Методика расчета сварных соединений
Сварка является самым простым из всех существующих сегодня способов соединения металлических заготовок. Технология дает возможность получать прочные и надежные соединения. Она востребована в создании металлоконструкций разного уровня сложности, в укладке трубопроводов, строительстве, машиностроении и других отраслях. Характеристики сварных соединений зависят от множества факторов. Наиболее значимые из них: толщина заготовок, условия выполнения работ, расходные материалы, оборудование, состав металла. Чтобы предварительно определить, насколько прочным получится соединение, нужно расчет сварного шва.
Он делается, как правило, в процессе проектирования и позволяет правильно выбрать материалы для выполнения конкретного вида операций. Предварительные вычисления необходимы для того, чтобы добиться нужного запаса прочности конструкции. Таким образом достигается нужная степень надежности готовых изделий.
СОДЕРЖАНИЕ
- Методика расчета
- Исходные параметры для вычислений
- Расчет изделий с угловым стыком
- Расчет стыков, выполненных внахлест
- Длина сварочного шва в зависимости от массы металла
- Порядок расчета сварных стыков
- Дефекты, возникающие в результате неправильных расчетов
- Калькуляторы сварочных швов
- Контроль размеров сварных швов
Методика расчета
Существуют разные варианты сцепления металла. Расчет сварных соединений для каждого из них выполняется отдельно. В зависимости от пространственного расположения свариваемых деталей различаются и сварные соединения. Соответственно они могут быть:
- угловыми. Соединяемые заготовки одна по отношению к другой располагаются перпендикулярно. Чтобы конструкция получилась максимально прочной, следует определить предельные усилия, которые будут воздействовать на швы;
- стыковыми. Заготовки располагаются в одной плоскости таким образом, что одна из них является продолжением другой. Свариваются торцы деталей. Такой вариант соединения принято считать оптимальным, так как он характеризуется минимальными показателями напряженности на стыке. Шов может быть косым или прямым;
- внахлест. Плоскости соединяемых заготовок перекрывают одна другую. Такая технология лучше всего подходит для соединения деталей, толщина стенок которых не превышает 5 мм. Также метод используется в ситуациях, если требуется укрепить сварной шов;
- тавровым сварочным швом.
Внешним видом очень похожи на угловые. Детали по отношению одна к другой тоже располагаются под углом в 90 градусов, но соединяются торцами. Такие виды стыков достаточно востребованы и часто используются. Среди основных достоинств методы – простота исполнения, надежность и экономичность. К тому же, используя специально разработанные методические указания, по тавровому соединению несложно выполнить расчеты с безупречной точностью.
Итак, пришло время детально рассмотреть методику расчета сварного шва. Специалисты вывели специальные формулы, которые упрощают выполнение необходимых вычислений. Помимо этого, в сети Интернет есть специальные программы. Они находятся в свободном доступе. От пользователя требуется только ввести нужные параметры, чтобы получить точный результат.
Исходные параметры для вычислений
Чтобы при расчете погрешность исключить или хотя бы свести к минимуму, нужно определиться с параметрами, которые окажут влияние на прочность стыка. Процесс сжатия и растяжения металла рассчитывается при помощи формулы
где:
- Yс – коэффициент, отражающий условия, которые преобладают на рабочем месте. Данный показатель общепринят и отражен в справочных таблицах. Достаточно найти нужный показатель и подставить его в формулу;
- Rу – индекс, обозначающий сопротивление металла с учетом предела его текучести. Отражен в справочных материалах сварщика;
- Ru – еще один показатель сопротивления металла, который несложно найти в таблицах;
- N – максимально допустимая нагрузка на сварочный шов;
- T – наименьшая толщина стенок свариваемых заготовок;
- Максимальная длина сварного стыка. При вычислениях данный параметр следует уменьшить на 2t;
- Rwу – сопротивление, зависящее от предела прочности соединения.
Когда сваривать приходится разные металлы, то значения Ru и Ry берутся того материала, прочность которого меньше. точно так же поступают и в случаях, когда выполняются расчеты сварочного шва на срез.
Для улучшения качества и увеличения скорости работ, вы всегда можете воcпользоваться нашими верстаками собственного производства от компании VTM.
Проектирование металлоконструкций осуществляется с учетом требований по безопасности сварного соединения, его способности выдерживать определенный уровень нагрузок стабильности соединенных с их помощью элементов. В случаях, когда для создания металлоконструкции необходимо наложить несколько сварных соединений, то важно грамотно их расположить. Важно, чтобы нагрузка при сварке была распределена равномерно между всеми стыками.
Определить параметры можно путем математических вычислений. В случае, когда полученный результат будет неудовлетворительным, то в конструктив следует внести изменения и рассчитать снова.
Расчет изделий с угловым стыком
Определение допустимой длины сварного соединения на отрыв выполняется с учетом силы, направленной к центру тяжести. При подсчетах такого рода выбирается сечение с высокой степенью опасности.
Каждый из показателей формулы влияет на прочностные характеристики шва, вне зависимости от вида свариваемых металлов. Условные обозначения:
- N – максимальное значение силы, которая оказывает давление на стык;
- ßf, ßz – коэффициенты, которые берутся в справочных таблицах и не зависят от типа свариваемых металлов. В большинстве своем ßz = 1, а ßf = 0,7;
- Rwf – показатель, отражающий сопротивление срезу. Определен справочными материалами. Проще всего найти в таблицах ГОСТа;
- Rwz – сопротивление по линии стыка. Значения берутся из справочной таблицы;
- Ywf – коэффициент, зависящий от сопротивления материала. К примеру, если для металла этот показатель составляет 4200 кгс/см², то поправочный коэффициент составит 0,85;
- С – еще один коэффициент, обозначающий условия рабочей среды. Как и большинство значений, определяется по справочным таблицам;
- Kf – толщина сварного шва по линии сплавления;
- Lw – общая длина стыка, уменьшенная на 10 мм.
Расчет стыков, выполненных внахлест
При вычислениях важно учесть пространственное положение и тип сварного соединения. Ведь при сваривании внахлест стыки могут быть и угловыми, и фланговыми, и лобовыми. Расчеты дают возможность получить данные по минимально допустимой площади сечения и проектной прочности линии соприкосновения. При вычислении площади сварного соединения за основу принимается наименьшая высота условного треугольного стыка. Для ручной сварки при условии, что катеты равны, данный коэффициент будет составлять 0,7.
Если сварочные работы выполняются автоматическими или полуавтоматическими аппаратами, то глубина прогрева материала будет большей. Поэтому показатели следует брать в справочных таблицах.
Длина сварочного шва в зависимости от массы металла
Длина сварного соединения определяется по формуле, определяющей соотношение массы наплава на один метр стыка: L = G/F × Y, где
- L – длина самого шва;
- G – вес наплава;
- F – площадь сечения;
- Y – удельный вес присадочного материала.
В результате вычислений будет получен коэффициент, который следует умножить на длину катета сварного шва.
Чтобы вычисления выполнять правильно, следует попрактиковаться. Важно понимать, что точный результат не дает возможности получить ни одна формула. Поэтому приобретать расходные материалы желательно с небольшим запасом. Это примерно 5-7% от общего количества. Правда, иногда получается и сэкономить присадку. Но такое случается нечасто и к тому же при условии, что у сварщика за плечами большой опыт выполнения аналогичной работы.
Порядок расчета сварных стыков
Чтобы вычислить нагрузку, которую сможет выдержать сварное соединение, следует внимательно отобрать исходные данные. Предотвратить или хотя бы минимизировать вероятность ошибки при вычислениях можно при условии соблюдения алгоритма работы:
- Максимально точно определить размеры, форму и пространственное расположение сварного соединения.
- Опасное сечение необходимо повернуть в сторону контактируемой со сварным стыком площади.
Этот прием актуален в случаях, когда плоскость стыка на исследуемой конструкции не соответствует проектному сечению. После поворота образуется новое расчетное сечение с более благоприятными параметрами.
- После этого вычисляется новый центр масс, который образовался в результате поворота сечения.
- Следующим шагом станет перемещение внешней нагрузки в предопределенный центр масс.
- Настало время определить расчетное значение нагрузок, которые воздействуют на сечение. А именно – крутящего и изгибающего момента, усилий поперечной и продольной направленности.
- После того, как найден модуль напряжения, следует определить точку, на которую воздействуют самые высокие нагрузки. Именно в такой точке все внешние силы работают одновременно, что дает возможность определить их суммарное значение. Это тот максимум, который будет воздействовать на сечение.
- Определяется максимально допустимое усилие, которое может воздействовать на шов без каких-либо последствий: деформации, разрушения и т.
п.
- На завершающем этапе сравниваются показатели допустимого и максимального фактического значений. В результате определяется расчетное сопротивление сварочного шва и его оптимальные размеры, которые необходимы для сопротивляемости нагрузкам.
Только так можно рассчитывать на полноценную и безопасную эксплуатацию будущей металлоконструкции. Для контроля можно выполнить проверочные расчеты. Желательно, чтобы ими занялся другой специалист, что повышает объективность полученного результата.
Прочность сварного шва будет достоверной и соответствующей расчетам только в том случае, если соблюдаются технология формирования соединений. Тем не менее стыки рассчитывать следует в любом случае. Только точно установленные параметры и векторы нагрузок обеспечивают прочное и надежное сварное соединение.
Дефекты, возникающие в результате неправильных расчетов
Прежде всего, нужно твердо усвоить, что теоретический расчет угловых, тавровых, нахлесточных или стыковых швов и практическая надежность, равно как и срок службы металлоконструкции являются звеньями одной цепи.
Наиболее часто возникают дефекты такого характера:
- подрезы. Они представляют собой канавки, которые образуются по линии соединения или возле нее. Приводят к быстрому разрушению стыка;
- поры. Визуально заметить их невозможно (кроме поверхностных). Образуются из-за проникновения газов, которые являются побочным продуктом плавления металла и электрода;
- непровары. Результат недостаточного прогрева стали, вследствие чего на стыке образуются пробелы;
- сторонние включения. Очень опасная ошибка, которая приводит к существенному снижению прочности сварного шва. Со временем в месте содержания примесей возникают трещины;
- горячие или холодные трещины.
первый тип дефекта образуется в результате нарушения технологии выполнения сварочных работ. Самый простой пример – неправильный подбор расходных материалов. Холодная трещина является результатом окисления металла и возникает после его остывания.
Вычисления по формулам помогают избежать брака в работе. Они позволяют создавать качественные сварные соединения, выдерживающие большие нагрузки во время эксплуатации металлических конструкций.
Калькуляторы сварочных швов
Необходимые расчеты можно выполнить, не имея на то каких-либо навыков. Для этого существуют специализированные калькуляторы, позволяющие вычислить параметры стыковых, точечных или угловых соединений; рассчитать оптимальную длину сварного шва. С помощью такого калькулятора несложно проверить все существующие сегодня стыки с разными силовыми нагрузками и направленностью прилагаемых усилий.
Математические расчеты помогут выбрать оптимальный для конкретной конструкции тип и размер сварного шва, точно определиться с металлом и расходными материалами. При помощи расчетов можно безошибочно определить геометрию сварного соединения и проверить степень его прочности.
Не рекомендуется для точечных соединений, электрозаклепок и стыков с разделкой кромок использовать значения усталостной нагрузки. Расчет для таких видов швов не поддерживается и полученные результаты будут весьма приблизительными. Еще следует иметь ввиду, что при вычислениях не принимаются во внимание изменения характеристик металлических заготовок, которые имеют место в результате изменения температуры и возникновения остаточных напряжений.
Контроль размеров сварных швов
Для контроля и определения фактических геометрических параметров сварных стыков применяются специальные инструменты. Они дают возможность точно измерить характеристики и показатели соединений, выполненных методом сваривания. Набор инструментария включает шаблоны и ряд измерителей, которые «заточены» под определение конкретного параметра.
youtube.com/embed/UiVykcMCA58″ frameborder=»0″ allowfullscreen=»allowfullscreen»>Поведение сварных конструкций при динамических нагрузках
Расчет на усталость производится при действии переменных (или вибрационных) нагрузок, характеризующихся большой повторяемостью (не менее 1000 раз). При этом расчет на выносливость сводится к определению прочности конструкций при действии таких переменных нагрузок. Для проведения расчета на выносливость необходимо знать соответствующее значение предела выносливости. Предел выносливости элемента конструкции — σr,k зависит от характеристики цикла изменения нагрузки, от свойств материала и от формы самого элемента. Значение предела выносливости определяется экспериментально. Рассмотрим некоторые общие понятия на примере действия вибрационной нагрузки на различные конструкции машиностроительного типа. В этом случае изменение величины нагрузки, происходящее от воздействия вращающихся частей машин, характеризуется определенной закономерностью, подобно той, которая показана на этом рисунке.
При действии переменной нагрузки разрушение элементов конструкций может произойти при нагружениях, меньших предела текучести. При этом наибольшая величина напряжений переменной нагрузки, вызывающей разрушение (σmax) будет зависеть от количества циклов нагрузки. Зависимость величины разрушающих напряжений от количества циклов выражается кривой линией, называемой кривой Веллера, показанная на рисунке справа. Эта зависимость показывает, что при некотором предельном значении напряжений разрушение не будет происходить даже при весьма большом количестве циклов. Это напряжение, определяемое для некоторого заданного количества циклов (называемого базой испытания), называется пределом выносливости (или пределом усталости).
Для стальных образцов база испытания принимается равной N = 107. Для образцов из алюминия она значительно больше и равна N = 5*107. Такое большое значение базы испытания целесообразно для деталей конструкций машиностроительного типа, которые в процессе своей работы могут подвергаться воздействию весьма большого количества циклов переменной нагрузки. Для металлических конструкций многих других отраслей промышленности и строительства количество циклов переменной нагрузки может быть значительно меньшим. Так, например, считают, что для корпусных судовых конструкций количество циклов переменной нагрузки за весь период их службы не превышает N = 106; для мостовых конструкций N = 2*106. Это же значение характерно и для крановых металлических конструкций. В связи с этим для таких конструкций определяют условный предел выносливости при значительно меньшей базе. Обычно в этих случаях принята база N = 2*106.
В зависимости от характеристики цикла r, представляющей собой отношение минимального значения напряжений от вибрационной нагрузки к максимальному их значению , величина предела выносливости σmах меняется. Это изменение может быть выражено графиком, показанном на рисунке выше (б).
Обычно при повышении температуры пределы выносливости сталей понижаются. В агрессивных средах предел выносливости значительно уменьшается. Прочность деталей конструкций при переменных нагрузках зависит от концентрации напряжений.
Эффективным коэффициентом концентрации напряжений Кэ называется отношение предела выносливости гладкого образца к пределу выносливости образца при наличии концентратора; Кэ ≥ 1; причем, чем ближе Кэ к единице, тем лучше работает изделие. У хрупких материалов эффективный коэффициент концентрации Кэ близок к теоретическому, у пластичных — он значительно меньше.
Решающее влияние на усталостную прочность оказывает качество технологического процесса. При наличии технологических дефектов (шлаковых включений, пор, окислов, трещин, непроваров и т.д.) прочность сварных соединений при переменных нагрузках резко падает. Даже небольшой непровар корня шва образует надрез и концентрацию напряжений, что может существенно снижать прочность стыковых соединений при переменных нагрузках. Влияние непровара на уменьшение усталостной прочности зависит от рода материала. Очень чувствительны к непроварам сварные соединения из аустенитных сталей типа 12Х18Н9Т и титановых сплавов. Помимо концентраторов напряжений, вызванных непроварами, на понижение усталостной прочности оказывает влияние наличие пор и шлаковых включений. Большое влияние на предел выносливости оказывает очертание поверхности швов. У выпуклых стыковых швов он более низкий, чем у гладких; весьма хорошие результаты получаются при снятии усилений стыковых швов или при их обработке, обеспечивающей плавный переход от шва к основному металлу, Получить соединения с хорошей прочностью можно не только при сварке прокатных элементов, но и при сварке литых деталей или прокатных с литыми.
Прочность при переменных нагрузках тавровых соединений в значительной степени зависит от подготовки кромок. Экспериментально доказано, что предел выносливости таврового соединения, сваренного с подготовкой кромок, выше, чем того же соединения без подготовки кромок. Причиной этого является концентрация напряжений из-за непровара кромок. При сварке тавровых соединений на автоматах под флюсом глубина проплавления больше, чем при других видах сварки. Это обстоятельство улучшает работу соединений, подвергавшихся переменным нагрузкам.
Остаточные напряжения могут быть не только вредными, но и полезными. Если в зоне наибольших растягивающих напряжений от внешних нагрузок создать сжимающие остаточные напряжения, то последние будут способствовать повышению усталостной прочности сварных соединений. Благоприятные остаточные напряжения сжатия можно создать местной пластической деформацией. С этой целью сварные соединения иногда подвергают поверхностной механической обработке: прокатке роликами или, что является более простым и удобным, обдувкой дробью, обработке пневматическим молотком или пучком проволок ударными методами. При этом в поверхностных слоях металла происходит пластическая деформация, которая вызывает наклеп металла, сопровождающийся повышением σт и, кроме того, образуются остаточные напряжения сжатия. Чем выше коэффициент концентрации напряжений в сварном соединении, тем более эффективно применение поверхностной обработки швов.
Эффект повышения предела выносливости сварных точечных соединений достигается их обжатием ковочным давлением при остывании. Проковка повышает сопротивляемость усталостным разрушениям в 1,4 … 2,0 раза, а при обработке специальным инструментом и скоростной проковке — в большей степени.
