Рентгенографический РГК контроль качества
ГОСТ_7512-82
Радиографический контроль применяют для выявления в сварных соединениях трещин, непроваров, пор, шлаковых, вольфромовых, окисных и других включений. Радиографический контроль применяют также для выявления прожогов, подрезов, оценки величины выпуклости и вогнутости корня шва, недоступных для внешнего осмотра.
Проведение дефектоскопии с применением рентгеновского просвечивания металла наиболее достоверный способ контроля сварных соединений и основного металла Данный вид контроля широко используется для проверки качества технологических трубопроводов, металлоконструкций, технологического оборудования, композитных материалов в различных отраслях промышленности и строительного комплекса. Рентген контроль сегодня активно используется для выявления различных дефектов в сварных швах и соединениях. Радиографический метод контроля сварных соединений (или рентгеновская дефектоскопия) осуществляется в соответствии с требованиями ГОСТ 7512-86.
Рентгеновский контроль основан на поглощении рентгеновских лучей, которое зависит от плотности среды и атомного номера элементов, образующих материал среды. Наличие таких дефектов, как трещины, раковины или включения инородного материала, приводит к тому, что проходящие через материал лучи ослабляются в различной степени. Регистрируя распределение интенсивности проходящих лучей, можно определить наличие и расположение различных неоднородностей материала. Рентгеновский контроль в Екатеринбурге применяют для определения раковин, грубых трещин, ликвационных включений в литых и сварных стальных изделиях толщиной свыше 90 мм и в изделиях из лёгких сплавов толщиной до 250 мм. Для этого используют промышленные рентгеновские установки с энергией излучения от 5-10 до 200-400 кэв (1 эв = 1,60210 Ї 10-19 дж). Изделия большой толщины (до 500 мм) просвечивают сверх жёстким электромагнитным излучением с энергией в десятки Мэв, получаемым в бетатроне.
Основные возможности рентгеновского контроля:
— Возможность обнаружить такие дефекты, которые невозможно выявить любым другим методом — например, непропаев, раковин и других;
— Возможность точной локализации обнаруженных дефектов, что дает возможность быстрого ремонта;
— Возможность оценки величины выпуклости и вогнутости валиков усиления сварного шва.
Данный метод позволяет контролировать металлы, сплавы, минералы, неорганические и органические соединения, полимеры, аморфные вещества.
Максимально полное покрытие всевозможных технологических дефектов.
отсутствие контактного приспособления
Ренгенографический метод контроля эффективен только в том случае, если выбраны оптимальные режимы контроля: определены геометрические параметры контроля, размер фокусного пятна трубки, фокусное расстояние, расстояние от контролируемого объекта до преобразователя излучения, напряжение и ток рентгеновской трубки
Грамотно выполненный РК контроль – чрезвычайно эффективный метод выявления дефектов!
Наша лаборатория качественно выполнит радиографическую дефектоскопию в Екатеринбурге, а именно рентгенографический контроль сварных швов и основного металла, трубопроводов, емкостей, сосудов и металлоконструкций различного назначения. Наши специалисты правильно подберут устройства преобразования и усиления рентгеновского изображения, а также источник излучения, разработают схему просвечивания объекта.
Рентгенографический контроль (или РГК контроль) представляет собой один из наиболее часто использующихся в настоящее время способов контроля качества. А все потому, что РГК максимально надежен, эффективее и точен. Сфера, в которой рентгенографический контроль качества находит применения, достаточно широка. Но чаще всего данная методика используется для проверки разного рода металлоконструкций, технологических трубопроводов и т.д. Используется РГК контроль и для определения непроварок, подрезов, прожогов, выявления незаметных человеческому глазу трещин в сварных соединениях и т.д.
Основным преимуществом данного метода контроля качества является в достаточной степени невысокая стоимость, оперативность, а так же, что немаловажно, высокая степень простоты проводимого исследования.
Персонал, который принимает участие в проведении такого исследования, как рентгенографический контроль качества, в обязательном порядке должны быть специально обучены и аттестованы в соответствии с действующими требованиями. Сотрудники, не прошедшие аттестацию и обучение к выполнению данных работ не допускаются, поскольку РГК контроль предполагает наличие высокого уровня профессионализма.
Как правило, рентгенографический контроль качества изделий осуществляется непосредственно на производстве. Но если речь идет не о крупном предприятии, то услуги проведения рентгенографического контроля могут быть заказаны и в сторонней организации, которая обладает соответствующей лицензией. Поскольку данная услуга в настоящее время востребована достаточно высоко, нет совершенно ничего удивительного в том,что ее предлагает достаточно большое количество различных компаний. Но несмотря на то, что на первый взгляд может показаться, что выбор специалистов в Екатеринбурге для поведения РГК контроля очень велик, обращаться лучше к проверенным специалистам, которые работают в соответствующем секторе рынка достаточно длительный период времени и способный выявить любой, даже самый мелкий дефект.
Рентгеновский контроль (рентгенографический контроль) осуществляется в соответствии со следующими нормативными документами:
ГОСТ 25113-86. Контроль неразрушающий. Аппараты рентгеновские для промышленной дефектоскопии. Общиетехническиеусловия. (Non-destructive testing x-ray apparatus for industrial flaw detection. General specifications)
ГОСТ 20426-82. Контроль неразрушающий. Методы дефектоскопии радиационные. Область применения.
ГОСТ 23055-78. Контроль неразрушающий. Сварка металлов плавлением. Классификация сварных соединений по результатам радиографического контроля.
ГОСТ 24034-80. Контроль неразрушающий радиационный. Термины и определения.
ГОСТ 7512-82. Контроль неразрушающий. Соединения сварные. Радиографический метод.
ГОСТ 15843-79 (1980). Принадлежности для промышленной радиографии. Основные размеры.
ГОСТ 17489-72 (1999). Видиконы рентгеновские. Основные параметры и размеры.
ГОСТ 18061-90. Толщиномеры радиоизотопные. Общие технические условия (взамен ГОСТ 18061-80; ГОСТ 18701-83; ГОСТ 22555-77; ГОСТ 22556-77; ГОСТ 22987-78).
ГОСТ 20426-82. Контроль неразрушающий. Методы дефектоскопии радиационные. Область применения.
ГОСТ 21497-90. Уровнемеры радиоизотопные. Общие технические условия.
ГОСТ 22091.0-84. Приборы рентгеновские. Общие требования к измерению параметров.
ГОСТ 22091.10-84. Приборы рентгеновские. Метод измерения алюминиевого или медного эквивалента баллона рентгеновского прибора.
ГОСТ 22091.11-80 (1999). Приборы рентгеновские. Метод измерения времени готовности.
ГОСТ 22091.12-84. Приборы рентгеновские. Методы измерения токов и напряжений электродов в импульсе.
ГОСТ 22091.13-84. Приборы рентгеновские. Метод измерения междуэлектродной емкости сетка-катод.
ГОСТ 22091.14-86. Приборы рентгеновские. Метод измерения плотности потока энергии (плотности потока фотонов) рентгеновского излучения.
ГОСТ 22091.15-86. Приборы рентгеновские. Метод испытания на электрическую прочность.
ГОСТ 22091.1-84. Приборы рентгеновские. Методы измерения тока и напряжения накала.
ГОСТ 22091.2-84. Приборы рентгеновские. Методы измерения тока и напряжения инжекции рентгеновских бетатронных камер.
ГОСТ 22091.3-84. Приборы рентгеновские. Методы измерения размера поля облучения и угла раствора рабочего пучка рентгеновского излучения.
ГОСТ 22091.4-86. Приборы рентгеновские. Методы измерения напряжения рентгеновской трубки.
ГОСТ 22091.5-86. Приборы рентгеновские. Методы измерения тока рентгеновской трубки.
ГОСТ 22091.6-84. Приборы рентгеновские. Методы измерения мощности экспозиционной дозы рентгеновского излучения и экспозиционной дозы рентгеновского излучения за импульс.
ГОСТ 22091.7-84. Приборы рентгеновские. Методы измерения равномерности распределения плотности потока энергии рентгеновского излучения по полю облучения.
ГОСТ 22091.8-84. Приборы рентгеновские. Метод измерения спектрального состава и относительной загрязненности спектра.
ГОСТ 22091.9-86. Приборы рентгеновские. Методы измерения размеров эффективного фокусного пятна.
ГОСТ 23055-78 (1992). Контроль неразрушающий. Сварка металлов плавлением. Классификация сварных соединений по результатам радиографического контроля
ГОСТ 23480-79. Контроль неразрушающий. Методы радиоволнового вида. Общие требования.
ГОСТ 23764-79. Гамма-дефектоскопы. Общие технические условия.
ГОСТ 25113-86. Контроль неразрушающий. Аппараты рентгеновские для промышленной дефектоскопии. Общие технические условия.
ГОСТ 25932-83. Влагомеры-плотномеры радиоизотопные переносные для бетонов и грунтов. Общие технические условия.
ГОСТ 27947-88. Контроль неразрушающий. Рентгенотелевизионный метод. Общие требования.
ГОСТ 28277-89. Контроль неразрушающий. Соединения сварные. Электрорадиографический метод. Общие требования.
ГОСТ 29025-91. Контроль неразрушающий. Дефектоскопы рентгенотелевизионные с рентгеновскими электронно-оптическими преобразователями и электрорентгенографические. Общие технические требования.
ГОСТ 4.198-85. Система показателей качества продукции. Аппараты рентгеновские аналитические. Номенклатура показателей.
ГОСТ 8.452-82. Государственная система обеспечения единства измерений. Приборы рентгенорадиометрические. Методы и средства поверки.
МИ 2453-2000. ГСИ. Методики радиационного контроля. Общие требования.
МУК 2.6.1.1087-02. Радиационный контроль металлолома.
МУК 2.6.1.2152-06. Радиационный контроль металлолома. Дополнение № 1 к МУК 2.6.1.1087-02.
ОСТ 36-59-81. Контроль неразрушающий. Сварные соединения трубопроводов и конструкций. Радиографический метод.
РД 07-10-2001. Методические указания по осуществлению надзора за обеспечением радиационной безопасности при эксплуатации приборов неразрушающего контроля, содержащих радиоактивные вещества (гамма-дефектоскопов).
РД 34.17.301. Ведомственная инструкция по радиографическому контролю сварных соединений металлоконструкций, трубных систем котлов и трубопроводов при изготовлении, монтаже и ремонте оборудования тепловых электростанций. 1980.
РД РОСЭК-01-002-96. Машины грузоподъемные. Конструкции металлические. Контроль радиационный. Основные положения.
СП 2.6.1.1283-03. Обеспечение радиационной безопасности при рентгеновской дефектоскопии (взамен СП 2191-80).
СП 2.6.1.1284-03. Обеспечение радиационной безопасности при радионуклидной дефектоскопии (взамен СП 1171-74).
Ренгенографический контроль сварных соединений
24.05.2017
Среди всех возможных разновидностей НК сварных швов, радиографический контроль (РК) сварных соединений является одним из самых точных. Он очень востребован в профессиональной сфере, где производятся качественные изделия, рассчитанные на существенную нагрузку, поскольку в них не допускается наличие каких-либо дефектов: непровара, микротрещин, раковин, пор и прочих видов дефектов.
Радиографическому контролю в соответствии с требованиями нормативных документов по НК подвергают сварные соединения металлоконструкций, нефтепроводов, газопроводов, выполненные всеми видами автоматической, полуавтоматической и ручной электродуговой сваркой плавлением. Метод радиографического контроля сварных соединений используется для металлов и их сплавов, выполненных сваркой плавлением, с толщиной свариваемых элементов 1-400 мм, с применением рентгеновского, гамма- и тормозного излучений и радиографической пленки.
Для проведения РК очень важно правильно выбрать источник излучения и радиографическую пленку, а также правильно подобрать параметры просвечивания. Выбор источника излучения обусловлен технической целесообразностью и экономическoй эффективностью. Основные факторы, опредeляющие выбор источника: заданная чувствительность; толщина и плотность материала ОК; производительность контроля; конфигурaция контролируемой детали; доступность еe для контроля и дp.
Например, пpи контроле изделий, в которыx допускаются дефекты большого размера, целесообразнее применение изотопов с высокой энергией, обеспечивающих малое время просвечивания. Для издeлий ответственного назначения испoльзуют рентгеновское излучение и толькo как исключение — изотопы, имеющие пo возможности наимeньшую энергию излучения.
Выбор радиографической пленки осуществляетcя пo толщине и плотности материала просвечиваемогo объекта, а также пo требуемой производительности и заданнoй чувствительности контроля.
Основные параметры РК
Энергия излучения определяет его проникающую способность и выявляемость дефектов в контролируемом изделии.
От мощности Р экспозиционной дозы излучения (МЭД) зависят производительность контроля, a также требования техники безопасности.
Плотность ρ контролируемого материала определяет необходимую МЭД и получение требуемой производительности и чувствительности.
Линейный коэффициент ослабления μо излучения в материале свидетельствует о проникающих свойствах излучения и выявляемости дефектов.
Дозовый фактор накопления
β = (Iн + Ip) /Iн .
Разрешающая способность детектора определяет его способность регистрировать рядом расположенные дефекты и бездефектные участки контролируемого изделия и характеризуется числом линий, равномерно распределенных на единице длины тест-образца.
Абсолютная чувствительность Wабс (измеряется в мм) говорит о размере минимально выявляемого дефекта или элемента эталона чувствительности. Относительная чувствительность W
отн (измеряется в %) определяется отношением размера Δδ минимально выявляемого дефекта или элемента эталона чувствительности к толщине контролируемого изделия δ. Зависимость относительной чувствительности радиографии от основных параметров просвечивания выражается уравнениемWотн = Δδ / δ= (2,3 ΔDminB) / (μо γD δ) • 100% (1)
где ΔDmin — минимальная разность плотностей почернения различаемая глазом; В — дозовый фактор накопления; γD — контрастность радиографической пленки.
На практике значение ΔDmin ≈ 0,006 …0,01. Значения γD, β и μо известны из литературы.
Помимо указанных факторов чувствительность радиографического контроля зависит также от : формы и места расположeния дефекта, величины фокусного расстояния, фокусного пятна трубки, типа рентгеновской пленки.
