Дефектоскопия сварных швов — виды контроля качества
Окончание сварных работ – это начало контроля качества сварных соединений. Ведь понятно, что от качества проведенных работ зависит долгосрочная эксплуатация сборной конструкции. Дефектоскопия сварных швов – это методы контроля сварных соединений. Их несколько, поэтому стоит разобраться в теме досконально.
Содержание страницы
- 1 Виды контроля сварных соединений
- 2 Визуальный осмотр
- 3 Магнитный контроль сварных швов
- 4 Радиационный контроль
- 5 Ультразвуковая дефектоскопия
- 6 Капиллярный контроль
- 7 Пенетранты
- 8 Керосин
- 9 Методы контроля качества сварных соединений на проницаемость
Виды контроля сварных соединений
Существует видимые дефекты сварочного шва и невидимые (скрытые). Первые легко можно увидеть глазами, некоторые из них не очень большие, но при помощи лупы обнаружить их не проблема. Вторая группа более обширная, и располагаются такие дефекты внутри тела сварного шва.
Обнаружить скрытые дефекты можно двумя способами. Способ первый – неразрушающий. Второй – разрушающий. Первый вариант, по понятным причинам, используется чаще всего.
Неразрушающий способ контроля качества сварных швов
В этой категории несколько способов, использующихся для проверки качества сварных швов.
- Визуальный осмотр (внешний).
- Магнитный контроль.
- Дефектоскопия радиационная.
- Ультразвуковая.
- Капиллярная.
- Контроль сварных соединений на проницаемость.
Есть и другие способы, но используются они нечасто.
Визуальный осмотр
С помощью внешнего осмотра можно выявить не только видимые дефекты швов, но и невидимые. К примеру, неравномерность шва по высоте и ширине говорит о том, что в процессе сварки были прерывания дуги. А это гарантия, что шов внутри имеет непровары.
Как правильно проводится осмотр.
- Шов очищается от окалин, шлака и капель металла.
- Затем его обрабатывают техническим спиртом.
- После еще одна обработка десятипроцентным раствором азотной кислоты. Она называется травление.
- Поверхность шва получается чистой и матовой. На ней хорошо видны самые мелкие трещинки и поры.
Внимание! Азотная кислота – материал, разъедающий металл. Поэтому после осмотра металлический сварной шов надо обработать спиртом.
О лупе уже упоминалось. С помощью этого инструмента можно обнаружить мизерные изъяны в виде тонких трещин толщиною меньше волоса, пережоги, мелкие подрезы и прочие. К тому же при помощи лупы можно проконтролировать – растет ли трещина или нет.
При осмотре можно также пользоваться штангенциркулем, шаблонами, линейкой. Ими замеряют высоту и ширину шва, его ровное продольное месторасположение.
Магнитный контроль сварных швов
Магнитные методы дефектоскопии основаны на создании магнитного поля, которое пронизывает тело сварного шва. Для этого используется специальный аппарат, в принцип работы которого вложено явления электромагнетизма.
Есть два способа, как определить дефект внутри соединения.
- С использованием ферромагнитного порошка, обычно это железо. Его можно использовать как в сухом виде, так и во влажном. Во втором случае железный порошок смешивают с маслом или керосином. Его посыпают на шов, а с другой стороны устанавливают магнит. В местах, где есть дефекты, порошок будет собираться.
- С помощью ферромагнитной ленты. Ее укладывают на шов, а с другой стороны устанавливают прибор. Все дефекты, которые оказываются в стыке двух металлических заготовок, будут отображаться на этой пленке.
Этот вариант дефектоскопии сварных соединений можно использовать для контроля только ферромагнитных стыков. Цветные металлы, стали с хромникелевым покрытием и другие таким способом не контролируются.
Радиационный контроль
Это, по сути, рентгеноскопия. Здесь используются дорогие приборы, да и гамма-излучение вредно для человека. Хотя это самый верный вариант обнаружения дефектов в сварочном шве. Они четко видны на пленке.
Ультразвуковая дефектоскопия
Это еще один точный вариант обнаружения изъянов в сварочном шве. В его основе лежит свойство ультразвуковых волн отражаться от поверхности материалов или сред с разными плотностями. Если сварной шов не имеет внутри себя дефектов, то есть, его плотность однородна, то звуковые волны пройдут сквозь него без помех. Если внутри дефекты есть, а это полости, наполненные газом, то внутри получаются две разные среды: металл и газ.
Поэтому ультразвук будет отражаться от металлической плоскости поры или трещины, и вернется обратно, отображаясь на датчике. Необходимо отметить, что разные изъяны отражают волны по-разному. Поэтому можно итог дефектоскопии классифицировать.
Это самый удобный и быстрый способ контроля сварных соединений трубопроводов, сосудов и других конструкций. Единственный у него минус – сложность расшифровки полученных сигналов, поэтому с такими приборами работают только высококвалифицированные специалисты.
Капиллярный контроль
Методы контроля сварных швов капиллярным способом основаны на свойствах некоторых жидкостей проникать в тело материалов по самым мельчайшим трещинкам и порам, структурным каналам (капиллярам). Самое главное, что этим способом можно контролировать любые материалы, разной плотности, размеров и формы. Неважно, это металл (черный или цветной), пластик, стекло, керамика и так далее.
Проникающие жидкости просачиваются в любые изъяны поверхности, а некоторые из них, к примеру, керосин, могут проходить сквозь достаточно толстые изделия насквозь. И самое главное, чем меньше размер дефекта и выше впитываемость жидкости, тем быстрее протекает процесс обнаружения изъяна, тем глубже жидкость проникает.
Сегодня специалисты пользуются несколькими видами проникающих жидкостей.
Пенетранты
С английского это слово переводится, как впитывающий. В настоящее время существует более десятка составов пенетрантов (водные или на основе органических жидкостей: керосин, масла и так далее). Все они обладают малым поверхностным натяжением и сильной цветовой контрастностью, что позволяет их легко увидеть. То есть, суть метода такова: наносится пенетрант на поверхность сварочного шва, он проникает внутрь, если есть дефект, окрашивается с этой же стороны после очистки нанесенного слоя.
Сегодня производители предлагают разные проникающие жидкости с разным эффектом обнаружения изъяном.
- Люминесцентные. Из названия понятно, что в их состав входят люминесцентные добавки. После нанесения такой жидкости на шов нужно посветить на стык ультрафиолетовой лампой. Если дефект есть, то люминесцентные вещества будут отсвечивать, и это будет видно.
- Цветные. В состав жидкостей входят специальные светящиеся красители. Чаще всего это красители ярко-красные. Они хорошо видны даже при дневном свете. Наносите такую жидкость на шов, и если с другой стороны появились красные пятнышки, то дефект обнаружен.
Есть разделение пенетрантов по чувствительности. Первый класс – это жидкости, с помощью которых можно определить дефекты с поперечным размером от 0,1 до 1,0 микрона. Второй класс – до 0,5 микрон. При этом учитывается, что глубина изъяна должна превосходить его ширину в десять раз.
Наносить пенетранты можно любым способом, сегодня предлагаются баллончики с этой жидкостью. В комплект к ним прилагаются очистители для зачистки дефектуемой поверхности и проявитель, с помощью которого выявляется проникновение пенетранта и показывается рисунок.
Как это надо делать правильно.
- Шов и околошовные участки необходимо хорошо очистить. Нельзя использовать механические методы, они могут стать причиной занесения грязи в сами трещины и поры. Используют теплую воду или мыльный раствор, последний этап – очистка очистителем.
- Иногда появляется необходимость протравить поверхность шва. Главное после этого кислоту убрать.
- Вся поверхность высушивается.
- Если контроль качества сварных соединений металлоконструкций или трубопроводов проводится при минусовой температуре, то сам шов перед нанесением пенетрантов надо обработать этиловым спиртом.
- Наносится впитывающая жидкость, которую через 5-20 минут надо удалить.
- После чего наносится проявитель (индикатор), который из дефектов сварного шва вытягивает пенетрант. Если дефект небольшой, то придется вооружиться лупой. Если никаких изменений на поверхности шва нет, то и дефектов нет.
Керосин
Этот способ можно обозначить, как самый простой и дешевый, но от этого эффективность его не снижается. Его проводят по этой технологии.
- Очищают стык двух металлических заготовок от грязи и ржавчины с двух сторон шва.
- С одной стороны на шов наносится меловой раствор (400 г на 1 л воды). Необходимо дождаться, чтобы нанесенный слой просох.
- С обратной стороны наносится керосин. Смачивать надо обильно в несколько подходов в течение 15 минут.
- Теперь нужно наблюдать за стороной, где был нанесен меловой раствор. Если появились темные рисунки (пятна, линии), то значит, в сварочном шве присутствует дефект. Эти рисунки со временем будут только расширяться.
Здесь важно точно определить места выхода керосина, поэтому после первого нанесения его на шов, нужно сразу проводить наблюдение. Кстати, точки и мелкие пятнышки будут говорить о наличие свищей, линии – о наличии трещин.
Очень эффективен этот метод при стыковочных вариантах соединение, к примеру, труба к трубе. При сварке металлов, уложенных внахлест, он менее эффективен.
Методы контроля качества сварных соединений на проницаемость
В основном этот способ контроля используется для емкостей и резервуаров, которые изготовлены методом сварки. Для этого можно использовать газы или жидкости, которыми заполняется сосуд. После чего внутри создается избыточное давление, выталкивающее материалы наружу.
И если в местах сварки емкостей есть дефекты, то жидкость или газ тут же начнут через них проходить. В зависимости от того, какой контрольный компонент используется в проверочном процессе, различаются четыре варианта: гидравлический, пневматический, пневмогидравлический и вакуумный.
При пневматическом способе внутрь сосуда закачивается газ, давление которого превышает номинальный в 1,5 раза. С внешней стороны на шов наносится мыльный раствор. Пузырьки покажут наличие дефектов. При гидравлической дефектоскопии в сосуд заливается жидкость под давлением в 1,5 раза превышающее рабочее, производится обстукивание околошовного участка. Появление жидкости говорит о наличии изъяна.
Вот такие варианты дефектоскопии трубопроводов, резервуаров и металлоконструкций сегодня используют для определения качества сварного шва. Некоторые из них достаточно сложные и дорогие. Но основные просты, поэтому и часто используемые.
