Резка кислородным копьём
- Просмотров: 3326
При частичном разрушении конструкций кроме механизированного инструмента (отбойных молотков, отрезных дисков) применяют установки термического воздействия — кислородное копье, порошково-кислородный резак и так далее.
Для прожигания отверстий в бетоне и железобетоне, а также для разделительной резки в промышленной практике используют кислородное или кислородно-порошковое копье.
Например, с помощью копьевой резки прожигались отверстия в бетонной плите, на которой был установлен реактор Чернобыльской атомной станции. Отверстия были необходимы для размещения датчиков, контролирующих температуру, радиационный фон и другие параметры в разрушенном реакторе.
Кислородное копье — стальная трубка необходимой длины, по которой пропускается кислород. Будучи предварительно нагретым до температуры 1350–1400 °С, рабочий конец копья после пуска кислорода начинает интенсивно окисляться (гореть), развивая температуру до 2000 °С.
Рис. 1. Прутковые копья
Для начального нагрева копья используют обычно посторонние источники нагрева, например сварочную дугу или подогревающее пламя резака. В начальный момент, при зажигании копья, давление кислорода устанавливают небольшим, не более 0,05 МПа (0,5 кгс/см2), после же воспламенения трубки и установления устойчивого процесса давление кислорода поднимают до рабочего.
В процессе горения копье непрерывно укорачивается, причем в зависимости от толщины прожигаемого материала длина сгоревшей части трубки копья может быть в 5–25 раз больше длины прожигаемого отверстия. Обычно процесс прожигания кислородным копьем отверстий производят без применения подогревающего пламени.
Особенность прожигания отверстий в бетоне и железобетоне состоит в том, что для поддержания материала в месте контакта с копьем в расплавленном состоянии копье необходимо прижимать к обрабатываемому бетону с силой до 300–500 Н (30–50 кгс), преодолевая сопротивление густоплавких шлаков.
Последнее вызвано тем, что бетон, состоящий из оксидов (Al2O3, CaO и SiО2), кислородной струей не окисляется и теплоты не выделяет, в связи с чем быстро застывает при удалении от его поверхности горящего конца копья. Поэтому прожигать отверстия в бетоне и других неметаллических материалах следует без возвратно–поступательных движений копья, а лишь периодически поворачивая копье на угол 10–15° в обе стороны.
Порошково-кислородное (кислородно-флюсовое) копье
Так же, как и при кислородном копье, рабочий конец порошково-кислородного копья в начале процесса нагревают источником теплоты до температуры 1350–1400 °С, после чего в копье подают кислород и флюс.
На выходе из копья порошок воспламеняется, образуя ярко светящийся факел длиной до 50 мм с температурой 4000 °С и выше. Направляя факел копья на поверхность обрабатываемого материала, ее расплавляют и кислородной струей удаляют образующиеся шлаки. При резке металлов наряду с расплавлением имеет место и окисление основного металла.
В отличие от кислородного порошково-кислородное копье во избежание закупорки его шлаком не прижимают к прожигаемому материалу, а выдерживают на расстоянии 30–50 мм от торца образуемого отверстия. Достигается это периодической с интервалом в несколько секунд подачей копья вперед до упора в торец отверстия.
Промежутки времени между очередными подачами копья вперед зависят от скорости сгорания трубки копья. В процессе прожигания отверстий копью иногда придают вращательные движения, поворачивая его рукой на угол 10–15° в обе стороны.
Отверстия в бетоне и железобетоне порошково-кислородным копьем прожигают обычно в горизонтальном или наклонном снизу вверх направлении. Диаметр образуемого порошковым копьем отверстия зависит от диаметра копья, наличия или отсутствия вращательных движений копья и от удельных расходов кислорода и флюса. В результате получаются отверстия приблизительно круглой формы и составляет 30–90 мм.
Разделительную резку начинают от края разрезаемого материала или от начального сквозного отверстия внутри контура. Сущность процесса состоит в том, что, направляя факел копья на поверхность разрезаемого материала и совершая копьем возвратно–поступательных движения по касательной к передней грани реза (рис. 2), расплавляют поверхность материала факелом и удаляют расплавленный материал и шлаки струей кислорода.
Углубляя постепенно копье в разрез, прорезают материал насквозь, т. е. осуществляют разделительную резку. Ширина образуемого щелевого разреза в зависимости от толщины материала и диаметра копья может составлять 25–70 мм.
Рис. 2. Разделительная порошково–копьевая резка в нижнем положении
Резка порошковым копьем возможна во всех пространственных положениях независимо от толщины материала (для бетона и железобетона в пределах 3–3,5 м).
В зависимости от толщины разрезаемого железобетона резку можно выполнять по одной из схем, представленных на рис.
В этом случае копье совершает возвратно–поступательные движения на всю толщину разрезаемого материала, смывая расплавленный бетон в шлаки. Резка железобетона большей толщины этим способом не может быть производительной, так как жидкая ванна шлака на передней грани (длина которой может составлять не более 300 мм) по мере продвижения копья в глубь железобетона застывает.
Последнее вызывает необходимость повторного разогрева передней грани реза до расплавления, что сильно снижает производительность процесса.
Рис. 3. Резка бетона и железобетона толщиной до 300 мм:
а — при направлении копья сверху вниз; б — при горизонтальном направлении
Для лучшего удаления шлака из образуемого разреза и достижения большей производительности резку железобетона толщиной более 300 мм следует проводить по схемам рис. 4.
В этом случае резку начинают от нижней (рис. 4, а) или боковой, задней (рис. 4, б) поверхности разрезаемого железобетона, причем для поддержания шлаковой ванны на всей длине в жидком состоянии максимальная длина передней грани реза не должна превышать 300 мм. Сказанное в полной мере относится к резке в вертикальной плоскости и вертикальном направлении (рис. 5).
Рис. 4. Резка бетона и железобетона толщиной более 200 мм:
а — в горизонтальной плоскости и вертикальном направлении;
б — в вертикальной плоскости и горизонтальном направлении
Рис. 5. Резка бетона и железобетона в вертикальной плоскости и вертикальном направлении:
а — при толщине разрезаемого материала до 300 мм;
б — при толщине разрезаемого материала более 200 мм
Резку железобетона толщиной более 200 мм по схемам рис. 4, 5 осуществляют участками (рис. 6). Резку в пределах одного участка выполняют послойно (рис. 7).
Рис. 6. Схема резки «участками» бетона и железобетона толщиной более 200 мм
Рис. 7. Схема послойной резки бетона и железобетона толщиной до 200–300 мм и послойной резки отдельных участков при толщине материала более 200 мм
При разделительной резке железобетона важно начало процесса. В простейшем случае резку железобетона начинают от внешней кромки. Однако в практике весьма часты случаи, когда процесс приходится начинать внутри контура железобетонной стены или перекрытия.
Для этого необходимо иметь начальное отверстие диаметром 70–100 мм, которое можно получить как кислородным, так и порошково–кислородным копьем. При порошково–копьевой резке применяют стальные водо–газопроводные трубки с внутренними диаметрами 10 и 15 мм (ГОСТ 3262).
Один из основных параметров режима резки — удельный расход кислорода — зависит от удельного расхода и состава флюса, сечения копья, насыщенности бетона арматурой, а также от толщины разрезаемого железобетона.
При порошково–копьевой разделительной резке железобетона с применением флюса, состоящего из 80–85% Fe и 15–20% Al (по объему), на окисление трубки копья и флюса ориентировочно расходуется до 40% кислорода. Остальное количество его идет на удаление образующихся шлаков и непроизводительные потери.
Коэффициент полезного действия процесса прожигания в большей мере зависит от толщины разрезаемого железобетона, с увеличением которой наблюдается более полное использование кислорода и флюса за счет увеличения времени протекания реакций окисления. Следовательно, удельный расход части кислорода, идущей на окисление трубки копья и флюса при разделительной порошково–копьевой резке, уменьшается с увеличением толщины железобетона.
Однако практически для лучшего удаления шлака при резке больших толщин железобетона давление кислорода увеличивают, в результате чего (при сохранении постоянства проходных сечений кислородопровода) удельный расход кислорода с увеличением толщины разрезаемого железобетона возрастает.
Давление кислорода определяет в основном степень трудности удаления шлака, зависящая, в свою очередь, от толщины железобетона и направления процесса резки.
Так, если при резке железобетона толщиной 1500 мм в вертикальном направлении сверху вниз рабочее давление кислорода составляет 0,6 МПа (6 кгс/см
Однако во избежание чрезмерно большого охлаждающего действия струи и непроизводительных потерь кислорода давление его даже при резке в горизонтальном направлении бетона толщиной до 2000 мм не должно превышать 1,4 МПа (14 кгс/см2).
Большое влияние на производительность резки оказывает также удельный расход флюса, изменение которого в пределах 24–48 кг/ч и более (при резке железобетона толщиной 150–1500 мм) изменяет скорость резки до 25–30%.
Материал статьи представлен только для ознакомления с данной технологией производства работ.
В данный момент ЧУП «ДОЛБО» не использует описываемый выше метод в своей работе.
Резка кислородным копьем — Энциклопедия по машиностроению XXL
Резка кислородным копьем — копье образуется тонкостенной стальной трубкой, присоединенной к рукоятке и свободным концом прижатой к прожигаемому металлу. Резка начинается с подогрева конца заготовки сварочной дугой или горелкой. При пропускании кислорода через трубку (копье) ее конец быстро загорается и дальнейший подогрев не нужен. Копье прижимают к металлу и углубляют в него. Таким образом, выжигают отверстия круглого сечения. Кислородным копьем отрезают прибыли крупных отливок, прожигают летки в металлургических печах, отверстия в бетоне и т. п. [c.209]Резка кислородным копьем (рис. 62). Резку кислородным копьем выполняют тонкостенной стальной трубкой (копьем) с наружным диаметром 20—35 мм. Трубку подсоединяют к рукоятке с вентилем [c.104] Своеобразным способом является резка кислородным копьем (прожигание отверстий).
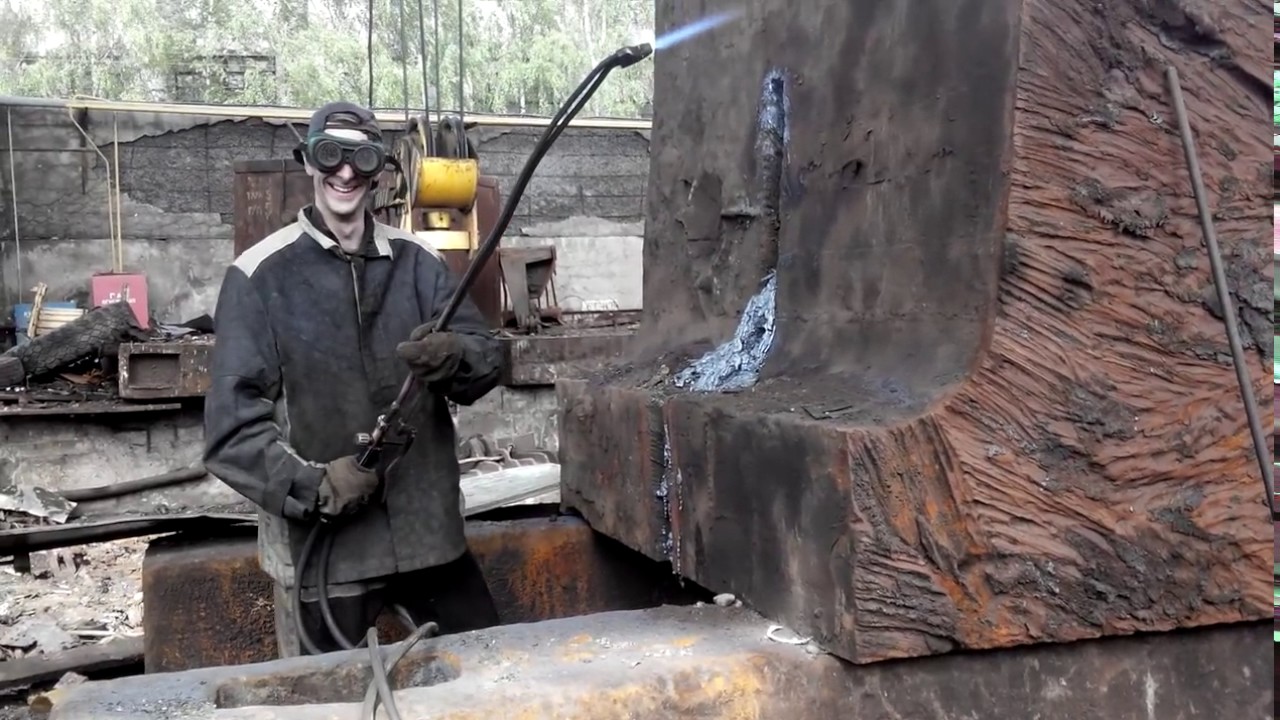
Резка копьем. В последнее время на металлургических заводах для ликвидации настылей в печах, при обрезке прибылей крупных стальных отливок и при других работах применяется новый способ газовой резки — резка кислородным копьем . При резке кислородным копьем в обыкновенную трубку диаметром до 25 мм подается кислород под давлением 3—5 ат из кислородного баллона через редуктор. На другом конце трубки имеется толстостенная стальная труба-копье с внутренним диаметром 3— 8 мм. На конце трубки имеется муфта, к которой привертывается отрезок трубки такого же диаметра.
