стационарные сварочные аппараты и зажимы. Применение зажимов позволяет более точно собрать конструкцию перед подготовкой к сварке. Этот способ сборки бывает как автоматизированным, так и ручным.

Способы крепления деталей перед сваркой.
Ручной способ основан на сделанных перед сборкой разметках, где в последующем будут производиться прихватки. Использование зажимов значительно упрощает саму сборку, также зажимы делают ее точной, а наносить прихватки с ними удобнее. Высота механизации процесса сборки зависит от количества деталей, которые входят в свариваемую конструкцию.
От правильно выполненных прихваток зависит правильность и удобство дальнейшей работы с будущей конструкцией. К качеству прихваток предъявляются некоторые требования:
- Особое внимание нужно уделить электродам, которыми выполняются прихватки. Они должны быть той марки, что и материал, которым будет выполняться дальнейшая сварка. Если работы по сварке в дальнейшем будут производиться с применением проволоки, то электрод должен соответствовать виду проволоки.
- По длине прихватки выполняются не более 2 см, а что касается толщины, то она делается в 2 раза меньше, чем будущий шов.
- Немаловажным является в этом процессе и сварной ток. Значение тока нужно правильно подобрать, учитывая значение тока, которое будет использоваться при сварке готовой конструкции. Устанавливая прихватки, нужно выполнить прочный провар мест, где их выполняют. Для надежности ток выбирается на 20% больше, чем ток, который будет использоваться в дальнейшем.
- Прихватки размещают в тех местах, где при сварке конструкции будет возникать самое большое внутреннее напряжение, и в том месте, где возможна деформация. Прихватку нельзя располагать на перекрестке сварных швов.
Если работы будут производиться автоматической сваркой, то прихватки располагаются с противоположной стороны по отношению к первому проходу. Но иногда технические характеристики требуют выполнение этих работ именно со стороны первого прохода. В данном процессе будет нужным соблюдать определенное количество прихваток.
Самое главное, на что обращается внимание перед сваркой, — это внешний вид самих прихваток. Перед тем как начать основную сварку, их нужно полностью привести в надлежащий вид — произвести очистку от шлаков и застывших металлических брызг, одним словом, место прихватки должно быть практически ровным.
Следовательно, места с остальными прихватками, имеющими наружные дефекты, такие как трещины или шлаковые «наросты», должны быть полностью очищены механическим путем.
ПРОЕКТ на тему «Подготовка металла к сварке»/
Описание презентации по отдельным слайдам:
1 слайд
ПРОЕКТ на тему «Подготовка металла к сварке» Исполнитель: Студент СВ-16 гр. Крутилин Д.Е. Кашира, 2018 год Государственное автономное профессиональное образовательное учреждение московской области «профессиональный КОЛЛЕДЖ «московия»
2 слайд
Содержание: 1. Введение 2. Ручная механическая подготовка металла к сварке 2.1. Правка металлических заготовок 2.2. Разметка заготовок 2.3. Резка металла 2.4. Подготовка кромок под сварку 2.5. Сборка деталей 3. Заключение Литература и источники информации
3 слайд
1. ВВЕДЕНИЕ Основанием выбора такой темы, как «Подготовка металла под сварку» обусловлено тем, что это один из главных этапов сварочного процесса при любом методе сварки. Тщательная подготовка изделий в итоге поможет получить качественный, прочный и надежный шов. Подготовка металла под сварку очень актуальный в настоящее время вопрос. Обработка металла в настоящее время классифицируется по видам и методам. Причем, в основе большинства видов лежит механический метод (точение, растачивание, фрезерование, сверление, шлифование, полирование и пр.). Главным их недостатком является большое количество образующейся металлической стружки, угара, опилок, что очень неблагоприятно сказывается на здоровье человека при производстве работ, требует значительных трудозатрат. Цель проекта: рассмотреть существующие методы и способы подготовки металла под сварку.
