Как уменьшить разбрызгивание металла при сварке
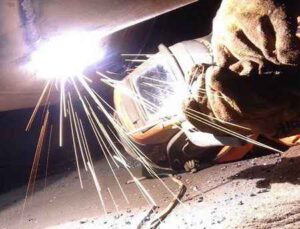
Разбрызгивание металла при сварке характеризуется появлением мелких шариков на поверхности, а это существенно портит внешний вид свариваемого изделия. Вследствие этого перед многими новичками сварщиками остро стоит вопрос, как снизить разбрызгивание металла при сварке электродом или полуавтоматом.
Сильное разбрызгивание металла во время сварки может говорить, как о проблемах в работе сварочного аппарата, так и о некачественных расходных материалах. Очень часто причины возникают и по вине самого сварщика, как правило, из-за неправильно выставленных регулировок инвертора.
Как избежать разбрызгивание металла при сварке? Что нужно знать, и на что, в первую очередь, обратить собственное внимание? Читайте об этом ниже, на сайте mmasvarka.ru.
Из-за чего происходит сильное разбрызгивание металла при сварке
Рассмотрим основные причины, из-за которых может происходить сильное разбрызгивание расплавленного металла. В первую очередь следует обратить внимание на сварочный ток.
В том случае, когда брызги металла при сварке появляются всё чаще и чаще, стоит обязательно проверить сварочный аппарат. Возможно, оборудование для сварки выдаёт ток низкого качества. Часто такое происходит из-за скачков напряжения в электросети.
Если речь идёт о сварочном полуавтомате, то, скорее всего виной износившийся токовый наконечник или сопло. Стоит заметить, что брызг при сварке металла электродом намного меньше, если использовать инвертор постоянного тока. Практически не избежать разбрызгивания металла на старых, однофазных сварочных аппаратах переменного тока.
Что же касается полуавтоматов, то здесь разбрызгивание металла происходит по причине износившегося сопла или токового наконечника. В таком случае очень трудно добиться стабильной дуги, а качество сварочного шва снижается в разы.
Плохие расходные материалы для сварки
Расходными материалами принято называть: электроды, флюс, газ и т. д. Если их качество будет низким, то также пострадает и качество сварки. Вследствие этого мы может наблюдать не только разбрызгивание металла, но и его непровар, грязный и неаккуратный сварочный шов с большим количеством шлака.
Уменьшить разбрызгивание металла при полуавтоматической сварке можно, если использовать:
- Качественные порошкообразные флюсы;
- В качестве защитной среды применять только аргоновые смеси и смеси на основе углекислого газа.
Что же касается ручной дуговой сварки, то здесь снизить разбрызгивание металла помогают рутиловые электроды. Однако это не правило, а скорее личный опыт и предпочтение каждого. Также сырые электроды приводят к тому, что металл ложится плохо, и все время разбрызгивается. Обязательно нужно прокалить отсыревшие электроды перед применением.
Кроме того, уменьшить количество брызг можно, следующим образом:
- Качественной подготовкой свариваемых поверхностей;
- Использованием специальных средств обработки металла;
- Специальной техникой сварки.
Если металл сильно разбрызгивается во время сварки электродами, то обязательно попробуйте уменьшить сварочную дугу. Ну а избежать загрязнения деталей сваркой можно, если защитить их поверхность от раскалённого металла.
Поделиться в соцсетях
Как и чем защитить металл от сварочных брызг
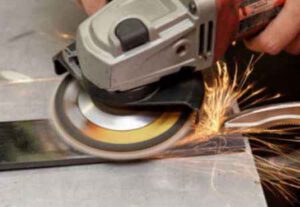
При сварке ответственных изделий очень важно уберечь их поверхность от брызг раскалённого металла. В некоторых случаях налипшие капли от сварки будут восприниматься как довольно серьёзный дефект.
Сварочные брызги возникают по разным причинам. В основном происходит это явление, когда зажигается дуга, и в результате завышенных параметров сварочного тока.
Для устранения подобного рода дефекта сварщики прибегают к болгарке с зубилом. Болгаркой они стачивают капли металла, а зубилом убирают их с поверхности.
Чтобы такого не происходило, важно защитить поверхность свариваемого изделия от брызг металла. Как и чем это лучше сделать, будет рассказано в статье.
Причины прилипания брызг металла
Существует достаточно большое количество причин, из-за которых сварочные брызги прилипают к металлу. В первую очередь это неправильный режим сварки: ток имеет слишком завышенные значения.
Также на появление брызг влияет и качество электродов. Если электроды будут плохими или отсыревшими, то все это приведёт к разбрызгиванию металла при сварке, а значит и к появлению капель.
Кроме того, недостаточная подготовка изделия перед сваркой, может привести к тому, что электрод все время будет прилипать к металлу, а это также приведёт к появлению брызг. Только избавившись полностью или частично от данных проблем, можно обеспечить высочайшее качество сварного соединения.
Как и чем защитить металл от сварочных брызг
Чтобы каждый раз не счёсывать брызги расплавленного металла механическим путём, следует защитить поверхность изделия. Сделать это можно различным способами, например, обработкой околошовных зон сварки мелом. В таком случае брызги не будут прилипать к металлу.
Также можно защитить части изделия асбестовой тканью или другим материалом, который не горит. Что же касается покупных средств, то на сегодняшний день их существует достаточно большое разнообразие в виде жидкостей и паст.
Наиболее хорошо себя зарекомендовали средства защиты от брызг таких производителей, как: ИНДУСВАР, BINZEL, E-WELD и ESAB.
По способу использования они подразделяются на:
- Жидкости, которые наносятся на свариваемую заготовку кисточкой или пульверизатором;
- Аэрозоли, которые распыляются с помощью специального флакона;
- Пасты, которые наносятся на поверхность металла, предотвращая тем самым прилипание брызг от сварки.
Чтобы защитить поверхность изделия от брызг раскалённого металла можно использовать различные средства. Однако важно понимать причину возникновения проблемы, если брызг слишком много. Часто она кроется в отсыревших и некачественных электродах, плохой работе инвертора, а также, ввиду сильно ржавой и плохо подготовленной поверхности.
Поделиться в соцсетях
К образованию брызг расплавленного металла при дуговой сварке в среде углеродистого газа Текст научной статьи по специальности «Технологии материалов»
УДК 621.791.72:621.791.052:620.17 В. В. 621ИТРШС,д-ртехн.наук, проф.
А. В. ГДЛРТ1КО
Наци ональныйтехнически йуниверситет «Харьковский политехнический институт», а Харьков
К ОБРАЗОВАНИЮ БРЫЗГ РАСПЛАВЛЕННОГО МЕТАЛЛА ПРИ ДУГОВОЙСВАРКЕ ВСРЕДЕУРЛЕРОДИСТОГОГАЗА
Изучены особенности механизма образования брызг расплавленного металла при дуговой сварке вередеуглекислогогазаизабрызгиваниярабочихповерхностейсопелитокоподводящих мундштуковеварочных горосои.
Вивчетоио0л1ичост1 мгхоти1адтвоШвноабрток розплавленого металу при дуговому зварювхнры в егредолитг зувиеквзлогогавыг зиихилеувлннярыдлхлх ыоиврхеих соехглта втнумотдв1Хнох ммндштухехзеарюкхльхив палвинтв.
Введение
Н процессе дугсвсй сварки в среде углекислсгс газа, исесльзуемсй преимущественно для изготовления соединений из углеродистых конструкционных сталей, образуются брызгираселавленного металла. Такие брызги еутем налипания и приваривания к рабочим поверхностям соеел и токоеодводящис мундштуков сварочных горелок вызывают ис засорение, что снижает степень защиты расплавленного металла от взаимодействия с атмосферными газами. Соответственно увеличивается количество исходных дефектов в металле шва, что снижает качественные характеристики сварных соединений.
Представляется целесообразным изучение особенностей образования брызг, что актуально для уменьшения забрызгивания сварочного оборудования.
Разбрызгивание обусловлено разрывом струи жидкого металла, переносимого из торцевого участка плавящегося электрода в сварочную ванну, а также взрывообразным выделением пузырьков газов из струи и расплава ванны [—Д].Выплески жидкого металла из расплава ванны также вызывают его разбрызгивание. В условиях изготовления сварных соединений разбрызгивание из расплава ванны при сварке в нижнем горизонтальном положении является менее интенсивным, чем при сварке угловых и круговых швов. При сварке в СОД основной причиной разбрызгивания электродного металла является сильное и неравномерно распределенное сжатие столба дуги, вызванное высокой теплопроводностью СОД в области температур дуги, а также интенсивным отбором теплоты на диссоциацию СОД. В зависимости от технологических условий сварки образующиеся брызги расплавленного металла могут быть мелкими (< 0,Д мм), средними (0,Д-0,5 мм) и крупными (> 0,5 мм) [3-4].
Основная часть
Потери металла на разбрызгивание (преимущественно электродного) при дуговой сварке в среде СОД составляют около -0—5 %, а при сварке в СОД+Аг — 5-Р %. Примерно -0-30 % образующихся брызг расплавленного металла при сварке на средних режимах в зависимости от физических условий сварки (химсостава электродного металла, длины дуги, угла разделки кромок и др. параметров) налипают и привариваются к рабочим участкам сопел, токоеодводящис мундштуков (НМ), входящих в состав сварочных горелок, а также следящих устройств сварочных автоматов и роботов. Из-за интенсивного забрызгивания рабочих участков сопел, токоеодводящис мундштуков и следящих устройств снижается стабильность процесса сварки и появляються дефекты в наплавленном металле. Средняя температура брызг в момент их контакта с поверхностью сопел или НМ имеет существенный разброс: может быть ниже, выше или соответствовать температуре плавления сплава брызг [4-Г]. Температура зависит от времени пребывания брызг в воздухе, их химсостава, массы, сварочного тока и других параметров. При сварке низкоуглеиодистыс, низколегированных
теплоустойчивых сталей перлитного класса электродными проволоками марки 10ХГ2СМА и 08ХМФА установили наличие в металле брызг соединений БеО, Бе203, Бе304, а также МпО и БЮ2. Причем при увеличении сварочного тока количество Бе304, МпО и БЮ2 в составе брызг возрастает [2-3].
Сопла преимущественно изготавливают из меди, характеризующейся более высоким, по сравнению с другими конструкционными материалами, коэффициентом теплопроводности, что соответственно обеспечивает в них меньшую степень аккумуляции теплоты, чем в соплах из других элементов и сплавов. Соответственно происходит и меньшее их забрызгивание.
Наличие брызг в полости канала сопла вызывает частичную турбулизацию формирующегося здесь потока защитного газа, снижает эффективность защиты расплавленного металла от взаимодействия с атмосферными газами, что способствует образованию пор, газовых пузырей и других дефектов. Приварившиеся и налипшие брызги вызывают ускоренный износ сопел, ТМ и следящих устройств. Снижается стабильность процесса сварки. В сварочных роботах удаление брызг связано с необходимостью использования дополнительных программ, обеспечивающих позиционирование горелок относительно оси свариваемых изделий. Следовательно, снижение интенсивности налипания и приваривания брызг расплавленного металла к рабочим поверхностям сварочных горелок роботов, автоматов и полуавтоматов представляется актуальным.
