Сварной метод соединения конструкций против болтового
04.02.2018
Почему в производстве металлоконструкций делается акцент на сварной метод соединения конструкций против болтового? Потому что он является современным аналогом геометрически точного процесса, в результате которого происходит соединение металлоконструкций.
При помощи сварки можно присоединить элемент любой формы. У болтовых соединений тоже есть несомненный плюс — монтаж на месте. Если же брать оба метода и «с нуля» разбирать их применение в строительном производстве, как определить почему сварной метод соединения конструкций против болтового проще и технологичной? Давайте, разбираться вместе.
- На разработку технологий уходят годы времени и миллионы денег. А все дело в вычислениях, которыми мы называем необходимые расчеты. Вместе с болтовыми и сварными методами были изобретены пайка и клёпка, на сегодняшний день используемые не так часто.
Оказывается, все дело в расчетах и повышенных требованиях к геометрической точности сопрягаемых частей конструкции. Сваркой можно соединить элементы металлоконструкций, изготовленных из металла, даже в положениях, которые являются достаточно сложными с точки зрения свободного пространства. Болтовые соединения используется в тех случаях, когда сварка просто невозможна – в том числе, при соединении неметаллических элементов.
Сварной метод соединения конструкций против болтового способен обеспечивать качество крепёжных отверстий — герметичность, точность, надежность. Болтами, зачастую, стягивается сразу несколько деталей и определить геометрию отверстий иногда очень трудно, из-за сложности форм.
Функциональность метода соединения металлоконструкций должна учитываться в любых условиях. Оперировать болтовыми процессами бывает очень сложно. Поэтому в труднодоступных и неудобных местах, где нет речи об использовании болтов, из-за сложности форм и креплений, применяется сварной метод соединения металлоконструкций.
- Что нужно сделать, чтобы точно и правильно осуществить соединение металлоконструкций болтами? Сделать герметичное и плотное отверстие для болтов, вымерить, просверлить его и проштамповать болты, после чего произвести болтовое соединение, обработав его дополнительно защитными средствами. В противном случае соединенные элементы не спасти от коррозии.
Первоначально, когда о сварке не знали, металлоконструкции соединяли клепками. Этот метод используется и в наши дни, ответственные конструкции и силовые элементы самолетов клепают до сих пор. В начале XX века сварка считалась «дорогим удовольствием», но более дешевым, чем соединение на клепках, поэтому человечеству потребовались дополнительные технологии, между которыми можно было бы поставить знак равенства по прочности, максимально снизив стоимость работ.
Сварной метод соединения конструкций против болтового стал использоваться раньше. К нашему времени он заметно подешевел и стал доступным для всех категорий потребителей. Но по-прежнему остался досягаемым для полноценного осуществления специалистам соответствующей категории, у которых есть специальное оборудование — аппарат, источник тока, кабеля и щиток, и, конечно же, навык работы.
Для болтовых соединений понадобятся гаечные ключи и метизы, к рабочим-исполнителям никаких требований по квалификации не предъявляется. Некоторые типы конструкций, например, мосты, собирают на высокопрочных болтах. В таких соединениях усилие передается не за счет прочности болта, а за счет силы трения между элементами, которые стягивает болт. В остальных случаях о надежности болтовых соединений говорить трудно.
У обычного болта есть всегда зазор между соединенными элементами, и, соответственно, люфт (дословно: зазор, промежуток, свободный ход, из-за чего одна деталь свободно, в небольших пределах движется в разные стороны без сцепления или контакта с другой деталью). Поэтому произвести болтовое соединение сложных по форме металлоконструкций — невозможно. Точно также как невозможно выполнить на одних болтах крепеж крупных строительных металлоконструкций — балок, ферм, рам, состоящих из различных прокатов.
По прочности сварной метод соединения конструкций против болтового не противопоставляются. Прочность болтового соединения определяется диаметром используемых болтов, в сварочных соединениях сварочный шов, выполненный качественно, почти на все 100% соответствует структуре того металла, который при сварке является основным. При малом числе точек креплений оптимальным считается болтовое соединение, во всех остальных случаях специалистами в строительном производстве используется сварное соединение.
Более подробно узнать сварной метод соединения конструкций против болтового будет лучше в вашем проекте или наоборот можно у специалистов компании по телефону 391 215-25-35. Обращайтесь!
Вернуться к списку
Виды сварных соединений — Сварные соединения
Виды сварных соединений
Категория:
Сварные соединения
Виды сварных соединений
Сварным соединением называют неразъемное соединение нескольких деталей, выполненное сваркой. При сварке плавлением применяют стыковое, нахлесточное, угловое и тавровое соединения. Применяются также соединения прорезные, торцовые, с накладками и электрозаклепочные.
В стыковом соединении составляющие его элементы расположены в одной плоскости или на одной поверхности. Оно наиболее распространено в сварных изделиях, так как имеет следующие преимущества перед остальными:
1. Неограниченная толщина свариваемых элементов.
Рис. 1. Основные виды сварных соединений: а — стыковые, б — стыковые с отбортовкой, в — стыковые листов разной толщины, г — нахлесточные, д — угловые, е — тавровые, ж — прорезные, з — торцовые, и — с накладками, к — электрозаклепочные; 1, 3 — свариваемые детали, 2 — накладки
2. Более равномерное распределение силовых линий (напряжений) при передаче усилий от одного элемента к другому.
3. Минимальный расход металла на образование сварного соединения.
4. Надежность и удобство контроля качества соединения рентгеновским излучением с определением места, размеров и характера дефекта сварки.
Недостатками стыковых соединений перед другими видами являются:
1. Необходимость более точной сборки элементов под сварку.
2. Сложность обработки кромок под стыковую сварку профильного металла (уголки, швеллеры, тавры, двутавры).
Угловое соединение — сварное соединение двух элементов, расположенных под прямым углом и сваренных в месте примыкания их краев (рис. 38, д).
Тавровое соединение — сварное соединение, в котором к боковой поверхности одного элемента примыкает под углом и приварен торцом другой элемент (рис. 38, е), как правило, угол между элементами прямой.
Угловые и тавровые соединения широко используются при сварке балок, колонн, стоек, каркасов, ферм и др., обеспечивая увеличение жесткости и уменьшение деформаций изделия.
Нахлесточное соединение представляет собой сварное соединение, в котором свариваемые элементы расположены параллельно и перекрывают друг друга. Эти соединения имеют недостатки: 1. Расход основного металла на перекрытия в соединении. Необходимость экономии металла ограничивает применение нахлесточных соединений для элементов толщиной до 20 мм. Величина нахлестки (перекрытия) должна быть не менее 5 толщин наиболее тонкого из свариваемых элементов.
2. Распределение силового потока в нахлесточном соединении является нелинейным, поэтому оно хуже работает на переменную или динамическую нагрузку, чем стыковое. В конструкциях, работающих при низких температурах и подвергающихся действию переменных или динамических нагрузок, следует избегать нахлесточных соединений.
3. Возможность проникновения влаги в щель между перекрываемыми листами (при односторонней сварке), что вызывает ржавление сварного соединения.
4. Сложность определения дефектов сварки.
Преимуществами нахлесточного соединения являются:
1. Отсутствие скоса кромок под сварку.
2. Простота сборки соединения (возможность подгонки размеров за счет величины нахлестки).
Прорезные соединения применяются тогда, когда длина шва нахлесточного соединения не обеспечивает достаточной прочности.
Соединения с накладками применяют только в тех случаях, когда не могут быть выполнены стыковые или на-хлесточные соединения.
Рис. 2. Распределение силовых линий в соединениях: а — стыковом, б —- нахлесточном
Накладки применяются также для соединения элементов из профильного металла и для усиления стыковых соединений.
Соединения электрозаклепками применяют в нахлесточных и тавровых соединениях. При помощи электрозаклепок получают прочные, но не плотные соединения. Верхний лист пробивается или просверливается, а отверстие заваривается так, чтобы был частично проплавлен нижний лист (или профиль). При толщине верхнего листа до 6 мм его можно предварительно не просверливать, а проплавлять дугой, горящей под флюсом или в защитном газе, при этом можно применять и неплавящиеся электроды.
Основные типы и конструктивные элементы электрозаклепоч-ных швов сварных соединений устанавливаются ГОСТ 14776—69.
Реклама:
Читать далее:
Классификация сварных швов
Статьи по теме:
Сварные соединения.

ООО ПКФ «ЧМП» представляет Вашему вниманию статьи на различные темы, связанные с обработкой металлов. В нашем справочнике Вы найдете большое колличество статей на различные темы:
- Резка металлов
- Токарная обработка металла
- Фрезеровка металла
- Шлифовальные работы
- Штамповка металлов и разновидность штамповой оснастки
- Термическая обработка
- Гальваническая обработка металла
- Сварочные работы
Сварные соединения. Достоинства и недостатки.Достоинства и недостатки сварных соединений по сравнению с заклепочными
соединениями. Достоинства: 1) простота конструкции сварного шва и меньшая трудоемкость; 2) снижение массы конструкции; 3) возможность соединения деталей любых форм; 4) герметичность соединения; 5) малошумность технологического процесса; 6) сравнительно легкая возможность автоматизации процесса; 7) в целом сварное соединение дешевле заклепочного. Недостатки: 1) возникновение остаточных напряжений в свариваемых элементах; 2) коробление деталей; 3) недостаточная надежность при значительных вибрационных и ударных нагрузках. Мы выполняем сварочные работы, газопламенную резку металла, токарные работы ЧПУ, фрезерные работы ЧПУ, шлифовальные работы, сверлильные работы, термообработку изделий, гальваническую обработку деталей.![]() Разделы / Полезная информация |
|
Если Вы желаете стать автором статей на тему обработка металлов, то просим написать администратору сайта (Написать администратору)
Какое соединение лучше и надежнее: сварное или болтовое
Необходимость делать подобный выбор сегодня обусловлена тем, что практически все современные металлоконструкции собираются по частям. Сегодня не меньше 95% металлических конструкций делаются именно сборными. Чем обоснован такой подход?