Контроль качества сварных швов
Для своевременного выявления дефектов необходим тщательный и систематический контроль сварных соединений трубопроводов на всех стадиях производства сварки. В зависимости от требований проекта или технических условий контроль сварных соединений технологических трубопроводов осуществляется путем наружного осмотра всех стыков, механических испытаний и физических методов контроля (металлографического исследования, просвечивания рентгеновскими или гамма-лучами, ультразвука, магнитографического способа), а также проверки плотности сварных стыков гидравлическим или пневматическим испытанием. В отдельных случаях в зависимости от материала труб и назначения трубопровода сварные швы проверяют на коррозионную стойкость.
Наружному осмотру подвергают каждый сваренный стык трубопровода. Путем осмотра выявляют внешние дефекты шва: наплывы, подрезы, кратеры, прожоги, трещины, свищи, наружные поры.
Механические испытания сварных соединений производят, чтобы определить их прочность и пластичность. Обязательными, видами механических испытаний являются испытания на растяжение, загиб или сплющивание и на ударную вязкость. Для проведения механических испытаний каждый сварщик одновременно со сваркой трубопровода осуществляет сварку контрольных (пробных) стыков, из которых вырезают образцы. Механические испытания контрольных стыков выполняют только при сварке трубопроводов, подведомственных органам Госгортехнадзора, на газопроводах, подведомственных органам газовой инспекции, а также на внутризаводских трубопроводах, транспортирующих огне- и взрывоопасные или токсичные газообразные и жидкие продукты. Механические испытания производят в соответствии с ГОСТ 6996—54.
Металлографическое исследование осуществляют, чтобы определить структуру металла шва и околошовной зоны, выявить в сварном шве газовые или шлаковые включения, волосяные трещины, непровары. При металлографическом исследовании проверяют излом сварного шва и определяют его макро- и микроструктуру. Эти исследования обязательны только для паропроводов первой и второй категорий, подведомственных Госгортехнадзору, и трубопроводов специального назначения. Исследованию подвергаются образцы, вырезанные из контрольного стыка.
Просвечивание рентгено- и гамма-лучами — наиболее распространенный способ контроля сварных швов без разрушения. Просвечивание позволяет обнаружить внутренние дефекты сварки — трещины, непровар, шлаковые включения и поры. Для просвечивания сварных швов применяют стационарные (РУП-200, РУП-400-5) и переносные (РУП-120-5-1 иИРА-1д) рентгеновские установки. Стационарные установки из-за больших габаритных размеров используют на заводах и в лабораториях; переносные — в монтажных условиях.
Гамма-лучи возникают в результате процессов, происходящих при распаде ядер элементов или изотопов, обладающих искусственной или естественной радиоактивностью. Эти лучи способны проникать через слой металла значительной толщины и действовать на рентгенопленку, приложенную к шву с обратной стороны. В тех местах, где имеются дефекты, поглощение лучей металлом будет меньше, и они окажут более сильное воздействие на эмульсию пленки. В данном месте на пленке появится темное пятно, по форме соответствующее дефекту шва. Для просвечивания пользуются гамма-лучами радиоактивных элементов цезия-137,. туллия-170, кобальта-60, иридия-192, европия-152. Для просвечивания радиоактивные вещества, излучающие гамма-лучи, помещают в специальные ампулы, заключенные в свинцовые кожухи (контейнеры). Рентгеновское и гамма-просвечивание проводят в соответствии с ГОСТ 7512—55. Недостатком способа контроля гамма-лучами является его вредность, требующая особых мер к охране людей от их воздействия.
Магнитографический способ контроля сварных швов основан на принципе изменения магнитного рассеивания, возникающего во время намагничивания контролируемого изделия в местах расположения дефектов. Особенностью этого способа является «запись» обнаруживаемых дефектов на специальную магнитофонную пленку (ленту).
Данный способ контроля применяют для труб толщиной до 20 мм, он позволяет четко выявить такие дефекты сварных швов, как продольные трещины, непровар, шлаковые включения и поры.
Ультразвуковой способ контроля сварных швов основан на различном отражении направленного пучка высокочастотных звуковых колебаний от металла (сварного шва) и имеющихся в нем дефектов.
Ультразвуковой контроль применяют для труб с внутренним диаметром 80 мм и более и стенками толщиной свыше 10 мм. Наибольшее применение для контроля нашли ультразвуковые дефектоскопы УЗД-7Н, НИИМ-5 и УЗД-39.
Недостатком данного способа контроля является то, что он позволяет определить лишь место дефекта, а не его характер.
Контролю физическими методами подвергают наихудшие стыки из отобранных по внешнему осмотру, в количестве:
Для трубопроводов I и II категорий…………………….. 3%
Для трубопроводов III категории ……………………….. 2%
Для трубопроводов IV категории…………………………. 1%
Количество стыков определяется от общего числа сваренных каждым сварщиком стыков, но оно должно быть не менее одного. Контролю необходимо подвергать весь периметр стыка.
При физических методах контроля сварные швы полагается браковать, если в них обнаружены следующие дефекты: трещины любых размеров; непровар глубиной более 15% от толщины стенки трубы, если она не превышает 20 мм, а при толщине стенки свыше 20 мм — более 3 мм; шлаковые включения и поры глубиной более 10% от толщины стенки трубы, если она не превышает 20 мм и 3 мм — при толщине стенки свыше 20 мм; скопления включений и пор в виде сплошной сетки дефектов в шве независимо от их глубины. Шлаковые включения глубиной до 10% от толщины стенки и длиной не более 30 мм, а также скопления пор длиной не более 15 мм не являются признаками брака.
Исправление дефектов сварных стыков трубопроводов допускается, если при условном диаметре трубопровода до 100 мм длина трещин меньше 20 мм и при условном диаметре свыше 100 мм — меньше 50 мм, а также если протяженность участков с недопустимыми дефектами меньше ¼окружности стыка. В процессе исправления необходимо вырубить дефектные места и вновь их заварить. В остальных случаях дефектный стык должен быть удален из трубопровода и на его место вварена катушка. Все подвергавшиеся исправлению участки стыков должны быть проверены физическими методами контроля.
1. Какие применяют способы контроля сварных швов?
2. В чем сущность просвечивания гамма-лучами? Какие радиоактивные элементы используются при этом?
3. Как производится исправление дефектов сварного шва?
Все материалы раздела «Сварка труб» :
● Способы сварки трубопроводов и виды сварных соединений
● Подготовка труб под сварку
● Технология газовой сварки и резки
● Кислородно-флюсовая и дуговая резка
● Технология ручной электродуговой сварки, электроды
● Источники питания сварочной дуги
● Автоматическая и полуавтоматическая сварка под флюсом
● Автоматическая и полуавтоматическая сварка в защитных газах
● Сварка трубопроводов из легированной стали
● Сварка трубопроводов высокого давления, термообработка сварных соединений
● Сварка трубопроводов из алюминия и его сплавов, из меди и ее сплавов
● Пайка трубопроводов, дефекты сварных швов
● Контроль качества сварных швов
● Виды сварки и применяемое оборудование
● Сварка и склеивание винипластовых труб
● Сварка полиэтиленовых трубопроводов
● Правила техники безопасности при резке и сварке трубопроводов
Сварной шов и методы проведения радиографического контроля сварных соединений
Содержание
- 1 Радиографический контроль и цели его проведения
- 2 Преимущества рентгенографического метода:
- 3 Радиографический контроль не используют при:
- 4 Принцип работы радиографической установки
- 5 Главные требования к рентгеновским аппаратам
- 6 Виды радиометрических аппаратов:
Производство и установка сварочных конструкций осуществляется в строгом соответствии со строительными нормами, техническими условиями и правилами, обозначенными в ГОСТе. Все существующие сегодня способы контролировать сварной шов, а также другие металлические изделия дают возможность выявлять всевозможные дефекты, которые можно повстречать на практике сварки.
Соответствующие методы контроля применяются в зависимости от ответственности сварных швов и конструкций. Самыми целесообразными комплексными испытаниями на сегодняшний день считают те, что включают целый ряд параллельно использующихся методов контроля, например, ультразвуковой контроль сварных швов и радиографическая дефектоскопия.
Радиографический контроль и цели его проведения
Рентгеновская дефектоскопия или же радиографический контроль сварочных швов, соединений чаще всего применяется с целью проверки уровня качества магистральных газо- и нефтепроводов, технологических трубопроводов, промышленных трубопроводов, металлоконструкций, а также композитных материалов и технологического оборудования в самых разных отраслях промышленности.
Рентгенографический контроль производят с целью выявления поверхностных и внутренних дефектов, к примеру, шлаковых включений, газовых пор, микротрещин, подрезов и шлаковых включений.
Наряду с другими физическими методами контроля радиографический выступает одним из самых эффективных и надёжных средств выявления всевозможных дефектов.
Выявленные дефекты: искусственные включения, нарушения геометрииОснован данный метод дефектоскопии на различном поглощении рентгеновских лучей материалами.
Такие дефекты, как включения инородных материалов, различные трещины, поры и шлаки проводят к ослаблению в той или иной степени рентгеновских лучей. Регистрация интенсивности лучей при помощи рентгенографического контроля помогает определить не только наличие, а и расположение разнообразных неоднородностей проверяемого материала.
Данный метод показал свой высокий уровень эффективности на практике в процессе контроля качества, которому подвергаются сварочные швы и соединения.
Преимущества рентгенографического метода:
- Максимально точная локализация даже самых мельчайших дефектов;
- Молниеносное обнаружение дефектов сварочных соединений и швов;
- Возможность произведения чёткой оценки микроструктуры: величины вогнутости, выпуклости корня шва даже в самых недоступных местах для внешнего осмотра.
Радиографическая дефектоскопия, контролирующая сварочные конструкции также даёт возможность обнаруживать внутренние дефекты в виде пор, непроваров, вольфрамовых, шлаковых, окисных и других включений, подрезов и трещин, усадочных раковин и прочего.
Согласно общим положениям ГОСТа 7512 82
Установки неразрушающего контрольРадиографический контроль не используют при:
- Наличии непроваров и трещин, величина раскрытия которых меньше стандартных значений, а плоскость раскрытия не соответствует направлению просвечивания;
- Любых несплошностях и включениях, имеющих размер в направлении просвечивания меньше удвоенной чувствительности контроля;
- Всяческих несплошностях и включениях в случае, когда их изображения на снимках совершенно не соответствуют изображениям построенных деталей, резких перепадов трещин металла, который просвечивается, а также острых углов.
