Подготовка под сварку кромок и поверхностей свариваемых деталей
Вырезку деталей и выполнение скосов кромок под сварку следует производить термической или механической резкой в соответствии с требованиями СНиП III-18-75. Разделка кромок под сварку должна соответствовать способу и технологии сварки, толщине свариваемых элементов и положению швов в пространстве. Конструктивные элементы кромок должны соответствовать требованиям ГОСТ 5264—80, ГОСТ 11534—75, ГОСТ 11533—75, ГОСТ 14771—76, ГОСТ 14776—79, ГОСТ 15164—78, ГОСТ 23518—79.
Кромки деталей из низколегированной стали классов до С60/45 включительно, не подлежащие сварке или не полностью проплавляемые при сварке, после ручной кислородной резки, а также кромки аналогичных деталей из сталей всех классов после воздушно-дуговой резки подлежат механической обработке (строжке, фрезеровке, обработке абразивным инструментом).
Механическая обработка производится на глубину, обеспечивающую удаление дефектов поверхности, при этом после воздушно-дуговой резки не менее 2 мм.
Кромки деталей из углеродистой стали класса С38/23 после ручной кислородной резки должны быть очищены и не иметь шероховатостей, превышающих 1 мм, а для конструкций, возводимых или эксплуатируемых в районах с расчетной температурой ниже минус 40° и до минус 65 °С включительно, не более 0,5 мм.
Кромки деталей после машинной кислородной и плазменно-дуговой резки, не подлежащие сварке или не полностью проплавляемые при сварке, не должны иметь неровностей, превышающих 0,3 мм.
Точность деталей и заготовок и качество поверхности реза при газовой и плазменно-дуговой резке сталей должны соответствовать ГОСТ 14792—80.
Кромки работающих на растяжение деталей из низколегированных сталей класса до С60/45 включительно всех толщин и из углеродистой стали толщиной свыше 10 мм, фасонок из низколегированной стали класса до С60/45 включительно, всех расчетных деталей в конструкциях, воспринимающих динамические нагрузки, либо возводимых и эксплуатируемых в районах с расчетной температурой ниже минус 65 °С, после резки с помощью ножниц подлежат механической обработке с тем, чтобы удалить дефекты поверхности.
Остальные кромки после резки на ножницах не должны иметь неровностей, заусенцев и завалов, превышающих 0,3 мм, и трещин.
При подготовке кромок под сварку допускается применение (без последующей обработки) резки способами, обеспечивающими требуемую форму кромок и соблюдение допусков по размерам. При этом отклонения прямолинейности кромок от проектного очертания определяются допусками на зазоры, установленными ГОСТ 5264— 80, ГОСТ 8713—79 и ГОСТ 14771—76.
После воздушно-дуговой резки стали классов С52/40 и С60/45 и после кислородной резки стали класса С60/45 необходима зачистка кромок абразивным инструментом.
Скосы по толщине на концах растянутых деталей (при сопряжении деталей разной толщины) в конструкциях, воспринимающих динамическую нагрузку, должны выполняться машинной кислородной резкой или механической обработкой и не должны иметь ступенек. Неровности и риски в детали должны быть сглажены абразивным инструментом вдоль усилия.
На подготовленных под сварку кромках и поверхностях не допускается наличие влаги, ржавчины, окалины, масла, краски и других загрязнений.
При использовании металлопроката, не подвергнутого консервации, проплавляемые поверхности и прилегающие к ним зоны металла шириной не менее 20 мм, а также кромки листов в местах примыкания выводных планок перед сборкой должны быть очищены до чистого металла. Продукты очистки не должны оставаться в зазорах между собранными деталями.
Допускается производить сварку без предварительной зачистки при отсутствии на кромках и поверхностях свариваемых деталей загрязнений, а также при наличии покрытия — защитного грунта, слоя цинка или алюминия и т. п., если металл шва и сварное соединение по своим свойствам отвечают требованиям строительных норм, а выделение вредных газов и аэрозолей при сварке не превышает санитарных норм.
Разделка кромок под сварку — виды, ГОСТ, формы, углы
Студентам-сварщикам на лекциях рассказывают основы и важность каждого подготовительного этапа перед сваркой. Ученики знают, с какой целью выполняют разделку кромок, а на практических занятиях тренируются с различными видами сварных соединений и их подготовкой.
Меню статьи:
Эта статья расскажет о базовых особенностях сварки: о правильной подготовке кромок металла, видах соединений и способах подготовки согласно ГОСТу.
Блок: 1/4 | Кол-во символов: 431
Источник: http://UkrAbraziv.com.ua/novosti/45-razdelka-kromok-pod-svarku-vidy-razdelki-dlya-trub-i-s-kakoj-tselyu-ee-vypolnyayut
Обязательная подготовка
Единственной задачей разделки кромок является желание получить качественный надежный шов. Разделку проводят так, чтобы электрод легко мог достать до нижних слоев и проварить изделие по всей толщине.
Подготовка кромок перед сваркой проводится в любом случае. Она может быть:
- без разделки;
- с отбортовкой;
- с разделкой.
Обязательный подготовительный этап заключается в очистке торцовой и прилегающей области от всевозможных механических и жировых загрязнений, оксидных пленок, ржавчины на расстояние не менее 20 мм в соответствии с ГОСТ.
Зачистка стыков под сварку может производиться вручную с использованием наждачки, щетки с металлической щетиной, напильника, шлифовальной машинки или с применением химических реагентов.
После того как детали собраны в узел, который предстоит варить, и зафиксированы, правильно обработать кромки уже не получится.
Подготовку стыков рекомендуется делать при толщине стенок свариваемых деталей 5 мм и более. Односторонняя отбортовка выполняется при сварке стыковых и угловых соединений.
Двухсторонняя отбортовка производится при стыковой сварке. В целом разделка заключается в придании кромкам определенной формы, в результате чего они становятся тоньше.
Блок: 2/6 | Кол-во символов: 1211
Источник: https://svaring.com/welding/teorija/razdelka-kromok-pod-svarku
Условные обозначения соединений
В стандарте описаны три типа сварных соединений трубопроводов:
- стыковые, обозначаются литерой С
- угловые, литерой У
- нахлесточные, обозначаются литерой Н.
Внутри каждого типа актуальный стандарт детализирует множество подтипов в зависимости от:
- вида сварного шва;
- числа сторон проварки;
- конфигурации подкладки;
- ее съемности;
- без скоса, со скосом одной или двух кромок;
- формы сечения кромок
- формы сечения шовного материала
- способа сварки;
- толщины стенок;
- диаметра трубы.
Пример обозначения типа С13.
В условное обозначение, кроме типа, входит признак замкнутости линии, способ сварки, параметры катета и вспомогательные символы. В соответствии с ГОСТ 16037 80 используется сварка аргоном, под флюсом и газом.
Блок: 2/8 | Кол-во символов: 983
Источник: https://svarka.guru/tehnika/detaley/gost-16037-80.html
Формы скосов кромок
Существуют разные виды разделки кромок под сварку. Но корректнее называть их видами формы скосов кромок. Каждая форма имеет свои характерные особенности, поэтому форма подбирается индивидуально для каждой детали. Нельзя бездумно выбирать произвольную форму просто потому, что вы научились делать только ее. Обучитесь выполнять скосы всех форм, чтобы расширить свои возможности. Итак, существуют следующие формы скосов кромок.
V-образная форма
V-образный скос кромок под сварку — самый популярный тип скоса, поскольку делается проще всего и широко применяется в большом диапазоне толщин.
X-образная форма
X-образный скос — выполняется с двух сторон, применяется при разделке толстых металлов. Рекомендуемый угол скосов — 60 градусов.
U-образная форма
U-образный скос — самый сложно выполнимый для многих новичков за счет непростой формы. Выполняется с двух сторон, подходит для сварки толстых металлов от 20 миллиметров. Зачастую кромки разделывают таким образом, когда нужно выполнить РДС сварку. Это связано с тем, что при такой форме скосов металл меньше наплавляется и электроды расходуются медленнее.
Это основные формы скосов. Бывают и другие (например, К-образный скос), но они применяются в редких случаях.
Блок: 3/5 | Кол-во символов: 1452
Источник: https://svarkaed.ru/svarka/obuchenie-svarke/razdelka-kromok-pod-svarku. html
Типы готовых кромок — какие бывают и как выбирать
Виды разделки кромок по Госстандартам учитывают массу параметров, которые имеют свои термины:
Угол разделки кромки (α) — его наличие обеспечивает плотный шов и качественную сварную ванну.
Длина скоса кромки (L) — обеспечивает плавный переход толщины металла.
Размер притупления кромок (S) — начинается там, где заканчивается скос и обеспечивает устойчивость сварки, равномерное наложение шва.
Зазор между двумя кромками (а) — требует внимательности и правильного подхода, т.к. от его величины зависит полнота провара.
Смещение кромок относительно друг друга (δ) — влияет на прочность соединения и допускается не более 10% от толщины металла.
Опытный сварщик знает все виды разделки кромок под сварку по ГОСТу и умеет их подобрать в зависимости от толщины металла, типа соединения и способа сварки. Стандарт для наиболее распространенной ручной дуговой сварки (ГОСТ 5264-80) включает по 4 и более типов форм кромок для каждого типа соединения:
Для стыкового — 15 видов кромок;
Для углового — 5 видов кромок;
Для таврового — 4 вида кромок;
Для нахлесточного — один вид: без скоса кромок.
Такие линейные типы сварных соединений, где требуется предварительная разделка кромок, встречаются на каждом шагу:
Металлоконструкции;
Металлические инсталляции — предметы искусства;
Винтовые и пожарные лестницы;
Отдельные виды перил и ограждений;
В судостроении и ремонте.
Блок: 3/4 | Кол-во символов: 1470
Источник: http://UkrAbraziv.com.ua/novosti/45-razdelka-kromok-pod-svarku-vidy-razdelki-dlya-trub-i-s-kakoj-tselyu-ee-vypolnyayut
В данном случае обе детали соединяются торцами, которые заранее специальным образом обрабатывают, либо оставляют необработанными. Это зависит от толщины металла деталей, стыковое соединение которых предполагается выполнить.
Также стоит обратить внимание (рис) на то, что может быть обработан торец только одной детали, что позволяет уменьшить расход металла, сварочной проволоки при солидной толщине деталей. Кроме этого, виды стыковых соединений могут быть обработаны с одной стороны – для односторонней сварки и с двух сторон – для двусторонней сварки.
Соединение без разделки не обрабатывается каким-либо образом, только возможно убираются зазубрины, неровности и шероховатости, чтобы совершить состыковку с зазором не более 2 мм, как положено по ГОСТ. Бывает односторонним и двухсторонним, соответственно рассчитано на сварные стыковые соединения деталей, толщина металла которых не превышает 4 мм и 8 мм соответственно.