Разбираемся какое соединение лучше: сварное или болтовое
- Во-первых, сборные металлоконструкции позволяют быстро заменить деталь, вышедшую из строя.
- Во-вторых, на изготовление сборной конструкции требуется гораздо меньше металла, чем на изготовление цельной. Таким образом, вся конструкция получается намного дешевле.
- В-третьих, сборные металлические конструкции гораздо проще транспортировать, так их можно разобрать и тем самым сократить размеры. Выгодная логистика – очень важный фактор в производстве.
В связи с этим возникает вопрос: какой из существующих типов соединения конструкций использовать лучше всего? В полной мере об этом можно судить, только имея представление о каком-то конкретном строительном случае. Однако, в любом случае есть некоторые особенности двух методов, справедливые для любой ситуации. Основываясь на них, мы дадим вам несколько советов.
Наиболее популярные сегодня техники соединения металлоконструкций – это сварная и болтовая. Есть также клёпка и пайка, но они используются далеко не так часто.
Сварное соединение
Неоспоримое преимущество сварного метода соединения – это герметичность шва, которая предохраняет конструкцию от попадания влаги между деталями. Сварка хороша тем, что, имея соответствующие навыки, вы можете прикрепить к основной конструкции детали совершенно любой формы и в самых разных положениях. Болтовое соединение такой вариативности не обеспечит, так как у него есть свои пространственные ограничения. И, наконец, сварное соединение – достаточно дешевый процесс.
Что касается недостатков сварки, здесь нужно сказать о том, что от сильного локального нагрева увеличивается подверженность коррозии, и металл может повести. Кроме того, сварочное соединение невозможно без наличия определенного инструментария: тут и сварочный аппарат, и кабели, и щиток, и надежный источник тока. И, что самое главное – соответствующий высокоразвитый навык.
Болтовое соединение
В чем состоит преимущество болтового соединения перед сварным? Прежде всего, это возможность разобрать конструкцию. Это особенно важно, когда мы говорим о соединении элементов водопровода или других конструкций, элементы в которых требуется регулярно заменять. Ведь для того, чтобы проникнуть в конструкцию, она должна легко разбираться – но при этом все же быть очень прочной. Болты это обеспечивают.
К недостаткам болтового соединения можно причислить геометрическую ограниченность. Соединяемые элементы должны идеально совпадать поверхностями, все углы должны быть ровными – иначе прочность крепежных отверстий обеспечить невозможно.
Что надежнее?
На самом деле, если все условия соблюдаются на сто процентов – сварка делается профессионально, а болты скрепляют геометрически правильные элементы – то прочность двух соединений получается почти равной. Особенно, если конструкция делается для исключительно бытовых целей и не будет в будущем подвержена особо сильным нагрузкам.
Выводы
В конце концов, выбор метода соединения вы все равно сделаете, исходя из целей металлоконструкции. Собираете конструкцию сложных форм из различного проката? Выбираем сварное соединение. Если хотите иметь возможность разобрать конструкцию, тогда болтовое соединение – идеальный вариант.
Сварные соединения.
Сварные соединения
Способы сварки деталей конструкций
Сварка — это технологический процесс соединения твёрдых материалов (металлов и некоторых неметаллов) в результате действия межатомных сил, которое происходит при местном сплавлении или совместном пластическом деформировании свариваемых деталей конструкций.
Современные способы сварки металлов можно разделить на две большие группы: сварка плавлением (сварка в жидкой фазе, термическая сварка), и сварка давлением (сварка в твёрдой фазе, механическая, термомеханическая).
При сварке плавлением материал соединяемых деталей самопроизвольно, без приложения внешних сил соединяется в одно целое в результате расплавления, смачивания и взаимного растворения в зоне сварки.
К сварке плавлением относятся: дуговая, плазменная, электрошлаковая, газовая, лучевая и др.
При сварке давлением для образования соединения без расплавления требуется значительное давление на контактную поверхность свариваемых деталей.
К сварке давлением относятся холодная, ультразвуковая, сварка трением, взрывом и др.
Граница между этими группами не всегда достаточно чёткая, например возможна сварка с частичным оплавлением деталей и последующим сдавливанием их (контактная электросварка).
Виды и способы сварки можно классифицировать и по другим признакам, например, по роду энергии: электрическая (дуговая, контактная, электрошлаковая, плазменная, индукционная и т. д.), механическая (трением, холодная, ультразвуковая и т. п.), химическая (газовая, термитная), лучевая (фотонная, электронная, лазерная).
Наиболее распространенными видами сварки являются электродуговая, электронно-лучевая, газовая (термическая сварка плавлением); контактная и термокомпрессионная (термомеханическая сварка); трением, холодная и ультразвуковая (сварка давлением или механическая сварка).
Электродуговая сварка
Электросварка — один из способов сварки, использующий для нагрева и расплавления металла электрическую дугу, образующуюся между электродом и свариваемым металлом.
Температура электрической дуги (до 7000°С) значительно выше температуры плавления всех известных металлов, поэтому процесс дуговой сварки сопровождается быстрым и эффективным расплавлением свариваемых деталей в зоне соединения.
В процессах электродуговой сварки применяются как плавящиеся, так и неплавящиеся электроды (угольные, графитовые, вольфрамовые). В первом случае формирование сварного шва происходит плавящимся электродом, во втором случае — расплавлением присадочного материала (проволоки, прутков и т. п.), которую вводят непосредственно в сварочную ванну.
Электродуговую сварку часто выполняют в среде защитного газа (аргона, гелия, углекислоты или их смесей) для защиты металла сварного шва от окисления. Газы подаются в зону дуги из сварочной головки в процессе электросварки.
Различают электродуговую сварку переменным и постоянным током. Сварка постоянным током меньше разбрызгивает металл, поскольку отсутствует амплитудное колебание напряжения, инициирующие разбрызгивание.
Электродуговую сварку классифицируют по разным технологическим признакам: по степени механизации (ручная, полуавтоматическая, автоматическая, по роду используемого электрического тока (постоянный с плюсом на электроде, постоянный с минусом на электроде, переменный), по типу дуги (зависимая дуга, независимая дуга), по свойствам электрода (плавящийся, неплавящийся), по свойствам материала покрытия электродов и некоторым другим показателям.
Дуговая электрическая сварка — важнейшее российское изобретение. Угольно-дуговая сварка впервые предложена Н. И. Бенардосом в 1882 г. Н. Г. Славянов в 1888 г. предложил сварку металлическим электродом.
Газовая сварка
Газовая сварка сопровождается местным расплавлением металла пламенем горючих газов сварочной горелки. Для повышения температуры пламени применяют смесь горючего газа с технически чистым кислородом. В качестве горючего газа чаще всего используется ацетилен, поскольку ацетилено-кислородное пламя даёт очень высокую температуру горения (3100 — 3200°С). Водородно-кислородная, бензино-кислородная и другие виды газовой сварки применяются реже.
Ацетилен получают разложением карбида кальция в воде с помощью ацетиленовых генераторов или промышленным способом. Кислород и ацетилен по шлангам подводятся к сварочной горелке, смешиваются в ней и сгорают на выходе из мундштука горелки, образуя сварочное пламя, которое одновременно оплавляет кромки соединяемых деталей и пруток присадочного металла, создавая сварной шов.
Газовая сварка применяется для стали, чугуна, меди, алюминия, всевозможных сплавов, при толщине свариваемых деталей от 0,1 до 6 мм, реже до 40 — 50 мм, так как при большой толщине заготовок выгоднее использовать более дешёвые и удобные способы сварки.
Широко распространена также наплавка всевозможных деталей с помощью газовой сварки.
Технология газовой сварки плохо поддается автоматизации и механизации, поэтому этот вид сварки обычно выполняется вручную.
Газовая сварка даёт удовлетворительное качество шва, однако при этом способе сварки нередки случаи коробления свариваемых деталей вследствие нагрева большой площади металла.
Преимущества газовой сварки: портативность и невысокая стоимость аппаратуры.
Недостатками этого вида сварки является высокая стоимость и взрывоопасность работ.
Лазерная сварка
Лазерная сварка — технологический процесс получения неразъемного соединения частей изделия путем местного расплавления металлов посредством нагрева по примыкающим поверхностям с помощью лазерного луча.
Когда лазерный луч попадает на металл, энергия излучения поглощается, металл нагревается и плавится. В результате такого плавления и последующей кристаллизации возникает прочное сцепление, образующее сварной шов. Сцепление свариваемых поверхностей основано на межатомном взаимодействии в металле.
Таким образом, лазерная сварка относится к методам сварки плавлением.
Как и любой технологический процесс, лазерная сварка имеет свои преимущества и недостатки. К основным преимуществам лазерной сварки можно отнести: локальность обработки материала, высокую производительность, технологическую гибкость и удобство.
Электронно-лучевая сварка
Электронно-лучевая сварка имеет сходную с лазерной сваркой принципиальную технологию. При этом способе соединения деталей нагрев осуществляется потоком заряженных частиц, поэтому для эффективности процесса необходим вакуум.
Лазерная сварка, в отличие от электронно-лучевой, может осуществляться в атмосфере или любой газовой среде, хотя для уменьшения окислительных процессов в свариваемом металле обычно применяют аргон.