Наиболее достоверный способ проконтролировать основной металл и сварной шов – провести дефектоскопию с рентгеновским просвечиванием металлов. Только так можно определить и вид, и характер обнаруженных дефектов, с высокой точностью определить их месторасположение и заархивировать результаты контроля в конечном итоге.
Принцип работы радиографической установки
Радиографический контроль относится, в первую очередь, к системам цифровой дефектоскопии радиационного типа. Радиационное изображение в данных системах превращается в цифровой массив (изображение), который впоследствии подвергается разным видам цифровой обработки, а затем выводится на монитор персонального компьютера в виде полутонового изображения. К слову, нередко металлография (классически метод) использует для исследования, а также контроля металлических материалов радиометрические установки.
Поскольку метод базируется на принципе измерения рентгеновского излучения или гамма-излучения, которое проходит сквозь материал контролируемого объекта, детектором для контроля выступает фотодиод со сцинтиллятором, наклеенным на него. Сцинтиллятор под воздействием излучений испускает видимый свет, выход которого пропорционален квантовой энергии. В конечном итоге исходящее световое излучение вызывает ток внутри фотодиода.
Таким образом, детектор преобразовывает проходящее сквозь контролируемое изделие излучение в электрические сигналы, величина которых прямо пропорциональна интенсивности лучей гамма.
Приёмник излучения рентгена – это линейка сцинтилляционных детекторов, которые по отдельности оснащены собственными усилителями, образующими единый независимый канал с детекторами. Количество детекторов в линейке строго зависит от необходимой ширины контролируемой зоны. Все каналы детекторного блока опрашиваются по очереди, а с помощью АЦП (аналого-цифровой преобразователь) все полученные сигналы приобретают цифровой вид. Впоследствии полученный в ходе опроса детекторных блоков цифровой массив передаётся на ПК.
Радиографический контроль трубыПосредством перемещения детекторных блоков по отношению к контролируемому сварочному соединению получают непрерывно считываемый массив данных, записывающийся в память ПК с целью последующего и более детального исследования, архивирования. Для оперативной оценки качества в лаборатории контроля в реальном времени эти данные выводятся в виде полутонового изображения прямо на монитор.
Если вы хотите стать профессиональным сварщиком, вам стоит для начала посмотреть уроки газовой и электросварки.
Для обработки металла резанием необходимо приобрести несколько типов станков. Подробнее о том, как происходит процесс, читайте в этой статье.
Хотите сделать бизнес в сфере металлообработки? О том, какие материалы и оборудование для этого нужно приобрести, читайте по https://elsvarkin.ru/prakticheskoe-primenenie/kak-samomu-sdelat-metallicheskij-karkas-dlya-karkasnogo-doma-i-garazha/ ссылке.
Главные требования к рентгеновским аппаратам
В процессе радиометрическом методе флуктуации интенсивности проходящего сквозь объект энергетического спектра не оказывают никакого воздействия на чувствительность контроля, так как изображение, фиксируемое на пленке рентгена изображение определяют посредством интегральной дозы излучения в период экспозиции.
Именно поэтому во время радиографического контроля разрешается применять рентгеновские аппараты любого существующего типа. В большинстве случаев изготовители рентген-аппаратов не приводят никаких данных о флуктуации интенсивности излучений, поскольку данная величина не является критичной.
Стоит отметить, что радиометрия представляет собой метод измерения при построчном сборе данных в режиме реального времени.
Для сканирования одной строки могут потребоваться десятые доли секунды. Исходя из этого рентген аппарату предъявляются 2 основных требования, а именно:
1) Плотность потока гамма-излучения, проходящего сквозь контролируемую толщину проверяемого объекта, должна быть настолько велика, чтобы этого времени было достаточно для регистрации изменения толщины объекта вдоль просканированной области
2) Интенсивность гамма-излучения обязательно должна быть постоянной
Таким образом, для качественного радиометрического контроля необходимы высокостабильные источники ионизирующего излучения, имеющего максимально возможную плотность лучевого потока, а также максимальный энергетический спектр.
С целью сравнения современных рентгеновских аппаратов панорамного типа с постоянным потенциалом разработан специальный переносной прибор, обеспечивающий проведение измерений интенсивности излучения в полевых условиях.
Виды радиометрических аппаратов:
- Аппараты, которые обладают фиксированной частотой флуктуаций интенсивности гамма-излучения. Регулярные перемены интенсивности рентгеновского излучения создают на изображении поперечные полосы. При этом среднеквадратичные отклонения в интенсивности излучения в несколько раз превышают статистические шумы. Возможно ослабление данных флуктуаций программным способом. С этой целью радиометрическую установку оснащают программами, определяющими спектральную долю флуктуаций для каждого аппарата. Подобные рентгеновские аппараты считаются условно применимыми для радиометрического контроля сварочных швов и соединений.
- Рентгеновские аппараты с постоянным потенциалом, которые обладают высокочастотными флуктуациями, случайными во времени. У таких приборов величина отклонений интенсивности гамма-излучения более одного процента. В радиометрическом контроле сварочных конструкций не рекомендуется применять такие устройства.
- Идеальным вариантом является оборудование, стабильность излучения которого превышает 0,5 процентов, а частота флуктуаций имеет показатель не более 0,1 Гц. Низкочастотные изменения интенсивности излучения столь незначительной величины можно легко устранить на изображении программным способом.
Специалисты рекомендуют рентгеновский программный аппарат модели РПД200П, который после соответствующей модификации системы питания показал, что может успешно применяться в процессе проведения радиометрического контроля высокого качества.
Развивающаяся стремительными темпами вычислительная и электронная техника открывает широкие возможности для удешевления и усовершенствования радиометрической аппаратуры.
Проведённые с помощью аппарата РПД200П панорамного типа измерения доказывают, что на базе оборудования этого типа можно создать целые радиометрические комплексы.
(рис. 63.1 – Операционный контроль Операционный контроль – это проверка качества во время реализации технологической операции и по её окончанию. В процессе подготовки к работе и сварке стальных газопроводов на соответствие стандартам ревизуют подготовку труб, правку концов, очистку, форму и размеры швов, число и расположение прихваток, порядок нанесения слоёв. После дуговой или газовой сварки труб стыки подвергаются внешнему осмотру. Проверяется выполнение следующих условий:
Сваренные стыки выборочно проверяются механическими испытаниями и физическими методами. Для стыков, соединённых дуговой или газовой сваркой, устраивают испытания на статическое сплющивание, изгиб или растяжение. Неудовлетворительными следует считать следующие результаты:
Трубы с диаметром ≤ 50 мм проходят механические испытания на сплющивание (50% контрольной выборки) и растяжение (оставшиеся 50 %). Сварной стык не проходит проверку на растяжение, если величина предела прочности на растяжение меньше нижнего предела прочности основного трубного металла. При испытании на сплющивание труба сжимается до возникновения первой трещины на шве. После измеряется величина просвета между рабочими поверхностями пресса. Она не должна превышать величину стенки трубы, умноженную на пять (5S). К физическим методам относятся: радиографический и ультразвуковой. Первым методом проверяются допускные стыки. Обоими – стыки внутренних и наружных газопроводов. (рис. 63.2 – Ультразвуковой контроль Ультразвуковой метод обязательно дублируется радиографическим методом: ≥ 10% отобранных для проверки стыков проходят страхующий контроль. Если хоть один стык, проверенный радиографическим методом, дал неудовлетворительный результат – объём радиографического контроля повышают до 50%. Выборку стыков на проверку формируют из сварных стоков наиболее худшего внешнего вида.
Ультразвуковой метод призван не допустить к эксплуатации сварные соединения труб со стыками, имеющими дефекты длиной > 25 мм на 300 мм протяжённости шва (если длина соединения < 300 мм, то протяжённость дефекта не должна превышать 10% периметра). Результаты проверки радиографическим и ультразвуковым методом оформляются протоколом. Запрещается: повторный ремонт и исправление дефектов стыков подчеканкой. При выявлении повторной физической проверкой хоть одного дефектного стыка, абсолютно все стыки, выполненные сварщиком в течение месяца на объекте, проходят радиографический контроль. В случае обнаружения повторной механической проверкой хотя бы одного дефектного стыка, абсолютно все стыки, выполненные сварщиком в течение месяца на объекте, удаляются (если сварены газовой сваркой) или проверяются радиографическим методом (если сварены дуговой сваркой). Похожие статьи:
|
Непровар корня сварного шва: причины дефекта, метод устранения
В технологическом процессе сварочных работ появляется непровар сварного шва, который ухудшает технологические свойства материала. Оценка приёмки работы требует проверки сварных соединений, где необходимо высокое качество обработки поверхности соединяемых плоскостей. Все образования на поверхности, имеющие неоднородную структуру и форму, именуются как дефект сварного шва непровар. В свою очередь существует разделение степени и уровни непровара, которые имеют следующие характеристики дефектов:
- Горячие или холодные микротрещины.
- Горячите или холодные макротрещины.
- Непровар корня сварного шва.
- Явные поры.
- Включения различных групп.
В целом, сварочные работы, в независимости от уровня и сложности, допускают появление непроваров, но при этом, необходимо устранить имеющиеся дефекты доступными средствами и технологиями.
Пример непровара сварного шва
Способы проверки появления дефектов
Визуально определить место можно только в том случае, если сварщик имеет достаточный опыт работы в данной сфере и знает причины непровара сварного шва. Появление дефектов возможно в любом месте, и мастеру необходимо своевременно устранить проблему, используя разрешённые методы для сварочной технологии. Наличие дефекта может в дальнейшем вызвать разрушение, снизить сопряжение сварных участков, а также привести к выходу из строя конструкционного элемента.
Основные причины непровара сварного шва возникшей проблемы, выглядят следующими критериями:
- Сварочный ток имеет малые показатели.
- Электрод перемещается достаточно интенсивно и с большой скоростью.
- Очень большая длина размерного ряда дуги.
- Для кромок имеет место малого угла скоса.
- В кромках есть явные изъяны большого угла притупления.
- Свариваемые элементы для кромки или перемещены неправильно, или значительно смещены.
- Между расположенными кромками имеет место малой величины зазора.
- В процессе сварки используют электрод с большим диаметром, не предназначенный для проведения этапа сварочных мероприятий.
- Между свариваемыми кромками происходит затекания шлака.