Соединение со скосом торцов выполняется во многих вариациях, как показано на рис. Это может быть и односторонний ровный/овальный скос кромки, и двусторонняя разделка, так называемый V-образный, U-образный скос. Применяются все эти типы стыковых соединений для деталей с толщиной металла 4-25 мм с зазором 1-2 мм.
Соединение с двусторонней разделкой имеет смысл выполнять при толщине свариваемой детали от 12 мм, так как именно с этой величины начиная можно заметить снижение расхода материала для сварки, металла. При этом и сама сварка стыковых соединений происходит быстрее, чем в случае с односторонней разделкой кромок по V-образному или U-образному способу, а расход сварочных материалов уменьшается в два раза как минимум.
Блок: 2/5 | Кол-во символов: 1718
Источник: https://mastery-of-building.org/vidy-i-sposoby-soedinenij-svarnyx-detalej/
Способы выполнения обработки (разделки кромок)
Как уже было сказано ранее существует несколько способов выполнения разделки кромок:
- газовая резка требует последующей механической или ручной обработки;
- механическая резка осуществляется на ножницах, после необходимо произвести механическую или ручную доработку.
Для тел вращения механическая обработка проводится на расточном станке; для прямолинейных элементов предназначена фрезерная обработка, механическая строжка, использование метода пневмошлифовки, угловой шлифовальной машинки (болгарки).
Ручная обработка подразумевает рубку зубилом или доработку напильником.
Блок: 4/12 | Кол-во символов: 618
Источник: https://WeldElec.com/svarka/nauchitsya/razdelka-kromok/
Для чего выполняется: цель подготовки и зачистки
Прежде чем приступать к разделке кромок, необходимо произвести очистку поверхности. Присутствие загрязнений отрицательно сказывается на качестве, надежности и прочности шва: в соединении формируются поры, трещины и шлаковые отложения. Как следует проводить зачистку рассказано в следующем подразделе. После зачистки поверхности осуществляется разделка. Данная процедура производится для достижения следующих целей:
- осуществление провара по всей толщине свариваемых изделий;
- обеспечение доступа к корню шва сварочного инструмента.
Подготовка свариваемых поверхностей
Предварительная подготовка свариваемых металлических поверхностей включает выполнение нескольких процедур:
Вальцы
Правка может выполняться вручную на специальных правильных плитах из стали или чугуна с помощью пресса или посредством ударов молотка. Механическая правка производится на листоправильных вальцах. Правка осуществляется с целью избавления от дефектов и кривизны.
Предварительная зачистка. В процессе подготовки металл необходимо очистить от масел, красок и лаков с помощью бензина или любого растворителя. Грязь и ржавчина удаляются кордщеткой, абразивными кругами или болгаркой. Изделия из высоколегированных сталей необходимо вычищать до блеска.
Кордщетки, насадки на болгарку
Разметка позволяет определить формы и размеры будущего изделия. Выполнять разметку нужно внимательно, так как даже небольшая неточность приведет к дефекту. Важно помнить о припуске на обработку.
Небольшой подогрев деталей.
Механическая резка металлических листов осуществляется с помощью роликовых ножниц, которые оборудованы ножами. Резка деталей из углеродистых сталей проводится плазменно-дуговой или газокислородной технологиями, легированные стали — кислородно-флюсовый и плазменно-дуговой методы.
При необходимости изделия подвергаются гибке.
После выполнения данных процедур, можно приступать к разделке кромок. Грамотно выполненный скос обеспечивает плавность перехода между свариваемыми заготовками, снизит возможное напряжение на область шва. О том, как правильно это сделать расскажем далее.
Важно! Общая информация для всех видов соединений. Обязательно нужно оставлять притупление. Величина притупления — 2,0-2,5 мм, зазор — 0-4 мм. Отсутствие притупления может привести к прожогам, а отсутствие зазора — к непровару.
Скос под сварку труб, трубопроводов
Сваривание труб осуществляется в различных сферах деятельности: в быту и промышленности, на производстве. Потребность в соединении труб возникает и при первоначальной прокладке и при ремонтных работах. Поэтому важно знать, в каких случаях следует осуществлять разделку, а когда можно обойтись без этой процедуры.
Под отводы
Отвод представляет собой фитинг, использующийся для изменения направления потока жидкости, газа или пара в трубопроводе. Для получения качественного стыкового соединения отвода с трубой, исполнителю необходимо выполнить односторонний скос одной или двух кромок под углом в 45 градусов относительно оси трубы.
Важно! При стыковом соединении детали должны иметь одинаковую толщину.
Кроме этого, сварщик может сделать угловое соединение, которое осуществляется без скоса.
Под штуцеры
Штуцер — это патрубок (небольшое отрезок трубы), привариваемый к любой конструкции и служащий для подключения к ней трубопровода с целью отвода жидкости, газа или пара.
Штуцер с трубопроводом может соединяться следующими способами:
- угловое соединение ответвительного штуцера с трубой односторонним швом без скоса кромок;
- нахлесточное соединение промежуточного штуцера с трубой односторонним швом без скоса кромок.
Скосы с торцов труб можно снимать с помощью механической обработки или газовой резкой.
Для сосудов и резервуаров
При разделке кромок под сварку различного рода сосудов и резервуаров следует следовать следующим рекомендациям:
- если толщина стенок изделия составляет 3-26 мм., то следует применять V-образный или X-образный скос;
- при толщине стенок, не превышающей 60 мм., следует выполнить U-образный скос кромок.
Стыкового соединения
Стыковое соединение (сварка встык) — тип соединения, при котором заготовки расположены в одной плоскости и примыкают друг к другу торцами. Такой тип соединения обеспечивает высокие прочностные характеристики, поэтому применяется при работе с ответственными конструкциями.
Изделия толщиной 1,0-3,0 мм. свариваются встык после отбортовки кромок.
Для деталей с толщиной стенок до 26 мм. следует выполнить односторонний скос одной или обеих кромок, с толщиной до 60 мм. — двухсторонний скос каждой кромки.
Угловых соединений
Угловое соединение — тип соединения, в котором угол между рабочими поверхностями двух заготовок в месте примыкания кромок превышает 30 градусов.
При толщине стенок изделия до 3 мм. рекомендуется выполнять отбортовку кромок.
При работе с большими толщинами (до 20 мм.) необходимо проводить односторонний скос одной кромки, значительные толщины требуют двухстороннего скоса.
Под сварку двутавра (двутавровой балки)
Двутавр (двутавровая балка) — стандартный профиль, имеющий сечение близкое по форме к букве «Н». Приваривание балки к различным конструкциям осуществляется посредством таврового соединения, при котором заготовки располагаются под прямым углом друг к другу.
Сварка деталей, толщина которых от 4 до 26 мм. осуществляется с односторонним скосом, толстостенные изделия (до 60 мм.) варятся после проведения двухстороннего скоса.
Блок: 2/12 | Кол-во символов: 5393
Источник: https://WeldElec.com/svarka/nauchitsya/razdelka-kromok/
Фаски под сварку
При соединении толстых трубных заготовок сформированный шов следует делать толще, чем сама деталь. Для формирования соединения с заданными геометрическими параметрами требуется выполнить разделку кромок, сняв фаску. После этого электроду будет обеспечен доступ для качественной проварки шва на всю глубину.
Основными параметрами фаски являются:
- Зазор b. расстояние меду заготовками, до 2-3 мм.
- Притупление C. Не скошенная часть кромки. ее оставляют, чтобы снизить вероятность прожога корня шва..
- Угол скоса β. При двусторонней разделке острый угол принимает значения 15-30 о, при односторонней- до 45о.
- Угол разделки α. Тупой угол равен двойному значению угла скоса, обеспечивает должный доступ к корню шва для сварочного оборудования.
Параметры фаски.
Если значение притупления невелико или его вовсе нет, то прожог предотвращают такими методами, как:
- использование подкладок, препятствующих вытеканию расплавленного металла;
- сварка на флюсовой подушке;
- предварительное подваривание;
- выполнение замка.
Технологам следует обращать особое внимание на корректный расчет и соблюдение оптимальных значений параметров разделки. Это позволяет снизить трудоемкость, экономно расходовать материалы и сохранять контроль над себестоимостью.
При подготовке стыковых соединений вид фаски зависит от толщины деталей:
- 3-25мм: одностороння фаска;
- 26-60мм: двухсторонняя;
Для угловых устанавливаются следующие границы:
- 3-20мм: одностороння;
- 21-50 мм: двухстороння.
Исходя из геометрической формы профиля поперечного сечения, выделяют такие типы разделки:
- обычный скос, профиль представляет собой трапецию,
- Х-образная, два скоса сделаны навстречу друг другу таким образом, что профиль поперечного сечения двусторонней разделки визуально напоминает очертания буквы Х;
- U-образная, профиль поперечного сечения криволинейный и напоминает очертания буквы U.
ГОСТ на сварку труб рекомендует применять U-образную разделку при больших толщинах заготовок, с целью снизить площадь сечения шва и, следовательно, снизить расход материалов и повысить скорость работы.
Форму разделки выбирают, руководствуясь толщиной труб:
- 3-25мм: Х-образная или V–образная;
- 26-60мм- U–образная;
- более 60 мм- специальные формы.
Они представляют собой:
- уступы;
- сложные криволинейные профили, призванные сохранить доступ электрода к корню шва и понизить площадь поперечного сечения.
Для разделки используются следующие способы:
- Газовый резак. Характеризуется низкой точностью и недостаточным качеством поверхности. Требует дополнительной обработки механическими способами.
- Мехобработка. Строгальная или фрезерная обработка дает достаточную чистоту и форму поверхности. Долбежная обработка также требует финишной мехобработки.
При разделке кромок труб большого диаметра используются специальные торцовочные аппараты. Во время ремонтных работ на магистралях отопления разделка часто выполняется вручную шлифмашинами.
Блок: 7/8 | Кол-во символов: 2883
Источник: https://svarka. guru/tehnika/detaley/gost-16037-80.html
Особенности методов резки
При газовой кислородной резке легированных сталей свободный углерод образует карбиды, удалить которые очень трудно. Поэтому подготовку таких сплавов, как хромированная нержавейка, например, проводят другими способами. Газовую разделку кромок применяют в основном к углеродистым сталям.
Качество термической резки, проведенной вручную, почти всегда оставляет желать лучшего, поэтому требуется дополнительно обрабатывать срез абразивом. К тому же изменяется состав и свойства верхнего слоя, что приводит к деформации изделий.