Выносливость сварных соединений может быть увеличена предварительным их нагруженном при одновременном устранении вредных растягивающих остаточных напряжений в зоне концентраторов. Иногда считают полезным создание предварительных напряжений в тонкостенных конструкциях и подвержение их вибрации. При этом остаточные растягивающие напряжения уменьшаются на несколько десятков процентов, а сопротивление усталостным нагрузкам повышается.
как производится, формула для разных типов, правила и нюансы
Если вам приходилось соединять детали металлические или из другого материала, то вы наверняка знаете, что самые прочные соединена выходят при работе со сваркой.
Такая надежность объясняется тем, что из-за высокой температуры, молекулы металла крепко соединяются между собой.
Но для того чтобы ваши швы были цельные и прочные важно хорошо рассчитать как сварить метал.
Содержание статьиПоказать
- Какие бывают сварочные швы
- Как провести расчет с помощью формул прочность разных соединений
- На что нужно опираться проводя расчет
- Как подсчитать такой показатель для углового шва
- Соединение, что делаются внахлест
- Самые распространенные проблемы, что возникают при формировании швов
Какие бывают сварочные швы
В наше время придумано большое количество методов сварки, но самым распространенным остаётся сварка электричеством, она в свою очередь делить на контактную и дуговую. Чаще всего для формирования швов используют два таких метода.
Но чтобы ваш шов был долговечен нужно провести расчет, где вы должны учесть и провести расчет характеристик выбранного вами шва, так же не забывайте учитывать особые характеристики стали с которой работаете.
Когда вы формируете сварочный шов на отрыв, то он может быль не качественным, разрываться и растрескиваться, все это возникает из-за неправильного подсчета его прочности.
Самыми прочными считаются швы, что отвечают по своей плотности и свойствам металлу над которым проводится работа. Проблемы возникают обычно на том участке, который больше всего нагревается, он наиболее уязвим.
Обычно это та часть изделия что находиться максимально близко ко шву. Металл изменяет свою химию при температурном воздействии, это и есть основной причиной по которой вам следовало бы посчитать прочность шва.
Ведь без такого расчета вы не будете знать способ ли данный металл выдерживать определенные нагрузки, а если нет, то вам будет о чем задуматься.
Когда речь заходит про угловые швы там все немного сложнее. Там все зависти от того какого качества вами выбран металл. Весь расчет должен быть направлен на самую горячую точку, то есть на тот участок который более чем другие подвержен трещинам.
Угловым соединением называют такой шов при котором две части шва расположены одна к другой под углом. Катет поперечного сечения(k) и периметр шва(L), это все данные которыми вам нужно будет владеть для подсчета надежности шва.
Просто занесите свои числа вот в эту формулу и посчитайте A = k·sin45*L = 0,7k·L.
Также ещё существуют точечные соединения, при работе с ними существуют свои нюансы.
- Формировать такой шов можно только на плоской поверхности для сварки.
- Все точки должны быть равномерно нагружены, нельзя делать точку опоры.
- В формуле, по которой мы подсчитывали силу углового шва можно допустить оплошность до 20 % в напряжении среза.
Как провести расчет с помощью формул прочность разных соединений
Для каждого отдельного вида сварочного соединения, а таких много, нужно производить подсчет отдельно, поскольку каждый имеет свои индивидуальные особенности.
Существует несколько подборов, например есть та, что делит швы по тому как расположены делали сварки:
- Швы на стыках, это таких соединения при которых две стороны металла соединяются торцами. Тогда одна часть продолжает другую. Такой вид шва считается самым популярным и оптимальным по исполнению. То есть он прост. Такой шов можно сделать двумя методами – косым и прямым соединениями.
- Сварка на углу-это когда два пласта металла расположены под наклоном.
- Соединение внахлест, такой способ соединения характерен тем, что один элемент сварки немного находит на другой и в таком виде они закрепляются. Но вам не удастся использовать такой вид сварки с толстыми металлами, это может быть металл с толщиной до 5 миллиметров, тогда такой шов будет себя оправдывать и укрепит соединение.
- Тавровые соединения, они вполне могут быть подвидом угловых, поскольку метал находиться под углом так же как и в угловых, но тут особенность в том, что они соединяются непосредственно торцами.
Но конечно каждый вид может ещё иметь в себе множество подвидов, так что при расчете прочности шва нужно обратить на это внимание. Все перечисленные виды сварки производиться по методу углового соединения.
Существует много формул по расчету таких соединений. Ну а если вы не дружите с математикой, то, в интернете есть программы, где вам нужно будет только ввести параметры и размеры и вам выдаст нужный результат.
На что нужно опираться проводя расчет
Для того чтобы рассчитать надежность соединения нужно выяснить некоторые характеристики которые и влияют на то, на сколько хорошо, скреплены ваши элементы.
Ниже мы привели формулу по которой вы можете рассчитать нужный вам параметр.
И так мы расскажем вам об этом:
- Сокращение УС – это те условиях в которых проводиться работа. Этот сокращение стало константой, и его можно удивить во всех основных книгах где проводятся подобные расчеты.
- RU- так обозначают параметр сопротивления, именно он показывает уровень качества металла. Такие данные вы можете найти в таблицах.
- RY- этот параметр обозначает тоже сопротивление, но он рассчитывается по отношению к текучести материала. Это так же табличные данные.
- RWY- как и два предыдущих обозначает сопротивление, но оно уже рассчитывается относительно того насколько прочный используемый металл. Иногда можно видеть, что вместо такой отметки используют (Rwu Yu), пусть это не сбивает вас с толка, этот то же параметр.
- N- этот знак показывает какую максимальную нагрузку способен перенести соединение, он этого показателя много чего зависит.
- t- эта буква указывает на то какую толщину имеет деталь над которой будет проводиться сварка.
- lw- это показатель, что определяет какую наибольшую длину соединения мы можем формировать, часто это вдвое больше чем толщина материала.
Если вы проводите работу с элементами, которые сделаны из разного металла, то сопротивление относительно текучести и просто сопротивление нужно определит отталкиваясь от того метала, что менее прочный.
Когда вам нужно подсчитать сварочный шов на срезе, то посмотрите на свои заготовки и отталкивайтесь от материала с низкой прочностью.
Свойства расчетного сопротивление для сварочной детали таково, что на прямую связано с растяжением сварочного соединения.
Именно из-за такой особенности соединения часто расположен немного под углом, и именно это дает возможность надежно соединить два металла разной природы.
Как подсчитать такой показатель для углового шва
Но если вам нужно провести расчет показателя качества прочности соединения для угловых соединений, то предыдущая формула вам не подойдет. Для угловых соединений нужно учитывать силу, что расположена в центре тяжести.
А это уже совсем другая формула. Когда вы введете все данные формулу проследите, что вы взяли данные показателя самой не надежной части сечения.
А подсчитать качество сварочного соединения на срезе вы можете по стандартной формуле, что мы привели снизу.
Будьте внимательны ведь каждый показатель в данной формуле крайне важен при расчёте качества прочности соединения, так же на это не влияет то какой вид металла используется. Итак, приступим.
N- это показатель наибольшей нагрузки, что в самой большей степени влияет на соединение, те показатели, что приведены в скобочках рядом постоянные и вы можете найти их в таблицах.
Чаще всего выходит такая картина.
- Bf- приблизительно 0,7
- BZ-приблизительно 1
- И тут так же не имеет какой фирмы и характеристик сталь, эти показатели часто приблизительно столько.
- RWF- это показатель из гостовского документа, и он указывает на сопротивление на срезе.
- RWZ- это также табличный показатель которой описывается как сопротивление на линии.
- C- тоже табличное число, которое имеет показатель рабочих условий.
- Ywf-этот показатель приблизительно 0,85, но это только с учетом того, что вы работаете с нормальным металлом, сопротивление которого до 4200 кгс на см.
- Ywz-этот показатель константа, что равняться 0,85 и не важно какой это вид стали.
- Kf- этот показатель нужно измерять по линии сопротивление, обозначает длину соединения, что у вас выйдет.
- Lw-это длинна, которую нужно уменьшить на 10 миллиметров.
Соединение, что делаются внахлест
Мы уже немного говорили о таком виде соединения ранее, соединение в внахлёст это такой метод при котором один пласт металла накрадывается на другой и в таком виде они свариваются, так же помине, что такая технология работает только с тонкими металлами с толстыми она будет не эффективна.
Расчёты проводятся по-разному потому что у такого шва тоже существуют свои разновидности, как например шов лобовой или под углом, фланговый шов. Ниже мы напишем формулу по которой вы можете посчитать.
N / (z kf lw) ≤ Rwz wz c.
Когда вы приступаете к расчету прочности длинны шва при соединении деталей из металла по технологии внахлест, вам нужно взять в расчет наименьшее сечение, оно должно быть расположено на самой меньшей высоте треугольника, что у нас визуализируется, при этом не нужно учитывать наплыв. Если вы пользуетесь ручной сваркой и ваши катеты приблизительно разны, то у вас выйдет показатель 0,7.
Мы должны так рассчитывать сечение по минимальной расчетной площади, потому что она связана с тем, что мы используем расходные сварочные материалы, и ещё связана с прочностью, что превышать прочность главного материала из которого состоят наши детали, что мы соединяем.
Если вы варите с помощью полуавтомата или автомата, то шов у углу обычно выходит немного толще и грубее, чем вы варили бы обычной ручной сваркой с дугой. А то как вам рассчитать высоту и подобрать правильную смотрите в таблице выше.
Самые распространенные проблемы, что возникают при формировании швов
Очень важно все правильно расчитать при работе с угловыми швами, или при работе может возникнут масса проблем, которые приведут к тому ,что ваш результат будет далеко е идеальным. Давайте поговорим про самые частые проблемы ,что возникают при сварке:
- Часто так бывает, что возникают поры – оно возникают из-за пагубного влияния кислорода и газов в среде, это возникает из-за плавления металла и электродов.
- Ещё иногда появляются подрезы-это такие просевшие участки, которые появляются на детали с боку от стыка, металл истончается и может треснуть.
- Следующая часта проблема непровары-это зоны в которых не удалось скрепить метал и между ним просто образовались дыры, это возникает из-за не правильной проплавки металла.
- Желательно чтобы в зону стыка не попадали другие включения не из метала, это может быть что угодно грязь, пыль или даже шлаки с электродов. Что качается шлаков можно сказать, что часто они не успевают выйти на поверхность шва чтобы вы их просто зачистили металлической щеткой. А если шлаки образовываются во время вашей работы с тонкими металлами-это достаточно критично, так как соединение будет хлипкое и в бедующем обязательно пойдут трещины.
- Далее вы узнаете о том, что возможно возникновение горячих трещин-это происходит из-за разращения соединения между кристаллами и тогда металл трескается под воздействием температуры, когда начинает плавиться сразу растрескивается.
Холодные трещины – они уже могут появиться после того как металл остыл. Этот процесс происходит из-за того что метал окислился ещё в процессе сварки. Для защиты от влияния кислородной среды используются специальные газы, что защищают участок.
В конце хочется добавить, что вы сможете найти в интернете много разных формул по расчёту прочности соединения.
Ещё используются разные показатели длинны, ширины шва, материала который свариваться и материалов расходных. Ещё учитывается площадь, толщина, и много других параметров.
Все это зависит от того каким видом соединения вы решили сваривать металл. Ещё важно учесть те усилия, что будут нагружены на шов из вне.
Выше вы можете посмотреть видео, где мастер проводит такие расчёты, вы сможете почерпнуть оттуда много полезного! Надеемся вам понравилась наша статья!
Как рассчитать прочность сварного соединения?
Очень важно знать, насколько прочным является сварной шов. Вы должны знать, насколько хорош ваш сварной шов. В противном случае сварка может выйти из строя, и у вас будут большие неприятности. Чтобы убедиться, что сварное соединение имеет достаточную прочность, чтобы выдержать приложенную нагрузку, необходимо рассчитать прочность сварного соединения. Позвольте нам сделать это, определив тип выполненной вами сварки и тип нагрузки, которую он испытывает.
Тип сварных соединений
В основном, типы сварных соединений сгруппированы в два типа
- Соединение внахлестку
- Соединение встык
Эти две группы сварных соединений могут иметь дополнительную классификацию. давайте обсудим их каждый.
Соединение внахлестку
Соединение внахлест можно выполнить, когда необходимо сварить две пластины, тогда они будут сварены внахлест одна на другую. сварка производится по краям двух пластин. теперь если сварка производится с одной кромки она называется Одинарная поперечная галтель, аналогично сварка производится по двум торцевым кромкам то она называется Двойная поперечная галтель, если две сварки выполняются с одной стороны одной паштетом то это называется параллельным угловым швом. Эти 3 типа сварки внахлестку показаны на рисунке выше.
Стыковое соединение
Стыковое соединение можно выполнить, поместив край двух пластин к краю, как показано на рисунке выше. для пластин толщиной 5 мм и менее фаску делать не нужно. если толщина больше 5 мм и меньше 12,5 мм, то края должны быть скошены до V или U-образной канавки с обеих сторон для добавления наполнителя. на основе этого скоса формы на краях пластины стыковые соединения могут быть выполнены различными способами, как показано на приведенных выше изображениях. это квадратное стыковое соединение, одинарное V-образное стыковое соединение, двойное V-образное стыковое соединение, одинарное U-образное стыковое соединение и двойное U-образное стыковое соединение.
Другими доступными типами соединений являются угловое угловое соединение, краевое соединение и Т-образное соединение, как показано на рисунке ниже.
Но как мы можем выбрать один из этих типов сварных соединений для наших приложений. Какие факторы мы должны учитывать?
- Требуемая форма свариваемой детали
- Толщина свариваемых листов
- Направление приложенных сил
Как читать паспортную табличку сварного…
Пожалуйста, включите JavaScript
Это основные факторы, которые необходимо учитывать при выборе типа сварного шва. Мы также обсудили различные типы сварочных процессов, такие как сварка TIG, сварка MIG, дуговая сварка и газовая сварка. Перед выбором типа сварного соединения необходимо также выбрать метод сварки.
Расчет прочности сварного соединения
Для следующих сварных соединений мы собираемся рассчитать прочность сварного соединения.
- Прочность поперечных угловых сварных соединений
- Прочность параллельных угловых сварных швов
- Прочность комбинированного поперечного и параллельного угловых сварных швов
- Прочность кругового углового сварного шва на кручение
- Прочность кругового углового шва на изгибающий момент Кручение
- Прочность стыкового соединения
1. Прочность поперечных угловых сварных соединений
Поперечные угловые соединения получают путем наложения двух пластин друг на друга внахлест и сварки кромок пластин. эти поперечные наполнители способны выдерживать высокую растягивающую нагрузку. Давайте рассчитаем прочность сварного соединения для одинарного и двойного поперечного углового шва, как показано на рисунках ниже.
Мы должны принять, что угловое сечение представляет собой прямоугольный треугольник, чтобы определить прочность углового соединения. В этом прямоугольном треугольнике ABC с гипотенузой AC образуют равные углы с двумя другими сторонами AB и BC .
Увеличенный вид скругления показан на рисунке ниже. Длина каждой стороны называется катетом или размером сварного шва, а перпендикулярное расстояние гипотенузы от пересечения катетов (, т. е. BD ) называется толщиной горловины. Минимальная площадь сварного шва получается на стыке BD , который дается произведением толщины шва и длины шва. Рис. Угловой шов, увеличенный вид или размер сварного шва ( AB ) = толщина листа ( BC )
l = длина сварного шва
Из приведенного выше рисунка видно, что толщина шва t = с × sin 45° = 0,707 с
Теперь нам нужно рассчитать максимальную площадь сварного шва. Мы должны учитывать минимальную площадь сварного шва, потому что напряжение максимально на минимальной площади.
Минимальная площадь площади сварного шва или горла, A = Толщина горла × Длина сварного шва
A = T × L = 0,707 S × L
Если σ 12121212212122122122122122122122122122122122122122122121221221221212122н 2
. — допустимое растягивающее напряжение для металла шва, то по формуле напряжения можно рассчитать предел прочности соединения для одиночного углового шва. (Напряжение = нагрузка/площадь)
нагрузка (P) = область горла × Допустимое растяжение напряжения
P = 0,707 S × L × σ T ……………………………………………………………………………………………………………………………………………… Уравнение (1a)
Это формула для расчета прочности одинарного углового поперечного соединения.
Для двойного углового поперечного соединения прочность на растяжение можно рассчитать, просто удвоив ее,
P = 2 × 0,707 с × л × σ t
P = 1,414 с × l × σ t ……………………. Уравнение (1b)
с этой формулой, мы можем рассчитать прочность поперечного соединения двойной галтели.
Очень важным примечанием является то, что сварной шов слабее листа из-за шлака и пузырей, поэтому сварной шов получает усиление, которое можно принять за 10% толщины листа. Для усиленных угловых швов размер шва может быть принят равным 0,85 9.0067 т .
Чтобы можно было начинать и останавливать сварной шов, к длине каждого сварного шва, полученной с помощью приведенного выше выражения, следует добавить 12,5 мм.
Пример задачи на расчет прочности поперечного углового соединения
Пластину шириной 100 мм и толщиной 5 мм необходимо приварить к другой пластине с помощью двойных поперечных угловых швов. Пластины подвергаются статической нагрузке 80 кН. Найти длину шва, если допускаемое растягивающее напряжение в шве не превышает 75 МПа.
Решение:
Данные:
Ширина пластины = 100 мм
Толщина (s ) = 5 мм (также известна как размер сварного шва) N
σ t = 75 МПа = 75 Н/мм 2
Пусть l = Длина сварного шва.
