Технология радиографического контроля armtorg.ru
Усиливающие экраны. Из рис. 2.34 видно, что применение металлических экранов обеспечивает некоторое повышение чувствительности, обусловленное уменьшением воздействия вторичного излучения, источником которого является сам контролируемый материал. Рассеянное вторичное излучение уменьшает резкость и контрастность изображения объекта. Рассеянное излучение от тяжелых элементов, подобных свинцу, сравнительно невелико, они выполняют роль своеобразного фильтра, особенно для первичного излучения низких энергий.Тип пленки. В зависимости от типа пленки, обусловленного размером зерна и реакцией к излучению, чувствительность радиографического контроля при прочих равных условиях (энергий излучения, рода и толщины материала) может изменяться от 0,5% (РТ-5) до 3% (РТ). Пленки, обеспечивающие лучшую чувствительность, имеют мелкозернистую структуру и слабую реакцию к излучению, но требуют большего времени для просвечивания.
С учетом изложенных факторов, влияющих на чувствительность контроля, кратко рассмотрим операции радиографического контроля на примере сварных соединений.
При радиографировании изделий соблюдают такую последовательность выполнения основных операций. Выбирают источник излучения, радиографическую пленку и определяют оптимальные режимы просвечивания, просвечивают объект, производят фотообработку снимков и их расшифровку, оформляют результаты контроля.
Выбор источника излучения обусловливается технической целесообразностью и экономической эффективностью. Основными факторами, определяющими выбор источника, являются заданная чувствительность, плотность и толщина материала контролируемого изделия, производительность контроля, конфигурация контролируемой детали, доступность ее для контроля и др.
Например, при контроле изделий, в которых допускаются дефекты большого размера, наиболее целесообразно применять изотопы с высокой энергией, обеспечивающие малое время просвечивания. Для изделий ответственного назначения используют рентгеновское излучение и только как исключение — изотопы, имеющие по возможности наименьшую энергию излучения, например 1г (табл. 2.8).
Выбор радиографической пленки осуществляется по толщине и плотности материала просвечиваемого объекта, а также по требуемой производительности и заданной чувствительности контроля.
Пленку РТ-1 используют, главным образом, для контроля сварных соединений больших толщин, так как она обладает высокой контрастностью и чувствительностью к излучению. Универсальную экранную пленку РТ-2 применяют при просвечивании деталей различной толщины, при этом время просвечивания по сравнению с другими типами пленок наименьшее. Для контроля изделий из алюминиевых сплавов и сплавов черных металлов небольшой толщины можно использовать высококонтрастную пленку РТ-3 и РТ-4.
При дефектоскопии ответственных соединений применяют пленку РТ-5. Эта пленка обладает весьма высокой контрастностью, позволяет выявлять незначительные дефекты, хотя и имеет наименьшую чувствительность к излучению, что приводит к увеличению времени экспозиции при контроле. Ориентировочно выбор радиографической пленки целесообразно производить пономограммам (рис. 2.35).
Для контроля сварных соединений различных типов выбирают одну из схем просвечивания, приведенных на рис. 2.36. Стыковые односторонние соединения без разделки кромок, а также с V-образной разделкой просвечивают, как правило, по нормали к плоскости свариваемых элементов (рис. 2.36, схема 1).
Швы, выполненные двусторонней сваркой с К-образной разделкой кромок, наиболее целесообразно просвечивать по схеме 2 с применением в ряде случаев двух экспозиций. В этом случае направление центрального луча должно совпадать с линией разделки кромок. Допускается просвечивать эти швы также и по схеме 1 .
При контроле швов нахлесточных, угловых и тавровых соединений центральный луч направляют, как правило, под углом 45° к плоскости листа (схемы 3, 4, 5, 6, 7, 8). Трубы большого диаметра (>200 мм) просвечивают через одну стенку, а источник излучения устанавливают снаружи или внутри изделий с направлением оси рабочего пучка перпендикулярно шву (схемы 9, 11). (Ф1и+\) (S+H), где 5 — толщина сварного соединения в направлении просвечивания, мм; Н — расстояние от пленки до обращенной к пленке поверхности — изделия. Обычно фокусное расстояние выбирают в диапазоне от 300 до 750 мм.
Время экспозиции и длина контролируемого за одну экспозицию участка при контроле по приведенным выше схемам должны быть такими, чтобы: плотность почернения изображения контролируемого участка шва, околошовной зоны и эталонов чувствительности была не менее 1,0 и не более 3,0 единиц оптической плотности; уменьшение плотности почернения любого участка сварного шва на снимке по сравнению с плотностью почернения в месте, установки эталона чувствительности было не более 0,4 — 0,6 единиц оптической плотности в зависимости от коэффициента контрастности пленки, но нигде плотность почернения не должна быть менее 1,5 единиц; искажение изображения дефектов на краях снимка по отношений) к изображениям их в его центре не превышало 10% для прямолинейных и 25% для криволинейных участков, и Обычно длина прямолинейных и близких к прямолинейным участков, контролируемых за одну экспозицию, должна быть не более /^0,8/, где / — расстояние от источника излучения до поверхности контролируемого участка.
Блог о контроле качества металла
Содержание | Блог о контроле качества металла Перейти к содержимомуПо рубрикам:
Контроль сварных швов (111) ↑
- 2020/05/24 Расшифровка радиографических снимков (Часть 3)
- 2020/05/03 Расшифровка радиографических снимков (Часть 2).
- 2018/11/03 Определение понятия технологические свойства и требования к ним. Технико-экономические показатели источников питания. Критерий выбора источников питания для сварки.
- 2018/04/09 Количество металла, испаряющегося с катодного пятна (Часть 2).
- 2017/06/30 Классификационные признаки источника питания. Распределение потенциала в дуге. Свойства сварочной дуги (Часть 1).
- 2017/06/21 Контроль на отсутствие дефектов в сварных швах (Часть 3).
- 2017/06/09 Контроль на отсутствие дефектов в сварных швах (Часть 2).
- 2017/05/29 Зависимость энергии ионизации атомов от температуры плазмы (Часть 2).
- 2017/05/24 Остатки сварочной проволоки в сварном шве.
- 2017/05/12 Зависимость энергии ионизации атомов от температуры плазмы (Часть 1).
- 2017/04/28 Распределение плотности тока, температуры и скорости газовых потоков в реальной сварочной дуге (Часть 3).
- 2017/04/26 Несплавление между слоями.
- 2017/04/14 Распределение плотности тока, температуры и скорости газовых потоков в реальной сварочной дуге (Часть 2).
- 2017/04/12 Непровар по кромке.
- 2017/04/03 Распределение плотности тока, температуры и скорости газовых потоков в реальной сварочной дуге (Часть 1).
- 2017/03/17 Деление столба реальной сварочной дуги на две части (Часть 2).
- 2017/03/01 Деление столба реальной сварочной дуги на две части (Часть 1).
- 2017/02/03 Методы оценки склонности металла шва к образованию горячих трещин (Часть 2).
- 2017/01/27 Методы оценки склонности металла шва к образованию горячих трещин (Часть 1).
- 2017/01/18 Поры в сварном шве (Часть 2).
- 2017/01/09 Методы оценки стойкости сварных соединений против холодных трещин (Часть 2).
- 2016/12/28 Поры в сварном шве (Часть 1).
- 2016/12/09 Непровар корня сварного шва.
- 2016/12/07 Методы оценки технологической прочности материалов.
- 2016/12/03 Смешение облицовочного слоя в сварном шве.
- 2016/10/17 Радиографический контроль. Дефекты сварных швов. Дефектограмма №20.
- 2016/10/05 Непровар (Часть 2).
- 2016/09/28 Радиографический контроль. Дефекты сварных швов. Дефектограмма №19.
- 2016/09/26 Непровар (Часть 1).
- 2016/09/16 Радиографический контроль. Дефекты сварных швов. Дефектограмма №18.
- 2016/09/02 Радиографический контроль. Дефекты сварных швов. Дефектограмма №17.
- 2016/08/31 Вспомогательные знаки для швов с разделкой кромок.
- 2016/08/22 Сварка и сварные соединения. Факторы размера шва и высоты скоса кромок.
- 2016/08/17 Радиографический контроль. Дефекты сварных швов. Дефектограмма №16.
- 2016/08/10 Сварка и сварные соединения. Сварные швы с разделкой кромок (Часть 2).
- 2016/08/03 Сварка и сварные соединения.
Сварные швы с разделкой кромок (Часть 1).
- 2016/07/27 Методы определения дефектов сварных швов (Продолжение, часть 2).
- 2016/07/25 Радиографический контроль. Дефекты сварных швов. Дефектограмма №15.
- 2016/07/20 Сварка и сварные соединения. Вспомогательные знаки. Способы чистовой обработки. Условные обозначения монтажной сварки. Условные знаки сварных швов со сквозным проплавлением.
- 2016/07/17 С ДНЕМ МЕТАЛЛУРГА!
- 2016/07/13 Радиографический контроль. Дефекты сварных швов. Дефектограмма №14.
- 2016/07/11 Сварка и сварные соединения. Роликовый шов; подварочный шов и подкладной валик.
- 2016/07/04 Радиографический контроль. Дефекты сварных швов. Дефектограмма №13.
- 2016/07/01 Сварка и сварные соединения. Прорезные сварные швы.
- 2016/06/27 Радиографический контроль. Дефекты сварных швов. Дефектограмма №12.
- 2016/06/22 Сварка и сварные соединения. Пробочные и прорезные сварные швы.
- 2016/06/17 Радиографический контроль.
Дефекты сварных швов. Дефектограмма №11.
- 2016/06/15 Сварка и сварные соединения. Терминология описания размерных параметров шва
- 2016/06/08 Радиографический контроль. Дефекты сварных швов. Дефектограмма №10.
- 2016/06/06 Сварка и сварные соединения. Терминология описания наложения сварных швов.
- 2016/05/30 Металловедение. Дефекты кристаллов (продолжение, часть 2).
- 2016/05/27 Сварка и сварные соединения. Условные знаки вида шва и условные обозначения сварки (продолжение, часть 2).
- 2016/05/20 Радиографический контроль. Дефекты сварных швов. Дефектограмма №9.
- 2016/05/18 Сварка и сварные соединения. Условные знаки вида шва и условные обозначения сварки (продолжение, часть 1).
- 2016/05/09 Радиографический контроль. Дефекты сварных швов. Дефектограмма №8.
- 2016/05/06 Сварка сварные соединения. Условные знаки вида шва и условные обозначения сварки.
- 2016/04/25 Сварка и сварные соединения. Наплавка поверхности.
- 2016/04/20 Радиографический контроль.
Дефекты сварных швов. Дефектограмма №7.
- 2016/04/11 Сварка и сварные соединения. Законченные сваркой швы.
- 2016/04/06 Радиографический контроль. Дефекты сварных швов. Дефектограмма №6.
- 2016/03/30 Сварные соединения. Условные обозначения подкладок и проставок.
- 2016/03/23 Радиографический контроль. Дефекты сварных швов. Дефектограмма №5.
- 2016/03/18 Сварные соединения. Обозначения подварочного шва и подкладного валика.
- 2016/03/04 Радиографический контроль. Дефекты сварных швов. Дефектограмма №4.
- 2016/03/02 Виды сварных швов.
- 2016/02/22 Сварные соединения и наплавка.
- 2016/02/19 Радиографический контроль. Дефекты сварных швов. Дефектограмма №3.
- 2016/02/15 Сварка и сварные соединения.
- 2016/02/05 Радиографический контроль. Дефекты сварных швов. Дефектограмма №2.
- 2016/02/01 Виды сварных соединений.
- 2016/01/25 Радиографический контроль. Дефекты сварных швов и соединений. Дефектограмма №1.
- 2016/01/22 Сварка и сварные соединения.
- 2016/01/11 Термины, описывающие процессы сплавления и проплавления.
- 2015/12/28 Контактная сварка (RW).
- 2015/12/21 Угловые сварные швы.
- 2015/12/16 Виды сварных швов.
- 2015/12/09 Сварные соединения. Контроль качества.
- 2015/12/05 Покрытые сварочные электроды. Сварка ММА.