[c.352]
Преимуществом резки кислородным копьем является то, что с помощью очень простой аппаратуры (обычной трубки при низком давлении кислорода) можно произвести резку металла любой толщины. [c.353]
Существуют три основные виды резки разделительная, поверхностная и резка кислородным копьем. [c.385]
Существует три основных вида резки разделительная, поверхностная и резка кислородным копьем. Разделительную резку, образующую сквозные резы, применяют для раскроя листов, вырезки отверстий, фланцев и фасонных заготовок. Поверхностная резка — это грубая строжка или обточка металла. Ее применяют для удаления поверхностных дефектов литья, вырезки поверхностных кана-470 [c.470]
В металлургических цехах широко применяется резка кислородным копьем затвердевшего металла в летках плавильных печей или в литейных ковшах.

Газокислородная резка делится на разделительную поверхностную и резку кислородным копьем. Разделительная резка применяется при раскрое листовой стали, резке профильного материала, вырезке различных деталей, отрезке прибылей литых [c.340]
Резка кислородным копьем. Этот вид резки применяется для образования отверстий круглой формы специальным копьем. Материалом копья служит трубка из малоуглеродистой стали. Прожигание Б металле или породе отверстий осуществляется благодаря одновременному сгоранию в струе режущего кислорода материала обрабатываемой заготовки и стальной трубки, по которой подается струя кислорода, и удалению этой струей образующихся окислов. Другой конец копья присоединяется при помощи резиновой трубки через редуктор к кислородной рампе. В процессе резки копье непрерывно, по мере его сгорания, совершает возвратно-поступательные движения.
[c.346]
РЕЗКА КИСЛОРОДНЫМ КОПЬЕМ [c.269]
Резка кислородным копьем — это процесс прожигания металла или породы струей кислорода, подаваемого к месту реза по стальной трубке (копью) небольшого диаметра, которая при этом сгорает. При прожигании отверстий в стальную трубку, конец которой предварительно нагревают пламенем газовой горелки, подают кислород, в результате чего происходит воспламенение конца труб- [c.269]
Газокислородная резка основана на способности металла сгорать в струе технически чистого кислорода с выделением значительного количества теплоты. Для нормального протекания процесса кислородной резки необходимо, чтобы температура плавления металла была бы выше температуры его воспламенения температура плавления окислов, образующихся при резке, была бы ниже температуры плавления металла, а образовавшиеся окислы достаточно жидкотекучими. Теплопроводность металла должна быть низкой. Указанным требованиям отвечает большинство марок углеродистой стали с содержанием углерода не более 0,7%. Однако высокохромистые стали, чугун, медь, магний, алюминий и их сплавы не поддаются обычной кислородной резке. Газокислородная резка делится на разделительную, поверхностную и резку кислородным копьем.
[c.335]
Резка кислородным копьем. Способ заключается в следующем. В стальную трубку (копье) после нагрева ее конца газовой горелкой подают кислород, вследствие чего происходит воспламенение конца трубки. Одновременно производят подогрев мест, где намечено пробить отверстие. Горящий конец трубки вплотную подводят к металлу и производят резку. Резка осуществляется за счет сгорания металла трубки и изделия в струе кислорода. Образующиеся окислы удаляют из зоны разреза струей кислорода. [c.338]
Резку кислородным копьем выполняют тонкостенной стальной трубкой диаметром 25—30 мм, по которой но-
[c. 431]
Фиг- 13. Процесс резки кислородным копьем [c.502]
ОРИЕНТИРОВОЧНЫЕ ПАРАМЕТРЫ РЕЗКИ КИСЛОРОДНЫМ КОПЬЕМ [34] [c.392]
Резка кислородным копьем. Сущность резки кислородным копьем заключается в прожигании отверстий [c.197]
Сущность резки кислородным копьем заключается в прожигании отверстий струей кислорода. Копье представляет собой толстостенную трубку наружным диаметром 20—35 мм. Возможно также использование тонкостенных газовых трубок, обмотанных снаружи стальной проволокой диаметром 3—4 мм, а также заполненными изнутри стальными прутками. Трубку подсоединяют к рукоятке с вентилем для кислорода и по ней подается кислород к месту резки. До начала резки конец трубки нагревают газовой горелкой, угольным электродом или электрической дугой до температуры воспламенения. В качестве копья применяют стальные трубы с наружным диаметром 10,2—21,3 мм. При прожигании бетона используют трубы, имеющие наибольшую толщину стенки. Для сгорания 1 кг железа расхо-
[c.191]
Резка кислородным копьем (рис. 220) заключается в прожигании в металле отверстий струей кислорода, подаваемого по стальной трубке, один конец которой упирается в прорезаемый [c.403]
КИСЛОРОДНОЕ КОПЬЕ — см. Резка кислородным копьем. [c.60]
При резке кислородным копьем кислород под давлением 3—5 ати подается из кислородного баллона через редуктор в стальную трубку диаметром 3—12 мм. Место, где нужно начать резку, а также конец трубки подогревают до температуры воспламенения, пользуясь нефтяной форсункой или сварочной горелкой. Затем на место резки направляют струю кислорода из трубки и подают трубку вперед. Она при этом углубляется в металл, прорезая его словно копьем. [c.222]
Поступают и так сперва обычным резаком разрезают деталь на глубину 150—200 мм, затем, не прерывая работы, продолжают резку кислородным копьем . Эти.м способом прорезают за 2 мин. отверстие диаметром 60 м.ч на глубину 300 мм.
[c.222]
У нас процесс резки кислородным копьем исследовался в сварочной лаборатории МВТУ им. Баумана. [c.223]
Следует, однако, подчеркнуть, что главная доля тепла, расходуемого при кислородной резке стали, получается за счет теплового эффекта реакций окисления металла. В некоторых случаях резка может идти целиком за счет окисления металла, без подогрева (например, резка кислородным копьем). [c.93]
Ориентировочные режимы резки кислородным копьем по данным МВТУ [c.193]Резку кислородным копьем выполняют тонкостенной стальной трубкой (коньем), присоединенной к рукоятке. Кислород проходит через стальную трубку, прижатую свободным концом к прожигаемому металлу. Начинается резка с подогрева конца отливки или места реза на металле сварочной дугой или горелкой. При пропускании кислорода конец копья быстро загорается, и дальнейший подогрев не нужен. Конье прижимают к металлу и углубляют в него. Таким образом, выжигают отверстие круглого сечения. Кислородным коньем прожигают летки в металлургических печах, отверстия в бетоне и т. п.
[c.312]
Резку больших металлических массивов можно производить с применением кислородного копья. Резка кислородным копьем заключается в прожигании (сверлении) в металле отверстий струей кислорода, подаваемого по стальной трубке. Перед началом резки конец трубки нагревают до температуры воспламенения. Затем прижимают конец трубки к прожигаемому металлу, повышая давление кислорода до 5—6 кПсм . По мере сгорания трубки и углубления прожигаемого отверстия трубка подается вперед. Сгоревшая трубка заменяется новой. [c.210]
Резка кислородным копьем — процесс прожигания металла или породы струей кислорода, подаваемого к месту реза по стальной трубе (копью) небольшого диаметра. При прожигании отверстий в стальную трубку, конец которой предварительно нагревают пламенем газовой горелки, подают кислород, в результате чего происходит вэс. пламенение конца трубки. Одновременно подогревают место для отверстия. Затем горящий конец копья приближают вплотную к изделию, и происходит резка, т. е, прошивка отверстия. Резка копьем находит применение при пробивке леток доменных и сталеплавильных печей, обработке крупных металлических отливок, раздел се металлического лома, пробгшке отверстий в толстых металлических или бетонных заготовках перед началом разделительной резки.
[c.304]
Краткий справочник газосварщика и газорезчика содержит основные данные о газах, газах-эаменителях и горючих жидкостях, применяемых при газопламенной обработке металла. В книге сообщены технические и технологические характеристики аппаратуры и оборудования для газовой сварки и резки, приведены правила эксплуатации и методы ремонта аппаратуры и оборудования, а также изготовления быстроизпашивающихся деталей. Приведены некоторые данные о материалах для ремонта и эксплуатации оборудования. По вопросам технологии сообщаются сведения о газовой сварке малоуглеродистых,средне- и высокоуглеродистых сталей, высоколегированных нержавеющих и жаропрочных сталей и сплавов с высоким омическим сопротивлением, а также о сварке чугуна и цветных металлов и сплавов сообща ются краткие сведения о сварке пластических материалов. Подробно освещены вопросы машинной и ручной кислородной разделительной резки сталей разной толщины, резки кислородом низкого давления, кислородно-флюсовой резки, резки кислородным копьем и поверхностно-кислородной резки. Приводятся данные о методах контроля сварных соединений.
[c.2]
РЕЗКА КИСЛОРОДНЫМ КОПЬЕМ — кислородная резка, основанная на сжигании металла в струе кислорода, проходящего через стальную трубку (кислородное копье), прижатую свободным концом к поверхности металла, без использования газового подогревательного пламени, которое заменяется довольно быстрым сгоранием самой трубки — копья. Резка начинается с подогрева места реза или, что удобнее, с подогрева конца копья, например сварочной горелкой или дугой при пропускании кислорода конец копья быст- [c.124]
ФЛЮСОВАЯ РЕЗКА КИСЛОРОДНЫМ КОПЬЕМ — резка кислородным копьем, при которой в зону реза подается флюс. Испольяуется для спепиальных сталей. [c.174]
Во время резки кислородным копьем трубка обгорает образующееся при этом тепло используется для подогрева металла. Для увеличепня количества тепла реко-222
[c.222]
Резка металла кислородным копьем
Газокислородная резка используется в металлургической промышленности довольно давно. Она успела доказать свою эффективность и высокие значения многих технологических показателей. Однако промышленный мир не стоит на месте. Одной из разновидностей процессов, предполагающих использование кислорода для разрезания заготовок, является резка кислородным копьём. Данный вид механической обработки возможен практически в любом пространственном положении.
При прожигании стальных заготовок в роли копья может выступать стальная водо- и газопроводная трубка с низкоуглеродистой проволокой внутри. Прожигание отверстий в заготовках из такого материала, как чугун, может использоваться при выполнении шпуров в зашлакованных массивах, предназначающихся для разрушения во взрывных ямах перед переплавкой. При этом производительность данного процесса будет довольно низкой: отверстие диаметром до 60 мм можно получить не менее чем за минуту. Иногда для повышения эффективности резки осуществляется подача железного порошка вместе с кислородом. Это позволяет выполнять не только прожигание отверстия нужного диаметра, но и разделительную резку бетона и стали.
Так же, как и плазменная резка, данный вид механической обработки металлических заготовок имеет ряд технологических особенностей. Рабочий конец копья предварительно нагревается до температуры около 1375°С при помощи одного из посторонних источников: сварочной горелки, дуги или пламени резака. В результате данной манипуляции он начинает интенсивно гореть, за счёт чего его температура повышается до 2000°С.
Для непосредственной резки заготовки копьё прижимают к обрабатываемому материалу, повышая давление подаваемого кислорода до необходимой величины. Необходимо при этом осуществлять вращательные и возвратно-поступательные движения, при которых копьё можно ненадолго отрывать от поверхности. Шлаки, которые образуются при данном процессе, поступают в зазор между трубкой и стенкой получаемого отверстия.
Форма готовых отверстий, как правило, круглая, а их диаметр во многом зависит от диаметра инструмента и осуществлённых движений копьём. Главная особенность процесса прожигания отверстий в бетоне заключается в том, что копьё должно быть прижато к обрабатываемой поверхности с усилием до 500 Н. При этом необходимо преодолевать сопротивление появляющихся шлаков. Эта трудность вызвана тем, что бетон не окисляется под воздействием струи кислорода и тепла, соответственно, не выделяет, поэтому при отдалении копья от поверхности оно очень быстро застывает. Таким образом, технология прожигания отверстий в неметаллических материалах типа бетона по этой причине исключает выполнение возвратно-поступательных движений, допуская только периодические движения по кругу в обе стороны.