Плазменная резка позволяет получить качественный срез практически любых металлов. В роли плазмообразующего газа применяют воздух. Переносные устройства терморезки оснащаются газовыми и плазменными горелками. При установке трех горелок можно делать скосы кромок К-образной формы.
При машинной термической резке, качество кромок получается высоким, и удовлетворяет требованиям ГОСТов. Лазерная разделка кромок используется, когда ее нечем заменить, стоит она очень дорого.
Механическая резка обеспечивает получение качественных скосов кромок. К достоинствам относится создание скосов сложной формы. Но есть и существенные недостатки, среди которых невысокая производительность и трудность формирования кромок на крупных заготовках.
При формировании двусторонних скосов механическим методом требуется кантовка заготовок. Резка стыков абразивами является вредным производством и требует много ручного труда. Элементы абразива вызывают трещины.
Блок: 5/6 | Кол-во символов: 1491
Источник: https://svaring.com/welding/teorija/razdelka-kromok-pod-svarku
Правила подготовки изделий
Подготовка изделий для последующего проведения сварки — один из важнейших этапов, независимо от используемого метода.
Обязательно проведение нескольких процедур: правка, зачистка, разметка, резка. Проведение каждого процесса гарантирует исключение различного вида дефектов заготовок.
В зависимости от типа обрабатываемых изделий и их толщины возможен нагрев деталей, который обеспечит более качественное соединение.
Блок: 5/12 | Кол-во символов: 445
Источник: https://WeldElec.com/svarka/nauchitsya/razdelka-kromok/
Требования к готовым поверхностям
Перед выполнением сварки кромки должны соответствовать следующим требованиям:
- очищены от различных загрязнений: пыль, грязь, ржавчина, краски, лаки, масла;
- иметь ровную поверхность, без кривизны;
- не должно быть перепадов или изменения угла скоса.
Блок: 6/12 | Кол-во символов: 281
Источник: https://WeldElec.com/svarka/nauchitsya/razdelka-kromok/
Под каким углом
Угол скоса — острый угол между плоскостью скоса кромки и торца.
Угол скоса зависит от следующих факторов:
- от вида применяемого вида сварки: газовая сварка — 40-45 градусов, притупление — 0,5-1,0 мм.
; электродуговая — 30-35 градусов и такая же величина притупления;
- от диаметра электрода или другого расходного материала, размеры кромки должны обеспечивать доступ стержня к корню шва;
- от толщины заготовок, чем она больше, тем больше должен быть угол открытия кромок.
Блок: 7/12 | Кол-во символов: 483
Источник: https://WeldElec.com/svarka/nauchitsya/razdelka-kromok/
Технология (разделки кромок)
Сущность технологии разделки кромок состоит в снятии части металла под определенным углом (углом скоса) с изделия, который в последствии будет подвергаться свариванию.
При снятии необходимо оставить притупление. Оно нужно для того, чтобы во время процессов прихватки и сварки расплавляющиеся кромки не создавали щель, которую будет сложно заварить.
Блок: 9/12 | Кол-во символов: 378
Источник: https://WeldElec.com/svarka/nauchitsya/razdelka-kromok/
Разделка трещин в металле перед сваркой
Трещины обязательно разделывать полностью, чтобы имелась возможность проварить их на всю глубину. Разделка осуществляется строго по всей длине трещины, с одной или с двух сторон, в зависимости от толщины детали и удобства проведения процесса.
Разделка может проводиться следующими способами:
- механические: вырубка или шлифовка;
- термические: дуговая или кислородная строжка или резка.
После разделки углы трещины необходимо засверлить по краям, чтобы предотвратить появление подобных дефектов.
Блок: 10/12 | Кол-во символов: 534
Источник: https://WeldElec.com/svarka/nauchitsya/razdelka-kromok/
Для элементов различной толщины
стыковое соединение с отбортовкой кромок (для тонкого металла)
Различные конструкции и элементы имеют разную толщину стенок:
- при работе с тонкостенными изделиями (до 5 мм.) разделка кромок не требуется;
- наличие отбортовки кромок также не требует их разделки;
- если толщина стенок деталей составляет от 5 до 20 мм. рекомендуется осуществлять односторонний скос;
- при толщине изделий от 20 до 60 мм.
следует производить двухстороннюю разделку.
Данные правила являются стандартными для разных деталей и для различных типов соединений.
Блок: 11/12 | Кол-во символов: 562
Источник: https://WeldElec.com/svarka/nauchitsya/razdelka-kromok/
Количество использованных доноров: 6
Информация по каждому донору:
- https://svaring.com/welding/teorija/razdelka-kromok-pod-svarku: использовано 2 блоков из 6, кол-во символов 2702 (12%)
- https://svarka.guru/tehnika/detaley/gost-16037-80.html: использовано 3 блоков из 8, кол-во символов 4092 (18%)
- https://WeldElec.com/svarka/nauchitsya/razdelka-kromok/: использовано 8 блоков из 12, кол-во символов 8694 (39%)
- https://svarkaed.ru/svarka/obuchenie-svarke/razdelka-kromok-pod-svarku.html: использовано 1 блоков из 5, кол-во символов 1452 (6%)
- http://UkrAbraziv.com.ua/novosti/45-razdelka-kromok-pod-svarku-vidy-razdelki-dlya-trub-i-s-kakoj-tselyu-ee-vypolnyayut: использовано 3 блоков из 4, кол-во символов 3822 (17%)
- https://mastery-of-building.
org/vidy-i-sposoby-soedinenij-svarnyx-detalej/: использовано 1 блоков из 5, кол-во символов 1718 (8%)
Сварка Подготовка кромок — Размеры
Для различных способов сварки требования к конструктивным элементам подготовки кромок и размерам швов регламентируются соответствующим ГОСТом (см. гл. 1). [c.271]На рис. А, А приведена конструктивная схема сферического резерву а-р а, составленного из лепестков небольшого размера. Лепестки соединяются в монтажные блоки при помощи ручней дуговой, автоматической под флюсом или электрошлаковой сварки. Подготовка кромок под эти виды сварки показаны на схемах а, а, б, б и S. Монтажные швы между блоками выполняются вручную, при этом кромки в верхней части резервуара обращены разделкой внутрь разделка кромок в [c.495]
При сварке швов стыковых соединений деталей неодинаковой толщины, когда разность не превышает величин, указанных в табл.
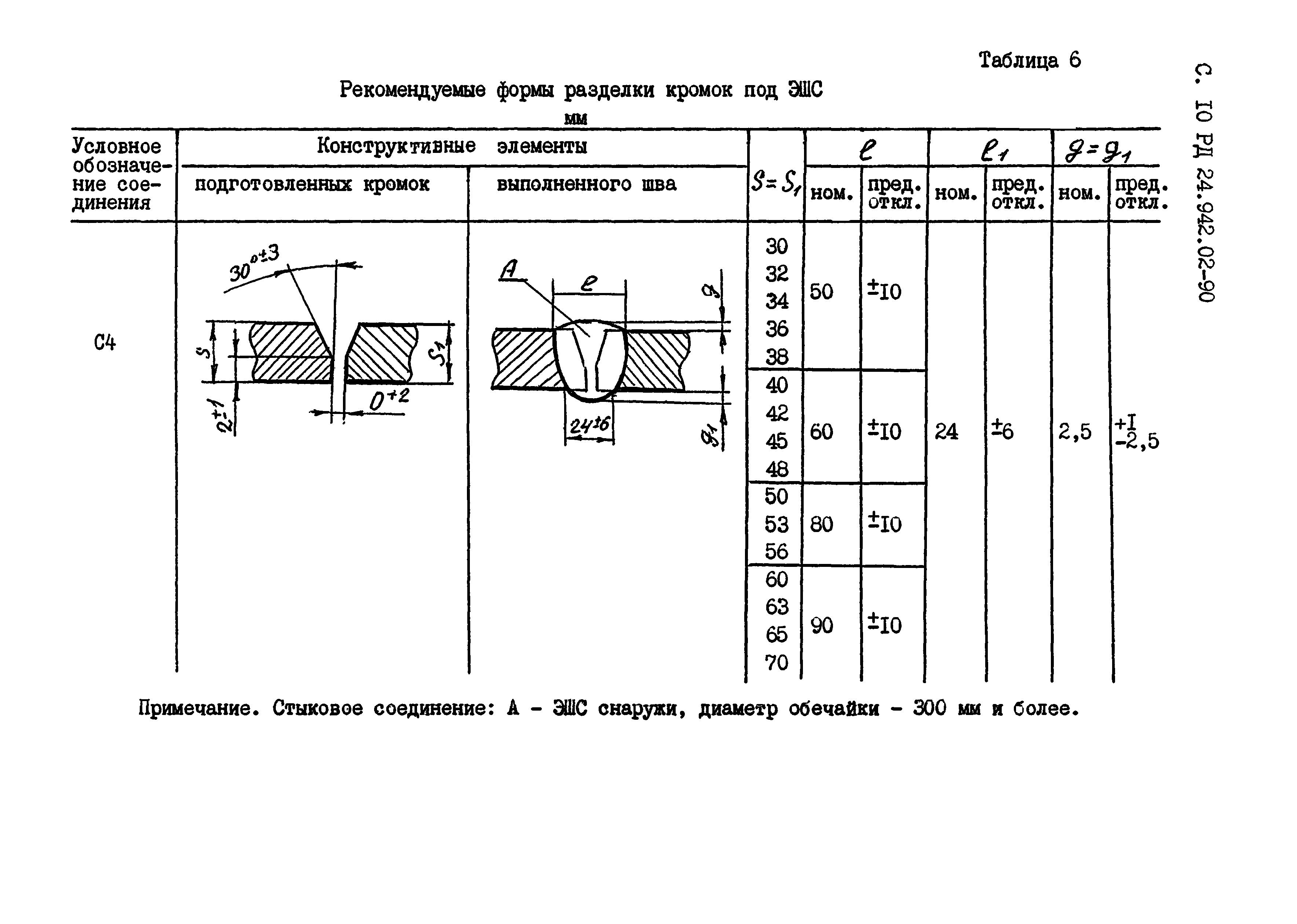
Подготовка кромок и размеры швов. Подготовка кромок и размеры сварных швов при ручной дуговой сварке должны соответствовать ГОСТ 5264-50. [c.260]
При практических испытаниях сварщиков необходимо установить размеры пластин для сварки, подготовку кромок, порядок их сварки, технологию изготовления образцов для механических испытаний и проведение испытаний. [c.383]
В связи с важностью правильной подготовки свариваемых кромок с точки зрения качества, экономичности, прочности и работоспособности сварного соединения созданы государственные стандарты на подготовку кромок под сварку. Стандарты регламентируют форму и конструктивные элементы разделки и сборки кромок под сварку и размеры готовых сварных швов.
