Режимы в защитных газах — Энциклопедия по машиностроению XXL
Таблица 10в. Режимы сварки титана и его сплавов плавящимся электродом в защитных газах |
Проведение этих мероприятий во многом зависит от габаритных размеров и конструктивного оформления сварных заготовок. Для сложных заготовок с элементами больших толщин и размеров при наличии криволинейных швов в различных пространственных положе-йиях можно применять только хорошо свариваемые металлы. Последние сваривают универсальными видами сварки, например ручной дуговой покрытыми электродами или полуавтоматической в защитных газах в широком диапазоне режимов. При сварке не нужны, например, подогрев, затрудненный вследствие больших толщин и размеров элементов, а также высокотемпературная термическая обработка, часто невозможная ввиду отсутствия печей и закалочных ванн соответствующего размера.
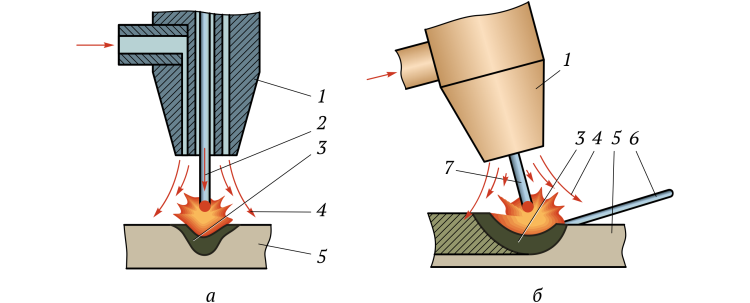
Участки I и II ВАХ соответствуют режимам сварки, применяемым при ручной сварке плавящимся покрытым электродом, а также неплавящимся электродом в среде защитных газов. Механизированная сварка под флюсом соответствует II области и частично захватывает III область при использовании тонких электродных проволок и повышенной плотности тока, сварка плавящимся электродом в защитных газах соответствует III области ВАХ. Для питания дуги с падающей или жесткой ВАХ применяют источники питания с падающей или пологопадающей внешней характеристикой. Для питания дуги с возрастающей ВАХ применяют источники тока с жесткой или возрастающей внешней характеристикой.
Для питания дуги на участке II с жесткой характеристикой применяют источники с падающей или пологопадающей характеристикой (ручная дуговая сварка, автоматическая под флюсом, сварка в защитных газах неплавящимся электродом). Режим горения дуги определяется точкой пересечения характеристик дуги б и источника тока I (рис. 5.4, б). Точка В соответствует режиму неустойчивого горения дуги, точка С — режиму устойчивого горения дуги (/св и f/д), точка А — режиму холостого хода в работе источника тока в период, когда дуга не горит и сварочная цепь разомкнута. Режим холостого хода характеризуется повышенным напряжением (60. .. 80 В). Точка D соответствует режиму короткого замыкания при зажигании дуги и ее замыкании каплями жидкого электродного металла. Короткое замыкание характеризуется малым напряжением, стремящимся к нулю, и повышенным, но ограниченным током.
Сварку осуществляют на режимах, ориентируясь на справочную литературу, производственные инструкции, операционные технологические карты и личный производственный опыт.
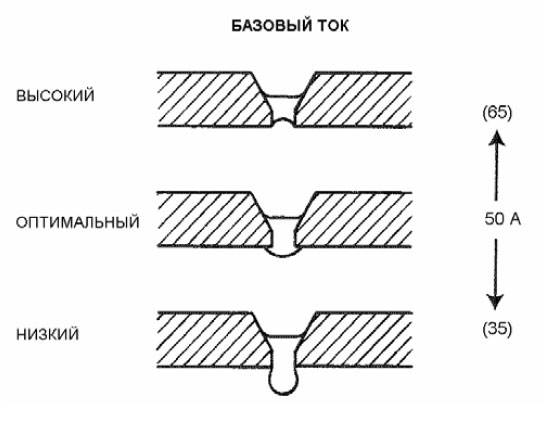
Каковы основные параметры режима сварки в защитных газах
[c. 179]
Цилиндрический корпус изделия собирают из обечаек путем последовательной стыковки на роликовых стендах или на механизированном рабочем месте, оснащенном сборочным устройством с гидравлическими прижимами. До начала сборки измеряют рулеткой периметры смежных торцов обечаек, определяют разность диаметров с целью равномерного расположения смещения кромок по всему контуру кольцевого стыка. При большой толщине кромок кольцевые стыки скрепляют прихватками, которые выполняют ручной дуговой сваркой, и затем сваривают их автоматической дуговой сваркой под флюсом на установках, оснащенных роликовыми вращателями с обрези-ненными роликами. При толщине кромок менее 3 мм стыки обечаек собирают на разжимных кольцах с подкладками для формирования проплава. В этом случае автоматическую сварку кольцевого стыка под флюсом или в защитном газе ведут без прихваток. Иногда, для предотвращения местных деформаций кромок в процессе сварки, применяют сплощную скоростную прихватку по всему периметру кольцевого стыка обечаек.
Коэффициент потерь зависит от способа сварки, типа электрода и параметров режима. На потери значительное влияние оказывает характер переноса электродного металла в сварочной дуге. Так, при сварке покрытыми электродами коэффициент потерь, %, составляет 5… 20, под флюсом — 1… 5, а в защитных газах — 1… 10. В тех случаях, когда в составе электродных покрытий или наполнителей порошковой проволоки содержится значительное количество металлических составляющих, коэффициент Ч отрицателен, поскольку Дн больше Др. [c.21]
При сварке плавящимся электродом в защитных газах зависимости формы и размеров шва от основных параметров режима такие же, как и при сварке под флюсом (см. рис. 3.29). Для сварки используют электродные проволоки малого диаметра (до 3 мм). Поэтому швы имеют узкую форму провара и в них может наблюдаться повышенная зональная ликвация. Применяя поперечные колебания электрода, изменяют форму шва и условия кристаллизации металла сварочной ванны и уменьшают вероятность зональной ликвации. Имеется опыт применения для сварки в углекислом газе электродных проволок диаметром 3. .. 5 мм. Сварочный ток в этом случае достигает 2000 А, что значительно повышает производительность сварки. Однако при подобных форсированных режимах наблюдается ухудшенное формирование стыковых швов и образование в них подрезов. Формирование и качество угловых швов вполне удовлетворительны.
Дуговая сварка в защитных газах. Состав защитного газа, марка и диаметр сварочной проволоки, основные параметры режима полуавтоматической и автоматической сварки выбираются по справочным данным, с [c.242]
Автоматическая сварка под слоем флюса.
Приемы выбора параметров режима сварки покрытыми электродами, в защитных газах, под флюсом. [c.249]
S. Рекомендуемые режимы сварки плавящимся электродом в защитных газах алюминиевых сплавов типа АМг [c.446]
Аналогично может влиять и применение при наплавке, выполняемой под флюсом или в защитных газах, электродной ленты, спрессованной из порошков, по сравнению с прокатной. Большее электрическое сопротивление спрессованной ленты и ее меньшая теплопроводность приводят к более быстрому ее расплавлению (большему а при том же, как при прокатанной ленте, режиме наплавки) и возможному уменьшению доли основного металла в наплавленном слое.
Основным оборудованием для дуговой сварки и наплавки являются источники сварочного тока для ручной сварки штучными электродами, полуавтоматы, автоматы, станки и установки для сварки плавящимся электродом без внешней защиты дуги, под флюсом и в защитных газах, оборудование для импульсно-дуговой сварки плавящимся электродом в инертных газах, установки для ру шой и автоматической сварки вольфрамовым электродом, специальное оборудование для сварки конкретных изделий. Универсальное оборудование имеет различные степень сложности и эксплуатационные возможности от простых полуавтоматов и источников со ступенчатым регулированием режимов до сложных с микропроцессорным управлением.
[c.53]
Универсальные тиристорные сварочные выпрямители выполнены с тиристорным регулированием и имеют универсальные жесткие и падающие внешние характеристики, предназначены для механизированной сварки в среде углекислого газа, под флюсом, резки металлов. Выпрямители на силу тока до 630 А могут быть использованы для ручной дуговой сварки штучными электродами. Выпрямители типов ВДУ-505 и 506 обеспечивают сварку в углекислом газе на силе тока 60 А сварочной проволокой диаметром 1,2 мм, имеют бесступенчатое автоматическое изменение индуктивности в сварочной цепи в зависимости от режима сварки. В схему управления выпрямителей на силу тока 500 и 630 А введено устройство, обеспечивающее форсирование зажигания дуги при сварке в защитных газах, а на силу тока 1250 А — в защитных газах и под флюсом.
Газовые поры образуются в случае применения отсыревших электродов, большой скорости сварки и длинной дуги, загрязненных кромок разделки, недостаточной зашиты шва при сварке в защитных газах. Равномерная пористость обычно возникает при постоянно действующих факторах — загрязненность свариваемых кромок (ржавчина, масло, влага), непостоянная толщина покрытия электродов, влажные электроды. Поры могут быть одиночными, в виде цепочки по продольной оси шва или отдельных групп, равномерно распределенных по шву. Одиночные поры образуются за счет действия случайных факторов — колебания напряжения в сети, местного дефекта в покрытии электрода, случайном удлинении дуги. Цепочки пор образуются, когда газообразные продукты проникают в металл по оси шва на всем его протяжении — подварка корня шва произведена некачественными электродами, подсос воздуха через зазор между кромками, сварка ржавого металла. Скопления пор возникают при местных загрязнениях илп при отклонениях от установленного режима сварки при сварке в начале шва, случайных изменениях длины дуги или ее обрыва, при сварке электродами с нарушенным покрытием.
Технологические режимы дуговой сварки в защитных газах. Для сварки углеродистых и низколегированных сталей широко применяют углекислый газ. Предупреждение появления пор в сварных швах и высокие механические свойства сварных соединений достигаются за счет применения сварочных проволок, содержащих повышенное количество кремния и марганца (табл. 10). [c.328]
Технология и режимы сварки в защитных газах алюминия и различных алюминиевых сплавов, в том числе и литейных, примерно одинаковы. Отсутствие флюса снимает ограничение в выборе типов соединений. Сварка в защитных газах — высокопроизводительный процесс, обеспечивающий получение наиболее качественных сварных соединений в любом пространственном положении материалов различной толщины, начиная от 0,5 мм.
[c. 438]
Приведены сведения о химическом составе, структуре и механических свойствах низколегированных сталей с пределом текучести свыше 586 МПа. Рассмотрены вопросы свариваемости этих сталей и рекомендованы меры борьбы с холодными трещинами. Описаны особенности подготовки деталей под сварку, технология ручной и механизированной сварки под флюсом и в защитных газах, сварочное оборудование. Даны рекомендации по режимам сварки в зависимости от толщины и конструкции соединений. Приведен опыт изготовления и эксплуатации сварных конструкций из высокопрочных низколегированных сталей. [c.2]
Сварка в защитных газах имеет ряд преимуществ по сравнению с другими способами, из которых главные наличие благоприятных условий для визуального, в том числе и дистанционного, наблюдения за процессом сварки широкий диапазон рабочих параметров режима сварки [c.6]
ТЕХНИКА И РЕЖИМЫ СВАРКИ В ЗАЩИТНЫХ ГАЗАХ
[c. 150]
При сварке в вертикальном положении кромки соединяемых элементов располагают вертикально на вертикальной плоскости. Перенос дополнительного металла в сварочную ванну обычно осуществляется в направлении, перпендикулярном к силе тяжести (рис. 5-13, а). В связи с указанными особенностями удовлетворительное формирование шва достигается только при небольшом объеме сварочной ванны. В этих условиях силы поверхностного натяжения удерживают жидкий металл от стекания. Сварку в вертикальном положении можно вьшолнять покрытыми электродами вручную или механизированным способом в защитном газе на режимах, обеспечивающих малый объем сварочной ванны. Сварку ведут, как правило, снизу вверх. Применяется также сварка сверху вниз. [c.177]
Изменение величины сварочного тока оказывает влияние на эффективность использования тепла дуги, разбрызгивание расплавленного металла, устойчивость горения дуги, производительность процесса сварки, площадь иоперечного сгчения наплавки и проплавления, химический состав металла шва. При сварке а одинаковых режимах в защитных газах и под флюсом количество тепла, затрачиваемого на расплавление основного и электродного металла, т. е. эффективность использования тепла дуги, выше при сварке в защитных газах. С увгли-чением тока при сварке в защитных газах уменьшается размер капель и при некотором критическом тока капельный перенос металла переходит в струйный. Изменение характера переноса капель металла в дуге оказывает влияние на величину разбрызгивания металла. С увеличением тока при сварке в защитных газах потгри металла на разбрызгивание снижаются, повышается устойчивость горения дуги, а производительность процесса наплавки возрастает. С дальнейшим увеличением тока выше определенных пределов разбрызгивание снова увеличивается, что определяет верхний предел тока. Нижний предел тока определяет устойчивость горения дуги.
[c.16]
Основные параметры режима механизированной сварки (автоматической и полуавтоматической) под флюсом и в защитных газах, оказывающие существенное влияние на размеры и форму швов, — сила сварочного тока, плотность тока в электроде, напряжение дуги, скорость сварки, химический состав (марка) и граггуляция флюса, род тока и ого полярность.
[c.185]
Аналогично может влиять и примепепие при поплавке, выполняемой под флюсом НЛП в защитных газах, электродной лепты, спрессованной из порошков, но сравнению с прокатной. ]Зольшее электрическое сопротивление спрессованной ленты и се меньшая теплопрозо/нюсть приводят к более быстрому ее расплавлению (большему а,1 при том же, как при прокатанной ленте, режиме [c.397]
Наиболее часто встречаются дефекты типа пор и непро-плавления. При сварке на мягких режимах (малых токах сварки и напряжениях дуги) возникают непроплавления между слоями, либо между первым слоем и основным металлом (рис. 5.7, а). Причиной появления непроплавлений и пор является недостаточно качественная зачистка поверхности каверны от ржавчины (рис. 5.7, б-г). Поры, как правило, возникают из-за содержащейся в защитном газе влаги. Наличие пор не привело к существенному снижению пластичности. При мягких режимах сварки и повышенной влажности защитного газа наличие одновременно общирного непроплавления и пор (рис. 5.7, а) привело к снижению пластичности до пяти раз. При таких условиях угол загиба образцов не превышал 24 градусов.
[c.306]
Для сварки ряда сталей созданы также композиции чисто аустенитного металла шва типа Х15Н25М6 (электроды ЦТ-10, НИАТ-5) [35], типа Х25Н15Г7ВЗ (сварочные проволоки для автоматической сварки стали Х23Н18 [36]. Имеются данные о заметном повышении технологической прочности однофазного аустенитного металла шва в случае перехода к сварке в защитных газах (аргоне или углекислом газе). Необходимо, однако, подчеркнуть, что во всех случаях сварка сталей второй группы представляет заметно более сложную задачу и требует ведения ряда технологических ограничений, связанных прежде всего с введением процесса на пониженных режимах тока, применением электродов малого диаметра, недопущением разогрева детали при сварке и т. п. Длительная прочность сварных соединений сталей этого типа может уступать соответствующим показателям для основного металла. [c.39]
Техника и технология механизированной сварки плавящимся электродом имеет много общего при использовании обычной стальной, имеющей сплошное сечение, порошковой газозащитной и порошковой са-мозащитной электродной проволоки. Различия в основном касаются значений параметров режима, рекомендуемых для сварки различных классов сталей той или иной толщины, величины вылета электродной проволоки, длины дугового промежутка. Основные типы и конструктивные элементы выполняемых дуговой сваркой в защитном газе швов сварных соединений регламентированы ГОСТ 14771-76, которым предусмотрены четыре типа соединений стыковые, угловые, тавровые и нахлесточные. [c.169]
Пример оформления технологического процесса сборки и сварки на операционных картах согласно ЕСТД показан на рис. 185. В операционных картах применены следующие условные обозначения ОК -операционная карта О — переход операции К/М — комплектующие детали и материалы Р — режимы МИ — масса изделия Т — инструмент То — основное время на переход Тв — вспомогательное время на переход ОПП — обозначение подразделения (кладовой, склада), откуда поступают детали, сборочные единицы, материалы или куда поступают обработанные детали, узлы ЕВ — единицы измерения величины (массы, длины и т.п.) ЕН — единица нормирования, на которую устанавливается норма расхода материала (например, 1,10,100) КИ — количество деталей, сборочных единиц, применяемых при сборке изделия Н. расх. — норма расхода материала P — режим сварки ПС -обозначение положения сварки по ГОСТ 11969-79 ДС — диаметр сопла для сварки в защитных газах со струйной защитой, мм 4 — расстояние от торца сопла до поверхности свариваемых деталей /э — вылет электрода, мм U — напряжение дуги I — сила сварочного тока Ус -скорость сварки V — скорость подачи присадочного материала доз -расход защитного газа. [c.369]
Сварка в защитных газах. Высокое качество сварных соединений толщиной 3. .. 5 мм достигается при аргонодуговой сварке неплавящим-ся электродом. При выборе присадочного материала (электродной проволоки) для дуговой сварки в среде защитных газов следует руководствоваться табл. 7.6. Первый слой выполняют без присадки с полным проваром кромок стыка и обратным валиком, второй — с поперечными низкочастотными колебаниями электрода и механической подачей присадочной проволоки. Возможен и третий слой с поперечными колебаниями электрода без присадочной проволоки со стороны обратного формирования на небольшом режиме для обеспечения плавного перехода от шва к основному металлу. [c.310]
АРНД). Аналогично для устранения отклонений силы тока и напряжения дуги для большинства применяемых режимов сварки свободно расширяющейся дугой — (область II) эффективным является использование явления саморегулирования дуги (системы АРДС), регуляторов типа АРНД с воздействием на скорость подачи электродной проволоки, либо систем совместного регулирования силы тока и напряжения дуги с воздействием на подачу электродной проволоки и на источник сварочного тока. Возрастающая статическая характеристика сжатой дуги, например, при сварке тонкой электродной проволокой в защитном газе в сочетании с жесткой внешней характеристикой источника сварочного тока (область III) требует применения автоматических регуляторов силы тока дуги типа АРТД. [c.101]
Применение основного металла переменного состава. В ряде случаев требуется исследовать влияние содержания в металле одного или нескольких легирующих элементов или примесей на структуру и свойства (твердость, прочность, пластичность, ударную вязкость, коррозионную стойкость и др.) стали. С эой целью одним из способов, указанных в п. 1, изготовляют слиток из этой стали ПС с содержанием исследуемого элемента в требуемых пределах. Из слитка отковывается пластина, которую используют в качестве основного металла. Технология ковки должна обеспечивать- непрерывное изменение — содержания- — исследуемого- здемента. по длине пластины и постоянное содержание этого элемента по ее ширине. В пластине выстрагиваются продольные и поперечные канавки, имитирующие разделку кромок. Эти канавки завариваются однослойными швами выбранным способом сварки (под флюсом, в защитных газах) с применением обычных присадочных Материалов и режимов сварки (рис. 8, а). Изменение содержания исследуемого элемента в металле швов будет достигаться путем его перехода из основного металла. При этом продольные швы (1) будут иметь металл переменного состава, а поперечные швы 12) — металл постоянного состава, но с различным содержанием [c.12]
Реализация приведенных мероприятий во многом зависит от габаритных размеров и конструктивного оформления сварных заготовок и узлов. Для сложных узлов с элементами больших толщин и размеров при наличии криволинейных швов в различных пространственных положениях можно применять только хорошо свариваемые материалы. Последние сваривают самыми универсальными способами, например ручной дуговой сваркой покрытыми электродами или полуавтоматической в защитных газах в широком диапазоне режимов. При их сварке не нужны, например, подогрев, затрудненный вследствие больших толщин и размеров элементов, а также высокотемпературная термическая обработка, часто невозможная из-за отсутствия печей и закалочных ванн соответствующего размера. Для простых малогаба-372 [c.372]
Механизированную сварку медных заготовок в защитных газах (аргоне и азоте) выполняют неплавящимся вольфрамовым или плавящимся электродом. В качестве материала для присадочного прутка или плавящегося электрода применяют проволоку из бронзы марок БрЦ0,8 БрКМцЗ-1 БрОЦ4-3, а также из меди М1 и М2. Ориентировочные режимы аргонодуговой сварки приведены в табл. 17.3. [c.273]
Сварка вольфрамовым электродом осуществляется преимущественно в инертных газах или их смесях, она целесообразна для материала толщиной до 5—7 мм. Хорошее формирование обратного валика позволяет рекомендовать вольфрамовый электрод для сварки корневых швов на сталях повышенных толщин (остальные валики могут выполняться под флюсом, покрытыми электродами или в защитных газах). Сварка может вестись непрерывно горящей или импульсной дугой, вручную, полуавтоматически или автоматически, иа режимах, приведенных в табл. XVI. 16. [c.396]
ПОДГОТОВКА ДЕТАЛЕЙ И РЕЖИМЫ СВАРКИ В ЗАЩИТНЫХ ГАЗАХ
Требования на подготовку деталей под сварку в защитных газах в основном аналогичны, как и для сварки под флюсом.