Таким образом, непровар сварного шва это дефект который представляет особую угрозу и опасность при проведении дальнейших работ с конструкционными изделиями.
Терминология непровара
В среде специалистов существует особые трактования, указывающее на что это такое непровар сварного шва – это видимый или скрытый участок места соединения, где отсутствует эффект сплавления, который обязателен в данной ситуации. Чаще всего конструктивный непровар сварного шва можно встретить в корневой части места соединения, в кромках между соединениями, между смежными параметрами слоёв наплавляемого шва по кромке.
Видимый непровар на детали
Далее, определение непровара сварного шва указывает на то, что значительно уменьшается рабочее сечение конструкционного соединения шва. В свою очередь это приводит к естественному снижению работоспособности имеющегося сварного соединения.
Технологическая просветка сварных швов, признана своеобразным концентратором напряжений, вследствие чего появляются трещины различной глубины и жёсткости. Выявляется снижение коррозийной стойкости готового сварного соединения.
Пористость, основные моменты дефектов
Не менее важным элементом дефекта допуска непровара сварного шва является выявление ее пористости. Появление этой структуры вызвано маленькими пузырьками, которые образуются в виде газов в металле. Как правило, структура имеет сферическую, или близкую к этой форме круглую структуру. Для углеродистых сталей непровары в этих местах имеют не сферическую, а трубчатую форму исполнения. Первоначально, сферические образования появляются в жидком металле во время проведения сварочных работ. В течение определённого времени сварки, а точнее интенсивного газообразования, не все задействованные пузырьки технологического процесса успевают выйти на поверхность. Какая-то часть остаётся внутри конструкции сварного соединения. Габаритные объёмы и размеры таких «шариков» колеблются в различных диапазонах, начиная с микроскопических, и заканчивая полноценными большими сферами в диаметре 2-3 мм. Если проходит диффузия газов, сферы начинают еще больше расти внутри сварного соединения до момента полного затвердевания.
Такие дефектные явления могут образовывать цепочки, группы и прочие фактуры. В целом, чтобы правильно использовать рекомендуемый метод устранения непровар сварного шва, обращаем внимание на следующие причины возникновения проблемы:
- Наличие газовых соединений, которые не успевают выйти, и происходит кристаллизация структуры.
- Взаимодействие окиси железа с углеродом, вследствие чего возникает углекислый газ и окись углерода.
- Есть влага во флюсе или в процессе автоматической сварки.
- Возникновение ржавчин, как на концах сварных технологических соединений, так и на проволоке.
Появление трещин
Это дополнительный дефект непровара, критерий связан, прежде всего, с образованием микроскопических или макроскопических компонентов межкристаллического разрушения, вследствие чего образуются малые полости с микроскопическими параметрами раскрытия. Наличие остаточных явлений напряжений на соединяемых участках приводит к тому, что в дальнейшем трещины с небывалой скоростью могут расширяться до невиданных размеров. Это процесс очень опасный, и в ряде случаев может привести к печальным последствиям эксплуатации значимых металлических узлов и компонентов. Причины возникновения трещин:
- Есть место повышенного усадочного напряжения, где происходит превышение предела прочности металла.
- Происходит жёсткий режим закрепления свариваемых элементов металла.
- В металле возникает так называемый эффект мартенсита, характерный для явления структурного напряжения.
- Во всех металлах есть место повышенное содержание серы, фосфора, а также углерода.
- Сварочные мероприятия проходили при очень низких температурах.
- На одном участке сосредоточено большое количество швов, которые вызывают комплексное сопряжение.
Группы непровара по ГОСТ
Существует единая классификация стандартов непровара дефектов сварных швов которые отражены в действующем регламентом положении ГОСТ 30242-97, где определено 6 основных групп или зон, характерные для каждого процесса и металла
Номер группы | Характер непровара |
1 | Трещина |
2 | Пора, а также полости |
3 | Включения твёрдой группы |
4 | Эффект несплавления или непровара по техническим параметрам |
5 | Техническое нарушение формы шва |
6 | Дефекты и группы, которые не включены в вышеназванные критерии дефектов. |
Виды непровара сварного шва
В техническом стандарте также даётся подробное описание того, как маркируется тот или иной тип непровара или технологического дефекта, связанные со сварочными работами. Все дефекты маркируются цифровыми значениями или маркировкой МИС (буквенное). Каждый дефект имеет собственную маркировку, причём группа маркировки зависит от номера группы в диапазоне от 1 до 6. Цифровое значение имеет 3 или 4 знака, буквенное значение 1-2 литеры английского алфавита, или отсутствует буквенное значение (числовое обязательное присутствует в списке). Для визуального определения варианта исполнения дефекта, в регламенте присутствует подробный рисунок, с объяснениями и разъяснениями дефектов непровара. Неполный провар имеет числовое значение 402, а буквенный ряд D.
Видео: описание непровара сварного соединения
Обзор дефектов и контроль качества сварных соединений | Новосибирск
Дефекты и контроль качества сварных соединений
Общие сведения и организация контроля
По ГОСТ 15467-79 качество продукции есть совокупность свойств продукции, обусловливающих ее пригодность удовлетворять определенные потребности в соответствии с ее назначением. Качество сварных изделий зависит от соответствия материала техническим условиям, состояния оборудования и оснастки, правильности и уровня отработки технологической документации, соблюдения технологической дисциплины, а также квалификации работающих. Обеспечить высокие технические и эксплуатационные свойства изделий можно только при условии точного выполнения технологических процессов и их стабильности. Особую роль здесь играют различные способы объективного контроля как производственных процессов, так и готовых изделий. При правильной организации технологического процесса контроль должен быть его неотъемлемой частью. Обнаружение дефектов служит сигналом не только к отбраковке продукции, но и оперативной корректировке технологии.
Сварные конструкции контролируют на всех этапах их изготовления. Кроме того, систематически проверяют приспособления и оборудование. При предварительном контроле подвергаются проверке основные и вспомогательные материалы, устанавливается их соответствие чертежу и техническим условиям.
После заготовительных работ детали подвергают чаще всего наружному осмотру, т.е. проверяют внешний вид детали, качество поверхности, наличие заусенцев, трещин, забоин и т.п., а также измеряют универсальными и специальными инструментами, шаблонами, с помощью контрольных приспособлений. Особенно тщательно контролируют участки, подвергающиеся сварке. Профиль кромок, подготовленных под сварку плавлением, проверяют специальными шаблонами, а качество подготовки поверхности — с помощью оптических приборов или специальными микрометрами.
Во время сборки и прихватки проверяют расположение деталей друг относительно друга, величину зазоров, расположение и размер прихваток, отсутствие трещин, прожогов и других дефектов в местах прихваток и т.д. Качество сборки и прихватки определяют главным образом наружным осмотром и обмером.
Наиболее ответственным моментом является текущий контроль выполнения сварки. Организация контроля сварочных работ может производиться в двух направлениях: контролируют сами процессы сварки либо полученные изделия.
Контроль процессов позволяет предотвратить появление систематических дефектов и особенно эффективен при автоматизированной сварке (автоматическая и механизированная дуговая, электрошлаковая и др.). Существуют следующие способы контроля сварочных процессов.
Контроль по образцам технологических проб. В этом случае периодически изготовляют образцы соединений из материала той же марки и толщины, что и свариваемое изделие, и подвергают их всесторонней проверке: внешнему осмотру, испытаниям на прочность соединений, просвечиванию рентгеновскими лучами, металлографическому исследованию и т.д. К недостаткам такого способа контроля следует отнести некоторое различие между образцом и изделием, а также возможность изменения сварочных условий с момента изготовления одного образца до момента изготовления следующего.
Контроль с использованием обобщающих параметров, имеющих прямую связь с качеством сварки, например использование дилатометрического эффекта в условиях точечной контактной сварки. Однако в большинстве случаев сварки плавлением трудно или не всегда удается выявить наличие обобщающего параметра, позволяющего достаточно надежно контролировать качество соединений.
Контроль параметров режима сварки. Так как в большинстве случаев определенных обобщающих параметров для процессов сварки плавлением нет, то на практике контролируют параметры, непосредственно определяющие режим сварки. При дуговой сварке такими параметрами в первую очередь являются сила тока, дуговое напряжение, скорость сварки, скорость подачи проволоки и др. Недостаток такого подхода заключается в необходимости контролирования многих параметров, каждый из которых в отдельности не может характеризовать непосредственно уровень качества получаемых соединений.
Контроль изделий производят пооперационно или после окончания изготовления. Последним способом обычно контролируют несложные изделия. Качество выполнения сварки на изделии оценивают по наличию наружных или внутренних дефектов. Развитие физики открыло большие возможности для создания высокоэффективных методов дефектоскопии с высокой разрешающей способностью, позволяющих проверять без разрушения качество сварных соединений в ответственных конструкциях.
В зависимости от того, нарушается или не нарушается целостность сварного соединения при контроле, различают неразрушающие и разрушающие методы контроля.
Дефекты сварных соединений и причины их возникновения
В процессе образования сварных соединений в металле шва и зоне термического влияния могут возникать различные отклонения от установленных норм и технических требований, приводящие к ухудшению работоспособности сварных конструкций, снижению их эксплуатационной надежности, ухудшению внешнего вида изделия. Такие отклонения называют дефектами. Дефекты сварных соединений различают по причинам возникновения и месту их расположения (наружные и внутренние). В зависимости от причин возникновения их можно разделить на две группы. К первой группе относятся дефекты, связанные с металлургическими и тепловыми явлениями, происходящими в процессе образования, формирования и кристаллизации сварочной ванны и остывания сварного соединения (горячие и холодные трещины в металле шва и околошовной зоне, поры, шлаковые включения, неблагоприятные изменения свойств металла шва и зоны термического влияния).
Ко второй группе дефектов, которые называют дефектами формирования швов, относят дефекты, происхождение которых связано в основном с нарушением режима сварки, неправильной подготовкой и сборкой элементов конструкции под сварку, неисправностью оборудования, недостаточной квалификацией сварщика и другими нарушениями технологического процесса. К дефектам этой группы относятся несоответствия швов расчетным размерам, непровары, подрезы, прожоги, наплывы, незаваренные кратеры и др. Виды дефектов приведены на рис. 1. Дефектами формы и размеров сварных швов являются их неполномерность, неравномерные ширина и высота, бугристость, седловины, перетяжки и т. п.