- 2015/11/19 Сущность процесса сварки ММА.
- 2015/11/11 Сварка стали в условиях окружающей температуры ниже нуля.
- 2015/10/18 Как изобреталась сварка.
- 2015/10/13 Воздействие газовых смесей на сварочный процесс.
- 2015/10/07 Особенности сварки алюминия.
- 2015/09/30 Сварка МИГ/МАГ — как влияет полярность тока на процесс.
- 2015/09/20 МИГ/МАГ — разновидности процесса сварки.
- 2015/09/14 Функции флюса сердечника порошковой проволоки.
- 2015/09/03 Сварка МИГ/МАГ порошковой проволокой
- 2015/08/25 Достоинства и недостатки сварки МИГ/МАГ
- 2015/08/01 Дефекты сварных швов.
Неравномерная ширина шва
- 2015/07/26 Контроль сварных соединений.
- 2015/07/22 Все о контроле сварных швов
- 2015/07/20 Спецификация процесса сварки (Welding Procedure Specification)
- 2015/07/16 Параметры режима сварки и влияние полярности тока на процесс сварки МИГ/МАГ
- 2015/06/22 Импульсный перенос электродного металла.
- 2015/04/09 Типы переноса металла при сварке МИГ/МАГ.
- 2015/03/09 Сущность процесса сварки МИГ/МАГ.
- 2015/03/02 Достоинства и недостатки процесса ручной сварки ТИГ
- 2015/02/17 Определение размеров включений в сварных швах и расстояний между ними.
- 2015/02/16 Сварка ТИГ. Блоки управления установками ТИГ.
- 2014/10/30 Положения сварки согласно EN 287, EN ISO 6947 и ASME IX
- 2014/07/24 Техника сварки ТИГ
- 2014/07/18 Основные международные обозначения, относящиеся к сварке ТИГ.
- 2014/07/14 Влияние полярности тока на процесс сварки ТИГ
- 2014/07/01 Сварка ТИГ (продолжение)
- 2014/06/19 Сущность процесса сварки ТИГ
- 2014/06/15 Присадочная проволока для сварки алюминия и его сплавов
- 2014/06/05 Присадочные материалы для сварки сталей.
- 2014/04/28 Дуговая сварка в защитных газах. Активные газы.
- 2014/04/24 Дуговая сварка в защитных газах
- 2014/04/11 Краткая информация о сварочных трансформаторах и сварочных выпрямителях
- 2014/04/08 Структура и характеристики электрической дуги
Металловедение и термическая обработка металлов (93) ↑
Начинающему техническому инспектору (235) ↑
Неразрушающий контроль (78) ↑
Новости металлургии (9) ↑
Технические инспекции (11) ↑
Информация:
Scroll Up
Автоматизация рентгеноскопических систем для контроля кольцевых сварных соединений магистральных трубопроводов
Автоматизация рентгеноскопических систем для контроля кольцевых сварных соединений магистральных трубопроводов
05.06.2012 / «Научно-технический и производственный журнал нефтегазового строительства, №2 за 2012 год»
Один из авторов статьи — Ксендзов Илья Дмитриевич — главный специалист отдела по контролю качества Дирекции по строительству ООО «СГМ»
Ф.
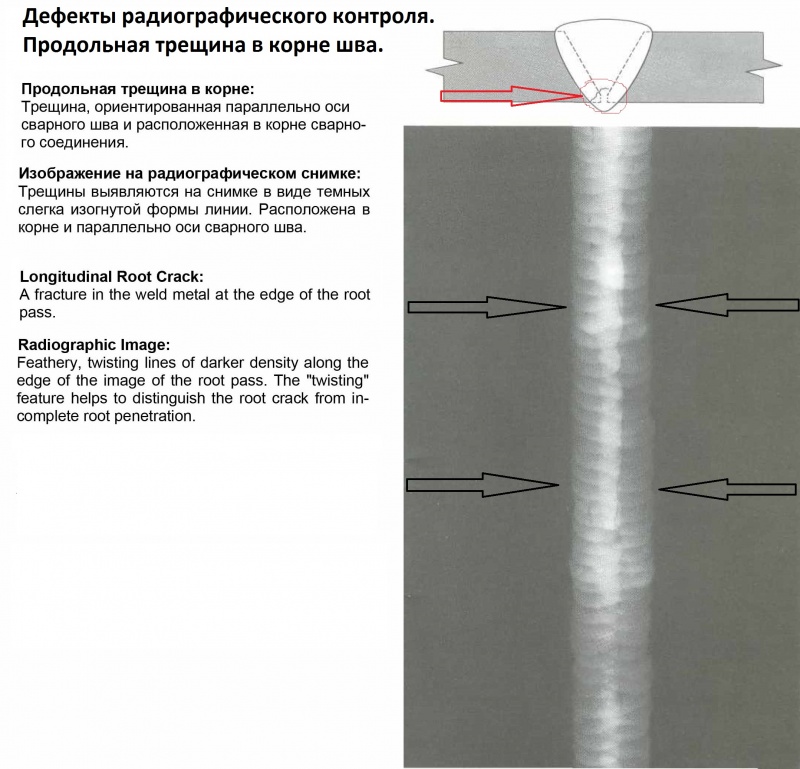
Повышение технического уровня сварочного производства во многом определяется развитием направления по неразрушающему контролю качества сварных соединений. В настоящее время при строительстве ремонте и реконструкции нефтегазопроводов используются в обязательном порядке визуальный и измерительный контроль для выявления поверхностных дефектов сварных соединений. Для обнаружения внутренних дефектов используют ультразвуковой и радиографический методы контроля, как раздельно, так и в дополнении друг друга.
Рисунок 1 — Схема радиографического контроля: 1 — источник излучения; 2 — объект контроля; 3 — детектор излучения; 4 — средства расшифровки и оценки результатов контроля.
Наибольшее применение в практике строительства нашел радиографический метод контроля, основанный на регистрации ионизирующего излучения (гамма или рентгеновского в зависимости от применяемого оборудования) после взаимодействия с контролируемым объектом и преобразовании его в радиографическое изображение или записи этого изображения на запоминающее устройство с последующим преобразованием в световое изображение (Рис.
Для регистрации результатов контроля используют специальную рентгеновскую пленку, в эмульсионном слое которой под действием ионизирующего излучения формируется скрытое изображение сварного соединения. Для его визуализации требуется специальная фотохимическая обработка, включающая проявление и фиксацию и некоторые промежуточные операции. После сушки снимки поступают на ручную расшифровку по результатам которой выдается заключение о годности/не годности сварного соединения.
Достоинствами этого метода является наглядность и возможность документирования его результатов, высокая чувствительность. К основным недостаткам следует отнести: низкая производительность, радиационная опасность поражения персонала, высокая стоимость работ, получение результатов контроля с большим отставанием от процесса сварки, ограниченный срок хранения результатов контроля на пленке, плохая чувствительность к плоскостным дефектам с расположением их плоскости более 35–40° от оси плоскости излучения.
До настоящего времени существовало два основных направления, устранения недостатков пленочной радиографии можно было разделить на две группы. Первое — применение многоразовых фосфорных (люминофорных) запоминающих пластин, в которых под действием ионизирующего излучения накапливается заряд, формируя, подобно рентгеновской пленке, скрытое изображение. Далее пластина загружается в сканер, который сканирует экспонированную пластину лазерным пучком, высвобождая наколенную энергию виде света. Этот свет собирается фотоприемником и конвертируется в цифровой сигнал, преобразуемый в цифровое изображение. Фосфорные пластины обладают большей чувствительностью, что позволяет уменьшить время экспозиции и дозовую нагрузку на персонал, однако высокая стоимость и чувствительность к механическим повреждениям не позволяет применять данные детекторы в трассовых условиях.
Другим направлением служило создание комплексов автоматической расшифровки радиографических изображений сварных соединений путём их сканирования. Данные комплексы позволяют решить задачи архивации радиографических снимков, а также поддерживает все основные операции расшифровки: поиска, определения размеров, классификации и оценки изображений дефектов, оценки наихудшего участка сварного соединения, оценки качества сварного соединения в целом, выпуска заключения о качестве сварного соединения (изделия). Применение данных комплексов упрощает архивацию и увеличивает объективность радиографических изображений, однако в месте с этим увеличивается время контроля за счет дополнительных операций.
В последнее время разработчиками оборудования уделяется большое внимание системам основанным на детекторах, позволяющих напрямую преобразовывать рентгеновское излучение в цифровое изображение (без использования расходных материалов). Данный метод контроля получил название цифровая радиометрия. Суть его заключается в измерении экспозиционной дозы или дозы излучения после взаимодействия с объектом контроля.
Рисунок 2. Схема регистрации рентгеновского излучения
Детектором для радиометрического контроля был выбран фотодиод с нанесенным на него слоем сцинтиллятора (Рисунок 2) . Рентгеновские кванты сначала взаимодействуют со сцинтиллятором, с образованием фотонов света, а затем свет преобразуется в электрический сигнал.
Радиометрический контроль относится к системам цифровой радиационной дефектоскопии. Отличием от радиографии является то, что радиометрия работает в режиме построчного сбора (сканирования), а не накопления информации.
В рамках исследовательской работы ОАО «Стройтрансгаз» и ООО «Нефтегазстройконтроль» была создана опытно-промышленная радиометрическая установка РМУ-1. В нее входят (Рисунок 3.):
- Блоки детектирования;
- Блок сбора и передачи информации;
- Бандаж c фиксирующей застежкой;
- Каретки перемещения блоков сбора и передачи информации;
- Механизм перемещения установки к сварным соединениям с шаговым двигателем;
- Транспортная тележка с аккумулятором и кабелем питания;
- Персональный компьютер;
- Кабель передачи информации от РМУ-1 к ПК;
- Рентгеновский аппарат РПД-250 с возможностью установки на кроулер;
- Маячок, сигнализирующий о наличии рентгеновского излучения;
Рисунок 3. Установка радиометрического контроля РМУ-1
Принципиальная схема проведения контроля представлена на рисунке 4. Источник рентгеновского излучения размещается по панорамной схеме просвечивания внутри трубы напротив контролируемого сварного шва. В качестве источника излучения для радиометрического контроля применяют рентгеновские аппараты только постоянного напряжения с отклонением не более 1% от номинальной величины напряжения; рентгеновские аппараты могут быть установлены на «кроулеры» (самоходные установки) или ручные тележки.
Рисунок 4. Схема просвечивания трубы с использованием РМУ-1
Для повышения производительности контроля радиометрическую РМУ-1 оснащают несколькими, параллельно работающими, детекторными блоками. Каждый детекторный блок считывает информацию со своего участка кольцевого сварного соединения. В установке в качестве рентгеночувствительных элементов были применены фотодиодные линейные массивы (128 пикселей на 0.4 мм).
Для точного позиционирования начала и конца участков сканирования в механизм перемещения включен шаговый двигатель, позволяющий точно устанавливать систему в начало просвечивания и возвращать ее в исходное положение автоматически.
При перемещении детекторов, изображение с них регистрируется в реальном времени с каждого датчика, что позволяет оператору отслеживать формирование снимка и оценивать параметры контроля.
Перемещая блоки детектирования относительно контролируемого сварного соединения, получаем непрерывно считываемый массив данных (Рисунок 5.). Этот массив записывается на жесткий диск для последующего более детального исследования и архивирования, а в обработанном виде выводится в виде полутонового изображения на монитор для оперативной оценки качества контролируемого участка в реальном времени.
Рисунок 5. Процесс контроля сварных соединений с применением РМУ-1
При сканировании сварного шва, оператор должен производить текущий просмотр результатов контроля на мониторе, установленном в кунге автолаборатории. При несоответствии фактических параметров контроля установленным требованиям (недостаточная чувствительность контроля, нестабильная и сомнительная идентификация дефектов сварки и т. д.) оператор должен произвести повторный контроль для получения результатов, соответствующих установленным требованиям.