Основные типы и конструктивные элементы выполняемых дуговой сваркой в защитных газах швов сварных соединений из сталей, а также сплавов на никелевой и железоникелевой основах регламентированы ГОСТ 14771-76, которым предусмотрено четыре типа соединений при сварке металла толщиной от 0,5 до 100 мм и более. В зависимости от формы подготовки кромок и толщины свариваемых деталей швы выполняются в соединениях: с отбортовкой кромок, без скоса кромок, со скосом кромок одной или двух кромок как с одной, так и с двух сторон. По характеру выполнения швов они могут быть одно — и двусторонними. Односторонние швы могут выполняться как на весу, так и на различного рода съемных и остающихся подкладках.
Стандартом установлены следующие обозначения способов сварки в защитных газах: ИН — в инертных газах неплавящимся электродом без присадочного материала, ИНП — в инертных газах неплавящимся электродом с присадочным металлом, ИП — в инертных газах и их смесях с углекислым газом и кислородом плавящимся электродом, УП — в углекислом газе и его смеси с кислородом плавящимся электродом.
К основным параметрам сварочных режимов сварки в защитных газах относятся диаметр электрода или электродной проволоки, сварочный ток, напряжение дуги, скорость подачи электродной проволоки, скорость сварки, вылет электрода, расход защитного газа, наклон электрода вдоль оси шва, род тока и полярность.
Диаметр электродной проволоки. Выбирается в пределах 0,5-3 мм в зависимости от толщины свариваемого металла и положения шва в пространстве. С уменьшением диаметра проволоки при прочих равных условиях повышается устойчивость горения дуги, увеличиваются глубина проплавления и коэффициент наплавки, уменьшается разбрызгивание жидкого металла.
С увеличением диаметра проволоки должна быть увеличена сила
тока.
Сварочный ток. С увеличением сварочного тока повышается глубина проплавления. Это приводит к увеличению доли основного металла в шве. Ширина шва сначала несколько увеличивается, а затем уменьшается. Сварочный ток устанавливают в зависимости от диаметра электрода и толщины свариваемого металла.
Напряжение дуги. С увеличением напряжения дуги глубина проплавления уменьшается, а ширина шва увеличивается. Чрезмерное увеличение напряжения дуги сопровождается повышенным разбрызгиванием жидкого металла, ухудшением газовой защиты и образованием пор в наплавленном металле. Напряжение дуги устанавливается в зависимости от выбранного сварочного тока.
Скорость подачи электродной проволоки. Скорость подачи связана со сварочным током. Ее устанавливают с таким расчетом, чтобы в процессе сварки не происходило коротких замыканий и обрывов дуги, а протекал устойчивый процесс плавления электрода.
Скорость сварки. С увеличением скорости сварки уменьшаются все геометрические размеры шва. Она устанавливается в зависимости от толщины свариваемого металла и с учетом обеспечения хорошего формирования шва. Сварку металла большой толщины лучше выполнять более узкими валиками на большей скорости. При слишком большой скорости сварки конец электрода может выйти из зоны защиты и окислиться на воздухе. Медленная скорость сварки вызывает чрезмерное увеличение сварочной ванны и повышает вероятность образования пор в металле шва.
Вылет электрода. С увеличением вылета электрода ухудшаются устойчивость горения дуги и формирование шва, а также увеличивается разбрызгивание жидкого металла. Очень малый вылет затрудняет наблюдение за процессом сварки, вызывает частое подгорание газового сопла и токоподводящего контактного наконечника. Кроме вылета электрода, необходимо выдерживать определенное расстояние от сопла горелки до поверхности свариваемого металла, так как с увеличением этого расстояния ухудшается газовая защита зоны сварки и возможно попадание кислорода и азота воздуха в расплавленном металле. Величину вылета электрода, а также расстояние от сопла горелки до поверхности металла устанавливают в зависимости от выбранного диаметра электродной проволоки. Некоторые значения параметров при сварке в углекислом газе приведены в таблице 14.1.
Таблица 14.1 Параметры сварки в углекислом газе
|
Расход защитного газа определяют в основном в зависимости от выбранного диаметра электродной проволоки и тепловой мощности дуги, зависящей от силы тока. Но на него оказывают также влияние скорость сварки, конфигурация изделия и наличие движения воздуха в цехе, ветра и т. п. Для улучшения газовой защиты в этих случаях приходится увеличивать расход защитного газа, уменьшать скорость сварки, приближать сопло к поверхности металла или пользоваться защитными щитами и другими устройствами.
Наклон электрода вдоль оси шва оказывает влияние на глубину проплавления и качество шва. При сварке углом вперед труднее вести наблюдение за формированием шва, но лучше видны свариваемые кромки и легче управлять электродом. Ширина шва при этом возрастает, а глубина проплавления уменьшается. Сварку углом вперед рекомендуется применять при небольших толщинах металла, когда существует опасность появления сквозных прожогов. При сварке углом назад улучшается видимость зоны сварки, повышается глубина проплавления и наплавленный металл получается более плотным.
Дуговая сварка в защитном газе: описание технологии, режимы, способы
Дуговая сварка в защитном газе представляет собой метод, который значительно повышает качество результата работы. Эта технология имеет ряд особенностей. Прежде чем применять ее, мастер должен ознакомиться с основами дуговой сварки, которая проводится в среде защитных газов. Об особенностях этой технологии будет рассказано далее.
Особенности методики
Одним из подвидов дугового соединения металлических изделий, заготовок является дуговая сварка в защитных газах. ГОСТом регламентирован процесс, во время которого в точку плавления подается газ. Это может быт аргон, кислород, азот или прочие разновидности. Существуют определенные особенности подобного процесса.
Каждый сварщик знает, что качество сварного шва зависит не только от умений мастера, а еще и от условий в точке плавления. В идеальном случае здесь должны присутствовать только электрод и присадочные материалы. Если сюда попадают иные элементы, они способны оказать негативное воздействие на сварку. Место спайки будет из-за этого недостаточно прочным.
Технология ручной дуговой сварки в защитном газе появилась еще в 1920 году. Применение подобных субстанций позволяет сделать швы без шлака. Они характеризуются высокой чистотой, не покрываются микротрещинами. Этот метод активно применяется в промышленности при создании разных элементов из металла.
Особые пропорции защитных газов позволяют снять напряжение в зоне расплава. Здесь не возникают поры, что заметно повышает качество спайки. Шов становится прочнее.
В промышленных условиях в ходе сварочных работ применяют стержни, смешанные с аргоном и диоксидом углерода. Благодаря такой комбинации дуга становится постоянной, оберегая зону расплава от сквозняков. Это позволяет соединить тонкие листы металла.
Если же требуется выполнить глубокую проплавку, смешивают углекислый газ и кислород. Этот состав обладает окислительными свойствами, защищает шов от пористости. Существует множество методик, которые предполагают применять разные газы в ходе сварочных работ. Выбор зависит от особенностей проведения этого процесса.
Техника сварки
Существуют разные режимы дуговой сварки в среде защитного газа. Применяется две основные методики. Первая из них предполагает применение плавящихся шпилей. По ним проходит ток, а стержень из-за этого расплавляется, образуя прочный шов. Этот материал обеспечивает прочное соединение.
Вторая методика предполагает проведение дуговой сварки в защитном газе неплавящимся электродом. В этом случае ток также проходит по стержню, но материал соединяется благодаря расплавлению краев металлических деталей, заготовок. Материал электрода не становится частью шва.
В ходе проведения подобных манипуляций применяются разные газы:
- Инертные. Такие субстанции не имеют запаха и цвета. У атомов присутствует плотная оболочка из электродов. Это обуславливает их инертность. К инертным газам относятся аргон, гелий и т. д.
- Активные. Растворяются в металлической заготовке, вступая с ней в реакцию. К таким средам относятся диоксид углерода, водород, азот и т. д.
- Комбинированные. В ходе определенных процессов нужно применять обе разновидности газов. Поэтому сварка проходит в среде как активных, так и инертных газов.
Чтобы выбрать газовую среду, учитывают состав металла, экономичность самой процедуры, а также свойства спайки. Могут учитываться и прочие нюансы.
В ходе применения инертных газов устойчивость дуги повышается, что позволяет выполнить глубокую расплавку. Подобные вещества подаются в зону расплава несколькими потоками. Если он идет параллельно стержню, это центральный поток. Также есть боковые и концентрические струи. Также газ может подаваться в подвижную насадку, установленную над рабочей средой.
Стоит отметить, что при дуговой сварке, которая происходит в газовой ванне, тепловые параметры приемлемые для производства шва требуемой модели, качества и размера. Выбор режима Чтобы соответствовать требованиям ГОСТ, дуговая сварка в защитных газах может проводиться в разных режимах. Для этого в большинстве случаев требуется применение инверторов полуавтоматического типа. При помощи такой аппаратуры становится возможным регулировать поток электричества, его напряжения.
Инверторные полуавтоматы служат источником питания. Они могут отличаться мощностью, а также опциями. Эксплуатационные качества зависят от модели. Для большинства стандартных операций, в ходе которых не требуется проведение сварки толстых или нечасто используемых сплавов, применяются простые аппараты.
Автоматическая дуговая сварка в среде защитных газов различается массой параметров:
- Радиус проволоки.
- Диаметр проволоки.
- Сила электричества.
- Напряжение.
- Скорость подачи контакта.
- Расход газа.
Существующие полуавтоматические режимы дуговой сварки в защитных газах также разделяют на локальные и общие. В первом случае защитный газ поступает из сопла в зону сварки. Этот вариант применяется чаще. При помощи локальной сварки можно соединить разные материалы, но результат не всегда может быть удовлетворительным.
При использовании локальной подачи газа в зону расплава может попадать воздух. Это снижает качество шва. Чем больше заготовка, которую нужно сварить, тем хуже будет результат при использовании такой методики.
Если нужно сварить крупногабаритные детали, применяются камеры, в которых регулируется атмосфера. Из них откачивается воздух, создается вакуум. Дальше в камеру закачивают нужный по технологии газ. При помощи дистанционного управления производится сварка.
Подготовка к сварке
Чтобы правильно выполнить процедуру соединения металлических заготовок, нужно понимать сущность дуговой сварки в защитном газе. Сварка требует правильной подготовки. Эта процедура всегда одинаковая, независимо от технологии сварки. Сначала кромкам придают правильную геометрию. Это определяется ГОСТом 14771-76.
Механизированная дуговая сварка в защитном газе применяется для полной проварки сплава, что позволяет полностью соединить края заготовки. Зазора между ними не остается. Если же присутствует определенный отступ, разделка краев, проварку можно провести для заготовки, толщина которой не превышает 11 мм.
Для увеличения производительности в процессе автоматической сварки проводится разделка краев заготовок без откосов.
После проведения сварки в углекислом газе потребуется очищать всю плоскость шва от грязи и шлака. Чтобы загрязнение было менее значительным, поверхности обрабатывают особыми составами. Чаще всего это аэрозоли, которые распыляют на металл. Ждать его высыхания не нужно.
В ходе последующей сборки применяются стандартные запчасти, например, клинья, прихватки, скобы и т. д. Конструкция перед началом работы требует тщательного осмотра.
Преимущества и недостатки
Ручная и автоматическая дуговая сварка в защитных газах имеет как преимущества, так и недостатки.
К положительным качествам этого метода относятся:
- Качество шва получается очень высокое. Этого не могут обеспечить иные методики сварки.
- Большинство защитных газов стоит относительно недорого, поэтому процесс сварки не удорожается сильно. Даже дешевые газы обеспечивают качественную защиту.
- Опытный сварщик, который ранее применял иные методики, легко освоит и эту технологию, поэтому поменять специфику маневров сможет даже крупное предприятие с большим количеством сотрудников в штате.
- Процесс универсальный, позволяет сварить как тонкие, так и толстые листы металла.
- Производительность высокая, что положительно сказывается на результатах работы производства.
- Методика применяется не только для сварки черных, но и цветных металлов и сплавов.
- Процесс сварки при использовании газовой защитной ванны легко поддается модернизации. Его можно переделать из ручного в автоматический.
- Процесс сварки можно приспособить ко всем тонкостям производства.
Автоматическая и ручная дуговая сварка в среде защитных газов имеет и определенные недостатки:
- Если сварка производится на открытом участке, нужно обеспечить хорошую герметичность камеры. В противном случае защитные газы могут выветриваться.
- Если же сварка проводится в помещении, здесь обязательно должна быть обустроена качественная система вентиляции.
- Некоторые разновидности газов стоят дорого (например, аргон). Это повышает себестоимость продукции, удорожает весь процесс производства.
Разновидности газов
Дуговая сварка в среде защитных газов производится в разных средах. Они могут быть активными или инертными. К последним относятся такие вещества как Ar, He и прочее. Они не растворяются в железе, не вступают с ним в реакцию.
Инертные газы применяют для сварки алюминия, титана и прочих популярных материалов. Дуговая сварка в защитном газе неплавящимся электродом применяется для стали, которая плохо поддается плавлению.
Активные газы также применяются в ходе проведения подобных работ. Но в этом случае чаще используют дешевые разновидности, например, азот, водород, кислород. Одним из самых популярных веществ, которые применяются в ходе сварки, является двуокись углерода. По цене это самый выгодный вариант.
Особенности газов, чаще всего применяемых в ходе процесса сварки, следующие:
- Аргон не воспламеняется, а также не взрывоопасен. Он обеспечивает качественную защиту сварного шва от неблагоприятных внешних воздействий.
- Гелий поставляется в баллонах с повышенной устойчивостью к давлению, которое здесь достигает 150 атм. Сжижается газ при очень низкой температуре, достигающей -269ºС.
- Двуокись углерода является неядовитым газом, который не имеет запаха и цвета. Это вещество добывают из дымовых газов. Для этого применяется специальное оборудование.
- Кислород является веществом, которое способствует горению. Его получают при помощи охлаждения из атмосферы.
- Водород при контакте с воздухом становится взрывоопасным. При обращении с таким веществом важно соблюдать все требования безопасности. Газ не обладает цветом и запахом, помогает процессам воспламенения.
Особенности сварки в углекислоте, азоте
Дуговая сварка в защитном газе плавящимся электродом проводится при использовании углекислоты. Это самая дешевая методика, которая сегодня пользуется большим спросом. Под воздействием сильного нагрева в зоне плавления СО₂ превращается в СО и О. Чтобы уберечь поверхность от окислительной реакции, в проволоке присутствуют кремний и марганец.
Это также приводит к некоторым неудобствам. Кремний и марганец вступают между собой в реакцию, образуя шлак. Он проступает на поверхности шва, требуя устранения. Это выполнить несложно. На качество сварного шва это обстоятельство никакого воздействия не имеет.
Перед началом работы из баллона удаляют воду, для чего его переворачивают. Это нужно делать с определенной периодичностью. Если не выполнить такую манипуляцию, шов станет пористым. Его прочностные качества будут невысокими.
Дуговая сварка в защитном газе может выполняться при помощи азота. Эта технология применяется для спайки медных заготовок или деталей из нержавейки. С этими сплавами азот не вступает в химическую реакцию. В ходе проведения сварки применяются графитовые или угольные электроды. Если применять для этих целей вольфрамовые контакты, это вызывает их перерасход.
Важно правильно настраивать оборудование. Это зависит от сложности сварки, типа материала и прочих условий. Чаще всего применяется оборудование с напряжением 150-500 А. Оно создает дугу 22-30 В, а расход газа при этом составляет 10 л/мин.
Процесс сварки
Дуговая сварка в защитном газе является эффективной методикой. Но чтобы этого добиться, мастер должен выполнять все требования, выдвигаемые стандартами к этому процессу. Эта методика несколько отличается от иных техник, что мастер должен обязательно учитывать.