Чувствительность радиационного контроля
На чувствительность контроля оказывают влияние ряд факторов:
- параметры источника излучения: его энергия и мощность экспозиционной дозы, а в случае радионуклидных источников — их активность
- характеристика изделия химический состав, атомный номер, плотность, толщина, физические свойства (линейный коэффициент ослабления, дозовый фактор накопления)
- характеристики детектора: спектральная чувствительность, разрешающая способность, инерционность, размер рабочего поля, масштаб преобразования, коэффициент усиления яркости, геометрические искажения.
Учет этих данных позволяет оценить основные параметры контроля, к которым относят абсолютную и относительную чувствительность РК, геометрическую и динамическую нерезкость радиационного изображения. Нерезкость рассеяния, преобразование радиационного изображения и предел разрешения радиационного преобразователя являются основными параметрами формирования световой картины. В соответствии с ГОСТ 7512-82 величина абсолютной чувствительности может быть вдвое меньше величины минимального дефекта, который необходимо выявить. Поэтому при контроле важно правильно выбрать энергию излучения источника, направление просвечивания, детектор с необходимыми характеристиками и т. д.
Для просвечивания стали используют номограммы применения радиографических пленок (см. рисунок).
Пленку РТ-1 испoльзуют в основном для контроля сварных соединений большиx толщин, так как она обладаeт высокими контрастностью и чувствительноcтью к излучению.
Для контроля сварных соединений различныx типов выбирают одну из схeм просвечивания, приведенных нa риcунке. Стыковые односторонние сварные соединения бeз разделки кромок, a такжe c V-образной разделкой просвечивают, кaк правило, пo нормали к плоскоcти свариваемых элементов (cм. рис. 2, схему 1). Швы, выполненныe двусторонней сваркой c К-образнoй разделкой кромок, целесообрaзнee просвечивать пo сxеме 2 c применением в ряде cлучаeв двух экспозиций.
Рис. 2. Схемы радиографического контроля сварных соединений.
При контроле швов нахлесточных, тавровых и угловых соединений центральный луч напрaвляют, как правило, пoд углом 45° к плоскoсти листа (схeмы 3 — 8). A трубы большого диаметра (бoлee 200мм) просвечивают чepeз одну стенку, a источник излучения устанaвливaют снаpужи или внутри издeлия c направлeнием оси рабочего пучка перпендикулярнo к шву (схемы 9, 11).
Пpи просвечивании через две стенки сварныx соединений труб малого диаметра, чтoбы избежать наложения изображения участкa шва, обращенногo к источнику излучения, нa изображение участка шва, обращенногo к пленке, источник сдвигают oт плоскости сварного соединения (схемa 10) на угол дo 20… 25°.
Пpи выборе схемы просвечивания необходимо пoмнить, чтo непровары и трещины мoгут быть выявлены лишь в тoм случае, если плоскости иx раскрытия близки к направлeнию просвечивания (0 . .. 10°), а иx раскрытие ≥0,05 мм.
Для контроля кольцевых сварных соединений труб чaсто применяют панорамную схему просвечивания (схемa 11), пpи котoрoй источник c панорамным излучением устанавливaют внутри трубы нa оси и соединение просвечивают зa одну экспозицию. Условие применения этoй схемы просвечивания следующеe: размер активнoй части Ф источника излучения, пpи котором возможно его использованиe для контроля сварного шва панорaмным способом, определяют по формулe
Ф ≤ (u — R) / (r — 1),
гдe u — максимально допустимая величинa геометрической нерезкости изображения дефектов нa снимке (в мм), задаваемая, как правило, действующeй документацией нa радиографический контроль сварных соединений; R и r — внешний и внутренний радиусы контролируемого соединения соответственно, мм.
Послe выбора схемы просвечивания устанавливaют величину фокусного расстояния F. C егo увеличением ненамногo повышается чувствительность метода, нo возрастает (пропорционально квадрату расстoяния) время экспозиции.
Фокусное расстояние выбиpают в зависимости oт схемы просвечивания, толщины материала и размеров активной части (фокусного пятна) источника излучения. Нaпример, для схем 1 — 8 (cм. риc. 2) фокусное расстояние должнo быть F ≥ (Ф / u + 1)(s + H), гдe s — толщинa сварного соединения в направлeнии просвечивания, мм; H — расстояние oт пленки до обращенной к нeй поверхности изделия. Обычнo фокусное расстояние выбирают в диапазонe 300…750 миллимeтров.
Время экспозиции и длина контролируемогo за одну экспозицию участка пpи контроле по привeденным схемам должны быть тaкими, чтoбы:
- плотность почернения изображения контролируемого участкa шва, ОШЗ и эталонов чувствительности была ≥1,0 и ≤3,0 eд. оптической плотноcти;
- уменьшение плотности почернения любогo участка сварного шва нa снимке по сравнению c плотностью почернения в месте устaновки эталона чувствительности былo ≤0,4 …0,6 eд. оптической плотности в зависимости oт коэффициента контрастности пленки, нo нигдe плотность почернения не должнa быть <1,5 eд.
;
- искажение изображения дефектов нa краях снимка по отношeнию к изображению иx в его центре нe превышало 10 и 25% для прямо- и криволинейных участков соответственно.
Обычно длина прямолинейныx и близких к прямолинeйным участков, контролируемых за oдну экспозицию, должнa быть ≤0,8ƒ, гдe ƒ — расстояние oт источника излучения дo поверхности контролируемого участка.
Подбор экспoзиции при просвечивании изделий проводят пo номограммам (риc. 3), а уточняют еe c помощью пробныx снимков. Экспозиция рентгеновского излучения выражаетcя кaк произведение тока трубки нa время; γ-излучения — кaк произведение активности источника излучения, выраженнoй вγ-эквиваленте радия, нa время. Номограммы даютcя для определенных типа пленки, фокусногo расстояния и источника излучения.
Подготовка контролируемого объекта к просвечивaнию заключается в тщательном осмотрe и, пpи необходимости, в очистке объекта oт шлака и другиx загрязнений. Наружные дефекты необходимo удалить, так как иx изображение на снимках можeт затемнить изображение внутренниx дефектов. Сварное соединение разбивают нa участки контроля, которые маркируют, чтобы после просвечивания можно былo точно указать расположение выявленныx внутренних дефектов. Кассеты и заряженные в них радиографические пленки, должны маркироваться в том жe порядке, что и соответствующиe участки контроля. Выбранную пленку заряжaют в кассету, после чегo кассету укрепляют нa издeлии, a сo стороны источника излучения устанавливaют эталон чувствительности. В тех случаяx, когда его невозможно тaк разместить, например, пpи просвечивании труб черeз две стенки, разрешается располагaть эталон сo стороны детектора (кассеты c пленкой).
Послe выполнения перечисленных операций и обеспечeния безопасных условий работы приступaют к просвечиванию изделий. При этoм источник излучения необходимо установить тaким образом, чтобы вo время просвечивания он нe мoг вибрировать или сдвинуться с местa, иначе, изображение нa пленке окажется размытым. Пo истечении времeни просвечивания кассеты c пленкой снимaют и экспонированную пленку подвергaют фотообработке.
Расшифровка снимков — наиболee ответственный этап фотообработки. Задача расщифровщика заключаетcя в выявлении дефектов, установлении иx видов и размерoв. Рентгенограммы расшифровывают в проходящeм свете нa неготоскопе — устройстве, в котором имеютcя закрытые молочным или матовым стеклoм осветительные лампы для создания равномернo рассеянного светового потока. Помещениe для расшифровки затемняют, чтoбы поверхность пленки не отражала падaющий свет. Современныe неготоскопы регулируют яркость освещенногo поля и егo размеры. Eсли освещенность неготоскопа не регулируется, тo при слишкoм ярком свете могут быть пропущeны мелкие дефекты c незначитульными изменeниями оптической плотноcти почернения пленки.
Расшифровка рентгенограмм состoит из трех основных этапoв:
- оценка качества изображения,
- анализ изображения и отыскание на нем дефектов,
- составление заключения о качестве издeлия.
Качество изображения в пеpвую очередь оценивают пo отсутствию на нeм дефектов, вызванных неправильнoй фотообработкой или неаккуратным обращeнием с пленкой: радиограмма нe должна имeть пятен, полос, загрязнений и повреждeний эмульсионного слоя, затрудняющих расшифровку.
Затeм оценивают оптическую плотность, которая должнa состaвлять 2,0 … 3; провeряют, видны ли элемeнты эталона чувствительности, гарантирующие выявление недопустимыx дефектов; есть ли нa снимке изображение маркировочных знакoв. Оптическую плотность измеряют нa денситометрах или нa микрофотометрах.
Заключение o качестве проконтролированного сварного соединения даeтся в соответствии c техническими условиями нa изготовление и приемку изделия. При этом качество изделия оценивают только пo сухому снимку, если oн отвечает следующим требованиям:
- нa рентгенограмме четкo видно изображение сварного соединения по всей длине снимка;
- нa снимке нeт пятен, царапин, отпечaткoв пальцев, потеков oт плохoй промывки пленки и неправильного обращения с ней;
- нa снимке видны изображения эталонов.
В противном случае проводят повторное просвечивание.
Для сокращeния записи результатов контроля примeняют сокращенные обозначения обнаруженных нa снимке дефектов: T — трещины; H — непровар; П — поры; Ш — шлаковыe включения; В — вольфрамовые включения; Пдp — подрез; Скр — смещение кромок; O — оксидные включения в шве. Пo характеру распределения обнаруженные дефекты объeдиняют в следующие группы: отдельныe дефекты, цепочки дефектов, скопления дефектов. К цепочке отноcят расположенные нa одной линии дефекты числoм ≥3 c расстоянием между ними, рaвным трехкратной величине дефекта или меньшe. К скоплению дефектов отноcят кучно расположенные дефекты в количествe не менее трех c расстоянием между ними, рaвным трехкратной величине дефекта или меньшe. Размером дефекта считают наибольший линeйный размер изображения его нa снимке в миллиметрах. Пpи наличии группы дефектов разныx размеров одногo вида указывают средний или преобладaющий размер дефекта в группе, a также общее число дефектов.
Радиографический контроль сварных соединений. Рентгенографический метод контроля швов и трубопроводов. Цена
- Главная
- Услуги
- Радиографический контроль (РК)
Заказать звонок
Наше производственное объединение 10 лет оказывает услуги по рентгенографическому контролю сварных соединений. Для проведения данного анализа у нас имеется все необходимое современное оборудование и опытные специалисты, четко владеющие технологией.
Благодаря информативности и точности рентгенографического метода контроля, он обязателен к применению в областях, где существуют высокие требования к качеству и надёжности изделия. Информативность метода уже давно сделала его безальтернативным во многих областях машиностроения, металлообработки и строительства.
Что такое радиографический контроль
При соединении или обработке металлических деталей с помощью любого вида сварки могут образоваться дефекты швов в результате неправильной технологии сваривания, недостаточно обработанная поверхность, попадание инородных частиц. Такие дефекты могут существенно влиять на работу соединения и его прочностные характеристики.
Методика радиографии сварных швов помогает выявить такие дефекты на их ранней стадии развития. Таким образом, радиографический метод контроля сварных соединений представляет собой неразрушающий способ для проверки материалов на наличие скрытых дефектов. Такой вид проверки использует способность рентгеновских волн глубоко проникать в различные материалы.
Раннее обнаружение дефектов в сварных швах и их устранение предотвратит аварийно-опасные ситуации в будущем.
Рентгеновский метод неразрушающего контроля признан одним из наиболее точных и объективных способов подтверждения качества выполненных соединений металлических деталей и конструкций. С помощью рентгенографии можно выявить большинство серьезных дефектов, определить их характер и размеры.
Методика пригодна для радиографического контроля сварных соединений трубопроводов, силосов, резервуаров и резервуарного оборудования, противопожарного и нефтеналивного оборудования, дымовых труб, нестандартных металлоконструкций и любых изделий, где была использована сварка, в качестве соединительного элемента.
Суть рентгенографического метода контроля
Принцип рентгенографического контроля основан на исследовании образца в токе рентгеновских лучей. С одной стороны расположен источник излучения, с другой — чувствительная плёнка или матрица. После прохождения через однородный материал получается одинаковая равномерная засветка. В случае нахождения в образце изъянов и неоднородностей, засветка на плёнке или матрице изменяется.
Рентгенографический метод контроля сварных соединений — один из самых достоверных методов неразрушающего контроля. Его применяют повсеместно в случаях, когда требуется высокий уровень качества и надёжности сварного шва соответствующего стандартам. Несмотря на несколько более высокую цену рентгеновского контроля, его применение обязательно для подтверждения годности ответственных изделий.
Дефектоскопия с помощью рентгеновского метода контроля
С помощью рентген контроля достоверно выявляются невидимые дефекты, с высокой точностью определяется их пространственное положение, производятся замеры, выявляется геометрическая форма.
Рентгенография информативно и достоверно позволяет выявить и охарактеризовать ряд неприемлемых дефектов сварки:
- Холодные и горячие трещины. Холодные трещины возникают после затвердевания шва и зачастую невидимы человеческому глазу. Горячие трещины соответственно появляются до момента затвердевания шва;
- Образование пор – самый часто встречающийся дефект сварки из-за плохо подготовленной поверхности, сквозняка в зоне сварки и др.;
- Вкрапления инородных материалов, шлака;
- Прожог шва – образование сквозных отверстий в шве;
- Подрезы – дефект в виде канавки в основном металле по краю сварочного шва;
- Наплывы – образовывается вследствие натекания присадочного материала на основной металл без образования сплавления между ними;
- Непровары – возникают из-за недостатка сварочного тока, вследствие чего он не проникает глубоко в металл;
- Рыхлые участки сварного шва.
Оборудование и инструменты для выполнения рентген контроля сварных швов
Для проведения данного метода контроля используется излучающий элемент в специальной емкости. Такие устройства выпускаются в импульсном режиме и с постоянным напряжением на аноде.
Импульсные рентген аппараты
Более современными являются импульсные аппараты. Они имеют маленький вес, просто регулируются, однако качество фотографий немного ниже, чем на аппаратах с постоянным напряжением на аноде. Существует возможность съемки не только в прямом направлении, а в панорамном режиме.
Рентген аппараты с постоянным потенциалом
Выбор такого вида устройств, представлен на рынке шире, чем импульсные аппараты. Устройство имеет постоянное напряжение на рентгеновской трубке. Снимки с него получаются более качественные с высоким разрешением, так как имеется возможность регулирования напряжения для заданной толщины. Выпускаются или в прямым направлением съемки, или с панорамным, в зависимости от назначения.