4 слайд
2. РУЧНАЯ МЕХАНИЧЕСКАЯ ПОДГОТОВКА МЕТАЛЛА К СВАРКЕ Прежде, чем приступить к свариванию металлических изделий, необходимо их подготовить. Непосредственно подготовка металла под сварку состоит из нескольких этапов. Вначале металл подвергается правке, затем осуществляется разметка и резка изделия, его зачистка и подогрев. На заключительной стадии производятся гибка и обработка кромок. Эти процедуры необходимы для того, чтобы добиться качественного соединения элементов конструкции. Стоит помнить: ржавчина, частички металла, прочие элементы, оставшиеся на поверхности, препятствуют качественной сварке. Поэтому важна правильная подготовка деталей к сварке, которая позволяет улучшить свариваемость. Количество процедур, которые необходимо выполнить при подготовке деталей под сварку, может различаться в зависимости от конкретной ситуации – степени загрязненности, деформации заготовок, объема работ и прочее. При этом все этапы подготовки регулируются согласно ГОСТ 5264-80.
5 слайд
2.1. ПРАВКА МЕТАЛЛИЧЕСКИХ ЗАГОТОВОК Металлические заготовки при транспортировке или по иной причине могут деформироваться. В этом случае возникают сложности с их стыковкой в области сваривания, что приводит к снижению качества сварного шва. Поэтому подготовительно выполняется правка изделия. В зависимости от размеров заготовок и сложности искривленных участков применяется холодная или горячая правка. Она выполняется вручную или специальными приспособлениями. Плиты из чугуна и стали вручную исправляют молотком или кувалдой. При необходимости создать большее давление применяется ручной пресс. Он представляет собой винтовой аппарат с двумя плитами, между которыми укладывают детали с деформированными участками, и выправляют их под высоким давлением. Если вручную исправить деформацию невозможно, используются специальные приспособления – в частности, листоплавильные станки или прессы различных типов. Данные устройства работают на электродвигателях, вырабатывающих необходимую для работы мощность, для передачи которой используются редукторы. Таким образом удается увеличить давление на искривленные участки.
6 слайд
2.2 РАЗМЕТКА ЗАГОТОВОК Подготовка деталей под сварку включает в себя такой важный этап, как разметка заготовок. Необходимость его выполнения связана с несовпадением размеров профилей с параметрами деталей, которые будут использованы в конструкции. Поэтому профиль необходимо подрезать. А перед этим – разметить, задав необходимые размеры. Выделяют несколько способов разметки: ручная, оптическая, мерная резка. При ручной разметке используются простые инструменты для измерений – например, линейка или штангенциркуль. Если размечается небольшая партия однотипных заготовок, применяются изготовленные из алюминия или профилируемых листов шаблоны. Ручной способ отличается трудоемкостью и низкой скоростью выполнения работы.
7 слайд
При оптическом способе нанесения разметки применяются разметно-маркировочные машины. Их преимущество заключается в высокой скорости – до 10 метров в минуту. Чтобы разметить заготовку, необходимо запрограммировать аппарат под установленные параметры. Для нанесения разметки в данных устройствах используется пневматический крен. Технология мерной резки не предполагает нанесение разметки на профили – в этом случае в специальные машины закладывается программа с указанием конфигурации и размеров заготовок. В результате аппарат сразу режет изделие под заданную форму.
8 слайд
2.3. РЕЗКА МЕТАЛЛА Это один из важнейших этапов, который предполагает подготовку металла под сварку, поскольку иначе не получится добиться нужного размера заготовок. Выделяют механическую и термическую резку. При механической резке используются ручные и механические инструменты.
9 слайд
Процесс термической резки представляет собой плавление металла по предварительно нанесенным отметкам. Этот тип работ также может быть ручным и автоматизированным. Для выполнении операции применяются кислородный резак, дуговая сварка, плазматрон. Также термическая резка осуществляется с применением станков, аппаратов, работающих в полу- или в автоматическом режиме. Стоит отметить, что термическая резка – это универсальная технология, которая позволяет разрезать изделия в различных направлениях, как прямолинейно, так и криволинейно.