Из приведенного выше уравнения (1b) имеем P = 1,414 с × l × σ t
80×10 3 = 1,414 × 5 × L × 75
L = (80 × 10 3 ) ÷ 530,25
L = 150,87
Длина WELD. и остановку валика шва к длине каждого шва следует добавить 12,5 мм.
Таким образом, окончательная общая длина сварного шва будет 150,87+12,5 = 163,4 мм
Теперь для каждой стороны пластины длина одной галтели составит 81,7 мм (половина общей длины) по ширине пластины 100 мм выдерживать нагрузку 80кН.
2. Прочность параллельных угловых сварных соединений
Прочность параллельных угловых сварных соединений в основном способна выдерживать нагрузку сдвига. Вместо прочности на растяжение, как мы рассматривали в поперечном угловом соединении, мы должны учитывать прочность на сдвиг присадочного материала для параллельного углового сварного шва. Рис. Двойной параллельный угловой шов
. металл шва.
Мы уже обсуждали в приведенном выше расчете прочности поперечного сварного шва, что минимальная площадь сварного шва или площадь горловины составляет A = 0,707 S × L
Прочность на сдвиг однополушного сварка из филе составит
P = область горла × Допустимое напряжение Shear = 0,707 S × L 333333333333 гг.
P = 0,707 S × L × τ
Для параллельного сустава с двойным филом можно рассчитать прочность на сдвиг.0067 л × τ
P = 1,414 с × л × τ …………………………………. Уравнение (2)
3. Прочность комбинации поперечного и параллельного углового сварного шва
Теперь давайте объединим поперечный угловой сварной шов с параллельным угловым сварным швом. Рис. Комбинация поперечного и параллельного углового шва
Мы можем совместите одинарный поперечный угловой сварной шов с двойным угловым параллельным сварным швом, как показано на рисунке выше. Мы уже знали формулы для одноуглового поперечного сварного соединения и двойного углового параллельного сварного соединения. нам нужно просто суммировать это.
P = 0,707 S × L 1 × σ T + 1,414 S × L 9008 212 111111199. 1111ком. …. Уравнение (3)
Пример задачи по расчету прочности поперечного углового соединения
Пластину шириной 70 мм и толщиной 5 мм необходимо приварить к другой пластине, используя одинарные поперечные галтели и двойной угловой параллельный стык. Пластины подвергаются статической нагрузке 80 кН. Найти длину шва, если допускаемое растягивающее напряжение в шве не превышает 75 МПа, а допустимое касательное напряжение в шве не превышает 55 МПа.
Решение:
Данные данные:
Ширина = 70 мм
Толщина (S ) = 5 мм (также известный как размер Weld)
P = 80K = 80 × 3 N
= 80kn = 80 × 100195 3 N
5 = 80 кН = 80 × 3 N
5 = 80 кН = 80 × 3 N
. σ T = 75 МПа = 75 Н/мм 2
τ = 55 МПа = 55 Н/мм 2
Пусть л 1 9968 BE — длина начинки L 1 2 BE THENET ARTET TRANPARSERENGER. l 2 двойной угловой параллельный шов.
then From the above equation (3)
P = (0.707 s × l 1 × σ t )+ (1.414 s × l 2 × τ )
80×10 3 = 0,707×5× l 1 ×75) + (1,414×5× l 2 ×55)
длина одиночного углового поперечного шва длина l 1 = 70 мм
80×10 3 = (0,707 × 5 × 70 × 75) + (1,414 × 5 × л 2 × 55)
80×10 3 9086 + 8 (15)558,8. 2 )
388,86 × L 2 = 61441,25
L 2 = 158 мм
, как мы упомянули выше, чтобы позволить для начала и остановки для WELD. каждого сварного шва.
Длина одиночного углового параллельного соединения будет ( л 2 ) 170,5 мм. это будет на каждой стороне краев пластины.
4.

В этом случае к пластине будет привариваться сплошной круглый стержень. затем сварка выполняется вокруг круглой кромки стержня, как показано на рисунке ниже. Для этого типа сварного соединения нам необходимо рассчитать прочность сварного соединения скручиваемого сплошного стержня и создать нагрузку на кручение.
Рис. Круговой угловой шов, подвергнутый кручениюИз приведенного выше рисунка
d = Диаметр стержня
r = Радиус стержня
T = Крутящий момент, действующий на стержень
s = Размер (или катет) сварного шва 5 = Толщина шва
J = Полярный момент инерции участка сварного шва
Из уравнения кручения
Мы можем записать напряжение сдвига
Это напряжение сдвига возникает в горизонтальной плоскости вдоль стороны углового шва. Максимальный сдвиг приходится на горловину сварного шва, наклоненного под углом 45° к горизонтальной плоскости.
Толщина горловины будет t = с sin45° = 0,707 с
, тогда приведенное выше уравнение будет
……………………………. Уравнение (4)
С помощью этой формулы мы можем рассчитать допустимую либо скручивающую нагрузку (крутящий момент), либо диаметр стержня с другими известными параметрами.
Пример Задача на прочность кругового углового сварного шва, подвергнутого кручению
Сплошной вал диаметром 50 мм приваривается к плоской пластине угловым швом толщиной 10 мм. Найти максимальный крутящий момент, который может выдержать сварное соединение, если максимальная интенсивность касательных напряжений в материале шва не превышает 80 МПа.
Решение:
Данные данные:
D = 50 мм
S = 10 мм
τ MAX = 80 мкА = 80N/мм 2
T = Максимум, который может быть повешен, может быть, с Swidded Sivide Shipded с помощью Стетского Стетского Стетского Стеаса.
Мы знаем из. приведенное выше уравнение (4)
80 = (2,83 × T) ÷ ( π × 10 × 50 2 )
T = 80 × 78550/2,83
90T = 2, -мм
T = 2,22 кН-м ~ Ответ
Сварное соединение выдерживает крутящий момент до 2,22 кН-м.
5. Прочность круглого углового шва под действием изгибающего момента
Подобно описанной выше сварке круглого цельного стержня на пластине, когда стержень подвергается изгибающему моменту, как показано на рисунке ниже, необходимо учитывать модуль сечения сварного шва вместо полярного момента инерции.
Рис.: Круговой угловой шов под действием изгибающего моментаВсе параметры остаются прежними, за исключением модуля сопротивления (Z) вместо полярного момента инерции и изгибающего момента (M) вместо крутящего момента.
Мы знаем напряжение изгиба σ B = M/Z
σ B = M/(π TD 2 /4)
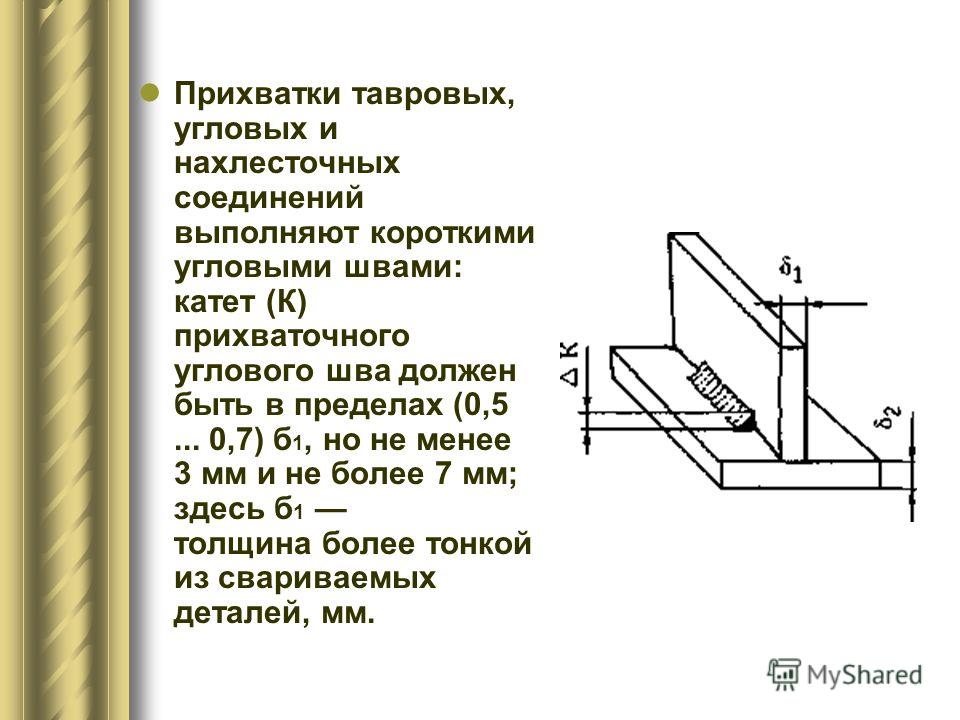
Это изгибающее напряжение возникает в горизонтальной плоскости вдоль стороны углового сварного шва. Максимальное изгибающее напряжение возникает в шейке шва, наклоненной под углом 45° к горизонтальной плоскости.
Толщина горловины составит t = с sin45° = 0,707 с
, тогда приведенное выше уравнение будет
………………………………. Уравнение (5)
С помощью этой формулы мы можем рассчитать допустимую изгибающую нагрузку (момент) или диаметр стержня с другими известными параметрами.
6. Прочность длинного углового шва на кручение
Теперь рассмотрим вертикальную пластину, прикрепленную к горизонтальной пластине двумя одинаковыми угловыми швами, как показано на рисунке.
Рис.: Длинный угловой шов, подвергнутый кручению Для этого типа сварного соединения, если вертикальная пластина скручивается по оси Z в ее средней точке. затем нам нужно рассчитать прочность сварного соединения.
Из вышеуказанного рисунка
T = крутящий момент, действуя на вертикальной пластине
L = длина сварка,
S = размер (или нога) сварки
T = горло. = Полярный момент инерции участка сварного шва (Проверьте здесь)
Как мы упоминали выше, вал скручивается по оси Z, и этому вращению противодействует напряжение сдвига, изменяющееся от нуля на оси Z и максимальное на концы пластины.
Это изменение касательного напряжения аналогично изменению нормального напряжения по глубине ( l ) балки, подвергнутой чистому изгибу.
Напряжение сдвига τ = (T × ( l /2))÷(t ×( l 3 /6))
τ = 3T ÷ t l 2
Максимальный сдвиг напряжение, возникающее в горловине, определяется как
……………………………. Уравнение (6)
Пример задачи на прочность длинного углового шва, подвергнутого кручению
Пластина длиной 1 м и толщиной 60 мм приваривается к другой пластине под прямым углом друг к другу угловым швом 15 мм. Найти максимальный крутящий момент, который может выдержать сварное соединение, если допустимая интенсивность касательных напряжений в материале шва не превышает 80 МПа.
Решение:
. Поседы даны данные
Длина Weld L = 1 м = 1000 мм
Толщина = 60 мм
S = 15 мм
τ MAX 2 = 80MPA = MAX = 80MPA = .0195 2
T = Максимальный крутящий момент, который может выдержать сварное соединение =?
Из приведенного выше уравнения (6) мы знаем, что максимальное напряжение сдвига (τ макс. )
τ макс. 0,283 T ÷ 10 6
T = 283 × 10 6 Н-мм = 283 кН-м
Сварное соединение выдерживает крутящий момент до 283 кН-м.
7. Прочность стыкового соединения
Сварное стыковое соединение рассчитано на растяжение и сжатие.
Рассмотрим одиночное V-образное стыковое соединение, как показано на рисунке ниже.
В случае стыкового соединения длина катета или размер сварного шва равны толщине шва, которая равна толщине листов.
Прочность на растяжение прикладного соединения (одно- V или квадратный приклад),
P = T × L × σ T
Whed 9008 L
Whed 9008 L 668 = ДЛИНА
Прочность на растяжение для двойного V Butt Saint, как показано на приведенной выше рисунке (правая сторона), задается
P = ( T 1 + T 2 ) L × σ σ σ σ σ σ 2 ) L × σ σ σ σ 2 ) L × σ σ σ 2 ) L × σ 2 ) L × σ σ 2 ) L × σ 2 )
, где
T 1 = Толщина горла в верхней части
T 2 = Горная толщина в нижней части
. толщина пластины, но может быть и меньше. В следующей справочной таблице показаны рекомендуемые минимальные размеры сварных швов для стыковых соединений.
The thickness of the plate (mm) | 3-5 | 6-8 | 10-16 | 18-24 | 26-55 | over 58 |
Minimum size of the Weld (MM) | 3 | 5 | 6 | 10 | 14 | 20 |
Заключение
We были обсуждены We Dirting Wis Tips. А также описано, как рассчитать прочность сварного соединения для 7 различных типов сварных соединений. Это поперечные угловые сварные соединения, параллельные угловые сварные соединения, комбинация поперечных и параллельных угловых сварных швов, круговой угловой сварной шов, подверженный кручению, круговой угловой сварной шов, подверженный изгибающему моменту, длинный угловой сварной шов, подверженный кручению, а также одинарное и двойное V-образное стыковое соединение. . Дайте нам знать, что вы думаете об этой статье в разделе комментариев ниже.
Расчет напряжения в угловых и стыковых сварных соединениях
Что такое напряжение?
Внешние силы, действующие на компонент, вызывают внутренние деформации, называемые напряжениями. Напряжение, действующее перпендикулярно поверхности сечения, описывается как нормальное напряжение, при этом следует различать растягивающее и сжимающее напряжение.
Греческая буква Σ (сигма) используется для обозначения нормального напряжения. Напряжения, действующие по касательной к наблюдаемой поверхности сечения, называются напряжениями сдвига и обозначаются греческой буквой 9.0130 Τ (Тау).
Касательные напряжения всегда возникают парами и направлены либо в сторону, либо в сторону от соединенных
ребер перпендикулярных плоскостей. Одноосное касательное напряженное состояние отсутствует.
Принципы проектирования сварных соединений являются основой хорошего сварного шва. Конструкция сварных соединений имеет решающее значение для общей прочности и устойчивости конструкции. Есть несколько факторов, которые необходимо учитывать при проектировании сварных соединений.
- Угловые сварные швы всегда рассчитываются на основе касательного напряжения в горловине (а).
- Должен быть выбран тип сварного соединения, для которого потребуется минимальное количество наплавленного металла. Используйте уменьшенное практическое раскрытие корня и угол паза для проектирования стыкового сварного шва.
- Например, если 20-градусная разделка может быть удовлетворительно сварена, нет необходимости в большем угле разделки. Это не только уменьшит деформацию и остаточные напряжения, но также уменьшит необходимость и стоимость PWHT и любых доработок из-за деформации.
- Сварка встык на толстых компонентах должна выполняться с использованием сварных швов с двойной V-образной или U-образной разделкой для уменьшения количества металла шва и остаточных напряжений, а также для контроля деформации.
- Соединения должны выполняться с максимально возможной подгонкой, так как соединения с большим зазором требуют дополнительных затрат и ресурсов.
Напряжение в угловых сварных швах
Угловые сварные швы Соединения могут быть нагружены напряжениями растяжения, сжатия или сдвига. Но из этих трех типов только напряжение сдвига отвечает за разрушение углового сварного шва под нагрузкой. Угловой сварной шов всегда не работает при сдвигающей нагрузке.
Критический размер в отношении прочности углового или стыкового сварного шва – это размер поперечного сечения (a) для углового и размер поперечного сечения (s) для стыкового сварного соединения.
Это минимальная толщина сварного шва на прямой линии, проходящей через его корень. Для расчета напряжения углового шва под углом 45° с длиной катета (L) теоретическое значение толщины шва составляет 1/√2 или 0,707L, где L — длина катета углового шва. На практике толщина шва угловых швов должна быть в пределах 0,6L и 0,9L.
Напряжение в угловых сварных швах должно рассматриваться как сдвиг, приложенный к эффективной площади для любого направления приложенной нагрузки. Поток напряжения происходит через стык шва в угловом шве, и шейка шва выдерживает максимальное напряжение.
При приложении напряжения к угловому сварному соединению горловина будет местом разрушения, если нагрузка превысит максимальную грузоподъемность. По этой причине в проектных расчетах угловых сварных швов учитывается расчет размера шва.
Для непрофессионального расчета уровня напряжения в скруглении ниже вы можете использовать приведенное ниже уравнение/формулу, чтобы помочь вам найти значение напряжения, размер прохода (a) или эффективную длину сварного шва (L), если вы знаете любой из этих 2 компоненты:
Испытание на сдвиг соединений точечной сварки
Пожалуйста, включите JavaScript
Испытание на сдвиг соединений точечной сварки
Напряжение (Н/мм 2 ) = (Нагрузка, P) / (Длина сварного шва x Раструб сварного шва, a)
Вы можете использовать это Формула для расчета уровня напряжения, размера горловины (a) или эффективной длины сварного шва (L) для угловых швов при сдвиговом напряжении, см. рисунок ниже.
В инженерной практике расчеты угловых сварных швов выполняются с учетом их приложения к сдвиговой нагрузке (поскольку угловые сварные швы в основном подвергаются напряжению сдвига).
Наиболее важным фактором является определение допустимого напряжения сдвига или расчетного напряжения сдвига. Как правило, расчетное напряжение сдвига можно считать равным половине предела текучести основного материала.
Причина рассмотрения значения половины предела текучести в конструкции углового сварного шва заключается в присущей конструкции соединения. Угловые швы всегда имеют недостаточное проплавление корня (они не являются швами с полным проплавлением) и большую общую толщину по сравнению со стыковыми швами.
Как объяснялось выше, в стандартах ISO для расчета углового сварного шва используется размер стыка (a), однако в наших американских нормах для расчетов конструкции учитывается размер длины катета (z).