Электронно-лучевой и лазерной сваркой чаще всего сваривают тугоплавкие и сильно окисляющиеся металлы и сплавы.
Контактная сварка
Контактная сварка осуществляется путем нагрева металла проходящим через него электрическим током в сочетании с пластической деформацией, вызываемой сжимающим усилием между свариваемыми поверхностями. Различают следующие виды контактной сварки: точечную, стыковую, роликовую (шовную) и конденсаторную.
Основные параметры режима всех способов контактной сварки — это сила сварочного тока, длительность его импульса и усилие сжатия деталей.
Контактная сварка – самый производительный способ сварки в промышленном производстве, допускающий широкую автоматизацию и механизацию процессов.
Осуществляется этот вид сварки на контактных сварочных машинах, которые бывают стационарными, передвижными и подвесными, универсальными и специализированными.
Термокомпрессионная сварка
Термокомпрессионная сварка осуществляется под давлением с местным нагревом участка соединения за счет теплопередачи от нагретого электрода.
Термокомпрессия — это процесс соединения двух материалов, находящихся в твердом состоянии, при воздействии на них теплоты и давления.
Температура нагрева соединяемых термокомпрессией материалов не должна превышать температуру образования их эвтектики (точки перехода от твердой к жидкой фазе любого из материалов), кроме того, один из материалов обязательно должен быть пластичным.
Получение прочного соединения термокомпрессиоиной сваркой можно объяснись следующим образом. На поверхностях контактной площадки и электродной проволоки имеется множество микровыступов и микровпадин, которые под действием давления и нагрева деформируются. При этом материал электрода и детали взаимно затекают в микровпадины, соединяя детали сплавлением.
В машиностроении и приборостроении термокомпрессионной сваркой чаще всего соединяют следующие пары материалов: золото — германий, золото — кремний, золото — алюминий, золото — золото, алюминий — алюминий, золото — серебро и алюминий — серебро.
Сварка трением
Сварка трением является разновидностью сварки давлением, при которой механическая энергия, подводимая к одной из свариваемых деталей, преобразуется в тепловую; при этом генерирование теплоты происходит непосредственно в месте будущего соединения.
Теплота может выделяться при вращении одной детали относительно другой или вставки между деталями, при возвратно-поступательном движении деталей в плоскости стыка с относительно малыми амплитудами и при звуковой частоте. Детали при этом прижимаются постоянным или возрастающим во времени давлением.
Сварка завершается осадкой и быстрым прекращением вращения или относительного перемещения свариваемых деталей.
В зоне стыка при сварке протекают следующие процессы.
По мере увеличения частоты вращения свариваемых заготовок при наличии сжимающего давления происходит притирка контактных поверхностей и разрушение жировых пленок, присутствующих на них в исходном состоянии. Граничное трение уступает место сухому.
Далее в контакт вступают отдельные микровыступы, происходит их деформация и образование ювенильных участков с ненасыщенными связями поверхностных атомов, между которыми мгновенно формируются металлические связи и немедленно разрушаются вследствие относительного движения поверхностей.
Разновидностью сварки трением является инерционная сварка.
При этом способе вращаемую деталь располагают в маховике, который раскручивают до заданной скорости и далее она вместе с маховиком вращается по инерции. Свариваемые детали соединяют и сварка завершается остановкой вращения маховика.
Холодная сварка
Этот вид сварки осуществляется сильным сжатием соединяемых деталей. Холодная сварка — сложный физико-химический процесс, протекающий только в условиях пластической деформации соединяемых деталей. Без пластической деформации в обычных атмосферных условиях практически невозможно получить полноценное монолитное соединение.
Роль деформации при холодной сварке заключается в предельном утонении или удалении слоя оксидов, в сближении свариваемых поверхностей до расстояния, соизмеримого с параметром кристаллической решетки, а также в повышении энергетического уровня поверхностных атомов, обеспечивающем возможность образования химических связей.
В зависимости от схемы пластической деформации заготовок различают точечную, шовную и стыковую разновидности холодной сварки.
Холодной сваркой можно соединять, например, алюминий, медь, свинец, цинк, никель, серебро, кадмий, железо. Особенно велико преимущество холодной сварки перед другими способами сварки при соединении разнородных металлов, чувствительных к нагреву или образующих интерметаллиды.
Для получения прочных и плотных швов необходимо предварительно очистить поверхности контакта от окислов. Прочность соединения при точечной холодной сварке может быть выше, чем при точечной контактной сварке, но при этом значительно хуже внешний вид соединения из-за вмятин и пластической деформации.
Ультразвуковая сварка
Ультразвуковая сварка — способ сварки деталей конструкций с применением ультразвука для сообщения колебаний инструменту, прижимаемому к поверхностям свариваемых материалов. При этом соединение металлов осуществляется в твердой фазе (без расплавления) — металл разогревается до температуры 200…600°С в результате действия сил трения между инструментом и металлом. Пластическая деформация металла облегчается благодаря снижению предела текучести при пропускании через свариваемые детали ультразвуковых колебаний.
Поскольку колебания инструмента способствуют очистке свариваемой поверхности, шов получается высокого качества. Этим способом соединяют отдельными точками или непрерывным швом главным образом листовые металлы (алюминий, титан, медь), некоторые сплавы, пластмассы.
***
Достоинства сварных соединений
Малая масса. По сравнению с заклепочными соединениями экономия металла составляет 15–20%, т.к. в заклепочных соединениях отверстия под заклепки ослабляют материал и обязательно применение накладок или частичное перекрытие соединяемых деталей. По сравнению с литыми стальными конструкциями экономия по массе составляет до 30%. Сваркой можно получить более совершенную конструкцию (литье не допускает большие перепады размеров) с малыми припусками на механическую обработку.
Малая стоимость. Стоимость сварной конструкции из проката примерно в два раза ниже стоимости литья и поковок.
Экономичность процесса сварки, возможность его автоматизации. Это связано с малой трудоемкостью процесса, сравнительной простотой и дешевизной оборудования: не нужны одновременное плавление большого количества металла, как при литье, и мощные дыропробивальные машины для установки заклепок большого диаметра.
Плотность и герметичность соединения. Герметичность сварных соединений используется в различных трубопроводах, газопроводах, металлических сосудах и т. п.
Соединение крупногабаритных деталей. Сварка дает возможность получения конструкций очень больших размеров, что невозможно, например, при литье. Примеры: сварной мост через реку Днепр, антенны радиотелескопов.
К достоинствам сварки следует отнести, также, возможность соединения различных материалов и деталей разных форм. Такие способы сварки, как лазерная, холодная, электронно-лучевая обладают рядом достоинств, которые позволяют использовать их при изготовлении высокоточных деталей и соединений.
***
Недостатки сварных соединений
Возможность получения скрытых дефектов сварного шва (трещины, непровары, шлаковые включения). Применение автоматической сварки в значительной мере устраняет этот недостаток.
Трудность контроля качества сварного шва. Существующие рентгеноскопические и ультразвуковые методы сложны.
Коробление деталей из–за неравномерности нагрева в процессе сварки.
Невысокая прочность при переменных режимах нагружения. Сварной шов является сильным концентратором напряжений.
***
Область применения сварных соединений
Сварные соединения широко применяют в строительстве. В машиностроении сварку применяют для получения заготовок деталей из проката в мелкосерийном и единичном производстве.
Сварными выполняют станины, рамы, корпуса редукторов, шкивы, зубчатые колеса, коленчатые валы, корпуса судов, кузова автомобилей, обшивку железнодорожных вагонов, трубопроводы, мосты, антенны радиотелескопов и др.
В массовом производстве применяют штампосварные детали.
Наибольшее распространение получили соединения электродуговой и газовой сваркой. Хорошо свариваются низко– и среднеуглеродистые стали. Высокоуглеродистые стали, чугуны и сплавы цветных металлов свариваются хуже.
***
Типы сварных швов и их расчет на прочность
Главная страница
Дистанционное образование
Специальности
Учебные дисциплины
Олимпиады и тесты
Усталостная долговечность сварных соединений | Инженерные расчеты
Конструкции со сварными соединениями склонны к разрушению под действием повторяющихся нагрузок, что обусловлено зарождением и ростом трещин в сварном соединении. В статье обсуждаются подходы к оценке усталостной долговечности сварных соединений.
Существует ряд причин, по которым наличие сварного соединения ограничивает ресурс конструкции:
- Материал сварного шва более хрупкий, нежели чем основной материал детали.
- Геометрия сварного шва содержит локальные неоднородности, которые могут являться концентраторами напряжений.
- Сварной шов может содержать полости и трещины, которые являются зоной начала разрушения.
- После сварки в сварном шве действуют высокие остаточные напряжения.
- Сварной шов зачастую расположен в месте резкого изменения сечения детали.
Основываясь на данных факторах, предсказание усталостной прочности и ресурса сварного соединения может быть достаточно сложной задачей. Однако, на эту тему существует большое количество исследований, а также разработаны нормы и стандарты, описывающие процедуры оценки долговечности сварных соединений. Все стандарты описывают два основных шага процедуры оценки:
- Метод расчета напряжений в сварном шве.
- Применение усталостной S-N кривой, описывающей зависимость уровня напряжений от количества циклов до разрушения, в логарифмических масштабах.