Для удаления приварившихся и налипших к поверхности сопел брызг расплавленного металла применяют различные механические и пневматические способы [7-9]. Например, в автоматах [7] подвод сжатого воздуха производится устройством, расположенным под бухтой. Имеет смысл продувку сопел сжатым воздухом осуществлять при давлении >0,5 МПа [3]. Представляется целесобразым разработка систем продувки и обдувки сопел горелок автоматов и роботов, позволяющих удалять возможно большее количество брызг расплавленного металла, налипших на их рабочие поверхности.
Налипание брызг расплавленного металла к рабочим поверхностям сопел и ТМ, входящих в состав горелок, а также следящих устройств, обусловлено адгезией, возникающей в течение их физического контакта. Адгезия представляет собой эффект на граничных участках поверхностей двух фаз: брызг расплавленного металла и рабочей поверхности сопел, ТМ, входящих в состав горелок, а также следящих устройств сварочных роботов и автоматов. Потенциал адгезии распространяется также и на когезию.
На поверхности сопел и ТМ, серийно изготовляемых из химически активных меди, латуни, реже из других сплавов, керамики, образуются различные
адсорбционные и оксидные пленки. При соударении брызг расплавленного металла с поверхностью сопел или ТМ на участках контакта такие пленки разрушаются и в результате адгезии брызги прилипают к рабочим поверхностям сопел или ТМ. Величина работы адгезии обусловлена физическими условиями процесса сварки, в т. ч. химсоставом, температурой, шероховатостью рабочей поверхности, структурой контактирующих сплавов и другими факторами.
Процесс забрызгивания рабочих участков сопел и ТМ включает активацию их рабочей поверхности, обусловленную нагревом теплом дуги и налипших брызг. Активация поверхности оказывает каталитическое воздействие на адгезию, когезию и на приваривание брызг, а также обеспечивает на участке контакта брызг с поверхностью (подложки) образование новой фазы. В условиях активации поверхности увеличение скорости реакции между жидкой и твердой фазами находили из уравнения Аррениуса [10]:
1 1 _ЕА /ЯТ
кс.р.= к0 •е А ■ (1)
где к — константа скорости реакции с размерностью обратного времени;
Ср
к0 — постоянная, определяемая физическими условиями контакта брызги с подложкой;
Бд — энергия активации;
Я — универсальная газовая постоянная;
Т — температура.
Химическое взаимодействие жидкой фазы (расплав брызг) и твердой (сплав сопел или ТМ), подвергается температурной и механической активации.
Путем моделирования физических условий налипания брызг определяли свободную энергию твердой фазы на участке ее контакта с жидкой фазой. Допускали, что условия налипания брызг на рабочую поверхность сопел и ТМ являются одинаковыми и брызги в момент контакта не подвергаются деформации. Работу адгезии определяли с использованием данных о смачивании поверхности подложки, учитывали равновесный (краевой) угол смачивания ¥, рис. 1.
Механизм действующих сил между твердой и жидкой фазами рассматривали в одинаковой размерности. При соударении брызг расплавленного металла с рабочей поверхностью образуется краевой угол смачивания ¥, зависящий от химсостава брызг и рабочей поверхности, их температуры, пленок, пылевидного слоя и других факторов, оказывающих влияние на межфазную энергию на границе раздела фаз.
В течение контакта брызг с поверхностью протекает энергетическое взаимодействие между жидкой и твердой фазами, определяемое работой адгезии, характеризуемое свободной энергией на участке их контакта £ тф./жф., что обеспечивает взаимодействие удельных свободных поверхностных энергий твердой фазы отв.ф.. и расплава брызг ож.ф. относительно поверхности. В расчетах учитывали уменьшение удельной свободной межфазной энергии на границе твердая фаза — жидкая фаза у тв.ф./ж.ф . Данная величина входит в энергетический баланс со знаком минус.
Г
Рис. 1. Схема смачивания рабочей поверхности расплавом брызги (капли): 1-рабочая поверхность сопел или ТМ; 2-слой мелких частиц сварочного аэрозоля;
3-брызга (капля)
Запишем
(2)
При £ тв.фУжф < 2 ож.ф происходит неполное смачивание.
С учетом (2) находили
ств.ф -Утв.ф./ж.ф. < сж.ф • отв.ф , определяли из уравнения Юнга, рис. 1.
°тв.ф у тв.ф./ж.ф + h ‘ kc.n.’ аж.ф -ста (3)
где kcn — коэффициент, учитывающий состояние поверхности, в том числе ее
шероховатость;
h — коэффициент, учитывающий химсостав поверхности, ее пористость и особенности слоя сварочного аэрозоля.
Величина ¥ зависит не только от взаимодействия отдельных компонентов, входящих в состав брызг (РеО, Fe2O3, Fe3O4 , Fе и др.), но и от взаимодействия между жидкой и твердой фазами [10].
Определение величины адгезии для конкретных условий сварки определяли с учетом данных о поверхностной и свободных энергиях контактирующих фаз, рассматриваемых сплавов. Допускали, что нет существенных отличий между значениями поверхностных энергий сплавов в жидком и твердом состояниях. Установленные данные учитывали при оценке поверхностных энергий контактирующих пар — брызг расплавленного металла и сопел с предлагаемыми термостойкими покрытиями [6, 11-12]. Взаимодействие
поверхностных энергий контактирующих участков может также способствовать активации адгезии. Наличие на рабочей поверхности сопел или ТМ частиц сварочного аэрозоля, оксидных пленок и других веществ незначительно уменьшает взаимодействие поверхностных энергий и повышает энергию активации поверхности. При значениях шероховатости поверхности сопел или ТМ ~ Rz >20 мкм может происходить деформация брызг и локальное оплавление гребней рабочей поверхности сопел и ТМ, рис.2, что существенно увеличивает интенсивность их забрызгивания.
1
Рис. 2. Схема приваривания брызг к рабочей поверхности сопел и ТМ. Реальная рабочая поверхность с определенными параметрами шероховатости: а) > 20 мкм; б) Я^< 20 мкм; 1 — участки поверхности; 2 — брызга (капля) расплавленного металла;
3 — участки гребней и впадин на рабочей поверхности
Можно показать, что интенсивность приваривания и налипания брызг расплавленного металла на подложку (рабочая поверхность сопел и ТМ) обусловлена степенью различия их химсостава, структуры, а также каталитическим влиянием температуры.
Одновременно возможно меньшая шероховатость поверхности подложки обеспечивает соответственно и уменьшенную интенсивность приваривания и налипания к ней брызг. Считаем, что для предотвращения налипания брызг на рабочую поверхность
подложки следует наносить термостойкое покрытие выдерживающее температуру 1500 °С и более [11-12]. Структура такого покрытия должна оставаться стабильной в условиях физического контакта с брызгами расплавленного металла и не разрушаться при механическом их удалинии.
При уменьшении значений шероховатости от 15 мкм наблюдали соответственно увеличение энергии границ зерен. Интенсивность приваривания и налипания брызг при высоких значениях шероховатости была примерно на 20-25 % больше, чем при низких [3]. Известно, что степень поверхностной энергии контактирующих фаз обусловлена когерентностью их кристаллических структур, а также их ориентацией.
При сварке в СО2 на средних режимах брызги имеют преимущественно сферическую или близкую к ней форму [3, 10]. Отмечали наличие градиента температур по сечению брызг [5, 10]. При значениях температур брызг близких к температуре плавления их сплавов, в момент столкновения брызг с поверхностью сопел или ТМ, наблюдали увеличение контактных участков по сравнению с брызгами, имеющими более низкую температуру. В первом случае отмечали определенную деформацию брызг, т. е. отличие их формы от шаровидной [3].
Незначительная растворимость железа в меди не предотвращает работу адгезии и приваривание брызг к поверхности сопел или ТМ. Интенсивности адгезии способствует также и более высокая поверхностная энергия, локализованная на границах зерен сплавов сопел или ТМ, значение которой несколько повышается в зависимости от уменьшения шероховатости. Для уменьшения адгезии и предотвращения приваривания брызг на поверхность сопел и ТМ целесообразно наносить специальные термостойкие покрытия, не обладающие сродством к сплаву брызг [10-12]
Учитывая, что адгезию при контакте брызг с поверхностью сопел или ТМ можно представить как функцию температуры, работу адгезии определяли с учетом допущений: поверхность брызг являлась окисленной, т. е., в состав поверхностной пленки входили соединения FеО, Fe2Oз, FeзO4 [3, 10]; брызги расплавленного металла имели сферическую форму; на участке раздела фаз, контактирующим с оксидной пленкой, структура металла брызг имела незначительные отличия от структуры по их сечению; увеличение £ при повышении температуры, характеризуемое взаимодействием оксидов железа с медью или ее сплавами обясняли энтальпией связи.
Считая, что пропорция между связями Fе-О и Fе-Сu на поверхности раздела фаз фиксирована и соответствует отношению стехиометрических коэффициентов в оксидах FеО, Fe2Oз, FeзO4 , работу адгезии можно выразить:
£ = 77^(АН 0(Бе) + — • АН Fe(Cu) X ,
^те п
где ^те — площадь, занимаемая молем металла на поверхности раздела фаз;
АН0(Бе) АНре(Си)
, — удельные энтальпии при внедрении кислорода в железо и
железа в медь;
а , п — коэффициенты, определяемые из условий процесса адгезии.
Приваривание брызг расплавленного металла к поверхности сопел или ТМ происходит при сближении их поверхностных участков на расстояния действия межатомных сил сцепления. На участках приваривания разрушаются термически нестойкие или отсутствуют термически стойкие соединения а также покрытия, препятствующие сближению поверхностей контактирующих фаз.
Выводы
С учетом физических условий налипания и приваривания брызг к рабочим поверхностям сопел и ТМ, а также расчетных значений представляется
неободимым использование защитных термостойких покритий, в состав которых входят нитриды и карбиды 11-й группы [11-12], что позволяет предотвратить забрызгивание сопел и ТМ, рис. 3, а также соответственно уменьшить количество исходных дефектов в металле шва сварных соединений.
ш,г
Рис. 3. Зависимость массы брызг расплавленного металла, налипших на рабочую поверхность неохлаждаемых сопел от времени и эксплуатации. Полуавтоматическая сварка в среде СО2 на средних режимах в нижнем горизонтальном положении: 1-штатные сопла из меди; 2-сопла с покрытием [13]; 3-с покрытием [11]; 4-с покрытием [12]
Список литературы
1. Заруба И. И. Механизм разбрызгивания металла при дуговой сварке // Автоматическая сварка. — 1970. — С. 12-18.
2. Кицуки М., Хасигути К. Об образовании брызг при электродуговой сварке в среде углекислого газа//Есэцу гидзюцу. — 1984. — № 2. — С. 76-78.
3. Дмитрик В. В., Акулов А. И. Снижение забрызгивания сопл горелок для сварки в углекислом газе//Сварочное производство. — 1991. — № 2. — С. 27.
4. Федько В. Т., Киянов С. С. Формирование и теплообмен брызг расплавленного металла в процессе сварки в СО2 //Сварочное производство. — 1992. — № 3. — С. 29-31.
5. Походня И. К., Суптель А. М. Теплосодержание капель при сварке в углекислом газе//Автоматическая сварка. — 1970. — № 7. — С. 12-18.