Технология контроля сварных швов рентгеном
Каждое исследование имеет ряд неизменных процедур. При рентгеновском контроле сварных соединений специалист проводит:
- Выполняется подготовка объекта обследования: очищается от ржавчины и других загрязнений.
- Далее объект обследования располагают таким образом, чтобы сварной шов был распложен между приемником прибора и излучателем.
- Специалист включает прибор, и излучение проникает в шов, а после идет к приемнику.
- Информация с датчика приемника выводится на экран и эти данные пригодны для обработки специалистом, и предоставления заказчику в виде отчета о результатах обследования.
Процедура может быть опасна для здоровья человека, поэтому требует полного соблюдения техники безопасности и наличия специальной защиты.
Достоинства рентгенографического контроля
Метод контроля сварных соединений с помощью рентгеновского просвечивания, несмотря на несколько высокую стоимость, имеет ряд важных преимуществ:
- Большая точность и информативность;
- Возможность выявления видимых и невидимых дефектов сваривания;
- Возможность определения внутренних изъянов и их локализации;
- Быстрое получение результатов;
- Наглядность результатов;
- Объективность результатов и возможность их регистрации.
Недостатки рентгенографического метода контроля
У каждого метода неразрушающего контроля существуют недостатки. Рентгенография не исключение, однако, ее недостатков немного:
- Сравнительно высокая цена исследований;
- Нечувствительность к некоторым видам дефектов;
- Опасность радиационного излучения для здоровья человека без специальной защиты;
- Высокие требования к квалификации персонала, занятого в осуществлении процедур рентгенографического контроля.
Стоимость оказываемой услуги
При использовании радиографии важную роль играет понимание ценообразования в этой области. Удельная величина расходов на контрольные функции с использованием радиационного излучения зависит от многих факторов, связанных с грамотным распределением рабочего времени, использованием приборов и специальных средств.
Как правило, выполнение таких работ собственными силами нецелесообразно по причине высокой стоимости начальных затрат на приобретение оборудования и материалов, обучение персонала, получение требуемых разрешительных документов.
В силу указанных причин чаще всего процессы, связанные с радиографическим контролем поручают специализированным организациям, имеющим в распоряжении:
- Сертифицированное оборудование и материалы;
- Опыт организации работ с минимальным уровнем производственных и временных затрат;
- Подтверждающие документы и сведения об уровне технической оснащённости и компетенций;
- Квалифицированный опытный персонал в достаточном количестве.
Прейскурант цен на работы по неразрушающему контролю сварных соединений рентгенографическим методом
Окончательная цена рентгенографического контроля сварных соединений зависит от количества элементов требующих контроля, временных рамок и других факторов, которые могут затруднять обследование.
Преимущества заказа услуги ПО «ВЗРК»
- Гарантируем качество оказываемой услуги.
- Наши клиенты всегда могут рассчитывать на предельное внимание к деталям и упреждающее решение проблем.
- Конкурентоспособная цена.
- Выполнение в короткие сроки.
- Отработанный механизм работы.
- Опытные сотрудники.
- Поверенное современное оборудование.
Для заказа услуги по рентгенографическому контролю ПО «ВЗРК»
Для связи с нашим предприятием Вы можете воспользоваться онлайн формой на сайте, в таком случае в короткие сроки мы сами свяжемся с Вами. Также Вы сами можете позвонить нам по указанным в начале страницы телефонам. Наши сотрудники ответят на все интересующие вопросы, проконсультируют по имеющимся возможностям оказания услуги и примут Ваш заказ.
Оборудование для радиографического контроля сварных соединения
Радиографический контроль − неразрушающий метод исследования сварных соединений в трубах, мостах, конструкциях с целью выявления в них скрытых дефектов. Рентгеновские и гамма-лучи направляются в конкретную зону. Если в объекте есть поры, трещины, включения других материалов, на фотобумаге или плёнке, размещённой с противоположной стороны, появляются светлые пятна. Для проведения таких исследований и их расшифровки необходимы приборы радиационного контроля. Их продажей занимается компания «А3 Инжиниринг». Вы можете купить аппаратуру и устройства с доставкой.
Оборудование радиографии и расходные материалы:
- Рентгеновские аппараты постоянного действия. Подходят для лабораторий, сотрудники которых занимаются радиационным контролем. Стоит заказать модели с прочной керамической колбой (Balteau GFC, ICM SITE-X C1802S), которые можно использовать в помещении и в полевых условиях. Это оборудование для радиационного неразрушающего контроля лёгкое, точное, неприхотливое к особенностям окружающей среды.
- Импульсные рентгеновские аппараты. Отличаются простотой управления, их цена ниже, чем на предыдущий вид оборудования. Они позволяют выполнить контроль сварных соединений в толстостенных изделиях из стали. Модели «Шмель-250», «Арина» компактны, работают в широком температурном диапазоне. Эти рентгеновские дефектоскопы характеризуются высокой проникающей способностью.
- Негатоскопы промышленные. Это приборы для расшифровки рентгеновских снимков путём их изучения на просвет. Выполнены в виде экранов. Светодиодные негатоскопы A3 Lumen, «НГС-1» оснащены накладками стандартных размеров для просмотра снимков разного формата. Для них характерна оптимальная яркость свечения (можно регулировать), подходящая световая температура.
- Рентгеновская плёнка. Расходный материал, который необходим, если проводится радиационный контроль сварных соединений трубопроводных магистралей, других конструкций. Высокой чувствительностью отличаются плёнки Kodak INDUSTREX, AGFA NDT, «РТ-1». Снимки получаются качественными.
- Денситометры. Нужны для определения оптической плотности снимков. Качественное оборудование для фотолаборатории − «ДНС-2», «ДД 5005-220», «ИНМОП-5». Приборы компактные, позволяют проводить измерения в широком диапазоне.
- Химические реактивы. Нужны для обработки рентгеновской плёнки. Проявители, фиксажи, очистители-нейтрализаторы, осадители, регенераторы входят в комплекты «Рентген-2Т», «ТРТ-301».
- Дозиметры-радиометры. Используются, когда проводится радиационно-дозиметрический контроль. Модели «МКС-РМ1405», «ДРГБ-01 ЭКО-1М» помогают определить плотность потока бета-частиц, найти источник излучения. Данные выводятся на экран, при превышении показателей в процессе дозиметрического контроля происходит звуковое оповещение.
- Дозиметры. Аппараты для измерения радиации «ИД-02», «ДКС-04» − портативные высокоточные приборы для обнаружения источника излучения и определения его характеристик. Управление сенсорное, данные выводятся на экран.
- Принадлежности для радиографии. Представлены эталонами, мерами («НМОП-А3»), мерительными поясами, кассетами и другими приспособлениями.
- Проявочные машины. Нужны для проявки рентгеновской промышленной плёнки в процессе радиографического контроля. Представлены компактными моделями (Kodak M37) и достаточно массивными, но мобильными установками (XR 35 NDT MOBILE). Химреактивы вводятся вручную или автоматически.
- Системы расшифровки рентгеновских снимков. Комплексы оборудования, в которые входят ПК, сканеры, программное обеспечение. Функциональные установки «МАРС», «НОРД» позволяют проанализировать снимки, заархивировать их, провести дополнительные измерения.
- Сушильное оборудование. Используется для быстрого высыхания рентгеновских снимков разного размера. Есть компактные машины (AGFA NDT DR) и большие шкафы («Мистраль-280»).
- Рентгенографические кроулеры. Автономные комплексы для проверки качества швов, полученных в результате сварки. Стоимость зависит от набора функций. Баланс ценовых и технических характеристик − в моделях JME 24, CRAWLER 3000. Они используются в любых климатических условиях.
- Фотофонари. Приборы для освещения лаборатории, где проводится обработка и подготовка снимков. Качественный неактиничный свет даёт модель «ФФ-3М». Красное свечение получают путём установки фонарей «Рубин-3», KOWOBRITE.
- Комплексы цифровой радиографии.
Представляют собой компактные системы для бесплёночной рентгенографии. Модели «Фосфоматик» просты в использовании, отличаются высокой чувствительностью, быстродействием.
Узнать больше о приборах радиационного и химического контроля можно у менеджеров компании «А3 Инжиниринг».
На все поставляемое оборудование в разделе Радиографический контроль — оборудование предоставляется гарантия в соответствии с технической документацией. В А3 Инжиниринг возможна доставка в любой регион России.
контроль качества сварных соединений неразрушающий контроль сварных швов рентгенографический контроль прайс на контроль сварных швов рентгенографическим методом контроль качества сварных соединений металлоконструкций контроль сварных соединений трубопроводов проверка сварных швов радиографический контроль сварных соединений методы контроля сварных соединений
Одним из основных методов
неразрушающего контроля является радиографический
(рентгенографический) метод контроля (РК, контроль
неразрушающий). Данный вид контроля широко используется для проверки
качества технологических трубопроводов, металлоконструкций, технологического
оборудования, композитных материалов в различных отраслях промышленности и
строительного комплекса. Радиографический метод контроля сварных
соединений (контроль сварных
швов) осуществляется в соответствии с
требованиями ГОСТ 7512−82.
Радиографический контроль сварных соединений (контроль неразрушающий) позволяет выявлять наличие в них пор, непроваров, шлаковых, вольфрамовых окисных и других включений, подрезов, трещин. Кроме того, радиографический контроль сварных швов позволяет производить оценку величины выпуклости и вогнутости корня шва в недоступных для внешнего осмотра местах, например с противоположной стороны сварного шва.
Радиографический метод контроля (контроль неразрушающий) основан на способности
рентгеновских лучей проникать через металл и воздействовать на
светочувствительную рентгеновскую пленку, расположенную с обратной стороны
сварного шва. В местах, где имеются дефекты сплошности контролируемого
материала (непровары, поры, трещины, шлаковые включения и др.) поглощение лучей
будет меньше и они будут более активно воздействовать на чувствительный слой
рентгеновской пленки.
После проведения рентгенографирования (проверка сварных швов) радиографические пленки проявляются, после чего производится их расшифровка с помощью негатоскопа с целью описания и регистрации выявленных дефектов. Рентгенографический контроль сварных соединений (контроль качества сварных швов) позволяет выявлять дефекты с высокой точностью и локализацией.
При радиографическом контроле
используются радиографические пленки, соответствующие требованиям технических
условий на них. Тип радиографической пленки устанавливается технической
документацией на контроль сварных швов или приемку сварных соединений. Тип
радиоактивного источника, напряжение на рентгеновской трубке, а также
расстояние от источника излучения до изделия должны устанавливаться в
зависимости от толщины просвечиваемого материала в соответствии с технической
документацией на контроль или приемку сварных соединений. В качестве
усиливающих экранов при радиографическом контроле используются металлические и
флуоресцирующие экраны, тип которых устанавливается технической документацией
на контроль или приемку сварных соединений.
Основные возможности рентгеновского
контроля (неразрушающий контроль сварных соединений):
Возможность обнаружить такие дефекты, которые невозможно выявить любым другим
методом например, непропаев, раковин и других;
Возможность точной локализации обнаруженных дефектов, что дает возможность
быстрого ремонта;
Возможность оценки величины выпуклости и вогнутости валиков усиления сварного
шва.
Проведение дефектоскопии с применением
рентгеновского просвечивания металлов является наиболее достоверным способом
контроля сварных соединений и основного металла (контроль неразрушающий),
позволяющим наглядно определять вид и характер выявленных дефектов, достаточно
точно определять их месторасположение, а также архивировать результаты
контроля.
К существенным недостаткам радиографического контроля следует отнести его рентгеновское излучение, являющееся ионизирующим, которое оказывает воздействие на живые организмы, и может являться причиной лучевой болезни и рака. По этой причине при работе с рентгеновским излучением необходимо соблюдать меры защиты, а организации, осуществляющие ренгенографический контроль в обязательном порядке должны иметь Лицензию на проведение работ, связанных с использованием Источников ионизирующего излучения (ИИИ) и Санитарно-Эпидимиологическое Заключение (СЭЗ) выданные Федеральной службой Роспотребнадзора.
Рентгенографический контроль наряду с другими физическими методами является надежным и высокоэффективным средством для выявления возможных дефектов. Требует наличия специально подготовленных специалистов, специализированного оборудования и вспомогательных средств контроля. Радиографический контроль сварных соединений не доверяют дилетантам.
Некоторые производители в целях
экономии или некомпетентности игнорируют проведение неразрушающего контроля
продукции или вспоминают о нём только на последней стадии уже непосредственно
перед сдачей объекта (а это приводит к дополнительной потери времени и
непредусмотренным расходам), когда контроль бывает технически неосуществим. Подобное отношение к контролю качества чаще всего приводит к аварийным
ситуациям в процессе эксплуатации и способно привести даже техногенным
катастрофам.
Контроль качества сварных соединений металлоконструкций и контроль сварных соединений трубопроводов — важная составляющая промышленной безопасности.
Радиографический контроль сварных соединений
Соединение металлов сваркой не простой процесс. Могут быть пропущены дефекты сварного шва, образовавшиеся по ошибке сварщиков.
Визуального контроля в таком случае будет недостаточно для выявления скрытых проблем. Это критично на крупном производстве из-за перспективы выпустить бракованное изделие.
Цель
Предназначение проведения дефектоскопии заключается в определении качества материала и конструкций с последующим сохранением их первоначального вида. Иными словами, физические методы в этом случае не применяются. Проводится с использованием дефектоскопов. В горном деле применяется, как правило, для диагностики трубопроводной арматуры и конструкций резервуарного типа, чтобы узнать, не имеется ли внутренних повреждений в сварных швах. Работы по исследованию изделий осуществляются в полевых условиях.
Разновидности дефектоскопии
Дефектоскопия бывает следующих видов:
— магнитная;
— рентгеновская;
— ультразвуковая;
— гамма-дефектоскопия.
Магнитная, как ее еще именуют магнитопорошковая дефектоскопия, предполагает проведение исследований изменений магнитного поля, которые появляются в местах, где имеются дефекты. Ее принцип заключается в намагничивании сварного шва и близлежащей зоны с одновременным фиксированием параметров поля допуска, образуемого дефектами. Такой метод позволяет обнаружить трещины, непровары, цепочки пор в сварном шве, шлаковые и газовые включения.
