Сварка металлоконструкций вертикального резервуара
Версия для печати
18.1 Общие требования
Требования настоящего раздела распространяются на сварку конструкций резервуаров при изготовлении и монтаже.
18.1.1. Технологические процессы заводской и монтажной сварки должны обеспечивать получение сварных соединений, в полной мере удовлетворяющих требованиям проекта КМ по всему комплексу физико-механических характеристик и геометрических параметров, а также по предельным размерам и видам дефектов, допускаемых настоящим Стандартом.
18.1.2. Заводскую сварку резервуарных конструкций следует выполнять в соответствии с утвержденным технологическим процессом (процедурами), в котором должны быть предусмотрены:
— требования к форме и подготовке кромок деталей, подлежащих сварке;
— способы и режимы сварки, сварочные материалы, а также последовательность выполнения технологических операций;
— конкретные указания по закреплению деталей перед сваркой;
— мероприятия, исключающие образование прожогов, смещение шва от его оси на величину более 2 мм для толщины деталей до 10 мм и на величину более 3 мм для толщины деталей свыше 10 мм;
— мероприятия, направленные на снижение сварочных деформаций.
18.1.3. Монтажную сварку резервуарных конструкций следует выполнять в соответствии с указаниями ППР, в котором должны быть предусмотрены:
— наиболее эффективные способы сварки монтажных соединений с учетом их пространственного положения;
— сварочные материалы, удовлетворяющие требованиям проекта КМ по уровню механических свойств;
— требуемая форма подготовки кромок монтируемых элементов под сварку;
— последовательность сварки и порядок выполнения каждого шва, обеспечивающих минимальные деформации и перемещения свариваемых элементов;
— режимы и указания по технике сварки, которые должны обеспечить необходимый уровень механических свойств сварных соединений, а также получение требуемых структур металла шва и околошовных зон;
— необходимая технологическая оснастка и оборудование для выполнения сварных соединений;
— допускаемая температура металла, при которой возможна сварка соединений без их подогрева, а также допускаемая скорость ветра в зоне сварки;
— указания по технологии производства сварочных работ в зимних условиях (если это предусматривается в соответствии с графиком работ).
18.1.4. В ППР должны быть предусмотрены мероприятия, направленные на обеспечение требуемой геометрической точности резервуарных конструкций, включая меры по компенсации или подавлению термодеформационных процессов усадки сварных швов, которые могут привести к потере устойчивости тонкостенной оболочки корпуса резервуара и образованию вмятин или выпуклостей его поверхности.
18.1.5. Руководство сварочными работами должно возлагаться на специалиста, имеющего специальное образование и прошедшего аттестацию на знание настоящего Стандарта и ПБ 03-273-99.
Руководитель сварочными работами назначается приказом по предприятию: заводу-изготовителю или монтажной организации.
18.1.6. Руководитель сварочных работ перед началом монтажа резервуара обязан:
— изучить проектную документацию на монтаж и сварку резервуара;
— укомплектовать объект в соответствии с ППР оборудованием и материалами;
— отобрать для сварки резервуара сварщиков, имеющих допуск к сварке ответственных конструкций, провести их инструктаж и организовать сварку каждым сварщиком пробных образцов соединений, которые им предстоит выполнять.
18.1.7. Сварщики должны быть аттестованы в соответствии с действующими Правилами аттестации, утвержденными Росгортехнадзором, что должно быть подтверждено удостоверениями.
Окончательное решение о допуске сварщиков к сварке соответствующих типов сварных соединений на резервуаре принимается руководителем сварочных работ на основании результатов контроля образцов, выполненных каждым сварщиком.
Каждому сварщику, допущенному к сварке резервуаров, приказом по заводу (монтажной организации) присваивается личное клеймо.
18.2. Рекомендуемые способы сварки
18.2.1. Применяемые способы и технология сварки резервуарных конструкций должны обеспечивать:
— высокую производительность и экономическую эффективность сварочных процессов;
— высокий уровень однородности и сплошности металла сварных соединений с учетом требований прочности, пластичности, твердости, ударной вязкости и хладостойкости;
— минимальный уровень деформаций свариваемых конструкций.
18. 2.2. При заводском изготовлении резервуарных конструкций основными способами сварки должна быть автоматизированная сварка под флюсом и механизированная сварка в углекислом газе или в смеси газов на основе аргона, при этом рекомендуется следующее соотношение газов: аргон — 82 %; углекислый газ — 18 %.
18.2.3. Рекомендуемые способы сварки для различных типов сварных соединений при монтаже резервуаров методами рулонной, полистовой или комбинированной сборки, приведены в таблицах 18.1 и 18.2.
Учитывая, что ручная дуговая сварка характеризуется относительно высоким уровнем удельного тепловложения, приводящим к повышенным сварочным деформациям, а также сравнительно низкой производительностью, применение этого способа сварки при монтаже резервуаров должно быть ограничено.
Таблица 18.1
Рекомендуемые способы монтажной сварки резервуаров рулонной сборки |
|
---|---|
Сварное соединение |
Рекомендуемый способ сварки |
Стыковые соединения окраек днища |
1. |
Соединения элементов центральной части днища |
1. Автоматизированная сварка под флюсом. |
Монтажные стыки стенки |
1. Механизированная сварка в углекислом газе |
Уторные швы в сопряжении стенки и днища |
1. Механизированная сварка в углекислом газе. |
Сварные соединения каркаса крыши при укрупнении в блоки |
1. |
Сварные соединения люков и патрубков на стенке и крыше |
1. Механизированная сварка в углекислом газе |
Сварные соединения в сопряжении крыши со стенкой и колец жесткости со стенкой |
1. Механизированная сварка в углекислом газе. |
Сварные соединения настила крыши |
1. Механизированная сварка в углекислом газе. |
Сварные соединения понтонов и плавающих крыш |
1. Механизированная сварка в углекислом газе. |
Примечания:
1. При сварке в углекислом газе в условиях ветра необходимо применять технологию, 2. Для всех типов сварных соединений возможно применение ручной дуговой сварки. |
Таблица 18.2
Рекомендуемые способы монтажной сварки резервуаров полистовой и комбинированной сборки |
|
---|---|
Сварное соединение |
Рекомендуемый способ сварки |
Вертикальные соединения |
1. |
Горизонтальные соединения стенки |
1. Автоматизированная сварка под флюсом. |
Прочие сварные соединения |
В соответствии с таблицей 18.1 |
Примечания: 1. При сварке в углекислом газе в условиях ветра необходимо применять технологию, обеспечивающую повышение устойчивости защитной струи газа и стойкости к порообразованию, или применять заграждения от ветра;
2. |
18.3. Требования к подготовке и сборке конструкций под сварку
18.3.1. До начала сварочных работ любые соединения резервуаров должны фиксироваться в проектном положении, что может быть обеспечено применением кондукторов, специальных сборочных приспособлений, привариваемых к деталям соединений, или постановкой прихваток.
Сборочные приспособления должны иметь достаточную прочность и жесткость, чтобы исключить чрезмерную усадку швов и перемещения свариваемых элементов.
Если при сварке соединений ожидаются значительные деформации, приводящие к изменению проектной формы, тогда при сборке деталей или узлов конструкций необходимо предусматривать соответствующие компенсирующие мероприятия (предварительный прогиб, строительный подъем, переменный зазор и пр.).
18.3.2. Прихватки, предназначенные для соединения свариваемых деталей, должны располагаться в местах расположения основных швов.
Размеры сечения прихваток должны быть минимально необходимыми для обеспечения расплавления их при наложении швов проектного сечения.
Наложение шва поверх прихваток допускается производить только после зачистки последних от шлака и брызг металла.
Прихватки с порами, раковинами и трещинами должны быть удалены и вновь заварены.
При необходимости постановки электроприхваток на монтажных стыках стенки их рекомендуется располагать с противоположной стороны от части сечения шва, выполняемой первой. Размер прихваток должен быть минимально необходимым. При выполнении зачистки корня шва такие прихватки удаляются.
Прихватки должны выполняться сварочными материалами и с использованием технологий, рекомендуемых для сварки основных швов сварных соединений.
Постановка прихваток при монтажной сборке конструкций должна выполняться аттестованными сварщиками.
18.4. Требования к технологии сварки
18.4.1. Способы, режимы и техника сварки резервуарных конструкций должны обеспечивать:
— требуемый уровень механических свойств и хладостойкости сварных соединений, предусмотренный проектом КМ;
— необходимую однородность и сплошность металла сварных соединений;
— минимальную величину сварочных деформаций и перемещений свариваемых элементов;
— коэффициент формы каждого наплавленного шва (прохода) в пределах от 1,3 до 2,0 (при сварке со свободным формированием шва).
18.4.2. При сварке резервуарных конструкций в зимнее время необходимо систематически контролировать температуру металла и, если расчетная скорость охлаждения металла шва превышает допускаемое значение для данной марки стали, необходимо организовать предварительный, сопутствующий или послесварочный подогрев свариваемых кромок. Требуемая температура и схема подогрева должны быть определены в ППР. Как правило, при осуществлении подогрева кромок следует нагревать металл на всю толщину в обе стороны от стыка на ширину 100 мм. Контроль температуры подогрева следует выполнять термокрасками, термокарандашами, контактным термопарным термометром, оптическим пирометром.
При сварке в зимнее время, независимо от температуры воздуха и марки стали, свариваемые кромки необходимо просушивать от влаги.
18.4.3. При использовании способов сварки с открытой дугой в зоне производства сварочных работ следует систематически контролировать скорость ветра. При превышении допускаемой скорости ветра, величина которой указывается в ППР, сварка должна быть прекращена или устроены соответствующие защитные укрытия.
18.4.4. Сварка должна производиться при стабильном режиме. Колебания величины сварочного тока и напряжения в сети, к которой подключается сварочное оборудование, не должны превышать ±5 %.
18.4.5. Последовательность выполнения сварных соединений конструкций резервуара и схемы выполнения каждого сварного шва в отдельности должны соблюдаться в соответствии с заводскими процедурами или указаниями ППР, исходя из условий обеспечения минимальных сварочных деформаций и перемещений элементов конструкций.
18.4.6. Не допускается выполнение каких-либо сварочных работ по поверхностям или соединениям, покрытых влагой, маслом, скоплениями окалины, шлака или другого рода загрязнениями. Не допускается выполнение сварочных работ на резервуаре при дожде, снеге, если кромки элементов, подлежащих сварке, не защищены от попадания влаги в зону сварки.
18.4.7. Все сварные соединения на днище и стенке резервуаров при ручной или механизированной сварке должны выполняться, как правило, не менее чем в два слоя. Каждый слой сварных швов должен проходить контроль внешним осмотром, а обнаруженные дефекты должны устраняться. Не допускается возбуждать дугу и выводить кратер на основной металл за пределы шва.
18.4.8. Удаление дефектных участков сварных швов должно выполняться механическим методом (шлифмашинками или пневмозубилом) или воздушно-дуговой строжкой с последующей зашлифовкой поверхности реза.
18.4.9. Заварку дефектных участков сварных швов следует выполнять способами и материалами, предусмотренными технологией. Исправленные участки сварного шва должны быть подвергнуты повторному контролю внешним осмотром или физическими методами. Если в исправленном участке вновь будут обнаружены дефекты, ремонт сварного шва должен выполняться при обязательном контроле всех технологических операций руководителем сварочных работ.
Выполнение троекратного ремонта сварных соединений в одной и той же зоне конструкций группы А должно согласовываться с разработчиком технологического процесса.
18. 4.10. Удаление технологических приспособлений, закрепленных сваркой к корпусу резервуара, должно производиться, как правило, механическим способом или кислородной резкой с последующей зачисткой мест их приварки заподлицо с основным металлом и контролем качества поверхности в этих зонах. Вырывы основного металла или подрезы в указанных местах недопустимы.
18.4.11. После сварки швы и прилегающие зоны должны быть очищены от шлака и брызг металла.
18.4.12. Каждый сварщик должен ставить личное клеймо на расстоянии 40…60 мм от границы выполненного им шва сварного соединения: одним сварщиком в одном месте; при выполнении несколькими сварщиками — в начале и в конце шва. Взамен постановки клейм допускается составление исполнительных схем с подписями сварщиков.
Руководителем сварочных работ по каждому резервуару ведется «Журнал сварочных работ».
18.5. Термообработка врезок в стенку резервуаров
18.5.1. Термообработке после сварки должны подвергаться врезки с условным проходом 300 мм и более в листы стенки резервуаров толщиной:
— свыше 25 мм для стали с пределом текучести менее 295 МПа;
— свыше 18 мм для стали с пределом текучести от 295 МПа до 345 МПа;
— свыше 12 мм для стали с пределом текучести свыше 345 МПа.
В состав врезки (термообрабатываемого узла) входит:
— лист стенки;
— усиливающий лист;
— обечайка (труба) люка или патрубка, утолщенная окрайка днища (только для придонного очистного люка по п. 8.12.3).
Примечание: Сварной шов приварки фланца к обечайке люка или патрубка термообработке может не подвергаться.
Термообработка врезок должна осуществляться до приварки термообрабатываемых узлов к смежным листам стенки и днищу резервуара.
Термообработка должна производиться в печах по технологическому процессу, разработанному с учетом следующих требований:
— термообрабатываемый узел должен быть полностью собран на заводе и термообработан при температуре от 590°С до 640°С из расчета 25 минут на каждые 10 мм толщины листа стенки;
— температура печи в момент помещения в нее узла не должна превышать 315°С, повышение температуры нагрева, начиная с 315°С, не должно превышать 200°С в час;
— во время нагрева перепад температуры узла не должен превышать 150°С;
— во время нагрева и периода выдержки атмосфера печи должна контролироваться, чтобы избежать чрезмерного окисления поверхности обрабатываемого материала, не должно быть непосредственного воздействия пламени на материал;
— узел должен охлаждаться в печи до температуры 400°С со скоростью не более 240°С в час. Ниже температуры 400°С узел может охлаждаться на открытом воздухе при температуре не ниже 5°С;
— после термообработки сварные швы узла должны быть проконтролированы методом магнитопорошковой или цветной дефектоскопии.
<< назад / к содержанию СТО-СА-03-002-2009 / вперед >>
Сварка при отрицательных температурах Категория: Сварка металлов При низких температурах получение сварных соединений высокого качества затрудняется. Сварка при низких температурах имеет свои особенности. 1. При низкой температуре снижается важнейший показатель механических свойств стали — ударная вязкость, сталь делается хрупкой. Это способствует возникновению в конструкциях больших остаточных напряжений, которые могут вызвать появление трещин в сварных соединениях в процессе сварки или при эксплуатации конструкции. 2. В процессе сварки повышается скорость охлаждения и кристаллизация жидкого металла сварочной ванны, что затрудняет удаление из него газов и неметаллических включений. Это увеличивает содержание в металле шва газов (кислород, водород, азот), окислов и частичек шлака. В результате снижаются механические показатели металла шва, а также увеличивается вероятность появления в нем трещин. 3. Повышенный отвод тепла от зоны сварки ухудшает проплавление кромок основного металла, что увеличивает вероятность получения серьезного дефекта сварных швов — непроваров. 4. Качество металла шва может быть снижено нз-за попадания в зону сварки влаги. Источником влаги служат: холодный окружающий воздух; иней на свариваемых кромках; электроды, длительное время хранившиеся на холоде. Наибольшие трудности возникают при сварке на холоде сталей с повышенным содержанием углерода, а также сталей, легированных марганцем, хромом, молибденом. Такие стали склонны к за- Калке и при быстром охлаждении в сварном соединении могут появиться трещины. Сварку сталей при низких температурах следует выполнять с соблюдением ряда мероприятий, направленных на снижение остаточных сварочных напряжений и уменьшение степени закалки свар, ного соединения. Основные из этих мероприятий: 7. Сварку вести до выполнения швов проектного размера без перерывов, за исключением времени, необходимого на смену электродов. В случае вынужденного перерыва сварку возобновлять после подогрева основного металла в соответствии с разработанным технологическим процессом. 8. Стремиться к максимальному уменьшению объема наплавленного металла. Избегать концентрации напряжений в виде чрезмерных усилий шва, резких переходов, пересечений швов, непроваров. Угловые швы выполнять с наименьшей выпуклостью. Сварку многослойных швов выполнять «каскадом», «горкой», секциями. 9. При сварке сталей, склонных к закалке, применять предварительный, сопутствующий, последующий подогрев. ![]() Согласно СНиП III—18—75 ручную и механизированную сварку металлоконструкций из стали классов до С52/40 включительно при температурах, ниже указанных, следует производить с предварительным подогревом стали до 120—160 °С на ширину 100 мм с каждой стороны соединения. Сварку конструкций из стали класса С60/45 следует производить при температуре не ниже —15°С при толщине стали до 16 мм и не ниже 0 °С при толщине стали 17—25 мм. При более низких температурах сварку такой стали указанных толщин следует производить с предварительным подогревом до температуры 120— 160 °С. При толщине стали свыше 25 мм предварительный подогрев. Примечание: при температуре окружающего воздуха ниже минус 20 °С сварка трубопроводов из углеродистых и легированных сталей должна выполняться по техническим условиям и технологическим инструкциям. Реклама:Читать далее:Требования электробезопасности при сварочных работах
Статьи по теме:
Главная → Справочник → Статьи → Блог → Форум |
Cварка металлоконструкций: технология, требования, расценки
Автор admin На чтение 5 мин. Просмотров 895 Опубликовано
В наши дни сварка используется в производстве, как мелкосерийных, так и массовых изделий различной степени сложности. Ведь с ее помощью можно «собрать» и угловое, и тавровое, и нахлесточное, и торцевое сопряжение деталей. Причем технологические приемы, с помощью которых осуществляется сварка металлоконструкций, со временем, становятся еще более изощренными и эффективными.