Рисунок 1 — Виды дефектов сварных швов:
а — ослабление шва. б — неравномерность ширины, в — наплыв, г — подрез, с — непровар, с — трещины и поры, ж — внутренние трещины и поры, з — внутренний непровар, и — шлаковые включения
Эти дефекты снижают прочность и ухудшают внешний вид шва. Причины их возникновения при механизированных способах сварки — колебания напряжения в сети, проскальзывание проволоки в подающих роликах, неравномерная скорость сварки из-за люфтов в механизме перемещения сварочного автомата, неправильный угол наклона электрода, протекание жидкого металла в зазоры, их неравномерность по длине стыка и т.п. Дефекты формы и размеров швов косвенно указывают на возможность образования внутренних дефектов в шве.
Наплывы образуются в результате натекания жидкого металла на поверхность холодного основного металла без сплавления с ним. Они могут быть местными — в виде отдельных застывших капель, а также иметь значительную протяженность вдоль шва. Чаще всего наплывы образуются при выполнении горизонтальных сварных швов на вертикальной плоскости. Причины образования наплывов — большой сварочный ток, слишком длинная дуга, неправильный наклон электрода, большой угол наклона изделия при сварке на спуск. При выполнении кольцевых швов наплывы образуются при недостаточном или излишнем смещении электрода с зенита. В местах наплывов часто могут выявляться непровары, трещины и др.
Подрезы представляют собой продолговатые углубления (канавки), образовавшиеся в основном металле вдоль края шва. Они возникают в результате большого сварочного тока и длинной дуги. Основной причиной подрезов при выполнении угловых швов является смещение электрода в сторону вертикальной стенки. Это вызывает значительный разогрев металла вертикальной стенки и его стекание при оплавлении на горизонтальную стенку. Подрезы приводят к ослаблению сечения сварного соединения и концентрации в нем напряжений, что может явиться причиной разрушения.
Прожоги — это сквозные отверстия в шве, образованные в результате вытекания части металла ванны. Причинами их образования могут быть большой зазор между свариваемыми кромками, недостаточное притупление кромок, чрезмерный сварочный ток, недостаточная скорость сварки. Наиболее часто прожоги образуются при сварке тонкого металла и выполнении первого прохода многослойного шва. Прожоги могут также образовываться в результате недостаточно плотного поджатая сварочной подкладки или флюсовой подушки.
Непроваром называют местное несплавление кромок основного металла или несплавление между собой отдельных валиков при многослойной сварке. Непровары уменьшают сечение шва и вызывают концентрацию напряжений в соединении, что может резко снизить прочность конструкции. Причины образования непроваров — плохая зачистка металла от окалины, ржавчины и загрязнений, малый зазор при сборке, большое притупление, малый угол скоса кромок, недостаточный сварочный ток, большая скорость сварки, смещение электрода от центра стыка. Непровары выше допустимой величины подлежат удалению и последующей заварке.
Трещины, также как и непровары, являются наиболее опасными дефектами сварных швов. Они могут возникать как в самом шве, так и в околошовной зоне и располагаться вдоль или поперек шва. По своим размерам трещины могут быть макро- и микроскопическими. На образование трещин влияет повышенное содержание углерода, а также примеси серы и фосфора.
Шлаковые включения, представляющие собой вкрапления шлака в шве, образуются в результате плохой зачистки кромок деталей и поверхности сварочной проволоки от оксидов и загрязнений. Они возникают при сварке длинной дугой, недостаточном сварочном токе и чрезмерно большой скорости сварки, а при многослойной сварке — недостаточной зачистке шлаков с предыдущих слоев. Шлаковые включения ослабляют сечение шва и его прочность.
Газовые поры появляются в сварных швах при недостаточной полноте удаления газов при кристаллизации металла шва. Причины пор — повышенное содержание углерода при сварке сталей, загрязнения на кромках, использование влажных флюсов, защитных газов, высокая скорость сварки, неправильный выбор присадочной проволоки. Поры могут располагаться в шве отдельными группами, в виде цепочек или единичных пустот. Иногда они выходят на поверхность шва в виде воронкообразных углублений, образуя так называемые свищи. Поры также ослабляют сечение шва и его прочность, сквозные поры приводят к нарушению герметичности соединений.
Микроструктура шва и зоны термического влияния в значительной степени определяет свойства сварных соединений и характеризует их качество.
К дефектам микроструктуры относят следующие: повышенное содержание оксидов и различных неметаллических включений, микропоры и микротрещины, крупнозернистость, перегрев, пережог металла и др. Перегрев характеризуется чрезмерным укрупнением зерна и огрублением структуры металла. Более опасен пережог — наличие в структуре металла зерен с окисленными границами. Такой металл имеет повышенную хрупкость и не поддаетсяисправлению. Причиной пережога является плохая защита сварочной ванны при сварке, а также сварка на чрезмерно большой силе тока.
Методы неразрушающего контроля сварных соединений
К неразрушающим методам контроля качества сварных соединений относят внешний осмотр, контроль на непроницаемость (или герметичность) конструкций, контроль для обнаружения дефектов, выходящих на поверхность, контроль скрытых и внутренних дефектов.
Внешний осмотр и обмеры сварных швов — наиболее простые и широко распространенные способы контроля их качества. Они являются первыми контрольными операциями по приемке готового сварного узла или изделия. Этим видам контроля подвергают все сварные швы независимо от того, как они будут испытаны в дальнейшем.
Внешним осмотром сварных швов выявляют наружные дефекты: непровары, наплывы, подрезы, наружные трещины и поры, смещение свариваемых кромок деталей и т. п. Визуальный осмотр производят как невооруженным глазом, так и с применением лупы с увеличением до 10 раз.
Обмеры сварных швов позволяют судить о качестве сварного соединения: недостаточное сечение шва уменьшает его прочность, слишком большое — увеличивает внутренние напряжения и деформации. Размеры сечения готового шва проверяют по его параметрам в зависимости от типа соединения. У стыкового шва проверяют его ширину, высоту, размер выпуклости со стороны корня шва, в угловом — измеряют катет. Замеренные параметры должны соответствовать ТУ или ГОСТам. Размеры сварных швов контролируют обычно измерительными инструментами или специальными шаблонами.
Внешний осмотр и обмеры сварных швов не дают возможности окончательно судить о качестве сварки. Они устанавливают только внешние дефекты шва и позволяют определить их сомнительные участки, которые могут быть проверены более точными способами.
Контроль непроницаемости сварных швов и соединений. Сварные швы и соединения ряда изделий и сооружений должны отвечать требованиям непроницаемости (герметичности) для различных жидкостей и газов. Учитывая это, во многих сварных конструкциях (емкости, трубопроводы, химическая аппаратура и» т.д.) сварные швы подвергают контролю на непроницаемость. Этот вид контроля производится после окончания монтажа или изготовления конструкции. Дефекты, выявленные внешним осмотром, устраняются до начала испытаний. Непроницаемость сварных швов контролируют следующими методами: капиллярным (керосином), химическим (аммиаком), пузырьковым (воздушным или гидравлическим давлением), вакуумированием или газоэлектрическими течеискателями.
Контроль керосином основан на физическом явлении капиллярности, которое заключается в способности керосина подниматься по капиллярным ходам — сквозным порам и трещинам. В процессе испытания сварные швы покрываются водным раствором мела с той стороны, которая более доступна для осмотра и выявления дефектов. После высушивания окрашенной поверхности с обратной стороны шов обильно смачивают керосином. Неплотности швов выявляют по наличию на меловом покрытии следов проникшего керосина. Появление отдельных пятен указывает на поры и свищи, полос — сквозных трещин и непроваров в шве. Благодаря высокой проникающей способности керосина обнаруживаются дефекты с поперечным размером 0,1 мм и менее.
Контроль аммиаком основан на изменении окраски некоторых индикаторов (раствор фенолфталеина, азотнокислой ртути) под воздействием щелочей. В качестве контролирующего реагента применяется газ аммиак. При испытании на одну сторону шва укладывают бумажную ленту, смоченную 5%-ным раствором индикатора, а с другой стороны шов обрабатывают смесью аммиака с воздухом. Аммиак, проникая через неплотности сварного шва, окрашивает индикатор в местах залегания дефектов.
Контроль воздушным давлением (сжатым воздухом или другими газами) подвергают сосуды и трубопроводы, работающие под давлением, а также резервуары, цистерны и т. п. Это испытание проводят с целью проверки общей герметичности сварного изделия. Малогабаритные изделия полностью погружают в ванну с водой, после чего в него подают сжатый воздух под давлением, на 10 — 20% превышающим рабочее. Крупногабаритные конструкции после подачи внутреннего давления по сварным швам покрывают пенным индикатором (обычно раствор мыла). О наличии неплотностей в швах судят по появлению пузырьков воздуха. При испытании сжатым воздухом (газами) следует соблюдать правила безопасности.
Контроль гидравлическим давлением применяют при проверке прочности и плотности различных сосудов, котлов, паро-, водо- и газопроводов и других сварных конструкций, работающих под избыточным давлением. Перед испытанием сварное изделие полностью герметизируют водонепроницаемыми заглушками. Сварные швы с наружной поверхности тщательно просушивают обдувом воздухом. Затем изделие заполняют водой под избыточным давлением, в 1,5 — 2 раза превышающим рабочее, и выдерживают в течение заданного времени. Дефектные места определяют по проявлению течи, капель или увлажнению поверхности швов.
Вакуумному контролю подвергают сварные швы, которые невозможно испытать керосином, воздухом или водой и доступ к которым возможен только с одной стороны. Его широко применяют при проверке сварных швов днищ резервуаров, газгольдеров и других листовых конструкций. Сущность метода заключается в создании вакуума на одной стороне контролируемого участка сварного шва и регистрации на этой же стороне шва проникновения воздуха через имеющиеся неплотности. Контроль ведется с помощью переносной вакуум-камеры, которую устанавливают на наиболее доступную сторону сварного соединения , предварительно смоченную мыльным раствором (рис. 2).
Рисунок 2 — Вакуумный контроль шва: 1 – вакуумметр, 2 — резиновое уплотнение, 3 — мыльный раствор, 4 — камера.
В зависимости от формы контролируемого изделия и типа соединения могут применяться плоские, угловые и сферические вакуум-камеры. Для создания вакуума в них применяют специальные вакуум-насосы.