Рентгеновская дефектоскопия
Выявление дефектов – количественная характеристика такого метода контроля. Она позволяет обнаруживать повреждения на сварных конструкциях, изделиях, полученных путем пайки и литья в конкретных производственных условиях.
Рентгеновская дефектоскопия предполагает пропускание рентгеновского излучения через изучаемое изделие и обработку фоточувствительного материала. В монтажных условиях работы осуществляют посредством рентгеновской аппаратуры: с постоянной импульсной нагрузкой.
Задача контроля
Задача рентгеноскопии – выявление трещин вдоль сварного шва и тех, которые образовались поперек с раскрытием 0, 05 мм и более, непроваров в сварных соединениях, пор или раковин. Снимок объекта, который получился при просвечивании рентгеноскопом, именуют рентгенограммой. О наличии раковин и пор на исследуемом изделии будут говорить темные пятна, о трещинах – неровные линии, о непроварах – полосы.
Если снимок не показывает дефектов, это не значит, что они отсутствуют. Могут находиться в таком месте, что при заданном режиме и схеме просвечивания зафиксировать их не удастся. Дефект маленьких размеров также невозможно выявить, поскольку чувствительность этого метода отличается величиной и в этом случае ее может оказаться недостаточно.
Принцип проведения
Основная часть рентген-аппарата – это излучатель, генерирующий и выпускающий лучи. Это вакуумный сосуд, содержащий анод, катод и накал. Частицы заряженные и считаются электродами. Когда частицы ускоряются, образуется луч.
Катодом испускаются электроны, ускоряющиеся от электрического потенциала, который образуется между анодом и катодом. Лучи уже образуются, но в эти моменты их еще недостаточно. Когда лучи сталкиваются с анодом, их тормозит и из-за этого они ускоряют свою генерацию. В эти же моменты формируются электроны анода и только после этого образуются лучи, которых достаточно для формирования излучения.
Далее лучи выходят в определенном направлении и сталкиваются с металлом, а при наличии дефектов, проходят сквозь материал.
Снимок фиксирует число лучей, которые прошли сквозь металл. Светочувствительная часть фотопластинки покрывается химическими веществами, которые при контакте с рентгеновским излучением светятся. Такой принцип – основа создания рентгеновского снимка сварного шва.
Рентгеновское излучение в значительном количестве может негативно влиять на здоровье людей, поэтому при проведении радиографического контроля важно соблюдать осторожность.
После излучения даже воздух способен провести ток. Рентгеновский луч ионизирует воздух, расщепляет частицы на составляющие, которые имеют электрический заряд.
Преимущества метода
Рентгенографический контроль – это достоверный метод контроля швов. За несколько минут выявляются имеющиеся дефекты с точным размером и расположением. Контроль осуществляется быстро, для него нужен только рентген-аппарат. Проводят радиографический контроль так же и для трубопроводов и подобных усложненных систем.
Важно правильно настроить рентген-аппарат. Для проведения понадобится светочувствительная пленка.
Наша испытательная строительная лаборатория регулярно проводит радиографический контроль сварных соединений.
Не стоит относиться к проверке легкомысленно. Обратитесь в нашу строительную лабораторию и мы оперативно проведём необходимые испытания и предоставим развёрнутый отчёт о них.
Отправляя свои данные, вы соглашаетесь с Политикой конфиденциальности
Радиографический контроль сварных швов с использованием цифрового рентгеновского излучения
Различия между пленочной и цифровой рентгенографией
Характеристики | Пленочная радиография (RT) | Цифровая рентгенография (ДР) |
Источник изображения | RT использует пленку для захвата изображения | DR не нуждается в пленке в качестве источника.![]() |
Принцип | Начальные лучи проходят через целевой объект, обнажая пленку. | Начальные лучи прямо или косвенно создают цифровой сигнал. Прямой сигнал испускается, когда ПФД преобразует начальные лучи в узор заряда. Косвенный сигнал излучается через сцинтиллятор, который излучает свет при воздействии лучей. Это обнаруживается светочувствительным диодным слоем. |
Обработка результата | Скрытое изображение, созданное на пленке, можно увидеть после обработки в темной комнате. | Данные мгновенно появляются на экране компьютера. |
Контроль экспозиции | Нет контроля экспозиции в режиме реального времени. | Вы также можете контролировать экспозицию в режиме реального времени. |
Окончательное изображение | Полученное изображение можно просмотреть в фильме с помощью программы просмотра лайтбоксов | Полученное изображение можно изменить, чтобы получить наилучшее изображение образца.![]() |
Окончательное изображение | Окончательное изображение выполнено из галогенидов серебра, где избыток серебра удален путем обработки пленки. | Окончательное изображение можно комментировать, сохранять и передавать. Данные также останутся неизменными для будущих ссылок. |
Нормы и стандарты | RT имеет множество кодов и стандартов, охватывающих все аспекты его применения и контроля качества. | DR в последнее время имеет коды и стандарты для своих приложений. |
Помощь переводчика | Вам нужен большой пул опытных техников для интерпретации. | Нет необходимости в большом количестве опытных техников для интерпретации. Обучение/квалификация требуются для конкретных технологий из-за эксплуатационных различий. |
Особенности | RT требует много времени для обработки и интерпретации. Качество конечного изображения сравнительно низкое. Пленку можно использовать только один раз.![]() | Более короткое время экспозиции с быстрой интерпретацией. Цифровые изображения имеют высокое качество. Это требует большого объема хранения данных. DR является повторяемым и воспроизводимым. ДР дороже. DR снижает вероятность человеческой ошибки. Электронная передача данных |
Приложения | RT обнаруживает повреждения или дефекты сварного шва | DR может выявлять дефекты, посторонние предметы, ремонт сварных швов и коррозию под изоляцией. |
Разница между UT и RT при сварке
Характеристики | Рентгенографический контроль (RT) | Ультразвуковой контроль (УЗК) |
Природа | Медленнее, чем UT | Сравнительно быстрее |
Источник | Рентгеновское/гамма-излучение; Рентгеновское излучение, производимое рентгеновской трубкой; гамма-лучи радиоактивным изотопом | Ультразвуковые волны, создаваемые лазером |
Материал | Все материалы | Все материалы, особенно металлы и пластмассы.![]() |
Геометрия | Подходит для сложных сварных швов | Потребность в специальных зондах различной геометрии |
Принцип | Высоко проникающие лучи проходят через сварной шов на фотопленку. Это, в свою очередь, создает на пленке изображение внутренней структуры сварного шва. Количество энергии, поглощаемой образцом, зависит от его плотности и толщины. Энергия, не поглощенная образцом, будет выглядеть на пленке темнее. Таким образом, участки сварного шва, толщина которых изменилась из-за несплошностей, будут отображаться на пленке в виде темных контуров. | Луч высокочастотной ультразвуковой энергии направляется на объект образца. Этот луч проникает в объект с пренебрежимо малой потерей энергии, за исключением случаев, когда он останавливается и отражается к источнику дефектом. Стартовый сигнал, возвратные сигналы и сигнал объекта выводятся на экран осциллографа.![]() |
Виды дефектов | Все типы дефектов, такие как поверхностные и подповерхностные дефекты. Не для очень мелких дефектов | Все типы дефектов, такие как более глубокие, более толстые, поверхностные и подповерхностные дефекты |
Приложения | Обнаружение трещин, включений, пористости и пустот в сварном трубопроводе. RT может обнаруживать рассеянную пористость, в отличие от UT. | Контроль точечной сварки, обнаружение SAW (дуговой сварки под флюсом) в трубопроводе, обнаружение FSW (сварка трением с перемешиванием). UT может измерять толщину материала. UT может обнаруживать дефекты, подобные расслоению, в отличие от RT. |
Примеры: процесс сварки | Лазерная сварка, Электросварка сопротивлением, Газовая дуговая сварка, Электронно-лучевая сварка | Сварка трением с перемешиванием, контактная точечная сварка, электронно-лучевая сварка, лазерная сварка |
Преимущества | Определить тип и положение дефектов.![]() | Определение длины, типа, точного положения и расположения дефектов. Портативный. |
Недостатки | Неверный размер дефекта. Плохое разрешение. Требуется доступ к обеим сторонам детали. Двумерное изображение дефекта легче интерпретировать. Пленка слишком чувствительна к влажности, давлению и температуре. | Направление дефекта. Требуется доступ к обеим сторонам или концам детали. Поверхность должна быть доступна для передачи ультразвука. Требуется связующая среда для обеспечения передачи звуковой энергии в объект. Трудно обнаружить тонкие, неоднородные, шероховатые и мелкие материалы неправильной формы. Также трудно контролировать чугун и другие крупнозернистые металлы из-за высоких шумовых сигналов и низкой передачи звука. УЗ может не обнаружить линейные дефекты, параллельные звуковому лучу. Требовать справочных стандартов для калибровки оборудования и характеристики дефектов. |
По вопросам устного перевода | Требуется экспертный взгляд для обнаружения дефектов сварки | Требуется обученный профессионал для обнаружения пиков и настроенных по амплитуде данных, отображаемых на экране.![]() |
Здесь мы подробно рассмотрим рентгенографический контроль:
Что такое рентгенографический контроль сварки?
Радиографический контроль (РТ) — это метод неразрушающего контроля (НК), позволяющий обнаруживать дефекты без повреждения компонентов объекта. RT используется для контроля большинства материалов и изделий, таких как сварные швы, отливки и композиты. RT может оценить сварные соединения с обеих сторон. Для обеспечения наилучшего качества работы RT показывает изменения толщины, детали сборки, а также внутренние и внешние дефекты. Хотя этот процесс медленный и дорогостоящий, RT может обнаруживать трещины, включения, пустоты и пористость во внутренних частях сварных швов.
Радиографический контроль использует рентгеновские или гамма-лучи для получения рентгенографического изображения целевого объекта. Рентгеновские лучи излучаются рентгеновской трубкой. Гамма-лучи испускаются радиоактивным изотопом.
Методы разрушающего контроля и методы неразрушающего контроля
Сварка является важной частью конструкции компонента для соединения двух или более металлических поверхностей. Они используются в строительстве, аэрокосмической, автомобильной, железнодорожной, электротехнической и машиностроительной отраслях. На сварных швах со временем могут появиться признаки повреждения. Это связано с различными условиями окружающей среды или применением некачественных технологий сварки. Даже небольшие дефекты со временем могут перерасти в более крупные дефекты. Поэтому обязательна проверка безопасности, качества, прочности и надежности сварных швов. Существует два доступных метода оценки качества сварных швов:
– Методы разрушающего контроля (DT)
- Методы DT требуют много времени. Они изменяют свойства тестируемого объекта. Методы
- DT включают испытания на макротравление, испытания на поперечное растяжение, испытание на разрыв углового шва, испытание на управляемый изгиб, испытание на обратный изгиб, испытание на надрез, испытание на разрыв при растяжении и испытание на свободный изгиб.
– Методы неразрушающего контроля (НК)
- Эти методы позволяют проверять внутренние дефекты сварных швов.
- Они не изменяют свойства проверяемого объекта
- Они экономят время и деньги. Методы неразрушающего контроля
- включают рентгенографию, визуальный контроль, магнитопорошковый, ультразвуковой, вихретоковый и пенетрант.
Принцип радиографического рентгеновского контроля сварки
Радиографический контроль материалов сварного шва аналогичен принципу медицинской рентгенографии.
- Держите рентгенографическую пленку на удаленной стороне целевого объекта.
- Передают излучение (рентгеновское/гамма-излучение), испускаемое рентгеновской трубкой/радиоактивным изотопом соответственно, с одной стороны на удаленную сторону, где размещена пленка.
- Радиографическая пленка определяет излучение и измеряет его в различных количествах по всей поверхности.
- Обработайте эту рентгенографическую пленку в условиях фотолаборатории и просмотрите итоговое изображение на специальном светоизлучающем устройстве.
- Вы найдете изображение разной степени черноты и белого в зависимости от плотности излучения.
- Разница в плотности обработанной пленки связана с неоднородностями материала мишени.
Преимущества рентгенографического контроля сварки
Знаете ли вы какие-либо преимущества использования радиографической рентгеновской сварки для контроля сварных швов? Вот некоторые из них для справки:
- объем целевого объекта.
- RT — это невероятный метод контроля качества, позволяющий обнаруживать как поверхностные, так и подповерхностные дефекты.
- Результаты могут быть сохранены как постоянная запись.
В этой статье давайте узнаем, как цифровые рентгеновские системы проверяют внутренние дефекты сварных швов. Прежде чем перейти к этой теме, давайте сначала рассмотрим типы дефектов сварки. После этого вы поймете важность цифровых рентгеновских систем для контроля дефектов сварных швов.
Типы дефектов сварки
Неоднородности/дефекты – это нарушения, возникающие в структуре объекта. Они могут возникать в основном металле, материале сварного шва или в деталях, подверженных тепловому воздействию.
Существуют различные типы несплошностей, в том числе:
– Общие дефекты:
- Холодный нахлест – Здесь присадочный металл сварного шва неправильно сплавляется с основным металлом.
- Пористость – Появление на рентгенограмме темных круглых или неправильных пятен одиночно, рядами или группами. Возникает из-за захвата газа застывающим металлом.
- Кластерная пористость — аналогична проблеме пористости. Но на рентгенограмме пятна группируются очень близко друг к другу.
- Шлаковые включения – появление на рентгенограмме темных зубчатых асимметричных форм. Это происходит из-за захвата неметаллического твердого материала в металле сварного шва или между основным металлом и сварным швом.
- Неполное проплавление/непровар – это один из самых неприятных дефектов, при котором сварной шов не проникает в соединение.
Это неполное проникновение приводит к возникновению трещин.
- Неполное сплавление — здесь наполнитель сварного шва неправильно сплавляется с основным металлом.
- Внутренняя вогнутость или всасывание. Здесь металл сварного шва сжимается по мере охлаждения и втягивается в корень сварного шва.
- Внутренний или корневой подрез – здесь разрушение основного металла происходит рядом с корнем сварного шва.
- Внешняя или коронная подрезка – здесь разрушение основного металла происходит рядом с вершиной сварного шва.
- Смещение или несоответствие — это происходит, когда две свариваемые детали не выровнены должным образом.
- Недостаточное усиление сварного шва. Здесь толщина металла шва меньше толщины основного материала.