В этой статье мы познакомим наших читателей с наиболее рациональными способами сваривания элементов металлических конструкций. Эта информация будет полезна всем заказчикам сварных работ.
Содержание
- Общие требования к сварке металлоконструкций
- Классические способы сварки металлоконструкций
- Технологические новинки
Общие требования к сварке металлоконструкций
Общий перечень требований к сварке конструкций из металла состоит из нескольких разделов, а именно:
- Требований к выбору деталей металлоконструкции, регулируемых СНИП II 23-81 и ГОСТ 27772-88.
Этот раздел указывает на возможность использования того или иного сортамента металлопроката в процессе сборки конструкции. Причем в требованиях учитываются не только геометрические параметры и прочностные характеристики, но и такое понятие, как свариваемость металла.
- Требований по схеме сварки конструкции. Этот раздел указывает на порядок наложения сварных швов, соблюдение которого удерживает конструкцию от возможной деформации. Ну а сама схема сварки зависит от прочностных характеристик, размеров и сложности (присутствия большого количества деталей) конструкции. Точную схему может просчитать только опытный проектировщик.
- Требований к квалификации исполнителей сварных работ. Эти требования указаны в особых руководящих документах, издаваемых профильными министерствами. Например, указанные требования содержатся в РД 34 15.132—96 подготовленном Минтопэнерго РФ.
- Требований к контролю качества сварочных работ. Сведения для этого раздела содержит любой ГОСТ на сварку металлоконструкций (8713-79, 5264-80, 15164-78 и так далее).
В итоге, решившись на соединение деталей металлоконструкции сваркой, вы должны решить: из чего вы будете собирать вашу конструкцию, как вы будете соединять детали, кто займется этой работой, и как будет осуществляться процесс контроля.
Словом, вам есть куда приложить свои знания и умения. Ну а если у вас недостает опыта, то просто наймите проектировщика. Впрочем, сейчас нас интересует только сварка, поэтому далее по тексту мы познакомим вас с классическими и современными технологиями сварочных работ.
Классические способы сварки металлоконструкций
Общеизвестные способы сварки деталей из металла предполагают применение в техпроцессе всего двух источников энергии: электрической дуги и газового пламени.
Дуговая и газовая сварка может быть ручной, автоматической или полуавтоматической. Причем первый вариант предполагает формирование сварочного шва только «своими руками. Кроме того, вручную осуществляется и управление процессом сваривания и подача электрода (присадочной проволоки).
В «ручном» режиме можно использовать технологию классической электродуговой сварки, сварки под флюсом, сварки-пайки газосварочным аппаратом. Ручной режим хорош только в быту.
Второй вариант – автоматическая сварка – основан на процессе наложения шва без участия человека (сварщика). Всю работу выполняет специальный механизм, настраиваемый на конкретную операцию. Разумеется, перечень подобных операций ограничен функциональностью механизма, но низкие расценки на сварку металлоконструкций подобным способом делают автоматическую сварку очень популярной, особенно в крупносерийном производстве.
В «автоматическом» режиме можно использовать технологию контактной сварки (нагрев и опрессовка деталей), электрошлаковой сварки, и все технологии «ручного» типа (только вместо руки сварщика аппаратом будет управлять робот).
Третий вариант – полуавтоматический «режим» — предполагает наложение шва «вручную», но проволока или электроды подаются в зону сваривания автоматический, что повышает производительность работ практически на порядок.
В «полуавтоматическом режиме» работают все технологии, использующие газовые флюсы, неплавкие электроды и автоматизированную подачу присадочной проволоки в зону прогрева. В мелкосерийном и бытовом применении сварка полуавтоматом металлоконструкций – это самый выгодный вариант техпроцесса.
Технологические новинки
Кроме электрической дуги или пламени перегретого газа в процессе соединения деталей металлоконструкции современные сварщики используют энергию лазера, тепловой эффект трения, силу пучка электронов и даже ультразвук.
Словом, технология сварки металлоконструкций не стоит на месте. Новые способы реализации этого техпроцесса появляются с завидной регулярностью. И среди технологических новинок можно выделить следующие типы сварки: термитную, плазменную и электронно-лучевую.
С помощью термитной технологии осуществляется сварка и монтаж металлоконструкций, элементы которых расплавляются (по контуру) шва при горении особой смеси, вводимой в место стыка. Причем термитом можно заделать даже трещины в готовой металлоконструкции, выполнив «наплыв» материала.
Плазменная сварка выполняется в среде ионизированного газа, пропускаемого между двумя электродами. По сути, такой газ играет роль электрической дуги. Однако эффективность у плазменной струи выше на несколько порядков. Перегретым газом можно не только плавить металл любой толщины, но и резать заготовку, что дает возможность выстроить вокруг плазменного генератора многофункциональную, автоматическую, сварочную систему.
Электронно-лучевые технологии позволяют заваривать глубокие швы (до 20 сантиметров) при соотношении погружения луча и ширины шва 20 к 1. То есть шов глубиной в 20 сантиметров по ширине будет не более одного сантиметра. Однако манипуляции с генератором (пушкой) электронных лучей возможны только в вакууме. Поэтому такая технология используется только для решения узкоспециализированных задач.
Если вам нужно собрать небольшую металлоконструкцию, то обратите внимание на ручную электродуговую или газовую сварку. Сборка мелкосерийных объектов оправдывает покупку полуавтоматического аппарата. Ну а в серийном производстве вам понадобятся современные технологии сваривания.
Сварка металлоконструкций: как варить металлоконструкции?
Требования к сварке
Перед тем, как варить конструкцию из металла, необходимо ознакомиться с технологическими особенностями процесса, тогда конструкция получится прочной, долговечной, а риск ее деформации – нулевым.
Для получения качественных сварных швов нужно учитывать следующие требования:
- зазор между свариваемыми деталями – необходим при сварке изделий простой геометрии без применения кондуктора, а также для выполнения сложных швов с кондуктором. Для прочности соединения зазор должен соответствовать допустимой норме;
- строгое соответствие деталей по виду/размеру конструкторской документации – позволит сохранить функциональные возможности изделия;
- строгое соответствие установленной детали своему местоположению, согласно карте – особенно важное требование при работе с ответственными металлоконструкциями;
- нижнее расположение конструкции является преимущественным при наложении швов – это обеспечит сварщика безопасными условиями работы;
- при ручной дуговой сварке корневые слои шва важно накладывать электродами с диаметром, не более 3-4 мм;
- применение специальных инструментов/кондуктора при варке угловых соединений – во избежание перекоса, углы между плоскостями должны соответствовать проекту, иначе возможно нарушение целостности механизма, потеря функциональности;
- соблюдение стабильного режима (разброс значений тока/напряжения не должен превышать 5%) – это даст конструкции минимальные усадочные напряжения и деформации;
- проведение технологической пробы – прежде чем приступать к основной работе, важно сварить тестовый образец в условиях, полностью совпадающих с условиями варки конструкций на месте производства, и провести его механические испытания;
Технологическую пробу также важно проводить при выполнении сварки ответственных конструкций с применением новых марок сталей или новых расходников, условия производства контрольного образца должны быть идентичны реальным условиям работы, это позволит сварщику исключить возможные ошибки, риски.
Приведенные выше требования рекомендуется учитывать перед непосредственным выполнением сварочных работ, а также на этапе сборки деталей в целостную конструкцию.
Чтобы стандартизировать все сварные соединения, обеспечив им необходимые требования прочности, их классифицировали по следующим признакам:
- толщина соединяемых элементов – тонкостенные/толстостенные;
- материал свариваемых элементов – сталь, алюминий, титан, медь и т.д.;
- целевое назначение металлоконструкции – строительные, авиационные, вагонные, судовые и прочие;
- способ получения заготовки – литье, штамповка, профильный металлопрокат.
Рекомендации по каждому сварному соединению указываются в технологической карте/чертежах проекта. Требования по сварке ответственных конструкций, прописаны в нормативных документах:
- металлоконструкции сварные, применяемые в строительстве – ГОСТ 27772, СНИП II 23-81;
- ручная сварка – ГОСТа 5264-80;
- сварка в защитном газе — ГОСТа 14771-76.
Подготовка к сварке
Сначала нужно подготовить детали в соответствии с технологической картой. Общие этапы подготовки:
- нарезка стандартного металлопроката (листовой металл, трубы, швеллеры, уголки), согласно чертежу;
- обработка кромок: по периметру детали снимают фаски под углом 45 градусов, углы притупляют;
- в необходимых местах сверлят отверстия;
- места соединения очищаются: с поверхности металла удаляется масло, грязь, краска, ржавчина.
Качественная сборка металлоконструкций напрямую зависит от грамотного составления чертежей, поэтому работа над любой металлоконструкцией начинается с проектирования, создания рабочего чертежа с указанием на нем требований к деталям, способу соединения.
Сначала разрабатываются чертежи конструкции общего вида, а итоговым документом считается детализированный чертеж конструкции, в состав которого входят все чертежи каждой детали, участвующей в этом виде соединения.
Для чего нужна технологическая карта?
Технологическая карта выполняет роль инструкции, по которой сварщик, работая в определенной последовательности, может изготовить деталь любой сложности.
В этом документе подробно расписана технология сварки металлоконструкций, ее этапы, произведены необходимые расчеты, выбраны оптимальные параметры соединений, правила контроля получившихся сварных соединений, способы фиксации элементов конструкции, данные сварочных параметров, допустимые отклонения качественных показателей.
Единого образца технологической карты не существует, она разрабатывается, исходя из типа и сложности изготавливаемой металлоконструкции, оборудования, технического задания, бюджета, иных факторов.
В технологической карте также оговариваются меры безопасности, с которыми сварщик обязан ознакомиться перед началом работы, чтобы следовать рекомендациям.
Технология сварки металлических конструкций
В основе всех современных способов сварки лежит классическая технология, которая позволяет использовать рациональные типы сечений в металлоконструкциях для снижения показателей металлоемкости в несколько раз, по сравнению с применением иных технологий.
Сегодня наибольшее распространение получили автоматическая, полуавтоматическая и ручная технологии.
Автоматическая
Процесс сварки полностью механизирован, ведется без задействования ручного труда. Сварочный аппарат производит работу автономно, в соответствии с заданными настройками режима функционирования с учетом конкретного вида выполняемой операции.
Плавка металла происходит за счет высокотемпературной электрической дуги. По направлению шва размещается проволока и флюсовая смесь, расплавляемые под воздействием пламени горелки. По завершении работы на шве остается слой флюсовой смеси (шлака), которая удаляется механической обработкой.
В отличие от полуавтоматической сварки, в которой активно участвует сварщик, автоматическая не предполагает участия специалиста в процессе, направление движения и скорость перемещения электрода регулируется автоматом.
Преимущества автоматической сварки:
- высокое качество шва – сварное соединение имеет большую прочность по сравнению с соединением, получаемым другими методами;
- высокая скорость работ – сварочная ванна имеет оптимальную величину, а электрическая дуга поджигается быстрее, от этого увеличивается производительность;
- экономия основного металла – происходит из-за отсутствия металлических брызг;
- экономия флюса – автомат использует меньшее количество флюса, качество шва сохраняется, так как положительный эффект достигается за счет отличного сцепления свариваемых металлов;
- минимальное образование оксидной пленки – благодаря флюсу, сварочная ванна защищена от окисления, не нужно использовать иные защитные приспособления для заготовок;
- эстетичность – ровное пламя электрической дуги дает красивый, ровный шов с мелкочешуйчатой структурой;
- устойчивое соединение деталей – достигается за счет интенсивного охлаждения шва по окончании процесса.
К недостаткам технологии можно отнести высокую стоимость, жесткие требования к фиксации заготовок, возможность применения только на предприятиях.
Полуавтоматическая
При сварке в полуавтоматическом режиме сварные швы формируются вручную, а электроды подаются автоматом. Технология подходит для обработки различных металлов – алюминия, углеродистых и низкоуглеродистых сталей, их сплавов, никеля, меди, магния.
Достоинства полуавтоматической сварки:
- высокое качество шва;
- простота работы;
- относительно невысокий нагрев областей, граничащих с местом соединения.
В зависимости от материала свариваемых заготовок, в полуавтоматической сварке применяются разные виды газов. От того, какой защитный газ используется, зависит форма и характеристики шва, скорость плавления, разбрызгивание металла, глубина проникновения дуги.
Скорость перемещения горелки в соответствии со скоростью подачи присадочной проволоки и напряжением дуги контролирует сварщик, от его опыта зависит форма и качество шва.
Ручная
При ручной сварке специалист контролирует все действия вручную: от подачи электрода до формирования самого соединения. Ручным методом можно проводить пайку газосварочным устройством, электродуговую сварку или под флюсом.
Ручной метод наиболее доступен для работы в домашних условиях. Для этого понадобится стандартный набор оборудования и расходных материалов: болгарка, дрель, отрезные/зачистные диски, инструмент для отбивания шлака, корщетка, сварочный аппарат, электроды, защитная маска со светофильтром, краги или рукавицы.
Сварка решетчатых конструкций
Решетка/ферма – это сваренные между собой в плоскую или объемную форму стержни арматуры. В зависимости от расположения стержней, решетка может состоять из сегментов разной формы (треугольник, трапеция, сегмент).
Соединение стержней должно быть таким, чтобы они испытывали только воздействия на растяжение или сжатие. Элементы металлоконструкций выполняют из уголков, швеллеров и двутавров.
При изготовлении ферм большое значение имеет последовательность: сварку узлов фермы ведут от середины к их краям, вначале выполняют стыковые швы, а затем угловые. Напряжение в узлах будет минимальным, если сварку вести от середины к краям.
Сварка балок
Сварка балок позволяет возведение конструкций высотой несколько метров, в которых толстые широкие пояса сочетаются с высокими тонкими стенками, что позволяет снижать затраты на металл и делает возводимые конструкции более экономичными.
Чаще других применяется сварка балок двутаврового сечения, поскольку у них есть много преимуществ:
- минимизация отходов;
- снижение веса конструкций, уменьшение давления на фундамент;
- возможность применения в быстровозводимых конструкциях;
- повышение способности выдерживать статические и динамические нагрузки.
Технология сварки балочных конструкций должна обеспечивать прочность, плотность, жесткость и подобные требования. В качестве подготовки необходимо осуществить расчет на жесткость и прочность.
Заказать услугу сварки металлоконструкций, узнать стоимость вы можете по телефону в Санкт-Петербурге: +7 (812) 209-54-04, либо оставить заявку на нашем сайте. Наши менеджеры оперативно свяжутся с вами, уточнят детали, рассчитают смету.
ТКП 45-1.03-236-2011. Строительно-монтажные работы сварочные работы (32482)
6.1.15 После сборки конструкции на прихватках она подлежит контролю на соответствие геометрических размеров проектной документации, отсутствие трещин и других дефектов. Результаты контроля записывают в журнал сварочных работ.
6.2 Требования к производству сварочных работ
6.2.1 В проектной документации на металлоконструкции должны быть указаны:
— сварочные материалы;
— требования к механическим свойствам сварных соединений в зависимости от уровня расчетных напряжений и условий работы;
— объем контроля сварных соединений физическими методами;
— требуемый уровень качества сварных соединений.
6.2.2 В ППР или ППСР должны быть предусмотрены:
— наиболее эффективные способы сварки монтажных соединений с учетом их пространственного положения;
— требуемая форма подготовки кромок монтируемых элементов под сварку;
— последовательность сварки и порядок выполнения каждого шва, обеспечивающие минимальные деформации и перемещения свариваемых элементов;
— режимы сварки и указания по технике сварки, которые должны обеспечить получение требуемых структур металла шва и околошовной зоны;
— необходимая технологическая оснастка и сварочное оборудование;
— меры по обеспечению требуемого качества подготовки и сборки конструкций под сварку, а также схема их закрепления и необходимая для этого оснастка;
— допустимая температура металла, при которой возможна сварка соединений без их подогрева, а также допустимая скорость ветра в зоне сварки;
— условия обеспечения требуемого диапазона скоростей охлаждения сварных соединений металлоконструкций при сварке;
— указания по технологии производства сварочных работ в зимних условиях (если это предусматривается в соответствии с календарным планом строительства).
6.2.3 В ППР или ППСР должны быть предусмотрены меры по обеспечению требуемой геометрической точности металлоконструкций при сварке, включая меры по компенсации или подавлению термодеформационных процессов усадки сварных швов, способных привести к потере устойчивости конструкций или изменению геометрической формы.
6.2.4 В случаях, когда в проектной документации предусмотрена термическая обработка каких-либо сварных соединений, в ППР или ППСР следует разработать технологию ее выполнения, включая способ, режимы термообработки, указания по контролю качества термообработанных соединений.