[c. 11]
ГОСТ 14771—69 Швы сварных соединений. Электродуговая сварка в защитных газах регламентирует форму и размеры подготовки кромок и сварных швов при сварке сталей в защитных газах активных ( Oj), инертных (Аг, Не) и смесях газов. [c.12]
ГОСТ 14806—69 Швы сварных соединений. Дуговая сварка алюминия и алюминиевых сплавов регламентирует форму и размеры подготовки кромок и выполненных сварных швов при ручной и механизированной сварке в защитных газах конструкций из алюминия и его сплавов, [c.12]
При предварительном контроле основного и сварочных материалов устанавливают, удовлетворяют ли сертификатные данные в документах заводов-поставщиков требованиям, предъявляемым к материалам в соответствии с назначением и ответственностью сварных узлов и конструкций. Осматривают поверхности основного материала, сварочной проволоки н покрытий электродов в целях обнаружения внешних дефектов. Перед сборкой и сваркой заготовок проверяют, соответствуют ли их форма и габаритные размеры установленным, а также контролируют качество подготовки кромок и свариваемых поверхностей. При изготовлении ответственных конструкций сваривают контрольные образцы. Из них вырезают образцы для механических испытаний. По результатам испытаний оценивают качество основного и сварочных материалов, а также квалификацию сварщиков, допущенных к сварке данных конструкций.
[c.243]
Дефекты формы шва. Отклонения размеров и формы сварного шва от проектных чаще всего наблюдаются в угловых швах и связаны с нарушением режимов сварки, неправильной подготовкой кромок под сварку, неравномерной скоростью сварки, а также с несвоевременным контрольным обмером шва. [c.146]
Зная конструктивные размеры зоны сварки и способ сварки, по соответствующим стандартам назначают тип сварного шва. Конструктивные элементы сварных швов приведены в справочниках [34], Типы сварных соединений, указанные в стандартах, могут сохраняться и для других методов сварки, для которых стандарты еще не разработаны, например, лазерная или электронно-лучевая. Но в этом случае конструктивные элементы подготовки кромок, форма и размеры сварных швов и допуски на них корректируются с учетом технологических особенностей этих способов сварки.
[c.156]
Все детали и элементы изготовляемого объекта перед сборкой под сварку проверяют на соответствие форм, размеров и качества подготовки кромок, перпендикулярности подготовленных под сварку торцов цилиндрических элементов, качества зачистки поверхностей элементов на прилегающих к кромкам участках, а также плавности и углов наклона переходов требованиям технологического процесса. Необходимая точность сопряжения труб может быть обеспечена в отдельных случаях применением раздачи или обжатия их концов на специальной оправке. [c.322]
ГОСТ 15164-78 «Электрошлаковая сварка. Соединения сварные» устанавливает основные типы, конструктивные элементы и размеры сварных соединений из сталей (кроме коррозионно-стойких) при сварке проволочным электродом, плавящимся мундштуком и электродом, сечение которого соответствует по форме поперечному сечению сварочного пространства (рис. 1.12, г) для толщины 30. .. 800 мм при длине прямолинейных и кольцевых щвов до 10000 мм. При электрошлаковой сварке используют наиболее простые формы подготовки кромок (рис. 1.12). Сварные соединения переменного сечения и переменной кривизны (рис. 1.12, г) допускается сваривать с выравниванием до прямоугольника.
[c.19]
ГОСТ 16098-80 «Соединения сварные из двухслойной коррозионно-стойкой стали» устанавливает основные типы, форму и размеры подготовки кромок и выполненных сварных швов, выполняемых ручной дуговой сваркой, автоматической сваркой под флюсом на весу и на флюсовой подушке, дуговой сваркой в защитных газах и электрошлаковой сваркой. [c.20]
Неправильное ведение горелки и прутка. Неточная сборка. Небрежная подготовка кромок. Неправильный выбор режима сварки. Нарушение нормальных размеров и формы газового пламени [c.279]
Швы сварные, выполненные специальными методами сварки (сварка в среде защитных газов, сварка методом глубокого провара и др. ), их форма и размеры, а также конструктивные элементы подготовки кромок свариваемых деталей, не предусмотренные этим стандартом, должны быть особо отмечены на чертеже или в технических условиях на изделие.
[c.295]
Конструктивные элементы подготовки кромок свариваемых деталей основных типов швов сварных соединений и допуски на их размеры в случае сварки встык металла равных толшин, когда S = S , должны соответствовать данным, приведенным в табл. 30. [c.303]
Подготовка кромок при сварке стыковых соединений показана на рис. 23. При толщине листов 5 [c.174]
В этом случае подготовку кромок под сварку производят так же, как для листов одинаковой толщины конструктивные элементы подготовленных кромок и размеры выполненного шва сварного соединения выбирают по большей толщине [c.36]
Подготовка элементов и сборка их в определенную конструкцию для последующей сварки влияют не только на производительность, но и на качество сварки. С этой целью проверяют качество подготовки кромок и сборки заготовок — чистоту кромок, соответствие угла разделки, зазора, притупления, количества и размеров прихваток допускаемым значениям. Для этого применяют специальные шаблоны или универсальный измерительный инструмент.
[c.245]
Сварка стыковых соединений конструктивные элементы подготовки кромок, размеры выполненных швов, режимы сварки [c.43]
При расположении свариваемых деталей под острыми и тупыми углами основные типы и конструктивные элементы швов регламентированы ГОСТ 11534—65 (ручная электродуговая сварка) и ГОСТ 11533—65 (автоматическая и полуавтоматическая сварка под флюсом). Этими стандартами предусмотрены формы подготовки кромок и размеры выполняемых швов угловых и тавровых соединений с углом наклона между стенками от 45 до 135° [от 0,785 до 2,355 рад] при толш,ине металла до 40 мм.
[c. 55]
ГОСТ 15164—69 Сварные соединения и Н1вы. Электрошлако-вая сварка регламентирует форму и размеры подготовки кромок и выполненных швов при электрошлаковой сварке. [c.12]
ГОСТ 16038—70 Швы сварных соединений трубопроводов из меди и медно-никелевого сплава регламептируе формуй размеры подготовки кромок и выполненных сварных швов при механизированной сварке в защитных газах труб из меди и се сплавов. [c.12]
При ручной дуговой Bapjie плавящимся электродом размеры сварного шва в большинстве случаев определяются размерами разделки кромок соединений, подготовленных под сварку. Поэтому необходимости определения глубины провара при ручной дуговой сварке, как правило, не возникает. Исключение может составлять только сварка стыковых соединений без разделки кромок, диапазон толщин которых согласно ГОСТ 5264—69 ограничен. Этим ГОСТом регламентированы также конструктивные элементы подготовки кромок соединений различных видов исходя из условий получения необходимой величины проплавления и формы шва при использовании режимов сварки в ншроком диапазоне.
[c.183]
На основе проведенных исследований и результатов опытно-промышленного опробования подготовлены нормативные технологические инструкции по ручной электроду го-вой сварке, по полуавтоматической сварке в среде углекис.то го газа и по автоматической сварке под флюсом регламентирующие применение разработанных технологий сварки, [5 этих руководящих документах регламентированы конструктивные формы и размеры элементов подготовки кромок, последовательность и требования к сборке, допустимые параметры твердых прослоек во взаимосвязи с геометрическими размерами и степенью их механической неоднородности, порядок выполнения сварки, выбор сварочных материалов и ре комендуемые режимы сварки, параметры сопутствую щег ) охлаждения с учетом толщины металла свариваемых элементов и рабочих условий эксплуатации. [c.106]
Основное (технологическое) время Наплавка шва Химический состав и физи-ко-м еханические свойства свариваемого металла. Толщина свариваемого металла. Вид соединения. Способ подготовки кромок под сварку (зазор, угол разделки, высота нескошениой части и т. п.). Размеры сечения шва. Число наплавленных слоев. Длина шва. Диаметр электродов. Тип (марка) электродов. Толш,ина покрытия. Род и сила тока Пространственное расположение шва во время сварки. Положение сварщика во время сварки, Наличие контроля собранных узлов перед сваркой
[c.466]
Размеры UJBOB, их форма и подготовка кромок под сварку должны отвечать требованиям ГОСТ 5264-56 Швы сварных соединений. Ручная электродуговая сварка. Конструктивные элементы . [c.65]
При проектировании элементов швов сварных стыковых соединений из лвстов разной толщины наибольшую предельную разность толщин выбирают в аависимостн от толщины S тонкого листа и метода сварки по табл. VH-I. При этом подготовку кромок под сварку производят так же, как и для листов одинаковой толщины. Конструктивные элементы подготовленных кромок и размеры выполненного шва сварного соединения выбирают по большей толщине листа S .
[c.327]
При конструировании сварной аппаратуры необходимо правильно назначить способ сварки, выбрать тип шва, определить подготовку кромок. Способ сварки выбирается в зависимости от материала свариваемых частей, их геометрических размеров и от оснащенности завода. Основными способами можно считать электродуговую автоматическую сварку под слоем флюса, а также полуавтоматическую и ручную дуговые сварки. По типу сварного шва применяются соединения встык, втавр и внахлестку. Основным и лучшим видом сварного соединения пищевых аппаратов является стыковой шов. Обработка кромок перед сваркой зависит от метода сварки и толщины свариваемых листов. Чаще всего применяются бесскосные швы, V-образные швы с подрубкой кромок и швы с подкладкой. [c.138]
Угольные электроды предназначены для воздушно-дуговой резки и сварки металлов, удаления прибылей и дефектов литья, строжки электроприхваток и сварных швов, поверхностной резки металлов, срезки заклепок и подготовки кромок под сварку. Выпускаемые электроды могут быть омедненными и неомедненны-ми, круглыми, диаметром 4… 18 мм, и плоскими с сечением размером 12×5 или 18×5 мм.
[c.90]
Процесс плазменной резки в отличие от воздушно-дуговой легко механизировать и приспособить для удаления сварных швов значительной протяженности, а также для подготовки кромок деталей под сварку и т. п. Недостатком является то, что плазмотрон имеет относительно большие по сравнению с резаком для воздушно-дуговой строжки габаритные размеры и ограничивает доступ в зауженнные места для обработки. Высокое нап- [c.145]
Бес кондуктор ная сборка балок под автоматическую сварку производится по разметке на нивелированных сборочных козелках с помощью крана. Балки собирают из предварительно состыкованных и сваренных листов. Затем по струне проверяют размеры деталей, их прямолинейность и подготовку кромок под сварку. Срубают усилгния на стыковых швах горизонтальных листов в месте примыкания вертикального листа. Выкладывают верхний горизонтальный лист элемента на козелки и намечают на нем шнуром линию установки вертикального листа.