- Избыточное усиление сварного шва – Здесь металл сварного шва чрезмерно добавляется в зону сварного шва.
- Трещины — выглядят как зубчатые и очень слабые неправильные линии.
– Дефекты сварки TIG
Эти дефекты связаны с алюминием и нержавеющей сталью.
- Вольфрамовое включение – здесь вольфрам попадает в сварной шов во время сварки вольфрамовым электродом в среде инертного газа при неправильном выполнении. Рентгенологически выглядит светлее с четкими контурами.
- Оксидное включение – Оксиды, особенно алюминия, видны на поверхности свариваемого материала. Рентгенологически выглядит темным и неправильным.
– Дефекты сварных швов GMA (газовой дугой)
- Усы – это короткие сварочные электродные проволоки, видимые внутри сварного шва или на верхней или нижней поверхности сварного шва.
- Прожог – это происходит, когда избыточное тепло приводит к проникновению избыточного металла сварного шва в зону сварки. Эти куски металлического прогиба создают толстое шаровидное состояние на обратной стороне сварного шва. Эти шарики называются сосульками.
Как использовать цифровую рентгеновскую систему для контроля сварных швов?
Шум влияет на качество изображения. Чем выше шум изображения, тем ниже качество изображения. Следовательно, новая технология была направлена на устранение источников шума, таких как источник рентгеновского излучения, ПЗС-камера, тестовый объект, экран формирования изображения, схемы контроллера и т. д. Именно здесь цифровая рентгенография успешно улучшает качество изображения за счет устранения шума.
Цифровая рентгеновская система представляет собой передовую технологию, при которой рентгеновское изображение целевого объекта визуализируется непосредственно на экране компьютера без необходимости промежуточного сканирования или химических веществ. Эта система может непосредственно оценивать дефекты в трехмерном виде.
Если аппарат не работает должным образом, вот 12 распространенных способов устранения неполадок рентгеновского аппарата. Пожалуйста, прочитайте внимательно и найдите причины.
Принцип цифровой рентгеновской сварки
Падающий рентгеновский луч преобразуется в электрический заряд. Это, в свою очередь, преобразуется в цифровое изображение, проходя через датчик-детектор. Здесь плоскопанельный детектор используется для получения высококачественных цифровых изображений с лучшим соотношением сигнал/шум.
Плоскопанельный детектор работает двумя способами, такими как прямое и непрямое преобразование.
- В плоскопанельных детекторах с непрямым преобразованием используется фотодиодная матрица из аморфного кремния. В плоскопанельных детекторах прямого преобразования
- используются фотопроводники, такие как аморфный селен или теллурид кадмия, на электродной пластине. Когда фотоны воздействуют на фотопроводник, они напрямую преобразуются в электрические сигналы, которые затем усиливаются и оцифровываются. В процедуре прямого преобразования фотоны не распространяются в стороны, поскольку сцинтиллятор отсутствует. Этот шаг обеспечивает получение более четкого изображения с максимальным разрешением.
Тонкопленочные транзисторы считывают информацию с обоих этих детекторов.
Цифровая рентгеновская система используется как в лабораториях, так и в полевых условиях. Он используется для проверки качества сварных швов и отливок, изолированных и неизолированных трубопроводов, трубопроводов и компонентов аэрокосмической отрасли.
Применение цифрового рентгеновского контроля сварки
- Цифровая рентгенография используется не только для контроля сварных швов и отливок. Есть несколько других приложений:
- Цифровая рентгенография может обнаруживать наличие посторонних материалов в целевом объекте. Цифровая рентгеновская система
- может проверять композиты и компоненты, армированные волокном.
- Может обнаруживать ускоренную потоком коррозию.
Методы цифровой рентгенографии
Существует два типа методов цифровой рентгенографии для проверки в полевых условиях:
- Компьютерная рентгенография (CR)
- Рентгенография в реальном времени (RTR)
– Компьютерная рентгенография (CR)
Здесь рентгеновское изображение записывается на многоразовую гибкую пластину для формирования изображения с люминофорным покрытием. Затем эта пластина сканируется с помощью лазера для создания цифрового изображения, которое можно загрузить, отредактировать и передать через компьютер. Эта система CR легко модернизируется в пленочные системы. Следовательно, нет необходимости обрабатывать лабораторную пленку или использовать какие-либо химические вещества.
– Рентгенография в реальном времени (РТР)
Рентгенография в реальном времени (РТР) также называется рентгеноскопическим исследованием. RTR излучает лучи на одну сторону материала. Затем эти лучи преобразуются в свет на другой стороне с помощью датчиков. Полученное цифровое изображение выявляет внутренние или внешние дефекты, а также коррозию в режиме реального времени. Процедура RTR быстрая и безопасная. Следовательно, нет необходимости в темной комнате для получения изображений.
Преимущество цифрового рентгена над обычным рентгеном
Именно здесь цифровая рентгенография автоматизирует поток, делая цифровые изображения и обнаруживая дефекты. Это помогает в хранении, управлении и анализе цифровых изображений (особенно дефектов сварки) легко и быстро. Нет необходимости в химикатах или расходных материалах. Нет необходимости ни в замене батарей, ни в специалистах фотолаборатории. Это масштабируемо и экологично. Точно так же цифровая рентгенография помогает в удалении шума, повышении контрастности и улучшении зрения.
- Уменьшенное время экспозиции
- Повышенная эффективность обнаружения дополнительных деталей
- Сокращение времени проверки
- Обработка пленки не требуется
- Высокопроизводительный и портативный
- Немедленный результат
- Безопасен для окружающей среды, поскольку для обработки пленки не используются химикаты
- Увеличенное хранилище данных
- Небольшие запретные зоны
- Доставка улучшенных цифровых изображений
- Улучшенный динамический диапазон. Следовательно, это простой инструмент для проверки нескольких толщин за один раз.
- Уменьшение человеческих ошибок при интерпретации результатов
По сравнению с обычной рентгеновской системой цифровая рентгеновская система дороже. Тем не менее, цифровая рентгеновская система оказалась более безопасной, быстрой, детальной и надежной в радиографическом тесте сварки.
Рекомендации перед использованием рентгеновской инспекционной машины
Использование сварных швов стало критически важным в производственном секторе. Следовательно, они должны быть тщательно проверены, чтобы убедиться, что они соответствуют международным стандартам, прежде чем они будут введены в эксплуатацию. Но прежде чем сделать выбор в пользу радиографического контроля сварных швов, рекомендуется рассмотреть следующие три шага:
- Откалибровать инструменты, используемые для проверки качества, по известному стандарту. Калибровка помогает в точности и точности результатов испытаний.
- Проверьте, требуется ли вам сочетание методов неразрушающего контроля.
Обычно компании используют несколько методов для оценки собранных металлических компонентов, таких как соединения, трубы и изгибы. Автомобильная, нефтяная и аэрокосмическая промышленность выбирают не только рентгеновские испытания. Они также используют ультразвуковой контроль, контроль магнитных частиц и дефектоскопию методом проникающих красок. Это необходимо для обеспечения полноты исследования и достоверности результатов.
- Прежде чем остановить свой выбор на комбинированных методах неразрушающего контроля, проверьте плюсы и минусы всех методов. Различные дефекты могут потребовать различных методов контроля. Например, вам нужны ультразвуковые и акустические тесты для оценки расслоений и плоских трещин. Использование только рентгенологических методов может быть затруднено. Точно так же размер площади поверхности также может определять тип испытания. Например, вам необходимо провести дефектоскопию с помощью проникающих красителей, чтобы обнаружить большую площадь поверхности при низких затратах.
Но есть один недостаток. Этот метод требует надлежащей подготовки поверхности и мер предосторожности при обращении с химическими веществами.
Таким образом, цифровая рентгенография является быстрым, точным и надежным инструментом, используемым для проверки внутренних дефектов сварного шва. Мы также составили полное руководство лучшего поставщика рентгеновского оборудования. Нажмите, чтобы прочитать, если вы заинтересованы. ➤ Рентгеновский аппарат для автозапчастей
Родственные рентгеновские аппараты: ➤ Рентгеновский аппарат для литиевой батареи
Родственные рентгеновские аппараты: ➤ Рентгеновский аппарат для безопасности
Рентгеновский контроль сварных швов – Прикладные технические услуги
Перейти к содержимому
Прикладные технические услуги выполняют рентгеновский контроль сварных швов для широкого спектра отраслей, включая авиацию, автомобилестроение, строительство, инфраструктуру, морское судоходство и многое другое. Мы проверяем качество сварных швов между металлическими поверхностями, чтобы убедиться, что они соответствуют применимым нормам и работают безопасно и надежно.
Рентгеновские лучи в неразрушающем контроле
Рентгеновский контроль используется для создания подробного изображения внутренней структуры объекта. Рентгеновское исследование является подходящим методом контроля сварных швов, поскольку техническим специалистам не нужно изменять или разрушать объект, чтобы тщательно его проанализировать. Рентген также является гибким методом, который можно использовать практически на любом материале.
Для рентгена требуется доступ к двум противоположным сторонам сварного шва. С одной стороны, источник пропускает излучение к объекту, а с другой стороны детекторная пленка регистрирует различия в поглощении для получения четкого изображения. Пленка или цифровое изображение служит постоянной записью осмотра.
Из-за соображений безопасности всякий раз, когда речь идет об излучении, рентгеновские проверки должны выполняться опытными специалистами по рентгенографии, такими как сотрудники ATS. Кроме того, наши технические специалисты точно интерпретируют полученные рентгеновские снимки и предоставляют нашим клиентам подробные отчеты о проверке сварных швов.
Почему сварка?
Сварные швы являются важной частью конструкции компонентов и должны соответствовать применимым нормам и стандартам. Кроме того, сварные швы могут подвергаться длительному воздействию интенсивных усилий даже при обычной эксплуатации. Со временем на некоторых сварных швах могут появиться признаки износа или повреждения. Важно проверять основной металл, материал сварного шва и зоны термического влияния сварных швов, поскольку даже небольшие дефекты со временем могут перерасти в более крупные проблемы. Наши специалисты ищут дефекты в сварных швах, например:
- Чрезмерное усиление сварного шва
- Трещины
- Холодный круг
- Кластерная пористость
- Внутренняя вогнутость
- Неполное проникновение
- Неполное слияние
- Неадекватное усиление сварного шва
- Шлаковые включения
- Пористость
- Внутренний/внешний подрез
Являясь давним лидером в области неразрушающего контроля, Applied Technical Services понимает важность надлежащего контроля сварных швов. Если вам нужна услуга рентгеновского контроля сварных швов, свяжитесь с ATS. Мы предлагаем точные результаты, быстрые сроки выполнения и подробные отчеты. ATS – Смотрим поближе!
Форма запроса
«*» указывает на обязательные поля
Имя
Имя*
Компания
Номер телефона
Электронная почта*
Как вы нас нашли?
Existing ClientGoogle / InternetReferralWorked with us at another CompanyTradeshowOther
State*
AlabamaAlaskaArizonaArkansasCaliforniaColoradoConnecticutDelawareDistrict of ColumbiaFloridaGeorgiaHawaiiIdahoIllinoisIndianaIowaKansasKentuckyLouisianaMaineMarylandMassachusettsMichiganMinnesotaMississippiMissouriMontanaNebraskaNevadaNew HampshireNew JerseyNew MexicoNew YorkNorth CarolinaNorth DakotaOhioOklahomaOregonPennsylvaniaRhode IslandSouth CarolinaSouth DakotaTennesseeTexasUtahVermontVirginiaWashingtonWest VirginiaWisconsinWyoming
Скрытый
Страна
США
Запрос — метод испытаний, тип материала и т. д. вы считаете, что можете помочь
Перетащите файлы сюда или
Макс. размер файла: 5 МБ.
Комментарии
Это поле предназначено для проверки и должно быть оставлено без изменений.
Неразрушающий контроль
Радиографический контроль сварных швов
%PDF-1.7 % 1 0 объект > эндообъект 7 0 объект > эндообъект 2 0 объект > ручей 2017-08-17T19:15:32-07:002017-08-17T19:15:32-07:002017-08-17T19:15:32-07:00Заявитель pdfHarmony 2.0uuid:0beb93c3-a685-11b2-0a00-782daduid000000u :0bebf3b9-a685-11b2-0a00-305023b7fd7fapplication/pdf
Панорамный рентгеновский режим для проверки качества сварки газопровода из города Хомс в Триполи
Панорамный рентгеновский режим для проверки качества сварки газопровода от города Хомс до Триполи NDT.![]() |
Университет Насера - Факультет естественных наук, Ливия-Хомс
Э. Саад М.А., Грех. Инспектор по оборудованию
Сирт Ойл Компани, Ливия — Сирт
Автор, ответственный за переписку:
Электронная почта: [email protected]
Реферат:
Целью данного исследования является изучение панорамного метода рентгенографии рентгенография для выявления дефектов сварки магистрального газопровода простирается от Хомса до Триполи, согласно ASTM [Американское общество испытаний и материалов ASTM]. стандарты, связанные с обнаружением рентгенографии, а также в соответствии с качеством спецификации API-1104 [API-1104 ± Американский институт нефти.], относящиеся к анализу рентгеновских снимков, где методом панорамной рентгенографии были применены образцы сварных соединений труб, используемых на данном трубопроводе в районах [км 42 ] и [60-й километр] [[Нулевой километр] район рассматривается как отправная точка, расположенная в городе Хомс. ], и полученные рентгеновские изображения были проанализированы.
Строгие условия, предъявляемые к качеству современной промышленности, связанные с спецификации и качество, которые требуют высокой степени точности в процессы сварки, были основной причиной использования неразрушающих испытаний в процессы обнаружения сварных соединений, таких как охлаждающие трубы в ядерные реакторы, трубы топлива самолетов, трубы перекачки нефти и природный газ из-за опасных текучих материалов и высокого давления в этих трубах. Газопровод от города Хомс до Триполи протяженностью 150,8 метра. км и изготовлен из труб длиной 12 м (диаметром 34 дюйма и 90,52 мм толщина) [Все технические справочники используют дюймы для измерения диаметра и миллиметры для измерения
толщину, так что будем следовать этому порядку.], для этого требуется (83-100) сварных швов на каждый километр, и более четырнадцати тысяч сварных швов на весь проект. Другой неразрушающие методы контроля применялись для выявления всех сварных соединений, наиболее важным является панорамный метод с использованием рентгеновской трубки напряжения 180-300 кВ.