6.2.5 Способы, режимы и техника сварки металлоконструкций должны обеспечивать:
— требуемый уровень механических свойств сварных соединений, предусмотренный проектом;
— необходимую однородность и сплошность металла сварных соединений;
— оптимальную скорость охлаждения выполненных сварных соединений;
— минимальный коэффициент концентрации напряжений;
— минимальное значение сварочных деформаций и перемещений свариваемых элементов;
— коэффициент формы каждого наплавленного слоя шва (прохода) в пределах от 1,3 до 2,0 (при сварке со свободным формированием шва).
6.2.6 Механические свойства металла сварных соединений должны соответствовать следующим требованиям:
— угол статического изгиба должен быть равен:
для углеродистых сталей толщиной до — не менее 100??, свыше — не менее 80??;
для низколегированных сталей толщиной до — не менее 80??, свыше — не менее 60??;
— статическое растяжение: временное сопротивление разрыву должно быть не менее нижнего предела временного сопротивления основного металла, регламентированного требованиями ТНПА;
— ударный изгиб металла шва: ударная вязкость должна быть не менее величины, указанной в технологической документации на монтажную сварку данной конструкции.
6.2.7 К сварке металлоконструкций следует приступать после приемки сборочных работ руководителем сварочных работ.
6.2.8 Последовательность выполнения сварных швов должна быть такой, чтобы деформации конструкции были минимальные и предотвращалось появление трещин в сварных соединениях.
Сварку всех узлов металлоконструкций, в том числе особо сложных (двутавровых балок большого сечения, монтажных стыков подкрановых балок, узлов соединения балок с колонами), следует выполнять согласно ППСР и технологической карте, в которых должны быть указаны последовательность наложения швов и приемы, обеспечивающие минимальные деформации и остаточные напряжения в конструкциях.
6.2.9 Подключение постов автоматической и механизированной сварки, а также однопостовых источников питания сварочной дуги должно быть произведено к распределительным шкафам (сборкам), соединенным с трансформаторной подстанцией отдельным фидером. Подключение к этим шкафам грузоподъемных и иных механизмов не допускается. Источник питания подключается к сети через индивидуальную пусковую аппаратуру (рубильник).
6.2.10 В зоне производства сварочных работ следует систематически контролировать скорость ветра. Допустимую скорость ветра в зоне сварки необходимо указывать в ППР или ППСР. При превышении допустимой скорости ветра более чем 2 м/с сварка должна быть прекращена или устроены соответствующие защитные укрытия.
6.2.11 Сварка должна производиться при стабильном режиме. Колебания величины напряжения в сети, к которой подключается сварочное оборудование, не должны превышать ??5 %.
Последовательность выполнения сварных соединений металлоконструкций и схема выполнения каждого сварного шва в отдельности должны соблюдаться в соответствии с указаниями ППР или ППСР, исходя из условий обеспечения минимальных сварочных деформаций и перемещений элементов конструкций.
6.2.12 Не допускается выполнение сварочных работ при дожде, снеге, если кромки элементов, подлежащих сварке, не защищены от попадания влаги в зону сварки.
6.2.13 Сварные соединения металлоконструкций при ручной или механизированной сварке следует выполнять не менее чем в два слоя согласно таблице 6.1.
Таблица 6.1 — Число проходов (слоев) сварного соединения в зависимости от толщины металла
Толщина металла, мм |
Число проходов (слоев) |
До 6 включ. |
До 2 включ. |
Св. 6 до 8 включ. |
Св. 2 до 3 включ. |
Св. 8 до 12 включ. |
Св. 3 до 4 включ. |
Св. 12 до 15 включ. |
Св. 4 до 5 включ. |
Св. |
Св. 5 до 6 включ. |
Св. 20 до 25 включ. |
Св. 6 до 7 включ. |
Св. 25 до 34 включ. |
Св. 7 до 8 включ. |
6.2.14 При сварке металлоконструкций в зимнее время необходимо систематически контролировать температуру металла и, если расчетная скорость охлаждения металла шва превышает допустимое значение для данной марки стали, необходимо организовать предварительный, сопутствующий или послесварочный подогрев; требуемая температура и схема подогрева должны быть определены в ППР или ППСР. Рабочие диапазоны скоростей охлаждения сталей, а также минимальные температуры, не требующие подогрева кромок при сварке, которые зависят от углеродного эквивалента, толщины металла, способа сварки, также следует указывать в ППР или ППСР (технологической карте). При сварке в зимнее время, независимо от температуры воздуха и марки стали, свариваемые кромки необходимо просушивать от влаги.
6.2.15 Сварные соединения (швы) длиной более при толщине стали до , выполняемые ручной или механизированной сваркой, следует сваривать обратноступенчатым способом.
6.2.16 При толщине стали от 15 до и более следует применять сварку способом «двойного слоя». Заваривают на участке длиной от 250 до первый слой шва, сбивают с него шлак и заваривают на этом же участке второй слой, далее в таком же порядке заваривают последующие участки. Сварку второго слоя выполняют по горячему первому слою. Остальные слои (проходы) выполняют обычным обратноступенчатым способом.
6.2.17 Сварка листовых объемных конструкций из стали толщиной более , особенно из стали с пределом текучести 390 МПа и более, должна производиться способами, обеспечивающими уменьшение скорости охлаждения — каскадом или горкой.
6.2.18 При производстве сварочных работ следует создавать условия для наиболее удобного выполнения сварки: в нижнем положении, с поворотом изделия; тавровые соединения необходимо выполнять «в лодочку» с кантовкой или поворотом изделия.
6.2.19 При сварке перекрещивающихся швов в первую очередь необходимо сваривать швы, выполнение которых не создает жесткого контура для остальных швов. Очередность выполнения швов должна указываться в ППР или ППСР и технологической карте. Недопустимо прерывать сварку в местах пересечения и сопряжения швов.
В первую очередь необходимо выполнять стыковые швы, во вторую — угловые швы.
6.2.20 При перерыве процесса сварки под флюсом возобновлять ее можно только после очистки конца шва на длину не менее и кратера от шлака. Этот участок и кратер следует перекрыть новым швом.
6.2.21 Многослойную сварку необходимо выполнять слоями высотой от 2 до согласно таблице 6.1. Каждый слой шва перед наложением последующего слоя должен быть тщательно очищен сварщиком от шлака и брызг металла, после чего производится внешний осмотр шва. Участки слоев шва с наружными порами, раковинами и трещинами должны быть удалены механическим способом. Допускается выборка дефектного участка огневым способом с последующей механической зачисткой мест выборки.
6.2.22 При сварке стыки участков (замки швов) в соседних слоях должны быть смещены не менее чем на .
6.2.23 При двусторонней ручной и механизированной сварке стыковых, угловых и тавровых соединений необходимо перед выполнением шва с обратной стороны удалить корень шва до чистого металла.
6.2.24 Придание угловым швам вогнутого профиля и плавного перехода к основному металлу необходимо осуществлять подбором режимов и механизированной зачисткой.
6.2.25 Минимальные катеты сварных швов не должны превышать толщины более тонкой детали в соединении.
Катет углового шва должен соответствовать указанному в проектной документации и составлять, мм:
4— для деталей толщиной от 4 до ;
не менее 5— для деталей большей толщины (определяется расчетом или конструктивно).
6.2.26 Нахлесточные соединения допускаются с величиной нахлестки не менее .
6.2.27 После окончания сварки со шва и околошовной зоны должен быть удален шлак и брызги металла. Снятие части усиления шва, зачистку корня шва и мест установки выводных планок необходимо выполнять с применением высокооборотных электрических шлифовальных машинок с абразивным кругом, исключающим образование грубых рисок.
Удаление технологических приспособлений, закрепленных сваркой к металлоконструкциям, должно производиться согласно 6.1.13. Проводится последующая зачистка мест приварки заподлицо с основным металлом и контроль поверхности в этих зонах. Не допускаются вырывы основного металла, подрезы, разного рода углубления в металле.
6.2.28 Методы контроля качества швов и сварных соединений должны соответствовать требованиям, приведенным в таблицах 6.2 – 6.6.
Таблица 6.2 — Методы контроля качества сварных соединений конструкций
Методы контроля |
Тип конструкций, объем контроля |
Внешний осмотр с проверкой геометрических размеров и формы швов |
Все типы конструкции в 100 %-ном объеме |
Контроль швов неразрушающими методами (радиографическим, ультразвуковым или др.) в соответствии с ГОСТ 3242 |
Все типы конструкций в объеме не менее 0,5 % длины швов, а также конструкции, методы и объемы контроля которых предусмотрены дополнительными правилами или рабочими чертежами марки основного комплекта КМ |
Испытания на непроницаемость и герметичность |
Конструкции (резервуарные и т. |
Механические испытания контрольных образцов |
Конструкции, для которых требования механических свойств сварных соединений предусмотрены чертежами КМ |
Металлографические исследования макрошлифов на торцах швов контрольных образцов или на торцах стыковых швов сварных соединений |
Конструкции, для которых требования металлографии, химанализа и других испытаний сварных соединений предусмотрены чертежами КМ |
Таблица 6.3 — Требования к качеству сварных соединений конструкций по внешнему виду
Наружные дефекты в сварных соединениях |
Требования к качеству, допустимые размеры дефектов |
Поверхность шва |
Мелкочешуйчатая, без прожогов, наплывов, сужений и перерывов. |
Трещины всех видов и направлений |
Не допускаются |
Незаваренные прожоги в металле шва |
Не допускаются |
Незаваренные кратеры |
Не допускаются |
Наплывы (натеки) на основной металл |
Не допускаются |
Подрезы |
Глубина — до 5 % толщины свариваемого проката, но не более |
Дефекты удлиненные и сферические одиночные |
Глубина — до 10 % толщины свариваемого проката, но не более . Длина — до 20 % длины оценочного участка* |
Дефекты удлиненные сферические в виде цепочки или скопления |
Глубина — до 5 % толщины свариваемого проката, но не более . |
Дефекты (непровары, цепочки и скопления пор) соседние по длине шва |
Расстояние между близлежащими концами — не менее |
* Здесь и далее длину оценочного участка следует принимать по таблице 6.5. |
Скачать бесплатно
Гост на сварку металлоконструкций
МИНИСТЕРСТВО ТОПЛИВА И ЭНЕРГЕТИКИ
РОССИЙСКОЙ ФЕДЕРАЦИИ
(МИНТОПЭНЕРГО РОССИИ)
ГОСУДАРСТВЕННЫЙ КОМИТЕТ РОССИЙСКОЙ ФЕДЕРАЦИИ ПО
ЖИЛИЩНОЙ И СТРОИТЕЛЬНОЙ ПОЛИТИКЕ
(ГОССТРОЙ РОССИИ)
РУКОВОДЯЩИЙ ДОКУМЕНТ
РД 34.15.132-96
СВАРКА И КОНТРОЛЬ
КАЧЕСТВА СВАРНЫХ СОЕДИНЕНИЙ
МЕТАЛЛОКОНСТРУКЦИЙ ЗДАНИЙ
ПРИ СООРУЖЕНИИ
ПРОМЫШЛЕННЫХ ОБЪЕКТОВ
14 марта 1996 г.
Разработчик: ОАО «Оргэнергострой»
Составители: С.С. Якобсон, канд. техн. наук;
Н.Д. Курносова, канд. техн. наук; Г.С. Зислин, канд. техн. наук;
М.Л. Эльяш, канд. техн. наук
Руководящий документ (РД) определяет организацию и технологию производства сварочных работ при сооружении металлических конструкций зданий промышленных объектов, а также объем, порядок контроля и нормы оценки качества сварных соединений.
РД 34.15.132-96 охватывает следующие виды сварки: ручную дуговую штучными электродами, механизированную (полуавтоматическую) сварку самозащитной порошковой проволокой и в углекислом газе, автоматическую и механизированную под флюсом.
РД 34.15.132-96 рассчитан на работников, занимающихся сваркой и сборкой крупных строительных объектов.
1.1. Назначение и область применения
1.1.1. Настоящий руководящий документ (РД) предназначен для персонала, осуществляющего производство сборочных и сварочных работ при укрупнении и монтаже металлоконструкций зданий промышленных объектов.
Выполнение требований настоящего РД по организации и технологии сборки и сварки металлоконструкций обеспечивает получение сварных соединений, удовлетворяющих установленным нормативами показателям качества, с минимальными затратами труда. РД является руководящим документом при разработке проектов производства работ и другой технологической документации.
1.1.2. РД распространяется на ручную дуговую сварку штучными электродами, механизированную (полуавтоматическую) сварку самозащитной порошковой проволокой и в углекислом газе, автоматическую и механизированную сварку под флюсом в условиях строительно-монтажной площадки.
1.1.3. Настоящий РД определяет технологию сборочно-сварочных работ при укрупнении и монтаже металлоконструкций, изготовленных из углеродистых и низколегированных сталей по ГОСТ 27772 :
фасонный прокат (уголки, двутавры, швеллеры) – из стали С235, С245, С255, С275, С285, С345, С345К, С375;
листовой, универсальный прокат и гнутые профили – из стали С235, С245, С255, С275, С285, С345, С345К, С375, С390, С390К, С440.
Обозначение сталей по ГОСТ 27772 (по пределу текучести) и соответствующие им марки сталей по другим действующим стандартам приведены в приложении 1.
РД действует совместно со следующими нормативно-техническими документами (НТД):
СНиП 3.03.01-87. Несущие и ограждающие конструкции;
СНиП II-23-81*. Нормы проектирования. Стальные конструкции. М., 1991.
1.1.4. В руководящем документе приведены основные положения по организации сварочных работ на строительных площадках, указания о выборе сварочных материалов и оборудования; требования, предъявляемые к сборке и сварке элементов конструкций, режимы сварки, порядок контроля и нормы оценки качества сварных соединений.
Кроме того, в настоящем РД даны рекомендации по технологии сварки отдельных типовых, наиболее часто встречающихся узлов стальных конструкций.
1.2. Требования к квалификации сварщиков, контролеров и ИТР
1.2.1. Сварка металлоконструкций зданий промышленных объектов должна проводиться сварщиками, имеющими удостоверения на право производства соответствующих сварочных работ, выданные им согласно требованиям «Правил аттестации сварщиков», утвержденных Госгортехнадзором России.
К сварке конструкций из сталей с пределом текучести 390 МПа (40 кгс/мм 2 ) и более допускаются сварщики, имеющие удостоверение на право работ по сварке этих сталей.
К механизированным способам сварки допускаются сварщики-операторы, прошедшие специальный курс теоретической и практической подготовки и сдавшие испытания на право производства этих работ.
Сварщики всех специальностей и квалификаций должны сдать испытания на 2-ю квалификационную группу по электробезопасности. Кроме того, все сварщики должны сдать испытания по противопожарным мероприятиям и технике безопасности.
1.2.2. Сварщик, впервые приступающий к сварке в данной организации, должен перед допуском к работе независимо от наличия у него удостоверения на право производства соответствующих работ сварить пробные (допускные) образцы. Сварка пробных образцов должна проводиться в условиях, тождественных с теми, в которых будет выполняться сварка конструкций.
Конструкция и число пробных образцов устанавливаются руководителем сварочных работ в зависимости от типов производственных соединений и квалификации сварщика. Качество пробных сварных соединений определяется путем визуального контроля на предмет определения сплошности и формирования шва, а при необходимости (по усмотрению руководителя сварочных работ) – с помощью неразрушающих физических методов контроля.
Качество пробных сварных соединений необходимо оценивать по нормам, предусмотренным для таких же производственных соединений. Пробные соединения должны быть идентичными или однотипными по отношению к тем производственным соединениям, которые будет сваривать проверяемый сварщик. Характеристика однотипных сварных соединений дана в «Правилах аттестации сварщиков».
1.2.3. Сварщики допускаются к тем видам работ, которые указаны в удостоверении. В удостоверении должны быть перечислены марки сталей или группы марок сталей в соответствии с «Правилами аттестации сварщиков», к сварке которых допускается сварщик.
1.2.4. Для сварки при температуре ниже минус 30 °С сварщик должен предварительно сварить пробные стыковые образцы при температуре не выше указанной. При удовлетворительных результатах механических испытаний пробных образцов сварщик может быть допущен к сварке при температуре на 10 °С ниже температуры сварки пробных образцов.
1.2.5. Руководство сварочными работами должно осуществлять лицо, имеющее документ о специальном образовании или подготовке в области сварки.
К руководству работами по сварке, контролю сварных соединений и операционному контролю допускаются ИТР, изучившие настоящий РД, соответствующие СНиП, рабочие чертежи изделий, производственно-технологическую документацию (ПТД) по сварке и методические инструкции по контролю. Знания ИТР и их профессиональная подготовка по сварочному производству должны быть проверены комиссией, назначенной приказом руководителя предприятия. Знания ИТР проверяются не реже одного раза в три года.
1.2.6. К выполнению работ по контролю качества сварных соединений допускаются контролеры, прошедшие специальную программу теоретического и практического обучения и получившие удостоверение на право выполнения работ по дефектоскопии сварных соединений соответствующим видом (способом) контроля. Контролеры по физическим методам контроля должны аттестовываться в соответствии с «Правилами аттестации специалистов неразрушающего контроля», утвержденными Госгортехнадзором России 18.08.92 г.