Сначала металл готовят для проведения процесса сварки. При использовании такой технологии эта процедура оказывает меньшее воздействие на результат, но проводить ее нужно. Далее проводится настройка оборудования в соответствии с параметрами сварки. Учитывается толщина и тип материала.
Когда оборудование будет готово, производится розжиг дуги. При этом подпаливают пламя горелки. Некоторые разновидности сварки предполагают проведение предварительного прогрева заготовки. Для этого сначала включают горелку, при помощи которой производится предварительная обработка металла.
Когда вокруг дуги начнет образовываться сварочная ванна, начинают подавать проволоку. Для этого оборудование оснащают специальным подающим устройством. Оно поставляет проволоку в зону расплава с определенной скоростью. Если нужно сделать длинный шов, это удобно, так как дугу не придется разрывать. Для этого применяется неплавкий электрод, который поддерживает дугу длительное время.
Если сварка происходит при использовании постоянного тока, его полярность должна быть обратной. Это сокращает вероятность разбрызгивания, но повышается расход металла. Коэффициент наплавления при использовании подобной методики заметно снижается. При прямой полярности он возрастает в 1,5 раз.
Ванну желательно вести слева направо (если мастер правша). Так будет видно процесс формирования шва. Также все действия нужно выполнять по направлению к себе. Шов создается просто, от мастера требуется только ровно вести аппарат на перманентной скорости.
Дуга отрывается от заготовки в обратном направлении относительно движения сварки. В некоторых случаях после такой манипуляции может потребоваться дополнительный прогрев.
Оборудование
Дуговая сварка в защитном газе производится при помощи специального оборудования. Оно применяет стандартные источники электропитания, а также обладает функцией регулировки напряжения.
Агрегаты для сварки оснащаются устройством, передающим проволоку. Также здесь предусмотрены узлы для подачи газов в зону плавления при помощи шлангов из баллонов. Процедура сварки производится при постоянной высокой частотности тока. От правильности регулировки зависит стабильность дуги. Также настраивается скорость подачи проволоки. Наиболее популярными агрегатами для проведения подобной сварки являются:
- «Импульс 3А». Применяется для сварки алюминия, но недостатком является малая функциональность прибора. Его также можно применять для сварки черных металлов, а также создания потолочных швов.
- «ПДГ-502». Применяется для проведения спайки в углекислом газе. Аппарат надежный и производительный. Работает от сети как 220 В, так и 380 В. Электричество может регулироваться от 100 А до 500 А.
- «УРС 62А». Применяется при сварке в полевых условиях. Преимущественно используется для сварки алюминия, но может и обработать титан.
Средства защиты
Сварочные работы при использовании газа отличаются высокой степенью опасности, особенно при использовании взрывоопасных веществ. Поэтому сварщик должен применять в работе индивидуальные средства защиты. Они должны закрывать кожу, глаза, не позволять мастеру вдыхать вредные пары.
Даже если проводится кратковременная сварка в собственном гараже, мастер должен применять специальную маску, респиратор и термоустойчивые краги. В этом случае работа будет выполняться в безопасном режиме, что также сильно отражается на качестве результата.
Обзор современного методического обеспечения расчета размеров шва при механизированной сварке в смеси газов
АННОТАЦИЯ
Современное крупное машиностроение трудно представить без повсеместного применения сварки в защитных газах. Отечественный и зарубежный опыт иллюстрирует, что одним из эффективных путей совершенствования сварки сталей плавящимся электродом в окислительных защитных газах является использование смесей газов. Однако обзор существующих методик по расчету геометрических размеров шва при механизированной сварке в защитных газовых смесях показал их полное отсутствие. Необходимы дальнейшие исследования и экспериментальные данные для создания качественных методик по расчету размеров шва при сварке в смесях.
ABSTRACT
Modern large-scale engineering is difficult to imagine without the widespread use of welding in protective gases. Domestic and foreign experience illustrates that one of the most effective ways to improve steels welding with a melting electrode in oxidizing protective gases is the use of gas mixtures. However, a survey of existing methods for calculating the geometric dimensions of the seam during mechanized welding in protective gas mixtures has showed their complete absence. Further research and experimental data are necessary to create high-quality methods for calculating the seam size during welding in mixtures.
Ключевые слова: дуговая сварка, механизированная сварка, смесь газов, защита шва, форма шва, расчет размеров шва.
Keywords: spark welding; mechanized welding; gas mixtures; seam protection; seam form; size calculation of a seam.
Дуговая сварка плавящимся электродом в среде защитных газов благодаря своей универсальности, возможности механизации и автоматизации процесса является одним из самых распространенных способов сварки в машиностроительном производстве.
Несмотря на широкую распространенность способа, при реализации технологии механизированной сварки зачастую сталкиваются с проблемой обеспечения требуемого качества сварных соединений.
Равнопрочность сварного шва основному металлу – одно из главных требований, предъявляемых к сварному соединению. Прочность, отсутствие дефектов, и требуемая работоспособность сварного соединения в значительной мере определяется правильно рассчитанными размерами и формой шва [3, 11], что, в свою очередь, ведет к существенному снижению расхода сварочных материалов и электроэнергии при производстве сварных конструкций.
Форму шва характеризуют основными параметрами – ширина, высота усиления и глубина проплавления основного металла.
Изменяя химический состава защитной среды, можно эффективно влиять на параметры дуги и глубину проплавления металла. К примеру, добавление к аргону газов с высоким потенциалом ионизации или газов с большой энергией диссоциации молекул ведет к увеличению напряжения дуги, плотности тока и глубины проплавления металла [12].
При сварке углеродистых и низколегированных сталей в качестве защитного газа чаще всего применяется углекислый газ. Однако процесс сварки в этом газе наряду с неоспоримыми достоинствами имеет существенные недостатки, которые ограничивают его использование при изготовлении металлоконструкции ответственного назначения.
Знание свойств компонентов защитных газов и их влияние на сварочный процесс позволяет создать оптимальную защитную среду с точки зрения оптимизации процесса сварки — повышение показателей качества и служебных характеристик сварных изделий, улучшения условий труда и повышения его производительности, а также соблюдения экологических норм при работе. При использовании смесей наблюдается существенная экономия за счет снижения расхода сварочной проволоки, вследствие уменьшения потерь на разбрызгивание, снижение трудозатрат на зачистку сварных соединений от брызг, повышение производительности труда сварщиков на 10 — 20 процентов. [9, 15].
В ближайшем и более отдаленном будущем использование газовых смесей станет одним из ведущих способов защиты сварного шва при соединении материалов [13].
Вопрос о влиянии отдельных параметров режима сварки в СО2 на размеры шва подробно рассматривался в 60-70х годах во многих работах [1, 6, 14], однако обобщенных зависимостей для расчета предложено не было, что сильно затрудняло применение данных исследований в производстве.
Данную проблему в 1973 году решил ассистент на кафедре конструкции судов ДВГТУ Луценко В.Т. За основу в своей работе [10] он использовал методы, применяемые для расчета размеров шва при сварке под флюсом [7]. Однако, данные методики сравнительно сложны и могли быть использованы только после установления многих эмпирических коэффициентов.
В работе [10] предложен метод расчета ширины шва при сварке под флюсом с использованием комплексного параметра, характеризующего давление дуги и удельную ширину шва.
Данный метод, позволяющий при минимальном количестве экспериментов получить зависимость для расчета ширины шва, был принят за основу при расчете ширины и усиления шва, а также глубины проплавления основного металла при механизированной и автоматической сварке в СО2. Это позволило одновременно учесть тепловое и механическое воздействие сварочной дуги, которые и определяют размеры шва [4].
Интерес представляет известная, вообще говоря, общепринятая методика расчета режимов при двусторонней сварке и геометрических размеров шва при автоматической и механизированной сварке под флюсом [2]. В расчетной методике рассматривается только проблема расчета высоты углового шва в зависимости от режима сварки, однако вопрос определения размеров минимального сечения и глубины проплавления остался открытым.
В работе [8] Н.Л. Зайцев усовершенствовал эту методику, основываясь на подтвержденных экспериментами допущениях: зона проплавления при сварке углового шва описывается с помощью уравнения эллипса, а площадь поперечного сечения шва остается постоянной при заданных параметрах режима сварки независимо от его положения. Предлагаемая методика позволила оптимизировать расчет геометрических размеров угловых швов.
В 2014 году Д.С. Бузорина [5] успешно исследовала влияние положение электрода в разделке, угла разделки, скорости сварки, состава защитной среды и вылета электрода на площадь сечения шва и полный тепловой КПД процесса сварки в зависимости от состава защитного газа. Полученные экспериментальные данные Д.С. Бузориной могут быть дополнены и использованы при оптимизации существующих методик для расчета размеров шва.
Данные методики чаще других используются в литературе и приняты за основу при преподавании основ сварки плавлением во всех университетах РФ. Наблюдается потребность в качественных методиках по расчету параметров режима и геометрических размеров шва при механизированной сварке, учитывающих современные тенденции по внедрению защитных смесей. Необходимо экспериментально, на большом количестве образцов при сварке в смеси газов, проследить за изменением конфигурации швов в зависимости от химического состава защитной среды, сопоставить результаты эксперимента с результатами расчёта по методикам [2, 10] и попытаться развить и усовершенствовать эти методики.
Список литературы:
1. Акулов, А. И. Влияние режима и пространственного положения на размеры шва при сварке в СО2 / А. И. Акулов, В. В. Спицын // Сварочное производство. – 1971. – №2. – С. 27-39.
2. Акулов, А. И. Технология и оборудование сварки плавлением : учебник для студентов вузов / А. И. Акулов, Г. А. Бельчук, В. П. Демянцевич. – М.: Машиностроение, 1977. – 432 с
3. Бельчук, Г. А. Сварные соединения в корпусных конструкциях / Г. А. Бельчук. – Л. : Судостроение, 1969. – 279 с.
4. Бродский, А. Я. Давление дуги при сварке электрозаклепками с глубоким проплавлением / А. Я. Бродский, Л. Н. Скороходов // Сварочное производство. – 1966. – №6.
5. Бузорина, Д. С. Исследование условий формирования шва и разработка методики расчета режимов дуговой сварки в защитных газах: автореф. дис. … канд. техн. наук: 05.02.10 / Д. С. Бузорина. — Екатеринбург, 2014. — 22 с.
6. Влияние режима сварки и положения шва в пространстве на их размеры при полуавтоматической сварке в СО2 / В. С. Головченко [и др.]. – Технология судостроения. – 1967. – №2.
7. Дятлов, В. И. Методика расчета автоматической сварки / В. И. Дятлов. – Киев: Облиздат, 1959. – 73 с.
8. Зайцев, Н. Л. Совершенствование методики расчета размеров угловых швов // Вестник ЮУрГУ. Серия Металлургия. – 2015. – №1. – С. 48-50.
9. Кайдалов, А. А. Эффективность применения защитных газовых смесей при дуговой сварке сталей / А. А. Кайдалов, А. Н. Гаврик // Сварщик. – 2011. – № 4. – С. 28–31.
10. Луценко, В. Т. Методика приближенного расчета параметров шва при сварке (наплавке) в СО2 // Сварочное производство. – 1973. – № 1. – С. 20-22.
11. Навроцкий, Д. И. Прочность сварных соединений / Д. И. Навроцкий. – М.: Машгиз, 1961. – 178 с.
12. Паршин, С. Г. Электродуговая сварка сталей и сплавов с применением активирующих материалов: дис. … д-ра техн. наук: 05.03.06 / С. Г Паршин. – Тольятти, 2006. – 404 с.
13. Патон Б. Е. Применение защитных газов в сварочном производстве : обзор / Б. Е Патон, С. Т. Римский, В. И. Галинич // Автоматическая сварка. – 2014. – №6-7. – С. 17-25.
14. Повышение производительности сварки в СО2 / В. Т. Золотых [и др.] // Сварочное производство. – 1966. – №8. – С. 16-19.
15. Синица, А. Н. Сравнение экономической эффективности применения углекислого газа и смеси Ar + СО2 в качестве защитных сред при сварке / А. Н. Синица, М. А. Синица, М. Ж. Солодков // Материалы, оборудование и ресурсосберегающие технологии: материалы междунар. научно-техн. конф. – Могилев: Изд – во Белорусско-Российского университета, 2017 – Ст. 153.
Режимы полуавтоматической сварки среде защитных газов
Использование сварочного полуавтомата в сочетании с защитным газом — почти всегда выигрышный вариант. Благодаря такому комплекту оборудования вам становится доступна качественная и быстрая сварка сталей, алюминия, меди и прочих металлов. Но есть и особенности, которые сварщик должен учитывать перед тем, как выберет данный метод сварки.
Прежде всего, полный новичок вряд ли сможет выполнить работу качественно. Это связано не только с отсутствием опыта, но и с тем фактом, что полуавтомат нужно правильно настроить и выбрать необходимые расходники. Опытные мастера говорят: «Чтобы настроить режимы сварки полуавтоматом в среде защитных газов нужно потратить несколько лет на изучение литературы, ГОСТов и кропотливую работу. Без практики ничего не получится».
Мы полностью согласны с этим утверждением. Но не спешим сбрасывать со счетов начинающих сварщиков. Специально для них мы подготовили краткую статью, которая поможет разобрать с режимами сварки и начать применять полученную информацию на практике. При составлении этой статьи мы руководствовались не только собственным опытом, но и справочной литературой.
Основные параметры
Чтобы правильно подобрать режимы полуавтоматической сварки нужно четко понимать, из чего состоят эти режимы. Далее мы перечислим основные параметры режимов сварки, зная которые вы сможете правильно выбрать настройки полуавтомата.
Диаметр и марка проволоки
Начнем с диаметра проволоки. Он может колебаться в пределах от 0.5 до 3 миллиметров. Обычно, диаметр проволоки подбирается исходя из толщины свариваемого металла. Но в любом случае у каждого диаметра есть свои характерные признаки. Например, при работе с проволокой малого диаметра мастера отмечают более устойчивое горение дуги и меньший коэффициент разбрызгивания металла. А при работе с проволокой большего диаметра всегда требуется увеличивать силу тока.
Не стоит забывать и о марке применяемой проволоки. А точнее, металле, из которого проволока изготовлена и какие вещества входят в ее состав. Например, для сварки низкоуглеродистой или низколегированной стали рекомендуется использовать проволоку с раскислителями, а в составе должен присутствовать марганец и кремний.
Но, справедливости ради, в среде защитного газа зачастую либо легированную, либо высоколегированную сталь. В таких случаях используют проволоку, изготовленную из того же металла, что и деталь, которую нужно сварить. Обратите внимание на выбор проволоки, ведь при неправильном выборе шов может получиться пористым и хрупким.
Сила, полярность и род сварочного тока
Помимо выбора комплектующих нам также нужно настроить сам полуавтомат. В типичном полуавтомате даже самого низкого ценового сегмента вы сможете настроить силу, полярность и род сварочного тока. У каждого параметра также есть свои особенности. Например, если увеличить силу тока, то глубина провара увеличиться. Силу тока устанавливают, опираясь на диаметр электрода и особенности металла, с которым собираются работать.
Теперь о полярности и роде тока. Общепринято выполнять полуавтоматическую сварку в среде защитного газа, установив постоянный ток и обратную полярность. Переменный род тока или прямая полярность применяются очень редко, поскольку такие настройки не обеспечивают устойчивое горение дуги и способствуют ухудшению качества сварного соединения. Но есть исключение из правил. Так переменный ток показан при сварке алюминия, например.
Также многие новички забывают о таком параметре, как напряжение сварочной дуги. А вместе с тем именно напряжение дуги влияет на глубину провара металла и размер сварочного соединения. Не стоит устанавливать слишком большое напряжение, иначе металл начнем разбрызгиваться, в шве образуются поры, а газ не сможет в должной мере защитить сварочную зону. Чтобы правильно настроить напряжение дуги ориентируйтесь на силу сварочного тока.
Скорость подачи проволоки
Как вы знаете, в полуавтоматической сварке проволока подается с помощью специального механизма. Он работает очень точно, поэтому необходимо заранее установить оптимальную скорость подачи присадочной проволоки, чтобы она вовремя плавилась и способствовала формированию качественного шва. Настраивайте скорость с учетом силы тока. В идеале проволока должна подаваться так, чтобы дуга сохраняла свою устойчивость, а шов формировался постепенно.
Скорость сварки
Не менее важна и скорость сварки. От нее во многом зависят физические размеры шва. Скорость регулируется ГОСТами, но ее можно выбрать и по своему усмотрению, опираясь на особенности металла и его толщину. Учтите, что толстый металл нужно варить быстрее, а шов должен быть узким. Но не стоит слишком спешить, иначе электрод может просто выйти из зоны защитного газа и окислиться под воздействием кислорода. Ну а слишком медленная скорость способствует формированию непрочного пористого шва.
Наклон электрода
И последний важный параметр, а именно угол наклона электрода при сварке. Наиболее частая ошибка у новичков — держать электрод так, как физически удобно. Это грубейшее нарушение. Ведь угол наклона электрода напрямую влияет на то, какова будет глубина провара и насколько качественным получится шов в конечном итоге.
Существует два типа наклона: углом назад и углом вперед. У каждого положения есть свои достоинства и недостатки. При сварке углом вперед зона сварки видна хуже, зато лучше видны кромки. Также глубина провара меньше. А при сварке углом назад наоборот зона сварки видна намного лучше, но глубина провара увеличивается.
Мы рекомендуем варить углом вперед только тонкий металл, поскольку данное положение наиболее удачно. А вот углом назад можно варить металлы любой другой толщины.
Таблицы
Да, опытные мастера с ходу способны подобрать правильный режим сварки, поскольку их опыт и знания позволяют. Но что делать новичкам? Им поможет специальная таблица для настройки режима. Точнее, таблицы, для каждого типа сварки. Но не стоит злоупотреблять готовыми настройками, экспериментируйте и не бойтесь применять на практике свой опыт.
Таблица №1. Рекомендуемые настройки для формирования стыкового шва в нижнем пространственном положении и сварки низкоуглеродистой и низколегированной стали в среде защитного газа (углекислого газа, смеси углекислоты с кислородом, а также смеси аргона с углекислым газом) током обратной полярности.
Таблица №2. Рекомендуемые настройки для формирования поворотно-стыковых соединений с применением углекислоты, смеси аргона с углекислотой и аргона с углекислотой и кислородом, ток обратной полярности.