Оценка напряжений в сварном шве может быть выполнена в упрощенной постановке или более детально методом конечных элементов. При упрощенной оценке усилия, действующие в дальней зоне детали вдали от сварного соединения, делятся на характерную площадь сечения сварного соединения для получения номинальных усредненных напряжений. Данный подход не учитывает особенности геометрии сварного шва и концентрацию напряжений. При оценке методом конечных элементов может быть построена идеализированная геометрия сварного шва и получены локальные значения напряжений в зоне корня и у границы наружной поверхности. При этом необходимо в подобной модели острые углы в зоне сварного соединения заменять на скругления, чтобы избежать сингулярности напряжений, или отступать от зоны сингулярности при оценке напряженного состояния. Многие стандарты и нормы расчета сварных соединений допускают не моделировать детально геометрию сварного шва, а определяют зоны вблизи сварного соединения, в которых необходимо определить напряжения, и далее способ их линеаризации для экстраполяции в зону сварного шва. Обзор подходов с применением линеаризации приведен в работе С.
В. Петинова, Р. В. Гучинского. S-N-критерии усталости материалов для расчетов ресурса конструкций: проблемы применения.
После того как значения напряжений определены, их можно использовать для оценки усталостной долговечности соединения. В зависимости от применяемого метода оценки напряжений на шаге 1, S-N кривая может быть скорректирована. Для стальных сварных соединений усталостные кривые имеют следующие характеристики:
- S-N кривая принимается линейной в логарифмической шкале по обеим осям с наклоном, равным -1/3.
- В зависимости от метода расчета напряжений, кривая может быть сдвинута вниз или вверх, как указано в применяемом стандарте.
- Типовое обозначение усталостных кривых для сварных соединений – FATххх, где ххх – значение напряжений в МПа, приводящее к разрушению при определенном числе циклов, обычно 2 миллиона. Кривая FAT225, применяемая при оценке напряжений методом конечных элементов, представлена на рисунке ниже.
- Для количества циклов более 2 миллионов, вторая ветка кривой либо становится параллельной оси Х (что соответствует пределу выносливости), либо более пологой.
На приведенном рисунке задан наклон -1/22 при количестве циклов более 10 миллионов.
- Для определения долговечности используется значение размаха напряжений, при этом средние напряжения (при несимметричном цикле нагружения) не учитываются. Исследования показали, что средний уровень напряжений не оказывает влияния на долговечности, вероятнее всего вследствие наличия высоких остаточных напряжений в зоне сварки, которые нивелируют эффект несимметричности цикла нагружения.
Используя знания в области расчетов методом конечных элементов и механики разрушения, становится возможным провести детальные расчеты усталостной прочности и долговечности сварных соединений, включая прогнозирование направления роста трещины с применением автоматических процедур перестроения конечно-элементной сетки.
Блог сварщика
Альтернативные источники энергии
2021-02-13
…
Владимир Будянов. Альтернативные технологии, Россия и Новый мировой порядок.

2021-02-11
Доктора наук Сергей Салль, Анатолий Конев, Валерий Дудышев (акад. Российской экологической академии) и ряд других учёных работают над созданием эффективных технологий, направленных на решение ключевых проблем человечества. Но на их пути стоит Всемирное мировое правительство… Передовые русские учёные обоснованно связывают современную мировую политику, направленную на установление Нового мирового порядка на основе всесилия «золотого тельца», с повсеместным обязательным подавлением новых технологий, в первую очередь энергетических и…
Альтернативная энергия своими руками: обзор лучших возобновляемых источников электричества
2017-12-21
Сегодня всем известно, что запасы углеводородов на Земле имеют свой предел. С каждым годом все труднее становится добывать нефть и газ из недр. Кроме того, их сжигание наносит непоправимый ущерб экологии нашей планеты. Несмотря на то, что технологии производства возобновляемой энергии сегодня очень эффективны, государства не спешат отказываться от сжигания топлива. При этом, цены на энергоносители растут с каждым годом, заставляя простых граждан все больше и больше раскошеливаться. В связи с этим, производство альтернативной энергии сегодня…
Альтернативные виды энергии. Обзор источников электичесива
2017-12-21
Ограниченные запасы ископаемого топлива и глобальное загрязнение окружающей среды заставило человечество искать возобновляемые альтернативные источники такой энергии, чтобы вред от ее переработки был минимальным при приемлемых показателях себестоимости производства, переработки и транспортировки энергоресурсов. Современные технологии позволяют использовать имеющиеся альтернативные энергетические ресурсы, как в масштабе целой планеты, так и в пределах энергосети квартиры или частного дома. Буйное развитие жизни на протяжении нескольких…
Альтернативные технологии — Россия и Новый мировой порядок.
2017-12-21
http://www.dal.by/news/89/28-08-12-25/
Альтернативные технологии, Россия и Новый мировой порядок
Доктора наук Сергей Салль, Анатолий Конев, Валерий Дудышев (акад. Российской экологической академии) и ряд других учёных работают над созданием эффективных технологий, направленных на решение ключевых проблем человечества. Но на их пути стоит Всемирное мировое правительство…
Передовые русские учёные обоснованно связывают современную мировую политику, направленную на установление Нового мирового порядка на основе всесилия «золотого…
Аккумуляторы для солнечных батарей
2017-12-21
Аккумуляторы для солнечных батарей — это буфер, обеспечивающий накопление энергии посредством обратимых химических реакций, благодаря чему гарантируется работа в циклическом режиме.
В солнечных системах используются аккумуляторные батареи герметичные и малообслуживаемые , а также Никель-солевые накопители энергии которые обладают большим ресурсом и предназначены специально для циклической работы. В настоящий момент самые востребованные свинцово-кислотные аккумуляторы для солнечных батарей , т.к это самый доступный класс накопителей. ..
Аккумуляторы для рынка возобновляемых источников энергии
2017-12-21
Журнал РАДИОЛОЦМАН, июнь 2014 Bruce Dorminey Renewable Energy World Magazine Как развивающиеся, так и развитые страны мира имеют веские основания задуматься об использовании аккумуляторных технологий. И вот почему. С тех дней, когда ваш дедушка вынужден был периодически открывать капот, чтобы добавить воды в свинцово-кислотную батарею, технология аккумуляторов прошла долгий путь. Всего десять лет назад идея, что блоки аккумуляторов скоро будут «сглаживать потоки энергии», текущей от ветряных и солнечных ферм в электрические сети, казалась почти фантастической….
Безтопливные генераторы — уже реальность (+видео) — Форум Izhcommunal.ru
2017-06-30
Гидроэнергоблок для безплотинных ГЭС Изобретатель Ленёв Николай Иванович. Патент №2166664
В изобретении предлагается оригинальный, ранее не использовавшийся ни в одной из существующих конструкций, способ использования энергии как водного потока любого вида (рек, ручьёв, приливов, морской волны и т. д.) так и движения воздушных масс. При этом используется естественный поток, без предварительного преобразования (строительства дамб, каналов, напорных труб).
Данный способ отъёма мощности водного потока является наиболее выгодным и с экологической…
Альтернативная энергетика
2017-06-22
содержание презентации «Альтернативная энергетика.ppt» № Слайд Текст 1 Альтернативная энергия в помощь Экологии и Энергосбережению Псков 2010г. Автономная некоммерческая организация Cоциально-консультационный центр «ПсковРегионИнфо» Альтернативная Энергия 2 Возобновляемые источники энергии Автономная некоммерческая организация Cоциально-консультационный центр «ПсковРегионИнфо» Альтернативная Энергия. Возобновляемые источники энергии – это не альтернатива существующей энергетике, а ее будущее, и вопрос лишь в том, когда…
Типы сварных соединений
СВАРНЫЙ СОЕДИНЕНИЕ
ВВЕДЕНИЕ
Когда два члена соединены
средствами сварки, такое соединение известно как сварное соединение. Предложения по сварке
возможность для дизайнера добиться более эффективного использования
материалы. Ранее конструкторы считали сварные швы менее устойчивыми к усталости. Это было
считал, что добиться хороших сварных швов на стройплощадке невозможно.Теперь день, с
достижения в области методов неразрушающего контроля (NDT), тестирования и
стало проще контролировать качество сварных швов. Это придает дизайнерам достаточно смелости.
изучить возможности и возможности сварных соединений. Быстрый
конструкция облегчается применением сварных соединений. Масса сварного
количество подключений относительно невысокое и, следовательно, снижает стоимость строительства. С тех пор
нет сокращения отверстий, общее поперечное сечение эффективно переносит
нагрузки.
ВИДЫ СВАРНЫХ СОЕДИНЕНИЙ
Основные виды сварных соединений
можно классифицировать в зависимости от типов сварных швов, положения сварных швов и типа
сустава.
1. На основе по типу сварного шва
По типу сварного шва сварные швы можно классифицировать по для углового шва, шва с разделкой кромок (или стыкового шва), электрозаклепки, щелевого шва, точечной сварки и Т. Д.На рисунке 15 показаны различные типы сварных швов.
1.1. Стыковые швы (стыковые)
Швы с разделкой кромок (стыковые швы) и угловые швы выполняются, когда соединяемые элементы выровнены. Канавка сварка обходится дороже, так как требует подготовки кромок. Швы с разделкой кромок могут быть безопасно использовать в сильно нагруженных членах. Предусмотрены квадратные стыковые швы. только для плиты толщиной 8 мм.Различные типы стыковых швов показаны на Рисунок 16.
1.2. Угловые швы
Угловые швы выполняются при
два соединяемых стержня находятся в разных плоскостях. Поскольку такая ситуация возникает
чаще угловые швы встречаются чаще, чем стыковые. Угловые швы
легче сделать, так как требует меньше подготовки поверхности. Тем не менее они
не такой прочный, как швы с разделкой кромок, и вызывает концентрацию напряжений.Филе
сварные швы предпочтительнее для слабо нагруженных элементов, где жесткость, а не
сила определяет дизайн. Различные типы угловых швов показаны на
Рисунок 17.
1.3. Слот и электрозаклепки
Щелевые и электрозаклепочные швы используются для дополнять угловые швы там, где невозможно обеспечить требуемую длину углового шва. достигнуто.