КИСЛОРОДНО-ФЛЮСОВАЯ КОПЬЕВАЯ РЕЗКА
Кислородно-флюсовое копье
Кислородно-флюсовая пробивка отверстий является совокупностью обычной техники кислородной пробивки с кислородно-флюсовым процессом; этот способ отличается от кислородно-флюсовой разделительной резки, тем что резак заменен специальным держателем, снабженным тонкостенной трубкой из малоуглеродистой стали соответствующей длины, через которую подают кислород и флюс, и используется для сверления и резки таких материалов и изделий, обработка которых ранее из-за их размера и жароустойчивости считалась невозможной или неэкономичной.
Для осуществления этого процесса необходимы кислород высокого давления, сжатый воздух или азот, трубчатое копье, флюсопитатель, копьедержатель, редуктор и шланги.
Флюсопитатели служат для подачи флюса в режущую струю. Азот или воздух от баллона или компрессора по шлангу поступает на вход редуктора, который установлен на флюсопитателе. Нажимным винтом редуктора устанавливается рабочее давление во флюсопитателе в пределах 0,5 — 1,0 кгс\см2, которое контролируется по манометру на редукторе. С выхода редуктора флюсонесущий газ подается под уплотнительную крышку бачка, создавая давление над порошком, и в циклонную камеру. Из циклонной камеры смесь флюсонесущего газа и порошка через выходной штуцер и рукав поступает в копьедержатель, а затем через копье в зону пробивки отверстий или реза.
Количество флюса, подаваемого в копьедержатель, определяется величиной давления в бачке и зазором в циклонной камере.
Копьедержатель состоит из держателя трубы с фиксирующими винтами, смесителя, инжектора, корпуса с вентилями подачи.
В качестве копья рекомендуется применять трубу по ГОСТ 3262 или ГОСТ 8734 с наружным диаметром 16 мм, длиной от 3 до 6 м. Длина трубы зависит от местных условий работы. При необходимости изготовления очень глубоких отверстий можно одновременно работать двумя или несколькими трубками.кислорода и флюса, плотнительных колец, штуцеров подачи кислорода и порошка, клапана с разрывной мембраны.
Практика резки кислородно-флюсовым копьем
Для начала пробивки отверстий необходимо нагреть выходной конец трубы газовой горелкой или резаком до температуры воспламенения. Предварительный подогрев места начала реза не требуется. Конец трубки копья должен находиться на расстоянии 50-150 мм от поверхности обрабатываемого изделия. При меньшем расстоянии увеличивается интенсивность сгорания трубки. Расплавленный металл вытекает из отверстия в виде жидкотекучего шлака. При горизонтальном сверлении рекомендуется пробивать отверстие и держать копье под углом 5-100, чтобы облегчить вытекание шлака. Кислородно-флюсовым копьем производят разделительную резку, перемещая его конец с одной стороны изделия на другую.
Кислородно-флюсовая пробивка отверстий копьем в металлургической промышленности
Обработка копьем отливок большого сечения
При помощи кислородно-флюсового копья можно удалять прибыли и литники с отливок из нержавеющей и малоуглеродистой сталей. Применяя копье, с поверхности отливок можно удалять песочины и другие дефекты.
Удаление из печи «козлов»
«Козлами» обычно называют остатки железа и стали в шлаковых камерах открытых мартеновских печей, металла и шлака в доменных, электрических печах и т.д. Эти «козлы» постепенно увеличиваются, и их нужно регулярно удалять из печи. Часто в их состав входят жаропрочные шлаки и цемент. Удаляют «козлы» с помощью кислородно-флюсовой резки копьем.
Пробивка леток в печах
Летки в доменных и сталеплавильных печах могут быть вскрыты в минимальное время кислородно-флюсовым копьем. Трубку копья для облегчения работы сгибают по плавной кривой. Такая форма не снижает эффективности копья. Давление кислорода обычно поддерживают приблизительно до 7 кгс/см2.
Пробивка копьем жаропрочных материалов
Кислородно-флюсовая резка применяется для разделения или сверления бетона и других жаропрочных материалов, особенно в тех случаях, когда не допускается шума и вибраций, вызываемых пневматическим инструментом и обычным сверлением. Для повышения температуры и мощности пламени обычно смешивают железный и алюминиевый порошки. Процесс при этом протекает медленнее, чем, например, пробивка чугуна, но кислорода и флюса расходуется больше. Расход жаростойких материалов при резке копьем изменяется в широких пределах в зависимости от состава материала и условий работы.
Инструкционная карта 36 — Резка порошково-кислородным копьем
Инструкционная карта 36 — Резка порошково-кислородным копьем
Категория:
Руководство газосварщика газорезчика
Инструкционная карта 36 — Резка порошково-кислородным копьем
Учебно-производственные задания. I — прожигание отверстий в металле и неметаллических материалах с помощью установки УФР-5, II — разделительная резка материалов.
Цель заданий: научиться пробивать отверстия и выполнять разделительную резку порошково-кислородным копьем.
Организационные указания. Подготовить стальные трубки диаметром 1/4” и 1/2”, длиной 3—6 м, баллоны с кислородом, флюс, состоящий из 80—85% железного порошка и 15—20% алюминиевого порошка, сварочные горелки (резаки) для нагрева копья перед началом резки. Подготовить образцы из стали, чугуна, бетона (железобетона толщиной от 100 мм и более).
I. Прожигание отверстий в металле и неметаллических материалах с помощью установки УФР-5
1. Установить образец из стали, чугуна или железобетона на подставки.
2. Проверить техническое состояние копьедержателя
3. Открыть вентиль и убедиться в том, что кислород выходит из камеры Закрыть кислородный вентиль.
4. Вставить стальную трубку (копье) в камеру так, чтобы ее конец плотно прижался к уплотнитель-ной прокладке.
5. Закрепить копье зажимами, размещенными на кожухе.
6. Открыть вентиль подачи кислорода, убедиться в отсутствии утечки газа между уплотняющей прокладкой и копьем. Если утечка есть, то газ выходит через втулку из камеры и легко обнаруживается на слух.
7. Убедившись в отсутствии утечки, закрыть вентиль кислорода.
8. Зажечь факел порошково-кислородного копья.
8.1. Нагреть рабочий конец трубки пламенем горелки (подогревающим пламенем резака, рис. 3) до температуры порядка 1350—1400 °С.
8.2. Подать в копье кислород, затем флюс (открыть вентиль подачи флюса) под давлением 0,2 МПа. Кислород, выходя с большой скоростью из инжектора, обеспечивает подсос флюса и подачу его к разогретому концу копья. На выходе из копья порошок воспламеняется, образуя ярко светящийся факел длиной до 50 мм с температурой 4000 °С и выше.
9. Прожечь отверстие в образце.
9.1. Направить факел порошково-кислородного копья на поверхность образца так, чтобы расстояние от торца копья до поверхности составляло 30—50 мм
9. 2. По мере расплавления материала и частичного окисления (при резке металла) подавать копье в направлении отверстия.
9.3. После заглубления копья в отверстие повысить давление кислорода до рабочего 0,6—0,7 МПа (для рассматриваемого случая).
9.4. Наклонить копье на угол примерно 5° от горизонтали для лучшего стекания шлаков и увеличения скорости прожигания отверстия.
9.5. В процессе прожигания отверстия выдерживать расстояние от торца трубки до торца образуемого отверстия в пределах 30—50 мм. Достигается это периодической, с интервалом в несколько секунд, подачей копья вперед до упора в торец отверстия, задерживания в этом положении на несколько секунд (столько, сколько нужно для сгорания трубки копья на величину 30— 50 мм) и подачей копья вновь до упора в торец отверстия. Промежутки времени между очередными подачами копья вперед зависят от скорости сгорания трубки (копья).
9.6. С целью увеличения диаметра отверстия и лучшего стекания шлака поворачивать копье на угол 10 — 15° в стороны.
9.7. После прожигания отверстия прекратить подачу кислорода и флюса путем закрытия соответствующих вентилей.
II. Разделительная резка материалов
1. Начинать процесс разделительной резки нужно от края разрезаемого материала или от начального сквозного отверстия, образуемого внутри контура.
2. Направлять факел копья на поверхность разрезаемого материала и совершать копьем возвратно-посту-пательные движения на всю толщину разрезаемого материала по касательной к передней грани реза.
3. Ширина образуемого щелевого разреза b может составлять 25—70 мм в зависимости от толщины материала и диаметра копья.
4. Резку бетона и железобетона толщиной более 300 мм осуществлять по схеме рис. 6. Резку начинать от нижней поверхности и поддерживать шлаковую ванну на всей длине в жидком состоянии (максимально возможная длина ванны 300 мм).
5. Резку бетона и железобетона можно осуществлять и послойно.
Реклама:
Читать далее:
Инструкционная карта 37 — Дуговая резка угольным и металлическим электродами
Статьи по теме:
Газовая резка: технология, виды, металлы
Метод газовой резки основан на экзотермической окислительной реакции. Для нагревания используют смесь (газ плюс кислород), для разделения металла по заданному контуру — направленную кислородную струю.
Рисунок 1 — Процесс газовой резки
Процесс подробно показан на рисунке 1:
- Ацетилено-кислородное пламя (3) нагревает заготовку (2) в исходной точке до необходимой температуры.
- На подготовленный металл направляют режущую струю (1).
- При горении зона реза производит высокий объем тепловой энергии.
- Пламя резака в совокупности с полученным теплом повышает температуру всей заготовки.
- Контакт расплавленного металла с кислородом вызывает химическую реакцию окисления. Кинетическая энергия направленной струи удаляет полученные оксиды.
Чем толще обрабатываемый слой, тем меньшее значение имеет мощность пламени горелки в общем количестве индуцируемого тепла. При обработке листа толщиной 5 мм тепловая энергия подогрева занимает около 80%, с толщиной 50 мм этот показатель снижается до 10 %.
Условия для газовой резки
Стабильный процесс газовой резки возможен только при использовании мощного источника тепла. Заготовку доводят до необходимой температуры, а сгорающий металл выделяет энергию в крупном объеме.
Химический состав обрабатываемого материала должен соответствовать следующим характеристикам:
- Температура реакции окисления ниже температуры плавления.
- Температура плавления выше температуры образующихся оксидов.
- Низкая теплопроводность.
- Хорошая текучесть оксидов.
Перечисленные ограничения не позволяют применять газовую резку по отношению к ряду металлов. Для меди подходит лазерная резка, поскольку высокая теплопроводность не позволяет ей разогреться до нужной температуры.
Оксиды чугуна, образующиеся при плавлении металлов, характеризуются низкой текучестью и высокой температурой, поэтому их сложно удалить из рабочей зоны. То же самое происходит со сплавами, содержащими магний, никель, хром или алюминий.
Идеальным металлом для газовой резки является углеродистая сталь.
Воздействие примесей стали
Воздействие примесей стали на непрерывность процесса газовой резки напрямую зависит от их процентного содержания:
- Алюминий. Допустимый уровень составляет 0,5%.
- Медь. Содержание примеси до 0,7% от общей массы на процесс не влияет.
- Ванадий, фосфор, сера. Не оказывают отрицательного влияния при допустимых значениях.
- Вольфрам. Не нарушает непрерывность резки при показателе до 10%. Более высокий процент делает работу затруднительной, при 20% процесс прерывается.
- Молибден. Допускается содержание 0,25%.
- Никель. Верхняя планка – 7-8%.
- Хром. Максимум – 4-5 % отрицательного влияния. Повышенный уровень резко ухудшает условия резки. Требуется применение флюса.
- Кремний.
При стандартных показателях не мешает процессу. При 4% резка невозможна.
- Углерод. Показатели колеблются от 0,4 % (норма) до 1-1,25 % (остановка работы).
- Марганец. Стандарт – до 0,4%. По мере повышения резка затрудняется, при достижении 14% — становится невозможной.
Особенности технологии газовой резки
Рисунок 2 — Газовая резка по прямой линии.
Технология газовой резки напоминает сварку (см. рисунок 2). При использовании вставного резака соблюдают следующую последовательность:
- Присоединение вставного резака к стволам горелки.
- Установка рекомендованного рабочего давления газов (зависит от типа мундштука).
- Розжиг факела (для этого вентиль подачи кислорода открывают полностью, вентиль подачи ацетилена – наполовину).
- Регулировка мощности пламени.
- Обозначение линии реза.
- Закрепление детали на верстаке.
- Формирование линии реза (несколько медленных проходов горелкой).
- Обработка металла (сначала заготовку разогревают до ярко-красного цвета, затем перемещают пламя резака по заданной черте).
Рисунок 3 — Резка по криволинейному контуру.
Метод криволинейного реза представлен на рисунке 3. Сначала намечают контуры отверстия, затем прожигают заготовку по центру и доводят разрез до заданных границ. Мундштук нужно поддерживать левой рукой.