6. Дмитрик В. В., Пузиков В. М., Семенов А .В. К разработке термостойких покрытий сопл и мундштуков сварочных горелок// Сварочное производство. -1993. — № 7. — С. 25-27.
7. Масек А. Н1а]еп]е іп і2рікауап]е уогііпе §1ауе 2а ші§-ша§ уаце^е па ауіюшаїи іп гоЬоШ//Уагі1па/-1983. — № 3. — Р. 73-76.
8. Способ очистки сопл горелок: А. с.1504029 СССР, МКИ В23К 9/16/М. Г. Фридлянд, А. К. Сторчак, Н. В. Потанина, В. А. Першин, П. А. Новыш, А. В. Пилипенко (СССР), -№4217637/27-27; Заявлено 31.03.87; — 0публ.30.08.89; Бюл. № 32. — 3 с.
9. Устройство для удаления брызг с горелки при дуговой сварке: Заявка 63309379, Япония, МКИ В23К 9/16/Мацуи Хитосия (Япония) № 63309379; -Заявлено 12.01.87; -Опубл. 16.12.88/Кокай токе кохо. — Сер.2(2). — 1988. — № 78. — С. 455-458.
10. Данильченко Б. В., Дмитрик В. В. Способы уменьшения забрызгивания сопл и токоподводящих мундштуков сварочных горелок//Сварочное производство. -1995. — № 9.- С. 22-24.
11. Патент на винахід № 65027, МКИ В23К 35/36. Термостійке покриття і спосіб його одержання //Семенов О. В., Пузіков В. М., Дмитрик В. В. (Україна), Бюл. № 4, 2006 р., 4 с.
12. Патент на винахід № 93108, МКИ В23К 35/36. Термостійке покриття і спосіб його одержання// Лобанов Л. М., Пузіков В. М., Семенов О. В., Дмитрик В. В., Царюк А. К., (Україна), Бюл. № 1, 2011р., 5 с.
13. Aerodag CERAMISШELD //Сварщик. — 2011. — № 1 (77). — С. 27.
TO FORMATION OF SPARKS OF MOLTEN METAL AT ARC/W IN ENVIRONMENT OF CARBON GAZA
V. V DMITRIK, D-r Scie. Tech, Pf.
A. V GLUSCHKO
The features of the formation mechanism of the spray of molten metal during arc welding of carbon dioxide in the environment and splashing on the working surfaces of the nozzles and welding current-supplying mouthpieces burners.
Поступила в редакцию 15.11 2011 г.
КЛАССИФИКАЦИЯ МЕТОДОВ СНИЖЕНИЯ РАЗБРЫЗГИВАНИЯ ПРИ СВАРКЕ
Рис. 14.3. Схемы постов для сварки в защитных газах: а — неплавящимся электродом в инертных газах на постоянном токе прямой полярности; б — то же, на переменном токе; в — плавящимся электродом на постоянном токе обратной полярности |
В УГЛЕКИСЛОМ ГАЗЕ
Разбрызгивание электродного металла при сварке в СО2 является одним из основных недостатков этого способа сварки. Разбрызгивание сопровождается увеличением расхода электродной проволоки и защитного газа, забрызгиванием поверхности свариваемых деталей и деталей сварочной горелки. Все это приводит к увеличению себестоимости сварочных работ за счет увеличения затрат на материалы и повышению трудоемкости вследствие затрат труда на зачистку от брызг.
Основными причинами разбрызгивания является:
*■ увеличение размера капель электродного металла при повышении напряжения;
* недостаточная стабильность процесса сварки;
* реактивные силы, выталкивающие каплю металла из зоны сварки в начале короткого замыкания;
* интенсивное газовыделение в объеме жидкого металла капли и сварочной ванны, сопровождающееся взрывообразными выбросами расплавленного металла из сварочной ванны;
* газодинамический удар при разрушении перемычки между электродом и переходящей в сварочную ванну каплей при сварке с короткими замыканиями.
В настоящее время проблема снижения разбрызгивания является актуальной и работы, направленные на ее решение, ведутся в различных направлениях.
Все известные методы снижения разбрызгивания можно разделить на два направления.
1. Химические методы:
* использование газовых смесей для защиты зоны сварки;
* двухслойная защита;
* использование активированных и порошковых проволок.
2. Энергетические методы (методы, влияющие на энергетические процессы сварки):
* подбор режимов;
* импульсно-дуговая сварка;
* сварка пульсирующей дугой;
* сварка с принудительными короткими замыканиями;
* синергетические системы управления параметрами режима;
* импульсная подача сварочной проволоки.
Сварка в смесях защитных газов. Сущность способа состоит в том, что при изменении химического состава защитного газа в существенной степени изменяются физические и металлургические процессы сварки. Это проявляется, во-первых, через окислительную способность защитной среды, во-вторых, через ее теплофизические свойства, влияющие на дугу.
Инертные газы обладают рядом особенностей: отсутствием диссоциации и отрицательных ионов, низким напряжением горения дуги благодаря наличию метастабильных уровней возбуждения и ступенчатой ионизации. В зависимости от применяемого инертного газа изменяются поверхностное натяжение и размер капель электродного металла. А также коэффициент расплавления электрода.
Для дуги в углекислом газе характерны высокие значения теплопроводности и градиента потенциала в столбе дуги. Применение СО2 связано с нестабильностью горения дуги, вызванной силой, отталкивающей каплю вверх и в сторону, действующей против направления переноса металла и создаваемой высоким давлением газа внутри столба струями пара с поверхности сварочной ванны, ударяющими в каплю.
Рассмотрим влияние компонентов газовой среды на примере смеси для высокого производительного процесса TIME. Обычно используют 65 % Аг + 26,5 % Не + 8 % С02 + 0,5 % О2.
Добавка гелия увеличивает потенциал ионизации и градиент потенциала в столбе дуги. Благодаря этому возрастают напряжение и энергия дуги. Плазменный поток становится более мощным и стабилизирует дугу.
Добавка О2 к аргону повышает стабильность горения дуги и улучшает перенос металла, уменьшая разбрызгивание. Добавка кислорода к углекислому газу улучшает отделение брызг от основного металла, улучшает внешний вид шва и снижает склонность к образованию пор при сварке металла, покрытого ржавчиной.
Предлагается рассмотривать действие парамагнитных сил и положительной магнитной восприимчивости кислорода и других газов на критическое значение тока перехода к струйному переносу. Предполагается, что наличие парамагнитного газа усиливает действие электродинамической силы, что приводит к уменьшению критического значения тока. Кроме того, существует возможность сепарации компонентов газовой смеси и концентрация кислорода вблизи расплавленной капли под воздействием магнитного поля, что снижает поверхностное натяжение металла.
Преимущества данного способа:
1) снижение уровня разбрызгивания;
2) переход к струйному переносу;
3) снижение уровня критического тока;
4) меньшая восприимчивость к качеству поверхности свариваемых
изделий.
Недостатками же сварки в смесях защитных газов являются:
1) смеси на основе аргона дорогостоящие;
2) невозможность длительного хранения готовых смесей газов;
3) повышенная окислительная способность атмосферы;
4) отсутствие управляемости процесса (отсутствие управляемого переноса).
Двухслойная защита. Сущность заключается в использовании двух потоков защитного газа: внутреннего, по которому подают аргон, для улучшения защиты и уменьшения сжатия столба дуги и наружного, по которому подают углекислый газ. Подобная защита сварочной дуги обеспечивает стабильность горения дуги с минимальным разбрызгиванием.
Использование активированных и порошковых проволок.
Сущность процесса состоит в том, что в зону сварки посредством проволоки вносятся некоторые химические элементы, влияющие на теплофизические свойства сварочной дуги.
При сварке проволоками различных систем легирования наибольшее влияние на характеристики переноса электродного металла оказывает кремний. Другие элементы, как алюминий, титан, молибден, марганец, хром, никель и т. п., располагаются в соответствии с их способностью изменять поверхностное натяжение расплавленного металла.
При нанесении на поверхность проволоки покрытий, состоящих из тонкого слоя солей щелочных и щелочноземельных металлов (соли цезия + соли калия; соли цезия + соли натрия; растворов углекислого калия, а также оксиды других металлов Fe304, СеО2), расширяются технологические возможности процесса сварки в результате повышения стабильности горения дуги и снижения разбрызгивания.
Наличие в сварочной дуге легкоионизируемых щелочных металлов резко уменьшает диаметр столба дуги, а площадь активных пятен расширяется. Электромагнитная сила способствует отрыву капель электродного металла.
Введение в электродную проволоку шихты, состоящей из 10 % К2С03; 10 % Ка2СОз; 5 % CaF2 (остальное двуокись титана) благоприятно сказывается на стабильности горения дуги и характере переноса металла. Применение активаторов на основе титана снижает разбрызгивание до 50 %.
К недостаткам активированных покрытий можно отнести его осыпание с поверхности проволоки. Эта проблема решается нанесением покрытия в процессе сварки при помощи специального устройства, устанавливаемого на сварочную горелку.
Существуют технологии изготовления проволок, поверхность которых насыщена кислородом, который увеличивает стабильность горения дуги и уменьшает разбрызгивание до 3% за счет снижения силы поверхностного натяжения.
С целью повышения стойкости против атмосферной коррозии, на проволоку наносят покрытие черный хром. Данное покрытие не только защищает проволоку от коррозии, но и снижает разбрызгивание и потери электродного металла.
Порошковые проволоки широко применяются для производства сварных изделий благодаря хорошим технологическим свойствам. Это направление сварочной техники широко развивается как в нашей стране, так и за рубежом. Флюс, входящий в состав порошковых проволок позволяет вводить в зону сварки компоненты, улучшающие стабильность горения дуги, улучшающие формирование шва, обеспечивающие минимальные потери металла на угар и разбрызгивание, и позволяет применять различные системы легирования.
Подбор режимов. Стабильность процесса, качество формирования шва и разбрызгивание электродного металла зависят от правильного выбора параметров режима сварки. При правильно подобранных режимах, когда скорость подачи равна скорости плавления, разбрызгивание не превышает 6-10 %.
Для каждого диаметра проволоки имеется диапазон так называемого критического тока, при котором разбрызгивание увеличивается примерно в два раза. Эти режимы применять нерационально.
Импульсно-дуговая сварка. Способ заключается в наложении на дежурную дугу импульсов большого тока. Применяются два основных способа управления переносом металла при импульсно-дуговой сварке плавящимся электродом. В первом случае расплавление конца электрода и формирование на его торце капли необходимого размера происходят во время протекания, так называемого, базового тока. При наложении тока на дугу он только отрывает образовавшуюся ранее каплю от электрода. Во втором случае плавление и отрыв капли осуществляются одним и тем же импульсом тока. Базовый ток в этом случае служит только для поддержания горения дуги в промежутках между импульсами тока и практически не расплавляет проволоку. Само наложение импульсов, представляющих собой управляющие воздействия, существенно стабилизирует процесс сварки, так как компенсирует действие возмущений, вызываемых капельным переносом металла, блужданием активного пятна (особенно при малых токах) вследствие электромагнитных, тепловых и других влияний газовых потоков в дуге. Однако наблюдаются колебания основных энергетических параметров процесса — средних значений напряжения на дуге и сварочного тока. Эти изменения происходят при действии на дугу как внешних возмущений (колебания напряжения питающей сети, скорости подачи электродной проволоки из-за несовершенства подающих механизмов, неравномерность движения руки сварщика), так и закономерно возникающих в зоне сварки во время плавления электродной проволоки. В результате могут нарушаться стабильность процесса и геометрические размеры шва. Это, в конечном счете, ухудшает качество и уменьшает производительность сварки, а также не дает возможности вести процесс во всех пространственных положениях.