Таблица №3. Рекомендуемые настройки для формирования нахлесточного шва с током обратной полярности, с применением углекислого газа или смеси углекислоты с аргоном.
Таблица №4. Рекомендуемые настройки для сварки углеродистой стали, пространственное положение вертикальное, применяется обратная полярность, а также углекислый газ или смесь углекислоты с аргоном.
Таблица №5. Рекомендуемые настройки для формирования горизонтального соединения на обратной полярности, с использованием углекислого защитного газа.
Таблица №6. Рекомендуемые настройки для формирования потолочных швов на обратной полярности с применением углекислого газа.
Таблица №7. Рекомендуемые режимы сварки в углекислом газе методом «точка», работа с углеродистой сталью.
Вместо заключения
Конечно, мы многие темы не затронули. Например, мы не рассказали, каково оптимальное рабочее давление углекислоты при сварке полуавтоматом, как производить расчет режима сварки в углекислом газе (или любом другом защитном газе). Это лишь краткий экскурс в тему выбора режима сварки. На нашем сайте вы найдете много полезного материала о полуавтоматической сварке и не только, обязательно прочтите, чтобы лучше разбираться в теме. И не забывайте практиковаться, ведь без практики теория теряют свою силу. Желаем удачи в работе!
Режимы сварки в защитных газах имеют такие основные параметры :
- род, сила и полярность тока;
- напряжение сварки,
- диаметр проволоки;
- скорость подачи электродной проволоки;
- вылет, наклон и колебания электрода;
- скорость сварки;
- расход газа;
- состав газа.
Таблица 1. Режимы сварки в в защитных газах (СO2,СO2+O2 и Ar+25%СO2 ) стыковых соединений низкоуглеродистых и низколегированных сталей в нижнем положении проволокой Св-08Г2СА (ток обратной полярности)
Диаметр детали, мм | Толщина стенки, мм | Зазор, мм | Смещение кромок, мм | Диаметр проволоки, мм | Сила сварочного тока, А | Напря- жение сварки, В | Скорость сварки, м/ч | Вылет электрода, мм | Расход газа, л/мин |
50* | 1-1,5 | 0-1 | 0-1 | 0,8-1,2 | 100-150 | 18-19 | 80-90 | 10-12 | 7-8 |
100-150** | 2-2,5 | 0-1.5 | 0-1 | 0,8-1,2 | 130-180 | 18-19 | 70-80 | 10-13 | 7-8 |
200-500** | 8-15 | 0-1 | 0-1 | 1-1,2 | 150-190 | 19-21 | 20-30 | 10-15 | 7-8 |
200-400** | 30-60 | 0-1 | 0-1 | 2-3 | 350-450 | 32-36 | 25-35 | 25-60 | 15-18 |
* Смещение электрода согласно Рис .1.
** Сварка корневого шва при V- или U-образной разделке
Рис. 1. Схемы расположения электрода при сварке в СO2 поворотных кольцевых швов тонкой стали 1 на весу.
Толщина металла, мм | Положение сварки | Защитный газ | Зазор, мм | Диаметр проволоки, мм | Сила сварочного тока, А | Напряжение сварки, В | Скорость сварки, м/ч | Вылет электрода, мм | Расход газа, л/мин | Примечание |
0,8+0,8 | В | СO2 | 0-0,5 | 0,8-1 | 100-120 | 17,5-19 | 40-80 | 8 | 6-7 | На медной прокладке |
1+1 | Н | 0,8-1,2 | 110-135 | 18-20 | 30-50 | 8-12 | 7-8 | |||
1+1 | В | 0,8-1,2 | 120-150 | 18-20 | 40-80 | 8-12 | 7-8 | На весу или на медной прокладке | ||
1,2+1,2 | Н | СO2 ,Ar+ 25%СO2 | 0-0,5 | 0,8-1,2 | 120-145 | 18-20 | 30-50 | 8-12 | 6-8 | На медной прокладке |
В | 130-160 | 40-80 | 7-8 | На весу или на медной прокладке | ||||||
2+2 | Н и В | 0-0,5 | 1-1,4 | 160-220 | 19-22 | 30-70 | 10-14 | 8-9 | На весу | |
5+5 | Н | 0-1 | 1,2-2 | 200-500 | 21-35 | 30-45 | 10-20 | 9-15 | ||
1,5+5 | Н и В | 0-1 | 1-1,4 | 130-180 | 19-22 | 30-65 | 8-14 | 7-9 |
* Н – нижнее, В – вертикальное положение сварки.
Таблица 4. Режимы сварки в в защитных газах ( СO2 и Ar+25%СO2 ) углеродистых сталей в вертикальном положении проволокой Св-08Г2С (сварка сверху вниз, обратная полярность).
Толщина металла, мм | Соединение | Зазор, мм | Номер прохода | Диаметр проволоки, мм | Сила сварочного тока, А | Напря- жение сварки, В | Скорость сварки, м/ч | Вылет электрода, мм | Расход газа, л/мин |
0,8-1 | 0-1 | 1 | 0,8-1,2 | 90-130 | 17-18 | 40-60 | 8-11 | 6-7 | |
1,2-2 | 0-1 | 0,8-1,2 | 140-200 | 18-22 | 40-55 | 8-12 | 6-7 | ||
2,2-4 | 0-1,5 | 1,2-1,5 | 180-260 | 21-24 | 35-55 | 9-12 | 7-8 | ||
3-6 | 1±1 | 1 | 1,2-1,4 | 160-200 | 20-23 | 25-45 | 9-12 | 8-9 | |
2 | 1,2-1,4 | 200-260 | 23-25 | 20-40 | 9-12 | 8-9 | |||
8-10 | 2±1/2 | 1 | 1,2-1,4 | 160-200 | 20-23 | 25-45 | 9-12 | 9-10 | |
2-3 | 1,2-1,4 | 200-260 | 23-35 | 20-35 | 9-12 | 9-10 | |||
0,8-1 | 0-0,05 | 1 | 0,8-1 | 90-130 | 17-18 | 40-55 | 8-11 | 5-7 | |
1,5-3 | 1 | 0,8-1,2 | 140-200 | 18-22 | 40-50 | 8-12 | 6-7 | ||
3,2-5,5 | 0-1 | 1-2 | 1,2-1,4 | 160-240 | 20-23 | 35-55 | 9-12 | 7-8 | |
6-12 | 0-1,5 | 1-2 | 1,2-1,4 | 200-260 | 22-26 | 25-35 | 10-12 | 8-10 |
Режимы сварки в защитных газах ( СO
2)горизонтальных швов проволокой Св-08Г2С (обратная полярность).
Толщина металла, мм | Соединение | Зазор, мм | Диаметр проволоки, мм | Сила сварочного тока, А | Напря- жение сварки, В | Скорость сварки, м/ч | Вылет электрода, мм | Расход газа, л/мин |
0,8-1 | 0-0,5 | 0,8-1 | 70-130 | 17-18,5 | 25-30 | 8-10 | 6-7 | |
1,5 | 1-1,5 | 0,8-1,2 | 100-150 | 17,5-19,5 | 19-24 | 8-12 | 6-8 | |
3 | 1,5-2 | 1-1,4 | 140-190 | 20-23 | 16-18 | 10-12 | 7-9 | |
5-6 | 0-1 | 1-1,4 | 150-250 | 20-23 | 10-14 | 12-14 | 8-10 |
Режимы сварки в защитных газах ( СO
2)швов в потолочном положении проволокой Св-08Г2С (обратная полярность).
Толщина металла, мм | Катет шва | Соединение | Зазор, мм | Диаметр проволоки, мм | Число проходов | Сила сварочного тока, А | Напря- жение сварки, В | Скорость сварки, м/ч | Расход газа, л/мин |
1,5-2 | 1,5-2 | 0-1 | 0,8-1,2 | 1 | 150-190 | 18,5-20 | 23-35 | 7 | |
3-5 | 3-5 | 0-1,5 | 1-1,2 | 1 | 160-260 | 18-22,5 | 20-30 | 8 | |
7-8 | 6-8 | 2 | 160-270 | 19,5-22,5 | 17-25 | 8-9 |
Режимы сварки (ориентировочные) углеродистых сталей в углекислом газе
электрозаклепками и точками.
Толщина листов, мм | Диаметр проволоки, мм | Сила сварочного тока, А | Напря- жение сварки, В | Длительность сварки, с | Вылет электрода, мм | Расход газа, л/мин | Наличие отверстия в верхнем листе | |
верхнего | нижнего | |||||||
0,5 | 0,5-2,0 | 0,8 | 100-140 | 18-21 | 0,6-1,1 | 6-10 | 5-6 | нет |
0,8 | 0,8-3,0 | 0,8 | 120-160 | 19-22 | 0,5-1,2 | 8-10 | 5-6 | нет |
1,0 | 1,0-4,0 | 0,8-1,0 | 150-190 | 20-23 | 1,0-1,8 | 8-12 | 5-7 | нет |
1,5 | 1,5-4,0 | 1,0-1,2 | 200-210 | 21-24 | 1,4-1,8 | 10-12 | 6-7 | нет |
1,5 | 1,5-4,0 | 1,0-1,2 | 190-210 | 21-23 | 1,3-1,6 | 10-12 | 6-7 | есть |
2,0 | 2,0-5,0 | 1,0-1,4 | 220-300 | 22-27 | 2,0-3,0 | 10-14 | 6-8 | нет |
2,0 | 2,0-5,0 | 1,0-1,4 | 210-250 | 22-25 | 1,6-2,0 | 10-14 | 6-7 | есть |
3,0 | 3,0-6,0 | 1,2-1,6 | 320-380 | 30-35 | 2,0-3,0 | 12-14 | 7-8 | нет |
3,0 | 3,0-6,0 | 1,2-1,6 | 300-350 | 28-32 | 1,9-2,5 | 12-14 | 7-8 | есть |
4,0 | 4,0-6,0 | 1,4-1,6 | 380-420 | 33-37 | 3,0-3,5 | 13-15 | 8-9 | нет |
4,0 | 4,0-6,0 | 1,4-1,6 | 350-380 | 32-35 | 2,2-3,0 | 13-15 | 8-9 | есть |
5,0 | 5,0-7,0 | 1,4-2,0 | 400-450 | 34-40 | 3,5-4,0 | 14-16 | 9-10 | нет |
6,0 | 6,0-8,0 | 1,6-2,4 | 420-550 | 38-44 | 3,0-4,0 | 14-18 | 9-10 | нет |
8,0 | 8,0-10,0 | 2,0-2,4 | 550-600 | 43-48 | 3,0-4,0 | 16-18 | 11-12 | нет |
Примечание к Табл.7: постоянный ток обратной полярности; режимы сварки точками принимают текими же, как при сварке без отверстия для толщины верхнего листа.
Сварка MIG / MAG была изобретена в 1950‑х годах и основные принципы используются, в современных сварочных аппаратах по сей день. Она является самой универсальной и часто применяемой в кузовном ремонте. Когда речь идёт о полуавтоматической сварке, то, имеют ввиду, именно эту сварку. В отличие от других видов ручной сварки она отличается лёгкостью применения, при этом даёт качественный результат.
p, blockquote 1,0,0,0,0 –>
Более правильное и полное название этого вида сварки GMAW (Gas metal arc welding – электродуговая сварка металла в среде защитного газа), но чаще используют именно аббревиатуру MIG / MAG (Metal Inert Gas/ Metal Active Gas).
p, blockquote 2,0,0,0,0 –>
MIG /MAG-сварка – это электро-дуговая сварка, использующая постоянный ток ( DC ). В качестве электрода в этом виде сварке используется проволока, которая поступает в место сварки с определённой заданной скоростью. Обычно такая сварка используется вместе с защитным газом. MIG – полуавтоматическая сварка, где в качестве защитного газа используется инертный газ (аргон, гелий..), а MAG – полуавтоматическая сварка, где в качестве защитного газа используется активный газ ( CO2 и смеси).
p, blockquote 3,0,0,0,0 –>
Первоначально использовался только аргон для сварки всех металлов, что было дорого и недоступно. В дальнейшем стали применять двуокись углевода ( CO2 ) и смеси и этот вид сварки стал более доступным и получил широкое распространение.
p, blockquote 4,0,0,0,0 –>
MIG /MAG-сваркой можно сваривать различные виды металла: алюминий и его сплавы, углеродистую и низкоуглеродистую сталь и сплавы, никель, медь и магний.
p, blockquote 5,0,0,0,0 –>
Учитывая высокое качество сварки и лёгкость применения, она, в дополнение к этому, распространяет сравнительно небольшой нагрев зоны, вокруг места сварки.
p, blockquote 6,0,0,0,0 –>
Принцип действия
p, blockquote 7,0,0,0,0 –>
Сварка MIG / MAG (Metal Inert Gas/ Metal Active Gas) осуществляется посредством электрической дуги, защищённой газом, образуемой между рабочей поверхностью и проволокой (электродом), которые автоматически поступают к месту сварки при нажатии на курок. Скорость подачи проволоки, напряжение сварки и количество газа устанавливаются заранее. Из-за того, что сварочная проволока автоматически поступает к месту сварки, а от сварщика зависят только манипуляции со сварочной горелкой, такой вид сварки часто и называют полуавтоматической.
p, blockquote 8,0,0,0,0 –>
При MIG /MAG-сварке очень важна настройка сварочного аппарата. При электродуговой сварке электродами и при сварке TIG настройки не так критичны. Также важна чистота металла перед началом сварки.
p, blockquote 9,0,0,0,0 –>
Конец проволоки должен выступать на определённое расстояние, иначе слишком длинная проволока-электрод не позволит защитному газу нормально действовать. Этот параметр мы рассмотрим ниже в этой статье.
p, blockquote 10,0,0,0,0 –>
Оборудование для сварки MIG / MAG
Сварочный аппарат MIG / MAG содержит генератор электрической дуги (трансформатор или инвертер), механизм подачи проволоки, кабель «массы» с зажимом, баллон для защитного газа.
p, blockquote 11,0,0,0,0 –>
Защитный газ
Основная задача защитного газа – защита расплавленного металла от атмосферного воздействия (кислород окисляет, а азот и влага из воздуха вызывают пористость шва) и обеспечить благоприятные условия зажигания сварочной дуги.
p, blockquote 12,0,0,0,0 –>
Тип защитного газа влияет на скорость плавления, проникновение сварочной дуги, на количество брызг при сварке, форму и механические свойства сварочного шва. Определённая смесь газов даёт существенный эффект стабильности электрической дуги и уменьшает количество брызг при сварке. Состав газа влияет на то, как расплавленный металл от проволоки передаётся к месту сварки.
p, blockquote 13,0,0,0,0 –>
Инертные газы и их смеси в качестве защитного газа ( MIG ) используются для сварки алюминия и цветных металлов. Обычно применяются аргон и гелий.
p, blockquote 14,0,0,0,0 –>
Активные газы и смеси ( MAG ) применяется для сварки сталей. Чаще всего это чистая двуокись углерода ( CO2 ), а также в смеси с аргоном.
p, blockquote 15,0,1,0,0 –>
Рассмотрим виды и смеси защитных газов подробнее:
p, blockquote 16,0,0,0,0 –>
- Чистая двуокись углерода ( CO2 ) или двуокись углерода с аргоном, а также аргон в смеси с кислородом обычно используются, для сварки стали. Если использовать двуокись углерода ( CO2 ) в качестве защитного газа, то получите высокую скорость плавления, лучшую проникаемость дуги, широкий и выпуклый профиль сварочного шва. Когда используется чистая двуокись углерода, то происходит сложное взаимодействие сил вокруг расплавленных металлических капель на кончике насадки. Эти несбалансированные силы становятся причиной образования больших нестабильных капель, которые передаются в зону сварки случайными движениями. Это является причиной увеличения брызг вокруг сварочного шва. Также чистый карбон диоксид образует больше испарений.
- Аргон, гелий и аргонно-гелиевая смесь используются при сварке цветных металлов и их сплавов. Эти смеси инертных газов дают более низкую скорость плавления, меньшее проникновение и более узкий сварочный шов. Аргон дешевле гелия и смеси гелия с аргоном, а также даёт меньшее количество брызг при сварке. В отличие от аргона, гелий даёт лучшее проникновение, более высокую скорость плавления и выпуклый профиль сварочного шва. Но когда используется гелий, сварочное напряжение возрастает при такой же длине сварочной дуги и расход защитного газа возрастает в сравнении с аргоном. Чистый аргон не подходит для сварки стали, так как дуга становится слишком нестабильной.
- Универсальная смесь для углеродистой стали состоит из 75% аргона и 25% двуокиси углерода (может обозначаться 74/25 или C25 ). При использовании такого защитного газа образуется наименьшее количество брызг и уменьшается вероятность прожига насквозь тонких металлов.
Металл должен быть зачищен от краски и ржавчины. Даже остатки краски при сварке будут ухудшать качество и прочность сварочного соединения. Место под зажим для массы также должно быть зачищено.
p, blockquote 17,0,0,0,0 –>
Как держать сварочную горелку
p, blockquote 18,0,0,0,0 –>
Сварочной горелкой полуавтомата MIG / MAG можно управлять одной рукой, но использование двух рук облегчит контроль и увеличит аккуратность и качество сварочного шва. Смысл в том, чтобы одной рукой держать горелку и опираться ей на другую руку. Так можно легче контролировать расстояние от свариваемой поверхности и угол, а также делать горелкой нужные движения при формировании шва.
p, blockquote 19,0,0,0,0 –>
Чтобы работать двумя руками, необходимо использовать полноразмерную сварочную маску (лучше с автозатемнением), которая удерживается на голове и руки остаются свободными.
p, blockquote 20,0,0,0,0 –>
Движение сварочной горелкой во время сварки
p, blockquote 21,0,0,0,0 –>
- Прямой шов, без каких-либо движений в сторону можно применять на металлах, имеющих практически любую толщину, но здесь нужен определённый опыт, чтобы удостовериться, что сварочная дуга равномерно действует на оба свариваемых металла.
- При сварке металлических деталей, имеющих толщину меньше 1мм, лучше использовать электродную проволоку меньшего диаметра, уменьшить параметры силы тока, а также скорость подачи проволоки. Нужно варить короткими импульсами, делая перерыв между ними в пределах 1 секунды, чтобы металл успевал охладиться. Короткий перерыв нужен, чтобы следующий сегмент сливался с предыдущим и получался монолитный герметичный шов.