[c.31]
Эскизы разделки кромок под сварку. Подготовка металла к сварке
TO категория:
Сварка металлов
Элементы подготовки кромок под сварку
ГОСТ(«Ручная дуговая сварка. Сварные соединения») устанавливает основные элементы геометрической формы подготовки кромок под сварку. Рассмотрим эти элементы на примере стыкового соединения.
Угол скоса кромки а — острый угол между плоскостью скоса кромки и плоскостью торца.При установке скоса обеих кромок в пределах а = 25 ± 2°. При скосе одной кромки угол скоса принимается равным а = 45 ± 2°. Скос кромок может быть односторонним и двусторонним, прямолинейным и криволинейным.
Угол режущих кромок (3) образован скошенными поверхностями двух соединяемых частей изделия. Угол разделки кромок выполняют при толщине металла более 3 мм. Отсутствие угла разделки кромок может привести к непровару участка сварного соединения, а также к перегреву и прогоранию металла.
Рис. 1. Элементы подготовки кромок под сварку:
а — угол скоса кромки; P — угол режущих кромок; в — притупление кромки; в — зазор между стыкуемыми кромками; s — толщина листа (детали) —
При сварке толстого металла угол разделки кромок позволяет производить сварку отдельными слоями, что улучшает структуру шва и снижает сварочные напряжения и деформации.
Притупление кромки (с) представляет собой неперекошенную часть торца кромки, подлежащей сварке.Выполняется для обеспечения стабильного процесса сварки при выполнении первого (корневого) слоя шва. Отсутствие притупления кромок облегчило бы течение металла при сварке (прожог). Величину притупления кромки чаще всего принимают равной 2 ± 1 мм.
Зазор между соединяемыми кромками (в) обеспечивает полное проплавление по сечению шва при наложении первого (корневого) слоя шва. Отсутствие зазора может привести к непровару корня шва и способствовать увеличению сварочных напряжений.Большое значение для качества сварки имеет равномерность зазора по всей длине шва, т. е. соблюдение параллельности свариваемых кромок. Величину зазора чаще всего принимают равной 2 ± 1 мм.
Сварку стыковых соединений деталей неодинаковой толщины с разностью, не превышающей значений, указанных в таблице, следует производить так же, как и деталей одинаковой толщины; конструктивные элементы подготовленных кромок и размеры сварного шва следует выбирать большей толщины.
Для плавного перехода одной детали в другую допускается наклонное расположение поверхности шва.
Если разница в толщине свариваемых деталей больше значений, указанных в таблице, скосы на одной детали и более должны выполняться с одной или двух сторон на толщину тонкой детали.
Рис. 2. Сварка и подготовка кромок листов разной толщины:
а — наклонное расположение поверхности шва; б — односторонний скос листа; в — двухсторонний скос листа; г — скос листа с последующей разделкой кромок
При этом конструктивные элементы подготовленных кромок и размеры сварного шва следует выбирать меньшей толщины.
Скос кромки (листа) регулирует плавный переход от толстой свариваемой детали к тонкой, снижая напряжения в сварной конструкции.
В стыковых, тавровых и угловых соединениях толщиной более 16 мм, выполненных в монтажных условиях, допускается увеличение зазора между соединяемыми кромками (в) до 4 мм с одновременным уменьшением значения угла скоса краев (а) на 3°.
Допускается смещение свариваемых кромок перед сваркой относительно друг друга, не более:
0.5 мм — для деталей толщиной до 4 мм;
1,0 мм — для деталей толщиной 4-10 мм;
, но не более 3 мм — для деталей толщиной 10-100 мм.
ОТРЕЗ ДЛЯ СВАРКИ
Обрезка кромки — придание свариваемым кромкам необходимой формы.
Разделка кромок под сварку выполняется с целью обеспечения:
Провара по всей толщине свариваемых элементов;
Доступ сварочного инструмента к корню шва.
По форме разделки кромок под сварку различают сварные соединения без разделки кромок, с отбортовкой и с разделкой кромок под сварку. Кроме того, сварные соединения с разделкой разделки подразделяют на сварные соединения с односторонней разделкой одной или двух кромок (односторонняя разделка одной или двух кромок) и сварные соединения с двусторонней разделкой одной или двух кромок (двусторонняя разделка кромок). канавка одной или двух кромок).
При выборе формы разделки кромок следует учитывать, что наиболее экономичным является сварное соединение без скоса кромок.В случае разделки кромок более простой в исполнении по сравнению с П-образной является разделка кромок с прямыми скошенными кромками (V, К, Х-образные). По сравнению с односторонней разделкой кромок К- и Х-образная двусторонняя более технологичны. Однако К- и Х-образные двухсторонние могут быть реализованы, если доступ к сварочному инструменту возможен с обеих сторон изделия.
Элементы конструкции в виде режущих кромок.
Конструктивные элементы формы разделки кромок зависят от конструктивных особенностей свариваемых элементов, а также от диаметра материала электрода (размеры разделки кромок должны обеспечивать доступ электрода или сварочная проволока к корню шва).
Форма режущих кромок характеризуется следующими основными конструктивными элементами: зазором В, притуплением С, углом наклона кромки β и углом наклона режущих кромок α.
Угол скоса β.
Скос кромки — прямой срез свариваемой кромки.
Угол скоса — острый угол между плоскостью скоса кромки и плоскостью торца.
Угол скоса β варьируется от 30 ± 5 до 10 ± 5 градусов. При резке одной кромки угол скоса кромки может составлять 45 градусов.
Угол кромки — угол между скошенными кромками свариваемых деталей. Угол режущих кромок α = 2 β. Угол режущих кромок выполняют для обеспечения доступа электрода к основанию шва.
Тупая кромка — нескошенная часть торца кромки, подлежащая сварке. Цель притупления – обеспечить правильное формирование сварного шва и предотвратить прижоги в корне шва. Тупая кромка ОТ обычно 2 мм ± 1 мм.Иногда из-за конструктивных особенностей сварного соединения величину притупления можно принять равной нулю (С = 0). В этом случае необходимо предусмотреть технологические мероприятия, исключающие возникновение прожога (футеровочная сварка, сварка под флюсом, укладка сварного шва, применение замкового соединения).
Зазор — кратчайшее расстояние между кромками деталей, собираемых под сварку. Зазор б обычно равен 1,0 — 3 мм, так как при принятых углах разделки необходимо наличие зазора для проплавления корня шва, но в ряде случаев при той или иной технологии зазор может быть нулевой или достигать 8-10 мм и более.Если зазор b = 0, то выполненную сварку называют сваркой без зазора, если b ≠ 0 — сваркой с зазором (или по зазору).
БЕЗ КРОМКИ Двутавровая (без фаски) | С КРОМКОЙ КРАЙ (без скошенных кромок) |
Односторонняя резка Односторонняя резка прямая фаска прямая фаска одна кромка две кромки | |
Кромочная форма |
Кромки нарезаны для полного провара заготовки по сечению, что является одним из условий равнопрочности сварного соединения с основным металлом. По формам подготовки кромок под сварку различают V, К, Х — образные
При ручной электродуговой сварке основными видами сварных соединений являются стыковые, угловые, тавровые и нахлесточные соединения. Стыковые соединения в зависимости от толщины свариваемых листов подразделяются на несколько видов. Для листов толщиной от 1 до 3 мм применяют стыковые соединения с отбортовкой кромок.
Листы толщиной от 1 до 8 мм свариваются между собой без подготовки кромок. Для листов толщиной от 1 до 6 мм применяют одностороннюю сварку, иногда с оставшимися или съемными подкладками; листы толщиной 3-3.5 мм до 8 мм приварены с обеих сторон. Предельная толщина металла в этом случае определяется возможностью проплавления всего сечения с одной или двух сторон. Для обеспечения провара всего сечения при сварке листов большей толщины делают скос кромок, называемых разделочными кромками.
Для металла толщиной от 3 до 26 мм предусмотрена так называемая V-образная односторонняя или двусторонняя фаска. С этими соединениями также могут использоваться остающиеся или съемные накладки.Металл толщиной от 12 до 40 мм можно сваривать К-образным стыком, при котором производится двусторонняя фаска только одной кромки. Для толщин от 20 до 60 мм в целях экономии наплавленного металла может применяться П-образное соединение с криволинейным скосом одной или двух кромок.
Для металла толщиной от 12 до 60 мм делают Х-образную заготовку ксмок, при которой делается двусторонний скос каждой кромки. При Х-образном стыковом соединении для металла толщиной от 30 до 60 мм может применяться и двухсторонний криволинейный скос двух кромок.Основными конструктивными элементами разделки являются: угол режущих кромок, притупление и зазор на стыке. Угол кромок для V- и Х-образных соединений принимают равным 60°, а для V-образного соединения со скосом одной кромки, а также для К-образного соединения — равным 50°.
Размер несрезанной части или так называемого притупления 1-2 мм, а зазор принимают 2 мм. Угловые соединения с толщиной металла не более 3 мм могут быть фланцевыми. При больших толщинах, в зависимости от вида углового соединения и толщины свариваемых листов, сварку производят без фаски, а также с односторонней или двусторонней фаской кромок вертикального листа.
Тавровые соединения, применяемые для металла толщиной от 2 до 60 мм, также выполняются без фаски или со фаской кромок вертикального листа. Соединения без скоса кромок применяются для толщин от 2 до 30 мм. Такие стыки свариваются как односторонними, так и двусторонними швами. При этом зазор может быть от 0 до 4 мм. Размер ножки выбирается в зависимости от толщины листов и условий работы.
Соединения с односторонним скосом кромок выполняются при толщине листа от 4 до 26 мм и двусторонним скосом для металла толщиной от 12 до 60 мм.Угол режущих кромок принимают равным 50°, а притупление от 1 до 2 мм, величина зазора обычно около 2 мм. Нахлесточные соединения бывают односторонними или двусторонними. Швы сплошные или прерывистые. Соединения внахлест также могут быть выполнены с круглыми или удлиненными отверстиями.
- Правка металла и резка деталей
- Зачистка деталей: нюансы
- Подготовка кромок под сварку
- Гибка металла: рекомендации
- Основные требования к сборке конструкции перед сваркой деталей
Перед сваркой металлических поверхностей их необходимо хорошо очистить.Подготовка металла к сварке – важнейший этап, качественное выполнение которого позволит получить прочный, надежный шов.
Во избежание дефектов сварки металлические предметы перед сваркой необходимо тщательно очистить от ржавчины и грязи.
При контакте с воздухом металл реагирует с кислородом с образованием оксидов. Появляется ржавчина и другие загрязнения, которые приводят к образованию различных дефектов сварки. Также нежелательно попадание масла, окалины, влаги в место сварки.Кроме того, для плотного прилегания металлических листов их необходимо предварительно расправить, если это необходимо. Наконец, необходима разметка деталей, резка и подготовка кромок листов для последующей сварки закладных деталей и других соединений.