Сварка пульсирующей дугой. Сущность процесса заключается в том, что скорость и количество вводимой в изделие энергии определяется не только режимом сварки, но и периодичностью пульсации сварочного тока. Последний, в свою очередь, задается в зависимости от теплофизических характеристик металла, типа соединения, геометрии и пространственного положения шва. При этом сварочный ток может изменяться от максимальной величины до минимальной или до нуля, а частота пульсации — от десятых долей до нескольких секунд. Это обуславливает следующие преимущества данного способа сварки:
а) возможность реализации на стандартном оборудовании;
б) электрические параметры дуги изменяются плавно по показательной функции, что способствует более рациональной отдаче тепла изделию;
в) плавная пульсация мощности дуги обуславливает плавное изменение ее давления: чем больше объем сварочной ванны, тем медленнее нарастает давление на жидкий металл, что предотвращает выплески его, прожоги, снижает разбрызгивание;
г) благодаря периодическому снижению мощности дуги и кристаллизации, в этот период ванны облегчается сварка в различных пространственных положениях;
д) специфические условия структурообразования сварных соединений при сварке пульсирующей дугой обеспечивают высокие пластические свойства сварных соединений.
Но также можно выделить следующие недостатки.
Процесс сварки пульсирующей дугой протекает с многократными повторами нагревов и охлаждений в интервале температур превращений аустенита, которые усугубляют химическую и структурную неоднородность металла ЗТВ. Усиление неоднородности происходит в результате того, что в условиях многократных охлаждений периодически образуются и растворяются сложные агрегаты, включающие различные структурные составляющие. В общем случае могут образовываться феррит с различной степенью перенасыщения углеродом, карбиды, выделяющиеся как из феррита, так и из аустенита.
При сварке с пульсирующей дугой воздействие в основном ориентировано на сварную ванну. Процесс не управляет переносом металла. Снижение разбрызгивания является косвенным следствием.
Сварка плавящимся электродом с принудительными короткими замыканиями. Сущность данного способа заключается в том, что на интервале горения дуги в импульсе происходит интенсивное расплавление торца электрода и свариваемой детали. При этом вследствие силового воздействия дуги металл сварочной ванны вытесняется в хвостовую часть и удерживается там в течении всей стадии плавления. По истечении заданного времени горения дуги в импульсе производят ступенчатое уменьшение сварочного тока до значения тока паузы. Это приводит к соответствующему снижению скорости плавления электрода и ослаблению силового воздействия дуги на сварочную ванну, которая стремится в этот момент заполнить кратер, образовавшийся под торцом электрода на стадии действия импульса тока. Одновременно с этим капля под действием сил тяжести и поверхностного натяжения стремится занять соосное с проволокой положение.
В результате этих встречных взаимонаправленных движений происходит принудительное короткое замыкание, в начальный момент которого в сварочной цепи производят увеличение тока, что позволит значительно повысить скорость нарастания тока короткого замыкания и тем самым ускорить образование и разрушение жидкой перемычки, причем на протяжении всей стадии короткого замыкания.
К преимуществам данного способа можно отнести: данный способ реализует управляемый перенос металла, что позволит управлять параметрами определяющими его; снижение объема сварочной ванны, а, значит, облегчение сварки в различных пространственных положениях; стабилизируется процесс горения дуги;
снижается перегрев капли, что снижает выгорание элементов из металла;
снижаются сварочные деформации;
ширина зоны разупрочнения снижается в ряде случаев 3…4 раза.
К недостаткам можно отнести:
1) необходимость использования в комплекте сварочного образования специальных сильноточных импульсных регуляторов сварочного тока с малой инерцией;
2) необходимость использования большого количества обратных связей для управления каплеобразованием.
Имульсно-дуговая сварка с синергетическим управлением параметрами режимов. Выбор оптимальных параметров импульсов тока при сварке с синергетическим управлением базируется на следующих трех основных требованиях:
* для любой скорости подачи электродной проволоки параметры являются целью поддержания постоянной длины дуги;
*■ базовый ток должен обеспечивать стабильное горение дуги в паузе;
* для заданной скорости подачи электродной проволоки амплитуда, длительность и частота следования импульсов тока, а также значение базового тока автоматически устанавливаются таким образом, чтобы за каждый импульс тока отделялась одна капля электродного материала.
Таким образом, можно сказать, что сущность данного процесса заключается в том, что для любой скорости подачи электродной проволоки параметры импульсов тока, а также значения базового тока и длительность паузы строго соответствуют скорости плавления электрода.
При этом обеспечивается мелкокапельный перенос металла по принципу: один импульс — одна капля электродного металла. Применение синергетического управления обеспечивает: простоту выбора и переналадки оптимальных параметров режима сварки;
стабильность горения дуги при изменении скорости подачи проволоки, вылета электрода и напряжения сети;
облегчение формирования шва во всех пространственных положениях;
качественную заварку кратера и благоприятное начало шва; меньшую чувствительность сварных соединений к термическому разупрочнению металла околошовной зоны; возможность использования проволок увеличенного диаметра; меньший расход электродной проволоки на единицу длины шва.
К недостаткам импульсно-дуговой сварки с синергетическими системами управления параметрами режимов можно отнести: использование относительно низкой погонной энергии; необходимость в тщательной зачистке кромок от ржавчины, окалины, масла и краски во избежание образования дефектов сварного соединения;
* более высокая стоимость оборудования и затрат на его эксплуатацию, ремонт.
Импульсная подача сварочной проволоки. Сущность процесса сварки с импульсной подачей сварочной проволоки заключается в программировании скорости подачи электродной проволоки по законам, обеспечивающим контролируемый перенос капли расплавленного электродного металла в жидкую сварочную ванну.
В основу процесса дуговой сварки с импульсной подачей электродной проволоки положено использование дополнительной силы, которая прикладываясь к капле, резко изменяет характер плавления и переноса электродного металла аналогично импульсу электродинамической силы при импульсно-дуговом процессе. В данном случае дополнительной силой выступает сила инерции, действующая в период торможения электрода.
Дозирование переносимого металла происходит за счет установки оптимальных значений шага подачи и частоты следования импульсов.
Данный способ имеет ряд преимуществ по сравнению с постоянной подачей электродной проволоки:
1) осуществляется управляемый перенос металла;
2) меньшее выгорание элементов из расплавленного металла в результате уменьшения времени пребывания капли на торце электрода;
3) снижение разбрызгивания происходит за счет совместного действия силы поверхностного натяжения, действующей со стороны сварочной ванны, и остатков кинетической энергии капли, которая способствует увеличению скорости втягивания капли и одновременно утонению перемычки, вследствие чего при ее взрыве вместо брызг образуются искры.
Вследствие вышесказанного можно сделать вывод, что наиболее перспективными методами снижения разбрызгивания в настоящее время являются методы, обеспечивающие управляемый перенос расплавленного металла, а именно: импульсно-дуговые процессы и процесс сварки с импульсной подачей сварочной проволоки.
Аксессуары для ухода за сварочными столами Siegmund
Сварочно-сборочные столы Siegmund обладают высокой, а в некоторых сериях экстремально высокой устойчивостью к негативным воздействиям. Однако, чтобы сохранять их в хорошем состоянии долгие годы, необходим регулярный уход и очистка поверхности.
Это касается даже самых стойких моделей, ведь грязь не должна сопровождать качественный монтажный и сварочный процесс. Разработчики Siegmund предлагают доступные и удобные средства ухода за сварочными столами, которые помогут продлить срок их эксплуатации на долгие годы и обеспечат правильные производственные условия.
Основные мероприятия по уходу за поверхностью стола
Уход за сборочно-сварочным столом состоит из нескольких важных компонентов:
— защита от сварочных брызг;
— очистка от жирных загрязнений;
— выравнивание поверхности;
— ежедневный уход.
Ни один из компонентов невозможно исключить из повседневных задач. Однако, Sigmund понимает, что тратить на них много времени является нецелесообразным, поэтому предлагает линейку высокоэффективных средств для защиты и очистки сварочного стола. Все жидкие средства могут доставляться в удобных бутылках с распылителем или насосом. Если на предприятии используются собственные емкости для распыления, то возможно приобретение жидких средств в экономичных канистрах до 33 кг.
Средства не содержат агрессивных компонентов, способных повредить металлическую поверхность. Напротив, их использование усиливает антикоррозийную защиту сварочно-монтажного стола. Высокая эффективность обеспечивает небольшой расход и быстрое удаление загрязнений без тяжелых усилий.
Финансовые затраты на закупку компенсируются долгим сроком эксплуатации и минимальным временем, которое потребуется на уход за поверхностью стола. Не менее важным является забота о безопасности рабочих при использовании средств ухода и защита окружающей среды.
Защита от сварочных брызг
Сварочные брызги – неизбежный источник негативных воздействий на материал столешницы. Брызги представляют собой маленькие частицы расплавленного металла, которые твердеют при застывании, а значит, удалить их с поверхности стола или изделия становится очень трудно. Перед выполнением работ необходимо заранее обработать столешницу специальным раствором против прилипания.
Siegmund предлагает не горючее и не токсичное средство, которое разбавляется водой. Оно предназначено для обработки столешницы и свариваемых деталей из стали, оцинкованной стали, нержавеющей стали, алюминия. После выполнения сварки брызги будут легко удаляться с поверхности стола и изделия.
Особыми преимуществами средства от брызг Siegmund являются:
— эффективность даже в сухом состоянии: не требуется постоянно сбрызгивать поверхность во время длительных сварочных процессов.
— дополнительная защита поверхности от коррозии.
Для нанесения можно использовать распылитель, кисть или щетку. При условии ежедневного использования расход средства на 1 кв. метр составит всего 20-30 евро в год. В качестве емкостей предлагаются: бутылка, бутылка с распылителем, бутылка с насосом (емкость 1 кг), канистра (емкость 5 кг), канистра (емкость 33 кг).
Очистка стола
1. Удаление жира. При сварке и сборке деталей на поверхность стола нередко попадает техническое масло и другие жирные загрязнения. Для удаления подобных компонентов Siegmund разработали специальное средство, которое можно разбрызгивать на поверхности. Его сильный чистящий эффект позволит удалять загрязнения за считаные минуты, не тормозя производство.
При длительном хранении средство частично диффундирует в пластиковые емкости, что приводит к небольшому уменьшению объема. Гарантия эффективности состава составляет 1 год. В качестве емкостей можно выбрать бутылку с распылителем (500 мл), канистру (5 л).
2. Ежедневный уход. Простое средство ежедневного ухода CleanBasic на водной основе дополнено антикоррозийными компонентами. Внимание! При высокой влажности, когда возникновение коррозии неизбежно следует прекратить использовать средство на водной основе. Емкости: бутылка (1 кг), бутылка с распылителем (1 кг), канистра (5 кг), канистра (33 кг).