10 слайд
2.4. ПОДГОТОВКА КРОМОК ПОД СВАРКУ Сварочные работы необходимо проводить на предварительно подготовленных поверхностях – очищенных от механических загрязнений, и химических пленок. Присутствие даже небольших частичек загрязнений может привести к растрескиванию конструкции, пористости, напряжению в металле. В результате сварное соединение утрачивает свои качественные характеристики.
11 слайд
Не стоит забывать об оксидной пленке, которая образуется на поверхности металлов при их контакте с воздухом. Она является жаростойкой, препятствует качественной сварке. Удалить ее можно как болгаркой, так и вручную, щеткой из металла. На производстве детали зачищаются пескоструйными и дробеструйными аппаратами. Также производится химическая чистка – путем погружения изделий на определенное время в ванну с химическими реагентами. Этот тип очистки в основном используется при подготовке деталей из цветных металлов, а черные, стальные заготовки зачищаются вручную. Кромки заготовок, особенно большой толщины, предварительно необходимо зачистить и придать им нужную геометрическую форму. Выделяют плоские, V-образные и Х-образные кромки. Плоские кромки используются при соединении тонких изделий, вторые два вида – при стыковке толстых заготовок. Важно: кромки не обрабатываются, если толщина детали не более 3 мм.
12 слайд

Подготовка кромок под сварку состоит из обработки ширины зазора, угла разделки, регулировки длины откоса. При подготовке кромок под сварку труб различной толщины их обработка особенно актуальна – в противном случае металл не провариться. Поэтому важно подобрать правильный скос, благодаря которому переход между деталями будет плавным. А это снимет напряжение нагрузки во время использования готового изделия. Для подрезки кромок при подготовке труб к сварке холодным способом используются станки или ручные инструменты. Термический способ предполагает использование горелок – ручных или автоматических. Холодная подготовка металла к сварке считается более качественной. В этом случае в разы повышается точность сборки конечного изделия. А после термической обработки фаски зачастую нужно довести до правильных размеров и формы, особенно когда осуществляется подготовка труб под сварку.
14 слайд
2.5 СБОРКА ДЕТАЛЕЙ Сборка под сварку – это заключительный этап подготовки. В этом случае отдельные детали фиксируются, чтобы они после сварки остались в нужном положении. Зачастую недостаточно просто расположить их рядом или зафиксировать специальным устройством – необходимо выполнить точечную приварку двух деталей. Это обеспечивает надежность конструкции и сохраняет ее форму. Такую заготовку можно расположить так, чтобы было удобно сделать горизонтальный шов. Сборка осуществляется после того, как полностью завершена подготовка поверхности металла под сварку. К местам соединения деталей нужно обеспечить свободный доступ. Все заготовки должны быть надежно скреплены, чтобы избежать деформации при сварке.
15 слайд
3. ЗАКЛЮЧЕНИЕ Раскрой металла – это технологический процесс, позволяющий получить металлические заготовки или детали необходимой формы и размеров. На сегодняшний день существует несколько методов раскроя металлических листов. Среди них заметное место занимают плазменная резка для раскроя металла. Данные способы дают возможность выполнять обработку любых типов металла и получать высококачественный результат в самые короткие сроки. При этом процедура является безопасной, экономичной и не наносит вред экологической среде.
16 слайд
Литература и источники информации : Лупачев В. Г. Сварочные работы. Мн.: Высшая школа, 1997 Лупачев В. Г. Ручная дуговая сварка. Мн.: Высшая школа,2006. Справочник сварщика / под ред. В. В. Степанова. – М.: машиностроение, 1983 Опорный конспект по предмету. ГОСТ 5264-80. Ручная дуговая сварка. Соединения сварные. Основные типы, конструктивные элементы и размеры». Интернет сайт: https://svarkalegko.com/
17 слайд
Спасибо за внимание!