Просмотр, расшифровка и оценка качества сварного соединения проводится по изображению контролируемого соединения на мониторе персонального компьютера с применением прикладных программ, которые позволяют улучшить изображение и провести его анализ (Рис. 6). Просмотр изображения контролируемого участка проводится в двух основных режимах:
В режиме «реального времени»(on line) — изображение выводится на монитор ПК одновременно с процессом считывания информации с контролируемых участков сварного соединения (четыре участка).
В режиме «стоп — кадр», когда записанная ранее информация считывается с жесткого носителя.
Рисунок 6. Изображение сварного шва на экране оператора
Скорость перемещения и масштаб изображения в режиме «стоп — кадр» регулируются с помощью специальных программ, работающих в диалоговом режиме. Привязкой для определения местоположения обнаруженных дефектов служит изображение мерного пояса, установленного на контролируемое сварное соединение.
Чувствительность контроля соответствует 2 классу по ГОСТ 7512. Ее значения зависят от скорости сканирования. При уменьшении скорости сканирования, чувствительность возрастает.
Машинное время контроля кольцевого сварного соединения труб 1420*12–25 мм. составляет не более 5 минут в зависимости от контролируемой толщины, а время перемещения от стыка к стыку (11 — 12 м.) не более 6 минут. Время подготовки к работе не превышает 10–15 минут.
В связи с появлением на рынке новых детекторов в рамках научно-исследовательской работы для ОАО «Газпром» в РГУ нефти и газа им. И. М. Губкина была проведена замена линейных детекторов на матричные массивы 100×50 мм с размером пикселя 100 мкм. Сравнительные данные характеритстик детекторов представлены в таблице 1.
Таблица 1. Сравнительные данные применяемых детекторов
Сравнивая изображения, полученные при применении матричного детектора (Рис. 7) следует обратить внимание на проволочные эталоны чувствительности по ГОСТ 7512: на изображенном слева снимке (фотодиодная линейка) сварного соединения просматриваются 4 индикатора-проволоки, что свидетельствуют о чувствительности 0,63 мм., а для изображения справа (матричный детектор) — 7 индикаторов-проволоки (чувствительность 0,32 мм.).
Рисунок 7 Сравнение изображений сварных соединений одинаковой толщины на диодную линейку (слева) и на матрицу (справа).
Была также проведена адаптация программного обеспечения аппаратно-программного комплекса «КАРС» (АПК «КАРС») для расшифровки изображений, получаемых с помощью радиометрии с применением матричных детекторов. Для подтверждения результатов повышения чувствительности проводился сравнительный анализ результатов автоматической расшифровки АПК «КАРС» изображений, полученных сканированием радиографических снимков (далее изображений радиографических снимков), и изображений, сформированных РМУ-1 (далее РМУ-изображений). Для этого были проконтролированы образцы сварных соединений толщиной стенки 13 мм с характерными дефектами, различного типа. Далее были изготовлены радиографические снимки этих образцов.
Затем после сканирования радиографических снимков были получены их изображения. Были также сформированы РМУ-изображения указанных образцов.
На рисунке 1 представлены соответственно фрагмент изображения радиографического снимка и фрагмент РМУ-изображения одного из образцов, на которых выделены контуры обнаруженных дефектов.
Рисунок. 7. Фрагмент изображения радиографического и радиометрического снимков
Следует отметить, что, с одной стороны, количество и расположение обнаруженных (выделенных на рис. 7) дефектов совпадает, с другой стороны, дефекты отличаются формой контуров и размерами.
Проводилось количественное сравнение результатов расшифровки изображений радиографических снимков и РМУ-изображений. В качестве примера, на рис. 3 и рис. 4 приведены таблицы с результатами поиска одиночных ИД, на фрагментах, изображения которых представлены соответственно на рисунках 8 и рисунках 9. Изображения всех образцов были расшифрованы. Затем были вычислены средние по множеству дефектов всех образцов относительные разности их соответствующих размеров. В результате вычислений было установлено, что средняя относительная разность трёх основных размеров (длина, ширина и глубина) не превышает 10%, а её предельные значения (отдельные выбросы) могут достигать 30%. Отличия в результатах расшифровки можно несколько уменьшить, если при получении изображений разными способами, во-первых, использовать один экземпляр эталона чувствительности контроля. Во-вторых, точно фиксировать его расположение на поверхности образца. Однако на практике выполнить эти условия было достаточно сложно, так как изображения были сформированы в разное время и в различных организациях.
Рис. 8. Результаты расшифровки фрагмента изображения радиографического снимка
Рис. 9. Результаты расшифровки фрагмента изображения, сформированного РМУ
На основании проведённого сравнительного анализа можно сделать вывод о том, что результаты расшифровки радиографических изображений образцов, которые (изображения) получены по разным технологиям на различном оборудовании, являются согласованными.
В настоящее время идут работы по конструктивному оформлению установки на новых детекторах. В перспективе ведется разработка установки, позволяющей контролировать сварные соединения по схеме «Черед две стенки» (при отсутствии внутреннего доступа к стыку).
Развитие цифровых радиометрических методов неразрушающего для непосредственного преобразования ионизирующего излучения в цифровое изображение является перспективным направлением в области рентгеноскопии сварных соединений. Применение радиометрических комплексов повысит производительность контроля, позволит значительно сократить затраты на расходные материалы и оборудование для фотохимической обработки, а также упростит архивацию результатов контроля.
Радиографический контроль – обзор
5.2.4 Радиографический контроль
Радиографический контроль (РТ) считается наиболее широко применяемым методом контроля. Расслоение как наиболее критическое и часто сообщаемое повреждение, которое испытывают композитные материалы FRP, часто приводит к повреждению воздушного кармана. Расслоение отчетливо выявляется только во время RT, при условии, что луч рентгеновского излучения и его ориентация не перпендикулярны друг другу. Существует множество типов рентгенографии с различными уникальными приложениями.Если детали не слишком тонкие или толстые, то лучше всего подходит традиционная RT. Когда детали тонкие, в диапазоне 1–5 мм, подходящим типом рентгенографии является рентгенография с низким напряжением. Гамма-лучи (γ-лучи) применяются для толстых деталей, поскольку они проникают через композиты и имеют более короткие длины волн. Другим типом рентгенографии, используемым специально для обнаружения расслоения и незначительных трещин матрицы образца FRP, является рентгенография с усилением пенетранта. Эти виды рентгенографии помогают обнаружить неравномерное распределение волокон, большие пустоты, трансламинарные трещины, включения, а также дезориентацию волокон.Дефекты/повреждения связаны с линиями сварки и складками волокон.
Кроме того, существует несколько типов методов рентгенографического контроля, каждый из которых имеет свое конкретное применение. Эти методы включают компьютерную рентгенографию, цифровую рентгенографию, пленочную рентгенографию и компьютерную томографию. Рентгеновскую компьютерную томографию (XCT) можно описать как неразрушающий метод исследования внутренней структуры твердых материалов/композитных образцов FRP, а также для получения в цифровом виде информации об их трехмерных (3D) характеристиках и свойствах. XCT имеет сравнительное преимущество по сравнению с проекционной радиологией благодаря 3D-микрофотографии образцов композита FRP, которые она предоставляет, т. е. проекционная радиология генерирует только 2-D изображение. Таким образом, данные XCT просты и легко читаемы. Его результаты также надежны, потому что XCT изменяет масштаб наблюдения с макроскопического на микроскопический. Более подробное обсуждение XCT можно найти в последующих подразделах.
Например, с помощью рентгеновского радиографического исследования с усилением пенетранта были определены механизмы местного повреждения и прочность болтовых соединений в композитных ламинатах из углеродного FRP с различной ориентацией (Atas and Soutis, 2013) (рис.5.6). Это было сделано в попытке уменьшить вызванное сверлением расслоение на просверленных отверстиях рассматриваемых образцов. Сообщалось о другом всестороннем исследовании, в ходе которого одновременно применялись три различных метода рентгеновской визуализации (микрокомпьютерная томография, компьютерная и цифровая рентгенография) для изучения наличия пустот в образце стеклопластикового композита (Rique et al. , 2015).
Рисунок 5.6. (i) Образец поврежденного болтового соединения [90°/45°/−45°/0] с, показывающий (ii) различные рентгенографические изображения повреждений, вызванных бурением, при предельной нагрузке: (a) поперечные трещины матрицы, (c ) расслоение, (б) 0° и (г) осевые расщепления ±45° соответственно (Atas and Soutis, 2013).
Неразрушающий контроль сварных швов
Азбука неразрушающего контроля сварных швовПерепечатано с разрешения журнала Welding Journal
Понимание преимуществ и недостатков каждой формы неразрушающего контроля может помочь вам выбрать лучший метод для вашего приложения.
Философия, которой часто руководствуются при изготовлении сварных узлов и конструкций, заключается в «обеспечении качества сварки». Однако понятие «качество сварки» относительно.Приложение определяет, что хорошо, а что плохо. Как правило, любой сварной шов имеет хорошее качество, если он соответствует требованиям к внешнему виду и будет продолжать выполнять работу, для которой он предназначен, в течение неопределенного времени. Первым шагом в обеспечении качества сварки является определение степени, требуемой приложением. Стандарт должен быть установлен на основе требований к обслуживанию.
Стандарты, разработанные для обеспечения качества сварки, могут различаться в зависимости от задания, но использование соответствующих методов сварки может гарантировать соблюдение применимых стандартов.Каким бы ни был стандарт качества, все сварные швы должны быть проверены, даже если проверка включает в себя не что иное, как контроль сварщиком своей работы после каждого прохода сварки. Хороший внешний вид поверхности сварного шва часто считается показателем высокого качества сварного шва. Однако внешний вид сам по себе не гарантирует хорошего качества изготовления или внутреннего качества.
Методы неразрушающего контроля (NDE) позволяют постоянно проверять соответствие стандартам путем изучения поверхности и подповерхности сварного шва и окружающего основного материала.Для контроля готовых сварных швов обычно используются пять основных методов: визуальный, проникающая жидкость, магнитопорошковый, ультразвуковой и радиографический (рентгеновский). Растущее использование компьютеризации с некоторыми методами обеспечивает дополнительное улучшение изображения и позволяет просматривать в реальном времени или почти в реальном времени, проводить сравнительные проверки и архивировать возможности. Обзор каждого метода поможет решить, какой процесс или комбинацию процессов использовать для конкретной работы и наиболее эффективно провести обследование.
Визуальный контроль (VT)
Визуальный контроль часто является наиболее экономичным методом, но он должен проводиться до, во время и после сварки.Многие стандарты требуют его использования перед другими методами, потому что нет смысла подвергать явно плохой сварной шов сложным методам контроля. В стандарте ANSI/AWS D1.1 «Сварка конструкций — сталь» говорится: «Сварные швы, подлежащие неразрушающему контролю, должны быть признаны приемлемыми при визуальном осмотре». Визуальный осмотр требует небольшого оборудования. Помимо хорошего зрения и достаточного освещения, все, что потребуется, — это карманная линейка, измеритель размера сварного шва, увеличительное стекло и, возможно, поверочная линейка и угольник для проверки прямолинейности, выравнивания и перпендикулярности.
Перед тем, как зажечь первую сварочную дугу, материалы должны быть проверены на соответствие требованиям по качеству, типу, размеру, чистоте и отсутствию дефектов. Жир, краска, масло, оксидная пленка или тяжелая окалина должны быть удалены. Соединяемые детали должны быть проверены на плоскостность, прямолинейность и точность размеров. Точно так же следует проверить выравнивание, подгонку и подготовку соединения. Наконец, следует проверить переменные процесса и процедуры, включая размер и тип электрода, настройки оборудования и условия для предварительного или последующего нагрева.Все эти меры предосторожности применяются независимо от используемого метода проверки.
Во время изготовления визуальный осмотр сварного шва и концевой лунки может выявить такие проблемы, как трещины, недостаточное проплавление и включения газа или шлака. Среди дефектов сварки, которые можно распознать визуально, можно выделить трещины, поверхностные шлаковые включения, поверхностную пористость и подрезы.