Виды резки
В зависимости от направленности и характера струи различают три основных вида газовой резки:
- разделительная (сквозная),
- поверхностная (снятие верхнего слоя),
- кислородное копье (формирование отверстий).
Скоростная газовая резка
Для скоростной высококачественной газовой резки используют тройные мундштуки. Их выходные отверстия расположены в виде равнобедренного треугольника. Основная струя, проходящая сквозь вершину угла, формирует надрезы. Вспомогательные струи проводят зачистку кромки. Недостатки метода – невозможность обработки сложного контура и значительная ширина полученного разреза.
Использование флюса
Рисунок 4 — Установка для кислородной резки под флюсом.
Для обработки легированных сталей используют порошкообразный флюс. При его сгорании выделяется дополнительный объем тепла, необходимый для нормальной работы газовой установки. Флюсопитатель, заполненный железным порошком, обеспечивает непрерывную подачу расходного материала и регулировку его объема. Полученные в процессе сгорания продукты вступают в химическую реакцию с оксидами и образуют жидкотекучие шлаки.
Кислородно-флюсовый способ подходит для чугуна, хромоникелевых и хромистых сталей. Медные и алюминиевые составы резать сложнее, они требуют дополнительной механической обработки.
Установка УГПР (на рисунке 4) предназначена для упрощения газовой флюсовой резки. В ее конфигурацию входит бачок флюсопитателя с редуктором модели ДКС-66 (на тележке), узел подачи флюса и универсальный резак марки Р2А-01. Флюс (железный порошок ПЖ) подается кислородом.
В процессе работы образуется вредная смесь пара и газов, из-за чего в помещении необходимо обеспечить хорошую вентиляцию. Рекомендовано использовать респиратор.
Поверхностная резка
Рисунок 5 — Поверхностная резка.
Для снятия верхнего слоя (рис. 5) мундштук располагают под углом от 15 до 40 градусов. Более низкая (по сравнению с разделительным способом) скорость подачи струи обеспечивает сгорание поверхностных слоев металла.
Кислородное копье
Резка кислородным копьем (на рисунке 6) подходит для металла, железобетона и бетона. К подающему кислород устройству присоединяют тонкостенную стальную трубку небольшого диаметра (20-35 мм). Перед началом работы ее нагревают до нужной температуры. При прохождении сквозь горячую трубку кислород воспламеняется и образует так называемое копье. Его прижимают к нужному месту заготовки с большим усилием, одновременно придавая вращательные и возвратно-поступательные движения.
Газовая резка металлов | Строительный справочник | материалы — конструкции
Под газопламенной резкой (чаще ее называют кислородной) понимают способ разделения металла по прямому или криволинейному контуру. Метод основан на использовании для нагрева смесь горючих газов с кислородом и экзотермической (с выделением тепла) реакции окисления металла. Суть кислородной резки заключается в сгорании железа в струе чистого кислорода, нагретом до температуры, близкой к плавлению. Для удаления оксидов железа из зоны реза используется кинетическая энергия режущего кислорода. Сам процесс резки включает в себя стадию подогрева металла ацетиленовым (или другим заменителем) пламенем и непосредственную резку струей режущего кислорода.
По характеру и направленности кислородной струи различают три основных вида резки: разделительная, при которой образуются сквозные резы, поверхностная, при которой снимают поверхностный слой металла, кислородное копье, заключающееся в прожигании в металле глубоких отверстий. Процесс кислородной резки представлен на рис.1. Металл 3 нагревается в начальной точке реза до температуры воспламенения (в кислороде для стали до 1000 — 1200°С) подогревающим ацетилено-кислородным пламенем 2, после «его направляется струя режущего кислорода 1 и металл начинает гореть с выделением значительного количества тепла.
Выделяемое тепло Q вместе с пламенем резака разогревают нижние слои металла на всю его толщину. Роль подогревающего пламени в процессе резки меняется в зависимости от толщины разрезаемого металла. Так, при толщине металла до 5 мм подогревающее пламя занимает до 80% в общем количестве тепла, участвующего в процессе резки.
С увеличением толщины металла роль подогревающего пламени в балансе температур падает, и при толщине 50 мм и более доля подогревающего пламени падает до 10%. В результате взаимодействия расплавленного металла с кислородом образуются оксиды железа 5, которые вместе с расплавленным металлом удаляются из зоны реза кинетической энергией струи кислорода 1.
Для обеспечения стабильности процесса и нормальной резки металла необходимо, чтобы в зоне реза выполнялись следующие условия:
- мощность источника тепла должна быть достаточной для нагрева металла до температуры, при которой происходит реакция сгорания металла;
- количество тепла, выделяемое при сгорании металла в струе кислорода, должно обеспечивать непрерывность процесса;
- реакция окисления металла должна происходить при температуре меньшей, чем требуется для плавления;
- температура плавления металла должна быть выше температуры образовавшихся оксидов. В противном случае пленка тугоплавких оксидов изолирует металл от кислорода;
- текучесть образовавшихся оксидов должна быть такой, чтобы они легко выдувались струей режущего кислорода;
- теплопроводность металла не должна быть высокой, иначе процесс резки может прерваться из-за интенсивного теплообмена.
Далеко не все металлы обладают свойствами, удовлетворяющими все эти условия, поэтому кислородная резка для некоторых из них становится невозможной. К примеру, большая теплопроводность меди не обеспечивает условий для нагрева до температуры реакции сгорания металла, что затрудняет начальный этап резки. Поэтому мощности газовых резаков недостаточно для разрезания меди, которую режут дуговой сваркой. Стали с большим содержанием хрома, магния и никеля, а также алюминий образуют тугоплавкую пленку оксидов, которая препятствует контакту металла с кислородом, что затрудняет кислородную резку.
Чугун, содержащий более 1,7% углерода, кислородной резкой не обрабатывается. Это. объясняется тем, что температура плавления чугуна ниже температуры плавления образующихся оксидов, поэтому металл удаляется из зоны реза без характерного окисления. Кроме того, образующиеся при нагреве оксиды имеют низкую текучесть и с трудом удаляются струей кислорода.
Лучше всего подходит для кислородной резки углеродистая сталь, которая удовлетворяет всем условиям, необходимым для поддержания непрерывности процесса. Влияние примесей в стали на процесс кислородной резки отражено таблице.
Влияние примесей стали на процесс кислородной резки
Элемент | Влияние на процесс резки |
Углерод | При содержании до 0, 4% процесс резки не гсудаается, при более высоком содержании ухудшается, а при содержании 1-1,25%- становится невозможным |
Марганец | Содержание до 0,4% на процесс резки заметно не ыгаяет. При более высоком содержании процесс резки затрудняется, а при 14% становится |
Кремний | Содержание в количестве, обычном для сталей отрицательного влияния на процесс резки не оказывает. При повышенном содержании процесс усложняется, а при содержании более 4% -становиться невозможным |
Фосфор и сера | В обычных количествах отрицательного влияния не оказывает |
Хром | Содержание до 4-5% отрицательного влияния на процесс резки не оказывает. При большем Содержании процесс резки становится невозможным и требует применения флюса.![]() |
Никель | Содержание до 7-8% отрицательного влияния на процесс резки не оказывает. С увеличением содержания процесс резки услажняется. |
Молибден | Содержание до 0,25% отрицательного влияния на процесс резки не оказьвает. |
Вольфрам | Содержание до 10% отрицательного влияния на Процесс резки не оказывает. При более вьсоком содержании процесс резки затрудняется, а при 20% |
Ванадий | В обычных количествах отрицательного влияния не оказывает |
Медь | Содержание до 0,7% влияния на процесс резки не оказывает |
Алюминий | Содержание до 0,5 % влияния на процесс резки не оказавает |
Рис. 1. Кислородная резка: 1 — струя кислорода; 2 — подогревающее пламя; 3 — металл; 4 — зона реза; 5 — оксиды железа | Рис. 2. Резка по прямой линии |
Технология газокислородной резки
Технологию газокислородной резки рассмотрим на примере использования вставного резака. Установку для газокислородной резки готовят так же, как и для газовой сварки. Вставной резак присоединяют к стволам горелки и устанавливают рабочее давление кислорода и ацетилена, равное значениям, рекомендуемым для данного размера мундштука. Для зажигания факела полностью открывают вентили подачи кислорода и примерно наполовину — вентиль подачи ацетилена. Пламя устанавливают, вращая вентиль подачи кислорода на вставном резаке. Пламя проверяют, нажимая на секунду рычаг подачи кислорода, и при необходимости выполняют регулировку.
На разрезаемой детали мелом наносят линию реза и устанавливают ее на верстак, закрепив при необходимости струбцинами или другим доступным способом. Для удобства можно укрепить вдоль линии реза (на расстоянии примерно 6 мм) направляющий уголок (рис. 2). Прижав боковую сторону горелки к направляющему уголку, делают два — три медленных прохода вдоль линии реза. Для обеспечения устойчивости можно опереться предплечьем рабочий верстак. Металл в начале реза разогрева до ярко-красного цвета, затем, полностью открыв рычагом (или вентилем в другой конструкции) подачу кислорода и начинают медленно перемещать пламя резака вдоль нанесенной линии.
Криволинейные контуры или отверстия режут методике, показанной на рис. 3. Для удобства перемещения резака его устанавливают на лев руку. Для резки отверстий сначала намечают её контуры, а затем прожигают внутри отверстие, из которого проводят рез до контуров, обведенных линией. После этого продолжают резку окружности.
Рис. 3. Резка криволинейного контура | Рис. 4. УГПР — Установка кислородно-флюсовой резки. 1 — тележка; 2 — циклон; 3 — флюсопитатель; 4 — редуктор кислорода; 5 — резак; 6 — шланги |
Высококачественная скоростная резка достигается наклоном резака под острым углом и применением специальных мундштуков, у которых имеется три отверстия для режущего кислорода. Центры этих отверстий образуют равнобедренный треугольник, вершиной которого служит отверстие, предназначенное для основной режущей струи. Режущая струя осуществляет резку и проходит первой. Две вторые струи, перемещаясь вслед за основной, осуществляют зачистку образовавшихся кромок. К недостаткам этого вида резки относят большую ширину реза и невозможность прохода по криволинейным контурам.
Кислородно-флюсовую резку выполняют при резке легированных сталей. Для этого вместе с кислородом вводят порошкообразный флюс, при сгорании которого выделяется дополнительное тепло, что увеличивает температуру в зоне резки. В качестве флюса чаще всего используют железный порошок, которым заполняют специальный флюсопитатель, обеспечивающий подачу и регулировку расхода. Продукты сгорания флюса взаимодействуют с оксидами, образуя жидкотекучие шлаки, которые легко удаляются из зоны реза. Лучше всего подаются кислородно-флюсовой резке хромистые и хромоникелевые стали. Этим же методом можно резать и чугун. Резка сплавов на медной и алюминиевой основе затруднительна и требует последующей механической обработки. Для механизации работ по кислородно-флюсовой резке существует установка УГПР (рис. 4). Сама установка состоит из бачка флюсопитателя с редуктором ДКС-66, смонтированных на тележке, универсального резака Р2А-01 в блоке с узлом подачи флюса. Флюс подается кислородом. Применяемая марка флюса — ПЖ (железный порошок). При резке подобных сплавов выделяется большое количество вредных паров и газов, что может оказать отрицательное влияние на здоровье резчика. Поэтому рабочее место должно хорошо вентилироваться, а при больших объемах работ может применяться дополнительная защита органов дыхания респиратором. Поверхностная резка (рис. 5) позволяет снять с основного металла слой нужной толщины.
Рис. 5. Поверхностная резка: 1 — мундштук; 2 — шлак; 3 — канавка | Рис. 6. Прожигание бетона кислородным копьем: 1 — бетон; 2 — копье; 3 — защитный экран; 4 — ручка подачи и вращения копья; 5 — подача кислорода; 6 — подача воздуха с флюсом. |
Для этого мундштук резака направляют к поверхности под углом 15 — 40°. Металл, расположенный вперед кислородной струи, нагревается перемещающимся нагретым шлаком и выдувается из зоны реза. Струю режущего кислорода подают с меньшей скорость чем при разделительной резке, что обеспечивает сгорание лишь поверхностных слоев металл Подобной резкой можно снимать полностью слой ил вырезать канавки, нужные для технологических целей.
Резку кислородным копьем (рис.6) можно выполнять по металлу, бетону или железобетон. Для этого к рукоятке с вентилем для кислород подсоединяют тонкостенную стальную трубку наружным диаметром 20 — 35 мм и подают к месту реза. До начала реза трубку нагревают газовой горелкой или электрической дугой до температуры, при которой происходит воспламенение кислорода.