- При сварке длинного сегмента, во избежание перегрева металла и тепловой деформации, можно сваривать небольшими сегментами или точками с интервалами, поочерёдно, то с одного, то с другого конца свариваемого отрезка. Таким образом, можно проварить весь сегмент, без получения тепловой деформации листового металла.
Скорость сварки
p, blockquote 22,0,0,0,0 –>
Скорость сварки – это скорость, с которой электрическая дуга проходит вдоль места сварки. Она контролируется сварщиком.
p, blockquote 23,0,0,0,0 –>
Скорость движения сварочной горелки должна контролироваться сварщиком и соответствовать скорости подачи проволоки и напряжению электрической арки, выбранных, в соответствии с толщиной свариваемого металла и формы шва.
p, blockquote 24,0,0,0,0 –>
Важно добиться правильной скорости сварки. Слишком высокая скорость может вызвать слишком много брызг расплавленного металла. Защитный газ может остаться в быстро застывающем расплавленном металле, образуя поры. Слишком медленная скорость сварки может стать причиной излишнего проникновения сварочной дуги в свариваемый металл.
p, blockquote 25,0,0,0,0 –>
Скорость движения сварочной горелки влияет на форму и качество сварочного шва. Многие опытные сварщики определяют с какой скоростью нужно двигать сварочную горелку, глядя на толщину и ширину шва в процессе сварки.
p, blockquote 26,0,0,0,0 –>
Скорость потока защитного газа
Может значительно влиять на качество сварки. Скорость потока защитного газа должна строго соответствовать скорости подачи проволоки. Слишком медленный поток не даёт нормальной защиты от окисления, в то время как слишком высокая скорость потока защитного газа может создать завихрения, которые также помешают нормальной защите. Все отклонения ведут к пористости сварочного шва. Важно создать ровный поток воздуха, без завихрений. На это может влиять наличие застывших брызг на насадке.
p, blockquote 27,0,0,0,0 –>
Угол сварочной горелки во время сварки
Сварка MIG / MAG может сваривать разные детали под разными углами, поэтому не существует универсального угла, который нужно соблюдать при сварке. При сварке деталей, лежащих в одной плоскости идеальным будет угол в 15–20 градусов (от вертикального положения). При сварке двух деталей под углом удобнее держать горелку под углом 45 градусов. Практикуясь, можно для себя определить наиболее удобный угол в конкретной ситуации.
p, blockquote 28,0,0,0,0 –>
Сварочное напряжение (длина электрической дуги)
Длина дуги одна из самых важных переменных в сварке MIG / MAG , которую нужно контролировать. Нормальное напряжение сварочной дуги в двуокиси углерода ( CO2 ) и гелии (He) намного выше, чем в Ароне (Ar). Напряжение дуги влияет на проникновение, прочность и ширину шва.
p, blockquote 29,0,0,0,0 –>
С увеличением напряжения электрической дуги, шов становится более плоским и широким и до определённых пределов увеличивается проникновение. Низкое напряжение даёт более узкий и выпуклый шов и уменьшается проникновение.
p, blockquote 30,1,0,0,0 –>
Слишком большое и слишком маленькое напряжение вызывает нестабильность дуги. Избыточное напряжение является причиной образования брызг и пористости шва.
p, blockquote 31,0,0,0,0 –>
Сварочная проволока
Сварочная проволока служит присадочным материалом. При сварке проволока поступает к месту шва и расплавляется вместе с кромками металлов, заполняя шов. У неё должен быть химический состав, схожий с составом свариваемых материалов. К примеру, содержание углерода, от которого зависит пластичность шва.
p, blockquote 32,0,0,0,0 –>
Температура плавления электродной проволоки должна быть чуть ниже или такой же, как металлов, которые свариваются. Если проволока будет плавиться позже, чем свариваемый металл, то увеличивается вероятность прожжения металла насквозь.
p, blockquote 33,0,0,0,0 –>
Для сварки алюминия и его сплавов применяется проволока из чистого алюминия или с примесью магния и кремния.
p, blockquote 34,0,0,0,0 –>
Диаметр сварочной проволоки
p, blockquote 35,0,0,0,0 –>
Диаметр сварочной проволоки влияет на размер шва, глубину проникновения сварочной дуги, прочность шва и на скорость сварки.
p, blockquote 36,0,0,0,0 –>
Больший диаметр электрода (проволоки) создаёт шов с меньшим проникновением, но более широкий. Выбор диаметра проволоки зависит от толщины свариваемого металла и положения свариваемых деталей.
p, blockquote 37,0,0,0,0 –>
В большинстве случаев маленький диаметр проволоки подходит для тонкого металла и для сварки в вертикальном положении.
p, blockquote 38,0,0,0,0 –>
Проволока большего диаметра желательна для более толстого металла. Ей нужно работать с уменьшенной скоростью подачи проволоки, из-за более низкого проникновения.
p, blockquote 39,0,0,0,0 –>
Длина выхода сварочной проволоки
p, blockquote 40,0,0,0,0 –>
До касания свариваемого металла проволока должна выступать из наконечника на определённую длину.
p, blockquote 41,0,0,0,0 –>
Этот сегмент проволоки проводит сварочный ток. Таким образом, увеличение длины этого сегмента увеличивает электрическое сопротивление и температуру этого отрезка проволоки. Чем больше выступает проволока, тем меньше будет электрическая дуга. При длинном выходе проволоки из наконечника получается узкий шов, низкое проникновение и повышенная толщина шва.
p, blockquote 42,0,0,0,0 –>
При уменьшении длины выхода отрезка сварочной проволоки даёт противоположный эффект. Увеличивается проникновение сварочной дуги, получается более широкий и тонкий шов.
p, blockquote 43,0,0,0,0 –>
Типичная длина выхода сварочной проволоки варьируется от 6 до 13 мм.
p, blockquote 44,0,0,0,0 –>
При использовании порошковой проволоки без газа длина выхода сварочной проволоки должна быть больше, чем с газом (30 – 45 мм).
p, blockquote 45,0,0,1,0 –>
Cварка самозащитной проволокой без газа
Порошковая самозащитная проволока, которую также называют флюсовой имеет сердечник, содержащий в себе все необходимые присадки для защиты шва и сварочной дуги в процессе сварки без газа.
p, blockquote 46,0,0,0,0 –>
Такая проволока содержит компоненты, образующие газ во время сварки, антиокислители, очистители, а также присадки, улучшающие электрическую дугу. Таким образом, при возникновении дуги образуется газ, который защищает расплавленный металл, а также специальные компоненты образуют подобие шлака поверх металла во время остывания, который защищает его во время затвердевания.
p, blockquote 47,0,0,0,0 –>
p, blockquote 48,0,0,0,0 –>
Такую проволоку удобно использовать, когда сварочный аппарат нужен не часто. Преимуществом является лучшая мобильность оборудования (не требуется баллон с газом) и возможность использования на улице (даже в ветреную погоду, ввиду отсутствия притока защитного газа).
p, blockquote 49,0,0,0,0 –>
При сварке самозащитной проволокой образуется много дыма и испарений и сложно визуально контролировать процесс сварки. Сварочный флюс, который остаётся поверх готового шва, не проводит электричества, поэтому после охлаждения, чтобы сваривать поверх готового шва, его необходимо сначала зачистить.
p, blockquote 50,0,0,0,0 –>
При помощи порошковой проволоки можно сваривать более толстый металл, чем при помощи проволоки, используемой с газом.
p, blockquote 51,0,0,0,0 –>
Сварка при помощи этого типа проволоки «прощает» недостаточно хорошо подготовленную поверхность.
p, blockquote 52,0,0,0,0 –>
Полярность при сварке без газа
Полярность – это направление потока электричества в цепи сварочного аппарата.
p, blockquote 53,0,0,0,0 –>
При прямой полярности электрод (проволока) – это минус, а свариваемый металл (заземление) – это плюс. При обратной полярности электрод – плюс, а свариваемый металл – минус.
p, blockquote 54,0,0,0,0 –>
Для сварки при помощи порошковой проволоки используется прямая полярность (проволока – минус, заземление — плюс).
p, blockquote 55,0,0,0,0 –>
При сварке с газом – электрод (+), масса (-).
p, blockquote 56,0,0,0,0 –>
Полярность, с которой будет нормально работать порошковая проволока, зависит от её состава. Бывают и такие, которые будут нормально сваривать с любой полярностью.
p, blockquote 57,0,0,0,0 –>
В большинстве случаев, при сварке без газа сварочный аппарат должен быть настроен с позитивным заземлением и негативным электродом. Это даст больше мощности для плавления порошковой проволоки.
p, blockquote 58,0,0,0,0 –>
Звук правильной сварки полуавтоматом
При обучении сварки MIG / MAG , важно слушать звуки, издаваемые при сварке и, конечно же, контролировать процесс сварки визуально (через затемнённую маску). При правильной сварке полуавтоматом издаётся звук, напоминающий жарку мяса на сковороде. Этот «шипяще-жужжащий» звук говорит о хорошем балансе между скоростью подачи проволоки, подаче газа и настройками напряжения. Застывшие брызги на насадке или наконечнике сварочной горелки ухудшают поток защитного газа, плохой контакт зажима массы, плохо очищенная область сварки, всё это может ухудшать формирование сварочной дуги, и будет отражаться на звуке сварки. Также можете прочитать статью “как настроить сварочный полуавтомат” для большего понимания правильной настройки аппарата перед сваркой.
“>
Качество процесса сварки в защитных газах Текст научной статьи по специальности «Технологии материалов»
УДК 621. 791
В. М. Белоконь, канд. техн. наук, доц.
КАЧЕСТВО ПРОЦЕССА СВАРКИ В ЗАЩИТНЫХ ГАЗАХ
В статье рассмотрены вопросы, связанные с качеством сварки в защитных газах. Исследовано влияние состава защитной атмосферы, диаметра электродной проволоки, режимов сварки на перенос электродного металла и разбрызгивание. Показано, что сварка в смеси защитных газов имеет преимущества перед сваркой в углекислом газе. Дополнительное введение в защитный газ кислорода увеличивает выгорание углерода в поверхностном слое, снижает силы поверхностного натяжения, измельчает капли электродного металла и улучшает формирование швов. При сварке без коротких замыканий дугового промежутка магнитные методы, проволоки с переменным диаметром и вибрация электрода снижают потери и улучшают перенос металла через дугу.
Качество процесса сварки в среде углекислого газа — устойчивость горения дуги, производительность и разбрызгивание, характер переноса электродного металла и т. д. — исследовано в широком диапазоне режимов применительно к определенным диаметрам проволок [1, 2]. Масштабы применения сварки в углекислом газе в промышленности делают особенно чувствительными те недостатки, которыми она обладает: не всегда удовлетворительный внешний вид швов, в некоторых случаях недостаточная производительность процесса, повышенное разбрызгивание электродного металла. При сварке теряется в среднем 10 % электродного металла. Капли расплавленного металла прилипают или сплавляются со свариваемой деталью, соплом горелки и токосъемником. Попадание крупных брызг в разделку кромок увеличивает возможность появления непроваров и шлаковых включений в металле шва. Возникает необходимость введения дополнительной, трудоемкой непроизводительной операции — зачистки.
Нами проведены сравнительные исследования качественных показателей процесса сварки проволоками диаметрами 1,6-2,5 мм [3].
Установлено, что с увеличением
плотности тока коэффициент расплавления и наплавки увеличивается. Более сложной зависимостью определяется коэффициент потерь.
При плотностях тока значительное количество энергии дуги расходуется на диссоциацию углекислого газа. Дуга сжимается, и анодное пятно не занимает всей поверхности торца электрода. При этом быстрое накопление большого количества тепловой энергии в небольшой по объему активной области приводит к последовательно возникающим тепловым микровзрывам. Это является одной из важных причин, вызывающих блуждание пятна. Причем ввиду того, что накопление энергии зависит от протяженности активной области, падения напряжения в ней, блуждания анодного и катодного пятен происходят с различной скоростью. Возникает тангенциальная по отношению к поверхности сила, действующая в плоскости, перпендикулярной оси электрода, и вызывающая смещение капли от оси электрода и ее отрыв [4]. Подъему капли способствует реактивное давление пара испаряющегося электрода, действие которого возрастает пропорционально квадрату тока. Поэтому при низких плотностях тока капля формируется на боковой поверхности элек-
трода, часто ее перенос происходит вне столба дуги [4]. Наблюдается интенсивное разбрызгивание металла, повышение коэффициента потерь и тем больше, чем больше диаметр проволоки.
По мере увеличения плотности тока увеличивается охват торца электрода активным пятном. Одновременно повышаются силы, отрывающие капли. Перенос металла становится мелкокапельным и при определенной плотности тока потери металла уменьшаются до уровня 7-9 %, улучшается стабильность горения дуги. Наличие некоторого количества мелких брызг рядом со сварным швом вызвано действием тангенциальной и реактивных сил испаряющегося металла, отрывающих и перемещающих часть капли в плоскости, перпендикулярной оси электрода.
Дальнейшее повышение плотности тока увеличивает испарение и угар расплавленного электродного металла, а также содержание окислов в окружающей атмосфере и их налет около шва. Потери металла растут. Удельное испарение металла с активного пятна электрода при сварке в углекислом газе на обратной полярности
тока можно приближенно рассчитать.6 ‘*3 ‘ ,(1)
8 п1 •
где Д1 — коэффициент пропорциональности, Д1 = 3,02-103; иэ — эффективное падение напряжения у электрода, В; Ее —
сечение столкновения частиц с электро-
20 2
нами, Ее = 25-10′ м ; Еп1 — скрытая теплота испарения, В-с/г.
По полученному уравнению рассчитаем удельное испарение металла в зависимости от плотности тока и диаметра электрода. Результаты расчета сведем в табл. 1.
Табл. 1. Удельное испарение металла при сварке проволоками диаметром 1,6-2,5 мм
19
Плотность тока, А/см2 Диаметр электрода, мм Удельное испарение металла, г/(см2-с)
1,90 1,6 3,38
2,0 3,64
2,5 3,905
2,00 1,6 3,4
2,0 3,67
2,5 3,95
2,10 1,6 3,44
2,0 3,70
2,5 3,98
2,20 1,6 3,47
2,0 3,74
2,5 4,02
Проведенные расчеты и эксперименты показывают, что потери металла зависят от диаметра электродной проволоки и при малых плотностях тока связаны, в основном, с разбрызгиванием, а при высоких — с испа-
рением и угаром. При оптимальных напряжениях на дуге при одинаковых плотностях тока потери металла могут не определяться диаметром проволоки (рис. 1).
100
130
160
190
У
2 0 А/мм2 і::
I —
Рис. 1. Влияние плотности тока на производительность процесса сварки: ар, ан, ¥ — коэффициенты расплавления, наплавки и потерь соответственно
Исследовано влияние напряжения на дуге на качество сварки. Увеличение напряжения на дуге при постоянной плотности тока вызывает сначала плавное, а затем более резкое снижение коэффициентов расплавления и наплавки (рис. 2). Потери электродного металла на угар и разбрызгивание растут. Такое изменение определяемых коэффициентов объясняется увеличением внешней составляющей дуги в соответствии с жесткой характеристикой источника и возрастающей характеристикой дуги, уменьшением подогрева вылета электродной проволоки, перераспределением теплового баланса в дуге. Изменяется размер капель электродного металла. Результаты скоростной киносъемки показывают, что с ростом напряжения дуги размер капель увеличивается, что ухудшает условия теплопередачи из анодной области к торцу электрода. Коэффициент потерь возрастает, в основном, из-за повышения разбрызгивания.
Стабильность горения дуги зависит от скорости сварки. При малой скорости
сварки устойчивость дуги ухудшается. При увеличении плотности тока и постоянном напряжении длина дуги уменьшается в соответствии со статической характеристикой. Стабильность горения дуги ухудшается. Увеличение скорости сварки сдвигает границу максимальных плотностей тока, допускающих устойчивое горение дуги. Оптимальная скорость при сварке проволоками диаметрами 1,6-2,5 мм составляет 30-70 м/ч. Этим же скоростям соответствует и лучшее формирование шва, хорошая защита сварочной ванны газом. Рекомендуемое соотношение значений тока и напряжения, обеспечивающее хороший внешний вид швов, устойчивое горение дуги, примерно одинаковые потери электродного металла приведены на рис. 3.
Для всех исследованных диаметров проволок диапазон сварочных токов расширяется с увеличением напряжения на дуге.
60
%
40
А
V
20
О
35 40 45 50 В
и————->■
Рис. |/
‘ X* ‘ •>
70
В
60
50
40
и
30
2Ь0 иьо 5ь0 8Ь0 а ;сьс
I ————►
Рис. 3. Области оптимальных режимов сварки проволоками диаметрами 1,6—2,5 мм.
Величина вылета электродной проволоки оказывает существенное влияние на производительность процесса сварки и параметры шва. Увеличение вылета электрода повышает эффективность процесса, спо-
собствует рациональному использованию тепла от нагрева проволоки на вылете. Одновременно уменьшается глубина проплавления. Возникают затруднения и в зажигании дуги — наблюдаются взрывы
и выбросы кусочков проволоки.
Производительность процесса сварки при увеличении вылета может быть повышена в 1,5-3,5 раза по сравнению со сваркой на коротких вылетах.
Применение сварки на повышенных плотностях тока требует заполнения кратера шва металлом. С этой целью в конце сварки изменяли ток, напряжение дуги и скорость сварки. При этом определено, что раздельное плавное уменьшение исследуемых факторов режима не позволяет полностью заварить кратер. Уменьшение напряжения дуги и скорости сварки приводит к уменьшению длины кратера, но увеличению его ширины. Уменьшается глубина кратера с уменьшением скорости подачи сварочной проволоки от номинальной до нуля. Однако и в этом случае конец шва имел ослабленное усиление.
Качественная заварка кратера возможна при переходе в конце сварки на меньшие значения тока, напряжения, скорости сварки. Программное управление режимом сварки позволяет решить эту задачу.
Применительно к полуавтоматической сварке исследовалась возможность заварки кратера с помощью возвратноэллиптических манипуляций концом электрода. Этот способ позволяет осуществить заварку кратера, но при этом необходимо не допускать растягивания дуги путем отвода держателя от изделия, т. к. в этом случае ухудшается защита расплавленного защитным газом. Решается данная задача применением двухрежимных полуавтоматов или программированием [6]. Проведенные исследования показывают, что изменением основных параметров режима сварки можно получить требуемые производительность процесса и характер переноса электродного металла, а также качественное формирование сварных швов при минимальных потерях.