Для простых сварных швов может быть достаточно проверки в начале каждой операции и периодически по ходу работы.Однако при нанесении более чем одного слоя металлического наполнителя может быть желательным проверять каждый слой перед нанесением следующего. Корневой проход многопроходной сварки наиболее важен для надежности сварного шва. Он особенно подвержен растрескиванию, а поскольку он быстро затвердевает, он может задерживать газ и шлак. При последующих проходах условия, вызванные формой наплавленного валика или изменением конфигурации шва, могут вызвать дальнейшее растрескивание, а также подрезы и захваты шлака. Затраты на ремонт могут быть сведены к минимуму, если визуальный осмотр обнаружит эти дефекты до начала сварки.
Визуальный контроль на ранней стадии производства также может предотвратить недоварку и переварку. Сварные швы меньшего размера, чем указано в спецификациях, не допускаются. Слишком большие валики излишне увеличивают затраты и могут вызвать деформацию из-за дополнительной усадочной нагрузки.
После сварки визуальный осмотр позволяет выявить различные дефекты поверхности, включая трещины, пористость и незаполненные кратеры, независимо от последующих процедур контроля. Могут быть оценены отклонения в размерах, коробление и дефекты внешнего вида, а также характеристики размера сварного шва.
Перед проверкой поверхностных дефектов сварные швы должны быть очищены от шлака. Дробеструйную очистку не следует проводить перед осмотром, потому что наклеп может запечатать мелкие трещины и сделать их невидимыми. Например, Кодекс структурной сварки AWS D1.1 не разрешает упрочнение «корня или поверхностного слоя сварного шва или основного металла по краям сварного шва».
Визуальный осмотр позволяет обнаружить дефекты только на поверхности сварного шва. Спецификации или применимые нормы могут требовать, чтобы внутренняя часть сварного шва и прилегающие металлические зоны также были исследованы.Неразрушающий контроль может быть использован для определения наличия дефекта, но он не может измерить его влияние на пригодность изделия к эксплуатации, если только он не основан на корреляции между дефектом и какой-либо характеристикой, влияющей на срок службы. В противном случае разрушающие испытания являются единственным надежным способом определения работоспособности сварного шва.
Рентгенографический контроль
Рентгенография (рентген) является одним из наиболее важных, универсальных и широко распространенных методов неразрушающего контроля — Рис.1. Рентгенологическое исследование используется для определения внутренней прочности сварных швов. Термин «рентгеновское качество», широко используемый для обозначения высокого качества сварных швов, происходит от этого метода контроля.
Рентгенография основана на способности рентгеновских и гамма-лучей проходить через металл и другие материалы, непрозрачные для обычного света, и производить фотографические записи переданной лучистой энергии. Все материалы будут поглощать известное количество этой лучистой энергии, поэтому рентгеновские и гамма-лучи можно использовать для выявления разрывов и включений в непрозрачном материале.Постоянная видеозапись внутренних условий покажет основную информацию, по которой определяется надежность сварного шва.
Рентгеновские лучи производятся генераторами высокого напряжения. По мере увеличения высокого напряжения, подаваемого на рентгеновскую трубку, длина волны испускаемого рентгеновского излучения становится короче, что обеспечивает большую проникающую способность. Гамма-лучи образуются при распаде атомов радиоизотопов. Радиоактивными изотопами, наиболее широко используемыми в промышленной радиографии, являются кобальт 60 и иридий 192.Гамма-лучи, испускаемые этими изотопами, похожи на рентгеновские лучи, за исключением того, что их длина волны обычно короче. Это позволяет им проникать на большую глубину, чем рентгеновские лучи той же мощности, однако время воздействия значительно больше из-за большей интенсивности.
Когда рентгеновские или гамма-лучи направляются на участок сварного шва, не все лучи проходят через металл. Различные материалы, в зависимости от их плотности, толщины и атомного номера, будут поглощать лучистую энергию с различной длиной волны.
Степень, в которой различные материалы поглощают эти лучи, определяет интенсивность лучей, проникающих через материал. Когда записываются вариации этих лучей, становится доступным средство заглянуть внутрь материала. Изображение на проявленной фотосенсибилизированной пленке известно как рентгенограмма. Более толстые участки образца или материала с более высокой плотностью (включения вольфрама) будут поглощать больше излучения, и соответствующие им участки на рентгенограмме будут светлее — рис. 2.
Будь то в магазине или в полевых условиях, надежность и интерпретационная ценность рентгенографических изображений зависят от их резкости и контрастности.Способность наблюдателя обнаружить дефект зависит от резкости его изображения и контраста с фоном. Чтобы убедиться, что рентгенографическое облучение дает приемлемые результаты, на деталь помещают датчик, известный как индикатор качества изображения (IQI), чтобы его изображение было воспроизведено на рентгенограмме.
IQI, используемые для определения радиографического качества, также называются пенетраметрами. Стандартный пенетраметр с отверстиями представляет собой прямоугольный кусок металла с тремя просверленными отверстиями заданного диаметра. Толщина куска металла выражается в процентах от толщины рентгенографируемого образца. Диаметр каждого отверстия различен и кратен толщине пенетраметра. Пенетраметры проводного типа также широко используются, особенно за пределами США. Они состоят из нескольких отрезков проволоки разного диаметра. Чувствительность определяется наименьшим диаметром проволоки, который хорошо виден на рентгенограмме.
Пенетраметр не является индикатором или прибором для измерения размера несплошности или минимального обнаруживаемого размера дефекта.Это показатель качества рентгенографической техники.
Рентгенографические изображения не всегда легко интерпретировать. Следы от обработки пленки и полосы, туман и пятна, вызванные ошибками проявления, могут затруднить выявление дефектов. Такие артефакты пленки могут маскировать несплошности сварного шва.
Поверхностные дефекты будут видны на пленке и должны быть распознаны. Поскольку угол экспонирования также влияет на рентгенограмму, анализ угловых швов с помощью этого метода затруднен или невозможен. Поскольку рентгенограмма сжимает все дефекты, возникающие по всей толщине сварного шва, в одну плоскость, она имеет тенденцию создавать преувеличенное впечатление дефектов рассеянного типа, таких как пористость или включения.
Рентгеновское изображение внутренней части сварного шва можно просматривать на флуоресцентном экране, а также на проявленной пленке. Это позволяет проверять детали быстрее и с меньшими затратами, но разрешение изображения хуже. Компьютеризация позволила преодолеть многие недостатки рентгенографического изображения, связав флуоресцентный экран с видеокамерой.Вместо того, чтобы ждать проявления пленки, изображения можно просматривать в режиме реального времени. Это может повысить качество и снизить затраты на производственные операции, такие как сварка труб, где проблема может быть быстро выявлена и устранена.
Оцифровав изображение и загрузив его в компьютер, изображение можно улучшить и проанализировать до невиданной прежде степени. Можно накладывать несколько изображений. Значения пикселей можно регулировать для изменения оттенка и контраста, выявляя небольшие дефекты и неоднородности, которые не будут видны на пленке.Разным оттенкам серого можно назначить цвета, чтобы еще больше улучшить изображение и лучше выделить недостатки. Процесс оцифровки изображения, снятого с флуоресцентного экрана, после обработки этого изображения компьютером и передачи его на монитор для просмотра занимает всего несколько секунд. Однако из-за временной задержки мы больше не можем считать это «реальным временем». Это называется «радиоскопические изображения».
Существующие пленки можно оцифровать для достижения тех же результатов и улучшения процесса анализа.Еще одним преимуществом является возможность архивирования изображений на лазерных оптических дисках, которые занимают гораздо меньше места, чем хранилища старых фильмов, и их гораздо легче вызвать при необходимости.
Промышленная радиография, таким образом, представляет собой метод контроля, использующий рентгеновские и гамма-лучи в качестве проникающей среды и уплотненную пленку в качестве носителя записи для получения фотографической записи внутреннего качества. Как правило, дефекты сварных швов состоят либо из пустот в самом металле шва, либо из включений, плотность которых отличается от плотности окружающего металла шва.
Радиографическое оборудование производит излучение, которое в чрезмерных количествах может нанести вред тканям тела, поэтому необходимо строго соблюдать все меры предосторожности. Все инструкции должны быть тщательно соблюдены для достижения удовлетворительных результатов. Только персонал, прошедший обучение по радиационной безопасности и имеющий квалификацию промышленного рентгенолога, должен иметь право проводить рентгенографические испытания.
Магнитопорошковая дефектоскопия (МТ)
Магнитопорошковая дефектоскопия — это метод обнаружения и определения несплошностей в магнитных материалах.Он отлично подходит для обнаружения поверхностных дефектов сварных швов, в том числе несплошностей, которые слишком малы, чтобы их можно было увидеть невооруженным глазом, а также дефектов, расположенных чуть глубже поверхности.
Этот метод может использоваться для проверки кромок листов перед сваркой, контроля в процессе каждого прохода или слоя сварки, оценки после сварки и проверки
ремонтов — рис. 3.
Это хороший метод для обнаружения поверхностных трещин всех размеров как в сварном шве, так и в прилегающем основном металле, подповерхностных трещин, непроваров, подрезов и непроваров в сварном шве, а также дефектов на отремонтированных кромках основного металла.Хотя магнитопорошковая дефектоскопия не должна заменять радиографию или ультразвук для подповерхностных оценок, она может иметь преимущество перед их методами при обнаружении узких трещин и дефектов поверхности.
При этом методе щупы обычно размещают с каждой стороны обследуемой зоны, а через рабочее место между ними пропускают большую силу тока. Магнитный поток создается под прямым углом к потоку тока — рис. 3. Когда эти силовые линии сталкиваются с неоднородностью, такой как продольная трещина, они отклоняются и просачиваются через поверхность, создавая магнитные полюса или точки притяжения. Магнитный порошок, напыленный на поверхность, будет цепляться за место утечки более прочно, чем где-либо еще, формируя указание на несплошность.
Для развития этого признака разрыв должен быть расположен под углом к магнитным силовым линиям. Таким образом, когда ток проходит через заготовку в продольном направлении, будут видны только продольные дефекты. Помещение заготовки внутрь катушки соленоида создаст продольные силовые линии (рис. 3), из-за которых при нанесении магнитного порошка становятся видны поперечные и угловые трещины.
Несмотря на то, что магнитопорошковый метод гораздо проще в использовании, чем радиографический, он ограничен использованием ферромагнитных материалов и не может использоваться для аустенитных сталей. Соединение между основным металлом и сварным швом с различными магнитными характеристиками создаст магнитные неоднородности, которые могут быть ложно интерпретированы как ненадежные. С другой стороны, истинный дефект может быть скрыт порошком, налипшим на безвредный магнитный разрыв. Чувствительность уменьшается с размером дефекта, а также с круглыми трещинами, такими как газовые карманы.Это лучше всего подходит для удлиненных форм, таких как трещины, и ограничено поверхностными дефектами и некоторыми подповерхностными дефектами, в основном на более тонких материалах.
Поскольку поле должно быть искажено в достаточной степени, чтобы создать внешнюю утечку, необходимую для выявления дефектов, мелкие удлиненные несплошности, такие как микротрещины, швы или включения, параллельные магнитному полю, не будут видны. Их можно развивать, изменяя направление поля, причем поле желательно накладывать с двух направлений, желательно под прямым углом друг к другу.
Магнитные порошки можно наносить сухим или влажным способом. Метод сухого порошка популярен для проверки тяжелых сварных конструкций, а мокрый метод часто используется для проверки компонентов самолетов. Сухой порошок равномерно напыляют на работу с помощью пульверизатора, мешка для пыли или распылителя. Мелкодисперсные магнитные частицы имеют покрытие для повышения их подвижности и доступны в сером, черном и красном цветах для улучшения видимости. При мокром методе очень мелкие красные или черные частицы суспендируют в воде или легком нефтяном дистилляте.Это можно облить или распылить, или деталь можно окунуть в жидкость. Влажный метод более чувствителен, чем сухой, потому что он позволяет использовать более мелкие частицы, которые могут обнаруживать чрезвычайно мелкие дефекты. Флуоресцентные порошки могут быть использованы для повышения чувствительности и особенно полезны для обнаружения несплошностей в углах, шпоночных канавках, шлицах и глубоких отверстиях.