Затем по трубке к месту реза направляют кислород, который, воспламеняясь, образует копье. Кислородное копье с большим усилием прижимают к нужному месту, прожигая отверстие. В процессе прожигания копью придают возвратно-поступательное и вращательное движение. Образовавшиеся при этом шлаки выдуваются через зазоры, образованные между стенками отверстия и копьем.
Как сделать спартанское копье за 15 долларов или меньше
Поднимите свое обучение на новый уровень с советами по устранению препятствий своими руками от создателей препятствий Спартанца. Получите пошаговые инструкции и разбивку материалов для создания собственного оборудования — и доминируйте в OCR как чемпион.
Препятствие «Бросок копья» может стать одним из самых разрушительных ударов на трассе спартанских гонок. Многие из нас пережили последствия того, что упустили единственный шанс поразить эту цель — лицо, полное бурпи! Знаменитый футбольный тренер Винс Ломбарди сказал об этом лучше всего: « Практика не ведет к совершенству. Только безупречная практика ведет к совершенству. Итак, вам нужны идеальные инструменты для безупречной практики. Самая важная часть практики метания копья — это правильный инструмент. В игру вступают вес, длина, наконечник и длина наконечника (не говоря уже о привязи и расстоянии до цели). Вот как сделать идеальную (читай: точную для расы) версию Spartan Spear.
Связано: 5 самых сложных спартанских препятствий — и как их преодолевать
Что вам понадобится:Материалы для копья:
1-60 дюймовРукоятка грабли ($ 9,48)
Оцинкованные гвозди с шипами размером 1–3 / 8 x 12 дюймов (0,75 доллара США)
1 — Интерьерные проекты 10 унций. Желто-коричневый строительный клей из латекса (1,77 доллара США). Этот материал лучше всего подходит для этого, поскольку он высыхает, обладает эластичными свойствами и не разрушается при использовании копья.
или
1 — Power Grab Express 6 эт. унция. Универсальная трубка для строительного клея (4,68 доллара США)
Инструменты:
* Угловая шлифовальная машина (с отрезным кругом по металлу) OR Ножовка по металлу Сабельная пила OR Ленточная пила OR Болторез (или любой другой инструмент, используемый для резки металла)
* Пистолет для уплотнения (при использовании строительного клея для несжимаемых трубок)
* СИЗ: Защита глаз и ушей при резке металла
* Клещи для захвата или тиски для удержания шипа при снятии головки
* Рулетка
* Дополнительный привязь:
Нейлоновая веревка Paracord 550 длиной 30–5/32 дюйма.Чтобы установить цель для копья на расстоянии 25 футов от «линии забора»
Проушина из нержавеющей стали размером 1–3 / 16 дюйма x шарнирная проушина. Чтобы веревка не заедала.
6 ”- Лента для защиты копья при сверлении отверстия для паракордового троса
1 — Сверло со сверлом ¼ ”
1 — Зажигалка для оплавления концов троса после обрезки до длины
1 — Письменный стол для разметки отверстия перед сверлением
Связано: Как тренироваться для гонки с полосой препятствий
Как сделать спартанское копье
Шаг 1:Найдите и разложите инструменты и материалы, необходимые для изготовления копья
Шаг 2:Закрепите 3/8 дюйма12 дюймов. Оцинкованные гвозди в тисках (зажимы) с головкой гвоздя, легко доступной для резки и снятия с стержня гвоздя
Шаг 3: С соответствующей защитой для ушей и глаз снимите шляпку гвоздя с вала, убедитесь, что лезвие работает безопасно, а в случае угловой шлифовальной машины с отходами металла. Прежде чем брать в руки металл, дайте ему остыть.
Заполнить цилиндрическое отверстие в рукоятке граблей строительным клеем.Для облегчения очистки скотчем с конца ручки граблей, где вы будете добавлять строительный клей, так как клей выльется через край, когда вы добавите шип.
Шаг 5:Вставьте обрезанный конец металлической иглы в цилиндр со строительным клеем и поверните, чтобы он полностью покрылся клеем. Удалите излишки клея и ленты, оставьте на 24 часа перед первым использованием (для достижения наилучших результатов укажите время высыхания клея).
Связано: от идей к курсам распознавания текста: как создаются спартанские препятствия
Как сделать дополнительный шнур: Шаг 1: Отмерьте и отметьте точку 1.5 дюймов вниз от закругленного (без шипа) конца копья. Для достижения наилучшего результата и чистого законченного вида снимите клейкую ленту. С помощью дрели и сверла для дерева диаметром ¼ дюйма проделайте отверстие в валу, используя вашу отметку для справки. Когда закончите, удалите ленту.
Отмерьте и разрежьте веревку Nylon Paracord 550 5/32 дюйма на 1 и 25 дюймов. С помощью зажигалки расплавьте концы веревки, чтобы снова соединиться. Вы можете аккуратно придать расплавленному нейлону острие форму, чтобы обеспечить его закрепление через Копье на следующих этапах.Причина использования Paracord 550 заключается в его исключительной прочности; оболочка веревки заполнена другими веревками меньшего размера, которые имеют номинальную прочность на разрыв 550 фунтов (отсюда и название Paracord 550)
Шаг 3: Пропустите 1-дюймовую секцию Parachord через отверстие, которое вы только что просверлили в своем копье. Отсюда вы будете протягивать одну сторону вашего вертлюга через конец веревки, привязывая ее обратно к себе. Этот шаг предохраняет вашу веревку от наматывания и трудностей при распутывании, поскольку ваше копье вращается, как футбольный мяч в полете.
Привяжите поводок к противоположному концу троса. Вот как Спартанец делает свои копья, и теперь вы тоже можете. Чтобы практиковаться в истинно спартанском стиле, вы должны установить цель на расстоянии 25 футов от того места, откуда вы бросаете (забор, к которому нужно привязать — ваш лучший подход, но проявляйте творческий подход к идеям и знайте, что у вас есть дополнительная длина на поводке, если вы хотите привязать к дереву или чему-то большему).
Заключительный этап:Попрактикуйтесь и НАСЛАЖДАЙТЕСЬ !!!
Купите спартанское снаряжение и получите БЕСПЛАТНУЮ ГОНКУ.Доступны спринты, суперспособности, звери и тройки. Щелкните здесь, чтобы начать делать покупки.
Инструмент для формирования пикета — Превратите квадратную трубу в пикет
Из трубок каких размеров можно формировать пикеты?
Наши инструменты подходят для квадрата минимум 1/2 ″, максимум 1 ″ квадрата. Толщина от 14 [для алюминия] от 16 [для стали] до 18 [для любого материала]. Инструмент настраивается на один размер квадратной трубы и требует сменного пуансона и матрицы при изменении размеров трубы.Некоторые размеры можно использовать с одним и тем же инструментом, см. Таблицу ниже.
Что мне нужно для самостоятельного пикета?
Вам потребуются квадратные трубки, способ обрезать трубку до желаемой длины пикета (или приобрести предварительно отрезанный кусок), наш инструмент для формирования пикета и пресс для привода инструмента.
Из трубок каких размеров можно формировать пикеты?
Наши инструменты подходят для квадрата минимум 1/2 ″, максимум 1 ″ квадрата. От 14 до 18 калибра. Инструмент настраивается на один размер квадратной трубы и требует сменного пуансона и матрицы при изменении размеров трубы.Некоторые размеры можно использовать с одним и тем же инструментом, см. Таблицу ниже.
Датчик размера трубки Используйте приспособление для:
1/2 ″ квадрат 14 ~ 18 1/2 ″
5/8 ″ квадрат 14 ~ 18 3/4 ″
3/4 ″ квадрат 14 ~ 18 3/4 ″
7/8 ″ квадрат 14 ~ 18 1 ″
1 ″ квадрат 14 ~ 18 1 ″
Вы показываете на своем сайте разные фигуры, что мне взять?
Острый (PC75) и радиусный (PC75R) — наши стандартные конструкции. Вы можете купить любой дизайн и позже преобразовать его в другой стиль. Мы предупреждаем, что многие местные строительные нормы и правила могут ограничивать или запрещать использование конструкции с острым концом по соображениям безопасности.Радиусный наконечник — безусловно, наша самая популярная конструкция. Две другие конструкции с выемками по бокам изготавливаются по индивидуальному заказу. Возможно, мы сможем предложить другие дополнительные нестандартные конструкции, поэтому, пожалуйста, отправьте нам по факсу или электронной почте свои идеи!
Сколько ударов нужно, чтобы разбить, обрезать и сформировать пикет?
Нашему инструменту требуется всего один ход пресса, чтобы создать пикет из отрезанной до нужной длины квадратной трубы. Обратите внимание, что во время обрезки кончика наконечника образуется небольшой кусочек обрезка, поэтому вам действительно нужно будет обрезать трубки немного длиннее, чтобы это компенсировать.
У меня нет пресса для приработки ваших инструментов, могу ли я работать с ручным прессом Vogel?
Тоннаж, необходимый для формирования пикетов, превышает то, что может произвести наш ручной пресс. Вам понадобится наш CSP-25-SA, простой гидравлический силовой агрегат. Этот пресс имеет напряжение 110 В, достаточно мал, чтобы поместиться на верстаке, и оснащен педальным переключателем для переключения пресса каждый раз, когда вы готовы сформировать пикет. С монтажным адаптером за 80,00 долларов вы также можете использовать блок питания для работы со всеми инструментами для надрезания, с которыми вы в настоящее время работаете с помощью ручного пресса.
Что мне сделать, чтобы сформировать горизонтальные рельсы в целую панель?
Мы предлагаем три инструмента, которыми можно проткнуть рельсы. Мы предлагаем два инструмента для пробивки каналов (с разной максимальной производительностью) и один инструмент для пробивки труб.
Проспект— За кулисами — Часть восьмая — Копье Зеда
Проспект , фильм, над которым мы работали в 2017 году, занимаясь строительством и отделкой реквизита и декораций, теперь доступен на Netflix в США! Prospect — это научно-фантастический вестерн, полный практических эффектов, в котором Педро Паскаль играет главную роль в шлеме. Он также доступен на Blu-ray, если вам нужна физическая копия! Эта серия постов из 8 частей не содержит спойлеров, поэтому вы можете проверить их все, не опасаясь испортить что-либо, если вы еще не видели фильм!
Одна из худших вещей в работе над фильмом — это то, что иногда никто не видит вашу тяжелую работу — вещи все время остаются на полу. Хотя это не единственное, над чем я работал и не попало на экран, это то, чем я больше всего гордился, что было вырезано, образно и буквально — винтовка Zed’s Spear.Это единственный герой, который мне нужно было сделать, и все это было сделано вручную с нуля! Наш оружейник разработал большую часть (а может и все) энергетическое оружие для проспекта . Он даже сделал большинство из них сам, но мне посчастливилось получить этот. Мне дали эту базовую 3D-модель / план дизайна, дали бюджет и сказали, чтобы она выглядела круто и утилитарно — чтобы соответствовать персонажу и внешнему виду в мире.
На первом этапе был проведен тест с использованием обрезков древесины, чтобы убедиться, что я могу выполнить все фаски и металлические вставки так, как я был уверен, прежде чем разрезать окончательную древесину. Одна вещь, о которой мы, вероятно, недостаточно говорим, — это то, сколько мы делаем макеты и прототипы перед тем, как сделать готовые изделия, которые вы видите, как мы публикуем, но почти всегда в ваших интересах тестировать и прототипировать, терпеть неудачу и учиться, прежде чем вы перейдете к финальному кусок. Как видите, оружие состоит из 6 деревянных кусков шестиугольной формы с металлическими вставками по длине древка. Я делал каждый скос дерева и алюминиевых полос настольной пилой (это шесть продольных разрезов на полосу дерева).
Имея бюджет, который мне был предоставлен, и желание получить экзотический вид, я потратил около 30 минут, пуская слюни над выбором твердых пород дерева в Rockler, прежде чем выбрать (с одобрения арт-директора) фиолетовое сердечное дерево. Слева — лес в моей машине, когда я возвращался в магазин. Справа — все полосы, обрезанные, рифленые и готовые к сборке.
Для лезвий, поскольку это был реквизит героя, а не для косплея, я мог использовать настоящий металл. Для простоты резки и отделки, а также для снижения веса я выбрал.Я вырезал базовые формы спиральной пилой, а затем отшлифовал изгибы на шпиндельной шлифовальной машине, чтобы получить основания лезвий.
После использования ленточной шлифовальной машины для снятия фаски на лезвиях, я склеил лезвия, куски дерева и алюминиевые полоски вместе с помощью клея для дерева и гориллы.
Как только это было сделано, мне впервые пришлось использовать мельницу и вырезать плоские и закругленные части древка и наконечника копья, чтобы они соответствовали дизайну.Изучение нового инструмента, особенно такого мощного и универсального, открыло глаза!