1.2.7. Подготовку контролеров должны осуществлять специальные учебные заведения или подразделения профессиональной подготовки (учебные комбинаты, центры, курсы и т.п.) предприятий, выполняющие работы по контролю качества сварки и имеющие лицензию на право проведения таких работ.
Подготовка контролеров должна быть специализирована по методам контроля (ультразвуковая дифектоскопия, радиографирование и др.), а при необходимости – по типам сварных соединений, что должно быть указано в их удостоверениях. Каждый контролер может быть допущен только к тем методам контроля, которые указаны в его удостоверении. Контролер, имевший перерыв в работе (по данному виду контроля) свыше 6 месяцев, должен вновь сдать экзамены в полном объеме.
1.3. Основные положения организации сварочных работ
1. 3.1. При разработке проекта производства работ (ППР) по монтажу металлоконструкций зданий должны быть учтены и отражены условия сборки конструкций под сварку, сварка и контроль сварных соединений.
В ППР должна быть заложена наиболее прогрессивная технология сборочно-сварочных работ с оптимальным уровнем механизации.
1.3.2. При организации и выполнении работ по сборке, сварке и контролю качества сварных соединений должны быть созданы все условия для соблюдения правил техники безопасности и пожарной безопасности в соответствии с требованиями следующих нормативных документов:
СНиП III-4-80. Техника безопасности в строительстве;
ГОСТ 12.3.003. Система стандартов безопасности труда. Работы электросварочные. Требования безопасности;
«Правил устройства электроустановок»;
«Правил технической эксплуатации электроустановок потребителей»;
«Правил техники безопасности при эксплуатации электроустановок потребителей»;
«Санитарных правил при проведении рентгеновской дефектоскопии», № 2191-80;
«Санитарных правил при радиоизотопной дефектоскопии», № 1171-74;
«Санитарных правил по сварке, наплавке и резке металлов», № 1009-73;
«Правил пожарной безопасности при проведении сварочных и других огневых работ на объектах народного хозяйства»;
«Правил пожарной безопасности при производстве строительно-монтажных работ. ППБ 05- 86».
1.3.3. Организация, выполняющая сборочно-сварочные работы, должна обеспечить надлежащее качество сварных соединений за счет:
применения исправного оборудования;
использования сварочных материалов надлежащего качества, прошедших соответствующий контроль;
выполнения технологических требований по сборке и сварке изделий, регламентированных ПТД;
выполнения операционного контроля процессов сборки и сварки;
своевременного выполнения контроля качества готовых сварных соединений.
1.3.4. Применение основных материалов (листов, профильного проката) и сварочных материалов (электродов, сварочной проволоки и флюсов), отличающихся от указанных в производственно-технологической документации (ПТД), может быть допущено по совместному техническому решению организации-разработчика ПТД, отраслевой специализированной организации и организации – производителя работ.
1.3.5. Порядок сборки и укрупнения монтажных блоков и последовательность работ должны обеспечивать возможность применения наиболее прогрессивных методов сварки. Для обеспечения надлежащего качества сварных соединений и повышения производительности труда при выполнении работ по сборке, сварке и контролю качества сварных соединений следует руководствоваться положениями, изложенными в настоящем разделе.
1.3.6. Способ сварки металлоконструкций на разных этапах их укрупнения и монтажа должен быть определен проектом производства работ (ППР).
При выборе способа сварки следует иметь в виду:
целесообразность применения механизированных способов сварки должна подтверждаться тех нико-экономическим расчетом;
автоматическую сварку под флюсом следует применять при укрупнительной сборке конструкций для швов значительной протяженности;
механизированная (полуавтоматическая) сварка самозащитной порошковой проволокой может быть применена при укрупнении и монтаже металлоконструкций для сварки швов в нижнем, наклонном и вертикальном положениях;
механизированную (полуавтоматическую) сварку в углекислом газе (проволокой сплошного сечения) следует использовать для укрупнительной и монтажной сварки металлоконструкций в любом положении шва при условии защиты места сварки от ветра.
В случаях, где не может быть использована автоматическая и механизированная сварка, должна применяться ручная дуговая сварка.
1.3.7. Численность инженерно-технических работников по сварке и наладчиков оборудования для механизированной сварки на строительно-монтажной площадке зависит от объема сварочных работ и числа работающих сварщиков. Она устанавливается в соответствии с положением о службе сварки строительно-монтажной организации.
1.3.8. Снабжение укрупнительной площадки и территории монтируемого или реконструируемого здания электропитанием для целей сварки следует выполнять с помощью разводок электросварочного тока на все участки укрупнительной площадки и монтируемого здания.
1.3.9. Сечение провода для присоединения источника питания для сварки к сети следует подбирать по данным табл. 1.1. При ручной дуговой сварке электрододержатель соединяют со сварочной цепью гибким медным проводом с резиновой изоляцией марок ПРД, ПРИ, КОГ 1, КОГ 2, сечение которого необходимо выбирать в зависимости от сварочного тока: при токе до 100 А – не менее 16 мм 2 , при 250 А – 25 мм 2 , при 300 А – 50 мм 2 . Длина гибкого провода должна быть не менее 5 м.
Сечение провода для подсоединения к сети источников сварочного тока
Максимальный сварочный ток источника питания, А
Сечение медного* провода, мм 2 , при напряжении сети, В
Сварка металлов, осуществляемая посредством локального плавления кромок соединяемых деталей, является основной технологией, используемой для выполнения неразъемных соединений.
Развитие и совершенствование сварочного процесса привели к появлению разновидностей этой технологии, отличающихся сферой применения, используемой аппаратурой и расходными материалами, а также характером самого сварочного процесса.
В силу традиции все сколько-нибудь значимые производственные процедуры стандартизуются в государственном масштабе. Стандарт является неотъемлемой частью плановой экономики.
По этой причине, существует целый ряд государственных стандартов (ГОСТ), определяющих нормы при выполнении различных видов сварочных процессов.
Ручной электродуговой сварочный процесс
Более всего в быту и мелкосерийном производстве распространена ручная дуговая сварка. Это разновидность сварочного процесса, при котором используются штучные сменяемые электроды, покрытые специальным составом, при сгорании образующем защитную газовую среду.
Тип применяемого покрытия электрода определяется свариваемым материалом и характером сварочного тока. Выпускаемые электроды делятся на те, которые предназначены для работы на переменном сварочном токе, и использующие при сварке аппарат постоянного тока.
Порядок выполнения работ с применением данной технологии регламентируется двумя ГОСТами.
ГОСТ 5264 – 80 устанавливает правила выполнения и графическое обозначение на чертежах основных видов соединений стальных элементов конструкций с использованием ручной сварки. К основным видам сварных соединений относятся:
- стыковые, при выполнении которых, элементы соединяются торцами, совмещёнными в одной плоскости;
- угловые, характеризующиеся тем, что соединяемые торцы деталей расположены в плоскостях, перпендикулярных друг другу;
- тавровые, заключающиеся в соединении торца одной заготовки с плоской поверхностью другой под прямым углом;
- нахлёсточные, соединяющие заготовки в параллельных плоскостях с наложением одной на другую.
Государственным стандартом устанавливается порядок подготовки поверхностей к выполнению сварного неразъемного соединения, включающий точную геометрию срезов кромок заготовок. Отдельные разделы стандарта посвящены свариванию заготовок разной толщины.
ГОСТ 11534 – 75 относится к соединениям, при которых заготовки образуют между собой острые или тупые углы. Описываются различные способы предварительной подготовки к сварке кромок изделий с указанием точных геометрических размеров.
Есть нормативные документы и для электродов. ГОСТ 9467 – 75 определяет требования к составу покрытия стальных электродов в зависимости от свойств свариваемых материалов, а также механических характеристик, которыми должны обладать сварные швы.
Важнейшими из этих характеристик являются показатели пластичности сварного соединения и величины разрушающих напряжений, возникающих при определенных видах нагрузки этого соединения.
Под слоем флюса
Технология сварки под слоем флюса широко применяется при сборке крупных стальных конструкций. Флюс может быть порошкообразным либо иметь жидкую консистенцию. К этому же типу процесса относится сварка в среде защитного газа.
ГОСТ 8713 – 79 определяет порядок выполнения работ с различными вариантами применения флюсов. Данный государственный стандарт описывает выполнение работ с применением механизированной и автоматической сварки.
ГОСТ 1533 – 75 посвящается свариванию заготовок под флюсом с использованием автоматических и полуавтоматических сварочных аппаратов. Рассматриваются типы сварных соединений с расположением кромок соединяемых элементов в плоскостях, образующих между собой острые и тупые углы.
ГОСТ 14771 – 76 описывает процессы создания сварных соединений в среде инертных газов или их смеси плавящимся и неплавящимся электродом. Показаны точные геометрические размеры скосов, выполняемых на соединяемых торцах изделий из стали и сплавов на основе железа и никеля.
При соединении труб
Ввиду высокой ответственности работ, осуществляемых при строительстве трубопроводов, выполнению сварных соединений на них посвящен отдельный ГОСТ 16037 – 80.
Действие этого ГОСТа распространяется на элементы стальных трубопроводов, неразъемное сварное соединение которых производится с применением различных технологий. Могут быть задействованы ручные, полуавтоматически и полностью автоматизированные электродуговые процессы, а также применяться газовая сварка.
В последней материал трубы плавится от тепла, получаемого при сгорании смеси газов. Для безопасной работы с газами важно соблюдать соответствующие инструкции.
Для заготовок из алюминия
Алюминий, являющийся легкоплавким металлом, требует особого подхода при выборе технологии производства сварных соединений.
Этот металл при плавлении легко разбрызгивается, что препятствует созданию качественного шва. ГОСТ 14806 – 80 определяет дуговой процесс сварки алюминия и его сплавов в среде инертных газов.
Существуют государственные стандарты, нормирующие порядок производства работ по таким видам сварки, как точечная, импульсная лазерная, контактная.
ГОСТами охвачены практически все применяемые в сварочных процессах материалы и само используемое оборудование.
Условные обозначения сварочных соединительных швов, применяемые в конструкторской технической документации, также определяются ГОСТом.
Кроме ГОСТов, регламентирующих проведение сварки и применяемое для этого оборудование, действует несколько строительных норм и правил (СНиП), имеющих отношение к процессам создания сварных соединений.
Эти документы устанавливают нормы при производстве строительных и монтажных работ по возведению стальных конструкций разного назначения, требующих применения технологий сваривания металла.
Английское название: Gas-shielded arc welding. Welded joints. Main types, design elements and dimensions
Настоящий стандарт устанавливает основные типы, конструктивные элементы и размеры сварных соединений из сталей, а также сплавов на железоникелевой и никелевой основах, выполняемых дуговой сваркой в защитном газе.
Стандарт не устанавливает основные типы, конструктивные элементы и размеры сварных соединений стальных трубопроводов по ГОСТ 16037-80
Дата издания: 01.12.2006
Дата введения в действие: 01.07.1977
Что такое структурная сварка? — Штаб-квартира по сварке
Сварка конструкций включает в себя создание различных сварных швов с использованием различных материалов компонентов для создания, изготовления и возведения сварных конструкций. Структурная сварка имеет свой собственный набор кодов, чертежей и типов сварных соединений.
Сварщикам конструкций требуется определенный набор навыков, включающий сбалансированные измерения и точность, чтобы выполнять свою работу эффективно. В этой статье я рассмотрю несколько вопросов, касающихся структурной сварки, ее требований и результатов.
Где применяется структурная сварка?
Конструкционная сварка используется для создания металлических каркасов зданий, мостов, транспортных средств и множества других сложных конструкций. Конструкционная сварка также используется для резки и ремонта балок, колонн и балок.
Сварка конструкций используется в различных отраслях промышленности, включая строительство, производство, судостроение, горнодобывающую промышленность, распределение нефти и газа, автомобилестроение, аэрокосмическую, военную и тяжелую промышленность.
Типы сварочных процессов, используемых при сварке конструкций
Товарная сталь является наиболее широко используемым металлом для сварки конструкций. Он предлагает гораздо лучшую долговечность и более устойчив к нагрузкам, чем большинство других металлов.
Еще одним преимуществом является то, что он довольно легкий по сравнению с другими металлами, такими как алюминий и железо. Сталь также достаточно экономична.
При сварке стальных конструкций используются в основном три типа сварочных процессов; сварка стержнем, сварка шпилек и дуговая сварка под флюсом.
Ручная сварка
Сварка стержнем также широко известна как дуговая сварка металлическим электродом в среде защитного газа (SMAW). Это наиболее широко используемый процесс сварки стальных конструкций.
В этом методе дуга зажигается между плавящимся электродом с флюсовым покрытием и металлом, который необходимо сварить.
Флюс создается из компонента на минеральной основе, который покрывает расплавленную сварочную ванну и защищает ее от окружающей среды. После того, как сварной шов остынет и затвердеет, отложения шлака удаляются с помощью инструмента для рубки или проволочной щетки.
Сварка SMAW используется для сварки или соединения двух металлических деталей, например стали, со сталью для создания более сложных конструкций. Электрический ток, используемый при сварке электродами, может быть как переменным, так и постоянным.
Сварка стержнем считается самым простым и недорогим способом сварки стальных конструкций. Многие отрасли производства и сварки металлов предпочитают использовать этот процесс сварки из-за его простоты.
Сварка электродами дает несколько преимуществ при создании конструкций:
- Этот процесс сварки можно использовать внутри и снаружи помещений
- Ручная сварка недорога по сравнению с другими типами сварки конструкций
- Предлагает широкий выбор сварных швов
- SMAW может использоваться для многих типов металлов, кроме стали .
- Для электродуговой сварки можно использовать разные электроды
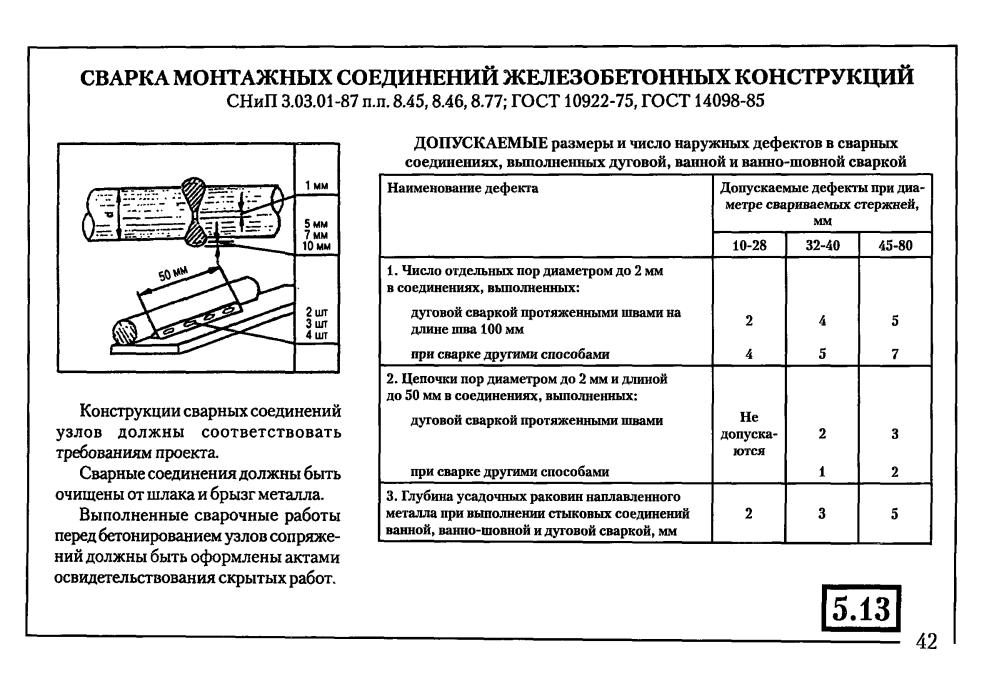
Приварка шпилек
Приварка шпилек также используется для изготовления стальных конструкций. Этот процесс также называется приваркой шпилек вытянутой дугой (DASW).
В этом методе крепеж или шпилька закрепляются на основном металле в процессе сварки. Крепеж бывает разных типов, например, с резьбой, с резьбой или без резьбы.
В методе приварки шпилек используется специальный тип флюса. И крепеж, и соединяемая вместе подложка могут быть из разных материалов, включая сталь, нержавеющую сталь или алюминий и т. д.
Сварка шпилек также очень популярна для создания более сложных металлических конструкций. Сварщики конструкций выбирают приварку шпилек по следующим причинам:
- Этот тип сварки выполняется только с одной стороны, поэтому вам не нужен доступ к другой стороне. Иногда это единственный вариант, который у вас есть.
- Приварка шпилек достаточно надежна.
В отличие от периферийных сварных швов, которые используются для приваривания болтов на место, соединение DASW представляет собой полный сварной шов в поперечном сечении.
- С точки зрения внешнего вида конструкционный сварной шов превосходит сварку электродами. Поскольку вам нужно использовать застежку только с одной стороны, индикаторов того, что вы прикрепили застежку с другой стороны, может и не быть.