Этот стенд практически подходит для углового сварного шва, где мы можем доказать взаимосвязь между размером стыка (a) и размером длины ноги (z), как указано ниже:
Размер стыка (a) = 0,7 x размер длины ноги (z) или длина ноги (z) = 1,4 x размер горловины (a)
соотношение размера горловины a и длины ноги z Хотя это уравнение не будет работать в случае вогнутого углового шва или выпуклого углового шва, поскольку размер горловины практически не будет представлять длину стороны или наоборот.
Как рассчитать напряжение сдвига в угловом сварном шве
Угловые швы рассчитаны на нагрузку сдвига. В тех случаях, когда приложенная нагрузка не перпендикулярна угловому сварному шву, сварной шов будет испытывать напряжение сдвига.
Это значительно снижает несущую способность сварного шва. Из-за этой проблемы на этапе проектирования сварного соединения предполагается, что к сварным швам будет приложена сдвигающая нагрузка (напряжение), как показано на рисунке ниже.
Здесь сварной шов параллелен приложенной нагрузке. Силы натяжения тянут соединяемые пластины в противоположных направлениях, и образовавшаяся область сварного шва испытывает напряжение сдвига, аналогичное соединению внахлестку.
В сварном компоненте, нагружающем сдвигом, нельзя учитывать свойства сварочной проволоки или электрода при растяжении. потому что прочность на растяжение снижается на коэффициент (обычно снижается на 70%), чтобы обеспечить безопасность.
Как указано в AWS D1. 1, минимальная прочность на растяжение металла сварного шва умножается на коэффициент 0,30, чтобы получить допустимое напряжение сдвига на сварном шве, как указано в приведенном ниже уравнении:
Допустимое напряжение, F V = 0,30 F EXX (1,0 + 0,50 SIN 1,5 θ )
, где
F V = Допустимый единичный напряжение
F EXX, I. Electrice Number. класс прочности электрода
θ = угол между направлением силы и осью сварочного элемента, градусы
Принимая во внимание приведенный выше коэффициент безопасности в нашем расчете напряжения, где напряжения представляют собой напряжение сдвига, τ, а не напряжение растяжения, мы можем видеть:
Где,
τ: максимально допустимое напряжение сдвига в сварном шве,
F: несущая способность сварного шва
A : эффективная площадь сварки.
Предположим, что сварной шов длиной 10 дюймов в двух местах с обеих сторон выполнен сварочными электродами E7018 с минимальным пределом прочности при растяжении 70 000 фунтов на квадратный дюйм, как показано ниже.
Таким образом, допустимое напряжение сдвига для сварных швов будет = 70 000 фунтов на квадратный дюйм x 0,30 = 21 000 фунтов на квадратный дюйм. (уменьшение на 70%)
Если размер сварных швов составляет 1/2 дюйма, как показано на приведенном выше рисунке, то прочность на сдвиг (несущая способность) сварных швов будет:
, как было рассчитано ранее, допустимое напряжение сдвига составляет 70 000 x 0,30 = 21 000 фунтов на квадратный дюйм.
Чтобы получить A (эффективная площадь сварного шва), сначала нам нужно преобразовать длину участка в размер горловины. как мы знаем, a = z x 0,707, поэтому нам нужно умножить длину ноги как (1/2 x 0,707 = 0,3535 дюйма) на длину (10 дюймов) на 2 сварных шва.
Эффективная площадь всего сварного шва будет: 10 дюймов x 0,3535 дюйма x 2 = 7,07 кв.дюйма.
Теперь мы можем решить на Ф .
F = 21 000 x 7,07 = 148 470 фунтов силы
Поскольку сварка выполняется параллельно нагрузке, напряжение на семьдесят процентов меньше по сравнению со сваркой, выполняемой перпендикулярно приложенной нагрузке.
Расчет альтернативного допустимого напряжения углового сварного шва
В случае одного линейного углового соединения или сварного шва с несколькими угловыми швами, состоящими из параллельных линейных угловых швов, нагруженных под одним углом и нагруженных в плоскости через центр тяжести сварного шва группа,
Допустимое напряжение может быть определена по формуле:
F V = 0,30 F EXX (1,0 + 0,50 SIN 1,5 θ )
, где
F V = Allable Mit Unit Press Press
F. 1111111112112111111111111111111111111111 гг. классификационный номер, т. е. класс прочности электрода
θ = угол между направлением силы и осью сварочного элемента, градусы предыдущего угла заготовки перед сваркой до 45°, образующегося посередине сварочного шва.
Боковина – соединение между сварным швом и основным материалом называется – «z». Размер «а» — это не что иное, как гипотенуза равнобедренного треугольника.
Для углового сварного шва с равными длинами катетов треугольник поперечного сечения представляет собой прямоугольный треугольник с углами 45 градусов в каждом углу. Соотношение между сварочным швом a и длиной участка z определяется следующим образом:
a ≈ 0,7z и z ≈ 1,4 a
(для математических умов 0,7 равно 1/√2, а 1,4 равно √2).
На приведенном ниже рисунке дан расчет различных напряжений в сварных швах.
Похожие сообщения
- Как рассчитать размер горловины или длины катета в угловом шве?
- Символы угловых швов, типы угловых швов
- Что такое сварной шов CJP, PJP, значение, символы, различия и примеры?
- Минимальное расстояние или близость между двумя кольцевыми сварными соединениями труб
Расчет прочности сварки с использованием Excel Sheet
Семинары
Проекты
Блоги
Карьера
Наем от US
для бизнеса / Университеты
.
Выберите категорию
Загрузка…
Все курсы / undefined
Все курсы / undefined / undefined
Загрузка…
Семинары
ДЛЯ БИЗНЕСА
Корпоративное повышение квалификации
ДЛЯ ВУЗОВ
Академическое обучение
Аренда у нас
Проекты
Мы нанимаем!
РЕЗЮМЕ: Сварка является наиболее распространенным процессом, который широко используется, когда требуется соединить две металлические детали для какого-либо технического применения. В некоторых случаях требуется расчет прочности сварных соединений. Допустимые напряжения для сварных соединений в некоторых конструкциях, например безогневое давление…
BIM
CAE
CFD
CSS
Подробная информация о проекте
Загрузка …
Оставьте комментарий
Благодарность за выбор. Пожалуйста, имейте в виду, что все комментарии модерируются в соответствии с нашей политикой комментариев, и ваш адрес электронной почты не будет опубликован по соображениям конфиденциальности. Пожалуйста, оставьте личный и содержательный разговор.
Пожалуйста, войдите, чтобы добавить комментарий
Другие комментарии…
Комментариев пока нет!
Будьте первым, кто оставит комментарий
Подробнее Проекты Манаса Патила (45)
Дизайн задней двери
Задача:
ЦЕЛЬ: Спроектировать заднюю дверь для автомобиля, используя предоставленную поверхность для укладки и следуя соответствующим методологиям проектирования. также, обеспечивая необходимые подкрепления и тиснения. Компоненты сборки задней двери: задняя дверь расположена в задней части автомобиля и обеспечивает доступ к багажнику для хранения…
29 июля 2022 18:48 IST
Подробнее
Задача по крыше
Цель:
ЦЕЛЬ: Спроектировать крышу со всеми ее компонентами, т. е. передней рейкой, носовой частью крыши, центральной рейкой и задней рейкой следуя основным разделам и проверив анализ осадки, также выполните исследование инерции и кривизны сечения. КРЫША: Крыша или верхняя часть — это часть автомобиля, которая находится над пассажиром…
25 мая 2022 г. 10:12 IST
Подробнее
Расчет и оптимизация модуля сечения
Цель:
ЦЕЛЬ: Рассчитать модуль сечения, используя сечение из конструкции капота, и придумать новое сечение, которое улучшило модуль сечения предыдущего сечения. МОДУЛИ СЕЧЕНИЯ: Модуль сечения — это геометрическое свойство заданного поперечного сечения любого вала или балочной конструкции. Это прямая мера прочности…
06 мая 2022 г. 18:50 IST
Подробнее
Fender Design Challenge
Цель:
ЦЕЛЬ: Спроектировать крыло, создав крепление порога, крепление бампера, крепление передней стойки и водослив с помощью мастер-сектора. КРЫЛО: Fender — это английский термин, обозначающий часть автомобиля (корпус транспортного средства), которая обрамляет колесную нишу (нижняя часть крыла). Его основная цель состоит в том, чтобы предотвратить попадание песка, грязи, камней, жидкостей,…0003
ВЫДЕРЖКА: Сварка является наиболее распространенным процессом, который широко используется, когда необходимо соединить две металлические детали для какого-либо технического применения. В некоторых случаях требуется расчет прочности сварных соединений. The permissible stresses for welded joints in certain structures, such as unfired pressure…
02 May 2022 08:10 AM IST
- BIM
- CAE
- CFD
- CSS
- FEA
- GIS
- HEV
- MBD
Читать далее
Конструкция крыла — испытание колесной арки
Цель:
ЦЕЛЬ: Рассчитать площадь колесной арки и решить, будет ли автомобиль соответствовать европейским стандартам. КРЫЛО: Fender — это английский термин, обозначающий часть автомобиля (корпус транспортного средства), которая обрамляет колесную нишу (нижняя часть крыла). Его основная цель — предотвратить попадание песка, грязи, камней, жидкостей и других…
28 апр. 2022 06:57 IST
Подробнее
Дизайн капота — неделя 2
Цель:
ЦЕЛЬ: Спроектировать внешнюю панель капота, внутреннюю панель и необходимое усиление, следуя основному разделу, и создать сборку из внутренней панели капота, внешней панели, защелки, петли и подкрепление. КАПОТ: Капот или капот автомобиля считается компонентом передней части корпуса. Капот — это отверстие…
20 апр. 2022 20:20 IST
Подробнее
Покрытие днища
Цель:
ПОКРЫТИЕ ДНИЩА: днище автомобиля подвергается наибольшему износу из-за грязной воды, выбоин на дорогах, камней и других препятствий на дороге, и поскольку оно не находится на виду, мы часто не видим повреждений. В индийских дорожных условиях днище автомобилей наиболее подвержено коррозии. Покрытие днища кузова…
06 апр. 2022 20:04 IST
Подробнее
Сравнительный анализ
Цель:
СРАВНИТЕЛЬНЫЙ СТАНДАРТ: Сравнительный анализ — это процесс сравнения вашей собственной организации, ее операций или процессов с другими организациями в вашей отрасли или в более широкий рынок. Сравнительный анализ может применяться к любому продукту, процессу, функции или подходу в бизнесе. Общие координаторы инициатив по сравнительному анализу…
04 апр. 2022 07:57 IST
Читать дальше
Неделя 11 — Окончательный проект
Цель:
ЦЕЛЬ: Разработать панель обивки двери из данного класса A и основных секций, а также создать элементы крепления. ЗАДАЧА: Создать поверхности класса B и C из заданной поверхности класса A для всех компонентов дверной отделки. Сформировать твердое тело, т. е. утолщенную часть для всех компонентов. Подробнее
ПРОЕКТ ШАССИ ДЛЯ СТУДЕНЧЕСКОЙ ФОРМУЛЫ SUPRA SAEINDIA
Цель:
ДИЗАЙН ШАССИ ДЛЯ СТУДЕНЧЕСКОЙ ФОРМУЛЫ SUPRA SAEINDIA ПРЕДСТАВЛЕНО — НАСТАВНИКОМ ПРОЕКТА МАНАС ПАТИЛ — ЧИККАМ СРИКАНТ . Со всей Индии отобраны студенты бакалавриата и аспирантуры инженеров…
21 марта 2022 г. 06:29 IST
- CATIA
- DESIGN
Подробнее
Неделя 10- Сборочный верстак
Цель:
ЦЕЛЬ: Создать отдельные детали из предоставленного 2D-чертежа, а затем создать полную сборку файлов этих деталей на сборочном верстаке. ОТЧЕТ: Загрузите 2D-чертежи компонентов по предоставленным ссылкам. Создайте отдельные файлы деталей для каждого компонента. Нарисуйте профиль для моделей и…
17 марта 2022 г. 07:42 IST
Подробнее
Неделя 9 — Проект — Мастер Раздел Развитие
Задача:
ЦЕЛЬ: Разработать цельнопластиковый компонент из заданных основных разделов вместе с техническими особенностями, а также выполнить анализ эскиза. ОТЧЕТ: Изучите предоставленные входные данные, т. е. основные сечения и поверхность класса A, чтобы разработать компонент. Чтобы создать ось инструмента, извлеките противоположные грани…
07 марта 2022 г. 18:43 IST
Подробнее
Неделя 9 — Проект 1 — Дизайн дверной аппликации с техническими характеристиками
Задача:
ОТЧЕТ: чтобы создать ось инструмента, извлеките базовую поверхность дверной аппликации класса A, создайте точку в центре и создайте линию, перпендикулярную поверхности и от точки, и мы получим ось инструмента. Чтобы создать экстракт поверхности класса B
28 февраля 2022 г. 19:23 IST
Читать далее
Неделя 9. Создание вложенных элементов — Задача 2
Цель:
ОТЧЕТ: При проектировании выступов следует соблюдать следующие требования: Уклон – 0,5 градуса на стенках выступа. Толщина – обычно 40%* номинальной стенки у основания. Отношение высоты к диаметру – радиусы 3:1 – максимальный радиус 0,25 мм. …
26 февраля 2022 г. 12:13 IST
Читать подробности
Неделя 9 — Создание функций вложения — Задача 1
Цель:
Отчет: Правила дизайна, которые следует соблюдать для создания ребер…
24 Feb 2022 06: 40 PM IST
Подробнее
Подлокотник двери Неделя 8 Задача
Задача:
ЦЕЛЬ: Разработать пластиковый компонент подлокотника двери и увеличить его толщину. ОТЧЕТ: Для данной части подлокотника двери, т.е. поверхности класса А, сначала нам нужно выполнить основные проверки, т.е. проверить непрерывность детали, убедиться, что между поверхностями нет зазора, для этого мы можем воспользоваться помощью команды поверхности…
23 фев. 2022 07:37 IST
Подробнее
Неделя 8 — Задача 5 — Проектирование сердечника и полости
Цель:
ЦЕЛЬ: Создание блоков сердечника и полости для пластикового компонента лицевой панели переключателя. ОТЧЕТ: Для данной детали панели переключателя сначала нам нужно выполнить основные проверки, т. Е. Проверить непрерывность детали, убедиться, что между поверхностями нет зазора, для этого мы можем воспользоваться помощью команды поверхности. Чтобы получить инструмент…
21 февраль 2022 г., 07:48 IST
- ДИЗАЙН
Подробнее
Неделя 8 — Задача 4 — Дизайн монетницы
Цель:
что между поверхностями нет зазора, мы можем воспользоваться помощью команды поверхности для этого. Чтобы создать ось инструмента, создайте систему осей и сформируйте пересечение держателя монет класса A…
20 февраля 2022 г. 12:31 IST
Подробнее
Неделя 8. Задача 3. Дизайн лицевой панели переключателя
Цель:
ЦЕЛЬ: Изготовить пластиковый компонент лицевой панели переключателя с помощью заданной поверхности класса A. базовые проверки, т. е. проверка непрерывности детали, убедитесь, что между поверхностями нет зазора, для этого мы можем воспользоваться помощью команды поверхности Чтобы получить…
17 фев. Задача 2 — Конструкция опорного кронштейна
Цель:
ОТЧЕТ: Для данной базовой части кронштейна сначала нам нужно выполнить основные проверки, т.е. проверить непрерывность детали, убедиться, что между поверхностями нет зазора, для этого мы можем воспользоваться помощью команды поверхности. Следующим шагом является создание фиктивной оси инструмента из центральной точки круговой геометрии на…
16 фев. 2022 18:05 IST
Читать далее
Неделя 8 — Задача 1 — Анализ проекта крышки вентилятора
Цель:
ОТЧЕТ: Для данной детали крышки вентилятора сначала нам нужно выполнить основные проверки, т. Е. Проверить непрерывность детали, убедиться, что между поверхностями нет зазора, для этого мы можем воспользоваться помощью команды поверхности. Следующим шагом является создание фиктивной оси инструмента от центральной точки поверхности крышки вентилятора класса A до…
15 фев.