На этом базовое копье было завершено и идеально соответствовало оригинальному дизайну. В качестве копья это уже было довольно грозное оружие. НО, как и большинство оружия на проспекте , это было одновременно энергетическое и холодное оружие. Мне пришлось разобраться в функциональности энергетического оружия. Единственное другое направление, которое я получил, заключалось в том, что на базе должен быть какой-то механизм, который мог бы заряжать оружие кинетической энергией.Остальное было до меня.
Частично проблема заключалась в том, что Зед однорукий, и хотя оружие должно было использоваться одной рукой, оно также должно было быть разработано для двуручного человека. Я остановился на спусковом механизме средней оси вместе с дополнительными захватами возле головки и хвоста вала. Это позволило бы использовать копье правой или левой рукой, под рукой, над рукой и в качестве колющего оружия ближнего боя, быстро меняя положение рук. Он также мог заряжаться и стрелять с одной руки.Кроме того, я хотел, чтобы рукоятки выглядели естественно и органично, а не были просто кожаными обертками на голенище. Я впервые использую Worbla! Я сделал три рукоятки и вставил спусковой крючок и провода под рукоятки, чтобы удерживать их на месте, затем покрасил и протер их.
У меня нет отличных фотографий зарядного механизма, но здесь вы можете его увидеть, плюс мне нравится удивление на лице моего сына, проверяющее его. У основания есть подкладка, соединенная с валом с помощью 5 больших пружин и конденсатор в центре.Идея состоит в том, что копье ударяется о землю, генерируя энергию, которая сохраняется там до тех пор, пока спусковой крючок не будет нажат, и она будет выпущена вниз по древку и из головы.
Вот я на съемочной площадке во время съемок в день, когда должны были сниматься сцены с Зедом и моим копьем. Режиссер не был уверен, нравится ли ему больше дизайн копья, и считал, что это не совсем вписывается в эстетику фильма. Он попросил меня вернуться в фургон и добавить еще несколько бонусов, чтобы попытаться сделать его более технологичным / очевидно энергетическим оружием.
Используя то, что я смог выудить из грузовика, я наложил на копье еще несколько вопиющих электронных устройств, но этого ему все равно было недостаточно. У режиссера была идея — давайте просто отрежем наконечник копья и сделаем из него древковое ружье — примитивно, но все же экзотично. В удивительном даре щедрости (вероятно, из-за того, что мое лицо отразилось на моем лице от такого предложения), он сказал, что позволит мне решить, отрубим ли мы острие копья. Я мог оставить копье в покое, гарантируя, что оно не будет использовано (сцена НЕ ТРЕБУЕТСЯ, чтобы у Зеда было какое-то конкретное оружие), или я мог отрубить его, и он использовал его в тот же день во время съемок.
Убить своих любимых всегда будет труднее всего. Поверьте мне. Это разбило мне сердце, но, в конце концов, я хотел, чтобы в фильме было оружие моего героя. Лучшим инструментом, который у меня был в грузовике, был лобзик, поэтому, поставив копье под ногу на воротах грузовика, я глубоко вздохнул и отрубил голову.
И это последняя форма оружия Зеда, которую фактически использовали и сняли в тот день. Хотя он не был полностью вырезан из фильма, сцена, в которой он находится, довольно темная и полная дыма, так что вы не можете ее увидеть, но я знаю, что она там!
Я должен был забрать домой острие в тот день.После того, как он был удален и не использовался на экране, это был просто еще один кусок мусора, но я был слишком горд им, чтобы отправить его в мусорное ведро истории. Он благополучно поселился в нашем доме. А затем, через несколько месяцев после того, как фильм был закончен, мне подарили остальное копье. Я не могу объяснить, как много для меня значило иметь копье. Но я решил восстановить копье в его первоначальном законченном виде.
Я удалил все грилы последней минуты. Мне пришлось серьезно отремонтировать базовую площадку (актеры, особенно когда задействованы трюки, могут плохо справляться с реквизитом — не ждите, что вещи выживут!).Я вставил небольшой металлический стержень в конец отрезанного копья и затем склеил его вместе с наконечником копья. Я размышлял, пытаясь залатать и отремонтировать разрезанный алюминий и дерево, а также попытаться покрасить и смешать их, чтобы они выглядели идеально. Я уверена, что могла бы сделать его безупречным, но потом мне пришла идея обвязать шов тканью. Я полностью заполнил разрез и даже добавил немного дополнительного армирования, так как он не должен был выглядеть идеально, а затем обработал и потрепал кусок ткани, который у меня был, который был близок к ткани костюма Зеда, и привязал его к сварному шву. .
Мы надеемся, что вам понравилась восьмая и последняя часть нашей серии «За кадром» Prospect . Если еще нет, смотрите проспект !
Если вы хотите помочь нам продолжать создавать отличные материалы и контент, вы можете поддержать нас, сделав пожертвование через нашу ko-fi или сделав покупки на нашей странице Amazon, где мы перечисляем все наши любимые и наиболее часто используемые инструменты и принадлежности! И, как всегда, мы готовы заняться дизайном и изготовлением декораций, декораций, костюмов.
Ассоциация подводных аквалангистов и рыболовов
24 июня Рубящие копья
Отправлено в 14:00 в оборудовании по USFA Зачем кому-то рубить копьем? У вас когда-нибудь отламывался наконечник в отверстии для дискеты? Согнул копье по флоперу на длинном ружье? Что ж, теперь вы сможете переработать эти старые куски стали для другого оружия и, надеюсь, еще одной рыбы.Вы также можете добавить хлыстики к копьям, например, копья-бабочки, или поменять хлысты сверху вниз. Какой бы ни была причина, по которой вам нужно рубить копье, вот как это сделать.
Во-первых, копья из пружинной стали НАМНОГО сложнее сверлить и обрабатывать, чем копья из пружинной нержавеющей стали. Но я не встречал копья, которое бы я никогда не пробил… в конце концов. Особенно прочными являются копья из пружинной стали фридайверов и копья из пружинной стали Rabitech. Копья Роба Аллена достаточно средние для сверления, Riffe так же просты, а туфы Torres похожи на резку масла.
Первая часть рубки копья — это отрубание флоппера. Это может быть немного сложно в зависимости от производителя. Копья Riffe практически невозможны, и вы также можете купить новый флоппер! Вот копье фридайвера в тисках, готовое к удалению флоппера.
Теперь все, что вам нужно сделать, это отпилить заклепку заподлицо с диском и выбить ее кернером. Это не всегда работает, поэтому вам, возможно, придется перевернуть его, подпилить с другой стороны и таким образом вырубить.В любом случае, после небольшого набивания, вы получите копье без флопа, например:
Теперь следующая часть сверлит копье. Если вы снимаете 10 см от копья, очевидно, поставьте красивую большую ручку на 10 см от конца. Теперь возьмите флоппер и поместите его примерно в 1 см от этой отметки. Где находится конец флоппера, это то место, где вы хотите сделать свою дырочку. Кончик всегда должен быть немного больше, чем длина флоппера.
Итак, вы не знаете, где вы хотите просверлить отверстие, как вы собираетесь просверливать эти закаленные биты из пружинной стали? Ну, первый шаг — это буровая кондукторка.Все это удерживает копье на месте винтом из нержавеющей стали, и у него есть небольшие закаленные вставки, чтобы сверло удерживалось в центре копья. У вас должна быть возможность купить что-то подобное в магазине для дайвинга, если у вас есть токарный станок, вы можете подделать его в обеденный перерыв. Я использовал кусочки серебряной стали для вставок, выполнил всю механическую обработку, а затем закалил их. У меня есть два размера отверстия: 3/32 дюйма и 7/64 дюйма. Я использую меньшее для 7-миллиметровых копий, а большее для 8-миллиметровых копий.
Хватит джига, вот как можно разметить копье.Поместите отметку там, где должно быть отверстие на маленьком отверстии на приспособлении, и отметьте еще одну линию, чтобы, когда вы протолкнете копье в кишки, вы знали, где остановиться!
А теперь не затягивайте копье в кондукторе. Возможно, вы захотите выровнять копье так, чтобы ваш флопер двигался прямо вверх и вниз (да, у меня раньше они выходили под углом 90 °!). задняя часть копья находится вертикально, ЗАТЕМ затяните приспособление так, чтобы отверстие для флоппера было вверх и вниз.Кажется очевидным, но я делал это несколько раз!
Теперь, чтобы просверлить эти копья, я использую сверло Formula Cobalt диаметром 3/32 дюйма или 7/64 дюйма. Вам также понадобится режущий состав. Вы можете обойтись без копий из нержавеющей стали, но с копьями из пружинной стали забудьте об этом. Вот что я использую, «Rocol» — паста коричневого цвета, как какашка, но это работает.
Еще одно соединение, которое можно использовать, — «Моликут», но это жидкое вещество. Любой из них будет работать нормально и облегчит сверление. Поэтому установите сверло в сверлильный станок и убедитесь, что вы нанесли на сверло хороший мазок режущего состава.Используйте на дрели минимально возможную скорость. Не поддавайтесь соблазну: «Быстрее — значит быстрее закончить!» Вы никуда не денетесь. Если вы хотите использовать ручную дрель, вы можете попробовать, но вы, вероятно, защелкните несколько сверл. Сверлильный станок — это способ справиться с сильным нисходящим давлением и помнить МЕДЛЕННО!
Как только закончите, выньте копье из джига и альта! Если вы не можете пройти сквозь копье, что случается с нечетным копьем фридайвера, попробуйте новое сверло. Если это не сработает, вам, возможно, придется нагреть область для сверления вишнево-красного цвета, затем дать ей остыть, а затем сверлить.После просверливания верните закалку в копье, как показано ниже. Делайте это только в крайнем случае.
Вы должны пройтись по просверленному отверстию большим сверлом, чтобы как бы утопить его, чтобы удалить заусенцы. Следующая часть всего процесса — снова надеть наконечник на копье. К счастью, с копьями из пружинной стали их можно повторно закалить, что означает УГЛОВАЯ ШЛИФОВКА. Вам не нужно беспокоиться о том, чтобы он раскалился, потому что это все равно произойдет в будущем. Так что сходите с ума и наденьте тройной разрез на кончик.Работайте по одному краю за раз, чтобы получить основную форму и правильные углы. Через несколько минут вы получите такой хороший совет. Вы будете становиться все лучше и лучше, выполняя эти тройные удары, поэтому, если первая пара окажется немного менее привлекательной, чем свекровь, не волнуйтесь, просто потренируйтесь на старых копьях. Через некоторое время напильник действительно не понадобится, но он поможет немного очистить наконечник.
Примечание; Работайте шлифовальной машиной только на копьях из пружинной стали, на копьях из нержавеющей стали старайтесь не обесцветить или не покраснеть, потому что вы не можете вернуть им закалку.Это займет немного больше времени, но опять же, они не такие твердые, как копья из пружинной стали.
Теперь вернем закалку в кончик копья, чтобы он не стал мягким, как масло. Просто вырвите эту паяльную лампу из всех созданных вами приспособлений и нагрейте кончик вишнево-красного цвета. Когда все станет горячим, переложите его в банку с маслом. Подойдет любое масло; Я использовал старые вещи из машины, так что это не критично! Не используйте воду, иначе она остынет слишком быстро, и копье станет слишком хрупким. Немного дыма и запаха здесь — это нормально.
Теперь мы вернулись туда, где мы почти пустили копье без флопа. Закрепление флопперов — это само по себе искусство, которое нужно практиковать или демонстрировать. Что касается булавки для дискеты, я считаю, что защелка — это настоящее удовольствие. Не поддавайтесь соблазну использовать гвозди или что-то еще, булавка должна быть довольно твердой из нержавеющей стали. В некоторых марках копий используется 316 штифтов, и они очень быстро забиваются, так как штифт теряет форму. Защелкивающиеся зажимы и зажимы типа «акула» изготовлены из высокопрочной пружинной нержавеющей стали и отлично справляются со своей задачей, с ними никогда не было проблем. Вы также можете использовать подходящие штифты для флоппера из магазина дайвинга. Защелкивающиеся зажимы идеально подходят для отверстий 3/32 дюйма, большие зажимы типа «акула» подходят для отверстий 7/64 дюйма. Используйте несколько болторезных станков, чтобы отрезать немного шире флоппера примерно на 2,5 мм. Также убедитесь, что флоппер находится внизу (да, это тоже случалось со мной раньше!)
Теперь вам понадобится наковальня определенного описания, тисков работает нормально, но у меня есть небольшой железнодорожный путь, который идеально подходит для этого . Используя молоток с шариковой головкой, аккуратно заклепайте одну сторону.