Капиллярная дефектоскопия (PT)
Поверхностные трещины и точечные отверстия, невидимые невооруженным глазом, могут быть обнаружены при помощи капиллярной дефектоскопии.Он широко используется для обнаружения утечек в сварных швах и может применяться к аустенитным сталям и цветным материалам, где магнитопорошковая дефектоскопия бесполезна.
Контроль проникающих жидкостей часто называют расширением метода визуального контроля. Многие стандарты, такие как AWS D.1. Кодекса говорится, что «сварные швы, подлежащие капиллярной дефектоскопии, должны оцениваться на основании требований к визуальному контролю».
Используются два типа проникающих жидкостей — флуоресцентный и видимый краситель.При флуоресцентном пенетрантном контроле на поверхность исследуемой детали наносится сильно флуоресцентная жидкость с хорошими проникающими свойствами. Капиллярный эффект втягивает жидкость в поверхностные отверстия, после чего излишки удаляются. «Проявитель» используется для нанесения пенетранта на поверхность, и полученный результат просматривается в ультрафиолетовом (черном) свете. Высокий контраст между флуоресцентным материалом и объектом позволяет обнаруживать мельчайшие следы пенетранта, указывающие на дефекты поверхности.
Проверка методом проникающих красителей аналогична, за исключением того, что используются ярко окрашенные красители, видимые при обычном освещении — рис. 4. Обычно с пенетрантами используется белый проявитель, который создает резко контрастирующий фон с ярким цветом красителя. Это обеспечивает большую мобильность за счет устранения необходимости в ультрафиолетовом свете.
Деталь, подлежащая осмотру, должна быть чистой и сухой, так как любое постороннее вещество может закрыть трещины или проколы и исключить пенетрант. Пенетранты можно наносить погружением, распылением или кистью, но должно пройти достаточно времени, чтобы жидкость полностью впиталась в несплошности.Это может занять час или больше при очень требовательной работе.
Контроль проникающей жидкости широко используется для обнаружения утечек. Обычная процедура заключается в нанесении флуоресцентного материала на одну сторону сустава, ожидании достаточного времени для проявления капиллярного действия, а затем осмотре другой стороны в ультрафиолетовом свете. В тонкостенных сосудах этот метод выявит течи, которые обычно не обнаруживаются при обычном испытании воздухом при давлении 5–20 фунтов/дюйм2. Однако, когда толщина стенки превышает 10 дюйма, чувствительность испытания на герметичность снижается.
Ультразвуковой контроль (УЗК)
Ультразвуковой контроль — это метод обнаружения несплошностей путем направления высокочастотного звукового луча через опорную плиту и сварной шов по предсказуемой траектории. Когда траектория пластины звукового луча нарушает непрерывность материала, часть звука отражается обратно. Звук собирается прибором, усиливается и отображается в виде вертикального транса на видеоэкране — рис. 5.
Как поверхностные, так и подповерхностные дефекты в металлах могут быть обнаружены, локализованы и измерены с помощью ультразвукового контроля, включая дефекты, которые слишком малы, чтобы их можно было обнаружить другими методами.
Ультразвуковой блок содержит кристалл кварца или другого пьезоэлектрического материала, заключенный в преобразователь или зонд. При подаче напряжения кристалл быстро вибрирует. Когда ультразвуковой преобразователь прикладывается к проверяемому металлу, он передает механические колебания той же частоты, что и кристалл, через соединительный материал в основной металл и сварной шов. Эти колебательные волны распространяются по материалу до тех пор, пока не достигнут разрыва или изменения плотности.В этих точках часть колебательной энергии отражается обратно. Поскольку ток, вызывающий вибрацию, отключается и включается с частотой 60-1000 раз в секунду, кристалл кварца периодически действует как приемник, улавливающий отраженные вибрации. Они вызывают давление на кристалл и генерируют электрический ток. Поступая на видеоэкран, этот ток вызывает вертикальные отклонения горизонтальной базовой линии. Результирующий рисунок на поверхности трубки представляет собой отраженный сигнал и разрыв.Компактное портативное ультразвуковое оборудование доступно для осмотра в полевых условиях и обычно используется при проведении мостовых и строительных работ.
Ультразвуковой контроль менее подходит, чем другие методы неразрушающего контроля для определения пористости в сварных швах, потому что круглые газовые поры реагируют на ультразвуковые испытания как ряд точечных отражателей. Это приводит к низкоамплитудным откликам, которые легко спутать с «базовым шумом», присущим параметрам тестирования. Тем не менее, это предпочтительный метод испытаний для обнаружения несплошностей более гладкого типа и расслоения.
Портативное ультразвуковое оборудование доступно с цифровым управлением и микропроцессорным управлением. Эти приборы могут иметь встроенную память и обеспечивать распечатку или видеонаблюдение и запись. Они могут быть подключены к компьютерам, что позволяет проводить дальнейший анализ, документирование и архивирование, как и в случае рентгенографических данных. Ультразвуковое исследование требует экспертной интерпретации со стороны высококвалифицированного и хорошо обученного персонала.
Выбор Контроль качества
Хорошая программа контроля неразрушающего контроля должна учитывать присущие каждому процессу ограничения.Например, как рентгенография, так и ультразвук имеют различные ориентировочные факторы, которые могут определять выбор того, какой процесс использовать для конкретной работы. Их сильные и слабые стороны, как правило, дополняют друг друга. В то время как рентгенография не может надежно обнаружить дефекты, подобные расслоению, ультразвук делает это намного лучше. С другой стороны, ультразвук плохо подходит для обнаружения рассеянной пористости, тогда как рентгенография очень хороша.
Какие бы методы контроля ни использовались, соблюдение «пяти пунктов» качества сварного шва поможет свести последующий контроль к рутинной проверке.Затем правильное использование методов неразрушающего контроля послужит проверкой для поддержания переменных в соответствии и качества сварки в соответствии со стандартами.
Пять П:
1. Выбор процесса — Процесс должен быть правильным для работы.
2. Подготовка — t Конфигурация соединения должна быть правильной и совместимой с процессом сварки.
3. Процедуры — t Процедуры должны быть подробно описаны и неукоснительно соблюдаться во время сварки.
4. Предварительные испытания — f Для подтверждения того, что процесс и процедуры обеспечивают желаемый стандарт качества, следует использовать крупномасштабные макеты или смоделированные образцы.
5. Персонал — q На работу должны быть назначены квалифицированных специалистов.
Рентгенографический контроль (РТ) — обзор инсайдеров
Радиографический контроль (РТ) — это метод неразрушающего контроля (НК), используемый для исследования объема испытуемого образца и выявления несплошностей и дефектов, а также их расположения внутри испытуемого образца. В этом методе используются рентгеновские и гамма-лучи для получения изображения тестируемого материала. Изображение, называемое рентгенограммой, показывает любые изменения толщины, внутренние или внешние дефекты и другие заметные детали образца.
История рентгенографии
Рентгенографический контроль в основном использует пучок лучей для проверки качества материала. Рентген, первый в мире источник энергии для этого метода, был открыт в 1895 году немецким ученым по имени Вильгельм Конрад Рентген. Он впервые наблюдал флуоресцентное свечение своей электронно-лучевой трубки, которое может проходить сквозь плотную бумагу, отбрасывая тени от твердых предметов.
Это открытие привело к открытию другой формы проникающих лучей в 1896 году, когда французский ученый Анри Беккерель обнаружил естественную радиоактивность флуоресцентных минералов, а именно соединений урана.То же самое и с наблюдениями Рентгена: эти изображения материалов создаются, когда они помещаются между источником излучения и фотопленками. В 1898 году Мария и Пьер Кюри исследовали другие его работы, намереваясь открыть другие элементы, что привело к открытию радия. После этого он стал первым промышленным источником гамма-излучения. За этим последовало открытие искусственных источников гамма-излучения, таких как кобальт и иридий, которые были более сильными, но менее дорогими, чем радий.
Принцип и механизм радиографического контроля
В этом методе плотность материала и различия в толщине испытуемого образца определяют затухание или уменьшение обнаруживаемого проникающего излучения на другой стороне объекта, поскольку происходит поглощение или рассеяние лучей.
Образец для испытаний помещается между источником излучения и пленкой или детектором (см. рисунок ниже). Пучок лучей (рентгеновских или гамма-лучей) испускается и проникает сквозь материал.
Общий процесс радиографического контроля (вид установки сверху и рентгенограмма спереди)
Если луч сталкивается с дефектом, который обычно имеет меньшую плотность, чем основной материал, то через область проходит больше ожидаемого количества излучения, которое затем регистрируется на рентгенографической пленке, расположенной на противоположной стороне тестовый образец.Эта область на пленке будет темнее, что указывает на то, что через тестируемый материал прошло больше излучения. Различные степени от черного до белого, называемые плотностью пленки, указывают на интенсивность проникновения луча. Затем сертифицированные инспекторы могут легко интерпретировать полученную рентгенограмму, а также идентифицировать и локализовать неоднородности и дефекты в материале.
Рентген или гамма-излучение?
Метод радиографического контроля может использоваться для материалов толщиной от 6 до 230 миллиметров.Затем толщина испытуемого образца определяет тип источника излучения, который необходимо использовать в методе RT. Производство рентгеновских лучей требует более высоких энергий фотонов в диапазоне от 10 до 100 МэВ (мегаэлектронвольт). Таким образом, его предпочтительно использовать для материалов с более тонкими характеристиками и/или меньшей плотностью.
С другой стороны, большинству промышленных радиографических изотопов требуется только меньшая энергия для проникновения в материалы, поэтому они обычно используются для более толстых или плотных материалов. Иридий-192 с периодом полураспада 74 дня может проходить сквозь сталь толщиной 6–75 мм всего за 0,31–0,60 МэВ; Цезий-137 с периодом полураспада 30,1 года может проникать в сталь толщиной 13–100 мм всего за 0,66 МэВ; наконец, кобальт-60 с периодом полураспада 5,3 года может проходить через сталь толщиной 19–230 мм всего за 1,17–1,33 МэВ.
Требования к радиографическому методу контроля
Метод радиографического исследования требует использования нескольких материалов, и его выполнение должно осуществляться с соблюдением мер предосторожности, поскольку радиация представляет опасность для здоровья при воздействии большого количества.Перед выполнением этого метода необходимо получить и отметить следующее:
- Руководства, такие как Национальный совет по радиационной защите и измерениям (NCRP) 147, 116 и 144, могут использоваться для обеспечения безопасности и предотвращения получения экспертами более высоких доз радиации, чем обычно.
- Области радиографического облучения должны быть очищены в первую очередь для получения данных и результатов без наложений.
- Фотолаборатории должны иметь возможность производить однородные рентгенограммы.Это поможет предотвратить появление пятен или артефактов на полученных изображениях, обеспечивая точную интерпретацию области.
- В зону обзора при съемке не должно попадать постороннее освещение, чтобы избежать отражения бликов от поверхности пленки. Пленки
- следует выбирать на основе уровня энергии источника излучения, толщины и конфигурации испытуемого образца, а также ожидаемого качества изображения. Требования к классу могут относиться к методу испытаний E1815 Американского общества по испытаниям и материалам (ASTM) (Стандартный метод испытаний для классификации пленочных систем для промышленной радиографии).
- Решения для обработки пленки используются для получения последовательных рентгенограмм. В отношении обработки пленки можно обращаться к Руководству ASTM E999 (Стандартное руководство по контролю качества обработки промышленных рентгенографических пленок).
- Источники излучения классифицируются и идентифицируются по соответствующим уровням напряжения и тока рентгеновского излучения для рентгеновского излучения и типу изотопов для гамма-излучения, которые основаны на типе материала и толщине испытуемого образца, а также на длине контакт.
- Усиливающие экраны, такие как экраны из свинцовой фольги, флуоресцентные, фторметаллические и металлические экраны, необходимо выбирать в зависимости от требуемого диапазона напряжений и чувствительности пенетраметра.
- Другими необходимыми материалами являются непленочные носители записи (например, бумага и аналоговая лента), держатели для пленки и кассеты.
Типы и методы рентгенографического метода контроля
Радиографические методы контроля можно разделить на два (2) типа: обычная рентгенография и цифровая рентгенография .