Спецификация СР. НЕТ. ПРЕДМЕТ НОМЕР. DESCRIPTION QTY MAKE P003_Z03_ST03_01_00 BASE UNIT 1x 1 P003_Z03_ST03_01_01 WELD FRAME 1x 2 P003_Z03_ST03_01_01.1 BASE PLATE 1x MFG 3 P003_Z03_ST03_01_01.2 SQ TUBE 50×50×2×L810 2x 4 P003_Z03_ST03_01_01. 3 SQ TUBE 50×50×2×L1510 2x 5 P003_Z03_ST03_01_01 .4 SQ TUBE 50×50×2×L710 1x 6 P003_Z03_ST03_01_01.5…
13 января 2022 г. 12:37 IST
Подробнее
Неделя 9: задача 2D-детализации
Задача:
Что такое шаблоны чертежей? Шаблоны чертежей — это в основном стандарты чертежей в соответствии со спецификациями заказчика. Шаблоны чертежей — это формат, который используется для детализации различных частей или узлов приспособления. В шаблоне уже есть n номеров деталей, и…
06 января 2022 12:09 IST
Подробнее
Неделя 8: — Финишная 3D-задача 2
Цель:
ЦЕЛЬ: Выполнить 3D-чистовую обработку и спроектировать черновые локаторы для проектирования узла крепления. 3D FINISH: 3D Finish — это процесс, при котором конструкция полностью завершается и готовится к окончательному моделированию и 2D-детализации. Это процесс перед отправкой детали на окончательное моделирование. В этом процессе…
05 января 2022 г. 19:37 IST
Подробнее
Неделя 8: — 3D-финишная обработка — задачи 1
Цель:
Что вы понимаете под процессом 3D-финишной обработки? 3D-финиш — это процесс, при котором проект полностью завершается и готовится к окончательному моделированию и 2D-детализации. Это процесс перед отправкой детали для окончательного моделирования. В ходе этого процесса детали проверяются на надлежащий зазор и номинал…
02 января 2022 г. 14:08 IST
- КОНСТРУКЦИЯ
Подробнее
Неделя 7 – Проблемы проектирования базового блока 2
Цель:
ЦЕЛЬ: Спроектировать базовый блок с полной сборкой крепления. БАЗОВЫЙ БЛОК: Базовый блок — это блок, предназначенный для установки всех других блоков (зажимного блока, штифтового блока, опорного блока и т. д.) инструмента, а также других частей, необходимых для инструмента, таких как коробка пневматического клапана, магистральный кабельный тракт. монтироваться на базовый блок. The…
31 декабря 2021 г. 11:56 IST
Подробнее
Неделя 6: Задание по проектированию узла зажима и штифтового зажима
Задача:
ЦЕЛЬ: Разработать и понять концепцию узла поворотного зажима и узла штифтового зажима. ЗАЖИМНЫЙ БЛОК: Зажимной блок — это блок, предназначенный для зажима/удержания панели автомобиля с блоками ЧПУ/майларом/остатками с помощью пневматического зажимного цилиндра. Различные части узла зажима: Зажим Mylar/Finger: Finger is NC…
28 декабря 2021 г. 17:38 IST
Подробнее
Неделя 7: Проблемы проектирования базового блока 1
Цель:
Что такое базовый блок? Каковы типичные части базового блока? Базовый блок — это блок, предназначенный для установки всех других блоков (зажимного блока, штифтового блока, опорного блока и т. д.) инструмента, а также других частей, необходимых для инструмента, таких как коробка пневматического клапана, магистральный кабельный тракт. к базовому блоку. Части…
25 декабря 2021 г. 11:31 IST
Читать дальше
Неделя 5. Задача проектирования упора и зажимного устройства
Цель:
ЦЕЛЬ: Разработать и понять концепцию силового зажимного приспособления и опорного узла. ЗАЖИМНЫЙ БЛОК: Зажимной блок — это блок, предназначенный для зажима/удержания панели автомобиля с блоками ЧПУ/майларом/остатками с помощью пневматического зажимного цилиндра. Различные части узла зажима: Зажим майлар/палец: палец представляет собой блок ЧПУ…
18 декабря 2021 г. 10:57 IST
Читать дальше
Неделя 4:- Проектирование блока штифтов
Цель:
ЦЕЛЬ: Разработать и понять концепцию блока с фиксированными штифтами и блока с выдвижными штифтами. Компоненты блока штифтов: Штифт: штифт — это часть, которая фиксирует панель автомобиля. Штифт может быть как заводской, так и стандартной деталью. Штифт должен иметь шлифовальную поверхность на валу с посадками, на которые будет устанавливаться фиксатор штифта. Монтаж…
14 дек. 2021 18:25 IST
Подробнее
Неделя 3: Проблемы методологии проектирования приспособлений BiW
Задача:
Что такое методология проектирования? Методология проектирования — это шаги, выполняемые на этапах разработки концепции конструкции светильника. Заказ на покупку: Заказ на покупку — это заказ от клиента на начало работы. По сути, это подтверждение со стороны заказчика, что мы готовы приступить к проектированию или вперед. …
04 дек. 2021 08:33 IST
- ДИЗАЙН
Подробнее
Неделя 2: — BiW Fixture Basics Challenge
Задача:
Что представляет собой процесс выполнения проекта? RFQ (Запрос ценового предложения): RFQ — это запрос ценового предложения, при котором заказчик предоставляет свои требования, спецификации и т. д. в виде документа или данных для изучения или работы над ним, а также предоставляет коммерческое предложение, техническое предложение, сроки реализации проекта покупатель. 1st…
27 нояб. 2021 17:43 IST
Подробнее
Неделя 1: Введение в BiW and Fixtures Challenge
Цель:
Ответы в прикрепленном файле word
24 ноября 2021 18:43 IST
Подробнее
Проект 1
Цель:
.te.com Создайте необходимые геометрические параметры, такие как точки и система осей. Определить детали как соединители из инструментальных средств проектирования электрических деталей. Определить точку соединения жгута.0820 Подробнее
Проект 2
Задача:
Проверка целостности жгута: Выровняйте вид: Процедура прокладки жгута проводов на задней двери автомобиля: Загрузите 3D-данные соединителя и зажима с сайта www. te.com Создайте необходимые геометрические параметры таких как система точек и осей. Определение деталей как соединителей из инструментальных средств проектирования электрических деталей Определение пучка…
18 ноября 2021 г. 12:36 IST
Подробнее
Проектирование жгута проводов в CATIA V5 — 3D-моделирование Неделя 7 Задача
Цель:
Процедура, необходимая для выравнивания сборки жгута проводов: Откройте файл продукта сборки жгута проводов Создайте новый продукт и назовите его «сплющивание жгута» Перейдите к рабочему столу выравнивания жгута проводов Нажмите на параметры выравнивания жгута проводов и введите все параметры Извлеките жгут сборочный продукт…
31 окт. 2021 14:03 IST
Подробнее
Проектирование жгута проводов в CATIA V5 — 3D-моделирование. Неделя 5 и 6 Задача
Цель:
Процедура прокладки жгута проводов: Сначала загрузите 3D-данные соединителя для всех соединителей с сайта www.te.com. Создайте необходимые геометрические параметры, такие как точки и система координат. Определите детали как соединители из инструментария проектирования электрических деталей. точка соединения Определить соединение разъема…
29 окт. 2021 19:55 IST
Подробнее
Проектирование жгута проводов в CATIA V5 — 3D-моделирование Неделя 4 Задача
Цель:
Процедура, выполняемая для прокладки жгута проводов: Загрузите 3D-данные соединителя с сайта www.te.com. Создайте необходимые геометрические параметры, такие как точки и система координат. Определите детали как соединители из инструментария проектирования электрических деталей. Определите точку соединения пучка. Определите точку соединения соединителя. …
22 окт. 2021 18:35 IST
Подробнее
Прокладка и упаковка жгутов проводов Правила Неделя 3 Задание
Цель:
Процедура определения зажима P в качестве электрической опоры: Получите 3D-деталь зажима на сайте te.com Задайте геометрические параметры, такие как точки и плоскости. Задайте деталь как опору. Задайте точку входа и плоскость. Задайте базовую и выходную плоскости.0003
16 октября 2021 г. 17:40 IST
Читать подробности
Дизайн жгута проводки в Catia V5 — 3d Modeling Week 2 Challlenge
Цель:
12 октября 2021 06:12 IST
Подробнее
.
Цель:
Процедура создания блоков литейной формы лицевой панели вентилятора ЦП: Определите направление инструмента и проверьте расчет уклона Масштабируйте модель с учетом усадки 0,6%, т.е. и свяжите их Создайте разделительные поверхности…
30 сентября 2021 г. 18:23 IST
Подробнее
Неделя 12 Задача
Цель:
Процедура создания блоков пресс-формы с пластиковой ручкой: выбор направления обработки и проверка на предмет анализа уклона Масштабирование модели с учетом усадки 0,6 % т. е. 1.006 Закройте открытые поверхности с помощью запорных поверхностей, оставьте нижние открытые поверхности незаполненными. Используйте лофт-поверхности для закрытия незаполненной части и…
24 сентября 2021 г. 19:50 IST
Подробнее
Неделя 9 Задание
Цель:
Процедура создания пресс-формы: Определите направление инструмента и проверьте расчет уклона Масштабируйте модель с учетом усадки 0,6%, т. е. 1,006. Разделите модель с помощью команды «Разделить линию» и создайте линии разъема. Закройте окно поверхностей с использованием закрытых поверхностей. Используйте линейчатые и лофт-поверхности для закрытия реберной части…
18 сентября 2021 г. 14:12 IST
Подробнее
Project 1
Цель:
Процедура, выполняемая для создания пресс-формы: Определите направление инструмента. С помощью анализа уклона проверьте уклон на каждой поверхности. Определите сторону сердцевины и полости формы. Увеличьте модель с учетом усадки 0,6%, т.е. 1,006. отверстия в модели с использованием…
15 сент. 2021 14:32 IST
Подробнее
Показаны 1 из 45 проектов
Попробуйте наши лучшие инженерные курсы, проекты и семинары сегодня! Закажите БЕСПЛАТНУЮ демонстрацию
Как рассчитывается прочность сварного шва
by Axenics19 ноября 2019 г. Испытания сварных швов
Расчетное время чтения: 5 минут
Некоторые люди с удивлением узнают, что сварные соединения компонентов из нержавеющей стали на самом деле могут быть прочнее основного металла. Как рассчитывается прочность сварки? Один из способов — через прочность на растяжение.
Прочность на растяжение — это метод разрушающих испытаний, демонстрирующий максимальное напряжение, которое выдерживает материал, прежде чем он выйдет из строя или сломается. Натяжение или растяжение материала до точки разрыва — вот как рассчитывается прочность на растяжение. Неразрушающие испытания сварки труб из нержавеющей стали или множественные испытания также могут использоваться для сварных конструкций.
Мы выехали за пределы объекта, чтобы определить предел прочности нержавеющей стали на растяжение, поскольку обычно мы не проводим разрушающие испытания собственными силами. Цель этого испытания состояла в том, чтобы выяснить, как отсутствие проплавления шва может в конечном итоге повлиять на предел прочности при растяжении. Испытание должно было доказать нам и нашим клиентам ценность сварного шва с полным проплавлением по сравнению со швом без проплавления, когда речь идет о прочности на растяжение.
Нижние сварные соединения на трубных узлах из нержавеющей стали для газотранспортных систем имеют большую вероятность выхода из строя с течением времени. Техники-сварщики компании Axenics делают дополнительный шаг, чтобы полностью проварить все наши сварные швы. Испытание на прочность на растяжение — отличный способ продемонстрировать важность хороших методов сварки.
Мы протестировали нержавеющую сталь 316L диаметром 1,00 дюйма. x 0,065 дюйма в стенке трубы, проведенной на равной выборке сварных соединений с полным и непроваром.
Для подготовки образца мы разрезали трубку пополам, а затем сплющили ее. Чтобы измерить прочность сварного шва, мы использовали расчет общей площади сварного шва, деленной на силу, необходимую для разрыва этого сварного шва.
- Соответствие размеров сварного шва или трубы не имеет значения.
- Формула берет ширину образца сварного шва и измеряет его высоту, что дает в результате «площадь».
- Когда машина растягивает образец, величина прилагаемой силы измеряется в фунтах.
- Когда образец в конечном счете ломается, машина записывает измерение в фунтах.
- В этот момент разделите «площадь» на фунты силы.
- Рассчитывает количество фунтов на квадратный дюйм, необходимое для разрыва сварного шва.
- Результаты показывают, что образцы с полным просверливанием разрушаются при гораздо более высоком пределе прочности PSI, чем образцы с частичным просверливанием.
- На всех испытанных образцах точка разрыва непроплавленных сварных швов приходилась на сварной шов.
- На образцах с полным проплавлением место разрыва, как правило, располагалось вне самого сварного соединения, в зоне термического влияния НКТ.
Это упражнение показало, что процесс сварки различных размеров и типов трубных сборок, используемых в газотранспортных системах, а также во всех других случаях, должен выполняться на самом высоком уровне качества. Это гарантирует, что ни одно оборудование не будет скомпрометировано катастрофическим отказом трубы. Неразрушающий контроль обычно обеспечивает максимальную производительность сварных конструкций, но мы готовы провести разрушающий контроль, чтобы облегчить вам задачу.
Методы неразрушающего контроля (НК)Услуги компании Axenics по неразрушающему контролю сварных швов из нержавеющей стали включают, но не ограничиваются:
- Визуальный контроль
- Проверка герметичности гелием
- Ультразвуковой контроль 40 Жидкость
Визуальный контроль сварных швов является жизненно важным методом проверки потенциальных утечек, а также возможностью проверки стабильности производства. Визуальные проверки часто сочетаются с различными формами неразрушающего контроля, такими как проверка на утечку гелия. Будь то небольшая партия компонентов или множество повторяющихся деталей, мы тестируем, чтобы гарантировать качество и согласованность.
Во время визуального осмотра мы ищем ряд характеристик, и эти характеристики зависят от типа используемого материала. Хотя стандарты могут различаться для каждого проекта, мы часто ищем потенциальные проблемные области, такие как:
- Однородность материалов
- Коррозия материалов
- Трещины в сварных швах
- Дефекты на поверхности материалов
- Искажение полос
Гелий — идеальный элемент для обнаружения трещин в сварных швах, поскольку он представляет собой инертный газ, состоящий из атомов, и имеет низкую вязкость, поэтому атомы могут перемещаться быстро. Испытания под давлением и вакуумные испытания — это две формы испытаний на утечку гелием, которые используются для проверки отсутствия дефектов сварных швов в ваших компонентах.
Наша команда экспертов точно знает, где могут быть обнаружены дефекты сварного шва. Все инструменты, которые мы используем для неразрушающего контроля, регулярно проверяются и калибруются нашими штатными специалистами, чтобы убедиться, что машины работают идеально, обеспечивая 100% точные результаты испытаний для ваших систем управления технологическим процессом.
Ультразвуковой контрольНавыки и обучение ультразвуковому неразрушающему контролю более обширны, чем другие методы неразрушающего контроля, и контролируются нашим отделом контроля качества. Ультразвуковые лучи безопасны для испытателей, так как не содержат электромагнитного излучения. Ультразвуковой контроль определяет точное положение разрыва сварного шва более точно, чем даже радиографический контроль.
Мы устанавливаем внутреннюю целостность сварного шва с помощью ультразвукового контроля в следующем процессе:
- Ультразвуковой датчик пропускает луч высокочастотной ультразвуковой энергии в компонент или материал.
- Ультразвуковой луч проникает через весь компонент или материал.
- Затем датчик издает два звуковых сигнала, предупреждающих тестер.
- Если ультразвуковой луч пересекает неоднородность в компоненте, он отражает местоположение обратно в исходную точку и звучит третий звуковой сигнал
- Это указывает на то, что деформация превышает допустимые параметры. По этому сигналу мы знаем точное местоположение и размер деформации.
Достижения в области чистых технологий являются благом для производителей альтернативной энергии. Водородные топливные элементы обеспечивают более безопасные и чистые решения для компаний, производящих расходные материалы. Вода является побочным продуктом водородных топливных элементов, поэтому вилочные погрузчики и другие транспортные средства с установленной технологией могут работать вместе с пищевыми продуктами, не загрязняя их.
Axenics обеспечивает неразрушающий контроль материалов и сварных соединений для водородных топливных элементов с трехходовым теплообменником для различных транспортных средств, таких как автопогрузчики или автобусы. Ультразвуковой датчик посылает высокочастотные механические вибрации в компонент или материал. Как только волна проникает через весь компонент, датчик издает два звуковых сигнала. Если есть третий звуковой сигнал, деформация выходит за рамки допустимых параметров. Например, царапина на трубе не может быть больше 10% толщины стенки материала, либо она не соответствует стандартам качества.
Сварные швы на водородных топливных элементах часто имеют толщину одной пряди человеческого волоса, поэтому глубиномеры могут не обнаружить дефект в сварном шве. Испытание на проникновение красителя ищет крошечные трещины, которые не могут быть обнаружены визуальными и другими методами тестирования. Шаги для этого метода тестирования включают:
- Очистку материала от грязи, пыли или потенциальных загрязнителей и последующую сушку материала
- Тонкий слой краски покрывает материал, а затем краска стирается с материала
- Далее материал напыляется проявляющим порошком
- Порошок стирается с материала
- При наличии дефектов оставшийся порошок обнажает их
- В зависимости от типа используемого красителя дефект виден человеческому глазу при белом или черном свете
Также следует отметить, что неразрушающий контроль не имеет смысла, если другие этапы производственного процесса происходят в «грязной» среде. Контроль загрязнения на каждом этапе является главным приоритетом при работе с компонентами, используемыми для производства продуктов высокой чистоты. Чистые помещения, такие как чистые помещения класса 100 в Axenics, являются идеальным решением для очистки для каждого аспекта производства, от проверки материалов до окончательного тестирования и упаковки.
Design Part 2 — TWI
Статья в последнем выпуске Connect представила угловой шов, наименее затратный тип сварки, поскольку соединяемые компоненты не требуют газопламенной резки или механической обработки подготовки под сварку, детали могут быть прислонены друг к другу, и сварщик может затем наплавить металл сварного шва за один проход на твердую металлическую основу.
Хотя это звучит просто, необходимо учитывать некоторые аспекты выполнения углового сварного шва (в дополнение к уже упомянутым в предыдущей статье «Проектирование, часть 1»).
Щелкните здесь для просмотра наших последних технических подкастов на YouTube .