Не бейте его слишком сильно и постарайтесь сделать его как можно шире и шире. Повторите для другой стороны. Вероятно, у вас довольно жесткий дискет или что-то с ним не так. Не волнуйтесь, это можно исправить! Для жесткого флоппера обычно достаточно вдавить в него немного 8 мм нержавеющей стали, чтобы сделать его шире:
Это должно заставить флоппер открываться и закрываться волей-неволей. Если вы не попробуете 10-миллиметровую нержавеющую сталь или вытащите плоскогубцы и пошевелите ею, вы сможете выбрать точки трения, делающие ее жесткой.Итак, предполагая, что ваш флоппер хороший и свободный, осторожно постучите по этой области молотком:
Это, надеюсь, заставит флоппер раскрыться примерно на 30 °, а затем заблокируется до конца.
Лучший способ узнать, правильно ли настроен флоппер, — это вставить копье в ружье и перевернуть его так, чтобы флоппер сел на копье. Резко постучите по пистолету ладонью, и флоппер должен полностью раскрыться и остаться на месте. Вот каким должен быть идеальный флоппер.
Итак, теперь у вас есть отлично работающее копье, способное поймать еще несколько рыб.Это особенно удобно, если у вас есть оружие той же марки, и вы сгибаете копье на своем 1400, а затем просто срезаете его для получения запасного 900-го. Вы также можете надеть на копья два флоппера, если хотите. Кроме того, теперь вы, ребята, должны иметь возможность надевать флоперы на стержни с резьбой, чтобы у вас могли быть крутые копья с прыгунами или очки для соревнований!
Как это:
Нравится Загрузка . ..
Уловок: создание самодельных наконечников копий
У всех нас есть один друг.Каждый раз, когда вы ведете его в лес, первое, что он делает, это выламывает нож и хватает палку, чтобы заточить ее в «копье». Когда вы спрашиваете его, что он делает, он обычно отвечает: «Это на случай, если что-то выскочит на нас» или «Чтобы я мог зарезать медведя». Хотя эффективность такого копья сомнительна, нет никаких сомнений в том, что оно дает вашему другу чувство безопасности — и не зря.
Копье, пожалуй, первое рукотворное оружие; примеры заостренных палочек датируются сотнями тысяч лет.Сегодня копья столь же эффективны, как и во времена первобытного человека. Практичность и предназначение различных типов копий не изменились, хотя способ их представления с годами изменился. Мы провели исследование и разработали шесть различных типов заостренных палочек, которые можно использовать для защиты и сбора пищи.
Материалы
Прежде чем вы начнете, вам необходимо иметь базовые представления о древесине, с которой вы будете работать. Древесину можно разделить на две категории: зеленая или выдержанная, живая или мертвая, соответственно.Вы можете работать с любым из них, чтобы сделать свое копье, но поймите, что из зеленого дерева будет легче вырезать. Компромисс — водный вес и долговечность. Часть этого веса и прочности можно изменить закалкой огнем, но обычно это делается только до кончика.
Подпишитесь сегодня и сэкономьте!
Закаленное дерево будет труднее вырезать, так как оно будет более твердым, и оно также будет менее гибким. Также учтите, какую древесину вы используете. Для изготовления копий ищите хорошие лиственные породы (не вечнозеленые).Кроме того, помните, что слишком тонкий стержень легко сломается, а слишком толстый потребует слишком много резьбы, чтобы уменьшить его до тонкой точки.
Если бы у нас был выбор и время, мы бы выбрали необработанную древесину, которую можно было бы упрочнить, оставив при этом некоторую гибкость в шахте, чтобы предотвратить треск. Мы не будем снимать с вала всю кору, поскольку дополнительная текстура может служить рукояткой. Тем не менее, мы удалим все узлы и выступы, чтобы не повредить руки во время работы и не снизить скорость доставки, если она поскользнется в нашей руке.
Копье / Javelin
То, что тот друг, который у всех нас, вероятно, делает, когда точит палку, является действительно грубой версией копья или дротика. Как указывалось ранее, нет точной даты, когда первобытный человек впервые заострил палки в инструменте или оружии, но Clacton Spear, заостренное деревянное острие копья, выставлено в лондонском музее и насчитывает 400 000 лет. Со временем формы развивались и менялись по длине, толщине и используемому древесному материалу.
При изготовлении однонаправленного копья начните с больших сокращений мощности, чтобы удалить значительное количество материала при вращении наконечника копья.Четыре-шесть хороших отключений электроэнергии дадут вам грубую подсказку. Переместите лезвие к плечам, созданным там, где встречаются электрические удары, и сбейте их. Продолжайте снимать плечи, пока голова копья не станет круглой. В зависимости от породы дерева вы можете использовать заболонь («пятно» в центре древесины разной окраски) в качестве центральной точки. Продолжайте удалять кору вниз по валу до точки, где вы хотите, чтобы проникновение прекратилось.
Копья использовались для боя и защиты во многих цивилизациях.Со временем каменные, а затем стальные головки заменили заостренные палки. По сей день стальные копья все еще используются при охоте на кабанов и в руках коренных жителей Африки.
Прямой одинарный зазубрины
Неизвестно, когда к копью была добавлена инновация в виде зазубрины, но, вероятно, это было вдохновлено примерами из природы. У скатов, например, есть колючий шип, а у некоторых птичьи когти тоже есть. Где бы он ни был, зазубрины усиливают удерживающие свойства копий, зацепляясь за плоть и кость жертвы, не позволяя ей ускользнуть.
Carving зубца требуют знаний стоп разреза. Этот разрез проходит перпендикулярно древку копья, а его глубина зависит от размера зазубрины. Если у вас есть швейцарский армейский нож или мультитул с пилой, это значительно упростит процесс. После того, как на стержне будет вырезан упор, возьмите лезвие и сделайте рез к нему в направлении острия. Упорный разрез предотвратит прорезание ножом его, и зазубрина начнет принимать форму. На этом этапе вы можете оставить острие с выступом или подрезать его, чтобы получился крючок.
Многие охотничьи копья с Филиппин были изготовлены таким образом, и они очень разнообразны на более чем 7600 островах. Колючки можно создать из дерева, кости и стали. Оптимальный размер, форма и количество зазубрин в значительной степени определяется добычей, на которую охотятся.
Вверху: автор использует естественную вилку в древке копья в качестве опоры для большого пальца. Это значительно повышает комфорт и увеличивает силу, которую можно приложить.
Гарпун со съемной головкой
Копье с зазубринами значительно увеличивает шансы предотвратить побег жертвы. Если вам повезет или вы достаточно умелы, чтобы пронзить животное, вы не хотите отпускать его. Однако иногда отпускание — лучший вариант. Возьмем, к примеру, индейцев Туле, которые охотились на гренландских млекопитающих с байдарок. Мы не можем себе представить, насколько злым и жестоким становится тюлень или кит, когда его утыкают острой палкой. Вот почему была создана технология гарпуна. Гарпун — это причина, по которой Туле процветали в Северной Атлантике, а отсутствие технологии гарпуна, вероятно, является причиной того, что норвежцы отказались от своих попыток поселиться в Гренландии.
Чтобы создать гарпун, вам нужно сделать три составляющих части: острие гарпуна, древко гарпуна и прочную веревку. Наконечник закреплен на стержне гарпуна с трением. Этого можно достичь, заклинив его между щелью в стержне или полостью, сделанной в стержне, в которую стержень меньшего диаметра наконечника гарпуна скользит, как пробка в бутылку. Наконечник может быть прикреплен к древку с помощью веревки, или древко может быть «одноразовым» и вырываться, когда только гарпун застревает в добыче, а веревка находится в руках охотника, что очень похоже на рыбалку на удочку. Полость создается острием лезвия и требует относительно толстого гарпунного древка.
Ознакомьтесь с историческими примерами гарпунов из китобойного промысла Новой Англии, и вы увидите главные валы размером с флагшток. Гарпун с клиньями изготовить намного проще, хотя ему не хватает массы, как у полого гарпунного древка. Пример, который мы создали для этой статьи, сделан из дерева в демонстрационных целях. На самом деле, кость или сталь были бы лучшим вариантом для гарпуна.
Гарпун со съемной головкой следует использовать на животных, которые, вероятно, будут метаться при ударе.Ремешок для веревки позволит вам освободить место и позволить ему утомиться, когда вы сокращаете расстояние и отправляете его другими способами.
Расколотое копье
Двухзубое расколотое копье для рыбной ловли
Большие копья работают с крупными животными, но с крупными животными больше шансов нанести травму охотнику. Меньшую дичь не так легко проткнуть деревянными наконечниками; шкура и мех могут замедлить и ограничить проникновение наконечника копья. Нечестные изображения копья, брошенного через маленькую рыбу, подвешенную в воде, являются медвежьей услугой и повторяются снова и снова в фильмах и телешоу.Рыбаки скажут вам, что даже на заостренный металлический крючок ловить мелкую рыбу сложно. Деревянные наконечники не такие тонкие, острые и прочные, а плавающую рыбу не поддерживают так, как если бы ее держали в руке, как наживку. Лучшим вариантом для протыкания копья является приколоть копья.
Базовое копье-булавка изготавливается легко. Отрежьте древко копья шириной 1 дюйм до нужной длины. В идеале он должен быть такого же роста, как охотник, если не выше. Более компактные «ручные копья» могут быть полезны, если вы преследуете добычу, которая живет в тесноте и под камнями.После обрезки нужной длины оберните стержень веревкой, лентой или другим плотным связывающим материалом на расстоянии примерно 8–12 дюймов от более толстого конца.
Если вы оборачиваете кусок зеленого дерева, вам, скорее всего, придется перематывать его заново, так как древесина сохнет, усаживается и переплет становится неплотным. Используйте более толстый конец, чтобы при закреплении выдвинуть как можно больше массы. После связывания удалите кору от более толстого конца до кончика. В этот момент используйте лезвие с помощью деревянной дубинки, чтобы разрезать толстый конец до переплета.Заедание предотвратит перемещение шпагата слишком далеко вниз по валу. Сделайте скос на концах вилок, чтобы они не раскололись, и поместите в вилку небольшую веточку или резной клин, чтобы она оставалась открытой.
Варианты этого раздвоенного копья включают использование шипов боярышника в качестве зазубрин или тяжелых ежевичных колючек, прикрепленных смолой или тонким шпагатом. Копье используется для того, чтобы прижать добычу к земле, где ее можно поднять руками или отправить другим инструментом.
Копье с четырьмя зубцами-штифтами
Копье с четырьмя зубцами для рыбной ловли, мелких рептилий или мелкой дичи
Копье с раздвоенным наконечником позволяет приколоть животное между двумя точками.С помощью пары дополнительных шагов легко превратить копье с раздвоенным наконечником в копье с четырьмя зубцами, увеличивая ваши шансы заклинивать животное. Выполните те же действия, что и для копья с разрезным наконечником, пока древко не разделится пополам. В этот момент возьмите лезвие и поверните его на 90 градусов на разделенном кончике, чтобы следующий разделитель прошел перпендикулярно первому.
После того, как вы разделите наконечник до обернутой части, при этом обе трещины будут в древесине, сожмите наконечник и заострите его до нужной точки.Затем расстелите его парой веточек. Необязательный шаг — зазубриться на каждом из четырех зубцов. Этот тип копья-булавки немного менее прочен, чем копье с одним разрезом, но он очень эффективен против мелких рептилий и земноводных. Если четыре зубца заострить до конца и использовать против животного с тонкой кожей, это создаст четыре отдельных канала для ран.
Gaff Hook
Этот следующий не обязательно является копьем, но он работает на конце длинной древко и использует те же навыки, что и некоторые из ранее упомянутых советов.Крюк багра отличается от традиционного копья — вместо того, чтобы выталкивать его наружу и от вас, потяните его обратно на себя. Коммерческий рыбак использует крючок багра, когда крупная дичь приближается к их лодкам, и этот инструмент отлично подходит для ловли рыбы и диких растений, которые находятся вне досягаемости.
Самый важный материал, необходимый для создания крюка багра, — это вилка, встречающаяся в природе на дереве. Если вилка слишком широкая, ее можно крепче привязать и обработать паром или высушить в более параллельные крюк и стержень багра.Раздвоенную ветку дерева можно разрезать по месту соединения, сохранив две разветвленные ветви. Отрежьте одну ветку примерно на расстоянии 6–12 дюймов от стыка, оставив кусок дерева в форме буквы «J».
Иногда при росте ветвей образуются три ветви, исходящие из одного выступа, и вы можете использовать две из трех ветвей в качестве узловых точек. Иногда крючок будет работать так, как задумано, а в других случаях вместо этого он будет совать. В любом случае цель состоит в том, чтобы принести вам добычу или урожай.
Вверху: Crawford Survival Staff — современное многоцелевое копье. Доступные насадки для копий включают одинарное лезвие, тройной зубец и крюк-багор.