2. На основе на позиции шва
В зависимости от положения сварного шва, Сварные швы можно разделить на плоский шов, горизонтальный шов, вертикальный шов, колодец и пр.
На основе тип стыков
На основе
по типу соединений сварные швы можно разделить на стыковые, внахлестку
сварные соединения, тройники и угловые сварные соединения.
Угловые сварные швы — обзор практики
Угловые сварные соединения, такие как тройники, соединения внахлест и угловые соединения, являются наиболее распространенными соединениями в сварном производстве. В общей сложности на них, вероятно, приходится около 80% всех соединений, выполненных дуговой сваркой.
Вероятно, что в большом проценте других методов соединения также используется какая-либо форма углового сварного соединения, включая процессы без плавления, такие как пайка, сварка твердым припоем и пайка.Последние методы выходят за рамки данной статьи.
Нажмите здесь, чтобы увидеть наши последние подкасты по технической инженерии на YouTube . Хотя угловой сварной шов является очень распространенным явлением, существует ряд аспектов, которые необходимо учитывать перед выполнением такого сварного шва. В этой статье будет рассмотрен ряд тем, относящихся к угловым сварным швам, и есть надежда, что даже самый опытный изготовитель или сварщик извлечет пользу из этой статьи.
Распространенные конструкции стыков для угловых швов показаны ниже в Рис.1 .
Рис. 1. Типовые конструкции угловых швов
Элементы углового шва
BS EN ISO 2553 использует следующие обозначения как Рис. 2 и 3 показывают.
a = толщина горловины
z = длина ножки
s = толщина горловины глубокого проникновения
Рис. 2. Филе под углом
Рис 3.Филе глубокого проникновения
Формы угловых сварных швов
Угловые швы большего размера или угловые швы увеличенного размера
Рис. 4. Размеры сварного шва в зависимости от необходимой длины полки или толщины шва
Одной из самых серьезных проблем, связанных с угловыми сварными соединениями, является получение правильного размера сварного шва в соответствии с требуемой длиной полки или толщиной шва ( Рис. 4 ).
Разработчик может рассчитать размер и учесть «коэффициент безопасности», чтобы сварной шов, указанный на производственном чертеже, был больше, чем требуется по конструктивным соображениям.
Размер сварного шва указывается с помощью соответствующего символа сварного шва.
В Великобритании размер сварного шва часто указывается путем ссылки на длину плеча «z» в EN ISO 2553, где число означает размер сварного шва в миллиметрах, как показано на Рис. 5 .
Рис. 5. Спецификация размеров сварного шва (Великобритания)
В Европе обычно определяют расчетную толщину горловины, указанную «a» ( Рис. 6 ).
Рис. 6. Спецификация размеров сварного шва (Европа)
После выдачи чертежа в цех обычно обнаруживается, что сварщик или инспектор также применяет дополнительный коэффициент безопасности.Также часто можно услышать «добавь еще немного, и оно станет сильнее».
В результате получается сварной шов увеличенного размера с длиной опоры, возможно, 8 мм, а не 6 мм, указанным дизайнером. Эти дополнительные 2 мм представляют собой увеличение объема сварного шва более чем на 80%.
Это в сочетании с уже превышенным размером сварного шва из «запаса прочности» разработчика может привести к получению сварного шва, который в два раза превышает объем углового шва правильного размера.
Сохраняя размер сварного шва, указанный в чертежном бюро, можно достичь более высоких скоростей сварки, что приведет к увеличению производительности, снижению общего веса продукта, расхода расходных материалов и их стоимости.
Другое преимущество заключается в том, что в случае большинства процессов дуговой сварки небольшое увеличение скорости перемещения в большинстве случаев приводит к увеличению глубины проплавления корня, так что фактическая толщина горловины увеличивается:
Поэтому сварной шов увеличенного размера очень дорого производить, он может не иметь «лучшей прочности», требует больших затрат на сварочные материалы и может вызвать другие производственные проблемы, включая чрезмерную деформацию.
Соединения внахлест, сваренные угловыми швами.
Как обсуждалось ранее, сварные швы с увеличенным размером являются обычным явлением, и соединение внахлест не исключение.Дизайнер может указать длину ноги, равную толщине материала, как на Рис. 7 .
Рис. 7. Соединение внахлестку — длина ветви
Соображения прочности могут означать, что размер углового сварного шва не обязательно должен приближаться к толщине листа. На практике сварной шов может иметь другие дефекты, например:
Рис. 8. Пример, показывающий угловой шов меньшего размера, который в некоторых спецификациях часто называется «без сварки»
Из-за оплавления угла верхней пластины ( рис.8 ), длина вертикального участка уменьшена, что означает, что проектное горло также было уменьшено; поэтому был получен шов меньшего размера. Поэтому необходимо следить за тем, чтобы угол верхней пластины не расплавился. В идеале сварной шов должен быть на расстоянии 0,5-1 мм от верхнего угла ( Рис. 9 ).
Рис. 9. В идеале сварной шов должен быть на расстоянии 0,5–1 мм от верхнего угла
Поэтому разработчик может указать немного меньшую длину ножки по сравнению с толщиной компонента.
Чтобы компенсировать это уменьшение толщины горловины, может потребоваться задать угловой шов с глубоким проплавлением. Это количество дополнительного проплавления должно быть подтверждено соответствующими испытаниями сварных швов. Во время производственной сварки также могут потребоваться дополнительные меры контроля, чтобы гарантировать постоянное достижение этого дополнительного проплавления.
В дополнение к уменьшению толщины горловины существует вероятность возникновения дополнительных проблем, таких как перекрытие на носке сварного шва из-за большего размера сварочной ванны ( Рис.10 ) или чрезмерно выпуклая поверхность шва и, как следствие, острые надрезы на носке шва ( Рис. 11 ).
Рис. 10. Перекрытие на носке сварного шва из-за большего размера сварочной ванны
Рис. 11. Чрезмерно выпуклая поверхность шва и, как следствие, острые зазубрины на носке шва
Обе потенциальные проблемы, показанные на Рис. 10 и 11 , могут отрицательно повлиять на усталостную долговечность сварного соединения из-за увеличенного угла носка, который действует как большая концентрация напряжений.Корневой провар также обычно уменьшается в однопроходных сварных швах такой формы.
Плохая подгонка также может уменьшить толщину горловины, как в Рис. 12 . Угол вертикального компонента на эскизе был преувеличенно скошен, чтобы проиллюстрировать эту точку.
Рис. 12. Толщина горловины может быть уменьшена из-за плохой подгонки
Сводка
Угловые сварные соединения — это не только наиболее часто используемые сварные соединения, но и одни из самых сложных для сварки с любой реальной степенью прочности.Угловые сварные швы требуют большего количества тепла, чем стыковое соединение такой же толщины, и у менее квалифицированных сварщиков это может привести к отсутствию проплавления и / или дефектов плавления, которые невозможно обнаружить визуальным осмотром и другими методами неразрушающего контроля.
Угловые сварные швы не всегда доступны для объемного неразрушающего контроля, который может рассматриваться как необоснованный из-за трудностей контроля, таких как доступ к месту нахождения пленки в RT, и требующих много времени методов контроля с UT, результаты которых часто бывают трудно интерпретировать.
Методы контроля, такие как визуальный контроль, магнитное испытание и проникающее испытание, относятся только к методам проверки поверхности. При визуальном контроле большая часть усилий тратится на измерение размера сварного шва, а не на определение других аспектов качества.
Таким образом, угловые сварные соединения намного сложнее сваривать и контролировать объемно. Часто получаемые сварные швы больше, чем они должны быть, или они могут иметь плохую форму, что может отрицательно сказаться на их эксплуатационных характеристиках.
Чтобы преодолеть эти трудности, проектировщикам необходимо точно указать наиболее подходящий размер горловины (или длину опоры, или даже оба требования), а сварочный персонал должен стремиться к достижению указанного проектного размера с осторожностью. Сами сварщики также должны быть надлежащим образом обучены и иметь достаточную квалификацию, чтобы иметь возможность поддерживать приемлемое качество сварки, размер сварного шва и наиболее подходящий уровень мастерства.
Эта статья была написана Марком Козенсом Ценг Фвелди из Weld-Class Solutions Ltd .
Для получения дополнительной информации свяжитесь с нами.
Сравнение сварных и болтовых соединений
На стадии планирования и проектирования любого проекта инженеры должны решить, какой материал или инструмент лучше всего подходят для выполнения определенных задач. Типы соединений, используемых в конструкции, обычно зависят от общей конструкции, но необходимо учитывать несколько факторов: стоимость, время установки и общие характеристики. В этой статье сравниваются сварные соединения и болтовые соединения, обычно используемые для соединения элементов из металлов или термопластов.Конструкция шарниров — ключевой элемент стальной конструкции.
Сварные швы состоят из сплавления двух элементов, подвергающихся сильному нагреву, и обеспечения их остывания. В строительной отрасли используются различные методы сварки. По данным Американского общества сварки (AWS), некоммерческой организации, занимающейся изучением и развитием сварки, существует пять типов сварки: стыковая, угловая, кромочная, внахлест и тройник. Эти типы соединений определяются положением свариваемых элементов друг относительно друга.
В болтовых соединениях используются крепежные детали, удерживающие элементы конструкции в определенном положении, которые затем фиксируются с помощью винтовой резьбы. Болтовые соединения подразделяются на соединения, работающие на растяжение и соединения, работающие на сдвиг. Как и во многих инженерных решениях, у обоих вариантов есть достоинства и недостатки.
Держите ваши проекты в курсе с помощью службы управления строительством.