Правка металлических и режущих деталей
Править металл можно с помощью специальных валов, предназначенных для этого, или вручную. Ручное редактирование требует кувалды или пресса. Осуществляется на правильных плитах из чугуна или стали.На прессах выравниваются швеллеры, двутавры и уголки.
В результате разметки и последующей резки определяется будущая конфигурация готовой детали. Разметка или наметка требует предварительного грунтования поверхности металлического листа. Отличие их в том, что маркировка относится к индивидуальному производству, а маркировка – к промышленному. Для подготовки к массовому раскрою листов используется шаблон из фанеры или металла. Использование шаблона при разметке называется наметкой.
Механически операция выполняется при необходимости получения прямых резов. В основном такая резка осуществляется ножницами, если нужен прямой рез, а толщина листов не превышает 20 мм. Для производства в промышленных масштабах устанавливаются гильотинные ножницы с длиной ножа 1-3 м или пресс-ножницы с ножами до 70 см. Лист толщиной менее 6 мм можно резать по криволинейным линиям роликовыми ножницами, для чего используют газокислородную или плазменно-дуговую резку, которая применяется для легированных сталей и цветных металлов.По отношению к ним может применяться газовая флюсовая резка. Холодная резка прутков любого сечения осуществляется круглыми зубчатыми или фрикционными пилами.
Вернуться к содержанию
Детали зачистки: нюансы
Поверхности основного и присадочного металлов тщательно очищают от маслянистых жировых пятен, следов влаги, ржавчины, окалины и всевозможных загрязнений неметаллического происхождения. Подготовка металла к сварке не может обойтись без этого важного этапа.
Малейшие остатки таких явлений провоцируют появление в швах пор, включений шлака.Трещины, которые могут образоваться в результате этого, снижают надежность сварки, ее прочность и плотность.
Вернуться к содержанию
Подготовка кромок под сварку
Для получения максимально прочного сварного шва следует подготовить и кромки деталей. Они должны иметь определенную геометрическую форму, включающую в себя угол среза, притупление, зазор, длину фаски, если листы имеют разную толщину.
Разделку кромок под сварку под углом следует выполнять, если металлический лист имеет толщину более 3 мм.
В противном случае шов может не полностью провариться по всему сечению, даже при сварке мелких деталей. Кроме того, при попытке добраться до дальних слоев уже сваренный металл перегреется и сгорит.
Если разделки нет, то необходимо увеличить сварочный ток. При его наличии детали свариваются послойно, с малым сечением, благодаря чему соединение получает качественную структуру, деформации и напряжения в металле сводятся к минимуму.
Правильно подобранный зазор обеспечивает полное проникновение металла в соединение.
Наличие фаски позволяет сделать плавный переход от одной детали к другой, если они имеют разную толщину. В то же время его длина влияет на возникающее напряжение в конструкции или его отсутствие.
Острые кромки при сварке образуют неустойчивую конструкцию, из-за чего детали могут смещаться относительно друг друга, образуются прижоги, деформируется шов, возникают дополнительные напряжения, сварное соединение становится менее прочным.
Во избежание этого и обеспечения более комфортных условий работы при формировании корневого шва края затупляются. При смещении стыков и нахлестов кромкам придают наиболее подходящую геометрическую форму сечения в соответствии с ГОСТами или техническими регламентами. Это особенно важно при сварке закладных деталей.
Кромки под сварку обрабатывают механически, на фрезерных, продольно-строгальных и кромкорезных станках, газокислородным пламенем.Пропеллент, ацетилен и другие вещества могут быть горючими и вызывать пламя. Если работы не много, то достаточно пневматического зубила. Кроме того, на этом этапе работают на токарных станках (для подготовки кромок с торца трубы). Для работы с цветными металлами или нержавеющей сталью используется плазменная резка.
После кислородной резки завершается механическая обработка, особенно если шов должен быть отличного качества. Таким образом удается избежать попадания мелких зерен, провоцирующих образование микротрещин, воздуха и других дефектов, приводящих к разрушению шва.В сооружениях, возводимых на ответственных строительных площадках, это недопустимо.
Рис. 7С Форма разделки кромок под сварку
Параметры резки – важная характеристика, от которой зависит качество шва и общие эксплуатационные характеристики изделия. Поэтому для каждого способа сварки и группы изделий нормативные документы определяют требования к выполнению разделки кромок под сварку.
Форма режущих кромок характеризуется следующими основными конструктивными элементами: угол скоса β; угол кромки α = 2 β; притупление С; клиренс б.
Фаска — прямолинейный косой срез привариваемой кромки.
Угол скоса β — острый угол между плоскостью скоса кромки и плоскостью торца.
Угол разделки (раскрытия) кромок α — угол между скошенными кромками свариваемых деталей.
Угол косых кромок β с прорезными канавками варьируется от 0 до 8 градусов.
Стандартный угол разделки кромок α в зависимости от способа варки и вида сварного шва варьируется от 60±5 до 20±5 градусов. Угол разделки кромок выполняют для обеспечения доступа электрода к основанию формируемого шва.
Тупая кромка ИЗ — нескошенная часть торца привариваемой кромки.
Притупление кромок С обычно составляет 2 мм ± 1 мм. Цель притупления — обеспечить формирование шва без образования прижога (см. Дефекты сварки) .Иногда из-за конструктивных особенностей сварного соединения величину притупления можно принять равной нулю (С = 0). В этом случае необходимо предусмотреть технологические мероприятия, исключающие возникновение прожога (футеровочная сварка, сварка под флюсом, укладка сварного шва — см. Выполнение сварных швов ).
Зазор б — кратчайшее расстояние между кромками деталей, собранных под сварку .
Зазор b обычно равен 1.от 0 до 3,0 мм. При принятых углах разделки кромок необходим зазор для обеспечения провара на всю толщину свариваемых элементов в результате затекания расплавленного металла между их кромками. В некоторых случаях при той или иной технологии зазор может быть нулевым или достигать 8-10 мм и более. Если зазор b = 0, то выполненную сварку называют сваркой без зазора, если b ≠ 0 — сваркой с зазором (или по зазору).
R Предназначен для обеспечения плавного сопряжения вертикальной и горизонтальной секущих плоскостей.Величина R зависит от геометрических особенностей режущего профиля.
Форма разделки кромок определяет количество дополнительного металла, необходимого для заполнения разделки, а значит, и производительность сварки. Так, например, Х-образная разделка кромок по сравнению с V-образной позволяет уменьшить объем наплавленного металла в 1,6 — 1,7 раза.
Форма разделки кромок, а также размеры параметров разделки (профиль разделки кромок, угол разделки кромок, величина зазора и притупления) зависят от свариваемый материал, толщина свариваемых элементов и способ сварки.Параметры кромки – важная характеристика, от которой зависит качество шва и общие эксплуатационные характеристики изделия. Поэтому для каждого способа сварки и группы изделий нормативные документы определяют требования к выполнению разделки кромок под сварку.
(PDF) Сварка кольцевых соединений промысловых трубопроводов с внутренним антикоррозионным поверхностным слоем
Содержание данной работы может быть использовано на условиях лицензии Creative Commons Attribution 3.0.Любое дальнейшее распространение
этой работы должно содержать указание автора(ов) и название работы, цитирование в журнале и DOI.
Опубликовано по лицензии IOP Publishing Ltd
EMMFT 2019
Журнал по физике: конференция серии 1614 (2020) 012059
IOP Publishing
DOI: 10. 1088 / 1742-6596 / 1614/1 / 012059
1
Сварка кольцевых соединений промысловых трубопроводов с внутренним
коррозионностойким наплавленным слоем
Елагина О.Ю.1, Волков И.В.1*, Буклаков А.Г.1, Наконечная К.В. [email protected]
Аннотация. Целью данной работы явилось изучение вопросов обеспечения нормативных показателей качества
монтажа сварных труб промысловых трубопроводов с наплавленным слоем из высокохромистой стали
. Исследования проводились на трубах из стали 09Г2С категории прочности К48
диаметром 258 мм с толщиной стенки 6 мм. Формирование наплавленного слоя
на внутренней поверхности концов труб выполняли электродуговой сваркой
в защитных газах проволокой СВ-12Х13 диаметром 1.2 мм. Сварку кольцевых стыков труб
выполняли электродами ЛБ-52У типа Э50А по ГОСТ 9467 по
по разработанной технологии. Экспериментальная отработка технологии сварки
Оценка качества получаемых швов и их коррозионной стойкости оценивалась
с применением неразрушающих и разрушающих методов контроля. Результаты исследований
показали возможность получения коррозионностойкого сварного соединения с соответствующими стандартами качества.
Определены нормативные требования к сварному соединению труб с внутренним поверхностным слоем
, которые могут быть использованы при реализации проектов строительства промысловых
трубопроводов с данным исполнением. Показано, что для обеспечения нормативных значений механических
свойств сварных соединений труб с внутренним наплавленным слоем требуется разработка
дополнения к существующей технологии сварки по подготовке труб перед сваркой и
контролю температуры до и сопутствующей сварке. нагрев, во избежание охрупчивания металла корневого шва
при его легировании.
1. Введение
Одной из наиболее частых причин выхода из строя промысловых трубопроводов является углекислотная коррозия [1]. Использование труб
из углеродистых и низколегированных сталей с внутренним полимерным покрытием взамен труб
из коррозионностойких высоколегированных сталей значительно удешевляет строительство. Однако имеет
ряд трудностей, связанных с обеспечением антикоррозионной защиты внутренней поверхности кольцевых
сварных соединений.Эта проблема в настоящее время решается различными способами [3,4], и одним из наиболее перспективных способов обеспечения длительной антикоррозионной защиты соединений
является применение труб со слоем коррозионностойкой стали
, наплавленным на внутренней поверхности концевых секций.
Высоколегированное металлическое покрытие на концах труб должно защищать внутреннюю поверхность на участке
между антикоррозионным полимерным покрытием и монтажным швом, а также обеспечивать легирование корня шва
до добиться необходимой коррозионной стойкости.
Помимо наплавки, существует ряд других технологий защиты сварных соединений труб
, создающих в зоне сварного шва коррозионно-стойкий слой, такие как применение подкладочных колец, наконечников, наплавки
и напыление. Однако наплавка является более технологичным и легко реализуемым методом подготовки труб в заводских условиях, а также лучше подходит для неразрушающего контроля после сварки не-
Китай ГОСТ/ 12821-80 Пн1.