- Приварка шпилек проста в освоении и не требует специальных навыков.
- Приварка шпилек выполняется быстрее, чем другие методы изготовления конструкций. Приварка крепежа 3/4 дюйма занимает всего около одной секунды.
Метод приварки шпилек применяется в следующих отраслях промышленности:
- Здания, строительные площадки и мосты
- Компании по прокладке кабелей
- Предприятия общественного питания, включая кофейни, салат-бары, пекарни, гриль-бары в ресторанах и т. д.
- Оборудование электропитания
- Военные, судостроительные и авиационные приложения
- Производство движущихся транспортных средств в строительстве, автомобилестроении, сельском хозяйстве и т.
д.
Сварка под флюсом
Дуговая сварка под флюсом (FCAW) — это процесс полуавтоматической или электрической сварки, используемый для создания сложных конструкций. На практике этот процесс очень похож на сварку MIG, поскольку в обоих случаях в качестве электрода для дуги используется один и тот же тип присадочной проволоки.
Этот процесс использует сам флюс для защиты и покрытия сварочной ванны вместо защитного газа. Покрытие также дает сварочной ванне больше времени для охлаждения, создавая более стабильный сварной шов.
Для FCAW требуется машина для непрерывной подачи электрода в сварочную ванну, что делает ее относительно простой в использовании. Этот тип сварки более полезен для плотных свариваемых участков конструкции толщиной не менее одного дюйма, поскольку он имеет более высокую скорость осаждения металла шва.
Сварка под флюсом имеет несколько уникальных преимуществ, которые делают ее более предпочтительной по сравнению с другими видами сварки:
- Сварка под флюсом не требует дополнительного защитного газа
- Идеально подходит для сварки на открытом воздухе даже в ветреную погоду
- Другие типы структурной сварки имеют более высокую вероятность пористости, чем сварка под флюсом
- Когда у вас есть подходящий присадочный материал, FCAW сводится к позиционированию; довольно легко научиться и применять
- Сварка под флюсом широко используется в отраслях, где требуется высокоскоростная и однородная сварка
Поскольку сварка с флюсовым сердечником обеспечивает высокое проплавление и идеально подходит для наружных работ, вы обнаружите, что она чаще используется в тяжелой промышленности, включая строительство зданий и общественных сооружений.
Сварка конструкций в полевых условиях или в цеху
Сварка конструкций может выполняться в полевых условиях или в мастерской. Сварка на месте в полевых условиях потребует от вас учета множества элементов, таких как ветер, высота и угол работы.
Сварка в цеху сопряжена с трудностями, поскольку вам необходимо подготовить конструкцию таким образом, чтобы ее можно было доставить на строительную площадку.
Сварка конструкций в полевых условиях
Большинство опытных сварщиков предпочитают использовать электродуговую сварку для наружных работ, потому что она им удобна. Однако переход на FCAW действительно может повысить производительность.
Сварка FCAW не требует использования защитного газа и создает глубокие швы, идеально подходящие для строительной площадки.
Несмотря на то, что сварка электродом является знакомым процессом для многих, и сварщики предпочитают его, потому что он более портативный, он также очень медленный. Вам придется часто менять наполнители.
Вот почему, когда сварка конструкций в полевых условиях требует большого количества сварочных работ в одном месте, может быть гораздо более продуктивно переключиться на сварку проволокой FCAW.
В некоторых случаях сварки конструкций в полевых условиях может быть более эффективно использовать в одной и той же работе сочетание электродуговой сварки и сварки FCAW. Области, которые требуют большего количества сварки в одном месте, должны выполняться с помощью машины с флюсовым сердечником, в то время как небольшие сварные швы, распространяющиеся на большую площадь, должны выполняться с помощью электродной сварки.
Сварка металлоконструкций в цеху
Для сварки металлоконструкций в цеху подходит как FCAW, так и приварка шпилек, поскольку они просты в применении и могут выполняться во всех положениях. Вам не потребуется большого мастерства в работе с оборудованием.
Что вам нужно, так это правильные чертежи конструкции, понимание правил сварки и хорошая голова на плечах, чтобы подавать дугу.
Эти особенности делают оба метода полезными для сварщиков конструкций с разным уровнем квалификации. Проволока, используемая при сварке под флюсом, в частности, допускает очень большой параметр, при котором она может работать достаточно хорошо.
Они дают вам большую погрешность, и даже непоследовательные методы могут быстро выполнить работу.
Если вы хотите получить более гладкую поверхность, приварка шпилек может стать идеальным решением для проектов, которые вам нужно выполнить в магазине. Вы также можете использовать эти методы сварки на более грязных основных металлах без необходимости их очистки.
При сварке шпилек и FCAW образуется много шлака и брызг, которые необходимо удалять между проходами и после окончательной обработки сварной конструкции. Шлак может скапливаться и в цехе, что требует дополнительной очистки.
Это может быть новым для сварщиков, которые привыкли только к сварке в цеху.
Резюме
В этом посте я кратко рассмотрел структурную сварку и различные типы процессов, используемых для изготовления и соединения конструкций. Мы также рассмотрели различия между сваркой конструкций в цеху и на стройплощадке.
Типы процессов изготовления металла
Изготовление металла — это широкий термин, относящийся к любому процессу, который разрезает, формирует или отливает металлический материал в конечный продукт. Вместо того, чтобы собирать конечный продукт из готовых компонентов, производство создает конечный продукт из сырья или полуфабрикатов. Существует множество различных производственных процессов изготовления. Изготовление металла используется как для нестандартных, так и для стандартных изделий.
Большинство металлических изделий, изготовленных на заказ, изготавливаются из ряда широко используемых металлов и их сплавов. Производители металла часто начинают с стандартных металлических компонентов, таких как листовой металл, металлические стержни, металлические заготовки и металлические стержни, для создания нового продукта.
—> Заинтересованы в изготовлении листового металла на заказ? Попробуйте Xometry Instant Quoting Engine℠, чтобы воплотить свой проект в жизнь. Бесплатная доставка по США.
Специализированные производители металлоконструкций называются производственными мастерскими. Подрядчики, производители оборудования и торговые посредники заставляют производителей металла работать над различными проектами. Многие производители металлоконструкций участвуют в торгах, отправляя чертежи, и, если они получают контракт, строят проект. После присуждения контракта производители металла приступают к этапам планирования, заказывая нужные материалы и заставляя инженера программировать станки с ЧПУ для проекта.
Производственные цеха могут использовать несколько процессов для создания конечного продукта. Они также могут предоставлять услуги по отделке, такие как удаление заусенцев, полировка, покрытие и покраска продукта. Финишная обработка отличается от изготовления металла тем, что финишная обработка является вторичным процессом для обработки внешней поверхности продукта, а не для его придания формы или создания нового продукта.
В этой статье дается обзор некоторых наиболее распространенных методов изготовления металлоконструкций и соображений по выбору подходящего цеха для выполнения работ по изготовлению металлоконструкций.
Чугунное литье в песчаную форму.
Изображение предоставлено: Mr. 1/Shutterstock.com
Типы металлических изделий
Выбор метода изготовления металла, подходящего для данного проекта, зависит от геометрии детали, предполагаемого назначения изделия и материалов, используемых при его изготовлении. Общие процессы изготовления металла следующие:
- Литье
- Резка
- Чертеж
- Складной
- Поковка
- Экструзия
- Обработка
- Штамповка
- Стрижка
- Штамповка
- Сварка
Литье
Литье — это когда расплавленный металл заливают в форму или форму и дают ему остыть и затвердеть, приняв желаемую форму. Процесс изготовления металла идеально подходит для массового производства деталей с повторным использованием одной и той же пресс-формы для создания идентичных продуктов. Существует несколько различных видов литья. Литье под давлением — это когда жидкий металл нагнетается в форму, а не в форму, и там приложенное давление удерживает его на месте, пока он не затвердеет. Этот процесс известен высокоскоростными приложениями, которые он поддерживает. Литье в постоянную форму включает заливку расплавленного металла в форму.
Существует множество типов процессов литья. В некоторых случаях в этом процессе также используется вакуум. Литье в постоянную форму может создавать более прочные отливки, чем литье под давлением, но их может быть трудно удалить из конечного продукта. По этой причине также доступны полупостоянные отливки в формы. Эти формы имеют одноразовые сердечники, что делает их более управляемыми и менее затратными для удаления. Завершающим процессом литья является литье в песчаные формы. При литье в песчаные формы отливки изготавливаются путем вдавливания модели в мелкую смесь песка. Это формирует форму для заливки расплавленного металла. Этот процесс медленный, но, как правило, более экономичный, чем другие формы литья. Его также хорошо использовать, когда необходимы сложные конструкции или для изготовления крупных металлических изделий.
Вы можете использовать сайт Thomasnet.com, чтобы найти ближайшие к вам компании по кастингу.
Резка
Этот очень распространенный тип изготовления металла представляет собой резку заготовки, чтобы разделить ее на более мелкие части. В то время как распиловка является старейшим методом резки, современные методы включают лазерную резку, гидроабразивную резку, силовые ножницы и плазменно-дуговую резку. Существует множество различных методов резки, от ручных и электроинструментов до станков с числовым программным управлением (ЧПУ). Резка может быть первым этапом более длительного производственного процесса или единственным используемым процессом.
Высечка — это еще один процесс резки, в котором используется штамп для нарезки металла. Ротационная высечка использует вращающуюся цилиндрическую матрицу для резки материала, подаваемого через пресс. Планшетная высечка используется для более толстых металлических материалов и использует штампы на прессе для вырезания фигур, когда штамп штампует металл.
Вы можете использовать платформу Thomas’ Supplier Discover Platform, чтобы найти ближайшие к вам компании по высечке.
Чертеж
Чертеж использует силу растяжения для втягивания металла в коническую матрицу и через нее. Матрица растягивает металл в более тонкую форму. Обычно волочение производится при комнатной температуре и называется холодным волочением, но металлическую заготовку можно нагреть, чтобы уменьшить необходимое усилие.
Этот процесс считается глубокой вытяжкой, когда глубина конечного продукта равна или превышает его радиус. Обычно он используется при изготовлении листового металла для превращения листов в полые цилиндрические или коробчатые сосуды.
Вы можете использовать платформу Thomas’s Supplier Discover Platform, чтобы найти компании глубокой вытяжки.
Складной
Этот процесс изготовления металла заключается в том, что металл изгибается под углом. Наиболее распространенным средством является тормозной пресс, который создает складки на металле, зажимая его. Заготовка удерживается между пуансоном и матрицей и сгибается под давлением пуансона. Этот процесс обычно используется для формирования листового металла. Складывание также можно выполнить, забивая заготовку молотком, пока она не согнется, или с помощью фальцевальной машины, также известной как папка. Станок имеет плоскую поверхность, на которую помещается плоский листовой металл, прижимную планку, которая удерживает заготовку на месте, и переднюю панель, которая поднимается вверх и заставляет изгибаться натянутый на нее металл.
Изготовление ножей методом ковки. Изображение предоставлено Франческо де Марко/Shutterstock. com
Ковка
Ковка использует силу сжатия для придания формы металлу. Молоток или плашка ударяют по заготовке до тех пор, пока не будет сформирована желаемая форма. Этот производственный процесс может выполняться с металлом при комнатной температуре и называется холодной ковкой. Ковка также может выполняться с нагревом металла до температуры от выше комнатной до температуры ниже температуры рекристаллизации, и тогда это называется горячей ковкой. Когда металл нагревают до температуры рекристаллизации, которая зависит от металла, процесс называется горячей ковкой. Ковка — один из древнейших видов изготовления металла, кузнецы использовали ковку много веков назад.
Примеры поковок из нержавеющей сталиИзображение предоставлено: Cornell Forge
Экструзия
В процессе экструзионного производства заготовка проталкивается через открытую или закрытую головку или вокруг нее. При продавливании через открытую или закрытую матрицу диаметр заготовки уменьшается до поперечного сечения матрицы. При прессовании вокруг штампа внутри заготовки образуется полость. В обоих этих процессах обычно используется металлический стержень или цилиндр (заготовка) в качестве заготовки и плунжер для выполнения операции удара. Полученный продукт цилиндрической формы часто представляет собой электропроводку или трубопровод. Поперечное сечение штампа может иметь различную форму для изготовления деталей различной формы. Экструзия может быть непрерывной для создания очень длинных деталей или полунепрерывной для создания множества более коротких деталей.
Ударная экструзия, также называемая холодной экструзией, выполняется при комнатной температуре и повышает прочность детали, делая ее прочнее исходного материала. Когда к соответствующему металлу прикладывается достаточное усилие, он начинает течь в доступную форму, подобно движению вязкой жидкости. Холодное прессование обычно используется для изготовления стальных металлов.
Горячее прессование выполняется при повышенной температуре, чтобы предотвратить затвердевание металла и облегчить его проталкивание через матрицу. Обычно он используется для изготовления меди, а также для создания нестандартных алюминиевых деталей.
Обработка
Метод изготовления металла, называемый механической обработкой, относится к процессу придания металлу формы путем удаления из него ненужного материала. Этот процесс может выполняться различными способами. Существует множество различных процессов обработки, включая сверление, точение и фрезерование.
Сверление использует вращающийся режущий инструмент, сверло, для вырезания отверстия в материале. Сверло давит на металл, вращаясь очень быстро, чтобы создать круглое отверстие.
Токарная обработка использует токарный станок для вращения металла, в то время как режущий инструмент перемещается линейно для удаления металла по диаметру, создавая цилиндрическую форму. Режущий инструмент можно наклонять под разными углами для создания различных форм. Это можно сделать вручную или на токарном станке с ЧПУ. Обработка с ЧПУ обычно используется, когда размеры детали должны быть чрезвычайно точными.
Фрезерование использует вращающиеся многогранные режущие инструменты для постепенного удаления материала с заготовки, пока не будет достигнута желаемая форма. Металл медленно подается во вращающийся режущий инструмент, или инструмент перемещается по неподвижному металлу, или заготовка и инструмент перемещаются относительно друг друга. Этот процесс можно выполнять вручную или на фрезерном станке с ЧПУ. Фрезерование часто является вторичным или чистовым процессом, но его можно использовать и как единственный метод изготовления металла от начала до конца. Различные типы фрезерования включают торцевое фрезерование, плоское фрезерование, угловое фрезерование, попутное фрезерование и фасонное фрезерование.
Пробивной станок с ЧПУ изготавливает отверстия в листовом металле.Изображение предоставлено: BigBlueStudio/Shutterstock.com
Штамповка
Револьверные головки уникальной формы на пробивном прессе ударяют по металлу через или в матрицу, создавая отверстия. Конечным продуктом может быть либо кусок металла с отверстиями для крепления, либо это могут быть уже удаленные и фигурные металлические детали, называемые заготовкой. Большинство штамповочных прессов являются механическими, но меньшие и более простые штампы могут быть с ручным приводом. Пробивные прессы с ЧПУ также теперь широко распространены и используются как для тяжелых, так и для легких металлов при производстве металлов.
Стрижка
Этот тип обработки металла представляет собой один длинный прямой разрез, который достигается путем объединения двух инструментов, один из которых находится над металлом, а другой расположен ниже для приложения давления. Верхнее лезвие прижимает металл к неподвижному нижнему лезвию и ломает его. Затем перелом распространяется внутрь для полного разделения. Срезанные края обычно заусенцы. Он идеально подходит для резки материалов меньшей длины и материалов различной формы, поскольку лезвия могут быть установлены под углом для уменьшения требуемой силы.
Штамповка
Этот процесс изготовления металла похож на штамповку, за исключением того, что пресс создает в металле не отверстие, а углубление. Револьвер не проталкивает металл полностью через матрицу, а только поднимает ее. Штамповка используется для формирования фигур, букв или изображений на металлической панели или листе. Механический и гидравлический — это два типа штамповочных прессов. Металлоштамповочные машины отливают, штампуют, вырезают и формируют металлические листы. Листы толщиной до 1/4 дюйма формуются в заданные формы и размеры. Прессы, используемые для штамповки металла, могут создавать широкий ассортимент продукции, и они могут выполнять ряд операций, включая вырубку, чеканку металла и формование четырех слайдов. Чеканка монет (как следует из названия) может быть использована для создания монет, но у нее есть и другие применения, например, детали для электроники. Четырехшаговая формовка включает в себя различные процессы штамповки и формовки для создания более сложных изделий, и она особенно эффективна для небольших деталей.
Изображение предоставлено: Aumm graphixphoto/Shutterstock.com
Сварка
При сварке два или более куска металла соединяются вместе за счет сочетания тепла и давления. Это популярный процесс, потому что куски металла могут быть любой формы и размера. Четыре популярных типа сварочных процедур — это электродуговая сварка, сварка MIG, сварка TIG и дуговая сварка порошковой проволокой.
Сварка стержнем, также известная как дуговая сварка защищенным металлом (SMAW), использует стержневой электрод, который производит электрический ток, который образует электрическую дугу при контакте с металлом. Высокая температура дуги сваривает металл.
Сварка металла в среде инертного газа (MIG) или газовая дуговая сварка металлическим электродом (GMAW) использует подаваемый извне газ вместе со сплошным электродом из сплошной проволоки, чтобы защитить металл от реакции на факторы окружающей среды, чтобы сварка была более быстрой и непрерывной. Защитный газ также создает меньше сварочного дыма.