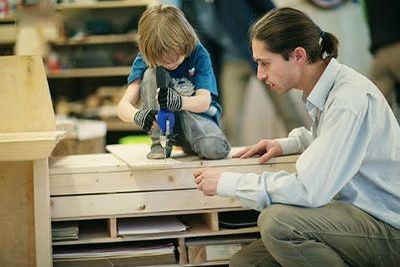
Курс профессиональной переподготовки
Учитель, преподаватель технологии
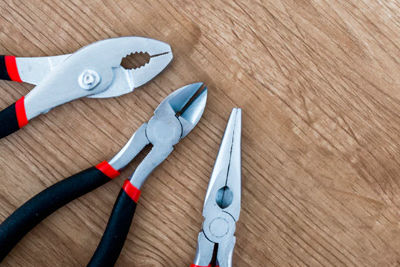
Курс повышения квалификации
Найдите материал к любому уроку,
указав свой предмет (категорию), класс, учебник и тему:
Выберите категорию: Все категорииАлгебраАнглийский языкАстрономияБиологияВсеобщая историяГеографияГеометрияДиректору, завучуДоп. образованиеДошкольное образованиеЕстествознаниеИЗО, МХКИностранные языкиИнформатикаИстория РоссииКлассному руководителюКоррекционное обучениеЛитератураЛитературное чтениеЛогопедия, ДефектологияМатематикаМузыкаНачальные классыНемецкий языкОБЖОбществознаниеОкружающий мирПриродоведениеРелигиоведениеРодная литератураРодной языкРусский языкСоциальному педагогуТехнологияУкраинский языкФизикаФизическая культураФилософияФранцузский языкХимияЧерчениеШкольному психологуЭкологияДругое
Выберите класс: Все классыДошкольники1 класс2 класс3 класс4 класс5 класс6 класс7 класс8 класс9 класс10 класс11 класс
Выберите учебник: Все учебники
Выберите тему: Все темы
также Вы можете выбрать тип материала:

Общая информация
Номер материала: ДБ-1520714
Похожие материалы
Вам будут интересны эти курсы:
Оставьте свой комментарийПодготовка и сборка деталей под сварку
Подготовка и сборка деталей под сварку подразумевает выполнение очистки, выравнивания, разметки, резания и сборки заготовок.[context]
Кромки и примыкающую зону, 20-30 мм с каждой стороны, очищают от ржавчины, краски, окалин, масла и других загрязнений. Качественно подготовленные кромки и прилегающая зона имеют металлический блеск, что достигается при использовании металлических щеток, пламя, а при ответственных соединениях используют травление, обезжиривание, пескоструйную обработку.
Более подробно об очистке заготовок перед сваркой смотрите в этой статье.
Детали с вмятинами, выпуклостями, волнистостью, искривлением обязательно выпрямляют. В холодном состоянии можно выпрямлять листы и прокат вручную или при помощи машин. При сильной деформации металла выпрямление делают в горячем состоянии. Для выпрямления используют молотки, прессы, правильные машины.
Следующий этап подготовки деталей перенесение размеров из чертежа на металл и его разметка. Для измерений и разметки используют метры, линейки, угольники, циркули, чертилки, маркеры, мел и специально изготовленные шаблоны. Во время сварки заготовки укорачиваются, что необходимо учитывать при разметке заготовок. Для этого используют припуск с расчета 1 мм на каждый поперечный стык и 0,1-0,2 мм на 1 м продольного шва.
После разметки детали разрезают термическими или механическими способами, для придания заготовкам необходимого размера и формы. Кромки на местах будущих сварных соединений делают напильником, зубилом или механическим способом на фрезерных станках, строгальных станках и др. Угол скоса зависит от способа сварки, химического состава металла и его толщины. Проверку угла скоса кромок делают при помощи шаблонов.