Обратите внимание! Очистку отверстий столов будет удобно выполнять специальным ершиком Siegmund, который разработан с учетом их диаметра.
Выравнивание поверхности
Комбинированный оселок – специальное приспособление, которое позволяет выравнивать поверхность стола и удалять повреждения от сварки. Для этих целей не подходят традиционные абразивы, угловые шлифовальные машины, зубчатые шайбы. Оселок состоит из двух слоев шлифовального материала: один – для очистки загрязнения, другой – для финишного выравнивания.
Средства по уходу за сварочными столами Siegmund разработаны с учетом огромного опыта производителя и сбора сведений по особенностям эксплуатации на самых разных производствах. В результате удалось добиться оптимального соотношения функциональности и предложить небольшое количество средств без лишних дорогостоящих компонентов.
Надежность сварочно-сборочных столов Siegmund подтверждена многочисленными испытаниями. Одно из них вы найдете на следующем видео:
о всем вопросам, касающимся нашего оборудования, специфике его работы, стоимости, а так же любым другим вопросам, обращайтесь к нашим специалистам
по телефонам +7 (495)787-49-12, 8-800-500-49-12
электронной почте [email protected]
Так же Вы можете связаться напрямую с интересующим Вас специалистом, посмотрев его контакты в разделе «Наши сотрудники» по ссылке
Будем рады ответить на все возникшие вопросы!
Объяснение брызг при сварке
У этого кошмара несколько причин. Наиболее известные:
- Качество сварочного материала.
- Качество свариваемого наполнителя
- Настройки сварочного аппарата
- Сварочная техника использовалась
- Сварочный газ
Давайте углубимся дальше и посмотрим, как каждая из этих причин приводит к разбрызгиванию, прежде чем мы посмотрим, как уменьшить это неудобство.
- Качество сварочного материала
Сварщики арматуры могут ошибочно подумать, что все сварочные материалы одинаковы.Это не правда. Качество свариваемого материала является основным фактором, определяющим величину разбрызгивания во время сварки.
Качество в этом контексте включает состав материала, степень его чистоты и качество материала, из которого он уголь. Давайте разберемся с этим.
i) Состав сварочного материала
Не все металлы предназначены для сварки. Некоторые материалы содержат дополнительные компоненты, которые не подходят для сварки. Вы также можете найти недорогой материал, продаваемый в качестве сварочного материала, хотя на самом деле это не так.Вместо этого такой материал содержит несколько дешевых добавок, добавляемых в процессе изготовления сердечника. Эти примеси и совершенно неподходящий материал являются основной причиной разбрызгивания.
Как уменьшить разбрызгивание по этой причине?
Не используйте такой материал. Вместо этого возьмите новый металлический материал, который будет давать как можно меньше брызг. Что произойдет, если это единственные материалы, которые у вас есть для выполнения работы? Прочтите и получите советы в разделе «Другие решения», которые помогут вам минимизировать эту угрозу.
ii) Качество металлического покрытия
Возможно, у вас правильный металл, но вы все равно будете разбрызгивать его. Проблема может заключаться в материале покрытия, используемом для покрытия металла. Оцинкованные покрытия, хром, резина, цинк и любые другие покрытия обязательно приведут к разбрызгиванию.
Чем больше вы избегаете металла с покрытием, тем лучше для вас. К сожалению, это не всегда так. Но обратите внимание, что предварительно загрунтованная сталь разработана без этих загрязнений и, следовательно, не добавит проблем с разбрызгиванием при сварке.
Решение
Используйте шлифовальный станок, чтобы избавиться от проблемного покрытия. Если сделать это перед сваркой, останется чистая поверхность, на которой будет гораздо меньше брызг. Чтобы быть в безопасности и добиться лучших результатов, отшлифуйте как минимум три четверти (¾) дюйма вокруг свариваемой поверхности.
iii) Грязный металл
Любые другие загрязнения на поверхности металла шва, кроме покрытия, вызовут разбрызгивание. Не имеет значения, является ли причиной оскорбления жир, грязь, пыль или линии маркера, пока оно находится на сварочном материале, оно вызывает разбрызгивание.
Решение
Загрязненный сварной шов — проблема. Итак, убедитесь, что ваш сварной шов чистый, прежде чем приступить к работе. Это действительно требует сложного процесса очистки; быстрое протирание чистым ковриком поможет и избавит вас от мучений из-за брызг.
Вы проверили качество материала, но это не гарантирует, что во время сварки не будет брызг. Вам нужно посмотреть на следующий компонент.
- Проблемы со свариваемым наполнителем
Это соединительный материал, размещенный в месте сварки.Это помогает соединить сварной шов. Если вы сделаете компромисс с качеством этого наполнителя, проблемы с разбрызгиванием все равно будут выглядеть некрасиво.
Некоторые проблемы с наполнителем могут привести к разбрызгиванию. К ним относятся:
i) Некачественный наполнитель
Пока вы используете некачественный наполнитель, вы еще не выбрались из леса. Будьте внимательны при выборе сварочного наполнителя. Некоторые производители этих расходных материалов выпускают недорогие наполнители. Многие из этих фильтров добавили компоненты, не имеющие отношения к сварке.
Хотя такие наполнители и будут служить цели, они будут вызывать дополнительное разбрызгивание из-за дополнительных компонентов.
Решение
Убедитесь, что применяемый свариваемый присадочный материал имеет хорошую репутацию и имеет правильный состав для получения чистых сварных швов. Неважно, что более качественные наполнители будут стоить дороже, но они того стоят.
Загрязненный наполнитель
Возможно, проблема с наполнителем не у производителя.На самом деле проблема даже не в оригинальном качестве наполнителя. У тебя могут быть проблемы.
Если вы оставите наполнитель без крышки, наполнитель будет загрязнен грязью, маслом, пылью и другими загрязнителями окружающей среды. Все эти нежелательные гости прикрепятся к сварному шву и шокируют вас.
Решение
Прикрывайте наполнитель и другие расходные материалы каждый раз, когда они не используются. Это предотвратит прилипание загрязнений к наполнителю.Один наполнитель, который может вас не так сильно беспокоить, — это стержни из нержавеющей стали. Эти наполнители не ржавеют. Однако, если вы продолжаете позволять им оставаться снаружи в течение некоторого времени, вам необходимо протереть их, прежде чем использовать их для сварки.
Стальная пыль, хотя и от стали, может вызвать ржавление стержней из нержавеющей стали и загрязнение сварных швов. Это загрязнение повлияет на работу вашего сварочного аппарата и приведет к образованию брызг. Во избежание этого рекомендуется держать стержни подальше при шлифовании стали.
Вы позаботились о сварочном материале и присадочном материале, но теперь можете ли вы успешно сваривать, не получая брызг от работы? Еще нет. Есть еще кое-что, что нужно учесть.
- Настройки сварщика
Сварочные аппараты MIG
У сварщиковесть настройки, которые используются для регулирования работы аппарата. Просматривая руководства пользователя для сварочных аппаратов MIG, , вы найдете рекомендации по скорости подачи проволоки, скорости потока газа и настройкам мощности.
Распространенной причиной разбрызгивания в настройках является неравномерность подачи проволоки в аппарате или чрезмерная скорость. Если присадочная проволока попадает в сварочную ванну, разбрызгивание становится неизбежным. Почему?
Сильный нагрев расплавляет сплошную проволоку, и при этом присадочная проволока становится жидкой и образует лужу. Если сталь будет достаточно холодной, это повлияет на реакцию проволоки на тепло. Когда проволока касается бассейна до того, как она расплавится и разбрызгивается, она вызывает хлопок и брызги.
Это означает, что для минимизации разбрызгивания сварочный аппарат должен быть достаточно горячим, чтобы расплавить проволоку перед попаданием в лужу в нужном месте.
Настройки SWAW
Необходимо правильно настроить параметры дуговой сварки экранированных металлов (SMAG). Нагрев должен быть подходящим для стержней и толщины металла. Слишком холодное оружие приведет к неправильной сварке. В этом случае это будет что-то среднее между наклеиванием и сваркой.Это, в свою очередь, вызовет чрезмерное разбрызгивание, ужасный сварной шов, не говоря уже о неприятном процессе.
Настройки скорости — важный вопрос, который следует учитывать. Установите скорость так, чтобы ее было достаточно, чтобы уменьшить разбрызгивание
Решение
Возьмите немного чистого металлолома и потренируйтесь, регулируя настройки MIG и SMG до уровня, который они не добавляют к получаемым брызгам. Помните, что рекомендации производителя не всегда могут уменьшить разбрызгивание в этом случае, поэтому доверьте свой метод проб и ошибок, чтобы получить наиболее удобные настройки для вашего проекта.
- Сварочная техника
Значит, даже после того, как все сделано правильно, у вас все еще есть личная роль? Большинство людей думают, что сварка — это просто направить сварщика к металлу, и вот оно что. Это не так. То, как вы свариваете, может иметь значение, получаете ли вы полное разбрызгивание или минимальное или почти нулевое разбрызгивание. Знание и использование правильных методов сварки имеет решающее значение, если вам приходится бороться с брызгами. Давайте выделим две категории методов, которые помогут вам добиться минимального разбрызгивания.
i) Методы сварки MIG
Стреляйте по металлу из горелки MIG, наклоненной под углом 20 градусов, и скажите мне, что вы не получите супер-брызг. Короче говоря, вам нужно выбрать правильный угол. Это не только изменяет глубину проплавления сварного шва, но также определяет величину разбрызгивания, которое вы производите.
Итак, какой угол лучше? Здесь нет жестких правил, но углы круче 15 градусов будут давать больше брызг.Вы можете себе представить, какое количество брызг можно получить при угле наклона 5 градусов.
Помимо постоянной скорости подачи проволоки, два других фактора определяют количество образующихся брызг. Это твердая рука и обезьяна движения газа. Если вы хотите уменьшить разбрызгивание, найдите правильную скорость, угол и линию и соблюдайте их.
ii) SWAW методы
СваркаSWAW требует меньшего количества методов для достижения меньшего количества брызг. Например, при нажатии будет меньше брызг, чем при нажатии.Так что знайте, когда нужно нажимать, и делайте это. Всегда используйте правильную скорость движения и придерживайтесь наилучшей скорости, обеспечивающей минимальное разбрызгивание.
- Сварочный газ
Все сварочные газы одинаковы? Не совсем. Есть разные газы, которые можно использовать для сварки. Все делают то, что должны, но результаты разные. Некоторые обычно используемые сварочные газы — это чистый аргон, чистый CO2 и смесь аргона и CO2.
Итак, в чем разница и как она влияет на брызги?
Чистый аргон
Этот газ в основном используется для сварки алюминия методом MIG и нержавеющей стали.Известно, что этот сварочный газ выделяет некоторое количество брызг. Если вы используете этот газ и заметили брызги, проблема может заключаться не во всех перечисленных выше причинах. Это могло быть виновником.
Чистый CO2
Этот газ довольно популярен благодаря относительно невысокой стоимости. Газовое оборудование глубокое проникновение и неплохо экранирует. Единственным недостатком является то, что он производит гораздо больше брызг, чем чистый аргон. Итак, опять же, если вы поддерживаете все остальные факторы постоянными, но все еще видите брызги, причиной может быть CO2.