Варианты самодельных голов
Помимо резных деревянных наконечников, выживший может изготовить несколько импровизированных голов из окружающих ресурсов. Ранний человек перешел от деревянных наконечников к камню, а затем к бронзе и стали. Даже мусор, который вы найдете в обычном походе, можно превратить в функциональные импровизированные наконечники для копий. Вот три идеи для наконечников копий, которые вы легко сможете создать, проявив изобретательность и практику.
Крышка металлической банки: Крышка металлической банки, в идеале стальная, а не алюминиевая, отлично подходит в качестве наконечников копий и стрел. Сложите и сломайте металл под углом, создав острие. Лезвие можно заточить или зазубрить с помощью камня и / или мультитула. Вставьте его между разрезанной веткой и привяжите на месте.
Вешалки: Лучшие вешалки для импровизированных голов — это тяжелые металлические химчистки, которые используют для подвешивания брюк. Используйте мультитул, чтобы разрезать ангар на 12-дюймовые отрезки.Используя один камень в качестве наковальни, а другой — в качестве молотка, разбейте концы отрезанных металлических стержней. Затем отрежьте кусок, который вы ударили, таким же образом, как крышка металлической банки, чтобы сформировать острие. Привяжите три или более металлических стержня к концу шеста, чтобы использовать его как копье с раздвоенным наконечником.
Пластмасса: Пластмасса может быть очень хрупкой, но ее также можно остро заточить и использовать с большой эффективностью против лягушек и рептилий с тонкой кожей. Даже полиэтиленовую пленку и пакеты можно расплавить и придать им очень острые концы.Стоит только взглянуть на некоторые хитрые тюремные хвостовики, которые изготавливаются, когда другого оружия нет в наличии. Необходимость — мать всех изобретений.
Процесс огневой закалки
Огнестойкая закалка — это процесс быстрого удаления влаги из сырого дерева, чтобы сделать его достаточно твердым для использования в качестве инструмента или оружия. Самый простой способ закалить деревянный наконечник копья — это положить его в золу (а не в угли) раскаленного костра. Внутри пепла дерево не может гореть, так как присутствует тепло, но нет кислорода.Тепло вытягивает влагу из дерева по мере его высыхания.
Закаленная от огня древесина имеет гораздо более отчетливый звук, чем зеленая необработанная древесина, если постучать тыльной стороной ножа. Мы используем закаленный в огне бук и хмель из граба, чтобы создать палки для копания и инструменты для выкапывания тесла, которые выдержали годы жестокого обращения с каменистой почвой. Наконечники копья могут выиграть от процесса закалки огнем, и если время и ресурсы позволяют, этот шаг стоит затраченных усилий.
Заключение
Настоящее копье — это гораздо больше, чем заостренная палка.Научитесь создавать различные наконечники и техники, чтобы получить максимальную отдачу от ваших затрат времени и энергии. Не делайте что-то просто «на случай, если вам придется что-то колоть». Сделайте специальное копье, которое будет действовать именно так, как вам нужно.
Подготовьтесь сейчас:
Военный противогаз 249,95 долларов mirasafety.com Ножи EDC от 7,99 долларов smkw.com Раскрытие информации: эти ссылки являются партнерскими ссылками. Caribou Media Group получает комиссию от соответствующих покупок. Спасибо!
ОСТАВАЙТЕСЬ В БЕЗОПАСНОСТИ: Загрузите бесплатную копию
OFFGRID Outbreak Issue В выпуске 12, Offgrid Magazine внимательно изучил, что вам следует знать в случае вирусной вспышки.Теперь мы предлагаем бесплатную цифровую копию проблемы OffGrid Outbreak при подписке на электронную рассылку OffGrid. Зарегистрируйтесь и получите бесплатную цифровую копию Нажмите, чтобы загрузить!Автор Кевин Эстела
Как выковать наконечник копья
Рекомендации и мысли по поводу наконечника копья — Я оставил наконечник так, как он вышел из кузницы и наковальни. Мне нравится средневековый почерневший вид. Но вы можете закончить свое копье с помощью точильного станка, ленточной шлифовальной машины или бумаги эмори, если вы предпочитаете серебро и блестящую. А если вам нужно более удобное копье, которое можно было бы использовать постоянно и надежно, я рекомендую вам использовать сталь с более высоким содержанием углерода. Но если вы начинающий кузнец и хотите простой проект, который даст вам возможность использовать различные методы кузнечного дела, тогда хорошим выбором будет низкоуглеродистая или мягкая сталь, которую легко обрабатывать и переделывать.
Обзор четырех шагов:
1.Сначала мы формируем талию в стальном куске, уменьшая ширину стали примерно на одну треть.
2. Формируем короткий конец стали в форме рыбьего хвоста
3. Формируем гнездо копья
4. Формируем клинок копья
Начнем с куска простой стали, который вы можете купить в любом магазине товаров для дома. Это плоский стальной пруток шириной 2 дюйма, толщиной 1/8 дюйма и длиной 48 дюймов. Мне это обошлось в 14 долларов.
Приступим к покупке, отрезав кусок стали. Я вырезал кусок длиной восемнадцать дюймов. Вы можете варьировать эту длину в зависимости от размера копья, которое вам нужно. По мере прохождения обучения вы поймете, как может измениться размер.
Хорошо, при кузнечном деле важно знать, если вы никогда ничего не делали, заключается в том, что вы нагреваете только части стали за раз и обрабатываете эти части.Это большую часть времени. Итак, мы начнем с нагрева нашей стали примерно здесь, на 1/3 расстояния от одного конца. И мы сделаем здесь свой первый шаг.
Хорошо! Это почти правильно. Немного больше.
Мы собираемся ввести этот кусок стали, чтобы сформировать фигуру в виде песочных часов.Для этого используем рог наковальни. Для этого потребуется многократный нагрев.
По мере того, как он начинает принимать форму от повторяющихся нагревов и ударов, я переключаюсь на молот меньшего размера, чтобы получить больше контроля.
По мере того, как вы создаете форму песочных часов, полоса будет искажаться и скручиваться.Используйте поверхность наковальни, чтобы снова выпрямить ее. Это нормальная часть процесса. Поскольку это наконечник копья, который мы делаем, важно, чтобы все оставалось точным и прямым.
Хорошо, выглядит отлично. Это форма песочных часов, которую мы ищем. Он красивый и симметричный. Шаг первый завершен.
Перейдем к шагу два
Посмотрите видеоинструкцию по этому проекту здесь:
Не могли бы вы пожертвовать 1 доллар в поддержку моей работы? Paypal делает это очень просто и безопасно.Щелкните здесь, чтобы пожертвовать 1 доллар — Каждый маленький кусочек помогает Уиллу продолжать создавать отличные учебные пособия и проекты. Спасибо!
Европейское копье холодного оружия —
Европейское копье — яркий пример эффективной и простой конструкции. Это просто правильно сделанное копье. Его дизайн очень мало изменился с бронзового века. Совершенная простота этого дизайна сделала его вневременной классикой. Каждый дюйм этого высококачественного инструмента для охоты и боя вопит о совершенстве.От полностью заточенного обоюдоострого лезвия до рукояти из американского ясеня, окрашенного в ореховый орех, — это прекрасное универсальное копье, которое займет почетное место в любой коллекции.
Мини-кузница Whitlox на древесном топливе — Кузница Whitlox на древесном топливе предназначена для использования необработанной древесины или древесного угля в качестве топлива для кузнечного дела. Форма канавки позволяет древесине наверху запекаться и опускаться в зону интенсивного нагрева в нижней части V. Корпус Mini Forge изготовлен из стали 11-го калибра и является чрезвычайно прочным.Kaowool (ватин из минерального волокна) защищает корпус кузницы от тепла и истирания, а огнеупорный кирпич обеспечивает дополнительную изоляцию и защиту. Требуется сборка. ПРИМЕЧАНИЕ: вентилятор в комплект не входит.
Вам нравится создавать проекты и заниматься различными хобби?
Подпишитесь на мою бесплатную рассылку новостей. Я регулярно сообщаю вам новости о хобби и проектах, которые вы можете реализовать.это совершенно бесплатно, и я никому не передаю вашу электронную почту.
Металлическое копье короля — Dragon Quest Wiki
Самое мощное копье. Способен проникать практически в любой материал.(Описание при выборе Копья Металлического короля в PS2 Dragon Quest VIII .

Металлическое королевское копье — повторяющееся оружие в серии Dragon Quest .Часто это одно из самых мощных копий в игре, а навык Multithrust означает, что это идеальный выбор для рубки металлических слизней. Наконечник копья украшен эмблемой Металлического короля слизи.
Появления [править]
Dragon Quest VIII: Путешествие проклятого короля [править]Металлическое королевское копье находится в конце Драговского Пути и имеет бонус атаки +120. Его можно продать за 24000 золотых монет или превратить в бумеранг с металлическим крылом, если смешать с бумерангом с крылом Бритвы в алхимическом горшке.Как и все оружие из металлической слизи, оно наносит 1-2 повреждения шарам.
- Начиная с версии игры для смартфонов, стало возможно превратить бумеранг с металлическим крылом обратно в копье в алхимическом горшке, объединив его со священным копьем. В версии для Nintendo 3DS второе металлическое королевское копье можно найти в Memories Lane, что позволяет игроку оставить одно и использовать другое, чтобы сделать металлический бумеранг крыла, если они того пожелают.
★★★★ ☆ |
+136 |
Паладины, Священники, Воины, Всеобщие копейщики |
НЕТ |
30 000 |
Великолепная рама с копьями, обладающая силой металлических королевских слизней. |
Рецепт: Копье жидкой слизи x 1, Орихалк x 1, Корона слизи x 1 1 ~ 2 урона металлическим слизням |
★★★★★ |
+221 (+231, +241, +251) |
+ 3% |
+ 12% |
Расплавленные глобулы x1, Корона слизи x1, Денсиниум x1, Красное дерево x2 |
Джейд, Серена |
НЕТ |
15 000 |
Великолепное копье, которое может разрезать металлических монстров и бесконечно очаровывать всех видов слизней.![]() |
+1 к урону металлическим слизням |
Руководство по ковке копья — это книга Making Things with Metal Kings , которая является наградой за изготовление 110 мини-медалей в L’Académie de Notre Maitre des Médailles.
Dragon Quest Heroes [править]Металлическое королевское копье имеет бонус атаки +126. Это самое сильное оружие Кирилла, и его можно получить, победив ветерана мрачного голема.
Dragon Quest Heroes II [править]Металлическое королевское копье получается после обработки 120 медалей.Он имеет бонус атаки +170.
Галерея [править]
Металлическое королевское копье из Dragon Quest IX
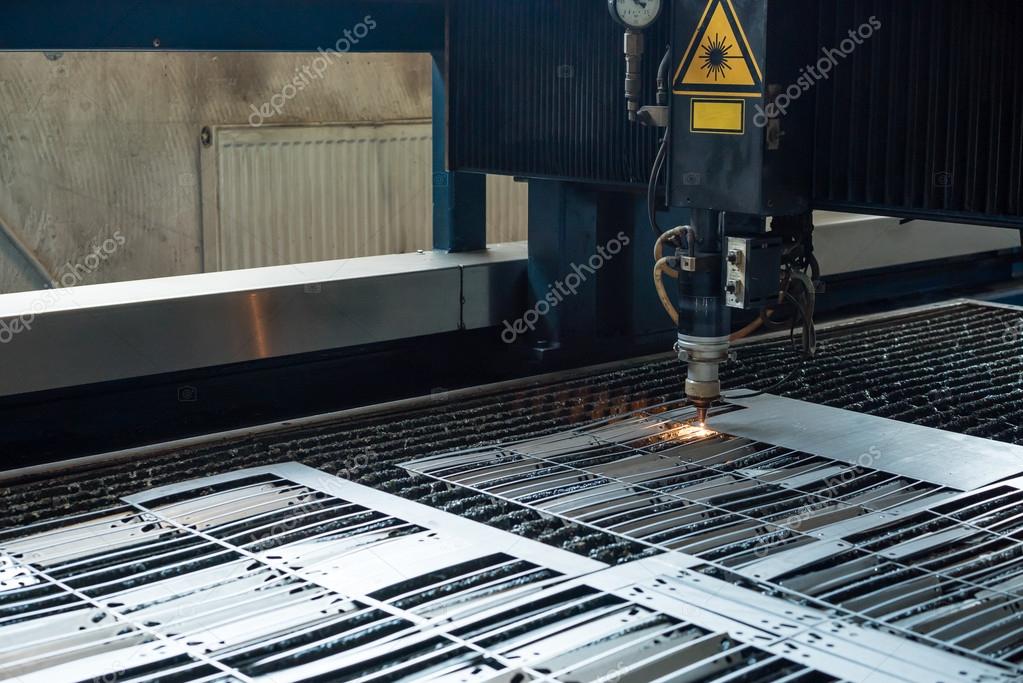