C Обычная рентгенография фиксирует изображение исследуемой области с помощью высокочувствительной рентгенографической пленки, которая реагирует на излучение, испускаемое в процессе RT. Это оставляет постоянную запись исследования, но фильмы можно использовать только один раз, и для их обработки и интерпретации требуется некоторое время.
С другой стороны, цифровая рентгенография использует цифровой детектор вместо пленки для отображения рентгенографических изображений.Это делается мгновенно. Таким образом, он предлагает лучшее время выполнения заказа, чем обычная рентгенография. Изображения, полученные с помощью этого метода, имеют более высокое качество и могут четко отражать дефекты, чем предыдущий метод. Существует четыре (4) методики этого типа RT:
- Компьютерная радиография использует люминофорную пластину вместо пленки. Однако отраженное изображение на люминофорной пластине передается в виде цифрового сигнала, который затем можно просмотреть на экране компьютера.Это намного быстрее, чем обычная рентгенография, но самая медленная среди методов цифровой рентгенографии.
- Подобно компьютерной рентгенографии, прямая рентгенография также использует плоскую панель, которая обнаруживает изображение. Однако это происходит почти мгновенно, поскольку изображение захватывается напрямую, а затем сразу же отображается на экране компьютера.
- Рентгенография в реальном времени позволяет получать мгновенные рентгенографические изображения, которые создаются при взаимодействии испускаемого излучения с люминофорным экраном или панельным детектором.Эти лучи создают цифровое изображение, которое можно одновременно перемещать и анализировать. Однако изображение, полученное с помощью этого метода, имеет низкий контраст и качество по сравнению с обычной рентгенографией.
- Компьютерная томография использует сотни тысяч двумерных отпечатков сканированного изображения, которые накладываются друг на друга для получения трехмерного рентгенографического изображения, которое можно легко изменить и проанализировать.
Для облегчения визуализации используется либо движущийся детектор со стационарным образцом, либо наоборот.Этот метод выгоден для образцов с небольшими и/или сложными конфигурациями. Это ограничивает человеческий фактор и, таким образом, обеспечивает более высокое качество изображения. Однако эти преимущества требуют более длительного времени рендеринга, являются дорогостоящими и требуют большего объема памяти для хранения данных.
Подробнее: Руководство по рентгенографическим пленкам и усиливающим экранам.
Общее использование радиографического контроля
Радиографический контроль — это подходящий метод неразрушающего контроля для обнаружения поверхностных и подповерхностных дефектов, таких как трещины, пористость, включения и пустоты в образце для испытаний.Это обычно используется при проверке качества отливок, поковок и сварных изделий.
Преимущества и недостатки радиографического контроля
Особенности метода тестирования ВУ следующие:
- RT можно использовать как с металлическими, так и с неметаллическими материалами.
- С помощью этого метода можно легко обнаружить поверхностные и подповерхностные дефекты.
- Он позволяет осуществлять контроль на объемном уровне, что означает, что он может оценивать внутреннюю часть испытуемого образца.
- Фотографические и визуальные графики могут быть сохранены и постоянно храниться в качестве протоколов испытаний для будущих справок.
Однако у этого метода есть и несколько недостатков, а именно:
- Для его выполнения требуется громоздкое и тяжелое оборудование. Однако новые технологии сделали возможным использование портативных систем в полевых условиях и на возвышенностях. Тем не менее, может быть компромисс в качестве изображения.
- Это оборудование также может быть дорогим из-за требований метода.
- Обе стороны образца должны быть легко доступны.
- Конфигурация материала (например, положение стыков, углов и т. д.) может повлиять на применимость метода, поскольку ориентация элемента может привести к множеству интерпретаций, как это отражено на изображении.
- Использование рентгеновских и гамма-лучей может представлять опасность для здоровья при более высоких дозах.
Каталожные номера:
- МакЭвили, А., 2013. Разрушения металлов: механизмы, анализ, предупреждение. Хобокен, Нью-Джерси: John Wiley & Sons, Inc.
- ASTM E1742 / E1742M-18, Стандартная практика рентгенографического исследования, ASTM International, West Conshohocken, PA, 2018.
Рентгенография – Служба инспекции RT
Радиографический контроль ( RT ) — это форма традиционного неразрушающего контроля ( NDT ), которая используется для проверки внутренней структуры активов в нефтегазовой, энергетической, обрабатывающей и аэрокосмической отраслях.
Радиографический контроль ( RT ) является чрезвычайно популярным методом контроля неразрушающего контроля ( NDT ) благодаря его универсальности в обнаружении широкого спектра дефектов на нескольких материалах и способности производить постоянную запись каждой проверки. .
Наш штат квалифицированных, сертифицированных профессиональных рентгенологов работает в строгом соответствии с параметрами безопасности. Мы производим высококачественные рентгенограммы, которые позволяют нам использовать наши навыки интерпретации, отточенные многолетним опытом, чтобы определить, действительно ли аномалия является дефектом или ее можно принять в соответствии с требованиями норм.
Радиографические испытания ( RT ) Применение для контроляMISTRAS оказывает услуги по инспекции RT в полевых условиях для нефтеперерабатывающих заводов, трубопроводов, атомных и ископаемых заводов и многих других промышленных клиентов. У нас также есть передовые возможности рентгенографии в наших собственных лабораториях для проверки новых компонентов для аэрокосмической, автомобильной и других производственных отраслей.
RT чувствительны к коррозии, изменениям толщины, пустотам, трещинам и изменениям плотности материала. MISTRAS проверяет на наличие этих повреждений широкий спектр крупных и мелких активов, в том числе:
- Трубопровод
- Трубопроводы
- Отливки
- Поковки
- Сварные швы
- Сосуды под давлением
- Клапаны
Рентгенография является распространенным методом проверки вновь построенных трубопроводов для обеспечения качества сварных швов. MISTRAS предоставляет опытных специалистов по инспекции для безопасного и экономичного проведения инспекций трубопроводов RT .
Мы проводим осмотр трубопроводов малого, среднего и большого диаметра, а также можем проводить оценку изолированных трубопроводов на наличие коррозии под изоляцией ( CUI ).
Наш парк трубопроводов включает в себя полностью автономные грузовики с переносными фотолабораториями, которые позволяют немедленно предоставлять нашим клиентам результаты инспекции, что позволяет им принимать незамедлительные меры в случае необходимости.
MISTRAS также предлагает запатентованные усовершенствованные услуги обхода трубопроводов с помощью цифровой радиографии (DR) для еще большей скорости проверки и лучшего понимания.
MISTRAS RT Технология и возможности контроляРентгенографический контроль можно проводить с использованием рентгеновского или гамма-излучения. Выбор источников излучения и их мощность зависят от множества факторов, включая размер компонента и толщину материала.
В обширной группе источников рентгеновского и гамма-излучения MISTRAS предлагает широкий выбор камер с различной интенсивностью излучения.
Рентгеновские возможностиMISTRAS варьируются от единиц 4 МэВ для рентгенографии очень больших или толстых отливок и поковок, до портативных рентгеновских камер, используемых для сварки в полевых условиях и контроля тонкостенных материалов.
Наши источники гамма-излучения включают в себя рентгеноскопические устройства очень низкого уровня для проведения исследований коррозии под изоляцией в режиме реального времени ( CUI ), источники иридия (Ir-192) и селена (Se-75), используемые для различных проверок сварных швов, к кобальту (Co 60) для испытаний толстых компонентов.
Рентгенография имеет много преимуществ, в том числе:
- Возможность контроля многих типов материалов с различной плотностью
- Возможность проверки собранных компонентов
- Требуется минимальная подготовка поверхности
- Определение роста трещин
- Обнаружение как поверхностных, так и подповерхностных дефектов
- Постоянная запись осмотра
Рентгенографический контроль (RT) | Инспекция
Радиографический контроль (RT) — это метод неразрушающего контроля (NDE) , который включает использование рентгеновских или гамма-лучей для просмотра внутренней структуры компонента.В нефтехимической промышленности RT часто используется для проверки оборудования, такого как сосудов под давлением и клапанов, для обнаружения дефектов. RT также используется для контроля ремонта сварных швов.
По сравнению с другими методами NDE рентгенография имеет ряд преимуществ. Он обладает высокой воспроизводимостью, может использоваться на различных материалах, а собранные данные могут быть сохранены для последующего анализа. Рентгенография является эффективным инструментом, требующим минимальной подготовки поверхности. Кроме того, многие рентгенографические системы являются портативными, что позволяет использовать их в полевых условиях и на возвышенности.
Виды рентгенографииСуществует множество типов методов RT, включая обычную рентгенографию и множественные цифровые рентгенографические исследования. Каждый из них работает немного по-разному и имеет свой набор преимуществ и недостатков.
Обычная рентгенография В традиционной рентгенографии используется чувствительная пленка, которая реагирует на испускаемое излучение для захвата изображения проверяемой детали. Затем это изображение можно проверить на наличие повреждений или дефектов.Самым большим ограничением этой техники является то, что пленки можно использовать только один раз, а их обработка и интерпретация занимают много времени.
В отличие от обычной рентгенографии, для цифровой рентгенографии не требуется пленка. Вместо этого он использует цифровой детектор для почти мгновенного отображения рентгенографических изображений на экране компьютера. Это позволяет использовать гораздо более короткое время экспозиции, чтобы изображения можно было интерпретировать быстрее. Кроме того, цифровые изображения имеют гораздо более высокое качество по сравнению с обычными рентгенографическими изображениями.Благодаря возможности получать изображения высокого качества, технологию можно использовать для выявления дефектов материала, посторонних предметов в системе, проверки ремонта сварных швов и проверки коррозии под изоляцией .
Четыре наиболее часто используемых метода цифровой рентгенографии в нефтегазовой и химической промышленности: компьютерная рентгенография, прямая рентгенография, рентгенография в реальном времени и компьютерная томография.
1) Компьютерная радиография
Компьютерная рентгенография (CR) использует люминофорную пластину, которая заменяет пленку в традиционных методах рентгенографии.Этот метод намного быстрее, чем пленочная рентгенография, но медленнее, чем прямая рентгенография. CR требует нескольких дополнительных шагов по сравнению с прямой рентгенографией. Сначала он косвенно фиксирует изображение компонента на люминофорной пластине, затем преобразует изображение в цифровой сигнал, который можно визуализировать на мониторе компьютера. Качество изображения удовлетворительное, но его можно улучшить с помощью соответствующих инструментов и методов (например, регулировка контрастности, яркости и т. д. без ущерба для целостности). Важно знать, как такие инструменты, как регулировка контрастности, влияют на изображение. Следует также позаботиться о том, чтобы незначительные дефекты не были скрыты после внесения улучшений.
2) Прямая рентгенография
Прямая рентгенография (DR) также является формой цифровой рентгенографии и очень похожа на компьютерную рентгенографию. Ключевое отличие заключается в том, как создается изображение. В DR плоскопанельный детектор используется для прямого захвата изображения и отображения этого изображения на экране компьютера. Хотя этот метод является быстрым и позволяет получать изображения более высокого качества, он более дорогостоящий, чем компьютерная рентгенография.
3) Рентгенография в режиме реального времени
Рентгенография в реальном времени (RTR), как следует из названия, представляет собой форму цифровой рентгенографии, которая выполняется в режиме реального времени. РТР работает, испуская излучение через объект. Затем эти лучи взаимодействуют либо со специальным люминофорным экраном, либо с плоскопанельным детектором, содержащим микроэлектронные датчики. Взаимодействие между панелью и излучением создает цифровое изображение, которое можно просматривать и анализировать в режиме реального времени.
Более яркие области изображения являются результатом более высоких уровней излучения, попадающего на экран.Это соответствует более тонкому или менее плотному участку компонента. И наоборот, более темные области являются результатом меньшего количества излучения, взаимодействующего с экраном, и указывают, где компонент толще.
Помимо возможности более быстрого доступа к изображениям и их анализа в режиме реального времени, RTR имеет ряд других преимуществ. Одним из них является то, что цифровые изображения не требуют физического места для хранения, и поэтому их легче хранить, передавать и архивировать, чем пленку.