Люминесцентный контроль и контроль методом красок, называемый также капиллярной дефектоскопией, проводят с помощью специальных жидкостей, которые наносят на контролируемую поверхность изделия. Эти жидкости, обладающие большой смачивающей способностью, проникают в мельчайшие поверхностные дефекты — трещины, поры, непровары. Люминесцентный контроль основан на свойстве некоторых веществ светиться под действием ультрафиолетового облучения. Перед контролем поверхности шва и околошовной зоны очищают от шлака и загрязнений, на них наносят слой проникающей жидкости, которая затем удаляется, а изделие просушивается. Для обнаружения дефектов поверхность облучают ультрафиолетовым излучением — в местах дефектов следы жидкости обнаруживаются по свечению.
Контроль методом красок заключается в том, что на очищенную поверхность сварного соединения наносится смачивающая жидкость, которая под действием капиллярных сил проникает в полость дефектов. После ее удаления на поверхность шва наносится белая краска. Выступающие следы жидкости обозначают места расположения дефектов.
Контроль газоэлектрическими течеискателям и применяют для испытания ответственных сварных конструкций, так как такие течеискатели достаточно сложны и дорогостоящи. В качестве газа-индикатора в них используется гелий. Обладая высокой проникающей способностью, он способен проходить через мельчайшие несплошности в металле и регистрируется течеискателем. В процессе контроля сварной шов обдувают или внутренний объем изделия заполняют смесью газа-индикатора с воздухом. Проникающий через неплотности газ улавливается щупом и анализируется в течеискателе.
Для обнаружения скрытых внутренних дефектов применяют следующие методы контроля.
Магнитные методы контроля основаны на обнаружении полей магнитного рассеяния, образующихся в местах дефектов при намагничивании контролируемых изделий. Изделие намагничивают, замыкая им сердечник электромагнита или помещая внутрь соленоида. Требуемый магнитный поток можно создать и пропусканием тока по виткам (3 — 6 витков) сварочного провода, наматываемого на контролируемую деталь. В зависимости от способа обнаружения потоков рассеяния различают следующие методы магнитного контроля: метод магнитного порошка, индукционный и магнитографический. При методе магнитного порошка на поверхность намагниченного соединения наносят магнитный порошок (окалина, железные опилки) в сухом виде (сухой способ) или суспензию магнитного порошка в жидкости (керосин, мыльный раствор, вода — мокрый способ). Над местом расположения дефекта создадутся скопления порошка в виде правильно ориентированного магнитного спектра. Для облегчения подвижности порошка изделие слегка обстукивают. С помощью магнитного порошка выявляют трещины, невидимые невооруженным глазом, внутренние трещины на глубине не более 15 мм, расслоение металла, а также крупные поры, раковины и шлаковые включения на глубине не более 3 — 5 мм. При индукционном методе магнитный поток в изделии наводят электромагнитом переменного тока.
Дефекты обнаруживают с помощью искателя, в катушке которого под воздействием поля рассеяния индуцируется ЭДС, вызывающая оптический или звуковой сигнал на индикаторе. При магнитографическом методе (рис. 3) поле рассеяния фиксируется на эластичной магнитной ленте, плотно прижатой к поверхности соединения. Запись воспроизводится на магнитографическом дефектоскопе. В результате сравнения контролируемого соединения с эталоном делается вывод о качестве соединения.
Рисунок 3 — Магнитная запись дефектов на ленту: 1 — подвижный электромагнит, 2 — дефект шва, 3 — магнитная лента.
Радиационные методы контроля являются надежным и широко распространенными методами контроля, основанными на способности рентгеновского и гамма-излучения проникать через металл. Выявление дефектов при радиационных методах основано на разном поглощении рентгеновского или гамма-излучения участками металла с дефектами и без них. Сварные соединения просвечивают специальными аппаратами. С одной стороны шва на некотором расстоянии от него помещают источник излучения, с противоположной стороны плотно прижимают кассету с чувствительной фотопленкой (рис. 4). При просвечивании лучи проходят через сварное соединение и облучают пленку. В местах, где имеются поры, шлаковые включения, непровары, крупные трещины, на пленке образуются темные пятна. Вид и размеры дефектов определяют сравнением пленки с эталонными снимками. Источниками рентгеновского излучения служат специальные аппараты (РУП-150-1, РУП-120-5-1 и др.).
Рисунок 4 — Схема радиационного просвечивания швов: а — рентгеновское, б — гамма-излучением: 1 — источник излучения, 2 — изделие, 3 — чувствительная пленка
Рентгенопросвечиванием целесообразно выявлять дефекты в деталях толщиной до 60 мм. Наряду с рентгенографированием (экспозицией на пленку) применяют и рентгеноскопию, т.е. получение сигнала о дефектах при просвечивании металла на экран с флуоресцирующим покрытием. Имеющиеся дефекты в этом случае рассматривают на экране. Такой способ можно сочетать с телевизионными устройствами и контроль вести на расстоянии.
При просвечивании сварных соединений гамма-излучением источником излучения служат радиоактивные изотопы: кобальт-60, тулий-170, иридий-192 и др. Ампула с радиоактивным изотопом помещается в свинцовый контейнер. Технология выполнения просвечивания подобна рентгеновскому просвечиванию. Гамма-излучение отличается от рентгеновского большей жесткостью и меньшей длиной волны, поэтому оно может проникать в металл на большую глубину. Оно позволяет просвечивать металл толщиной до 300 мм. Недостатками просвечивания гамма-излучением по сравнению с рентгеновским являются меньшая чувствительность при просвечивании тонкого металла (менее 50 мм), невозможность регулирования интенсивности излучения, большая опасность гамма-излучения при неосторожном обращении с гамма-аппаратами.
Ультразвуковой контроль основан на способности ультразвуковых волн проникать в металл на большую глубину и отражаться от находящихся в нем дефектных участков. В процессе контроля пучок ультразвуковых колебаний от вибрирующей пластинки-щупа (пьезокристалла) вводится в контролируемый шов. При встрече с дефектным участком ультразвуковая волна отражается от него и улавливается другой пластинкой-щупом, которая преобразует ультразвуковые колебания в электрический сигнал (рис. 5).
Рисунок 5 — Ультразвуковой контроль швов: 1 — генератор УЗК, 2 — щуп, 3 — усилитель, 4 — экран.
Эти колебания после их усиления подаются на экран электронно-лучевой трубки дефектоскопа, которые свидетельствуют о наличии дефектов. По характеру импульсов судят о протяженности дефектов и глубине их залегания. Ультразвуковой контроль можно проводить при одностороннем доступе к сварному шву без снятия усиления и предварительной обработки поверхности шва.
Ультразвуковой контроль имеет следующие преимущества: высокая чувствительность (1 — 2%), позволяющая обнаруживать, измерять и определять местонахождение дефектов площадью 1 — 2 мм2; большая проникающая способность ультразвуковых волн, позволяющая контролировать детали большой толщины; возможность контроля сварных соединений с односторонним подходом; высокая производительность и отсутствие громоздкого оборудования. Существенным недостатком ультразвукового контроля является сложность установления вида дефекта. Этот метод применяют и как основной вид контроля, и как предварительный с последующим просвечиванием сварных соединений рентгеновским или гамма-излучением.
Методы контроля с разрушением сварных соединений
К этим методам контроля качества сварных соединений относятся механические испытания, металлографические исследования, специальные испытания с целью получения характеристик сварных соединений. Эти испытания проводят на сварных образцах, вырезаемых из изделия или из специально сваренных контрольных соединений — технологических проб, выполненных в соответствии с требованиями и технологией на сварку изделия в условиях, соответствующих сварке изделия.
Целью испытаний является: оценка прочности и надежности сварных соединений и конструкций; оценка качества основного и присадочного металла; оценка правильности выбранной технологии; оценка квалификации сварщиков.
Свойства сварного соединения сопоставляют со свойствами основного металла. Результаты считаются неудовлетворительными, если они не соответствуют заданному уровню.
Механические испытания проводятся по ГОСТ 6996-66, предусматривающему следующие виды испытаний сварных соединений и металла шва: испытание сварного соединения в целом и металла разных его участков (наплавленного металла, зоны термического влияния, основного металла) на статическое растяжение, статистический изгиб, ударный изгиб, стойкость против старения, измерение твердости.
Контрольные образцы для механических испытаний выполняют определенных размеров и формы.
Испытаниями на статическое .растяжение определяют прочность сварных соединений. Испытаниями на статический изгиб определяют пластичность соединения по величине угла изгиба до образования первой трещины в растянутой зоне. Испытания на статический изгиб проводят на образцах с продольными и поперечными швами со снятым усилением шва заподлицо с основным металлом. Испытаниями на ударный изгиб, а также разрыв определяют ударную вязкость сварного соединения. По результатам определения твердости судят о структурных изменениях и степени подкалки металла при охлаждении после сварки.
Основной задачей металлографических исследований являются установление структуры металла и качества сварного соединения, выявление наличия и характера дефектов. Металлографические исследования включают в себя макро- и микроструктурный методы анализа металлов.
При макроструктурном методе изучают макрошлифы и изломы металла невооруженным глазом или с помощью лупы. Макроисследование позволяет определить характер и расположение видимых дефектов в разных зонах сварных соединений.
При микроструктурном анализе исследуется структура металла при увеличении в 50 — 2000 раз с помощью оптических микроскопов. Микроисследование позволяет установить качество металла, в том числе обнаружить пережог металла, наличие оксидов, засоренность металла шва неметаллическими включениями, величину зерен металла, изменение состава его, микроскопические трещины, поры и некоторые другие дефекты структуры. Методикаизготовления шлифов для металлографических исследований заключается в вырезке образцов из сварных соединений, шлифовке, полировке и травлении поверхности металла специальными травителями. Металлографические исследования дополняются измерением твердости и при необходимости химическим анализом металла сварных соединений. Специальные испытания проводят с целью получения характеристик сварных соединений, учитывающих условия эксплуатации сварных конструкций: определение коррозионной стойкости для конструкций, работающих в различных агрессивных средах; усталостной прочности при циклических нагружениях; ползучести при эксплуатации в условиях повышенных температур и др.
Применяют также и методы контроля с разрушением изделия. В ходе таких испытаний устанавливают способность конструкций выдерживать заданные расчетные нагрузки и определяют разрушающие нагружения, т.е. фактический запас прочности. При испытаниях изделий с разрушением схема нагружения их должна соответствовать условиям работы изделия при эксплуатации. Число изделий, подвергающихся испытаниям с разрушением, устанавливается техническими условиями и зависит от степени их ответственности, системы организации производства и технологической отработанности конструкции.