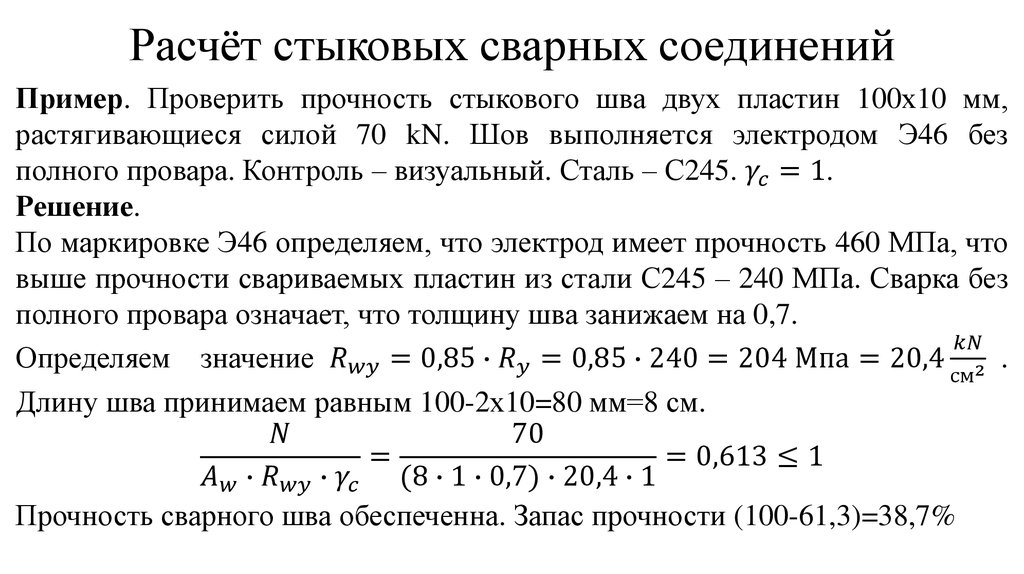
Скорость охлаждения в угловом шве выше, чем в стыковом шве такой же толщины. Есть три пути, по которым тепло будет теряться из сварного шва. Этот факт означает, что дефекты непровара/холодного пуска более вероятны, особенно в металлах с высокой теплопроводностью, таких как алюминий, а риск холодного растрескивания увеличивается в углеродистых и низколегированных сталях. То, что может быть приемлемым с точки зрения подводимого тепла и/или температуры предварительного нагрева для стыкового сварного шва, может быть неприемлемо для конфигурации углового шва. Этот момент иногда упускают из виду, особенно при сварке временных приспособлений, таких как крепостные опоры, где контроль качества может быть несколько слабым. Это привело к серьезным проблемам с растрескиванием для некоторых производителей.
В отличие от стыкового сварного шва, где требуемый размер сварочного шва обычно равен толщине основного металла, размер углового шва определяется ожидаемыми нагрузками. Следовательно, он может быть любого размера, который укажет проектировщик, хотя существуют практические ограничения в отношении как минимальной, так и максимальной толщины горловины.
При использовании обычных процессов дуговой сварки трудно наплавить угловой шов с шириной горла менее 2 мм. Это в дополнение к упомянутой выше возможности отсутствия плавления/холодного растрескивания из-за быстрого охлаждения, которому подвергаются небольшие угловые сварные швы. Максимальный размер углового шва, как правило, равен толщине более тонкого из двух соединяемых элементов, но очень большие угловые швы могут вызвать неприемлемую деформацию и/или чрезвычайно высокие остаточные напряжения. Кроме того, при размерах выше определенного может оказаться более экономичным выполнение Т-образного стыкового шва, а не углового шва.
Несмотря на то, что толщина шва считается наиболее важным параметром для целей проектирования, фактом является то, что механическое разрушение угловых сварных швов часто происходит по линии сплавления или по самому основному материалу. Одной из причин этого для углеродистых или низколегированных сталей является то, что металл сварного шва в основном значительно прочнее основного металла.
Как упоминалось в Connect , статья № 90, существует множество форм угловых швов, которые делают точное измерение толщины шва несколько более сложным, чем может показаться на первый взгляд.
Горловина — это кратчайшее расстояние от корня до поверхности сварного шва. Измерить этот размер в обычном угловом шве под углом или с плоской поверхностью относительно просто. Форма равнобедренного треугольника, горло составляет 0,7 длины ноги. Однако выпуклые, вогнутые швы и швы с глубоким проплавлением имеют толщину шва, как показано на рис. 1 .
Рис.1. Размеры стыка угловых швов
Таким образом, очевидно, что измерение только длины катета или фактической толщины стыка не является надежным при определении проектной толщины стыка сварного шва, но форма сварного шва необходимо учитывать. Избыток металла выпуклого шва не дает преимущества в отношении расчетной прочности, и с точки зрения затрат поверхность углового шва должна быть как можно более плоской.
Сварка с глубоким проплавлением является очень экономичным способом увеличения прочности соединения, поскольку только часть металла шва приходится на наплавленный присадочный металл. Однако измерить ширину шва глубокого провара невозможно. Чтобы гарантировать минимальное проектное сечение, необходимо контролировать параметры сварки и подгонки в очень жестких допусках. Поэтому этот тип сварки обычно выполняется с использованием автоматизированного или механизированного процесса сварки (дуговая сварка под флюсом или струйный перенос MIG/MAG), чтобы обеспечить достаточный и постоянный контроль параметров сварки.
При выборе размера углового шва следует помнить, что небольшое увеличение толщины шва приведет к значительному увеличению наплавленного металла шва, поскольку площадь поперечного сечения углового шва зависит от площади катета. длина (площадь = z 2 /2). Увеличение сечения, скажем, с 5 до 6 мм приводит к увеличению площади и, следовательно, металла шва примерно на 45%. Это соответствует почти 0,1 кг дополнительного металла шва на 1 метр длины сварного шва. Таким образом, необходимо заплатить существенные штрафы за стоимость и вес, если соединение либо завышено проектировщиком, либо сварено сварщиком. Не существует жестких и быстрых правил относительно точки, в которой более экономично перейти от углового шва к двухстороннему угловому шву или стыковому шву с частичным проплавлением. Области, указанные в Рис. 2 следует учитывать при выборе размеров углового сварного шва.
Рис.2. Относительные площади поперечного сечения
Для углового шва, нагруженного сдвигом (нагрузка параллельна сварному шву), расчет напряжения на сварной шов прост; это нагрузка, деленная на площадь сварного шва.
Рис.3. Расчет площади поперечного сечения углового шва
В целях проектирования предполагается, что угловой шов выходит из строя, поэтому можно легко рассчитать площадь поперечного сечения, способную выдержать эту приложенную нагрузку, когда известна прочность металла шва. .
Обратите внимание, что прочность металла на сдвиг обычно составляет от 70% до 80% прочности на растяжение. Эта цифра часто учитывается, чтобы дать приемлемый запас прочности. В Великобритании для простых углеродистых сталей часто используется прочность на сдвиг 115 Н/мм 2 , что позволяет рассчитать толщину шва по простой формуле шов: — шов ‘a’ = P/(L x 115).
Размеры поперечного сечения таврового соединения с двойным угловым швом, нагруженного растяжением, можно определить с использованием того же подхода. Обратите внимание, однако, что это очень упрощенный расчет, и он не принимает во внимание любые другие напряжения (изгиб, кручение и т. д.), которые могут испытывать сварной шов. Однако в рамки этих кратких статей не входит подробное рассмотрение анализа напряжений сварных швов.
Часть 3
Часть 4
Часть 5
Эта статья была написана Gene Mathers.
Численное прогнозирование прочности раструбных сварных труб с учетом компьютерного моделирования сварочных напряжений и деформаций
Материалы (Базель). 2022 май; 15(9): 3243.
Published online 2022 Apr 30. doi: 10.3390/ma15093243
, 1, * , 2 , 1 , 1 and 3
Shinichi Tashiro, академический редактор
Информация об авторе Примечания к статье Информация об авторских правах и лицензиях Отказ от ответственности
- Заявление о доступности данных
В статье представлена численная модель, основанная на методе конечных элементов (МКЭ) для прогнозирования деформаций и остаточных напряжений при сварке враструб. из нержавеющих труб различного диаметра из стали Х5ХН18-10. Следующая часть работы посвящена определению прочностных свойств сварного соединения в условиях испытания на сдвиг. С помощью программного обеспечения Abaqus FEA разработана численная термоупруго-пластическая модель для определения тепловых и механических явлений в сварном соединении. Этот подход требует реализации распределения мощности подвижного источника тепла на основе модели Голдака с движущимся по окружности источником тепла. Эта модель реализована в дополнительной подпрограмме DFLUX, написанной на языке программирования Fortran. Правильность принятой модели тепловых явлений подтверждается исследованиями формы и размеров зоны оплавления. Прочность сварного соединения, подвергаемого сдвигу, проверяется путем проведения испытаний на сжатие сварных труб, а также компьютерного моделирования с проверкой расчетной модели с использованием системы корреляции трехмерных изображений Dantec.
Ключевые слова: раструбная сварка, система корреляции изображений, численный анализ, термомеханические явления, деформации, сварные трубы
Сварка — неотъемлемый технологический процесс, осуществляемый при изготовлении многих элементов конструкций. Этот процесс оказывает непосредственное влияние на целостность, а также тепловое и механическое поведение конструкции в условиях эксплуатации. Сварные конструкции являются неотъемлемой частью многих зданий, мостов, кораблей, труб, сосудов высокого давления, ядерных реакторов и других инженерных сооружений [1,2,3,4].
Несомненно, одним из наиболее выгодных профилей, обычно используемых в стальных конструкциях, являются трубы. Применяются в качестве элементов для передачи жидкостей и газов (трубопроводы, а также различные виды опор конструкций и ферм). Это связано с тем, что они обеспечивают максимальную устойчивость к продольному изгибу (наибольший момент инерции) при минимальном использовании материала в конструкции [5,6]. В случае трубопроводов применяют два основных способа соединения — сварку встык и сварку в раструб [7,8].
Используемые в трубопроводах раструбные соединения одинакового диаметра требуют расширения поперечного сечения одного конца сегмента трубы до другого конца вставляемого соседнего сегмента трубы. С другой стороны, соединения внахлестку для труб разного диаметра (используемые в качестве переходника трубы или в длинных конструкциях с повышенной жесткостью) требуют соединения труб с контактной посадкой или аккуратной выточки внутреннего диаметра более широкого отрезка трубы для подгонки к более узкому отрезку трубы. [9,10].
Трубы сварные встык отличаются низкими затратами на строительство. С другой стороны, зона сварки раструбной трубы является слабой зоной по сравнению с зоной стыкового шва, особенно в случае усталостной прочности [11,12,13]. Правильно выполненная стыковая сварка обеспечивает оптимальную статическую и усталостную прочность соединения. Однако это требует большого мастерства сварщика и больших затрат, связанных с подготовкой труб перед сваркой. Сварка труб в раструб часто используется в качестве альтернативы стыковой сварке или сварке между трубой и фитингом, таким как клапан, штуцер, тройник, отверстие или колено.
Этот тип соединения используется, в частности, в случае, когда стыковые или фланцевые соединения не могут быть выполнены или когда конструкция требует снижения веса при сохранении требуемой жесткости (например, в уличном освещении) или в качестве ремонтных соединений на существующих трубопроводах. Кроме того, сварка с муфтой используется для труб малого диаметра (с номинальным диаметром менее 50,8 мм/2 дюйма) в системах вторичных трубопроводов на атомных электростанциях с особым условием, что они не должны использоваться в условиях щелевой коррозии между могут возникнуть трубы и фитинги. Обычно на одной типичной 1000-мегапиксельной электростанции с водо-водяным реактором (PWR) имеется около 40 000 сварных швов враструб [9].,10,11].
Механические параметры необходимы для правильной работы трубчатых конструкций, сваренных по окружности. Большое количество тепла, вводимого в соединение, оказывает существенное влияние на его прочностные свойства [14,15,16,17] сварных труб. Распознавание значений остаточных напряжений чрезвычайно важно при анализе развития трещин в сварных конструкциях [18,19]. Их оценка может помочь в решении проблем, связанных с межкристаллитным разрушением под напряжением или усталостной прочностью. Кроме того, важно определить деформационную способность стальных трубопроводов, особенно трубопроводов, сооружаемых в геоопасных зонах (например, в районах с сейсмической активностью) [20,21].
Численный прогноз тепломеханических свойств сварных соединений и подбор параметров сварки позволяют значительно ускорить выполнение и удешевить технологический процесс. За последнее десятилетие разработан ряд численных моделей для оценки распределения температуры и остаточных напряжений при сварке стальных труб [5,6,7,8,16,17,18,22]. Исследователи используют полную трехмерную численную модель [8,18,23,24,25] для анализа влияния изменения параметров при кольцевой сварке труб на распределение временных и остаточных напряжений, для анализа напряженного состояния, возникающего при соединении разнородных материалов. или для моделирования остаточных напряжений при многопроходной сварке трубы. Многие исследователи выбирают осесимметричные 2D модели для сокращения времени расчета и затрат при моделировании кольцевой сварки труб [4,5,26,27]. Большинство численных моделей проверяются реальными испытаниями сварки и прочностными испытаниями на соответствующих машинах для испытаний на прочность [19].,28,29,30]. До сих пор отсутствует верификация численных моделей на основе экспериментально определяемого поля значений (например, поля перемещений) на всей площади анализируемого образца.
Современные исследования в области численного моделирования сварки труб сосредоточены в основном на анализе термомеханических явлений в стыковых соединениях [8,14,15,16,17]. В литературе имеется всего несколько работ, посвященных численному анализу термомеханических явлений, происходящих в раструбных трубах.
В работе представлены физические аспекты сварки сосредоточенным подвижным источником тепла вокруг наружной поверхности труб и численный анализ сжатия свариваемых труб различного диаметра. Расчеты выполняются в программе расчета Abaqus FEA, дополненной дополнительными числовыми подпрограммами. Термомеханические свойства стали Х5ХН18-10, меняющиеся в зависимости от температуры, адаптированы в расчетах [16,31,32,33]. На основе [8,10,18,19,20,25] проверены энергетические параметры процесса. Численная модель основана на геометрии экспериментальных образцов труб различного диаметра, сваренных по окружности внахлестку методом GTAW. Проведено моделирование для определения температурного поля в стыке, формы и размера зоны расплава и напряженного состояния, а также поля перемещений. Для проверки правильности принятых моделей теплообмена полученные форму и размеры зоны расплава сравнивают с макроскопической картиной поперечного сечения стыка. Продольные нагрузки являются основной причиной разрушения раструбных соединений. Объем исследований по численному моделированию раструбных соединений должен включать также прочностной анализ. Испытание на сжатие труб, сваренных по окружности, представленное в документе, действительно является испытанием на сдвиг сварных соединений. Сварные трубы обжимали на универсальной испытательной машине Zwick/Roell для определения прочности сварного соединения при сжатии. Система корреляции изображений Dantec 3D использовалась при испытании на сжатие для измерения реального распределения смещения в различных зонах сварных труб. Полученные результаты численного моделирования испытания на сжатие сравнивались с результатами экспериментальных испытаний.
В ходе экспериментов по сварке GTAW две трубы разного диаметра из аустенитной стали были сварены по окружности внахлестку. Размеры: внутренняя труба диаметром 30 мм × 2 мм и длиной 66,5 мм и внешняя труба диаметром 33,7 мм × 2 мм и длиной 65,5 мм. Схема системы и размеры показаны на .
Открыть в отдельном окне
Схема анализируемой системы.
Трубы соединены внахлест 20 мм. Внешняя трубка была свернута до 0,15 мм на длину 20 мм для хорошей сборки соединения (). Процесс сварки осуществлялся с использованием дополнительного материала в виде стержня диаметром 1 мм. В качестве защитного газа использовался аргон. Параметры процесса сварки: сила тока 83 А, напряжение 20 В, скорость горелки 0,3 м/мин, угол отклонения сварочной горелки от вертикальной плоскости 20°. показывает полученное сварное соединение.
Открыть в отдельном окне
Труба кольцевая сварная различных диаметров: ( а ) общий вид, ( б ) макроскопический вид поперечного сечения сварного шва.
Металлографические испытания были проведены для определения размера и формы зоны расплава. Данные, полученные в результате экспериментальных испытаний, необходимы для проверки модели распределения мощности источника тепла. Макроскопическая картина сварного соединения позволила сравнить форму зоны оплавления с результатами численного моделирования. Точное определение тепловой нагрузки обеспечило правильное распределение температуры в соединении и соответствующий анализ сварочных напряжений и деформаций [19].,24].
Методы измерения с корреляцией изображений в настоящее время все чаще применяются для определения составляющих напряжений, деформаций или перемещений в лабораторных условиях, а также для выявления дефектов элементов конструкций или машин, возникающих при статических или динамических нагрузках [34,35,36 ,37,38]. Алгоритм корреляции отслеживает положение одних и тех же точек на исходном изображении и искаженном изображении ().
Открыть в отдельном окне
Схема анализа изображения поверхности до и после деформации [34].
Корреляционные алгоритмы позволяют определять максимальное смещение с точностью до 1/100 пикселя матрицы. Алгоритм корреляции отслеживает положение одних и тех же точек, видимых на исходном изображении и искаженном изображении. Для этого на исходном изображении идентифицируют квадратную поверхность, содержащую набор пикселей, и в положении, соответствующем изображению после деформации.
приведена схема исследовательской станции, на которой выделяются три основные группы элементов: объект контроля (образец с системой нагружения), измерительная система и система анализа результатов измерения. Измерительная система оснащена набором цифровых камер, установленных на общем штативе. Эта система соединена с компьютерным блоком, оснащенным программным обеспечением ISTRA 3D, которое собирает и анализирует результаты, зарегистрированные во время измерения.