Сравнение затрат
Стоимость болтовых и сварных соединений зависит от проекта, но болтовые соединения обычно являются менее дорогим вариантом. Цена на болтовые соединения более чувствительна к ценам на сталь, но процесс их изготовления более эффективен и автоматизирован по сравнению со сварными соединениями.
Сварные соединения могут выполнять только сертифицированные сварщики, и их почасовая оплата может быть высокой. С другой стороны, затраты на рабочую силу, связанные с затяжкой болтов, намного ниже. Если стоимость проекта является ключевым моментом, болтовые соединения обычно являются лучшим вариантом.
Сравнение структурных характеристик
Сварные соединения обычно прочнее болтовых соединений, главным образом потому, что их материал не имеет отверстий, необходимых для болтовых соединений.Когда речь идет о прочности соединения, процесс производства является определяющим: болтовые соединения просты, а сварные соединения обеспечивают более высокую прочность.
Сварные соединения рекомендуются, когда конструктивные характеристики проекта имеют больший приоритет, чем стоимость.
Сложность проверки с каждым вариантом
В болтовых соединениях инспекторы должны убедиться, что вылет болта положительный или нулевой — недопустимо, чтобы конец болта находился внутри гайки. Инспекторы также должны следить за тем, чтобы болты были затянуты, и при необходимости проверять, не отломаны ли концы.
Методы контроля сварки различаются в зависимости от проекта. Визуальный осмотр является наиболее распространенным и проводится до, во время и после сварки. Для других методов проверки требуется специализированное оборудование, которое стоит дороже и требует сертифицированных AWS инспекторов. Другими словами, контроль сварных соединений дороже и сложнее.
Сравнение гибкости суставов
Сварные соединения более жесткие, чем болтовые, из-за непрерывности поперечного сечения.С другой стороны, болтовые соединения соединяются пластинами или уголками, и прогиб этих элементов во время передачи нагрузки добавляет гибкости. По этой причине болтовые соединения допускают большее движение при меньшем структурном напряжении.
Недостатком болтовых соединений является дополнительное оборудование, необходимое для установки, что ограничивает их применение. Сварка более универсальна, так как почти любые две поверхности можно сваривать вместе, а новые элементы можно легко добавлять к существующим соединениям.
Процесс установки и безопасность
Между порядком монтажа болтовых и сварных соединений существуют важные различия.Руководители строительства должны знать о них, чтобы эффективно управлять проектом.
Болтовые соединения проще в обращении и обычно устанавливаются с помощью ударного ключа или обычного торцевого ключа. Их также легче ремонтировать, что помогает сэкономить время в непредвиденных ситуациях. Болтовые соединения также обеспечивают более быструю установку в полевых условиях.
Сварка обычно выполняется сертифицированным сварщиком вручную. В зависимости от типа сварного шва требуются разные типы оборудования и источники энергии.Дуговая сварка в защищенном металлическом корпусе (SMAW) является наиболее распространенной, когда электрическая дуга возникает между металлическим электродом с покрытием и стальными компонентами, которые необходимо сваривать. Сварка может выполняться на заводе или на строительной площадке, но в обоих случаях существуют строгие требования к безопасности и качеству.
Сварка — опасная задача, и необходимо соблюдать меры предосторожности, чтобы избежать ожогов, повреждения зрения, вдыхания дыма и газов, воздействия УФ-излучения и поражения электрическим током. С другой стороны, установка болтов не несет особого риска, кроме работы на высоте.Безопасность на рабочем месте важна независимо от типа соединения, но сварка сопряжена с большим количеством специфических рисков.
Заключительные замечания
В заключение, болтовые соединения имеют преимущество в стоимости и простоте, но имеют место потери конструктивных характеристик. С другой стороны, сварные соединения прочнее, но дороже и сложнее в обращении.
Ни один из вариантов не может считаться лучшим для всех случаев, поскольку наилучшее соответствие меняется в зависимости от проекта.В конце концов, тип указанного соединения будет зависеть от требований проекта и предпочтений владельца.
Многоплоскостные сварные соединения | Институт стальных труб
Джеффри А. Пакер
Бахен / Таненбаум Профессор гражданского строительства, Университет Торонто, Онтарио, Канада
AISC 360-16 Спецификация Раздел K1 начинается с упоминания его объема: «Для целей данной главы осевые линии элементов ответвления должны лежать в общей плоскости» (AISC, 2016).Однако на практике большое количество конструкций с полыми секциями имеет не только плоские сварные соединения, но и многоплоскостные соединения. Они могут возникать в башнях, морских сооружениях, крановых порталах, мостах, навесах, атриумах, решетчатых колоннах и конструкциях крыш. Архитектура произвольной формы высвободила и поощряла художественное самовыражение до такой степени, что дизайнеры теперь чувствуют, что почти любое трехмерное расположение элементов может быть определено и построено. Это может привести к серьезным производственным трудностям, таким как пример на Рисунке 1.
Большинство пространственных рам спроектированы как системы с штифтовым соединением, что приводит только к осевым силам элемента, поэтому конструкция многих многоплоскостных сварных соединений (с основным или «сквозным» элементом) может быть связана с их аналогами плоских соединений, нагруженных в осевом направлении . Терминология для многоплоскостных соединений была принята таким образом, что если вторая плоскость в узле содержит второе X- (или Cross-), T- или K-соединение, то соединение называется XX-, TT- или KK- подключение соответственно.Точно так же Т-образная ветвь в плоскости, ортогональной плоскому X-соединению, создаст многоплоскостное TX-соединение (или, альтернативно, его можно рассматривать как XT-соединение) и так далее. Однако такие метки соединений ферменного типа по-прежнему подпадают под действие правил классификации соединений, основанных на передаче силы, как описано в разделе комментариев K1 AISC 360-16 и в Руководстве по проектированию AISC № 24 (Packer et al. , 2010). Несколько основных типов многоплоскостных соединений по сравнению с их однолинейными аналогами показаны на рисунке 2.
AWS (2015) предоставляет средства обработки многоплоскостных эффектов для круглых соединений HSS, но правила проектирования относительно сложны и, в зависимости от конфигурации и загрузки соединений, они могут быть ненадежными для прогнозов прочности. Большое количество исследователей, как резюмируют Packer and Henderson (1997), Wardenier et al. (2008) и Packer et al. (2009), выполнил экспериментальные и численные исследования многоплоскостных, сварных, быстрорежущих соединений.Исследования все чаще показывают, что «мультипланарный эффект» вызывается как нагрузкой, так и геометрическими эффектами, причем последнее является функцией, в частности, отношения ширины (β) и гибкости стенки пояса (2γ), что касается плоских соединений. Простое добавление большего количества ответвлений к соединению (например, сварка большего количества стали) часто служит для придания жесткости области соединения и обеспечения увеличения прочности.
Рекомендуемый подход CIDECT (Wardenier et al., 2008; Packer et al., 2009) для проектирования многоплоскостных соединений состоит в том, чтобы рассмотреть тип соединения в одной плоскости, а затем отрегулировать прочность плоского соединения (на основе управляющего предельное состояние) для влияния ветвей, лежащих вне этой плоскости, на поправочный коэффициент µ.Учитывая положительный эффект приварных ответвлений и игнорируя влияние нагрузки, этот коэффициент µ во многих случаях может быть принят равным 0,9 или 1,0. Это имеет условие, что для расчета значения Qf плоского соединения используется общая хордовая сила; с использованием либо общего «предварительного напряжения» для круглых поясов из быстрорежущей стали, либо общего «максимального напряжения» для прямоугольных поясов из быстрорежущей стали. Поправочные коэффициенты для прочности плоского соединения (определены в главах J и K Спецификации AISC 360-16 или Руководстве по проектированию AISC No.24) приведены для распространенных типов соединений в таблице 1 для круглой HSS и в таблице 2 для прямоугольной HSS. Далее следуют особые замечания относительно соединений XX и KK.
Конструкция соединения XX
При плоском X- (или поперечном) соединении, как показано на рисунке 2, при равных и противоположных силах сжатия ветви, круглая хорда из быстрорежущей стали сглаживается и приобретает овальную форму.Для прямоугольной HSS поверхности нагруженного пояса изгибаются внутрь, а две ненагруженные стенки перемычки изгибаются наружу, в то время как углы имеют тенденцию приблизительно сохранять свои углы 90 °. Таким образом, для обеих форм стороны пояса выступают наружу. Если теперь добавить нагруженные сжатием неплоскостные ответвления (как в соединении ХХ на Рисунке 2), можно увидеть, что такие силы стремятся восстановить хордовую секцию до ее исходной формы и, таким образом, имеют положительный эффект в противодействии. деформация хорды. И наоборот, разветвления, нагруженные растяжением, находящиеся вне плоскости, будут иметь противоположный эффект и усугубить деформацию соединения.Таким образом, в таблицах 1 и 2 поправочный коэффициент плоской прочности µ сильно зависит от относительного значения сил в парах X-ветвей. XX-соединение с ортогональными плоскостями X-ответвлений, нагруженными в противоположном смысле, представляет собой единственный случай многоплоскостного соединения, который может привести к серьезному уменьшению (до 35%) по сравнению с его монопланарным аналогом.
Конструкция соединения KK
Для круглых соединений HSS KK простой коэффициент уменьшения µ = 0.9 может применяться для учета многоплоскостных эффектов, как указано в таблице 1. Это следует из Руководства по проектированию CIDECT № 1, 1-е. изд. (Wardenier et al., 1991), потому что это конкретное руководство CIDECT — как и спецификация AISC 360-16 — основано на «предварительном напряжении» хорды (нижнее напряжение хорды) для расчета коэффициента круглой HSS Q f . (Это можно увидеть в разделе «Функции» в таблице спецификаций AISC K3.1). Кроме того, две рекомендации (Руководство по проектированию CIDECT № 1, 1-е изд. И Спецификация AISC 360-16) имеют общие проверки предельного состояния для K-соединений с зазором и перекрытия.