Сварка вольфрамовым электродом в среде инертного газа (TIG), также называемая дуговой сваркой вольфрамовым электродом, использует стержень вольфрамового электрода, который создает короткую дугу для сварки более тяжелых металлов при изготовлении тяжелых изделий. Этот метод требует высокой квалификации сварщика, так как процесс более сложный, но его можно использовать для большинства металлических изделий и для сложных проектов.
Дуговая сварка порошковой проволокой (FCAW) имеет тот же процесс и оборудование, что и MIG. Используемый проволочный электрод содержит сердечник, который производит защитный газ, поэтому дополнительный источник газа не требуется. Этот метод более портативный, чем сварка MIG или Stick, но его нельзя использовать для более тонких металлов.
Выбор производителей металла
Выбор мастерской по изготовлению металлоконструкций на заказ или производителя металлоконструкций на заказ, который наилучшим образом удовлетворит потребности проекта, является важным решением, которое может повлиять на скорость производства, качество продукции и экономическую эффективность данного проекта. Вот несколько соображений, которые помогут вам в процессе выбора:
Опыт : Механические мастерские, которые работают в течение длительного времени или имеют хорошо зарекомендовавший себя сервис, могут представлять очевидные причины для выбора магазина.
Отрасли, обслуживаемые : может быть полезно отметить, какие отрасли обычно обслуживает магазин, а также виды продуктов или процессов, на которых он конкретно фокусируется, поскольку они лучше подходят для выполнения конкретных отраслевых требований. Также важно узнать об опыте производителя с типом металла, необходимого для проекта. Некоторые мастерские специализируются на одном или двух видах металлообработки. Если вы уже знаете, что лучшим материалом для проекта является алюминий, найдите специализированного производителя алюминия.
Ресурсы : Станки с ЧПУ могут быть лучшим вариантом для мелкодетализированного проекта, но ручные станки могут лучше подойти для проекта с ограниченным бюджетом. Размер оборудования имеет значение, если конечный продукт имеет большие размеры. Инструментальные возможности производителя металла могут иметь большое влияние на его возможности и качество его металлических изделий. Требуется ли точное изготовление? Прецизионное изготовление листового металла в значительной степени зависит от быстро развивающихся компьютерных технологий.
Многие компании, специализирующиеся на прецизионном производстве, используют программное обеспечение CAD/CAM для проектирования и компоновки изготавливаемых изделий. Компьютеры с ЧПУ запрограммированы для выполнения конкретных задач и достижения невероятно точных спецификаций, необходимых для производства множества металлических изделий, изготовленных по индивидуальному заказу.
Тип производства : Размер производственного цикла, будь то краткосрочный или долгосрочный, мелкосерийный или крупносерийный, должен быть одним из центральных соображений при выборе адекватной службы индивидуального изготовления.
Складские материалы : Наконец, важно убедиться, что производитель металла либо уже имеет, либо может сформировать конкретный металл, который будет использоваться для продукта. Если у них есть конкретный поставщик металла, которого они используют, также стоит изучить репутацию поставщика. Специализированный цех по производству нержавеющей стали может работать с одним и тем же поставщиком стали в течение длительного периода времени.
—> Заинтересованы в изготовлении листового металла на заказ? Попробуйте Xometry Instant Quoting Engine℠, чтобы воплотить свой проект в жизнь. Бесплатная доставка по США.
Изготовление металлоконструкций на заказ — сводка
Это руководство дает общее представление о производстве металла, различных методах и соображениях по выбору производителя. Для получения дополнительной информации о сопутствующих услугах обратитесь к другим нашим руководствам по продуктам или посетите платформу поиска поставщиков Thomas, чтобы найти потенциальные источники или просмотреть сведения о конкретных продуктах.
Источники:
- https://www.plasmacnc.co.uk/blog/understanding-fabrication-and-types-of-fabrication/
- https://www.thefabricator.com/article/bending/sheet-metal-folding-evolves
- https://www.themanufacturer.com/articles/different-types-of-welding-and-what-they-are-used-for/
- http://www.engineeringarticles.org/machining-operation-and-types-of-machining-tools/
- https://www.reinkeandschomann.com/blog/custom-metal-fabrication/
- https://www.cornellforge.com/forging-forged-parts-guide/
- http://www.pdf-inc.com/types-metal-fabrication-processes/
- https://alliedsinterings.com/products/
- https://www.ampflame.com/custom-metal-fabrication.html
- https://www.technoxmachine.com/metal-fabrication-services/
Другие изделия из металла
- Как предотвратить образование складок во время глубокой вытяжки
- Травмы, характерные для металлообработки
- Основное сырье, используемое при изготовлении металла
- Процессы изготовления нержавеющей стали
- Готовые изделия из нержавеющей стали
- Металлообработка на токарном станке
- Как глубоко вытянуть латунь
- История металлического прядения
- Алюминиевый профиль в строительстве
- Как работают станки для отделки металла
- Взрывной гидроформинг
- Технология гидроформовки металлов
- Применение ротационной штамповки в профилегибочном производстве
- Пластик против.
Изготовление металла — преимущества и недостатки
- Материалы, используемые при профилировании
- Гидроформинг в автомобильной промышленности
- Процесс экструзии алюминия и его применение
- Конструкционные алюминиевые профили
- Наплавка нержавеющей сталью
- Ведущие компании по производству штамповок глубокой вытяжки в США
- О формовке металлов — Краткое руководство
- Что такое ковка?
- Инструменты и оборудование для ковки металла, а также запасные части
- Понимание штамповки металлов
- Металлическая отделка – какие виды отделки существуют?
- Что такое глубокое рисование? Углубленный взгляд на формирование глубокой вытяжки
- Справочник по видам ковки — холодная и горячая ковка
- Что такое прецизионная штамповка? Взгляд на машину для штамповки металла
- Профилегибочная машина и процесс профилирования
Изображение предоставлено: Изображение предоставлено: Aumm graphixphoto/Shutterstock. com
Еще от Изготовление и изготовление на заказ
Архив избранных проектов — Сварочные работы
новыйадмин Избранные проекты
Известный художник Гилберт В. Боро создает потрясающие абстрактные скульптуры из самых разных материалов. Когда Боро понадобилась помощь в реализации его последнего видения, он обратился в Welding Works в Мэдисоне, штат Коннектикут. Результатом сотрудничества стала «Регата II»: медная работа из серии скульптур «Регата» Боро, вдохновленных парусником.
После того, как с художником связался Сварочный завод, он начал оценивать стоимость проекта. Шестифутовое произведение искусства должно было быть изготовлено из латуни, предоставленной художником, и должно было быть выполнено несколько уникальных требований. Как и в случае с большинством произведений искусства, особое внимание уделялось обращению с ними. Очистка на каждом этапе была необходима для поддержания безупречного внешнего вида скульптуры. Дизайн требовал гладкого, чистого внешнего вида, и любой незначительный дефект в изготовлении привлек бы нежелательное внимание.
Сварочные работы имели опыт оценки и изготовления скульптуры и получили задание. Планирование и строительство «Регаты II» требовало координации между художником, инженером-проектировщиком и сварочными работами.
Для обеспечения точности размеров материал был вырезан лазером по формам, указанным в шаблоне. Затем вырезы прокатывались до определенного радиуса на прокатном станке. Когда деталь приобрела форму, все сварные соединения были стратегически скрыты от глаз квалифицированными сварщиками Welding Works. Затем конструкция была прикреплена к основанию из бирюзового цвета с порошковым покрытием, что завершило еще один успешный проект паблик-арта.
newadmin Избранные проекты, главная страница-слайдер
Лошадь
◄ Назад
Далее ►
Изображение 1 из 32
Сварочные работы завершили крупный проект архитектурного орнамента, установленного на монументе арки Грейт-Платт-Ривер-Роуд. Этот 309-й маршрут проходит по межштатной автомагистрали 80 в Кирни, штат Небраска.Трехфутовая арка посвящена первопроходцам, которые 160 лет назад отправились на запад по Грейт-Платт-Ривер-Роуд, по чьему пути теперь следует межштатная автомагистраль.
Роль сварочного завода в этом грандиозном предприятии заключалась в изготовлении символического внешнего украшения конструкции. Орнамент, разработанный Кентом Блумером, включает в себя два набора алюминиевых крыльев высотой 25 футов, которые установлены на северной и южной башнях Арки. Крылья были выбраны Блумером как символ движения, транспорта и связи. Алюминиевая лошадь выпрыгивает из одного набора крыльев, символизируя Пони-Экспресс. Все украшения из алюминиевых пластин были очищены и оставлены в естественном виде. Орнаменты поддерживают около шести тонн конструкционной стали, подвергнутой пескоструйной обработке и окрашенной, также изготовленной Welding Works.
Кроме того, Welding Works завершила 370 футов 14-футовой решетки из алюминиевых труб и пластин, также разработанной Bloomer, и шестнадцать стоек из оцинкованной стали, поддерживающих секции решетки. Решетка тянется через вершину Арки в виде плетеной волны, вызывая ощущение реки Платт. Всего в проекте было использовано около 12 тонн готовых алюминиевых листов и труб. Украшения были изготовлены максимально крупными частями, чтобы ускорить окончательную сборку на месте и крепление к арке, спроектированной архитекторами Питером Х. Домиником-младшим, FAIA, и Робертом Э. Фицджеральдом из Urban Design Group, Inc. , Денвер, Колорадо.
Сварочные работы заключили контракт на выполнение работ с Кентом Блумером и первоначально определили объем работ. На этапе проектирования и проектирования проект крыльев был первым и наиболее важным шагом. Однако каждой паре крыльев требовалась независимая конструкция позади и внутри нее для поддержки и обеспечения взаимодействия произведения искусства с собой и стальной конструкцией здания. За проектирование этих конструкций отвечал Дуг Рутледж, инженер проекта в KL&A (инженер-строитель проекта), который предоставил грубые эскизы опорной конструкции. Какими бы завершенными они ни были, Welding Works столкнулись с бесчисленными проблемами, когда они стремились сочетать произведение искусства со структурой. Связь между Сварочным заводом и инженерами-конструкторами продолжалась, и инженеры-конструкторы также несколько раз посещали Сварочный завод.
Сварка для проекта выполнялась исключительно методом GMAW. Процедуры, сертифицированные Welding Works, а также восемь сварщиков по стандартам AWS для алюминиевого материала 5052-h42 и 6061-T6. Присадочная проволока Е-4043 диаметром 5/64″. Защитным газом был чистый аргон. Материал варьировался от листа толщиной 0,090 до пластины толщиной 1/2 дюйма, причем большинство из них имело толщину 0,190 и 1/2 дюйма. Welding Works использовала источники питания Miller с различными выходными потенциалами с механизмами подачи проволоки Miller XR-30. Эти современные устройства подачи позволили Welding Works подавать очень мягкую проволоку E-4043 диаметром 5/64″ на расстояние 30 футов. Это было важно для работы, так как различные формы и размеры произведений искусства были такими непохожими. Некоторые детали были размером 12 на 26 футов, а иногда сварщики работали на высоте 30 футов в воздухе. Подавляющее большинство сварных швов представляли собой галтели размером от 3/16″ до 1/4″.
Резка конструктивных элементов (балки, уголки, конструкционные трубы и т. д.) выполнялась обычной ленточной пилой. Формы пластин, которые составляли большую часть листвы, были вырезаны на машине для прожига оптических глаз AIRCO. Эта машина способна резать секции шириной шесть футов и длиной 16 футов. Сварочный завод модернизировал машину для резки с помощью Thermal Dynamics STAK-PAC с двумя силовыми модулями и механизированной горелкой. Это позволило компании разрезать лист толщиной 1 дюйм, что было самым толстым участком в проекте. Компания Welding Works добавила датчик высоты C&G для автоматизированной резки. Формы были взяты из моделей в масштабе 8 и четверти и увеличены до полномасштабных плоских моделей. Затем эти узоры были преобразованы в черно-белый шаблон, чтобы трассировщик оптического глаза мог повторять форму. Таким образом, оператор мог быстро и точно вырезать множество различных форм. В проекте было более 1000 различных форм.
Формовка представляла собой серьезную проблему. Модели в масштабе восемь или четверть были единственным источником информации о том, сколько элементов должно быть сформировано. Студия Блумера масштабировала модели и разработала шаблоны прокатки и формовки для Welding Works. Для получения окончательного вида каждой формы обычно использовался метод проб и ошибок. После того, как форма была разработана, Welding Works использовал листогибочный пресс, а также два прокатных станка. Лошадь была самым трудоемким элементом скульптуры из-за того, что многие детали требовали ручной обработки. Только кожи более 400 штук, еще 300 штук пошло на изготовление тела лошади.
Чтобы обеспечить посадку произведения искусства на арочном проходе, а также для разработки распорок, удерживающих произведение искусства, потребовались полномасштабные макеты как северной, так и южной башен здания. Сварочный завод использовал два типа макетов. Данные для размещения листвы были получены из обзора здания, сделанного на крыше в Небраске. Произведение искусства было выложено и поддержано в правильном отношении к зданию и к самому себе. Затем были разработаны стойки, чтобы удерживать всю листву. Чтобы еще больше убедиться, что произведение искусства подойдет, когда оно достигнет Небраски, был выполнен полный вертикальный макет всех сборок. Съемка использовалась для разработки пьедесталов, которые представляли собой пьедесталы зданий. Стальная опорная система была установлена во дворе Сварочного завода, а затем все художественные работы были повешены на сталь в натуральную величину. Каждый конец также был смоделирован в натуральную величину, со всеми элементами, расположенными в правильном соотношении. Для всех этих частей также были разработаны стойки.
Эта симуляция существующих условий на площадке и тестовая сборка были особенно важны. Из-за сложности и нестандартных форм сварщики должны были убедиться, что все узлы подходят друг к другу и будут работать без каких-либо помех. Инженеры-строители также смогли прояснить многие моменты, которые невозможно было рассчитать на бумаге. Пробная сборка также позволила Кенту Блумеру просмотреть готовые украшения и определить, были ли соблюдены художественные критерии. Короче говоря, это давало всем заинтересованным сторонам чувство безопасности, зная, что любые проблемы будут решены на сварочном заводе до отгрузки.
После пробной сборки на Сварочном заводе украшение было доставлено в Небраску. Пять грузовиков, большая часть которых имела большую ширину, доставили проект на площадку. Памятник арке Грейт-Платт-Ривер-Роуд приветствует посетителей на двух уровнях интерактивных экспонатов, размещенных в арке, которые помогают оживить дилижанс Wells Fargo и Pony Express.
newadmin Избранные проекты, главная страница-слайдер
Дубовый мост 035
◄ Назад
Далее ►
Фото 1 из 35
Охрана Центрального парка приняла решение заменить существующий утилитарный пешеходный мост копией Дубового моста, впервые построенного в 1860 году на том же месте. Первоначальный проект моста длиной 75 футов и шириной 13 футов будет приближен с использованием более современных и прочных материалов.
Команда «Сварочные работы» предоставила для этого проекта полный комплекс услуг, от предварительного рассмотрения планов и закупки материалов до решения проблем и монтажа. Некоторые основные моменты:
Наша команда превратила планы архитектора в готовые к изготовлению детали, которые прослужат долго. Наши работы по изготовлению включали декоративные литые алюминиевые концевые стойки; декоративные литые и сварные алюминиевые панели заполнения балюстрады; декоративные литые алюминиевые балюстрады; и декоративные литые алюминиевые медальоны. Нашей целью было убедиться, что все отдельные части и секции должным образом подходят друг к другу.
Welding Works тесно сотрудничала с нашим производителем моделей для создания моделей для большого количества отливок, необходимых для проекта. Это было особенно сложно, потому что многие отливки служили декоративной облицовкой для покрытия двутавровых балок, и каждое покрытие должно было иметь левый и правый рисунок, которые должны были идеально сочетаться друг с другом.
Мы помогли создать систему крепления, похожую на оригинальную. Поскольку новый мост должен был выглядеть так, как будто он был построен в 19 веке, металлические крепления и кронштейны не могли быть видны. Скрытая система крепления, которая была разработана, включала подвесные кронштейны из литого алюминия.
На нашем предприятии в Мэдисоне, штат Коннектикут, был собран макет. Для оценки была полностью собрана одна полная секция моста, состоящая из стальной двутавровой балки и соответствующих ей алюминиевых крышек и решеток.
Перед сборкой моста все алюминиевые отливки были покрыты порошковой краской. Коричневое покрытие с небольшой текстурой использовалось для имитации дерева. Декоративные панели между вертикальными стойками были покрыты черным цветом, чтобы они напоминали кованое железо.