Открыть в отдельном окне
Схема системы измерения деформации.
3.1. Система измерения
В исследовании используется универсальная испытательная машина Zwick & Roell Z100 с максимальной нагрузкой 100 кН и точностью 1 Н усилие/0,01 мм смещения (без экстензометра, ). Измерительная система связана с системой корреляции изображений Dantec 3D. Система Dantec оснащена оптическими камерами, используемыми для регистрации деформаций при испытании на растяжение с объективами диаметром 50 мм и имеющими максимальное разрешение 2048 × 2048 пикселей каждая. Это позволило определить полный размер анализируемого образца в рабочей зоне универсальной испытательной машины.
Открыть в отдельном окне
Измерительная система для определения перемещений с рабочей зоной и образцом.
В эксперименте использовалась система из трех камер. Поля деформации измерялись для всего цикла растяжения. Для измерения в программе Istra4D был создан триггерный механизм. Снимки делались для каждого шага времени Δt = 0,1 с.
3.2. Результаты измерений
Экспериментальные испытания проводились для проверки корректности численной модели [39,40] термомеханических явлений при сжатии сварных труб до 90 кН (а). б представлена диаграмма смещения верхней траверсы испытательной машины в зависимости от продолжительности нагрузки. Процесс сжатия фиксировался системой камер. Во время теста камеры сделали 471 контрольный снимок. Нагрузку прикладывали после достижения начального усилия, равного 100 Н. Процесс разгрузки происходил после превышения максимального усилия 90 кН. показывает значения перемещений в выбранных пяти контрольных точках вдоль z ось. содержит полные характеристики испытания на сжатие с отдельными зонами: основная нагрузка и разгрузка. Время нагружения начинается с шага 0 и заканчивается на шаге 375. В и отмечены характерные контрольные точки, для которых максимальное значение смещения, полученное от движения траверсы, соответствует значению, измеренному системой Dantec.
Открыть в отдельном окне
Характеристические параметры испытания на сжатие, ( a ) диаграмма нагрузки, ( б ) диаграмма перемещений верхней траверсы.
Открыть в отдельном окне
U z диаграмма перемещений для пяти выбранных точек измерения.
а показано поле перемещений по оси z (ось, соответствующая направлению нагрузки), где линия измерения отмечена сплошной линией. Для этой линии диаграмма перемещений показана на б. Измерительная линия находится на боковой поверхности свариваемых труб. Видно, что в области сварного шва; смещения имеют значительно меньшие значения по сравнению с основным материалом, что связано с увеличением жесткости этой области, возникающей в результате изменения механических свойств сварного шва.
Открыть в отдельном окне
Экспериментальное распределение смещения по оси z ( a ) на внешней поверхности, ( b ) вдоль осевых линий.
Распределение перемещений U x , U y за время 37,5 с (что соответствует действию удельной нагрузки) на боковой поверхности труб показано на . Видимое уменьшение величины смещения происходит внутри шва в перпендикулярном направлении к боковой поверхности (ось и ). Небольшой рост перемещений по оси х (горизонтальной) обусловлен небольшим прогибом образца, вызванным малым проскальзыванием прижимной пластины.
Открыть в отдельном окне
Смещение ( a ) по оси x, ( b ) по оси y.
4.1. Математические модели термомеханических явлений
Численный анализ термомеханических явлений подразделяется на тепловой и механический [19].,41,42].
Тепловые явления описываются уравнением теплопередачи в модуле моделирования Abaqus/Standard. Уравнение решения основано на законе сохранения энергии и законе Фурье [27]. Это уравнение описывается следующей формулой:
где λ = λ( T ) — теплопроводность (Вт/(м K)), U = U ( T ) — внутренняя энергия (Дж/кг), δT — вариационная функция, ρ — плотность (кг/м 3 ), q v — объемный источник тепла (Вт/м 3 ), q S — поверхностный тепловой поток. (Вт/м 2 ).
Уравнение (1) дополняется начальным условием и граничными условиями типа Дирихле, Неймана и Ньютона [19,33].
Численный анализ механических явлений в Abaqus FEA основан на классических уравнениях равновесия. В анализируемой системе преобладают термические деформации; поэтому при анализе предполагаются малые деформации [43,44,45]. Градиент смещения небольшой; следовательно, тензор деформации можно записать в виде:
ε=12[∇u+(∇u)T] when ∇u=∂u∂u≈1
(2)
Тензор напряжений Коши отождествляется с тензором номинальных напряжений согласно следующему уравнению:
∇∘σ(x)+Fb=0
(3)
где σ — тензор напряжений Коши, ∇ — оператор дивергенции, F b — плотность объемной силы относительно начальной конфигурации.
Приведенное выше уравнение равновесия дополняется граничными условиями, заданными как:
9для Suσ⋅n=Φ для SΦ(4)
где û — перемещение на участке S u граничной поверхности, а Φ — растяжение граничной поверхности на участке S Φ .
Тензор напряжений Коши, ∇, оператор дивергенции, F b плотность объемной силы относительно начальной конфигурации. Общая деформация описывается упруго-ископластической моделью согласно [19,43,44]:
ε=εtotal=εe+εp+εTh
(5)
где ε e — тензор скорости упругой деформации, ε p — тензор скорости пластической деформации и ε Th — скорость термической деформации.
Скорость напряжения зависит от скорости упругой деформации
σ˙=D=:(ε˙−ε˙p−ε˙Th)
(6)
где D= — тензор изотропной упругости четвертого порядка, «:» — внутреннее тензорное произведение.
D==2μI=+(kB−23μ)I⊗I
(7)
где мк , k B – модуль сдвига и объемный модуль, I=, I – тождественные тензоры четвертого и второго порядка, ⊗ – внешнее тензорное произведение.
Упругая деформация рассчитывается с использованием инвертированного обобщенного закона Гука, описываемого формулой [43,44]:
где E — модуль Юнга, ν — коэффициент Пуассона, σ ij — тензор напряжений и δ ij — дельта Кронекера.
Пластические деформации определяются на основе модели неизотермического пластического течения с условием пластичности Губера–Мизеса и изотропным упрочнением. Функция потока ( f ) определяется по следующей формуле:
f=σef−σ¯(εijp,T)=0
(9)
где σef — эффективное напряжение, σ¯(εijp,T) — пластифицирующее напряжение материала, зависящее от пластической деформации (εijp) и температуры T .
Эффективное напряжение и деформация описаны следующим образом: где S ij — тензор девиаторных напряжений (Sij=σij−13σmδij), σm — среднее напряжение.
Скорость пластической деформации можно выразить в следующей форме
ε˙ijp=32ε˙efpSijσef
(11)
где ε˙ijpl — составляющая скорости пластической деформации, λ — коэффициент пластической текучести, а S ij представляет девиаторное напряжение.
Термическая деформация возникает в результате изменения объема из-за разницы температур:
εijTh=∫T0Tα(T)dTδij
(12)
где α — зависящий от температуры коэффициент теплового расширения, T 0 — эталонная температура.
4.2. Моделирование источника тепла
В случае численного моделирования процесса электродуговой сварки в литературе для описания распределения мощности источника чаще всего используется модель Голдака [33,46,47]. Эта модель описывается двумя полуэллипсоидами, соединенными между собой осью симметрии [46]. Схема модели представлена на . Уравнение, описывающее модель Голдака, выражается следующим уравнением:
Q1(x,y,z)=63f1QAabc1ππexp(−3x2c12)exp(−3z2a2)exp(−3y2b2)Q2(x,y,z)=63f2QAabc2ππexp(−3x2c22)exp(−3z2a2)exp(−3y2b2)
(13)
где параметры a , b , c 1 и c 2 описывают размеры источника тепла Гольдака формы, коэффициенты f 1 2 , представляющие распределение тепла во фронте и источник тепла во фронте. коэффициенты f 2 , представляющие распределение энергии в задней части источника тепла, ( f 1 + f 2 = 2), satisfying the condition Q 1 ( x , y , z ) and Q 2 ( x , г , г ).
Открыть в отдельном окне
Схема модели Голдака (Уравнение (13)).
В уравнении (13) параметр Q A описывает значение мощности электрической дуги:
QA = I⋅U⋅η
(14)
где U — напряжение [В], I — сила тока [А] и η — КПД.
Дополнительная подпрограмма DEFLUX реализована в решателе Abaqus FEA для определения подвижного источника сварки [19,33]. Подпрограмма включает в себя математическую модель распределения мощности источника тепла, скорости и направления движения источника. Основным аспектом моделирования процесса кольцевой сварки в лагранжевых координатах является анализ движения источника по траектории окружности ().
Открыть в отдельном окне
Схема движения источника в цилиндрической системе [33].
Необходимо ввести уравнения преобразования, чтобы отразить положение источника тепла в декартовых координатах. В процедуру DFLUX вводятся уравнения перехода от цилиндрической системы к декартовой системе. Уравнения перехода описаны ниже:
где R z – внешний радиус трубы, t – время, ϕ0 – начальное положение оси балки, ω=v/Rz – угловая скорость, при которой v = const. — линейная скорость по периметру трубы, а z 0 — начальное положение на оси z .
Для включения в модель наклона источника необходимо внести в расчеты дополнительное преобразование по оси x. показывает схематическое изображение преобразований.
Открыть в отдельном окне
Схема системы преобразования распределения мощности источника Голдака [33].
Преобразование распределения мощности сварочного источника осуществляется с использованием модели преобразования [33]: =−cos α ⋅y′−sin α ⋅z′z=sinα ⋅y′−cosα ⋅z′
(17)
Уравнение (16) получается после решения представленной матрицы преобразования из базовой системы ( x , y , z ) в повернутую систему ( x 1 , y 1 , z 2 1 8 1 ). Открыть в отдельном окне Схема наклона источника тепла. Численная модель в Abaqus FEA разработана с использованием реальных сварных труб (показаны на ). Модель геометрии свариваемых труб представлена сеткой конечных элементов. Открыть в отдельном окне Дискретная модель анализируемого соединения. Меньший шаг сетки КЭ составляет около 0,25 мм и находится в зоне действия источника тепла. Общее количество конечных элементов 495100. Модель материала стали X5CrNi18-10 принята по литературным данным [32,33] как: температуры солидуса и ликвидуса T S = 1400 °С, T L = 1455 °С, скрытая теплота плавления H L = 260 × 10 3 Дж/кг, температура окружающей среды T 0 = 20 °C и тепловая конвекция α k = 50 Вт/м 5 2 90. Основные параметры источника Голдака предполагаются по данным эксперимента. Мощность источника тепла определяется на основании уравнения (13) при Q А = 996 Вт (при КПД процесса η = 60%). Скорость сварки задается равной v = 0,3 [м/мин], а угол отклонения сварочной горелки от вертикальной плоскости задается равным 20°. На основании численной проверки приняты следующие параметры источника Голдака: а = 4 мм, b = 2 мм, с 1 = 4 мм и с 2 = 4 мм. Коэффициенты равны f 1 = 1 и f 2 = 1 ( f 1 + f 2 = 2). При анализе тепловых явлений учитывается идеальный контакт между соединяемыми элементами. В случае анализа механических явлений предполагается «самоконтакт» [40] между внутренней плоскостью трубы большего диаметра и внешней плоскостью трубы меньшего диаметра. показывает место самоконтакта. Открыть в отдельном окне Схема контактной площадки и механических граничных условий. также показывает расположение и тип предполагаемых механических граничных условий. На конце трубы меньшего диаметра были отключены все степени свободы (переводы U X = U Y = U Z = 0 и повороты U RX Уравнения преобразования также были записаны в подпрограмме DFLUX. Численное моделирование кольцевой сварки двух труб разного диаметра также требует соответствующего угла наклона оси источника тепла. показывает наклон источника тепла, принятый в модели. Ось источника сварки повернута на угол α = 20° (направление наклона такое же, как и в эксперименте).
4.3. Численная модель
Проведено компьютерное моделирование на основе разработанных математических и численных моделей. Расчеты проводились в два этапа. Первый этап касается тепловых и механических явлений, связанных с процессом кольцевой сварки труб различного диаметра. На втором этапе проводились численные расчеты механических явлений при испытании на сжатие. Моделирование сжатия трубы производилось с учетом остаточных напряжений, возникающих в процессе сварки.
5.1. Результаты численного моделирования термомеханических явлений при сварочных процессах
Время перемещения сварочной горелки по внешней плоскости трубы зависит от радиуса и линейной скорости перемещения источника тепла. Для принятых данных это время составляет ок. 20 с. Общее время моделирования от начала нагрева до охлаждения до температуры окружающей среды составляет 150 с. Температура в стыке определяется для принятых энергетических параметров источника тепла. показывает температурное поле для двух разных длительностей моделирования ( т = 7 с; т = 17 с). Зона плавления отмечена на этом рисунке сплошной линией, определяемой температурой ликвидуса ( T L ).
Открыть в отдельном окне
Температурный профиль сварных труб для двух времен моделирования, t = 7 с; т = 17 с.
а показывает температурное поле в сечении стыка за время t = 10 с. Сплошной линией отмечена граница зоны оплавления. Результаты моделирования распределения температуры были проверены экспериментально. б показано поперечное сечение реального шва, где проходит граница зоны оплавления (сплошной линией отмечен диапазон зоны оплавления, T L ≈ 1455 °C) дано в рамке. Как видно, для допущений, принятых в модели, получается хорошее совпадение результатов.
Открыть в отдельном окне
Сечение стыка ( a ) результаты численных расчетов, ( b ) реальный сварной шов.
Численно определенная тепловая нагрузка, действующая на комбинированную систему из двух труб разного диаметра, позволила выполнить расчеты механических явлений. показывает распределение временного приведенного напряжения для двух разных периодов моделирования, t = 8 с и t = 17 с. Наибольшие временные напряжения возникают в зоне действия источника нагрева на материал величиной 255 МПа. Остаточное приведенное напряжение после охлаждения до температуры окружающей среды представлено за время t = 150 с.
Открыть в отдельном окне
Временные приведенные напряжения сварного соединения для двух разных времен моделирования, t = 8 с; т = 17 с.
Открыть в отдельном окне
Приведенные напряжения после сварки, за время t = 150 с.
Из сравнения и видно, что после понижения температуры соединения до температуры окружающей среды (t = 150 с) максимальные напряжения уменьшились.
Поле перемещений сварного соединения прогнозируется численно. показывает поле смещения в общем виде ( U z , U y , U z ). Для анализируемой сварной системы из двух труб наибольшее значение перемещений составляет ок. 0,03 см (0,3 мм).
Открыть в отдельном окне
Поле смещения в сварных трубах.
Для принятых механических граничных условий наибольшие значения перемещений направлены по оси z ( U z , c) в анализируемом стыке. На основании результатов, показанных на а, б, видно, что поперечное сечение стыка деформируется из-за работы источника сварки. Значения смещения в направлении x и и оси сопоставимы с приблизительным размером 0,2 мм.
Анализируемый способ сварки труб может быть использован для различных видов строительных крепей. Поэтому необходимо провести анализ прочности, такой как испытание на сжатие, чтобы определить механические свойства этого типа сварной конструкции.
5.2. Результаты численного моделирования испытаний на сжатие
В данной работе разработана численная модель испытаний на сжатие на основе экспериментальных испытаний, выполненных с использованием универсальной испытательной машины и системы корреляции изображений (см. раздел 3.1). В ходе численного моделирования был проведен прочностной анализ соединяемых труб. Принятая в расчетах дискретная модель показана на рис.
Образец был нагружен силами сжатия, как показано на диаграмме нагрузки (). Граничные условия принимались в соответствии с условиями, существовавшими во время эксперимента. Граничные условия, принятые при анализе, показаны на .
Открыть в отдельном окне
Схема анализируемой системы при испытании на сжатие.
Все поступательные и вращательные степени свободы получены на нижней поверхности образца, в месте контакта образца с нижним неподвижным компрессионным основанием: U x = U y = U z = 0, U Rx = U Ry = U Rz = 0 and U Rx = U Ry = U Rz = 0. С другой стороны, на верхней поверхности контакта с подвижной траверсой допускается движение по оси z ( U x = U у = 0 и U Rx = U Ry = U Rz = 0). Расчеты ведутся в упругопластическом диапазоне. Данные по материалам в области пластичности для стали Х5ХН18-10 приняты относительно литературных данных [48].
Численные расчеты проводились с учетом остаточных напряжений, возникающих в процессе сварки. В расчетах в качестве начального условия использовалось численно оцененное поле остаточных напряжений (). Численно оценивалось распределение напряжений, возникающих при осевом сжатии образца (), а также распределение перемещений ().
Открыть в отдельном окне
Распределение приведенных напряжений в сжатом образце за время ( a ) t = 1 с, ( b ) t = 37,5 с.
Открыть в отдельном окне
Поля смещения в сжатом образце: ( A ) U x , ( B ) U Y 9 , ( C ) 111111111111111111111111111121) y 2 , ( C ) y 2 , ( C ) y 2 , ( C ) 121). и ( d ) сравнение U z смещение с экспериментальным испытанием.
а показывает распределение приведенных напряжений в первую секунду моделирования ( t = 1 с). С другой стороны, b показывает распределение напряжения для максимальной сжимающей нагрузки на образец ( т = 37,5 с).
Из анализа прогноза напряженного состояния в сжатом образце () видно, что на начальном этапе нагружения наибольшая концентрация напряжений находится в сварном соединении, что связано с остаточными напряжениями от процесс сварки. Приведенные напряжения увеличиваются во всем элементе при нагружении сжимающей силой. При максимальной нагрузке максимальные значения напряжений возникают в зоне сварки (б). При заданной нагрузке 90 кН элемент не поврежден. Однако дальнейшее увеличение нагрузки могло привести к разрушению образца из-за трещины в сварном шве. показаны распределения смещения с учетом уменьшенных остаточных напряжений, возникающих в результате процесса сварки.