Мы обещаем обменять наш лучший качественный фланец из углеродистой стали, фланец из металлической трубы стандарта Ansi, тройник из углеродистой стали и внимательное обслуживание для успеха нашего сотрудничества со всеми клиентами! И индивидуальные заказы приемлемы. Только придавая большое значение международному обмену и сотрудничеству и осваивая самую передовую информацию в мире, компания может добиться быстрого развития лучше и быстрее.Наша продукция продается по всему миру и пользуется популярностью у новых и старых клиентов. Мы искренне надеемся установить хорошие отношения сотрудничества с нашими клиентами, и предоставить им качественную и удовлетворительную продукцию является нашей вечной целью.
Технические характеристики
● Фланцы для ковки и литья фланца
ГОСТ 12820-80 Пластинчатый фланец, 12821-80 Сварочная шея фланца
DN10-DN1600
PN6, PN10, PN16, PN25, PN40, PN63
ГОСТ Фланцем
Название продуктов | ГОСТ 12820-80 плоский фланец | |
Индивидуальный пакет и стандартный пакет | Фланцы в меньшем размере будут упакованы в фанерные чехлы, более крупные фланцы размера будут упакованы на поддоны с полиэтиленовой пленкой и упаковочным поясом. | |
Материал 9013 | 16мн, 20 #, 321 нержавеющая сталь, сплав сталь | |
стандарт | Gost Standard | |
тип | Шел Фланец из стального листа | |
Маркировка | По требованию заказчика | |
Срок поставки | 90 | |
Трансфер | FOB или FCA, товары могут быть доставлены морем или поездом в Россию. | |
Размер | DN15-DN2000 |
Наша фирма имеет отличную программу гарантии, которая уже была создана для ГОСТ / 12821-80 Pn1.6 MPa Dn125 20mn Фланец кованый с приварной горловиной. Мы искренне приветствуем отечественных и зарубежных клиентов посетить нашу компанию и поддерживать с нами долгосрочные контакты и сотрудничество. Искренне надеемся на взаимовыгодное сотрудничество!
Стальные конструкции Язык: английский | Фундаментные болты. Структура и размеры Язык: английский | Единая система конструкторской документации.Эксплуатационные документы Язык: английский | Болты с шестигранной головкой. Классы продукции А и В Язык: английский | Винты с шестигранной головкой. Язык: английский | Ширерс.Общие технические требования. Методы испытаний Язык: английский | Управление рисками. Анализ рисков технологических систем Язык: английский | Сталь. Методы испытаний и оценки макроструктуры Язык: английский | Основные нормы взаимозаменяемости.Эвольвентные шлицевые соединения с углом профиля 30°. Размеры, допуски и измеряемые размеры Язык: английский | Неразрушающий контроль. Сварные соединения. Язык: английский | Нефть и нефтепродукты. Методы отбора проб Язык: английский | Маркировка химических веществ.Общие требования Язык: английский | Высокопрочные конструкционные болтовые соединения для предварительной нагрузки. Общие требования Язык: английский | Технологический трубопровод. Стандарт на напряжения, вибрацию и сейсмический анализ Язык: английский | Базовая норма взаимозаменяемости.Цилиндрические передачи для общего и тяжелого машиностроения. Язык: английский | Клапаны трубопроводные. Методы контроля и испытаний Язык: английский | Неразрушающий контроль. Метод магнитопорошкового контроля. Стандартные технологические процессы Язык: английский | Составление и оформление паспорта безопасности химической продукции Язык: английский | Плиты прямоугольные для машин и аппаратов.Размеры Язык: английский | Вредные вещества. Классификация и общие требования безопасности Язык: английский |
Оценка влияния термических методов разделительной резки металла на качество сварки
[1]
Ю. А. Пыкин, С.В. Анахов, И.Ю. Пышминцев, Д.В. Овчинников, В.А. Элькин, Об эффективности применения плазменных технологий при резке трубчатых металлопродукции, Прокатное производство, 1 (2014) С. 38-45.
[2] СР 86.13330. 2014, Свод правил. Основные трубопроводы. Обновленная редакция СНиП III-42-80. Москва, проспект, (2016).
[3]
СТО-СА-03-002-2009, Правила проектирования, изготовления и монтажа вертикальных цилиндрических стальных резервуаров для нефти и нефтепродуктов, Коллектив авторов, Ассоциация Ростехэкспертиза, Москва, (2009).
[4] РД 34. 15. 132-96, Сварка и контроль качества сварных соединений металлоконструкций зданий при возведении промышленных объектов, НПО ОБТ, Москва (2001).
[5]
С.В. Анахов, К. Сингеп, Ю.А. Пыкин, С.А. Шакупов, Исследование поверхности реза при терморазделительной резке стали 09Г2С, Сварочное производство, 7 (2007) 17-21.
[6] А.К. Тингаев, А.К. Губайдулин, И.А. Ильин, Исследование влияния термической резки на микроструктуру и химический состав кромок заготовок из стали марок С345, С390, Procedia Engineering, 150 (2016) 1783-1790.
DOI: 10.1016/j.proeng.2016.07.171
[7]
Р. Янко, П. Элештос, Моделирование теплового поля ремонтной резьбы в отверстии в крышке сосуда высокого давления путем сварки с использованием sysweld, (2017).
DOI: 10.1007/978-3-319-44087-3_25
[8] Дж.Б. Джи, Дж.З. Чжан, Л. Чжан, Численное моделирование и испытания стали 45, сваренной на основе источника тепла Гаусса, (2014).
[9]
Я. Г. Ширшов, В.Н. Котиков, Плазменная резка, Машиностроение, Ленинград, (1987).
[10] ГОСТ 23118-2012, Конструкции строительные стальные. Общие технические условия, Стандартинформ, Москва, (2012).
[11]
СП 70. 13330. 2012, Несущие и ограждающие конструкции, Актуальная редакция СНиП 3. 03. 01-87, Проспект, Москва, (2016).
[12] ГОСТ 27772-2015, Прокат для строительных металлоконструкций. Общие технические условия, Стандартинформ, Москва, (2015).
[13]
С.В. Анахов, С.В. Гладковский, С.В. Лепихин, Ю. В.А. Пыкин, А.В. Матушкин, Механические и технологические свойства сварных соединений, полученных после применения плазменной резки, Сварочное производство, 6 (2016) 8-14.
DOI: 10.1080/09507116.2016.1268761
[14] С.В. Анахов, Ю.А. Пыкин, Д.А. Голотвин, А.В. Матушкин, Анализ прочности и пластичности сварных соединений, полученных с применением технологии плазменной резки, Сварка и диагностика, 1 (2016) С. 37-40.
ГОСТ 10705-80 ЭЛЕКТРОСВАРНЫЕ СТАЛЬНЫЕ ТРУБЫ Поставщики и производители — Фабрика Китая
Характеристики ГОСТ 10705-80 ЭЛЕКТРОСВАРНЫЕ СТАЛЬНЫЕ ТРУБЫ: высокая скорость сварки, небольшая зона термического влияния сварки, сварка без очистки заготовки, сварка тонкостенная труба и сварка металлической трубы.
Транзисторная высокочастотная машина энергосберегающая и экологически чистая. Он безопасен в использовании, имеет долгий срок службы и отличное качество сварки. Ему глубоко доверяют в трубной и других отраслях промышленности. изменять.
Производственный процесс в основном зависит от ассортимента продукции. От сырья до готовой продукции требуется ряд процессов. Для выполнения этих процессов требуется различное механическое оборудование и устройства для сварки, электрического контроля и тестирования.Эти устройства и устройства основаны на различных технологических требованиях. Разнообразие разумных компоновок, типичные процессы сварки высокочастотными сварными трубами: продольная резка-размотка полосы-выравнивание головки и хвоста-срезка полосы-стыковая сварка-накопление петли-формовка-сварка-удаление заусенцев-проклейка-дефектоскопия-обрезка на лету — предварительная проверка — Выпрямление стальных труб — Обработка секций труб — Гидравлические испытания — Дефектоскопия — Печать и нанесение покрытий — Готовая продукция.
Влияние операции на качество сварки при производстве труб с высокочастотной сваркой
Подведенное тепло?
Поскольку один из основных параметров процесса сварки, то есть сварочный ток (или температуру сварки), трудно измерить, вместо этого используется подводимое тепло, а подводимое тепло может быть выражено выходной мощностью генератора :
N = Ep · Ip
Где N — выходная мощность, кВт;
Эр-экранное напряжение, кВ;
Поток IP-экрана, A [1] ?.
После определения генератора, катушки индуктивности и резистора также определяется КПД лампы генератора, выходного трансформатора и катушки индуктивности. Изменение подводимой мощности примерно пропорционально изменению подводимого тепла.
Когда подводимого тепла недостаточно, нагретая кромка не может достичь температуры сварки, а твердая структура остается и не может быть сварена, образуя сварочную трещину. Когда подводимое тепло велико, нагретая кромка превышает температуру сварки и подвержена перегреву или даже перегреву. Растрескивание происходит после приложения силы; когда подводимое тепло слишком велико, температура сварки слишком высока, что приводит к разрушению сварного шва, в результате чего расплавленный металл выплескивается и образует отверстия. Температура сварки расплавом обычно составляет 1350 ~ 1400 ℃.
Давление сварки
Давление сварки является одним из основных параметров процесса сварки. После нагрева двух кромок трубной заготовки до температуры сварки под действием силы выдавливания образуется общее зерно металла, то есть кристаллизуются друг с другом для получения сварки.Сварочное давление влияет на прочность и ударную вязкость сварного шва. Если приложенное сварочное давление невелико, металлические свариваемые кромки не могут быть полностью прижаты, а оставшиеся неметаллические включения и оксиды металлов в сварном шве трудно удалить из-за низкого давления. В это время большая часть металла, достигшего температуры сварки, была выдавлена, что не только снизило прочность сварного шва, но и вызвало дефекты, такие как чрезмерные внутренние и внешние заусенцы или сварка внахлест. Поэтому оптимальное давление сварки, подходящее для него, должно быть получено на практике по разным разновидностям и спецификациям. Согласно практическому опыту, давление сварки на единицу обычно составляет 20 ~ 40 МПа.
Из-за возможных допусков по ширине и толщине трубной заготовки, а также колебаний температуры и скорости сварки возможны изменения усилия выдавливания при сварке. Количество сварочной экструзии обычно регулируется путем регулировки расстояния между экструзионными валками, а также может регулироваться разницей между окружностью трубы до и после экструзионных валков.
угол раскрытия
Угол раскрытия относится к углу между двумя краями заготовки трубы перед прижимным роликом. Величина угла раскрытия связана со стабильностью процесса обжига и оказывает большое влияние на качество сварки.