Все поручни, отливки и деревянный настил заказчика были собраны на месте. Когда началась сборка, полевые условия потребовали творческой подгонки секций моста. Алюминиевый материал имел некоторую степень «податливости», что позволяло выполнять эти регулировки при сохранении целостности конструкции.
newadmin Избранные проекты, главная страница-слайдер
ЦИФРОВАЯ КАМЕРА OLYMPUS
◄ Назад
Далее ►
Изображение 1 из 72
ЦИФРОВАЯ КАМЕРА OLYMPUS
Результат «Изобретательности янки» компании из Коннектикута теперь оценили тысячи людей, которые каждый день посещают и используют Центральный парк Нью-Йорка. Сварочные работы в Мэдисоне, штат Коннектикут, недавно завершили совершенно новый забор, чтобы воспроизвести тот, который окружал водохранилище Центрального парка с 1862 по 19 год.26. Первоначальный декоративный забор был уникальным по дизайну и конструкции, в отличие от любого забора, который обычно производится сегодня. Welding Works поставили задачу «нестандартно мыслить», чтобы справиться со сложностями проекта. Они использовали обратный инжиниринг и исследовали технологии, использовавшиеся в прошлом, чтобы разработать рабочий дизайн, план изготовления и установки.
Американская ассоциация оград недавно признала этот проект Welding Works наградой организации «Проект года в области оград». Компания Welding Works получила эту награду во время FENCETECH’04, ежегодного конгресса и торговой выставки Ассоциации, проходивших в Орландо, штат Флорида, с 25 по 27 февраля 2004 г. компания, которая продемонстрировала уникальное мастерство и образцовые знания в области установки ограждений».
Первоначальная декоративная ограда была уникальна по дизайну и конструкции – ее наконечники и декоративные соединения были отлиты вокруг, а не прикреплены к ее штакетникам и перилам. Единственными механическими креплениями, которые использовались для соединения панелей со стойками. Реплика будет установлена на существующем облицовочном камне и будет иметь размеры примерно 8 150 футов в длину и 48 дюймов в высоту (достаточная высота, поскольку водохранилище больше не используется для снабжения питьевой водой).
Поскольку этот проект должен был соответствовать оригинальному забору 1862 года, никаких крепежных деталей, штифтов или сварных швов не было видно. Новые панели должны были иметь сварную конструкцию, и это стало одной из самых сложных задач проекта — разработать методы производства, обеспечивающие экономически эффективное и производительное литье вокруг сварного шва. Чтобы убедиться, что пресс-форма плотно прилегает к каждому соединению для точного литья, первым шагом было создание точных сборочных приспособлений для точности. Сварные детали должны были быть ± 0,15 дюйма, чтобы гарантировать правильность отливки. Приспособление для сварки удерживало стальные стойки на месте с помощью пневматических зажимов и позволяло двум рабочим выполнять сварку одновременно.
Тем временем Welding Works также разработала план, чтобы отливки соответствовали оригинальному ограждению, и работала рука об руку с дизайнером пресс-форм Джимом Кейсом, чтобы разработать уникальную пресс-форму, состоящую из трех частей. Эта форма не только гарантировала попадание достаточного количества железа в форму и заполнила все зазоры, но также могла быть удалена без повреждения отливки. Так как чугун затвердевал почти мгновенно, получить хорошие, плотные, цельные отливки было непросто. Кейс создал резервуар для заливки песка, который позволял подавать в форму дополнительный металл, чтобы компенсировать усадку во время охлаждения.
В итоге было использовано более 1400 чугунных форм для изготовления 19 сборок панельных форм и 16 сборок стоечных форм. Перед заливкой соединений на панели были проведены всесторонние испытания под нагрузкой, чтобы убедиться, что ограждение соответствует последним нормам в 200 фунтов силы. Было определено, что стойки могут выдерживать давление более 900 фунтов без постоянного отклонения.
Сварочный завод подсчитал, что они изготовили 1535 панелей ограждения, каждая длиной 5 футов 6 дюймов, по 26 отливок на панель. К каждой панели присоединялся пост, всего 1538 постов, на каждом по 2 отливки. Всего в рамках проекта было проведено более 43 000 отливок.
Все процедуры установки были разработаны и протестированы на сварочном заводе перед попыткой установки на месте. Уолт Кэмп из Welding Works объяснил: «Как правило, при полевой установке у вас будет возможность решать проблемы и совершенствовать процедуру по мере ее продвижения. При таком плотном графике нам пришлось заранее усовершенствовать методы установки».
Ограждение было завершено и освящено в декабре 2003 года. Его называют «самым значительным изменением в парке за 100 лет». Отсюда открывается беспрепятственный вид на водохранилище, а также на горизонт Манхэттена. Отрицательных отзывов о проекте практически не было. Кристофер Нолан, вице-президент Central Park Conservancy по капитальному ремонту, сообщает: «Забор был очень хорошо принят. Он восстанавливает историческую эстетику водохранилища и полностью меняет представление людей о Центральном парке».
За дополнительной информацией обращайтесь: Welding Works, 32 New Road, Madison, CT 06443, телефон: 203-245-2731, факс: 203-245-0823, электронная почта: [email protected].
newadmin Избранные проекты, главная страница-слайдер
7wwlib
◄ Назад
Далее ►
Изображение 1 из 15
Более года Welding Works участвовала в грандиозном проекте: изготовлении семи алюминиевых декоративных конструкций для Библиотечного центра Гарольда Вашингтона в Чикаго. Мы изготовили более 90 отдельных украшений, разработанных Кентом Блумером, которые мы затем собрали в 7 основных конструкций, которые только что были установлены в 4 углах библиотеки и 3 входах. Эти конструкции шириной до 75 футов и высотой до 40 футов состоят из алюминиевой опорной рамы, к которой прикреплены отдельные узлы. По нашим оценкам, для завершения проекта потребовалось более 1 миллиона сварных швов. Всего было использовано 100 тонн листового, толстолистового и конструкционного алюминия. Алюминий был выбран из-за его прочности и долговечности, а также относительно легкого веса. 80 000 фунтов оцинкованной конструкционной стали также потребовалось для поддержки декоративных конструкций.
Архитектор Томас Биби из Hammond Beeby and Babka, фирмы, спроектировавшей библиотеку, разработал концепцию и архитектурную схему украшений для здания. Его идеи интерпретировали скульптор/орнаментер Кент Блумер и скульптор Рэймонд Каски. Блумер, профессор архитектуры Йельского университета, разработал декоративную листву. Он говорит: «Ботанические украшения для Чикагской библиотеки восходят к древней классической традиции, согласно которой важные элементы, найденные внутри или происходящие от природы… размещаются на видных местах важного здания, чтобы символизировать силы жизни и вечности».
Лиственные украшения состоят из крылатых листьев и вьющихся листьев. Кент Блумер и его помощник Уильям Джелли изготовили модели украшений из дерева и пенопласта, которые использовались для проектирования, ценообразования, проектирования и изготовления. Из них мы разработали полноразмерные шаблоны, которые использовались для вырезания сложных форм из листов и пластин толщиной до 1 дюйма. Таким образом было изготовлено около 1000 различных форм.
Формование оказалось одним из самых сложных аспектов проекта. Для получения окончательного вида каждой формы обычно использовался метод проб и ошибок. После того, как форма была разработана, для формовки использовались листогибочный пресс и 2 прокатных станка. Потребовалась также значительная ручная работа, чтобы привести элементы в их окончательные конфигурации.
В то время как 2 из основных структур имеют большие семенные коробочки в центре, остальные пять украшены совами, которые служат символами мудрости. Рогатая сова высотой 20 футов устроилась в листве над главным входом, а амбарные совы высотой 12 футов являются частью орнамента, установленного в четырех углах здания. Все совы были разработаны Рэймондом Каски из Вашингтона, округ Колумбия. Скульптуры сов были отлиты из песка по частям в Германии, а затем возвращены в Соединенные Штаты, где сварочные работы сварили вместе от 40 до 50 отдельных частей, из которых состоит каждая фигура.
Welding Works произвела пробную сборку каждой крупной конструкции на наших объектах, чтобы убедиться, что все сборки должным образом подходят друг к другу и что все художественные критерии соблюдены. Все непредвиденные проблемы были решены инженерами-строителями, и была разработана последовательность монтажа для использования на площадке в Чикаго.
В общей сложности 35 тягачей с прицепами были использованы для перевозки частично разобранных конструкций из Коннектикута в Чикаго, на расстоянии 900 миль. Когда они добрались до Чикаго, украшения были окрашены в зеленый цвет, чтобы имитировать выветренную медь. Поскольку установка требовала перекрытия городских улиц, большая часть этих работ выполнялась только по выходным, чтобы не мешать движению транспорта.
В прошлом почти вся наша работа была связана с производством. Тем не менее, этот проект дал Welding Works шанс доказать свое мастерство в создании архитектурных украшений.
Работа, выполненная Welding Works для этого проекта, была отмечена двумя крупными наградами. Первой была награда 1995 года за выдающееся мастерство обработки металлов на международном конкурсе, спонсируемом Национальной ассоциацией декоративных и прочих металлов (NOMMA). Второе признание было получено от Ассоциации инженеров-строителей штата Иллинойс, которая присудила проекту украшения награду за заслуги перед его вкладом в развитие современного строительства.
newadmin Избранные проекты, без категории
Когда поместье известного архитектора и скульптора Тони Смита (1918-1980) недавно заказало изготовление одного из его проектов под названием SMOG, компания Lippincotts, LLC заключила контракт на координацию всех аспектов проекта. Эта конструкция, которая состояла из 45 октаэдров, 15 верхних призм, 22 базовых призм, 21 узла накладок и изготовленных на заказ крепежных устройств, представляла множество проблем при изготовлении.
Липпинкоттс знал, что производителя нужно выбирать очень тщательно. Альфред Липпинкотт, президент компании, сказал, что критерии, по которым оценивались четыре фирмы-изготовителя, которые они рассмотрели, были следующими:
- способность выполнять точную, детальную работу с особым вниманием к эстетике;
- возможность строить в больших масштабах, с просторными помещениями и мостовыми кранами;
- способность руководства тщательно продумывать проект и решать проблемы, всегда имея в виду замысел художника и его имущество.
Дизайн SMOG состоял из очень точных геометрических форм и математических расчетов, поэтому мы решили подойти к этому проекту очень тщательно. После нескольких мозговых штурмов мы разработали уникальный дизайн и производственный план, который позволил решить все проблемы поместья и Липпинкотта по разумной цене. В результате мы получили контракт.
Мы обнаружили, что при изготовлении SMOG нам приходилось учитывать множество проблем. Важно было соблюдать точность. Если бы 45 октаэдров не были сделаны точно, в результате появились бы нежелательные промежутки и отверстия. Одним из ключей к созданию октаэдров была литая алюминиевая переборка, разработанная Welding Works. Отливки были легкими, но прочными. Обработка всех кромок и подготовка под сварку оказалась рентабельной. Эти факторы значительно сократили время шлифовки/шлифовки и обеспечили плотную посадку.
На этапе планирования было потрачено много часов. Компания Welding Works разработала полный набор подробных чертежей AutoCAD, а также тщательно спланировала производственные процессы. Было спроектировано и изготовлено специальное приспособление для сборки и сварки блоков. Это, наряду с другими нашими процедурами, позволило нам поддерживать допуски 0,020″, которые Альфред Липпинкотт назвал «замечательными для производственного предприятия».
Другие строгие требования проекта заключались в том, чтобы все поверхности были ровными и не имели неровностей; что все болтовые соединения имеют максимальный зазор 0,030 дюйма; и чтобы все соединительные края были четкими и четко очерченными. Наконец, отделка и покраска деталей оказались особенно сложными. Несмотря на более чем 3500 футов сварных швов, конечный продукт не мог иметь видимых сварных швов или фурнитуры.
После сварки и осмотра каждая деталь была помещена в специальную люльку для защиты, где она оставалась для шлифовки, шлифовки, грунтовки, окончательной окраски и загрузки в грузовик для отправки. Еще одной сложной задачей было нарисовать большие плоские панели скульптуры. Мы использовали двухслойную систему грунтовки, а также несколько финишных слоев черного полуматового покрытия.
В итоге СМОГ был выполнен в рамках бюджета и на месяц раньше срока. Были приняты меры по доставке в Вермонт, где он был установлен на территории кампуса Миддлбери-колледжа. Альфред Липпинкотт недавно заявил: «Готовность Welding Works реагировать на наши вызовы очень обнадеживает. Мы были особенно впечатлены их вниманием к деталям, и они уже работают над другими проектами Тони Смита для нас».
Руководство по материалам, используемым при изготовлении металлоконструкций
Зарегистрировано ITAR
Изготовление металлоконструкций определяется как процесс создания и изготовления металлических конструкций из необработанных металлических материалов. Он включает в себя резку, формование, сгибание и формование металлического материала в желаемый конечный продукт. Процессы изготовления металла включают в себя все, от тяжелых машин и оборудования до простых поручней. Конкретные процессы могут включать изготовление ручных инструментов, столовых приборов, конструкционных металлов, проволоки, производство пружин, ковку, производство винтов и болтов, штамповку и архитектурные металлы. Изготовление позволяет создавать конечный продукт из сырья вместо продукта, сделанного из готовых материалов. части.
Сырье, используемое в производстве металлов
Перед началом процесса изготовления металлов необходимо понять, какие материалы доступны, и определить, подходят ли они для вашего применения. За прошедшие годы использование общего сырья привело к стандартизации производственных деталей и их компонентов. Следующее изложенное сырье легко доступно у широкого круга поставщиков металлов, чтобы удовлетворить ваши производственные потребности.
Сырье для литья
Литье — это процесс, при котором жидкий металл заливают в форму, а затем дают ему остыть, чтобы он затвердел и принял желаемую форму. Литье — идеальный выбор для изготовления изделий сложной геометрии, поскольку оно обладает высокой степенью гибкости. В процессе литья обычно используется расплавленный металл, но также можно использовать бетон, глину и эпоксидные смолы.
Общие металлы, которые используются в процессе, включают:
- Железо является природным химическим элементом и одним из самых распространенных на Земле по своей массе.
Он в изобилии и является важным материалом, используемым в производстве стали.
- Алюминий — легкий, универсальный и долговечный элемент. Он также обладает отличной электро- и теплопроводностью. Алюминий плохо работает при температурах выше 400°F, но отлично работает при отрицательных температурах; следовательно, он идеально подходит для приложений, связанных с низкими температурами, таких как авиация или охлаждение.
- Сталь – это сплав, полученный из углерода и железа. Он включает в себя смесь железной руды, известняка, угля и некоторых других элементов. Это наиболее используемый металл в производстве, и он имеет множество применений в машиностроении, строительных материалах и даже в оружии.
- Нержавеющая сталь представляет собой сплав, обладающий высоким коэффициентом коррозионной стойкости. Он состоит из алюминия, хрома, углеродистой стали и других элементов. Металл имеет характерное серебристое зеркальное покрытие. Нержавеющая сталь используется в производстве кухонной посуды, хирургических изделий, приборов и фурнитуры для шкафов.
- Медь — это прочный, ковкий и прочный металл, который является отличным проводником электричества. Он обладает высокой устойчивостью к коррозии, что делает его полезным для промышленных и морских целей.
- Бронза представляет собой гораздо более прочный сплав меди и тяжелее стали с более низкой температурой плавления. Он используется для изготовления монет, доспехов, посуды и оружия.
- Магний представляет собой относительно легкий конструкционный металл с низкой плотностью. Идеально подходит для использования там, где требуется жесткость, а не прочность. Магний в основном используется в корпусах самолетов, вращающихся машинах и автомобильных деталях.
- Латунь – это сплав цинка и меди. Он обладает акустическими свойствами, что делает его полезным при литье музыкальных инструментов. Он также используется для производства болтов, гаек, дверных ручек, фитингов и деталей часов.
Типы металлоконструкций
- Литье — это метод изготовления, при котором расплавленный металл помещается в форму и охлаждается для затвердевания до требуемой формы.
Для получения желаемого дизайна используются различные инструменты для крафта.
- Резка – это тип изготовления, при котором металлическая деталь разрезается на более мелкие части в зависимости от желаемого размера.
- Волочение — это процесс, который включает в себя вытягивание металла в тонкую форму. Нанесение обычно проводят при комнатной температуре, но можно проводить нагрев, если есть необходимость уменьшить силу.
- Сгибание — это манипулирование металлом, чтобы заставить его сгибаться под определенным углом. В основном это делается с помощью тормозного пресса, который сжимает металл, чтобы образовались складки. Это также можно сделать с помощью фальцевальной машины или вручную забить металлическую деталь, пока она не согнется.
- Ковка — это использование силы сжатия для придания формы металлу. Молоток бьет по металлической детали до тех пор, пока не будет сформирована необходимая форма.
- Экструзия — это процесс, который используется для скручивания металлического листа в цилиндрическую форму для формирования конструкции проводки или трубопровода.
- Механическая обработка — это удаление ненужного материала с металлической детали для придания ей формы. Обработка может производиться фрезерованием или сверлением.
- Штамповка – это создание отверстий в металлической детали с помощью штамповочного пресса.
- Резка — это процесс, необходимый для получения длинных прямых пропилов в металле. Это включает в себя использование двух инструментов; лезвие в верхней части и неподвижное нижнее лезвие, оказывающее давление на металл.
- Штамповка — это процесс, аналогичный штамповке, за исключением того, что вместо отверстия делается углубление. Он используется для формирования букв, изображений или фигур на металлическом листе. Для штамповки можно использовать инструменты для крафта или пресс.
- Сварка — это процесс соединения двух или более металлических деталей с использованием тепла и давления.