Для прямоугольных HSS-соединений KK простой коэффициент уменьшения µ = 0,9 может также применяться для учета многоплоскостных эффектов, как указано в таблице 2. Это следует из Руководства по проектированию CIDECT № 3, 1-е. изд. (Packer et al., 1992), потому что это конкретное руководство CIDECT — как и спецификация AISC 360-16 — основано на хорде «максимальное напряжение» для расчета прямоугольного фактора HSS Qf, и обе рекомендации имеют общие проверки предельного состояния для зазоров и перекрытий K -соединения.
Усилие в одном элементе пояса может быть значительно выше в соединении KK, чем в соединении K, из-за составляющих силы, параллельных хорде, от ответвлений в двух плоскостях.Точно так же компоненты силы, перпендикулярные хорде от ответвлений в двух плоскостях, могут быть значительно выше в соединении KK, чем в соединении K. Таким образом, для соединений KK с зазором рекомендуется составить диаграмму свободного тела, показывающую силы пояса, действующие на участок, проходящий через область зазора, а затем выполнить проверку взаимодействия на предмет разрушения в области зазора при комбинированном нормальном и напряжение сдвига. Это показано в таблице 1 для круглой HSS и в таблице 2 для прямоугольной HSS. Для круглых HSS-соединений KK общая «вертикальная» поперечная сила в зазоре (V зазор ) применяется к круглому поперечному сечению, где площадь сдвига хорды принимается равной (2 / π) A (Wardenier et al., 2010). Для прямоугольного соединения KK с зазором из быстрорежущей стали, с углом между плоскостями ответвления φ = 90 °, соединение подвергается воздействию сдвигающей силы (0,5√2) V зазор в каждой плоскости. Сдвигающей силе в каждой плоскости противодействуют две стенки прямоугольной хорды из быстрорежущей стали. «Горизонтальные» составляющие двух плоскостей уравновешиваются. Как для круглой, так и для прямоугольной быстрорежущей стали предел текучести при сдвиге принимается равным 0,6F y в соответствии со спецификацией AISC 360-16 .
Аспекты изготовления с KK-соединениями
Круглый HSS
Обычная начальная компоновка для 3D-моделирования состоит в том, чтобы иметь одну рабочую точку для нескольких ветвей на средней линии хорды, но проектировщики должны знать, что это может потребовать более сложных процедур изготовления.В одной плоскости два элемента ответвления в K-соединении могут перекрывать друг друга, но в KK-соединении элементы ответвления из одной плоскости могут также перекрывать элементы из другой плоскости. Увеличение количества перекрывающихся ответвлений приводит к большему профилированию концов ответвлений, более сложной сборке и большему количеству проблем со сваркой. Чтобы избежать перекрытия элементов ответвления одной боковой плоскости на элементы другой, может потребоваться ввести «поперечный зазор» между соседними плоскостями, но это может привести к смещению рабочей точки перпендикулярно оси хорды.Этот эксцентриситет кодирования должен быть ≤ 0,25D, чтобы создаваемый изгибающий момент не учитывался с точки зрения его основного воздействия на конструкцию соединения. Момент эксцентриситета имеет некоторое влияние на прочность соединения, так как он влияет на значение Q f , фактора влияния напряжения хорды. Момент эксцентриситета всегда будет влиять на конструкцию элементов пояса, потому что они должны быть рассчитаны на комбинированное осевое усилие и изгиб.
В соединении KK, если два элемента сжатой перемычки перекрывают друг друга, а два элемента натяжной перемычки накладываются друг на друга, но по-прежнему существует зазор g вдоль хорды между сжимающими и растягивающими элементами перемычки (при симметричной нагрузке) , то объединенная «зона обслуживания» с двумя ветвями может рассматриваться как одно целое, а KK-соединение анализируется как K-соединение.
Прямоугольный HSS
Рисунок 3: Треугольная ферма из быстрорежущей стали с двумя поясами сжатия. Треугольные фермы или фермы «треугольник» (Δ) часто имеют форму буквы «V», которая объединяет один нижний пояс с двумя верхними поясами, как показано на Рисунке 3. Под действием силы тяжести это дает преимущество повышенной поперечной устойчивости, обеспечиваемой двойные, разделенные, но связанные компрессионные хорды. Эти фермы часто используются в качестве открытых конструкций и считаются эквивалентными по внешнему виду, но менее дорогими, чем космические каркасы.Квадратные аккорды HSS использовались с элементами перемычки, обрамляющими углы секции аккорда, путем придания формы концам перемычек для образования так называемых соединений «птичий клюв» (например, крыша конференц-центра Миннеаполиса, эстакада аэропорта Миннеаполис / Сент-Пол. ). Однако дешевле повернуть нижний пояс на 45 ° и скосить концы перемычки так, чтобы они попадали на плоские поверхности пояса (как показано для соединений KK в Таблице 2). При использовании в качестве стропильной фермы прогоны могут не потребоваться, поскольку верхние пояса могут быть разнесены на подходящем расстоянии друг от друга, чтобы можно было пролететь между ними.Затем настил можно прикрепить непосредственно к плоским поверхностям элементов верхнего пояса из быстрорежущей стали.
Список литературы
AISC. 2016. «Спецификация для зданий из конструкционной стали», ANSI / AISC 360-16 и комментарий, Американский институт стальных конструкций, Чикаго, Иллинойс.
AWS. 2015. «Нормы сварки конструкций — сталь», ANSI / AWS D1.1 / D1.1M: 2015, 23-е. изд., Американское общество сварки, Майами, Флорида.
Пакер, Дж.А. и Хендерсон, Дж. Э. 1997. «Соединения полых структурных секций и фермы — руководство по проектированию», 2-е. изд., Канадский институт стальных конструкций, Торонто, Канада.
Пакер, Дж. А., Шерман, Д. и Лечче, М. 2010. «Соединения полых структурных секций», Руководство по проектированию AISC № 24, 1-е. изд., Американский институт стальных конструкций, Чикаго, Иллинойс.
Packer, J.A., Wardenier, J., Kurobane, Y., Dutta, D. и Yeomans, N. 1992. «Руководство по проектированию соединений с полым прямоугольным сечением (RHS) при преимущественно статической нагрузке», CIDECT Design Guide No. 3, 1-й. изд., CIDECT (Ed.) и Verlag TÜV Rheinland, Кельн, Германия.
Packer, J.A., Wardenier, J., Zhao, X.L., van der Vegte, G.J. и Куробане, Ю. 2009. «Руководство по проектированию соединений с полым прямоугольным сечением (RHS) при преимущественно статической нагрузке», CIDECT Design Guide No. 3, 2nd. изд., CIDECT, Женева, Швейцария.
Wardenier, J., Kurobane, Y., Packer, J.A., Dutta, D. and Yeomans, N. 1991. «Руководство по проектированию соединений с полым круглым сечением (CHS) при преимущественно статической нагрузке», CIDECT Design Guide No.1, 1-й. изд., CIDECT (Ed.) и Verlag TÜV Rheinland, Кельн, Германия.
Wardenier, J., Kurobane, Y., Packer, J.A., van der Vegte, G.J. и Чжао, X.-L. 2008. «Руководство по проектированию соединений с полым круглым сечением (CHS) при преимущественно статической нагрузке», CIDECT Design Guide No. 1, 2nd. изд., CIDECT, Женева, Швейцария.
Wardenier, J., Packer, J. A., Zhao, X.-L. и ван дер Вегте, Г.Дж. 2010. «Полые профили в конструкционных приложениях», 2-е. изд., CIDECT, Женева, Швейцария
июнь 2018
Скачать PDF
Проектирование сварного соединения двутавра
Существует два метода расчета сварного шва в соответствии с EN 1993-1-8 [1].Инженер может использовать ориентированный или упрощенный метод проектирования.
В принципе, метод, связанный с направлением, более рентабелен, тогда как упрощенный метод дает идентичные результаты параллельно оси сварного шва в случае только касательных напряжений в области углового шва.
В данном примере поперечного сечения HEA расчет с использованием упрощенного метода в соответствии с EN 1993-1-8, пункт 4.5.3.3 будет выполнен быстро и легко с помощью автономной программы SHAPE-THIN.
Рисунок 01 — Схема системы
Действующие внутренние силы могут быть введены в таблицу 3.1:
N = -1,190 кН
V y = 180 кН
V z = 370 кН
M y = 225 кНм
M z = 26 кНм
Расчетное значение прочности на сдвиг для сварного шва рассчитывается по формуле
$ {\ mathrm f} _ {\ mathrm {VW}, \ mathrm d} \; = \; \ frac {{\ mathrm f} _ {\ mathrm u}} {\ sqrt3 \; \ cdot \; {\ mathrm \ beta} _ {\ mathrm w} \; \ cdot \; {\ mathrm \ gamma} _ {\ mathrm M2}}
$ до
$ {\ mathrm f} _ {\ mathrm {VW}, \ mathrm d} \; = \; \ frac {360} {\ sqrt3 \; \ cdot \; 0. 2} $
Это должно быть установлено в параметрах расчета в SHAPE-THIN, потому что настройка по умолчанию соответствует эквивалентному напряжению согласно Мизесу (см. Рисунок 03).
Рисунок 03 — Определение параметров расчета
Результат проектирования в SHAPE-THIN отображается непосредственно графически. Соотношение сварных швов на фланце и стенке можно быстро определить с помощью цветового градиента.