Предполагаемые параметры испытания на сжатие совпадают с параметрами, полученными в эксперименте (). Поэтому значения продольных перемещений U z согласуются с экспериментом. Максимальное значение этого смещения составляет до 1,6 мм (контрольная точка относится к величине смещения от испытательной машины за время испытания 37,5 с). Отрицательный знак смещения вдоль z Направление оси определяется принятой системой координат. Это направление оси z противоположно направлению в системе координат, найденному в экспериментальных исследованиях. Полученные перемещения по оси трубы сопоставимы; их максимальные значения колеблются около 0,2 мм. Численно оцененные значения перемещений по осям x и y сопоставимы с результатами эксперимента, полученными системой Dantec 3D (). г показывает сравнение перемещений вдоль z ось для линии измерения (c) с результатами, полученными в системе Dantec 3D (). На этом рисунке можно наблюдать высокую сходимость полученных результатов.
В отличие от большинства работ по моделированию процесса сварки, в данной работе моделируются термомеханические явления при сварке и проводятся испытания для определения механических свойств сварной конструкции. Численный анализ процесса сварки, а также моделирование механических нагрузок при испытаниях на сжатие позволили спрогнозировать прочность соединения.
Сравнение численно оцененной температуры ликвидуса с результатами эксперимента показывает, что расчетная зона сплавления хорошо согласуется с границей зоны оплавления в поперечном сечении полученного соединения. Приведенные сварочные напряжения, полученные при моделировании, не превышают значения 250 МПа, а значения смещения не превышают 0,3 мм. Полученные результаты моделирования процесса сварки используются в качестве исходных данных для прочностного анализа при испытании сварных труб на сжатие.
Экспериментальные результаты, полученные с помощью системы корреляции трехмерных изображений Dantec, согласуются как в поперечном направлении, так и вдоль оси z . Сравнение полей смещений в каждом направлении подтвердило правильность разработанных численных моделей.
На основании полученных результатов моделирования напряжений в сжатом образце (см. ) видно, что на начальном этапе нагружения наибольшая концентрация напряжений находится в стыке, что связано с остаточной сваркой стрессы. При нагружении остаточное напряжение во всем образце увеличивается. Максимальные значения напряжений возникают в зоне сварки при максимальной нагрузке 90 кН. Дальнейшее увеличение нагрузки могло привести к разрушению образца.
Разработанная численная модель позволяет прогнозировать влияние параметров сварки на распределение напряжений и деформаций и, таким образом, позволяет определять технологические параметры, используемые для получения хорошего качества соединения.
Это исследование не получило внешнего финансирования.
Концептуализация, Т.Д., В.П. и З.С.; Курирование данных, М.К.; Формальный анализ, Т.Д., В.П. и З.С.; Методология, В. П., М.К. и С.С.; Администрация проекта, Т.Д. и М.К.; Ресурсы, С.С.; Валидация, т.д.; Визуализация, З.С.; Письмо — первоначальный вариант, З.С.; Написание — обзор и редактирование, Т.Д., В.П., М.К. и S.S. Все авторы прочитали и согласились с опубликованной версией рукописи.
Неприменимо.
Неприменимо.
Данные содержатся в статье.
Авторы заявляют об отсутствии конфликта интересов.
Примечание издателя: MDPI сохраняет нейтралитет в отношении юрисдикционных претензий в опубликованных картах и институциональной принадлежности.
1. Вебстер С.Э., Ткач Ю., Лангенберг П., Нонн А., Кухарчижк П., Кристенсен Дж.К., Куртад П., Дебин Л., Петринг Д. Гиблас: Экономичная и безопасная лазерная гибридная сварка конструкционной стали. Бюро официальных публикаций Европейских сообществ; Люксембург: 2009 г.. [CrossRef] [Google Scholar]
2. Джеймс М.Н., Мэтьюз Л., Хаттинг Д.Г. Трещины от затвердевания сварного шва в резервуаре для воды из нержавеющей стали 304L. англ. Потерпеть неудачу. Анальный. 2020;115:104614. doi: 10.1016/j.engfailanal.2020.104614. [CrossRef] [Google Scholar]
3. Caccese V., Yorulmaz S. Лазерная сварка стальных сэндвич-панелей мостового настила: анализ методом конечных элементов и испытания на прочность сварных швов. Университет штата Мэн; Orono, ME, USA: 2009. [Google Scholar]
4. Чапек Дж., Троян К., Кец Дж., Черны И., Ганев Н., Немечек С. О свариваемости толстых стальных листов P355NL1 для сосудов высокого давления с использованием лазерная сварка. Материалы. 2021;14:131. дои: 10.3390/ma14010131. [Бесплатная статья PMC] [PubMed] [CrossRef] [Google Scholar]
5. Zhang Y., Shuai J., Ren W., Lv Z. Исследование реакции на растяжение кольцевого сварного шва высокопрочного стального трубопровода . Дж. Констр. Сталь Рез. 2022;188:107047. doi: 10.1016/j.jcsr.2021.107047. [CrossRef] [Google Scholar]
6. Пак Дж.Х., Мун Х.С. Усовершенствованная система автоматической сварки для морской трубопроводной системы с функцией отслеживания шва. заявл. науч. 2020;10:324. doi: 10.3390/app10010324. [Перекрестная ссылка] [Академия Google]
7. Доброта Д., Ротару И., Бондреа И. Проект сварной конструкции переходной арматуры с металлических труб на пластиковые. Металлы. 2020;10:1231. doi: 10.3390/met100
. [CrossRef] [Google Scholar]
8. Денг Д., Муракава Х. Численное моделирование температурного поля и остаточных напряжений в многопроходных сварных швах труб из нержавеющей стали и сравнение с экспериментальными измерениями. вычисл. Матер. науч. 2006; 37: 269–277. doi: 10.1016/j.commatsci.2005.07.007. [Перекрестная ссылка] [Академия Google]
9. Baek J., Jang Y., Kim I., Yoo J., Kim C., Kim J. Влияние сварочных процессов и конфигурации сварного шва на усталостное разрушение патрубка природного газа. Междунар. Дж. Прес. Весь. Пип. 2021;193:104474. doi: 10.1016/j.ijpvp.2021.104474. [CrossRef] [Google Scholar]
10. Чой Ю.Х., Чой С.Ю. Целостность раструбных сварных швов ядерных трубопроводов в условиях усталостного нагружения. Нукл. англ. Дес. 2007; 237: 213–218. doi: 10.1016/j.nucengdes.2006.06.005. [CrossRef] [Google Scholar]
11. Oh C.Y., Lee J.H., Kim D.W., Lee S.H. Экспериментальная оценка усталостной прочности раструбных сварных соединений малого диаметра в условиях вибрационного нагружения. Нукл. англ. Технол. 2021;53:3837–3851. doi: 10.1016/j.net.2021.05.036. [Перекрестная ссылка] [Академия Google]
12. Алиан А.Р., Шазлы М., Мегахед М.М. 3D конечно-элементное моделирование ремонтной сварки газопроводов в процессе эксплуатации. Междунар. Дж. Прес. Весь. Пип. 2019;146:216–229. doi: 10.1016/j.ijpvp.2016.09.002. [CrossRef] [Google Scholar]
13. Ли Д. М., Ким С. Дж., Ли Х. Дж., Ким Ю. Дж. Оценка усталостной долговечности раструбной сварной трубы с дефектом неполного провара: I-тест и анализ КЭ. Нукл. англ. Технол. 2021; 53: 3852–3859. doi: 10.1016/j.net.2021.05.033. [CrossRef] [Академия Google]
14. Комизо Ю. Обзор новейших технологий сварки при строительстве трубопроводов. Транс JWRI. 2008; 37:1–5. [Google Scholar]
15. Riffel K.C., Silva R.H.G., Dalpiaz G., Marques C., Schwedersky M.B. GTAW с замочной скважиной и динамической подачей проволоки применяется для орбитальной сварки труб из нержавеющей стали 304L. Soldagem Inspeçã 2019; 24:18. doi: 10.1590/0104-9224/si24.18. [CrossRef] [Google Scholar]
16. Акбари Д., Саттари-Фар И. Влияние погонной энергии сварки на остаточные напряжения в стыковых швах разнородных трубных соединений. Междунар. Дж. Прес. Весь. Пип. 2009 г.;86:769–776. doi: 10.1016/j.ijpvp.2009.07.005. [CrossRef] [Google Scholar]
17. Обейд О., Альфано Г., Бахай Х., Джухара Х. Параметрическое исследование полей термических и остаточных напряжений при сварке футерованных труб. Терм. науч. англ. прог. 2017;4:205–218. doi: 10.1016/j.tsep.2017.10.011. [CrossRef] [Google Scholar]
18. Xu J., Jia X., Fan Y., Liu A., Zhang C. Анализ остаточных напряжений при моделировании сварки труб: трехмерная труба в сравнении с осесимметричными моделями. Procedia Mater. науч. 2014;3:511–516. doi: 10.1016/j.mspro.2014.06.085. [Перекрестная ссылка] [Академия Google]
19. Сатернус З., Пекарска В., Кубяк М., Доманьски Т. Влияние наклона сварочного источника тепла на форму зоны расплава, деформации и напряженное состояние тройников, сваренных лазером. Материалы. 2021;14:5303. дои: 10.3390/ma14185303. [Бесплатная статья PMC] [PubMed] [CrossRef] [Google Scholar]
20. Хенгеш Дж. В., Энджелл М., Леттис В. Р., Баххубер Дж. Л. Системный подход к снижению геологических опасностей при проектировании и строительстве трубопроводов; Материалы Международной конференции по трубопроводам; Калгари, AB, Канада. 4–8 октября 2004 г .; стр. 2567–2576. МПК2004-0147. [Перекрестная ссылка] [Академия Google]
21. Ашрафи Х., Вассеги А., Хоссейни М., Базли М. Разработка функций хрупкости для газопроводов на границе якорных блоков. англ. Структура 2019;186:216–226. doi: 10.1016/j.engstruct.2019.02.020. [CrossRef] [Google Scholar]
22. Асади П., Алимохаммади С., Кохантораби О., Фазли А., Акбари М. Влияние типа материала, предварительного нагрева и числа проходов на остаточное напряжение сварных стальных труб при многократных сварках. проходная сварка TIG (C-Mn, SUS304, SUS316) Терм. науч. англ. прог. 2020;16:100462. doi: 10.1016/j.tsep.2019.100462. [CrossRef] [Google Scholar]
23. Варма Прасад В.М., Джой Варгезе В.М., Суреш М.Р., Сива Кумар Д. Трехмерное моделирование остаточных напряжений, возникающих при сварке труб из нержавеющей стали методом TIG. Процессия Технол. 2016; 24:364–371. doi: 10.1016/j.protcy.2016.05.049. [CrossRef] [Google Scholar]
24. Ариф А.Ф.М., Аль-Омари А.С., Йилбас Б.С., Аль-Нассар Ю.Н. Анализ термических напряжений спиральной лазерно-сварной трубы. Дж. Матер. Процесс. Тех. 2011;211:675–687. doi: 10.1016/j.jmatprotec.2010.12.002. [Перекрестная ссылка] [Академия Google]
25. Афзаал Малик М., Эджаз Куреши М., Наим Уллах Д., Икбал К. Анализ тонкостенных цилиндров с дуговой сваркой по окружности для исследования полей остаточных напряжений. J. Тонкостенная конструкция. 2008;46:1391–1401. doi: 10.1016/j.tws.2008.03.011. [CrossRef] [Google Scholar]
26. Yaghi A., Hyde T.H., Becker A.A., Sun W., Williams J.A. Моделирование остаточных напряжений в сварных швах тонкостенных и толстостенных труб из нержавеющей стали с учетом влияния диаметра трубы. Междунар. Дж. Прес. Весь. Пип. 2006; 83: 864–874. doi: 10.1016/j.ijpvp.2006.08.014. [Перекрестная ссылка] [Академия Google]
27. Сюй С., Ван В., Чанг Ю. Использование МКЭ для прогнозирования остаточных напряжений в кольцевом сварном соединении многослойных цилиндрических сосудов. Междунар. Дж. Пресс. Судно. Пип. 2014; 119:1–7. doi: 10.1016/j.ijpvp.2014.02.002. [CrossRef] [Google Scholar]
28. Górka J., Stano S. Микроструктура и свойства гибридных лазерно-дуговых сварных соединений (Laser Beam-MAG) при термомеханическом контроле обработанной стали S700MC. Металлы. 2018;8:132. doi: 10.3390/met8020132. [CrossRef] [Google Scholar]
29. Сапиета М., Сапиетова А. , Декис В. Сравнение выражений термоупругих явлений в нержавеющих сталях при циклическом нагружении. Металлургия. 2017;56:203–206. [Академия Google]
30. Валенса К., Малужда И., Таласка К., Вильчински Д. Анализ процесса сварки приводных ремней горячей пластиной. Акта Мех. Эт автомат. 2020;14:84–90. [Google Scholar]
31. Hu X., Yang Y., Song M. Экспериментальные и численные исследования термомеханического поведения сварного соединения композитной пластины из нержавеющей стали 304/Q345R. Материалы. 2019;12:3489. doi: 10.3390/ma12213489. [PMC free article] [PubMed] [CrossRef] [Google Scholar]
32. Джафарзадеган М., Тагиабади Р., Мофид М.А. Использование модели двойного эллипсоида источника тепла для прогнозирования роста зерен ЗТВ в GTAW нержавеющей стали 304. Матер. Сегодня коммун. 2022;31:103411. doi: 10.1016/j.mtcomm.2022.103411. [Перекрестная ссылка] [Академия Google]
33. Сатернус З., Пекарска В. Численный анализ термомеханических явлений при лазерной сварке плоских труб. Procedia англ. 2017; 177:196–203. doi: 10.1016/j.proeng.2017.02.220. [CrossRef] [Google Scholar]
34. Chu T.C., Ranson W.F., Sutton M.A., Peters W.H. Применение методов цифровой корреляции изображений к экспериментальной механике. Эксп. мех. 1985; 25: 232–244. doi: 10.1007/BF02325092. [CrossRef] [Google Scholar]
35. Кубяк М., Доманьски Т., Декиш В., Сапиетова А. Измерение деформации при испытании сварного соединения на растяжение с использованием многокамерной трехмерной корреляционной системы. Procedia англ. 2017; 177:107–113. doi: 10.1016/j.proeng.2017.02.197. [CrossRef] [Google Scholar]
36. Dan X., Li J., Zhao Q., Sun F., Wang Y., Yang L. Корреляция многоракурсных цифровых изображений на основе кросс-дихроичной призмы Система. заявл. науч. 2019;9:673. doi: 10.3390/app
73. [CrossRef] [Google Scholar]
37. Сиберт Т., Ван В., Моттерсхед Дж. Э., Пипино А. Применение высокоскоростной корреляции изображений для измерения форм колебаний капота автомобиля. заявл. мех. Матер. 2011;70:45–50. doi: 10.4028/www.scientific.net/AMM.70.45. [Перекрестная ссылка] [Академия Google]
38. Требуня Ф., Хуняди Р., Бобовский З., Хагара М. Результаты и опыт применения цифровой корреляции изображений в операционном модальном анализе. Акта Политех. Венгрия. 2013;10:159–174. [Google Scholar]
39. Фэн Л.-Дж., У Л.-З., Ю Г.-Ц. Оптимальное количество слоев сэндвич-колонн с многослойным пирамидальным сердечником при сжатии в плоскости. Теор. Приложение. мех. лат. 2016; 6: 65–68. doi: 10.1016/j.taml.2016.01.002. [CrossRef] [Google Scholar]
40. Войтковяк Д., Таласка К., Вильчински Д. Оценка эффективности процесса ленточной штамповки на основе силы сопротивления сжимаемого материала. Междунар. Дж. Адв. Произв. Технол. 2020;110:717–727. дои: 10.1007/s00170-020-05819-4. [CrossRef] [Google Scholar]
41. Доуден Дж. М. Математика теплового моделирования. Группа Тейлор и Фрэнсис; Нью-Йорк, штат Нью-Йорк, США: 2001. [Google Scholar]
42. Система Dassault. Руководство по теории Abaqus. Система Дассо; Велизи-Вилакубле, Франция: 2007 г. Версия 6.7, SIMULIA. [Google Scholar]
43. Корич С., Томас Б. Термомеханическая модель процессов затвердевания с помощью ABAQUS; Материалы конференции пользователей Abaqus; Париж, Франция. 22–24 мая 2007 г. [Google Scholar]
44. Гафури М., Ан Дж., Моуруярви Дж., Бьорк Т., Ларкиола Дж. Моделирование методом конечных элементов сварочных деформаций в сверхвысокопрочной стали S960 MC, включая комплексные модели термического и твердотельного фазового превращения. англ. Структура 2020;219:110804. doi: 10.1016/j.engstruct.2020.110804. [CrossRef] [Google Scholar]
45. Xu G., Wu C., Ma X., Wang X. Численный анализ сварочных остаточных напряжений и деформации при гибридной сварке Т-образного соединения из алюминиевого сплава лазером + GMAW. Акта Металл. Грех. англ. лат. 2013;26:352–360. дои: 10.1007/s40195-012-0166-5. [CrossRef] [Google Scholar]
46. Голдак Дж.А. Вычислительная механика сварки.