Профили
Профили изготовлены из стали и доступны в стандартных размерах и формах. В основном они предназначены для строительных и инженерных целей. Химические и физические свойства различных видов профильных металлов уже имеют заранее установленные стандарты. Общие типы включают в себя:
- Двутавровая балка представляет собой длинную стальную балку с поперечным сечением, напоминающим букву I. Обе полки балки имеют наклон на внутренней поверхности, который обычно составляет 1:6, что делает полки утолщенными внутри и тонкий снаружи. Двутавровая балка и балка с широкой полкой (WF) являются разновидностями этой категории балок.
- Z-образная балка представляет собой балку, напоминающую букву «Z», с половинной полкой, выступающей в противоположном направлении.
- Полый конструкционный профиль (HSS) представляет собой тип стальной балки с полым поперечным сечением. Они изготавливаются различных стандартных форм, то есть круглого, квадратного, эллиптического или прямоугольного сечения.
- Пруток представляет собой вид профильного металла с прямоугольным поперечным сечением, длинным и плоским.
- Стержень представляет собой кусок металла, имеющий длинную форму квадратного или круглого сечения.
Плоский металл
Это металл, прокатанный и спрессованный в тонкие плоские детали. Толщина плоского металла измеряется в калибрах и может варьироваться от нескольких сантиметров до менее миллиметра. Сырье из плоского металла можно разделить на три категории:
- Наиболее распространен листовой металл толщиной шесть миллиметров.
- Фольга или листовой металл имеют толщину бумаги и фактически являются самыми тонкими из плоских металлов.
- Листовой металл — это категория любого плоского металла толщиной более 0,25 дюйма.
Проволока сварочная
Проволока сварочная состоит из легко спаиваемых металлов, сформированных в круглые стержни. Они используются в процессе сварки, где они соединяют два или более металлических куска вместе. Сварочная проволока поджигается, чтобы сделать проволоку мягкой и создать нагретую дугу для соединения металлических деталей. Они изготавливаются в широком диапазоне размеров и металлических материалов, что позволяет выполнять сварку по индивидуальному заказу.
Формованный и расширенный металл
Расширенный металл формируется из стальных листов, одновременно расширяемых и разрезаемых в холодных условиях для создания ромбовидных отверстий одинаковой толщины и размера. Эти отверстия окружены металлическими нитями, которые соединены между собой для расширения до конечного размера. Полученные решетчатые листы используются для уличной мебели, дверей-ширм, ограждений и других архитектурных конструкций. Они также используются в промышленности в качестве ограждений, чтобы избежать прямого контакта с горячим оборудованием.
Метизы
Метизы определяются как различные детали или фитинги, используемые для того, чтобы сделать конкретный продукт более прочным и легким в изготовлении. К ним относятся такие материалы, как:
- Уголки представляют собой металлические детали, срезанные под углом, которые используются для соединения металлических деталей под углом 90°.
- Ручки используются для облегчения удерживания металлической пластины.
- Замки представляют собой механизм, размещенный на металлической конструкции для блокировки двух или более частей на месте.
- Ключи идут рука об руку с замками, обеспечивая механизм открывания.
- Цепи используются для связывания или подвешивания металлических деталей.
Инструменты, используемые в металлообработке
- Ленточная пила представляет собой электрическую пилу с острым длинным лезвием, состоящим из металлической ленты, зубчатой и натянутой на два или более колеса для резки предметов. Он идеально подходит для выполнения однородного, неровного или криволинейного разреза на различных материалах.
- Настольные ножницы используются для вырезания заготовок из металлических листов. Единственным недостатком является то, что они не могут выполнять деликатные разрезы.
- Электроножницы используются для быстрой резки металлических листов с минимальными ручными усилиями.
Они не способны вырезать узкие углы или замысловатые формы.
- Ножницы по металлу — это ручные ножницы, напоминающие ножницы с толстыми ручками и короткими, прочными и острыми лезвиями, используемые для резки тонких листов металла, например нержавеющей стали.
- Стамески — это режущие инструменты с заостренным клином на дне, которые часто используются с киянкой или молотком для резки или придания формы металлу. Долото считается частью ремесленных инструментов.
- Шлифовальные станки — это инструменты, которые используются для обработки материалов путем измельчения или измельчения их на более мелкие кусочки. Шлифовальные машины также используются для полировки металлических поверхностей.
- Крепеж Cleco представляет собой набор инструментов, которые временно скрепляют несколько металлических листов перед их постоянным соединением или сверлением.
- Диски шлифовальных станков изготовлены из грубого, грубого материала, склеенного вместе в круглую форму.
Эти круги используются в шлифовальных станках.
- Кусачки — это специальные плоскогубцы, предназначенные для перекусывания проводов своими губками.
- Стеклорезы используются для неглубокого проникновения на стеклянную поверхность, которую необходимо разбить. Стекло разбивается по бороздке, сделанной в зависимости от введенной формы.
- Зубофрезерные станки — это станки, которые используются для нарезания зубчатых колес, звездочек и шлицов.
- Фрезерные станки используются для удаления слоев материала в виде канавок с поверхности металлической детали с помощью многолезвийной фрезы.
- Хонинговальные станки используются для улучшения формы конкретной поверхности путем создания точной поверхности на металлической детали путем очистки шлифовальным кругом по контролируемой траектории.
- Строгальные станки — это станки, используемые для изготовления точных пазов и плоских поверхностей.
Краткий обзор металлоконструкций
В этом руководстве многое объясняется о сырье, используемом в производстве металлов, и, надеюсь, вы лучше понимаете, как это работает. Изготовление металлов имеет очень широкое применение во многих отраслях промышленности, а также в производстве потребительских товаров. В настоящее время большинство компаний внедрили передовое оборудование для увеличения скорости выполняемой работы. Поэтому для создания такого оборудования нужны специалисты по металлообработке.
Вернуться назад
Сварочные услуги в строительстве
Admin • 16 октября 2017 г.
Сварка — это процесс, в котором используется сплав для соединения металлов. Это самый прочный и долговечный способ соединения металлов, который используется во многих отраслях промышленности. В строительной отрасли сварщики являются квалифицированными специалистами, которые участвуют на каждом этапе строительства.
Сварщики используют различные сварочные процессы в цеху или на месте. Некоторые из наиболее известных процессов включают дуговую сварку в среде защитного газа, дуговую сварку под флюсом и дуговую сварку под флюсом. Каждый процесс сварки служит отдельной потребности и цели и выполняется сварщиком, который специализируется на этом конкретном типе сварки.
Вот некоторые из услуг, которые сварщики предоставляют в строительной отрасли.
Сварка несущих и ненесущих систем
Сварщик работает со строительным подрядчиком для соединения стальных двутавровых балок, колонн, ферм и нижних этажей, составляющих несущий каркас здания. Эти компоненты нарезаются по размеру, поднимаются на место с помощью крана или строительного домкрата, а затем свариваются вместе для поддержки полов, стен и крыши здания.
Сварщик также может сваривать ненесущие металлические элементы здания. К таким элементам относятся лестницы, поручни, мосты между комнатами, балки пола, стальные каркасные шпильки, брандмауэр и другие компоненты, которые слишком велики или являются неотъемлемой частью конструкции здания, чтобы их можно было закрепить болтами.
Сварка электрических систем
Сварщик работает в тесном сотрудничестве с трубомонтажником, чтобы установить и соединить вместе стальные трубы, называемые электрическими кабелепроводами, в соответствии с планами архитектора. Эта система передает электричество от источника питания за пределами здания в каждую часть здания, которая нуждается в электричестве.
Этот электрический кабелепровод скрепляет провода и защищает их от повреждений. Электрический кабель режется по размеру, сгибается, чтобы соответствовать размерам комнаты, а затем сваривается вместе сварщиком. Затем электрический кабелепровод надежно крепится к стенам или стойкам стены комнаты и проходит между блоками электропитания.
После того, как электрический кабелепровод сформирован, сварен и присоединен, электрические провода проталкиваются через него в электрические коробки, где электрик может подключить проводку к выключателям и вилкам для электрификации системы.
Сварка сантехнических систем
Сварщик работает в тесном контакте с сантехником, чтобы разрезать, сварить и установить водопроводные и канализационные трубы в каждую комнату здания, где будет водопровод. Водопроводные трубы подают питьевую воду из городского или сельского водопровода и распределяют ее по всему зданию.
Канализационные трубы устанавливаются для отвода использованной воды из здания и направления ее в дренажно-канализационную систему. Водопроводные и канализационные трубы нарезаются по размеру, свариваются вместе для обеспечения прочности и долговечности и закапываются под землю для обеспечения их безопасности.
Сварка системы отопления
Сварщик работает с трубомонтажником, чтобы установить систему циркуляции топлива, которая подает природный газ по всему зданию для отопления и приготовления пищи. Эти топливные трубы нарезаются по размеру и размещаются в стенах и полах жилого или коммерческого здания в соответствии с архитектурными чертежами здания.
Вспомогательная система вентиляции установлена рядом с топливной системой для улавливания выхлопных газов и удаления их из здания. Трубы топливной и вентиляционной системы свариваются вместе, чтобы соответствовать определенной форме помещения и предотвратить протечки.
Чтобы получить квалифицированную сварку для любого из этих строительных процессов, свяжитесь с 3-B Welding LLC. Их сварщики могут предложить свой опыт и знания независимо от того, строите ли вы жилое или коммерческое здание. Позвоните им или свяжитесь с ними через Интернет, и они посетят место, чтобы встретиться с вами и просмотреть ваши архитектурные чертежи, чертежи и спецификации. Благодаря их опыту у вас получится красивое здание, которое прослужит вам долгие годы.
Новое сообщение >
Поделиться
Твитнуть
Поделиться
Отправить по электронной почте
Как изготовление листового металла на заказ принесет вам пользу
По администратору
•
10 августа 2022 г. •
Изготовление изделий из листового металла на заказ может стать большим преимуществом для многих предприятий. Узнайте о некоторых преимуществах изготовления изделий из листового металла на заказ.
Что следует учитывать при найме службы мобильного крана
По администратору • 10 июня 2022 г. •
Аренда крана может быть более рентабельной, чем владение краном. Вот несколько вещей, которые следует учитывать при выборе идеального поставщика услуг крана.
Типичные ошибки, которые совершают люди при работе с крановой службой
03 апр, 2022 •
Вы должны знать распространенные ошибки, которые совершают люди при работе с крановой службой, чтобы ваш проект прошел гладко. Читайте дальше, чтобы узнать несколько советов.
4 способа, которыми сварщик может модернизировать кузов вашего грузовика
07 марта 2022 г. •
Если вы хотите модернизировать кузов грузовика, сварка — отличный способ сделать это. Прочтите этот блог, чтобы узнать, как сварщики могут модернизировать кузов вашего грузовика.
2 простых способа защитить конвейерную ленту от повреждений
По администратору • 02 фев, 2022 •
Во избежание повреждения конвейерной ленты ознакомьтесь с частями вашей системы, требующими обслуживания. Узнайте, как предотвратить повреждение конвейерной ленты.
Вопросы, которые следует задать своему монтажнику, прежде чем нанимать его
По администратору • 07 дек, 2021 •
Монтаж металлоконструкций является важным этапом строительства любого успешного здания. В этом блоге подробно рассказывается, что вы должны спросить, прежде чем нанимать монтажника металлоконструкций.
Причины нанять профессионального сварщика для ремонта оборудования
По администратору • 23 авг, 2021 •
Хотя металл является прочным материалом, не требующим особого ухода, он подвержен износу и повреждениям. Читайте дальше, чтобы узнать, почему наем профессионального сварщика может помочь.
Аренда мобильного крана для вашего начинающего бизнеса
По администратору • 25 июня 2021 г. •
Вы хотите арендовать или нанять мобильный кран для своего начинающего строительного бизнеса? Читайте дальше, чтобы узнать больше о том, как аренда мобильного телефона может помочь вашему бизнесу.
Преимущества и области применения точечной сварки
По администратору • 24 мая 2021 г. •
Точечная сварка – это вид сварки, при котором две металлические поверхности соединяются электричеством и давлением. Узнайте о преимуществах и применении этой техники.
4 Варианты услуг по сварке Идеально подходят для компаний, занимающихся вывозом мусора
По администратору • 17 марта 2021 г. •
Если вы хотите продлить срок службы и возможности использования мусорного контейнера, рассмотрите возможность использования профессиональных сварочных услуг. Сварочные услуги могут улучшить аренду вашего мусорного контейнера.
Показать больше
Сварочный аппарат — 7J40
Сварочный аппарат — 7J40ОБЩЕЕ ОПРЕДЕЛЕНИЕ
Это полноценные сварочные работы по ремонту, восстановлению или замене поврежденных деталей различных конструкций и оборудования из легких и тяжелых металлов. Работник этого класса осматривает поврежденные части металлических конструкций или оборудования для определения методов и приемов работы, а также ремонтирует, восстанавливает или заменяет металлические детали с использованием различного сварочного оборудования, инструментов и машин. Работа включает удаление поврежденных металлических деталей, а также проектирование и изготовление запасных частей. Работник этого класса может использовать в работе точные инструменты и машины.
Работа выполняется под руководством руководителя ремонтной группы и связана с физическими нагрузками и условиями, которые можно лишь частично контролировать.
КОЭФФИЦИЕНТ РАСПРЕДЕЛЕНИЯ: (Следующие условия должны быть выполнены для того, чтобы должность была отнесена к этому классу.)
- Должность должна осматривать поврежденные части металлических конструкций или оборудования, определять соответствующие методы и приемы работы, а также ремонтировать, восстанавливать или заменять металлические детали с использованием различного сварочного оборудования, инструментов и машин.
ТИПОВЫЕ ПРИМЕРЫ РАБОТ (ТОЛЬКО ИЛЛЮСТРАТИВНЫЕ)
- Осматривает поврежденные металлические детали, чтобы определить характер работы и типы используемых инструментов, оборудования и материалов.
- Выполняет сварку для ремонта или восстановления поврежденных частей различных алюминиевых, медных, стальных и других металлических конструкций или оборудования, таких как крылья, кузовные панели, кронштейны, резервуары, бункеры, радиаторы, заборы, ворота, замки , шарниры, трубы, насосы, клапаны, котлы и компрессоры; сваривает или удаляет поврежденные детали; использует ацетиленовый газ, металлический инертный газ (MIG), вольфрамовый инертный газ (TIG) и электрическое оборудование, такое как терморезка или кислородно-ацетиленовая горелка, для резки, расплавления, пайки, пайки и сборки деталей; использует молотки, гаечные ключи, инструменты и оборудование, такое как мостовые краны, гидравлические домкраты, прижимные планки, опорные столы и т.
д., для удаления, позиционирования, облегчения и выпрямления деталей; очищает и модифицирует детали, используя шлифовальные станки; может сваривать или удалять детали из пластика или стекловолокна, используя оборудование для сварки пластика или стекловолокна (ПВХ).
- Проектирует и производит запасные части; проектирует и изготавливает кузовные панели, кронштейны, болты, гайки, ступени, баки, ограждения, замки, петли, ограждения, экраны, трубы, валы, стержни клапанов, втулки и другие детали; макет или готовый металлопрокат для изготовления; выбирает инструменты, оборудование и машины, необходимые для выполнения задачи; снимает мерки с поврежденных деталей для изготовления; размещает металломатериал на станках для выполнения необходимых операций; сваривает или изготавливает детали с использованием точных инструментов и машин; прикрепляет изготовленные детали к основным конструкциям или оборудованию; могут использовать чертежи и письменные спецификации.
- Делает оценку времени и материалов.
- Может назначать работу и инструктировать других профессий и помощников по элементам профессии.
- Выполняет соответствующие работы по мере необходимости.
НЕОБХОДИМЫЕ ЗНАНИЯ, НАВЫКИ И СПОСОБНОСТИ
ЗНАНИЕ:
- Эксплуатация оборудования для электродуговой и ацетиленовой газовой сварки.
- использование оборудования для электродуговой и ацетиленовой газовой сварки для сварки, пайки, пайки, резки, наращивания и изготовления деталей.
- профессиональные опасности и меры предосторожности, применимые при сварке и изготовлении.
- Металлическое оборудование с инертным газом (MIG или Heli-Arc) и вольфрамовым инертным газом (TIG), процедуры и методы.
НАВЫК:
- уход и использование инструментов, машин и оборудования, используемых в торговле.
СПОСОБНОСТЬ:
- научиться технике сварки распылением.
- понимать и выполнять устные и письменные инструкции.
- осматривать поврежденные или дефектные детали металлоконструкций и оборудования и определять методы и приемы работ.
- сварка или изготовление деталей и конструкций с использованием измерений поврежденных деталей, чертежей и письменных спецификаций.
- сделать смету времени и материалов.
МИНИМАЛЬНАЯ ДОПУСТИМАЯ ПОДГОТОВКА И ОПЫТ
- ОБРАЗОВАНИЕ:
Образование, эквивалентное окончанию двенадцатого класса школы. - Три года обучения сварочному делу в качестве ученика или помощника, включая опыт работы в области электродуговой, ацетиленовой, гелиодуговой и/или другой сварки.
Или любое эквивалентное сочетание образования и опыта, признанное отделом кадров приемлемым.