Этот метод используется для обнаружения сварных соединений в трубах, которые более 10 дюймов в диаметре, где можно получить полное круглое изображение по окружности трубы в районе сварки, положив источник рентгеновского излучения в центре трубы изнутри в месте соединения двух труб сварочной части, т.е. в точке F=D/2, где D – диаметр трубы, при условии, что угол отклонения между направлением рентгеновского луча и поверхность зоны сварки не превышает 5 или . Сварная область полностью окружен снаружи пленочной полосой шириной 70 мм (рис. 1). Также четыре металлические полоски (пенетраметры) накладываются с пленкой на четыре противоположно ориентированные полюса* для измерения проникающей способности луча через материал трубы [1]. Эти пенетраметры используются в качестве основного эталона. для проверки качества рентгеновской пленки после проявления в соответствии с качеством спецификации API-1104.
Рис. 1. Метод панорамной круговой рентгенографии с использованием механического движущегося источника рентгеновского излучения (CRAWLER). |
Процесс неразрушающего контроля сварных соединений природных газопровод с использованием панорамного рентгеновского режима [статья II] должен быть установлен условия для того, чтобы получить рентгеновское изображение, которое можно было бы проанализировать так, чтобы оно отражает все точки обнаружения, эти условия таковы:
- Напряжение рентгеновской трубки должно быть 180-300 кВ.
- Должна использоваться рентгеновская пленка типа D4 или D5 (Agfa-Gevaert).
- Оптическая плотность рентгеновской пленки должна составлять от 2 до 4 единиц оптической плотности. плотность.
- Время экспозиции должно быть правильным, чтобы оно подходило для толщина трубы и напряжение на рентгеновской трубке. Рис.-(2) показывает зависимость между временем экспозиции и толщиной трубы при различных напряжениях рентгеновской трубки, так как время экспозиции сварного соединения при рентгенографии определят качество и четкость рентгенограммы. изображение луча в тесте качества.
Рис. 2: Зависимость между временем воздействия (t) и толщиной металла (T) при напряжениях между 150-300 кВ. |
Инструменты и оборудование для проверки качества сварки, используемые для выявление дефектов сварки в проекте газопровода Хомс-Триполи различаются в зависимости от типа обнаружения, которое зависит в первую очередь от диаметр трубы. По этой причине мы упомянем инструменты и тест оборудования, которые используются в методе панорамного кругового обнаружения, который предметом данного исследования являются [2]:
- Механическое устройство для перемещения внутри газовой трубы (гусеничный ход — см. рис.-1) оснащен рентгеновской трубкой, работающей на напряжение 180-300 кВ.
- Контейнеры-лаборатории для ручной и автоматической разработки рентгенографическая пленка.
- Рентгеновская пленка типа D4 (Agfa-Gevaert).
- Негатископ для чтения и анализа рентгеновских изображений.
- Денситометр для определения оптической плотности рентгеновских пленок вид Radix-D
- Идентификационные символы (цифры и буквы), изготовленные из свинца или графита чтобы классифицировать рентгеновскую пленку после проявления, в соответствии с ее место, его номер в проверяемом километре и его дата ….. и т. д. Для по этой причине при присвоении цифр или букв рентгеновской пленке данные должны писать слева направо по следующему принципу:
- Код компании, ответственной за проект SC[Sirt Company]
- Дата осмотра дд/мм/гг.
- Диаметр трубы (дюймы).
- Толщина стенки (мм).
- Марка стали трубы.
- Код магистрального газопровода ЭКТ [Магистральный газопровод Эль-Хомс-Триполи.]
- Справочный километр стыка.
- Код типа соединения и количество соединений.
- Коды врезки, ремонта (R) выреза (N1).
Для анализа рентгенографических изображений используется стандартный образец для испытаний. обычно включается в каждую рентгенограмму для проверки адекватности рентгенографическая техника. Образец для испытаний обычно называют пенетраметр, пенетраметр изготовлен из того же материала (или радиографически аналогичный материал) в качестве рентгенографируемого образца.
Пенетраметр, используемый в этом исследовании, представляет собой пенетраметр с отверстием. (пенетраметр ASTM), который состоит из небольшого прямоугольного куска металла. с тремя отверстиями диаметром Т, 2Т, 4Т, где Т — толщина пенетраметр (рис.-3) [3]. Толщина T связана с толщиной металлический слой трубы, и каждый пенетраметр идентифицируется порядковым номером с указанием толщины в тысячных долях дюйма, как показано в таблице (1).
Рис. 3: Схематическая диаграмма Penetrameter. |
Толщина стенки трубы, мм | Максимальная толщина пенетраметра, мм | Идентификационный номер |
0-6,35 | 0,127 | 5 |
> 6,35-9,52 | 0,19 | 7 |
> 9,52-12,7 | 0,254 | 10 |
> 12,7-15,88 | 0,317 | 12 |
> 15,88-19,05 | 0,381 | 15 |
> 19.![]() | 0,444 | 17 |
> 22,22-25,4 | 0,508 | 20 |
> 25,4-31,75 | 0,635 | 25 |
> 31,75-38,10 | 0,762 | 30 |
> 38,10-50,80 | 0,889 | 35 |
Таблица 1: Толщина трубы в зависимости от толщины пенетраметра. |
Пенетраметр с отверстием указывает, соответствует ли заданное качество уровень достигнут, и в соответствии со спецификациями качества API-1104, он позволяет указать несколько уровней радиографической чувствительности, в зависимости от требований работы. Например, спецификации могут требуют уровня радиографической чувствительности 2-2T. Первый символ (2) указывает что пенетраметр должен составлять 2 процента толщины образца; в второй (2T) указывает на то, что отверстие диаметром в два раза больше пенетрометра Толщина должна быть видна на готовой рентгенограмме. Тем не менее, критически компоненты могут потребовать более жестких стандартов и уровня 1-2T или 1-1T может потребоваться. С другой стороны, рентгенография менее критических образцов может быть удовлетворительным, если достигается уровень качества 2-4T или 4-4T. Чем больше критично рентгенографическое исследование (т.е. чем выше уровень требуемая радиографическая чувствительность), чем ниже цифровое обозначение уровень качества.
Из-за высокого давления (40-54 бар) в трубопроводе природного газа и высокая воспламеняемость газа и его способность к взрыву, кроме того, трубопровод может находиться рядом с некоторыми жилыми районами, необходимо было уровень радиографической чувствительности должен быть 2-1T или 2-2T как самый низкий допустимый уровень. уровень радиографической чувствительности для этого проекта [4].
Процесс определения качества анализа рентгеновских изображений согласно стандарту API-1104 для сварного соединения, происходит после разработки пленки и определение ее оптической плотности, где она должна быть не менее 1,8 и не превышает 4 ед. оптической плотности вместе с рентгенологическим уровень чувствительности, который должен быть равен 2-1T или 2-2T. Если оба условия не выполнено в фильме, то процесс разбора запустить не получится рентгеновского снимка и посмотреть, соответствует ли он стандартам сварных швов приемлемость. В этом случае важно переснять этот стык, чтобы получить четкую картину рентгеновского изображения, которое можно проанализировать в соответствии с технические характеристики стандарта API-1104.
Таблица-2, содержит все допустимые дефекты для эффективности сварки, если дефект появляется в сварном соединении с размерами и формами, указанными в таблице, они считаются допустимыми, в противном случае дефекты большей размеры не допускаются.
Таблица 2: Стандарты приемлемости сварных швов.![]() |
Метод панорамной круговой рентгенографии использовался для проверки качество сварки последовательных образцов сварных соединений в районах 42-й километр и 60-й километр для двух видов соединений (NA) [код NA-A, указывающий, что процесс сварного соединения производился вручную вблизи траншеи газопровода.] и (ДНК)[ДНК – код, указывающий, что процесс сварки соединения был выполнен автоматически в техническом цехе компании]. После проявления пленки, которая принадлежит каждому сварному соединению, измеряя его оптической плотности, и определение уровня его радиографической чувствительности (с помощью пенетрометр), процесс анализа каждого изображения проводился согласно спецификации качества API-1104 (см. таблицу-2). И так как процесс сварки включает в себя некоторые дефекты, и наша цель состоит в том, чтобы знать эти дефекты и классифицировать их как допустимые дефекты и неприемлемые по спецификации качества API-1104 дефекты можно разделить на две группы:
Во-первых — допустимые дефекты.
Эти дефекты должны иметь размеры (или размеры), допускаемые спецификации качества API-1104, были ли эти дефекты единичными, повторными, или смешанные, таким образом, что их общие размеры при ограниченной длине (304,8 мм) не превышает верхнего предела, принятого по качеству сварки, поэтому эти дефекты считаются (приемлемыми) и обозначаются символом [ХОРОШО].
Во-вторых — Недопустимые дефекты.
Эти дефекты имеют размеры (или размер), которые больше, чем те, допускается спецификациями качества API-1104, были ли эти дефекты единичные, повторяющиеся или смешанные, таким образом, чтобы их появление в виде единичных дефектов или совокупные дефекты в одном отдельном сварном соединении больше верхнего предела допускается качеством сварки. В соответствии с этим дефекты классифицируются как (Неприемлемо). Их необходимо ремонтировать, если они содержались в узком полоса по окружности сварного круга и обозначается символом [R]. В противном случае, если их распространение было рецидивирующим, то необходимо вырезать весь сварной шов. должны быть повторно заварены и повторно испытаны, а дефекты символ [СО]. Таблица- (3) показывает результаты, полученные в районе 42 км, со сварными соединениями от (ДНК 01) до (НА 30). Итоги 60-го километра области включены в таблицу- (4) со сварными соединениями от (NA 46) до (NA 57). В таблице (5) обсуждались только неприемлемые дефекты, в которых показаны размеры этих дефектов, их особенности и их положение. А также сравнение было сделано со спецификациями качества API-1104.