- Смесь аргона и CO2
Этот гибридный газ поставляется в различных смесях, каждая из которых лучше всего подходит для определенных видов сварки MIG. Как показывает практика, чем толще сталь, тем выше содержание CO2 в газе, используемом для сварки металла.
Методы, описанные выше, безусловно, помогут уменьшить разбрызгивание при правильном использовании. Однако это не единственные методы, которые вы можете использовать. При использовании с другими не менее мощными методами вы можете еще больше уменьшить количество брызг.Обратите внимание на следующее.
Используйте сварочные аппараты со специальными функциями
Достижения в технологии сварочных аппаратов привели к появлению сварочных аппаратов с функциями, которые минимизируют или практически исключают разбрызгивание. Ультравысокоскоростная электроника позволила разработать источники сварочного тока, ориентированные на уменьшение разбрызгивания.
.Лучшие 4 исправления • WelditU
0
Как начинающий сварщик-любитель, я получал больше брызг вокруг сварных швов, чем ожидалось — иногда на намного больше!
Мои навыки шлифования улучшились быстрее, чем навыки сварки, поэтому мне нужно было научиться уменьшить разбрызгивание при сварке MIG.
Я обнаружил, что основные причины чрезмерного разбрызгивания сварочного шва делятся на четыре категории. Ниже вы найдете дополнительные советы по устранению неполадок, а вот контрольный список, который я использую, чтобы уменьшить брызги при сварке MIG.
Контрольный список: как уменьшить разбрызгивание при сварке MIG
- Проверка на наличие загрязненных материалов: Тщательно очистите и подготовьте заготовку. Очистите или замените грязный или ржавый провод.
- Проверка техники сварки: Угол пистолета не должен превышать 5-15 ° от вертикали. Держите выступ на ⅜ дюйма. для MIG и ½ дюйма. для порошковой проволоки.
- Проверьте настройки сварочного аппарата: Используйте правильную полярность . Уменьшите скорость подачи проволоки и / или напряжение.
- Проверьте оборудование на наличие проблем: Неустойчивая подача проволоки, плохое соединение рабочего зажима, недостаточный защитный газ, изношенный или слишком большой контактный наконечник.
Что такое брызги при сварке MIG?
Брызги при сварке MIG, иногда называемые брызгами, содержат капли расплавленного сварочного материала. Некоторые капли, возникающие вокруг сварочной дуги, выбрасываются за пределы сварочной ванны. Когда расплавленные капли приземляются и остывают, остаются брызги.
Вот короткое 30-секундное видео, в котором крупным планом видна грубая дуга, образующая чрезмерное разбрызгивание.Когда вы видите бурную активность в сварочной ванне, легче понять, откуда взялись все эти брызги.
При сварке MIG, особенно в режиме короткого замыкания, вопрос не в том, будут ли брызги, а в их количестве.
Если ваша сварочная дуга стабильная и гладкая, капельки брызг могут быть настолько мелкими, что могут быть всего лишь помехой . Но если дуга излучает и лопается, количество брызг может быть значительным. Вы можете обнаружить капли брызг размером с BB, которые придется стачивать долотом или стачивать с заготовки.
Брызги сами по себе не повлияют на целостность сварного шва, если вы не приварите их к многопроходному стыку. В основном это косметическая проблема, но основная причина разбрызгивания может снизить прочность сварного шва.
Настройки машины для уменьшения брызг при сварке MIG
Легко забыть изменить полярность при переключении с порошковой проволоки на сплошную. Если у вас грубая дуга и за пределами сварного шва остается столько присадочного материала, сколько необходимо для сварки валика, еще раз проверьте полярность.Это случается со всеми.


Установка скорости подачи проволоки слишком быстро — основная причина чрезмерного разбрызгивания. Попробуй немного набрать его. То же самое и с настройками напряжения.
Точная настройка сварочного аппарата MIG для получения гладкой и стабильной дуги снизит количество сварочных брызг.
Эта способность приходит через опыт. Помогает общий опыт сварки, а также время, проведенное с вашим конкретным сварщиком.
В качестве отправной точки можно использовать таблицу настроек сварочного аппарата или программы.Но поскольку сварочные аппараты, материалы и условия различаются, им обычно требуется регулировка для получения наилучшей дуги.
Вот как я набираю настройки сварочного аппарата:
- Установите напряжение в соответствии с таблицей сварщика или там, где, как я думаю, это должно быть по опыту. Это грубая настройка, которую я больше не трогаю, если мне не удается получить правильную дугу с помощью следующих шагов.
- Установите скорость подачи проволоки в соответствии с таблицей настроек. Это прекрасная настройка, которую я немного увеличиваю или уменьшаю, чтобы получить плавную дугу.Небольшие корректировки не позволяют пропустить золотую середину.
- Если я пробежал весь диапазон скоростей подачи проволоки, но по-прежнему не могу получить хорошую дугу, пора грубо изменить напряжение, увеличивая или уменьшая его. Затем вернитесь к шагу 2 и повторяйте, пока дуга не станет стабильной.
- При стабильной дуге проверю сварной шов на проплавление. При необходимости я могу внести небольшие изменения в скорость подачи проволоки или скорость перемещения горелки, чтобы получить хороший профиль валика (индикатор проплавления) при сохранении гладкой дуги.
- Если дуга вспыхивает, а валик по-прежнему выглядит слишком холодным или горячим, я знаю, что я вне диапазона текущей настройки нагрева (напряжения). Я либо увеличиваю напряжение, либо уменьшаю его. Затем, после точной настройки скорости подачи проволоки, я должен быть готов к сварке.
Ключ для меня: Вносить одно изменение за раз и делать записи для дальнейшего использования.
Технология сварки влияет на разбрызгивание
Когда количество разбрызгиваний меняется во время сварки, я внимательно посмотрю, что я делаю, чтобы избежать ошибки оператора.Правильная техника сварки может иметь большое значение для уменьшения разбрызгивания.
Если держать пистолет под углом всего 5-15 ° от вертикали, защитный газ может покрыть зону сварки. Этот угол легко превысить, если вы пытаетесь держать сварочную лужу в поле зрения.
Но слишком большой угол наклона пистолета может подтолкнуть газ к одной стороне сварного шва, оставив другую незащищенной. Это может привести к разбрызгиванию и пористости сварного шва.
Если вылет электрода слишком большой, он может врезаться в сварочную ванну, вызывая разбрызгивание.Короткая дуга помогает уменьшить разбрызгивание, но если ваш электрод слишком короткий, дуга может разбрызгиваться. Это также может нарушить сварочную лужу и вызвать разбрызгивание.
Да, разбрызгивание вызывает разбрызгивание.
Вылет рекомендация дюйма. для MIG или ½ дюйма. для порошковой сварки у меня хорошо работает. Сохранение одинаковой длины электрода помогает мне делать стабильные сварные швы.
Поддержание согласованной формы поможет вам быстро настроить параметры сварки.
Чистые материалы уменьшают количество сварочных брызг


Ржавчина, краска, жир и прокатная окалина на вашей рабочей поверхности вызовут разбрызгивание дуги; брызги брызг из сварного шва.
Многие люди не любят красить, но мне нравится красить стены, двери и даже отделку. Что мне не нравится, так это вся подготовка, необходимая перед началом рисования.
У меня то же самое со сваркой. Но не нужно много времени, чтобы понять, что даже самый опытный сварщик (или маляр) не сможет добиться наилучших результатов без хорошо подготовленной поверхности .
Как бы мне ни не нравилась вся подготовительная работа при сварке, мне еще меньше нравятся переделки. Я трачу время на шлифовку паршивых сварных швов и брызг, а в итоге готовлю деталь, как и следовало делать с самого начала.
Сделайте себе одолжение, потратив время на подготовку деталей к сварке. Вы сэкономите время и на одну проблему меньше, если вы будете производить чрезмерное разбрызгивание.
К счастью, для удобных 4,5-дюймовых моделей доступны различные насадки. Угловая шлифовальная машина поможет быстро очистить практически любой предмет. Окончательная очистка ацетоном делает его готовым к сварке.
См. , соответствующие советы по подготовке : Как сваривать алюминий методом MIG без катушечного пистолета
Не забудьте проверить катушку с проволокой на предмет загрязнения.Может накапливаться пыль, а на проводе может образоваться ржавчина. Это может вызвать беспорядочную подачу и загрязнение сварного шва, что приведет к чрезмерному разбрызгиванию.


Удаление верхних слоев может привести к обнажению чистой проволоки под ними.
Некоторые используют продукт для очистки проволоки во время подачи под названием Lube-Matic от Weld-Aid. Я еще не пробовал это делать, но некоторые говорят, что это работает на слегка загрязненном проводе.
Если вы время от времени работаете на дому, между сварочными работами может пройти много времени. Вы можете снимать проволоку со сварочного аппарата между использованиями и помещать ее в пакет с застежкой-молнией.Это сохранит его сухим, чистым и готовым к использованию. Найдите теплое сухое место для хранения.
Проблемы оборудования, способствующие чрезмерному разбрызгиванию MIG
Многие вещи могут пойти не так со сварщиком, что приведет к плохим сварным швам с чрезмерным разбрызгиванием. Наиболее частые причины также легче всего исправить.
Проверка рабочего зажима


Слабое соединение здесь может вызвать колебания сварочной дуги. Убедитесь, что зажим плотно прилегает к заготовке или столу.
При необходимости ударьте по области контакта проволочным диском или щеткой. Проверьте зажим и машину на предмет ослабления кабельных соединений. Постарайтесь прикрепить зажим как можно ближе к сварному шву.
Некоторые производители сварочных аппаратов экономят на качестве зажимов для домовладельцев MIG. Если вы считаете, что ваш зажим хлипкий, его легко заменить на этот прочный литой медный зажим.
Проблемы с подачей проволоки
Неустойчивая подача проволоки приведет к повреждению сварных швов брызгами.
Убедитесь, что натяжение подачи проволоки не настолько слабое, чтобы приводные ролики не проскальзывали.Пока вы работаете, убедитесь, что вы установили приводной ролик, соответствующий размеру проволоки.


Вы видите много металлической пыли вокруг приводных роликов или направляющей для проволоки? Эта пыль также может накапливаться внутри кабельного лайнера.
При отключенном натяжителе механизма подачи проволоки проволока должна легко перемещаться вперед и назад по тросу вручную. В противном случае снимите пистолет и с помощью сжатого воздуха продуйте лайнер в направлении конца пистолета.
Гильза также может быть перекручена и повреждена.
Как упоминалось ранее, грязная или ржавая катушка с проволокой подается неравномерно и вызывает большое количество брызг.
Отсутствие защитного газа
Помимо защиты сварного шва от атмосферных примесей, защитный газ MIG помогает стабилизировать сварочную дугу. Таким образом, недостаток защитного газа может вызвать нестабильную дугу и дополнительное разбрызгивание.


Сначала убедитесь, что газ достигает пистолета. Если вы отключите натяжитель механизма подачи проволоки и нажмете на спусковой крючок, вы должны услышать газ, выходящий из сопла .