Характер плавления и переноса электродного металла влияет на интенсивность протекания физических и химических процессов при взаимодействии металлической и газовой фаз. Изменяются технологиче-
ские характеристики — производительность сварки, разбрызгивание, формирование швов и т. д.
Перенос электродного металла в сварочную ванну через газовую среду осуществляется в виде капель и паров. Размер переносимых капель может быть различным и определяется режимом сварки, защитной атмосферой, составом электродного металла и т. д. Уменьшение подвижности сварочной дуги, увеличение охвата дугой поверхности свариваемых деталей и измельчение переноса приводит к более равномерному по объему и более высокому нагреву капель [7]. Одновременно улучшается предварительный подогрев близлежащих к шву слоев металла, наблюдается более высокая температура поверхности сварочной ванны. Сила поверхностного натяжения снижается. Условия формирования шва улучшаются. Поэтому в большинстве случаев желателен мелкокапельный перенос.
В процессе образования капли на нее действуют силы, препятствующие и способствующие отрыву от торца электрода. Многочисленными исследованиями стран СНГ и зарубежных авторов установлены основные из них.
Сила поверхностного натяжения удерживает каплю на торце электрода в процессе ее формирования и зависит от легирующих элементов, окружающей каплю атмосферы, температуры и т. д.
Основные легирующие элементы проволоки для сварки в среде углекислого газа малоуглеродистых и низколегированных сталей — углерод, кремний, марганец. Кремний в количестве 0,17-0,5 % снижает, а в других — увеличивает поверхностное натяжение. Влияние марганца на поверхностное натяжение выражается кривой с максимумом при 0,8 %. Однако изменение содержания кремния и марганца ограничивается. Их соотношение и количество определяют металлургические процессы, протекающие при сварке, качество сварных швов.
Двоякое влияние на величину по-
верхностного натяжения оказывает содержание углерода. Увеличение или уменьшение углерода от 0,20 % снижает поверхностное натяжение. При этом повышение содержания углерода в металле швов приводит к образованию в них горячих трещин, а слишком заниженные — к потере прочностных свойств. Последнее может быть скомпенсировано дополнительным легированием проволоки соответствующими элементами. Следовательно, изменение содержания углерода в проволоке в разумных пределах может изменить характер переноса, разбрызгивания, формирование швов.
В зарубежных и странах СНГ проводились исследования в области разработки новых проволок для сварки в среде углекислого газа за счет дополнительного легирования такими элементами, как титан, никель, молибден, цирконий и др. Это позволяет стабилизировать горение дуги, повысить эксплуатационные характеристики сварных узлов. Такой путь удорожает сварочную проволоку и требует затрат дефицитных материалов.
В работах исследователей проверено влияние предварительного нанесения элементов — активаторов на поверхность сварочной проволоки в виде солей бария, калия, лития и др. Известно, что щелочные и щелочно-земельные металлы обладают способностью заполнять свободные связи на поверхности жидкости, тем самым ослаблять связь поверхностных атомов и молекул между собой. Резко изменяется эмиссия с катода, увеличивается площадь активного пятна, снижается плотность тока. Это уменьшает отталкивающее действие электромагнитной силы, осевая составляющая которой способствует отрыву капли. Обнаруженное повышение температуры капли при этом способствует уменьшению поверхностного натяжения металла и размера капли. Скорость же расплавления электрода снижается. Последнее объясняется тем, что элементы-активаторы снижают работу выхода электронов. Перед катодом образуется электронное облако, которое,
нейтрализуя сталкивающиеся с ним положительные ионы, уменьшает количество тепла, выделяющегося на катоде.
Оказывает влияние на процесс сварки состояние поверхности, способ изготовления проволоки [1].
Существенное влияние на перенос металла через дугу оказывает состав защитного газа. Положительно влияет кислород как активное вещество при сварке в смесях газов. К таким смесям следует отнести смеси: углекислого газа и кислорода, аргона; углекислого газа и кислорода, аргона и углекислого газа, аргона и кислорода.
Изменение состава защитного газа влияет на интенсивность охлаждения дуги, эффективный потенциал ионизации дугового промежутка и его температуру. При сварке на прямой полярности в среде многоатомных газов значительное количество тепла расходуется на диссоциацию. В результате — сжатие дуги, высокая подвижность катодного пятна, не охватывающего всю поверхность торца электрода. Это сказывается на величине и направлении электромагнитных сил, повышении реактивного давления паров, действующих на каплю. Перенос становится беспорядочным, потери металла увеличиваются, ухудшается формирование шва.
Влияет на характер переноса электродного металла и химическое взаимодействие капли с газовой фазой. В литературе рассматривается в основном окисление углерода.
Мнения исследователей о роли окисления углерода противоречивы. Одни считают, что образование пузырьков углекислого газа внутри капель является определяющим фактором в переносе металла, другие отводят этому процессу второстепенную роль [8]. Экспериментально в [9] показано, что: окисление углерода происходит в основном на поверхности капель; реактивное давление окиси углерода вызывает деформирование капли, отталкивание от ванны; увеличивается подвижность капли
на электроде и разбрызгивание металла; масса переходящих капель изменяется незначительно.
Положительное влияние на качество сварки оказывает подача в зону дуги вместе с защитным газом специального флюса, закладывание в разделку перед сваркой металлической крупки, обрезков прутков проволоки, электродов основного типа или подача дополнительной проволоки в зону дуги. При этом изменяется распределение теплового баланса в дуге, повышается производительность, улучшается качество швов.
При данных режимах сварки и конкретной защитной атмосфере перенос металла зависит от вылета электрода и его диаметра [10].
Увеличение вылета электрода позволяет рационально использовать нагрев вылета проходящим током. Теплосодержание капель уменьшается, а размер их, время пребывания на торце электрода и производительность расплавления увеличиваются. Так как повышенное количество электродного металла наплавляется, возможны наплывы, ухудшение формы шва. Это происходит при недостаточном прогреве поверхности свариваемых деталей.
Уменьшение диаметра электродной проволоки увеличивает температуру капель, охват дугой торца электрода, снижает силы, удерживающие капли. Перенос электродного металла измельчается.
При сварке без коротких замыканий для улучшения переноса металла через дугу используются способы искусственного сбрасывания капель с торца электродной проволоки. Для этой цели пригодна вибрация или предложенная
ВНИИАВТОГЕНМАШем для сварки пульсирующая подача электродной проволоки.
Уменьшается разбрызгивание и улучшается перенос капель через дугу при применении сечения проволоки с заранее сформированными каплями.
Положительный эффект в отношении переноса и разбрызгивания получен при применении магнитных методов
управления сварочными процессами.
Рассмотренные электрические и неэлектрические способы улучшения процесса сварки в большей или меньшей степени применяются в промышленности. Для более широкого применения требуется учитывать специфику данного производства, форму и конструкцию свариваемых узлов и т. д.
Выводы
1. Изменением состава защитной атмосферы, диаметра электродной проволоки, режимов сварки можно в определенных пределах воздействовать на качественные показатели процесса сварки: формирование швов, перенос электродного металла и разбрызгивание. Минимальные и примерно равные потери металла наблюдаются в широком диапазоне оптимальных соотношений плотностей тока напряжения на дуге.
2. Сварка в смесях газов имеет преимущества перед сваркой в углекислом газе. Изменение степени диссоциации защитного газа влияет на стабильность горения дуги, ее форму. Дополнительное введение в защитный газ кислорода интенсифицирует выгорание углерода в поверхностном слое, снижает силы поверхностного натяжения, измельчает капли электродного металла и способствует улучшению формирования швов.
3. При сварке без коротких замыканий дугового промежутка применение искусственного сбрасывания капель с торца электрода, вибрации и пульсирующей подачи электродной проволоки, проволоки переменного сечения, магнитных методов позволяет значительно снизить потери металла и улучшить процесс переноса капель через дугу.
СПИСОК ЛИТЕРАТУРЫ
1. Потапьевский, А. Г. Сварка в защитных газах плавящимся электродом / А. Г. Потапьевский. — М.. : Машиностроение, 1974. -240 с.
2. Новожилов, Н. М. Основы металлургии дуговой сварки в газах / Н. М. Новожилов. -М. : Машиностроение, 1974. — 231 с.
3. Сварка в углекислом газе проволокой диаметром 2,5 мм / В. М. Белоконь [и др.] / Сварочное производство. — 1974. — № і. — С. 43-44.
4. Белоконь, В. М. Качество сварки плавлением при различных составах защитного газа и сварочной проволоки / В. М. Белоконь // Вестн. Белорус.-Рос. ун-та. — 200В. — № 4. — С. 62-69.
5. Лесков, Г. И. Электрическая сварочная дуга / Г. И. Лесков. — М. : Машиностроение, 1970. -335 с.
6. Потапьевский, А. Г. Сварка в углекислом газе с программированием режима / А. Г.
Потапьевский, В. Я. Лаврищев, М. П. Дайнеко / Автоматическая сварка. — 1972. — № 4. — C. 44-46.
7. Походня, И. К. Газы в сварных швах / И. К. Походня. — М. : Машиностроение, 1972. -256 с.
В. Мазель, А. Г. Технологические свойства электросварочной дуги / А. Г. Мазель. — М. : Машиностроение, 1969. — 17В c.
9. Ерохин, А. А. Основы сварки плавлением / А. А. Ерохин. — М. : Машиностроение, 1973. — 44В с.
10. Куликов, В. П. Технология и оборудование сварки плавлением и термической резки / В. П. Куликов. — Минск : Экоперспектива, 2003. — 412 с.
Белорусско-Российский университет Материал поступил 21.12.2008
V. M. Belokon
The quality of the gas shielding welding process
The paper considers the problems connected with the welding quality in shielding gases. The influence of the composition of the protective atmosphere, the diameter of the electrode wire, the welding conditions on the electrode metal transfer and sputtering has been studied. It has been shown that welding in the mixture of shielding gases has some advantages over welding in carbon dioxide. Additional input of oxygen into the shielding gas increases carbon burning in the surface layer, lowers surface tension forces, breaks electrode metal drops and improves weld formation. In welding without short circuits of the arc gap, magnetic methods, wires with changeable diameters and electrode vibrations decrease losses and improve metal transfer across the arc.
Сварка конструкций в среде защитных газов
Сварка конструкции штучными электродами в заводских условиях применяется в тех случаях, когда использование механизированных способов сварки затруднено из-за чрезмерно малой длины выполняемых швов или когда по технико-экономическим соображениям механизированная сварка не рациональна (выполнение прихваток, приварка фиксирующих и монтажных приспособлений, сварка специальных сталей в ограниченных объемах и т. п.).
Из механизированных способов сварки при изготовлении основной номенклатуры сварных строительных конструкций наибольшее применение находит сварка в среде защитных газов.
Сущность сварки в защитных газах заключается в том, что электрическая дуга горит в струе газа, поступающего через сварочную горелку в зону сварки, оттесняющего воздух из зоны сварки и защищающего дугу и расплавленный металл от вредного влияния его составляющих.
Сварка может производиться как плавящимся, так и неплавящимся электродом.
При сварке неплавящимся электродом (см. рис. 6, б) электрическая дуга прямой полярности (минус на электроде) горит между угольным или вольфрамовым электродом и изделием. Шов сварного соединения образуется за счет расплавления отбортованных кромок или за счет подачи присадочной проволоки в зону горения дуги. .Этим способом сваривается металл толщиной до 1 мм. В качестве источников тока применяют сварочные выпрямители с повышенным напряжением холостого хода.
Сварка плавящимся электродом в среде углекислого газа по сравнению с другими способами дуговой сварки при изготовлении строительных металлоконструкций обладает рядом технико-экономических преимуществ. Этот способ сварки применяется при изготовлении изделий из углеродистых и низколегированных сталей толщиной свыше 0,8 мм во всех пространственных положениях при любой длине и конфигурации швов. Сварка плавящимся электродом может производиться полуавтоматами и автоматами.
Производительность полуавтоматической сварки в защитных газах в 2,5—4 раза, а автоматической — в 4— 10 раз выше ручной дуговой сварки.
Сварку швов в нижнем положении допускается выполнять на форсированных режимах (на токе до 650 А). Качество швов при этом, как правило, высокое, разбрызгивание малое, а производительность значительно выше, чем при сварке на обычных режимах.
Сварка в углекислом газе плавящимся электродом в соответствии с ГОСТ 14771—76 в технической документации может обозначаться буквами УП, а сварки в инертных газах и их смесях с активными газами плавящимся электродом обозначается буквами ИП. Эффективность газовой защиты зависит от типа соединения, скорости сварки, расстояния между соплом и изделием, расхода газа и скорости движения окружающего воздуха.
В качестве защитных газов применяют активные (азот, углекислый газ) и инертные (аргон, гелий) газы и смеси углекислого газа с кислородом, углекислого газа с аргоном и кислородом, аргона с углекислым газом. Наиболее высокое качество сварных швов можно получить при сварке в среде инертных газов, так как эти газы не реагируют с расплавленным металлом.
Из активных газов чаще применяют углекислый газ и его смесь с кислородом. При сварке в среде активных газов из основного и присадочного металла выгорает углерод, кремний и марганец. Для раскисления расплавляемого дугой металла и компенсации потерь выгорающих элементов в сварочную ванну вводят присадочный материал с повышенным содержанием марганца и кремния. Чаще при сварке в среде защитных газов применяют сварочную проволоку Св-08Г2С.
Влияние контроля защитного газа: свойства сварных швов при оптимизации процесса GMAW
Weber R (2003) Как сэкономить 20% на сварочных расходах. Корпус прицепа, сборка 44 (3): 46–50
Google Scholar
Филхо Д.Ф., Рейс Р.П., Феррарези В.А. (2011) Оценка влияния защитного газа на свариваемость ферритной нержавеющей стали. В кн .: Дуговая сварка. Риека, Ин. Tech., Pp 152–176
Ка П, Мартикайнен Дж. (2013) Влияние защитных газов при сварке металлов.Int J Adv Manuf Technol 64 (9): 1411–1421
Артикул Google Scholar
Little K, Stapon G (2005) Упрощение выбора защитного газа показывает, как различные газовые смеси влияют на вашу сварочную работу. J Pract Weld 9 (1)
Канг Б., Прасад Ю.К., Кан М.Дж., Ким Х.Дж., Ким И.С. (2009) Характеристики альтернативной подачи защитного газа при сварке алюминия GMA. J Mater Process Technol 209 (10): 4716–4721
Артикул Google Scholar
Sierwert E, Wilhelm M, Hässler M, Schein J, Hanson T., Schnick M, Füssel U (2014) Визуализация потоков газа в сварочных дугах с помощью измерительной техники Шлирена. Сварка J 1: 1–5
Google Scholar
Schnick M, Dreher M, Zschetzsche J, Füssel U, Spille-Kohoff A (2012) Визуализация и оптимизация потоков защитного газа при дуговой сварке. Weld World 56 (1-2): 54–61
Статья Google Scholar
Американское общество сварки (AWS) (2006) Передовой опыт: дуговая сварка вольфрамовым электродом в газовой среде. Weld J 80–82
Литтл К.А., Praxair I (1990) Справочник по ASM, том 6. ASM international
Ирвин Б. (1999) Защитные газы — ключ к инновациям в сварке. Сварка J 78 (1): 37–41
Google Scholar
Lozano J, Moreda P, Llorente CL, Bilmes PD (2003) Характеристики плавления сварных швов GMAW из аустенитной нержавеющей стали.Lat Am Res 33: 27–31
Google Scholar
EN ISO 14175 (2008) Сварочные материалы. Газы и газовые смеси для сварки плавлением и родственных процессов. EN ISO
A. CODE (2015) Квалификационный стандарт для процедур сварки, пайки и плавления; сварщики; мангалы; и операторы сварки, пайки и плавки. ASME
EN ISO 15614 (2004) Технические требования и аттестация процедур сварки металлических материалов — Испытание процедуры сварки — Часть 1: дуговая и газовая сварка сталей и дуговая сварка никеля и никелевых сплавов.EN ISO
Немецкое общество сварщиков DVS (2001) Сварка MIG / MAG: учебное пособие. Технологический центр Fronius, Дюссельдорф
Google Scholar
Уттрахи Г.Д. (2007) Системы управления потоком защитного газа GMAW. Сварка J 86 (4): 22–23
Google Scholar
Ким Л.С., Сон Дж.С., Ким Х.Дж., Чин Б.А. (2006) Исследование изменений защитного газа при GTA-сварке с использованием конечных элементов.J Achiev Mater Manuf Eng 17 (1-2): 249–252
Google Scholar
Накла Х., Яо Дж., Бетеа М. (2012) Воздействие на окружающую среду использования сварочного газа. J Technol Manag Appl Eng 28 (3): 1–11
Google Scholar
Campbell SW, Galloway AM, McPherson NA (2012) Технико-экономическая оценка снижения расхода защитного газа при GMAW при сохранении качества сварного шва. Int J Adv Manuf Technol 63 (9–12): 975–985
Статья Google Scholar
Campbell SW, Galloway AM, McPherson NA, Gillies A (2012) Оценка дуговой сварки металлическим электродом в газовой среде с чередованием защитных газов для использования на AA6082T6. Proc Inst Mech Eng B J Eng Manuf 226 (6): 992–1000
Артикул Google Scholar
Кэмпбелл В., Галлоуэй А., Рэмси Г., Макферсон Н. (2012) Потенциальное решение для оптимизации потока газа GMAW. В: 9-я международная конференция «Тенденции исследований в области сварки». Чикаго
Mvola B, Kah P, Martikainen J, Suoranta R (2015) Современные технологии дуговой сварки металлическим газом: сварка разнородных металлов. Proc Inst Mech Eng B J Eng Manuf 229 (10): 1694–1710
Артикул Google Scholar
Bell D (2011) Предотвращение путаницы со смесями защитных газов. [В сети]. Доступно: http://www.thefabricator.com. По состоянию на 23 июня 2015 г.