Другие статьи:
- Возможности современных источников серии S-XT
- Технология сварки чугуна
- Технология сварки MIG/MAG
Maven Plastics — полупрозрачные прозрачные пластиковые сварочные стержни, катушки и R из ПВХ — Perigee Direct
Maven Plastics
Артикул: MV_ROD_PVC_3MM_CLEAR_CIR_12IN_10PK
Круглые 3 мм (1/8 дюйма) / стержни-12 в упаковке по 10 штук — 11,99 долларов США Круглые 3 мм (1/8 дюйма) / стержни-12 в упаковке по 20 штук — 13,99 долларов США Круглые 3 мм (1/8 дюйма) / стержни -12 в упаковке из 40 штук — 18,68 долларов США Круглые 3 мм (1/8 дюйма) / Катушки-100 футов (около 0,5 фунта) — 27,99 долларов США Круглые 3 мм (1/8 дюйма) / Катушки (катушки) 10 фунтов — 129,99 долларов США Круглые 3 мм (1/8 дюйма) / Катушки (шпули) 20 фунтов — 219 долларов США0,80 долларов США Круглые 3 мм (1/8 дюйма) / катушки (шпули) 40 фунтов — 399,60 долларов США Круглые 4 мм (5/32 дюйма) / стержни-12 в упаковке из 10 — 11,99 долларов США Круглые 4 мм (5/32 дюйма) / стержни -12 шт.

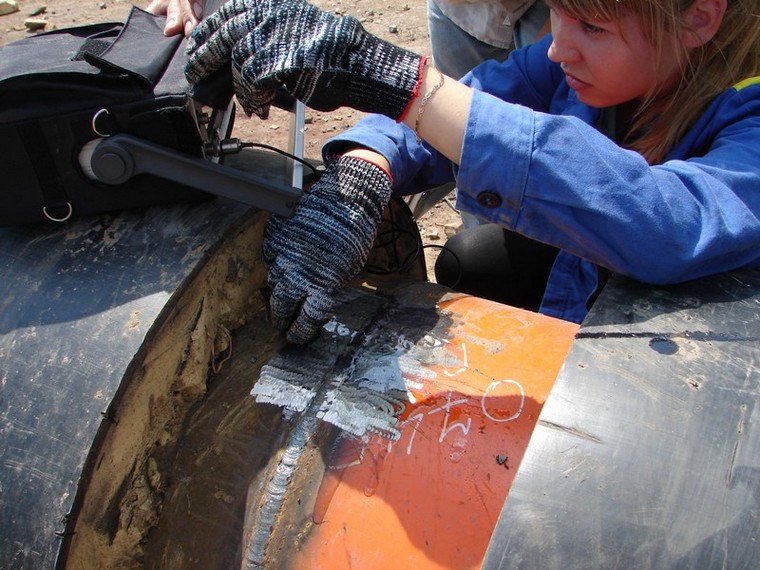
Maven Plastics — Сварочные и ремонтные стержни, катушки и катушки из ПВХ-пластика — полупрозрачный (полупрозрачный) ПВХ круглой формы (поливинилхлорид).
Технические характеристики пластикового сварочного стержня:
- 100 % чистый и однородный ПВХ-материал
- Варианты формы:
- Круглые 1/8 дюйма (3 мм), 5/32 дюйма (4 мм) и 3/16 дюйма (5 мм)
- Треугольник 7/32 дюйма (5,7 мм)
- Плоский 1/16 x 5/8 (1,6 мм x 16 мм)
- Варианты упаковки:
- Стержни поставляются в упаковках по 10, 20 и 40 стержней
- Катушки бывают длиной 100 футов (около 1/2 фунта) и 200 футов (около 1 фунта)
- Катушки бывают 500 футов (около 2,5 фунтов), 10 фунтов, 20 фунтов и 50 фунтов
Изготовлен из 100% чистого ПВХ пластика (поливинилхлорида), без примесей. Все пластиковые стержни, катушки и катушки следует использовать с соответствующим пластиковым сварочным утюгом, распределителем тепла или горелкой с соответствующими насадками.
Прутки, катушки и катушки из ПВХ можно использовать для нескольких популярных типов ремонтных работ, но каждая работа по ремонту пластика должна быть тщательно подобрана к тому же типу пластикового стержня или катушки. Эти стержни, катушки и катушки изготовлены из ПВХ-пластика.
Предупреждение: Смешивание различных видов пластика может привести к некачественному ремонту и снижению долговечности сварных швов. Проще говоря, подберите пластик, и все будет хорошо… разные пластики просто плохо сочетаются друг с другом.
Прутки, рулоны и катушки из ПВХ: используйте с любым пластиком, имеющим маркировку Recycling # 3. Также обычно включает водопроводные трубы, подземные горизонтальные трубы для полива газонов, игрушки
Сварочные одеяла, шторы и экраны а экраны удерживают брызги и искры, предотвращая пожары и повреждения. Они изготовлены из материалов, устойчивых к огню и устойчивых к теплу, выделяемому сварочным оборудованием. Сварочные покрывала накрывают поверхности и оборудование, создавая защитный экран. Сварные завесы и экраны образуют барьеры для ограждения горячих рабочих зон.
Сварочные одеяла, шторы и экраны удерживают брызги и искры, предотвращая пожары и повреждения. Они изготовлены из материалов, устойчивых к огню и устойчивых к теплу, выделяемому сварочным оборудованием. Сварочные покрывала накрывают поверхности и оборудование, создавая защитный экран. Сварные завесы и экраны образуют барьеры для ограждения горячих рабочих зон.
Выдерживаемая температура: не указано
Загрузка … |
СВЕТ ТЕМПЕС.


. | Загрузка … | |||||
Загрузка … | ||||||
Загрузка … | ||||||
Загрузка … | ||||||
Загрузка … | ||||||
Погрузка … | 999977777777777777777777777777777777777777777777777777777777777777777777777777777777 70077777777777777777777777777777777777777777777. …||||||
Loading… | ||||||
Loading… | ||||||
Loading… | ||||||
Loading… | ||||||
Loading… | ||||||
Loading… | ||||||
Загрузка .![]() | ||||||
Загрузка … | ||||||
Загрузка … | ||||||
Загрузка … | ||||||
Загрузка … | ||||||
Загрузка … | ||||||
Loading… | ||||||
Loading… | ||||||
Loading… | ||||||
Loading… | ||||||
Loading… | ||||||
Loading… | ||||||
Loading … | ||||||
Загрузка … | ||||||
Загрузка … | ||||||
Загрузка … | ||||||
Загрузка … | ||||||
нагрузка … | ||||||
Loading… | ||||||
Loading.![]() | ||||||
Loading… | ||||||
Loading… | ||||||
Loading… | ||||||
Loading… |
Withstand Temp.: 1,200 Degrees F
Loading… | ||||||
Загрузка … | ||||||
Загрузка … | ||||||
Загрузка … | ||||||
Загрузка … |

ВЫСОКАЯ ТЕМПЕР.0068
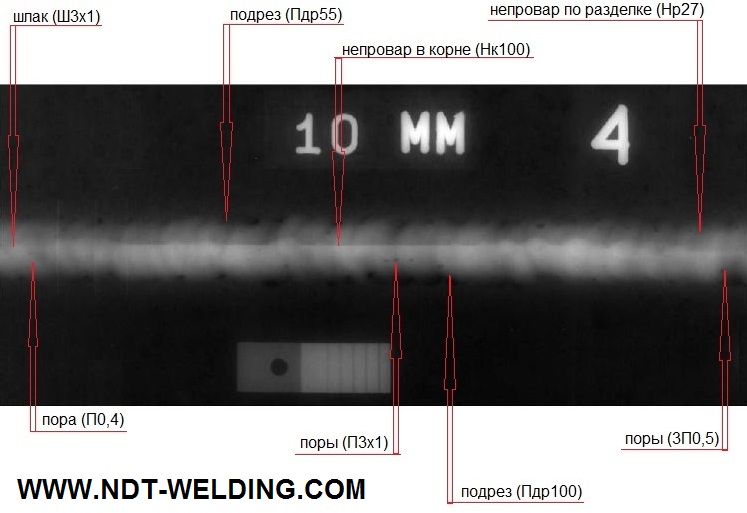
Удержание ТЕПЕР. Ширина по возрастанию

… | ||||||||||||||||||||||||||||||||||||||||||||||||||||||||||||||||||||||||||||||||||||||||||||||||||||||||||||||||||||||||||||||||||||||||||||||||||
… |
… | ||||||||||||||||||||||||||||||||||
… | ||||||||||||||||||||||||||||||||||
… | ||||||||||||||||||||||||||||||||||
878 | .![]() | |||||||||||||||||||||||||||||||||
78 | … | |||||||||||||||||||||||||||||||||
… | 70078. | Загрузка … | ||||||||||||||||||||||||||||||||
Загрузка … | ||||||||||||||||||||||||||||||||||
Загрузка … | ||||||||||||||||||||||||||||||||||
Загрузка … | ||||||||||||||||||||||||||||||||||
Загрузка … | ||||||||||||||||||||||||||||||||||
Погрузка … | 999977777777777777777777777777777777777777777777777777777777777777777777777777777777 70077777777777777777777777777777777777777777777. …||||||||||||||||||||||||||||||||||
Загрузка … | ||||||||||||||||||||||||||||||||||
Загрузка … |
ВЫСОКАЯ ТЕМПЕР.