Если нет, проверьте и при необходимости отрегулируйте газовый регулятор и убедитесь, что газовый клапан работает.
Также проверьте газовые линии и фитинги, включая соединения внутри сварочного аппарата. Они могут использовать пружинные зажимы на трубке, которые могут отсоединиться.
Брызги могут скапливаться внутри сопла пистолета и ограничивать поток газа. Очистите или замените. При сварке порошковой проволокой без сопла или с использованием сопла MIG брызги могут достигнуть и накрыть отверстия для газа.
Очистите или замените переходник контактного наконечника.Форсунки с флюсовой сердцевиной, защищающие отверстия для газа от брызг, доступны для многих пистолетов.
Защищайте место сварки от ветра, который может рассеять защитный газ. Переставьте вентиляторы или повесьте сварочные одеяла или занавески, чтобы перекрыть поток воздуха.
При добавлении к сварочному газу аргона, CO2 (2-25%) стабилизирует сварочную дугу и уменьшает разбрызгивание. Хотя и дешевле, сварка со 100% CO2 приводит к большему разбрызгиванию, чем традиционная смесь C25 MIG из 75% аргона и 25% CO2.
Изношенные или негабаритные наконечники для контактов
У меня никогда не изнашивались контактные наконечники, но я понимаю, как это может происходить.Тонкая стальная проволока тверже меди и действует как тонкое пильное полотно. Вы когда-нибудь замечали пилообразные отпечатки, оставленные роликом с флюсовым сердечником с накаткой?
Более высокие температуры сварки только усиливают эффект резки. У Бернарда больше информации об износе контактных наконечников.
Вот что я сделал, , . Поскольку контактные наконечники разного размера выглядят одинаково, а маркировка плохо читается, легко установить неправильный наконечник .
При слишком большом отверстии проволочный электрод может потерять контакт с наконечником, что приведет к разбрызгиванию дуги.Замените, если проход для провода выглядит овальным, а не круглым, или если его размер не подходит для провода. Легкое исправление.
Управление разбрызгиванием
Хотя эти продукты не уменьшают разбрызгивание, легкий слой сварочного спрея для предотвращения разбрызгивания или моего любимого геля для форсунок может предотвратить прилипание брызг. Облегчает очистку пистолета и недрагоценных металлов.
Также может помочь хорошая сварочная рубашка с длинными рукавами.


Before You Go
Машины MIG — это лучшие сварщики для начинающих, а иногда и домашнего сварщика. Но чтобы овладеть основами, нужна определенная практика.
По мере накопления опыта в сварке вы лучше узнаете своего сварочного аппарата MIG. Настройка машины для ваших проектов станет вашей второй натурой. Ваши навыки обращения с пистолетом MIG улучшатся, как и ваша способность подготовить заготовку.
Со временем вы устраните большинство причин чрезмерного количества брызг при сварке MIG .Тогда качественные сварные швы станут нормой, а не исключением.
.7 причин появления брызг и способы их устранения
Сварка МИГ характеризуется искрами и брызгами, разлетающимися повсюду. В фильмах это выглядит отлично, но когда мы делаем сварку, мы понимаем, что брызги — это плохо. Это создает больше работы за счет увеличения времени очистки, расходует материал и может обжечься, если вы не носите подходящие СИЗ. Устранить разбрызгивание при сварке MIG практически невозможно, но мы, безусловно, можем уменьшить его, понимая, что в первую очередь вызывает их.
У большинства из нас нет возможности покупать новейшее сварочное оборудование для устранения разбрызгивания. Мы должны сваривать то, что у нас есть. Поэтому мы не будем говорить о том, как оборудование может помочь устранить брызги. Этот список — это элементы, которые вы можете изменить прямо сейчас и бесплатно.
7 причин разбрызгивания:
1. Неправильные настройки — неисправные процедуры вызовут разбрызгивание. Сила тока, напряжение и электрические характеристики имеют решающее значение.
Сила тока в GMAW определяется скоростью подачи проволоки. Слишком высокий рабочий ток вызовет разбрызгивание. Чтобы исправить это, либо уменьшите силу тока, уменьшив скорость подачи проволоки, либо увеличив напряжение.
Как указано выше, если ваше напряжение слишком низкое, уровень разбрызгивания увеличится. Увеличивайте напряжение, пока брызги не уменьшатся.
- Электрическое вылетание (ESO):
Вылет — это расстояние от контактного наконечника до обрабатываемой детали.При сварке с миграцией вы хотите быть около 3/4 дюйма. Немного больше для большой силы тока. Чрезмерный вылет несколько увеличивает разбрызгивание, но создает более серьезные проблемы (пористость из-за отсутствия защитного газа и непроницаемости).
2. Слишком большой рабочий угол — ведутся споры о том, следует ли толкать или перетаскивать при сварке MIG. Независимо от того, что вы предпочитаете, убедитесь, что ваш рабочий угол перетаскивания (тяги) или толкания не превышает 15 градусов. Иногда нет выбора, если охват является проблемой.Но когда вы можете контролировать, не превышайте 15 градусов. Крутые углы создают много брызг.
3. Поверхностные загрязнения — ржавчина, масло, краска и другие поверхностные загрязнения образуют брызги. Как можно лучше очистите поверхности перед сваркой.
4. Режим переноса металла — Короткая дуга и сферический перенос — это режимы переноса металла, при которых образуется много брызг. Чтобы значительно уменьшить разбрызгивание, необходимо добиться распыления. Для этого вам потребуется как минимум 83% аргона в вашей защитной смеси (обычно 90/10).Тем не менее, вы также должны быть выше переходных токов для диаметра используемого вами провода. Меньшие машины на это не способны.
5. Беспорядочная подача — когда механизм подачи проволоки не может подавать проволоку с постоянной скоростью, будут колебания силы тока, которые сильно повлияют на дугу, вызывая большое количество брызг. Убедитесь, что у вас нет проблем с кормлением. Чтобы получить помощь в решении этой проблемы, см. «Устранение неполадок при нестабильной подаче проволоки».
6.Качество расходных материалов — некоторые приложения могут жить с большим количеством брызг, другие — нет. В роботизированных приложениях и других ситуациях, когда стабильность проводов критична, избегайте дешевых проводов низкого качества. Одна катушка или барабан могут быть одинаковыми, но для нескольких катушек или барабанов могут быть различия в диаметре проволоки, медном покрытии и химическом составе. К сожалению, AWS позволяет использовать такой широкий спектр химикатов, что даже вешалку для одежды можно превратить в мигрирующую проволоку. Лучшие производители придерживаются собственных диапазонов и допусков и, таким образом, производят лучший продукт.
7. Плохой защитный газ — Это очень редко, но защитные газы низкого качества могут повлиять на уровень разбрызгивания. Чаще встречается неправильная маркировка (то есть получение 75/25 на баллоне с этикеткой 90/10), но даже это бывает редко. Чем выше содержание аргона, тем ровнее дуга. 100% углекислый газ дешев и обеспечивает хороший профиль проникновения, но создает много брызг.
Если вам кажется, что избавиться от брызг кажется слишком сложным, посмотрите, во что это может вам обойтись: Реальная стоимость сварочных брызг
Напоследок пару слов о защите от брызг.Антибрызгивание не устраняет и не предотвращает разбрызгивание. Он просто позволяет брызгам соскальзывать с материала, а не прилипать к нему. Использование чрезмерного количества может вызвать другие проблемы, такие как пористость. Это неплохо использовать, но в первую очередь выясните, что вызывает разбрызгивание, и позаботьтесь об этом.
Источники: AWS D1.1 / D1.1M: 2015 Кодекс структурной сварки (сталь)
Руководство по дуговой сварке, 14-е издание
.Welding Anti Spatter Spray and Nozzle Gel, что это такое &
Зачем он вам?
Вы можете разочароваться в очистке места сварки после сварки или раздражаться тем, сколько времени уходит на очистку брызг с детали, которую вы так тщательно сварили.
Независимо от того, что вызвало у вас интерес к сварочному спрею для защиты от брызг, оставайтесь со мной, и я объясню, что это такое, зачем он вам нужен и как его использовать. У меня даже есть несколько предложений по использованию хороших продуктов.
Что такое Spatter?
Spatter — это красивые искры радужного цвета, которые можно увидеть во время классических сварочных швов.

Сварка с образованием брызг
Посмотрите внимательно, сварочные брызги состоят из крошечных кусочков расплавленного металла, выбрасываемых в процессе сварки.
И эти сварочные брызги попадают на всю зону сварки.
Свариваемая деталь, сварочный стол, пол, вы и ваша одежда, вверх и внутрь головки сварочной горелки.
У меня есть статья, в которой более подробно рассказывается о Spatter. Если вам интересно и вы хотите узнать больше о тех небольших характеристиках, которые доставляют вам все эти проблемы, ознакомьтесь с моей статьей «Что такое разбрызгивание при сварке?» И почему это отстой »
Проблемы, вызванные сварочными брызгами MIG
Сварочные брызги MIG, также известные как bb, остывают и прилипают к вашей работе, и их трудно удалить. Сварочные брызги портят вашу работу, блокируют головку горелки и могут вызвать короткое замыкание, когда сварочные брызги забивают сопло и контактный наконечник.

Скопление брызг на сопле и контактном наконечнике
Когда эти сварочные брызги препятствуют вытеканию проволоки и / или блокируют подачу защитного газа, это может привести к провалу сварного шва, если брызги не будут удалены.
Последнее, что вам нужно, когда вы только начинаете сварку, — это тонна брызг по всей поверхности вашего начинающего борта.
Но именно тогда вы получите больше всего брызг.
Потому что у вас недостаточно опыта в настройке MIG и вы будете производить много брызг, пока не узнаете достаточно, чтобы уменьшить разбрызгивание до минимума.
Причины появления брызг при сварке MIG
- Обычно при сварке проволокой с флюсовым сердечником в аппарате для сварки сердечником. Проволока с сердечником из флюса известна тем, что производит больше брызг.
- При использовании 100% углекислого газа с вашей MIG — 100% углекислый газ часто используется, потому что защитный газ дешевле купить. Побочным продуктом этой экономии денег часто является более частое разбрызгивание.
- Если настройки сварочного шва MIG не совсем правильные, слишком высокая или низкая скорость подачи проволоки, слишком высокая или слишком низкая концентрация газа или загрязнение сварной детали.
Моя статья о разбрызгивании охватывает 7 других причин разбрызгивания. Стоит взглянуть и понять, что может вызвать разбрызгивание.
Как уменьшить количество брызг при сварке
Давайте взглянем на некоторые области, где образуются брызги.
- Правильная настройка сварочного аппарата MIG для металла, который вы свариваете, уменьшит разбрызгивание сварочного шва, но вряд ли полностью избавит от него.
- Прочтите таблицу параметров сварки, прилагаемую к сварочной проволоке, еще раз, чтобы узнать правильные настройки для используемой проволоки.
- Используйте защитный газ, подходящий для свариваемого металла.
- Используйте сварочную проволоку с флюсовым сердечником с низким или уменьшающим разбрызгивание от ESAB или Lincoln Electric.
У меня есть документ, который включает 20 пунктов, на которые вы можете обратить внимание, пытаясь свести к минимуму разбрызгивание, производимое сваркой. Обязательно посмотрите, если хотите узнать, как бороться с брызгами при сварке.