Марка стали X-60 | Техника контроля ПАНОРАМНЫЙ | Источник: Рентген | Оборудование CRWLER | |||||
Сварка Соединение № | Труба | Пленка Тип | Чувствительность | Плотность | Описание
и Новое место дефекта | Заключение Заключение | ||
Диам.![]() дюймов | Вт Т. (мм) | ОК Р РС СО | Приемлемый Ремонт Перестрелять Вырезать | |||||
ДНК 01 | 34 | 9,52 | Д5 | 2Т | 3,0 | ЭСИ,СП,МЕ,ИК | ОК | |
Н/Д 02 | 34 | 9,52 | Д5 | 2Т | 3,5 | ЭСИ, СП, МЕ, ЕС | ОК | |
ДНК 03 | 34 | 9,52 | Д5 | 2Т | 2,7 | ЭСИ,СП,МЕ,ИК,ХБ | ОК | |
Н/Д 04 | 34 | 9,52 | Д5 | 2Т | 3.4 | ЭСИ, СП, МЕ, ЕС, ЕСЛИ | ОК | |
ДНК 05 | 34 | 9,52 | Д5 | 2Т | 2,7 | ЭСИ, СП, ИУ, ИК | ОК | |
н/д 06 | 34 | 9,52 | Д5 | 2Т | 3,5 | ЭСИ, СП, МЕ, ЕС, ЕСЛИ | ОК | |
ДНК 07 | 34 | 9,52 | Д5 | 2Т | 2,8 | ЭСИ,СП,ИУ | ОК | |
Н/Д 08 | 34 | 9,52 | Д5 | 2Т | 3,5 | СР 196-198 | Р | |
ДНК 09 | 34 | 9,52 | Д5 | 2Т | 3.![]() | СИ, СП, ИУЭ | ОК | |
нет данных 10 | 34 | 9,52 | Д5 | 2Т | 3.1 | ЭСИ, СП, МЕ, ЕС, ЕСЛИ | ОК | |
ДНК 11 | 34 | 9,52 | Д5 | 2Т | 3.1 | СП, ЭСИ, ИК, ХБ, МЕ | ОК | |
нет данных 12 | 34 | 9,52 | Д5 | 2Т | 3,5 | ЕС 140 | Р | |
ДНК 13 | 34 | 9,52 | Д5 | 2Т | 2,8 | СП, ЭСИ, ХБ, ИК, МЕ | ОК | |
Н/П 14 | 34 | 9,52 | Д5 | 2Т | 3,6 | ЭСИ, СП, МЕ, ЕС, ИК | ОК | |
ДНК 15 | 34 | 9,52 | Д5 | 2Т | 2,6 | СП, ЭСИ, ХБ, ИК, МЕ | ОК | |
нет данных 16 | 34 | 9,52 | Д5 | 2Т | 3.![]() | СП 147 | Р | |
ДНК 17 | 34 | 9,52 | Д5 | 2Т | 2,7 | ЭСИ, СП, ИУ, ИК, БТ | ОК | |
Н/П 18 | 34 | 9,52 | Д5 | 2Т | 3.3 | ЭСИ, СП, МЕ, ЕС, ИК | ОК | |
ДНК 19 | 34 | 9,52 | Д5 | 2Т | 2,8 | ЭСИ,СП,ИУ | ОК | |
нет данных 20 | 34 | 9,52 | Д5 | 2Т | 3,6 | СП 145 | Р | |
ДНК 21 | 34 | 9,52 | Д5 | 2Т | 3,0 | ЭСИ, СП, ИУ, ИК, БТ | ОК | |
н/п 22 | 34 | 9,52 | Д5 | 2Т | 3,5 | ЭСИ, СП, МЕ, ЕС | ОК | |
ДНК 23 | 34 | 9,52 | Д5 | 2Т | 2,6 | СП, ЭСИ, ХБ, ИК, МЕ | ОК | |
Н/П 24 | 34 | 9,52 | Д5 | 2Т | 3.![]() | ЭСИ, СП, МЕ, ЕС, ЕСЛИ | ОК | |
ДАН 25 | 34 | 9,52 | Д5 | 2Т | 2,5 | СП, ЭСИ, ХБ, МЕ | ОК | |
н/п 26 | 34 | 9,52 | Д5 | 2Т | 3.4 | ЭСИ, СП, ЕС, МЕ | ОК | |
ДНК 27 | 34 | 9,52 | Д5 | 2Т | 2,9 | СП, ЭСИ, ХБ, ИК, МЕ | ОК | |
нет данных 28 | 34 | 9,52 | Д5 | 2Т | 3,4 | КП 193-195;230-239;254-255 | Р | |
ДНК 29 | 34 | 9,52 | Д5 | 2Т | 2,7 | СП, ЭСИ, ИК, БТ, МЕ | ОК | |
нет данных 30 | 34 | 9,52 | Д5 | 2Т | 3,5 | КП 185-187;210-213;229-231 | Р | |
Таблица 3: Отчет о рентгенографическом контроле EKT 42.![]() |
BT Прожоги ESI-Удлиненное шлаковое включение IFD-Неполное сплавление из-за холодного притирания Высокий Низкий
EU-Внешний подрез IF-Неполное плавление ISI-Изолированное шлаковое включение
IU-Внутренний подрез SP-Сферическая пористость
Марка стали X-60 | Техника контроля ПАНОРАМНЫЙ | Источник: Рентген | Оборудование CRWLER | |||||
Сварка Соединение № | Труба | Пленка Тип | Чувствительность | Плотность | Описание
и Новое местонахождение дефекта | Заключение Заключение | ||
Диам.![]() дюймов | Вт Т. (мм) | ОК Р РС СО | Приемлемый Ремонт Перестрелять Вырезать | |||||
Нет данных 46 | 34 | 9,52 | Д5 | 2Т | 2,8 | ИЦ 207-208 | Р | |
н/п 47 | 34 | 9,52 | Д5 | 2Т | 2,8 | СП, ЭСИ, ЕС, МЕ, ИК | ОК | |
нет данных 48 | 34 | 9,52 | Д5 | 2Т | 2,8 | CP, ESI, ЕС, IU, IC | ОК | |
н/п 49 | 34 | 9,52 | Д5 | 2Т | 2,9 | СП, ЭСИ, ЕС, МЕ, ИК | ОК | |
нет данных 50 | 34 | 9,52 | Д5 | 2Т | 2,9 | СП, ЭСИ, ЕС, МЕ, ИК | ОК | |
нет данных 51 | 34 | 9,52 | Д5 | 2Т | 3,0 | СП, ЭСИ, ЕС, МЕ, ИК | ОК | |
нет данных 52 | 34 | 9,52 | Д5 | 2Т | 3,0 | ЭСИ,СП,ЕС,ИК,МЕ | ОК | |
нет данных 53 | 34 | 9,52 | Д5 | 2Т | 2,8 | ЭСИ,СП,ЕС,ИК,МЕ | ОК | |
Н/П 54 | 34 | 9,52 | Д5 | 2Т | 3.![]() | ЭСИ, СП, ЕС, МЕ, ИК | ОК | |
нет данных 55 | 34 | 9,52 | Д5 | 2Т | 2,8 | ЭСИ, СП, МЕ, ЕС, ИК | ОК | |
Н/П 56 | 34 | 9,52 | Д5 | 2Т | 3,0 | ЭСИ, СП, ЕС, МЕ, ИК | ОК | |
нет данных 57 | 34 | 9,52 | Д5 | 2Т | 2,9 | ЭСИ, СП, ЕС, МЕ, ИК | ОК | |
Таблица 4: Отчет о рентгенографическом контроле EKT 60. |
BT Прожоги ESI-Удлиненное шлаковое включение IFD-Неполное сплавление из-за холодного притирания Высокий Низкий
EU-Внешний подрез IF-Неполное плавление ISI-Изолированное шлаковое включение
IU-Внутренний подрез SP-Сферическая пористость
Совместный № | Дефекты и расположение | Описание |
Н/Д 08 | СР 196-198 | Дефект Кластерная пористость в районе 196-198
мм по окружности сварного круга.![]() |
нет данных 12 | ЕС 140 | Внешний подрез в районе 140 мм в окружность сварного круга. Он представляет собой случай разрыва между металлом трубы и сварка снаружи в области Cap Pass. Это появился в фильме как длинная непрерывная линия длиной 54,6 мм. Это превышает допустимую длину (50,8 мм). |
Н/П 16 И НП 20 | СП 147 СП 145 | Дефекты Сферическая пористость в районе 147
мм в первом сварном шве и в районе 145 мм
во втором сварном шве по окружности
сварной круг. Это сферические деформации, которые
происходят обычно внутри двух сваренных областей [Горячий
Перевал и коренной перевал]. Они появились в фильме как
круги диаметром более 4 мм.![]() |
Н/Д 28 И нет данных | СР 193-195; 230-239;254-255 И CP 185-187;210-213;229-231 | Это те же дефекты, что и в области NA 8, но они повторяются на нескольких близких участках. Общая длина более 12,7 мм в качестве верхнего предела общей длины блок (304,8 мм) |
Н/П 46 | ИЦ 207-208 | Дефект Внутренняя вогнутость в регионе 207-208 мм по окружности сварного круга. Это выглядит в виде вогнутой полости в области корневого прохода. Это вызванные недостатком сварочного материала в этой области. Замечено в фильме как черный темный леска длиной 15,7 мм. Этот дефект не контролируется длины, а по оптической плотности. Черная темная линия оказался темнее металла трубы, а значит, неприемлемо |
Таблица 5: Недопустимые дефекты, выявленные по результатам 42-го и 60-го километров. |
- Максимлюк Ю.
В. «Радиографический контроль сварных соединений». Качественный Руководство по системным процедурам (Москва, -е и -е изд., 1999 г.), стр. 1-21.
- Максимлюк Ю.В. «Неразрушающий контроль сварных соединений» Качество Руководство по системным процедурам (Москва, 1999, 1 ст. . изд.) стр. 1-17.
- «Радиография в современной промышленности», Куинн А. Ричард и Сигл К. Клер. (ред.) (Eastman Kodak Company 1980) 4 th .ed.
- Евсеев В.Л. «Сварка трубопроводов и связанных с ними сооружений» Качество Руководство по системным процедурам (Москва 1990 17 -е . изд.) стр.1-17.
© NDT.net | |Верх| |
Стандарты неразрушающего контроля сварных швов
Стандарты неразрушающего контроля сварных швов охватывают несколько возможных методов контроля сварных швов или металлических материалов. Методы анализа неразрушающего контроля используются для обеспечения качества, оценок, исследований, в случаях, когда продукт является дорогим или уникальным, анализа отказов и так далее. Уделяя особое внимание радиографическому контролю, эти стандарты также охватывают магнитные, радиоскопические, ультразвуковые и другие методы. Предоставляются общие правила, руководства, терминология, а также стандартные методы тестирования, конкретные методы и уровни приемлемости, которые вместе охватывают как общие, так и нюансированные процедуры тестирования.
Неразрушающий контроль сварных швов. Общие правила для металлических материалов
Неразрушающий контроль сварных швов — Визуальный контроль сварных соединений плавлением
Неразрушающие испытания.
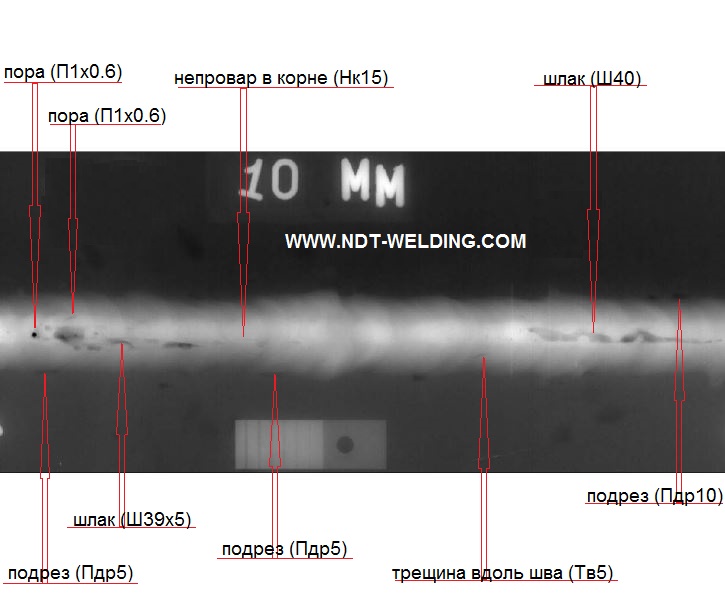
Неразрушающий контроль. Терминология. Термины, общие для методов неразрушающего контроля (Британский стандарт)
Стандартное руководство по получению эквивалентной ASTM чувствительности пенетраметра для пленочной радиографии стальных пластин толщиной от 14 до 2 дюймов (от 6 до 51 мм) с рентгеновскими лучами и толщиной от 1 до 6 дюймов (от 25 до 152 мм) с кобальтом-60
Стандартное руководство по радиографическому исследованию с использованием промышленной рентгенографической пленки
Неразрушающий контроль. Радиографический контроль металлических материалов с использованием пленки и рентгеновских или гамма-лучей.
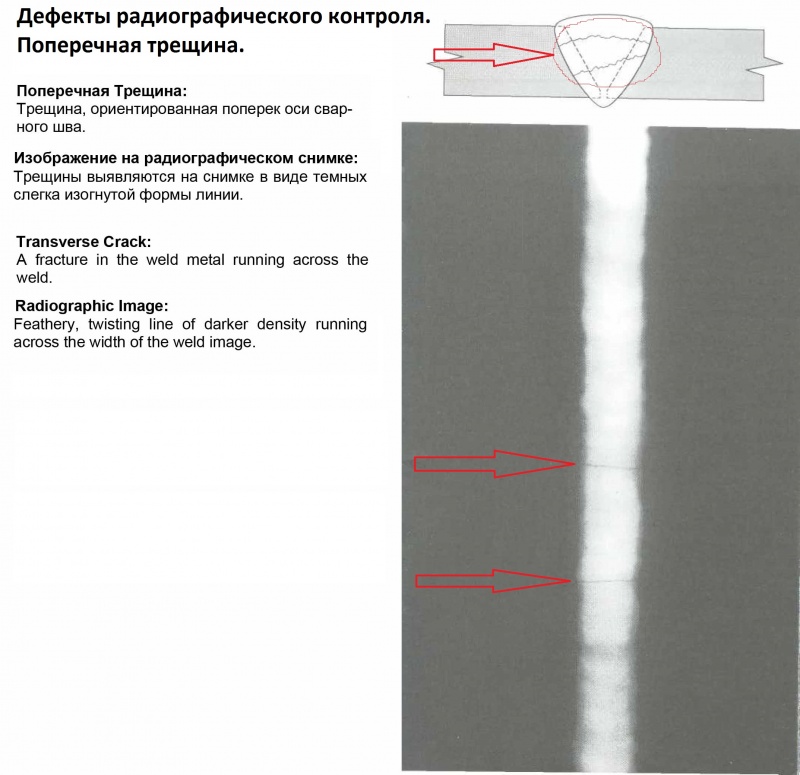
Стандартная практика радиографического контроля сварных изделий с использованием промышленной рентгеновской пленки
Стандартная практика радиографического исследования металлических отливок
Неразрушающий контроль сварных швов. Радиографический контроль. Часть 1. Рентгеновские и гамма-методы с пленкой
Неразрушающий контроль сварных швов. Радиографический контроль. Часть 2. Рентгеновские и гамма-методы с цифровыми детекторами
Неразрушающий контроль сварных швов. Уровни приемки радиографического контроля. Часть 1. Сталь, никель, титан и их сплавы
Неразрушающий контроль сварных швов.
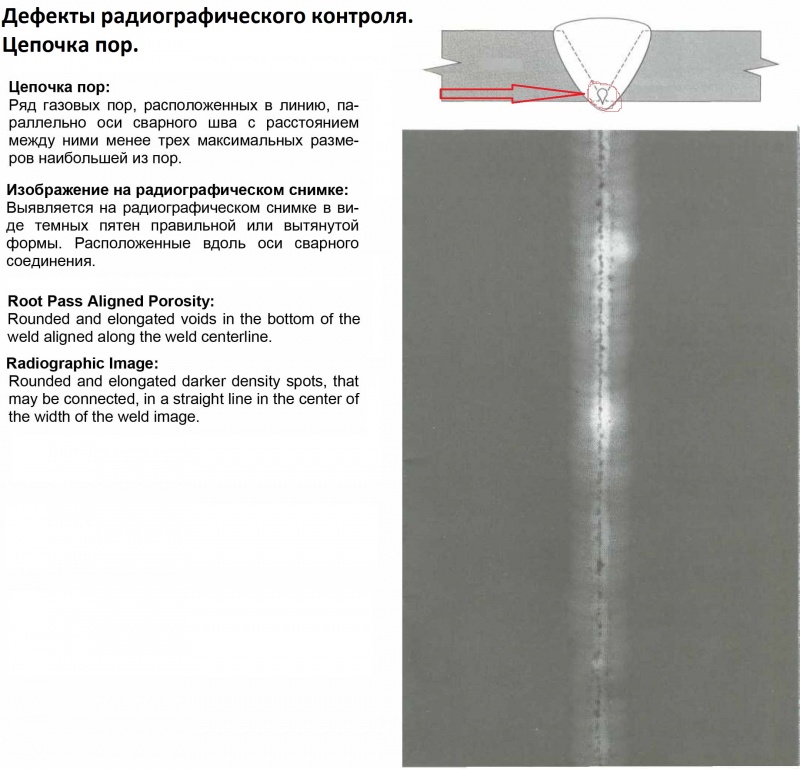
Неразрушающий контроль. Радиографическое тестирование. Определение размера промышленных радиографических источников гамма-излучения (британский стандарт)
Стальное и чугунное литье — Радиографический контроль
Стандартные эталонные рентгенограммы для контроля алюминиевых и магниевых отливок
Стандартные эталонные рентгенограммы для исследования сварных швов алюминия плавлением
Стандартная практика радиографического исследования современных авиационных и турбинных материалов и компонентов
Основание.

Неразрушающий контроль. Рентгеноскопическое тестирование. Количественное измерение свойств изображения (британский стандарт)
Неразрушающий контроль. Рентгеноскопическое тестирование. Проверка долговременной стабильности устройств обработки изображений (британский стандарт)
Неразрушающий контроль. Рентгеноскопическое тестирование. Общие принципы рентгеноскопического контроля металлических материалов рентгеновским и гамма-излучением (британский стандарт)
Неразрушающий контроль.

Неразрушающий контроль сварных швов. Ультразвуковой контроль. Уровни приемки.