Rhee S, Kannatey-Asibu JE (1992) Наблюдение за переносом металла при газовой дуговой сварке.Сварка J 71: 381–386
Google Scholar
Зелинское МО (2008) Влияние газа на форму дуги при сварке MIG-MAG. Eur Phys J Appl Phys 43 (1): 111–122
Статья Google Scholar
Church JG, Imaizumi H (1990) Сварочные характеристики нового процесса сварки, процесс TIME. IIW, тт. Doc XII-1199-90
Субан М., Тусек Дж. (2001) Зависимость скорости плавления при сварке MIG / MAG от типа используемого защитного газа.J Mater Process Technol 119: 185–192
Статья Google Scholar
Хан К.Х., Хан Дж.М., Ли М.В., Ли Э.Б., Хан Ю.С. (1995) Влияние защитного газа на свариваемость высокоэффективного процесса GMAW. J KWS 13 (1): 559–569
Google Scholar
Гауда М., Такахаши М., Икеучи К. (2005) Микроструктуры металла сварного шва, выполненного в газовой среде, из стали класса 950 МПа. Sci Technol Weld Join 10 (3): 369–377
Статья Google Scholar
Menzel M (2003) Влияние отдельных компонентов промышленной газовой смеси на процесс сварки и свойства сварных соединений. Weld Int 17 (4): 262–264
Артикул Google Scholar
Эбрахимния М., Гударзи М., Нури М., Шейхи М. (2009) Исследование влияния состава защитного газа на механические свойства сварного шва стали ST 37–2 при газовой дуговой сварке металла. Mater Des 30 (9): 3891–3895
Артикул Google Scholar
Жерносеков А.М., Сидорец В.Н., Шевчук С.А. (2014) Комбинированное импульсное воздействие защитных газов и сварочного тока при сварке плавящимся электродом. Weld Int 66 (12): 9–13
Google Scholar
Гадаллах Р., Фахми Р., Халифа Т., Садек А. (2012) Влияние состава защитного газа на свойства порошковой дуговой сварки простой углеродистой стали. Int J Eng Technol Innov 2 (1): 01–12
Google Scholar
Латабай С., Стаут Р.Д. (1985) Влияние защитного газа и тепла на свойства металла сварного шва с флюсовой сердцевиной. Weld J 303–313
Катерасан Д., Сатья П., Раджа А. (2013) Влияние защитного газа на сварку сваркой порошковой проволокой соединений аустенитной нержавеющей стали AISI 316L (N). Mater Des 45: 43–51
Статья Google Scholar
Мухопадхяй С., Пал Т.К. (2006) Влияние смеси защитного газа на газовую дуговую сварку стали HSLA сплошной и порошковой проволокой.Int J Adv Manuf Technol 3–4 (29): 262–268
Статья Google Scholar
Ляо М.Т., Чен В.Дж. (1999) Сравнение дуговой сварки в газовой среде с порошковой проволокой и сплошной проволокой с использованием защитного газа. Int J Adv Manuf Technol 15 (1): 49–53
Статья Google Scholar
Моравец Дж., Рохан П. (2011) Влияние различных типов газовой защиты на геометрию сварочной ванны для метода сварки MIG.В кн .: 20-я Международная конференция по металлургии и материалам. Брно, Чешская Республика
Lucas W (1992) Защитные газы для дуговой сварки. Weld Met Fabr 60: 218–225
Google Scholar
Kim W-G, Um K-K, An Y-H, Lee C-S (2009) Механические свойства стального листа YS 460MPa TMCP для больших контейнеровозов. В: Материалы девятнадцатой (2009 г.) международной конференции по морской и полярной инженерии.Осака, Япония
Гю Б., Рю К.М., Сик П.Дж., Чон Бай, Ким Т.С., Ли Дж.С. (2010) Устойчивость к хрупким трещинам в толстых стальных листах для судостроения. J KWJS 28 (1): 47–53
Google Scholar
Kim HJ, Jang TW, Yoon DR (2008) Тандемная электрогазовая сварка высокопрочной конструкционной стали корпуса. В: Материалы восемнадцатой (2008 г.) международной конференции по морской и полярной инженерии. Ванкувер, Британская Колумбия, Канада
Sasaki K, Motomatsu R-I, Ohkita S, Suda K, Hashiba Y, Imai S (2004) Разработка процесса двухэлектродной электрогазовой дуговой сварки. Nippon Steel Technical Report № 90, Токио, Япония
Pires I, Rosado T, Costa A, Quintino L (2007) Влияние защитного газа GMAW на производительность и газообразные выбросы. В: 10-я международная аахенская конференция по сельскому хозяйству. Ахен, Германия
Migatronic (2012) IGC-Intelligent Gas Control. Мигатроник. [В сети]. Доступно: http: // www.migatronic.com. По состоянию на 9 мая 2016 г.
Влияние защитных газов в GMAW
Использование подходящего защитного газа необходимо не только для предотвращения пористости, но и для обеспечения надлежащего проплавления, желаемых механических свойств, включая прочность сварного шва, и общего качества сварки. Чтобы правильно выбрать защитный газ, необходимо учитывать следующее:
— Сплав присадочного металла
— Толщина материала
— Режим GMAW (спрей, короткая дуга и т. Д.)
— Сварочная позиция
— Желаемый профиль проникновения
— Стоимость
Типичными сварочными газами являются : диоксид углерода, аргон и смеси аргона (с диоксидом углерода, гелием, азотом, водородом и кислородом).
Газы можно разделить на две категории: инертные и реактивные.
Инертные газы
Аргон и гелий — инертные газы. Это означает, что ни один из газов не вступит в химическую реакцию с расплавленной сварочной ванной. Аргон является наиболее широко используемым инертным газом, поскольку он легко доступен и недорого по сравнению с гелием. Он создает профиль проникновения, похожий на палец (см. Изображения ниже). Гелий имеет очень высокую теплопроводность по сравнению с аргоном и используется для получения более горячей дуги.Он также используется для газовой смеси из нержавеющей стали. Гелий обеспечивает широкое, но неглубокое проникновение. Гелий и аргон обычно смешивают при сварке алюминия толщиной 1 дюйм или более или в более тонких секциях, чтобы компенсировать недостаточный размер источника питания.
Реактивные газы
Двуокись углерода, кислород, азот и водород являются реактивными защитными газами. Эти газы химически соединяются со сварочной ванной, влияя на механические и химические свойства металла шва. Двуокись углерода — единственное, что можно использовать отдельно.Все это можно комбинировать с аргоном для получения бинарных смесей защитных газов. За исключением трехкомпонентных смесей из нержавеющей стали, большинство из них представляют собой только комбинацию аргона и одного из реактивных газов.
На изображении 1 ниже показано влияние на контур валика и проникновение различных газов. На рис. 2 показано влияние кислорода на двуокись углерода при использовании в смесях аргона и 100% двуокиси углерода.
В таблице ниже приведены наиболее распространенные сварочные газы, используемые при дуговой сварке, в зависимости от типа материала.Он также показывает, какой газ использовать в соответствии с желаемым режимом переноса металла (например, короткое замыкание или распыление). Могут использоваться и другие газы, особенно в смесях аргона, но они наиболее распространены.
Существуют буквально сотни смесей защитных газов. Небольшое изменение процентного содержания каждого компонента в некоторых случаях может дать очень желаемый эффект. Некоторые смеси будут содержать такие компоненты, как азот, в диапазоне миллионных долей, но это будет иметь значительный эффект.Какой защитный газ вы используете? Вы думали об использовании другого защитного газа? Если да, то может быть полезно прочитать, стоит ли вам рассматривать другой защитный газ. Также может быть интересен вопрос, влияет ли смесь защитного газа на прочность сварного шва.
Ссылка: Руководство Lincoln Electric по сварке GMAW — Джефф Надзам
Как выбрать типы защитного газа для GMAW
- Гелий имеет более низкую плотность, чем аргон, что требует более высоких скоростей потока.Гелий также является газом с одним атомом, который обычно используется для более толстых материалов. Это также хороший выбор для сварки алюминия. Потому что, несмотря на ограниченную высокую цену, гелий уже редко встречается в отрасли.
- Двуокись углерода (CO 2 ) редко используется отдельно, потому что она дает широкий сварной шов и часто приводит к образованию большого количества брызг. CO 2 чаще всего сочетается с аргоном для получения наилучшего конечного результата. CO 2 также является химически активным газом, что означает, что он имеет высокий потенциал ионизации.
Газы, используемые в смесях
- Кислород представляет собой двухатомную молекулу, обычно добавляемую в газовые смеси GTAW в количестве 10% или меньше. Его можно рассматривать как дополнение к аргону для GMAW, поскольку он может помочь создать глубокий и узкий проплавленный сварной шов в специализированных приложениях.
- Водород — активный защитный газ, который также обычно используется в смесях GMAW в количестве 10% или меньше.Эта двухатомная молекула имеет тенденцию давать горячие бусинки с широкой поверхностью. Водород в основном используется в материалах из нержавеющей стали для улучшения текучести и увеличения скорости движения.
При выборе защитного газа для GMAW необходимо учитывать три основных компонента: тип материала, тип наполнителя и режим переноса.
- Тип материала : Наиболее важным фактором является соответствие вашего газа типу материала.Например, сталь намного плотнее алюминия, поэтому для достижения желаемого результата сварки требуется другой защитный газ. Также важно учитывать толщину материала, поскольку более толстые материалы потребуют более высоких тепловложений.
- Присадочный металл Тип : дважды проверьте, соответствует ли присадочный металл основному материалу. Это даст вам уверенность, когда дело доходит до выбора наилучшего защитного газа.
- Режим переноса сварки : определите, используете ли вы короткое замыкание, дугу со струйным переносом, импульсную дугу или глобальный перенос.Каждый режим передачи будет лучше работать с определенными защитными газами, чем с другими.
Когда дело доходит до защитного газа для GMAW, есть еще много чего. Следите за новостями в следующих статьях, в которых мы рассмотрим правильный поток защитного газа и подробно расскажем о процессе GMAW с каждым типом материала!
GMAW Welding Equipment BuildersВыбор подходящего защитного газа — важный шаг на пути к успеху сварки.При правильной оптимизации это не только улучшит качество сварки, но и сэкономит деньги и время. Команда Bancroft Engineering может помочь вам выбрать подходящий защитный газ и убедиться, что ваша автоматизированная или полуавтоматическая сварочная система дает наилучшие результаты. Свяжитесь с нашими инженерами-сварщиками сегодня!
Выбор подходящего защитного газа и системы подачи для GMAW
Выбор защитного газа и системы подачи газа для дуговой сварки металлическим электродом (GMAW) требует анализа затрат и возможностей для определения наиболее экономичных и эффективных решений для вашего предприятия. операция.Стоимость выбранного сварочного газа может составлять небольшой процент от общей стоимости процесса, но правильный газ может снизить трудозатраты и накладные расходы или обеспечить более высокую скорость сварки.
Затраты, которые вы должны оценить, включают трудозатрат и накладные расходы , защитный газ , расходные материалы (проволока и / или электроды) и газоснабжение .
Трудозатраты и накладные расходы
Правильный выбор защитного газа может снизить трудозатраты, накладные расходы и чистые затраты за счет увеличения скорости сварки и рабочего цикла при одновременном сокращении времени очистки.
Максимальное увеличение скорости сварки в значительной степени зависит от комбинации свойств теплопередачи , , окислительного потенциала , и характеристик переноса металла выбранного газа. Газы с высокой теплопроводностью создают самые горячие лужи с максимальной текучестью. Сильноокисляющие газы более эффективно снижают поверхностное натяжение валика сварного шва и улучшают слипание металла шва. Смеси инертных газов, которые обеспечивают перенос распылением, обеспечивают высочайший уровень эффективности осаждения и, как правило, более высокие скорости перемещения.
Например, за тот же период времени смесь аргона в режиме струйной дуги дает сварной шов, который примерно на 17-20 процентов длиннее, чем сварной шов, выполненный с использованием диоксида углерода в глобулярном режиме (для сварных швов размером 0,025 дюйма и более при прочих равных). Самая частая ошибка при выборе защитного газа — выбор наименее дорогостоящего; другие факторы влияют на общую стоимость процесса сварки и зависят от качества используемого защитного газа.
Помимо защитного газа и размера сварного шва, другие факторы, влияющие на скорость сварки, включают ток, напряжение, положение сварного шва, подгонку стыка и режим движения (механизированный или ручной).Максимально возможные скорости сварки для любого защитного газа более достижимы в механизированных применениях с чистой пластиной и хорошей подгонкой. При работе вручную квалификация оператора часто является ограничивающим фактором. Сварщик обычно может постоянно отслеживать сварной шов, и наплавка приемлемого сварного шва обычно составляет примерно от 35 до 40 дюймов в минуту. Автоматические и / или роботизированные приложения обеспечивают более высокую скорость сварки; однако максимальная скорость зависит от используемой системы.
Что касается ручной сварки более тонких материалов, все защитные газы могут выдерживать более высокие скорости сварки, чем могут обеспечить операторы.При механизированной операции углекислый газ может обеспечить более быструю сварку тонкого материала, когда прожог не является проблемой. Однако, когда проблемы с подгонкой или прожогом очевидны, смеси аргона с более низким процентным содержанием углекислого газа могут обеспечить более стабильные результаты. Иногда даже снижение уровня углекислого газа с 25 до 8 процентов может значительно улучшить линейную скорость движения. В большинстве цехов, где можно сваривать различные материалы и толщину, могут потребоваться различные смеси газов.
Влияние защитного газа на рабочий цикл и очистку
Рабочий цикл оператора — это время, в течение которого оператор фактически выполняет сварку, в отличие от времени, затрачиваемого на связанные функции, такие как настройка, очистка или другие несварочные действия.
Когда черный металл сваривается с использованием диоксида углерода в качестве защитного газа, брызги накапливаются в газовом сопле, нарушая потоки газа, или собираются на конце контактной трубки, вызывая проблемы с подачей проволоки. Использование газовых смесей на основе аргона значительно снижает разбрызгивание при сварке, во многих случаях полностью устраняя разбрызгивание.В результате операторы могут дольше проводить сварку перед остановкой, чтобы смыть брызги с сопел и контактных наконечников. Любой фактор, снижающий разбрызгивание сварочного шва, может повысить эффективность наплавки в процессе сварки.
Пары и газы также образуются в результате химической реакции между горячим металлом и активными газами, такими как кислород или углекислый газ. Использование смесей аргона, которые производят меньше дыма и газов, может снизить затраты на контроль загрязнения и очистку.
Использование подходящего защитного газа помогает обеспечить максимальную эффективность осаждения для используемого процесса.Например, эффективность осаждения при операции GMAW с использованием чистого диоксида углерода обычно составляет 89 процентов. Когда защитный газ заменяется смесью аргона с 25% диоксида углерода, эффективность осаждения может возрасти до 97%.
Стоимость защитного газа. Стоимость защитного газа не должна превышать 5 процентов от общей стоимости. Даже несмотря на то, что аргон или смеси аргона стоят значительно больше, чем диоксид углерода, с учетом увеличения рабочего цикла оператора и эффективности наплавки общая стоимость на фут сварного шва меньше для смеси аргона, чем для диоксида углерода.Стоимость газа варьируется в зависимости от географического региона, но в среднем аргон или смеси аргона стоят в пять раз дороже, чем прямой диоксид углерода.
Расходные материалы. При определении стоимости расходных материалов следует учитывать цены на проволоку и защитный газ вместе, поскольку защитный газ влияет на эффективность наплавки. Помните, что самые дешевые проволока и газ также могут дать самую низкую эффективность наплавки. Хотя начальная цена может быть выше, рекомендуемая комбинация проволоки и газа может повысить эффективность наплавки и снизить общую стоимость.
Для использования высокоокислительных защитных газов, таких как чистый диоксид углерода, необходима сварочная проволока с дополнительными раскислителями для предотвращения потерь сплава в сварочной дуге. Если защиту от углекислого газа заменить на аргон с 20-процентным содержанием двуокиси углерода, можно будет заменить менее дорогостоящую сварочную проволоку из-за хорошего удерживания сплава защитным газом аргоном. Благодаря этому изменению цех может сэкономить до 15% затрат на проволоку, сохранив при этом механические свойства, упростив работу и увеличив скорость сварки.
Система подачи газа
Защитный газ доступен в баллонах высокого давления, жидкостных баллонах или в объемных жидкостях. Выбор зависит от используемых вами газовых смесей, характера потребления, расположения вашего оборудования и наличия системы распределения трубопроводов. Следует учитывать затраты на продукцию и стоимость аренды систем хранения, амортизируемых из расчета ежемесячного потребления продукции. Когда используются различные газовые смеси, может потребоваться инвентаризация большого количества баллонов.
Один из методов получения газовой смеси — использование газового смесителя на месте.Однако стоимость оборудования для хранения и смешивания необходимо сравнивать со стоимостью предварительно смешанных продуктов в цилиндрах, чтобы определить, какая форма поставки более экономична.
Управление потоком газа в точках использования требует целенаправленных и постоянных усилий по предотвращению потерь. Рекомендации по правильному определению размеров системы, правильному использованию регулирующего и смесительного оборудования, а также расходомеров для обеспечения экономичного потребления газа можно получить у поставщика газа.
После того, как вы выбрали защитный газ, рассмотрите различные доступные системы подачи газа.
Системы хранения цилиндров. Если требуется небольшой объем газа, можно использовать отдельные баллоны с аргоном, гелием, диоксидом углерода, кислородом или смесями этих газов непосредственно в процессе сварки. Если скорость потребления увеличивается, два или более цилиндра могут быть объединены вместе в группы, чтобы обеспечить большую подачу и уменьшить количество манипуляций с цилиндрами. Коллектор обычно имеет два независимых набора элементов управления, позволяющих поочередно или одновременно работать с двумя рядами цилиндров.Пустые цилиндры можно заменить полными после отключения одного или обоих рядов цилиндров.
Если вы используете предварительно смешанные смешанные газы даже в небольших объемах, ваши затраты могут быть выше, чем ожидалось, потому что смешанный газ обычно оценивается на уровне более дорогих компонентов. Смесь 75/25 аргона / диоксида углерода стоит столько же, сколько 100-процентный аргон, что сводит на нет любую экономию, полученную за счет более дешевого диоксида углерода.
Газовое смешение. Защитные газы часто используются в смесях для оптимизации процесса дуговой сварки.Блендеры могут предоставлять смеси с жесткими допусками, гарантируя пользователям, что они постоянно получают правильную смесь. Вы можете покупать и смешивать чистые газы в соответствии с меняющимися производственными требованиями, изменяя настройки смесителя. При использовании блендера вы можете выбирать различные смеси, и никаких дополнительных цилиндров не потребуется; Кроме того, может быть реализована более низкая стоимость диоксида углерода. Даже в небольших объемах (5000 кубических футов в месяц) стоимость оборудования может быть компенсирована более низкой стоимостью газа.В более крупных приложениях криогенные цилиндры или системы для массовых грузов на месте могут добавить к экономии затрат.