При уменьшении угла раскрытия расстояние между краями также уменьшается, что усиливает эффект близости. При тех же условиях температура нагрева кромок может быть увеличена для увеличения скорости сварки. Если угол открытия слишком мал, расстояние от точки встречи до центральной линии прижимного ролика будет увеличено, что приведет к тому, что кромка не будет обжиматься при самой высокой температуре, что снизит качество сварки и повысит энергопотребление. . ?
Реальный производственный опыт показывает, что продольное положение подвижного направляющего ролика можно регулировать для регулировки угла раскрытия, который обычно колеблется в пределах от 2 до 6°. Если направляющий ролик невозможно отрегулировать в продольном направлении, для регулировки угла раскрытия можно использовать толщину направляющего кольца или закрытую форму отверстия.
Требования к геометрии и форме трубной заготовки
ГОСТ 10705-80 ТРУБЫ СТАЛЬНЫЕ ЭЛЕКТРОСВАРНЫЕ Геометрия заготовки
Отклонение ширины и толщины трубной заготовки изменяет температуру нагрева и величину выдавливания кромки. Квалифицированный продукт должен требовать, чтобы ширина и толщина трубной заготовки находились в пределах допустимого диапазона.
Форма трубы и форма соединения
Если на краю заготовки трубы имеются изгибы, серповидные изгибы и гофры, они будут отклоняться от центра отверстия при прохождении формовочной машины, вызывая изгиб двух сторон полосы .Плохая регулировка ролика также может вызвать такие дефекты, как прогиб полосы или деформация трубной заготовки, приводящие к последствиям, влияющим на качество сварки или вообще к невозможности сварки.
При сварке двух концов трубной заготовки все толщины двух концов должны быть соединены. Два края заготовки трубы должны быть прямыми и параллельными. При разрезании полосы зазор между режущими кромками диска слишком велик или износ лезвия значителен, что приводит к слишком большому заусенцу на кромке полосы, и после сварки легко образуются трещины.
Качество кромки полосы
Качество кромки полосы влияет на результат нагрева высокочастотной индукцией и, следовательно, на качество сварного шва. После того, как трубчатая заготовка сформирована, следите за параллельностью двух краев полосы, иначе возникнет эффект острого угла, что повлияет на качество сварного шва.
видов швов и соединений
В процессе выполнения сварочных работ различные соединения. Сварочные швы способны соединять не только металлы, но и другие разнородные материалы. Состыкованные в единое целое элементы представляют собой соединение, которое можно разделить на несколько секций.
Зоны сварки
Соединение, полученное в процессе сварки, делится на следующие зоны:
- Место сплавления — граница между основным металлом и металлом полученного шва.В этой зоне находятся зерна, отличающиеся по своей структуре от состояния основного металла. Это связано с частичным расплавлением в процессе сварки.
- Зона термического влияния – это зона основного металла, не подвергшаяся плавлению, хотя ее структура была изменена в процессе нагрева металла.
- Сварка — участок, образовавшийся при кристаллизации в процессе охлаждения металла.
Виды сварных соединений
В зависимости от расположения соединяемых изделий друг относительно друга соединения подразделяются на следующие виды:
- Встык.Стыковка элементов конструкции осуществляется в одной плоскости торцами друг к другу. В зависимости от разной толщины соединяемых деталей торцы могут перемещаться относительно друг друга по вертикали.
- Косынка. В этом случае выравнивание торцов производится под углом. Процесс сварки осуществляется на прилегающих кромках деталей.
- Соединение внахлест. Детали для сварки располагаются параллельно с частичным нахлестом.
- Концевое соединение. Свариваемые элементы выравниваются параллельно друг другу и состыковываются по концам.
- Тавровая связь.
При этом конец одной детали прилегает к стороне другой под углом.
Сварные соединения также характеризуют типы сварных швов, которые можно квалифицировать по определенным критериям.
Значения сварки
Существует несколько параметров, по которым можно охарактеризовать все полученные сварочные швы:
- ширина — размер между кромками шва, которые проведены видимыми линиями сплавления;
- корнем шва является его изнаночная сторона, расположенная на максимальном расстоянии от лицевой части;
- выпуклость — определяется в наиболее выпуклой части шва и обозначается расстоянием от плоскости основного металла до границы наибольшего выступа
- вогнутость — этот показатель актуален, если она имеет место в шве, т.к. факт, является дефектом; этот параметр определяется в том месте, где шов имеет наибольший прогиб – от него до плоскости основного металла измеряется размер вогнутости;
- фальцевая ножка — выполняется только в угловом и тавровом стыке; этот показатель измеряется наименьшим расстоянием от боковой поверхности одной свариваемой детали до граничной линии шва на поверхности второй.
Виды швов по способу выполнения
- Швы односторонние сварные. Их выполняют с полным проваром металла по всей длине.
- Двустороннее исполнение. По технологии после односторонней сварки удаляют корень шва, и только после этого производят сварку с другой стороны.
- Однослойные швы. Выполняется однопроходной сваркой с одним наплавленным валиком.
- Многослойные швы. Их применение целесообразно при большой толщине металла, т. е. когда выполнить сварку за один проход не представляется возможным по технологии.Шовный слой будет состоять из нескольких валиков (проходов). Это позволит ограничить распространение зоны термического воздействия и получить прочный и качественный сварной шов.
Виды сварных швов по пространственному положению и длине
Различают такие положения сварки:
- днище, когда шов находится в нижней горизонтальной плоскости, т.е. под углом 0º относительно земли;
- горизонтальный, направление сварки горизонтальное, угол наклона детали может быть от 0º до 60º;
- вертикальное, в этом положении свариваемая поверхность находится в плоскости от 60º до 120º, а сварка ведется в вертикальном направлении;
- потолочный, когда работы ведутся под углом 120-180º, то есть швы располагаются над мастером;
- «в лодочку», это положение относится только к угловым или тавровым соединениям, деталь устанавливается под углом, а сварка ведется «в угол».
Разбивка по длине:
- непрерывные, так выполняются почти все швы, но есть исключения;
- прерывистые швы, встречаются только в угловых соединениях; возможно выполнение двухсторонних швов этого типа как в шахматном, так и в цепном порядке
Кромка
Данная конструктивная особенность применяется в том случае, когда толщина металла, используемого для сварки, больше 7 мм. Кромка – снятие металла с кромок определенной формы. пройти стыковые швы.Это необходимо для того, чтобы получить правильный сварочный шов. Что касается толстого материала, резка необходима для того, чтобы расплавить сначала корень корня, а затем следующими роликами, равномерно заполняя полость, проварить металл по всей толщине. Кромку можно делать, если толщина металла не менее 3 мм. Потому что его более низкое значение приведет к прожогам. Резка характеризуется такими конструктивными параметрами: зазор — R; угол резания — α; притупление — с. Расположение этих параметров показывает чертеж сварного шва.
Кромка увеличивает количество расходных материалов. Поэтому они стараются минимизировать это значение. Делится на несколько видов исполнения:
- V-образный;
- Х-образный;
- Y-образный;
- U-образный;
- щель.
Особенности разделки кромок
Для малых толщин свариваемого материала от 3 до 25 мм обычно применяется односторонняя V-образная резка. Скос может быть выполнен на обоих концах или на одном из них. Металл толщиной 12-60 мм целесообразно сваривать двусторонней Х-образной разделкой.Угол α при резке в форме X, V равен 60º, если скос выполняется только на одной кромке, то значение α будет равно 50º. При толщине 20-60 мм расход наплавляемого металла при П-образной разделке будет наиболее экономным. Фаска также может быть выполнена на одном или обоих концах. Матовость составит 1-2 мм, а зазор будет равен 2 мм. При большой толщине металла (свыше 60 мм) наиболее эффективным способом будет щелевая проточка. Эта процедура очень важна для сварного соединения; влияет на несколько факторов шва:
- производительность соединения;
- прочность и качество сварного шва;
- эконом.
Стандарты и ГОСТы
- Ручная дуговая сварка. Сварочные швы и соединения по ГОСТ 5264-80 включают типы, конструктивные размеры для сварки, покрытые электродами во всех пространственных положениях. Сюда не входят только стальные трубопроводы.
- Сварка стальных трубопроводов. ГОСТ 16037-80 — определяет основные виды, разделку кромок, конструктивные размеры при механизированном способе сварки.
- Сварка трубопроводов из меди и медно-никелевых сплавов.ГОСТ 16038-80.
- Дуговая сварка алюминия. Сварные швы. ГОСТ 14806-80 — Форма, размер, подготовка кромок под ручную и механизированную сварку алюминия и его сплавов, процесс проводят в защитной среде.
- Под флюсом. ГОСТ 8713-79 — сварочные швы и стыки выполняются автоматической или механизированной сваркой на массе, на флюсовой подушке. Растекается по металлу толщиной от 1,5 до 160 мм.
- Сварка алюминия в инертных газах. ГОСТ 27580-88 — стандарт на ручную, полуавтоматическую и автоматическую сварку.
Выполняется неплавящимся электродом в инертных газах с добавкой материала и распространяется на толщину алюминия от 0,8 до 60 мм.
Обозначение сварного шва
Согласно нормативным документам наличие сварных швов показывают на сборочных чертежах или в общем виде. Изображают сварные швы сплошными линиями, если они видны. А если наоборот — то штриховые отрезки. Листочки с односторонними стрелками отводятся от этих строк. Условное обозначение сварных швов выполняется на полке от выноски.Надпись делается над полочкой, если шов с лицевой стороны. В обратном варианте обозначение будет под полкой. Сюда включается информация о шве в следующей последовательности:
- Вспомогательные знаки. На пересечении выноски с полкой может быть значок:
○ — закрытый шов;
┐ — сварной шов выполняется при монтаже.
- Обозначение сварных швов, их конструктивных элементов и соединений ГОСТ.
- Наименование шва по стандарту.
- Метод сварки в соответствии с нормативными стандартами.
- Указана ножка, этот пункт относится только к угловым соединениям.
- Прерывистый шов, если таковой имеется. Это указывает на шаг и расположение сегментов сварки.
- Дополнительные значки вспомогательных значений. Считайте их отдельным пунктом.
Вспомогательное обозначение
Эти клейма наносят также сверху полки, если на чертеже виден сварочный шов, и под ним, когда невидим:
- снятие усиления шва;
- обработка поверхности, которая обеспечит плавный переход к основному металлу, устраняя наплывы и неровности;
- шов выполняется по открытой линии; этот знак распространяется только на видимые на чертеже сварочные швы;
- обработка поверхности сварного соединения.
Для простоты, если все конструкционные швы выполнены по одному ГОСТу, они имеют одинаковые кромочные раскройные и конструктивные размеры, обозначение и стандарт на сварку указываются в технических требованиях. Дизайн может быть не весь, а большое количество одинаковых швов.