Сборка деталей под сварку производится одним из трех подходов:
предварительно собрать всю деталь и сварить все необходимые швы;
сварить часть конструкции и к ней постепенно присоединять недостающие детали;
предварительная сборка и сварка изделия с отдельных узлов конструкции;
Продуктивность и качество изготовления сварных конструкций во многом зависит от базовых поверхностей (баз) для сборки сварных конструкций. Базовыми считаются поверхности с наибольшими размерами; в качестве направляющей базы — самую длинную поверхность; опорной базой считают любого размера поверхность в нормальном состоянии и неизменной форме (без резов, капель, швов).
Выбирать базу стоит исходя из наличия сборочных приспособлений, вида заготовок, жесткости деталей и точности из размещения, зазора между кромками. Важно учитывать сварочные напряжения и деформации.
Приспособления для сборки и сварки
Для более продуктивного и качественного изготовления сварных конструкций используют специальные приспособления для сборки и сварки:
- универсальный зажим для монтажа и сборки цилиндрических деталей;
- ручная скоба для сборки профильного и листового металла;
- ручная пружинная скоба для сборки профильного металла;
- поворотный винтовой зажим для сборки и крепления деталей в массовом производстве;
- струбцина для сборки деталей разного профиля;
- угловой прихват из болтом для сборки крупных контрукций с листового металла;
- скоба прихваточная с ломом для конструкций, которые собирают внахлест в монтажных условиях;
- гребенка на прихватках для крупных листовых конструкций;
- прихваточные шайбы с планками и клиньями для листовых конструкций;
- винтовая стяжка для притягивания деталей;
- стягивательное кольцо для трубопроводов большого диаметра;
- гибкий хомут с эксцентрическим зажимом для цилиндрических деталей;
- винтовой распорно-стягивательный механизм для листовых конструкций и плоскостных изделий;
- крюк с ломом для стягивания кромок;
- винтовая распорка для цилиндрических деталей;
- распор для сборки деталей машиностроительных конструкций;
- винтовая упорная скоба для деталей ограниченных размеров;
- односторонний винтовой упор для сборки профилей ферм и других конструкций;
- односторонний упор для сборки конструкций на стационарных постах.
Выполнение прихваток после сборки конструкции
[context] Собранные детали прихватывают. Длина прихваток и расстояния между ними зависит от толщины металла и длины шва. Ставят прихватки для фиксации деталей и сохрани зазора между ними в процессе сварки. Прихватка должна проваривать корень шва, потому что в процессе сварки сама прихватка может полностью не переплавится.
Толщина металла, мм | ≤ 5 | ≤ 5 |
Длина металла, мм | ≤ 150-200 | ≤ 200 |
Длина прихваток, мм | ≤ 5 | 20-30 |
Расстояние между прихватками, мм | 50-100 | 300-500 |
Нужно делать прихватки максимально низкими, лучше если они будут вогнутыми. Прихватки ставят на режимах аналогичных режимам сварки. Иногда прихватку заменяют цельным швом небольшого разреза.
При сварки меди необходимо обходиться без прихваток, зажимать детали в кондукторах или других приспособлениях, потому что они вызывают трещины при повторном нагревании.
Прихватки нагревают металл и при последующем передвижении деталей возможно возникновение трещин. Чем больше толщина деталей, тем больше растягивающая усадка в прихватках и возможность появления трещин. Поэтому прихватки целесообразно использовать для деталей небольшой толщины (до 6-8 мм). При большей толщине листов безопасность передвижения узлов можно достичь при помощи гребенок (эластичных прихваток) или собирают изделие из гибкими деталями (решетки, фермы и т.п.)
Подготовка под сварку деталей разной толщины
L= 5×(S1-S)
L1=2,5×(S1-S)
При стыковом соединении деталей разной толщины можно обойтись без дополнительных операций и сваривать их как детали одинаковой толщины, если разница между ними не выше чем значения указанные в таблице ниже
Толщина тонкой детали, мм | 1-4 | 4-20 | 20-30 | больше 30 |
Допустимая разница, мм | 1 | 2 | 3 | 4 |
Для плавного перехода между деталями допускается наклонное размещение поверхности шва.