Системы бестарного хранения. Если вы потребляете более 50 000 куб. Ft. газа в месяц, считают системы массового криогенного хранения, потому что они предлагают такую значительную экономию места и затрат. Резервуары для хранения сыпучих материалов довольно распространены, со стандартной емкостью от 1500 до 11000 галлонов.
Системы распределения инертного газа. Когда для подачи газа используются отдельные баллоны, к баллону присоединяется регулятор давления для снижения давления выходящего газа.Расходомер, подсоединенный к сварочному оборудованию с помощью трубок с соответствующими фитингами, используется для поддержания заданного расхода газа.
Когда требуются большие объемы газа или имеется несколько сварочных станций, может быть предпочтительнее установить систему распределительных трубопроводов. Система этого типа содержит основные и второстепенные распределительные линии. Обратите внимание, что требуется подача газа, смеситель, главная распределительная линия и запорная арматура.
Типичная вторичная линия имеет клапан станции, который соединен со сварочными аппаратами через регулятор давления и расходомер (часто комбинированный блок).Он соединен со сварочными аппаратами шлангом или трубкой инертного газа с соответствующими фитингами и запорным клапаном с электромагнитным управлением.
Рекомендуется, чтобы конструкция, материалы, изготовление, осмотр и испытания соответствовали стандартам, установленным в брошюре Ассоциации сжатого газа «Промышленная практика для газотранспортных и распределительных систем трубопроводов ».
Защитные газы для сварки и их влияние на свойства нержавеющей стали
Защитные газы являются неотъемлемой частью всех традиционных сварочных процессов.
Они выполняют несколько функций, но в первую очередь предназначены для защиты сварочной ванны от атмосферы и обеспечения среды, которая может пропускать электрический ток от электрода к заготовке. Даже процессы, не имеющие внешнего источника газа, такие как ручная дуговая сварка металла (MMAW, MMA или SMAW) и безгазовая порошковая сварка (FCAW), имеют защитный газ, который образуется при разложении флюса в присутствии сварочной дуги.
Защитный газ также может влиять на стабильность дуги, форму сварного шва и глубину проплавления, а также на механические свойства и металлургию сварных деталей из нержавеющей стали.
В процессах в среде защитных газов, таких как газовая дуговая сварка вольфрамом (GTAW или TIG) и газовая дуговая сварка металла (GMAW или MIG), используются защитные газы различного состава в зависимости от области применения. Поскольку электрод в GTAW изготовлен из вольфрама, в качестве защитного газа обычно используется аргон или гелий, чтобы предотвратить окисление электрода. Это ограничение не распространяется на GMAW, поэтому в состав газа могут входить такие активные газы, как диоксид углерода и кислород. В обоих этих процессах можно использовать небольшие количества других газов, таких как азот и водород, поскольку они особенно полезны для сварки нержавеющей стали.Хотя ни один из газов не является инертным по определению, их можно использовать с GTAW, поскольку они не вступают в реакцию с вольфрамом.
Существует три основных свойства защитного газа, которые определяют поведение сварочной ванны; потенциал ионизации (насколько легко атом отдает электрон), теплопроводность газа и, наконец, поверхностное натяжение между сварочной ванной и защитным газом.
Потенциал ионизации
Защитный газ обеспечивает перенос электронов между электродом и заготовкой.При зажигании дуги электроны испускаются либо из заготовки, либо из электрода, в зависимости от того, какой из них заряжен положительно. Эти электроны сталкиваются с газовыми атомами, в результате чего эти атомы высвобождают один из своих электронов, что приводит к цепной реакции, поддерживающей дугу. Потенциал ионизации газа — это легкость, с которой они отдают электрон. «Более горячие» газы — это те, которым требуется больше энергии для ионизации или высвобождения электрона. Гелий имеет более высокий потенциал ионизации, чем аргон, поэтому имеет более высокое напряжение дуги и, следовательно, более высокий подвод тепла при том же токе и длине дуги.
Аналогичный принцип применяется к молекулярным газам (H 2 , N 2 , O 2 , CO 2 ), которые диссоциируют в дуге на отдельные атомы, а затем рекомбинируют при охлаждении, высвобождая при этом энергию. Аргон часто смешивают с небольшими количествами других газов для улучшения проплавления шва.
Теплопроводность
Теплопроводность защитного газа влияет на его способность передавать тепло по дуге. Он влияет на радиальные потери тепла от центра к периферии столба дуги, а также на передачу тепла от дуги к расплавленной сварочной ванне.Газы с низкой теплопроводностью, такие как аргон, будут иметь узкую горячую сердцевину в центре дуги и значительно более холодную внешнюю зону. В результате получается сварной шов с узким «пальцем» в основании сварного шва и более широким верхом. С другой стороны, гелий обладает высокой теплопроводностью, поэтому тепло более равномерно распределяется по дуге, но в результате глубина проникновения меньше. Смешивание газов позволяет сочетать полезные свойства каждого газа, ограничивая при этом недостатки.
Поверхностное натяжение
Поверхностное натяжение влияет на профиль валика сварного шва.Представьте себе, как вода капает на только что отполированную машину. Это нежелательно при сварке, так как создает крутой угол между сварным швом и исходным швом, что может привести к таким дефектам, как поднутрение, отсутствие плавления боковых стенок и снижение усталостных характеристик. Это еще одна причина, по которой чистый аргон не используется в качестве защитного газа для процесса GMAW.
Компоненты газа
Кислород
Хотя это может показаться нелогичным, поскольку хорошо известно, что горячие металлы окисляются, небольшие количества кислорода часто добавляют в защитные газы для процесса GMAW.Небольшие количества кислорода снижают поверхностное натяжение между расплавленной сварочной ванной и окружающей атмосферой. Более низкая поверхностная энергия приводит к более плоскому и гладкому сварному шву с меньшей склонностью к подрезанию основного металла. Чтобы свести к минимуму потери сплава при окислении, содержание кислорода обычно ограничивают до 2%. Тепловой оттенок будет более сильным, чем при сварке без добавления кислорода в защитный газ.
Двуокись углерода
GMAW также использует CO 2 в качестве компонента защитного газа.Общей проблемой для нержавеющих сталей является охрупчивание и коррозия из-за сенсибилизации из-за образования карбида хрома, но было продемонстрировано, что поглощение углерода из CO 2 достаточно низкое, чтобы полученный металл сварного шва все еще достиг необходимого (≤0,03%) содержания углерода. для обозначения класса L. Таким образом, выбранное содержание CO 2 больше связано с проникновением и смачиванием, чем с улавливанием углерода. Содержание углекислого газа в GMAW обычно составляет 2-5%, в то время как в порошковой проволоке используется 20% смеси с аргоном или даже 100% CO 2 .
Водород
Уникальной особенностью аустенитных нержавеющих сталей является их невосприимчивость к водородному растрескиванию, за исключением, возможно, очень сильно обработанных холодным способом материалов. Это позволяет добавлять водород в защитный газ в количестве от 2 до 15%, обеспечивая больший нагрев дуги и лучшее проплавление. Количество водорода для ручной сварки обычно ограничивается до 5%, а более высокие концентрации ограничиваются автоматизированным процессом, таким как орбитальная GTAW. Водород нельзя использовать в качестве компонента защитного газа для ферритных, мартенситных или дуплексных нержавеющих сталей из-за риска растрескивания.
Азот
Азот — полезная добавка к защитному газу для дуплексных нержавеющих сталей, содержащих растворенный азот. Его добавляют для увеличения сопротивления точечной коррозии и в качестве стабилизатора аустенита для создания сбалансированной «дуплексной» микроструктуры в сварном шве, особенно для тонких материалов, которые охлаждаются слишком быстро, чтобы образовалось достаточное количество аустенита. Азот можно добавлять как в сварочный, так и в продувочный газ, чтобы предотвратить потери азота во время сварки.
В этой статье рассматриваются газы для активной стороны сварного шва. При сварке трубы или трубы, нормально подавать инертный газ, такой как аргон или азот, в трубу или трубу, чтобы поддерживать низкий уровень кислорода и минимизировать образование теплового оттенка до уровня бледной соломы. Обычно для этого требуется чувствительный кислородный измеритель или, возможно, ранее проверенные методы продувки. На толстых участках продувка должна продолжаться для всех проходов. Азотная продувка двойных корневых проходов улучшит коррозионную стойкость, но также может нарушить фазовый баланс.Добавки водорода использовались в продувочных газах как для аустенитных, так и для дуплексных сварных швов, чтобы минимизировать тепловые оттенки.
Защитные газы для сварки MIG
Основной функцией защитного газа при сварке GMAW является защита расплавленной сварочной ванны от атмосферного загрязнения. Эти загрязнения находятся в форме кислорода, азота и водорода, которые содержатся в атмосфере. Реакция этих элементов на сварочную ванну может создать множество проблем, включая пористость (отверстия в сварном шве) и чрезмерное разбрызгивание.Различные защитные газы также влияют на следующее:
- Характеристики дуги
- Режим переноса металла
- Профиль проплавления и сварного шва
- Скорость сварки
- Тенденция к подрезанию
- Очистка
- Механические свойства наплавленного металла
Аргон, гелий, CO2 и кислород — наиболее распространенные защитные газы, используемые в процессе сварки MIG. Некоторые газы лучше других подходят для наиболее часто используемых основных материалов, будь то алюминий, углеродистая сталь или нержавеющая сталь.
CO2 и кислород являются химически активными газами, то есть они влияют на то, что происходит в сварочной ванне. Электроны этих газов вступают в реакцию со сварочной ванной, приобретая различные характеристики. Аргон и гелий — инертные газы, поэтому они не вступают в реакцию с основным материалом или сварочной ванной. Например, чистый CO2 обеспечивает очень глубокое проплавление сварного шва, что полезно для сварки толстого материала, однако 100% CO2 дает менее стабильную дугу и большее количество брызг и может использоваться только в режиме переноса металла с короткой дугой.Если качество и внешний вид шва важны, смесь аргона и CO2 может обеспечить стабильность дуги, контроль сварочной ванны и уменьшение разбрызгивания. В зависимости от свариваемого основного материала могут использоваться следующие газы и газовые смеси.
АлюминийДля алюминия следует использовать 100% аргон. Смесь аргона и гелия хорошо работает, если вам требуется более глубокое проникновение или более высокая скорость движения.
Низкоуглеродистая стальСуществует множество вариантов защитного газа, включая 100% CO2 или смесь CO2 / аргона.По мере того, как материал становится толще, добавление кислорода в газообразный аргон может помочь в проникновении.
Углеродистая стальЗащитные газы, используемые для этой стали с более высоким содержанием углерода, хорошо работают со 100-процентным CO2 или смесью CO2 / аргона. Низколегированная сталь. Для этого материала хорошо подходит смесь 98% аргона и 2% кислорода.
Нержавеющая стальАргон, смешанный с 2–5% CO2, является нормой. Если вам требуется очень низкое содержание углерода в сварном шве, используйте аргон с 1-2% кислорода.Для наилучшего соответствия цвета материала серии 300 также можно использовать смесь гелия / аргона / СО2.
Выбранный вами защитный газ может влиять на многие сварочные характеристики. Как только вы поймете, какие свойства наиболее важны для вашего приложения, вы сможете выбрать лучшую смесь для работы. Для выбора наилучшего варианта рекомендуется проконсультироваться с поставщиком газа или другими специалистами в области сварки.
Различные типы сварочных процессов
Сегодня существует множество видов сварочных услуг, которые используются как любителями, так и профессионалами.Учитывая универсальность и квалификацию, необходимые для сварочных работ, неудивительно, что сварщики должны проходить серьезную подготовку, чтобы стать квалифицированными в своем деле. Поскольку сварка относится к соединению металлических сплавов, важно увидеть, как сварщики используют для этой цели различные методы. Вот некоторые из различных типов сварочных процессов, используемых сегодня для нержавеющей стали и других металлических сплавов.
Газовая вольфрамовая дуговая сварка (GTAW)
Газовая дуговая сварка вольфрамом — это разновидность дуговой сварки с использованием неплавящегося вольфрамового электрода.Окисление не влияет на электрод или зону сварного шва через инертный защитный газ, особенно аргон или гелий, и присадочный металл. Когда используется гелий, это называется гелиарной сваркой, но процесс такой же. Сварочный источник постоянного тока обеспечивает электрическую энергию, которая проходит через дугу через ионизированный газ и пары металлов. GTAW обычно используется для нержавеющей стали, алюминия, магния и меди, поскольку сварщик может выполнять более прочные и качественные сварные швы.
Дуговая сварка порошковой проволокой (FCAW)
Дуговая сварка порошковой проволокой — это еще один тип дуговой сварки, при котором расходуемый трубчатый электрод, содержащий флюс, непрерывно подается через источник сварочного тока постоянного тока.Иногда используется внешний защитный газ, но не обязательно для завершения сварки. Сам флюс обеспечивает защиту, так как образует газообразный и жидкий шлак, который защищает его. Благодаря естественным защитным барьерам, высокой скорости сварки и портативности FCAW часто используется в строительных проектах. Первоначально разработанный как альтернатива дуговой сварке защищенным металлом, FCAW использует стержневые электроды, которые снижают многие ограничения, характерные для SMAW.
Дуговая сварка экранированных металлов (SMAW)
SMAW эффективен для процесса ручной дуговой сварки, в которой используются плавящиеся электроды, покрытые флюсом.Переменный или постоянный электрический ток от источника сварочного тока образует электрическую дугу между электродом и соединяемыми металлами. Это плавит электрод и заготовку, образуя расплавленный металл, который затем охлаждается и образует соединение. Затем флюсовое покрытие распадается, оставляя пары, которые действуют как защитный газ и образуют слой жидкого шлака, используемый для защиты от атмосферного загрязнения. Поскольку операции SMAW просты, но требуют относительно небольшого количества оборудования, они являются сегодня одним из самых популярных видов сварки, особенно в отраслях технического обслуживания и ремонта.С помощью этого метода можно использовать железо, нержавеющую сталь, алюминий, никель и медь.
Газовая дуговая сварка металлов (GMAW)
Дуговая сварка металлическим электродом в газовой среде — это процесс сварки, при котором возникает электрическая дуга между плавящимися электродами из проволоки MIG и металлами детали. Этот тип сварки нагревает металлы, заставляя их плавиться и соединяться. Защитный газ проходит через сварочную горелку и защищает от атмосферного загрязнения. Автоматическая или полуавтоматическая система постоянного тока использует четыре основных метода переноса для переноса металла: шаровидный, короткозамкнутый, распылительный и импульсный.Метод GMAW первоначально использовался для алюминия и цветных металлов, но в настоящее время он используется для сталей из-за короткого времени сварки и большей универсальности. Это наиболее распространенная форма промышленного процесса сварки, учитывая эти преимущества и возможность адаптации к роботизированной автоматизации. Тем не менее, отсутствие защитного экрана делает его непригодным для использования на открытом воздухе.
Лазерная сварка
Лазерная сварка — это новая технология, при которой лазеры соединяют детали из металла или термопласта.Луч действует как концентрированный источник тепла, что позволяет выполнять узкие и глубокие сварные швы с высокой скоростью сварки. Процессы лазерной сварки часто используются в больших объемах, особенно в автомобильной промышленности, где часто используется сварка с отверстием или проплавлением. Высокая удельная мощность приводит к уменьшению зон термического влияния и более высокой скорости нагрева и охлаждения. Размер пятна может варьироваться, а глубина проникновения пропорциональна количеству подаваемой мощности и зависит от местоположения точки фокусировки.Сварка лазерным лучом обычно используется для углеродистой стали, нержавеющей стали, алюминия и титана, но высокая скорость охлаждения может привести к растрескиванию.
Электронно-лучевая сварка (EBM)
Одним из видов сварки плавлением, отличающимся от других видов сварки, является электронно-лучевая сварка. В этом процессе используется пучок высокоскоростных электронов, применяемый для соединения двух материалов. Когда детали плавятся, кинетическая энергия при ударе преобразуется в тепло и соединяет материалы. Процессы обычно проходят в условиях вакуума, чтобы предотвратить рассеяние электронного луча.EBM обычно представляют собой тонкостенные компоненты, чтобы обеспечить идеальную точку контакта и предотвратить смещение во время сварки. Некоторые материалы, такие как цинк, кадмий, магний и любые неметаллы, не могут подвергаться процессам EBM с учетом их температур плавления. Кроме того, процесс EBM не может соединить два разнородных материала с разными составами сплава. Электронные лучи могут создать атмосферу с высоким вакуумом и локализовать нагрев в точной точке, если для луча напрямую доступна более низкая точка плавления.
Дуговая сварка под флюсом (SAW)
Сварка под флюсом — это обычный процесс, используемый при непрерывной подаче плавящегося твердого или трубчатого электрода и погружении расплавленного сварного шва и зоны дуги в плавкий флюс. Затем поток становится проводящим и обеспечивает пути прохождения тока между электродом и заготовкой. Поскольку толстый слой флюса покрывает расплавленный металл, он предотвращает брызги и искры. Он также подавляет интенсивное ультрафиолетовое излучение и пары. Процессы SAW обычно автоматические и механизированные, но существуют способы подачи флюса под давлением или самотеком, ограниченные положениями плоской или горизонтальной угловой сварки.Токи варьируются от 300 до 5000 А при использовании одного или нескольких электродов. Комбинации постоянного и переменного тока обычно используются для процессов SAW и других многоэлектродных систем.
В CMPI мы понимаем важность сварочных услуг ASME. для любой производственной системы. Независимо от причины, мы вам поможем. Мы обеспечиваем надежность наших продуктов и услуг для любой отрасли, от продуктов питания и напитков до фармацевтики, до производства резервуаров и емкостей.Вместо того, чтобы создавать продукт для продажи, мы хотим действовать как расширение вашего магазина. Поэтому, когда в дело вступают ваши сварочные конструкции, мы учитываем передовой опыт и соображения, которые соответствуют вашим конкретным потребностям. Позвоните нам сегодня, если у вас возникнут вопросы или проблемы, и мы будем рады ответить вам. В противном случае ознакомьтесь с нашими различными продуктами и услугами на нашем веб-сайте, чтобы узнать, какие из них подходят вам.
.