… | ||||||||||||||||||||||||||||||||||||||||||||||||||||||||||||||||||||||||||||||||||||||||||||||||||||||||||||||||||||||||||||||||||||||||||||||||||||||||||||||||||||||||||||||||||||||||||||||||||||||||||||||||||||||||||||||||||||||||||||||||||||||||||||||||||||||||||||||||||||||||||||||||||||||||||||||||||||||||||||||||||||||||||||||||||||||||||||||||||||||||||||||||||||||||||||||||||||||||||||||||||||||||||||||||||||||||||||||||||||||||||||||||||||||||||||||||||||||||||||||||||||||||||||||||||||||||||||||||||||||||||||||||||||||||||||||||||||||||
… |
… | |||||||||||||||||||||||||||||||||||||||||||||||||||||||||||||||||||||||||||||||||||||||||||||||||||||||||||||||||||||||||||||||||||||||||||||||||||||||||
… | |||||||||||||||||||||||||||||||||||||||||||||||||||||||||||||||||||||||||||||||||||||||||||||||||||||||||||||||||||||||||||||||||||||||||||||||||||||||||
.![]() | |||||||||||||||||||||||||||||||||||||||||||||||||||||||||||||||||||||||||||||||||||||||||||||||||||||||||||||||||||||||||||||||||||||||||||||||||||||||||
878 | … | ||||||||||||||||||||||||||||||||||||||||||||||||||||||||||||||||||||||||||||||||||||||||||||||||||||||||||||||||||||||||||||||||||||||||||||||||||||||||
78 | … | ||||||||||||||||||||||||||||||||||||||||||||||||||||||||||||||||||||||||||||||||||||||||||||||||||||||||||||||||||||||||||||||||||||||||||||||||||||||||
… | 70078. | Loading… | |||||||||||||||||||||||||||||||||||||||||||||||||||||||||||||||||||||||||||||||||||||||||||||||||||||||||||||||||||||||||||||||||||||||||||||||||||||||
Loading… | |||||||||||||||||||||||||||||||||||||||||||||||||||||||||||||||||||||||||||||||||||||||||||||||||||||||||||||||||||||||||||||||||||||||||||||||||||||||||
Loading… | |||||||||||||||||||||||||||||||||||||||||||||||||||||||||||||||||||||||||||||||||||||||||||||||||||||||||||||||||||||||||||||||||||||||||||||||||||||||||
Loading… | |||||||||||||||||||||||||||||||||||||||||||||||||||||||||||||||||||||||||||||||||||||||||||||||||||||||||||||||||||||||||||||||||||||||||||||||||||||||||
Loading… | |||||||||||||||||||||||||||||||||||||||||||||||||||||||||||||||||||||||||||||||||||||||||||||||||||||||||||||||||||||||||||||||||||||||||||||||||||||||||
Loading… | |||||||||||||||||||||||||||||||||||||||||||||||||||||||||||||||||||||||||||||||||||||||||||||||||||||||||||||||||||||||||||||||||||||||||||||||||||||||||
Loading … | |||||||||||||||||||||||||||||||||||||||||||||||||||||||||||||||||||||||||||||||||||||||||||||||||||||||||||||||||||||||||||||||||||||||||||||||||||||||||
Загрузка … | |||||||||||||||||||||||||||||||||||||||||||||||||||||||||||||||||||||||||||||||||||||||||||||||||||||||||||||||||||||||||||||||||||||||||||||||||||||||||
Загрузка … | |||||||||||||||||||||||||||||||||||||||||||||||||||||||||||||||||||||||||||||||||||||||||||||||||||||||||||||||||||||||||||||||||||||||||||||||||||||||||
Загрузка … | |||||||||||||||||||||||||||||||||||||||||||||||||||||||||||||||||||||||||||||||||||||||||||||||||||||||||||||||||||||||||||||||||||||||||||||||||||||||||
Загрузка … | |||||||||||||||||||||||||||||||||||||||||||||||||||||||||||||||||||||||||||||||||||||||||||||||||||||||||||||||||||||||||||||||||||||||||||||||||||||||||
Загрузка … | |||||||||||||||||||||||||||||||||||||||||||||||||||||||||||||||||||||||||||||||||||||||||||||||||||||||||||||||||||||||||||||||||||||||||||||||||||||||||
. | |||||||||||||||||||||||||||||||||||||||||||||||||||||||||||||||||||||||||||||||||||||||||||||||||||||||||||||||||||||||||||||||||||||||||||||||||||||||||
Загрузка… | |||||||||||||||||||||||||||||||||||||||||||||||||||||||||||||||||||||||||||||||||||||||||||||||||||||||||||||||||||||||||||||||||||||||||||||||||||||||||
Загрузка … | |||||||||||||||||||||||||||||||||||||||||||||||||||||||||||||||||||||||||||||||||||||||||||||||||||||||||||||||||||||||||||||||||||||||||||||||||||||||||
Загрузка … | |||||||||||||||||||||||||||||||||||||||||||||||||||||||||||||||||||||||||||||||||||||||||||||||||||||||||||||||||||||||||||||||||||||||||||||||||||||||||
Загрузка … | |||||||||||||||||||||||||||||||||||||||||||||||||||||||||||||||||||||||||||||||||||||||||||||||||||||||||||||||||||||||||||||||||||||||||||||||||||||||||
Загрузка .![]() | |||||||||||||||||||||||||||||||||||||||||||||||||||||||||||||||||||||||||||||||||||||||||||||||||||||||||||||||||||||||||||||||||||||||||||||||||||||||||
Загрузка … | |||||||||||||||||||||||||||||||||||||||||||||||||||||||||||||||||||||||||||||||||||||||||||||||||||||||||||||||||||||||||||||||||||||||||||||||||||||||||
. | |||||||||||||||||||||||||||||||||||||||||||||||||||||||||||||||||||||||||||||||||||||||||||||||||||||||||||||||||||||||||||||||||||||||||||||||||||||||||
Loading… | |||||||||||||||||||||||||||||||||||||||||||||||||||||||||||||||||||||||||||||||||||||||||||||||||||||||||||||||||||||||||||||||||||||||||||||||||||||||||
Loading… | |||||||||||||||||||||||||||||||||||||||||||||||||||||||||||||||||||||||||||||||||||||||||||||||||||||||||||||||||||||||||||||||||||||||||||||||||||||||||
Loading… | |||||||||||||||||||||||||||||||||||||||||||||||||||||||||||||||||||||||||||||||||||||||||||||||||||||||||||||||||||||||||||||||||||||||||||||||||||||||||
Loading… | |||||||||||||||||||||||||||||||||||||||||||||||||||||||||||||||||||||||||||||||||||||||||||||||||||||||||||||||||||||||||||||||||||||||||||||||||||||||||
Loading… | |||||||||||||||||||||||||||||||||||||||||||||||||||||||||||||||||||||||||||||||||||||||||||||||||||||||||||||||||||||||||||||||||||||||||||||||||||||||||
Loading… | |||||||||||||||||||||||||||||||||||||||||||||||||||||||||||||||||||||||||||||||||||||||||||||||||||||||||||||||||||||||||||||||||||||||||||||||||||||||||
Загрузка… | |||||||||||||||||||||||||||||||||||||||||||||||||||||||||||||||||||||||||||||||||||||||||||||||||||||||||||||||||||||||||||||||||||||||||||||||||||||||||
Загрузка … | |||||||||||||||||||||||||||||||||||||||||||||||||||||||||||||||||||||||||||||||||||||||||||||||||||||||||||||||||||||||||||||||||||||||||||||||||||||||||
Загрузка … | |||||||||||||||||||||||||||||||||||||||||||||||||||||||||||||||||||||||||||||||||||||||||||||||||||||||||||||||||||||||||||||||||||||||||||||||||||||||||
Загрузка … | |||||||||||||||||||||||||||||||||||||||||||||||||||||||||||||||||||||||||||||||||||||||||||||||||||||||||||||||||||||||||||||||||||||||||||||||||||||||||
Загрузка … | |||||||||||||||||||||||||||||||||||||||||||||||||||||||||||||||||||||||||||||||||||||||||||||||||||||||||||||||||||||||||||||||||||||||||||||||||||||||||
Загрузка … |
. | Loading… | |||||
Loading.![]() | ||||||
Loading… | ||||||
Loading… | ||||||
Loading… | ||||||
Loading… | ||||||
Загрузка… | ||||||
Загрузка … | ||||||
Загрузка … | ||||||
Загрузка … | ||||||
Загрузка … | ||||||
Загрузка … | ||||||
. | ||||||
Loading… | ||||||
Loading… | ||||||
Loading… | ||||||
Loading… | ||||||
Loading… | ||||||
Loading.![]() | ||||||
Загрузка… |
ВЫСОКАЯ ТЕМПЕР.
ТЕМПЕР. , sorted by Protective Width, ascending

ВЫПУСКА.
с Temp. Выдержанный температура: 150 градусов по Фаренгейту, сортируется по защитной ширине, восхождение
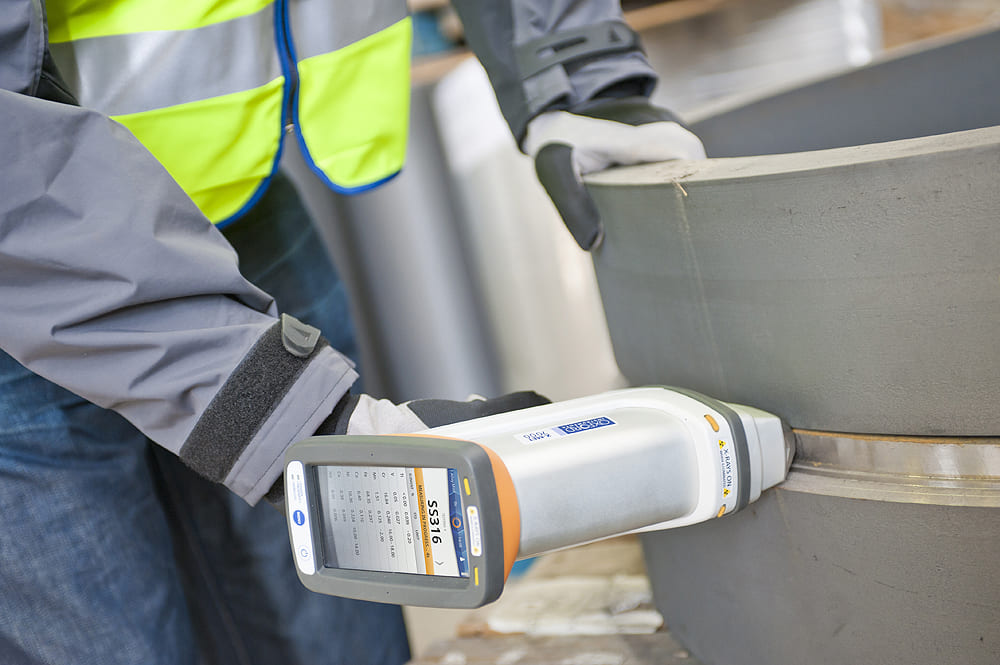