С другой стороны, этот метод также имеет ряд недостатков.По сравнению с обычной рентгенографией РТР имеет более низкую контрастную чувствительность и ограниченное разрешение изображения. Изображения, созданные с помощью RTR, часто страдают неравномерным освещением, ограниченным разрешением, недостаточной резкостью и шумами. Эти факторы сильно влияют на качество изображения.
4) Компьютерная томография
Компьютерная томография (КТ) — это метод, который берет от сотен до тысяч (в зависимости от размера компонента) двухмерных рентгенографических изображений и накладывает их для создания трехмерного рентгенографического изображения.
В промышленных условиях КТ можно получить двумя способами. В одном методе проверяемый компонент остается неподвижным, в то время как источник излучения и детектор рентгеновского излучения вращаются вокруг компонента. Этот метод, скорее всего, будет использоваться для крупных компонентов. Второй метод состоит в том, что источник излучения и детектор рентгеновского излучения остаются неподвижными, в то время как компонент поворачивается на 360 градусов. Этот второй метод более полезен, когда компонент небольшой или имеет сложную геометрию.
Хотя эта технология является своевременной, дорогой и требует хранения большого объема данных, КТ обеспечивает высокоточные изображения, повторяемость и воспроизводимость и сводит к минимуму человеческий фактор.
Связанные темы
Тема Инструменты
Поделись этой темой
Вклад в определение
Мы приветствуем обновления этого определения Integripedia от Inspectioneering. сообщество.Нажмите на ссылку ниже, чтобы отправить любые рекомендуемые изменения для Inspectioneering. команда редакторов для проверки.
Вклад в определениеДефекты — [Документ в формате PDF]
Просмотр и интерпретация рентгенограмм
Страница 1 из 36
Просмотр и интерпретация рентгенограмм Указатель тем1. 2. 3. 4. 5. 6. 7. 8. 9. 10. 11. 12. 13. Назад к предметному указателю Введение Требования к проверке рентгенограмм Интерпретация несплошностей сварных швов Поверхностные несплошности сварных швов Внутренние несплошности сварных швов Интерпретация несплошностей литья Отчетность о несплошностях литья Резюме несоответствий Основные этапы интерпретации рентгенограммы Проверьте свой прогресс Ваша задача Глоссарий
Введение Заключительный этап рентгенографического контроля — это просмотр, интерпретация и отчет о результатах рентгенографического контроля.В конце концов, настоящая цель радиографического контроля состоит в том, чтобы предоставить информацию о приемлемости или неприемлемости тестируемого продукта. После выполнения этой задачи вы должны быть в состоянии:
настроить и проверить условия для правильного просмотра рентгенограммы; интерпретировать рентгенограммы сварных швов на наличие дефектов в соответствии с австралийскими стандартами; интерпретировать рентгенограммы отливок в соответствии с ASME и австралийскими стандартами. Наверх
Требования к проверке рентгенограмм
http://onlineshowcase.tafensw.edu.au/ndt/content/radiographic/task8/accessible.htm
04.05.2010
Просмотр и интерпретация рентгенограмм
Стр. 2 из 36
В средстве просмотра должен быть равномерно освещенный рассеивающий экран. что исследование рентгенограмм следует проводить при рассеянном свете в затемненном помещении. Большинство осветителей также имеют реостат, который позволяет регулировать яркость для получения рентгенограмм различной плотности. Кроме того, должна быть предусмотрена возможность маскировки наблюдателя, чтобы исключить попадание в глаза инспектора яркого прямого света.Осветитель для просмотра рентгенограмм (щелкните фото, чтобы увеличить)
Очень важным требованием является яркость устройства просмотра AS3998 требует, чтобы минимальная интенсивность света, проходящего через исследуемую рентгенограмму, составляла 30 кандел на квадратный метр (кд/м2). Для этого яркость средства просмотра должна быть не ниже указанной в следующей таблице: Минимальная яркость осветителя, необходимая для плотности рентгенограммы Плотность рентгенограммы Минимальная яркость осветителя (кд/м2) 1. 5 2,0 2,5 3,0 3,5 1000 3000 10000 30000 100000
Отсюда следует, что верхний предел плотности пленки определяется яркостью имеющегося осветителя. Вышеуказанные значения являются минимальной яркостью для просмотра пленки при интенсивности проходящего света 30 кд/м2. Стандарт предполагает, что 100 кд/м2 является более разумным значением. Яркость осветителя можно проверить с помощью фотометра, выполнив следующие действия:
http://onlineshowcase.tafensw.edu.au/ndt/content/radiographic/task8/accessible.htm
04.05.2010
Просмотр и интерпретация рентгенограмм
Стр. 3 из 36
1. 2. 3. 4.
Установите индикатор светочувствительности пленки до 100 ASA или 200 ASA Поместите чувствительный элемент измерителя близко к экрану осветителя. Запишите экспозицию в сотых долях секунды при настройке диафрагмы камеры f10, f14,3 или f20. Используйте приведенную ниже таблицу, чтобы соотнести время фотографической экспозиции. к яркости экрана.Фотографический измеритель яркости (щелкните фото, чтобы увеличить)
В следующей таблице представлена информация о взаимосвязи между яркостью экрана и показаниями экспозиции, полученными с использованием описанного выше метода. Соотношение между яркостью экрана и показаниями экспозиции f число Экспозиция (секунды) 10 10 10 14,3 14,3 14,3 20 20 20 20 20 1/100 1/500 1/1000 1/100 1/500 1/1000 1/100 1/500 1/1000 1/1500 1/2000 Яркость экрана (кд/м2) 100 ASA 1000 5000 10 000 10 000 10 000 20 000 3 000 15 000 30 000 45 000 60 000 200 ASA 200 000 10 000 в 400 000 4000 до 20 000 40 000 6 000 30 000 60 000
120 000
Этот осветитель должны использоваться в затемненной комнате
http: // onlineshowcase.tafensw.edu.au/ndt/content/radiographic/task8/accessible.htm
04.05.2010
Просмотр и интерпретация рентгенограмм
Стр. 4 из 36
Фонового освещения должно быть достаточно для записи Подробности в записи просмотра. Слишком яркое фоновое освещение может привести к отражениям от пленки, эффективно снижая контрастность и затрудняя интерпретацию. Кроме того, комната, используемая в качестве смотровой, должна быть тихой и удобной, чтобы избежать ненужных отвлекающих факторов.Рентгенограммы просматриваются через короткие промежутки времени. Эта практика используется, чтобы предотвратить напряжение глаз и максимально повысить уровень концентрации внимания. Хотя каждый интерпретатор будет отличаться, рекомендуется не более пяти минут тратить на просмотр рентгенограммы. Приступая к сеансу просмотра, переводчик должен дать достаточно времени своим глазам, чтобы привыкнуть к затемненным условиям. Рентгенограммы следует высушивать перед просмотром Промывочная вода на рентгенограмме оказывает значительное влияние на чувствительность и затрудняет обнаружение мелких несплошностей.Обязательно высушите рентгенограммы перед просмотром. Проверка качества рентгенограммы Перед тем, как приступить к надлежащему осмотру, рентгенограмму проверяют на обработку и обращение с артефактами и плотность пленки, а также определяют чувствительность IQI. Лицо, интерпретирующее рентгенограмму, должно быть уверено в том, что качество рентгенограммы адекватно и соответствует требованиям правил или спецификаций, чтобы можно было обнаружить соответствующие неоднородности.
Результаты этих предварительных проверок и измерений должны быть зафиксированы в акте осмотра.Оценка разрывов проводится методично. Вы должны сопротивляться искушению просто обнаружить дефект. Тщательное обследование достигается тщательным сканированием рентгенограммы с одной стороны на другую, концентрируя внимание на каждой области рентгенограммы при ее просмотре. Чтобы сделать это должным образом, переводчик должен понимать:
изделие, которое было подвергнуто рентгенографии, включая тип материала метод изготовления или литья тип несплошностей, которые могут возникнуть при получении рентгенограммы.
Другими очень важными критериями, которые переводчик должен четко понимать, являются критерии приемки/отбраковки проверяемой области или части. Эта информация обычно содержится в спецификациях или кодах, а иногда и в собственных спецификациях компонентов. Радиографическая интерпретация — это навык, которым можно овладеть только благодаря знанию тестируемого материала и опыту. Многие индикаторы дают слабоконтрастные или нечеткие изображения, которые трудно интерпретировать.Материальные знания и опыт являются наиболее важными. из 36
ценных пособий, которыми может воспользоваться переводчик. Вернуться к началу
Интерпретация несплошностей сварки Несплошности сварки обозначаются стандартными аббревиатурами Для описания большинства несплошностей сварки используется стандартный набор аббревиатур.Эти аббревиатуры перечислены в AS4749-2001 «Терминология неразрушающего контроля и аббревиатуры дефектов сварки плавлением, выявленные с помощью рентгенографии». Предоставляется описание каждой несплошности, а также отпечатки, сделанные с реальной рентгенограммы или эскиза для описания несплошности. Вам настоятельно рекомендуется получить копию этого стандарта от Standards Australia, если вы вообще связаны с рентгенографией сварных швов. Дефекты сварки бывают поверхностными или внутренними. Существует два класса дефектов сварного шва:
дефекты поверхности внутренние дефекты.
Стандартные сокращения для несплошностей сварного шва приведены в таблицах ниже. Сокращения для обозначения дефектов поверхности Несовершенство Чрезмерное проникновение Неполное заполнение канавки Подрез След шлифовки След молотка Точечная коррозия на поверхности Линейное смещение Впадина Вогнутость Усадочная канавка Чрезмерная правка След от инструмента Разорванная поверхность Брызги Код SXP SGI SUC SMG SMH SPT HiLo SRC SGS SED SMT STS SSP Аббревиатуры внутренних дефектов Несовершенство Продольная трещина Кратерная трещина Непроплавление корня Неполное проваривание корня Линейное включение Вольфрамовое включение Газовая пора Кратерная трубка Линейная пористость Равномерная пористость Дифракционная пятнистость Поперечная трещина Отсутствие бокового сплавления Отсутствие межпроходного сплавления Код KL KC LR LP IL IT GP CP PL PU DM KT LS LI
http://onlineshowcase.tafensw.edu.au/ndt/content/radiographic/task8/accessible.htm
04.05.2010
Просмотр и интерпретация рентгенограмм
Страница 6 из 36
Включение Оксидное включение Медное включение Червоточина Локализованная пористость Прожигание насквозь
IN IO IC WH PG EC BT
Все рентгенограммы следует интерпретировать для определения их соответствия коду или стандарту Типичным стандартом является австралийский стандарт AS4037, который включает допустимые уровни для различных дефектов сварки в сосудах под давлением. В нем указано:
Плоские дефекты (например, трещины или дефекты непровара) не допускаются. В основных стыковых швах (сосуды класса 1) шлаковые включения могут иметь: максимальную длину 6 мм для толщин до 18 мм максимальную длину Т/3 для толщин от 18 мм до 60 мм максимальную длину 20 мм для толщиной более 60 мм.
Некоторые стандарты включают диаграммы пористости, которые обычно являются иллюстрациями для обеспечения визуального сравнения, помогающего определить приемлемость неоднородностей пористости.Несовершенства пористости можно классифицировать как:
изолированные поры (максимальный диаметр 0,3Т, но не более 6 мм) однородная пористость групповая пористость линейная пористость. Вернуться к началу
Неровности поверхности сварных швов Следующие изображения были предоставлены Agfa Gevaert Pty Ltd. На этих репродукциях рентгенограмм показаны различные дефекты сварных швов, как они могут выглядеть на рентгенограмме. Чрезмерное проплавление (SXP) Металл шва выступает через корень
120174253 TWI Радиографическая интерпретация Ремонт дефектов сварки
M. S.Rogers Copyright 2004 TWI Ltd
сварные дефекты и ремонт
радиографические интерпретации
Msrogers Copyright 2004 TWI Ltd
Неисправности в сварках
Msrogers Copyright 2004 TWI LTD
Дефекты, которые могут быть обнаружены По визуальной проверке
может быть сгруппирован под следующие заголовки
трещины
твердые включения
поверхность и профили
Миссилирование
(набор
неровности)
Газные поры и пористость
Отсутствие слияния
Механический ущерб
Повреждение основного материала
Разное
Неисправности сварных швов плавлением
M.S.rogers Copyright 2004 TWI Ltd
TWI
36
MSROGers Copyright 2004 TWI Ltd
Классифицированы по форме
Longitudental
Transverse
Разветвленные
Chevron
Chevron
CAR
Centreline
Кратер
Зона сплавления
Основной металл
Трещины, которые могут возникать в свариваемых материалах,
обычно вызваны многими факторами и могут быть классифицированы по
форме и положению, трещины классифицируются как плоские.