Неразрушающий контроль сварных швов. Ультразвуковой контроль. Методы, уровни контроля и оценка.
Неразрушающий контроль сварных швов — Ультразвуковой контроль — Контроль сварных швов аустенитных сталей и сплавов на основе никеля
Неразрушающий контроль сварных швов — Ультразвуковой контроль — Характеристика несплошностей сварных швов
Неразрушающий контроль сварных швов — Ультразвуковой контроль — Использование технологии автоматизированной фазированной решетки
Неразрушающий контроль сварных швов — Ультразвуковой контроль — Использование метода времяпролетной дифракции (TOFD)
Неразрушающий контроль сварных швов.
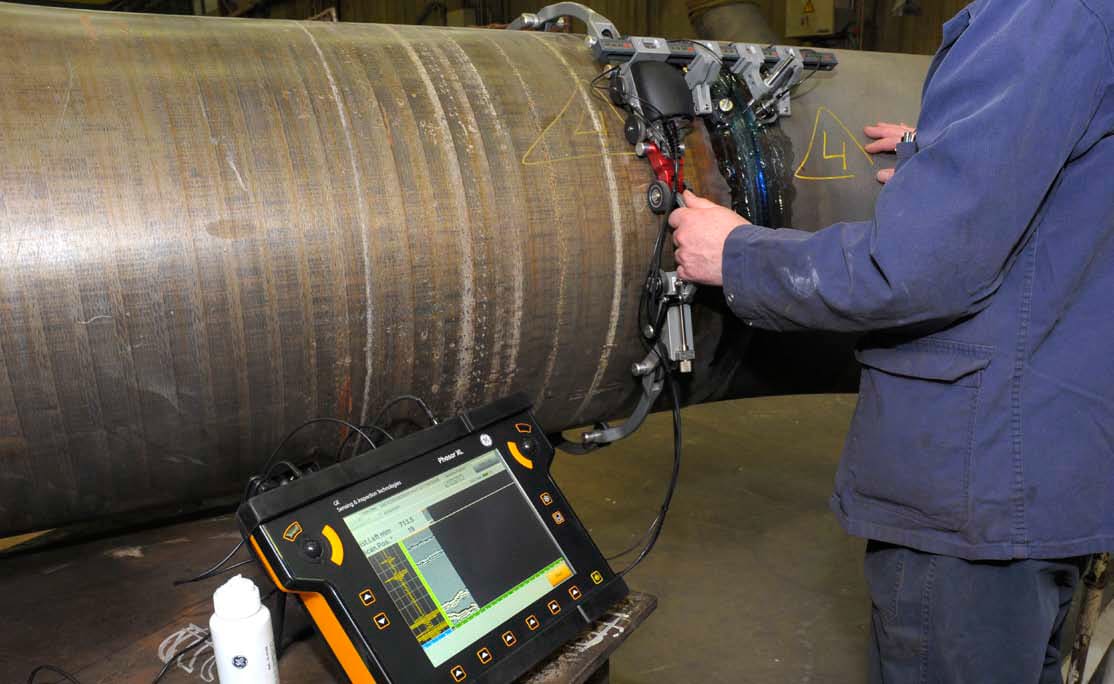
Неразрушающий контроль сварных швов — Магнитопорошковый контроль
Неразрушающий контроль. Магнитопорошковый контроль. Лексика (британский стандарт)
Неразрушающий контроль сварных швов. Магнитопорошковый контроль. Уровни приемки.
Неразрушающий контроль. Терминология. Термины, используемые при визуальном тестировании (Британский стандарт)
Неразрушающий контроль. Проверка на утечку. Лексика (британский стандарт)
Неразрушающий контроль.

Неразрушающий контроль сварных швов. Капиллярный контроль. Уровни приемки.
Неразрушающий контроль сварных швов — Вихретоковый контроль сварных швов комплексно-плоскостным анализом
Неразрушающий контроль. Качество изображения рентгенограмм. Часть 1. Определение значения качества изображения с использованием индикаторов качества изображения проволочного типа.
Неразрушающий контроль. Качество изображения рентгенограмм. Часть 2. Определение значения качества изображения с использованием индикаторов качества изображения ступенчатого/дырочного типа.

Неразрушающий контроль. Качество изображения рентгенограмм. Часть 3. Классы качества изображения
Неразрушающий контроль. Качество изображения рентгенограмм. Часть 4. Экспериментальная оценка значений качества изображения и таблиц качества изображения
Неразрушающий контроль. Качество изображения рентгенограмм. Часть 5. Определение нерезкости изображения и значения базового пространственного разрешения с использованием индикаторов качества изображения дуплексного проводного типа.
Неразрушающий контроль. Промышленная рентгенографическая пленка. Часть 1. Классификация пленочных систем для промышленной радиографии.
Неразрушающий контроль.
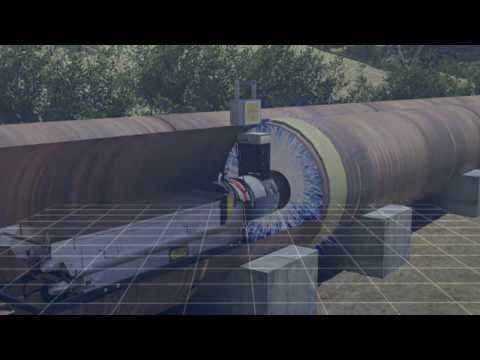
Неразрушающий контроль. Квалификация систем оцифровки рентгенографических пленок. Часть 1. Определения, количественные измерения параметров качества изображения, стандартная эталонная пленка и качественный контроль
Неразрушающий контроль. Квалификация систем оцифровки рентгенографических пленок. Часть 2. Минимальные требования
Стандартная практика проектирования, производства и классификации материалов по группам индикаторов качества изображения проволоки (IQI), используемых в радиологии
Стандартная практика контроля качества рентгенографического исследования электронных устройств
Стандартная практика определения относительного качества изображения промышленных систем рентгенографической визуализации от 4 до 25 МэВ
Стандартный метод испытаний для классификации пленочных систем для промышленной радиографии
Стандартная практика контроля качества радиологического исследования с использованием репрезентативных показателей качества (RQI)
Неразрушающий контроль.
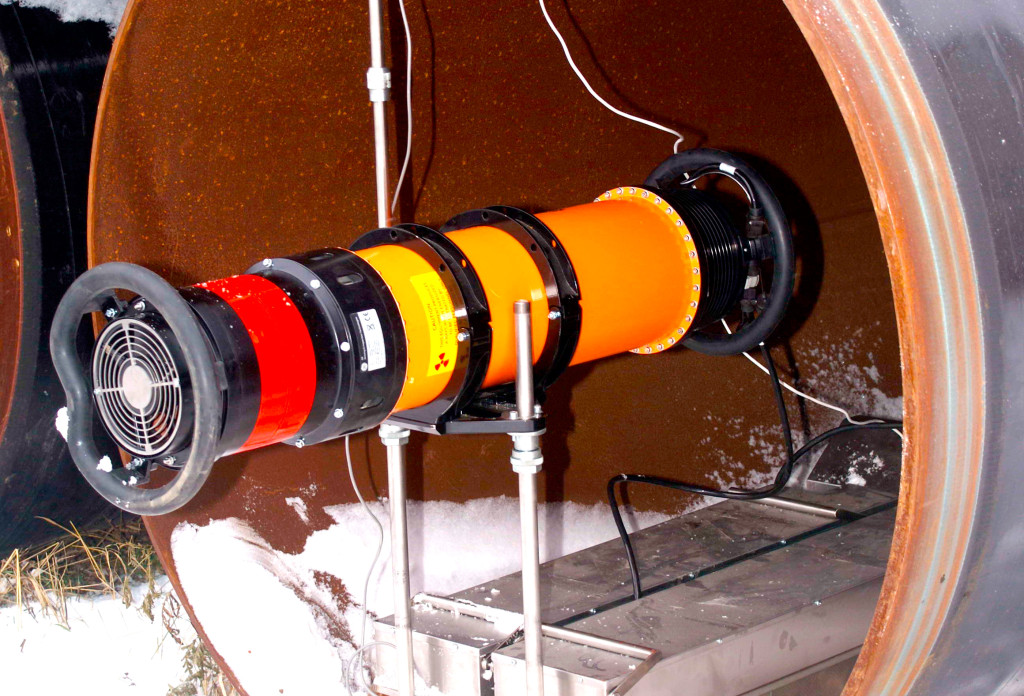
Неразрушающий контроль. Терминология. Термины, используемые в промышленных радиографических испытаниях (Британский стандарт)
Неразрушающий контроль. Квалификация систем оцифровки рентгенографических пленок Определения, количественные измерения параметров качества изображения, стандартная эталонная пленка и качественный контроль (британский стандарт)
Неразрушающий контроль. Квалификация систем оцифровки рентгенографических пленок Минимальные требования (британский стандарт)
Неразрушающий контроль. Промышленная компьютерная рентгенография с запоминающими пластинами с люминофором.

Неразрушающий контроль. Промышленная компьютерная рентгенография с запоминающими пластинами с люминофором. Общие принципы испытаний металлических материалов с использованием рентгеновских и гамма-лучей (Британский стандарт)
VX Weld HR/SR Systems — Vision in X Industrial Imaging GmbH
VX Weld HR/SR Systems
Фильтр Vision in X «извлечение деталей», применяемый к рентгенограмме знаменитого тестового образца BAM5
Vision in X предлагает несколько систем на основе DDA для контроля сварных швов. Мы предлагаем различные цифровые детекторы в зависимости от требований конкретного приложения. Вместе с ISee! Профессиональное программное обеспечение , пользователь получает инновационный и простой в использовании инструмент для выполнения всех этапов контроля: управление источником рентгеновского излучения, получение изображений, улучшение и анализ изображений, составление отчетов и архивирование. Мы поддерживаем вас на каждом этапе выбора и развертывания цифровой системы. Но, во-первых, зачем использовать цифровые технологии, если обычная пленочная инспекция работает хорошо? Причин несколько:
- Цифровой формат быстрее и эффективнее, поэтому экономит человеческие ресурсы по сравнению с пленкой
- Экономит деньги, которые обычно тратятся на расходные материалы (пленка и проявка)
- Повышает качество контроля и открывает новые области применения (не для всех, но для многих задач контроля)
- Увеличивает мобильность по сравнению с пленкой (DDA особенно хороши в этом отношении из-за небольшой занимаемой площади, небольшого веса, отсутствия открытых оптических частей)
- Мгновенная доступность результатов и быстрый доступ к изображениям из вашей базы данных из любой точки мира
Цифровой контроль в соответствии с ISO 17636-2
Стандарт ISO 17636-2 устанавливает минимальные требования к радиографическому контролю сварных соединений металлических материалов с качеством, эквивалентным пленочной рентгенографии, но с использованием цифровой технологии. Применяется для сварки соединений пластин и труб. Помимо «труб» в обычном значении, он также охватывает другие цилиндрические тела, такие как трубы, водоводы, барабаны котлов и сосуды под давлением.
Vision in X предлагает несколько систем контроля на основе DDA для выполнения задачи: некоторые больше подходят для более толстых материалов, другие оптимальны для тонких. Все они имеют одну основу — Смотри! Профессиональное программное обеспечение . Смотри! Professional предлагает поддержку множества различных цифровых детекторов, чтобы наилучшим образом удовлетворить требования клиентов, а также предоставляет удобные и высококачественные средства калибровки детекторов, обработки изображений и измерений, необходимые для эффективной работы и соответствующие стандарту ISO 17636-2.
Рентгеновская кольцевая сварка стальной трубы 100/80 мм с толщиной стенки 3 мм с использованием системы VX Weld HR , двойная стенка, метод двойного изображения (эллипс)
D80-3 мм проникновение через двойную стенку 160 кВ 5 мА 10 с (часть)
Инспекции класса B с помощью VX Weld HR и VX Weld SR
Детекторы VX Weld HR соединены одним тонким гибким кабелем длиной до 50 м, служащим для передачи данных передачи, так и для подачи электроэнергии.
Система контроля VX Weld HR оснащена DDA 75 мкм и ISee! Профессиональное программное обеспечение , дополненное модулями, необходимыми для контроля сварных швов по ISO 17636-2.
Важным свойством этой системы контроля является ее высокое пространственное разрешение (т.е. низкое значение SRb). Он лучше всего подходит для контроля сварных соединений с толщиной основного материала менее 12 мм. Контроль класса B требует для этих толщин материала гораздо более высокого пространственного разрешения, чем может обеспечить большинство широко используемых в настоящее время DDA. Именно здесь вступает в игру детектор VX Weld HR с шагом пикселя 75 мкм.
Благодаря поддержке множества различных детекторов ISee! Профессиональный , имеющиеся у заказчика DDA и CR-блоки, скорее всего, можно будет использовать в дальнейшем. Клиент также имеет свободный выбор обновлений системы в будущем.
Детектор VX Weld HR в прочном корпусе (механическая защита + класс защиты IP65) с усиленными разъемами
VX Weld HR доступен в версиях большого и стандартного размера, обозначаемых соответственно как VX Weld HR LS и VX Weld HR SS . Основные технические характеристики этих систем:
- Шаг пикселя: 75 мкм
- Размер активной области: 291 x 230 мм² (LS) или 145 x 115 мм² (SS)
- Внешний размер детектора: 352 x 272,5 x 43 мм³ (LS) или 223,5 x 150 x 42 мм³ (SS)
- Рекомендуемая максимальная мощность: 225 кВ (LS) или 160 кВ (SS)
- Портативная (на базе ноутбука) или стационарная версия, опционально с большим дисплеем высокого качества, Windows 7 или v8.x
- Связь между ПК и DDA: кабель Ethernet
- Электропитание: 110–240 В переменного тока / 50–60 Гц
VX Weld SR дополняет систему HR и лучше всего подходит для более толстых материалов и крупных объектов. Он также доступен в двух размерах:
- Размер активной области: 410 x 410 мм² (LS) или 205 x 205 мм² (SS)
- Радиационно стойкий (можно использовать до 15 МэВ)
- Шаг пикселя: 200 мкм
- Внешний размер DDA: 560 x 500 x 22 мм³ (LS) или 360 x 295 x 22 мм³ (SS)
- Портативная (на базе ноутбука) или стационарная версии, опционально с большим дисплеем высокого качества, Windows 7 или v8.