Если разница в толщине свариваемых деталей больше чем указаны в таблице, то на деталях большей толщины делают скос кромок с одной или обеих сторон. При этом элементы разделки и толщину шва выбирают исходя их размеров меньшей детали. Допускается смещение кромок не более: 0,5 мм — для деталей толщиной до 4 мм; 1,0 мм — для деталей толщиной 4-10 мм; 0,1 × S, но не более 3 мм — для деталей толщиной 10-100 мм; 0,01 × S + 2 мм, но не более 4 мм — для деталей толщиной более 100 мм.
Катеты углового шва должны указываться при проектировании изделия, но не более 3 мм для деталей толщиной до 3 мм включительно и 1,2 толщины тонкой детали при сварке деталей толщиной более 3 мм.
Правильная подготовка металла под сварку
Прежде чем сваривать металлические поверхности, их нужно хорошо зачистить. Подготовка металла под сварку – это наиболее важный этап, качественное выполнение которого позволит получить прочный, надежный шов.

Во избежание дефектов шва, металлические предметы перед сваркой необходимо тщательно очищать от ржавчины и грязи.
При соприкосновении с воздухом металл реагирует с кислородом, образуя окислы. Появляется ржавчина и другие загрязнения, которые приводят к образованию различных дефектов шва. Попадание масла, окалины, влаги на место сварки также нежелательно. Кроме того, для плотного соприкосновения листов металла их нужно предварительно выправить, если это требуется. Наконец, необходима разметка деталей, нарезка и подготовка кромок листа под последующую сварку закладных деталей и других соединений.
Правка металла и нарезка деталей
Править металл можно с применением специальных валов, предназначенных для этого, либо вручную. Для ручной правки необходима кувалда или пресс. Она выполняется на правильных плитах из чугуна или стали. На прессах же выравниваются швеллеры, двутавры и угловая сталь.

Последовательность ручной правки металлического листа.
В результате проведения разметки и последующей нарезки определяется будущая конфигурация готовой детали. Разметка или наметка требуют предварительного грунтования поверхности металлического листа. Их отличие состоит в том, что разметка имеет отношение к индивидуальному производству, а наметка – к промышленному. Для подготовки к массовой нарезке листов используется шаблон из фанеры или металла. Применение шаблона при разметке называется наметкой.
Механически операция производится в случае необходимости получения прямолинейных резов. В основном такая резка осуществляется ножницами, если нужен прямолинейный рез, а листы по толщине не превышают 20 мм. Для промышленных масштабов производства устанавливаются гильотинные ножницы, имеющие длину ножей 1-3 м или пресс-ножницы с ножами до 70 см. По изогнутым линиям лист толщиной меньше 6 мм можно разрезать роликовыми ножницами, для них же применяется газокислородная или плазменно-дуговая резка, которая используется и с легированной сталью, и с цветными металлами. В отношении них может использоваться газофлюсовая резка. Холодная резка стержней любого сечения производится круглыми зубчатыми или фрикционными пилами.
Вернуться к оглавлению
Зачистка деталей: нюансы
Поверхности основного и присадочного металлов с особой тщательностью очищаются от маслянистых жирных пятен, следов влаги, ржавчины, окалин и всяческих загрязнений неметаллического происхождения. Подготовка металла под сварку не может обойтись без этого важного этапа.
Малейшие остатки таких явлений провоцируют появление пор в швах, включений шлака. Трещины, которые могут образовываться в результате этого, снижают надежность сварки, ее прочность и плотность.
Вернуться к оглавлению
Подготовка кромок под сварку
Для достижения наиболее прочного сварного шва следует подготовить и кромки деталей. Они должны иметь определенную геометрическую форму, в которую входит угол разделки, притупление, зазор, длина скоса, если листы имеют разную толщину.
Разделка кромок под сварку под углом должна производиться, если металлический лист имеет толщину свыше 3 мм.

Виды подготовки кромок под сварку.
В противном случае шов может не провариться полностью по всему сечению даже при сварке мелких деталей. Кроме того, при попытке достать дальние слои уже сваренный металл будет перегреваться и пережжется.