трещины
MSROGERS Copyright 2004 TWI Ltd
водорода, вызванные холодным крекингом (HICC)
затвердевание (HICC)
затвердевающее крекинг (горячая разрывая)
Re Team Tracking
процесса трещины
процесса
MSROGERS авторские права 2004 TWI Ltd.S.rogers Copyright 2004 TWI Ltd
поперечные трещины продольные трещины
Msrogers Copyright 2004 TWI Ltd
включения
MSROGERS COPYRICE 2004 TWI LTD
COOT COOT
кластерная пористость газовой порой
ударов
Errringbone Пористость
Потеря газового щита
Влажные электроды
Загрязнение
Длина дуги Слишком большая
Поврежденного электродного потока
Влажность на родительский материал
Сварочный ток Слишком низкая
газовый потер 1.6mm
газовых полостей
Msrogers Copyright 2004 TWI Ltd
Root Piping
пористость
MSROGERS Copyright 2004 TWI Ltd
кластер пористость Errdbone
Msrogers Copyright 2004 TWI Ltd
Шлак от сварочного флюса
В процессе сварки MAG и TIG образуется кремнезем
Включения
Шлак образуется из-за недостаточной очистки
Другие включения включают вольфрам и медь
включения от процесса сварки TIG и TIG
5 90
Шлаковые включения определяются как неметаллические включения
, вызванные каким-либо сварочным процессом
Шлаковые включения
Параллельные шлаковые линии Отсутствие проплавления + шлак
Непровар боковых стенок с
связанный шлак
5
М. S.Rogers Copyright 2004 TWI Ltd
Удлиненные шлаковые линии Interpass Slag Inclusions
Msrogers Copyright 2004 TWI Ltd
Отсутствие Fusion
Msrogers Copyright 2004 TWI Ltd
Неполная заполненная канавция
+ отсутствие Sidewall Fusion
1
1
2
1. Отсутствие боковины Fusion
2. Отсутствие межпровода Sifion
Бедный сварщик
Неверный электрод
Манипуляция
дуговой удар
Неправильная сварка
Ток / напряжение
Неправильная скорость движения
Неправильная межпроходная очистка
Отсутствие сварки
M.S.Rogers Copyright 2004 TWI Ltd
Дефект на кромке или в корне сварного шва, вызванный
натеканием металла на поверхность основного металла
без сплавления с ним
Загрязнение
Низкая скорость перемещения
Неверно технология сварки
Слишком низкий ток
Нахлест
MSRogers Copyright 2004 TWI Ltd
Носок внахлест Угловой шов
Носок внахлест Стыковой шов
6 M Внахлест
5
5S. Rogers Copyright 2004 TWI Ltd
Неполное корневое Fusion
Неполное корневое проникновение
Низкие AMPS / VOLTS
Большой корневой корень
Небольшой корневой пробел
Быстрая скорость движения
Неправильный электрод Угол
Загрязнение
дуговой удар М.S.Rogers Copyright 2004 TWI Ltd
Недостаточное проникновение корня Недостаточное срастание корня
MSRogers Copyright 2004 TWI Ltd
Поверхность и профиль
MSRogers Copyright 20904 Заполненный профиль
Чрезмерная высота крышки
Плохое крышные профили и чрезмерные
CAP-подкрепления могут привести к
точкам концентрации напряжений при
сварных пальцев и будет также
вносят вклад в общее количество бедных носок
Blend
.
М.S.Rogers Copyright 2004 TWI Ltd
Неполная заполненная канавтика избыток Cap Rearmerce
MSROGERS Copyright 2004 TWI Ltd
Плохое остановка / начала
сварной профиль
36
Msrogers Copyright 2004 TWI LTD
Разное дефекты
Msrogers Copyright 2004 TWI Ltd
разбрызгивает чрезмерное текущее
влажные электроды
загрязнение
неверная скорость подачи проводов
при сварке с процессом сварки MAG
дуговой удар
разные дефекты
М. S.rojers Copyright 2004 TWI Ltd
Случайные поразительные удары дуги
на родительский материал
Неисправный держатель электрода
Плохое изоляция кабеля
Плохое возврата зажима
Arc Strike
Разное дефекты
Msrogers Copyright 2004 TWI Ltd
Нерегулярная канавция на носке сварного сварного шва в родительском металле
избыточные усилители / вольт
Чрезмерная скорость перемещения
Неправильный Угол электрода
Чрезмерное плетение
Неправильная сварная техника
электрод слишком большой
Подрез крышки и корня
M.S.Rogers Copyright 2004 TWI Ltd
прерывистой CAP undercut
CAP undercut
Msrogers Copyright 2004 TWI Ltd Msrogers Copyright 2003 TWI Ltd
CAP undercut Root undercut
Msrogers Copyright 2004 TWI Ltd
Усадочная канавка
Недостаточное количество металла шва
В корневом шве
Слишком высокая скорость охлаждения во время
Нанесение корневого шва
Наплавка валика
Плохая техника сварки
Неглубокая канавка, вызванная усадкой в
металл вдоль каждой стороны проплавляющего валика
Дефект корня сварного шва
M. S.Rogers Copyright 2004 TWI Ltd. проход
Неглубокая канавка, которая может образоваться в корне стыкового сварного шва
Дефект корня сварного шва
MSRogers Copyright 2004 TWI Ltd
Вогнутый корень
Дефект корня сварного шва 5
5 90.2305 90.005
S.Rogers Copyright 2004 TWI Ltd. используется
Дефект корня шва
MSRogers Copyright 2004 TWI Ltd
Дефект корня шва
Чрезмерный корень
Провар
вогнутые корневые избыточные корневые проникновения
Msrogers Copyright 2004 TWI Ltd
High AmPS / VOLTS
маленький корневой лицевой сторона
большой корневой пробел
медленное путешествие Скорость Прожог
Локальное разрушение сварочной ванны из-за чрезмерного
проплавления, приводящее к образованию отверстия в корневом стыке
Дефект корня шва
M. S.rogers Copyright 2004 TWI Ltd
WELD CORT Defect
Burn через
MSROGERS Copyright 2004 TWI LtdУбыток или недостаточный Back
Чувственный газ
Чаще всего читает
при сварке нержавеющей стали
сталей
продувочные газы включают
аргон, гелий и
изредка азота
окисленный корень (коквинг)
MSROGERS Copyright 2004 TWI LTD
Crater Pipe
сварки Crater
Crater Tips
M.S.Rogers Copyright 2004 TWI Ltd
Кратерная труба является дефектом усадки, а не газовым дефектом, имеет вид газовой поры в кратере сварного шва
Слишком высокая скорость охлаждения
Раскисление
реакции и жидкость до
твердого объема изменения
загрязнение
кратер трещины
(звезды трещин)
(звезды трещины)
Crater Tips
Crater Tips
Crater Tips
Msrogers Copyright 2004 TWI LTD
Механический урон
M. S.Rogers Copyright 2004 TWI Ltd
Механическое повреждение может быть определено как любое повреждение материала поверхности
в процессе производства.
Это может включать в себя ущерб, вызванный:
шлифование
Charting
Chammering
Chiselling
Разрыва сварных вложений (порванные поверхности)
с использованием игл пушки для сжимания сварки Coapt Run
м .S.Rogers Copyright 2004 TWI Ltd
Механический урон
Механический урон
Механический ущерб / шлифовальный марки
Chipping Marks
MSROGERS Copyright 2004 TWI LTDНастройки неровности
36
Msrogers Copyright 2004 TWI LTD
Изменение длин участков углового сварного шва
Примечание. Неравные длины участков углового сварного шва могут быть указаны
как часть конструкции, и в этом случае это не будет считаться дефектом.
Ноги разной длины
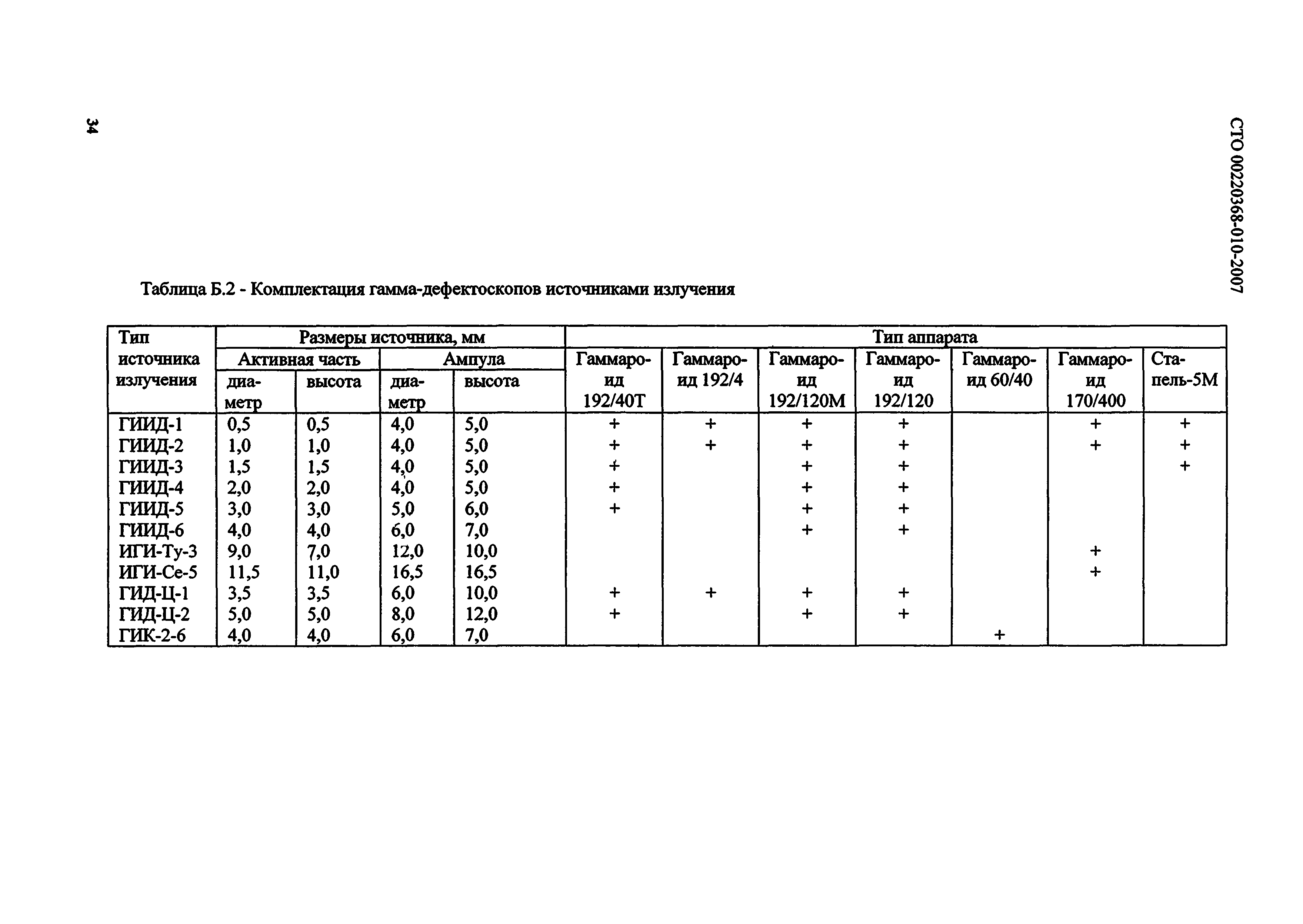