Рисунок 04 — Коэффициент использования сварного шва
Болты против сварных швов против заклепок для стальных соединений
В наше время наиболее распространенным способом соединения стальных конструкционных элементов является использование болтов или сварных швов.Исторически заклепки использовались в качестве соединительной среды, однако по ряду причин их в основном заменяли болтами. В следующей статье мы обсудим различия между заклепками, болтами и сварными швами в качестве крепежа / приспособлений для соединений конструкционной стали.
Заклепочные соединения
Заклепки имеют долгую историю в качестве соединительного средства для стальных соединений. Они состоят из головки и гибкого стержня.Процесс установки потребовал предварительного нагрева заклепки и приложения пневматического давления. Это имело ряд недостатков, включая необходимость предварительного нагрева (дополнительные затраты энергии и технологический процесс, а также риск пожара), высокий уровень шума во время установки и сложность замены заклепок во время технического обслуживания.Болтовые соединения
Болты в значительной степени заменили заклепки из-за их более низкой стоимости установки, простоты установки и обслуживания. В стальных конструкциях обычно используются два типа болтов: высокопрочная конструкционная сталь и болты A307 (обычные болты).Болты из конструкционной стали делятся на подкатегории A325 (Группа A) и A490 (Группа B) и обладают высокой прочностью.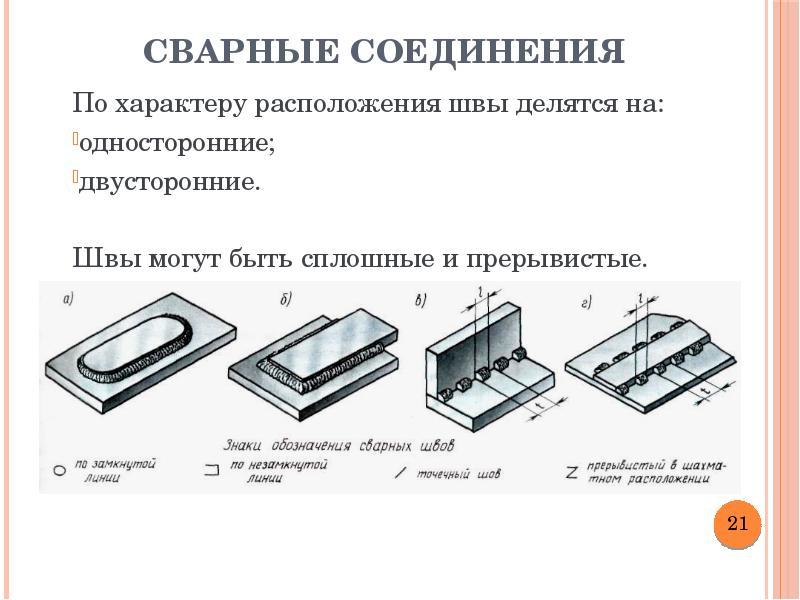
Сварные соединения
Основное преимущество сварных соединений — простота конструкции, требующая меньшего количества деталей и материалов. Однако сварные швы дают усадку, и этот эффект необходимо учитывать при проектировании, особенно для больших сварных швов. Кроме того, проверка сварных швов сложнее и, следовательно, дороже и сложнее в обслуживании.Различия существуют в отношении качества сварного шва, выполняемого монтажником. К наиболее распространенным типам сварных швов относятся угловые швы, швы с разделкой кромок, заглушки и пазы. Программное обеспечение SkyCiv Connection Design Уильям КуангИнженер и разработчик программного обеспечения
BEng Механический (Hons1)
Сварные соединения из высокопрочных сталей для строительства
org/ScholarlyArticle»> [1]EN 1993-1-8: 2005, Еврокод 3: Проектирование стальных конструкций — Часть 1-8: Проектирование соединений и EN 1993-1- 8: 2005 / AC: 2005: Еврокод 3: Проектирование стальных конструкций — Часть 1-8: Проектирование соединений, Исправления к EN 1993-1-8: 2005-07.
EN 1993-1-10: 2005, Еврокод 3: Проектирование стальных конструкций — Часть 1-10: Прочность материала и свойства по всей толщине.
EN 1993-1-12: 2007, Еврокод 3: Проектирование стальных конструкций — Часть 1-12: Дополнительные правила для расширения EN 1993 до марок стали S700.
EN 10025-1 до -6: 2005, Горячекатаный прокат из конструкционных сталей.
Исходная документация D.03: 1990, Оценка результатов испытаний сварных соединений из FeE 460 с целью получения прочностных функций и подходящих коэффициентов модели, Редакционная группа Еврокода 3.
Греснигт А.М .: Обновление правил проектирования для угловых сварных швов, Труды 3 -й Европейской конференции по стальным конструкциям, Коимбра, Португалия, 2002, стр. 919–927.
EN 1993-1-9: 2005, Еврокод 3: Проектирование стальных конструкций — Часть 1-9: Усталость.
Кюн Б.: Beitrag zur Vereinheitlichung europäischer Regelungen zur Vermeidung von Sprödbruch, Вклад в стандартизацию европейских правил хрупкого разрушения, Диссертация, Lehrstuhl für Stahlbau, 2004 (в Германии, Ахен).
Милн И., Эйнсворт Р.А., Доулинг А.Р. и Стюарт А.Т.: Оценка целостности конструкций, содержащих дефекты, British Energy (ранее CEGB), R / H / R6-Revision 3, 1998.
EN ISO 14341: 2008, Сварочные материалы. Проволочные электроды и наплавки для дуговой сварки нелегированных и мелкозернистых сталей в среде защитных газов. Классификация.
EN ISO 16834: 2007, Сварочные материалы. Проволока, электроды, проволока, прутки и наплавки для дуговой сварки высокопрочных сталей в среде защитного газа. Классификация.
ISO 4063: 1998, Сварка и родственные процессы. Номенклатура процессов и ссылочные номера.
Федер Д., Вернер Г .: Ansätze zur Traglastberechnung von Schweißverbindungen, Подход к прогнозированию несущей способности сварных конструкций, Schweißen und Schneiden, 1977, vol. 29, нет. 4. С. 125–132 (на немецком языке).
Google ученый
EN 1011-2: 2001, Сварка — Рекомендации по сварке металлических материалов, Часть 2: Дуговая сварка ферритных сталей.
http://www.uni-weimar.de/Bauing/stahlbau/aif_14195bg.
Kuhlmann U., Vormwald M., Werner F., Köhler G., Heinemann H., Günther H.-P., Beier T. , Hildebrand J., Rasche C., Versch C. and Wudtke I .: Forschungsvorhaben P 652: Wirtschaftliche Schweißverbindungen höherfester Baustähle, Экономичные сварные соединения высокопрочных сталей для строительного сектора, Дюссельдорф: Verlag und Vertriebsgesellschaft, ed. FOSTA Forschungsvereinigung Stahlanwendung e.В., 2008 (на немецком языке).
DIN 18800-1: Stahlbauten, Teil 1: Bemessung und Konstruktion, Проектирование стальных конструкций, Deutsches Institut für Normung e.V. (DIN), Ausgabe 1990-11 (на немецком языке).
E 1820-99: Стандартный метод испытаний для измерения вязкости разрушения, Annual Book of ASTM Standards Vol. 03.01, Американское общество по испытаниям и материалам, 1999.
Калиновски Б.: Experimentelle Überprüfung des Sprödbruchkonzeptes des EC 3 an bauteilähnlichen Großzugproben mit aufgeschweißten, основанный на правилах крупномасштабной проверки хрупкости EC 3 Versteifungen. образцы для испытаний, Диссертация, Berichte aus dem Institut für Eisenhüttenkunde, RWTH Aachen, 1999 (на немецком языке).
Кокельманн Х. и Шварц Т.: Quantifizierung der teilzerstörenden Eigenspannungsmessverfahren (Bohrloch-und Ringkernverfahren) для анизотропных Werkstoffe und Mehrachsiguredes — определение остаточных напряжений с использованием метода количественной оценки деструктивно-деструктурного анализа скважин. анизотропные материалы и многоосное остаточное напряженное состояние, Abschlussbericht, Штутгарт: MPA Stuttgart 1991 (на немецком языке).
EN 1043-1: 1995: Разрушающие испытания сварных швов металлических материалов. Испытания на твердость. Часть 1: Испытания на твердость сварных соединений.
ANSYS®, Release 11.0, ANSYS, Inc. Саутпойнт, Канонсбург, 2007.
Процедура SINTAP, Процедуры оценки структурной целостности для европейской промышленности, Заключительный отчет, Программа Европейского Союза Brite-Euram , Проект ЕС № BE 95-1462, Брюссель, 1999.
DIN EN ISO 5817: 2006, Сварка — Сварные соединения плавлением стали, никеля, титана и их сплавов (за исключением лучевой сварки). Уровни качества для недостатков.
EN 1990: 2002, Еврокод: Основы проектирования конструкций.
DIN EN 1993-1-8 / NA: Национальное приложение — Параметры, определяемые на национальном уровне — Еврокод 3: Проектирование стальных конструкций — Часть 1-8: Расчет соединений, DIN Deutsches Institut für Normung, 2010.
Коллин Р. и Йоханссон Б.: Расчет сварных швов в высокопрочной стали, Труды 4 -й Европейской конференции по стали и композитным конструкциям, Маастрихт, 2005 г., Том C, стр. 4.10–89– 4.10-98.
Кульман У., Гюнтер Х.-П. и Раше С.: Высокопрочные стальные угловые сварные соединения, Стальная конструкция — проектирование и исследования, Ernst & Sohn, сентябрь 2008 г., т. 1. С. 77–84.
Артикул Google ученый