Если разделка кромок отсутствует, то сила сварочного тока должна быть увеличена. При ее наличии сварка деталей ведется послойно, с небольшим сечением, благодаря чему соединение получает качественную структуру, минимизируются деформации и напряжения в металле.
Грамотно подобранный зазор обеспечивает полноценный провар металла в соединении.
Наличие скоса позволяет осуществить плавный переход от одной детали к другой, если они имеют разную толщину. Его длина при этом влияет на возникающее напряжение в конструкции или его отсутствие.
Острые кромки при проварке образуют неустойчивую конструкцию, из-за чего детали могут съезжать относительно друг друга, образуются прожоги, шов деформируется, возникает дополнительное напряжение, сварное соединение становится менее прочным.

Схема притупления кромки.
Чтобы этого избежать и обеспечить более комфортные условия работы в процессе образования корневого шва, кромки притупляют. При стыковых соединениях и внахлест производится смещение, кромкам придают наиболее подходящую геометрическую форму сечения в соответствии с ГОСТами или техническим регламентом. Особенно это важно, когда производят сварку закладных деталей.
Кромки под сварку обрабатываются механически, с использованием фрезерных, продольнострогательных и кромкострогательных станков, газокислородным пламенем. Горючим для получения пламени может быть пропан, ацетилен и другие. Если работы немного, то бывает достаточно пневматического зубила. Кроме того, на этом этапе работают на токарных станках (для подготовки кромки с торца трубы). Для работы с цветными металлами или нержавеющей сталью используется плазменная резка.
После газокислородной резки в завершение проводится механическая обработка, особенно если шов должен быть отменного качества. Таким образом удается избежать попадания мелких крупинок, которые провоцируют образование микротрещин, попадание воздуха и другие дефекты, приводящие к разрушению шва. В конструкциях, возводимых на ответственных участках строительства, это недопустимо.
Вернуться к оглавлению
Гибка металла: рекомендации

Радиусы гибки листового металла.
Листы, полосы пропускаются через листогибочные вальцы, трехвалковые и четырехвалковые. Холодной гибке подлежат листы, у которых кромки металла к сварке уже подготовлены, а также вырезаны небольшие отверстия, если они необходимы по проекту. Профильный металл гнется под правильно-гибочными прессами или пускается на роликовые гибочные станы. Ограничения по радиусу гибки на холодную напрямую зависят от толщины листа или высоты профиля. Он должен быть в 25 раз больше значения этих параметров. При уменьшении радиуса деформации будут появляться трещины или надломы.
Если необходим малый радиус или толщина листа слишком большая, то применяется горячий метод в цехах с технологиями, используемыми кузнецами. При температуре свыше 1000 градусов металл податлив и легче принимает нужную форму. В этом случае подготовка кромок производится следующим этапом после гибки, а не наоборот.
Большие отверстия проделываются после гибки, если они необходимы. Этот этап завершает подготовку деталей под сварку, после чего они отправляются на сборку всей конструкции.
Вернуться к оглавлению
Основные требования к сборке конструкции перед сваркой деталей
Сборка изделий под сварку должна производиться в соответствии со следующими требованиями, чтобы обеспечить выполнение качественного соединения:
- К месту соединения деталей должен быть обеспечен свободный доступ, даже если для их фиксации используются дополнительные приспособления.
- Детали должны быть закреплены жестко, с высокой точностью в требуемом положении, чтобы в процессе не возникало дополнительных деформаций, которые можно избежать.
- Все повороты, изменения положения конструкции в пространстве сводятся к минимуму, чтобы не возникало случайных перекосов и смещений.
- Сборку деталей под сварку на каждом этапе осуществляют таким образом, чтобы она не приводила к затруднениям для выполнения последующего. Все должно быть максимально доступно и грамотно спланировано.
Готовое изделие проверяется, сверяются размеры, просматриваются швы, для чего также необходим свободный доступ и его легкое высвобождение после этого из удерживающих приспособлений.