И когда вы сделаете все возможное, вы можете …Защита от брызг при сварке — это защита от брызг для сварки
Учитывая, что у вас будут брызги — особенно для новичков, лучшая защита — это остановить брызги от брызг. прилипание к металлическим поверхностям вокруг вас.
Не позволяйте ей прилипать к контактному наконечнику, соплу, заготовке и сварочному столу. Лучший способ сделать это — использовать средства защиты от брызг при сварке.
Что такое спрей от брызг?
Хотя антибрызгивание называется антибрызгиванием, оно на самом деле не останавливает образование брызг — этих красивых брызг радужных искр. Только правильная настройка сварочного аппарата MIG может уменьшить это.
Что такое спрей для защиты от брызг, — это продукт, который вы распыляете.Скажите на сварочном столе и на частях сварочного проекта, чтобы предотвратить прилипание брызг. Эти горячие куски металла, пятнающие ваш проект и рабочий стол, дадут вам часы на уборку.
Чтобы брызги не прилипали к вам? Вот для чего нужны перчатки, сварочные шлемы и подходящий комбинезон. Бандана на шее и беруши могут предотвратить попадание неприятных брызг в места, где им быть не должно.
Спрей против разбрызгивания содержит активные ингредиенты, обычно силикон, растворитель и чаще всего на основе нефти.Он также может быть на водной основе.
Спрей для защиты от брызг также доступен в виде гелей или капель, специально предназначенных для предотвращения прилипания брызг к концу сопла MIG и контактному наконечнику, вызывающему короткое замыкание.
Продукты для защиты от брызг для сварки
Продукты для защиты от брызг доступны в виде спрея, окунания или геля. Они не предотвращают разбрызгивание — только правильная настройка сварочного аппарата MIG может сделать это или, по крайней мере, минимизировать образование брызг.
Они предотвращают прилипание брызг или шариков к поверхностям, на которые нанесено средство защиты от брызг.
Как пользоваться спреем, гелем или окунанием от брызг?
Все средства защиты от брызг необходимо наносить в качестве профилактики, то есть перед началом сварки.
Любые брызги, прилипшие к заготовке или соплу, должны быть легко удалены щеткой.
Где использовать средства защиты от брызг сварки?
Защита от брызг для сварки MIG используется на металлических объектах в зоне сварного шва и вокруг нее, где вы не хотите, чтобы брызги прилипали.

Стол для сварки распылением с защитой от разбрызгивания
Вы можете использовать там, где хотите, и ваша готовая работа должна выглядеть хорошо.
Распыляйте и, конечно же, не забывайте, что в дополнение вы можете использовать физический щит, чтобы брызги не попадали в места вокруг мастерской.
Как можно лучше закройте и защитите участки заготовки, которые не подлежат сварке.
Распылите и используйте на сварочном столе перед укладкой свариваемой детали. Это уменьшит прилипание брызг к сварочному столу.
Используйте гель для сопел для сварки MIG или окуните сопло головки горелки и контактный наконечник.
Брызги должны быть легко удалены после завершения сварочных работ.

Сотрите брызги со сварочного стола
После нанесения покрытия для предотвращения разбрызгивания и сварки вы можете очистить контакт и сопло щеткой или стучать, чтобы удалить брызги.
Лучший способ удалить брызги — не допустить их прилипания к вашей заготовке и окружающей области с помощью профилактических методов, которые я предложил.
Гораздо труднее удалить, когда он застрял, и тогда вам понадобится угловая шлифовальная машина, чтобы удалить его.
Возможные проблемы с использованием сварочного спрея против брызг
Боюсь, это не все хорошо.
Активными ингредиентами спрея для защиты от брызг для сварки, как правило, являются силикон, растворитель, нефть или вода. Защита от брызг при сварке MIG может быть вредной для вас и окружающей среды, поэтому стоит внимательно выбирать продукт, который вы используете.
Есть некоторые проблемы с использованием некоторых сварочных спреев для защиты от брызг.
Они есть;
- Трудности при снятии — они могут оставлять жирные остатки, которые трудно полностью удалить без химикатов, жирная поверхность затрудняет покраску вашей работы в дальнейшем
- Окрашивание металлов — некоторые сварочные спреи для защиты от брызг могут потемнить и оставить пятна
- Загрязнение сварного шва, ведущее к пористости — если в продукте специально не указано, что он не вызывает пористости, безопаснее предположить, что это так.Держите сварочный спрей для защиты от брызг вдали от самого стыка.
- Опасность для окружающей среды — некоторые сварочные спреи не являются экологически безопасными. На самом деле некоторые из них содержат метиленхлорид, который, как было доказано, вызывает рак у лабораторных животных. Если вас это беспокоит, используйте респиратор или избегайте использования баллончиков с этим химическим веществом.
- Жалобы на распыление брызг при сварке на водной основе, ржавление деталей, особенно в более влажных частях страны
Точно такие же материалы в распылителе сварочных брызг, который предотвращает налипание брызг и может повредить сварное соединение.Распылите средство по всей поверхности, защитите стык, который вы планируете сваривать. Не распыляйте непосредственно на свариваемое соединение.
Все сказанное выше, если вы тщательно выбираете средство для распыления сварочных брызг, которое вы используете в своих конкретных обстоятельствах; они — благо для использования.
Сварка Распылительная сварка с защитой от разбрызгивания
Распылительная сварка с защитой от разбрызгивания легко выполняется, если следовать нескольким советам.
Встряхивайте баллончик от 30 секунд до минуты, чтобы полностью распределить и перемешать материалы внутри.
Используется путем распыления легкого слоя сварочного брызга на область сварки. Например;
ваш сварочный стол или
при сварке детали в полевых условиях или при ремонте автомобилей, нанесите распылением на металлические поверхности вокруг соединения, которое необходимо отремонтировать, чтобы предотвратить прилипание брызг.
Распылите на свариваемую деталь, но избегайте попадания брызг на сам сварной шов.
Если на сварном шве будет нанесено покрытие, предотвращающее разбрызгивание, существует риск загрязнения сварного шва.
Лучший спрей для защиты от разбрызгивания для сварки
При написании этой статьи я провел для вас небольшое исследование, в соответствии с которым спрей от разбрызгивания отлично подходит на рынке. Вот моя продуманная коллекция. Вы можете зайти на Amazon, проверить их сами и узнать, что вы думаете.
(комиссионные, полученные через ссылки Amazon)
Hobart 82113 Anti Spatter Spray Без хлорированных растворителей, нетоксичный, банка 20 унций | |
Lincoln Electric Spatter Lincol спрей для защиты от брызг в хорошо проветриваемом помещении и используйте средства защиты глаз, так как может вызвать раздражение глаз и дыхательных путей, негорючий, биоразлагаемый | |
Cantesco AS-16-A | |
CRC Anti Spatter Water Based | |
Weld-Aid Weld Kleen |
Вот минутное видео на YouTube, сделанное Cantesco, демонстрирующее, как используется спрей для защиты от брызг для сварки.
Cantesco Anti-Spatter на основе растворителя
Видео предоставлено: Cantesco Welding Chemical Products
Гель для защиты от брызг
Также известен как гель для сварочных сопел или гель для окунания.
Что это?
В то время как сварочный спрей для защиты от брызг обычно используется в зоне сварки.Гель для сварочных сопел используется специально для предотвращения прилипания брызг к соплу и контактному наконечнику головки горелки.
Гель для сварочного сопла
Перед использованием убедитесь, что все имеющиеся брызги удалены с ваших наконечников и сопла с помощью сварочных плоскогубцев, щетки для очистки проволоки или напильника.
Нанесите несколько дюймов стартовых шариков на запасной кусок металла, чтобы нагреть контактный наконечник и сопло. Эти гели наносятся на горячую насадку и контактный наконечник.
Погрузите насадку в ванну с гелем примерно на дюйм.

Окуните сопло в гель для сварочного сопла
Выньте сопло и оставьте сопло лицевой стороной вниз над ванной, чтобы излишки стекали обратно в ванну.
В качестве альтернативы вы можете
Нанесите гель для сварочного сопла с помощью небольшой кисточки
, окунанием или кистью;
Положите еще один дюймовой бусинку на запасной кусок металла, чтобы израсходовать проволоку, которая контактировала с погружением.
Затем сваривайте как обычно.
Проверьте перерывы в сварке на предмет разбрызгивания.
Постучите соплом по сварочному столу, чтобы выпали ножки, или
счистите любые ножки из сопла.Они должны легко выходить и раскрываться.
По завершении сеанса сварки произведите последнюю чистку, чтобы сопло и контактный наконечник горелки были готовы к следующему сеансу сварки.
Лучшие примеры гелевых сварочных сопел
Щелкните ссылки, чтобы узнать текущую цену на Amazon.
(комиссионные, полученные через ссылки Amazon)
Hobart 770074 Гель для форсунок | |
Lincoln Electric Dip Gel | |
Blue Demon Nozzle Gel | |
Forney 37031 Гель для форсунок | |
Cantesco TD-16 | |
Сопло для сварочных аппаратов Kleen |
Керамический спрей для защиты от разбрызгивания для сварки
Существует третий тип средства от разбрызгивания, которое вы можете использовать, на керамической основе.Это намного дороже, чем традиционный спрей или гель для защиты от брызг MIG. Это особенно полезно для сварочного сопла и контактного наконечника, продлевая срок службы этих компонентов и потенциально уменьшая загрязнение сварного шва.

Распыление керамического спрея
Одноразовое использование этих продуктов может продлить вам весь сварочный сеанс, что делает их экономичными в использовании.
Как говорится, получаешь то, за что платишь.
Керамические сварочные спреи для защиты от брызг обладают отличными характеристиками при их высокой цене и отлично подходят для сварки алюминия.

Распыление керамических распылителей на сопло
Лучшие примеры распылителей для защиты от брызг для сварки на керамической основе
После обширных исследований и моего опыта керамических распылителей для защиты от брызг, которые, кажется, действительно работают, стали Loctite, Vibra-Tite и Walter Surface Technologies. Я считаю, что из трех лучше всех выходит Loctite SF 7900. Я предоставил ссылку, чтобы вы могли увидеть, как сравниваются цены на Amazon.
(комиссионные, полученные через ссылки Amazon)
Loctite SF 7900 Керамическое покрытие против брызг при сварке |
Вот видеоролик на YouTube продолжительностью менее трех минут, сделанный Loctite, демонстрирующий, как используется керамический спрей для защиты от брызг Loctite SF 7900 и его преимущества. Наслаждайтесь!
Loctite SF 7900
Видео Кредит: Loctite North America
Мне нравится это 1-минутное 20-секундное видео от Walter Surface Technologies, демонстрирующее их протектор для сварного сопла E-Weld Nozzle на керамической основе. Многие люди в сварочном сообществе любят этот продукт.
Сопло E-Weld
Видео предоставлено: WalterSurfaceTechnologies
Я также предоставил ссылку на два керамических спрея для защиты от брызг, которые мне нравятся как занявшие второе место. Вы можете взглянуть на отзывы и увидеть, какая цена по сравнению с вашей покупкой на месте.
(комиссионные, полученные через ссылки Amazon)